Kameramodul ragasztók
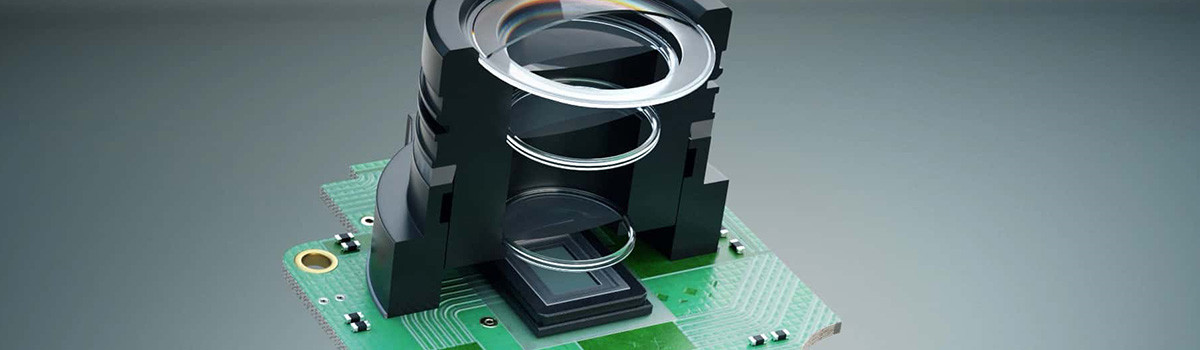
A kameramodul-ragasztó kritikus szerepet játszik a modern okostelefon-kamerák összeszerelésében és teljesítményében. A ragasztó felelős a kameramodul biztonságos rögzítéséért, megakadályozva, hogy használat közben elmozduljon vagy elmozduljon. Ez az átfogó útmutató mindent tartalmaz, amit a kameramodul ragasztójáról tudni kell, beleértve annak típusait, alkalmazási módjait, előnyeit, hátrányait és még sok mást.
Mi az a kameramodul ragasztó?
A kameramodul ragasztója egyfajta ragasztó vagy kötőanyag, amellyel a kameramodult egy eszköz, például okostelefon vagy táblaszámítógép fő áramköri lapjához rögzítik. A kameramodul ragasztója alapvető szerepet játszik annak biztosításában, hogy a modul biztonságosan a helyén maradjon, és ne mozduljon el vagy mozduljon el az idő múlásával, ami befolyásolhatja a kamerával rögzített képek vagy videók minőségét.
A kameramodulok ragasztói jellemzően erős és tartós anyagból készülnek, amely ellenáll a napi használat során fellépő igénybevételeknek és igénybevételeknek. A készülék speciális követelményeitől és a tervezett alkalmazástól függően hőálló, vízálló vagy ütésálló kivitelben készülhetnek.
A kameramodul ragasztójának felhordása jellemzően precíz és körültekintő folyamatot igényel, mivel a kameramodult megfelelően kell az áramköri laphoz igazítani a megfelelő működés érdekében. A gyártók speciális berendezéseket vagy technikákat használhatnak a ragasztó felvitelére, és robusztus és megbízható kötést biztosítanak a kameramodul és az áramköri lap között.
Miért fontos a kameramodul ragasztója?
A kameramodul-ragasztó elengedhetetlen eleme a kameramodulokat tartalmazó elektronikus eszközök, például okostelefonok, táblagépek, laptopok és kamerák gyártásának. A kameramodul rögzítésére szolgál az eszköz nyomtatott áramköri lapjához (PCB) vagy fedőlencséhez, biztosítva a kamera biztonságos rögzítését.
A ragasztó döntő fontosságú a kameramodul helyzetének és beállításának megőrzésében, ami kritikus fontosságú a kiváló minőségű képek és videók készítéséhez. A kameramodul ragasztójának robusztus és tartós kötést kell biztosítania, amely kibírja a mindennapi használat megterhelését, beleértve az ütéseket, rezgéseket és hőmérsékletváltozásokat.
A kameramodul ragasztó funkcionális tulajdonságain túl esztétikai célt is szolgál, és precízen felhordható, hogy a kameramodul és a készülék felülete között zökkenőmentes, tiszta felület jöjjön létre.
Összességében a kameramodul-ragasztó elengedhetetlen a kameramodulokat tartalmazó elektronikus eszközök megbízhatóságához, teljesítményéhez és megjelenéséhez.
A kameramodul ragasztójának típusai
A kameramodul-ragasztó egy speciális ragasztó, amelyet a kameramodulok elektronikus eszközökhöz, például okostelefonokhoz, táblagépekhez, laptopokhoz és egyéb eszközökhöz való rögzítésére használnak. Különféle kameramodul-ragasztók léteznek, többek között:
- Akril ragasztó: Az akril ragasztó egy kameramodul ragasztó, amely nagy tapadási szilárdságot és kiváló környezeti ellenállást biztosít. Ezt a ragasztót általában olyan kameramodulokhoz használják, amelyek nagy kötési szilárdságot és hosszú távú tartósságot igényelnek.
- Epoxi ragasztó: Az epoxi ragasztó egy kétkomponensű ragasztó, nagy tapadási szilárdsággal és kiváló környezeti ellenállással. Ezt a ragasztót általában olyan kameramodulokhoz használják, amelyek nagy kötési szilárdságot és hosszú távú tartósságot igényelnek.
- Szilikon ragasztó: A szilikon ragasztó egy kameramodul ragasztó, amely jó tapadási szilárdságot és rugalmasságot biztosít. Ezt a ragasztót általában olyan kameramodulokhoz használják, amelyek rugalmasságot és rezgéscsillapítást igényelnek.
- UV-re keményedő ragasztó: Az UV-re keményedő ragasztó egy kameramodul ragasztó, amely UV fény hatására megköt. Ez a ragasztó gyors kötési időt és kiváló tapadási szilárdságot biztosít. Általában olyan kameramodulokhoz használják, amelyek gyors kötési időt igényelnek.
- Nyomásérzékeny ragasztó: A nyomásérzékeny ragasztó egy kameramodul ragasztó, amely jó tapadási szilárdsággal és könnyen alkalmazható. Ezt a ragasztót általában olyan kameramodulokhoz használják, amelyek könnyű felhordást és ideiglenes ragasztást igényelnek.
A kameramodul ragasztójának kiválasztása az alkalmazás speciális követelményeitől és a használt kameramodul típusától függ.
Folyékony ragasztó vs. szalagragasztó
A folyékony ragasztót és a szalagragasztót általában anyagok egymáshoz ragasztására használják, de van néhány lényeges különbség.
A folyékony ragasztó vagy ragasztó egy viszkózus folyékony anyag, amelyet közvetlenül a felületekre visznek fel a kötés érdekében. Különféle formákban lehet, például fehér, átlátszó, szuper és epoxi. A folyékony ragasztó erős, tartós kötést hoz létre, és alkalmas papírra, fára, fémre és műanyagokra. Felhordási módok tekintetében is sokoldalú, mint például ecsettel, hengerrel vagy szórással, a ragasztó típusától függően.
Másrészt a szalagragasztó vékony ragasztóanyagréteg, amely egy rugalmas hátlapra, például papírra, filmre vagy szövetre van bevonva. A szalagragasztók leggyakoribb típusai a kétoldalas ragasztószalag és a maszkolószalag. A kétoldalas szalag mindkét oldalán ragasztóval rendelkezik, amely lehetővé teszi két felület egymáshoz ragasztását, míg a maszkoló videó egyik oldalán ragasztó van, és főleg tárgyak ideiglenes helyben tartására szolgál festés, díszítés vagy egyéb alkalmazások során. A ragasztószalag gyorsan és egyszerűen felvihető, és a legtöbb esetben maradék nélkül eltávolítható.
Vezetőképes ragasztó vs. nem vezető ragasztó
A vezetőképes és nem vezető ragasztók kétféle ragasztóanyag, amelyeket különböző alkalmazásokban használnak.
A vezetőképes ragasztó olyan ragasztó, amely képes vezetni az elektromosságot. Ezt a fajta ragasztót általában olyan elektronikai alkalmazásokban használják, ahol elektromos vezetőképességre van szükség, például elektronikus alkatrészek nyomtatott áramköri lapokhoz (PCB-k) történő rögzítéséhez vagy elektródák rögzítéséhez az orvosbiológiai érzékelőkhöz. A vezetőképes ragasztók általában vezetőképes töltőanyagokat, például ezüst-, réz- vagy nikkelrészecskéket tartalmaznak.
A nem vezető ragasztó viszont olyan ragasztó, amely nem vezet áramot. Ezt a fajta ragasztót olyan alkalmazásokban használják, ahol nincs szükség elektromos vezetőképességre, például építőipari vagy csomagolóanyagok ragasztására. A nem vezető ragasztók különféle anyagokból készülhetnek, beleértve az akrilokat, epoxikat vagy cianoakrilátokat.
A ragasztó kiválasztásakor feltétlenül figyelembe kell venni az alkalmazási követelményeket. Ha elektromos vezetőképességre van szükség, vezetőképes ragasztót kell használni. A nem vezető ragasztó alkalmasabb lehet, ha nincs szükség elektromos vezetőképességre. Más tényezőket is figyelembe kell venni, mint például a kötési szilárdságot, a kötési időt és a környezeti feltételeket, hogy biztosítsa a ragasztó az elvárásoknak megfelelő teljesítményt.
UV-re keményedő ragasztó vs. hőre keményedő ragasztó
Az UV-re keményedő és a hőre keményedő ragasztók két különböző típusú ragasztók, amelyeket általánosan használnak az ipari és gyártási folyamatokban.
Ahogy a neve is sugallja, az UV-re keményedő ragasztó megkeményedik, ha UV fénynek van kitéve. Az ilyen típusú ragasztók jellemzően gyors kötési idővel rendelkeznek, ami nagy áteresztőképességet tesz lehetővé a gyártási folyamatokban. Az UV-re keményedő ragasztót általában elektronikában, optikában és orvosi eszközökben használják.
A hőre keményedő ragasztó viszont hő hatására megköt, és az ilyen típusú ragasztók általában hosszabb kötési időt igényelnek, mint az UV-sugárzással keményedő ragasztók. A hőre keményedő ragasztó azonban erősebb kötést és magasabb hőmérsékletállóságot biztosíthat, így alkalmas olyan alkalmazásokra, mint a repülőgépipar és az autóipar.
Mindkét ragasztótípusnak megvannak az előnyei és hátrányai az alkalmazási követelményektől függően. Az UV-re keményedő ragasztót olyan alkalmazásokhoz részesítik előnyben, amelyek gyors kötési időt és alacsony hőtermelést igényelnek, míg a hőre keményedő ragasztót olyan alkalmazásokhoz, amelyek nagy szilárdságot és hőállóságot igényelnek.
A kameramodul-ragasztó előnyei
A kameramodul-ragasztó számos előnnyel jár az elektronikai eszközök gyártásához és összeszereléséhez, különösen azok esetében, amelyekhez kameramodulra van szükség. Néhány ilyen előny a következőket tartalmazza:
- Erős tapadás: A kameramodul ragasztóját úgy tervezték, hogy robusztus és megbízható tapadást biztosítson a kameramodul és a készülék hordozója között. Ez biztosítja, hogy a kamera biztonságosan a helyén maradjon még kemény vagy erős vibrációjú környezetben is.
- Jobb kamerateljesítmény: A kameramodul ragasztója a vibráció, az ütés és a képminőséget befolyásoló egyéb tényezők csökkentésével is javíthatja a kamera teljesítményét. Ez jobb képstabilizációt, élesebb képeket és jobb általános kamerateljesítményt eredményezhet.
- Költséghatékony: A kameramodul ragasztója gyakran költséghatékonyabb, mint a hagyományos mechanikus rögzítők vagy kapcsok, mivel kevesebb alkatrészt igényel, és könnyebben összeszerelhető.
- Csökkentett vastagság: A kameramodul ragasztója segíthet csökkenteni az eszköz teljes vastagságát, így kompaktabbá és könnyebbé válik.
- Fokozott gyártási hatékonyság: A kameramodul ragasztója gyorsan és egyszerűen felhordható, ami gyorsabb gyártási és összeszerelési időt tesz lehetővé. Ez segíthet csökkenteni a termelési költségeket és javítani az általános hatékonyságot.
Összességében a kameramodul-ragasztó megbízható és költséghatékony megoldás a kameramodulok rögzítésére elektronikus eszközökben, jobb teljesítményt és gyártási hatékonyságot kínálva.
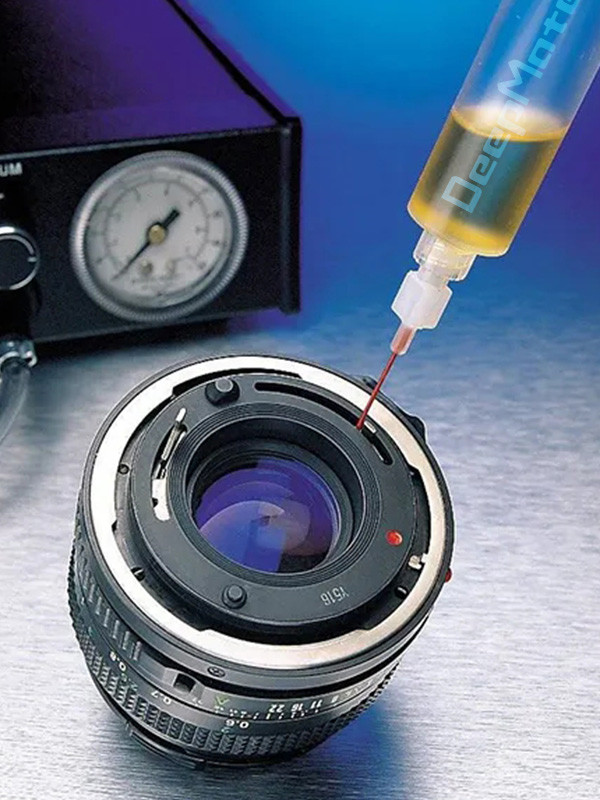
A kameramodul-ragasztó hátrányai
Van néhány hátránya annak, ha kameramodul ragasztót használ a kameramodul eszközhöz vagy felülethez való rögzítéséhez. Ezek közül néhány a következőket tartalmazza:
- Korlátozott rugalmasság: A kameramodul a ragasztó felhordása után tartósan a felülethez van rögzítve. A kameramodul bármilyen beállítása vagy javítása nehézkessé vagy lehetetlenné válik.
- Nehéz eltávolítani: Ha a kameramodult el kell távolítani, akkor kihívást jelenthet anélkül, hogy károsítaná a csatlakoztatott eszközt vagy felületet. A ragasztó eltávolításához oldószerek vagy egyéb vegyszerek használatára lehet szükség, amelyek károsíthatják a készüléket vagy a felületet.
- Inkonzisztens felhordás: A ragasztó felhordása bizonyos szintű készségeket és tapasztalatokat igényel. A tapasztalatlan vagy képzetlen személyek túl sok vagy túl kevés ragasztót alkalmazhatnak, ami problémákat okozhat a kameramodul beállításában, stabilitásában és általános teljesítményében.
- Érzékeny a környezeti tényezőkre: A kameramodul ragasztóját befolyásolhatják olyan környezeti tényezők, mint a hőmérséklet, a páratartalom és az UV-sugárzás. Ez idővel a ragasztó lebomlását vagy hatékonyságának csökkenését okozhatja, ami problémákat okozhat a kameramodul stabilitásával vagy teljesítményével kapcsolatban.
- Korlátozott tartósság: Előfordulhat, hogy a kameramodul rögzítésére szolgáló ragasztó nem olyan tartós, mint más rögzítési módok, például csavarok vagy kapcsok. Ez azt jelenti, hogy a kameramodul idővel leválhat, különösen, ha gyakori vagy jelentős mozgásnak vagy rezgésnek van kitéve.
Tényezők, amelyeket figyelembe kell venni a kameramodul ragasztójának kiválasztásakor
A kameramodul ragasztójának kiválasztásakor több szempontot is figyelembe kell venni:
- Ragasztási szilárdság: A ragasztónak elég erősnek kell lennie ahhoz, hogy a helyén tartsa a kameramodult, és ellenálljon a használat során fellépő rezgéseknek és ütéseknek.
- Kompatibilitás: A ragasztónak kompatibilisnek kell lennie mind a kameramodul, mind a rögzített eszköz anyagával. Ez biztosítja, hogy ne reagáljon, és ne károsítsa az alkatrészeket.
- Hőmérsékletállóság: A ragasztónak el kell viselnie azt a hőmérsékleti tartományt, amelynek a készülék használat közben ki van téve. Ez különösen fontos azoknál a készülékeknél, amelyek szélsőséges körülmények között is használhatók.
- Nedvességállóság: A ragasztónak ellenállónak kell lennie a nedvességgel és a nedvességgel szemben, mivel ez idővel lebomolhat, és potenciálisan befolyásolhatja a kameramodul teljesítményét.
- Felhordási mód: A ragasztónak könnyen felhordhatónak kell lennie, és nem igényel speciális felszerelést vagy képzést.
- Kötési idő: A ragasztónak ésszerű kötési időnek kell lennie ahhoz, hogy megfelelően és biztonságosan tapadjon az eszközhöz.
- Költség: A ragasztó költségét figyelembe kell venni, mivel egyes opciók drágábbak lehetnek, mint mások.
Összességében alapvető fontosságú, hogy olyan ragasztót válasszunk, amely megfelel az eszköz és a rendeltetésszerű használat speciális követelményeinek, miközben figyelembe kell venni az olyan tényezőket is, mint a tapadási szilárdság, kompatibilitás, hőmérséklet- és nedvességállóság, felhordási mód, kötési idő és költség.
Kompatibilitás a kameramodul anyagokkal
A kameramodul anyagok kompatibilitása számos tényezőtől függ, például a kameramodul típusától, a környezeti feltételektől, amelyeknek a kamerát ki kell téve, és a kameramodul tervezett felhasználásától.
Például, ha a kameramodult zord környezeti feltételekre, például magas hőmérsékletre vagy páratartalomra szánják, olyan anyagokat kell választani, amelyek ellenállnak ezeknek a feltételeknek. Hasonlóképpen UV-álló anyagokra lehet szükség, ha a kameramodult kültéri használatra tervezték.
A kameramodul anyagainak optikai tisztaságot, mechanikai stabilitást és tartósságot kell biztosítaniuk. A kameramodulokhoz általánosan használt anyagok közé tartozik az üveg, a műanyag és a kerámia.
Az üveg optikai tisztasága és karcállósága miatt népszerű, de nehéz és törékeny is lehet. A műanyagok, például a polikarbonát és az akril könnyűek és tartósak, de könnyen megkarcolódhatnak, és idővel lebomlanak az UV-sugárzás hatására.
A kerámia anyagok jó egyensúlyt biztosítanak az optikai tisztaság és a tartósság között, de gyártásuk kihívást jelenthet, és drágábbak lehetnek, mint más anyagok.
Végső soron a kameramodulok anyagának megválasztása az alkalmazás speciális követelményeitől, valamint az optikai teljesítmény, a mechanikai stabilitás és a tartósság közötti kompromisszumoktól függ.
Viszkozitás és reológia
A viszkozitás a folyadék áramlással szembeni ellenállásának mértéke. Ez a folyadékok olyan tulajdonsága, amely leírja a belső súrlódásukat vagy a molekulák egymás melletti elmozdulásával szembeni ellenállását. A nagy viszkozitású folyadékok vastagok és lassan áramlanak, míg az alacsony viszkozitású folyadékok vékonyak és gyorsan áramlanak.
A reológia az anyagok alakváltozását és áramlását vizsgálja, beleértve a folyadékokat, szilárd anyagokat és gázokat. Ez magában foglalja mind a viszkozitás, mind a rugalmasság, valamint az egyéb tulajdonságok, például a folyási feszültség, a nyírófeszültség és az alakváltozási sebesség tanulmányozását.
A viszkozitás és a reológia szorosan összefüggenek, mivel a konzisztencia a reológiai vizsgálatok egyik kritikus paramétere. Egy anyag reológiája leírja, hogyan viselkedik feszültség vagy feszültség hatására, és hogyan reagál a hőmérséklet, nyomás és egyéb változók változásaira. A reológiai mérésekkel meg lehet határozni a folyadék áramlási tulajdonságait, a szilárd anyag mechanikai tulajdonságait, és más lényeges jellemzőket, amelyek befolyásolják annak teljesítményét különböző alkalmazásokban.
Kötési idő és hőmérséklet
A kikeményedési idő és a hőmérséklet alapvető tényezők a különböző iparágakban, mint például a gyártás, az építőipar és a bevonatok.
A kikeményedés azt jelenti, hogy lehetővé teszik az anyag megkötését vagy megkeményedését kémiai reakció vagy fizikai folyamat során. A kikeményítéshez szükséges idő és hőmérséklet az anyag típusától és a késztermék kívánt tulajdonságaitól függ.
Például a kompozitok gyártása során a kikeményedési idő és a hőmérséklet kritikus tényezők, amelyek befolyásolják a végtermék szilárdságát, merevségét és tartósságát. A kikeményedési folyamat során hőt és nyomást alkalmaznak a kompozit anyagra, ami aktiválja a gyantát és megkeményedik. A kikeményedési folyamat hőmérséklete és időtartama az alkalmazott gyantarendszertől, valamint a kompozit alkatrészek méretétől és vastagságától függ.
A kikeményedési idő és a hőmérséklet szintén kritikus tényező a bevonatiparban a tartós és hosszú élettartamú felület elérésében. A kikeményedési folyamat során a bevonat és az aljzat között kémiai reakció lép fel, ami szilárd kötést hoz létre. A kikeményedési idő és hőmérséklet a bevonat típusától és a bevonat felvitelének körülményeitől függ.
Az építőiparban a kötési idő és a hőmérséklet lényeges tényezők a beton megkötésében és megkeményedésében. A kikeményedési folyamat magában foglalja a beton nedvesen és állandó hőmérsékleten tartását egy meghatározott ideig, hogy lehetővé tegye a cement hidratálását és megkeményedését. A kötési idő és hőmérséklet a felhasznált cement típusától, a környezeti feltételektől, valamint a beton méretétől és vastagságától függ.
A megfelelő kikeményedési idő és hőmérséklet kritikus fontosságú a különböző anyagok és termékek kívánt tulajdonságainak és teljesítményének biztosításához.
A kötés erőssége és tartóssága
A kötési szilárdság a ragasztó azon képességére utal, hogy két felületet összetart. Általában font per négyzethüvelykben (psi) mérik, és olyan tényezőktől függ, mint a ragasztó típusa, a ragasztandó anyagok és a felület előkészítése.
A tartósság a kötés azon képességét jelenti, hogy ellenáll a külső igénybevételeknek, például hőmérséklet-változásoknak, nedvességnek és mechanikai erőknek anélkül, hogy idővel elveszítené szilárdságát vagy integritását.
A ragasztó kötési szilárdsága és tartóssága szorosan összefügg. Az erős kötés általában tartósabb, mivel nagyobb igénybevételnek ellenáll anélkül, hogy eltörne. A kötés tartóssága azonban más tényezőktől is függ, például a felhasználási környezettől és a ragasztandó anyagoktól.
Az erős és tartós kötés biztosításához elengedhetetlen a ragasztandó anyagokhoz megfelelő ragasztó kiválasztása, a felületek megfelelő előkészítése, valamint a gyártó felhordási és kötési előírásainak betartása. A kötés rendszeres karbantartása és ellenőrzése is biztosíthatja annak hosszú távú tartósságát.
Egyszerű alkalmazás és adagolás
A könnyű felvitel és adagolás a termék felvitelének vagy adagolásának kényelmét és egyszerűségét jelenti. Elengedhetetlen számos fogyasztási cikkhez, különösen a gyakran használt termékekhez, például a testápolási cikkekhez, tisztítószerekhez és élelmiszerekhez.
Az alkalmazás és az adagolás egyszerűségét számos tényező befolyásolhatja, beleértve a termék csomagolásának kialakítását, a termék viszkozitását és textúráját, valamint az alkalmazott adagoló mechanizmus típusát.
Például egy pumpás flakonban lévő testápolót könnyebb lehet felvinni, mint egy tégelyben lévőt, mivel így nem kell a felhasználónak az ujjaival kikanalazni a terméket. Hasonlóképpen, egy szórófejes palackban lévő tisztítószert könnyebb lehet adagolni és felvinni, mint egy nagyobb tartályból kiönteni.
A gyártók arra törekszenek, hogy könnyen felvihető és adagolható termékeket hozzanak létre, mivel ezek javíthatják a felhasználói élményt és növelhetik a vásárlók elégedettségét. Ugyanakkor az is fontos, hogy a könnyű használhatóságot más tényezőkkel, például a termékbiztonsággal, a hatékonysággal és a költségekkel egyensúlyba hozzuk.
Költség és rendelkezésre állás
A könnyű felvitel és adagolás a termék felvitelének vagy adagolásának kényelmét és egyszerűségét jelenti. Elengedhetetlen számos fogyasztási cikkhez, különösen a gyakran használt termékekhez, például a testápolási cikkekhez, tisztítószerekhez és élelmiszerekhez.
Az alkalmazás és az adagolás egyszerűségét számos tényező befolyásolhatja, beleértve a termék csomagolásának kialakítását, a termék viszkozitását és textúráját, valamint az alkalmazott adagoló mechanizmus típusát.
Például egy pumpás flakonban lévő testápolót könnyebb lehet felvinni, mint egy tégelyben lévőt, mivel így nem kell a felhasználónak az ujjaival kikanalazni a terméket. Hasonlóképpen, egy szórófejes palackban lévő tisztítószert könnyebb lehet adagolni és felvinni, mint egy nagyobb tartályból kiönteni.
A gyártók arra törekszenek, hogy könnyen felvihető és adagolható termékeket hozzanak létre, mivel ezek javíthatják a felhasználói élményt és növelhetik a vásárlók elégedettségét. Ugyanakkor az is fontos, hogy a könnyű használhatóságot más tényezőkkel, például a termékbiztonsággal, a hatékonysággal és a költségekkel egyensúlyba hozzuk.
Hogyan alkalmazzák a kameramodul ragasztóját?
A ragasztónak a kameramodulra történő felvitelének folyamata a használt ragasztó konkrét típusától és a kameramodul gyártási folyamatától függően változhat. Íme azonban egy általános áttekintés a ragasztó kameramodulra történő felvitelének lépéseiről:
- Készítse elő a kameramodult: A ragasztó felhordása előtt a modulnak tisztának és száraznak kell lennie. A kameramodul felületén lévő por, szennyeződés vagy nedvesség befolyásolhatja a ragasztó tapadását.
- A ragasztó felhordása: A használt ragasztó típusától függően manuálisan vagy automata adagoló segítségével is felhordható. A ragasztó egy meghatározott mintázatban van jelen, így biztosítva, hogy lefedje azokat a területeket, ahol a kameramodult az eszközhöz rögzítik.
- A kameramodul elhelyezése: A ragasztó felhordása után a kameramodult óvatosan helyezze rá a készülékre. A kameramodult helyesen kell beállítani, hogy biztosítsa a tökéletes elhelyezkedését.
- A ragasztó kikeményítése: A használt ragasztótól függően előfordulhat, hogy a kameramodul használata előtt meg kell kötni. A kikeményedés különféle módszerekkel történhet, például hővel vagy UV-fénnyel.
- Tesztelje a kameramodult: Miután a ragasztó megkötött, meg kell vizsgálni, hogy biztosan rögzítve van-e a készülékhez, és megfelelően működik-e.
Összességében a ragasztó felhordása a kameramodulra pontosságot és a részletekre való odafigyelést igényel, hogy biztosítsa a kameramodul biztonságos rögzítését és megfelelő működését.
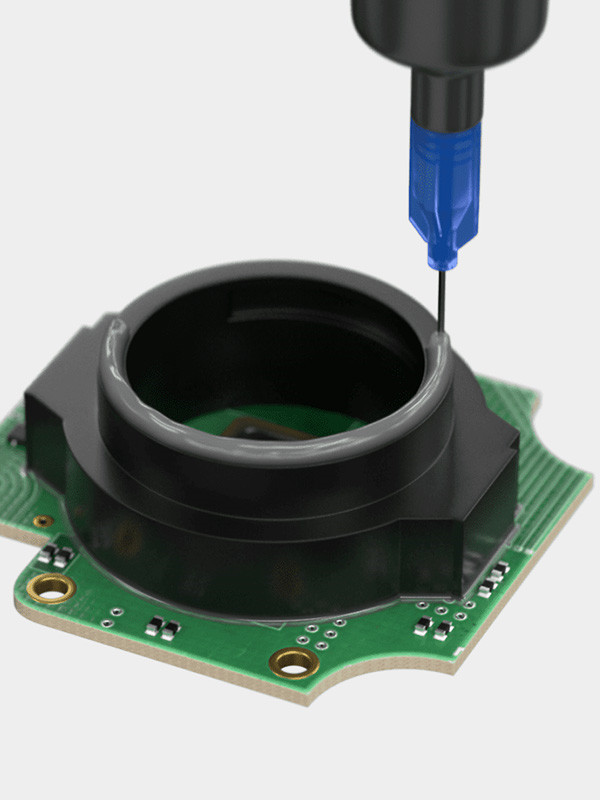
Kézi alkalmazás kontra automatizált alkalmazás
A kézi és automatizált alkalmazások egy feladat vagy folyamat két különböző módszerére utalnak, az egyik emberi munkával, a másik pedig szoftverrel vagy gépekkel. Íme néhány fő különbség a kézi és az automatizált alkalmazások között:
Kézi alkalmazás:
- Emberi munkával készült
- Ez időigényes lehet, és hajlamos a hibákra
- Magas fokú szaktudást vagy képzettséget igényelhet
- Rugalmasságot kínál az egyedi vagy változó helyzetekhez való alkalmazkodásban
- Nehéz lehet skálázni vagy több példányban replikálni
Automatizált alkalmazás:
- Szoftverrel vagy gépekkel
- Gyorsabb és pontosabb lehet, mint a kézi alkalmazás
- Programozható összetett feladatok elvégzésére
- Konzisztens eredményeket kínál, és csökkenti a hibák valószínűségét
- Nagy mennyiségű adatot vagy feladatot tud kezelni
- Ennek fejlesztése és karbantartása költséges lehet
- Lehet, hogy nem olyan rugalmas, mint a manuális alkalmazás az egyedi vagy változó helyzetekhez való alkalmazkodásban
Felület előkészítés és tisztítás
A felület előkészítése és tisztítása kritikus fontosságú a különböző iparágakban, például a gyártásban, az építőiparban és az autóiparban. Ezek a lépések szükségesek annak biztosításához, hogy a felületek mentesek legyenek a szennyeződésektől, és megfelelően előkészítve legyenek a további feldolgozáshoz vagy bevonáshoz.
Íme néhány szabványos felület-előkészítési és -tisztítási módszer:
- A mechanikai tisztítás magában foglalja a szennyeződések fizikai eltávolítását a felületről olyan módszerekkel, mint a homokfúvás, a szemcseszórás vagy a csiszolókorongokkal végzett súrolás. Ez a módszer gyakran eltávolítja a rozsdát, a festéket és más bevonatokat a fémfelületekről.
- A kémiai tisztítás során vegyszereket használnak a felületen lévő szennyeződések feloldására vagy lebontására. Az ebben a módszerben használt vegyszerek példái közé tartoznak a savak, lúgok és oldószerek. A kémiai tisztítást gyakran használják olajok, zsírok és egyéb szerves szennyeződések eltávolítására.
- Az elektrokémiai tisztítás során elektromos áramot használnak a szennyeződések eltávolítására a felületről. Ezt a módszert gyakran használják rozsda és más fémoxidok eltávolítására.
- Hőtisztítás: Ez hő használatával eltávolítja a szennyeződéseket a felületről. A termikus tisztítási módszerek közé tartozik a lángos tisztítás és a sütés. Ez a módszer gyakran eltávolítja a festéket és egyéb bevonatokat a fémfelületekről.
- A nagynyomású víztisztítás során nagynyomású vízsugárral távolítják el a felületről a szennyeződéseket. Ezt a módszert gyakran használják beton és más bonyolult karakterek más módszerekkel történő tisztítására.
Elengedhetetlen a megfelelő felület-előkészítési és tisztítási módszer kiválasztása a felület típusa és a jelenlévő szennyeződések típusa alapján. A felület megfelelő előkészítése és tisztítása javíthatja a bevonatok tapadását és biztosíthatja a karakter hosszú élettartamát.
Adagolási technikák és berendezések
Az adagolási technikák és berendezések elengedhetetlenek a gyógyszerek pontos és hatékony adagolásához. Íme néhány standard technika és berendezés, amelyet a gyógyszeradagolás során használnak:
- Automatizált adagolórendszerek (ADS): Ezek a számítógépes rendszerek vonalkódok és szkennerek segítségével adagolják a gyógyszereket a pontosság biztosítása érdekében.
- A gyógyszeres kocsik mozgatható kocsik, amelyeket gyógyszerek tárolására és egyik helyről a másikra történő szállítására használnak, és gyakran használják egészségügyi intézményekben.
- Egyedi dózisú csomagolás: Ez magában foglalja a gyógyszer egyes adagjainak a gyógyszerre vonatkozó információval ellátott, egyedi csomagolásba történő kiadását.
- Többadagos csomagolás: Ez azt jelenti, hogy több adag gyógyszert egyetlen tartályba kell kiadni, amelyen fel van tüntetve a gyógyszerre és az adagolási rendre vonatkozó információ.
- Fecskendők és tűk: Ezeket a gyógyszerek felszívására és beadására használják szájon át vagy injekció formájában.
- Orális fecskendők: Orális adagolásra szánt folyékony gyógyszerek mérésére és adagolására szolgálnak.
- Pillazúzók és pirulavágók: Ezeket a pirulák aprítására vagy kisebb darabokra vágására használják, hogy könnyebben lenyeljék őket.
- Elektronikus receptírás (e-recept): Ez a technológia lehetővé teszi az egészségügyi szolgáltatók számára, hogy elektronikus úton küldjék el a recepteket a gyógyszertárakba, így nincs szükség papírreceptre.
- IV pumpák: Ezeket arra használják, hogy a gyógyszert intravénás (IV) vezetéken keresztül közvetlenül a páciens véráramba adják be.
- Inhalátorok és porlasztók: Ezeket a gyógyszereket közvetlenül a tüdőbe juttatják légzési betegségek esetén.
Ezek a technikák és berendezések segítenek biztosítani a pontos és biztonságos gyógyszeradagolást, ami elengedhetetlen a betegek egészségéhez és jólétéhez.
A kameramodul ragasztójának kezelése és tárolása
A kameramodul-ragasztó egy speciális ragasztó, amellyel kameramodulokat rögzítenek elektronikus eszközökhöz, például okostelefonokhoz, laptopokhoz és táblagépekhez. A kameramodul ragasztójának kezelése és tárolása elengedhetetlen a hatékony és biztonságos megőrzéshez. Íme néhány irányelv a kameramodul ragasztójának kezelésére és tárolására:
- Kezelés: A kameramodul ragasztójának kezelésekor elengedhetetlen a megfelelő egyéni védőfelszerelés (PPE), például kesztyű és védőszemüveg viselése. Ez segít megelőzni a bőrrel való érintkezést és a ragasztó szembe jutását. Mindig kövesse a gyártó utasításait a ragasztó kezelésére és felhordására vonatkozóan.
- Tárolás: A kameramodul ragasztóját hűvös, száraz helyen, közvetlen napfénytől és hőforrásoktól védve kell tárolni. A hőnek és napfénynek való kitettség a ragasztó károsodását és hatékonyságának elvesztését okozhatja. A ragasztót szorosan lezárt tartályban is kell tárolni, hogy elkerüljük a szennyeződést és a nedvesség felszívódását.
- Eltarthatóság: A kameramodul ragasztójának eltarthatósága a gyártótól és az adott terméktől függően változik. A ragasztó használata előtt mindig ellenőrizze a lejárati dátumot a tartályon. A lejárt ragasztót megfelelően ártalmatlanítani kell.
- Alkalmazás: Gondosan kövesse a gyártó utasításait a kameramodul ragasztójának felhordásakor. Csak az ajánlott mennyiségű ragasztót használja a megfelelő ragasztás érdekében. A ragasztó túlzott felhordása hiányos ragasztáshoz vezethet, és károsíthatja a készüléket.
- Ártalmatlanítás: A kameramodul fel nem használt vagy lejárt ragasztóját a helyi előírásoknak megfelelően kell megsemmisíteni. Ne dobja a ragasztót a szokásos szemétbe, és ne öntse a lefolyóba.
A kameramodul ragasztójának megfelelő kezelése és tárolása elengedhetetlen a hatékony és biztonságos megőrzéshez. Mindig kövesse a gyártó utasításait, és tegye meg a megfelelő óvintézkedéseket a ragasztó kezelése és felhordása során.
Eltarthatóság és lejárat
A kameramodul ragasztójának eltarthatósága és lejárati ideje számos tényezőtől függően változhat, például a ragasztó típusától, a tárolási körülményektől és a gyártási dátumtól függően.
Általánosságban elmondható, hogy a legtöbb kameramodul-ragasztó eltarthatósága körülbelül hat hónap és egy év közötti a gyártástól számítva, amennyiben hűvös, száraz helyen, közvetlen napfénytől és szélsőséges hőmérsékletektől védve tárolják. Azonban bizonyos típusú ragasztók eltarthatósági ideje hosszabb vagy rövidebb lehet.
Fontos megjegyezni, hogy a kameramodul ragasztójának eltarthatósága nem feltétlenül jelzi a lejárati idejét, hanem arra az időtartamra vonatkozik, ameddig a ragasztó tárolható és felhasználható megfelelő tulajdonságainak és teljesítményének megőrzése mellett. A lejárt eltarthatósági idő után a ragasztó leromolhat és elveszítheti hatékonyságát, ami csökkenti a ragasztási szilárdságot és egyéb problémákat.
A kameramodul ragasztójának tényleges lejárati dátumának meghatározásához javasoljuk, hogy ellenőrizze a termék címkéjét, vagy olvassa el a gyártó dokumentációját a konkrét útmutatásért. A megfelelő tárolási és kezelési eljárások betartása elengedhetetlen ahhoz, hogy a ragasztó a lehető leghosszabb ideig megőrizze hatékonyságát.
Óvintézkedések és biztonsági intézkedések
A kameramodul ragasztója veszélyes lehet, ha nem megfelelően kezelik és használják. Az óvintézkedések és biztonsági intézkedések betartása elengedhetetlen a ragasztó biztonságos és hatékony felhasználásához. Íme néhány szükséges óvintézkedés és biztonsági intézkedés, amelyet szem előtt kell tartania, amikor kameramodul ragasztóval dolgozik:
- Viseljen védőfelszerelést: Mindig viseljen védőfelszerelést, például kesztyűt, védőszemüveget és maszkot a kameramodul ragasztójának kezelésekor. Ez megvédi Önt az alkalmazás során felszabaduló gőzöktől vagy irritáló anyagoktól.
- Jól szellőző helyen végzett munka: Jól szellőző helyen használjon kameramodul ragasztót, hogy elkerülje a káros gőzök belélegzését. Nyissa ki az ablakokat vagy használjon elszívó ventilátorokat a megfelelő szellőzés érdekében.
- Kerülje a bőrrel való érintkezést: Kerülje a ragasztó közvetlen bőrrel való érintkezését, mert bőrirritációt vagy allergiás reakciókat okozhat. Ha bőrrel érintkezik, azonnal mossa le az érintett területet szappannal és vízzel.
- A ragasztót megfelelően tárolja: A ragasztót hűvös, száraz helyen, közvetlen napfénytől és szélsőséges hőmérséklettől védve tárolja. A megfelelő tárolás és kezelés érdekében kövesse a gyártó utasításait.
- A ragasztót rendeltetésszerűen használja: Csak rendeltetésszerűen használja, és gondosan kövesse a gyártó utasításait.
- A ragasztóanyag megfelelő ártalmatlanítása: A fel nem használt ragasztót vagy csomagolóanyagot a helyi előírások és irányelvek szerint semmisítse meg.
Ezen óvintézkedések és biztonsági intézkedések betartásával minimalizálhatja a kameramodul ragasztójával kapcsolatos kockázatokat, és biztosíthatja annak biztonságos és hatékony használatát.
Gyakori problémák a kameramodul ragasztójával
A kameramodul ragasztója a kameragyártás alapvető összetevője, és bármilyen probléma hatással lehet a végtermék minőségére és megbízhatóságára. Íme néhány gyakori probléma a kameramodul ragasztójával kapcsolatban, amelyekkel a gyártók találkozhatnak:
- Rossz tapadás: A kameramodul ragasztójával kapcsolatos egyik leggyakoribb probléma a rossz kötés. Ennek oka lehet a nem megfelelő alkalmazás, a nem megfelelő kötési idő, vagy a kameramodul anyagához nem kompatibilis ragasztó használata.
- Egyenetlen ragasztóeloszlás: Az egyenetlen ragasztóeloszlás inkonzisztens kötést eredményezhet, és problémákat okozhat a képminőségben. Ez akkor fordulhat elő, ha a ragasztót nem egyenletesen alkalmazzák, vagy ha a kameramodul nincs erősen a ragasztóhoz nyomva a ragasztási folyamat során.
- Légbuborékok: A ragasztórétegbe szorult légbuborékok ragasztási problémákat okozhatnak, és befolyásolhatják a képminőséget. Ez akkor fordulhat elő, ha a ragasztót megfelelően össze kell keverni vagy ellenőrzött környezetben kell felhordani.
- Delamináció akkor következik be, amikor a kameramodul és a készülékház közötti ragasztókötés meghibásodik, ami szétválást eredményez. Ez történhet olyan környezeti tényezők miatt, mint a magas hőmérséklet vagy a páratartalom.
- Szennyeződés: A ragasztó porral, olajjal vagy egyéb részecskékkel való szennyeződése befolyásolhatja a ragasztási teljesítményt, és rossz képminőséget eredményezhet.
- Kompatibilitási problémák: Nem kompatibilis ragasztóanyag használata a kameramodul anyagával ragasztási problémákat okozhat, és befolyásolhatja a kameramodul általános minőségét és megbízhatóságát.
Ezen problémák minimalizálása érdekében elengedhetetlen a kameramodul anyagával kompatibilis, kiváló minőségű ragasztó használata, a megfelelő felhordási eljárások betartása, és a gyártás során alapos minőségellenőrzési tesztek elvégzése.
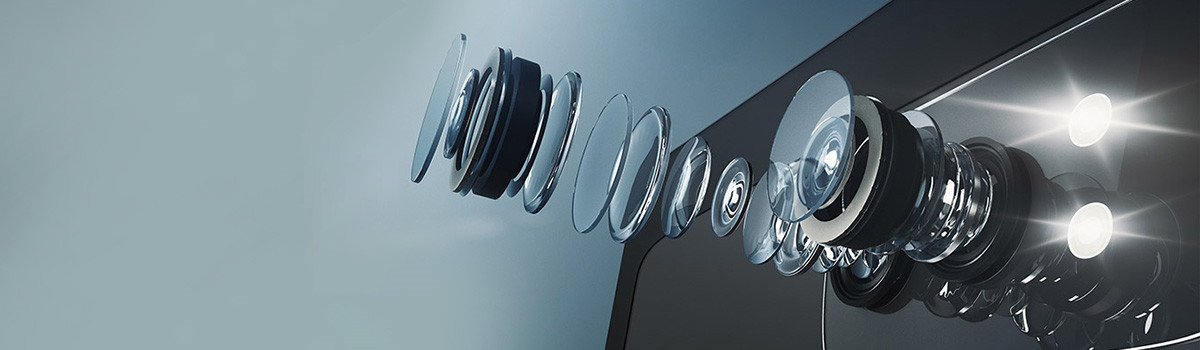
Ragasztómaradványok és szennyeződés
A ragasztómaradványok és a szennyeződés gyakori a különböző iparágakban, beleértve a gyártást, az autógyártást és az építőiparban. A ragadós maradvány az a ragasztóanyag-maradvány, amely a korábban felvitt ragasztó eltávolítása után visszamarad. Szennyezés viszont akkor következik be, amikor nem kívánt idegen részecskék vagy anyagok tapadnak egy felületre vagy anyagra, ami befolyásolja annak minőségét és teljesítményét.
A ragasztómaradványok nagy kihívást jelenthetnek, és speciális tisztítószereket és eszközöket igényelnek. Néhány szabványos módszer a ragasztómaradványok eltávolítására: oldószerek, kaparás, csiszolás vagy melegítés. A megfelelő biztonsági óvintézkedések betartása az oldószerek vagy a hő kezelésekor elengedhetetlen, mivel ezek veszélyesek lehetnek az Ön egészségére.
A szennyeződés különböző okokból következhet be, például nem megfelelő kezelés, tárolás vagy feldolgozás miatt. A szennyező anyagok lehetnek por, szennyeződés, olaj vagy vegyszerek, és befolyásolhatják a termék vagy az anyag teljesítményét és biztonságát. A szennyeződés megelőzése magában foglalja a megfelelő kezelési eljárások betartását, a megfelelő védőfelszerelés használatát, valamint a munkaterületek és eszközök tisztaságának fenntartását.
Összességében kulcsfontosságú a ragasztómaradványok és a szennyeződés gyors és hatékony kezelése a termék vagy anyag biztonságának és minőségének biztosítása érdekében.
Inkonzisztens kötődési erősség
A kameramodul ragasztójának inkonzisztens kötési szilárdságát számos tényező okozhatja, beleértve a gyártási folyamat eltéréseit, a felhasznált anyagok különbségeit vagy a környezeti tényezőket, például a hőmérsékletet és a páratartalmat.
Az egyik lehetséges megoldás a gyártási folyamat gondos ellenőrzése a konzisztens ragasztófelvitel biztosítása és a környezeti feltételek gyártás közbeni figyelemmel kísérése. Ez csökkentheti a ragasztó kötési szilárdságának változékonyságát.
Egy másik megoldás egy másik típusú ragasztó használata, amely kevésbé hajlamos a kötési szilárdság változékonyságára. Egyes gyártók például áttérhetnek az oldószer alapú ragasztóról a hőre keményedő ragasztóra, ami egyenletesebb eredményt biztosíthat.
Ugyancsak alapvető fontosságú a ragasztó kötési szilárdságának tesztelése és érvényesítése különböző körülmények között, például hőmérsékleten és páratartalomban, hogy biztosítsa a ragasztó tartós működését. Ez segíthet a lehetséges problémák korai felismerésében, és megelőzheti a későbbi problémákat.
Összességében a kameramodul ragasztójának ellentmondásos kötési szilárdsága nagy kihívást jelenthet. Ennek ellenére a gyártási folyamat gondos ellenőrzésével és a ragasztó különböző körülmények között történő tesztelésével lehetőség van a változékonyság minimalizálására és az egyenletes teljesítmény biztosítására.
Termikus és környezeti degradáció
A termikus és a környezeti degradáció kétféle anyagromlás, amely idővel előfordul, és negatívan befolyásolhatja az anyag tulajdonságait és teljesítményét.
A termikus lebomlás akkor következik be, amikor egy anyag a magas hőmérsékletnek való kitettség következtében elbomlik vagy elveszti szilárdságát és integritását. Ez több okból is megtörténhet, például hőnek, sugárzásnak vagy magas hőmérsékleten lejátszódó kémiai reakcióknak. Például, ha egy műanyag magas hőmérsékletnek van kitéve, lebomolhat és mérgező gázokat bocsáthat ki.
Másrészt a környezeti leromlás az a folyamat, amelynek során az anyag lebomlik olyan környezeti tényezők hatására, mint a nedvesség, napfény és vegyszerek. Ennek több oka is lehet, például UV-sugárzás, vegyszerek vagy vízzel való érintkezés. Például, ha egy fémanyagot víz ér, korrodálódhat, és elveszítheti szilárdságát és integritását.
Mindkét típusú leromlás károsíthatja az anyagokat, és csökkenti a teljesítményt és a tartósságot. A termikus és környezeti degradáció megelőzése érdekében elengedhetetlen a megfelelő anyagok és védőbevonatok kiválasztása, amelyek ellenállnak az adott környezeti feltételeknek és hőmérsékleti tartományoknak. A megfelelő karbantartási és tárolási gyakorlatok szintén segíthetnek megelőzni vagy minimalizálni az idő múlásával bekövetkező károsodást.
Hibamódok és -elemzés
A kameramodulok ragasztásával kapcsolatos problémák különböző meghibásodási módokhoz vezethetnek, mint például rossz képminőség, kameramodul leválása és a kamerarendszer teljes meghibásodása. Meghibásodási módok és hatások elemzése (FMEA) elvégezhető a lehetséges meghibásodási módok és okok azonosítására, valamint stratégiák kidolgozására ezek megelőzésére vagy enyhítésére.
Az alábbiakban felsorolunk néhány lehetséges hibamódot és azok okait:
- Gyenge képminőség fordulhat elő, ha a kameramodul nincs biztonságosan rögzítve az eszközhöz, ami mozgást vagy vibrációt eredményezhet a képrögzítés során. Ennek oka lehet az elégtelen tapadási szilárdság, rossz fedőképesség vagy nem megfelelő kötés.
- Kameramodul leválása: Ez akkor fordulhat elő, ha a ragasztó nem biztosít megfelelő kötési szilárdságot, vagy ha szennyeződések tapadnak a felületekre. A szennyeződések megakadályozhatják a megfelelő kötést és gyengíthetik a tapadási szilárdságot.
- A kamerarendszer teljes meghibásodását okozhatja, ha a kameramodul leválik a készülékről, vagy ha a ragasztóanyag idővel lebomlik. Ezt magas hőmérsékletnek, páratartalomnak vagy olyan vegyszereknek való kitettség okozhatja, amelyek gyengíthetik vagy ronthatják a ragasztót.
E meghibásodási módok megelőzésére vagy enyhítésére többféle stratégia alkalmazható, többek között:
- Az adott alkalmazásnak és környezeti feltételeknek megfelelő nagy szilárdságú ragasztó használata.
- A felület megfelelő előkészítésének biztosítása, beleértve a tisztítást és a ragasztandó felületek szennyeződéseinek eltávolítását.
- A ragasztó megfelelő kikeményítésének és kezelésének biztosítása a kívánt kötési szilárdság elérése érdekében.
- A rendszeres minőség-ellenőrzések biztosítják, hogy a ragasztó a vártnak megfelelően működik.
- Fontolja meg további mechanikus rögzítők vagy más kötési módszerek használatát a redundancia biztosítása és az általános megbízhatóság javítása érdekében.
A lehetséges meghibásodási módok azonosításával és azok megelőzésére vagy enyhítésére irányuló stratégiák végrehajtásával a kameramodulok ragasztási problémái minimalizálhatók vagy kiküszöbölhetők, ami javítja a kamera teljesítményét és megbízhatóságát.
A kameramodul ragasztási problémáinak elhárítása
Ha ragasztási problémákat tapasztal a kameramodullal, több lépést is megtehet a probléma elhárításához. Íme néhány lehetséges megoldás:
- Tisztítsa meg a ragasztófelületet: Először győződjön meg arról, hogy az a felület, amelyen a ragasztónak fel kell tapadnia, tiszta és szennyeződésmentes. Használjon puha, szöszmentes kendőt és némi izopropil-alkoholt a felület tisztításához.
- Használjon erősebb ragasztót: Ha a jelenlegi ragasztó nem tartja biztonságosan a helyén a kameramodult, próbáljon meg erősebb ragasztót használni. Erősebb ragasztókat vásárolhat hardverboltokban vagy online. Azonban győződjön meg arról, hogy a választott ragasztó biztonságos az elektronikus alkatrészekhez, és nem károsítja a kameramodult.
- Cserélje ki a ragasztót: Ha régi vagy szélsőséges hőmérsékletnek volt kitéve, elveszítheti hatékonyságát. Ebben az esetben előfordulhat, hogy a ragasztót újra kell cserélnie.
- Vigye fel újra a ragasztót: Ha a ragasztó még mindig jó állapotban van, de a kameramodul nem tapad megfelelően, próbálja meg újra felvinni a ragasztót. Távolítsa el a régi ragasztót a kameramodulról és a felületről, amelyhez ragaszkodnia kell. Vigyen fel új ragasztóréteget, biztosítva az egyenletes eloszlást és a teljes felületet.
- Kérjen szakember segítségét: Ha a fenti megoldások egyike sem működik, ideje lehet szakember segítségét kérni. Vidd el a kameramodult egy tapasztalt technikushoz, aki felméri a problémát, és megoldást kínál.
Összességében elengedhetetlen, hogy legyen óvatos a kameramodul ragasztási problémáinak elhárítása során. A kameramodul helytelen kezelése vagy nem megfelelő típusú ragasztó használata károsíthatja a kameramodult vagy használhatatlanná teheti azt.
A kameramodul ragasztójának eltávolítása és cseréje
A kameramodul ragasztójának eltávolítása és cseréje kényes folyamat lehet, mivel a kameramodul érzékeny alkatrész a legtöbb elektronikus eszközben, például okostelefonokban, táblagépekben és laptopokban. A kameramodul-ragasztó eltávolításának és cseréjének lépései a következők:
- Kapcsolja ki a készüléket, és lehetőség szerint távolítsa el az akkumulátort. Ez megakadályozza, hogy elektromos áram folyjon át a gépen, és minimálisra csökkenti a károsodás kockázatát.
- Használjon műanyag kifeszítő eszközt vagy vékony fém pálcát, hogy finoman húzza le a kameramodult az eszközről. Ügyeljen arra, hogy ne sértsen meg semmilyen más alkatrészt vagy hajlékony kábelt, amely útban lehet.
- Használjon hőpisztolyt vagy hajszárítót a ragasztó felmelegítéséhez a kameramodul körül. Ezáltal a ragasztó rugalmasabb lesz, és könnyebben eltávolítható.
- Óvatosan emelje le a kameramodult a ragasztóról. Ha a ragasztó különösen makacs, akkor egy műanyag feszítőeszköz segítségével eltávolíthatja.
- Tiszta ruhával vagy alkoholos törlőkendővel tisztítsa meg a kameramodul környékét. Győződjön meg róla, hogy nem maradt maradék vagy törmelék.
- Vigyen fel egy kis mennyiségű új ragasztót a kameramodul hátuljára. Ügyeljen arra, hogy ne alkalmazzon túl sokat, mert ez a modul elcsúszását okozhatja, vagy kihívást jelenthet az újracsatlakoztatás.
- Óvatosan csatlakoztassa újra a kameramodult a készülékhez, ügyelve a megfelelő beállításra. Erősen nyomja le a biztonságos illeszkedés érdekében.
- Hagyja pihenni a készüléket legalább 24 órán át, mielőtt újra használná. Ez időt ad a ragasztónak a megkötéshez és a megfelelő megkötéshez.
Fontos megjegyezni, hogy a fenti lépések általános iránymutatások, és nem feltétlenül vonatkoznak minden eszközre. Mindig javasoljuk, hogy olvassa el a gyártó utasításait, vagy forduljon szakemberhez, ha pontosításra van szüksége a folyamattal kapcsolatban.
A kameramodul ragasztójának újrahasznosítása és ártalmatlanítása
A kameramodul ragasztójának újrahasznosítása és ártalmatlanítása a használt ragasztótól függ. A kameramodul ragasztója általában termikus és optikai ragasztókra osztható.
A hőragasztót általában a kameramodulokban használják az objektívtartó és a képérzékelő összeragasztására. Ezt a ragasztót úgy távolíthatja el, hogy a kameramodult magas hőmérsékletre melegíti, felpuhítja, és hagyja lekaparni. Az eltávolított ragasztóanyag szokásos hulladékként kezelhető.
Az optikai ragasztót a lencse lencsetartóhoz való rögzítésére használják, és nehezebb eltávolítani, mint a termikus ragasztót. Ennek a ragasztónak a feloldásához speciális oldószerek szükségesek, és az eljárást óvatosan kell elvégezni, nehogy a lencse vagy más alkatrészek sérüljenek. A ragasztó eltávolítása után az oldószert és a maradékot veszélyes hulladékként megfelelően ártalmatlanítani kell.
Általában a legjobb, ha konzultál a gyártóval vagy a professzionális újrahasznosító szolgálattal, hogy meghatározzák a megfelelő újrahasznosítási módszert vagy a kameramodul ragasztójának ártalmatlanítását. A környezet és az emberi egészség védelme érdekében minden veszélyes hulladék gondos kezelése és a helyi előírások betartása elengedhetetlen.
A kameramodul-ragasztótechnológia jövőbeli trendjei és fejlesztései
A kameramodulok ragasztási technológiája kritikus szempont az okostelefonok gyártásában. Mivel a fogyasztók fejlettebb kamerafunkciókat igényelnek, a kameramodul ragasztótechnológiájának fejlődnie kell, hogy megfeleljen ezeknek az igényeknek. Íme néhány lehetséges jövőbeli trend és fejlesztés a kameramodul-ragasztótechnológiában:
- Vékonyabb ragasztók: Ahogy az okostelefonok vékonyabbak és kompaktabbak lesznek, a kameramodulok ragasztóinak is vékonyodniuk kell. Ehhez új ragasztóanyagok kifejlesztésére lesz szükség, amelyek erősítik a kötést, miközben elég könnyűek ahhoz, hogy szűk helyeken is elférjenek.
- Erősebb ragasztók: A fejlettebb kamerafunkcióknál, mint például a nagyobb felbontás és az optikai zoom, a kameramodul ragasztóinak robusztusabbnak kell lenniük, hogy a kameramodul stabil maradjon, és ne mozduljon el használat közben.
- Magasabb hőállóság: Ahogy az okostelefon processzorai egyre erősebbek, több hőt termelnek, ami hatással lehet a kameramodult a helyén tartó ragasztóra. Nagyobb hőmérsékletállóságú kameramodul ragasztókra lesz szükség, hogy a modul magas üzemi hőmérséklet mellett is biztonságos maradjon.
- Továbbfejlesztett rezgésállóság: A rezgések a kameramodul elmozdulását okozhatják, ami elmosódott képeket vagy egyéb problémákat okozhat. A kameramodulok ragasztóinak javított rezgésállósága segíthet a kamera stabilitásában még erős vibrációs körülmények között is.
- Környezetbarátabb ragasztók: A fogyasztókat egyre jobban aggasztják termékeik környezeti hatásai. A környezetbarátabb anyagokat, például bioalapú vagy könnyen újrahasznosítható ragasztókat használó kameramodulos ragasztótechnológiára a jövőben nagyobb lesz az igény.
- Továbbfejlesztett automatizált gyártási folyamatok: Az okostelefonok gyártási volumenének növekedésével a kameramodul-ragasztó alkalmazásoknak automatizáltabbá és hatékonyabbá kell válniuk. Új gyártási eljárásokra lesz szükség, mint például a robotizált ragasztó alkalmazások, hogy lépést tudjunk tartani a fejlett kamerafunkciókkal rendelkező okostelefonok iránt.
Összességében a kameramodul-ragasztó technológia tovább fog fejlődni, válaszul a fejlettebb okostelefon-kamerafunkciók iránti keresletre. A vékonyabb, erősebb és környezetbarátabb ragasztók kifejlesztése, valamint a hőmérséklet- és rezgésállóság javítása elengedhetetlen lesz ahhoz, hogy az okostelefon-gyártók a jövőben kielégíthessék a fogyasztók igényeit.