Bonding with Confidence: The Best Glue for Electronics
Bonding with Confidence: The Best Glue for Electronics
Are you tired of dealing with loose wires and malfunctioning gadgets? Do you wish there was a way to fix your electronics without having to constantly replace them? If so, then you’re in luck! Today, we will be discussing the best glue for electronics – a game-changer that will revolutionize the way you bond your devices. We understand the frustration that comes with broken gadgets, and we want to help you find a solution that will give you peace of mind and confidence in your repairs. So, sit back, relax, and let us guide you through the world of electronic bonding with confidence.
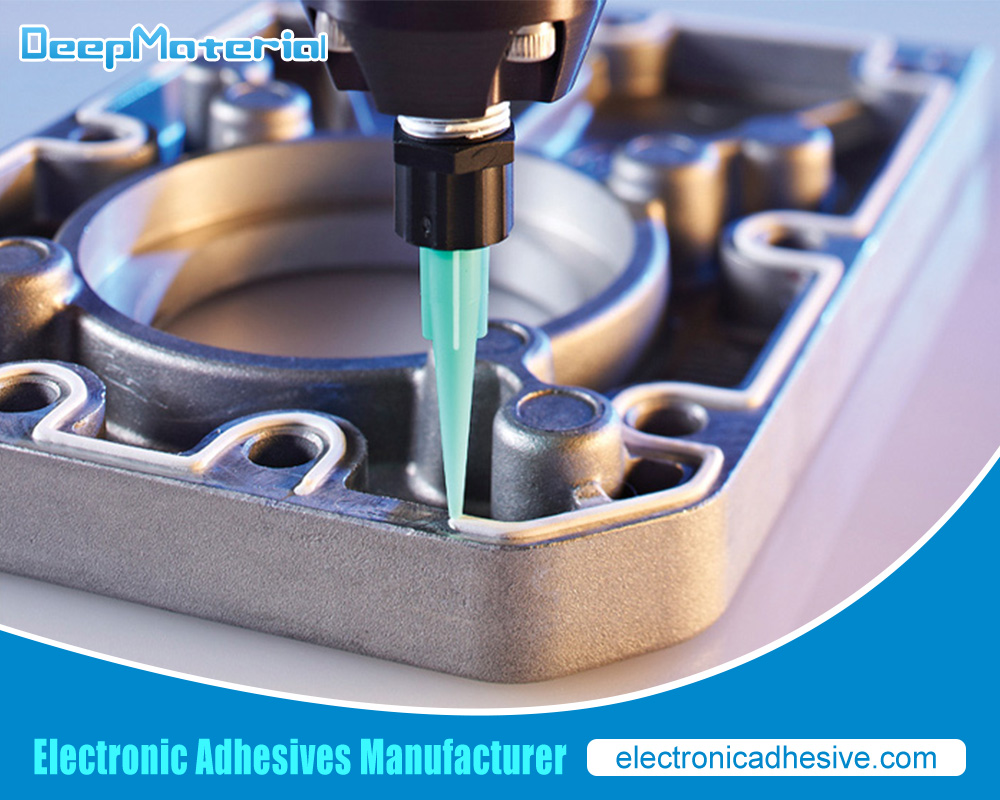
Importance of Choosing the Right Glue for Electronics
The role of glue in electronics is to provide a strong and durable bond between two or more components. This bond must be able to withstand various stresses such as temperature changes, vibrations, and exposure to chemicals. Using the wrong glue can result in weak bonds that can break easily, leading to malfunctioning or non-functional electronic devices.
The consequences of using the wrong glue can be severe. For example, if a non-conductive glue is used to bond two conductive components, it can interfere with the electrical conductivity of the circuit and cause it to malfunction. Similarly, if a glue that is not resistant to high temperatures is used in an application that requires it, it can melt or break down under heat stress and cause the device to fail.
Types of Glue Commonly Used in Electronics
There are several types of glue commonly used in electronics. These include:
Epoxy: Epoxy is a two-part adhesive that is known for its high strength and durability. It is commonly used in applications that require a strong bond between two or more components.
Silicone: Silicone is a flexible adhesive that is resistant to high temperatures and chemicals. It is commonly used in applications that require a flexible bond that can withstand temperature changes.
Cyanoacrylate: Cyanoacrylate, also known as superglue, is a fast-drying adhesive that is commonly used in applications that require a quick bond.
Acrylic: Acrylic adhesive is known for its high strength and resistance to chemicals. It is commonly used in applications that require a strong bond between two or more components.
Polyurethane: Polyurethane adhesive is known for its flexibility and resistance to impact and vibration. It is commonly used in applications that require a flexible bond that can withstand stress.
Factors to Consider When Selecting the Best Glue for Electronics
When selecting the best glue for electronics, there are several factors to consider. These include:
Temperature resistance: When selecting a glue for a particular application, it is important to consider the temperature range that the glue will be exposed to. If the glue is not able to withstand the temperature range, it may melt or break down, causing the bond to weaken or fail completely.
Chemical resistance: When selecting a glue for a particular application, it is important to consider its ability to withstand exposure to chemicals. This is especially important in industrial settings where chemicals are commonly used. The glue must be able to maintain its strength and integrity even when exposed to harsh chemicals such as acids, bases, solvents, and oils.
Electrical conductivity: When an application requires electrical conductivity, it is important to ensure that the glue used is conductive or at least does not interfere with the electrical conductivity of the circuit. This is because the glue can act as an insulator and prevent the flow of electricity through the circuit, leading to malfunction or failure. Conductive glues are specially formulated to allow for the flow of electricity, and they typically contain conductive particles such as silver or copper.
Bond strength: The glue must provide a strong bond between two or more components that can withstand various stresses such as temperature changes, vibrations, and exposure to chemicals.
Tips for Preparing Surfaces Before Bonding
Proper surface preparation is crucial for ensuring a strong and durable bond between two or more components. Some tips for preparing surfaces before bonding include:
Cleaning: The surfaces must be clean and free from dirt, dust, oil, and other contaminants that can interfere with bonding.
Sanding: Sanding can help roughen up smooth surfaces and provide better adhesion.
Degreasing: If the surfaces are oily or greasy, they must be degreased before bonding.
Common Mistakes to Avoid When Bonding Electronics
Some common mistakes to avoid when bonding electronics include:
Using too much glue: Using too much glue can result in weak bonds and excess glue that can interfere with other components.
Not allowing enough drying time: Not allowing enough drying time can result in weak bonds that can break easily.
Not following manufacturer instructions: Not following manufacturer instructions can result in improper bonding and weak bonds.
Best Practices for Curing and Drying Glue in Electronics
It is crucial to known some of the best practices for curing and drying glue in electronics. These include:
Temperature and humidity considerations: The temperature and humidity must be appropriate for the type of glue being used.
Time required for curing and drying: The time required for curing and drying must be appropriate for the type of glue being used and the application.
Testing the Strength and Durability of Bonded Electronics
Testing the strength and durability of bonded electronics is crucial for ensuring their reliability and longevity. Some tests that can be performed include:
Pull test: A pull test involves applying force to one component while holding another component stationary to test the strength of the bond.
Shear test: A shear test involves applying force parallel to the surface of one component while holding another component stationary to test the strength of the bond.
Environmental testing: Environmental testing involves exposing bonded components to various environmental stresses such as temperature changes, humidity changes, vibration, shock, etc., to test their durability under real-world conditions.
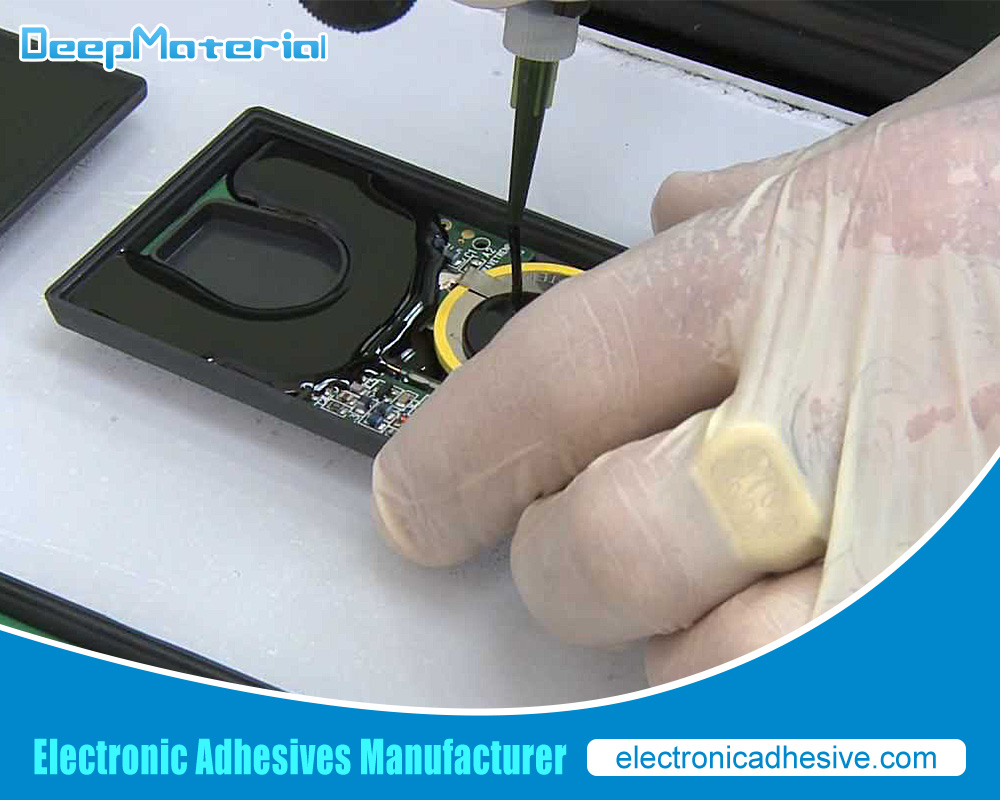
Conclusion and Recommendations for Bonding Electronics with Confidence
Bonding with confidence in electronics requires selecting the right type of glue based on factors such as temperature resistance, chemical resistance, electrical conductivity, bond strength, and drying time; preparing surfaces properly before bonding; applying glue correctly using appropriate techniques; avoiding common mistakes such as using too much glue or not allowing enough drying time; following best practices for curing and drying; and testing bonded components thoroughly before use under real-world conditions.
For more about choosing the best glue for electronics, you can pay a visit to DeepMaterial at https://www.electronicadhesive.com/about/ for more info.