Sottoriempimento epossidico
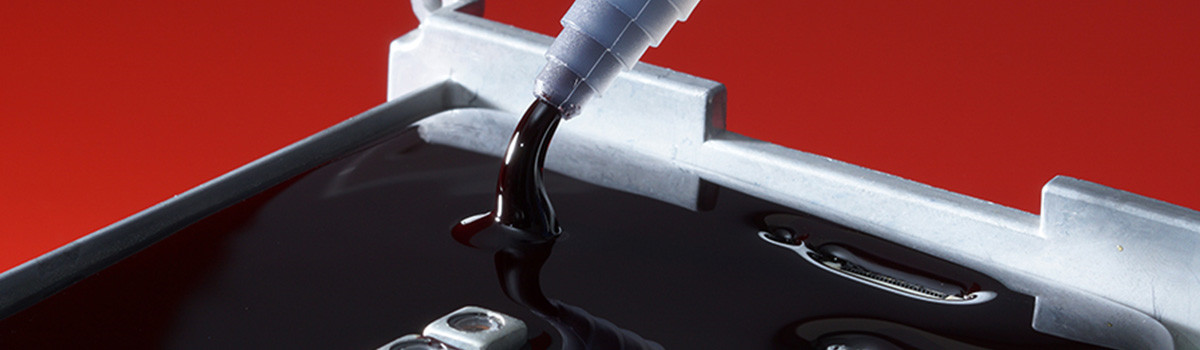
La resina epossidica Underfill è un tipo di adesivo utilizzato per migliorare l'affidabilità dei componenti elettronici, in particolare nelle applicazioni di imballaggio dei semiconduttori. Colma il divario tra il contenitore e il circuito stampato (PCB), fornendo supporto meccanico e riduzione delle sollecitazioni per prevenire danni da espansione termica e contrazione. La resina epossidica Underfill migliora anche le prestazioni elettriche del pacchetto riducendo l'induttanza parassita e la capacità. In questo articolo, esploriamo le varie applicazioni della resina epossidica underfill, i diversi tipi disponibili e i loro vantaggi.
L'importanza della resina epossidica Underfill negli imballaggi dei semiconduttori
La resina epossidica Underfill è fondamentale nell'imballaggio dei semiconduttori, poiché fornisce rinforzo meccanico e protezione ai delicati componenti microelettronici. È un materiale adesivo specializzato utilizzato per colmare il divario tra il chip semiconduttore e il substrato del pacchetto, migliorando l'affidabilità e le prestazioni dei dispositivi elettronici. Qui, esploreremo l'importanza della resina epossidica non riempita negli imballaggi dei semiconduttori.
Una delle funzioni principali della resina epossidica non caricata è quella di migliorare la resistenza meccanica e l'affidabilità della confezione. Durante il funzionamento, i chip semiconduttori sono soggetti a varie sollecitazioni meccaniche, come espansione e contrazione termica, vibrazioni e shock meccanici. Queste sollecitazioni possono portare alla formazione di crepe nei giunti di saldatura, che possono causare guasti elettrici e ridurre la durata complessiva del dispositivo. La resina epossidica Underfill agisce come un agente di riduzione dello stress distribuendo lo stress meccanico in modo uniforme su chip, substrato e giunti di saldatura. Riduce efficacemente al minimo la formazione di cricche e previene la propagazione di cricche esistenti, garantendo l'affidabilità a lungo termine del pacchetto.
Un altro aspetto critico della resina epossidica underfill è la sua capacità di migliorare le prestazioni termiche dei dispositivi a semiconduttore. La dissipazione del calore diventa una preoccupazione significativa in quanto i dispositivi elettronici si riducono di dimensioni e aumentano la densità di potenza e il calore eccessivo può degradare le prestazioni e l'affidabilità del chip semiconduttore. La resina epossidica Underfill ha eccellenti proprietà di conduttività termica, che le consentono di trasferire in modo efficiente il calore dal chip e di distribuirlo in tutto il pacchetto. Questo aiuta a mantenere temperature operative ottimali e previene i punti caldi, migliorando così la gestione termica complessiva del dispositivo.
La resina epossidica Underfill protegge anche dall'umidità e dai contaminanti. L'ingresso di umidità può portare a corrosione, dispersione elettrica e crescita di materiali conduttivi, con conseguenti malfunzionamenti del dispositivo. La resina epossidica Underfill funge da barriera, sigillando le aree vulnerabili e impedendo all'umidità di entrare nella confezione. Offre inoltre protezione contro polvere, sporco e altri contaminanti che possono influire negativamente sulle prestazioni elettriche del chip semiconduttore. Salvaguardando il chip e le sue interconnessioni, la resina epossidica underfill garantisce l'affidabilità e la funzionalità a lungo termine del dispositivo.
Inoltre, la resina epossidica non riempita consente la miniaturizzazione negli imballaggi dei semiconduttori. Con la costante richiesta di dispositivi più piccoli e compatti, la resina epossidica con riempimento insufficiente consente di utilizzare tecniche di imballaggio flip-chip e su scala di chip. Queste tecniche comportano il montaggio diretto del chip sul substrato del pacchetto, eliminando la necessità di incollaggio dei cavi e riducendo le dimensioni del pacchetto. La resina epossidica Underfill fornisce supporto strutturale e mantiene l'integrità dell'interfaccia chip-substrato, consentendo l'implementazione di successo di queste tecnologie di imballaggio avanzate.
In che modo la resina epossidica Underfill affronta le sfide
L'imballaggio dei semiconduttori svolge un ruolo cruciale nelle prestazioni, nell'affidabilità e nella longevità dei dispositivi elettronici. Implica l'incapsulamento di circuiti integrati (IC) in involucri protettivi, la fornitura di collegamenti elettrici e la dissipazione del calore generato durante il funzionamento. Tuttavia, l'imballaggio dei semiconduttori deve affrontare diverse sfide, tra cui lo stress termico e la deformazione, che possono avere un impatto significativo sulla funzionalità e sull'affidabilità dei dispositivi imballati.
Una delle sfide principali è lo stress termico. I circuiti integrati generano calore durante il funzionamento e una dissipazione inadeguata può aumentare le temperature all'interno del contenitore. Questa variazione di temperatura si traduce in stress termico poiché diversi materiali all'interno della confezione si espandono e si contraggono a velocità diverse. L'espansione e la contrazione non uniformi possono causare sollecitazioni meccaniche, con conseguenti guasti ai giunti di saldatura, delaminazione e crepe. Lo stress termico può compromettere l'integrità elettrica e meccanica del pacchetto, influenzando in ultima analisi le prestazioni e l'affidabilità del dispositivo.
La deformazione è un'altra sfida critica nel packaging dei semiconduttori. La deformazione si riferisce alla flessione o alla deformazione del substrato della confezione o dell'intera confezione. Può verificarsi durante il processo di confezionamento oa causa di stress termico. La deformazione è principalmente causata dalla mancata corrispondenza del coefficiente di dilatazione termica (CTE) tra i diversi materiali nella confezione. Ad esempio, il CET della matrice di silicio, del substrato e del composto dello stampo può differire in modo significativo. Se sottoposti a variazioni di temperatura, questi materiali si espandono o si contraggono a velocità diverse, provocando deformazioni.
Warpage pone diversi problemi per i pacchetti di semiconduttori:
- Può provocare punti di concentrazione delle sollecitazioni, aumentando la probabilità di guasti meccanici e riducendo l'affidabilità della scatola.
- La deformazione può portare a difficoltà nel processo di assemblaggio, poiché influisce sull'allineamento del pacchetto con altri componenti, come il circuito stampato (PCB). Questo disallineamento può compromettere i collegamenti elettrici e causare problemi di prestazioni.
- La deformazione può influire sul fattore di forma complessivo del pacchetto, rendendo difficile l'integrazione del dispositivo in applicazioni con fattore di forma ridotto o PCB densamente popolati.
Varie tecniche e strategie sono impiegate nel packaging dei semiconduttori per affrontare queste sfide. Questi includono l'utilizzo di materiali avanzati con CTE corrispondenti per ridurre al minimo lo stress termico e la deformazione. Vengono condotte simulazioni e modelli termomeccanici per prevedere il comportamento del pacchetto in diverse condizioni termiche. Modifiche di progettazione, come l'introduzione di strutture antistress e layout ottimizzati, vengono implementate per ridurre lo stress termico e la deformazione. Inoltre, lo sviluppo di processi e attrezzature di produzione migliorati aiuta a ridurre al minimo il verificarsi di deformazioni durante l'assemblaggio.
Vantaggi della resina epossidica Underfill
La resina epossidica Underfill è un componente critico nell'imballaggio dei semiconduttori che offre numerosi vantaggi. Questo materiale epossidico specializzato viene applicato tra il chip semiconduttore e il substrato del pacchetto, fornendo rinforzo meccanico e affrontando varie sfide. Ecco alcuni dei vantaggi fondamentali della resina epossidica non riempita:
- Affidabilità meccanica migliorata: uno dei principali vantaggi della resina epossidica con riempimento insufficiente è la sua capacità di migliorare l'affidabilità meccanica dei pacchetti di semiconduttori. La resina epossidica Underfill crea un legame coesivo che migliora l'integrità strutturale complessiva riempiendo gli spazi e i vuoti tra il chip e il substrato. Questo aiuta a prevenire la deformazione della confezione, riduce il rischio di guasti meccanici e migliora la resistenza alle sollecitazioni esterne come vibrazioni, urti e cicli termici. La maggiore affidabilità meccanica porta a una maggiore durata del prodotto e una maggiore durata del dispositivo.
- Dissipazione dello stress termico: la resina epossidica sottoriempimento aiuta a dissipare lo stress termico all'interno del pacchetto. I circuiti integrati generano calore durante il funzionamento e una dissipazione inadeguata può provocare variazioni di temperatura all'interno del contenitore. Il materiale epossidico underfill, con il suo coefficiente di dilatazione termica (CTE) inferiore rispetto ai materiali del chip e del substrato, funge da strato tampone. Assorbe le sollecitazioni meccaniche causate dallo stress termico, riducendo il rischio di rotture dei giunti di saldatura, delaminazione e crepe. Dissipando lo stress termico, la resina epossidica sottoriempita aiuta a mantenere l'integrità elettrica e meccanica della confezione.
- Prestazioni elettriche migliorate: la resina epossidica sottoriempimento ha un impatto positivo sulle prestazioni elettriche dei dispositivi a semiconduttore. Il materiale epossidico riempie gli spazi tra il chip e il substrato, riducendo la capacità parassita e l'induttanza. Ciò si traduce in una migliore integrità del segnale, minori perdite di segnale e una migliore connettività elettrica tra il chip e il resto del pacchetto. Gli effetti parassiti ridotti contribuiscono a migliori prestazioni elettriche, velocità di trasferimento dati più elevate e maggiore affidabilità del dispositivo. Inoltre, la resina epossidica sottoriempita fornisce isolamento e protezione da umidità, contaminanti e altri fattori ambientali che possono degradare le prestazioni elettriche.
- Riduzione dello stress e assemblaggio migliorato: la resina epossidica sottoriempimento funge da meccanismo di riduzione dello stress durante l'assemblaggio. Il materiale epossidico compensa il disallineamento CTE tra il chip e il substrato, riducendo lo stress meccanico durante le variazioni di temperatura. Ciò rende il processo di assemblaggio più affidabile ed efficiente, riducendo al minimo il rischio di danneggiamento o disallineamento della confezione. La distribuzione controllata dello stress fornita dalla resina epossidica underfill aiuta anche a garantire il corretto allineamento con altri componenti sul circuito stampato (PCB) e migliora la resa complessiva dell'assemblaggio.
- Miniaturizzazione e ottimizzazione del fattore di forma: la resina epossidica Underfill consente la miniaturizzazione di pacchetti di semiconduttori e l'ottimizzazione del fattore di forma. Fornendo rinforzo strutturale e riduzione delle sollecitazioni, la resina epossidica underfill consente di progettare e produrre confezioni più piccole, sottili e compatte. Ciò è particolarmente importante per applicazioni come i dispositivi mobili e l'elettronica indossabile, dove lo spazio è prezioso. La capacità di ottimizzare i fattori di forma e ottenere densità di componenti più elevate contribuisce a dispositivi elettronici più avanzati e innovativi.
Tipi di resina epossidica Underfill
Diversi tipi di formulazioni epossidiche underfill sono disponibili in imballaggi per semiconduttori, ciascuno progettato per soddisfare requisiti specifici e affrontare sfide diverse. Ecco alcuni tipi comunemente usati di resina epossidica underfill:
- Resina epossidica per riempimento capillare: la resina epossidica per riempimento capillare è il tipo più tradizionale e ampiamente utilizzato. Una resina epossidica a bassa viscosità scorre nello spazio tra il chip e il substrato attraverso un'azione capillare. Il riempimento capillare viene generalmente erogato sul bordo del chip e, quando la confezione viene riscaldata, la resina epossidica scorre sotto il chip, riempiendo i vuoti. Questo tipo di sottoriempimento è adatto per confezioni con piccole fessure e fornisce un buon rinforzo meccanico.
- Resina epossidica No-Flow Underfill: La resina epossidica No-flow underfill è una formulazione ad alta viscosità che non scorre durante l'indurimento. Viene applicato come resina epossidica pre-applicata o come pellicola tra il truciolo e il substrato. La resina epossidica underfill senza flusso è particolarmente utile per i pacchetti flip-chip, in cui le protuberanze di saldatura interagiscono direttamente con il substrato. Elimina la necessità di flusso capillare e riduce il rischio di danni ai giunti di saldatura durante l'assemblaggio.
- Wafer-Level Underfill (WLU): l'underfill a livello di wafer è una resina epossidica underfill applicata a livello di wafer prima che i singoli chip vengano isolati. Implica l'erogazione del materiale di riempimento su tutta la superficie del wafer e la polimerizzazione. Il riempimento insufficiente a livello di wafer offre numerosi vantaggi, tra cui una copertura uniforme del riempimento insufficiente, tempi di assemblaggio ridotti e un migliore controllo del processo. È comunemente usato per la produzione di grandi volumi di dispositivi di piccole dimensioni.
- Molded Underfill (MUF): l'underfill modellato è una resina epossidica underfill applicata durante lo stampaggio per incapsulamento. Il materiale di sottoriempimento viene erogato sul substrato, quindi il truciolo e il substrato vengono incapsulati in un composto per stampi. Durante lo stampaggio, la resina epossidica scorre e riempie lo spazio tra il chip e il substrato, fornendo sottoriempimento e incapsulamento in un unico passaggio. Il sottopiede stampato offre un eccellente rinforzo meccanico e semplifica il processo di assemblaggio.
- Underfill non conduttivo (NCF): la resina epossidica underfill non conduttiva è specificatamente formulata per fornire l'isolamento elettrico tra i giunti di saldatura sul chip e il substrato. Contiene cariche isolanti o additivi che impediscono la conduttività elettrica. NCF viene utilizzato in applicazioni in cui il cortocircuito elettrico tra giunti di saldatura adiacenti è un problema. Offre sia il rinforzo meccanico che l'isolamento elettrico.
- Underfill termicamente conduttivo (TCU): la resina epossidica underfill termicamente conduttiva è progettata per migliorare le capacità di dissipazione del calore del pacchetto. Contiene riempitivi termicamente conduttivi, come particelle di ceramica o metallo, che migliorano la conducibilità termica del materiale di riempimento. La TCU viene utilizzata in applicazioni in cui è fondamentale un efficiente trasferimento di calore, come i dispositivi ad alta potenza o quelli che operano in ambienti termici esigenti.
Questi sono solo alcuni esempi dei diversi tipi di resina epossidica underfill utilizzati negli imballaggi dei semiconduttori. La selezione della resina epossidica underfill appropriata dipende da fattori quali il design della confezione, il processo di assemblaggio, i requisiti termici e considerazioni elettriche. Ogni resina epossidica underfill offre vantaggi specifici ed è adattata per soddisfare le esigenze uniche di varie applicazioni.
Underfill capillare: bassa viscosità e alta affidabilità
L'underfill capillare si riferisce a un processo utilizzato nell'industria dell'imballaggio dei semiconduttori per migliorare l'affidabilità dei dispositivi elettronici. Consiste nel riempire gli spazi tra un chip microelettronico e il suo pacchetto circostante con un materiale liquido a bassa viscosità, tipicamente una resina a base epossidica. Questo materiale di riempimento fornisce supporto strutturale, migliora la dissipazione termica e protegge il chip da sollecitazioni meccaniche, umidità e altri fattori ambientali.
Una delle caratteristiche critiche del riempimento capillare è la sua bassa viscosità. Il materiale di sottoriempimento è formulato per avere una densità relativamente bassa, che gli consente di fluire facilmente negli stretti spazi tra il chip e la confezione durante il processo di sottoriempimento. Ciò garantisce che il materiale di sottoriempimento possa penetrare efficacemente e riempire tutti i vuoti e le intercapedini d'aria, riducendo al minimo il rischio di formazione di vuoti e migliorando l'integrità complessiva dell'interfaccia chip-package.
I materiali di riempimento capillare a bassa viscosità offrono anche molti altri vantaggi. In primo luogo, facilitano il flusso efficiente del materiale sotto il truciolo, il che comporta una riduzione dei tempi di processo e un aumento della produttività. Ciò è particolarmente importante negli ambienti di produzione ad alto volume in cui l'efficienza in termini di tempo e costi è fondamentale.
In secondo luogo, la bassa viscosità consente migliori proprietà di bagnatura e adesione del materiale di riempimento. Consente al materiale di distribuirsi uniformemente e di formare forti legami con il chip e la confezione, creando un incapsulamento affidabile e robusto. Ciò garantisce che il chip sia protetto in modo sicuro da sollecitazioni meccaniche come cicli termici, urti e vibrazioni.
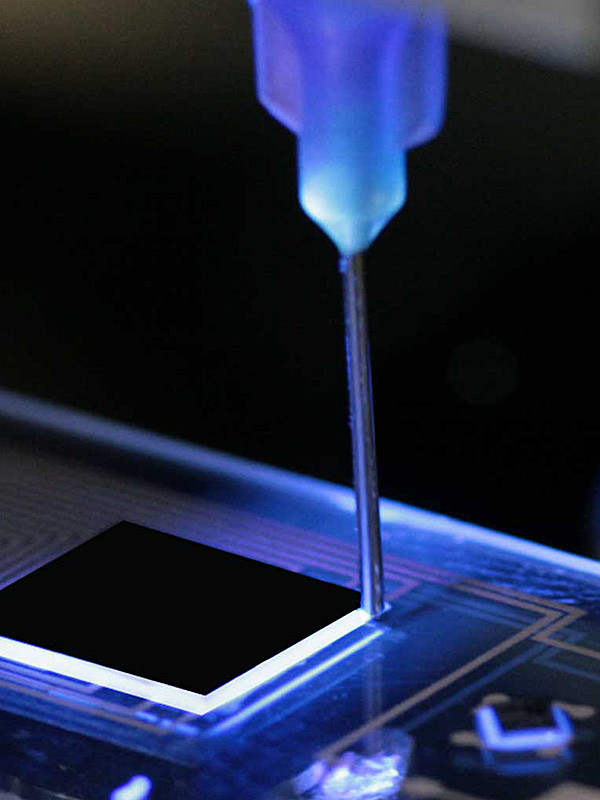
Un altro aspetto cruciale dei sottoriempimenti capillari è la loro elevata affidabilità. I materiali di riempimento a bassa viscosità sono specificamente progettati per esibire un'eccellente stabilità termica, proprietà di isolamento elettrico e resistenza all'umidità e agli agenti chimici. Queste caratteristiche sono essenziali per garantire le prestazioni e l'affidabilità a lungo termine dei dispositivi elettronici confezionati, in particolare in applicazioni impegnative come quelle automobilistiche, aerospaziali e delle telecomunicazioni.
Inoltre, i materiali di riempimento capillare sono progettati per avere un'elevata resistenza meccanica e un'eccellente adesione a vari materiali di substrato, inclusi metalli, ceramiche e materiali organici comunemente utilizzati negli imballaggi dei semiconduttori. Ciò consente al materiale del sottoriempimento di fungere da ammortizzatore delle sollecitazioni, assorbendo e dissipando efficacemente le sollecitazioni meccaniche generate durante il funzionamento o l'esposizione ambientale.
No-Flow Underfill: Autoerogazione e produttività elevata
No-flow underfill un processo specializzato utilizzato nell'industria dell'imballaggio dei semiconduttori per migliorare l'affidabilità e l'efficienza dei dispositivi elettronici. A differenza dei riempimenti insufficienti capillari, che si basano sul flusso di materiali a bassa viscosità, i riempimenti inferiori senza flusso utilizzano un approccio di autoerogazione con materiali ad alta viscosità. Questo metodo offre numerosi vantaggi, tra cui l'autoallineamento, un'elevata produttività e una maggiore affidabilità.
Una delle caratteristiche fondamentali del riempimento insufficiente senza flusso è la sua capacità di autoerogazione. Il materiale di riempimento utilizzato in questo processo è formulato con una viscosità più elevata, che ne impedisce il libero scorrimento. Invece, il materiale di sottoriempimento viene erogato sull'interfaccia chip-pacchetto in modo controllato. Questa erogazione controllata consente il posizionamento preciso del materiale di riempimento, assicurando che venga applicato solo alle aree desiderate senza traboccare o diffondersi in modo incontrollabile.
La natura auto-erogazione del riempimento insufficiente senza flusso offre diversi vantaggi. In primo luogo, consente l'autoallineamento del materiale di riempimento. Man mano che il sottoriempimento viene erogato, si autoallineerà naturalmente con il chip e la confezione, riempiendo uniformemente gli spazi e i vuoti. Ciò elimina la necessità di posizionamento e allineamento precisi del truciolo durante il processo di sottoriempimento, risparmiando tempo e fatica nella produzione.
In secondo luogo, la funzione di erogazione automatica dei riempimenti inferiori senza flusso consente un'elevata produttività nella produzione. Il processo di erogazione può essere automatizzato, consentendo un'applicazione rapida e coerente del materiale di riempimento su più chip contemporaneamente. Ciò migliora l'efficienza produttiva complessiva e riduce i costi di produzione, rendendolo particolarmente vantaggioso per gli ambienti di produzione ad alto volume.
Inoltre, i materiali di riempimento senza flusso sono progettati per fornire un'elevata affidabilità. I materiali di riempimento ad alta viscosità offrono una migliore resistenza ai cicli termici, alle sollecitazioni meccaniche e ai fattori ambientali, garantendo le prestazioni a lungo termine dei dispositivi elettronici confezionati. I materiali presentano un'eccellente stabilità termica, proprietà di isolamento elettrico e resistenza all'umidità e agli agenti chimici, contribuendo all'affidabilità complessiva dei dispositivi.
Inoltre, i materiali di sottoriempimento ad alta viscosità utilizzati nel sottoriempimento no-flow hanno una maggiore resistenza meccanica e proprietà di adesione. Formano forti legami con il chip e il pacchetto, assorbendo e dissipando efficacemente le sollecitazioni meccaniche generate durante il funzionamento o l'esposizione ambientale. Questo aiuta a proteggere il chip da potenziali danni e migliora la resistenza del dispositivo a urti e vibrazioni esterni.
Sottopiede modellato: alta protezione e integrazione
Il sottoriempimento stampato è una tecnica avanzata utilizzata nell'industria degli imballaggi dei semiconduttori per fornire livelli elevati di protezione e integrazione per i dispositivi elettronici. Implica l'incapsulamento dell'intero chip e della sua confezione circostante con un composto per stampi che incorpora materiale di riempimento. Questo processo offre vantaggi significativi in termini di protezione, integrazione e affidabilità complessiva.
Uno dei vantaggi fondamentali del sottoriempimento stampato è la sua capacità di fornire una protezione completa per il chip. Il composto dello stampo utilizzato in questo processo funge da robusta barriera, racchiudendo l'intero chip e la confezione in un guscio protettivo. Ciò fornisce una schermatura efficace contro fattori ambientali come umidità, polvere e contaminanti che potrebbero influire sulle prestazioni e sull'affidabilità del dispositivo. L'incapsulamento aiuta anche a proteggere il chip da sollecitazioni meccaniche, cicli termici e altre forze esterne, garantendone la durata a lungo termine.
Inoltre, il sottoriempimento stampato consente elevati livelli di integrazione all'interno del pacchetto semiconduttore. Il materiale di riempimento viene miscelato direttamente nel composto dello stampo, consentendo una perfetta integrazione dei processi di riempimento e incapsulamento. Questa integrazione elimina la necessità di una fase di sottoriempimento separata, semplificando il processo di produzione e riducendo tempi e costi di produzione. Garantisce inoltre una distribuzione del sottoriempimento coerente e uniforme in tutto il pacchetto, riducendo al minimo i vuoti e migliorando l'integrità strutturale complessiva.
Inoltre, il sottoriempimento stampato offre eccellenti proprietà di dissipazione termica. Il composto dello stampo è progettato per avere un'elevata conduttività termica, che gli consente di trasferire il calore lontano dal chip in modo efficiente. Questo è fondamentale per mantenere la temperatura operativa ottimale del dispositivo e prevenire il surriscaldamento, che può portare a un degrado delle prestazioni e problemi di affidabilità. Le migliorate proprietà di dissipazione termica del sottoriempimento stampato contribuiscono all'affidabilità complessiva e alla longevità del dispositivo elettronico.
Inoltre, il sottoriempimento stampato consente una maggiore miniaturizzazione e ottimizzazione del fattore di forma. Il processo di incapsulamento può essere adattato per adattarsi a varie dimensioni e forme di confezioni, comprese strutture 3D complesse. Questa flessibilità consente di integrare più chip e altri componenti in un pacchetto compatto ed efficiente in termini di spazio. La capacità di raggiungere livelli più elevati di integrazione senza compromettere l'affidabilità rende il sottoriempimento stampato particolarmente prezioso nelle applicazioni in cui i vincoli di dimensioni e peso sono fondamentali, come i dispositivi mobili, i dispositivi indossabili e l'elettronica automobilistica.
Chip Scale Package (CSP) Underfill: miniaturizzazione e alta densità
L'underfill Chip Scale Package (CSP) è una tecnologia critica che consente la miniaturizzazione e l'integrazione di dispositivi elettronici ad alta densità. Poiché le dimensioni dei dispositivi elettronici continuano a ridursi fornendo al contempo una maggiore funzionalità, il CSP svolge un ruolo cruciale nel garantire l'affidabilità e le prestazioni di questi dispositivi compatti.
CSP è una tecnologia di packaging che consente di montare il chip semiconduttore direttamente sul substrato o sul circuito stampato (PCB) senza bisogno di un pacchetto aggiuntivo. Ciò elimina la necessità di un tradizionale contenitore in plastica o ceramica, riducendo le dimensioni e il peso complessivi del dispositivo. CSP underfill un processo in cui viene utilizzato un materiale liquido o incapsulante per riempire lo spazio tra il chip e il substrato, fornendo supporto meccanico e proteggendo il chip da fattori ambientali quali umidità e sollecitazioni meccaniche.
La miniaturizzazione si ottiene attraverso il sottoriempimento CSP riducendo la distanza tra il chip e il substrato. Il materiale di riempimento riempie lo stretto spazio tra il truciolo e il substrato, creando un solido legame e migliorando la stabilità meccanica del truciolo. Ciò consente dispositivi più piccoli e sottili, consentendo di racchiudere più funzionalità in uno spazio limitato.
L'integrazione ad alta densità è un altro vantaggio dell'underfill CSP. Eliminando la necessità di un pacchetto separato, CSP consente di montare il chip più vicino ad altri componenti sul PCB, riducendo la lunghezza delle connessioni elettriche e migliorando l'integrità del segnale. Il materiale di riempimento funge anche da conduttore termico, dissipando efficacemente il calore generato dal chip. Questa capacità di gestione termica consente densità di potenza più elevate, consentendo l'integrazione di chip più complessi e potenti nei dispositivi elettronici.
I materiali di riempimento CSP devono possedere caratteristiche specifiche per soddisfare le esigenze di miniaturizzazione e integrazione ad alta densità. Devono avere una bassa viscosità per facilitare il riempimento di spazi ristretti, nonché eccellenti proprietà di flusso per garantire una copertura uniforme ed eliminare i vuoti. I materiali dovrebbero inoltre avere una buona adesione al truciolo e al substrato, fornendo un solido supporto meccanico. Inoltre, devono presentare un'elevata conduttività termica per trasferire il calore lontano dal chip in modo efficiente.
Underfill CSP a livello di wafer: conveniente e ad alto rendimento
Il sottoriempimento WLCSP (Wafer-level chip scale package) è una tecnica di confezionamento economica e ad alto rendimento che offre numerosi vantaggi in termini di efficienza di produzione e qualità complessiva del prodotto. WLCSP underfill applica materiale underfill a più chip contemporaneamente mentre sono ancora in forma di wafer prima che vengano separati in singoli pacchetti. Questo approccio offre numerosi vantaggi in termini di riduzione dei costi, migliore controllo del processo e maggiori rese di produzione.
Uno dei vantaggi fondamentali del sottoriempimento WLCSP è il suo rapporto costo-efficacia. L'applicazione del materiale di riempimento a livello del wafer rende il processo di confezionamento più snello ed efficiente. Il materiale sottoriempito viene erogato sul wafer utilizzando un processo controllato e automatizzato, riducendo lo spreco di materiale e minimizzando i costi di manodopera. Inoltre, l'eliminazione delle singole fasi di gestione e allineamento delle confezioni riduce il tempo e la complessità complessivi della produzione, con conseguenti risparmi significativi rispetto ai metodi di imballaggio tradizionali.
Inoltre, il sottoriempimento WLCSP offre un migliore controllo del processo e maggiori rese di produzione. Poiché il materiale di sottoriempimento viene applicato a livello di wafer, consente un migliore controllo sul processo di erogazione, garantendo una copertura di sottoriempimento coerente e uniforme per ogni chip sul wafer. Ciò riduce il rischio di vuoti o riempimento incompleto, che può portare a problemi di affidabilità. La capacità di ispezionare e testare la qualità del sottoriempimento a livello di wafer consente anche il rilevamento tempestivo di difetti o variazioni di processo, consentendo azioni correttive tempestive e riducendo la probabilità di pacchetti difettosi. Di conseguenza, il sottoriempimento WLCSP consente di ottenere rese di produzione più elevate e una migliore qualità complessiva del prodotto.
L'approccio a livello di wafer consente anche migliori prestazioni termiche e meccaniche. Il materiale di riempimento utilizzato in WLCSP è tipicamente un materiale a flusso capillare a bassa viscosità che può riempire in modo efficiente gli spazi ristretti tra i chip e il wafer. Ciò fornisce un solido supporto meccanico ai trucioli, migliorandone la resistenza alle sollecitazioni meccaniche, alle vibrazioni e ai cicli di temperatura. Inoltre, il materiale di riempimento funge da conduttore termico, facilitando la dissipazione del calore generato dai trucioli, migliorando così la gestione termica e riducendo il rischio di surriscaldamento.
Flip Chip Underfill: densità e prestazioni I/O elevate
Il flip chip underfill è una tecnologia critica che consente un'elevata densità di input/output (I/O) e prestazioni eccezionali nei dispositivi elettronici. Svolge un ruolo cruciale nel migliorare l'affidabilità e la funzionalità del packaging flip-chip, ampiamente utilizzato nelle applicazioni avanzate dei semiconduttori. Questo articolo esplorerà l'importanza del riempimento insufficiente del flip chip e il suo impatto sul raggiungimento di densità e prestazioni I/O elevate.
La tecnologia flip chip prevede la connessione elettrica diretta di un circuito integrato (IC) o di un die semiconduttore al substrato, eliminando la necessità di un collegamento a filo. Ciò si traduce in un pacchetto più compatto ed efficiente, poiché i pad I/O si trovano sulla superficie inferiore del die. Tuttavia, l'imballaggio flip-chip presenta sfide uniche che devono essere affrontate per garantire prestazioni e affidabilità ottimali.
Una delle sfide critiche nell'imballaggio dei flip chip è prevenire lo stress meccanico e il disadattamento termico tra la matrice e il substrato. Durante il processo di fabbricazione e il successivo funzionamento, le differenze nei coefficienti di dilatazione termica (CTE) tra lo stampo e il substrato possono causare stress significativi, con conseguente degrado delle prestazioni o addirittura guasti. Flip chip underfill è un materiale protettivo che incapsula il chip, fornendo supporto meccanico e riduzione dello stress. Distribuisce efficacemente le sollecitazioni generate durante i cicli termici e impedisce loro di intaccare le delicate interconnessioni.
L'elevata densità di I/O è fondamentale nei dispositivi elettronici moderni, dove sono essenziali fattori di forma più piccoli e una maggiore funzionalità. Il riempimento insufficiente del flip chip consente densità di I/O più elevate offrendo un isolamento elettrico superiore e capacità di gestione termica. Il materiale di riempimento riempie lo spazio tra la matrice e il substrato, creando un'interfaccia robusta e riducendo il rischio di cortocircuiti o dispersioni elettriche. Ciò consente una distanza più ravvicinata dei pad I/O, con conseguente aumento della densità I/O senza sacrificare l'affidabilità.
Inoltre, il riempimento insufficiente del flip chip contribuisce a migliorare le prestazioni elettriche. Riduce al minimo i parassiti elettrici tra il die e il substrato, riducendo il ritardo del segnale e migliorando l'integrità del segnale. Il materiale di riempimento presenta anche eccellenti proprietà di conduttività termica, dissipando in modo efficiente il calore generato dal chip durante il funzionamento. Un'efficace dissipazione del calore assicura che la temperatura rimanga entro limiti accettabili, prevenendo il surriscaldamento e mantenendo prestazioni ottimali.
I progressi nei materiali underfill del flip chip hanno consentito densità di I/O e livelli prestazionali ancora più elevati. I sottoriempimenti nanocompositi, ad esempio, sfruttano i riempitivi su scala nanometrica per migliorare la conduttività termica e la resistenza meccanica. Ciò consente una migliore dissipazione del calore e affidabilità, consentendo dispositivi con prestazioni più elevate.
Ball Grid Array (BGA) Underfill: elevate prestazioni termiche e meccaniche
Ball Grid Array (BGA) è una tecnologia critica che offre elevate prestazioni termiche e meccaniche nei dispositivi elettronici. Svolge un ruolo cruciale nel migliorare l'affidabilità e la funzionalità dei pacchetti BGA, ampiamente utilizzati in varie applicazioni. In questo articolo, esploreremo l'importanza del sottoriempimento BGA e il suo impatto sul raggiungimento di elevate prestazioni termiche e meccaniche.
La tecnologia BGA prevede un design del contenitore in cui il circuito integrato (IC) o il die del semiconduttore è montato su un substrato e le connessioni elettriche sono realizzate tramite una serie di sfere di saldatura situate sulla superficie inferiore del contenitore. Il BGA riempie in modo insufficiente un materiale erogato nello spazio tra il die e il substrato, incapsulando le sfere di saldatura e fornendo supporto meccanico e protezione all'assieme.
Una delle sfide critiche nel packaging BGA è la gestione delle sollecitazioni termiche. Durante il funzionamento, il circuito integrato genera calore e l'espansione e la contrazione termica possono causare una pressione significativa sui giunti di saldatura che collegano il die e il substrato. Il BGA svolge un ruolo cruciale nel mitigare queste sollecitazioni formando un solido legame con lo stampo e il substrato. Agisce come un tampone di sollecitazione, assorbendo l'espansione e la contrazione termica e riducendo la tensione sui giunti di saldatura. Ciò aiuta a migliorare l'affidabilità complessiva del pacchetto e riduce il rischio di guasti ai giunti di saldatura.
Un altro aspetto critico dell'underfill BGA è la sua capacità di migliorare le prestazioni meccaniche del pacchetto. I pacchetti BGA sono spesso soggetti a sollecitazioni meccaniche durante la manipolazione, l'assemblaggio e il funzionamento. Il materiale di riempimento riempie lo spazio tra il die e il substrato, fornendo supporto strutturale e rinforzo ai giunti di saldatura. Ciò migliora la resistenza meccanica complessiva dell'assieme, rendendolo più resistente a urti meccanici, vibrazioni e altre forze esterne. Distribuendo efficacemente le sollecitazioni meccaniche, il sottoriempimento BGA aiuta a prevenire rotture, delaminazioni o altri guasti meccanici della confezione.
Elevate prestazioni termiche sono essenziali nei dispositivi elettronici per garantire la corretta funzionalità e affidabilità. I materiali BGA underfill sono progettati per avere eccellenti proprietà di conduttività termica. Ciò consente loro di trasferire in modo efficiente il calore lontano dallo stampo e di distribuirlo sul substrato, migliorando la gestione termica complessiva della confezione. Un'efficace dissipazione del calore aiuta a mantenere temperature operative più basse, prevenendo i punti caldi termici e il potenziale degrado delle prestazioni. Contribuisce inoltre alla longevità della scatola riducendo lo stress termico dei componenti.
I progressi nei materiali di riempimento BGA hanno portato a prestazioni termiche e meccaniche ancora più elevate. Formulazioni migliorate e materiali di riempimento, come nanocompositi o riempitivi ad alta conducibilità termica, hanno consentito una migliore dissipazione del calore e resistenza meccanica, migliorando ulteriormente le prestazioni dei pacchetti BGA.
Quad Flat Package (QFP) Underfill: grande numero di I/O e robustezza
Quad Flat Package (QFP) è un pacchetto di circuiti integrati (IC) ampiamente utilizzato nell'elettronica. Presenta una forma quadrata o rettangolare con cavi che si estendono da tutti e quattro i lati, fornendo molte connessioni di ingresso/uscita (I/O). Per migliorare l'affidabilità e la robustezza dei pacchetti QFP, vengono comunemente impiegati materiali di riempimento.
Underfill è un materiale protettivo applicato tra l'IC e il substrato per rafforzare la resistenza meccanica dei giunti di saldatura e prevenire guasti indotti dallo stress. È particolarmente importante per i QFP con un elevato numero di I/O, in quanto l'elevato numero di connessioni può portare a sollecitazioni meccaniche significative durante i cicli termici e le condizioni operative.
Il materiale di sottoriempimento utilizzato per le confezioni QFP deve possedere caratteristiche specifiche per garantire robustezza. In primo luogo, dovrebbe avere un'adesione eccellente sia all'IC che al substrato per creare un forte legame e ridurre al minimo il rischio di delaminazione o distacco. Inoltre, dovrebbe avere un basso coefficiente di dilatazione termica (CTE) per corrispondere al CTE dell'IC e del substrato, riducendo i disallineamenti delle sollecitazioni che potrebbero portare a crepe o fratture.
Inoltre, il materiale di sottoriempimento dovrebbe avere buone proprietà di flusso per garantire una copertura uniforme e il completo riempimento dello spazio tra l'IC e il substrato. Questo aiuta a eliminare i vuoti, che possono indebolire i giunti di saldatura e comportare una ridotta affidabilità. Il materiale dovrebbe anche avere buone proprietà di polimerizzazione, che gli consentano di formare uno strato protettivo rigido e duraturo dopo l'applicazione.
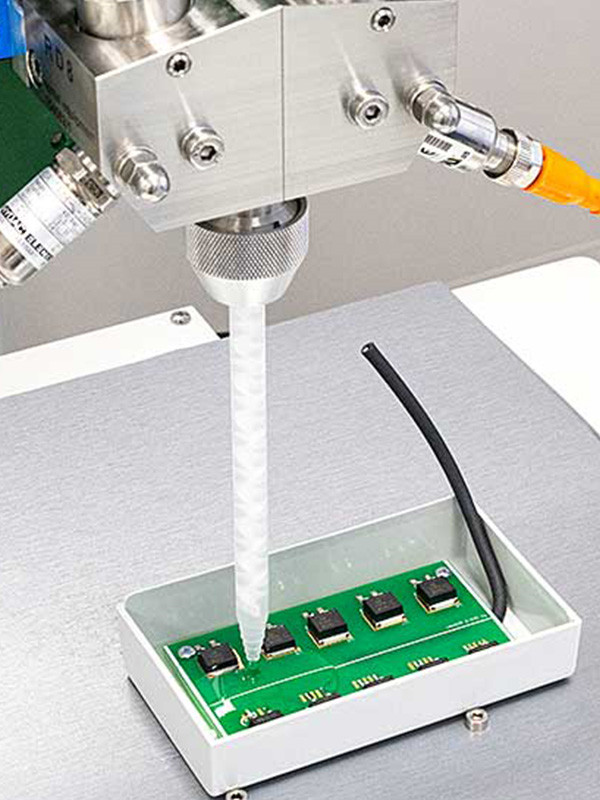
In termini di robustezza meccanica, il sottoriempimento dovrebbe possedere un'elevata resistenza al taglio e alla pelatura per resistere alle forze esterne e prevenire la deformazione o la separazione della confezione. Dovrebbe inoltre mostrare una buona resistenza all'umidità e ad altri fattori ambientali per mantenere le sue proprietà protettive nel tempo. Ciò è particolarmente importante nelle applicazioni in cui il pacchetto QFP può essere esposto a condizioni difficili o subire variazioni di temperatura.
Sono disponibili vari materiali di riempimento per ottenere queste caratteristiche desiderate, comprese le formulazioni a base epossidica. A seconda dei requisiti specifici dell'applicazione, questi materiali possono essere erogati utilizzando diverse tecniche, come il flusso capillare, il getto o la serigrafia.
Underfill System-in-Package (SiP): integrazione e prestazioni
System-in-Package (SiP) è una tecnologia di packaging avanzata che integra più chip semiconduttori, componenti passivi e altri elementi in un unico pacchetto. SiP offre numerosi vantaggi, tra cui un fattore di forma ridotto, prestazioni elettriche migliorate e funzionalità potenziate. Per garantire l'affidabilità e le prestazioni degli assemblaggi SiP, vengono comunemente utilizzati materiali di riempimento.
Il riempimento insufficiente nelle applicazioni SiP è fondamentale per fornire stabilità meccanica e connettività elettrica tra i vari componenti all'interno del pacchetto. Aiuta a ridurre al minimo il rischio di guasti indotti da stress, come crepe o fratture dei giunti di saldatura, che possono verificarsi a causa delle differenze nei coefficienti di dilatazione termica (CTE) tra i componenti.
L'integrazione di più componenti in un pacchetto SiP porta a un'interconnettività complessa, con molti giunti di saldatura e circuiti ad alta densità. I materiali underfill aiutano a rafforzare queste interconnessioni, migliorando la resistenza meccanica e l'affidabilità dell'assieme. Supportano i giunti di saldatura, riducendo il rischio di affaticamento o danni causati da cicli termici o sollecitazioni meccaniche.
In termini di prestazioni elettriche, i materiali di riempimento sono fondamentali per migliorare l'integrità del segnale e ridurre al minimo il rumore elettrico. Riempiendo gli spazi tra i componenti e riducendone la distanza, l'underfill contribuisce a ridurre la capacità e l'induttanza parassite, consentendo una trasmissione del segnale più rapida ed efficiente.
Inoltre, i materiali di riempimento per le applicazioni SiP dovrebbero avere un'eccellente conduttività termica per dissipare in modo efficiente il calore generato dai componenti integrati. Un'efficace dissipazione del calore è essenziale per prevenire il surriscaldamento e mantenere l'affidabilità e le prestazioni complessive dell'assieme SiP.
I materiali underfill negli imballaggi SiP devono avere proprietà specifiche per soddisfare questi requisiti di integrazione e prestazioni. Devono avere una buona fluidità per garantire una copertura completa e riempire gli spazi tra i componenti. Il materiale di riempimento dovrebbe anche avere una formulazione a bassa viscosità per consentire una facile erogazione e riempimento in fori stretti o piccoli spazi.
Inoltre, il materiale di riempimento dovrebbe mostrare una forte adesione a diverse superfici, inclusi chip semiconduttori, substrati e componenti passivi, per garantire un legame affidabile. Dovrebbe essere compatibile con vari materiali di imballaggio, come substrati organici o ceramica, e presentare buone proprietà meccaniche, inclusa un'elevata resistenza al taglio e alla pelatura.
La scelta del materiale di sottoriempimento e del metodo di applicazione dipende dalla specifica progettazione del SiP, dai requisiti dei componenti e dai processi di produzione. Le tecniche di erogazione come il flusso capillare, il getto o i metodi assistiti da pellicola applicano comunemente il riempimento insufficiente negli assemblaggi SiP.
Optoelettronica Underfill: allineamento ottico e protezione
L'underfill dell'optoelettronica include l'incapsulamento e la protezione dei dispositivi optoelettronici, garantendo al tempo stesso un allineamento ottico preciso. I dispositivi optoelettronici, come laser, fotorivelatori e interruttori ottici, richiedono spesso un delicato allineamento dei componenti ottici per ottenere prestazioni ottimali. Allo stesso tempo, devono essere protetti da fattori ambientali che potrebbero comprometterne la funzionalità. Optoelectronics underfill soddisfa entrambi questi requisiti fornendo allineamento ottico e protezione in un unico processo.
L'allineamento ottico è un aspetto critico della produzione di dispositivi optoelettronici. Implica l'allineamento di elementi visivi, come fibre, guide d'onda, lenti o reticoli, per garantire un'efficiente trasmissione e ricezione della luce. L'allineamento preciso è necessario per massimizzare le prestazioni del dispositivo e mantenere l'integrità del segnale. Le tecniche di allineamento tradizionali includono l'allineamento manuale mediante ispezione visiva o l'allineamento automatizzato mediante fasi di allineamento. Tuttavia, questi metodi possono essere dispendiosi in termini di tempo, laboriosi e soggetti a errori.
Optoelettronica underfill una soluzione innovativa incorporando caratteristiche di allineamento direttamente nel materiale underfill. I materiali di riempimento sono in genere composti liquidi o semiliquidi che possono scorrere e riempire gli spazi tra i componenti ottici. Aggiungendo caratteristiche di allineamento, come microstrutture o segni fiduciali, all'interno del materiale di riempimento, il processo di allineamento può essere semplificato e automatizzato. Queste caratteristiche fungono da guida durante l'assemblaggio, garantendo un allineamento preciso dei componenti ottici senza la necessità di complesse procedure di allineamento.
Oltre all'allineamento ottico, i materiali di riempimento proteggono i dispositivi optoelettronici. I componenti optoelettronici sono spesso esposti ad ambienti difficili, tra cui fluttuazioni di temperatura, umidità e sollecitazioni meccaniche. Questi fattori esterni possono degradare le prestazioni e l'affidabilità dei dispositivi nel tempo. I materiali underfill fungono da barriera protettiva, incapsulando i componenti ottici e proteggendoli dai contaminanti ambientali. Forniscono inoltre rinforzo meccanico, riducendo il rischio di danni dovuti a urti o vibrazioni.
I materiali di riempimento utilizzati nelle applicazioni optoelettroniche sono generalmente progettati per avere un basso indice di rifrazione e un'eccellente trasparenza ottica. Ciò garantisce un'interferenza minima con i segnali ottici che passano attraverso il dispositivo. Inoltre, presentano una buona adesione a vari substrati e hanno bassi coefficienti di dilatazione termica per ridurre al minimo lo stress del dispositivo durante i cicli termici.
Il processo di sottoriempimento prevede l'erogazione del materiale di sottoriempimento sul dispositivo, consentendogli di fluire e riempire gli spazi tra i componenti ottici e quindi polimerizzarlo per formare un incapsulamento solido. A seconda dell'applicazione specifica, il materiale di riempimento può essere applicato utilizzando diverse tecniche, come il flusso capillare, l'erogazione a getto o la serigrafia. Il processo di indurimento può essere ottenuto mediante calore, radiazione UV o entrambi.
Underfill dell'elettronica medica: biocompatibilità e affidabilità
L'elettronica medica non soddisfa un processo specializzato che prevede l'incapsulamento e la protezione dei componenti elettronici utilizzati nei dispositivi medici. Questi dispositivi svolgono un ruolo cruciale in varie applicazioni mediche, come dispositivi impiantabili, apparecchiature diagnostiche, sistemi di monitoraggio e sistemi di somministrazione di farmaci. L'underfill dell'elettronica medica si concentra su due aspetti critici: biocompatibilità e affidabilità.
La biocompatibilità è un requisito fondamentale per i dispositivi medici che entrano in contatto con il corpo umano. I materiali di riempimento utilizzati nell'elettronica medica devono essere biocompatibili, il che significa che non devono causare effetti dannosi o reazioni avverse a contatto con tessuti viventi o fluidi corporei. Questi materiali devono essere conformi a norme e standard rigorosi, come ISO 10993, che specifica le procedure di test e valutazione della biocompatibilità.
I materiali di riempimento per l'elettronica medica sono accuratamente selezionati o formulati per garantire la biocompatibilità. Sono progettati per essere atossici, non irritanti e anallergici. Questi materiali non devono rilasciare sostanze nocive o degradarsi nel tempo, in quanto ciò potrebbe causare danni ai tessuti o infiammazioni. I materiali di riempimento biocompatibili hanno anche un basso assorbimento d'acqua per prevenire la crescita di batteri o funghi che potrebbero causare infezioni.
L'affidabilità è un altro aspetto critico del sottoriempimento dell'elettronica medica. I dispositivi medici devono spesso affrontare condizioni operative difficili, tra cui temperature estreme, umidità, fluidi corporei e stress meccanico. I materiali di riempimento devono proteggere i componenti elettronici, garantendone l'affidabilità e la funzionalità a lungo termine. L'affidabilità è fondamentale nelle applicazioni mediche in cui il guasto del dispositivo potrebbe compromettere gravemente la sicurezza e il benessere del paziente.
I materiali di riempimento per l'elettronica medica devono avere un'elevata resistenza all'umidità e alle sostanze chimiche per resistere all'esposizione ai fluidi corporei o ai processi di sterilizzazione. Dovrebbero inoltre mostrare una buona adesione a vari substrati, garantendo un incapsulamento sicuro dei componenti elettronici. Le proprietà meccaniche, come i bassi coefficienti di dilatazione termica e la buona resistenza agli urti, sono fondamentali per ridurre al minimo lo stress sui dettagli durante i cicli termici o il caricamento automatico.
Il processo di sottoriempimento per l'elettronica medicale comporta:
- Erogazione del materiale di riempimento sui componenti elettronici.
- Colmare le lacune.
- Polimerizzazione per formare un incapsulamento protettivo e meccanicamente stabile.
Occorre prestare attenzione per garantire la completa copertura delle caratteristiche e l'assenza di vuoti o sacche d'aria che potrebbero compromettere l'affidabilità del dispositivo.
Inoltre, vengono prese in considerazione ulteriori considerazioni in caso di riempimento insufficiente dei dispositivi medici. Ad esempio, il materiale di riempimento deve essere compatibile con i metodi di sterilizzazione utilizzati per il dispositivo. Alcuni materiali possono essere sensibili a specifiche tecniche di sterilizzazione, come vapore, ossido di etilene o radiazioni, e potrebbe essere necessario selezionare materiali alternativi.
Elettronica aerospaziale Underfill: resistenza alle alte temperature e alle vibrazioni
L'elettronica aerospaziale è al di sotto di un processo specializzato per incapsulare e proteggere i componenti elettronici nelle applicazioni aerospaziali. Gli ambienti aerospaziali pongono sfide uniche, tra cui temperature elevate, vibrazioni estreme e sollecitazioni meccaniche. Pertanto, l'underfill dell'elettronica aerospaziale si concentra su due aspetti cruciali: resistenza alle alte temperature e resistenza alle vibrazioni.
La resistenza alle alte temperature è fondamentale nell'elettronica aerospaziale a causa delle temperature elevate riscontrate durante il funzionamento. I materiali di riempimento utilizzati nelle applicazioni aerospaziali devono resistere a queste temperature elevate senza compromettere le prestazioni e l'affidabilità dei componenti elettronici. Dovrebbero presentare un'espansione termica minima e rimanere stabili in un ampio intervallo di temperature.
I materiali di riempimento per l'elettronica aerospaziale sono selezionati o formulati per elevate temperature di transizione vetrosa (Tg) e stabilità termica. Un'elevata Tg assicura che il materiale mantenga le sue proprietà meccaniche a temperature elevate, prevenendo deformazioni o perdite di adesione. Questi materiali possono resistere a temperature estreme, come durante il decollo, il rientro atmosferico o il funzionamento in vani motore caldi.
Inoltre, i materiali di riempimento per l'elettronica aerospaziale dovrebbero avere bassi coefficienti di dilatazione termica (CTE). Il CTE misura quanto un materiale si espande o si contrae con le variazioni di temperatura. Avendo un CTE basso, i materiali di riempimento possono ridurre al minimo lo stress sui componenti elettronici causato dai cicli termici, che possono portare a guasti meccanici o affaticamento del giunto di saldatura.
La resistenza alle vibrazioni è un altro requisito fondamentale per il sottoriempimento dell'elettronica aerospaziale. I veicoli aerospaziali sono soggetti a varie vibrazioni, tra cui il motore, le vibrazioni indotte dal volo e gli shock meccanici durante il lancio o l'atterraggio. Queste vibrazioni possono compromettere le prestazioni e l'affidabilità dei componenti elettronici se non adeguatamente protetti.
I materiali di riempimento utilizzati nell'elettronica aerospaziale dovrebbero presentare eccellenti proprietà di smorzamento delle vibrazioni. Dovrebbero assorbire e dissipare l'energia generata dalle vibrazioni, riducendo lo stress e la tensione sui componenti elettronici. Questo aiuta a prevenire la formazione di crepe, fratture o altri guasti meccanici dovuti all'eccessiva esposizione alle vibrazioni.
Inoltre, nelle applicazioni aerospaziali sono preferiti i materiali di riempimento con elevata adesione e forza coesiva. Queste proprietà assicurano che il materiale di riempimento rimanga saldamente legato ai componenti elettronici e al substrato, anche in condizioni di vibrazioni estreme. La forte adesione impedisce al materiale di riempimento di delaminarsi o separarsi dagli elementi, mantenendo l'integrità dell'incapsulamento e proteggendo dall'ingresso di umidità o detriti.
Il processo di sottoriempimento per l'elettronica aerospaziale prevede in genere l'erogazione del materiale di sottoriempimento sui componenti elettronici, consentendogli di scorrere e riempire gli spazi vuoti e quindi polimerizzarlo per formare un robusto incapsulamento. Il processo di indurimento può essere realizzato utilizzando metodi di indurimento termico o UV, a seconda dei requisiti specifici dell'applicazione.
Elettronica automobilistica Underfill: durata e resistenza ai cicli termici
L'elettronica automobilistica non soddisfa un processo critico che prevede l'incapsulamento e la protezione dei componenti elettronici nelle applicazioni automobilistiche. Gli ambienti automobilistici presentano sfide uniche, tra cui variazioni di temperatura, cicli termici, sollecitazioni meccaniche ed esposizione a umidità e sostanze chimiche. Pertanto, l'underfill dell'elettronica automobilistica si concentra su due aspetti critici: durata e resistenza ai cicli termici.
La durabilità è un requisito cruciale per l'elettronica automobilistica con riempimento insufficiente. Durante il normale funzionamento, i veicoli automobilistici sono soggetti a vibrazioni, urti e sollecitazioni meccaniche costanti. I materiali di riempimento utilizzati nelle applicazioni automobilistiche devono proteggere i componenti elettronici in modo robusto, garantendone la durata e la longevità. Dovrebbero resistere alle condizioni difficili e ai carichi meccanici incontrati sulla strada e resistere all'ingresso di umidità, polvere e sostanze chimiche.
I materiali di riempimento per l'elettronica automobilistica sono selezionati o formulati per un'elevata resistenza meccanica e resistenza agli urti. Dovrebbero mostrare un'eccellente adesione ai componenti elettronici e al substrato, impedendo la delaminazione o la separazione sotto sollecitazioni meccaniche. I durevoli materiali di riempimento aiutano a ridurre al minimo il rischio di danni ai componenti elettronici dovuti a vibrazioni o urti, garantendo prestazioni affidabili per tutta la vita utile del veicolo.
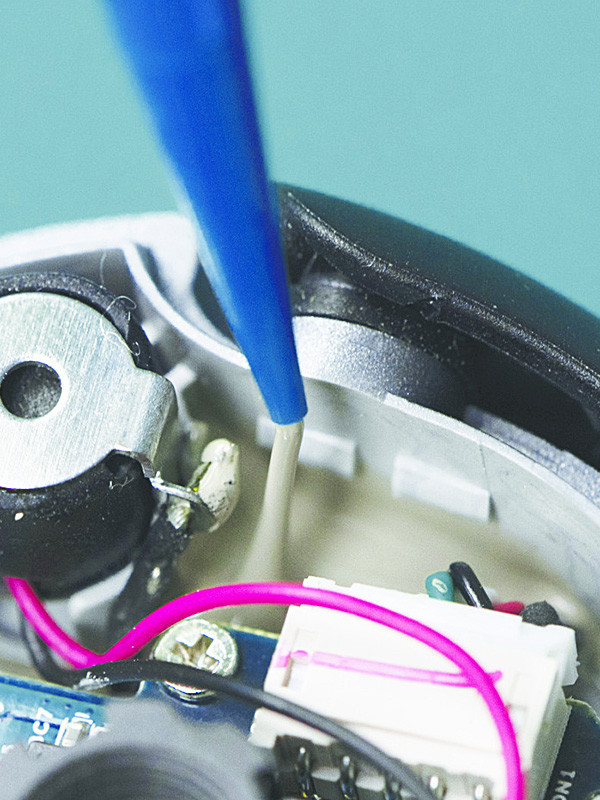
La resistenza ai cicli termici è un altro requisito fondamentale per il sottoriempimento dell'elettronica automobilistica. I veicoli automobilistici sono soggetti a frequenti variazioni di temperatura, specialmente durante l'avvio e il funzionamento del motore, e questi cicli di temperatura possono indurre sollecitazioni termiche sui componenti elettronici e sul materiale di riempimento circostante. I materiali di riempimento utilizzati nelle applicazioni automobilistiche devono avere un'eccellente resistenza ai cicli termici per resistere a queste fluttuazioni di temperatura senza comprometterne le prestazioni.
I materiali di riempimento per l'elettronica automobilistica dovrebbero avere bassi coefficienti di espansione termica (CTE) per ridurre al minimo lo stress dei componenti elettronici durante i cicli termici. Un CTE ben abbinato tra il materiale di riempimento e gli ingredienti riduce il rischio di affaticamento del giunto di saldatura, incrinature o altri guasti meccanici causati dallo stress termico. Inoltre, i materiali di riempimento dovrebbero presentare una buona conduttività termica per dissipare il calore in modo efficiente, prevenendo punti caldi localizzati che potrebbero influire sulle prestazioni e sull'affidabilità dei componenti.
Inoltre, i materiali di sottoriempimento dell'elettronica automobilistica dovrebbero resistere all'umidità, alle sostanze chimiche e ai fluidi. Dovrebbero avere un basso assorbimento d'acqua per prevenire la formazione di muffe o la corrosione dei componenti elettronici. La resistenza chimica assicura che il materiale di riempimento rimanga stabile quando esposto a fluidi automobilistici, come oli, carburanti o detergenti, evitando il degrado o la perdita di adesione.
Il processo di sottoriempimento per l'elettronica automobilistica in genere comporta l'erogazione del materiale di sottoriempimento sui componenti elettronici, consentendogli di fluire e riempire gli spazi vuoti e quindi polimerizzarlo per formare un incapsulamento durevole. Il processo di indurimento può essere realizzato mediante metodi di indurimento termico o UV, a seconda dei requisiti specifici dell'applicazione e del materiale di riempimento utilizzato.
Scegliere la giusta resina epossidica per il riempimento
La scelta della resina epossidica underfill giusta è una decisione cruciale nell'assemblaggio e nella protezione dei componenti elettronici. Gli epossidici underfill forniscono rinforzo meccanico, gestione termica e protezione contro i fattori ambientali. Ecco alcune considerazioni chiave quando si seleziona la resina epossidica underfill appropriata:
- Proprietà termiche: una delle funzioni principali della resina epossidica underfill è la dissipazione del calore generato dai componenti elettronici. Pertanto, è essenziale considerare la conduttività termica e la resistenza termica della resina epossidica. L'elevata conducibilità termica favorisce un efficiente trasferimento del calore, prevenendo i punti caldi e mantenendo l'affidabilità dei componenti. La resina epossidica dovrebbe anche avere una bassa resistenza termica per ridurre al minimo lo stress termico sui componenti durante i cicli di temperatura.
- Corrispondenza CTE: il coefficiente di dilatazione termica (CTE) della resina epossidica underfill deve essere ben abbinato al CTE dei componenti elettronici e del substrato per ridurre al minimo lo stress termico e prevenire guasti ai giunti di saldatura. Un CTE molto simile aiuta a ridurre il rischio di guasti meccanici dovuti ai cicli termici.
- Capacità di flusso e riempimento degli spazi: la resina epossidica non riempita dovrebbe avere buone caratteristiche di flusso e la capacità di riempire efficacemente gli spazi tra i componenti. Ciò garantisce una copertura completa e riduce al minimo i vuoti o le sacche d'aria che potrebbero influire sulla stabilità meccanica e sulle prestazioni termiche dell'assieme. La viscosità della resina epossidica deve essere adatta all'applicazione specifica e al metodo di assemblaggio, che si tratti di flusso capillare, erogazione a getto o serigrafia.
- Adesione: una forte adesione è fondamentale per il riempimento insufficiente della resina epossidica per garantire un legame affidabile tra i componenti e il substrato. Dovrebbe mostrare una buona adesione a vari materiali, inclusi metalli, ceramica e plastica. Le proprietà di adesione della resina epossidica contribuiscono all'integrità meccanica dell'assieme e all'affidabilità a lungo termine.
- Metodo di polimerizzazione: considera il metodo di polimerizzazione più adatto al tuo processo di produzione. Le resine epossidiche sottoriempimento possono essere polimerizzate mediante calore, radiazioni UV o una combinazione di entrambi. Ogni metodo di polimerizzazione presenta vantaggi e limiti e scegliere quello che si allinea alle proprie esigenze di produzione è essenziale.
- Resistenza ambientale: valutare la resistenza della resina epossidica di riempimento a fattori ambientali come umidità, sostanze chimiche e temperature estreme. La resina epossidica dovrebbe essere in grado di resistere all'esposizione all'acqua, prevenendo la crescita di muffe o corrosione. La resistenza chimica garantisce la stabilità a contatto con fluidi per autoveicoli, detergenti o altre sostanze potenzialmente corrosive. Inoltre, la resina epossidica dovrebbe mantenere le sue proprietà meccaniche ed elettriche in un ampio intervallo di temperature.
- Affidabilità e longevità: considerare i dati di affidabilità e track record della resina epossidica con riempimento insufficiente. Cerca materiali epossidici testati e dimostrati per funzionare bene in applicazioni simili o avere certificazioni del settore e conformità agli standard pertinenti. Considera fattori come il comportamento all'invecchiamento, l'affidabilità a lungo termine e la capacità della resina epossidica di mantenere le sue proprietà nel tempo.
Quando si seleziona la giusta resina epossidica di riempimento, è fondamentale considerare i requisiti specifici della propria applicazione, tra cui gestione termica, stabilità meccanica, protezione ambientale e compatibilità del processo di produzione. La consulenza con i fornitori di resine epossidiche o la ricerca di una consulenza esperta può essere utile per prendere una decisione informata che soddisfi le esigenze della tua applicazione e garantisca prestazioni e affidabilità ottimali.
Tendenze future nella resina epossidica sottoriempimento
La resina epossidica Underfill è in continua evoluzione, guidata dai progressi nelle tecnologie elettroniche, dalle applicazioni emergenti e dalla necessità di migliorare le prestazioni e l'affidabilità. Diverse tendenze future possono essere osservate nello sviluppo e nell'applicazione della resina epossidica underfill:
- Miniaturizzazione e imballaggi ad alta densità: poiché i dispositivi elettronici continuano a ridursi e presentano densità di componenti più elevate, le resine epossidiche sottoriempimento devono adattarsi di conseguenza. Le tendenze future si concentreranno sullo sviluppo di materiali di riempimento che penetrano e colmano spazi più piccoli tra i componenti, garantendo una copertura completa e una protezione affidabile in gruppi elettronici sempre più miniaturizzati.
- Applicazioni ad alta frequenza: con la crescente domanda di dispositivi elettronici ad alta frequenza e ad alta velocità, le formulazioni epossidiche underfill dovranno soddisfare i requisiti specifici di queste applicazioni. I materiali di riempimento con bassa costante dielettrica e tangenti a bassa perdita saranno essenziali per ridurre al minimo la perdita di segnale e mantenere l'integrità dei segnali ad alta frequenza nei sistemi di comunicazione avanzati, nella tecnologia 5G e in altre applicazioni emergenti.
- Gestione termica migliorata: la dissipazione del calore rimane un problema critico per i dispositivi elettronici, in particolare con l'aumento della densità di potenza. Le future formulazioni epossidiche underfill si concentreranno su una migliore conducibilità termica per migliorare il trasferimento di calore e gestire efficacemente i problemi termici. Filler e additivi avanzati saranno incorporati nelle resine epossidiche underfill per ottenere una maggiore conduttività termica pur mantenendo le altre proprietà desiderate.
- Elettronica flessibile ed estensibile: l'ascesa dell'elettronica flessibile ed estensibile apre nuove possibilità per il riempimento insufficiente di materiali epossidici. Le resine epossidiche sottoriempimento flessibili devono dimostrare un'adesione eccellente e proprietà meccaniche anche sotto ripetute flessioni o allungamenti. Questi materiali consentiranno l'incapsulamento e la protezione dell'elettronica in dispositivi indossabili, display pieghevoli e altre applicazioni che richiedono flessibilità meccanica.
- Soluzioni rispettose dell'ambiente: la sostenibilità e le considerazioni ambientali giocheranno un ruolo sempre più significativo nello sviluppo di materiali epossidici underfill. Ci si concentrerà sulla creazione di formulazioni epossidiche prive di sostanze pericolose e con un impatto ambientale ridotto durante tutto il loro ciclo di vita, compresa la produzione, l'utilizzo e lo smaltimento. Anche i materiali a base biologica o rinnovabili possono acquisire importanza come alternative sostenibili.
- Processi di produzione migliorati: le tendenze future nella resina epossidica underfill si concentreranno sulle proprietà dei materiali e sui progressi nei processi di produzione. Saranno esplorate tecniche come la produzione additiva, l'erogazione selettiva e metodi di polimerizzazione avanzati per ottimizzare l'applicazione e le prestazioni della resina epossidica con riempimento insufficiente in vari processi di assemblaggio elettronico.
- Integrazione di tecniche avanzate di test e caratterizzazione: con la crescente complessità e i requisiti dei dispositivi elettronici, sarà necessario disporre di metodi avanzati di test e caratterizzazione per garantire l'affidabilità e le prestazioni della resina epossidica non riempita. Tecniche come prove non distruttive, monitoraggio in situ e strumenti di simulazione contribuiranno allo sviluppo e al controllo di qualità dei materiali epossidici non riempiti.
Conclusione
La resina epossidica Underfill svolge un ruolo fondamentale nel migliorare l'affidabilità e le prestazioni dei componenti elettronici, in particolare negli imballaggi dei semiconduttori. I diversi tipi di resina epossidica underfill offrono una serie di vantaggi, tra cui elevata affidabilità, autoerogazione, alta densità ed elevate prestazioni termiche e meccaniche. La scelta della resina epossidica sottoriempimento giusta per l'applicazione e la confezione garantisce un legame robusto e duraturo. Man mano che la tecnologia avanza e le dimensioni delle confezioni si riducono, ci aspettiamo soluzioni epossidiche sottoriempimento ancora più innovative che offrano prestazioni, integrazione e miniaturizzazione superiori. La resina epossidica Underfill è destinata a svolgere un ruolo sempre più importante nel futuro dell'elettronica, consentendoci di raggiungere livelli più elevati di affidabilità e prestazioni in vari settori.