Composto per impregnazione PCB
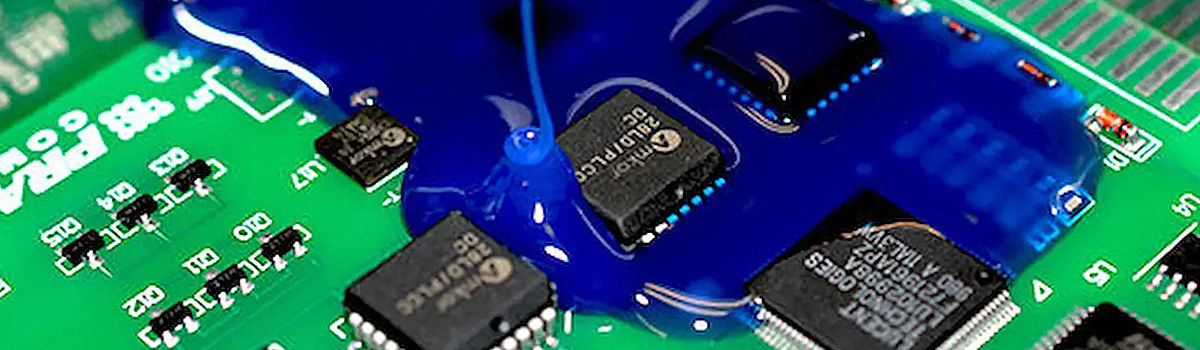
Il composto per impregnazione PCB, noto anche come incapsulante, è un materiale utilizzato per proteggere e isolare i componenti elettronici sui circuiti stampati (PCB). Il composto per impregnazione viene applicato agli elementi e al PCB e quindi polimerizzato per formare un guscio duro e protettivo. Questo processo protegge l'elettronica da fattori ambientali come umidità, polvere e vibrazioni e può migliorare le prestazioni termiche. In questo articolo, esploreremo i vantaggi dell'utilizzo di composti per impregnazione PCB e come possono migliorare la longevità e l'affidabilità dei sistemi elettronici.
Che cos'è il composto per impregnazione PCB?
Il composto per impregnazione PCB è una resina protettiva che incapsula i componenti elettronici su un circuito stampato (PCB). Forma una solida barriera, proteggendo il PCB da fattori ambientali come umidità, polvere e fluttuazioni di temperatura. Il composto di impregnazione migliora la resistenza meccanica del PCB, fornisce l'isolamento elettrico e ne aumenta l'affidabilità complessiva. È comunemente utilizzato nella produzione elettronica, automobilistica, aerospaziale e delle telecomunicazioni per garantire la longevità e le prestazioni di dispositivi e sistemi elettronici.
Come funziona il composto per impregnazione PCB?
Il composto per impregnazione PCB è un materiale specializzato che incapsula e protegge i componenti elettronici su un circuito stampato (PCB). Ecco come funziona il composto per impregnazione PCB:
- incapsulamento: Il composto per impregnazione PCB viene applicato al PCB versandolo o erogandolo sui componenti. Scorre intorno agli elementi e riempie i vuoti, creando un involucro solido e protettivo.
- Protezione ambientale: Una volta indurito, il composto per impregnazione forma una robusta barriera che protegge i componenti da fattori ambientali come umidità, polvere e sostanze chimiche. Impedisce a questi elementi di raggiungere l'elettronica sensibile, proteggendola da corrosione, cortocircuiti e altri potenziali danni.
- Isolamento: Il composto per impregnazione PCB offre eccellenti proprietà di isolamento elettrico. Isola i componenti l'uno dall'altro, prevenendo i cortocircuiti elettrici e mantenendo l'integrità dei circuiti. Questo isolamento è fondamentale nelle applicazioni con caratteristiche ravvicinate o differenziali ad alta tensione.
- Stabilità meccanica: Il composto per impregnazione migliora la stabilità meccanica del gruppo PCB. Migliora l'integrità strutturale, smorza le vibrazioni e riduce il rischio di spostamento dei componenti o danni dovuti a sollecitazioni meccaniche. È particolarmente importante considerare questo fattore in situazioni in cui il circuito stampato può subire condizioni difficili, vibrazioni o impatti.
- Gestione termica: Il composto per impregnazione PCB può anche fornire un'efficace gestione termica. Aiuta a dissipare il calore generato dai componenti, prevenendone il surriscaldamento e prolungandone la durata. Alcune miscele per impregnazione hanno un'elevata conducibilità termica, trasferendo efficacemente il calore dagli elementi.
- Proprietà dielettriche:I composti per impregnazione PCB sono formulati con proprietà dielettriche, che consentono loro di resistere ad alte tensioni senza condurre elettricità. Questa caratteristica è fondamentale nelle applicazioni critiche di isolamento elettrico, come gli alimentatori ad alta tensione o le apparecchiature elettriche.
- Compatibilità e adesione: I composti per impregnazione PCB aderiscono bene a vari substrati utilizzati nella produzione di PCB, come resina epossidica, FR-4 o metallo. Formano un forte legame con i componenti e il PCB, fornendo una protezione affidabile e garantendo prestazioni a lungo termine.
Vantaggi dell'utilizzo del composto per impregnazione PCB
L'uso di composti per impregnazione PCB offre numerosi vantaggi nella produzione e protezione di dispositivi elettronici. Ecco alcuni vantaggi chiave:
- Protezione ambientale:Il composto per impregnazione PCB forma una barriera protettiva che protegge i componenti elettronici da umidità, polvere, sostanze chimiche e altri fattori ambientali. Aiuta a prevenire corrosione, cortocircuiti e danni causati dall'esposizione a condizioni difficili.
- Isolamento elettrico: I composti per impregnazione forniscono un eccellente isolamento elettrico, isolando i componenti e prevenendo i cortocircuiti elettrici. L'isolamento è fondamentale nelle applicazioni con elementi ravvicinati o tensioni elevate.
- Stabilità meccanica: Il composto per impregnazione migliora la stabilità meccanica del gruppo PCB. Migliora l'integrità strutturale, riduce le vibrazioni e protegge dalle sollecitazioni meccaniche, garantendo prestazioni affidabili anche in ambienti difficili.
- Resistenza alle vibrazioni e agli urti: Il composto impregnante aiuta a smorzare le vibrazioni e ad assorbire gli urti, proteggendo i componenti dai danni dovuti alle sollecitazioni meccaniche. I continui movimenti in applicazioni come l'industria automobilistica o aerospaziale rendono particolarmente importante la presenza di questo isolamento.
- Dissipazione di calore: Alcuni composti per impregnazione hanno un'elevata conducibilità termica, consentendo un'efficiente dissipazione del calore. Aiutano a dissipare il calore generato dai componenti, prevenendo il surriscaldamento e prolungandone la durata.
- Resistenza chimica:I composti per impregnazione PCB resistono a vari prodotti chimici, proteggendo i componenti dall'esposizione a sostanze corrosive o solventi. Questa resistenza garantisce l'affidabilità a lungo termine del gruppo PCB.
- Flessibilità di personalizzazione e progettazione: La formulazione di composti per impregnazione consente di soddisfare requisiti specifici, fornendo personalizzazione e flessibilità di progettazione. La personalizzazione dei composti per impregnazione consente di fornire le proprietà desiderate come durezza, flessibilità, resistenza alla fiamma o tolleranze ambientali precise.
- Protezione da danni fisici: Il composto per impregnazione crea uno strato protettivo attorno ai componenti, proteggendoli da danni fisici causati da urti o maneggiamenti bruschi durante il trasporto o l'installazione.
- Facile applicazione:I composti per impregnazione PCB sono in genere facili da applicare. Il versamento, l'iniezione o l'erogazione di composti per impregnazione sul gruppo PCB consente loro di conformarsi alla forma dei componenti e di riempire efficacemente i vuoti.
- Affidabilità a lungo termine: Fornendo protezione e isolamento robusti, i composti per impregnazione contribuiscono all'affidabilità a lungo termine di dispositivi e sistemi elettronici. Aiutano a prolungare la durata dei componenti, riducendo i costi di manutenzione e sostituzione.
Protezione dai fattori ambientali
La protezione dai fattori ambientali è fondamentale nella produzione di dispositivi elettronici e il composto per invasatura PCB fornisce adeguate protezioni contro vari elementi. Ecco alcuni punti chiave che evidenziano la protezione offerta dal composto per impregnazione PCB:
- Barriera anti-umido: Il composto sigillante per PCB crea una barriera resistente all'umidità che impedisce all'acqua o all'umidità di raggiungere i componenti elettronici sensibili. Questa protezione è fondamentale nelle applicazioni esposte ad ambienti ricchi di umidità, come l'elettronica esterna o le impostazioni industriali.
- Protezione da polvere e particelle: I composti sigillanti sigillano i componenti e il PCB, impedendo l'ingresso di polvere, sporco e altre particelle. Questa barriera aiuta a mantenere prestazioni ottimali riducendo il rischio di contaminazione o intasamento dei circuiti elettronici sensibili.
- Resistenza chimica:I produttori formulano spesso composti per impregnazione con eccellenti proprietà di resistenza chimica. Possono resistere all'esposizione a vari prodotti chimici, inclusi solventi, acidi, oli e detergenti. Questa protezione è essenziale negli ambienti in cui l'esposizione chimica è prevalente, come gli ambienti industriali o di laboratorio.
- Prevenzione della corrosione: I composti per impregnazione PCB forniscono uno strato protettivo che protegge i componenti dalle sostanze corrosive. Riducono al minimo il rischio di corrosione, che può degradare le prestazioni e portare al guasto dei componenti nel tempo.
- Resistenza ai raggi UV: I produttori progettano composti di impregnazione specifici per offrire resistenza contro le radiazioni ultraviolette (UV). Questa protezione è fondamentale per applicazioni all'aperto o dispositivi esposti alla luce solare diretta, poiché le radiazioni UV possono causare scolorimento, degrado o invecchiamento precoce dei materiali.
- Stabilità termica: I composti impregnanti possono fornire stabilità termica resistendo alle fluttuazioni di temperatura. Aiutano a proteggere i componenti dal caldo o dal freddo eccessivo, garantendone il funzionamento affidabile in caso di variazioni di temperatura estreme.
- Protezione meccanica:I composti di impregnazione migliorano la protezione automatica dei componenti elettronici fornendo un incapsulamento durevole e resistente. Questa protezione protegge i componenti da impatti fisici, vibrazioni o sollecitazioni meccaniche, riducendo il rischio di danni o guasti.
- Isolamento elettrico: I composti per impregnazione PCB offrono eccellenti proprietà di isolamento elettrico. Prevengono cortocircuiti elettrici e perdite fornendo una barriera non conduttiva tra i componenti o tracce conduttive sul PCB.
- Schermatura EMI/RFI: Alcuni composti per impregnazione possono incorporare materiali che offrono schermatura contro le interferenze elettromagnetiche (EMI) o contro le interferenze in radiofrequenza (RFI). Questa funzione aiuta a prevenire interferenze o disturbi indesiderati causati da radiazioni o segnali elettromagnetici.
- Conformità ambientale: I produttori progettano determinati composti per impregnazione per soddisfare specifici standard o regolamenti ambientali, come RoHS (Restriction of Hazardous Substances) o REACH (Registration, Evaluation, Authorization, and Restriction of Chemicals). Questi composti garantiscono la conformità alle linee guida ambientali e contribuiscono a pratiche di produzione sostenibili.
Il composto per impregnazione PCB fornisce una protezione completa da vari fattori ambientali, tra cui umidità, polvere, sostanze chimiche, corrosione, radiazioni UV, fluttuazioni di temperatura, sollecitazioni meccaniche, problemi elettrici e interferenze elettromagnetiche. Questa protezione aiuta a garantire la longevità, l'affidabilità e le prestazioni dei dispositivi elettronici in diverse applicazioni e ambienti.
Prestazioni termiche migliorate
La progettazione e il funzionamento dei dispositivi elettronici si basano in modo critico su prestazioni termiche migliorate, che i progettisti possono ottenere attraverso varie tecniche e materiali. Ecco alcuni punti chiave che evidenziano i vantaggi e i metodi per ottenere prestazioni termiche migliorate:
- Dissipazione del calore efficiente:Un'efficace dissipazione del calore è fondamentale per prevenire il surriscaldamento e mantenere temperature operative ottimali per i componenti elettronici. Utilizzando soluzioni di raffreddamento avanzate come dissipatori di calore, tubi di calore o pad termici, l'energia termica può essere trasferita in modo efficiente lontano dagli elementi, riducendo il rischio di degrado delle prestazioni o guasti.
- Materiali dell'interfaccia termica: I materiali di interfaccia termica, come paste termiche, pastiglie o materiali a cambiamento di fase, migliorano il trasferimento di calore tra il componente e il sistema di raffreddamento. Questi materiali aiutano a riempire i vuoti d'aria o le imperfezioni microscopiche sull'interfaccia, riducendo la resistenza termica e migliorando la conduttività termica.
- Tecniche di diffusione del calore:Le tecniche di diffusione del calore prevedono l'utilizzo di materiali con elevata conducibilità termica, come rame o alluminio, per distribuire uniformemente il calore attraverso il dispositivo. Mantenere una distribuzione uniforme della temperatura è essenziale per evitare il surriscaldamento di aree specifiche.
- Considerazioni sulla progettazione termica:Una progettazione termica efficace implica un'attenta considerazione di fattori come il posizionamento dei componenti, il dimensionamento e il posizionamento del dissipatore di calore e il flusso d'aria complessivo all'interno del dispositivo. L'ottimizzazione di questi aspetti riduce al minimo i punti caldi e migliora la dissipazione del calore.
- Gestione della ventilazione e del flusso d'aria: Un'adeguata ventilazione e gestione del flusso d'aria sono fondamentali per rimuovere il calore dal dispositivo e mantenere un ambiente operativo più fresco. Mantenere un flusso continuo di aria fresca è essenziale per dissipare il calore in modo efficace. Un modo per raggiungere questo obiettivo è utilizzare ventole, prese d'aria o condotti.
- Simulazione termica e test:L'utilizzo di software di simulazione termica e metodologie di test consente agli ingegneri di analizzare e ottimizzare le prestazioni termiche dei dispositivi elettronici. Miglioramenti iterativi nella progettazione, nella selezione dei componenti e nelle soluzioni di raffreddamento consentirebbero agli ingegneri di ottenere una migliore gestione termica.
- Tecnologie di raffreddamento avanzate:Tecnologie di raffreddamento innovative, come le soluzioni con camera di liquido o vapore, possono migliorare significativamente le prestazioni termiche in applicazioni ad alta potenza o con vincoli di spazio. Queste tecnologie forniscono capacità di dissipazione del calore superiori e possono gestire efficacemente le richieste termiche dei sistemi elettronici avanzati.
- Selezione del materiale: La scelta di materiali con elevata conduttività termica, bassa resistenza termica ed eccellenti proprietà di dissipazione del calore può migliorare le prestazioni termiche. Per garantire una gestione termica efficiente, gli ingegneri dovrebbero scegliere substrati, adesivi e incapsulanti appositamente progettati per questo scopo.
- Gestione termica attiva:Le tecniche di gestione termica attiva, come il controllo dinamico della velocità della ventola o la limitazione della potenza basata sulla temperatura, possono aiutare a regolare le temperature in base alle condizioni in tempo reale. L'abilitazione della massima dissipazione del calore garantisce che i componenti funzionino entro limiti di temperatura sicuri.
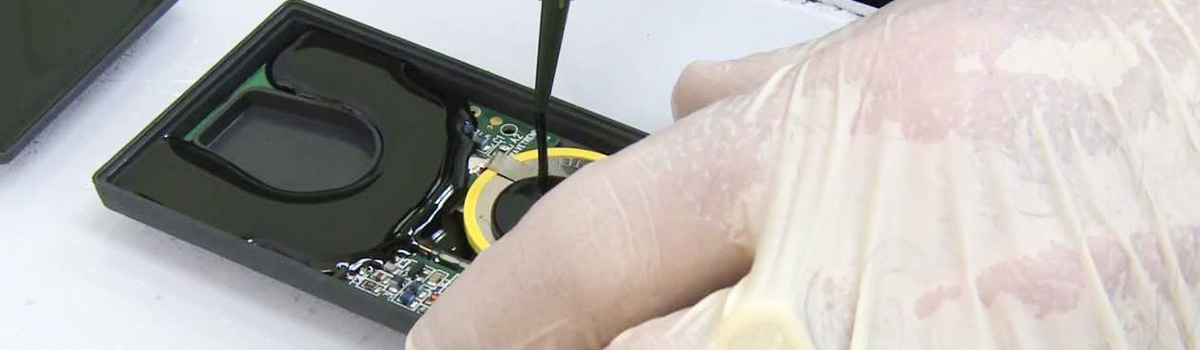
Resistenza meccanica migliorata
Una migliore resistenza meccanica è un fattore critico per garantire la durata e l'affidabilità dei dispositivi elettronici. Ecco alcuni punti chiave che evidenziano i vantaggi e i metodi per ottenere una migliore resistenza meccanica:
- Recinzioni rinforzate: Un approccio per migliorare la resistenza meccanica consiste nell'utilizzare involucri rinforzati, come involucri rinforzati o resistenti agli urti. I progettisti creano questi involucri per resistere a sollecitazioni fisiche, vibrazioni e potenziali impatti, proteggendo i componenti interni da eventuali danni.
- Ottimizzazione della progettazione strutturale:Utilizzando tecniche di progettazione avanzate, come l'analisi degli elementi finiti (FEA) o la progettazione assistita da computer (CAD), gli ingegneri possono ottimizzare l'integrità strutturale dei dispositivi elettronici. Individuare le aree che necessitano di miglioramenti per alleviare le concentrazioni di stress e rafforzare i punti critici sono essenziali per migliorare la resistenza meccanica.
- Materiali di alta qualità:La selezione di materiali di alta qualità è fondamentale per migliorare la resistenza meccanica. La scelta di materiali con resistenza alla trazione, resistenza agli urti e stabilità dimensionale superiori può migliorare significativamente la robustezza e l'affidabilità dei dispositivi elettronici.
- Rinforzi e rinforzi:Nelle applicazioni che richiedono maggiore resistenza meccanica, i progettisti possono incorporare puntoni ed elementi di rinforzo. Questi possono includere staffe metalliche, travi di supporto o nervature che forniscono ulteriore integrità strutturale e resistenza alla flessione o alla torsione.
- Collante adesivo:L'utilizzo di robuste tecniche di incollaggio adesivo può migliorare la resistenza meccanica dei gruppi di dispositivi. Gli adesivi ad alta resistenza garantiscono un legame sicuro tra i componenti, prevenendo la separazione o l'allentamento dovuto a sollecitazioni meccaniche o vibrazioni.
- Connettori rinforzati e punti di montaggio: I connettori e i punti di montaggio, come viti o elementi di fissaggio, possono essere rinforzati per migliorare la resistenza meccanica. Utilizzando materiali più consistenti o incorporando un supporto aggiuntivo, questi componenti possono resistere meglio alle forze meccaniche e mantenere connessioni affidabili.
- Assorbimento degli urti e resistenza agli urti: L'incorporazione di materiali o strutture che assorbono e dissipano l'energia d'urto può migliorare la resistenza meccanica. I progettisti possono utilizzare misure protettive come materiali che assorbono gli urti, elementi di ammortizzazione o rivestimenti per salvaguardare i componenti e prevenire danni da urti o cadute improvvisi.
- Conformità agli standard di settore: La conformità agli standard del settore, come quelli definiti da organizzazioni come la Commissione elettrotecnica internazionale (IEC) o l'Institute of Electrical and Electronics Engineers (IEEE), garantisce che i dispositivi elettronici soddisfino i requisiti di resistenza meccanica specificati. Il rispetto di questi standard aiuta a garantire prestazioni costanti e affidabili in varie condizioni operative.
- Imballaggio e manipolazione robusti: Tecniche di imballaggio e manipolazione adeguate durante la produzione, il trasporto e l'installazione svolgono un ruolo cruciale nel mantenimento della resistenza meccanica. L'imballaggio protettivo, le misure antistatiche e le procedure di manipolazione sicure riducono al minimo il rischio di danni fisici e mantengono l'integrità del dispositivo.
Riduzione del rumore elettrico
La riduzione del rumore elettrico è fondamentale per la progettazione e il funzionamento dei dispositivi elettronici per garantire prestazioni affidabili e integrità del segnale. Ecco alcuni punti chiave che evidenziano i vantaggi e i metodi per ridurre il rumore elettrico:
- Messa a terra e schermatura:Tecniche di messa a terra e meccanismi di schermatura adeguati aiutano a ridurre al minimo il rumore elettrico fornendo un percorso a bassa impedenza per correnti elettriche indesiderate. Gli schermi di messa a terra e gli involucri conduttivi aiutano a contenere e reindirizzare le interferenze elettromagnetiche (EMI) e le interferenze di radiofrequenza (RFI), riducendone l'impatto sui componenti sensibili.
- Filtraggio e disaccoppiamento:Filtri e componenti di disaccoppiamento, come condensatori, induttori e perline di ferrite, aiutano a sopprimere il rumore elettrico attenuando i componenti ad alta frequenza. Questi componenti sono strategicamente posizionati vicino a circuiti sensibili o linee di alimentazione per evitare che il rumore si propaghi ulteriormente.
- Isolamento del segnale: Le tecniche di isolamento del segnale, come optoaccoppiatori o trasformatori, interrompono la connessione elettrica tra i circuiti per ridurre al minimo il trasferimento del rumore elettrico. L'isolamento dei segnali sensibili dalle fonti di rumore aiuta a mantenere l'integrità del segnale e riduce il rischio di danneggiamento o interferenza dei dati.
- Layout e instradamento PCB: Un'attenta disposizione dei circuiti stampati e pratiche di instradamento sono fondamentali per ridurre il rumore elettrico. La corretta separazione dei circuiti analogici e digitali, la riduzione al minimo delle lunghezze delle tracce e l'utilizzo di piani di massa o tecniche di isolamento del segnale possono aiutare a mitigare gli effetti dell'accoppiamento del rumore e della radiazione elettromagnetica.
- Cavi e connettori schermati: Cavi e connettori schermati aiutano a ridurre al minimo la captazione o l'emissione di rumore. La protezione dei cavi con materiali conduttivi, come schermature intrecciate o laminate, fornisce una barriera contro le interferenze elettromagnetiche esterne.
- Tecniche di messa a terra:L'implementazione di tecniche di messa a terra adeguate, come la messa a terra a stella o piani di massa, assicura un punto di riferimento comune per i segnali elettrici e aiuta a prevenire loop di terra che possono introdurre rumore elettrico.
- Filtri EMI/RFI: L'inclusione di filtri EMI/RFI negli stadi di ingresso o di uscita degli alimentatori o delle linee di segnale può ridurre significativamente il rumore elettrico. Questi filtri attenuano i componenti del rumore ad alta frequenza e ne impediscono la propagazione nei circuiti sensibili.
- Selezione dei componenti:La scelta di componenti con caratteristiche di basso rumore, come amplificatori a basso rumore o riferimenti di tensione di precisione, può aiutare a ridurre il rumore elettrico alla fonte. Anche la selezione di componenti con un'elevata immunità al rumore o alle interferenze contribuisce alla riduzione del rumore.
- Test di compatibilità elettromagnetica (EMC): L'esecuzione di test EMC durante le fasi di progettazione e produzione aiuta a identificare potenziali fonti di rumore elettrico e valutare la conformità del dispositivo agli standard di compatibilità elettromagnetica. Questo test garantisce che il dispositivo funzioni entro limiti di rumore accettabili e riduce al minimo le interferenze con altre apparecchiature elettroniche.
- Pratiche di messa a terra e collegamento:Pratiche adeguate di messa a terra e collegamento equipotenziale durante l'installazione e il funzionamento del dispositivo aiutano a ridurre il rumore elettrico. È essenziale creare solide connessioni di messa a terra, collegare i componenti metallici a una terra condivisa e utilizzare metodi di gestione dei cavi per ridurre le interferenze.
Aumento della durata della vita dell'elettronica
Aumentare la durata dell'elettronica è una considerazione cruciale sia per i produttori che per i consumatori. Ecco alcuni punti chiave che evidenziano i vantaggi e i metodi per aumentare la durata dell'elettronica:
- Gestione termica efficiente: Adeguate tecniche di gestione termica, come un'adeguata dissipazione del calore, possono prolungare significativamente la durata dei componenti elettronici. Il mantenimento di temperature operative ottimali riduce al minimo lo stress termico sugli elementi, riducendo il rischio di degrado o guasto.
- Design e costruzione robusti: La progettazione di componenti elettronici con componenti potenti e durevoli, come connettori, resistori, condensatori e circuiti integrati di alta qualità, può aumentarne la longevità. Quando si scelgono i componenti, è essenziale considerare la loro longevità, affidabilità e capacità di gestire i livelli di tensione e temperatura corretti.
- Buona alimentazione e regolazione della tensione: Garantire un'alimentazione stabile e pulita è essenziale per aumentare la durata dell'elettronica. Una corretta regolazione della tensione, protezione contro le sovratensioni e alimentatori o regolatori di tensione di alta qualità aiutano a prevenire la sovratensione o le fluttuazioni di tensione che possono danneggiare i componenti sensibili.
- Adeguata protezione ESD:L'implementazione di adeguate misure di protezione contro le scariche elettrostatiche (ESD) salvaguarda l'elettronica dai danni causati dall'elettricità statica. L'utilizzo di postazioni di lavoro sicure ESD, cinghie di messa a terra e imballaggi schermati ESD garantisce la sicurezza durante la produzione, la manipolazione e l'installazione.
- Manutenzione e pulizia regolari: La manutenzione regolare, inclusa la pulizia e l'ispezione, può aiutare a identificare e risolvere potenziali problemi prima che si intensifichino. Rimuovere polvere, detriti e contaminanti dai dispositivi elettronici e garantire un flusso d'aria e una ventilazione adeguati può prevenire il surriscaldamento e il guasto dei componenti.
- Protezione adeguata dai fattori ambientali: Proteggere l'elettronica da fattori ambientali, come umidità, umidità, temperature estreme e sostanze corrosive, è fondamentale per la longevità. I progettisti possono raggiungere questo obiettivo utilizzando involucri adeguati, rivestimenti conformi o composti per impregnazione che forniscono isolamento e protezione da condizioni difficili.
- Manipolazione e conservazione corrette:Maneggiare con cura i componenti elettronici, seguire procedure di installazione ragionevoli e conservarli in ambienti controllati quando non vengono utilizzati può aiutare a prevenire danni fisici e prolungarne la durata. Proteggiamo da urti fisici, scariche statiche, calore eccessivo, umidità o esposizione alla polvere.
- Aggiornamenti firmware e software:Mantenere firmware e software aggiornati aiuta a garantire prestazioni, compatibilità e sicurezza ottimali. Gli aggiornamenti regolari spesso includono correzioni di bug, miglioramenti delle prestazioni e maggiore compatibilità, prolungando così la vita utile dell'elettronica.
- Considerazioni ambientali:Progettare l'elettronica tenendo conto di considerazioni ecologiche, come l'utilizzo di componenti ad alta efficienza energetica, la riduzione del consumo energetico in modalità standby e l'implementazione di programmi di riciclaggio o smaltimento, contribuisce alla loro durata complessiva. Inoltre promuove la sostenibilità e riduce i rifiuti elettronici.
- Controllo e test di qualità: L'implementazione di rigorose misure di controllo della qualità e test approfonditi durante la produzione aiuta a identificare e correggere potenziali difetti o problemi. Possiamo migliorare la loro durata garantendo che siano disponibili solo componenti elettronici affidabili e di alta qualità.
Tipi di composti per impregnazione
I progettisti utilizzano composti per impregnazione per incapsulare e proteggere i componenti elettronici, fornendo isolamento, resistenza ambientale e supporto meccanico. Sono disponibili vari composti per impregnazione, ognuno dei quali offre proprietà e vantaggi specifici. Ecco alcuni tipi comuni di composti per impregnazione:
- Resina epossidica: La resina epossidica è una scelta popolare per le applicazioni di impregnazione grazie alle sue eccellenti proprietà di isolamento elettrico, elevata resistenza e resistenza agli agenti chimici e alle variazioni di temperatura. Fornisce una buona adesione a molti substrati e una protezione affidabile contro l'umidità e i contaminanti ambientali.
- Poliuretano: I composti per riempimento in poliuretano offrono flessibilità, resistenza agli urti ed eccellente resistenza alle vibrazioni. Forniscono una protezione adeguata contro l'umidità, i prodotti chimici e le radiazioni UV. I composti poliuretanici utilizzano frequentemente applicazioni che richiedono assorbimento degli urti o cicli termici.
- Silicone: I composti siliconici per impregnazione hanno un'eccezionale stabilità termica, resistenza alle alte temperature ed eccellente flessibilità in un ampio intervallo di temperature. Offrono un buon isolamento elettrico e sono altamente resistenti all'umidità, agli agenti chimici e all'esposizione ai raggi UV. I progettisti utilizzano comunemente composti siliconici in applicazioni che richiedono un'estrema resistenza alle temperature o l'esposizione ad ambienti difficili.
- Acrilico:Le persone apprezzano i composti per impregnazione acrilici per il loro tempo di indurimento rapido, il basso ritiro e le buone proprietà di isolamento elettrico. Forniscono una soluzione conveniente per molte applicazioni di impregnazione e offrono resistenza all'umidità, alle sostanze chimiche e ai cicli termici. Le persone usano spesso composti acrilici quando desiderano un equilibrio tra costo, prestazioni e facilità d'uso.
- Poliammide: I compound in poliammide, noti come compound a base di nylon, offrono un'eccellente resistenza alle alte temperature, agli agenti chimici e alle sollecitazioni meccaniche. Forniscono una buona adesione a vari substrati e offrono una protezione affidabile in ambienti difficili. I produttori utilizzano comunemente composti di poliammide nelle applicazioni automobilistiche, aerospaziali e industriali.
- Polimerizzazione UV:I composti per invasatura a polimerizzazione UV possiedono una caratteristica unica: polimerizzano utilizzando la luce ultravioletta. Offrono tempi di polimerizzazione rapidi, consentendo un'elevata produttività nei processi di produzione. I composti a polimerizzazione UV forniscono un'eccellente adesione, isolamento elettrico e resistenza all'umidità e agli agenti chimici. Trovano spesso impiego in applicazioni che richiedono un indurimento rapido e un controllo preciso del processo di indurimento.
- Materiali di interfaccia termica (TIM): I materiali di interfaccia termica, come grassi termici, cuscinetti termici o materiali a cambiamento di fase, vengono utilizzati per applicazioni di impregnazione in cui il trasferimento efficiente del calore è fondamentale. Questi materiali aiutano a migliorare la conduttività termica e assicurano un'efficace dissipazione del calore, prevenendo il surriscaldamento dei componenti elettronici.
È essenziale considerare i requisiti specifici dell'applicazione quando si seleziona un composto per impregnazione. Per scegliere il composto di resinatura più adatto per prestazioni e protezione ottimali dei componenti elettronici, è necessario considerare fattori quali l'intervallo di temperatura, l'esposizione chimica, lo stress meccanico, l'isolamento elettrico e il tempo di indurimento.
Composto epossidico per impregnazione
Varie industrie utilizzano ampiamente composti epossidici per impregnazione grazie alle loro eccezionali proprietà e applicazioni versatili. Ecco alcuni punti chiave che evidenziano le caratteristiche e i vantaggi dei composti epossidici per impregnazione:
- Adesione superiore: I composti epossidici per impregnazione presentano un'eccellente adesione a vari substrati, inclusi metalli, ceramica, plastica e circuiti stampati (PCB). Questo forte legame fornisce stabilità meccanica e impedisce l'ingresso di umidità, migliorando l'affidabilità complessiva dei dispositivi elettronici.
- Isolamento elettrico:I composti epossidici per impregnazione offrono eccellenti proprietà di isolamento elettrico, isolando e proteggendo efficacemente i componenti elettronici sensibili da correnti elettriche e potenziali cortocircuiti. Questo isolamento aiuta a prevenire malfunzionamenti, degrado delle prestazioni e danni causati da dispersioni elettriche.
- Resistenza alle alte temperature:I composti epossidici per impregnazione possono resistere a temperature di esercizio elevate, rendendoli adatti per applicazioni in ambienti difficili o con componenti che generano calore. Mantengono la loro integrità strutturale e le loro prestazioni anche a temperature elevate, garantendo l'affidabilità a lungo termine dell'elettronica incapsulata.
- Resistenza chimica e ambientale: I composti epossidici per impregnazione resistono a vari prodotti chimici, inclusi solventi, carburanti, oli e acidi. Questa resistenza aiuta a proteggere i componenti elettronici dalla corrosione chimica o dal degrado, prolungandone la durata in ambienti difficili.
- Resistenza meccanica:I composti epossidici per impregnazione forniscono un'eccellente resistenza meccanica e integrità strutturale, rendendoli adatti per applicazioni che richiedono resistenza alle vibrazioni e assorbimento degli urti. Aiutano a proteggere i componenti delicati da sollecitazioni meccaniche, urti e vibrazioni, garantendo prestazioni affidabili anche in condizioni difficili.
- Ritiro basso: I composti per impregnazione epossidici hanno tipicamente un basso ritiro durante il processo di indurimento. Questa caratteristica fornisce uno stress minimo sui componenti incapsulati e riduce il rischio di incrinature o delaminazione, migliorando la stabilità complessiva e la durata dell'elettronica incapsulata.
- Applicazione Versatile:I composti epossidici trovano applicazione in vari settori, tra cui elettronica, automotive, aerospaziale e telecomunicazioni. Trovano impiego nell'incapsulamento e nella protezione di più dispositivi, come alimentatori, sensori, motori, moduli LED e unità di controllo elettronico (ECU).
- Elaborazione facile: I composti epossidici per impregnazione sono in genere facili da maneggiare e lavorare. Offrono la comodità di essere facilmente miscelati, versati o erogati in stampi o su componenti, consentendo processi di produzione e assemblaggio efficienti. La loro viscosità gestibile e il tempo di polimerizzazione consentono un'applicazione precisa e facilitano la produzione di grandi volumi.
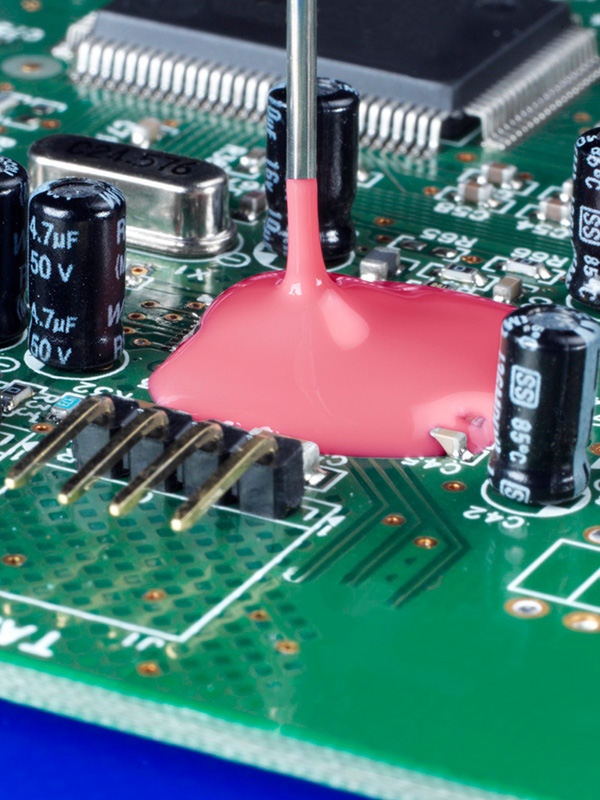
Composto per impregnazione in silicone
I composti siliconici per impregnazione sono materiali altamente versatili per un uso estensivo in vari settori. Ecco alcuni punti chiave che evidenziano le caratteristiche e i vantaggi dei composti siliconici per impregnazione:
- Flessibilità e prestazioni a bassa temperatura: I composti siliconici per impregnazione offrono flessibilità ed elasticità eccezionali, rendendoli adatti per applicazioni che richiedono movimenti dinamici o resistenza alle vibrazioni. Possono mantenere le loro proprietà anche a basse temperature, garantendo prestazioni affidabili in ambienti freddi.
- Eccellente resistenza all'umidità: I composti siliconici per impregnazione presentano un'eccellente resistenza all'umidità e all'ingresso di acqua. Creano una barriera affidabile contro l'umidità, proteggendo i componenti elettronici sensibili dalla corrosione e dai danni causati dall'esposizione all'umidità o ad ambienti umidi.
- Resistenza ai raggi UV e agli agenti atmosferici: I composti per impregnazione in silicone hanno una resistenza intrinseca ai raggi UV e agli agenti atmosferici, che consente loro di resistere all'esposizione prolungata alla luce solare e agli elementi esterni. L'invasatura in silicone è perfetta per l'uso esterno in quanto protegge dai raggi UV e dai fattori ambientali. Inoltre, vanta buone proprietà dielettriche. I composti possiedono buone proprietà dielettriche, che li rendono isolanti efficaci per i componenti elettrici. Possono prevenire perdite elettriche e fornire un isolamento affidabile, riducendo il rischio di cortocircuiti e guasti elettrici.
- Stabilità termica: I composti siliconici per impregnazione presentano un'eccellente stabilità termica e possono resistere a varie temperature. Rimangono flessibili e mantengono le loro proprietà in un ampio intervallo di temperature, garantendo prestazioni costanti in ambienti caldi e freddi.
- Resistenza chimica: I composti siliconici per impregnazione resistono a vari prodotti chimici, inclusi oli, solventi e molti prodotti chimici industriali comuni. Questa resistenza protegge i componenti elettronici dalla corrosione chimica e dal degrado, migliorandone la durata e l'affidabilità in ambienti difficili.
- Elaborazione e cura facili:I composti per impregnazione in silicone sono in genere facili da maneggiare e lavorare. Hanno una viscosità gestibile, che consente un'applicazione precisa e un facile riempimento di forme o vuoti complessi. Offrono anche un tempo di polimerizzazione relativamente rapido, consentendo processi di produzione e assemblaggio efficienti.
- Compatibilità con componenti sensibili:I composti sigillanti in silicone sono noti per la loro compatibilità con un'ampia gamma di componenti sensibili, come sensori, connettori e delicati circuiti elettronici. La loro natura delicata e non abrasiva protegge i componenti incapsulati senza comprometterne la funzionalità.
- Ampia gamma di applicazioni:Vari settori, tra cui l'elettronica, l'automotive, l'aerospaziale, i dispositivi medici e l'energia rinnovabile, utilizzano ampiamente composti per impregnazione in silicone. Trovano impiego nell'incapsulamento e nella protezione di moduli elettronici, illuminazione a LED, sensori, alimentatori e altri componenti critici.
Queste proprietà li rendono la scelta preferita per l'invasatura e l'incapsulamento, garantendo una protezione affidabile e prestazioni a lungo termine dei dispositivi elettronici in diversi settori.
Composto per impregnazione poliuretanico
Varie industrie utilizzano ampiamente i composti di impregnazione in poliuretano per le loro proprietà uniche e applicazioni versatili. Ecco alcuni punti chiave che evidenziano le caratteristiche e i vantaggi dei composti poliuretanici per impregnazione:
- Eccellente resistenza meccanica: I composti poliuretanici per impregnazione forniscono un'eccezionale resistenza meccanica, rendendoli adatti per applicazioni che richiedono una robusta protezione contro sollecitazioni meccaniche, vibrazioni e impatti. Offrono un'eccellente resistenza alla deformazione, garantendo la stabilità e la durata a lungo termine dei componenti incapsulati.
- Smorzamento delle vibrazioni e assorbimento degli urti:I composti di riempimento in poliuretano presentano eccellenti proprietà di smorzamento delle vibrazioni, consentendo loro di assorbire e dissipare le vibrazioni. In ambienti difficili, le vibrazioni possono avere un impatto negativo sui componenti elettronici sensibili. Avere misure di protezione in atto è fondamentale per garantire prestazioni affidabili.
- Resistenza chimica e ambientale:I composti per impregnazione in poliuretano resistono a vari prodotti chimici, inclusi oli, solventi e sostanze industriali comuni. Forniscono inoltre resistenza all'umidità, all'umidità e ad altri fattori ambientali, salvaguardando i componenti elettronici dalla corrosione e dal degrado.
- Stabilità termica:I composti di riempimento in poliuretano dimostrano un'eccellente stabilità termica, che consente loro di resistere a temperature di esercizio elevate senza comprometterne le proprietà o l'integrità. Questa caratteristica li rende adatti per applicazioni che coinvolgono componenti che generano calore o esposizione a temperature elevate.
- Isolamento elettrico: I composti isolanti in poliuretano presentano buone proprietà di isolamento elettrico, isolando e proteggendo efficacemente i componenti elettronici da correnti elettriche, potenziali cortocircuiti e interferenze elettriche. Contribuiscono alle prestazioni affidabili e alla longevità dei dispositivi incapsulati.
- Adesione a vari substrati:I composti per impregnazione in poliuretano aderiscono bene a vari substrati, inclusi metalli, plastica, ceramica e PCB. Questo forte legame migliora la stabilità meccanica complessiva dei componenti incapsulati, impedendo l'ingresso di umidità e promuovendo un funzionamento affidabile.
- Ritiro basso:I composti di impregnazione poliuretanici hanno generalmente un basso ritiro durante il processo di indurimento. Questa caratteristica riduce al minimo lo stress sui componenti incapsulati, riducendo il rischio di cricche, delaminazione o danni causati da sollecitazioni interne.
- Applicazione Versatile: I composti per impregnazione in poliuretano trovano applicazione in diversi settori, come l'elettronica, l'automotive, l'aerospaziale e le energie rinnovabili. Lo usano per incapsulare e proteggere vari dispositivi, inclusi sensori, connettori, elettronica di potenza e moduli di controllo.
- Facilità di elaborazione:I composti per impregnazione in poliuretano sono in genere facili da maneggiare e lavorare. Offrono la comodità di essere facilmente miscelati, versati o erogati in stampi o su componenti, consentendo processi di produzione e assemblaggio efficienti. La loro viscosità gestibile e il tempo di polimerizzazione consentono un'applicazione precisa e facilitano la produzione di grandi volumi.
Fattori da considerare quando si sceglie un composto per impregnazione
Si dovrebbero considerare diversi fattori quando si sceglie un composto per impregnazione per un'applicazione specifica. Ecco alcuni punti chiave da considerare quando si sceglie un mix per l'invasatura:
- Requisiti delle applicazioni: Valutare i requisiti specifici dell'applicazione, inclusi intervallo di temperatura, esposizione chimica, resistenza all'umidità, resistenza ai raggi UV, stress meccanico e proprietà di isolamento elettrico. Determinare il livello di protezione necessario per i componenti per garantire che il composto per impregnazione possa soddisfare gli standard prestazionali desiderati.
- Compatibilità:Assicurarsi che il composto per impregnazione sia compatibile con i materiali incapsulati, come PCB, connettori, sensori o altri componenti elettronici. Considera fattori come l'adesione, il coefficiente di dilatazione termica (CTE) e le potenziali interazioni tra il composto di riempimento e i materiali incapsulati.
- Tempo e processo di polimerizzazione:Valuta il tempo di indurimento e il processo del composto per impregnazione. Prendere in considerazione fattori come la durata utile, la temperatura di polimerizzazione e il tempo di polimerizzazione. Determinare se il processo di polimerizzazione è in linea con il processo di produzione o assemblaggio e se consente una produzione efficiente e tempi di manipolazione adeguati.
- Resistenza meccanica:Considerare i requisiti di resistenza meccanica dell'applicazione. Valuta il potenziale di vibrazioni, urti o sollecitazioni meccaniche e scegli un composto per impregnazione in grado di fornire la resistenza e la durata necessarie per resistere a tali condizioni.
- Conduttività termica:Valutare i requisiti di conducibilità termica dell'applicazione. Scegli un composto di impregnazione in grado di trasferire efficacemente il calore lontano dai componenti che generano calore a seconda delle esigenze di dissipazione del calore, garantendo una gestione termica ottimale.
- Proprietà elettriche: Considera le proprietà di isolamento elettrico del composto per impregnazione. Assicurarsi che offra la rigidità dielettrica e la resistenza necessarie per prevenire perdite elettriche o cortocircuiti. Se l'interferenza elettromagnetica (EMI) è un problema, prendere in considerazione composti per impregnazione con proprietà di schermatura EMI migliorate.
- Considerazioni ambientali: Valutare le condizioni ecologiche a cui sarà esposto il composto per invasatura. Valuta fattori come umidità, umidità, radiazioni UV ed esposizione chimica. Scegli un composto per impregnazione in grado di proteggere e resistere a specifiche sfide ambientali.
- Compatibilità di processo: Considerare la compatibilità del composto di impregnazione con il processo di produzione o assemblaggio. Valuta la viscosità, la durata utile, i requisiti di miscelazione, i metodi di erogazione e le condizioni di polimerizzazione. Garantire che il composto per impregnazione possa integrarsi facilmente nei processi di produzione esistenti.
- Conformità normativa: Assicurarsi che il composto per impregnazione scelto sia conforme agli standard e alle normative del settore pertinenti, come RoHS (Restriction of Hazardous Substances) o REACH (Registration, Evaluation, Authorization and Restriction of Chemicals). In questo modo, garantiamo che il prodotto finale sia sicuro e conforme.
Considerando questi fattori, si può prendere una decisione informata quando si seleziona un composto di impregnazione che soddisfi al meglio i requisiti dell'applicazione, garantendo protezione e prestazioni ottimali dei componenti elettronici incapsulati.
Compatibilità con l'elettronica
La compatibilità con l'elettronica è un fattore cruciale da considerare quando si sceglie un composto per impregnazione per l'incapsulamento di componenti elettronici. Ecco alcuni punti chiave da considerare per quanto riguarda la compatibilità dei composti di impregnazione con l'elettronica:
- Compatibilità chimica:Assicurarsi che il composto di impregnazione sia chimicamente compatibile con i materiali utilizzati nei componenti elettronici, come PCB, connettori e circuiti elettronici sensibili. La compatibilità garantisce che il composto per impregnazione non reagisca o degradi gli ingredienti, causando malfunzionamenti o danni.
- Adesione: Considera le proprietà di adesione del composto di riempimento alle superfici dei componenti elettronici. Dovrebbe aderire bene ai materiali incapsulati, fornendo un forte legame e prevenendo eventuali lacune o vuoti che potrebbero compromettere la protezione offerta dal composto di impregnazione.
- Proprietà dielettriche: Valutare le proprietà dielettriche del composto impregnante. Dovrebbe possedere buone proprietà di isolamento elettrico per garantire che i componenti incapsulati siano efficacemente isolati l'uno dall'altro e dalle correnti elettriche esterne. In questo modo si evita la possibilità di cortocircuiti o interferenze elettriche.
- Conduttività termica: Considerare i requisiti di conducibilità termica dell'elettronica. A seconda dell'applicazione, il composto sigillante dovrebbe avere la conduttività termica appropriata per dissipare il calore generato dai componenti. Il mantenimento di temperature operative ottimali è fondamentale per prevenire il surriscaldamento, che può causare problemi di prestazioni o guasti ai componenti.
- Coefficiente di espansione termica: Considera il coefficiente di dilatazione termica (CTE) del composto di impregnazione e la sua compatibilità con i componenti elettronici. Valori CET simili tra il composto di sigillatura e i materiali incapsulati riducono il rischio di fessurazioni o delaminazioni indotte da sollecitazioni dovute ai cicli termici.
- Resistenza all'umidità e all'ambiente:Valuta la resistenza del composto per impregnazione all'umidità, all'umidità e ad altri fattori ambientali. L'elettronica è spesso esposta ad ambienti difficili, che richiedono che il composto per impregnazione fornisca una protezione affidabile contro l'ingresso di umidità. Questa protezione aiuta a prevenire la corrosione e il danneggiamento dei componenti.
- Compatibilità con i processi di produzione:Considerare la compatibilità del composto di impregnazione con i processi di produzione o assemblaggio. Valuta la viscosità, la durata utile, i requisiti di miscelazione e le condizioni di polimerizzazione. Garantire che il composto di impregnazione si integri facilmente nei processi di produzione esistenti senza causare ritardi o complicazioni.
- Conformità normativa:Assicurarsi che il composto per impregnazione sia conforme alle normative e agli standard del settore pertinenti, come RoHS (Restriction of Hazardous Substances) o REACH (Registration, Evaluation, Authorization and Restriction of Chemicals). La conformità garantisce che il composto per impregnazione non contenga sostanze nocive che potrebbero danneggiare la salute umana o l'ambiente.
Tempo di indurimento
Il tempo di indurimento è un fattore essenziale da considerare quando si sceglie un composto per incapsulamento per l'incapsulamento di componenti elettronici. Ecco alcuni punti chiave da considerare per quanto riguarda il tempo di polimerizzazione:
- Pot life: Il pot life si riferisce alla durata durante la quale il composto per impregnazione rimane lavorabile dopo la miscelazione dei componenti. È essenziale comprendere la durata utile del composto per garantire un tempo sufficiente per l'applicazione e il posizionamento corretti dei componenti prima che il materiale inizi a polimerizzare.
- Tempo di cura:Il tempo di indurimento è necessario affinché il composto per impregnazione si indurisca e raggiunga completamente le proprietà desiderate. È fondamentale selezionare un composto per impregnazione con un tempo di polimerizzazione che si allinei con il programma di produzione o il processo di assemblaggio. Tempi di polimerizzazione lunghi possono causare ritardi nella produzione, mentre tempi di polimerizzazione brevi possono richiedere una lavorazione rapida.
- Condizioni ambientali: Considerare l'effetto delle condizioni ambientali, come la temperatura e l'umidità, sul tempo di indurimento del composto per impregnazione. Alcuni composti possono richiedere condizioni di temperatura o umidità specifiche per una polimerizzazione ottimale. Assicurarsi che le condizioni ambientali durante il processo di indurimento possano essere facilmente controllate e mantenute.
- Tecniche di accelerazione:Alcuni composti per impregnazione offrono opzioni di indurimento accelerato tramite calore, luce UV o additivi chimici. Questo metodo porta a tempi di indurimento più rapidi, rendendolo vantaggioso per le impostazioni di produzione ad alto volume o quando è necessario un rapido turnaround.
- Considerazioni post-cura:Capire se il composto per impregnazione richiede passaggi post-polimerizzazione, come ulteriore trattamento termico o esposizione ai raggi UV, per raggiungere le sue proprietà complete. Quando si valuta la praticità del composto per impregnazione, è essenziale considerare come le misure post-polimerizzazione possono influire sulla tempistica complessiva della produzione.
- Tempo di manipolazione e lavorabilità:Considerare il tempo di manipolazione e lavorabilità del composto di colata, che si riferisce alla durata durante la quale il materiale rimane in uno stato adatto per la miscelazione, la colata o l'erogazione; scegliendo un composto per impregnazione che fornisca un tempo di manipolazione adeguato per un'applicazione efficiente, garantendo al tempo stesso una qualità costante.
- È importante Curare il restringimento: Valutare il potenziale restringimento del composto di impregnazione durante il processo di polimerizzazione. Un restringimento eccessivo può causare stress sui componenti incapsulati e può portare a crepe o delaminazione. La scelta di un composto sigillante con restringimento minimo aiuta a mantenere l'integrità e l'affidabilità dell'elettronica incapsulata.
- Ottimizzazione e test:Si consiglia di condurre test approfonditi e di ottimizzare il processo di indurimento per il composto di impregnazione selezionato. È necessario considerare le dimensioni del componente, la complessità, la resistenza meccanica desiderata e le prestazioni termiche per garantire il tempo di indurimento appropriato per un'applicazione specifica.
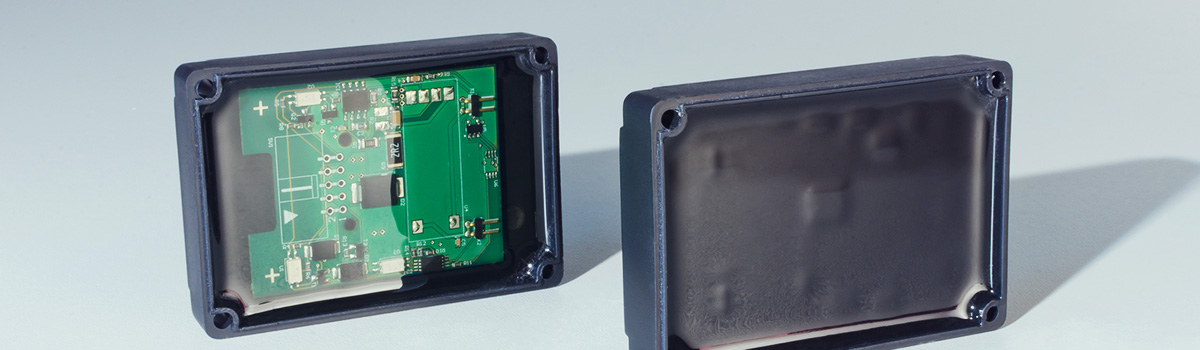
Resistenza alla temperatura
Quando si seleziona un composto sigillante per componenti elettronici, è fondamentale considerare la resistenza alla temperatura, specialmente nelle applicazioni in cui i materiali saranno esposti a temperature estreme. Ecco alcuni punti chiave da considerare per quanto riguarda la resistenza alla temperatura:
- Range di temperatura: Valuta l'intervallo di temperatura di funzionamento previsto dei componenti elettronici e scegli un composto per impregnazione in grado di resistere a tali temperature senza degrado o perdita di prestazioni. Considera gli estremi di alta e bassa temperatura che gli elementi possono incontrare durante il funzionamento.
- Ciclismo termico: Valutare la capacità del composto di impregnazione di resistere ai cicli termici, che comportano ripetute fluttuazioni di temperatura. I componenti che subiscono variazioni di temperatura possono espandersi e contrarsi, portando potenzialmente a stress sul materiale incapsulante. Scegliere un composto per impregnazione con un coefficiente di dilatazione termica (CTE) adeguato per ridurre al minimo lo stress e prevenire crepe o delaminazioni.
- Resistenza alle alte temperature:Selezionare un composto per impregnazione con un'eccellente resistenza al calore se l'applicazione coinvolge ambienti ad alta temperatura. Cerca un composto in grado di mantenere la sua resistenza meccanica, le proprietà di isolamento elettrico e altre caratteristiche prestazionali a temperature elevate.
- Resistenza alle basse temperature:Scegliere un composto per impregnazione con buona resistenza alle basse temperature per applicazioni che richiedono il funzionamento in condizioni di ghiaccio. Dovrebbe rimanere flessibile e mantenere la sua funzionalità anche a temperature sotto lo zero, garantendo l'integrità dei componenti incapsulati.
- Conduttività termica:Considerare la conduttività termica del composto di impregnazione, specialmente nelle applicazioni in cui la dissipazione del calore è fondamentale. Un composto sigillante con una buona conduttività termica può trasferire efficacemente il calore lontano dai componenti incapsulati, contribuendo a mantenere temperature operative ottimali e prevenendo il surriscaldamento.
- Proprietà di isolamento: Assicurarsi che il composto per impregnazione mantenga le sue proprietà di isolamento elettrico nell'intervallo di temperatura dell'applicazione. Dovrebbe isolare efficacemente i componenti elettronici e prevenire il rischio di perdite elettriche o cortocircuiti, anche in condizioni di temperatura estreme.
- Compatibilità con le soluzioni di gestione termica:Se si utilizzano soluzioni di gestione termica come dissipatori di calore o cuscinetti termici con il composto per impregnazione, verificare la compatibilità tra il composto per impregnazione e questi componenti. Garantendo un trasferimento di calore efficiente, possiamo ottenere la massima efficienza termica.
- Test e convalida: Condurre test approfonditi e convalidare la resistenza alla temperatura del composto di impregnazione. Per garantire l'affidabilità e le prestazioni del materiale, potrebbe essere necessario sottoporlo a cicli di temperatura, shock termici o esposizione prolungata a temperature estreme.
Considerazioni sui costi
Le considerazioni sui costi sono significative quando si seleziona un composto per invasatura per componenti elettronici, in quanto incidono direttamente sul budget complessivo del progetto. Ecco alcuni punti chiave da considerare per quanto riguarda le considerazioni sui costi:
- Costo materiale: Valuta il costo del composto per invasatura stesso. Diversi tipi di composti per impregnazione, come resina epossidica, silicone o poliuretano, variano nel prezzo. Considera il materiale necessario per il progetto e confronta il costo per unità di volume per ogni tipo.
- Efficienza dell'applicazione:Valuta la facilità di applicazione e la lavorabilità del composto per impregnazione. Alcuni composti possono richiedere attrezzature specializzate o manodopera qualificata per una corretta applicazione, aumentando i costi complessivi della manodopera. Scegli un composto per impregnazione che puoi facilmente applicare utilizzando i processi di produzione esistenti o con un investimento aggiuntivo minimo in attrezzature.
- Rifiuti e pulizia: Considera la quantità di rifiuti generati durante il processo di invasatura e la facilità di pulizia. Alcuni composti per impregnazione possono avere requisiti di smaltimento specifici, che possono aumentare il costo complessivo del progetto. Optare per materiali che generano rifiuti minimi e hanno procedure di pulizia semplici.
- Tempi di produzione: Analizza il tempo di indurimento e la durata utile del composto per invasatura. Tempi di polimerizzazione più lunghi possono aumentare la produzione, comportando costi di manodopera aggiuntivi e potenziali ritardi. Seleziona un composto per impregnazione con un tempo di polimerizzazione che si allinea con il programma di produzione per ottimizzare l'efficienza e ridurre i costi.
- Requisiti di prestazione: Bilancia il costo del composto di resinatura con i requisiti prestazionali desiderati dei componenti elettronici. Le opzioni più economiche possono offrire protezione o prestazioni diverse rispetto a quelle più costose. Valutare la criticità dell'applicazione e selezionare un composto per impregnazione che soddisfi gli standard prestazionali necessari senza inutili specifiche eccessive.
- Affidabilità e longevità: Considera le implicazioni di costo a lungo termine del composto per impregnazione. L'investimento in un composto per impregnazione di qualità superiore e più costoso può aumentare l'affidabilità e la longevità dell'elettronica incapsulata. La riduzione di guasti, riparazioni e sostituzioni per tutta la durata del progetto può far risparmiare sui costi.
- Supporto e garanzia del fornitore:Valutare il supporto fornito dal fornitore del composto per impregnazione e qualsiasi garanzia o garanzia associata. Un fornitore affidabile con un eccellente servizio clienti può offrire assistenza tecnica, risoluzione dei problemi e copertura della garanzia, contribuendo a risparmiare sui costi in caso di problemi o preoccupazioni.
- Conformità normativa: Considera le implicazioni in termini di costi della conformità alle normative. Assicurarsi che il composto per impregnazione scelto sia conforme alle normative e agli standard del settore pertinenti. La non conformità può comportare sanzioni o battute d'arresto del progetto, che possono comportare costi aggiuntivi.
Considerando attentamente le considerazioni sui costi e i fattori correlati, è possibile selezionare un composto di impregnazione che bilanci l'accessibilità economica e soddisfi i requisiti di prestazioni e affidabilità necessari per i componenti elettronici incapsulati.
Tecniche applicative
Le tecniche di applicazione dei composti per impregnazione comportano l'incapsulamento di componenti elettronici con il materiale scelto. Ecco alcuni punti chiave da considerare per quanto riguarda le tecniche di applicazione:
- Erogazione: L'erogazione è una tecnica di applicazione comune in cui il composto di impregnazione viene erogato direttamente sui componenti elettronici. Puoi farlo manualmente usando le siringhe o automatizzarlo usando l'attrezzatura di erogazione. L'erogazione consente un'applicazione precisa e il controllo sulla quantità di materiale utilizzato.
- Invasatura sottovuoto: L'impregnazione sottovuoto comporta il posizionamento dei componenti elettronici in una camera a vuoto e quindi l'introduzione del composto di impregnazione. Il vuoto aiuta a rimuovere le bolle d'aria e garantisce una corretta penetrazione e copertura del composto attorno agli elementi. Questa tecnica consente di ottenere un incapsulamento privo di vuoti.
- Stampaggio a iniezione: Lo stampaggio a iniezione è una tecnica di applicazione più automatizzata e ad alto volume. Il composto di impregnazione viene riscaldato e iniettato in una cavità dello stampo contenente i componenti elettronici. Dopo l'indurimento, aprire lo stampo e rimuovere le parti incapsulate. Lo stampaggio a iniezione offre un incapsulamento efficiente e uniforme, che lo rende adatto alla produzione su larga scala.
- Borse per invasatura:I sacchetti per invasatura sono sacchetti preformati in plastica o silicone riempiti con il composto per invasatura. Posizionare i componenti elettronici all'interno del sacchetto e sigillarlo prima di iniziare il processo di polimerizzazione. Questa tecnica è appropriata quando si ha a che fare con forme o caratteristiche complesse che richiedono un orientamento specifico durante l'incapsulamento.
- Rivestimento conforme:Il conformal coating comporta l'applicazione di un sottile strato di composto impregnante sulla superficie dei componenti elettronici. Protegge dai fattori ambientali senza incapsulare completamente i componenti. Il rivestimento conforme è adatto per applicazioni in cui l'accessibilità o la rilavorabilità degli ingredienti è essenziale.
- Incapsulamento sottovuoto: L'incapsulamento sottovuoto prevede la combinazione di invasatura sottovuoto con il posizionamento di una pellicola protettiva o di un sacchetto attorno ai componenti elettronici. Il vuoto rimuove l'aria dalla confezione, introducendo il composto di riempimento per riempire i vuoti. Quindi sigillare la pellicola o il sacchetto per creare un contenitore ermeticamente chiuso. Questa tecnica è utile per le applicazioni che richiedono una protezione di alto livello dall'umidità e da altri contaminanti.
- Cast cinematografico: La colata di pellicola comporta il versamento o la diffusione di un composto per impregnazione liquido su una superficie piana e la sua polimerizzazione in una pellicola sottile. La pellicola viene quindi tagliata e sagomata per adattarsi alle dimensioni dei componenti elettronici. Questa tecnica è adatta alle applicazioni che desiderano uno strato di incapsulamento flessibile e sottile.
- Applicazione robotica:L'applicazione robotica prevede l'utilizzo di sistemi meccanici per applicare il composto di impregnazione sui componenti elettronici. Bracci robotici o sistemi di erogazione automatizzati assicurano un'applicazione precisa e uniforme. Questa tecnica trova un uso comune negli ambienti di produzione ad alto volume.
Applicazioni comuni del composto per impregnazione PCB
I composti per impregnazione PCB trovano ampio uso in varie applicazioni in cui la protezione, l'isolamento e una maggiore affidabilità dei componenti elettronici sono essenziali. Ecco alcune applicazioni tipiche dei composti per impregnazione PCB:
- Elettronica automobilistica:L'elettronica automobilistica utilizza ampiamente composti per impregnazione PCB, inclusi moduli di controllo, sensori, sistemi di accensione e illuminazione. Proteggono da vibrazioni, umidità e fluttuazioni di temperatura, garantendo la durata e le prestazioni dei componenti elettronici in ambienti automobilistici difficili.
- Elettronica di consumo: L'elettronica di consumo come smartphone, tablet, laptop ed elettrodomestici utilizza composti per impregnazione. Offrono protezione contro sollecitazioni meccaniche, umidità, polvere e urti, prolungando la durata e l'affidabilità dei dispositivi elettronici.
- Equipaggiamento industriale:Apparecchiature industriali come alimentatori, azionamenti per motori, pannelli di controllo e sistemi di automazione utilizzano composti per impregnazione PCB. Proteggono i componenti elettronici sensibili dai rischi ambientali, tra cui l'esposizione chimica, le vibrazioni, le temperature estreme e le interferenze elettriche.
- Sistemi di energia rinnovabile: I composti per impregnazione sono vitali nei sistemi di energia rinnovabile come pannelli solari, turbine eoliche e dispositivi di accumulo di energia. Proteggono l'elettronica sensibile dalle condizioni esterne, comprese le radiazioni UV, l'umidità e le variazioni di temperatura, garantendo la funzionalità e le prestazioni a lungo termine dei sistemi di energia rinnovabile.
- Illuminazione a LED:Le applicazioni di illuminazione a LED utilizzano ampiamente composti per impregnazione PCB, inclusi driver LED, moduli e dispositivi di illuminazione per esterni. Offrono protezione da calore, umidità e vibrazioni, consentendo un funzionamento affidabile e una durata prolungata dei sistemi di illuminazione a LED.
- Aerospazio e Difesa:I composti di impregnazione trovano applicazione nell'elettronica aerospaziale e della difesa, inclusi avionica, sistemi di comunicazione, apparecchiature radar e veicoli militari. Proteggono da temperature estreme, urti, vibrazioni e ingresso di umidità, garantendo il funzionamento affidabile di componenti elettronici critici in ambienti difficili.
- Dispositivi medici: I dispositivi medici come le apparecchiature diagnostiche, i sistemi di monitoraggio dei pazienti e i dispositivi impiantabili utilizzano composti per impregnazione di PCB. Offrono protezione contro l'umidità, le sostanze chimiche e i processi di sterilizzazione, garantendo l'integrità e la longevità dei componenti elettronici sensibili negli ambienti medici.
- Attrezzature marine e offshore:I composti per impregnazione trovano impiego in applicazioni marine e offshore, inclusi sistemi di navigazione, sensori subacquei e apparecchiature di comunicazione. Proteggono dall'ingresso di acqua, dalla corrosione dell'acqua salata e dalle vibrazioni, garantendo prestazioni affidabili e longevità in ambienti marini difficili.
- Telecomunicazioni:Le apparecchiature di telecomunicazione, comprese le stazioni base, gli switch di rete e i dispositivi di comunicazione, utilizzano composti di impregnazione. Offrono protezione contro umidità, polvere e variazioni di temperatura, garantendo il funzionamento ininterrotto dell'infrastruttura di comunicazione critica.
- Moduli e gruppi elettronici:Vari settori utilizzano composti per impregnazione PCB per incapsulare moduli e assiemi elettronici. Questi includono l'elettronica di potenza, i sistemi di controllo, i gruppi PCB e i sottogruppi elettronici. I composti di impregnazione proteggono i fattori ambientali, migliorando l'affidabilità e le prestazioni dell'elettronica incapsulata.
L'importanza dell'uso del composto per impregnazione PCB
Il composto per impregnazione PCB è un materiale cruciale per la protezione dei componenti elettronici e l'affidabilità a lungo termine. L'invasatura o l'incapsulamento di un dispositivo elettronico può salvaguardarlo dall'ambiente, dallo stress termico, dallo shock fisico e dall'esposizione chimica. Ecco alcuni motivi per cui l'utilizzo del composto per impregnazione PCB è essenziale:
- Protezione ambientale:Il composto isolante crea una barriera che protegge i componenti elettronici da umidità, polvere e altri fattori ambientali che possono portare a corrosione o cortocircuiti.
- Durata migliorata: L'impregnazione può aggiungere forza fisica e resistenza agli urti ai componenti elettronici, rendendoli più durevoli e meno soggetti a danni da vibrazioni o urti.
- Maggiore affidabilità: Eliminando le sacche d'aria, i composti per impregnazione possono ridurre il rischio di shock termico e migliorare l'affidabilità complessiva dell'elettronica.
- Gestione termica migliorata: I composti per impregnazione possono migliorare la dissipazione del calore, il che può aiutare a prolungare la vita dei componenti che generano molto calore.
- Rumore ridotto: Il potting può aiutare a ridurre il rumore elettrico, migliorando le prestazioni complessive dell'elettronica.
- Risparmi:Proteggendo i componenti elettronici dai danni, l'invasatura può aiutare a ridurre i costi di riparazione e sostituzione. Inoltre, l'uso di composti per impregnazione può aiutare a ridurre la probabilità di reclami in garanzia e migliorare la soddisfazione del cliente.
L'utilizzo di composti per impregnazione PCB può aiutare a garantire l'affidabilità e le prestazioni a lungo termine dei componenti elettronici, il che è fondamentale in un'ampia gamma di settori e applicazioni.
Conclusione
Il composto per impregnazione PCB è un componente cruciale per garantire la longevità e l'affidabilità dei sistemi elettronici. Fornisce protezione dai fattori ambientali, migliora le prestazioni termiche, migliora la resistenza meccanica e riduce il rumore elettrico. Il tipo di impregnante scelto dipenderà da diversi fattori, tra cui la compatibilità con l'elettronica, il tempo di indurimento, la resistenza alla temperatura e il costo. Selezionando e applicando correttamente il composto di impregnazione adatto, i componenti elettronici possono essere protetti da condizioni difficili, aumentandone in ultima analisi la durata e l'affidabilità.