Optikai ragasztó ragasztó
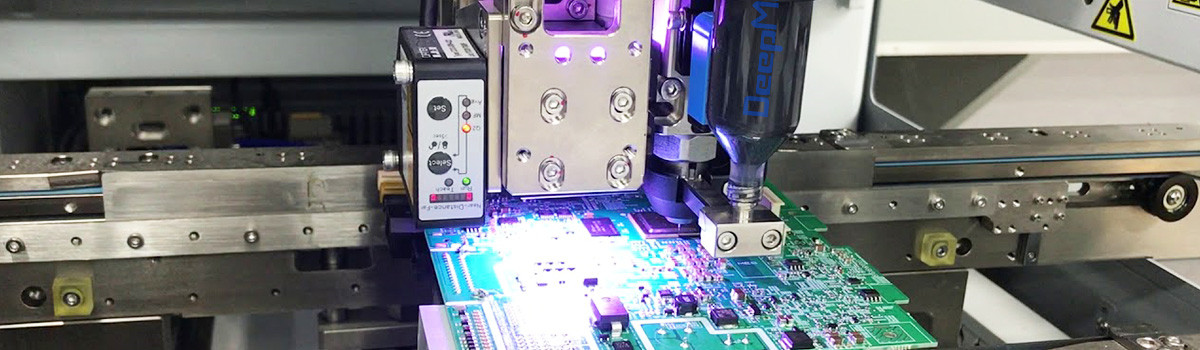
Az optikai kötőragasztó olyan technológia, amely érintőképernyős kijelzőket állít elő a teljesítmény és a funkcionalitás javítása érdekében. Ez egy védőréteg vagy fedőüveg rögzítésének folyamata az érintőpanelre egyedi ragasztó segítségével.
A ragasztó javítja a kijelző optikai teljesítményét azáltal, hogy csökkenti a visszaverődés, a tükröződés és a színeltolódás mértékét, ami jobb képminőséget és olvashatóságot eredményez. Ezt a technológiát széles körben használják különféle alkalmazásokban, beleértve az autóipari, orvosi, katonai, repülési, ipari, fogyasztói elektronikai és hordható eszközöket. Ez a cikk az érintőképernyős kijelzőkhöz használható optikai ragasztóanyag előnyeivel, típusaival, alkalmazási területeivel és jövőbeli trendjeivel foglalkozik.
Megvitatjuk továbbá az optikai kötőragasztó kiválasztásakor figyelembe veendő tényezőket, valamint ennek a technológiának a korlátait és költségszempontjait. Végül kiemeljük az optikai kötőragasztó fontosságát a kijelzőtechnológiában és szerepét a felhasználói élmény javításában.
Mi az az optikai ragasztóanyag?
Az optikai kötőragasztó olyan ragasztóanyag, amelyet optikai alkatrészek egymáshoz ragasztására használnak. Az optikai kötés célja a két felület közötti légrés megszüntetése, amely visszaverődést, fénytörést és egyéb vizuális torzulásokat okozhat.
Az optikai ragasztáshoz használt ragasztó jellemzően átlátszó epoxi- vagy szilikon alapú anyag, amely átlátszó és alacsony törésmutatóval rendelkezik a vizuális torzítás minimalizálása érdekében. Vékonyan felhordják az egyik vagy mindkét optikai komponensre, és hő vagy UV fény hatására kikeményítik.
Az optikai kötőragasztót általában elektronikus eszközök, például okostelefonok, táblagépek és tévék kijelzőinek gyártására használják, ahol elengedhetetlen a kiváló képminőség és tisztaság. Az optikai kötés csökkenti a tükröződést és javítja a kontrasztot, így a kijelző könnyebben olvasható és látható erős fényviszonyok mellett is.
Hogyan működik az optikai ragasztóanyag?
Az optikai ragasztóanyag fedőüveget vagy érintőképernyőt rögzít a kijelzőmodulhoz. A fedőüveg és a kijelzőmodul közötti rést egy átlátszó ragasztóval tölti ki, amely megkeményedik, így egységes darabot alkot.
Íme egy rövid áttekintés az optikai kötőragasztó működéséről:
- Tisztítás és előkészítés: A fedőüveget és a kijelzőmodult alaposan meg kell tisztítani a ragasztó felhordása előtt az erős kötés biztosítása érdekében. Bármilyen por, olaj vagy törmelék gyengítheti a kötést, és később problémákat okozhat.
- Ragasztó alkalmazása: A ragasztó vékony, egyenletes rétegben kerül felhasználásra a kijelző modul felületén. A ragasztó általában egy optikailag átlátszó epoxigyanta, amelyet arra terveztek, hogy kitöltse a fedőüveg és a kijelzőmodul közötti réseket.
- Takaróüveg elhelyezése: A ragasztó felhordása után a fedőüveget óvatosan helyezzük a kijelzőmodul tetejére. A fedőüveget erősen meg kell nyomni, hogy érintkezzen a ragasztóval.
- Kikeményedés: A ragasztót ezután hővel vagy ultraibolya fénnyel kikeményítik. Ez a folyamat megkeményíti a ragasztót, és erős kötést hoz létre a fedőüveg és a kijelzőmodul között.
- Minőségellenőrzés: Végül megvizsgálják a ragasztott szerelvényt, hogy vannak-e olyan hibák, mint például buborékok, rétegválás vagy nem megfelelő beállítás. Bármilyen problémát orvosolnak, mielőtt az összeállítást az ügyfélhez szállítanák.
Az optikai kötő ragasztó számos előnnyel jár, beleértve a jobb vizuális teljesítményt, a nagyobb tartósságot, valamint a nedvességgel, porral és egyéb környezeti tényezőkkel szembeni ellenállást.
Az optikai ragasztóanyag előnyei
Az optikai kötés egy olyan folyamat, amelynek során egyedi ragasztót visznek fel két felület, jellemzően egy kijelző és egy védőburkolat közé a tisztaság, a tartósság és a teljesítmény fokozása érdekében. Íme néhány előnye az optikai kötőragasztó használatának:
- Továbbfejlesztett optikai teljesítmény: Az optikai kötés segít megszüntetni a kijelző és a burkolat közötti légrést, ami csökkenti a tükröződést és a tükröződést, valamint javítja a kontrasztot, a színek pontosságát és az általános láthatóságot.
- Megnövelt tartósság: Az optikai ragasztáshoz használt ragasztó erős kötést képez a kijelző és a burkolat között, javítva az eszköz általános szerkezeti integritását. Ez ellenállóbbá teszi az ütésekkel, rezgésekkel és egyéb mechanikai igénybevételekkel szemben, ami segít megelőzni a kijelző sérülését és meghosszabbítja élettartamát.
- Továbbfejlesztett érintőképernyő funkcionalitás: Az optikai kötés javítja az érintőképernyős kijelzők pontosságát és válaszkészségét azáltal, hogy csökkenti az érintésérzékelő és a műsor közötti távolságot. Ez megkönnyíti a használatát, és csökkenti a hibák vagy félreértelmezések valószínűségét.
- Jobb ellenállás a környezeti tényezőkkel szemben: Az optikai kötés javíthatja a kijelző azon képességét, hogy ellenálljon a környezeti tényezőknek, például a hőmérséklet-változásoknak, a páratartalomnak és a napfénynek való kitettségnek, amelyek idővel a gyűjtemény romlását vagy károsodását okozhatják.
- Jobb esztétika: Az optikai kötés javíthatja a kijelző általános megjelenését azáltal, hogy csökkenti a bemutató és a borító közötti határ láthatóságát, ami elegáns és zökkenőmentes megjelenést kölcsönöz.
Összességében az optikai kötőragasztó számos olyan előnyt kínál, amelyek hozzájárulhatnak a különféle alkalmazásokban használt kijelzők teljesítményének, tartósságának és esztétikájának javításához, a fogyasztói elektronikától az ipari és orvosi eszközökig.
Az optikai ragasztóanyag típusai
A piacon többféle optikai ragasztóanyag kapható, többek között:
- Epoxi ragasztók: Ezek kétkomponensű ragasztók, amelyek összekeverve megkeményednek. Nagy szilárdságukról és tartósságukról ismertek, így népszerű választás az optikai kötésekhez.
- Az UV-re keményedő ragasztók ultraibolya fény hatására megkötnek, így az epoxi ragasztók gyorsabb alternatívája. Magas átlátszóságukról és alacsony sárgulásukról is ismertek.
- Szilikon ragasztók: A szilikon ragasztók rugalmasak és jól ellenállnak a hőmérsékletnek és a nedvességnek. Népszerű választás a kijelzők ívelt felületekhez való ragasztására.
- Akril ragasztók: Ezek a ragasztók jó optikai tisztaságot biztosítanak, és kiválóan ellenállnak az UV sugárzásnak és az időjárás viszontagságainak. Nagy szilárdságukról és különböző felületekhez való jó tapadásukról is ismertek.
- Cianoakrilát ragasztók: Ezek a ragasztók gyorsan kikeményednek és jól tapadnak különböző felületekhez. Kijelzők ragasztására azonban nem ajánlottak, mivel magas savasságuk miatt károkat okozhatnak.
A ragasztó kiválasztása az alkalmazás speciális követelményeitől függ, beleértve olyan tényezőket, mint a kijelző mérete és alakja, az eszköz típusa és a környezeti feltételek, amelyek között az eszközt használni fogják.
Az optikai ragasztóanyag alkalmazásai
Az optikai ragasztót különféle alkalmazásokban használják, ahol kijelzőket vagy érintőképernyőket kell csatlakoztatni az eszközhöz. Az optikai kötőragasztók szabványos alkalmazásai közé tartozik:
- Ipari kijelzők: Az optikai kötést széles körben használják ipari kijelzőkben, például gyártó létesítményekben vagy vezérlőtermekben. A ragasztó segít megvédeni a gyűjteményt olyan környezeti tényezőktől, mint a por, nedvesség és hőmérséklet-ingadozások.
- Orvosi eszközök: Az optikai kötést gyakran használják orvosi eszközökben, például ultrahangos gépekben vagy betegfigyelő rendszerekben. A ragasztó javítja a kijelző tisztaságát, és megóvja a gyakori tisztítás miatti sérülésektől.
- Repülési kijelzők: Az optikai kötést repülési kijelzőkben használják, például a repülőgépek pilótafülkéiben vagy navigációs rendszerekben. A ragasztó javítja a láthatóságot és csökkenti a tükröződést erős napfényben.
- Kültéri kijelzők: Az optikai kötést kültéri kijelzőkön, például digitális jelzéseken vagy kioszkban használják. A ragasztó segít megvédeni a kollekciót olyan környezeti tényezőktől, mint az eső, szél és napfény.
- Szórakoztató elektronika: Az optikai kötést az elektronikában, például okostelefonokban és táblagépekben használják. A ragasztó javítja a kijelző tisztaságát és megvédi a mindennapi használatból eredő sérülésektől.
Összességében az optikai kötőragasztót olyan alkalmazásokban használják, ahol jobb láthatóság, tartósság és kijelzővédelem szükséges.
Optikai ragasztóanyag érintőképernyős kijelzőkhöz
Az optikai ragasztóanyagot érintőképernyős kijelzők gyártására használják, hogy javítsák azok teljesítményét és tartósságát. Ez a folyamat magában foglalja az érintőpanelt az előadáshoz rögzítve a két felület közötti légrést átlátszó ragasztóval kitöltve. Ez erősíti a kijelzőt, javítja annak vizuális tisztaságát, és csökkenti a belső tükröződés vagy a tükröződés esélyét.
Az optikai ragasztáshoz használt ragasztó típusa az adott alkalmazástól és a kívánt eredménytől függ. A leggyakrabban használt ragasztók közé tartoznak az akrilok, a szilikonok és a poliuretánok. Az akrilokat széles körben használják, mivel kiváló optikai tisztasággal rendelkeznek, és könnyű velük dolgozni. A szilikonok rugalmasságuk és magas hőmérsékletekkel szembeni ellenállásuk miatt is népszerűek, a poliuretánok pedig nagy szilárdságukról és tartósságukról ismertek.
Az optikai ragasztóanyagot gondosan kell kiválasztani és felhordani, hogy elkerüljük az érintőképernyő teljesítményére gyakorolt negatív hatásokat. Ez szakértelmet és precizitást igényel, ezért a legjobb, ha tapasztalt ragasztógyártóktól vagy beszállítóktól kér szakmai segítséget. A ragasztó megfelelő kezelése, tárolása és felhordása kulcsfontosságú az érintőképernyős kijelző minőségének és megbízhatóságának biztosításához.
Optikai ragasztó ragasztó autóipari kijelzőkhöz
Az optikai kötő ragasztó az autóipari kijelzők gyártásában általánosan használt ragasztótípus. A kijelzőpanelt a fedőüveghez vagy az érintőképernyőhöz köti, erős, optikailag tiszta kötést biztosítva a két alkatrész között.
Az autóipari kijelzőkhöz többféle optikai kötőragasztó áll rendelkezésre, beleértve a szilikon-, akril- és poliuretán alapú ragasztókat. Minden ragasztótípusnak megvannak a maga előnyei és hátrányai, és a ragasztó kiválasztása a kijelző speciális követelményeitől függ.
A szilikon alapú ragasztók a leggyakrabban használt optikai kötőragasztók az autóipari kijelzőkhöz. Kiváló optikai tisztaságot biztosítanak, ellenállnak az UV-sugárzásnak és a hőmérséklet-változásoknak, valamint nagy rugalmassággal rendelkeznek. Ellenállnak a nedvességnek és a vegyszereknek is, így ideálisak a zord autóipari környezetekhez.
Az akril alapú ragasztók egy másik népszerű lehetőség az autóipari kijelzők számára. Kiváló optikai tisztaságukról és kiváló tapadási tulajdonságaikról ismertek. Ellenállnak az UV-sugárzásnak és a hőmérséklet-változásoknak is, így jó választás autóipari kijelzőkhöz.
A poliuretán alapú ragasztókat ritkábban használják autóipari kijelzőkben, de számos előnnyel rendelkeznek a többi ragasztóval szemben. Kiváló vegyszerállósággal, víz- és nedvességállósággal, valamint kiváló tapadási tulajdonságokkal rendelkeznek. Ezenkívül nagyon rugalmasak, ezért ideálisak olyan kijelzőkhöz, amelyek erős vibrációnak vagy mozgásnak vannak kitéve.
Összességében az optikai ragasztóanyag kiválasztása az autóipari kijelzőkhöz számos tényezőtől függ, beleértve a gyártás speciális követelményeit, a működési környezetet és a kívánt teljesítményjellemzőket. Az adott alkalmazáshoz megfelelő ragasztó kiválasztásához elengedhetetlen, hogy szakképzett szakemberrel konzultáljon.
Optikai ragasztó ragasztó kültéri kijelzőkhöz
A kültéri kijelzők optikai kötőanyagának kiválasztásakor néhány kulcsfontosságú tényezőt figyelembe kell venni:
- UV-ellenállás: A kültéri kijelzők napfénynek és egyéb UV-sugárzásnak vannak kitéve. Az UV-álló ragasztó elengedhetetlen annak biztosításához, hogy a ragasztóanyag idővel ne romoljon, és ne okozza a kijelző meghibásodását.
- Hőmérsékletállóság: A kültéri kijelzők különféle hőmérsékleteknek vannak kitéve, a forró nyári napoktól a hideg téli éjszakákig. A ragasztóanyagnak ki kell bírnia ezeket a szélsőséges hőmérsékleteket anélkül, hogy elveszítené kötési szilárdságát.
- Ütésállóság: A kültéri kijelzők érzékenyebbek az ütések és rezgések okozta károsodásokra. A jó ütésállóságú ragasztó segíthet megvédeni a gyűjteményt, és megakadályozza a repedéseket vagy egyéb sérüléseket.
- Tisztaság: Az optikai ragasztáshoz használt ragasztónak a lehető legegyszerűbbnek kell lennie, hogy elkerülhető legyen a torzítás vagy homályosság, amely befolyásolhatja a kijelző olvashatóságát.
- Tapadási szilárdság: A ragasztóanyagnak elegendő erősségűnek kell lennie ahhoz, hogy szilárd és tartós kötést biztosítson a kijelző és a fedőüveg között.
Számos különféle optikai ragasztóanyag kapható a piacon, és elengedhetetlen, hogy a kültéri kijelzőkkel szemben támasztott követelményeknek megfelelőt válasszuk. Néhány népszerű lehetőség közé tartozik a szilikon, epoxi és akril alapú ragasztók. Javasoljuk, hogy konzultáljon egy ragasztási szakértővel vagy a ragasztó gyártójával, hogy meghatározza a legjobb választást az adott alkalmazáshoz.
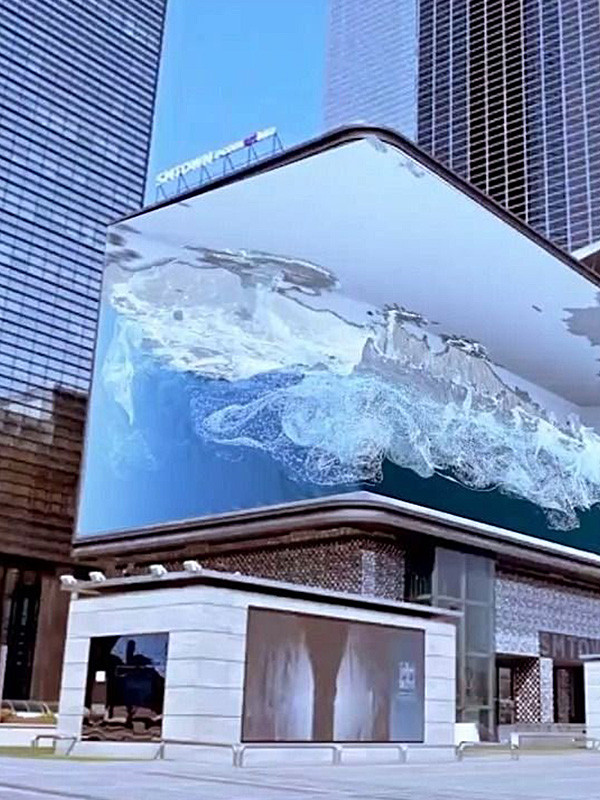
Optikai ragasztó ragasztó orvosi kijelzőkhöz
Az optikai kötőragasztó olyan eljárás, amellyel a fedőüveget vagy az érintőpanelt a kijelző LCD-paneléhez rögzítik. Ez magában foglalja a két felület közötti rés kitöltését az üveghez hasonló optikai tulajdonságokkal rendelkező átlátszó ragasztóval. Az optikai kötőragasztót gyakran használják az orvosi kijelzőkben, hogy javítsák a kijelző tartósságát, olvashatóságát és biztonságát.
Az orvosi kijelzők optikai kötőragasztójának kiválasztásakor számos tényezőt figyelembe kell venni, mint például a biokompatibilitást, a vegyszerállóságot és az optikai tisztaságot. A ragasztónak biológiailag kompatibilisnek kell lennie, és nem kell károsítania a pácienst vagy a felhasználót, valamint ellenállnia kell az orvosi környezetben általánosan használt durva vegyszereknek és fertőtlenítőszereknek.
Ezenkívül a ragasztónak kiváló optikai tisztasággal kell rendelkeznie, hogy a kijelző könnyen leolvasható legyen, és pontos információkat adjon. Fontos figyelembe venni a ragasztó kötési idejét is, mivel ez befolyásolhatja a kijelző teljes gyártási idejét.
Az orvosi kijelzőkhöz alkalmas optikai kötőragasztókra néhány példa a szilikon alapú ragasztók, a poliuretán alapú ragasztók és az akril alapú ragasztók. Elengedhetetlen, hogy konzultáljon egy képzett szállítóval, hogy meghatározza a legjobb ragasztót egy adott alkalmazáshoz.
Optikai ragasztó ragasztó katonai kijelzőkhöz
Az optikai kötés egy optikailag átlátszó ragasztóréteg rögzítése a kijelzőpanel és a fedőüveg vagy az érintőképernyő közé. Ez a folyamat segít megszüntetni a két felület közötti légréseket, amelyek visszaverődéshez, kontrasztcsökkenéshez és egyéb optikai torzulásokhoz vezethetnek.
Katonai alkalmazásokban a kijelzőknek masszívnak és tartósnak kell lenniük, és képesnek kell lenniük ellenállni a szélsőséges környezetnek és a zord körülményeknek. Ezért a katonai kijelzőkben használt optikai kötőragasztónak ellenállnia kell a magas hőmérsékletnek, páratartalomnak, vibrációnak és ütésnek.
A katonai kijelzőkhöz gyakran használt optikai kötőragasztók közé tartozik a szilikon, az epoxi és az akril. A szilikon ragasztók magas hőmérséklettel szembeni ellenállásukról és rugalmasságukról ismertek, így ideálisak a szélsőséges környezetnek kitett katonai kijelzőkhöz. Az epoxi ragasztók nagy szilárdságukról és ütés- és rezgésállóságukról ismertek, míg az akril ragasztók optikai tisztaságukról és alacsony zsugorodásukról ismertek.
A katonai kijelzők optikai kötőragasztójának kiválasztásakor elengedhetetlen olyan tényezőket figyelembe venni, mint a hőmérséklet-tartomány, a nedvességállóság, a ragasztási szilárdság és a vizuális teljesítmény. Gondoskodni kell arról is, hogy a ragasztó megfeleljen a katonai előírásoknak és a megbízhatóságra és tartósságra vonatkozó szabványoknak.
Optikai ragasztó ragasztó repülőgépekhez
Az optikai kötés egy védőüveg vagy műanyag burkolat rögzítése az elektronikus kijelzőhöz ragasztó segítségével. Az optikai kötést általában az űrrepülőgép-kijelzőkben használják, hogy megvédjék a kollekciót a vibráció, hőmérséklet-változások és egyéb környezeti tényezők okozta károsodásoktól.
Az optikai ragasztáshoz használt ragasztónak meg kell felelnie az űrrepülési alkalmazásokra vonatkozó szigorú követelményeknek, beleértve a magas hőmérsékleti ellenállást, az alacsony gázkibocsátást, valamint a kijelző és a burkolat anyagaival való kompatibilitást. Az űrrepülésben használt ragasztók néhány gyakori típusa az epoxi, a szilikon és az akril.
Az epoxi ragasztók szilárdságukról és tartósságukról ismertek, és általában olyan repülőgép-ipari alkalmazásokban használatosak, ahol nagy szilárdságú ragasztásra van szükség. A szilikon ragasztók rugalmasságukról ismertek, és gyakran használják olyan alkalmazásokban, ahol a rezgés- és ütésállóság kritikus fontosságú. Az akril ragasztók alacsony gázkibocsátó tulajdonságaikról ismertek, és gyakran használják olyan alkalmazásokban, ahol a kijelző szennyeződése aggodalomra ad okot.
Az űrrepülőgép-kijelzők optikai ragasztásához szükséges ragasztó kiválasztásakor elengedhetetlen, hogy figyelembe vegyék az alkalmazás speciális követelményeit, és olyan kötést válasszanak, amely megfelel ezeknek a követelményeknek. Szükséges továbbá olyan beszállítóval dolgozni, aki tapasztalattal rendelkezik a repülési alkalmazások terén, és útmutatást tud adni a ragasztó kiválasztásához és alkalmazásához.
Optikai ragasztóanyag hordható eszközökhöz
Az optikai kötés olyan eljárás, amellyel fedőüveget vagy érintőpanelt rögzítenek egy LCD- vagy OLED-kijelzőhöz, hogy javítsák az eszköz vizuális teljesítményét. Az optikai kötésnél használt ragasztó kritikus, mivel erős kötést és nagy optikai tisztaságot kell biztosítania.
A nagy teljesítményű ragasztó elengedhetetlen a hordható eszközökhöz, ahol a kijelző gyakran kisebb, és az eszköz nagyobb fizikai igénybevételnek lehet kitéve. Optikai ragasztáshoz többféle ragasztó használható, beleértve a szilikont, az akrilt és a poliuretánt.
A szilikon ragasztókat gyakran használják hordható eszközökben, mert jó optikai tisztaságot és rugalmasságot biztosítanak, ami segíthet megelőzni a repedést vagy a kijelző károsodását. Jól tapadnak a különféle aljzatokhoz is, ami kulcsfontosságú lehet hordható eszközöknél, ahol a kollekció ívelt vagy szabálytalan felülethez rögzíthető.
Az akril ragasztók egy másik lehetőség, amelyek nagy optikai tisztaságukról és kiváló tapadási szilárdságukról ismertek. Ellenállnak a sárgulásnak és ellenállnak az UV-sugárzásnak is, így jó választás a napfénynek kitett hordható eszközökhöz.
A poliuretán ragasztókat ritkábban használják optikai kötéseknél, de kiváló kötési szilárdságot, tartósságot és jó optikai tulajdonságokat kínálnak. Gyakran használják olyan alkalmazásokban, ahol a kijelző szélsőséges hőmérsékletnek vagy zord környezetnek lehet kitéve.
Végső soron a ragasztó kiválasztása a hordható eszköz sajátos követelményeitől függ, beleértve a kijelző méretét és alakját, a ragasztandó anyagokat és a környezeti feltételeket, amelyek között az eszközt használni fogják. Alapvető fontosságú, hogy egy képzett szállítóval dolgozzon együtt, aki útmutatást nyújt az alkalmazáshoz legjobb ragasztó kiválasztásához.
Optikai ragasztó ragasztó virtuális valóság fejhallgatókhoz
Az optikai kötés az a folyamat, amikor egy anyagréteget rögzítenek a kijelzőpanel felületére, jellemzően egy érintőképernyőre vagy LCD-képernyőre, hogy csökkentsék a fényvisszaverődés és a tükröződés mértékét. A virtuális valóság fejhallgatóival összefüggésben az optikai kötést a vizuális minőség javítására és a VR-élmény elmerülésére használják azáltal, hogy csökkentik a headset kijelzőpaneleinek felületéről visszaverődő fény mennyiségét.
Az optikai kötés végrehajtásához egy adott típusú ragasztóra van szükség. Ennek a ragasztónak átlátszónak, rugalmasnak kell lennie, és képesnek kell lennie különféle anyagokhoz, köztük üveghez, műanyaghoz és fémhez tapadni. A ragasztónak jó hőstabilitással is rendelkeznie kell, mivel a VR fejhallgatók jelentős hőt termelhetnek használat közben.
A VR headsetek optikai ragasztására általában néhány típusú ragasztót használnak:
- Optikai átlátszó ragasztó (OCA): Ezt a vékony, átlátszó filmet a kijelzőpanel felületére hordják fel. Az OCA kiváló optikai tulajdonságokkal rendelkezik, és javíthatja a kijelző kontrasztját, színét és fényerejét.
- Folyékony optikailag átlátszó ragasztó (LOCA): Ezt a folyékony ragasztót a kijelzőpanel és a fedőüveg vagy műanyag közé kell felhordani. A LOCA-t jellemzően ívelt kijelzőkhöz használják, mivel gyorsabban tud alkalmazkodni az ívelt felülethez, mint az OCA.
- Epoxi: Az epoxi ragasztókat gyakran használják üveg fémhez vagy műanyaghoz való ragasztására, és robusztus és tartós kötést biztosítanak. Ritkábban használják azonban VR fejhallgatók optikai kötésére, mivel légbuborékokat vagy más olyan hibákat vezethetnek be, amelyek befolyásolhatják a kijelző optikai tulajdonságait.
Optikai ragasztó ragasztó ipari kijelzőkhöz
Az optikai kötés egy védőüveg vagy műanyag burkolat rögzítése a kijelzőhöz ragasztó segítségével annak optikai tulajdonságainak, például a kontraszt és a tisztaság javítása érdekében. Ipari környezetben a kiállítások zord körülményeknek vannak kitéve, például magas hőmérsékletnek, páratartalomnak és pornak, ami befolyásolja teljesítményüket és élettartamukat. Az optikai ragasztóanyag segíthet megvédeni a kijelzőt ezektől a körülményektől, és növelheti annak tartósságát.
Különféle típusú optikai kötőragasztók állnak rendelkezésre a piacon, amelyek mindegyike egyedi tulajdonságokkal és előnyökkel rendelkezik. Az ipari kijelzőkhöz általánosan használt ragasztótípusok közül néhány:
- Epoxi ragasztó: Az epoxi ragasztó népszerű választás az optikai ragasztáshoz kiváló tapadószilárdsága és tartóssága miatt. Ellenáll a vegyszereknek és ellenáll a magas hőmérsékletnek, így alkalmas a kemény ipari környezetben való használatra.
- UV-re keményedő ragasztó: Az UV-re keményedő ragasztó egy gyorsan keményedő ragasztó, amely UV fény hatására gyorsan megkeményedik. Ideális olyan alkalmazásokhoz, amelyek gyors gyártási időt és nagy kötési szilárdságot igényelnek.
- Szilikon ragasztó: A szilikon ragasztó rugalmasságáról és kiváló ellenálló képességéről ismert a magas hőmérséklettel, páratartalommal és UV sugárzással szemben. Általában ipari környezetben használják, ahol a kijelzők extrém körülményeknek vannak kitéve.
- Akril ragasztó: Az akril ragasztó sokoldalú, kiváló kötési szilárdságot és tartósságot biztosít. Ellenáll az időjárásnak, a vegyszereknek és az UV sugárzásnak, így alkalmas ipari környezetben való használatra.
Optikai ragasztó ragasztó szórakoztató elektronikai cikkekhez
Az optikai kötőragasztó egy ragasztóanyag-réteg két optikai felület, például kijelzőpanel és fedőüveg közé való ragasztásának folyamata a kijelző láthatóságának és tartósságának javítása érdekében. A fogyasztói elektronikában az optikai kötést általában okostelefonokban, táblagépekben, laptopokban és más hordozható eszközökben használják a kijelző minőségének és a felhasználói élmény javítása érdekében.
Különféle típusú optikai kötőragasztók állnak rendelkezésre a piacon, például szilikon, akril és poliuretán ragasztók. Minden ragasztó egyedi jellemzőkkel és tulajdonságokkal rendelkezik; a kiválasztás a konkrét alkalmazási követelményektől függ.
A szilikon ragasztó kiváló optikai tisztasága, magas hőmérsékleti ellenállása és rugalmassága miatt híres a fogyasztói elektronikáról. Jó kötési szilárdságot is biztosít, és könnyen felhordható. Ez azonban drágább lehet, mint a többi ragasztó.
Az akril ragasztó egy másik lehetőség, amely jó optikai tisztaságot és kötési szilárdságot biztosít. Megfizethetőbb is, mint a szilikon ragasztó, így a pénztárcabarát gyártók kedvelt választása. Előfordulhat azonban, hogy nem olyan rugalmas, mint a szilikon ragasztó, és a kötési szilárdsága idővel csökkenhet az UV fény hatására.
A poliuretán ragasztó egy tartós és robusztus ragasztó, amely ellenáll a szélsőséges hőmérsékleteknek és a zord környezetnek. Kiváló kötési szilárdságot biztosít, és különböző anyagok ragasztására használható. Előfordulhat azonban, hogy jobb optikai tisztaságot biztosít, mint a szilikon vagy akril ragasztók.
A gyártóknak figyelembe kell venniük az optikai tisztaságot, a kötési szilárdságot, a hőmérséklet-állóságot, a rugalmasságot és a tartósságot a ragasztó kiválasztásakor.
Tényezők, amelyeket figyelembe kell venni az optikai ragasztóragasztó kiválasztásakor
Az optikai ragasztóanyag kiválasztásakor a következőket kell figyelembe venni:
- Kompatibilitás: A választott ragasztónak kompatibilisnek kell lennie a ragasztandó anyagokkal. Egyes ragasztók bizonyos anyagokkal jól működnek, míg mások nem. Győződjön meg arról, hogy a ragasztó illeszkedik a burkolathoz és a kijelzőpanelhez.
- Törésmutató: A ragasztó törésmutatója döntő jelentőségű az optikai kötésben. A törésmutatónak meg kell egyeznie a kijelzőpanel törésmutatójával, hogy csökkentse a fényvisszaverődés és -törés mértékét, ami torzulást vagy tükröződést okozhat.
- Kötési idő: A ragasztó kötési ideje az az idő, amely szükséges ahhoz, hogy a ragasztó elérje teljes szilárdságát. A kötési idő a ragasztó kémiai összetételétől függ, néhány perctől több óráig terjedhet. Vegye figyelembe a kötési időt, amikor kiválasztja a ragasztót a projekthez.
- Működési hőmérséklet: A ragasztó működési hőmérséklete az a hőmérséklet-tartomány, amelyben a ragasztó optimálisan működik. A ragasztó kiválasztásakor feltétlenül figyelembe kell venni az alkalmazási környezet hőmérsékleti tartományát.
- Mechanikai tulajdonságok: A ragasztónak jó mechanikai tulajdonságokkal kell rendelkeznie, például nagy szakítószilárdsággal, valamint nyírással és hámlással szembeni ellenállással. Ezek a tulajdonságok biztosítják, hogy a ragasztó ellenálljon a mechanikai igénybevételnek, és idővel megőrizze a kötést.
- Környezeti ellenállás: A ragasztónak ellenállnia kell az olyan ökológiai tényezőknek, mint a nedvesség, az UV fény és a hőmérséklet-változások. Ezek a tényezők a ragasztó károsodását okozhatják, ami meggyengül a kötés.
- Költség: Végül vegye figyelembe a ragasztó költségét. Válasszon olyan kötvényt, amely egyensúlyt kínál a teljesítmény és a költséghatékonyság között.
Az optikai ragasztó ragasztó erőssége
Az optikai kötőragasztó ragasztási szilárdsága általában különböző tényezőktől függ, beleértve a használt ragasztó típusát, a ragasztott anyagokat, a felület előkészítését és a kikeményedési folyamatot.
Általában az optikai kötőragasztókat úgy tervezték, hogy nagy kötési szilárdságot és tartósságot biztosítsanak az optikai tisztaság megőrzése mellett. Úgy vannak kialakítva, hogy robusztus és megbízható kötést biztosítsanak az optikai alkatrészek, például a kijelző és a fedőüveg között anélkül, hogy befolyásolnák optikai tulajdonságaikat.
A ragasztó kötési szilárdságát általában nyíróereje vagy szakítószilárdsága alapján mérik. A nyírószilárdság a ragasztó azon képességére utal, hogy ellenáll a csúszó- vagy nyíróerőknek, míg a húzószilárdság arra a képességére utal, hogy ellenáll az izmok húzásának vagy nyújtásának.
A kötési szilárdságot a ragasztott anyagok felület-előkészítése befolyásolhatja. Fontos, hogy a felületek tiszták, szárazak és szennyeződésektől, például olajoktól, portól vagy ujjlenyomatoktól mentesek legyenek. A felületkezelések, például a plazmatisztítás vagy a koronakisülés szintén fokozhatják a kötési szilárdságot.
A ragasztó keményedési folyamata szintén kritikus fontosságú a szilárd kötés eléréséhez. A kötési idő és hőmérséklet a ragasztó típusától és a ragasztandó anyagoktól függően változhat. Az optimális kötési szilárdság biztosítása érdekében elengedhetetlen a gyártó kikeményedési ajánlásainak betartása.
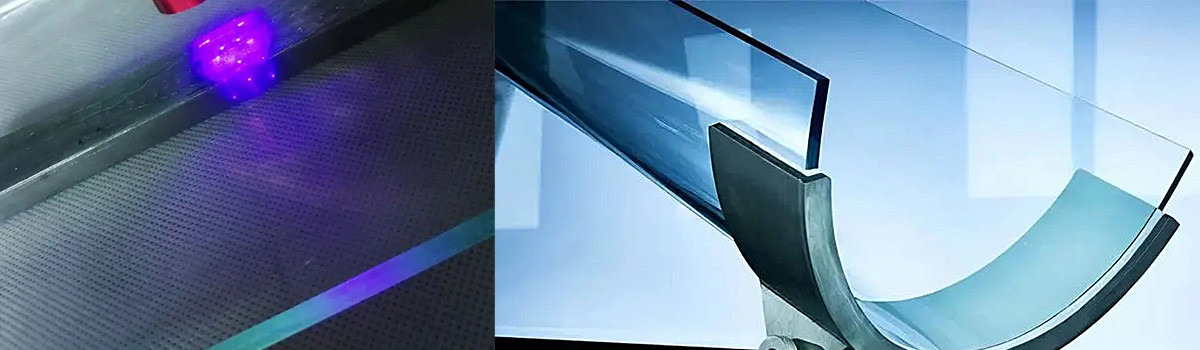
Az optikai ragasztóanyag optikai tisztasága
Az optikai kötőanyag-ragasztó optikai tisztasága arra utal, hogy képes átengedni a fényt anélkül, hogy jelentős szórást vagy abszorpciót okozna. Más szóval azt méri, hogy a ragasztó mennyire átlátszó a látható fény számára.
A ragasztó optikai tisztaságát számos tényező befolyásolja, beleértve a törésmutatóját, viszkozitását és vastagságát. A magas törésmutatójú ragasztók általában jobb optikai tisztasággal rendelkeznek, mivel jobban illeszkednek az általuk ragasztott anyagok törésmutatójához, ami kisebb fényvisszaverődést és fénytörést eredményez.
A viszkozitás az optikai tisztaságban is szerepet játszik, mivel az alacsony sűrűségű ragasztók hajlamosak egyenletesebben oszlani el, és vékonyabb kötési vonalat hoznak létre, ami kisebb torzulást és fényszórást eredményez. A nagyon alacsony viszkozitású ragasztók kezelése és felhordása azonban nagyobb kihívást jelenthet.
A ragasztóréteg vastagsága egy másik fontos tényező, mivel a vastagabb rétegek több torzítást okozhatnak, és csökkentik az optikai tisztaságot. Ezért elengedhetetlen a megfelelő mennyiségű ragasztó használata a kötési vonal vastagságának minimalizálása érdekében.
Összességében a nagy optikai tisztaságú optikai ragasztóanyag kiválasztása elengedhetetlen a kritikus átlátszósággal és láthatósággal rendelkező alkalmazásokhoz, például érintőképernyőkhöz, kijelzőkhöz és optikai szűrőkhöz.
Az optikai ragasztóanyag kémiai ellenállása
Az optikai kötőanyag kémiai ellenállása a használt ragasztó típusától függ. Általában az optikai kötő ragasztókat úgy tervezték, hogy ellenálljanak a különféle vegyszereknek, beleértve az oldószereket, savakat és lúgokat, de bizonyos vegyszerekkel szembeni ellenállásuk változhat.
Például egyes optikai kötőragasztók ellenállhatnak az alkoholnak és bizonyos típusú olajoknak, míg mások nem. A vegyszerállóság meghatározásához elengedhetetlen, hogy tanulmányozza a gyártó specifikációit és ajánlásait az adott ragasztóra vonatkozóan.
Az optikailag kötő ragasztó kémiai ellenállását befolyásoló tényezők közé tartozik a ragasztó összetétele, a kikeményedési folyamat és a hordozó típusa, amelyhez ragasztják. Alapvető fontosságú a megfelelő ragasztó kiválasztása az adott alkalmazáshoz és felhasználási feltételekhez, beleértve a különböző vegyi anyagoknak való kitettséget is.
Általánosságban elmondható, hogy a használat befejezése előtt ajánlott tesztelni az optikai kötőanyag kémiai ellenállását az adott alkalmazási területen és felhasználási körülmények között. Ez segíthet abban, hogy a ragasztó az elvárásoknak megfelelően működjön, és biztosítsa a szükséges szintű vegyszerállóságot.
Az optikai ragasztóanyag hőállósága
Az optikai kötőragasztó hőmérsékletállósága a használt ragasztótól és a tervezett alkalmazástól függően változhat. Az optikai kötőragasztókat általában úgy tervezték, hogy ellenálljanak a hőmérséklet széles tartományának, beleértve a szélsőséges hőmérsékleteket is, amelyek más típusú kötések károsodását okozhatják.
Egyes optikai kötőragasztók akár -55°C (-67°F) és 150°C (302°F) hőmérsékletet is képesek ellenállni. Fontos azonban megjegyezni, hogy ezek az értékek nagymértékben változhatnak az adott ragasztó összetételétől, a ragasztott anyagoktól és a felhasználási körülményektől függően.
A hőmérsékletállóságon kívül az optikai kötőanyag kiválasztásakor figyelembe veendő egyéb alapvető tényezők közé tartozik annak optikai tulajdonságai, adhéziós szilárdsága, kötési ideje és a ragasztott anyagokkal való kémiai kompatibilitása. Mindig a legjobb, ha konzultál a ragasztó gyártójával vagy egy hozzáértő műszaki szakértővel, hogy megbizonyosodjon arról, hogy a kiválasztott ragasztó megfelel a tervezett alkalmazásnak és a környezeti feltételeknek.
Az optikai ragasztóanyag UV-állósága
Az optikai kötőragasztó UV-állósága fontos szempont, amikor olyan kültéri vagy egyéb alkalmazásokhoz választunk ragasztót, amelyek napfénynek vagy más UV-sugárzásnak vannak kitéve. Egyes optikai kötőragasztókat úgy tervezték, hogy nagyon ellenálljanak az UV-sugárzásnak, míg mások idővel lebomlanak vagy megsárgulhatnak, ha UV-sugárzásnak vannak kitéve.
Az UV-ellenállást gyakran a ragasztókészítményben lévő speciális adalékokkal érik el, amelyek elnyelik vagy visszaverik az UV-sugárzást. Egyes ragasztók olyan inhibitorokat is tartalmazhatnak, amelyek megakadályozzák a ragasztó UV-sugárzás miatti lebomlását.
Amikor kiválasztunk egy optikai kötőanyagot kültéri vagy egyéb UV-sugárzásnak kitett alkalmazásokhoz, feltétlenül figyelembe kell venni a ragasztó UV-állóságát és általános teljesítményjellemzőit. A nagy UV-állóságú ragasztóknak eltérő optikai vagy mechanikai tulajdonságaik lehetnek, mint a nem UV-álló ragasztóké. Ezenkívül a ragasztandó konkrét anyagok és a felhordási mód befolyásolhatja a ragasztó UV-állóságát.
Mint minden ragasztó kiválasztásánál, mindig a legjobb, ha konzultál a gyártóval vagy egy hozzáértő műszaki szakértővel, hogy megbizonyosodjon arról, hogy a kiválasztott ragasztó megfelel a tervezett alkalmazásnak és a környezeti feltételeknek.
Az optikai ragasztóanyag nedvességállósága
Az optikai kötő ragasztók a használt ragasztótól függően különböző fokú nedvességállósággal rendelkezhetnek. Az optikai kötő ragasztókat azonban általában úgy tervezték, hogy jó nedvességállóak legyenek, mivel gyakran használják kültéri vagy zord környezetben, ahol valószínű a nedvességnek való kitettség.
Az optikai kötő ragasztó nedvességállóságának egyik döntő tényezője az alkalmazott ragasztó kémia típusa. Egyes ragasztók, például az akrilok vagy a poliuretánok, természetüknél fogva nedvességállóbbak, mint mások, például az epoxik. Ezenkívül a ragasztó speciális összetétele is befolyásolhatja annak nedvességállóságát.
Egy másik tényező, amely befolyásolhatja az optikai kötő ragasztó nedvességállóságát, a ragasztóréteg vastagsága. A vastagabb ragasztórétegek hajlamosabbak lehetnek a nedvesség behatolására, mivel több anyag jut a nedvesség behatolására. Ezért a ragasztási folyamat során elengedhetetlen a ragasztóréteg vastagságának gondos ellenőrzése.
Összességében elmondható, hogy az optikai kötőanyagú ragasztók úgy tervezhetők, hogy kiváló nedvességállósággal rendelkezzenek, de elengedhetetlen az adott ragasztó kémiájának és összetételének, valamint a ragasztási folyamat paramétereinek gondos mérlegelése, hogy az optimális teljesítményt zord környezetben is biztosítsák.
Az optikai ragasztó ragasztó eltarthatósága
Az optikai kötő ragasztó eltarthatósága a ragasztó adott típusától és márkájától függően változhat. A legtöbb gyártó azonban azt javasolja, hogy a ragasztót a gyártástól számított 6-12 hónapon belül használja fel az optimális teljesítmény érdekében.
Fontos megjegyezni, hogy az eltarthatósági időt számos tényező befolyásolhatja, például a tárolási feltételek, valamint a hőnek, páratartalomnak és fénynek való kitettség. Ha a ragasztót nem megfelelően tárolják, vagy kedvezőtlen körülményeknek van kitéve, az eltarthatósága jelentősen csökkenhet.
Annak érdekében, hogy az optikai kötőanyag továbbra is használható legyen, mindig ajánlott használat előtt ellenőrizni annak konzisztenciáját és tulajdonságait, különösen, ha hosszabb ideig tárolták. Ha a ragasztó szerkezete vagy megjelenése megváltozik, vagy már nem tapad megfelelően, el kell dobni, és új tételre kell cserélni.
Az optikai ragasztóanyag tárolása és kezelése
Az optikai ragasztóanyag megfelelő tárolása és kezelése biztosítja annak hatékonyságát és hosszú élettartamát. Íme néhány követendő irányelv:
- Tárolási hőmérséklet: Az optikai ragasztót hűvös, száraz helyen, 5°C és 25°C (41°F és 77°F) közötti hőmérsékleten kell tárolni. Az ezen a tartományon kívüli hőmérsékleten történő tárolás befolyásolhatja a ragasztó tulajdonságait és csökkentheti annak hatékonyságát.
- Eltarthatósági idő: Az optikai ragasztó ragasztó eltarthatósága típustól és gyártótól függően változhat. Mindig ellenőrizze a gyártó ajánlásait az ajánlott eltarthatósági időre vonatkozóan.
- Kezelés: Az optikai ragasztóanyagot óvatosan kell kezelni a szennyeződés elkerülése érdekében. Mindig viseljen kesztyűt és használjon tiszta eszközöket a ragasztó felhordásakor.
- Keverés: Bizonyos típusú optikai kötőragasztókat használat előtt össze kell keverni. Gondosan kövesse a gyártó utasításait, és alaposan keverje össze a ragasztót a megfelelő ragasztás érdekében.
- Felhasználás: Az optikai kötő ragasztót egyenletesen és vékonyan kell felvinni a ragasztandó felületekre. A túlzott ragasztóanyag buborékokat vagy egyéb hibákat okozhat a kötésben.
- Kikeményedés: Az optikai kötő ragasztó általában meghatározott hőmérsékleten és páratartalom mellett, meghatározott ideig kikeményíti. A megfelelő ragasztás érdekében kövesse a gyártó kikeményedési útmutatásait.
- Ártalmatlanítás: A fel nem használt vagy lejárt optikai ragasztóanyagokat a helyi előírások szerint megfelelően ártalmatlanítani kell.
Ezen irányelvek betartása elősegíti az optikai kötőragasztó megfelelő tárolását és kezelését, ami jobb teljesítményt és a kötés hosszabb élettartamát eredményezi.
Optikai ragasztóanyag előkészítése és felhordása
Az optikai kötési folyamat javítja a kijelző tartósságát és láthatóságát azáltal, hogy csökkenti a levegő mennyiségét a fedőüveg és a kijelzőpanel között, ezáltal minimálisra csökkenti a visszaverődést, a tükröződést és a fénytörést. Íme az optikai ragasztóanyag előkészítésének és felhordásának lépései:
Elkészítés:
- A felületek tisztítása: Tisztítsa meg a fedőüveget és a kijelzőpanel felületeit a szennyeződés, a por és a törmelék eltávolításához. Használjon szöszmentes rongyot és a ragasztóval kompatibilis tisztítóoldatot.
- Az alapozó felhordása: Vigyen fel vékony réteg alapozót a fedőüvegre és a kijelzőpanel felületére is. Az alapozó növeli a ragasztó tapadási szilárdságát.
- Keverje össze a ragasztót: Keverje össze az optikai kötőanyagot a gyártó utasításai szerint. Viseljen kesztyűt, és kövesse az ajánlott biztonsági óvintézkedéseket.
Alkalmazás:
- A ragasztó adagolása: A ragasztót az egyik felületre egy folyamatos, egyenletes gyöngyben adagolja. Használjon olyan adagolóeszközt, amely lehetővé teszi a ragasztó áramlásának pontos szabályozását.
- A ragasztó felhordása: Hengerrel vagy terítővel egyenletesen terítse el a ragasztót a felületen. Ügyeljen arra, hogy a ragasztót egyenletesen hordja fel, hogy elkerülje a buborékok vagy üregek kialakulását.
- A felületek igazítása: Óvatosan igazítsa a fedőüveget a kijelzőpanelhez, ügyelve arra, hogy a ragasztó egyenletesen oszlik el közöttük.
- Nyomja meg a felületeket: Egyenletes nyomást gyakoroljon a fedőüveg felületére, hogy rányomja a kijelzőpanelre. A szükséges nyomás kifejtéséhez használjon laminálógépet vagy vákuumos laminálógépet.
- A ragasztó kikeményítése: Kösítse ki a ragasztót a gyártó utasításai szerint. A kikeményedési folyamat hőt vagy UV-fényt igényelhet, ami több órát is igénybe vehet.
- Vizsgálja meg a kötést: Vizsgálja meg a fedőüveg és a kijelzőpanel közötti kötést, hogy megbizonyosodjon arról, hogy egyenletes, buborékok vagy üregek nélkül.
Az optikai ragasztóanyag minőség-ellenőrzése
Az optikai ragasztóanyag minőségellenőrzése elengedhetetlen az optikai kijelzők, érintőképernyők és egyéb optikai alkatrészek gyártásához. Íme néhány kritikus lépés az optikai ragasztóanyag minőségének biztosításához:
- Nyersanyag-ellenőrzés: A minőség-ellenőrzési folyamat a ragasztó gyártásához használt alapanyagok ellenőrzésével kezdődik. A kívánt előírások teljesítése érdekében az anyagok tisztaságát, viszkozitását és egyéb tulajdonságait ellenőrizni kell.
- Keverési folyamat: A keverési folyamatot szorosan figyelemmel kell kísérni annak biztosítására, hogy a ragasztó alaposan és a megfelelő arányban keveredjen. A megadott keverési eljárástól való bármilyen eltérés a ragasztó tulajdonságok eltéréseit eredményezheti.
- Kikeményedési folyamat: A folyamat kritikus fontosságú annak biztosításához, hogy a ragasztó a kívánt szilárdsággal és optikai tulajdonságokkal rendelkezzen. A kötési időt, a hőmérsékletet és a páratartalmat gondosan ellenőrizni kell, hogy biztosítsa a ragasztó megfelelő megkötését.
- Ragasztóvizsgálat: A ragasztót tesztelni kell, hogy megbizonyosodjon arról, hogy megfelel a kívánt optikai, mechanikai és termikus tulajdonságoknak. A megbízható eredmények biztosítása érdekében a tesztelést szabványos eljárásokkal és berendezésekkel kell elvégezni.
- Szemrevételezés: Miután a ragasztóanyagot felvitték az optikai alkatrészre, szemrevételezéssel meg kell vizsgálni, hogy nincsenek hibák, például buborékok vagy egyenetlen felhordás.
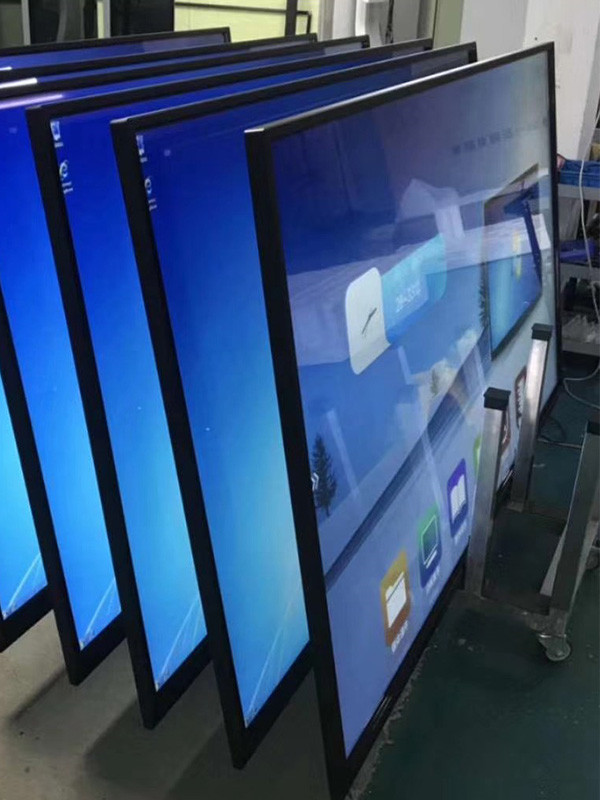
Optikai ragasztóanyag tesztelése és tanúsítása
Az optikai ragasztóanyag tesztelése és tanúsítása több lépésből áll, többek között:
- Ragasztóanyag vizsgálata: A ragasztóanyag fizikai tulajdonságait, viszkozitását, keménységét és tapadási szilárdságát vizsgálják. A tesztelés biztosítja, hogy a ragasztó ellenálljon a valós alkalmazások során tapasztalható igénybevételeknek és igénybevételeknek.
- Kompatibilitási vizsgálat: A ragasztót különböző aljzatokkal és bevonatokkal való kompatibilitás szempontjából teszteljük, hogy megbizonyosodjunk arról, hogy nem okoz semmilyen sérülést vagy elszíneződést a ragasztott felületen.
- Optikai teljesítmény vizsgálata: A ragasztó optikai teljesítményét spektrofotométerrel vizsgálják a ragasztón keresztül visszavert és áteresztett fény mennyiségének mérésére. A tesztelés annak biztosítása érdekében történik, hogy a ragasztóanyag ne befolyásolja-e a készülék megjelenítési minőségét.
- Környezeti vizsgálat: A ragasztót tesztelték, hogy ellenáll-e a különböző környezeti feltételeknek, például hőmérsékletnek, páratartalomnak és UV-sugárzásnak. A tesztelés biztosítja, hogy a ragasztó stabil marad, és nem romlik az idő múlásával.
- Tanúsítvány: Miután a ragasztó átesett az összes szükséges vizsgálaton, független tesztelő ügynökségek, például Underwriters Laboratories (UL), Intertek vagy TUV Rheinland tanúsítja. A tanúsítás biztosítja, hogy a ragasztó megfelel az előírt szabványoknak, és biztonságosan használható elektronikus eszközökben.
Optikai ragasztóanyag költségmegfontolások
Az optikai ragasztóanyag költsége több tényezőtől függően változhat, beleértve a ragasztó típusát és minőségét, a kijelzőegység méretét és összetettségét, valamint a gyártási folyamathoz szükséges mennyiséget.
Néhány további költségmegfontolás az optikai kötőragasztóval kapcsolatban:
- Anyagköltség: Maga a ragasztóanyag költsége a ragasztó típusától és minőségétől függően változhat. Például egyes ragasztók magasabb tisztasági szintet vagy összetettebb gyártási folyamatot igényelhetnek, ami növelheti a költségeket.
- Munkaköltség: Az optikai kötési folyamat szakképzett munkaerőt igényel a ragasztó felviteléhez és az alkatrészek egymáshoz ragasztásához. A munkaerő költsége az összeszerelés összetettségétől és a munkaerő tapasztalati szintjétől függően változhat.
- Berendezés költsége: Az optikai kötőberendezések drágák lehetnek, különösen nagyobb vagy összetettebb kijelzők esetén. A berendezés költsége befolyásolhatja a gyártási folyamat összköltségét.
- Garancia és javítási költségek: Az optikai ragasztás javíthatja a kijelzőegység tartósságát, de növelheti a javítási költségeket vagy a jótállási igényeket is, ha a ragasztás meghibásodik, vagy az alkatrészeket ki kell cserélni.
Az optikai ragasztóanyag jövőbeli trendjei
A technológia fejlődésével az optikai kötőragasztók jövőbeli trendjei valószínűleg a következőket foglalják magukban:
- Fejlődés az anyagok terén: Valószínűleg továbbra is az optikai kötőanyagú ragasztókhoz használható új és továbbfejlesztett anyagok, például új polimerek és ragasztók fejlesztésére kell összpontosítani, amelyek jobb optikai tulajdonságokat és tartósságot biztosítanak.
- A rugalmas kijelzők fokozottabb használata: A rugalmas műsorok növekvő népszerűségével valószínűleg megnő az igény az olyan optikai kötőragasztókra, amelyek képesek rugalmas anyagok egymáshoz ragasztására, miközben megőrzik a kiváló optikai tisztaságot és tartósságot.
- Kisebb és vékonyabb eszközök: Ahogy az eszközök egyre kisebbek és könnyebbek, az optikai ragasztóanyagnak finomabbá és pontosabbá kell válnia, hogy alkalmazkodjon a trendhez. Ez magában foglalhatja új alkalmazási módszerek és berendezések kifejlesztését.
- Jobb UV-állóság: Mivel az UV-sugárzás idővel ronthatja az optikai kötőanyagot, valószínűleg megnő az igény a fokozott UV-állóságú ragasztók iránt, hogy meghosszabbítsák az optikai eszközök élettartamát.
- Integráció más technológiákkal: Ahogy az optikai eszközök jobban integrálódnak más technológiákkal, például érzékelőkkel és érintőképernyőkkel, szükség lehet olyan optikai kötőragasztóra, amely ezeket a kiegészítő alkatrészeket is össze tudja kötni.
Összességében az optikai kötőragasztók jövőbeli trendjei valószínűleg az anyagok fejlődését, a rugalmas kijelzők fokozottabb használatát, a kisebb és vékonyabb eszközöket, a jobb UV-állóságot és más technológiákkal való integrációt foglalják magukban.
Az optikai ragasztóanyag korlátai
Míg az optikai kötő ragasztónak számos előnye van, például jobb láthatóság, nagyobb tartósság és csökkentett visszaverődés, számos korlátja is van. Néhány ilyen korlátozás a következőket tartalmazza:
- Költség: Az optikai kötőragasztók drágák lehetnek más kötésekhez képest, így egyes gyártók számára megfizethetetlenek.
- Összetettség: Az optikai ragasztóanyag megfelelő felhordásához magas szintű szakértelem és speciális felszerelés szükséges. Ez időigényesebbé és költségesebbé teheti a ragasztási folyamatot.
- Korlátozott felhasználás: Az optikai ragasztóanyag nem alkalmas minden kijelzőre vagy érintőpanelre. Előfordulhat, hogy nem hatékony bizonyos anyagok vagy aljzatok ragasztásában, ami korlátozhatja az alkalmazását.
- Hőmérsékletérzékenység: Az optikai ragasztó érzékeny lehet a magas vagy alacsony hőmérsékletre, ami befolyásolja a teljesítményt. A szélsőséges hőmérséklet a ragasztó meggyengüléséhez vagy tönkremeneteléhez vezethet, ami a kijelző vagy az érintőpanel meghibásodásához vezethet.
- Karbantartás: Az optikai ragasztóanyag rendszeres karbantartást igényel, hogy hatékony maradjon. A ragasztó bármilyen sérülése vagy romlása veszélyeztetheti a ragasztási szilárdságát, és csökkentheti a kijelző vagy az érintőpanel tartósságát.
Következtetés: Az optikai ragasztóanyag jelentősége a kijelzőtechnológiában
Az optikai kötőragasztó kritikus szerepet játszik a kijelzőtechnológiában azáltal, hogy javítja a kijelzők vizuális teljesítményét és tartósságát. Ez a ragasztó segít megszüntetni a légrést a kijelzőpanel és a fedőüveg vagy érintőpanel között, ami minimálisra csökkenti a tükröződést, a tükröződést és a torzítást, ami jobb képtisztaságot, kontrasztot és színpontosságot eredményez.
Ezenkívül az optikai ragasztóanyag védőréteget képez a környezeti tényezőkkel, például nedvességgel, porral és karcokkal szemben, ezáltal növelve a kijelző tartósságát és élettartamát. Az optikai ragasztóanyag elengedhetetlen az optimális megjelenítési teljesítmény eléréséhez és a kiváló minőségű felhasználói élmény biztosításához.