Elektromos motor epoxi ragasztó
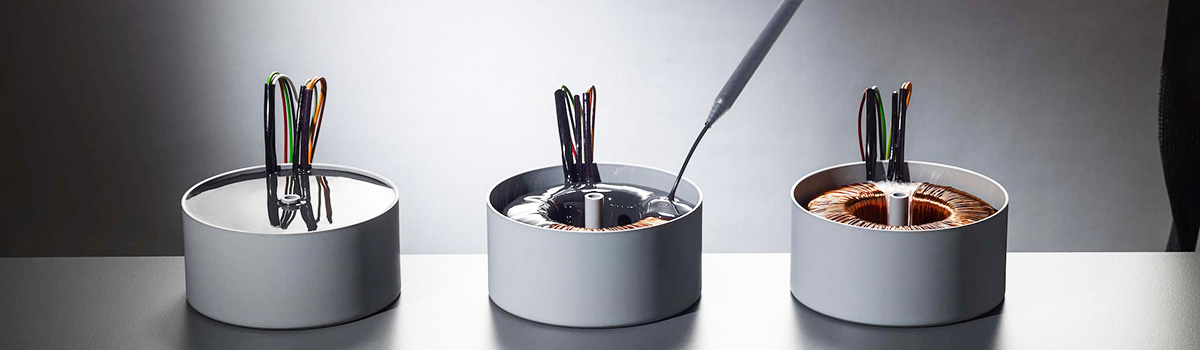
Az elektromotoros epoxi ragasztó egy speciális típus, amelyet elektromos motorokhoz terveztek. Ez a ragasztó a motor különféle alkatrészeit, például mágneseket, tekercseket és rétegelt lemezeket köt össze, és tömíti és védi a motort az olyan környezeti tényezőktől, mint a nedvesség és a hő. Ebben a cikkben megvizsgáljuk az elektromotoros epoxi ragasztó előnyeit és alkalmazásait, valamint azokat a tényezőket, amelyeket figyelembe kell venni egy adott munkához megfelelő ragasztó kiválasztásakor.
Mi az elektromos motor epoxi ragasztója?
Az elektromos motorok epoxi ragasztója egy speciális ragasztó, amelyet kifejezetten az elektromos motorok alkatrészeinek ragasztására és rögzítésére terveztek. Ez egy nagy szilárdságú ragasztó, amely kiváló tapadást és elektromos szigetelési tulajdonságokat biztosít. Ez az epoxi ragasztó ellenáll a magas hőmérsékletnek, vibrációnak és az elektromos motoroknál gyakran előforduló zord működési feltételeknek. Hatékonyan ragaszt különféle anyagokat, köztük fémeket, kerámiákat és műanyagokat, biztosítva a motor alkatrészek szerkezeti integritását. Az elektromos motorok epoxi ragasztója döntő szerepet játszik az elektromos motorok megbízhatóságának és teljesítményének növelésében, mivel tartós és elektromosan szigetelő kötést biztosít a különböző alkatrészek között, ezáltal minimalizálva az elektromos rövidzárlatok és a mechanikai meghibásodások kockázatát.
Hogyan működik az elektromos motor epoxi ragasztója?
Az elektromos motorok epoxi ragasztója kémiai és fizikai mechanizmusok kombinációját alkalmazva erős és tartós kötéseket hoz létre a motoralkatrészek között. Íme a kulcsfontosságú pontok, amelyek elmagyarázzák az elektromotoros epoxi ragasztó működését:
- Kémiai reakció: Az elektromotoros epoxi ragasztó egy gyantát és egy keményítőt tartalmaz, amelyek keveréséhez meghatározott arányra van szükség. A komponensek kémiai reakciót indítanak el, aminek következtében az epoxi megkeményedik és megkeményedik. Ez a kémiai reakció térhálósított szilárd polimer láncokat hoz létre, hozzájárulva a ragasztó nagy szilárdságához és stabilitásához.
- Ragasztó tulajdonságai:A kikeményedett epoxi ragasztó kiváló tulajdonságokkal rendelkezik, lehetővé téve az elektromos motorokban általánosan előforduló anyagokhoz való kötődését, beleértve a fémeket, kerámiákat és műanyagokat. A ragasztó bensőséges érintkezést képez a komponensek felületével, erős molekuláris szintű kölcsönhatásokat hozva létre és elősegíti a tapadást.
- Felület előkészítése:Az epoxi ragasztó felhordása előtt kulcsfontosságú a motoralkatrészek felületének megfelelő előkészítése. Az optimális tapadás érdekében a felületeket alaposan meg kell tisztítani és zsírtalanítani kell a szennyeződések eltávolítása érdekében. A felületek csiszolással vagy maratással történő érdesítése szintén növelheti a kötés szilárdságát azáltal, hogy megnöveli a tapadáshoz rendelkezésre álló felületet.
- Hőálló: Az elektromotoros epoxi ragasztókészítmény ellenáll a motor működése során fellépő magas hőmérsékletnek. Szélsőséges hőviszonyok között is megőrzi szerkezeti integritását és tapadószilárdságát, biztosítva, hogy a ragasztott alkatrészek biztonságosan rögzítve maradjanak.
- Elektromos szigetelés: Az elektromotoros epoxi ragasztó a szilárd kötés mellett kiváló elektromos szigetelési tulajdonságokkal is rendelkezik. Gátként működik, megakadályozza, hogy az elektromos áram áthaladjon a ragasztott területen, és minimálisra csökkenti a rövidzárlat kockázatát. Ez a szigetelési tulajdonság kulcsfontosságú az elektromos motorok megbízható és biztonságos működésének fenntartásához.
- Rezgés- és ütésállóság: Az elektromos motorok működése során gyakran jelentős rezgéseket és ütéseket tapasztalnak. Az epoxi ragasztó nagy rugalmassága és mechanikai feszültségelnyelő képessége segít megakadályozni a ragasztott alkatrészek kilazulását vagy szétválását ilyen dinamikus körülmények között. Ezt a gyakorlatot követve a motor hosszabb ideig tart és megbízhatóbb lesz.
Az elektromos motoros epoxi ragasztó előnyei
Az elektromos motorok epoxi ragasztója számos előnnyel rendelkezik, amelyek előnyös választássá teszik az elektromos motorok alkatrészeinek ragasztására és rögzítésére. Íme az elektromos motoros epoxi ragasztó használatának legfontosabb előnyei:
- Erős kötelék: Az elektromos motorok epoxi ragasztója erős és tartós kötést hoz létre a motor alkatrészek között, biztosítva azok stabilitását és integritását. Bensőséges érintkezést képez a felületekkel, elősegítve a kiváló tapadást és minimalizálva az alkatrészek szétválásának vagy elmozdulásának kockázatát.
- Hőstabilitás: Elektromos motor epoxi ragasztót készítünk, hogy ellenálljon a motor működése során fellépő magas hőmérsékletnek. Szélsőséges hőviszonyok között is megőrzi szerkezeti integritását és tapadószilárdságát, így biztosítja a tartós teljesítményt és megbízhatóságot.
- Elektromos szigetelés: Az epoxi ragasztó hatékony elektromos szigetelést biztosít, megakadályozva, hogy az elektromos áram áthaladjon a ragasztott területen. Ez a szigetelési tulajdonság csökkenti az elektromos rövidzárlat kockázatát, és javítja az elektromos motorok biztonságát és megbízhatóságát.
- Kémiai ellenállás: Az elektromotoros epoxi ragasztó kiválóan ellenáll a különféle vegyszereknek és oldószereknek. Ellenáll az olajoknak, üzemanyagoknak, kenőanyagoknak és más, a motoros környezetben gyakran előforduló anyagoknak anélkül, hogy a tapadási tulajdonságait vagy szerkezeti integritását veszélyeztetné.
- Rezgés és lengéscsillapítás: Az elektromos motorok működése során rezgéseket és ütéseket tapasztalnak, amelyek meglazíthatják vagy gyengíthetik az alkatrészek közötti kötéseket. Az elektromotoros epoxi ragasztó jó rugalmassággal és ütéselnyelő tulajdonságokkal rendelkezik, hatékonyan csillapítja a rezgéseket és minimálisra csökkenti a kötés meghibásodásának kockázatát.
- Sokoldalúság: Az elektromos motor epoxi ragasztója különféle anyagokkal kompatibilis, beleértve a fémeket, kerámiákat és műanyagokat. Alkotórészek, például állórészek, rotorok, mágnesek és tekercsek összeragasztására alkalmas, sokoldalúságot kínálva a motor-összeszerelési és -javítási alkalmazásokban.
- Könnyű alkalmazás:Az elektromotoros epoxi ragasztó jellemzően kétkomponensű kiszerelésben kapható, amelyek könnyen keverhetők és felhordhatók. Keverés után megfelelő működési ideje van, mielőtt elkezd kikeményedni, lehetővé téve az alkatrészek megfelelő elhelyezését és beállítását. Ez az egyszerű alkalmazás hozzájárul a hatékony motor-összeszerelési és karbantartási folyamatokhoz.
- Hosszú élet:Nagy szilárdságának, termikus stabilitásának és a környezeti tényezőkkel szembeni ellenálló képességének köszönhetően az elektromotoros epoxi ragasztó segít meghosszabbítani az elektromos motorok élettartamát. Ez biztosítja a ragasztott alkatrészek tartósságát és megbízhatóságát, minimálisra csökkentve a gyakori javítások vagy cserék szükségességét.
Kivételes ragasztási szilárdság
A kiváló tapadási szilárdság a kiváló minőségű ragasztók alapvető jellemzője, amely megbízható és tartós kapcsolatot biztosít a különböző anyagok között. Íme a legfontosabb pontok, amelyek megmagyarázzák a kivételes kötési szilárdság jelentőségét és tényezőit:
- Felület előkészítése: A megfelelő felület-előkészítés kulcsfontosságú a kivételes tapadási szilárdság eléréséhez. Az optimális tapadás érdekében a karaktereket alaposan meg kell tisztítani, zsírtalanítani, és ha szükséges, érdesíteni kell. A szennyeződések eltávolítása és az érdes felület kialakítása növeli a ragasztó és az aljzat közötti érintkezési felületet, javítva a kötési szilárdságot.
- Molekuláris szintű kölcsönhatások: A kivételes kötési szilárdságú ragasztók molekuláris szintű szilárd kölcsönhatásokat hoznak létre a hordozóanyagokkal. A kémiai kötések, az elektrosztatikus kölcsönhatások és az intermolekuláris erők (mint például Van der Waals) mind ennek elérésének módjai. Ezek a kölcsönhatások növelik a ragasztó azon képességét, hogy ellenálljon a külső erőknek és feszültségeknek.
- Ragasztó összetétel:A ragasztó összetétele létfontosságú szerepet játszik a ragasztó szilárdságának meghatározásában. A nagy szilárdságú összetételű ragasztók, mint például az epoxi vagy poliuretán ragasztók, kiváló ragasztóképességet kínálnak. A megfelelő ragasztótípus kiválasztása a ragasztott anyagok és a tervezett alkalmazás alapján elengedhetetlen a kivételes ragasztási szilárdság eléréséhez.
- Kikeményedési folyamat:A ragasztó kikeményedési folyamata jelentősen befolyásolja a ragasztó végső kötési szilárdságát. Amikor a ragasztók, például az epoxi keményedési folyamaton mennek keresztül, térhálós polimer hálózatokat képeznek, amelyek robusztusabbá és stabilabbá teszik őket. A megfelelő kikeményedés, beleértve a hőmérsékletet, a páratartalmat és az időt, elengedhetetlen a ragasztó tapadásának maximalizálásához.
- Anyagkompatibilitás: A rendkívüli tapadási szilárdság megköveteli a ragasztó és az aljzat anyagainak kompatibilitását. A gyártók ragasztókat készítenek bizonyos típusú anyagok, például fémek, műanyagok vagy kompozitok ragasztására. Az optimális tapadási szilárdság eléréséhez elengedhetetlen annak biztosítása, hogy a ragasztó kompatibilis a ragasztott aljzatokkal.
- Környezeti tényezők:A környezeti tényezők, mint például a hőmérséklet, a páratartalom és a vegyszereknek vagy UV-sugárzásnak való kitettség, befolyásolhatják a ragasztók tapadási szilárdságát. A speciális környezetekhez, például autóipari vagy repülőgépipari alkalmazásokhoz tervezett kiváló minőségű ragasztók úgy vannak kialakítva, hogy megőrizzék kötési szilárdságukat még kihívásokkal teli körülmények között is.
- Tesztelés és minőségellenőrzés:A ragasztógyártók szigorú vizsgálatokat és minőség-ellenőrzési intézkedéseket hajtanak végre a kivételes ragasztási szilárdság biztosítása érdekében. Különböző értékeléseken kell átesnie, például nyírási, lehúzási vagy szakítószilárdsági teszteken, hogy meghatározzák, mennyire működik a ragasztó. Azok a ragasztók, amelyek megfelelnek vagy meghaladják a ragasztási szilárdságra vonatkozó iparági szabványokat, megbízhatóságot és megbízhatóságot biztosítanak teljesítményükben.
A kivételes kötési szilárdság elengedhetetlen a biztonságos és tartós csatlakozást igénylő alkalmazásokhoz. Legyen szó az építőiparról, a gyártásról vagy a mindennapi termékekről, a rendkívüli tapadási szilárdságú ragasztók biztosítják a ragasztott szerelvények integritását és tartósságát, hozzájárulva a termék általános minőségéhez és megbízhatóságához.
Magas hőmérsékleti ellenállás
A magas hőmérséklettel szembeni ellenállás bizonyos anyagok és termékek döntő jellemzője, különösen a magas hőmérsékletnek kitett alkalmazásokban. Íme a kulcsfontosságú pontok, amelyek megmagyarázzák a magas hőmérséklettel szembeni ellenállás jelentőségét és tényezőit:
- Anyagválasztás:A magas hőmérsékletnek kitett alkalmazásokhoz magas hőmérsékletnek ellenálló anyagokat, például kerámiákat, tűzálló fémeket és speciális polimereket választanak. Ezek az anyagok olyan jellemző tulajdonságokkal rendelkeznek, amelyek lehetővé teszik számukra, hogy ellenálljanak a hőterhelésnek, és megőrizzék szerkezeti integritásukat szélsőséges hőségben is.
- Hőstabilitás: Az anyagok akkor érik el a magas hőmérsékleti ellenállást, ha kiváló hőstabilitást mutatnak. A kiváló hőstabilitású anyagok még magas hőmérsékleten is megőrzik fizikai és mechanikai tulajdonságaikat anélkül, hogy jelentős alakváltozást, sérülést vagy kémiai változást okoznának.
- Olvadáspont:Az anyag olvadáspontja alapvető tényező a magas hőmérséklettel szembeni ellenállásának meghatározásában. A magas olvadáspontú anyagok, mint például a volfrám vagy bizonyos kerámiák, ellenállnak a szélsőséges hőmérsékleteknek anélkül, hogy megolvadnának vagy elveszítenék szilárdságukat.
- Oxidációs ellenállás:A magas hőmérsékletnek való kitettség gyakran oxidatív környezettel jár. A magas hőmérsékletnek ellenálló anyagok jó oxidációs ellenállást mutatnak, ami azt jelenti, hogy magas hőmérsékleten ellenállnak az oxigén és más reaktív gázok káros hatásainak. Az oxidatív körülményeknek való kitettség az anyag lebomlásához vagy korróziójához vezethet. Ennek megakadályozása érdekében elengedhetetlen az oxidációnak ellenálló intézkedések végrehajtása vagy olyan anyagok alkalmazása.
- Hőtágulás: A magas hőmérséklettel szembeni ellenállás szorosan összefügg az anyag hőtágulásnak és összehúzódásnak ellenálló képességével. Az alacsony hőtágulási együtthatójú anyagok jobban ellenállnak a hőterhelésnek, így minimálisra csökken a repedések vagy a szerkezeti tönkremenetel kockázata, ha hőmérséklet-ingadozásoknak vannak kitéve.
- Hőleadás: A magas hőmérséklettel szembeni ellenállás egyes alkalmazásokban a hatékony hőelvezetéssel korrelál. Azok az anyagok, amelyek hatékonyan képesek vezetni és elvezetni a hőt, mint például bizonyos fémek vagy termikus interfész anyagok, hozzájárulnak az eszközök vagy rendszerek alacsonyabb üzemi hőmérsékletének fenntartásához, általános teljesítményük és megbízhatóságuk javításához.
- Tesztelés és tanúsítás:A gyártók gyakran szigorú tesztelési és tanúsítási folyamatoknak vetik alá az anyagokat vagy termékeket, hogy meghatározzák magas hőmérséklettel szembeni ellenállásukat. Ezek a tesztek szélsőséges hőmérsékleti viszonyokat szimulálnak, és értékelik az anyag azon képességét, hogy ellenáll-e a hőterhelésnek, megőrizze a stabilitást, és megfelel-e az ipari szabványoknak vagy követelményeknek.
Kémiai ellenállás
A vegyszerállóság bizonyos anyagok és bevonatok kritikus tulajdonsága, lehetővé téve, hogy ellenálljanak a különféle vegyi anyagoknak anélkül, hogy lebomlanának vagy károsodnának. Íme a legfontosabb pontok, amelyek elmagyarázzák a vegyszerállóság jelentőségét és tényezőit:
- Anyagválasztás: Bizonyos anyagok, mint például a fluorpolimerek (pl. PTFE), kerámiák vagy bizonyos fémek (pl. rozsdamentes acél) ismertek a benne rejlő vegyi ellenállásukról. A kompatibilis és az adott vegyi anyagokkal szemben ellenálló kiválasztása elengedhetetlen a vegyi anyagokkal való érintkezést igénylő alkalmazásokhoz való anyagok kiválasztásakor.
- Kémiai tehetetlenség: A vegyszerállóság gyakran az anyag tehetetlenségével függ össze a különböző vegyi anyagokkal szemben. Az inert anyagok minimális mértékben reagálnak a vegyi anyagokkal, így kevésbé valószínű, hogy kémiai reakciókon mennek keresztül vagy lebomlanak, ha korrozív vagy reaktív anyagoknak vannak kitéve.
- Polimerizáció vagy térhálósítás:Egyes anyagok, például az epoxik vagy poliuretánok polimerizációs vagy térhálósodási reakciókon mennek keresztül, sűrű és kémiailag ellenálló hálózatot képezve. Az iparágak ezeket az anyagokat általában bevonatként vagy ragasztóként használják olyan alkalmazásokban, amelyek vegyszerállóságot igényelnek.
- Az akadály tulajdonságai: A vegyszerállóság az anyag azon képességének is tulajdonítható, hogy gátként működik, megakadályozva a vegyszerek áthatolását vagy behatolását. Az alacsony áteresztőképességű anyagok, mint például az üveg vagy bizonyos műanyagok, megvédhetik az alatta lévő felületeket vagy szubsztrátumokat a vegyi hatásoktól.
- Hőmérsékleti szempontok: A vegyszerállóság változhat, mivel bizonyos vegyszerek fokozott reakciókészséget vagy agresszivitást mutathatnak magasabb hőmérsékleten. Ezért létfontosságú, hogy figyelembe vegyük a kémiai expozíció hőmérsékleti tartományát az anyag kémiai ellenállásának értékelésekor.
- Tesztelés és tanúsítás:A gyártók az anyagokat vagy bevonatokat szigorú vizsgálati és tanúsítási folyamatoknak vetik alá, hogy meghatározzák vegyi ellenállásukat. Ezek a vizsgálatok általában magukban foglalják az anyagot külön-külön és kombinációkban különféle vegyszerek hatásának kitéve, valamint teljesítményének és stabilitásának időbeli értékelését. Iparági szabványok vagy speciális követelmények irányítják ezeket a vizsgálati eljárásokat.
- Kompatibilitási táblázatok: A kémiai kompatibilitási táblázatok vagy adatbázisok értékes források az anyagok vegyszerállóságának meghatározásához. Ezek a referenciák információt nyújtanak bizonyos anyagok kompatibilitásáról különböző vegyi anyagokkal, segítve a mérnököket és a szakembereket, hogy megalapozott döntéseket hozzanak a vegyi környezethez szükséges anyagok kiválasztásakor.
A vegyszerállóság kulcsfontosságú az olyan iparágakban, mint a vegyipar, a gyógyszeripar, az olaj- és gázipar, valamint a gyártás, ahol az anyagok vagy bevonatok agresszív vagy korrozív anyagokkal érintkeznek. A kiváló vegyszerálló anyagok biztosítják a berendezések, szerkezetek és termékek hosszú élettartamát, biztonságát és teljesítményét, csökkentve a vegyszer okozta lebomlás vagy meghibásodás kockázatát.
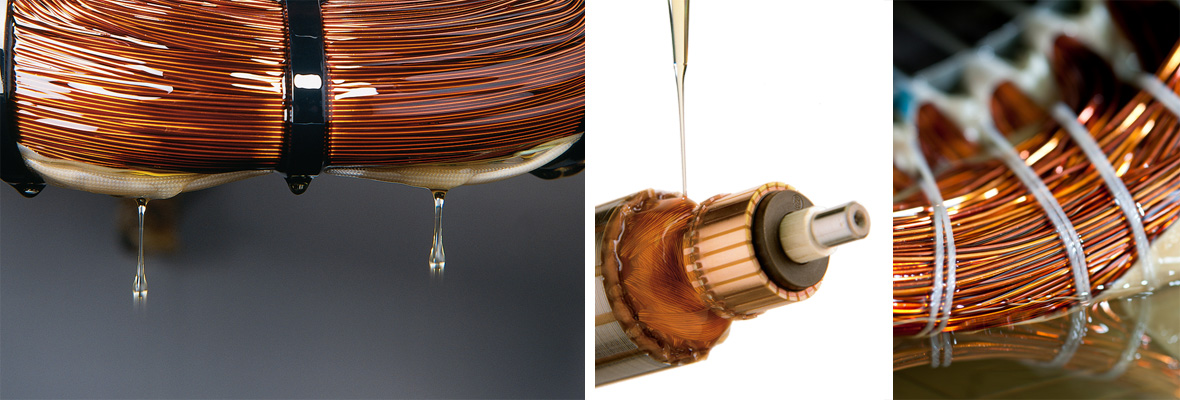
Nedvességállóság
A nedvességállóság az anyagok és bevonatok kritikus tulajdonsága, amely lehetővé teszi, hogy ellenálljanak a nedvességnek vagy nedves környezetnek anélkül, hogy leromlanak vagy károsodnának. Íme a legfontosabb pontok, amelyek elmagyarázzák a nedvességállóság jelentőségét és tényezőit:
- Anyagválasztás: Bizonyos anyagokat, például korrózióálló tulajdonságokkal rendelkező fémeket (pl. rozsdamentes acél), nedvességálló polimereket (pl. polietilén) vagy nedvességálló bevonatokat (pl. epoxi vagy poliuretán) kifejezetten a nedvességálló képességük alapján választanak ki. vagy vízbehatolás.
- Átjárhatatlanság: A nedvességállóság gyakran magában foglalja egy anyag vagy bevonat azon képességét, hogy áthatolhatatlan gátként működjön, megakadályozva a víz vagy nedvesség behatolását vagy felszívódását. Az át nem eresztő anyagok, mint például az üveg vagy bizonyos műanyagok, hatékonyan blokkolják a vízmolekulák átjutását, és védik az alatta lévő felületeket vagy szubsztrátumokat.
- Nedvesség páraátbocsátási sebesség (MVTR): Egy anyag nedvességállóságát is jellemzi, hogy gátolja a páraáteresztést. Az alacsony MVTR azt jelzi, hogy az anyagnak alacsony a nedvesség diffúziós sebessége, ami minimálisra csökkenti a vízgőz átjutását és csökkenti a nedvesség okozta károsodások lehetőségét.
- Hidrofóbicitás: A hidrofób anyagok taszítják vagy ellenállnak a víz felszívódásának. Alacsony affinitásuk van a vízmolekulákhoz, így a vízcseppek felfelé gördülnek és legördülnek a felületről. A hidrofób bevonatok vagy felületkezelések növelik a nedvességállóságot azáltal, hogy megakadályozzák a nedvesség felhalmozódását az anyag felületén.
- Nedvesség felszívódás: A nedvességálló anyagok általában alacsony nedvességelnyelő tulajdonságokkal rendelkeznek. Ezek az anyagok csak kis mennyiségű vizet tudnak felszívni a környezetükből, vagy csak meghatározott körülmények között tudnak vizet inni. Az alacsony nedvességfelvétel segít megőrizni az anyag méretstabilitását, és megakadályozza a nedvesség okozta duzzadást vagy vetemedést.
- Tesztelés és tanúsítás: A gyártók az anyagokat vagy bevonatokat szigorú tesztelési és tanúsítási folyamatoknak vetik alá, hogy értékeljék nedvességállóságukat. Ezek a tesztek gyakran magukban foglalják az anyagot szabályozott páratartalomnak vagy hosszabb ideig tartó vízbemerítésnek, valamint a teljesítmény és a stabilitás értékelését. Iparági szabványok vagy speciális követelmények irányítják ezeket a vizsgálati eljárásokat.
- Környezetvédelmi szempontok:A környezeti tényezők, például a hőmérséklet, a páratartalom és az expozíció időtartama befolyásolják az anyagok nedvességállóságát. Azok az anyagok, amelyek az egyik környezetben jó nedvességállóságot mutatnak, másképpen teljesíthetnek a másikban. Azok az anyagok, amelyek az egyik környezetben jó nedvességállóságot mutatnak, másképpen teljesíthetnek a másikban. Alapvetően figyelembe kell venni azokat a specifikus nedvességviszonyokat, amelyekkel az anyag az alkalmazás vagy a használat során találkozik.
A nedvességállóság alapvető fontosságú a különböző iparágakban és alkalmazásokban, beleértve az építőiparban, az elektronikában, a csomagolásban és a kültéri berendezésekben. A kiváló nedvességállósággal rendelkező anyagok vagy bevonatok biztosítják a szerkezetek, termékek és rendszerek tartósságát, megbízhatóságát és hosszú élettartamát, megóvják azokat a nedvességgel kapcsolatos problémáktól, például a korróziótól, a penészedéstől vagy az anyagromlástól.
Sokoldalú alkalmazások
A sokoldalú alkalmazások egy termék vagy anyag felhasználásának széles skáláját és alkalmazkodóképességét jelentik különböző iparágakban és kontextusokban. Íme a kulcsfontosságú pontok, amelyek elmagyarázzák a sokoldalú alkalmazások jelentőségét és tényezőit:
- Anyag rugalmassága:A sokoldalú anyagok különféle tulajdonságokkal rendelkeznek, amelyek lehetővé teszik számukra, hogy különféle területeken alkalmazzák őket. Erősséget, rugalmasságot, hőstabilitást és vegyszerállósági jellemzőket mutathatnak, így alkalmasak különböző környezetekre és követelményekre.
- Kompatibilitás különböző szubsztrátumokkal:A sokoldalú anyagok különféle szubsztrátumokhoz köthetnek vagy kölcsönhatásba léphetnek, beleértve a fémeket, műanyagokat, kerámiákat és kompozitokat. Ez a kompatibilitás lehetővé teszi, hogy többféle alkalmazásban is használhatók legyenek, kezdve a különböző anyagok összeillesztésétől az építőiparban az alkatrészek ragasztásáig az elektronikában vagy az autóipari szerelvényekben.
- Alkalmazható formulák:Egyes anyagok, mint például a polimerek vagy ragasztók, azzal az előnnyel rendelkeznek, hogy speciális követelményeknek vagy alkalmazási igényeknek megfelelően vannak kialakítva. Ezek az anyagok testre szabhatók összetételük, kikeményedési folyamatuk vagy adalékanyagaik módosításával, lehetővé téve, hogy különféle alkalmazásokban felhasználják őket, miközben megőrzik alapvető tulajdonságaikat.
- Széles hőmérsékleti tartomány:A sokoldalú anyagok gyakran széles skálán teljesítenek. Szélsőséges meleg vagy hideg körülmények között is megőrizhetik integritásukat és funkcionalitásukat, így alkalmasak repülési, autóipari vagy ipari gyártási alkalmazásokra.
- Több iparág: A sokoldalú anyagokat különféle iparágakban alkalmazzák, beleértve az építőiparban, az elektronikában, az egészségügyben, a csomagolásban, az autóiparban és a fogyasztási cikkekben. Az emberek különféle célokra használják őket, mint például szerkezeti elemek, szigetelés, tapadás, tömítés, csomagolás stb.
- Testreszabási lehetőségek:A sokoldalú anyagok gyakran testreszabhatók vagy módosíthatók, hogy megfeleljenek az adott alkalmazási követelményeknek. Az iparágak módosíthatják az olyan tulajdonságokat, mint az erő, a rugalmasság, a szín vagy a felületi textúra, hogy testreszabott megoldásokat hozzanak létre, amelyek megfelelnek az igényeiknek.
- A technológia fejlődése:A technológiai fejlesztések és az anyagi innovációk hozzájárulnak az anyagok sokoldalúságához és alkalmazási területeihez. A folyamatos kutatás-fejlesztési erőfeszítések új, javított tulajdonságokkal rendelkező anyagok bevezetéséhez vezetnek, bővítve azok felhasználási lehetőségeit.
A sokoldalú anyagok létfontosságúak az innováció ösztönzésében és a különféle iparágakban történő előrehaladás elősegítésében, lehetővé téve az összetett kihívások kreatív és hatékony megoldásait.
Az elektromos motorok epoxi ragasztójának típusai
Az elektromotoros epoxi ragasztó különböző típusokban kapható, amelyek mindegyike sajátos tulajdonságokkal és jellemzőkkel rendelkezik, amelyek megfelelnek az elektromos motorok alkalmazási követelményeinek. Íme az elektromotoros epoxi ragasztó legfontosabb típusai:
- Hőálló epoxi ragasztó: Ezt az epoxi ragasztókészítményt úgy terveztük, hogy ellenálljon a motor működése során fellépő magas hőmérsékletnek. Szélsőséges hőviszonyok között is megőrzi kötési szilárdságát és szerkezeti integritását, így alkalmas olyan alkalmazásokra, ahol elengedhetetlen a magas hőmérsékleti ellenállás.
- Elektromos szigetelő epoxi ragasztó:Elektromos motor epoxi ragasztót tervezünk elektromos szigetelő tulajdonságokkal, hogy megfelelő szigetelést biztosítsunk a motor alkatrészek között. Megakadályozza az elektromos áram áthaladását a ragasztott területen, csökkenti az elektromos rövidzárlat kockázatát és biztosítja az elektromos motorok biztonságos és megbízható működését.
- Gyorsan kötő epoxi ragasztó: Gyorskötésű epoxi ragasztókat készítünk rövid kötési időre, lehetővé téve az elektromos motor alkatrészek gyors összeszerelését és javítását. Ez a fajta ragasztó előnyös nagy mennyiségű gyártási környezetben vagy olyan helyzetekben, amelyek gyors átfutási időt igényelnek.
- Nagy szilárdságú epoxi ragasztó:A nagy szilárdságú epoxi ragasztó kivételes ragasztási képességeket kínál, szilárd és tartós kötést biztosítva a motor alkatrészei között. Ellenáll a motor működése során fellépő mechanikai igénybevételeknek, rezgéseknek és ütéseknek, így biztosítja a motorszerelvény hosszú távú stabilitását és megbízhatóságát.
- Vegyszerálló epoxi ragasztó:Vegyszerálló elektromos motor-epoxi ragasztót tervezünk, hogy ellenálljon a motoros környezetben gyakran előforduló vegyszereknek, oldószereknek, olajoknak és üzemanyagoknak. Megőrzi tapadó tulajdonságait és szerkezeti integritását, még akkor is, ha agresszív anyagokkal érintkezik.
- Alacsony gázkibocsátású epoxi ragasztó: Az alacsony gázképződésű epoxi ragasztó minimális mennyiségű illékony anyagot bocsát ki hőnek vagy vákuumnak kitéve. Az elektromos motorok általában ezt a fajta ragasztót használják vákuum környezetben vagy olyan alkalmazásokban, ahol az illékony vegyületek gázkibocsátása teljesítménybeli problémákat okozhat.
- Rugalmas epoxi ragasztó: A rugalmas epoxi ragasztó jó rugalmasságot és rugalmasságot biztosít, lehetővé téve a rezgések elnyelését és a hőtágulást/összehúzódást az elektromos motor alkatrészekben. Ez a rugalmasság segít megelőzni a kötés meghibásodását vagy repedését dinamikus körülmények között, hozzájárulva a motorszerelvény általános tartósságához és megbízhatóságához.
Ezek az elektromotoros epoxi ragasztótípusok számos lehetőséget kínálnak, amelyek megfelelnek a különböző motorterveknek, működési feltételeknek és speciális alkalmazási követelményeknek. A gyártók olyan tényezők alapján választhatják ki a megfelelő ragasztóválasztékot, mint a hőmérséklet-tartomány, az elektromos szigetelési igények, a kötési szilárdság, a vegyi expozíció és a rugalmasság, így biztosítva az elektromos motorok optimális teljesítményét és hosszú élettartamát.
Kétkomponensű epoxi ragasztó
A kétkomponensű epoxi ragasztó használat előtt a felhasználónak két komponenst, egy gyantát és egy keményítőt meghatározott arányban össze kell kevernie. Íme a kétkomponensű epoxi ragasztó tulajdonságait és előnyeit magyarázó legfontosabb pontok:
- Keverés és kikeményítés: A kétkomponensű epoxi ragasztókhoz a gyanta és a keményítő komponenseinek alapos összekeverését igénylik a kikeményedési folyamat elindításához. Miután összekeverték, a kötés kikeményedni kezd, jellemzően exoterm reakció révén, folyadékból vagy pasztából szilárd anyaggá alakulva. A kötési idő a ragasztó adott összetételétől és a környezeti feltételektől függően változhat.
- Sokoldalúság: A kétkomponensű epoxi ragasztók sokoldalúságot kínálnak különféle anyagok, köztük fémek, műanyagok, kompozitok, kerámiák és egyebek ragasztásában. Erős és tartós kötéseket tudnak létrehozni a különböző anyagok között, így különféle alkalmazásokhoz alkalmasak.
- Kötés erőssége: A kétkomponensű epoxi ragasztók kivételes kötési szilárdságukról ismertek. Molekuláris szintű szilárd kölcsönhatásokat alakítanak ki az aljzattal, megbízható és tartós tapadást biztosítva. A kikeményedett ragasztó nagy szakító-, nyíró- és leválási erővel rendelkezik, ami biztosítja a ragasztott szerelvények integritását.
- Hiánypótlás: A kétkomponensű epoxi ragasztók kiváló hézagkitöltő képességgel rendelkeznek. Kitömhetik és ragaszthatják a szabálytalan vagy egyenetlen felületeket, kompenzálva a kis hézagokat vagy felületi hibákat. Ez a tulajdonság előnyös a különböző formájú vagy méretű alkatrészek összeillesztésekor.
- Hőmérséklet-ellenállás: A kétkomponensű epoxi ragasztók jó hőállóságot mutatnak, megőrzik kötési szilárdságukat még magas hőmérsékleten is. Az adott összetételtől függően széles hőmérséklet-tartományban ellenállnak, így alkalmasak a magas hőmérsékletű környezetben történő alkalmazásokra.
- Kémiai és nedvességállóság: A kétkomponensű epoxi ragasztók ellenállnak a különféle vegyszereknek, beleértve az oldószereket, az üzemanyagokat és az olajokat, valamint a nedvességnek és páratartalomnak. Ez az ellenállás segít megvédeni a kötést a lebomlástól vagy gyengüléstől, amikor zord környezetnek vagy vegyi anyagoknak van kitéve.
- Alkalmazási sokoldalúság: A kétkomponensű epoxi ragasztók különféle módszerekkel alkalmazhatók, mint például kézi keveréssel, automatizált adagolással vagy injekcióval. Használhatók ragasztásra, tömítésre, öntözésre, kapszulázásra vagy bevonó alkalmazásokra, így alkalmasak különféle iparágakra, beleértve az autógyártást, az elektronikát, a repülőgépgyártást és az építőiparban.
A kétkomponensű epoxi ragasztók robusztus, tartós és sokoldalú ragasztási megoldásokat kínálnak különféle alkalmazásokhoz. A nagy szilárdságú kötések létrehozására, a hézagok kitöltésére és a kihívásokkal teli környezetben való ellenálló képességük miatt számos iparágban előnyben részesítik őket, amelyek megbízható és tartós tapadást igényelnek.
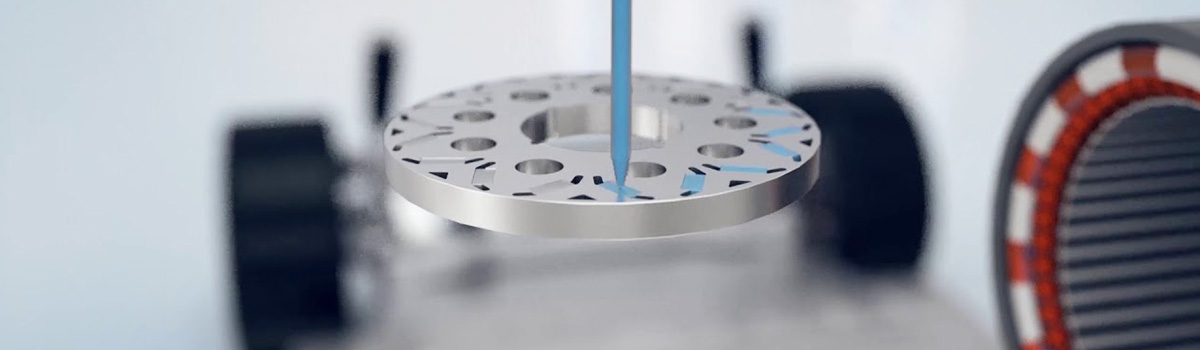
Egykomponensű epoxi ragasztó
Az egykomponensű epoxi ragasztó olyan típusú ragasztó, amely előre összekevert és további komponensek vagy keverés nélkül használatra kész. Íme az egykomponensű epoxi ragasztó tulajdonságait és előnyeit magyarázó legfontosabb pontok:
- Kényelem: Az egykomponensű epoxi ragasztó kényelmes és könnyű használatot biztosít, mivel nem igényel keverést vagy mérést. A ragasztót előre összeállítottuk, és közvetlenül a tartályból felhordható, így időt és erőfeszítést takarít meg az előkészítés során.
- Azonnali tapadás: Az egykomponensű epoxi ragasztók gyors kezdeti tapadást biztosítanak. Általában rövid nyitvatartási idejük van, ami lehetővé teszi az alkatrészek gyors pozícionálását és összeszerelését. Felhordás után a ragasztó azonnal tapadni kezd, azonnali tapadást és kezdeti szilárdságot biztosítva.
- Hosszú eltarthatóság: Az egykomponensű epoxi ragasztók eltarthatósága hosszabb, mint a kétkomponensű epoxi ragasztóké. Hosszú ideig stabilak és használhatók maradnak az idő előtti kikeményedés vagy lebomlás veszélye nélkül, rugalmas tárolást és felhasználást biztosítva.
- Hőaktiválás: Egyes egykomponensű epoxi ragasztók hőaktiválást igényelnek a teljes kikeményedéshez és az optimális kötési szilárdság eléréséhez. Ezeket a ragasztókat úgy terveztük, hogy magas hőmérsékleten kikeményedjenek, így nagyobb teljesítményt és tartósságot biztosítanak a magas hőmérsékletű alkalmazásokban.
- Sokoldalúság: Az egykomponensű epoxi ragasztók különféle anyagokhoz köthetők, beleértve a fémeket, műanyagokat, kerámiákat és kompozitokat. Sokoldalúságot kínálnak az erős és tartós kötéseket igénylő alkalmazásokban, mint például az autóipar, az elektronika, az építőipar és a gyártás.
- Kémiai és nedvességállóság:Az egykomponensű epoxi ragasztók jól ellenállnak a vegyszereknek, beleértve az oldószereket, az üzemanyagokat és az olajokat, valamint a nedvességgel és páratartalommal szemben. Ez az ellenállás segít megvédeni a kötést a lebomlástól vagy gyengüléstől, amikor zord környezetnek vagy vegyi anyagoknak van kitéve.
- Alkalmazási rugalmasság: Az egykomponensű epoxi ragasztókat különféle módszerekkel alkalmazhatja, beleértve a kézi adagolást, ecsettel vagy automatizált rendszerekkel. Használhatók ragasztásra, tömítésre, ültetésre, kapszulázásra vagy bevonásra, rugalmasságot biztosítva a különböző gyártási folyamatokban.
Az egykomponensű epoxi ragasztók kényelmes és hatékony megoldást nyújtanak a ragasztási alkalmazásokhoz. Könnyű használhatóságuk, azonnali tapadásuk és sokoldalúságuk különféle iparágaknak és alkalmazásoknak megfelel. Legyen szó összeszerelésről, javításról vagy tömítésről, az egykomponensű epoxi ragasztók megbízható tapadást és teljesítményt nyújtanak, miközben leegyszerűsítik a ragasztási folyamatot.
Gyorsan kötő epoxi ragasztó
A gyorsan kötő epoxi ragasztó egy olyan típusú ragasztó, amely gyorsított kötési időt biztosít, lehetővé téve az alkatrészek gyors ragasztását és összeszerelését. Íme a kulcsfontosságú pontok, amelyek elmagyarázzák a gyorsan kötő epoxi ragasztó tulajdonságait és előnyeit:
- Gyors kötés:A gyorsan kötő epoxi ragasztók keményedési ideje jelentősen lerövidül a standard epoxi ragasztókhoz képest. Az adott készítménytől és a környezeti feltételektől függően úgy tervezzük meg őket, hogy gyorsan, gyakran perceken vagy akár másodperceken belül kikeményedjenek. Ez a gyors kikeményedés gyorsabb gyártási folyamatokat tesz lehetővé, növeli a termelékenységet, és csökkenti az összeszerelési vagy ragasztási ciklusidőt.
- Azonnali erő:A gyorsan kötő epoxi ragasztók a kezdeti kötési szilárdság gyors fejlődését biztosítják. Azonnali tapadást és tapadást biztosítanak, lehetővé téve a ragasztott részek azonnali kezelését vagy további feldolgozását. Ez a gyors szilárdságfejlesztés minimálisra csökkenti a szorítás vagy rögzítés szükségességét, így időt takarít meg és javítja a hatékonyságot.
- Magas kötési erősség: Gyorsan kötődő jellegük ellenére a gyorsan kötő epoxi ragasztók továbbra is nagy kötési szilárdságot biztosítanak. Erős és tartós kötéseket képeznek, amelyek ellenállnak a különféle alkalmazások során tapasztalható igénybevételeknek és terheléseknek. A kikeményedett tömítőanyag kiváló szakító-, nyíró- és lefejtőszilárdságot biztosít, biztosítva a ragasztott szerelvények integritását és megbízhatóságát.
- Sokoldalúság:A gyorsan kötő epoxi ragasztók különféle anyagokhoz köthetők, beleértve a fémeket, műanyagokat, kerámiákat, kompozitokat stb. Sokoldalúságot kínálnak a gyors összeszerelést, javítást vagy ragasztást igénylő alkalmazásokban. Az autóipar, az elektronika, a repülőgépipar és a gyártóipar általában használja ezeket a ragasztókat.
- Hőmérséklet-ellenállás:A gyorsan kötő epoxi ragasztók gyakran jó hőállóságot mutatnak. Különböző hőmérsékleteken is megőrzik kötési szilárdságukat és teljesítményüket, megbízható tapadást biztosítva alacsony és magas hőmérsékletű környezetben is.
- Kémiai és nedvességállóság: A gyorsan kötő epoxi ragasztók ellenállnak a különféle vegyszereknek, beleértve az oldószereket, üzemanyagokat, olajokat és nedvességet. Ez az ellenállás segít megvédeni a kötést a lebomlástól vagy gyengüléstől, amikor zord környezetnek vagy vegyi anyagoknak van kitéve.
- Alkalmazási rugalmasság:Különféle módszerek, mint például kézi adagolás, automatizált rendszerek vagy adagolóberendezések teszik lehetővé a gyorsan kötődő epoxi ragasztók alkalmazását. Használhatók ragasztásra, tömítésre, ültetésre vagy kapszulázásra, rugalmasságot biztosítva a különböző gyártási folyamatokban.
A gyorsan kötő epoxi ragasztók jelentős előnyöket kínálnak olyan alkalmazásokban, ahol az idő kritikus. A gyártási ciklusidő csökkentésével és a hatékonyság javításával a gyorsan kötő epoxi ragasztók növelik a termelékenységet és a költségmegtakarítást a különböző iparágakban.
Magas hőmérsékletű epoxi ragasztó
A tervezők olyan magas hőmérsékletű epoxi ragasztót hoznak létre, amely ellenáll a magas hőmérsékletnek anélkül, hogy a ragasztási tulajdonságait vagy integritását veszélyeztetné. Íme a kulcsfontosságú pontok, amelyek elmagyarázzák a magas hőmérsékletű epoxi ragasztó tulajdonságait és előnyeit:
- Hőmérséklet-ellenállás: A magas hőmérsékletű epoxi ragasztógyártók úgy tervezik a termékeket, hogy megőrizzék a kötési szilárdságot és a szerkezeti integritást magas hőmérsékleten. Kibírják a szélsőséges hőt anélkül, hogy meglágyulnának, leromlanak, vagy elveszítenék tapadási tulajdonságaikat. Ezek a ragasztók általában 150 °C-ot (300 °F) meghaladó hőmérséklet-tartományban működhetnek, és akár 300 °C-ig (572 °F) vagy magasabb hőmérsékleten is működhetnek, az adott készítménytől függően.
- Hőstabilitás: A magas hőmérsékletű epoxi ragasztók kiváló hőstabilitást mutatnak, ami azt jelenti, hogy hőhatásnak kitéve nem változnak jelentős fizikai vagy kémiai tulajdonságaik. Megőrzik méretstabilitásukat, keménységüket, szilárdságukat és rugalmasságukat hosszan tartó magas hőmérsékleti körülmények között is.
- Kötés erőssége: A magas hőmérsékletű epoxi ragasztók kivételes kötési szilárdságot biztosítanak, lehetővé téve a rendkívüli hőterhelésnek kitett anyagok megbízható ragasztását. Erős és tartós kötéseket hoznak létre, amelyek ellenállnak a hőtágulásnak, összehúzódásnak, valamint a ciklikus felmelegedésnek és lehűlésnek anélkül, hogy veszélyeztetnék a ragasztott szerelvény integritását.
- Sokoldalúság:A magas hőmérsékletű epoxi ragasztók különféle anyagokhoz köthetők, beleértve a fémeket, kerámiákat, üveget, kompozitokat és műanyagokat. Alkalmazásukat az autóiparban, a repülőgépiparban, az elektronikai iparban és a gyártóiparban találják, amelyek megbízható tapadást igényelnek magas hőmérsékletű környezetben.
- Kémiai ellenállás:A magas hőmérsékletű epoxi ragasztók gyakran ellenállnak a különféle vegyszereknek, beleértve az oldószereket, üzemanyagokat, olajokat és bizonyos savakat. Ez a vegyszerállóság biztosítja a kötés stabilitását és tartósságát még akkor is, ha kemény kémiai környezetnek és magas hőmérsékletnek van kitéve.
- Alkalmazási rugalmasság: A magas hőmérsékletű epoxi ragasztókat különféle módszerekkel alkalmazhatja, például kézi adagolással, automatizált rendszerekkel vagy adagolóberendezésekkel. Használhatók ragasztásra, tömítésre, ültetésre vagy kapszulázásra, rugalmasságot biztosítva a különböző gyártási folyamatokban.
A magas hőmérsékletű epoxi ragasztók kritikusak olyan alkalmazásokban, ahol extrém hőhatásnak kitett ragasztóanyagokra van szükség. Az a képességük, hogy ellenállnak a magas hőmérsékletnek, miközben megtartják a kötési szilárdságot és stabilitást, alkalmassá teszik őket igényes környezetben való használatra.
Alacsony gázkibocsátású epoxi ragasztó
Az alacsony gázképződésű epoxi ragasztó egy speciális típus, amelyet úgy alakítottak ki, hogy minimalizálja vagy megszüntesse az illékony anyagok felszabadulását, amelyet gázkibocsátásnak neveznek a kötési folyamat során és után. Íme a kulcsfontosságú pontok, amelyek elmagyarázzák az alacsony gázkibocsátású epoxi ragasztó tulajdonságait és előnyeit:
- Kibocsátás csökkentése:A tervezők alacsony gázképződésű epoxi ragasztókat hoznak létre, hogy minimálisra csökkentsék az illékony vegyületek szintjét, amelyek az alkalmazás után kikerülhetnek a kötésből. Ez a jellemző különösen fontos azokban az alkalmazásokban, ahol a gázkibocsátás szennyeződést okozhat, vagy befolyásolhatja az érzékeny alkatrészek teljesítményét, például a repülésben, az optikában vagy az elektronikában.
- Alacsony illékony tartalom: Az alacsony gázkibocsátású epoxi ragasztók alacsony illékonyságúak, és csökkentett mennyiségben tartalmaznak olyan anyagokat, amelyek elpárologhatnak vagy elpárologhatnak. Az alacsony gázkibocsátású epoxi ragasztók megvédik a közeli alkatrészeket az esetleges károsodástól, és mentesítik az érzékeny környezetet a szennyeződéstől azáltal, hogy megakadályozzák a káros vagy reakcióképes vegyületek felszabadulását.
- Kompatibilitás kényes anyagokkal:A gyártók gyakran alacsony gázkibocsátású epoxi ragasztókat állítanak elő, hogy biztosítsák a kényes vagy érzékeny anyagokkal való kompatibilitást. Minimálisra csökkentik a károsodás vagy nemkívánatos reakciók kockázatát, ha olyan anyagokhoz kötődnek, mint az optika, érzékelők, elektronikus alkatrészek vagy precíziós műszerek.
- Magas kötési erősség: Alacsony gázkibocsátó tulajdonságaik ellenére ezek a ragasztók még mindig nagy kötési szilárdságot biztosítanak. Erős és tartós kötéseket hoznak létre, amelyek ellenállnak a különféle alkalmazások során fellépő feszültségeknek és terheléseknek. A kikeményedett ragasztó kiváló szakító-, nyíró- és leválási szilárdságot mutat, ami megbízható tapadást biztosít.
- Hő- és kémiai ellenállás: Az alacsony gázképződésű epoxi ragasztók általában jó hő- és vegyszerállóságot mutatnak. Ellenállnak a hőmérsékletnek és ellenállnak a különféle vegyszereknek, beleértve az oldószereket, az üzemanyagokat és az olajokat, anélkül, hogy veszélyeztetnék alacsony gázkibocsátó tulajdonságaikat.
- Alkalmazási rugalmasság:Az alacsony gázkibocsátású epoxi ragasztókat különféle módszerekkel alkalmazhatja, például kézi adagolással, automatizált rendszerekkel vagy adagolóberendezésekkel. Használhatók ragasztásra, tömítésre, ültetésre vagy kapszulázásra, rugalmasságot biztosítva a különböző gyártási folyamatokban.
Tényezők, amelyeket figyelembe kell venni az elektromos motorok epoxi ragasztójának kiválasztásakor
Az optimális teljesítmény és az adott alkalmazási követelményekkel való kompatibilitás biztosítása érdekében az elektromotorokhoz használt epoxi ragasztó kiválasztásakor több tényezőt is figyelembe kell venni. Íme a legfontosabb tényezők, amelyeket figyelembe kell venni:
- Hőmérséklet-ellenállás: Értékelje azt a hőmérsékleti tartományt, amelyet a ragasztónak el kell viselnie az elektromos motoron belül. Vegye figyelembe az üzemi hőmérsékletet és a lehetséges hőmérséklet-ugrásokat a motor működése vagy a közeli hőforrások során.
- Ragasztási szilárdság: Határozza meg a kívánt kötési szilárdságot a tervezett alkalmazáshoz. Vegye figyelembe a feszültségeket, terheléseket és rezgéseket, amelyeket a ragasztónak el kell viselnie a tartós és megbízható kötés érdekében.
- Aljzatkompatibilitás: Mérje fel a ragasztandó anyagokat, például fémeket, műanyagokat, kompozitokat vagy kerámiákat, és ellenőrizze, hogy a ragasztó kompatibilis-e ezekkel az aljzatokkal. Egyes ragasztókhoz felület-előkészítésre vagy alapozóra lehet szükség az optimális ragasztáshoz.
- Az elektromos szigetelés tulajdonságai:Az elektromos motor epoxi ragasztójának szigetelést kell biztosítania, hogy megakadályozza az elektromos áram szivárgását vagy rövidzárlatát. Ellenőrizze, hogy a kötés megfelelő dielektromos tulajdonságokkal rendelkezik-e, hogy megfeleljen az elektromos szigetelési követelményeknek.
- Kémiai ellenállás:A ragasztó motoron belüli felhasználásának értékelésekor elengedhetetlen figyelembe venni a kémiai környezetet, amelynek ki lesz téve. Értékelje az olajokkal, üzemanyagokkal, oldószerekkel és egyéb jelen lévő vegyi anyagokkal szembeni ellenállását, biztosítva ezzel, hogy a kötés megőrizze teljesítményét és integritását.
- Keményedési idő:Határozza meg a kívánt kötési időt az adott alkalmazáshoz. Egyes ragasztók gyors kikeményedést tesznek lehetővé a gyorsabb összeszerelési vagy javítási folyamatok érdekében, míg mások hosszabb kötési időt igényelhetnek a pontos igazításhoz vagy összetett ragasztási követelményekhez.
- Alkalmazási módszer: Fontolja meg a gyártási folyamatnak leginkább megfelelő alkalmazási módot. Határozza meg, hogy a megfelelő alkalmazáshoz kézi adagolás, automatizált rendszerek vagy speciális berendezések szükségesek.
- Környezetvédelmi szempontok: Mérje fel a ragasztóra esetlegesen érvényben lévő ökológiai előírásokat vagy korlátozásokat, mint például a VOC (illékony szerves vegyület) tartalma vagy az adott iparági szabványoknak való megfelelés.
- Eltarthatósági idő és tárolási feltételek:Ellenőrizze a ragasztó eltarthatóságát és az ajánlott tárolási feltételeket, hogy biztosítsa a ragasztó stabilitását és használhatóságát az idő múlásával. Egyes kötések tárolása speciális hőmérsékleti vagy páratartalmi feltételeket igényelhet.
Ezeket a tényezőket gondosan mérlegelve kiválasztható a legmegfelelőbb villanymotoros epoxi ragasztó, amely megfelel az adott teljesítménykövetelményeknek, biztosítva az optimális ragasztást, a tartósságot és a megbízhatóságot az elektromos motorokon belül.
Kompatibilitás a motor alkatrészekkel
Az elektromos motor epoxi ragasztójának kiválasztásakor a motor alkatrészekkel való kompatibilitása lényeges szempont, amelyet figyelembe kell venni. A ragasztó nem okozhat semmilyen károsodást vagy károsodást a motor alkatrészeiben, például szigetelőanyagokban, mágnesekben, tekercsekben vagy csapágyakban. Íme néhány fontos szempont a kompatibilitás biztosításához:
- Szigetelő anyagok: A ragasztó nem ronthatja vagy gyengítheti a motorban használt szigetelőanyagokat, például lakkokat vagy gyantákat. Győződjön meg arról, hogy a ragasztó megfelelő elektromos szigetelési tulajdonságokkal rendelkezik, hogy elkerülje az elektromos áram szivárgását vagy rövidzárlatát.
- Mágnesek és tekercsek: A ragasztó nem zavarhatja a motoron belüli vonzások vagy tekercsek mágneses vagy elektromos tulajdonságait. Ellenőrizze, hogy a kötés megfelelő mágneses permeabilitással és dielektromos tulajdonságokkal rendelkezik-e a motor teljesítményének fenntartásához.
- Csapágyak és tengelyek:A ragasztó nem befolyásolhatja a motor csapágyainak vagy tengelyeinek forgását vagy mozgását. Vegye figyelembe a ragasztó viszkozitását, folyási tulajdonságait és kopásállóságát, hogy megbizonyosodjon arról, hogy nem zavarja a motor mozgását.
- Hőleadás: A ragasztó nem akadályozhatja a motor hőelvezetési folyamatát. Vegye figyelembe a ragasztó hővezető tulajdonságait annak biztosítására, hogy ne akadályozza a motor hőelvezetését és az optimális üzemi hőmérséklet fenntartását.
- Rozsdásodás elleni védelem: A ragasztónak korrózióvédelmet kell biztosítania a motor alkatrészei számára. Ellenőrizze, hogy a kötés megfelelő korrózióálló tulajdonságokkal rendelkezik-e a rozsda, oxidáció vagy a motor teljesítményét befolyásoló egyéb korróziós formák megelőzésére.
A motorkomponensekkel való kompatibilitás biztosításával az elektromos motor epoxi ragasztója optimális kötést, tartósságot és megbízhatóságot biztosít, miközben megőrzi a motor teljesítményét és integritását.
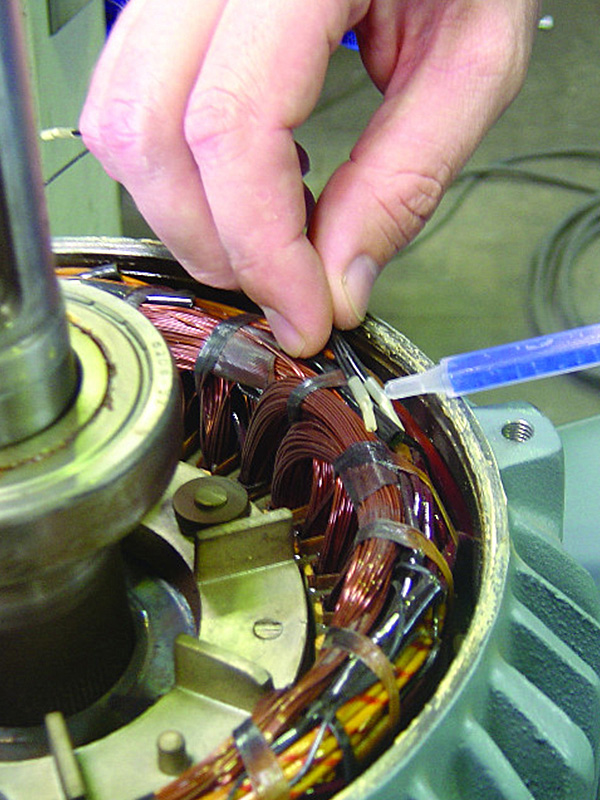
Keményedési idő
A kötési idő kulcsfontosságú tényező, amelyet figyelembe kell venni az elektromotoros epoxi ragasztó kiválasztásakor. Arra az időtartamra vonatkozik, amely szükséges ahhoz, hogy a kötés elérje teljes szilárdságát és kötési tulajdonságait az alkalmazás után. Íme néhány fontos szempont, amelyet figyelembe kell venni a gyógyulási idővel kapcsolatban:
- Nyitva tartás:Nyitott idő alatt azt értjük, amikor a ragasztót el lehet helyezni vagy beállítani, mielőtt elkezdene kikeményedni, és továbbra is használható marad. Értékelje ki a kívánt rendelkezésre álló időt az adott alkalmazási követelmények alapján, és hagyjon elegendő időt a motoralkatrészek megfelelő beállítására és összeszerelésére.
- Kötési sebesség: Vegye figyelembe a ragasztó kívánt kötési sebességét. Egyes ragasztók gyorsan kötő tulajdonságokkal rendelkeznek, lehetővé téve a gyors ragasztást és csökkentve az összeszerelési időt. Másoknál hosszabb kikeményedési időre lehet szükség az optimális kötési szilárdság eléréséhez vagy további feldolgozási lépések elvégzéséhez.
- Környezeti feltételek: A környezeti feltételek, például a hőmérséklet és a páratartalom befolyásolhatják az epoxi ragasztó kötési idejét. Vegye figyelembe a gyártó által ajánlott keményedési feltételeket, és győződjön meg arról, hogy azok kompatibilisek a gyártási környezettel.
- Gyorsítási módszerek:Az alkalmazási követelményektől függően szükség lehet a ragasztó kötési idejének felgyorsítására. Egyes epoxi ragasztók hőaktiválhatók, vagy előnyös lehet gyorsítók vagy térhálósítószerek használata a kötési folyamat felgyorsítása érdekében.
- Feldolgozhatóság:A fazékidő azt az időtartamot jelenti, amely alatt a ragasztó felhasználható marad, miután összekeverték vagy levegővel érintkeztek. Értékelje az epoxi ragasztó felhasználhatósági idejét annak biztosítására, hogy az elegendő a felhordási folyamathoz, figyelembe véve az olyan tényezőket, mint a keverés, az adagolás és a felhordási idő.
- Utókezelés:Egyes epoxi ragasztókhoz utólagos kötési eljárásra lehet szükség a maximális kötési szilárdság és a kívánt tulajdonságok elérése érdekében. Fontolja meg, hogy szükség van-e utókezelésre, és fontolja meg az utókezelési folyamat javasolt időtartamát vagy feltételeit.
A kötési idő és a kapcsolódó tényezők figyelembevételével kiválasztható az elektromotoros epoxi ragasztó, amely megfelel az alkalmazás speciális követelményeinek. A rendelkezésre álló idő, a kikeményedési sebesség, a környezeti feltételek, a gyorsítási módszerek, a fazékidő és a lehetséges utókezelési követelmények megfelelő felmérése biztosítja a motoralkatrészek hatékony és eredményes ragasztását, miközben betartja a gyártási határidőket.
Hőmérsékleti követelmények
A hőmérsékleti követelmények kritikus szempontok az elektromos motor epoxi ragasztójának kiválasztásakor. A ragasztónak ki kell bírnia a motor üzemi hőmérsékletét anélkül, hogy a teljesítmény, az integritás vagy a kötési szilárdság csökkenne. Íme néhány fontos szempont, amelyet figyelembe kell venni a hőmérsékleti követelményekkel kapcsolatban:
- Működési hőmérséklet tartomány:Értékelje az elektromos motor várható üzemi hőmérséklet-tartományát. Vegye figyelembe az átlagos üzemi hőmérsékletet, valamint a motor működése közben fellépő esetleges hőmérsékleti kiugrásokat vagy ingadozásokat. A ragasztónak meg kell őriznie kötési szilárdságát és stabilitását ezen a hőmérséklet-tartományon belül.
- Hőstabilitás: Értékelje az epoxi ragasztó termikus stabilitását. Ellen kell állnia a megemelkedett hőmérsékletnek anélkül, hogy megpuhulna, megolvadna vagy lebomlana. Kérjük, ellenőrizze, hogy a ragasztó megőrzi-e fizikai és kémiai tulajdonságait, például keménységét, rugalmasságát és tapadási szilárdságát, még akkor is, ha a megadott működési hőmérsékleti tartománynak van kitéve.
- Hőmérséklet-ellenállás: A ragasztónak magas hőmérsékleten ellenállónak kell lennie, lehetővé téve a megbízható működést nehéz körülmények között is. Győződjön meg arról, hogy a kiválasztott ragasztó elviseli a motor maximális üzemi hőmérsékletét anélkül, hogy káros hatással lenne a ragasztási szilárdságra vagy szerkezeti integritásra.
- Termál kerékpározás: Az elektromos motorok gyakran hőcikluson mennek keresztül, ami ismétlődő fűtési és hűtési ciklusokat foglal magában. A ragasztónak ellenállnia kell a hőtágulásnak és összehúzódásnak ezekben a ciklusokban anélkül, hogy veszélyeztetné a motorkomponensek közötti kötést.
- Hőleadás:Vegye figyelembe a ragasztó hatását a motor hőelvezetési folyamatára. Nem akadályozhatja a motor által termelt hő átadását. Ellenőrizze, hogy a kötés megfelelő hővezető tulajdonságokkal rendelkezik-e, ami lehetővé teszi a hatékony hőelvezetést és megakadályozza a kritikus alkatrészek túlmelegedését.
- Hideg hőmérsékleti teljesítmény:A magas hőmérséklet mellett vegye figyelembe a ragasztó teljesítményét hideg környezetben is. A ragasztónak meg kell őriznie kötési szilárdságát és rugalmasságát alacsony hőmérsékleten is, biztosítva a megbízható teljesítményt még fagypont alatti körülmények között is.
- Hőmérséklet vizsgálat: Javasoljuk, hogy végezzen hőmérsékleti tesztet, vagy olvassa el a ragasztó gyártójának specifikációit, hogy ellenőrizze, hogy a ragasztó megfelel-e a várható hőmérsékleti követelményeknek. Keresse meg a releváns teljesítményadatokat, például a hőmérséklet-állóságot, a hőstabilitást és a hőmérséklettel kapcsolatos egyéb tulajdonságokat.
Biztonsági szempontok
Az elektromos motorok epoxi ragasztóival végzett munka során a biztonsági szempontok rendkívül fontosak. Íme néhány kulcsfontosságú szempont, amelyeket figyelembe kell venni a biztonság biztosítása érdekében a ragasztó kiválasztása és alkalmazása során:
- Anyagbiztonsági adatlapok (MSDS): Szerezze be és tekintse át a ragasztó gyártója által biztosított anyagbiztonsági adatlapokat. Ezek a dokumentumok fontos biztonsági információkat tartalmaznak, beleértve a veszélyeket, a kezelési óvintézkedéseket és az ajánlott egyéni védőfelszereléseket (PPE).
- Veszélyes anyagok: Azonosítsa a veszélyes anyagokat a ragasztókészítményben, például az illékony szerves vegyületeket (VOC) vagy más potenciálisan káros vegyi anyagokat. Mérje fel ezen anyagok egészségügyi kockázatait, és gondoskodjon a megfelelő szellőzésről és védőintézkedésekről.
- Személyi védőfelszerelés (PPE):Kövesse az MSDS-ben szereplő ajánlásokat az egyéni védőeszközök, például kesztyű, védőszemüveg vagy légzésvédő használatára vonatkozóan. Gondoskodjon arról, hogy a ragasztóanyag felvitelében részt vevő személyzet megfelelő egyéni védőfelszerelést kapjon.
- Szellőztetés:Gondoskodjon a munkaterület megfelelő szellőzéséről, hogy minimálisra csökkentse a potenciálisan káros gőzöknek vagy gőzöknek való kitettséget. Ha szükséges, használjon helyi elszívást, vagy végezzen ragasztóanyagot jól szellőző helyen, hogy megakadályozza a levegőben lévő szennyeződések felhalmozódását.
- Bőrrel való érintkezés:Tegyen óvintézkedéseket, hogy elkerülje a ragasztóval való közvetlen érintkezést a bőrrel. Használjon kesztyűt és egyéb védőruházatot, ahogyan azt a ragasztó gyártója javasolja, hogy megelőzze a bőrirritációt vagy túlérzékenységet.
- Szemvédelem:Viseljen védőszemüveget vagy védőszemüveget, hogy megvédje a szemet a véletlen kifröccsenéstől vagy a ragasztóval való érintkezéstől. Szembe kerülés esetén azonnal öblítse ki tiszta vízzel, és szükség esetén forduljon orvoshoz.
- Kezelés és tárolás: Kövesse a ragasztó gyártójának megfelelő kezelési és tárolási eljárásait. Tárolja a ragasztót az ajánlott hőmérsékleti és páratartalom mellett, távol gyújtóforrásoktól vagy összeférhetetlen anyagoktól.
- Vészhelyzeti készültség:Készüljön fel az esetleges vészhelyzetekre. Rendelkezésre álljon a megfelelő kiömlés-elhárítási intézkedések, például nedvszívó anyagok és kiömlési készletek. A személyzet oktatása a vészhelyzeti eljárásokról, beleértve az elsősegélynyújtási intézkedéseket és az események jelentését.
- Előírásoknak való megfelelés: Gondoskodjon a vonatkozó biztonsági előírásoknak, például a Munkahelyi Biztonsági és Egészségügyi Hivatal (OSHA) szabványainak vagy a helyi szabályozási követelményeknek való megfelelésről. Legyen naprakész az epoxi ragasztók használatával kapcsolatos szabályozási változásokkal vagy irányelvekkel kapcsolatban.
- Képzés és oktatás: Biztosítson megfelelő képzést és oktatást a ragasztóanyag felviteli folyamatában részt vevő személyzet számára. Győződjön meg arról, hogy ismerik a ragasztóval kapcsolatos lehetséges veszélyeket, biztonságos kezelési gyakorlatokat és vészhelyzeti eljárásokat.
Ezen biztonsági szempontok figyelembe vételével, a megfelelő kezelési eljárások végrehajtásával és a vonatkozó biztonsági irányelvek betartásával minimálisra csökkenthető az elektromotoros epoxi ragasztó használatával kapcsolatos kockázat, és biztonságosabb munkakörnyezet teremthető az alkalmazási folyamatban részt vevő személyzet számára.
Alkalmazási technikák
A felhordási technika kulcsfontosságú az optimális kötés eléréséhez és a ragasztó hatékonyságának biztosításához, amikor elektromotoros epoxi ragasztóval dolgozunk. Íme néhány kulcsfontosságú szempont, amelyet figyelembe kell venni az alkalmazási technikák kiválasztása és alkalmazása során:
- Kiadási mód: Válassza ki a legmegfelelőbb módszert az adott ragasztóösszetétel és az alkalmazás követelményei alapján. A standard technikák közé tartozik a kézi adagolás fecskendőkkel vagy patronokkal, automatizált adagolórendszerekkel vagy mérő-keverő-adagoló berendezéssel kétkomponensű ragasztókhoz.
- Keverés: Kétkomponensű epoxi ragasztók esetén alaposan keverje össze a gyanta és a keményítő komponenseit a gyártó utasításai szerint. A homogén keverék eléréséhez kövesse az ajánlott keverési arányokat és technikákat.
- Felület előkészítése:A megfelelő felület-előkészítés kulcsfontosságú a szilárd ragasztó kötések eléréséhez. Alaposan tisztítsa meg és zsírtalanítsa a ragasztandó karaktereket, hogy eltávolítsa a tapadást akadályozó szennyeződéseket. Dörzsölje le a felületeket, ha szükséges, hogy elősegítse a mechanikai reteszelést és javítsa a tapadást.
- Alkalmazási eszközök: Használjon megfelelő eszközöket, például ecsetet, spatulákat vagy precíziós adagolóhegyeket, a ragasztó jellegétől és az alkalmazási követelményektől függően. Győződjön meg arról, hogy a szerszámok tiszták és kompatibilisek a ragasztóval, hogy megelőzze a teljesítményre gyakorolt káros hatásokat.
- Fedőképesség és vastagság: A megfelelő ragasztás érdekében vigye fel a ragasztót az ajánlott tartományban és vastagságban. Az optimális teljesítmény érdekében kövesse a gyártó útmutatásait az egységnyi felületre vonatkozó ragasztásra és az ajánlott vastagságra vonatkozóan.
- Bond Line Control: A ragasztó felhordása közben tartsa fenn az ellenőrzést a kötési vonal vastagsága felett. Használjon távtartókat, alátéteket vagy más megfelelő technikákat, hogy egyenletes és egyenletes kötési vonalvastagságot érjen el a ragasztott felületeken.
- Befogás vagy rögzítés:A ragasztóanyagtól és az alkalmazástól függően szükség lehet befogásra vagy rögzítésre, hogy az alkatrészek a helyükön maradjanak a kikeményedési folyamat során. Kövesse az ajánlott szorítási nyomást és időtartamot, hogy biztosítsa az egyenletes nyomáseloszlást és megakadályozza a kötést veszélyeztető mozgást.
- Kikeményedés körülményei: Hozzon létre ideális kötési feltételeket a ragasztó számára. Vegye figyelembe az olyan tényezőket, mint a hőmérséklet, páratartalom és a ragasztó gyártója által megadott kötési idő. Győződjön meg arról, hogy a kikeményedési környezet állandó és megfelelő marad ahhoz, hogy a kötés elérje teljes szilárdságát és teljesítményét.
- Minőség-ellenőrzés:Végezzen minőség-ellenőrzési intézkedéseket a ragasztó felhordási folyamata során. Rendszeresen ellenőrizze a ragasztókötéseket, hogy biztosítsa a megfelelő fedést, vastagságot és integritást. Végezzen tapadási teszteket vagy más megfelelő minőség-ellenőrzési vizsgálatokat a kötés szilárdságának és teljesítményének ellenőrzésére.
Ezen alkalmazási technikák figyelembe vételével, a gyártói irányelvek betartásával és a következetes minőség-ellenőrzési intézkedések betartásával optimalizálható az elektromos motorok epoxi ragasztója, biztosítva a megbízható ragasztást, a tartósságot és az általános teljesítményt az elektromos motoros alkalmazásokban.
Következtetés
Az elektromotoros epoxi ragasztó egy speciális ragasztó, amely elengedhetetlen az elektromos motor alkatrészeinek ragasztásához és védelméhez. Kivételes kötési szilárdságot, magas hőmérsékletű, vegyszer- és nedvességállóságot biztosít. A választott ragasztó típusa számos tényezőtől függ, beleértve a motorkomponensekkel való kompatibilitást, a kötési időt, a hőmérsékleti követelményeket és a biztonsági szempontokat. A megfelelő villanymotoros epoxi ragasztó kiválasztásával és a megfelelő felhordási technikák követésével megbízható és hosszan tartó kötést biztosíthat, amely ellenáll az elektromos motorok szigorú körülményeinek.