Elektromos ragasztó ragasztó
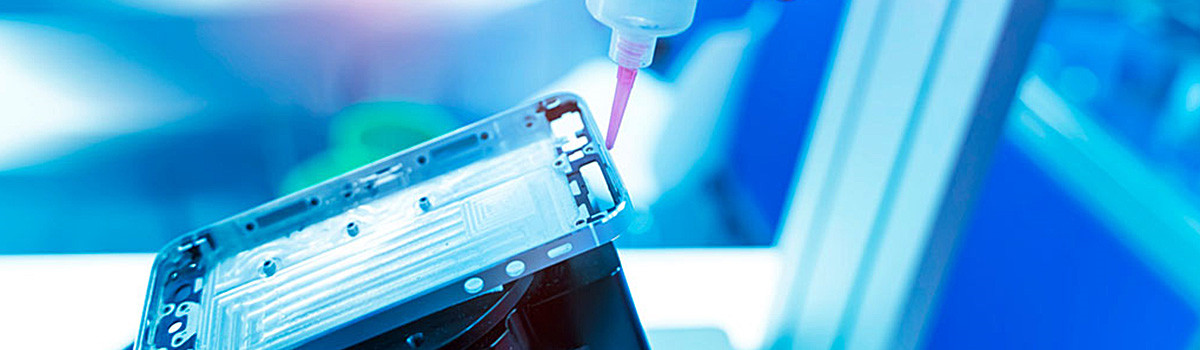
Az elektromos kötőragasztók speciális ragasztók, amelyeket elektromos alkalmazások ragasztására és tömítésére használnak. A következőket biztosítják:
- Kiváló elektromos vezetőképesség és hőstabilitás.
- Ideálissá teszi őket elektronikus eszközökhöz.
- Autóipari alkatrészek.
- Repülési alkalmazások.
Ezek a ragasztók döntő szerepet játszanak az elektromos rendszerek biztonságának és megbízhatóságának biztosításában azáltal, hogy biztonságos kötést biztosítanak, és megakadályozzák az elektromos ív vagy szikrák kialakulását.
Mik azok az elektromos ragasztók?
Az elektromos kötőragasztók speciális ragasztók, amelyeket elektromos és elektronikus alkalmazásokban használnak, hogy biztonságos kötést hozzanak létre a különböző vezetőképes alkatrészek között. Ezeket a ragasztókat úgy tervezték, hogy megbízható elektromos csatlakozásokat biztosítsanak, biztosítsák a földelést és védjenek az elektromágneses interferencia (EMI) ellen. Kulcsfontosságúak a különböző iparágakban, beleértve az autógyártást, a repülőgépgyártást, a távközlést és a fogyasztói elektronikát.
Az elektromos kötőragasztók elsődleges funkciója, hogy alacsony ellenállású utat hozzon létre két vagy több vezetőképes felület, például fém alkatrészek vagy áramköri lapok között. Ez az út lehetővé teszi az elektromos áram hatékony átvitelét, segít megelőzni a statikus kisülést, és csökkenti az elektromos meghibásodások kockázatát. Azáltal, hogy szilárd kötést hoznak létre, ezek a ragasztók mechanikai alátámasztást is nyújtanak, és növelik az összeszerelt alkatrészek általános tartósságát.
Számos létfontosságú tulajdonság teszi alkalmassá az elektromos kötőragasztókat a tervezett alkalmazási területeikre. Először is kiváló elektromos vezetőképességgel rendelkeznek, ami azt jelenti, hogy hatékonyan vezetik az elektromosságot, minimálisra csökkentve az ellenállást és megbízható kapcsolatot biztosítanak. Vezetőképes töltőanyagokat, például ezüstöt, rezet vagy grafitot gyakran beépítenek a ragasztókészítménybe a vezetőképesség fokozása érdekében.
Másodszor, az elektromos kötő ragasztók jellemzően jó hővezető tulajdonságokkal rendelkeznek. Ez lehetővé teszi számukra az elektromos alkatrészek által termelt hő elvezetését, megakadályozva a túlmelegedést és az érzékeny elektronikus eszközök esetleges károsodását.
Ezen túlmenően ezek a ragasztók úgy vannak kialakítva, hogy nagy szilárdsággal és kötési integritással rendelkezzenek. Ellenállnak a mechanikai igénybevételeknek, a vibrációnak és a hőciklusnak anélkül, hogy veszélyeztetnék az elektromos csatlakozást. Ez döntő jelentőségű, különösen azokban az alkalmazásokban, ahol a ragasztott komponensek zord környezeti feltételeknek lehetnek kitéve.
Az elektromos kötőragasztók különféle formákban kaphatók, beleértve a pasztákat, filmeket, szalagokat vagy folyadékokat. A ragasztó kiválasztása olyan tényezőktől függ, mint az alkalmazási követelmények, a ragasztandó anyagok típusa és az összeszerelési folyamat. Például vezetőképes öntapadó fóliákat vagy szalagokat általában hajlékony áramkörök összeállítására használnak. Ezzel szemben vezetőképes paszta ragasztókat gyakran használnak nyomtatott áramköri lapokon lévő felületre szerelhető alkatrészek ragasztására.
Amellett, hogy elektromos és mechanikai kötést biztosítanak, egyes ragasztók EMI-árnyékoló tulajdonságokkal is rendelkeznek. Vezetőképes töltőanyagokat tartalmaznak, amelyek vezető gátat hoznak létre, megakadályozva, hogy az elektromágneses sugárzás megzavarja a közeli elektronikus alkatrészek működését.
A megfelelő felület-előkészítés kulcsfontosságú elektromos kötőragasztók használatakor az optimális kötési szilárdság és teljesítmény biztosítása érdekében. A felületeket alaposan meg kell tisztítani, szennyeződésektől mentesen, és bizonyos esetekben felületaktiválást vagy alapozást igényelhet a tapadás fokozása érdekében.
Az elektromos kötőanyag-ragasztók elengedhetetlenek a modern elektromos és elektronikai gyártásban. Megbízható és hatékony elektromos csatlakozásokat tesznek lehetővé, miközben mechanikus támogatást és EMI elleni védelmet nyújtanak. Az anyagok és ragasztótechnológiák folyamatos fejlődésével ezek a ragasztók létfontosságú szerepet játszanak az innovatív és megbízható elektronikus eszközök és rendszerek fejlesztésében.
Az elektromos ragasztók típusai
Az elektromos kötőragasztók biztonságos és megbízható elektromos kapcsolatokat hoznak létre a vezetőképes alkatrészek között. Ezeket a ragasztókat úgy tervezték, hogy kiváló elektromos vezetőképességet biztosítsanak, miközben erős mechanikai kötési tulajdonságokat kínálnak. Íme néhány általános elektromos ragasztótípus:
- Vezetőképes epoxi ragasztók: A vezetőképes epoxi ragasztókat széles körben használják elektromos ragasztási alkalmazásokban. Két részből álló rendszerből állnak, jellemzően egy gyantából és egy keményítőből, amelyeket használat előtt össze kell keverni. Ezek a ragasztók vezetőképes töltőanyagokat tartalmaznak, mint például ezüst, réz vagy grafit, amelyek lehetővé teszik az elektromos áram áramlását. A vezetőképes epoxi ragasztók kiváló tapadást biztosítanak a különböző aljzatokhoz, elektromos vezetőképességet és mechanikai szilárdságot biztosítanak.
- Elektromosan vezető ragasztószalagok: Az elektromosan vezető ragasztószalagok vezetőképes részecskéket tartalmazó ragasztóval bevont hátlapból állnak. A hátlap anyaga mechanikai tartást és szigetelést biztosít, míg a vezetőképes ragasztó biztosítja az elektromos folytonosságot. Ezek a szalagok könnyen felhordhatók, sokoldalúak, és egyenetlen felületekhez is alkalmazkodnak. Általában rugalmas áramkörök, földelési alkalmazások és EMI/RFI-árnyékolás kötésére használják.
- Vezetőképes ezüst ragasztók: A vezetőképes ezüst ragasztók polimer mátrixban szuszpendált ezüstrészecskéket tartalmaznak. Az ezüst kiváló elektromos vezető, nagy elektromos vezetőképességgel rendelkezik. Ezek a ragasztók erős tapadást biztosítanak különféle felületeken, beleértve a fémeket, kerámiákat és műanyagokat. Általában elektronikus összeszerelésben, elektromos alkatrészek ragasztásában és elektromos áramkörök javításában használják.
- Elektromosan vezető szilikon ragasztók: Az elektromosan vezető szilikon ragasztók szilikon polimerekkel és vezetőképes töltőanyagokkal, például ezüsttel, nikkellel vagy szénnel vannak összeállítva. Jó elektromos vezetőképességet, rugalmasságot és hőstabilitást kínálnak. Ezeket a ragasztókat gyakran használják olyan alkalmazásokban, amelyek rugalmasságot és környezeti ellenállást igényelnek, például rugalmas áramkörök, tömítő csatlakozók és elektronikus alkatrészek ragasztására.
- Elektromosan vezető poliuretán ragasztók: Az elektromosan vezető poliuretán ragasztókat úgy tervezték, hogy elektromos vezetőképességet és erős kötési tulajdonságokat biztosítsanak. Poliuretán polimerekkel és vezetőképes töltőanyagokkal, például szén- vagy fémrészecskékkel készülnek. Ezek a ragasztók jó tapadást biztosítanak különféle aljzatokhoz, ellenállnak a környezeti tényezőknek és tartósak. Általában elektronikai gyártásban, földelési alkalmazásokban és különböző anyagok ragasztásában használják.
- Vezetőképes pillanatragasztók: A vezetőképes pillanatragasztók, más néven cianoakrilát ragasztók, egykomponensű ragasztók, amelyek nedvességgel érintkezve gyorsan kikeményednek. Ezek a ragasztók, például fém- vagy grafitrészecskék, vezetőképes töltőanyagokat tartalmaznak, amelyek elektromos vezetőképességet biztosítanak. Gyors kötést és nagy szilárdságot kínálnak, így alkalmasak olyan alkalmazásokhoz, amelyek gyors összeszerelést és jó elektromos teljesítményt igényelnek.
Fontos megjegyezni, hogy az elektromos kötőanyag megválasztása az alkalmazás speciális követelményeitől függ, mint például a hordozóanyagtól, a környezeti feltételektől és a kívánt elektromos vezetőképességtől. A ragasztógyártókkal vagy a terület szakértőivel folytatott konzultáció segíthet kiválasztani az adott alkalmazáshoz legmegfelelőbb ragasztót.
Vezetőképes és nem vezető ragasztók
A vezetőképes és a nem vezető ragasztók két különböző kategóriát alkotnak, amelyeket különféle alkalmazásokban használnak, és az elsődleges különbség köztük az elektromos vezetőképességi tulajdonságaikban rejlik. Íme a vezetőképes és nem vezető ragasztók áttekintése:
Vezetőképes ragasztók: A vezetőképes ragasztók úgy vannak kialakítva, hogy lehetővé teszik az elektromos áram áramlását. Vezetőképes töltőanyagokat, például fém- vagy szénrészecskéket tartalmaznak, amelyek elektromos vezetőképességet biztosítanak. A vezetőképes ragasztókat általában olyan alkalmazásokban használják, ahol elektromos folytonosságra van szükség. A vezetőképes ragasztók néhány fő jellemzője:
- Elektromos vezetőképesség: A vezetőképes ragasztók kiváló elektromos vezetőképességet biztosítanak a vezetőképes töltőanyagok jelenlétének köszönhetően. Megbízható elektromos kapcsolatokat hozhatnak létre a vezetőképes alkatrészek között, például az áramköri kártyákon lévő elektromos nyomokat vagy a földelést.
- Ragasztás és mechanikai szilárdság: A vezetőképes ragasztók elektromos vezetőképességet és mechanikai szilárd kötési tulajdonságokat biztosítanak. Erős kötéseket hozhatnak létre a hordozók között, biztosítva a szerkezeti integritást és a hosszú távú megbízhatóságot.
- Alkalmazási rugalmasság: A vezetőképes ragasztók különféle formákban kaphatók, beleértve az epoxit, a szilikont és a poliuretánt, amelyek rugalmasságot biztosítanak az alkalmazási módok és az aljzatok tekintetében. Folyadékként, filmként vagy pasztaként adagolhatók, ami sokoldalúságot tesz lehetővé a különböző összeszerelési folyamatokban.
- EMI/RFI árnyékolás: A vezetőképes ragasztókat gyakran használják az elektromágneses interferencia (EMI) és a rádiófrekvenciás interferencia (RFI) árnyékolására. Vezető utakat hozhatnak létre, hatékonyan minimalizálva az elektromágneses sugárzás hatását az érzékeny elektronikai alkatrészekre.
Nem vezető ragasztók: A nem vezető vagy szigetelő ragasztók nem vezetnek áramot, és úgy vannak kialakítva, hogy elektromos szigetelést biztosítsanak az alkatrészek vagy a hordozók között. A nem vezető ragasztókat széles körben használják olyan alkalmazásokban, ahol elektromos szigetelésre van szükség. Íme a nem vezető ragasztók néhány kritikus jellemzője:
- Elektromos szigetelés: A nem vezető ragasztók nagy ellenállással rendelkeznek, megakadályozva az elektromos áram áramlását. Elektromos akadályok létrehozására használják őket, amelyek szigetelik az alkatrészeket egymástól vagy a környező környezettől.
- Dielektromos szilárdság: A nem vezető ragasztók nagy dielektromos szilárdságot mutatnak, amelyek meghibásodás nélkül ellenállnak az elektromos igénybevételnek. Ez a tulajdonság döntő fontosságú a nagyfeszültségű alkalmazásokban, mint például a teljesítményelektronika vagy az elektromos szigetelés.
- Hőstabilitás: A nem vezető ragasztók gyakran kiváló hőstabilitással rendelkeznek, lehetővé téve, hogy megőrizzék elektromos szigetelési tulajdonságaikat magas hőmérsékleten. Ez a jellemző elengedhetetlen azokban az alkalmazásokban, ahol a hőelvezetés aggodalomra ad okot.
- Környezeti ellenállás: A nem vezető ragasztókat úgy tervezték, hogy ellenálljanak a különféle környezeti tényezőknek, beleértve a nedvességet, a vegyszereket és a hőmérséklet-ingadozásokat. Hosszú távú megbízhatóságot kínálnak kihívást jelentő üzemi körülmények között is.
A nem vezető ragasztók különféle formákban találhatók, például epoxi-, akril- vagy szilikon alapú készítményekben, rugalmasságot biztosítva az alkalmazásban és az alapfelülettel való kompatibilitásban.
Az elektromos ragasztóragasztók használatának előnyei
Az elektromos kötőragasztók számos előnnyel járnak a biztonságos és megbízható elektromos csatlakozások létrehozása során. Íme néhány fő előnye az elektromos kötőragasztók használatának:
- Elektromos vezetőképesség: Az elektromos kötőragasztók úgy vannak kialakítva, hogy kiváló elektromos vezetőképességet biztosítsanak. Lehetővé teszik az elektromos áram áramlását, biztosítva a megbízható elektromos kapcsolatokat a vezetőképes alkatrészek között. Ez döntő fontosságú az alapvető elektromos folytonosságot igénylő alkalmazásokban, mint például az elektronikus összeszerelés, az áramköri lapok csatlakoztatása vagy a földelés.
- Ragasztási szilárdság: Az elektromos vezetőképesség mellett a ragasztók erős mechanikai kötési tulajdonságokat is kínálnak. Robusztus és tartós kötéseket hozhatnak létre az aljzatok között, javítva az összeállítás általános szerkezeti integritását. Ez különösen fontos olyan alkalmazásokban, ahol vibráció, hőciklus vagy mechanikai igénybevétel léphet fel.
- Kompatibilitás különféle aljzatokkal: Az elektromos kötőragasztókat különféle hordozókhoz való ragasztásra tervezték, beleértve a fémeket, kerámiákat, műanyagokat és kompozitokat. Ez a sokoldalúság lehetővé teszi különböző anyagok összekapcsolását és leegyszerűsíti az összeszerelési folyamatot. Nincs szükség további mechanikus rögzítőkre, például csavarokra vagy forrasztásra, csökkentve az összeszerelési időt és a költségeket.
- Feszültségeloszlás: A ragasztó ragasztók egyenletesebben osztják el a feszültséget a ragasztott területen, mint más rögzítési módok. Eloszlathatják a feszültséget és csökkenthetik a koncentrációs pontokat, minimalizálva a helyi meghibásodások vagy repedések kockázatát az egységben.
- Javított hőelvezetés: Egyes elektromos kötőragasztók, például a hővezető ragasztók, fokozhatják a hőelvezetést az elektronikus eszközökben. Hővezető utat biztosítanak a hőtermelő alkatrészek és a hűtőbordák között, lehetővé téve a hatékony hőátadást és a jobb hőkezelést.
- Környezeti ellenállás: Az elektromos kötőragasztókat úgy alakították ki, hogy ellenálljanak a különböző környezeti tényezőknek, beleértve a hőmérséklet-ingadozásokat, a nedvességet, a vegyszereket és az UV-sugárzást. Jól ellenállnak az öregedésnek és a leépülésnek, így biztosítják a hosszú távú megbízhatóságot különböző üzemi körülmények között.
- Tervezési rugalmasság: A ragasztók rugalmasságot biztosítanak a tervezésben, lehetővé téve összetett formák vagy szabálytalan felületek ragasztását. Alkalmazkodhatnak a kontúrokhoz, kitölthetik a hézagokat, és erős kötéseket hozhatnak létre a nehezen elérhető helyeken, ami sokoldalúbb és hatékonyabb tervezést tesz lehetővé.
- Költséghatékony megoldás: Sok esetben az elektromos kötőragasztók használata költséghatékony lehet más hagyományos ragasztási módszerekkel összehasonlítva. Kiküszöböli a további hardverek vagy összetett összeszerelési folyamatok szükségességét, csökkentve az anyag- és munkaerőköltségeket.
- EMI/RFI árnyékolás: A vezetőképes kötőragasztók hatékony elektromágneses interferencia (EMI) és rádiófrekvenciás interferencia (RFI) árnyékolást biztosítanak. Vezető utakat hoznak létre, minimalizálva az elektromágneses sugárzás hatását az érzékeny elektronikai alkatrészekre.
Összességében az elektromos kötőragasztók számos előnnyel rendelkeznek, beleértve az elektromos vezetőképességet, az izomkötési szilárdságot, a különféle hordozókkal való kompatibilitást, a feszültségeloszlást, a hőelvezetést, a környezeti ellenállást, a tervezési rugalmasságot, a költséghatékonyságot és az EMI/RFI árnyékolást. Ezek az előnyök fontos választássá teszik őket számos elektromos és elektronikus alkalmazáshoz.
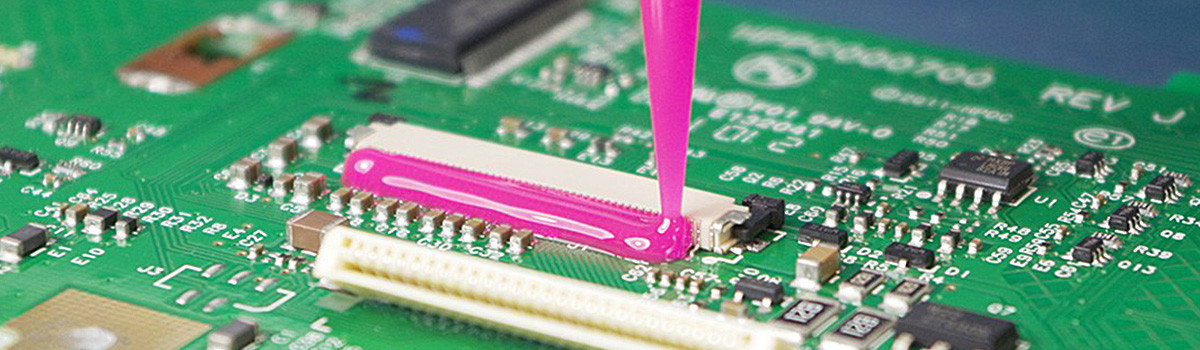
Elektromos kötőragasztók alkalmazásai
Az elektromos kötőragasztók számos alkalmazást találnak a különböző iparágakban, ahol biztonságos és megbízható elektromos csatlakozásokra van szükség. Ezek a ragasztók olyan egyedi tulajdonságokkal rendelkeznek, amelyek többféle alkalmazásra is alkalmassá teszik őket. Íme néhány tipikus alkalmazási terület az elektromos ragasztók számára:
- Elektronikai gyártás: Az elektromos kötőragasztók létfontosságú szerepet játszanak az elektronikus alkatrészek összeszerelésében és ragasztásában. Elektromos kapcsolatokat hoznak létre az áramköri kártyák között, összekötik a huzalvezetékeket, és rögzítik a felületre szerelt darabokat és az érzékeny elektronikus eszközöket. Ezek a ragasztók elektromos vezetőképességet és mechanikai kötési szilárdságot biztosítanak, biztosítva az elektronikus eszközök teljesítményét és hosszú távú tartósságát.
- Gépjárműipar: Az autóipar különféle alkalmazásokhoz támaszkodik elektromos kötőragasztókra. Elektromos alkatrészek, például érzékelők, csatlakozók és kábelkötegek összekötésére és földelésére használják. Ezek a ragasztók biztonságos elektromos csatlakozást biztosítanak, ellenállnak a vibrációnak és a hőciklusnak, valamint környezeti ellenállást biztosítanak az autóipari alkalmazásokban.
- Repülés és repülés: A repülési és légiközlekedési ágazatban az elektromos kötőragasztók elengedhetetlenek a repülőgépek, műholdak és űrhajók elektromos alkatrészeinek ragasztásához. Repüléselektronikai rendszerek, antennák, érzékelők és földelési alkalmazások összekapcsolására használják. Ezeknek a ragasztóknak nagy megbízhatóságot, tartósságot, valamint szélsőséges hőmérséklet-ingadozásokkal és rezgésekkel szembeni ellenállást kell kínálniuk.
- Orvosi eszközök: Az elektromos kötőragasztók orvosi eszközöket és berendezéseket gyártanak. Elektródák, csatlakozók, érzékelők és vezetékek ragasztására használják különféle orvosi alkalmazásokban, beleértve a monitorozó eszközöket, diagnosztikai berendezéseket és beültethető eszközöket. Ezeknek a ragasztóknak meg kell felelniük a biokompatibilitás, a sterilizálási ellenállás és a hosszú távú megbízhatóság szigorú követelményeinek.
- Megújuló energia: Az elektromos kötőanyagokat a megújuló energia szektorban használják, különösen a napelemek gyártásában. Napelemeken belüli elektromos csatlakozások ragasztására és földelésére használják, például napelemek ragasztására, sínek rögzítésére és elektromos kábelek csatlakoztatására. Ezeknek a ragasztóknak megbízható elektromos vezetőképességet, időjárásállóságot és hosszú távú tartósságot kell biztosítaniuk kültéri környezetben.
- Távközlés: A távközlési iparban elektromos kötőragasztókat használnak kommunikációs eszközök, antennák, csatlakozók és száloptikai alkatrészek elektromos csatlakozásainak ragasztására. Ezek a ragasztók biztosítják a biztonságos elektromos csatlakozásokat, az EMI/RFI árnyékolást és a környezeti tényezőkkel szembeni ellenállást, mint például a nedvesség és a hőmérséklet ingadozása.
- Szórakoztató elektronika: Az elektromos kötőragasztók fogyasztói elektronikai cikkeket szerelnek össze, beleértve az okostelefonokat, táblagépeket, laptopokat és hordható eszközöket. Elektromos alkatrészek ragasztására, kijelzők rögzítésére, rugalmas áramkörök csatlakoztatására és földelésre használják. Ezek a ragasztók megbízható elektromos vezetőképességet, mechanikai kötési szilárdságot és rugalmasságot biztosítanak a miniatűr kialakításokhoz.
- Ipari berendezések: Az elektromos kötőragasztókat különféle ipari berendezésekben, például vezérlőpanelekben, ipari érzékelőkben, motorokban és transzformátorokban alkalmazzák. Elektromos csatlakozások, földelő alkatrészek és EMI/RFI-árnyékolás összekötésére használják. Ezeknek a ragasztóknak ellenállniuk kell a zord ipari környezetnek, beleértve a szélsőséges hőmérsékleteket, a vibrációt és a vegyi hatásokat.
Ez csak néhány példa az elektromos kötőragasztók széles köréből. Ezek a ragasztók sokoldalúsága, megbízhatósága és teljesítménye nélkülözhetetlenné teszik őket azokban az iparágakban, ahol a biztonságos elektromos csatlakozások kritikusak az optimális működés és biztonság szempontjából.
Ragasztás és tömítés elektronikus eszközökben
A ragasztás és a tömítés két alapvető folyamat az elektronikai eszközök összeszerelése és gyártása során, és döntő szerepet játszanak az elektronikus alkatrészek megbízhatóságának, funkcionalitásának és védelmének biztosításában. Íme az elektronikus eszközök ragasztásának és tömítésének áttekintése:
A ragasztás két vagy több komponens ragasztóanyag segítségével történő összekapcsolását jelenti. Az elektronikus eszközökben a kötést különféle célokra használják, beleértve az elektromos csatlakozásokat, a mechanikai támogatást és a hőkezelést. Íme néhány kritikus szempont az elektronikus eszközök ragasztásával kapcsolatban:
- Elektromos csatlakozások: A ragasztó ragasztók elektromos kapcsolatokat hoznak létre az alkatrészek között, például a vezetékeket az áramköri lapokon lévő párnákhoz kötik, vagy vezető nyomokat rögzítenek. Ezek a ragasztók elektromos vezetőképességet biztosítanak, biztosítva a megbízható elektromos folytonosságot a készülékben.
- Alkatrészek rögzítése: A ragasztással az alkatrészeket áramköri lapokhoz vagy hordozókhoz rögzítik. A ragasztóanyagok közé tartoznak az epoxi- vagy szilikon alapú ragasztók, a ragasztóelemek, például a felületre szerelt eszközök (SMD), csatlakozók, érzékelők vagy kijelzők. Ez biztosítja az alkatrészek biztonságos és mechanikailag erős tapadását.
- Szerkezeti támogatás: A ragasztó ragasztók szerkezeti támogatást nyújtanak az elektronikus alkatrészeknek. Erős kötéseket hoznak létre, amelyek segítenek ellenállni a mechanikai igénybevételeknek, a rezgéseknek és a hőciklusnak. Ez különösen fontos olyan elemeknél, amelyek mechanikai igénybevételnek vagy külső erőknek lehetnek kitéve.
- Hőleadás: A kritikus hőleadású készülékekben hővezető tulajdonságokkal rendelkező kötőragasztókat használnak. Ezek a ragasztók segítik a hőt a hőt termelő alkatrészekről, például teljesítménytranzisztorokról vagy LED-ekről a hűtőbordákhoz vagy más hőkezelési megoldásokhoz továbbítani.
tömítő: A tömítés során olyan védőanyagot kell alkalmazni, amely megakadályozza a nedvesség, por vagy egyéb szennyeződések bejutását az elektronikus eszközökbe. A tömítés elengedhetetlen az elektronikus alkatrészek és rendszerek megbízhatóságának és hosszú élettartamának növeléséhez. Íme néhány kritikus szempont az elektronikus eszközök lezárásával kapcsolatban:
- Környezetvédelem: A tömítő ragasztók, mint például a szilikon alapú anyagok, olyan gátat képeznek, amely megvédi az elektronikus alkatrészeket a nedvességtől, nedvességtől és környezeti szennyeződésektől. Ez különösen fontos a zord környezetnek kitett eszközök, például kültéri elektronikai vagy autóipari alkalmazások esetében.
- Vízszigetelés: A tömítés kritikus fontosságú az elektronikus eszközök víz- és porállóságának eléréséhez, különösen kültéri vagy zord környezetben. Tömítőanyagokat alkalmaznak a burkolatokra, csatlakozókra vagy nyílásokra, hogy megakadályozzák a víz vagy a por behatolását, biztosítva az eszköz teljesítményét és hosszú élettartamát.
- Vegyi ellenállás: A tömítőragasztók ellenállnak a vegyi expozíciónak, megvédik az elektronikus alkatrészeket a korrozív anyagoktól vagy a vegyi gőzöktől. Ez olyan alkalmazásokban fontos, ahol az elektronikus eszközök vegyszerekkel vagy agresszív környezettel érintkezhetnek.
- Szigetelés és dielektromos tulajdonságok: A tömítőanyagok gyakran kiváló szigetelő tulajdonságokkal rendelkeznek, elektromos szigetelést biztosítva az alkatrészek vagy nyomok között. Ez segít megelőzni a rövidzárlatokat és az elektromos meghibásodásokat. A nagy dielektromos szilárdságú tömítőragasztókat elektromos szigetelést igénylő alkalmazásokban használják.
- Rezgés- és ütésállóság: A tömítőragasztók javítják az elektronikus eszközök mechanikai stabilitását azáltal, hogy ellenállnak a rezgéseknek és ütéseknek. Megakadályozzák a belső alkatrészek mechanikai igénybevétel miatti kilazulását vagy elmozdulását, biztosítva a készülék hosszú távú megbízhatóságát.
A ragasztás és tömítés kulcsfontosságú folyamatok az elektronikai eszközök összeszerelésében és gyártásában, és biztosítják a megbízható elektromos csatlakozásokat, a mechanikai stabilitást, a környezeti tényezők elleni védelmet és az eszközök hosszú élettartamát. A ragasztó- és tömítőanyagok kiválasztása a készülék alkalmazási területétől, az üzemi feltételektől és a kívánt teljesítményjellemzőktől függ.
Járműipari alkalmazások
Az elektromos kötőanyag-ragasztóknak számos felhasználási területük van az autóiparban, ahol döntő szerepet játszanak a megbízható elektromos csatlakozások, a szerkezeti integritás és az általános teljesítmény biztosításában. Íme az elektromos kötőragasztók néhány kritikus autóipari alkalmazása:
- Kábelköteg-szerelvény: A kábelköteg az autók elektromos rendszereinek alapvető alkatrészei, amelyek elektromos jeleket és áramot továbbítanak a járműben. Az elektromos kötőragasztók rögzítik és védik a kábelkötegeket, mechanikai támasztást, feszültségmentességet, valamint rezgés- és hőmérséklet-ingadozásokkal szembeni ellenállást biztosítanak. Ezek a ragasztók biztosítják a kábelköteg hosszú élettartamát és megbízhatóságát kihívást jelentő autóipari környezetben.
- Érzékelők rögzítése: Különféle érzékelőket alkalmaznak az autóipari rendszerekben, beleértve a motorérzékelőket, a helyzetérzékelőket és a közelségérzékelőket. Az elektromos kötőragasztók rögzítik ezeket az érzékelőket a rögzítési helyükhöz, biztonságos rögzítést és pontos és megbízható érzékelőleolvasást biztosítva. Ezek a ragasztók mechanikai stabilitást, rezgés elleni védelmet, valamint hőmérséklet- és nedvességállóságot biztosítanak.
- Csatlakozók kötése: A csatlakozók kritikus alkatrészek az autóipari elektromos rendszerekben, megkönnyítve az elektromos kapcsolatokat az alrendszerek és alkatrészek között. Az elektromos kötőragasztók a csatlakozókat áramköri lapokhoz vagy más rögzítési felületekhez kötik, biztosítva a biztonságos elektromos csatlakozásokat és a mechanikai stabilitást. Ezek a ragasztók ellenállnak az ütéseknek, a vibrációnak és a hőmérséklet-ciklusoknak, amelyek általánosak az autóipari alkalmazásokban.
- Elektronikus vezérlőegységek (ECU): Az ECU-k a modern autóipari rendszerek központi elemei, amelyek különféle funkciók vezérléséért felelősek, mint például a motorvezérlés, a fékrendszer és a biztonsági rendszerek. Az elektromos kötőragasztók ECU-kat szerelnek össze, biztosítva az elektromos csatlakozásokat, a mechanikai támogatást és a környezeti tényezők elleni védelmet. Ezek a ragasztók kiváló elektromos vezetőképességet, hőkezelést, valamint nedvességgel, vegyszerekkel és hőmérséklet-ingadozásokkal szembeni ellenállást biztosítanak.
- Világítási rendszerek: Az autóipari világítási rendszerek, beleértve a fényszórókat, a hátsó lámpákat és a belső világítást, biztonságos kötést igényelnek az elektromos csatlakozásokhoz és a mechanikai stabilitáshoz. Az elektromos kötőragasztók rögzítik a világítási alkatrészeket, például a LED-eket a szerelési helyükre, biztosítva a megbízható elektromos csatlakozásokat, valamint a rezgésekkel és hőciklusokkal szembeni ellenállást. Ezek a ragasztók nagy átlátszóságot biztosítanak, optimális fényáteresztést és hosszú távú tartósságot biztosítanak.
- Akkumulátoregység összeállítás: Az elektromos és hibrid járművekben az akkumulátorcsomagok kritikus alkatrészek, amelyek biztonságos rögzítést igényelnek az elektromos csatlakozásokhoz és a szerkezeti integritáshoz. Elektromos kötőragasztókat használnak az akkumulátor-csomag összeszerelésében, amelyek adhéziós és tömítő tulajdonságokat biztosítanak a megbízható elektromos vezetőképesség, a rezgésállóság, valamint a nedvesség és a hőciklus elleni védelem érdekében. Ezek a ragasztók hozzájárulnak az elektromos járművek akkumulátorainak biztonságához és teljesítményéhez.
- EMI/RFI árnyékolás: A vezető tulajdonságokkal rendelkező elektromos kötőragasztókat elektromágneses interferencia (EMI) és rádiófrekvenciás interferencia (RFI) árnyékolására használják autóipari alkalmazásokban. Vezető utakat hoznak létre, csökkentve az elektromágneses sugárzás hatását az érzékeny elektronikai alkatrészekre. Az EMI/RFI árnyékoló ragasztókat olyan területeken használják, mint például az elektronikus modulok, antennák és vezetékek, hogy biztosítsák az autóelektronika megfelelő működését.
- Szerkezeti ragasztás: Egyes autóipari alkalmazásokban elektromos kötőragasztókat használnak szerkezeti ragasztási célokra. Erős tapadást biztosítanak a különböző aljzatok között, javítva az autóipari alkatrészek általános szerkezeti integritását. A szerkezeti kötőragasztókat például járműkarosszéria-panelek, erősítő tartókonzolok vagy kompozit anyagok ragasztására használják, hozzájárulva a súlycsökkentéshez és a jármű teljesítményének javításához.
Ez csak néhány példa az elektromos ragasztóragasztók autóipari alkalmazásainak széles skálájából. Ezeknek a ragasztóknak az olyan tulajdonságai, mint az elektromos vezetőképesség, a mechanikai szilárdság, a környezeti ellenállás és a hőkezelés, elengedhetetlenek az autóelektromos rendszerek és alkatrészek összeszereléséhez és teljesítményéhez.
Repülési alkalmazások
Az elektromos kötőragasztók kritikus szerepet játszanak a repülési alkalmazásokban, ahol különféle célokra használják őket, beleértve az elektromos kötést, a földelést, a szerkezeti kötést és a környezeti tényezők elleni védelmet. Íme az elektromos kötőragasztók néhány kritikus űrrepülési alkalmazása:
- Repüléselektronikai rendszerek: A repüléstechnikai rendszerek, beleértve a repülésirányító rendszereket, a kommunikációs rendszereket és a navigációs rendszereket, biztonságos elektromos csatlakozásokon és földelésen alapulnak. Az elektromos kötőragasztók összekötik és földelik a repüléselektronikai házakban lévő alkatrészeket, biztosítva a megbízható elektromos folytonosságot, a mechanikai stabilitást, valamint védelmet a rezgések, hőmérséklet-ingadozások és elektromágneses interferencia ellen.
- Repülőgép vezetékei és kábelkötegei: A repülőgép vezetékei és kábelkötegei elektromos kábelek és csatlakozók összetett hálózatai, amelyek áramot és jeleket továbbítanak a repülőgépen. Az elektromos kötőragasztók védik a vezetékeket és a kábelkötegeket, biztosítva a feszültségmentesítést, a mechanikai támasztást, valamint rezgés- és környezeti tényezőkkel szembeni ellenállást. Ezek a ragasztók biztosítják az elektromos csatlakozások hosszú élettartamát és megbízhatóságát igényes légi közlekedési környezetben.
- Antennaszerelés: Az antennák kulcsfontosságúak az űrhajózási alkalmazásokban, lehetővé téve a kommunikációt, a navigációt és az adatátvitelt. Az elektromos kötőragasztók az antennákat a rögzítési felületükhöz kötik, biztonságos rögzítést, elektromos folytonosságot és mechanikai igénybevétellel, rezgésekkel és hőmérséklet-ingadozásokkal szembeni ellenállást biztosítva. Ezek a ragasztók hozzájárulnak a repülőgép-antennarendszerek teljesítményéhez és tartósságához.
- Kompozit ragasztás: Az űrrepülőgép-szerkezetek egyre gyakrabban tartalmaznak kompozit anyagokat, amelyek nagy szilárdság-tömeg arányt kínálnak. Az elektromos kötőragasztókat kompozit alkatrészekhez, például törzspanelekhez, szárnyrendszerekhez és vezérlőfelületekhez használják. Ezek a ragasztók erős és tartós kötést biztosítanak, hozzájárulva a repülőgép szerkezeti integritásához és csökkentve a súlyt.
- Műholdak és űrhajók elektronikája: A műholdak és űrhajók megbízható elektromos csatlakozásokat és védelmet igényelnek a zord űrviszonyok ellen. Az elektromos kötőragasztók műholdak és űrhajók elektronikáját, például elektronikus vezérlőegységeket, érzékelőket és kommunikációs rendszereket szerelnek össze. Ezek a ragasztók elektromos vezetőképességet, mechanikai stabilitást, hőciklusokkal és vákuumviszonyokkal szembeni ellenállást, valamint sugárzás elleni védelmet nyújtanak.
- Villámcsapás elleni védelem: A villámcsapás jelentős kockázatot jelent a repülőgépekre. A villámcsapás elleni védelmi rendszerekben elektromos kötőragasztókat és vezető anyagokat használnak. Ezek a ragasztók segítenek vezető utakat létrehozni, amelyek biztonságosan elvezetik a villámáramot a kritikus alkatrészektől, csökkentve a sérülések kockázatát és biztosítva a repülőgép és az utasok biztonságát.
- EMI/RFI-árnyékolás: A repülési alkalmazásokban az elektromágneses interferencia (EMI) és a rádiófrekvenciás interferencia (RFI) árnyékolása kulcsfontosságú az érzékeny elektronikus rendszerekkel való interferencia megelőzésében. Az EMI/RFI árnyékoláshoz vezető tulajdonságú elektromos kötőragasztókat használnak. Vezető utat biztosítanak, csökkentve az elektromágneses sugárzás hatását az elektronikus alkatrészekre, és biztosítva a megfelelő működést.
- Hőkezelés: Az űrrepülési rendszerek gyakran szélsőséges hőmérséklet-ingadozásokkal szembesülnek. A hővezető tulajdonságokkal rendelkező elektromos kötőragasztókat hatékony hőelvezetésre és hőkezelésre használják. Segítik a hő elvezetését a hőt termelő alkatrészektől, például a teljesítményelektronikától vagy a termikus interfészektől, hogy javítsák a repülőgép-rendszerek általános teljesítményét és megbízhatóságát.
Ez csak néhány példa az elektromos kötőragasztók repülőgép- és űrkutatási alkalmazásainak széles skálájából. Ezeknek a ragasztóknak az olyan tulajdonságai, mint az elektromos vezetőképesség, a mechanikai szilárdság, a környezeti ellenállás és a hőkezelés, kritikus fontosságúak a repülőgép-alkatrészek és -rendszerek megbízhatósága, funkcionalitása és biztonsága szempontjából.
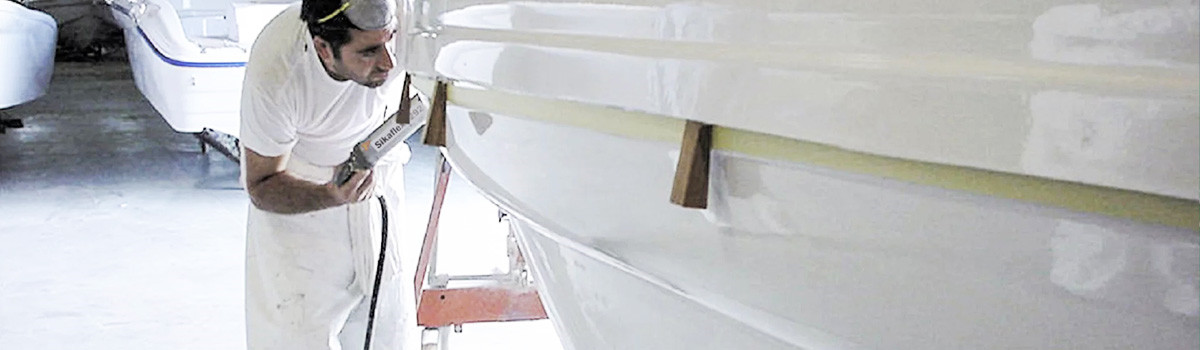
Tengerészeti alkalmazások
Az elektromos kötőragasztóknak jelentős alkalmazásai vannak a tengeri iparban, ahol különféle célokra használják őket, beleértve az elektromos kötést, a földelést, a korrózióvédelmet és a tömítést. Íme az elektromos kötőragasztók néhány kritikus tengeri alkalmazása:
- Elektromos kötés és földelés: Az elektromos kötőragasztók megbízható elektromos csatlakozásokat és földelést hoznak létre a tengeri hajókban. Összeragasztják és rögzítik az elektromos kábeleket, csatlakozókat és földelő hevedereket, biztosítva a megfelelő elektromos folytonosságot és minimalizálva az elektromos hibák vagy meghibásodások kockázatát. Ezek a ragasztók kiváló vezetőképességet, korrózióállóságot és mechanikai stabilitást biztosítanak tengeri környezetben.
- Elektronika és műszerek: A tengeri hajók összetett elektronikus rendszerekre támaszkodnak a navigációhoz, kommunikációhoz, vezérléshez és megfigyeléshez. Az elektromos kötőragasztókat elektronikus alkatrészek, például vezérlőpanelek, műszerrendszerek és kommunikációs eszközök összeszerelésére és telepítésére használják. Ezek a ragasztók biztonságos kötést, elektromos csatlakozásokat és védelmet biztosítanak a környezeti tényezőkkel, például nedvességgel, rezgéssel és hőmérséklet-ingadozásokkal szemben.
- Világítási rendszerek: Az elektromos ragasztóanyagokat tengeri világítási rendszerekben alkalmazzák, beleértve a navigációs lámpákat, a belső világításokat és a víz alatti lámpákat. Világítótesteket, LED-modulokat vagy világítási alkatrészeket kötnek a hajó szerkezetéhez, biztosítva az elektromos csatlakozásokat és a mechanikai stabilitást. Ezek a ragasztók ellenállnak a víz behatolásának, a korróziónak és a vibrációnak, hozzájárulva a tengeri világítási rendszerek élettartamához és teljesítményéhez.
- Korrózióvédelem: A tengeri hajók folyamatosan ki vannak téve korrozív tengervíznek, amely károsíthatja a fém alkatrészeket és szerkezeteket. A korróziógátló tulajdonságokkal rendelkező elektromos kötőragasztók védik a fémfelületeket a korróziótól. Ezek a ragasztók védőréteget képeznek, megakadályozva a tengervízzel való közvetlen érintkezést, és ellenállnak a korróziónak. Olyan területeken alkalmazzák őket, mint a hajótestek, fedélzeti szerelvények és víz alatti berendezések, hogy növeljék a tengeri hajók tartósságát és élettartamát.
- Tömítés és vízszigetelés: A tömítő ragasztókat tengeri alkalmazásokban használják vízszigetelő és tömítő tulajdonságok biztosítására. Lezárják a kábelbemeneteket, csatlakozókat, átmenő hajótest szerelvényeket és egyéb nyílásokat a hajó szerkezetében. Ezek a ragasztók megakadályozzák a víz behatolását, védik az érzékeny elektromos alkatrészeket és megőrzik az edény épségét. Ellenállnak a sós víznek, az UV-sugárzásnak és a hőmérséklet-ingadozásoknak, így biztosítják a hosszú távú tömítési hatékonyságot.
- Üvegszálas és kompozit alkatrészek ragasztása: Könnyű és nagy szilárdságú tulajdonságaik miatt az üvegszálas és kompozit anyagokat széles körben használják a tengeri hajók építésében. Az elektromos kötőragasztókat üvegszálas és kompozit alkatrészek, például hajótestek, fedélzetek és szerkezeti megerősítések ragasztására és rögzítésére használják. Ezek a ragasztók erős és tartós kötést biztosítanak, javítva az edény szerkezeti integritását.
- EMI/RFI árnyékolás: A tengeri hajókon gyakran vannak érzékeny elektronikus berendezések, amelyek védelmet igényelnek az elektromágneses interferencia (EMI) és a rádiófrekvenciás interferencia (RFI) ellen. A vezető tulajdonságokkal rendelkező elektromos kötőragasztókat EMI/RFI-árnyékolásra használják tengeri alkalmazásokban. Vezető utakat hoznak létre, csökkentve az elektromágneses sugárzás hatását az elektronikus alkatrészekre, és biztosítják a megfelelő működést és megbízhatóságot.
- Javítás és karbantartás: Az elektromos kötőragasztókat a hajóiparban javítási és karbantartási célokra is használják. Javíthatják az elektromos csatlakozásokat, rögzíthetik a meglazult alkatrészeket, megjavíthatják a sérült vezetékeket és megerősíthetik a meggyengült szerkezeteket. Ezek a ragasztók gyors és megbízható ragasztási megoldásokat kínálnak, lehetővé téve a hatékony javítást és minimalizálva az állásidőt.
Ez csak néhány példa az elektromos ragasztóragasztók tengeri alkalmazásainak széles skálájából. Ezeknek a ragasztóknak az olyan tulajdonságai, mint az elektromos vezetőképesség, a korrózióállóság, a tömítési hatékonyság és a mechanikai szilárdság, elengedhetetlenek a megbízható elektromos csatlakozások biztosításához, a környezeti tényezők elleni védelemhez, valamint a tengeri hajók és berendezések általános teljesítményéhez.
Orvosi alkalmazások
Az elektromos kötőragasztóknak alapvető alkalmazásai vannak az orvostudomány területén, ahol különféle célokra használják őket, beleértve az elektródák rögzítését, az orvosi eszközök összeszerelését, a betegek megfigyelését és az elektromos stimulációt. Íme az elektromos kötőragasztók néhány kritikus orvosi alkalmazása:
- Elektródák rögzítése: Az elektromos kötőragasztók elektródákat rögzítenek a bőrhöz orvosi megfigyelési és diagnosztikai célokra. Ezek a ragasztók biztonságos kötést biztosítanak, biztosítva a megbízható elektromos érintkezést az elektróda és a bőr között. Kiváló biokompatibilitást, konformitást és tapadási tulajdonságokat kínálnak az elektródák megfelelő elhelyezésének megőrzéséhez, javítják a jelminőséget és minimalizálják a beteg kényelmetlenségét.
- Orvosi eszközök összeszerelése: Az elektromos kötőragasztók kulcsfontosságúak a különböző orvosi eszközök összeszerelésében. Rögzítik és rögzítik az olyan alkatrészeket, mint az érzékelők, csatlakozók, nyomtatott áramköri lapok és kábelek az orvosi eszközökön belül. Ezek a ragasztók elektromos vezetőképességet, mechanikai stabilitást és védelmet nyújtanak a környezeti tényezőkkel szemben, hozzájárulva az eszközök általános teljesítményéhez és megbízhatóságához.
- Betegmonitorozás: Elektromos kötőragasztókat használnak a betegfelügyeleti rendszerekben, mint például az EKG (elektrokardiogram), az EEG (elektroencefalogram) és az EMG (elektromiogram) eszközök. Elektródák vagy érzékelők rögzítésére szolgálnak a páciens testére, biztosítva a megfelelő elektromos csatlakozásokat és a jelfelvételt. Ezek a ragasztók erős kötést, megbízható elektromos vezetőképességet és hosszú távú tapadást tesznek lehetővé, lehetővé téve a beteg pontos és folyamatos monitorozását.
- Elektromos stimuláció: Az elektromos kötőragasztók szerepet játszanak az elektromos stimulációs terápiákban, például a transzkután elektromos idegstimulációban (TENS) vagy a neuromuszkuláris elektromos stimulációban (NMES). Stimulációs elektródák rögzítésére szolgálnak a bőrre, elektromos áramot juttatva a megcélzott területekre. Ezek a ragasztók biztonságos kötést, megbízható elektromos érintkezést és a páciens kényelmét biztosítják a stimulációs kezelések során.
- Sebzárás: Az elektromos kötőragasztókat olyan technikákban alkalmazzák, mint az elektromos sebzárás (EWC) vagy az elektrosebészeti eljárások. Biztosítják a seb széleit, és megkönnyítik az elektromos áram áramlását a gyógyulási folyamat során. Ezek a ragasztók erős kötést, elektromos vezetőképességet és kompatibilitást biztosítanak a környező szövetekkel, elősegítve a sebek bezárását és gyógyulását.
- Orvosi érzékelők és hordható eszközök: Az elektromos kötőragasztók orvosi érzékelőket és hordható eszközöket, például bioszenzorokat, glükózmonitorokat és egészségügyi nyomkövetőket állítanak össze. Biztosítják az érzékelők bőrhöz vagy más felületekhez való biztonságos rögzítését, biztosítva a megfelelő jelgyűjtést és megbízható adatátvitelt. Ezek a ragasztók biológiai kompatibilitást, rugalmasságot és hosszú távú tapadást biztosítanak a kényelmes és pontos monitorozás megkönnyítése érdekében.
- Rehabilitáció és protetika: Az elektromos kötőragasztók szerepet játszanak a javítási és protetikai eszközökben. Elektródák, érzékelők vagy segédeszközök alkatrészeinek testhez vagy protézis interfészekhez való rögzítésére szolgálnak. Ezek a ragasztók megbízható elektromos csatlakozásokat, mechanikai stabilitást és hosszan tartó tapadást biztosítanak, hozzájárulva a rehabilitációs és protetikai rendszerek működőképességéhez és használhatóságához.
- Orvosi kutatás és fejlesztés: Az elektromos kötőragasztókat az orvosi kutatás és fejlesztés területén alkalmazzák. Prototípus készítésére, tesztelésére és egyedi elektronikus áramkörök, érzékelők vagy kísérleti beállítások összeállítására használják. Ezek a ragasztók rugalmasságot, könnyű használatot és megbízható elektromos csatlakozásokat kínálnak, lehetővé téve a kutatók számára, hogy innovatív orvosi eszközöket és rendszereket hozzanak létre.
Ez csak néhány példa az elektromos kötőragasztók orvosi alkalmazásainak széles skálájából. Ezeknek a ragasztóknak az olyan tulajdonságai, mint a biokompatibilitás, az elektromos vezetőképesség, a tapadási szilárdság és a környezeti ellenállás, kritikus fontosságúak a biztonságos és megbízható teljesítmény biztosításához orvosi környezetben.
Tényezők, amelyeket figyelembe kell venni az elektromos ragasztók kiválasztásakor
Az elektromos kötőanyag-ragasztók kiválasztásakor több tényezőt is figyelembe kell venni annak érdekében, hogy a ragasztó megfeleljen és hatékony legyen a tervezett alkalmazáshoz. Íme néhány kulcsfontosságú tényező, amelyet figyelembe kell venni:
- Elektromos vezetőképesség: A ragasztó elektromos vezetőképessége döntő fontosságú olyan alkalmazásokban, ahol elektromos csatlakozásokra vagy földelésre van szükség. Az egyedi követelményektől függően, mint például az alacsony ellenállás vagy a fajlagos vezetőképesség szintje, a ragasztónak megfelelő vezetőképességi tulajdonságokkal kell rendelkeznie a megbízható elektromos teljesítmény biztosítása érdekében.
- Az aljzat kompatibilitása: Vegye figyelembe a ragasztás során használt hordozótípusokat. A ragasztónak kompatibilisnek kell lennie olyan ragasztott anyagokkal, mint a fémek, műanyagok, kompozitok vagy üveg. A kompatibilitás magában foglalja mind a kémiai összeférhetőséget, amellyel elkerülhető az aljzat degradációja vagy korróziója, mind a mechanikai kompatibilitás az alapfelülethez való erős tapadás biztosítása érdekében.
- Környezeti ellenállás: Értékelje azokat a környezeti feltételeket, amelyeknek a ragasztó ki lesz téve. Vegye figyelembe az olyan tényezőket, mint a hőmérséklet-ingadozások, nedvesség, vegyszerek, UV-sugárzás és egyéb, az alkalmazás szempontjából releváns környezeti feltételek. A ragasztónak ellenállnia kell ezeknek a feltételeknek, hogy idővel megőrizze teljesítményét és adhéziós szilárdságát.
- Ragasztási szilárdság és tartósság: Mérje fel az adott alkalmazáshoz szükséges kötési szilárdságot és tartósságot. Figyelembe kell venni az olyan tényezőket, mint a teherbíró képesség, rezgésállóság, ütésállóság és ciklikus igénybevétel. A ragasztónak elegendő kötési szilárdságot és tartósságot kell biztosítania a hosszú távú megbízhatóság és működési feltételek melletti teljesítmény biztosítása érdekében.
- Kötési idő és folyamat: Vegye figyelembe a ragasztó kötési mechanizmusát és kötési idejét. Az alkalmazási követelményektől függően válasszon olyan ragasztók közül, amelyek szobahőmérsékleten kötődnek (környezeti térhálósodás), vagy olyan ragasztók közül, amelyek kikeményítéséhez hőt, nedvességet vagy UV-sugárzást igényelnek. A keményedési időnek meg kell egyeznie a gyártási vagy összeszerelési folyamattal, hogy lehetővé tegye a hatékony ragasztást és minimalizálja a gyártási időt.
- Felhordási mód: Vegye figyelembe a ragasztó felhordásához rendelkezésre álló felhordási módot és eszközöket. Egyes ragasztók kézi felhordásra alkalmasak, míg mások speciális adagoló- vagy felhordó berendezést igényelhetnek. A ragasztó viszkozitásának és reológiai tulajdonságainak kompatibilisnek kell lenniük a választott felhordási módszerrel, hogy biztosítsák a megfelelő ragasztófedést és ragasztást.
- Szabályozási megfelelőség: Bizonyos alkalmazásokhoz, például orvostechnikai eszközökhöz vagy repülőgép-alkatrészekhez, meghatározott iparági szabványok és előírások betartására lehet szükség. Győződjön meg arról, hogy a kiválasztott ragasztó megfelel a vonatkozó ipari szabványoknak, mint például a biokompatibilitási, gyúlékonysági vagy biztonsági előírásoknak, hogy megfeleljen az alkalmazás speciális követelményeinek.
- Szerviz és támogatás: Értékelje a műszaki támogatás, a termékdokumentáció és a ragasztó gyártója vagy szállítója által nyújtott segítség elérhetőségét. Vegye figyelembe az adott területen szerzett szakértelmüket és képességüket, hogy útmutatást nyújtsanak, vagy megválaszoljanak bármilyen kérdést vagy aggályt a ragasztó kiválasztásával, felvitelével vagy teljesítményével kapcsolatban.
Ezen tényezők gondos mérlegelésével kiválaszthatja az adott alkalmazáshoz legmegfelelőbb elektromos kötőragasztót, amely biztosítja a ragasztott alkatrészek vagy rendszerek optimális teljesítményét, megbízhatóságát és hosszú élettartamát.
Kötési idő és hőmérséklet
A kötési idő és a hőmérséklet fontos szempontok az elektromos ragasztóanyagokkal végzett munka során. A kötési idő arra az időtartamra vonatkozik, amely szükséges ahhoz, hogy a kötés elérje teljes szilárdságát és kötési tulajdonságait. A hőmérséklet viszont befolyásolja a kötési sebességet és a ragasztó általános teljesítményét. Íme néhány kulcsfontosságú pont az elektromos kötőragasztók kötési idejével és hőmérsékletével kapcsolatban:
Keményedési idő:
- A kötési idő a ragasztó típusától és összetételétől függően jelentősen változhat. Ez néhány perctől több óráig vagy akár napig is terjedhet.
- A gyorsabb kikeményedési idő sok alkalmazásban kívánatos, mivel csökkenti az összeszerelési időt, és lehetővé teszi a ragasztott alkatrészek gyors kezelését és további feldolgozását.
- Hosszabb kötési időre lehet szükség olyan alkalmazásoknál, ahol pontos igazításra vagy beállításra van szükség, mielőtt a ragasztó megköt.
- A kötési időt olyan tényezők befolyásolhatják, mint a ragasztó vastagsága, a környezeti feltételek (nedvesség, hőmérséklet), valamint a gyorsítók vagy térhálósítószerek jelenléte.
Hőmérsékleti szempontok:
- A ragasztógyártók termékeikhez ajánlott kikeményedési hőmérséklet-tartományokat biztosítanak. Az optimális ragasztóteljesítmény érdekében elengedhetetlen ezen irányelvek betartása.
- A hőmérséklet befolyásolja a gyógyulás sebességét. A magasabb hőmérséklet általában felgyorsítja a kikeményedési folyamatot, míg az alacsonyabb hőmérséklet lassítja. A túl magas hőmérséklet azonban a ragasztóanyag lebomlását vagy nemkívánatos mellékhatásokat okozhat.
- A ragasztók kikeményedési hőmérséklete minimális és maximális lehet. Ha ezeken a hőmérsékleti határokon kívül működik, az tökéletlen vagy károsodott kikeményedést eredményezhet, ami csökkenti a kötési szilárdságot és a tartósságot.
- Egyes ragasztókhoz speciális kötési hőmérsékleti profilok szükségesek, amelyek magukban foglalják a hőmérséklet fokozatos emelését vagy csökkentését az optimális kötési tulajdonságok elérése érdekében.
- Nagyon fontos figyelembe venni a ragasztandó aljzat hőmérsékleti korlátait. Egyes anyagok érzékenyek lehetnek a magas hőmérsékletre, és deformálódhatnak vagy hőkárosodást szenvedhetnek.
Hőkezelés vs. szobahőmérsékleten történő kikeményedés:
- Egyes elektromos kötőragasztók hőkezelést igényelnek, és a kötést meghatározott időtartamig megemelkedett hőmérsékletnek teszik ki. A hőkezelés gyorsabb kötési időt és jobb tapadási tulajdonságokat biztosít.
- A szobahőmérsékleten térhálósodó ragasztók vagy a környezeti hőmérsékleten kikeményedő ragasztók természetesen, további hő nélkül kötnek ki. Átlagos szobahőmérsékleten kikeményednek, és jellemzően hosszabb kötési időt igényelnek, mint a hőre keményedő kötéseknél.
- A hőkezelés és a szobahőmérsékletű térhálósítás közötti választás a konkrét alkalmazási követelményektől, a gyártási folyamatoktól és a berendezések rendelkezésre állásától függ.
Elengedhetetlen, hogy gondosan kövesse a gyártó utasításait és ajánlásait az adott ragasztó kötési idejére és hőmérsékletére vonatkozóan. Az ajánlott irányelvektől való eltérés ronthatja a ragasztó teljesítményét, ami meggyengülhet a kötéseknél vagy a ragasztó meghibásodását eredményezheti. A megfelelő kötési idő és a hőmérséklet-szabályozás hozzájárul a ragasztott szerelvények vagy alkatrészek kívánt kötési szilárdságának, tartósságának és általános megbízhatóságának eléréséhez.
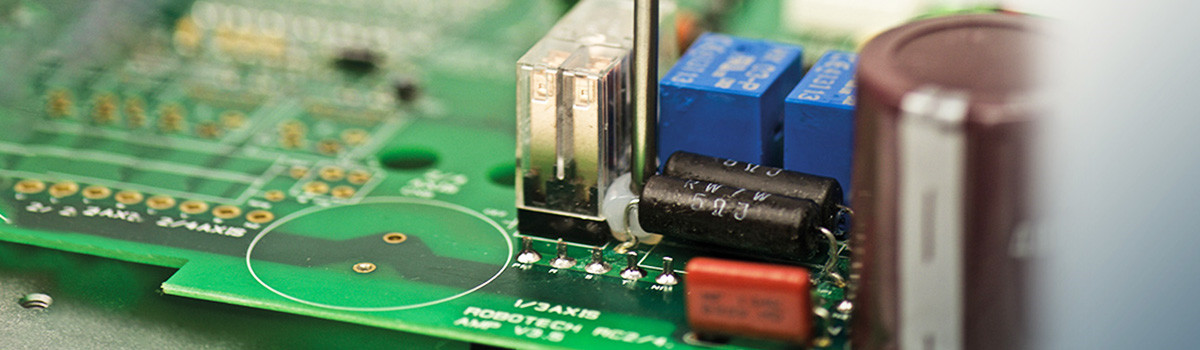
Kémiai ellenállás
A vegyszerállóság fontos szempont az elektromos kötőanyag-ragasztók kiválasztásakor, különösen olyan alkalmazásokban, ahol a ragasztó különféle vegyszereknek, oldószereknek vagy agresszív környezetnek van kitéve. A kötés vegyszerállósága határozza meg azt a képességét, hogy megőrizze sértetlenségét, tapadási szilárdságát és általános teljesítményét meghatározott vegyi anyagokkal való érintkezéskor. Íme néhány kulcsfontosságú pont az elektromos kötőragasztók vegyi ellenállásának megértéséhez:
- Kémiai kompatibilitás: A különböző ragasztók eltérő mértékben ellenállnak bizonyos vegyi anyagokkal szemben. Kulcsfontosságú, hogy felmérjük a ragasztó kompatibilitását azokkal a vegyszerekkel, amelyekkel az élettartama során érintkezésbe kerülhet. Ez magában foglalja a vegyi anyagok típusának, koncentrációjuknak és az expozíció időtartamának figyelembevételét.
- Kémiai típusok: A vegyszerállóság az adott vegyszertípustól függően változhat, például savak, lúgok, oldószerek, olajok, üzemanyagok, tisztítószerek vagy ipari vegyszerek. Egyes ragasztók jól ellenállnak bizonyos vegyi anyagoknak, de érzékenyek lehetnek másokra. Alapvető fontosságú a ragasztó kompatibilitása az alkalmazás szempontjából releváns vegyi anyagokkal.
- Duzzanat és lebomlás: Ha a ragasztót vegyszereknek teszik ki, megduzzadhat, meglágyulhat vagy lebomolhat, ami a tapadási szilárdság és az általános teljesítmény elvesztéséhez vezet. Alapvető fontosságú, hogy olyan ragasztót válasszunk, amely minimális vagy egyáltalán nem duzzad és nem bomlik a várható vegyszerekkel érintkezve.
- Hőmérsékleti szempontok: A vegyszerállóságot a hőmérséklet is befolyásolhatja. Egyes ragasztók jó ellenállást mutathatnak bizonyos vegyi anyagokkal szemben környezeti hőmérsékleten, de kevésbé ellenállóak magasabb hőmérsékleten. Az üzemi hőmérséklet-tartomány figyelembe vétele és a ragasztó vegyszerállóságának felmérése ilyen körülmények között elengedhetetlen.
- Tesztelés és adatok: A ragasztógyártók általában adatlapokat vagy műszaki információkat szolgáltatnak, amelyek meghatározzák termékeik vegyszerállósági tulajdonságait. Ezek az erőforrások segíthetnek a ragasztó adott vegyi anyagokkal való kompatibilitásának értékelésében, és segíthetnek a kívánt alkalmazáshoz megfelelő ragasztó kiválasztásában.
- Bevonatok és tömítőanyagok: Bizonyos esetekben további védőbevonatokat vagy tömítőanyagokat lehet felvinni a ragasztóra a vegyi ellenállás fokozása érdekében. Ezek a bevonatok extra védelmet nyújtanak a vegyszerek ellen, és tovább javítják a ragasztott szerelvény általános tartósságát és vegyi kompatibilitását.
- Alkalmazás-specifikus követelmények: A különböző alkalmazásokhoz eltérő vegyi expozíciós követelmények vonatkoznak. Például az autóiparban az üzemanyagrendszer alkatrészeiben használt ragasztóknak kiválóan kell ellenállniuk az üzemanyagoknak és a szénhidrogéneknek. Alapvető fontosságú, hogy megértsük az alkalmazás speciális kémiai expozíciós feltételeit, és olyan ragasztót válasszunk, amely megfelel ezeknek a követelményeknek.
Az elektromos kötőanyag-ragasztók vegyi ellenállásának figyelembevétele döntő fontosságú a ragasztott szerelvények vagy alkatrészek hosszú távú megbízhatóságának és teljesítményének biztosítása érdekében. Az adott alkalmazáshoz megfelelő vegyszerállósági tulajdonságokkal rendelkező ragasztó kiválasztása segít megelőzni a ragasztó tönkremenetelét, fenntartani az erős kötéseket, és biztosítja a rendszer általános integritását agresszív kémiai környezetben.
Elektromos vezetőképesség
Az elektromos kötőragasztók elektromos vezetőképessége kritikus tulajdonság az olyan alkalmazásokban, ahol elektromos csatlakozásokra vagy földelésre van szükség. Az elektromos vezetőképesség egy anyag azon képességére utal, hogy lehetővé teszi az elektromos áram áramlását. Íme néhány kulcsfontosságú pont az elektromos kötőragasztók elektromos vezetőképességének megértéséhez:
Vezetőképes és nem vezető ragasztók: Az elektromosan kötő ragasztók alapvetően két típusba sorolhatók elektromos vezetőképességük alapján: vezetőképes és nem vezető ragasztókra.
- Vezetőképes ragasztók: Ezek a ragasztók vezetőképes töltőanyagokkal, például fémrészecskékkel vagy szálakkal vannak összeállítva, amelyek megkönnyítik az elektromos áram áramlását. A vezetőképes ragasztók alacsony elektromos ellenállást biztosítanak, ami hatékony elektromos vezetést tesz lehetővé a ragasztott alkatrészek között. Általában olyan alkalmazásokban használják, amelyek elektromos folytonosságot igényelnek, mint például a földelés, az elektromágneses interferencia (EMI) árnyékolás vagy az elektromos csatlakozások.
- Nem vezető ragasztók: A nem vezető ragasztók, ahogy a neve is sugallja, nem rendelkeznek elektromos vezetőképességgel. Ezeket a ragasztókat általában olyan alkalmazásokban használják, amelyek elektromos leválasztást vagy szigetelést igényelnek. Megakadályozzák az elektromos áram áramlását a ragasztott alkatrészek között, és elektromos szigetelést vagy dielektromos tulajdonságokat biztosítanak.
- Elektromos ellenállás: A ragasztó elektromos vezetőképességét gyakran elektromos ellenállásban vagy ellenállásban fejezik ki. Az elektromos ellenállás az anyagon áthaladó elektromos áram ellenállásának mértéke. Az alacsonyabb ellenállásértékek jobb elektromos vezetőképességet jeleznek.
- Töltőanyagok és adalékok: A vezetőképes ragasztók olyan töltőanyagokat vagy adalékanyagokat tartalmaznak, amelyek javítják az elektromos vezetőképességet. Ezek a töltőanyagok, mint például az ezüst-, réz-, szén- vagy grafitrészecskék, vezető utakat hoznak létre a ragasztómátrixon belül, megkönnyítve az elektromos áram áramlását. Ezen töltőanyagok típusa, mérete és koncentrációja befolyásolhatja a ragasztó elektromos vezetőképességét.
- Elektromos csatlakozás és földelés: A vezetőképes ragasztókat általában az alkatrészek közötti elektromos csatlakozások létrehozására vagy a földelésre használják. Különféle iparágakban alkalmazzák őket, beleértve az elektronikát, az autógyártást, a repülőgépgyártást és a távközlést, ahol a megbízható elektromos vezetőképesség elengedhetetlen az eszközök megfelelő működéséhez és teljesítményéhez.
- EMI árnyékolás: Az elektromágneses árnyékolási alkalmazásokban jó elektromos vezetőképességű, vezetőképes ragasztókat használnak. Vezető utat biztosítanak az elektromágneses interferencia eloszlatásához, megvédik az érzékeny elektronikus eszközöket vagy áramköröket a külső elektromágneses sugárzástól vagy zajtól.
- Elektromos érintkezők megbízhatósága: A ragasztó ragasztók elektromos vezetőképessége közvetlenül befolyásolja az elektromos érintkezők megbízhatóságát. A vezetőképes ragasztók megfelelő és állandó elektromos érintkezést biztosítanak a ragasztott felületek között, minimalizálva az érintkezési ellenállást, és megakadályozzák a szakaszos vagy megbízhatatlan csatlakozásokat.
- Ragasztóvastagság és érintkezési felület: A ragasztó elektromos vezetőképességét a ragasztóréteg vastagsága és a ragasztott felületek érintkezési felülete befolyásolhatja. A vékonyabb ragasztórétegek és a nagyobb érintkezési felületek általában jobb elektromos vezetőképességet biztosítanak.
- Tesztelés és ellenőrzés: A ragasztók elektromos vezetőképessége különféle technikákkal mérhető, beleértve a négypontos vagy kétpontos szondás módszereket is. Ezek a tesztek segítenek felmérni a ragasztó vezetőképességi tulajdonságait, és biztosítják a szükséges elektromos előírásoknak való megfelelést.
Elengedhetetlen a megfelelő típusú elektromos kötőragasztó kiválasztása az alkalmazás specifikus elektromos vezetőképességi követelményei alapján. A vezetőképes ragasztók akkor alkalmasak, ha elektromos folytonosságra vagy földelésre van szükség, míg a nem vezető ragasztók elektromos leválasztást vagy szigetelést biztosítanak. A ragasztó elektromos vezetőképességi tulajdonságainak megértése elősegíti az optimális teljesítményt, megbízhatóságot és biztonságot az elektromos ragasztási alkalmazásokban.
Hőstabilitás
A hőstabilitás az elektromos kötőragasztók alapvető jellemzője, különösen olyan alkalmazásokban, ahol a kötés magas hőmérsékletnek van kitéve. A ragasztó hőstabilitása arra utal, hogy képes megőrizni integritását, tapadási szilárdságát és általános teljesítményét magas hőmérsékleti körülmények között. Íme néhány kulcsfontosságú pont az elektromos kötőragasztók hőstabilitásának megértéséhez:
- Hőmérséklet-tartomány: A ragasztóknak meghatározott hőmérsékletük van teljesítményük és stabilitásuk megőrzése érdekében. A ragasztó termikus stabilitását gyakran a maximális folyamatos üzemi hőmérséklettel vagy a csúcshőmérséklet-ellenállással írják le. Lényeges olyan kötés kiválasztása, amely ellenáll az alkalmazás várható hőmérsékleti tartományának.
- Termikus lebomlás: A túlzott hőhatás a ragasztóanyag lebomlását, megváltoztatja a fizikai és kémiai tulajdonságokat. Ez csökkentheti a tapadási szilárdságot, a mechanikai tulajdonságok elvesztését és az általános teljesítmény csökkenését. A termikusan stabil ragasztó még magas hőmérsékleten is ellenáll a lebomlásnak, megőrzi eredeti tulajdonságait.
- A kötési szilárdság megtartása: A ragasztó hőstabilitása szorosan összefügg azzal a képességével, hogy megőrizze kötési szilárdságát magas hőmérsékleten. Ha magas hőmérsékletnek van kitéve, a termikusan stabil ragasztónak minimális kötési szilárdságcsökkenést kell mutatnia. Szilárd, tartós kötést kell biztosítania a ragasztott felületek között, még nehéz hőviszonyok között is.
- Üvegesedési hőmérséklet (Tg): Az üvegesedési hőmérséklet fontos paraméter, amelyet figyelembe kell venni a ragasztó termikus stabilitásának értékelésekor. Ez az a hőmérséklet, amelyen a ragasztó merev, üveges állapotból lágyabb, gumiszerű állapotba megy át. A magasabb Tg értékű ragasztók általában jobb hőstabilitást biztosítanak, mivel magasabb hőmérsékletet is elviselnek, mielőtt meglágyulnának vagy elveszítenék mechanikai tulajdonságaikat.
- Hőciklus: Egyes alkalmazások ismételt hőciklusoknak vannak kitéve, ahol a ragasztó váltakozó magas és alacsony hőmérsékletet tapasztal. Ilyen esetekben elengedhetetlen a hőstabilitás, mivel a ragasztónak el kell viselnie ezeket a hőmérséklet-ingadozásokat anélkül, hogy jelentős romlása vagy a tapadási szilárdság csökkenése csökkenne. A hőstabil ragasztó megőrzi teljesítményét többszöri hőkezelési ciklus után is.
- Hőállóság: A hőt termelő alkatrészeket vagy környezetet érintő alkalmazásokban, például elektronikában, teljesítményelektronikában vagy világítási rendszerekben használt ragasztók jó hőállóságot igényelnek. A hőálló ragasztók ellenállnak az ezen alkatrészek által keltett hőnek, és megőrzik teljesítményüket anélkül, hogy meglágyulnának, megolvadnának vagy elveszítenék a tapadási erejét.
- Hővezetőképesség: Egyes alkalmazásokban a hővezető képesség fontos szempont. A hővezető képesség egy anyag hővezető képességére utal. A nagy hővezető képességű ragasztók hatékonyan tudják elvezetni a hőt a hőérzékeny alkatrészektől, így biztosítva a hatékony hőelvezetést és megelőzve a hőkárosodást.
- Tesztelés és adatok: A ragasztógyártók jellemzően műszaki adatlapokat bocsátanak rendelkezésre, amelyek meghatározzák termékeik hőstabilitási tulajdonságait. Ez az információ tartalmazza az ajánlott üzemi hőmérséklet-tartományt, a hőellenállást és egyéb releváns termikus tulajdonságokat. Alapvető fontosságú ezen adatok áttekintése annak biztosítása érdekében, hogy a ragasztó megfelel-e az alkalmazás speciális hőstabilitási követelményeinek.
A hőstabil ragasztó kiválasztása kulcsfontosságú a hosszú távú megbízhatóság és teljesítmény biztosítása érdekében, különösen a magas hőmérséklettel vagy termikus ciklusokkal járó alkalmazásoknál. A termikusan stabil ragasztó megőrzi adhéziós szilárdságát, mechanikai tulajdonságait és általános teljesítményét magas hőmérsékleti körülmények között, hozzájárulva a ragasztott szerelvények vagy alkatrészek tartósságához és integritásához.
Viszkozitás
A viszkozitás az elektromos kötőanyagú ragasztók alapvető tulajdonsága, amely meghatározza folyási viselkedésüket és alkalmazási jellemzőit. A ragasztó vastagságára vagy folyási ellenállására utal. A viszkozitás megértése döntő fontosságú a ragasztó megfelelő kiválasztásához és felhordási folyamatához. Íme néhány kulcsfontosságú pont az elektromos kötőragasztók viszkozitásának megértéséhez:
- Meghatározás és mérés: A viszkozitás a folyadék áramlással szembeni ellenállását méri. Meghatározza a ragasztó szétterülési, nedves felületi és hézagkitöltő képességét. A viszkozitást általában olyan mértékegységekben mérik, mint a centipoise (cP) vagy Pascal-másodperc (Pa·s).
- Viszkozitási tartomány: Az elektromos kötőragasztók különböző viszkozitásúak lehetnek, az alacsony viszkozitású folyadékoktól a nagy viszkozitású pasztákig vagy gélekig. A megfelelő viszkozitás az alkalmazási követelményektől függ, például a kötési vonal méretétől, a hézagkitöltő képességtől és az alkalmazás egyszerűségétől.
- Folyási viselkedés: A ragasztók viszkozitásuktól függően eltérő folyási viselkedést mutathatnak. A newtoni folyadékok vastagsága állandó, függetlenül az alkalmazott nyírási sebességtől. Másrészt a nem newtoni folyadékok nyírási elvékonyodást (sűrűség csökkenés a nyírási sebesség növekedésével) vagy nyírási vastagodást (viszkozitás növekedése a nyírási sebesség növekedésével) mutathatnak. A folyási viselkedés megértése segít megjósolni a ragasztó viselkedését az alkalmazás során és különböző körülmények között.
- Alkalmazási módok: A viszkozitás befolyásolja a ragasztók alkalmazhatóságát különböző módszerekkel, mint például a kézi adagolás, az automatizált adagolás, a szitanyomás vagy a fecskendőadagolás. Az alacsony viszkozitású ragasztók könnyen folynak, és alkalmasak automatikus adagolásra, míg a nagy viszkozitású ragasztókhoz kézi felhordási módszerekre vagy vastagabb anyagok kezelésére alkalmas adagolóberendezésre lehet szükség.
- Hézagkitöltő képesség: A viszkozitás szerepet játszik abban, hogy a ragasztó képes kitölteni hézagokat vagy szabálytalan kötési felületeket. Az alacsonyabb viszkozitású ragasztók hatékonyabban tudnak befolyni szűk helyekre vagy szűkebb résekbe, míg a nagyobb viszkozitású ragasztók általában a helyükön maradnak, és jobb hézagkitöltő képességet biztosítanak.
- Az alapfelület kompatibilitása: A viszkozitás akkor is fontos, ha figyelembe vesszük a ragasztó és a ragasztandó aljzat kompatibilitását. A megfelelő viszkozitású ragasztók jó nedvesedést és érintkezést biztosítanak az aljzat felületeivel, elősegítve az erős tapadást.
- Tixotrópia: Egyes ragasztók tixotróp viselkedést mutatnak, ahol a viszkozitásuk csökken nyírófeszültségnek vagy keverésnek kitéve, de nyugalmi állapotban helyreáll. A tixotróp ragasztók könnyen felvihetők és eloszlanak a felhordás során, de felhordás után gyorsan visszanyeri vastagságát, megakadályozva a nem kívánt folyást vagy megereszkedést.
- Hőmérsékletfüggőség: A viszkozitás hőmérsékletfüggő lehet, vagyis a hőmérséklettel változik. Egyes ragasztók magasabb hőmérsékleten kevésbé viszkózussá válhatnak, így könnyebben felvihetők vagy adagolhatók. Mások alacsonyabb hőmérsékleten magasabb viszkozitást mutathatnak, ami előmelegítést vagy melegítést igényel az optimális áramlás és megmunkálhatóság érdekében.
- Anyagkezelés: A viszkozitás befolyásolja az anyagmozgatás egyszerűségét, például a keverést, keverést vagy a ragasztók átvitelét. A nagyobb viszkozitású ragasztókhoz további keverést vagy felszerelést igényelhet az egyenletesség és homogenitás biztosítása érdekében.
Az elektromos kötőragasztók viszkozitásának megértése kulcsfontosságú a sikeres alkalmazáshoz és a kívánt kötési minőség eléréséhez. A megfelelő viszkozitás kiválasztása biztosítja a megfelelő nedvesedést és tapadást az aljzatokhoz, hatékony hézagkitöltést és könnyű felhordást. Az optimális teljesítmény biztosítása érdekében elengedhetetlen a speciális alkalmazási követelmények figyelembe vétele, és a ragasztógyártó ajánlásaiban a viszkozitási specifikációk figyelembevétele.
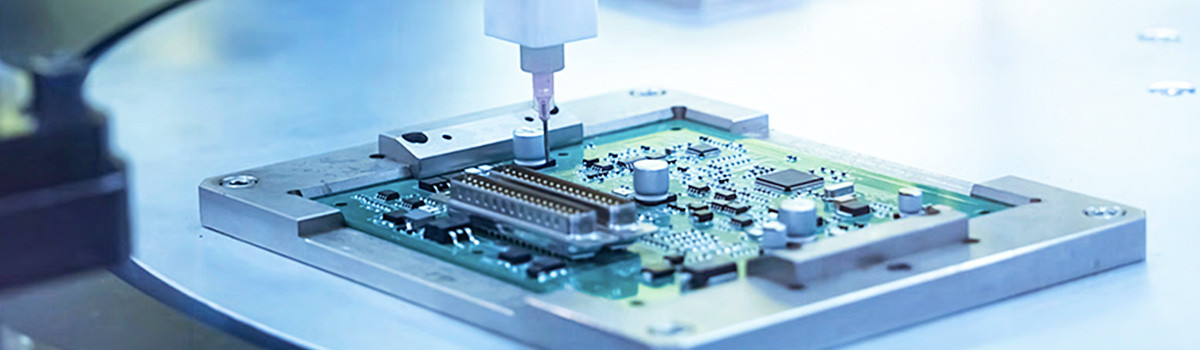
Szavatossági idő
Az elektromos kötőanyag ragasztók eltarthatósága arra az időtartamra vonatkozik, ameddig a ragasztó tárolható és használatra alkalmas marad. Alapvető fontosságú a ragasztók eltarthatóságának megértése, hogy biztosítsuk hatékonyságukat és megbízhatóságukat felhordáskor. Íme néhány fontos tudnivaló az elektromos ragasztóragasztók eltarthatóságáról:
- Definíció: Az eltarthatósági idő az az időtartam, ameddig a ragasztó meghatározott körülmények között tárolható anélkül, hogy a tulajdonságai, teljesítménye vagy minősége jelentősen megváltozna.
- Lejárati idő: A ragasztógyártók általában megadják a lejárati dátumot vagy a termék ajánlott eltarthatóságát. Ez a dátum azt a pontot jelzi, amely után a ragasztó leromolhat vagy elveszítheti hatékonyságát. Az optimális teljesítmény biztosítása érdekében elengedhetetlen ennek a lejárati dátumnak a betartása.
- Az eltarthatóságot befolyásoló tényezők: Számos tényező befolyásolhatja az elektromos kötőanyag ragasztók eltarthatóságát:
- Tárolási feltételek: A ragasztókat ellenőrzött körülmények között kell tárolni a stabilitás megőrzése érdekében. Az olyan tényezők, mint a hőmérséklet, a páratartalom és a fényhatás befolyásolhatják a ragasztó eltarthatóságát. A ragasztókat hűvös, száraz helyen kell tárolni, védve a közvetlen napfénytől vagy szélsőséges hőmérséklet-ingadozásoktól.
- Csomagolás: A megfelelő csomagolás döntő fontosságú a ragasztó eltarthatóságának megőrzésében. A ragasztókat szorosan lezárt tartályokban kell tárolni, hogy megakadályozzuk a nedvesség bejutását, elpárolgását vagy szennyeződését. A könnyű azonosítás érdekében a tartályokat megfelelően fel kell címkézni a ragasztó típusával, a tételszámmal és a lejárati dátummal.
- Kémiai stabilitás: A ragasztók idővel kémiai reakciókon menhetnek keresztül, amelyek tulajdonságaik megváltozásához vezethetnek. Az olyan tényezők, mint a nedvesség, az oxigén vagy a reaktív anyagoknak való kitettség felgyorsíthatják ezeket a reakciókat és csökkenthetik az eltarthatósági időt. A stabilizátorokat vagy antioxidánsokat tartalmazó ragasztók javított kémiai stabilitást és hosszabb eltarthatóságot eredményezhetnek.
- Tárolási javaslatok: A gyártók konkrét tárolási ajánlásokat adnak ragasztótermékeikhez. Ezek az ajánlások magukban foglalhatják a hőmérséklet-tartományokat, a páratartalom szintjét és az átlátszó tárolóedényeket vagy feltételeket. A ragasztó minőségének és hosszú élettartamának biztosítása érdekében elengedhetetlen ezen irányelvek betartása.
- Tesztelés és ellenőrzés: Ha egy ragasztót hosszabb ideig vagy a lejárati időn túl tároltak, ajánlatos ragasztóvizsgálatot végezni az alkalmasság ellenőrzésére. Ezek a tesztek magukban foglalhatják a viszkozitás és a tapadási szilárdság mérését vagy a ragasztási próbák elvégzését a ragasztó teljesítményének értékelésére.
- Termékek szétválasztása: A ragasztókat a „first in, first out” alapon kell tárolni és használni annak érdekében, hogy a régebbi anyagok kerüljenek felhasználásra az újabbak előtt. Ez a gyakorlat segít megelőzni a lejárt vagy leromlott ragasztók megjelenését, és a legjobb eredményt biztosítja.
- Gyártói útmutató: A ragasztó eltarthatósági idejére vonatkozó konkrét információkért feltétlenül olvassa el a gyártó dokumentációját, például a termék adatlapjait vagy a műszaki közleményeket. A gyártó útmutatása figyelembe veszi a ragasztó összetételét, a tárolási körülményeket és a várható teljesítményt az idő múlásával.
Az elektromos kötőanyag-ragasztók eltarthatóságának megértése alapvető fontosságú hatékonyságuk megőrzéséhez és a megfelelő teljesítmény biztosításához. Az eltarthatósági idejüket meghaladó ragasztók csökkentett tapadási szilárdságot, viszkozitásváltozást vagy egyéb káros hatásokat mutathatnak. A megfelelő tárolási gyakorlatok betartása, a gyártói irányelvek betartása és a ragasztók lejárati idejének rendszeres ellenőrzése segíti a ragasztók megbízhatóságát és egyenletes teljesítményét felhordáskor.
Felület előkészítése
A felület előkészítése kritikus lépés az elektromos kötőragasztók alkalmazásában. A megfelelő felület-előkészítés biztosítja az optimális tapadást és tapadási szilárdságot a ragasztó és az aljzat között. Íme néhány kulcsfontosságú pont az elektromos ragasztók felületének előkészítésével kapcsolatban:
- Tisztítás: A felület-előkészítés első lépése az alapfelületek alapos megtisztítása. A felületeknek mentesnek kell lenniük olyan szennyeződésektől, mint a szennyeződés, por, zsír, olaj, nedvesség vagy oxidáció. A tisztítás történhet oldószerekkel, tisztítószerekkel vagy a ragasztó gyártója által ajánlott speciális tisztítószerekkel. A tisztítási folyamat az aljzattól és a szennyeződések természetétől függően törlést, kefét vagy ultrahangos tisztítási technikákat foglalhat magában.
- Felület érdesítése: Bizonyos esetekben szükség lehet az aljzat felületének érdesítésére a ragasztó kötési szilárdságának növelése érdekében. Ezt általában mechanikus módszerekkel, például csiszolással, csiszolással vagy szemcseszórással végzik. A felület érdesítése megnöveli a felületet és mechanikai reteszelést biztosít, ami lehetővé teszi a ragasztó erősebb kötést.
- Felületi aktiválás: Egyes hordozók, például fémek vagy bizonyos műanyagok felületaktiválást igényelhetnek a tapadás elősegítése érdekében. A felületaktiválási módszerek közé tartoznak a kémiai kezelések, a plazmakezelések, az alapozók vagy a tapadást elősegítő anyagok. Ezek a kezelések módosítják a felület tulajdonságait, javítva a ragasztó nedvesítési és tapadási tulajdonságait.
- Oxidáció eltávolítása: Az oxidációs rétegek eltávolítása kulcsfontosságú a fémes felületeknél a jó tapadás biztosítása érdekében. Az oxidáció akadályozhatja a ragasztónak az aljzathoz való kötődését. A mechanikai módszerek, például a csiszolás vagy a kémiai kezelések, például a savas pácolás eltávolíthatják az oxidrétegeket, és tiszta felületet tesznek lehetővé a ragasztáshoz.
- Szárítás és zsírtalanítás: Tisztítás és felületkezelés után elengedhetetlen az aljzatfelületek alapos szárítása a nedvesség és a tisztítószerek eltávolítása érdekében. A nedvesség megzavarhatja a ragasztó kötési folyamatát, és veszélyeztetheti a kötés szilárdságát. Ezenkívül a felületek zsírtalanítása segít eltávolítani a visszamaradt olajokat vagy szennyeződéseket, amelyek gátolhatják a ragasztó hatékony tapadását.
- Felületi kompatibilitás: A ragasztó és az alapfelület közötti kompatibilitás figyelembevétele elengedhetetlen. Egyes kötések speciális felületi jellemzőket vagy kezelési módszereket igényelhetnek a megfelelő kötés biztosításához. A megfelelő felület-előkészítési technikák meghatározásához az adott ragasztó és aljzat kombinációjához a ragasztó gyártójának ajánlásait kell követni.
- Ragasztó felhordása: A felület-előkészítés befejezése után a ragasztót fel lehet vinni az előkészített felületekre. A ragasztó gyártójának a felhordási módszerre vonatkozó utasításainak betartása elengedhetetlen a ragasztó vastagságára és a rendelkezésre álló időre vonatkozóan. A megfelelő felhordási technikák, mint például az egyenletes szórás vagy az ellenőrzött adagolás, egyenletes fedést és kötési szilárdságot biztosítanak.
A megfelelő felület-előkészítés kulcsfontosságú a szilárd és tartós kötések eléréséhez elektromos kötőragasztók használatakor. Elősegíti az optimális tapadást, minimalizálja a ragasztás meghibásodásának kockázatát, és biztosítja a ragasztott szerelvények hosszú távú megbízhatóságát. A ragasztó gyártója által megadott ajánlott felület-előkészítési eljárások betartása segít a ragasztó teljesítményének maximalizálásában és a sikeres ragasztásban.
Kezelés és tárolás
Az elektromos kötőanyag-ragasztók megfelelő kezelése és tárolása elengedhetetlen azok hatékonyságának, minőségének és eltarthatóságának megőrzéséhez. A nem megfelelő kezelés vagy tárolás károsíthatja a ragasztót, ami rontja a teljesítményt és csökkenti a kötés szilárdságát. Íme néhány kulcsfontosságú pont az elektromos kötőanyag-ragasztók kezelésével és tárolásával kapcsolatban:
Kezelési óvintézkedések: A ragasztók kezelésekor elengedhetetlen bizonyos óvintézkedések betartása a biztonság és a szennyeződés elkerülése érdekében:
- Viseljen megfelelő egyéni védőfelszerelést (PPE) a ragasztó gyártója által javasoltak szerint. Ez magában foglalhatja a kesztyűt, a védőszemüveget és a védőruházatot.
- Kerülje a bőrrel, szemmel vagy ruházattal való érintkezést. Véletlen érintkezés esetén alaposan öblítse le vízzel, és szükség esetén forduljon orvoshoz.
- Használjon megfelelő szellőzést a munkaterületen, hogy biztosítsa a megfelelő légáramlást, és minimalizálja a gőzöknek és gőzöknek való kitettséget.
- Kövesse a gyártó utasításait a megfelelő kezelési technikákra vonatkozóan, beleértve a keverési arányokat (ha van), és minden speciális óvintézkedést.
Tárolási feltételek: A ragasztóanyag tárolási körülményei kulcsfontosságúak a minőség és a hatékonyság megőrzésében. Az elektromos ragasztók tárolása során vegye figyelembe a következő tényezőket:
- Hőmérséklet: A ragasztókat a gyártó által javasolt hőmérsékleti tartományon belül kell tárolni. Az extrém magas és alacsony hőmérséklet befolyásolhatja a ragasztó teljesítményét és eltarthatóságát. Általában ajánlott a ragasztókat hűvös, száraz helyen, közvetlen napfénytől és hőforrásoktól távol tartani.
- Páratartalom: A nedvesség negatívan befolyásolhatja a ragasztó tulajdonságait, és idő előtti kikeményedést vagy lebomlást okozhat. A ragasztókat alacsony páratartalmú környezetben kell tárolni, hogy megakadályozzuk a nedvesség felszívódását. A tartályokat tartsa szorosan lezárva, hogy minimalizálja a nedvesség bejutását.
- Eltarthatósági idő figyelése: A ragasztós tartályokon fel kell tüntetni a tételszámot, a gyártási dátumot és a lejárati dátumot. Valósítson meg egy FIFO (first in, first out) rendszert, hogy először használja a régebbi ragasztókészletet, és megakadályozza a lejárt anyagok felhasználását.
- Kompatibilitás: Egyes ragasztóknak összetételüktől függően különleges tárolási követelmények lehetnek. A ragasztó minőségének megőrzése érdekében kövesse a gyártó tárolási hőmérsékletre, páratartalomra vonatkozó ajánlásait és egyéb utasításokat.
Tartálykezelés: A ragasztós tartályokat óvatosan kell kezelni, hogy elkerüljük a szivárgást, kiömlést vagy szennyeződést:
- Használat után győződjön meg arról, hogy a tartályokat szorosan lezárja, hogy elkerülje a levegő expozícióját és a nedvesség bejutását. Kövesse a gyártó utasításait a megfelelő zárási technikákhoz.
- Kerülje a ragasztótartályok leejtését vagy helytelen kezelését, mert ez károsíthatja a csomagolást vagy veszélyeztetheti a ragasztó sértetlenségét.
- Tisztítsa meg a tartályok külső felületeit, mielőtt kinyitná őket, hogy elkerülje a szennyeződések bejutását a ragasztóba.
- Elkülönítés és címkézés: A ragasztókat az összeférhetetlen anyagoktól elkülönítve tárolja a keresztszennyeződés vagy reakciók elkerülése érdekében. A tartályok megfelelő címkézése a ragasztó típusával, tételszámával és egyéb releváns információkkal segíti a készlet pontos azonosítását és nyomon követését.
- Szállítás: Ragasztók szállítása során ügyeljen arra, hogy megfelelően csomagolják és rögzítsék, hogy elkerüljék a szivárgást és a károsodást. Kövesse a ragasztóanyagok biztonságos szállítására vonatkozó vonatkozó előírásokat vagy irányelveket.
Az elektromos kötőragasztók megfelelő kezelése és tárolása döntő fontosságú minőségük, teljesítményük és eltarthatóságuk megőrzéséhez. Az ajánlott tárolási feltételek, a kezelési óvintézkedések és a gyártó utasításainak betartása biztosítja, hogy a ragasztó hatékony és megbízható maradjon a ragasztási alkalmazásokhoz.
Biztonsági óvintézkedések
Biztonsági óvintézkedéseket kell tenni az elektromos ragasztóanyagokkal végzett munka során az egyének védelme és a biztonságos munkakörnyezet biztosítása érdekében. A ragasztók olyan vegyi anyagokat tartalmazhatnak, amelyek nem megfelelő kezelés esetén veszélyesek lehetnek. Íme néhány alapvető biztonsági óvintézkedés, amelyeket figyelembe kell venni az elektromos ragasztóanyagokkal végzett munka során:
- Személyi védőfelszerelés (PPE): Viseljen megfelelő PPE-t, hogy megvédje magát a lehetséges veszélyektől. Ez magában foglalhat kesztyűt, védőszemüveget vagy védőszemüveget, laborköpenyt vagy védőruházatot, és szükség esetén légzésvédőt. A PPE követelményeket a ragasztó anyagbiztonsági adatlapja (MSDS) és a gyártó ajánlásai alapján kell meghatározni.
- Szellőztetés: Gondoskodjon megfelelő szellőzésről a munkaterületen, hogy minimalizálja a ragasztó felhordása vagy kötése során keletkező gőzöknek, gőzöknek vagy levegőben lévő részecskéknek való kitettséget. Használjon helyi elszívó szellőztetést, vagy dolgozzon jól szellőző helyen a levegő minőségének megőrzése érdekében.
- Veszélyes vegyi anyagok: Az elektromos kötőragasztók olyan vegyi anyagokat tartalmazhatnak, amelyek veszélyesek lehetnek az egészségre. Ismerkedjen meg a ragasztó MSDS-ével, hogy megértse a termékkel kapcsolatos konkrét veszélyeket. Kövesse a gyártó ajánlásait a ragasztó biztonságos kezelésére, tárolására és ártalmatlanítására vonatkozóan.
- Bőrrel való érintkezés: Kerülje a ragasztó közvetlen bőrrel való érintkezését. Egyes ragasztók bőrirritációt vagy allergiás reakciókat okozhatnak. A bőrrel való érintkezés elkerülése érdekében viseljen az adott ragasztónak ellenálló védőkesztyűt. Véletlen érintkezés esetén mossa le az érintett területet szappannal és vízzel, és szükség esetén forduljon orvoshoz.
- Szemvédelem: A ragasztók szemirritációt vagy sérülést okozhatnak, ha szembe kerülnek. Viseljen védőszemüveget vagy védőszemüveget, hogy megvédje a szemet, amikor ragasztóval dolgozik. Véletlen szemmel való érintkezés esetén öblítse ki a szemet vízzel legalább 15 percig, és azonnal forduljon orvoshoz.
- Belélegzés: Minimalizálja a ragasztógőzök vagy gőzök belélegzését. Jól szellőző helyen dolgozzon, vagy ha szükséges, használjon légzésvédőt. Kövesse a gyártó ajánlásait a megfelelő légzésvédő felszerelésre vonatkozóan.
- Tűz- és gyújtóforrások: Egyes ragasztók gyúlékonyak lehetnek, vagy sajátos gyúlékonysági jellemzőkkel rendelkeznek. Tegyen óvintézkedéseket annak megakadályozására, hogy a ragasztó nyílt lánggal, szikrával vagy más gyújtóforrással érintkezzen. Tárolja és használja a ragasztót hőforrásoktól távol, és kövesse a megfelelő tűzvédelmi intézkedéseket.
- Kémiai kompatibilitás: Ügyeljen arra, hogy a ragasztó más anyagokkal vagy anyagokkal kompatibilis. Kerülje a ragasztók összekeverését inkompatibilis vegyszerekkel vagy anyagokkal, amelyek veszélyes reakciókat okozhatnak.
- Tárolás és ártalmatlanítás: A ragasztókat a gyártó utasításait követve tárolja, hogy elkerülje a szivárgást, kiömlést vagy a véletlen expozíciót. Kövesse a megfelelő irányelveket a ragasztós tartályok és hulladékanyagok biztonságos tárolására és ártalmatlanítására vonatkozóan.
- Vészhelyzeti felkészültség: Készüljön fel a vészhelyzetekre úgy, hogy a munkaterületen vészhelyzeti szemmosó állomások, biztonsági zuhanyok és tűzoltó berendezések állnak rendelkezésre. Ismerkedjen meg a megfelelő vészhelyzeti eljárásokkal és protokollokkal.
Feltétlenül olvassa el a ragasztógyártó speciális biztonsági adatait és utasításait. A megfelelő biztonsági óvintézkedések és irányelvek betartása segít megóvni az egyéneket, megelőzni a baleseteket, és biztonságos munkakörnyezetet biztosítani az elektromos kötőragasztókkal.
Következtetés
Összefoglalva, az elektromos kötőragasztók kritikus szerepet játszanak az elektromos rendszerek megbízhatóságának és biztonságának biztosításában. Kiváló ragasztási és tömítési megoldást nyújtanak különféle alkalmazásokhoz, az elektronikai eszközöktől a repülőgép-alkatrészekig. A megfelelő ragasztó kiválasztásához számos tényező gondos mérlegelése szükséges, beleértve a kötési időt, a vegyszerállóságot és az elektromos vezetőképességet. Megfelelő kezeléssel és tárolással az elektromos kötőragasztók tartós és biztonságos kötést biztosítanak, biztosítva az elektromos rendszerek optimális teljesítményét.