Félvezető ragasztó
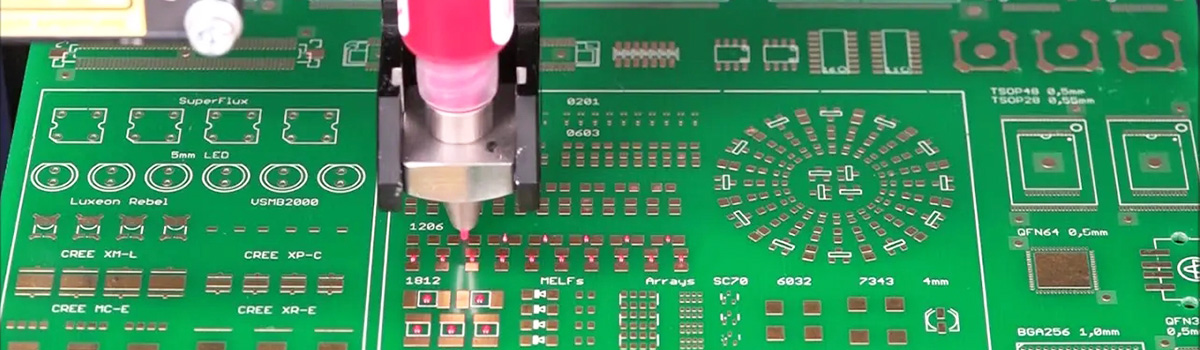
A félvezető ragasztó kritikus komponens a félvezető eszközök, például mikroprocesszorok, memóriachipek és más integrált áramkörök gyártásában és összeszerelésében. Ezek a ragasztók robusztus és megbízható kötési képességet, valamint védelmet nyújtanak a környezeti tényezőkkel és a hőterheléssel szemben. A kisebb, gyorsabb és összetettebb félvezető eszközök iránti növekvő kereslet következtében a nagy teljesítményű és megbízható ragasztómegoldások kritikusabbá váltak, mint valaha. Ez a cikk a félvezető ragasztók különféle típusait, alkalmazásait és kihívásait tárja fel, kiemelve kulcsfontosságú szerepüket a félvezető eszközök miniatürizálásában és nagy teljesítményében.
A félvezető ragasztók típusai
A félvezető ragasztók döntő szerepet játszanak az elektronikai eszközök gyártási és összeszerelési folyamataiban. Ezeket a ragasztókat úgy tervezték, hogy robusztus és megbízható kötést biztosítsanak a félvezető eszközök különböző összetevői között, például chipek, hordozók és csomagok között. Ellenállnak a zord környezeti feltételeknek, a termikus ciklusoknak és a mechanikai igénybevételeknek. A félvezető ragasztók többféle típusa is elérhető a piacon, mindegyik egyedi tulajdonságokkal és alkalmazási területtel. Nézzünk meg néhány általánosan használt félvezető ragasztót:
- Epoxi ragasztók: Az epoxi alapú ragasztókat széles körben használják félvezető alkalmazásokban kiváló kötési szilárdságuk, nagy vegyszerállóságuk és jó elektromos szigetelési tulajdonságaik miatt. Erős tapadást biztosítanak különféle anyagokhoz, köztük fémekhez, kerámiákhoz és műanyagokhoz. Az epoxi ragasztók szobahőmérsékleten vagy hő hatására megkeményednek, így merev és tartós kötést képeznek.
- Szilikon ragasztók: A szilikon alapú ragasztók rugalmasságukról, hőstabilitásukról és szélsőséges hőmérsékletekkel szembeni ellenállásukról ismertek. Kiszereléstől függően széles hőmérsékleti tartományban, -50°C-tól 200°C-ig vagy még ennél is magasabb hőmérsékletet bírnak. A szilikon ragasztók kiváló elektromos szigetelő tulajdonságokkal rendelkeznek, és gyakran használják olyan alkalmazásokban, ahol a hőkezelés kulcsfontosságú, például teljesítményelektronikai eszközökben.
- Akril ragasztók: Az akril ragasztók gyors kikeményedést, nagy kötési szilárdságot és jó hőmérséklet- és nedvességállóságot biztosítanak. Sokoldalúságukról ismertek, és különféle hordozókhoz köthetők, beleértve a fémeket, műanyagokat és üvegeket. Az akril ragasztókat, például az autóelektronikát és a LED-es szerelvényeket gyakran használják olyan alkalmazásokban, amelyek nagy szilárdságot és tartósságot igényelnek.
- Poliuretán ragasztók: A poliuretán alapú ragasztók egyensúlyt biztosítanak a rugalmasság és az erősség között. Jó tapadást biztosítanak különféle anyagokhoz, köztük fémekhez, műanyagokhoz és üvegekhez. A poliuretán ragasztók ellenállnak az ütéseknek, a vibrációnak és a hőciklusnak, így alkalmasak olyan alkalmazásokra, ahol mechanikai igénybevétel is érintett, például az autóiparban és a repülőgépiparban.
- Vezetőképes ragasztók: A vezetőképes ragasztók vezetőképes töltőanyagokkal, például ezüsttel, rézzel vagy szénnel vannak összeállítva, hogy lehetővé tegyék az elektromos vezetőképességet a ragasztott kötésekben. Általában elektronikus eszközök szerszámos rögzítésére, flip-chip ragasztására és alkatrészek összekapcsolására használják. A vezetőképes ragasztók alacsony ellenállást és kiváló tapadást biztosítanak, megbízható elektromos csatlakozást biztosítva.
- Underfill ragasztók: Az alátöltő ragasztókat kifejezetten flip-chip alkalmazásokhoz tervezték, ahol a forgács fejjel lefelé van felszerelve egy hordozóra. Ezek a ragasztók a kikeményedés során a forgács alá folynak, kitöltve a forgács és az aljzat közötti hézagokat. Az alátöltő ragasztók mechanikai támaszt nyújtanak, növelik a hővezető képességet, és megakadályozzák a forrasztási kötések hőterhelés okozta meghibásodását.
- UV-sugárzással térhálósítható ragasztók: Az UV-sugárzással térhálósítható ragasztók gyorsan megkeményednek ultraibolya fény hatására. Nagy kötési szilárdságot, optikai tisztaságot és vegyszerállóságot kínálnak. Az UV-sugárzással keményedő ragasztókat gyakran használják olyan alkalmazásokban, amelyek gyors feldolgozást és precíziós ragasztást igényelnek, mint például a kijelző-összeállítás, a száloptika és az optoelektronikai eszközök.
Epoxi ragasztók: a leggyakoribb választás
Az epoxi ragasztókat széles körben elismerik, mint az egyik leggyakoribb és legsokoldalúbb típust. Kivételes kötési szilárdságuk, tartósságuk és sokoldalúságuk miatt széles körben használják különféle iparágakban és alkalmazásokban. Itt megvizsgáljuk, miért az epoxi ragasztók a leggyakoribb választás egy korlátozott szószámon belül.
- Ragasztási szilárdság: Az epoxi ragasztók kivételes tapadási szilárdságot biztosítanak, így alkalmasak különféle anyagokhoz. Legyen szó fémről, műanyagról, kerámiáról, fáról vagy kompozitokról, az epoxi ragasztók szilárd és megbízható kötéseket biztosítanak, biztosítva az összeillesztett alkatrészek hosszú élettartamát és stabilitását.
- Sokoldalúság: Az epoxi ragasztók kiváló sokoldalúságot mutatnak az alkalmazási módszerek és a kikeményedési lehetőségek tekintetében. Különböző formákban kaphatók, például egy- vagy kétrészes rendszerekben, ami rugalmasságot tesz lehetővé a használatukban. Ezenkívül az epoxi ragasztók szobahőmérsékleten vagy hővel térhálósíthatók, az alkalmazás speciális követelményeitől függően.
- Vegyi ellenállás: Az epoxi ragasztók kivételes vegyszerállósággal rendelkeznek, így ideálisak olyan alkalmazásokhoz, ahol aggodalomra ad okot a kemény vegyszereknek vagy oldószereknek való kitettség. Szerkezeti integritásukat akkor is megőrzik, ha különféle vegyszereknek, olajoknak, üzemanyagoknak és savaknak vannak kitéve, biztosítva a ragasztott szerelvények tartósságát.
- Hőmérsékletállóság: Az epoxi ragasztók széles hőmérsékleti tartományban ellenállnak, így alkalmasak olyan alkalmazásokra, amelyek magas vagy alacsony hőmérséklettel szembeni ellenállást igényelnek. Legyen szó az autóiparról, a repülőgépiparról vagy az elektronikai iparról, az epoxi ragasztók még szélsőséges hőmérsékleten is megbízható kötést biztosítanak.
- Hézagkitöltő képesség: Az epoxi ragasztók másik előnye, hogy képesek kitölteni az illeszkedő felületek közötti hézagokat és egyenetlenségeket. Ez a jellemző erős kötést biztosít még akkor is, ha az érintkezési felületek nem illeszkednek ideálisan, így fokozott szerkezeti integritást biztosít az összekapcsolt alkatrészeknek.
- Mechanikai tulajdonságok: Az epoxi ragasztók kiváló mechanikai tulajdonságokkal rendelkeznek, mint például a nagy szakító- és nyírószilárdság, valamint jó ütésállóság. Ezek a tulajdonságok alkalmassá teszik teherhordó alkalmazásokhoz, ahol a ragasztónak jelentős igénybevételnek vagy ütésnek kell ellenállnia a kötési szilárdság veszélyeztetése nélkül.
- Elektromos szigetelés: Az epoxi ragasztók kiváló elektromos szigetelési tulajdonságokkal rendelkeznek, így népszerűek az elektronikai és elektromos alkalmazásokban. Hatékony szigetelést biztosítanak, megvédik az érzékeny elektronikai alkatrészeket az elektromos áramoktól és rövidzárlatoktól.
- Könnyű használat: Az epoxi ragasztók használata és felhordása viszonylag egyszerű. Pontosan adagolhatók, lehetővé téve az ellenőrzött alkalmazást és minimalizálva a pazarlást. Ezenkívül az epoxi ragasztók hosszú nyitott idővel rendelkeznek, így elegendő munkaidőt biztosítanak az alkatrészek összeszereléséhez, mielőtt a ragasztó megköt.
Vezetőképes ragasztók: lehetővé teszik az elektromos csatlakozást
A vezetőképes ragasztók speciális ragasztóanyag-típusok, amelyek tapadó és vezető tulajdonságokkal is rendelkeznek. Úgy tervezték, hogy lehetővé tegyék az elektromos csatlakoztatást különböző alkalmazásokban, ahol a hagyományos forrasztási módszerek esetleg nem megvalósíthatók vagy nem kívánatosak. Ezek a ragasztók számos előnnyel rendelkeznek, beleértve a könnyű használatot, a környezetbarátságot és a sokoldalúságot.
A vezetőképes ragasztók egyik kritikus előnye a könnyű használat. Ellentétben a forrasztással, amely hőigényes és összetett is lehet, a vezetőképes ragasztók egyszerűen felvihetők a ragasztónak a kívánt felületekre történő adagolásával vagy eloszlatásával. Ezáltal a felhasználók széles köre számára alkalmasak, a szakemberektől a hobbiig, és nincs szükség speciális felszerelésre.
A környezetbarátság a vezetőképes ragasztók másik előnye. A forrasztástól eltérően, amely jellemzően ólomalapú forrasztóanyagokat tartalmaz, a vezetőképes ragasztók nem mérgező anyagokkal is előállíthatók. Ez környezetbarátabbá és biztonságosabbá teszi őket, csökkentve ezzel a felhasználók egészségügyi kockázatait. Ezenkívül az ólom hiánya miatt ezek a ragasztók megfelelnek a veszélyes anyagok használatát korlátozó előírásoknak.
A vezetőképes ragasztók sokoldalúságot kínálnak az összeragasztható anyagok tekintetében is. Csatlakozhatnak vezető anyagokhoz, például fémekhez és nem vezető anyagokhoz, például műanyagokhoz, kerámiákhoz és üvegekhez. Ez a széles körű kompatibilitás lehetővé teszi több anyagból álló összeállítások létrehozását integrált elektromos csatlakozással, ami új tervezési lehetőségeket nyit meg a különböző iparágakban.
Ezeknek a ragasztóknak a vezetőképességét úgy érik el, hogy vezetőképes töltőanyagokat, például ezüst- vagy szénrészecskéket adnak a ragasztómátrixba. Ezek a töltőanyagok vezető utakat képeznek, amelyek lehetővé teszik az elektromos áram áramlását a ragasztott felületeken. A töltőanyag és a koncentráció kiválasztása a speciális vezetőképességi követelményekhez igazítható, lehetővé téve a ragasztó elektromos tulajdonságainak finomhangolását.
A vezetőképes ragasztók alkalmazása széles körben elterjedt. Általában az elektronikai iparban használják alkatrészek ragasztására, forrasztási folyamatok helyettesítésére vagy kiegészítésére. A vezetőképes ragasztók különösen előnyösek olyan kényes elektronikus alkatrészek összeillesztésekor, amelyek nem bírják a forrasztással járó magas hőmérsékletet. Rugalmas áramkörök, RFID-címkék és érintőképernyők gyártására is használják őket, ahol előnyös a különféle hordozókhoz való kötődési képességük.
Az autóiparban a vezetőképes ragasztók érzékelőket, vezérlőegységeket és világítási rendszereket szerelnek össze. Nem mechanikus kötési képességeik csökkentik a feszültségkoncentrációs pontokat, javítva az elektromos csatlakozás megbízhatóságát és hosszú élettartamát. Ezenkívül a vezetőképes ragasztók lehetővé teszik a járművek tömegének csökkentését, mivel nincs szükség nehézfém csatlakozókra.
Az elektronikán és az autóipari alkalmazásokon túl a vezetőképes ragasztókat orvosi eszközökben, repülőgép-alkatrészekben és még olyan fogyasztói termékekben is használják, mint a hordható elektronika. Sokoldalúságuk, egyszerű használatuk és környezeti előnyeik vonzóvá teszik az ipari tervezők és mérnökök számára.
Rögzítőszerszámok: Félvezető chipek ragasztása az aljzatokhoz
Az öntapadó ragasztók döntő szerepet játszanak a félvezetőiparban, mivel megbízható és hatékony módszert biztosítanak a félvezető chipek hordozókhoz való ragasztására. Ezek a ragasztók interfészként szolgálnak a chip és a hordozó között, biztosítva a biztonságos és elektromosan vezető kapcsolatot.
A préselt ragasztók elsődleges funkciója a mechanikai támaszték és az elektromos összeköttetés biztosítása a chip és a hordozó között. Kiváló adhéziós tulajdonságokkal kell rendelkezniük annak biztosításához, hogy a forgács biztonságosan rögzítve maradjon az aljzathoz különféle működési körülmények között, beleértve a hőciklust, a mechanikai igénybevételt és a környezeti hatásokat.
A stancolt ragasztókkal szembeni egyik kritikus követelmény a magas hőmérsékletnek való ellenálló képességük. A forgács-összeállítási folyamatok során, mint például a forrasztási újrafolyatás vagy a hőkompressziós kötés, a ragasztónak meg kell őriznie integritását és adhéziós szilárdságát. A stancolt ragasztókat általában úgy tervezték, hogy ellenálljanak a 200 °C feletti hőmérsékletnek, így biztosítva a kötés megbízhatóságát.
Az öntapadó ragasztókat általában epoxi alapú és forrasztó alapú ragasztókra osztják. Az epoxi alapú ragasztók hőre keményedő anyagok, amelyek hő hatására megkeményednek. Kiváló tapadást, magas hővezető képességet és elektromos szigetelést biztosítanak. Másrészt a forrasztó alapú ragasztók olyan fémötvözetből állnak, amely a kötési folyamat során megolvad. Alacsony ellenállású elektromos utat és magas hővezető képességet biztosítanak, így alkalmasak nagy teljesítményű disszipációs alkalmazásokhoz.
A préselt ragasztó kiválasztása számos tényezőtől függ, beleértve a konkrét alkalmazást, a működési feltételeket és a hordozóanyagot. A ragasztónak kompatibilisnek kell lennie azokkal az anyagokkal, amelyekhez ragasztják, biztosítva a megfelelő tapadást és megakadályozva a káros kölcsönhatásokat. A ragasztónak jó adagolási és folyási jellemzőkkel is kell rendelkeznie, hogy megkönnyítse a ragasztást, és minimalizálja az üregeket vagy hézagokat a forgács és a hordozó között.
A megbízható kötés eléréséhez elengedhetetlen a felület előkészítése. Az aljzat és a forgácsfelületeket alaposan meg kell tisztítani a szennyeződések, oxidok és egyéb, a tapadást akadályozó szennyeződések eltávolítása érdekében. A felületkezelési technikákat, például a plazmatisztítást, a kémiai maratást vagy az ultrahangos tisztítást gyakran alkalmazzák a ragasztó ragasztási teljesítményének javítására.
Miután a szerszámhoz rögzítő ragasztót felvitték, a forgácsot óvatosan helyezik el és igazítják az alapfelületre. Nyomás vagy hő használható a megfelelő nedvesítés és érintkezés biztosítására a ragasztó és a ragasztandó felületek között. A ragasztó ezután kikeményedik vagy megszilárdul, és ezzel befejeződik a kötési folyamat.
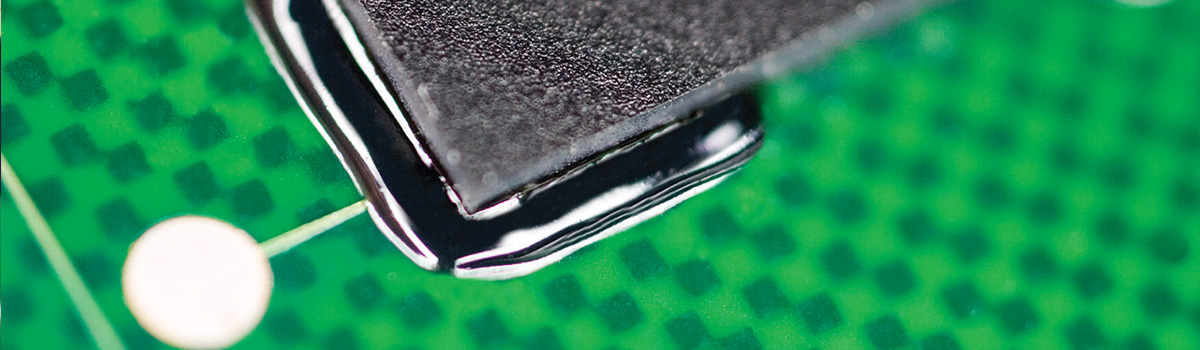
Alultöltő ragasztók: védelem a hőterhelés ellen
Az alátöltő ragasztók alapvető anyagok, amelyeket az elektronikus csomagolásban használnak a hőterhelés elleni védelem érdekében. Mechanikai megerősítést biztosítanak, és javítják az elektronikus eszközök megbízhatóságát azáltal, hogy minimalizálják a hőciklusok és a mechanikai ütések hatását.
A hőfeszültség jelentős aggodalomra ad okot az elektronikai szerelvényekben a különböző anyagok közötti hőtágulási együttható (CTE) eltérése miatt. Amikor egy eszköz hőmérséklet-ingadozáson megy keresztül, az anyagok különböző sebességgel tágulnak és zsugorodnak, és olyan feszültségeket fejlesztenek ki, amelyek meghibásodhatnak. Az alátöltő ragasztók segítenek enyhíteni ezt a problémát azáltal, hogy pufferként működnek a forgács és a hordozó között, elnyelve és elosztva a hőciklus okozta feszültséget.
Az alátöltő ragasztók elsődleges funkciója az integrált áramköri (IC) chipet a hordozóval összekötő forrasztási kötések megerősítése. A gyártás során a chipet forraszanyag segítségével rögzítik az alapfelületre, amely kötést hoz létre a két alkatrész között. A chip és a hordozó közötti CTE eltérés azonban feszültségkoncentrációt okozhat a forrasztási kötéseknél. Az alátöltő ragasztókat a forgács és az aljzat közötti résbe fecskendezik, kitöltve az üregeket, és robusztus és rugalmas réteget képeznek. Ez a réteg csökkenti a feszültségkoncentrációt, javítva a szerelvény általános mechanikai integritását.
Az alátöltő ragasztók kiváló hővezető képességgel is rendelkeznek, ami elengedhetetlen az elektronikus alkatrészek által termelt hő elvezetéséhez. A hatékony hőelvezetés létfontosságú a túlmelegedés megelőzéséhez, valamint a készülék teljesítményének és élettartamának megőrzéséhez. A forgácsról az aljzatra való hőátadás elősegítésével az alátöltő ragasztók segítenek fenntartani a stabil működési hőmérsékletet, és megakadályozzák, hogy a hőterhelés károsítsa az IC-t.
Ezenkívül az alátöltő ragasztók védenek a nedvességtől és a szennyeződésektől. Az elektronikus eszközök gyakran vannak kitéve zord környezetnek, beleértve a nedvességet és a különféle vegyi anyagokat, amelyek ronthatják teljesítményüket és megbízhatóságukat. Az alátöltő anyagok gátat képeznek, megakadályozzák a nedvesség bejutását és a káros anyagok bejutását a forgácscsomagba. Ez a védelem segít megőrizni az elektromos teljesítményt és meghosszabbítja a készülék élettartamát.
Flip Chip ragasztók: Miniatürizálás engedélyezése
A flip chip ragasztók kulcsfontosságúak a különféle elektronikus eszközök miniatürizálásának lehetővé tételében. A technológia fejlődésével folyamatosan igény mutatkozik a kisebb, könnyebb és erősebb gépekre. A flip-chip kötés az ilyen eszközökben a nagy sűrűségű összeköttetések megvalósításának kedvelt módszereként jelent meg. Ezek a ragasztók megkönnyítik a közvetlen elektromos és mechanikai kapcsolatot a chip és a hordozó között, számos előnyt kínálva a miniatürizáláshoz.
A flip-chip ragasztók egyik kritikus előnye, hogy képesek csökkenteni az elektronikus csomagok teljes méretét. A hagyományos huzalkötési technikák helyet igényelnek a huzalhurkok számára, ami korlátozza az elérhető eszközméretet. Ezzel szemben a flip-chip kötés megszünteti a huzalhurkok szükségességét, jelentősen csökkentve a csomagolás méretét. A kisebb helyigény jelentős a hordozható elektronikai eszközökben, például okostelefonokban, táblagépekben és hordható eszközökben, ahol a hely prémium.
Ezenkívül a flip-chip ragasztók növelik az eszköz teljesítményét. A chip és a hordozó közötti közvetlen elektromos kapcsolat csökkenti a jelút hosszát és az induktivitást, javítva az elektromos teljesítményt. Ez különösen fontos a nagy sebességű alkalmazásoknál, például mikroprocesszoroknál és memóriachipeknél, ahol kritikus a jelkésleltetés és -veszteség minimalizálása. A flip chip kötés hozzájárul a gyorsabb adatátviteli sebességhez, az alacsonyabb energiafogyasztáshoz és az eszköz fokozott megbízhatóságához a parazita hatások csökkentésével.
Ezenkívül a flip-chip ragasztók kiváló hőkezelési képességeket kínálnak. A hőleadás kezelése jelentős kihívássá válik, mivel az elektronikus alkatrészek erősebbek és sűrűbben vannak csomagolva. A flip chip ragasztás lehetővé teszi a forgács közvetlen rögzítését az aljzathoz, ami javítja a hőátadás hatékonyságát. Ez hatékony hőelvezetést tesz lehetővé, megakadályozza a túlmelegedést és javítja a készülék általános megbízhatóságát és élettartamát. A hatékony hőkezelés elengedhetetlen az olyan nagy teljesítményű eszközökhöz, mint a grafikus feldolgozó egységek (GPU-k) és a központi feldolgozó egységek (CPU-k).
A flip-chip ragasztók másik előnye a mechanikai stabilitásuk. A flip-chip ragasztáshoz használt ragasztóanyagok szilárd és megbízható összeköttetéseket biztosítanak. A huzalkötések hiánya kiküszöböli a huzaltörés vagy kifáradás kockázatát, így biztosítva a hosszú távú mechanikai integritást. A flip-chip ragasztók robusztussága alkalmassá teszi őket olyan nehéz üzemi körülményeknek kitett alkalmazásokhoz, mint például az autóelektronika vagy az űrrepülési rendszerek.
Ezenkívül a flip-chip ragasztók támogatják a nagy sűrűségű összekapcsolásokat. A flip-chip kötés segítségével kis területen nagyszámú csatlakozást lehet elérni, ami több funkcionalitás integrálását teszi lehetővé korlátozott helyen. Ez különösen előnyös olyan összetett elektronikus eszközök esetében, amelyek számos bemeneti/kimeneti kapcsolatot igényelnek, mint például integrált áramkörök, érzékelők vagy mikroelektromechanikai rendszerek (MEMS). A flip-chip ragasztók által lehetővé tett nagy sűrűségű összekapcsolások hozzájárulnak az eszköz általános miniatürizálásához.
Kapszulázó ragasztók: Az érzékeny komponensek védelme
A kapszulázó ragasztók nélkülözhetetlenek az érzékeny elektronikus alkatrészek különféle környezeti tényezőktől, mechanikai igénybevételtől és vegyi expozíciótól való védelmében. Ezek a ragasztók védőréteget képeznek, beágyazzák az elemeket, és biztosítják azok hosszú élettartamát és megbízhatóságát. Ez a cikk feltárja a kapszulázó ragasztók fontosságát és szerepüket az érzékeny alkatrészek védelmében.
Az érzékeny elektronikus alkatrészek, mint például az integrált áramkörök, érzékelők és a kényes vezetékek érzékenyek a nedvesség, por, hőmérséklet-ingadozások és fizikai hatások által okozott károsodásokra. A kapszulázó ragasztók megbízható megoldást kínálnak azáltal, hogy védőréteget képeznek ezen alkatrészek körül. Gátként működnek, megvédik az alkatrészeket a külső elemektől, amelyek veszélyeztethetik a működést vagy idő előtti meghibásodáshoz vezethetnek.
A kapszulázó ragasztók egyik kritikus tulajdonsága, hogy ellenállnak a nedvesség behatolásának. A nedvesség korróziót, rövidzárlatot és elektromos szivárgást okozhat, ami a készülék meghibásodásához vezethet. A kapszulázó ragasztók kiváló nedvességállóságot biztosítanak, meggátolva a víz vagy páragőz bejutását az érzékeny alkatrészekbe. Ez a funkció döntő fontosságú a magas páratartalmú vagy nedves környezetben lévő alkalmazásokban, például az autóelektronikában vagy a kültéri ipari berendezésekben.
A nedvesség elleni védelem mellett a kapszulázó ragasztók kiváló vegyszerállóságot is biztosítanak. Ellenállnak a különféle vegyszereknek, beleértve az oldószereket, savakat, lúgokat és tisztítószereket. Ez az ellenállás biztosítja, hogy az érzékeny komponensekre ne legyenek hatással a kémiai kölcsönhatások, megőrizve integritásukat és funkcionalitásukat.
A kapszulázó ragasztók mechanikai védelmet is nyújtanak az érzékeny alkatrészeknek. Lengéscsillapítóként működnek, eloszlatják a mechanikai igénybevételt és a rezgéseket, amelyek károsíthatják az alkatrészeket. Ez a funkció létfontosságú a gyakori mozgásnak kitett alkalmazásokban, mint például a repülőgépipar, az autóipar és a fogyasztói elektronika.
Ezenkívül a kapszulázó ragasztók kiváló hőkezelési tulajdonságokat kínálnak. Nagy hővezető képességgel rendelkeznek, lehetővé téve a hatékony hőelvezetést az érzékeny alkatrészekről. Ezek a ragasztók segítenek fenntartani az optimális működési hőmérsékletet azáltal, hogy hatékonyan elvezetik a hőt, megakadályozzák a hőterhelést és biztosítják a hosszú távú megbízhatóságot.
A kapszulázó ragasztók másik előnye, hogy képesek javítani az elektronikus szerelvények szerkezeti integritását. A különböző alkatrészek kapszulázása és összekapcsolása további szilárdságot és stabilitást biztosít a teljes rendszer számára. Ez a funkció különösen előnyös olyan alkalmazásokban, ahol elengedhetetlen a mechanikai robusztusság, mint például az ipari vezérlőrendszerek vagy a katonai minőségű elektronika.
A kapszulázó ragasztók különféle összetételűek, hogy megfeleljenek a különböző alkalmazási követelményeknek. Lehetnek szobahőmérsékleten keményedő folyékony ragasztók vagy nagy teljesítményű alkalmazásokhoz használt hővezető vegyületek. A megfelelő ragasztó kiválasztása olyan tényezőktől függ, mint a kívánt védelmi szint, működési feltételek, kötési idő és összeszerelési folyamat.
Alacsony gázkibocsátású ragasztók: kritikus fontosságú űripari alkalmazásokhoz
Az alacsony gázkibocsátású ragasztók kritikus szerepet játszanak az űralkalmazásokban, ahol elengedhetetlen a tiszta és ellenőrzött környezet fenntartása. A gázkibocsátás az illékony szerves vegyületek (VOC) és egyéb szennyeződések anyagokból, köztük a ragasztókból való vákuum vagy alacsony nyomás alatti kibocsátását jelenti. A gázkibocsátás károsíthatja az érzékeny berendezéseket, optikai rendszereket és űrhajók felületeit az űr szélsőséges körülményei között, ahol nincs légköri nyomás. Ezért az alacsony gázkibocsátású ragasztók használata kiemelten fontos az űrmissziók megbízható teljesítményének és hosszú élettartamának biztosításához.
A gázkibocsátással kapcsolatos egyik elsődleges probléma a szennyeződések kritikus felületekre, például optikai lencsékre és érzékelőkre való lerakódása. A szennyeződések vékony filmréteget képezhetnek ezeken a felületeken, csökkentve átlátszóságukat, rontva a teljesítményt, és megzavarva a tudományos méréseket. Az optikai rendszerek esetében a nyitottság enyhe csökkenése is jelentősen befolyásolhatja az űrből gyűjtött képek és adatok minőségét. Az alacsony gázkibocsátású ragasztókat úgy tervezték, hogy minimalizálják az illékony vegyületek felszabadulását, csökkentve a szennyeződés kockázatát és megőrizzék az érzékeny műszerek működőképességét.
Az alacsony gázkibocsátású ragasztók másik kritikus szempontja az elektronikus alkatrészekre és áramkörökre gyakorolt hatás. A gázkibocsátás során felszabaduló illékony szerves vegyületek korrodálhatják vagy leronthatják az érzékeny elektronikus rendszereket, ami meghibásodásokhoz vagy teljes meghibásodáshoz vezethet. Ez különösen vonatkozik az űrhajókra, ahol az elektronikus alkatrészek a tér vákuumának, szélsőséges hőmérséklet-ingadozásoknak és sugárzásnak vannak kitéve. Az alacsony gázkibocsátású ragasztók alacsony gőznyomású anyagokból készülnek, minimálisra csökkentve a korrozív anyagok felszabadulását és védve az elektronikus rendszerek integritását.
Ezenkívül a gázkibocsátás az űrhajósok egészségét és a legénységgel rendelkező űrhajók lakhatóságát is veszélyeztetheti. Zárt környezetben, például űrkapszulákban vagy űrállomásokon a gázkibocsátásból származó VOC-ok felhalmozódása kellemetlen vagy veszélyes légkört hozhat létre. Az alacsony gázkibocsátású ragasztók segítenek csökkenteni ezt a kockázatot az illékony vegyületek kibocsátásának csökkentésével, biztonságos és egészséges környezetet biztosítva az űrhajósok számára küldetésük során.
Az alacsony gázkibocsátási tulajdonságok elérése érdekében az űralkalmazásokban használt ragasztók szigorú tesztelési és minősítési folyamatokon mennek keresztül. Ezek a folyamatok magukban foglalják a ragasztók szimulált térviszonyoknak való kitételét, beleértve a vákuumkamrákat, a szélsőséges hőmérsékleteket és a különböző környezeti terheléseket. Azok a ragasztók, amelyek megfelelnek az alacsony gázkibocsátás szigorú követelményeinek, tanúsítvánnyal és jóváhagyással rendelkeznek az űrmissziókban való használatra.
Ostyaszintű ragasztó ragasztók: a költségek csökkentése és a hozam növelése
Az ostyaszintű kötés kulcsfontosságú folyamat a félvezetőiparban, ahol több chipet vagy lapkát kapcsolnak össze, hogy összetett integrált áramköröket képezzenek. Hagyományosan ez a kötési folyamat forrasztási dudorokat vagy huzalkötési technikákat tartalmazott, amelyek precíz igazítást és minden chip egyedi ragasztását igényelnek, ami magasabb költségeket és alacsonyabb hozamot eredményez. A ragasztótechnológiák fejlődése azonban megnyitotta az utat az ostyaszintű kötőragasztók számára, amelyek költségcsökkentést és nagyobb hozamot kínálnak a félvezetőgyártásban.
Az ostyaszintű kötőragasztókat úgy tervezték, hogy megbízható és robusztus kötést biztosítsanak az ostyák vagy forgácsok között ostyaszinten, így nincs szükség egyedi ragasztási eljárásokra. Ezeket a ragasztókat jellemzően vékony rétegként alkalmazzák az ostyák közé, és ellenőrzött körülmények között keményítik a kívánt kötési szilárdság elérése érdekében. Íme néhány kulcsfontosságú tényező, amelyek hozzájárulnak a költségcsökkentéshez és a jobb hozamhoz:
- Folyamategyszerűsítés: Az ostyaszintű kötőragasztók leegyszerűsítik a ragasztási folyamatot azáltal, hogy lehetővé teszik több chip vagy lapka egyidejű ragasztását egyetlen lépésben. Ezzel szükségtelenné válik az egyes chipek bonyolult igazítása és egyedi ragasztása, ami időt takarít meg és csökkenti a gyártási költségeket. Ezenkívül a ragasztó egyenletesen felvihető nagy felületre, biztosítva az egyenletes tapadást az ostyán.
- Nagy kötési szilárdság és megbízhatóság: Az ostyaszintű kötőragasztók kiváló tapadási tulajdonságokat kínálnak, ami nagy kötési szilárdságot eredményez az ostyák között. Ez a robusztus kötés megbízható összekapcsolhatóságot biztosít, és minimalizálja a rétegvesztés vagy meghibásodás kockázatát a következő gyártási lépések vagy az eszköz működése során. A ragasztó mechanikai, termikus és elektromos tulajdonságai a speciális alkalmazási követelményekhez szabhatók, tovább növelve a megbízhatóságot.
- Költséghatékony anyagok: Az ostyaszintű kötőragasztók gyakran költséghatékony anyagokat használnak a hagyományos ragasztási technikákhoz képest. Ezeket a ragasztókat különféle polimerek, például epoxik, poliimidek vagy akrilátok felhasználásával állíthatjuk elő, amelyek könnyen beszerezhetők és jó teljesítményt nyújtanak elfogadható áron. A különféle anyagok közötti választás lehetővé teszi a gyártók számára, hogy a teljesítmény, az ár és a különböző aljzatokkal való kompatibilitás alapján optimalizálják a ragasztó kiválasztását.
- Termésjavítás: Az ostyaszintű kötőragasztók hozzájárulnak a jobb hozamhoz a félvezetőgyártásban. A ragasztó egyenletes felhordása az ostyán minimálisra csökkenti az üregek, a levegő beszorulásának vagy az egyenetlen ragasztásnak a kockázatát, ami hibákhoz vagy meghibásodásokhoz vezethet. Ezen túlmenően, az egyedi forgácstapadások kiküszöbölése csökkenti a kötési folyamat során bekövetkező eltérések vagy sérülések esélyét, ami magasabb hozamot és kisebb selejt arányt eredményez.
- Kompatibilitás a fejlett csomagolási technológiákkal: Az ostyaszintű kötőragasztók kompatibilisek a különféle fejlett csomagolási technológiákkal, mint például az ostyaszintű chip-méretű csomagolással (WLCSP), az ostyaszintű csomagolással (FOWLP) vagy a 3D-s integrációs folyamatokkal. Ezek a ragasztók lehetővé teszik több chip vagy különböző komponensek integrálását egy kompakt formába, megkönnyítve a miniatürizálást és lehetővé téve az elektronikus eszközök fejlett funkcionalitását.

UV-re keményedő ragasztók: Gyors és precíz ragasztás
Az UV-re keményedő ragasztók olyan forradalmi ragasztók, amelyek gyors és precíz ragasztást tesznek lehetővé. Különböző iparágakban népszerűségre tettek szert egyedi tulajdonságaik és a hagyományos ragasztókkal szembeni előnyeik miatt. Az UV-re keményedő ragasztók jellemzően monomerből, fotoiniciátorból és stabilizátorból állnak. Ultraibolya (UV) fénynek kitéve ezek a ragasztók fotokémiai reakción mennek keresztül, ami gyors kikeményedést és kötést eredményez.
Az UV-sugárzással keményedő ragasztók egyik kritikus előnye a gyors kötési idő. Ellentétben a hagyományos kötésekkel, amelyeknél órákra vagy akár napokra van szükség a teljes kikeményedéshez, az UV-re keményedő ragasztók másodpercek vagy percek alatt megkeményednek. Ez a gyors kikeményedési idő jelentősen növeli a termelés hatékonyságát és csökkenti a futószalag várakozási idejét, ami jelentős költségmegtakarítást eredményez a gyártók számára. Az azonnali kötésképzés lehetővé teszi a ragasztott komponensek azonnali kezelését és további feldolgozását is.
Az UV-re keményedő ragasztók precíz ragasztóképessége további jelentős előny. A ragasztó folyékony marad mindaddig, amíg UV fénynek nem teszik ki, így elegendő időt biztosít a ragasztandó részek igazítására és pozicionálására. Miután a ragasztó UV fénynek van kitéve, gyorsan megszilárdul, így szilárd és tartós kötést hoz létre. Ez a precíz ragasztási képesség a nagy pontosságot és szűk tűrést igénylő alkalmazások számára előnyös, mint például az elektronika, az optika és az orvosi eszközök.
Az UV-re keményedő ragasztók kiváló kötési szilárdságot és tartósságot is biztosítanak. A kikeményedett ragasztó erős kötést képez, amely ellenáll a különböző környezeti tényezőknek, beleértve a szélsőséges hőmérsékleteket, a nedvességet és a vegyszereket. Ez biztosítja a ragasztott alkatrészek hosszú élettartamát és megbízhatóságát, így az UV-re keményedő ragasztók alkalmasak az igényes alkalmazásokhoz.
Ezenkívül az UV-re keményedő ragasztók oldószermentesek és alacsony illékony szerves vegyület (VOC) kibocsátással rendelkeznek. A száradást igénylő és potenciálisan káros gőzöket kibocsátó oldószer alapú ragasztókkal ellentétben az UV-re keményedő ragasztók környezetbarátak és biztonságosak. Ez vonzó választássá teszi azokat az iparágak számára, amelyek célja, hogy csökkentsék környezeti lábnyomukat, és megfeleljenek az előírásoknak.
Az UV-re keményedő ragasztók sokoldalúsága egy másik figyelemre méltó szempont. Különböző anyagokat, köztük üveget, fémet, műanyagot, kerámiát és még eltérő felületeket is képesek ragasztani. Ez a széles körű kompatibilitás teszi az UV-re keményedő ragasztókat alkalmassá az autóipar, a repülőgépipar, az elektronikai és az orvosi ipar különféle felhasználási területeire.
Vezetőképes paszta ragasztók: rugalmas és nyomtatott elektronika lehetővé tétele
A vezetőképes pasztaragasztók a rugalmas és nyomtatott elektronika fejlesztésének kritikus technológiájaként jelentek meg. Ezek az innovatív anyagok ötvözik a hagyományos ragasztók tulajdonságait a fémek vezetőképességével, és új lehetőségeket nyitnak meg az elektronikus eszközök különféle hordozókon történő gyártásához és integrálásához.
A vezetőképes pasztaragasztók egyik fő előnye, hogy mind mechanikai tapadást, mind elektromos vezetőképességet biztosítanak. A hagyományos ragasztók jellemzően szigetelők, ami korlátozza az elektronikus alkalmazásokban való felhasználásukat. A vezetőképes pasztaragasztók viszont vezetőképes részecskéket, például ezüstöt, rezet vagy szenet tartalmaznak, amelyek megkönnyítik az elektromos áram áramlását. Ez a kettős funkció lehetővé teszi, hogy ragasztóként és vezető útként is szolgáljanak, így ideálisak elektronikus alkatrészek ragasztására vagy vezető nyomok létrehozására rugalmas hordozókon.
A vezetőképes pasztaragasztók rugalmassága egy másik kritikus jellemző, amely alkalmassá teszi őket rugalmas elektronikához. Ezek a ragasztók megőrzik elektromos vezetőképességüket még hajlításnak, nyújtásnak vagy csavarásnak kitéve is. Ez a rugalmasság kulcsfontosságú az olyan alkalmazásoknál, mint a hordható eszközök, a rugalmas kijelzők és a konform elektronika, ahol a hagyományos merev áramkörök kivitelezhetetlenek vagy lehetetlenek lennének. A vezetőképes paszta ragasztók robusztus és megbízható elektromos csatlakozások létrehozását teszik lehetővé rugalmas felületeken, biztosítva a rugalmas elektronikus eszközök teljesítményét és tartósságát.
Ezenkívül a vezetőképes pasztaragasztók kompatibilisek különféle nyomtatási technikákkal, például szitanyomással, tintasugaras nyomtatással és flexonyomtatással. Ez a kompatibilitás lehetővé teszi a nyomtatott elektronika nagy volumenű és költséghatékony gyártását. A nyomtatási eljárások lehetővé teszik a vezetőképes paszta ragasztók precíz mintázatú lerakódását, ami lehetővé teszi összetett áramkörök és elektronikus tervek létrehozását minimális anyagveszteséggel. A vezetőképes nyomok közvetlenül rugalmas hordozóra történő nyomtatásának lehetősége leegyszerűsíti a gyártási folyamatot és csökkenti a gyártási időt, így a nyomtatott elektronika életképes megoldást jelent a nagyméretű gyártáshoz.
A vezetőképes pasztaragasztók a hőkezelés szempontjából is előnyöket kínálnak. A vezetőképes részecskék jelenléte ezekben a ragasztókban elősegíti az elektronikus alkatrészek által generált hőelvezetést. Ez a tulajdonság döntő fontosságú a jelentős hőt termelő eszközök, például a teljesítményelektronika vagy a nagy teljesítményű LED-ek megbízhatóságának és teljesítményének biztosításához. Vezetőképes pasztaragasztók termikus interfészként történő felhasználásával a hő hatékonyan továbbítható a hőt termelő komponensről a hűtőbordára, javítva az eszköz általános teljesítményét és élettartamát.
Forrasztópaszták: az öntapadó ragasztás alternatívája
A forrasztópaszták, más néven forrasztópaszták, alternatívát kínálnak a ragasztással szemben különféle alkalmazásokban. Míg a ragasztós kötés során ragasztót használnak az anyagok összekapcsolására, a forrasztópaszták más mechanizmust alkalmaznak a robusztus és megbízható kötés eléréséhez. Ebben a válaszban a forrasztópasztákat vizsgáljuk meg, mint a ragasztás alternatíváját 450 szóban.
A forrasztópaszták fémötvözet részecskék, folyasztószer és kötőanyag keverékéből állnak. A fémötvözet részecskéi általában ónból, ólomból, ezüstből vagy ezek kombinációjából állnak. A változás elősegíti a forrasztási folyamatot azáltal, hogy eltávolítja az oxidokat a fémfelületekről, és elősegíti a nedvesedést és a tapadást. A kötőanyag összetartja a pasztát, és lehetővé teszi annak könnyű felvitelét.
A forrasztópaszták egyik elsődleges előnye a ragasztással szemben a kötés szilárdsága és tartóssága. A forrasztás kohászati kötést hoz létre az összekapcsolt anyagok között, így erős kötés jön létre, amely ellenáll a különféle mechanikai, hő- és elektromos igénybevételeknek. A forrasztott kötés gyakran robusztusabb és megbízhatóbb, mint az öntapadó kötések, amelyek idővel vagy bizonyos körülmények között leépülhetnek.
A forrasztópaszták gyorsabb és hatékonyabb kötési folyamatot is kínálnak. A paszta precízen felhordható a kívánt területekre, és a kötést úgy alakíthatjuk ki, hogy a szerelvényt a forrasztás olvadáspontjára melegítjük. Ez a folyamat gyakran gyorsabb, mint az öntapadós ragasztás, ami kikeményedési vagy száradási időt igényelhet. Ezenkívül a forrasztópaszták lehetővé teszik több alkatrész egyidejű összekapcsolását, csökkentve az összeszerelési időt és növelve a termelékenységet.
További előnye a forrasztópaszták sokoldalúsága a különböző anyagok összekapcsolásában. A ragasztásnak korlátai lehetnek különböző anyagok vagy eltérő hőtágulási együtthatójú anyagok ragasztása esetén. A forrasztópaszták megbízható kötéseket képezhetnek különböző anyagok, köztük fémek, kerámiák és egyes műanyagok között, így sokféle alkalmazásra alkalmasak.
Ezenkívül a forrasztópaszták javíthatják a hő- és elektromos vezetőképességet a ragasztáshoz képest. Ez a tulajdonság különösen előnyös azokban az alkalmazásokban, ahol a hőelvezetés vagy az elektromos folytonosság döntő fontosságú, mint például az elektronikus szerelvények – a forrasztott csatlakozás közvetlen fémpályát képez, elősegítve a hatékony hőátadást és az elektromos vezetést.
Fontos azonban megjegyezni, hogy a forrasztópasztáknak is vannak megfontolásai és korlátai. Például egyes forrasztóötvözetek ólmot tartalmaznak, ami környezetvédelmi és egészségügyi megfontolások miatt korlátozott lehet. Alternatív megoldásként ólommentes forrasztópasztákat fejlesztettek ki, de eltérő tulajdonságokkal rendelkezhetnek, és speciális eljárási megfontolásokat igényelnek.
Ragasztóadagolási technikák: pontosság és hatékonyság
A ragasztóanyag-adagolási technikák kulcsfontosságúak a különböző iparágakban, a gyártástól az építőiparig. A ragasztófelvitel pontossága és hatékonysága elengedhetetlen a megbízható kötések biztosításához, a hulladék minimalizálásához és az általános termelékenység javításához. Ez a cikk olyan kritikus technikákat tár fel, amelyek elősegítik a ragasztóanyag-adagolás pontosságát és hatékonyságát.
- Automatizált adagolórendszerek: Az automatizált adagolórendszerek robotkarokat vagy számítógép által vezérelt berendezéseket használnak a ragasztók pontos felviteléhez. Ezek a rendszerek nagy megismételhetőséget, pontosságot és sebességet kínálnak, biztosítva a folyamatos ragasztófelvitelt több alkatrészen vagy terméken. Az emberi hibák kiküszöbölésével az automatizált rendszerek minimalizálják a pazarlást és javítják a ragasztóanyag-adagolási folyamatok hatékonyságát.
- Adagoló- és keverőrendszerek: Egyes alkalmazásokhoz két vagy több komponens adagolása szükséges, amelyeket meghatározott arányban kell összekeverni. Az adagoló- és keverőrendszerek precízen mérik és kombinálják a ragasztókomponenseket az elosztás előtt, így biztosítva a pontos arányokat és az egyenletes minőséget. Ezek a rendszerek különösen előnyösek kétkomponensű epoxik, poliuretánok és más reaktív ragasztók esetében.
- Nyomásvezérelt adagolás: A nyomásvezérelt adagolási technikák során pneumatikus vagy hidraulikus rendszereket használnak a ragasztó áramlási sebességének és nyomásának szabályozására. A ragasztó adagolása szabályozott sebességgel történik az állandó erő fenntartásával, a pontos felvitel biztosításával és a felesleges ragasztóanyag minimalizálásával. A nyomásvezérelt adagolást általában olyan alkalmazásokhoz használják, amelyek finom vonalakat, pontokat vagy bonyolult mintákat igényelnek.
- Fúvóka és tűadagolás: A fúvókás és tűadagolási technikák olyan alkalmazásokhoz alkalmasak, amelyek nagy sebességű és precíz ragasztófelhelyezést igényelnek. A sugárzó rendszerek nyomásimpulzusokat használnak az apró cseppek vagy folyamatos ragasztóvonalak adagolására. Másrészt a tűadagolás során tűt vagy fúvókát használnak a ragasztó szabályozott mennyiségben történő felhordására. Ezeket a technikákat általában az elektronikai összeszerelésben használják, ahol kicsi, precíz ragasztólerakódásokra van szükség.
- Permetező- és bevonórendszerek: Nagy felületű ragasztási vagy bevonatolási alkalmazásokhoz a permetező- és bevonórendszerek hatékony ragasztóadagolást biztosítanak. Ezek a rendszerek porlasztási technikákat alkalmaznak, hogy finom permetet vagy ragasztópermetet hozzanak létre, egyenletes fedést és minimális hulladékot biztosítva. A permetező- és bevonórendszereket széles körben használják az autóiparban, a repülőgépiparban és a bútorgyártásban.
- Adagolószelepek és fúvókák: Az adagolószelepek és fúvókák kiválasztása kulcsfontosságú a ragasztóanyag-adagolás pontosságának eléréséhez. A különböző típusú szelepek és fúvókák, például tűszelepek, membránszelepek vagy kúpos fúvókák, különböző szabályozást kínálnak az áramlási sebesség, a minta és a cseppméret felett. A precíz és hatékony adagolás eléréséhez elengedhetetlen a megfelelő szelep vagy fúvóka kiválasztása az adott ragasztó- és alkalmazási követelményeknek megfelelően.
- Látásvezérelt rendszerek: A látásvezérelt adagolórendszerek kamerákat és fejlett szoftvereket használnak az alkatrészek vagy hordozók helyzetének észlelésére és nyomon követésére. A rögzített képeket elemezve a rendszer valós időben állítja be a ragasztóadagolási paramétereket, így biztosítva a pontos elhelyezést egyenetlen felületeken vagy változó alkatrészméreteken is. A látásvezérelt rendszerek növelik a pontosságot és a hatékonyságot, miközben alkalmazkodnak a folyamatváltozatokhoz.
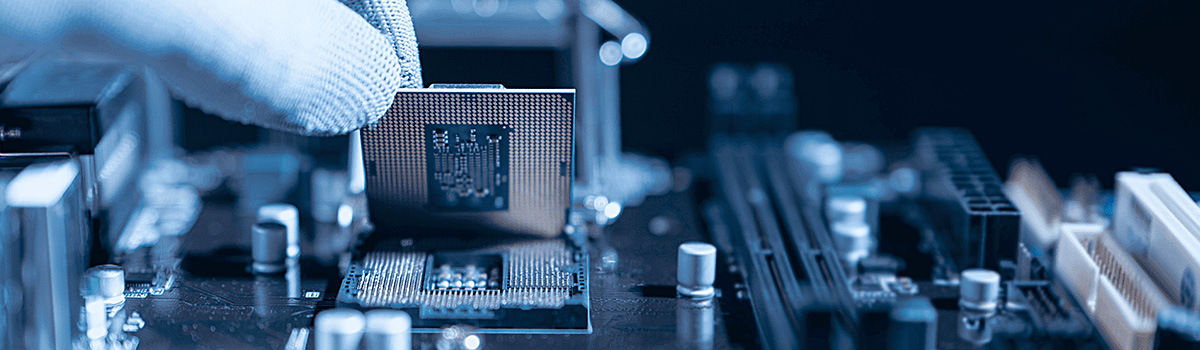
Kihívások a félvezető ragasztók alkalmazásában
A félvezető ragasztó alkalmazása számos olyan kihívással néz szembe, amelyek hatással lehetnek az elektronikus eszközök teljesítményére és megbízhatóságára. Ezek a kihívások a félvezetőkkel szemben támasztott egyedi követelmények és jellemzők, valamint a velük szemben támasztott szigorú működési feltételek miatt merülnek fel. Íme néhány kritikus kihívás a félvezető ragasztók alkalmazásában:
- Hőkezelés: A félvezetők működés közben hőt termelnek, és a hatékony hőkezelés kulcsfontosságú a túlmelegedés elkerülése érdekében. A félvezetőkben használt ragasztóanyagoknak kiváló hővezető képességgel kell rendelkezniük ahhoz, hogy hatékonyan átadják a hőt az eszközből. A megfelelő tapadás biztosítása a hőteljesítmény veszélyeztetése nélkül jelentős kihívás.
- Kémiai kompatibilitás: A félvezetők élettartamuk során különféle vegyszereknek vannak kitéve, beleértve a tisztítószereket, oldószereket és folyasztószereket. A ragasztóanyagoknak kémiailag kompatibilisnek kell lenniük ezekkel az anyagokkal, hogy elkerüljék a lebomlást vagy a tapadás elvesztését az idő múlásával. Az olyan ragasztóanyagok kiválasztása, amelyek ellenállnak bizonyos vegyi anyagoknak, összetett feladat.
- Mechanikai igénybevétel: Az elektronikus eszközök gyakran mechanikai igénybevételnek vannak kitéve a hőtágulás, a rezgések és a külső erők miatt. Ahhoz, hogy ellenálljon ezeknek az igénybevételeknek, a ragasztóanyagoknak megfelelő mechanikai tulajdonságokkal kell rendelkezniük, mint például a rugalmasság és a szilárdság. A rossz tapadási teljesítmény a félvezető eszköz leválásához, repedéséhez vagy mechanikai meghibásodásához vezethet.
- Miniatürizálás: A miniatürizálás folyamatos tendenciájával a félvezető eszközök egyre kisebbek és bonyolultabbak. Az ilyen miniatűr szerkezetek ragasztása nagy pontosságot és ellenőrzést igényel. Az egyenletes fedés biztosítása, az üregek elkerülése és az egyenletes kötési vonalvastagság fenntartása kritikus kihívássá válik.
- A folyamat kompatibilitása: A félvezető gyártás több feldolgozási lépést foglal magában, beleértve a tisztítást, a lerakást és a csomagolást. A ragasztóanyagoknak kompatibilisnek kell lenniük ezekkel a folyamatokkal anélkül, hogy negatívan befolyásolnák a teljesítményüket. Kihívások merülnek fel olyan ragasztók megtalálásában, amelyek ellenállnak a magas hőmérsékleti folyamatoknak, ellenállnak a nedvességnek, és megőrzik a stabilitást a gyártási ciklus során.
- Megbízhatóság és öregedés: A félvezető eszközöktől hosszú élettartammal és megbízható teljesítménnyel kell rendelkezniük különféle működési körülmények között. A ragasztóanyagoknak hosszú távú stabilitást, öregedésállóságot és megbízható tapadást kell mutatniuk hosszabb ideig. A kihívás a lehetséges leromlási mechanizmusok előrejelzésében és mérséklésében rejlik, amelyek hatással lehetnek a félvezető eszköz teljesítményére és megbízhatóságára.
- Környezetvédelmi szempontok: A félvezető alkalmazásokhoz használt ragasztóanyagoknak meg kell felelniük a környezetvédelmi előírásoknak és szabványoknak.
- Ez magában foglalja a veszélyes anyagok, például az ólom és más mérgező anyagok korlátozását. Kihívást jelenthet olyan környezetbarát ragasztómegoldások kifejlesztése, amelyek megfelelnek a szabályozási követelményeknek a teljesítmény csökkenése nélkül.
- Költség és méretezhetőség: A ragasztóanyagoknak költséghatékonynak és méretezhetőnek kell lenniük, hogy megfeleljenek a nagy volumenű félvezetőgyártás követelményeinek. A költségmegfontolások és a teljesítménykövetelmények egyensúlyba hozása kihívást jelent a megfelelő ragasztóanyagok kiválasztásában és az alkalmazási folyamat optimalizálása során.
Megbízhatósági vizsgálat: A ragasztó teljesítményének értékelése
A megbízhatósági vizsgálat elengedhetetlen folyamat a ragasztók teljesítményének értékeléséhez. A ragasztókat gyakran használják különféle iparágakban, beleértve az autógyártást, a repülőgépgyártást, az elektronikát és az építőiparban, ahol kritikus szerepet játszanak a különböző anyagok összekapcsolásában. A ragasztóanyagok megbízhatósága kulcsfontosságú a ragasztott szerelvények tartósságának és hosszú távú működésének biztosításához.
A megbízhatósági vizsgálat egyik kulcsfontosságú szempontja a ragasztó szilárdságának és tapadási tulajdonságainak értékelése. Ez magában foglalja a ragasztómintákat különböző feszültségi feltételeknek kitéve, hogy szimulálják a valós forgatókönyveket, és meghatározzák a teljesítményüket különböző terhelések, hőmérsékletek és környezeti feltételek mellett. Szakító-, nyíró- és leválási teszteket általában végeznek a ragasztó mechanikai tulajdonságainak és a különböző irányú erők ellenálló képességének felmérésére.
A ragasztási teljesítményben a mechanikai vizsgálatok mellett a környezeti tényezők is jelentős szerepet játszanak. A ragasztók élettartama során extrém hőmérsékletnek, páratartalomnak, vegyi anyagoknak és UV-sugárzásnak lehetnek kitéve. Ezért a megbízhatósági vizsgálat során a ragadós mintákat gyorsított öregítési teszteknek vetik alá, ahol hosszabb ideig durva környezeti feltételeknek vannak kitéve. Ez segít megjósolni a ragasztó hosszú távú teljesítményét, és felmérni a degradációval szembeni ellenállását, például a tapadási szilárdság elvesztését vagy a kémiai károsodást.
A megbízhatósági vizsgálat másik fontos szempontja a ragasztó ciklikus terhelés melletti tartósságának értékelése. Sok alkalmazásban a ragasztók ismétlődő mechanikai igénybevételnek vannak kitéve, például vibrációnak vagy hőciklusnak. A kifáradásteszt értékeli a ragasztó tönkremenetelével szembeni ellenállását ezen ciklikus terhelések mellett. A mintákat jellemzően meghatározott számú terhelési ciklusnak vetik alá, és teljesítményüket figyelik a ragasztási hiányosságok, például a repedés terjedésének vagy a kötés leválásának jelei miatt.
Ezenkívül a megbízhatósági vizsgálat magában foglalja a ragasztó valós körülmények közötti teljesítményének értékelését. Ez magában foglalhatja a ragasztó azon képességének tesztelését, hogy képes-e ragasztani az iparban általánosan használt anyagokat, például fémeket, műanyagokat, kompozitokat vagy üveget. A mintákat szabványosított eljárásokkal készítik elő, és olyan tesztelési protokolloknak vetik alá, amelyek szimulálják a konkrét alkalmazási követelményeket. Ez lehetővé teszi a mérnökök számára, hogy felmérjék a ragasztó kompatibilitását a különböző aljzatokkal, és értékeljék a kötési szilárdságát, rugalmasságát és a környezeti tényezőkkel szembeni ellenállását.
A megbízhatósági vizsgálat magában foglalja a ragasztó kémiai összeférhetőségének értékelését is más anyagokkal, amelyekkel érintkezésbe kerülhet alkalmazása vagy élettartama során. Ez magában foglalja a kompatibilitási tesztek elvégzését annak megállapítására, hogy a ragasztó károsan reagál-e oldószerekkel, tisztítószerekkel, üzemanyagokkal vagy más vegyi anyagokkal, amelyek jelen lehetnek a környezetben. A kémiai kompatibilitási tesztelés segít azonosítani azokat a lehetséges problémákat, amelyek a ragasztóanyag meghibásodásához vagy leromlásához vezethetnek.
Összefoglalva, a megbízhatóság vizsgálata döntő lépés a ragasztó teljesítményének értékelésében. Ez magában foglalja a mechanikai tulajdonságok értékelését, a gyorsított öregedési tesztek elvégzését, a ciklikus terhelés melletti tartósság értékelését, a valós körülmények közötti teljesítmény értékelését és a kémiai kompatibilitás vizsgálatát. Átfogó megbízhatósági tesztek elvégzésével a gyártók és mérnökök biztosíthatják a ragasztók alkalmasságát és hosszú távú teljesítményét a tervezett alkalmazási területeken.
Környezetvédelmi szempontok a félvezető ragasztóknál
A félvezető ragasztók kritikus szerepet játszanak az elektronikus eszközök összeszerelésében és csomagolásában, különösen a félvezetőiparban. Noha ezek a ragasztók olyan alapvető funkciókat látnak el, mint a kötés és a hőkezelés, létfontosságú, hogy figyelembe vegyük környezeti hatásukat az életciklusuk során. Íme néhány kulcsfontosságú környezetvédelmi szempont a félvezető ragasztóval kapcsolatban:
- Toxicitás: Sok félvezető ragasztó tartalmaz veszélyes anyagokat, beleértve az illékony szerves vegyületeket (VOC), nehézfémeket és más mérgező vegyi anyagokat. Ezek az anyagok káros hatással lehetnek az emberi egészségre és a környezetre. A káros összetevők minimalizálása vagy megszüntetése a ragasztókészítményekben kulcsfontosságú a környezeti hatások csökkentése érdekében.
- Kibocsátások: A félvezető ragasztók gyártása és felhordása során illékony komponensek kerülhetnek a levegőbe, ami hozzájárul a légszennyezéshez. A VOC-kibocsátás például hozzájárulhat a talajközeli ózon és a káros részecskék képződéséhez. A gyártóknak törekedniük kell alacsony VOC-tartalmú ragasztókészítmények kifejlesztésére, és szigorú kibocsátáscsökkentő intézkedéseket kell bevezetniük e környezeti hatások mérséklése érdekében.
- Energiafogyasztás: A félvezető ragasztók előállítása energiaigényes folyamatokat igényel, beleértve a szintézist, a keverést és a kikeményítést. Az energiafogyasztás csökkentése folyamatoptimalizálással és energiahatékony technológiák alkalmazásával minimalizálhatja a ragasztógyártással kapcsolatos környezeti lábnyomot.
- Hulladéktermelés: A félvezetőipar jelentős hulladékot termel, és a ragasztók hozzájárulnak ehhez a hulladékáramhoz. A hulladék tartalmazhat fel nem használt vagy lejárt ragasztókat, csomagolóanyagokat és gyártási melléktermékeket. A hulladékkezelési gyakorlatok, például a ragasztóhulladék újrahasznosítása, újrafelhasználása vagy biztonságos ártalmatlanítása elengedhetetlen a környezetszennyezés és az erőforrások kimerülésének minimalizálása érdekében.
- Életciklus-elemzés: A félvezető ragasztók teljes életciklusának figyelembevétele kulcsfontosságú a környezeti hatásuk átfogó értékeléséhez. Ez az elemzés magában foglalja a nyersanyag-kitermelés, a gyártás, a szállítás, az alkalmazás és az életciklus végén történő ártalmatlanítás ökológiai lábnyomának értékelését. A fejlesztési lehetőségek azonosítása minden szakaszban fenntarthatóbb ragasztómegoldásokhoz vezethet.
- Fenntartható alternatívák: A fenntartható alternatívák feltárása és elfogadása alapvető fontosságú a félvezető ragasztók környezeti hatásának csökkentése érdekében. Ez magában foglalhatja bioalapú vagy megújuló nyersanyagok használatát, vízbázisú vagy oldószermentes készítmények kifejlesztését, valamint környezetbarát gyártási eljárások alkalmazását. A ragasztóanyagok újrahasznosításának elősegítése vagy a körkörös gazdaság gyakorlatának megvalósítása szintén hozzájárulhat az erőforrások megőrzéséhez.
- Szabályozási megfelelőség: A ragasztógyártóknak be kell tartaniuk a vegyszerek felhasználására, ártalmatlanítására és címkézésére vonatkozó környezetvédelmi előírásokat és szabványokat. Az ökológiai és az emberi egészség védelmének biztosítása érdekében kulcsfontosságú, hogy naprakészek maradjanak a vonatkozó szabályozásokkal, mint például a REACH (Registration, Evaluation, Authorization, and Restriction of Chemicals) az Európai Unióban, és a hasonló szabályozások a különböző régiókban.
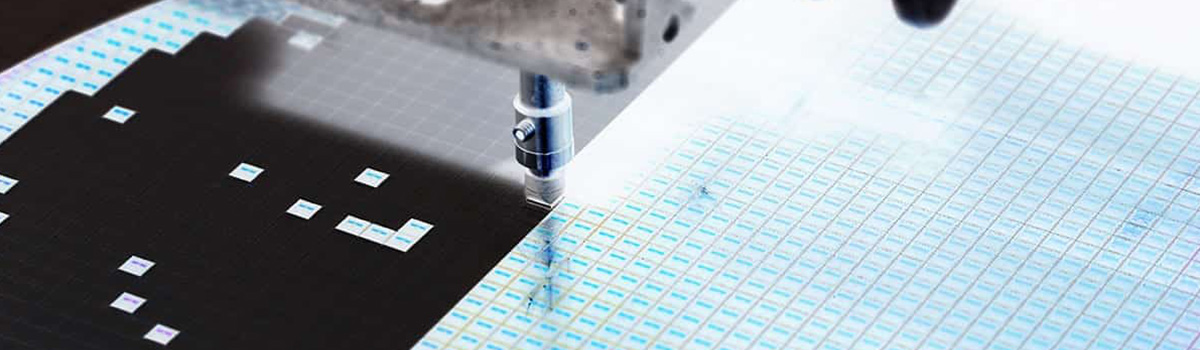
Trendek és innovációk a félvezető ragasztóval kapcsolatban
A félvezető ragasztó döntő szerepet játszik az elektronikai eszközök összeszerelésében és csomagolásában, biztosítva a félvezető alkatrészek megfelelő ragasztását és stabilitását. A technológia fejlődésével számos kulcsfontosságú trend és innováció jelenik meg a félvezető ragasztók területén.
- Miniatürizálás és magasabb készülékkomplexitás: A félvezetőipar egyik jelentős tendenciája az elektronikus eszközök folyamatos miniatürizálása és tervezésük egyre bonyolultabbá válása. Ez a tendencia javított tulajdonságokkal rendelkező ragasztókat igényel, mint például alacsonyabb viszkozitás, nagyobb kötési szilárdság és fokozott hővezető képesség, hogy a kisebb és sűrűbben csomagolt komponensekhez illeszkedjenek.
- Speciális csomagolási technikák: A fejlett csomagolási technikák, mint például a rendszerben csomagolt (SiP), a kifújható ostyaszintű csomagolás (FOWLP) és a 3D-s csomagolás egyre népszerűbbek, mivel képesek javítani az eszköz teljesítményét és csökkenteni az alaktényezőt. Ezek a technikák gyakran speciális ragasztókat igényelnek, amelyek képesek megbirkózni a több szerszám és alkatrész kis helyigényű összekapcsolásával járó egyedi kihívásokkal.
- Hőkezelés: Ahogy az elektronikus eszközök egyre erősebbek és kompaktabbak, a hatékony hőkezelés egyre kritikusabbá válik. A kiváló hővezető tulajdonságokkal rendelkező félvezető ragasztók fejlesztése a félvezető eszközök hőelvezetésének elősegítése, a túlmelegedés megakadályozása és az optimális teljesítmény biztosítása érdekében folyik.
- Alacsony hőmérsékleten történő kikeményedés: A hagyományos félvezető ragasztók gyakran magas hőmérsékleten történő kikeményedési eljárást igényelnek, ami problémát okozhat a hőmérsékletre érzékeny alkatrészek vagy aljzatok esetében. Az alacsony hőmérsékleten keményedő ragasztók innovációi lényegesen alacsonyabb hőmérsékleten is lehetővé teszik a ragasztást, csökkentve a kényes félvezető anyagok hőkárosodásának kockázatát.
- Új anyagösszetételek: A kutatók új anyagösszetételeket kutatnak félvezető ragasztókhoz, hogy megfeleljenek a változó követelményeknek. Ez magában foglalja az elektromosan vezető ragasztók (ECA) kifejlesztését, amelyek kötést és elektromos vezetőképességet biztosítanak, kiküszöbölve a forrasztás szükségességét bizonyos alkalmazásokban. Ezenkívül új anyagokat, például rugalmas ragasztókat vezetnek be, hogy megfeleljenek a rugalmas és hajlítható elektronikus eszközök iránti növekvő keresletnek.
- Környezeti megfontolások: A fenntarthatóság és a környezeti hatás egyre nagyobb figyelmet kap a félvezetőiparban. A ragasztógyártók a környezetbarát, csökkentett illékony szerves vegyületeket (VOC) és veszélyes anyagokat tartalmazó készítmények fejlesztésére összpontosítanak, miközben megőrzik a kiváló teljesítményjellemzőket.
- Folyamatoptimalizálás és automatizálás: A félvezető eszközök iránti kereslet növekedésével egyre nagyobb az igény a hatékony és automatizált gyártási folyamatokra. A ragasztógyártók együttműködnek a berendezések beszállítóival, hogy optimalizálják a ragasztóadagolási és térhálósodási folyamatokat, biztosítva a következetes és megbízható eredményeket, miközben csökkentik a gyártási ciklusidőket.
- Megbízhatóság és tartósság: A félvezető eszközök várhatóan hosszú ideig megbízhatóan működnek, gyakran zord környezetben. A ragasztó innovációk célja a készülék megbízhatóságának javítása a tapadási szilárdság, a nedvességgel, hőmérséklettel és különböző környezeti tényezőkkel szembeni ellenállás fokozása révén.
Alkalmazási területek: fogyasztói elektronika, autóipar, repülőgépipar és egyebek
A fogyasztói elektronika:
A szórakoztató elektronika a technológiai fejlesztések egyik legkiemelkedőbb alkalmazási területe. Számos eszközt magában foglal, például okostelefonokat, táblagépeket, laptopokat, okostévéket, hordható eszközöket és háztartási gépeket. Az elmúlt években a fogyasztói elektronika jelentős teljesítmény-, funkcionalitás- és kapcsolódási fejlesztéseken ment keresztül. Például az okostelefonok erősebbek lettek, és olyan fejlett funkciókat kínálnak, mint a nagy felbontású kamerák, a mesterséges intelligencia integrációja és a kiterjesztett valóság képességei. Az intelligens tévék mostantól támogatják a 4K, sőt a 8K felbontást és az intelligens otthoni integrációt a jobb szórakozás érdekében. A hordható eszközök, például az okosórák és a fitneszkövetők egészségfigyelő és fitneszkövető képességeik miatt váltak népszerűvé.
Autóipari:
Az autóipar jelentős fejlődésen ment keresztül, elsősorban a technológia által. A modern járművek kifinomult elektronikai és szoftverrendszerekkel rendelkeznek, amelyek fokozzák a biztonságot, a hatékonyságot és a felhasználói élményt. A fejlesztés egyik kritikus területe az autonóm vezetés, az önvezető autók valósággá válnak. Ezek a járművek fejlett érzékelőkre, mesterséges intelligencia algoritmusokra és csatlakoztathatóságra támaszkodnak az utakon való navigáláshoz és intelligens döntések meghozatalához. Ezenkívül az autóipari alkalmazások közé tartoznak:
- Infotainment rendszerek.
- Fejlett vezetőtámogató rendszerek (ADAS).
- Autós csatlakozás.
- Elektromos jármű technológia.
- Jármű-jármű kommunikáció.
Aerospace:
A repülőgépipar nagymértékben támaszkodik a fejlett technológiákra a biztonság, a hatékonyság és a teljesítmény javítása érdekében. A repülési alkalmazások közé tartozik a repülőgép-tervezés és -gyártás, az űrkutatás, a műholdas rendszerek és a légiforgalom-irányítás. A számítógéppel segített tervezés (CAD) és a szimulációs eszközök segítenek a mérnököknek aerodinamikusabb és üzemanyag-hatékonyabb repülőgépek tervezésében. A műholdas rendszerek globális kommunikációs, időjárás-figyelő és navigációs szolgáltatásokat nyújtanak. A repülőgépipar a fejlett anyagokat, például a kompozitokat és a könnyű ötvözeteket is kihasználja a súly csökkentése és az üzemanyag-hatékonyság növelése érdekében. Az űrkutatásban a robotika, a távérzékelés és a meghajtórendszerek lehetővé teszik az égitestek feltárását és tudományos adatok gyűjtését.
Egészségügy:
A technológia döntő szerepet játszik az egészségügyben, különféle módokon átalakítva az ipart. Az orvosi eszközök és berendezések, mint például az MRI gépek, az ultrahang szkennerek és a robotsebészeti rendszerek forradalmasították a diagnosztikai és kezelési eljárásokat. Az elektronikus egészségügyi nyilvántartások (EHR) és a távorvoslás lehetővé teszik az egészségügyi szakemberek számára, hogy hozzáférjenek a betegek információihoz, és távoli ellátást nyújtsanak. A hordható eszközök és az egészségfigyelő rendszerek lehetővé teszik az egyének számára, hogy nyomon kövessék életjeleiket, és személyre szabott egészségügyi ajánlásokat kapjanak. Mesterséges intelligenciát és gépi tanulási algoritmusokat alkalmaznak a betegségek diagnosztizálására, a gyógyszerkutatásra és a prediktív elemzésekre, amelyek jobb betegek kimeneteléhez és személyre szabott orvosláshoz vezetnek.
Ipari automatizálás:
Az ipari automatizálás magában foglalja a fejlett technológiák alkalmazását a gyártási folyamatok automatizálására és a termelékenység javítására. A robotokat és a robotkarokat széles körben használják olyan feladatokhoz, mint az összeszerelés, a hegesztés és az anyagmozgatás. A dolgok internete (IoT) eszközei és érzékelői valós idejű adatok gyűjtésére és a működési hatékonyság optimalizálására szolgálnak. A gépi látórendszerek lehetővé teszik a minőség-ellenőrzést és -ellenőrzést, biztosítva, hogy a termékek megfeleljenek a szigorú szabványoknak. A fejlett vezérlőrendszerek és a prediktív karbantartási algoritmusok segítenek minimalizálni az állásidőt és maximalizálni a termelési teljesítményt. Az ipari automatizálás növelheti a hatékonyságot, csökkentheti a költségeket és növelheti a biztonságot a különböző iparágakban, beleértve a gyártást, a logisztikát és az energiát.
Jövőbeli kilátások és lehetőségek
A jövő tele van izgalmas kilátásokkal és lehetőségekkel, amelyeket a gyors technológiai fejlődés, a változó társadalmi igények és a változó globális trendek hajtanak. Itt feltárunk néhány kulcsfontosságú területet, amelyek jelentős növekedési és fejlődési potenciállal rendelkeznek.
- Mesterséges intelligencia (AI) és automatizálás: A mesterséges intelligencia átfogóan átalakítja az iparágakat, fokozza a hatékonyságot, a termelékenységet és a döntéshozatalt. Ahogy az AI-technológiák érnek, egyre több lehetőség nyílik az AI-specialisták, adattudósok és mérnökök számára. Az automatizálás továbbra is racionalizálja a folyamatokat, ami munkahelyteremtéshez vezet a robotika, a gépi tanulás és az intelligens rendszerek terén.
- Megújuló energia és fenntarthatóság: Az éghajlatváltozás miatti növekvő aggodalom miatt hatalmas kereslet mutatkozik a megújuló energia megoldások iránt. A tisztább forrásokra, például a nap-, szél- és vízenergiára való átállás számos perspektívát rejt magában. A megújuló energia mérnöki, energiagazdálkodási és fenntartható fejlődési karrierje kulcsfontosságú lesz a zöldebb jövő kialakításában.
- Egészségügy és biotechnológia: Az orvosi kutatás, a személyre szabott orvoslás és a génszerkesztés fejlődése forradalmasítja az egészségügyi ágazatot. Rengeteg lehetőség kínálkozik a bioinformatika, a genetikai tanácsadás, a telemedicina és a gyógyszerfejlesztés területén. A technológia és az egészségügy metszéspontja ösztönzi az innovációt, ami jobb betegellátáshoz és jobb eredményekhez vezet.
- Kiberbiztonság és adatvédelem: Ahogy egyre növekszik a digitális rendszerektől való függésünk, úgy nő az igény a robusztus kiberbiztonsági intézkedésekre. A kiberfenyegetések egyre kifinomultabbak, igényt teremtve kiberbiztonsági szakértőkre, etikus hackerekre és adatvédelmi szakértőkre. Az érzékeny információk védelme és a biztonságos infrastruktúra fejlesztése kulcsfontosságú lesz a szervezetek és az egyének számára.
- E-kereskedelem és digitális marketing: Az e-kereskedelem megváltoztatta vásárlásainkat, új utakat teremtve a vállalkozások számára. Az online kiskereskedelmi platformok, a digitális marketing és a közösségi médiában történő hirdetés elengedhetetlenné vált a virágzó cégek számára. Az e-kereskedelmi menedzsment, a digitális tartalomkészítés és az ügyfélélmény-optimalizálás terén továbbra is nagy kereslet mutatkozik majd.
- Űrkutatás és kereskedelmi forgalomba hozatal: Az űrkutatás a kormány által irányított kezdeményezésekről a kereskedelmi vállalkozások felé tolódott el, lehetőségeket nyitva a repülőgépgyártás, a műholdas technológia és az űrturizmus terén. Magánvállalatok fektetnek be az űrutazásokba, az erőforrás-bányászatba és a műholdas kommunikációba, megnyitva ezzel az utat az űrkutatás új korszaka előtt.
- Fenntartható mezőgazdaság és élelmiszerrendszerek: Mivel a világ népessége 9-re várhatóan eléri a 2050 milliárd főt, az élelmezésbiztonság és a fenntartható mezőgazdasági gyakorlatok biztosítása kritikus fontosságú. A vertikális gazdálkodás, a precíziós mezőgazdaság és az alternatív fehérjeforrások innovációs lehetőséget kínálnak. A mezőgazdasági technológiai, agronómiai és élelmiszertudományi karrier létfontosságú szerepet fog játszani a jövőbeni élelmiszerigények kielégítésében.
- Virtuális valóság (VR), kiterjesztett valóság (AR) és kiterjesztett valóság (XR): Ezek a technológiák forradalmasíthatják a szórakoztatást, az oktatást, a képzést és a különféle iparágakat. A VR/AR fejlesztők, tartalomkészítők és magával ragadó élménytervezők alakítják a szórakoztatás, a játékok és a virtuális együttműködés jövőjét.
- Pénzügyi technológia (Fintech): A technológia és a pénzügyek integrációja a Fintech felemelkedését eredményezte, amely új pénzügyi szolgáltatásokat, digitális fizetési megoldásokat és blokklánc technológiát kínál. Várhatóan nagy kereslet mutatkozik a pénzügyi analitikus, a banki kiberbiztonság és a blokklánc-fejlesztés területén.
- Fenntarthatósági tanácsadás és zöld építészet: Ahogy a fenntarthatóság prioritássá válik, a vállalatok és magánszemélyek útmutatást kérnek szénlábnyomuk csökkentéséről és a környezetbarát gyakorlatok alkalmazásáról. Fenntartható tanácsadók, zöld építészek és környezetvédelmi mérnökök fontos szerepet fognak játszani a fenntartható megoldások tervezésében és megvalósításában.
Az együttműködés jelentősége a félvezető ragasztótechnológia fejlesztésében
Az együttműködés létfontosságú a félvezető ragasztótechnológia fejlesztésében, az innováció előmozdításában és annak sikeres megvalósításában a különböző iparágakban. A félvezetőipar rendkívül összetett és gyorsan fejlődik, interdiszciplináris szakértelmet és az érdekelt felek együttműködését igényli.
- Változatos szakértelem: A félvezető ragasztótechnológia több tudományágat is felölel, beleértve az anyagtudományt, a kémiát, a mérnöki tudományt és a gyártást. Az együttműködés különböző területek szakértőit fogja össze, mindegyik speciális tudással és készségekkel járul hozzá. A sokrétű szakértelem ötvözésével a partnerség olyan újszerű ragasztóanyagok és technikák kifejlesztését teszi lehetővé, amelyek javíthatják a félvezető eszközök teljesítményét, megbízhatóságát és tartósságát.
- Tudáscsere: Az együttműködés elősegíti a tudás- és információcserét kutatók, mérnökök és iparági szakemberek között. Együttműködési erőfeszítések révén az egyének megoszthatják meglátásaikat, tapasztalataikat és kutatási eredményeiket, ami a ragasztóanyagok és alkalmazásaik mélyebb megértéséhez vezet. Ez a tudáscsere segíthet azonosítani a kialakuló trendeket, kezelni a technikai kihívásokat, és felgyorsítani az innovatív megoldások fejlesztését.
- Továbbfejlesztett kutatás és fejlesztés: Az együttműködésen alapuló kutatási és fejlesztési erőfeszítések lehetővé teszik a források összevonását a finanszírozás és a felszerelés tekintetében. Ez kiterjedtebb kísérletezést, tesztelést és elemzést tesz lehetővé, ami gyorsabb felfedezéshez és innovációhoz vezet. A közös munkával a kutatók olyan speciális létesítményekhez, élvonalbeli technológiákhoz és fejlett jellemzési eszközökhöz férhetnek hozzá, amelyek külön-külön nem biztos, hogy elérhetők. Az ilyen erőforrások jelentősen hozzájárulhatnak a félvezető ragasztótechnológia fejlődéséhez.
- Ipari és egyetemi együttműködés: Az ipar és a tudományos körök közötti együttműködés kulcsfontosságú a kutatási eredmények gyakorlati alkalmazásokba való átültetéséhez. Az egyetemek alapkutatást folytathatnak és új koncepciókat fedezhetnek fel, míg az ipari partnerek valós perspektívákat és gyakorlati megfontolásokat hoznak. Ez az együttműködés biztosítja, hogy a ragasztótechnológiai fejlesztések igazodjanak a piaci igényekhez, és integrálhatók legyenek az ipari folyamatokba. Az ipari-egyetemi szövetség a technológiatranszfert is támogatja, lehetővé téve, hogy az akadémiai kutatás kézzelfogható hatást gyakoroljon a kereskedelmi alkalmazásokra.
- Szabványosítás és minőségbiztosítás: Az iparág szereplői közötti együttműködés elősegíti a félvezető ragasztótechnológiára vonatkozó szabványok és irányelvek kidolgozását. A szabványok segítenek biztosítani a konzisztenciát, a kompatibilitást és a megbízhatóságot a különböző termékek és gyártási folyamatok között. Az együttműködési erőfeszítések bevált gyakorlatokat, tesztelési módszereket és minőség-ellenőrzési eljárásokat hozhatnak létre, amelyek elengedhetetlenek a félvezető eszközök teljesítményének és hosszú távú megbízhatóságának garantálásához.
- Piacbővítés és versenyképesség: A félvezetőiparban tevékenykedő vállalatok közötti együttműködés piacbővüléshez és versenyképesség növekedéséhez vezethet. A vállalatok egyesíthetik erőforrásaikat, tudásukat és piaci betekintéseiket azáltal, hogy közösen dolgoznak ki olyan ragasztómegoldásokat, amelyek megfelelnek az iparági követelményeknek. Az együttműködési erőfeszítések elősegíthetik a ragasztótechnológia új alkalmazásokban és feltörekvő piacokon történő átvételét is, tovább mozdítva a félvezetőipar növekedését.
Következtetés:
A félvezető ragasztó létfontosságú szerepet játszik a félvezető eszközök miniatürizálásának és nagy teljesítményének lehetővé tételében. Ezeknek a ragasztóknak az a képessége, hogy erős kötési képességet biztosítsanak, védelmet nyújtanak a környezeti tényezőkkel és a hőterheléssel szemben, valamint az elektromos vezetőképességük döntő fontosságú a mikroprocesszorok, memóriachipek és egyéb integrált áramkörök gyártása és összeszerelése során. Ahogy a technológia folyamatosan fejlődik, az innovatív ragasztómegoldások fejlesztése, valamint a gyártók, kutatók és végfelhasználók közötti együttműködés kulcsfontosságú lesz a félvezetőipar növekvő igényeinek és kihívásainak kielégítésében. A félvezető ragasztóban rejlő lehetőségek kiaknázásával még kisebb, gyorsabb és bonyolultabb félvezető eszközök előtt nyithatjuk meg az utat, amelyek modern világunkat irányítják.