FPC接合用接着剤
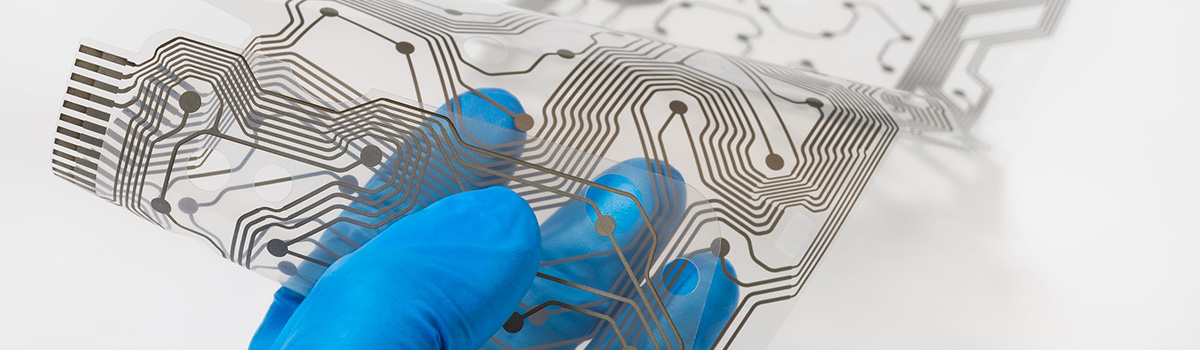
FPC 接着剤は、スマートフォン、ウェアラブル、自動車用途などのさまざまな電子機器で広く使用されているフレキシブル プリント回路 (FPC) 基板の製造および組み立てにおいて重要なコンポーネントです。 これらの接着剤は、FPC ボードの柔軟性と耐久性を確保しながら、強力な接着能力、電気絶縁性、および環境要因からの保護を提供します。 フレキシブルで信頼性の高い電子デバイスへの需要が高まるにつれ、高性能で信頼性の高い FPC 接着剤の重要性がますます高まっています。 この記事では、FPC 接合用接着剤のさまざまな種類、用途、課題を探り、電子デバイスの柔軟性と信頼性を実現する上での重要な役割に焦点を当てます。
FPC接着剤の種類
FPC(フレキシブルプリント回路)接着剤は、さまざまな電子機器のフレキシブル回路の組み立てや接続に不可欠です。 これらの接着剤は、フレキシブル回路とターゲット基板間の信頼性と耐久性のある接着を保証します。 数種類の FPC 接着剤が市場で入手可能であり、それぞれに独自の特性と用途があります。 この回答では、いくつかの一般的なタイプの FPC 接着剤の概要を説明します。
- アクリル系接着剤: アクリル系接着剤は、金属、プラスチック、ガラスなどのさまざまな基材への優れた接着力により人気があります。 柔軟性、熱安定性、湿気や化学薬品に対する耐性を備えています。 アクリル系接着剤は、テープ、フィルム、液状接着剤などさまざまな形態で入手可能であり、さまざまな FPC 接着用途に多用途に使用できます。
- エポキシベースの接着剤: エポキシベースの接着剤は高い接着強度を提供し、FPC の接着に広く使用されています。 さまざまな基材に対して優れた接着力を示し、良好な電気絶縁特性を提供します。 エポキシ接着剤は、XNUMX 液系や XNUMX 液系などのさまざまな配合で入手でき、複数の接着プロセスと硬化条件のオプションを提供します。
- シリコーンベースの接着剤: シリコーンベースの接着剤は、柔軟性、耐高温性、および優れた電気絶縁特性で知られています。 極端な温度に耐え、耐湿性に優れているため、要求の厳しい環境に適しています。 シリコーン接着剤は、熱管理と信頼性が重要な用途によく使用されます。
- 感圧接着剤 (PSA): PSA は、圧力が加わると瞬時に接着を形成する接着材料です。 他の硬化プロセスが不要になるため、FPC ボンディング用途に便利です。 PSA はさまざまな基材に優れた接着力を示し、残留物を残さずに簡単に剥がすことができるため、一時的な接着や再加工に最適です。
- UV 硬化型接着剤: UV 硬化型接着剤は、紫外線にさらされると急速に硬化する液体接着剤です。 硬化時間が速く、接着強度が高く、さまざまな基材に優れた接着力を発揮します。 UV 硬化型接着剤は、迅速な組み立てと生産性の向上が必要な FPC 接合用途によく使用されます。
- 導電性接着剤: 導電性接着剤は、接着と導電性のために特別に配合されています。 これらには銀やカーボンなどの導電性フィラーが含まれており、これにより接着剤が回路コンポーネント間の電気接続を確立できるようになります。 導電性接着剤は、EMI シールド、接地、電気相互接続などの用途の FPC 接合に広く使用されています。
- 熱伝導性接着剤: 熱伝導性接着剤は、接着特性と効率的な熱伝達特性の両方を提供するように設計されています。 これらは、フレキシブル回路をヒートシンクやその他の熱伝導性基板に接着するなど、熱管理が重要な FPC 接着用途に使用されます。
FPC 接着剤の選択は、特定のアプリケーション要件、基板材料、環境条件、製造プロセスなどのさまざまな要因に依存することに注意することが重要です。 接着剤のメーカーまたはサプライヤーに問い合わせると、特定の FPC 接合用途に最適な接着剤を選択するためのより詳細な情報とガイダンスが提供されます。
アクリル系接着剤: 最も一般的な選択
アクリル接着剤は、その多用途性、強力な接着能力、使いやすさにより、さまざまな業界で人気があります。 これらの接着剤はアクリルポリマーで構成されており、幅広い基材に優れた接着力を発揮します。 ここでは、アクリル系接着剤が最も一般的な選択肢である理由を 450 語以内で探っていきます。
アクリル接着剤の重要な利点の XNUMX つは、異なる材料を接着できることです。 アクリル接着剤は、プラスチック、金属、セラミック、木材、さらにはガラスを接着する場合でも、耐久性と信頼性の高い接着を実現します。 この多用途性により、自動車、建設、電子機器、看板などのさまざまな用途に適しています。
アクリル接着剤は優れた接着強度も備えており、高い応力、温度変化、環境条件に耐える強力な接着を形成できます。 そのため、耐久性と長期的なパフォーマンスが重要な用途に最適です。
アクリル接着剤の人気のもう XNUMX つの理由は、硬化時間が速いことです。 他のタイプの接着剤と比較して、アクリル接着剤は硬化時間が比較的短いため、より速い生産サイクルが可能になります。 多くの場合、数分で取り扱い強度を達成できるため、組み立て時間が短縮され、生産性が向上します。
さらに、アクリル接着剤は湿気、化学物質、紫外線に耐性があることで知られています。 耐水性に優れ、湿った環境でも粘着力を維持します。 この特性により、過酷な条件にさらされることが予想される屋外用途や環境に適しています。
アクリル系接着剤は優れた熱安定性も備えています。 接着強度を損なうことなく、極寒から高温までの広い温度範囲に耐えることができます。 この熱抵抗により、自動車産業やエレクトロニクス産業など、温度変動が頻繁に起こる用途に適しています。
物理的特性に加えて、アクリル接着剤は取り扱いや塗布が簡単です。 液状、ペースト状、フィルム状、テープ状などさまざまな形状があり、施工方法に柔軟に対応できます。 これらは、アプリケーションの特定の要件に応じて、自動塗布システムを使用して塗布することも、手動で塗布することもできます。
さらに、アクリル接着剤は一般に無臭で、揮発性有機化合物 (VOC) 含有量が低いです。 そのため、強い臭気を発したり、有害な化学物質が含まれる可能性がある溶剤ベースの接着剤よりも安全です。
シリコーン系接着剤:優れた耐環境性
シリコーン接着剤は、優れた耐環境性で知られる接着剤の一種です。 これらはさまざまな用途で優れた性能と耐久性を提供し、自動車、エレクトロニクス、航空宇宙、建設、医療業界で非常に人気があります。
シリコーン接着剤の重要な利点の XNUMX つは、極端な温度に耐えられることです。 接着特性を失ったり脆くなったりすることなく、高温や低温に耐えることができます。 そのため、自動車のエンジンや電子機器など、温度変動が頻繁に起こる用途に適しています。
シリコーン接着剤は、湿気や水に対しても優れた耐性を示します。 他の多くの接着剤タイプとは異なり、水や湿気の多い環境にさらされても強度と完全性を維持できます。 この特性は、ガスケットのシール、水中コンポーネントの接着、湿気による損傷からの電子回路の保護など、耐水性が必要な用途において非常に重要です。
さらに、シリコーン接着剤は、紫外線や耐候性に対して優れた耐性を備えています。 接着特性が劣化したり失われたりすることなく、日光、雨、雪、その他の環境要因に長時間さらされても耐えることができます。 そのため、屋外看板のシール、ソーラーパネルの接着、屋外電子機器の保護などの屋外用途に最適です。
耐薬品性もシリコーン接着剤が優れている分野です。 溶剤、油、燃料、酸などのさまざまな化学薬品に耐性があります。 この耐性は、毎日複数の化学物質にさらされる自動車や航空宇宙などの業界では顕著です。 攻撃的な化学薬品の中でも、シリコーン接着剤は完全性と接着性を維持し、長期的な性能と信頼性を保証します。
シリコーン接着剤は、耐環境性に加えて、優れた電気絶縁特性も備えています。 高い絶縁耐力を持ち、電流に対して絶縁を提供します。 そのため、電気的な絶縁と保護が重要な電子部品の接着と封止に最適です。
シリコーン接着剤は、一液型または二液型システム、熱硬化、湿気硬化、UV 硬化などのさまざまな硬化メカニズムを含むさまざまな形式で入手できます。 この多用途性により、幅広い用途と接着要件に対応できます。
シリコーン接着剤は優れた耐環境性を備えていますが、他の種類の接着剤ほど高い初期接着強度を持たない可能性があることに注意してください。 ただし、柔軟性、耐久性、過酷な条件下での長期的なパフォーマンスによってこれを補います。
UV 硬化型接着剤: 迅速かつ正確な接着
UV 硬化接着剤は、紫外線硬化接着剤とも呼ばれ、迅速かつ正確に接着できるため、さまざまな業界で非常に人気があります。 これらの接着剤は従来の接着剤システムに比べて多くの利点を備えているため、迅速かつ信頼性の高い接着が必要な用途に最適です。
UV 硬化接着剤には、紫外線にさらされるとプロセスを開始する特殊な光開始剤が配合されています。 硬化反応はほぼ瞬時に起こり、迅速な結合形成が可能になります。 硬化に熱や化学反応を使用する従来の接着剤とは異なり、UV 硬化接着剤は事実上瞬時に接着するため、貴重な生産時間を節約し、効率を向上させます。
UV 硬化接着剤の重要な利点の XNUMX つは、正確な接着能力です。 硬化反応は高度に制御され、局所的に行われるため、接着剤は必要な領域のみで硬化します。 これにより、複雑なアセンブリであっても、コンポーネントの正確な位置決めと位置合わせが可能になります。 メーカーは、UV 硬化接着剤を使用することで、厳しい公差を達成し、高い製品品質を維持できます。
UV 接着剤の硬化時間の速さは、迅速な生産ターンアラウンドが重要な産業において特に有利です。 たとえば、エレクトロニクス製造では、UV 硬化接着剤を使用するとコンポーネントを迅速に接着できるため、組み立て時間が短縮され、生産性が向上します。 同様に、医療機器業界でも、UV 接着剤はさまざまな材料を迅速かつ確実に接着し、複雑な医療機器の迅速な組み立てを可能にします。
UV 硬化型接着剤は優れた接着強度と耐久性を備えています。 これらの接着剤は硬化すると、温度変動、湿気、化学物質などのさまざまな環境条件に耐える強力な結合を形成します。 この結合は、経時的な黄変や劣化に対して高い耐性を示し、長期的な性能と信頼性を保証します。
UV 硬化接着剤は多用途で、プラスチック、金属、ガラス、セラミックなどのさまざまな基材と互換性があります。 異種材料を接着できるため、使用できる用途の範囲が広がります。 自動車産業におけるプラスチック部品のクリックから電子機器の組み立てに至るまで、UV 硬化接着剤は、多様な接着ニーズに対する信頼性の高いソリューションを提供します。
さらに、UV 硬化接着剤は溶剤を含まないため、揮発性有機化合物 (VOC) が不要となり、環境への影響が軽減されます。 また、有害な化学物質への曝露を最小限に抑えることで、健康と安全の利点も提供します。 溶剤や VOC が存在しないため、オペレーターにとってよりクリーンで健康的な作業環境が実現します。
エポキシ接着剤: 高い接着強度と耐薬品性
エポキシ接着剤は、高い接着強度と優れた耐薬品性により、さまざまな業界で人気があります。 他の接着剤オプションに比べて多くの利点があり、複数の用途に多用途で信頼性が高くなります。
エポキシ接着剤の重要な利点の XNUMX つは、その優れた接着強度です。 これらは、適切に適用されると大きな応力や荷重に耐えることができる強力な結合を生成するため、耐久性と長期持続する結合を必要とする用途に適しています。 エポキシ接着剤は、金属、プラスチック、セラミック、ガラス、複合材料などのさまざまな材料を接着でき、さまざまな業界に信頼性の高い接合ソリューションを提供します。
エポキシ接着剤は、高い接着強度に加えて、優れた耐薬品性を示します。 溶剤、酸、塩基、油、燃料などのさまざまな化学薬品に耐えることができます。 この化学的攻撃に対する耐性により、接着剤は安定した状態を保ち、過酷な環境でも接着強度が維持されます。 そのため、エポキシ接着剤は、化学物質への曝露が懸念される自動車、航空宇宙、エレクトロニクス、化学処理産業で一般的に使用されています。
エポキシ接着剤の耐薬品性は、その独特の分子構造に起因します。 エポキシ接着剤は、化学反応して架橋ネットワークを形成する樹脂と硬化剤で構成されています。 この架橋構造により、接着剤に強度と耐薬品性が与えられます。 エポキシ接着剤の硬化プロセスは、さまざまなレベルの耐薬品性を実現するように調整できるため、特定の用途要件に基づいてカスタマイズできます。
さらに、エポキシ接着剤は優れた耐熱性を備えており、これも多くの産業にとって重要な要素です。 高温および低温でも接着強度と完全性を維持できるため、極端な温度変化にさらされる用途に適しています。 この特性は、コンポーネントが大幅な温度変動を受ける可能性がある航空宇宙や自動車などの業界では基本的なものです。
エポキシ接着剤のもう XNUMX つの利点は、塗布方法の多様性です。 手動分注、シリンジ分注、スプレー塗布、自動分注システムなどのさまざまな技術を適用できます。 この塗布方法の柔軟性により、さまざまな製造環境において効率的かつ正確な接合が可能になります。
エポキシ接着剤で最適な接着強度と耐薬品性を実現するには、適切な表面処理と接着剤塗布技術が不可欠であることに注意することが重要です。 最大限の接着力を確保するには、表面は清潔で乾燥しており、汚染物がない必要があります。 さらに、接着剤は、樹脂と硬化剤の正しい比率と適切な硬化条件を考慮して、メーカーの指示に従って混合する必要があります。
結論として、エポキシ接着剤は高い接着強度と優れた耐薬品性を備えているため、さまざまな用途に理想的な選択肢となります。 さまざまな材料を接着し、過酷な化学物質に耐え、極端な温度下でも優れた性能を発揮するその能力により、自動車、航空宇宙、エレクトロニクス、および化学処理産業において不可欠なものとなっています。 適切な表面処理と塗布技術により、エポキシ接着剤は耐久性と信頼性の高い接着を実現し、組み立てられたコンポーネントの全体的な性能と寿命に貢献します。
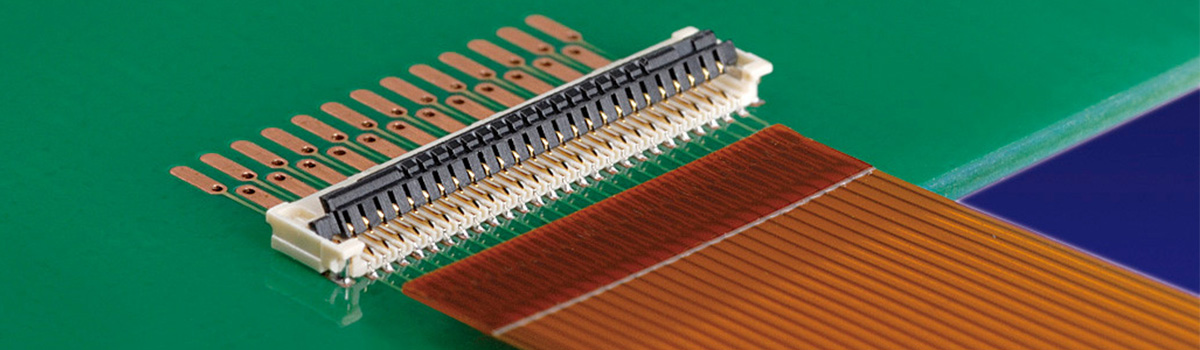
導電性接着剤: 電気接続を可能にする
導電性接着剤は、さまざまな用途で電気接続を可能にする上で重要な役割を果たします。 これらの革新的な材料は、優れた導電性、使いやすさ、多用途性を備え、従来のはんだ付けまたは機械的固定方法に代わる効果的な代替手段となります。 この記事では、導電性接着剤の主な特徴と用途について説明します。
導電性接着剤は、銀、銅、カーボンなどの導電性フィラーとポリマーバインダーを組み合わせて配合されます。 導電性フィラーは電流の流れを促進し、バインダーはさまざまな基材への接着を保証します。 この独自の組成により、導電性接着剤は困難な環境でも信頼性の高い電気接続を提供できます。
導電性接着剤の主な利点の XNUMX つは、幅広い材料との適合性です。 金属、セラミック、ガラス、プラスチック、さらにはフレキシブル基板を接着できるため、さまざまな産業に適しています。 異種材料の接続は、異なる熱膨張係数を持つコンポーネントを結合する必要があるエレクトロニクス産業において特に有利です。
導電性接着剤は、従来のはんだ付けに匹敵する優れた導電性を備えています。 この特性により、特定の用途においてはんだ接合部を効果的に置き換えることができます。 さらに、導電性接着剤は、はんだ付け接続よりも熱サイクル、機械的ストレス、振動に対して優れた耐性を示します。 これらの特性により、頻繁な温度変動や自動動作を伴うアプリケーションに最適です。
塗布が容易であることも、導電性接着剤の大きな利点です。 これらは通常、注射器などの便利な形状で入手できるか、フィルムやテープとして分配されます。 これにより、正確かつ制御された塗布が可能になり、自動および手動の組み立てプロセスに適しています。 特殊な機器と専門知識が必要なはんだ付けとは異なり、導電性接着剤は最小限のトレーニングで簡単に塗布できます。
導電性接着剤はさまざまな業界で応用されています。 エレクトロニクス分野では、コンポーネントの取り付け、ダイボンディング、ワイヤボンディング、およびプリント基板 (PCB) アセンブリにおけるはんだ付けの代替として使用されます。 また、基板の柔軟性により従来のはんだ付け方法が使用できないフレキシブルエレクトロニクスの製造にも使用されます。
自動車産業では、センサー、アンテナ、照明システムの接着に導電性接着剤が使用されています。 プラスチックや複合材など、自動車用途に使用される材料に対して優れた接着力を発揮します。 さらに、温度変化、湿度、化学薬品への曝露などの過酷な環境条件に耐える能力があるため、自動車エレクトロニクスにとって理想的な選択肢となります。
導電性接着剤は医療分野でも重要な役割を果たしています。 センサー、電極、埋め込み型デバイスなどの医療機器を組み立てます。 導電性接着剤の生体適合性のあるバリアントにより、人間の組織と接触しても安全です。
低アウトガス接着剤: 宇宙用途に不可欠
低アウトガス接着剤は、材料が宇宙環境の極限条件に耐えなければならない宇宙用途において重要な役割を果たします。 アウトガスとは、真空または高温にさらされたときに材料から揮発性化合物が放出されることを指します。 宇宙では、これらの揮発性化合物は、敏感な機器や機器の機能と信頼性に重大なリスクをもたらす可能性があります。
真空の宇宙空間では、ガスを放出した物質が光学レンズやセンサーなどの近くの表面に凝縮し、汚染や性能の低下を引き起こす可能性があります。 汚染は測定の精度を損ない、信号品質を低下させ、さらには重要なコンポーネントの故障につながる可能性があります。 さらに、凝縮したガス放出物質は時間の経過とともに蓄積し、光を吸収または散乱させる可能性のある層を形成し、光学システムや撮像装置に影響を与える可能性があります。
低ガス放出接着剤は、揮発性化合物の放出を最小限に抑えるように特別に配合されています。 これらは蒸気圧が低くなるように設計されており、真空条件にさらされたときに放出されるガスや蒸気の量が少なくなります。 この特性は、傷つきやすい表面やコンポーネントの汚染や劣化を防ぐのに役立ちます。
宇宙船や人工衛星は、さまざまな用途に低ガス放出接着剤を使用しています。 重要な用途の XNUMX つは、電子部品の接着とカプセル化です。 これらの接着剤は、汚染やガス放出関連の問題のリスクを最小限に抑えながら、異なる材料間に強固で信頼性の高い接着を提供します。 これらはコンポーネントの構造的完全性と電気的接続を保証し、宇宙での打ち上げや運用中に経験する振動や衝撃に耐えることができます。
低アウトガス接着剤は、宇宙望遠鏡、カメラ、センサーで使用される光学システムにも不可欠です。 これらのシステムで使用される接着剤は、レンズ、ミラー、検出器の透明度や性能への影響を最小限に抑える必要があります。 これらの接着剤はガスの放出を減らすことで光学特性を維持し、画質を低下させたり、正確な測定を妨げたりする可能性のある汚染層の形成を防ぎます。
さらに、宇宙用途では熱管理が重要な考慮事項となります。 低アウトガス接着剤は、ヒートシンク、サーマルインターフェイスマテリアル、および熱放散に関与するその他のコンポーネントを接着します。 これらの接着剤は、熱管理システムの性能を損なう可能性のある汚染のリスクを最小限に抑えながら、効率的な熱伝達を保証します。
宇宙用途の厳しい要件を満たすために、低ガス放出接着剤は厳格なテストと認証プロセスを受けています。 材料は熱サイクル、真空暴露、および分析を受けて、ガス放出特性を評価します。 NASA のガス放出要件 (ASTM E595 など) などの組織によって設定された基準を満たす接着剤は、宇宙ミッションに適していると考えられます。
熱伝導性接着剤: 電子機器の熱を管理する
熱伝導性接着剤は、電子デバイスの熱を管理する上で重要な役割を果たします。 電子部品のサイズは縮小し続け、より高い電力密度で動作するため、最適なパフォーマンスと信頼性を確保するには効果的な熱放散がますます重要になっています。 熱伝導性接着剤は、発熱コンポーネントからヒートシンクやその他の熱放散機構に熱を効率的に伝達することにより、実行可能な解決策を提供します。 この記事では、熱伝導性接着剤の重要な側面と、電子デバイスの熱管理におけるその役割について説明します。
熱伝導性接着剤は、接着特性と高い熱伝導性の両方を備えた特別に配合された材料です。 これらは、集積回路やパワーデバイスなどの発熱コンポーネントとヒートシンクやその他の冷却要素の間に強力な結合を形成するように設計されています。 これらの材料の粘着性により確実な取り付けが保証され、高い熱伝導率により効率的な熱伝達が可能になります。
熱伝導性接着剤の主な利点の XNUMX つは、合わせ面間の小さな隙間や凹凸を埋めることができるため、熱抵抗が最小限に抑えられることです。 この機能は、平坦でない表面を持つコンポーネントを取り付ける場合や、熱の流れを妨げる微細な空隙に対処する場合に特に有益です。 これらの隙間を埋めることで、熱伝導性接着剤がキャラクター間に緊密な接触を確立し、熱伝達を強化し、熱ホットスポットのリスクを軽減します。
電子デバイスの熱管理におけるもう XNUMX つの重要な側面は、温度サイクルや機械的ストレスに耐えられるかどうかです。 電子デバイスは、動作中にさまざまな温度条件や機械的振動にさらされます。 熱伝導性接着剤は、広い温度範囲にわたって接着強度と熱性能を維持するように配合されており、困難な条件下でも確実な放熱を保証します。
さらに、熱伝導性接着剤は電気絶縁特性を提供し、コンポーネント間の電気的短絡を防ぎます。 この機能は、複数の部品が密に詰め込まれており、導電性要素間で偶発的に接触するリスクがある電子デバイスでは非常に重要です。
熱伝導性接着剤は、ディスペンス、スクリーン印刷、フィルムラミネートなどのさまざまな方法を使用して塗布できます。 これらの接着剤はさまざまな粘度および硬化メカニズムで利用できるため、製造プロセスでの柔軟性が可能になります。 熱伝導性接着剤の中には室温で硬化するものもありますが、高温または UV 光を必要とするものもあります。 メーカーは、特定の生産要件に最も適したボンドを選択できます。
剥がして貼れる接着剤: 使いやすく、貼りやすい
剥がして貼れる接着剤は、接着材料を必要とするさまざまなプロジェクトやタスクへの取り組み方に革命をもたらしました。 これらの接着剤は非常に使いやすく、塗布しやすいため、専門家や DIY 愛好家の間で人気があります。 利便性と多用途性により、剥がして貼れる接着剤は多くの用途で頼りになるソリューションとなっています。
剥がして貼れる接着剤の主な利点の XNUMX つは、その簡単さです。 多くの場合混合や特殊なツールが必要な従来の接着剤とは異なり、剥がして貼るだけの接着剤は裏材にあらかじめ塗布されており、パッケージからすぐに使用できます。 これにより、追加の機器や大規模な準備が不要になり、時間と労力が節約されます。
剥がして貼れる接着剤の塗布プロセスは簡単で使いやすいです。 裏紙を剥がして粘着面を露出させ、目的の面にしっかりと押し付けるだけです。 接着剤は素早く確実に接着し、クランプや乾燥時間なしで瞬時に接着します。 このため、剥がして貼るタイプの接着剤は、迅速な修理、一時的な設置、または時間に制約のあるプロジェクトに最適です。
剥がして貼れる接着剤のもう XNUMX つの利点は、その多用途性です。 用途や材質に合わせて、テープ状、シート状、ドット状などさまざまな形状をご用意しております。 軽量の物体を取り付ける必要がある場合でも、装飾品を取り付ける必要がある場合でも、特定の頑丈なアイテムを取り付ける必要がある場合でも、剥がして貼れる接着剤はその作業に適しています。 木材、金属、ガラス、プラスチック、布地などのさまざまな表面によく接着し、さまざまな素材との柔軟性と互換性を提供します。
剥がして貼るタイプの接着剤は、きれいに貼れることでも知られています。 汚れやすく後片付けが必要な従来の接着剤とは異なり、剥がして貼るタイプの接着剤は、適切に貼り付けたり剥がしたりすると残留物を残しません。 これは、損傷から保護したいデリケートな表面や仕上げ表面を作業する場合に特に有利です。
使いやすさに加えて、ピールアンドスティック接着剤は多くの場合、強力な接着能力を示します。 接着剤は信頼性が高く耐久性のある接着を提供するように設計されており、取り付けたアイテムが確実に所定の位置に留まります。 ただし、最適な結果を得るには、プロジェクトに適したタイプの接着剤を選択し、メーカーのガイドラインに従うことが不可欠です。
粘着フィルム: 効率と一貫性の向上
粘着フィルムは、さまざまな業界でさまざまな用途を提供する多用途の素材です。 これらは、紙、プラスチック、布地などの裏材にコーティングされた粘着性物質の薄い層です。 これらのフィルムは多くの利点をもたらし、さまざまなプロセスの効率と一貫性を高めます。 この記事では、接着フィルムがさまざまな用途で効率と一貫性をどのように向上させるかを検討します。
粘着フィルムの重要な利点の XNUMX つは、貼り付けの容易さです。 混合や特殊な装置が必要な従来の接着剤とは異なり、接着フィルムはすぐに使用できる状態で提供されます。 希望の形状やサイズに簡単にカットできるため、素早く正確に貼り付けるのに最適です。 これにより、製造および組立プロセスの時間とリソースが節約され、全体的な効率が向上します。
さらに、粘着フィルムは安定した接着性能を提供します。 均一な厚さと制御された接着特性により、異なる素材間でも信頼性の高い接着が保証されます。 XNUMX つの表面を接合する場合でも、層を積層する場合でも、コンポーネントを取り付ける場合でも、粘着フィルムは一貫した接着強度を提供し、失敗ややり直しのリスクを最小限に抑えます。 この一貫性により、製品の品質が向上し、無駄が削減され、生産性が向上します。
粘着フィルムが効率を高めるもう XNUMX つの方法は、自動システムとの互換性によるものです。 さまざまな業界でオートメーション化の傾向が高まる中、接着フィルムはロボットによる組み立ておよび包装プロセスに適合するように設計されています。 自動化された生産ラインに簡単に組み込むことができ、高速かつ正確な接合作業が可能になります。 これにより、効率が向上するだけでなく、人件費や人的ミスも削減されます。
さらに、粘着フィルムにより、シールおよび保護用途の効率が向上します。 湿気、ほこり、汚染物質に対するバリアを提供し、敏感なコンポーネントや製品への損傷を防ぎます。 電子機器のシール、食品の包装、または表面の腐食からの保護のいずれの場合でも、粘着フィルムは信頼性が高く一貫した保護を提供します。 これにより、製品の寿命と信頼性が向上し、頻繁なメンテナンスや交換の必要性が軽減されます。
さらに、粘着フィルムにより、効率的なカスタマイズと設計の柔軟性が可能になります。 さまざまな接着強度、耐熱性、光学特性などの特定の要件に合わせてカスタマイズできます。 これにより、メーカーは用途のニーズに基づいて接着特性を最適化し、最高の性能と信頼性を確保することができます。 さらに、粘着フィルムは簡単に印刷または装飾できるため、ブランド化の機会と美的魅力が得られます。
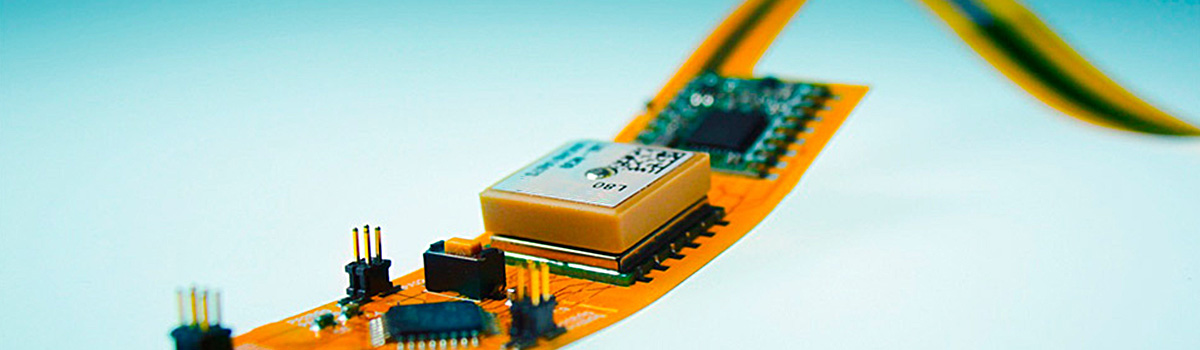
ホットメルト接着剤: 素早く耐久性のある接着
ホットメルト接着剤 (HMA) は、さまざまな業界や用途に迅速かつ耐久性のある接着ソリューションを提供する多用途の接着剤です。 これらの接着剤、またはホットグルーは、液体状態に溶かして塗布する熱可塑性材料です。 冷却すると固化し、基材間に強力な結合が形成されます。 ここでは、ホットメルト接着剤の特徴、メリット、用途について詳しく見ていきます。
HMA の重要な利点の XNUMX つは、迅速な接着機能です。 これらの接着剤は加熱するとすぐに液化するため、効率的かつ高速に塗布できます。 他のタイプの接着剤とは異なり、溶媒の蒸発や化学反応の必要がありません。 ホットメルト接着剤は急速に固化するため、組み立て時間と生産時間が短縮され、生産性が向上し、コストが削減されます。
さらに、ホットメルト接着剤は、接着接合部に優れた耐久性をもたらします。 湿気、化学薬品、温度変化に対して優れた耐性を示します。 この弾力性により、耐久性と信頼性の高い接着を必要とする要求の厳しい環境や用途に適しています。 HMA は柔軟性と耐衝撃性も備えているため、接着の完全性を損なうことなく振動や衝撃に耐えることができます。
HMA は、包装、木工、自動車、エレクトロニクス、繊維、建設など、さまざまな業界で応用されています。 ホットメルト接着剤は、ケースやカートンの封止、不正開封防止用の蓋、ラベルやテープの接着などの包装に広く使用されています。 安全で改ざん防止のシールを提供し、製品の完全性を保証し、盗難を防ぎます。
HMA の木工用途には、エッジバンディング、ベニヤ加工、ラミネート加工などがあります。 ホットメルト接着剤の急速硬化の性質により、効率的な組み立てラインプロセスが促進されます。 これらは木の接合部に強い結合を生み出し、家具やキャビネットの構造的完全性と寿命を高めます。
自動車メーカーは、内外装トリムの接着、ワイヤーハーネス、ガスケットのシールにホットメルト接着剤を使用しています。 これらの接着剤の耐久性と耐熱性により、極端な条件下での性能が不可欠な自動車用途に最適です。
電子機器の組み立てと製造では、コンポーネントの接着、ワイヤーの仮止め、および封止にホットメルト接着剤がよく使用されます。 プラスチック、金属、ガラスなどの異種材料を接着できるため、さまざまな電子用途に適しています。
繊維産業のホットメルト接着剤の用途には、生地のラミネート、ヘミング、アップリケの接着などがあります。 これらにより、縫製、ステッチング、またはその他の機械的な固定方法を使用せずに、正確かつきれいな接着が可能になります。
建設分野では、HMA は床材の設置、パネル、断熱材、タイルの接着に使用されます。 急速硬化特性により、迅速な施工プロセスが容易になり、さまざまな建材で確実に接着します。
感圧接着剤: 一貫した接着力を確保
感圧接着剤 (PSA) は、自動車やエレクトロニクスから包装や医療機器に至るまで、さまざまな業界で使用される多用途の材料です。 これらの接着剤は、塗布の容易さ、即時接着、広範囲の表面に接着できるなどの独自の利点を備えています。 ただし、PSA を使用する場合、一貫した接着を確保することが課題となる場合があります。 感圧接着剤で信頼性が高く一貫した接着を実現するための重要な考慮事項をいくつか示します。
- 表面処理: PSA との一貫した接着を実現するには、適切な表面処理が不可欠です。 表面は清潔で乾燥しており、ほこり、油、グリース、湿気による汚染物があってはなりません。 適切な溶剤やクリーナーで表面を洗浄し、研磨やプラズマ処理などの技術を使用すると、表面エネルギーが強化され、結合に対する潜在的な障壁が除去されるため、接着力が向上します。
- 材料の適合性: PSA が基材の材料と適合することを確認することが不可欠です。 一部の PSA は、特定の表面との接着力の低下や適合性の問題を示す場合があります。 接着剤と基材の両方の化学組成と特性を理解することは、特定の用途に適切な接着剤を選択するのに役立ち、一貫した接着を確保できます。
- 塗布技術: 塗布技術は、一貫した接着を実現する上で重要な役割を果たします。 塗布時の圧力、温度、滞留時間は接着強度に影響を与える可能性があります。 適用する適切な圧力や接着に推奨される温度範囲など、塗布パラメーターに関するメーカーの推奨事項に従うことが重要です。
- 硬化時間: PSA は通常、完全な接着強度を発揮するまでに一定の時間を必要とします。 この硬化時間または「滞留」時間により、接着剤が流動し、基材との強力な接着が形成されます。 接着されたアセンブリに応力や負荷がかかる前に、十分な硬化時間を確保することが重要です。 プロセスを急いで行うと、接着力が弱くなったり、接着不良が発生したりする可能性があります。
- 環境要因: 環境条件は PSA のパフォーマンスに影響を与える可能性があります。 温度、湿度、化学物質や紫外線への曝露などの要因が、接着剤の特性や接着性能に影響を与える可能性があります。 接着剤がさらされる特定の環境条件を理解し、これらの要因に対する適切な耐性を持つ接着剤を選択することは、長期間にわたって一貫した接着を確保するのに役立ちます。
- テストと品質管理: 一貫した接着を確保するには、定期的なテストと品質管理措置が不可欠です。 剥離接着力、せん断強度、粘着性などのさまざまな試験方法で、接着剤の性能を評価できます。 適切なテストプロトコルを確立し、生産中に定期的な品質チェックを実施することで、不一致や問題を早期に特定し、最終製品の一貫した接着を確保することができます。
- 保管と保管期間: 接着剤の性能を維持するには、適切な保管条件と保管期間のガイドラインを順守することが不可欠です。 PSA は熱、光、または空気への曝露により時間の経過とともに劣化し、粘着特性に影響を与える可能性があります。 管理された環境でボンドを保管し、推奨される保存期間内に使用すると、一貫した接着力を維持することができます。
接着剤塗布技術: 精度と効率
接着剤塗布技術はさまざまな業界で重要であり、接着用途の精度と効率を確保します。 製造、組み立て、修理のいずれの場合でも、適切な塗布方法は接着剤の品質と信頼性に大きな影響を与える可能性があります。 この記事では、限られた文字数内で接着剤塗布の精度と効率を達成するのに役立つ重要なテクニックについて説明します。
- 手動による接着剤の塗布: 手動による接着剤の塗布は、小規模な作業や複雑な用途でよく使用されます。 接着剤を正確に塗布するには、注射器、スクイーズ ボトル、ブラシなどの手持ちデバイスを使用します。 この方法は柔軟性と制御性を備えていますが、オペレーターのスキルと一貫性に依存します。
- 時間/圧力ディスペンス: 時間/圧力ディスペンスは、接着剤を一貫して制御して塗布するために広く使用されている技術です。 これには、圧力調整器とタイマーを備えた空気式または電動ディスペンサーを使用することが含まれます。 塗布時間と圧力を調整することで、オペレータは塗布する接着剤の量を正確に制御できます。 この技術は中粘度から高粘度の接着剤に適しています。
- ジェッティング: ジェッティングは、接着剤の高速流を利用してターゲット表面に正確かつ少量の接着剤を塗布するディスペンス技術です。 電子機器のアセンブリやマイクロボンディングなど、高速かつ正確な配置が必要なアプリケーションで一般的に使用されます。 ジェッティング システムは、圧電または空気圧による作動を使用して、制御された接着剤の液滴を作成します。
- スプレー塗布: スプレー塗布は、広い領域をカバーしたり、均一にカバーしたりするための効率的な手法です。 これには、接着剤を細かい液滴に噴霧し、空気圧または自動スプレーガンを使用して表面に噴射することが含まれます。 スプレー塗布は、高速かつ均一な塗布が必要な自動車、木工、包装業界で一般的に使用されています。
- ロボットによるディスペンス: ロボットによるディスペンス システムは、プログラム可能な自動化を通じて、正確で再現性のある接着剤の塗布を実現します。 これらには、複雑なパターンや輪郭に従うようにプログラムできる高度なセンサーと分配バルブが装備されています。 ロボットによる塗布により一貫性と精度が確保され、大量生産ラインや複雑な組み立てプロセスに最適です。
- フィルム/スワール コーティング: フィルムまたはスワール コーティングは、接着剤の均一な層を基材上に塗布するために使用される技術です。 これには、回転機構またはアプリケーターを使用して接着剤を薄い連続フィルムに広げることが含まれます。 この方法は自動車、航空宇宙、建設業界で一般的に採用されており、最適な性能を得るには接着剤の厚さを制御することが重要です。
FPC接着剤塗布における課題
FPC (フレキシブルプリント回路) 接着剤の塗布には、接着を成功させ信頼性の高い性能を得るために対処しなければならないいくつかの課題があります。 これらの課題は主に、FPC の固有の特性と要件に起因します。 この回答では、FPC 接着剤の塗布で遭遇するいくつかの重要な課題について概説します。
- 基板の互換性: FPC は、ポリイミド、ポリエステル、薄い銅などの柔軟な材料で作られており、リジッド基板とは異なる表面特性を備えています。 接着剤は、層間剥離や基板への損傷を引き起こすことなく適切な接着を保証するために、FPC 材料と適合する必要があります。
- 表面処理: 接着剤による接着には、適切な表面処理が重要です。 FPC 表面には、接着を妨げる可能性のある残留物、油、または汚染物質が付着していることがよくあります。 課題は、FPC の完全性を損なうことなくこれらの不純物を除去するための正しい洗浄方法または表面処理を選択することにあります。
- ボンドラインの厚さの制御: 信頼性の高いパフォーマンスを得るには、ボンドラインの厚さを均一にすることが不可欠です。 接着剤の厚さが不均一であると、導電性、機械的強度、熱管理にばらつきが生じる可能性があります。 FPC は柔軟な性質を持っているため、ボンド ラインの厚さを正確に制御することは困難な場合があります。
- 熱管理: FPC は、温度変化が予想されるアプリケーションでよく使用されます。 接着に使用される接着剤は、熱を効果的に放散し、FPC やそのコンポーネントに損傷を与える可能性のある局所的なホットスポットを防ぐために良好な熱伝導性を備えている必要があります。 FPC の柔軟性と電気的特性を損なうことなく最適な熱管理を達成することは課題です。
- 接着剤の硬化: FPC 接着剤は通常、熱や UV などの硬化プロセスを必要とします。 課題は、特に複雑な、または高密度に実装された FPC 設計において、ボンド ライン全体で均一かつ完全な硬化を保証することでした。 硬化が不十分な場合、接着力が強くなったり、接着が不完全になったりして、信頼性の問題が発生する可能性があります。
- 柔軟性と耐久性: FPC は柔軟になるように設計されており、接着剤はその完全性を損なうことなくこの柔軟性に対応する必要があります。 接着は、亀裂、剥離、または接着強度の低下なしに、繰り返しの曲げ、曲げ、および伸びに耐える必要があります。 柔軟性と耐久性の両方を維持できる接着を見つけるのは難しい場合があります。
- 導電性: FPC は電気信号を伝送することが多いため、導電性が重要な要件となります。 接着剤は、回路の性能を妨げる可能性のある高い抵抗を生じさせてはなりません。 機械的完全性を確保しながらボンドライン全体で良好な導電性を達成することは課題となります。
- プロセスの自動化: FPC ボンディングが大規模に行われる業界では、接着剤塗布プロセスの自動化が必要になります。 課題は、FPC のサイズ、形状、設計の変動を考慮して、一貫して精度と効率で接着剤を塗布できる自動システムを開発することにあります。
これらの課題に対処するには、FPC 材料、接着剤、およびアプリケーションの特定の要件を包括的に理解する必要があります。 多くの場合、FPC ボンディング用途における接着剤の適合性、性能、信頼性を確保するために、慎重な材料の選択、プロセスの最適化、テストが必要になります。
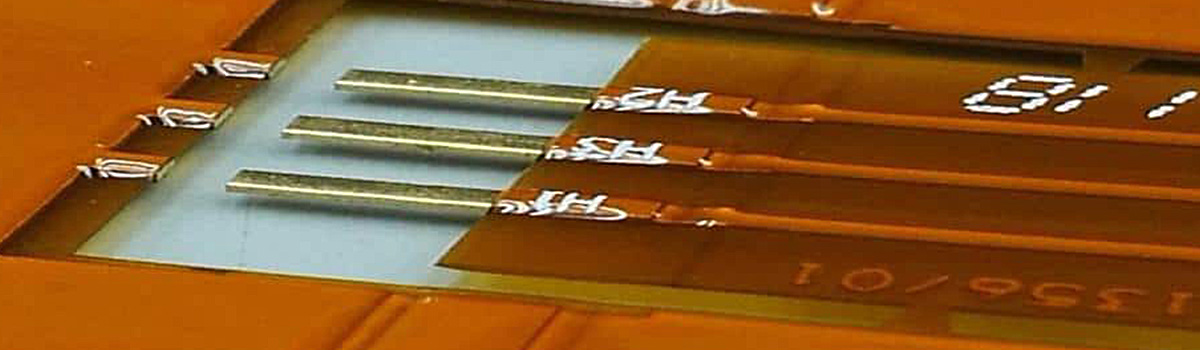
信頼性試験: 接着性能の評価
信頼性試験は、接着剤の性能を評価する上で重要なステップです。 接着剤は、自動車、航空宇宙、エレクトロニクス、建設などのさまざまな業界で、さまざまな材料を接着するために広く使用されています。 接着剤の信頼性は、最終製品の安全性、耐久性、全体的なパフォーマンスを確保するために不可欠です。
信頼性テストには、実際の環境や使用シナリオをシミュレートするさまざまな条件やストレス要因に接着剤をさらすことが含まれます。 目標は、接着強度と完全性を長期間にわたって維持する接着剤の能力を評価することです。 信頼性試験で接着剤の性能を評価する際に考慮すべき重要な側面をいくつか示します。
- 接着強度: 接着剤の初期接着強度は、重ね剪断試験、剥離試験、引張試験などの標準化された試験を使用して評価されます。 これらのテストでは、接着結合を破壊するのに必要な力を測定します。 これは、さまざまな条件にさらした後の接着強度と比較するためのベースラインを提供します。
- 環境への暴露: 接着剤は、極端な温度、湿度、紫外線、化学物質などの過酷な環境条件にさらされることがよくあります。 信頼性試験では、接着剤サンプルを加速老化試験に供し、これらの条件を長期間にわたってシミュレートします。 これは、接着剤の環境劣化に対する耐性と、悪条件下で接着強度を維持する能力を評価するのに役立ちます。
- 熱サイクル: 温度変化により材料の膨張と収縮が引き起こされ、接着結合にストレスがかかる可能性があります。 熱サイクル試験では、接着剤のサンプルを低温から高温まで繰り返し温度サイクルにさらし、熱応力に対する接着剤の耐性と接着の完全性を維持する能力を評価します。
- 機械的ストレス: 接着剤結合は、使用中に引張、圧縮、せん断、振動などのさまざまな種類の機械的ストレスを受ける可能性があります。 信頼性試験には、繰り返し疲労、衝撃、または曲げ試験を通じて接着剤サンプルに機械的ストレスを与えることが含まれます。 これらのテストは、接着が破壊されることなく自動荷重に耐える接着剤の能力を評価するのに役立ちます。
- 耐久性と経年劣化: 接着剤結合は長期耐久性が期待され、時間の経過による劣化に耐える必要があります。 信頼性テストには、製品の予想寿命をシミュレートする長期エージングテストが含まれます。 これには、接着剤サンプルを温度、湿度、紫外線などの環境要因に長時間曝露し、接着強度と完全性を定期的に評価することが含まれる場合があります。
- 適合性: 接着剤は、接着する材料と適合性がなければなりません。 信頼性テストには、金属、プラスチック、複合材料、業界で一般的に使用されるその他の材料など、さまざまな基材と接着剤の適合性を評価することが含まれます。 適合性テストでは、接着剤の接着強度、化学的相互作用に対する耐性、および基材に対する悪影響を評価します。
信頼性テストは、さまざまな条件下での接着剤の性能と限界に関する貴重な情報を提供します。 これは、メーカーが用途に最適な接着剤を選択するのに役立ち、実際のシナリオでの信頼性と耐久性を保証します。 厳格な信頼性テストを実施することで、メーカーは接着不良のリスクを軽減し、製品の品質を向上させ、顧客満足度を向上させることができます。
FPC接着剤における環境への配慮
FPC (フレキシブルプリント回路) 接着剤は、電子デバイスの組み立てと信頼性において重要な役割を果たします。 環境意識と持続可能性がますます重要になるにつれ、これらの接着剤が環境に与える影響を考慮することが不可欠です。 FPC 接着剤に関連する環境に関する重要な考慮事項をいくつか示します。
- 毒性: 主な懸念事項の XNUMX つは、接着剤とその成分の毒性です。 接着剤には、揮発性有機化合物 (VOC) や有害大気汚染物質 (HAP) などの有害な化学物質が含まれる場合があります。 これらの物質は人間の健康や環境に悪影響を与える可能性があります。 メーカーは、接着剤配合物中の有毒化学物質を最小限に抑えるか排除するよう努める必要があります。
- 排出ガスと大気質: 製造および適用プロセス中に、FPC 接着剤から VOC やその他の大気汚染物質が大気中に放出される可能性があります。 これらの排出物は大気汚染の一因となり、大気の質に悪影響を与える可能性があります。 環境に配慮した接着剤メーカーは、低 VOC またはゼロ VOC 接着剤を配合することで、これらの排出量を削減することを目指しています。
- エネルギー消費: FPC 接着剤の製造にはエネルギーが必要ですが、その多くは再生不可能な資源から得られます。 環境への影響を最小限に抑えるために、メーカーはエネルギー効率の高いプロセスを導入し、再生可能エネルギー源の使用を検討する必要があります。
- 廃棄物の発生: 接着剤の塗布プロセスでは、余分な接着剤、梱包材、清掃用資材などの廃棄物が発生する可能性があります。 可能な限り廃棄物をリサイクルまたは再利用するなど、適切な廃棄物管理慣行に従う必要があります。 さらに、製造業者は、期限切れまたは未使用の製品からの廃棄物を削減するために、より長い保存期間を持つ接着剤の開発を検討する必要があります。
- 耐用年数終了に関する考慮事項: FPC 接着剤を含む電子デバイスの廃棄は、重大な環境問題です。 分解しにくい接着剤や危険な成分を含む接着剤は、デバイスが廃棄されるときに汚染の原因となる可能性があります。 接着剤メーカーは、リサイクル時に回路基板から簡単に分離できる接着剤など、リサイクルまたは廃棄プロセスに適合する環境に優しい製品の開発に努める必要があります。
- 持続可能性とグリーンへの取り組み: 接着剤メーカーは持続可能性を自社のビジネス慣行に組み込む必要があります。 これには、再生可能な原材料の使用、環境に優しい製造プロセスの導入、認められた環境基準や認証の順守などが含まれます。 さらに、企業は製品の回収プログラムやリサイクル施設との提携などのグリーンイニシアチブに参加できます。
- ライフサイクル評価: FPC 接着剤の包括的なライフサイクル評価 (LCA) を実施することは、原材料の抽出から廃棄までの環境への影響を理解するために重要です。 LCA は、温室効果ガス排出量の削減、資源消費の最小限化、リサイクル可能性の強化など、改善できる領域を特定するのに役立ちます。
FPC接着剤のトレンドとイノベーション
FPC (フレキシブルプリント基板) 接着剤は、電子機器の高性能化、小型化、信頼性の向上への要求に応え、常に進化しています。 FPC 接着剤の注目すべきトレンドと革新をいくつか紹介します。
- 小型化と薄さ: 電子デバイスが小型化および薄型化するにつれて、これらのフォームファクター要件に対応する FPC 接着剤の必要性が高まっています。 メーカーは、アセンブリ全体の厚さを最小限に抑えながら強力な接着を実現する、極薄で薄型の接着剤を開発しています。
- 高温耐性: 多くの電子デバイス、特に自動車、航空宇宙、産業用途の電子デバイスは高温環境で動作します。 耐熱性を強化した FPC 接着剤は、極端な温度条件下でも信頼性の高い性能を確保し、層間剥離や接着不良を防止するために開発されています。
- 低圧硬化: 従来の接着剤硬化プロセスでは多くの場合、高温または長時間の硬化時間が必要ですが、熱に弱いコンポーネントやデリケートな基材にとっては困難な場合があります。 UV 硬化または湿気硬化接着剤などの低圧技術の革新により、より穏やかな硬化オプションが提供され、温度に敏感なコンポーネントや基板との互換性が可能になります。
- 導電性接着剤: 回路要素間の電気接続が必要な用途において、導電性を備えた FPC 接着剤の需要が増加しています。 導電性接着剤を使用すると、さまざまなはんだ付けプロセスが不要になるため、より迅速な組み立てが可能になり、敏感なコンポーネントへの熱損傷のリスクが軽減されます。
- 柔軟性と耐久性の向上: フレキシブル電子デバイスの曲げ、ねじれ、振動に耐える FPC 接着剤にとって、柔軟性と耐久性は非常に重要です。 ポリマー化学と配合技術の進歩により、接着剤の柔軟性、伸び、機械的応力に対する耐性が向上し、動的環境でも信頼性の高い接着が保証されます。
- 環境への配慮:接着剤の開発においては、持続可能な原材料の使用や有害物質の削減など、環境への配慮がより重要になってきています。 メーカーは、石油ベースの原料の代替品として、バイオベースの再生可能な材料を模索しています。 さらに、環境への影響を最小限に抑えるために、環境に優しい製造プロセスとリサイクル可能な接着剤配合が開発されています。
- 塗布と塗布の改善: 接着剤を効率的かつ正確に塗布することは、安定した信頼性の高い接着を実現するために非常に重要です。 自動ディスペンス システムやジェッティング方法などのディスペンス技術の革新により、微妙なピッチ コンポーネントを備えた複雑な FPC 設計でも、制御された正確な接着剤の塗布が可能になります。
- 接着フィルム技術: 接着フィルムは、その取り扱いの容易さと正確な配置により、FPC ボンディングで人気を集めています。 これらの予備成形フィルムは、均一な接着剤の厚さ、優れた濡れ特性、および簡素化された組み立てプロセスを提供します。 メーカーは接着フィルムの配合を継続的に改良して、接着性能とさまざまな基材との適合性を強化しています。
- 信頼性の向上: 長期的な信頼性を確保するために、湿気、化学物質、老化などの要因に対する耐性を向上させた FPC 接着剤が開発されています。 これらの接着剤は、過酷な環境条件下での性能を評価するための厳格なテストを受けており、製品の寿命にわたって一貫した機能と接着の完全性を保証します。
- カスタマイズおよびアプリケーション固有のソリューション: FPC 接着剤は、自動車、家庭用電化製品、医療機器、ウェアラブル技術など、さまざまなアプリケーションの特定の要件を満たすように調整されています。 メーカーはデバイス設計者やメーカーと緊密に連携して、各アプリケーション固有の課題や性能要求に対応するカスタマイズされた接着剤ソリューションを開発しています。
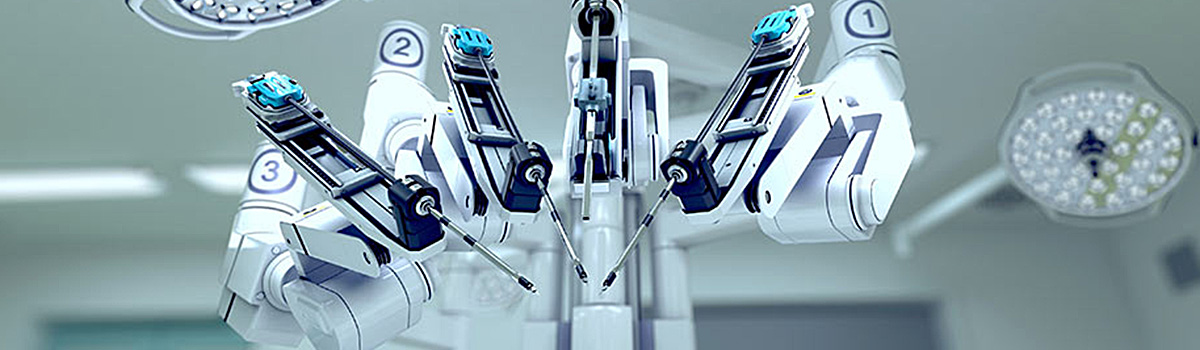
応用分野: 家庭用電化製品、自動車、医療機器など
家電: 家庭用電化製品には、個人使用や娯楽のために設計された幅広い製品が含まれます。 これらには、スマートフォン、タブレット、ラップトップ、ゲーム機、スマート TV、スマート ホーム デバイス、ウェアラブルなどが含まれます。 家庭用電化製品の応用は、人々のコミュニケーション、仕事、娯楽の方法に革命をもたらしました。 技術の進歩により、家庭用電化製品はより強力、コンパクト、そして手頃な価格になり、ユーザーにシームレスな接続、没入型体験、利便性を提供しています。
オートモーティブ・ソリューション : 自動車産業は近年、主に技術統合によって大きな進歩を遂げてきました。 電気自動車 (EV) から自動運転システムに至るまで、自動車アプリケーションは私たちの移動方法を変えてきました。 電気自動車は、環境に優しく、二酸化炭素排出量が削減できるため、人気が高まっています。 さらに、自動車メーカーは、運転体験を向上させ、安全性を向上させ、効率的な車両管理を可能にするために、先進運転支援システム (ADAS)、コネクティビティ、インフォテインメント システム、テレマティクスなどの革新的な機能を組み込んでいます。
医療機器: 医療機器は、さまざまな病状の診断、監視、治療において重要な役割を果たしてきました。 その範囲は、体温計や血圧計などの単純な機器から、MRI 装置やロボット手術システムなどの高度な機器まで多岐にわたります。 医療機器を使用すると、医療専門家は正確な診断を提供し、低侵襲処置を実行し、患者の健康状態を遠隔監視することができます。 これらは医療業界に革命をもたらし、患者の転帰を改善し、入院期間を短縮し、全体的なケアの質を向上させてきました。
モノのインターネット(IoT): モノのインターネット (IoT) は、センサー、ソフトウェア、接続機能が組み込まれた相互接続されたデバイスのネットワークです。 デバイス間のデータ交換と通信が可能になり、自動化、データ分析、意思決定の向上につながります。 IoT は、医療、農業、製造、エネルギーなど、さまざまな業界に応用されています。 医療分野では、IoT デバイスは患者のバイタルを監視し、服薬遵守を追跡し、遠隔での患者監視を可能にします。 IoT デバイスは、灌漑を最適化し、土壌状態を監視し、農業における作物管理を強化できます。 IoT は、産業をより効率的で持続可能かつデータ駆動型にすることで、産業に革命を起こす可能性を秘めています。
産業自動化: 産業オートメーションには、テクノロジーと制御システムを使用して産業プロセスとタスクを自動化することが含まれます。 これには、ロボット、マシン ビジョン システム、センサー、プログラマブル ロジック コントローラー (PLC) が含まれます。 産業オートメーションは生産性を向上させ、安全性を向上させ、運用コストを削減し、製造、物流、エネルギー、その他の分野で応用されています。 人工知能 (AI) と機械学習 (ML) の統合により、産業オートメーションはプロセスを最適化し、異常を検出し、予知保全を可能にし、効率を向上させ、ダウンタイムを削減します。
将来の展望と機会
FPC (フレキシブルプリント回路) 接着剤は、電子デバイスの製造において重要なコンポーネントです。 これは、フレキシブル回路と他の部品間の信頼性の高い堅牢な接続を確保するために非常に重要です。 将来に目を向けると、FPC 接着剤に関するいくつかの見通しと機会を検討する価値があります。
- フレキシブル エレクトロニクスの進歩: フレキシブル エレクトロニクスの分野は急速に進化しており、フレキシブル ディスプレイ、ウェアラブル デバイス、インテリジェント テキスタイルの需要が高まっています。 FPC 接合用接着剤は、これらの革新的な用途におけるフレキシブル回路の組み立てと相互接続を可能にするために、今後も高い地位を占め続けるでしょう。
- デバイスの小型化とスリム化: 家電製品のコンパクト化とスリム化が進むにつれ、より薄く、より柔軟な相互接続ソリューションが最も重要になっています。 FPC 接着剤を使用すると、極薄のフレキシブル回路の組み立てが容易になり、より滑らかで軽量なデバイスを作成できます。
- 強化された接着性能: メーカーは、高いせん断強度、優れた導電性、熱安定性など、優れた接着性能を提供する接着剤ソリューションを継続的に求めています。 将来の FPC 接着剤には、これらの厳しい要件を満たすために、先進的な材料と配合物が組み込まれる可能性があります。
- 高度な製造プロセスとの統合: 3D プリンティング、ロールツーロール処理、ハイブリッド統合などの新興製造テクノロジーは、フレキシブル回路製造の新たな可能性を切り開きます。 FPC 接合用接着剤は、これらの製造プロセスに適合し、互換性があり、最適化された接着力と信頼性を提供する必要があります。
- フレキシブル ハイブリッド エレクトロニクス (FHE): FHE は、従来のリジッド エレクトロニクスと適応性のあるコンポーネントを組み合わせて、独自のフォーム ファクターと機能を備えたデバイスを作成します。 FPC 接着剤は、これらのハイブリッド システムの組み立てに役立ち、柔軟な要素と硬い要素をシームレスに接続します。
- 持続可能性と環境への配慮: 持続可能性と環境責任への注目の高まりにより、環境に優しい FPC 接着剤を開発する機会が生まれています。 将来の配合には、再生可能またはリサイクル可能な材料が組み込まれ、電子廃棄物の環境への影響が軽減される可能性があります。
- スマート機能の統合: モノのインターネット (IoT) と相互接続デバイスの台頭により、FPC 接着剤には埋め込みセンサー、自己修復機能、熱管理特性などのインテリジェントな機能を組み込むことができる可能性があります。 これらの進歩により、電子機器の機能と信頼性が向上します。
- 医療およびヘルスケア アプリケーション: 医療分野では、ウェアラブル デバイス、埋め込み型センサー、インテリジェント ヘルスケア テクノロジーが急増しています。 生体適合性があり、滅菌可能で、さまざまな基板に接着できる FPC 接着剤は、この分野で重要な用途が見出されます。
- 自動車および航空宇宙産業: 自動車および航空宇宙産業では、軽量化と省スペース化の利点を目的として、フレキシブル回路の採用が増えています。 極端な温度、振動、機械的ストレスに耐えることができる FPC 接着剤は、これらの厳しい環境で高い需要が見込まれます。
- 研究開発:FPC接合用接着剤の継続的な研究開発努力は、さらなる進歩につながります。 接着剤の化学、製造技術、プロセスの最適化における革新が業界を前進させ、新しい用途と性能の向上を可能にします。
FPC接合用接着剤技術の進歩におけるコラボレーションの重要性
FPC (フレキシブルプリント回路) 接合用接着剤技術の進歩においては、コラボレーションが極めて重要です。 これにより、さまざまな関係者間での知識、リソース、専門知識の交換が可能になり、イノベーションと進歩の加速につながります。 FPC 接合用接着剤技術の進歩におけるコラボレーションの重要性を強調する主な理由は次のとおりです。
- 専門分野を超えた専門知識: FPC 接着剤技術には、材料科学、化学、エレクトロニクス製造、エンジニアリングなどのさまざまな領域が含まれます。 コラボレーションにより、これらの多様な分野の専門家が集まり、問題解決への学際的なアプローチが促進されます。 研究者と業界の専門家は、知識と視点を組み合わせることで、複雑な課題に対処し、新しいソリューションをより効果的に開発できます。
- 知識の共有: コラボレーションにより、さまざまな組織間での情報、調査結果、ベスト プラクティスの共有が促進されます。 メーカー、サプライヤー、研究者、学術機関は協力して、FPC 接合用接着剤技術に関する貴重な洞察と技術的知識を広めることができます。 この共有された知識は、冗長な作業を回避し、標準化を促進し、開発全体を加速するのに役立ちます。
- リソースへのアクセス: 共同の取り組みにより、資金、設備、施設、資材などのより幅広いリソースへのアクセスが可能になります。 組織、研究機関、または政府機関と提携すると、個別には利用できない専門リソースへのアクセスが提供されます。 このアクセスにより、より広範な実験、テスト、プロトタイピングが可能になり、FPC 接着剤の配合と製造プロセスの改善につながります。
- イノベーションの加速: コラボレーションは、オープン イノベーションと創造性の環境を促進します。 多様な視点と専門知識を結集することで、新しいアイデアやコンセプトが生まれ、FPC 接合用接着剤技術の限界を押し広げることができます。 共同プロジェクトでは、各パートナーの強みを活用し、それぞれの独自の能力とリソースを組み合わせて革新的なソリューションを加速的に開発することもできます。
- 市場洞察と業界トレンド: 業界パートナーやエンドユーザーと協力することで、市場の需要、新たなトレンド、顧客の要件に関する貴重な洞察が得られます。 この理解は、FPC 接合用接着剤技術の開発を業界の進化するニーズに合わせるのに役立ちます。 共同作業により、早期のフィードバックと検証が可能になり、開発されたソリューションが実用的で関連性があり、商業的に実行可能であることが保証されます。
- 品質保証と標準化: コラボレーションにより、FPC 接合用接着剤技術の品質保証手段と業界標準の確立が促進されます。 標準化団体や規制機関と提携することで、開発された接着剤が安全性、信頼性、性能要件を確実に満たすことができます。 また、コラボレーションにより、テスト方法と検証プロトコルの共有が可能になり、より一貫性のある標準化された結合プロセスが可能になります。
- 検証と現実世界のアプリケーション: エンドユーザー、メーカー、システムインテグレーターと協力することで、現実世界のアプリケーションにおける FPC 接合用接着剤技術の確認が可能になります。 接着剤メーカーは協力することで、性能、使いやすさ、製造可能性に関する貴重なフィードバックを得ることができます。 このフィードバック ループは、接着剤配合の改良と改善に役立ち、さまざまな用途や環境への適合性を確保します。
- リスクの軽減: コラボレーションにより、研究開発の取り組みに関連するリスクが分散されます。 パートナーは、リソースと専門知識を共有することで、共同して課題に取り組み、個々のリスクを軽減できます。 コラボレーションにより、知的財産や特許権の共有も可能になり、より協力的で競争の少ない環境が促進されます。
まとめ
FPC 接着剤は、電子機器の柔軟性と信頼性を実現するために不可欠です。 FPC 基板の柔軟性と耐久性を確保しながら、強力な接着能力、電気絶縁性、および環境要因からの保護を提供するこれらの接着剤の能力は、さまざまな電子デバイスの製造および組み立てにおいて非常に重要です。 技術が進歩するにつれて、エレクトロニクス業界の増大する需要と課題に対応するには、革新的な接着剤ソリューションの開発と、メーカー、研究者、エンドユーザー間の協力が重要になります。 FPC 接着剤の可能性を活用することで、現代社会を支える、さらに柔軟で耐久性があり、信頼性の高い電子デバイスへの道を切り開くことができます。