Az elektronikus ragasztók teljes útmutatója
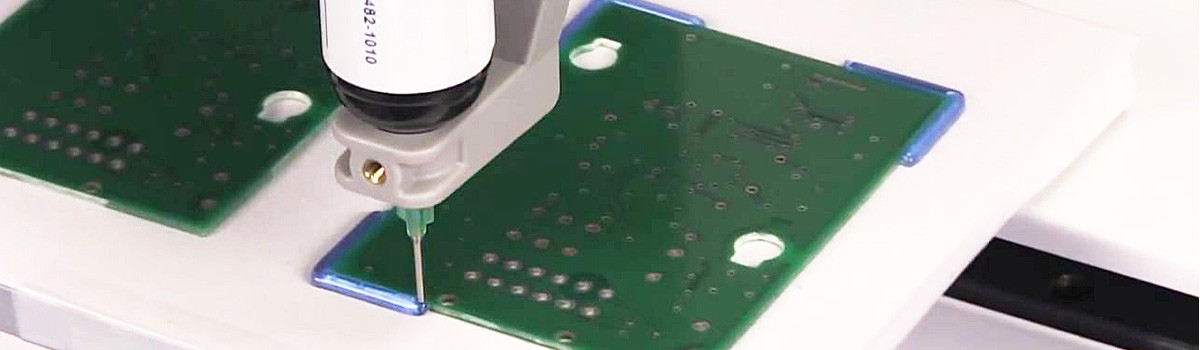
Elektronikus ragasztók
Az elektronikus ragasztók olyan speciális anyagok, amelyek elektronikus alkatrészeket, például integrált áramköröket, ellenállásokat, kondenzátorokat és tranzisztorokat kötnek áramköri lapokhoz, hordozókhoz és más elektronikus eszközökhöz. Ezek a ragasztók biztosítják az elektronikai termékek megbízhatóságát, teljesítményét és hosszú élettartamát.
Az elektronikus ragasztóknak különféle típusai vannak, beleértve a vezetőképes és nem vezető ragasztókat, a hő- és elektromosan vezető ragasztókat, valamint az UV-sugárzással keményedő ragasztókat. Úgy alakítottuk ki őket, hogy ellenálljanak a szélsőséges hőmérsékleteknek, vegyszereknek, nedvességnek, vibrációnak és egyéb környezeti tényezőknek, amelyekkel az elektronikai eszközök élettartamuk során találkozhatnak.
Különböző iparágak széles körben használnak elektronikus ragasztókat, beleértve az autógyártást, a repülőgépgyártást, a távközlést, az orvosi és a fogyasztói elektronikát. Lehetővé teszik az elektronikus eszközök miniatürizálását, sebességét és funkcionalitását, valamint a zord körülményekkel szembeni ellenállásukat.
Az elektronikus ragasztók jelentősége a modern technológiában
Az elektronikus ragasztók a modern technológia elengedhetetlen alkotóelemei. Létfontosságú szerepet játszanak az elektronikus eszközök megbízhatóságának és hosszú élettartamának, valamint miniatürizálásának, sebességének és funkcionalitásának biztosításában. Íme néhány ok, amiért az elektronikus ragasztók olyan fontosak a modern technológiában:
Miniatürizálás: Mivel a gyártók miniatürizálják az elektronikai eszközöket, az összeszerelésükhöz használt alkatrészeket is miniatürizálniuk kell. Az elektronikus ragasztók lehetővé teszik a gyártók számára, hogy ezeket a kis alkatrészeket precízen és stabilan ragasszák, lehetővé téve kisebb, összetettebb eszközök fejlesztését.
Tartósság: A zord környezeti feltételek, beleértve a hőmérséklet-változásokat, a páratartalmat és az ütéseket, gyakran teszik ki az elektronikus eszközöket. Elektronikus ragasztókat készítünk, hogy ellenálljanak ezeknek a feltételeknek, biztosítva az alkatrészek biztonságos rögzítését és a készülék megfelelő működését.
funkcionalitás: Elektronikus ragasztókkal is lehet vezető utakat létrehozni az alkatrészek között, lehetővé téve az elektromos áram átáramlását az eszközön. Lehetővé teszi bonyolultabb áramkörök fejlesztését és megnövelt funkcionalitást az elektronikus eszközökben.
Sebesség: Az elektronikus ragasztók használata a gyártásban elősegíti a gyártás egyszerűsítését és csökkenti az összeszerelési időt. Az elektronikus tömítőanyagok gyorsan és pontosan alkalmazhatók, így időt takaríthatunk meg és növeljük a hatékonyságot.
Megbízhatóság: Már egy kisebb meghibásodás is jelentős problémákat okozhat az elektronikai eszközökben. Az elektronikus ragasztók megbízható és biztonságos kötést biztosítanak az alkatrészek között, csökkentve a veszteség kockázatát és biztosítva a készülék megfelelő működését.
Elektronikus ragasztók típusai: Átfogó áttekintés
Az elektronikus ragasztók többféle típusban kaphatók, mindegyik egyedi tulajdonságokkal és előnyeivel. A ragasztó kiválasztása az eszköz konkrét alkalmazásától és követelményeitől függ, és a gyártóknak megfelelő ragasztót kell választaniuk a megbízhatóság, a funkcionalitás és a hosszú élettartam érdekében. Íme az iparban általánosan használt különféle típusú elektronikus ragasztók:
- Vezetőképes ragasztók:Az elektronikai gyártók vezetőképes ragasztókat használnak az elektronikus alkatrészek közötti elektromos kapcsolatok létrehozására. Vezetőképes részecskéket, például ezüstöt vagy rezet tartalmaznak, amelyek lehetővé teszik az elektromosság áramlását a ragasztón keresztül. A gyártók ezeket a ragasztókat általában érintőképernyők, érzékelők és egyéb elektronikus eszközök gyártására használják.
- Nem vezető ragasztók:A gyártók nem vezető ragasztót használnak az elektromos csatlakozást nem igénylő elektronikus alkatrészekhez. Gyakran használják az áramköri lapok összeszerelésében, mechanikai stabilitást és szigetelést biztosítva az elemek között.
- Hővezető ragasztók: A hővezető ragasztók elvezetik a hőt az elektronikus alkatrészekről. Hővezető részecskéket tartalmaznak, például kerámiát vagy szenet, amelyek lehetővé teszik a hő átáramlását a ragasztón. A gyártók ezeket a ragasztókat tápegységek, LED-es világítás és egyéb jelentős mennyiségű hőt termelő berendezések gyártására használják.
- Elektromosan vezető ragasztók:Az elektromosan vezető ragasztók hasonlóak a vezetőképes ragasztókhoz, de nagyobb az elektromos vezetőképességük. Gyakran használják nagy teljesítményű elektronikus eszközök, például mikroprocesszorok és memóriachipek összeszerelésére.
- UV-re keményedő ragasztók: Az UV-sugárzással keményedő ragasztókat ultraibolya fénnyel lehet kikeményíteni. Gyorsan kikeményednek, és kiváló tapadást biztosítanak különféle aljzatokhoz. A gyártók ezeket a ragasztókat általában orvosi eszközök, optikai berendezések és egyéb olyan eszközök gyártására használják, amelyek gyors kötési időt igényelnek.
- Epoxi ragasztók: Az epoxi ragasztók nagy szilárdságukról és tartósságukról ismertek. Általában olyan elektronikus eszközöket szerelnek össze, amelyek erős kötést igényelnek, például okostelefonokat, táblagépeket és laptopokat.
Vezetőképes ragasztók: szerepük az elektromos áramkörökben
A vezetőképes ragasztók nélkülözhetetlen anyagok az elektronikai eszközök gyártásában. Módszert biztosítanak az elektronikus alkatrészek közötti elektromos kapcsolatok létrehozására, ami kulcsfontosságú ezen eszközök működőképessége szempontjából. Ez a blogbejegyzés a vezetőképes ragasztók szerepét tárgyalja az elektromos áramkörökben.
A vezetőképes ragasztók olyan vezetőképes részecskéket tartalmaznak, mint az ezüst, réz vagy nikkel, ami lehetővé teszi az elektromosság átáramlását a ragasztón. Ezek a részecskék vezető utat hoznak létre az elektronikus alkatrészek között, biztosítva a készülék megfelelő működését. A gyártók általában vezetőképes ragasztókat használnak érintőképernyők, érzékelők és egyéb elektronikus eszközök gyártásához.
A vezetőképes ragasztók elektromos áramkörökben való használatának egyik előnye, hogy biztonságos kötést biztosítanak az alkatrészek között. Ezek a ragasztók robusztus és stabil kapcsolatot hoznak létre, amely ellenáll az elektronikus eszközök környezeti igénybevételének. A ragasztó egyenletesen osztja el az áramot az áramkörben, megakadályozva a forró pontok kialakulását, és biztosítja, hogy minden alkatrész a megfelelő áramot kapja.
Vezetőképes ragasztók segítségével rugalmas áramkörök hozhatók létre, ami elengedhetetlen a flexibilis eszközökhöz, például hordható elektronikához vagy orvosi eszközökhöz. A vezetőképes ragasztók rugalmas aljzatokra hordhatók fel, így hajlékony, csavarodó vagy nyúló rétegek jönnek létre.
A vezetőképes ragasztók használatának egyik kihívása, hogy vezetőképességük idővel romolhat, különösen akkor, ha zord környezeti feltételeknek vannak kitéve. A gyártók folyamatosan új készítményeket fejlesztenek ki jobb tartóssággal és vezetőképességgel a probléma megoldására.
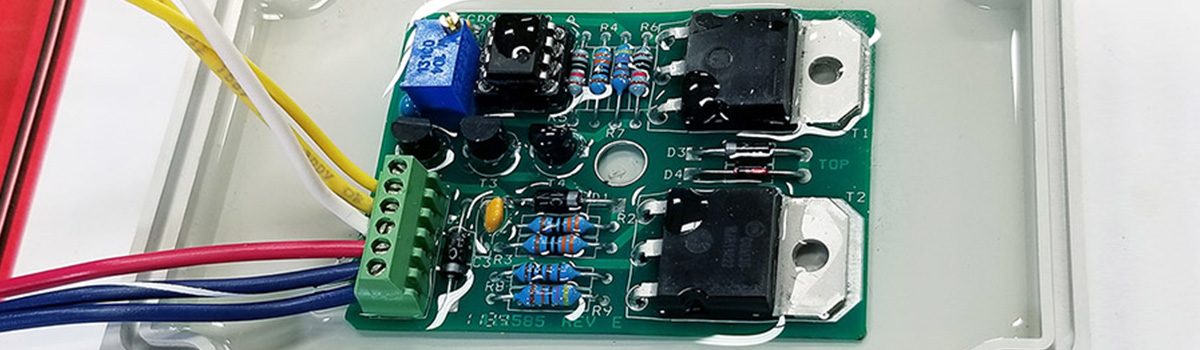
A hővezető ragasztók ismerete
A hővezető ragasztók számos modern elektronikai eszköz alapvető alkotóelemei. Ezek a ragasztók megkötik és átadják a hőt két felület között, javítva a hőkezelést és megakadályozva a túlmelegedést. Ebben a bejegyzésben megvizsgáljuk, mik azok a hővezető ragasztók, tulajdonságaik és alkalmazásaik.
A hővezető ragasztók olyan ragasztófajták, amelyek nagy hővezető képességgel rendelkeznek, és ez azt jelenti, hogy hatékonyan képesek átadni a hőt két felület között. A vezetőképes ragasztók tipikus összetétele polimer mátrix, például epoxi vagy szilikon, és vezetőképes részecskék, például alumínium-oxid vagy bór-nitrid kombinációját tartalmazza.
A hővezető ragasztók tulajdonságai a polimer mátrix típusától és a használt vezetőképes részecskéktől függenek. Az alapvető tulajdonságok közé tartozik a hővezető képesség, a viszkozitás és a kikeményedési idő. A ragasztó legkritikusabb tulajdonsága a hővezető képessége, amely meghatározza, hogy a felületek között mennyire hatékony a hőátadás. A ragasztó viszkozitása határozza meg, hogy mennyire könnyű felhordani, a kikeményedési idő pedig azt, hogy mennyi idő alatt köt ki a ragasztó, és éri el maximális hővezető képességét.
A hővezető ragasztóknak számos felhasználási területük van, többek között az autóiparban, a repülőgépiparban és az elektronikai iparban. Az elektronikai iparban a hővezető ragasztók az alkatrészeket hűtőbordákhoz és szórófejekhez kötik, javítva a hőkezelést és megakadályozva a túlmelegedést. A LED-es világítási alkatrészek hordozókhoz való ragasztására is szolgálnak, amelyek sok hőt termelnek.
Az autóiparban hővezető ragasztókat használnak a teljesítményelektronikai alkatrészek hűtőbordákhoz való ragasztására, ami javítja a hőkezelést. Szenzorokat is csatlakoztatnak a motor alkatrészeihez, amelyeknek magas hőmérsékletű környezetben kell működniük.
Dielektromos ragasztók: Az elektromos alkatrészek szigetelésének biztosítása
A dielektromos ragasztók alapvető anyagok, amelyeket az elektronikai iparban használnak az elektromos alkatrészek szigetelésére és védelmére. Azokban az alkalmazásokban, ahol az elektromos vezetőképesség aggodalomra ad okot, vagy nagyfokú szigetelésre van szükség, hővezető ragasztókat használnak a hagyományos ragasztók helyett, amelyek nem felelnek meg ezeknek a követelményeknek. A dielektromos ragasztók kiváló szigetelő tulajdonságokkal rendelkeznek, és ellenállnak a magas hőmérsékletnek, így ideálisak elektronikus eszközökben való használatra.
Íme néhány előnye a dielektromos ragasztók használatának:
- Szigetelés:A dielektromos ragasztók kiváló szigetelési tulajdonságokat biztosítanak, meggátolva az elektromos áram átfolyását, és biztosítják, hogy a kötőelemeik elektromosan le legyenek szigetelve.
- Hőellenállás:A dielektromos ragasztók ellenállnak a magas hőmérsékletnek, és idővel megőrzik tulajdonságaikat, így kiválóan alkalmasak jelentős hőt termelő alkalmazásokhoz, például motorokhoz és transzformátorokhoz.
- Kémiai ellenállás: A dielektromos ragasztók ellenállnak a vegyszereknek, így alkalmasak olyan zord környezetben való használatra, ahol más ragasztók tönkremennek.
- Tartósság: A dielektromos ragasztók kiváló kötési tulajdonságokkal rendelkeznek, és ellenállnak a nagy igénybevételnek és igénybevételnek, így ideálisak a mechanikai igénybevételnek kitett alkalmazásokhoz.
- Könnyű alkalmazás:A dielektromos ragasztók gyorsan és hatékonyan alkalmazhatók, ami lehetővé teszi a gyors összeszerelést és gyártást.
- Sokoldalúság:A dielektromos ragasztókat különféle alkalmazásokban használhatja, például elektronikus eszközökben, autóalkatrészekben és orvosi berendezésekben.
A dielektromos ragasztók különféle formákban állnak rendelkezésre, beleértve az epoxit, szilikont és akrilt. Minden készítményt egyedi tulajdonságokkal tervezünk, amelyek megfelelnek az adott alkalmazásoknak.
UV-sugárzással keményedő ragasztók: Gyors javítás az elektronikus összeszereléshez
Az elektronikus eszközök életünk szerves részévé váltak. Szinte minden elektronikára támaszkodunk, az okostelefonoktól a laptopokig, az autóktól az orvosi eszközökig. Az elektronikus összeszerelés különböző alkatrészek összekapcsolását foglalja magában, és a ragasztók döntő szerepet játszanak. Az UV-sugárzással keményedő ragasztók egyre népszerűbbek a különféle ragasztók között gyors kötési idejük és nagy kötési szilárdságuk miatt.
Az UV-sugárzással keményedő ragasztók olyan reaktív ragasztók, amelyek ultraibolya fény hatására megkeményednek. A kikeményedés másodpercek alatt megtörténik, így ideális választás nagy mennyiségű gyártási környezethez. Az UV-re keményedő ragasztók szükségtelenné teszik a melegítést vagy szárítást, csökkentve az összeszerelési időt és a gyártási költségeket.
Az UV-sugárzással kikeményedő ragasztók nagy tapadási szilárdsága miatt alkalmasak különféle felületekre, beleértve a fémeket, műanyagokat és üvegeket. Kiváló tapadást biztosítanak a nehezen ragasztható anyagokhoz, például polipropilénhez, polietilénhez és polikarbonáthoz. Az UV-sugárzással kikeményedő ragasztók által kialakított ragasztókötés szilárd és tartós, és ellenáll a zord környezeteknek is, például magas hőmérsékletnek, vegyszereknek és nedvességnek.
Az UV-sugárzással keményedő ragasztók másik előnye, hogy egy adott területen kikeményednek. A ragasztó pontosan felhordható a ragasztási területre, és a kikeményedési folyamat elindítható azáltal, hogy a helyet UV fénynek tesszük ki. Ez a tulajdonság ideálissá teszi őket olyan alkalmazásokhoz, amelyek precíz pozícionálást és alkatrészek beállítását igényelnek.
Az UV-sugárzással keményedő ragasztók környezetbarátak, és nem tartalmaznak oldószert, és nem bocsátanak ki illékony szerves vegyületeket (VOC) a kötés során. Biztonságossá teszi használatukat szűk helyeken, és csökkenti a környezetterhelést.
A megfelelő elektronikus ragasztó kiválasztása: fontos szempontok
A megfelelő elektronikus ragasztók kiválasztása kulcsfontosságú az elektronikus eszközök hosszú élettartamának és megbízhatóságának biztosításában. Az elektronikus ragasztók összeragasztják az alkatrészeket, és védenek a külső tényezőktől, például nedvességtől, portól és hőmérséklet-ingadozásoktól. Itt megvitatjuk azokat a kulcsfontosságú tényezőket, amelyeket figyelembe kell venni a megfelelő elektronikus ragasztó kiválasztásakor.
Kémiai tulajdonságok
Kompatibilitás: A ragasztónak kompatibilisnek kell lennie azokkal az anyagokkal, amelyekhez tapad, beleértve a fémeket, műanyagokat és üvegeket.
Kémiai ellenállás: A ragasztónak ellenállnia kell az elektronikus eszközzel érintkező vegyszereknek, például tisztítószereknek vagy oldószereknek.
Termikus tulajdonságok: A ragasztónak ellenállnia kell az üzemi hőmérsékleteknek és ingadozásoknak.
Alkalmazás tulajdonságai
Viszkozitás: A megfelelő felhordás érdekében figyelembe kell venni a ragasztó vastagságát, mivel annak egyenletesen kell folynia és fednie kell a ragasztandó felületeket.
Keményedési idő: A ragasztónak az összeszerelési folyamattal kompatibilis kötési idővel kell rendelkeznie. A hosszú kikeményedési idő lelassíthatja a termelést, míg a rövid kikeményedési idő nem teszi lehetővé a megfelelő kötést.
Tapadási szilárdság: A ragasztónak elegendő tapadószilárdsággal kell rendelkeznie ahhoz, hogy az eszköz alkatrészeit összeragassza és hosszú élettartamot biztosítson.
Környezeti tulajdonságok
Nedvességállóság: A ragasztónak védenie kell a nedvességtől, amely károsíthatja az elektronikus alkatrészeket.
UV ellenállás: A ragasztónak védenie kell az UV sugárzástól, amely elszíneződést és az anyagok lebomlását okozhatja.
Ütésállóság: A ragasztónak védenie kell a fizikai behatásoktól, például leejtéstől vagy ütéstől.
A megfelelő elektronikus ragasztók kiválasztása kulcsfontosságú az elektronikus eszközök hosszú élettartamának és megbízhatóságának biztosításában. A ragasztó kémiai, alkalmazási és környezeti tulajdonságainak figyelembevételével a gyártók biztosíthatják, hogy a ragasztó megfelelően tapadjon az alkatrészekhez, és védjen a külső tényezőktől.
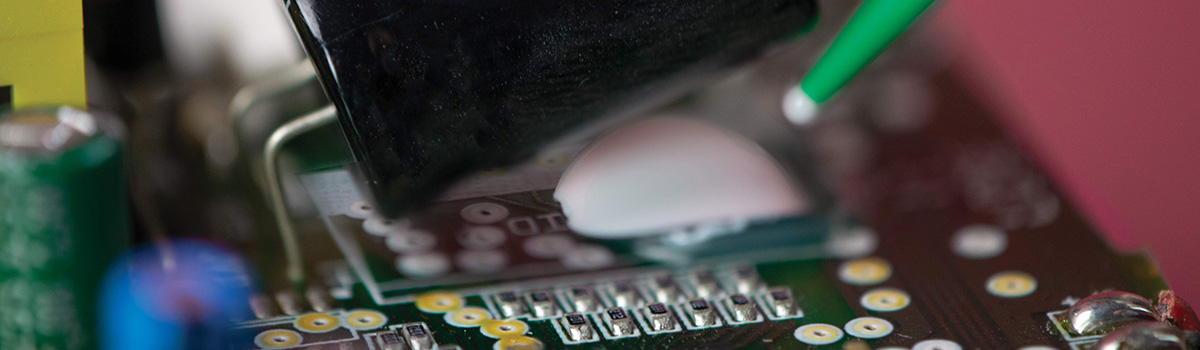
Kompatibilitás a szubsztrátumokkal: Tapadás és stabilitás biztosítása
Az aljzatokkal való kompatibilitás biztosítja a tapadást és a stabilitást a különböző iparágakban, például az autóiparban, az építőiparban és a csomagolásban. A bevonat vagy ragasztó hordozóra történő felhordásának sikere attól függ, hogy a két anyag mennyire kompatibilis. Ebben a beszélgetésben hangsúlyozni fogjuk a szubsztrátumokkal való kompatibilitás biztosításának jelentőségét, és felvázoljuk az ennek eléréséhez szükséges lépéseket.
A szubsztrátumokkal való kompatibilitás fontossága
Tapadás: Annak érdekében, hogy a bevonat vagy ragasztó a helyén maradjon, felhordáskor hozzá kell tapadnia az aljzat felületéhez. Az aljzatokkal való kompatibilitás elengedhetetlen annak biztosításához, hogy a bevonat vagy a ragasztó tapadjon az aljzathoz, és stabil maradjon.
Stabilitás: Az aljzattal összeférhetetlen bevonat vagy ragasztó instabilitáshoz vezethet, és a bevonat vagy a tömítőanyag meghibásodását okozhatja. Ez jelentős problémákhoz vezethet, például az épület szerkezeti meghibásodásához vagy a termék elvesztéséhez a használat során.
A szubsztrátumokkal való kompatibilitás biztosítása
Felület előkészítés: Az aljzat felületének előkészítéséhez bevonat vagy ragasztó felhordásához tisztítsa meg és távolítsa el a szennyeződéseket. Lehetővé teszi, hogy a bevonat vagy tömítőanyag megfelelően tapadjon az aljzathoz.
Tesztelés: A bevonat vagy ragasztó felhordása előtt kompatibilitási vizsgálatot kell végezni, hogy megbizonyosodjon arról, hogy a két anyag kompatibilis. A kompatibilitási teszteléshez különféle módszereket használhat, például lehúzási vagy lapnyírási tesztet.
Anyagválasztás: Elengedhetetlen az aljzathoz megfelelő bevonat vagy ragasztó kiválasztása. Vegye figyelembe a réteg vagy ragasztóanyag és az aljzat kémiai és fizikai tulajdonságait.
A hordozókkal való kompatibilitás hiányának súlyos következményei lehetnek, ami meghibásodásokhoz, valamint magas idő- és pénzköltségekhez vezethet. Az aljzatokkal való kompatibilitás biztosításával a tapadást és a stabilitást, valamint a sikeres és tartós felhordást biztosíthatja.
Környezeti ellenállás: figyelembe veendő tényezők
A környezeti ellenállás azokra a természetes tényezőkre utal, amelyek korlátozzák az élőlények növekedését, eloszlását és bőségét az ökoszisztémában. Ezek a tényezők lehetnek biotikusak (élő) vagy abiotikusak (nem élő), és számos fizikai, kémiai és biológiai körülményt foglalnak magukban. Ebben a blogbejegyzésben megvitatjuk azokat a tényezőket, amelyek hozzájárulnak a környezeti ellenálláshoz, és ezeknek a tényezőknek az ökoszisztéma egészségére gyakorolt hatásait.
Biotikus tényezők
- Verseny: Az élőlények versenyeznek élelemért, vízért és menedékforrásokért. Az erőforrások elérhetőségének csökkentésével korlátozhatja a népesség növekedését.
- Predáció: A ragadozók az egyedek elfogyasztásával korlátozhatják a személy méretét. Ez egy faj teljes populációméretének csökkenéséhez is vezethet.
- Betegség: A betegségek gyorsan terjedhetnek a populációban, ami idővel az egyedek számának csökkenését okozza.
Abiotikus tényezők
- Hőmérséklet:Az élőlények optimális hőmérsékleti tartománya van a túléléshez és a szaporodáshoz. A szélsőséges hőmérséklet korlátozhatja az élőlények növekedését és elterjedését.
- Víz: A víz nélkülözhetetlen az élethez, és az élőlényeknek bizonyos mennyiségű vízre van szükségük a túléléshez. A vízhiány korlátozhatja az élőlények növekedését és eloszlását.
- light: A fény szükséges a fotoszintézishez a növényekben, így termelnek táplálékot. A napfény hiánya korlátozhatja a növények fejlődését és elterjedését.
A környezeti ellenállás következményei
- Az egyensúly fenntartása: A környezeti ellenállás segít fenntartani az egyensúlyt az ökoszisztémákban azáltal, hogy megakadályozza, hogy egy faj domináljon és egyensúlyhiányt okozzon.
- Biodiverzitás: A környezeti ellenállás elősegíti a biológiai sokféleséget azáltal, hogy fülkéket hoz létre a különböző fajok számára, ezáltal növeli a fajok számát az ökoszisztémában.
- Ökoszisztéma egészsége:A környezeti ellenállás döntő szerepet játszik az ökoszisztéma egészségének megőrzésében. E tényezők megzavarása a fajok hanyatlásához vagy kipusztulásához vezethet, ami lépcsőzetes hatást gyakorolhat az egész ökoszisztémára.
Alkalmazási mód: A megfelelő adagolási technika kiválasztása
A gyártás során kulcsfontosságú a termék megfelelő alkalmazási módjának kiválasztása. A fejlesztés kiadagolási folyamata nagymértékben befolyásolhatja annak teljesítményét és megjelenését.
Éppen ezért elengedhetetlen, hogy gondosan mérlegelje lehetőségeit, és válassza ki az igényeinek leginkább megfelelő technikát.
Íme néhány szempont, amelyeket figyelembe kell venni a megfelelő adagolási technika kiválasztásakor:
- Viszkozitás: Az adagolt anyag viszkozitása fontos szempont. Az alacsony viszkozitású anyagok, például a víz vagy az oldószerek eltérő adagolási módot igényelhetnek, mint a nagy viszkozitású anyagok, például ragasztók vagy paszták. Alacsony viszkozitású anyagok esetén a permetezési vagy porlasztási technikák hatékonyabbak lehetnek, míg a nagy viszkozitású anyagok ellenőrzöttebb megközelítést igényelhetnek, például a precíziós adagolást.
- Anyag tulajdonságai: Az adagolási mód kiválasztásakor figyelembe kell vennie az adagolni kívánt anyag tulajdonságait. Például egyes anyagok érzékenyek lehetnek a levegő vagy a hőmérséklet változásaira, és olyan adagolási módszereket igényelnek, amelyek minimálisra csökkentik ezeknek a tényezőknek való kitettséget. Hasonlóképpen, azokhoz az anyagokhoz, amelyek bizonyos szintű pontosságot vagy pontosságot igényelnek, speciálisabb adagolóberendezésre lehet szükség.
- Termék dizájn: A termék kialakítása is befolyásolhatja az adagolási technika megválasztását. Például, ha a terméke bonyolult vagy kényes jellemzőkkel rendelkezik, a kézi adagolási folyamat megfelelőbb lehet, mint az automatizált. Másrészt, ha a terméke nagy mennyiségű kimenetet igényel, mechanikus vagy robotizált adagolási technikára lehet szükség.
- Környezeti tényezők: Végül a környezeti tényezők is befolyásolhatják az adagolási mód kiválasztását. Ha tisztatéri környezetben kell kiadnia a terméket, akkor például speciális berendezésre lehet szüksége, amely megfelel bizonyos tisztasági szabványoknak. Hasonlóképpen, ha az Ön terméke gyúlékony vagy veszélyes, előfordulhat, hogy olyan adagolási technikát kell választania, amely minimálisra csökkenti a balesetek vagy tüzek kockázatát.
Kikeményedési folyamat: A hő és az idő hatásának megértése
A kikeményedés döntő fontosságú folyamat, amely számos iparágban biztosítja a termékek hosszú élettartamát és tartósságát. Az autóipartól az építőiparig a kikeményítés elengedhetetlen annak biztosításához, hogy a végtermékek szilárdak és ellenálljanak a környezeti tényezőknek. A kikeményedési folyamat során hőt és időt alkalmaznak a fejlesztéshez, ami befolyásolja a mechanikai tulajdonságait és az általános minőséget.
A hő az egyik kritikus tényező, amely befolyásolja a kikeményedési folyamatot. A hőmérséklet-tartomány és a hőkezelés időtartama jelentősen befolyásolja a termék szilárdságát és merevségét. A hő aktiválja azokat a kémiai reakciókat, amelyek keresztkötések kialakulásához vezetnek az anyagban. Ezek a keresztkötések növelik az anyag erejét azáltal, hogy kötéseket hoznak létre a molekulaláncok között.
A keményedési folyamat időtartama egy másik kritikus tényező. Minél hosszabb a kikeményedési idő, annál több térháló képződik, ami robusztusabb és merevebb terméket eredményez. A túl hosszú kötési idő azonban törékenységhez és csökkent rugalmassághoz vezethet. A megfelelő egyensúly megtalálása a kikeményedési idő és a szilárdság között, a termék követelményeitől függően.
A megfelelő kikeményítési mód a termék típusától és a kívánt tulajdonságoktól függ. Például az autóiparban egy festékkeményítő kemencét használnak az autó karosszériájának hőkezelésére, biztosítva, hogy a festék megszáradjon és tapadjon a fémhez. Az építőiparban a betont víz hozzáadásával térhálósítják, és hagyják, hogy idővel megkeményedjen, növelve a szilárdságát.
A kikeményedési folyamat nemcsak a termék mechanikai tulajdonságai, hanem megjelenése szempontjából is elengedhetetlen. A kikeményedés során alkalmazott hő és idő befolyásolja a termék textúráját, színét és felületét. Ezért a kikeményedési folyamat ellenőrzése kulcsfontosságú annak biztosításához, hogy a termék megfeleljen a kívánt esztétikai és funkcionális követelményeknek.
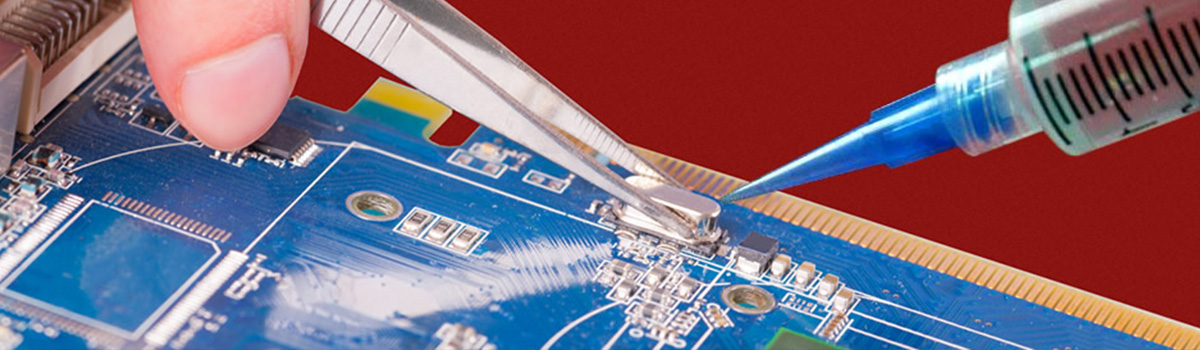
Tárolás és kezelés: Tippek a ragasztóminőség megőrzéséhez
A megfelelő tárolás és kezelés kulcsfontosságú a ragasztók hatékonyságának biztosításához. A nem megfelelő tárolás és kezelés a ragasztó minőségének romlásához vezethet, és végső soron a termék meghibásodásához vezethet. Íme néhány tipp a ragasztó minőségének megőrzéséhez:
- Hőmérséklet-szabályozás: A ragasztóanyagok érzékenyek a hőmérséklet-változásokra, és az extrém hőmérsékleteknek való kitettség károsíthatja a minőségüket. A magas hőmérséklet hatására a ragasztóanyagok elveszíthetik viszkozitásukat és tapadási szilárdságukat, míg alacsony hőmérsékleten törékennyé és nehezen használhatóvá válhatnak. Ezért a ragasztókat hűvös, száraz helyen, közvetlen napfénytől védve és állandó hőmérsékleten kell tárolni.
- Páratartalom szabályozás: A páratartalom is befolyásolhatja a ragasztóanyagok minőségét. A nedvesség a ragasztók tönkremenetelét okozhatja, ami csökkenti a ragasztó erejét. A ragasztó minőségének megőrzése érdekében a ragadós tartályokat szorosan lezárva kell tárolni, és szabályozott páratartalmú helyen kell tárolni.
- Megfelelő kezelés: A ragasztóanyagok megfelelő kezelése kulcsfontosságú a hosszú élettartamuk szempontjából. Elengedhetetlen a ragadós edények leejtése vagy felrázása, mert ez légbuborékok kialakulásához vezethet, ami befolyásolja a ragasztó minőségét. Ezenkívül elengedhetetlen a ragasztók megfelelő összekeverése használat előtt, mivel a nem megfelelő keverés a ragasztó minőségének és teljesítményének egyenetlenségéhez vezethet.
- Shelf Life: A ragasztóanyagok eltarthatósági ideje korlátozott, és a megadott időkereten belüli felhasználásuk elengedhetetlen. Idővel a ragasztóanyagok elkezdhetnek lebomlani, aminek következtében elveszíthetik ragasztóerejüket és viszkozitásukat. Hatékonyságuk biztosítása érdekében kulcsfontosságú, hogy a ragasztókat lejárat előtt használjuk.
- Kompatibilitás: A gyártók különböző ragasztóanyagokat terveznek bizonyos felületekhez és alkalmazásokhoz. Elengedhetetlen annak biztosítása, hogy a ragasztóanyag kompatibilis legyen a textúrával és az alkalmazási követelményekkel. Nem összeférhető ragasztóanyagok használata a termék meghibásodásához és a felületek károsodásához vezethet.
Az elektronikus ragasztók általános alkalmazásai
Az elektronikus ragasztók olyan speciális ragasztók, amelyek elektronikus alkatrészeket és rendszereket ragasztanak és tömítenek. A repülőgépipar és az autóipar, valamint a fogyasztói elektronika az ezeket hasznosító különféle alkalmazások közé tartozik. Íme néhány az elektronikus ragasztók leggyakoribb alkalmazásai:
- A fogyasztói elektronika:Az elektronikus ragasztókat széles körben használják a fogyasztói elektronikában, beleértve az okostelefonokat, laptopokat és táblagépeket. Összeragasztják és lezárják az elektronikus alkatrészeket, például a kijelzőket, az érintőképernyőket és az akkumulátorokat. Az elektronikus ragasztók védelmet nyújtanak a nedvesség és az elektronikus alkatrészeket károsító egyéb környezeti tényezők ellen is.
- Autóipar: Az autóipar nagymértékben támaszkodik az elektronikus ragasztókra, hogy biztosítsa a modern autók megbízhatóságát és biztonságát. Elektronikus ragasztók rögzítik és tömítik az elektronikus alkatrészeket, szerkezeti elemeket és elektromos csatlakozásokat. A gyártók a modern autógyártásban egyre elterjedtebb kompozit anyagok, például szénszálak ragasztására és tömítésére is használják őket.
- Repülőipar: A repülőgépipar speciális ragasztókat igényel, amelyek ellenállnak a szélsőséges környezeti igénybevételeknek, beleértve a magas hőmérséklet-változásokat és a sós víznek való kitettséget. Az elektronikus ragasztókat széles körben használják a repülőgépiparban elektronikus alkatrészek, szerkezeti elemek és elektromos csatlakozások ragasztására és tömítésére.
- Orvosi eszközök: Az orvosi eszközök gyártói elektronikus ragasztókat használnak olyan termékekben, mint a pacemakerek, defibrillátorok és inzulinpumpák. Elektronikus alkatrészek ragasztására és tömítésére szolgálnak, biztosítva azok helyes és megbízható működését.
- LED világítás:A gyártók elektronikus ragasztókat használnak LED-világítások gyártásához, beleértve az autóvilágítást és az utcai lámpákat. Ezek a ragasztók összeragasztják és lezárják az elektronikus alkatrészeket, hogy megvédjék azokat a nedvességtől és más környezeti tényezőktől, amelyek károkat okozhatnak.
- Megújuló energia: Az ipar elektronikus ragasztókat használ napelemek, szélturbinák és akkumulátorok ragasztására és lezárására. Arra szolgálnak, hogy megvédjék az elektronikus alkatrészeket a nedvességtől és más környezeti tényezőktől, biztosítva, hogy megbízhatóak és működőképesek maradjanak a berendezés élettartama alatt.
Autóipar: Az elektronikai ragasztók szerepe az autógyártásban
Az autóipar folyamatosan fejlődik, és az autógyártók mindig keresik a módját, hogy javítsák járműveik biztonságát, megbízhatóságát és hatékonyságát. Az egyik kritikus elem, amely létfontosságú szerepet játszik a modern autók építésében, az elektronikus ragasztók. Az elektronikus ragasztókat széles körben használják az autóiparban különféle alkalmazásokhoz, beleértve az elektronikus alkatrészek, szerkezeti elemek és elektromos csatlakozások ragasztását és tömítését.
Az elektronikus ragasztók számos kulcsfontosságú módon alkalmazhatók az autógyártás során:
- Elektronikus alkatrészek ragasztása és tömítése:Az elektronikus ragasztók megragasztják és kitöltik az elektronikus részleteket, például érzékelőket, vezérlőrendszereket és kijelzőket. Az elektronikus ragasztók garantálják, hogy ezek az alkatrészek megfelelően működnek még szélsőséges körülmények között is.
- Szerkezeti elemek ragasztása és tömítése:Az elektronikus ragasztók megragasztják és kitöltik a szerkezeti elemeket, például a karosszériaelemeket és az alvázat. Az elektronikus ragasztók használata garantálja, hogy az autó alkatrészei biztonságosan rögzítve maradnak, még akkor is, ha a mindennapi vezetési igénybevételnek vannak kitéve.
- Elektromos vezetőképesség: Az autógyártók elektronikus ragasztókat használnak az autóalkatrészek közötti megbízható elektromos vezetőképesség garantálására. Az alkatrészek közötti biztonságos elektromos csatlakozások különösen fontosak a hibrid és elektromos járműveknél, mivel ezek biztosítják az autó biztonságos és hatékony működését.
- Rezgésállóság:Az EDesigners olyan elektronikus ragasztókat hoz létre, amelyek elnyelik a rezgéseket és ütéseket, megakadályozva az alkatrészek kilazulását vagy meghibásodását. Az elemek kilazulásának vagy elhalásának megakadályozása elengedhetetlen a nagy teljesítményű járművekben, ahol az alkatrészek nagy igénybevételnek vannak kitéve.
- Környezetvédelem:A tervezők elektronikus ragasztókat hoznak létre, hogy megvédjék az alkatrészeket a környezeti tényezőktől, például nedvességtől, portól és egyéb olyan anyagoktól, amelyek károsíthatják vagy lebonthatják azokat. Az elektronikus kötések garantálják, hogy az alkatrészek megbízhatóak és működőképesek maradjanak a jármű teljes élettartama során.
Az autógyártók kritikus alkalmazásaik mellett elektronikus ragasztókat is használnak a gyártási folyamat során. Az autógyártók elektronikus ragasztókat használnak a modern autógyártásban egyre elterjedtebb kompozit anyagok, például szénszálak ragasztására és tömítésére. A kompozit anyagok használata könnyebb, erősebb és üzemanyag-hatékonyabb járműveket eredményez, de speciális ragasztórendszerekre is szükség van az alkatrészek megfelelő ragasztásához és tömítéséhez.
Repülési ipar: Hogyan biztosítják az elektronikus ragasztók a biztonságot a repülőgépekben
A repülőgépipar a világ egyik legösszetettebb és legigényesebb iparága. A repülőgép fedélzetén az utasok és a személyzet tagjainak biztonsága a legfontosabb, és a repülőgép építésénél használt anyagok vagy alkatrészek meghibásodása katasztrofális következményekkel járhat. A gyártók, tervezők és mérnökök nem becsülhetik túl az elektronikus ragasztók jelentőségét a repülőgépek biztonságának biztosításában.
Az elektronikus ragasztókat széles körben használják a repülőgépiparban különféle alkalmazásokhoz. Elektronikus alkatrészek, például érzékelők és vezérlőrendszerek ragasztására és tömítésére használják, hogy biztosítsák azok megfelelő működését extrém körülmények között is. Ezenkívül összekapcsolják és tömítik a szerkezeti elemeket, például a szárnyakat és a törzsrészeket, hogy biztosítsák, hogy szilárdan a helyükön maradjanak repülés közben.
A repülőgépgyártás során az egyik elsődleges szempont a nedvesség és más környezeti tényezők hatása az alkatrészek épségére. A tervezők olyan elektronikus ragasztókat hoznak létre, amelyek ellenállnak a környezeti igénybevételeknek, például szélsőséges hőmérséklet-változásoknak és magas páratartalomnak, amelyek veszélyeztethetik a repülőgép teljesítményét. A tervezők az elektronikus ragasztókat is úgy tervezik, hogy hosszan tartó védelmet nyújtsanak a korrózió ellen, ami jelentős probléma a korrozív környezetnek, például sós víznek kitett síkoknál.
Az elektronikus ragasztók a repülőgépek gyártási folyamatában is döntő szerepet játszanak. Az elektronikus ragasztók, például a szénszálas kompozit anyagokat megragasztják és tömítik, egyre gyakoribbak a modern repülőgépgyártásban. A kompozit anyagok használata könnyebb, erősebb és üzemanyag-hatékonyabb repülőgépeket eredményez, de speciális ragasztórendszerekre is szükség van az alkatrészek megfelelő ragasztásához és tömítéséhez.
A repülőgépipar a szerkezeti és védelmi célokon túl elektronikus ragasztókat is alkalmaz az elektromos vezetőképesség növelésére. Elektronikus áramkörök és alkatrészek ragasztására és tömítésére szolgálnak, biztosítva azok megfelelő és megbízható működését. Az elektronikus ragasztók garantálják, hogy a repülőgép elektromos csatlakozásai biztonságosak maradjanak, minimálisra csökkentve az elektromos meghibásodás kockázatát.
Orvosi ipar: A ragasztók szerepe az orvosi eszközökben
Az orvosi ipar a technológiára támaszkodik, hogy hatékony és eredményes betegkezelést biztosítson. Az orvosi eszközök kulcsfontosságúak a különböző egészségügyi állapotok diagnosztizálásában, kezelésében és monitorozásában. A ragasztók nélkülözhetetlenek az orvosi eszközökhöz, mivel megbízható és biztonságos módot kínálnak az alkatrészek ragasztására és az eszköz működőképességének biztosítására. Itt megvizsgáljuk a ragasztók szerepét az orvosi eszközökben.
Íme néhány mód, ahogyan a ragasztók döntő szerepet játszanak az orvosi eszközökben:
- Ragasztás: A ragasztókat az orvosi eszközök alkatrészeinek egymáshoz ragasztására használják, biztosítva, hogy azok a helyükön maradjanak és rendeltetésszerűen működjenek. Az alkatrészek helyes elhelyezése és működése kulcsfontosságú az olyan eszközökben, mint a szívritmus-szabályozók és az inzulinpumpák, mivel ez élet-halál kérdése lehet, így az elektronikus ragasztók elengedhetetlenek a biztonságos elhelyezés és a megbízható működés biztosításához.
- tömítő: Az orvostechnikai eszközök gyártói ragasztókat használnak az eszközök lezárására, valamint a szivárgás és szennyeződés megakadályozására. Például a katéterekben és az IV vezetékekben tömítőanyagokat használnak az eszköz és a páciens bőre közötti kapcsolat lezárására, megakadályozva a baktériumok bejutását.
- Tartósság:Az orvostechnikai eszközöknek elég tartósnak kell lenniük ahhoz, hogy ellenálljanak a napi használat során fellépő igénybevételeknek. A ragasztók döntő szerepet játszanak az orvostechnikai eszközök tartósságának biztosításában, mivel szilárd és hosszan tartó kötést biztosítanak az alkatrészek között.
- Biokompatibilitás: Az orvosi eszközökben használt ragasztóknak biológiailag kompatibilisnek kell lenniük, ami azt jelenti, hogy biztonságosan használhatók az emberi szervezetben, és nem okoznak sérülést vagy irritációt. A gyártóknak az orvostechnikai eszközökben való használatra bevizsgált és jóváhagyott ragasztókat kell használniuk.
- Rugalmasság: Egyes orvosi eszközöknek meg kell felelniük a test alakjának. A gyártók ragasztókat használnak a rugalmas alkatrészek ragasztására, miközben megőrzik az eszköz rugalmasságát.
Szórakoztató elektronika: A mindennapi eszközök tartósságának biztosítása
A szórakoztató elektronikai termékek mindennapi életünk elengedhetetlen részévé váltak, és a kommunikációtól a szórakoztatásig mindenben támaszkodunk rájuk. Ilyen intenzív használat mellett a tartósság kritikus tényező annak biztosításában, hogy készülékeink ellenálljanak a mindennapi használat során felmerülő kopásnak. Itt megvizsgálunk néhány módszert, amellyel a gyártók biztosíthatják a fogyasztói elektronika tartósságát.
- Robusztus kialakítás: A fogyasztói elektronika tartósságának biztosításának egyik alapvető tényezője a tervezés. A gyártóknak szilárd anyagokból és alkatrészekből kell olyan eszközöket készíteniük, amelyek ellenállnak a mindennapi használat igénybevételének. Figyelembe kell venniük a víz-, csepp- és karcállósági tényezőket is.
- Tesztelés:A tesztelés elengedhetetlen része a fogyasztói elektronikai cikkek tartósságának biztosításának. A gyártóknak szigorú tesztelést kell végezniük eszközeiken, hogy megbizonyosodjanak arról, hogy ellenállnak a különböző környezeti feltételeknek és használati forgatókönyveknek. A gyártók különféle teszteket végezhetnek, beleértve a vízállóságot, az ejtésállóságot, a hőmérsékletállóságot és egyebeket, hogy biztosítsák a termékek tartósságát és megbízhatóságát.
- Minőség-ellenőrzés: A minőség-ellenőrzés kulcsfontosságú annak biztosításában, hogy minden eszköz megfeleljen a gyártó tartóssági szabványainak. A gyártóknak szigorú minőség-ellenőrzési folyamatot kell alkalmazniuk, hogy azonosítsák azokat a hibákat vagy problémákat, amelyek befolyásolhatják az eszköz tartósságát.
- Javítás és karbantartás: A fogyasztók számára lehetővé kell tenni a készülékek egyszerű javítását és karbantartását. A gyártóknak olyan eszközöket kell tervezniük, amelyek könnyen szét- és újra összeszerelhetők, és cserealkatrészek könnyen elérhetők. E tesztek elvégzésével a gyártók biztosítják, hogy a fogyasztók hosszabb ideig megőrizhessék készülékeik jó munkakörülményeit.
- Felhasználói oktatás: Végül a gyártóknak fel kell tanítaniuk a fogyasztókat arra, hogyan használják eszközeiket a tartósság előmozdítása érdekében. A gyártók utasításokat tartalmazhatnak a gép megfelelő tisztítására és karbantartására vonatkozóan, valamint a károsodások gyakori okainak elkerülésére vonatkozó információkat, például a készülék leejtését vagy víznek való kitételét.
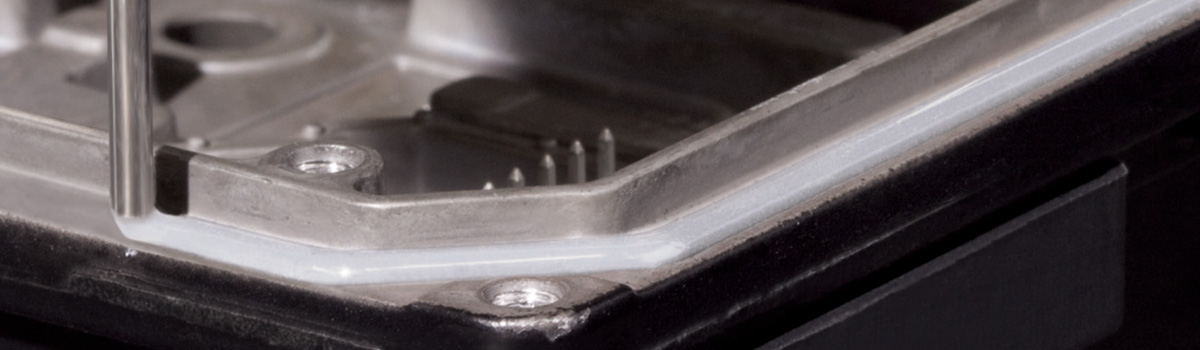
Az elektronikus ragasztók jövője: feltörekvő trendek és innovációk
Ahogy a technológia soha nem látott ütemben fejlődik, az elektronikus ragasztók jövője is átalakulóban van. A feltörekvő trendek és innovációk alakítják az iparágat, új lehetőségeket kínálva az elektronikai eszközök gyártóinak termékeik teljesítményének és tartósságának javítására. Ez a blogbejegyzés az elektronikus ragasztók legígéretesebb fejlesztéseit és azok lehetséges hatásait vizsgálja meg.
Íme néhány feltörekvő trend és innováció az elektronikus ragasztók területén:
- Magas hővezető képességű ragasztók:A nagy teljesítményű elektronikai eszközök iránti növekvő kereslet miatt egyre nagyobb az igény a hőt hatékonyan elvezetni képes ragasztókra. A nagy hővezető képességű ragasztók megoldást kínálnak a hőkezelés javításával és a nagyobb teljesítmény lehetővé tételével.
- Rugalmas ragasztók:A rugalmas tömítőanyagok egyre népszerűbbek a rugalmas elektronikában, a hordható eszközökben és az orvosi alkalmazásokban. Ezek a ragasztók rugalmasságot, szilárdságot és tartósságot kínálnak, így ideálisak olyan eszközökhöz, amelyek hajlítanak, csavarodnak vagy alkalmazkodnak különféle alakzatokhoz.
- Környezetbarát ragasztók:A környezetvédelmi szempontok egyre hangsúlyosabbá válásával egyre nagyobb az igény a környezetbarát és fenntartható ragasztókra. Ezen a területen az innovációk közé tartoznak a megújuló anyagokból, például természetes gumiból és könnyen újrahasznosítható vagy újrafelhasználható ragasztók.
- Miniatürizálás: Mivel az elektronikai eszközök mérete folyamatosan csökken, szükség van olyan ragasztókra, amelyek lépést tudnak tartani a trenddel. Egyre népszerűbbek a nagy tapadási szilárdságú miniatür tömítőanyagok, amelyek lehetővé teszik a kisebb, kompaktabb eszközök használatát.
- Innovatív ragasztók:A fejlesztők innovatív ragasztókat készítenek öngyógyító, alakmemóriával és vezetőképességgel. Ezek a ragasztók lehetővé teszik az elektronikai eszközök gyártói számára, hogy intelligensebb és érzékenyebb termékeket fejlesszenek ki.
Az elektronikus ragasztótechnológia jövőbeli trendjei és innovációi
Az elektronikus ragasztótechnológia folyamatosan fejlődik, és új trendek és innovációk jelennek meg, amelyek megfelelnek az elektronikai ipar változó igényeinek. Íme néhány az elektronikus ragasztótechnológia jövőbeli trendjei és innovációi:
- Miniatürizálás:Ahogy az elektronika egyre kisebb és kompaktabb lesz, úgy növekszik a kereslet a mikroméretekben is működő ragasztók iránt. Egyre kritikusabbak azok a ragasztók, amelyek képesek a kis és kényes alkatrészek megkötésére anélkül, hogy károsítanák azokat.
- Vezetőképes ragasztók: Az elektronikai gyártók egyre gyakrabban használnak vezetőképes ragasztókat a forrasztás alternatívájaként. Az előnyök közé tartozik az alacsonyabb üzemi hőmérséklet, az egyszerűsített összeszerelési folyamatok és a nagyobb megbízhatóság.
- Hőkezelés: Az elektronikus eszközök megnövekedett teljesítménysűrűsége miatt a hőelvezetés kritikus kihívássá vált. Az alkatrészektől hőt elvezetni képes ragasztók elengedhetetlenek az elektronikus eszközök élettartamának és megbízhatóságának növeléséhez.
- Rugalmas ragasztók: Ahogy az elektronika rugalmasabbá és hordhatóbbá válik, a rugalmas ragasztók egyre fontosabbá válnak. Ezek a ragasztók repedés nélkül ellenállnak a hajlításnak és csavarodásnak, így biztosítják, hogy az elektronikus alkatrészek még feszültség alatt is ragaszkodjanak.
- Környezetbarát ragasztók:Ahogy a fenntarthatóság egyre fontosabbá válik, egyre nagyobb az igény a környezetbarát ragasztók iránt. Egyre elterjedtebbek a biológiailag lebomló vagy újrahasznosított anyagokból készült ragasztók.
- Innovatív ragasztók:A kutatók olyan intelligens ragasztókat fejlesztenek, amelyek megváltoztathatják tulajdonságaikat külső ingerekre, például hőmérsékletre vagy fényre reagálva. Ezek a ragasztók potenciálisan alkalmazhatók érzékelőkben, aktuátorokban és más elektronikus eszközökben.
Az elektronikus ragasztó használata során felmerülő gyakori kihívások és azok leküzdése
Az elektronikai ragasztók az elektronikai eszközök gyártásában nélkülözhetetlenek, de számos kihívást is jelenthetnek. Íme néhány, az elektronikus ragasztó használata során felmerülő gyakori kihívások és azok leküzdése:
- Gyenge tapadás:Gyenge tapadás fordulhat elő, ha a ragasztó nem tapad megfelelően az aljzathoz, ami az alkatrész meghibásodásához vezethet. A megoldás az, hogy a felület tiszta és szennyeződésmentes legyen a ragasztó felhordása előtt. Ezenkívül alapozó vagy felületkezelés javíthatja a kötés tapadását.
- Keményedési idő:A ragasztók keményedése sokáig tarthat, ami a gyártás késéséhez vezethet. A megoldás a gyorsan kötő ragasztók használata vagy a kötési feltételek, például a hőmérséklet és a páratartalom optimalizálása a folyamat felgyorsítása érdekében.
- Nedvesség érzékenység:A nedvességre érzékeny ragasztók lebomlanak, ha nedvességnek vannak kitéve, ami a tapadás és az elektromos teljesítmény elvesztéséhez vezethet. A megoldás a nedvességálló ragasztók használata vagy a ragasztó megfelelő tárolása és kezelése, például száraz környezetben való tárolás és zárt csomagolás használata.
- Hőtágulás: A ragasztók hőtágulást és összehúzódást tapasztalhatnak, ami mechanikai igénybevételhez és az alkatrészek meghibásodásához vezethet. A megoldás az alacsony hőtágulási együtthatójú ragasztók használata, vagy a hőtágulást és -összehúzódást alkalmazó elektronikus rendszer tervezése.
- Kompatibilitás: A ragasztók nem kompatibilisek bizonyos anyagokkal, például műanyagokkal vagy fémekkel, ami gyenge tapadáshoz vagy kémiai reakcióhoz vezethet. A megoldás az elektronikus rendszer anyagaival kompatibilis ragasztók használata, vagy a ragasztó felhordása előtt kompatibilitási vizsgálat elvégzése.
A ragasztók adagolása kihívást jelenthet, különösen akkor, ha kicsi és kényes alkatrészekkel foglalkozik. Meg tudjuk oldani a problémát precíziós adagolóberendezések vagy előre gyártott öntapadó fóliák vagy szalagok használatával, amelyeket az egyének könnyen felhelyezhetnek az alkatrészekre.
Az elektronikus ragasztók szerepe a viselhető technológiában
A hordható technológia az elmúlt évtizedben egyre népszerűbb lett, ma már eszközök széles választéka áll a fogyasztók rendelkezésére. Ezek az eszközök, például az okosórák és a fitneszkövetők elektronikus alkatrészekre támaszkodnak, amelyeket biztonságosan kell rögzíteni a hordható eszközhöz. Az elektronikus alkatrészek erős és megbízható ragasztását igénylő helyzetekben az elektronikus ragasztók döntő szerepet játszanak.
A gyártók elektronikus ragasztókkal ragasztják az érzékelőket, a LED-eket, az akkumulátorokat és más alkatrészeket a hordható eszközökhöz, biztosítva azok megfelelő működését és tartósságát. Ezeknek a ragasztóknak ellenállniuk kell a mindennapi használat igénybevételének, beleértve a nedvességnek, hőnek és fizikai hatásoknak való kitettséget. A hordható technológiának köszönhetően rugalmasnak kell lenniük, hogy lehetővé tegyék a hajlítást és a nyújtást.
Az elektronikus ragasztók egyik legfontosabb előnye a hordható technológiában, hogy zökkenőmentes és áramvonalas megjelenést biztosítanak. Ha nem lennének kötések, a gyártóknak csavarokat vagy más mechanikus rögzítőelemeket kellene használniuk az alkatrészek rögzítéséhez, ami növelheti az eszköz súlyát és méretét. Másrészt a gyártók a ragasztókat vékony, egyenletes, szabad szemmel szinte láthatatlan rétegben is felvihetik.
Egy másik fontos szempont a hordható technológiához használt elektronikus ragasztók kiválasztásakor a biokompatibilitás. Annak biztosítása érdekében, hogy a hordható eszközök ne okozzanak irritációt vagy allergiás reakciókat közvetlenül a bőrön viselve, a gyártóknak nem irritáló és hipoallergén ragasztót kell használniuk. Az olyan orvosi hordható eszközök esetében, mint a glükóz- vagy EKG-monitorok, amelyeket speciális egészségi állapotú emberek használnak, különösen fontos annak biztosítása, hogy a ragasztó ne okozzon irritációt vagy allergiás reakciókat, mivel azok közvetlenül érintkeznek a bőrrel.
Ahogy a hordható technológia folyamatosan fejlődik, az ilyen eszközök egyedi igényeit kielégítő elektronikus ragasztók iránti kereslet tovább fog növekedni. A ragasztógyártók már új készítményeket fejlesztenek, amelyek ellenállnak a szélsőséges hőmérsékleteknek, ellenállnak a nedvességnek, és nagyobb rugalmasságot biztosítanak. Ennek eredményeként a hordható technológia még kényelmesebbé, megbízhatóbbá és funkcionálisabbá válik.
Elektronikus ragasztók adagolási technikái: tippek és bevált gyakorlatok
Az elektronikus ragasztók elengedhetetlenek az elektronikus eszközök gyártásában. Az adagolásuk azonban nagy kihívást jelenthet, különösen, ha kicsi és bonyolult alkatrészekről van szó. Íme néhány tipp és bevált gyakorlat az elektronikus ragasztók adagolásához:
- Válassza ki a megfelelő adagolási módot: Az elektronikus ragasztókhoz többféle adagolási mód is rendelkezésre áll, beleértve a kézi adagolást, a fecskendős adagolást és az automatizált adagolást. Válassza ki az alkalmazásának leginkább megfelelő módot.
- Használja a megfelelő adagolási tippet: Az adagolóhegynek meg kell egyeznie a ragasztó viszkozitásával és a ragasztott rész méretével. A kisebb információ ideális kisebb adagokhoz, míg a jelentősebb információ a fontosabb részletekhez.
- Adagolás tiszta környezetben: A tiszta környezet megakadályozza a szennyeződést és erős kötést biztosít. Használjon tiszta munkaterületet, és viseljen kesztyűt, hogy megakadályozza, hogy bőrolajok kerüljenek a ragasztóra.
- Biztosítsa a megfelelő tárolást: A megfelelő tárolás kulcsfontosságú az elektronikus ragasztók hosszú élettartama szempontjából. Tartsa a tárgyakat kiválóan és szárazon, és szorosan zárja le a tartályt.
- Egyenletesen vigye fel a ragasztót:Győződjön meg arról, hogy a ragasztó egyenletesen kerül felhordásra, hogy elkerülje a légzsákok kialakulását, amelyek gyengíthetik a kötést. Használjon biztos kézzel, és folyamatos mozdulatokkal vigye fel a ragasztót.
- Az áramlási sebesség szabályozása: Szabályoznia kell a ragasztó áramlási sebességét, hogy elkerülje a felesleges ragasztó kiszivárgását és a rendetlenséget. Használjon lassú és egyenletes áramlási sebességet, különösen, ha kis alkatrészekkel dolgozik.
- Rendszeresen tisztítsa meg az adagolócsúcsot:Tisztítsa meg rendszeresen az adagolócsúcsot, hogy elkerülje az eltömődéseket és biztosítsa a ragasztó egyenletes folyását. Használjon megfelelő tisztítóoldatot, és kövesse a gyártó utasításait.
- Gyakorolja a biztonsági óvintézkedéseket:A gyártók gyakran használnak vegyi anyagokat az elektronikus ragasztókban, amelyek egészségügyi kockázatot jelenthetnek. A kezelés során használjon védőfelszerelést, például kesztyűt és védőszemüveget.
Ezen tippek és bevált gyakorlatok követésével sikeresen adagolhatja az elektronikus ragasztókat, és erős kötést biztosíthat elektronikus eszközei között.
Következtetés
Összefoglalva, az elektronikus ragasztók kritikus szerepet játszanak a modern technológiában. Elengedhetetlenek az elektronikus alkatrészek közötti megbízható és tartós kötések kialakításához, megvédve azokat a környezeti tényezőktől, például nedvességtől, hőtől és vibrációtól. Az elektronikus ragasztók lehetővé teszik az elektronikus eszközök miniatürizálását is, ezáltal kisebbek és hordozhatóbbak.
A technológia fejlődésével az elektronikus ragasztók még kritikusabbá válnak. Nekik lépést kell tartaniuk a robusztusabb és kompaktabb elektronikus eszközök iránti növekvő kereslettel, miközben foglalkozniuk kell a fenntarthatósággal és a környezeti hatásokkal kapcsolatos aggályokkal is.
Ezenkívül az elektronikus ragasztóknak meg kell felelniük a különböző iparágak és alkalmazások speciális követelményeinek, az orvosi eszközöktől az autóelektronikán át a repülőgépiparig és a védelmi rendszerekig. Ezért ezen a területen folyamatos kutatásra és fejlesztésre lesz szükség a változó igények kielégítéséhez.