OLED kijelző modul ragasztó
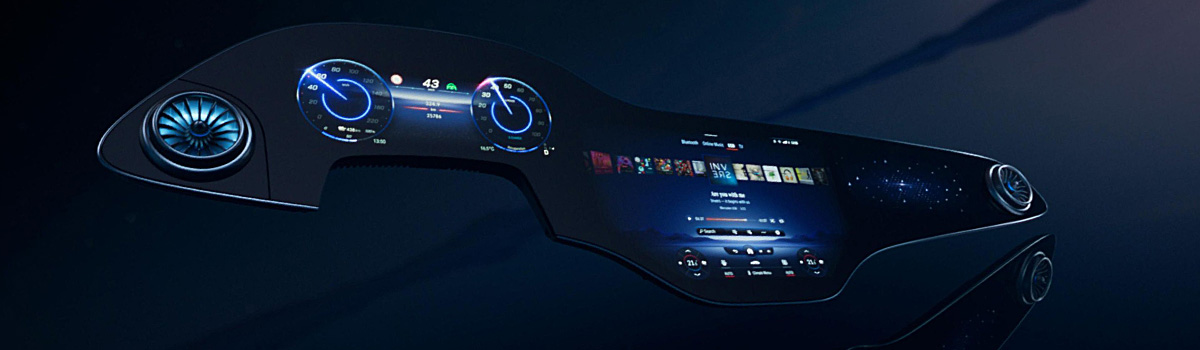
Bevezetés: Az OLED (Organic Light-Emitting Diode) kijelzőmodul számos elektronikai eszközről vált híressé magas kontrasztaránya, élénk színei és vékonysága miatt. Az OLED-kijelző modulok egyik kulcsfontosságú összetevője azonban, amelyet gyakran figyelmen kívül hagynak, az a ragasztó, amely a modult a helyén tartja. A megfelelő ragasztó javíthatja az eszköz tartósságát és megbízhatóságát, valamint javíthatja a kijelző teljesítményét. Ez a cikk az OLED kijelzőmodul ragasztójának fontosságát, valamint annak különböző típusait és alkalmazásait vizsgálja meg.
Mi az OLED kijelzőmodul ragasztó?
Az OLED kijelzőmodul egy speciális ragasztó, amelyet OLED (Organic Light-Emitting Diode) kijelzőpanelek gyártására és összeszerelésére használnak. Kulcsfontosságú szerepet játszik a különböző kijelzőmodul-rétegek összekapcsolásában, biztosítva a szerkezeti integritást, az elektromos csatlakozást és az optikai teljesítményt.
Az OLED kijelzők vékonyságukról, rugalmasságukról és kiváló képminőségükről ismertek. Több réteget tartalmaznak, beleértve a szubsztrátumot, a szerves bevonatokat, az elektródákat és a kapszulát. Ezeket a rétegeket biztonságosan össze kell kötni, hogy biztosítsák a kijelző megfelelő működését, és megóvják a külső tényezőktől, például nedvességtől, portól és fizikai sérülésektől.
Az OLED kijelző modul ragasztóját úgy tervezték, hogy megfeleljen az OLED kijelzők speciális követelményeinek. Ez jellemzően átlátszó vagy áttetsző ragasztóanyag, amely jelentős interferencia nélkül engedi át a fényt. Ez kulcsfontosságú a kijelző optikai tulajdonságainak megőrzéséhez, beleértve a fényerőt, a színpontosságot és a kontrasztot.
A ragasztó egyik kritikus funkciója, hogy elektromos kapcsolatot biztosítson a kijelző modul különböző rétegei között. Biztosítja a megfelelő érintkezést az elektródák és a szerves rétegek között, lehetővé téve az OLED pixelek fénykibocsátásához szükséges elektromos áram áramlását. Ez az elektromos csatlakozás elengedhetetlen ahhoz, hogy a kijelző megfelelően működjön és kiváló minőségű képeket készítsen.
Ezenkívül az OLED kijelzőmodul ragasztója szerkezeti támogatást is nyújt az érzékeny OLED rétegekhez. A ragasztó segít összeragasztani a rétegeket, megakadályozza a rétegvesztést, és biztosítja, hogy a kijelző sértetlen marad még mechanikai igénybevétel vagy hőmérséklet-ingadozás esetén is. Növeli a kijelzőmodul általános tartósságát és megbízhatóságát.
Az OLED kijelzőmodul ragasztójának másik alapvető jellemzője, hogy kompatibilis a kijelzőmodulban használt anyagokkal. Képesnek kell lennie különféle hordozókhoz tapadni, beleértve az üveget és a rugalmas műanyagokat, valamint különféle típusú elektródaanyagokat, például indium-ón-oxidot (ITO) vagy grafént. A ragasztónak jó tapadást kell mutatnia a szerves rétegekhez is, megelőzve az idő múlásával történő szétválást vagy lebomlást.
Az OLED kijelző modul ragasztójának a tapadó tulajdonságain kívül más kívánatos tulajdonságokkal is kell rendelkeznie. Jó hőstabilitásúnak kell lennie, hogy ellenálljon a kijelző működése során keletkező hőnek. Ellen kell állnia a nedvességnek és a környezeti tényezőknek, hogy hosszú távú védelmet nyújtson az OLED rétegeknek. Ezenkívül alacsony gázkibocsátási sebességgel kell rendelkeznie, hogy minimalizálja a kijelző teljesítményére vagy élettartamára gyakorolt esetleges hatásokat.
Összességében az OLED-kijelzőmodulok ragasztója kritikus komponens az OLED-kijelzők gyártásában. Átlátszó és elektromosan vezető tulajdonságai, valamint a különböző rétegek összekapcsolásának képessége hozzájárul az OLED-kijelzők funkcionalitásához, tartósságához és optikai teljesítményéhez, lehetővé téve a kiváló minőségű és vizuálisan lenyűgöző eszközök előállítását.
A ragasztó szerepe az OLED kijelzőmodulokban
A ragasztó döntő szerepet játszik az OLED (Organic Light Emitting Diode) kijelzőmodulokban, hozzájárulva szerkezeti integritásukhoz, optikai teljesítményükhöz és általános megbízhatóságukhoz. Az OLED technológia jelentős népszerűségre tett szert olyan előnyeinek köszönhetően, mint a nagy kontrasztarány, a széles színskála, a gyors válaszidő és a vékony forma. Az OLED kijelzőmodulokban használt ragasztóanyagok számos, az alábbiakban vázolt létfontosságú funkciót látnak el.
Szerkezeti integritás: Ragasztóanyagot használnak az OLED kijelző modulok különböző rétegeinek és alkatrészeinek egymáshoz ragasztására, biztosítva azok stabilitását és mechanikai szilárdságát. Ezek a rétegek általában magukban foglalják az üveg vagy műanyag hordozót, az átlátszó vezetőréteget, a fénykibocsátásért felelős szerves rétegeket és a kapszulázó réteget. A ragasztóanyagok erős kötést biztosítanak, megakadályozzák a rétegvesztést és megőrzik a kijelző modul szerkezeti integritását.
Optikai teljesítmény: A ragasztóanyagok szintén hozzájárulnak az OLED kijelzőmodulok vizuális teljesítményéhez. Úgy tervezték, hogy nagy átlátszósággal és alacsony homályossággal rendelkezzenek, minimálisra csökkentve a fényszóródást és maximalizálva az OLED-pixelekből kibocsátott fényt. Ez jobb képminőséget, élénk színeket és magas kontrasztarányt eredményez. A kiváló optikai tulajdonságokkal rendelkező ragasztóanyagok kulcsfontosságúak az optimális megjelenítési teljesítmény eléréséhez.
Hőkezelés: Az OLED kijelzők működés közben hőt termelnek, a hatékony hőelvezetés pedig elengedhetetlen a túlmelegedés megelőzése és a hosszú távú megbízhatóság érdekében. Az OLED modulokban használt ragasztóanyagok gyakran jó hővezető tulajdonságokkal rendelkeznek. Megkönnyítik a hőátadást az OLED rétegekről más alkatrészekre, például hűtőbordákra vagy a készülékházra, hatékonyan elvezetik a keletkezett hőt, és az OLED működési hőmérsékletét elfogadható határokon belül tartják.
Környezetvédelem: Az OLED kijelzők érzékenyek a nedvességre és az oxigénre, ami ronthatja teljesítményüket és élettartamukat. A ragasztóanyagok létfontosságúak az OLED rétegek tokozásában, védőréteget képezve a környezeti tényezőkkel szemben. Ezeket az anyagokat úgy tervezték, hogy magas záró tulajdonságokkal rendelkezzenek, minimálisra csökkentve a nedvesség és az oxigén bejutását a kijelzőmodulba. A megfelelő ökológiai védelmet biztosítva a ragasztóanyagok hozzájárulnak az OLED-kijelzők hosszú élettartamához és megbízhatóságához.
Gyártási folyamat: A ragasztóanyagok az OLED kijelzőmodulok összeszerelését is megkönnyítik. Megfelelő reológiai tulajdonságokkal rendelkeznek, lehetővé téve a pontos adagolást és az egyenletes kötést a gyártás során. A megfelelő térhálósodási kinetikájú ragasztók hatékony feldolgozást tesznek lehetővé, csökkentve a gyártási időt és a költségeket.
A ragasztóanyagok az OLED kijelzőmodulok kritikus alkotóelemei, amelyek több funkciót is ellátnak. Szerkezeti integritást biztosítanak, optimalizálják az optikai teljesítményt, segítik a hőkezelést, környezetvédelmet kínálnak és támogatják a gyártást. Az OLED technológia folyamatos fejlődésével az OLED-kijelzőkre szabott speciális ragasztóanyagok fejlesztése továbbra is kulcsszerepet játszik a teljesítményük, megbízhatóságuk és élettartamuk növelésében.
A kiváló minőségű ragasztó OLED-kijelzők használatának előnyei
Az OLED-kijelzők kiváló minőségű ragasztójának használata számos előnnyel jár, hozzájárulva az eszközök általános teljesítményéhez, tartósságához és felhasználói élményéhez. Nézzünk meg néhányat az alábbi előnyök közül:
- Továbbfejlesztett megjelenítési minőség: A kiváló minőségű ragasztóanyagokat úgy tervezték, hogy kiváló optikai tulajdonságokkal rendelkezzenek, mint például a nagy átlátszóság és az alacsony homályosság. A gyártók minimális fényszórást és maximális fényáteresztést biztosítanak az OLED rétegeken ezekkel a ragasztókkal. Ez jobb megjelenítési minőséget eredményez, beleértve az élénk színeket, a magas kontrasztarányt és az éles képmegjelenítést.
- Továbbfejlesztett szerkezeti integritás: Az OLED-kijelzők több rétegből állnak, amelyeket biztonságosan össze kell kötni. A kiváló minőségű ragasztók kiváló tapadási szilárdságot biztosítanak, biztosítva a kijelző modul szerkezeti integritását. Hatékonyan megakadályozzák a rétegvesztést, és minimálisra csökkentik a mechanikai igénybevétel, például ütések vagy hajlítás miatti sérülések kockázatát. Ennek eredményeként a kijelzőmodul sértetlen és tartós marad még kihívásokkal teli körülmények között is.
- Fokozott megbízhatóság: Az OLED kijelzők érzékenyek a környezeti tényezőkre, például a nedvességre és az oxigénre. A kiváló minőségű ragasztóanyagokat kifejezetten úgy alakították ki, hogy kiváló záró tulajdonságokkal rendelkezzenek, hatékony kapszulázó réteget hozva létre, amely megvédi az OLED rétegeket a nedvességtől és az oxigén behatolásától. Ez az akadály megakadályozza az OLED-kijelző leromlását és meghosszabbítja az élettartamot, ami jobb megbízhatóságot és hosszabb élettartamot eredményez.
- Hatékony hőkezelés: Az OLED-kijelzők működés közben hőt termelhetnek, a hatékony hőkezelés pedig kulcsfontosságú a teljesítményromlás vagy az idő előtti meghibásodás megelőzése érdekében. A jó minőségű ragasztók gyakran jó hővezető tulajdonságokkal rendelkeznek, megkönnyítve a hő hatékony elvezetését az OLED rétegekről. Ez segít fenntartani a kijelző optimális működési hőmérsékletét, biztosítva a stabil teljesítményt és meghosszabbítja az OLED-eszköz élettartamát.
- Zökkenőmentes integráció: A kiváló minőségű ragasztóanyagokat úgy tervezték, hogy megfelelő reológiai tulajdonságokkal rendelkezzenek, így könnyen felhordhatók és egyenletes kötést biztosítanak az OLED kijelzőmodulon. Ezek a ragasztók kiváló nedvesítési tulajdonságokat biztosítanak, lehetővé téve a precíz adagolást, és minimálisra csökkentik az üregek vagy inkonzisztenciák kialakulásának kockázatát a ragasztásban. Ez a zökkenőmentes integráció hozzájárul az OLED-eszköz általános esztétikájához és funkcionalitásához.
- Gyártási hatékonyság: A kiváló minőségű ragasztók javíthatják az OLED-kijelzők gyártási folyamatát. Kiszerelésük lehetővé teszi a hatékony kikeményedést, csökkentve a gyártási időt és a költségeket. Az optimalizált kikeményedési kinetikájú kötések gyorsabb összeszerelést, nagyobb termelési hozamokat és egyszerűsített gyártási műveleteket tesznek lehetővé.
Tényezők, amelyeket figyelembe kell venni az OLED kijelzőmodul ragasztójának kiválasztásakor
Az OLED kijelzőmodul ragasztójának kiválasztásakor több lényeges tényezőt is figyelembe kell venni az optimális teljesítmény és tartósság érdekében. Íme néhány fontos szempont, amelyet szem előtt kell tartani:
- Optikai tisztaság: Az OLED-kijelzők magas szintű optikai tisztaságot igényelnek a képernyő vizuális minőségének és fényerejének megőrzéséhez. A ragasztónak kiváló átlátszósági tulajdonságokkal kell rendelkeznie, minimálisra csökkentve a kijelző láthatóságát.
- Hővezető képesség: Az OLED-kijelzők működés közben hőt termelnek, a hatékony hőelvezetés pedig kulcsfontosságú a sérülések megelőzése és a teljesítmény megőrzése érdekében. A ragasztónak jó hővezető tulajdonságokkal kell rendelkeznie ahhoz, hogy a hőt a kijelzőről távolítsa el és hatékonyan eloszlassa.
- Tapadási szilárdság: A ragasztónak erősen meg kell tapadnia a kijelző modul és a hordozó vagy a fedőüveg között. Megfelelő tapadási szilárdságúnak kell lennie ahhoz, hogy megbízható és tartós kapcsolatot biztosítson, még változó hőmérsékleti viszonyok és mechanikai igénybevétel esetén is.
- Rugalmasság: Az OLED-kijelzőket gyakran használják rugalmas vagy ívelt alkalmazásokban, például okostelefonokban vagy hordható eszközökben. A ragasztónak elég rugalmasnak kell lennie ahhoz, hogy alkalmazkodjon a bemutató hajlításához vagy íveléséhez anélkül, hogy veszélyeztetné annak integritását.
- Nedvesség- és környezetállóság: Az OLED-kijelzők érzékenyek a nedvességre, és megsérülhetnek, ha túlzott nedvességnek vagy folyadéknak vannak kitéve. A ragasztónak jó nedvességálló tulajdonságokkal kell rendelkeznie, hogy megvédje a kijelzőmodult a környezeti tényezőktől, és biztosítsa a hosszú távú megbízhatóságot.
- Kémiai kompatibilitás: Alapvetően fontos figyelembe venni a ragasztó kompatibilitását a kijelzőmodulban használt egyéb anyagokkal, például a fedőüveggel vagy a polarizátorral. A ragasztó nem reagálhat vagy ronthatja ezen alkatrészek teljesítményét, biztosítva a harmonikus integrációt.
- Folyamat-kompatibilitás: A ragasztónak kompatibilisnek kell lennie az OLED kijelzőmodul gyártási folyamatával. Könnyen kezelhetőnek, adagolhatónak és kikeményíthetőnek kell lennie a hatékony és költséghatékony gyártás érdekében.
- Öregedés és sárgás: Idővel egyes ragasztók elöregedhetnek vagy sárgulhatnak, ami befolyásolhatja a kijelző vizuális minőségét. Alapvető fontosságú, hogy olyan kötést válasszunk, amely jó hosszú távú stabilitással rendelkezik, és nem sárgul el vagy nem romlik el hosszabb időn keresztül.
- Elektromos szigetelés: A ragasztónak elektromos szigetelést kell biztosítania az OLED kijelzőmodul vezető alkatrészei között, megelőzve a rövidzárlatokat és megbízható elektromos teljesítményt biztosítva.
- Szabályozási megfelelőség: A környezeti és egészségügyi biztonság biztosítása érdekében vegye figyelembe a vonatkozó ipari előírásokat vagy szabványokat, amelyeknek a ragasztónak meg kell felelnie, például a RoHS (veszélyes anyagok korlátozása) megfelelőségét.
Ezeket a tényezőket gondosan mérlegelve kiválaszthatja azt az OLED kijelző modul ragasztót, amely megfelel az alkalmazás speciális követelményeinek, és biztosítja az optimális teljesítményt, tartósságot és vizuális minőséget. Gyakran tanácsos konzultálni a ragasztógyártókkal vagy -beszállítókkal, hogy részletes műszaki specifikációkat és ajánlásokat kaphasson az Ön egyedi igényei alapján.
Ragasztótípusok OLED kijelző modulokhoz
Az OLED (Organic Light-Emitting Diode) kijelzőmodulokat nagy kontrasztjuk, széles betekintési szögük és energiahatékonyságuk miatt széles körben használják különféle elektronikus eszközökben, például okostelefonokban, televíziókban és hordható eszközökben. Az OLED-kijelző modulok összeszerelése magában foglalja a különböző rétegek és alkatrészek ragasztását. Ezek a ragasztók kritikus szerepet játszanak az OLED-kijelzők teljesítményének, tartósságának és megbízhatóságának biztosításában. Nézzünk meg néhány általánosan használt ragasztótípust, amelyeket az OLED kijelzőmodulokhoz használnak.
- Optikai átlátszó ragasztók (OCA): Az optikai átlátszó ragasztókat széles körben használják OLED-kijelzőkben nagy optikai átlátszóságuk és kiváló tapadási tulajdonságaik miatt. Általában a fedőüveget vagy az érintőpanelt az OLED-modulhoz kötik. Az OCA-k törésmutatója hasonló az italokhoz, ami segít minimalizálni a fényveszteséget és javítja a kijelző tisztaságát. Ezenkívül védenek a nedvességtől és a portól.
- Folyékony optikailag átlátszó ragasztók (LOCA): A LOCA-k optikai tulajdonságaikban hasonlítanak az OCA-khoz. Azonban folyékony formában szállítják, majd szilárd ragasztóvá keményítik. A LOCA-kat általában rugalmas OLED-kijelzők fedőüveghez vagy érintőpanelhez való ragasztására használják. Jó optikai tisztaságot, rugalmasságot és tapadási szilárdságot kínálnak.
- Vezetőképes ragasztók: Az OLED-kijelzőkben vezetőképes ragasztókat használnak az elektromos csatlakozások ragasztására, például az OLED-panel és a meghajtó áramkör csatlakoztatására. Ezek a ragasztók vezetőképes részecskéket (pl. ezüst vagy réz) tartalmaznak, amelyek lehetővé teszik az elektromos vezetést, miközben tapadó tulajdonságokat biztosítanak. A vezetőképes ragasztók megbízható elektromos csatlakozást biztosítanak, és ellenállnak a hőtágulásnak és összehúzódásnak a készülék működése során.
- Szerkezeti ragasztók: A szerkezeti ragasztók az OLED-kijelzők különféle alkatrészeit, például a keretet, a háttérvilágítási egységet és más szerkezeti elemeket rögzítik. Ezek a ragasztók nagy tapadási szilárdságot, tartósságot és ellenállást biztosítanak a környezeti tényezőkkel szemben, mint például a hőmérséklet, a páratartalom és a vibráció. A szerkezeti ragasztók jellemzően epoxi alapúak vagy akril alapúak, a konkrét alkalmazási követelményektől függően.
- Nyomásérzékeny ragasztók (PSA): A PSA-k általában OLED-kijelzőket szerelnek össze ideiglenes ragasztás vagy pozicionálás céljából. Általában ragasztószalagként vagy filmként szállítják őket, és felülettel érintkezve azonnali tapadást biztosítanak. A PSA-k jó tapadást biztosítanak számos aljzathoz, és könnyen eltávolíthatók anélkül, hogy maradványokat hagynának.
- Thermal Interface Materials (TIM-ek): A TIM-eket az OLED-kijelzőkben használják a hőelvezetés és a hőkezelés javítására. Ezeket az OLED panel és a hűtőborda vagy a hűtőrendszer közé helyezik, hogy fokozzák a hőátadást a kijelzőmodultól. A TIM-ek gyakran hővezető ragasztók vagy párnák formájában vannak, amelyek ragasztó- és termikus tulajdonságokkal is rendelkeznek.
- UV-sugárzással keményedő ragasztók: Az UV-sugárzással keményedő ragasztókat olyan OLED-kijelző-összeállítási folyamatokban használják, amelyek gyors kötést és nagy tapadási szilárdságot igényelnek. Ezeket a ragasztókat folyékony formában alkalmazzák, majd ultraibolya (UV) fénynek kitéve gyorsan kikeményednek. Az UV-re keményedő kötések kiváló tapadást, gyors kötési időt és nagy mechanikai szilárdságot biztosítanak.
Fontos megjegyezni, hogy az OLED kijelzőmodulok ragasztójának konkrét megválasztása a kijelző szerkezetétől, a felhasznált anyagoktól, a kívánt optikai tulajdonságoktól, az összeszerelési folyamat követelményeitől és a környezeti feltételektől függ. A gyártók olyan ragasztókat választanak ki, amelyek megfelelnek az OLED-kijelző alkalmazásaik teljesítményének, megbízhatóságának és gyártási hatékonyságának kritériumainak.
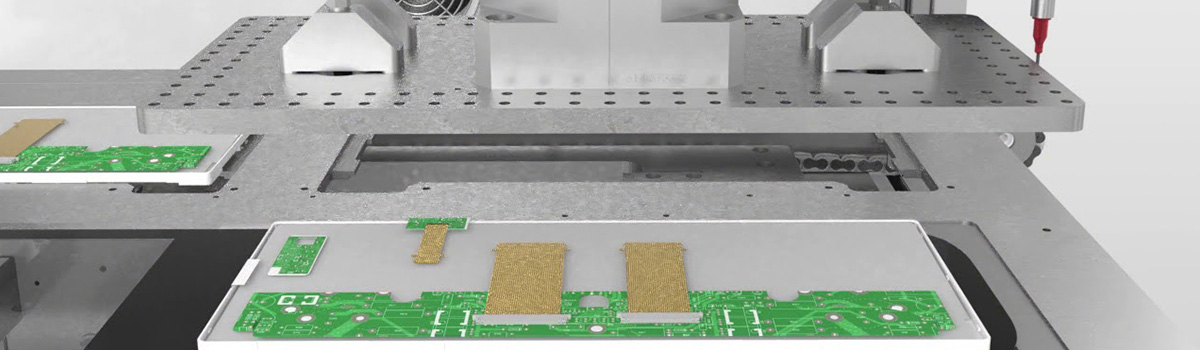
Vezetőképes ragasztó OLED kijelzőkhöz
A vezetőképes ragasztó döntő szerepet játszik az OLED (Organic Light Emitting Diode) kijelzők összeszerelésében és gyártásában. Az OLED kijelzők vékonyságukról, rugalmasságukról és energiahatékonyságukról ismertek, így népszerűek különféle elektronikus eszközökben, például okostelefonokban, televíziókban és hordható eszközökben. Az OLED-kijelzőkben vezetőképes ragasztókat használnak a különböző alkatrészek közötti elektromos kapcsolatok létrehozására, így biztosítva a megbízható teljesítményt és funkcionalitást.
Az OLED-kijelzőkben lévő vezetőképes ragasztó elsődleges célja, hogy elektromos kapcsolatokat hozzon létre a gyártás szerves rétegei és az alatta lévő áramkörök között. A hagyományos forrasztási módszerek nem alkalmasak az OLED bemutatókra, mivel érzékenyek a magas hőmérsékletre, ami a szerves anyagok károsodását vagy lebomlását okozhatja. A vezetőképes ragasztók alacsony hőmérsékletű ragasztási megoldást nyújtanak a hatékony és biztonságos összeszerelési folyamatokhoz.
Az OLED-kijelzők vezetőképes ragasztójának egyik legfontosabb jellemzője az elektromos vezetőképesség. Jó vezetőképességgel kell rendelkeznie, hogy biztosítsa az elektromos jelek hatékony átvitelét az alkatrészek között. Az ezüsttel töltött vezetőképes ragasztókat nagy elektromos vezetőképességük miatt gyakran használják OLED prezentációkban. Ezek a ragasztók apró ezüstrészecskéket tartalmaznak egy polimer mátrixban diszpergálva, amelyek két felület között felhordva vezető utakat képeznek. Az ezüst részecskék megkönnyítik az elektromos áram áramlását, lehetővé téve a kijelző megfelelő működését.
Az elektromos vezetőképességen kívül a ragasztónak más kívánatos tulajdonságokat is kell mutatnia. Az egyik döntő szempont a tapadási szilárdság. A ragasztónak erős kötést kell kialakítania az OLED kijelző különböző rétegei és alkatrészei között, hogy biztosítsa a mechanikai stabilitást és a hosszú távú megbízhatóságot. Ezenkívül a ragasztónak jó termikus stabilitással kell rendelkeznie, hogy ellenálljon a bemutató üzemi körülményeinek degradáció vagy rétegvesztés nélkül.
Egy másik fontos tulajdonság a ragasztó viszkozitása vagy folyóképessége. A ragasztót az összeszerelés során ki kell adagolni és egyenletesen el kell oszlatni a kívánt területen. Megfelelő vastagságúnak kell lennie, hogy könnyű legyen felhordani, és megakadályozza a túlzott szétterülést vagy csöpögést. A ragasztónak ésszerű kötési idővel kell rendelkeznie, amely lehetővé teszi a hatékony gyártási folyamatokat szükségtelen késedelmek nélkül.
Ezenkívül a vezetőképes ragasztónak kompatibilisnek kell lennie az OLED-kijelzőkben használt anyagokkal. Jól kell tapadnia különféle felületekhez, például üveghez vagy rugalmas műanyaghoz, és hatékonyan kell működnie a kijelzőrétegekben jelen lévő szerves anyagokkal. A kapszulázó anyagokkal való kompatibilitás szintén elengedhetetlen az OLED szerkezet megfelelő tömítéséhez és védelméhez a környezeti tényezőkkel, például nedvességgel és oxigénnel szemben.
Nem vezető ragasztó OLED kijelzőkhöz
Míg a vezetőképes ragasztó elengedhetetlen az OLED (Organic Light Emitting Diode) kijelzők elektromos csatlakozásainak kialakításához, a nem vezető ragasztó az összeszerelésben és a gyártásban is döntő szerepet játszik. A nem vezető ragasztók megragasztják és rögzítik az OLED-kijelzők különböző alkatrészeit, mechanikai stabilitást, védelmet és szigetelést biztosítva. Ezek a ragasztók számos alapvető tulajdonságot kínálnak, amelyeket kifejezetten az OLED technológia egyedi követelményeihez szabtak.
Az OLED-kijelzőkben a nem vezető ragasztó egyik alapvető célja a különböző rétegek és alkatrészek összetartása. Az OLED-prezentációk több rétegből állnak, beleértve a szerves emissziót, az átlátszó vezetőképes réteget és a hordozót. A nem vezető ragasztó megköti ezeket a rétegeket, és robusztus és megbízható szerkezetet hoz létre. Biztosítja, hogy a rétegek biztonságosan rögzítve maradjanak, megakadályozva a rétegvesztést vagy a szétválást működés közben.
A nem vezető ragasztó egyik kritikus tulajdonsága a mechanikai szilárdsága. A ragasztónak robusztus kötést kell biztosítania, lehetővé téve az OLED-kijelző számára, hogy ellenálljon a különféle mechanikai igénybevételeknek, például hajlításnak vagy hajlításnak. Hozzájárul a kijelző tartósságának növeléséhez, különösen a rugalmasságot igénylő alkalmazásokban, mint például az ívelt vagy összecsukható kijelzők.
A nem vezető ragasztó másik lényeges jellemzője az optikai tisztaság. Az OLED kijelzők fényt bocsátanak ki a szerves rétegeken keresztül, és minden homályos vagy átlátszatlan ragasztó akadályozhatja a fényáteresztést, ami negatívan befolyásolja a kijelző teljesítményét. A nem vezető ragasztókat úgy tervezték, hogy nagy átlátszóságúak legyenek, minimális interferenciát biztosítva a kibocsátott fénnyel, és megőrizzék a kijelző fényerejét és képminőségét.
A hőstabilitás szintén kulcsfontosságú szempont az OLED-kijelzők nem vezető ragasztói esetében. Ezeknek a ragasztóknak ki kell bírniuk a prezentáció üzemi hőmérsékletét anélkül, hogy a tapadás romlása vagy elvesztése lennének. Az OLED-kijelzők működés közben hőt termelhetnek, különösen nagy felbontású vagy nagy fényerejű alkalmazások esetén. A ragasztónak jó hőállósággal kell rendelkeznie ahhoz, hogy ilyen körülmények között megőrizze szerkezeti integritását és ragasztó tulajdonságait.
Ezenkívül az OLED-kijelzőkben használt nem vezető ragasztóknak kompatibilisnek kell lenniük az anyagokkal. Jól kell tapadniuk olyan felületekhez, mint az üveg vagy a rugalmas műanyag, erős kötést biztosítva a különböző rétegek között. A kijelző szerves anyagaival való kompatibilitás elengedhetetlen a káros kémiai kölcsönhatások elkerülése érdekében, amelyek teljesítményromláshoz vagy az eszköz meghibásodásához vezethetnek.
Ezenkívül a nem vezető ragasztóknak megfelelő viszkozitással és kötési idővel kell rendelkezniük a hatékony gyártási folyamatokhoz. Könnyen adagolhatónak, egyenletesen eloszlathatónak kell lenniük, és lehetővé kell tenni a komponensek megfelelő beállítását a kikeményedés előtt. A ragasztónak ésszerű kikeményedési idővel is rendelkeznie kell, hogy szükségtelen késedelem nélkül időben lehessen gyártani.
Hővezető ragasztó OLED kijelzőkhöz
A hővezető ragasztó létfontosságú szerepet játszik az OLED (Organic Light Emitting Diode) kijelzők hatékony hőelvezetésében és hőkezelésében. Az OLED-kijelzők működés közben hőt termelnek, különösen a nagy felbontású vagy nagy fényerejű alkalmazásoknál, és a hatékony hőelvezetés kulcsfontosságú az optimális teljesítmény fenntartásához, a túlmelegedés megelőzéséhez és a kijelző élettartamának meghosszabbításához. A hővezető ragasztókat kifejezetten úgy tervezték, hogy kiváló hőátadási tulajdonságokat biztosítsanak, miközben megfelelnek az OLED-kijelzők ragasztási követelményeinek.
Az OLED-kijelzők hővezető ragasztójának elsődleges feladata, hogy megkönnyítse a hőátadást a hőt termelő alkatrészekről a környező környezetbe vagy a hűtőbordákba. Ezeket a ragasztókat hővezető töltőanyagokkal, például kerámia vagy fém részecskékkel állítják elő, amelyek javítják a ragasztó hővezető képességét. A töltőanyagok vezető utat képeznek a ragasztóban, lehetővé téve a hő hatékony átáramlását a ragasztórétegen.
A hővezető ragasztó egyik kritikus jellemzője a hővezető képessége. A ragasztónak nagy hővezető képességgel kell rendelkeznie ahhoz, hogy hatékonyan elvezetje a hőt a hőforrástól. Az OLED-kijelzők hővezető ragasztóinak hővezető képessége általában több W/m·K-tól több tíz W/m·K-ig terjed. Ez biztosítja a hatékony hőelvezetést, megakadályozza a lokális forró pontok kialakulását, és fenntartja a hőmérséklet egyenletes eloszlását a kijelzőn.
A hővezető képességen kívül a hővezető ragasztóknak más kívánatos tulajdonságokkal is kell rendelkezniük. Az adhéziós szilárdság kulcsfontosságú a hőt termelő alkatrészek, például a kijelző-meghajtó IC-k és a hűtőbordák vagy a kijelző hátlapja közötti megfelelő kötés biztosításához. A ragasztónak megbízható mechanikai kötést kell biztosítania, amely ellenáll a hőtágulásnak és összehúzódásnak anélkül, hogy a hőátadási útvonalat veszélyeztetné.
A hőstabilitás szintén létfontosságú szempont a hővezető ragasztók esetében. Az OLED-kijelzők magas hőmérsékleten is működhetnek, és a ragasztónak ki kell bírnia ezeket a feltételeket anélkül, hogy a ragasztó tulajdonságai romlana vagy elveszne. Meg kell őriznie hővezető képességét és tapadási szilárdságát széles hőmérséklet-tartományban, biztosítva a hosszú távú megbízhatóságot és a teljesítmény stabilitását.
Egy másik fontos tulajdonság az elektromos szigetelés. Az OLED-kijelzőkben használt hővezető ragasztóknak jó elektromos szigetelési jellemzőkkel kell rendelkezniük, hogy megakadályozzák az alkatrészek közötti rövidzárlatot vagy elektromos interferenciát. Ez különösen fontos, ha a ragasztót elektromos csatlakozások vagy áramkörök közelében használják.
Ezenkívül a ragasztónak megfelelő viszkozitással és kötési idővel kell rendelkeznie a hatékony gyártási folyamatokhoz. Könnyen felvihetőnek, egyenletesen eloszlathatónak kell lennie, és lehetővé kell tennie a komponensek megfelelő összehangolását a kikeményedés előtt. A kikeményedési időnek ésszerűnek kell lennie ahhoz, hogy jelentős késedelem nélkül lehetővé tegye az időben történő gyártást.
UV-re keményedő ragasztó OLED kijelzőkhöz
Az UV-re keményedő ragasztó az OLED-kijelzők gyártásában kulcsfontosságú összetevő, jelentős szerepet játszik a különböző rétegek összeragasztásában, valamint a kijelző teljesítményének és tartósságának biztosításában. Az OLED (Organic Light Emitting Diode) kijelzőket élénk színeik, magas kontrasztarányuk és energiahatékonyságuk miatt széles körben használják olyan alkalmazásokban, mint például okostelefonok, televíziók és hordható eszközök. Az UV-re keményedő ragasztó számos előnnyel jár az OLED kijelző gyártási folyamatában, így ideális választás a kiváló minőségű kijelzők eléréséhez.
Az UV-re keményedő ragasztók polimer alapú anyagok, amelyek gyorsan megkötnek ultraibolya (UV) fény hatására. Ezek a ragasztók jellemzően oligomerekből, monomerekből, fotoiniciátorokból és adalékanyagokból állnak. A fotoiniciátor elindítja a kikeményedési folyamatot, amely elnyeli az UV fényt, és kémiai reakciót vált ki, amely gyors polimerizációhoz vezet. Ez lehetővé teszi az OLED rétegek gyors ragasztását, csökkentve a gyártási időt és növelve a hatékonyságot.
Az UV-re keményedő ragasztó egyik kritikus előnye, hogy igény szerint kikeményedik. Más, időt vagy hőt igénylő ragasztótípusoktól eltérően az UV-re keményedő ragasztók másodpercek alatt megkeményednek UV fény hatására. Ez a funkció gyorsabb összeszerelést és nagyobb gyártási teljesítményt tesz lehetővé, így kiválóan alkalmas OLED-kijelzők tömeggyártására.
Az UV-re keményedő ragasztók kiváló tapadási szilárdságot és tartósságot is biztosítanak. Erős kötéseket hoznak létre az OLED kijelző különböző rétegei között, biztosítva a stabilitást és megakadályozva a rétegvesztést. A kikeményedett tömítőanyag mechanikai támaszt nyújt, és megvédi az érzékeny OLED alkatrészeket a környezeti tényezőktől, például nedvességtől, portól és vibrációtól. Ez növeli a kijelző általános megbízhatóságát és élettartamát.
Ezenkívül az UV-re keményedő ragasztók a kikeményedés során csekély zsugorodást mutatnak, így minimálisra csökkentik az OLED-rétegek feszültség okozta károsodásának kockázatát. Ez kulcsfontosságú, mivel az OLED-kijelzők érzékeny szerves anyagokból állnak, amelyeket a túlzott igénybevétel vagy terhelés hátrányosan érinthet. Az UV-re keményedő ragasztók alacsony zsugorodási tulajdonsága segít megőrizni a kijelző szerkezeti integritását, és megakadályozza a teljesítmény idővel történő romlását.
További jelentős előny a precíz és egyenletes ragasztórétegvastagság elérése. Az UV-re keményedő ragasztók szabályozottan felvihetők, biztosítva a következetes és egyenletes eloszlást a kijelzőn. Ez az egységesség létfontosságú az optikai tisztaság megőrzéséhez, a fényszórás csökkentéséhez és a kijelző teljesítményének maximalizálásához.
A környezeti hatásokat tekintve az UV-re keményedő ragasztók általában környezetbarátabbak, mint az oldószer alapú ragasztók. Nem bocsátanak ki káros illékony szerves vegyületeket (VOC) a kikeményedés során, és a gyors térhálósodási folyamatnak köszönhetően alacsonyabb energiaigényük van. Az UV-re keményedő ragasztók összeállíthatók veszélyes anyagoktól mentesen, így megfelelnek a különböző környezetvédelmi előírásoknak.
Epoxi ragasztó OLED kijelzőkhöz
Az UV-re keményedő ragasztó az OLED-kijelzők gyártásában kulcsfontosságú összetevő, jelentős szerepet játszik a különböző rétegek összeragasztásában, valamint a kijelző teljesítményének és tartósságának biztosításában. Az OLED (Organic Light Emitting Diode) kijelzőket élénk színeik, magas kontrasztarányuk és energiahatékonyságuk miatt széles körben használják olyan alkalmazásokban, mint például okostelefonok, televíziók és hordható eszközök. Az UV-re keményedő ragasztó számos előnnyel jár az OLED kijelző gyártási folyamatában, így ideális választás a kiváló minőségű kijelzők eléréséhez.
Az UV-re keményedő ragasztók polimer alapú anyagok, amelyek gyorsan megkötnek ultraibolya (UV) fény hatására. Ezek a ragasztók jellemzően oligomerekből, monomerekből, fotoiniciátorokból és adalékanyagokból állnak. A fotoiniciátor elindítja a kikeményedési folyamatot, amely elnyeli az UV fényt, és kémiai reakciót vált ki, amely gyors polimerizációhoz vezet. Ez lehetővé teszi az OLED rétegek gyors ragasztását, csökkentve a gyártási időt és növelve a hatékonyságot.
Az UV-re keményedő ragasztó egyik kritikus előnye, hogy igény szerint kikeményedik. Más, időt vagy hőt igénylő ragasztótípusoktól eltérően az UV-re keményedő ragasztók másodpercek alatt megkeményednek UV fény hatására. Ez a funkció gyorsabb összeszerelést és nagyobb gyártási teljesítményt tesz lehetővé, így kiválóan alkalmas OLED-kijelzők tömeggyártására.
Az UV-re keményedő ragasztók kiváló tapadási szilárdságot és tartósságot is biztosítanak. Erős kötéseket hoznak létre az OLED kijelző különböző rétegei között, biztosítva a stabilitást és megakadályozva a rétegvesztést. A kikeményedett tömítőanyag mechanikai támaszt nyújt, és megvédi az érzékeny OLED alkatrészeket a környezeti tényezőktől, például nedvességtől, portól és vibrációtól. Ez növeli a kijelző általános megbízhatóságát és élettartamát.
Ezenkívül az UV-re keményedő ragasztók a kikeményedés során csekély zsugorodást mutatnak, így minimálisra csökkentik az OLED-rétegek feszültség okozta károsodásának kockázatát. Ez kulcsfontosságú, mivel az OLED-kijelzők érzékeny szerves anyagokból állnak, amelyeket a túlzott igénybevétel vagy terhelés hátrányosan érinthet. Az UV-re keményedő ragasztók alacsony zsugorodási tulajdonsága segít megőrizni a kijelző szerkezeti integritását, és megakadályozza a teljesítmény idővel történő romlását.
További jelentős előny a precíz és egyenletes ragasztórétegvastagság elérése. Az UV-re keményedő ragasztók szabályozottan felvihetők, biztosítva a következetes és egyenletes eloszlást a kijelzőn. Ez az egységesség létfontosságú az optikai tisztaság megőrzéséhez, a fényszórás csökkentéséhez és a kijelző teljesítményének maximalizálásához.
A környezeti hatásokat tekintve az UV-re keményedő ragasztók általában környezetbarátabbak, mint az oldószer alapú ragasztók. Nem bocsátanak ki káros illékony szerves vegyületeket (VOC) a kikeményedés során, és a gyors térhálósodási folyamatnak köszönhetően alacsonyabb energiaigényük van. Az UV-re keményedő ragasztók összeállíthatók veszélyes anyagoktól mentesen, így megfelelnek a különböző környezetvédelmi előírásoknak.
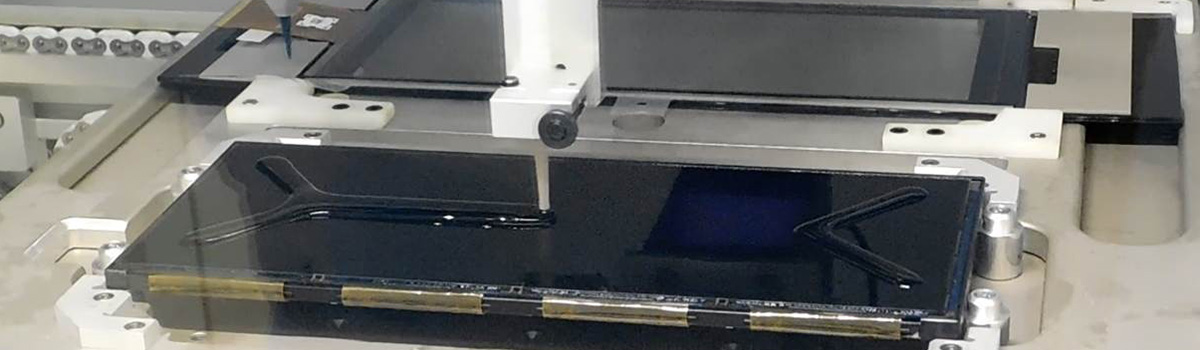
Szilikon ragasztó OLED kijelzőkhöz
Egyedülálló tulajdonságainak és előnyeinek köszönhetően a szilikon ragasztót széles körben használják az OLED (Organic Light Emitting Diode) kijelzők összeszerelésénél és gyártásánál. Kivételes képminőségük, rugalmasságuk és energiahatékonyságuk miatt az OLED-kijelzőket különféle elektronikus eszközökben, például okostelefonokban, televíziókban és hordható eszközökben használják. A szilikon ragasztók számos kulcsfontosságú előnyt kínálnak az OLED kijelző egység számára.
Az OLED kijelzőkhöz készült szilikon ragasztók egyik jelentős előnye a rugalmasságuk. Az OLED-kijelzőket gyakran hajlékonynak vagy íveltnek tervezik, és olyan ragasztóanyagokra van szükség, amelyek képesek ellenállni a bemutató hajlításának és hajlításának. A szilikon ragasztók kiváló rugalmassággal rendelkeznek, és ellenállnak az OLED-kijelzők rugalmasságával járó mechanikai igénybevételnek anélkül, hogy elveszítenék a tapadást vagy a kollekció integritását.
Ezenkívül a szilikon ragasztók kiváló hőstabilitással rendelkeznek. Az OLED-kijelzők működés közben hőt termelhetnek, és a ragasztónak ellenállnia kell a megemelkedett hőmérsékletnek, anélkül, hogy leromlana. A szilikon ragasztók ellenállnak a magas hőmérsékletnek, így hőben is megőrzik tapadásukat és szerkezeti integritásukat. Ez kulcsfontosságú az OLED-kijelzők hosszú távú megbízhatósága és teljesítménye szempontjából.
A szilikon ragasztók másik lényeges tulajdonsága az optikai tisztaságuk. A szilikon ragasztók az átlátszóságukról ismertek, ami az OLED kijelzők vizuális minőségének megőrzéséhez szükséges. A ragasztó nem tartalmazhat szennyeződéseket, homályosodást vagy elszíneződést, ami befolyásolhatja a kijelző tisztaságát és képminőségét. A szilikon ragasztók kiváló optikai tisztaságot és minimális interferenciát biztosítanak a fényáteresztésben, biztosítva a kijelző optimális teljesítményét.
A szilikon ragasztók jó ellenállást biztosítanak a nedvességgel és a környezeti tényezőkkel szemben is. A nedvesség jelentős aggodalomra adhat okot az OLED-kijelzők számára, mivel korrózióhoz, elektromos rövidzárlathoz vagy az érzékeny alkatrészek károsodásához vezethet. A szilikon ragasztók kiváló nedvességállóságot biztosítanak, védik a kijelzőt a környezeti tényezőktől, és növelik annak tartósságát és megbízhatóságát.
Ezenkívül a szilikon ragasztóknak alacsony a gázkibocsátási hajlama. A gázkibocsátás azt jelenti, hogy a ragasztókból illékony vegyületeket szabadítanak fel, amelyek megzavarhatják az érzékeny elektronikus alkatrészek teljesítményét. A szilikon ragasztók gyakori illékony vegyületekkel rendelkeznek, így alkalmasak olyan alkalmazásokhoz, amelyek minimális gázkibocsátást igényelnek, mint például az OLED kijelzők.
Ami a gyártási hatékonyságot illeti, a szilikon ragasztók gyors kötési időt biztosítanak, a gyors kikeményedés pedig gyorsabb gyártási ciklust tesz lehetővé, és csökkenti az összeszerelési költségeket. A szilikon ragasztók alacsonyabb hőmérsékleten kikeményedhetnek, csökkentve a kijelző alkatrészekre ható hőterhelést az összeszerelés során.
Összességében a szilikon ragasztókat részesítik előnyben az OLED-kijelzők összeszerelésénél rugalmasságuk, hőstabilitásuk, optikai tisztaságuk, nedvességállóságuk, alacsony gázkibocsátásuk és gyors kötési tulajdonságaik miatt. Ezek a tapadási jellemzők hozzájárulnak az OLED-kijelzők megbízhatóságához, hosszú élettartamához és teljesítményéhez különböző elektronikus eszközökben. Ahogy az OLED technológia folyamatosan fejlődik, a speciális megjelenítési követelményekhez szabott, speciális szilikon ragasztók fejlesztése tovább javítja az OLED-kijelzők minőségét és funkcionalitását.
Akril ragasztó OLED kijelzőkhöz
Az akril ragasztót széles körben használják OLED (Organic Light-Emitting Diode) kijelzők összeszerelésénél és ragasztásánál kiváló optikai tulajdonságai, erős tapadása és könnyű felhordása miatt. Az OLED-kijelzők vékonyak, könnyűek, nagy kontrasztot és élénk színeket kínálnak, így egyre népszerűbbek a különféle elektronikus eszközökben, például okostelefonokban, televíziókban és hordható eszközökben. A gyártásuk során használt ragasztó kritikus szerepet játszik a kijelzők teljesítményének, tartósságának és általános minőségének biztosításában.
Az OLED-kijelzőkben használt ragasztókkal szemben támasztott egyik kritikus követelmény az optikai tisztaság. Az akril ragasztók kivételes átlátszóságot biztosítanak, lehetővé téve, hogy az OLED pixelek által kibocsátott fény torzulás vagy szóródás nélkül áthaladjon. Ez a tulajdonság kulcsfontosságú a kiváló minőségű vizuális élmény fenntartásához, és az OLED-kijelzők erről ismertek.
Ezenkívül az akril ragasztók kiváló tapadást mutatnak az OLED-kijelzőkben gyakran használt különféle hordozókhoz, beleértve az üveget, a műanyagot és a fémet. Ez az erős kötés biztosítja a kijelző egység integritását, megakadályozva a rétegleválást vagy a kritikus rétegek leválását. Ezenkívül növeli a kijelző ellenálló képességét a mechanikai igénybevételekkel, például hajlítással vagy hajlítással szemben, ami különösen fontos a rugalmas OLED-kijelzők esetében.
Az akril ragasztók könnyű felhordásukról ismertek, és jellemzően folyékony készítményekként szállítják őket, amelyek könnyen adagolhatók a kívánt területre. Az adott ragasztókészítménytől függően, miután felvitték, különféle módszerekkel térhálósíthatók, beleértve az ultraibolya (UV) fénnyel, hővel vagy nedvességgel. A gyors kikeményedési folyamat elősegíti a gyártási folyamat egyszerűsítését és a termelékenység javítását.
Az OLED-kijelzők akril ragasztóit gyakran úgy alakítják ki, hogy ellenálljanak az életciklusuk során előforduló megerőltető körülményeknek, így biztosítva a megbízható teljesítményt. Ezek a ragasztók ellenállnak a magas hőmérsékletnek, stabilitást biztosítanak és megőrzik a kötés integritását még magasabb hőmérsékleten is. Úgy is tervezhetők, hogy ellenálljanak a nedvességnek és a nedvességnek, megvédve az OLED alkatrészeket a teljesítményüket rontó környezeti tényezőktől.
Ezenkívül az akril ragasztók kiváló elektromos szigetelési tulajdonságokat biztosíthatnak, ami döntő fontosságú az OLED-kijelzők esetében a nem kívánt elektromos interferencia vagy a különböző alkatrészek közötti rövidzárlatok elkerülése érdekében.
Nyomásérzékeny ragasztó OLED kijelzőkhöz
A nyomásérzékeny ragasztó (PSA) technológia egyre fontosabbá vált az OLED-kijelzők gyártásában. Az OLED (organic light-emitting diode) kijelzők számos előnnyel rendelkeznek a hagyományos LCD-kkel szemben, többek között jobb színvisszaadást, nagyobb kontrasztarányt és gyorsabb válaszidőt. Az OLED-kijelzők optimális teljesítménye és tartóssága érdekében a speciális nyomásérzékeny ragasztók elengedhetetlenekké váltak.
A PSA-k egyedi ragasztók, amelyek kötést képeznek, amikor nyomást gyakorolnak rájuk. Gyakran használják különféle alkalmazásokban, például autóiparban, elektronikában és orvosi eszközökben. A PSA-k kulcsfontosságúak a különböző kijelzőrétegek összeragasztásában és az OLED-kijelzők alapjához való rögzítésében.
Az OLED-kijelzők PSA-k fejlesztésének egyik elsődleges kihívása a szilárd tapadás és a kényes OLED-anyagok minimális igénybevétele közötti egyensúly megteremtése. Az OLED prezentációk több rétegből állnak, beleértve a fényt kibocsátó szerves réteget is. A ragasztási folyamat alatti túlzott nyomás károsíthatja ezeket a rétegeket, és befolyásolhatja a kijelző általános teljesítményét. Ezért az OLED-kijelzőkhöz tervezett PSA-knak megfelelő kötési szilárdságot kell biztosítaniuk, miközben meg kell őrizniük a gyengéd érintést a sérülések elkerülése érdekében.
Az OLED-kijelzőkben használt PSA-k másik döntő tényezője az optikai tulajdonságaik. A ragasztórétegnek minimálisan kell befolyásolnia a kijelző optikai tisztaságát, fényerejét és színpontosságát. Az alacsony homályosságú és kiváló fényáteresztési jellemzőkkel rendelkező PSA-kat részesítik előnyben, hogy a kijelző vizuális minősége ne sérüljön.
Ezenkívül az OLED-kijelzők PSA-inak kiváló hőstabilitással és környezeti tényezőkkel szembeni ellenállással kell rendelkezniük. Az OLED bemutatók változó hőmérsékletnek, páratartalomnak és egyéb külső körülményeknek vannak kitéve. A ragasztónak stabilnak kell maradnia és meg kell őriznie tulajdonságait ilyen körülmények között, hogy biztosítsa a kijelző élettartamát és megbízhatóságát.
A gyártók folyamatosan fejlesztik és fejlesztik a kifejezetten OLED-kijelzőkre szabott PSA-készítményeket. Ezeket a speciális ragasztókat gyakran fejlett polimertechnológiák felhasználásával tervezték, amelyek nagy rugalmasságot, alacsony gázkibocsátást és kiváló alkalmazkodóképességet tartalmaznak. Úgy tervezték, hogy kompatibilisek legyenek az OLED-kijelzőkben használt egyedi hordozókkal és anyagokkal.
A ragasztó tulajdonságok mellett az alkalmazási folyamat is döntő jelentőségű. Az OLED-kijelzők PSA-megoldásai általában előre kivágott szalagok vagy filmek formájában készülnek, lehetővé téve a precíz és hatékony összeszerelést. A videók testreszabhatók, hogy illeszkedjenek a kijelző méretéhez és alakjához, lehetővé téve a könnyű integrációt a gyártási folyamatba.
A megfelelő ragasztó kiválasztása OLED kijelzőmodulhoz
Az OLED kijelzőmodul összeszerelésekor a megfelelő ragasztó kiválasztása kulcsfontosságú az optimális teljesítmény, tartósság és hosszú élettartam érdekében. A ragasztó kritikus fontosságú a különböző alkatrészek egymáshoz való ragasztásában és a mechanikai stabilitás biztosításában. Ez a cikk megvizsgálja azokat a kulcsfontosságú tényezőket, amelyeket figyelembe kell venni az OLED kijelzőmodul tömítőanyagának kiválasztásakor.
- Optikai átlátszóság: Az OLED kijelzők élénk színeikről és kiváló kontrasztarányukról ismertek. Ezért elengedhetetlen olyan ragasztó kiválasztása, amely megőrzi a kijelző vizuális tisztaságát. Keressen olyan ragasztókat, amelyeket kifejezetten OLED alkalmazásokhoz terveztek, biztosítva a nagy átlátszóságot és a fényáteresztésre gyakorolt minimális hatást.
- Hőstabilitás: Az OLED-kijelzők működés közben hőt termelnek, és a ragasztónak ellenállnia kell a megnövekedett hőmérsékletnek a teljesítmény csökkenése nélkül. Győződjön meg arról, hogy a ragasztó jó hőstabilitással rendelkezik, és képes kezelni a kijelzőmodul által termelt hőt. Ez különösen fontos, ha az alkalmazás nagy fényerő-beállításokat vagy hosszan tartó használatot igényel.
- Tapadási szilárdság: A ragasztónak erősen meg kell ragasztania az OLED panelt, a fedőüveget és a modul egyéb alkatrészeit. Leválás vagy leválás nélkül ki kell bírnia a mechanikai igénybevételt, például hajlítást vagy hajlítást. Fontolja meg a nagy hámlási és nyírószilárdságú ragasztókat a hosszú távú tapadási megbízhatóság biztosítása érdekében.
- Nedvesség- és környezetállóság: Az OLED-kijelzők érzékenyek a nedvességre és a környezeti tényezőkre, például a páratartalomra és a hőmérséklet-változásokra. A ragasztónak kiváló nedvességállóságot kell biztosítania, megakadályozva a nedvesség behatolását, amely károsíthatja az OLED panelt. Keressen olyan ragasztókat, amelyek magas védelmet nyújtanak a nedvesség és a környezeti tényezők ellen.
- Kompatibilitás: Fontolja meg a ragasztó kompatibilitását az OLED kijelzőmodulban használt anyagokkal. Győződjön meg arról, hogy a ragasztó alkalmas a modulban található adott anyagok, például üveg, fém vagy műanyag ragasztására. Az OLED alkalmazásokhoz tervezett ragasztók általában kiválóan kompatibilisek a különféle felületekkel.
- Feldolgozhatóság: A könnyű alkalmazhatóság egy másik fontos tényező. A ragasztónak könnyen adagolhatónak, egyenletesen eloszlathatónak és a kívánt időn belül megkeményedőnek kell lennie. Ezenkívül kompatibilisnek kell lennie az összeszerelési folyamattal, akár kézi, akár automatizált alkalmazási módszerekről van szó. Vegye figyelembe a gyártási folyamathoz megfelelő viszkozitású, kötési idővel és adagolási követelményekkel rendelkező ragasztókat.
- Megbízhatóság és tartósság: A megbízható ragasztó elengedhetetlen az OLED kijelzőmodul hosszú távú működéséhez. Idővel meg kell őriznie adhéziós tulajdonságait, ellenállva az öregedés, a hőmérséklet-ingadozások és a fénynek való kitettség okozta lebomlásnak. Keressen olyan ragasztókat, amelyek teszteltek és bizonyítottan hosszú távú megbízhatóságot és tartósságot kínálnak az OLED alkalmazásokban.
Az OLED kijelzőmodul ragasztójának megfelelő alkalmazási technikái
Az OLED-kijelző modulok ragasztójának felhordása gondos odafigyelést igényel a sikeres ragasztás és a megbízható teljesítmény biztosítása érdekében. A nem megfelelő alkalmazási technikák olyan problémákat okozhatnak, mint a rossz tapadás, légbuborékok vagy egyenetlen terjedés, ami befolyásolhatja a modul optikai tisztaságát és tartósságát. Ez a cikk az OLED kijelzőmodul ragasztójának néhány alapvető alkalmazási technikáját vizsgálja meg.
- Felület-előkészítés: A megfelelő felület-előkészítés kritikus fontosságú a szilárd kötés eléréséhez. Győződjön meg arról, hogy minden ragasztandó héj tiszta, száraz, és portól, olajtól vagy bármilyen szennyeződéstől mentes. Használjon megfelelő tisztítószert vagy oldószert, amelyet a ragasztó gyártója javasol a maradványok eltávolításához. Az alapos felület-előkészítés javítja a ragasztó azon képességét, hogy hatékonyan tapadjon az aljzathoz.
- Adagolás és felhordás: A ragasztót egyenletesen kell elosztani, hogy egyenletes fedést biztosítson a ragasztási területen. Használjon a ragasztójának megfelelő adagolási módot, például fecskendőt, adagolót vagy automata rendszert. Ügyeljen a gyártó által megadott ragasztógyöngy-méretre és adagolási mintára.
- A levegő beszorulásának elkerülése: A ragasztó és az aljzatok közé szorult légbuborékok veszélyeztethetik az optikai tisztaságot és a tapadási szilárdságot. A levegő beszorulásának minimalizálása érdekében alkalmazza a ragasztókontrollt, elkerülve a gyors vagy túlzott felhordást, amely légzsákokat okozhat. Használjon szerszámot, például görgőt vagy gumibetétet a ragasztó szétterítéséhez, miközben óvatosan eltávolítja a benne rekedt levegőt.
- Kikeményedés: Kövesse a ragasztó gyártója által ajánlott kötési utasításokat. Győződjön meg arról, hogy a környezeti feltételek, például a hőmérséklet és a páratartalom a megadott tartományon belül vannak a kikeményedési folyamat során. A nem megfelelő kikeményedés tökéletlen ragasztást vagy csökkent ragasztási teljesítményt eredményezhet. Hagyjon elegendő kikeményedési időt, mielőtt a modult további kezelésnek vagy tesztelésnek veti alá.
- Igazítás és rögzítés: Az alkatrészek megfelelő igazítása és rögzítése kulcsfontosságú a pontos pozicionálás és az egyenletes kötési vonalvastagság eléréséhez. Az OLED-panel, a fedőüveg és más alkatrészek pontos elhelyezéséhez használjon igazítószerszámokat vagy beállítóeszközöket. Alkalmazzon megfelelő nyomást, vagy használjon rögzítési módszereket, hogy fenntartsa az igazítást a ragasztó kikeményítése során.
- Minőségellenőrzés: Végezzen minőség-ellenőrzési intézkedéseket a ragasztófelvitel és a ragasztás minőségének ellenőrzésére. Szemrevételezéssel ellenőrizze a hibákat, például az egyenetlen ragasztóterjedést vagy üregeket. Végezzen tapadási vizsgálatot a kötés szilárdságának és tartósságának ellenőrzésére. Dokumentálja és kezelje a jelentkezési folyamat során tapasztalt eltéréseket vagy problémákat.
- Ragasztótárolás: A ragasztó megfelelő tárolása elengedhetetlen az integritás és a teljesítmény megőrzéséhez. Kövesse a gyártó által megadott tárolási előírásokat, beleértve a hőmérsékletet és az eltarthatósági szempontokat. A ragasztót ellenőrzött környezetben, közvetlen napfénytől és szélsőséges hőmérséklettől védve tárolja.
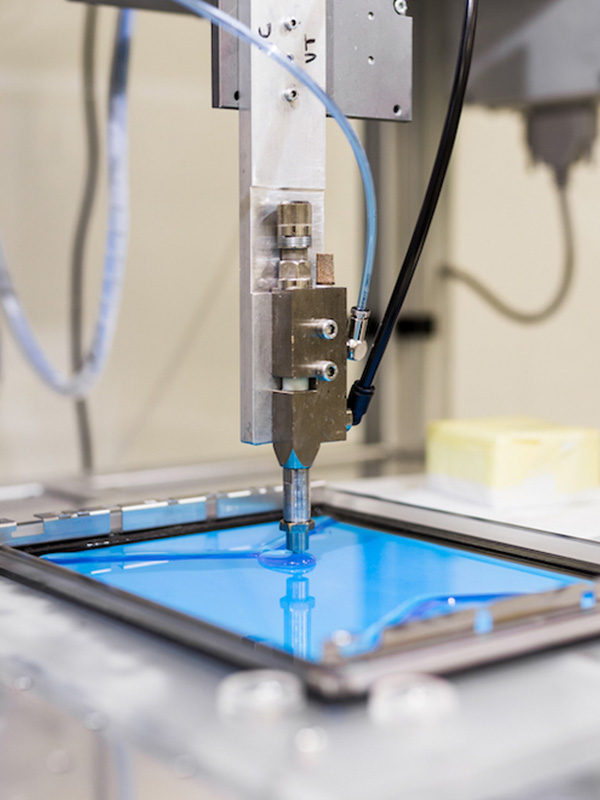
Gyakori hibák az OLED-kijelzők ragasztójának felhordásakor
Amikor OLED-kijelzőkre ragasztót visz fel, a megfelelő eljárások betartása kulcsfontosságú a sikeres és tartós kötés biztosításához. Vannak azonban olyan mindennapi dolgok, amelyeket az embereknek ki kell javítaniuk a folyamat során, és íme néhány ezek közül:
- Nem megfelelő tisztítás: Az egyik leggyakoribb hiba a ragasztandó felületek nem megfelelő tisztítása. A ragasztó felhordása előtt feltétlenül távolítson el minden port, olajat és szennyeződést a kijelzőről és az aljzatról. Ennek elmulasztása gyenge tapadást és a kijelző esetleges meghibásodását eredményezheti.
- Pontatlan felhordás: A ragasztó egyenetlenül vagy nem megfelelő területeken történő felhordása ragasztási problémákhoz vezethet, és befolyásolhatja a kijelző általános teljesítményét. Alapvetően fontos betartani a gyártó útmutatásait a felhordási móddal kapcsolatban, beleértve az ajánlott mennyiséget, a szórási technikát és a kikeményedési időt.
- Rossz ragasztó használata: Az OLED-kijelzők speciális ragasztókat igényelnek egyedi tulajdonságaik, például a rugalmasság és az átlátszóság miatt. A megfelelő ragasztó használata kompatibilitási problémákat, megfelelő kötési szilárdságot vagy a kijelző károsodását okozhatja. Mindig győződjön meg arról, hogy a kiválasztott ragasztó kifejezetten OLED alkalmazásokhoz készült.
- Helytelen kötési idő: A ragasztó kikeményedési ideje kulcsfontosságú az optimális kötési szilárdság eléréséhez. Vannak, akik elsietik a folyamatot, mivel nem hagynak elegendő időt a ragasztó teljes megkötésére. Hasonlóképpen, mások nyomást gyakorolhatnak vagy túl korán manipulálják a kijelzőt, megzavarva a kikeményedési folyamatot. Mindig tartsa be a ragasztó gyártója által megadott ajánlott kötési időt.
- Környezeti tényezők figyelmen kívül hagyása: A környezeti feltételek, például a hőmérséklet és a páratartalom jelentősen befolyásolhatják a ragasztó teljesítményét. Ha ezeket a tényezőket nem veszi figyelembe a ragasztási folyamat során, az rossz tapadáshoz, kötési problémákhoz vagy akár a ragasztás meghibásodásához vezethet. Kövesse a ragasztó gyártójának útmutatásait az ideális környezeti feltételekkel kapcsolatban a felhordáshoz és a kötéshez.
- A biztonsági óvintézkedések figyelmen kívül hagyása: A ragasztók gyakran tartalmaznak vegyi anyagokat, amelyek rossz kezelés esetén károsak lehetnek. Vannak, akik figyelmen kívül hagyják a biztonsági óvintézkedéseket, például kesztyűt, védőszemüveget viselnek, vagy jól szellőző helyen dolgoznak. A ragasztók kezelésekor mindig tartsa szem előtt a biztonságot, és kövesse az ajánlott irányelveket saját és mások védelme érdekében.
- Nem megfelelő tesztelés és minőségellenőrzés: A tömeggyártás vagy a végső összeszerelés előtt alapvető fontosságú, hogy alapos tesztelést és minőség-ellenőrzési intézkedéseket hajtsanak végre. Előfordulhat, hogy egyes személyeknek nagyobb figyelmet kell fordítaniuk ezekre a lépésekre, ami ragasztóval kapcsolatos problémákhoz vezethet a késztermékben. Mindig végezzen megfelelő vizsgálatokat, mint például a tapadási szilárdság, a hőciklus és a megbízhatóság vizsgálata, hogy megbizonyosodjon arról, hogy a ragasztó megfelel az előírt szabványoknak.
E gyakori hibák elkerülése jelentősen javíthatja az OLED-kijelzők ragasztási folyamatát. A gyártó utasításainak betartása, a környezeti feltételekre való odafigyelés és a megfelelő biztonsági intézkedések végrehajtása elősegíti a megbízható és tartós tapadás elérését, biztosítva a kijelzők minőségét és teljesítményét.
OLED kijelzőmodulok karbantartása és javítása
Az OLED kijelzőmodulok karbantartása és javítása elengedhetetlen az optimális teljesítmény biztosításához és e fejlett kijelzőtechnológiák élettartamának meghosszabbításához. Az OLED (Organic Light-Emitting Diode) kijelzők kiváló képminőségükről, élénk színeikről és magas kontrasztszintjükről ismertek. Az OLED-kijelzők azonban idővel problémákat vagy minőségromlást tapasztalhatnak, mint bármely elektronikus eszköz esetében. A rendszeres karbantartás és a javítási igények azonnali kezelése segíthet enyhíteni ezeket a problémákat és maximalizálni az OLED kijelzőmodulok élettartamát.
Az OLED kijelzőmodulok karbantartása elsősorban a megfelelő tisztítást és gondos kezelést foglalja magában. Az OLED-kijelzők tisztítása során döntő fontosságú a puha, szöszmentes kendő és kifejezetten az elektronikus kijelzőkhöz tervezett, karcmentes tisztítószerek használata. A durva vegyszerek vagy durva anyagok károsíthatják az OLED panel érzékeny felületét. Óvatosan, körkörös mozdulatokkal törölje le a képernyőt a por, az ujjlenyomatok és a szennyeződések eltávolításához. Fontos, hogy ne alkalmazzon túlzott nyomást vagy karcolja meg a felületet.
Ezenkívül tanácsos az OLED-kijelzőket távol tartani a közvetlen napfénytől vagy erős hőforrásoktól, mivel ez károsíthatja a gyűjteményben lévő szerves anyagokat. Az OLED panelek érzékenyek a hőre, és a hosszan tartó expozíció pixelbeégést vagy a színpontosság romlását okozhatja. Hasonlóképpen, az extrém hideg hőmérséklet is befolyásolhatja az OLED teljesítményét, ezért nagyon fontos, hogy ne tegye ki a kijelzőt fagyos hatásoknak.
Az OLED kijelző modullal kapcsolatos problémák esetén javasoljuk, hogy szakképzett technikussal vagy a gyártó ügyfélszolgálatával forduljon a javításhoz. A barkács javítás kockázatos lehet, és érvénytelenítheti a garanciát. Ha a kijelzőn tartós képvisszamaradás vagy beégés tapasztalható, a korábbi képek maradványai továbbra is a képernyőn maradnak, és a gyártó speciális eszközöket vagy szoftvereket biztosíthat a probléma megoldásához. Elengedhetetlen, hogy jelentse az esetleges hibákat vagy rendellenességeket az időben történő megoldás érdekében.
A javítás néha magában foglalhatja az OLED-kijelző modul hibás alkatrészeinek cseréjét. Az OLED panelek bonyolult szerkezetek, és az egyes képpontok vagy alpixelek cseréje nem praktikus. Ezért, ha a kijelzőmodul jelentős károsodást vagy meghibásodást szenved, teljes cserére lehet szükség. A gyártók vagy a felhatalmazott szervizközpontok jellemzően javítási vagy csereszolgáltatásokat kínálnak az OLED kijelzőmodulokhoz, biztosítva a kompatibilitást és megőrizve az eszköz teljesítményét.
A lehetséges problémák elkerülése és az OLED-kijelző modulok élettartamának optimalizálása érdekében tanácsos betartani a gyártó használati és karbantartási irányelveit. A gyártó által biztosított rendszeres szoftverfrissítések optimalizálást és az ismert problémák javítását is tartalmazhatják, javítva az OLED-kijelző általános teljesítményét.
Tippek az OLED kijelzőmodulok élettartamának meghosszabbításához
Az OLED kijelzőmodulok élettartamának meghosszabbítása kulcsfontosságú a hosszú távú teljesítmény és tartósság biztosítása érdekében. Íme néhány tipp az OLED-kijelzők élettartamának maximalizálásához:
- Fényerő-beállítások módosítása: Az OLED-kijelzők érzékenyek a fényerőszintre. A magas fényerő-beállítások felgyorsíthatják a szerves anyagok lebomlását. Fontolja meg a fényerő szintjének ésszerű és kényelmes szintre csökkentését a kopás csökkentése és a kijelző élettartamának növelése érdekében.
- Képernyővédők és alvó mód használata: Ha a kijelző nincs használatban, aktiválja a képernyővédőket, vagy használja az alvó üzemmódot. Az OLED-show-k hajlamosak a beégésre, ahol a statikus képek maradandó károsodást okozhatnak. A képernyővédők segítenek megakadályozni, hogy a statikus elemek hosszabb ideig a képernyőn maradjanak, így minimálisra csökkentik a beégés kockázatát.
- Kerülje a statikus képek megjelenítését: az OLED-kijelzők hajlamosak beégni, ha statikus képeket hosszabb ideig jelenítenek meg. Ennek megelőzése érdekében kerülje a statikus elemek, például logók, ikonok vagy menük hosszabb ideig tartó megjelenítését a képernyőn. Használjon dinamikus tartalmat, és időnként mozgassa vagy frissítse a megjelenített elemeket.
- Képponteltolás engedélyezése: A pixeleltolás egy olyan technika, amely kissé elmozdítja a képernyőn megjelenő tartalom helyzetét, hogy megakadályozza a statikus képek beégését. Egyes OLED-kijelzők beépített pixeleltolási funkciókkal rendelkeznek, amelyek automatikusan rendszeresen mozgatják a tartalmat. Engedélyezze ezt a funkciót a kopás egyenletes elosztásához a kollekcióban.
- Az energiagazdálkodás megvalósítása: Az OLED-kijelzők kevesebb energiát fogyasztanak, amikor sötétebb tartalmat jelenítenek meg, mivel az egyes képpontok fényt bocsátanak ki. Fontolja meg a sötét témák használatát vagy az energiatakarékos módok alkalmazását az általános energiafogyasztás csökkentése érdekében. Az alacsonyabb energiafogyasztás növelheti az OLED-kijelző élettartamát.
- Kerülje a közvetlen napfény hatását: az OLED-kijelzők érzékenyek a hőre, és a hosszan tartó expozíció károsodást okozhat. Helyezze a kijelzőket távol a közvetlen napfénytől, és gondoskodjon megfelelő szellőzésről a túlmelegedés elkerülése érdekében. A magas hőmérséklet felgyorsíthatja az OLED anyagok öregedési folyamatát.
- Óvatosan tisztítsa meg a kijelzőt: Az OLED-kijelzők tisztításához használjon puha, szöszmentes mikroszálas kendőt, hogy elkerülje a felület megkarcolását. Kerülje a túlzott nyomás alkalmazását vagy a kemény vegyszerek használatát, amelyek károsíthatják a műsort. Finoman törölje le a képernyőt, hogy eltávolítsa a port, az ujjlenyomatokat vagy a szennyeződéseket, amelyek befolyásolhatják a vizuális minőséget.
- Rendszeresen frissítse a firmware-t: A gyártók gyakran adnak ki frissítéseket a teljesítmény javítása és az OLED-kijelzőkkel kapcsolatos lehetséges problémák megoldása érdekében. Legyen naprakész a legújabb firmware-kiadásokkal, és alkalmazza azokat a gyártó ajánlása szerint. Ezek a frissítések olyan optimalizálásokat tartalmazhatnak, amelyek növelik a kijelző élettartamát.
- Óvatosan tárolja és szállítsa: Ha OLED-kijelzőket kell tárolnia vagy szállítania, győződjön meg arról, hogy megfelelően védi azokat a fizikai sérülésektől, szélsőséges hőmérsékletektől és nedvességtől. Használjon megfelelő csomagolási és kezelési eljárásokat, hogy elkerülje a lehetséges károkat, amelyek befolyásolhatják a kijelző élettartamát.
- Használjon megfelelő elalvásidőzítőket: Az OLED-kijelzők számára előnyösek az elalváskapcsolók, amelyek bizonyos tétlenség után automatikusan kikapcsolják a műsort. Ez a funkció segít csökkenteni a használaton kívüli kijelző felesleges kopását, meghosszabbítva az élettartamát.
Ha követi ezeket a tippeket, jelentősen meghosszabbíthatja OLED kijelzőmoduljai élettartamát, így biztosítva az optimális teljesítményt és hosszú élettartamot.
Az OLED kijelzőmodul-ragasztók jövőbeli fejlesztései
Az OLED kijelzőmodul-ragasztó fejlesztése a folyamatos kutatás és innováció területe. Az OLED technológia fejlődésével a gyártók javítják az ezekben a kijelzőkben használt ragasztóanyagokat. Íme néhány lehetséges jövőbeli fejlesztés az OLED-kijelzőmodul-ragasztóval kapcsolatban:
- Javított tapadási szilárdság: A jövőbeni ragasztófejlesztés egyik fókuszában az OLED kijelzőmodul különböző rétegei közötti kötési szilárdság javítása áll. Az erősebb ragasztók jobb tapadást biztosítanak, és minimálisra csökkentik a rétegek leválásának vagy leválásának kockázatát idővel. Ez a fejlesztés hozzájárul az OLED-kijelzők általános tartósságához és élettartamához.
- Rugalmasság és nyújthatóság: Az OLED-kijelzőket egyre gyakrabban használják rugalmas és hajlítható eszközökben, például okostelefonokban, hordható eszközökben és ívelt kijelzőkben. A jövőbeni ragasztókészítményeknek nagyobb rugalmasságot és nyújthatóságot kell mutatniuk, hogy megfeleljenek ezeknek a hajlítási és hajlítási követelményeknek. Az ilyen alkalmazásokhoz elengedhetetlenek olyan ragasztók, amelyek megtartják kötésüket különböző hajlítási szögek és ismételt hajlítás mellett.
- Hőkezelés: Az OLED-kijelzők működés közben hőt termelhetnek, ami befolyásolja a teljesítményt és a hosszú élettartamot. A jövő ragasztóanyagai a jobb hőkezelési tulajdonságokra fognak összpontosítani. A javított hőelvezetési képességgel rendelkező ragasztók segítenek csökkenteni az OLED-kijelzők hőterhelését, megelőzve a túlmelegedést és az esetleges károsodást.
- Optikai átlátszóság: Az OLED kijelzők kiváló vizuális minőségükről és élénk színeikről ismertek. A ragasztók jövőbeli fejlesztésének célja az OLED-bemutatókban használt ragasztók optikai tisztaságának fenntartása vagy javítása. Az átlátszó és átlátszó ragasztók minimális interferenciát biztosítanak a fényáteresztéssel, lehetővé téve az OLED pixelek pontos és élénk színek megjelenítését.
- Ultravékony és könnyű: A technológia fejlődésével folyamatosan igyekeznek csökkenteni az elektronikus eszközök vastagságát és súlyát. Az OLED-kijelzők jövőbeli ragasztóanyagait ultravékonyra és könnyűre tervezik, minimálisra csökkentve a kijelzőmodul teljes vastagságát. A vékonyabb és könnyebb ragasztók hozzájárulnak az eszközök karcsúságához és hordozhatóságához, miközben megtartják a szükséges ragasztási szilárdságot.
- Környezetvédelmi megfontolások: A fenntartható és környezetbarát ragasztós megoldások, köztük az OLED-kijelzők egyre fontosabbak az elektronikus eszközök fejlesztésében. A jövőbeni ragasztóanyagok valószínűleg a veszélyes anyagok, például az illékony szerves vegyületek (VOC) vagy a nehézfémek használatának csökkentésére vagy megszüntetésére fognak összpontosítani. A környezetbarát ragasztási lehetőségek kielégítik a környezetbarátabb és fenntarthatóbb elektronika iránti növekvő keresletet.
- Gyártási hatékonyság: Az OLED-kijelzőket összetett folyamatok segítségével gyártják, amelyek magukban foglalják több réteg precíz igazítását és ragasztását. A jövőbeni ragasztófejlesztések racionalizálják és optimalizálják a gyártási folyamatot, javítva a hatékonyságot és csökkentve a gyártási költségeket. A gyorsabb kötési időt, nagyobb hozamot és könnyebb kezelhetőséget biztosító ragasztók növelik a gyártás termelékenységét.
- Hosszú távú stabilitás: A stabilitás döntő tényező az OLED-kijelzők ragasztóanyagaiban. A jövőbeni fejlesztések a javított hosszú távú stabilitású ragasztók előállítására összpontosítanak, amelyek ellenállnak a környezeti tényezőknek, például a hőmérsékletnek, a páratartalomnak és az UV-sugárzásnak. A tulajdonságaikat hosszú ideig megőrző ragasztók biztosítják az OLED-kijelzők hosszú élettartamát és megbízhatóságát.
Következtetés: Az OLED-kijelző modulok a különféle elektronikus eszközök nélkülözhetetlen alkotóelemeivé váltak, és az őket a helyükön tartó ragasztó ugyanolyan fontos. A kiváló minőségű ragasztó javíthatja a készülék tartósságát, megbízhatóságát és teljesítményét. Mivel az OLED-kijelzőkhöz nagyon sokféle ragasztó áll rendelkezésre, elengedhetetlen, hogy figyelembe vegyük az alkalmazás speciális követelményeit, és válasszuk ki a megfelelőt. A megfelelő alkalmazási technikák és karbantartás azt is biztosítják, hogy az OLED kijelzőmodul hosszabb ideig optimálisan működjön. Ha megérti az OLED kijelzőmodul ragasztó fontosságát, megalapozott döntéseket hozhat, és javíthatja eszköze teljesítményét.