Adesivo per collegamento elettrico
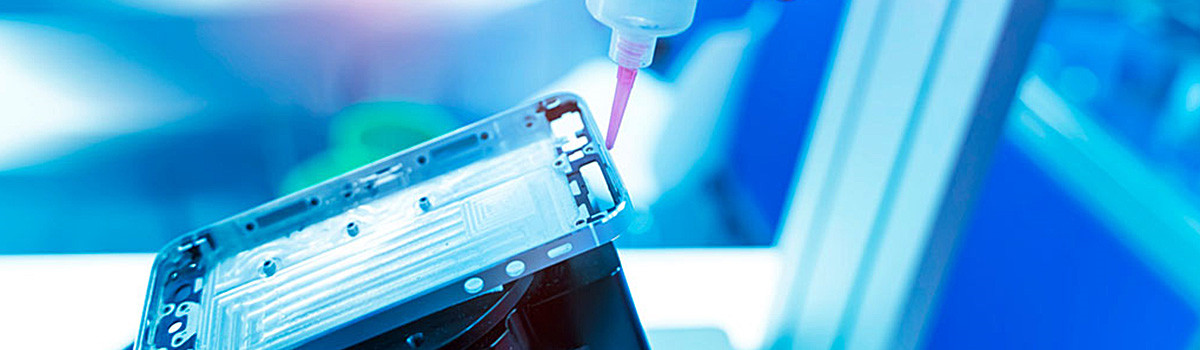
Gli adesivi per l'incollaggio elettrico sono adesivi specializzati utilizzati per l'incollaggio e la sigillatura di applicazioni elettriche. Loro forniscono:
- Eccellente conduttività elettrica e stabilità termica.
- Rendendoli ideali per dispositivi elettronici.
- Componenti automobilistici.
- Applicazioni aerospaziali.
Questi adesivi svolgono un ruolo cruciale nel garantire la sicurezza e l'affidabilità dei sistemi elettrici fornendo un legame sicuro e prevenendo la formazione di archi elettrici o scintille.
Cosa sono gli adesivi per il collegamento elettrico?
Gli adesivi per il collegamento elettrico sono adesivi specializzati utilizzati nelle applicazioni elettriche ed elettroniche per creare un legame sicuro tra diversi componenti conduttivi. Questi adesivi sono progettati per fornire collegamenti elettrici affidabili, garantire la messa a terra e proteggere dalle interferenze elettromagnetiche (EMI). Sono cruciali in vari settori, tra cui quello automobilistico, aerospaziale, delle telecomunicazioni e dell'elettronica di consumo.
La funzione principale degli adesivi per il collegamento elettrico è stabilire un percorso a bassa resistenza tra due o più superfici conduttive, come componenti metallici o circuiti stampati. Questo percorso consente il trasferimento efficiente della corrente elettrica, aiuta a prevenire le scariche statiche e riduce il rischio di guasti elettrici. Creando un solido legame, questi adesivi offrono anche supporto meccanico e migliorano la durata complessiva dei componenti assemblati.
Diverse caratteristiche vitali rendono gli adesivi per l'incollaggio elettrico adatti alle applicazioni previste. In primo luogo, hanno un'eccellente conducibilità elettrica, il che significa che possono condurre l'elettricità in modo efficace, riducendo al minimo la resistenza e garantendo una connessione affidabile. I riempitivi conduttivi come argento, rame o grafite sono spesso incorporati nella formulazione dell'adesivo per migliorare la conduttività.
In secondo luogo, gli adesivi per il collegamento elettrico hanno tipicamente buone proprietà di conduttività termica. Ciò consente loro di dissipare il calore generato dai componenti elettrici, prevenendo il surriscaldamento e potenziali danni ai dispositivi elettronici sensibili.
Inoltre, questi adesivi sono formulati per avere un'elevata resistenza e integrità del legame. Possono sopportare sollecitazioni meccaniche, vibrazioni e cicli termici senza compromettere il collegamento elettrico. Questo è fondamentale, specialmente nelle applicazioni in cui i componenti incollati possono essere esposti a condizioni ambientali difficili.
Gli adesivi per il collegamento elettrico sono disponibili in varie forme, tra cui paste, pellicole, nastri o liquidi. La scelta dell'adesivo dipende da fattori quali i requisiti dell'applicazione, il tipo di materiali da incollare e il processo di assemblaggio. Ad esempio, pellicole o nastri adesivi conduttivi sono comunemente usati per assemblare circuiti flessibili. Al contrario, gli adesivi in pasta conduttiva sono spesso utilizzati per incollare componenti a montaggio superficiale su circuiti stampati.
Oltre a fornire un collegamento elettrico e meccanico, alcuni adesivi offrono proprietà di schermatura EMI. Contengono riempitivi conduttivi che creano una barriera conduttiva, impedendo alle radiazioni elettromagnetiche di interferire con il funzionamento dei componenti elettronici vicini.
Una corretta preparazione della superficie è fondamentale quando si utilizzano adesivi per l'incollaggio elettrico per garantire forza e prestazioni ottimali dell'incollaggio. Le superfici devono essere accuratamente pulite, prive di contaminanti e, in alcuni casi, potrebbe essere necessaria l'attivazione della superficie o l'applicazione di primer per migliorare l'adesione.
Gli adesivi per il collegamento elettrico sono essenziali nella moderna produzione elettrica ed elettronica. Consentono connessioni elettriche affidabili ed efficienti offrendo al contempo supporto meccanico e protezione contro le interferenze elettromagnetiche. Con i continui progressi nei materiali e nelle tecnologie adesive, questi adesivi svolgono un ruolo fondamentale nello sviluppo di dispositivi e sistemi elettronici innovativi e affidabili.
Tipi di adesivi per il collegamento elettrico
Gli adesivi per il collegamento elettrico creano connessioni elettriche sicure e affidabili tra componenti conduttivi. Questi adesivi sono progettati per fornire un'eccellente conduttività elettrica offrendo allo stesso tempo forti proprietà di legame meccanico. Ecco alcuni tipi comuni di adesivi per il collegamento elettrico:
- Adesivi epossidici conduttivi: gli adesivi epossidici conduttivi sono ampiamente utilizzati nelle applicazioni di collegamento elettrico. Sono costituiti da un sistema in due parti, tipicamente una resina e un indurente, che devono essere miscelati prima dell'uso. Questi adesivi contengono riempitivi conduttivi, come argento, rame o grafite, che consentono il flusso di corrente elettrica. Gli adesivi epossidici conduttivi offrono un'eccellente adesione a vari substrati, fornendo conduttività elettrica e resistenza meccanica.
- Nastri adesivi elettricamente conduttivi: i nastri adesivi elettricamente conduttivi sono costituiti da un materiale di supporto rivestito con un adesivo che contiene particelle conduttive. Il materiale di supporto fornisce supporto meccanico e isolamento, mentre l'adesivo conduttivo garantisce la continuità elettrica. Questi nastri sono facili da applicare, versatili e possono adattarsi a superfici irregolari. Sono comunemente usati per collegare circuiti flessibili, applicazioni di messa a terra e schermatura EMI/RFI.
- Adesivi conduttivi all'argento: gli adesivi conduttivi all'argento sono formulati con particelle d'argento sospese in una matrice polimerica. L'argento è un ottimo conduttore di elettricità, offrendo un'elevata conduttività elettrica. Questi adesivi forniscono una forte adesione a vari substrati, inclusi metalli, ceramica e plastica. Sono comunemente usati nell'assemblaggio elettronico, nell'incollaggio di componenti elettrici e nella riparazione di circuiti elettrici.
- Adesivi siliconici elettricamente conduttivi: gli adesivi siliconici elettricamente conduttivi sono formulati con polimeri siliconici e riempitivi conduttivi, come argento, nichel o carbonio. Offrono una buona conduttività elettrica, flessibilità e stabilità termica. Questi adesivi sono spesso utilizzati in applicazioni che richiedono flessibilità e resistenza ambientale, come l'incollaggio di circuiti flessibili, la sigillatura di connettori e l'invasatura di componenti elettronici.
- Adesivi poliuretanici elettricamente conduttivi: gli adesivi poliuretanici elettricamente conduttivi sono progettati per fornire sia conduttività elettrica che forti proprietà di adesione. Sono formulati con polimeri poliuretanici e cariche conduttive, come particelle di carbonio o metalliche. Questi adesivi offrono una buona adesione a vari substrati, resistenza ai fattori ambientali e durata. Sono comunemente usati nella produzione elettronica, nelle applicazioni di messa a terra e nell'incollaggio di materiali diversi.
- Adesivi istantanei conduttivi: gli adesivi istantanei conduttivi, noti anche come adesivi cianoacrilici, sono adesivi monocomponenti che polimerizzano rapidamente a contatto con l'umidità. Questi adesivi, come particelle di metallo o grafite, contengono riempitivi conduttivi che forniscono conduttività elettrica. Offrono un incollaggio rapido e un'elevata resistenza, rendendoli adatti per applicazioni che richiedono un montaggio rapido e buone prestazioni elettriche.
È importante notare che la scelta dell'adesivo per il collegamento elettrico dipende dai requisiti specifici dell'applicazione, come i materiali del substrato, le condizioni ambientali e la conduttività elettrica desiderata. La consulenza con produttori di adesivi o esperti del settore può aiutare a selezionare l'adesivo più appropriato per una particolare applicazione.
Adesivi conduttivi e non conduttivi
Gli adesivi conduttivi e non conduttivi sono due categorie distinte utilizzate in varie applicazioni e la differenza principale tra loro risiede nelle loro proprietà di conduttività elettrica. Ecco una panoramica degli adesivi conduttivi e non conduttivi:
Adesivi conduttivi: Gli adesivi conduttivi sono formulati per consentire il flusso di corrente elettrica. Contengono cariche conduttive, come particelle metalliche o di carbonio, che forniscono conduttività elettrica. Gli adesivi conduttivi sono comunemente usati nelle applicazioni in cui è richiesta la continuità elettrica. Alcune caratteristiche chiave degli adesivi conduttivi includono:
- Conduttività elettrica: gli adesivi conduttivi offrono un'eccellente conducibilità elettrica grazie alla presenza di riempitivi conduttivi. Possono creare connessioni elettriche affidabili tra componenti conduttivi, come l'incollaggio di tracce elettriche su circuiti stampati o applicazioni di messa a terra.
- Incollaggio e resistenza meccanica: gli adesivi conduttivi forniscono conduttività elettrica e proprietà meccaniche solide di adesione. Possono creare legami robusti tra i substrati, garantendo l'integrità strutturale e l'affidabilità a lungo termine.
- Flessibilità dell'applicazione: gli adesivi conduttivi sono disponibili in varie forme, tra cui resina epossidica, silicone e poliuretano, offrendo flessibilità per quanto riguarda i metodi di applicazione e i substrati. Possono essere erogati come liquidi, pellicole o paste, consentendo versatilità in diversi processi di assemblaggio.
- Schermatura EMI/RFI: gli adesivi conduttivi sono spesso utilizzati per schermare le interferenze elettromagnetiche (EMI) e le interferenze di radiofrequenza (RFI). Possono creare percorsi conduttivi, riducendo efficacemente al minimo l'impatto delle radiazioni elettromagnetiche sui componenti elettronici sensibili.
Adesivi non conduttivi: Gli adesivi non conduttivi o isolanti non conducono elettricità e sono formulati per fornire isolamento elettrico tra componenti o substrati. Gli adesivi non conduttivi sono ampiamente utilizzati nelle applicazioni in cui è richiesto l'isolamento elettrico. Ecco alcune caratteristiche critiche degli adesivi non conduttivi:
- Isolamento elettrico: gli adesivi non conduttivi hanno un'elevata resistività, impedendo il flusso di corrente elettrica. Sono utilizzati per creare barriere elettriche, isolando i componenti l'uno dall'altro o dall'ambiente circostante.
- Rigidità dielettrica: gli adesivi non conduttivi presentano un'elevata rigidità dielettrica, che può sopportare sollecitazioni elettriche senza guasti. Questa proprietà è fondamentale nelle applicazioni con tensioni elevate, come l'elettronica di potenza o l'isolamento elettrico.
- Stabilità termica: gli adesivi non conduttivi spesso possiedono un'eccellente stabilità termica, che consente loro di mantenere le loro proprietà di isolamento elettrico a temperature elevate. Questa caratteristica è essenziale nelle applicazioni in cui la dissipazione del calore è un problema.
- Resistenza ambientale: gli adesivi non conduttivi sono progettati per resistere a vari fattori ambientali, tra cui umidità, sostanze chimiche e fluttuazioni di temperatura. Offrono affidabilità a lungo termine in condizioni operative difficili.
Gli adesivi non conduttivi possono essere trovati in varie forme, come formulazioni epossidiche, acriliche o a base di silicone, fornendo flessibilità nell'applicazione e compatibilità con il substrato.
Vantaggi dell'utilizzo di adesivi per il collegamento elettrico
Gli adesivi per il collegamento elettrico offrono numerosi vantaggi nella creazione di collegamenti elettrici sicuri e affidabili. Ecco alcuni vantaggi chiave dell'utilizzo di adesivi per il collegamento elettrico:
- Conduttività elettrica: gli adesivi per il collegamento elettrico sono formulati per fornire un'eccellente conduttività elettrica. Consentono il flusso di corrente elettrica, garantendo collegamenti elettrici affidabili tra componenti conduttivi. Questo è fondamentale nelle applicazioni con continuità elettrica essenziale, come l'assemblaggio elettronico, il collegamento di circuiti stampati o le applicazioni di messa a terra.
- Forza di adesione: oltre alla conduttività elettrica, gli adesivi di unione offrono forti proprietà di adesione meccanica. Possono creare legami robusti e durevoli tra i substrati, migliorando l'integrità strutturale complessiva dell'assieme. Ciò è particolarmente importante nelle applicazioni in cui possono verificarsi vibrazioni, cicli termici o sollecitazioni meccaniche.
- Compatibilità con vari substrati: gli adesivi per l'incollaggio elettrico sono progettati per aderire a vari substrati, inclusi metalli, ceramica, plastica e compositi. Questa versatilità consente di collegare materiali diversi e semplifica il processo di assemblaggio. Elimina la necessità di ulteriori fissaggi meccanici, come viti o saldature, riducendo tempi e costi di assemblaggio.
- Distribuzione dello stress: gli adesivi per incollaggio distribuiscono lo stress in modo più uniforme nell'area incollata rispetto ad altri metodi di fissaggio. Possono dissipare le sollecitazioni e ridurre i punti di concentrazione, riducendo al minimo il rischio di guasti o crepe localizzate nell'assieme.
- Migliore dissipazione del calore: alcuni adesivi per il collegamento elettrico, come gli adesivi termicamente conduttivi, possono migliorare la dissipazione del calore nei dispositivi elettronici. Forniscono un percorso termicamente conduttivo tra i componenti che generano calore e i dissipatori di calore, consentendo un efficiente trasferimento del calore e una migliore gestione termica.
- Resistenza ambientale: gli adesivi per il collegamento elettrico sono formulati per resistere a vari fattori ambientali, tra cui fluttuazioni di temperatura, umidità, sostanze chimiche ed esposizione ai raggi UV. Offrono una buona resistenza all'invecchiamento e al degrado, garantendo affidabilità a lungo termine in diverse condizioni operative.
- Flessibilità di progettazione: gli adesivi offrono flessibilità di progettazione, consentendo l'incollaggio di forme complesse o superfici irregolari. Possono conformarsi ai contorni, colmare le lacune e creare forti legami in aree difficili da raggiungere, consentendo progetti più versatili ed efficienti.
- Soluzione conveniente: in molti casi, l'utilizzo di adesivi per l'incollaggio elettrico può essere conveniente rispetto ad altri metodi di incollaggio tradizionali. Eliminano la necessità di hardware aggiuntivo o complessi processi di assemblaggio, riducendo i costi di materiale e manodopera.
- Schermatura EMI/RFI: gli adesivi conduttivi possono fornire un'efficace schermatura contro le interferenze elettromagnetiche (EMI) e le interferenze in radiofrequenza (RFI). Creano percorsi conduttivi, riducendo al minimo l'impatto delle radiazioni elettromagnetiche sui componenti elettronici sensibili.
Nel complesso, gli adesivi per il collegamento elettrico offrono numerosi vantaggi, tra cui conduttività elettrica, forza del legame muscolare, compatibilità con vari substrati, distribuzione delle sollecitazioni, dissipazione del calore, resistenza ambientale, flessibilità di progettazione, economicità e schermatura EMI/RFI. Questi vantaggi li rendono una scelta importante per molte applicazioni elettriche ed elettroniche.
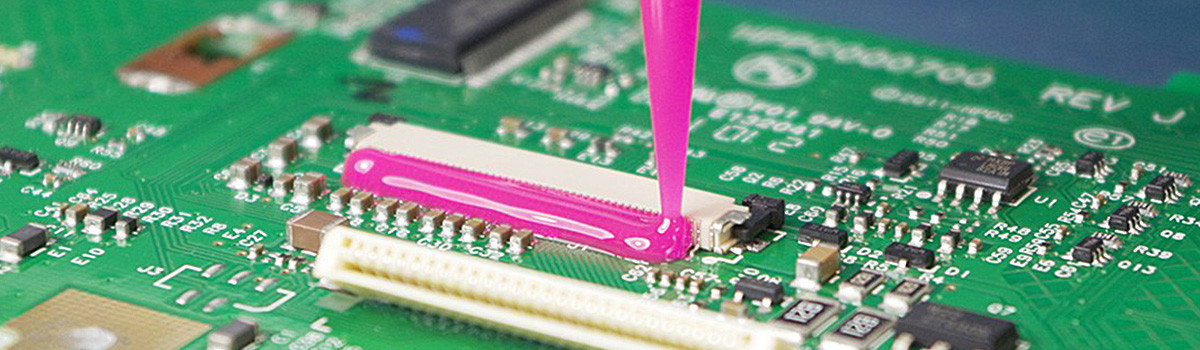
Applicazioni degli adesivi per il collegamento elettrico
Gli adesivi per il collegamento elettrico trovano numerose applicazioni in vari settori in cui sono richieste connessioni elettriche sicure e affidabili. Questi adesivi offrono proprietà uniche che li rendono adatti a molteplici applicazioni. Ecco alcune applicazioni tipiche degli adesivi per l'incollaggio elettrico:
- Produzione elettronica: gli adesivi per l'incollaggio elettrico svolgono un ruolo fondamentale nell'assemblaggio e nell'incollaggio di componenti elettronici. Creano connessioni elettriche tra circuiti stampati, conduttori di cavi di collegamento e collegano pezzi montati in superficie e dispositivi elettronici sensibili all'invasatura. Questi adesivi forniscono conduttività elettrica e forza di adesione meccanica, garantendo prestazioni dei dispositivi elettronici e durata a lungo termine.
- Industria automobilistica: l'industria automobilistica fa affidamento sugli adesivi per l'incollaggio elettrico per varie applicazioni. Sono utilizzati per il collegamento e la messa a terra di componenti elettrici, come sensori, connettori e cablaggi. Questi adesivi garantiscono connessioni elettriche sicure, resistono alle vibrazioni e ai cicli termici e forniscono resistenza ambientale nelle applicazioni automobilistiche.
- Aerospaziale e aeronautica: nei settori aerospaziale e aeronautico, gli adesivi per l'incollaggio elettrico sono fondamentali per l'incollaggio di componenti elettrici in aerei, satelliti e veicoli spaziali. Sono utilizzati per il collegamento di sistemi avionici, antenne, sensori e applicazioni di messa a terra. Questi adesivi devono offrire elevata affidabilità, durata e resistenza a variazioni estreme di temperatura e vibrazioni.
- Dispositivi medici: gli adesivi per il collegamento elettrico producono dispositivi e apparecchiature mediche. Sono utilizzati per l'incollaggio di elettrodi, connettori, sensori e cablaggi in varie applicazioni mediche, inclusi dispositivi di monitoraggio, apparecchiature diagnostiche e dispositivi impiantabili. Questi adesivi devono soddisfare severi requisiti di biocompatibilità, resistenza alla sterilizzazione e affidabilità a lungo termine.
- Energia rinnovabile: gli adesivi per l'incollaggio elettrico sono utilizzati nel settore delle energie rinnovabili, in particolare nella produzione di pannelli solari. Sono utilizzati per l'incollaggio e la messa a terra dei collegamenti elettrici all'interno dei pannelli solari, come l'incollaggio di celle solari, il collegamento di sbarre collettrici e il collegamento di cavi elettrici. Questi adesivi devono fornire conduttività elettrica affidabile, resistenza agli agenti atmosferici e durata a lungo termine in ambienti esterni.
- Telecomunicazioni: nel settore delle telecomunicazioni, gli adesivi per l'incollaggio elettrico vengono utilizzati per unire i collegamenti elettrici in dispositivi di comunicazione, antenne, connettori e componenti in fibra ottica. Questi adesivi assicurano connessioni elettriche sicure, schermatura EMI/RFI e resistenza a fattori ambientali, come umidità e variazioni di temperatura.
- Elettronica di consumo: gli adesivi per il collegamento elettrico assemblano l'elettronica di consumo, inclusi smartphone, tablet, laptop e dispositivi indossabili. Sono utilizzati per collegare componenti elettrici, collegare display, collegare circuiti flessibili e applicazioni di messa a terra. Questi adesivi forniscono conduttività elettrica affidabile, forza di adesione meccanica e flessibilità per adattarsi a progetti miniaturizzati.
- Apparecchiature industriali: gli adesivi per l'incollaggio elettrico trovano applicazione in varie apparecchiature industriali, come pannelli di controllo, sensori industriali, motori e trasformatori. Sono utilizzati per collegare collegamenti elettrici, componenti di messa a terra e schermatura EMI/RFI. Questi adesivi devono resistere ad ambienti industriali difficili, comprese temperature estreme, vibrazioni ed esposizione chimica.
Questi sono solo alcuni esempi dell'ampia gamma di applicazioni degli adesivi per l'incollaggio elettrico. La versatilità, l'affidabilità e le prestazioni di questi adesivi li rendono indispensabili nelle industrie in cui i collegamenti elettrici sicuri sono fondamentali per una funzionalità e una sicurezza ottimali.
Incollaggio e sigillatura nei dispositivi elettronici
L'incollaggio e la sigillatura sono due processi essenziali nell'assemblaggio e nella produzione di dispositivi elettronici e svolgono un ruolo cruciale nel garantire l'affidabilità, la funzionalità e la protezione dei componenti elettronici. Ecco una panoramica dell'incollaggio e della sigillatura nei dispositivi elettronici:
L'incollaggio si riferisce all'unione di due o più componenti mediante un materiale adesivo. Nei dispositivi elettronici, il collegamento viene utilizzato per vari scopi, tra cui collegamenti elettrici, supporto meccanico e gestione termica. Ecco alcuni aspetti critici del collegamento nei dispositivi elettronici:
- Connessioni elettriche: gli adesivi per l'incollaggio creano connessioni elettriche tra i componenti, come l'incollaggio di fili a piazzole su circuiti stampati o il collegamento di tracce conduttive. Questi adesivi forniscono conduttività elettrica, garantendo una continuità elettrica affidabile nel dispositivo.
- Attaccamento dei componenti: l'incollaggio collega i componenti ai circuiti stampati o ai substrati. I materiali adesivi includono adesivi epossidici o a base di silicone, componenti di fissaggio come dispositivi a montaggio superficiale (SMD), connettori, sensori o display. Ciò garantisce un'adesione sicura e meccanicamente forte dei componenti.
- Supporto strutturale: gli adesivi di fissaggio forniscono un supporto strutturale ai componenti elettronici. Creano forti legami che aiutano a resistere a sollecitazioni meccaniche, vibrazioni e cicli termici. Ciò è particolarmente importante per le caratteristiche che possono subire sollecitazioni meccaniche o forze esterne.
- Dissipazione del calore: nei dispositivi con dissipazione del calore critica, vengono utilizzati adesivi con proprietà di conduttività termica. Questi adesivi aiutano a trasferire il calore dai componenti che generano calore, come transistor di potenza o LED, ai dissipatori di calore o ad altre soluzioni di gestione termica.
Guarnizione: La sigillatura comporta l'applicazione di un materiale protettivo per impedire l'ingresso di umidità, polvere o altri contaminanti nei dispositivi elettronici. La sigillatura è essenziale per migliorare l'affidabilità e la longevità dei componenti e dei sistemi elettronici. Ecco alcuni aspetti critici della sigillatura dei dispositivi elettronici:
- Protezione ambientale: gli adesivi sigillanti, come i materiali a base di silicone, creano una barriera che protegge i componenti elettronici da umidità, umidità e contaminanti ambientali. Ciò è particolarmente importante per i dispositivi esposti ad ambienti difficili, come l'elettronica esterna o le applicazioni automobilistiche.
- Impermeabilità: la tenuta è fondamentale per ottenere la resistenza all'acqua o alla polvere nei dispositivi elettronici, specialmente in ambienti esterni o difficili. I materiali di tenuta vengono applicati a custodie, connettori o aperture per impedire la penetrazione di acqua o polvere, garantendo prestazioni e longevità del dispositivo.
- Resistenza chimica: gli adesivi sigillanti possono resistere all'esposizione chimica, proteggendo i componenti elettronici da sostanze corrosive o vapori chimici. Questo è importante nelle applicazioni in cui i dispositivi elettronici possono entrare in contatto con sostanze chimiche o ambienti aggressivi.
- Isolamento e proprietà dielettriche: i materiali di tenuta spesso possiedono eccellenti proprietà isolanti, fornendo isolamento elettrico tra componenti o tracce. Questo aiuta a prevenire cortocircuiti e guasti elettrici. Gli adesivi sigillanti con elevata rigidità dielettrica sono utilizzati in applicazioni che richiedono l'isolamento elettrico.
- Resistenza a vibrazioni e urti: gli adesivi sigillanti aiutano a migliorare la stabilità meccanica dei dispositivi elettronici fornendo resistenza a vibrazioni e urti. Impediscono l'allentamento o lo spostamento dei componenti interni a causa di sollecitazioni meccaniche, garantendo l'affidabilità a lungo termine del dispositivo.
L'incollaggio e la sigillatura sono processi cruciali nell'assemblaggio e nella produzione di dispositivi elettronici e garantiscono connessioni elettriche affidabili, stabilità meccanica, protezione da fattori ambientali e longevità dei dispositivi. La scelta dei materiali di incollaggio e sigillatura dipende dall'applicazione del dispositivo, dalle condizioni operative e dalle caratteristiche prestazionali desiderate.
Applicazioni Automotive
Gli adesivi per il collegamento elettrico hanno numerose applicazioni nell'industria automobilistica, dove svolgono un ruolo cruciale nel garantire collegamenti elettrici affidabili, integrità strutturale e prestazioni complessive. Ecco alcune applicazioni automobilistiche critiche di adesivi per il collegamento elettrico:
- Assemblaggio del cablaggio: i cablaggi sono componenti essenziali nei sistemi elettrici automobilistici che trasmettono segnali elettrici e potenza in tutto il veicolo. Gli adesivi per il collegamento elettrico fissano e proteggono i cablaggi, fornendo supporto meccanico, pressacavo e resistenza alle vibrazioni e alle fluttuazioni di temperatura. Questi adesivi garantiscono la longevità e l'affidabilità dei cablaggi in ambienti automobilistici difficili.
- Sensor Bonding: vari sensori sono impiegati nei sistemi automobilistici, inclusi sensori del motore, sensori di posizione e sensori di prossimità. Gli adesivi per il collegamento elettrico uniscono questi sensori alle loro posizioni di montaggio, fornendo un fissaggio sicuro e garantendo letture del sensore accurate e affidabili. Questi adesivi offrono stabilità meccanica, protezione dalle vibrazioni e resistenza alla temperatura e all'umidità.
- Incollaggio dei connettori: i connettori sono componenti critici nei sistemi elettrici automobilistici, poiché facilitano i collegamenti elettrici tra sottosistemi e componenti. Gli adesivi per il collegamento elettrico fissano i connettori ai circuiti stampati o ad altre superfici di montaggio, garantendo connessioni elettriche sicure e stabilità meccanica. Questi adesivi resistono agli urti, alle vibrazioni e ai cicli di temperatura, comuni nelle applicazioni automobilistiche.
- Unità di controllo elettronico (ECU): le ECU sono componenti centrali nei moderni sistemi automobilistici, responsabili del controllo di varie funzioni, come la gestione del motore, la frenata e i sistemi di sicurezza. Gli adesivi per il collegamento elettrico assemblano le ECU, fornendo collegamenti elettrici, supporto meccanico e protezione contro i fattori ambientali. Questi adesivi offrono un'eccellente conduttività elettrica, gestione termica e resistenza all'umidità, agli agenti chimici e alle variazioni di temperatura.
- Sistemi di illuminazione: i sistemi di illuminazione per autoveicoli, compresi i fari, le luci posteriori e l'illuminazione interna, richiedono un collegamento sicuro per i collegamenti elettrici e la stabilità meccanica. Gli adesivi per il collegamento elettrico collegano i componenti di illuminazione, come i LED, alle loro posizioni di montaggio, garantendo collegamenti elettrici affidabili e resistenza alle vibrazioni e ai cicli termici. Questi adesivi offrono un'elevata trasparenza, consentendo una trasmissione della luce ottimale e una lunga durata.
- Assemblaggio del pacco batteria: nei veicoli elettrici e ibridi, i pacchi batteria sono componenti critici che richiedono un collegamento sicuro per i collegamenti elettrici e l'integrità strutturale. Gli adesivi per il collegamento elettrico vengono utilizzati nell'assemblaggio del pacco batteria, fornendo proprietà di adesione e sigillatura per garantire conduttività elettrica affidabile, resistenza alle vibrazioni e protezione dall'umidità e dai cicli termici. Questi adesivi contribuiscono alla sicurezza e alle prestazioni delle batterie dei veicoli elettrici.
- Schermatura EMI/RFI: gli adesivi per il collegamento elettrico con proprietà conduttive vengono utilizzati per la schermatura delle interferenze elettromagnetiche (EMI) e delle interferenze in radiofrequenza (RFI) nelle applicazioni automobilistiche. Creano percorsi conduttivi, riducendo l'impatto delle radiazioni elettromagnetiche sui componenti elettronici sensibili. Gli adesivi di schermatura EMI/RFI vengono utilizzati in aree come moduli elettronici, antenne e cablaggi per garantire il corretto funzionamento dell'elettronica automobilistica.
- Incollaggio strutturale: in alcune applicazioni automobilistiche, gli adesivi per l'incollaggio elettrico vengono utilizzati per l'incollaggio strutturale. Forniscono una forte adesione tra diversi substrati, migliorando l'integrità strutturale complessiva dei componenti automobilistici. Gli adesivi per l'incollaggio strutturale, ad esempio, vengono utilizzati per l'incollaggio di pannelli della carrozzeria dei veicoli, staffe di rinforzo o materiali compositi per l'incollaggio, contribuendo alla riduzione del peso e al miglioramento delle prestazioni del veicolo.
Questi sono solo alcuni esempi dell'ampia gamma di applicazioni automobilistiche per gli adesivi per l'incollaggio elettrico. Le proprietà di questi adesivi, come la conduttività elettrica, la resistenza meccanica, la resistenza ambientale e la gestione termica, li rendono essenziali nell'assemblaggio e nelle prestazioni di sistemi e componenti elettrici automobilistici.
Applicazioni aerospaziali
Gli adesivi per l'incollaggio elettrico svolgono un ruolo fondamentale nelle applicazioni aerospaziali, dove vengono utilizzati per vari scopi, tra cui l'incollaggio elettrico, la messa a terra, l'incollaggio strutturale e la protezione da fattori ambientali. Ecco alcune applicazioni aerospaziali critiche di adesivi per il collegamento elettrico:
- Sistemi avionici: i sistemi avionici, compresi i sistemi di controllo del volo, i sistemi di comunicazione e i sistemi di navigazione, si basano su connessioni elettriche e messa a terra sicure. Gli adesivi per il collegamento elettrico fissano e mettono a terra i componenti all'interno degli involucri avionici, garantendo continuità elettrica affidabile, stabilità meccanica e protezione da vibrazioni, variazioni di temperatura e interferenze elettromagnetiche.
- Cablaggi e cablaggi per aeromobili: i cablaggi e i cablaggi per aeromobili sono reti complesse di cavi elettrici e connettori che trasmettono potenza e segnali in tutto l'aeromobile. Gli adesivi per il collegamento elettrico proteggono il cablaggio e i cablaggi, fornendo scarico della trazione, supporto meccanico e resistenza alle vibrazioni e ai fattori ambientali. Questi adesivi garantiscono la longevità e l'affidabilità dei collegamenti elettrici in ambienti aerospaziali esigenti.
- Montaggio dell'antenna: le antenne sono fondamentali nelle applicazioni aerospaziali, consentendo la comunicazione, la navigazione e la trasmissione dei dati. Gli adesivi per il collegamento elettrico fissano le antenne alle loro superfici di montaggio, fornendo un fissaggio sicuro, continuità elettrica e resistenza alle sollecitazioni meccaniche, alle vibrazioni e alle variazioni di temperatura. Questi adesivi contribuiscono alle prestazioni e alla durata dei sistemi di antenne aerospaziali.
- Incollaggio composito: le strutture aerospaziali incorporano sempre più materiali compositi che offrono un elevato rapporto resistenza/peso. Gli adesivi per il collegamento elettrico vengono utilizzati per i componenti compositi, come i pannelli della fusoliera, i sistemi alari e le superfici di controllo. Questi adesivi forniscono legami forti e durevoli, contribuendo all'integrità strutturale del velivolo e riducendone il peso.
- Elettronica per satelliti e veicoli spaziali: i satelliti e i veicoli spaziali richiedono collegamenti elettrici affidabili e protezione da condizioni spaziali difficili. Gli adesivi per il collegamento elettrico assemblano l'elettronica di satelliti e veicoli spaziali, come unità di controllo elettroniche, sensori e sistemi di comunicazione. Questi adesivi offrono conducibilità elettrica, stabilità meccanica, resistenza ai cicli termici e condizioni di vuoto e protezione contro le radiazioni.
- Protezione dai fulmini: i fulmini rappresentano un rischio significativo per gli aerei. Gli adesivi per il collegamento elettrico e i materiali conduttivi sono utilizzati nei sistemi di protezione contro i fulmini. Questi adesivi aiutano a creare percorsi conduttivi che incanalano in modo sicuro la corrente dei fulmini lontano dai componenti critici, riducendo il rischio di danni e garantendo la sicurezza del velivolo e dei suoi occupanti.
- Schermatura EMI/RFI: nelle applicazioni aerospaziali, la schermatura delle interferenze elettromagnetiche (EMI) e delle interferenze in radiofrequenza (RFI) è fondamentale per prevenire le interferenze con i sistemi elettronici sensibili. Gli adesivi per il collegamento elettrico con proprietà conduttive vengono utilizzati per la schermatura EMI/RFI. Forniscono un percorso conduttivo, riducendo l'impatto delle radiazioni elettromagnetiche sui componenti elettronici e garantendo la corretta funzionalità.
- Gestione termica: i sistemi aerospaziali devono spesso affrontare variazioni di temperatura estreme. Gli adesivi per l'incollaggio elettrico con proprietà di conduttività termica vengono utilizzati per un'efficace dissipazione del calore e gestione termica. Aiutano a trasferire il calore lontano dai componenti che generano calore, come l'elettronica di potenza o le interfacce termiche, per migliorare le prestazioni complessive e l'affidabilità dei sistemi aerospaziali.
Questi sono solo alcuni esempi dell'ampia gamma di applicazioni aerospaziali per gli adesivi per l'incollaggio elettrico. Le proprietà di questi adesivi, come la conduttività elettrica, la resistenza meccanica, la resistenza ambientale e la gestione termica, sono fondamentali per garantire l'affidabilità, la funzionalità e la sicurezza dei componenti e dei sistemi aerospaziali.
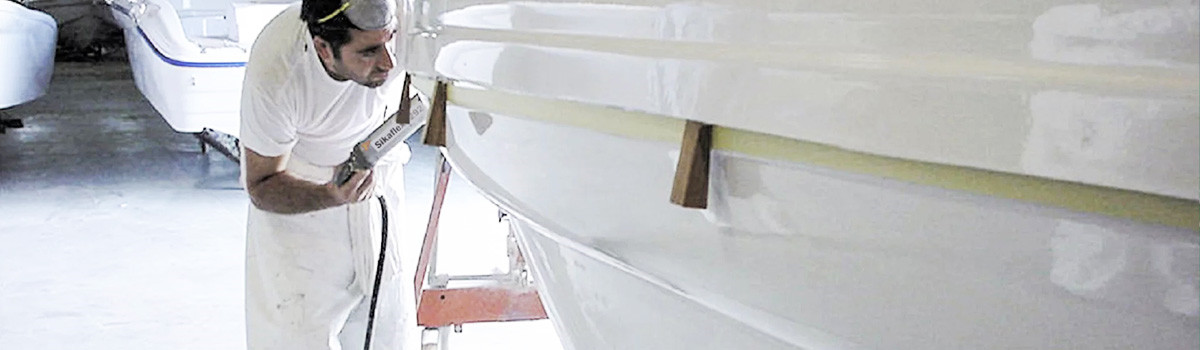
Applicazioni marine
Gli adesivi per l'incollaggio elettrico hanno applicazioni significative nell'industria navale, dove vengono utilizzati per vari scopi, tra cui l'incollaggio elettrico, la messa a terra, la protezione dalla corrosione e la sigillatura. Ecco alcune applicazioni marine critiche di adesivi per il collegamento elettrico:
- Collegamento elettrico e messa a terra: gli adesivi per il collegamento elettrico creano collegamenti elettrici e messa a terra affidabili nelle imbarcazioni marine. Collegano e fissano cavi elettrici, connettori e fascette di messa a terra, garantendo un'adeguata continuità elettrica e riducendo al minimo il rischio di guasti o guasti elettrici. Questi adesivi forniscono un'eccellente conduttività, resistenza alla corrosione e stabilità meccanica in ambienti marini.
- Elettronica e strumentazione: le navi marittime si affidano a complessi sistemi elettronici per la navigazione, la comunicazione, il controllo e il monitoraggio. Gli adesivi per il collegamento elettrico vengono utilizzati per assemblare e installare componenti elettronici, come pannelli di controllo, sistemi di strumentazione e dispositivi di comunicazione. Questi adesivi assicurano un legame sicuro, connessioni elettriche e protezione da fattori ambientali come umidità, vibrazioni e variazioni di temperatura.
- Sistemi di illuminazione: gli adesivi per l'incollaggio elettrico trovano applicazione nei sistemi di illuminazione marina, comprese le luci di navigazione, le luci interne e le luci subacquee. Collegano corpi illuminanti, moduli LED o componenti di illuminazione alla struttura dell'imbarcazione, garantendo collegamenti elettrici e stabilità meccanica. Questi adesivi resistono all'ingresso di acqua, alla corrosione e alle vibrazioni, contribuendo alla longevità e alle prestazioni dei sistemi di illuminazione marini.
- Protezione anticorrosione: le imbarcazioni sono costantemente esposte all'acqua di mare corrosiva, che può danneggiare componenti e strutture metalliche. Gli adesivi per l'incollaggio elettrico con proprietà anticorrosione proteggono le superfici metalliche dalla corrosione. Questi adesivi formano una barriera protettiva, impedendo il contatto diretto con l'acqua di mare e offrendo resistenza alla corrosione. Vengono applicati ad aree come scafi, accessori di coperta e attrezzature subacquee per migliorare la durata e la durata delle imbarcazioni marine.
- Sigillatura e impermeabilizzazione: gli adesivi sigillanti sono impiegati nelle applicazioni marine per fornire proprietà impermeabilizzanti e sigillanti. Sigillano ingressi cavi, connettori, raccordi passascafo e altre aperture nella struttura dell'imbarcazione. Questi adesivi impediscono l'ingresso di acqua, proteggendo i componenti elettrici sensibili e mantenendo l'integrità della nave. Resistono all'acqua salata, ai raggi UV e alle fluttuazioni di temperatura, garantendo un'efficacia di tenuta a lungo termine.
- Incollaggio di componenti in fibra di vetro e compositi: la fibra di vetro e i materiali compositi sono ampiamente utilizzati nella costruzione di imbarcazioni marine grazie alle loro proprietà leggere e ad alta resistenza. Gli adesivi per l'incollaggio elettrico vengono utilizzati per incollare e fissare componenti in fibra di vetro e compositi, come scafi, ponti e rinforzi strutturali. Questi adesivi forniscono legami forti e durevoli, migliorando l'integrità strutturale della nave.
- Schermatura EMI/RFI: le imbarcazioni dispongono spesso di apparecchiature elettroniche sensibili che richiedono protezione contro le interferenze elettromagnetiche (EMI) e le interferenze di radiofrequenza (RFI). Gli adesivi per il collegamento elettrico con proprietà conduttive vengono utilizzati per la schermatura EMI/RFI nelle applicazioni marine. Creano percorsi conduttivi, riducendo l'impatto delle radiazioni elettromagnetiche sui componenti elettronici e garantendo la corretta funzionalità e affidabilità.
- Riparazione e manutenzione: gli adesivi per l'incollaggio elettrico sono utilizzati anche per scopi di riparazione e manutenzione nell'industria marittima. Possono riparare collegamenti elettrici, fissare componenti sciolti, riparare cavi danneggiati e rinforzare strutture indebolite. Questi adesivi offrono soluzioni di incollaggio rapide e affidabili, consentendo riparazioni efficienti e riducendo al minimo i tempi di inattività.
Questi sono solo alcuni esempi dell'ampia gamma di applicazioni marine per gli adesivi per l'incollaggio elettrico. Le proprietà di questi adesivi, come la conduttività elettrica, la resistenza alla corrosione, l'efficacia della tenuta e la resistenza meccanica, li rendono essenziali per garantire collegamenti elettrici affidabili, protezione contro fattori ambientali e prestazioni complessive di imbarcazioni e apparecchiature marine.
Applicazioni mediche
Gli adesivi per l'incollaggio elettrico hanno applicazioni essenziali in campo medico, dove vengono utilizzati per vari scopi, tra cui il fissaggio di elettrodi, l'assemblaggio di dispositivi medici, il monitoraggio dei pazienti e la stimolazione elettrica. Ecco alcune applicazioni mediche critiche degli adesivi per il collegamento elettrico:
- Collegamento degli elettrodi: gli adesivi per il collegamento elettrico fissano gli elettrodi alla pelle per il monitoraggio medico e per scopi diagnostici. Questi adesivi forniscono un legame sicuro, garantendo un contatto elettrico affidabile tra l'elettrodo e la pelle. Offrono eccellenti proprietà di biocompatibilità, conformabilità e adesione per mantenere il corretto posizionamento degli elettrodi, migliorare la qualità del segnale e ridurre al minimo il disagio del paziente.
- Assemblaggio di dispositivi medici: gli adesivi per il collegamento elettrico sono fondamentali per l'assemblaggio di vari dispositivi medici. Collegano e fissano componenti come sensori, connettori, circuiti stampati e cavi all'interno di dispositivi medici. Questi adesivi forniscono conducibilità elettrica, stabilità meccanica e protezione contro i fattori ambientali, contribuendo alle prestazioni e all'affidabilità complessive dei dispositivi.
- Monitoraggio del paziente: gli adesivi per il collegamento elettrico sono utilizzati nei sistemi di monitoraggio del paziente, come i dispositivi ECG (elettrocardiogramma), EEG (elettroencefalogramma) ed EMG (elettromiogramma). Sono utilizzati per collegare elettrodi o sensori al corpo del paziente, garantendo collegamenti elettrici e acquisizione del segnale corretti. Questi adesivi offrono un forte legame, una conduttività elettrica affidabile e un'adesione a lungo termine, consentendo un monitoraggio accurato e continuo del paziente.
- Stimolazione elettrica: gli adesivi per il legame elettrico svolgono un ruolo nelle terapie di stimolazione elettrica, come la stimolazione nervosa elettrica transcutanea (TENS) o la stimolazione elettrica neuromuscolare (NMES). Sono utilizzati per attaccare gli elettrodi di stimolazione alla pelle, fornendo correnti elettriche alle aree mirate. Questi adesivi forniscono un legame sicuro, un contatto elettrico affidabile e il comfort del paziente durante i trattamenti di stimolazione.
- Chiusura della ferita: gli adesivi per il legame elettrico trovano applicazione in tecniche come la chiusura elettrica della ferita (EWC) o le procedure elettrochirurgiche. Proteggono i bordi della ferita e facilitano il flusso di corrente elettrica durante il processo di guarigione. Questi adesivi offrono un forte legame, conducibilità elettrica e compatibilità con i tessuti circostanti, favorendo la chiusura della ferita e la guarigione.
- Sensori medici e dispositivi indossabili: gli adesivi per il collegamento elettrico assemblano sensori medici e dispositivi indossabili, come biosensori, misuratori di glucosio e tracker sanitari. Forniscono un fissaggio sicuro dei sensori alla pelle o ad altre superfici, garantendo una corretta acquisizione del segnale e una trasmissione affidabile dei dati. Questi adesivi offrono biocompatibilità, flessibilità e adesione a lungo termine per facilitare un monitoraggio comodo e accurato.
- Riabilitazione e protesi: gli adesivi per l'incollaggio elettrico svolgono un ruolo nella riparazione e nei dispositivi protesici. Sono utilizzati per collegare elettrodi, sensori o componenti di dispositivi di assistenza al corpo o alle interfacce protesiche. Questi adesivi forniscono connessioni elettriche affidabili, stabilità meccanica e adesione duratura, contribuendo alla funzionalità e all'usabilità dei sistemi riabilitativi e protesici.
- Ricerca e sviluppo medico: gli adesivi per l'incollaggio elettrico sono impiegati nelle impostazioni di ricerca e sviluppo medico. Sono utilizzati per la prototipazione, il test e l'assemblaggio di circuiti elettronici personalizzati, sensori o configurazioni sperimentali. Questi adesivi offrono flessibilità, facilità d'uso e collegamenti elettrici affidabili, consentendo ai ricercatori di creare dispositivi e sistemi medici innovativi.
Questi sono solo alcuni esempi dell'ampia gamma di applicazioni mediche degli adesivi per l'incollaggio elettrico. Le proprietà di questi adesivi, come la biocompatibilità, la conduttività elettrica, la forza di adesione e la resistenza ambientale, sono fondamentali per garantire prestazioni sicure e affidabili in ambito medico.
Fattori da considerare nella scelta degli adesivi per il collegamento elettrico
Quando si scelgono gli adesivi per il collegamento elettrico, è necessario considerare diversi fattori per garantire l'idoneità e l'efficacia dell'adesivo per l'applicazione prevista. Ecco alcuni fattori chiave da considerare:
- Conducibilità elettrica: la conducibilità elettrica dell'adesivo è fondamentale per le applicazioni in cui sono richiesti collegamenti elettrici o messa a terra. A seconda dei requisiti specifici, come bassa resistenza o livelli di conduttività specifici, l'adesivo dovrebbe avere proprietà di conduttività appropriate per garantire prestazioni elettriche affidabili.
- Compatibilità del substrato: considerare i tipi di substrati coinvolti nell'applicazione dell'incollaggio. L'adesivo deve essere compatibile con materiali incollati come metalli, plastica, compositi o vetro. La compatibilità comprende sia la compatibilità chimica per evitare il degrado o la corrosione del supporto, sia la compatibilità meccanica per garantire una forte adesione alla superficie del supporto.
- Resistenza ambientale: valutare le condizioni ambientali a cui sarà esposto l'adesivo. Considerare fattori quali variazioni di temperatura, umidità, sostanze chimiche, radiazioni UV e altre condizioni ambientali specifiche rilevanti per l'applicazione. L'adesivo deve resistere a queste condizioni per mantenere le sue prestazioni e la forza di adesione nel tempo.
- Forza di adesione e durata: valutare la forza di adesione e la durata necessarie per l'applicazione specifica. Devono essere considerati fattori come la capacità portante, la resistenza alle vibrazioni, agli urti e alle sollecitazioni cicliche. L'adesivo dovrebbe fornire forza di adesione e durata sufficienti per garantire affidabilità e prestazioni a lungo termine in condizioni operative.
- Tempo e processo di polimerizzazione: considerare il meccanismo di polimerizzazione dell'adesivo e il tempo di polimerizzazione. A seconda dei requisiti dell'applicazione, scegliere tra adesivi che polimerizzano a temperatura ambiente (polimerizzazione ambiente) o quelli che richiedono calore, umidità o esposizione ai raggi UV per la polimerizzazione. Il tempo di indurimento deve essere allineato con il processo di produzione o assemblaggio per consentire un incollaggio efficiente e ridurre al minimo i tempi di produzione.
- Metodo di applicazione: considerare il metodo di applicazione e l'attrezzatura disponibile per l'applicazione dell'adesivo. Alcuni adesivi sono adatti per l'applicazione manuale, mentre altri possono richiedere attrezzature speciali per l'erogazione o l'applicazione. La viscosità e le proprietà reologiche dell'adesivo devono essere compatibili con il metodo di applicazione prescelto per garantire una copertura e un'adesione adeguate dell'adesivo.
- Conformità alle normative: per determinate applicazioni, come dispositivi medici o componenti aerospaziali, può essere richiesta l'adesione a specifici standard e regolamenti del settore. Assicurarsi che l'adesivo scelto sia conforme agli standard del settore pertinenti, come biocompatibilità, infiammabilità o norme di sicurezza, per soddisfare i requisiti specifici dell'applicazione.
- Assistenza e supporto: valutare la disponibilità di supporto tecnico, documentazione del prodotto e assistenza da parte del produttore o fornitore dell'adesivo. Considerare la loro esperienza nel campo e la capacità di fornire indicazioni o rispondere a qualsiasi domanda o dubbio relativo alla selezione, all'applicazione o alle prestazioni dell'adesivo.
Considerando attentamente questi fattori, è possibile selezionare l'adesivo per l'incollaggio elettrico più adatto alla propria applicazione specifica, garantendo prestazioni, affidabilità e longevità ottimali dei componenti o dei sistemi incollati.
Tempo di polimerizzazione e temperatura
Il tempo e la temperatura di indurimento sono considerazioni importanti quando si lavora con adesivi elettrici. Il tempo di indurimento si riferisce alla durata necessaria affinché l'incollaggio raggiunga la sua piena forza e le sue proprietà adesive. La temperatura, d'altra parte, influisce sulla velocità di polimerizzazione e sulle prestazioni complessive dell'adesivo. Di seguito sono riportati alcuni punti chiave da comprendere sul tempo e sulla temperatura di polimerizzazione negli adesivi per l'incollaggio elettrico:
Tempo di cura:
- Il tempo di polimerizzazione può variare notevolmente a seconda del tipo di adesivo e della sua formulazione. Può variare da pochi minuti a diverse ore o addirittura giorni.
- Tempi di polimerizzazione più rapidi sono desiderabili in molte applicazioni in quanto riducono i tempi di assemblaggio e consentono una manipolazione rapida e un'ulteriore lavorazione dei componenti incollati.
- Potrebbero essere necessari tempi di polimerizzazione più lunghi per le applicazioni in cui sono richiesti allineamenti o regolazioni precisi prima che l'adesivo faccia presa.
- Il tempo di indurimento può essere influenzato da fattori quali lo spessore dell'adesivo, le condizioni ambientali (umidità, temperatura) e la presenza di acceleranti o agenti indurenti.
Considerazioni sulla temperatura:
- I produttori di adesivi forniscono intervalli di temperatura di polimerizzazione consigliati per i loro prodotti. È essenziale seguire queste linee guida per ottenere prestazioni adesive ottimali.
- La temperatura influisce sulla velocità di guarigione. Temperature più elevate generalmente accelerano il processo di indurimento, mentre temperature più basse lo rallentano. Tuttavia, temperature eccessivamente elevate possono causare il degrado dell'adesivo o effetti collaterali indesiderati.
- Gli adesivi possono avere un intervallo di temperatura minimo e massimo per l'indurimento. Il funzionamento al di fuori di questi limiti di temperatura può comportare una polimerizzazione incompleta o compromessa, riducendo la forza di adesione e la durata.
- Alcuni adesivi richiedono specifici profili di temperatura di polimerizzazione che comportano un graduale aumento o diminuzione della temperatura per ottenere proprietà di adesione ottimali.
- È fondamentale considerare i limiti di temperatura dei substrati da incollare. Alcuni materiali possono essere sensibili alle alte temperature e deformarsi o subire danni termici.
Indurimento a caldo rispetto a indurimento a temperatura ambiente:
- Alcuni adesivi per l'incollaggio elettrico richiedono l'indurimento a caldo, sottoponendo l'incollaggio a specifiche temperature elevate per una durata definita. L'indurimento a caldo può fornire tempi di indurimento più rapidi e migliori proprietà adesive.
- Gli adesivi a polimerizzazione a temperatura ambiente, o adesivi a polimerizzazione a temperatura ambiente, polimerizzano naturalmente senza calore aggiuntivo. Polimerizzano a temperatura ambiente media e in genere richiedono tempi di polimerizzazione più lunghi rispetto agli adesivi polimerizzati a caldo.
- La scelta tra indurimento a caldo e indurimento a temperatura ambiente dipende dai requisiti specifici dell'applicazione, dai processi di produzione e dalla disponibilità delle attrezzature.
È essenziale seguire attentamente le istruzioni e le raccomandazioni del produttore in merito al tempo e alla temperatura di polimerizzazione per l'adesivo specifico. La deviazione dalle linee guida consigliate può compromettere le prestazioni dell'adesivo, con conseguente indebolimento dei legami o cedimento dell'adesivo. Il tempo di indurimento e il controllo della temperatura adeguati contribuiscono a ottenere la forza di adesione desiderata, la durata e l'affidabilità complessiva degli assemblaggi o dei componenti incollati.
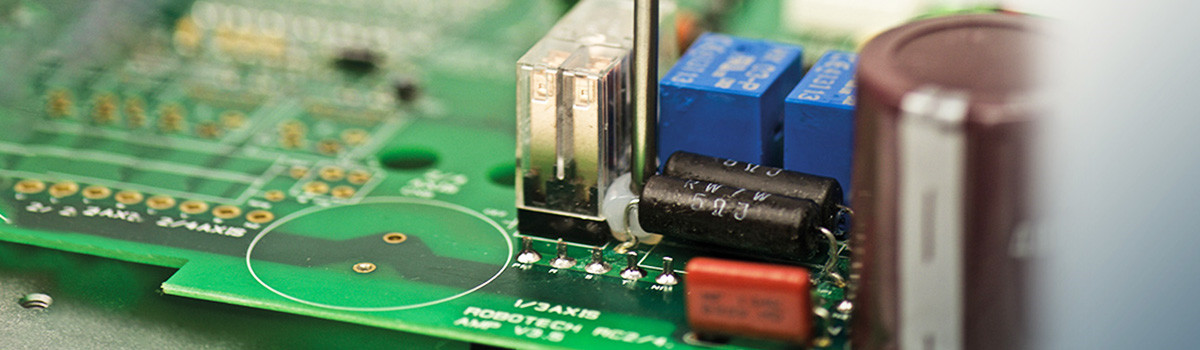
Resistenza chimica
La resistenza chimica è una considerazione importante nella scelta degli adesivi per il collegamento elettrico, specialmente nelle applicazioni che espongono l'adesivo a vari prodotti chimici, solventi o ambienti aggressivi. La resistenza chimica di un legame determina la sua capacità di mantenere la sua integrità, forza di adesione e prestazioni complessive a contatto con sostanze chimiche specifiche. Ecco alcuni punti chiave da comprendere sulla resistenza chimica degli adesivi per il collegamento elettrico:
- Compatibilità chimica: diversi adesivi hanno diversi livelli di resistenza a sostanze chimiche specifiche. È fondamentale valutare la compatibilità dell'adesivo con le sostanze chimiche con cui può entrare in contatto durante la sua vita utile. Ciò include considerare i tipi di sostanze chimiche, le loro concentrazioni e la durata dell'esposizione.
- Tipi chimici: la resistenza chimica può variare a seconda dei tipi chimici specifici, come acidi, basi, solventi, oli, carburanti, detergenti o prodotti chimici industriali. Alcuni adesivi possono mostrare una buona resistenza a determinate sostanze chimiche ma possono essere suscettibili ad altre. È essenziale valutare la compatibilità dell'adesivo con le sostanze chimiche specifiche rilevanti per l'applicazione.
- Rigonfiamento e degradazione: quando un adesivo viene esposto a sostanze chimiche, può gonfiarsi, ammorbidirsi o subire un degrado, con conseguente perdita della forza di adesione e delle prestazioni complessive. È essenziale selezionare un adesivo che mostri un rigonfiamento e un degrado minimi o nulli quando viene a contatto con le sostanze chimiche previste.
- Considerazioni sulla temperatura: la resistenza chimica può anche essere influenzata dalla temperatura. Alcuni adesivi possono mostrare una buona resistenza a determinate sostanze chimiche a temperatura ambiente, ma possono essere meno resistenti a temperature elevate. È essenziale considerare l'intervallo di temperatura di esercizio e valutare la resistenza chimica dell'adesivo in tali condizioni.
- Test e dati: i produttori di adesivi in genere forniscono schede tecniche o informazioni tecniche che specificano le proprietà di resistenza chimica dei loro prodotti. Queste risorse possono aiutare a valutare la compatibilità dell'adesivo con prodotti chimici specifici e aiutare a selezionare l'adesivo appropriato per l'applicazione prevista.
- Rivestimenti e sigillanti: in alcuni casi, sull'adesivo possono essere applicati ulteriori rivestimenti protettivi o sigillanti per migliorare la resistenza chimica. Questi rivestimenti possono fornire un ulteriore livello di protezione contro le sostanze chimiche e migliorare ulteriormente la durata complessiva e la compatibilità chimica dell'assieme incollato.
- Requisiti specifici dell'applicazione: diverse applicazioni hanno diversi requisiti di esposizione chimica. Ad esempio, nell'industria automobilistica, gli adesivi utilizzati nei componenti del sistema di alimentazione devono presentare un'eccellente resistenza ai carburanti e agli idrocarburi. È essenziale comprendere le specifiche condizioni di esposizione chimica dell'applicazione e scegliere un adesivo che soddisfi tali requisiti.
Considerare la resistenza chimica degli adesivi per il collegamento elettrico è fondamentale per garantire l'affidabilità e le prestazioni a lungo termine degli assemblaggi o dei componenti incollati. La selezione di un adesivo con proprietà di resistenza chimica appropriate per l'applicazione specifica aiuta a prevenire il cedimento dell'adesivo, a mantenere legami forti ea garantire l'integrità complessiva del sistema in presenza di ambienti chimici aggressivi.
Conduttività elettrica
La conduttività elettrica degli adesivi per il collegamento elettrico è una proprietà critica nelle applicazioni in cui sono richiesti collegamenti elettrici o messa a terra. La conducibilità elettrica si riferisce alla capacità di un materiale di consentire il flusso di corrente elettrica. Ecco alcuni punti chiave da comprendere sulla conduttività elettrica degli adesivi per il collegamento elettrico:
Adesivi conduttivi e non conduttivi: gli adesivi per il collegamento elettrico possono essere ampiamente classificati in due tipi in base alla loro conduttività elettrica: adesivi conduttivi e non conduttivi.
- Adesivi conduttivi: questi adesivi sono formulati con riempitivi conduttivi, come particelle metalliche o fibre, che facilitano il flusso di corrente elettrica. Gli adesivi conduttivi offrono una bassa resistenza elettrica, consentendo un'efficiente conduzione elettrica tra i componenti incollati. Sono comunemente usati in applicazioni che richiedono continuità elettrica, come messa a terra, schermatura contro le interferenze elettromagnetiche (EMI) o collegamenti elettrici.
- Adesivi non conduttivi: gli adesivi non conduttivi, come suggerisce il nome, non possiedono una conduttività elettrica intrinseca. Questi adesivi sono generalmente utilizzati in applicazioni che richiedono isolamento o isolamento elettrico. Impediscono il flusso di corrente elettrica tra i componenti collegati e possono fornire isolamento elettrico o proprietà dielettriche.
- Resistenza elettrica: la conducibilità elettrica di un adesivo è spesso espressa in termini di resistenza elettrica o resistività. La resistenza elettrica è una misura dell'opposizione al flusso di corrente elettrica attraverso il materiale. Valori di resistenza inferiori indicano una migliore conduttività elettrica.
- Riempitivi e additivi: gli adesivi conduttivi contengono riempitivi o additivi che migliorano la conduttività elettrica. Questi riempitivi, come particelle di argento, rame, carbonio o grafite, stabiliscono percorsi conduttivi all'interno della matrice adesiva, facilitando il flusso di corrente elettrica. Il tipo, le dimensioni e la concentrazione di questi riempitivi possono influenzare la conducibilità elettrica dell'adesivo.
- Collegamento elettrico e messa a terra: gli adesivi conduttivi sono comunemente usati per creare collegamenti elettrici tra i componenti o per la messa a terra. Sono impiegati in vari settori, tra cui l'elettronica, l'automotive, l'aerospaziale e le telecomunicazioni, dove una conduttività elettrica affidabile è essenziale per il corretto funzionamento e le prestazioni del dispositivo.
- Schermatura EMI: nelle applicazioni di schermatura elettromagnetica vengono utilizzati adesivi conduttivi con buone proprietà di conduttività elettrica. Forniscono un percorso conduttivo per la dissipazione delle interferenze elettromagnetiche, proteggendo dispositivi o circuiti elettronici sensibili da radiazioni o rumori elettromagnetici esterni.
- Affidabilità dei contatti elettrici: la conduttività elettrica degli adesivi di fissaggio influisce direttamente sull'affidabilità dei contatti elettrici. Gli adesivi conduttivi assicurano un contatto elettrico corretto e costante tra le superfici incollate, riducendo al minimo la resistenza di contatto e prevenendo connessioni intermittenti o inaffidabili.
- Spessore adesivo e area di contatto: la conduttività elettrica di un adesivo può essere influenzata dallo spessore dello strato adesivo e dall'area di contatto tra le superfici incollate. Strati adesivi più sottili e aree di contatto più grandi offrono generalmente una migliore conduttività elettrica.
- Test e verifica: la conduttività elettrica degli adesivi può essere misurata utilizzando varie tecniche, compresi i metodi con sonda a quattro o due punti. Questi test aiutano a valutare le proprietà di conduttività dell'adesivo ea garantire la conformità alle specifiche elettriche richieste.
È essenziale selezionare il tipo appropriato di adesivo per il collegamento elettrico in base ai requisiti specifici di conducibilità elettrica dell'applicazione. Gli adesivi conduttivi sono adatti quando è necessaria la continuità elettrica o la messa a terra, mentre gli adesivi non conduttivi forniscono isolamento o isolamento elettrico. Comprendere le proprietà di conduttività elettrica dell'adesivo aiuta a garantire prestazioni, affidabilità e sicurezza ottimali nelle applicazioni di collegamento elettrico.
Stabilità termica
La stabilità termica è una caratteristica essenziale degli adesivi per l'incollaggio elettrico, in particolare nelle applicazioni in cui l'incollaggio sarà esposto a temperature elevate. La stabilità termica di un adesivo si riferisce alla sua capacità di mantenere la sua integrità, forza di adesione e prestazioni complessive in condizioni di alta temperatura. Ecco alcuni punti chiave da comprendere sulla stabilità termica degli adesivi per l'incollaggio elettrico:
- Intervallo di temperatura: gli adesivi hanno temperature specifiche per mantenere le loro prestazioni e stabilità. La stabilità termica di un adesivo è spesso descritta dalla sua massima temperatura operativa continua o dalla resistenza alla temperatura di picco. La scelta di un legame in grado di resistere all'intervallo di temperatura previsto dell'applicazione è essenziale.
- Degradazione termica: il calore eccessivo può causare la degradazione dell'adesivo, modificando le proprietà fisiche e chimiche. Ciò può comportare una ridotta forza di adesione, perdita di proprietà meccaniche e prestazioni complessive ridotte. Un adesivo termicamente stabile resiste al degrado anche alle alte temperature, mantenendo le sue proprietà originali.
- Mantenimento della forza di adesione: la stabilità termica di un adesivo è strettamente correlata alla sua capacità di mantenere la forza di adesione a temperature elevate. Se esposto a temperature elevate, un adesivo termicamente stabile dovrebbe presentare una riduzione minima della forza di adesione. Dovrebbe possedere un legame solido e duraturo tra le superfici aderite, anche in condizioni termiche difficili.
- Temperatura di transizione vetrosa (Tg): la temperatura di transizione vetrosa è un parametro importante da considerare quando si valuta la stabilità termica di un adesivo. È la temperatura alla quale l'adesivo passa da uno stato rigido e vetroso a uno stato più morbido e gommoso. Gli adesivi con valori Tg più elevati offrono generalmente una migliore stabilità termica, in quanto possono resistere a temperature più elevate prima di rammollirsi o perdere le loro proprietà meccaniche.
- Cicli termici: alcune applicazioni comportano l'esposizione a cicli termici ripetuti, in cui l'adesivo subisce un'alternanza di temperature alte e basse. La stabilità termica è essenziale in questi casi, poiché l'adesivo deve resistere a queste fluttuazioni di temperatura senza degrado significativo o perdita di forza di adesione. Un adesivo termicamente stabile mantiene le sue prestazioni anche dopo più cicli termici.
- Resistenza al calore: gli adesivi utilizzati in applicazioni che coinvolgono componenti o ambienti che generano calore, come l'elettronica, l'elettronica di potenza o i sistemi di illuminazione, richiedono una buona resistenza al calore. Gli adesivi resistenti al calore possono resistere al calore generato da questi componenti e mantenere le loro prestazioni senza ammorbidirsi, sciogliersi o perdere forza di adesione.
- Conducibilità termica: in alcune applicazioni, la conducibilità termica è una considerazione importante. La conducibilità termica si riferisce alla capacità di un materiale di condurre il calore. Gli adesivi con elevata conduttività termica possono trasferire efficacemente il calore lontano dai componenti sensibili al calore, garantendo un'efficiente dissipazione del calore e prevenendo danni termici.
- Test e dati: i produttori di adesivi in genere forniscono schede tecniche che specificano le proprietà di stabilità termica dei loro prodotti. Queste informazioni includono l'intervallo di temperatura di esercizio consigliato, la resistenza termica e altre proprietà termiche rilevanti. È essenziale rivedere questi dati per garantire che l'adesivo soddisfi i requisiti specifici di stabilità termica dell'applicazione.
La scelta di un adesivo termicamente stabile è fondamentale per garantire affidabilità e prestazioni a lungo termine, soprattutto in applicazioni che prevedono alte temperature o cicli termici. Un adesivo termicamente stabile mantiene la forza di adesione, le proprietà meccaniche e le prestazioni complessive in condizioni di alta temperatura, contribuendo alla durata e all'integrità degli assemblaggi o dei componenti incollati.
Viscosità
La viscosità è una proprietà essenziale degli adesivi per l'incollaggio elettrico che ne determina il comportamento di scorrimento e le caratteristiche applicative. Si riferisce allo spessore o alla resistenza allo scorrimento dell'adesivo. Comprendere la viscosità è fondamentale per la corretta selezione dell'adesivo e il processo di applicazione. Ecco alcuni punti chiave da comprendere sulla viscosità degli adesivi per il collegamento elettrico:
- Definizione e misurazione: la viscosità misura la resistenza di un fluido allo scorrimento. Determina la capacità dell'adesivo di stendersi, bagnare le superfici e riempire i vuoti. La viscosità è tipicamente misurata in unità come centipoise (cP) o Pascal-secondi (Pa·s).
- Intervallo di viscosità: gli adesivi per incollaggio elettrico possono avere varie viscosità, da liquidi a bassa viscosità a paste o gel ad alta viscosità. La viscosità appropriata dipende dai requisiti dell'applicazione, come la dimensione della linea di giunzione, la capacità di riempimento degli spazi e la facilità di applicazione.
- Comportamento del flusso: gli adesivi possono presentare diversi comportamenti del flusso a seconda della loro viscosità. I fluidi newtoniani hanno uno spessore costante indipendentemente dalla velocità di taglio applicata. D'altra parte, i fluidi non newtoniani possono presentare un comportamento di assottigliamento al taglio (diminuzione della densità con l'aumento della velocità di taglio) o di ispessimento del taglio (aumento della viscosità con l'aumento della velocità di taglio). Comprendere il comportamento del flusso aiuta a prevedere il comportamento dell'adesivo durante l'applicazione e in condizioni diverse.
- Metodi di applicazione: la viscosità influisce sull'applicabilità degli adesivi utilizzando vari metodi come l'erogazione manuale, l'erogazione automatica, la serigrafia o l'erogazione con siringa. Gli adesivi a bassa viscosità scorrono facilmente e sono adatti per l'erogazione automatica, mentre gli adesivi ad alta viscosità possono richiedere metodi di applicazione manuali o apparecchiature di erogazione in grado di gestire materiali più spessi.
- Capacità di riempimento degli spazi vuoti: la viscosità gioca un ruolo nella capacità dell'adesivo di riempire gli spazi vuoti o le superfici di unione irregolari. Gli adesivi a bassa viscosità possono fluire in spazi ristretti o spazi ristretti in modo più efficiente, mentre gli adesivi a viscosità più elevata tendono a rimanere in posizione e fornire una migliore capacità di riempimento degli spazi.
- Compatibilità del substrato: anche la viscosità è importante quando si considera la compatibilità dell'adesivo con i substrati da incollare. Adesivi con livelli di viscosità adeguati assicurano una buona bagnatura e contatto con le superfici del supporto, favorendo una forte adesione.
- Tissotropia: alcuni adesivi presentano un comportamento tixotropico, in cui la loro viscosità diminuisce se sottoposta a sollecitazione di taglio o agitazione, ma si ripristina quando è a riposo. Gli adesivi tixotropici sono facili da applicare e stendere durante l'applicazione, ma riacquistano spessore rapidamente dopo l'applicazione, prevenendo colature o colature indesiderate.
- Dipendenza dalla temperatura: la viscosità può essere dipendente dalla temperatura, nel senso che cambia con la temperatura. Alcuni adesivi possono diventare meno viscosi a temperature più elevate, rendendoli più facili da applicare o erogare. Altri possono mostrare una maggiore viscosità a temperature più basse, richiedendo il preriscaldamento o il riscaldamento per un flusso e una lavorabilità ottimali.
- Manipolazione dei materiali: la viscosità influisce sulla facilità di manipolazione dei materiali, come la miscelazione, l'agitazione o il trasferimento di adesivi. Gli adesivi a viscosità più elevata possono richiedere miscelazione o attrezzature aggiuntive per garantire uniformità e omogeneità.
Comprendere la viscosità degli adesivi per l'incollaggio elettrico è fondamentale per un'applicazione di successo e per ottenere la qualità dell'incollaggio desiderata. L'appropriata selezione della viscosità garantisce un'adeguata bagnatura e adesione ai substrati, un efficace riempimento degli spazi vuoti e facilità di applicazione. È essenziale considerare i requisiti specifici dell'applicazione e consultare le raccomandazioni del produttore dell'adesivo per le specifiche di viscosità per garantire prestazioni ottimali.
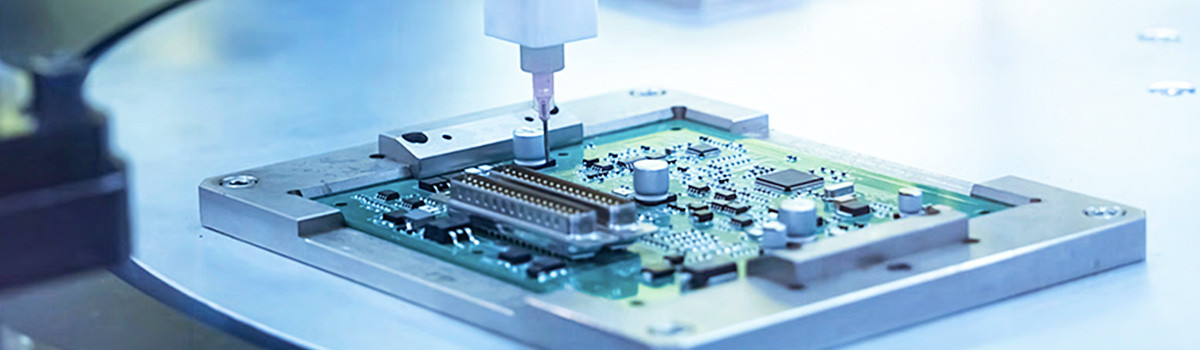
Data di scadenza
La durata di conservazione degli adesivi per l'incollaggio elettrico si riferisce al periodo durante il quale l'adesivo può essere conservato e rimanere idoneo all'uso. È essenziale conoscere la durata di conservazione degli adesivi per garantirne l'efficacia e l'affidabilità una volta applicati. Ecco alcuni punti chiave da sapere sulla durata di conservazione degli adesivi per il collegamento elettrico:
- Definizione: la durata di conservazione è la durata in cui l'adesivo può essere conservato in condizioni specificate senza cambiamenti significativi nelle sue proprietà, prestazioni o qualità.
- Data di scadenza: i produttori di adesivi in genere forniscono una data di scadenza o una durata di conservazione consigliata del prodotto. Questa data indica il punto dopo il quale l'adesivo può degradarsi o perdere efficacia. È essenziale rispettare questa data di scadenza per garantire prestazioni ottimali.
- Fattori che influenzano la durata di conservazione: diversi fattori possono influenzare la durata di conservazione degli adesivi per il collegamento elettrico:
- Condizioni di stoccaggio: gli adesivi devono essere conservati in condizioni controllate per mantenerne la stabilità. Fattori come la temperatura, l'umidità e l'esposizione alla luce possono influire sulla durata di conservazione dell'adesivo. Gli adesivi devono essere conservati in aree fresche e asciutte, lontano dalla luce solare diretta o da sbalzi di temperatura estremi.
- Imballaggio: un imballaggio adeguato è fondamentale per preservare la durata di conservazione dell'adesivo. Gli adesivi devono essere conservati in contenitori ermeticamente chiusi per evitare l'ingresso di umidità, l'evaporazione o la contaminazione. I contenitori devono essere etichettati in modo appropriato con il tipo di adesivo, il numero di lotto e la data di scadenza per una facile identificazione.
- Stabilità chimica: gli adesivi possono subire reazioni chimiche nel tempo che possono portare a cambiamenti nelle loro proprietà. Fattori come l'umidità, l'ossigeno o l'esposizione a sostanze reattive possono accelerare queste reazioni e ridurre la durata di conservazione. Gli adesivi formulati con stabilizzanti o antiossidanti possono avere una migliore stabilità chimica e una maggiore durata.
- Raccomandazioni per la conservazione: i produttori forniscono raccomandazioni specifiche per la conservazione dei loro prodotti adesivi. Queste raccomandazioni possono includere intervalli di temperatura, livelli di umidità e contenitori o condizioni di conservazione trasparenti. È essenziale seguire queste linee guida per garantire la qualità e la longevità dell'adesivo.
- Test e verifica: se un adesivo è stato conservato per un lungo periodo o oltre la data di scadenza, si consiglia di eseguire test dell'adesivo per verificarne l'idoneità. Questi test possono includere la misurazione della viscosità e della forza di adesione o l'esecuzione di prove di incollaggio per valutare le prestazioni dell'adesivo.
- Segregazione del prodotto: gli adesivi devono essere conservati e utilizzati in base all'ordine di entrata per garantire che i materiali più vecchi vengano utilizzati prima di quelli più nuovi. Questa pratica aiuta a prevenire adesivi scaduti o degradati e fornisce i migliori risultati.
- Guida del produttore: è essenziale fare riferimento alla documentazione del produttore, come schede tecniche del prodotto o bollettini tecnici, per informazioni specifiche relative alla durata di conservazione dell'adesivo. La guida del produttore considera la formulazione dell'adesivo, le condizioni di conservazione e le prestazioni previste nel tempo.
Comprendere la durata di conservazione degli adesivi per il collegamento elettrico è fondamentale per mantenerne l'efficacia e garantire prestazioni adeguate. Gli adesivi che hanno superato la durata di conservazione possono presentare una forza di adesione ridotta, variazioni di viscosità o altri effetti dannosi. Aderendo alle pratiche di conservazione appropriate, seguendo le linee guida del produttore e monitorando regolarmente le date di scadenza degli adesivi, contribuiamo a garantirne l'affidabilità e le prestazioni costanti quando vengono applicati.
Preparazione della superficie
La preparazione della superficie è un passaggio fondamentale nell'applicazione di adesivi per l'incollaggio elettrico. Una corretta preparazione della superficie garantisce un'adesione ottimale e una forza di adesione tra l'adesivo e il supporto. Ecco alcuni punti chiave da comprendere sulla preparazione della superficie per gli adesivi per l'incollaggio elettrico:
- Pulizia: il primo passaggio nella preparazione della superficie è la pulizia accurata delle superfici del supporto. Le superfici devono essere prive di contaminanti come sporcizia, polvere, grasso, olio, umidità o ossidazione. La pulizia può essere effettuata utilizzando solventi, detergenti o detergenti specifici consigliati dal produttore dell'adesivo. Il processo di pulizia può comportare la pulizia, la spazzolatura o l'utilizzo di tecniche di pulizia ad ultrasuoni a seconda del substrato e della natura dei contaminanti.
- Irruvidimento della superficie: in alcuni casi, potrebbe essere necessario irruvidire la superficie del substrato per migliorare la forza di adesione dell'adesivo. Questo viene in genere fatto utilizzando metodi meccanici come levigatura, molatura o sabbiatura abrasiva. L'irrruvidimento della superficie aumenta la superficie e fornisce un incastro meccanico, consentendo all'adesivo di formare un legame più forte.
- Attivazione della superficie: alcuni substrati, come metalli o alcune plastiche, possono richiedere l'attivazione della superficie per favorire l'adesione. I metodi di attivazione superficiale includono trattamenti chimici, trattamenti al plasma, primer o promotori di adesione. Questi trattamenti modificano le proprietà superficiali, migliorando le caratteristiche di bagnabilità e adesione dell'adesivo.
- Rimozione dell'ossidazione: la rimozione degli strati di ossidazione è fondamentale per i substrati metallici per garantire una buona adesione. L'ossidazione può ostacolare la capacità dell'adesivo di aderire al substrato. Metodi meccanici come la sabbiatura o trattamenti chimici come il decapaggio acido possono rimuovere gli strati di ossido ed esporre una superficie pulita per l'incollaggio.
- Asciugatura e sgrassaggio: Dopo la pulizia e il trattamento superficiale, è essenziale asciugare accuratamente le superfici del supporto per rimuovere l'eventuale umidità o agenti detergenti. L'umidità può interferire con il processo di indurimento dell'adesivo e compromettere la forza di adesione. Inoltre, lo sgrassaggio delle superfici aiuta a eliminare gli oli residui oi contaminanti che possono ostacolare la capacità dell'adesivo di aderire efficacemente.
- Compatibilità della superficie: è essenziale considerare la compatibilità tra l'adesivo e la superficie del supporto. Alcuni incollaggi possono richiedere specifiche caratteristiche della superficie o metodi di trattamento per garantire un corretto incollaggio. È necessario seguire le raccomandazioni del produttore dell'adesivo per determinare le tecniche di preparazione della superficie appropriate per la particolare combinazione di adesivo e substrato.
- Applicazione dell'adesivo: Una volta completata la preparazione della superficie, l'adesivo può essere applicato alle superfici preparate. È essenziale seguire le istruzioni del produttore dell'adesivo in merito al metodo di applicazione, lo spessore dell'adesivo consigliato e il tempo disponibile. Tecniche di applicazione adeguate, come la diffusione uniforme o l'erogazione controllata, assicurano una copertura e una forza di adesione costanti.
Una corretta preparazione della superficie è fondamentale per ottenere legami solidi e durevoli quando si utilizzano adesivi per l'incollaggio elettrico. Promuove un'adesione ottimale, riduce al minimo il rischio di rottura dell'adesivo e garantisce l'affidabilità a lungo termine degli assemblaggi incollati. Seguire le procedure consigliate per la preparazione della superficie specificate dal produttore dell'adesivo aiuta a massimizzare le prestazioni dell'adesivo e garantisce un'adesione efficace.
Manipolazione e stoccaggio
La manipolazione e lo stoccaggio corretti degli adesivi elettrici sono essenziali per mantenerne l'efficacia, la qualità e la durata. La manipolazione o lo stoccaggio impropri possono danneggiare l'adesivo, comprometterne le prestazioni e ridurre la forza di adesione. Di seguito sono riportati alcuni punti chiave da comprendere sulla manipolazione e lo stoccaggio degli adesivi per l'incollaggio elettrico:
Precauzioni per la manipolazione: quando si maneggiano gli adesivi, è essenziale seguire alcune precauzioni per garantire la sicurezza ed evitare la contaminazione:
- Indossare dispositivi di protezione individuale (DPI) adeguati come raccomandato dal produttore dell'adesivo. Ciò può includere guanti, occhiali di sicurezza e indumenti protettivi.
- Evitare il contatto con la pelle, gli occhi o i vestiti. In caso di contatto accidentale, sciacquare abbondantemente con acqua e consultare un medico se necessario.
- Utilizzare una ventilazione adeguata nell'area di lavoro per garantire un flusso d'aria adeguato e ridurre al minimo l'esposizione a fumi o vapori.
- Seguire le istruzioni del produttore per le corrette tecniche di manipolazione, compresi i rapporti di miscelazione (se applicabili) e le eventuali precauzioni specifiche.
Condizioni di conservazione: le condizioni di conservazione dell'adesivo sono cruciali per il mantenimento della qualità e dell'efficacia. Considerare i seguenti fattori quando si conservano gli adesivi per il collegamento elettrico:
- Temperatura: gli adesivi devono essere conservati entro l'intervallo di temperatura consigliato dal produttore. Temperature estremamente alte e basse possono influire sulle prestazioni e sulla durata dell'adesivo. Si consiglia generalmente di conservare gli adesivi in un luogo fresco e asciutto, lontano dalla luce diretta del sole e da fonti di calore.
- Umidità: l'umidità può influire negativamente sulle proprietà dell'adesivo e causare un indurimento o un degrado prematuri. Gli adesivi devono essere conservati in ambienti a bassa umidità per evitare l'assorbimento di umidità. Mantenere i contenitori ben chiusi per ridurre al minimo l'ingresso di umidità.
- Monitoraggio della durata di conservazione: i contenitori adesivi devono essere etichettati con il numero di lotto, la data di produzione e la data di scadenza. Implementa un sistema FIFO (first-in, first-out) per utilizzare prima l'inventario di adesivi meno recenti e prevenire l'uso di materiali scaduti.
- Compatibilità: alcuni adesivi possono avere requisiti di conservazione specifici in base alla loro formulazione. Seguire le raccomandazioni del produttore per la temperatura di conservazione, i livelli di umidità e altre istruzioni per mantenere la qualità dell'adesivo.
Manipolazione dei contenitori: i contenitori adesivi devono essere maneggiati con cura per evitare perdite, versamenti o contaminazioni:
- Assicurarsi che i contenitori siano ben chiusi dopo l'uso per evitare l'esposizione all'aria e l'ingresso di umidità. Seguire le istruzioni del produttore per le corrette tecniche di chiusura.
- Evitare di far cadere o maneggiare in modo improprio i contenitori di adesivo, in quanto ciò può causare danni all'imballaggio o compromettere l'integrità dell'adesivo.
- Pulire le superfici esterne dei contenitori prima di aprirli per evitare che la contaminazione penetri nell'adesivo.
- Segregazione ed etichettatura: conservare gli adesivi separatamente dai materiali incompatibili per evitare contaminazioni incrociate o reazioni. La corretta etichettatura dei contenitori con tipo di adesivo, numero di lotto e altre informazioni pertinenti aiuta a identificare e tracciare accuratamente l'inventario.
- Trasporto: durante il trasporto di adesivi, assicurarsi che siano adeguatamente imballati e fissati per evitare perdite o danni. Seguire tutte le normative o le linee guida applicabili per il trasporto sicuro dei materiali adesivi.
La manipolazione e lo stoccaggio corretti degli adesivi elettrici sono fondamentali per mantenerne la qualità, le prestazioni e la durata. Il rispetto delle condizioni di conservazione raccomandate, le precauzioni di manipolazione e il rispetto delle istruzioni del produttore assicurano che l'adesivo rimanga efficace e affidabile per le applicazioni di incollaggio.
Misure di sicurezza
È necessario adottare precauzioni di sicurezza quando si lavora con adesivi elettrici per proteggere le persone e garantire un ambiente di lavoro sicuro. Gli adesivi possono contenere sostanze chimiche che possono essere pericolose se non maneggiate correttamente. Ecco alcune precauzioni di sicurezza essenziali da considerare quando si lavora con adesivi per il collegamento elettrico:
- Dispositivi di protezione individuale (DPI): Indossare DPI adeguati per proteggersi da potenziali pericoli. Ciò può includere guanti, occhiali o occhiali protettivi, camici da laboratorio o indumenti protettivi e protezione respiratoria, se necessario. I requisiti DPI devono essere determinati in base alla scheda di sicurezza dei materiali (MSDS) dell'adesivo e alle raccomandazioni del produttore.
- Ventilazione: garantire un'adeguata ventilazione nell'area di lavoro per ridurre al minimo l'esposizione a fumi, vapori o particelle sospese nell'aria generate durante l'applicazione o l'indurimento dell'adesivo. Utilizzare un sistema di ventilazione locale o lavorare in aree ben ventilate per mantenere la qualità dell'aria.
- Sostanze chimiche pericolose: gli adesivi per il collegamento elettrico possono contenere sostanze chimiche pericolose per la salute. Acquisire familiarità con la scheda di sicurezza dell'adesivo per comprendere i pericoli specifici associati al prodotto. Seguire le raccomandazioni del produttore per la manipolazione, la conservazione e lo smaltimento sicuri dell'adesivo.
- Contatto con la pelle: evitare il contatto diretto della pelle con l'adesivo. Alcuni adesivi possono causare irritazioni cutanee o reazioni allergiche. Indossare guanti protettivi resistenti all'adesivo specifico per evitare il contatto con la pelle. In caso di contatto accidentale, lavare l'area interessata con acqua e sapone e consultare un medico se necessario.
- Protezione degli occhi: gli adesivi possono causare irritazione o lesioni agli occhi se entrano in contatto con gli occhi. Indossa occhiali o occhiali di sicurezza per proteggere gli occhi quando lavori con gli adesivi. In caso di contatto accidentale con gli occhi, sciacquare gli occhi con acqua per almeno 15 minuti e consultare immediatamente un medico.
- Inalazione: Ridurre al minimo l'inalazione di fumi o vapori adesivi. Lavorare in un'area ben ventilata o utilizzare una protezione respiratoria se necessario. Seguire le raccomandazioni del produttore per l'attrezzatura di protezione respiratoria appropriata.
- Incendio e fonti di ignizione: alcuni adesivi possono essere infiammabili o avere specifiche caratteristiche di infiammabilità. Prendere precauzioni per evitare che l'adesivo entri in contatto con fiamme libere, scintille o altre fonti di accensione. Conservare e utilizzare gli adesivi lontano da fonti di calore e seguire adeguate misure di sicurezza antincendio.
- Compatibilità chimica: essere consapevoli della compatibilità dell'adesivo con altri materiali o sostanze. Evitare di miscelare adesivi con prodotti chimici o materiali incompatibili che potrebbero causare reazioni pericolose.
- Stoccaggio e smaltimento: conservare gli adesivi seguendo le istruzioni del produttore per evitare perdite, fuoriuscite o esposizione accidentale. Seguire le linee guida appropriate per conservare e smaltire in modo sicuro i contenitori adesivi e i materiali di scarto.
- Preparazione alle emergenze: prepararsi alle emergenze disponendo di postazioni per il lavaggio oculare di emergenza, docce di sicurezza e attrezzature antincendio prontamente disponibili nell'area di lavoro. Acquisire familiarità con le procedure e i protocolli di emergenza appropriati.
È essenziale consultare i dati e le istruzioni di sicurezza specifici del produttore dell'adesivo. Seguire le precauzioni e le linee guida di sicurezza adeguate aiuta a proteggere le persone, prevenire gli incidenti e garantire un ambiente di lavoro sicuro con gli adesivi per il collegamento elettrico.
Conclusione
In conclusione, gli adesivi per il collegamento elettrico svolgono un ruolo fondamentale nel garantire l'affidabilità e la sicurezza dei sistemi elettrici. Forniscono un'eccellente soluzione di incollaggio e sigillatura per varie applicazioni, dai dispositivi elettronici ai componenti aerospaziali. La scelta di un adesivo adatto richiede un'attenta considerazione di diversi fattori, tra cui il tempo di polimerizzazione, la resistenza chimica e la conduttività elettrica. Con una corretta manipolazione e conservazione, gli adesivi per il collegamento elettrico possono fornire un legame duraturo e sicuro, garantendo prestazioni ottimali dei sistemi elettrici.