The Role of Non Conductive Coating for Electronics in Preventing Electrical Failures
The Role of Non Conductive Coating for Electronics in Preventing Electrical Failures
The non-conductive coating for electronics, also known as an insulating coating or dielectric coating, is a protective layer that prevents the flow of electricity between components. It serves as a barrier against potential electrical shorts and other malfunctions that could lead to catastrophic system failures.
In this blog post, we will delve into the critical role that non-conductive coatings play in safeguarding electronic devices from electrical failures. We will explore their function, their importance in various applications, and how they contribute to the longevity and reliability of electronic systems.
Whether you are an electronics enthusiast, an engineering student, or a seasoned professional in the field, this comprehensive guide will provide valuable insights into the unsung role of non-conductive coatings in preventing electrical failures.
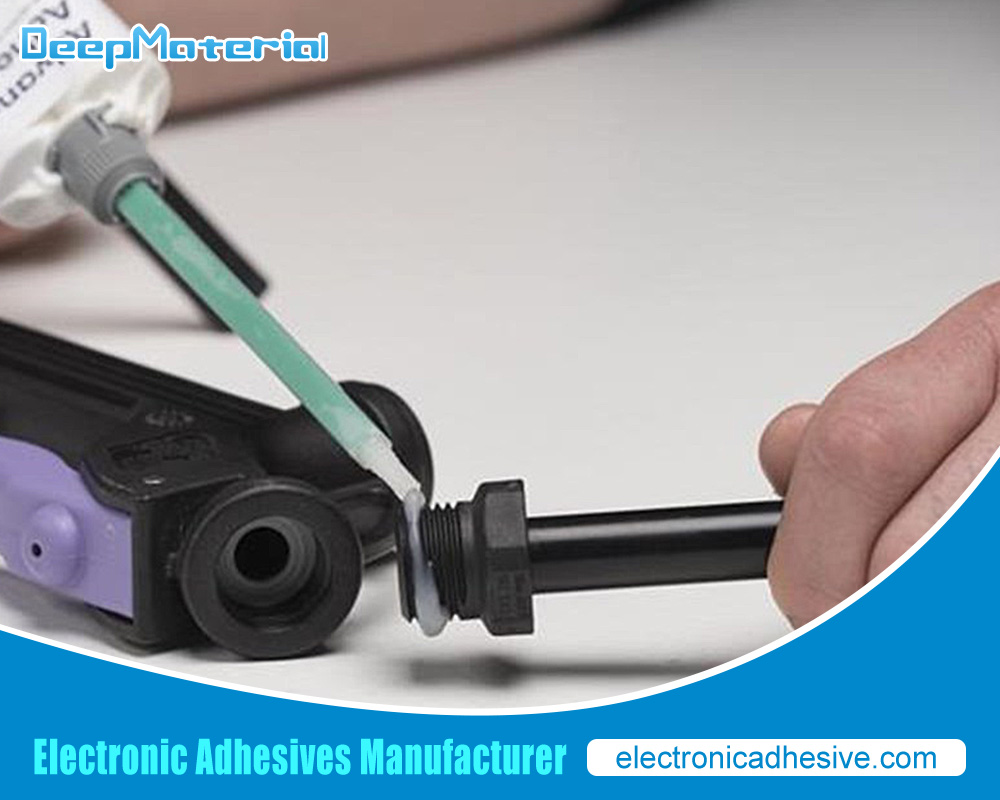
Understanding Electrical Failures in Electronics
Electrical failures in electronics can be caused by a variety of factors. One common cause is moisture, which can seep into the electronic components and cause short circuits or corrosion. Dust and other contaminants can also accumulate on the surface of the electronic devices and interfere with their proper functioning. In addition, electrical failures can occur due to physical damage, such as dropping the device or exposing it to extreme temperatures.
These electrical failures can have a significant impact on electronic devices. They can lead to malfunctions, reduced performance, or even complete failure of the device. This can result in costly repairs or replacements, as well as downtime for businesses that rely on these devices for their operations.
Introduction to Non Conductive Coating for Electronics
Non conductive coating for electronics is a protective layer that is applied to the surface of electronic devices. It is designed to prevent electrical failures by providing a barrier against moisture, dust, and other contaminants. This coating is typically made of a non conductive material, such as silicone or acrylic, which does not allow electricity to pass through.
The non conductive coating works by creating a protective barrier between the electronic components and the external environment. It prevents moisture from seeping into the device and causing short circuits or corrosion. It also repels dust and other contaminants, keeping the device clean and free from interference.
How Non Conductive Coating Prevents Electrical Failures
Non conductive coating plays a crucial role in preventing electrical failures in electronic devices. It protects the devices from moisture, dust, and other contaminants that can cause malfunctions or damage. By creating a barrier between the electronic components and the external environment, the coating ensures that the devices can operate reliably and efficiently.
One of the main ways that non conductive coating prevents electrical failures is by repelling moisture. Moisture can be a major cause of electrical failures, as it can cause short circuits or corrosion. The non conductive coating creates a waterproof barrier that prevents moisture from seeping into the device and coming into contact with the electronic components.
In addition to repelling moisture, non conductive coating also repels dust and other contaminants. Dust can accumulate on the surface of electronic devices and interfere with their proper functioning. By preventing dust from settling on the device, the coating ensures that the device can operate at its optimal performance.
Types of Non Conductive Coating for Electronics
There are several different types of non conductive coating available for electronics. Each type has its own pros and cons, and the choice of coating depends on the specific requirements of the application.
One common type of non conductive coating is silicone-based coating. Silicone is known for its excellent water resistance and durability, making it an ideal choice for protecting electronic devices from moisture. However, silicone-based coatings can be difficult to apply evenly and may require multiple coats for optimal protection.
Another type of non conductive coating is acrylic-based coating. Acrylic coatings are known for their excellent adhesion and flexibility, making them suitable for a wide range of applications. They are also easy to apply and provide good protection against moisture and dust. However, acrylic coatings may not be as durable as silicone coatings and may require more frequent reapplication.
Epoxy-based coatings are another option for non conductive coating. Epoxy coatings are known for their excellent adhesion and chemical resistance, making them suitable for harsh environments. They provide good protection against moisture, dust, and other contaminants. However, epoxy coatings can be more difficult to apply and may require specialized equipment.
Benefits of Using Non Conductive Coating for Electronics
Using non conductive coating for electronics offers several benefits. One of the main advantages is that it can extend the lifespan of electronic devices. By protecting the devices from moisture, dust, and other contaminants, the coating ensures that they can operate reliably and efficiently for a longer period of time. This can result in cost savings for businesses, as they can avoid costly repairs or replacements.
Another benefit of using non conductive coating is that it can improve the performance of electronic devices. By preventing moisture and dust from interfering with the device’s operation, the coating ensures that it can function at its optimal level. This can be especially important for devices that are used in critical applications, such as medical equipment or aerospace systems.
Non conductive coating also provides a cosmetic benefit by keeping electronic devices clean and free from fingerprints or smudges. This can be particularly important for devices that are used in consumer-facing applications, such as smartphones or tablets. The coating can help maintain the appearance of the device and enhance the user experience.
Application Process of Non Conductive Coating for Electronics
The application process of non conductive coating for electronics typically involves several steps. The first step is to prepare the surface of the electronic device by cleaning it thoroughly. This ensures that the coating can adhere properly to the surface and provide optimal protection.
Once the surface is clean, the next step is to apply the coating. This can be done using a variety of methods, such as spraying, brushing, or dipping. The specific method depends on the type of coating and the size and shape of the device.
After the coating is applied, it needs to be allowed to dry or cure. This typically takes a certain amount of time, depending on the type of coating and the environmental conditions. It is important to follow the manufacturer’s instructions for drying or curing to ensure that the coating provides optimal protection.
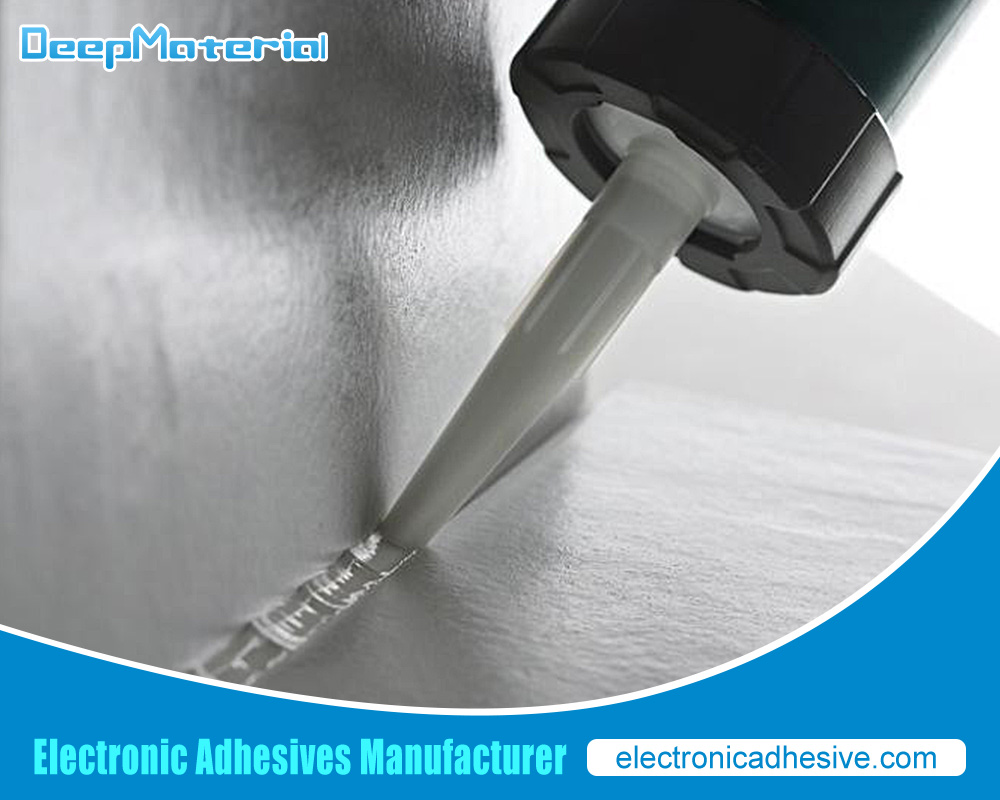
Final Thoughts
Non conductive coating for electronics plays a crucial role in protecting electronic devices from electrical failures. It prevents moisture, dust, and other contaminants from interfering with the operation of the devices, ensuring that they can operate reliably and efficiently. By extending the lifespan of electronic devices and improving their performance, non conductive coating offers a cost-effective solution for businesses and consumers alike.
For more about choosing the Role of Non Conductive Coating for Electronics in Preventing Electrical Failures, you can pay a visit to DeepMaterial at https://www.electronicadhesive.com/about/ for more info.