Can Electronic Potting Material Be Used For Both Rigid And Flexible PCBs?
Can Electronic Potting Material Be Used For Both Rigid And Flexible PCBs?
Electronic potting material is essential for providing insulation and protecting electronic components and circuitry from damaging environmental factors – moisture, dust, vibrations – and giving the PCB (Printed Circuit Board) that extra bit of mechanical support. It’s all about offering reliability and durability to enhance our everyday electronics.
The market offers a range of potting materials, each with special properties that make them suitable for unique applications. Epoxy resins bring flexibility; polyurethane resins deliver thermal conductivity; silicone rubber offers solid chemical resistance, while thermoplastic materials stand out in curing time. To ensure you find the right fit for your project, consider operating temperatures, protection levels or those must-have mechanical qualities.
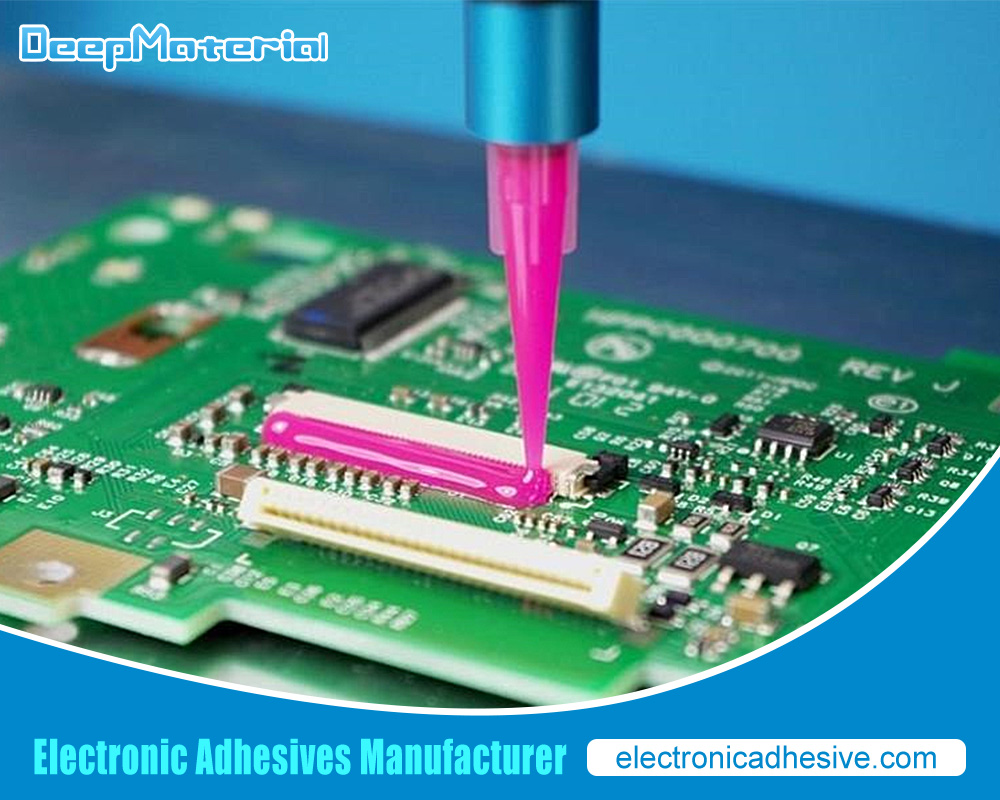
Can Electronic Potting Material Be Used For Both Rigid And Flexible PCBs?
Cruising straight to the heart of the matter – can one electronic potting material hold its own with rigid and flexible PCBs? Rigid PCBs hitched up from rigid materials like fibreglass or epoxy resin, while supple flexi-PCBs spring forth from more malleable mediums. It truly is a night-and-day difference between them – their suppleness or hardness.
The obvious ease brought on by finding universal potting material for both endued us with the ability to simplify our manufacturing process drastically, at once cutting costs and alleviating inventory management woes, all while ensuring we get consistent performance & reliability across different types of PCBs.
Traditional potting materials for rigid PCBs
Over the years, epoxy resins have proven to be a reliable potting material for various rigid PCBs. They’ve got everything: from strength and chemical resistance to thermal stability and affordability – hardy stuff! Yet, this all-star packaging protector has some drawbacks; being stiff and brittle makes them ill-suited when flexibility is critical, while their higher curing temperatures can quickly become problematic with heat-sensitive components.
Polyurethane resins tick the box if you need something more malleable, while silicone rubber maximizes your electrical insulation properties and provides excellent deals with high-heat situations. Although both options might increase the price slightly compared to epoxy resin, they still offer unique benefits.
Challenges in potting flexible PCBs
Potting flex PCBs is a tricky prospect – they can bend and twist, so the potting material needs to hold firm, even in the face of all that stretching and shifting. Plus, it has to stay glued tight with no blisters or bubbles!
The adhesive on flexible placements presents a bit of an issue, too; if your potting material isn’t compatible with it (i.e., won’t adhere properly), you’re out of luck regarding effective encapsulation.
And that’s no small risk considering what kind of dangers lingering moisture can bring. Bottom line: if you plan on potting flex PCBs, ensuring you have the suitable materials is critical.
Advantages of using electronic potting material for flexible PCBs
Flexible PCBs come with their fair share of struggles; nevertheless, having electronic potting material on your side can bring in several advantages – flexibility being the main one. Electronic potting materials are made to bend and twist repeatedly without cracking or separating, far better than traditional epoxy resins. Ensuring all components and circuitry remain unharmed even when flexed gives it an edge over others.
For extra protection against environmental harm such as moisture, dust, and vibrations – there’s nothing quite like electronic potting material! As it creates a shield around the parts collective, water is denied entrance, reducing any jeopardy towards corrosion; plus, it subtly masks vibrations, which helps minimize damage caused by mechanical stress.
Electronic potting material stands out when paired with different kinds of substrates – polyimide and polyester-derived flexible PCB, for instance- stick easily due to their adhesive nature. This produces a reliable connection between both substrates, preventing separation at any cost.
Differences between rigid and flexible PCBs
Rigid and flexible PCBs are practically night and day – one as solid as stone, the other bending like a serpent. The material they’re made from affects their properties in some striking ways. If you get my drift, what works for rigid boards won’t necessarily do on flexibles.
These differences mean picking out a potting material is no easy ride: your choice will largely depend on how rigid or bendy it needs to be when all’s said and done! For steps that must stay strong – think PCBs of the rigid kind – we need something offering mechanical robustness with extra defence against environmental harm.
But where flexibility matters most, we’ll go for something more pliant to withstand repeated twisting without succumbing to damage.
Lastly, spare us a thought about temperature resistance, too. At the same time, very hot conditions might not faze stiffer materials; their supplier cousins can’t take much heat, so pick curing temperatures accordingly or else expect less-than-ideal results once complete.
Testing and validation of electronic potting material for flexible PCBs
Testing and validating are critical for ensuring the best performance of electronic potting material used in flexible PCBs. Getting a handle on potential material limitations helps ensure it meets all necessary standards.
A thermal cycling test is a surefire way to evaluate the reliability of these materials under different temperature ranges. It allows us to bring out capabilities – or lack thereof – that may not have been revealed otherwise.
The flexibility test also has to be done regarding PCBs meant to bend or flex during use! This helps determine if those pieces can handle repeated bending without showing damage like cracking or delamination.
Finally, there’s also moisture resistance testing, chemical resistance testing and electrical insulation tests as crucial components for determining whether this stuff can adequately protect from repercussions like water intrusion.
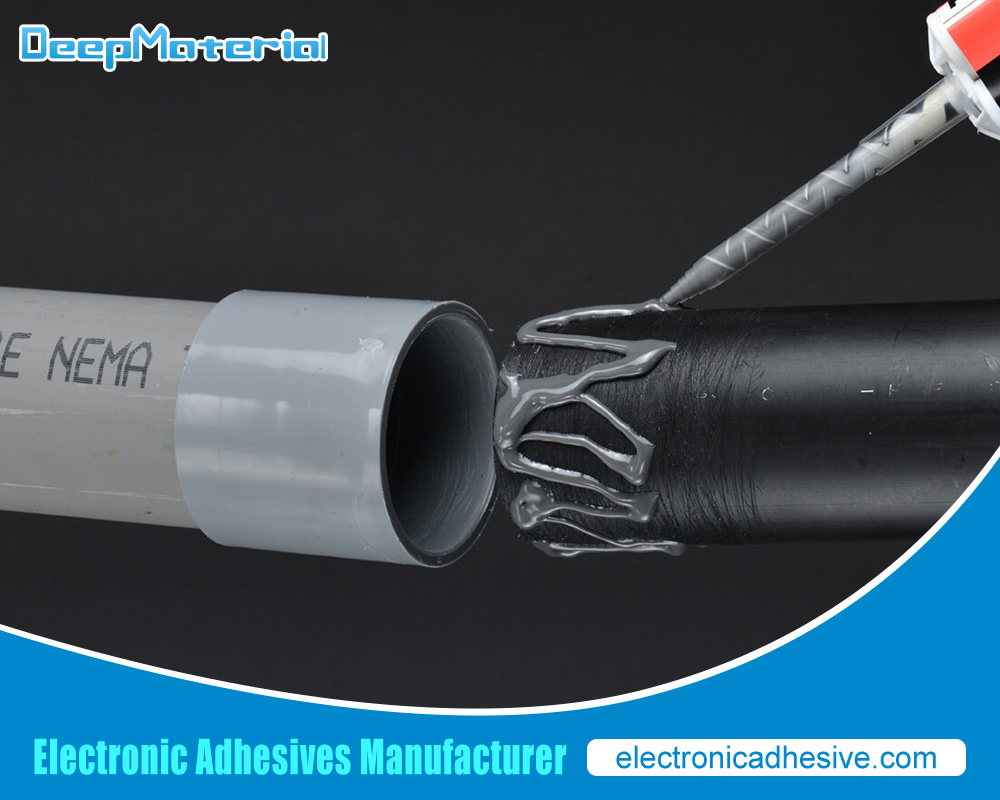
Last Words
Electronic potting material rocks the house for inflexible and flexible PCBs. While old-school goopy stuff was awesome on inflexible PCBs, it won’t cut it with bendable ones. Electronic potting materials can do it all—offering incredible flexibility and toughness that meets each board’s needs head-on.
This type of material pays off because you get unbeatable protection against environmental disturbances, no more compatibility issues (thanks to its wide array of substrates) and super stellar reliability. Even though some hiccups like air bubbles or adhesion issues may briefly appear along your PCB journey, knock them back with some testing before they become serious.
For more about choosing the Electronic Potting Material, you can pay a visit to DeepMaterial at https://www.electronicadhesive.com/about/ for more info.