Bring your production designs to life by using consumer electronics bonding adhesive
Bring your production designs to life by using consumer electronics bonding adhesive
The world that we live in today is driven by various modern and advanced electronics. Thanks to modern electronic designs, our lifestyles have been improved. We are now surrounded by electronic vehicles, smartphones, electronic personal assistants, smart TVs, and so on. Even smart homes and smart cities are driven by electronics. The quest for people to live smartly powered by technology has increased the need for more electronic devices. New and innovative electronic devices are made possible due to the ability of electronic engineers to interpret complex designs. These industrial engineers usually face tough challenges when it comes to designing and developing various types of consumer electronics.
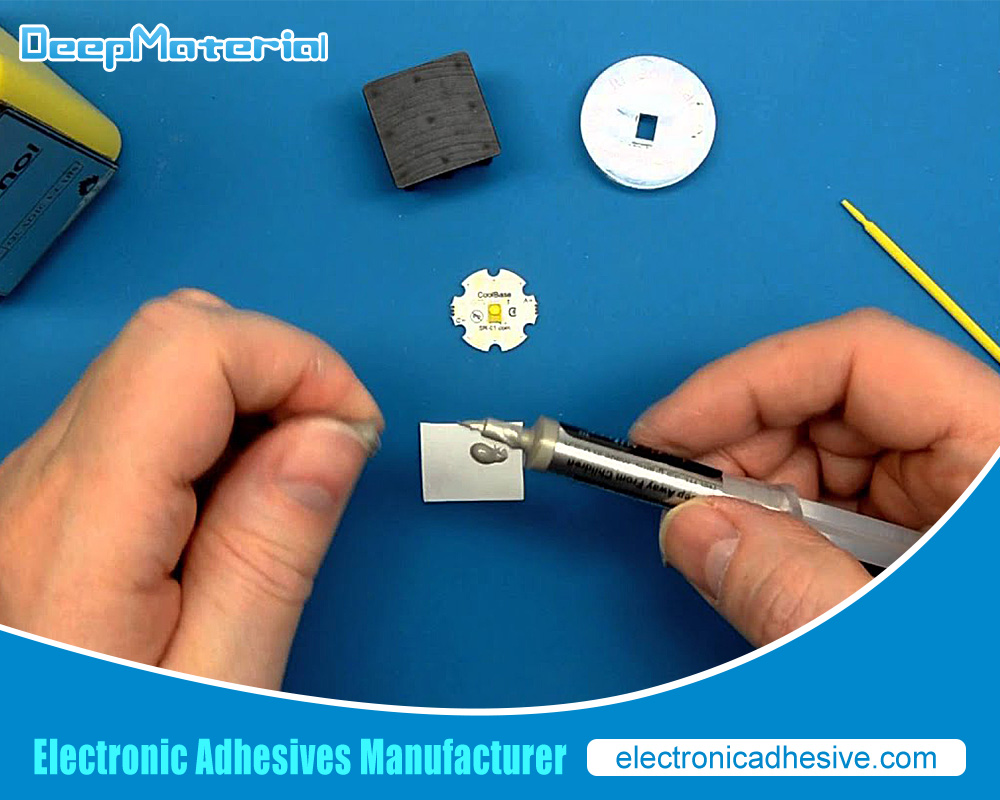
Electronics bonding adhesives: Enhancing product performance and reducing costs
From the perspective of a designer, adhesives can be used in the electronics industry to open up a world of innovation. Industrial glues help bring electronic product components together, thereby producing consumer goods that are bigger than the sum of all individual parts. The use of innovative engineering adhesives in the electronics industry paves the way for increased cost savings and new design specifications. Adhesives help electronics makers to access a wealth of design options with their products. Apart from enhancing product service life and reliability, adhesives have a way of helping designers interpret their design intents. Adhesives can be used to achieve design geometry and sizes while still enhancing performance and load distribution. In addition, they also help manufacturers of consumer electronics to reduce the weight and size of the goods.
Liquid adhesive provides more efficiencies with product designs
liquid adhesives are used to fill up surface irregularities and make up for design errors and shortcomings. When used to bond substrates in the electronic industry, they can help fill up the clearance gaps between substrates like metals, and so on. When they cure, they usually create a high-strength and very dense adhesive bond. This bond is typically used for maximum load distribution and increased joint strength. The consumer electronics bonding adhesive usually forms a fully cured resin. This resin helps enhance the surface contact area to 100%. This ensures that the joint reliability and stress distribution is enhanced. It also partly enhances the life of the product.
Why soldering and welding are less favored with consumer electronics bonding
Soldering and welding are used in the electronics industry but in a limited capacity. These mechanical fastening methods are not as important when it comes to the many benefits that engineering adhesives provide electronic makers. Welding and soldering are limited to specific applications in the industry. This is because they usually require the application of very high temperatures which can distort or deform the electronics components. The substrates can get excessively heated which can easily cause structural degradation and residual stresses. This can cause both short- and long-term defects in the final electronics product.
The importance of adhesives in enhancing electronic designs
Thanks to engineered consumer electronics bonding adhesive products, product engineers are now able to produce electronic products with more complicated designs. Adhesives help electronic designers meet the size and dimensional requirements easily. This way, the performance of the final product is not compromised. Engineering glues like the consumer electronics bonding adhesive make it easier for manufacturers to produce more lighter and compact products. This is opposed to other available options like bolting and laser welding which are known to increase the size and weight of electronics products. Adhesives usually provide instant bonds that are as good as laser welds without causing any stress to the finished products. Many electronics manufacturers have used adhesives in replacement for more costly fastening methods. When they introduce engineering adhesives to assemble electronics, they discover that they usually need lightweight housing for each product. This helps them save up on a lot of money.
Electronics bonding adhesives and product material selection
A consumer electronics bonding adhesive is an engineering glue that helps enhance the final designs of the product. This is because they allow product assemblers to use the right substrates to interpret the designs from the design engineers. With engineering adhesives, electronic product manufacturers can increase the number of product substrates for production. Without the use of engineering adhesives, it can be very difficult to choose the right substrate for each production process. Many joined components usually have great stress levels at the joints. With many other fastening methods, various substrates will easily fail, however, while adhesives help enhance the rigidity of many substrates. In addition, engineering adhesives help to strengthen the full electronic assembly – this way, it makes the selection of substrates less critical to the performance of the parts.
Consumer electronics bonding adhesive: Easily achieve design intent
Thanks to recent advances in engineering adhesive technology, glues for assembling consumer electronics are becoming more robust. Many of these adhesives are formulated with special ingredients to help product designers achieve their various design aims. In addition, these adhesives can also be produced to make product assembly very simple. This means that in many cases, they do not need activators, primers, or cleaners to strengthen bonds and boost curing speed. Many of these adhesives also come with various other custom mechanical properties that help the electronics to resist extreme temperatures after assembly. Weight and size are key parameters that drive production designers. The use of the right type of consumer electronics bonding adhesive helps the designers easily achieve this intent. In addition, adhesives can also help product fabricators to increase the efficiency of the final product.
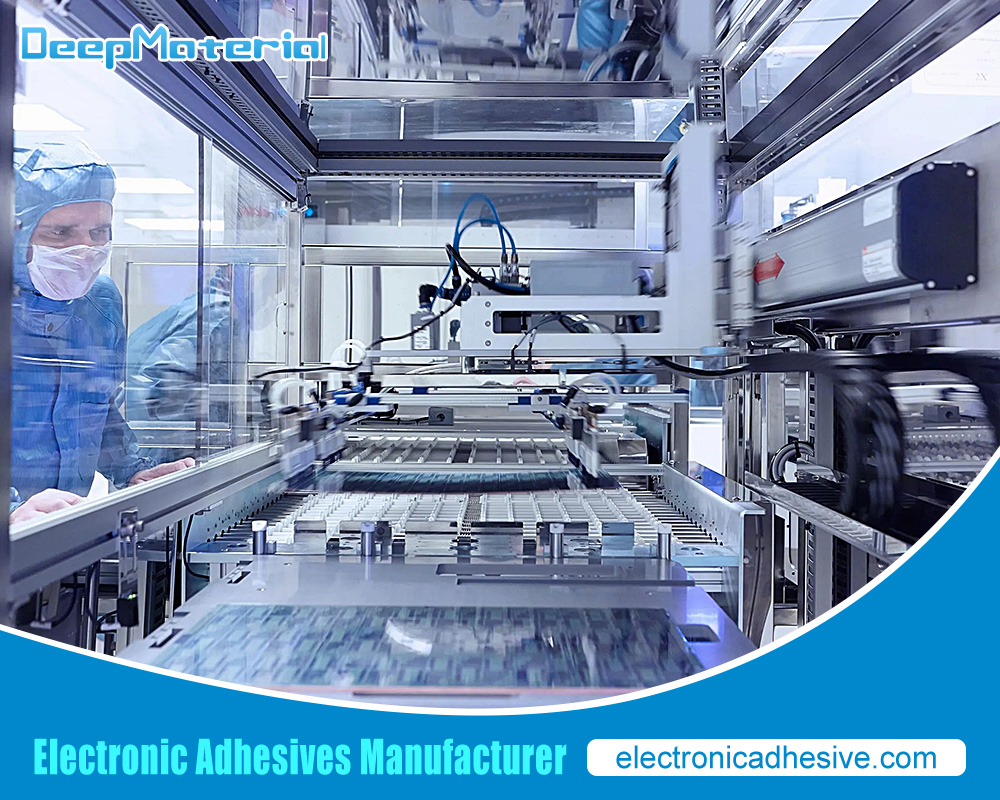
The benefits of using consumer electronics bonding adhesives
Thanks to advanced adhesive technology, electronics manufacturers have been able to experiment with innovative product designs. There are now numerous innovative electronic products in the market. This is a result of the availability of innovative engineering adhesives that were formulated to help product designers to overcome basic design challenges. These are some of the benefits that consumer electronics bonding adhesives provide for manufacturers of electronics:
- They help product designers interpret complex designs.
- They are more suitable for other fastening methods and products.
- They provide string and durable bonds.
- They can be cured easily to increase daily product throughput
- Adhesives can be customized to provide special properties such as temperature resistance, thermal resistance, water resistance, and so on.
- They help reduce the general weight of the final product.
- They make it easier for manufacturers to choose the right substrate for each fabrication job.
For more about choosing the electronics bonding adhesive, you can pay a visit to DeepMaterial at https://www.electronicadhesive.com/about/ for more info.