Konformális bevonatok elektronikához
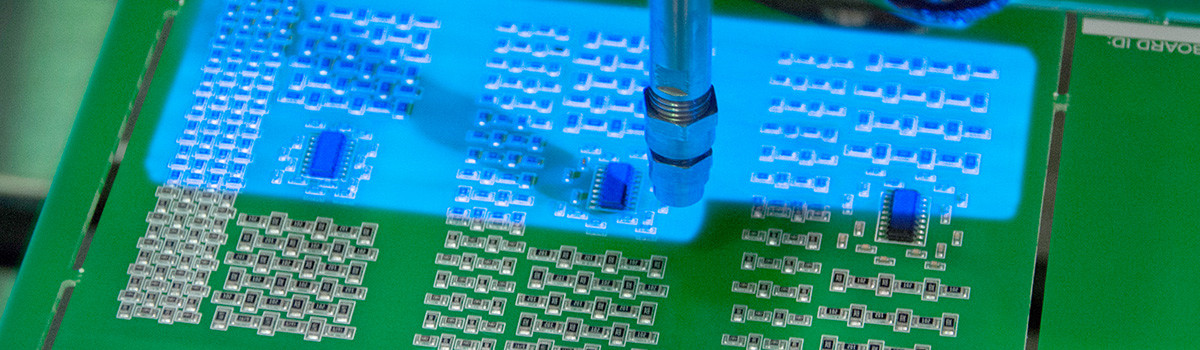
A mai világban az elektronikus eszközök mindennapi életünk szerves részét képezik. Ahogy az elektronikus eszközök egyre összetettebbé és miniatürizáltabbá válnak, egyre kritikusabbá válik a környezeti tényezők, például a nedvesség, a por és a vegyszerek elleni védelem szükségessége. Itt jönnek be a konform bevonatok. A konform bevonatok olyan speciálisan kialakított anyagok, amelyek megvédik az elektronikus alkatrészeket a teljesítményüket és funkcionalitásukat veszélyeztető külső tényezőktől. Ez a cikk feltárja a konform bevonatok előnyeit és fontosságát az elektronika számára.
Mik azok a konform bevonatok az elektronikához?
A konformális bevonatok speciális védőbevonatok, amelyeket az elektronikai iparban használnak, hogy megvédjék az elektronikus alkatrészeket és áramköri lapokat olyan környezeti tényezőktől, mint a nedvesség, por, vegyszerek és szélsőséges hőmérsékleti viszonyok. Ezeket a bevonatokat vékony, egyenletes rétegben hordják fel az elektronika felületére, igazodva az alkatrészek kontúrjához, így biztosítva a teljes fedést és védelmet.
A konform bevonatok elsődleges célja az elektronikus eszközök külső elemek által okozott károsodásának vagy hibás működésének megelőzése. A nedvesség és a pára például korróziót és rövidzárlatot okozhat, míg a por és törmelék ronthatja az érzékeny alkatrészek teljesítményét. A megfelelő bevonat megvédi az elektronikai egységet ezektől a veszélyektől, biztosítva annak megbízhatóságát és hosszú élettartamát.
A konform bevonatok általában különféle kémiai összetételekből készülnek, beleértve az akrilokat, szilikonokat, uretánokat és epoxikat. Minden típusú bevonat különböző tulajdonságokkal és előnyökkel rendelkezik. Az akril bevonatokat sokoldalúságuk, könnyű felhordásuk és költséghatékonyságuk miatt széles körben használják. Jó nedvességállóságot biztosítanak, és viszonylag egyszerűen eltávolíthatók és szükség esetén újra felvihetők. A szilikonok kiváló rugalmasságukról, hőstabilitásukról és magas hőmérséklettel szembeni ellenállásukról ismertek. Az uretán bevonatok kivételes vegyszerállóságot és védelmet nyújtanak az oldószerek és üzemanyagok ellen. Az epoxik kiváló keménységet és tartósságot biztosítanak, így alkalmasak a zord környezetben való használatra.
A konform bevonatok gondos odafigyelést igényelnek, hogy biztosítsák a megfelelő fedést és tapadást. A különféle technikák közé tartozik a kefe, a permetezés, a bemártás és a szelektív bevonat. Különböző módszerek alkalmazhatók a speciális követelményektől és az összeállítás összetettségétől függően. Egyes bevonatokat manuálisan hordnak fel, míg másokat automatizált eljárásokkal, például robotizált szórással vagy merítési rendszerekkel hajtanak végre.
Felhordás után a konform bevonat védőréteget hoz létre, amely befogja az elektronikus alkatrészeket anélkül, hogy akadályozná működésüket. Védőfóliát képez, amely a felülethez tapad, és idővel megőrzi védő tulajdonságait. A bevonatok jellemzően átlátszóak vagy áttetszőek, lehetővé téve az összeszerelés vizuális ellenőrzését.
A környezeti tényezők elleni védelem mellett a konform bevonatok más előnyöket is kínálnak. Elektromos szigetelést biztosítanak, megakadályozva az áramszivárgást és a rövidzárlatot. A rétegek növelhetik az összeállítás rezgésekkel és mechanikai igénybevételekkel szembeni ellenállását is, csökkentve a szállítás vagy működés közbeni sérülések kockázatát. Ezenkívül védelmet nyújthatnak a gombák, penészgombák és egyéb szennyeződések ellen, amelyek veszélyeztethetik az elektronikus eszközök teljesítményét.
A konform bevonatok jelentősége az elektronikai eszközöknél
A konform bevonatok döntő szerepet játszanak az elektronikus eszközök megbízhatóságának és tartósságának növelésében, és számos alapvető előnyt kínálnak az optimális teljesítmény és hosszú élettartam biztosításában. Íme néhány fő ok, amiért konform bevonat szükséges az elektronikus eszközökhöz:
- Nedvesség és nedvesség elleni védelem: A konform bevonatok egyik elsődleges célja, hogy megóvja az elektronikus alkatrészeket a nedvességtől és a nedvességtől. A víz korrózióhoz, oxidációhoz és vezető utak kialakulásához vezethet, ami rövidzárlatokhoz és az eszközök hibás működéséhez vezethet. A konform bevonatok gátként működnek, megakadályozva, hogy a nedvesség elérje az érzékeny alkatrészeket, és csökkentse a károsodás kockázatát.
- A por és törmelék felhalmozódásának megelőzése: Az elektronika gyakran ki van téve pornak, szennyeződésnek és levegőben lévő szennyeződéseknek. Ezek a részecskék lerakódhatnak az áramköri lapokon és alkatrészeken, ami szigetelési problémákhoz, fokozott hőtermeléshez és lehetséges rövidzárlatokhoz vezethet. A konform bevonatok védőréteget képeznek, amely megakadályozza a por és törmelék felhalmozódását, megőrzi az elektronika tisztaságát és teljesítményét.
- Vegyszerállóság: Számos konform bevonat ellenáll a különféle vegyszereknek, beleértve az oldószereket, üzemanyagokat, savakat és lúgokat. Ez különösen fontos olyan környezetben, ahol az elektronikus eszközök érintkezésbe kerülhetnek korrozív anyagokkal. A bevonatok pajzsként működnek, megakadályozzák a kémiai reakciókat és biztosítják az alkatrészek hosszú élettartamát.
- Hővédelem: Az elektronikus eszközök működés közben hőt termelnek, a túlzott hő pedig ronthatja az alkatrészek teljesítményét és megbízhatóságát. A konform bevonatok hőgátat képezhetnek, elvezetik a hőt és csökkentik a túlmelegedés kockázatát. Az egyes rétegek, például a szilikon alapúak kiváló hőstabilitásukról ismertek, és ellenállnak a magas hőmérsékletnek anélkül, hogy védő tulajdonságaik sérülnének.
- Elektromos szigetelés: A konform bevonatok elektromos szigetelést biztosítanak, megakadályozva az áramszivárgást és a rövidzárlatokat. Segítenek fenntartani az alkatrészek kívánt elektromos jellemzőit, és csökkentik a környezeti tényezők vagy szennyeződések által okozott elektromos meghibásodások lehetőségét.
- Mechanikai védelem: Az elektronika mechanikai igénybevételnek lehet kitéve, mint például rezgés, ütés vagy ütés. A konform bevonatok növelik az elektronikus eszközök mechanikai robusztusságát azáltal, hogy további védelmi réteget biztosítanak. Segítenek elnyelni a rezgéseket és az ütközési erőket, csökkentve a kényes alkatrészek károsodásának kockázatát és biztosítva a megbízható működést.
- Környezetvédelmi ellenállás: A konform bevonatok lehetővé teszik az elektronikus eszközök számára, hogy ellenálljanak a különböző környezeti feltételeknek. Ellenállnak a szélsőséges hőmérsékleteknek, az UV-sugárzásnak, a sópermetnek és más durva elemeknek. Ez különösen fontos a kültéri vagy ipari alkalmazásokban használt eszközök esetében, ahol kihívást jelentő környezeteknek lehetnek kitéve.
A konform bevonatok használatának előnyei
Az elektronikus eszközök konform bevonatainak használata számos előnnyel jár, amelyek hozzájárulnak azok általános megbízhatóságához és hosszú élettartamához. Íme néhány fő előnye a konform bevonat használatának:
- Környezetvédelem: A konform bevonatok védőréteget képeznek, amely megvédi az elektronikus alkatrészeket a környezeti tényezőktől, például nedvességtől, portól, szennyeződéstől és vegyszerektől. Megakadályozzák a víz bejutását, ami korróziót és rövidzárlatot okozhat, valamint védenek a por és törmelék felhalmozódásától, ami ronthatja a teljesítményt. Ez a környezetvédelem meghosszabbítja az elektronikus eszközök élettartamát.
- Megnövelt megbízhatóság: A környezeti veszélyek elleni védelem révén a konform bevonatok növelik az elektronikus eszközök megbízhatóságát. Minimalizálják a nedvességgel kapcsolatos problémák, például a korrózió okozta alkatrészkárosodás vagy az elektrokémiai migráció által okozott meghibásodások kockázatát. Ezenkívül a bevonatok védelmet nyújtanak a por és törmelék ellen, amelyek elektromos rövidzárlatot vagy szigetelési meghibásodást okozhatnak, így biztosítva az egyenletes és megbízható teljesítményt.
- Elektromos szigetelés: A konform bevonatok elektromos szigetelési tulajdonságokat kínálnak, megakadályozva az áramszivárgást és a rövidzárlatot. Segítenek fenntartani az alkatrészek kívánt elektromos jellemzőit, csökkentve a szennyeződésből vagy nedvességfelvételből eredő elektromos meghibásodások vagy meghibásodások lehetőségét. Az elektromos szigetelés a biztonsági és szabályozási követelmények teljesítését is segíti.
- Hőkezelés: Egyes konform bevonatok hőkezelési tulajdonságokkal rendelkeznek, amelyek lehetővé teszik az elektronikus alkatrészek által termelt hő elvezetését. Ez a hővédelem segít megelőzni a túlmelegedést, ami ronthatja a teljesítményt és csökkentheti az érzékeny eszközök élettartamát. A hőmérséklet hatékony kezelésével a konform bevonatok hozzájárulnak az elektronika általános megbízhatóságához.
- Vegyi ellenállás: Sok konform bevonat kiváló vegyszerállóságot mutat. Gátat képeznek a korrozív anyagokkal, oldószerekkel, üzemanyagokkal és más vegyi anyagokkal szemben, amelyek leronthatják az elektronikus alkatrészeket. Ez a vegyszerállóság megakadályozza a kémiai reakciókat, az anyagok lebomlását és a zord környezetnek való kitettség vagy a vegyi anyagokkal való érintkezés által okozott esetleges meghibásodásokat.
- Rezgés- és ütésvédelem: A konform bevonatok mechanikai védelmet nyújtanak a rezgések elnyelésével és az ütések és a mechanikai igénybevételek hatásának csökkentésével. Ez különösen előnyös a szállítási vagy zord működési feltételeknek kitett elektronikus eszközök esetében. A konform bevonatok segítenek megelőzni a kényes alkatrészek, forrasztási kötések és csatlakozások károsodását azáltal, hogy minimalizálják a rezgések és ütések hatását.
- Könnyű ellenőrzés és javítás: A konform bevonatok gyakran átlátszóak vagy áttetszőek, lehetővé téve az alatta lévő alkatrészek szemrevételezését. Ez megkönnyíti az olyan lehetséges problémák könnyebb észlelését, mint a forrasztási hézag hibái, az alkatrészek sérülése vagy az idegen anyaggal való szennyeződés. Ezenkívül a megfelelő bevonatok eltávolíthatók és újra felhordhatók, ha javításra vagy módosításra van szükség, ami egyszerűsíti a karbantartást.
Hogyan működnek a konform bevonatok?
A konform bevonatok védőréteget képeznek az elektronikus alkatrészek és áramköri lapok felületén. Ezeket a bevonatokat jellemzően vékony, egyenletes rétegekben hordják fel, amelyek alkalmazkodnak az eszközök körvonalához, biztosítva a teljes fedést és védelmet. A bevonatok a felülethez tapadnak, és folyamatos filmet képeznek, amely megvéd a környezeti tényezőktől és a lehetséges szennyeződésektől.
A konform bevonatok felhordása több lépésből áll:
- Felület előkészítés: A megfelelő bevonat felhordása előtt az elektronikai egység felületét megfelelően elő kell készíteni. Ez általában a szennyeződések, például por, olajok és maradékok tisztítását és eltávolítását jelenti. A burkolatot oldószerrel, ultrahangos tisztítással vagy más megfelelő módszerrel lehet tisztítani, hogy tiszta és sima aljzatot biztosítsunk a bevonat tapadásához.
- Bevonatanyag kiválasztása: Különféle típusú konform bevonatok állnak rendelkezésre, mint például akrilok, szilikonok, uretánok és epoxik, mindegyiknek megvan a maga tulajdonságai és előnyei. A bevonat anyagának megválasztása olyan tényezőktől függ, mint a környezeti feltételek, a kívánt védelmi szint, az elektromos szigetelési követelmények és a speciális alkalmazási szempontok.
- Alkalmazási mód: A konform bevonatok különféle módszerekkel hordhatók fel, beleértve az ecsettel, szórással, mártással és szelektív bevonattal. Az alkalmazási mód kiválasztása olyan tényezőktől függ, mint az összeszerelés összetettsége, a bevonóanyag típusa és a kívánt pontosság. A kézi felhordási módszerek alkalmasak kisebb méretű gyártáshoz vagy meghatározott területekre, ahol célzott bevonat szükséges. A nagyobb léptékű gyártáshoz gyakran alkalmaznak automatizált eljárásokat, mint például a robotizált permetező vagy mártogató bevonatrendszereket, hogy biztosítsák a konzisztens és egyenletes bevonatfedést.
- Kikeményedés és száradás: A bevonat felhordása után kikeményedésnek vagy szárítási folyamatnak kell alávetni. Ez az eljárás lehetővé teszi a bevonóanyag megszilárdulását és védőfólia kialakítását. A kikeményedési idő és feltételek az adott bevonóanyagtól és a gyártó ajánlásaitól függenek. A kikeményedési módszerek közé tartozhat a levegőn történő szárítás, a hőkezelés kemencékben, vagy bizonyos típusú bevonatok esetében UV-fénynek való kitétel.
Felhordás és kikeményedés után a konform bevonat védőréteget hoz létre, amely befogja az elektronikus alkatrészeket. A réteg gátat képez a nedvességgel, porral, vegyi anyagokkal és egyéb környezeti tényezőkkel szemben, amelyek károsíthatják vagy lebonthatják az alkatrészeket. Segít megelőzni a korróziót, az elektromos rövidzárlatokat és a szigetelés meghibásodását, biztosítva az elektronikus eszközök megbízhatóságát és hosszú élettartamát.
A konform bevonatok idővel megőrzik védő tulajdonságaikat, folyamatos védelmet nyújtva az elektronikus összeszereléshez. Javítások vagy módosítások esetén a réteg szelektíven eltávolítható és újra felhordható, ami lehetővé teszi a karbantartást vagy a komponensek cseréjét anélkül, hogy a bevonat általános védelmét veszélyeztetné.
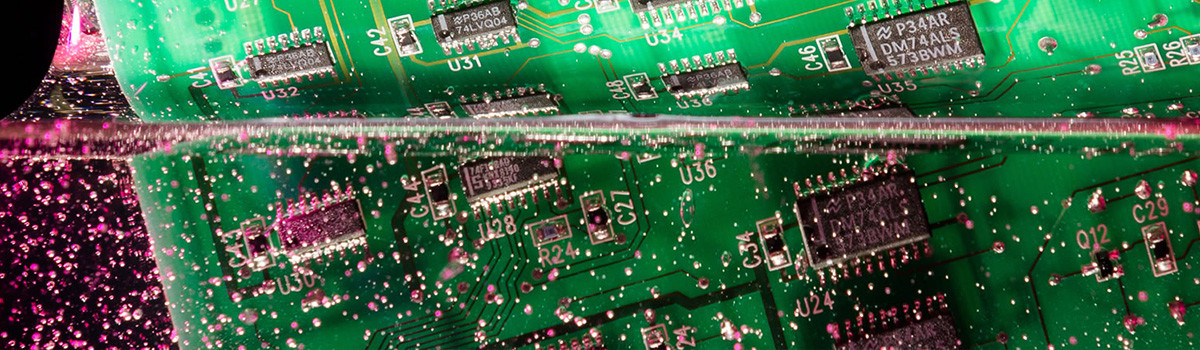
A konform bevonatok típusai
Többféle konform bevonat áll rendelkezésre, mindegyiknek megvan a maga tulajdonságai, előnyei és alkalmazásai. A bevonat típusának kiválasztása olyan tényezőktől függ, mint az elektronikus szerelvény speciális követelményei, a környezeti feltételek, a kívánt védelmi szint és a gyártási folyamatok. Íme néhány gyakran használt konform bevonat:
- Akril konform bevonatok: Sokoldalúságuk és költséghatékonyságuk miatt az akril bevonatok az egyik legszélesebb körben használt típusok. Jó nedvességállóságot, elektromos szigetelést és védelmet nyújtanak a környezeti tényezőkkel szemben. Az akril bevonatok könnyen felhordhatók, eltávolíthatók és átdolgozhatók. Különféle alkalmazásokhoz alkalmasak, és jó általános célú védelmet nyújtanak.
- Szilikon konform bevonatok: A szilikon bevonatok kiváló rugalmassággal, hőstabilitással és magas hőmérséklettel szembeni ellenállással rendelkeznek. Ellenállnak a szélsőséges hőmérsékleti ingadozásoknak anélkül, hogy elveszítenék védő tulajdonságaikat. A szilikon bevonatok kiváló nedvességállóságot és elektromos szigetelést biztosítanak. Gyakran használják olyan alkalmazásokban, ahol a nagy hőstabilitás és rugalmasság kritikus fontosságú, például autóiparban, repülőgépiparban és kültéri elektronikai eszközökben.
- Urethane Conformal bevonatok: Az uretán bevonatok kivételes vegyszerállóságot biztosítanak, így alkalmasak olyan alkalmazásokra, ahol az oldószereknek, üzemanyagoknak vagy más erős vegyi anyagoknak való kitettség aggodalomra ad okot. Jó nedvességvédelmet, elektromos szigetelést és mechanikai tartósságot biztosítanak. Az uretán bevonatokat gyakran használják igényes környezetben, például autóiparban, ipari és katonai alkalmazásokban.
- Epoxy Conformal bevonatok: Az epoxi bevonatok kiváló keménységükről és tartósságukról ismertek. Szilárd mechanikai védelmet, valamint kopás- és ütésállóságot kínálnak. Az epoxi bevonatok jó vegyszerállóságot és nedvességvédelmet biztosítanak. Általában olyan alkalmazásokban használatosak, amelyek erős védelmet és mechanikai szilárdságot igényelnek, például ipari vezérlőrendszerekben, robusztus elektronikában és nagy igénybevételű környezetekben.
- Parylene Conformal Coatings: A Parylene egy egyedülálló típusú konform bevonat, amely gőz formájában van lerakva, és vékony, tűlyukmentes polimer filmet képez. A Parylene rétegek kiváló nedvességzáró tulajdonságokat, elektromos szigetelést, vegyszerállóságot és biokompatibilitást biztosítanak. Magas szintű védelmet kínálnak, és megfelelnek az összetett geometriáknak. A parylene bevonatokat gyakran használják orvosi eszközökben, repülésben és érzékeny elektronikai alkalmazásokban.
- UV-keményíthető konform bevonatok: Az UV-re keményedő bevonatokat folyadékként hordják fel, majd UV-fénnyel térhálósítják. Gyors kikeményedési időt kínálnak, ami növelheti a termelés hatékonyságát. Az UV-sugárzással keményedő rétegek jó nedvességállóságot, elektromos szigetelést és vegyszerállóságot biztosítanak. Gyors kikeményedést, nagy áteresztőképességet és egyenletes bevonatminőséget igénylő alkalmazásokhoz alkalmasak.
Fontos megjegyezni, hogy a megfelelő konform bevonat kiválasztása az elektronikus szerelvény speciális követelményeitől és a tervezett alkalmazástól függ. A konform bevonat típusának kiválasztásakor figyelembe kell venni a környezeti feltételeket, az üzemi hőmérséklet-tartományt, a vegyi expozíciót és a kívánt védelmi szintet, hogy biztosítsák az elektronikus eszközök optimális teljesítményét és hosszú élettartamát.
Akril konform bevonatok
Az akril konform bevonatok széles körben használatosak az elektronikai iparban sokoldalúságuk, költséghatékonyságuk és egyszerű alkalmazásuk miatt. Számos előnyt biztosítanak, és alkalmasak különféle elektronikai összeállításokhoz és alkalmazásokhoz. Íme az akril konform bevonatok néhány fő jellemzője és előnyei:
- Nedvesség elleni védelem: Az akril bevonatok jó nedvességállóságot biztosítanak, így megakadályozzák a víz vagy nedvesség behatolását az elektronikus alkatrészekbe. A nedvesség korróziót, elektromos rövidzárlatot és a teljesítmény romlását okozhatja. Az akril bevonatok gátként működnek, védenek a nedvességgel kapcsolatos problémáktól, és növelik az elektronikus eszközök megbízhatóságát és élettartamát.
- Elektromos szigetelés: Az akril bevonatok elektromos szigetelést biztosítanak, megakadályozva az áramszivárgást és a rövidzárlatot. Segítenek megőrizni az alkatrészek kívánt elektromos jellemzőit, és csökkentik a szennyeződés vagy nedvességfelvétel által okozott elektromos meghibásodások vagy meghibásodások kockázatát. Ez az elektromos szigetelési tulajdonság elengedhetetlen az elektronikus áramkörök integritásának megőrzéséhez.
- Környezetvédelem: Az akril konform bevonatok védik az elektronikus részegységeket a környezeti tényezőktől, például portól, szennyeződéstől, vegyszerektől és hőmérséklet-ingadozásoktól. Gátat képeznek a levegőben lebegő szennyeződésekkel szemben, meggátolva azok lerakódását az alkatrészek felületén. Az akril bevonatok bizonyos fokú vegyszerállóságot is biztosítanak, így további védelmet nyújtanak a korrozív anyagokkal szemben.
- Könnyű felhordás: Az akril bevonatok könnyű felhordásukról ismertek. Különféle módszerekkel alkalmazhatók, beleértve az ecsettel, szórással, mártással vagy szelektív bevonattal. Ez a rugalmasság lehetővé teszi a kézi és automatizált alkalmazási folyamatokat, az egyedi követelményektől és a gyártási méretektől függően. Az akrilbevonatok általában jó nedvesítő képességgel rendelkeznek, egyenletes fedést és tapadást biztosítanak az elektronikus alkatrészek felületén.
- Javítási és utómunkálási képesség: Az akril bevonatok egyik előnye az újradolgozhatóságuk. Ha javításra vagy módosításra van szükség, az akril bevonatok könnyen eltávolíthatók megfelelő oldószerekkel, lehetővé téve az alatta lévő alkatrészek javítását. Az akrilbevonatok eltávolításának és újrafelvitelének lehetősége leegyszerűsíti a javítási folyamatot és megkönnyíti a karbantartási tevékenységeket.
- Átlátszó vagy áttetsző: Az akril konform bevonatok általában átlátszóak vagy áttetszőek. Ez a funkció lehetővé teszi az alatta lévő alkatrészek szemrevételezését a bevonat eltávolítása nélkül. A vizuális ellenőrzés azonosítja a lehetséges problémákat, például a forrasztási hézag hibáit, az alkatrészek sérülését vagy az idegen anyaggal való szennyeződést.
- Költséghatékonyság: Az akril konform bevonatok költséghatékony megoldást kínálnak az elektronikai egységek védelmére. Jól egyensúlyozzák a teljesítményt és a megfizethetőséget, így sokféle alkalmazásra alkalmasak. Az akrilbevonatok viszonylag alacsony költsége költséghatékony gyártási folyamatokat tesz lehetővé anélkül, hogy az elektronikus eszközök kívánt védelmét és megbízhatóságát veszélyeztetné.
Míg az akril konform bevonatok számos előnnyel járnak, a bevonat típusának kiválasztásakor elengedhetetlen, hogy figyelembe vegyék az elektronikai egység sajátos követelményeit és a környezeti feltételeket. Az optimális védelem és teljesítmény biztosítása érdekében figyelembe kell venni az olyan tényezőket, mint az üzemi hőmérséklet-tartomány, a kémiai expozíció és a mechanikai igénybevételek.
Szilikon konform bevonatok
A szilikon konform bevonatok széles körben használatosak az elektronikai iparban egyedülálló tulajdonságaik és a kihívást jelentő környezeti feltételeknek való ellenálló képességük miatt. Számos előnyt kínálnak, amelyek alkalmassá teszik őket különféle elektronikai összeállításokhoz és alkalmazásokhoz. Íme a konform szilikon bevonatok néhány fő jellemzője és előnyei:
- Hőstabilitás: A szilikon bevonatok kiváló hőstabilitásukról ismertek, lehetővé téve, hogy ellenálljanak a magas üzemi hőmérsékletnek anélkül, hogy elveszítenék védő tulajdonságaikat. Hatékonyabban kezelik a hőmérséklet-ingadozásokat, mint sok más konform bevonattípus. Emiatt a szilikon bevonatok kiválóan alkalmasak nagy hőstabilitású alkalmazásokhoz, például autóiparban, repülőgépiparban és ipari elektronikában.
- Rugalmasság és alkalmazkodóképesség: A szilikon konform bevonatok rendkívül rugalmasak, és képesek alkalmazkodni az összetett elektronikus szerelvények formájához. Vékony, egyenletes rétegekben alkalmazhatók, amelyek teljes fedést biztosítanak még bonyolult áramkörökön és alkatrészeken is. A szilikon bevonatok rugalmassága és alkalmazkodóképessége biztosítja a kritikus területek megfelelő védelmét, csökkentve a sérülések vagy meghibásodások kockázatát.
- Nedvesség és környezetvédelem: A szilikon bevonatok kiváló nedvességállóságot biztosítanak, így praktikus gátat képeznek a víz és a nedvesség behatolása ellen. Ez a nedvesség elleni védelem segít megelőzni a korróziót, az oxidációt és a nedvességgel kapcsolatos problémák által okozott elektromos rövidzárlatokat. A szilikon bevonatok ellenállnak az olyan környezeti tényezőknek is, mint a por, szennyeződés és vegyszerek, növelve az elektronikus eszközök élettartamát és megbízhatóságát.
- Elektromos szigetelés: A szilikon konform bevonatok elektromos szigetelési tulajdonságokat biztosítanak, megakadályozva az áramszivárgást és a rövidzárlatot. Megőrzik az alkatrészek elektromos integritását, és védelmet nyújtanak a szennyeződés vagy nedvességfelvétel okozta elektromos meghibásodások ellen. A szilikon bevonatok által kínált elektromos szigetelés kulcsfontosságú az elektronikus áramkörök megbízhatóságának és teljesítményének megőrzéséhez.
- Vegyi ellenállás: A szilikon bevonatok jól ellenállnak a különféle vegyszereknek, beleértve az oldószereket, üzemanyagokat, savakat és lúgokat. Ez a vegyszerállóság teszi a szilikon bevonatokat olyan alkalmazásokra, ahol aggodalomra ad okot a korrozív anyagoknak való kitettség. A rétegek védőgátként működnek, megakadályozzák a kémiai reakciókat és az anyagromlást, és biztosítják az elektronikus alkatrészek hosszú élettartamát.
- UV- és időjárásállóság: A szilikon bevonatok kiválóan ellenállnak az ultraibolya (UV) sugárzásnak és az időjárás viszontagságainak. Kibírják a hosszan tartó napfénynek és kültéri környezetnek való kitettséget anélkül, hogy jelentős mértékben romlanak vagy elveszítenék védő tulajdonságaikat. Ez teszi a szilikon bevonatokat ideálissá kültéri alkalmazásokhoz vagy UV sugárzásnak kitett elektronikus eszközökhöz.
- Dielektromos tulajdonságok: A szilikon konform bevonatok jó dielektromos tulajdonságokkal rendelkeznek, ami azt jelenti, hogy hatékony elektromos szigetelést biztosítanak anélkül, hogy jelentősen befolyásolnák az alkatrészek elektromos teljesítményét. Ez a tulajdonság elengedhetetlen a kívánt elektromos jellemzők megőrzéséhez és az elektronikus áramkörök elektromos meghibásodásának megakadályozásához.
A konform szilikon bevonatok különböző összetételekben állnak rendelkezésre, hogy megfeleljenek az egyedi alkalmazási követelményeknek. Különféle módszerekkel alkalmazhatók, beleértve az ecsettel, szórással vagy mártással. A szilikon bevonatok megbízható és tartós védőréteget biztosítanak az elektronikai szerelvények számára, biztosítva azok működőképességét és megbízhatóságát még zord üzemi körülmények között is.
A konform szilikon bevonatok mérlegelésekor az olyan tényezők értékelése, mint az üzemi hőmérséklet-tartomány, a vegyi anyagoknak való kitettség és a mechanikai igénybevétel, elengedhetetlen az adott alkalmazáshoz legmegfelelőbb bevonatformuláció meghatározásához.
Epoxi konform bevonatok
Az epoxi konform bevonatokat széles körben használják az elektronikában kiváló keménységük, tartósságuk és vegyszerállóságuk miatt. Számos előnyt kínálnak, amelyek alkalmassá teszik őket különféle elektronikai összeállításokhoz és alkalmazásokhoz. Íme az epoxi konform bevonatok néhány fő jellemzője és előnyei:
- Keménység és mechanikai védelem: Az epoxi bevonatok kivételes keménységet és mechanikai védelmet biztosítanak, így rendkívül ellenállóak a kopással, ütésekkel és fizikai sérülésekkel szemben. Robusztus gátat kínálnak, amely megvédi az elektronikus alkatrészeket a mechanikai igénybevételektől, biztosítva azok hosszú élettartamát és megbízhatóságát. Az epoxi bevonatok különösen alkalmasak fokozott automatikus védelmet igénylő alkalmazásokhoz, például ipari vezérlőrendszerekhez és robusztus elektronikához.
- Vegyi ellenállás: Az epoxi konform bevonatok kiválóan ellenállnak a különféle vegyszereknek, beleértve az oldószereket, üzemanyagokat, savakat és lúgokat. Ez a vegyszerállóság megvédi az elektronikus alkatrészeket a korrozív anyagoknak való kitettség által okozott leromlástól vagy károsodástól. Az epoxi bevonatok gátként működnek, megakadályozzák a kémiai reakciókat és biztosítják az alatta lévő komponensek integritását.
- Nedvesség és környezetvédelem: Az epoxi bevonatok megfelelő nedvesség- és környezetvédelmet biztosítanak. Gátat képeznek a vízzel, nedvességgel, porral és egyéb környezeti szennyeződésekkel szemben, amelyek károsíthatják az elektronikus alkatrészeket. Az epoxi bevonatok megakadályozzák a korróziót, az elektromos rövidzárlatokat és a teljesítmény romlását azáltal, hogy megakadályozzák a nedvesség bejutását.
- Elektromos szigetelés: Az epoxi konform bevonatok kiváló elektromos szigetelési tulajdonságokat kínálnak, megakadályozva az áramszivárgást és a rövidzárlatot. Fenntartják az alkatrészek kívánt elektromos jellemzőit, csökkentve a szennyeződés vagy nedvességfelvétel által okozott elektromos meghibásodások vagy meghibásodások kockázatát. Az epoxi bevonatok által biztosított elektromos szigetelés kulcsfontosságú az elektronikus áramkörök megbízhatóságának és teljesítményének megőrzéséhez.
- Hőállóság: Az epoxi bevonatok jó hőállósággal rendelkeznek, lehetővé téve, hogy ellenálljanak a megnövekedett hőmérsékletnek anélkül, hogy jelentős mértékben romlanak vagy elveszítenék a védő tulajdonságait. Segítenek elvezetni az elektronikus alkatrészek által termelt hőt, hozzájárulnak a hőkezeléshez és megakadályozzák a túlmelegedést. Ez a hőállóság teszi az epoxi bevonatokat olyan alkalmazásokra, ahol a hőmérséklet-ingadozások és a hőelvezetés kritikus szempontok.
- Tapadás és fedőképesség: Az epoxi konform bevonatok kiváló tapadást mutatnak különféle aljzatokhoz, beleértve a fémet, műanyagot és PCB anyagokat. Jól tapadnak az elektronikai szerelvények felületére, egységes és folyamatos védőréteget képezve. Az epoxi bevonatok teljes lefedettséget biztosítanak, biztosítva, hogy minden kritikus terület és alkatrész megfelelően védett legyen.
- Javíthatóság: Az epoxi bevonatok előnye, hogy újradolgozhatók és javíthatók. Ha javításra vagy módosításra van szükség, az epoxi bevonatok szelektíven eltávolíthatók megfelelő oldószerekkel, lehetővé téve az alatta lévő alkatrészek javítását. Ez a javíthatósági funkció leegyszerűsíti a karbantartási tevékenységeket, és szükség esetén megkönnyíti az alkatrészek cseréjét.
Az epoxikonformális bevonatokat általában ecsettel, szórással vagy szelektív bevonási módszerekkel hordják fel. A bevonatok kémiai reakcióval vagy hőkezelési eljárással kikeményednek, és tartós védőfóliát képeznek. Hosszan tartó védelmet nyújtanak az elektronikus szerelvények számára, biztosítva azok működőképességét és megbízhatóságát a kihívásokkal teli környezetben.
Az epoxikonformális bevonatok mérlegelésekor az olyan tényezők értékelése, mint az üzemi hőmérséklet-tartomány, a vegyszereknek való kitettség, a mechanikai igénybevételek, valamint a mechanikai és vegyi védelem kívánt szintje, elengedhetetlen az adott alkalmazáshoz legmegfelelőbb bevonat készítmény kiválasztásához.
Konform uretán bevonatok
Az uretán konform bevonatok, más néven poliuretán bevonatok kivételes vegyszerállóságuk és mechanikai tartósságuk miatt széles körben használatosak az elektronikai iparban. Számos előnyt kínálnak, amelyek alkalmassá teszik őket különféle elektronikai összeállításokhoz és alkalmazásokhoz. Íme az uretán konform bevonatok néhány fő jellemzője és előnyei:
- Vegyi ellenállás: Az uretán bevonatok ellenállnak a különféle vegyszereknek, beleértve az oldószereket, üzemanyagokat, olajokat, savakat és lúgokat. Ez a vegyszerállóság teszi az uretán bevonatokat olyan alkalmazásokhoz, ahol aggodalomra ad okot az agresszív vegyszereknek való kitettség. Gátként működnek, megvédik az elektronikus alkatrészeket a kémiai lebomlástól, a korróziótól és egyéb károsodásoktól.
- Nedvességvédelem: Az uretán konform bevonatok hatékony nedvességállóságot biztosítanak, megakadályozva a víz vagy nedvesség behatolását az elektronikus alkatrészekbe. A nedvesség korróziót, elektromos rövidzárlatot és a teljesítmény romlását okozhatja. Az uretán bevonatok gátként működnek, védenek a nedvességgel kapcsolatos problémáktól, és növelik az elektronikus eszközök megbízhatóságát és élettartamát.
- Mechanikai tartósság: Az uretán bevonatok kiváló mechanikai tartósságot biztosítanak, ellenállnak a kopásnak, az ütéseknek és a fizikai sérüléseknek. Kemény védőréteget biztosítanak, amely ellenáll a kemény kezelésnek és a környezeti feltételeknek. Az uretán bevonatok olyan alkalmazásokra alkalmasak, ahol fokozott mechanikai védelemre van szükség, például ipari környezetben vagy nagy kopásnak kitett eszközökben.
- Hőállóság: Az uretán bevonatok jó hőállósággal rendelkeznek, lehetővé téve, hogy ellenálljanak a megemelkedett hőmérsékletnek anélkül, hogy jelentős mértékben romlanak vagy elveszítenék a védő tulajdonságait. Segítenek elvezetni az elektronikus alkatrészek által termelt hőt, hozzájárulnak a hőkezeléshez és megakadályozzák a túlmelegedést. Ez a hőállóság teszi az uretán bevonatokat olyan alkalmazásokra, ahol a hőmérséklet-ingadozások és a hőelvezetés kritikus szempontok.
- Rugalmasság: Az uretán konform bevonatok egyensúlyt biztosítanak a keménység és a rugalmasság között. Van némi rugalmasságuk, ami lehetővé teszi számukra, hogy alkalmazkodjanak a kisebb mozgásokhoz és feszültségekhez az elektronikus egységben. Ez a rugalmasság segít csökkenteni a bevonat repedésének vagy leválásának kockázatát, biztosítva az alkatrészek hosszú távú védelmét.
- UV-stabilitás: Az uretán bevonatok jól ellenállnak az ultraibolya (UV) sugárzásnak, védve a napfény és más UV-források potenciálisan káros hatásaitól. Ellenállnak a sárgulásnak vagy lebomlásnak UV fény hatására, így alkalmasak kültéri használatra vagy UV sugárzásnak kitett eszközökre.
- Tapadás és fedettség: Az uretán bevonatok kiváló tapadást mutatnak különféle aljzatokhoz, beleértve a fémeket, műanyagokat és PCB anyagokat. Jól tapadnak az elektronikai szerelvények felületére, egységes és folyamatos védőréteget képezve. Az uretán bevonatok teljes lefedettséget biztosítanak, biztosítva, hogy minden kritikus terület és alkatrész megfelelően védett legyen.
Az uretán konform bevonatokat általában ecsettel, szórással vagy szelektív bevonási módszerekkel hordják fel. A rétegek hőkezeléssel vagy nedvességkötési eljárással kikeményíthetők, tartós és védőfóliát képezve. Hosszan tartó védelmet nyújtanak az elektronikus szerelvények számára, biztosítva azok funkcionalitását és megbízhatóságát igényes környezetben.
Az uretán konform bevonatok használatának mérlegelésekor elengedhetetlen a specifikus vegyi expozíció, az üzemi hőmérséklet-tartomány, a mechanikai igénybevételek, valamint a kémiai és mechanikai védelem kívánt szintjének értékelése, hogy az adott alkalmazáshoz a legmegfelelőbb bevonatkészítményt válasszuk ki.
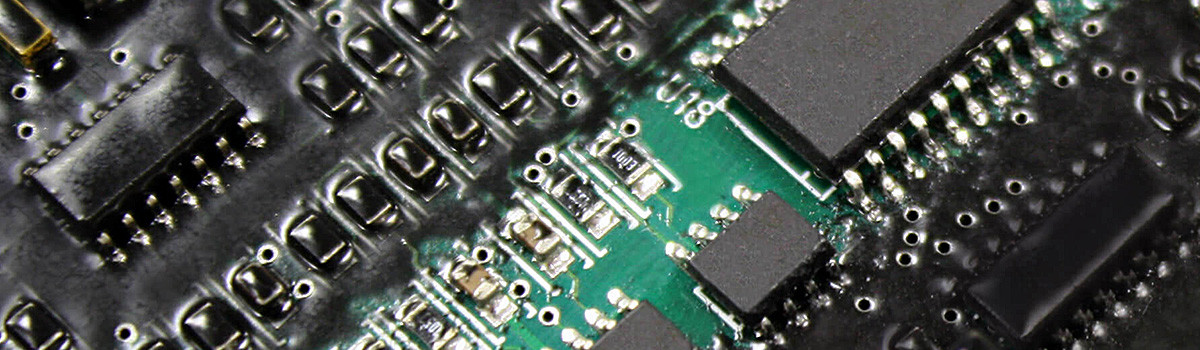
Parylene konform bevonatok
A Parylene konform bevonatok egyedülállóak és kivételes védelmet nyújtanak az elektronikus eszközök számára. A parilén bevonatok gőz formájában rakódnak le, és vékony, tűlyukmentes polimer filmet képeznek. Számos előnyt kínálnak, amelyek kiválóan alkalmassá teszik őket különféle elektronikai szerelvényekhez és alkalmazásokhoz. Íme a Parylene konform bevonatok legfontosabb jellemzői és előnyei:
- Nedvesség- és kémiai gát: A Parylene bevonatok kiváló védelmet nyújtanak a nedvességgel, gázokkal és vegyi anyagokkal szemben. A Parylene bevonatok által alkotott vékony, egyenletes film rendkívül hatékony nedvességzáró gátat biztosít, megakadályozva a víz és a nedvesség bejutását az elektronikus alkatrészekbe. Kivételes ellenállást biztosítanak a vegyszerekkel szemben is, beleértve az oldószereket, savakat, lúgokat és maró anyagokat. Ez a nedvesség- és vegyszerállóság megvédi az elektronikus eszközöket a korróziótól, az oxidációtól és a lebomlástól, így biztosítja azok hosszú távú megbízhatóságát.
- Konformitás és fedettség: A Parylene bevonatok kiemelkedő alakformáló tulajdonságokkal rendelkeznek, vagyis alkalmazkodnak az összetett és szabálytalan felületek formájához. A gőzleválasztási eljárás lehetővé teszi, hogy a réteg egyenletesen fedje le a teljes elektronikus szerelvényt, beleértve a bonyolult jellemzőket, az éles széleket és a repedéseket. A parylene bevonatok mélyen behatolnak szűk helyekre is, így biztosítva a teljes fedést és védelmet minden kritikus területen.
- Elektromos szigetelés: A Parylene konform bevonatok kiváló elektromos szigetelési tulajdonságokat biztosítanak. Nagy dielektromos szilárdsággal rendelkeznek, hatékonyan szigetelik az elektromos alkatrészeket, és megakadályozzák az áramszivárgást vagy a rövidzárlatot. A parylene bevonatok megőrzik a részletek kívánt elektromos jellemzőit, csökkentve a szennyeződés vagy nedvességfelvétel okozta elektromos meghibásodások vagy meghibásodások kockázatát.
- Biokompatibilitás: A Parylene bevonatok biológiailag kompatibilisek és kémiailag semlegesek, így alkalmasak orvosi eszközökhöz és beültethető elektronikához. Nem okoznak káros reakciókat, ha biológiai szövetekkel vagy folyadékokkal érintkeznek. A parylene bevonatokat olyan alkalmazásokban használják, mint például pacemakerek, idegi implantátumok és bioszenzorok, ahol a biokompatibilitás kritikus.
- Hőstabilitás: A Parylene bevonatok kiváló hőstabilitást mutatnak, és széles hőmérséklet-tartományban ellenállnak. Alacsony és magas hőmérsékleten is stabilak maradnak, jelentős lebomlás nélkül megőrzik védő tulajdonságaikat. Ez a hőstabilitás a Parylene bevonatokat alkalmassá teszi olyan alkalmazásokra, ahol a hőmérséklet-ingadozások és a hőelvezetés alapvető szempontok.
- Alacsony súrlódási együttható: A Parylene bevonatok alacsony súrlódási tényezőjűek, így biztosítják a kenést és csökkentik az alkatrészek közötti felületi súrlódást. Ez az alacsony súrlódási együttható segít minimalizálni a kopást, megakadályozni a ragadást vagy megtapadást, valamint javítja a bevonatos elektronikus eszközök általános teljesítményét és élettartamát.
- Átláthatóság és nyomon követhetőség: A Parylene konform bevonatok átlátszóak, lehetővé téve az alatta lévő alkatrészek szemrevételezését a bevonat eltávolítása nélkül. Ez az átlátszóság lehetővé teszi az olyan lehetséges problémák felmérését és azonosítását, mint a forrasztási kötések hibái, az alkatrészek sérülése vagy az idegen anyagokkal való szennyeződés. Ezenkívül a Parylene bevonatok adalékolhatók vagy nyomon követhető elemekkel jelölhetők, megkönnyítve a minőség-ellenőrzést, a nyomon követést és az azonosítást.
A konformális parylene bevonatokat általában speciális gőzleválasztási eljárással alkalmazzák. A rétegek kialakítása kémiai gőzleválasztásos (CVD) eljárással történik, amely egyenletes és lyukmentes fedést biztosít. A Parylene bevonatok hosszan tartó védelmet biztosítanak az elektronikus szerelvények számára, még zord környezetben és igényes alkalmazások esetén is.
A Parylene konform bevonatok mérlegelésekor alapvető fontosságú olyan tényezők értékelése, mint az elektronikus szerelvény speciális követelményei, a környezeti feltételek és a kívánt védelmi szint a megfelelő Parylene típus és leválasztási eljárás kiválasztásához.
Tényezők, amelyeket figyelembe kell venni a konform bevonat kiválasztásakor
Az elektronikus eszközök megfelelő bevonatának kiválasztásakor több tényezőt is figyelembe kell venni annak biztosítására, hogy a bevonat megfeleljen az alkalmazás speciális követelményeinek. Íme néhány kulcsfontosságú tényező, amelyet figyelembe kell venni:
- Környezeti feltételek: A környezeti feltételek, amelyek között az elektronikus eszköz működni fog, döntő szerepet játszanak a megfelelő konform bevonat kiválasztásában. Vegye figyelembe az olyan tényezőket, mint a szélsőséges hőmérséklet, páratartalom, vegyi expozíció, sópermet és UV-sugárzás. A különböző rétegek eltérő mértékben ellenállnak ezeknek a környezeti tényezőknek, és a hosszú távú megbízhatóság szempontjából elengedhetetlen egy olyan bevonat kiválasztása, amely ellenáll bizonyos feltételeknek.
- Elektromos tulajdonságok: Vegye figyelembe az elektronikus összeállításhoz szükséges elektromos tulajdonságokat. Egyes bevonatok jobb elektromos szigetelési tulajdonságokkal rendelkeznek, mint mások. Értékelje a dielektromos szilárdságot, a felületi ellenállást és a szigetelés fenntartásának képességét még nedvesség vagy szennyeződések jelenlétében is. Győződjön meg arról, hogy a kiválasztott bevonat nem befolyásolja negatívan az alkatrészek elektromos teljesítményét.
- Vastagság és fedés: A konform bevonat vastagságára és fedésére vonatkozó követelmények alapvető szempontok. A vékony rétegek olyan alkalmazásokban kívánatosak, ahol a korlátozott hely vagy a szoros tűrések fenntartása kritikus. Azonban vastagabb bevonatra lehet szükség az olyan alkalmazásokhoz, amelyek fokozott védelmet igényelnek a mechanikai igénybevétel vagy a zord környezet ellen. A rétegnek egységesen le kell fednie az összes kritikus területet, beleértve az összetett geometriákat és alkatrészeket is.
- Felhordási mód: Vegye figyelembe a rendelkezésre álló módszereket, és válasszon a kiválasztott móddal kompatibilis bevonatot. A szabványos felhordási módszerek közé tartozik a permetezés, ecsettel, merítéssel és szelektív bevonattal. Egyes rétegek jobban megfelelnek bizonyos felhordási módszereknek, míg mások speciális felszerelést vagy technikát igényelhetnek.
- Átdolgozás és javítás: Értékelje a bevonat átdolgozhatósági és javíthatósági követelményeit. Egyes esetekben a réteg eltávolítása vagy javítása szükséges lehet az alkatrészek cseréjéhez, javításához vagy módosításához. Egyes bevonatok könnyen átdolgozhatók vagy eltávolíthatók, míg mások nehezebbek lehetnek, vagy speciális oldószereket vagy módszereket igényelnek.
- Az alapfelület kompatibilitása: Vegye figyelembe a bevonat kompatibilitását az elektronikus összeszerelésben használt anyagokkal és hordozókkal. A bevonatnak hozzá kell tapadnia az aljzathoz, és jól kompatibilisnek kell lennie az alkatrészekkel, forrasztási kötésekkel és más anyagokkal. A kompatibilitási problémák leváláshoz, csökkent tapadáshoz vagy gyenge bevonatteljesítményhez vezethetnek.
- Szabályozási megfelelőség: Vegye figyelembe az elektronikus eszközre vagy az alkalmazási ágazatra vonatkozó speciális szabályozási követelményeket. A tipikus alkalmazások, például az orvosi eszközök vagy a repülőgép-elektronika speciális szabályozási szabványokkal rendelkezhetnek a megfelelő bevonatokra vonatkozóan. Győződjön meg arról, hogy a kiválasztott bevonat megfelel a vonatkozó előírásoknak és szabványoknak.
- Költség és elérhetőség: Értékelje a bevonat költségét és elérhetőségét a szükséges mennyiségben. Vegye figyelembe a bevonat költséghatékonyságát, a kívánt védelmi szintet és a projekt teljes költségvetését. Ezenkívül gondoskodjon arról, hogy a bevonat könnyen elérhető legyen megbízható beszállítóktól, hogy elkerülje a késéseket vagy az ellátási lánc problémáit.
Ezeket a tényezőket figyelembe véve olyan konform bevonatot választhat, amely optimális védelmet, teljesítményt és megbízhatóságot biztosít az elektronikus eszköz és a működési környezet specifikus követelményeihez.
Alkalmazási módok konform bevonatokhoz
A konform bevonatok vékony védőrétegek az elektronikus áramköri lapokon és alkatrészeken, hogy szigetelést biztosítsanak, és megvédjék azokat a környezeti tényezőktől, például nedvességtől, portól, vegyszerektől és hőmérséklet-ingadozásoktól. Ezeket a bevonatokat úgy tervezték, hogy „alkalmazkodjanak” az aljzat formájához, egységes és folyamatos védőréteget biztosítva. A konform bevonatok felvitelére számos módszer létezik, amelyek mindegyikének megvannak az előnyei és megfontolásai. Ez a cikk a konform bevonatok néhány szokásos alkalmazási módját vizsgálja meg.
- Ecsetelés/mártás: A kefés vagy bemártás az egyik legegyszerűbb és leghagyományosabb módszer a konform bevonatok felvitelére. A bevonóanyagot kézzel kefélik, vagy a komponenseket a bevonóoldatot tartalmazó edénybe mártják. Ez a módszer költséghatékony és alkalmas kis mennyiségű gyártásra. Ez azonban inkonzisztens bevonatvastagságot eredményezhet, és felhordás utáni kikeményítést igényelhet.
- Permetező bevonat: A permetezés során sűrített levegőt vagy speciális permetezőrendszert használnak a bevonóanyag finom köd formájában történő felhordásához az aljzatra. Ez a módszer gyorsabb alkalmazást tesz lehetővé, és alkalmas kézi és automatizált folyamatokhoz. A permetező bevonat jobban szabályozza a bevonat vastagságát és egyenletességét, de megfelelő szellőző- és szűrőrendszereket igényel a túlpermetezés szabályozása és a kezelő biztonsága érdekében.
- Szelektív bevonat: Szelektív bevonat akkor használatos, ha csak bizonyos aljzatterületek igényelnek védelmet. Ez magában foglalja egy vezérelt adagolórendszer vagy egy precíziós applikátorral ellátott robotkar használatát, hogy a bevonóanyagot pontosan a kívánt helyekre vigyék fel. A szelektív bevonat minimálisra csökkenti a veszteséget, csökkenti a maszkolás szükségességét, és célzott védelmet tesz lehetővé. Általában érzékeny alkatrészeket tartalmazó összetett áramköri kártyákhoz használják.
- Gőzleválasztás: A gőzfázisú leválasztási módszerek, mint például a kémiai gőzfázisú leválasztás (CVD) és a fizikai gőzfázisú leválasztás (PVD), egy konform bevonatréteget vonnak le a hordozóra egy gőzfázison keresztül. Ezek a módszerek jellemzően speciális berendezéseket és ellenőrzött környezetet igényelnek. A gőzleválasztási technikák kiváló bevonat egyenletességet, vastagságszabályozást és lefedettséget biztosítanak összetett geometriákon. Általában nagy teljesítményű alkalmazásokhoz és fejlett elektronikus eszközökhöz használják.
- Parylene bevonat: A Parylene bevonat egy egyedülálló módszer, amely egy vékony konform polimer filmréteget von fel az aljzatra gőzleválasztással. A Parylene bevonatok kivételes védelmet, szigetelést és biokompatibilitást kínálnak. A bevonóanyag behatol a résekbe, és egyenletesen befedi a teljes felületet, még bonyolult alkatrészeken is. A parylene bevonatokat gyakran használják orvosi eszközökben, repülésben és nagy megbízhatóságú alkalmazásokban.
A megfelelő bevonatok alkalmazási módjának kiválasztásakor több tényezőt is figyelembe kell venni, beleértve az aljzat összetettségét, a gyártási mennyiséget, a bevonóanyag tulajdonságait, a költségeket és a környezeti követelményeket. Elengedhetetlen az optimális bevonatfedést, egyöntetűséget és megbízhatóságot biztosító módszer kiválasztása, figyelembe véve az alkalmazás speciális igényeit.
Konform bevonatvastagság
A konform bevonat vastagsága kritikus az elektronikus alkatrészekre és áramköri lapokra alkalmazott védőbevonat hatékonyságának és megbízhatóságának biztosításában. A bevonat vastagsága közvetlenül befolyásolja a környezeti tényezők, például nedvesség, por, vegyszerek és hőmérséklet-ingadozások elleni védelem szintjét. Ez a cikk a megfelelő bevonatvastagság fontosságát és a kívánt bevonatvastagság elérésével kapcsolatos szempontokat fogja feltárni.
A konform bevonatok elsődleges célja, hogy egységes és folyamatos védőréteget hozzanak létre az aljzaton. A bevonat vastagságának elegendőnek kell lennie ahhoz, hogy szigetelést biztosítson, és megakadályozza az esetleges elektromos rövidzárlatokat vagy szivárgó áramokat, miközben nem lehet olyan vastag, hogy elektromos interferenciát vagy hőproblémát okozzon. Az ideális bevonatvastagság olyan tényezőktől függ, mint a bevonat anyaga, az adott alkalmazás és a környezeti feltételek, amelyekkel a bevont elektronika találkozik.
A konform bevonatokat általában vékony rétegként hordják fel, jellemzően néhány mikrométertől (µm) több tíz mikrométerig terjedő vastagságban. A bevonatanyag gyártója gyakran határozza meg az ajánlott bevonatvastagságot, vagy az ipari szabványok, például az IPC-CC-830 meghatározzák a megfelelő bevonatok esetében.
A kívánt bevonatvastagság eléréséhez több tényezőt is figyelembe kell venni:
- Bevonóanyag: A különböző konform bevonóanyagoknak eltérő viszkozitása és folyási jellemzői vannak. Ezek a tulajdonságok befolyásolják, hogy a bevonat hogyan oszlik el és hogyan oszlik el az aljzat felületén, befolyásolva a kapott vastagságot. Alapvető fontosságú a konkrét alkalmazási követelmények megértése és a kívánt vastagságszabályozással felhordható bevonóanyag kiválasztása.
- Felhordási mód: A választott felhordási mód a bevonat vastagságának meghatározásában is jelentős szerepet játszik. Az olyan gyakorlatok, mint az ecsettel vagy mártással, a bevonat vastagságának változását eredményezhetik a kézi felhordási technikák miatt. Az olyan automatizált eljárások, mint a permetezés vagy a szelektív bevonat, jobban szabályozhatják a bevonat vastagságát, egyenletesebb és egyenletesebb réteget eredményezve.
- Folyamatszabályozás: A megfelelő folyamatszabályozás kulcsfontosságú a kívánt bevonatvastagság eléréséhez. Az olyan tényezőket, mint a permetezési nyomás, a fúvóka mérete, a szórási távolság és a bevonóanyag viszkozitása, gondosan ellenőrizni kell a felhordási folyamat során. Előfordulhat, hogy a folyamat paramétereit módosítani kell az aljzat geometriája és a kívánt bevonatvastagság alapján.
- Kikeményedés/zsugorodás: Néhány konform bevonóanyag a felhordás után keményedési vagy száradási folyamaton megy keresztül. A bevonóanyag a folyamat során összezsugorodhat, ami befolyásolja a bevonat végső vastagságát. A kezdeti bevonatvastagság meghatározásakor feltétlenül figyelembe kell venni a lehetséges zsugorodást.
- Ellenőrzés és ellenőrzés: A bevonat felhordása után feltétlenül ellenőrizni kell a vastagságát, hogy megbizonyosodjon arról, hogy megfelel a szükséges előírásoknak. Különféle vizsgálati technikák használhatók, mint például a szemrevételezés, a keresztmetszetek, vagy speciális mérőberendezések, mint a profilométerek vagy az optikai mikroszkópia kalibrált mérőszoftverrel.
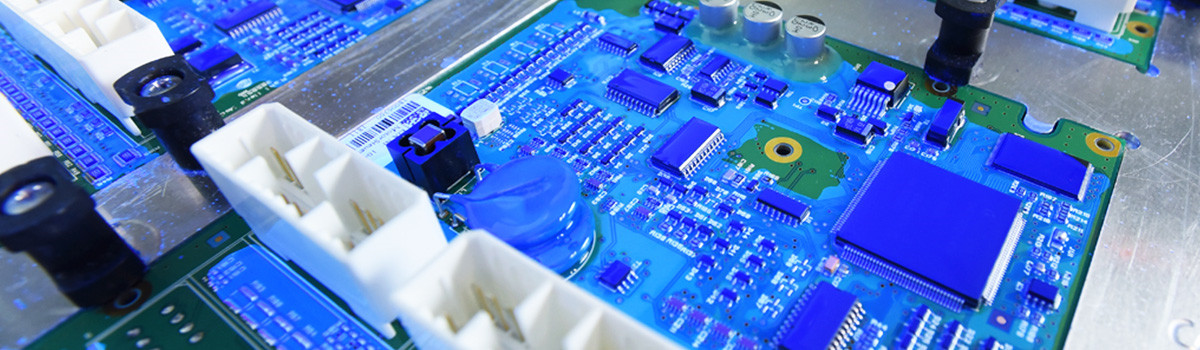
Gyakori problémák a konform bevonatokkal
Míg a megfelelő bevonatok elengedhetetlenek az elektronikus alkatrészek és az áramköri lapok védelméhez, időnként problémákba ütközhetnek, amelyek befolyásolhatják teljesítményüket és megbízhatóságukat. Ez a cikk a konform bevonatokkal kapcsolatos néhány gyakori problémát és azok lehetséges okait tárgyalja.
- Nem megfelelő fedés: Nem megfelelő fedés akkor fordul elő, ha a bevonat nem fedi le az aljzat teljes felületét, vagy hézagokat és üregeket hagy maga után. Ez a probléma a nem megfelelő felhordási technikákból eredhet, mint például az egyenetlen szórás vagy a bevonat elégtelen viszkozitása. Felszíni szennyeződés, nem megfelelő száradás vagy térhálósodás, vagy nem megfelelő bevonatvastagság-szabályozás miatt is előfordulhat.
- Vastagságváltozás: Egy másik gyakori probléma az egyenetlen bevonatvastagság. Az inkonzisztens felhordási technikák, mint például az egyenetlen permetezés vagy a folyamatparaméterek nem megfelelő ellenőrzése okozhatja. Több száradási vagy térhálósodási időre van szükség, a bevonóanyag nem megfelelő viszkozitása vagy a felület elégtelen előkészítése szintén hozzájárulhat a vastagság változásához.
- Hólyagosodás és rétegvesztés: Hólyagosodás és rétegválás akkor következik be, amikor a konform bevonat buborékokat képez, vagy elválik az aljzattól. Ezt a problémát a felület nem megfelelő tisztítása és előkészítése, a felület nedvessége vagy szennyeződése, nem megfelelő kikeményedés vagy száradás, illetve a bevonóanyag és az alapfelület nem megfelelő kompatibilitása okozhatja.
- Repedés és áthidalás: A repedés a konform bevonatban repedések vagy törések kialakulását jelenti, míg az áthidalás akkor következik be, amikor a bevonóanyag átnyúlik a hézagokon vagy a szomszédos alkatrészeken, ami nem kívánt elektromos csatlakozásokat eredményez. Ezeket a problémákat okozhatja a túlzott bevonatvastagság, a nem megfelelő térhálósodás vagy száradás, a termikus igénybevétel, a nem megfelelő bevonóanyag-választás vagy a bevonat nem megfelelő rugalmassága.
- Gyenge tapadás: Gyenge a tapadás, ha a bevonat nem tapad az aljzathoz, ami csökkenti a védelmet és a bevonat leválását. A felület nem megfelelő tisztítása és előkészítése, szennyeződések, összeférhetetlen bevonó-alapanyagok, vagy elégtelen kikeményedés vagy száradás okozhatja.
- Elektrokémiai migráció: Az elektrokémiai migráció az ionok vagy szennyeződések mozgása a bevont hordozó felületén, ami rövidzárlatokhoz és korrózióhoz vezethet. Előfordulhat nem megfelelő bevonatvastagság, vezetőképes szennyeződések jelenléte, illetve nedvesség vagy páratartalom miatt.
- Nem megfelelő vegyszerállóság: A konform bevonatoknak ellenállniuk kell a különféle vegyszereknek és oldószereknek. Ha a bevonóanyag nem rendelkezik kellő vegyszerállósággal, bizonyos anyagoknak kitéve lebomolhat vagy feloldódhat, ami veszélyezteti védőképességét. A megfelelő anyagválasztás kulcsfontosságú a várható kémiai környezettel való kompatibilitás biztosításához.
E problémák mérséklése érdekében elengedhetetlen a konform bevonat felvitelére vonatkozó legjobb gyakorlatok és irányelvek követése, beleértve a megfelelő felülettisztítást és -előkészítést, a folyamatparaméterek pontos ellenőrzését, a megfelelő bevonóanyag kiválasztását és a megfelelő kikeményedést vagy szárítást. Rendszeres ellenőrzési és minőség-ellenőrzési intézkedéseket kell végrehajtani a lehetséges bevonatproblémák korai felismerése és kezelése érdekében. Az ipari szabványok, például az IPC-CC-830 betartása szintén hozzájárulhat a megfelelő bevonatok megbízhatóságának és teljesítményének biztosításához.
Konform bevonatok karbantartása
A megfelelő bevonatok védik az elektronikus alkatrészeket és az áramköri lapokat a környezeti tényezőktől, például nedvességtől, portól, vegyszerektől és hőmérséklet-ingadozásoktól. Azonban, mint minden védőbevonat, a konform bevonatok is megfelelő karbantartást igényelnek, hogy biztosítsák hosszú távú hatékonyságukat. Íme néhány kulcsfontosságú szempont, amelyeket figyelembe kell venni a konform bevonatok karbantartásakor:
- Rendszeres ellenőrzés: Végezze el a bevont felületek rutinszerű ellenőrzését, hogy ellenőrizze a sérülés, kopás vagy rétegvesztés jeleit. Keressen repedéseket, forgácsokat vagy területeket, ahol a bevonat lekopott. Az ellenőrzéseket rendszeres időközönként el kell végezni, különösen kezelés, szállítás vagy zord körülményeknek való kitettség után.
- Tisztítás: Tartsa tisztán a bevont felületeket, hogy megakadályozza a szennyeződések felhalmozódását, amelyek veszélyeztethetik a bevonat hatékonyságát. Használjon kímélő tisztítási módszereket, például puha kefét vagy sűrített levegőt a por, törmelék vagy részecskék eltávolítására. Kerülje a durva oldószerek vagy dörzsölő anyagok használatát, amelyek károsíthatják a bevonatot.
- Sérült területek javítása: Ha az ellenőrzés során bármilyen sérülést vagy kopást észlelnek, akkor azt azonnal orvosolni kell. Javítsa meg a sérült területeket ugyanazzal a konform bevonóanyaggal. Az új bevonat felhordása előtt győződjön meg arról, hogy a sérült terület megfelelően meg van tisztítva és előkészítve. Ez segít megőrizni a védőréteg integritását.
- Hőmérséklet és páratartalom szabályozása: Fenntartja a megfelelő hőmérsékletet és páratartalmat abban a környezetben, ahol a bevont alkatrészeket tárolják vagy üzemeltetik. A szélsőséges hőmérséklet vagy a magas páratartalom befolyásolhatja a bevonat teljesítményét, és leváláshoz vagy csökkentett védelemhez vezethet. Kövesse a gyártó ajánlásait az adott konform bevonóanyag elfogadható hőmérsékleti és páratartalmi tartományaira vonatkozóan.
- Kerülje el a vegyszerekkel való érintkezést: Kerülje el, hogy a bevont felületeket durva vegyszerek vagy oldószerek érjék, amelyek ronthatják a bevonatot. Legyen óvatos, amikor tisztítószereket használ vagy karbantartási műveleteket végez a fedett alkatrészek közelében. Tegye meg a szükséges óvintézkedéseket, hogy megvédje a konform bevonatot a vegyi anyagokkal való közvetlen érintkezéstől.
- Újratesztelés és újratanúsítás: Egyes iparágakban, például a repülőgépiparban vagy az orvostudományban, a megfelelő bevonatok rendszeres újratesztelést és újratanúsítást igényelhetnek annak biztosítása érdekében, hogy megfeleljenek a szükséges szabványoknak és előírásoknak. Kövesse a vonatkozó ipari szabványok irányelveit, és rendszeres időközönként végezze el a szükséges vizsgálatokat vagy ellenőrzéseket.
- Dokumentáció és nyilvántartás: Vezessen részletes nyilvántartást a megfelelő bevonat felviteléről, a karbantartási tevékenységekről, az ellenőrzésekről és a javításokról. Ez a dokumentáció segít nyomon követni a karbantartási előzményeket, azonosítani a meghibásodásokat vagy kopási mintákat, és biztosítja az ipari előírásoknak és szabványoknak való megfelelést.
Konform bevonatok tesztelése és ellenőrzése
A megfelelő bevonatok tesztelése és ellenőrzése elengedhetetlen az elektronikus alkatrészek és részegységek védelmének hatékonyságának és megbízhatóságának biztosításához. Íme néhány általánosan használt módszer a konform bevonatok tesztelésére és ellenőrzésére:
- Szemrevételezés: A szemrevételezés elengedhetetlen lépés a megfelelő bevonatok minőségének értékelésében. Ez magában foglalja a bevonat felületének látható hibákat, például lyukakat, buborékokat, repedéseket vagy egyenetlen fedést.
- Vastagságmérés: A konform bevonat vastagsága döntő jelentőségű, mivel befolyásolja a megfelelő védelmet nyújtó képességét. A konzisztencia mérhető örvényáramú, mágneses indukciós vagy optikai profilometriai technikákkal. A mérést össze kell hasonlítani a meghatározott bevonatvastagsági követelményekkel.
- Tapadásvizsgálat: A tesztek a konform bevonat és az aljzat közötti tapadási szilárdságot értékelik. A tapadásvizsgálati módszerek közé tartoznak a szalagtesztek, a keresztirányú sraffozási tesztek és a lehúzási tesztek. Ezek a tesztek meghatározzák, hogy a réteg megfelelően tapad-e a felülethez, és ellenáll-e az üzemelés és kezelés során fellépő feszültségeknek.
- Szigetelési ellenállás vizsgálata: Ez a teszt a konform bevonat elektromos ellenállását értékeli. Biztosítja, hogy a réteg hatékony elektromos szigetelést biztosít a szivárgás vagy a rövidzárlat elkerülése érdekében. A szigetelési ellenállás vizsgálatát általában nagyfeszültségű teszterrel vagy megohmméterrel végzik.
- Dielektromos ellenállás-tesztelés: A dielektromos ellenállás-tesztelés, más néven nagy potenciál vagy hipoteteszt, ellenőrzi a bevonat azon képességét, hogy meghibásodás nélkül ellenáll-e a nagyfeszültségnek. A konform bevonatot meghatározott ideig meghatározott feszültségnek vetik alá annak biztosítása érdekében, hogy megfeleljen a szükséges elektromos szigetelési szabványoknak.
- Termikus ciklus tesztelése: A hőciklus a konform bevonatot hőmérséklet-ingadozásoknak teszi ki, hogy felmérje a hőterheléssel szembeni ellenállását. A réteget ismétlődő szélsőséges hőmérsékleti ciklusoknak vetik alá, és minden változást, például repedést vagy leválást megfigyelnek.
- Nedvesség- és nedvességállósági vizsgálat: Ezek a tesztek értékelik a konform bevonat nedvesség- és nedvességálló képességét. A réteg meghatározott ideig magas páratartalomnak vagy nedvességnek van kitéve, és teljesítményét a korrózió és az elektromos meghibásodások elleni védelem szempontjából értékelik.
- Vegyszerállósági vizsgálat: A vegyszerállósági vizsgálat azt ellenőrzi, hogy a konform bevonat mennyire ellenáll a különféle vegyi anyagoknak, például oldószereknek vagy tisztítószereknek. A réteget meghatározott ideig tesszük ki az anyagok hatásának, és megvizsgáljuk megjelenését, tapadását és működőképességét.
- Sóspray-teszt: A sóspray-teszt a bevonat korrózióállóságát sóval terhelt környezetben értékeli. A konform bevonatot meghatározott ideig sóködnek vagy ködnek teszik ki, és megvizsgálják a korrózió vagy a degradáció minden jelét.
Fontos megjegyezni, hogy a speciális vizsgálati követelmények az iparágtól, az alkalmazástól és a megfelelő bevonatra vonatkozó szabványoktól függően változhatnak. A gyártók vagy az ipari szabványügyi szervezetek gyakran adnak útmutatást vagy előírásokat a tesztelési és ellenőrzési eljárásokhoz.
A konform bevonatok ipari szabványai
Számos iparági szabvány és előírás létezik a megfelelő bevonatokra, hogy biztosítsák azok minőségét, megbízhatóságát és teljesítményét. Íme néhány gyakran hivatkozott szabvány:
- IPC-CC-830: Ezt a szabványt, amelyet az Association of Connecting Electronics Industries (IPC) adott ki, széles körben használják a megfelelő bevonóanyagokhoz és az alkalmazási követelményekhez. Tartalmazza a megfelelő bevonatok általános feltételeit, anyagtulajdonságait, felhordási módjait és ellenőrzési kritériumait.
- MIL-STD-883: Ez a katonai szabvány a mikroelektronikai eszközök vizsgálati módszereit és eljárásait írja le, beleértve a megfelelő bevonatokat is. Tartalmazza a tapadásra, a szigetelési ellenállásra, a hősokkra, a páratartalomra és a megfelelő bevonatokra vonatkozó egyéb tesztekre vonatkozó előírásokat.
- MIL-STD-810: Ez a szabvány környezetmérnöki szempontokat és laboratóriumi vizsgálati módszereket biztosít az anyagok, berendezések és rendszerek teljesítményének szimulálásához és értékeléséhez különféle környezeti feltételek mellett. Tartalmazza a megfelelő bevonatok vizsgálati eljárásait a hőmérséklet, páratartalom, vibráció, ütés stb.
- IEC 61086: Ez a nemzetközi szabvány az elektronikus szerelvényekben használt megfelelő bevonatok követelményeit és vizsgálati módszereit határozza meg. Lefedi a bevonó anyagokat, a vastagságot, a tapadást, a rugalmasságot, a hőállóságot és a vegyszerállóságot.
- UL 746E: Ez az Underwriters Laboratories (UL) által kiadott szabvány az elektromos berendezésekben használt polimer anyagok értékelésére összpontosít. Tartalmazza a megfelelő bevonatok vizsgálati követelményeit a gyúlékonyság, az öregedési jellemzők és az elektromos teljesítmény tekintetében.
- ISO 9001: Noha nem jellemző a megfelelő bevonatokra, az ISO 9001 a minőségirányítási rendszerek nemzetközileg elismert szabványa. Biztosítja, hogy a szervezetek következetes minőség-ellenőrzési folyamatokat kövessenek, beleértve a megfelelő bevonatok előállítását és ellenőrzését.
Fontos megjegyezni, hogy a különböző iparágaknak és alkalmazásoknak lehetnek egyedi szabványai vagy specifikációi, amelyek egyedi követelményeikhez igazodnak. Ezen túlmenően sok konform bevonat gyártó műszaki adatlapokat vagy alkalmazási útmutatókat biztosíthat, amelyek értékes referenciaként szolgálhatnak a megfelelő bevonat kiválasztásához és teszteléséhez.
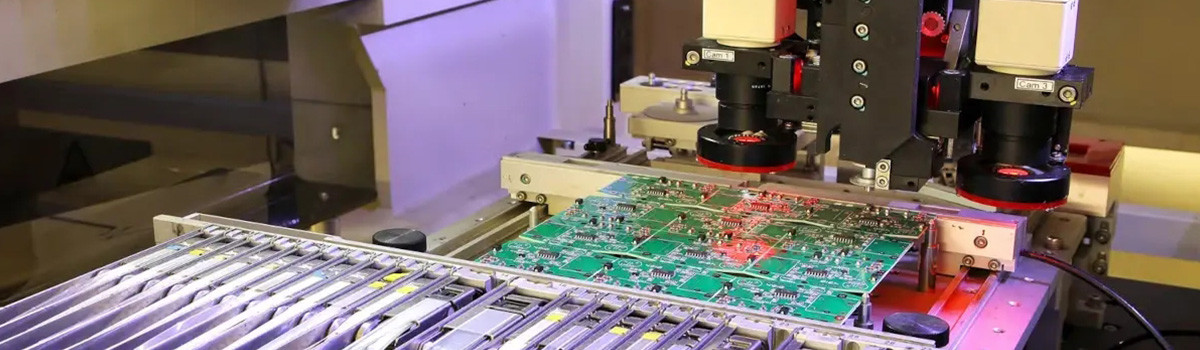
Fejlődés a konform bevonat technológiájában
Az elmúlt években jelentős előrelépések történtek a konform bevonat technológiájában, ami az elektronikus alkatrészek és szerelvények jobb védelmének, megbízhatóságának és teljesítményének szükségessége miatt következett be. Íme néhány főbb fejlesztés:
- Nanobevonatok: A nanobevonatok ígéretes előrelépésként jelentek meg a konform bevonat technológiájában. Ezek a bevonatok ultravékony, jellemzően nanoméretű rétegekből állnak, amelyek kiváló nedvesség- és korrózióállóságot biztosítanak, miközben megőrzik az elektromos teljesítményt. A nanobevonatok kiváló lefedettséget és konformitást biztosítanak, megfelelő védelmet biztosítva még bonyolult és sűrűn csomagolt elektronikus szerelvényeken is.
- Többfunkciós bevonatok: A többfunkciós tulajdonságokkal rendelkező, konform bevonatokat fejlesztik, hogy egyszerre több kihívást is kezeljenek. Például egyes bevonatok nedvesség- és vegyszerállóságot, valamint fokozott elektromos vezetőképességet vagy hőkezelési képességeket kínálnak. Ezek a többfunkciós bevonatok csökkentik a további védőrétegek szükségességét, és javítják az általános teljesítményt.
- Öngyógyuló bevonatok: Az öngyógyuló konform bevonatok a kisebb sérülések automatikus javítására szolgálnak. Ezek a bevonatok kapszulázott gyógyító anyagokat tartalmaznak, amelyek a sérülés hatására felszabadulnak, kitöltik a repedéseket vagy üregeket, és visszaállítják a bevonat védő tulajdonságait. Az öngyógyító bevonatok meghosszabbítják az elektronikai alkatrészek élettartamát azáltal, hogy mérséklik a kopás és a környezeti terhelés hatásait.
- Rugalmas és nyújtható bevonatok: A rugalmas elektronika és a hordható eszközök térnyerésével a konform bevonatoknak alkalmazkodniuk kell a hordozók hajlításához, nyújtásához és csavarodásához. A rugalmas és nyújtható rétegeket úgy fejlesztették ki, hogy robusztus védelmet nyújtsanak, miközben megőrzik épségüket mechanikai igénybevétel esetén is. Ezek a bevonatok konform lefedettséget tesznek lehetővé rugalmas aljzatokon, kibővítve az alkalmazások körét.
- Alacsony VOC-tartalmú és környezetbarát bevonatok: Egyre nagyobb hangsúlyt kapnak a csökkentett illékony szerves vegyületeket (VOC) tartalmazó konform bevonatok és a környezetbarát készítmények fejlesztése. Ezeknek a bevonatoknak az a célja, hogy minimálisra csökkentsék a környezetre gyakorolt hatást az alkalmazás és a használat során, miközben megőrzik a nagy teljesítményű jellemzőket. A hagyományos oldószerbázisú bevonatok alternatívájaként vízbázisú vagy oldószermentes bevonatokat fejlesztenek ki.
- UV-re keményedő bevonatok: Az UV-sugárzással keményedő konform bevonatok gyors kikeményedési időt biztosítanak, ami nagyobb teljesítményt tesz lehetővé a gyártási folyamatokban. Ezek a bevonatok ultraibolya (UV) fényt használnak a kikeményedési reakció elindításához, ami gyorsabb gyártási ciklust és csökkentett energiafogyasztást tesz lehetővé. Az UV-sugárzással keményedő bevonatok kiváló fedést és tapadást is biztosítanak, növelve a bevont szerelvények általános megbízhatóságát.
- Konformális bevonat-ellenőrzési technológiák: Az ellenőrzési technológiák fejlődése segít a konform bevonat minőségének és teljesítményének értékelésében. Az automatizált optikai ellenőrző (AOI) rendszerek nagy felbontású kamerákkal és képelemző algoritmusokkal képesek észlelni az olyan hibákat, mint a tűlyukak, buborékok vagy a bevonat vastagságának változásai. Ez javítja az ellenőrzés hatékonyságát és megbízhatóságát, biztosítva az egyenletes bevonatminőséget.
- Vékonyabb és könnyebb bevonatok: Az elektronikus eszközök miniatürizálása és könnyű kialakítása iránti kereslet a vékonyabb és könnyebb konform bevonatok kifejlesztését ösztönözte. Ezek a bevonatok megfelelő védelmet nyújtanak, miközben minimálisra csökkentik a bevont alkatrészek tömegére és méretére gyakorolt hatást. A vékonyabb rétegek jobb hőelvezetést is kínálnak, ami kritikus a nagy teljesítményű alkalmazásoknál.
Ezek a konform bevonat technológiai fejlesztések hozzájárulnak a megbízhatóbb és tartósabb elektronikus eszközök kifejlesztéséhez. Ahogy az elektronikai ipar folyamatosan fejlődik, a konform bevonatokkal kapcsolatos, folyamatban lévő kutatások és innovációk várhatóan választ adnak a felmerülő kihívásokra, és fokozott védelmet tesznek lehetővé a különböző alkalmazásokban.
Környezetvédelmi szempontok és megfelelő bevonatok
A környezeti szempontok jelentős szerepet játszanak a konform bevonatok kifejlesztésében és használatában. Mivel az elektronikai ipar folyamatosan növekszik, egyensúlyba kell hozni a konform bevonatok előnyeit a lehetséges környezeti hatásaival. Íme néhány kritikus szempont a környezetvédelmi szempontokkal és a megfelelő bevonatokkal kapcsolatban:
- Illékony szerves vegyületek (VOC): A hagyományos oldószer alapú konform bevonatok gyakran nagy mennyiségben tartalmaznak illékony szerves vegyületeket, ami hozzájárul a levegő szennyezéséhez és károsítja az emberi egészséget. Erre válaszul egyre nagyobb az igény az alacsony VOC-tartalmú vagy VOC-mentes készítmények iránt. A környezetterhelés csökkentésére alternatívaként vízbázisú és alacsony VOC-tartalmú bevonatokat fejlesztenek ki.
- Veszélyes anyagok: Egyes konform bevonatok veszélyes anyagokat, például nehézfémeket vagy perzisztens szerves szennyező anyagokat (POP) tartalmazhatnak. Ezeknek az anyagoknak hosszan tartó környezeti hatásai lehetnek, és kockázatot jelenthetnek a gyártás, az alkalmazás és az élettartam végén történő ártalmatlanítás során. Ennek megoldására a szabályozások és szabványok, például a veszélyes anyagok korlátozásáról szóló (RoHS) irányelv korlátozzák bizonyos veszélyes anyagok használatát az elektronikai termékekben.
- Életciklus-értékelés (LCA): Az életciklus-értékelés értékeli a megfelelő bevonatok környezeti hatásait azok teljes életciklusa során, a nyersanyag kitermelésétől az ártalmatlanításig. Segít azonosítani a javítandó területeket, és irányítja a környezetbarát rétegek kialakítását. Az LCA figyelembe veszi az energiafogyasztást, az erőforrások kimerülését, a kibocsátást és a hulladéktermelést.
- Környezetbarát készítmények: A konform bevonatok gyártói aktívan fejlesztenek környezetbarát készítményeket, amelyek minimálisra csökkentik a környezetre gyakorolt hatást. Ez magában foglalja a bioalapú anyagok, a megújuló erőforrások és a környezetbarát oldószerek használatát. A természetes forrásokból származó bioalapú bevonatok potenciális előnyöket kínálnak a csökkentett ökológiai lábnyom és a jobb fenntarthatóság tekintetében.
- Újrahasznosítás és hulladékkezelés: A megfelelő bevonatok megfelelő ártalmatlanítása és újrahasznosítása elengedhetetlen a környezetszennyezés megelőzéséhez. Az elektronikus alkatrészek és szerelvények újrahasznosítása során meg kell fontolni a megfelelő bevonatok eltávolítását vagy leválasztását a hatékony anyagvisszanyerés érdekében. Az újrahasznosítási technológiák és folyamatok fejlesztései segítenek a bevonat eltávolításával és a hulladékkezeléssel kapcsolatos kihívások kezelésében.
- Környezetvédelmi előírások: A szabályozási keretek és szabványok, mint például az Európai Unió vegyi anyagok regisztrálására, értékelésére, engedélyezésére és korlátozására vonatkozó rendelet (REACH) célja, hogy megvédje az emberi egészséget és a környezetet a potenciálisan káros anyagoktól. Ezen előírások betartása biztosítja, hogy a megfelelő bevonatok megfeleljenek a speciális környezetvédelmi követelményeknek és biztonsági szabványoknak.
- Fenntartható gyártási gyakorlatok: A fenntartható gyártási gyakorlatok alkalmazása csökkenti a megfelelő bevonatok előállításával kapcsolatos környezeti hatásokat. Ez magában foglalja az erőforrás-felhasználás optimalizálását, a hulladékkeletkezés minimalizálását, az energiahatékony folyamatok megvalósítását és a megújuló energiaforrások népszerűsítését.
- Környezetvédelmi tanúsítások: A környezetvédelmi tanúsítványok, mint például az ISO 14001, keretet biztosítanak a szervezetek számára környezeti teljesítményük irányításához és folyamatos javításához. A megfelelő bevonatok gyártói tanúsítványt kérhetnek, hogy bizonyítsák elkötelezettségüket a környezeti felelősségvállalás és a fenntartható gyakorlatok iránt.
Ahogy az ipar folyamatosan fejlődik, egyre nagyobb hangsúlyt kap a konform bevonatok fejlesztése, amelyek megfelelő védelmet nyújtanak, miközben minimálisra csökkentik környezeti hatásukat. A gyártók, a szabályozó testületek és a végfelhasználók együtt dolgoznak a környezetbarát bevonatok használatának előmozdításán és a felelős és fenntartható gyakorlatok biztosítása érdekében az elektronikai termékek teljes életciklusa során.
A konform bevonatok jövőbeli kilátásai az elektronikában
Az elektronikai konform bevonatok jövőbeli kilátásai ígéretesek a technológiai fejlődésnek, a nagy teljesítményű elektronikai eszközök iránti növekvő keresletnek és az iparágban kialakuló trendeknek köszönhetően. Íme néhány kulcsfontosságú szempont, amelyek a konform bevonatok jövőjét alakítják:
- Miniatürizálás és nagyobb integráció: A kisebb és kompaktabb, magasabb integrációs szinttel rendelkező elektronikus eszközök irányába mutató tendencia kihívások elé állítja a konform bevonatokat. A jövőbeni bevonatoknak megfelelő védelmet kell nyújtaniuk, miközben meg kell őrizniük sértetlenségüket a miniatürizált alkatrészeken és a sűrűn csomagolt szerelvényeken. Ez magában foglalja a vékonyabb rétegek fejlesztését, jobb fedettséggel és konformációval.
- Rugalmas és nyújtható elektronika: A rugalmas és nyújtható elektronika térnyerése, beleértve a hordható eszközöket is, olyan konform bevonatokat igényel, amelyek ellenállnak a mechanikai igénybevételnek és az ismételt hajlításnak anélkül, hogy veszélyeztetnék védő tulajdonságaikat. A jövőbeli rétegek a rugalmasságra, a tartósságra és a tapadásra fognak összpontosítani, hogy megfeleljenek ezeknek a feltörekvő alkalmazásoknak az egyedi követelményeinek.
- Speciális anyagok: A továbbfejlesztett tulajdonságokkal rendelkező új anyagok kifejlesztése a konform bevonatok jövőjét vezérli. Ez magában foglalja a nanoanyagok, például nanorészecskék és nanokompozitok használatát a bevonat teljesítményének javítására a nedvességállóság, az elektromos vezetőképesség, a hőkezelés és a záró tulajdonságok tekintetében. A fejlett anyagok lehetővé teszik, hogy a bevonatok megfeleljenek az elektronikus eszközök változó igényeinek.
- Többfunkciós bevonatok: Tovább fog nőni a kereslet a többfunkciós bevonatok iránt, amelyek a védelem mellett többféle előnnyel is járnak. A jövőbeli rétegek tartalmazhatnak öngyógyító képességeket, hővezető képességet, antisztatikus tulajdonságokat, antimikrobiális tulajdonságokat vagy energiagyűjtő tulajdonságokat. A többfunkciós bevonatok jobb teljesítményt, csökkentett összetettséget és nagyobb megbízhatóságot kínálnak az elektronikus szerelvényekben.
- Környezetvédelmi megfontolások: Az ökológiai fenntarthatóságra való összpontosítás és a veszélyes anyagokra vonatkozó előírások befolyásolják a megfelelő bevonatok jövőjét. Elterjedtebbé válik a környezetbarát, csökkentett VOC-tartalmú készítmények fejlesztése és a bioalapú anyagok használata. A megfelelő bevonatok újrahasznosítási és hulladékkezelési stratégiái szintén jelentős szerepet fognak játszani a környezeti hatások minimalizálásában.
- Fejlett felhordási technikák: Az alkalmazási technikák innovációi javítják a konform bevonatolási eljárások hatékonyságát és minőségét. Ez magában foglalja a robotizált adagolórendszereket, a szelektív bevonási módszereket és a fejlett permetezési technológiákat, amelyek biztosítják a precíz és egyenletes bevonatfedést, csökkentik az anyagpazarlást és javítják a termelékenységet.
- Speciális vizsgálati és tesztelési módszerek: Az elektronikus szerelvények összetettségének növekedésével kifinomultabb vizsgálati és vizsgálati módszerekre lesz szükség a megfelelő bevonatokhoz. Ez magában foglalja az automatizált optikai ellenőrző (AOI) rendszerek fejlesztését, amelyek fejlett képalkotási és elemzési képességekkel rendelkeznek a bevonathibák, a vastagságváltozások és a tapadási minőség észlelésére és értékelésére.
- Ipari szabványok és tanúsítványok: Az ipari szabványok és tanúsítványok folyamatos fejlesztése továbbra is formálja a megfelelő bevonatok jövőjét. A gyártók és a végfelhasználók a frissített szabványokra támaszkodnak, hogy biztosítsák a rétegek minőségét, megbízhatóságát, valamint a változó követelményeknek és előírásoknak való megfelelést.
Összességében a konform bevonatok jövője az elektronikában ígéretesnek tűnik, a jobb teljesítményre, az új technológiákhoz való alkalmazkodóképességre, a környezeti fenntarthatóságra, valamint a fejlett anyagok és alkalmazási technikák fejlesztésére összpontosítva. Ezek a fejlesztések lehetővé teszik, hogy a konform bevonatok robusztus védelmet nyújtsanak az elektronikus eszközök számára változatos és kihívásokkal teli környezetben.
Következtetés: A konformális elektronikus bevonatok kiváló megoldást kínálnak az elektronikus eszközök védelmére a környezeti tényezőktől, amelyek meghibásodásukhoz vagy meghibásodásukhoz vezethetnek. A technológia fejlődésével a hatékonyabb és megbízhatóbb konform bevonatok iránti igény csak növekedni fog. A gyártóknak, tervezőknek és mérnököknek lépést kell tartaniuk a terület legújabb fejlesztéseivel, hogy biztosítsák elektronikus eszközeik optimális védelmét. A konform bevonatok az elektronikai gyártási folyamat döntő részét képezik, és segíthetnek meghosszabbítani az elektronikai eszközök élettartamát és teljesítményét.