FPC ragasztó ragasztó
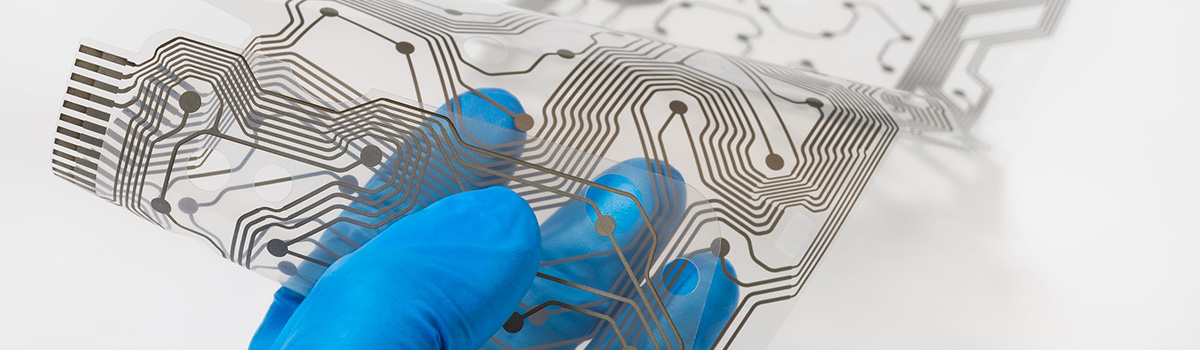
Az FPC kötőragasztó kulcsfontosságú eleme a rugalmas nyomtatott áramköri (FPC) kártyák gyártásának és összeszerelésének, amelyeket széles körben használnak különféle elektronikus eszközökben, beleértve az okostelefonokat, hordható eszközöket és autóipari alkalmazásokat. Ezek a ragasztók erős ragasztási képességet, elektromos szigetelést és védelmet nyújtanak a környezeti tényezőkkel szemben, miközben biztosítják az FPC táblák rugalmasságát és tartósságát. A rugalmas és megbízható elektronikus eszközök iránti kereslet növekedésével a nagy teljesítményű és megbízható FPC kötőragasztók jelentősége egyre kritikusabbá vált. Ez a cikk az FPC kötőragasztók különféle típusait, alkalmazásait és kihívásait vizsgálja, kiemelve kulcsfontosságú szerepüket az elektronikus eszközök rugalmasságának és megbízhatóságának lehetővé tételében.
Az FPC ragasztó ragasztó típusai
Az FPC (Flexible Printed Circuit) kötőragasztók nélkülözhetetlenek a különféle elektronikus eszközök rugalmas áramköreinek összeszereléséhez és csatlakoztatásához. Ezek a ragasztók megbízható és tartós kötést biztosítanak a rugalmas áramkör és a célfelület között. Az FPC kötőragasztók többféle típusa is elérhető a piacon, mindegyik egyedi jellemzőkkel és alkalmazási területtel. Ez a válasz áttekintést nyújt az FPC kötőragasztók néhány általános típusáról.
- Akril alapú ragasztók: Az akril alapú kötőragasztók népszerűek, mivel kiválóan tapadnak különféle aljzatokhoz, beleértve a fémeket, műanyagokat és üvegeket. Rugalmasságot, hőstabilitást, valamint nedvességgel és vegyszerekkel szembeni ellenállást kínálnak. Az akril ragasztók különféle formákban, például szalagok, fóliák és folyékony ragasztók formájában állnak rendelkezésre, így sokoldalúak a különböző FPC ragasztási alkalmazásokhoz.
- Epoxi alapú ragasztók: Az epoxi alapú ragasztók nagy kötési szilárdságot biztosítanak, és széles körben használják FPC ragasztáshoz. Kiváló tapadást biztosítanak különféle aljzatokhoz és jó elektromos szigetelési tulajdonságokat biztosítanak. Az epoxi ragasztók különböző összetételekben állnak rendelkezésre, beleértve az egy- és kétkomponensű rendszereket, amelyek többféle ragasztási folyamathoz és kikeményedési feltételekhez nyújtanak lehetőséget.
- Szilikon alapú ragasztók: A szilikon alapú ragasztók rugalmasságukról, magas hőmérsékleti ellenállásukról és kiváló elektromos szigetelési tulajdonságaikról ismertek. Ellenállnak a szélsőséges hőmérsékleteknek és jó nedvességállóságot biztosítanak, így alkalmasak az igényes környezetben való használatra. A szilikon ragasztókat gyakran használják kritikus hőkezeléssel és megbízhatósággal rendelkező alkalmazásokban.
- Nyomásérzékeny ragasztók (PSA): A PSA-k olyan ragasztóanyagok, amelyek nyomás hatására azonnali kötést képeznek. Kiküszöbölik az egyéb kikeményítési folyamatok szükségességét, így kényelmessé teszik őket az FPC ragasztási alkalmazásokhoz. A PSA-k jó tapadást biztosítanak a különböző aljzatokhoz, és könnyen eltávolíthatók anélkül, hogy maradványokat hagynának, így ideálisak ideiglenes ragasztáshoz vagy újrafeldolgozáshoz.
- UV-sugárzással keményedő ragasztók: Az UV-sugárzással keményedő ragasztók folyékony ragasztók, amelyek ultraibolya fény hatására gyorsan kikeményednek. Gyors kötési időt, nagy tapadási szilárdságot és kiváló tapadást biztosítanak a különböző aljzatokhoz. Az UV-sugárzással keményedő ragasztókat általában FPC ragasztási alkalmazásokban használják, ahol gyors összeszerelés és fokozott termelékenység szükséges.
- Vezetőképes ragasztók: A vezetőképes ragasztókat kifejezetten a ragasztásra és az elektromos vezetőképességre tervezték. Vezetőképes töltőanyagokat, például ezüstöt vagy szenet tartalmaznak, amelyek lehetővé teszik, hogy a ragasztó elektromos kapcsolatot hozzon létre az áramköri alkatrészek között. A vezetőképes ragasztókat széles körben használják az FPC-kötéseknél olyan alkalmazásokhoz, mint az EMI-árnyékolás, a földelés és az elektromos összeköttetések.
- Hővezető ragasztók: A hővezető ragasztókat úgy tervezték, hogy mind a tapadást, mind a hatékony hőátadási tulajdonságokat biztosítsák. FPC ragasztási alkalmazásokban használják, ahol a hőkezelés kritikus fontosságú, például rugalmas áramkörök hűtőbordákhoz vagy más hővezető hordozókhoz való ragasztásakor.
Fontos megjegyezni, hogy az FPC kötőragasztó kiválasztása számos tényezőtől függ, beleértve a speciális alkalmazási követelményeket, az aljzat anyagait, a környezeti feltételeket és a gyártási folyamatokat. A ragasztógyártókkal vagy -beszállítókkal konzultálva részletesebb információkat és útmutatást nyújthat az adott FPC ragasztási alkalmazáshoz legmegfelelőbb ragasztó kiválasztásához.
Akril ragasztók: a leggyakoribb választás
Az akril ragasztók sokoldalúságuk, erős ragasztóképességük és egyszerű használatuk miatt népszerűek a különböző iparágakban. Ezek a ragasztók akril polimerekből állnak, amelyek kiváló tapadást biztosítanak az aljzatok széles körében. Itt megvizsgáljuk, miért a legáltalánosabb választás az akril ragasztók 450 szón belül.
Az akril ragasztók egyik kritikus előnye, hogy képesek különböző anyagokat egymáshoz kötni. Az akril ragasztók tartós és megbízható kötéseket hozhatnak létre, legyen szó műanyagok, fémek, kerámiák, fa vagy akár üveg ragasztásáról. Ez a sokoldalúság alkalmassá teszi őket különféle autóipari, építőipari, elektronikai és jelzőtáblás alkalmazásokhoz.
Az akril ragasztók kiváló kötési szilárdságot is nyújtanak, és erős kötéseket képezhetnek, amelyek ellenállnak a nagy igénybevételnek, a hőmérséklet-ingadozásoknak és a környezeti feltételeknek. Ez ideálissá teszi őket olyan alkalmazásokhoz, ahol a tartósság és a hosszú távú teljesítmény döntő fontosságú.
Az akril ragasztók népszerűségének másik oka a gyors kötési idő. A többi ragasztótípushoz képest az akril ragasztók viszonylag rövid kötési idővel rendelkeznek, ami gyorsabb gyártási ciklust tesz lehetővé. Gyakran percek alatt elérik a kezelhetőséget, csökkentve az összeszerelési időt és növelve a termelékenységet.
Ezenkívül az akril ragasztók nedvességnek, vegyszereknek és UV-sugárzásnak ellenálló tulajdonságairól ismertek. Kiváló vízállósággal rendelkeznek, és nedves környezetben is megőrzik tapadó tulajdonságaikat. Ez a tulajdonság alkalmassá teszi őket kültéri alkalmazásokhoz és olyan környezetekhez, ahol zord körülményeknek való kitettség várható.
Az akril ragasztók kiváló hőstabilitást is biztosítanak. Széles hőmérsékleti tartományban ellenállnak, az extrém hidegtől a nagy melegig, anélkül, hogy rontják a kötési szilárdságukat. Ez a hőellenállás alkalmassá teszi azokat az alkalmazásokhoz, ahol gyakori a hőmérséklet-ingadozás, például az autóiparban és az elektronikai iparban.
Az akril ragasztók fizikai tulajdonságaikon túlmenően könnyen kezelhetők és felhordhatók. Különböző formákban állnak rendelkezésre, beleértve a folyadékokat, pasztákat, fóliákat és szalagokat, amelyek rugalmasságot biztosítanak az alkalmazási módszerekben. Alkalmazhatók automatizált adagolórendszerekkel vagy manuálisan, az alkalmazás speciális követelményeitől függően.
Ezenkívül az akril ragasztók általában szagtalanok és alacsony illékony szerves vegyület (VOC) tartalommal rendelkeznek. Ez biztonságosabbá teszi őket, mint az oldószer alapú ragasztók, amelyek erős szagot bocsáthatnak ki vagy káros vegyszereket tartalmazhatnak.
Szilikon ragasztók: Kiváló környezeti ellenállás
A szilikon ragasztók a ragasztók egy osztálya, amelyek kiváló környezeti ellenállásukról ismertek. Különböző alkalmazásokban kivételes teljesítményt és tartósságot kínálnak, így rendkívül keresettek az autóiparban, az elektronikában, a repülőgépiparban, az építőiparban és az orvosi iparban.
A szilikon ragasztók egyik kritikus előnye, hogy képesek ellenállni a szélsőséges hőmérsékleteknek. Ellenállnak a magas és alacsony hőmérsékletnek anélkül, hogy elveszítenék tapadó tulajdonságaikat vagy törékennyé válnának. Ez alkalmassá teszi őket olyan alkalmazásokhoz, ahol gyakori a hőmérséklet-ingadozás, például autómotorokban vagy elektronikus berendezésekben.
A szilikon ragasztók kiválóan ellenállnak a nedvességnek és a víznek is. Ellentétben sok más ragasztótípussal, akkor is megőrzik szilárdságát és integritását, ha víznek vagy nedves környezetnek vannak kitéve. Ez a tulajdonság döntő fontosságú a vízállóságot igénylő alkalmazásokban, mint például a tömítések tömítése, a víz alatti alkatrészek ragasztása vagy az elektronikus áramkörök nedvesség által okozott károktól való védelme.
Ezenkívül a szilikon ragasztók kivételesen ellenállnak az UV sugárzásnak és az időjárás viszontagságainak. Kibírják a napfénynek, esőnek, hónak és egyéb környezeti tényezőknek való hosszan tartó kitettséget anélkül, hogy rontanának vagy elveszítenék ragasztó tulajdonságaikat. Emiatt ideálisak kültéri alkalmazásokhoz, például kültéri táblák lezárására, napelemek ragasztására vagy kültéri elektronikai eszközök védelmére.
A vegyszerállóság egy másik terület, ahol a szilikon ragasztók kiválóak. Ellenállnak különféle vegyszereknek, beleértve az oldószereket, olajokat, üzemanyagokat és savakat. Ez az ellenállás jelentős az olyan iparágakban, mint az autóipar és a repülőgépipar, ahol naponta több vegyszernek van kitéve. A szilikon ragasztók még agresszív vegyszerekben is megőrzik sértetlenségüket és tapadásukat, így biztosítják a hosszú távú teljesítményt és megbízhatóságot.
A szilikon ragasztók környezeti ellenállásuk mellett kiváló elektromos szigetelő tulajdonságokkal is rendelkeznek. Nagy a dielektromos szilárdságuk és szigetelést biztosítanak az elektromos áram ellen. Ez ideálissá teszi őket elektronikus alkatrészek ragasztására és tömítésére, ahol az elektromos leválasztás és védelem kulcsfontosságú.
A szilikon ragasztók különféle formákban állnak rendelkezésre, beleértve az egy- vagy kétrészes rendszereket, valamint különféle kötőmechanizmusokat, például hőkezelést, nedvességkötést vagy UV-kötést. Ez a sokoldalúság az alkalmazások és a ragasztási követelmények széles skáláját teszi lehetővé.
Érdemes megjegyezni, hogy bár a szilikon ragasztók kivételes környezeti ellenállást biztosítanak, előfordulhat, hogy nem olyan magas a kezdeti kötési szilárdságuk, mint néhány más ragasztótípus. Ezt azonban rugalmasságukkal, tartósságukkal és zord körülmények között nyújtott hosszú távú teljesítményükkel kompenzálják.
UV-re keményedő ragasztók: Gyors és precíz ragasztás
Az UV-re keményedő ragasztók, más néven ultraibolya sugárzással keményedő ragasztók, a gyors és pontos kötési képességük miatt jelentős népszerűségre tettek szert a különböző iparágakban. Ezek a ragasztók számos előnnyel rendelkeznek a hagyományos ragasztórendszerekkel szemben, így előnyben részesítik őket a gyors és megbízható tapadást igénylő alkalmazásokhoz.
Az UV-re keményedő ragasztók speciális fotoiniciátorokkal készülnek, amelyek ultraibolya fény hatására elindítják a folyamatot. A keményedési reakció szinte azonnal lezajlik, lehetővé téve a gyors kötés kialakulását. A hagyományos ragasztókkal ellentétben, amelyek hő- vagy kémiai reakciókat alkalmaznak a térhálósodáshoz, az UV-sugárzással keményedő ragasztók gyakorlatilag azonnali kötést biztosítanak, értékes gyártási időt takarítanak meg és növelik a hatékonyságot.
Az UV-re keményedő ragasztók egyik kritikus előnye a precíz ragasztási képességük. A kötési reakció erősen szabályozott és lokalizált, így a ragasztó csak a kívánt területen köt ki. Ez lehetővé teszi az alkatrészek pontos pozícionálását és igazítását, még összetett összeállítások esetén is. A gyártók szigorú tűréshatárokat érhetnek el, és magas termékminőséget tarthatnak fenn UV-sugárzással keményedő ragasztókkal.
Az UV-ragasztók gyors kötési ideje különösen előnyös azokban az iparágakban, ahol a gyártás gyors átfutása döntő fontosságú. Például az elektronikai gyártásban az UV-re keményedő ragasztók lehetővé teszik az alkatrészek gyors ragasztását, csökkentve az összeszerelési időt és növelve a termelékenységet. Hasonlóképpen, az orvostechnikai eszközök iparában az UV-ragasztók gyors és megbízható ragasztást biztosítanak különböző anyagokhoz, lehetővé téve bonyolult orvosi eszközök gyors összeszerelését.
Az UV-re keményedő ragasztók kiváló kötési szilárdságot és tartósságot biztosítanak. Kikeményedést követően ezek a ragasztók erős kötéseket képeznek, amelyek ellenállnak a különböző környezeti feltételeknek, beleértve a hőmérséklet-ingadozásokat, a nedvességet és a vegyszereket. A kötések nagy ellenállást mutatnak az idő múlásával szembeni sárgulással vagy leromlással szemben, így biztosítják a hosszú távú teljesítményt és megbízhatóságot.
Az UV-re keményedő ragasztók sokoldalúak, és különféle felületekkel kompatibilisek, beleértve a műanyagokat, fémeket, üvegeket és kerámiákat. Különböző anyagokat tudnak egymáshoz ragasztani, kibővítve az alkalmazások körét, ahol felhasználhatók. Az UV-re keményedő ragasztók az autóipari műanyag alkatrészek kattanásától az elektronikai eszközök összeszereléséig megbízható megoldást kínálnak a különféle ragasztási igényekre.
Ezenkívül az UV-re keményedő ragasztók oldószermentesek, így nincs szükség illékony szerves vegyületekre (VOC) és csökkentik a környezeti hatást. Egészségügyi és biztonsági előnyöket is kínálnak azáltal, hogy minimalizálják a veszélyes vegyi anyagoknak való kitettséget. Az oldószerek és az illékony szerves vegyületek hiánya tisztább és egészségesebb munkakörnyezethez járul hozzá a kezelők számára.
Epoxi ragasztók: nagy kötési szilárdság és vegyszerállóság
Az epoxi ragasztók nagy kötési szilárdságuk és kiváló vegyszerállósági tulajdonságaik miatt népszerűek a különböző iparágakban. Számos előnnyel rendelkeznek a többi ragasztóval szemben, így sokoldalúak és megbízhatóak több alkalmazáshoz.
Az epoxi ragasztók egyik kritikus előnye a kivételes kötési szilárdság. Erőteljes kötéseket hoznak létre, amelyek megfelelő alkalmazás esetén jelentős igénybevételnek és terhelésnek is ellenállnak, így alkalmasak olyan alkalmazásokhoz, amelyek tartós és tartós kötést igényelnek. Az epoxi ragasztók különféle anyagok, köztük fémek, műanyagok, kerámiák, üvegek és kompozitok ragasztására alkalmasak, megbízható illesztési megoldást biztosítva a különböző iparágakban.
A nagy tapadási szilárdságukon kívül az epoxi ragasztók kiváló vegyszerállóságot mutatnak. Ellenállnak különféle vegyszereknek, beleértve az oldószereket, savakat, lúgokat, olajokat és üzemanyagokat. Ez a vegyi hatásokkal szembeni ellenállás biztosítja, hogy a ragasztó stabil marad, és megőrzi kötési szilárdságát még zord környezetben is. Következésképpen az epoxi ragasztókat általánosan használják az autóiparban, a repülőgépiparban, az elektronikai iparban és a vegyipari feldolgozóiparban, ahol a vegyi anyagoknak való kitettség aggodalomra ad okot.
Az epoxi ragasztók vegyszerállóságát egyedi molekulaszerkezetüknek tulajdonítják. Az epoxi ragasztók gyantából és keményítőből állnak, amelyek kémiai reakcióba lépve térhálós hálózatot alkotnak. Ez a térhálós szerkezet biztosítja a ragasztó szilárdságát és vegyszerállóságát. Az epoxi ragasztók kikeményedési folyamata beállítható a vegyszerállóság különböző szintjei eléréséhez, lehetővé téve az egyedi alkalmazási követelmények alapján történő testreszabást.
Ezenkívül az epoxi ragasztók kiváló hőállóságot biztosítanak, ami számos iparágban egy másik döntő tényező. Megőrizhetik kötési szilárdságukat és integritásukat magas és alacsony hőmérsékleten is, így alkalmasak az extrém hőmérséklet-ingadozásoknak kitett alkalmazásokhoz. Ez a tulajdonság alapvető fontosságú az olyan iparágakban, mint a repülőgépgyártás és az autóipar, ahol az alkatrészek jelentős hőmérséklet-ingadozásokat tapasztalhatnak.
Az epoxi ragasztók másik előnye az alkalmazási módok sokoldalúsága. Különféle technikák alkalmazhatók, beleértve a kézi adagolást, a fecskendős adagolást, a permetezést és az automatizált adagolórendszereket. Az alkalmazási módszerek rugalmassága hatékony és precíz ragasztást tesz lehetővé különböző gyártási környezetekben.
Fontos megjegyezni, hogy a megfelelő felület-előkészítés és a ragasztó felhordási technikák elengedhetetlenek az epoxi ragasztókkal történő optimális kötési szilárdság és vegyszerállóság eléréséhez. A felületeknek tisztának, száraznak és szennyeződésmentesnek kell lenniük a maximális tapadás biztosítása érdekében. Ezenkívül a ragasztót a gyártó utasításai szerint kell keverni, figyelembe véve a gyanta és a keményítő megfelelő arányát és a megfelelő kikeményedési feltételeket.
Összefoglalva, az epoxi ragasztók nagy kötési szilárdságot és kiváló vegyszerállóságot kínálnak, így ideális választás a különféle alkalmazásokhoz. Különböző anyagok ragasztására, kemény vegyszerekkel szembeni ellenálló képességük, valamint szélsőséges hőmérsékleti körülmények között is jól teljesítő képességük nélkülözhetetlenné teszi őket az autóiparban, a repülőgépiparban, az elektronikai iparban és a vegyi feldolgozóiparban. Megfelelő felület-előkészítési és felhordási technikákkal az epoxi ragasztók tartós és megbízható kötéseket biztosíthatnak, hozzájárulva az összeszerelt alkatrészek általános teljesítményéhez és hosszú élettartamához.
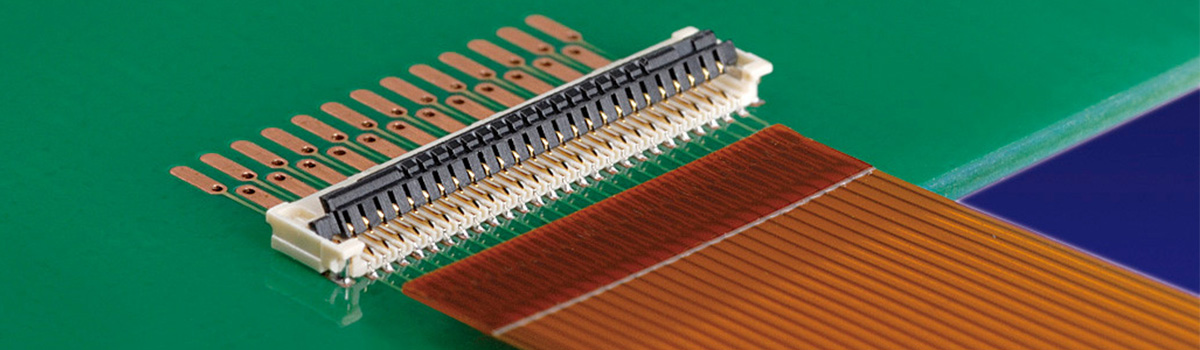
Vezetőképes ragasztók: lehetővé teszik az elektromos csatlakozást
A vezetőképes ragasztók döntő szerepet játszanak az elektromos csatlakoztatás lehetővé tételében különböző alkalmazásokban. Ezek az innovatív anyagok hatékony alternatívát jelentenek a hagyományos forrasztási vagy mechanikus rögzítési módokhoz képest, mivel kiváló elektromos vezetőképességet, könnyű használhatóságot és sokoldalúságot kínálnak. Ez a cikk a vezetőképes ragasztók legfontosabb jellemzőit és alkalmazásait vizsgálja meg.
A vezetőképes ragasztókat vezetőképes töltőanyagok, például ezüst, réz vagy szén és polimer kötőanyag kombinációjával állítják elő. A vezetőképes töltőanyagok elősegítik az elektromos áram áramlását, míg a kötőanyag biztosítja a tapadást a különböző aljzatokhoz. Ez az egyedülálló összetétel lehetővé teszi, hogy a vezetőképes ragasztók megbízható elektromos csatlakozásokat biztosítsanak még kihívásokkal teli környezetben is.
A vezetőképes ragasztók egyik elsődleges előnye, hogy sokféle anyaggal kompatibilisek. Fémeket, kerámiákat, üvegeket, műanyagokat és még rugalmas aljzatokat is képesek ragasztani, így különféle iparágakban használhatók. Különböző anyagok összekapcsolása különösen előnyös az elektronikai iparban, ahol különböző hőtágulási együtthatójú alkatrészeket kell összeilleszteni.
A vezetőképes ragasztók kiváló elektromos vezetőképességet biztosítanak, összehasonlítva a hagyományos forrasztással. Ez a tulajdonság lehetővé teszi számukra, hogy hatékonyan cseréljék ki a forrasztási kötéseket speciális alkalmazásokban. Ezenkívül a vezetőképes ragasztók jobban ellenállnak a hőciklusnak, a mechanikai igénybevételnek és a vibrációnak, mint a forrasztott csatlakozások. Ezek a tulajdonságok ideálissá teszik őket a gyakori hőmérséklet-ingadozásokkal vagy automatikus mozgásokkal járó alkalmazásokhoz.
A vezetőképes ragasztók másik jelentős előnye a könnyű felhordás. Általában kényelmes formában, például fecskendőben, vagy filmek vagy szalagok formájában kaphatók. Ez precíz és ellenőrzött adagolást tesz lehetővé, így alkalmasak automatizált és kézi összeszerelési folyamatokra. A speciális felszerelést és szakértelmet igénylő forrasztással ellentétben a vezetőképes ragasztók minimális képzéssel könnyen felhordhatók.
A vezetőképes ragasztókat különféle iparágakban alkalmazzák. Az elektronikai szektorban az alkatrészek rögzítésére, stancolásra, huzalkötésre, valamint a forrasztás alternatívájaként használják a nyomtatott áramköri lapok (PCB) összeszerelésében. Rugalmas elektronika gyártásánál is alkalmazzák, ahol a hagyományos forrasztási módszerek nem kivitelezhetők a hordozók rugalmassága miatt.
Az autóiparban vezetőképes ragasztókat használnak érzékelők, antennák és világítási rendszerek ragasztására. Kiváló tapadást biztosítanak az autóipari alkalmazásokban használt anyagokhoz, beleértve a műanyagokat és a kompozitokat. Ezen túlmenően, mivel képesek ellenállni a szélsőséges környezeti feltételeknek, például a hőmérséklet-ingadozásoknak, a páratartalomnak és a vegyi anyagoknak való kitettségnek, ideális választássá teszik őket az autóelektronika számára.
A vezetőképes ragasztók az orvostudományban is jelentős szerepet játszanak. Orvosi eszközöket, például érzékelőket, elektródákat és beültethető eszközöket állítanak össze. A vezetőképes ragasztók biokompatibilis változatai biztosítják, hogy biztonságosan érintkezzenek az emberi szövetekkel.
Alacsony gázkibocsátású ragasztók: kritikus fontosságú űripari alkalmazásokhoz
Az alacsony gázkibocsátású ragasztók kritikus szerepet játszanak az űralkalmazásokban, ahol az anyagoknak ellenállniuk kell az űrkörnyezet szélsőséges feltételeinek. A gázkibocsátás illékony vegyületek felszabadulását jelenti az anyagokból, amikor vákuumnak vagy magas hőmérsékletnek vannak kitéve. Az űrben ezek az illékony vegyületek jelentős kockázatot jelenthetnek az érzékeny berendezések és műszerek működőképességére és megbízhatóságára nézve.
A tér vákuumában a kigázosodott anyagok lecsapódhatnak a közeli felületekre, például optikai lencsékre vagy érzékelőkre, ami szennyeződést és a teljesítmény romlását okozza. A szennyeződés ronthatja a mérések pontosságát, ronthatja a jel minőségét, és akár a kritikus alkatrészek meghibásodásához is vezethet. Ezenkívül a kondenzált kigázosodott anyagok idővel felhalmozódhatnak, és olyan réteget képezhetnek, amely képes elnyelni vagy szórni a fényt, és hatással lehet az optikai rendszerekre és a képalkotó eszközökre.
Az alacsony gázkibocsátású ragasztókat kifejezetten az illékony vegyületek felszabadulásának minimalizálására tervezték. Alacsony gőznyomásra tervezték, ami azt jelenti, hogy kevesebb gázt és gőzt bocsátanak ki, ha vákuumnak vannak kitéve. Ez a tulajdonság segít megelőzni az érzékeny felületek és alkatrészek szennyeződését és leépülését.
Az űrhajók és a műholdak alacsony gázkibocsátású ragasztókra támaszkodnak különféle alkalmazásokhoz. Az egyik fontos felhasználási terület az elektronikus alkatrészek ragasztása és tokozása. Ezek a ragasztók szilárd és megbízható kötést biztosítanak a különböző anyagok között, miközben minimálisra csökkentik a szennyeződés és a gázkibocsátással kapcsolatos problémák kockázatát. Biztosítják az alkatrészek szerkezeti integritását és elektromos csatlakoztatását, lehetővé téve számukra, hogy ellenálljanak az indításkor és az űrben történő működés során tapasztalt rezgéseknek és ütéseknek.
Az alacsony gázkibocsátású ragasztók az űrtávcsövekben, kamerákban és szenzorokban használt optikai rendszerekben is elengedhetetlenek. Az ezekben a rendszerekben használt ragasztóknak minimális hatást kell gyakorolniuk a lencsék, tükrök és detektorok tisztaságára és teljesítményére. Azáltal, hogy csökkentik a gázkibocsátást, ezek a ragasztók megőrzik optikai tulajdonságait, és megakadályozzák a szennyeződési rétegek kialakulását, amelyek ronthatják a képminőséget vagy megzavarhatják a pontos mérést.
Ezenkívül a hőkezelés kritikus szempont az űralkalmazásokban. Az alacsony gázkibocsátású ragasztók megragasztják a hűtőbordákat, a hőfelületi anyagokat és a hőelvezetésben részt vevő egyéb alkatrészeket. Ezek a ragasztók hatékony hőátadást biztosítanak, miközben minimálisra csökkentik a szennyeződés kockázatát, amely ronthatja a hőkezelési rendszerek teljesítményét.
Az űralkalmazások szigorú követelményeinek való megfelelés érdekében az alacsony gázkibocsátású ragasztók szigorú tesztelési és tanúsítási folyamatokon mennek keresztül. Az anyagokat hőciklusnak, vákuumnak vetik alá, és elemzésnek vetik alá a gázkibocsátási jellemzőik felmérésére. Azok a ragasztók, amelyek megfelelnek az olyan szervezetek által meghatározott szabványoknak, mint a NASA gázkibocsátási követelményei (mint például az ASTM E595), alkalmasnak tekinthetők űrmissziókra.
Hővezető ragasztók: hőkezelés az elektronikus eszközökben
A hővezető ragasztók döntő szerepet játszanak az elektronikus eszközök hőkezelésében. Mivel az elektronikus alkatrészek mérete folyamatosan csökken, és nagyobb teljesítménysűrűséggel működnek, a hatékony hőelvezetés egyre fontosabbá válik az optimális teljesítmény és megbízhatóság biztosításához. A hővezető ragasztók életképes megoldást kínálnak azáltal, hogy hatékonyan továbbítják a hőt a hőtermelő alkatrészekről a hűtőbordákra vagy más hőleadó mechanizmusokra. Ez a cikk megvizsgálja a hővezető ragasztók kritikus szempontjait és szerepüket az elektronikus eszközök hőkezelésében.
A hővezető ragasztók speciálisan összeállított anyagok, amelyek mind ragasztó tulajdonságokkal, mind magas hővezető képességgel rendelkeznek. Úgy tervezték, hogy erős kötéseket hozzanak létre a hőt termelő alkatrészek, például integrált áramkörök vagy tápegységek, valamint a hűtőbordák vagy más hűtőelemek között. Ezeknek az anyagoknak a tapadó jellege megbízható rögzítést, magas hővezető képességük pedig hatékony hőátadást tesz lehetővé.
A hővezető ragasztók egyik elsődleges előnye, hogy képesek kitölteni az illeszkedő felületek közötti kis hézagokat és egyenetlenségeket, ezáltal minimálisra csökkentik a hőellenállást. Ez a tulajdonság különösen előnyös nem sík felületű alkatrészek rögzítésekor, vagy ha mikroszkopikus légrésekkel kell foglalkozni, amelyek akadályozzák a hőáramlást. E hézagok kitöltésével a hővezető ragasztók bensőséges érintkezést hoznak létre a karakterek között, javítva a hőátadást és csökkentve a hőforrások kialakulásának kockázatát.
Az elektronikus eszközök hőkezelésének másik kritikus szempontja a hőmérséklet-ciklusnak és a mechanikai igénybevételeknek való ellenálló képesség. Az elektronikus eszközök működése során változó hőmérsékleti feltételeknek és mechanikai rezgéseknek vannak kitéve. A hővezető ragasztók úgy vannak kialakítva, hogy megőrizzék tapadási szilárdságukat és hőteljesítményüket széles hőmérséklet-tartományban, biztosítva a megbízható hőelvezetést még nehéz körülmények között is.
Ezenkívül a hővezető ragasztók elektromos szigetelő tulajdonságokkal rendelkeznek, megakadályozva az elektromos rövidzárlatokat az alkatrészek között. Ez a funkció kulcsfontosságú az olyan elektronikus eszközökben, ahol több darab sűrűn van összecsomagolva, és fennáll a véletlen érintkezés veszélye a vezető elemek között.
A hővezető ragasztók különféle módszerekkel alkalmazhatók, beleértve az adagolást, a szitanyomást vagy a film laminálást. Ezek a ragasztók különböző viszkozitásban és térhálósodási mechanizmusban állnak rendelkezésre, lehetővé téve a gyártási folyamat rugalmasságát. Egyes hővezető ragasztók szobahőmérsékleten keményednek, míg mások magasabb hőmérsékletet vagy UV-fényt igényelnek. A gyártók kiválaszthatják azt a kötést, amely a legjobban megfelel sajátos gyártási követelményeinek.
Lehúzható és tapadó ragasztók: Könnyen használható és felvihető
A lehúzható ragasztók forradalmasították a különböző, ragasztóanyagot igénylő projektek és feladatok megközelítését. Ezek a ragasztók hihetetlenül könnyen használhatók és felhordhatók, így népszerűek a szakemberek és a barkácsolás szerelmesei körében. Kényelmük és sokoldalúságuk révén a lehúzható és tapadó ragasztók számos alkalmazás számára kitűnő megoldássá váltak.
A lehúzható ragasztók egyik fő előnye az egyszerűségük. A hagyományos ragasztókkal ellentétben, amelyek gyakran keverést vagy speciális eszközöket igényelnek, a lehúzható és tapadó ragasztókat előre felhordják a hordozóanyagra, és a csomagolásból felhasználásra készen állnak. Ezáltal nincs szükség további felszerelésre vagy alapos előkészítésre, így időt és erőfeszítést takarít meg.
A lehúzható és tapadó ragasztók felhordási folyamata egyszerű és felhasználóbarát. Mindössze annyit kell tennie, hogy le kell húznia a hordozópapírt, hogy szabaddá tegye a ragasztós oldalt, és erősen rá kell nyomnia a kívánt felületre. A ragasztó gyorsan és biztonságosan tapad, azonnali tapadást biztosítva kapcsok és száradási idő nélkül. Ennek köszönhetően a lehúzható ragasztók ideálisak gyors javításokhoz, ideiglenes telepítésekhez vagy időérzékeny projektekhez.
A lehúzható ragasztók másik előnye a sokoldalúságuk. Különféle formákban állnak rendelkezésre, például szalagok, lapok vagy pontok formájában, hogy megfeleljenek a különböző alkalmazásoknak és anyagoknak. Legyen szó könnyű tárgyak rögzítéséről, dekorációk rögzítéséről vagy bizonyos nagy teherbírású tárgyakról, a lehúzható ragasztó megfelel a feladatnak. Jól tapadnak különféle felületekre, beleértve a fát, fémet, üveget, műanyagot és szövetet, rugalmasságot és kompatibilitást biztosítva a különböző anyagokkal.
A lehúzható és tapadó ragasztók tiszta felhordásukról is ismertek. A hagyományos ragasztókkal ellentétben, amelyek rendetlenek lehetnek és tisztítást igényelnek, a lehúzható és tapadó ragasztók nem hagynak maradékot, ha megfelelően alkalmazzák és eltávolítják. Ez különösen akkor előnyös, ha olyan finom vagy kész felületeken dolgozik, amelyeket meg akar óvni a sérülésektől.
Könnyű használhatóságuk mellett a lehúzható és tapadó ragasztók gyakran erős kötési képességet is mutatnak. A ragasztókat úgy tervezték, hogy megbízható és tartós kötést biztosítsanak, biztosítva, hogy a rögzített elemek biztonságosan a helyükön maradjanak. Az optimális eredmény elérése érdekében azonban elengedhetetlen a megfelelő típusú ragasztó kiválasztása a projekthez, és a gyártó útmutatásainak betartása.
Ragasztófóliák: a hatékonyság és a konzisztencia fokozása
A ragasztófóliák sokoldalú anyagok, amelyek különféle alkalmazásokat kínálnak a különböző iparágakban. Vékony rétegek ragadós anyagok, amelyek egy hátlapra, például papírra, műanyagra vagy szövetre vannak bevonva. Ezek a fóliák számos előnnyel járnak, növelve a hatékonyságot és a konzisztenciát a különböző folyamatokban. Ez a cikk megvizsgálja, hogyan javítják a ragasztófóliák a hatékonyságot és a konzisztenciát a különböző alkalmazásokban.
A ragasztófóliák egyik legfontosabb előnye a könnyű felhordás. A hagyományos ragasztókkal ellentétben, amelyek keverést vagy speciális felszerelést igényelhetnek, a ragasztófóliák használatra készek. Könnyedén vághatók a kívánt formára és méretre, így ideálisak a gyors és precíz alkalmazáshoz. Ez időt és erőforrást takarít meg a gyártási és összeszerelési folyamatokban, növelve az általános hatékonyságot.
Ezenkívül a ragasztófóliák egyenletes ragasztási teljesítményt biztosítanak. Egyenletes vastagságuk és szabályozott tapadási tulajdonságaik megbízható tapadást biztosítanak a különböző anyagok között. Legyen szó két felület összekapcsolásáról, laminálásról vagy alkatrészek rögzítéséről, a ragasztófóliák egyenletes kötési szilárdságot biztosítanak, minimálisra csökkentve a meghibásodás vagy az utómunkálatok kockázatát. Ez az összhang javítja a termék minőségét, csökkenti a hulladék mennyiségét és növeli a termelékenységet.
Az öntapadó fóliák egy másik módja a hatékonyság növelésének az automatizálási rendszerekkel való kompatibilitásuk. A különféle iparágakban az automatizálás növekvő tendenciája miatt a ragasztófóliákat úgy tervezték, hogy kompatibilisek legyenek a robotizált összeszerelési és csomagolási folyamatokkal. Könnyen integrálhatók automatizált gyártósorokba, ami nagy sebességű és precíz ragasztási műveleteket tesz lehetővé. Ez nemcsak a hatékonyságot javítja, hanem csökkenti a munkaerőköltségeket és az emberi hibákat is.
Ezenkívül a ragasztófóliák fokozott hatékonyságot kínálnak a tömítési és védelmi alkalmazásokban. Gátat biztosítanak a nedvesség, a por és a szennyeződések ellen, megakadályozva az érzékeny alkatrészek vagy termékek károsodását. Legyen szó elektronikus eszközök lezárásáról, élelmiszerek csomagolásáról vagy felületek korrózió elleni védelméről, a ragasztófóliák megbízható és egyenletes védelmet nyújtanak. Ez hozzájárul a termékek hosszú élettartamához és megbízhatóságához, csökkentve a gyakori karbantartás vagy csere szükségességét.
Ezenkívül a ragasztófóliák hatékony testreszabást és tervezési rugalmasságot tesznek lehetővé. Testreszabhatók a speciális követelményekhez, például a különböző kötési szilárdságokhoz, hőmérséklet-állósághoz vagy optikai tulajdonságokhoz. Ez lehetővé teszi a gyártók számára, hogy alkalmazási igényeik alapján optimalizálják a ragasztó tulajdonságait, biztosítva a legjobb teljesítményt és megbízhatóságot. Ezenkívül a ragasztófóliák könnyen nyomtathatók vagy díszíthetők, így márkaépítési lehetőségeket és esztétikai vonzerőt kínálnak.
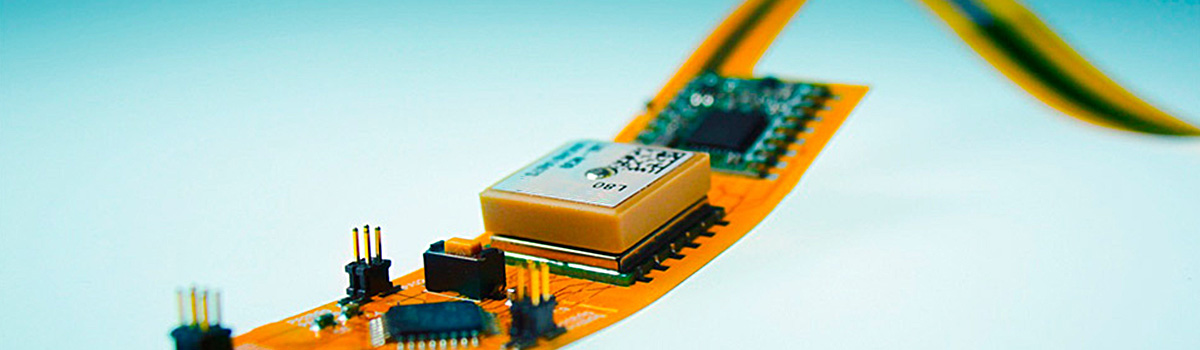
Hot Melt ragasztók: Gyors és tartós ragasztás
A melegen olvadó ragasztók (HMA) sokoldalú ragasztók, amelyek gyors és tartós ragasztási megoldásokat kínálnak különféle iparágakban és alkalmazásokban. Ezek a ragasztók vagy forró ragasztók hőre lágyuló anyagok, amelyeket folyékony halmazállapotúvá olvasztanak és olvadt formában alkalmaznak. Lehűléskor megszilárdulnak és erős kötést hoznak létre az aljzatok között. Íme közelebbről a forró olvadékragasztók jellemzői, előnyei és alkalmazásai.
A HMA-k egyik kritikus előnye a gyors kötési képességük. Ezek a ragasztók hevítés hatására gyorsan cseppfolyósodnak, ami hatékony és nagy sebességű felhordást tesz lehetővé. A többi ragasztótípustól eltérően szükségtelenné teszik az oldószer elpárolgását vagy a kémiai reakciókat. A forró olvadékragasztók gyors megszilárdulása rövidebb összeszerelési és gyártási időt eredményez, növelve a termelékenységet és költségmegtakarítást.
Ezenkívül a forró olvadékragasztók kivételes tartósságot biztosítanak a ragasztott illesztéseknél. Kiválóan ellenállnak a nedvességnek, a vegyszereknek és a hőmérséklet-ingadozásoknak. Ez a rugalmasság teszi őket alkalmassá olyan igényes környezetekhez és alkalmazásokhoz, amelyek hosszan tartó és megbízható kötést igényelnek. A HMA-k rugalmasságot és ütésállóságot is kínálnak, lehetővé téve számukra, hogy ellenálljanak a rezgéseknek és ütéseknek a kötés integritásának veszélyeztetése nélkül.
A HMA-kat különféle iparágakban alkalmazzák, beleértve a csomagolást, a fafeldolgozást, az autógyártást, az elektronikát, a textilgyártást és az építőiparban. A melegen olvadó ragasztókat széles körben használják tokok és kartondobozok lezárására, hamisításbiztos záróelemekre, valamint címkék és szalagok ragasztására. Biztonságos és illetéktelen tömítéseket biztosítanak, biztosítva a termék sértetlenségét és megakadályozva az ellopást.
A HMA-k famegmunkálási alkalmazásai közé tartozik az élszalagozás, a furnérozás és a laminálás. A forró olvadékragasztók gyorsan kötődő jellege megkönnyíti a hatékony összeszerelősor-folyamatokat. Erős kötéseket hoznak létre a fa illesztésekben, növelve a bútorok és szekrények szerkezeti integritását és hosszú élettartamát.
Az autógyártók forró olvadékragasztókat használnak a belső és külső kárpitok ragasztásához, kábelkötegekhez és tömítések tömítéséhez. Ezek a ragasztók tartóssága és hőállósága ideálissá teszik őket autóipari alkalmazásokhoz, ahol elengedhetetlen a szélsőséges körülmények közötti teljesítmény.
Az elektronikai összeszerelés és gyártás gyakran forró olvadékragasztókat használ az alkatrészek ragasztására, huzalragasztására és kapszulázására. Különböző anyagok, például műanyagok, fémek és üvegek ragasztására való képességük alkalmassá teszi őket különféle elektronikus alkalmazásokhoz.
A textilipar melegen olvadó ragasztóinak alkalmazásai közé tartozik a szövet laminálás, szegés és rátétragasztás. Pontos és tiszta ragasztást tesznek lehetővé varrás, varrás vagy egyéb mechanikus rögzítési módok nélkül.
Az építőiparban a HMA-kat padlóburkolatok beépítésére, burkolásra, szigetelésre és csempe ragasztására használják. Gyors kötési tulajdonságaik elősegítik a gyors építési folyamatokat és megbízható tapadást biztosítanak különböző építőanyagokban.
Nyomásérzékeny ragasztók: egyenletes tapadás biztosítása
A nyomásérzékeny ragasztók (PSA) sokoldalú anyagok, amelyeket különféle iparágakban használnak, az autóipartól és az elektronikától a csomagolásig és az orvosi eszközökig. Ezek a ragasztók olyan egyedülálló előnyöket kínálnak, mint az egyszerű felhordás, azonnali ragasztás és a felületek széles skálájához való tapadhatóság. A konzisztens tapadás biztosítása azonban kihívást jelenthet a PSA-kkal való munka során. Íme néhány kulcsfontosságú szempont a nyomásérzékeny ragasztókkal való megbízható és egyenletes tapadás eléréséhez.
- Felület-előkészítés: A megfelelő felület-előkészítés kulcsfontosságú a PSA-kkal való egyenletes tapadás eléréséhez. A felületeknek tisztának, száraznak és portól, olajtól, zsírtól és nedvességszennyeződéstől mentesnek kell lenniük. A felület megfelelő oldószerekkel vagy tisztítószerekkel történő megtisztítása, valamint olyan technikák alkalmazása, mint a kopás vagy plazmakezelés, javíthatja a tapadást azáltal, hogy növeli a felületi energiát és eltávolítja a ragasztás előtti potenciális akadályokat.
- Anyagkompatibilitás: Alapvető fontosságú annak biztosítása, hogy a PSA kompatibilis legyen a hordozóanyaggal. Egyes PSA-k gyenge tapadási vagy kompatibilitási problémákat mutathatnak bizonyos felületekkel. Mind a ragasztó, mind az aljzat kémiai összetételének és tulajdonságainak megismerése segíthet kiválasztani az adott alkalmazáshoz megfelelő ragasztót, biztosítva az egyenletes tapadást.
- Felhordási technika: Az alkalmazási technika jelentős szerepet játszik a konzisztens tapadás elérésében. Az alkalmazás során a nyomás, a hőmérséklet és a tartózkodási idő befolyásolhatja a kötés szilárdságát. Alapvetően fontos betartani a gyártó ajánlásait az alkalmazási paraméterekkel kapcsolatban, beleértve a megfelelő nyomást és a ragasztáshoz javasolt hőmérsékleti tartományt.
- Kikeményedési idő: A PSA-knak jellemzően bizonyos időre van szükségük ahhoz, hogy teljes tapadási szilárdságukat kifejlesszék. Ez a kikeményedési vagy „tartási” idő lehetővé teszi, hogy a ragasztó folyjon, és erős kötéseket hozzon létre az aljzattal. Elengedhetetlen, hogy elegendő kikeményedési időt biztosítsunk, mielőtt a ragasztott szerelvényt feszültségnek vagy terhelésnek tennénk ki. A folyamat siettetése gyengébb tapadást vagy akár a ragasztás meghibásodását is eredményezheti.
- Környezeti tényezők: A környezeti feltételek befolyásolhatják a PSA-k teljesítményét. Az olyan tényezők, mint a hőmérséklet, a páratartalom és a vegyszereknek vagy UV-sugárzásnak való kitettség befolyásolhatják a ragasztó tulajdonságait és tapadási teljesítményét. Ha megértjük, hogy a ragasztó milyen speciális környezeti feltételeknek lesz kitéve, és az ezekkel a tényezőkkel szembeni ellenálló képességgel rendelkező ragasztót választja ki, ez elősegítheti a folyamatos tapadást az idő múlásával.
- Tesztelés és minőség-ellenőrzés: A rendszeres tesztelés és minőség-ellenőrzés elengedhetetlen az egyenletes tapadás biztosításához. Különböző vizsgálati módszerek, mint például a leválási tapadás, a nyírószilárdság és a tapadás, értékelhetik a ragasztó teljesítményét. A megfelelő vizsgálati protokollok felállítása és a rendszeres minőségellenőrzés a gyártás során segíthet az inkonzisztenciák vagy problémák korai felismerésében, és biztosítja a konzisztens tapadást a végtermékben.
- Tárolás és eltarthatóság: A megfelelő tárolási feltételek és az eltarthatósági irányelvek betartása elengedhetetlen a ragasztó teljesítményének megőrzéséhez. A PSA-k idővel lebomlanak a hő, a fény vagy a levegő hatására, ami befolyásolja a tapadási tulajdonságaikat. A kötések ellenőrzött környezetben történő tárolása és az ajánlott eltarthatósági időn belüli felhasználása segíthet fenntartani a konzisztens tapadást.
Ragasztóadagolási technikák: pontosság és hatékonyság
A ragasztóadagolási technikák kulcsfontosságúak a különböző iparágakban, biztosítva a ragasztási alkalmazások pontosságát és hatékonyságát. Legyen szó gyártásról, összeszerelésről vagy javításról, a megfelelő adagolási mód jelentősen befolyásolhatja a ragasztószalagok minőségét és megbízhatóságát. Ez a cikk azokat a kritikus technikákat vizsgálja meg, amelyek segítenek elérni a ragasztóanyag-adagolás pontosságát és hatékonyságát korlátozott szószámon belül.
- Kézi adagolás: A kézi ragasztóadagolást általában kis léptékű műveleteknél vagy összetett alkalmazásoknál alkalmazzák. Ez magában foglalja a kézi eszközök, például fecskendők, kinyomható palackok vagy ecsetek használatát a ragasztó pontos felviteléhez. Bár ez a módszer rugalmasságot és ellenőrzést kínál, ez a kezelő készségétől és következetességétől függ.
- Idő/nyomás adagolás: Az idő/nyomás adagolás egy széles körben használt technika, amely egyenletes és ellenőrzött ragasztófelhordást biztosít. Ez magában foglalja a pneumatikus vagy elektromos adagolók használatát nyomásszabályozókkal és időzítőkkel. Az adagolási idő és a nyomás beállításával a kezelők pontosan szabályozhatják a felvitt ragasztó mennyiségét. Ez a technika közepes és nagy viszkozitású ragasztókhoz alkalmas.
- Sugárzás: A jetting olyan adagolási technika, amely nagy sebességű ragasztóáramot használ, hogy precíz és kis mennyiségű ragasztót vigyen fel a célfelületre. Általában olyan alkalmazásokban használják, amelyek gyors és pontos elhelyezést igényelnek, mint például az elektronikai összeszerelés vagy a mikro kötés. A sugárzó rendszerek piezoelektromos vagy pneumatikus működtetést alkalmaznak, hogy szabályozott ragasztócseppeket hozzanak létre.
- Permetezés: A spray-adagolás hatékony technika nagy területek lefedésére vagy egyenletes fedés elérésére. Ez abból áll, hogy a ragasztót finom cseppekre porlasztják, és levegőnyomással vagy automata szórópisztollyal a felületre irányítják. A permetező adagolást általában az autóiparban, a fafeldolgozó vagy a csomagolóiparban használják, ahol gyors és egyenletes fedés szükséges.
- Robot adagolás: A robotadagoló rendszerek precíz és megismételhető ragasztó alkalmazásokat kínálnak a programozható automatizálás révén. Fejlett érzékelőkkel és adagolószelepekkel vannak felszerelve, amelyek programozhatók a bonyolult minták és kontúrok követésére. A robotadagolás biztosítja a konzisztenciát és a pontosságot, így ideális nagy mennyiségű gyártósorokhoz és összetett összeszerelési folyamatokhoz.
- Film/örvénybevonat: A film vagy az örvénybevonat egy olyan technika, amellyel egyenletes ragasztóréteget visznek fel az alapfelületre. Ez magában foglalja egy forgó mechanizmus vagy applikátor használatát a ragasztó vékony, folyamatos filmben történő eloszlatására. Ezt a módszert általában az autóiparban, a repülőgépiparban és az építőiparban alkalmazzák, ahol az ellenőrzött ragasztóvastagság kritikus az optimális teljesítményhez.
Kihívások az FPC ragasztóragasztó alkalmazásában
Az FPC (Flexible Printed Circuit) ragasztóragasztó alkalmazása számos kihívást jelent, amelyeket meg kell oldani a sikeres ragasztás és a megbízható teljesítmény érdekében. Ezek a kihívások elsősorban az FPC-k egyedi tulajdonságaiból és követelményeiből fakadnak. Ebben a válaszban felvázolok néhány kulcsfontosságú kihívást, amelyekkel az FPC ragasztóragasztó alkalmazása során találkoztunk.
- Aljzatkompatibilitás: Az FPC-k rugalmas anyagokból, például poliimidből, poliészterből vagy vékony rézből készülnek, amelyek felületi jellemzői eltérnek a merev hordozóktól. A ragasztónak kompatibilisnek kell lennie az FPC anyaggal, hogy biztosítsa a megfelelő tapadást anélkül, hogy az aljzat leválását vagy károsodását okozná.
- Felület előkészítés: A megfelelő felület-előkészítés kritikus fontosságú a ragasztáshoz. Az FPC felületeken gyakran vannak maradványok, olajok vagy szennyeződések, amelyek gátolhatják a tapadást. A kihívás a megfelelő tisztítási módszer vagy felületkezelés kiválasztásában rejlik, hogy eltávolítsák ezeket a szennyeződéseket az FPC integritásának veszélyeztetése nélkül.
- Ragasztási vonalvastagság szabályozása: Az egyenletes ragasztási vonalvastagság elérése elengedhetetlen a megbízható teljesítményhez. Az inkonzisztens ragasztóvastagság eltéréseket okozhat az elektromos vezetőképességben, a mechanikai szilárdságban és a hőkezelésben. A kötési vonal vastagságának pontos szabályozása az FPC-k rugalmas jellege miatt kihívást jelenthet.
- Hőkezelés: Az FPC-ket gyakran használják olyan alkalmazásokban, ahol hőmérséklet-ingadozások várhatók. A ragasztáshoz használt ragasztónak jó hővezető képességgel kell rendelkeznie, hogy hatékonyan elvezesse a hőt, megelőzve a helyi forró pontok kialakulását, amelyek károsíthatják az FPC-t vagy annak alkatrészeit. Az optimális hőszabályozás elérése az FPC rugalmasságának és elektromos tulajdonságainak veszélyeztetése nélkül kihívást jelent.
- Ragasztó kikeményítése: Az FPC ragasztó ragasztók általában keményedési folyamatokat igényelnek, például hőt vagy UV-t. A kihívás az egységes és teljes kikeményedés biztosításában rejlett a kötési vonalon, különösen összetett vagy sűrűn csomagolt FPC-konstrukciók esetén. A nem megfelelő kikeményedés erősebb tapadást vagy tökéletlen ragasztást eredményezhet, ami megbízhatósági problémákhoz vezethet.
- Rugalmasság és tartósság: Az FPC-ket rugalmasra tervezték, és a ragasztó ragasztónak alkalmazkodnia kell ehhez a rugalmassághoz anélkül, hogy az integritását veszélyeztetné. A kötésnek ellenállnia kell az ismételt hajlításnak, hajlításnak és nyújtásnak anélkül, hogy megrepedne, elválik vagy elveszítené a tapadási erejét. A rugalmasságot és a tartósságot egyaránt megőrző kötés megtalálása kihívást jelenthet.
- Elektromos vezetőképesség: Az FPC-k gyakran hordoznak elektromos jeleket, így az elektromos vezetőképesség kritikus követelmény. A ragasztóanyag nem okozhat olyan nagy ellenállást, amely megzavarhatja az áramkör teljesítményét. A jó elektromos vezetőképesség elérése a kötési vonalon a mechanikai integritás biztosítása mellett kihívást jelent.
- Folyamatautomatizálás: A ragasztófelhordási folyamat automatizálása szükségessé válik azokban az iparágakban, ahol az FPC kötést nagy méretekben végzik. A kihívás az olyan automatizált rendszerek fejlesztésében rejlik, amelyek következetesen pontosan és hatékonyan tudják felvinni a ragasztót, figyelembe véve az FPC méretek, formák és kialakítások eltéréseit.
Ezeknek a kihívásoknak a megoldásához az FPC anyagok, a ragasztó ragasztók és az alkalmazás specifikus követelményeinek átfogó ismerete szükséges. Ez gyakran gondos anyagválasztást, folyamatoptimalizálást és tesztelést igényel, hogy biztosítsa a ragasztó kompatibilitását, teljesítményét és megbízhatóságát az FPC ragasztási alkalmazásokban.
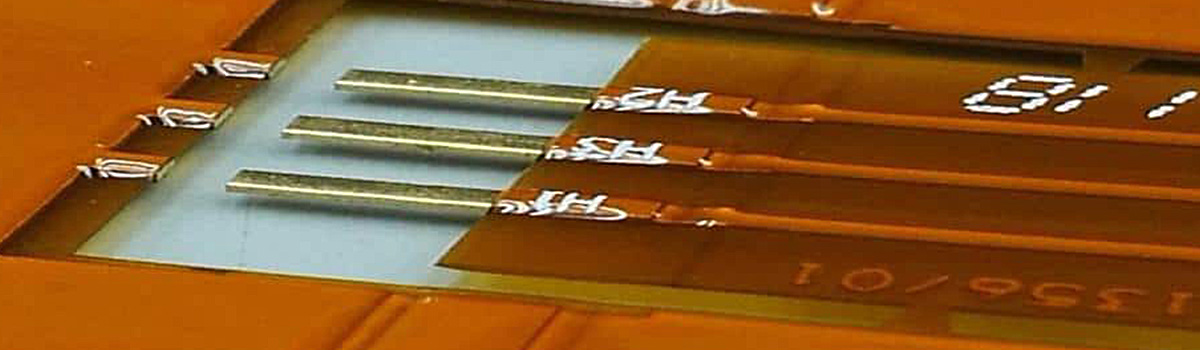
Megbízhatósági vizsgálat: A ragasztó teljesítményének értékelése
A megbízhatósági vizsgálat döntő lépés a ragasztók teljesítményének értékelésében. A ragasztókat széles körben használják különféle iparágakban, beleértve az autógyártást, a repülőgépgyártást, az elektronikát és az építőiparban, különböző anyagok ragasztására. Az öntapadó kötések megbízhatósága elengedhetetlen a végtermék biztonságának, tartósságának és általános teljesítményének biztosításához.
A megbízhatósági tesztelés során a ragasztókötéseket különféle feltételeknek és stresszhatásoknak vetik alá, amelyek valós környezeteket és használati forgatókönyveket szimulálnak. A cél annak értékelése, hogy a ragasztó mennyire képes megőrizni kötési szilárdságát és integritását az idő múlásával. Íme néhány kulcsfontosságú szempont, amelyet figyelembe kell venni a ragasztó teljesítményének megbízhatósági vizsgálat során történő értékelése során:
- Kötési szilárdság: A ragasztó kezdeti kötési szilárdságát szabványos tesztekkel, például átlapolási nyírási, lehúzási vagy szakítószilárdsági tesztekkel értékelik. Ezek a tesztek mérik a ragasztó kötés megszakításához szükséges erőt. Kiindulási alapot nyújt a kötési szilárdsággal való összehasonlításhoz a különböző körülményeknek való kitettség után.
- Környezeti expozíció: A ragasztók gyakran vannak kitéve zord környezeti feltételeknek, például szélsőséges hőmérsékleti hatásoknak, páratartalomnak, UV-sugárzásnak és vegyszereknek. A megbízhatósági vizsgálat során a ragasztómintákat gyorsított öregedési teszteknek vetik alá, amelyek ezeket a feltételeket hosszabb ideig szimulálják. Ez segít felmérni a ragasztó ellenálló képességét a környezeti károsodásokkal szemben, valamint azt, hogy képes-e fenntartani a ragasztó szilárdságát kedvezőtlen körülmények között.
- Termikus ciklus: A hőmérséklet-változások az anyagok tágulását és összehúzódását okozhatják, ami megterhelheti a ragasztókötéseket. A hőciklusos tesztek során a ragasztómintákat ismételt hőmérsékleti ciklusoknak vetik alá, az alacsonytól a magas szélsőségig, hogy felmérjék a ragasztó hőterheléssel szembeni ellenállását és a kötés integritását fenntartó képességét.
- Mechanikai igénybevétel: A ragasztókötések különböző típusú mechanikai igénybevételnek lehetnek kitéve a használat során, mint például a feszültség, a nyomás, a nyírás és a vibráció. A megbízhatósági vizsgálat során a ragasztómintákat mechanikai igénybevételnek vetik alá ciklikus kifáradási, ütési vagy hajlítási tesztekkel. Ezek a tesztek segítenek értékelni a ragasztó azon képességét, hogy ellenáll-e az automatikus terhelésnek a kötés meghibásodása nélkül.
- Tartósság és öregedés: Az öntapadó kötések várhatóan hosszú távú tartóssággal rendelkeznek, és ellenállnak az idő múlásával történő leromlásnak. A megbízhatósági vizsgálat magában foglalja a hosszú távú öregedési teszteket, amelyek szimulálják a termék várható élettartamát. Ez magában foglalhatja a ragasztómintákat hosszan tartó környezeti tényezőknek, például hőmérsékletnek, páratartalomnak és UV-sugárzásnak kitéve, valamint a kötés erősségének és integritásának időszakos értékelését.
- Kompatibilitás: A ragasztóknak kompatibilisnek kell lenniük azokkal az anyagokkal, amelyekhez ragasztják. A megbízhatósági vizsgálat magában foglalja a ragasztó különböző hordozókkal való kompatibilitásának felmérését, beleértve a fémeket, műanyagokat, kompozitokat és más, az iparban általánosan használt anyagokat. A kompatibilitási tesztek értékelik a ragasztó kötési szilárdságát, a kémiai kölcsönhatásokkal szembeni ellenállását és az aljzatra gyakorolt esetleges káros hatásokat.
A megbízhatósági vizsgálat értékes információkat nyújt a ragasztók teljesítményéről és korlátairól különböző körülmények között. Segíti a gyártókat az alkalmazásukhoz legmegfelelőbb ragasztó kiválasztásában, és biztosítja annak megbízhatóságát és tartósságát a valós körülmények között. Szigorú megbízhatósági tesztek elvégzésével a gyártók csökkenthetik a ragasztóanyag tönkremenetelének kockázatát, javíthatják a termék minőségét és javíthatják a vevők elégedettségét.
Környezetvédelmi megfontolások az FPC kötőragasztónál
Az FPC (Flexible Printed Circuit) kötőragasztók kritikus szerepet játszanak az elektronikus eszközök összeszerelésében és megbízhatóságában. Mivel a környezettudatosság és a fenntarthatóság egyre fontosabbá válik, elengedhetetlen figyelembe venni ezen ragasztók ökológiai hatását. Íme néhány kritikus környezetvédelmi szempont az FPC ragasztóanyagokkal kapcsolatban:
- Toxicitás: Az egyik elsődleges szempont a ragasztó és összetevőinek toxicitása. A ragasztók tartalmazhatnak káros vegyszereket, például illékony szerves vegyületeket (VOC) vagy veszélyes légszennyező anyagokat (HAP). Ezek az anyagok káros hatással lehetnek az emberi egészségre és a környezetre. A gyártóknak törekedniük kell a mérgező vegyszerek minimalizálására vagy kiküszöbölésére ragasztókészítményeikben.
- Kibocsátások és levegőminőség: A gyártási és alkalmazási folyamatok során az FPC kötőragasztók VOC-okat és egyéb légszennyező anyagokat bocsáthatnak ki a légkörbe. Ezek a kibocsátások hozzájárulnak a levegőszennyezéshez, és hátrányosan befolyásolhatják a levegő minőségét. A környezettudatos ragasztógyártók célja, hogy csökkentsék ezeket a kibocsátásokat alacsony VOC vagy nulla VOC-tartalmú ragasztók kialakításával.
- Energiafogyasztás: Az FPC kötőragasztók előállítása energiát igényel, amely gyakran nem megújuló forrásokból származik. A környezeti hatások minimalizálása érdekében a gyártóknak energiahatékony folyamatokat kell bevezetniük, és meg kell vizsgálniuk a megújuló energiaforrások használatát.
- Hulladékképződés: A ragasztófelhordási folyamatok során hulladék keletkezhet, beleértve a felesleges ragasztóanyagot, csomagolóanyagot és tisztítóanyagokat. Követni kell a megfelelő hulladékkezelési gyakorlatokat, például a hulladékanyagok újrahasznosítását vagy újrafelhasználását, amikor csak lehetséges. Ezenkívül a gyártóknak meg kell vizsgálniuk a hosszabb eltarthatósági idejű ragasztók fejlesztését, hogy csökkentsék a lejárt vagy fel nem használt termékekből származó hulladék mennyiségét.
- Élettartam végével kapcsolatos megfontolások: Az FPC kötőragasztókat tartalmazó elektronikus eszközök ártalmatlanítása jelentős környezetvédelmi szempont. A nem könnyen lebomló vagy veszélyes összetevőket tartalmazó ragasztók hozzájárulhatnak a környezetszennyezéshez, amikor az eszközöket eldobják. A ragasztógyártóknak törekedniük kell olyan környezetbarát termékek kifejlesztésére, amelyek kompatibilisek az újrahasznosítási vagy ártalmatlanítási folyamatokkal, például olyan ragasztókat, amelyek az újrahasznosítás során könnyen leválaszthatók az áramköri lapokról.
- Fenntarthatóság és zöld kezdeményezések: A ragasztógyártóknak be kell építeniük a fenntarthatóságot üzleti gyakorlatukba. Ez magában foglalhatja a megújuló nyersanyagok használatát, a környezetbarát gyártási folyamatok megvalósítását, valamint az elismert környezetvédelmi szabványok és tanúsítványok betartását. Ezenkívül a vállalatok részt vehetnek zöld kezdeményezésekben, például termék-visszavételi programokban vagy partnerségekben az újrahasznosító létesítményekkel.
- Életciklus-értékelés: Az FPC kötőragasztók átfogó életciklus-értékelésének (LCA) elvégzése alapvető fontosságú a környezeti hatások megértéséhez a nyersanyag kitermelésétől az ártalmatlanításig. Az LCA-k segítenek azonosítani azokat a területeket, ahol javítani lehet, mint például az üvegházhatású gázok kibocsátásának csökkentése, az erőforrás-felhasználás minimalizálása és az újrahasznosíthatóság javítása.
Trendek és innovációk az FPC ragasztóragasztó terén
Az FPC (Flexible Printed Circuit) kötőragasztók folyamatosan fejlődnek, a nagyobb teljesítmény, a miniatürizálás és az elektronikus eszközök fokozott megbízhatósága iránti igény vezérelve. Íme néhány figyelemre méltó trend és újítás az FPC kötőragasztók terén:
- Miniatürizálás és vékonyság: Ahogy az elektronikus eszközök egyre kisebbek és vékonyabbak, egyre nagyobb az igény az FPC kötőragasztókra, hogy megfeleljenek ezeknek a formai követelményeknek. A gyártók ultravékony és alacsony profilú ragasztókat fejlesztenek, amelyek erős kötést biztosítanak, miközben minimálisra csökkentik az összeállítás teljes vastagságát.
- Magas hőmérséklettel szembeni ellenállás: Sok elektronikai eszköz, különösen az autóiparban, a repülőgépiparban és az ipari alkalmazásokban, magas hőmérsékletű környezetben működik. A fokozott hőállósággal rendelkező FPC kötőragasztókat fejlesztik, hogy megbízható teljesítményt biztosítsanak szélsőséges hőmérsékleti viszonyok között, megelőzve a rétegvesztést vagy a kötés meghibásodását.
- Alacsony nyomású kikeményedés: A hagyományos ragasztós kikeményedési eljárások gyakran magas hőmérsékletet vagy hosszú kikeményedési időt igényelnek, ami kihívást jelenthet hőérzékeny alkatrészek vagy kényes aljzatok esetében. Az alacsony nyomású technikák innovációi, mint például az UV-re vagy nedvességre keményedő ragasztók, kíméletesebb kötési lehetőségeket kínálnak, lehetővé téve a kompatibilitást a hőmérséklet-érzékeny alkatrészekkel és aljzatokkal.
- Vezetőképes ragasztók: Az elektromos vezetőképességgel rendelkező FPC kötőragasztók iránti kereslet növekszik azokban az alkalmazásokban, amelyek elektromos csatlakozást igényelnek az áramköri elemek között. A vezetőképes ragasztók szükségtelenné teszik a különböző forrasztási folyamatokat, lehetővé téve a gyorsabb összeszerelést és csökkentve az érzékeny alkatrészek hőkárosodásának kockázatát.
- Fokozott rugalmasság és tartósság: A rugalmasság és a tartósság döntő fontosságú az FPC kötőragasztók számára, hogy ellenálljanak a hajlításnak, csavarodásnak és vibrációnak a rugalmas elektronikus eszközökben. A polimerkémia és a formulázási technikák fejlődése jobb rugalmasságot, nyúlást és mechanikai igénybevétellel szembeni ellenálló képességet eredményez, így megbízható kötést biztosít dinamikus környezetben.
- Környezetbarátság: A környezeti megfontolások, beleértve a fenntartható nyersanyagok felhasználását és a mérgező anyagok csökkentését, egyre hangsúlyosabbak a ragasztók fejlesztésében. A gyártók bioalapú és megújuló anyagokat keresnek a kőolaj alapú összetevők alternatívájaként. Ezenkívül környezetbarát gyártási folyamatokat és újrahasznosítható ragasztókészítményeket fejlesztenek ki a környezeti hatás minimalizálása érdekében.
- Továbbfejlesztett adagolás és felhordás: A hatékony és precíz ragasztófelvitel kulcsfontosságú az egyenletes és megbízható kötések eléréséhez. Az adagolási technológiák újításai, mint például az automatizált adagolórendszerek és a jetting módszerek lehetővé teszik a ragasztók ellenőrzött és pontos felhordását, még az összetett FPC-konstrukciókban is, finom osztású alkatrészekkel.
- Ragasztófólia-technológia: A ragasztófóliák egyre népszerűbbek az FPC-ragasztásban, köszönhetően a könnyű kezelhetőségnek és a pontos elhelyezésüknek. Ezek az előre kialakított fóliák egyenletes ragasztóvastagságot, kiváló nedvesítési tulajdonságokat és egyszerűsített összeszerelési folyamatokat kínálnak. A gyártók folyamatosan fejlesztik a ragasztófólia-készítményeket, hogy javítsák ragasztási teljesítményüket és kompatibilitásukat a különböző hordozókkal.
- Megbízhatósági fejlesztések: A hosszú távú megbízhatóság biztosítása érdekében FPC kötőragasztókat fejlesztenek ki, amelyek jobban ellenállnak az olyan tényezőknek, mint a nedvesség, a vegyszerek és az öregedés. Ezek a ragasztók szigorú tesztelésen esnek át, hogy felmérjék teljesítményüket zord környezeti feltételek mellett is, biztosítva a következetes funkcionalitást és a kötés integritását a termék élettartama alatt.
- Testreszabás és alkalmazás-specifikus megoldások: Az FPC kötőragasztókat úgy alakítják ki, hogy megfeleljenek a különböző alkalmazások speciális követelményeinek, mint például az autóipar, a fogyasztói elektronika, az orvosi eszközök és a hordható technológia. A gyártók szorosan együttműködnek az eszközök tervezőivel és gyártóival, hogy személyre szabott ragasztómegoldásokat dolgozzanak ki, amelyek megfelelnek az egyes alkalmazások egyedi kihívásainak és teljesítményigényeinek.
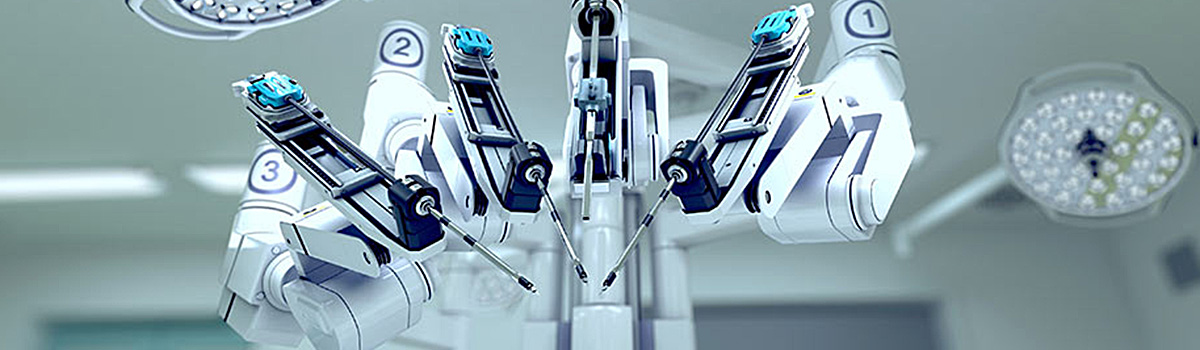
Alkalmazási területek: fogyasztói elektronika, autóipar, orvosi eszközök és egyebek
A fogyasztói elektronika: A fogyasztói elektronika a személyes használatra és szórakoztatásra tervezett termékek széles skáláját öleli fel. Ide tartoznak az okostelefonok, táblagépek, laptopok, játékkonzolok, okostévék, intelligens otthoni eszközök, hordható eszközök stb. A fogyasztói elektronika alkalmazása forradalmasította az emberek kommunikációját, munkáját és szórakoztatását. A technológiai fejlesztések a fogyasztói elektronikát erősebbé, kompaktabbá és megfizethetőbbé tették, zökkenőmentes csatlakozást, magával ragadó élményt és kényelmet biztosítva a felhasználók számára.
Autóipari: Az autóipar az elmúlt években jelentős fejlődésen ment keresztül, elsősorban a technológiai integrációnak köszönhetően. Az elektromos járművektől az autonóm vezetési rendszerekig az autóipari alkalmazások megváltoztatták az utazásunkat. Az elektromos autók egyre népszerűbbek környezetbarát jellegüknek és a szén-dioxid-kibocsátás csökkentésének köszönhetően. Ezen túlmenően az autógyártók olyan innovatív funkciókat építenek be, mint a fejlett vezetőtámogató rendszerek (ADAS), a csatlakoztathatóság, az infotainment rendszerek és a telematika, hogy javítsák a vezetési élményt, javítsák a biztonságot és lehetővé tegyék a hatékony járműkezelést.
Orvosi eszközök: Az orvostechnikai eszközök döntő szerepet játszanak a különböző egészségügyi állapotok diagnosztizálásában, monitorozásában és kezelésében. Az egyszerű eszközöktől, például hőmérőktől és vérnyomásmérőktől a fejlett berendezésekig, például MRI-gépekig és robotsebészeti rendszerekig terjednek. Az orvosi eszközök lehetővé teszik az egészségügyi szakemberek számára, hogy pontos diagnózist állítsanak fel, minimálisan invazív eljárásokat hajtsanak végre, és távolról nyomon kövessék a betegek egészségét. Forradalmasították az egészségügyi ágazatot, javították a betegek kimenetelét, csökkentették a kórházi tartózkodások számát, és javították az ellátás általános minőségét.
A dolgok internete (IoT): Az Internet of Things (IoT) érzékelőkkel, szoftverrel és csatlakozási lehetőségekkel beágyazott, egymással összekapcsolt eszközök hálózata. Lehetővé teszi az adatcserét és az eszközök közötti kommunikációt, ami automatizáláshoz, adatelemzéshez és jobb döntéshozatalhoz vezet. Az IoT-nek számos iparágban van alkalmazása, beleértve az egészségügyet, a mezőgazdaságot, a gyártást és az energiát. Az egészségügyben az IoT-eszközök figyelemmel kísérhetik a betegek életfontosságát, nyomon követhetik a gyógyszeres kezelést, és lehetővé teszik a betegek távoli megfigyelését. Az IoT-eszközök optimalizálhatják az öntözést, nyomon követhetik a talajviszonyokat, és javíthatják a termésgazdálkodást a mezőgazdaságban. Az IoT képes forradalmasítani az iparágakat azáltal, hogy hatékonyabbá, fenntarthatóbbá és adatközpontúbbá teszi azokat.
Ipari automatizálás: Az ipari automatizálás magában foglalja a technológia és a vezérlőrendszerek használatát az ipari folyamatok és feladatok automatizálására. Ide tartozik a robotika, a gépi látórendszerek, az érzékelők és a programozható logikai vezérlők (PLC). Az ipari automatizálás növeli a termelékenységet, növeli a biztonságot, csökkenti a működési költségeket, és alkalmazásokat talál a gyártásban, a logisztikában, az energetikában és más ágazatokban. A mesterséges intelligencia (AI) és a gépi tanulás (ML) integrációjával az ipari automatizálás optimalizálhatja a folyamatokat, észlelheti az anomáliákat, és lehetővé teszi a prediktív karbantartást, javítva a hatékonyságot és csökkentve az állásidőt.
Jövőbeli kilátások és lehetőségek
Az FPC (Flexible Printed Circuit) kötőragasztó az elektronikai eszközök gyártásában kritikus komponens. Kulcsfontosságú a rugalmas áramkörök és más alkatrészek közötti megbízható és robusztus kapcsolatok biztosításában. Ahogy a jövőbe tekintünk, érdemes megfontolni az FPC kötőragasztó számos kilátását és lehetőségét.
- Fejlődések a rugalmas elektronikában: A rugalmas elektronika területe gyorsan fejlődik, és egyre nagyobb az igény a rugalmas kijelzők, hordható eszközök és intelligens textíliák iránt. Az FPC kötőragasztók továbbra is jó minőségűek lesznek, hogy lehetővé tegyék a rugalmas áramkörök összeszerelését és összekapcsolását ezekben az innovatív alkalmazásokban.
- Miniatürizálás és karcsúbb eszközök: Ahogy a fogyasztói elektronika egyre kompaktabb és vékonyabb, a vékonyabb és rugalmasabb összekapcsolási megoldások kulcsfontosságúak. Az FPC kötőragasztók megkönnyíthetik az ultravékony, rugalmas áramkörök összeszerelését, így karcsúbb és könnyebb eszközöket hozhat létre.
- Fokozott ragasztási teljesítmény: A gyártók folyamatosan keresik azokat a ragasztómegoldásokat, amelyek kiváló kötési teljesítményt, például nagy nyírószilárdságot, kiváló elektromos vezetőképességet és hőstabilitást kínálnak. A jövőbeni FPC kötőragasztók valószínűleg fejlett anyagokat és összetételeket fognak tartalmazni, hogy megfeleljenek ezeknek a szigorú követelményeknek.
- Integráció fejlett gyártási folyamatokkal: Az olyan feltörekvő gyártási technológiák, mint a 3D nyomtatás, a tekercsről tekercsre történő feldolgozás és a hibrid integráció új lehetőségeket nyitnak meg a rugalmas áramkörök előállításában. Az FPC kötőragasztóknak alkalmazkodniuk kell ezekhez a gyártási folyamatokhoz, és kompatibilisnek kell lenniük azokkal, optimalizált tapadást és megbízhatóságot kínálva.
- Flexible Hybrid Electronics (FHE): Az FHE a hagyományos merev elektronikát alkalmazkodó alkatrészekkel ötvözi, egyedi formai tényezőkkel és funkciókkal rendelkező eszközöket hozva létre. Az FPC kötőragasztók fontos szerepet játszanak majd ezeknek a hibrid rendszereknek az összeszerelésében, zökkenőmentesen összekapcsolva a rugalmas és merev elemeket.
- Fenntarthatósági és környezetvédelmi megfontolások: A fenntarthatóságra és a környezeti felelősségvállalásra való növekvő figyelem lehetőséget kínál környezetbarát FPC kötőragasztók kifejlesztésére. A jövőbeni készítmények megújuló vagy újrahasznosítható anyagokat tartalmazhatnak, csökkentve az elektronikai hulladék környezeti hatását.
- Intelligens funkciók integrálása: A dolgok internete (IoT) és az összekapcsolt eszközök térnyerésével az FPC kötőragasztók olyan intelligens funkciókat tartalmazhatnak, mint a beágyazott érzékelők, öngyógyító képességek vagy hőkezelési tulajdonságok. Ezek a fejlesztések javítanák az elektronikus eszközök funkcionalitását és megbízhatóságát.
- Orvosi és egészségügyi alkalmazások: Az orvosi területen a hordható eszközök, a beültethető érzékelők és az intelligens egészségügyi technológiák felfutása tapasztalható. A biológiailag kompatibilis, sterilizálható és különféle szubsztrátumokhoz tapadni képes FPC kötőragasztók jelentős alkalmazási területet fognak találni ezen a területen.
- Autóipar és repülőgépipar: Az autóipar és a repülőgépipar egyre gyakrabban alkalmaz rugalmas áramköröket könnyű és helytakarékos előnyei miatt. Az extrém hőmérsékleteknek, rezgéseknek és mechanikai igénybevételeknek ellenálló FPC ragasztóanyagokra nagy igény lesz ezekben az igényes környezetekben.
- Kutatás és fejlesztés: Az FPC kötőragasztókkal kapcsolatos folyamatos kutatási és fejlesztési erőfeszítések további előrelépésekhez vezetnek. A ragasztókémiával, a gyártási technikákkal és a folyamatoptimalizálással kapcsolatos innovációk előre fogják vinni az iparágat, új alkalmazásokat és jobb teljesítményt tesz lehetővé.
Az együttműködés jelentősége az FPC ragasztóragasztó technológia fejlesztésében
Az együttműködés kulcsfontosságú az FPC (Flexible Printed Circuit) ragasztóragasztó technológia fejlesztésében. Lehetővé teszi a tudás, az erőforrások és a szakértelem cseréjét a különböző érdekelt felek között, ami felgyorsítja az innovációt és a fejlődést. Íme a legfontosabb okok, amelyek rávilágítanak az együttműködés fontosságára az FPC ragasztóragasztó technológia fejlesztésében:
- Több tudományágat átívelő szakértelem: Az FPC ragasztóragasztó technológia különböző területeket foglal magában, beleértve az anyagtudományt, a kémiát, az elektronikai gyártást és a mérnöki tudományt. Az együttműködés ezen különböző területek szakértőit hozza össze, elősegítve a problémamegoldás interdiszciplináris megközelítését. Tudásuk és perspektíváik ötvözésével a kutatók és az iparági szakemberek komplex kihívásokat kezelhetnek, és hatékonyabban dolgozhatnak ki új megoldásokat.
- Tudásmegosztás: Az együttműködés megkönnyíti az információmegosztást, a kutatási eredményeket és a legjobb gyakorlatokat a különböző entitások között. A gyártók, beszállítók, kutatók és akadémiai intézmények együttműködhetnek, hogy értékes ismereteket és műszaki ismereteket terjeszthessenek az FPC ragasztóragasztó technológiáról. Ez a megosztott tudás segít elkerülni a felesleges erőfeszítéseket, elősegíti a szabványosítást és felgyorsítja az általános fejlődést.
- Hozzáférés az erőforrásokhoz: Az együttműködési erőfeszítések lehetővé teszik a források szélesebb köréhez való hozzáférést, beleértve a finanszírozást, felszereléseket, létesítményeket és anyagokat. A szervezetekkel, kutatóintézetekkel vagy kormányzati szervekkel való partnerség hozzáférést biztosíthat olyan speciális erőforrásokhoz, amelyek külön-külön nem biztos, hogy elérhetők. Ez a hozzáférés kiterjedtebb kísérletezést, tesztelést és prototípuskészítést tesz lehetővé, ami továbbfejlesztett FPC ragasztóanyag-összetételekhez és gyártási folyamatokhoz vezet.
- Felgyorsított innováció: Az együttműködés elősegíti a nyitott innováció és kreativitás környezetét. A különböző nézőpontok és szakértelem egyesítése révén új ötletek és koncepciók születhetnek, feszegetve az FPC ragasztóragasztó technológia határait. Az együttműködési projektek az egyes partnerek erősségeit is kiaknázhatják, egyesítve egyedi képességeiket és erőforrásaikat, hogy innovatív megoldásokat fejlesszenek ki gyorsított ütemben.
- Piaci betekintések és iparági trendek: Az iparági partnerekkel és végfelhasználókkal való együttműködés értékes betekintést nyújt a piaci igényekbe, a kialakuló trendekbe és az ügyfelek igényeibe. Ez a megértés segít az FPC ragasztóragasztó-technológia fejlesztésének összehangolásában az iparág változó igényeivel. Az együttműködési erőfeszítések lehetővé teszik a korai visszacsatolást és érvényesítést, biztosítva, hogy a kifejlesztett megoldások praktikusak, relevánsak és üzletileg életképesek legyenek.
- Minőségbiztosítás és szabványosítás: Az együttműködés megkönnyíti a minőségbiztosítási intézkedések és az ipari szabványok kialakítását az FPC ragasztóragasztó technológiára vonatkozóan. A szabványügyi szervezetekkel és szabályozó testületekkel való együttműködés biztosítja, hogy a kifejlesztett ragasztók megfeleljenek a biztonsági, megbízhatósági és teljesítménykövetelményeknek. Az együttműködés lehetővé teszi a tesztelési módszerek és érvényesítési protokollok megosztását is, ami következetesebb és szabványosabb kötési folyamatokhoz vezet.
- Érvényesítés és valós alkalmazás: A végfelhasználókkal, gyártókkal és rendszerintegrátorokkal való együttműködés lehetővé teszi az FPC ragasztóragasztó technológia megerősítését a valós alkalmazásokban. Együttműködéssel a ragasztógyártók értékes visszajelzéseket kaphatnak a teljesítményről, a használhatóságról és a gyárthatóságról. Ez a visszacsatoló hurok segít finomítani és javítani a ragasztókészítményeket, biztosítva azok alkalmasságát a különböző alkalmazásokhoz és környezetekhez.
- Kockázatcsökkentés: Az együttműködés szétteríti a kutatási és fejlesztési erőfeszítésekkel kapcsolatos kockázatokat. A partnerek közösen kezelhetik a kihívásokat és mérsékelhetik az egyéni kockázatokat az erőforrások és a szakértelem összevonásával. Az együttműködés lehetővé teszi a szellemi tulajdon és a szabadalmi jogok megosztását is, elősegítve az együttműködőbb és kevésbé versenyképes környezetet.
Következtetés
Az FPC kötőragasztó létfontosságú az elektronikus eszközök rugalmasságának és megbízhatóságának biztosításához. Ezeknek a ragasztóknak az a képessége, hogy erős ragasztási képességet, elektromos szigetelést és védelmet nyújtanak a környezeti tényezőkkel szemben, miközben biztosítják az FPC-lapok rugalmasságát és tartósságát, döntő fontosságú a különféle elektronikus eszközök gyártása és összeszerelése során. A technológia fejlődésével az innovatív ragasztómegoldások fejlesztése, valamint a gyártók, kutatók és végfelhasználók közötti együttműködés kulcsfontosságú lesz az elektronikai ipar növekvő igényeinek és kihívásainak kielégítésében. Az FPC kötőragasztóban rejlő lehetőségek kiaknázásával még rugalmasabb, tartósabb és megbízhatóbb elektronikus eszközök előtt nyithatjuk meg az utat, amelyek modern világunkat táplálják.