Alultöltő epoxi
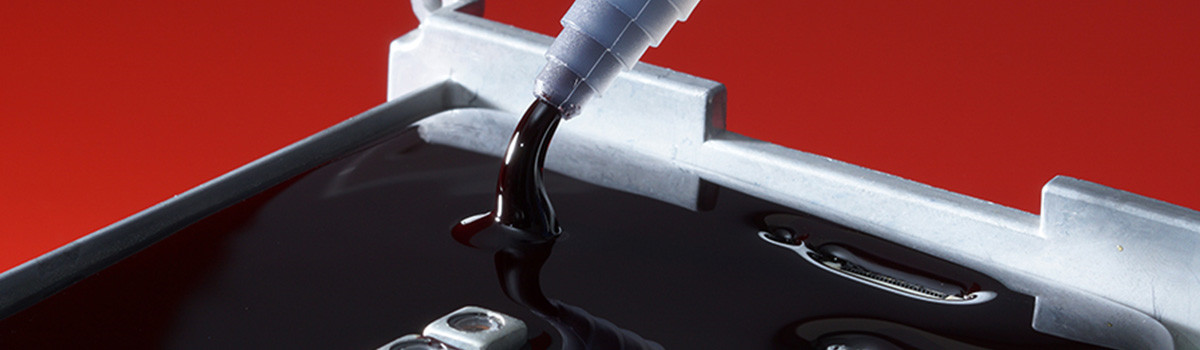
Az alátöltő epoxi egyfajta ragasztó, amelyet az elektronikus alkatrészek megbízhatóságának növelésére használnak, különösen a félvezető csomagolási alkalmazásokban. Kitölti a csomagolás és a nyomtatott áramköri lap (NYÁK) közötti rést, mechanikai támasztást és feszültségmentesítést biztosítva megakadályozza a hőtágulást és az összehúzódást. Az alátöltő epoxi javítja a csomag elektromos teljesítményét is a parazita induktivitás és kapacitás csökkentésével. Ebben a cikkben megvizsgáljuk az alátöltő epoxi különböző alkalmazásait, a különböző típusokat és azok előnyeit.
Az alátöltő epoxi jelentősége a félvezető csomagolásban
Az alátöltő epoxi kulcsfontosságú a félvezető csomagolásban, mivel mechanikai megerősítést és védelmet nyújt a finom mikroelektronikai alkatrészeknek. Ez egy speciális ragasztóanyag, amelyet a félvezető chip és a csomag hordozója közötti rés kitöltésére használnak, növelve az elektronikus eszközök megbízhatóságát és teljesítményét. Itt megvizsgáljuk az alultöltött epoxi jelentőségét a félvezető csomagolásban.
Az alátöltött epoxi egyik elsődleges funkciója a csomagolás mechanikai szilárdságának és megbízhatóságának javítása. Működés közben a félvezető chipek különféle mechanikai igénybevételeknek vannak kitéve, mint például hőtágulás és összehúzódás, vibráció és mechanikai ütés. Ezek a feszültségek forrasztási repedések kialakulásához vezethetnek, amelyek elektromos meghibásodásokat okozhatnak, és csökkentik az eszköz teljes élettartamát. Az alátöltő epoxi feszültségcsökkentő szerként működik azáltal, hogy a mechanikai feszültséget egyenletesen oszlatja el a forgácson, a hordozón és a forrasztási kötéseken. Hatékonyan minimalizálja a repedések kialakulását és megakadályozza a meglévő repedések továbbterjedését, biztosítva a csomagolás hosszú távú megbízhatóságát.
Az alátöltő epoxi másik kritikus szempontja, hogy képes javítani a félvezető eszközök hőteljesítményét. A hőleadás jelentős aggodalomra ad okot, mivel az elektronikus eszközök mérete csökken, és megnő a teljesítménysűrűség, a túlzott hő pedig ronthatja a félvezető chip teljesítményét és megbízhatóságát. Az alátöltő epoxi kiváló hővezető tulajdonságokkal rendelkezik, lehetővé téve, hogy hatékonyan átadja a hőt a forgácsról, és elosztja azt a csomagolásban. Ez segít fenntartani az optimális működési hőmérsékletet, és megakadályozza a forró pontok kialakulását, ezáltal javítja a készülék általános hőkezelését.
Az alátöltő epoxi véd a nedvességtől és a szennyeződésektől is. A nedvesség behatolása korrózióhoz, elektromos szivárgáshoz és vezető anyagok növekedéséhez vezethet, ami a készülék meghibásodásához vezethet. Az alátöltő epoxi gátként működik, lezárja a sérülékeny területeket, és megakadályozza a nedvesség bejutását a csomagolásba. Ezenkívül védelmet nyújt a por, szennyeződés és egyéb szennyeződések ellen, amelyek hátrányosan befolyásolhatják a félvezető chip elektromos teljesítményét. A chip és összekapcsolásai védelmével az alátöltő epoxi biztosítja a készülék hosszú távú megbízhatóságát és működőképességét.
Ezenkívül az alultöltött epoxi lehetővé teszi a félvezető csomagolások miniatürizálását. A kisebb és kompaktabb eszközök iránti állandó kereslet miatt az alultöltött epoxi lehetővé teszi a flip-chip és chip-scale csomagolási technikák alkalmazását. Ezek a technikák magukban foglalják a chipet közvetlenül a csomag hordozójára szerelik, így nincs szükség huzalkötésre, és csökkentik a csomagolás méretét. Az Underfill epoxi szerkezeti támogatást nyújt, és megőrzi a chip-szubsztrát interfész integritását, lehetővé téve ezen fejlett csomagolási technológiák sikeres megvalósítását.
Az Underfill Epoxy hogyan kezeli a kihívásokat
A félvezető csomagolás döntő szerepet játszik az elektronikus eszközök teljesítményében, megbízhatóságában és hosszú élettartamában. Ez magában foglalja az integrált áramkörök (IC-k) védőburkolatokba zárását, az elektromos csatlakozásokat és a működés során keletkező hő elvezetését. A félvezető csomagolás azonban számos kihívással néz szembe, beleértve a hőterhelést és a vetemedést, amelyek jelentősen befolyásolhatják a csomagolt eszközök funkcionalitását és megbízhatóságát.
Az egyik fő kihívás a termikus stressz. Az integrált áramkörök működés közben hőt termelnek, és a nem megfelelő disszipáció növelheti a hőmérsékletet a csomagoláson belül. Ez a hőmérséklet-változás termikus feszültséget eredményez, mivel a csomagoláson belüli különböző anyagok különböző sebességgel tágulnak és zsugorodnak. Az egyenetlen tágulás és összehúzódás mechanikai igénybevételt okozhat, ami a forrasztási kötések meghibásodásához, leváláshoz és repedésekhez vezethet. A hőterhelés veszélyeztetheti a csomagolás elektromos és mechanikai integritását, ami végső soron befolyásolja az eszköz teljesítményét és megbízhatóságát.
A vetemedés egy másik kritikus kihívás a félvezető csomagolásban. A vetemedés a csomag hordozójának vagy a teljes csomagnak a meghajlását vagy deformációját jelenti. Előfordulhat a csomagolási folyamat során vagy termikus igénybevétel miatt. A vetemedést elsősorban a hőtágulási együttható (CTE) eltérése okozza a csomagolásban lévő különböző anyagok között. Például a szilícium szerszám, a szubsztrátum és a formakeverék CTE értéke jelentősen eltérhet. Amikor hőmérséklet-változásoknak vannak kitéve, ezek az anyagok különböző sebességgel kitágulnak vagy összehúzódnak, ami vetemedéshez vezet.
A vetemedés számos problémát vet fel a félvezető csomagoknál:
- Feszültségkoncentrációs pontokat eredményezhet, növelve a mechanikai meghibásodások valószínűségét és csökkentve a doboz megbízhatóságát.
- A vetemedés nehézségeket okozhat az összeszerelési folyamat során, mivel befolyásolja a csomagolás más alkatrészekhez, például a nyomtatott áramköri laphoz (PCB) való illeszkedését. Ez az eltolódás ronthatja az elektromos csatlakozásokat és teljesítménybeli problémákat okozhat.
- A vetemedés hatással lehet a csomag általános alaktényezőjére, és megnehezíti az eszköz integrálását kis méretű alkalmazásokba vagy sűrűn lakott PCB-kbe.
A félvezető csomagolásban különféle technikákat és stratégiákat alkalmaznak ezeknek a kihívásoknak a kezelésére. Ezek közé tartozik a fejlett anyagok és a megfelelő CTE-k használata a hőfeszültség és a vetemedés minimalizálása érdekében. Termomechanikai szimulációkat és modellezéseket végeznek a csomag viselkedésének előrejelzésére különböző hőviszonyok között. A tervezési módosítások, például a feszültségmentesítő szerkezetek és az optimalizált elrendezések bevezetése a hőfeszültség és a vetemedés csökkentése érdekében valósul meg. Ezenkívül a továbbfejlesztett gyártási folyamatok és berendezések fejlesztése segít minimalizálni a vetemedés előfordulását az összeszerelés során.
Az Underfill Epoxy előnyei
Az alátöltő epoxi a félvezető csomagolás kritikus összetevője, amely számos előnnyel jár. Ezt a speciális epoxianyagot a félvezető chip és a csomag hordozója közé alkalmazzák, mechanikai megerősítést biztosítva és különféle kihívásokat kezelve. Íme az alultöltött epoxi kritikus előnyei:
- Megnövelt mechanikai megbízhatóság: Az alátöltő epoxi egyik elsődleges előnye, hogy képes növelni a félvezető csomagok mechanikai megbízhatóságát. Az alátöltő epoxi kohéziós kötést hoz létre, amely javítja az általános szerkezeti integritást azáltal, hogy kitölti a réseket és üregeket a forgács és az alapfelület között. Ez segít megelőzni a csomagolás elhajlását, csökkenti a mechanikai meghibásodások kockázatát, és növeli a külső feszültségekkel, például rezgéssel, ütésekkel és hőciklussal szembeni ellenállást. A jobb mechanikai megbízhatóság növeli a termék tartósságát és meghosszabbítja az eszköz élettartamát.
- Hőfeszültség-eloszlás: Az alátöltő epoxi segít eloszlatni a hőfeszültséget a csomagoláson belül. Az integrált áramkörök működés közben hőt termelnek, és a nem megfelelő disszipáció hőmérséklet-ingadozásokat eredményezhet a tartályon belül. Az alátöltő epoxi anyag a forgácshoz és a szubsztrátumhoz képest alacsonyabb hőtágulási együtthatójával (CTE) pufferrétegként működik. Elnyeli a termikus igénybevétel okozta mechanikai igénybevételt, így csökkenti a forrasztási kötések meghibásodásának, rétegvesztésének és repedéseinek kockázatát. A hőfeszültség eloszlatásával az alultöltött epoxi segít megőrizni a csomag elektromos és mechanikai integritását.
- Fokozott elektromos teljesítmény: Az alátöltő epoxi pozitívan befolyásolja a félvezető eszközök elektromos teljesítményét. Az epoxi anyag kitölti a chip és a hordozó közötti hézagokat, csökkentve a parazita kapacitást és induktivitást. Ez javítja a jelintegritást, csökkenti a jelveszteséget, és javítja az elektromos kapcsolatot a chip és a csomag többi része között. A csökkent parazita hatások hozzájárulnak a jobb elektromos teljesítményhez, nagyobb adatátviteli sebességhez és az eszköz megbízhatóságához. Ezenkívül az alultöltött epoxi szigetelést és védelmet nyújt a nedvesség, szennyeződések és egyéb környezeti tényezők ellen, amelyek ronthatják az elektromos teljesítményt.
- Feszültségmentesítés és jobb összeszerelés: Az alátöltő epoxi feszültségoldó mechanizmusként működik az összeszerelés során. Az epoxi anyag kompenzálja a CTE eltérést a forgács és a hordozó között, csökkentve a mechanikai feszültséget a hőmérsékletváltozások során. Ez megbízhatóbbá és hatékonyabbá teszi az összeszerelési folyamatot, minimálisra csökkentve a csomagolás sérülésének vagy eltolódásának kockázatát. Az alátöltő epoxi által biztosított ellenőrzött feszültségeloszlás elősegíti a nyomtatott áramköri kártya (PCB) többi alkatrészéhez való megfelelő illeszkedést is, és javítja az összeszerelés összteljesítményét.
- Miniatürizálás és alaktényező optimalizálása: Az alátöltő epoxi lehetővé teszi a félvezető csomagok miniatürizálását és a formai tényező optimalizálását. A szerkezeti megerősítés és a feszültségmentesítés révén az alátöltő epoxi lehetővé teszi kisebb, vékonyabb és kompaktabb csomagok tervezését és gyártását. Ez különösen fontos az olyan alkalmazásoknál, mint például a mobileszközök és a hordható elektronika, ahol a hely rendkívüli. Az alaktényezők optimalizálásának és a nagyobb alkatrészsűrűség elérésének képessége hozzájárul a fejlettebb és innovatívabb elektronikus eszközökhöz.
Az alátöltő epoxi típusai
Az alátöltő epoxi készítmény többféle típusa is elérhető félvezető csomagolásban, amelyek mindegyike úgy lett megtervezve, hogy megfeleljen a speciális követelményeknek és különböző kihívásokat kezeljen. Íme néhány gyakran használt alultöltő epoxi típus:
- Kapilláris alátöltő epoxi: A kapilláris alátöltő epoxi a leghagyományosabb és legszélesebb körben használt típus. Alacsony viszkozitású epoxigáz áramlik a forgács és a hordozó közötti résbe kapilláris hatás révén. A kapilláris alátöltést általában a forgács szélére adagolják, és ahogy a csomagot felmelegítik, az epoxi a forgács alá folyik, kitöltve az üregeket. Ez a fajta alátöltés alkalmas kis hézagokkal rendelkező csomagokhoz, és jó mechanikai megerősítést biztosít.
- No-Flow Underfill Epoxy: A No-Flow Underfill Epoxy egy nagy viszkozitású készítmény, amely nem folyik a kikeményedés során. Előre felvitt epoxiként vagy filmként hordják fel a forgács és az aljzat közé. A folyásmentes alátöltő epoxi különösen hasznos a flip-chip csomagoknál, ahol a forrasztási dudorok közvetlenül érintkeznek a hordozóval. Kiküszöböli a kapilláris áramlás szükségességét, és csökkenti a forrasztási kötés sérülésének kockázatát az összeszerelés során.
- Wafer-Level Underfill (WLU): Az ostyaszintű alátöltés egy alátöltő epoxi, amelyet az ostya szintjén alkalmaznak az egyes forgácsok elkülönítése előtt. Ez magában foglalja az alátöltő anyag szétosztását az ostya teljes felületén, és kikeményíti. Az ostyaszintű alátöltés számos előnnyel jár, beleértve az egyenletes alátöltési lefedettséget, a csökkentett összeszerelési időt és a jobb folyamatvezérlést. Általában kis méretű készülékek nagy volumenű gyártására használják.
- Molded Underfill (MUF): A fröccsöntött alátét egy alultöltő epoxi, amelyet a kapszulázó öntés során alkalmaznak. Az alátöltő anyagot a hordozóra adagolják, majd a forgácsot és a hordozót egy formakeverékbe kapszulázzák. A fröccsöntés során az epoxi megfolyik, és kitölti a forgács és az aljzat közötti rést, egyetlen lépésben biztosítva az alátöltést és a kapszulázást. Az öntött alátét kiváló mechanikai megerősítést kínál, és leegyszerűsíti az összeszerelési folyamatot.
- Non-Conductive Underfill (NCF): A nem vezetőképes alátöltő epoxi speciálisan úgy lett kialakítva, hogy elektromos szigetelést biztosítson a forrasztási kötések között a forgácson és az alapfelület között. Szigetelő töltőanyagokat vagy adalékokat tartalmaz, amelyek megakadályozzák az elektromos vezetőképességet. Az NCF-et olyan alkalmazásokban használják, ahol a szomszédos forrasztási csatlakozások közötti elektromos rövidzárlat aggodalomra ad okot. Mechanikai megerősítést és elektromos szigetelést egyaránt kínál.
- Hővezető alátöltés (TCU): A hővezető alátöltő epoxit úgy tervezték, hogy fokozza a csomag hőelvezetési képességét. Hővezető töltőanyagokat, például kerámia- vagy fémrészecskéket tartalmaz, amelyek javítják az alátöltő anyag hővezető képességét. A TCU-t olyan alkalmazásokban használják, ahol kulcsfontosságú a hatékony hőátadás, például nagy teljesítményű eszközökben vagy olyanokban, amelyek magas hőmérsékleti viszonyok között működnek.
Ez csak néhány példa a félvezető csomagolásban használt különböző típusú alátöltő epoxikra. A megfelelő alátöltő epoxi kiválasztása olyan tényezőktől függ, mint a csomagolás kialakítása, az összeszerelési folyamat, a hőmérsékleti követelmények és az elektromos megfontolások. Mindegyik alátöltő epoxi speciális előnyökkel jár, és a különféle alkalmazások egyedi igényeinek megfelelően lett kialakítva.
Kapilláris alátöltés: Alacsony viszkozitás és nagy megbízhatóság
A kapilláris alátöltés olyan eljárásra utal, amelyet a félvezető-csomagolóiparban használnak az elektronikus eszközök megbízhatóságának növelésére. Ez magában foglalja a mikroelektronikai chip és a környező csomagolás közötti rések kitöltését alacsony viszkozitású folyékony anyaggal, jellemzően epoxi alapú gyantával. Ez az alátöltő anyag szerkezeti támogatást nyújt, javítja a hőelvezetést, és megvédi a forgácsot a mechanikai igénybevételtől, a nedvességtől és egyéb környezeti tényezőktől.
A kapilláris alátöltés egyik kritikus jellemzője az alacsony viszkozitása. Az alátöltő anyag viszonylag kis sűrűségűre van kialakítva, lehetővé téve, hogy az alátöltési folyamat során könnyen befolyjon a forgács és a csomag közötti szűk résekbe. Ez biztosítja, hogy az alátöltő anyag hatékonyan behatoljon és kitöltse az összes üreget és légrést, minimálisra csökkentve az üregképződés kockázatát és javítva a forgács-csomag interfész általános integritását.
Az alacsony viszkozitású kapilláris alátöltő anyagok számos egyéb előnyt is kínálnak. Először is megkönnyítik az anyag hatékony áramlását a forgács alatt, ami csökkenti a folyamatidőt és növeli a gyártási teljesítményt. Ez különösen fontos a nagy volumenű gyártási környezetekben, ahol az idő- és költséghatékonyság kritikus fontosságú.
Másodszor, az alacsony viszkozitás lehetővé teszi az alátöltő anyag jobb nedvesítési és tapadási tulajdonságait. Lehetővé teszi az anyag egyenletes eloszlását, és erős kötéseket alakít ki a chippel és a csomagolással, megbízható és robusztus kapszulát hozva létre. Ez biztosítja, hogy a chip biztonságosan védve legyen az olyan mechanikai igénybevételekkel szemben, mint a hőciklus, ütések és rezgések.
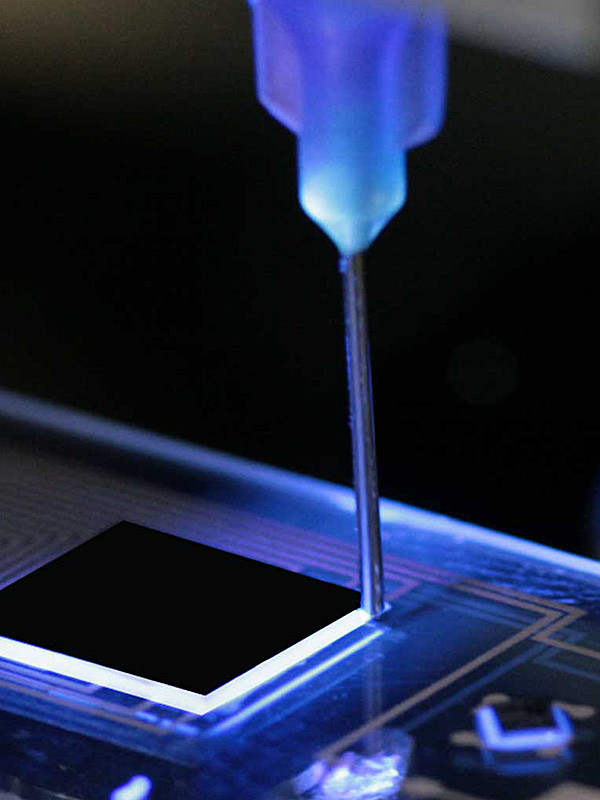
A kapilláris alátöltések másik fontos szempontja a nagy megbízhatóság. Az alacsony viszkozitású alátöltő anyagokat kifejezetten úgy tervezték, hogy kiváló hőstabilitást, elektromos szigetelési tulajdonságokat, valamint nedvességgel és vegyszerekkel szembeni ellenállást mutassanak. Ezek a jellemzők elengedhetetlenek a csomagolt elektronikus eszközök hosszú távú teljesítményének és megbízhatóságának biztosításához, különösen az olyan igényes alkalmazásokban, mint az autóipar, a repülőgépipar és a távközlés.
Ezen túlmenően a kapilláris alátöltő anyagokat úgy tervezték, hogy nagy mechanikai szilárdsággal és kiváló tapadásúak legyenek különféle hordozóanyagokhoz, beleértve a fémeket, kerámiákat és a félvezető csomagolásban általánosan használt szerves anyagokat. Ez lehetővé teszi, hogy az alátöltő anyag feszültségpufferként működjön, hatékonyan elnyeli és eloszlatja a működés vagy a környezeti hatások során keletkező mechanikai feszültségeket.
No-Flow Underfill: Önadagoló és nagy áteresztőképesség
A folyásmentes alátöltés egy speciális eljárás, amelyet a félvezető-csomagolóiparban használnak az elektronikus eszközök megbízhatóságának és hatékonyságának növelésére. Ellentétben a kapilláris alátöltésekkel, amelyek az alacsony viszkozitású anyagok áramlásán alapulnak, az áramlásmentes alátöltések önadagoló megközelítést alkalmaznak a nagy viszkozitású anyagokkal. Ez a módszer számos előnnyel jár, beleértve az önbeállítást, a nagy áteresztőképességet és a nagyobb megbízhatóságot.
Az áramlásmentes alátöltés egyik kritikus jellemzője az önadagoló képessége. Az ebben az eljárásban használt alátöltő anyag nagyobb viszkozitású, ami megakadályozza a szabad áramlását. Ehelyett az alátöltő anyagot szabályozott módon adagolják a chip-csomag interfészre. Ez az ellenőrzött adagolás lehetővé teszi az alátöltő anyag pontos elhelyezését, biztosítva, hogy csak a kívánt területekre kerüljön felhordás nélkül, túlfolyás vagy ellenőrizhetetlen szétterülés nélkül.
Az áramlásmentes alátöltés önadagoló jellege számos előnnyel jár. Először is lehetővé teszi az alátöltő anyag önbeállítását. Az alátöltés kiadagolása során természetesen magától illeszkedik a forgácshoz és a csomagoláshoz, egyenletesen kitöltve a hézagokat és üregeket. Ezzel szükségtelenné válik a forgács pontos pozicionálása és igazítása az alátöltési folyamat során, így időt és erőfeszítést takarít meg a gyártás során.
Másodszor, az áramlásmentes alátöltések önadagoló tulajdonsága nagy termelési teljesítményt tesz lehetővé. Az adagolási folyamat automatizálható, ami lehetővé teszi az alátöltő anyag gyors és következetes felvitelét több forgácson egyszerre. Ez javítja az általános gyártási hatékonyságot és csökkenti a gyártási költségeket, így különösen előnyös a nagy volumenű gyártási környezetekben.
Ezenkívül a folyásmentes alátöltő anyagokat úgy tervezték, hogy nagy megbízhatóságot biztosítsanak. A nagy viszkozitású alátöltő anyagok jobban ellenállnak a hőciklusnak, a mechanikai igénybevételeknek és a környezeti tényezőknek, így biztosítják a csomagolt elektronikus eszközök hosszú távú teljesítményét. Az anyagok kiváló hőstabilitást, elektromos szigetelési tulajdonságokat, nedvességgel és vegyszerekkel szembeni ellenállást mutatnak, ami hozzájárul az eszközök általános megbízhatóságához.
Ezenkívül az áramlásmentes alátöltésben használt nagy viszkozitású alátöltő anyagok fokozott mechanikai szilárdsággal és tapadási tulajdonságokkal rendelkeznek. Erős kötéseket képeznek a chippel és a csomagolással, hatékonyan elnyelve és eloszlatva a működés vagy a környezeti hatások során keletkező mechanikai feszültségeket. Ez segít megvédeni a chipet az esetleges sérülésektől, és növeli a készülék ellenállását a külső ütésekkel és rezgésekkel szemben.
Öntött alátöltés: magas szintű védelem és integráció
A fröccsöntött alátöltés egy fejlett technika, amelyet a félvezető csomagolóiparban használnak az elektronikus eszközök magas szintű védelmére és integrációjára. Ez magában foglalja a teljes chipet és a környező csomagolást egy alátöltő anyagot tartalmazó formakeverékkel. Ez a folyamat jelentős előnyöket kínál a védelem, az integráció és az általános megbízhatóság tekintetében.
Az öntött alátöltés egyik kritikus előnye, hogy átfogó védelmet nyújt a forgács számára. Az ebben a folyamatban használt formakeverék robusztus gátként működik, védőburkolatba zárva a teljes forgácsot és a csomagot. Ez hatékony árnyékolást biztosít az olyan környezeti tényezőkkel szemben, mint a nedvesség, por és szennyeződések, amelyek befolyásolhatják a készülék teljesítményét és megbízhatóságát. A tokozás emellett segít megvédeni a chipet a mechanikai igénybevételektől, a hőciklustól és más külső erőktől, így biztosítja a chip hosszú távú tartósságát.
Ezenkívül az öntött alátöltés magas szintű integrációt tesz lehetővé a félvezető csomagban. Az alátöltő anyagot közvetlenül a formakeverékbe keverik, lehetővé téve az alátöltési és kapszulázási folyamatok zökkenőmentes integrációját. Ez az integráció szükségtelenné teszi külön alultöltési lépést, leegyszerűsíti a gyártási folyamatot és csökkenti a gyártási időt és költségeket. Ezenkívül biztosítja az alultöltés egyenletes és egyenletes eloszlását a csomagban, minimálisra csökkentve az üregeket és javítva az általános szerkezeti integritást.
Ezenkívül a fröccsöntött alátét kiváló hőelvezetési tulajdonságokat kínál. A formakeveréket úgy tervezték, hogy magas hővezető képességgel rendelkezzen, lehetővé téve a hő hatékony elvezetését a forgácsról. Ez kulcsfontosságú a készülék optimális üzemi hőmérsékletének megőrzéséhez és a túlmelegedés elkerüléséhez, ami teljesítményromláshoz és megbízhatósági problémákhoz vezethet. Az öntött alátöltés fokozott hőelvezetési tulajdonságai hozzájárulnak az elektronikus eszköz általános megbízhatóságához és hosszú élettartamához.
Ezenkívül a fröccsöntött alátöltés több miniatürizálást és alaktényező-optimalizálást tesz lehetővé. A kapszulázási folyamat különféle méretű és formájú csomagokhoz szabható, beleértve a bonyolult 3D-s struktúrákat is. Ez a rugalmasság lehetővé teszi több chip és egyéb alkatrészek integrálását egy kompakt, helytakarékos csomagba. A magasabb szintű integráció elérésének képessége a megbízhatóság veszélyeztetése nélkül különösen értékessé teszi a fröccsöntött alátöltést olyan alkalmazásokban, ahol a méret- és súlykorlátozások kritikusak, mint például a mobileszközök, a hordható eszközök és az autóelektronika.
Chip Scale Package (CSP) alátöltés: Miniatürizálás és nagy sűrűség
A Chip Scale Package (CSP) alátöltés egy kritikus technológia, amely lehetővé teszi a miniatürizálást és a nagy sűrűségű elektronikus eszközök integrációját. Mivel az elektronikus eszközök mérete folyamatosan csökken, miközben megnövekedett funkcionalitást biztosít, a CSP kulcsfontosságú szerepet tölt be e kompakt eszközök megbízhatóságának és teljesítményének biztosításában.
A CSP egy olyan csomagolási technológia, amely lehetővé teszi, hogy a félvezető chipet közvetlenül a hordozóra vagy a nyomtatott áramköri lapra (PCB) szereljük fel anélkül, hogy további csomagra lenne szükség. Ezzel szükségtelenné válik a hagyományos műanyag vagy kerámia edény, ami csökkenti az eszköz teljes méretét és súlyát. A CSP alátöltés egy olyan folyamat, amelyben folyékony vagy kapszulázó anyagot használnak a forgács és az aljzat közötti rés kitöltésére, mechanikai alátámasztást biztosítva és megvédve a chipet az olyan környezeti tényezőktől, mint a nedvesség és a mechanikai igénybevétel.
A miniatürizálás a CSP alátöltés révén érhető el a chip és a hordozó közötti távolság csökkentésével. Az alátöltő anyag kitölti a forgács és az aljzat közötti szűk rést, így szilárd kötést hoz létre és javítja a forgács mechanikai stabilitását. Ez lehetővé teszi a kisebb és vékonyabb eszközök használatát, így korlátozott helyen több funkcionalitás is elfér.
A nagy sűrűségű integráció a CSP alátöltés másik előnye. Azáltal, hogy nincs szükség külön csomagra, a CSP lehetővé teszi, hogy a chip közelebb kerüljön a NYÁK-on lévő többi komponenshez, csökkentve az elektromos csatlakozások hosszát és javítva a jel integritását. Az alátöltő anyag hővezetőként is működik, hatékonyan elvezetve a forgács által termelt hőt. Ez a hőkezelési képesség nagyobb teljesítménysűrűséget tesz lehetővé, lehetővé téve bonyolultabb és erősebb chipek integrálását elektronikus eszközökbe.
A CSP alátöltő anyagoknak sajátos jellemzőkkel kell rendelkezniük, hogy megfeleljenek a miniatürizálás és a nagy sűrűségű integráció követelményeinek. Alacsony viszkozitásúaknak kell lenniük, hogy megkönnyítsék a szűk rések kitöltését, valamint kiváló folyási tulajdonságokkal kell rendelkezniük az egyenletes fedés biztosítása és az üregek megszüntetése érdekében. Az anyagoknak jó tapadásúaknak kell lenniük a forgácshoz és az aljzathoz is, így szilárd mechanikai tartást kell biztosítaniuk. Ezenkívül nagy hővezető képességgel kell rendelkezniük ahhoz, hogy hatékonyan elvezetjék a hőt a chipről.
Ostyaszintű CSP alátöltés: Költséghatékony és magas hozam
A wafer-level chip scale pack (WLCSP) alátöltés egy költséghatékony és nagy hozamú csomagolási technika, amely számos előnnyel jár a gyártási hatékonyság és az általános termékminőség terén. A WLCSP alátöltés több chipre alkalmazza az alátöltő anyagot egyidejűleg, miközben még ostya formában van, mielőtt azokat külön csomagokba helyezné. Ez a megközelítés számos előnnyel jár a költségcsökkentés, a jobb folyamatszabályozás és a magasabb termelési hozam tekintetében.
A WLCSP alátöltés egyik kritikus előnye a költséghatékonyság. Az alátöltő anyag ostyaszinten történő felhordása leegyszerűsíti és hatékonyabbá teszi a csomagolási folyamatot. Az alultöltött anyagot ellenőrzött és automatizált eljárással adagolják az ostyára, csökkentve az anyagpazarlást és minimalizálva a munkaerőköltségeket. Ezen túlmenően, az egyes csomagkezelési és igazítási lépések kiiktatása csökkenti a teljes gyártási időt és a bonyolultságot, ami jelentős költségmegtakarítást eredményez a hagyományos csomagolási módszerekhez képest.
Ezenkívül a WLCSP alátöltés jobb folyamatszabályozást és magasabb termelési hozamokat kínál. Mivel az alátöltő anyagot az ostya szintjén alkalmazzák, ez lehetővé teszi az adagolási folyamat jobb irányítását, biztosítva a konzisztens és egyenletes alátöltési lefedettséget az ostyán lévő minden egyes chip számára. Ez csökkenti az üregek vagy a hiányos alultöltés kockázatát, ami megbízhatósági problémákhoz vezethet. Az alátöltés minőségének szeletszinten történő vizsgálata és tesztelése lehetővé teszi a hibák vagy folyamateltérések korai felismerését is, lehetővé téve az időben történő korrekciós intézkedéseket, és csökkenti a hibás csomagok valószínűségét. Ennek eredményeként a WLCSP alátöltés segít magasabb termelési hozamok és jobb általános termékminőség elérésében.
Az ostyaszintű megközelítés jobb termikus és mechanikai teljesítményt is lehetővé tesz. A WLCSP-ben használt alátöltő anyag jellemzően alacsony viszkozitású, kapillárison folyó anyag, amely hatékonyan képes kitölteni a forgács és az ostya közötti szűk réseket. Ez szilárd mechanikai alátámasztást biztosít a forgácsoknak, növelve a mechanikai igénybevétellel, rezgéssel és hőmérséklet-ciklussal szembeni ellenállásukat. Ezenkívül az alátöltő anyag hővezetőként működik, megkönnyítve a forgácsok által termelt hő elvezetését, ezáltal javítva a hőkezelést és csökkentve a túlmelegedés kockázatát.
Flip Chip Underfill: Nagy I/O sűrűség és teljesítmény
A flip chip alátöltés egy kritikus technológia, amely nagy bemeneti/kimeneti (I/O) sűrűséget és kivételes teljesítményt tesz lehetővé az elektronikus eszközökben. Döntő szerepet játszik a flip-chip csomagolás megbízhatóságának és funkcionalitásának fokozásában, amelyet széles körben használnak a fejlett félvezető alkalmazásokban. Ez a cikk a flip-chip alátöltés jelentőségét és a nagy I/O sűrűség és teljesítmény elérésére gyakorolt hatását vizsgálja.
A flip chip technológia magában foglalja egy integrált áramkör (IC) vagy egy félvezető szerszám közvetlen elektromos csatlakoztatását a hordozóhoz, így nincs szükség huzalkötésre. Ez kompaktabb és hatékonyabb csomagot eredményez, mivel az I/O-párnák a szerszám alsó felületén találhatók. A flip-chip csomagolás azonban egyedi kihívásokat jelent, amelyekkel az optimális teljesítmény és megbízhatóság biztosítása érdekében foglalkozni kell.
A flip chip csomagolás egyik kritikus kihívása a mechanikai igénybevétel és a termikus eltérés megelőzése a szerszám és az aljzat között. A gyártási folyamat és az azt követő művelet során a szerszám és a hordozó közötti hőtágulási együttható (CTE) különbségei jelentős feszültséget okozhatnak, ami teljesítményromláshoz vagy akár meghibásodáshoz vezethet. A flip chip alátöltés egy védőanyag, amely magába zárja a chipet, mechanikai támasztást és feszültségcsökkentést biztosítva. Hatékonyan osztja el a hőciklus során keletkező feszültségeket, és megakadályozza, hogy azok befolyásolják a kényes összeköttetéseket.
A nagy I/O-sűrűség kritikus fontosságú a modern elektronikai eszközökben, ahol a kisebb mérettényezők és a megnövelt funkcionalitás elengedhetetlenek. A flip chip alátöltés nagyobb I/O sűrűséget tesz lehetővé, mivel kiváló elektromos szigetelést és hőkezelési képességeket kínál. Az alátöltő anyag kitölti a szerszám és a hordozó közötti rést, robusztus interfészt hozva létre, és csökkenti a rövidzárlat és az elektromos szivárgás kockázatát. Ez lehetővé teszi az I/O-padok közötti szorosabb távolságot, ami megnöveli az I/O-sűrűséget a megbízhatóság feláldozása nélkül.
Ezenkívül a flip chip alátöltés hozzájárul a jobb elektromos teljesítményhez. Minimalizálja az elektromos parazitákat a szerszám és a hordozó között, csökkenti a jel késleltetését és javítja a jel integritását. Az alátöltő anyag kiváló hővezető tulajdonságokkal is rendelkezik, hatékonyan vezeti el a forgács által működés közben keletkező hőt. A hatékony hőelvezetés biztosítja, hogy a hőmérséklet az elfogadható határokon belül maradjon, megakadályozza a túlmelegedést és fenntartja az optimális teljesítményt.
A flip chip alátöltő anyagok fejlesztése még nagyobb I/O sűrűséget és teljesítményszintet tesz lehetővé. A nanokompozit alultöltők például nanoméretű töltőanyagokat használnak fel a hővezető képesség és a mechanikai szilárdság növelésére. Ez jobb hőelvezetést és megbízhatóságot tesz lehetővé, ami nagyobb teljesítményű eszközöket tesz lehetővé.
Ball Grid Array (BGA) alátöltés: nagy termikus és mechanikai teljesítmény
A Ball Grid Array (BGA) egy kritikus technológia alátámasztása, amely magas hő- és mechanikai teljesítményt kínál az elektronikus eszközökben. Döntő szerepet játszik a különböző alkalmazásokban széles körben használt BGA-csomagok megbízhatóságának és funkcionalitásának fokozásában. Ebben a cikkben megvizsgáljuk a BGA alátöltés jelentőségét és hatását a magas termikus és mechanikai teljesítmény elérésére.
A BGA technológia egy olyan csomagkialakítást foglal magában, amelyben az integrált áramkör (IC) vagy a félvezető matrica egy hordozóra van szerelve, és az elektromos csatlakozások a csomagolás alsó felületén található forrasztógolyókon keresztül jönnek létre. A BGA alátölti a szerszám és a hordozó közötti résbe adagolt anyagot, beágyazza a forrasztógolyókat, és mechanikai alátámasztást és védelmet biztosít a szerelvénynek.
A BGA csomagolás egyik kritikus kihívása a termikus igénybevételek kezelése. Működés közben az IC hőt termel, a hőtágulás és összehúzódás pedig jelentős nyomást gyakorolhat a szerszámot és a hordozót összekötő forrasztási kötésekre. A BGA döntő szerepet játszik ezen feszültségek mérséklésében azáltal, hogy szilárd kötést hoz létre a szerszámmal és az aljzattal. Feszültségpufferként működik, elnyeli a hőtágulást és összehúzódást, és csökkenti a forrasztási kötések terhelését. Ez segít javítani a csomag általános megbízhatóságát, és csökkenti a forrasztási kötések meghibásodásának kockázatát.
A BGA alátöltés másik kritikus szempontja, hogy képes javítani a csomag mechanikai teljesítményét. A BGA csomagok gyakran vannak kitéve mechanikai igénybevételnek a kezelés, az összeszerelés és a működés során. Az alátöltő anyag kitölti a szerszám és az aljzat közötti rést, szerkezeti alátámasztást és megerősítést biztosítva a forrasztási kötéseknek. Ez javítja a szerelvény általános mechanikai szilárdságát, így jobban ellenáll a mechanikai ütéseknek, rezgéseknek és egyéb külső erőknek. A mechanikai igénybevételek hatékony elosztásával a BGA alátöltés segít megelőzni a csomagolás repedését, rétegválását vagy egyéb mechanikai hibákat.
A magas hőteljesítmény elengedhetetlen az elektronikus eszközök megfelelő működéséhez és megbízhatóságához. A BGA alátöltő anyagokat úgy tervezték, hogy kiváló hővezető tulajdonságokkal rendelkezzenek. Ez lehetővé teszi számukra, hogy hatékonyan továbbítsák a hőt a szerszámból, és elosztják azt a hordozón, javítva a csomagolás általános hőkezelését. A hatékony hőelvezetés segít fenntartani az alacsonyabb üzemi hőmérsékletet, megelőzve a hőforrások kialakulását és a teljesítmény esetleges romlását. Ezenkívül hozzájárul a doboz élettartamához azáltal, hogy csökkenti az alkatrészek hőterhelését.
A BGA alátöltő anyagok fejlesztése még magasabb hő- és mechanikai teljesítményt eredményezett. A továbbfejlesztett készítmények és töltőanyagok, például a nanokompozitok vagy a nagy hővezető képességű töltőanyagok jobb hőelvezetést és mechanikai szilárdságot tettek lehetővé, tovább javítva a BGA-csomagok teljesítményét.
Quad Flat Package (QFP) alátöltés: nagy I/O-szám és robusztusság
A Quad Flat Package (QFP) egy integrált áramköri (IC) csomag, amelyet széles körben használnak az elektronikában. Négyzet vagy téglalap alakú, mind a négy oldalról kinyúló vezetékekkel, sok bemeneti/kimeneti (I/O) csatlakozást biztosítva. A QFP-csomagok megbízhatóságának és robusztusságának növelése érdekében általában alátöltő anyagokat használnak.
Az alátöltés egy védőanyag, amelyet az IC és a hordozó között alkalmaznak, hogy megerősítsék a forrasztási kötések mechanikai szilárdságát és megakadályozzák a feszültség okozta meghibásodásokat. Ez különösen fontos a nagy I/O-számmal rendelkező QFP-k esetében, mivel a csatlakozások nagy száma jelentős mechanikai igénybevételekhez vezethet a termikus ciklus és az üzemi körülmények során.
A QFP csomagokhoz használt alátöltő anyagnak sajátos jellemzőkkel kell rendelkeznie a robusztusság biztosítása érdekében. Először is, kiválóan tapadnia kell mind az IC-hez, mind az aljzathoz, hogy erős kötést hozzon létre, és minimalizálja a delamináció vagy leválás kockázatát. Ezenkívül alacsony hőtágulási együtthatóval (CTE) kell rendelkeznie, hogy megfeleljen az IC és a hordozó CTE-jének, csökkentve a feszültségi eltéréseket, amelyek repedésekhez vagy törésekhez vezethetnek.
Ezenkívül az alátöltő anyagnak jó folyási tulajdonságokkal kell rendelkeznie, hogy biztosítsa az egyenletes fedést és az IC és az aljzat közötti rés teljes kitöltését. Ez segít megszüntetni az üregeket, amelyek gyengíthetik a forrasztási kötéseket, és csökkenthetik a megbízhatóságot. Az anyagnak jó kötési tulajdonságokkal is rendelkeznie kell, hogy a felhordás után merev és tartós védőréteget képezzen.
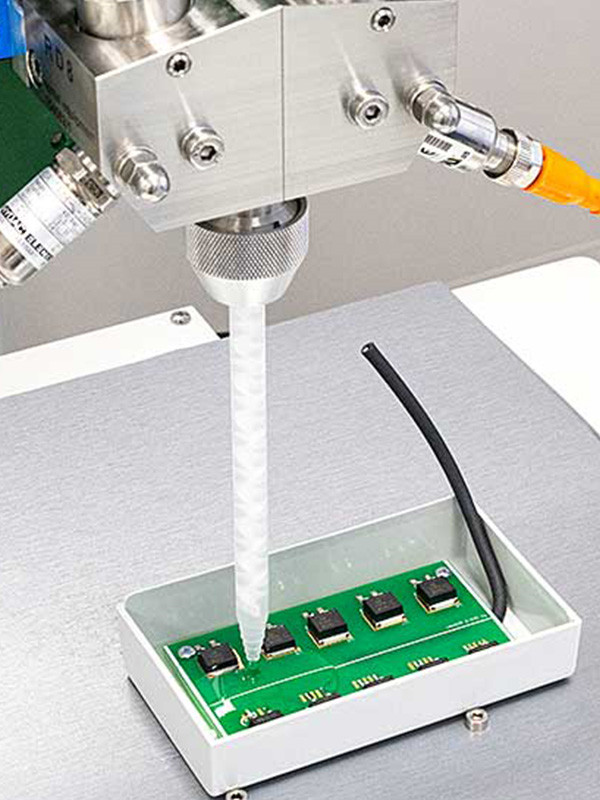
A mechanikai robusztusság szempontjából az alátöltésnek nagy nyíró- és leválási szilárdsággal kell rendelkeznie, hogy ellenálljon a külső erőknek, és megakadályozza a csomagolás deformálódását vagy szétválását. Jó ellenálló képességgel kell rendelkeznie a nedvességgel és más környezeti tényezőkkel szemben is, hogy idővel megőrizze védő tulajdonságait. Ez különösen fontos azokban az alkalmazásokban, ahol a QFP-csomag zord körülményeknek van kitéve, vagy hőmérséklet-ingadozásoknak lehet kitéve.
Különféle alátöltő anyagok állnak rendelkezésre a kívánt tulajdonságok eléréséhez, beleértve az epoxi alapú készítményeket is. Az alkalmazás speciális követelményeitől függően ezek az anyagok különböző technikákkal adagolhatók, például kapilláris áramlással, sugárhajtással vagy szitanyomással.
System-in-Package (SiP) alátöltés: integráció és teljesítmény
A System-in-Package (SiP) egy fejlett csomagolási technológia, amely több félvezető chipet, passzív komponenseket és egyéb elemeket integrál egyetlen csomagba. A SiP számos előnnyel rendelkezik, beleértve a csökkentett alaktényezőt, a jobb elektromos teljesítményt és a továbbfejlesztett funkcionalitást. A SiP-szerelvények megbízhatóságának és teljesítményének biztosítása érdekében általában alátöltő anyagokat használnak.
Az alultöltés a SiP-alkalmazásokban kulcsfontosságú a mechanikai stabilitás és az elektromos csatlakozás biztosításában a csomagon belüli különböző alkatrészek között. Segít minimalizálni a feszültség okozta meghibásodások kockázatát, mint például a forrasztási csatlakozások repedései vagy törései, amelyek az alkatrészek közötti hőtágulási együttható (CTE) különbségei miatt fordulhatnak elő.
Több komponens integrálása egy SiP-csomagba összetett összekapcsolhatósághoz vezet, sok forrasztási csatlakozással és nagy sűrűségű áramkörrel. Az alátöltő anyagok segítenek megerősíteni ezeket az összeköttetéseket, növelve az összeszerelés mechanikai szilárdságát és megbízhatóságát. Megtámasztják a forrasztási kötéseket, csökkentve a kifáradás vagy a hőciklus vagy a mechanikai igénybevétel által okozott károsodás kockázatát.
Az elektromos teljesítmény szempontjából az alátöltő anyagok kritikusak a jel integritásának javítása és az elektromos zaj minimalizálása szempontjából. Az alkatrészek közötti hézagok kitöltésével és a köztük lévő távolság csökkentésével az alátöltés segít csökkenteni a parazita kapacitást és induktivitást, ami gyorsabb és hatékonyabb jelátvitelt tesz lehetővé.
Ezenkívül a SiP alkalmazásokhoz használt alátöltő anyagoknak kiváló hővezető képességgel kell rendelkezniük, hogy hatékonyan elvezessék az integrált alkatrészek által termelt hőt. A hatékony hőelvezetés elengedhetetlen a túlmelegedés megelőzéséhez, valamint a SiP-szerelvény általános megbízhatóságának és teljesítményének fenntartásához.
A SiP csomagolásban lévő alátöltő anyagoknak meghatározott tulajdonságokkal kell rendelkezniük ahhoz, hogy megfeleljenek ezeknek az integrációs és teljesítménykövetelményeknek. Jó folyóképességűeknek kell lenniük, hogy biztosítsák a teljes fedést és kitöltsék az alkatrészek közötti hézagokat. Az alátöltő anyagnak alacsony viszkozitású összetételűnek kell lennie, hogy lehetővé tegye a könnyű adagolást és a szűk lyukakban vagy kis helyeken való kitöltést.
Ezenkívül az alátöltő anyagnak erősen tapadnia kell a különböző felületekhez, beleértve a félvezető chipeket, hordozókat és passzív anyagokat, hogy biztosítsa a megbízható kötést. Kompatibilisnek kell lennie különféle csomagolóanyagokkal, például szerves anyagokkal vagy kerámiákkal, és jó mechanikai tulajdonságokkal kell rendelkeznie, beleértve a nagy nyíró- és lefejtőszilárdságot.
Az alátöltő anyag és a felhordási módszer megválasztása a konkrét SiP-tervezéstől, az alkatrészek követelményeitől és a gyártási folyamatoktól függ. Az olyan adagolási technikák, mint a kapilláris áramlás, a fúvóka vagy a fóliával segített módszerek általában alultöltést alkalmaznak a SiP-szerelvényekben.
Optoelektronikai alátöltés: optikai igazítás és védelem
Az optoelektronikai alátöltés magában foglalja az optoelektronikai eszközök tokozását és védelmét, miközben biztosítja a pontos optikai igazítást. Az optoelektronikai eszközök, például a lézerek, fotodetektorok és optikai kapcsolók gyakran az optikai alkatrészek finom beállítását igénylik az optimális teljesítmény elérése érdekében. Ugyanakkor meg kell védeni azokat a környezeti tényezőktől, amelyek befolyásolhatják működésüket. Az optoelektronikai alátöltés mindkét követelményt kielégíti azáltal, hogy egyetlen folyamatban biztosítja az optikai igazítást és védelmet.
Az optikai igazítás az optoelektronikai eszközök gyártásának kritikus szempontja. Ez magában foglalja a vizuális elemek, például szálak, hullámvezetők, lencsék vagy rácsok összehangolását a hatékony fényátvitel és -vétel érdekében. Pontos igazítás szükséges az eszköz teljesítményének maximalizálásához és a jel integritásának megőrzéséhez. A hagyományos igazítási technikák közé tartozik a szemrevételezéssel végzett kézi igazítás vagy az igazítási szakaszokat használó automatizált igazítás. Ezek a módszerek azonban idő-, munkaigényesek és hibákra hajlamosak lehetnek.
Az optoelektronika innovatív megoldást jelent az igazítási funkciók közvetlenül az alátöltő anyagba történő beépítésével. Az alátöltő anyagok jellemzően folyékony vagy félfolyékony vegyületek, amelyek képesek folyni és kitölteni az optikai alkatrészek közötti hézagokat. Igazítási jellemzők, például mikrostruktúrák vagy kiindulási jelek hozzáadásával az alátöltő anyagon belül az igazítási folyamat egyszerűsíthető és automatizálható. Ezek a jellemzők vezetőként működnek az összeszerelés során, biztosítva az optikai alkatrészek pontos beállítását anélkül, hogy bonyolult igazítási eljárásokra lenne szükség.
Az optikai beállítás mellett az alátöltő anyagok védik az optoelektronikai eszközöket. Az optoelektronikai alkatrészek gyakran vannak kitéve zord környezetnek, beleértve a hőmérséklet-ingadozásokat, a nedvességet és a mechanikai igénybevételt. Ezek a külső tényezők idővel ronthatják az eszközök teljesítményét és megbízhatóságát. Az alátöltő anyagok védőgátként működnek, beburkolják az optikai alkatrészeket, és megvédik őket a környezeti szennyeződésektől. Mechanikai megerősítést is biztosítanak, csökkentve az ütés vagy rezgés okozta sérülések kockázatát.
Az optoelektronikai alkalmazásokban használt alátöltő anyagokat általában úgy tervezték, hogy alacsony törésmutatókkal és kiváló optikai átlátszósággal rendelkezzenek. Ez minimális interferenciát biztosít a készüléken áthaladó optikai jelekkel. Ezenkívül jó tapadást mutatnak a különböző felületekhez, és alacsony hőtágulási együtthatóval rendelkeznek, hogy minimalizálják az eszköz feszültségét a hőciklus során.
Az alátöltési folyamat során az alátöltő anyagot kiadagolják az eszközre, lehetővé téve az áramlást, és kitöltik az optikai alkatrészek közötti réseket, majd kikeményítik, hogy szilárd kapszulát képezzenek. A konkrét alkalmazástól függően az alátöltő anyagot különböző technikákkal lehet felvinni, például kapilláris áramlással, sugáradagolással vagy szitanyomással. A keményedési folyamat hővel, UV-sugárzással vagy mindkettővel megvalósítható.
Orvosi elektronikai alátöltés: biokompatibilitás és megbízhatóság
Az orvosi elektronika egy speciális folyamat alá tartozik, amely magában foglalja az orvosi eszközökben használt elektronikus alkatrészek tokozását és védelmét. Ezek az eszközök döntő szerepet játszanak különböző orvosi alkalmazásokban, például beültethető eszközökben, diagnosztikai berendezésekben, megfigyelőrendszerekben és gyógyszeradagoló rendszerekben. Az orvosi elektronikai alátöltés két kritikus szempontra összpontosít: a biokompatibilitásra és a megbízhatóságra.
A biokompatibilitás alapvető követelmény az emberi testtel érintkező orvostechnikai eszközökkel szemben. Az orvosi elektronikában használt alátöltő anyagoknak biokompatibilisnek kell lenniük, azaz élő szövetekkel vagy testnedvekkel érintkezve nem okozhatnak káros hatásokat vagy mellékhatásokat. Ezeknek az anyagoknak meg kell felelniük a szigorú előírásoknak és szabványoknak, például az ISO 10993 szabványnak, amely meghatározza a biokompatibilitás vizsgálati és értékelési eljárásait.
Az orvosi elektronika alátöltőanyagait gondosan választják ki vagy alakítják ki, hogy biztosítsák a biokompatibilitást. Úgy tervezték, hogy nem mérgezőek, nem irritálnak és nem okoznak allergiát. Ezek az anyagok nem szivároghatnak ki semmilyen káros anyagot, és nem bomlanak le idővel, mivel ez szövetkárosodáshoz vagy gyulladáshoz vezethet. A biokompatibilis alátöltő anyagok alacsony vízfelvétellel rendelkeznek, hogy megakadályozzák a fertőzést okozó baktériumok vagy gombák növekedését.
A megbízhatóság egy másik kritikus szempont az orvosi elektronika alátöltésénél. Az orvosi eszközök gyakran kihívást jelentő működési feltételekkel szembesülnek, beleértve a szélsőséges hőmérsékleteket, nedvességet, testfolyadékokat és mechanikai igénybevételt. Az alátöltő anyagoknak meg kell védeniük az elektronikus alkatrészeket, biztosítva azok hosszú távú megbízhatóságát és működőképességét. A megbízhatóság kiemelkedően fontos az orvosi alkalmazásokban, ahol az eszköz meghibásodása súlyosan befolyásolhatja a betegek biztonságát és jólétét.
Az orvosi elektronika alátöltő anyagainak nagy ellenállásúaknak kell lenniük a nedvességgel és a vegyi anyagokkal szemben, hogy ellenálljanak a testnedveknek vagy a sterilizálási folyamatoknak. Ezenkívül jó tapadást kell mutatniuk a különböző felületekhez, biztosítva az elektronikus alkatrészek biztonságos tokozását. A mechanikai tulajdonságok, mint például az alacsony hőtágulási együttható és a jó ütésállóság, kulcsfontosságúak a hőciklus vagy az automatikus terhelés során a részletekre nehezedő feszültség minimalizálásában.
Az orvosi elektronika alátöltési folyamata a következőket tartalmazza:
- Az alátöltő anyag adagolása az elektronikus alkatrészekre.
- Hiánypótlás.
- Kikeményítve védő és mechanikailag stabil kapszulát képez.
Gondoskodni kell arról, hogy a funkciók teljes mértékben lefedjenek, és ne legyenek olyan üregek vagy légzsákok, amelyek veszélyeztethetik a készülék megbízhatóságát.
Ezenkívül az orvostechnikai eszközök alátöltésénél további szempontokat is figyelembe kell venni. Például az alátöltő anyagnak kompatibilisnek kell lennie az eszköz sterilizálási módszereivel. Egyes anyagok érzékenyek lehetnek bizonyos sterilizációs technikákra, például gőzre, etilén-oxidra vagy sugárzásra, és előfordulhat, hogy más anyagokat kell kiválasztani.
Aerospace Electronics Underfill: Magas hőmérséklet- és rezgésállóság
Az űrrepülési elektronika egy speciális folyamatot tölt be az űrrepülési alkalmazásokban használt elektronikus alkatrészek beágyazására és védelmére. A repülési környezet egyedi kihívásokat jelent, beleértve a magas hőmérsékletet, a szélsőséges rezgéseket és a mechanikai igénybevételeket. Ezért a repülőgép-elektronikai alátöltés két kulcsfontosságú szempontra összpontosít: a magas hőmérséklettel szembeni ellenállásra és a rezgésállóságra.
A repülési elektronikában a magas hőmérséklettel szembeni ellenállás az üzemeltetés során tapasztalható megemelkedett hőmérséklet miatt kiemelkedően fontos. Az űrhajózási alkalmazásokban használt alátöltő anyagoknak ellenállniuk kell ezeket a magas hőmérsékleteket anélkül, hogy az elektronikus alkatrészek teljesítményét és megbízhatóságát veszélyeztetnék. Minimális hőtágulást kell mutatniuk, és széles hőmérsékleti tartományban stabilnak kell maradniuk.
A repülőgép-elektronika alátöltőanyagait magas üvegesedési hőmérsékletre (Tg) és hőstabilitásra választják vagy alakítják ki. A magas Tg biztosítja, hogy az anyag megőrizze mechanikai tulajdonságait magas hőmérsékleten, megakadályozva a deformációt vagy a tapadás elvesztését. Ezek az anyagok ellenállnak a szélsőséges hőmérsékleti hatásoknak, például felszállás, légköri visszatérés vagy forró motorterekben történő üzemeltetés során.
Ezenkívül a repülőgép-elektronika alátöltő anyagainak alacsony hőtágulási együtthatóval (CTE) kell rendelkezniük. A CTE azt méri, hogy egy anyag mennyit tágul vagy zsugorodik össze a hőmérséklet változásával. Az alacsony CTE-értékkel az alátöltő anyagok minimálisra csökkenthetik az elektronikus alkatrészek hőciklusa által okozott feszültségét, ami mechanikai meghibásodásokhoz vagy a forrasztási kötések kifáradásához vezethet.
A rezgésállóság egy másik kritikus követelmény a repülőgép-elektronika alátöltésénél. Az űrrepülőgépek különféle rezgéseknek vannak kitéve, beleértve a hajtóművet, a repülés okozta rezgéseket és a mechanikai ütéseket az indulás vagy leszállás során. Ezek a rezgések veszélyeztethetik az elektronikus alkatrészek teljesítményét és megbízhatóságát, ha nincsenek megfelelően védve.
A repülőgép-elektronikában használt alátöltő anyagoknak kiváló rezgéscsillapító tulajdonságokkal kell rendelkezniük. El kell nyelniük és el kell adniuk a rezgések által generált energiát, csökkentve az elektronikus alkatrészek feszültségét és feszültségét. Ez segít megelőzni a repedések, törések vagy más mechanikai hibák kialakulását a túlzott vibráció miatt.
Ezenkívül a nagy tapadású és kohéziós szilárdságú alátöltő anyagokat előnyben részesítik az űrhajózási alkalmazásokban. Ezek a tulajdonságok biztosítják, hogy az alátöltő anyag szilárdan tapadjon az elektronikus alkatrészekhez és az aljzathoz, még szélsőséges vibrációs körülmények között is. Az erős tapadás megakadályozza, hogy az alátöltő anyag rétegesedjék vagy elváljon az elemektől, megőrzi a tokozás integritását és véd a nedvesség vagy törmelék behatolásától.
A repülőgép-elektronika alátöltési folyamata jellemzően abból áll, hogy az alátöltő anyagot az elektronikai alkatrészekre adagolják, lehetővé téve az áramlást, és kitöltik a hézagokat, majd kikeményítik, hogy robusztus kapszulát képezzenek. A kikeményedési folyamat termikus vagy UV térhálósítási módszerekkel hajtható végre, az alkalmazás speciális követelményeitől függően.
Autóelektronikai alátöltés: tartósság és hőállóság
Az autóelektronika alátámasztja azt a kritikus folyamatot, amely magában foglalja az autóipari alkalmazásokban használt elektronikai alkatrészek tokozását és védelmét. Az autóipari környezet egyedi kihívásokat jelent, beleértve a hőmérséklet-ingadozásokat, a hőciklusokat, a mechanikai igénybevételeket, valamint a nedvességnek és vegyszereknek való kitettséget. Ezért az autóelektronikai alátöltés két kritikus szempontra összpontosít: a tartósságra és a hőciklussal szembeni ellenállásra.
A tartósság alapvető követelmény az autóelektronika alátöltésénél. A rendszeres működés során a gépjárművek állandó rezgéseket, ütéseket és mechanikai igénybevételeket tapasztalnak. Az autóipari alkalmazásokban használt alátöltő anyagoknak robusztusan meg kell védeniük az elektronikus alkatrészeket, biztosítva azok tartósságát és hosszú élettartamát. Ellen kell állniuk a zord körülményeknek és az úton előforduló mechanikai terheléseknek, és ellenállniuk kell a nedvesség, por és vegyszerek behatolásának.
Az autóelektronika alátöltőanyagait úgy választják ki vagy alakítják ki, hogy nagy mechanikai szilárdságot és ütésállóságot biztosítsanak. Kiváló tapadást kell mutatniuk az elektronikus alkatrészekhez és a hordozóhoz, megakadályozva a mechanikai igénybevétel hatására a rétegvesztést vagy a szétválást. A tartós alátöltő anyagok segítenek minimalizálni az elektronikus alkatrészek vibráció vagy ütés miatti károsodásának kockázatát, így biztosítva a megbízható teljesítményt a jármű teljes élettartama alatt.
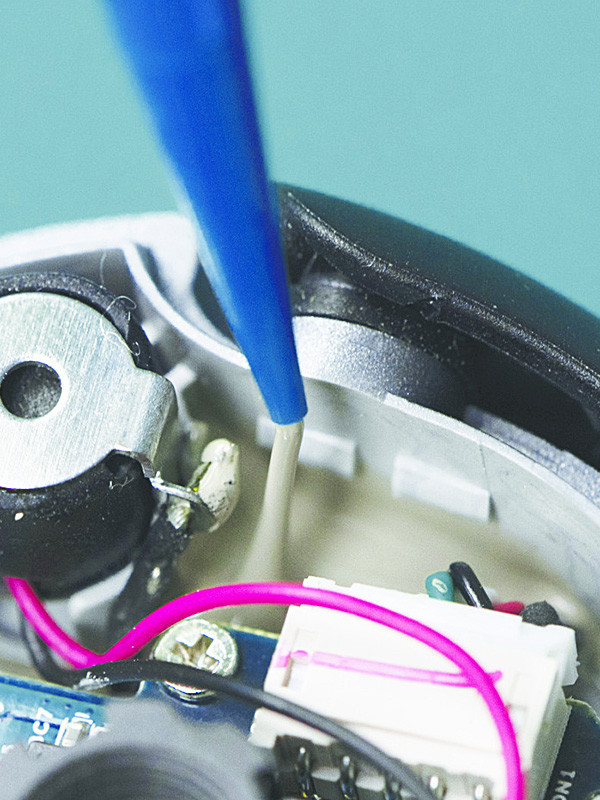
A hőciklus-ellenállás egy másik kritikus követelmény az autóelektronika alátöltésénél. A gépjárművek hőmérséklete gyakori ingadozásokon megy keresztül, különösen a motor indítása és működése során, és ezek a hőmérsékleti ciklusok hőterhelést válthatnak ki az elektronikus alkatrészeken és a környező alátöltő anyagon. Az autóipari alkalmazásokban használt alátöltő anyagoknak kiváló hőciklus-ellenállással kell rendelkezniük, hogy ellenálljanak ezeknek a hőmérséklet-ingadozásoknak anélkül, hogy a teljesítményük csökkenne.
Az autóelektronika alátöltő anyagainak alacsony hőtágulási (CTE) együtthatóval kell rendelkezniük, hogy minimálisra csökkentsék az elektronikai alkatrészek feszültségét a hőciklus során. Az alátöltő anyag és az összetevők közötti jól illeszkedő CTE csökkenti a forrasztási kötések kifáradásának, repedésének vagy egyéb mechanikai meghibásodásának kockázatát, amelyet a hőterhelés okoz. Ezenkívül az alátöltő anyagoknak jó hővezető képességgel kell rendelkezniük, hogy hatékonyan elvezessék a hőt, megakadályozva a helyi forró pontok kialakulását, amelyek befolyásolhatják az alkatrészek teljesítményét és megbízhatóságát.
Ezenkívül az autóelektronikai alátöltő anyagoknak ellenállniuk kell a nedvességnek, a vegyszereknek és a folyadékoknak. Alacsony vízfelvevő képességgel kell rendelkezniük, hogy megakadályozzák a penészképződést vagy az elektronikus alkatrészek korrózióját. A vegyszerállóság biztosítja, hogy az alátöltő anyag stabil maradjon, amikor autóipari folyadékoknak, például olajoknak, üzemanyagoknak vagy tisztítószereknek van kitéve, elkerülve a leromlást vagy a tapadás elvesztését.
Az autóelektronika alátöltési folyamata általában abból áll, hogy az alátöltő anyagot az elektronikai alkatrészekre adagolják, lehetővé téve az áramlást és kitöltik a hézagokat, majd kikeményítik, hogy tartós kapszulát képezzenek. A kikeményedési folyamat termikus vagy UV-keményítési módszerekkel valósítható meg, az alkalmazás speciális követelményeitől és a felhasznált alátöltő anyagtól függően.
A megfelelő alátöltő epoxi kiválasztása
A megfelelő alátöltő epoxi kiválasztása kulcsfontosságú döntés az elektronikai alkatrészek összeszerelése és védelme során. Az alátöltő epoxik mechanikai megerősítést, hőkezelést és védelmet nyújtanak a környezeti tényezőkkel szemben. Íme néhány fő szempont a megfelelő alátöltő epoxi kiválasztásakor:
- Termikus tulajdonságok: Az alátöltő epoxi egyik elsődleges funkciója az elektronikus alkatrészek által termelt hő elvezetése. Ezért fontos figyelembe venni az epoxi hővezető képességét és hőállóságát. A magas hővezető képesség elősegíti a hatékony hőátadást, megakadályozza a forró pontok kialakulását és fenntartja az alkatrészek megbízhatóságát. Az epoxinak alacsony hőellenállással is rendelkeznie kell, hogy minimalizálja az alkatrészek hőterhelését a hőmérséklet-ciklus során.
- CTE Match: Az alátöltő epoxi hőtágulási együtthatójának (CTE) jól illeszkednie kell az elektronikus alkatrészek és a hordozó CTE értékéhez, hogy minimalizálja a hőfeszültséget és megelőzze a forrasztási kötések meghibásodását. A szorosan illeszkedő CTE segít csökkenteni a hőciklusból eredő mechanikai meghibásodások kockázatát.
- Áramlási és hézagkitöltő képesség: Az alultöltött epoxinak jó folyási jellemzőkkel kell rendelkeznie, és képesnek kell lennie az alkatrészek közötti hézagok hatékony kitöltésére. Ez biztosítja a teljes lefedettséget, és minimálisra csökkenti az üregeket vagy légzsákokat, amelyek befolyásolhatják az egység mechanikai stabilitását és hőteljesítményét. Az epoxi viszkozitásának meg kell felelnie az adott alkalmazási és összeszerelési módnak, legyen szó kapilláris áramlásról, sugáradagolásról vagy szitanyomásról.
- Tapadás: Az erős tapadás kulcsfontosságú az epoxi alátöltetnél, hogy biztosítva legyen az alkatrészek és az aljzat közötti megbízható kötés. Jó tapadást kell mutatnia különféle anyagokhoz, beleértve a fémeket, kerámiákat és műanyagokat. Az epoxi adhéziós tulajdonságai hozzájárulnak a szerelvény mechanikai integritásához és hosszú távú megbízhatóságához.
- Kikeményedési módszer: Fontolja meg a gyártási folyamatának leginkább megfelelő kikeményítési módszert. Az alátöltő epoxik hővel, UV-sugárzással vagy a kettő kombinációjával térhálósíthatók. Mindegyik kikeményítési módszernek megvannak az előnyei és korlátai, és elengedhetetlen a gyártási követelményeknek megfelelő módszer kiválasztása.
- Környezeti ellenállás: Értékelje az alátöltő epoxi ellenállását olyan környezeti tényezőkkel szemben, mint a nedvesség, a vegyszerek és a szélsőséges hőmérséklet. Az epoxinak ellenállnia kell a víznek, meggátolva a penész vagy a korrózió kialakulását. A vegyszerállóság biztosítja a stabilitást autóipari folyadékokkal, tisztítószerekkel vagy más potenciálisan korrozív anyagokkal való érintkezéskor. Ezenkívül az epoxinak meg kell őriznie mechanikai és elektromos tulajdonságait széles hőmérséklet-tartományban.
- Megbízhatóság és hosszú élettartam: Vegye figyelembe az alátöltő epoxi múltbeli és megbízhatósági adatait. Keressen olyan epoxi anyagokat, amelyeket teszteltek és bizonyítottan jól teljesítenek hasonló alkalmazásokban, vagy amelyek rendelkeznek ipari tanúsítvánnyal és megfelelnek a vonatkozó szabványoknak. Vegye figyelembe az olyan tényezőket, mint az öregedési viselkedés, a hosszú távú megbízhatóság és az epoxi azon képessége, hogy idővel megőrizze tulajdonságait.
A megfelelő alátöltő epoxi kiválasztásakor kulcsfontosságú, hogy figyelembe vegye az alkalmazás speciális követelményeit, beleértve a hőkezelést, a mechanikai stabilitást, a környezetvédelmet és a gyártási folyamat kompatibilitását. Az epoxi beszállítókkal folytatott konzultáció vagy szakértői tanácsok kérése hasznos lehet egy olyan megalapozott döntés meghozatalában, amely megfelel az alkalmazás igényeinek, és biztosítja az optimális teljesítményt és megbízhatóságot.
Az alultöltő epoxi jövőbeli trendjei
Az alátöltő epoxi folyamatosan fejlődik, az elektronikai technológiák fejlődésének, a feltörekvő alkalmazásoknak, valamint a jobb teljesítmény és megbízhatóság iránti igénynek köszönhetően. Az alátöltő epoxi fejlesztésében és alkalmazásában számos jövőbeli trend figyelhető meg:
- Miniatürizálás és nagyobb sűrűségű csomagolás: Mivel az elektronikus eszközök folyamatosan zsugorodnak, és nagyobb alkatrészsűrűséggel rendelkeznek, az alátöltő epoxiknak ennek megfelelően kell alkalmazkodniuk. A jövőbeli trendek olyan alátöltő anyagok fejlesztésére összpontosítanak, amelyek behatolnak és kitöltik az alkatrészek közötti kisebb réseket, biztosítva a teljes lefedettséget és a megbízható védelmet az egyre miniatürizáltabb elektronikus szerelvényekben.
- Nagyfrekvenciás alkalmazások: A nagyfrekvenciás és nagysebességű elektronikus eszközök iránti növekvő kereslet miatt az alátöltő epoxi készítményeknek meg kell felelniük ezen alkalmazások speciális követelményeinek. Az alacsony dielektromos állandóval és alacsony veszteségű érintőkkel rendelkező alátöltő anyagok elengedhetetlenek a jelveszteség minimalizálásához és a magas frekvenciájú jelek integritásának megőrzéséhez a fejlett kommunikációs rendszerekben, az 5G technológiában és más feltörekvő alkalmazásokban.
- Továbbfejlesztett hőkezelés: A hőelvezetés továbbra is kritikus aggodalomra ad okot az elektronikus eszközök számára, különösen a növekvő teljesítménysűrűség miatt. A jövőbeni alátöltő epoxi készítmények a jobb hővezető képességre fognak összpontosítani, hogy javítsák a hőátadást és hatékonyan kezeljék a termikus problémákat. Fejlett töltőanyagokat és adalékanyagokat építenek be az alátöltő epoxikba, hogy magasabb hővezető képességet érjenek el, miközben más kívánt tulajdonságokat is megtartanak.
- Rugalmas és nyújtható elektronika: A rugalmas és nyújtható elektronika térnyerése új lehetőségeket nyit meg az epoxi anyagok alátöltésében. A rugalmas alátöltő epoxiknak kiváló tapadást és mechanikai tulajdonságokat kell mutatniuk még ismételt hajlítás vagy nyújtás esetén is. Ezek az anyagok lehetővé teszik az elektronika tokozását és védelmét hordható eszközökbe, hajlítható kijelzőkbe és más, mechanikai rugalmasságot igénylő alkalmazásokba.
- Környezetbarát megoldások: A fenntarthatóság és a környezetvédelmi szempontok egyre jelentősebb szerepet fognak játszani az alátöltő epoxi anyagok fejlesztésében. A hangsúly a veszélyes anyagoktól mentes epoxikészítmények létrehozására fog összpontosítani, amelyek életciklusuk során, beleértve a gyártást, a felhasználást és az ártalmatlanítást is, csökkentik a környezetterhelést. A bioalapú vagy megújuló anyagok fenntartható alternatívaként is előtérbe kerülhetnek.
- Továbbfejlesztett gyártási folyamatok: Az alátöltő epoxi jövőbeli trendjei az anyagok tulajdonságaira és a gyártási folyamatok fejlődésére összpontosítanak. Olyan technikákat vizsgálnak meg, mint az additív gyártás, a szelektív adagolás és a fejlett térhálósítási módszerek, hogy optimalizálják az alultöltő epoxi alkalmazását és teljesítményét a különböző elektronikai összeszerelési folyamatokban.
- Fejlett tesztelési és jellemzési technikák integrációja: Az elektronikus eszközök növekvő összetettsége és követelményei miatt fejlett tesztelési és jellemzési módszerekre lesz szükség az alultöltött epoxi megbízhatóságának és teljesítményének biztosítása érdekében. Az olyan technikák, mint a roncsolásmentes tesztelés, a helyszíni megfigyelés és a szimulációs eszközök, segítik az alultöltött epoxi anyagok fejlesztését és minőségellenőrzését.
Következtetés
Az alátöltő epoxi kritikus szerepet játszik az elektronikus alkatrészek megbízhatóságának és teljesítményének növelésében, különösen a félvezető csomagolásban. A különböző típusú alátöltő epoxik számos előnyt kínálnak, beleértve a nagy megbízhatóságot, az önadagolást, a nagy sűrűséget, valamint a magas hő- és mechanikai teljesítményt. Az alkalmazáshoz és a csomagoláshoz megfelelő alátöltő epoxi kiválasztása robusztus és hosszan tartó kötést biztosít. A technológia fejlődésével és a csomagok méretének csökkenésével még innovatívabb alátöltő epoxi megoldásokat várunk, amelyek kiváló teljesítményt, integrációt és miniatürizálást kínálnak. Az Underfill epoxy egyre fontosabb szerepet fog játszani az elektronika jövőjében, lehetővé téve számunkra, hogy magasabb szintű megbízhatóságot és teljesítményt érjünk el a különböző iparágakban.