SMT ragasztó

Az elektronikai gyártás folyamatosan fejlődő világában a Surface Mount Technology (SMT) ragasztó a játék megváltoztatójaként jelent meg. Ez a fejlett ragasztó döntő szerepet játszik az elektronikus alkatrészek nyomtatott áramköri kártyákra (PCB-k) történő zökkenőmentes integrálásának biztosításában. A termékmegbízhatóság növelésétől a gyártási folyamatok egyszerűsítéséig az SMT ragasztó a gyártók nélkülözhetetlen eszközévé vált. Ez a blogbejegyzés az SMT ragasztó különböző aspektusait és az elektronikai iparban betöltött jelentőségét vizsgálja meg.
Az SMT ragasztó megértése: Rövid áttekintés
Az SMT ragasztót vagy felületre szerelhető technológiás ragasztót az elektronikai iparban használják felületre szerelhető eszközök (SMD) nyomtatott áramköri lapokhoz (PCB-k) történő rögzítésére.
Az SMT ragasztó általában szintetikus gyantákból, oldószerekből és adalékanyagokból készül. A ragasztót adagolóval vagy sablonnal kell felvinni a PCB-re. Ezután az SMD-ket a ragasztóra helyezik, mielőtt megszáradna.
Többféle SMT ragasztó kapható, beleértve az epoxi-, akril- és szilikon alapú ragasztókat. Mindegyik típusnak megvannak a maga sajátosságai és előnyei. Például az epoxi ragasztók nagy szilárdságukról és tartósságukról ismertek, míg az akril ragasztók kiváló elektromos szigetelő tulajdonságokkal rendelkeznek.
Az SMT ragasztó kulcsfontosságú az SMT gyártás sikere szempontjából, mivel segít a helyükön tartani az SMD-ket az összeszerelési folyamat során. A ragasztó javítja a végtermék megbízhatóságát és tartósságát is az SMD-k mechanikai támogatásával.
Az SMT ragasztó kiválasztásakor az egyik kritikus szempont a kötési idő. A kikeményedési idő arra az időre vonatkozik, amely szükséges ahhoz, hogy a ragasztó teljesen megkeményedjen, és megtapadjon a PCB-hez és az SMD-hez. A kötési idő a ragasztó típusától és a környezeti feltételektől függően változhat, amelyek között a ragasztót alkalmazzák.
A kötési időn kívül az SMT ragasztó kiválasztásakor figyelembe kell venni a viszkozitást, a tixotrópiát, valamint a hő- és kémiai ellenállást.
Összességében az SMT ragasztó az SMT gyártási folyamatának kritikus összetevője, segítve az elektronikus eszközök megbízhatóságát és tartósságát. A megfelelő ragasztó kiválasztása hozzájárulhat az SMT összeszerelés sikeréhez és a végtermék teljesítményének javításához.
Az SMT ragasztó jelentősége az elektronikai gyártásban
Az SMT ragasztó kulcsfontosságú az elektronikai gyártásban, különösen a felületre szerelhető eszközök (SMD) nyomtatott áramköri kártyákra (PCB-kre) történő összeszerelésénél. Az SMT ragasztó használata biztosítja, hogy az SMD-k biztonságosan rögzítve legyenek a NYÁK-hoz, így mechanikai támaszt nyújtanak, és javítják a végtermék megbízhatóságát és tartósságát.
Az SMT ragasztó egyik fő előnye, hogy az SMD-ket a helyén tartja az összeszerelési folyamat során. Ragasztó nélkül az SMD-k elmozdulhatnak vagy elmozdulhatnak a gyártás során, ami a végtermék hibáihoz vagy meghibásodásához vezethet. Az SMT ragasztó segít megelőzni ezeket a problémákat azáltal, hogy az SMD-ket a helyükön tartja, amíg fel nem forrasztják őket a PCB-re.
Az SMT ragasztó az SMD-k mechanikai támogatásával is javítja az elektronikus eszközök teljesítményét. Ez különösen fontos azokban az alkalmazásokban, ahol a készüléket vibrációnak vagy egyéb mechanikai igénybevételnek tehetik ki. A ragasztó segít elnyelni ezeket a feszültségeket és megakadályozza az SMD-k károsodását, biztosítva, hogy az eszköz továbbra is megfelelően működjön az idő múlásával.
A mechanikai alátámasztás mellett az SMT ragasztó elektromos szigetelést és hővezető képességet biztosít. Ez fontos azokban az alkalmazásokban, ahol az SMD-k hőt termelnek, mivel a ragasztó segíthet ennek a hőnek az elvezetésében, és megakadályozhatja a túlmelegedést és az eszköz károsodását.
A megfelelő SMT ragasztó kiválasztása kulcsfontosságú az elektronikai gyártás sikeréhez. A ragasztó kiválasztásakor figyelembe kell venni olyan tényezőket, mint a kikeményedési idő, viszkozitás, tixotrópia, valamint vegyi és hőállóság. A nem megfelelő ragasztó kiválasztása a végtermék hibáihoz vagy meghibásodásához vezethet, ami költséges és időigényes lehet.
Az SMT ragasztók típusai: A változatok áttekintése
Az SMT (Surface Mount Technology) ragasztó többféle típusa elérhető, mindegyik egyedi tulajdonságokkal és előnyeivel. A megfelelő típusú ragasztó kiválasztása az alkalmazás speciális követelményeitől függ, beleértve a ragasztandó felületek típusát, a környezeti feltételeket és a kötési időt.
- Epoxi ragasztó: Az epoxi ragasztók a leggyakrabban használt SMT ragasztók az elektronikai gyártásban. Nagy szilárdságot és kiváló tartósságot kínálnak, így ideálisak olyan alkalmazásokhoz, ahol mechanikai igénybevétel és magas hőmérséklet várható. Az epoxi ragasztók gyorsan kikeményednek, ezért a nagy volumenű gyártási környezetek kedvelt választása.
- Akril ragasztó: Az akril ragasztók kiváló elektromos szigetelő tulajdonságaikról ismertek. Jó kötési szilárdságot biztosítanak, és szobahőmérsékleten kikeményednek, így alkalmasak olyan alkalmazásokra, ahol nincs szükség magas hőmérsékletre. Az akril ragasztók ellenállnak a környezeti tényezőknek is, például nedvességnek, vegyszereknek és UV-sugárzásnak.
- Szilikon ragasztó: A szilikon ragasztók kiváló rugalmasságot biztosítanak, így ideálisak olyan alkalmazásokhoz, ahol hőtágulás és összehúzódás várható. Jól ellenállnak a nedvességnek, a vegyszereknek és az UV sugárzásnak is. A szilikon ragasztóknak azonban kisebb a tapadási szilárdsága, mint az epoxi és akril ragasztóké.
- UV-sugárzással térhálósítható ragasztó: Az UV-sugárzással térhálósítható ragasztók UV fény hatására kikeményednek, így előnyben részesítik azokat az alkalmazásokhoz, ahol gyors kötésre van szükség. Kiváló kötési szilárdságot biztosítanak, és ideálisak olyan alkalmazásokhoz, ahol nem várható magas hőmérséklet és mechanikai igénybevétel.
- Hot Melt ragasztó: A melegen olvadó ragasztók hőre lágyuló anyagok, amelyeket olvadt állapotra hevítenek és a felületre visznek fel. Gyorsan kikeményednek és jó kötési szilárdságot biztosítanak. Nem alkalmasak azonban olyan alkalmazásokra, ahol magas hőmérséklet várható.
Tényezők, amelyeket figyelembe kell venni az SMT ragasztó kiválasztásakor
A megfelelő SMT (Surface Mount Technology) ragasztó kiválasztása kulcsfontosságú az elektronikai gyártás sikere szempontjából. A kötvény kiválasztásakor számos tényezőt figyelembe kell venni, többek között:
- Aljzatanyag: A ragasztandó aljzatok típusai döntő szerepet játszanak a felhasználandó ragasztó típusának meghatározásában. Egyes ragasztók jobban megfelelnek bizonyos anyagok, például üveg, kerámia vagy fém ragasztására.
- Környezeti feltételek: A végtermék felhasználási környezetét is figyelembe kell venni. Az olyan tényezők, mint a hőmérséklet, a páratartalom és a vegyszereknek való kitettség befolyásolhatják a ragasztó teljesítményét. Fontos, hogy olyan ragasztót válasszunk, amely ellenáll az adott környezeti feltételeknek.
- Kötési idő: A ragasztó kötési ideje alapvető fontosságú tényező, amelyet figyelembe kell venni. A kikeményedési időnek összeegyeztethetőnek kell lennie a termék gyártási ciklusával. A gyorsan kötő ragasztók ideálisak nagy mennyiségű gyártási környezethez. Ezzel szemben a lassabban keményedő ragasztók alkalmasak lehetnek kis mennyiségű gyártásra.
- Viszkozitás és tixotrópia: A ragasztó vastagsága és tixotrópiája kulcsfontosságú tényezők, amelyeket figyelembe kell venni, különösen kis alkatrészek vagy egyenetlen felületek ragasztásánál. Az alacsony viszkozitású ragasztó ideális kis alkatrészek csatlakoztatására. Ezzel szemben a magas tixotrópiájú ragasztó egyenetlen felületek ragasztására alkalmas.
- Kémiai és hőállóság: A ragasztónak ellenállnia kell a termék életciklusa során várható vegyi anyagoknak és hőviszonyoknak. Ez különösen fontos a magas hőmérsékletű alkalmazásoknál, ahol a ragasztónak ellenállnia kell az extrém hőnek és a hőciklusnak.
- Alkalmazási mód: Az alkalmazás módja egy másik kritikus tényező, amelyet figyelembe kell venni. Egyes ragasztókat adagolókkal, míg másokat stencilnyomtatással vagy sugáradagoló módszerrel alkalmaznak. A kiválasztott ragasztónak kompatibilisnek kell lennie az alkalmazási móddal.
Az SMT ragasztó szerepe az alkatrészek elhelyezésében
Felületi szerelési technológia (SMT) A ragasztó kritikus fontosságú az alkatrészek elhelyezésében az elektronikai gyártásban. A ragasztót a nyomtatott áramköri lap (PCB) felületére kell felhordani, hogy az alkatrészek a helyükön maradjanak forrasztás előtt.
Az SMT ragasztó kritikus szerepei az alkatrészek elhelyezésében a következők:
- Biztonságos alkatrészek elhelyezése: SMT ragasztó rögzíti az alkatrészeket a PCB-re. Ez azért fontos, mert az alkatrészek nagyon kicsik és könnyűek, és a gyártás során elmozdulhatnak vagy elmozdulhatnak. A ragasztó segít a helyükön tartani az alkatrészeket, és megakadályozza, hogy elmenjenek vagy leesjenek a tábláról.
- A forrasztási áthidalás megakadályozása: Az SMT ragasztót az elektronikai gyártásban gyakori probléma, a forrasztási áthidalás elkerülésére is használják. Forrasztási áthidalás akkor következik be, amikor egy nem szándékos csatlakozás két szomszédos forrasztási kötést összekapcsol. Ez rövidzárlatot okozhat, és károsíthatja az alkatrészeket. A ragasztó segít elválasztani az alkatrészeket, és megakadályozza a forrasztási áthidalást.
- A forrasztási kötés minőségének javítása: Az SMT ragasztó javíthatja a forrasztási kötés minőségét is. A ragasztó a helyükön tartja a darabokat, ami csökkenti a forrasztási folyamat közbeni elmozdulás kockázatát. Ez egyenletesebb és megbízhatóbb forrasztást eredményez.
- Növelje a gyártási hatékonyságot: Az SMT ragasztó a gyártás hatékonyságát is növelheti. A ragasztót az alkatrészek PCB-re való felhelyezése előtt alkalmazzák, ami csökkenti a kézi igazításhoz és elhelyezéshez szükséges időt. Ez gyorsabb és hatékonyabb gyártási folyamatot eredményez.
- A termék megbízhatóságának javítása: Az SMT ragasztó javíthatja a végtermék megbízhatóságát. Azáltal, hogy a gyártási folyamat során az alkatrészeket a helyükön tartja, a ragasztó segít biztosítani, hogy a részletek megfelelően illeszkedjenek és biztonságosan rögzítsék a nyomtatott áramkört. Ez csökkenti az alkatrészek meghibásodásának vagy hibás működésének kockázatát mozgás vagy vibráció miatt.
Erős és megbízható kötések elérése SMT ragasztóval
Az SMT (Surface Mount Technology) ragasztóval szilárd és megbízható kötések elérése kritikus fontosságú az elektronikai gyártás sikere szempontjából. Az SMT ragasztó a helyükön tartja az alkatrészeket a nyomtatott áramköri lapon (PCB), mielőtt forrasztják őket. Íme néhány tipp a szilárd és megbízható kötések eléréséhez SMT ragasztóval:
- Válassza ki a megfelelő ragasztót: A megfelelő SMT ragasztó kiválasztása elengedhetetlen. A ragasztó kiválasztásakor figyelembe kell venni az aljzat anyagát, a környezeti feltételeket, a kikeményedési időt, a viszkozitást, a tixotrópiát, a vegyi és hőállóságot, valamint az alkalmazási módot. A projekt sajátos követelményeinek megfelelő tömítőanyag kiválasztása elősegíti a robusztus és megbízható kötést.
- A felület előkészítése: A PCB felületének tisztának és szennyeződésektől, például olajoktól, szennyeződésektől és portól mentesnek kell lennie. Ezt tisztítószerrel és szöszmentes kendővel vagy plazmatisztítóval lehet elérni. A megfelelő felület-előkészítés kritikus fontosságú a robusztus és megbízható kötés eléréséhez.
- Helyesen alkalmazza a ragasztót: A ragasztót a megfelelő mennyiségben és a megfelelő helyre kell felhordani. A ragasztó felviteléhez adagolóeszközök, például fecskendők, tűk és adagolók használhatók. A ragasztót egyenletesen és megfelelő mennyiségben kell felhordani, hogy az alkatrészek biztonságosan a helyükön maradjanak.
- Gondoskodjon a megfelelő kikeményedésről: A ragasztónak elegendő időt kell adni a megkötéshez, mielőtt az alkatrészeket forrasztják. A kötési idő a ragasztóanyagtól és a környezeti feltételektől függően változhat. Kövesse a gyártó utasításait a megfelelő kikeményedés biztosítása érdekében.
- Figyelje a környezeti feltételeket: A gyártási környezet környezeti feltételei befolyásolhatják a ragasztó teljesítményét. A hőmérséklet, a páratartalom és a vegyszereknek való kitettség egyaránt befolyásolhatja a kötés szilárdságát és megbízhatóságát. Figyelje ezeket a feltételeket, és tegye meg a megfelelő intézkedéseket annak biztosítására, hogy az ajánlott tartományon belül legyenek.
- Használjon minőségi alkatrészeket: A minőségi alkatrészek elengedhetetlenek a robusztus és megbízható kötés eléréséhez. A rossz minőségű alkatrészeken szabálytalanságok vagy inkonzisztenciák lehetnek, amelyek befolyásolhatják a ragasztási folyamatot. Olyan összetevőket használjon, amelyek megfelelnek a szükséges előírásoknak, és jó hírű beszállítóktól származnak.
- Tesztelje a kötést: A kötés tesztelése elengedhetetlen annak biztosításához, hogy a ragasztó robusztus és megbízható kötést képezzen. Különféle módszerek használhatók a kötés tesztelésére, beleértve a húzóvizsgálatot, a nyírási tesztet és a hőciklusos vizsgálatot. A tesztelés segíthet a ragasztási folyamattal kapcsolatos problémák azonosításában, és biztosíthatja, hogy a végtermék megbízható és tartós legyen.
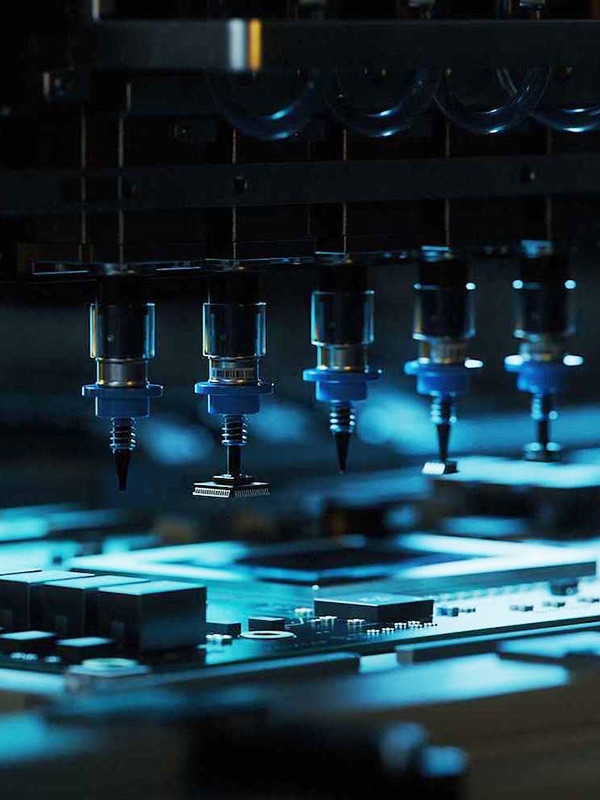
SMT ragasztóadagolási technikák és legjobb gyakorlatok
Az SMT (Surface Mount Technology) ragasztóadagolás kritikus fontosságú az elektronikai gyártásban. A ragasztó a helyükön tartja az alkatrészeket a nyomtatott áramköri lapon (PCB), mielőtt forrasztják őket. Íme néhány adagolási technika és bevált gyakorlat az SMT ragasztóhoz:
- Kézi adagolás: A kézi adagolás költséghatékony technika, amelyhez szakképzett kezelőre van szükség. A kézi adagolás történhet fecskendővel vagy adagolótollal. Ez a technika lehetővé teszi az adagolt ragasztó mennyiségének pontos szabályozását, így ideális kis projektekhez.
- Automatizált adagolás: Az automatizált adagolás gyorsabb és hatékonyabb technika, amely ideális nagyüzemi gyártáshoz. Az automatizált adagolórendszerek olyan berendezéseket használnak, mint a robotok, szivattyúk és szelepek a ragasztónak a PCB-re való felhordásához. Ez a technika lehetővé teszi az egyenletes adagolást és növelheti a termelés hatékonyságát.
- Fúvókás adagolás: A sugáradagolás egy nagy sebességű adagolási technika, amely pneumatikus adagolót használ a ragasztó finom sugárban történő felhordására. Ez a technika ideális nagy mennyiségű gyártáshoz, és kis mennyiségű ragasztót nagy pontossággal adagolhat.
- Szitanyomás: A szitanyomás egy széles körben használt adagolási technika, amely magában foglalja a ragasztó stencilen keresztüli felvitelét. Ez a technika ideális számos ragasztó PCB-re történő felhordásához. A szitanyomás egy költséghatékony és hatékony adagolási módszer, amely kis- és nagyüzemi gyártáshoz egyaránt alkalmazható.
- Bevált gyakorlatok: Az SMT ragasztó adagolásához elengedhetetlen a bevált gyakorlatok követése. Néhány bevált gyakorlat:
- Győződjön meg arról, hogy az adagoló berendezés tiszta és szennyeződésmentes.
- Használja a használt ragasztónak megfelelő adagolócsúcsot vagy fúvókát.
- Győződjön meg arról, hogy az adagolási információ vagy a fúvóka a ragasztott alkatrésznek megfelelő méretű.
- Tartsa be a megfelelő távolságot az adagolócsúcs vagy fúvóka és a nyomtatott áramkör között.
- Tartsa az adagolócsúcsot vagy a fúvókát merőlegesen a PCB felületére.
- Folyamatos mozdulatokkal, megállás nélkül adagolja a ragasztót.
- Győződjön meg arról, hogy a ragasztót egyenletesen és a megfelelő mennyiségben adagolja.
- A megfelelő adagolás érdekében ellenőrizze a ragasztó viszkozitását és tixotrópiáját.
Kihívások leküzdése az SMT ragasztó alkalmazásban
Az SMT (Surface Mount Technology) ragasztó alkalmazása számos tényező miatt kihívást jelenthet, mint például a ragasztó viszkozitása, az alkatrészek mérete és alakja, valamint a PCB elrendezés összetettsége. Íme néhány gyakori kihívás az SMT ragasztó alkalmazása során, és hogyan lehet ezeket leküzdeni:
- A ragasztó viszkozitása: Az SMT ragasztók különböző viszkozitásokban kaphatók, az alacsonytól a magasig. A ragasztó konzisztenciája befolyásolhatja az adagolási folyamatot és a kötési szilárdságot. Az alacsony viszkozitású ragasztók hatékonyabban folynak, míg a nagy viszkozitású ragasztók nagyobb adagolási nyomást igényelhetnek. Ennek a kihívásnak a leküzdése érdekében a gyártóknak az adott alkalmazáshoz megfelelő viszkozitású ragasztót kell kiválasztaniuk, és ennek megfelelően kell beállítaniuk az adagolási paramétereket.
- Alkatrészek mérete és alakja: Az SMT alkatrészek különböző méretűek és formájúak, és néhányat nehéz lehet ragasztani kis méretük vagy szabálytalan formájuk miatt. Ezenkívül az egymáshoz túl közel eső elemek speciális adagolási technikákat igényelhetnek, hogy elkerüljék a ragasztó kivérzést vagy áthidalást. Ennek a kihívásnak a leküzdése érdekében a gyártóknak olyan adagolási technikát kell választaniuk, amely képes kezelni az alkatrészek méretét és alakját, például finom adagolócsúcsot vagy fúvókát a kis elemekhez, vagy fúvóka-adagoló rendszert az egymáshoz közeli elemekhez.
- PCB elrendezés: A PCB elrendezés összetettsége az SMT ragasztó alkalmazását is befolyásolhatja. A NYÁK széléhez túl közel elhelyezett alkatrészek speciális adagolási technikákat igényelhetnek a ragasztó túlfolyásának elkerülése érdekében. Ezenkívül a nagy komponenssűrűségű PCB-k olyan adagolási megközelítést igényelhetnek, amely precíz és ellenőrzött módon alkalmazza a ragasztót. Ennek a kihívásnak a leküzdése érdekében a gyártóknak gondosan át kell tekinteniük a nyomtatott áramköri lapok elrendezését, és olyan adagolási technikát kell választaniuk, amely megfelel az elrendezésnek.
- Környezeti tényezők: A környezeti tényezők, például a hőmérséklet, a páratartalom és a légnyomás befolyásolhatják az SMT ragasztó felhordási folyamatát. Például a magas páratartalom a ragasztó túl gyors megkötését okozhatja. Ezzel szemben az alacsony páratartalom a ragasztó túl lassú megkötését okozhatja. E kihívás leküzdése érdekében a gyártóknak gondosan figyelemmel kell kísérniük a környezeti feltételeket, és ennek megfelelően módosítaniuk kell az adagolási paramétereket.
- Ragasztó kikeményedés: Az SMT ragasztók keményedést igényelnek a kívánt kötési szilárdság eléréséhez. A kikeményedési folyamatot olyan tényezők befolyásolhatják, mint a hőmérséklet, a páratartalom és a ragasztóréteg vastagsága. Ennek a kihívásnak a leküzdése érdekében a gyártóknak követniük kell a ragasztógyártó kötési időre és hőmérsékletre vonatkozó ajánlásait, és biztosítaniuk kell, hogy a környezeti feltételek az ajánlott tartományon belül legyenek.
Az SMT ragasztó hatása a hőkezelésre
A felületre szerelhető technológiás (SMT) ragasztók alapvető szerepet játszanak az elektronikus eszközök hőkezelésében. Az elektronikus eszközök hőkezelése kulcsfontosságú, mivel ez biztosítja a gép hatékony és megbízható működését, valamint megakadályozza a túlzott hő okozta károkat. Az SMT ragasztók többféle módon is befolyásolhatják a hőkezelést, amint azt alább tárgyaljuk.
Először is, az SMT ragasztók hővezető utat biztosítanak a hőelvezetéshez. Ezeket a ragasztókat úgy tervezték, hogy magas hővezető képességgel rendelkezzenek, lehetővé téve, hogy a hőt a hőt termelő alkatrészektől a készülék hűtőbordájába továbbítsák. Ez a hőátadás segít fenntartani a készülék hőmérsékletét a biztonságos működési határokon belül.
Másodszor, az SMT ragasztók a hőszigetelést is befolyásolhatják a hőkezelésre. Ezek a ragasztók hőszigetelőként működhetnek, megakadályozva a hő távozását a készülékből. Ez akkor lehet hasznos, ha az állandó hőmérséklet fenntartása kritikus fontosságú, például orvosi berendezésekben vagy tudományos műszerekben.
Harmadszor, az SMT ragasztók kötési jellemzőik révén befolyásolhatják a hőkezelést. Egyes ragasztók magasabb hőmérsékleten megkeményednek, ami hőterhelést okozhat a készüléken. Ez mechanikai meghibásodásokhoz, például a ragasztó megrepedéséhez vagy leválásához vezethet. Ezért elengedhetetlen, hogy olyan ragasztót válasszunk, amely nem haladja meg a készülék üzemi hőmérsékletét.
Negyedszer, a ragasztó vastagsága is befolyásolhatja a hőkezelést. A vastagabb ragasztóréteg hőgátat képezhet, amely akadályozhatja a hőelvezetést, növelve a hőmérsékletet a készülékben. Másrészt a vékonyabb ragasztóréteg hatékonyabb hőátadást tesz lehetővé, javítva a hőkezelést.
Végül az SMT ragasztó hatással lehet az eszköz általános hőteljesítményére. A különböző kötések eltérő hővezető képességgel, keményedési jellemzőkkel és vastagsággal rendelkeznek. A kifejezetten hőkezelésre tervezett ragasztó kiválasztása segíthet a készülék optimális teljesítményének biztosításában.
Az SMT ragasztóanyag és hozzájárulása a rezgés- és ütésállósághoz
A felületre szerelhető technológiájú (SMT) ragasztók befolyásolják a hőkezelést, és jelentősen hozzájárulnak az elektronikus készülék rezgés- és ütésállóságához. A vibráció és az ütés károsíthatja az elektronikus eszközöket, és az SMT ragasztók elengedhetetlenek e kockázat csökkentéséhez.
Az SMT ragasztók mechanikai támasztást és megerősítést biztosítanak a forrasztott alkatrészeknek. Pufferként működnek a részletek és a hordozó között, szélesebb területen osztva el a vibrációt és az ütési erőket. Ez csökkenti a forrasztási kötések feszültségét, és megakadályozza, hogy az alkalmazott nyomás hatására megrepedjenek vagy eltörjenek.
Az SMT alkalmazásokban használt ragasztóanyag szintén kritikus szerepet játszik a vibráció- és ütésállóságban. A ragasztónak elég szilárdnak és tartósnak kell lennie ahhoz, hogy törés vagy repedés nélkül ellenálljon az eszközre ható erőknek. Ezenkívül a ragasztónak bizonyos fokú rugalmassággal kell rendelkeznie, hogy lehetővé tegye a mozgást és a rugalmasságot a gépben anélkül, hogy a szerkezeti integritását veszélyeztetné.
Az SMT ragasztó hozzájárulhat a készülék rezgésének csillapításához is. A csillapítás az energia disszipációja, amely csökkenti a rendszer rezgési amplitúdóját. A ragasztó képes elnyelni és eloszlatni a vibrációból származó erő egy részét, csökkentve a rezgések amplitúdóját, és megakadályozva, hogy kárt okozzanak a készülékben.
A ragasztóréteg vastagsága is befolyásolhatja a készülék rezgés- és ütésállóságát. A vastagabb ragasztóréteg párnázást és ütéselnyelést biztosíthat. A vékonyabb réteg merevebb lehet, és kisebb ütésállóságot biztosít. A ragasztóréteg vastagságát az eszköz sajátos igényei, valamint a rezgés és ütés mértéke alapján kell megválasztani.
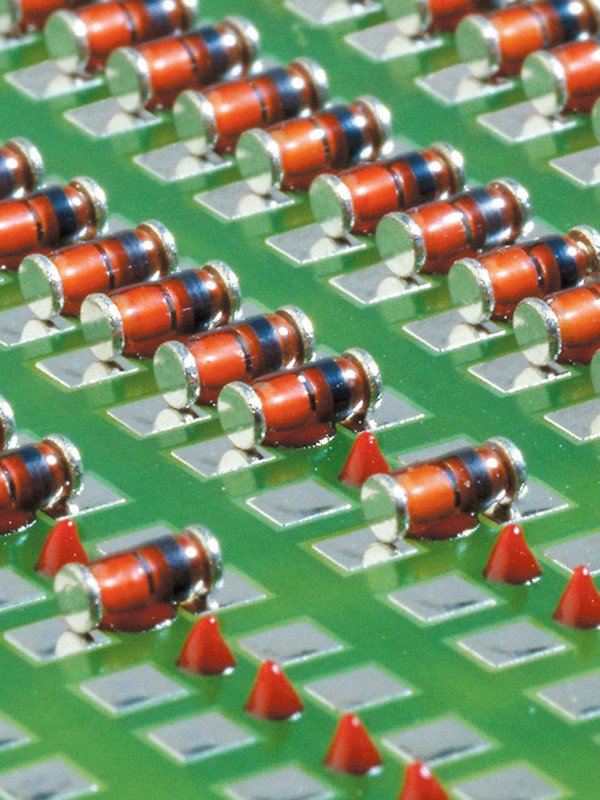
Az SMT ragasztó előnyei
Felületi szerelési technológia (SMT) A ragasztó kritikus eleme az elektronikai eszközök gyártásának. Ez egy olyan ragasztótípus, amelyet kifejezetten a felületre szerelt alkatrészek nyomtatott áramköri kártyákhoz (PCB-k) történő ragasztására terveztek a gyártás során. Íme az SMT ragasztó használatának néhány előnye:
- Megnövelt megbízhatóság: Az SMT ragasztó erős kötést biztosít a felületre szerelhető alkatrészek és a PCB-k között, javítva az elektronikus eszközök megbízhatóságát és teljesítményét. Segít megelőzni az alkatrészek elmozdulását vagy sérülését működés közben, ami meghibásodásokhoz vagy hibás működéshez vezethet.
- Csökkentett utómunkálatok és javítások: SMT ragasztóval az alkatrészek rögzítésére a gyártók csökkenthetik az utómunkálatok és javítások szükségességét. Ezzel időt és pénzt takaríthat meg a gyártási folyamat során, és javíthatja a késztermék általános minőségét.
- Továbbfejlesztett hőkezelés: Az SMT ragasztó javíthatja az elektronikus eszközök hőkezelését azáltal, hogy hűtőbordát biztosít az alkatrészek és a PCB között. Ez segít a hő elvezetésében és megakadályozza a túlmelegedést, ami meghibásodásokhoz vagy hibás működéshez vezethet.
- Miniatürizálás: Az SMT ragasztóval kisebb és kompaktabb elektronikai eszközöket lehet gyártani. Lehetővé teszi kisebb alkatrészek használatát. Csökkenti az alkatrészek elhelyezéséhez szükséges helyet, ami hatékonyabb és költséghatékonyabb tervezést eredményezhet.
- Jobb elektromos teljesítmény: Az SMT ragasztó javíthatja az elektronikus eszközök elektromos teljesítményét azáltal, hogy csökkenti az alkatrészek és a PCB közötti ellenállást. Ez jobb jelintegritást, csökkentett zajt és jobb általános teljesítményt eredményezhet.
- Sokoldalúság: Az SMT ragasztó különféle összetételekben és viszkozitásokban kapható, hogy megfeleljen a különböző alkalmazások speciális igényeinek. Ez sokoldalú kötést biztosít több elektronikus eszközhöz, beleértve a fogyasztói elektronikát, az orvosi készülékeket és az autóelektronikát.
Összességében az SMT ragasztó használata számos előnnyel jár az elektronikai eszközök gyártásában. A felületre szerelhető alkatrészek és a nyomtatott áramköri lapok közötti robusztus és megbízható kötés javíthatja az elektronikus eszközök teljesítményét, megbízhatóságát és hatékonyságát, miközben csökkenti az utómunkálatok és javítások szükségességét. Ez egy sokoldalú ragasztó, amelyet különféle alkalmazásokban használnak, így az elektronikai ipar elengedhetetlen alkotóeleme.
Az SMT ragasztó hátrányai
A Surface Mount Technology (SMT) ragasztó egyfajta ragasztó, amelyet általában elektronikus áramkörök és eszközök gyártásában használnak. Ez egy ragasztó, amely a felületre szerelhető alkatrészeket a helyén tartja a forrasztás során. Bár az SMT ragasztónak megvannak a maga előnyei, számos hátránya is van az ilyen típusú ragasztó használatának.
- Eltávolítási nehézségek: Az SMT ragasztó egyik fő hátránya, hogy nehéz eltávolítani. Miután a ragasztó megkötött, a felületre szerelhető alkatrész eltávolítása kihívást jelenthet anélkül, hogy károsítaná az áramköri lapot. Ez kihívást jelenthet a jövőben az alkatrészek javításában vagy cseréjében.
- Költség: Az SMT ragasztó drága lehet, ami megnehezíti a használatát nagy mennyiségű gyártási környezetben. Ez különösen igaz, ha a ragasztó kiváló minőségű, ami az alkatrészek megbízható tapadásának biztosításához szükséges.
- Kikeményedési idő: Az SMT ragasztónak bizonyos időre van szüksége a kötéshez, mielőtt a darabokat a helyükre lehet forrasztani. Ez növelheti az elektronikus eszközök és áramkörök teljes gyártási idejét.
- Felhasználhatósági idő: Az SMT ragasztónak korlátozott az eltarthatósága, ezért meghatározott időkereten belül kell felhasználni. Ez pazarláshoz vezethet, ha a ragasztót lejárata előtt nem használják fel.
- Minőségellenőrzés: Az SMT ragasztó kihívást jelenthet nagy mennyiségű gyártási környezetben. A kötés alkalmazásának eltérései az alkatrészek tapadásának inkonzisztenciájához vezethetnek, ami a végtermék hibáihoz vezethet.
- Környezetvédelmi szempontok: Az SMT ragasztó olyan vegyi anyagokat tartalmaz, amelyek károsíthatják a környezetet, ha nem megfelelően ártalmatlanítják. Ez a fenntartható és környezettudatos gyártási gyakorlatok mellett elkötelezett vállalatokat érintheti.
- Az alkatrészek sérülésének lehetősége: Az SMT ragasztó károsíthatja azokat a jellemzőket, amelyeket a helyén kell tartani. Ez akkor fordulhat elő, ha a ragasztót túl vastagon vagy nem egyenletesen alkalmazzák.
- Rugalmasság hiánya: Az SMT ragasztó törékeny lehet, ami azt jelenti, hogy nem alkalmas a rugalmasságot igénylő alkatrészekhez. Ez korlátozhatja az elektronikus eszközökben és áramkörökben használt funkciók típusait.
Környezetvédelmi szempontok: Ólommentes SMT ragasztómegoldások
Az ólommentes felületre szerelhető technológia (SMT) ragasztómegoldásai a környezetvédelmi szempontok miatt egyre fontosabbá váltak. Az EU-ban a RoHS (Restriction of Hazardous Substances) irányelv és más országok hasonló szabályozása korlátozza az ólom használatát az elektronikai eszközökben. Ezért az ólommentes SMT ragasztók a hagyományos ólomtartalmú kötések népszerű alternatívájává váltak.
Az ólommentes SMT ragasztók jellemzően más fémeket, például ezüstöt, rezet vagy ónt tartalmaznak, amelyek kevésbé károsak a környezetre, mint az ólom. Ezek az alternatív fémek egyre elterjedtebbek, mivel a gyártók igyekeznek csökkenteni a környezetre gyakorolt hatásukat, miközben megőrzik a kiváló minőségű termékteljesítményt.
Az ólommentes SMT ragasztók gyártása kisebb környezetterheléssel jár, mint a hagyományos ólomtartalmú kötések. Az ólomtartalmú ragasztók előállítása gyakran mérgező vegyi anyagok alkalmazását igényli, ami káros lehet a dolgozókra és a környezetre. Ezzel szemben az ólommentes ragasztókat tisztább, környezetbarátabb módszerekkel állítják elő.
Az ólommentes SMT ragasztók másik környezetvédelmi szempontja az ártalmatlanításuk. A hagyományos ólomtartalmú ragasztók veszélyes hulladéknak minősülnek, és különleges ártalmatlanítási eljárásokat igényelnek. Ezzel szemben az ólommentes ragasztók nem minősülnek veszélyes hulladéknak. A szokásos hulladékkezelési módszerekkel ártalmatlaníthatók.
Kimutatták, hogy az ólommentes SMT ragasztók a hagyományos ólomtartalmú kötésekhez hasonlóan teljesítenek a hőkezelés, a vibráció és az ütésállóság tekintetében. Ezért az ólomtartalmú ragasztók közvetlen helyettesítésére használhatók anélkül, hogy az eszköz teljesítményét veszélyeztetnék.
SMT ragasztó a miniatürizált elektronikában: a pontosság biztosítása
A felületre szerelhető technológiás (SMT) ragasztók kritikus szerepet játszanak a miniatürizált elektronika pontosságának biztosításában. Ahogy az elektronikus eszközök mérete folyamatosan csökken, az alkatrészek elhelyezése és ragasztása egyre kritikusabbá válik. Az SMT ragasztók mechanikus alátámasztást és megerősítést biztosítanak a forrasztott részeknek, megakadályozva azok elmozdulását vagy elmozdulását működés közben.
A miniatürizált elektronikában az alkatrészek elhelyezése döntő fontosságú a megfelelő működés érdekében. Az SMT ragasztók módszert biztosítanak az alkatrészek rögzítésére az összeszerelés és a működés során. A ragasztót pontosan kell felhordani, hogy az alkatrészek a megfelelő helyen és tájolásban legyenek. Még a legkisebb eltérés is teljesítményproblémákat okozhat, vagy használhatatlanná teheti az eszközt.
Az SMT ragasztófelvitel pontossága fejlett adagolási technológiákkal javítható. Ezek a technológiák nagy pontosságú adagolókat használnak, hogy a ragasztót pontosan az egyes komponensekhez szükséges mennyiségben és helyen alkalmazzák. Ez biztosítja, hogy az összeszerelés során a részletek megfelelően rögzítve legyenek és illeszkedjenek.
A ragasztóanyag megválasztása a miniatürizált elektronika precizitása szempontjából is elengedhetetlen. A ragasztónak alacsony viszkozitásúnak és nagyfokú felhelyezési pontossággal kell rendelkeznie. Gyors kötési idővel is kell rendelkeznie, ami lehetővé teszi a gyors összeszerelést és átfutási időt.
A pontos elhelyezés mellett az SMT ragasztók a miniatürizált elektronika teljesítményét is befolyásolhatják. A ragasztónak kiváló hővezető képességgel kell rendelkeznie, hogy biztosítsa a hatékony hőátadást az alkatrészekről az aljzatra. A ragasztónak magas elektromos szigetelési tulajdonságokkal kell rendelkeznie a rövidzárlatok és egyéb teljesítményproblémák elkerülése érdekében.
Összességében az SMT ragasztók kritikus szerepet játszanak a miniatürizált elektronika pontosságának és teljesítményének biztosításában. A ragasztót precízen, nagy pontossággal kell felhordani, és az anyagválasztást alaposan meg kell fontolni, hogy megfeleljen az alkalmazás speciális igényeinek. A fejlett adagolási technológiák javíthatják a ragasztó felvitelének pontosságát, biztosítva, hogy az alkatrészek megfelelően rögzítve legyenek és az összeszerelés során egy vonalba kerüljenek. A megfelelő ragasztó kiválasztásával a gyártók biztosíthatják miniatürizált elektronikus eszközeik teljesítményét és hosszú élettartamát.
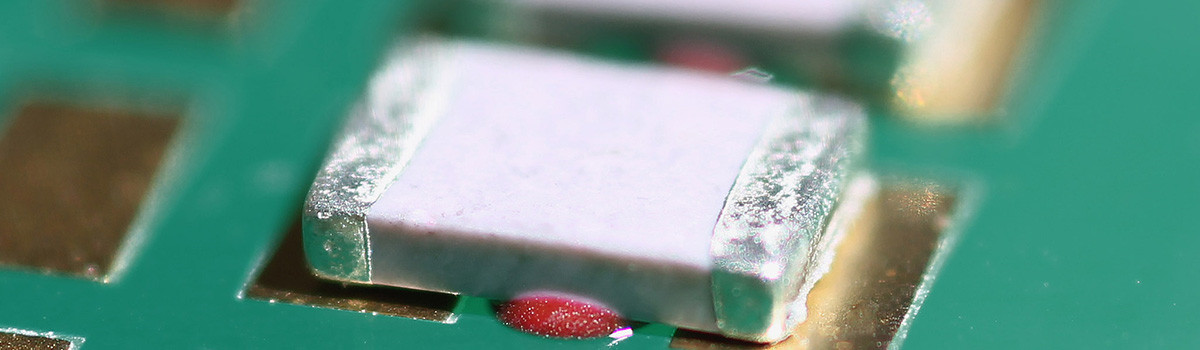
A hozam és a hatékonyság növelése SMT ragasztóval
A felületre szerelhető technológiás (SMT) ragasztók kritikus szerepet játszanak a miniatürizált elektronika pontosságának biztosításában. Ahogy az elektronikus eszközök mérete folyamatosan csökken, az alkatrészek elhelyezése és ragasztása egyre kritikusabbá válik. Az SMT ragasztók mechanikus alátámasztást és megerősítést biztosítanak a forrasztott részeknek, megakadályozva azok elmozdulását vagy elmozdulását működés közben.
A miniatürizált elektronikában az alkatrészek elhelyezése döntő fontosságú a megfelelő működés érdekében. Az SMT ragasztók módszert biztosítanak az alkatrészek rögzítésére az összeszerelés és a működés során. A ragasztót pontosan kell felhordani, hogy az alkatrészek a megfelelő helyen és tájolásban legyenek. Még a legkisebb eltérés is teljesítményproblémákat okozhat, vagy használhatatlanná teheti az eszközt.
Az SMT ragasztófelvitel pontossága fejlett adagolási technológiákkal javítható. Ezek a technológiák nagy pontosságú adagolókat használnak, hogy a ragasztót pontosan az egyes komponensekhez szükséges mennyiségben és helyen alkalmazzák. Ez biztosítja, hogy az összeszerelés során a részletek megfelelően rögzítve legyenek és illeszkedjenek.
A ragasztóanyag megválasztása a miniatürizált elektronika precizitása szempontjából is elengedhetetlen. A ragasztónak alacsony viszkozitásúnak és nagyfokú felhelyezési pontossággal kell rendelkeznie. Gyors kötési idővel is kell rendelkeznie, ami lehetővé teszi a gyors összeszerelést és átfutási időt.
A pontos elhelyezés mellett az SMT ragasztók a miniatürizált elektronika teljesítményét is befolyásolhatják. A ragasztónak kiváló hővezető képességgel kell rendelkeznie, hogy biztosítsa a hatékony hőátadást az alkatrészekről az aljzatra. A ragasztónak magas elektromos szigetelési tulajdonságokkal kell rendelkeznie a rövidzárlatok és egyéb teljesítményproblémák elkerülése érdekében.
Összességében az SMT ragasztók kritikus szerepet játszanak a miniatürizált elektronika pontosságának és teljesítményének biztosításában. A ragasztót precízen, nagy pontossággal kell felhordani, és az anyagválasztást alaposan meg kell fontolni, hogy megfeleljen az alkalmazás speciális igényeinek. A fejlett adagolási technológiák javíthatják a ragasztó felvitelének pontosságát, biztosítva, hogy az alkatrészek megfelelően rögzítve legyenek és az összeszerelés során egy vonalba kerüljenek. A megfelelő ragasztó kiválasztásával a gyártók biztosíthatják miniatürizált elektronikus eszközeik teljesítményét és hosszú élettartamát.
A megbízhatósági aggályok kezelése az SMT ragasztóval
Felületi szerelési technológia (SMT) A ragasztó alapvető szerepet játszik az elektronikus eszközök megbízhatóságának biztosításában. A ragasztó rögzíti az alkatrészeket a helyükön, megakadályozza a mozgást, és minimálisra csökkenti a károsodás vagy meghibásodás kockázatát működés közben. Az SMT ragasztókkal kapcsolatban azonban számos megbízhatósági aggály is felmerül, amelyekkel a gyártóknak foglalkozniuk kell termékeik hosszú távú teljesítményének biztosítása érdekében.
Az SMT ragasztók egyik fő megbízhatósági szempontja a hosszú távú tartóssága. A ragasztónak ellenállnia kell a különféle környezeti tényezőknek, például hőmérséklet-változásoknak, páratartalomnak és mechanikai igénybevételnek. Idővel ezeknek a tényezőknek való kitettség a ragasztó károsodását okozhatja, ami az alkatrészek elmozdulásához és esetleges meghibásodásához vezethet. Ezért a gyártóknak olyan ragasztót kell választaniuk, amely kiváló tartósságú és ellenáll a környezeti tényezőknek, hogy biztosítsák a hosszú távú megbízhatóságot.
Egy másik probléma az SMT ragasztóval kapcsolatban, hogy a felhordás során üregeket vagy légbuborékokat képezhet. Ezek az üregek hőátadási problémákat okozhatnak, és az alkatrészek idő előtti meghibásodásához vezethetnek. A gyártóknak gondosan ellenőrizniük kell a ragasztó felhordási folyamatát, hogy megakadályozzák az üregképződést és fenntartsák a megbízható hőátadást.
A tárolási körülmények és a kezelés is befolyásolhatja az SMT ragasztó megbízhatóságát. Tegyük fel, hogy a ragasztót nem megfelelően tárolják, vagy nem megfelelően kezelik a gyártás során. Ebben az esetben szennyeződhet vagy leromolhat, ami csökkenti a teljesítményt és a megbízhatóságot.
E megbízhatósági aggályok megoldása érdekében a gyártók több lépést is megtehetnek. Olyan ragasztót választhatnak, amely bizonyítottan tartós és ellenáll a környezeti tényezőknek, így biztosítva, hogy ellenálljon a hosszú távú igénybevételnek. A ragasztó felhordási folyamata is gondosan ellenőrizhető az üregképződés megelőzése és a megbízható hőátadás fenntartása érdekében. A ragasztó megfelelő tárolása és kezelése szintén hozzájárulhat a teljesítmény és a megbízhatóság megőrzéséhez.
Ezenkívül a gyártók kiterjedt tesztelési és minőség-ellenőrzési intézkedéseket hajthatnak végre termékeik megbízhatóságának biztosítása érdekében. Ez magában foglalhatja a gyorsított öregedési teszteket, a környezeti tesztelést és a funkcionális tesztelést, hogy azonosítsák a lehetséges problémákat, és biztosítsák, hogy a ragasztó megfelelően működjön.
Az SMT ragasztó és szerepe az átdolgozási és javítási folyamatokban
Felületi szerelési technológia (SMT) A ragasztó elengedhetetlen az elektronikai eszközök átdolgozásához és javításához. Az utómunkálati és javítási folyamatok szabványosak az elektronikai iparban, mivel a gyártás vagy a használat során hibák és problémák léphetnek fel. Az SMT ragasztó használható a meglazult vagy leváló alkatrészek újrarögzítésére vagy a sérült alkatrészek javítására.
Az SMT ragasztóval végzett utómunkálatok vagy javítások során elengedhetetlen az alkalmazáshoz megfelelő Ragasztó kiválasztása. A ragasztónak megfelelő tulajdonságokkal kell rendelkeznie ahhoz, hogy erős tapadást biztosítson a komponenshez és az aljzathoz. Ezenkívül a ragasztónak könnyen felhordhatónak kell lennie, gyors kötési idővel az állásidő minimalizálása és a javítási költségek csökkentése érdekében.
Az SMT ragasztó mindennapos használata az utómunkálatok és javítások során a meglazult vagy leváló alkatrészek visszahelyezése. Ezt mechanikai igénybevétel, hőmérséklet-ingadozások vagy más környezeti tényezők okozhatják. A ragasztó vissza tudja rögzíteni a darabot a helyére, és megakadályozza a további elmozdulást vagy leválást. Ez meghosszabbíthatja az elektronikus eszköz élettartamát, és csökkentheti a csere szükségességét.
Az SMT ragasztó javíthatja a sérült alkatrészeket is, például repedt vagy törött forrasztási kötéseket. A ragasztó felvihető a sérült területre, hogy további támogatást és megerősítést biztosítson, segítve az alkatrész eredeti funkciójának helyreállítását. Egyes esetekben az SMT ragasztó a sérült áramköri lapok javítására is használható, hatékony megoldást nyújtva kisebb sérülésekre vagy problémákra.
Az utómunkálási és javítási folyamatokban való felhasználása mellett az SMT ragasztó megakadályozza az utómunkálatok vagy javítások szükségességét is. A ragasztó a kezdeti gyártási folyamat során használható az alkatrészek megfelelő elhelyezésének biztosítására, valamint az elmozdulás vagy leválás elkerülésére. Ez segíthet minimalizálni a hibák vagy problémák kockázatát, amelyek átdolgozást vagy javítást igényelnek.
Az SMT Adhesive jövője: Fejlődések és innovációk
A felületre szerelhető technológia (SMT) ragasztópiaca várhatóan jelentősen növekedni fog az elkövetkező években a ragasztótechnológia fejlődésének és innovációinak köszönhetően. A gyártók folyamatosan új és továbbfejlesztett ragasztómegoldásokat keresnek, hogy megfeleljenek az egyre növekvő elektronikai ipar igényeinek.
Az SMT ragasztók egyik innovációs területe a környezetbarátabb megoldások kifejlesztése. A fenntarthatóságra és a csökkentett környezetterhelésre fokozottan összpontosítva a gyártók olyan ragasztókat keresnek, amelyek megfelelnek ezeknek a követelményeknek. Olyan új ragasztómegoldásokat fejlesztenek ki, amelyek kevesebb káros vegyszert használnak, és könnyebben újrahasznosíthatók, csökkentve a hulladékot és javítva a fenntarthatóságot.
Az innováció másik területe a javított hőkezelési tulajdonságokkal rendelkező ragasztók fejlesztése. A hatékony hőkezelés egyre fontosabbá válik a kisebb, kompaktabb elektronikus eszközök irányába mutató tendencia miatt. A hőelvezetést és hőátadást javító kötések javíthatják az elektronikus eszközök teljesítményét és megbízhatóságát.
Emellett egyre nagyobb az érdeklődés a javított elektromos tulajdonságokkal rendelkező ragasztók iránt. A vezetőképességet javító vagy elektromos szigetelést biztosító kötések javíthatják az elektronikus eszközök teljesítményét és megbízhatóságát. Ide tartozhatnak a nagy dielektromos szilárdságú vagy alacsony elektromos ellenállású kötések.
A nanotechnológia fejlődése az SMT-ragasztók innovációját is ösztönzi. Nanorészecskéket lehet hozzáadni a ragasztókhoz, hogy javítsák azok tulajdonságait, például a hővezető képességet, a tapadási szilárdságot és az elektromos vezetőképességet. Ez megnövelt teljesítményű és megbízhatóságú ragasztókhoz vezethet a különböző alkalmazásokban.
Végül az adagolási és felhordási technológiai fejlesztések az SMT-ragasztók innovációját is ösztönzik. Az új adagolóberendezések és módszerek segíthetnek javítani a ragasztófelvitel pontosságán és konzisztenciáján, ami javítja az elektronikus eszközök minőségét és megbízhatóságát.
Iparági reflektorfényben: Esettanulmányok és sikertörténetek
Számos sikertörténet és esettanulmány rávilágít az SMT ragasztók fontosságára és hatékonyságára az elektronikai iparban. Íme néhány példa:
- Mobiltelefon-gyártás: Egy jelentős mobiltelefon-gyártó készülékproblémákkal küzdött, beleértve az alkatrészek meglazulását és a szélsőséges hőmérsékleten való gyenge teljesítményt. Nagy teljesítményű SMT ragasztót kezdtek használni az alkatrészek rögzítésére és a hőkezelés javítására. Ez az eszközök megbízhatóságának és teljesítményének jelentős javulását eredményezte, valamint csökkentette az utómunkálatok és javítások szükségességét.
- Gépjárműelektronika: Az autóelektronikai termékek egyik gyártója olyan problémákat tapasztalt, hogy az alkatrészek a rezgések és ütések miatt elmozdultak. Elkezdtek használni egy rendkívül rugalmas SMT ragasztót, amelyet kifejezetten úgy terveztek, hogy ellenálljon ezeknek a környezeti tényezőknek. Ez az alkatrészek meghibásodásának jelentős csökkenéséhez és az elektronikus rendszerek általános megbízhatóságának növekedéséhez vezetett.
- Orvosi eszközök: Az orvostechnikai eszközök gyártója a gyártási folyamat során problémákat tapasztalt az alkatrészek tapadásával kapcsolatban. Speciális SMT ragasztót kezdtek használni a nagy tapadási szilárdság és a kiváló elektromos tulajdonságok biztosítása érdekében. Ez az orvostechnikai eszközök minőségének és megbízhatóságának javulásához, valamint a gyártási hibák és az utómunkálatok számának csökkenéséhez vezetett.
- Szórakoztató elektronika: Egy szórakoztatóelektronikai gyártónak problémái voltak az eszközei túlmelegedésével a rossz hőkezelés miatt. Elkezdtek nagy teljesítményű SMT ragasztót használni a hőelvezetés és -átadás javítására. Ez az eszköz teljesítményének és megbízhatóságának javulásához, valamint a javítások és cserék szükségességének csökkenéséhez vezetett.
Ezek az esettanulmányok és sikertörténetek rávilágítanak az SMT ragasztók fontosságára és hatékonyságára az elektronikai ipar különböző alkalmazásaiban. Az alkalmazáshoz megfelelő ragasztó kiválasztásával, valamint a megfelelő felvitel és kikeményedés biztosításával a gyártók javíthatják elektronikus eszközeik megbízhatóságát és teljesítményét, miközben csökkentik az utómunkálatok és javítások szükségességét.
Az SMT ragasztók kezelésének, tárolásának és ártalmatlanításának legjobb gyakorlatai
A felületre szerelhető technológiájú (SMT) ragasztó megfelelő kezelése, tárolása és ártalmatlanítása elengedhetetlen a hatékonyságának biztosításához és a lehetséges veszélyek minimalizálásához. Íme néhány követendő bevált gyakorlat:
- Kezelés: Az SMT ragasztó kezelésekor elengedhetetlen a megfelelő egyéni védőfelszerelés (PPE), például kesztyű, védőszemüveg és szükség esetén légzőkészülék viselése. Ez segít minimalizálni a káros vegyi anyagoknak való kitettséget. Ugyancsak elengedhetetlen a gyártó használati utasításának betartása, beleértve a megfelelő keverést, felhordást és kikeményítést.
- Tárolás: Az SMT ragasztót hűvös, száraz helyen, közvetlen napfénytől, hőtől és nedvességtől védve kell tárolni. A hőmérsékleti és páratartalmi feltételeknek meg kell felelniük a gyártó ajánlásainak, hogy a ragasztó hatékony maradjon. Ezenkívül az SMT ragasztót az eredeti tartályában, szorosan lezárt fedéllel kell tárolni a szennyeződés és a párolgás elkerülése érdekében.
- Ártalmatlanítás: Az SMT ragasztó megfelelő ártalmatlanítása elengedhetetlen a lehetséges környezeti hatások minimalizálása érdekében. Minden fel nem használt vagy lejárt ragasztót a helyi előírások és irányelvek szerint kell megsemmisíteni. Ez magában foglalhatja a veszélyeshulladék-ártalmatlanító létesítménybe vitelét vagy egy speciális hulladékkezelő céggel való kapcsolatfelvételt a megfelelő ártalmatlanítás érdekében.
- Kiömlések és szivárgások: Esés vagy szivárgás esetén a terület azonnali tisztítása elengedhetetlen a további szennyeződés elkerülése érdekében. Ez magában foglalhatja abszorbens anyagok, például homok vagy agyag használatát a kiömlés megfékezésére, és a terület megfelelő oldószerrel vagy tisztítószerrel történő megtisztítását.
- Képzés: Az SMT-ragasztókat kezelő alkalmazottakat megfelelő képzésben és oktatásban kell részesíteni. Ennek tartalmaznia kell a ragasztó megfelelő kezelésével, tárolásával és ártalmatlanításával kapcsolatos információkat, valamint az egyéni védőeszközök megfelelő használatát és a vészhelyzeti reagálási eljárásokat baleset vagy kiömlés esetén.
Az SMT ragasztó kezelésére, tárolására és ártalmatlanítására vonatkozó ezen bevált gyakorlatok követésével a gyártók biztosíthatják a ragasztó biztonságát és hatékonyságát, miközben minimalizálják a lehetséges veszélyeket vagy környezeti hatásokat. A konkrét ajánlásokhoz és követelményekhez feltétlenül olvassa el a gyártó utasításait, a helyi előírásokat és az irányelveket.
Következtetés:
Az SMT ragasztó forradalmasította az elektronikai gyártást azáltal, hogy javította a termék megbízhatóságát és lehetővé tette az alkatrészek pontos elhelyezését. A rendelkezésre álló ragasztó opciók széles skálája, az adagolási technikák fejlődése és a környezetvédelmi megfontolások az SMT ragasztót a modern gyártási folyamatok alapvető összetevőjévé tették. Az iparág fejlődésével a gyártóknak naprakésznek kell lenniük az SMT ragasztókkal kapcsolatos legújabb fejlesztésekkel és bevált gyakorlatokkal, hogy maximalizálják a hatékonyságot, a hozamot és az általános termékminőséget. Az SMT ragasztó erejének kihasználásával a gyártók új lehetőségeket nyithatnak meg az elektronikai gyártásban, ami jobb teljesítményt és a vevők elégedettségét eredményezi.