Composé d'enrobage PCB
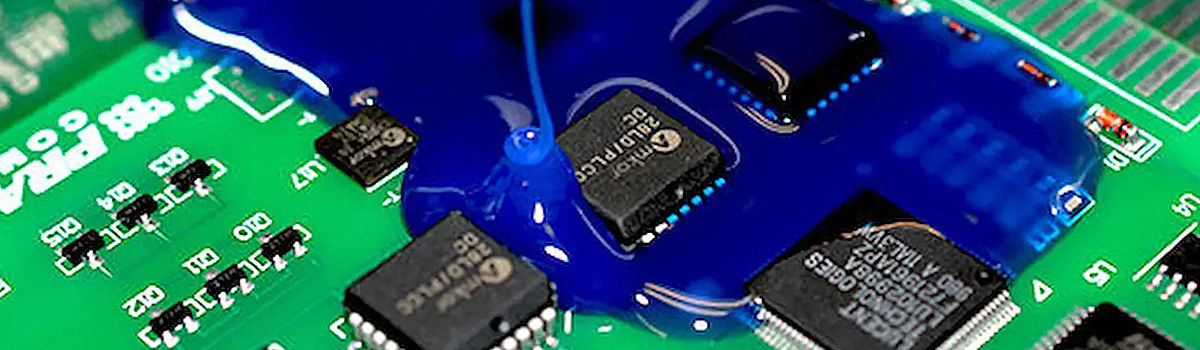
Le composé d'enrobage de PCB, également connu sous le nom d'encapsulant, est un matériau utilisé pour protéger et isoler les composants électroniques sur les cartes de circuits imprimés (PCB). Le composé d'enrobage est appliqué sur les éléments et le PCB, puis durci pour former une coque dure et protectrice. Ce processus protège l'électronique des facteurs environnementaux tels que l'humidité, la poussière et les vibrations et peut améliorer les performances thermiques. Dans cet article, nous explorerons les avantages de l'utilisation de composés d'enrobage de PCB et comment ils peuvent améliorer la longévité et la fiabilité des systèmes électroniques.
Qu'est-ce que le composé d'enrobage pour PCB ?
Le composé d'enrobage PCB est une résine protectrice encapsulant des composants électroniques sur une carte de circuit imprimé (PCB). Il forme une barrière solide, protégeant le PCB des facteurs environnementaux tels que l'humidité, la poussière et les fluctuations de température. Le composé d'enrobage améliore la résistance mécanique du PCB, fournit une isolation électrique et améliore sa fiabilité globale. Il est couramment utilisé dans la fabrication électronique, l'automobile, l'aérospatiale et les télécommunications pour assurer la longévité et les performances des appareils et systèmes électroniques.
Comment fonctionne le composé d'enrobage pour PCB ?
Le composé d'enrobage pour PCB est un matériau spécialisé qui encapsule et protège les composants électroniques sur une carte de circuit imprimé (PCB). Voici comment fonctionne le composé d'enrobage PCB :
- Encapsulation: Le composé d'enrobage de PCB est appliqué sur le PCB en le versant ou en le distribuant sur les composants. Il coule autour des éléments et remplit les vides, créant une enceinte solide et protectrice.
- Protection environnementale: Une fois durci, le composé d'enrobage forme une barrière robuste qui protège les composants des facteurs environnementaux tels que l'humidité, la poussière et les produits chimiques. Il empêche ces éléments d'atteindre l'électronique sensible, les protégeant contre la corrosion, les courts-circuits et autres dommages potentiels.
- Isolation: Le composé d'enrobage PCB offre d'excellentes propriétés d'isolation électrique. Il isole les composants les uns des autres, empêchant les courts-circuits électriques et maintenant l'intégrité des circuits. Cette isolation est cruciale dans les applications avec des caractéristiques étroitement espacées ou des différentiels à haute tension.
- Stabilité mécanique : Le composé d'enrobage améliore la stabilité mécanique de l'assemblage PCB. Il améliore l'intégrité structurelle, amortit les vibrations et réduit le risque de déplacement des composants ou de dommages dus aux contraintes mécaniques. Il est particulièrement crucial de prendre en compte ce facteur dans les situations où la carte de circuit imprimé peut subir des conditions difficiles, des vibrations ou des chocs.
- Gestion de la chaleur: Le composé d'enrobage de PCB peut également fournir une gestion thermique efficace. Il aide à dissiper la chaleur générée par les composants, évitant ainsi la surchauffe et prolongeant leur durée de vie. Certains terreaux ont une conductivité thermique élevée, transférant efficacement la chaleur des éléments.
- Propriétés diélectriques :Les composés d'enrobage de PCB sont formulés avec des propriétés diélectriques, leur permettant de résister à des tensions élevées sans conduire l'électricité. Cette caractéristique est essentielle dans les applications d'isolation électrique critiques, telles que les alimentations haute tension ou les équipements électriques.
- Compatibilité et adhérence : Les composés d'enrobage de PCB adhèrent bien à divers substrats utilisés dans la fabrication de PCB, tels que l'époxy, le FR-4 ou le métal. Ils forment une liaison solide avec les composants et le circuit imprimé, offrant une protection fiable et garantissant des performances à long terme.
Avantages de l'utilisation d'un composé d'enrobage pour PCB
L'utilisation de composés d'enrobage de PCB offre plusieurs avantages dans la fabrication et la protection des appareils électroniques. Voici quelques avantages clés :
- Protection environnementale:Le composé d'enrobage PCB forme une barrière protectrice qui protège les composants électroniques de l'humidité, de la poussière, des produits chimiques et d'autres facteurs environnementaux. Il aide à prévenir la corrosion, les courts-circuits et les dommages causés par l'exposition à des conditions difficiles.
- Isolation électrique: Les composés d'enrobage offrent une excellente isolation électrique, isolant les composants et empêchant les courts-circuits électriques. L'isolation est cruciale dans les applications avec des éléments étroitement espacés ou des tensions élevées.
- Stabilité mécanique : Le composé d'enrobage améliore la stabilité mécanique de l'assemblage PCB. Il améliore l'intégrité structurelle, réduit les vibrations et protège contre les contraintes mécaniques, garantissant des performances fiables même dans des environnements difficiles.
- Résistance aux vibrations et aux chocs : Le composé d'enrobage aide à amortir les vibrations et à absorber les chocs, protégeant les composants des dommages dus aux contraintes mécaniques. Les mouvements constants dans des applications telles que les industries automobile ou aérospatiale rendent particulièrement important la mise en place de cette isolation.
- Dissipation de la chaleur: Certains composés d'enrobage ont une conductivité thermique élevée, permettant une dissipation thermique efficace. Ils aident à dissiper la chaleur générée par les composants, empêchant la surchauffe et prolongeant leur durée de vie.
- Résistance chimique:Les composés d'enrobage de PCB résistent à divers produits chimiques, protégeant les composants de l'exposition aux substances corrosives ou aux solvants. Cette résistance assure la fiabilité à long terme de l'ensemble PCB.
- Flexibilité de personnalisation et de conception : La formulation de composés d'enrobage permet de répondre à des exigences spécifiques, offrant une personnalisation et une flexibilité de conception. La personnalisation des composés d'enrobage permet de fournir les propriétés souhaitées telles que la dureté, la flexibilité, la résistance aux flammes ou des tolérances environnementales précises.
- Protection contre les dommages physiques : Le composé d'enrobage crée une couche protectrice autour des composants, les protégeant des dommages physiques causés par des impacts ou une manipulation brutale pendant le transport ou l'installation.
- Application facile:Les composés d'enrobage de PCB sont généralement faciles à appliquer. Verser, injecter ou distribuer des composés d'enrobage sur l'assemblage PCB leur permet de se conformer à la forme des composants et de remplir efficacement les vides.
- Fiabilité à long terme : En fournissant une protection et une isolation robustes, les composés d'enrobage contribuent à la fiabilité à long terme des appareils et systèmes électroniques. Ils contribuent à prolonger la durée de vie des composants, en réduisant les coûts de maintenance et de remplacement.
Protection contre les facteurs environnementaux
La protection contre les facteurs environnementaux est cruciale dans la fabrication d'appareils électroniques, et le composé d'enrobage de PCB fournit des garanties adéquates contre divers éléments. Voici quelques points clés soulignant la protection offerte par le composé d'enrobage PCB :
- Barrière d'humidité: Le composé d'enrobage PCB crée une barrière résistante à l'humidité qui empêche l'eau ou l'humidité d'atteindre les composants électroniques sensibles. Cette protection est essentielle dans les applications exposées à des environnements riches en humidité, tels que l'électronique extérieure ou les environnements industriels.
- Protection contre la poussière et les particules : Les composés d'enrobage scellent les composants et le PCB, empêchant la pénétration de poussière, de saleté et d'autres particules. Cette barrière permet de maintenir des performances optimales en réduisant le risque de contamination ou de colmatage des circuits électroniques sensibles.
- Résistance chimique:Les fabricants formulent souvent des composés d'enrobage avec d'excellentes propriétés de résistance chimique. Ils peuvent résister à l'exposition à divers produits chimiques, notamment les solvants, les acides, les huiles et les agents de nettoyage. Cette protection est essentielle dans les environnements où l'exposition aux produits chimiques est répandue, comme les environnements industriels ou de laboratoire.
- Prévention de la corrosion : Les composés d'enrobage de PCB fournissent une couche protectrice qui protège les composants des substances corrosives. Ils minimisent le risque de corrosion, qui peut dégrader les performances et entraîner une défaillance des composants au fil du temps.
- Résistance aux UV: Les fabricants conçoivent des composés d'enrobage spécifiques pour offrir une résistance aux rayons ultraviolets (UV). Cette protection est cruciale pour les applications extérieures ou les appareils exposés à la lumière directe du soleil, car les rayons UV peuvent provoquer une décoloration, une dégradation ou un vieillissement prématuré des matériaux.
- Stabilité thermique: Les composés d'enrobage peuvent fournir une stabilité thermique en résistant aux fluctuations de température. Ils aident à protéger les composants contre la chaleur ou le froid excessifs, assurant leur fonctionnement fiable dans des variations de température extrêmes.
- Protections mécaniques :Les composés d'enrobage améliorent la protection automatique des composants électroniques en fournissant une encapsulation durable et résistante. Cette protection protège les composants contre les impacts physiques, les vibrations ou les contraintes mécaniques, réduisant ainsi le risque de dommages ou de défaillance.
- Isolation électrique : Les composés d'enrobage de PCB offrent d'excellentes propriétés d'isolation électrique. Ils empêchent les courts-circuits électriques et les fuites en fournissant une barrière non conductrice entre les composants ou les traces conductrices sur le PCB.
- Blindage EMI/RFI : Certains composés d'enrobage peuvent incorporer des matériaux qui offrent un blindage contre les interférences électromagnétiques (EMI) ou les interférences radiofréquences (RFI). Cette fonctionnalité permet d'éviter les interférences ou les perturbations indésirables causées par des rayonnements ou des signaux électromagnétiques.
- Respect de l'environnement: Les fabricants conçoivent certains composés d'empotage pour répondre à des normes ou réglementations environnementales spécifiques, telles que RoHS (Restriction of Hazardous Substances) ou REACH (Registration, Evaluation, Authorization, and Restriction of Chemicals). Ces composés garantissent le respect des directives environnementales et contribuent à des pratiques de fabrication durables.
Le composé d'enrobage pour PCB offre une protection complète contre divers facteurs environnementaux, notamment l'humidité, la poussière, les produits chimiques, la corrosion, le rayonnement UV, les fluctuations de température, les contraintes mécaniques, les problèmes électriques et les interférences électromagnétiques. Cette protection permet d'assurer la longévité, la fiabilité et les performances des appareils électroniques dans diverses applications et environnements.
Performances thermiques améliorées
La conception et le fonctionnement des dispositifs électroniques reposent essentiellement sur des performances thermiques améliorées, que les concepteurs peuvent obtenir grâce à diverses techniques et matériaux. Voici quelques points clés mettant en évidence les avantages et les méthodes pour atteindre des performances thermiques améliorées :
- Dissipation thermique efficace :Une dissipation thermique efficace est cruciale pour éviter la surchauffe et maintenir des températures de fonctionnement optimales pour les composants électroniques. En utilisant des solutions de refroidissement avancées telles que des dissipateurs de chaleur, des caloducs ou des tampons thermiques, l'énergie thermique peut être efficacement transférée loin des éléments, réduisant ainsi le risque de dégradation ou de défaillance des performances.
- Matériaux d'interface thermique : Les matériaux d'interface thermique, tels que les pâtes thermiques, les tampons ou les matériaux à changement de phase, améliorent le transfert de chaleur entre le composant et le système de refroidissement. Ces matériaux aident à combler les vides d'air ou les imperfections microscopiques sur l'interface, réduisant la résistance thermique et améliorant la conductivité thermique.
- Techniques de propagation de la chaleur :Les techniques de propagation de la chaleur impliquent l'utilisation de matériaux à haute conductivité thermique, tels que le cuivre ou l'aluminium, pour répartir la chaleur uniformément sur l'appareil. Le maintien d'une répartition uniforme de la température est essentiel pour éviter la surchauffe de zones spécifiques.
- Considérations de conception thermique :Une conception thermique efficace implique de prendre soigneusement en compte des facteurs tels que le placement des composants, le dimensionnement et le positionnement du dissipateur thermique et le flux d'air global à l'intérieur de l'appareil. L'optimisation de ces aspects minimise les points chauds et améliore la dissipation de la chaleur.
- Gestion de la ventilation et du flux d'air : Une ventilation et une gestion du flux d'air adéquates sont essentielles pour évacuer la chaleur de l'appareil et maintenir un environnement de fonctionnement plus frais. Maintenir un flux continu d'air frais est essentiel pour dissiper efficacement la chaleur. Une façon d'y parvenir consiste à utiliser des ventilateurs, des évents ou des conduits.
- Simulation thermique et tests :L'utilisation de logiciels de simulation thermique et de méthodologies de test permet aux ingénieurs d'analyser et d'optimiser les performances thermiques des appareils électroniques. Des améliorations itératives dans la conception, la sélection des composants et les solutions de refroidissement permettraient aux ingénieurs d'obtenir une meilleure gestion thermique.
- Technologies de refroidissement avancées :Les technologies de refroidissement innovantes, telles que les solutions de chambre à liquide ou à vapeur, peuvent améliorer considérablement les performances thermiques dans les applications à haute puissance ou à espace restreint. Ces technologies offrent des capacités de dissipation thermique supérieures et peuvent gérer efficacement les exigences thermiques des systèmes électroniques avancés.
- Sélection du matériau: Choisir des matériaux avec une conductivité thermique élevée, une faible résistance thermique et d'excellentes propriétés de dissipation thermique peut améliorer les performances thermiques. Pour assurer une gestion thermique efficace, les ingénieurs doivent choisir des substrats, des adhésifs et des encapsulants spécialement conçus à cet effet.
- Gestion Thermique Active :Les techniques de gestion thermique active, telles que le contrôle dynamique de la vitesse du ventilateur ou la limitation de la puissance en fonction de la température, peuvent aider à réguler les températures en fonction des conditions en temps réel. L'activation de la dissipation thermique maximale garantit que les composants fonctionnent dans des limites de température sûres.
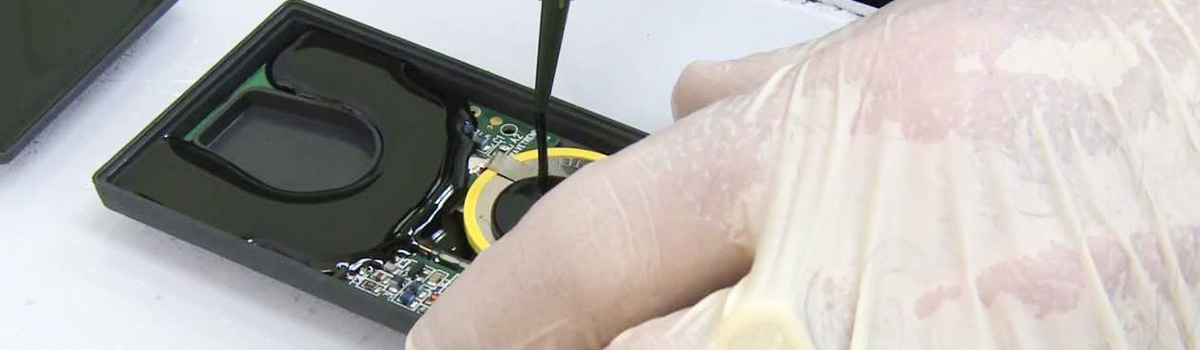
Résistance mécanique améliorée
L'amélioration de la résistance mécanique est un facteur critique pour assurer la durabilité et la fiabilité des appareils électroniques. Voici quelques points clés mettant en évidence les avantages et les méthodes pour obtenir une meilleure résistance mécanique :
- Enceintes renforcées : Une approche pour améliorer la résistance mécanique consiste à utiliser des boîtiers renforcés, tels que des boîtiers renforcés ou résistants aux chocs. Les concepteurs créent ces boîtiers pour résister aux contraintes physiques, aux vibrations et aux impacts potentiels, protégeant ainsi les composants internes des dommages.
- Optimisation de la conception structurelle :En utilisant des techniques de conception avancées, telles que l'analyse par éléments finis (FEA) ou la conception assistée par ordinateur (CAO), les ingénieurs peuvent optimiser l'intégrité structurelle des appareils électroniques. L'identification des zones nécessitant des améliorations, la réduction des concentrations de contraintes et la consolidation des points critiques sont essentielles pour améliorer la résistance mécanique.
- Matériaux de haute qualité:La sélection de matériaux de haute qualité est cruciale pour améliorer la résistance mécanique. Le choix de matériaux dotés d'une résistance à la traction, d'une résistance aux chocs et d'une stabilité dimensionnelle supérieures peut améliorer considérablement la robustesse et la fiabilité des appareils électroniques.
- Renforts et contreventement :Dans les applications nécessitant une résistance mécanique supplémentaire, les concepteurs peuvent incorporer des entretoises et des éléments de contreventement. Ceux-ci peuvent inclure des supports métalliques, des poutres de support ou des nervures qui offrent une intégrité structurelle supplémentaire et une résistance à la flexion ou à la torsion.
- Collage:L'utilisation de techniques de liaison adhésive robustes peut améliorer la résistance mécanique des ensembles de dispositifs. Les adhésifs à haute résistance assurent une liaison sûre entre les composants, empêchant la séparation ou le desserrage dû aux contraintes mécaniques ou aux vibrations.
- Connecteurs renforcés et points de montage : Les connecteurs et les points de montage, tels que les vis ou les fixations, peuvent être renforcés pour améliorer la résistance mécanique. En utilisant des matériaux plus substantiels ou en incorporant un support supplémentaire, ces composants peuvent mieux résister aux forces mécaniques et maintenir des connexions fiables.
- Absorption des chocs et résistance aux chocs : L'incorporation de matériaux ou de structures qui absorbent et dissipent l'énergie d'impact peut améliorer la résistance mécanique. Les concepteurs peuvent utiliser des mesures de protection telles que des matériaux absorbant les chocs, des éléments de rembourrage ou des revêtements pour protéger les composants et éviter les dommages causés par des impacts ou des chutes soudains.
- Conformité aux normes de l'industrie : La conformité aux normes de l'industrie, telles que celles définies par des organisations telles que la Commission électrotechnique internationale (CEI) ou l'Institut des ingénieurs électriciens et électroniciens (IEEE), garantit que les appareils électroniques répondent aux exigences de résistance mécanique spécifiées. Le respect de ces normes permet de garantir des performances constantes et fiables dans diverses conditions de fonctionnement.
- Emballage et manutention robustes : Des techniques d'emballage et de manutention appropriées pendant la fabrication, le transport et l'installation jouent un rôle crucial dans le maintien de la résistance mécanique. L'emballage protecteur, les mesures antistatiques et les procédures de manipulation sûres minimisent le risque de dommages physiques et préservent l'intégrité de l'appareil.
Réduction du bruit électrique
La réduction du bruit électrique est essentielle à la conception et au fonctionnement des appareils électroniques pour garantir des performances fiables et l'intégrité du signal. Voici quelques points clés mettant en évidence les avantages et les méthodes de réduction du bruit électrique :
- Mise à la terre et blindage :Des techniques de mise à la terre et des mécanismes de blindage appropriés aident à minimiser le bruit électrique en fournissant un chemin à faible impédance pour les courants électriques indésirables. Les blindages de mise à la terre et les boîtiers conducteurs aident à contenir et à rediriger les interférences électromagnétiques (EMI) et les interférences de radiofréquence (RFI), réduisant ainsi leur impact sur les composants sensibles.
- Filtrage et découplage :Les composants de filtrage et de découplage, tels que les condensateurs, les inducteurs et les perles de ferrite, aident à supprimer le bruit électrique en atténuant les composants haute fréquence. Ces composants sont stratégiquement placés à proximité de circuits sensibles ou de lignes d'alimentation pour empêcher le bruit de se propager davantage.
- Isolation des signaux : Les techniques d'isolation de signal, telles que les optocoupleurs ou les transformateurs, rompent la connexion électrique entre les circuits pour minimiser le transfert de bruit électrique. Isoler les signaux sensibles des sources de bruit aide à maintenir l'intégrité du signal et réduit le risque de corruption ou d'interférence des données.
- Disposition et routage du circuit imprimé : Des pratiques soigneuses de disposition et de routage des circuits imprimés sont essentielles pour réduire le bruit électrique. Une séparation appropriée des circuits analogiques et numériques, la minimisation des longueurs de trace et l'utilisation de plans de masse ou de techniques d'isolation des signaux peuvent aider à atténuer les effets du couplage du bruit et du rayonnement électromagnétique.
- Câbles et connecteurs blindés : Les câbles et connecteurs blindés aident à minimiser la captation ou l'émission de bruit. La protection des câbles avec des matériaux conducteurs, tels que des blindages tressés ou en feuille, fournit une barrière contre les interférences électromagnétiques externes.
- Techniques de mise à la terre :La mise en œuvre de techniques de mise à la terre appropriées, telles que la mise à la terre en étoile ou les plans de masse, garantit un point de référence commun pour les signaux électriques et aide à prévenir les boucles de masse qui peuvent introduire du bruit électrique.
- Filtres EMI/RFI : L'inclusion de filtres EMI/RFI aux étages d'entrée ou de sortie des alimentations ou des lignes de signal peut réduire considérablement le bruit électrique. Ces filtres atténuent les composantes de bruit haute fréquence et empêchent leur propagation dans les circuits sensibles.
- Sélection des composants :Le choix de composants à faible bruit, tels que des amplificateurs à faible bruit ou des références de tension de précision, peut contribuer à réduire le bruit électrique à la source. La sélection de composants à haute immunité au bruit ou aux interférences contribue également à la réduction du bruit.
- Test de compatibilité électromagnétique (CEM) : La réalisation de tests CEM pendant les étapes de conception et de fabrication permet d'identifier les sources potentielles de bruit électrique et d'évaluer la conformité de l'appareil aux normes de compatibilité électromagnétique. Ce test garantit que l'appareil fonctionne dans des limites de bruit acceptables et minimise les interférences avec d'autres équipements électroniques.
- Pratiques de mise à la terre et de liaison :Des pratiques de mise à la terre et de liaison appropriées tout au long de l'installation et du fonctionnement de l'appareil aident à réduire le bruit électrique. Il est essentiel de créer des connexions de mise à la terre solides, de connecter les composants métalliques à une terre partagée et d'utiliser des méthodes de gestion des câbles pour réduire les interférences.
Augmentation de la durée de vie de l'électronique
L'augmentation de la durée de vie de l'électronique est une considération cruciale pour les fabricants et les consommateurs. Voici quelques points clés mettant en évidence les avantages et les méthodes pour augmenter la durée de vie de l'électronique :
- Gestion thermique efficace : Des techniques de gestion thermique appropriées, telles qu'une dissipation thermique adéquate, peuvent prolonger considérablement la durée de vie des composants électroniques. Le maintien de températures de fonctionnement optimales minimise les contraintes thermiques sur les éléments, réduisant ainsi le risque de dégradation ou de défaillance.
- Conception et construction robustes : Concevoir des composants électroniques avec des composants puissants et durables, tels que des connecteurs, des résistances, des condensateurs et des circuits intégrés de haute qualité, peut améliorer leur longévité. Lors du choix des pièces, il est essentiel de prendre en compte leur longévité, leur fiabilité et leur capacité à gérer les niveaux de tension et de température appropriés.
- Bonne alimentation et régulation de tension : Assurer une alimentation électrique stable et propre est essentiel pour augmenter la durée de vie de l'électronique. Une régulation de tension appropriée, une protection contre les surtensions et des alimentations ou régulateurs de tension de haute qualité aident à prévenir les surtensions ou les fluctuations de tension qui peuvent endommager les composants sensibles.
- Protection ESD adéquate :La mise en œuvre de mesures de protection contre les décharges électrostatiques (ESD) appropriées protège l'électronique contre les dommages causés par l'électricité statique. L'utilisation de postes de travail protégés contre les décharges électrostatiques, de bandes de mise à la terre et d'emballages protégés contre les décharges électrostatiques garantit la sécurité lors de la fabrication, de la manipulation et de l'installation.
- Entretien et nettoyage réguliers : Un entretien régulier, y compris le nettoyage et l'inspection, peut aider à identifier et à résoudre les problèmes potentiels avant qu'ils ne s'aggravent. L'élimination de la poussière, des débris et des contaminants des appareils électroniques et la garantie d'une circulation d'air et d'une ventilation appropriées peuvent éviter la surchauffe et la défaillance des composants.
- Protection adéquate contre les facteurs environnementaux : La protection de l'électronique contre les facteurs environnementaux, tels que l'humidité, les températures extrêmes et les substances corrosives, est cruciale pour la longévité. Les concepteurs peuvent y parvenir en utilisant des boîtiers appropriés, des revêtements conformes ou des composés d'enrobage qui offrent une isolation et une protection contre les conditions difficiles.
- Manipulation et stockage appropriés :Manipuler les appareils électroniques avec soin, suivre des procédures d'installation raisonnables et les stocker dans des environnements contrôlés lorsqu'ils ne sont pas utilisés peut aider à prévenir les dommages physiques et à prolonger leur durée de vie. Nous protégeons contre les chocs physiques, les décharges statiques, la chaleur excessive, l'humidité ou l'exposition à la poussière.
- Mises à jour du micrologiciel et du logiciel :La mise à jour du micrologiciel et des logiciels permet de garantir des performances, une compatibilité et une sécurité optimales. Les mises à jour régulières incluent souvent des corrections de bogues, des améliorations de performances et une compatibilité améliorée, prolongeant ainsi la durée de vie utile de l'électronique.
- Considérations environnementales:Concevoir des appareils électroniques en tenant compte de considérations écologiques, telles que l'utilisation de composants économes en énergie, la réduction de la consommation d'énergie en mode veille et la mise en œuvre de programmes de recyclage ou d'élimination, contribue à leur durée de vie globale. Il favorise également la durabilité et réduit les déchets électroniques.
- Contrôle de qualité et tests : La mise en œuvre de mesures de contrôle qualité rigoureuses et de tests approfondis pendant la fabrication permet d'identifier et de corriger les défauts ou problèmes potentiels. Nous pouvons améliorer leur durée de vie en veillant à ce que seuls des composants électroniques fiables et de haute qualité soient disponibles.
Types de composés d'enrobage
Les concepteurs utilisent des composés d'enrobage pour encapsuler et protéger les composants électroniques, offrant une isolation, une résistance environnementale et un support mécanique. Divers composés d'empotage sont disponibles, chacun offrant des propriétés et des avantages spécifiques. Voici quelques types courants de composés d'empotage :
- Une résine époxy: La résine époxy est un choix populaire pour les applications d'enrobage en raison de ses excellentes propriétés d'isolation électrique, de sa haute résistance et de sa résistance aux produits chimiques et aux variations de température. Il offre une bonne adhérence à de nombreux substrats et une protection fiable contre l'humidité et les contaminants environnementaux.
- Polyuréthane: Les composés d'enrobage en polyuréthane offrent une flexibilité, une résistance aux chocs et une excellente résistance aux vibrations. Ils offrent une protection adéquate contre l'humidité, les produits chimiques et les rayons UV. Les composés de polyuréthane utilisent fréquemment des applications nécessitant une absorption des chocs ou un cycle thermique.
- Silicone: Les composés d'enrobage en silicone ont une stabilité thermique exceptionnelle, une résistance aux hautes températures et une excellente flexibilité sur une large plage de températures. Ils offrent une bonne isolation électrique et sont très résistants à l'humidité, aux produits chimiques et à l'exposition aux UV. Les concepteurs utilisent couramment des composés de silicone dans des applications qui nécessitent une résistance aux températures extrêmes ou une exposition à des environnements difficiles.
- Acrylique:Les gens apprécient les composés d'enrobage acryliques pour leur temps de durcissement rapide, leur faible retrait et leurs bonnes propriétés d'isolation électrique. Ils offrent une solution rentable pour de nombreuses applications d'empotage et offrent une résistance à l'humidité, aux produits chimiques et aux cycles thermiques. Les gens utilisent souvent des composés acryliques lorsqu'ils souhaitent un équilibre entre le coût, les performances et la facilité d'utilisation.
- Polyamide: Les composés d'enrobage en polyamide, connus sous le nom de composés à base de nylon, offrent une excellente résistance aux températures élevées, aux produits chimiques et aux contraintes mécaniques. Ils offrent une bonne adhérence sur divers substrats et offrent une protection fiable dans les environnements exigeants. Les fabricants utilisent couramment des composés de polyamide dans les applications automobiles, aérospatiales et industrielles.
- Séchage UV :Les composés d'enrobage à durcissement UV possèdent une caractéristique unique : ils durcissent à l'aide de lumière ultraviolette. Ils offrent des temps de durcissement rapides, permettant une productivité élevée dans les processus de fabrication. Les composés de durcissement UV offrent une excellente adhérence, une isolation électrique et une résistance à l'humidité et aux produits chimiques. Ils trouvent souvent une utilisation dans des applications qui nécessitent un durcissement rapide et un contrôle précis du processus de durcissement.
- Matériaux d'interface thermique (TIM) : Les matériaux d'interface thermique, tels que les graisses thermiques, les tampons thermiques ou les matériaux à changement de phase, sont utilisés pour les applications d'enrobage où le transfert efficace de la chaleur est crucial. Ces matériaux contribuent à améliorer la conductivité thermique et assurent une dissipation thermique efficace, empêchant la surchauffe des composants électroniques.
Il est essentiel de tenir compte des exigences spécifiques de l'application lors de la sélection d'un composé d'enrobage. Pour choisir le composé d'enrobage le plus approprié pour des performances et une protection optimales des composants électroniques, il convient de prendre en compte des facteurs tels que la plage de température, l'exposition chimique, les contraintes mécaniques, l'isolation électrique et le temps de durcissement.
Composé d'enrobage époxy
Diverses industries utilisent largement les composés d'enrobage époxy en raison de leurs propriétés exceptionnelles et de leurs applications polyvalentes. Voici quelques points clés mettant en évidence les caractéristiques et les avantages des composés d'enrobage époxy :
- Adhésion supérieure : Les composés d'enrobage époxy présentent une excellente adhérence à divers substrats, y compris les métaux, la céramique, les plastiques et les cartes de circuits imprimés (PCB). Cette liaison solide offre une stabilité mécanique et empêche la pénétration d'humidité, améliorant ainsi la fiabilité globale des appareils électroniques.
- Isolation électrique:Les composés d'enrobage époxy offrent d'excellentes propriétés d'isolation électrique, isolant et protégeant efficacement les composants électroniques sensibles des courants électriques et des courts-circuits potentiels. Cette isolation permet d'éviter les dysfonctionnements, la dégradation des performances et les dommages causés par les fuites électriques.
- Résistance aux hautes températures :Les composés d'enrobage époxy peuvent résister à des températures de fonctionnement élevées, ce qui les rend adaptés aux applications dans des environnements difficiles ou avec des composants générant de la chaleur. Ils conservent leur intégrité structurelle et leurs performances même à des températures élevées, garantissant la fiabilité à long terme de l'électronique enrobée.
- Résistance chimique et environnementale : Les composés d'enrobage époxy résistent à divers produits chimiques, notamment les solvants, les carburants, les huiles et les acides. Cette résistance aide à protéger les composants électroniques contre la corrosion chimique ou la dégradation, prolongeant leur durée de vie dans des environnements exigeants.
- Force mécanique:Les composés d'enrobage époxy offrent une excellente résistance mécanique et une intégrité structurelle, ce qui les rend adaptés aux applications nécessitant une résistance aux vibrations et une absorption des chocs. Ils aident à protéger les composants délicats des contraintes mécaniques, des impacts et des vibrations, garantissant des performances fiables même dans des conditions difficiles.
- Faible rétrécissement: Les composés d'enrobage époxy ont généralement un faible retrait pendant le processus de durcissement. Cette caractéristique fournit une contrainte minimale sur les composants enrobés et réduit le risque de fissuration ou de délaminage, améliorant la stabilité et la durabilité globales de l'électronique encapsulée.
- Polyvalence:Les composés d'enrobage époxy trouvent une application dans diverses industries, notamment l'électronique, l'automobile, l'aérospatiale et les télécommunications. Ils trouvent une utilisation dans l'encapsulation et la protection de plusieurs appareils, tels que les alimentations, les capteurs, les moteurs, les modules LED et les unités de commande électroniques (ECU).
- Traitement facile : Les composés d'enrobage époxy sont généralement faciles à manipuler et à traiter. Ils offrent la commodité d'être facilement mélangés, versés ou distribués dans des moules ou sur des composants, permettant des processus de production et d'assemblage efficaces. Leur viscosité et leur temps de durcissement gérables permettent une application précise et facilitent la fabrication à grand volume.
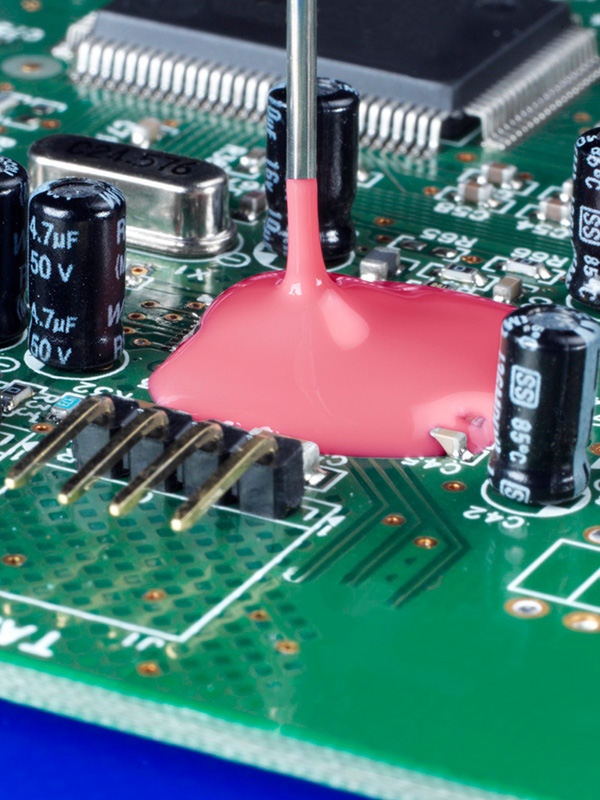
Composé d'enrobage de silicone
Les composés d'enrobage en silicone sont des matériaux très polyvalents pour une utilisation intensive dans diverses industries. Voici quelques points clés mettant en évidence les caractéristiques et les avantages des composés d'enrobage en silicone :
- Flexibilité et performances à basse température : Les composés d'enrobage en silicone offrent une flexibilité et une élasticité exceptionnelles, ce qui les rend adaptés aux applications nécessitant des mouvements dynamiques ou une résistance aux vibrations. Ils peuvent conserver leurs propriétés même à basse température, garantissant des performances fiables dans les environnements froids.
- Excellente résistance à l'humidité : Les composés d'enrobage en silicone présentent une excellente résistance à l'humidité et à l'eau. Ils créent une barrière fiable contre l'humidité, protégeant les composants électroniques sensibles de la corrosion et des dommages causés par l'exposition à l'humidité ou aux environnements humides.
- Résistance aux UV et aux intempéries : Les composés d'enrobage en silicone ont une résistance inhérente aux UV et aux intempéries, ce qui leur permet de résister à une exposition prolongée à la lumière du soleil et aux éléments extérieurs. Le rempotage en silicone est parfait pour une utilisation en extérieur car il protège contre les rayons UV et les facteurs environnementaux. De plus, il possède de bonnes propriétés diélectriques. Les composés possèdent de bonnes propriétés diélectriques, ce qui en fait des isolants efficaces pour les composants électriques. Ils peuvent empêcher les fuites électriques et fournir une isolation fiable, réduisant ainsi le risque de courts-circuits et de pannes électriques.
- Stabilité thermique: Les composés d'enrobage en silicone présentent une excellente stabilité thermique et peuvent résister à diverses températures. Ils restent flexibles et conservent leurs propriétés sur une large plage de températures, garantissant des performances constantes dans les environnements chauds et froids.
- Résistance chimique: Les composés d'enrobage en silicone résistent à divers produits chimiques, notamment les huiles, les solvants et de nombreux produits chimiques industriels courants. Cette résistance protège les composants électroniques de la corrosion chimique et de la dégradation, améliorant leur durée de vie et leur fiabilité dans des environnements difficiles.
- Traitement et durcissement faciles :Les composés d'enrobage en silicone sont généralement faciles à manipuler et à traiter. Ils ont une viscosité gérable, permettant une application précise et un remplissage facile de formes complexes ou de vides. Ils offrent également un temps de durcissement relativement rapide, permettant des processus de production et d'assemblage efficaces.
- Compatibilité avec les composants sensibles :Les composés d'enrobage en silicone sont connus pour leur compatibilité avec une large gamme de composants sensibles, tels que les capteurs, les connecteurs et les circuits électroniques délicats. Leur nature douce et non abrasive protège les composants enrobés sans compromettre leur fonctionnalité.
- Large gamme d'applications:Diverses industries, notamment l'électronique, l'automobile, l'aérospatiale, les dispositifs médicaux et les énergies renouvelables, utilisent largement les composés d'enrobage en silicone. Ils trouvent un emploi dans l'encapsulation et la protection des modules électroniques, de l'éclairage LED, des capteurs, des alimentations et d'autres composants critiques.
Ces propriétés en font un choix privilégié pour l'enrobage et l'encapsulation, garantissant une protection fiable et des performances à long terme des appareils électroniques dans diverses industries.
Composé d'enrobage en polyuréthane
Diverses industries utilisent largement les composés d'enrobage en polyuréthane pour leurs propriétés uniques et leurs applications polyvalentes. Voici quelques points clés mettant en évidence les caractéristiques et les avantages des composés d'enrobage en polyuréthane :
- Excellente résistance mécanique : Les composés d'enrobage en polyuréthane offrent une résistance mécanique exceptionnelle, ce qui les rend adaptés aux applications qui nécessitent une protection robuste contre les contraintes mécaniques, les vibrations et les impacts. Ils offrent une excellente résistance à la déformation, assurant la stabilité et la durabilité à long terme des composants encapsulés.
- Amortissement des vibrations et absorption des chocs :Les composés d'enrobage en polyuréthane présentent d'excellentes propriétés d'amortissement des vibrations, leur permettant d'absorber et de dissiper les vibrations. Dans les environnements exigeants, les vibrations peuvent avoir un impact négatif sur les composants électroniques sensibles. La mise en place de mesures de protection est essentielle pour garantir des performances fiables.
- Résistance chimique et environnementale :Les composés d'enrobage en polyuréthane résistent à divers produits chimiques, y compris les huiles, les solvants et les substances industrielles courantes. Ils offrent également une résistance contre l'humidité, l'humidité et d'autres facteurs environnementaux, protégeant les composants électroniques de la corrosion et de la dégradation.
- Stabilité thermique:Les composés d'enrobage en polyuréthane présentent une excellente stabilité thermique, ce qui leur permet de résister à des températures de fonctionnement élevées sans compromettre leurs propriétés ou leur intégrité. Cette caractéristique les rend adaptés aux applications impliquant des composants générant de la chaleur ou exposés à des températures élevées.
- Isolation électrique: Les composés d'enrobage en polyuréthane présentent de bonnes propriétés d'isolation électrique, isolant et protégeant efficacement les composants électroniques des courants électriques, des courts-circuits potentiels et des interférences électriques. Ils contribuent aux performances fiables et à la longévité des dispositifs encapsulés.
- Adhésion à divers substrats :Les composés d'enrobage en polyuréthane adhèrent bien à divers substrats, y compris les métaux, les plastiques, la céramique et les PCB. Cette liaison solide améliore la stabilité mécanique globale des composants encapsulés, empêchant la pénétration d'humidité et favorisant un fonctionnement fiable.
- Faible rétrécissement:Les composés d'enrobage en polyuréthane ont généralement un faible retrait pendant le processus de durcissement. Cette caractéristique minimise les contraintes sur les composants encapsulés, réduisant ainsi le risque de fissuration, de délaminage ou de dommages causés par des contraintes internes.
- Polyvalence: Les composés d'enrobage en polyuréthane trouvent une application dans diverses industries, telles que l'électronique, l'automobile, l'aérospatiale et les énergies renouvelables. Ils l'utilisent pour encapsuler et protéger divers appareils, notamment des capteurs, des connecteurs, des composants électroniques de puissance et des modules de contrôle.
- Facilité de traitement :Les composés d'enrobage en polyuréthane sont généralement faciles à manipuler et à traiter. Ils offrent la commodité d'être facilement mélangés, versés ou distribués dans des moules ou sur des composants, permettant des processus de production et d'assemblage efficaces. Leur viscosité et leur temps de durcissement gérables permettent une application précise et facilitent la fabrication à grand volume.
Facteurs à prendre en compte lors du choix d'un composé d'empotage
Il faut tenir compte de plusieurs facteurs lors du choix d'un composé d'empotage pour une application spécifique. Voici quelques points clés à considérer lors du choix d'un terreau :
- Conditions d'application: Évaluez les exigences spécifiques de l'application, y compris la plage de température, l'exposition aux produits chimiques, la résistance à l'humidité, la résistance aux UV, les contraintes mécaniques et les propriétés d'isolation électrique. Déterminez le niveau de protection nécessaire pour les composants afin de vous assurer que le composé d'enrobage peut répondre aux normes de performance souhaitées.
- Compatibilité:Assurez-vous que le composé d'enrobage est compatible avec les matériaux encapsulés, tels que les PCB, les connecteurs, les capteurs ou d'autres composants électroniques. Tenez compte de facteurs tels que l'adhérence, le coefficient de dilatation thermique (CTE) et les interactions potentielles entre le composé d'enrobage et les matériaux encapsulés.
- Temps et processus de durcissement :Évaluez le temps de durcissement et le processus du composé d'enrobage. Tenez compte de facteurs tels que la durée de vie en pot, la température de durcissement et le temps de durcissement. Déterminez si le processus de durcissement s'aligne sur le processus de fabrication ou d'assemblage et s'il permet une production efficace et un temps de traitement adéquat.
- Force mécanique:Tenez compte des exigences de résistance mécanique de l'application. Évaluez le potentiel de vibration, d'impact ou de contrainte mécanique et choisissez un composé d'enrobage qui peut fournir la résistance et la durabilité nécessaires pour résister à de telles conditions.
- Conductivité thermique:Évaluer les exigences de conductivité thermique de l'application. Choisissez un composé d'enrobage capable de transférer efficacement la chaleur des composants générant de la chaleur en fonction des besoins de dissipation de la chaleur, assurant une gestion thermique optimale.
- Propriétés électriques: Considérez les propriétés d'isolation électrique du composé d'enrobage. Assurez-vous qu'il offre la rigidité diélectrique et la résistance requises pour éviter les fuites électriques ou les courts-circuits. Si les interférences électromagnétiques (EMI) sont un problème, envisagez des composés d'enrobage avec des propriétés de blindage EMI améliorées.
- Considérations environnementales: Évaluer les conditions écologiques auxquelles le composé d'empotage sera exposé. Évaluez les facteurs tels que l'humidité, l'humidité, le rayonnement UV et l'exposition aux produits chimiques. Choisissez un composé d'empotage qui peut protéger et résister à des défis environnementaux spécifiques.
- Compatibilité de processus : Tenez compte de la compatibilité du composé d'enrobage avec le processus de fabrication ou d'assemblage. Évaluez la viscosité, la durée de vie en pot, les exigences de mélange, les méthodes de distribution et les conditions de durcissement. Assurez-vous que le composé d'enrobage peut s'intégrer facilement dans les processus de production existants.
- Conformité réglementaire: Assurez-vous que le composé d'empotage choisi est conforme aux normes et réglementations pertinentes de l'industrie, telles que RoHS (Restriction of Hazardous Substances) ou REACH (Registration, Evaluation, Authorization, and Restriction of Chemicals). Ce faisant, nous garantissons que le produit final est à la fois sûr et conforme.
Compte tenu de ces facteurs, on peut prendre une décision éclairée lors de la sélection d'un composé d'enrobage qui répond le mieux aux exigences de l'application, assurant une protection et des performances optimales des composants électroniques encapsulés.
Compatibilité avec l'électronique
La compatibilité avec l'électronique est un facteur crucial à prendre en compte lors du choix d'un composé d'enrobage pour encapsuler des composants électroniques. Voici quelques points clés à considérer concernant la compatibilité des composés d'enrobage avec l'électronique :
- Compatibilité chimique :Assurez-vous que le composé d'enrobage est chimiquement compatible avec les matériaux utilisés dans les composants électroniques, tels que les PCB, les connecteurs et les circuits électroniques sensibles. La compatibilité garantit que le composé d'empotage ne réagira pas avec les ingrédients ou ne les dégradera pas, entraînant un dysfonctionnement ou des dommages.
- Adhérence: Considérez les propriétés d'adhérence du composé d'enrobage aux surfaces des composants électroniques. Il doit bien adhérer aux matériaux encapsulés, offrant une liaison solide et empêchant tout espace ou vide qui pourrait compromettre la protection offerte par le composé d'enrobage.
- Propriétés diélectriques : Évaluer les propriétés diélectriques du composé d'enrobage. Il doit posséder de bonnes propriétés d'isolation électrique pour garantir que les composants encapsulés sont efficacement isolés les uns des autres et des courants électriques externes. Cela évite la possibilité de courts-circuits ou d'interférences électriques.
- Conductivité thermique: Considérez les exigences de conductivité thermique de l'électronique. Selon l'application, le composé d'enrobage doit avoir la conductivité thermique appropriée pour dissiper la chaleur générée par les composants. Le maintien de températures de fonctionnement optimales est essentiel pour éviter la surchauffe, qui peut entraîner des problèmes de performances ou une défaillance des composants.
- Coefficient de dilatation thermique: Tenez compte du coefficient de dilatation thermique (CTE) du composé d'enrobage et de sa compatibilité avec les composants électroniques. Des valeurs CTE similaires entre le composé d'enrobage et les matériaux encapsulés réduisent le risque de fissuration ou de délaminage induit par la contrainte en raison du cycle thermique.
- Résistance à l'humidité et à l'environnement :Évaluez la résistance du composé d'empotage à l'humidité, à l'humidité et à d'autres facteurs environnementaux. L'électronique est fréquemment exposée à des environnements difficiles, nécessitant que le composé d'enrobage fournisse une protection fiable contre la pénétration d'humidité. Cette protection aide à prévenir la corrosion et les dommages aux composants.
- Compatibilité avec les procédés de fabrication :Considérez la compatibilité du composé d'enrobage avec les processus de fabrication ou d'assemblage. Évaluez la viscosité, la durée de vie en pot, les exigences de mélange et les conditions de durcissement. Assurez-vous que le composé d'enrobage s'intègre facilement dans les processus de production existants sans entraîner de retards ni de complications.
- Conformité réglementaire:Assurez-vous que le composé d'enrobage est conforme aux réglementations et normes pertinentes de l'industrie, telles que RoHS (Restriction of Hazardous Substances) ou REACH (Registration, Evaluation, Authorization, and Restriction of Chemicals). La conformité garantit que le composé d'empotage ne contient aucune substance nocive qui pourrait nuire à la santé humaine ou à l'environnement.
Temps de durcissement
Le temps de durcissement est un facteur essentiel à prendre en compte lors du choix d'un composé d'enrobage pour encapsuler des composants électroniques. Voici quelques points clés à considérer concernant le temps de durcissement :
- Vie en pot: La durée de vie en pot fait référence à la durée pendant laquelle le composé d'enrobage reste utilisable après le mélange des composants. Il est essentiel de comprendre la durée de vie en pot du composé pour garantir un temps suffisant pour une application et un positionnement corrects des composants avant que le matériau ne commence à durcir.
- Temps de durcissement:Un temps de durcissement est nécessaire pour que le composé d'enrobage durcisse et atteigne pleinement les propriétés souhaitées. La sélection d'un composé d'enrobage avec un temps de durcissement qui s'aligne sur le calendrier de production ou le processus d'assemblage est cruciale. Des temps de durcissement longs peuvent entraîner des retards de production, tandis que des temps de durcissement courts peuvent nécessiter un traitement rapide.
- Conditions ambiantes: Considérez l'effet des conditions ambiantes, telles que la température et l'humidité, sur le temps de durcissement du composé d'enrobage. Certains composés peuvent nécessiter des conditions de température ou d'humidité spécifiques pour un durcissement optimal. Assurez-vous que les conditions ambiantes pendant le processus de durcissement peuvent être facilement contrôlées et maintenues.
- Techniques d'accélération :Certains composés d'enrobage offrent des options de durcissement accéléré par la chaleur, la lumière UV ou des additifs chimiques. Cette méthode conduit à des temps de durcissement plus rapides, ce qui la rend avantageuse pour les paramètres de production à volume élevé ou lorsqu'un délai d'exécution rapide est nécessaire.
- Considérations post-durcissement :Comprenez si le composé d'empotage nécessite des étapes de post-durcissement, telles qu'un traitement thermique supplémentaire ou une exposition aux UV, pour atteindre ses propriétés complètes. Lors de l'évaluation de l'aspect pratique du composé d'empotage, il est essentiel de tenir compte de l'impact des mesures de post-durcissement sur le calendrier de production global.
- Temps de manipulation et de maniabilité :Considérez le temps de manipulation et de maniabilité du composé d'empotage, qui fait référence à la durée pendant laquelle le matériau reste dans un état approprié pour le mélange, le versement ou la distribution ; choisir un composé d'enrobage qui offre un temps de manipulation adéquat pour une application efficace tout en garantissant une qualité constante.
- Est important de guérir le rétrécissement : Évaluer le retrait potentiel du composé d'enrobage pendant le processus de durcissement. Un rétrécissement excessif peut provoquer une contrainte sur les composants encapsulés et peut entraîner une fissuration ou un délaminage. Le choix d'un composé d'enrobage avec un retrait minimal aide à maintenir l'intégrité et la fiabilité de l'électronique encapsulée.
- Optimisation et tests :Il est conseillé d'effectuer des tests approfondis et d'optimiser le processus de durcissement du composé d'enrobage sélectionné. Il faut tenir compte de la taille des composants, de la complexité, de la résistance mécanique souhaitée et des performances thermiques pour garantir le temps de durcissement approprié pour une application spécifique.
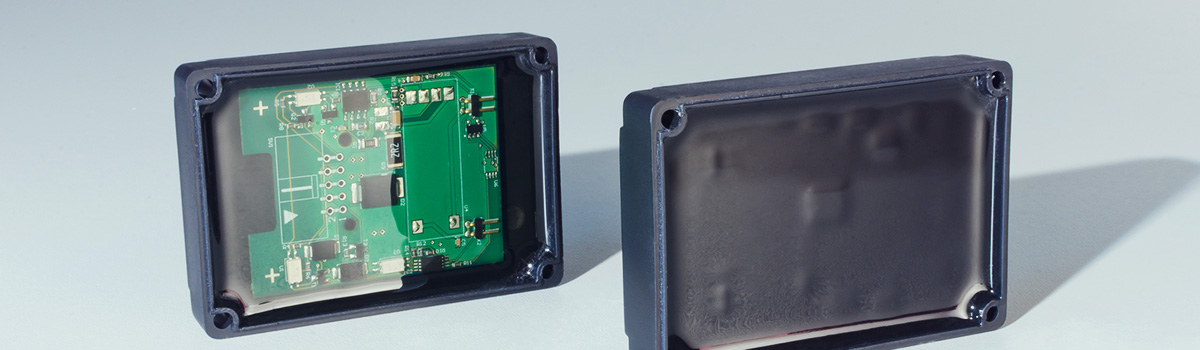
Résistance à la température
Lors de la sélection d'un composé d'enrobage pour composants électroniques, il est crucial de prendre en compte la résistance à la température, en particulier dans les applications où les matériaux seront exposés à des températures extrêmes. Voici quelques points clés à considérer concernant la résistance à la température :
- Température de fonctionnement: Évaluez la plage de températures de fonctionnement attendue des composants électroniques et choisissez un composé d'enrobage capable de résister à ces températures sans dégradation ni perte de performances. Tenez compte des températures extrêmes élevées et basses que les éléments peuvent rencontrer pendant le fonctionnement.
- Cyclisme thermique: Évaluer la capacité du composé d'enrobage à résister aux cycles thermiques, ce qui implique des fluctuations de température répétées. Les composants qui subissent des changements de température peuvent se dilater et se contracter, entraînant potentiellement une contrainte sur le matériau d'encapsulation. Choisissez un composé d'enrobage avec un coefficient de dilatation thermique (CTE) approprié pour minimiser les contraintes et éviter les fissures ou le délaminage.
- Résistance aux hautes températures :Sélectionnez un composé d'enrobage avec une excellente résistance à la chaleur si l'application implique des environnements à haute température. Recherchez un composé capable de conserver sa résistance mécanique, ses propriétés d'isolation électrique et d'autres caractéristiques de performance à des températures élevées.
- Résistance aux basses températures :Choisissez un composé d'enrobage avec une bonne résistance aux basses températures pour les applications qui nécessitent un fonctionnement dans des conditions glaciales. Il doit rester flexible et conserver sa fonctionnalité même à des températures inférieures à zéro, garantissant l'intégrité des composants encapsulés.
- Conductivité thermique:Tenez compte de la conductivité thermique du composé d'enrobage, en particulier dans les applications où la dissipation thermique est critique. Un composé d'enrobage avec une bonne conductivité thermique peut efficacement transférer la chaleur des composants encapsulés, aidant à maintenir des températures de fonctionnement optimales et à prévenir la surchauffe.
- Propriétés d'isolation : Assurez-vous que le composé d'enrobage conserve ses propriétés d'isolation électrique sur toute la plage de température de l'application. Il doit isoler efficacement les composants électroniques et prévenir les risques de fuites électriques ou de courts-circuits, même dans des conditions de températures extrêmes.
- Compatibilité avec les solutions de gestion thermique :Si vous utilisez des solutions de gestion thermique telles que des dissipateurs thermiques ou des tampons thermiques avec le composé d'enrobage, vérifiez la compatibilité entre le composé d'enrobage et ces composants. En assurant un transfert de chaleur efficace, nous pouvons atteindre une efficacité thermique maximale.
- Test et Validation : Effectuez des tests approfondis et validez la résistance à la température du composé d'enrobage. Pour garantir la fiabilité et les performances du matériau, vous devrez peut-être le soumettre à des cycles de température, à un choc thermique ou à une exposition prolongée à des températures extrêmes.
Considérations de coûts
Les considérations de coût sont importantes lors de la sélection d'un composé d'enrobage pour les composants électroniques, ce qui a un impact direct sur le budget global du projet. Voici quelques points clés à considérer concernant les considérations de coût :
- Coût matériel: Évaluez le coût du composé d'empotage lui-même. Différents types de composés d'enrobage, tels que l'époxy, le silicone ou le polyuréthane, varient en prix. Considérez le matériel nécessaire pour le projet et comparez le coût par unité de volume pour chaque type.
- Efficacité des applications :Évaluer la facilité d'application et la maniabilité du composé d'empotage. Certains composés peuvent nécessiter un équipement spécialisé ou une main-d'œuvre qualifiée pour une application appropriée, ce qui augmente les coûts de main-d'œuvre globaux. Choisissez un composé d'enrobage que vous pouvez facilement appliquer en utilisant les processus de fabrication existants ou avec un investissement supplémentaire minimal en équipement.
- Déchets et nettoyage : Tenez compte de la quantité de déchets générés pendant le processus d'empotage et de la facilité de nettoyage. Certains composés d'empotage peuvent avoir des exigences d'élimination spécifiques, ce qui peut augmenter le coût global du projet. Optez pour des matériaux qui génèrent un minimum de déchets et qui ont des procédures de nettoyage simples.
- Temps de production: Analysez le temps de durcissement et la durée de vie en pot du composé d'enrobage. Des temps de durcissement plus longs peuvent augmenter la production, entraînant des coûts de main-d'œuvre supplémentaires et des retards potentiels. Sélectionnez un composé d'enrobage avec un temps de durcissement qui s'aligne sur le calendrier de production pour optimiser l'efficacité et réduire les coûts.
- Exigences de performances : Équilibrez le coût du composé d'enrobage avec les exigences de performance souhaitées des composants électroniques. Les options moins chères peuvent offrir une protection ou des performances différentes de celles plus chères. Évaluez la criticité de l'application et sélectionnez un composé d'enrobage qui répond aux normes de performance nécessaires sans sur-spécifications inutiles.
- Fiabilité et longévité : Considérez les implications financières à long terme du composé d'empotage. Investir dans un composé d'enrobage de meilleure qualité et plus cher peut augmenter la fiabilité et la longévité de l'électronique encapsulée. La réduction des pannes, des réparations et des remplacements tout au long de la durée de vie du projet peut réduire les coûts.
- Assistance et garantie du fournisseur :Évaluez l'assistance fournie par le fournisseur de composé d'enrobage et toute garantie ou garantie associée. Un fournisseur réputé avec un excellent service client peut offrir une assistance technique, un dépannage et une couverture de garantie, contribuant ainsi à réduire les coûts en cas de problème ou de préoccupation.
- Conformité réglementaire: Tenez compte des implications financières de la conformité réglementaire. Assurez-vous que le composé d'empotage choisi est conforme aux réglementations et normes pertinentes de l'industrie. La non-conformité peut entraîner des pénalités ou des revers de projet, ce qui peut entraîner des coûts supplémentaires.
En examinant attentivement les considérations de coût et les facteurs connexes, on peut sélectionner un composé d'enrobage qui équilibre l'abordabilité et répond aux exigences de performance et de fiabilité nécessaires pour les composants électroniques encapsulés.
Techniques d'application
Les techniques d'application des composés d'enrobage impliquent l'encapsulation de composants électroniques avec le matériau choisi. Voici quelques points clés à considérer concernant les techniques d'application :
- Distribution : La distribution est une technique d'application courante dans laquelle le composé d'enrobage est distribué directement sur les composants électroniques. Vous pouvez le faire manuellement à l'aide de seringues ou l'automatiser à l'aide d'un équipement de distribution. La distribution permet une application précise et un contrôle sur la quantité de matériau utilisé.
- Rempotage sous vide : L'enrobage sous vide consiste à placer les composants électroniques dans une chambre à vide, puis à introduire le composé d'enrobage. Le vide aide à éliminer les bulles d'air et assure une bonne pénétration et couverture du composé autour des éléments. Cette technique permet d'obtenir une encapsulation sans vide.
- Moulage par injection: Le moulage par injection est une technique d'application plus automatisée et à grand volume. Le composé d'enrobage est chauffé et injecté dans une cavité de moule contenant les composants électroniques. Après durcissement, ouvrez le moule et retirez les pièces encapsulées. Le moulage par injection offre une encapsulation efficace et cohérente, ce qui le rend adapté à une production à grande échelle.
- Sacs de rempotage :Les sacs de rempotage sont des sacs préformés en plastique ou en silicone remplis de composé de rempotage. Placez les composants électroniques à l'intérieur du sac et scellez-le avant de commencer le processus de durcissement. Cette technique est appropriée lorsqu'il s'agit de formes ou de caractéristiques complexes qui nécessitent une orientation spécifique lors de l'encapsulation.
- Revêtement enrobant:Le revêtement conforme consiste à appliquer une fine couche de composé d'enrobage sur la surface des composants électroniques. Il protège contre les facteurs environnementaux sans encapsuler complètement les composants. Le revêtement conforme convient aux applications où l'accessibilité ou la possibilité de retravailler les ingrédients est essentielle.
- Encapsulation sous vide : L'encapsulation sous vide consiste à combiner l'enrobage sous vide avec la mise en place d'un film ou d'un sac protecteur autour des composants électroniques. Le vide élimine l'air de l'emballage, introduisant le composé d'enrobage pour remplir les vides. Ensuite, scellez le film ou le sac pour créer un récipient hermétiquement fermé. Cette technique est utile pour les applications qui nécessitent une protection de haut niveau contre l'humidité et d'autres contaminants.
- Casting de films : La coulée de film consiste à verser ou à étaler un composé d'enrobage liquide sur une surface plane et à le laisser durcir en un film mince. Le film est ensuite découpé et façonné pour correspondre aux dimensions des composants électroniques. Cette technique convient aux applications qui souhaitent une couche d'encapsulation flexible et fine.
- Application robotique :L'application robotique implique l'utilisation de systèmes mécaniques pour appliquer le composé d'enrobage sur les composants électroniques. Des bras robotisés ou des systèmes de distribution automatisés garantissent une application précise et cohérente. Cette technique trouve une utilisation courante dans les environnements de production à volume élevé.
Applications courantes du composé d'enrobage pour PCB
Les composés d'enrobage de PCB sont largement utilisés dans diverses applications où la protection, l'isolation et la fiabilité accrue des composants électroniques sont essentielles. Voici quelques applications typiques des composés d'enrobage de PCB :
- Électronique automobile :L'électronique automobile utilise largement les composés d'enrobage de PCB, y compris les modules de commande, les capteurs, les systèmes d'allumage et l'éclairage. Ils protègent contre les vibrations, l'humidité et les fluctuations de température, garantissant la durabilité et les performances des composants électroniques dans les environnements automobiles difficiles.
- Électronique grand public: Les appareils électroniques grand public tels que les smartphones, les tablettes, les ordinateurs portables et les appareils ménagers utilisent des composés d'enrobage. Ils offrent une protection contre les contraintes mécaniques, l'humidité, la poussière et les chocs, prolongeant la durée de vie et la fiabilité des appareils électroniques.
- Équipement industriel:Les équipements industriels tels que les alimentations électriques, les entraînements de moteur, les panneaux de commande et les systèmes d'automatisation utilisent des composés d'enrobage de PCB. Ils protègent les composants électroniques sensibles contre les risques environnementaux, notamment l'exposition aux produits chimiques, les vibrations, les températures extrêmes et les interférences électriques.
- Systèmes d'énergie renouvelable : Les composés d'enrobage sont essentiels dans les systèmes d'énergie renouvelable tels que les panneaux solaires, les éoliennes et les dispositifs de stockage d'énergie. Ils protègent les appareils électroniques sensibles des conditions extérieures, y compris les rayons UV, l'humidité et les variations de température, garantissant la fonctionnalité et les performances à long terme des systèmes d'énergie renouvelable.
- Éclairage LED:Les applications d'éclairage LED utilisent largement les composés d'enrobage de PCB, y compris les pilotes LED, les modules et les luminaires extérieurs. Ils offrent une protection contre la chaleur, l'humidité et les vibrations, permettant un fonctionnement fiable et une durée de vie prolongée des systèmes d'éclairage à LED.
- Aéronautique et Défense :Les composés d'enrobage trouvent une application dans l'aérospatiale et l'électronique de défense, y compris l'avionique, les systèmes de communication, les équipements radar et les véhicules militaires. Ils protègent contre les températures extrêmes, les chocs, les vibrations et la pénétration d'humidité, assurant le fonctionnement fiable des composants électroniques critiques dans des environnements exigeants.
- Équipement médical: Les dispositifs médicaux tels que les équipements de diagnostic, les systèmes de surveillance des patients et les dispositifs implantables utilisent des composés d'enrobage de PCB. Ils offrent une protection contre l'humidité, les produits chimiques et les processus de stérilisation, garantissant l'intégrité et la longévité des composants électroniques sensibles dans les environnements médicaux.
- Équipement marin et offshore :Les composés d'enrobage trouvent une utilisation dans les applications marines et offshore, y compris les systèmes de navigation, les capteurs sous-marins et les équipements de communication. Ils protègent contre les infiltrations d'eau, la corrosion par l'eau salée et les vibrations, garantissant des performances et une longévité fiables dans les environnements marins difficiles.
- Télécommunications:Les équipements de télécommunications, y compris les stations de base, les commutateurs de réseau et les dispositifs de communication, utilisent des composés d'enrobage. Ils offrent une protection contre l'humidité, la poussière et les variations de température, assurant le fonctionnement ininterrompu de l'infrastructure de communication critique.
- Modules et assemblages électroniques :Diverses industries utilisent des composés d'enrobage de PCB pour encapsuler des modules et des assemblages électroniques. Ceux-ci incluent l'électronique de puissance, les systèmes de contrôle, les assemblages de circuits imprimés et les sous-assemblages électroniques. Les composés d'enrobage protègent les facteurs environnementaux, améliorant la fiabilité et les performances de l'électronique encapsulée.
L'importance d'utiliser un composé d'enrobage pour PCB
Le composé d'enrobage PCB est un matériau crucial pour la protection et la fiabilité à long terme des composants électroniques. L'empotage ou l'encapsulation d'un appareil électronique peut le protéger contre l'environnement, les contraintes thermiques, les chocs physiques et l'exposition aux produits chimiques. Voici quelques raisons pour lesquelles l'utilisation d'un composé d'enrobage pour PCB est essentielle :
- Protection environnementale:Le composé d'enrobage crée une barrière qui protège les composants électroniques de l'humidité, de la poussière et d'autres facteurs environnementaux pouvant entraîner de la corrosion ou des courts-circuits.
- Durabilité améliorée : L'enrobage peut ajouter de la force physique et de la résistance aux chocs aux composants électroniques, les rendant plus durables et moins sujets aux dommages causés par les vibrations ou les chocs.
- Fiabilité accrue : En éliminant les poches d'air, les composés d'enrobage peuvent réduire le risque de choc thermique et améliorer la fiabilité globale de l'électronique.
- Gestion thermique améliorée : Les composés d'enrobage peuvent améliorer la dissipation de la chaleur, ce qui peut aider à prolonger la durée de vie des composants qui génèrent beaucoup de chaleur.
- Bruit réduit : L'empotage peut aider à réduire le bruit électrique, améliorant ainsi les performances globales de l'électronique.
- Économies de coûts:En protégeant les composants électroniques contre les dommages, l'empotage peut aider à réduire les coûts de réparation et de remplacement. De plus, l'utilisation de composés d'enrobage peut aider à réduire la probabilité de réclamations au titre de la garantie et à améliorer la satisfaction des clients.
L'utilisation de composés d'enrobage de PCB peut aider à garantir la fiabilité et les performances à long terme des composants électroniques, ce qui est crucial dans un large éventail d'industries et d'applications.
Conclusion
Le composé d'enrobage de PCB est un composant crucial pour assurer la longévité et la fiabilité des systèmes électroniques. Il offre une protection contre les facteurs environnementaux, améliore les performances thermiques, améliore la résistance mécanique et réduit le bruit électrique. Le type de composé d'enrobage choisi dépendra de plusieurs facteurs, notamment la compatibilité avec l'électronique, le temps de durcissement, la résistance à la température et le coût. En sélectionnant et en appliquant correctement le composé d'enrobage approprié, les composants électroniques peuvent être protégés des conditions difficiles, augmentant ainsi leur durée de vie et leur fiabilité.