Rivestimento epossidico isolante
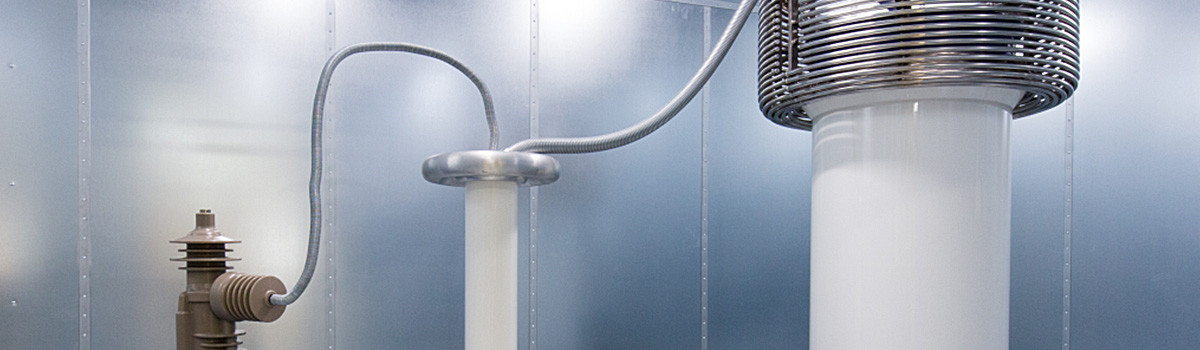
Il rivestimento isolante epossidico è un materiale versatile e ampiamente utilizzato con eccellenti proprietà di isolamento elettrico. Varie industrie lo impiegano comunemente per proteggere componenti elettrici, circuiti stampati e altre apparecchiature sensibili da umidità, polvere, sostanze chimiche e danni fisici. Questo articolo si propone di approfondire il rivestimento isolante epossidico, evidenziandone le applicazioni, i vantaggi e le considerazioni critiche per la selezione dello strato adatto per esigenze specifiche.
Comprensione del rivestimento epossidico isolante
Il rivestimento epossidico isolante è un rivestimento protettivo che fornisce isolamento e resistenza alla conduttività elettrica a varie superfici. È comunemente utilizzato nelle industrie elettronica, elettrica, automobilistica e aerospaziale per proteggere e migliorare le prestazioni dei componenti elettrici.
Lo scopo principale dei rivestimenti epossidici isolanti è impedire il flusso di corrente elettrica tra materiali conduttivi. Questi rivestimenti vengono applicati a superfici vulnerabili a cortocircuiti elettrici, corrosione o danni causati da fattori ambientali. Il materiale epossidico funge da isolante, impedendo il trasferimento di elettroni e riducendo al minimo il rischio di guasti elettrici o malfunzionamenti.
I rivestimenti epossidici isolanti sono tipicamente realizzati da una combinazione di resina epossidica, un polimero termoindurente e un agente indurente. La resina epossidica fornisce un'eccellente adesione, resistenza chimica e forza meccanica, mentre l'agente indurente innesca la reazione di reticolazione che converte la resina epossidica liquida in un rivestimento solido e duraturo.
L'applicazione di rivestimenti epossidici isolanti prevede diversi passaggi. Innanzitutto, la superficie da rivestire viene accuratamente pulita e preparata per garantire una corretta adesione. Qualsiasi sporco, grasso o contaminante deve essere rimosso per creare una superficie di incollaggio pulita. Quindi, il rivestimento epossidico viene miscelato secondo le istruzioni del produttore e applicato alla superficie mediante tecniche di spruzzatura, pennello o immersione.
Una volta applicato, il rivestimento epossidico subisce un processo di indurimento, durante il quale si indurisce e forma una barriera protettiva. L'indurimento può essere ottenuto attraverso vari metodi, tra cui calore, prodotti chimici o entrambi. L'indurimento migliora le proprietà meccaniche, la forza di adesione e la resistenza chimica del rivestimento.
I rivestimenti epossidici isolanti offrono diversi vantaggi:
- Forniscono isolamento elettrico, impedendo il flusso di corrente elettrica e riducendo il rischio di cortocircuiti o guasti elettrici.
- Questi rivestimenti offrono un'eccellente protezione contro fattori ambientali come umidità, sostanze chimiche e abrasione, prolungando la durata dei componenti rivestiti.
- I rivestimenti epossidici isolanti possono migliorare la stabilità termica e la resistenza alla fiamma delle superfici, rendendole adatte per applicazioni in ambienti ad alta temperatura.
L'importanza dell'isolamento elettrico
L'isolamento elettrico svolge un ruolo cruciale nel mantenimento della sicurezza, dell'affidabilità e dell'efficienza dei sistemi elettrici. Implica l'utilizzo di materiali e tecniche per impedire il flusso di corrente elettrica tra componenti o superfici conduttive. Ecco alcuni motivi chiave che evidenziano l'importanza dell'isolamento elettrico:
- Protezione contro le scosse elettriche: l'isolamento elettrico impedisce il contatto diretto con conduttori sotto tensione, riducendo il rischio di scosse elettriche. Agisce come una barriera che inibisce il flusso di corrente elettrica attraverso materiali non conduttivi, salvaguardando le persone da potenziali danni.
- Prevenzione di cortocircuiti e incendi elettrici: l'isolamento aiuta a prevenire il contatto elettrico involontario tra materiali conduttivi, che può causare cortocircuiti e incendi elettrici. Fili, cavi e componenti elettrici isolanti riducono al minimo la probabilità di archi elettrici, scintille e surriscaldamento, riducendo significativamente il rischio di incendi e danni alle apparecchiature.
- Prestazioni elettriche migliorate: i materiali isolanti con elevata rigidità dielettrica e bassa conduttività elettrica migliorano le prestazioni complessive dei sistemi elettrici. Mantengono livelli di tensione adeguati, prevengono le correnti di dispersione e riducono l'interferenza o la distorsione del segnale, garantendo il funzionamento ottimale dei circuiti e dei dispositivi elettrici.
- Protezione contro i fattori ambientali: i materiali di isolamento elettrico resistono all'umidità, agli agenti chimici, alla polvere e ad altri contaminanti. Questa protezione aiuta a prevenire la corrosione, il degrado e la rottura dell'isolamento causati da fattori esterni, mantenendo così la longevità e l'affidabilità dei componenti elettrici.
- Maggiore efficienza energetica: l'isolamento riduce la perdita di energia e migliora l'efficienza dei sistemi elettrici. Prevenendo la dispersione di corrente, l'isolamento riduce al minimo lo spreco di energia e migliora la trasmissione e la distribuzione dell'energia elettrica, con conseguente riduzione del consumo energetico e minori costi operativi.
- Conformità agli standard e alle normative di sicurezza: l'isolamento elettrico è essenziale per soddisfare gli standard e le normative di sicurezza stabiliti dalle autorità e dalle organizzazioni del settore. La conformità a questi requisiti garantisce che le installazioni e le apparecchiature elettriche siano progettate e gestite in modo da ridurre al minimo i rischi per il personale, la proprietà e l'ambiente.
- Protezione delle apparecchiature sensibili: l'isolamento è fondamentale per proteggere le apparecchiature elettriche ed elettroniche sensibili da disturbi elettrici e picchi di tensione. I materiali isolanti, come vernici o rivestimenti, proteggono i componenti delicati dalle interferenze elettromagnetiche (EMI) e dalle scariche elettrostatiche (ESD), preservandone la funzionalità e prolungandone la durata.
Applicazioni del rivestimento epossidico isolante
Il rivestimento epossidico isolante è un rivestimento specializzato che offre eccellenti proprietà di isolamento elettrico, rendendolo adatto a varie applicazioni. Questo rivestimento comprende tipicamente una resina epossidica, che fornisce capacità isolanti e qualità protettive. Ecco alcune delle applicazioni critiche del rivestimento epossidico isolante:
- Componenti elettronici ed elettrici: il rivestimento epossidico isolante è ampiamente utilizzato nell'industria elettronica ed elettrica. Viene applicato a componenti come circuiti stampati, trasformatori, condensatori e bobine per fornire isolamento elettrico, prevenire cortocircuiti e migliorare l'affidabilità complessiva e la durata di vita di questi componenti. Il rivestimento protegge anche da umidità, polvere e altri contaminanti ambientali.
- Generazione e trasmissione di energia: i rivestimenti epossidici isolanti sono fondamentali nei sistemi di generazione e trasmissione di energia. Vengono applicati a isolatori, quadri, sbarre collettrici e altre apparecchiature ad alta tensione per prevenire dispersioni elettriche, scariche a corona e scariche elettriche. Fornendo un'elevata rigidità dielettrica, il rivestimento aiuta a mantenere l'integrità e la sicurezza dell'infrastruttura elettrica.
- Motori e generatori: i motori e i generatori elettrici richiedono un isolamento per evitare guasti elettrici e garantire prestazioni efficienti. Rivestimenti epossidici isolanti vengono applicati agli avvolgimenti di queste macchine e ad altre parti critiche. Il rivestimento migliora l'isolamento elettrico, migliora la dissipazione del calore e offre protezione contro sostanze chimiche, umidità e sollecitazioni meccaniche.
- Industria automobilistica: i rivestimenti epossidici isolanti trovano varie applicazioni nel settore automobilistico. Isolano collegamenti elettrici, terminali e cablaggi nei veicoli. Lo strato aiuta a mantenere l'integrità elettrica, previene i cortocircuiti e protegge da corrosione, vibrazioni e cicli termici. Viene utilizzato anche per l'isolamento di componenti in veicoli ibridi ed elettrici.
- Aerospaziale e difesa: i rivestimenti epossidici isolanti sono vitali nei settori aerospaziale e della difesa. Vengono applicati a sistemi elettronici, avionici, apparecchiature radar e sistemi di comunicazione per garantire prestazioni affidabili in ambienti difficili. Il rivestimento protegge da interferenze elettriche, radiazioni, umidità e temperature estreme.
- Rivestimento per circuiti stampati (PCB): i PCB sono la spina dorsale dei dispositivi elettronici. I rivestimenti epossidici proteggono i circuiti e i giunti di saldatura dei PCB da umidità, polvere e altri contaminanti. Il rivestimento fornisce anche isolamento tra gli strati conduttivi, prevenendo i cortocircuiti e migliorando la durata complessiva delle schede.
- Resistenza chimica e alla corrosione: i rivestimenti epossidici isolanti offrono un'eccellente resistenza chimica e possono proteggere le superfici da sostanze corrosive. Sono utilizzati nella lavorazione chimica, petrolio e gas e trattamento delle acque reflue. Il rivestimento previene gli attacchi chimici, aumenta la longevità delle apparecchiature e riduce al minimo i requisiti di manutenzione.
- Incapsulamento elettrico: i rivestimenti epossidici isolanti vengono utilizzati per l'incapsulamento elettrico, in particolare nelle applicazioni in cui l'umidità o altri contaminanti rappresentano un rischio. È comunemente usato per incapsulare e incapsulare componenti elettronici, sensori e connettori. Il rivestimento forma una barriera protettiva contro i fattori ambientali e le sollecitazioni meccaniche.
Protezione per componenti elettronici
La protezione dei componenti elettronici è fondamentale per garantirne il corretto funzionamento e la longevità. I componenti elettronici sono spesso sensibili a fattori ambientali come temperatura, umidità, rumore elettrico e stress fisico. Con una protezione adeguata, questi componenti possono essere protetti e persino resi inutilizzabili. Ecco alcuni metodi e tecniche standard utilizzati per salvaguardare i componenti elettronici:
- Custodie: i componenti elettronici possono essere alloggiati in custodie protettive, come custodie, armadi o scatole. Le sezioni forniscono protezione fisica contro polvere, umidità e altri contaminanti. Proteggono inoltre i componenti da urti accidentali o maltrattamenti.
- Schermatura EMI/RFI: le interferenze elettromagnetiche (EMI) e le interferenze in radiofrequenza (RFI) possono interrompere il normale funzionamento dei componenti elettronici. La schermatura EMI/RFI prevede l'utilizzo di materiali conduttivi, come rivestimenti metallici o guarnizioni conduttive, per creare un effetto gabbia di Faraday. Questa schermatura impedisce ai segnali elettromagnetici esterni di interferire con l'elettronica sensibile.
- Gestione termica: i componenti elettronici generano calore durante il funzionamento e un calore eccessivo può degradarne le prestazioni e l'affidabilità. Tecniche di gestione termica come dissipatori di calore, ventole e cuscinetti termici aiutano a dissipare il calore e a mantenere temperature operative ottimali. I dissipatori di calore assorbono e dissipano il calore, mentre le ventole facilitano il flusso d'aria. I pad termici forniscono un'interfaccia termica tra il componente e il dissipatore di calore per un efficiente trasferimento di calore.
- Protezione contro le sovratensioni: le sovratensioni causate da fulmini, guasti elettrici o transitori di commutazione possono danneggiare i componenti elettronici. I dispositivi di protezione contro le sovratensioni, come soppressori di sovratensioni o varistori in ossido di metallo (MOV), deviano la tensione in eccesso per proteggere i membri. Questi dispositivi limitano i livelli di tensione e impediscono ai picchi transitori di raggiungere i componenti sensibili.
- Sigillatura ambientale: in applicazioni specifiche, i componenti elettronici necessitano di protezione da condizioni ambientali difficili, come umidità, sostanze chimiche o temperature estreme. Le tecniche di sigillatura ambientale, come i conformal coating, i composti per impregnazione o la sigillatura ermetica, creano una barriera che salvaguarda i componenti da questi elementi.
- Protezione del circuito: i componenti elettronici possono essere vulnerabili a sovratensione, sovracorrente e scariche elettrostatiche (ESD). I dispositivi di protezione del circuito, come fusibili, interruttori automatici, soppressori di tensioni transitorie (diodi TVS) e diodi di protezione ESD, vengono impiegati per limitare e reindirizzare corrente, tensione o cariche statiche eccessive lontano dai componenti.
- Messa a terra e collegamento equipotenziale: tecniche adeguate di messa a terra e collegamento equipotenziale sono essenziali per proteggere i componenti elettronici dai disturbi elettrici e garantire la sicurezza. La messa a terra fornisce un percorso per la dissipazione di cariche elettriche indesiderate. Al contrario, l'incollaggio riduce le differenze di potenziale che potrebbero causare danni. Le tecniche di messa a terra e di collegamento comprendono l'utilizzo di piani di massa, fili e connessioni di terra tipiche.
- Filtraggio: il rumore elettrico e le interferenze provenienti da varie fonti possono influire sulle prestazioni dei componenti elettronici. Filtri come passa-basso, passa-alto o filtri di interferenza elettromagnetica possono eliminare o ridurre i segnali indesiderati e garantire un'erogazione di potenza pulita ai membri.
- Misure antistatiche: le scariche elettrostatiche (ESD) possono causare danni significativi ai componenti elettronici. Le misure antistatiche, come le postazioni di lavoro, i cinturini da polso e i materiali di imballaggio protetti da scariche elettrostatiche, impediscono l'accumulo e la scarica di cariche elettrostatiche nelle parti sensibili.
- Manutenzione e test regolari: manutenzione, ispezione e test regolari sono essenziali per identificare potenziali problemi con i componenti elettronici. Controlli periodici garantiscono il corretto funzionamento delle misure di protezione e la tempestiva risoluzione di eventuali guasti o guasti.
I componenti elettronici possono essere protetti da rischi ambientali, disturbi elettrici e danni fisici utilizzando queste tecniche di protezione. Ciò garantisce il loro funzionamento affidabile e ne prolunga la durata, migliorando le prestazioni e riducendo i tempi di inattività.
Rivestimento del circuito stampato
Il rivestimento di circuiti stampati è un processo cruciale nella produzione di componenti elettronici che prevede l'applicazione di uno strato protettivo sul circuito stampato (PCB). Questo rivestimento fornisce isolamento, protezione da fattori ambientali e migliora l'affidabilità e la longevità dei circuiti. In questo articolo esploreremo l'importanza del rivestimento dei circuiti stampati e i diversi tipi di rivestimenti utilizzati.
Lo scopo principale del rivestimento del circuito è quello di salvaguardare i delicati componenti elettronici da vari stress ambientali. Queste sollecitazioni includono umidità, polvere, sporcizia, prodotti chimici e fluttuazioni di temperatura, che possono portare a corrosione, cortocircuiti e altri guasti. Il rivestimento funge da barriera, impedendo a questi elementi dannosi di raggiungere i circuiti e causare danni.
Sono disponibili diversi tipi di rivestimenti per circuiti stampati, ognuno dei quali offre vantaggi specifici a seconda dei requisiti dell'applicazione. Un tipo comune è il conformal coating, che è una sottile pellicola protettiva applicata direttamente sulla superficie del PCB. I rivestimenti conformi possono essere realizzati con vari materiali, inclusi acrilici, uretani, siliconi e resine epossidiche. Questi rivestimenti si adattano alla forma del circuito, coprendo tutti i componenti e le tracce esposte e forniscono un'eccellente protezione contro umidità, polvere e contaminanti chimici.
Un altro tipo di rivestimento è l'incapsulamento o potting compound, che è un materiale più spesso che ricopre l'intero PCB, incapsulandolo completamente. I composti per impregnazione sono tipicamente realizzati in resina epossidica o poliuretano e offrono una protezione superiore contro sollecitazioni meccaniche, vibrazioni e temperature estreme. Sono comunemente utilizzati in applicazioni in cui i circuiti stampati sono esposti ad ambienti difficili o ad alti livelli di stress fisico.
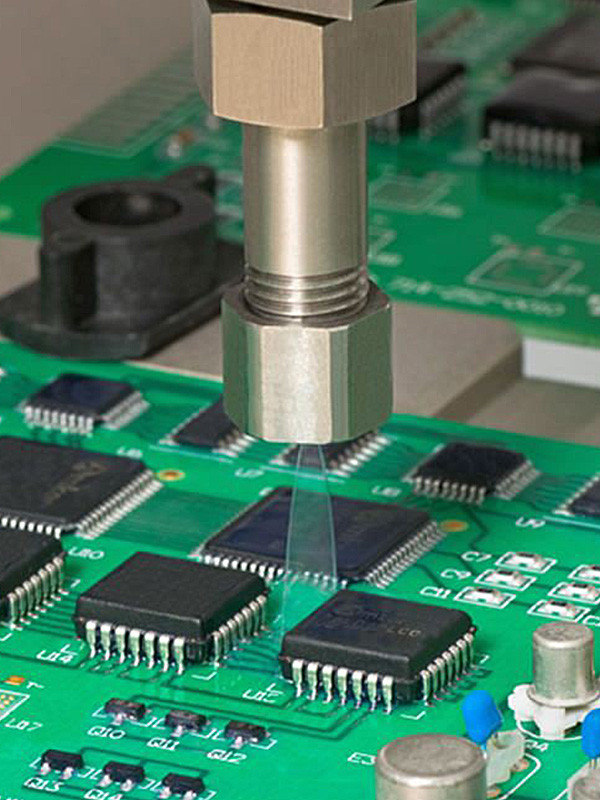
Il processo di rivestimento stesso prevede tecniche di applicazione attente per garantire una copertura uniforme e un'adesione adeguata. Possono essere impiegati diversi metodi, come il rivestimento a spruzzo, il rivestimento per immersione o il rivestimento selettivo. Il rivestimento a spruzzo prevede l'uso di una pistola a spruzzo o di un atomizzatore per applicare una sottile nebbia del materiale di rivestimento sul PCB. Il rivestimento per immersione, d'altra parte, immerge il PCB in un bagno di materiale di rivestimento, permettendogli di ricoprire completamente la scheda. Il rivestimento selettivo è un metodo preciso che applica il rivestimento solo ad aree specifiche del PCB, lasciando gli altri componenti non rivestiti per l'accessibilità.
Oltre alla protezione ambientale, i rivestimenti per circuiti stampati offrono anche proprietà di isolamento elettrico. Il materiale di rivestimento ha un'elevata rigidità dielettrica, che impedisce la dispersione di corrente tra tracce o componenti ravvicinati. Ciò è particolarmente importante nelle applicazioni ad alta tensione in cui l'isolamento elettrico è fondamentale.
Isolamento del motore e del trasformatore
La protezione dei componenti elettronici è fondamentale per garantirne il corretto funzionamento e la longevità. I componenti elettronici sono spesso sensibili a fattori ambientali come temperatura, umidità, rumore elettrico e stress fisico. Con una protezione adeguata, questi componenti possono essere protetti e persino resi inutilizzabili. Ecco alcuni metodi e tecniche standard utilizzati per salvaguardare i componenti elettronici:
- Custodie: i componenti elettronici possono essere alloggiati in custodie protettive, come custodie, armadi o scatole. Le sezioni forniscono protezione fisica contro polvere, umidità e altri contaminanti. Proteggono inoltre i componenti da urti accidentali o maltrattamenti.
- Schermatura EMI/RFI: le interferenze elettromagnetiche (EMI) e le interferenze in radiofrequenza (RFI) possono interrompere il normale funzionamento dei componenti elettronici. La schermatura EMI/RFI prevede l'utilizzo di materiali conduttivi, come rivestimenti metallici o guarnizioni conduttive, per creare un effetto gabbia di Faraday. Questa schermatura impedisce ai segnali elettromagnetici esterni di interferire con l'elettronica sensibile.
- Gestione termica: i componenti elettronici generano calore durante il funzionamento e un calore eccessivo può degradarne le prestazioni e l'affidabilità. Tecniche di gestione termica come dissipatori di calore, ventole e pad aiutano a dissipare il calore e a mantenere temperature operative ottimali. I dissipatori di calore assorbono e dissipano il calore, mentre le ventole facilitano il flusso d'aria. I pad termici forniscono un'interfaccia termica tra il componente e il dissipatore di calore per un efficiente trasferimento di calore.
- Protezione contro le sovratensioni: le sovratensioni causate da fulmini, guasti elettrici o transitori di commutazione possono danneggiare i componenti elettronici. I dispositivi di protezione contro le sovratensioni, come soppressori di sovratensioni o varistori in ossido di metallo (MOV), deviano la tensione in eccesso per proteggere i membri. Questi dispositivi limitano i livelli di tensione e impediscono ai picchi transitori di raggiungere i componenti sensibili.
- Sigillatura ambientale: in applicazioni specifiche, i componenti elettronici necessitano di protezione da condizioni ambientali difficili, come umidità, sostanze chimiche o temperature estreme. Le tecniche di sigillatura ambientale, come i conformal coating, i composti per impregnazione o la sigillatura ermetica, creano una barriera che salvaguarda i componenti da questi elementi.
- Protezione del circuito: i componenti elettronici possono essere vulnerabili a sovratensione, sovracorrente e scariche elettrostatiche (ESD). I dispositivi di protezione del circuito, come fusibili, interruttori automatici, soppressori di tensioni transitorie (diodi TVS) e diodi di protezione ESD, vengono impiegati per limitare e reindirizzare corrente, tensione o cariche statiche eccessive lontano dai componenti.
- Messa a terra e collegamento equipotenziale: tecniche adeguate di messa a terra e collegamento equipotenziale sono essenziali per proteggere i componenti elettronici dai disturbi elettrici e garantire la sicurezza. La messa a terra fornisce un percorso per la dissipazione di cariche elettriche indesiderate. Al contrario, l'incollaggio riduce le differenze di potenziale che potrebbero causare danni. Le tecniche di messa a terra e di collegamento comprendono l'utilizzo di piani di massa, fili e connessioni di terra tipiche.
- Filtraggio: il rumore elettrico e le interferenze provenienti da varie fonti possono influire sulle prestazioni dei componenti elettronici. Filtri come passa-basso, passa-alto o filtri di interferenza elettromagnetica possono eliminare o ridurre i segnali indesiderati e garantire un'erogazione di potenza pulita ai membri.
- Misure antistatiche: le scariche elettrostatiche (ESD) possono causare danni significativi ai componenti elettronici. Le misure antistatiche, come le postazioni di lavoro, i cinturini da polso e i materiali di imballaggio protetti da scariche elettrostatiche, impediscono l'accumulo e la scarica di cariche elettrostatiche nelle parti sensibili.
- Manutenzione e test regolari: manutenzione, ispezione e test regolari sono essenziali per identificare potenziali problemi con i componenti elettronici. Controlli periodici garantiscono il corretto funzionamento delle misure di protezione e la tempestiva risoluzione di eventuali guasti o guasti.
I componenti elettronici possono essere protetti da rischi ambientali, disturbi elettrici e danni fisici utilizzando queste tecniche di protezione. Ciò garantisce il loro funzionamento affidabile e ne prolunga la durata, migliorando le prestazioni e riducendo i tempi di inattività.
Isolamento di cavi e fili
L'isolamento di cavi e fili svolge un ruolo cruciale nei sistemi elettrici fornendo protezione, isolamento e sicurezza. Si riferisce al rivestimento o rivestimento esterno che circonda i conduttori elettrici, impedendo il flusso di corrente elettrica verso aree non previste e proteggendo i conduttori da fattori ambientali. La scelta del materiale isolante dipende da fattori quali la tensione nominale, l'intervallo di temperatura, le condizioni ambientali e l'applicazione prevista.
Uno dei materiali isolanti comunemente usati è il termoplastico. L'isolamento termoplastico è flessibile, durevole e resistente all'abrasione e agli agenti chimici. Il cloruro di polivinile (PVC) è un popolare materiale termoplastico noto per la sua convenienza e l'ampia gamma di applicazioni. È comunemente utilizzato in applicazioni a bassa tensione come il cablaggio domestico e i cavi per uso generico. L'isolamento in PVC offre buone proprietà elettriche ed è ignifugo.
Un altro materiale isolante molto utilizzato è il termoindurente. A differenza dei termoplastici, l'isolamento termoindurente non può essere rifuso o riformato una volta indurito. Il polietilene reticolato (XLPE) è un materiale termoindurente comunemente usato noto per le sue eccellenti proprietà elettriche, resistenza alle alte temperature e resistenza all'umidità e agli agenti chimici. L'isolamento XLPE viene spesso utilizzato nei cavi di alimentazione a media e alta tensione, compresi i sistemi di trasmissione e distribuzione sotterranei.
Oltre ai termoplastici e ai termoindurenti, altri materiali isolanti specializzati sono progettati per applicazioni specifiche. Ad esempio, l'isolamento in gomma siliconica è noto per la sua resistenza alle alte temperature, che lo rende adatto per applicazioni in ambienti estremi come l'industria aerospaziale e automobilistica. I fluoropolimeri, come il politetrafluoroetilene (PTFE), sono utilizzati in applicazioni ad alta temperatura e ad alta frequenza grazie alle loro eccellenti proprietà elettriche e alla resistenza agli agenti chimici e al calore.
La tensione nominale e l'uso previsto del cavo o del filo determinano lo spessore dello strato isolante. Le applicazioni a tensione più elevata richiedono strati isolanti più spessi per resistere ai campi elettrici più elevati e prevenire guasti elettrici. Lo spessore dell'isolamento influisce anche sul diametro complessivo e sulla flessibilità del cavo.
I materiali isolanti sono sottoposti a vari test per garantirne le prestazioni e la sicurezza. Questi test possono includere la misurazione di proprietà elettriche come rigidità dielettrica e resistenza di isolamento, valutazione della resistenza alle variazioni di temperatura, resistenza alla fiamma e proprietà meccaniche come flessibilità e resistenza all'abrasione. La conformità agli standard e alle normative del settore è essenziale per garantire l'affidabilità e la sicurezza degli impianti elettrici.
Industrie aerospaziali e automobilistiche
I rivestimenti epossidici isolanti trovano applicazioni essenziali sia nell'industria aerospaziale che in quella automobilistica. Questi rivestimenti offrono numerosi vantaggi, tra cui l'isolamento elettrico, la resistenza alla corrosione e la protezione termica. Questa risposta esplorerà gli usi critici dei rivestimenti epossidici isolanti nei settori aerospaziale e automobilistico, rispettando il limite di 450 parole.
Industria aerospaziale:
- Strutture degli aeromobili: i rivestimenti epossidici isolanti proteggono le strutture degli aeromobili da fattori ambientali, come umidità, sostanze chimiche e radiazioni UV. Questi rivestimenti fungono da barriera, prevenendo la corrosione e prolungando la durata dei componenti critici. Inoltre, forniscono isolamento elettrico, riducendo il rischio di interferenze elettriche e migliorando la sicurezza.
- Componenti elettronici: i rivestimenti epossidici isolanti vengono applicati ai componenti elettronici nei sistemi aerospaziali, inclusi circuiti stampati, connettori e sensori. Questi rivestimenti offrono eccellenti proprietà di isolamento elettrico, proteggendo l'elettronica sensibile da scariche statiche, umidità e contaminanti. Gli strati aiutano anche con la dissipazione del calore, garantendo prestazioni ottimali e affidabilità dei sistemi elettronici.
- Radome: i radome, che sono involucri protettivi per antenne radar, richiedono rivestimenti epossidici isolanti per garantire la trasparenza del segnale e la protezione dagli elementi ambientali. Questi rivestimenti forniscono isolamento contro le interferenze elettromagnetiche (EMI) mantenendo l'integrità strutturale del radome. Offrono inoltre resistenza all'erosione e agli agenti atmosferici, mantenendo le prestazioni del sistema radar.
Industria automobilistica:
- Batterie per veicoli elettrici (EV): i rivestimenti epossidici isolanti sono fondamentali per proteggere le batterie dei veicoli elettrici. Questi rivestimenti impediscono la penetrazione di umidità e contaminanti, garantendo l'integrità e la longevità delle celle della batteria. Forniscono inoltre isolamento elettrico, riducendo al minimo il rischio di cortocircuiti e migliorando la sicurezza dei veicoli elettrici.
- Componenti del motore: i rivestimenti epossidici isolanti vengono utilizzati sui componenti del motore per proteggerli dalla corrosione, dal calore e dall'esposizione chimica. Questi rivestimenti migliorano la durata e le prestazioni delle parti del motore, come testate, collettori di aspirazione e sistemi di scarico. Gli strati forniscono anche isolamento termico, riducendo il trasferimento di calore e migliorando l'efficienza del motore.
- Impianti elettrici: i rivestimenti epossidici isolanti vengono applicati agli impianti elettrici all'interno dei veicoli, inclusi cablaggi, connettori e circuiti stampati. Questi rivestimenti offrono isolamento elettrico, prevenendo i cortocircuiti e garantendo prestazioni affidabili. Proteggono inoltre da umidità, sostanze chimiche e variazioni di temperatura, aumentando la durata dei componenti elettrici.
- Protezione del telaio e del sottoscocca: i rivestimenti epossidici isolanti proteggono il telaio e il sottoscocca dei veicoli dalla corrosione causata da umidità, sale e detriti stradali. Questi rivestimenti formano una robusta barriera, impedendo la penetrazione di sostanze corrosive e prolungando la vita del veicolo. Inoltre, forniscono isolamento termico, riducendo il trasferimento di calore e migliorando il comfort dei passeggeri.
Applicazioni marine e offshore
I rivestimenti epossidici isolanti svolgono un ruolo cruciale nelle applicazioni marine e offshore fornendo una barriera protettiva contro la corrosione, l'abrasione e la conduttività elettrica. Questi rivestimenti specializzati offrono numerosi vantaggi e sono ampiamente utilizzati in ambienti marini e offshore.
- Imbarcazioni marittime: i rivestimenti epossidici isolanti sono ampiamente utilizzati su imbarcazioni marittime, comprese navi, chiatte e piattaforme offshore. Questi rivestimenti proteggono gli scafi dagli effetti corrosivi di acqua salata, sostanze chimiche e organismi marini. Forniscono una barriera protettiva duratura che prolunga la durata della nave e riduce i requisiti di manutenzione.
- Piattaforme petrolifere e di gas offshore: nell'esplorazione e produzione di petrolio e gas offshore, i rivestimenti epossidici isolanti sono essenziali per mantenere l'integrità delle piattaforme e delle apparecchiature. Proteggono le strutture da condizioni ambientali difficili, tra cui acqua salata corrosiva, alte temperature ed esposizione chimica. I rivestimenti isolanti forniscono anche isolamento elettrico, impedendo alle correnti elettriche di interferire con apparecchiature sensibili e garantendo la sicurezza.
- Condutture e applicazioni sottomarine: i rivestimenti epossidici isolanti vengono applicati a canali e apparecchiature sottomarine per proteggerli dalla corrosione causata da acqua di mare, umidità e sostanze chimiche. Questi rivestimenti fungono da barriera, impedendo la penetrazione di sostanze corrosive e mantenendo l'integrità dell'infrastruttura. Forniscono inoltre isolamento elettrico, riducendo il rischio di interferenze elettriche o danni.
- Parchi eolici offshore: i rivestimenti epossidici isolanti sono utilizzati nella costruzione e manutenzione di parchi eolici offshore. Proteggono le strutture delle turbine eoliche, tra cui torri, fondazioni e cavi sottomarini, dalla corrosione e dal degrado ambientale. Questi rivestimenti forniscono anche isolamento elettrico, garantendo una trasmissione di potenza sicura ed efficiente.
- Attrezzature marine e offshore: i rivestimenti epossidici vengono applicati a varie attrezzature marine e offshore, come pompe, valvole, serbatoi e sistemi di ormeggio. Questi rivestimenti proteggono le apparecchiature dalla corrosione, dall'abrasione e dall'esposizione chimica, prolungandone la durata e riducendo i costi di manutenzione. Le proprietà isolanti di questi rivestimenti prevengono anche problemi di conducibilità elettrica, migliorando la sicurezza e l'affidabilità delle apparecchiature.
- Navi FPSO (Floating Production Storage and Offloading): le FPSO sono ampiamente utilizzate nella produzione offshore di petrolio e gas. I rivestimenti epossidici isolanti vengono applicati agli scafi e alle strutture interne degli FPSO per proteggerli dalla corrosione, dall'abrasione e dall'esposizione chimica. Questi rivestimenti forniscono una protezione a lungo termine e garantiscono l'integrità strutturale della nave.
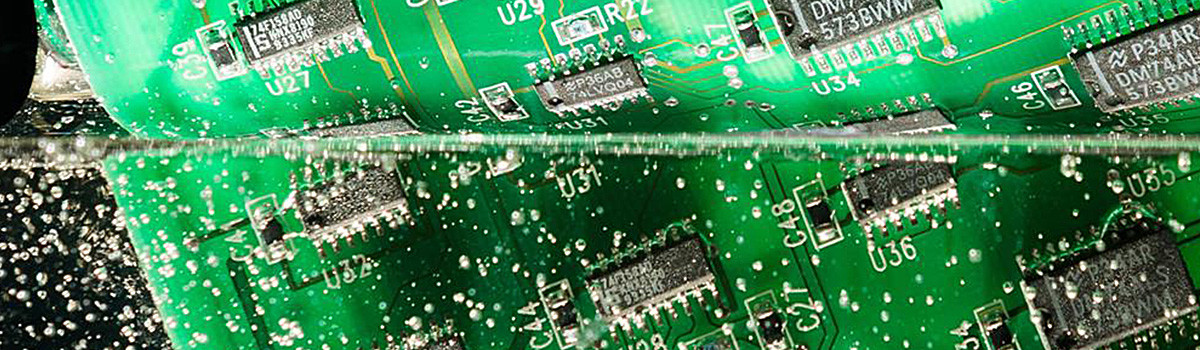
Resistenza chimica e alla corrosione
I rivestimenti epossidici isolanti sono ampiamente utilizzati in vari settori per la protezione dalla corrosione e l'isolamento elettrico. Questi rivestimenti offrono un'eccellente resistenza chimica, rendendoli adatti per ambienti difficili dove l'esposizione a sostanze corrosive è un problema.
La resistenza chimica è fondamentale per i rivestimenti epossidici isolanti, poiché sono spesso esposti a un'ampia gamma di sostanze chimiche, inclusi acidi, alcali, solventi e combustibili. I rivestimenti epossidici resistono a molte sostanze corrosive grazie alla loro densa struttura molecolare e alla rete polimerica reticolata. Questa struttura crea una barriera che impedisce la penetrazione di agenti corrosivi, proteggendo così il supporto sottostante.
Uno dei principali fattori che contribuiscono alla resistenza chimica dei rivestimenti epossidici è la loro elevata densità di reticolazione. La reticolazione si riferisce al legame chimico tra le molecole di resina epossidica, risultando in una rete tridimensionale. Questa rete aumenta la resistenza del rivestimento all'attacco chimico creando una barriera che impedisce la diffusione di sostanze corrosive. Di conseguenza, il substrato rivestito rimane protetto dalla corrosione.
Inoltre, i rivestimenti epossidici possono essere formulati con vari additivi e rinforzi per migliorare la loro resistenza chimica. Ad esempio, l'aggiunta di inibitori di corrosione può migliorare ulteriormente le proprietà protettive del rivestimento inibendo il processo di corrosione e riducendo il degrado della resina epossidica. Rinforzi come fibre di vetro o nanoparticelle possono anche migliorare la resistenza meccanica e chimica del rivestimento.
Oltre alla resistenza chimica, i rivestimenti epossidici isolanti offrono un'eccellente resistenza alla corrosione. La corrosione si verifica quando un materiale reagisce con il suo ambiente, portando al suo deterioramento e potenziale guasto. I rivestimenti epossidici fungono da barriera tra l'ambiente corrosivo e il substrato, impedendo il contatto di umidità, ossigeno e altri agenti corrosivi con la superficie metallica sottostante.
I rivestimenti epossidici forniscono anche un'eccellente adesione a vari substrati, garantendo una protezione a lungo termine contro la corrosione. Il forte legame tra lo strato e il substrato impedisce l'ingresso di umidità e sostanze corrosive, riducendo la probabilità di inizio e progressione della corrosione.
È importante notare che la resistenza chimica e alla corrosione dei rivestimenti epossidici isolanti può essere influenzata dalla temperatura, dal tempo di esposizione e dall'ambiente chimico specifico. Sebbene i rivestimenti epossidici offrano un'eccellente resistenza a vari prodotti chimici, le sostanze altamente aggressive possono comunque causare danni per periodi prolungati o in condizioni estreme.
Per garantire prestazioni ottimali, è essenziale selezionare la formulazione appropriata del rivestimento epossidico in base ai requisiti specifici dell'applicazione. Quando si sceglie il giusto sistema di rivestimento epossidico, è necessario considerare l'ambiente operativo, l'esposizione chimica, la temperatura e la durata prevista.
Conducibilità termica e dissipazione del calore
La conduttività termica e la dissipazione del calore sono essenziali in vari campi, tra cui l'ingegneria, l'elettronica e la scienza dei materiali. Sono fondamentali per determinare l'efficienza e l'affidabilità dei sistemi che generano o gestiscono il calore. Esploriamo ulteriormente questi concetti entro il limite di parole dato.
La conducibilità termica si riferisce alla capacità di un materiale di condurre il calore ed è una proprietà che caratterizza la facilità con cui il calore può trasferirsi attraverso una sostanza. I materiali con elevata conducibilità termica consentono al calore di fluire rapidamente, mentre quelli con bassa conducibilità termica impediscono il trasferimento di calore. L'unità di misura della conducibilità termica è il watt per metro-kelvin (W/mK).
Vari fattori influenzano la conduttività termica di un materiale. Uno dei fattori critici è la struttura molecolare o atomica. Le sostanze con atomi o molecole strettamente imballati tendono ad avere una conduttività termica più elevata. Metalli come il rame e l'alluminio sono noti per la loro elevata conduttività termica dovuta al legame metallico e alle strutture cristalline compatte.
D'altra parte, i materiali con strutture molecolari complesse o grandi vuoti, come polimeri o isolanti come il legno o la gomma, hanno una conducibilità termica relativamente inferiore. L'aria e altri gas sono cattivi conduttori di calore, motivo per cui i materiali con sacche d'aria intrappolate, come i materiali isolanti, presentano una bassa conduttività termica.
La dissipazione del calore, tuttavia, si riferisce al trasferimento o alla dissipazione del calore lontano da un sistema o componente per prevenire il surriscaldamento e mantenere condizioni operative ottimali. Un'efficiente dissipazione del calore è fondamentale per la longevità e le prestazioni dei dispositivi, in particolare quelli che generano quantità significative di calore, come componenti elettronici, sistemi di alimentazione e motori.
Esistono vari metodi di dissipazione del calore, a seconda dell'applicazione specifica. Alcune tecniche standard includono conduzione, convezione e radiazione.
La conduzione comporta il trasferimento di calore attraverso il contatto fisico diretto tra oggetti. Materiali conduttori di calore efficienti, come metalli o materiali con elevata conduttività termica, facilitano il trasferimento di calore tra i componenti che generano calore e i dissipatori di calore o i sistemi di raffreddamento.
La convezione comporta il trasferimento di calore attraverso il movimento di fluidi, come aria o liquido. Questo processo si basa sulla circolazione del fluido, naturale o con ventilatori o pompe, per portare via il calore dalla sorgente. Dissipatori di calore con superfici estese sono spesso utilizzati per aumentare la superficie per il trasferimento di calore convettivo.
La radiazione si riferisce all'emissione e all'assorbimento della radiazione termica, che è la radiazione elettromagnetica emessa dagli oggetti a causa della loro temperatura. Tutti gli oggetti al di sopra della temperatura dello zero assoluto emettono radiazioni termiche. La dissipazione del calore per irraggiamento si verifica quando la radiazione emessa trasporta il calore dalla sorgente verso un ambiente più rilassato.
Varie tecniche e tecnologie vengono impiegate per migliorare la dissipazione del calore, inclusi dissipatori di calore, tubi di calore, materiali di interfaccia termica, ventole, sistemi di raffreddamento a liquido e soluzioni avanzate di gestione termica.
Prestazioni di isolamento elettrico
I rivestimenti epossidici isolanti sono fondamentali per fornire isolamento elettrico in vari settori, tra cui l'elettronica, le apparecchiature elettriche e i sistemi di alimentazione. Questi rivestimenti sono progettati per impedire il flusso di corrente elettrica e proteggere da guasti elettrici o cortocircuiti. Esploriamo le prestazioni di isolamento elettrico dei rivestimenti epossidici isolanti entro il limite di parole specificato.
Una delle proprietà fondamentali che contribuiscono alle prestazioni di isolamento elettrico dei rivestimenti epossidici è la loro elevata rigidità dielettrica. La rigidità dielettrica si riferisce al campo elettrico massimo che un materiale può sopportare senza subire un guasto elettrico. I rivestimenti epossidici isolanti sono formulati per avere un'elevata rigidità dielettrica, che consente loro di resistere a livelli di tensione elevati e prevenire perdite elettriche o archi.
Diversi fattori, tra cui la formulazione della resina, il processo di indurimento e i materiali di riempimento, influenzano la rigidità dielettrica dei rivestimenti epossidici isolanti. Le resine epossidiche ad alto peso molecolare e densità di reticolazione presentano una maggiore rigidità dielettrica. Anche il processo di polimerizzazione gioca un ruolo importante, poiché una corretta polimerizzazione garantisce la formazione di un rivestimento denso e uniforme in grado di resistere alle sollecitazioni elettriche.
I materiali di riempimento possono essere aggiunti ai rivestimenti epossidici per migliorare le prestazioni di isolamento elettrico. I riempitivi, come fibre di vetro o cariche minerali, possono aumentare la rigidità dielettrica riducendo la presenza di vuoti o punti deboli all'interno del rivestimento. Questi riempitivi migliorano l'omogeneità complessiva e l'integrità strutturale del rivestimento, riducendo al minimo il rischio di guasti elettrici.
I rivestimenti epossidici isolanti offrono anche una buona resistività elettrica, che si riferisce alla capacità del materiale di resistere al flusso di corrente elettrica. L'elevata resistività elettrica è fondamentale per prevenire le correnti di dispersione e mantenere l'integrità dell'isolamento elettrico. I rivestimenti epossidici hanno tipicamente valori di resistività elevati, che contribuiscono alla loro efficacia come isolanti elettrici.
Un altro aspetto importante delle prestazioni di isolamento elettrico è la capacità dei rivestimenti epossidici isolanti di resistere a fattori ambientali che possono influire sulle loro proprietà elettriche. Fattori come l'umidità, le variazioni di temperatura e l'esposizione a sostanze chimiche possono influenzare la rigidità dielettrica e la resistività del rivestimento. Pertanto, è essenziale selezionare rivestimenti epossidici con formulazioni e additivi appropriati per fornire prestazioni di isolamento elettrico a lungo termine in condizioni ambientali specifiche.
Inoltre, i rivestimenti epossidici isolanti dovrebbero presentare una buona adesione al substrato per garantire un isolamento elettrico a lungo termine. Un forte legame tra lo strato e la superficie sottostante impedisce la formazione di vuoti o intercapedini che potrebbero compromettere le prestazioni di isolamento elettrico. La preparazione della superficie, le tecniche di applicazione del rivestimento e la compatibilità tra il rivestimento e il substrato influenzano l'adesione.
Per riassumere, i rivestimenti epossidici isolanti offrono eccellenti prestazioni di isolamento elettrico fornendo elevata rigidità dielettrica, resistività elettrica e buona adesione al substrato. La loro formulazione, il processo di polimerizzazione e l'uso di riempitivi contribuiscono alla loro capacità di resistere allo stress elettrico e prevenire guasti elettrici. La corretta selezione e applicazione di rivestimenti epossidici isolanti è fondamentale per garantire un efficace isolamento elettrico in varie applicazioni, dall'elettronica ai sistemi di alimentazione.
Tipi di rivestimenti epossidici isolanti
Sono disponibili diversi tipi di rivestimenti epossidici isolanti, ciascuno progettato per soddisfare requisiti specifici e fornire diversi livelli di isolamento elettrico. Ecco alcuni tipi comuni di rivestimenti epossidici protettivi:
- Rivestimenti epossidici isolanti standard: si tratta di rivestimenti epossidici per uso generico formulati per fornire un isolamento elettrico primario. Offrono una buona rigidità dielettrica e resistività elettrica, che li rende adatti a varie applicazioni.
- Rivestimenti epossidici isolanti per alte temperature: questi rivestimenti sono specificatamente formulati per resistere a temperature elevate senza compromettere le loro prestazioni di isolamento elettrico. Possono essere utilizzati in applicazioni in cui è prevista l'esposizione a calore elevato, come motori, trasformatori o componenti elettrici nell'industria automobilistica o aerospaziale.
- Rivestimenti epossidici isolanti termici conduttivi: questi rivestimenti forniscono isolamento elettrico e hanno la proprietà aggiuntiva della conduttività termica. Sono progettati per dissipare il calore in modo efficiente mantenendo l'isolamento elettrico. Questi rivestimenti sono comunemente usati in applicazioni che richiedono isolamento elettrico e un'efficace dissipazione del calore, come nell'elettronica di potenza.
- Rivestimenti epossidici isolanti ignifughi: i rivestimenti epossidici ignifughi sono formulati per fornire isolamento elettrico offrendo resistenza alla propagazione della fiamma e alla combustione. Questi rivestimenti sono comunemente usati in applicazioni in cui la sicurezza antincendio è un problema, come quadri elettrici, quadri o cablaggi.
- Rivestimenti epossidici isolanti resistenti agli agenti chimici: questi rivestimenti sono progettati per fornire isolamento elettrico offrendo al tempo stesso un'eccellente resistenza a vari prodotti chimici e sostanze corrosive. Sono adatti per applicazioni in cui è prevista l'esposizione a sostanze chimiche aggressive o ambienti corrosivi, come negli impianti di lavorazione chimica o nelle applicazioni marine.
- Rivestimenti epossidici isolanti resistenti ai raggi UV: i rivestimenti resistenti ai raggi UV sono formulati per fornire isolamento elettrico offrendo protezione contro gli effetti dannosi delle radiazioni ultraviolette (UV). Questi rivestimenti sono comunemente utilizzati in applicazioni esterne o ambienti in cui l'esposizione alla luce solare è significativa, come pannelli solari o apparecchiature elettriche esterne.
- Rivestimenti epossidici isolanti flessibili: i rivestimenti epossidici flessibili sono progettati per fornire isolamento elettrico in applicazioni in cui il substrato rivestito è sottoposto a sollecitazioni meccaniche o movimenti. Questi rivestimenti offrono una buona adesione e flessibilità, consentendo loro di resistere alla flessione o all'allungamento senza incrinarsi o compromettere l'isolamento elettrico.
È importante notare che la selezione del tipo di rivestimento epossidico isolante appropriato dipende dai requisiti specifici dell'applicazione, dai fattori ambientali e dalle aspettative prestazionali. La consulenza con produttori di rivestimenti o esperti del settore può aiutare a determinare il rivestimento epossidico isolante più adatto per una particolare applicazione.
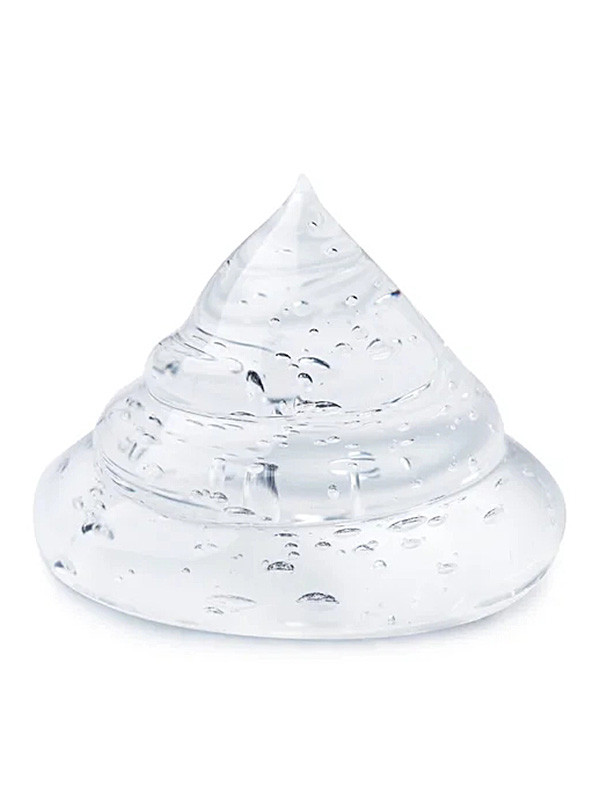
Rivestimenti epossidici bicomponenti
I rivestimenti epossidici bicomponenti sono ampiamente utilizzati in vari settori per la loro eccezionale durata, resistenza chimica e versatilità. Questi rivestimenti sono costituiti da due componenti: una resina e un indurente. Se combinati nel rapporto corretto, subiscono una reazione chimica nota come indurimento, che si traduce in un rivestimento solido e protettivo. Qui esploreremo le principali caratteristiche, applicazioni e vantaggi dei rivestimenti epossidici bicomponenti.
caratteristiche: I rivestimenti epossidici bicomponenti offrono diverse caratteristiche chiave che li rendono altamente desiderabili in molte applicazioni. In primo luogo, forniscono un'eccellente adesione a vari substrati, tra cui cemento, metallo, legno e fibra di vetro. Questa adesione garantisce prestazioni di lunga durata e previene problemi come desquamazione o delaminazione. Inoltre, i rivestimenti epossidici presentano un'elevata resistenza chimica, che li rende adatti per l'uso in ambienti esposti a sostanze corrosive, sostanze chimiche o solventi. Sono anche noti per la loro eccezionale durezza, resistenza all'abrasione e resistenza agli urti, contribuendo alla loro longevità e durata. Inoltre, a seconda dei requisiti estetici e funzionali desiderati, i rivestimenti epossidici possono essere formulati per avere varie finiture, tra cui lucido, opaco o strutturato.
applicazioni: I rivestimenti epossidici bicomponenti trovano applicazione in vari settori grazie alla loro versatilità e alle loro caratteristiche prestazionali. Nel settore industriale sono comunemente utilizzate per proteggere le pavimentazioni in calcestruzzo di stabilimenti produttivi, magazzini e garage. Il rivestimento epossidico crea una superficie continua e resistente in grado di resistere a traffico intenso, urti e fuoriuscite di sostanze chimiche. Nell'industria nautica, i rivestimenti epossidici vengono utilizzati per scafi, ponti e altre strutture di barche, proteggendo da infiltrazioni d'acqua, radiazioni UV e corrosione. Questi rivestimenti sono impiegati anche nell'industria automobilistica per fornire uno strato protettivo su carrozzerie, componenti del motore e rivestimenti sottoscocca, migliorandone la resistenza all'abrasione, agli agenti chimici e agli agenti atmosferici. Inoltre, i rivestimenti epossidici bicomponenti sono ampiamente utilizzati nel settore delle costruzioni per l'impermeabilizzazione, le riparazioni del calcestruzzo e i sistemi di pavimentazione decorativa.
Vantaggi: L'utilizzo di rivestimenti epossidici bicomponenti offre numerosi vantaggi agli utenti industriali e commerciali. In primo luogo, la loro eccezionale durata e resistenza all'usura garantiscono una maggiore durata delle superfici rivestite, riducendo i costi di manutenzione e sostituzione. I rivestimenti epossidici sono anche relativamente facili da applicare, consentendo un'installazione efficiente e riducendo al minimo i tempi di fermo negli ambienti industriali. La loro natura continua e non porosa li rende igienici e facili da pulire, ideali per ambienti che richiedono elevati livelli di pulizia, come strutture sanitarie o impianti di trasformazione alimentare. Inoltre, i rivestimenti epossidici possono essere personalizzati per soddisfare requisiti specifici, tra cui proprietà antiscivolo, resistenza al calore o conduttività elettrica. Questa versatilità consente soluzioni su misura in varie applicazioni. Infine, i rivestimenti epossidici bicomponenti sono rispettosi dell'ambiente in quanto sono a basso contenuto di composti organici volatili (VOC), il che li rende più sicuri per i lavoratori e per l'ambiente.
Rivestimenti epossidici monocomponenti
I rivestimenti epossidici monocomponenti sono rivestimenti monocomponenti che offrono molti vantaggi rispetto ai tradizionali rivestimenti epossidici bicomponenti, ma con processi di applicazione semplificati. Questi rivestimenti sono formulati con una resina che contiene sia la resina epossidica che l'agente indurente, eliminando la necessità di un indurente separato. Questo articolo esplorerà le caratteristiche, le applicazioni e i vantaggi dei rivestimenti epossidici monocomponenti.
caratteristiche: I rivestimenti epossidici monocomponenti possiedono diverse caratteristiche chiave che li rendono popolari in vari settori. Questi rivestimenti presentano un'eccellente adesione a diversi substrati, tra cui cemento, metallo e legno, garantendo un legame solido e una protezione di lunga durata. Forniscono una buona resistenza chimica, offrendo protezione contro sostanze corrosive, prodotti chimici e solventi. Inoltre, i rivestimenti epossidici monocomponenti offrono una buona resistenza all'abrasione e durata, rendendoli adatti per superfici soggette a traffico intenso o usura. Possono anche essere formulati con diverse finiture, come lucide o opache, per ottenere l'aspetto estetico desiderato.
applicazioni: I rivestimenti epossidici monocomponenti trovano applicazioni in vari settori e superfici. Nel settore delle costruzioni, sono comunemente usati per proteggere e migliorare i pavimenti in cemento, fornendo una copertura continua e duratura in ambienti come magazzini, spazi commerciali ed edifici commerciali. Questi rivestimenti trovano applicazione anche nell'industria automobilistica, dove vengono utilizzati per la protezione dalla corrosione su telai di veicoli, componenti di telai e altre superfici metalliche. Inoltre, i rivestimenti epossidici monocomponenti sono utilizzati nell'industria nautica per i ponti delle barche, le piscine e le strutture marine, fornendo resistenza all'acqua, ai raggi UV e alle sostanze chimiche. Possono essere utilizzati anche su superfici metalliche, come macchinari, attrezzature o serbatoi di stoccaggio, per proteggere dalla corrosione e dall'usura.
Vantaggi: I rivestimenti epossidici monocomponenti offrono numerosi vantaggi che li rendono vantaggiosi per molte applicazioni. Uno dei principali vantaggi è la facilità d'uso e di applicazione. Poiché vengono premiscelati, non è necessario misurare e miscelare più componenti, semplificando il processo di rivestimento e riducendo il rischio di errori. Questo li rende ideali per progetti più piccoli o utenti con esperienza limitata con i rivestimenti epossidici. Inoltre, i rivestimenti epossidici monocomponenti hanno spesso una durata utile maggiore rispetto ai sistemi bicomponenti, consentendo un tempo di lavorazione prolungato e un'applicazione più semplice. Offrono inoltre un'eccellente adesione, durata e resistenza chimica, garantendo una protezione duratura per le superfici rivestite. Inoltre, i rivestimenti epossidici monocomponenti sono tipicamente a basso contenuto di composti organici volatili (VOC), il che li rende rispettosi dell'ambiente e più sicuri per gli utenti.
Selezione del giusto rivestimento epossidico isolante
La selezione del rivestimento epossidico isolante è fondamentale per garantire un adeguato isolamento e protezione per varie applicazioni. I rivestimenti epossidici isolanti sono progettati per fornire isolamento elettrico e resistenza termica, impedendo la conduttività elettrica e il trasferimento di calore. Ecco alcuni fattori chiave da considerare nella scelta del rivestimento epossidico isolante adatto:
- Proprietà elettriche: la funzione primaria di un rivestimento epossidico isolante è quella di fornire isolamento elettrico. Pertanto, è essenziale considerare le proprietà elettriche del rivestimento, come rigidità dielettrica, resistività di volume e resistività superficiale. La rigidità dielettrica determina la tensione massima che il rivestimento può sopportare prima della rottura, mentre la resistività misura la capacità del materiale di resistere al flusso di corrente elettrica. Assicurarsi che lo strato soddisfi gli standard elettrici richiesti per l'applicazione specifica.
- Resistenza termica: si prevede inoltre che i rivestimenti epossidici isolanti offrano resistenza termica per prevenire il trasferimento di calore. Considera la capacità del rivestimento di resistere alle alte temperature e fornire un efficace isolamento termico. Cerca strati con bassa conduttività termica per ridurre al minimo il trasferimento di calore e mantenere la stabilità della temperatura.
- Compatibilità del substrato: valutare la compatibilità del rivestimento epossidico con il materiale del substrato. I rivestimenti epossidici isolanti sono comunemente usati su metalli in rame, alluminio o acciaio. Assicurarsi che il rivestimento sia formulato per aderire bene allo specifico materiale del substrato, fornendo un forte legame e prestazioni a lungo termine.
- Metodo di applicazione: considerare il metodo di applicazione e la facilità di applicazione per il rivestimento epossidico isolante scelto. Alcuni rivestimenti sono adatti per l'applicazione a spruzzo, mentre altri sono più adatti per l'applicazione a pennello oa rullo. Scegli un livello che si allinei con l'attrezzatura dell'applicazione disponibile e i requisiti del progetto.
- Resistenza ambientale: valutare le condizioni ecologiche a cui sarà esposto il rivestimento, come umidità, umidità, sostanze chimiche o radiazioni UV. I rivestimenti epossidici isolanti dovrebbero offrire un'eccellente resistenza a questi fattori ambientali per garantire prestazioni e protezione a lungo termine. Prendere in considerazione rivestimenti con elevata resistenza chimica e stabilità ai raggi UV se esposti ad ambienti difficili.
- Certificazioni e standard: alcune certificazioni o standard possono essere richiesti a seconda dell'applicazione. Ad esempio, i rivestimenti epossidici isolanti potrebbero dover soddisfare specifici standard o certificati elettrici nel settore elettrico. Assicurarsi che il rivestimento scelto soddisfi gli standard e le certificazioni del settore per garantire conformità e prestazioni.
- Prestazioni e durata: considerare le prestazioni complessive e la durata del rivestimento epossidico isolante. Cerca strati con eccellente adesione, resistenza all'abrasione e durata a lungo termine per garantire isolamento e protezione prolungati. Valutare la resistenza del rivestimento a danni fisici, come urti o graffi, che potrebbero compromettere le proprietà isolanti.
- Costo e valore: infine, valutare il costo e il valore del rivestimento epossidico isolante. Considera fattori come il costo iniziale, la durata prevista del layer e i potenziali costi di manutenzione o sostituzione nel tempo. Bilanciare l'investimento iniziale con le prestazioni e la durata a lungo termine contribuirà a determinare il valore complessivo del rivestimento.
Considerazioni ambientali
Le considerazioni ambientali giocano un ruolo significativo nella selezione e nell'uso di rivestimenti epossidici isolanti. La scelta di rivestimenti che forniscano un adeguato isolamento e riducano al minimo l'impatto ambientale durante tutto il loro ciclo di vita è essenziale. Ecco alcune considerazioni ecologiche critiche da tenere a mente quando si selezionano rivestimenti epossidici isolanti:
- Contenuto di COV: i composti organici volatili (COV) sono sostanze chimiche che possono contribuire all'inquinamento atmosferico e avere potenziali effetti sulla salute. Quando si scelgono rivestimenti epossidici isolanti, optare per formulazioni a basso VOC o prive di VOC. Questi rivestimenti emettono meno fumi nocivi durante l'applicazione e contribuiscono a migliorare la qualità dell'aria interna ed esterna.
- Sostanze pericolose: valutare la presenza di sostanze pericolose nella formulazione del rivestimento epossidico. Alcuni additivi, solventi o metalli pesanti possono danneggiare la salute umana o l'ambiente. Cerca rivestimenti privi o con livelli ridotti di sostanze pericolose, che garantiscano una manipolazione, uno smaltimento e un impatto ambientale più sicuri a lungo termine.
- Biodegradabilità: considerare la biodegradabilità del rivestimento epossidico isolante. I rivestimenti biodegradabili si degradano naturalmente nel tempo, riducendo il loro impatto sull'ambiente. Cerca strati derivati da risorse rinnovabili o che sono stati testati e certificati per la loro biodegradabilità.
- Efficienza energetica: i rivestimenti epossidici isolanti spesso migliorano l'efficienza energetica riducendo il trasferimento di calore. Selezionando rivestimenti con elevate proprietà di resistenza termica, è possibile migliorare l'efficienza energetica in applicazioni come l'isolamento elettrico, l'isolamento degli edifici o le barriere termiche. Ciò può portare a un ridotto consumo di energia ea un minore impatto ambientale.
- Durata e longevità: scegli rivestimenti epossidici isolanti con eccellente durata e longevità. I rivestimenti più resistenti all'usura, alla corrosione o al degrado richiedono manutenzione, riapplicazione e smaltimento meno frequenti. Ciò riduce l'impatto ambientale complessivo associato all'uso dei rivestimenti.
- Imballaggio e rifiuti: considerare l'imballaggio dei rivestimenti epossidici isolanti e la generazione di rifiuti durante il loro utilizzo. Optare per rivestimenti confezionati in materiali riciclabili o ecologici. Inoltre, i rivestimenti che riducono al minimo la generazione di rifiuti durante l'applicazione, come quelli con ridotto overspray o requisiti di miscelazione minimi, possono contribuire a ridurre l'impatto ambientale.
- Certificazioni ambientali: cercare rivestimenti epossidici isolanti che abbiano ottenuto certificazioni ecologiche o rispettino standard ambientali riconosciuti. Gli esempi includono certificati come LEED (Leadership in Energy and Environmental Design) o l'adesione agli standard di gestione ambientale ISO 14001. Queste certificazioni assicurano che i rivestimenti siano stati sottoposti a rigorosi test e rispondano a specifici criteri di prestazione ambientale.
- Smaltimento e riciclaggio corretti: considerare le opzioni di smaltimento e riciclaggio appropriate per i rivestimenti epossidici isolanti. Verificare le normative e le linee guida locali per garantire che i rivestimenti possano essere smaltiti o riciclati in modo appropriato al termine del loro ciclo di vita. Per alcuni rivestimenti possono essere disponibili programmi o opzioni di riciclaggio specifici.
Considerando queste considerazioni ambientali, è possibile selezionare rivestimenti epossidici isolanti che forniscano un adeguato isolamento e riducano al minimo il loro impatto ecologico. La scelta di rivestimenti rispettosi dell'ambiente contribuisce agli sforzi di sostenibilità, riduce l'inquinamento e promuove un ecosistema più sano.
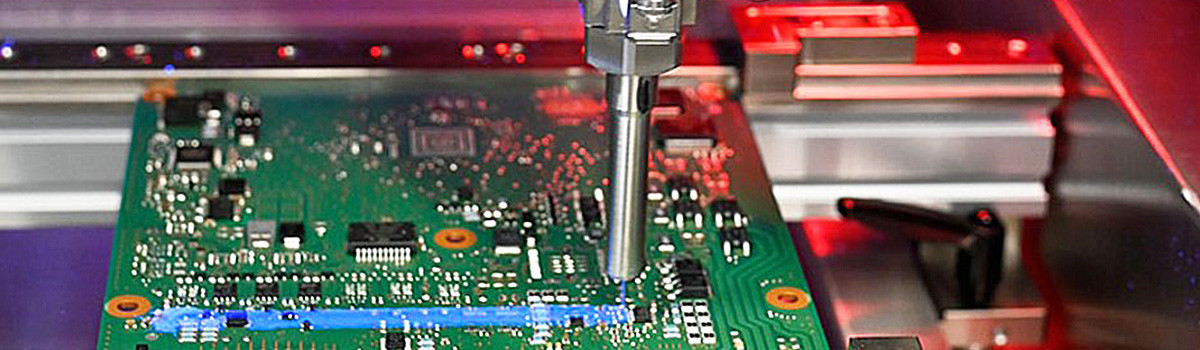
Tecniche e suggerimenti per l'applicazione
Tecniche di applicazione adeguate sono essenziali per ottenere risultati ottimali durante l'isolamento dei rivestimenti epossidici. I seguenti suggerimenti contribuiranno a garantire un'applicazione corretta e a migliorare le prestazioni del livello:
- Preparazione della superficie: Pulire accuratamente e preparare la superficie prima di applicare il rivestimento epossidico isolante. Rimuovere sporco, polvere, grasso o rivestimenti esistenti che potrebbero interferire con l'adesione. Le tecniche di preparazione della superficie possono includere la carteggiatura, lo sgrassaggio o l'uso di detergenti appropriati. Seguire le linee guida del produttore per la preparazione della superficie specifica per il rivestimento e il substrato.
- Rapporti di miscelazione e pot life: Seguire attentamente le istruzioni del produttore relative ai rapporti di miscelazione e al pot life. I rivestimenti epossidici isolanti sono in genere sistemi in due parti che richiedono un'accurata miscelazione di resina e componenti indurenti. Una miscelazione impropria può causare una polimerizzazione incompleta o prestazioni compromesse. Prestare attenzione al pot life e al tempo di lavorazione a disposizione una volta miscelati gli ingredienti. Evitare di superare il pot life per garantire una corretta applicazione.
- Metodo di applicazione: scegliere il metodo di applicazione appropriato per il rivestimento epossidico isolante in base alla superficie e ai requisiti del progetto. I metodi di applicazione standard includono l'applicazione a pennello, rullo o spruzzo. Utilizzare pennelli e rulli per aree più piccole o quando è richiesta precisione. L'applicazione a spruzzo è adatta per ambienti più grandi o per una finitura più uniforme. Seguire le raccomandazioni del produttore per il rivestimento specifico per quanto riguarda il metodo di applicazione e l'attrezzatura.
- Temperatura e umidità: considerare la temperatura ambiente e le condizioni di umidità durante l'applicazione. I rivestimenti epossidici isolanti possono avere requisiti specifici di temperatura e umidità per prestazioni ottimali. Seguire le linee guida del produttore per quanto riguarda l'intervallo di temperatura e le condizioni di umidità consigliate durante l'applicazione e l'indurimento. Temperature estreme o umidità elevata possono influire sul tempo di indurimento del rivestimento e sulle prestazioni complessive.
- Applicazione Spessore: Applicare il rivestimento epossidico isolante allo spessore consigliato per l'isolamento e la protezione desiderati. Uno spessore sufficiente del rivestimento può compromettere le proprietà isolanti, mentre uno spessore eccessivo può portare a problemi di polimerizzazione o adesione non corretta. Utilizzare uno spessimetro a film umido per garantire uno spessore del rivestimento uniforme e accurato durante l'intera applicazione.
- Ventilazione e sicurezza: garantire un'adeguata ventilazione nell'area di applicazione per ridurre al minimo l'inalazione di fumi o vapori. Utilizzare dispositivi di protezione individuale (DPI) adeguati come raccomandato dal produttore, come guanti, occhiali o protezione respiratoria. Segui le linee guida e le normative sulla sicurezza per proteggere te stesso e gli altri durante il processo di candidatura.
- Tempo di indurimento e asciugatura: consentire un tempo di indurimento e asciugatura sufficiente per il rivestimento epossidico isolante. Seguire le istruzioni del produttore per quanto riguarda il tempo di indurimento consigliato e le condizioni ambientali per una corretta adesione e prestazioni. Evitare di sottoporre la superficie rivestita a umidità eccessiva o sollecitazioni meccaniche fino a quando il rivestimento non è completamente indurito.
- Ispezione e manutenzione: ispezionare regolarmente la superficie rivestita per eventuali segni di danni o usura. Eseguire la manutenzione ordinaria per garantire la continua efficacia del rivestimento epossidico isolante. Affrontare tempestivamente eventuali problemi per evitare ulteriori lesioni o deterioramento.
Seguendo queste tecniche e suggerimenti di applicazione, è possibile ottenere risultati positivi quando si applicano rivestimenti epossidici isolanti. Un'adeguata preparazione della superficie, un'accurata miscelazione, metodi di applicazione adeguati e il rispetto delle linee guida sulla polimerizzazione contribuiranno a garantire l'isolamento e la protezione desiderati per l'applicazione.
Processo di indurimento e asciugatura
Il processo di indurimento e asciugatura per rivestimenti epossidici isolanti è un passaggio critico che determina le proprietà finali e le prestazioni del rivestimento. Una corretta polimerizzazione garantisce uno strato forte, durevole e completamente isolante. Ecco i fattori chiave e le considerazioni per il processo di indurimento e asciugatura dei rivestimenti epossidici isolanti:
- Seguire le istruzioni del produttore: fare sempre riferimento alle istruzioni del produttore e alla scheda tecnica per indicazioni specifiche sui tempi di indurimento e asciugatura e sulle condizioni ambientali richieste per il rivestimento. Diversi rivestimenti epossidici possono avere diversi processi di indurimento e tempi di asciugatura consigliati.
- Temperatura ambiente: il processo di indurimento dei rivestimenti epossidici dipende dalla temperatura. La maggior parte dei rivestimenti epossidici richiede un intervallo di temperatura ambiente minimo e massimo per una corretta polimerizzazione. Assicurarsi che la temperatura ambiente rientri nell'intervallo specificato durante tutto il processo di indurimento e asciugatura. Temperature estremamente calde e fredde possono influire negativamente sul processo di indurimento e sulle prestazioni finali del rivestimento.
- Umidità relativa: i livelli di umidità possono anche influenzare l'indurimento e l'asciugatura dei rivestimenti epossidici isolanti. In ambienti molto umidi, il tempo di indurimento può essere prolungato a causa della lenta evaporazione dell'umidità dallo strato. Al contrario, una bassa umidità può causare una polimerizzazione troppo rapida del rivestimento, compromettendone l'integrità. Mantenere i livelli di umidità consigliati specificati dal produttore per una polimerizzazione ottimale.
- Ventilazione: un'adeguata ventilazione è fondamentale durante l'indurimento e l'asciugatura per garantire una corretta circolazione dell'aria e la dissipazione di fumi o vapori. Una buona ventilazione aiuta a facilitare il processo di polimerizzazione e riduce il rischio di intrappolamento di solventi, che potrebbe influire sulle prestazioni del rivestimento.
- Tempo di indurimento: il tempo di indurimento per i rivestimenti epossidici isolanti può variare a seconda della formulazione specifica, dello spessore dello strato applicato e delle condizioni ambientali. È essenziale consentire il tempo di polimerizzazione consigliato specificato dal produttore per garantire una reticolazione completa e lo sviluppo delle proprietà desiderate. L'esposizione prematura a umidità, polvere o sollecitazioni meccaniche durante il processo di indurimento può compromettere le prestazioni del rivestimento.
- Tempo di asciugatura: il tempo di asciugatura si riferisce a quando il solvente evapora dal rivestimento. Il tempo di asciugatura può variare in base allo spessore del rivestimento, alla temperatura, all'umidità e alla ventilazione. È fondamentale consentire il tempo di asciugatura consigliato affinché il rivestimento raggiunga un'adeguata formazione del film ed eviti la manipolazione o l'esposizione prematura.
- Indurimento completo: sebbene il rivestimento possa sembrare asciutto al tatto dopo il tempo di asciugatura consigliato, è essenziale notare che l'indurimento completo potrebbe richiedere più tempo. La cura completa si riferisce alla completa reticolazione chimica e all'indurimento del rivestimento epossidico. Seguire le istruzioni del produttore per quanto riguarda il tempo di indurimento completo consigliato prima di sottoporre la superficie rivestita a carichi pesanti, abrasione o altri fattori di stress.
- Post-indurimento: alcuni rivestimenti epossidici isolanti possono beneficiare del post-indurimento per migliorare ulteriormente le loro proprietà. Il post-indurimento prevede di sottoporre lo strato indurito a temperature elevate per una durata specificata. Questo processo può migliorare la resistenza chimica, la durezza e l'adesione del rivestimento. Se applicabile, fare riferimento alle linee guida del produttore relative al processo di polimerizzazione post-stampa consigliato.
Seguendo attentamente le istruzioni del produttore, mantenendo condizioni ambientali adeguate, consentendo tempi di indurimento e asciugatura adeguati e garantendo un'adeguata ventilazione, è possibile ottenere risultati ottimali nei rivestimenti epossidici isolanti. I rivestimenti opportunamente polimerizzati ed essiccati forniranno l'isolamento elettrico e la resistenza termica desiderati per l'applicazione prevista.
Manutenzione e riparazione di rivestimenti epossidici isolanti
I rivestimenti isolanti epossidici sono ampiamente utilizzati in vari settori per proteggere e isolare apparecchiature elettriche e infrastrutture. Questi rivestimenti forniscono una barriera protettiva duratura che impedisce a umidità, sostanze chimiche e altri contaminanti di raggiungere le superfici sottostanti. Tuttavia, come qualsiasi altro sistema di rivestimento, i rivestimenti epossidici isolanti possono richiedere manutenzione e riparazione per garantirne l'efficacia e la longevità.
La manutenzione dei rivestimenti epossidici isolanti comporta principalmente un'ispezione e una pulizia regolari. Ispezionare periodicamente le superfici rivestite per identificare eventuali segni di danneggiamento, come crepe, bolle o desquamazione. Si prega di prestare molta attenzione alle aree esposte a condizioni difficili o sollecitazioni meccaniche, in quanto sono più soggette a danni. Se vengono rilevati problemi, risolverli prontamente per evitare un ulteriore deterioramento.
La pulizia delle superfici rivestite è essenziale per rimuovere sporco, polvere, oli e altri contaminanti che possono accumularsi nel tempo. Utilizzare detergenti delicati e non abrasivi e spazzole o panni morbidi per pulire delicatamente le superfici. Evitare prodotti chimici aggressivi o materiali abrasivi che graffiano o degradano il rivestimento. Una pulizia regolare aiuta a mantenere le proprietà isolanti del rivestimento epossidico e previene l'accumulo di materiali conduttivi che potrebbero comprometterne l'efficacia.
Quando si tratta di riparare, l'approccio può variare a seconda dell'entità del danno. È possibile utilizzare kit di riparazione epossidici appositamente progettati per rivestimenti isolanti per lesioni minori come piccole crepe o scheggiature. Questi kit in genere includono stucco epossidico e istruzioni per applicarlo correttamente. Pulire accuratamente l'area danneggiata, seguire le istruzioni fornite con l'attrezzatura e utilizzare lo stucco epossidico sulla parte danneggiata. Lasciare polimerizzare secondo le raccomandazioni del produttore.
Nei casi in cui il danno è più significativo, può essere necessario rimuovere la parte danneggiata del rivestimento o applicare un nuovo strato di resina epossidica isolante. Ciò richiede un'attenta preparazione della superficie, compresa la pulizia e l'irruvidimento dell'area circostante il danno per garantire la corretta adesione del nuovo rivestimento. Seguire le linee guida del produttore relative all'applicazione del nuovo rivestimento epossidico, compresi i tempi di indurimento e i requisiti di temperatura.
In alcuni casi, può essere più pratico cercare assistenza professionale per mantenere e riparare rivestimenti epossidici isolanti. Appaltatori esperti o specialisti del rivestimento possono valutare l'entità del danno, consigliare il metodo di riparazione più adatto e garantire che il rivestimento migliorato soddisfi gli standard e i requisiti necessari.
Ricorda che l'ispezione regolare e la manutenzione preventiva sono fondamentali per prolungare la durata dei rivestimenti epossidici isolanti. Affrontando tempestivamente problemi minori e seguendo procedure di pulizia adeguate, è possibile ridurre al minimo la necessità di riparazioni estese e garantire la continua efficacia del rivestimento nella protezione e nell'isolamento di apparecchiature elettriche e infrastrutture.
Conclusione
I rivestimenti epossidici isolanti sono fondamentali per proteggere i componenti e le apparecchiature elettriche da vari fattori esterni. Con applicazioni che vanno da componenti elettronici a circuiti stampati, motori e cavi, questi rivestimenti forniscono una protezione essenziale contro umidità, sostanze chimiche e danni fisici. La corretta selezione del rivestimento epossidico isolante dipende dalle condizioni ambientali, dai requisiti prestazionali e dalle tecniche di applicazione. Comprendendo i vantaggi e le considerazioni associate ai rivestimenti epossidici isolanti, le industrie possono fare scelte informate per migliorare la durata, l'affidabilità e la longevità dei loro sistemi elettrici e delle apparecchiature.