半導体用接着剤
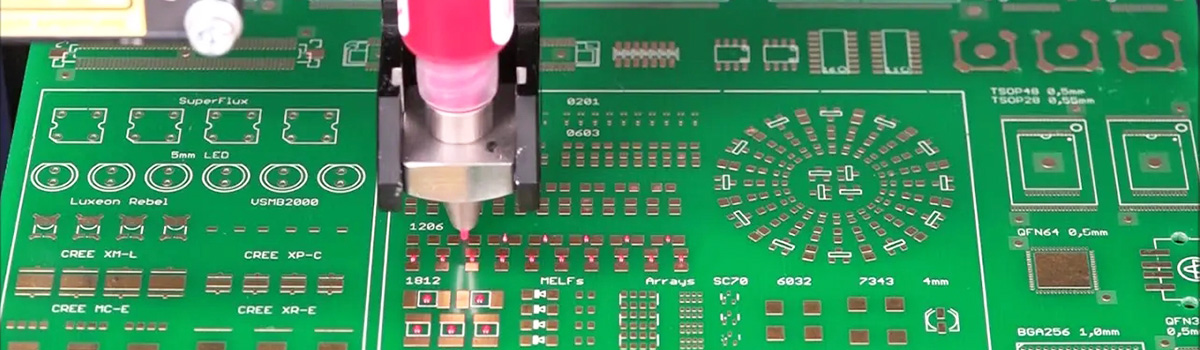
半導体接着剤は、マイクロプロセッサ、メモリチップ、その他の集積回路などの半導体デバイスの製造および組み立てにおいて重要な部品です。 これらの接着剤は、堅牢で信頼性の高い接着能力を提供し、環境要因や熱ストレスに対する保護を提供します。 より小さく、より高速で、より複雑な半導体デバイスに対する需要が高まるにつれ、高性能で信頼性の高い接着剤ソリューションがこれまで以上に重要になっています。 この記事では、半導体接着剤のさまざまな種類、用途、課題を探り、半導体デバイスの小型化と高性能化を可能にする上での重要な役割に焦点を当てます。
半導体用接着剤の種類
半導体接着剤は、電子デバイスの製造および組み立てプロセスにおいて重要な役割を果たします。 これらの接着剤は、チップ、基板、パッケージなどの半導体デバイスのさまざまなコンポーネント間に堅牢で信頼性の高い接着を提供するように設計されています。 過酷な環境条件、熱サイクル、機械的ストレスに耐えることができます。 数種類の半導体接着剤が市場で入手可能であり、それぞれに独自の特性と用途があります。 一般的に使用される半導体接着剤のいくつかを見てみましょう。
- エポキシ接着剤: エポキシベースの接着剤は、優れた接着強度、高い耐薬品性、良好な電気絶縁特性により、半導体用途で広く使用されています。 金属、セラミックス、プラスチックなど、さまざまな素材に強力に接着します。 エポキシ接着剤は室温または加熱下で硬化し、硬くて耐久性のある接着を形成します。
- シリコーン接着剤: シリコーンベースの接着剤は、柔軟性、熱安定性、および極端な温度に対する耐性で知られています。 配合に応じて、-50°C ~ 200°C、またはそれ以上の広い温度範囲に耐えることができます。 シリコーン接着剤は優れた電気絶縁特性を示し、パワー エレクトロニクス デバイスなど、熱管理が重要な用途によく使用されます。
- アクリル系接着剤: アクリル系接着剤は、硬化が早く、接着強度が高く、温度や湿気に対する優れた耐性を備えています。 これらは多用途性で知られており、金属、プラスチック、ガラスなどのさまざまな基材に接着できます。 アクリル接着剤は、自動車エレクトロニクスや LED アセンブリなど、高い強度と耐久性が必要な用途によく使用されます。
- ポリウレタン接着剤: ポリウレタンベースの接着剤は、柔軟性と強度のバランスを提供します。 金属、プラスチック、ガラスなどのさまざまな素材に優れた接着力を発揮します。 ポリウレタン接着剤は衝撃、振動、熱サイクルに対する耐性があり、自動車や航空宇宙エレクトロニクスなど、機械的ストレスが関係する用途に適しています。
- 導電性接着剤: 導電性接着剤には銀、銅、カーボンなどの導電性フィラーが配合されており、接着接合部の導電性を実現します。 これらは、電子デバイスのダイアタッチ、フリップチップボンディング、およびコンポーネントの相互接続に一般的に使用されます。 導電性接着剤は抵抗が低く、接着力に優れているため、信頼性の高い電気接続が可能です。
- アンダーフィル接着剤: アンダーフィル接着剤は、チップが基板上に上下逆に取り付けられるフリップチップ用途向けに明確に設計されています。 これらの接着剤は硬化中にチップの下に流れ、チップと基板の間の隙間を埋めます。 アンダーフィル接着剤は機械的サポートを提供し、熱伝導率を高め、熱応力によるはんだ接合の破損を防ぎます。
- UV 硬化型接着剤: UV 硬化型接着剤は、紫外線にさらされると急速に硬化します。 高い接着強度、光学的透明性、耐薬品性を備えています。 UV 硬化型接着剤は、ディスプレイ アセンブリ、光ファイバー、光電子デバイスなど、高速処理と精密な接着が必要な用途によく使用されます。
エポキシ接着剤: 最も一般的な選択
エポキシ接着剤は、最も一般的で多用途なタイプの XNUMX つとして広く認識されています。 優れた接着強度、耐久性、汎用性により、さまざまな産業や用途で幅広く使用されています。 ここでは、限られた文字数の中で、エポキシ接着剤が最も一般的な選択肢である理由を探っていきます。
- 接着強度:エポキシ接着剤は優れた接着強度を示し、さまざまな材料に適しています。 金属、プラスチック、セラミック、木材、複合材料のいずれであっても、エポキシ接着剤は強固で信頼性の高い接着を提供し、接合部品の寿命と安定性を保証します。
- 多用途性: エポキシ接着剤は、塗布方法と硬化オプションにおいて優れた多用途性を示します。 これらは XNUMX 液型または XNUMX 液型システムなど、さまざまな形式で利用できるため、柔軟に使用できます。 さらに、エポキシ接着剤は、用途の特定の要件に応じて、室温または加熱で硬化できます。
- 耐薬品性: エポキシ接着剤は優れた耐薬品性を備えているため、過酷な化学薬品や溶剤への曝露が懸念される用途に最適です。 さまざまな化学薬品、油、燃料、酸にさらされた場合でも構造の完全性を維持し、接着アセンブリの耐久性を確保します。
- 温度耐性: エポキシ接着剤は広い温度範囲に耐えることができるため、高温または低温に対する耐性が必要な用途に適しています。 自動車産業、航空宇宙産業、電子産業のいずれにおいても、エポキシ接着剤は極端な温度下でも信頼性の高い接着を実現します。
- 隙間充填能力: エポキシ接着剤のもう XNUMX つの利点は、合わせ面間の隙間や凹凸を埋める能力です。 この特性により、接触面が理想的に一致していない場合でも強力な接合が保証され、接合部品の構造的完全性が強化されます。
- 機械的特性: エポキシ接着剤は、高い引張強度とせん断強度、優れた耐衝撃性など、優れた機械的特性を備えています。 これらの特性により、接着剤は接着強度を損なうことなく大きな応力や衝撃に耐える必要がある耐荷重用途に適しています。
- 電気絶縁: エポキシ接着剤は優れた電気絶縁特性を示し、電子および電気用途で広く使用されています。 効果的な絶縁を提供し、敏感な電子部品を電流や短絡から保護します。
- 使いやすさ: エポキシ接着剤は使用と塗布が比較的簡単です。 正確に塗布できるため、塗布の制御が可能になり、無駄を最小限に抑えることができます。 さらに、エポキシ接着剤はオープンタイムが長いため、接着剤が硬化する前に部品を組み立てるのに十分な作業時間が得られます。
導電性接着剤: 電気接続を可能にする
導電性接着剤は、粘着性と導電性の両方の特性を備えた特殊なタイプの接着材料です。 これらは、従来のはんだ付け方法が実行不可能または望ましくないさまざまな用途で電気接続を可能にするように設計されています。 これらの接着剤には、使いやすさ、環境への優しさ、多用途性など、多くの利点があります。
導電性接着剤の重要な利点の XNUMX つは、使いやすさです。 熱が必要で複雑な場合があるはんだ付けとは異なり、導電性接着剤は、接着剤を目的の表面に塗布または塗布するだけで簡単に塗布できます。 これにより、専門家から愛好家まで幅広いユーザーに適しており、専用の機器は必要ありません。
環境に優しいことも導電性接着剤の利点です。 通常、鉛ベースのはんだを使用するはんだ付けとは異なり、導電性接着剤は毒性のない材料を配合できます。 これにより、より環境に優しく、より安全に取り扱うことができ、ユーザーの健康リスクが軽減されます。 さらに、鉛が含まれていないため、これらの接着剤は有害物質の使用を制限する規制に準拠しています。
導電性接着剤は、接着できる材料の多様性も提供します。 金属などの導電性材料と、プラスチック、セラミック、ガラスなどの非導電性材料を接合できます。 この幅広い互換性により、統合された電気接続を備えたマルチマテリアル アセンブリの作成が可能になり、さまざまな業界で新しい設計の可能性が開かれます。
これらの接着剤の導電性は、銀や炭素粒子などの導電性フィラーを接着剤マトリックス内に含めることによって実現されます。 これらのフィラーは、接着表面全体に電流が流れることを可能にする導電性経路を形成します。 フィラーの材料と濃度の選択は、特定の導電率要件を満たすように調整できるため、接着剤の電気特性を微調整することができます。
導電性接着剤の用途は広く普及しています。 これらは、エレクトロニクス業界でコンポーネントの接合、はんだ付けプロセスの代替または補完に一般的に使用されています。 導電性接着剤は、はんだ付けに伴う高温に耐えられない繊細な電子部品を接合するのに特に有益です。 これらは、フレキシブル回路、RFID タグ、およびタッチスクリーンの製造にも使用され、さまざまな基板に接着できるという利点があります。
自動車産業では、導電性接着剤はセンサー、制御ユニット、照明システムを組み立てます。 非機械的接合機能により応力集中点が減少し、電気接続の信頼性と寿命が向上します。 さらに、導電性接着剤を使用すると、重金属コネクタが不要になるため、車両の軽量化が可能になります。
導電性接着剤は、エレクトロニクスや自動車の用途を超えて、医療機器、航空宇宙部品、さらにはウェアラブル電子機器などの消費者製品にも使用されています。 多用途性、使いやすさ、環境上の利点により、工業デザイナーやエンジニアにとって魅力的です。
ダイアタッチ接着剤: 半導体チップを基板に接着
ダイアタッチ接着剤は、半導体チップを基板に接着する信頼性の高い効率的な方法を提供することで、半導体産業において重要な役割を果たしています。 これらの接着剤はチップと基板の間のインターフェースとして機能し、安全で導電性の接続を確保します。
ダイアタッチ接着剤の主な機能は、チップと基板の間に機械的サポートと電気的接続を提供することです。 熱サイクル、機械的ストレス、環境暴露などのさまざまな動作条件下でチップが基板にしっかりと取り付けられた状態を維持するには、優れた接着特性を備えている必要があります。
ダイアタッチ接着剤の重要な要件の 200 つは、高温に耐えられる能力です。 はんだリフローや熱圧着などのチップ組み立てプロセス中、接着剤はその完全性と接着強度を維持する必要があります。 通常、ダイアタッチ接着剤は XNUMX°C を超える温度に耐えるように設計されており、接着の信頼性が確保されています。
ダイアタッチ接着剤は一般に、エポキシベースの接着剤とはんだベースの接着剤に分類されます。 エポキシベースの接着剤は、熱にさらされると硬化する熱硬化性材料です。 優れた接着性、高い熱伝導性、電気絶縁性を備えています。 一方、はんだベースの接着剤は、接合プロセス中に溶ける金属合金で構成されています。 これらは低抵抗の電気経路と高い熱伝導率を提供するため、高電力損失のアプリケーションに適しています。
ダイアタッチ接着剤の選択は、特定の用途、動作条件、基板材質などのいくつかの要因によって決まります。 接着剤は、適切な接着を確保し、有害な相互作用を防ぐために、接着される材料と適合する必要があります。 また、接着剤は、接着を容易にし、チップと基板の間の空隙や隙間を最小限に抑えるために、良好な塗布特性と流動特性を備えていなければなりません。
信頼性の高い接合を実現するには、表面処理が不可欠です。 基板とチップの表面は、接着を妨げる汚染物質、酸化物、その他の不純物を除去するために徹底的に洗浄する必要があります。 接着剤の接着性能を高めるために、プラズマ洗浄、化学エッチング、超音波洗浄などの表面処理技術が一般的に使用されます。
ダイアタッチ接着剤を塗布したら、チップを慎重に基板上に配置し、位置合わせします。 圧力または熱を使用して、接着剤と接着面の間の適切な湿潤と接触を確保することができます。 その後、接着剤が硬化または固化し、接着プロセスが完了します。
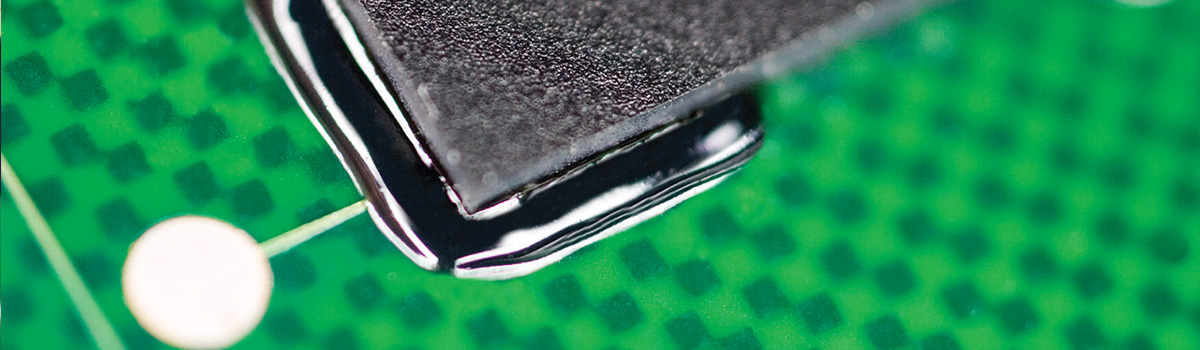
アンダーフィル接着剤: 熱応力からの保護
アンダーフィル接着剤は、熱ストレスから保護するために電子パッケージングに使用される必須の材料です。 これらは機械的な強化を提供し、熱サイクルや機械的衝撃の影響を最小限に抑えることで電子デバイスの信頼性を向上させます。
熱応力は、異なる材料間の熱膨張係数 (CTE) の不一致により、電子アセンブリにおいて重大な懸念事項となります。 デバイスが温度変動を受けると、材料はさまざまな速度で膨張および収縮し、破損する可能性のある応力が発生します。 アンダーフィル接着剤は、チップと基板の間の緩衝材として機能し、熱サイクルによって生じる応力を吸収および分散することで、この問題を軽減します。
アンダーフィル接着剤の主な機能は、集積回路 (IC) チップを基板に接続するはんだ接合を強化することです。 製造中、チップははんだを使用して基板に取り付けられ、これにより XNUMX つのコンポーネント間に接合が形成されます。 ただし、チップと基板の間の CTE の不一致により、はんだ接合部に応力集中が発生する可能性があります。 アンダーフィル接着剤はチップと基板の間のギャップに注入され、空隙を埋めて堅牢で弾性のある層を形成します。 この層は応力集中を軽減し、アセンブリの全体的な機械的完全性を高めます。
アンダーフィル接着剤は、電子部品から発生する熱を放散するために重要な優れた熱伝導性も備えています。 過熱を防ぎ、デバイスの性能と寿命を維持するには、効率的な熱放散が不可欠です。 アンダーフィル接着剤は、チップから基板への熱伝達を促進することで、安定した動作温度を維持し、熱ストレスによる IC の損傷を防ぎます。
さらに、アンダーフィル接着剤は湿気や汚染物質から保護します。 電子デバイスは、湿気やさまざまな化学薬品などの過酷な環境にさらされることが多く、その性能や信頼性が低下する可能性があります。 アンダーフィル材料はバリアとなり、水分の侵入やチップ パッケージへの有害物質の拡散を防ぎます。 この保護は、電気的性能を維持し、デバイスの寿命を延ばすのに役立ちます。
フリップチップ接着剤: 小型化を可能にする
フリップチップ接着剤は、さまざまな電子機器の小型化を可能にするために重要です。 技術の進歩に伴い、より小型、軽量、より強力な機械に対する需要が常にあります。 フリップチップボンディングは、このようなデバイスで高密度の相互接続を実現するための好ましい方法として浮上しています。 これらの接着剤は、チップと基板間の直接的な電気的および機械的接続を容易にし、小型化に多くの利点をもたらします。
フリップチップ接着剤の重要な利点の XNUMX つは、電子パッケージの全体サイズを縮小できることです。 従来のワイヤボンディング技術ではワイヤループのためのスペースが必要であり、実現可能なデバイスサイズが制限されていました。 対照的に、フリップチップボンディングではワイヤループが不要になり、パッケージサイズが大幅に縮小されます。 設置面積が小さいことは、スペースが重要視されるスマートフォン、タブレット、ウェアラブルなどのポータブル電子デバイスにおいて重要です。
さらに、フリップチップ接着剤によりデバイスのパフォーマンスが向上します。 チップと基板間の直接電気接続により、信号経路長とインダクタンスが短縮され、電気的性能が向上します。 これは、信号の遅延や損失を最小限に抑えることが重要なマイクロプロセッサやメモリ チップなどの高速アプリケーションにとって特に重要です。 フリップチップボンディングは、寄生効果を低減することにより、データ転送速度の高速化、消費電力の低減、デバイスの信頼性の向上に貢献します。
さらに、フリップチップ接着剤は優れた熱管理機能を提供します。 電子部品の高性能化と高密度化に伴い、熱放散の管理が重要な課題となっています。 フリップチップボンディングにより、チップを基板に直接取り付けることができるため、熱伝達効率が向上します。 これにより、効率的な熱放散が可能になり、過熱が防止され、デバイス全体の信頼性と寿命が向上します。 グラフィックス プロセッシング ユニット (GPU) や中央処理装置 (CPU) などの高性能デバイスには、効果的な熱管理が不可欠です。
フリップチップ接着剤のもう XNUMX つの利点は、機械的安定性です。 フリップチップボンディングに使用される接着材料は、強固で信頼性の高い相互接続を提供します。 ワイヤーボンドがないため、ワイヤーの破損や疲労のリスクがなくなり、長期にわたる機械的完全性が保証されます。 フリップチップ接着剤は堅牢であるため、自動車エレクトロニクスや航空宇宙システムなど、過酷な動作条件にさらされる用途に適しています。
さらに、フリップチップ接着剤は高密度の相互接続をサポートします。 フリップチップボンディングを使用すると、狭い面積で多数の接続を実現できるため、限られたスペース内により多くの機能を統合できます。 これは、集積回路、センサー、微小電気機械システム (MEMS) など、多数の入出力接続を必要とする複雑な電子デバイスにとって特に有益です。 フリップチップ接着剤によって実現された高密度の相互接続は、デバイス全体の小型化に貢献します。
封止用接着剤: 敏感なコンポーネントの保護
封止用接着剤は、傷つきやすい電子部品をさまざまな環境要因、機械的ストレス、化学物質への曝露から保護するために不可欠です。 これらの接着剤は保護バリアを提供し、要素をカプセル化し、その寿命と信頼性を保証します。 この記事では、封止接着剤の重要性と、敏感なコンポーネントの保護におけるその役割について説明します。
集積回路、センサー、繊細な配線などの繊細な電子コンポーネントは、湿気、ほこり、温度変動、物理的衝撃によって引き起こされる損傷を受けやすいです。 封止接着剤は、これらのコンポーネントの周囲に保護層を形成することで、信頼性の高いソリューションを提供します。 これらはバリアとして機能し、機能を損なったり早期故障につながる可能性のある外部要素からコンポーネントを保護します。
カプセル化接着剤の重要な特性の XNUMX つは、湿気の侵入に抵抗する能力です。 湿気は腐食、ショート、漏電の原因となり、機器の故障につながる可能性があります。 カプセル化接着剤は優れた耐湿性を備え、敏感なコンポーネントへの水や水蒸気の侵入を防ぎます。 この機能は、自動車エレクトロニクスや屋外産業機器など、高湿度または湿気の多い環境にさらされるアプリケーションでは非常に重要です。
封止用接着剤は、湿気から保護するだけでなく、優れた耐薬品性も備えています。 溶剤、酸、塩基、洗浄剤などのさまざまな化学物質への暴露に耐えることができます。 この耐性により、敏感なコンポーネントは化学的相互作用による影響を受けず、その完全性と機能が維持されます。
カプセル化接着剤は、傷つきやすいコンポーネントを機械的に保護します。 これらはショックアブソーバーとして機能し、コンポーネントに損傷を与える可能性のある機械的ストレスや振動を分散します。 この機能は、航空宇宙、自動車、家庭用電化製品など、頻繁に移動するアプリケーションでは不可欠です。
さらに、封止接着剤は優れた熱管理特性を提供します。 高い熱伝導率を備えているため、敏感なコンポーネントからの効率的な熱放散が可能になります。 これらの接着剤は、熱を効果的に放散し、熱ストレスを防止し、長期的な信頼性を確保することにより、最適な動作温度を維持するのに役立ちます。
封止接着剤のもう XNUMX つの利点は、電子アセンブリの構造的完全性を強化できることです。 さまざまなコンポーネントをカプセル化して結合することで、システム全体の強度と安定性が向上します。 この機能は、産業用制御システムや軍事グレードの電子機器など、機械的な堅牢性が不可欠なアプリケーションで特に有益です。
封止用接着剤には、さまざまな用途要件に応えるさまざまな配合があります。 これらは、室温で硬化する液体接着剤、または高出力用途に使用される熱伝導性化合物です。 適切な接着剤の選択は、必要な保護レベル、動作条件、硬化時間、組み立てプロセスなどの要因によって異なります。
低アウトガス接着剤: 宇宙用途に不可欠
低アウトガス接着剤は、清潔で管理された環境を維持することが不可欠な宇宙用途で重要な役割を果たします。 ガス放出とは、真空または低圧条件下で接着剤などの材料から揮発性有機化合物 (VOC) やその他の汚染物質を放出することを指します。 大気圧のない極限状態の宇宙では、ガスの放出により、敏感な機器、光学システム、宇宙船の表面に損傷を与える可能性があります。 したがって、宇宙ミッションの信頼できる性能と寿命を確保するには、低ガス放出接着剤を使用することが最も重要です。
ガス放出に関する主な懸念事項の XNUMX つは、光学レンズやセンサーなどの重要な表面への汚染物質の堆積です。 不純物はこれらの表面に薄膜を形成し、透明性を低下させ、性能を低下させ、科学的測定を妨げる可能性があります。 光学システムの場合、開放性がわずかに低下するだけでも、宇宙から収集される画像やデータの品質に大きな影響を与える可能性があります。 低アウトガス接着剤は、揮発性化合物の放出を最小限に抑え、汚染のリスクを軽減し、敏感な機器の機能を維持するように設計されています。
低アウトガス接着剤のもう XNUMX つの重要な側面は、電子部品や回路への影響です。 ガス放出中に放出される VOC は、繊細な電子システムを腐食または劣化させ、誤動作や完全な故障につながる可能性があります。 これは、電子部品が宇宙の真空、極端な温度変化、放射線にさらされる宇宙船では特に懸念されます。 低ガス放出接着剤は低蒸気圧材料で配合されており、腐食性化合物の放出を最小限に抑え、電子システムの完全性を保護します。
さらに、ガスの放出は宇宙飛行士の健康や有人宇宙船の居住性を脅かす可能性もあります。 宇宙カプセルや宇宙ステーションなどの閉鎖環境では、ガスの放出による VOC の蓄積により、不快または危険な雰囲気が生じる可能性があります。 低アウトガス接着剤は、揮発性化合物の排出を削減することでこのリスクを軽減し、ミッション中の宇宙飛行士にとって安全で健康的な環境を確保します。
低ガス放出特性を達成するために、宇宙用途で使用される接着剤は厳格なテストと認定プロセスを受けます。 これらのプロセスには、接着剤を真空チャンバー、極端な温度、さまざまな環境ストレスなどの模擬空間条件にさらすことが含まれます。 低アウトガスの厳しい要件を満たす接着剤は、宇宙ミッションでの使用が認定および承認されています。
ウェーハレベル接着用接着剤: コスト削減と歩留まり向上
ウェーハレベルのボンディングは、複数のチップまたはウェーハを相互接続して複雑な集積回路を形成する、半導体産業において重要なプロセスです。 従来、このボンディングプロセスにははんだバンプまたはワイヤボンディング技術が含まれており、正確な位置合わせと各チップの個別のボンディングが必要であり、その結果、コストが高くなり歩留まりが低下していました。 しかし、接着技術の進歩により、半導体製造におけるコスト削減と歩留まりの向上を実現するウェーハレベルの接着接着剤への道が開かれました。
ウェーハレベルの接着剤は、ウェーハレベルでウェーハまたはチップ間に信頼性の高い堅牢な接着を提供するように設計されており、個別の接着プロセスが不要になります。 これらの接着剤は通常、ウェーハ間に薄層として塗布され、制御された条件下で硬化されて、所望の接着強度が得られます。 コスト削減と歩留まりの向上に貢献する主な要因を以下に示します。
- プロセスの簡素化: ウェーハレベルの接着剤は、単一のステップで複数のチップまたはウェーハを同時に接着できるため、接着プロセスが簡素化されます。 これにより、複雑な位置合わせや各チップの個別のボンディングが不要になり、時間が節約され、生産コストが削減されます。 さらに、接着剤を広い領域に均一に塗布できるため、ウェハ全体に一貫した接着が保証されます。
- 高い接着強度と信頼性: ウェーハレベルの接着剤は優れた接着特性を提供し、ウェーハ間の高い接着強度を実現します。 この強固な接着により、信頼性の高い相互接続が保証され、後続の製造ステップやデバイス動作中の層間剥離や故障のリスクが最小限に抑えられます。 接着剤の機械的、熱的、電気的特性は、特定の用途要件に合わせて調整できるため、信頼性がさらに向上します。
- コスト効率の高い材料: ウェーハレベルの接着剤には、従来の接着技術と比較してコスト効率の高い材料が使用されることがよくあります。 これらの接着剤は、エポキシ、ポリイミド、アクリレートなどのさまざまなポリマーを使用して配合でき、これらは容易に入手でき、手頃なコストで優れた性能を発揮します。 さまざまな材料から選択することで、メーカーは性能、価格、さまざまな基材との互換性に基づいて接着剤の選択を最適化できます。
- 歩留まりの向上: ウェーハレベルの接着剤は、半導体製造における歩留まりの向上に貢献します。 ウェーハ全体に接着剤を均一に塗布することで、欠陥や故障につながる可能性のあるボイド、空気の閉じ込め、不均一な接合のリスクを最小限に抑えます。 さらに、個々のチップのボンディングを排除することで、ボンディングプロセス中の位置ずれや損傷の可能性が減り、その結果、歩留まりが向上し、スクラップ率が低下します。
- 高度なパッケージング技術との互換性: ウェーハレベル接着剤は、ウェーハレベルチップスケールパッケージング (WLCSP)、ファンアウトウェーハレベルパッケージング (FOWLP)、または 3D 統合プロセスなど、さまざまな高度なパッケージング技術と互換性があります。 これらの接着剤を使用すると、複数のチップやさまざまなコンポーネントをコンパクトなフォームファクター内に統合できるため、小型化が促進され、電子デバイスの高度な機能が可能になります。

UV 硬化型接着剤: 迅速かつ正確な接着
UV 硬化接着剤は、迅速かつ正確な接着機能を提供する革新的な接着剤です。 これらは、そのユニークな特性と従来の接着剤を超える利点により、さまざまな業界で人気を集めています。 UV 硬化接着剤は通常、モノマー、光開始剤、安定剤で構成されます。 紫外線 (UV) 光にさらされると、これらの接着剤は光化学反応を起こし、急速に硬化して接着します。
UV 硬化接着剤の重要な利点の XNUMX つは、硬化時間が速いことです。 完全に硬化するまでに数時間、場合によっては数日を要する従来の接着剤とは異なり、UV 硬化型接着剤は数秒から数分で硬化します。 この迅速な硬化時間により、生産効率が大幅に向上し、組立ラインの待ち時間が短縮され、製造業者にとって大幅なコスト削減につながります。 また、瞬時に接着が形成されるため、接着したコンポーネントを即座に取り扱い、さらに加工することも可能になります。
UV 硬化接着剤の正確な接着能力も、大きな利点です。 接着剤は UV 光にさらされるまで液体のままであるため、接着する部品の位置合わせと位置決めに十分な時間がかかります。 接着剤が紫外線にさらされるとすぐに固まり、強固で耐久性のある接着が形成されます。 この正確な接着能力は、エレクトロニクス、光学機器、医療機器など、高精度と厳しい公差を必要とする用途に役立ちます。
UV 硬化型接着剤は優れた接着強度と耐久性を備えています。 硬化した接着剤は、極端な温度、湿気、化学物質などのさまざまな環境要因に耐えられる強力な結合を形成します。 これにより、接着されたコンポーネントの寿命と信頼性が確保され、UV 硬化型接着剤が要求の厳しい用途に適したものになります。
さらに、UV 硬化接着剤は溶剤を含まず、揮発性有機化合物 (VOC) の排出量が低くなります。 乾燥が必要で潜在的に有害な蒸気を放出する溶剤ベースの接着剤とは異なり、UV 硬化型接着剤は環境に優しく安全です。 このため、環境フットプリントを削減し、規制に準拠することを目指す業界にとって、これらは魅力的な選択肢となります。
UV 硬化接着剤の多用途性も注目すべき点です。 ガラス、金属、プラスチック、セラミック、さらには異種基板など、さまざまな材料を接着できます。 この幅広い互換性により、UV 硬化接着剤は自動車、航空宇宙、エレクトロニクス、医療業界にわたるさまざまな用途に適しています。
導電性ペースト接着剤: フレキシブルエレクトロニクスおよびプリンテッドエレクトロニクスを可能にする
導電性ペースト接着剤は、フレキシブルエレクトロニクスやプリンテッドエレクトロニクスの開発を可能にする重要な技術として浮上しています。 これらの革新的な材料は、従来の接着剤の特性と金属の導電性を組み合わせており、さまざまな基板上での電子デバイスの製造と統合の新たな可能性を切り開きます。
導電性ペースト接着剤の主な利点の XNUMX つは、機械的接着力と導電性の両方を提供できることです。 従来の接着剤は通常絶縁性であるため、電子用途での使用は制限されています。 逆に、導電性ペースト接着剤には、電気の流れを促進する銀、銅、カーボンなどの導電性粒子が含まれています。 この二重の機能により、接着剤と導電経路の両方として機能することができるため、電子部品を接着したり、フレキシブル基板上に導電性トレースを作成したりするのに最適です。
導電性ペースト接着剤の柔軟性も、フレキシブルエレクトロニクスに適したものにする重要な特性です。 これらの接着剤は、曲げ、伸ばし、ねじりを受けても導電性を維持できます。 この柔軟性は、ウェアラブル デバイス、フレキシブル ディスプレイ、コンフォーマル エレクトロニクスなど、従来のリジッド回路では実装が非現実的または不可能であるアプリケーションにとって非常に重要です。 導電性ペースト接着剤を使用すると、フレキシブル基板上に堅牢で信頼性の高い電気接続を作成でき、フレキシブル電子デバイスの性能と耐久性が保証されます。
さらに、導電性ペースト接着剤は、スクリーン印刷、インクジェット印刷、フレキソ印刷などのさまざまな印刷技術と互換性があります。 この互換性により、プリンテッド エレクトロニクスの大量生産とコスト効率の高い製造が可能になります。 印刷プロセスにより、導電性ペースト接着剤を正確なパターンで堆積できるため、材料の無駄を最小限に抑えながら複雑な回路や電子設計を作成することが可能になります。 導電性トレースをフレキシブル基板上に直接印刷できるため、製造プロセスが簡素化され、生産時間が短縮され、プリンテッド エレクトロニクスが大規模製造にとって実行可能なソリューションになります。
導電性ペースト接着剤には、熱管理の面でも利点があります。 これらの接着剤に導電性粒子が存在すると、電子部品によって発生する熱の放散が促進されます。 この特性は、パワー エレクトロニクスや高出力 LED など、大量の熱を発生するデバイスの信頼性とパフォーマンスを確保するために非常に重要です。 導電性ペースト接着剤を熱インターフェースとして使用すると、熱を発熱コンポーネントからヒートシンクに効率的に伝達でき、デバイス全体の性能と寿命が向上します。
はんだペースト: 接着剤による接合の代替
はんだペーストとも呼ばれるはんだペーストは、さまざまな用途で接着剤による接合の代替手段となります。 接着接合では接着剤を使用して材料を接合しますが、はんだペーストでは異なるメカニズムを利用して、堅牢で信頼性の高い接合を実現します。 この回答では、接着剤接合の代替手段としてのはんだペーストについて 450 語の制限内で検討します。
はんだペーストは、金属合金粒子、フラックス、およびバインダーの混合物で構成されています。 金属合金粒子は通常、スズ、鉛、銀、またはこれらの金属の組み合わせで構成されます。 この変更により、金属表面から酸化物が除去され、濡れと接着が促進されるため、はんだ付けプロセスが促進されます。 バインダーはペーストを保持し、簡単に塗布できます。
接着剤による接合に対するペーストはんだ付けの主な利点の XNUMX つは、接合の強度と耐久性です。 はんだ付けにより、接合された材料間に金属結合が形成され、さまざまな機械的、熱的、電気的ストレスに耐えられる強力な接合が得られます。 はんだ付け接合は、時間の経過や特定の条件下で劣化する可能性がある接着接合よりも堅牢で信頼性が高いことがよくあります。
はんだペーストは、より迅速かつ効率的な接合プロセスも提供します。 ペーストは必要な領域に正確に塗布でき、アセンブリをはんだの溶融温度まで加熱することで接合を形成できます。 このプロセスは多くの場合、硬化時間や乾燥時間を必要とする接着よりも高速です。 さらに、はんだペーストを使用すると、複数のコンポーネントを同時に接合できるため、組み立て時間が短縮され、生産性が向上します。
もう XNUMX つの利点は、異なる材料を接合する際のはんだペーストの多用途性です。 異種の材料または異なる熱膨張係数を持つ材料を接着する場合、接着剤による接着には制限がある場合があります。 はんだペーストは、金属、セラミック、一部のプラスチックなどのさまざまな材料間に信頼性の高い接合を形成できるため、さまざまな用途に適しています。
さらに、はんだペーストは、接着剤による接合と比較して、熱伝導性と電気伝導性を向上させることができます。 この特性は、電子アセンブリなど、熱放散や電気的連続性が重要な用途で特に有益です。はんだ付けされた接合部が直接的な金属経路を形成し、効率的な熱伝達と電気伝導が促進されます。
ただし、はんだペーストにもいくつかの考慮事項と制限があることに注意することが重要です。 たとえば、一部のはんだ合金には鉛が含まれており、環境や健康上の懸念から鉛が制限される場合があります。 代替品として鉛フリーはんだペーストが開発されていますが、それらは異なる特性を持ち、特定のプロセスの考慮が必要になる場合があります。
接着剤塗布技術: 精度と効率
接着剤塗布技術は、製造から建設に至るまで、さまざまな業界で重要です。 接着剤塗布の精度と効率を達成することは、信頼性の高い接着を確保し、無駄を最小限に抑え、全体的な生産性を向上させるために不可欠です。 この記事では、接着剤塗布の精度と効率を達成するのに役立つ重要なテクニックについて説明します。
- 自動塗布システム: 自動塗布システムは、ロボット アームまたはコンピュータ制御の機器を利用して、接着剤を正確に塗布します。 これらのシステムは高い再現性、精度、速度を提供し、複数の部品または製品にわたって一貫した接着剤の塗布を保証します。 自動化システムは人的エラーを排除することで無駄を最小限に抑え、接着剤塗布プロセスの効率を高めます。
- 計量および混合システム: 一部のアプリケーションでは、特定の比率で混合する必要がある XNUMX つ以上のコンポーネントを分注する必要があります。 計量および混合システムは、配布前に接着剤成分を正確に測定して組み合わせ、正確な比率と一貫した品質を保証します。 これらのシステムは、二液型エポキシ、ポリウレタン、その他の反応性接着剤に特に有益です。
- 圧力制御によるディスペンス: 圧力制御によるディスペンス技術では、空気圧または油圧システムを使用して接着剤の流量と圧力を制御します。 接着剤は、一定の力を維持し、正確な塗布を保証し、余分な接着剤を最小限に抑えることにより、制御された速度で塗布されます。 圧力制御によるディスペンスは、細い線、ドット、または複雑なパターンを必要とするアプリケーションによく使用されます。
- ジェッティングおよびニードル ディスペンス: ジェッティングおよびニードル ディスペンス技術は、高速かつ正確な接着剤の配置が必要な用途に適しています。 ジェッティング システムは、圧力パルスを使用して小さな液滴や連続した接着剤のラインを吐出します。 一方、ニードルディスペンスでは、ニードルまたはノズルを使用して接着剤を制御された量で塗布します。 これらの技術は、少量で正確な接着剤の塗布が必要な電子機器の組み立てでよく使用されます。
- スプレーおよびコーティング システム: 大面積の接着またはコーティング用途の場合、スプレーおよびコーティング システムは効率的な接着剤塗布を実現します。 これらのシステムは霧化技術を利用して接着剤の細かいミストまたはスプレーを生成し、均一な被覆と最小限の無駄を確保します。 スプレーおよびコーティング システムは、自動車、航空宇宙、家具製造業界で広く使用されています。
- 塗布バルブとノズル: 塗布バルブとノズルの選択は、接着剤塗布の精度を達成するために非常に重要です。 ニードル バルブ、ダイヤフラム バルブ、テーパー ノズルなどのさまざまなタイプのバルブやノズルにより、流量、パターン、液滴サイズをさまざまに制御できます。 正確かつ効率的な塗布を実現するには、特定の接着剤や用途の要件に応じて適切なバルブやノズルを選択することが不可欠です。
- 視覚誘導システム: 視覚誘導塗布システムは、カメラと高度なソフトウェアを使用して、部品または基板の位置を検出および追跡します。 キャプチャした画像を分析することで、システムは接着剤塗布パラメータをリアルタイムで調整し、凹凸のある表面やさまざまな部品寸法でも正確に配置できるようにします。 ビジョン誘導システムは、プロセスの変動に対応しながら、精度と効率を向上させます。
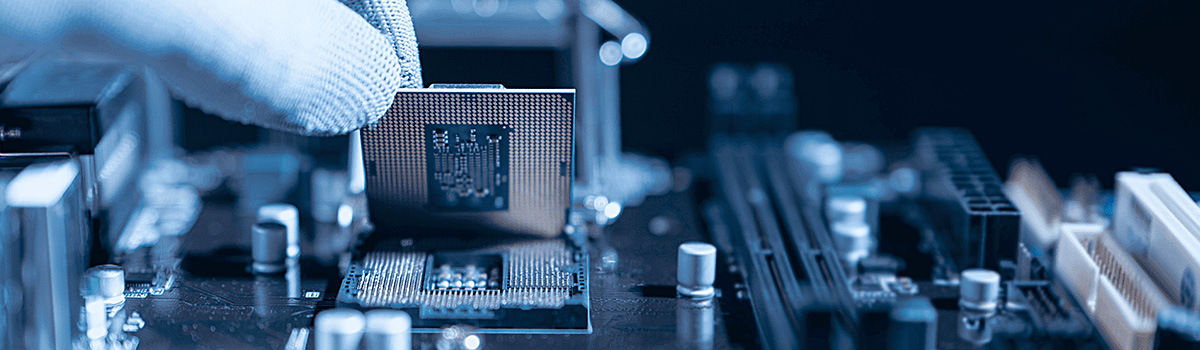
半導体接着剤塗布における課題
半導体接着剤の塗布は、電子デバイスの性能と信頼性に影響を与える可能性のあるいくつかの課題に直面しています。 これらの課題は、半導体固有の要件と特性、およびそれらがさらされる厳しい動作条件によって発生します。 半導体接着剤の塗布における重要な課題のいくつかを以下に示します。
- 熱管理: 半導体は動作中に熱を発生するため、過熱を防ぐには効果的な熱管理が重要です。 半導体で使用される接着材料は、デバイスからの熱を効率的に伝達するために優れた熱伝導率を備えている必要があります。 熱性能を損なうことなく適切な接着を確保することは重要な課題です。
- 化学的適合性: 半導体は、その寿命の間、洗浄剤、溶剤、フラックスなどのさまざまな化学物質にさらされます。 接着材料は、時間の経過による劣化や接着力の低下を避けるために、これらの物質と化学的に適合する必要があります。 特定の化学物質への曝露に耐えられる接着剤材料を選択することは、複雑な作業です。
- 機械的ストレス: 電子デバイスは、熱膨張、振動、外力による機械的ストレスを受けることがよくあります。 これらの応力に耐えるために、接着材料は柔軟性や強度などの適切な機械的特性を備えていなければなりません。 接着性能が低いと、半導体デバイスの剥離、亀裂、または機械的故障が発生する可能性があります。
- 小型化: 小型化の傾向が続く中、半導体デバイスはますます小型化、複雑化しています。 このような小型構造物への接着剤の塗布には、高い精度と制御が必要です。 均一な被覆を確保し、ボイドを回避し、一貫したボンドラインの厚さを維持することが重要な課題となります。
- プロセスの互換性: 半導体製造には、洗浄、成膜、パッケージングなどの複数の処理ステップが含まれます。 接着材料は、その性能に悪影響を与えることなく、これらのプロセスに適合する必要があります。 高温プロセスに耐え、湿気に強く、製造サイクル全体を通じて安定性を維持できる接着剤を見つける際に課題が生じます。
- 信頼性と経年劣化: 半導体デバイスには、さまざまな動作条件下で長寿命と信頼性の高いパフォーマンスが期待されます。 接着材料は、長期安定性、耐老化性、および長期間にわたる信頼性の高い接着性を示さなければなりません。 課題は、半導体デバイスの性能と信頼性に影響を与える可能性のある潜在的な劣化メカニズムを予測し、軽減することにあります。
- 環境への配慮: 半導体用途で使用される接着材料は、環境規制および基準に準拠する必要があります。
- これには、鉛やその他の有毒物質などの有害物質の制限が含まれます。 性能を損なうことなく規制要件を満たし、環境に優しい接着剤ソリューションを開発することは困難な場合があります。
- コストと拡張性: 接着材料は、半導体の大量生産の需要を満たすために、コスト効率が高く、拡張性がある必要があります。 コストの考慮事項と性能要件のバランスをとることは、適切な接着材料の選択と塗布プロセスの最適化に課題をもたらします。
信頼性試験: 接着性能の評価
信頼性試験は、接着剤の性能を評価するために不可欠なプロセスです。 接着剤は自動車、航空宇宙、エレクトロニクス、建設などのさまざまな業界で一般的に使用されており、異なる材料を接合する際に重要な役割を果たしています。 接着剤の信頼性は、接着アセンブリの耐久性と長期的な機能を確保するために非常に重要です。
信頼性試験の重要な側面の XNUMX つは、接着剤の強度と接着特性を評価することです。 これには、接着剤サンプルをさまざまな応力条件にさらして現実世界のシナリオをシミュレートし、さまざまな荷重、温度、環境条件下での性能を測定することが含まれます。 接着剤の機械的特性と、さまざまな方向の力に耐える能力を評価するために、引張、せん断、剥離試験が一般的に行われます。
機械的試験に加えて、環境要因も接着剤の性能に重要な役割を果たします。 接着剤は、耐用期間中、極端な温度、湿度、化学物質、紫外線にさらされる可能性があります。 したがって、信頼性試験には、粘着性のあるサンプルを加速老化試験に供し、過酷な環境条件に長期間さらすことが含まれます。 これは、接着剤の長期的な性能を予測し、接着強度の低下や化学的劣化などの劣化に対する耐性を評価するのに役立ちます。
信頼性試験のもう XNUMX つの重要な側面は、繰り返し荷重下での接着剤の耐久性を評価することです。 多くの用途において、接着剤は振動や熱サイクルなどの繰り返しの機械的ストレスにさらされます。 疲労試験では、これらの繰り返し荷重下での接着剤の破損に対する耐性を評価します。 通常、サンプルは指定された回数の負荷サイクルにさらされ、亀裂の伝播や接着層の剥離など、接着剤の欠陥の兆候がないかどうかその性能が監視されます。
さらに、信頼性試験には、実際の条件における接着剤の性能を評価することが含まれます。 これには、金属、プラスチック、複合材料、ガラスなど、業界で一般的に使用されているさまざまな材料を接着する接着剤の能力のテストが含まれる場合があります。 サンプルは標準化された手順を使用して準備され、特定のアプリケーション要件をシミュレートするテストプロトコルを受けます。 これにより、エンジニアは接着剤のさまざまな基材との適合性を評価し、接着強度、柔軟性、環境要因に対する耐性を評価できるようになります。
信頼性テストには、接着剤の使用中または耐用年数中に接触する可能性のある他の物質との化学的適合性を評価することも含まれます。 これには、接着剤が環境中に存在する可能性のある溶剤、洗浄剤、燃料、またはその他の化学物質と悪反応するかどうかを判断するための適合性テストの実施が含まれます。 化学的適合性テストは、接着剤の破損や劣化につながる可能性のある潜在的な問題を特定するのに役立ちます。
結論として、信頼性試験は接着剤の性能を評価する上で重要なステップです。 これには、機械的特性の評価、加速老化試験の実施、繰り返し荷重下での耐久性の評価、現実世界の条件での性能の評価、および化学的適合性の試験が含まれます。 包括的な信頼性テストを実施することで、メーカーやエンジニアは、意図した用途における接着剤の適合性と長期的な性能を保証できます。
半導体接着剤における環境への配慮
半導体接着剤は、特に半導体産業において、電子デバイスの組み立てとパッケージングにおいて重要な役割を果たします。 これらの接着剤は接着や熱管理などの重要な機能を提供しますが、ライフサイクル全体を通じて環境への影響を考慮することが重要です。 半導体接着剤における環境に関する重要な考慮事項は次のとおりです。
- 毒性: 多くの半導体接着剤には、揮発性有機化合物 (VOC)、重金属、その他の有毒化学物質などの有害物質が含まれています。 これらの物質は人間の健康や環境に悪影響を与える可能性があります。 環境への影響を軽減するには、接着剤配合物中の有害な成分を最小限に抑えるか排除することが重要です。
- 排出物: 半導体接着剤の製造および塗布中に、揮発性成分が空気中に放出され、大気汚染の原因となる可能性があります。 たとえば、VOC の排出は、地上でのオゾンや有害な粒子状物質の形成に寄与する可能性があります。 メーカーは、低 VOC 接着剤配合の開発に努め、これらの環境への影響を軽減するために厳格な排出規制措置を実施する必要があります。
- エネルギー消費: 半導体接着剤の製造には、合成、混合、硬化など、エネルギーを大量に消費するプロセスが必要です。 プロセスの最適化とエネルギー効率の高い技術の使用によりエネルギー消費を削減し、接着剤の製造に伴う環境フットプリントを最小限に抑えることができます。
- 廃棄物の発生: 半導体産業では大量の廃棄物が発生しており、接着剤もこの廃棄物の流れの一因となっています。 廃棄物には、未使用または期限切れの接着剤、梱包材、製造副産物などが含まれます。 環境汚染や資源の枯渇を最小限に抑えるには、接着剤廃棄物のリサイクル、再利用、安全な処分などの廃棄物管理慣行の実施が不可欠です。
- ライフサイクル分析: 半導体接着剤の環境への影響を包括的に評価するには、半導体接着剤のライフサイクル全体を考慮することが重要です。 この分析には、原材料の抽出、製造、輸送、使用、使用後の廃棄におけるエコロジカル フットプリントの評価が含まれます。 各段階で改善の機会を特定することで、より持続可能な接着剤ソリューションを実現できます。
- 持続可能な代替品: 半導体接着剤の環境への影響を軽減するには、持続可能な代替品を探索して採用することが不可欠です。 これには、バイオベースまたは再生可能な原材料の使用、水ベースまたは無溶剤配合物の開発、環境に優しい製造プロセスの採用などが含まれます。 接着剤のリサイクルを促進したり、循環経済の実践を実践したりすることも、資源の節約に貢献できます。
- 規制の遵守: 接着剤メーカーは、化学物質の使用、廃棄、およびラベル表示を管理する環境規制および基準を遵守する必要があります。 生態系と人間の健康を確実に保護するには、欧州連合の REACH (化学物質の登録、評価、認可、制限) やさまざまな地域の同様の規制など、関連する規制を常に最新の状態に保つことが重要です。
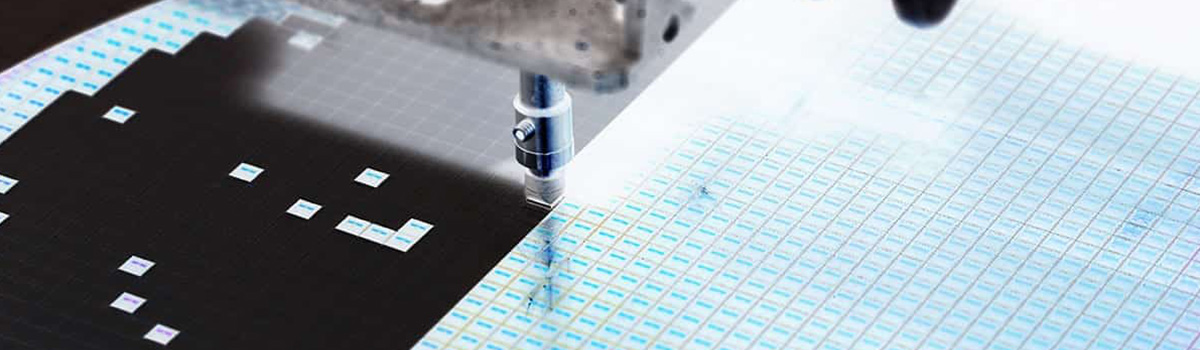
半導体接着剤のトレンドとイノベーション
半導体接着剤は、電子デバイスの組み立てとパッケージングにおいて重要な役割を果たし、半導体コンポーネントの適切な接着と安定性を確保します。 技術の進歩に伴い、半導体接着剤分野ではいくつかの重要なトレンドと革新が生まれています。
- 小型化とデバイスの複雑さの増大: 半導体業界における重要な傾向の XNUMX つは、電子デバイスの小型化とその設計の複雑さの増大です。 この傾向により、より小型でより高密度に充填されたコンポーネントに対応するために、より低い粘度、より高い接着強度、および強化された熱伝導率など、改良された特性を備えた接着剤が必要とされています。
- 高度なパッケージング技術: システムインパッケージ (SiP)、ファンアウトウェーハレベルパッケージング (FOWLP)、3D パッケージングなどの高度なパッケージング技術は、デバイスのパフォーマンスを向上させ、フォームファクターを削減できるため、人気が高まっています。 これらの技術では、多くの場合、小さな設置面積内で複数のダイやコンポーネントを相互接続するという特有の課題に対処できる特殊な接着剤が必要になります。
- 熱管理: 電子デバイスがより強力かつコンパクトになるにつれて、効果的な熱管理がますます重要になります。 半導体デバイスからの熱放散を促進し、過熱を防ぎ、最適な性能を確保するために、優れた熱伝導特性を備えた半導体接着剤が開発されています。
- 低温硬化: 従来の半導体接着剤は多くの場合高温硬化プロセスを必要とし、これは温度に敏感なコンポーネントや基板にとっては問題となる可能性があります。 低温硬化型接着剤の革新により、大幅に低い温度での接着が可能となり、デリケートな半導体材料への熱損傷のリスクが軽減されます。
- 新しい材料配合: 研究者は、進化する要件を満たすために、半導体接着剤の新しい材料配合を模索しています。 これには、接着と導電性を提供し、特定の用途ではんだ付けの必要性を排除する導電性接着剤 (ECA) の開発が含まれます。 さらに、柔軟で曲げ可能な電子デバイスに対する需要の高まりに対応するために、柔軟な接着剤などの新しい材料が導入されています。
- 環境への配慮: 半導体業界では、持続可能性と環境への影響に対する注目が高まっています。 接着剤メーカーは、優れた性能特性を維持しながら、揮発性有機化合物 (VOC) や有害物質を削減した環境に優しい配合物の開発に重点を置いています。
- プロセスの最適化と自動化: 半導体デバイスの需要の増加に伴い、効率的で自動化された製造プロセスの必要性が高まっています。 接着剤メーカーは、装置サプライヤーと協力して接着剤の塗布および硬化プロセスを最適化し、生産サイクル時間を短縮しながら一貫した信頼性の高い結果を保証します。
- 信頼性と耐久性: 半導体デバイスは、多くの場合過酷な環境で長期間にわたって確実に動作することが期待されます。 接着剤のイノベーションは、接着強度、湿気、温度、およびさまざまな環境要因に対する耐性を強化することにより、デバイスの信頼性を向上させることを目的としています。
応用分野: 家庭用電化製品、自動車、航空宇宙など
家電:
家庭用電子機器は、技術進歩の最も顕著な応用分野の 4 つです。 スマートフォン、タブレット、ラップトップ、スマート TV、ウェアラブル デバイス、家電製品などの多くのデバイスが含まれます。 近年、家庭用電化製品の性能、機能、接続性が大幅に進歩しています。 たとえば、スマートフォンはより強力になり、高解像度カメラ、人工知能の統合、拡張現実機能などの高度な機能を提供します。 インテリジェント TV は、8K、さらには XNUMXK 解像度とスマート ホーム統合をサポートし、エンターテインメント体験を強化します。 スマートウォッチやフィットネス トラッカーなどのウェアラブル デバイスは、健康モニタリングやフィットネス トラッキング機能で人気を集めています。
オートモーティブ・ソリューション :
自動車産業は、主にテクノロジーによって目覚ましい進歩を遂げてきました。 現代の車両には、安全性、効率性、ユーザー エクスペリエンスを向上させる高度な電子機器およびソフトウェア システムが搭載されています。 開発の重要な分野の XNUMX つは自動運転であり、自動運転車が現実のものとなります。 これらの車両は、高度なセンサー、人工知能アルゴリズム、接続性を利用して道路を移動し、インテリジェントな意思決定を行います。 さらに、自動車用途には次のようなものがあります。
- インフォテイメント システム。
- 先進運転支援システム (ADAS)。
- 車内接続。
- 電気自動車技術。
- 車車間通信。
航空宇宙:
航空宇宙産業は、安全性、効率、パフォーマンスを向上させるために高度なテクノロジーに大きく依存しています。 航空宇宙アプリケーションには、航空機の設計と製造、宇宙探査、衛星システム、航空交通管理が含まれます。 コンピュータ支援設計 (CAD) およびシミュレーション ツールは、エンジニアが航空機設計においてより空力効率と燃料効率の高い航空機を作成するのに役立ちます。 衛星システムは、地球規模の通信、気象監視、およびナビゲーション サービスを提供します。 航空宇宙産業では、複合材料や軽量合金などの先進的な材料を活用して、重量を軽減し、燃料効率を向上させています。 宇宙探査では、ロボット工学、リモート センシング、推進システムにより、天体を探索して科学データを収集するミッションが可能になります。
健康管理:
テクノロジーはヘルスケアにおいて重要な役割を果たしており、さまざまな形で業界を変革しています。 MRI 装置、超音波スキャナー、ロボット手術システムなどの医療機器や医療機器は、診断と治療手順に革命をもたらしました。 電子医療記録 (EHR) と遠隔医療により、医療専門家は患者情報にアクセスし、遠隔医療を提供できるようになります。 ウェアラブル デバイスと健康監視システムにより、個人は自分のバイタル サインを追跡し、パーソナライズされたヘルスケアの推奨事項を受け取ることができます。 人工知能と機械学習アルゴリズムは疾患の診断、創薬、予測分析に採用されており、患者の転帰の改善とカスタマイズされた医療につながります。
産業自動化:
産業オートメーションには、高度なテクノロジーを使用して製造プロセスを自動化し、生産性を向上させることが含まれます。 ロボット工学とロボット アームは、組み立て、溶接、マテリアル ハンドリングなどの作業に広く使用されています。 モノのインターネット (IoT) デバイスとセンサーは、リアルタイム データを収集し、運用効率を最適化するために導入されています。 マシンビジョンシステムは品質管理と検査を可能にし、製品が厳しい基準を満たしていることを保証します。 高度な制御システムと予知保全アルゴリズムにより、ダウンタイムを最小限に抑え、生産量を最大化できます。 産業オートメーションは、製造、物流、エネルギーなどのさまざまな業界で効率を高め、コストを削減し、安全性を強化できます。
将来の展望と機会
未来には、急速な技術の進歩、社会ニーズの変化、世界的なトレンドの進化によって刺激的な見通しと機会が溢れています。 ここでは、大きな成長と発展の可能性があるいくつかの主要分野を探ります。
- 人工知能 (AI) と自動化: AI は業界全体を変革し、効率、生産性、意思決定を強化しています。 AI テクノロジーが成熟するにつれて、AI スペシャリスト、データ サイエンティスト、エンジニアのチャンスが増大します。 自動化は今後もプロセスを合理化し、ロボット工学、機械学習、インテリジェント システムにおける雇用の創出につながります。
- 再生可能エネルギーと持続可能性: 気候変動に対する懸念が高まる中、再生可能エネルギー ソリューションに対する大きな需要が生じています。 太陽光、風力、水力発電などのよりクリーンな電源への移行には、多くの展望が見えてきます。 再生可能エネルギーエンジニアリング、エネルギー管理、持続可能な開発におけるキャリアは、より環境に優しい未来を形作る上で極めて重要になります。
- ヘルスケアとバイオテクノロジー: 医学研究、個別化医療、遺伝子編集の進歩により、ヘルスケア業界に革命が起きています。 バイオインフォマティクス、遺伝カウンセリング、遠隔医療、医薬品開発にはチャンスがたくさんあります。 テクノロジーとヘルスケアの交差点はイノベーションを推進し、より良い患者ケアと転帰の改善につながります。
- サイバーセキュリティとデータプライバシー: デジタルシステムへの依存度が高まるにつれ、堅牢なサイバーセキュリティ対策の必要性も高まっています。 サイバー脅威はますます巧妙化しており、サイバーセキュリティの専門家、倫理的なハッカー、データプライバシーの専門家に対する需要が生じています。 機密情報を保護し、安全なインフラストラクチャを開発することは、組織や個人にとって非常に重要です。
- E コマースとデジタル マーケティング: E コマースは私たちの買い物方法を変革し、ビジネスに新しい道を生み出しました。 オンライン小売プラットフォーム、デジタル マーケティング、ソーシャル メディア広告は、企業の成長にとって不可欠なものとなっています。 eコマース管理、デジタルコンテンツ作成、カスタマーエクスペリエンス最適化の分野でのキャリアは、今後も高い需要があり続けます。
- 宇宙探査と商業化: 宇宙探査は政府主導の取り組みから商業ベンチャーへと移行し、航空宇宙工学、衛星技術、宇宙観光の機会が開かれています。 民間企業は宇宙旅行、資源採掘、衛星通信に投資し、宇宙探査の新時代への道を切り開いています。
- 持続可能な農業と食料システム: 世界人口は9年までに2050億人に達すると予想されており、食料安全保障と持続可能な農業実践を確保することが重要です。 垂直農業、精密農業、代替タンパク質源は、イノベーションの可能性をもたらします。 農業技術、農学、食品科学の分野でのキャリアは、将来の食料需要を満たす上で重要な役割を果たすでしょう。
- 仮想現実 (VR)、拡張現実 (AR)、拡張現実 (XR): これらのテクノロジーは、エンターテイメント、教育、トレーニング、およびさまざまな業界に革命をもたらす可能性があります。 VR/AR 開発者、コンテンツ クリエーター、没入型エクスペリエンス デザイナーは、エンターテインメント、ゲーム、仮想コラボレーションの未来を形作ります。
- 金融テクノロジー (フィンテック): テクノロジーと金融の統合により、新しい金融サービス、デジタル決済ソリューション、ブロックチェーン テクノロジーを提供するフィンテックが台頭しました。 金融分析、銀行業界のサイバーセキュリティ、ブロックチェーン開発の分野でのキャリアは、高い需要が見込まれています。
- サステナビリティ コンサルティングとグリーン アーキテクチャ: サステナビリティが優先事項になるにつれ、企業や個人は二酸化炭素排出量を削減し、環境に優しい慣行を導入するためのガイダンスを求めています。 持続可能なコンサルタント、グリーンアーキテクト、環境エンジニアは、持続可能なソリューションの設計と実装に貢献します。
半導体接着技術の進歩におけるコラボレーションの重要性
半導体接着技術を進歩させ、イノベーションを推進し、さまざまな業界で確実に導入を成功させるには、協力が不可欠です。 半導体業界は非常に複雑で急速に進化しており、学際的な専門知識と関係者の協力が必要です。
- 多様な専門知識: 半導体接着技術は、材料科学、化学、エンジニアリング、製造などの複数の分野を網羅しています。 コラボレーションでは、さまざまな分野の専門家が集まり、それぞれが専門的な知識とスキルを提供します。 この提携により、多様な専門知識を組み合わせることで、半導体デバイスの性能、信頼性、耐久性を向上できる新しい接着材料と技術の開発が可能になります。
- 知識の交換: コラボレーションにより、研究者、エンジニア、業界専門家間の知識と情報の交換が促進されます。 共同作業を通じて、個人は自分の洞察、経験、研究結果を共有することができ、接着材料とその用途についてのより深い理解につながります。 この知識交換は、新たなトレンドを特定し、技術的な課題に対処し、革新的なソリューションの開発を加速するのに役立ちます。
- 研究開発の強化: 共同研究開発の取り組みにより、資金と設備の面でリソースをプールすることが可能になります。 これにより、より広範な実験、テスト、分析が可能になり、発見とイノベーションの迅速化につながります。 研究者は協力することで、個別には利用できない特殊な施設、最先端の技術、高度な特性評価ツールにアクセスできます。 このようなリソースは、半導体接着技術の進歩に大きく貢献する可能性があります。
- 産学連携: 研究成果を実用化するためには、産学間の連携が不可欠です。 大学は基礎研究を実施し、新しい概念を探求できますが、業界パートナーは現実世界の視点と実践的な考慮事項をもたらします。 この提携により、接着技術の開発が市場のニーズに確実に適合し、産業プロセスに統合できるようになります。 産学連携は技術移転も促進し、学術研究が商業応用に具体的な影響を与えることを可能にします。
- 標準化と品質保証: 業界関係者間の協力により、半導体接着技術の標準とガイドラインの開発が促進されます。 標準は、さまざまな製品や製造プロセスにわたって一貫性、互換性、信頼性を確保するのに役立ちます。 共同の取り組みにより、半導体デバイスの性能と長期信頼性を保証するために不可欠なベスト プラクティス、テスト方法、品質管理手順を確立できます。
- 市場の拡大と競争力: 半導体業界で活動する企業間の協力は、市場の拡大と競争力の向上につながる可能性があります。 企業は、特定の業界要件を満たす接着剤ソリューションを開発するために協力することで、自社のリソース、知識、市場に関する洞察を組み合わせることができます。 共同の取り組みにより、新しい用途や新興市場での接着技術の導入が促進され、半導体産業の成長がさらに促進されます。
結論:
半導体接着剤は、半導体デバイスの小型化・高性能化を実現するために重要な役割を果たしています。 これらの接着剤が強力な接着能力、環境要因や熱応力に対する保護、導電性を提供できることは、マイクロプロセッサ、メモリ チップ、その他の集積回路の製造と組み立てにおいて非常に重要です。 技術が進歩し続けるにつれて、革新的な接着剤ソリューションの開発と、メーカー、研究者、エンドユーザー間の協力は、半導体業界の増大する需要と課題に対応する上で非常に重要になります。 半導体接着剤の可能性を活用することで、現代世界を推進するさらに小型、高速、より複雑な半導体デバイスへの道を切り開くことができます。