Adesivo MEMS
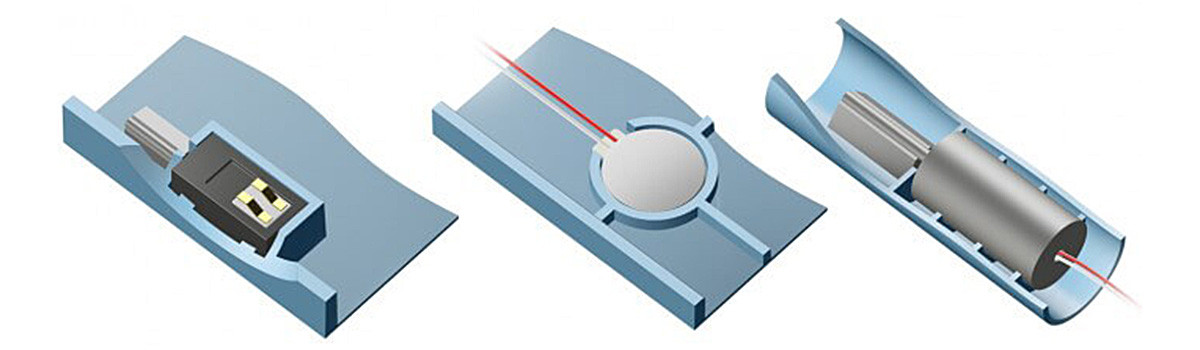
I sistemi microelettromeccanici (MEMS) hanno rivoluzionato vari settori consentendo lo sviluppo di dispositivi più piccoli ed efficienti. Un componente fondamentale che ha contribuito al successo della tecnologia MEMS è l'adesivo MEMS. L'adesivo MEMS svolge un ruolo cruciale nell'incollaggio e nel fissaggio di microstrutture e componenti nei dispositivi MEMS, garantendone la stabilità, l'affidabilità e le prestazioni. In questo articolo, esploriamo il significato dell'adesivo MEMS e delle sue applicazioni, evidenziando i sottotitoli chiave che fanno luce sui suoi vari aspetti.
Comprensione dell'adesivo MEMS: fondamenti e composizione
I sistemi microelettromeccanici (MEMS) hanno rivoluzionato vari settori consentendo la produzione di piccoli dispositivi con potenti capacità. L'adesivo MEMS svolge un ruolo fondamentale nell'assemblaggio e nel confezionamento di questi dispositivi miniaturizzati. Comprendere i fondamenti e la composizione dell'adesivo MEMS è essenziale per ottenere un legame affidabile e robusto nella fabbricazione di MEMS. Questo articolo approfondisce l'adesivo MEMS per far luce sulla sua importanza e considerazioni critiche.
I fondamenti dell'adesivo MEMS
L'adesivo MEMS è specificamente progettato per facilitare legami robusti e durevoli tra i vari componenti dei microdispositivi. Questi adesivi possiedono proprietà uniche per soddisfare i severi requisiti delle applicazioni MEMS. Una delle proprietà fondamentali dell'adesivo MEMS è la sua capacità di resistere a condizioni ambientali difficili, comprese le fluttuazioni di temperatura, l'umidità e l'esposizione chimica. Inoltre, gli adesivi MEMS dovrebbero presentare eccellenti proprietà meccaniche, come elevata forza di adesione, basso ritiro e scorrimento minimo, per garantire affidabilità a lungo termine.
Composizione dell'adesivo MEMS
La composizione dell'adesivo MEMS è accuratamente formulata per soddisfare le esigenze specifiche dell'imballaggio MEMS. In genere, gli adesivi MEMS sono costituiti da diversi componenti chiave, ciascuno con uno scopo particolare:
Matrice polimerica: La matrice polimerica costituisce la maggior parte dell'adesivo e fornisce la necessaria integrità strutturale. I polimeri comuni utilizzati negli adesivi MEMS includono resina epossidica, poliimmide e acrilico. Questi polimeri offrono eccellenti proprietà di adesione, resistenza chimica e stabilità meccanica.
Materiali di riempimento: Per migliorare le proprietà adesive, i riempitivi sono incorporati nella matrice polimerica. Riempitivi come silice, allumina o particelle metalliche possono migliorare la conducibilità termica, la conduttività elettrica e la stabilità dimensionale dell'adesivo.
Agenti indurenti: Gli adesivi MEMS richiedono spesso un processo di polimerizzazione per raggiungere le loro proprietà finali. Gli agenti indurenti, come ammine o anidridi, avviano reazioni di reticolazione nella matrice polimerica, determinando un forte legame adesivo.
Promotori di adesione: Alcuni adesivi MEMS possono includere promotori di adesione per migliorare il legame tra l'adesivo e i substrati. Questi promotori sono tipicamente composti a base di silano che migliorano l'adesione a vari materiali, come metalli, ceramiche o polimeri.
Considerazioni per la selezione dell'adesivo MEMS
L'adesivo MEMS adatto garantisce prestazioni e affidabilità a lungo termine dei dispositivi MEMS. Quando si sceglie un'obbligazione, è necessario considerare diversi fattori:
Compatibilità: L'adesivo deve essere compatibile con i materiali da incollare, nonché con l'ambiente operativo del dispositivo MEMS.
Compatibilità di processo: L'adesivo deve essere compatibile con i processi di produzione coinvolti, come i metodi di erogazione, polimerizzazione e incollaggio.
Proprietà termiche e meccaniche: L'adesivo dovrebbe presentare un'adeguata stabilità termica, un basso coefficiente di dilatazione termica (CTE) ed eccellenti proprietà meccaniche per resistere alle sollecitazioni incontrate durante il funzionamento del dispositivo.
Forza di adesione: L'adesivo deve fornire una forza sufficiente per garantire un legame robusto tra i componenti, prevenendo la delaminazione o il cedimento.
Tipi di adesivi MEMS: una panoramica
I dispositivi MEMS (Microelectromechanical Systems) sono dispositivi miniaturizzati che combinano componenti meccanici ed elettrici su un singolo chip. Questi dispositivi richiedono spesso tecniche di incollaggio precise e affidabili per garantire la corretta funzionalità. Gli adesivi MEMS svolgono un ruolo cruciale nell'assemblaggio e nel confezionamento di questi dispositivi. Forniscono un legame solido e durevole tra i diversi componenti, soddisfacendo al tempo stesso i requisiti unici della tecnologia MEMS. Ecco una panoramica di alcuni tipi comuni di adesivi MEMS:
- Adesivi epossidici: gli adesivi a base epossidica sono ampiamente utilizzati nelle applicazioni MEMS. Offrono un'eccellente forza di adesione e una buona resistenza chimica. Gli adesivi epossidici sono tipicamente termoindurenti e richiedono calore o un agente indurente. Forniscono un'elevata integrità strutturale e possono resistere a condizioni operative difficili.
- Adesivi siliconici: gli adesivi siliconici sono noti per la loro flessibilità, resistenza alle alte temperature ed eccellenti proprietà di isolamento elettrico. Sono particolarmente adatti per dispositivi MEMS sottoposti a cicli termici o che richiedono uno smorzamento delle vibrazioni. Gli adesivi siliconici offrono una buona adesione a vari substrati e possono mantenere le loro proprietà in un ampio intervallo di temperature.
- Adesivi acrilici: gli adesivi a base acrilica sono popolari per i tempi di polimerizzazione rapidi, la buona forza di adesione e la trasparenza ottica. Sono spesso utilizzati in applicazioni che richiedono chiarezza visiva, come i dispositivi MEMS ottici. Gli adesivi acrilici forniscono un legame affidabile e possono aderire a diversi substrati, inclusi vetro, metalli e plastica.
- Adesivi a polimerizzazione UV: gli adesivi a polimerizzazione UV sono progettati per polimerizzare rapidamente se esposti alla luce ultravioletta (UV). Offrono tempi di polimerizzazione rapidi, che possono migliorare l'efficienza produttiva. Gli adesivi UV sono comunemente usati nelle applicazioni MEMS dove è necessario un allineamento preciso perché rimangono liquidi finché non vengono esposti alla luce UV. Forniscono un'adesione eccellente e sono adatti per l'incollaggio di componenti delicati.
- Adesivi conduttivi anisotropi (ACA): gli adesivi ACA sono progettati per l'incollaggio di componenti microelettronici che richiedono supporto meccanico e conduttività elettrica. Sono costituiti da particelle conduttive disperse all'interno di una matrice adesiva non conduttiva. Gli adesivi ACA forniscono connessioni elettriche affidabili pur mantenendo la stabilità meccanica, rendendoli ideali per dispositivi MEMS che coinvolgono interconnessioni elettriche.
- Adesivi sensibili alla pressione (PSA): gli adesivi PSA sono caratterizzati dalla loro capacità di formare un legame all'applicazione di una leggera pressione. Non richiedono calore o agenti indurenti per l'incollaggio. Gli adesivi PSA offrono facilità d'uso e possono essere riposizionati se necessario. Sono comunemente usati nei dispositivi MEMS che richiedono un legame temporaneo o dove si desidera una separazione non distruttiva.
Gli adesivi MEMS sono disponibili in varie forme, inclusi adesivi liquidi, pellicole, paste e nastri, consentendo flessibilità nella scelta dell'opzione più adatta per specifici processi di assemblaggio e confezionamento. La scelta di un particolare adesivo dipende da fattori quali i materiali del substrato, le condizioni ambientali, i requisiti termici e considerazioni sulla conducibilità elettrica.
È essenziale considerare la compatibilità dell'adesivo con i materiali MEMS e i requisiti e i vincoli di elaborazione per garantire l'integrazione riuscita e l'affidabilità a lungo termine dei dispositivi MEMS. I produttori spesso eseguono numerosi test e processi di qualificazione per convalidare le prestazioni e l'idoneità dell'adesivo per specifiche applicazioni MEMS.
Tecniche di incollaggio: energia superficiale e adesione
L'energia superficiale e l'adesione sono concetti fondamentali nelle tecniche di incollaggio e la comprensione di questi concetti è fondamentale per legami solidi e affidabili tra i materiali. Ecco una panoramica dell'energia superficiale e dell'adesione nell'incollaggio:
Energia superficiale: L'energia superficiale è una misura dell'energia richiesta per aumentare l'area superficiale di un materiale. È una proprietà che determina come un materiale interagisce con altre sostanze. L'energia superficiale deriva dalle forze coesive tra atomi o molecole sulla superficie di un materiale. Può essere pensato come la tendenza di un materiale a ridurre al minimo la sua area superficiale e formare una forma con la minor quantità di energia superficiale.
Materiali diversi mostrano diversi livelli di energia superficiale. Alcuni materiali hanno un'elevata energia superficiale, il che significa che hanno una forte affinità per altre sostanze e formano facilmente legami. Esempi di materiali ad alta energia superficiale includono metalli e materiali polari come il vetro o alcune plastiche. D'altra parte, alcuni materiali hanno una bassa energia superficiale, che li rende meno inclini a legarsi con altre sostanze. Esempi di materiali a bassa energia superficiale includono polimeri specifici, come polietilene o polipropilene.
Adesione: L'adesione è il fenomeno di attrazione molecolare tra materiali diversi che li fa aderire quando vengono a contatto. La forza tiene insieme due superfici e l'adesione è essenziale per ottenere legami solidi e durevoli nelle tecniche di incollaggio.
L'adesione può essere classificata in diversi tipi in base ai meccanismi coinvolti:
- Adesione meccanica: l'adesione meccanica si basa sull'incastro o sull'incastro fisico tra le superfici. Si verifica quando due materiali hanno superfici ruvide o irregolari che si incastrano tra loro, creando un solido legame. L'adesione meccanica è spesso potenziata da adesivi o tecniche che aumentano l'area di contatto tra i caratteri, come i nastri adesivi ad alta conformabilità.
- Adesione chimica: L'adesione chimica si verifica quando c'è un'interazione chimica tra le superfici di due materiali. Implica la formazione di legami chimici o forze attrattive all'interfaccia. L'adesione chimica è comunemente ottenuta attraverso adesivi che reagiscono chimicamente con le superfici o mediante trattamenti superficiali che promuovono l'adesione chimica, come il trattamento al plasma o i primer.
- Adesione elettrostatica: L'adesione elettrostatica si basa sull'attrazione tra cariche positive e negative su diverse superfici. Si verifica quando un personaggio si carica elettricamente, attirando la superficie caricata in modo opposto. L'adesione elettrostatica è comunemente utilizzata nelle tecniche di fissaggio o incollaggio elettrostatico che coinvolgono particelle cariche.
- Adesione molecolare: L'adesione molecolare coinvolge le forze di van der Waals o le interazioni dipolo-dipolo tra le molecole all'interfaccia di due materiali. Queste forze intermolecolari possono contribuire all'adesione tra le superfici. Il legame molecolare è particolarmente rilevante per i materiali con bassa energia superficiale.
Per ottenere un'adesione adeguata, è essenziale considerare l'energia superficiale dei materiali da incollare. I materiali con energie superficiali simili tendono a mostrare una migliore adesione, tuttavia, quando si uniscono materiali con energie superficiali significativamente diverse, possono essere necessari trattamenti superficiali o promotori di adesione per migliorare l'adesione.
Vantaggi dell'adesivo MEMS nella miniaturizzazione
I sistemi microelettromeccanici (MEMS) hanno rivoluzionato il campo della miniaturizzazione, consentendo lo sviluppo di dispositivi compatti e sofisticati in vari settori. L'adesivo MEMS svolge un ruolo cruciale nell'integrazione e nell'assemblaggio di successo dei dispositivi MEMS, offrendo numerosi vantaggi che contribuiscono alla loro miniaturizzazione. In questa risposta, illustrerò in 450 parole i principali vantaggi dell'adesivo MEMS nella miniaturizzazione.
- Incollaggio preciso: l'adesivo MEMS offre capacità di incollaggio precise e affidabili, consentendo il fissaggio sicuro di microcomponenti con elevata precisione. Con i dispositivi miniaturizzati, in cui la dimensione dei singoli componenti è spesso su scala micron o submicron, l'adesivo deve essere in grado di formare legami forti e coerenti tra strutture delicate. Le formulazioni adesive MEMS sono progettate per fornire eccellenti proprietà di adesione, garantendo l'integrità strutturale e la funzionalità dei dispositivi MEMS assemblati.
- Basso degassamento: i dispositivi miniaturizzati spesso operano in ambienti ad alte prestazioni o sensibili, come applicazioni aerospaziali, automobilistiche o mediche. In tali casi, l'adesivo utilizzato deve presentare un degassamento minimo per prevenire la contaminazione, il degrado o l'interferenza con i componenti o le superfici circostanti. Gli adesivi MEMS sono formulati per avere caratteristiche di basso degassamento, riducendo al minimo il rilascio di composti volatili e riducendo il rischio di effetti negativi sulle prestazioni del dispositivo.
- Stabilità termica: i dispositivi MEMS spesso incontrano condizioni di temperatura variabili durante il loro funzionamento. I materiali adesivi MEMS sono progettati per esibire un'eccellente stabilità termica, resistere a temperature estreme e cicli termici senza compromettere la forza di adesione. Questa caratteristica è essenziale nei sistemi miniaturizzati in cui lo spazio è limitato e l'adesivo deve sopportare ambienti termici impegnativi senza degrado.
- Flessibilità meccanica: la capacità di resistere a sollecitazioni meccaniche e vibrazioni è fondamentale per i dispositivi miniaturizzati che possono essere soggetti a forze esterne. Le formulazioni adesive MEMS offrono flessibilità meccanica, consentendo loro di assorbire e dissipare lo stress, riducendo la probabilità di danni strutturali o cedimenti. Questa flessibilità garantisce l'affidabilità e la durata a lungo termine dei dispositivi MEMS miniaturizzati, anche in ambienti dinamici.
- Isolamento elettrico: molti dispositivi MEMS incorporano componenti elettrici, come sensori, attuatori o interconnessioni. I materiali adesivi MEMS possiedono eccellenti proprietà di isolamento elettrico, prevenendo efficacemente i cortocircuiti o le interferenze elettriche tra i diversi componenti. Questa caratteristica è particolarmente importante nei dispositivi miniaturizzati, dove la vicinanza di percorsi elettrici può aumentare il rischio di accoppiamenti elettrici indesiderati.
- Compatibilità chimica: le formulazioni adesive MEMS sono progettate per essere chimicamente compatibili con un'ampia gamma di materiali comunemente usati nella fabbricazione di MEMS, come silicio, polimeri, metalli e ceramica. Questa compatibilità consente l'integrazione versatile di diversi componenti, consentendo la miniaturizzazione di complessi sistemi MEMS. Inoltre, la resistenza chimica dell'adesivo garantisce la stabilità e la longevità delle interfacce incollate, anche se esposte ad ambienti operativi difficili o sostanze corrosive.
- Compatibilità del processo: i materiali adesivi MEMS sono sviluppati per essere compatibili con vari processi di assemblaggio, tra cui l'incollaggio di flip-chip, l'imballaggio a livello di wafer e l'incapsulamento. Questa compatibilità facilita processi di produzione semplificati per dispositivi miniaturizzati, migliorando la produttività e la scalabilità. Le formulazioni adesive MEMS possono essere personalizzate per soddisfare requisiti di lavorazione specifici, consentendo un'integrazione perfetta nelle tecniche di fabbricazione esistenti.
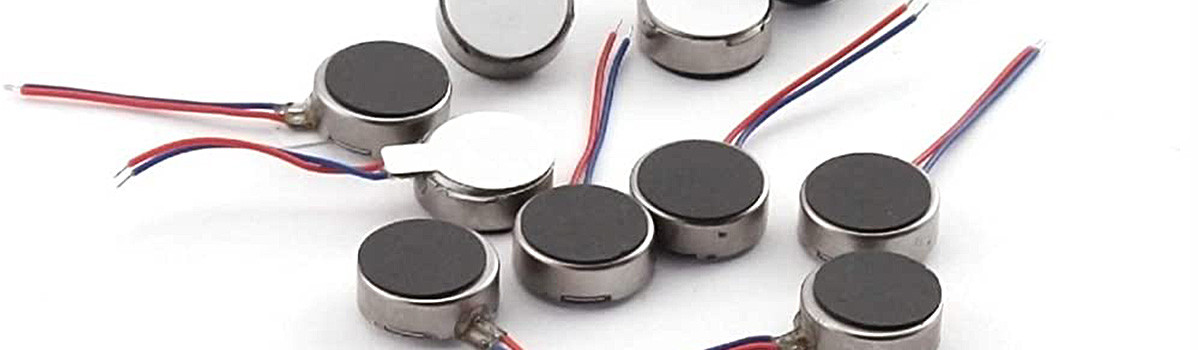
Adesivo MEMS per applicazioni con sensori
I sensori MEMS (Micro-Electro-Mechanical Systems) sono ampiamente utilizzati in varie applicazioni come i settori automobilistico, elettronico di consumo, sanitario e industriale. Questi sensori sono in genere dispositivi miniaturizzati che combinano componenti elettrici e meccanici per misurare e rilevare fenomeni fisici come pressione, accelerazione, temperatura e umidità.
Un aspetto critico della fabbricazione e dell'integrazione dei sensori MEMS è il materiale adesivo utilizzato per unire il sensore al substrato target. L'adesivo garantisce prestazioni del sensore affidabili e robuste, fornendo stabilità meccanica, connettività elettrica e protezione dai fattori ambientali.
Quando si tratta di selezionare un adesivo per le applicazioni dei sensori MEMS, è necessario considerare diversi fattori:
Compatibilità: il materiale adesivo deve essere compatibile con il sensore e il substrato per garantire una corretta adesione. Diversi sensori MEMS possono avere materiali distinti, come silicio, polimeri o metalli, e l'adesivo dovrebbe aderire efficacemente a queste superfici.
Proprietà meccaniche: l'adesivo deve possedere proprietà meccaniche adeguate per sopportare le sollecitazioni incontrate durante il funzionamento del sensore MEMS. Dovrebbe mostrare una buona resistenza al taglio, resistenza alla trazione e flessibilità per resistere all'espansione termica, alle vibrazioni e agli urti meccanici.
Stabilità termica: i sensori MEMS possono essere esposti a temperature variabili durante il funzionamento. Il materiale adesivo deve avere un'elevata temperatura di transizione vetrosa (Tg) e mantenere la sua forza adesiva in un ampio intervallo di temperature.
Conduttività elettrica: in alcune applicazioni dei sensori MEMS, è necessaria la connettività elettrica tra il sensore e il substrato. Un adesivo con buona conduttività elettrica o bassa resistenza può garantire una trasmissione affidabile del segnale e ridurre al minimo le perdite elettriche.
Resistenza chimica: l'adesivo deve resistere all'umidità, agli agenti chimici e ad altri fattori ambientali per fornire stabilità a lungo termine e proteggere i componenti del sensore dal degrado.
Gli adesivi a base di silicone sono comunemente usati nelle applicazioni dei sensori MEMS grazie alla loro eccellente compatibilità con vari materiali, al basso degassamento e alla resistenza ai fattori ambientali. Offrono una buona adesione ai dispositivi MEMS a base di silicio e forniscono isolamento elettrico se necessario.
Inoltre, gli adesivi a base epossidica sono ampiamente utilizzati per la loro elevata resistenza e l'eccellente stabilità termica. Offrono un solido legame a vari substrati e possono resistere a diverse temperature.
In alcuni casi, gli adesivi conduttivi vengono utilizzati quando è richiesta la connettività elettrica. Questi adesivi sono formulati con riempitivi conduttivi come argento o carbonio, che consentono loro di fornire sia legame meccanico che conduzione elettrica.
È essenziale considerare i requisiti specifici dell'applicazione del sensore MEMS e consultare produttori o fornitori di adesivi per selezionare l'adesivo più adatto. Devono essere considerati anche fattori come il tempo di indurimento, la viscosità e il metodo di applicazione.
Adesivo MEMS nei dispositivi medici: progressi e sfide
La tecnologia MEMS (Micro-Electro-Mechanical Systems) ha applicazioni significative nei dispositivi medici, consentendo progressi nella diagnostica, nel monitoraggio, nella somministrazione di farmaci e nei dispositivi impiantabili. I materiali adesivi utilizzati nei dispositivi medici basati su MEMS svolgono un ruolo cruciale nel garantire l'affidabilità, la biocompatibilità e le prestazioni a lungo termine di questi dispositivi. Esploriamo i progressi e le sfide degli adesivi MEMS nei dispositivi medici.
Avanzamenti:
- Biocompatibilità: i materiali adesivi utilizzati nei dispositivi medici devono essere biocompatibili per garantire che non provochino reazioni avverse o causino danni al paziente. Sono stati compiuti progressi significativi nello sviluppo di materiali adesivi con una migliore biocompatibilità, consentendo un'integrazione più sicura e affidabile dei sensori MEMS nei dispositivi medici.
- Miniaturizzazione: la tecnologia MEMS consente la miniaturizzazione dei dispositivi medici, rendendoli più portatili, minimamente invasivi e in grado di monitorare in tempo reale. I materiali adesivi progettati per le applicazioni MEMS sono avanzati per soddisfare la tendenza alla miniaturizzazione, fornendo un legame robusto e affidabile in spazi ristretti.
- Substrati flessibili: i dispositivi medici flessibili ed estensibili hanno acquisito importanza grazie alla loro capacità di conformarsi alle superfici curve e migliorare il comfort del paziente. Sono stati sviluppati materiali adesivi con elevata flessibilità ed estensibilità per consentire un legame sicuro tra sensori MEMS e substrati flessibili, ampliando le possibilità di dispositivi medici indossabili e impiantabili.
- Biodegradabilità: in applicazioni mediche specifiche in cui vengono utilizzati dispositivi temporanei, come sistemi di somministrazione di farmaci o scaffold di tessuti, gli adesivi biodegradabili hanno guadagnato attenzione. Questi adesivi possono degradarsi gradualmente nel tempo, eliminando la necessità di procedure di rimozione o espianto del dispositivo.
sfide:
- Test di biocompatibilità: garantire la biocompatibilità dei materiali adesivi utilizzati nei dispositivi medici basati su MEMS è un processo complesso che richiede test approfonditi e conformità normativa. I produttori di adesivi affrontano sfide nel soddisfare i severi standard stabiliti dagli organismi di regolamentazione per garantire la sicurezza dei pazienti.
- Affidabilità a lungo termine: i dispositivi medici spesso richiedono l'impianto a lungo termine o l'uso continuo. I materiali adesivi devono esibire un legame affidabile e mantenere le loro proprietà meccaniche e adesive per periodi prolungati, considerando le condizioni fisiologiche e i potenziali fattori di degrado presenti nel corpo.
- Stabilità chimica e termica: i dispositivi medici basati su MEMS possono incontrare ambienti chimici difficili, fluidi corporei e fluttuazioni di temperatura durante il funzionamento. Gli adesivi devono possedere un'eccellente resistenza chimica e stabilità termica per mantenere la loro integrità e forza di adesione.
- Compatibilità con la sterilizzazione: i dispositivi medici devono essere sottoposti a processi di sterilizzazione per eliminare potenziali agenti patogeni e garantire la sicurezza del paziente. I materiali adesivi devono essere compatibili con i metodi di sterilizzazione standard come la sterilizzazione in autoclave, la sterilizzazione con ossido di etilene (EtO) o l'irradiazione gamma senza comprometterne le proprietà adesive.
Adesivo MEMS per microfluidica: miglioramento del controllo dei fluidi
La microfluidica, la scienza e la tecnologia di manipolazione di piccoli volumi di fluidi, ha guadagnato un'attenzione significativa in vari campi, tra cui la ricerca biomedica, la diagnostica, la somministrazione di farmaci e l'analisi chimica. La tecnologia MEMS (Micro-Electro-Mechanical Systems) consente un controllo preciso dei fluidi nei dispositivi microfluidici. I materiali adesivi utilizzati in questi dispositivi sono fondamentali per ottenere connessioni fluidiche affidabili e mantenere il controllo del fluido. Esploriamo come gli adesivi MEMS migliorano la potenza fluida nella microfluidica e i progressi associati.
- Sigillatura senza perdite: i dispositivi microfluidici spesso richiedono più canali fluidici, valvole e serbatoi. I materiali adesivi con eccellenti proprietà di tenuta sono cruciali per connessioni senza perdite, prevenendo la contaminazione incrociata e garantendo un controllo preciso del fluido. Gli adesivi MEMS forniscono una tenuta robusta, consentendo il funzionamento affidabile dei dispositivi microfluidici.
- Incollaggio di materiali dissimili: i dispositivi microfluidici possono essere costituiti da vari materiali come vetro, silicio, polimeri e metalli. Gli adesivi MEMS sono formulati per avere una buona adesione a diversi materiali di substrato, consentendo l'incollaggio di materiali diversi. Questa capacità consente l'integrazione di diversi componenti e facilita la fabbricazione di complesse strutture microfluidiche.
- Elevata compatibilità chimica: gli adesivi MEMS utilizzati nella microfluidica devono presentare un'elevata compatibilità chimica con i fluidi e i reagenti manipolati. Devono resistere alla degradazione chimica e rimanere stabili, garantendo l'integrità dei canali fluidici e prevenendo la contaminazione. Gli adesivi MEMS avanzati sono progettati per resistere a varie sostanze chimiche comunemente utilizzate nelle applicazioni microfluidiche.
- Caratteristiche di flusso ottimali: nei dispositivi microfluidici, il controllo preciso del flusso del fluido e la riduzione al minimo delle interruzioni del flusso sono essenziali. Gli adesivi MEMS possono essere personalizzati per avere proprietà superficiali lisce e uniformi, riducendo la presenza di bolle, goccioline o modelli di flusso irregolari. Questa ottimizzazione migliora il controllo dei fluidi e migliora la precisione delle operazioni microfluidiche.
- Replica di caratteristiche su microscala: i dispositivi microfluidici richiedono spesso la replica di complesse caratteristiche su microscala, come canali, camere e valvole. Gli adesivi MEMS con bassa viscosità e proprietà bagnanti elevate possono riempire efficacemente le caratteristiche su microscala, garantendo la riproduzione accurata di strutture fluidiche complesse e mantenendo il controllo del fluido su piccola scala.
- Resistenza alla temperatura e alla pressione: i dispositivi microfluidici possono subire variazioni di temperatura e fluttuazioni di pressione durante il funzionamento. Gli adesivi MEMS progettati per la microfluidica offrono stabilità alle alte temperature e possono resistere alle pressioni sperimentate all'interno del sistema microfluidico, garantendo la durata e l'affidabilità del controllo del fluido.
- Integrazione con componenti funzionali: i dispositivi microfluidici spesso incorporano sensori, elettrodi e attuatori aggiuntivi. Gli adesivi MEMS possono facilitare l'integrazione di questi elementi funzionali, fornendo connessioni sicure e affidabili, consentendo funzionalità multimodali e migliorando le prestazioni complessive dei sistemi microfluidici.
I progressi nella tecnologia adesiva MEMS continuano a migliorare la precisione, l'affidabilità e la versatilità del controllo dei fluidi nei dispositivi microfluidici. La ricerca in corso si concentra sullo sviluppo di adesivi con proprietà su misura, come bioadesivi per microfluidica biocompatibile, adesivi sensibili agli stimoli per potenza fluida dinamica e adesivi autorigeneranti per una maggiore longevità del dispositivo. Questi progressi contribuiscono a migliorare la microfluidica e la sua vasta gamma di applicazioni.
Gestione termica e adesivo MEMS: gestione della dissipazione del calore
La gestione termica è fondamentale per i dispositivi MEMS (Micro-Electro-Mechanical Systems), poiché spesso generano calore durante il funzionamento. Un'efficiente dissipazione del calore è essenziale per mantenere prestazioni ottimali, prevenire il surriscaldamento e garantire l'affidabilità e la longevità dei dispositivi MEMS. Gli adesivi MEMS sono fondamentali per affrontare le sfide di dissipazione del calore fornendo soluzioni di gestione termica efficaci. Esploriamo come gli adesivi MEMS possono aiutare ad affrontare la dissipazione del calore nei dispositivi MEMS.
- Conduttività termica: gli adesivi MEMS con elevata conduttività termica possono trasferire in modo efficiente il calore dai componenti che generano calore ai dissipatori di calore o ad altri meccanismi di raffreddamento. Questi adesivi agiscono come efficaci ponti termici, riducendo la resistenza termica e migliorando la dissipazione del calore.
- Incollaggio ai dissipatori di calore: i dissipatori di calore sono comunemente usati nei dispositivi MEMS per dissipare il calore. Gli adesivi MEMS forniscono un legame affidabile tra i componenti che generano calore e i dissipatori di calore, garantendo un efficiente trasferimento di calore al dissipatore. Il materiale adesivo deve avere buone proprietà di adesione per resistere ai cicli termici e mantenere un forte legame a temperature elevate.
- Bassa resistenza termica: gli adesivi MEMS devono possedere una bassa resistenza termica per ridurre al minimo l'impedenza termica tra la fonte di calore e l'interfaccia di raffreddamento. La bassa resistenza termica consente un efficiente trasferimento del calore e migliora la gestione termica nei dispositivi MEMS.
- Stabilità termica: i dispositivi MEMS possono funzionare a temperature elevate o subire fluttuazioni di temperatura. Il materiale adesivo deve presentare un'eccellente stabilità termica per resistere a queste condizioni senza degradare o perdere le sue proprietà adesive. Questa stabilità garantisce prestazioni costanti di dissipazione del calore per tutta la durata del dispositivo MEMS.
- Proprietà dielettriche: in alcuni casi, i dispositivi MEMS possono richiedere l'isolamento elettrico tra i componenti che generano calore e i dissipatori di calore. Gli adesivi MEMS con proprietà dielettriche appropriate possono fornire conduttività termica e isolamento elettrico, consentendo un'efficace dissipazione del calore mantenendo l'integrità elettrica.
- Capacità di riempimento degli spazi: gli adesivi MEMS con una buona capacità di riempimento degli spazi possono eliminare gli spazi vuoti o i vuoti tra i componenti che generano calore e i dissipatori di calore, migliorando il contatto termico e riducendo al minimo la resistenza termica. Questa capacità garantisce un trasferimento e una dissipazione del calore più efficienti all'interno del dispositivo MEMS.
- Compatibilità con i materiali MEMS: i dispositivi MEMS incorporano silicio, polimeri, metalli e ceramica. Gli adesivi MEMS devono essere compatibili con questi materiali per garantire una corretta adesione e gestione termica. La compatibilità previene anche le interazioni chimiche avverse o il degrado che influisce sulle prestazioni di dissipazione del calore.
I progressi nella tecnologia adesiva MEMS si concentrano sullo sviluppo di materiali con una migliore conduttività termica, una migliore stabilità termica e proprietà su misura per soddisfare specifici requisiti di gestione termica. I ricercatori stanno esplorando nuove formulazioni adesive, come gli adesivi nanocompositi contenenti riempitivi termicamente conduttivi, per migliorare ulteriormente le capacità di dissipazione del calore.
Adesivo MEMS nei sistemi ottici: garantire un allineamento preciso
Nei sistemi ottici, l'allineamento preciso è fondamentale per ottenere prestazioni e funzionalità ottimali. Un componente chiave che svolge un ruolo fondamentale nel garantire un allineamento preciso è l'adesivo dei sistemi microelettromeccanici (MEMS). L'adesivo MEMS si riferisce al materiale adesivo utilizzato per fissare dispositivi MEMS, come specchi, lenti o microattuatori, ai rispettivi substrati nei sistemi ottici. Consente il posizionamento e l'allineamento accurati di questi dispositivi, migliorando così le prestazioni complessive e l'affidabilità del sistema visivo.
Quando si tratta di garantire un allineamento preciso nei sistemi ottici, è necessario considerare diversi fattori nella scelta e nell'applicazione degli adesivi MEMS. In primo luogo, il materiale adesivo dovrebbe possedere eccellenti proprietà ottiche, come un basso indice di rifrazione e una diffusione o un assorbimento della luce minimi. Queste caratteristiche aiutano a ridurre al minimo i riflessi o le distorsioni indesiderate, che possono degradare le prestazioni del sistema ottico.
Inoltre, l'adesivo MEMS dovrebbe presentare un'elevata stabilità meccanica e durata. I sistemi ottici sono spesso soggetti a varie condizioni ambientali, tra cui fluttuazioni di temperatura, variazioni di umidità e sollecitazioni meccaniche. Il materiale adesivo deve resistere a queste condizioni senza compromettere l'allineamento dei componenti ottici. Inoltre, dovrebbe avere un basso coefficiente di dilatazione termica per ridurre al minimo l'impatto dei cicli termici sulla stabilità dell'allineamento.
Inoltre, l'adesivo dovrebbe offrire un controllo preciso sul processo di incollaggio. Ciò include bassa viscosità, buone proprietà bagnanti e tempo di polimerizzazione o indurimento controllato. La bassa densità garantisce una copertura adesiva uniforme e affidabile tra il dispositivo MEMS e il substrato, facilitando un migliore contatto e allineamento. Buone proprietà bagnanti consentono una corretta adesione e prevengono la formazione di vuoti o bolle d'aria. Il tempo di polimerizzazione controllato consente una regolazione e un allineamento sufficienti prima che l'adesivo faccia presa.
In termini di applicazione, è necessario prestare particolare attenzione alle tecniche di erogazione e manipolazione dell'adesivo. Gli adesivi MEMS vengono generalmente applicati in piccole quantità con elevata precisione. È possibile utilizzare sistemi di erogazione automatizzati o strumenti specializzati per garantire un'applicazione accurata e ripetibile. Tecniche di manipolazione adeguate, come l'utilizzo di camere bianche o ambienti controllati, aiutano a prevenire la contaminazione che potrebbe influire negativamente sull'allineamento e sulle prestazioni ottiche.
Per convalidare e garantire l'allineamento preciso dei componenti ottici utilizzando adesivi MEMS, sono essenziali test approfonditi e caratterizzazione. Tecniche come l'interferometria, la microscopia ottica o la profilometria possono essere impiegate per misurare l'accuratezza dell'allineamento e valutare le prestazioni del sistema visivo. Questi test aiutano a identificare deviazioni o disallineamenti, consentendo regolazioni o perfezionamenti per ottenere l'allineamento desiderato.
Adesivo MEMS nell'elettronica di consumo: consentire design compatti
Gli adesivi MEMS sono diventati sempre più importanti nell'elettronica di consumo, consentendo lo sviluppo di design compatti e sottili per vari dispositivi. Questi adesivi sono fondamentali per l'incollaggio e il fissaggio di componenti di sistemi microelettromeccanici (MEMS) all'interno di dispositivi elettronici di consumo, come smartphone, tablet, dispositivi indossabili ed elettrodomestici intelligenti. Garantendo un fissaggio affidabile e un allineamento preciso, gli adesivi MEMS contribuiscono alla miniaturizzazione di questi dispositivi e al miglioramento delle prestazioni.
Un vantaggio chiave degli adesivi MEMS nell'elettronica di consumo è la loro capacità di fornire un legame robusto e duraturo occupando uno spazio minimo. Man mano che i dispositivi elettronici di consumo diventano più piccoli e più portatili, i materiali adesivi devono offrire un'elevata forza di adesione in uno strato sottile. Ciò consente design compatti senza compromettere l'integrità strutturale. Gli adesivi MEMS sono progettati per fornire un'adesione eccellente a vari substrati comunemente usati nell'elettronica di consumo, inclusi metalli, vetro e plastica.
Oltre alle loro capacità di incollaggio, gli adesivi MEMS offrono vantaggi in termini di gestione termica. I dispositivi elettronici di consumo generano calore durante il funzionamento e un'efficiente dissipazione del calore è fondamentale per prevenire il degrado delle prestazioni o il guasto dei componenti. Gli adesivi MEMS ad alta conduttività termica possono collegare componenti che generano calore, come processori o amplificatori di potenza, a dissipatori di calore o altre strutture di raffreddamento. Questo aiuta a dissipare il calore in modo efficace, migliorando la gestione termica complessiva del dispositivo.
Inoltre, gli adesivi MEMS contribuiscono all'affidabilità e alla durata complessive dei dispositivi elettronici di consumo. Questi adesivi resistono a fattori ambientali come variazioni di temperatura, umidità e sollecitazioni meccaniche e possono resistere alle condizioni rigorose incontrate durante l'uso quotidiano, comprese cadute, vibrazioni e cicli termici. Fornendo un legame robusto, gli adesivi MEMS aiutano a garantire la longevità e l'affidabilità dell'elettronica di consumo.
Un altro vantaggio degli adesivi MEMS è la loro compatibilità con i processi di produzione automatizzati. Poiché i dispositivi elettronici di consumo sono prodotti in serie, i metodi di assemblaggio efficienti e affidabili sono fondamentali. Gli adesivi MEMS possono essere erogati con precisione utilizzando sistemi di erogazione meccanici, consentendo un assemblaggio preciso e ad alta velocità. I materiali adesivi sono progettati per avere caratteristiche di viscosità e indurimento adeguate per la manipolazione automatizzata, consentendo processi di produzione semplificati.
Inoltre, la versatilità degli adesivi MEMS ne consente l'uso in un'ampia gamma di applicazioni di elettronica di consumo. Che si tratti di collegare sensori, microfoni, altoparlanti o altri componenti MEMS, questi adesivi offrono la flessibilità necessaria per adattarsi a vari design e configurazioni di dispositivi. Possono essere applicati a diversi materiali di supporto e finiture superficiali, fornendo compatibilità con vari prodotti elettronici di consumo.
Adesivo MEMS per applicazioni aerospaziali e di difesa
La tecnologia adesiva MEMS si è dimostrata estremamente preziosa nelle applicazioni aerospaziali e della difesa, dove la precisione, l'affidabilità e le prestazioni sono fondamentali. Le proprietà uniche degli adesivi MEMS li rendono adatti per l'incollaggio e il fissaggio di componenti di sistemi microelettromeccanici (MEMS) nei sistemi aerospaziali e di difesa, che vanno dai satelliti e aerei alle apparecchiature e sensori militari.
Un aspetto critico delle applicazioni aerospaziali e della difesa è la capacità degli adesivi di resistere a condizioni ambientali estreme. Gli adesivi MEMS sono progettati per offrire stabilità alle alte temperature, resistendo alle temperature elevate sperimentate durante le missioni spaziali, i voli supersonici o le operazioni in ambienti difficili. Presentano un'eccellente resistenza ai cicli termici, garantendo l'affidabilità e le prestazioni a lungo termine dei componenti incollati.
Inoltre, i sistemi aerospaziali e di difesa devono spesso affrontare elevate sollecitazioni meccaniche, tra cui vibrazioni, urti e forze di accelerazione. Gli adesivi MEMS forniscono stabilità meccanica e durata eccezionali, mantenendo l'integrità del legame in queste condizioni difficili. Ciò garantisce che i componenti MEMS, come sensori o attuatori, rimangano saldamente collegati e operativi, anche in ambienti di lavoro difficili.
Un altro fattore cruciale nelle applicazioni aerospaziali e della difesa è la riduzione del peso. Gli adesivi MEMS offrono il vantaggio di essere leggeri, consentendo di ridurre al minimo il peso complessivo del sistema. Ciò è particolarmente significativo nelle applicazioni aerospaziali, dove la riduzione del peso è essenziale per l'efficienza del carburante e la capacità di carico utile. Gli adesivi MEMS consentono di incollare materiali leggeri, come compositi in fibra di carbonio o film sottili, mantenendo l'integrità strutturale.
Inoltre, gli adesivi MEMS sono fondamentali nella miniaturizzazione dei sistemi aerospaziali e di difesa. Questi adesivi consentono l'incollaggio e il posizionamento unici dei componenti MEMS, che sono spesso piccoli e delicati. Facilitando i design compatti, gli adesivi MEMS contribuiscono all'ottimizzazione dello spazio all'interno di aree limitate di aerei, satelliti o attrezzature militari. Ciò consente di integrare più funzionalità e migliorare le prestazioni del sistema senza compromettere le dimensioni o i vincoli di peso.
La capacità degli adesivi MEMS di mantenere un allineamento preciso è fondamentale anche nelle applicazioni aerospaziali e della difesa. Il materiale adesivo deve garantire un posizionamento accurato, sia che si tratti di allineare componenti ottici, sensori basati su MEMS o microattuatori. Questo è fondamentale per ottenere prestazioni ottimali, come navigazione precisa, targeting o acquisizione dati. Gli adesivi MEMS con eccellente stabilità dimensionale e proprietà di basso degassamento aiutano a mantenere l'allineamento per periodi prolungati, anche in ambienti sottovuoto o ad alta quota.
Rigorosi standard di qualità e procedure di collaudo sono fondamentali nei settori aerospaziale e della difesa. Gli adesivi MEMS vengono sottoposti a test rigorosi per garantire la loro conformità ai requisiti del settore. Ciò include test meccanici per resistenza e durata, test termici per la stabilità a temperature estreme e test ambientali per umidità, sostanze chimiche e resistenza alle radiazioni. Questi test convalidano le prestazioni e l'affidabilità del materiale adesivo, garantendone l'idoneità per applicazioni aerospaziali e di difesa.
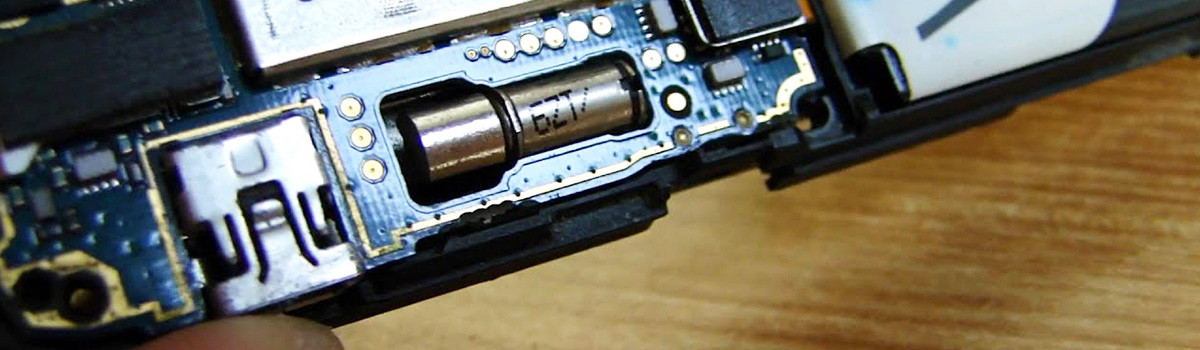
Adesivo MEMS per l'industria automobilistica: miglioramento della sicurezza e delle prestazioni
La tecnologia adesiva MEMS è emersa come una risorsa preziosa nell'industria automobilistica, fondamentale per migliorare la sicurezza, le prestazioni e l'affidabilità. Con la crescente complessità e sofisticazione dei sistemi automobilistici, gli adesivi MEMS forniscono soluzioni cruciali per l'incollaggio e il fissaggio dei componenti dei sistemi microelettromeccanici (MEMS), contribuendo alla funzionalità e all'efficienza complessive dei veicoli.
Una delle aree principali in cui gli adesivi MEMS migliorano la sicurezza automobilistica è nelle applicazioni dei sensori. I sensori MEMS, come quelli utilizzati nell'attivazione degli airbag, nel controllo della stabilità o nei sistemi avanzati di assistenza alla guida (ADAS), richiedono un collegamento preciso e affidabile. Gli adesivi MEMS assicurano il fissaggio sicuro di questi sensori a vari substrati all'interno del veicolo, come il telaio o il telaio della carrozzeria. Ciò fornisce prestazioni accurate del sensore, consentendo un'acquisizione dei dati tempestiva e accurata per le funzioni di sicurezza critiche.
Inoltre, gli adesivi MEMS contribuiscono alla durata e all'affidabilità complessive dei componenti automobilistici. Resistono ai fattori ambientali, comprese le variazioni di temperatura, l'umidità e le vibrazioni. Nelle applicazioni automobilistiche in cui i dettagli sono soggetti a sollecitazioni continue e variabili, gli adesivi MEMS forniscono un legame robusto, prevenendo il distacco o il guasto dei componenti. Ciò migliora la longevità e le prestazioni dei sistemi automobilistici, portando a una migliore affidabilità complessiva del veicolo.
Gli adesivi MEMS contribuiscono anche alla riduzione del peso e all'ottimizzazione del design nell'industria automobilistica. Poiché i produttori automobilistici si sforzano di migliorare l'efficienza del carburante e ridurre le emissioni, vengono sempre più utilizzati materiali leggeri. Gli adesivi MEMS offrono il vantaggio di essere leggeri, consentendo un incollaggio efficiente di materiali leggeri come compositi o film sottili. Questo aiuta a ridurre il peso complessivo del veicolo senza compromettere l'integrità strutturale oi requisiti di sicurezza.
Inoltre, gli adesivi MEMS contribuiscono alla miniaturizzazione dei sistemi automobilistici. Poiché i veicoli incorporano tecnologie e funzionalità più avanzate, i design compatti diventano cruciali. Gli adesivi MEMS consentono il fissaggio e il posizionamento precisi di componenti piccoli e delicati, come microsensori o attuatori. Ciò facilita l'ottimizzazione dello spazio all'interno del veicolo, consentendo l'integrazione di funzionalità aggiuntive pur mantenendo un fattore di forma più piccolo.
In termini di efficienza produttiva, gli adesivi MEMS offrono vantaggi nei processi di assemblaggio all'interno dell'industria automobilistica. Possono essere applicati utilizzando sistemi di erogazione automatizzati, garantendo un incollaggio accurato e uniforme, e questo semplifica i processi di produzione, riduce i tempi di assemblaggio e migliora i rendimenti di produzione. Le proprietà degli adesivi MEMS, come il tempo di indurimento controllato e le buone proprietà di bagnatura, contribuiscono a un incollaggio efficiente e affidabile durante la produzione di grandi volumi.
Infine, gli adesivi MEMS vengono sottoposti a rigorosi test e processi di controllo qualità per soddisfare gli standard dell'industria automobilistica. I test meccanici assicurano la resistenza e la durata del legame adesivo, mentre i test termici ne valutano la stabilità alle variazioni di temperatura. I test ambientali valutano la resistenza dell'adesivo agli agenti chimici, all'umidità e ad altri fattori. Soddisfacendo questi rigorosi requisiti, gli adesivi MEMS forniscono l'affidabilità e le prestazioni necessarie per le applicazioni automobilistiche.
Adesivo MEMS biocompatibile: abilitazione dei dispositivi impiantabili
La tecnologia adesiva MEMS biocompatibile ha rivoluzionato il campo dei dispositivi medici impiantabili consentendo un fissaggio sicuro e affidabile dei componenti dei sistemi microelettromeccanici (MEMS) all'interno del corpo umano. Questi adesivi svolgono un ruolo fondamentale nel garantire il successo e la funzionalità dei dispositivi impiantabili fornendo soluzioni di legame biocompatibili compatibili con tessuti e fluidi umani.
Uno dei requisiti critici per i dispositivi impiantabili è la biocompatibilità. Gli adesivi MEMS utilizzati in tali applicazioni sono attentamente formulati per essere atossici e non irritanti per i tessuti circostanti. Vengono sottoposti a test di biocompatibilità approfonditi per garantire che non inducano reazioni avverse o danneggino il paziente. Questi adesivi sono progettati per essere stabili in ambienti fisiologici e mantenere l'integrità senza rilasciare sostanze nocive nel corpo.
I dispositivi impiantabili richiedono spesso legami solidi e duraturi per garantire stabilità e funzionalità per periodi prolungati. Gli adesivi MEMS biocompatibili offrono un'adesione eccellente a vari substrati, inclusi metalli, ceramiche e polimeri biocompatibili comunemente usati nei dispositivi impiantabili. Questi adesivi forniscono un fissaggio sicuro dei componenti MEMS, come sensori, elettrodi o sistemi di somministrazione di farmaci, al dispositivo o al tessuto circostante, consentendo prestazioni accurate e affidabili.
Oltre alla biocompatibilità e alla forza di adesione, gli adesivi MEMS biocompatibili possiedono eccellenti proprietà meccaniche. I dispositivi impiantabili possono subire sollecitazioni meccaniche, come flessione, stiramento o compressione, a causa del movimento o dei processi naturali all'interno del corpo. Il materiale adesivo deve resistere a queste sollecitazioni senza compromettere l'integrità del legame. Gli adesivi MEMS biocompatibili offrono elevata stabilità meccanica e flessibilità, garantendo la durata del legame adesivo nell'ambiente dinamico del corpo umano.
Inoltre, gli adesivi MEMS biocompatibili consentono il posizionamento e l'allineamento precisi dei componenti MEMS all'interno del dispositivo impiantabile. Il posizionamento accurato è fondamentale per la funzionalità e le prestazioni ottimali del dispositivo. Il materiale adesivo consente la regolazione fine e il fissaggio sicuro di caratteristiche, come biosensori o microattuatori, garantendo il corretto posizionamento e allineamento rispetto al tessuto o all'organo target.
I dispositivi impiantabili richiedono spesso una chiusura ermetica per proteggere i componenti sensibili dai fluidi corporei circostanti. Gli adesivi MEMS biocompatibili possono fornire una tenuta affidabile e biocompatibile, impedendo l'ingresso di fluidi o contaminanti nel dispositivo. Questi adesivi presentano eccellenti proprietà barriera, garantendo l'integrità a lungo termine del dispositivo impiantabile e riducendo al minimo il rischio di infezione o guasto del dispositivo.
Infine, gli adesivi MEMS biocompatibili vengono sottoposti a test rigorosi per garantirne l'idoneità per le applicazioni impiantabili. Sono sottoposti a valutazioni di biocompatibilità secondo gli standard internazionali, tra cui valutazioni di citotossicità, sensibilizzazione e irritazione. I materiali adesivi sono inoltre testati per la stabilità in condizioni fisiologiche, comprese le variazioni di temperatura, pH e umidità. Questi test garantiscono la sicurezza, l'affidabilità e le prestazioni a lungo termine dell'adesivo all'interno del dispositivo impiantabile.
Test degli adesivi MEMS e considerazioni sull'affidabilità
I test sugli adesivi MEMS e le considerazioni sull'affidabilità sono fondamentali per garantire le prestazioni e la longevità dei dispositivi dei sistemi microelettromeccanici (MEMS). Questi dispositivi operano spesso in ambienti difficili e sono soggetti a varie sollecitazioni e condizioni. Test approfonditi e un'attenta considerazione dei fattori di affidabilità sono essenziali per convalidare le prestazioni dell'adesivo e garantire l'affidabilità dei dispositivi MEMS.
Un aspetto critico dei test sugli adesivi è la caratterizzazione meccanica. I legami adesivi devono essere valutati per la loro resistenza meccanica e durata per resistere alle sollecitazioni incontrate durante la vita del dispositivo. Test come taglio, trazione o peel test misurano la resistenza dell'adesivo a diverse forze meccaniche. Questi test forniscono informazioni sulla capacità dell'adesivo di mantenere un forte legame e resistere alle sollecitazioni meccaniche, garantendo l'affidabilità del dispositivo MEMS.
Un altro fattore cruciale nei test sugli adesivi è la prestazione termica. I dispositivi MEMS possono subire variazioni di temperatura significative durante il funzionamento. I materiali adesivi devono essere testati per garantirne la stabilità e l'integrità in queste condizioni di temperatura. I test sui cicli termici, in cui l'adesivo è sottoposto a ripetuti cicli di temperatura, aiutano a valutare la sua capacità di resistere all'espansione e alla contrazione termica senza delaminazione o degradazione. Inoltre, i test di invecchiamento termico valutano la stabilità e l'affidabilità a lungo termine dell'adesivo in caso di esposizione prolungata a temperature elevate.
I test ambientali sono inoltre essenziali per valutare la resistenza dell'adesivo a vari fattori ambientali. Umidità, sostanze chimiche e gas che si incontrano comunemente nelle applicazioni del mondo reale possono influire sulle prestazioni e sull'integrità dell'adesivo. I test di invecchiamento accelerato, in cui il legame è esposto a condizioni ambientali difficili per un periodo prolungato, aiutano a simulare gli effetti a lungo termine di questi fattori. Questi test forniscono preziose informazioni sulla resistenza dell'adesivo al degrado ambientale, garantendone l'affidabilità in diverse condizioni operative.
Le considerazioni sull'affidabilità vanno oltre i test, includendo fattori come le modalità di cedimento dell'adesione, i meccanismi di invecchiamento e le prestazioni a lungo termine. Comprendere le modalità di cedimento del legame adesivo è fondamentale per progettare dispositivi MEMS robusti. Le tecniche di analisi dei guasti, come la microscopia e la caratterizzazione dei materiali, aiutano a identificare i meccanismi di guasto, come la delaminazione dell'adesivo, il cedimento coesivo o il cedimento dell'interfaccia. Questa conoscenza guida il miglioramento delle formulazioni adesive e dei processi di incollaggio per mitigare i rischi di fallimento.
Anche i meccanismi di invecchiamento possono influire sulle prestazioni a lungo termine dell'adesivo e fattori come l'assorbimento di umidità, le reazioni chimiche o l'esposizione ai raggi UV possono degradare l'adesivo. Come accennato in precedenza, i test di invecchiamento accelerato aiutano a valutare la resistenza dell'adesivo a questi meccanismi di invecchiamento. I produttori possono progettare dispositivi MEMS con una durata operativa estesa e prestazioni affidabili comprendendo e affrontando potenziali problemi di invecchiamento.
Inoltre, le considerazioni sull'affidabilità includono la selezione di materiali adesivi appropriati per specifiche applicazioni MEMS. Diversi adesivi hanno proprietà diverse, come viscosità, tempo di indurimento e compatibilità con i substrati, e questi fattori devono essere attentamente considerati per garantire un'adesione ottimale e un'affidabilità a lungo termine. I produttori di adesivi forniscono dati tecnici e linee guida applicative per facilitare la selezione dei materiali, tenendo conto dei requisiti specifici e delle condizioni operative dei dispositivi MEMS.
Processi e tecniche di produzione di adesivi MEMS
I processi e le tecniche di produzione di adesivi MEMS comportano una serie di passaggi per produrre materiali adesivi di alta qualità per applicazioni di sistemi microelettromeccanici (MEMS). Questi processi garantiscono l'uniformità, l'affidabilità e le prestazioni dell'adesivo, soddisfacendo i requisiti specifici dei dispositivi MEMS. Di seguito sono riportati i passaggi critici coinvolti nella produzione di adesivi MEMS:
- Formulazione: il primo passo nella produzione dell'adesivo è la formulazione del materiale adesivo. Ciò comporta la selezione della resina di base e degli additivi appropriati per ottenere le proprietà desiderate come forza di adesione, flessibilità, stabilità termica e biocompatibilità. La formulazione tiene conto dei requisiti dell'applicazione, dei materiali del substrato e delle condizioni ambientali.
- Miscelazione e dispersione: una volta determinata la formulazione dell'adesivo, il passaggio successivo è la miscelazione e la dispersione degli ingredienti. Questo viene tipicamente fatto utilizzando attrezzature di miscelazione specializzate per garantire una miscela omogenea. Il processo di miscelazione è fondamentale per una distribuzione uniforme degli additivi e per mantenere proprietà costanti in tutto il materiale adesivo.
- Applicazione dell'adesivo: l'adesivo viene preparato per l'applicazione dopo le fasi di formulazione e miscelazione. La tecnica di applicazione dipende dalle specifiche esigenze e caratteristiche dell'adesivo. I metodi di applicazione standard includono l'erogazione, la serigrafia, il rivestimento a rotazione o la spruzzatura. L'obiettivo è applicare uniformemente l'adesivo alle superfici o ai componenti desiderati con precisione e controllo.
- Indurimento: l'indurimento è un passaggio fondamentale nella produzione di adesivi, trasformando l'adesivo da uno stato liquido o semiliquido a una forma solida. L'indurimento può essere ottenuto attraverso varie tecniche come il calore, i raggi UV o l'indurimento chimico. Il processo di polimerizzazione attiva reazioni di reticolazione all'interno dell'adesivo, sviluppando forza e proprietà di adesione.
- Controllo di qualità: durante tutto il processo di produzione dell'adesivo, vengono implementate rigorose misure di controllo della qualità per garantire la consistenza e l'affidabilità del materiale adesivo. Ciò include il monitoraggio di parametri come viscosità, forza adesiva, tempo di polimerizzazione e composizione chimica. Le procedure di controllo della qualità aiutano a identificare deviazioni o incoerenze, consentendo aggiustamenti o azioni correttive per mantenere l'integrità del prodotto.
- Imballaggio e stoccaggio: una volta che l'adesivo è stato prodotto e la qualità è stata testata, viene confezionato e preparato per lo stoccaggio o la distribuzione. Un imballaggio adeguato protegge l'adesivo da fattori esterni come umidità, luce o agenti contaminanti. Le condizioni di conservazione dell'adesivo, comprese la temperatura e l'umidità, sono considerate attentamente per mantenere la stabilità e le prestazioni dell'adesivo durante la sua durata di conservazione.
- Ottimizzazione del processo e scale-up: i produttori di adesivi si impegnano continuamente per ottimizzare il processo di produzione e scalare la produzione per soddisfare la crescente domanda. Ciò comporta perfezionamento del processo, automazione e miglioramenti dell'efficienza per garantire una qualità costante, ridurre i costi di produzione e migliorare la produttività complessiva.
Vale la pena notare che i processi e le tecniche di produzione specifici possono variare a seconda del tipo di adesivo, dell'applicazione prevista e delle capacità del produttore. I produttori di adesivi spesso dispongono di metodi e competenze proprietarie per adattare il processo di produzione alle loro specifiche formulazioni di prodotto e alle esigenze dei clienti.
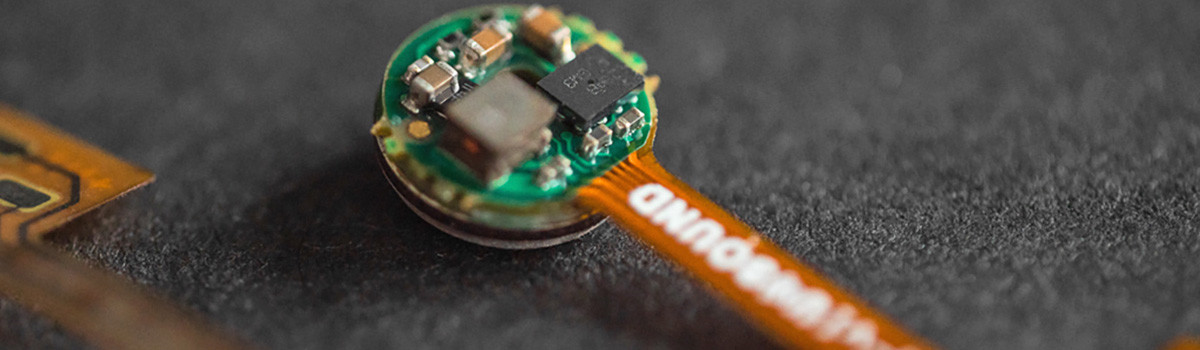
Sfide nell'incollaggio adesivo MEMS: compatibilità dei materiali e gestione dello stress
L'incollaggio MEMS presenta diverse sfide, in particolare per quanto riguarda la compatibilità dei materiali e la gestione delle sollecitazioni. Queste sfide sorgono a causa della vasta gamma di materiali utilizzati nei dispositivi dei sistemi microelettromeccanici (MEMS) e delle complesse condizioni di stress che subiscono. Superare queste sfide è fondamentale per garantire legami adesivi affidabili e durevoli nelle applicazioni MEMS.
La compatibilità dei materiali è una considerazione critica nell'incollaggio MEMS. I dispositivi MEMS sono spesso costituiti da vari materiali, come silicio, vetro, polimeri, metalli e ceramica, ciascuno con proprietà uniche. L'adesivo deve essere compatibile con questi materiali per stabilire un legame forte e affidabile. La selezione dell'adesivo comporta la considerazione di fattori quali i coefficienti di dilatazione termica, l'adesione a diversi materiali e la compatibilità con le condizioni operative del dispositivo.
Le differenze nei coefficienti di dilatazione termica possono portare a sollecitazioni e deformazioni significative durante i cicli di temperatura, causando delaminazione o fessurazione all'interfaccia dell'adesivo. La gestione di queste sollecitazioni termiche richiede un'attenta selezione dei materiali e considerazioni di progettazione. Gli adesivi con modulo inferiore e coefficienti di dilatazione termica più vicini ai materiali incollati possono aiutare a ridurre il disallineamento delle sollecitazioni e migliorare l'affidabilità a lungo termine dell'incollaggio.
Un'altra sfida nell'incollaggio MEMS è la gestione delle sollecitazioni meccaniche subite dal dispositivo. I dispositivi MEMS possono essere soggetti a varie sollecitazioni meccaniche, tra cui flessione, stiramento e compressione. Queste sollecitazioni possono derivare da condizioni ambientali, funzionamento del dispositivo o processi di assemblaggio. I materiali adesivi devono possedere resistenza e flessibilità sufficienti per resistere a queste sollecitazioni senza delaminazione o cedimenti.
Per affrontare le sfide della gestione dello stress, possono essere impiegate diverse tecniche. Un approccio utilizza adesivi conformi o elastomerici che assorbono e distribuiscono le sollecitazioni nell'area incollata. Questi adesivi forniscono una maggiore flessibilità, consentendo al dispositivo di resistere alle deformazioni meccaniche senza compromettere il legame adesivo. Inoltre, l'ottimizzazione della progettazione dei dispositivi MEMS, come l'incorporazione di funzionalità antistress o l'introduzione di interconnessioni flessibili, può aiutare ad alleviare le concentrazioni di stress e ridurre al minimo l'impatto sui legami adesivi.
Garantire un'adeguata preparazione della superficie è fondamentale anche per affrontare le sfide relative alla compatibilità dei materiali e alla gestione delle sollecitazioni. I trattamenti superficiali, come la pulizia, l'irruvidimento o l'applicazione di primer o promotori di adesione, possono migliorare l'adesione tra l'adesivo e i materiali del substrato. Questi trattamenti promuovono una migliore bagnatura e adesione all'interfaccia, migliorando la compatibilità dei materiali e la distribuzione delle sollecitazioni.
Inoltre, un controllo preciso sull'applicazione dell'adesivo è vitale per il successo dell'incollaggio. Fattori come la tecnica di erogazione dell'adesivo, le condizioni di polimerizzazione ei parametri di processo possono influenzare la qualità e le prestazioni del legame adesivo. L'uniformità dello spessore dell'adesivo, la copertura uniforme e la corretta polimerizzazione sono essenziali per ottenere incollaggi affidabili in grado di resistere alle sfide di compatibilità dei materiali e alle sollecitazioni meccaniche.
Il superamento delle sfide relative alla compatibilità dei materiali e alla gestione dello stress nell'incollaggio MEMS richiede un approccio multidisciplinare che coinvolga la scienza dei materiali, la progettazione dei dispositivi e l'ottimizzazione dei processi. La collaborazione tra produttori di adesivi, progettisti di dispositivi MEMS e ingegneri di processo è essenziale per affrontare efficacemente queste sfide. Attraverso un'attenta selezione dei materiali, considerazioni di progettazione, preparazione della superficie e controllo del processo, l'incollaggio adesivo nelle applicazioni MEMS può essere ottimizzato per ottenere legami affidabili e durevoli, garantendo le prestazioni e la longevità dei dispositivi MEMS.
Progressi nella tecnologia adesiva MEMS: nanomateriali e adesivi intelligenti
I progressi nella tecnologia adesiva MEMS sono stati guidati dalla necessità di migliorare le prestazioni, la miniaturizzazione e migliorare la funzionalità nelle applicazioni dei sistemi microelettromeccanici (MEMS). Due importanti aree di avanzamento nella tecnologia adesiva MEMS includono l'integrazione di nanomateriali e lo sviluppo di adesivi intelligenti. Questi progressi offrono capacità uniche e migliori prestazioni nell'incollaggio di dispositivi MEMS.
I nanomateriali hanno svolto un ruolo cruciale nell'avanzamento della tecnologia adesiva MEMS. L'integrazione di nanomateriali, come nanoparticelle, nanofibre o nanocompositi, nelle formulazioni adesive ha migliorato le proprietà e le funzionalità. Ad esempio, l'aggiunta di nanoparticelle può migliorare la resistenza meccanica, la stabilità termica e la conducibilità elettrica del materiale adesivo. Le nanofibre come i nanotubi di carbonio o il grafene possono fornire un rinforzo potenziato e migliori proprietà elettriche o termiche. L'utilizzo di nanocompositi negli adesivi offre una combinazione unica di proprietà, tra cui elevata resistenza, flessibilità e compatibilità con vari materiali di substrato. L'integrazione di nanomateriali negli adesivi MEMS consente lo sviluppo di soluzioni di incollaggio ad alte prestazioni per applicazioni MEMS impegnative.
Un altro progresso significativo nella tecnologia adesiva MEMS è lo sviluppo di adesivi intelligenti. Gli adesivi innovativi sono progettati per esibire proprietà o funzionalità uniche in risposta a stimoli esterni, come temperatura, luce o sollecitazioni meccaniche. Questi adesivi possono subire cambiamenti reversibili o irreversibili nelle loro proprietà, consentendo risposte dinamiche e adattabilità in diverse condizioni operative. Ad esempio, gli adesivi a memoria di forma possono cambiare forma o recuperare la loro forma originale in seguito all'esposizione a variazioni di temperatura, offrendo capacità di incollaggio reversibile. Gli adesivi attivati dalla luce possono essere attivati per incollare o staccare da specifiche lunghezze d'onda della luce, fornendo controllo e rilavorabilità precisi. Gli adesivi innovativi possono abilitare funzionalità avanzate nei dispositivi MEMS, come la riconfigurabilità, l'autoriparazione o le capacità di rilevamento, migliorandone le prestazioni e la versatilità.
L'integrazione di nanomateriali e tecnologie adesive innovative offre vantaggi sinergici nelle applicazioni MEMS. I nanomateriali possono essere incorporati in adesivi intelligenti per migliorarne ulteriormente le proprietà e le funzionalità. Ad esempio, i nanomateriali possono essere utilizzati per sviluppare adesivi nanocompositi sensibili agli stimoli che mostrano un comportamento unico basato su stimoli esterni. Questi sistemi adesivi possono fornire capacità di rilevamento automatico, consentendo il rilevamento di sollecitazioni meccaniche, temperatura o altri cambiamenti ambientali. Possono anche offrire proprietà di autoriparazione, in cui l'adesivo può riparare microfessure o danni in caso di esposizione a condizioni specifiche. La combinazione di nanomateriali e tecnologie adesive innovative apre nuove possibilità per dispositivi MEMS avanzati con prestazioni, durata e adattabilità migliorate.
Questi progressi nella tecnologia adesiva MEMS hanno implicazioni in vari settori. Consentono lo sviluppo di dispositivi MEMS più piccoli e affidabili con funzionalità avanzate. Nel settore sanitario, gli adesivi potenziati con nanomateriali possono supportare la fabbricazione di dispositivi impiantabili con migliore biocompatibilità e affidabilità a lungo termine. Gli adesivi innovativi possono abilitare dispositivi autoriparanti o riconfigurabili nell'elettronica di consumo, migliorando l'esperienza dell'utente e la longevità del prodotto. I legami potenziati con nanomateriali possono offrire soluzioni di incollaggio leggere con resistenza e durata migliorate nelle applicazioni automobilistiche e aerospaziali.
Considerazioni ambientali: adesivo MEMS per la sostenibilità
Le considerazioni ambientali stanno diventando sempre più importanti nello sviluppo e nell'utilizzo di materiali adesivi per dispositivi di sistemi microelettromeccanici (MEMS). Poiché la sostenibilità e la coscienza ecologica continuano a guadagnare terreno, è fondamentale affrontare l'impatto dei materiali adesivi MEMS durante il loro ciclo di vita. Ecco alcuni fattori chiave da considerare quando si punta alla sostenibilità nelle applicazioni adesive MEMS:
- Selezione dei materiali: la scelta di materiali adesivi ecologici è il primo passo verso la sostenibilità. La scelta di adesivi a basso impatto ambientale, come formulazioni a base acqua o prive di solventi, può aiutare a ridurre le emissioni e minimizzare l'uso di sostanze pericolose. Inoltre, la selezione di obbligazioni con una durata di conservazione più lunga o derivate da risorse rinnovabili può contribuire agli sforzi di sostenibilità.
- Processi di produzione: la valutazione e l'ottimizzazione dei processi di produzione associati alla produzione di adesivi MEMS è vitale per la sostenibilità. L'utilizzo di tecniche di produzione ad alta efficienza energetica, la riduzione al minimo della produzione di rifiuti e l'implementazione di pratiche di riciclaggio o riutilizzo possono ridurre significativamente l'impatto ambientale della produzione di adesivi. L'ottimizzazione dei processi può anche portare a risparmi di risorse e maggiore efficienza, contribuendo agli obiettivi di sostenibilità.
- Considerazioni sulla fine del ciclo di vita: comprendere le implicazioni sulla fine del ciclo di vita dei materiali adesivi MEMS è essenziale per la sostenibilità. Gli adesivi compatibili con i processi di riciclo o facilmente rimovibili durante lo smontaggio del dispositivo favoriscono la circolarità e riducono gli sprechi. Considerare la riciclabilità o la biodegradabilità dei materiali adesivi consente uno smaltimento o un recupero responsabile dal punto di vista ambientale di componenti di valore.
- Valutazione dell'impatto ambientale: condurre una valutazione completa dell'impatto ambientale dei materiali adesivi MEMS aiuta a identificare potenziali rischi ecologici e valutare le prestazioni di sostenibilità. Le metodologie di valutazione del ciclo di vita (LCA) possono essere impiegate per analizzare l'impatto ambientale dei materiali adesivi durante l'intero ciclo di vita, compresa l'estrazione delle materie prime, la produzione, l'uso e lo smaltimento. Questa valutazione fornisce informazioni sui punti critici e sulle aree di miglioramento, guidando lo sviluppo di soluzioni adesive più sostenibili.
- Conformità alle normative: il rispetto delle normative e degli standard pertinenti relativi alla protezione ambientale è fondamentale per applicazioni adesive sostenibili. La conformità a leggi come REACH (registrazione, valutazione, autorizzazione e restrizione delle sostanze chimiche) garantisce l'uso e la manipolazione sicuri dei materiali adesivi, riducendo i potenziali danni all'ambiente e alla salute umana. Inoltre, l'adesione a schemi o certificazioni di etichettatura ecologica può dimostrare un impegno di sostenibilità e fornire trasparenza agli utenti finali.
- Ricerca e innovazione: la continua ricerca e innovazione nella tecnologia adesiva può guidare la sostenibilità nelle applicazioni MEMS. L'esplorazione di materiali adesivi alternativi, come adesivi a base biologica o di ispirazione biologica, può offrire opzioni più sostenibili. Lo sviluppo di materiali adesivi con migliore riciclabilità, biodegradabilità o minore impatto ambientale può portare a dispositivi MEMS più ecologici e sostenibili.
Tendenze future nello sviluppo di adesivi MEMS
Negli ultimi anni, la tecnologia dei sistemi microelettromeccanici (MEMS) ha guadagnato un'attenzione significativa ed è diventata parte integrante di vari settori, tra cui l'elettronica, la sanità, l'automotive e l'aerospaziale. I dispositivi MEMS sono generalmente costituiti da componenti meccanici ed elettrici miniaturizzati che richiedono un collegamento preciso per garantire affidabilità e funzionalità. I materiali adesivi sono fondamentali nell'assemblaggio MEMS, fornendo legami forti e durevoli tra le parti.
Guardando al futuro, si possono identificare diverse tendenze nello sviluppo di adesivi per applicazioni MEMS:
- Miniaturizzazione e integrazione: si prevede che la tendenza alla miniaturizzazione nei dispositivi MEMS continuerà, portando alla domanda di materiali adesivi in grado di unire componenti più piccoli e complessi. Gli adesivi con capacità ad alta risoluzione e la capacità di creare forti legami su superfici in microscala saranno cruciali per fabbricare dispositivi MEMS miniaturizzati. Inoltre, i materiali adesivi che consentono l'integrazione di più componenti all'interno di un singolo dispositivo MEMS saranno molto richiesti.
- Maggiore affidabilità e durata: i dispositivi MEMS sono spesso esposti a condizioni operative difficili, tra cui fluttuazioni di temperatura, umidità e sollecitazioni meccaniche. I futuri sviluppi degli adesivi si concentreranno sul miglioramento dell'affidabilità e della durata dei legami in tali condizioni. Gli adesivi con una maggiore resistenza ai cicli termici, all'umidità e alle vibrazioni meccaniche saranno essenziali per garantire le prestazioni e la stabilità a lungo termine dei dispositivi MEMS.
- Indurimento a bassa temperatura: molti materiali MEMS, come polimeri e componenti elettronici delicati, sono sensibili alle alte temperature. Di conseguenza, vi è una crescente domanda di adesivi in grado di polimerizzare a basse temperature senza compromettere la forza di adesione. Gli adesivi indurenti a bassa temperatura consentiranno l'assemblaggio di componenti MEMS sensibili alla temperatura e ridurranno il rischio di danni termici durante la fabbricazione.
- Compatibilità con più substrati: i dispositivi MEMS spesso comportano l'incollaggio di diversi materiali, come metalli, ceramiche e polimeri. Saranno molto ricercati materiali adesivi che presentano un'eccellente adesione a vari substrati. Inoltre, lo sviluppo di adesivi in grado di unire materiali dissimili con coefficienti di espansione termica non corrispondenti contribuirà a mitigare il potenziale di guasto indotto dallo stress nei dispositivi MEMS.
- Adesivi biocompatibili: il campo dei MEMS biomedici sta avanzando rapidamente, con applicazioni nella somministrazione di farmaci, ingegneria tissutale e dispositivi impiantabili. I materiali adesivi, biocompatibili e non tossici saranno fondamentali per queste applicazioni, garantendo la sicurezza e la compatibilità dei dispositivi MEMS con i sistemi biologici. Gli sviluppi futuri si concentreranno sulla progettazione e la sintesi di adesivi che presentano un'eccellente biocompatibilità pur mantenendo una forte adesione e proprietà meccaniche.
- Adesivi rilasciabili e riutilizzabili: in alcune applicazioni MEMS, è auspicabile la capacità di rilasciare e riposizionare o riutilizzare i componenti dopo l'incollaggio. Gli adesivi rilasciabili e riutilizzabili forniranno flessibilità durante i processi di fabbricazione e assemblaggio di MEMS, consentendo regolazioni e correzioni senza danneggiare le parti oi substrati.
Conclusione: l'adesivo MEMS come forza trainante nel progresso della microelettronica
I materiali adesivi MEMS sono diventati una forza trainante nel progresso della microelettronica, svolgendo un ruolo fondamentale nell'assemblaggio e nella funzionalità dei dispositivi MEMS. Questi minuscoli componenti meccanici ed elettrici richiedono un legame speciale per garantire affidabilità e prestazioni. Si prevede che le tendenze future nello sviluppo di adesivi MEMS miglioreranno ulteriormente le capacità e le applicazioni di questi dispositivi.
La miniaturizzazione e l'integrazione continueranno a spingere i confini della tecnologia MEMS. I materiali adesivi con capacità ad alta risoluzione saranno cruciali per l'incollaggio di componenti più piccoli e complessi. Inoltre, gli adesivi che consentono l'integrazione di più componenti all'interno di un singolo dispositivo MEMS guideranno l'innovazione in questo campo.
Affidabilità e durata sono fondamentali nelle applicazioni MEMS, poiché questi dispositivi sono esposti a condizioni operative difficili. I futuri sviluppi degli adesivi miglioreranno i cicli termici, l'umidità e la resistenza allo stress meccanico. L'obiettivo è garantire le prestazioni e la stabilità a lungo termine dei dispositivi MEMS in vari ambienti.
Gli adesivi a bassa temperatura affronteranno la sensibilità dei materiali MEMS alle alte temperature. La polimerizzazione a temperature più basse senza compromettere la forza di adesione faciliterà l'assemblaggio di componenti sensibili alla temperatura, riducendo il rischio di danni termici durante la fabbricazione.
La compatibilità con più substrati è fondamentale nell'assemblaggio MEMS, poiché spesso sono coinvolti materiali diversi. I materiali adesivi che presentano un'eccellente adesione a un'ampia gamma di substrati consentiranno l'incollaggio di materiali diversi e contribuiranno a mitigare il cedimento indotto dallo stress nei dispositivi MEMS.
Nei MEMS biomedici, la domanda di adesivi biocompatibili è in rapida crescita. Questi adesivi devono essere atossici e compatibili con i sistemi biologici pur mantenendo una forte adesione e proprietà meccaniche. Lo sviluppo di tali legami amplierà le applicazioni dei MEMS in aree quali la somministrazione di farmaci, l'ingegneria tissutale e i dispositivi impiantabili.
Infine, gli adesivi rilasciabili e riutilizzabili forniranno flessibilità durante i processi di fabbricazione e assemblaggio dei MEMS. La capacità di rilasciare e riposizionare i componenti o addirittura riutilizzarli dopo l'incollaggio supporta regolazioni e correzioni senza danneggiare le parti o i substrati.
In conclusione, i materiali adesivi MEMS stanno guidando i progressi nella microelettronica consentendo l'assemblaggio e la funzionalità dei dispositivi MEMS. I futuri sviluppi degli adesivi MEMS miglioreranno ulteriormente la miniaturizzazione, l'affidabilità, l'indurimento a bassa temperatura, la compatibilità del substrato, la biocompatibilità e la flessibilità dei processi di assemblaggio. Questi progressi sbloccheranno nuove possibilità e applicazioni per la tecnologia MEMS, rivoluzionando vari settori e plasmando il futuro della microelettronica.