Adesivo per incollaggio FPC
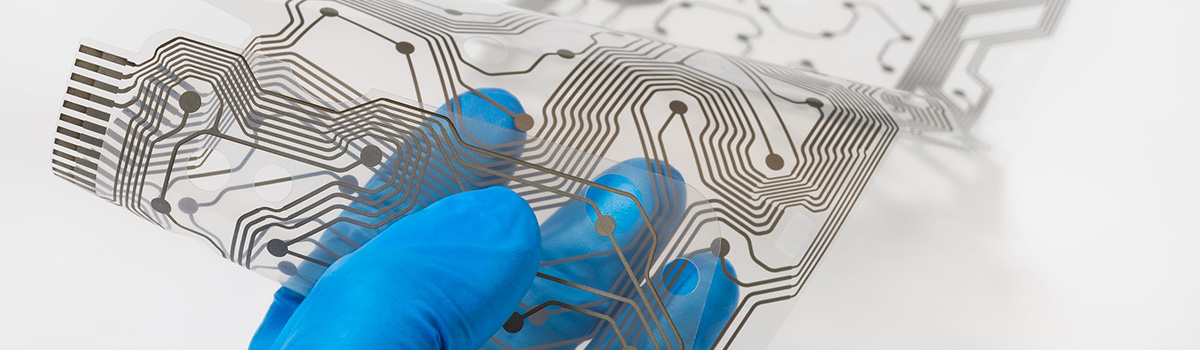
L'adesivo per incollaggio FPC è un componente cruciale nella produzione e nell'assemblaggio di schede per circuiti stampati flessibili (FPC), ampiamente utilizzate in vari dispositivi elettronici, inclusi smartphone, dispositivi indossabili e applicazioni automobilistiche. Questi adesivi forniscono forti capacità di adesione, isolamento elettrico e protezione contro i fattori ambientali, garantendo al tempo stesso la flessibilità e la durata delle schede FPC. Con l'aumentare della domanda di dispositivi elettronici flessibili e affidabili, l'importanza di adesivi per incollaggio FPC ad alte prestazioni e affidabili è diventata più critica. Questo articolo esplorerà i vari tipi, le applicazioni e le sfide degli adesivi per incollaggio FPC, evidenziando il loro ruolo cruciale nel consentire flessibilità e affidabilità nei dispositivi elettronici.
Tipi di adesivo per incollaggio FPC
Gli adesivi di fissaggio FPC (Flexible Printed Circuit) sono essenziali per l'assemblaggio e il collegamento di circuiti flessibili in vari dispositivi elettronici. Questi adesivi assicurano un legame affidabile e duraturo tra il circuito flessibile e il substrato target. Sul mercato sono disponibili diversi tipi di adesivi per incollaggio FPC, ciascuno con caratteristiche e applicazioni uniche. Questa risposta fornirà una panoramica di alcuni tipi comuni di adesivi per incollaggio FPC.
- Adesivi a base acrilica: gli adesivi a base acrilica sono popolari grazie alla loro eccellente adesione a vari substrati, inclusi metalli, plastica e vetro. Offrono flessibilità, stabilità termica e resistenza all'umidità e agli agenti chimici. Gli adesivi acrilici sono disponibili in varie forme, come nastri, pellicole e adesivi liquidi, che li rendono versatili per diverse applicazioni di incollaggio FPC.
- Adesivi a base epossidica: gli adesivi a base epossidica forniscono un'elevata forza di adesione e sono ampiamente utilizzati per l'incollaggio FPC. Offrono un'eccellente adesione a vari substrati e forniscono buone proprietà di isolamento elettrico. Gli adesivi epossidici sono disponibili in diverse formulazioni, inclusi sistemi monocomponenti e bicomponenti, offrendo opzioni per molteplici processi di incollaggio e condizioni di indurimento.
- Adesivi a base di silicone: gli adesivi a base di silicone sono noti per la loro flessibilità, resistenza alle alte temperature ed eccellenti proprietà di isolamento elettrico. Possono resistere a temperature estreme e fornire una buona resistenza all'umidità, rendendoli adatti ad ambienti difficili. Gli adesivi siliconici sono comunemente usati in applicazioni con gestione termica critica e affidabilità.
- Adesivi sensibili alla pressione (PSA): i PSA sono materiali adesivi che formano un legame istantaneo quando viene applicata la pressione. Eliminano la necessità di altri processi di polimerizzazione, rendendoli convenienti per le applicazioni di incollaggio FPC. I PSA offrono una buona adesione a vari substrati e possono essere facilmente rimossi senza lasciare residui, rendendoli ideali per l'incollaggio temporaneo o la rilavorazione.
- Adesivi a polimerizzazione UV: gli adesivi a polimerizzazione UV sono adesivi liquidi che polimerizzano rapidamente se esposti alla luce ultravioletta. Offrono tempi di indurimento rapidi, elevata forza adesiva ed eccellente adesione a diversi substrati. Gli adesivi a polimerizzazione UV sono comunemente utilizzati nelle applicazioni di incollaggio FPC in cui sono richiesti un assemblaggio rapido e una maggiore produttività.
- Adesivi conduttivi: gli adesivi conduttivi sono appositamente formulati per l'incollaggio e la conduttività elettrica. Contengono riempitivi conduttivi, come argento o carbonio, che consentono all'adesivo di stabilire collegamenti elettrici tra i componenti del circuito. Gli adesivi conduttivi sono ampiamente utilizzati nell'incollaggio FPC per applicazioni come la schermatura EMI, la messa a terra e le interconnessioni elettriche.
- Adesivi termicamente conduttivi: gli adesivi termicamente conduttivi sono progettati per fornire proprietà sia di adesione che di trasferimento termico efficiente. Sono utilizzati nelle applicazioni di incollaggio FPC in cui la gestione termica è fondamentale, come l'incollaggio di circuiti flessibili a dissipatori di calore o altri substrati termicamente conduttivi.
È importante notare che la scelta di un adesivo per incollaggio FPC dipende da vari fattori, inclusi i requisiti specifici dell'applicazione, i materiali del substrato, le condizioni ambientali e i processi di produzione. Consultare produttori o fornitori di adesivi può fornire informazioni e indicazioni più dettagliate sulla selezione dell'adesivo più adatto per una specifica applicazione di incollaggio FPC.
Adesivi acrilici: la scelta più comune
Gli adesivi acrilici sono popolari in vari settori grazie alla loro versatilità, alle forti capacità di adesione e alla facilità d'uso. Questi adesivi sono composti da polimeri acrilici, che forniscono un'eccellente adesione a un'ampia gamma di substrati. Qui, esploreremo perché gli adesivi acrilici sono la scelta più comune entro 450 parole.
Uno dei vantaggi fondamentali degli adesivi acrilici è la loro capacità di unire insieme diversi materiali. Gli adesivi acrilici possono creare legami durevoli e affidabili, sia che si tratti di incollare plastica, metalli, ceramica, legno o persino vetro. Questa versatilità li rende adatti a varie applicazioni automobilistiche, edili, elettroniche e di segnaletica.
Gli adesivi acrilici offrono anche un'eccellente forza di adesione e possono formare legami forti che resistono a sollecitazioni elevate, variazioni di temperatura e condizioni ambientali. Questo li rende ideali per applicazioni in cui la durata e le prestazioni a lungo termine sono cruciali.
Un altro motivo della popolarità degli adesivi acrilici è il loro rapido tempo di indurimento. Rispetto ad altri tipi di adesivi, gli adesivi acrilici hanno tempi di polimerizzazione relativamente brevi, consentendo cicli di produzione più rapidi. Spesso possono raggiungere la forza di movimentazione in pochi minuti, riducendo i tempi di assemblaggio e aumentando la produttività.
Inoltre, gli adesivi acrilici sono noti per resistere all'umidità, agli agenti chimici e ai raggi UV. Hanno un'eccellente resistenza all'acqua e possono mantenere le loro proprietà adesive anche in ambienti umidi. Questa caratteristica li rende adatti per applicazioni all'aperto e ambienti in cui è prevista l'esposizione a condizioni gravose.
Gli adesivi acrilici forniscono anche un'eccellente stabilità termica. Possono resistere a un'ampia gamma di temperature, dal freddo estremo al caldo elevato, senza compromettere la loro forza di adesione. Questa resistenza termica li rende adatti per applicazioni in cui le fluttuazioni di temperatura sono comuni, come nell'industria automobilistica ed elettronica.
Oltre alle loro proprietà fisiche, gli adesivi acrilici sono facili da maneggiare e applicare. Sono disponibili in varie forme, inclusi liquidi, paste, pellicole e nastri, offrendo flessibilità nei metodi di applicazione. Possono essere applicati utilizzando sistemi di erogazione automatizzati o manualmente, a seconda dei requisiti specifici dell'applicazione.
Inoltre, gli adesivi acrilici sono generalmente inodori e hanno un basso contenuto di composti organici volatili (VOC). Questo li rende più sicuri degli adesivi a base di solventi, che possono emettere forti odori o contenere sostanze chimiche nocive.
Adesivi siliconici: resistenza ambientale superiore
Gli adesivi siliconici sono una classe di adesivi noti per la loro superiore resistenza ambientale. Offrono prestazioni e durata eccezionali in varie applicazioni, rendendole molto ricercate nei settori automobilistico, elettronico, aerospaziale, edile e medico.
Uno dei vantaggi fondamentali degli adesivi siliconici è la loro capacità di resistere a temperature estreme. Possono resistere alle alte e basse temperature senza perdere le loro proprietà adesive o diventare fragili. Questo li rende adatti per applicazioni in cui le fluttuazioni di temperatura sono comuni, come nei motori automobilistici o nei dispositivi elettronici.
Gli adesivi siliconici presentano inoltre un'eccellente resistenza all'umidità e all'acqua. A differenza di molti altri tipi di adesivi, possono mantenere resistenza e integrità anche se esposti ad acqua o ambienti umidi. Questa proprietà è fondamentale nelle applicazioni che richiedono resistenza all'acqua, come la tenuta di guarnizioni, l'incollaggio di componenti sott'acqua o la protezione di circuiti elettronici dai danni causati dall'umidità.
Inoltre, gli adesivi siliconici offrono un'eccezionale resistenza ai raggi UV e agli agenti atmosferici. Possono resistere all'esposizione prolungata alla luce solare, alla pioggia, alla neve e ad altri fattori ambientali senza degradare o perdere le loro proprietà adesive. Questo li rende ideali per applicazioni esterne, come la sigillatura di segnaletica esterna, l'incollaggio di pannelli solari o la protezione di dispositivi elettronici esterni.
La resistenza chimica è un'altra area in cui eccellono gli adesivi siliconici. Possono resistere a vari prodotti chimici, inclusi solventi, oli, carburanti e acidi. Questa resistenza è significativa in settori come quello automobilistico e aerospaziale, dove l'esposizione a più sostanze chimiche è quotidiana. Anche in prodotti chimici aggressivi, gli adesivi siliconici possono mantenere la loro integrità e adesione, garantendo prestazioni e affidabilità a lungo termine.
Oltre alla loro resistenza ambientale, gli adesivi siliconici offrono eccellenti proprietà di isolamento elettrico. Hanno un'elevata rigidità dielettrica e possono fornire isolamento contro le correnti elettriche. Questo li rende ideali per l'incollaggio e la sigillatura di componenti elettronici, dove l'isolamento elettrico e la protezione sono cruciali.
Gli adesivi siliconici sono disponibili in varie forme, inclusi sistemi monocomponenti o bicomponenti, oltre a diversi meccanismi di polimerizzazione come polimerizzazione a caldo, polimerizzazione con umidità o polimerizzazione UV. Questa versatilità consente un'ampia gamma di applicazioni e requisiti di incollaggio.
Vale la pena notare che mentre gli adesivi siliconici offrono un'eccezionale resistenza ambientale, potrebbero non avere la stessa elevata forza di adesione iniziale di altri tipi di adesivi. Tuttavia, compensano questo con la loro flessibilità, durata e prestazioni a lungo termine in condizioni difficili.
Adesivi a polimerizzazione UV: incollaggio rapido e preciso
Gli adesivi a polimerizzazione UV, noti anche come adesivi a polimerizzazione ultravioletta, hanno guadagnato una notevole popolarità in vari settori grazie alla loro capacità di fornire un incollaggio rapido e preciso. Questi adesivi offrono numerosi vantaggi rispetto ai sistemi adesivi tradizionali, rendendoli la scelta preferita per le applicazioni che richiedono un'adesione rapida e affidabile.
Gli adesivi a polimerizzazione UV sono formulati con speciali fotoiniziatori che avviano il processo se esposti alla luce ultravioletta. La reazione di indurimento avviene quasi istantaneamente, consentendo una rapida formazione del legame. A differenza degli adesivi convenzionali che utilizzano il calore o reazioni chimiche per polimerizzare, gli adesivi a polimerizzazione UV forniscono un legame praticamente istantaneo, risparmiando tempo di produzione prezioso e aumentando l'efficienza.
Uno dei vantaggi fondamentali degli adesivi a polimerizzazione UV è la loro precisa capacità di incollaggio. La reazione di indurimento è altamente controllata e localizzata, assicurando che l'adesivo indurisca solo nell'area desiderata. Ciò consente un posizionamento e un allineamento precisi dei componenti, anche in assiemi complessi. I produttori possono ottenere tolleranze ristrette e mantenere un'elevata qualità del prodotto utilizzando adesivi a polimerizzazione UV.
Il rapido tempo di indurimento degli adesivi UV è particolarmente vantaggioso nelle industrie in cui è fondamentale un rapido ritorno alla produzione. Ad esempio, nella produzione elettronica, gli adesivi a polimerizzazione UV consentono il rapido incollaggio dei componenti, riducendo i tempi di assemblaggio e aumentando la produttività. Allo stesso modo, nel settore dei dispositivi medici, gli adesivi UV forniscono un incollaggio rapido e affidabile di vari materiali, consentendo un rapido assemblaggio di dispositivi medici complessi.
Gli adesivi a polimerizzazione UV offrono un'eccellente forza di adesione e durata. Una volta induriti, questi adesivi formano legami forti che resistono a varie condizioni ambientali, comprese le fluttuazioni di temperatura, l'umidità e le sostanze chimiche. I legami presentano un'elevata resistenza all'ingiallimento o al degrado nel tempo, garantendo prestazioni e affidabilità a lungo termine.
Gli adesivi a polimerizzazione UV sono versatili e compatibili con vari substrati, tra cui plastica, metalli, vetro e ceramica. Possono unire insieme materiali dissimili, ampliando la gamma di applicazioni in cui possono essere utilizzati. Dall'incollaggio di componenti in plastica nell'industria automobilistica all'assemblaggio di dispositivi elettronici, gli adesivi a polimerizzazione UV offrono una soluzione affidabile per diverse esigenze di incollaggio.
Inoltre, gli adesivi a polimerizzazione UV sono privi di solventi, eliminando la necessità di composti organici volatili (VOC) e riducendo l'impatto ambientale. Offrono anche benefici per la salute e la sicurezza riducendo al minimo l'esposizione a sostanze chimiche pericolose. L'assenza di solventi e COV contribuisce a un ambiente di lavoro più pulito e sano per gli operatori.
Adesivi epossidici: elevata forza adesiva e resistenza chimica
Gli adesivi epossidici sono popolari in vari settori grazie alla loro elevata forza adesiva e alle eccellenti proprietà di resistenza chimica. Offrono numerosi vantaggi rispetto ad altre opzioni adesive, rendendole versatili e affidabili per molteplici applicazioni.
Uno dei vantaggi fondamentali degli adesivi epossidici è la loro eccezionale forza di adesione. Creano legami potenti che possono sopportare stress e carichi significativi se applicati correttamente, rendendoli adatti per applicazioni che richiedono un legame durevole e duraturo. Gli adesivi epossidici possono unire diversi materiali, inclusi metalli, plastica, ceramica, vetro e compositi, fornendo una soluzione di giunzione affidabile per vari settori.
Oltre all'elevata forza adesiva, gli adesivi epossidici presentano un'eccellente resistenza chimica. Possono resistere a vari prodotti chimici, inclusi solventi, acidi, basi, oli e combustibili. Questa resistenza all'attacco chimico assicura che l'adesivo rimanga stabile e mantenga la sua forza adesiva anche in ambienti difficili. Di conseguenza, gli adesivi epossidici sono comunemente usati nelle industrie automobilistiche, aerospaziali, elettroniche e di trasformazione chimica, dove l'esposizione alle sostanze chimiche è un problema.
La resistenza chimica degli adesivi epossidici è attribuita alla loro struttura molecolare unica. Gli adesivi epossidici sono costituiti da una resina e un indurente che reagiscono chimicamente per formare una rete reticolata. Questa struttura reticolata conferisce all'adesivo forza e resistenza agli agenti chimici. Il processo di indurimento degli adesivi epossidici può essere regolato per ottenere diversi livelli di resistenza chimica, consentendo la personalizzazione in base a specifici requisiti applicativi.
Inoltre, gli adesivi epossidici offrono un'eccellente resistenza alla temperatura, un altro fattore cruciale in molti settori. Possono mantenere la forza di adesione e l'integrità ad alte e basse temperature, rendendole adatte per applicazioni esposte a variazioni di temperatura estreme. Questa proprietà è fondamentale in settori come quello aerospaziale e automobilistico, dove i componenti possono subire fluttuazioni di temperatura significative.
Un altro vantaggio degli adesivi epossidici è la loro versatilità in termini di metodi di applicazione. Varie tecniche, tra cui l'erogazione manuale, l'erogazione di siringhe, l'applicazione a spruzzo e i sistemi di erogazione automatizzati, possono applicarli. Questa flessibilità nei metodi di applicazione consente un incollaggio efficiente e preciso in diversi ambienti di produzione.
È importante notare che una corretta preparazione della superficie e tecniche di applicazione dell'adesivo sono essenziali per ottenere una forza adesiva e una resistenza chimica ottimali con gli adesivi epossidici. Le superfici devono essere pulite, asciutte e prive di contaminanti per garantire la massima adesione. Inoltre, l'adesivo deve essere miscelato secondo le istruzioni del produttore, considerando il corretto rapporto tra resina e indurente e le condizioni di polimerizzazione appropriate.
In conclusione, gli adesivi epossidici offrono un'elevata forza di adesione e un'eccellente resistenza chimica, rendendoli la scelta ideale per varie applicazioni. La loro capacità di unire materiali diversi, resistere a sostanze chimiche aggressive e funzionare bene a temperature estreme li rende indispensabili nell'industria automobilistica, aerospaziale, elettronica e di trasformazione chimica. Con un'adeguata preparazione della superficie e tecniche di applicazione, gli adesivi epossidici possono fornire legami durevoli e affidabili, contribuendo alle prestazioni complessive e alla longevità dei componenti assemblati.
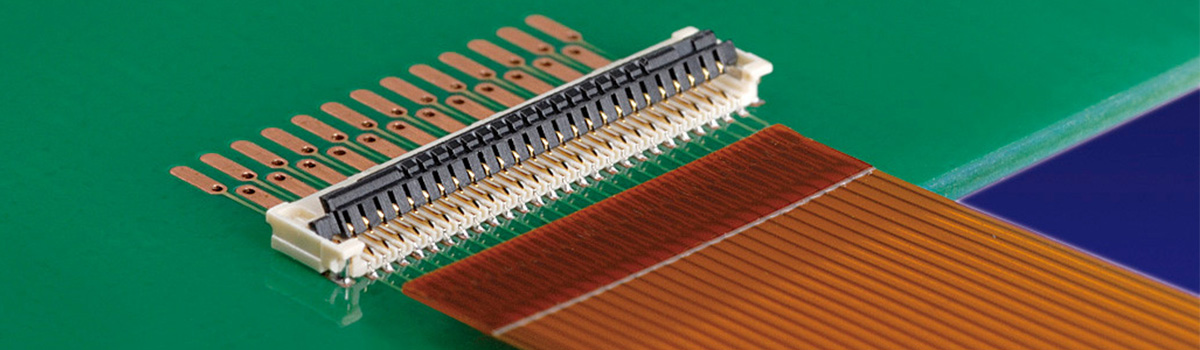
Adesivi conduttivi: consentire la connettività elettrica
Gli adesivi conduttivi svolgono un ruolo cruciale nel consentire la connettività elettrica in varie applicazioni. Questi materiali innovativi forniscono un'efficace alternativa ai tradizionali metodi di saldatura o fissaggio meccanico offrendo un'eccellente conduttività elettrica, facilità d'uso e versatilità. Questo articolo esplorerà le principali caratteristiche e applicazioni degli adesivi conduttivi.
Gli adesivi conduttivi sono formulati utilizzando una combinazione di riempitivi conduttivi, come argento, rame o carbonio, e un legante polimerico. I riempitivi conduttivi facilitano il passaggio della corrente elettrica, mentre il legante garantisce l'adesione a diversi substrati. Questa composizione unica consente agli adesivi conduttivi di fornire connessioni elettriche affidabili anche in ambienti difficili.
Uno dei principali vantaggi degli adesivi conduttivi è la loro compatibilità con un'ampia gamma di materiali. Possono incollare metalli, ceramica, vetro, plastica e persino substrati flessibili, rendendoli adatti a vari settori. Il collegamento di materiali dissimili è particolarmente vantaggioso nell'industria elettronica, dove è necessario unire insieme componenti con coefficienti di dilatazione termica diversi.
Gli adesivi conduttivi offrono un'eccellente conducibilità elettrica, paragonabile alla saldatura tradizionale. Questa proprietà consente loro di sostituire efficacemente i giunti di saldatura in applicazioni specifiche. Inoltre, gli adesivi conduttivi presentano una migliore resistenza ai cicli termici, alle sollecitazioni meccaniche e alle vibrazioni rispetto alle connessioni saldate. Questi attributi li rendono ideali per applicazioni con frequenti sbalzi di temperatura o movimenti automatici.
La facilità di applicazione è un altro vantaggio significativo degli adesivi conduttivi. Sono tipicamente disponibili in forme convenienti, come siringhe, o erogati come pellicole o nastri. Ciò consente un'erogazione precisa e controllata, rendendoli adatti a processi di assemblaggio automatizzati e manuali. A differenza della saldatura, che richiede attrezzature e competenze specializzate, gli adesivi conduttivi possono essere facilmente applicati con una formazione minima.
Gli adesivi conduttivi trovano applicazioni in vari settori. Nel settore dell'elettronica, vengono utilizzati per il fissaggio di componenti, l'incollaggio di die, l'incollaggio di fili e come alternativa alla saldatura nell'assemblaggio di circuiti stampati (PCB). Sono anche impiegati nella produzione di elettronica flessibile, dove i metodi di saldatura tradizionali non sono fattibili a causa della flessibilità dei substrati.
Nell'industria automobilistica, gli adesivi conduttivi vengono utilizzati per l'incollaggio di sensori, antenne e sistemi di illuminazione. Offrono un'eccellente adesione ai materiali utilizzati nelle applicazioni automobilistiche, tra cui plastica e compositi. Inoltre, la loro capacità di resistere a condizioni ambientali difficili, come variazioni di temperatura, umidità ed esposizione chimica, li rende la scelta ideale per l'elettronica automobilistica.
Gli adesivi conduttivi svolgono un ruolo significativo anche in campo medico. Assemblano dispositivi medici, come sensori, elettrodi e dispositivi impiantabili. Le varianti biocompatibili degli adesivi conduttivi assicurano che siano sicuri per il contatto con i tessuti umani.
Adesivi a basso degassamento: critici per le applicazioni spaziali
Gli adesivi a basso degassamento svolgono un ruolo fondamentale nelle applicazioni spaziali in cui i materiali devono resistere alle condizioni estreme dell'ambiente spaziale. Il degassamento si riferisce al rilascio di composti volatili dai materiali quando esposti al vuoto o alle alte temperature. Nello spazio, questi composti volatili possono comportare rischi significativi per la funzionalità e l'affidabilità di apparecchiature e strumenti sensibili.
Nel vuoto dello spazio, i materiali degassati possono condensarsi sulle superfici vicine, come lenti ottiche o sensori, causando contaminazione e degrado delle prestazioni. La contaminazione può compromettere l'accuratezza delle misurazioni, ridurre la qualità del segnale e persino portare al guasto di componenti critici. Inoltre, i materiali degassati condensati possono accumularsi nel tempo, formando uno strato in grado di assorbire o diffondere la luce, con effetti sui sistemi ottici e sui dispositivi di imaging.
Gli adesivi a basso degassamento sono specificatamente formulati per ridurre al minimo il rilascio di composti volatili. Sono progettati per avere una bassa tensione di vapore, il che significa che rilasciano meno gas e vapori se esposti a condizioni di vuoto. Questa caratteristica aiuta a prevenire la contaminazione e il degrado di superfici e componenti sensibili.
Veicoli spaziali e satelliti si affidano ad adesivi a basso degassamento per varie applicazioni. Un uso importante è nell'incollaggio e nell'incapsulamento di componenti elettronici. Questi adesivi forniscono legami solidi e affidabili tra materiali diversi, riducendo al minimo il rischio di contaminazione e problemi legati al degassamento. Garantiscono l'integrità strutturale e la connettività elettrica dei componenti, consentendo loro di resistere alle vibrazioni e agli urti sperimentati durante il lancio e il funzionamento nello spazio.
Gli adesivi a basso degassamento sono essenziali anche per i sistemi ottici utilizzati nei telescopi spaziali, nelle fotocamere e nei sensori. Gli adesivi utilizzati in questi sistemi devono avere un impatto minimo sulla chiarezza e sulle prestazioni di lenti, specchi e rilevatori. Riducendo il degassamento, questi adesivi mantengono le proprietà ottiche e prevengono la formazione di strati di contaminazione che potrebbero degradare la qualità dell'immagine o interferire con misurazioni precise.
Inoltre, la gestione termica è una considerazione critica nelle applicazioni spaziali. Gli adesivi a basso degassamento uniscono dissipatori di calore, materiali di interfaccia termica e altri componenti coinvolti nella dissipazione del calore. Questi adesivi garantiscono un efficiente trasferimento del calore riducendo al minimo il rischio di contaminazione che potrebbe compromettere le prestazioni dei sistemi di gestione termica.
Per soddisfare i severi requisiti delle applicazioni spaziali, gli adesivi a basso degassamento vengono sottoposti a rigorosi processi di test e certificazione. I materiali sono sottoposti a cicli termici, esposizione al vuoto e analisi per valutarne le caratteristiche di degassamento. Gli adesivi che soddisfano gli standard stabiliti da organizzazioni come i requisiti di degassamento della NASA (come ASTM E595) sono considerati idonei per le missioni spaziali.
Adesivi termicamente conduttivi: gestione del calore nei dispositivi elettronici
Gli adesivi termicamente conduttivi svolgono un ruolo cruciale nella gestione del calore nei dispositivi elettronici. Poiché le dimensioni dei componenti elettronici continuano a ridursi e funzionano a densità di potenza più elevate, un'efficace dissipazione del calore diventa sempre più essenziale per garantire prestazioni e affidabilità ottimali. Gli adesivi termicamente conduttivi forniscono una soluzione praticabile trasferendo in modo efficiente il calore dai componenti che generano calore ai dissipatori di calore o ad altri meccanismi di dissipazione del calore. Questo articolo esplorerà gli aspetti critici degli adesivi termicamente conduttivi e il loro ruolo nella gestione del calore nei dispositivi elettronici.
Gli adesivi termicamente conduttivi sono materiali appositamente formulati con proprietà adesive ed elevata conducibilità termica. Sono progettati per formare forti legami tra componenti che generano calore, come circuiti integrati o dispositivi di alimentazione, e dissipatori di calore o altri elementi di raffreddamento. La natura adesiva di questi materiali garantisce un fissaggio affidabile, mentre la loro elevata conducibilità termica consente un efficiente trasferimento di calore.
Uno dei principali vantaggi degli adesivi termicamente conduttivi è la loro capacità di riempire piccoli spazi e irregolarità tra le superfici di accoppiamento, riducendo così al minimo la resistenza termica. Questa caratteristica è particolarmente vantaggiosa quando si collegano componenti con superfici non piane o quando si ha a che fare con microscopiche intercapedini d'aria che ostacolano il flusso di calore. Colmando queste lacune, gli adesivi termicamente conduttivi stabiliscono un contatto intimo tra i personaggi, migliorando il trasferimento di calore e riducendo il rischio di hotspot termici.
Un altro aspetto critico della gestione del calore nei dispositivi elettronici è la capacità di resistere ai cicli di temperatura e alle sollecitazioni meccaniche. I dispositivi elettronici sono soggetti a condizioni di temperatura variabili e vibrazioni meccaniche durante il funzionamento. Gli adesivi termicamente conduttivi sono formulati per mantenere la forza adesiva e le prestazioni termiche in un ampio intervallo di temperature, garantendo una dissipazione del calore affidabile anche in condizioni difficili.
Inoltre, gli adesivi termicamente conduttivi offrono proprietà di isolamento elettrico, prevenendo i cortocircuiti elettrici tra i componenti. Questa caratteristica è fondamentale nei dispositivi elettronici in cui più pezzi sono densamente imballati e vi è il rischio di contatto accidentale tra elementi conduttivi.
Gli adesivi termicamente conduttivi possono essere applicati utilizzando vari metodi, tra cui l'erogazione, la serigrafia o la laminazione di pellicole. Questi adesivi sono disponibili in diverse viscosità e meccanismi di polimerizzazione, consentendo flessibilità nel processo di produzione. Alcuni adesivi termicamente conduttivi polimerizzano a temperatura ambiente, mentre altri richiedono temperature elevate o luce UV. I produttori possono selezionare il legame che meglio si adatta alle loro specifiche esigenze di produzione.
Adesivi Peel-and-Stick: facili da usare e da applicare
Gli adesivi peel-and-stick hanno rivoluzionato il modo in cui affrontiamo vari progetti e attività che richiedono materiali di fissaggio. Questi adesivi sono incredibilmente facili da usare e applicare, rendendoli popolari tra i professionisti e gli appassionati di fai da te. Con la loro praticità e versatilità, gli adesivi peel-and-stick sono diventati una soluzione ideale per molte applicazioni.
Uno dei principali vantaggi degli adesivi peel-and-stick è la loro semplicità. A differenza degli adesivi tradizionali che spesso richiedono la miscelazione o strumenti specializzati, gli adesivi peel-and-stick vengono pre-applicati su un materiale di supporto, pronti per l'uso dalla confezione. Ciò elimina la necessità di attrezzature aggiuntive o di una preparazione approfondita, risparmiando tempo e fatica.
Il processo di applicazione degli adesivi peel-and-stick è semplice e intuitivo. Tutto quello che devi fare è staccare la carta protettiva per esporre il lato adesivo e premerlo con decisione sulla superficie desiderata. L'adesivo aderisce in modo rapido e sicuro, fornendo un'adesione istantanea senza morsetti o tempi di asciugatura. Ciò rende gli adesivi peel-and-stick ideali per riparazioni rapide, installazioni temporanee o progetti urgenti.
Un altro vantaggio degli adesivi peel-and-stick è la loro versatilità. Sono disponibili in varie forme, come nastri, fogli o punti, per adattarsi a diverse applicazioni e materiali. Sia che tu abbia bisogno di attaccare oggetti leggeri, montare decorazioni o alcuni oggetti pesanti, un adesivo staccabile è adatto per il compito. Aderiscono bene a varie superfici, tra cui legno, metallo, vetro, plastica e tessuto, offrendo flessibilità e compatibilità con diversi materiali.
Gli adesivi peel-and-stick sono noti anche per la loro applicazione pulita. A differenza degli adesivi tradizionali che possono essere disordinati e richiedere la pulizia, gli adesivi peel-and-stick non lasciano residui se applicati e rimossi correttamente. Ciò è particolarmente vantaggioso quando si lavora su superfici delicate o finite che si desidera proteggere dai danni.
Oltre alla loro facilità d'uso, gli adesivi peel-and-stick spesso mostrano forti capacità di adesione. Gli adesivi sono progettati per fornire un legame affidabile e duraturo, assicurando che gli elementi attaccati rimangano saldamente in posizione. Tuttavia, è essenziale scegliere il giusto tipo di adesivo per il tuo progetto e seguire le linee guida del produttore per ottenere risultati ottimali.
Pellicole adesive: migliorare l'efficienza e la consistenza
Le pellicole adesive sono materiali versatili che offrono varie applicazioni in vari settori. Sono strati sottili di sostanze appiccicose rivestite su un materiale di supporto, come carta, plastica o tessuto. Questi film offrono numerosi vantaggi, migliorando l'efficienza e la coerenza in vari processi. Questo articolo esplorerà come le pellicole adesive migliorano l'efficienza e la coerenza in diverse applicazioni.
Un vantaggio chiave delle pellicole adesive è la loro facilità di applicazione. A differenza degli adesivi tradizionali, che possono richiedere la miscelazione o attrezzature specializzate, le pellicole adesive sono pronte per l'uso. Possono essere facilmente tagliati nelle forme e dimensioni desiderate, rendendoli ideali per un'applicazione rapida e precisa. Ciò consente di risparmiare tempo e risorse nei processi di produzione e assemblaggio, aumentando l'efficienza complessiva.
Inoltre, le pellicole adesive offrono prestazioni di incollaggio costanti. Il loro spessore uniforme e le proprietà adesive controllate garantiscono un'adesione affidabile tra diversi materiali. Che si tratti di unire due superfici, strati di laminazione o fissare componenti, le pellicole adesive forniscono una forza di adesione costante, riducendo al minimo il rischio di guasti o rilavorazioni. Questa uniformità migliora la qualità del prodotto, riduce gli sprechi e aumenta la produttività.
Un altro modo in cui le pellicole adesive migliorano l'efficienza è attraverso la loro compatibilità con i sistemi di automazione. Con la crescente tendenza dell'automazione in vari settori, le pellicole adesive sono progettate per essere compatibili con i processi di assemblaggio e confezionamento robotizzati. Possono essere facilmente integrati in linee di produzione automatizzate, consentendo operazioni di incollaggio precise e ad alta velocità. Ciò non solo migliora l'efficienza, ma riduce anche i costi di manodopera e gli errori umani.
Inoltre, le pellicole adesive offrono una maggiore efficienza nelle applicazioni di sigillatura e protezione. Forniscono una barriera contro umidità, polvere e contaminanti, prevenendo danni a componenti o prodotti sensibili. Che si tratti di sigillare dispositivi elettronici, imballare prodotti alimentari o proteggere le superfici dalla corrosione, le pellicole adesive offrono una protezione affidabile e costante. Ciò contribuisce alla longevità e all'affidabilità dei prodotti, riducendo la necessità di frequenti manutenzioni o sostituzioni.
Inoltre, le pellicole adesive consentono una personalizzazione efficiente e flessibilità di progettazione. Possono essere personalizzati in base a requisiti specifici, come diverse forze di adesione, resistenza alla temperatura o proprietà ottiche. Ciò consente ai produttori di ottimizzare le proprietà adesive in base alle loro esigenze applicative, garantendo le migliori prestazioni e affidabilità. Inoltre, le pellicole adesive possono essere facilmente stampate o decorate, offrendo opportunità di branding e fascino estetico.
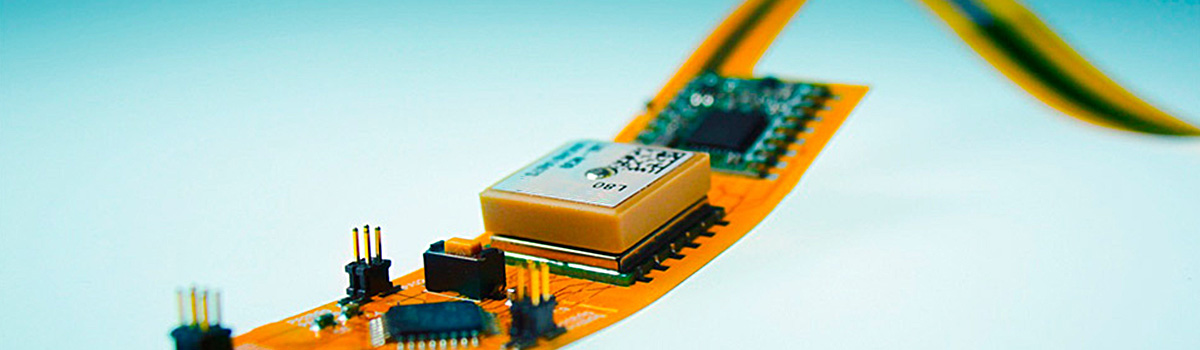
Adesivi hot melt: incollaggio rapido e durevole
Gli adesivi hot melt (HMA) sono adesivi versatili che offrono soluzioni di incollaggio rapide e durevoli in vari settori e applicazioni. Questi adesivi, o colla a caldo, sono materiali termoplastici che vengono fusi allo stato liquido e applicati fusi. Dopo il raffreddamento, si solidificano e creano un forte legame tra i substrati. Ecco uno sguardo più da vicino alle caratteristiche, ai vantaggi e alle applicazioni degli adesivi hot melt.
Uno dei vantaggi fondamentali degli HMA è la loro capacità di incollaggio rapido. Questi adesivi si liquefanno rapidamente quando riscaldati, consentendo un'applicazione efficiente e ad alta velocità. Eliminano la necessità di evaporazione del solvente o reazioni chimiche, a differenza di altri tipi di adesivi. La rapida solidificazione degli adesivi hot melt si traduce in tempi di assemblaggio e produzione più brevi, aumentando la produttività e risparmiando sui costi.
Inoltre, gli adesivi hot melt garantiscono una durata eccezionale nelle giunzioni incollate. Presentano un'eccellente resistenza all'umidità, agli agenti chimici e alle fluttuazioni di temperatura. Questa resilienza li rende adatti per ambienti e applicazioni esigenti che richiedono un incollaggio duraturo e affidabile. Gli HMA offrono anche flessibilità e resistenza agli urti, consentendo loro di resistere a vibrazioni e urti senza compromettere l'integrità del legame.
Gli HMA trovano applicazioni in vari settori, tra cui imballaggio, lavorazione del legno, automobilistico, elettronico, tessile e costruzioni. Gli adesivi hot melt sono ampiamente utilizzati negli imballaggi per sigillare casse e cartoni, chiusure antimanomissione e incollaggio di etichette e nastri. Forniscono sigilli sicuri e resistenti alla manomissione, garantendo l'integrità del prodotto e prevenendo il furto.
Le applicazioni per la lavorazione del legno degli HMA includono le operazioni di bordatura, impiallacciatura e laminazione. La natura a presa rapida degli adesivi hot melt facilita i processi efficienti della catena di montaggio. Creano forti legami nelle giunture in legno, migliorando l'integrità strutturale e la longevità di mobili e mobili.
I produttori automobilistici si affidano agli adesivi hot melt per l'incollaggio di finiture interne ed esterne, cablaggi e sigillatura di guarnizioni. La durabilità e la resistenza al calore di questi adesivi li rendono ideali per le applicazioni automobilistiche, dove le prestazioni in condizioni estreme sono essenziali.
L'assemblaggio e la produzione di componenti elettronici spesso utilizzano adesivi hot melt per l'incollaggio di componenti, l'incollaggio di cavi e l'incapsulamento. La loro capacità di unire materiali diversi, come plastica, metalli e vetro, li rende adatti a diverse applicazioni elettroniche.
Le applicazioni degli adesivi hot melt per l'industria tessile includono la laminazione di tessuti, l'orlatura e l'incollaggio di applicazioni. Consentono un incollaggio preciso e pulito senza cuciture, cuciture o altri metodi di fissaggio meccanico.
Nel settore delle costruzioni, gli HMA vengono utilizzati per l'installazione di pavimenti, pannellature, isolamento e incollaggio di piastrelle. Le loro caratteristiche di presa rapida facilitano processi di costruzione rapidi e garantiscono un'adesione affidabile in vari materiali da costruzione.
Adesivi sensibili alla pressione: garantiscono un'adesione uniforme
Gli adesivi sensibili alla pressione (PSA) sono materiali versatili utilizzati in vari settori, dall'automotive e dall'elettronica agli imballaggi e ai dispositivi medici. Questi adesivi offrono vantaggi unici come la facilità di applicazione, l'incollaggio immediato e la capacità di aderire a un'ampia gamma di superfici. Tuttavia, garantire un'adesione costante può essere una sfida quando si lavora con PSA. Ecco alcune considerazioni chiave per ottenere un'adesione affidabile e uniforme con adesivi sensibili alla pressione.
- Preparazione della superficie: un'adeguata preparazione della superficie è fondamentale per ottenere un'adesione uniforme con i PSA. Le superfici devono essere pulite, asciutte e prive di polvere, olio, grasso e umidità. La pulizia della superficie con solventi o detergenti adeguati e l'utilizzo di tecniche come l'abrasione o il trattamento al plasma possono migliorare l'adesione aumentando l'energia superficiale e rimuovendo potenziali barriere all'incollaggio.
- Compatibilità del materiale: è essenziale garantire che il PSA sia compatibile con il materiale del substrato. Alcuni PSA possono presentare scarsa adesione o problemi di compatibilità con determinate superfici. Comprendere la composizione chimica e le proprietà sia dell'adesivo che del substrato può aiutare a selezionare l'adesivo appropriato per l'applicazione specifica, garantendo un'adesione uniforme.
- Tecnica di applicazione: la tecnica di applicazione gioca un ruolo significativo nel raggiungimento di un'adesione uniforme. La pressione, la temperatura e il tempo di permanenza durante l'applicazione possono influire sulla forza di adesione. È essenziale seguire le raccomandazioni del produttore per quanto riguarda i parametri dell'applicazione, compresa la corretta pressione da applicare e l'intervallo di temperatura consigliato per l'incollaggio.
- Tempo di polimerizzazione: i PSA richiedono in genere un certo periodo di tempo per sviluppare la loro piena forza adesiva. Questo tempo di indurimento o di "riposo" consente all'adesivo di fluire e formare forti legami con il substrato. È essenziale consentire un tempo di polimerizzazione sufficiente prima di sottoporre l'assieme incollato a stress o carico. L'accelerazione del processo può comportare un'adesione più debole o addirittura un guasto dell'adesivo.
- Fattori ambientali: le condizioni ambientali possono influire sulle prestazioni dei PSA. Fattori come la temperatura, l'umidità e l'esposizione a sostanze chimiche o radiazioni UV possono influenzare le proprietà dell'adesivo e le prestazioni di adesione. Comprendere le condizioni ambientali specifiche a cui sarà esposto l'adesivo e selezionare un adesivo con un'adeguata resistenza a questi fattori può aiutare a garantire un'adesione costante nel tempo.
- Test e controllo qualità: test regolari e misure di controllo qualità sono essenziali per garantire un'adesione costante. Vari metodi di prova, come l'adesione alla pelatura, la resistenza al taglio e l'adesività, possono valutare le prestazioni dell'adesivo. Stabilire protocolli di test adeguati e condurre regolari controlli di qualità durante la produzione può aiutare a identificare eventuali incoerenze o problemi nella fase iniziale e garantire un'adesione costante nel prodotto finale.
- Conservazione e durata di conservazione: le condizioni di conservazione adeguate e il rispetto delle linee guida sulla durata di conservazione sono essenziali per mantenere le prestazioni dell'adesivo. I PSA possono degradarsi nel tempo a causa del calore, della luce o dell'esposizione all'aria, compromettendo le loro proprietà adesive. Conservare i legami in ambienti controllati e utilizzarli entro la durata di conservazione consigliata può aiutare a mantenere un'adesione costante.
Tecniche di erogazione dell'adesivo: precisione ed efficienza
Le tecniche di erogazione degli adesivi sono cruciali in vari settori, garantendo precisione ed efficienza nelle applicazioni di incollaggio. Che si tratti di produzione, assemblaggio o riparazione, il metodo di erogazione corretto può influire in modo significativo sulla qualità e l'affidabilità dei legami adesivi. Questo articolo esplorerà le tecniche critiche che aiutano a raggiungere la precisione e l'efficienza nell'erogazione dell'adesivo con un numero limitato di parole.
- Erogazione manuale: l'erogazione manuale dell'adesivo è comunemente impiegata in operazioni su piccola scala o applicazioni complesse. Implica l'utilizzo di dispositivi portatili come siringhe, flaconi da spremere o pennelli per applicare l'adesivo con precisione. Sebbene questo metodo offra flessibilità e controllo, dipende dall'abilità e dalla costanza dell'operatore.
- Erogazione tempo/pressione: l'erogazione tempo/pressione è una tecnica ampiamente utilizzata che fornisce un'applicazione uniforme e controllata dell'adesivo. Prevede l'utilizzo di erogatori pneumatici o elettrici con regolatori di pressione e temporizzatori. Regolando il tempo e la pressione di erogazione, gli operatori possono controllare con precisione la quantità di adesivo applicata. Questa tecnica è adatta per adesivi a media e alta viscosità.
- Jetting: il Jetting è una tecnica di erogazione che utilizza un flusso di adesivo ad alta velocità per applicare piccole quantità precise di adesivo sulla superficie target. È comunemente utilizzato in applicazioni che richiedono un posizionamento rapido e preciso, come l'assemblaggio di componenti elettronici o il micro incollaggio. I sistemi a getto utilizzano l'azionamento piezoelettrico o pneumatico per creare goccioline adesive controllate.
- Erogazione spray: l'erogazione spray è una tecnica efficiente per coprire grandi aree o ottenere una copertura uniforme. Si tratta di nebulizzare l'adesivo in goccioline fini e dirigerle sulla superficie utilizzando la pressione dell'aria o una pistola a spruzzo automatica. L'erogazione spray è comunemente utilizzata nell'industria automobilistica, della lavorazione del legno o dell'imballaggio, dove è richiesta una copertura rapida e uniforme.
- Erogazione robotica: i sistemi di erogazione robotica offrono applicazioni di adesivo precise e ripetibili attraverso l'automazione programmabile. Sono dotati di sensori avanzati e valvole di erogazione che possono essere programmate per seguire schemi e contorni complessi. L'erogazione robotizzata garantisce uniformità e precisione, rendendola ideale per linee di produzione ad alto volume e processi di assemblaggio complessi.
- Rivestimento a pellicola/a vortice: il rivestimento a pellicola o a vortice è una tecnica utilizzata per applicare uno strato uniforme di adesivo su un substrato. Implica l'utilizzo di un meccanismo rotante o di un applicatore per stendere l'adesivo in una pellicola sottile e continua. Questo metodo è comunemente impiegato nei settori automobilistico, aerospaziale e delle costruzioni, dove lo spessore adesivo controllato è fondamentale per prestazioni ottimali.
Sfide nell'applicazione dell'adesivo per incollaggio FPC
L'applicazione di adesivo per incollaggio FPC (Flexible Printed Circuit) pone diverse sfide che devono essere affrontate per un incollaggio di successo e prestazioni affidabili. Queste sfide derivano principalmente dalle proprietà e dai requisiti unici degli FPC. In questa risposta, illustrerò alcune sfide chiave incontrate nell'applicazione dell'adesivo di incollaggio FPC.
- Compatibilità del substrato: gli FPC sono realizzati con materiali flessibili come poliimmide, poliestere o rame sottile, con caratteristiche superficiali diverse rispetto ai substrati rigidi. L'adesivo di fissaggio deve essere compatibile con il materiale FPC per garantire una corretta adesione senza causare delaminazione o danni al substrato.
- Preparazione della superficie: una corretta preparazione della superficie è fondamentale per l'incollaggio. Le superfici FPC presentano spesso residui, oli o contaminanti che possono ostacolare l'adesione. La sfida sta nel selezionare il metodo di pulizia o il trattamento superficiale corretto per rimuovere queste impurità senza compromettere l'integrità dell'FPC.
- Controllo dello spessore della linea di giunzione: ottenere uno spessore uniforme della linea di giunzione è essenziale per prestazioni affidabili. Lo spessore adesivo incoerente può portare a variazioni di conduttività elettrica, resistenza meccanica e gestione termica. Garantire un controllo preciso sullo spessore della linea di giunzione può essere difficile a causa della natura flessibile degli FPC.
- Gestione termica: gli FPC sono spesso utilizzati in applicazioni in cui sono previste variazioni di temperatura. L'adesivo utilizzato per l'incollaggio deve avere una buona conducibilità termica per dissipare il calore in modo efficace, evitando punti caldi localizzati che potrebbero danneggiare l'FPC oi suoi componenti. Raggiungere una gestione termica ottimale senza compromettere la flessibilità e le proprietà elettriche dell'FPC è una sfida.
- Indurimento dell'adesivo: gli adesivi per incollaggio FPC richiedono in genere processi di indurimento come il calore o i raggi UV. La sfida consisteva nell'assicurare una polimerizzazione uniforme e completa su tutta la linea di giunzione, in particolare in progetti FPC complessi o densamente imballati. Una polimerizzazione inadeguata può comportare un'adesione più forte o un legame incompleto, con conseguenti problemi di affidabilità.
- Flessibilità e durata: gli FPC sono progettati per essere flessibili e l'adesivo di fissaggio deve adattarsi a questa flessibilità senza comprometterne l'integrità. Il legame deve resistere a ripetute flessioni, flessioni e stiramenti senza incrinarsi, delaminarsi o perdere la forza di adesione. Trovare un legame in grado di mantenere sia la flessibilità che la durata può essere difficile.
- Conducibilità elettrica: gli FPC spesso trasportano segnali elettrici, rendendo la conducibilità elettrica un requisito fondamentale. L'adesivo di fissaggio non deve introdurre elevate resistenze che potrebbero interferire con le prestazioni del circuito. Raggiungere una buona conduttività elettrica attraverso la linea di giunzione assicurando al tempo stesso l'integrità meccanica rappresenta una sfida.
- Automazione del processo: l'automazione del processo di applicazione dell'adesivo diventa necessaria nei settori in cui l'incollaggio FPC viene eseguito su larga scala. La sfida sta nello sviluppo di sistemi automatizzati in grado di applicare costantemente l'adesivo con precisione ed efficienza, tenendo conto delle variazioni nelle dimensioni, nelle forme e nei design degli FPC.
Affrontare queste sfide richiede una comprensione completa dei materiali FPC, degli adesivi di fissaggio e dei requisiti specifici dell'applicazione. Spesso comporta un'attenta selezione dei materiali, l'ottimizzazione del processo e il collaudo per garantire la compatibilità, le prestazioni e l'affidabilità dell'adesivo nelle applicazioni di incollaggio FPC.
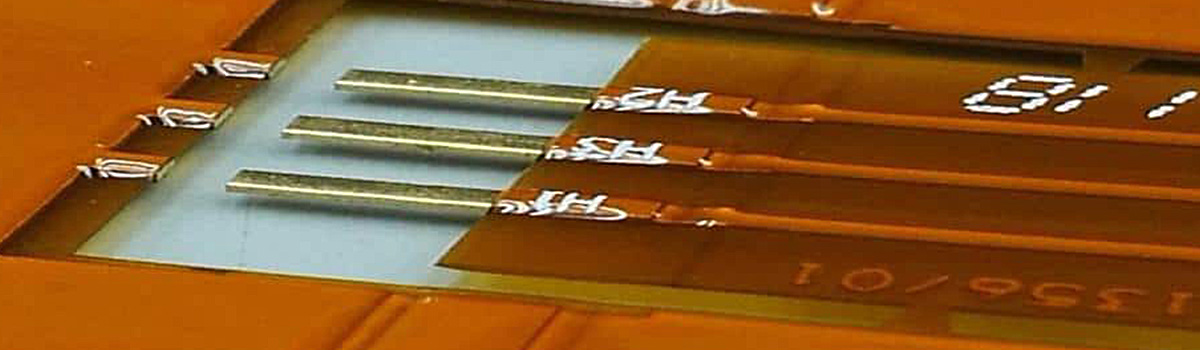
Test di affidabilità: valutazione delle prestazioni degli adesivi
I test di affidabilità sono un passaggio cruciale nella valutazione delle prestazioni degli adesivi. Gli adesivi sono ampiamente utilizzati in vari settori, tra cui automobilistico, aerospaziale, elettronico e edile, per incollare materiali diversi. L'affidabilità dei legami adesivi è essenziale per garantire la sicurezza, la durata e le prestazioni complessive del prodotto finale.
I test di affidabilità implicano il sottoporre i legami adesivi a varie condizioni e fattori di stress che simulano ambienti e scenari di utilizzo reali. L'obiettivo è valutare la capacità dell'adesivo di mantenere la forza di adesione e l'integrità nel tempo. Ecco alcuni aspetti chiave da considerare quando si valutano le prestazioni dell'adesivo nei test di affidabilità:
- Forza di adesione: la forza di adesione iniziale dell'adesivo viene valutata utilizzando test standardizzati come i test di taglio, pelatura o trazione. Questi test misurano la forza necessaria per rompere il legame adesivo. Fornisce una linea di base per il confronto con la forza di adesione dopo l'esposizione a diverse condizioni.
- Esposizione ambientale: gli adesivi sono spesso esposti a condizioni ambientali difficili come temperature estreme, umidità, radiazioni UV e sostanze chimiche. I test di affidabilità prevedono di sottoporre i campioni di adesivo a test di invecchiamento accelerato che simulano queste condizioni per un periodo prolungato. Questo aiuta a valutare la resistenza dell'adesivo al degrado ambientale e la sua capacità di mantenere la forza di adesione in condizioni avverse.
- Ciclo termico: le variazioni di temperatura possono causare l'espansione e la contrazione dei materiali, che possono stressare i legami adesivi. I test sui cicli termici prevedono di sottoporre i campioni di adesivo a ripetuti cicli di temperatura, da estremi bassi a estremi, per valutare la resistenza dell'adesivo allo stress termico e la sua capacità di mantenere l'integrità del legame.
- Stress meccanico: i legami adesivi possono subire diversi tipi di stress meccanico durante il servizio, come tensione, compressione, taglio e vibrazione. I test di affidabilità prevedono di sottoporre i campioni di adesivo a sollecitazioni meccaniche mediante prove cicliche di fatica, impatto o flessione. Questi test aiutano a valutare la capacità dell'adesivo di resistere al carico automatico senza cedimento del legame.
- Durata e invecchiamento: si prevede che i legami adesivi abbiano una durata a lungo termine e resistano al degrado nel tempo. I test di affidabilità includono test di invecchiamento a lungo termine che simulano la durata prevista del prodotto. Ciò può comportare l'esposizione prolungata di campioni di adesivo a fattori ambientali, come temperatura, umidità e radiazioni UV, e la valutazione periodica della forza e dell'integrità del legame.
- Compatibilità: gli adesivi devono essere compatibili con i materiali che intendono incollare. I test di affidabilità comportano la valutazione della compatibilità dell'adesivo con diversi substrati, inclusi metalli, plastica, compositi e altri materiali comunemente usati nel settore. I test di compatibilità valutano la forza di adesione dell'adesivo, la resistenza all'interazione chimica e qualsiasi effetto negativo sul substrato.
I test di affidabilità forniscono preziose informazioni sulle prestazioni e sui limiti degli adesivi in varie condizioni. Aiuta i produttori a selezionare l'adesivo più adatto per la loro applicazione e ne garantisce l'affidabilità e la durata in scenari reali. Conducendo rigorosi test di affidabilità, i produttori possono mitigare il rischio di fallimento del legame adesivo, migliorare la qualità del prodotto e migliorare la soddisfazione del cliente.
Considerazioni ambientali nell'adesivo per incollaggio FPC
Gli adesivi di fissaggio FPC (Flexible Printed Circuit) svolgono un ruolo fondamentale nell'assemblaggio e nell'affidabilità dei dispositivi elettronici. Poiché la consapevolezza ambientale e la sostenibilità diventano sempre più importanti, è essenziale considerare l'impatto ecologico di questi adesivi. Ecco alcune considerazioni ambientali critiche relative agli adesivi di incollaggio FPC:
- Tossicità: una delle preoccupazioni principali è la tossicità dell'adesivo e dei suoi componenti. Gli adesivi possono contenere sostanze chimiche nocive come composti organici volatili (COV) o inquinanti atmosferici pericolosi (HAP). Queste sostanze possono avere effetti dannosi sulla salute umana e sull'ambiente. I produttori dovrebbero sforzarsi di ridurre al minimo o eliminare le sostanze chimiche tossiche nelle loro formulazioni adesive.
- Emissioni e qualità dell'aria: durante i processi di produzione e applicazione, gli adesivi FPC possono rilasciare COV e altri inquinanti atmosferici nell'atmosfera. Queste emissioni contribuiscono all'inquinamento atmosferico e possono influire negativamente sulla qualità dell'aria. I produttori di adesivi attenti all'ambiente mirano a ridurre queste emissioni formulando adesivi a basso o zero COV.
- Consumo energetico: la produzione di adesivi FPC richiede energia, che spesso proviene da fonti non rinnovabili. Per ridurre al minimo l'impatto ambientale, i produttori dovrebbero implementare processi ad alta efficienza energetica ed esplorare l'utilizzo di fonti di energia rinnovabile.
- Generazione di rifiuti: i processi di applicazione dell'adesivo possono generare rifiuti, tra cui materiale adesivo in eccesso, imballaggi e materiali per la pulizia. Dovrebbero essere seguite adeguate pratiche di gestione dei rifiuti, come il riciclaggio o il riutilizzo dei materiali di scarto quando possibile. Inoltre, i produttori dovrebbero esplorare lo sviluppo di adesivi con una durata di conservazione più lunga per ridurre gli sprechi di prodotti scaduti o inutilizzati.
- Considerazioni sulla fine del ciclo di vita: lo smaltimento di dispositivi elettronici contenenti adesivi di fissaggio FPC è un problema ambientale significativo. Gli adesivi che non sono facilmente degradabili o hanno componenti pericolosi possono contribuire all'inquinamento quando i dispositivi vengono smaltiti. I produttori di adesivi dovrebbero sforzarsi di sviluppare prodotti ecocompatibili che siano compatibili con i processi di riciclaggio o smaltimento, come gli adesivi che possono essere facilmente separati dai circuiti stampati durante il riciclaggio.
- Sostenibilità e iniziative verdi: i produttori di adesivi dovrebbero incorporare la sostenibilità nelle loro pratiche commerciali. Ciò può includere l'utilizzo di materie prime rinnovabili, l'implementazione di processi di produzione ecologici e l'adesione a standard e certificazioni ambientali riconosciuti. Inoltre, le aziende possono partecipare a iniziative ecologiche, come programmi di ritiro dei prodotti o partnership con impianti di riciclaggio.
- Valutazione del ciclo di vita: condurre una valutazione completa del ciclo di vita (LCA) degli adesivi per incollaggio FPC è fondamentale per comprendere il loro impatto ambientale dall'estrazione delle materie prime allo smaltimento. Gli LCA aiutano a identificare le aree in cui è possibile apportare miglioramenti, come la riduzione delle emissioni di gas serra, la riduzione al minimo del consumo di risorse e il miglioramento della riciclabilità.
Tendenze e innovazioni nell'adesivo per incollaggio FPC
Gli adesivi per incollaggio FPC (Flexible Printed Circuit) si evolvono costantemente, guidati dalla domanda di prestazioni più elevate, miniaturizzazione e maggiore affidabilità nei dispositivi elettronici. Ecco alcune tendenze e innovazioni degne di nota negli adesivi per incollaggio FPC:
- Miniaturizzazione e sottigliezza: man mano che i dispositivi elettronici diventano sempre più piccoli, c'è una crescente necessità di adesivi FPC per soddisfare questi requisiti di fattore di forma. I produttori stanno sviluppando adesivi ultrasottili ea basso profilo che forniscono un forte legame riducendo al minimo lo spessore complessivo dell'assieme.
- Resistenza alle alte temperature: molti dispositivi elettronici, in particolare quelli nelle applicazioni automobilistiche, aerospaziali e industriali, operano in ambienti ad alta temperatura. Sono in fase di sviluppo adesivi per incollaggio FPC con resistenza al calore potenziata per garantire prestazioni affidabili in condizioni di temperatura estreme, prevenendo la delaminazione o il fallimento dell'incollaggio.
- Indurimento a bassa pressione: i tradizionali processi di indurimento degli adesivi richiedono spesso temperature elevate o lunghi tempi di indurimento, che possono essere difficili per componenti sensibili al calore o substrati delicati. Le innovazioni nelle tecniche a bassa pressione, come gli adesivi a polimerizzazione UV o a umidità, offrono opzioni di polimerizzazione più delicate, consentendo la compatibilità con componenti e substrati sensibili alla temperatura.
- Adesivi conduttivi: la domanda di adesivi per incollaggio FPC con conducibilità elettrica è in aumento nelle applicazioni che richiedono collegamenti elettrici tra elementi del circuito. Gli adesivi conduttivi eliminano la necessità di diversi processi di saldatura, consentendo un assemblaggio più rapido e riducendo il rischio di danni termici ai componenti sensibili.
- Flessibilità e durata migliorate: la flessibilità e la durata sono fondamentali per gli adesivi FPC per resistere a flessione, torsione e vibrazioni nei dispositivi elettronici flessibili. I progressi nella chimica dei polimeri e nelle tecniche di formulazione si traducono in adesivi con maggiore flessibilità, allungamento e resistenza alle sollecitazioni meccaniche, garantendo un legame affidabile in ambienti dinamici.
- Compatibilità ambientale: le considerazioni ambientali, incluso l'utilizzo di materie prime sostenibili e la riduzione delle sostanze tossiche, stanno diventando sempre più importanti nello sviluppo degli adesivi. I produttori stanno esplorando materiali a base biologica e rinnovabili come alternative agli ingredienti a base di petrolio. Inoltre, vengono sviluppati processi di produzione ecologici e formulazioni adesive riciclabili per ridurre al minimo l'impatto ambientale.
- Migliore erogazione e applicazione: l'applicazione efficiente e precisa dell'adesivo è fondamentale per ottenere incollaggi uniformi e affidabili. Le innovazioni nelle tecnologie di erogazione, come i sistemi di erogazione automatizzati e i metodi di getto, consentono la deposizione controllata e accurata degli adesivi, anche in progetti FPC complessi con componenti a passo delicato.
- Tecnologia delle pellicole adesive: le pellicole adesive stanno guadagnando popolarità nell'incollaggio FPC grazie alla loro facilità di manipolazione e posizionamento preciso. Questi film preformati offrono uno spessore adesivo uniforme, eccellenti proprietà bagnanti e processi di assemblaggio semplificati. I produttori migliorano continuamente le formulazioni delle pellicole adesive per migliorare le prestazioni di adesione e la compatibilità con vari substrati.
- Miglioramenti dell'affidabilità: per garantire l'affidabilità a lungo termine, sono stati sviluppati adesivi per incollaggio FPC con una migliore resistenza a fattori quali umidità, sostanze chimiche e invecchiamento. Questi adesivi vengono sottoposti a test rigorosi per valutare le loro prestazioni in condizioni ambientali difficili, garantendo funzionalità costante e integrità del legame per tutta la durata del prodotto.
- Personalizzazione e soluzioni specifiche per l'applicazione: gli adesivi di incollaggio FPC vengono adattati per soddisfare i requisiti specifici di diverse applicazioni, come l'automotive, l'elettronica di consumo, i dispositivi medici e la tecnologia indossabile. I produttori stanno collaborando a stretto contatto con i progettisti e i produttori di dispositivi per sviluppare soluzioni adesive personalizzate che rispondano alle sfide uniche e alle esigenze prestazionali di ciascuna applicazione.
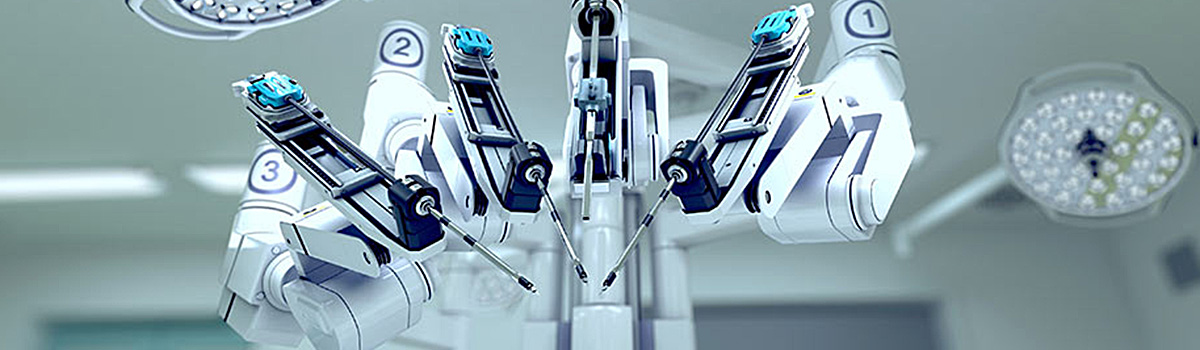
Aree di applicazione: elettronica di consumo, automotive, dispositivi medici e altro ancora
Elettronica di consumo: L'elettronica di consumo comprende una vasta gamma di prodotti progettati per l'uso personale e l'intrattenimento. Questi includono smartphone, tablet, laptop, console di gioco, smart TV, dispositivi domestici intelligenti, dispositivi indossabili e altro ancora. L'applicazione dell'elettronica di consumo ha rivoluzionato il modo in cui le persone comunicano, lavorano e si divertono. I progressi tecnologici hanno reso l'elettronica di consumo più potente, compatta e conveniente, fornendo agli utenti connettività senza interruzioni, esperienze coinvolgenti e praticità.
Settore automobilistico: L'industria automobilistica ha assistito a progressi significativi negli ultimi anni, guidati principalmente dall'integrazione tecnologica. Dai veicoli elettrici (EV) ai sistemi di guida autonoma, le applicazioni automobilistiche hanno trasformato il modo in cui viaggiamo. Le auto elettriche stanno guadagnando popolarità grazie alla loro natura ecologica e alla riduzione delle emissioni di carbonio. Inoltre, le case automobilistiche stanno incorporando funzionalità innovative come sistemi avanzati di assistenza alla guida (ADAS), connettività, sistemi di infotainment e telematica per migliorare l'esperienza di guida, migliorare la sicurezza e consentire una gestione efficiente del veicolo.
Dispositivi medici: I dispositivi medici hanno svolto un ruolo cruciale nella diagnosi, nel monitoraggio e nel trattamento di varie condizioni mediche. Si va da dispositivi semplici come termometri e monitor della pressione sanguigna ad apparecchiature avanzate come macchine per risonanza magnetica e sistemi chirurgici robotici. I dispositivi medici consentono agli operatori sanitari di fornire diagnosi accurate, eseguire procedure minimamente invasive e monitorare la salute dei pazienti da remoto. Hanno rivoluzionato il settore sanitario, migliorando i risultati dei pazienti, riducendo le degenze ospedaliere e migliorando la qualità complessiva dell'assistenza.
Internet delle cose (IoT): L'Internet of Things (IoT) è una rete di dispositivi interconnessi incorporati con sensori, software e capacità di connettività. Consente lo scambio di dati e la comunicazione tra dispositivi, portando all'automazione, all'analisi dei dati e a un migliore processo decisionale. L'IoT ha applicazioni in vari settori, tra cui sanità, agricoltura, produzione ed energia. Nel settore sanitario, i dispositivi IoT possono monitorare i parametri vitali dei pazienti, tenere traccia dell'aderenza ai farmaci e consentire il monitoraggio remoto dei pazienti. I dispositivi IoT possono ottimizzare l'irrigazione, monitorare le condizioni del suolo e migliorare la gestione delle colture in agricoltura. L'IoT ha il potenziale per rivoluzionare i settori rendendoli più efficienti, sostenibili e basati sui dati.
Automazione industriale: L'automazione industriale implica l'utilizzo di tecnologia e sistemi di controllo per automatizzare processi e attività industriali. Ciò include robotica, sistemi di visione artificiale, sensori e controllori logici programmabili (PLC). L'automazione industriale aumenta la produttività, migliora la sicurezza, riduce i costi operativi e trova applicazioni nella produzione, nella logistica, nell'energia e in altri settori. Con l'integrazione di intelligenza artificiale (AI) e machine learning (ML), l'automazione industriale può ottimizzare i processi, rilevare anomalie e consentire la manutenzione predittiva, migliorando l'efficienza e riducendo i tempi di inattività.
Prospettive e opportunità future
L'adesivo per incollaggio FPC (Flexible Printed Circuit) è un componente fondamentale nella produzione di dispositivi elettronici. È fondamentale per garantire connessioni affidabili e robuste tra circuiti flessibili e altre parti. Mentre guardiamo al futuro, vale la pena considerare diverse prospettive e opportunità per l'adesivo per incollaggio FPC.
- Progressi nell'elettronica flessibile: il campo dell'elettronica flessibile è in rapida evoluzione, con una crescente domanda di display flessibili, dispositivi indossabili e tessuti intelligenti. Gli adesivi di incollaggio FPC continueranno ad essere in ottimo stato per consentire l'assemblaggio e l'interconnessione di circuiti flessibili in queste applicazioni innovative.
- Miniaturizzazione e dispositivi più sottili: poiché l'elettronica di consumo diventa sempre più compatta e sottile, le soluzioni di interconnessione più sottili e flessibili sono fondamentali. Gli adesivi di incollaggio FPC possono facilitare l'assemblaggio di circuiti flessibili ultrasottili, creando dispositivi più eleganti e leggeri.
- Prestazioni di incollaggio migliorate: i produttori cercano continuamente soluzioni adesive che offrano prestazioni di incollaggio superiori, come un'elevata resistenza al taglio, un'eccellente conduttività elettrica e stabilità termica. I futuri adesivi di fissaggio FPC incorporeranno probabilmente materiali e formulazioni avanzati per soddisfare questi requisiti esigenti.
- Integrazione con processi di produzione avanzati: le tecnologie di produzione emergenti come la stampa 3D, l'elaborazione roll-to-roll e l'integrazione ibrida aprono nuove possibilità per la produzione di circuiti flessibili. Gli adesivi di incollaggio FPC devono adattarsi ed essere compatibili con questi processi di produzione, offrendo adesione e affidabilità ottimizzate.
- Elettronica ibrida flessibile (FHE): FHE combina l'elettronica rigida tradizionale con componenti adattabili, creando dispositivi con fattori di forma e funzionalità unici. Gli adesivi di incollaggio FPC saranno fondamentali per l'assemblaggio di questi sistemi ibridi, collegando senza soluzione di continuità elementi flessibili e rigidi.
- Sostenibilità e considerazioni ambientali: la crescente attenzione alla sostenibilità e alla responsabilità ambientale rappresenta un'opportunità per sviluppare adesivi FPC ecocompatibili. Le formulazioni future possono incorporare materiali rinnovabili o riciclabili, riducendo l'impatto ambientale dei rifiuti elettronici.
- Integrazione di funzionalità intelligenti: con l'ascesa dell'Internet of Things (IoT) e dei dispositivi interconnessi, gli adesivi di incollaggio FPC possono potenzialmente incorporare funzionalità intelligenti come sensori integrati, capacità di autoriparazione o proprietà di gestione termica. Questi progressi migliorerebbero la funzionalità e l'affidabilità dei dispositivi elettronici.
- Applicazioni mediche e sanitarie: il settore medico sta registrando un'ondata di dispositivi indossabili, sensori impiantabili e tecnologie sanitarie intelligenti. Gli adesivi di incollaggio FPC che sono biocompatibili, sterilizzabili e in grado di aderire a vari substrati troveranno applicazioni significative in questo dominio.
- Industrie automobilistiche e aerospaziali: i settori automobilistico e aerospaziale adottano sempre più circuiti flessibili per i loro vantaggi di leggerezza e risparmio di spazio. Gli adesivi per incollaggio FPC in grado di resistere a temperature estreme, vibrazioni e sollecitazioni meccaniche saranno molto richiesti per questi ambienti difficili.
- Ricerca e sviluppo: i continui sforzi di ricerca e sviluppo negli adesivi per incollaggio FPC porteranno a ulteriori progressi. Le innovazioni nei prodotti chimici degli adesivi, nelle tecniche di produzione e nell'ottimizzazione dei processi porteranno avanti il settore, consentendo nuove applicazioni e migliori prestazioni.
Importanza della collaborazione nell'avanzamento della tecnologia degli adesivi FPC Bonding
La collaborazione è fondamentale per l'avanzamento della tecnologia adesiva di incollaggio FPC (Flexible Printed Circuit). Consente lo scambio di conoscenze, risorse e competenze tra le diverse parti interessate, portando a innovazione e progresso accelerati. Ecco i motivi principali che evidenziano l'importanza della collaborazione nell'avanzamento della tecnologia adesiva di incollaggio FPC:
- Competenza interdisciplinare: la tecnologia adesiva di incollaggio FPC coinvolge vari domini, tra cui la scienza dei materiali, la chimica, la produzione elettronica e l'ingegneria. La collaborazione riunisce esperti di questi diversi campi, promuovendo approcci interdisciplinari alla risoluzione dei problemi. Combinando le loro conoscenze e prospettive, ricercatori e professionisti del settore possono affrontare sfide complesse e sviluppare nuove soluzioni in modo più efficace.
- Condivisione delle conoscenze: la collaborazione facilita la condivisione delle informazioni, i risultati della ricerca e le migliori pratiche tra entità diverse. Produttori, fornitori, ricercatori e istituzioni accademiche possono collaborare per diffondere preziose informazioni e conoscenze tecniche sulla tecnologia adesiva FPC. Questa conoscenza condivisa aiuta a evitare sforzi ridondanti, promuove la standardizzazione e accelera lo sviluppo complessivo.
- Accesso alle risorse: gli sforzi collaborativi consentono l'accesso a una gamma più ampia di risorse, inclusi finanziamenti, attrezzature, strutture e materiali. La collaborazione con organizzazioni, istituti di ricerca o agenzie governative può fornire l'accesso a risorse specializzate che potrebbero non essere disponibili individualmente. Questo accesso consente una sperimentazione, un test e una prototipazione più estesi, portando a migliori formulazioni di adesivi per incollaggio FPC e processi di produzione.
- Innovazione accelerata: la collaborazione favorisce un ambiente di innovazione aperta e creatività. Riunendo diverse prospettive e competenze, possono emergere nuove idee e concetti, spingendo i confini della tecnologia adesiva FPC. I progetti collaborativi possono anche sfruttare i punti di forza di ciascun partner, combinando le loro capacità e risorse uniche per sviluppare soluzioni innovative a un ritmo accelerato.
- Approfondimenti di mercato e tendenze del settore: la collaborazione con i partner del settore e gli utenti finali fornisce preziose informazioni sulle richieste del mercato, sulle tendenze emergenti e sui requisiti dei clienti. Questa comprensione aiuta ad allineare lo sviluppo della tecnologia adesiva di incollaggio FPC con le esigenze in continua evoluzione del settore. Gli sforzi collaborativi consentono un feedback e una convalida precoci, assicurando che le soluzioni sviluppate siano pratiche, pertinenti e commercialmente valide.
- Garanzia di qualità e standardizzazione: la collaborazione facilita la definizione di misure di garanzia della qualità e standard di settore per la tecnologia adesiva di incollaggio FPC. La collaborazione con organizzazioni di standardizzazione e organismi di regolamentazione garantisce che gli adesivi sviluppati soddisfino i requisiti di sicurezza, affidabilità e prestazioni. La collaborazione consente inoltre di condividere metodologie di test e protocolli di convalida, portando a processi di bonding più coerenti e standardizzati.
- Convalida e applicazione nel mondo reale: la collaborazione con utenti finali, produttori e integratori di sistema consente la conferma della tecnologia adesiva di incollaggio FPC nelle applicazioni del mondo reale. Lavorando insieme, i produttori di adesivi possono ottenere un prezioso feedback su prestazioni, usabilità e producibilità. Questo ciclo di feedback aiuta a perfezionare e migliorare le formulazioni adesive, garantendone l'idoneità per varie applicazioni e ambienti.
- Mitigazione del rischio: la collaborazione diffonde i rischi associati agli sforzi di ricerca e sviluppo. I partner possono affrontare collettivamente le sfide e mitigare i rischi individuali mettendo in comune risorse e competenze. La collaborazione consente inoltre la condivisione della proprietà intellettuale e dei diritti di brevetto, favorendo un ambiente più cooperativo e meno competitivo.
Conclusione
L'adesivo per incollaggio FPC è fondamentale per consentire flessibilità e affidabilità nei dispositivi elettronici. La capacità di questi adesivi di fornire forti capacità di adesione, isolamento elettrico e protezione contro i fattori ambientali, garantendo al tempo stesso la flessibilità e la durata delle schede FPC, è fondamentale nella produzione e nell'assemblaggio di vari dispositivi elettronici. Con l'avanzare della tecnologia, lo sviluppo di soluzioni adesive innovative e la collaborazione tra produttori, ricercatori e utenti finali saranno cruciali per soddisfare le crescenti richieste e le sfide dell'industria elettronica. Sfruttando il potenziale dell'adesivo adesivo FPC, possiamo aprire la strada a dispositivi elettronici ancora più flessibili, durevoli e affidabili che alimentano il nostro mondo moderno.