Una guida completa di adesivi elettronici
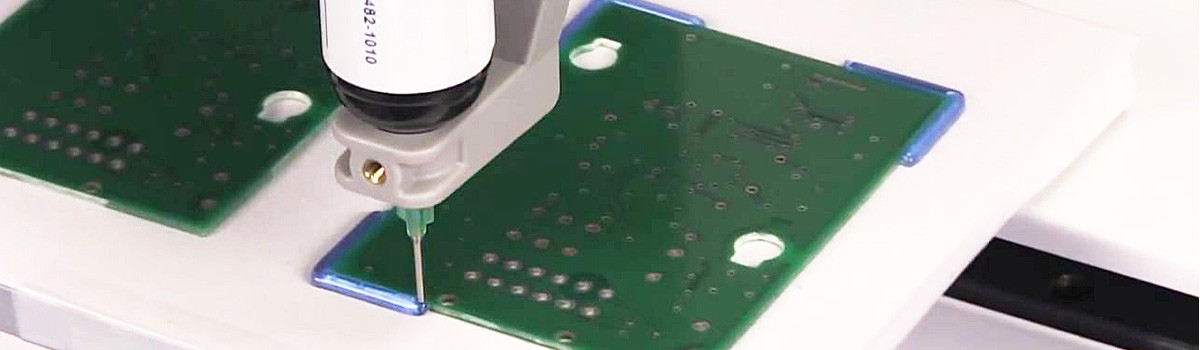
Adesivi elettronici
Gli adesivi elettronici sono materiali specializzati che uniscono componenti elettronici, come circuiti integrati, resistori, condensatori e transistor, a circuiti stampati, substrati e altri dispositivi elettronici. Questi adesivi garantiscono l'affidabilità, le prestazioni e la longevità dei prodotti elettronici.
Gli adesivi elettronici sono disponibili in vari tipi, inclusi adesivi conduttivi e non conduttivi, adesivi termici ed elettricamente conduttivi e adesivi a polimerizzazione UV. Li formuliamo per resistere a temperature estreme, sostanze chimiche, umidità, vibrazioni e altri fattori ambientali che i dispositivi elettronici possono incontrare durante il loro ciclo di vita.
Vari settori utilizzano ampiamente adesivi elettronici, tra cui quello automobilistico, aerospaziale, delle telecomunicazioni, medico e dell'elettronica di consumo. Consentono la miniaturizzazione, la velocità e la funzionalità dei dispositivi elettronici e la loro resistenza a condizioni difficili.
L'importanza degli adesivi elettronici nella tecnologia moderna
Gli adesivi elettronici sono una componente essenziale della tecnologia moderna. Svolgono un ruolo fondamentale nel garantire l'affidabilità e la longevità dei dispositivi elettronici, nonché la loro miniaturizzazione, velocità e funzionalità. Ecco alcuni dei motivi per cui gli adesivi elettronici sono così importanti nella tecnologia moderna:
Miniaturizzazione: Poiché i produttori miniaturizzano i dispositivi elettronici, devono anche miniaturizzare i componenti utilizzati nella loro costruzione. Gli adesivi elettronici consentono ai produttori di unire questi piccoli componenti con precisione e stabilità, consentendo lo sviluppo di dispositivi più piccoli e complessi.
Durabilità: Condizioni ambientali difficili, inclusi sbalzi di temperatura, umidità e urti, spesso espongono i dispositivi elettronici. Formuliamo adesivi elettronici per resistere a queste condizioni, assicurando che i componenti rimangano fissati saldamente e che il dispositivo continui a funzionare correttamente.
Funzionalità: È inoltre possibile utilizzare adesivi elettronici per creare percorsi conduttivi tra i componenti, consentendo il flusso di elettricità attraverso il dispositivo. Consente lo sviluppo di circuiti più complessi e una maggiore funzionalità nei dispositivi elettronici.
Velocità: L'utilizzo di adesivi elettronici nella produzione può aiutare a semplificare la produzione e ridurre i tempi di assemblaggio. I sigillanti elettronici possono essere applicati in modo rapido e preciso, risparmiando tempo e aumentando l'efficienza.
Affidabilità: Anche un guasto minore può causare problemi significativi ai dispositivi elettronici. Gli adesivi elettronici forniscono un legame affidabile e sicuro tra i componenti, riducendo il rischio di perdita e garantendo il corretto funzionamento del dispositivo.
Tipi di adesivi elettronici: una panoramica completa
Gli adesivi elettronici sono disponibili in vari tipi, ciascuno con proprietà e vantaggi unici. La scelta dell'adesivo dipende dall'applicazione e dai requisiti specifici del dispositivo e i produttori devono scegliere un adesivo adatto per garantire affidabilità, funzionalità e longevità. Ecco i diversi tipi di adesivi elettronici comunemente usati nel settore:
- Adesivi conduttivi:I produttori di elettronica utilizzano adesivi conduttivi per creare connessioni elettriche tra componenti elettronici. Contengono particelle conduttive, come argento o rame, che consentono il flusso di elettricità attraverso la colla. I produttori usano comunemente questi adesivi per produrre touchscreen, sensori e altri dispositivi elettronici.
- Adesivi non conduttivi:I produttori utilizzano adesivi non conduttivi per incollare componenti elettronici che non richiedono collegamenti elettrici. Sono spesso utilizzati nell'assemblaggio di circuiti stampati, fornendo stabilità meccanica e isolamento tra i membri.
- Adesivi termoconduttivi: Gli adesivi termoconduttivi dissipano il calore dai componenti elettronici. Contengono particelle termicamente conduttive, come la ceramica o il carbonio, che consentono al calore di fluire attraverso la colla. I produttori utilizzano questi adesivi per produrre alimentatori, illuminazione a LED e altri dispositivi che generano quantità significative di calore.
- Adesivi elettricamente conduttivi:Gli adesivi elettricamente conduttivi sono simili agli adesivi conduttivi ma hanno una maggiore conduttività elettrica. Sono spesso utilizzati per assemblare dispositivi elettronici ad alte prestazioni, come microprocessori e chip di memoria.
- Adesivi a polimerizzazione UV: Si possono polimerizzare adesivi induribili ai raggi UV utilizzando la luce ultravioletta. Essi sono a indurimento rapido e forniscono un'eccellente adesione a una varietà di substrati. I produttori utilizzano comunemente questi adesivi per fabbricare dispositivi medici, apparecchiature ottiche e altri dispositivi che richiedono tempi di polimerizzazione rapidi.
- Adesivi epossidici: Gli adesivi epossidici sono noti per la loro elevata resistenza e durata. Comunemente assemblano dispositivi elettronici che richiedono un forte legame, come smartphone, tablet e laptop.
Adesivi conduttivi: il loro ruolo nei circuiti elettrici
Gli adesivi conduttivi sono materiali essenziali nella produzione di dispositivi elettronici. Forniscono un metodo per creare connessioni elettriche tra componenti elettronici, che è fondamentale per la funzionalità di questi dispositivi. Questo post sul blog discuterà il ruolo degli adesivi conduttivi nei circuiti elettrici.
Gli adesivi conduttivi sono formulati con particelle conduttive come argento, rame o nichel, che consentono all'elettricità di fluire attraverso la colla. Queste particelle creano un percorso conduttivo tra i componenti elettronici, garantendo il corretto funzionamento del dispositivo. I produttori usano comunemente adesivi conduttivi per produrre touchscreen, sensori e altri dispositivi elettronici.
Un vantaggio dell'utilizzo di adesivi conduttivi nei circuiti elettrici è la loro capacità di fornire un legame sicuro tra i componenti. Questi adesivi creano una connessione robusta e stabile in grado di resistere alle sollecitazioni ambientali dei dispositivi elettronici. La colla può anche distribuire uniformemente la corrente attraverso il circuito, prevenendo i punti caldi e assicurando che tutti i componenti ricevano la corretta alimentazione.
Si possono anche utilizzare adesivi conduttivi per creare circuiti flessibili, essenziali per dispositivi flessibili, come l'elettronica indossabile o i dispositivi medici. Gli adesivi conduttivi possono essere applicati a substrati flessibili, creando corsi che si piegano, si attorcigliano o si allungano.
Una delle sfide dell'utilizzo di adesivi conduttivi è che la loro conduttività può degradarsi nel tempo, soprattutto se esposti a condizioni ambientali difficili. I produttori sviluppano continuamente nuove formulazioni con maggiore durata e conducibilità per affrontare questo problema.
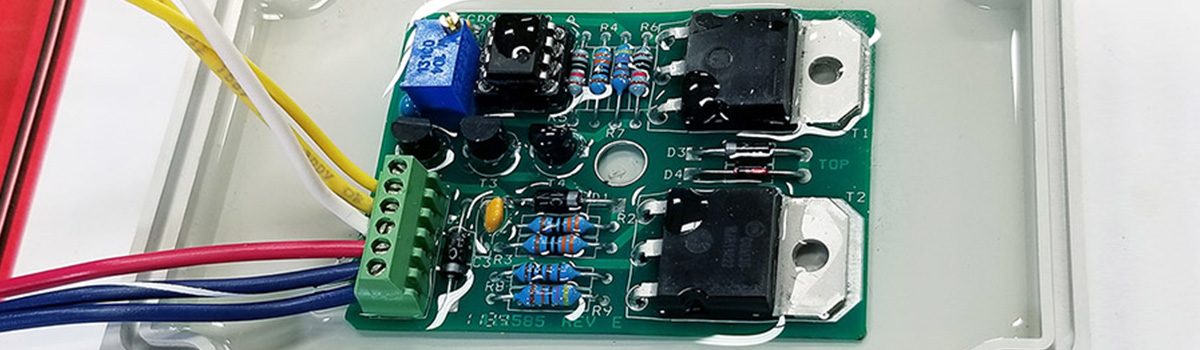
Comprensione degli adesivi termicamente conduttivi
Gli adesivi termicamente conduttivi sono un componente essenziale in molti dispositivi elettronici moderni. Questi adesivi uniscono e trasferiscono il calore tra due superfici, migliorando la gestione termica e prevenendo il surriscaldamento. In questo post, esploreremo cosa sono gli adesivi termicamente conduttivi, le loro proprietà e le loro applicazioni.
Gli adesivi termicamente conduttivi sono un tipo di adesivo che ha un'elevata conducibilità termica e ciò significa che possono trasferire il calore in modo efficiente tra due superfici. La composizione tipica degli adesivi conduttivi include una combinazione di una matrice polimerica, come resina epossidica o silicone, e particelle conduttive, come ossido di alluminio o nitruro di boro.
Le proprietà degli adesivi termicamente conduttivi dipendono dal tipo di matrice polimerica e dalle particelle conduttive utilizzate. Le proprietà fondamentali includono conducibilità termica, viscosità e tempo di indurimento. La proprietà più critica dell'adesivo è la sua conduttività termica, in quanto determina l'efficacia del trasferimento di calore tra le superfici. La viscosità dell'adesivo determina la facilità di applicazione e il tempo di indurimento determina il tempo necessario all'adesivo per indurirsi e raggiungere completamente la sua massima conducibilità termica.
Gli adesivi termicamente conduttivi hanno molte applicazioni, anche nell'industria automobilistica, aerospaziale ed elettronica. Nell'industria elettronica, gli adesivi termicamente conduttivi uniscono i componenti a dissipatori di calore e diffusori, migliorando la gestione termica e prevenendo il surriscaldamento. Sono anche utilizzati per incollare componenti di illuminazione a LED a substrati, che generano molto calore.
Nell'industria automobilistica, gli adesivi termicamente conduttivi vengono utilizzati per unire i componenti dell'elettronica di potenza ai dissipatori di calore, contribuendo a migliorare la gestione termica. Inoltre collegano i sensori ai componenti del motore, che devono funzionare in ambienti ad alta temperatura.
Adesivi dielettrici: garantire l'isolamento nei componenti elettrici
Gli adesivi dielettrici sono materiali essenziali utilizzati nell'industria elettronica per fornire isolamento e protezione ai componenti elettrici. Nelle applicazioni in cui la conducibilità elettrica è un problema o è necessario un elevato grado di isolamento, vengono utilizzati adesivi termicamente conduttivi al posto degli adesivi tradizionali che non possono soddisfare questi requisiti. Gli adesivi dielettrici hanno eccellenti proprietà di isolamento e possono resistere alle alte temperature, rendendoli ideali per l'uso in dispositivi elettronici.
Ecco alcuni dei vantaggi dell'utilizzo di adesivi dielettrici:
- Isolamento:Gli adesivi dielettrici forniscono eccellenti proprietà di isolamento, impedendo alla corrente elettrica di fluire attraverso di essi e assicurando che i loro componenti di collegamento siano elettricamente isolati.
- Resistenza al calore:Gli adesivi dielettrici possono resistere alle alte temperature e mantenere le loro proprietà nel tempo, il che li rende adatti per applicazioni che generano calore significativo, come motori e trasformatori.
- Resistenza chimica: Gli adesivi dielettrici resistono agli agenti chimici, rendendoli adatti per l'uso in ambienti difficili dove altri adesivi fallirebbero.
- Durabilità: Gli adesivi dielettrici hanno eccellenti proprietà di adesione e possono sopportare sollecitazioni e deformazioni elevate, il che li rende ideali per l'uso in applicazioni con sollecitazioni meccaniche.
- Facile applicazione:Gli adesivi dielettrici possono essere applicati in modo rapido ed efficiente, consentendo un rapido assemblaggio e produzione.
- Versatilità:È possibile utilizzare adesivi dielettrici in varie applicazioni, come dispositivi elettronici, componenti automobilistici e apparecchiature mediche.
Gli adesivi dielettrici sono disponibili in varie formulazioni, inclusi epossidici, siliconi e acrilici. Progettiamo ogni formulazione con proprietà uniche che si adattano ad applicazioni specifiche.
Adesivi a polimerizzazione UV: una soluzione rapida per l'assemblaggio elettronico
I dispositivi elettronici sono diventati parte integrante della nostra vita. Facciamo affidamento sull'elettronica per quasi tutto, dagli smartphone ai laptop, dalle automobili ai dispositivi medici. L'assemblaggio elettronico comporta l'unione di diversi componenti e gli adesivi svolgono un ruolo cruciale. Gli adesivi a polimerizzazione UV stanno guadagnando popolarità tra i vari adesivi grazie al loro rapido tempo di indurimento e all'elevata forza di adesione.
Gli adesivi a polimerizzazione UV sono adesivi reattivi che polimerizzano se esposti alla luce ultravioletta. La polimerizzazione avviene in pochi secondi, il che li rende la scelta ideale per gli ambienti di produzione ad alto volume. Gli adesivi a polimerizzazione UV eliminano la necessità di riscaldamento o asciugatura, riducendo i tempi di assemblaggio e i costi di produzione.
L'elevata forza di adesione degli adesivi a polimerizzazione UV li rende adatti a vari substrati, inclusi metalli, plastica e vetro. Offrono un'eccellente adesione a materiali difficili da incollare, come polipropilene, polietilene e policarbonato. Il legame adesivo formato da adesivi a polimerizzazione UV è solido e duraturo e può resistere ad ambienti difficili, come alte temperature, sostanze chimiche e umidità.
Un altro vantaggio degli adesivi a polimerizzazione UV è la loro capacità di polimerizzare in un'area specifica. L'adesivo può essere applicato con precisione sull'area di incollaggio e il processo di indurimento può essere attivato esponendo il sito alla luce UV. Questa caratteristica li rende ideali per applicazioni che richiedono un posizionamento preciso e l'allineamento dei componenti.
Gli adesivi a polimerizzazione UV sono anche rispettosi dell'ambiente e non contengono solventi né emettono composti organici volatili (COV) durante la polimerizzazione. Li rende sicuri da usare in spazi ristretti e riduce l'impatto ambientale.
Selezione dell'adesivo elettronico giusto: fattori chiave da considerare
La selezione di adesivi elettronici adatti è fondamentale per garantire la longevità e l'affidabilità dei dispositivi elettronici. Gli adesivi elettronici uniscono i componenti e proteggono da fattori esterni quali umidità, polvere e sbalzi di temperatura. Qui discuteremo i fattori chiave da considerare quando si seleziona un adesivo elettronico adatto.
Proprietà chimiche
Compatibilità: L'adesivo deve essere compatibile con i materiali a cui si legherà, inclusi metalli, plastica e vetro.
Resistenza chimica: L'adesivo deve resistere alle sostanze chimiche che possono entrare in contatto con il dispositivo elettronico, come detergenti o solventi.
Proprietà termali: L'adesivo deve resistere alle temperature e alle fluttuazioni di esercizio.
Proprietà dell'applicazione
Viscosità: Per garantire una corretta applicazione, è necessario considerare lo spessore dell'adesivo, poiché deve scorrere uniformemente e coprire le superfici che si desidera incollare.
Tempo di cura: L'adesivo deve avere un tempo di polimerizzazione compatibile con il processo di assemblaggio. Un tempo di polimerizzazione lungo può rallentare la produzione, mentre un tempo di polimerizzazione breve potrebbe non consentire un'adesione adeguata.
Forza di adesione: L'adesivo deve avere una forza di adesione sufficiente per unire i componenti del dispositivo e garantire la longevità.
Proprietà ambientali
Resistenza all'umidità: L'adesivo deve proteggere dall'umidità, che può danneggiare i componenti elettronici.
Resistenza ai raggi UV: L'adesivo deve proteggere dai raggi UV, che possono causare lo scolorimento e il degrado dei materiali.
Resistenza all'impatto: L'adesivo deve proteggere da impatti fisici come cadute o urti.
La selezione di adesivi elettronici adatti è fondamentale per garantire la longevità e l'affidabilità dei dispositivi elettronici. Considerando le proprietà chimiche, applicative e ambientali dell'adesivo, i produttori possono garantire che l'adesivo aderisca correttamente ai componenti e protegga da fattori esterni.
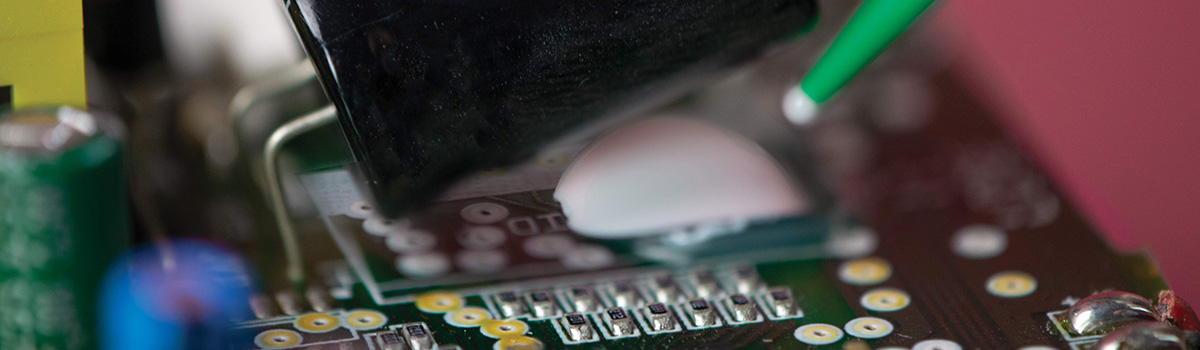
Compatibilità con i substrati: garanzia di adesione e stabilità
La compatibilità con i substrati garantisce adesione e stabilità in vari settori, come l'automotive, l'edilizia e l'imballaggio. Il successo dell'applicazione di un rivestimento o di un adesivo su un substrato dipende dalla compatibilità dei due materiali. In questa discussione, sottolineeremo l'importanza di garantire la compatibilità con i substrati e delineeremo i passaggi per raggiungerla.
Importanza della compatibilità con i substrati
Adesione: Per garantire che il rivestimento o l'adesivo rimangano in posizione, devono aderire alla superficie del supporto durante l'applicazione. La compatibilità con i substrati è essenziale per garantire che il rivestimento o l'adesivo aderisca al substrato e rimanga stabile.
Stabilità: Un rivestimento o un adesivo incompatibile con il substrato può causare instabilità e causare il cedimento del rivestimento o del sigillante. Può portare a problemi significativi, come il cedimento strutturale dell'edificio o la perdita del prodotto durante l'uso.
Garantire la compatibilità con i substrati
Preparazione della superficie: Per preparare la superficie del substrato per l'applicazione di un rivestimento o di un adesivo, pulirla e rimuovere i contaminanti. Consentirà al rivestimento o al sigillante di aderire correttamente al substrato.
Test: È necessario eseguire test di compatibilità prima di applicare un rivestimento o un adesivo per garantire che i due materiali siano compatibili. È possibile utilizzare vari metodi, come pull-off o lap shear test, per eseguire test di compatibilità.
Selezione del materiale: È essenziale selezionare il rivestimento o l'adesivo adatto per il substrato. Considerare le proprietà chimiche e fisiche dello strato o dell'adesivo e del substrato.
Le implicazioni di una mancanza di compatibilità con i substrati possono essere gravi, portando a guasti e costi elevati in termini di tempo e denaro. È possibile ottenere adesione e stabilità e garantire un'applicazione di successo e di lunga durata garantendo la compatibilità con i substrati.
Resistenza ambientale: fattori da considerare
La resistenza ambientale si riferisce ai fattori naturali che limitano la crescita, la distribuzione e l'abbondanza di organismi in un ecosistema. Questi fattori possono essere biotici (viventi) o abiotici (non viventi) e includono una serie di condizioni fisiche, chimiche e biologiche. In questo post del blog, discuteremo i fattori che contribuiscono alla resistenza ambientale e le implicazioni di questi fattori sulla salute dell'ecosistema.
Fattori biotici
- Concorso: Gli organismi competono per cibo, acqua e risorse di riparo. Può limitare la crescita di una popolazione riducendo la disponibilità delle risorse.
- Predazione: I predatori possono limitare le dimensioni di una persona consumando individui. Può anche portare a una diminuzione della dimensione complessiva della popolazione di una specie.
- Malattia: Le malattie possono diffondersi rapidamente in una popolazione, causando un declino degli individui nel tempo.
Fattori abiotici
- Temperatura:Gli organismi hanno una gamma di temperature ottimali per sopravvivere e riprodursi. Le temperature estreme possono limitare la crescita e la distribuzione degli organismi.
- Acqua: L'acqua è essenziale per la vita e gli organismi richiedono una certa quantità di acqua per sopravvivere. La mancanza di acqua può limitare la crescita e la distribuzione degli organismi.
- Light: La luce è necessaria per la fotosintesi nelle piante, che è il modo in cui producono cibo. La mancanza di luce solare può limitare lo sviluppo e la distribuzione delle piante.
Implicazioni della resistenza ambientale
- Mantenere l'equilibrio: La resistenza ambientale aiuta a mantenere l'equilibrio negli ecosistemi impedendo a una specie di dominare e causare squilibri.
- Biodiversità: La resistenza ambientale promuove la biodiversità creando nicchie per specie diverse, aumentando così il numero di specie in un ecosistema.
- Salute dell'ecosistema:La resistenza ambientale gioca un ruolo cruciale nel mantenimento della salute dell'ecosistema. L'interruzione di questi fattori può portare al declino o all'estinzione delle specie, che possono avere effetti a cascata sull'intero ecosistema.
Metodo di applicazione: scelta della giusta tecnica di erogazione
Durante la produzione, la scelta del metodo di applicazione corretto per il tuo prodotto è fondamentale. Il processo di erogazione dello sviluppo può influenzarne pesantemente le prestazioni e l'aspetto.
Ecco perché è fondamentale valutare attentamente le proprie opzioni e scegliere la tecnica più adatta alle proprie esigenze.
Ecco alcuni fattori da considerare quando si sceglie la corretta tecnica di erogazione:
- Viscosità: La viscosità del materiale che stai erogando è una considerazione importante. I materiali a bassa viscosità come acqua o solventi possono richiedere stili di erogazione diversi rispetto ai materiali ad alta viscosità come adesivi o paste. Per i materiali a bassa viscosità, le tecniche di spruzzatura o atomizzazione possono essere più efficaci, mentre i materiali ad alta viscosità possono richiedere un approccio più controllato, come l'erogazione di precisione.
- Proprietà dei materiali: Quando si seleziona un metodo di erogazione, è necessario considerare le proprietà del materiale che si intende erogare. Ad esempio, alcuni materiali possono essere sensibili all'aria o ai cambiamenti di temperatura e richiedere metodi di erogazione che riducano al minimo l'esposizione a questi fattori. Allo stesso modo, i materiali che richiedono un certo livello di precisione o accuratezza potrebbero richiedere attrezzature di erogazione più specializzate.
- Design del prodotto: Il design del tuo prodotto può anche influenzare la scelta della tecnica di erogazione. Ad esempio, se il tuo prodotto ha caratteristiche complesse o delicate, un processo di erogazione manuale potrebbe essere più appropriato di uno automatizzato. D'altra parte, se il tuo prodotto richiede volumi elevati, potrebbe essere necessaria una tecnica di erogazione meccanica o robotica.
- Fattori ambientali: Infine, anche i fattori ambientali possono influenzare la scelta del metodo di erogazione. Se hai bisogno di erogare il tuo prodotto in un ambiente di camera bianca, potresti aver bisogno di attrezzature specializzate che soddisfino particolari standard di pulizia, ad esempio. Analogamente, se il prodotto è infiammabile o pericoloso, potrebbe essere necessario scegliere una tecnica di erogazione che riduca al minimo il rischio di incidenti o incendi.
Processo di polimerizzazione: comprensione dell'impatto del calore e del tempo
La polimerizzazione è un processo cruciale che garantisce la longevità e la durata dei prodotti in diversi settori. Dall'automotive all'edilizia, la polimerizzazione è essenziale per garantire che i prodotti finali siano solidi e resistenti ai fattori ambientali. Il processo di polimerizzazione comporta l'applicazione di calore e tempo allo sviluppo, che ne influenza le proprietà meccaniche e la qualità complessiva.
Il calore è uno dei fattori critici che influenzano il processo di polimerizzazione. L'intervallo di temperatura e la durata dell'applicazione del calore influiscono in modo significativo sulla resistenza e sulla rigidità del prodotto. Il calore attiva le reazioni chimiche che portano alla formazione di reticolazioni nel materiale. Questi collegamenti incrociati aumentano la potenza del materiale creando legami tra le catene molecolari.
La durata del processo di polimerizzazione è un altro fattore critico. Più lungo è il tempo di indurimento, più reticoli si formano, risultando in un prodotto più robusto e rigido. Tuttavia, un tempo di indurimento eccessivo può portare a fragilità e ridotta flessibilità. Sta trovando il giusto equilibrio tra tempo di polimerizzazione e forza, a seconda dei requisiti del prodotto.
Il metodo di polimerizzazione appropriato dipende dal tipo di prodotto e dalle proprietà richieste. Ad esempio, nell'industria automobilistica, viene utilizzato un forno per la polimerizzazione della vernice per applicare calore alla carrozzeria dell'auto, assicurando che la vernice si asciughi e aderisca al metallo. Nel settore delle costruzioni, il calcestruzzo viene stagionato aggiungendo acqua e lasciandolo indurire nel tempo, aumentandone la resistenza.
Il processo di stagionatura è fondamentale non solo per le proprietà meccaniche del prodotto ma anche per il suo aspetto. Il calore e il tempo applicati durante l'indurimento influenzano la consistenza, il colore e la finitura del prodotto. Pertanto, il controllo del processo di polimerizzazione è fondamentale per garantire che il prodotto soddisfi i requisiti estetici e funzionali desiderati.
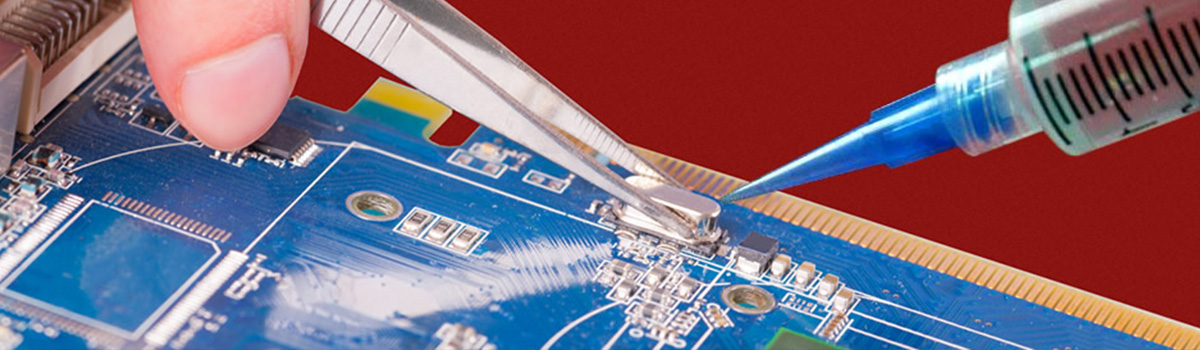
Stoccaggio e manipolazione: suggerimenti per mantenere la qualità dell'adesivo
La corretta conservazione e manipolazione sono fondamentali per garantire l'efficacia degli adesivi. Lo stoccaggio e la manipolazione impropri possono portare al degrado della qualità dell'adesivo e, in ultima analisi, al guasto del prodotto. Ecco alcuni consigli per mantenere la qualità dell'adesivo:
- Controllo della temperatura: I materiali adesivi sono sensibili alle variazioni di temperatura e l'esposizione a temperature estreme può danneggiarne la qualità. Le alte temperature possono causare la perdita di viscosità e forza di adesione dei materiali adesivi, mentre le basse temperature possono farli diventare fragili e difficili da usare. Pertanto, è essenziale conservare gli adesivi in un luogo fresco e asciutto, lontano dalla luce solare diretta ea una temperatura costante.
- Controllo dell'umidità: L'umidità può anche influire sulla qualità dei materiali adesivi. L'umidità può causare la rottura degli adesivi, riducendone la forza adesiva. Per mantenere la qualità dell'adesivo, è necessario mantenere i contenitori appiccicosi ben chiusi e conservarli in un'area con umidità controllata.
- Gestione corretta: La corretta gestione dei materiali adesivi è fondamentale per la loro longevità. È essenziale evitare di far cadere o scuotere i contenitori appiccicosi, in quanto ciò può portare alla formazione di bolle d'aria, compromettendo la qualità dell'adesivo. Inoltre, è essenziale miscelare correttamente gli adesivi prima dell'uso, poiché una miscelazione inadeguata può portare a prestazioni e qualità dell'adesivo non uniformi.
- Shelf Life: I materiali adesivi hanno una durata di conservazione limitata e il loro utilizzo entro il periodo di tempo specificato è essenziale. Nel corso del tempo, i materiali adesivi possono iniziare a rompersi, causando la perdita della forza adesiva e della viscosità. È fondamentale utilizzare gli adesivi prima della scadenza per garantirne l'efficacia.
- Compatibilità: I produttori progettano diversi materiali adesivi per superfici e applicazioni specifiche. È essenziale garantire che il materiale adesivo sia compatibile con la struttura e i requisiti dell'applicazione. L'uso di materiali adesivi incompatibili può causare guasti al prodotto e danni alle superfici.
Applicazioni comuni degli adesivi elettronici
Gli adesivi elettronici sono adesivi specializzati che incollano e sigillano componenti e sistemi elettronici. Le industrie aerospaziale e automobilistica e l'elettronica di consumo sono tra le varie applicazioni che li utilizzano. Ecco alcune delle applicazioni più comuni degli adesivi elettronici:
- Elettronica di consumo:Gli adesivi elettronici sono ampiamente utilizzati nell'elettronica di consumo, inclusi smartphone, laptop e tablet. Incollano e sigillano componenti elettronici come display, touchscreen e batterie. Gli adesivi elettronici proteggono anche dall'umidità e da altri fattori ambientali che danneggiano i componenti elettronici.
- Industria automobilistica: L'industria automobilistica fa molto affidamento sugli adesivi elettronici per garantire l'affidabilità e la sicurezza delle auto moderne. Gli adesivi elettronici incollano e sigillano componenti elettronici, componenti strutturali e collegamenti elettrici. I produttori li usano anche per incollare e sigillare materiali compositi, come la fibra di carbonio, che stanno diventando sempre più diffusi nella moderna costruzione di automobili.
- Industria aerospaziale: L'industria aerospaziale richiede adesivi specializzati in grado di resistere a sollecitazioni ambientali estreme, compresi i cambiamenti di temperatura elevata e l'esposizione all'acqua salata. Gli adesivi elettronici sono ampiamente utilizzati nell'industria aerospaziale per incollare e sigillare componenti elettronici, componenti strutturali e collegamenti elettrici.
- Dispositivi medici: I produttori di dispositivi medici utilizzano adesivi elettronici in prodotti come pacemaker, defibrillatori e pompe per insulina. Sono utilizzati per incollare e sigillare componenti elettronici, assicurando che funzionino correttamente e in modo affidabile.
- Illuminazione a LED:I produttori utilizzano adesivi elettronici per produrre illuminazione a LED, inclusa l'illuminazione automobilistica e i lampioni. Questi adesivi uniscono e sigillano i componenti elettronici per proteggerli dall'umidità e da altri fattori ambientali che possono causare danni.
- Energia rinnovabile: L'industria utilizza adesivi elettronici per incollare e sigillare pannelli solari, turbine eoliche e batterie. Sono utilizzati per proteggere i componenti elettronici dall'umidità e da altri fattori ambientali, assicurando che rimangano affidabili e funzionali per tutta la vita dell'apparecchiatura.
Industria automobilistica: il ruolo degli adesivi elettronici nella produzione automobilistica
L'industria automobilistica è in continua evoluzione e le case automobilistiche sono sempre alla ricerca di modi per migliorare la sicurezza, l'affidabilità e l'efficienza dei loro veicoli. Un componente critico che svolge un ruolo fondamentale nella costruzione delle auto moderne sono gli adesivi elettronici. Gli adesivi elettronici sono ampiamente utilizzati nell'industria automobilistica per varie applicazioni, tra cui l'incollaggio e la sigillatura di componenti elettronici, componenti strutturali e collegamenti elettrici.
Gli adesivi elettronici trovano applicazione in diversi modi cruciali durante la produzione di automobili:
- Incollaggio e sigillatura di componenti elettronici:Gli adesivi elettronici incollano e riempiono dettagli elettronici come sensori, sistemi di controllo e display. Gli adesivi elettronici garantiscono che questi componenti possano funzionare correttamente, anche se sottoposti a condizioni estreme.
- Incollaggio e sigillatura di componenti strutturali:Gli adesivi elettronici incollano e riempiono elementi strutturali, come i pannelli della carrozzeria e il telaio. L'utilizzo di adesivi elettronici garantisce che i componenti dell'auto rimangano saldamente fissati, anche se sottoposti alle sollecitazioni della guida quotidiana.
- Conduttività elettrica: Le case automobilistiche utilizzano adesivi elettronici per garantire una conduttività elettrica affidabile tra i componenti dell'auto. I collegamenti elettrici sicuri tra le parti sono particolarmente cruciali nei veicoli ibridi ed elettrici, in quanto garantiscono il funzionamento sicuro ed efficiente dell'auto.
- Resistenza alle vibrazioni:EI progettisti creano adesivi elettronici che assorbono vibrazioni e urti, impedendo che i componenti si allentino o si guastino. Prevenire che gli elementi si allentino o muoiano è essenziale nei veicoli ad alte prestazioni, dove le parti sono sottoposte a forti sollecitazioni.
- Protezione dell'ambiente:I progettisti creano adesivi elettronici per proteggere i componenti da fattori ambientali come umidità, polvere e altri agenti che possono danneggiarli o degradarli. I legami elettronici garantiscono che le parti rimangano affidabili e operative per tutta la vita del veicolo.
Le case automobilistiche utilizzano anche adesivi elettronici durante il processo di produzione, oltre alle loro applicazioni critiche. Le case automobilistiche utilizzano adesivi elettronici per incollare e sigillare materiali compositi, come la fibra di carbonio, che sono sempre più comuni nella moderna costruzione di automobili. L'utilizzo di materiali compositi si traduce in veicoli più leggeri, più resistenti e più efficienti in termini di consumo di carburante, ma richiede anche sistemi adesivi specializzati per garantire che i componenti siano correttamente incollati e sigillati.
Industria aerospaziale: come gli adesivi elettronici garantiscono la sicurezza negli aerei
L'industria aerospaziale è una delle industrie più complesse ed esigenti del mondo. La sicurezza dei passeggeri e dei membri dell'equipaggio a bordo degli aeromobili è fondamentale e qualsiasi guasto nei materiali o nei componenti utilizzati nella costruzione degli aeromobili può avere conseguenze catastrofiche. Produttori, progettisti e ingegneri non possono sopravvalutare l'importanza degli adesivi elettronici per garantire la sicurezza degli aerei.
Gli adesivi elettronici sono ampiamente utilizzati nell'industria aerospaziale per varie applicazioni. Sono utilizzati per incollare e sigillare componenti elettronici, come sensori e sistemi di controllo, per garantire che funzionino correttamente in condizioni estreme. Inoltre collegano e sigillano elementi strutturali, come ali e sezioni di fusoliera, per garantire che rimangano saldamente in posizione durante il volo.
Una delle principali preoccupazioni nella costruzione di aeromobili è l'impatto dell'umidità e di altri fattori ambientali sull'integrità dei componenti. I progettisti creano adesivi elettronici in grado di resistere a sollecitazioni ambientali, come sbalzi di temperatura estremi e umidità elevata, che possono compromettere le prestazioni del velivolo. I progettisti progettano anche adesivi elettronici per offrire una protezione duratura contro la corrosione, un problema significativo negli aerei esposti ad ambienti corrosivi come l'acqua salata.
Anche gli adesivi elettronici svolgono un ruolo cruciale nel processo di fabbricazione degli aerei. Gli adesivi elettronici incollano e sigillano i materiali compositi, come la fibra di carbonio, stanno diventando sempre più comuni nella moderna costruzione di aeromobili. L'utilizzo di materiali compositi si traduce in velivoli più leggeri, più resistenti e più efficienti in termini di consumo di carburante, ma richiede anche sistemi adesivi specializzati per garantire che i componenti siano correttamente incollati e sigillati.
Oltre a servire per scopi strutturali e protettivi, l'industria aerospaziale impiega adesivi elettronici per la conducibilità elettrica. Sono utilizzati per incollare e sigillare circuiti e componenti elettronici, assicurandone il corretto funzionamento e l'affidabilità. Gli adesivi elettronici garantiscono che i collegamenti elettrici del velivolo rimangano sicuri, riducendo al minimo il rischio di guasti elettrici.
Industria medica: il ruolo degli adesivi nei dispositivi medici
L'industria medica fa affidamento sulla tecnologia per fornire trattamenti ai pazienti efficaci ed efficienti. I dispositivi medici sono fondamentali per la diagnosi, il trattamento e il monitoraggio di varie condizioni mediche. Gli adesivi sono essenziali per i dispositivi medici, offrendo un modo affidabile e sicuro per unire i componenti e garantire la funzionalità del dispositivo. Qui esploreremo il ruolo degli adesivi nei dispositivi medici.
Ecco alcuni dei modi in cui gli adesivi svolgono un ruolo cruciale nei dispositivi medici:
- Incollaggio: Gli adesivi vengono utilizzati per unire insieme i componenti dei dispositivi medici, assicurando che rimangano in posizione e funzionino come previsto. Il corretto posizionamento e funzionamento dei componenti è fondamentale in dispositivi come pacemaker e pompe per insulina poiché può essere una questione di vita o di morte, rendendo gli adesivi elettronici essenziali per garantire un posizionamento sicuro e un funzionamento affidabile.
- Guarnizione: I produttori di dispositivi medici utilizzano adesivi per sigillare i dispositivi e prevenire perdite e contaminazioni. Ad esempio, nei cateteri e nelle linee IV, i sigillanti vengono utilizzati per sigillare la connessione tra il dispositivo e la pelle del paziente, impedendo l'ingresso di batteri.
- Durabilità:I dispositivi medici devono essere sufficientemente durevoli da resistere alle sollecitazioni dell'uso quotidiano. Gli adesivi svolgono un ruolo cruciale nel garantire la durata dei dispositivi medici fornendo un legame solido e duraturo tra i componenti.
- Biocompatibilità: Gli adesivi utilizzati nei dispositivi medici devono essere biocompatibili, il che significa che sono sicuri da usare nel corpo umano e non causano danni o irritazioni. I produttori devono utilizzare adesivi testati e approvati per l'uso nei dispositivi medici.
- Flessibilità: Alcuni dispositivi medici devono essere conformi alla forma del corpo. I produttori utilizzano adesivi per incollare componenti flessibili preservando la flessibilità del dispositivo.
Elettronica di consumo: garantire la durata nei dispositivi di tutti i giorni
L'elettronica di consumo è diventata una parte essenziale della nostra vita quotidiana e ci affidiamo a loro per tutto, dalla comunicazione all'intrattenimento. Con un utilizzo così intenso, la durabilità è un fattore critico per garantire che i nostri dispositivi possano resistere all'usura dell'uso quotidiano. Qui esploreremo alcuni modi in cui i produttori possono garantire la durata nell'elettronica di consumo.
- Design robusto: Uno dei fattori essenziali per garantire la durata nell'elettronica di consumo è il design. I produttori devono creare dispositivi con materiali e componenti solidi in grado di resistere alle sollecitazioni dell'uso quotidiano. Dovrebbero anche considerare i fattori di resistenza all'acqua, alle cadute e ai graffi.
- Test:I test sono una parte essenziale per garantire la durata nell'elettronica di consumo. I produttori dovrebbero condurre test rigorosi dei loro dispositivi per garantire che possano resistere a diverse condizioni ambientali e scenari di utilizzo. I produttori possono eseguire vari test, tra cui resistenza all'acqua, resistenza alle cadute, resistenza alla temperatura e altro ancora, per garantire la durata e l'affidabilità dei prodotti.
- Controllo di qualità: Il controllo di qualità è fondamentale per garantire che ogni dispositivo soddisfi gli standard di durata del produttore. I produttori dovrebbero disporre di un rigoroso processo di controllo della qualità per identificare difetti o problemi che potrebbero influire sulla durata del dispositivo.
- Riparazione e manutenzione: I consumatori dovrebbero anche essere in grado di riparare e mantenere facilmente i propri elettrodomestici. I produttori dovrebbero progettare dispositivi facili da smontare e rimontare, con parti di ricambio prontamente disponibili. Conducendo questi test, i produttori assicurano che i consumatori possano mantenere le buone condizioni di lavoro dei loro dispositivi più a lungo.
- Istruzione dell'utente: Infine, i produttori dovrebbero istruire i consumatori su come utilizzare i propri dispositivi per promuovere la durabilità. I produttori possono includere istruzioni sulla corretta pulizia e manutenzione della macchina e informazioni su come evitare cause comuni di danni, come la caduta o l'esposizione del dispositivo all'acqua.
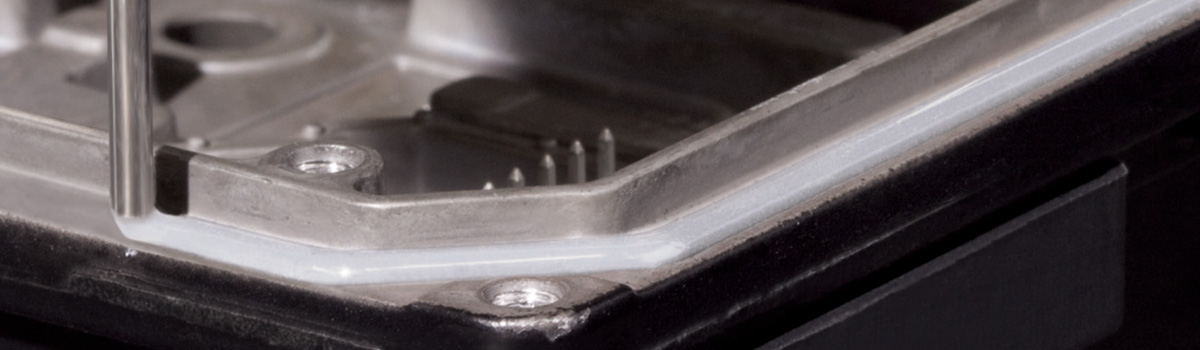
Il futuro degli adesivi elettronici: tendenze emergenti e innovazioni
Mentre la tecnologia continua ad evolversi a un ritmo senza precedenti, anche il futuro degli adesivi elettronici si sta trasformando. Le tendenze e le innovazioni emergenti stanno plasmando il settore, offrendo nuove possibilità ai produttori di dispositivi elettronici per migliorare le prestazioni e la durata dei loro prodotti. Questo post sul blog esplorerà alcuni degli sviluppi più promettenti negli adesivi elettronici e il loro potenziale impatto.
Ecco alcune delle tendenze emergenti e delle innovazioni nel campo degli adesivi elettronici:
- Adesivi ad alta conducibilità termica:Con la crescente domanda di dispositivi elettronici ad alta potenza, vi è una crescente necessità di adesivi in grado di dissipare efficacemente il calore. Gli adesivi ad alta conduttività termica offrono una soluzione migliorando la gestione termica e consentendo prestazioni più elevate.
- Adesivi flessibili:I sigillanti flessibili stanno diventando sempre più popolari nell'elettronica flessibile, nei dispositivi indossabili e nelle applicazioni mediche. Questi adesivi offrono flessibilità, resistenza e durata, rendendoli ideali per strumenti che si piegano, si torcono o si adattano a varie forme.
- Adesivi ecologici:Con le preoccupazioni ambientali che diventano sempre più importanti, c'è una crescente necessità di adesivi ecologici e sostenibili. Le innovazioni in questo settore includono legami realizzati con materiali rinnovabili come gomma naturale e colle che possono essere facilmente riciclate o riutilizzate.
- Miniaturizzazione: Poiché le dimensioni dei dispositivi elettronici continuano a ridursi, vi è la necessità di adesivi in grado di tenere il passo con la tendenza. I sigillanti miniaturizzati con elevata forza di adesione stanno diventando sempre più popolari, consentendo dispositivi più piccoli e compatti.
- Adesivi innovativi:Gli sviluppatori creano adesivi innovativi con caratteristiche di autoriparazione, memoria di forma e conduttività. Questi adesivi consentono ai produttori di dispositivi elettronici di sviluppare prodotti più intelligenti e reattivi.
Tendenze e innovazioni future nella tecnologia degli adesivi elettronici
La tecnologia degli adesivi elettronici è in continua evoluzione e stanno emergendo nuove tendenze e innovazioni per soddisfare le mutevoli esigenze dell'industria elettronica. Ecco alcune delle tendenze e innovazioni future nella tecnologia degli adesivi elettronici:
- Miniaturizzazione:Man mano che l'elettronica diventa più piccola e compatta, aumenta la domanda di adesivi in grado di funzionare su microscala. Gli adesivi in grado di unire componenti piccoli e delicati senza danneggiarli stanno diventando sempre più critici.
- Adesivi conduttivi: I produttori di elettronica utilizzano sempre più adesivi conduttivi come alternativa alla saldatura. I vantaggi includono temperature di esercizio inferiori, processi di assemblaggio semplificati e maggiore affidabilità.
- Gestione termica: Con l'aumento della densità di potenza dei dispositivi elettronici, la dissipazione del calore è diventata una sfida critica. Gli adesivi in grado di allontanare il calore dai componenti sono essenziali per migliorare la longevità e l'affidabilità dei dispositivi elettronici.
- Adesivi flessibili: Man mano che l'elettronica diventa più flessibile e indossabile, gli adesivi flessibili stanno diventando più critici. Questi adesivi possono resistere alla flessione e alla torsione senza incrinarsi, assicurando che i componenti elettronici rimangano incollati anche sotto stress.
- Adesivi ecocompatibili:Poiché la sostenibilità diventa sempre più importante, c'è una crescente domanda di adesivi ecologici. Gli adesivi realizzati con materiali biodegradabili o riciclati stanno diventando sempre più comuni.
- Adesivi innovativi:I ricercatori stanno sviluppando adesivi intelligenti in grado di modificare le proprie proprietà in risposta a stimoli esterni come la temperatura o la luce. Questi adesivi hanno potenziali applicazioni in sensori, attuatori e altri dispositivi elettronici.
Sfide comuni affrontate quando si utilizza l'adesivo elettronico e come superarle
Gli adesivi elettronici sono un componente essenziale nella produzione di dispositivi elettronici, ma possono anche presentare diverse sfide. Ecco alcune delle sfide comuni affrontate quando si utilizza l'adesivo elettronico e come superarle:
- Scarsa adesione:Una scarsa adesione può verificarsi quando l'adesivo non aderisce correttamente al substrato, causando il cedimento dei componenti. La soluzione è assicurarsi che la superficie sia pulita e priva di contaminanti prima di applicare l'adesivo. Inoltre, l'utilizzo di un primer o di un trattamento superficiale può migliorare l'adesione dell'incollaggio.
- Tempo di indurimento:Gli adesivi possono richiedere molto tempo per polimerizzare, causando ritardi nella produzione. La soluzione è utilizzare adesivi a polimerizzazione rapida o ottimizzare le condizioni di polimerizzazione, come temperatura e umidità, per accelerare il processo.
- Sensibilità all'umidità:Gli adesivi sensibili all'umidità possono degradarsi se esposti all'umidità, causando una perdita di adesione e prestazioni elettriche. La soluzione è utilizzare adesivi resistenti all'umidità o conservare e maneggiare correttamente la colla, ad esempio conservandola in un ambiente asciutto e utilizzando imballaggi sigillati.
- Dilatazione termica: Gli adesivi possono subire dilatazioni e contrazioni termiche, con conseguenti sollecitazioni meccaniche e guasti dei componenti. La soluzione è utilizzare adesivi con un basso coefficiente di dilatazione termica o progettare un sistema elettronico per adattarsi all'espansione e alla contrazione termica.
- Compatibilità: Gli adesivi possono essere incompatibili con determinati materiali, come plastica o metalli, causando una scarsa adesione o una reazione chimica. La soluzione è utilizzare adesivi compatibili con i materiali nel sistema elettronico o eseguire test di compatibilità prima di applicare la colla.
L'erogazione di adesivi può essere impegnativa, soprattutto quando si tratta di componenti piccoli e delicati. Possiamo risolvere il problema utilizzando apparecchiature di erogazione di precisione o pellicole o nastri adesivi prefabbricati che le persone possono facilmente applicare alle parti.
Il ruolo degli adesivi elettronici nella tecnologia indossabile
La tecnologia indossabile è diventata sempre più popolare nell'ultimo decennio, con una vasta gamma di dispositivi ora disponibili per i consumatori. Questi dispositivi, come smartwatch e fitness tracker, si basano su componenti elettronici che devono essere fissati saldamente al dispositivo indossabile. In situazioni che richiedono un legame forte e affidabile di componenti elettronici, gli adesivi elettronici svolgono un ruolo cruciale.
I produttori utilizzano adesivi elettronici per incollare sensori, LED, batterie e altri componenti ai dispositivi indossabili, assicurandosi che funzionino correttamente e rimangano durevoli. Questi adesivi devono resistere alle sollecitazioni dell'uso quotidiano, inclusa l'esposizione all'umidità, al calore e all'impatto fisico. Con la tecnologia indossabile, devono anche essere flessibili per consentire la flessione e l'allungamento.
Uno dei principali vantaggi degli adesivi elettronici nella tecnologia indossabile è la loro capacità di fornire un aspetto uniforme e aerodinamico. Se non ci fossero legami, i produttori dovrebbero utilizzare viti o altri elementi di fissaggio meccanici per fissare i componenti, il che potrebbe aumentare il peso e le dimensioni del dispositivo. D'altra parte, i produttori possono applicare gli adesivi in uno strato sottile e uniforme quasi invisibile a occhio nudo.
Un'altra considerazione importante nella scelta degli adesivi elettronici per la tecnologia indossabile è la biocompatibilità. Per garantire che i dispositivi indossabili non causino irritazioni o reazioni allergiche se indossati direttamente contro la pelle, i produttori devono utilizzare colla non irritante e ipoallergenica. Per i dispositivi medici indossabili, come i monitor del glucosio o dell'ECG utilizzati da persone con condizioni di salute specifiche, è particolarmente importante garantire che l'adesivo non provochi irritazioni o reazioni allergiche, dato il loro contatto diretto con la pelle.
Con la continua evoluzione della tecnologia indossabile, la domanda di adesivi elettronici in grado di soddisfare le esigenze specifiche di questi dispositivi continuerà a crescere. I produttori di adesivi stanno già sviluppando nuove formulazioni in grado di resistere a temperature estreme, resistere all'umidità e fornire una maggiore flessibilità. Di conseguenza, la tecnologia indossabile diventerà ancora più comoda, affidabile e funzionale.
Tecniche di erogazione per adesivi elettronici: suggerimenti e best practice
Gli adesivi elettronici sono essenziali nella produzione di dispositivi elettronici. Tuttavia, erogarli può essere un compito impegnativo, soprattutto quando si tratta di parti piccole e complesse. Ecco alcuni suggerimenti e best practice per l'erogazione di adesivi elettronici:
- Scegli il metodo di erogazione corretto: Sono disponibili diversi metodi di erogazione per gli adesivi elettronici, tra cui l'erogazione manuale, l'erogazione con siringa e l'erogazione automatica. Scegli il modo più adatto alla tua applicazione.
- Utilizzare la punta di erogazione corretta: La punta di erogazione deve corrispondere alla viscosità dell'adesivo e alle dimensioni della parte incollata. Informazioni minori sono ideali per porzioni più piccole, mentre informazioni più considerevoli sono adatte per dettagli più importanti.
- Erogare in un ambiente pulito: Un ambiente pulito previene la contaminazione e garantisce un forte legame. Utilizzare un'area di lavoro pulita e indossare guanti per evitare che gli oli della pelle penetrino nell'adesivo.
- Garantire una corretta conservazione: La corretta conservazione è fondamentale per la longevità degli adesivi elettronici. Mantieni gli oggetti puliti e asciutti e chiudi ermeticamente il contenitore.
- Applicare l'adesivo in modo uniforme:Assicurarsi che l'adesivo sia applicato in modo uniforme per evitare sacche d'aria, che possono indebolire il legame. Usa una mano ferma e applica la colla con un movimento continuo.
- Controlla la portata: È necessario controllare la portata dell'adesivo per evitare che la colla in eccesso fuoriesca e crei disordine. Utilizzare una portata lenta e costante, specialmente quando si lavora con piccole parti.
- Pulire regolarmente la punta di erogazione:Pulire regolarmente la punta di erogazione per evitare ostruzioni e garantire un flusso regolare di adesivo. Utilizzare una soluzione detergente appropriata e seguire le istruzioni del produttore.
- Praticare le precauzioni di sicurezza:I produttori utilizzano spesso sostanze chimiche negli adesivi elettronici che possono comportare rischi per la salute. Utilizzare indumenti protettivi come guanti e occhiali quando li si maneggia.
Seguendo questi suggerimenti e le migliori pratiche, puoi erogare con successo adesivi elettronici e garantire un forte legame per i tuoi dispositivi elettronici.
Conclusione
In conclusione, gli adesivi elettronici svolgono un ruolo fondamentale nella tecnologia moderna. Sono essenziali per creare legami affidabili e duraturi tra i componenti elettronici, proteggendoli da fattori ambientali quali umidità, calore e vibrazioni. Gli adesivi elettronici consentono anche la miniaturizzazione dei dispositivi elettronici, rendendoli più piccoli e più portatili.
Man mano che la tecnologia continua ad avanzare, gli adesivi elettronici diventeranno ancora più critici. Dovranno tenere il passo con la crescente domanda di dispositivi elettronici più robusti e compatti, affrontando al contempo le preoccupazioni sulla sostenibilità e l'impatto ambientale.
Inoltre, gli adesivi elettronici devono soddisfare i requisiti specifici di diversi settori e applicazioni, dai dispositivi medici all'elettronica automobilistica, ai sistemi aerospaziali e di difesa. Pertanto, la ricerca e lo sviluppo continui in questo campo saranno necessari per soddisfare queste mutevoli esigenze.