Revêtement Epoxy Isolant
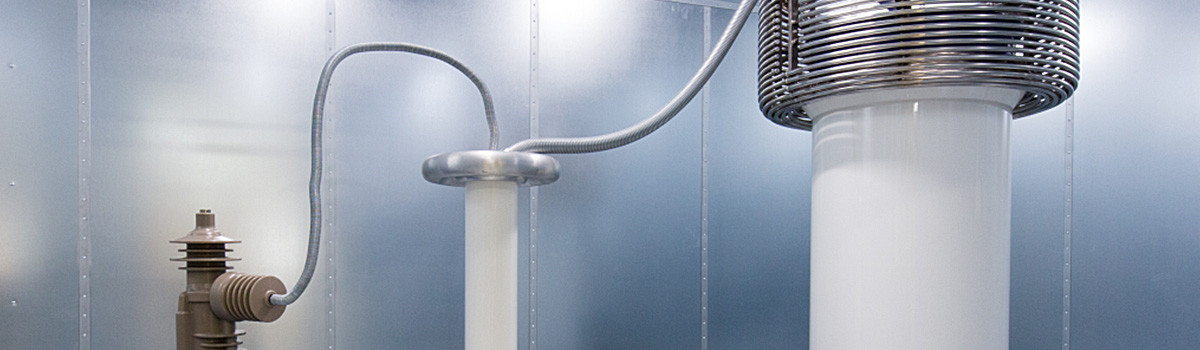
Le revêtement époxy isolant est un matériau polyvalent et largement utilisé avec d'excellentes propriétés d'isolation électrique. Diverses industries l'utilisent couramment pour protéger les composants électriques, les cartes de circuits imprimés et d'autres équipements sensibles contre l'humidité, la poussière, les produits chimiques et les dommages physiques. Cet article vise à approfondir le revêtement époxy isolant, en mettant en évidence ses applications, ses avantages et ses considérations essentielles pour sélectionner la couche appropriée pour des besoins spécifiques.
Comprendre le revêtement époxy isolant
Le revêtement époxy isolant est un revêtement protecteur qui fournit une isolation et une résistance à la conductivité électrique à diverses surfaces. Il est couramment utilisé dans les secteurs de l'électronique, de l'électricité, de l'automobile et de l'aérospatiale pour protéger et améliorer les performances des composants électriques.
L'objectif principal des revêtements époxy isolants est d'empêcher la circulation du courant électrique entre les matériaux conducteurs. Ces revêtements sont appliqués sur des surfaces vulnérables aux courts-circuits électriques, à la corrosion ou aux dommages causés par des facteurs environnementaux. Le matériau époxy agit comme un isolant, empêchant le transfert d'électrons et minimisant le risque de pannes ou de dysfonctionnements électriques.
Les revêtements époxy isolants sont généralement fabriqués à partir d'une combinaison de résine époxy, d'un polymère thermodurcissable et d'un agent durcissant. La résine époxy offre une excellente adhérence, résistance chimique et résistance mécanique, tandis que l'agent de durcissement déclenche la réaction de réticulation qui convertit l'époxy liquide en un revêtement solide et durable.
L'application de revêtements époxy isolants comporte plusieurs étapes. Tout d'abord, la surface à revêtir est soigneusement nettoyée et préparée pour assurer une bonne adhérence. Toute saleté, graisse ou contaminant doit être éliminé pour créer une surface de collage propre. Ensuite, le revêtement époxy est mélangé selon les instructions du fabricant et appliqué sur la surface à l'aide de techniques de pulvérisation, de brossage ou de trempage.
Une fois appliqué, le revêtement époxy subit un processus de durcissement au cours duquel il durcit et forme une barrière protectrice. Le durcissement peut être réalisé par diverses méthodes, y compris la chaleur, les produits chimiques ou les deux. Le durcissement améliore les propriétés mécaniques, la force d'adhérence et la résistance chimique du revêtement.
Les revêtements époxy isolants offrent plusieurs avantages :
- Ils assurent une isolation électrique, empêchant la circulation du courant électrique et réduisant les risques de courts-circuits ou de pannes électriques.
- Ces revêtements offrent une excellente protection contre les facteurs environnementaux tels que l'humidité, les produits chimiques et l'abrasion, prolongeant la durée de vie des composants revêtus.
- Les revêtements époxy isolants peuvent améliorer la stabilité thermique et la résistance aux flammes des surfaces, ce qui les rend adaptées aux applications dans des environnements à haute température.
L'importance de l'isolation électrique
L'isolation électrique joue un rôle crucial dans le maintien de la sécurité, de la fiabilité et de l'efficacité des systèmes électriques. Il s'agit d'utiliser des matériaux et des techniques pour empêcher la circulation du courant électrique entre des composants ou des surfaces conductrices. Voici quelques raisons clés soulignant l'importance de l'isolation électrique :
- Protection contre les chocs électriques : L'isolation électrique empêche le contact direct avec les conducteurs sous tension, réduisant ainsi le risque de choc électrique. Il agit comme une barrière qui inhibe la circulation du courant électrique à travers les matériaux non conducteurs, protégeant les individus contre les dommages potentiels.
- Prévention des courts-circuits et des incendies électriques : l'isolation aide à prévenir les contacts électriques involontaires entre les matériaux conducteurs, ce qui peut entraîner des courts-circuits et des incendies électriques. Les fils, câbles et composants électriques isolants minimisent la probabilité d'arc électrique, d'étincelles et de surchauffe, réduisant considérablement le risque d'incendie et de dommages matériels.
- Performances électriques améliorées : les matériaux d'isolation à haute résistance diélectrique et à faible conductivité électrique améliorent les performances globales des systèmes électriques. Ils maintiennent des niveaux de tension appropriés, empêchent les courants de fuite et réduisent les interférences ou la distorsion du signal, garantissant ainsi le fonctionnement optimal des circuits et appareils électriques.
- Protection contre les facteurs environnementaux : les matériaux d'isolation électrique résistent à l'humidité, aux produits chimiques, à la poussière et à d'autres contaminants. Cette protection aide à prévenir la corrosion, la dégradation et la rupture de l'isolation causées par des facteurs externes, maintenant ainsi la longévité et la fiabilité des composants électriques.
- Efficacité énergétique accrue : L'isolation réduit les pertes d'énergie et améliore l'efficacité des systèmes électriques. En empêchant les fuites de courant, l'isolation minimise le gaspillage d'énergie et améliore la transmission et la distribution de l'énergie électrique, ce qui entraîne une réduction de la consommation d'énergie et des coûts d'exploitation.
- Conformité aux normes et réglementations de sécurité : L'isolation électrique est essentielle pour respecter les normes et réglementations de sécurité établies par les autorités et les organisations industrielles. Le respect de ces exigences garantit que les installations et équipements électriques sont conçus et exploités de manière à minimiser les risques pour le personnel, les biens et l'environnement.
- Protection des équipements sensibles : L'isolation est essentielle pour protéger les équipements électriques et électroniques sensibles contre les perturbations électriques et les surtensions. Les matériaux isolants, tels que les vernis ou les revêtements, protègent les composants délicats des interférences électromagnétiques (EMI) et des décharges électrostatiques (ESD), préservant leur fonctionnalité et prolongeant leur durée de vie.
Applications du revêtement époxy isolant
Le revêtement époxy isolant est un revêtement spécialisé qui offre d'excellentes propriétés d'isolation électrique, ce qui le rend adapté à diverses applications. Ce revêtement comprend typiquement une résine époxy, apportant des capacités isolantes et des qualités protectrices. Voici quelques-unes des applications critiques du revêtement époxy isolant :
- Composants électroniques et électriques : Le revêtement époxy isolant est largement utilisé dans l'industrie électronique et électrique. Il est appliqué aux composants tels que les circuits imprimés, les transformateurs, les condensateurs et les bobines pour fournir une isolation électrique, prévenir les courts-circuits et améliorer la fiabilité et la durée de vie globales de ces composants. Le revêtement protège également contre l'humidité, la poussière et d'autres contaminants environnementaux.
- Production et transmission d'énergie : les revêtements époxy isolants sont cruciaux dans les systèmes de production et de transmission d'énergie. Ils sont appliqués aux isolateurs, aux appareillages de commutation, aux jeux de barres et à d'autres équipements haute tension pour éviter les fuites électriques, les décharges corona et les contournements. En offrant une résistance diélectrique élevée, le revêtement aide à maintenir l'intégrité et la sécurité de l'infrastructure électrique.
- Moteurs et générateurs : Les moteurs électriques et les générateurs nécessitent une isolation pour éviter les pannes électriques et garantir des performances efficaces. Des revêtements époxy isolants sont appliqués sur les bobinages et autres pièces critiques de ces machines. Le revêtement améliore l'isolation électrique, améliore la dissipation de la chaleur et offre une protection contre les produits chimiques, l'humidité et les contraintes mécaniques.
- Industrie automobile : Les revêtements époxy isolants trouvent diverses applications dans le secteur automobile. Ils isolent les connexions électriques, les bornes et les faisceaux de câbles des véhicules. La couche aide à maintenir l'intégrité électrique, empêche les courts-circuits et protège contre la corrosion, les vibrations et les cycles thermiques. Il est également utilisé pour isoler les composants des véhicules hybrides et électriques.
- Aéronautique et Défense : Les revêtements époxy isolants sont vitaux dans les secteurs de l'aérospatiale et de la défense. Ils sont appliqués aux systèmes électroniques, à l'avionique, aux équipements radar et aux systèmes de communication pour garantir des performances fiables dans des environnements difficiles. Le revêtement protège contre les interférences électriques, les radiations, l'humidité et les températures extrêmes.
- Revêtement pour cartes de circuits imprimés (PCB) : les PCB sont l'épine dorsale des appareils électroniques. Les revêtements époxy protègent les circuits et les joints de soudure des PCB de l'humidité, de la poussière et d'autres contaminants. Le revêtement fournit également une isolation entre les couches conductrices, empêchant les courts-circuits et améliorant la durabilité globale des cartes.
- Résistance chimique et à la corrosion : Les revêtements époxy isolants offrent une excellente résistance chimique et peuvent protéger les surfaces des substances corrosives. Ils sont utilisés dans le traitement chimique, le pétrole et le gaz et le traitement des eaux usées. Le revêtement empêche les attaques chimiques, améliore la longévité de l'équipement et minimise les besoins de maintenance.
- Encapsulation électrique : les revêtements époxy isolants sont utilisés pour l'encapsulation électrique, en particulier dans les applications où l'humidité ou d'autres contaminants présentent un risque. Il est couramment utilisé pour empoter et encapsuler des composants électroniques, des capteurs et des connecteurs. Le revêtement forme une barrière protectrice contre les facteurs environnementaux et les contraintes mécaniques.
Protection des composants électroniques
La protection des composants électroniques est cruciale pour assurer leur bon fonctionnement et leur longévité. Les composants électroniques sont souvent sensibles aux facteurs environnementaux tels que la température, l'humidité, le bruit électrique et le stress physique. Avec une protection adéquate, ces composants peuvent être protégés et même rendus inutilisables. Voici quelques méthodes et techniques standard utilisées pour protéger les composants électroniques :
- Boîtiers : les composants électroniques peuvent être logés dans des boîtiers de protection, tels que des boîtiers, des armoires ou des boîtes. Les sections offrent une protection physique contre la poussière, l'humidité et d'autres contaminants. Ils protègent également les composants contre les chocs accidentels ou les mauvaises manipulations.
- Blindage EMI/RFI : les interférences électromagnétiques (EMI) et les interférences radioélectriques (RFI) peuvent perturber le fonctionnement régulier des composants électroniques. Le blindage EMI/RFI implique l'utilisation de matériaux conducteurs, tels que des revêtements métalliques ou des joints conducteurs, pour créer un effet de cage de Faraday. Ce blindage empêche les signaux électromagnétiques externes d'interférer avec l'électronique sensible.
- Gestion thermique : les composants électroniques génèrent de la chaleur pendant le fonctionnement, et une chaleur excessive peut dégrader leurs performances et leur fiabilité. Les techniques de gestion thermique telles que les dissipateurs thermiques, les ventilateurs et les tampons thermiques aident à dissiper la chaleur et à maintenir des températures de fonctionnement optimales. Les dissipateurs thermiques absorbent et dissipent la chaleur, tandis que les ventilateurs facilitent la circulation de l'air. Les coussinets thermiques fournissent une interface thermique entre le composant et le dissipateur thermique pour un transfert de chaleur efficace.
- Protection contre les surtensions : les surtensions causées par la foudre, les pannes électriques ou les transitoires de commutation peuvent endommager les composants électroniques. Les dispositifs de protection contre les surtensions, comme les suppresseurs de surtension ou les varistances à oxyde métallique (MOV), détournent la tension excessive pour protéger les membres. Ces dispositifs limitent les niveaux de tension et empêchent les pointes transitoires d'atteindre les composants sensibles.
- Étanchéité environnementale : dans des applications spécifiques, les composants électroniques doivent être protégés contre les conditions environnementales difficiles, telles que l'humidité, les produits chimiques ou les températures extrêmes. Les techniques d'étanchéité environnementales, telles que les revêtements conformes, les composés d'enrobage ou l'étanchéité hermétique, créent une barrière qui protège les composants de ces éléments.
- Protection des circuits : les composants électroniques peuvent être vulnérables aux surtensions, aux surintensités et aux décharges électrostatiques (ESD). Les dispositifs de protection de circuit, tels que les fusibles, les disjoncteurs, les suppresseurs de tension transitoire (diodes TVS) et les diodes de protection ESD, sont utilisés pour limiter et rediriger le courant, la tension ou les charges statiques excessifs loin des composants.
- Mise à la terre et liaison : Des techniques de mise à la terre et de liaison appropriées sont essentielles pour protéger les composants électroniques du bruit électrique et assurer la sécurité. La mise à la terre fournit un chemin vers la dissipation des charges électriques indésirables. En revanche, le collage réduit les différences de potentiel qui pourraient causer des dommages. Les techniques de mise à la terre et de liaison comprennent l'utilisation de plans de masse, de fils et de connexions de masse typiques.
- Filtrage : Le bruit électrique et les interférences provenant de diverses sources peuvent affecter les performances des composants électroniques. Des filtres tels que les filtres passe-bas, passe-haut ou d'interférence électromagnétique peuvent éliminer ou réduire les signaux indésirables et assurer une alimentation électrique propre aux membres.
- Mesures antistatiques : Les décharges électrostatiques (ESD) peuvent endommager considérablement les composants électroniques. Les mesures antistatiques, telles que les postes de travail, les bracelets antistatiques et les matériaux d'emballage protégés contre les décharges électrostatiques, empêchent les charges statiques de s'accumuler et de se décharger dans les pièces sensibles.
- Maintenance et tests réguliers : une maintenance, une inspection et des tests réguliers sont essentiels pour identifier les problèmes potentiels avec les composants électroniques. Des contrôles périodiques garantissent que les mesures de protection fonctionnent correctement et que les défauts ou pannes sont rapidement corrigés.
Les composants électroniques peuvent être protégés contre les risques environnementaux, les perturbations électriques et les dommages physiques en utilisant ces techniques de protection. Cela garantit leur fonctionnement fiable et prolonge leur durée de vie, ce qui améliore les performances et réduit les temps d'arrêt.
Revêtement de circuit imprimé
Le revêtement de carte de circuit imprimé est un processus crucial dans la fabrication électronique qui consiste à appliquer une couche protectrice sur la carte de circuit imprimé (PCB). Ce revêtement fournit une isolation, une protection contre les facteurs environnementaux et améliore la fiabilité et la longévité des circuits. Dans cet article, nous explorerons l'importance du revêtement des circuits imprimés et les différents types de revêtements utilisés.
L'objectif principal du revêtement des cartes de circuits imprimés est de protéger les composants électroniques délicats des diverses contraintes environnementales. Ces contraintes comprennent l'humidité, la poussière, la saleté, les produits chimiques et les fluctuations de température, qui peuvent entraîner de la corrosion, des courts-circuits et d'autres défaillances. Le revêtement agit comme une barrière, empêchant ces éléments nocifs d'atteindre les circuits et de causer des dommages.
Il existe plusieurs types de revêtements disponibles pour les cartes de circuits imprimés, chacun offrant des avantages spécifiques en fonction des exigences de l'application. Un type courant est le revêtement conforme, qui est un film protecteur mince appliqué directement sur la surface du PCB. Les revêtements conformes peuvent être constitués de divers matériaux, notamment des acryliques, des uréthanes, des silicones et des résines époxy. Ces revêtements épousent la forme du circuit imprimé, couvrant tous les composants et les traces exposées, et offrent une excellente protection contre l'humidité, la poussière et les contaminants chimiques.
Un autre type de revêtement est le composé d'encapsulation ou d'enrobage, qui est un matériau plus épais qui recouvre tout le PCB, l'encapsulant complètement. Les composés d'enrobage sont généralement fabriqués en époxy ou en polyuréthane et offrent une protection supérieure contre les contraintes mécaniques, les vibrations et les températures extrêmes. Ils sont couramment utilisés dans les applications où les cartes de circuits imprimés sont exposées à des environnements difficiles ou à des niveaux élevés de contraintes physiques.
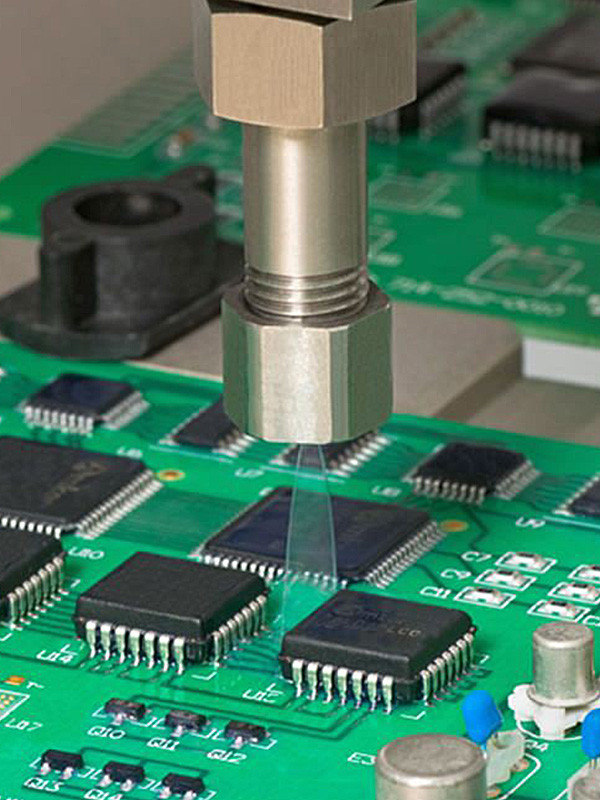
Le processus de revêtement lui-même implique des techniques d'application minutieuses pour assurer une couverture uniforme et une bonne adhérence. Différentes méthodes peuvent être utilisées, telles que le revêtement par pulvérisation, le revêtement par immersion ou le revêtement sélectif. Le revêtement par pulvérisation consiste à utiliser un pistolet pulvérisateur ou un atomiseur pour appliquer une fine brume du matériau de revêtement sur le PCB. Le revêtement par immersion, quant à lui, plonge le circuit imprimé dans un bain de matériau de revêtement, ce qui lui permet de recouvrir entièrement la carte. Le revêtement sélectif est une méthode précise qui applique le revêtement uniquement à des zones spécifiques du PCB, laissant les autres composants non revêtus pour l'accessibilité.
Outre la protection de l'environnement, les revêtements de circuits imprimés offrent également des propriétés d'isolation électrique. Le matériau de revêtement a une rigidité diélectrique élevée, ce qui empêche la fuite de courant entre des pistes ou des composants étroitement espacés. Ceci est particulièrement important dans les applications haute tension où l'isolation électrique est essentielle.
Isolation du moteur et du transformateur
La protection des composants électroniques est cruciale pour assurer leur bon fonctionnement et leur longévité. Les composants électroniques sont souvent sensibles aux facteurs environnementaux tels que la température, l'humidité, le bruit électrique et le stress physique. Avec une protection adéquate, ces composants peuvent être protégés et même rendus inutilisables. Voici quelques méthodes et techniques standard utilisées pour protéger les composants électroniques :
- Boîtiers : les composants électroniques peuvent être logés dans des boîtiers de protection, tels que des boîtiers, des armoires ou des boîtes. Les sections offrent une protection physique contre la poussière, l'humidité et d'autres contaminants. Ils protègent également les composants contre les chocs accidentels ou les mauvaises manipulations.
- Blindage EMI/RFI : les interférences électromagnétiques (EMI) et les interférences radioélectriques (RFI) peuvent perturber le fonctionnement régulier des composants électroniques. Le blindage EMI/RFI implique l'utilisation de matériaux conducteurs, tels que des revêtements métalliques ou des joints conducteurs, pour créer un effet de cage de Faraday. Ce blindage empêche les signaux électromagnétiques externes d'interférer avec l'électronique sensible.
- Gestion thermique : les composants électroniques génèrent de la chaleur pendant le fonctionnement, et une chaleur excessive peut dégrader leurs performances et leur fiabilité. Les techniques de gestion thermique telles que les dissipateurs thermiques, les ventilateurs et les coussinets aident à dissiper la chaleur et à maintenir des températures de fonctionnement optimales. Les dissipateurs thermiques absorbent et dissipent la chaleur, tandis que les ventilateurs facilitent la circulation de l'air. Les coussinets thermiques fournissent une interface thermique entre le composant et le dissipateur thermique pour un transfert de chaleur efficace.
- Protection contre les surtensions : les surtensions causées par la foudre, les pannes électriques ou les transitoires de commutation peuvent endommager les composants électroniques. Les dispositifs de protection contre les surtensions, comme les suppresseurs de surtension ou les varistances à oxyde métallique (MOV), détournent la tension excessive pour protéger les membres. Ces dispositifs limitent les niveaux de tension et empêchent les pointes transitoires d'atteindre les composants sensibles.
- Étanchéité environnementale : dans des applications spécifiques, les composants électroniques doivent être protégés contre les conditions environnementales difficiles, telles que l'humidité, les produits chimiques ou les températures extrêmes. Les techniques d'étanchéité environnementales, telles que les revêtements conformes, les composés d'enrobage ou l'étanchéité hermétique, créent une barrière qui protège les composants de ces éléments.
- Protection des circuits : les composants électroniques peuvent être vulnérables aux surtensions, aux surintensités et aux décharges électrostatiques (ESD). Les dispositifs de protection de circuit, tels que les fusibles, les disjoncteurs, les suppresseurs de tension transitoire (diodes TVS) et les diodes de protection ESD, sont utilisés pour limiter et rediriger le courant, la tension ou les charges statiques excessifs loin des composants.
- Mise à la terre et liaison : Des techniques de mise à la terre et de liaison appropriées sont essentielles pour protéger les composants électroniques du bruit électrique et assurer la sécurité. La mise à la terre fournit un chemin vers la dissipation des charges électriques indésirables. En revanche, le collage réduit les différences de potentiel qui pourraient causer des dommages. Les techniques de mise à la terre et de liaison comprennent l'utilisation de plans de masse, de fils et de connexions de masse typiques.
- Filtrage : Le bruit électrique et les interférences provenant de diverses sources peuvent affecter les performances des composants électroniques. Des filtres tels que les filtres passe-bas, passe-haut ou d'interférence électromagnétique peuvent éliminer ou réduire les signaux indésirables et assurer une alimentation électrique propre aux membres.
- Mesures antistatiques : Les décharges électrostatiques (ESD) peuvent endommager considérablement les composants électroniques. Les mesures antistatiques, telles que les postes de travail, les bracelets antistatiques et les matériaux d'emballage protégés contre les décharges électrostatiques, empêchent les charges statiques de s'accumuler et de se décharger dans les pièces sensibles.
- Maintenance et tests réguliers : une maintenance, une inspection et des tests réguliers sont essentiels pour identifier les problèmes potentiels avec les composants électroniques. Des contrôles périodiques garantissent que les mesures de protection fonctionnent correctement et que les défauts ou pannes sont rapidement corrigés.
Les composants électroniques peuvent être protégés contre les risques environnementaux, les perturbations électriques et les dommages physiques en utilisant ces techniques de protection. Cela garantit leur fonctionnement fiable et prolonge leur durée de vie, ce qui améliore les performances et réduit les temps d'arrêt.
Isolation des câbles et des fils
L'isolation des câbles et des fils joue un rôle crucial dans les systèmes électriques en assurant la protection, l'isolation et la sécurité. Il fait référence au revêtement extérieur ou à la gaine qui entoure les conducteurs électriques, empêchant la circulation du courant électrique vers des zones non intentionnelles et protégeant les conducteurs des facteurs environnementaux. Le choix du matériau d'isolation dépend de facteurs tels que la tension nominale, la plage de température, les conditions environnementales et l'application prévue.
L'un des matériaux d'isolation couramment utilisés est le thermoplastique. L'isolation thermoplastique est flexible, durable et résistante à l'abrasion et aux produits chimiques. Le chlorure de polyvinyle (PVC) est un matériau thermoplastique populaire connu pour son prix abordable et sa large gamme d'applications. Il est couramment utilisé dans les applications basse tension telles que le câblage domestique et les câbles à usage général. L'isolation en PVC offre de bonnes propriétés électriques et est ignifuge.
Un autre matériau d'isolation largement utilisé est le thermodurcissable. Contrairement aux thermoplastiques, l'isolant thermodurcissable ne peut pas être refondu ou reformé une fois durci. Le polyéthylène réticulé (XLPE) est un matériau thermodurcissable couramment utilisé, connu pour ses excellentes propriétés électriques, sa résistance aux températures élevées et sa résistance à l'humidité et aux produits chimiques. L'isolation XLPE est souvent utilisée dans les câbles électriques moyenne et haute tension, y compris les systèmes de transmission et de distribution souterrains.
En plus des thermoplastiques et des thermodurcissables, d'autres matériaux d'isolation spécialisés sont conçus pour des applications spécifiques. Par exemple, l'isolation en caoutchouc de silicone est connue pour sa résistance aux hautes températures, ce qui la rend adaptée aux applications dans des environnements extrêmes tels que les industries aérospatiale et automobile. Les fluoropolymères, tels que le polytétrafluoroéthylène (PTFE), sont utilisés dans les applications à haute température et haute fréquence en raison de leurs excellentes propriétés électriques et de leur résistance aux produits chimiques et à la chaleur.
La tension nominale et l'utilisation prévue du câble ou du fil déterminent l'épaisseur de la couche d'isolation. Les applications à haute tension nécessitent des couches d'isolation plus épaisses pour résister aux champs électriques plus élevés et éviter les pannes électriques. L'épaisseur de l'isolation affecte également le diamètre global et la flexibilité du câble.
Les matériaux d'isolation sont soumis à divers tests pour garantir leurs performances et leur sécurité. Ces tests peuvent inclure la mesure de propriétés électriques telles que la rigidité diélectrique et la résistance d'isolation, l'évaluation de la résistance aux variations de température, la résistance aux flammes et les propriétés mécaniques telles que la flexibilité et la résistance à l'abrasion. Le respect des normes et réglementations de l'industrie est essentiel pour assurer la fiabilité et la sécurité des systèmes électriques.
Industries aérospatiale et automobile
Les revêtements époxy isolants trouvent des applications essentielles dans les industries aérospatiale et automobile. Ces revêtements offrent de nombreux avantages, notamment l'isolation électrique, la résistance à la corrosion et la protection thermique. Cette réponse explorera les utilisations critiques des revêtements époxy isolants dans les secteurs de l'aérospatiale et de l'automobile tout en respectant la limite de 450 mots.
Industrie aérospaciale:
- Structures d'aéronefs : les revêtements époxy isolants protègent les structures d'aéronefs des facteurs environnementaux, tels que l'humidité, les produits chimiques et les rayons UV. Ces revêtements agissent comme une barrière, empêchant la corrosion et prolongeant la durée de vie des composants critiques. De plus, ils fournissent une isolation électrique, réduisant le risque d'interférences électriques et améliorant la sécurité.
- Composants électroniques : les revêtements époxy isolants sont appliqués sur les composants électroniques des systèmes aérospatiaux, notamment les cartes de circuits imprimés, les connecteurs et les capteurs. Ces revêtements offrent d'excellentes propriétés d'isolation électrique, protégeant les composants électroniques sensibles des décharges statiques, de l'humidité et des contaminants. Les couches contribuent également à la dissipation de la chaleur, garantissant des performances et une fiabilité optimales des systèmes électroniques.
- Radômes : les radômes, qui sont des enceintes de protection pour les antennes radar, nécessitent des revêtements époxy isolants pour assurer la transparence du signal et la protection contre les éléments environnementaux. Ces revêtements fournissent une isolation contre les interférences électromagnétiques (EMI) tout en maintenant l'intégrité structurelle du radôme. Ils offrent également une résistance à l'érosion et aux intempéries, maintenant les performances du système radar.
Industrie automobile:
- Batteries de véhicules électriques (EV) : les revêtements époxy isolants sont essentiels pour protéger les batteries des véhicules électriques. Ces revêtements empêchent la pénétration de l'humidité et des contaminants, garantissant l'intégrité et la longévité des cellules de la batterie. Ils fournissent également une isolation électrique, minimisant le risque de courts-circuits et améliorant la sécurité des véhicules électriques.
- Composants du moteur : Des revêtements époxy isolants sont utilisés sur les composants du moteur pour les protéger de la corrosion, de la chaleur et de l'exposition aux produits chimiques. Ces revêtements améliorent la durabilité et les performances des pièces du moteur, telles que les culasses, les collecteurs d'admission et les systèmes d'échappement. Les couches fournissent également une isolation thermique, réduisant le transfert de chaleur et améliorant l'efficacité du moteur.
- Systèmes électriques : les revêtements époxy isolants sont appliqués sur les systèmes électriques des véhicules, y compris les faisceaux de câbles, les connecteurs et les cartes de circuits imprimés. Ces revêtements offrent une isolation électrique, empêchent les courts-circuits et garantissent des performances fiables. Ils protègent également contre l'humidité, les produits chimiques et les variations de température, augmentant ainsi la durée de vie des composants électriques.
- Protection du châssis et du soubassement : Les revêtements époxy isolants protègent le châssis et le soubassement des véhicules de la corrosion causée par l'humidité, le sel et les débris de la route. Ces revêtements forment une barrière robuste, empêchant la pénétration de substances corrosives et prolongeant la durée de vie du véhicule. De plus, ils fournissent une isolation thermique, réduisant le transfert de chaleur et améliorant le confort des passagers.
Applications marines et offshore
Les revêtements époxy isolants jouent un rôle crucial dans les applications marines et offshore en fournissant une barrière protectrice contre la corrosion, l'abrasion et la conductivité électrique. Ces revêtements spécialisés offrent de nombreux avantages et sont largement utilisés dans les environnements marins et offshore.
- Navires marins : les revêtements époxy isolants sont largement utilisés sur les navires marins, y compris les navires, les barges et les plates-formes offshore. Ces revêtements protègent les coques des effets corrosifs de l'eau salée, des produits chimiques et des organismes marins. Ils fournissent une barrière de protection durable qui prolonge la durée de vie du navire et réduit les besoins d'entretien.
- Plates-formes pétrolières et gazières offshore : dans l'exploration et la production pétrolières et gazières offshore, les revêtements époxy isolants sont essentiels pour maintenir l'intégrité des plates-formes et des équipements. Ils protègent les structures contre les conditions environnementales difficiles, y compris l'eau salée corrosive, les températures élevées et l'exposition aux produits chimiques. Les revêtements isolants fournissent également une isolation électrique, empêchant les courants électriques d'interférer avec les équipements sensibles et garantissant la sécurité.
- Pipelines et applications sous-marines : des revêtements époxy isolants sont appliqués sur les canaux et les équipements sous-marins pour les protéger de la corrosion causée par l'eau de mer, l'humidité et les produits chimiques. Ces revêtements agissent comme une barrière, empêchant la pénétration de substances corrosives et maintenant l'intégrité de l'infrastructure. Ils fournissent également une isolation électrique, réduisant le risque d'interférences électriques ou de dommages.
- Parcs éoliens offshore : Les revêtements époxy isolants sont utilisés dans la construction et l'entretien des parcs éoliens offshore. Ils protègent les structures des éoliennes, y compris les tours, les fondations et les câbles sous-marins, contre la corrosion et la dégradation de l'environnement. Ces revêtements fournissent également une isolation électrique, assurant une transmission de puissance sûre et efficace.
- Équipement marin et offshore : Les revêtements époxy sont appliqués sur divers équipements marins et offshore, tels que les pompes, les vannes, les réservoirs et les systèmes d'amarrage. Ces revêtements protègent l'équipement de la corrosion, de l'abrasion et de l'exposition aux produits chimiques, prolongeant leur durée de vie et réduisant les coûts de maintenance. Les propriétés isolantes de ces revêtements évitent également les problèmes de conductivité électrique, améliorant ainsi la sécurité et la fiabilité de l'équipement.
- Navires flottants de production, de stockage et de déchargement (FPSO) : les FPSO sont largement utilisés dans la production pétrolière et gazière offshore. Des revêtements époxy isolants sont appliqués sur les coques et les structures internes des FPSO pour les protéger de la corrosion, de l'abrasion et de l'exposition aux produits chimiques. Ces revêtements offrent une protection à long terme et garantissent l'intégrité structurelle du navire.
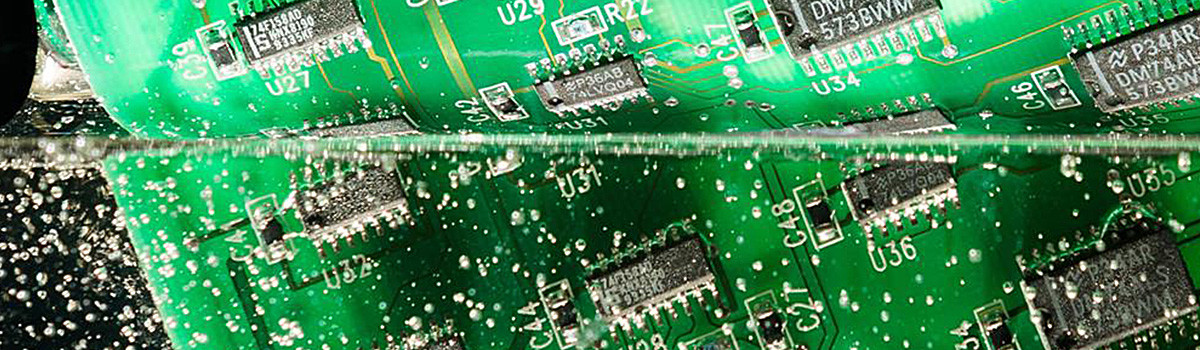
Résistance chimique et à la corrosion
Les revêtements époxy isolants sont largement utilisés dans diverses industries pour protéger contre la corrosion et l'isolation électrique. Ces revêtements offrent une excellente résistance chimique, ce qui les rend adaptés aux environnements difficiles où l'exposition à des substances corrosives est un problème.
La résistance chimique est cruciale pour les revêtements époxy isolants, car ils sont souvent exposés à une large gamme de produits chimiques, notamment des acides, des alcalis, des solvants et des carburants. Les revêtements époxy résistent à de nombreuses substances corrosives en raison de leur structure moléculaire dense et de leur réseau de polymères réticulés. Cette structure crée une barrière qui empêche la pénétration d'agents corrosifs, protégeant ainsi le substrat sous-jacent.
L'un des principaux facteurs contribuant à la résistance chimique des revêtements époxy est leur haute densité de réticulation. La réticulation fait référence à la liaison chimique entre les molécules d'époxy, résultant en un réseau tridimensionnel. Ce réseau renforce la résistance du revêtement aux agressions chimiques en créant une barrière empêchant la diffusion de substances corrosives. De ce fait, le substrat revêtu reste protégé contre la corrosion.
De plus, les revêtements époxy peuvent être formulés avec divers additifs et renforts pour améliorer leur résistance chimique. Par exemple, l'ajout d'inhibiteurs de corrosion peut encore améliorer les propriétés protectrices du revêtement en inhibant le processus de corrosion et en réduisant la dégradation de l'époxy. Des renforts tels que des fibres de verre ou des nanoparticules peuvent également renforcer la résistance mécanique et chimique du revêtement.
En plus de la résistance chimique, les revêtements époxy isolants offrent une excellente résistance à la corrosion. La corrosion se produit lorsqu'un matériau réagit avec son environnement, entraînant sa détérioration et sa défaillance potentielle. Les revêtements époxy agissent comme une barrière entre l'environnement corrosif et le substrat, empêchant le contact de l'humidité, de l'oxygène et d'autres agents corrosifs avec la surface métallique sous-jacente.
Les revêtements époxy offrent également une excellente adhérence à divers substrats, assurant une protection à long terme contre la corrosion. La forte liaison entre la couche et le substrat empêche la pénétration d'humidité et de substances corrosives, réduisant ainsi la probabilité d'initiation et de progression de la corrosion.
Il est important de noter que la résistance chimique et à la corrosion des revêtements époxy isolants peut être influencée par la température, le temps d'exposition et l'environnement chimique spécifique. Bien que les revêtements époxy offrent une excellente résistance à divers produits chimiques, des substances très agressives peuvent tout de même causer des dommages sur de longues périodes ou dans des conditions extrêmes.
Pour garantir des performances optimales, il est essentiel de sélectionner la formulation de revêtement époxy appropriée en fonction des exigences spécifiques de l'application. Lors du choix du bon système de revêtement époxy, l'environnement d'exploitation, l'exposition aux produits chimiques, la température et la durée de vie prévue doivent être pris en compte.
Conductivité thermique et dissipation thermique
La conductivité thermique et la dissipation thermique sont essentielles dans divers domaines, notamment l'ingénierie, l'électronique et la science des matériaux. Ils sont cruciaux pour déterminer l'efficacité et la fiabilité des systèmes qui génèrent ou gèrent de la chaleur. Explorons ces concepts plus en détail dans la limite de mots donnée.
La conductivité thermique fait référence à la capacité d'un matériau à conduire la chaleur, et c'est une propriété qui caractérise la facilité avec laquelle la chaleur peut être transférée à travers une substance. Les matériaux à haute conductivité thermique permettent à la chaleur de circuler rapidement, tandis que ceux à faible conductivité thermique empêchent le transfert de chaleur. L'unité de mesure de la conductivité thermique est le watt par mètre-kelvin (W/mK).
Divers facteurs affectent la conductivité thermique d'un matériau. L'un des facteurs critiques est la structure moléculaire ou atomique. Les substances avec des atomes ou des molécules étroitement emballés ont tendance à avoir une conductivité thermique plus élevée. Les métaux comme le cuivre et l'aluminium sont connus pour leur conductivité thermique élevée en raison de leur liaison métallique et de leurs structures cristallines compactes.
D'autre part, les matériaux avec des structures moléculaires complexes ou de grands vides, tels que les polymères ou les isolants comme le bois ou le caoutchouc, ont une conductivité thermique relativement plus faible. L'air et les autres gaz sont de mauvais conducteurs de chaleur, c'est pourquoi les matériaux avec des poches d'air emprisonnées, comme les matériaux d'isolation, présentent une faible conductivité thermique.
La dissipation thermique, cependant, fait référence au transfert ou à la dissipation de la chaleur d'un système ou d'un composant pour éviter la surchauffe et maintenir des conditions de fonctionnement optimales. Une dissipation thermique efficace est cruciale pour la longévité et les performances des appareils, en particulier ceux qui génèrent des quantités importantes de chaleur, tels que les composants électroniques, les systèmes d'alimentation et les moteurs.
Il existe différentes méthodes de dissipation de la chaleur, en fonction de l'application spécifique. Certaines techniques standard incluent la conduction, la convection et le rayonnement.
La conduction implique le transfert de chaleur par contact physique direct entre des objets. Les matériaux conducteurs de chaleur efficaces, tels que les métaux ou les matériaux à haute conductivité thermique, facilitent le transfert de chaleur entre les composants générant de la chaleur et les dissipateurs thermiques ou les systèmes de refroidissement.
La convection implique le transfert de chaleur par le mouvement de fluides, tels que l'air ou un liquide. Ce processus repose sur la circulation du fluide, soit naturellement, soit avec des ventilateurs ou des pompes, pour évacuer la chaleur de la source. Les dissipateurs thermiques avec des surfaces étendues sont souvent utilisés pour augmenter la surface pour le transfert de chaleur par convection.
Le rayonnement fait référence à l'émission et à l'absorption de rayonnement thermique, qui est un rayonnement électromagnétique émis par des objets en raison de leur température. Tous les objets au-dessus de la température du zéro absolu émettent un rayonnement thermique. La dissipation de la chaleur par rayonnement se produit lorsque le rayonnement émis évacue la chaleur de la source vers un environnement plus détendu.
Diverses techniques et technologies sont utilisées pour améliorer la dissipation de la chaleur, notamment les dissipateurs thermiques, les caloducs, les matériaux d'interface thermique, les ventilateurs, les systèmes de refroidissement liquide et les solutions avancées de gestion thermique.
Performances d'isolation électrique
Les revêtements époxy isolants sont essentiels pour fournir une isolation électrique dans diverses industries, notamment l'électronique, les équipements électriques et les systèmes d'alimentation. Ces revêtements sont conçus pour empêcher la circulation du courant électrique et protéger contre les pannes électriques ou les courts-circuits. Explorons les performances d'isolation électrique des revêtements époxy isolants dans la limite de mots donnée.
L'une des propriétés fondamentales contribuant aux performances d'isolation électrique des revêtements époxy est leur résistance diélectrique élevée. La rigidité diélectrique fait référence au champ électrique maximal qu'un matériau peut supporter sans subir de panne électrique. Les revêtements époxy isolants sont formulés pour avoir une résistance diélectrique élevée, ce qui leur permet de résister à des niveaux de tension élevés et d'empêcher les fuites électriques ou les arcs électriques.
Plusieurs facteurs, notamment la formulation de la résine, le processus de durcissement et les matériaux de remplissage, influencent la résistance diélectrique des revêtements époxy isolants. Les résines époxy à haut poids moléculaire et densité de réticulation présentent une résistance diélectrique plus élevée. Le processus de durcissement joue également un rôle, car un durcissement approprié assure la formation d'un revêtement dense et uniforme qui peut résister aux contraintes électriques.
Des matériaux de remplissage peuvent être ajoutés aux revêtements époxy pour améliorer les performances d'isolation électrique. Les charges, telles que les fibres de verre ou les charges minérales, peuvent augmenter la rigidité diélectrique en réduisant l'apparition de vides ou de points faibles dans le revêtement. Ces charges améliorent l'homogénéité globale et l'intégrité structurelle du revêtement, minimisant ainsi le risque de panne électrique.
Les revêtements époxy isolants offrent également une bonne résistivité électrique, qui fait référence à la capacité du matériau à résister au passage du courant électrique. Une résistivité électrique élevée est cruciale pour prévenir les courants de fuite et maintenir l'intégrité de l'isolation électrique. Les revêtements époxy ont généralement des valeurs de résistivité élevées, contribuant à leur efficacité en tant qu'isolants électriques.
Un autre aspect important des performances d'isolation électrique est la capacité des revêtements époxy isolants à résister aux facteurs environnementaux susceptibles d'avoir un impact sur leurs propriétés électriques. Des facteurs tels que l'humidité, les variations de température et l'exposition à des produits chimiques peuvent affecter la résistance diélectrique et la résistivité du revêtement. Par conséquent, il est essentiel de sélectionner des revêtements époxy avec des formulations et des additifs appropriés pour fournir des performances d'isolation électrique à long terme dans des conditions environnementales spécifiques.
De plus, les revêtements époxy isolants doivent présenter une bonne adhérence au substrat pour assurer une isolation électrique à long terme. Une liaison solide entre la couche et la surface sous-jacente empêche la formation de vides ou d'espaces qui pourraient compromettre les performances d'isolation électrique. La préparation de surface, les techniques d'application du revêtement et la compatibilité entre le revêtement et le substrat influencent l'adhérence.
En résumé, les revêtements époxy isolants offrent d'excellentes performances d'isolation électrique en offrant une résistance diélectrique élevée, une résistivité électrique et une bonne adhérence au substrat. Leur formulation, leur processus de durcissement et l'utilisation de charges contribuent à leur capacité à résister aux contraintes électriques et à prévenir les pannes électriques. Une sélection et une application appropriées des revêtements époxy isolants sont essentielles pour assurer une isolation électrique efficace dans diverses applications, allant de l'électronique aux systèmes d'alimentation.
Types de revêtements époxy isolants
Plusieurs types de revêtements époxy isolants sont disponibles, chacun conçu pour répondre à des exigences spécifiques et fournir différents niveaux d'isolation électrique. Voici quelques types courants de revêtements époxy protecteurs :
- Revêtements époxy isolants standard : il s'agit de revêtements époxy à usage général formulés pour fournir une isolation électrique primaire. Ils offrent une bonne rigidité diélectrique et une bonne résistivité électrique, ce qui les rend adaptés à diverses applications.
- Revêtements époxy isolants haute température : ces revêtements sont spécifiquement formulés pour résister à des températures élevées sans compromettre leurs performances d'isolation électrique. Ils peuvent être utilisés dans des applications où une exposition à une chaleur élevée est attendue, comme les moteurs, les transformateurs ou les composants électriques dans les industries automobile ou aérospatiale.
- Revêtements époxy isolants thermoconducteurs : ces revêtements fournissent une isolation électrique et ont la propriété supplémentaire de conductivité thermique. Ils sont conçus pour dissiper efficacement la chaleur tout en maintenant l'isolation électrique. Ces revêtements sont couramment utilisés dans les applications nécessitant une isolation électrique et une dissipation thermique efficace, comme dans l'électronique de puissance.
- Revêtements époxy isolants ignifuges : Les revêtements époxy ignifuges sont formulés pour fournir une isolation électrique tout en offrant une résistance à la propagation des flammes et à la combustion. Ces revêtements sont couramment utilisés dans les applications où la sécurité incendie est une préoccupation, telles que les panneaux électriques, les appareillages de commutation ou le câblage.
- Revêtements époxy isolants résistants aux produits chimiques : Ces revêtements sont conçus pour fournir une isolation électrique tout en offrant une excellente résistance à divers produits chimiques et substances corrosives. Ils conviennent aux applications où une exposition à des produits chimiques agressifs ou à des environnements corrosifs est attendue, comme dans les usines de traitement chimique ou les applications marines.
- Revêtements époxy isolants résistants aux UV : Les revêtements résistants aux UV sont formulés pour fournir une isolation électrique tout en offrant une protection contre les effets néfastes des rayons ultraviolets (UV). Ces revêtements sont couramment utilisés dans les applications extérieures ou les environnements où l'exposition au soleil est importante, comme les panneaux solaires ou les équipements électriques extérieurs.
- Revêtements époxy isolants flexibles : Les revêtements époxy flexibles sont conçus pour fournir une isolation électrique dans les applications où le substrat revêtu subit des contraintes mécaniques ou des mouvements. Ces revêtements offrent une bonne adhérence et flexibilité, leur permettant de résister à la flexion ou à l'étirement sans se fissurer ni compromettre l'isolation électrique.
Il est important de noter que la sélection du type de revêtement époxy isolant approprié dépend des exigences spécifiques de l'application, des facteurs environnementaux et des performances attendues. Consulter les fabricants de revêtements ou les experts de l'industrie peut aider à déterminer le revêtement époxy isolant le plus approprié pour une application particulière.
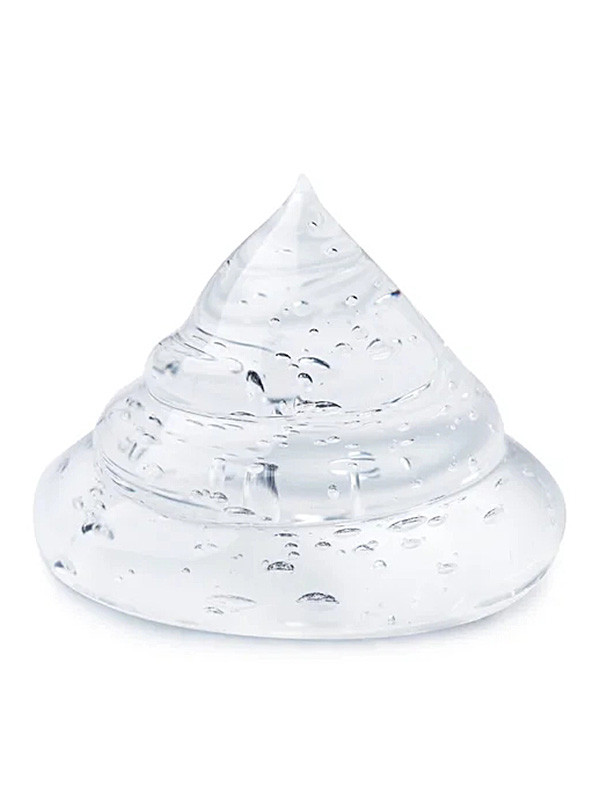
Revêtements époxy à deux composants
Les revêtements époxy à deux composants sont largement utilisés dans diverses industries pour leur durabilité, leur résistance chimique et leur polyvalence exceptionnelles. Ces revêtements sont constitués de deux composants : une résine et un durcisseur. Lorsqu'ils sont combinés dans le bon rapport, ils subissent une réaction chimique connue sous le nom de durcissement, résultant en un revêtement solide et protecteur. Ici, nous explorerons les principales caractéristiques, applications et avantages des revêtements époxy en deux parties.
Caractéristiques: Les revêtements époxy en deux parties offrent plusieurs caractéristiques clés qui les rendent hautement souhaitables dans de nombreuses applications. Premièrement, ils offrent une excellente adhérence à divers substrats, notamment le béton, le métal, le bois et la fibre de verre. Cette adhérence garantit des performances durables et évite des problèmes tels que le pelage ou le délaminage. De plus, les revêtements époxy présentent une résistance chimique élevée, ce qui les rend adaptés à une utilisation dans des environnements exposés à des substances corrosives, des produits chimiques ou des solvants. Ils sont également connus pour leur dureté, leur résistance à l'abrasion et leur résistance aux chocs exceptionnelles, contribuant à leur longévité et à leur durabilité. De plus, selon les exigences esthétiques et fonctionnelles souhaitées, les revêtements époxy peuvent être formulés pour avoir diverses finitions, notamment brillantes, mates ou texturées.
Applications : Les revêtements époxy en deux parties trouvent des applications dans diverses industries en raison de leur polyvalence et de leurs caractéristiques de performance. Dans le secteur industriel, ils sont couramment utilisés pour protéger les sols en béton des usines de fabrication, des entrepôts et des garages. Le revêtement époxy crée une surface homogène et durable qui peut résister à la circulation intense, aux impacts et aux déversements de produits chimiques. Dans l'industrie maritime, les revêtements époxy sont utilisés pour les coques de bateaux, les ponts et autres structures, protégeant contre l'intrusion d'eau, les rayons UV et la corrosion. Ces revêtements sont également utilisés dans l'industrie automobile pour fournir une couche protectrice sur les carrosseries de voitures, les composants de moteur et les revêtements de soubassement, améliorant leur résistance à l'abrasion, aux produits chimiques et aux intempéries. De plus, les revêtements époxy à deux composants sont largement utilisés dans le secteur de la construction pour l'imperméabilisation, les réparations de béton et les systèmes de revêtements de sol décoratifs.
Avantages : L'utilisation de revêtements époxy à deux composants offre de nombreux avantages aux utilisateurs industriels et commerciaux. Premièrement, leur durabilité exceptionnelle et leur résistance à l'usure garantissent une durée de vie plus longue des surfaces revêtues, réduisant ainsi les coûts d'entretien et de remplacement. Les revêtements époxy sont également relativement faciles à appliquer, permettant une installation efficace et minimisant les temps d'arrêt dans les environnements industriels. Leur nature homogène et non poreuse les rend hygiéniques et faciles à nettoyer, idéales pour les environnements qui nécessitent des niveaux de propreté élevés, tels que les établissements de santé ou les usines de transformation des aliments. De plus, les revêtements époxy peuvent être personnalisés pour répondre à des exigences spécifiques, notamment les propriétés antidérapantes, la résistance à la chaleur ou la conductivité électrique. Cette polyvalence permet des solutions sur mesure dans diverses applications. Enfin, les revêtements époxy à deux composants sont écologiques car ils contiennent peu de composés organiques volatils (COV), ce qui les rend plus sûrs pour les travailleurs et l'environnement.
Revêtements époxy monocomposant
Les revêtements époxy monocomposants sont des revêtements monocomposants qui offrent de nombreux avantages par rapport aux revêtements époxy bicomposants traditionnels mais avec des processus d'application simplifiés. Ces revêtements sont formulés avec une résine qui contient à la fois la résine époxy et l'agent de durcissement, éliminant ainsi le besoin d'un durcisseur séparé. Cet article explorera les caractéristiques, les applications et les avantages des revêtements époxy monocomposants.
Caractéristiques: Les revêtements époxy monocomposant possèdent plusieurs caractéristiques clés qui les rendent populaires dans diverses industries. Ces revêtements présentent une excellente adhérence sur différents substrats, y compris le béton, le métal et le bois, assurant une liaison solide et une protection durable. Ils offrent une bonne résistance chimique, offrant une protection contre les substances corrosives, les produits chimiques et les solvants. De plus, les revêtements époxy monocomposant offrent une bonne résistance à l'abrasion et une bonne durabilité, ce qui les rend adaptés aux surfaces soumises à un trafic intense ou à l'usure. Ils peuvent également être formulés avec différentes finitions, telles que brillantes ou mates, pour obtenir l'attrait esthétique souhaité.
Applications : Les revêtements époxy monocomposant trouvent des applications dans diverses industries et surfaces. Dans l'industrie de la construction, ils sont couramment utilisés pour protéger et améliorer les sols en béton, offrant une couverture homogène et durable dans des environnements tels que les entrepôts, les espaces de vente au détail et les bâtiments commerciaux. Ces revêtements trouvent également des applications dans l'industrie automobile, où ils sont utilisés pour la protection contre la corrosion sur les trains roulants de véhicules, les composants de châssis et d'autres surfaces métalliques. De plus, les revêtements époxy monocomposants sont utilisés dans l'industrie maritime pour les ponts de bateaux, les piscines et les structures marines, offrant une résistance à l'eau, aux rayons UV et aux produits chimiques. Ils peuvent également être utilisés sur des surfaces métalliques, telles que des machines, des équipements ou des réservoirs de stockage, pour les protéger contre la corrosion et l'usure.
Avantages : Les revêtements époxy monocomposant offrent plusieurs avantages qui les rendent avantageux pour de nombreuses applications. L'un des principaux avantages est leur facilité d'utilisation et d'application. Comme ils sont pré-mélangés, il n'est pas nécessaire de mesurer et de mélanger plusieurs composants, ce qui simplifie le processus de revêtement et réduit le risque d'erreurs. Cela les rend idéaux pour les petits projets ou les utilisateurs ayant une expérience limitée avec les revêtements époxy. De plus, les revêtements époxy à un composant ont souvent une durée de vie en pot plus longue que les systèmes à deux composants, ce qui permet un temps de travail prolongé et une application plus simple. Ils offrent également une excellente adhérence, durabilité et résistance chimique, assurant une protection durable des surfaces revêtues. De plus, les revêtements époxy monocomposants sont généralement faibles en composés organiques volatils (COV), ce qui les rend respectueux de l'environnement et plus sûrs pour les utilisateurs.
Choisir le bon revêtement époxy isolant
Le choix du revêtement époxy isolant est crucial pour assurer une isolation et une protection adéquates pour diverses applications. Les revêtements époxy isolants sont conçus pour fournir une isolation électrique et une résistance thermique, empêchant la conductivité électrique et le transfert de chaleur. Voici quelques facteurs clés à prendre en compte lors du choix du revêtement époxy isolant approprié :
- Propriétés électriques : La fonction principale d'un revêtement époxy isolant est de fournir une isolation électrique. Par conséquent, il est essentiel de prendre en compte les propriétés électriques du revêtement, telles que la rigidité diélectrique, la résistivité volumique et la résistivité superficielle. La rigidité diélectrique détermine la tension maximale que le revêtement peut supporter avant la panne, tandis que la résistivité mesure la capacité du matériau à résister au flux de courant électrique. Assurez-vous que la couche répond aux normes électriques requises pour votre application spécifique.
- Résistance thermique : Les revêtements époxy isolants doivent également offrir une résistance thermique pour empêcher le transfert de chaleur. Considérez la capacité du revêtement à résister à des températures élevées et à fournir une isolation thermique efficace. Recherchez des couches à faible conductivité thermique pour minimiser le transfert de chaleur et maintenir la stabilité de la température.
- Compatibilité du substrat : évaluez la compatibilité du revêtement époxy avec le matériau du substrat. Les revêtements époxy isolants sont couramment utilisés sur les métaux en cuivre, en aluminium ou en acier. Assurez-vous que le revêtement est formulé pour bien adhérer au matériau de substrat spécifique, offrant une adhérence solide et une performance à long terme.
- Méthode d'application : Tenez compte de la méthode d'application et de la facilité d'application du revêtement époxy isolant choisi. Certains revêtements conviennent à l'application par pulvérisation, tandis que d'autres conviennent mieux à l'application au pinceau ou au rouleau. Choisissez une couche qui correspond à l'équipement d'application disponible et aux exigences du projet.
- Résistance environnementale : évaluez les conditions écologiques auxquelles le revêtement sera exposé, telles que l'humidité, l'humidité, les produits chimiques ou les rayons UV. Les revêtements époxy isolants doivent offrir une excellente résistance à ces facteurs environnementaux pour assurer une performance et une protection à long terme. Envisagez des revêtements à haute résistance chimique et stabilité aux UV s'ils sont exposés à des environnements difficiles.
- Certifications et normes : Certaines certifications ou normes peuvent être exigées selon l'application. Par exemple, les revêtements époxy isolants peuvent devoir répondre à des normes électriques ou à des certificats spécifiques dans l'industrie électrique. Assurez-vous que le revêtement choisi respecte les normes et les certifications de l'industrie pour garantir la conformité et la performance.
- Performance et durabilité : Considérez la performance globale et la durabilité du revêtement époxy isolant. Recherchez des couches offrant une excellente adhérence, une résistance à l'abrasion et une durabilité à long terme pour assurer une isolation et une protection durables. Évaluer la résistance du revêtement aux dommages physiques, tels que les chocs ou les rayures, qui pourraient compromettre les propriétés d'isolation.
- Coût et valeur : Enfin, évaluez le coût et la valeur du revêtement époxy isolant. Tenez compte de facteurs tels que le coût initial, la durée de vie prévue de la couche et les coûts potentiels de maintenance ou de remplacement au fil du temps. Équilibrer l'investissement initial avec les performances et la durabilité à long terme aidera à déterminer la valeur globale du revêtement.
Considérations environnementales
Les considérations environnementales jouent un rôle important dans la sélection et l'utilisation des revêtements époxy isolants. Il est essentiel de choisir des revêtements qui offrent une isolation adéquate et minimisent l'impact environnemental tout au long de leur cycle de vie. Voici quelques considérations écologiques essentielles à garder à l'esprit lors de la sélection de revêtements époxy isolants :
- Teneur en COV : les composés organiques volatils (COV) sont des produits chimiques qui peuvent contribuer à la pollution de l'air et avoir des effets potentiels sur la santé. Lorsque vous choisissez des revêtements époxy isolants, optez pour des formulations à faible teneur en COV ou sans COV. Ces revêtements émettent moins de fumées nocives lors de l'application et contribuent à une meilleure qualité de l'air intérieur et extérieur.
- Substances dangereuses : évaluer la présence de substances dangereuses dans la formulation du revêtement époxy. Certains additifs, solvants ou métaux lourds peuvent nuire à la santé humaine ou à l'environnement. Recherchez des revêtements sans ou avec des niveaux réduits de substances dangereuses, garantissant une manipulation, une élimination et un impact environnemental à long terme plus sûrs.
- Biodégradabilité : tenir compte de la biodégradabilité du revêtement époxy isolant. Les revêtements biodégradables se décomposent naturellement au fil du temps, réduisant ainsi leur impact sur l'environnement. Recherchez des couches dérivées de ressources renouvelables ou qui ont été testées et certifiées pour leur biodégradabilité.
- Efficacité énergétique : Les revêtements époxy isolants améliorent souvent l'efficacité énergétique en réduisant le transfert de chaleur. En sélectionnant des revêtements à haute résistance thermique, vous pouvez améliorer l'efficacité énergétique dans des applications telles que l'isolation électrique, l'isolation des bâtiments ou les barrières thermiques. Cela peut entraîner une réduction de la consommation d'énergie et un impact environnemental moindre.
- Durabilité et longévité : Choisissez des revêtements époxy isolants avec une excellente durabilité et longévité. Les revêtements plus résistants à l'usure, à la corrosion ou à la dégradation nécessitent un entretien, une réapplication et une élimination moins fréquents. Cela réduit l'impact environnemental global associé à l'utilisation des revêtements.
- Emballage et déchets : Considérez l'emballage des revêtements époxy isolants et la génération de déchets lors de leur utilisation. Optez pour des revêtements emballés dans des matériaux recyclables ou respectueux de l'environnement. De plus, les revêtements qui minimisent la génération de déchets lors de l'application, tels que ceux avec une surpulvérisation réduite ou des exigences de mélange minimales, peuvent aider à réduire l'impact environnemental.
- Certifications environnementales : recherchez des revêtements époxy isolants qui ont obtenu des certifications écologiques ou qui sont conformes aux normes environnementales reconnues. Les exemples incluent des certificats tels que LEED (Leadership in Energy and Environmental Design) ou le respect des normes de gestion environnementale ISO 14001. Ces certifications garantissent que les revêtements ont subi des tests rigoureux et répondent à des critères de performance environnementale spécifiques.
- Élimination et recyclage appropriés : Considérez les options d'élimination et de recyclage appropriées pour les revêtements époxy isolants. Vérifiez les réglementations et directives locales pour vous assurer que les revêtements peuvent être éliminés ou recyclés de manière appropriée à la fin de leur cycle de vie. Certains revêtements peuvent avoir des programmes de recyclage spécifiques ou des options disponibles.
Compte tenu de ces considérations environnementales, vous pouvez sélectionner des revêtements époxy isolants qui offrent une isolation adéquate et minimisent leur impact écologique. Le choix de revêtements respectueux de l'environnement contribue aux efforts de durabilité, réduit la pollution et favorise un écosystème plus sain.
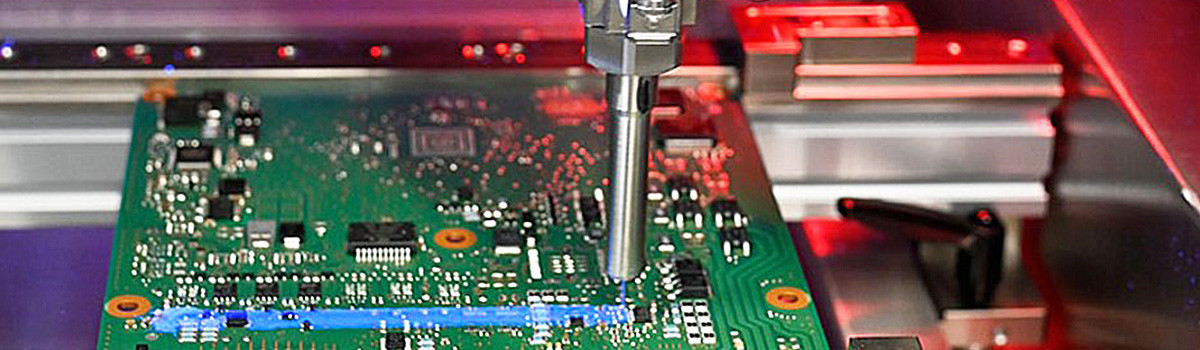
Techniques d'application et conseils
Des techniques d'application appropriées sont essentielles pour obtenir des résultats optimaux lors de l'isolation des revêtements époxy. Les conseils suivants vous aideront à garantir une application réussie et à améliorer les performances de la couche :
- Préparation de la surface : Nettoyer soigneusement et préparer la surface avant d'appliquer le revêtement époxy isolant. Enlevez la saleté, la poussière, la graisse ou les revêtements existants susceptibles d'interférer avec l'adhérence. Les techniques de préparation de surface peuvent inclure le ponçage, le dégraissage ou l'utilisation d'agents de nettoyage appropriés. Suivez les directives du fabricant pour la préparation de la surface spécifique au revêtement et au substrat.
- Rapports de mélange et durée de vie en pot : Suivez attentivement les instructions du fabricant concernant les rapports de mélange et la durée de vie en pot. Les revêtements époxy isolants sont généralement des systèmes en deux parties qui nécessitent un mélange précis des composants résine et durcisseur. Un mélange incorrect peut entraîner un durcissement incomplet ou des performances compromises. Faites attention à la durée de vie en pot et au temps de travail disponible une fois les ingrédients mélangés. Éviter de dépasser la durée de vie en pot pour garantir une application correcte.
- Méthode d'application : Choisissez la méthode d'application appropriée pour le revêtement époxy isolant en fonction de la surface et des exigences du projet. Les méthodes d'application standard comprennent l'application au pinceau, au rouleau ou au pistolet. Utilisez des brosses et des rouleaux pour les petites surfaces ou lorsque la précision est requise. L'application par pulvérisation convient aux grandes pièces ou à une finition plus uniforme. Suivez les recommandations du fabricant pour le revêtement spécifique concernant la méthode d'application et l'équipement.
- Température et humidité : tenir compte des conditions de température et d'humidité ambiantes lors de l'application. Les revêtements époxy isolants peuvent avoir des exigences spécifiques en matière de température et d'humidité pour des performances optimales. Suivez les directives du fabricant concernant la plage de température et les conditions d'humidité recommandées pendant l'application et le durcissement. Des températures extrêmes ou une humidité élevée peuvent affecter le temps de durcissement et les performances globales du revêtement.
- Épaisseur d'application : Appliquer le revêtement époxy isolant à l'épaisseur recommandée pour l'isolation et la protection souhaitées. Une épaisseur de revêtement suffisante peut compromettre les propriétés isolantes, tandis qu'une épaisseur excessive peut entraîner des problèmes de durcissement ou une mauvaise adhérence. Utilisez une jauge d'épaisseur de film humide pour assurer une épaisseur de revêtement constante et précise tout au long de l'application.
- Ventilation et sécurité : Assurer une ventilation adéquate dans la zone d'application afin de minimiser l'inhalation de fumées ou de vapeurs. Utilisez un équipement de protection individuelle (EPI) approprié tel que recommandé par le fabricant, comme des gants, des lunettes ou une protection respiratoire. Suivez les consignes de sécurité et les réglementations pour vous protéger et protéger les autres pendant le processus de candidature.
- Temps de durcissement et de séchage : Allouer un temps de durcissement et de séchage suffisant pour le revêtement époxy isolant. Suivez les instructions du fabricant concernant le temps de durcissement recommandé et les conditions environnementales pour une adhérence et une performance appropriées. Évitez de soumettre la surface revêtue à une humidité excessive ou à des contraintes mécaniques jusqu'à ce que le revêtement soit complètement durci.
- Inspection et entretien : Inspectez régulièrement la surface revêtue pour tout signe de dommage ou d'usure. Effectuez un entretien de routine pour assurer l'efficacité continue du revêtement époxy isolant. Résoudre tout problème rapidement pour éviter d'autres blessures ou détériorations.
En suivant ces techniques d'application et ces conseils, vous pouvez obtenir de bons résultats lors de l'application de revêtements époxy isolants. Une préparation de surface appropriée, un mélange précis, des méthodes d'application appropriées et le respect des directives de durcissement aideront à assurer l'isolation et la protection souhaitées pour votre application.
Processus de durcissement et de séchage
Le processus de durcissement et de séchage des revêtements époxy isolants est une étape critique qui détermine les propriétés finales et les performances du revêtement. Un durcissement approprié assure une couche solide, durable et entièrement isolante. Voici les principaux facteurs et considérations pour le processus de durcissement et de séchage des revêtements époxy isolants :
- Suivez les instructions du fabricant : reportez-vous toujours aux instructions et à la fiche technique du fabricant pour obtenir des conseils spécifiques sur les temps de durcissement et de séchage et les conditions environnementales requises pour le revêtement. Différents revêtements époxy peuvent avoir des processus de durcissement et des temps de séchage recommandés différents.
- Température ambiante : Le processus de durcissement des revêtements époxy dépend de la température. La plupart des revêtements époxy nécessitent une plage de température ambiante minimale et maximale pour un durcissement correct. Assurez-vous que la température ambiante se situe dans la plage spécifiée tout au long du processus de durcissement et de séchage. Des températures extrêmement chaudes et froides peuvent nuire au processus de durcissement et aux performances finales du revêtement.
- Humidité relative : Les niveaux d'humidité peuvent également avoir un impact sur le durcissement et le séchage des revêtements époxy isolants. Dans les environnements très humides, le temps de durcissement peut être prolongé en raison de la lente évaporation de l'humidité de la couche. À l'inverse, une faible humidité peut faire durcir le revêtement trop rapidement, compromettant ainsi son intégrité. Maintenir les niveaux d'humidité recommandés spécifiés par le fabricant pour un durcissement optimal.
- Ventilation : Une ventilation adéquate est cruciale pendant le durcissement et le séchage pour assurer une bonne circulation de l'air et la dissipation des fumées ou des vapeurs. Une bonne ventilation aide à faciliter le processus de durcissement et réduit le risque de piégeage de solvant, ce qui pourrait affecter les performances du revêtement.
- Temps de durcissement : Le temps de durcissement des revêtements époxy isolants peut varier en fonction de la formulation spécifique, de l'épaisseur de la couche appliquée et des conditions ambiantes. Il est essentiel de respecter le temps de durcissement recommandé spécifié par le fabricant pour assurer une réticulation complète et le développement des propriétés souhaitées. Une exposition prématurée à l'humidité, à la poussière ou à des contraintes mécaniques pendant le processus de durcissement peut compromettre les performances du revêtement.
- Temps de séchage : Le temps de séchage fait référence au moment où le solvant s'évapore du revêtement. Le temps de séchage peut varier en fonction de l'épaisseur du revêtement, de la température, de l'humidité et de la ventilation. Il est crucial de laisser le temps de séchage recommandé au revêtement pour obtenir une formation de film appropriée et éviter une manipulation ou une exposition prématurée.
- Durcissement complet : Bien que le revêtement puisse sembler sec au toucher après le temps de séchage recommandé, il est essentiel de noter que le durcissement complet peut prendre plus de temps. Le durcissement complet fait référence à la réticulation et au durcissement chimiques complets du revêtement époxy. Suivez les instructions du fabricant concernant le temps de durcissement complet recommandé avant de soumettre la surface revêtue à de lourdes charges, à l'abrasion ou à d'autres facteurs de stress.
- Post-durcissement : certains revêtements époxy isolants peuvent bénéficier d'un post-durcissement pour améliorer davantage leurs propriétés. Le post-durcissement consiste à soumettre la couche durcie à des températures élevées pendant une durée spécifiée. Ce processus peut améliorer la résistance chimique, la dureté et l'adhérence du revêtement. Le cas échéant, reportez-vous aux directives du fabricant concernant le processus de post-durcissement recommandé.
En suivant attentivement les instructions du fabricant, en maintenant des conditions ambiantes appropriées, en permettant des temps de durcissement et de séchage appropriés et en assurant une ventilation adéquate, vous pouvez obtenir des résultats optimaux dans l'isolation des revêtements époxy. Des revêtements correctement durcis et séchés fourniront l'isolation électrique et la résistance thermique souhaitées pour l'application prévue.
Entretien et réparation de revêtements époxy isolants
Les revêtements époxy isolants sont largement utilisés dans diverses industries pour protéger et isoler les équipements et infrastructures électriques. Ces revêtements fournissent une barrière protectrice durable qui empêche l'humidité, les produits chimiques et autres contaminants d'atteindre les surfaces sous-jacentes. Cependant, comme tout autre système de revêtement, les revêtements époxy isolants peuvent nécessiter un entretien et des réparations pour assurer leur efficacité et leur longévité.
L'entretien des revêtements époxy isolants implique principalement une inspection et un nettoyage réguliers. Inspectez périodiquement les surfaces revêtues pour identifier tout signe de dommage, tel que des fissures, des cloques ou un pelage. Veuillez prêter une attention particulière aux zones exposées à des conditions difficiles ou à des contraintes mécaniques, car elles sont plus sujettes aux dommages. Si des problèmes sont détectés, résolvez-les rapidement pour éviter toute détérioration supplémentaire.
Le nettoyage des surfaces revêtues est essentiel pour éliminer la saleté, la poussière, les huiles et autres contaminants qui peuvent s'accumuler avec le temps. Utilisez des nettoyants doux et non abrasifs et des brosses ou chiffons doux pour nettoyer les surfaces en douceur. Évitez les produits chimiques agressifs ou les matériaux abrasifs qui rayent ou dégradent le revêtement. Un nettoyage régulier aide à maintenir les propriétés isolantes du revêtement époxy et empêche l'accumulation de matériaux conducteurs qui pourraient compromettre son efficacité.
En matière de réparation, l'approche peut varier en fonction de l'étendue des dégâts. Vous pouvez utiliser des kits de réparation époxy spécialement conçus pour les revêtements isolants pour les blessures mineures telles que les petites fissures ou les éclats. Ces kits comprennent généralement un mastic époxy et des instructions pour l'appliquer correctement. Nettoyez soigneusement la zone endommagée, suivez les instructions fournies avec l'équipement et utilisez le mastic époxy sur la partie endommagée. Laisser durcir selon les recommandations du fabricant.
Dans les cas où les dommages sont plus importants, il peut être nécessaire d'enlever la partie endommagée du revêtement tout comme d'appliquer une nouvelle couche d'époxy isolant. Cela nécessite une préparation minutieuse de la surface, y compris le nettoyage et la rugosité de la zone entourant les dommages pour assurer une bonne adhérence du nouveau revêtement. Suivez les directives du fabricant concernant l'application du nouveau revêtement époxy, y compris les temps de durcissement et les exigences de température.
Dans certains cas, il peut être plus pratique de faire appel à un professionnel pour entretenir et réparer les revêtements époxy isolants. Des entrepreneurs expérimentés ou des spécialistes du revêtement peuvent évaluer l'étendue des dommages, recommander la méthode de réparation la plus appropriée et s'assurer que le revêtement amélioré répond aux normes et exigences nécessaires.
N'oubliez pas qu'une inspection régulière et un entretien préventif sont essentiels pour prolonger la durée de vie des revêtements époxy isolants. En traitant les problèmes mineurs dès le début et en suivant les procédures de nettoyage appropriées, vous pouvez minimiser le besoin de réparations importantes et assurer l'efficacité continue du revêtement dans la protection et l'isolation des équipements et infrastructures électriques.
Conclusion
L'isolation des revêtements époxy est cruciale pour protéger les composants et équipements électriques contre divers facteurs externes. Avec des applications allant des composants électroniques aux cartes de circuits imprimés, moteurs et câbles, ces revêtements offrent une protection essentielle contre l'humidité, les produits chimiques et les dommages physiques. Le choix d'un revêtement époxy isolant approprié dépend des conditions environnementales, des exigences de performance et des techniques d'application. En comprenant les avantages et les considérations associés aux revêtements époxy isolants, les industries peuvent faire des choix éclairés pour améliorer la durabilité, la fiabilité et la longévité de leurs systèmes et équipements électriques.