Rivestimenti conformi per l'elettronica
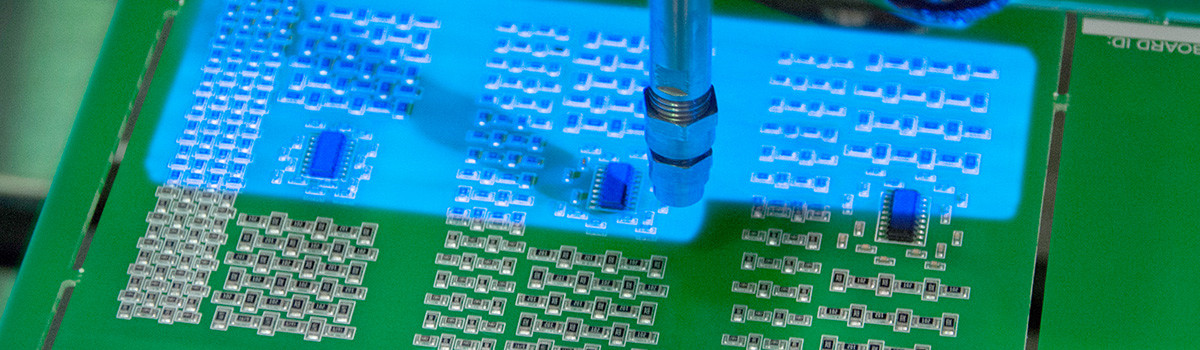
Nel mondo di oggi, i dispositivi elettronici sono parte integrante della nostra vita quotidiana. Man mano che i dispositivi elettronici diventano più complessi e miniaturizzati, la necessità di protezione da fattori ambientali come umidità, polvere e sostanze chimiche diventa più critica. È qui che entrano in gioco i conformal coating. I conformal coating sono materiali appositamente formulati che proteggono i componenti elettronici da fattori esterni che potrebbero comprometterne le prestazioni e la funzionalità. Questo articolo esplorerà i vantaggi e l'importanza dei conformal coating per l'elettronica.
Cosa sono i conformal coating per l'elettronica?
I rivestimenti conformi sono rivestimenti protettivi specializzati utilizzati nell'industria elettronica per salvaguardare i componenti elettronici e i circuiti stampati da fattori ambientali come umidità, polvere, sostanze chimiche e temperature estreme. Questi rivestimenti vengono applicati in uno strato sottile e uniforme sulla superficie dell'elettronica, adattandosi ai contorni dei componenti per fornire una copertura e una protezione complete.
Lo scopo principale dei conformal coating è prevenire danni o malfunzionamenti dei dispositivi elettronici causati da elementi esterni. Umidità e umidità, ad esempio, possono causare corrosione e cortocircuiti, mentre polvere e detriti possono compromettere le prestazioni di componenti sensibili. Un rivestimento protettivo protegge l'assieme elettronico da questi pericoli, garantendone l'affidabilità e la longevità.
I rivestimenti conformi sono generalmente realizzati con varie formulazioni chimiche, tra cui acrilici, siliconi, uretani ed epossidici. Ogni tipo di rivestimento offre proprietà e vantaggi distinti. I rivestimenti acrilici sono ampiamente utilizzati per la loro versatilità, facilità di applicazione ed economicità. Forniscono una buona resistenza all'umidità e sono relativamente semplici da rimuovere e riapplicare se necessario. I siliconi sono noti per la loro eccellente flessibilità, stabilità termica e resistenza alle alte temperature. I rivestimenti in uretano offrono un'eccezionale resistenza chimica e protezione contro solventi e carburanti. Gli epossidici forniscono una durezza e una durata superiori, rendendoli adatti per ambienti difficili.
I rivestimenti conformi richiedono un'attenzione particolare per garantire una copertura e un'adesione adeguate. Varie tecniche includono spazzolatura, spruzzatura, immersione e rivestimento selettivo. Diversi metodi possono essere impiegati a seconda delle esigenze specifiche e della complessità dell'assieme. Alcuni rivestimenti vengono applicati manualmente, mentre altri vengono eseguiti attraverso processi automatizzati, come la spruzzatura robotizzata o sistemi di rivestimento a immersione.
Una volta applicato, il conformal coating crea una barriera protettiva che incapsula i componenti elettronici senza ostacolarne la funzionalità. Forma un film protettivo che aderisce alla superficie e mantiene le sue proprietà protettive nel tempo. I rivestimenti sono tipicamente trasparenti o traslucidi, consentendo l'ispezione visiva dell'assemblaggio.
Oltre a proteggere dai fattori ambientali, i conformal coating offrono anche altri vantaggi. Possono fornire isolamento elettrico, prevenendo perdite di corrente e cortocircuiti. Gli strati possono anche migliorare la resistenza dell'assieme alle vibrazioni e alle sollecitazioni meccaniche, riducendo il rischio di danni durante il trasporto o il funzionamento. Inoltre, possono offrire protezione contro funghi, muffe e altri contaminanti che possono compromettere le prestazioni dei dispositivi elettronici.
L'importanza dei conformal coating per i dispositivi elettronici
I rivestimenti conformi svolgono un ruolo cruciale nel migliorare l'affidabilità e la durata dei dispositivi elettronici e offrono una serie di vantaggi essenziali per garantire prestazioni e longevità ottimali. Ecco alcuni dei motivi principali per cui i conformal coating sono necessari per i dispositivi elettronici:
- Protezione contro l'umidità e l'umidità: uno degli scopi principali dei rivestimenti conformi è proteggere i componenti elettronici dall'umidità e dall'umidità. L'acqua può causare corrosione, ossidazione e formazione di percorsi conduttivi, con conseguenti cortocircuiti e malfunzionamenti dei dispositivi. I conformal coating fungono da barriera, impedendo all'umidità di raggiungere i componenti sensibili e riducendo il rischio di danni.
- Prevenzione dell'accumulo di polvere e detriti: l'elettronica è spesso esposta a polvere, sporco e contaminanti presenti nell'aria. Queste particelle possono depositarsi su circuiti stampati e componenti, causando problemi di isolamento, aumento della generazione di calore e potenziali cortocircuiti. I conformal coating creano uno strato protettivo che inibisce l'accumulo di polvere e detriti, mantenendo la pulizia e le prestazioni dell'elettronica.
- Resistenza chimica: molti conformal coating resistono a varie sostanze chimiche, inclusi solventi, carburanti, acidi e alcali. Ciò è particolarmente importante negli ambienti in cui i dispositivi elettronici possono entrare in contatto con sostanze corrosive. I rivestimenti fungono da scudo, prevenendo le reazioni chimiche e garantendo la longevità dei componenti.
- Protezione termica: i dispositivi elettronici generano calore durante il funzionamento e un calore eccessivo può degradare le prestazioni e l'affidabilità dei componenti. I conformal coating possono fornire una barriera termica, dissipando il calore e riducendo il rischio di surriscaldamento. Strati specifici, come quelli a base di silicone, sono noti per la loro eccellente stabilità termica e possono resistere a temperature elevate senza compromettere le loro proprietà protettive.
- Isolamento elettrico: i rivestimenti conformi possono offrire isolamento elettrico, prevenendo perdite di corrente e cortocircuiti. Aiutano a mantenere le caratteristiche elettriche desiderate dei componenti e riducono il rischio di guasti elettrici causati da fattori ambientali o contaminazione.
- Protezione meccanica: l'elettronica può essere soggetta a sollecitazioni meccaniche, come vibrazioni, urti o impatti. I rivestimenti conformi migliorano la robustezza meccanica dei dispositivi elettronici fornendo un ulteriore livello di protezione. Aiutano ad assorbire le vibrazioni e le forze di impatto, riducendo il rischio di danni ai componenti delicati e garantendo un funzionamento affidabile.
- Resistenza ambientale: i rivestimenti conformi consentono ai dispositivi elettronici di resistere a diverse condizioni ambientali. Possono resistere a temperature estreme, radiazioni UV, nebbia salina e altri elementi aggressivi. Ciò è particolarmente importante per i dispositivi utilizzati in applicazioni esterne o industriali, dove possono essere esposti ad ambienti difficili.
Vantaggi dell'utilizzo di conformal coating
L'utilizzo di conformal coating per dispositivi elettronici offre numerosi vantaggi che contribuiscono alla loro affidabilità e longevità complessive. Ecco alcuni vantaggi chiave dell'utilizzo di conformal coating:
- Protezione ambientale: i rivestimenti conformi forniscono una barriera protettiva che protegge i componenti elettronici da fattori ambientali come umidità, polvere, sporco e sostanze chimiche. Impediscono l'ingresso di acqua, che può causare corrosione e cortocircuiti, e proteggono dall'accumulo di polvere e detriti che possono compromettere le prestazioni. Questa protezione ambientale estende la durata dei dispositivi elettronici.
- Maggiore affidabilità: salvaguardando dai rischi ambientali, i conformal coating migliorano l'affidabilità dei dispositivi elettronici. Riducono al minimo il rischio di guasti causati da problemi legati all'umidità, come danni ai componenti indotti dalla corrosione o migrazione elettrochimica. Inoltre, i rivestimenti proteggono da polvere e detriti che possono causare cortocircuiti elettrici o rotture dell'isolamento, garantendo prestazioni costanti e affidabili.
- Isolamento elettrico: i rivestimenti conformi offrono proprietà di isolamento elettrico, prevenendo perdite di corrente e cortocircuiti. Aiutano a mantenere le caratteristiche elettriche desiderate dei componenti, riducendo la possibilità di malfunzionamenti elettrici o guasti dovuti a contaminazione o assorbimento di umidità. L'isolamento elettrico aiuta anche a soddisfare i requisiti normativi e di sicurezza.
- Gestione termica: alcuni conformal coating hanno proprietà di gestione termica, che consentono loro di dissipare il calore generato dai componenti elettronici. Questa protezione termica aiuta a prevenire il surriscaldamento, che può degradare le prestazioni e ridurre la durata dei dispositivi sensibili. Gestendo efficacemente le temperature, i conformal coating contribuiscono all'affidabilità complessiva dell'elettronica.
- Resistenza chimica: molti conformal coating presentano un'eccellente resistenza chimica. Forniscono una barriera contro sostanze corrosive, solventi, carburanti e altre sostanze chimiche che possono degradare i componenti elettronici. Questa resistenza chimica previene le reazioni chimiche, il degrado del materiale e potenziali guasti causati dall'esposizione ad ambienti difficili o dal contatto con sostanze chimiche.
- Protezione da vibrazioni e urti: i rivestimenti conformi offrono protezione meccanica assorbendo le vibrazioni e riducendo l'impatto di urti e sollecitazioni meccaniche. Ciò è particolarmente vantaggioso per i dispositivi elettronici soggetti a trasporto o condizioni operative difficili. I conformal coating aiutano a prevenire danni a componenti delicati, giunti di saldatura e connessioni riducendo al minimo gli effetti di vibrazioni e urti.
- Facilità di ispezione e riparazione: i conformal coating sono spesso trasparenti o traslucidi, consentendo l'ispezione visiva dei componenti sottostanti. Ciò facilita il rilevamento più semplice di potenziali problemi come difetti dei giunti di saldatura, danni ai componenti o contaminazione da materiale estraneo. Inoltre, i conformal coating possono essere rimossi e riapplicati se sono necessarie riparazioni o modifiche, semplificando la manutenzione.
Come funzionano i conformal coating?
I conformal coating creano una barriera protettiva sulla superficie dei componenti elettronici e dei circuiti stampati. Questi rivestimenti vengono generalmente applicati come strati sottili e uniformi che si adattano ai contorni dei dispositivi, garantendo una copertura e una protezione complete. I rivestimenti aderiscono alla superficie e formano un film continuo che protegge da fattori ambientali e potenziali contaminanti.
L'applicazione di conformal coating prevede diverse fasi:
- Preparazione della superficie: prima di applicare il conformal coating, la superficie del gruppo elettronico deve essere adeguatamente preparata. Ciò comporta in genere la pulizia e la rimozione di contaminanti come polvere, oli e residui. La copertura può essere pulita utilizzando solventi, pulizia a ultrasuoni o altri metodi appropriati per garantire un substrato pulito e liscio per l'adesione del rivestimento.
- Selezione del materiale di rivestimento: sono disponibili diversi tipi di rivestimenti conformi, come acrilici, siliconi, uretani ed epossidici, ciascuno con le sue proprietà e vantaggi. La scelta del materiale di rivestimento dipende da fattori quali le condizioni ambientali, il livello di protezione desiderato, i requisiti di isolamento elettrico e considerazioni specifiche sull'applicazione.
- Metodo di applicazione: i rivestimenti conformi possono essere applicati utilizzando vari metodi, tra cui pennello, spruzzatura, immersione e rivestimento selettivo. La scelta del metodo di applicazione dipende da fattori quali la complessità dell'assemblaggio, il tipo di materiale di rivestimento e il livello di precisione desiderato. I metodi di applicazione manuale sono adatti per produzioni su piccola scala o aree specifiche che richiedono un rivestimento mirato. I processi automatizzati, come la spruzzatura robotizzata o i sistemi di rivestimento a immersione, vengono spesso utilizzati per la produzione su larga scala per garantire una copertura del rivestimento uniforme e uniforme.
- Polimerizzazione ed essiccazione: dopo l'applicazione del rivestimento, deve essere sottoposto a un processo di polimerizzazione o asciugatura. Questo processo consente al materiale di rivestimento di solidificarsi e formare un film protettivo. Il tempo e le condizioni di indurimento dipendono dal materiale di rivestimento specifico e dalle raccomandazioni del produttore. I metodi di polimerizzazione possono includere l'essiccazione all'aria, la polimerizzazione termica mediante forni o l'esposizione alla luce UV per alcuni tipi di rivestimenti.
Una volta applicato e indurito, il conformal coating crea una barriera protettiva che incapsula i componenti elettronici. Lo strato è una barriera contro umidità, polvere, sostanze chimiche e altri fattori ambientali che possono danneggiare o degradare i componenti. Aiuta a prevenire la corrosione, i cortocircuiti elettrici e la rottura dell'isolamento, garantendo l'affidabilità e la longevità dei dispositivi elettronici.
I rivestimenti conformi mantengono le loro proprietà protettive nel tempo, offrendo una protezione continua per l'assemblaggio elettronico. In caso di riparazioni o modifiche, lo strato può essere selettivamente rimosso e riapplicato, consentendo la manutenzione o la sostituzione dei componenti senza compromettere la protezione complessiva fornita dal rivestimento.
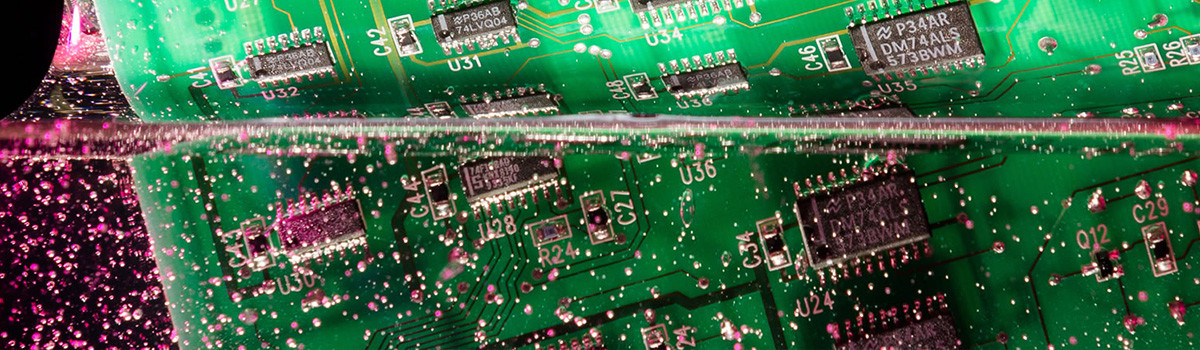
Tipi di conformal coating
Sono disponibili diversi tipi di conformal coating, ciascuno con le sue proprietà, vantaggi e applicazioni. La selezione del tipo di rivestimento dipende da fattori quali i requisiti specifici del gruppo elettronico, le condizioni ambientali, il livello di protezione desiderato e i processi di produzione. Ecco alcuni tipi comunemente usati di conformal coating:
- Rivestimenti conformi acrilici: i rivestimenti acrilici sono uno dei tipi più utilizzati grazie alla loro versatilità e convenienza. Forniscono una buona resistenza all'umidità, isolamento elettrico e protezione contro i fattori ambientali. I rivestimenti acrilici sono facili da applicare e possono essere rimossi e rielaborati. Sono adatti a varie applicazioni e offrono una buona protezione per tutti gli usi.
- Rivestimenti conformi in silicone: i rivestimenti in silicone hanno un'eccellente flessibilità, stabilità termica e resistenza alle alte temperature. Possono resistere a variazioni di temperatura estreme senza perdere le loro proprietà protettive. I rivestimenti in silicone forniscono un'eccellente resistenza all'umidità e un isolamento elettrico. Sono spesso utilizzati in applicazioni in cui l'elevata stabilità termica e flessibilità sono fondamentali, come nei dispositivi elettronici automobilistici, aerospaziali e per esterni.
- Rivestimenti conformi in uretano: i rivestimenti in uretano offrono un'eccezionale resistenza chimica, rendendoli adatti per applicazioni in cui l'esposizione a solventi, carburanti o altri prodotti chimici aggressivi rappresenta un problema. Forniscono una buona protezione dall'umidità, isolamento elettrico e durata meccanica. I rivestimenti in uretano sono spesso utilizzati in ambienti difficili come applicazioni automobilistiche, industriali e militari.
- Rivestimenti epossidici conformi: i rivestimenti epossidici sono noti per la loro eccellente durezza e durata. Offrono una solida protezione meccanica e resistenza all'abrasione e agli urti. I rivestimenti epossidici offrono una buona resistenza chimica e protezione dall'umidità. Sono comunemente usati in applicazioni che richiedono protezione robusta e resistenza meccanica, come nei sistemi di controllo industriale, elettronica rinforzata e ambienti ad alto stress.
- Parylene Conformal Coatings: il Parylene è un tipo unico di conformal coating depositato sotto forma di vapore e forma una sottile pellicola polimerica priva di microfori. Gli strati di parylene forniscono eccellenti proprietà di barriera contro l'umidità, isolamento elettrico, resistenza chimica e biocompatibilità. Offrono un alto livello di protezione e sono conformi a geometrie complesse. I rivestimenti in parylene sono comunemente usati nei dispositivi medici, nel settore aerospaziale e nelle applicazioni elettroniche sensibili.
- Rivestimenti conformi a polimerizzazione UV: i rivestimenti polimerizzabili a UV vengono applicati come liquido e quindi polimerizzati utilizzando la luce UV. Offrono tempi di polimerizzazione rapidi, che possono aumentare l'efficienza produttiva. Gli strati polimerizzabili ai raggi UV forniscono una buona resistenza all'umidità, isolamento elettrico e resistenza chimica. Sono adatti per applicazioni che richiedono un indurimento rapido, un'elevata produttività e una qualità di rivestimento costante.
È importante notare che la selezione del rivestimento conforme appropriato dipende dai requisiti specifici dell'assieme elettronico e dall'applicazione prevista. Le condizioni ambientali, l'intervallo di temperatura di esercizio, l'esposizione chimica e il livello di protezione desiderato devono essere considerati quando si sceglie il tipo di rivestimento protettivo per garantire prestazioni e longevità ottimali dei dispositivi elettronici.
Rivestimenti conformi acrilici
I conformal coating acrilici sono ampiamente utilizzati nell'industria elettronica grazie alla loro versatilità, economicità e facilità di applicazione. Offrono una serie di vantaggi e sono adatti a vari assemblaggi e applicazioni elettroniche. Ecco alcune caratteristiche e vantaggi chiave dei conformal coating acrilici:
- Protezione dall'umidità: i rivestimenti acrilici offrono una buona resistenza all'umidità, aiutando a prevenire la penetrazione di acqua o umidità nei componenti elettronici. L'umidità può causare corrosione, cortocircuiti elettrici e degrado delle prestazioni. I rivestimenti acrilici fungono da barriera, proteggendo dai problemi legati all'umidità e migliorando l'affidabilità e la durata dei dispositivi elettronici.
- Isolamento elettrico: i rivestimenti acrilici forniscono isolamento elettrico, prevenendo perdite di corrente e cortocircuiti. Aiutano a mantenere le caratteristiche elettriche desiderate dei componenti e riducono il rischio di malfunzionamenti elettrici o guasti causati da contaminazione o assorbimento di umidità. Questa proprietà di isolamento elettrico è essenziale per mantenere l'integrità dei circuiti elettronici.
- Protezione ambientale: i conformal coating acrilici proteggono i gruppi elettronici da fattori ambientali come polvere, sporco, sostanze chimiche e variazioni di temperatura. Creano una barriera contro i contaminanti presenti nell'aria, impedendo loro di depositarsi sulla superficie dei componenti. I rivestimenti acrilici offrono anche un certo livello di resistenza agli agenti chimici, fornendo una protezione aggiuntiva contro le sostanze corrosive.
- Facilità di applicazione: i rivestimenti acrilici sono noti per la loro facilità di applicazione. Possono essere applicati con vari metodi, tra cui pennello, spruzzatura, immersione o rivestimento selettivo. Questa flessibilità consente processi applicativi manuali e automatizzati, a seconda dei requisiti specifici e della scala di produzione. I rivestimenti acrilici hanno generalmente una buona capacità bagnante, garantendo una copertura uniforme e aderenza alle superfici dei componenti elettronici.
- Capacità di riparazione e rilavorazione: uno dei vantaggi dei rivestimenti acrilici è la loro rilavorabilità. Se sono necessarie riparazioni o modifiche, i rivestimenti acrilici possono essere facilmente rimossi utilizzando solventi appropriati, consentendo il lavoro di riparazione sui componenti sottostanti. La capacità di rimuovere e riapplicare i rivestimenti acrilici semplifica il processo di riparazione e facilita le attività di manutenzione.
- Trasparente o traslucido: i conformal coating acrilici sono generalmente trasparenti o traslucidi. Questa caratteristica consente l'ispezione visiva dei componenti sottostanti senza la necessità di rimuovere il rivestimento. L'ispezione visiva identifica potenziali problemi, come difetti dei giunti di saldatura, danni ai componenti o contaminazione da materiale estraneo.
- Economicità: i conformal coating acrilici offrono una soluzione conveniente per proteggere i gruppi elettronici. Bilanciano bene prestazioni e convenienza, rendendoli adatti a un'ampia gamma di applicazioni. Il costo relativamente basso dei rivestimenti acrilici consente processi di produzione economici senza compromettere la protezione e l'affidabilità desiderate dei dispositivi elettronici.
Sebbene i conformal coating acrilici offrano numerosi vantaggi, è essenziale considerare i requisiti specifici dell'assieme elettronico e le condizioni ambientali quando si sceglie un tipo di rivestimento. Fattori come l'intervallo di temperatura di esercizio, l'esposizione chimica e le sollecitazioni meccaniche devono essere considerati per garantire protezione e prestazioni ottimali.
Rivestimenti conformi in silicone
I rivestimenti conformi in silicone sono ampiamente utilizzati nell'industria elettronica grazie alle loro proprietà uniche e alla capacità di resistere a condizioni ambientali difficili. Offrono una serie di vantaggi che li rendono adatti a vari assemblaggi e applicazioni elettroniche. Ecco alcune caratteristiche e vantaggi chiave dei rivestimenti conformi in silicone:
- Stabilità termica: i rivestimenti in silicone sono noti per la loro eccellente stabilità termica, che consente loro di resistere a temperature di esercizio elevate senza perdere le loro proprietà protettive. Possono gestire le variazioni di temperatura in modo più efficace rispetto a molti altri tipi di conformal coating. Ciò rende i rivestimenti in silicone adatti per applicazioni con elevata stabilità termica, come l'elettronica automobilistica, aerospaziale ed industriale.
- Flessibilità e conformabilità: i conformal coating in silicone sono altamente flessibili e possono adattarsi alla forma di complessi assemblaggi elettronici. Possono essere applicati come strati sottili e uniformi che forniscono una copertura completa anche su circuiti e componenti complessi. La flessibilità e la conformabilità dei rivestimenti in silicone assicurano che le aree critiche siano adeguatamente protette, riducendo il rischio di danni o guasti.
- Umidità e protezione ambientale: i rivestimenti in silicone offrono un'eccellente resistenza all'umidità, rendendoli pratiche barriere contro la penetrazione di acqua e umidità. Questa protezione dall'umidità aiuta a prevenire corrosione, ossidazione e cortocircuiti causati da problemi legati all'umidità. I rivestimenti in silicone resistono anche a fattori ambientali come polvere, sporco e sostanze chimiche, migliorando la longevità e l'affidabilità dei dispositivi elettronici.
- Isolamento elettrico: i rivestimenti conformi in silicone forniscono proprietà di isolamento elettrico, prevenendo perdite di corrente e cortocircuiti. Mantengono l'integrità elettrica dei componenti e proteggono da guasti elettrici causati da contaminazione o assorbimento di umidità. L'isolamento elettrico offerto dai rivestimenti in silicone è fondamentale per mantenere l'affidabilità e le prestazioni dei circuiti elettronici.
- Resistenza chimica: i rivestimenti in silicone mostrano una buona resistenza a vari prodotti chimici, inclusi solventi, carburanti, acidi e alcali. Questa resistenza chimica rende i rivestimenti in silicone adatti per applicazioni in cui l'esposizione a sostanze corrosive è un problema. Gli strati fungono da barriera protettiva, prevenendo le reazioni chimiche e il degrado del materiale e garantendo la longevità dei componenti elettronici.
- Resistenza ai raggi UV e agli agenti atmosferici: i rivestimenti in silicone offrono un'eccellente resistenza alle radiazioni ultraviolette (UV) e agli agenti atmosferici. Possono resistere all'esposizione prolungata alla luce solare e agli ambienti esterni senza degrado significativo o perdita delle proprietà protettive. Ciò rende i rivestimenti in silicone ideali per dispositivi elettronici utilizzati in applicazioni esterne o esposti a radiazioni UV.
- Proprietà dielettriche: i conformal coating in silicone hanno buone proprietà dielettriche, il che significa che forniscono un efficace isolamento elettrico senza influire in modo significativo sulle prestazioni elettriche dei componenti. Questa proprietà è essenziale per mantenere le caratteristiche elettriche desiderate e prevenire guasti elettrici nei circuiti elettronici.
I conformal coating in silicone sono disponibili in diverse formulazioni per soddisfare requisiti applicativi specifici. Possono essere applicati con vari metodi, tra cui pennello, spruzzatura o immersione. I rivestimenti in silicone forniscono uno strato protettivo affidabile e duraturo per i gruppi elettronici, garantendone la funzionalità e l'affidabilità anche in condizioni operative difficili.
Quando si considerano i conformal coating in silicone, la valutazione di fattori come l'intervallo di temperatura di esercizio, l'esposizione a sostanze chimiche e le sollecitazioni meccaniche è essenziale per determinare la formulazione del rivestimento più adatta per l'applicazione specifica.
Rivestimenti epossidici conformi
I rivestimenti conformi epossidici sono ampiamente utilizzati nell'elettronica grazie alla loro eccellente durezza, durata e resistenza chimica. Offrono una serie di vantaggi che li rendono adatti a vari assemblaggi e applicazioni elettroniche. Ecco alcune caratteristiche e vantaggi chiave dei rivestimenti conformi epossidici:
- Durezza e protezione meccanica: i rivestimenti epossidici forniscono un'eccezionale durezza e protezione meccanica, rendendoli altamente resistenti all'abrasione, agli urti e ai danni fisici. Offrono una robusta barriera che protegge i componenti elettronici dalle sollecitazioni meccaniche, garantendone la longevità e l'affidabilità. I rivestimenti epossidici sono particolarmente adatti per applicazioni che richiedono una protezione automatica avanzata, come nei sistemi di controllo industriale e nell'elettronica rinforzata.
- Resistenza chimica: i conformal coating epossidici presentano un'eccellente resistenza a vari prodotti chimici, inclusi solventi, carburanti, acidi e alcali. Questa resistenza chimica protegge i componenti elettronici dal degrado o dai danni causati dall'esposizione a sostanze corrosive. I rivestimenti epossidici fungono da barriera, prevenendo le reazioni chimiche e garantendo l'integrità dei componenti sottostanti.
- Protezione dall'umidità e dall'ambiente: i rivestimenti epossidici forniscono un'adeguata protezione dall'umidità e dall'ambiente. Creano una barriera contro acqua, umidità, polvere e altri contaminanti ambientali che possono danneggiare i componenti elettronici. I rivestimenti epossidici aiutano a prevenire la corrosione, i cortocircuiti elettrici e il degrado delle prestazioni prevenendo l'ingresso di umidità.
- Isolamento elettrico: i rivestimenti conformi epossidici offrono eccellenti proprietà di isolamento elettrico, prevenendo perdite di corrente e cortocircuiti. Mantengono le caratteristiche elettriche desiderate dei componenti, riducendo il rischio di malfunzionamenti elettrici o guasti causati da contaminazione o assorbimento di umidità. L'isolamento elettrico fornito dai rivestimenti epossidici è fondamentale per mantenere l'affidabilità e le prestazioni dei circuiti elettronici.
- Resistenza termica: i rivestimenti epossidici hanno una buona resistenza termica, che consente loro di resistere a temperature elevate senza degrado significativo o perdita di proprietà protettive. Aiutano a dissipare il calore generato dai componenti elettronici, contribuendo alla gestione termica e prevenendo il surriscaldamento. Questa resistenza termica rende i rivestimenti epossidici adatti per applicazioni in cui le variazioni di temperatura e la dissipazione del calore sono fattori critici.
- Adesione e copertura: i conformal coating epossidici presentano un'eccellente adesione a vari substrati, tra cui metallo, plastica e materiali PCB. Aderiscono bene alla superficie dei gruppi elettronici, formando uno strato protettivo uniforme e continuo. I rivestimenti epossidici possono fornire una copertura completa, assicurando che tutte le aree e i componenti critici siano adeguatamente protetti.
- Riparabilità: i rivestimenti epossidici offrono il vantaggio di essere rilavorabili e riparabili. Se sono necessarie riparazioni o modifiche, i rivestimenti epossidici possono essere rimossi selettivamente utilizzando solventi appropriati, consentendo il lavoro di riparazione sui componenti sottostanti. Questa caratteristica di riparabilità semplifica le attività di manutenzione e facilita la sostituzione dei componenti se necessario.
I rivestimenti conformi alle resine epossidiche vengono generalmente applicati utilizzando metodi di pennello, spruzzatura o rivestimento selettivo. I rivestimenti polimerizzano attraverso una reazione chimica o un processo di indurimento termico, formando una pellicola protettiva durevole. Forniscono una protezione duratura per i gruppi elettronici, garantendone la funzionalità e l'affidabilità in ambienti difficili.
Quando si considerano i conformal coating epossidici, la valutazione di fattori come l'intervallo di temperatura operativa, l'esposizione a sostanze chimiche, le sollecitazioni meccaniche e il livello desiderato di protezione meccanica e chimica è essenziale per selezionare la formulazione del rivestimento più adatta per l'applicazione specifica.
Rivestimenti conformi in uretano
I conformal coating in uretano, noti anche come rivestimenti in poliuretano, sono ampiamente utilizzati nell'industria elettronica grazie alla loro eccezionale resistenza chimica e durata meccanica. Offrono una serie di vantaggi che li rendono adatti a vari assemblaggi e applicazioni elettroniche. Ecco alcune caratteristiche e vantaggi chiave dei rivestimenti conformi in uretano:
- Resistenza chimica: i rivestimenti in uretano resistono a vari prodotti chimici, inclusi solventi, carburanti, oli, acidi e alcali. Questa resistenza chimica rende i rivestimenti in uretano adatti per applicazioni in cui l'esposizione a sostanze chimiche aggressive è un problema. Agiscono come una barriera, proteggendo i componenti elettronici dal degrado chimico, dalla corrosione e da altre forme di danno.
- Protezione dall'umidità: i rivestimenti conformi in uretano forniscono un'efficace resistenza all'umidità, impedendo la penetrazione di acqua o umidità nei componenti elettronici. L'umidità può causare corrosione, cortocircuiti elettrici e degrado delle prestazioni. I rivestimenti in uretano fungono da barriera, proteggendo dai problemi legati all'umidità e migliorando l'affidabilità e la durata dei dispositivi elettronici.
- Durata meccanica: i rivestimenti in uretano offrono un'eccellente durata meccanica, con resistenza all'abrasione, agli urti e ai danni fisici. Forniscono uno strato protettivo resistente che resiste a condizioni ambientali e di manipolazione difficili. I rivestimenti in uretano sono adatti per applicazioni in cui è richiesta una maggiore protezione meccanica, come in ambienti industriali o dispositivi esposti a livelli elevati di usura.
- Resistenza termica: i rivestimenti in uretano presentano una buona resistenza termica, che consente loro di resistere a temperature elevate senza degrado significativo o perdita di proprietà protettive. Aiutano a dissipare il calore generato dai componenti elettronici, contribuendo alla gestione termica e prevenendo il surriscaldamento. Questa resistenza termica rende i rivestimenti in uretano adatti per applicazioni in cui le variazioni di temperatura e la dissipazione del calore sono fattori critici.
- Flessibilità: i conformal coating in uretano offrono un equilibrio tra durezza e flessibilità. Hanno una certa elasticità, che consente loro di adattarsi a piccoli movimenti e sollecitazioni nel gruppo elettronico. Questa flessibilità aiuta a ridurre il rischio di fessurazione o delaminazione del rivestimento, garantendo una protezione a lungo termine dei componenti.
- Stabilità ai raggi UV: i rivestimenti in uretano presentano una buona resistenza alle radiazioni ultraviolette (UV), proteggendo dagli effetti potenzialmente dannosi della luce solare e di altre fonti UV. Resistono all'ingiallimento o al degrado se esposti ai raggi UV, rendendoli adatti per applicazioni esterne o dispositivi esposti ai raggi UV.
- Adesione e copertura: i rivestimenti in uretano dimostrano un'eccellente adesione a vari substrati, inclusi metalli, plastica e materiali PCB. Aderiscono bene alla superficie dei gruppi elettronici, formando uno strato protettivo uniforme e continuo. I rivestimenti in uretano possono fornire una copertura completa, assicurando che tutte le aree e i componenti critici siano adeguatamente protetti.
I rivestimenti conformi in uretano vengono generalmente applicati utilizzando metodi di pennello, spruzzatura o rivestimento selettivo. Gli strati possono essere induriti mediante processi di indurimento a caldo o indurimento all'umidità, formando un film durevole e protettivo. Forniscono una protezione duratura per i gruppi elettronici, garantendone la funzionalità e l'affidabilità in ambienti difficili.
Quando si considera l'utilizzo di rivestimenti conformi in uretano, è essenziale valutare l'esposizione chimica specifica, l'intervallo di temperatura di esercizio, le sollecitazioni meccaniche e il livello desiderato di protezione chimica e meccanica per selezionare la formulazione del rivestimento più adatta per la particolare applicazione.
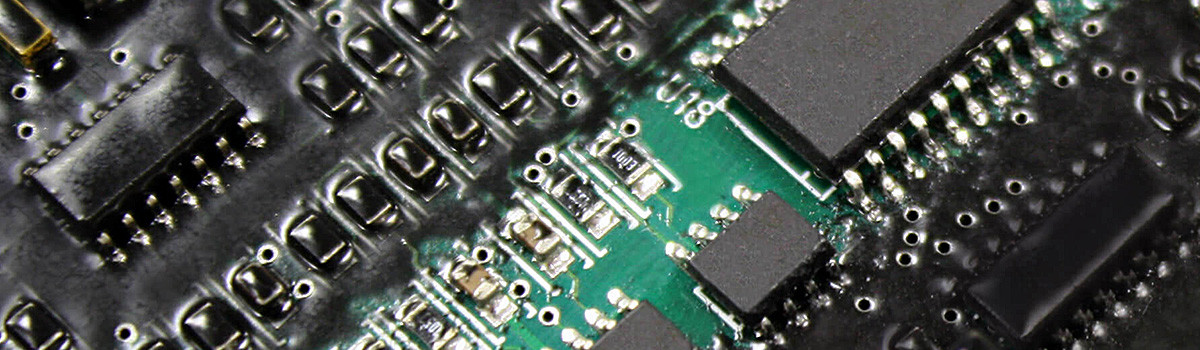
Rivestimenti conformi in parylene
I conformal coating in parylene sono unici e forniscono una protezione eccezionale per i dispositivi elettronici. I rivestimenti in parylene vengono depositati sotto forma di vapore e formano un sottile film polimerico privo di microfori. Offrono una serie di vantaggi che li rendono particolarmente adatti a vari assemblaggi e applicazioni elettroniche. Ecco alcune caratteristiche e vantaggi chiave dei rivestimenti conformi in Parylene:
- Barriera chimica e contro l'umidità: i rivestimenti in parylene forniscono un'eccellente barriera contro umidità, gas e sostanze chimiche. La pellicola sottile e uniforme formata dai rivestimenti in Parylene offre una barriera contro l'umidità altamente efficace, impedendo l'ingresso di acqua e umidità nei componenti elettronici. Forniscono inoltre un'eccezionale resistenza agli agenti chimici, inclusi solventi, acidi, basi e sostanze corrosive. Questa resistenza all'umidità e agli agenti chimici protegge i dispositivi elettronici dalla corrosione, dall'ossidazione e dal degrado, garantendone l'affidabilità a lungo termine.
- Conformità e copertura: i rivestimenti in parylene hanno eccezionali proprietà conformi, nel senso che si adattano alla forma di superfici complesse e irregolari. Il processo di deposizione da vapore consente allo strato di coprire uniformemente l'intero gruppo elettronico, comprese le caratteristiche complesse, gli spigoli vivi e le fessure. I rivestimenti in parylene possono penetrare in profondità in spazi ristretti, garantendo una copertura e una protezione complete per tutte le aree critiche.
- Isolamento elettrico: i rivestimenti conformi in parylene forniscono eccellenti proprietà di isolamento elettrico. Hanno un'elevata rigidità dielettrica e possono isolare efficacemente i componenti elettrici e prevenire perdite di corrente o cortocircuiti. I rivestimenti in parylene mantengono le caratteristiche elettriche desiderate dei particolari, riducendo il rischio di malfunzionamenti elettrici o guasti causati da contaminazione o assorbimento di umidità.
- Biocompatibilità: i rivestimenti in parylene sono biocompatibili e chimicamente inerti, il che li rende adatti per dispositivi medici ed elettronica impiantabile. Non provocano reazioni avverse a contatto con tessuti o fluidi biologici. I rivestimenti in parylene sono utilizzati in applicazioni come pacemaker, impianti neurali e biosensori, dove la biocompatibilità è fondamentale.
- Stabilità termica: i rivestimenti in parylene presentano un'eccellente stabilità termica e possono resistere a un'ampia gamma di temperature. Rimangono stabili alle basse e alle alte temperature, mantenendo le loro proprietà protettive senza degrado significativo. Questa stabilità termica rende i rivestimenti in Parylene adatti per applicazioni in cui le variazioni di temperatura e la dissipazione del calore sono considerazioni essenziali.
- Basso coefficiente di attrito: i rivestimenti in parylene hanno un basso coefficiente di attrito, fornendo lubrificazione e riducendo l'attrito superficiale tra i componenti. Questo basso coefficiente di attrito aiuta a ridurre al minimo l'usura, prevenire l'adesione o il grippaggio e migliorare le prestazioni complessive e la durata dei dispositivi elettronici rivestiti.
- Trasparenza e tracciabilità: i conformal coating in parylene sono trasparenti e consentono l'ispezione visiva dei componenti sottostanti senza la necessità di rimuovere il rivestimento. Questa trasparenza consente di valutare e identificare potenziali problemi come difetti dei giunti di saldatura, danni ai componenti o contaminazione da materiale estraneo. Inoltre, i rivestimenti in parylene possono essere drogati o contrassegnati con elementi tracciabili, facilitando il controllo della qualità, la tracciabilità e l'identificazione.
I rivestimenti conformi in parylene vengono generalmente applicati utilizzando un processo di deposizione da vapore specializzato. Gli strati sono formati attraverso un metodo di deposizione chimica in fase di vapore (CVD), che garantisce una copertura uniforme e priva di microfori. I rivestimenti in parylene forniscono una protezione duratura per i gruppi elettronici, anche in ambienti difficili e applicazioni impegnative.
Quando si considerano i conformal coating in Parylene, è essenziale valutare fattori quali i requisiti specifici dell'assieme elettronico, le condizioni ambientali e il livello di protezione desiderato per selezionare il tipo e il processo di deposizione di Parylene appropriati.
Fattori da considerare nella scelta di un conformal coating
Quando si sceglie un rivestimento conforme per dispositivi elettronici, è necessario considerare diversi fattori per garantire che il rivestimento soddisfi i requisiti specifici dell'applicazione. Ecco alcuni fattori chiave da considerare:
- Condizioni ambientali: le condizioni ambientali in cui opererà il dispositivo elettronico svolgono un ruolo cruciale nella selezione del rivestimento protettivo appropriato. Considerare fattori come temperature estreme, livelli di umidità, esposizione chimica, nebbia salina e radiazioni UV. Diversi strati hanno diversi gradi di resistenza a questi fattori ambientali e la scelta di un rivestimento in grado di resistere a condizioni specifiche è essenziale per l'affidabilità a lungo termine.
- Proprietà elettriche: considerare le proprietà elettriche richieste per l'assieme elettronico. Alcuni rivestimenti offrono migliori proprietà di isolamento elettrico rispetto ad altri. Valutare la rigidità dielettrica, la resistenza superficiale e la capacità di mantenere l'isolamento anche in presenza di umidità o agenti contaminanti. Assicurarsi che il rivestimento scelto non influisca negativamente sulle prestazioni elettriche dei componenti.
- Spessore e copertura: i requisiti di spessore e copertura del conformal coating sono considerazioni essenziali. Gli strati sottili sono desiderabili per le applicazioni in cui lo spazio limitato o il mantenimento di tolleranze strette è fondamentale. Tuttavia, possono essere necessari rivestimenti più spessi per le applicazioni che richiedono una maggiore protezione contro sollecitazioni meccaniche o ambienti difficili. Lo strato dovrebbe essere in grado di coprire uniformemente tutte le aree critiche, comprese geometrie e componenti complessi.
- Metodo di applicazione: considerare i metodi disponibili e scegliere un rivestimento compatibile con la modalità selezionata. I metodi di applicazione standard includono spruzzatura, pennello, immersione e rivestimento selettivo. Alcuni strati possono essere più adatti per metodi di applicazione specifici, mentre altri possono richiedere attrezzature o tecniche specializzate.
- Rilavorazione e riparazione: valutare i requisiti di rilavorazione e riparabilità del rivestimento. In alcuni casi, la rimozione o la riparazione dello strato può essere necessaria per la sostituzione, la riparazione o la modifica dei componenti. Alcuni rivestimenti possono essere facilmente rielaborati o rimossi, mentre altri possono essere più difficili o richiedere solventi o metodi specializzati.
- Compatibilità del substrato: considerare la compatibilità del rivestimento con i materiali e i substrati utilizzati nell'assieme elettronico. Il rivestimento deve aderire al substrato e presentare una buona compatibilità con componenti, giunti di saldatura e altri materiali. I problemi di compatibilità possono portare a delaminazione, ridotta adesione o scarse prestazioni del rivestimento.
- Conformità alle normative: prendere in considerazione eventuali requisiti normativi specifici che si applicano al dispositivo elettronico o al settore in cui verrà utilizzato. Applicazioni tipiche come i dispositivi medici o l'elettronica aerospaziale possono avere standard normativi specifici per i conformal coating. Assicurarsi che il rivestimento scelto sia conforme alle normative e agli standard pertinenti.
- Costo e disponibilità: valutare il costo del rivestimento e la sua disponibilità nelle quantità richieste. Considera l'efficacia in termini di costi del rivestimento, il livello di protezione desiderato e il budget complessivo del progetto. Inoltre, assicurati che il rivestimento sia prontamente disponibile presso fornitori affidabili per evitare ritardi o problemi della catena di fornitura.
Considerando questi fattori, è possibile selezionare un rivestimento protettivo che fornisca protezione, prestazioni e affidabilità ottimali per i requisiti specifici del dispositivo elettronico e del relativo ambiente operativo.
Metodi applicativi per conformal coating
I rivestimenti conformi sono sottili strati protettivi applicati a circuiti stampati e componenti elettronici per fornire isolamento e proteggerli da fattori ambientali come umidità, polvere, sostanze chimiche e fluttuazioni di temperatura. Questi rivestimenti sono progettati per “conformarsi” alla forma del supporto, fornendo una barriera protettiva uniforme e continua. Esistono diversi metodi per l'applicazione di conformal coating, ciascuno con vantaggi e considerazioni. Questo articolo esplorerà alcuni metodi di applicazione standard per rivestimenti conformi.
- Spazzolatura/immersione: la spazzolatura o immersione è uno dei metodi più semplici e tradizionali per l'applicazione di conformal coating. Il materiale di rivestimento viene spazzolato manualmente oppure i componenti vengono immersi in un contenitore della soluzione di rivestimento. Questo metodo è economico e adatto alla produzione di piccoli volumi. Tuttavia, può causare uno spessore del rivestimento incoerente e richiedere la polimerizzazione post-applicazione.
- Rivestimento a spruzzo: il rivestimento a spruzzo comporta l'uso di aria compressa o un sistema di spruzzatura specializzato per applicare il materiale di rivestimento come una nebbia sottile sul substrato. Questo metodo offre un'applicazione più rapida ed è adatto a processi manuali e automatizzati. Il rivestimento a spruzzo offre un maggiore controllo sullo spessore e sull'uniformità del rivestimento, ma richiede sistemi di ventilazione e filtrazione adeguati per controllare l'overspray e garantire la sicurezza dell'operatore.
- Rivestimento selettivo: il rivestimento selettivo viene utilizzato quando solo aree specifiche del substrato richiedono protezione. Implica l'utilizzo di un sistema di erogazione controllato o di un braccio robotico con un applicatore di precisione per applicare il materiale di rivestimento con precisione nelle posizioni desiderate. Il rivestimento selettivo riduce al minimo gli sprechi, riduce la necessità di mascheramento e consente una protezione mirata. È comunemente usato per circuiti stampati complessi con componenti sensibili.
- Deposizione da vapore: i metodi di deposizione da vapore, come la deposizione chimica da vapore (CVD) e la deposizione fisica da vapore (PVD), comportano il deposito di uno strato di rivestimento conforme sul substrato attraverso una fase vapore. Questi metodi richiedono in genere attrezzature specializzate e ambienti controllati. Le tecniche di deposizione in fase di vapore offrono un'eccellente uniformità del rivestimento, controllo dello spessore e copertura su geometrie complesse. Sono comunemente usati per applicazioni ad alte prestazioni e dispositivi elettronici avanzati.
- Rivestimento in parilene: il rivestimento in parilene è un metodo unico che prevede il deposito di un sottile film polimerico conforme sul substrato mediante deposizione da vapore. I rivestimenti in parylene offrono protezione, isolamento e biocompatibilità eccezionali. Il materiale di rivestimento penetra nelle fessure e copre uniformemente l'intera superficie, anche su componenti complessi. I rivestimenti in parylene sono comunemente usati nei dispositivi medici, nel settore aerospaziale e nelle applicazioni ad alta affidabilità.
Quando si seleziona un metodo di applicazione per rivestimenti conformi, è necessario considerare diversi fattori, tra cui la complessità del substrato, il volume di produzione, le proprietà del materiale di rivestimento, il costo e i requisiti ambientali. È essenziale scegliere il metodo che fornisce copertura, uniformità e affidabilità ottimali del rivestimento tenendo conto delle esigenze specifiche dell'applicazione.
Spessore del rivestimento conforme
Lo spessore del rivestimento conforme è fondamentale per garantire l'efficacia e l'affidabilità del rivestimento protettivo applicato a componenti elettronici e circuiti stampati. Lo spessore del rivestimento influisce direttamente sul livello di protezione fornito contro i fattori ambientali, quali umidità, polvere, sostanze chimiche e variazioni di temperatura. Questo articolo esplorerà l'importanza dello spessore del rivestimento conforme e le considerazioni necessarie per ottenere lo spessore del rivestimento desiderato.
Lo scopo principale dei conformal coating è quello di creare uno strato protettivo uniforme e continuo sul substrato. Lo spessore del rivestimento deve essere sufficiente a fornire isolamento e prevenire potenziali cortocircuiti elettrici o correnti di dispersione pur non essendo così spesso da causare interferenze elettriche o problemi termici. Lo spessore ideale del rivestimento dipende da fattori quali il materiale di rivestimento, l'applicazione specifica e le condizioni ambientali che l'elettronica rivestita incontrerà.
I rivestimenti conformi vengono generalmente applicati come strati sottili, in genere con uno spessore compreso tra pochi micrometri (µm) e decine di micrometri. Il produttore del materiale di rivestimento spesso specifica lo spessore del rivestimento consigliato o può essere definito da standard di settore come IPC-CC-830 per rivestimenti conformi.
Il raggiungimento dello spessore di rivestimento desiderato comporta la considerazione di diversi fattori:
- Materiale di rivestimento: diversi materiali di rivestimento conforme hanno viscosità e caratteristiche di flusso diverse. Queste proprietà influenzano il modo in cui il rivestimento si stende e si livella sulla superficie del substrato, influenzando lo spessore risultante. È essenziale comprendere i requisiti specifici dell'applicazione e selezionare un materiale di rivestimento che possa essere applicato con il controllo dello spessore desiderato.
- Metodo di applicazione: anche il metodo di applicazione scelto svolge un ruolo significativo nella determinazione dello spessore del rivestimento. Pratiche come la spazzolatura o l'immersione possono comportare variazioni nello spessore del rivestimento dovute alle tecniche di applicazione manuale. Processi automatizzati come lo spray o il rivestimento selettivo possono fornire un maggiore controllo sullo spessore del rivestimento, risultando in uno strato più uniforme e uniforme.
- Controllo del processo: un corretto controllo del processo è fondamentale per ottenere lo spessore di rivestimento desiderato. Fattori come la pressione di spruzzo, la dimensione dell'ugello, la distanza di spruzzo e la viscosità del materiale di rivestimento devono essere attentamente controllati durante il processo di applicazione. Potrebbe essere necessario regolare i parametri di processo in base alla geometria del substrato e allo spessore del rivestimento desiderato.
- Indurimento/ritiro: alcuni materiali di conformal coating subiscono un processo di indurimento o essiccazione dopo l'applicazione. Il materiale di rivestimento può restringersi durante questo processo, influenzando lo spessore finale del rivestimento. È essenziale considerare il potenziale restringimento quando si determina lo spessore iniziale del rivestimento.
- Verifica e ispezione: una volta applicato il rivestimento, è essenziale verificarne lo spessore per assicurarsi che soddisfi le specifiche richieste. È possibile utilizzare varie tecniche di ispezione, come l'ispezione visiva, la sezione trasversale o apparecchiature di misurazione specializzate come profilometri o microscopia ottica con software di misurazione calibrato.
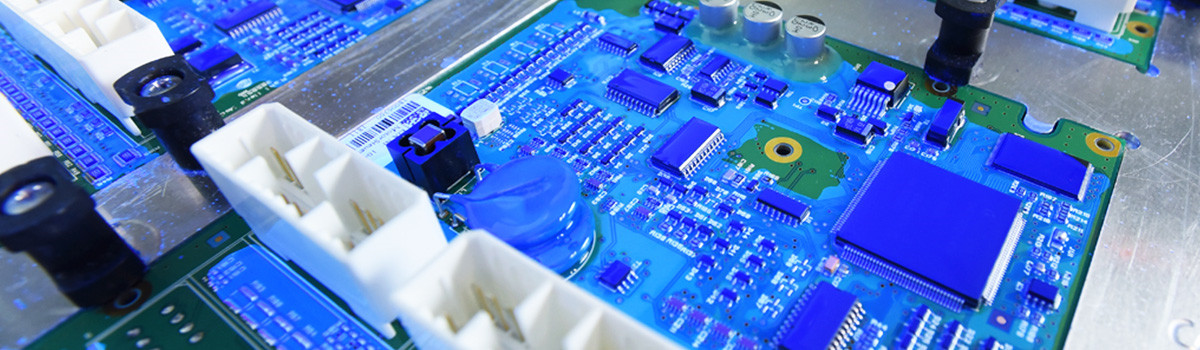
Problemi comuni con rivestimenti conformi
Sebbene i rivestimenti conformi siano essenziali per proteggere i componenti elettronici e le schede dei circuiti, a volte possono incontrare problemi che possono influire sulle loro prestazioni e affidabilità. Questo articolo discuterà alcuni problemi comuni con i conformal coating e le loro potenziali cause.
- Copertura inadeguata: una copertura inadeguata si verifica quando il rivestimento non riesce a coprire l'intera superficie del substrato o lascia spazi vuoti e vuoti. Questo problema può derivare da tecniche di applicazione improprie, come una spruzzatura irregolare o una viscosità del rivestimento insufficiente. Può anche verificarsi a causa di contaminazione superficiale, asciugatura o indurimento inadeguati o controllo inadeguato dello spessore del rivestimento.
- Variazione dello spessore: lo spessore del rivestimento non uniforme è un altro problema comune. Tecniche di applicazione incoerenti, come una spruzzatura irregolare o un controllo inadeguato dei parametri di processo, possono causarlo. Anche la necessità di tempi di asciugatura o indurimento più lunghi, una viscosità inadeguata del materiale di rivestimento o una preparazione superficiale insufficiente possono contribuire alle variazioni di spessore.
- Blistering e delaminazione: Blistering e delaminazione si verificano quando il conformal coating forma delle bolle o si separa dal substrato. Questo problema può sorgere a causa di un'errata pulizia e preparazione della superficie, umidità o contaminazione sulla superficie, indurimento o asciugatura inadeguati o compatibilità impropria tra il materiale di rivestimento e il substrato.
- Cracking e bridging: il cracking si riferisce allo sviluppo di fessure o fratture nel rivestimento conforme, mentre il bridging si verifica quando il materiale di rivestimento si estende su spazi o componenti adiacenti, con conseguenti collegamenti elettrici involontari. Questi problemi possono essere causati da uno spessore eccessivo del rivestimento, indurimento o asciugatura inadeguati, stress termico, selezione impropria del materiale di rivestimento o flessibilità del rivestimento inadeguata.
- Scarsa adesione: una scarsa adesione si verifica quando il rivestimento non aderisce al substrato, con conseguente riduzione della protezione e potenziale distacco del rivestimento. La pulizia e la preparazione inadeguate della superficie, i contaminanti, i materiali di rivestimento-substrato incompatibili o l'indurimento o l'asciugatura insufficienti possono causarlo.
- Migrazione elettrochimica: la migrazione elettrochimica è il movimento di ioni o contaminanti attraverso la superficie del substrato rivestito, che porta a potenziali cortocircuiti e corrosione. Può verificarsi a causa di uno spessore del rivestimento inadeguato, della presenza di contaminanti conduttivi o della presenza di umidità o umidità.
- Resistenza chimica insufficiente: potrebbe essere necessario che i rivestimenti conformi resistano all'esposizione a vari prodotti chimici e solventi. Se il materiale di rivestimento non ha una sufficiente resistenza chimica, può degradarsi o dissolversi se esposto a sostanze specifiche, compromettendone le capacità protettive. La corretta selezione del materiale è fondamentale per garantire la compatibilità con l'ambiente chimico previsto.
Per mitigare questi problemi, è essenziale seguire le migliori pratiche e le linee guida per l'applicazione del rivestimento conforme, compresa un'adeguata pulizia e preparazione della superficie, un controllo accurato dei parametri di processo, una selezione del materiale di rivestimento adatto e un'adeguata polimerizzazione o asciugatura. Dovrebbero essere implementate ispezioni regolari e misure di controllo della qualità per identificare e affrontare tempestivamente potenziali problemi di rivestimento. Anche il rispetto degli standard del settore, come IPC-CC-830, può contribuire a garantire l'affidabilità e le prestazioni dei conformal coating.
Manutenzione dei conformal coating
I rivestimenti protettivi proteggono i componenti elettronici e le schede dei circuiti da fattori ambientali come umidità, polvere, sostanze chimiche e fluttuazioni di temperatura. Tuttavia, come qualsiasi rivestimento protettivo, i rivestimenti conformi richiedono un'adeguata manutenzione per garantire la loro efficacia a lungo termine. Ecco alcuni punti chiave da considerare quando si tratta della manutenzione dei conformal coating:
- Ispezione regolare: eseguire ispezioni di routine delle superfici rivestite per verificare la presenza di eventuali segni di danni, usura o delaminazione. Cerca crepe, scheggiature o aree in cui il rivestimento potrebbe essersi consumato. Le ispezioni devono essere effettuate periodicamente, soprattutto dopo la manipolazione, il trasporto o l'esposizione a condizioni difficili.
- Pulizia: mantenere pulite le superfici rivestite per evitare l'accumulo di contaminanti che potrebbero compromettere l'efficacia del rivestimento. Utilizzare metodi di pulizia delicati, come una spazzola morbida o aria compressa, per rimuovere polvere, detriti o particolato. Evitare l'uso di solventi aggressivi o materiali abrasivi che possono danneggiare il rivestimento.
- Riparazione di aree danneggiate: se durante le ispezioni vengono rilevati danni o segni di usura, è essenziale affrontarli tempestivamente. Riparare le aree danneggiate ricoprendole con lo stesso materiale di rivestimento conforme. Assicurarsi che l'area danneggiata sia adeguatamente pulita e preparata prima di applicare il nuovo rivestimento. Ciò contribuirà a mantenere l'integrità dello strato protettivo.
- Controllo della temperatura e dell'umidità: mantenere condizioni di temperatura e umidità adeguate nell'ambiente in cui i componenti rivestiti vengono conservati o utilizzati. Temperature estreme o livelli di umidità elevati possono influire sulle prestazioni del rivestimento e portare alla delaminazione o alla riduzione della protezione. Seguire le raccomandazioni del produttore relative agli intervalli di temperatura e umidità accettabili per lo specifico materiale di rivestimento conforme.
- Evitare l'esposizione chimica: evitare l'esposizione delle superfici rivestite a sostanze chimiche o solventi aggressivi che possono deteriorare il rivestimento. Prestare attenzione durante l'utilizzo di detergenti o l'esecuzione di procedure di manutenzione in prossimità dei componenti coperti. Prendere le precauzioni necessarie per proteggere il rivestimento protettivo dal contatto diretto con sostanze chimiche.
- Nuovo test e ricertificazione: in alcuni settori, come quello aerospaziale o medico, i conformal coating possono richiedere periodici test e ricertificazioni per garantire che soddisfino gli standard e le specifiche necessarie. Seguire le linee guida degli standard di settore pertinenti ed eseguire i test o le ispezioni necessarie a intervalli regolari.
- Documentazione e registrazione: conservare registrazioni dettagliate dell'applicazione del conformal coating, delle attività di manutenzione, delle ispezioni e delle riparazioni. Questa documentazione aiuterà a tenere traccia della cronologia della manutenzione, identificare i modelli di guasto o usura e garantire la conformità alle normative e agli standard del settore.
Prove e ispezioni di conformal coating
I test e l'ispezione dei conformal coating sono essenziali per garantirne l'efficacia e l'affidabilità nella protezione di componenti e assiemi elettronici. Ecco alcuni metodi comunemente usati per testare e ispezionare i conformal coating:
- Ispezione visiva: l'ispezione visiva è un passaggio essenziale nella valutazione della qualità dei conformal coating. Implica l'esame della superficie del rivestimento per difetti visibili come fori di spillo, bolle, crepe o copertura irregolare.
- Misurazione dello spessore: lo spessore del rivestimento protettivo è fondamentale in quanto influisce sulla sua capacità di fornire una protezione adeguata. La coerenza può essere misurata utilizzando tecniche di corrente parassita, induzione magnetica o profilometria ottica. La misurazione deve essere confrontata con i requisiti di spessore del rivestimento specificati.
- Test di adesione: i test valutano la forza di adesione tra il conformal coating e il substrato. I metodi per i test di adesione includono test su nastro, test di tratteggio incrociato e test di pull-off. Questi test determinano se lo strato aderisce adeguatamente alla superficie e può resistere alle sollecitazioni durante il funzionamento e la manipolazione.
- Test di resistenza all'isolamento: questo test valuta la resistenza elettrica del rivestimento protettivo. Assicura che lo strato fornisca un efficace isolamento elettrico per evitare perdite o cortocircuiti. Il test della resistenza di isolamento viene generalmente condotto utilizzando un tester ad alta tensione o un megaohmmetro.
- Test della tensione di tenuta dielettrica: il test della tensione di tenuta dielettrica, noto anche come test ad alto potenziale o hipot, controlla la capacità del rivestimento di resistere all'alta tensione senza guasti. Il rivestimento protettivo è sottoposto a una tensione specificata per una durata fissa per garantire che soddisfi gli standard di isolamento elettrico richiesti.
- Test dei cicli termici: i cicli termici espongono il conformal coating a variazioni di temperatura per valutarne la resistenza allo stress termico. Lo strato è soggetto a cicli ripetuti di temperature estreme e si osservano eventuali cambiamenti, come fessurazioni o delaminazioni.
- Test di resistenza all'umidità e all'umidità: questi test valutano la capacità del rivestimento conforme di resistere all'umidità e all'umidità. Lo strato è esposto a umidità elevata o condizioni di umidità per un periodo specificato e le sue prestazioni vengono valutate per la protezione contro la corrosione o guasti elettrici.
- Test di resistenza chimica: i test di resistenza chimica controllano quanto bene il rivestimento protettivo resiste all'esposizione a vari prodotti chimici, come solventi o agenti di pulizia. Lo strato viene esposto alle sostanze per una durata specificata e ne vengono valutati l'aspetto, l'adesione e la funzionalità.
- Test in nebbia salina: il test in nebbia salina valuta la resistenza del rivestimento alla corrosione in un ambiente carico di sale. Il rivestimento protettivo viene esposto a nebbia salina o nebbia per una durata specificata e vengono esaminati eventuali segni di corrosione o degradazione.
È importante notare che i requisiti di test specifici possono variare a seconda del settore, dell'applicazione e degli standard applicabili al rivestimento protettivo. I produttori o le organizzazioni di standard di settore spesso forniscono linee guida o specifiche per le procedure di test e ispezione.
Standard di settore per conformal coating
Esistono diversi standard e specifiche del settore per i rivestimenti conformi per garantirne la qualità, l'affidabilità e le prestazioni. Ecco alcuni degli standard comunemente citati:
- IPC-CC-830: questo standard, pubblicato dall'Association of Connecting Electronics Industries (IPC), è ampiamente utilizzato per i materiali di rivestimento conforme e i requisiti delle applicazioni. Copre le condizioni generali, le proprietà dei materiali, i metodi di applicazione e i criteri di ispezione per i conformal coating.
- MIL-STD-883: questo standard militare delinea i metodi e le procedure di test dei dispositivi microelettronici, inclusi i conformal coating. Include le specifiche per l'adesione, la resistenza all'isolamento, lo shock termico, l'umidità e altri test relativi ai conformal coating.
- MIL-STD-810: questo standard fornisce considerazioni di ingegneria ambientale e metodi di test di laboratorio per simulare e valutare le prestazioni di materiali, apparecchiature e sistemi in varie condizioni ambientali. Include procedure di test per conformal coating riguardanti temperatura, umidità, vibrazioni, urti, ecc.
- IEC 61086: questo standard internazionale specifica i requisiti e i metodi di prova per i conformal coating utilizzati negli assemblaggi elettronici. Copre i materiali di rivestimento, lo spessore, l'adesione, la flessibilità, la resistenza termica e la resistenza chimica.
- UL 746E: questo standard, pubblicato da Underwriters Laboratories (UL), si concentra sulla valutazione dei materiali polimerici da utilizzare nelle apparecchiature elettriche. Include i requisiti di prova per i conformal coating riguardanti l'infiammabilità, le caratteristiche di invecchiamento e le prestazioni elettriche.
- ISO 9001: Sebbene non sia specifico per i conformal coating, ISO 9001 è uno standard riconosciuto a livello internazionale per i sistemi di gestione della qualità. Garantisce che le organizzazioni seguano processi di controllo della qualità coerenti, inclusa la produzione e l'ispezione di conformal coating.
È importante notare che diversi settori e applicazioni possono avere standard o specifiche specifici adattati ai loro requisiti unici. Inoltre, molti produttori di conformal coating possono fornire schede tecniche o linee guida applicative, che possono fungere da preziosi riferimenti per la selezione e il test del conformal coating.
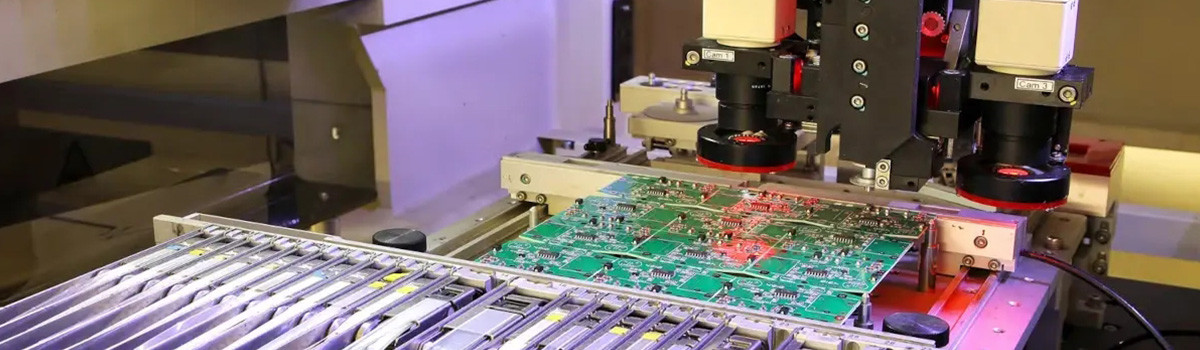
Progressi nella tecnologia del rivestimento conforme
Negli ultimi anni, ci sono stati progressi significativi nella tecnologia del conformal coating, spinti dalla necessità di migliorare la protezione, l'affidabilità e le prestazioni dei componenti e degli assiemi elettronici. Ecco alcuni miglioramenti chiave:
- Nano-rivestimenti: i nano-rivestimenti sono emersi come un promettente progresso nella tecnologia del rivestimento conforme. Questi rivestimenti sono costituiti da strati ultrasottili, tipicamente su scala nanometrica, che forniscono un'eccellente resistenza all'umidità e alla corrosione pur mantenendo le prestazioni elettriche. I nano-rivestimenti offrono una copertura e una conformabilità superiori, garantendo un'adeguata protezione anche su gruppi elettronici complessi e densamente imballati.
- Rivestimenti multifunzionali: i rivestimenti conformi vengono sviluppati con proprietà multifunzionali per affrontare più sfide contemporaneamente. Ad esempio, alcuni rivestimenti offrono resistenza all'umidità e agli agenti chimici e una migliore conduttività elettrica o capacità di gestione termica. Questi rivestimenti multifunzionali riducono la necessità di ulteriori strati protettivi e migliorano le prestazioni complessive.
- Rivestimenti autorigeneranti: i conformal coating autorigeneranti sono progettati per riparare automaticamente danni minori. Questi rivestimenti contengono agenti curativi incapsulati rilasciati in seguito al danno, che riempiono crepe o vuoti e ripristinano le proprietà protettive del rivestimento. I rivestimenti autorigeneranti prolungano la durata dei componenti elettronici mitigando gli effetti dell'usura o delle sollecitazioni ambientali.
- Rivestimenti flessibili ed estensibili: con l'ascesa dell'elettronica flessibile e dei dispositivi indossabili, i rivestimenti conformi devono adattarsi alla flessione, all'allungamento e alla torsione dei substrati. Gli strati flessibili ed estensibili sono stati sviluppati per fornire una protezione robusta pur mantenendo la loro integrità sotto sollecitazione meccanica. Questi rivestimenti consentono una copertura conforme su substrati flessibili, ampliando la gamma di applicazioni.
- Rivestimenti a basso contenuto di COV e rispettosi dell'ambiente: vi è una crescente attenzione allo sviluppo di rivestimenti conformi con composti organici volatili (COV) ridotti e formulazioni rispettose dell'ambiente. Questi rivestimenti mirano a ridurre al minimo l'impatto ambientale durante l'applicazione e l'uso mantenendo caratteristiche ad alte prestazioni. Si stanno sviluppando rivestimenti a base d'acqua o privi di solventi come alternative ai tradizionali rivestimenti a base di solventi.
- Rivestimenti a polimerizzazione UV: i conformal coating a polimerizzazione UV offrono tempi di polimerizzazione rapidi, consentendo una maggiore produttività nei processi di produzione. Questi rivestimenti utilizzano la luce ultravioletta (UV) per avviare la reazione di indurimento, consentendo cicli di produzione più rapidi e un consumo energetico ridotto. I rivestimenti a polimerizzazione UV forniscono anche un'eccellente copertura e adesione, migliorando l'affidabilità complessiva degli assemblaggi rivestiti.
- Tecnologie di ispezione del rivestimento conforme: i progressi nelle tecnologie di ispezione stanno aiutando a valutare la qualità e le prestazioni del rivestimento conforme. I sistemi di ispezione ottica automatizzata (AOI) con telecamere ad alta risoluzione e algoritmi di analisi delle immagini possono rilevare difetti quali microfori, bolle o variazioni dello spessore del rivestimento. Ciò migliora l'efficienza e l'affidabilità dell'ispezione, garantendo una qualità costante del rivestimento.
- Rivestimenti più sottili e più leggeri: la richiesta di miniaturizzazione e design leggeri nei dispositivi elettronici ha portato allo sviluppo di rivestimenti conformi più sottili e leggeri. Questi rivestimenti forniscono una protezione sufficiente riducendo al minimo l'impatto sul peso e sulle dimensioni dei componenti rivestiti. Gli strati più sottili offrono anche una migliore dissipazione del calore, fondamentale per le applicazioni ad alta potenza.
Questi progressi nella tecnologia del rivestimento conforme contribuiscono allo sviluppo di dispositivi elettronici più affidabili e durevoli. Mentre l'industria elettronica continua ad evolversi, la ricerca e l'innovazione in corso nei rivestimenti conformi dovrebbero affrontare le sfide emergenti e consentire una protezione migliorata in varie applicazioni.
Preoccupazioni ambientali e conformal coating
Le preoccupazioni ambientali giocano un ruolo significativo nello sviluppo e nell'utilizzo di conformal coating. Poiché l'industria elettronica continua a crescere, è necessario bilanciare i vantaggi dei conformal coating con i loro potenziali impatti ambientali. Ecco alcuni aspetti critici relativi alle preoccupazioni ambientali e ai conformal coating:
- Composti organici volatili (COV): i conformal coating tradizionali a base di solventi contengono spesso livelli elevati di COV, che contribuiscono all'inquinamento atmosferico e danneggiano la salute umana. In risposta, vi è una crescente domanda di formulazioni a basso VOC o prive di VOC. Vernici a base acqua e vernici a basso contenuto di COV sono in fase di sviluppo come alternative per ridurre l'impatto ambientale.
- Sostanze pericolose: alcuni conformal coating possono contenere sostanze pericolose, come metalli pesanti o inquinanti organici persistenti (POP). Queste sostanze possono avere effetti ambientali di lunga durata e comportare rischi durante la produzione, l'applicazione e lo smaltimento a fine vita. Per risolvere questo problema, normative e standard, come la direttiva RoHS (Restriction of Hazardous Substances), limitano l'uso di determinate sostanze pericolose nei prodotti elettronici.
- Valutazione del ciclo di vita (LCA): la valutazione del ciclo di vita valuta gli impatti ambientali dei conformal coating durante l'intero ciclo di vita, dall'estrazione delle materie prime allo smaltimento. Aiuta a identificare le aree di miglioramento e guida lo sviluppo di strati rispettosi dell'ambiente. LCA considera il consumo di energia, l'esaurimento delle risorse, le emissioni e la produzione di rifiuti.
- Formulazioni ecologiche: i produttori di rivestimenti conformi sviluppano attivamente formulazioni ecologiche che riducono al minimo l'impatto ambientale. Ciò include l'utilizzo di materiali a base biologica, risorse rinnovabili e solventi ecocompatibili. I rivestimenti a base biologica derivati da fonti naturali offrono potenziali vantaggi in termini di riduzione dell'impronta ecologica e maggiore sostenibilità.
- Riciclaggio e gestione dei rifiuti: il corretto smaltimento e il riciclaggio dei rivestimenti conformi sono essenziali per prevenire l'inquinamento ambientale. Il riciclaggio di componenti e assiemi elettronici dovrebbe prendere in considerazione la rimozione o la separazione dei conformal coating per consentire un efficiente recupero del materiale. Gli sviluppi nelle tecnologie e nei processi di riciclaggio stanno aiutando ad affrontare le sfide associate alla rimozione del rivestimento e alla gestione dei rifiuti.
- Regolamenti ambientali: i quadri normativi e gli standard, come il regolamento REACH (Registrazione, valutazione, autorizzazione e restrizione delle sostanze chimiche) dell'Unione europea, mirano a proteggere la salute umana e l'ambiente da sostanze potenzialmente dannose. La conformità a queste normative garantisce che i conformal coating soddisfino specifici requisiti ambientali e standard di sicurezza.
- Pratiche di produzione sostenibili: l'adozione di pratiche di produzione sostenibili riduce l'impatto ambientale associato alla produzione di conformal coating. Ciò include l'ottimizzazione dell'utilizzo delle risorse, la riduzione al minimo della produzione di rifiuti, l'implementazione di processi efficienti dal punto di vista energetico e la promozione delle fonti energetiche rinnovabili.
- Certificazioni ambientali: le certificazioni ambientali, come ISO 14001, forniscono un quadro per le organizzazioni per gestire e migliorare continuamente le proprie prestazioni ambientali. I produttori di rivestimenti conformi possono richiedere la certificazione per dimostrare il loro impegno nei confronti della responsabilità ambientale e delle pratiche sostenibili.
Mentre l'industria continua ad evolversi, c'è una crescente enfasi sullo sviluppo di rivestimenti conformi che offrano una protezione adeguata riducendo al minimo il loro impatto ambientale. Produttori, organismi di regolamentazione e utenti finali stanno lavorando insieme per promuovere l'uso di rivestimenti ecologici e garantire pratiche responsabili e sostenibili durante l'intero ciclo di vita dei prodotti elettronici.
Le prospettive future per i conformal coating nell'elettronica
Le prospettive future per i conformal coating nell'elettronica sono promettenti, guidate dai progressi tecnologici, dalla crescente domanda di dispositivi elettronici ad alte prestazioni e dalle tendenze emergenti nel settore. Ecco alcuni aspetti chiave che danno forma al futuro dei conformal coating:
- Miniaturizzazione e maggiore integrazione: la tendenza verso dispositivi elettronici più piccoli e compatti con livelli di integrazione più elevati pone sfide per i conformal coating. I futuri rivestimenti devono fornire una protezione adeguata pur mantenendo la loro integrità su componenti miniaturizzati e assiemi densamente imballati. Ciò include lo sviluppo di strati più sottili con una migliore copertura e conformabilità.
- Elettronica flessibile ed estensibile: l'ascesa dell'elettronica flessibile ed estensibile, compresi i dispositivi indossabili, richiede rivestimenti conformi in grado di resistere alla sollecitazione meccanica e alla flessione ripetuta senza comprometterne le proprietà protettive. Gli strati futuri si concentreranno su flessibilità, durata e adesione per soddisfare i requisiti unici di queste applicazioni emergenti.
- Materiali avanzati: lo sviluppo di nuovi materiali con proprietà migliorate guiderà il futuro dei conformal coating. Ciò include l'utilizzo di nanomateriali, come nanoparticelle e nanocompositi, per migliorare le prestazioni del rivestimento in termini di resistenza all'umidità, conduttività elettrica, gestione termica e proprietà barriera. I materiali avanzati consentiranno ai rivestimenti di soddisfare le esigenze in continua evoluzione dei dispositivi elettronici.
- Rivestimenti multifunzionali: la domanda di rivestimenti multifunzionali che offrono molteplici vantaggi oltre alla protezione continuerà a crescere. Gli strati futuri possono incorporare capacità di autoriparazione, conduttività termica, proprietà antistatiche, proprietà antimicrobiche o caratteristiche di raccolta di energia. I rivestimenti multifunzionali offrono prestazioni migliorate, complessità ridotta e maggiore affidabilità nei gruppi elettronici.
- Considerazioni ambientali: l'attenzione alla sostenibilità ecologica e alle normative in materia di sostanze pericolose influenzerà il futuro dei rivestimenti conformi. Lo sviluppo di formulazioni eco-compatibili con COV ridotti e l'uso di materiali a base biologica diventeranno sempre più diffusi. Anche le strategie di riciclaggio e di gestione dei rifiuti per i conformal coating svolgeranno un ruolo significativo nel ridurre al minimo l'impatto ambientale.
- Tecniche di applicazione avanzate: le innovazioni nelle tecniche di applicazione miglioreranno l'efficienza e la qualità dei processi di conformal coating. Ciò include sistemi di erogazione robotizzati, metodi di rivestimento selettivi e tecnologie di spruzzatura avanzate per garantire una copertura del rivestimento precisa e uniforme, ridurre lo spreco di materiale e migliorare la produttività.
- Metodi avanzati di ispezione e test: con l'aumentare della complessità degli assemblaggi elettronici, sarà necessario disporre di metodi di ispezione e test più sofisticati per i conformal coating. Ciò include lo sviluppo di sistemi di ispezione ottica automatizzata (AOI) con funzionalità avanzate di imaging e analisi per rilevare e valutare i difetti del rivestimento, le variazioni di spessore e la qualità dell'adesione.
- Standard e certificazioni del settore: i continui sviluppi negli standard e nelle certificazioni del settore continueranno a plasmare il futuro dei conformal coating. I produttori e gli utenti finali si affideranno a standard aggiornati per garantire la qualità, l'affidabilità e la conformità dei layer ai requisiti e alle normative in evoluzione.
Nel complesso, il futuro dei conformal coating nell'elettronica sembra promettente, concentrandosi sul miglioramento delle prestazioni, sull'adattabilità alle nuove tecnologie, sulla sostenibilità ambientale e sullo sviluppo di materiali avanzati e tecniche di applicazione. Questi progressi consentiranno ai conformal coating di fornire una solida protezione per i dispositivi elettronici in ambienti diversi e difficili.
Conclusione: I rivestimenti elettronici conformi offrono un'ottima soluzione per proteggere i dispositivi elettronici da fattori ambientali che possono portare al loro guasto o malfunzionamento. Con l'avanzare della tecnologia, la necessità di conformal coating più efficaci e affidabili non farà che aumentare. Produttori, progettisti e ingegneri devono stare al passo con gli ultimi sviluppi nel campo per garantire la protezione ottimale dei loro dispositivi elettronici. I rivestimenti conformi sono una parte cruciale del processo di produzione elettronica e possono aiutare a prolungare la durata e le prestazioni dei dispositivi elettronici.