Száloptikai ragasztók
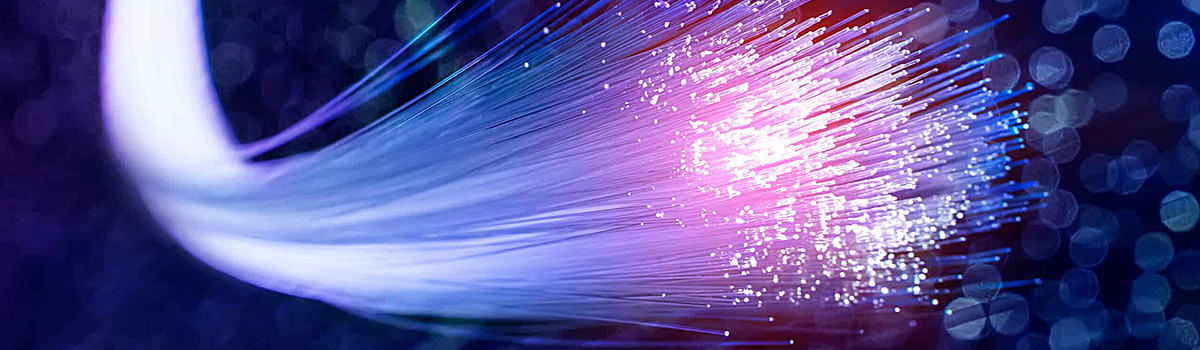
A száloptikai ragasztó kritikus komponens az optikai kábelek gyártásában és telepítésében. A száloptikai csatlakozók és érvéghüvelyek száloptikai kábelhez való rögzítésére szolgál, biztonságos és stabil csatlakozást biztosítva. A száloptikai ragasztó különféle formákban és összetételekben kapható, mindegyik saját tulajdonságokkal és alkalmazási területtel rendelkezik. Ebben a cikkben megvitatjuk mindazt, amit a száloptikai ragasztóról tudnia kell, beleértve annak típusait, tulajdonságait, alkalmazásait és a legjobb gyakorlatokat.
Mi az a száloptikai ragasztó?
A száloptikai ragasztó egy speciális ragasztó, amelyet az optikai kábelek összeszerelésére és telepítésére használnak. Ez egy kétkomponensű epoxigyanta, amelyet az optikai kábelek különböző alkatrészeinek összekapcsolására terveztek.
A száloptikai ragasztó jellemzően egy gyantából és egy keményítőből áll, amelyet meghatározott arányban kevernek össze közvetlenül a felhasználás előtt. A ragasztó összekeverése után megkeményedik és megkeményedik, erős kötést hozva létre az optikai komponensek között.
A ragasztót általában száloptikai csatlakozók száloptikai kábelhez való ragasztására és a csatlakozó különböző alkatrészeinek ragasztására használják. A ragasztó száloptikai patch vezetékeket és egyéb száloptikai alkatrészeket is előállít.
A száloptikai ragasztót kifejezetten alacsony zsugorodásra és alacsony gázkibocsátásra tervezték, ami segít biztosítani, hogy a kötés idővel erős maradjon. Alacsony viszkozitással is rendelkezik, ami megkönnyíti a felvitelt, és lehetővé teszi, hogy kis résekbe és résekbe folyjon.
A száloptikai ragasztó típusai
Számos típusú ragasztót használnak száloptikai alkalmazásokhoz, többek között:
- Epoxi alapú száloptikai ragasztó
- Akril alapú száloptikai ragasztó
- Szilikon alapú száloptikai ragasztó
- UV-re keményedő száloptikai ragasztó
- Kettős keményedésű száloptikai ragasztó
Epoxi alapú száloptikai ragasztó
Az epoxi alapú száloptikai ragasztók kétkomponensű ragasztók, amelyek gyantából és keményítőből állnak. Általában a távközlésben használják optikai szálak összekötésére és lezárására. Ezek a ragasztók nagy mechanikai szilárdsággal és kiváló vegyszerállósággal rendelkeznek, ami ideálissá teszi őket száloptikai alkalmazásokhoz.
Epoxi alapú száloptikai ragasztó használatakor a gyártó utasításainak gondos követése elengedhetetlen a megfelelő kikeményedés és ragasztás érdekében. A ragasztót vékony rétegben kell felhordani, és a szálat közvetlenül azelőtt kell behelyezni, hogy a ragasztó elkezdene megkötni. Szintén elengedhetetlen a szálak megfelelő beállításának biztosítása a ragasztókészletek előtt.
Egyes epoxi alapú száloptikai ragasztók speciális adalékanyagokkal vannak összeállítva, hogy javítsák optikai tulajdonságaikat, mint például az alacsony csillapítás és a magas törésmutató. Ezek a tulajdonságok segítenek a jelveszteség minimalizálásában és a száloptikai rendszer hatékonyságának maximalizálásában.
Akril alapú száloptikai ragasztó
Az akril alapú száloptikai ragasztót száloptikai kábelek összeszerelésére és beszerelésére használják. Ez egy kétkomponensű ragasztó, amely gyantából és keményítőből áll. Összekeverve a ragasztó erős kötést képez, amely ellenáll a nedvességnek, a hőnek és a vegyszereknek.
Az akril alapú száloptikai ragasztót általában az optikai kábelek csatlakozóinak rögzítésére és a szálak hordozókhoz való rögzítésére használják. Száloptikai alkatrészeket is gyárt, például csatolókat, csillapítókat és osztókat.
Az akril alapú száloptikai ragasztó egyik fő előnye a gyors kötési idő; jellemzően kevesebb, mint 10 perc alatt megköt, így népszerű választás a nagy volumenű gyártási környezetekben. Az akril alapú ragasztó viszonylag könnyen kezelhető, és nem igényel speciális felhordó felszerelést.
Az akril alapú száloptikai ragasztónak azonban vannak bizonyos korlátai. Nem alkalmas magas hőmérsékletű környezetre, mivel leromolhat és elveszítheti adhéziós tulajdonságait. Ezenkívül előfordulhat, hogy nem tapad jól bizonyos műanyagokhoz és fémekhez, ezért elengedhetetlen az adott alkalmazáshoz megfelelő ragasztó kiválasztása.
Szilikon alapú száloptikai ragasztó
A szilikon alapú száloptikai ragasztók optikai szálak ragasztására és rögzítésére specializálódtak különféle alkalmazásokban, beleértve a távközlést, adatközpontokat, orvosi berendezéseket és ipari automatizálást. Ezeket a ragasztókat kifejezetten úgy alakították ki, hogy erős kötést és kiváló tapadást biztosítsanak többféle felületen, beleértve az üveget, műanyagot és fémeket.
A szilikon alapú száloptikai ragasztók számos előnnyel rendelkeznek, mint például a magas hőmérséklet-állóság, a kiváló hőstabilitás, az alacsony zsugorodás és az alacsony gázkibocsátás. Kiváló mechanikai tulajdonságokkal is rendelkeznek, mint például a nagy szilárdság, nyúlás és rugalmasság, biztosítva a megbízható kötést és a hosszú távú tartósságot az optikai alkalmazásokban.
A szilikon alapú száloptikai ragasztók különféle formákban kaphatók, beleértve az egy- vagy kétrészes rendszereket is, amelyek hővel vagy UV-fénnyel kötődhetnek. Az alkalmazási követelményektől függően különféle módszerekkel alkalmazhatók, például mártással, ecsettel vagy fecskendővel.
A szilikon alapú száloptikai ragasztó kiválasztásakor elengedhetetlen olyan tényezőket figyelembe venni, mint a kötési idő, a kötési szilárdság, a termikus és mechanikai tulajdonságok, valamint az optikai szálakkal és hordozókkal való kompatibilitás. Az optimális teljesítmény és a hosszú távú megbízhatóság érdekében elengedhetetlen a gyártó tárolási, kezelési és alkalmazási előírásainak betartása is.
UV-re keményedő száloptikai ragasztó
Az UV-sugárzással keményedő száloptikai ragasztók egyfajta ragasztóanyag, amelyet optikai szálak összekapcsolására használnak különböző alkalmazásokban, beleértve a távközlést, adatközpontokat és orvosi eszközöket. Ezek a ragasztók jellemzően polimer gyantából és fotoiniciátorból állnak, amely UV-fénnyel reagálva megkeményedik és kikeményíti a ragasztót.
Az UV-sugárzással keményedő száloptikai ragasztók számos előnnyel rendelkeznek a hagyományos ragasztókhoz képest, beleértve a gyorsabb kötési időt, az alacsonyabb zsugorodási arányt és a nagyobb kötési szilárdságot. Az UV-re keményedő ragasztók környezetbarátabbak, mint az oldószer alapú ragasztók, mivel nem tartalmaznak káros illékony szerves vegyületeket (VOC).
Az UV-sugárzással keményedő száloptikai ragasztókkal végzett munka során az egyik fontos szempont a ragasztó kikeményítéséhez használt UV-fény hullámhossza. A ragasztóban lévő fotoiniciátort úgy tervezték, hogy az UV-fény meghatározott hullámhosszával, jellemzően 300-400 nm-rel reagáljon. A nem megfelelő hullámhosszú fény használata tökéletlen kikeményedést és gyengült kötéseket eredményezhet.
Összességében elmondható, hogy az UV-re keményedő száloptikai ragasztók megbízható és hatékony megoldást jelentenek az optikai szálak különböző alkalmazásokban történő ragasztására, és számos előnnyel rendelkeznek a hagyományos ragasztókkal szemben.
Kettős keményedésű száloptikai ragasztó
A kettős keményedésű száloptikai ragasztó egyfajta ragasztó, amelyet általában száloptikai alkalmazásokban használnak. Ezt a ragasztót úgy tervezték, hogy akár UV-fénnyel, akár hővel kötődjön, így rugalmasabb és sokoldalúbb kötési megoldást tesz lehetővé.
A ragasztó kettős térhálósodása azt jelenti, hogy UV-fénnyel és hővel is megköt, ami ideálissá teszi számos alkalmazáshoz. Például egyes alkalmazásokban az UV fény nem képes áthatolni a ragasztó minden területére, de a hő igen, és fordítva. A ragasztó teljesen és egyenletesen tud kikeményedni, ha mindkét kötési mód rendelkezésre áll, így biztosítva a szilárd kötést.
Ezenkívül gyakran használnak kettős térhálósodású optikai ragasztót, mivel a kikeményedés során alacsony a zsugorodási aránya. Ez azért fontos, mert a zsugorodás feszültséget okozhat a száloptikai alkatrészeken, ami olyan problémákhoz vezethet, mint például a jel elvesztése vagy törése.
A száloptikai ragasztó tulajdonságai
A száloptikai ragasztó, más néven optikai ragasztó vagy epoxi, egyfajta ragasztó, amelyet optikai szálak száloptikai rendszerek különböző alkatrészeihez való kötésére használnak. A száloptikai ragasztó néhány tulajdonsága:
- Alacsony zsugorodás: A száloptikai ragasztót úgy tervezték, hogy kötéskor nagyon alacsony zsugorodása legyen. Ez azért fontos, mert bármilyen zsugorodás feszültséget okozhat a szálon, és jelvesztéshez vagy károsodáshoz vezethet.
- Magas optikai tisztaság: A száloptikai ragasztót úgy alakították ki, hogy nagyon átlátszó legyen, így nem zavarja az optikai szálon keresztüli fényáteresztést.
- Magas hőmérséklettel szembeni ellenállás: A száloptikai ragasztót úgy tervezték, hogy ellenálljon a magas hőmérsékletnek anélkül, hogy a kötési szilárdság romlása vagy elvesztése lenne.
- Alacsony viszkozitás: A száloptikai ragasztónak jellemzően alacsony a sűrűsége, így könnyű vele dolgozni, és kis, pontos mennyiségben is felvihető.
- Alacsony gázkibocsátás: A száloptikai ragasztót úgy alakították ki, hogy alacsony gázkibocsátású legyen, ami nagyon kevés gázt bocsát ki a kötés során. Ez azért fontos, mert minden felszabaduló gáz szennyezheti az optikai rendszert.
- Jó tapadás: A száloptikai ragasztó úgy van kialakítva, hogy erős tapadást biztosítson az optikai szálhoz és a többi komponenshez, amelyhez ragasztja.
Keményedési idő
A kikeményedési idő azt az időt jelenti, amely alatt egy anyag, például bevonat, ragasztóanyag vagy beton teljesen megszárad vagy megkeményedik. A kikeményedési idő az anyag típusától, a környezet hőmérsékletétől és páratartalmától, valamint egyéb tényezőktől függően változhat.
Például a vízbázisú festéknek néhány órába telhet, amíg tapintásra megszárad, de több napig is eltarthat, amíg teljesen kikeményedik, és eléri maximális keménységét és tartósságát. A kétkomponensű epoxi ragasztó kötési ideje rövidebb lehet, általában néhány óra, de több napra is szükség lehet a teljes szilárdság eléréséhez.
A gyártó által javasolt kikeményedési idő betartása elengedhetetlen ahhoz, hogy az anyag elérje maximális szilárdságát és teljesítményét. A keményedési folyamat siettetése gyengébb és kevésbé tartós végterméket eredményezhet.
Szakítószilárdság
A szakítószilárdság azt a maximális húzófeszültséget jelenti, amelyet egy anyag képes ellenállni, mielőtt eltörne vagy eltörne, és méri az anyag széthúzásnak vagy nyújtásnak ellenálló képességét.
A szakítószilárdságot általában az egységnyi területre eső erő egységeiben fejezik ki, például font per négyzethüvelyk (psi) vagy newton per négyzetméter (N/m^2). Például az acél szakítószilárdsága 400 és 2,500 megapascal (MPa) vagy 58,000 363,000 és XNUMX XNUMX psi között lehet, az acél típusától és a gyártási folyamattól függően.
A szakítószilárdság alapvető tulajdonsága a nyújtó- vagy húzóerőknek kitett alkalmazásokban, például az építőiparban, a tervezésben és a gyártásban használt anyagok esetében. Általában szakítógéppel tesztelik, amely addig távolítja el az anyagmintát, amíg az el nem törik, miközben méri az erőt és a deformációt.
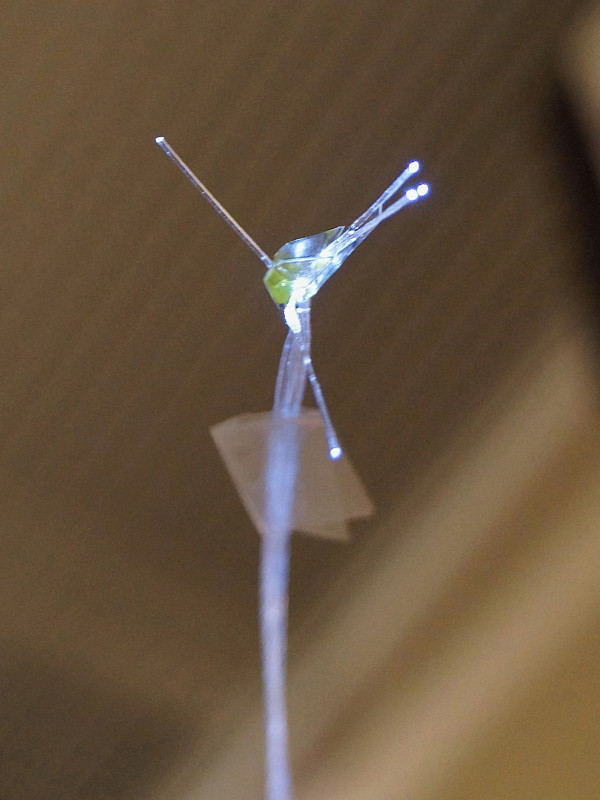
Nyírószilárdság
A nyírószilárdság az anyag azon képessége, hogy ellenálljon a felületével párhuzamosan vagy érintőlegesen kifejtett erőknek, amelyek az anyag egy részének elcsúszását vagy nyírását okozzák egy másik helyzethez képest. A fémek, polimerek és kompozitok fontos mechanikai tulajdonsága.
A nyírószilárdságot általában nyírópróbával mérik, amely során az anyag felületére merőleges erőt alkalmaznak, miközben az anyag felső és alsó felülete párhuzamosan elmozdul. A maximális nyírófeszültség, amelyet az anyag ellenállhat, mielőtt meghibásodik, a nyírószilárdsága.
A mérnöki és szerkezeti tervezésben az anyag nyírószilárdsága kritikus paraméter, amely meghatározza, hogy a szerkezet mekkora maximális terhelést tud ellenállni, mielőtt a nyíróerők miatt meghibásodik. Ugyancsak elengedhetetlen az anyagok viselkedésének megértése különböző terhelési körülmények között, valamint az ilyen erőknek ellenálló anyagok és szerkezetek tervezésénél.
Héj ereje
A leválási szilárdság az az erő, amely ahhoz szükséges, hogy két ragasztott anyagot egy felülettől, például ragasztószalagtól leválasztson. Egy anyag tapadási szilárdságát vagy két anyag közötti kötést méri. A leválási szilárdságot általában font per hüvelykben (lb/in) vagy newton per méterben (N/m) fejezik ki. Egy anyag vagy kötés leválási szilárdságát különböző tényezők befolyásolhatják, mint például a használt ragasztó típusa, a ragasztandó anyagok felület-előkészítése, a ragasztás alatti hőmérséklet és páratartalom, valamint a leválási szilárdság mérésére alkalmazott vizsgálati módszer.
Hőállóság
A hőmérsékletállóság egy anyag vagy anyag azon képességére utal, hogy megőrzi fizikai és kémiai tulajdonságait különböző hőmérsékleti viszonyok között. Más anyagok további hőálló képességgel rendelkeznek.
Például egyes anyagok, például fémek, kerámiák és bizonyos műanyagok ellenállnak a magas hőmérsékletnek, míg mások, mint például a szerves anyagok és egyes műanyagok, magas hőmérsékleten lebomlanak vagy megolvadhatnak.
A különböző alkalmazásokhoz szükséges anyagok kiválasztásakor figyelembe kell venni a hőmérsékletállóságot. Például a repülőgépiparban a motoralkatrészekhez használt anyagoknak rendkívül magas hőmérsékletnek kell ellenállniuk. Ezzel szemben az élelmiszeriparban a csomagoláshoz használt anyagoknak különféle hőmérsékleti tartományokat kell kibírniuk anélkül, hogy káros anyagok lebomlanak vagy kimosódnának.
A hőmérsékletállóságot befolyásoló tényezők közé tartozik az anyag összetétele és szerkezete, valamint a fűtési vagy hűtési sebesség. Általánosságban elmondható, hogy magasabb hőmérsékleti ellenállást magasabb olvadáspontú anyagok használatával vagy hőstabilizáló adalékok hozzáadásával érnek el.
Kémiai ellenállás
A vegyszerállóság egy anyag vagy anyag azon képességére utal, hogy ellenáll a különféle vegyi anyagoknak anélkül, hogy jelentős romláson, lebomláson vagy egyéb káros hatásokon menne keresztül. A vegyszerállóság számos ipari anyag, például bevonatok, műanyagok és fémek, valamint az egyéni védőfelszerelések (PPE), például kesztyűk és légzőkészülékek alapvető tulajdonsága.
A vegyszerállóságot számos tényező befolyásolhatja, beleértve a vegyszer típusát és koncentrációját, a hőmérsékleti és nyomásviszonyokat, valamint az expozíció időtartamát. Egyes anyagok ellenállhatnak bizonyos vegyi anyagoknak, másoknak viszont nem, és a különböző anyagok eltérő ellenállási szinttel rendelkeznek ugyanazzal a vegyszerrel szemben.
Egy anyag vegyszerállósága különféle módszerekkel végzett teszteléssel határozható meg, például merítési vizsgálattal, gőznek való kitettséggel vagy pontszerű vizsgálattal. E tesztek eredményei segítenek meghatározni az anyag alkalmasságát egy adott alkalmazáshoz, és útmutatást adnak a megfelelő PPE kiválasztásához a veszélyes vegyi anyagokat kezelő munkavállalók számára.
Index egyezés
Az indexillesztés olyan technika, amely csökkenti a reflexiós veszteségeket két különböző törésmutatójú anyag határfelületén. Amikor a fény egy magasabb törésmutatójú szövetről egy alacsonyabb törésmutatójú anyagra halad át, a fény egy része visszaverődik a felületen, ami energiaveszteséghez és a jelerősség csökkenéséhez vezet. Az indexillesztés során egy vékony anyagréteget helyeznek el közepes törésmutatóval a két anyag közé, hogy minimalizálják a törésmutató különbségét és csökkentsék a visszaverődési veszteségeket.
Az indexillesztést gyakran használják optikai alkalmazásokban, például lencsék, prizmák és szálak esetében, hogy javítsák az átviteli hatékonyságot és csökkentsék a nem kívánt visszaverődést. Az index-illesztő anyag kiválasztása az adott alkalmazástól és az illesztett anyagok törésmutatóitól függ. Néhány gyakori index-egyeztető anyag az optikai ragasztók, folyadékok, gélek és filmek.
A száloptikai ragasztó alkalmazásai
A száloptikai ragasztó egy speciális ragasztó, amelyet optikai kábelek gyártására és telepítésére használnak. Íme a száloptikai ragasztó néhány alkalmazása:
- Kábelgyártás: A száloptikai ragasztót a száloptikai kábelek gyártása során használják a száloptikai alkatrészek, például a szálak, puffercsövek és szilárdsági elemek összekapcsolására.
- Kábelszerelés: Száloptikai ragasztóval száloptikás kábeleket szerelnek fel, hogy a vezetéket rögzítsék a rögzítő hardverekhez, az illesztési burkolatokhoz és egyéb berendezésekhez.
- Üvegszálas lezárás: A száloptikai ragasztót az optikai kábelek lezárására használják, hogy a szálat a csatlakozókhoz, érvéghüvelyekhez vagy más lezáró eszközökhöz rögzítsék.
- Összeillesztés: A száloptikai ragasztót a száloptikai kábelek összeillesztésére használják, hogy folyamatos optikai utat hozzon létre két szál között.
- Karbantartás és javítás: A száloptikai ragasztót karbantartási és javítási tevékenységek során használják az optikai kábelek laza vagy sérült alkatrészeinek rögzítésére.
Száloptikai kábelek gyártása
Íme az optikai kábelgyártás fő lépései:
- Gyártás végrehajtása: Az első lépés egy üveg előforma gyártása, amely egy hengeres üvegrúd, amely az optikai kábel alapjául szolgál. Az előforma úgy készül, hogy nagy tisztaságú szilícium-dioxid-üveget olvasztnak egy speciális kemencében, majd óvatosan lehűtik szilárd, átlátszó rudat.
- Szálhúzás: Miután az előformát elkészítették, egy szálhúzó toronyba helyezik. A torony felmelegíti az előformát, és vékony, rugalmas optikai szálat húz. Ezt a folyamatot többször megismételjük, hogy több szálat hozzanak létre, amelyeket összecsavarva egy kábelt alkotnak.
- Bevonat: A szálszálakat ezután polimer anyagból készült védőréteggel vonják be, hogy megakadályozzák a beépítés és a használat során bekövetkező sérüléseket. A bevonóanyagot precíziós eljárással hordják fel, hogy biztosítsák, hogy egyenletesen oszlik el a szál körül.
- Kábelezés: Miután a szálszálakat bevonták, összecsavarják őket, hogy kábelt alkossanak. A vonal további védőanyagokkal, például kevlárral van megerősítve az erősség és a tartósság érdekében.
- Tesztelés: Végül a kész kábelt tesztelik, hogy megbizonyosodjon arról, hogy megfelel-e az adatátvitelhez szükséges előírásoknak. Ez magában foglalja a vonal tesztelését olyan paraméterek tekintetében, mint a csillapítás, a sávszélesség és a jel-zaj arány.
Száloptikai csatlakozó szerelvény
A száloptikai csatlakozó összeszerelése magában foglalja az optikai kábel lezárását egy csatlakozóval, amely összeköti más eszközökkel vagy kábelekkel. A folyamat általában a következő lépéseket tartalmazza:
- A kábel előkészítése: Az első lépés az optikai kábel előkészítése a külső burkolat és a védőbevonat eltávolításával, hogy szabaddá tegye a csupasz szálat.
- A szál hasítása: A következő lépés a szál hasítása, hogy tiszta, lapos homlokfelületet kapjunk.
- A szál tisztítása: A menet meghasadt végét ezután megmossák, hogy eltávolítsák a port, olajat vagy egyéb szennyeződéseket, amelyek befolyásolhatják a csatlakozás minőségét.
- A szál behelyezése: A szálat ezután behelyezik a csatlakozótestbe, és egy krimphüvellyel vagy más mechanizmussal rögzítik.
- A végfelület polírozása: Az utolsó lépés a szál végfelületének polírozása a sima felület elérése érdekében, amely minimális veszteséggel engedi át a fényt.
A teljes folyamatot körültekintően kell végrehajtani, hogy a csatlakozó megbízható, alacsony veszteségű kapcsolatot biztosítson.
Fúziós illesztés
A fúziós összeillesztés két optikai szálat egyesít a végük megolvasztásával és elektromos ív segítségével történő olvasztásával. Az így létrejövő illesztés vagy toldás állandó, és kis jelveszteséggel rendelkezik, így ideális nagy teljesítményű optikai hálózatokhoz.
A fúziós illesztési folyamat több lépésből áll. Először a szálakat úgy készítik elő, hogy eltávolítják a védőbevonatukat és megtisztítják őket, hogy tiszta felületet biztosítsanak a fúzióhoz. A szálakat ezután egy speciális, kamerákkal és mikroszkóppal felszerelt fúziós splicer gép segítségével igazítják a tökéletes igazítás érdekében. A beállítás után egy elektromos ív összeolvasztja a menetvégeket, és állandó kötést képez.
A fúziós illesztést előnyben részesítik más illesztési módszerekkel, például a mechanikus illesztéssel szemben, mivel jobb jelveszteséget és megbízhatósági teljesítményt nyújt. Általában hosszú távú és nagy sebességű száloptikai hálózatokban, valamint olyan alkalmazásokban használják, mint például száloptikai érzékelők és orvosi berendezések.
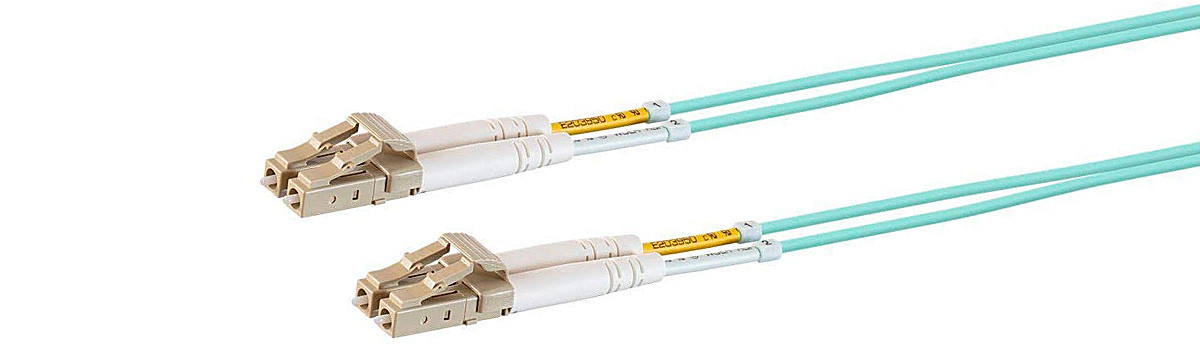
Száloptikai lezárás
A száloptikai lezárás az optikai kábelek végeinek lezárását vagy összekapcsolását jelenti különböző eszközökkel vagy alkatrészekkel, például adókkal, vevőkkel, kapcsolókkal és patch panelekkel.
A lezárási folyamat magában foglalja a védőbevonatot vagy köpeny óvatos eltávolítását az optikai kábel végéről, a szabadon lévő szál tisztítását és polírozását, majd egy csatlakozó vagy adapter rögzítését a menet végére. Ez a csatlakozó ezután csatlakoztatható a megfelelő eszközhöz vagy alkatrészhez.
Különféle típusú száloptikai csatlakozók állnak rendelkezésre, beleértve az SC, LC, ST és MTRJ csatlakozókat, amelyek mindegyikének megvannak az előnyei és hátrányai. A megfelelő lezárás kulcsfontosságú az optikai kábeleken keresztül történő jó minőségű adatátvitel biztosításához, mivel a kapcsolat bármilyen tökéletlensége vagy eltolódása jelvesztést, csillapítást vagy egyéb teljesítményproblémákat okozhat.
Száloptikai vizsgálat
A száloptikai vizsgálat az optikai kábel, a csatlakozó vagy a toldás fizikai állapotát vizsgálja. Ez az ellenőrzés kritikus fontosságú a száloptikai rendszer optimális működésének biztosításában, mivel a szál bármilyen sérülése vagy tökéletlensége negatívan befolyásolhatja a jelátvitelt és a minőséget.
A száloptikai vizsgálatnak számos módszere létezik, beleértve a szemrevételezést, a mikroszkópos vizsgálatot és a videós vizsgálatot. A szemrevételezés során szabad szemmel kell megnézni a csatlakozót vagy a kábel végfelületét, hogy nincs-e rajta látható hiba vagy sérülés. A mikroszkópos vizsgálat speciális mikroszkópot használ a csatlakozó vagy a kábel végfelületének nagyítására, és a gyengeségek vagy sérülések részletesebb azonosítására. A videóellenőrzés során speciális kamerát használnak a csatlakozó vagy a kábel végfelületének kép- vagy videófelvételére, valamint a felvételek elemzésére a hibák vagy sérülések szempontjából.
A száloptikás ellenőrzés számos alkalmazáshoz elengedhetetlen, beleértve a távközlést, az orvosi képalkotást, valamint a katonai és védelmi rendszereket. Az optikai rendszerek rendszeres ellenőrzése és karbantartása biztosíthatja az optimális teljesítményt és megelőzheti a költséges leállásokat.
Bevált gyakorlatok a száloptikai ragasztó használatához
Íme néhány bevált gyakorlat a száloptikai ragasztó használatához:
- Válassza ki a megfelelő ragasztót: Különféle típusú száloptikai ragasztók állnak rendelkezésre a piacon, és mindegyik típust egy adott alkalmazáshoz tervezték. Egyes kötések jobban megfelelnek az alacsony hőmérsékletű környezetnek, míg mások ellenállnak a magas hőmérsékletnek. A megfelelő ragasztó kiválasztása az adott alkalmazási követelmények alapján elengedhetetlen.
- Kövesse a gyártó utasításait: Mindig kövesse a gyártó utasításait, amikor száloptikai ragasztót használ. Ez magában foglalja a keverési arányokat, a kikeményedési időket és az alkalmazási módokat. Az utasítások be nem tartása rossz kötést eredményezhet, és veszélyeztetheti a száloptikai alkatrészek teljesítményét.
- Tisztítsa meg a felületeket: A ragasztandó felületeknek tisztának, szennyeződéstől, portól vagy olajtól mentesnek kell lenniük. A felületek tisztításához használjon szöszmentes kendőt és a gyártó által javasolt tisztítóoldatot. A felületeken maradó maradékok befolyásolhatják a kötés szilárdságát.
- Használja a megfelelő mennyiségű ragasztót: Használja a gyártó által megadott ajánlott mennyiségű ragasztót. A túl sok ragasztó a felesleg kinyomódását okozhatja, és az alkalmazás rendetlenségét eredményezheti. Túl kevés ragasztó használata gyenge kötést eredményezhet.
- Egyenletes nyomás alkalmazása: Egyenletes nyomást gyakoroljon a ragasztott felületekre, hogy biztosítsa a megfelelő érintkezést a felületek és a ragasztó között. Ez megtehető speciális szerszámmal vagy kézi nyomás alkalmazásával.
- Hagyja meg a megfelelő kötési időt: Hagyja a ragasztót az ajánlott ideig kikeményedni, mielőtt az optikai komponenst használná. Az idő előtti használat veszélyeztetheti a kötés szilárdságát és befolyásolhatja a száloptikai alkatrész teljesítményét.
- Megfelelő tárolás: A száloptikai ragasztót hűvös és száraz helyen, közvetlen napfénytől és hőforrásoktól távol tárolja. Kövesse a gyártó utasításait a tárolási feltételekre és az eltarthatóságra vonatkozóan.
Felület előkészítése
A felület előkészítéséhez sokféle technika és eszköz használható, a felület típusától és a kívánt eredménytől függően. Néhány szabványos módszer a következőket tartalmazza:
- Tisztítás: A felületet alaposan meg kell tisztítani a szennyeződések, zsírok, olajok és egyéb szennyeződések eltávolítása érdekében. Ezt megteheti oldószerek, tisztítószerek vagy más tisztítószerek segítségével.
- Csiszolás: A csiszolás durva felületek simítására és a régi bevonatok vagy festékek eltávolítására szolgál. Ezt csiszolópapírral vagy csiszológéppel lehet megtenni.
- Köszörülés: A köszörülés eltávolítja a magas foltokat vagy durva területeket a felületről. Ezt csiszolókoronggal vagy gyémánttárcsával lehet megtenni.
- A szemcseszórás eltávolítja a felületről a rozsdát, festéket és egyéb makacs szennyeződéseket. Ezt meg lehet tenni homokfúvással vagy más szemcseszórási technikával.
- Alapozás: Ha a felület tiszta és sima, egy alapozó segíti a bevonat vagy festék megfelelő tapadását. Az alkalmazott alapozó típusa a felület típusától és az alkalmazott bevonattól vagy festéktől függ.
A felületre felvitt bármilyen bevonat vagy festék hosszú élettartamához elengedhetetlen a megfelelő felület-előkészítés. Ha a felületet nem megfelelően készítik elő, előfordulhat, hogy a bevonat vagy a szín nem tapad megfelelően, ami hámlást, repedést vagy egyéb problémákat okozhat.
Keverési arány
A keverési arány, más néven tömeg- vagy nedvességkeverési arány, a levegő és vízgőz keverékében lévő vízgőz mennyiségét méri. Ez a keverékben lévő száraz levegő egységnyi vízgőz tömege.
A keverési arányt jellemzően vízgőz gramm/kg száraz levegőben (g/kg) vagy tömegrész per milliórészben (ppm) fejezik ki. Értékes mérték a meteorológiában és a légkörtudományban, mivel az adiabatikus folyamatokban konzervált mennyiség, ami azt jelenti, hogy állandó marad, amikor a levegő emelkedik vagy süllyed a légkörben.
A keverési arány a légkör nedvességtartalmának egyéb mérőszámaihoz kapcsolódik, mint például a relatív páratartalom és a harmatpont-hőmérséklet, de közvetlenebb mérést ad a levegőben lévő vízgőz tényleges mennyiségéről.
Adagolási technika
Íme néhány alapvető lépés a gyógyszeradagolás során:
- A recept ellenőrzése – A gyógyszerész vagy gyógyszertári technikus ellenőrzi a receptet, hogy megbizonyosodjon arról, hogy a gyógyszer, az adagolás és az utasítások pontosak és megfelelőek.
- A gyógyszer címkézése – A gyógyszerész vagy gyógyszerésztechnikus felcímkézi a gyógyszertartályt a beteg nevével, a gyógyszer nevével, az adagolással és a használati utasítással.
- A gyógyszermérés – A gyógyszerész vagy gyógyszerész technikus kalibrált mérőeszközzel, például fecskendővel, mérőhengerrel vagy elektronikus mérleggel pontosan méri a gyógyszert.
- A gyógyszer áthelyezése – A gyógyszer átkerül a páciens tartályába, például palackba, buborékcsomagolásba vagy inhalátorba.
- Minőségellenőrzés – A gyógyszer kiadása előtt a gyógyszerész vagy a gyógyszertári technikus ellenőrzi, hogy a gyógyszert pontosan kimérték és továbbították.
- Tanácsadás – A gyógyszerész vagy gyógyszerész technikus tanácsot ad a páciensnek a gyógyszer helyes használatára vonatkozóan, és válaszol a beteg esetleges kérdéseire.
Elengedhetetlen az adagolási technikák pontos követése a gyógyszerelési hibák elkerülése és a betegek biztonsága érdekében. A gyógyszerészek és gyógyszerésztechnikusok ki vannak képezve a szabványos eljárások követésére, hogy biztosítsák a gyógyszer biztonságos és pontos adagolását.
Kikeményedési feltételek
Bármilyen egészségügyi probléma esetén elengedhetetlen, hogy szakképzett egészségügyi szakemberrel forduljon orvoshoz. Megfelelő diagnózist tudnak felállítani, és megfelelő kezelést javasolnak az Ön igényei és kórtörténete alapján.
Az egészségügyi állapotok néhány gyakori kezelése magában foglalhatja a gyógyszeres kezelést, a műtétet, a fizikoterápiát, a tanácsadást és az életmódbeli változtatásokat, például az étrendet és a testmozgást. A kezelés hatékonysága az adott állapottól és az egyéni körülményektől függően változhat, ezért elengedhetetlen az egészségügyi szolgáltató útmutatásainak betartása.
Tárolás és kezelés
A tárolás és kezelés néhány közös alapelve:
- Hőmérséklet-szabályozás: Sok termékhez meghatározott hőmérsékleti tartományok szükségesek az optimális tároláshoz és kezeléshez, például a hűtést a romlandó élelmiszerek esetében, vagy a kiváló, száraz körülményeket a gyógyszerek esetében.
- Páratartalom szabályozása: A nedvességre érzékeny termékek, például az elektronikai vagy papírtermékek különleges csomagolást vagy tárolási feltételeket igényelhetnek a károsodás elkerülése érdekében.
- Fény elleni védelem: Egyes termékekre, például gyógyszerekre vagy bizonyos vegyszerekre hatással lehet a napfény, ezért átlátszatlan vagy fényzáró csomagolásra lehet szükség.
- Megfelelő csomagolás: A termékeket megfelelő anyagokban kell tárolni, hogy elkerüljük a kezelés és szállítás során bekövetkező sérüléseket vagy szennyeződéseket.
- Tiszta és rendezett tárolási területek: A tárolóterületeknek tisztának és rendezettnek kell lenniük, hogy megakadályozzák a keresztszennyeződést, és szükség esetén biztosítsák a könnyű hozzáférést a termékhez.
- Megfelelő eljárások: A termékeket óvatosan kell kezelni a sérülések vagy szennyeződések elkerülése érdekében, és minden szükséges biztonsági eljárást be kell tartani.
Ezen elvek követésével a vállalkozások és magánszemélyek hozzájárulhatnak termékeik biztonságos és hatékony tárolásához és kezeléséhez.
Egészségügyi és biztonsági óvintézkedések
Néhány mindennapi egészségügyi és biztonsági óvintézkedés:
- Személyi védőfelszerelés (PPE): Ide tartoznak a kesztyűk, maszkok és védőszemüvegek, amelyek segíthetnek megvédeni az egyéneket a káros anyagoknak vagy fertőző betegségeknek való kitettségtől.
- Megfelelő szellőzés: A megfelelő szellőzés elengedhetetlen a káros gázok, gőzök vagy részecskék felhalmozódásának megakadályozásához a zárt terekben.
- A tűzbiztonság olyan intézkedéseket foglal magában, mint a füstérzékelők, tűzoltó készülékek és a vészkijárati tervek a tüzek megelőzésére és az azokra való reagálásra.
- Ergonómia: A megfelelő ergonómia segíthet megelőzni a munkahelyi sérüléseket, például húzódásokat, ficamokat és ismétlődő mozgásos sérüléseket.
- Veszélyekkel kapcsolatos kommunikáció: A munkáltatóknak és más szervezeteknek közölniük kell a potenciális veszélyeket az alkalmazottakkal és a kitettekkel.
- Veszélyes anyagok megfelelő kezelése és ártalmatlanítása: Ez magában foglalja a vegyszerek, akkumulátorok és egyéb veszélyes anyagok kezelésére, tárolására és ártalmatlanítására vonatkozó megfelelő protokollok követését.
- Higiénia és higiénia: A felületek és létesítmények rendszeres tisztítása és fertőtlenítése segíthet megelőzni a fertőző betegségek terjedését.
- A biztonságos vezetési gyakorlatok közé tartozik a közlekedési szabályok betartása és a zavaró tényezők elkerülése vezetés közben a balesetek megelőzése érdekében.
Ezen és más egészségügyi és biztonsági óvintézkedések végrehajtásával az egyének és szervezetek segíthetnek megelőzni a sérüléseket, betegségeket és egyéb károkat önmagukban és másokban.
Gyakori problémák a száloptikai ragasztóval
A száloptikai ragasztó az optikai szálakat más alkatrészekhez, például csatlakozókhoz, érvéghüvelyekhez és illesztőtálcákhoz köti. A száloptikai ragasztóval azonban több gyakori probléma is előfordulhat:
- Gyenge kötési szilárdság: A száloptikai ragasztókkal kapcsolatos egyik leggyakoribb probléma a rossz kötési szilárdság, ami száltörést vagy jelvesztést okozhat. Ez akkor fordulhat elő, ha a ragasztót megfelelően össze kell keverni, vagy ha a felületet meg kell tisztítani és előkészíteni kell a ragasztó felhordása előtt.
- Kötési idő: A száloptikai ragasztó megkötéséhez meghatározott idő szükséges, ami a ragasztó típusától és a környezeti feltételektől függően változhat. Ha a ragasztó nem kap elég időt a kikeményedéshez, előfordulhat, hogy nem tapad megfelelően, vagy gyenge kötést eredményezhet.
- Szennyeződés: Még kis mennyiségű szennyeződés is befolyásolhatja a száloptikai ragasztó teljesítményét. A por, olaj és egyéb szennyeződések megzavarhatják a kötést, ami gyenge kötést vagy jelveszteséget eredményezhet.
- Eltarthatósági idő: A száloptikai ragasztó korlátozott eltarthatósági idővel rendelkezik, és idővel lejárhat vagy kevésbé hatékony. Használat előtt feltétlenül ellenőrizze a kötés lejárati idejét és a tárolási feltételeket.
- Kompatibilitás: A különböző típusú száloptikai ragasztókat speciális alkalmazásokhoz tervezték, és előfordulhat, hogy nem kompatibilisek bizonyos anyagokkal vagy alkatrészekkel. Lényeges, hogy az adott alkalmazáshoz megfelelő ragasztót válasszunk, és biztosítsuk a kompatibilitást az összes érintett komponenssel.
- Adagolás: A száloptikai ragasztó megfelelő adagolása kritikus fontosságú a szilárd kötés eléréséhez. A nem megfelelő adagolás, például a túl sok vagy túl kevés ragasztó felvitele gyenge kötést vagy jelveszteséget eredményezhet.
- Biztonság: A száloptikai ragasztó veszélyes lehet, ha nem megfelelően kezelik. A ragasztóval végzett munka során minden biztonsági előírás betartása és védőfelszerelés viselése elengedhetetlen.
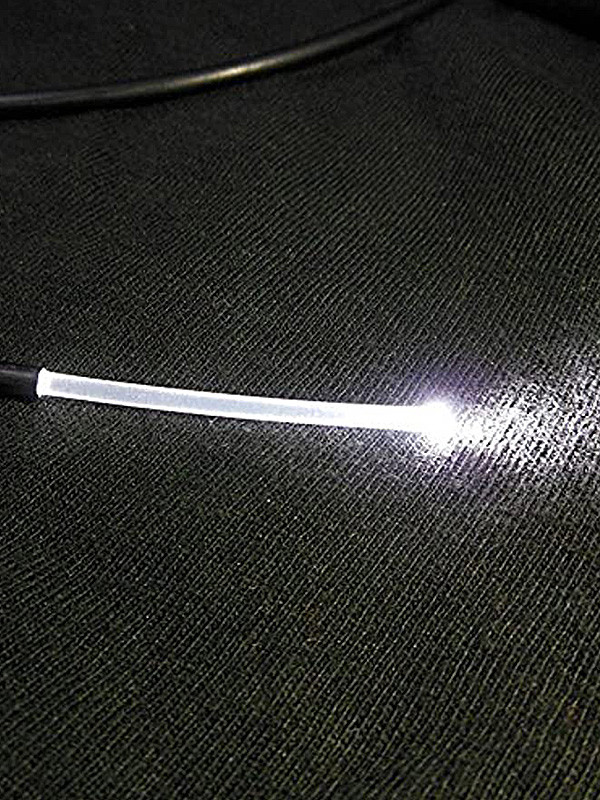
Hibaelhárítási tippek
Íme néhány általános hibaelhárítási tipp, amelyek különféle helyzetekben alkalmazhatók:
- Kezdje az alapokkal: Győződjön meg arról, hogy minden megfelelően van csatlakoztatva, be van kapcsolva és csatlakoztatva.
- Újraindítás: Néha az eszköz vagy a szoftver újraindítása megoldhatja a problémát.
- Frissítések keresése: Ellenőrizze, hogy elérhető-e frissítés az eszközhöz vagy szoftverhez, és szükség esetén telepítse azokat.
- Hibaüzenetek keresése: Keressen minden olyan hibaüzenetet vagy kódot, amely a problémára utalhat.
- Próbálkozzon más megközelítéssel: Ha az egyik módszer nem működik, próbáljon ki egy másik megközelítést vagy módszert, hogy megtudja, megoldja-e a problémát.
- Ellenőrizd az ütközéseket: Győződjön meg arról, hogy nincsenek ütközések más eszközökkel vagy szoftverekkel, amelyek okozhatják a problémát.
- Kérjen segítséget: Ha továbbra is segítségre van szüksége a probléma megoldásához, kérjen segítséget az ügyfélszolgálattól, online fórumokon vagy szakembertől.
- Dokumentálja a problémát: Kövesse nyomon a probléma elhárítása érdekében tett lépéseket, valamint az esetleges hibaüzeneteket vagy kódokat, hogy könnyebben közölje a problémát másokkal, akik segíthetnek.
A száloptikai ragasztó hatása a távközlési infrastruktúrára
A száloptikai ragasztó a távközlési infrastruktúra elengedhetetlen eleme, és jelentősen befolyásolja annak teljesítményét és megbízhatóságát. A ragasztó az optikai kábeleket a csatlakozókhoz köti, biztonságos és stabil kapcsolatot biztosítva, amely ellenáll a zord környezeti feltételeknek.
A száloptikai ragasztó egyik legjelentősebb előnye, hogy alacsony veszteségű kapcsolatot biztosít az optikai kábel és a csatlakozó között. Ez kulcsfontosságú a távközlési infrastruktúrában, ahol már kis veszteségek is jelentősen befolyásolhatják a jel minőségét és az adatátviteli sebességet.
A száloptikai ragasztó másik lényeges előnye, hogy biztonságos és stabil kapcsolatot tud biztosítani, amely számos környezeti tényezőnek ellenáll. Ez magában foglalja a szélsőséges hőmérsékleteket, a nedvességet, a vibrációt és a mechanikai igénybevételt. A ragasztó segít megelőzni a kábelek sérülését és a jelvesztést, biztosítva a távközlési infrastruktúra megbízható és hatékony működését.
A teljesítmény előnyei mellett a száloptikai ragasztó könnyen felhordható, és különféle alkalmazásokban használható. Ez ideális választássá teszi a távközlési infrastruktúrához, ahol az optikai kábelektől kezdve a csatlakozókig és az illesztőtálcákig mindenben használják.
Összességében az optikai ragasztónak a távközlési infrastruktúrára gyakorolt hatása jelentős. Hozzájárul a megbízható és hatékony adatátvitel biztosításához, még kihívást jelentő környezeti feltételek mellett is, és a modern távközlési hálózatok elengedhetetlen eleme.
A száloptikai ragasztó hatása az IoT-re és az intelligens eszközökre
A száloptikai ragasztó jelentősen befolyásolhatja az IoT-t (Internet of Things) és a fényes eszközöket. A száloptikai ragasztó a száloptikai csatlakozókat a szálakhoz köti, így robusztus és megbízható kapcsolatot biztosít az eszközök között. Íme néhány módszer, amellyel a száloptikai ragasztó hatással lehet az IoT-re és az intelligens eszközökre:
- Továbbfejlesztett csatlakoztathatóság: A száloptikai ragasztó javíthatja az eszközök közötti kapcsolatot. Robusztus és megbízható kapcsolatot biztosít, ami elengedhetetlen az IoT és a fényes eszközök zavartalan működéséhez. A száloptikai ragasztó jelentősen csökkenti az adatvesztés vagy a lassú adatátvitel kockázatát.
- Gyorsabb adatátvitel: A száloptikai ragasztó segíthet gyorsabb adatátviteli sebesség elérésében. Az optikai kábelek ugyanis igen nagy sebességgel tudnak adatot továbbítani, a száloptikai ragasztó által biztosított megbízható kapcsolattal pedig megszakítások és késések nélkül továbbíthatók az adatok.
- Megnövelt megbízhatóság: Az IoT-nek és az intelligens eszközöknek megbízhatónak kell lenniük a megfelelő működéshez. A száloptikai ragasztó javíthatja az eszközök megbízhatóságát azáltal, hogy biztosítja az eszközök közötti kapcsolat biztonságos és stabilitását. Ez csökkentheti az állásidőt és a karbantartási költségeket.
- Fokozott biztonság: Az optikai kábelek magas szintű védelemükről ismertek. Nehéz feltörni vagy elfogni őket, és a száloptikai ragasztó segíti az eszközök közötti kapcsolatot. Ez különösen fontos lehet az érzékeny információkat tartalmazó IoT és intelligens eszközök esetében.
Száloptikai ragasztó száloptikai érzékelő alkalmazásokhoz
Íme néhány szempont, amelyeket figyelembe kell venni, amikor száloptikai érzékelő alkalmazásokhoz ragasztót választunk:
- Törésmutató: A ragasztó törésmutatójának hasonlónak kell lennie a száloptikai anyagéhoz. Ez minimálisra csökkenti a fényveszteséget a ragasztószálas felületen, ami befolyásolhatja a mérési pontosságot.
- Hőmérséklet-stabilitás: A ragasztónak képesnek kell lennie arra, hogy megőrizze mechanikai és optikai tulajdonságait széles hőmérséklet-tartományban. Ez különösen fontos olyan alkalmazásoknál, amelyek magas hőmérsékletű környezetet vagy hőmérséklet-ciklusokat foglalnak magukban.
- Vegyszerállóság: A ragasztónak ellenállnia kell azoknak a vegyszereknek és környezeti tényezőknek, amelyeknek ki lehet téve az érzékelés során. Ez azért fontos, hogy megelőzzük a ragasztóanyag idővel történő leromlását, ami befolyásolhatja a mérés pontosságát.
- Kötési idő: A ragasztó kötési idejének meg kell felelnie az alkalmazásnak. Néha gyorsabb keményedési időre lehet szükség az állásidő minimalizálása vagy a feldolgozási idő csökkentése érdekében.
- Könnyű használat: A ragasztónak könnyen felvihetőnek és kezelhetőnek kell lennie. Ez azért fontos, hogy minimalizáljuk a hibákat a ragasztó felhordási folyamata során.
Néhány példa a száloptikai érzékelő alkalmazásokhoz általánosan használt ragasztókra: az UV-sugárzással keményedő ragasztók, az epoxi alapú ragasztók és a cianoakrilát alapú ragasztók. Végső soron az adott száloptikai érzékelő alkalmazáshoz a legjobb ragasztó kiválasztása az adott alkalmazás speciális követelményeitől függ.
A következetesség jelentősége a száloptikai ragasztógyártásban
A konzisztencia több okból is kulcsfontosságú a száloptikai ragasztógyártásban:
- Minőségbiztosítás: A száloptikai ragasztó kritikus az optikai kábelek gyártásában. A gyártási folyamat bármely következetlensége a végtermék minőségének változásához vezethet, ami veszélyeztetheti az optikai kábelek teljesítményét.
- Teljesítmény: A száloptikai ragasztó biztosítja, hogy a kábelben lévő optikai szálak biztonságosan a helyükön maradjanak. Az inkonzisztens ragasztó alkalmazása a szálak elmozdulását vagy meglazulását eredményezheti, ami befolyásolja a kábel általános teljesítményét.
- Költség: Az inkonzisztens gyártási folyamatok anyagpazarláshoz vezethetnek, ami a gyártási költségek növekedéséhez vezethet. Az inkonzisztens ragasztófelhordás a termék meghibásodásához is vezethet, ami szavatossági igényeket és visszaküldést eredményezhet, ami tovább növeli a költségeket.
- Hírnév: A következetesség elengedhetetlen egy jó hírű márka felépítéséhez az optikai iparban. Azok a vállalatok, amelyek folyamatosan jó minőségű termékeket állítanak elő, valószínűleg hűséges vásárlói bázist építenek ki, míg a következetlen gyártóknak segítségre lehet szükségük a piaci részesedés megszerzéséhez.
A száloptikai ragasztók jövője: feltörekvő technológiák és alkalmazások
A száloptikai ragasztótechnológia az elmúlt években jelentős fejlődésen ment keresztül, és továbbra is az optikai szálas kábelek gyártásának alapvető eleme. A száloptikai ragasztók feltörekvő technológiái és alkalmazásai a következők:
- Nanorészecskékkel javított ragasztó: A száloptikai ragasztók területén az egyik feltörekvő technológia a nanorészecskék használata a ragasztó tulajdonságainak javítására. Nanorészecskék, például szén nanocsövek és grafén adhatók a ragasztóhoz a mechanikai szilárdság, a hőstabilitás és az elektromos vezetőképesség javítása érdekében.
- UV-sugárzással keményedő ragasztó: A száloptikai ragasztók területén egy másik feltörekvő technológia az UV-sugárzással keményedő ragasztók használata. Ez a fajta ragasztó UV-fénnyel gyorsan megköthető, jelentősen csökkentve az optikai kábelek gyártási idejét.
- Alacsony hőmérsékletű ragasztó: Az alacsony hőmérsékletű ragasztó egy másik feltörekvő technológia, amely forradalmasíthatja az optikai kábelek gyártását. Ez a fajta ragasztó akár -40°C hőmérsékleten is kikeményedhet, csökkentve az energiafogyasztást és javítva a gyártási folyamat hatékonyságát.
- Ragasztó zord környezetekhez: Egyre nagyobb az igény olyan száloptikai kábelekre, amelyek ellenállnak a zord környezeteknek, például szélsőséges hőmérsékleteknek, páratartalomnak és vegyszereknek való kitettségnek. A ragasztógyártók olyan új készítményeket fejlesztenek ki, amelyek ellenállnak ezeknek a zord körülményeknek, például a magas hőmérsékletű epoxi- és szilikonragasztókat.
- Optikai alkatrészek 3D nyomtatása: A 3D nyomtatási technológia forradalmasíthatja a száloptikai alkatrészek gyártását. A ragasztógyártók olyan új készítményeket fejlesztenek ki, amelyek a 3D nyomtatásban használhatók testreszabott optikai komponensek gyors és hatékony létrehozásához.
- Orvosi alkalmazások: A száloptikai ragasztó az orvostudományban is új alkalmazásokat talál. Például optikai szálakat csatlakoztathat orvosi eszközökhöz, például endoszkópokhoz és katéterekhez.