アンダーフィルエポキシ
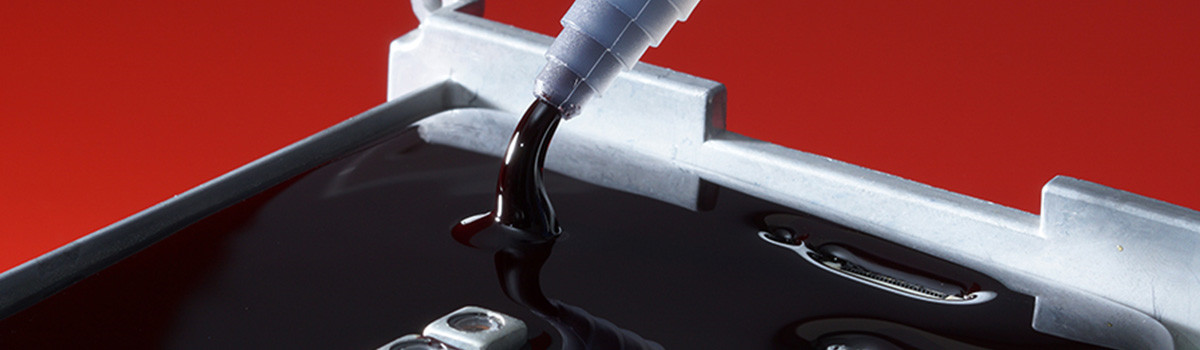
アンダーフィル エポキシは、特に半導体パッケージング用途において、電子部品の信頼性を高めるために使用される接着剤の一種です。 パッケージとプリント基板 (PCB) の間の隙間を埋め、機械的サポートと応力緩和を提供して、熱膨張と収縮による損傷を防ぎます。 アンダーフィル エポキシは、寄生インダクタンスと寄生容量を低減することにより、パッケージの電気的性能も向上させます。 この記事では、アンダーフィル エポキシのさまざまな用途、利用可能なさまざまな種類、およびそれらの利点について説明します。
半導体パッケージングにおけるアンダーフィルエポキシの重要性
アンダーフィル エポキシは半導体パッケージングにおいて極めて重要であり、繊細なマイクロエレクトロニクス部品に機械的補強と保護を提供します。 半導体チップとパッケージ基板の間の隙間を埋めるために使用される特殊な接着材料であり、電子機器の信頼性と性能を向上させます。 ここでは、半導体パッケージングにおけるアンダーフィルエポキシの重要性について探っていきます。
アンダーフィルエポキシの主な機能の XNUMX つは、パッケージの機械的強度と信頼性を向上させることです。 動作中、半導体チップは熱膨張や熱収縮、振動、機械的衝撃などのさまざまな機械的ストレスにさらされます。 これらの応力ははんだ接合部の亀裂の形成につながる可能性があり、これにより電気的故障が発生し、デバイスの全体的な寿命が短くなる可能性があります。 アンダーフィル エポキシは、チップ、基板、はんだ接合部全体に機械的応力を均等に分散することにより、応力を軽減する役割を果たします。 クラックの形成を効果的に最小限に抑え、既存のクラックの伝播を防ぎ、パッケージの長期信頼性を確保します。
アンダーフィル エポキシのもう XNUMX つの重要な側面は、半導体デバイスの熱性能を向上させる能力です。 電子デバイスのサイズが縮小し、電力密度が増加するにつれて、熱放散は重大な問題となり、過剰な熱は半導体チップの性能と信頼性を低下させる可能性があります。 アンダーフィル エポキシは優れた熱伝導特性を備えているため、チップからの熱を効率的に伝達し、パッケージ全体に熱を分散させることができます。 これにより、最適な動作温度が維持され、ホットスポットが防止され、デバイス全体の熱管理が向上します。
アンダーフィルエポキシは湿気や汚染物質からも保護します。 湿気の侵入は腐食、漏電、導電性物質の成長を引き起こし、デバイスの誤動作につながる可能性があります。 アンダーフィル エポキシはバリアとして機能し、脆弱な領域を密閉し、パッケージへの湿気の侵入を防ぎます。 また、半導体チップの電気的性能に悪影響を与える可能性のある塵、汚れ、その他の汚染物質に対する保護も提供します。 アンダーフィル エポキシはチップとその相互接続を保護することで、デバイスの長期的な信頼性と機能を保証します。
さらに、アンダーフィルドエポキシにより、半導体パッケージングの小型化が可能になります。 より小型でコンパクトなデバイスに対する絶え間ない需要により、アンダーフィルドエポキシにより、フリップチップおよびチップスケールのパッケージング技術の使用が可能になります。 これらの技術には、チップをパッケージ基板に直接実装することが含まれており、ワイヤボンディングの必要性がなくなり、パッケージサイズが縮小されます。 アンダーフィル エポキシは構造的なサポートを提供し、チップと基板のインターフェースの完全性を維持するため、これらの高度なパッケージング技術の実装を成功させることができます。
アンダーフィルエポキシが課題にどのように対処するか
半導体パッケージングは、電子デバイスの性能、信頼性、寿命において重要な役割を果たします。 これには、集積回路 (IC) を保護ケースに封入し、電気接続を提供し、動作中に発生する熱を放散することが含まれます。 しかし、半導体パッケージングは、パッケージ化されたデバイスの機能と信頼性に大きな影響を与える可能性がある、熱応力や反りなどのいくつかの課題に直面しています。
主な課題の XNUMX つは熱ストレスです。 集積回路は動作中に熱を発生し、放熱が不十分だとパッケージ内の温度が上昇する可能性があります。 パッケージ内のさまざまな材料がさまざまな速度で膨張および収縮するため、この温度変化により熱応力が発生します。 不均一な膨張と収縮により機械的歪みが生じ、はんだ接合部の破損、層間剥離、亀裂が発生する可能性があります。 熱ストレスはパッケージの電気的および機械的完全性を損ない、最終的にはデバイスの性能と信頼性に影響を与える可能性があります。
反りは、半導体パッケージングにおけるもう XNUMX つの重要な課題です。 反りとは、パッケージ基板またはパッケージ全体の曲がりや変形を指します。 これは、パッケージングプロセス中または熱応力によって発生する可能性があります。 反りは主に、パッケージ内の異なる材料間の熱膨張係数 (CTE) の不一致によって発生します。 たとえば、シリコン ダイ、基板、およびモールド コンパウンドの CTE は大幅に異なる場合があります。 温度変化を受けると、これらの材料は異なる速度で膨張または収縮し、反りが発生します。
反りは半導体パッケージにいくつかの問題を引き起こします。
- これにより応力集中点が生じ、機械的故障の可能性が高まり、ボックスの信頼性が低下する可能性があります。
- 反りは、プリント基板 (PCB) などの他のコンポーネントとパッケージの位置合わせに影響を与えるため、組み立てプロセスが困難になる可能性があります。 この位置ずれにより電気接続が損なわれ、パフォーマンス上の問題が発生する可能性があります。
- 反りはパッケージの全体的なフォームファクターに影響を与える可能性があり、デバイスを小さなフォームファクターのアプリケーションや高密度の PCB に統合することが困難になります。
これらの課題に対処するために、半導体パッケージングではさまざまな技術や戦略が採用されています。 これには、熱応力と反りを最小限に抑えるために、適合する CTE を備えた先進的な材料を使用することが含まれます。 熱機械シミュレーションとモデリングは、さまざまな熱条件下でのパッケージの動作を予測するために実行されます。 熱応力や反りを軽減するために、応力緩和構造の導入やレイアウトの最適化などの設計変更が実施されます。 さらに、改善された製造プロセスと装置の開発により、組み立て時の反りの発生を最小限に抑えることができます。
アンダーフィル エポキシの利点
アンダーフィル エポキシは、いくつかの利点をもたらす半導体パッケージングの重要なコンポーネントです。 この特殊なエポキシ材料は、半導体チップとパッケージ基板の間に適用され、機械的補強を提供し、さまざまな課題に対処します。 アンダーフィルエポキシの重要な利点のいくつかを次に示します。
- 機械的信頼性の向上: アンダーフィル エポキシの主な利点の XNUMX つは、半導体パッケージの機械的信頼性を向上できることです。 アンダーフィル エポキシは、チップと基板の間のギャップやボイドを埋めることで全体的な構造の完全性を向上させる凝集性の結合を作成します。 これにより、パッケージの反りを防止し、機械的故障のリスクを軽減し、振動、衝撃、熱サイクルなどの外部ストレスに対する耐性を強化します。 機械的信頼性の向上により、製品の耐久性が向上し、デバイスの寿命が長くなります。
- 熱応力の放散: アンダーフィル エポキシは、パッケージ内の熱応力の放散に役立ちます。 集積回路は動作中に熱を発生し、放熱が不十分だとコンテナ内の温度が変動する可能性があります。 アンダーフィルのエポキシ材料は、チップや基板の材料と比較して熱膨張係数 (CTE) が低く、バッファ層として機能します。 熱応力によって引き起こされる機械的歪みを吸収し、はんだ接合部の故障、層間剥離、亀裂のリスクを軽減します。 アンダーフィルされたエポキシは、熱応力を分散することにより、パッケージの電気的および機械的完全性を維持するのに役立ちます。
- 電気的性能の向上: アンダーフィル エポキシは、半導体デバイスの電気的性能にプラスの影響を与えます。 エポキシ材料はチップと基板の間のギャップを埋め、寄生容量とインダクタンスを低減します。 これにより、信号の完全性が向上し、信号損失が減少し、チップとパッケージの残りの部分の間の電気接続が強化されます。 寄生効果の低減により、電気的性能が向上し、データ転送速度が向上し、デバイスの信頼性が向上します。 さらに、アンダーフィルドエポキシは絶縁性を提供し、電気的性能を低下させる可能性のある湿気、汚染物質、その他の環境要因から保護します。
- 応力緩和と組立改善: アンダーフィル エポキシは、組立中に応力緩和機構として機能します。 エポキシ材料は、チップと基板間の熱膨張係数の不一致を補償し、温度変化時の機械的ストレスを軽減します。 これにより、組み立てプロセスの信頼性と効率が向上し、パッケージの損傷や位置ずれのリスクが最小限に抑えられます。 アンダーフィル エポキシによってもたらされる制御された応力分布は、プリント基板 (PCB) 上の他のコンポーネントとの適切な位置合わせを保証し、全体的なアセンブリ歩留まりを向上させるのにも役立ちます。
- 小型化とフォームファクターの最適化: アンダーフィルエポキシにより、半導体パッケージの小型化とフォームファクターの最適化が可能になります。 アンダーフィル エポキシは構造強化と応力緩和を提供することにより、より小さく、より薄く、よりコンパクトなパッケージの設計と製造を可能にします。 これは、スペースが貴重なモバイル デバイスやウェアラブル電子機器などのアプリケーションにとって特に重要です。 フォームファクターを最適化し、より高いコンポーネント密度を達成する能力は、より高度で革新的な電子デバイスに貢献します。
アンダーフィルエポキシの種類
半導体パッケージングでは数種類のアンダーフィル エポキシ配合が利用可能であり、それぞれが特定の要件を満たし、さまざまな課題に対処するように設計されています。 一般的に使用されるアンダーフィル エポキシのタイプをいくつか示します。
- キャピラリー アンダーフィル エポキシ: キャピラリー アンダーフィル エポキシは、最も伝統的で広く使用されているタイプです。 低粘度のエポキシが毛細管現象によってチップと基板の間の隙間に流れ込みます。 毛細管アンダーフィルは通常、チップの端に塗布され、パッケージが加熱されるとエポキシがチップの下に流れて空隙を埋めます。 このタイプのアンダーフィルは、隙間が小さいパッケージに適しており、優れた機械的補強を提供します。
- ノーフローアンダーフィルエポキシ: ノーフローアンダーフィルエポキシは、硬化中に流動しない高粘度配合です。 これは、事前に塗布されたエポキシとして、またはチップと基板の間にフィルムとして塗布されます。 ノーフローアンダーフィルエポキシは、はんだバンプが基板と直接相互作用するフリップチップパッケージに特に役立ちます。 これにより、毛細管の流れが不要になり、組み立て中のはんだ接合部が損傷するリスクが軽減されます。
- ウェハレベルアンダーフィル (WLU): ウェハレベルアンダーフィルは、個々のチップが個片化される前にウェハレベルで塗布されるアンダーフィルエポキシです。 これには、ウェーハ表面全体にアンダーフィル材料を塗布し、それを硬化することが含まれます。 ウェーハレベルのアンダーフィルには、均一なアンダーフィル被覆率、組み立て時間の短縮、プロセス制御の向上など、いくつかの利点があります。 小型デバイスの大量生産によく使用されます。
- モールド アンダーフィル (MUF): モールド アンダーフィルは、封止成形中に塗布されるアンダーフィル エポキシです。 アンダーフィル材料が基板上に塗布され、チップと基板がモールドコンパウンド内に封入されます。 成形中、エポキシが流れてチップと基板の間のギャップを埋め、単一のステップでアンダーフィルと封止が行われます。 成形アンダーフィルは優れた機械的補強を提供し、組み立てプロセスを簡素化します。
- 非導電性アンダーフィル (NCF): 非導電性アンダーフィル エポキシは、チップ上のはんだ接合部と基板の間に電気的絶縁を提供するために特別に配合されています。 導電性を妨げる絶縁フィラーまたは添加剤が含まれています。 NCF は、隣接するはんだ接合部間の電気的短絡が懸念される用途に使用されます。 機械的補強と電気的絶縁の両方を提供します。
- 熱伝導性アンダーフィル (TCU): 熱伝導性アンダーフィル エポキシは、パッケージの放熱機能を強化するように設計されています。 アンダーフィル材料の熱伝導率を向上させる、セラミックまたは金属粒子などの熱伝導性フィラーが含まれています。 TCU は、高出力デバイスや要求の厳しい熱環境で動作するデバイスなど、効率的な熱伝達が重要な用途に使用されます。
これらは、半導体パッケージに使用されるさまざまな種類のアンダーフィル エポキシのほんの一例です。 適切なアンダーフィル エポキシの選択は、パッケージ設計、組み立てプロセス、熱要件、電気的考慮事項などの要因によって異なります。 各アンダーフィル エポキシには特有の利点があり、さまざまな用途の固有のニーズを満たすように調整されています。
キャピラリアンダーフィル:低粘度、高信頼性
キャピラリ アンダーフィルとは、電子デバイスの信頼性を高めるために半導体パッケージング業界で使用されるプロセスを指します。 これには、マイクロ電子チップとその周囲のパッケージの間の隙間を低粘度の液体材料、通常はエポキシベースの樹脂で充填することが含まれます。 このアンダーフィル材料は構造的なサポートを提供し、熱放散を改善し、機械的ストレス、湿気、その他の環境要因からチップを保護します。
キャピラリ アンダーフィルの重要な特性の XNUMX つは、粘度が低いことです。 アンダーフィル材料は比較的低密度になるように配合されているため、アンダーフィルプロセス中にチップとパッケージの間の狭い隙間に容易に流れ込むことができます。 これにより、アンダーフィル材料がすべてのボイドとエアギャップに効果的に浸透して充填できるようになり、ボイド形成のリスクが最小限に抑えられ、チップとパッケージの境界面の全体的な完全性が向上します。
低粘度のキャピラリ アンダーフィル材料には、他にもいくつかの利点があります。 まず、チップ下の材料の効率的な流れが促進され、プロセス時間が短縮され、生産スループットが向上します。 これは、時間とコスト効率が重要な大量生産環境では特に重要です。
第二に、粘度が低いため、アンダーフィル材料の濡れ性と接着性が向上します。 これにより、材料が均一に広がり、チップとパッケージとの強力な結合が形成され、信頼性が高く堅牢なカプセル化が実現されます。 これにより、チップが熱サイクル、衝撃、振動などの機械的ストレスから確実に保護されます。
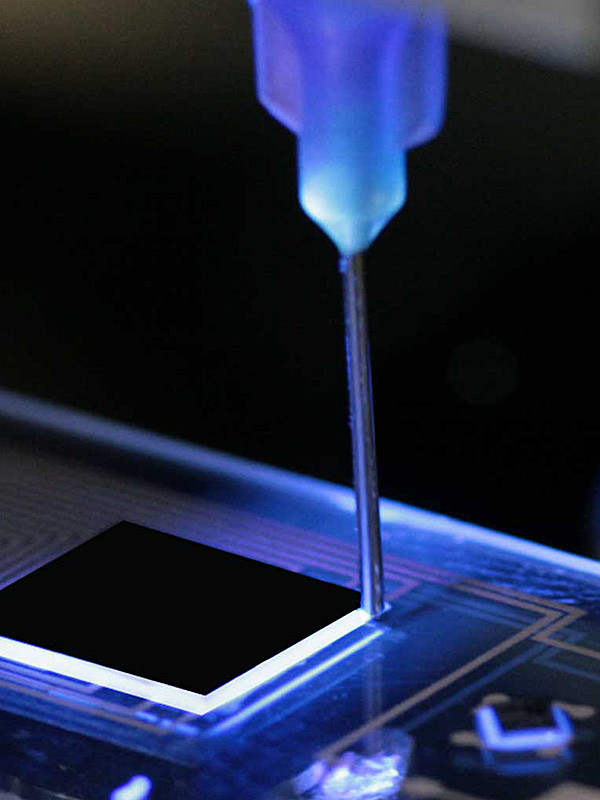
キャピラリ アンダーフィルのもう XNUMX つの重要な側面は、その高い信頼性です。 低粘度のアンダーフィル材料は、優れた熱安定性、電気絶縁特性、湿気や化学薬品に対する耐性を示すように特別に設計されています。 これらの特性は、特に自動車、航空宇宙、通信などの要求の厳しいアプリケーションにおいて、パッケージ化された電子デバイスの長期的な性能と信頼性を確保するために不可欠です。
さらに、キャピラリ アンダーフィル材料は、高い機械的強度と、半導体パッケージで一般的に使用される金属、セラミック、有機材料などのさまざまな基板材料への優れた接着性を持つように設計されています。 これにより、アンダーフィル材料が応力緩衝材として機能し、動作中または環境への曝露中に発生する機械的応力を効果的に吸収および消散することができます。
ノーフローアンダーフィル: 自動ディスペンスと高スループット
ノーフローアンダーフィルは、電子デバイスの信頼性と効率を高めるために半導体パッケージング業界で使用される特殊なプロセスです。 低粘度材料の流れに依存するキャピラリ アンダーフィルとは異なり、無流動アンダーフィルは高粘度材料の自動塗布アプローチを利用します。 この方法には、自動調整、高スループット、信頼性の向上など、いくつかの利点があります。
ノーフローアンダーフィルの重要な機能の XNUMX つは、自動塗布機能です。 このプロセスで使用されるアンダーフィル材料は粘度が高く配合されているため、自由に流れることができません。 代わりに、アンダーフィル材料が制御された方法でチップとパッケージの境界面に塗布されます。 この制御されたディスペンスにより、アンダーフィル材料の正確な配置が可能になり、あふれたり制御不能に広がることなく、必要な領域にのみ確実に適用されます。
ノーフローアンダーフィルの自動ディスペンス特性には、いくつかの利点があります。 まず、アンダーフィル材料の自動位置合わせが可能になります。 アンダーフィルが塗布されると、チップやパッケージと自然に自己位置合わせされ、ギャップやボイドを均一に埋めます。 これにより、アンダーフィルプロセス中にチップを正確に位置決めしたり位置合わせしたりする必要がなくなり、製造の時間と労力が節約されます。
次に、ノーフローアンダーフィルの自動塗布機能により、生産における高スループットが可能になります。 塗布プロセスは自動化できるため、複数のチップに同時にアンダーフィル材料を迅速かつ一貫して塗布できます。 これにより、全体的な生産効率が向上し、製造コストが削減され、特に大量生産環境にとって有利になります。
さらに、ノーフローアンダーフィル材料は高い信頼性を提供するように設計されています。 高粘度のアンダーフィル材料は、熱サイクル、機械的ストレス、環境要因に対する耐性を向上させ、パッケージ化された電子デバイスの長期的な性能を保証します。 この材料は優れた熱安定性、電気絶縁特性、湿気や化学薬品に対する耐性を示し、デバイスの全体的な信頼性に貢献します。
さらに、ノーフローアンダーフィルに使用される高粘度アンダーフィル材料は、機械的強度と接着特性が向上しています。 これらはチップおよびパッケージと強力な結合を形成し、動作中または環境への曝露中に発生する機械的応力を効果的に吸収および消散します。 これにより、チップを潜在的な損傷から保護し、外部の衝撃や振動に対するデバイスの耐性が強化されます。
成形アンダーフィル: 高い保護と一体化
成形アンダーフィルは、電子デバイスに高レベルの保護と統合を提供するために半導体パッケージング業界で使用される高度な技術です。 これには、アンダーフィル材料を組み込んだモールドコンパウンドでチップ全体とその周囲のパッケージを封止することが含まれます。 このプロセスは、保護、統合、全体的な信頼性に関して大きな利点をもたらします。
成形アンダーフィルの重要な利点の XNUMX つは、チップを包括的に保護できることです。 このプロセスで使用されるモールドコンパウンドは堅牢なバリアとして機能し、チップとパッケージ全体を保護シェルで包みます。 これにより、デバイスの性能や信頼性に影響を与える可能性のある湿気、ほこり、汚染物質などの環境要因から効果的にシールドされます。 カプセル化は、チップが機械的ストレス、熱サイクル、その他の外力から保護されるのにも役立ち、長期的な耐久性が保証されます。
さらに、成形アンダーフィルにより、半導体パッケージ内の高い集積レベルが可能になります。 アンダーフィル材料はモールドコンパウンドに直接混合されるため、アンダーフィルと封止プロセスのシームレスな統合が可能になります。 この統合により、個別のアンダーフィル工程が不要になり、製造プロセスが簡素化され、製造時間とコストが削減されます。 また、パッケージ全体にアンダーフィルを一貫して均一に分散させ、ボイドを最小限に抑え、全体の構造的完全性を高めます。
さらに、モールドアンダーフィルにより優れた放熱特性を実現します。 モールドコンパウンドは熱伝導率が高く、チップから効率的に熱を逃がすことができるように設計されています。 これは、デバイスの最適な動作温度を維持し、パフォーマンスの低下や信頼性の問題につながる可能性のある過熱を防ぐために非常に重要です。 成形アンダーフィルの強化された熱放散特性は、電子デバイスの全体的な信頼性と寿命に貢献します。
さらに、成形アンダーフィルにより、さらなる小型化とフォームファクターの最適化が可能になります。 カプセル化プロセスは、複雑な 3D 構造を含むさまざまなパッケージのサイズや形状に対応するように調整できます。 この柔軟性により、複数のチップやその他のコンポーネントをコンパクトでスペース効率の高いパッケージに統合することができます。 モールドアンダーフィルは、信頼性を損なうことなくより高いレベルの統合を達成できるため、モバイルデバイス、ウェアラブル、自動車エレクトロニクスなど、サイズと重量の制約が重要な用途で特に価値があります。
チップスケールパッケージ (CSP) アンダーフィル: 小型化と高密度化
チップ スケール パッケージ (CSP) アンダーフィルは、小型化と高密度の電子デバイスの統合を可能にする重要なテクノロジーです。 電子デバイスは機能を向上させながらサイズが縮小し続けるため、CSP はこれらのコンパクトなデバイスの信頼性とパフォーマンスを確保する上で重要な役割を果たしています。
CSP は、追加のパッケージを必要とせずに、半導体チップを基板またはプリント基板 (PCB) に直接実装できるパッケージング技術です。 これにより、従来のプラスチックやセラミックの容器が不要になり、デバイス全体のサイズと重量が軽減されます。 CSP アンダーフィルは、液体または封入材を使用してチップと基板の間のギャップを埋めるプロセスで、機械的サポートを提供し、湿気や機械的ストレスなどの環境要因からチップを保護します。
CSPアンダーフィルによりチップと基板間の距離を縮め、小型化を実現します。 アンダーフィル材料はチップと基板の間の狭い隙間を埋め、強固な接合を形成し、チップの機械的安定性を向上させます。 これにより、デバイスの小型化と薄型化が可能になり、限られたスペースにより多くの機能を詰め込むことが可能になります。
高密度実装が CSP アンダーフィルのもう XNUMX つの利点です。 CSP を使用すると、別個のパッケージが不要になるため、チップを PCB 上の他のコンポーネントの近くに実装できるようになり、電気接続の長さが短縮され、信号の完全性が向上します。 アンダーフィル材は熱伝導体としても機能し、チップから発生した熱を効率的に放散します。 この熱管理機能により、より高い電力密度が可能になり、より複雑で強力なチップを電子デバイスに統合できるようになります。
CSP アンダーフィル材料は、小型化と高密度集積化の要求を満たす特定の特性を備えている必要があります。 狭い隙間の充填を容易にする低粘度、および均一な被覆を確保して空隙を排除する優れた流動特性が必要です。 また、材料はチップと基板への良好な接着性を備え、強固な機械的サポートを提供する必要があります。 さらに、チップから熱を効率的に逃がすために、高い熱伝導率を示す必要があります。
ウェーハレベルの CSP アンダーフィル: コスト効率が高く、歩留まりが高い
ウェーハ レベル チップ スケール パッケージ (WLCSP) アンダーフィルは、製造効率と全体的な製品品質においていくつかの利点をもたらす、コスト効率が高く歩留まりの高いパッケージング技術です。 WLCSP アンダーフィルは、複数のチップが個別のパッケージに個片化される前に、ウェハの状態で同時にアンダーフィル材料を複数のチップに塗布します。 このアプローチは、コスト削減、プロセス制御の改善、生産歩留まりの向上に関して多くの利点をもたらします。
WLCSP アンダーフィルの重要な利点の XNUMX つは、その費用対効果です。 アンダーフィル材料をウェーハレベルで適用すると、パッケージングプロセスがより合理化され、効率的になります。 アンダーフィルされた材料は、制御された自動プロセスを使用してウェーハ上に塗布されるため、材料の無駄が削減され、人件費が最小限に抑えられます。 さらに、個別のパッケージの取り扱いと位置合わせのステップを排除することで、全体の生産時間と複雑さが軽減され、従来のパッケージング方法と比較して大幅なコスト削減につながります。
さらに、WLCSP アンダーフィルにより、プロセス制御が改善され、生産歩留まりが向上します。 アンダーフィル材料はウェーハレベルで適用されるため、ディスペンスプロセスをより適切に制御でき、ウェーハ上の各チップの一貫した均一なアンダーフィル被覆が保証されます。 これにより、信頼性の問題につながる可能性のあるボイドや不完全なアンダーフィルのリスクが軽減されます。 ウェハレベルでアンダーフィルの品質を検査およびテストできるため、欠陥やプロセスのばらつきを早期に検出することもでき、タイムリーな修正措置を可能にし、パッケージ欠陥の可能性を低減します。 その結果、WLCSP アンダーフィルは、より高い生産歩留まりと全体的な製品品質の向上に役立ちます。
ウェハレベルのアプローチにより、熱的および機械的性能の向上も可能になります。 WLCSP で使用されるアンダーフィル材料は通常、チップとウェハの間の狭いギャップを効率的に充填できる低粘度の毛細管流動材料です。 これにより、チップに強固な機械的サポートが提供され、機械的ストレス、振動、温度サイクルに対する耐性が強化されます。 さらに、アンダーフィル材料は熱伝導体として機能し、チップによって生成された熱の放散を促進するため、熱管理が改善され、過熱のリスクが軽減されます。
フリップチップアンダーフィル: 高い I/O 密度とパフォーマンス
フリップ チップ アンダーフィルは、電子デバイスの高い入出力 (I/O) 密度と卓越したパフォーマンスを可能にする重要な技術です。 これは、高度な半導体アプリケーションで広く使用されているフリップチップパッケージングの信頼性と機能性を向上させる上で重要な役割を果たします。 この記事では、フリップ チップ アンダーフィルの重要性と、高い I/O 密度とパフォーマンスの達成に対するその影響について説明します。
フリップチップ技術では、集積回路 (IC) または半導体ダイを基板に直接電気的に接続するため、ワイヤボンディングの必要がなくなります。 これにより、I/O パッドがダイの底面に配置されるため、よりコンパクトで効率的なパッケージが実現します。 ただし、フリップチップ パッケージには、最適なパフォーマンスと信頼性を確保するために対処する必要がある特有の課題があります。
フリップチップパッケージングにおける重要な課題の XNUMX つは、ダイと基板間の機械的ストレスと熱の不一致を防ぐことです。 製造プロセスおよびその後の動作中に、ダイと基板の間の熱膨張係数 (CTE) の違いにより大きな応力が発生し、性能の低下や故障につながる可能性があります。 フリップチップアンダーフィルはチップを封入する保護材料であり、機械的サポートと応力緩和を提供します。 熱サイクル中に発生する応力を効果的に分散し、繊細な相互接続への影響を防ぎます。
最新の電子デバイスでは、高い I/O 密度が重要であり、より小型のフォーム ファクターと機能の向上が不可欠です。 フリップ チップ アンダーフィルは、優れた電気絶縁機能と熱管理機能を提供することで、より高い I/O 密度を実現します。 アンダーフィル材料はダイと基板の間のギャップを埋め、堅牢なインターフェースを形成し、短絡や漏電のリスクを軽減します。 これにより、I/O パッドの間隔が狭くなり、信頼性を犠牲にすることなく I/O 密度が向上します。
さらに、フリップチップアンダーフィルは電気的性能の向上に貢献します。 ダイと基板間の電気的寄生を最小限に抑え、信号遅延を低減し、信号の完全性を高めます。 アンダーフィル材は優れた熱伝導特性も示し、動作中にチップから発生する熱を効率的に放散します。 効果的な熱放散により、温度が許容範囲内に維持され、過熱が防止され、最適なパフォーマンスが維持されます。
フリップチップアンダーフィル材料の進歩により、さらに高い I/O 密度と性能レベルが可能になりました。 たとえば、ナノコンポジットアンダーフィルは、ナノスケールフィラーを利用して熱伝導率と機械的強度を強化します。 これにより、放熱性と信頼性が向上し、デバイスの高性能化が可能になります。
ボール グリッド アレイ (BGA) アンダーフィル: 高い熱的および機械的性能
ボール グリッド アレイ (BGA) アンダーフィルは、電子デバイスに高い熱的および機械的性能を提供する重要な技術です。 さまざまなアプリケーションで広く使用されている BGA パッケージの信頼性と機能性を向上させる上で重要な役割を果たします。 この記事では、BGA アンダーフィルの重要性と、高い熱的および機械的性能の達成に対するその影響について探っていきます。
BGA テクノロジには、集積回路 (IC) または半導体ダイが基板に実装され、パッケージの底面にあるはんだボールのアレイを通じて電気接続が行われるパッケージ設計が含まれます。 BGA は、ダイと基板の間のギャップに塗布された材料をアンダーフィルし、はんだボールをカプセル化し、アセンブリに機械的なサポートと保護を提供します。
BGA パッケージングにおける重要な課題の XNUMX つは、熱ストレスの管理です。 動作中、IC は熱を発生し、熱膨張と熱収縮により、ダイと基板を接続するはんだ接合部に大きな圧力がかかる可能性があります。 BGA アンダーフィルは、ダイと基板との強固な結合を形成することで、これらのストレスを軽減するという重要な役割を果たします。 応力緩衝材として機能し、熱膨張と収縮を吸収し、はんだ接合部の歪みを軽減します。 これにより、パッケージ全体の信頼性が向上し、はんだ接合部の故障のリスクが軽減されます。
BGA アンダーフィルのもう XNUMX つの重要な側面は、パッケージの機械的性能を向上させる能力です。 BGA パッケージは、取り扱い、組み立て、操作中に機械的ストレスにさらされることがよくあります。 アンダーフィル材料はダイと基板の間のギャップを埋め、はんだ接合部に構造的なサポートと補強を提供します。 これにより、アセンブリの全体的な機械的強度が向上し、機械的衝撃、振動、その他の外力に対する耐性が高まります。 BGA アンダーフィルは機械的応力を効果的に分散することで、パッケージの亀裂、層間剥離、その他の機械的故障の防止に役立ちます。
電子機器の適切な機能と信頼性を確保するには、高い熱性能が不可欠です。 BGA アンダーフィル材料は、優れた熱伝導特性を持つように設計されています。 これにより、ダイから熱を効率的に逃がし、基板全体に分散させることができ、パッケージ全体の熱管理が強化されます。 効果的な熱放散により動作温度を低く維持し、熱ホットスポットや潜在的なパフォーマンス低下を防ぎます。 また、コンポーネントの熱応力を軽減することで、ボックスの寿命を延ばすことにも貢献します。
BGA アンダーフィル材料の進歩により、熱的および機械的性能がさらに向上しました。 ナノコンポジットや高熱伝導率フィラーなどの配合とフィラー材料の改良により、放熱性と機械的強度が向上し、BGA パッケージの性能がさらに向上しました。
クアッド フラット パッケージ (QFP) アンダーフィル: 大きな I/O 数と堅牢性
クアッド フラット パッケージ (QFP) は、電子機器で広く使用されている集積回路 (IC) パッケージです。 正方形または長方形の形状をしており、リード線が XNUMX つの側面すべてから伸びており、多くの入出力 (I/O) 接続を提供します。 QFP パッケージの信頼性と堅牢性を高めるために、アンダーフィル材料が一般的に使用されます。
アンダーフィルは、はんだ接合部の機械的強度を強化し、応力による故障を防ぐために、IC と基板の間に塗布される保護材です。 接続数が多いと、熱サイクルや動作条件中に重大な機械的ストレスが発生する可能性があるため、I/O 数が多い QFP にとってこれは特に重要です。
QFP パッケージに使用されるアンダーフィル材料は、堅牢性を確保するために特定の特性を備えている必要があります。 まず、強力な接着を実現し、層間剥離や剥離のリスクを最小限に抑えるために、IC と基板の両方に対して優れた接着力を備えている必要があります。 さらに、IC と基板の CTE に一致する低い熱膨張係数 (CTE) を備え、亀裂や破損につながる可能性のある応力の不一致を軽減する必要があります。
さらに、アンダーフィル材料は、IC と基板の間のギャップを均一に覆い、完全に埋めるために、良好な流動特性を備えている必要があります。 これは、はんだ接合部を弱め、信頼性を低下させる可能性があるボイドを排除するのに役立ちます。 また、材料は良好な硬化特性を備えており、塗布後に硬くて耐久性のある保護層を形成できる必要があります。
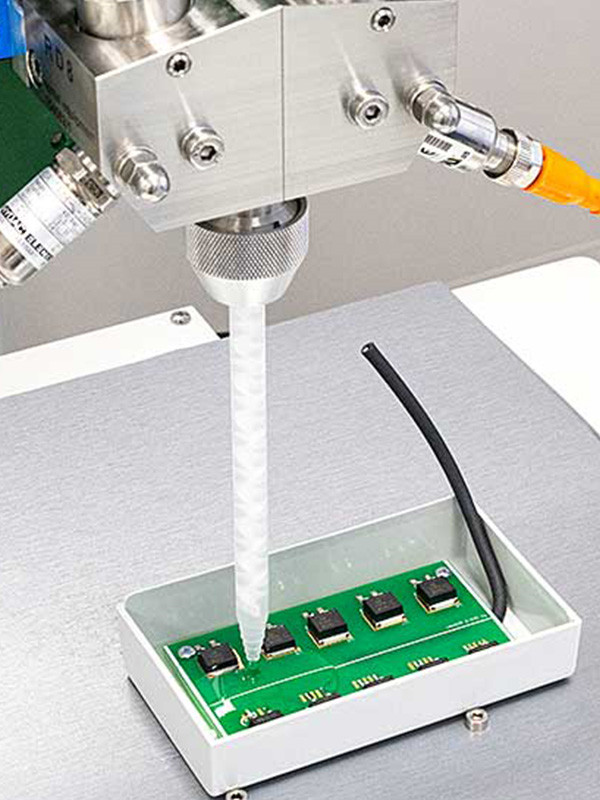
機械的堅牢性の観点から、アンダーフィルは外力に耐え、パッケージの変形や剥離を防ぐために、高いせん断強度と剥離強度を備えている必要があります。 また、保護特性を長期間維持するには、湿気やその他の環境要因に対して優れた耐性を示す必要があります。 これは、QFP パッケージが過酷な条件にさらされたり、温度変化を受ける可能性があるアプリケーションでは特に重要です。
これらの望ましい特性を達成するために、エポキシベースの配合物を含むさまざまなアンダーフィル材料が利用可能です。 アプリケーションの特定の要件に応じて、これらの材料は毛細管流、ジェッティング、スクリーン印刷などのさまざまな技術を使用して塗布できます。
システムインパッケージ (SiP) アンダーフィル: 統合とパフォーマンス
システムインパッケージ (SiP) は、複数の半導体チップ、受動部品、その他の要素を XNUMX つのパッケージに統合する高度なパッケージング技術です。 SiP には、フォームファクタの縮小、電気的性能の向上、機能の強化など、数多くの利点があります。 SiP アセンブリの信頼性と性能を確保するために、アンダーフィル材料が一般的に使用されます。
SiP アプリケーションのアンダーフィルは、パッケージ内のさまざまなコンポーネント間の機械的安定性と電気的接続を提供する上で非常に重要です。 これにより、コンポーネント間の熱膨張係数 (CTE) の違いによって発生する可能性のある、はんだ接合部の亀裂や破損などの応力による故障のリスクを最小限に抑えることができます。
複数のコンポーネントを SiP パッケージに統合すると、多くのはんだ接合と高密度回路による複雑な相互接続が可能になります。 アンダーフィル材料はこれらの相互接続を強化し、アセンブリの機械的強度と信頼性を向上させます。 これらははんだ接合部をサポートし、熱サイクルや機械的ストレスによって引き起こされる疲労や損傷のリスクを軽減します。
電気的性能の観点から見ると、アンダーフィル材料は信号の完全性を向上させ、電気ノイズを最小限に抑える上で重要です。 アンダーフィルはコンポーネント間の隙間を埋めてコンポーネント間の距離を縮めることにより、寄生容量と寄生インダクタンスを低減し、より高速かつ効率的な信号伝送を可能にします。
さらに、SiP アプリケーション用のアンダーフィル材料は、集積コンポーネントによって生成された熱を効率的に放散するために、優れた熱伝導率を備えている必要があります。 過熱を防ぎ、SiP アセンブリの全体的な信頼性とパフォーマンスを維持するには、効果的な熱放散が不可欠です。
SiP パッケージングのアンダーフィル材料は、これらの統合および性能要件を満たす特定の特性を備えている必要があります。 完全にカバーし、コンポーネント間の隙間を埋めるには、良好な流動性が必要です。 アンダーフィル材料は、狭い穴や小さなスペースへの塗布と充填を容易にするために、低粘度の配合でなければなりません。
さらに、アンダーフィル材料は、信頼性の高い接合を確保するために、半導体チップ、基板、受動部品などのさまざまな表面に対して強力な接着力を示す必要があります。 有機基材やセラミックなどのさまざまな包装材料と適合し、高いせん断強度や剥離強度などの良好な機械的特性を示す必要があります。
アンダーフィルの材料と塗布方法の選択は、特定の SiP 設計、コンポーネント要件、および製造プロセスによって異なります。 キャピラリ フロー、ジェッティング、またはフィルム支援法などのディスペンス技術は、通常、SiP アセンブリにアンダーフィルを適用します。
オプトエレクトロニクス アンダーフィル: 光学的位置合わせと保護
オプトエレクトロニクス アンダーフィルには、正確な光学的位置合わせを確保しながら、オプトエレクトロニクス デバイスを封入および保護することが含まれます。 レーザー、光検出器、光スイッチなどの光電子デバイスでは、最適なパフォーマンスを達成するために光学コンポーネントの繊細な位置合わせが必要になることがよくあります。 同時に、機能に影響を与える可能性のある環境要因から保護する必要があります。 オプトエレクトロニクス アンダーフィルは、単一プロセスで光学的な位置合わせと保護を提供することで、これらの両方の要件に対応します。
光学的位置合わせは、光電子デバイス製造の重要な側面です。 これには、効率的な光の送受信を確保するために、ファイバー、導波路、レンズ、回折格子などの視覚要素を位置合わせすることが含まれます。 デバイスのパフォーマンスを最大化し、信号の整合性を維持するには、正確な位置合わせが必要です。 従来の位置合わせ技術には、目視検査を使用した手動位置合わせや、位置合わせステージを使用した自動位置合わせが含まれます。 ただし、これらの方法は時間と労力がかかり、エラーが発生しやすい可能性があります。
オプトエレクトロニクス アンダーフィルは、位置合わせ機能をアンダーフィル材料に直接組み込むことにより、革新的なソリューションを実現します。 アンダーフィル材料は通常、流動して光学部品間の隙間を埋めることができる液体または半液体の化合物です。 微細構造や基準マークなどの位置合わせ機能をアンダーフィル材料内に追加することにより、位置合わせプロセスを簡素化および自動化できます。 これらの機能は組み立て中にガイドとして機能し、複雑な位置合わせ手順を必要とせずに光学コンポーネントの正確な位置合わせを保証します。
光学的位置合わせに加えて、アンダーフィル材料は光電子デバイスを保護します。 オプトエレクトロニクス部品は、温度変動、湿気、機械的ストレスなどの過酷な環境にさらされることがよくあります。 これらの外部要因により、時間の経過とともにデバイスのパフォーマンスと信頼性が低下する可能性があります。 アンダーフィル材料は保護バリアとして機能し、光学コンポーネントをカプセル化し、環境汚染物質から保護します。 また、機械的な補強も行い、衝撃や振動による損傷のリスクを軽減します。
オプトエレクトロニクス用途で使用されるアンダーフィル材料は、通常、屈折率が低く、光透過性に優れるように設計されています。 これにより、デバイスを通過する光信号との干渉が最小限に抑えられます。 さらに、さまざまな基板に対して優れた接着性を示し、熱膨張係数が低いため、熱サイクル中のデバイスの応力が最小限に抑えられます。
アンダーフィル プロセスには、アンダーフィル材料をデバイス上に塗布し、流動させて光学部品間のギャップを充填し、その後硬化して固体の封止を形成することが含まれます。 特定の用途に応じて、毛細管流、ジェット ディスペンス、スクリーン印刷などのさまざまな技術を使用してアンダーフィル材料を塗布できます。 硬化プロセスは、熱、UV 照射、またはその両方によって実現できます。
医療用電子機器のアンダーフィル: 生体適合性と信頼性
医療用電子機器のアンダーフィルは、医療機器で使用される電子部品の封入と保護を含む特殊なプロセスを実行します。 これらのデバイスは、埋め込み型デバイス、診断機器、モニタリング システム、薬物送達システムなどのさまざまな医療用途で重要な役割を果たしています。 医療用電子機器のアンダーフィルは、生体適合性と信頼性という XNUMX つの重要な側面に重点を置いています。
生体適合性は、人体に接触する医療機器の基本的な要件です。 医療用電子機器で使用されるアンダーフィル材料は生体適合性がなければなりません。つまり、生体組織や体液と接触したときに有害な影響や副作用を引き起こしてはなりません。 これらの材料は、生体適合性のテストと評価手順を規定する ISO 10993 などの厳格な規制と規格に準拠する必要があります。
医療用電子機器用のアンダーフィル材料は、生体適合性を確保するために慎重に選択または配合されています。 非毒性、非刺激性、非アレルギー性となるように設計されています。 これらの材料は、組織の損傷や炎症を引き起こす可能性があるため、有害な物質が浸出したり、時間の経過とともに劣化したりしてはなりません。 生体適合性アンダーフィル材料は吸水性が低く、感染症を引き起こす可能性のある細菌や真菌の増殖を防ぎます。
信頼性は、医療用電子機器のアンダーフィルのもう XNUMX つの重要な側面です。 医療機器は、極端な温度、湿気、体液、機械的ストレスなどの困難な動作条件に直面することがよくあります。 アンダーフィル材料は電子部品を保護し、長期的な信頼性と機能性を確保する必要があります。 機器の故障が患者の安全と健康に重大な影響を与える可能性がある医療用途では、信頼性が最も重要です。
医療用電子機器のアンダーフィル材料は、体液や滅菌プロセスへの曝露に耐えられるよう、湿気や化学薬品に対する高い耐性を備えている必要があります。 また、さまざまな基板に対して優れた接着性を示し、電子部品の確実な封止を保証する必要があります。 低い熱膨張係数や優れた耐衝撃性などの機械的特性は、熱サイクルや自動荷重中に細部にかかるストレスを最小限に抑えるために重要です。
医療用電子機器のアンダーフィル プロセスには以下が含まれます。
- 電子部品上にアンダーフィル材料を塗布します。
- 隙間を埋める。
- それを硬化させて、保護的で機械的に安定したカプセル化を形成します。
機能を完全にカバーし、デバイスの信頼性を損なう可能性のある空隙やエアポケットがないように注意する必要があります。
さらに、医療機器にアンダーフィルを充填する場合には、追加の考慮事項が考慮されます。 たとえば、アンダーフィル材料は、デバイスに使用される滅菌方法に適合する必要があります。 一部の材料は、蒸気、エチレンオキシド、放射線などの特定の滅菌技術に敏感な場合があり、代替の材料を選択する必要がある場合があります。
航空宇宙エレクトロニクスのアンダーフィル: 高温および耐振動性
航空宇宙エレクトロニクスのアンダーフィルは、航空宇宙用途の電子部品をカプセル化して保護するための特殊なプロセスです。 航空宇宙環境には、高温、極度の振動、機械的ストレスなどの特有の課題があります。 したがって、航空宇宙エレクトロニクスのアンダーフィルは、高温耐性と耐振動性という XNUMX つの重要な側面に重点を置いています。
航空宇宙エレクトロニクスでは、動作中に高温にさらされるため、高温耐性が最も重要です。 航空宇宙用途で使用されるアンダーフィル材料は、電子部品の性能と信頼性を損なうことなく、これらの高温に耐える必要があります。 熱膨張を最小限に抑え、広い温度範囲にわたって安定した状態を維持する必要があります。
航空宇宙エレクトロニクス用のアンダーフィル材料は、高いガラス転移温度 (Tg) と熱安定性を考慮して選択または配合されます。 Tg が高いため、高温でも材料の機械的特性が維持され、変形や接着力の低下が防止されます。 これらの材料は、離陸時、大気圏突入時、または高温のエンジン コンパートメントでの動作時などの極端な温度に耐えることができます。
さらに、航空宇宙エレクトロニクス用のアンダーフィル材料は、熱膨張係数 (CTE) が低い必要があります。 CTE は、温度変化に応じて材料がどの程度膨張または収縮するかを測定します。 アンダーフィル材料は CTE が低いため、機械的故障やはんだ接合部の疲労につながる可能性がある熱サイクルによって引き起こされる電子コンポーネントへのストレスを最小限に抑えることができます。
耐振動性は、航空宇宙エレクトロニクスのアンダーフィルのもう XNUMX つの重要な要件です。 航空宇宙ビークルは、エンジン、飛行中に誘発される振動、打ち上げや着陸時の機械的衝撃など、さまざまな振動にさらされます。 これらの振動は、適切に保護されていない場合、電子コンポーネントの性能と信頼性を危険にさらす可能性があります。
航空宇宙エレクトロニクスに使用されるアンダーフィル材料は、優れた振動減衰特性を示す必要があります。 振動によって発生するエネルギーを吸収および消散し、電子部品にかかる応力と歪みを軽減する必要があります。 これは、過度の振動にさらされることによる亀裂、亀裂、またはその他の機械的故障の形成を防ぐのに役立ちます。
さらに、航空宇宙用途では、高い接着力と凝集力を備えたアンダーフィル材料が好まれます。 これらの特性により、極端な振動条件下でもアンダーフィル材料が電子部品および基板にしっかりと接着された状態を維持します。 強力な接着力により、アンダーフィル材料の層間剥離や要素からの分離が防止され、封止の完全性が維持され、湿気や破片の侵入が防止されます。
航空宇宙エレクトロニクスのアンダーフィル プロセスでは通常、アンダーフィル材料を電子部品上に塗布し、流動させてギャップを埋め、その後硬化して堅牢な封止を形成します。 硬化プロセスは、用途の特定の要件に応じて、熱または UV 硬化方法を使用して実行できます。
自動車エレクトロニクスのアンダーフィル: 耐久性と熱サイクル耐性
自動車エレクトロニクスのアンダーフィルは、自動車用途の電子部品の封入と保護を含む重要なプロセスです。 自動車環境には、温度変化、熱サイクル、機械的ストレス、湿気や化学物質への曝露など、特有の課題があります。 したがって、自動車エレクトロニクスのアンダーフィルは、耐久性と熱サイクル耐性という XNUMX つの重要な側面に重点を置いています。
耐久性は、自動車エレクトロニクスのアンダーフィルにとって重要な要件です。 通常の運転中、自動車は継続的な振動、衝撃、機械的ストレスにさらされます。 自動車用途に使用されるアンダーフィル材料は、電子部品を堅牢に保護し、耐久性と寿命を確保する必要があります。 道路上で遭遇する過酷な条件や機械的負荷に耐え、湿気、埃、化学物質の侵入に耐える必要があります。
自動車エレクトロニクス用のアンダーフィル材料は、高い機械的強度と耐衝撃性を備えて選択または配合されています。 これらは、電子部品および基板に対して優れた接着力を示し、機械的ストレス下での層間剥離や分離を防止する必要があります。 耐久性のあるアンダーフィル素材により、振動や衝撃による電子コンポーネントの損傷のリスクが最小限に抑えられ、車両の耐用年数にわたって信頼性の高いパフォーマンスが保証されます。
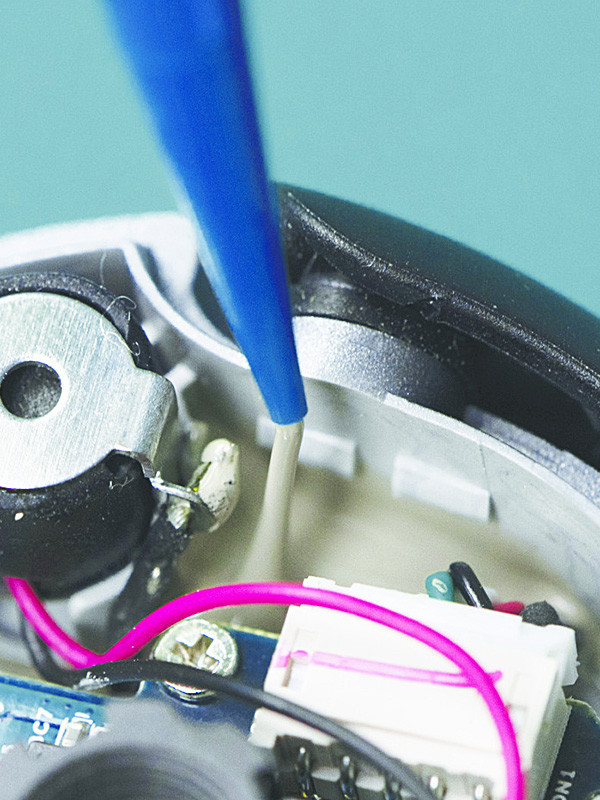
熱サイクル耐性は、自動車エレクトロニクスのアンダーフィルのもう XNUMX つの重要な要件です。 自動車は、特にエンジンの始動中および動作中に頻繁に温度変化にさらされ、これらの温度サイクルにより電子部品や周囲のアンダーフィル材料に熱応力が誘発される可能性があります。 自動車用途で使用されるアンダーフィル材料は、性能を損なうことなくこれらの温度変動に耐えられる優れた熱サイクル耐性を備えていなければなりません。
自動車エレクトロニクス用のアンダーフィル材料は、熱サイクル中の電子部品の応力を最小限に抑えるために、低い熱膨張 (CTE) 係数を持つ必要があります。 アンダーフィル材料とその成分の CTE が適切に一致していると、熱応力によって引き起こされるはんだ接合部の疲労、亀裂、またはその他の機械的故障のリスクが軽減されます。 さらに、アンダーフィル材料は熱を効率的に放散し、コンポーネントの性能と信頼性に影響を与える可能性のある局所的なホットスポットを防ぐために良好な熱伝導率を示す必要があります。
さらに、自動車エレクトロニクスのアンダーフィル材料は、湿気、化学薬品、および液体に耐性がある必要があります。 カビの発生や電子部品の腐食を防ぐために、吸水性が低い必要があります。 耐薬品性により、オイル、燃料、洗浄剤などの自動車用液体にさらされた場合でもアンダーフィル材料が安定した状態を保ち、劣化や接着力の低下を防ぎます。
自動車エレクトロニクスのアンダーフィル プロセスでは通常、アンダーフィル材料を電子部品上に塗布し、流動させてギャップを埋め、その後硬化して耐久性のある封止を形成します。 硬化プロセスは、アプリケーションの特定の要件と使用されるアンダーフィル材料に応じて、熱または UV 硬化方法によって実行できます。
適切なアンダーフィル エポキシの選択
適切なアンダーフィル エポキシを選択することは、電子部品の組み立てと保護において重要な決定です。 アンダーフィル エポキシは、機械的補強、熱管理、および環境要因からの保護を提供します。 適切なアンダーフィル エポキシを選択する際の重要な考慮事項をいくつか示します。
- 熱特性: アンダーフィル エポキシの主な機能の XNUMX つは、電子部品から発生する熱を放散することです。 したがって、エポキシの熱伝導率と熱抵抗を考慮することが重要です。 高い熱伝導率により効率的な熱伝達が可能になり、ホットスポットを防止し、コンポーネントの信頼性を維持します。 また、温度サイクル中のコンポーネントへの熱応力を最小限に抑えるために、エポキシは熱抵抗が低い必要があります。
- CTE の一致: 熱応力を最小限に抑え、はんだ接合の故障を防ぐために、アンダーフィル エポキシの熱膨張係数 (CTE) は電子部品および基板の CTE とよく一致している必要があります。 CTE が厳密に一致しているため、熱サイクルによる機械的故障のリスクが軽減されます。
- 流動性とギャップ充填能力: アンダーフィルされたエポキシは、良好な流動特性とコンポーネント間のギャップを効果的に充填する能力を備えている必要があります。 これにより、完全にカバーされ、アセンブリの機械的安定性や熱性能に影響を与える可能性のある空隙やエアポケットが最小限に抑えられます。 エポキシの粘度は、毛細管流、ジェット ディスペンス、スクリーン印刷など、特定の用途や組み立て方法に適している必要があります。
- 接着力: コンポーネントと基板間の確実な接着を確保するために、エポキシをアンダーフィルする場合、強力な接着力が非常に重要です。 金属、セラミック、プラスチックなどのさまざまな材料に対して優れた接着力を示す必要があります。 エポキシの接着特性は、アセンブリの機械的完全性と長期信頼性に貢献します。
- 硬化方法:製造プロセスに最適な硬化方法を検討してください。 アンダーフィル エポキシは、熱、UV 照射、またはその両方の組み合わせによって硬化できます。 各硬化方法には利点と制限があり、製造要件に合ったものを選択することが重要です。
- 環境耐性: 湿気、化学物質、極端な温度などの環境要因に対するアンダーフィル エポキシの耐性を評価します。 エポキシは水への暴露に耐え、カビや腐食の発生を防ぐ必要があります。 耐薬品性により、自動車用液体、洗浄剤、その他の潜在的な腐食性物質と接触した場合でも安定性が確保されます。 さらに、エポキシは広い温度範囲にわたって機械的および電気的特性を維持する必要があります。
- 信頼性と寿命: アンダーフィル エポキシの実績と信頼性データを考慮してください。 同様の用途でテストされ、優れた性能を発揮することが証明されているエポキシ材料、または業界認証を取得し、関連規格に準拠しているエポキシ材料を探してください。 経年劣化の挙動、長期的な信頼性、エポキシの特性を長期間にわたって維持する能力などの要素を考慮してください。
適切なアンダーフィル エポキシを選択する際には、熱管理、機械的安定性、環境保護、製造プロセスの適合性など、アプリケーションの特定の要件を考慮することが重要です。 エポキシのサプライヤーに相談したり、専門家のアドバイスを求めたりすることは、アプリケーションのニーズを満たし、最適なパフォーマンスと信頼性を確保するための情報に基づいた決定を下す上で有益です。
アンダーフィルエポキシの今後の動向
アンダーフィル エポキシは、電子技術の進歩、新たな用途、性能と信頼性の向上のニーズによって継続的に進化しています。 アンダーフィル エポキシの開発と応用では、いくつかの将来の傾向が観察されます。
- 小型化と高密度実装: 電子デバイスの小型化が進み、コンポーネント密度が高くなるにつれて、アンダーフィル エポキシもそれに応じて適応する必要があります。 今後のトレンドは、部品間の小さな隙間を貫通して埋めるアンダーフィル材料の開発に焦点が当てられ、小型化が進む電子アセンブリにおいて完全な被覆と信頼性の高い保護を確保することになるでしょう。
- 高周波アプリケーション: 高周波および高速電子デバイスに対する需要が高まる中、アンダーフィル エポキシ配合物はこれらのアプリケーションの特定の要件に対応する必要があります。 低誘電率と低損失正接を備えたアンダーフィル材料は、高度な通信システム、5G テクノロジー、その他の新興アプリケーションにおいて信号損失を最小限に抑え、高周波信号の完全性を維持するために不可欠です。
- 強化された熱管理: 熱放散は、特に電力密度の増加に伴い、電子デバイスにとって依然として重大な懸念事項です。 将来のアンダーフィル エポキシ配合物は、熱伝達を強化し、熱の問題を効果的に管理するために、熱伝導率の向上に重点を置くことになります。 高度なフィラーと添加剤がアンダーフィル エポキシに組み込まれ、他の望ましい特性を維持しながらより高い熱伝導率を実現します。
- フレキシブルで伸縮性のあるエレクトロニクス: フレキシブルで伸縮性のあるエレクトロニクスの台頭により、アンダーフィルエポキシ材料の新たな可能性が開かれています。 フレキシブルアンダーフィルエポキシは、繰り返し曲げたり伸ばしたりしても優れた接着力と機械的特性を発揮する必要があります。 これらの材料により、ウェアラブル デバイス、曲げ可能なディスプレイ、および機械的柔軟性を必要とするその他の用途における電子機器のカプセル化と保護が可能になります。
- 環境に優しいソリューション: アンダーフィル エポキシ材料の開発において、持続可能性と環境への配慮がますます重要な役割を果たします。 有害物質を含まず、製造、使用、廃棄を含むライフサイクル全体を通じて環境への影響を低減したエポキシ配合物の開発に重点が置かれます。 バイオベースまたは再生可能材料も、持続可能な代替品として注目を集める可能性があります。
- 製造プロセスの改善: アンダーフィル エポキシの今後の傾向は、材料特性と製造プロセスの進歩に焦点が当てられるでしょう。 さまざまな電子アセンブリプロセスにおけるアンダーフィルエポキシの用途と性能を最適化するために、積層造形、選択的ディスペンシング、高度な硬化方法などの技術が検討されます。
- 高度なテストおよび特性評価技術の統合: 電子デバイスの複雑さと要件が増大するにつれて、アンダーフィルド エポキシの信頼性と性能を確保するための高度なテストおよび特性評価方法が必要になります。 非破壊検査、現場モニタリング、シミュレーション ツールなどの技術は、アンダーフィルド エポキシ材料の開発と品質管理に役立ちます。
まとめ
アンダーフィル エポキシは、電子部品、特に半導体パッケージングの信頼性と性能を向上させる上で重要な役割を果たします。 さまざまなタイプのアンダーフィル エポキシは、高い信頼性、自動塗布、高密度、高い熱的および機械的性能など、さまざまな利点を提供します。 アプリケーションとパッケージに適切なアンダーフィル エポキシを選択すると、堅牢で長期にわたる接着が保証されます。 技術が進歩し、パッケージ サイズが縮小するにつれて、優れた性能、統合性、小型化を実現するさらに革新的なアンダーフィル エポキシ ソリューションが期待されます。 アンダーフィル エポキシはエレクトロニクスの将来においてますます重要な役割を果たし、さまざまな業界でより高いレベルの信頼性とパフォーマンスを達成できるようになります。