SMT මැලියම්

ඉලෙක්ට්රොනික නිෂ්පාදන නිෂ්පාදනයේ දිනෙන් දින පරිණාමය වෙමින් පවතින ලෝකය තුළ, මතුපිට සවි කිරීමේ තාක්ෂණය (SMT) මැලියම් ක්රීඩාව වෙනස් කරන්නෙකු ලෙස මතු වී තිබේ. මුද්රිත පරිපථ පුවරු (PCBs) මත ඉලෙක්ට්රොනික උපාංග බාධාවකින් තොරව ඒකාබද්ධ කිරීම සහතික කිරීම සඳහා මෙම උසස් මැලියම් තීරණාත්මක කාර්යභාරයක් ඉටු කරයි. නිෂ්පාදන විශ්වසනීයත්වය වැඩි දියුණු කිරීමේ සිට නිෂ්පාදන ක්රියාවලීන් විධිමත් කිරීම දක්වා, SMT මැලියම් නිෂ්පාදකයින් සඳහා අත්යවශ්ය මෙවලමක් බවට පත්ව ඇත. මෙම බ්ලොග් සටහන SMT මැලියම්වල විවිධ පැති සහ ඉලෙක්ට්රොනික කර්මාන්තයේ එහි වැදගත්කම ගවේෂණය කරනු ඇත.
SMT මැලියම් තේරුම් ගැනීම: කෙටි දළ විශ්ලේෂණයක්
මුද්රිත පරිපථ පුවරු (PCBs) වෙත මතුපිට සවි කිරීමේ උපාංග (SMDs) ඇමිණීම සඳහා ඉලෙක්ට්රොනික කර්මාන්තයේ SMT ඇලවුම් හෝ මතුපිට සවි කිරීමේ තාක්ෂණ මැලියම් භාවිතා වේ.
SMT මැලියම් සාමාන්යයෙන් කෘතිම දුම්මල, ද්රාවක සහ ආකලන වලින් සාදා ඇත. ඩිස්පෙන්සර් හෝ ස්ටෙන්සිල් භාවිතයෙන් මැලියම් PCB වෙත යොදනු ලැබේ. එවිට SMDs වියළීමට පෙර මැලියම් මත තබා ඇත.
ඉෙපොක්සි, ඇක්රිලික් සහ සිලිකොන් පාදක මැලියම් ඇතුළුව SMT මැලියම් වර්ග කිහිපයක් තිබේ. සෑම වර්ගයකටම එහි අද්විතීය ගුණාංග සහ වාසි ඇත. උදාහරණයක් ලෙස, ඉෙපොක්සි ඇලවුම් දව්ය ඉහළ ශක්තියක් සහ කල්පැවැත්මක් සඳහා ප්රසිද්ධ වන අතර ඇක්රිලික් මැලියම් විශිෂ්ට විදුලි පරිවාරක ගුණ ලබා දෙයි.
SMT මැලියම් SMT නිෂ්පාදනයේ සාර්ථකත්වය සඳහා ඉතා වැදගත් වේ, එය එකලස් කිරීමේ ක්රියාවලියේදී SMDs ස්ථානගත කිරීමට උපකාරී වේ. මැලියම් SMD වලට යාන්ත්රික සහාය ලබා දීමෙන් අවසාන නිෂ්පාදනයේ විශ්වසනීයත්වය සහ කල්පැවැත්ම වැඩි දියුණු කරයි.
SMT මැලියම් තෝරාගැනීමේදී තීරණාත්මක සලකා බැලීමක් වන්නේ එහි සුව කිරීමේ කාලයයි. Curing time යන්නෙන් අදහස් කරන්නේ මැලියම් සම්පූර්ණයෙන්ම දැඩි වීමට සහ PCB සහ SMD වෙත බන්ධනය වීමට අවශ්ය කාලයයි. ඇලවුම් වර්ගය සහ මැලියම් යොදන පාරිසරික තත්ත්වයන් අනුව සුව කිරීමේ කාලය වෙනස් විය හැක.
සුව කිරීමේ කාලයට අමතරව, SMT මැලියම් තෝරාගැනීමේදී සලකා බැලිය යුතු අනෙකුත් සාධක වන්නේ එහි දුස්ස්රාවීතාවය, තික්සොට්රොපි සහ තාප හා රසායනික ප්රතිරෝධයයි.
සමස්තයක් වශයෙන්, SMT මැලියම් යනු SMT නිෂ්පාදන ක්රියාවලියේ තීරණාත්මක අංගයක් වන අතර එය ඉලෙක්ට්රොනික උපාංගවල විශ්වසනීයත්වය සහ කල්පැවැත්ම සහතික කිරීමට උපකාරී වේ. සුදුසු මැලියම් තෝරාගැනීම SMT එකලස් කිරීමේ සාර්ථකත්වය සහතික කිරීමට සහ අවසාන නිෂ්පාදනයේ කාර්ය සාධනය වැඩි දියුණු කිරීමට උපකාරී වේ.
ඉලෙක්ට්රොනික නිෂ්පාදනයේදී SMT ඇලවුම් වල වැදගත්කම
SMT මැලියම් ඉලෙක්ට්රොනික නිෂ්පාදන නිෂ්පාදනයේදී, විශේෂයෙන්ම මුද්රිත පරිපථ පුවරු (PCBs) මත මතුපිට සවිකිරීම් උපාංග (SMDs) එකලස් කිරීමේදී ඉතා වැදගත් වේ. SMT මැලියම් භාවිතයෙන් SMDs PCB වෙත ආරක්ෂිතව සම්බන්ධ කර ඇති අතර, යාන්ත්රික සහාය ලබා දීම සහ අවසාන නිෂ්පාදනයේ විශ්වසනීයත්වය සහ කල්පැවැත්ම වැඩිදියුණු කිරීම සහතික කරයි.
SMT මැලියම්වල ඇති එක් ප්රධාන වාසියක් නම් එකලස් කිරීමේ ක්රියාවලියේදී SMD රඳවා තබා ගැනීමේ හැකියාවයි. අලවන ද්රව්ය නොමැතිව, නිෂ්පාදනයේදී SMD වලට මාරු වීමට හෝ චලනය වීමට හැකි වන අතර, එය අවසාන නිෂ්පාදනයේ දෝෂ හෝ අසාර්ථක වීමට හේතු වේ. SMT අලවන ද්රව්ය මෙම ගැටළු වළක්වා ගැනීමට SMDs PCB වෙත පාස්සන තෙක් රඳවා තබා ගැනීමට උපකාරී වේ.
SMT මැලියම් SMD වලට යාන්ත්රික සහාය ලබා දීමෙන් ඉලෙක්ට්රොනික උපාංග ක්රියාකාරිත්වය වැඩි දියුණු කිරීමට ද උපකාරී වේ. උපාංගය කම්පනය හෝ වෙනත් යාන්ත්රික ආතතීන්ට නිරාවරණය කළ හැකි යෙදුම් වලදී මෙය විශේෂයෙන් වැදගත් වේ. මැලියම් මෙම ආතතීන් අවශෝෂණය කර ගැනීමට සහ SMD වලට හානි වීම වැළැක්වීමට උපකාරී වේ, කාලයත් සමඟ උපාංගය නිවැරදිව ක්රියා කරන බව සහතික කරයි.
යාන්ත්රික ආධාරකයට අමතරව, SMT මැලියම් මගින් විද්යුත් පරිවාරක සහ තාප සන්නායකතා ගුණාංග සැපයිය හැකිය. SMDs තාපය ජනනය කරන යෙදුම් වලදී මෙය වැදගත් වේ, මැලියම් මගින් මෙම තාපය විසුරුවා හැරීමට සහ උපාංගයට අධික උනුසුම් වීම සහ හානි වැළැක්වීමට උපකාරී වේ.
ඉලෙක්ට්රොනික නිෂ්පාදනයේ සාර්ථකත්වය සඳහා සුදුසු SMT මැලියම් තෝරාගැනීම ඉතා වැදගත් වේ. ඇලවුම් ද්රව්යයක් තෝරාගැනීමේදී සුව කිරීමේ කාලය, දුස්ස්රාවීතාව, තික්සෝට්රොපි සහ රසායනික හා තාප ප්රතිරෝධය වැනි සාධක සලකා බැලිය යුතුය. වැරදි ඇලවුම් තෝරා ගැනීම අවසාන නිෂ්පාදනයේ දෝෂ හෝ අසාර්ථක වීමට හේතු විය හැකි අතර එය මිල අධික හා කාලය ගත විය හැකිය.
SMT ඇලවුම් වර්ග: ප්රභේද පිළිබඳ දළ විශ්ලේෂණයක්
SMT (Surface Mount Technology) මැලියම් වර්ග කිහිපයක් තිබේ, ඒ සෑම එකක්ම එහි අද්විතීය ගුණාංග සහ වාසි ඇත. නිවැරදි ඇලවුම් වර්ගය තෝරාගැනීම බන්ධනය කළ යුතු මතුපිට වර්ග, පාරිසරික තත්ත්වයන් සහ සුව කිරීමේ කාලය ඇතුළුව යෙදුමේ නිශ්චිත අවශ්යතා මත රඳා පවතී.
- ඉෙපොක්සි ඇලවුම්: ඉෙපොක්සි මැලියම් යනු ඉෙලක්ෙටොනික් නිෂ්පාදනෙය් බහුලව භාවිතා වන SMT මැලියම් වේ. ඔවුන් ඉහළ ශක්තියක් සහ විශිෂ්ට කල්පැවැත්මක් ලබා දෙයි, යාන්ත්රික ආතතිය සහ ඉහළ උෂ්ණත්වයන් අපේක්ෂා කරන යෙදුම් සඳහා ඒවා වඩාත් සුදුසු වේ. ඉෙපොක්සි අලවන ද්රව්ය ඉක්මනින් සුව වන අතර එමඟින් ඒවා ඉහළ පරිමාණ නිෂ්පාදන පරිසරයන් සඳහා වඩාත් කැමති තේරීමක් කරයි.
- ඇක්රිලික් මැලියම්: ඇක්රිලික් මැලියම් ඒවායේ විශිෂ්ට විද්යුත් පරිවාරක ගුණ සඳහා ප්රසිද්ධය. ඒවා හොඳ බන්ධන ශක්තියක් ලබා දෙන අතර කාමර උෂ්ණත්වයේ දී සුව කළ හැකි අතර, ඉහළ උෂ්ණත්වයන් අවශ්ය නොවන යෙදුම් සඳහා ඒවා සුදුසු වේ. ඇක්රිලික් මැලියම් තෙතමනය, රසායනික ද්රව්ය සහ පාරජම්බුල කිරණ වැනි පාරිසරික සාධකවලටද ප්රතිරෝධය දක්වයි.
- සිලිකොන් මැලියම්: සිලිකොන් මැලියම් විශිෂ්ට නම්යශීලී බවක් ලබා දෙයි, තාප ප්රසාරණය සහ හැකිලීම අපේක්ෂා කරන යෙදුම් සඳහා ඒවා වඩාත් සුදුසු වේ. ඔවුන් තෙතමනය, රසායනික ද්රව්ය සහ UV විකිරණ සඳහා හොඳ ප්රතිරෝධයක් ද සපයයි. කෙසේ වෙතත්, සිලිකොන් ඇලවුම් ඉෙපොක්සි සහ ඇක්රිලික් ඇලවුම් වලට වඩා අඩු බන්ධන ශක්තියක් ඇත.
- පාරජම්බුල කිරණ සුව කළ හැකි මැලියම්: පාරජම්බුල කිරණවලට නිරාවරණය වන විට UV සුව කළ හැකි මැලියම් සුව කරයි, වේගවත් සුව කිරීම අවශ්ය යෙදුම් සඳහා ඒවා වඩාත් කැමති තේරීමක් කරයි. ඒවා විශිෂ්ට බන්ධන ශක්තියක් ලබා දෙන අතර ඉහළ උෂ්ණත්වය සහ යාන්ත්රික ආතතිය අපේක්ෂා නොකරන යෙදුම් සඳහා වඩාත් සුදුසු වේ.
- Hot Melt ඇලවුම්: Hot Melt මැලියම් යනු උණු කළ තත්වයකට රත් කර මතුපිටට යොදන තාප ප්ලාස්ටික් ද්රව්ය වේ. ඔවුන් ඉක්මනින් සුව වන අතර හොඳ බන්ධන ශක්තියක් ලබා දෙයි. කෙසේ වෙතත්, ඉහළ උෂ්ණත්වයන් අපේක්ෂා කරන යෙදුම් සඳහා ඒවා සුදුසු නොවේ.
SMT මැලියම් තෝරාගැනීමේදී සලකා බැලිය යුතු සාධක
නිවැරදි SMT (Surface Mount Technology) මැලියම් තෝරාගැනීම ඉලෙක්ට්රොනික නිෂ්පාදනයේ සාර්ථකත්වය සඳහා ඉතා වැදගත් වේ. බැඳුම්කරයක් තෝරාගැනීමේදී සාධක කිහිපයක් සලකා බැලිය යුතුය, ඒවා අතර:
- උපස්ථර ද්රව්ය: බන්ධනය කළ යුතු උපස්ථර වර්ග භාවිතා කළ යුතු මැලියම් වර්ගය තීරණය කිරීමේදී තීරණාත්මක කාර්යභාරයක් ඉටු කරයි. වීදුරු, සෙරමික් හෝ ලෝහ වැනි විශේෂිත ද්රව්ය බන්ධනය කිරීම සඳහා සමහර මැලියම් වඩාත් සුදුසු වේ.
- පාරිසරික තත්ත්වයන්: අවසාන නිෂ්පාදනය භාවිතා කරන පරිසරය ද සලකා බැලිය යුතුය. උෂ්ණත්වය, ආර්ද්රතාවය සහ රසායනික ද්රව්යවලට නිරාවරණය වීම වැනි සාධක මැලියම්වල ක්රියාකාරිත්වයට බලපායි. විශේෂිත පාරිසරික තත්ත්වයන්ට ඔරොත්තු දෙන මැලියම් තෝරා ගැනීම අත්යවශ්ය වේ.
- සුව කිරීමේ කාලය: මැලියම්වල සුව කිරීමේ කාලය සැලකිල්ලට ගත යුතු අත්යවශ්ය සාධකයකි. සුව කිරීමේ කාලය නිෂ්පාදනයේ නිෂ්පාදන චක්රය සමඟ අනුකූල විය යුතුය. ඉක්මන් සුව කරන මැලියම් ඉහළ පරිමාවකින් යුත් නිෂ්පාදන පරිසරයන් සඳහා සුදුසු වේ. ඊට ප්රතිවිරුද්ධව, අඩු ප්රමාණයේ නිෂ්පාදනය සඳහා මන්දගාමී සුව කිරීමේ මැලියම් සුදුසු විය හැක.
- දුස්ස්රාවීතාවය සහ තික්සොට්රොපි: මැලියම්වල ඝනකම සහ තික්සෝට්රොපි සලකා බැලිය යුතු තීරණාත්මක සාධක වේ, විශේෂයෙන් කුඩා කොටස් හෝ අසමාන මතුපිට බන්ධනය කිරීමේදී. කුඩා සංරචක සම්බන්ධ කිරීම සඳහා අඩු දුස්ස්රාවිතතාවයකින් යුත් මැලියම් සුදුසු වේ. ඊට ප්රතිවිරුද්ධව, ඉහළ thixotropy සහිත මැලියම් අසමාන පෘෂ්ඨයන් බන්ධනය කිරීම සඳහා සුදුසු වේ.
- රසායනික සහ තාප ප්රතිරෝධය: නිෂ්පාදනයේ ජීවන චක්රය තුළ අපේක්ෂිත රසායනික ද්රව්ය සහ තාප තත්ත්වයට මැලියම් ප්රතිරෝධය දැක්විය යුතුය. මෙය විශේෂයෙන් වැදගත් වන්නේ අධි-උෂ්ණත්ව යෙදුම් වලදී, මැලියම් අධික තාපයට සහ තාප බයිසිකල් පැදීමේදී ඔරොත්තු දිය යුතුය.
- අයදුම් කිරීමේ ක්රමය: අයදුම් කිරීමේ ක්රමය සලකා බැලිය යුතු තවත් තීරණාත්මක සාධකයකි. සමහර ඇලවුම් ද්රව්ය ඩිස්පෙන්සර් භාවිතයෙන් යොදන අතර අනෙක් ඒවා ස්ටෙන්සිල් මුද්රණය හෝ ජෙට් බෙදා හැරීමේ ක්රම භාවිතා කරයි. තෝරාගත් මැලියම් යෙදුම් ක්රමයට අනුකූල විය යුතුය.
සංරචක ස්ථානගත කිරීමේදී SMT මැලියම්වල කාර්යභාරය
මතුපිට සවි කිරීමේ තාක්ෂණය (SMT) ඉලෙක්ට්රොනික නිෂ්පාදනයේ සංරචක ස්ථානගත කිරීමේදී මැලියම් ඉතා වැදගත් වේ. මුද්රිත පරිපථ පුවරුවේ (PCB) මතුපිටට අලවන ද්රව්ය පෑස්සීමට පෙර කොටස් රඳවා තබා ගැනීම සඳහා යොදනු ලැබේ.
සංරචක ස්ථානගත කිරීමේදී SMT මැලියම්වල තීරණාත්මක භූමිකාවන් පහත දැක්වේ:
- ආරක්ෂිත සංරචක ස්ථානගත කිරීම: SMT මැලියම් PCB මත සංරචක සුරක්ෂිත කරයි. සංරචක ඉතා කුඩා සහ සැහැල්ලු වන අතර නිෂ්පාදනයේදී චලනය වීමට හෝ මාරු වීමට ඉඩ ඇති නිසා මෙය වැදගත් වේ. අලවන ද්රව්යය සංරචක නිසි තැන තබා ගැනීමට සහ ඒවා පුවරුවෙන් යාමෙන් හෝ වැටීමෙන් වළක්වා ගැනීමට උපකාරී වේ.
- සොල්ඩර් පාලම් වැළැක්වීම: ඉලෙක්ට්රොනික නිෂ්පාදනයේ පොදු ගැටළුවක් වන පෑස්සුම් පාලම වැළැක්වීම සඳහා SMT මැලියම් ද භාවිතා වේ. අනපේක්ෂිත සම්බන්ධතාවයක් යාබද පෑස්සුම් සන්ධි දෙකක් එකට එකතු වූ විට පෑස්සුම් පාලම සිදු වේ. මෙය කෙටි පරිපථයක් හා සංරචක වලට හානි විය හැක. මැලියම් සංරචක වෙන් කර තබා ගැනීමට සහ පෑස්සුම් පාලම වැළැක්වීමට උපකාරී වේ.
- Solder Joint Quality වැඩි දියුණු කරන්න: SMT මැලියම් මගින් පෑස්සුම් සන්ධියේ ගුණාත්මකභාවය වැඩි දියුණු කළ හැකිය. ඇලවුම් ද්රව්යය කෑලි තබා ඇති අතර, පෑස්සුම් ක්රියාවලියේදී චලනය වීමේ අවදානම අඩු කරයි. මෙය වඩාත් ස්ථාවර සහ විශ්වසනීය පෑස්සුම් සන්ධියක් ඇති කරයි.
- නිෂ්පාදන කාර්යක්ෂමතාව වැඩි දියුණු කිරීම: SMT මැලියම් නිෂ්පාදන කාර්යක්ෂමතාව වැඩි දියුණු කළ හැක. සංරචක PCB මත තැබීමට පෙර මැලියම් යොදනු ලැබේ, එය අතින් පෙළගැස්වීම සහ ස්ථානගත කිරීම සඳහා අවශ්ය කාලය අඩු කරයි. මෙය වේගවත් හා වඩා කාර්යක්ෂම නිෂ්පාදන ක්රියාවලියක් ඇති කරයි.
- නිෂ්පාදන විශ්වසනීයත්වය වැඩි දියුණු කරන්න: SMT මැලියම් අවසන් නිෂ්පාදනයේ විශ්වසනීයත්වය වැඩි දියුණු කළ හැකිය. නිෂ්පාදන ක්රියාවලියේදී සංරචක රඳවා තබා ගැනීමෙන්, විස්තර නිවැරදිව පෙළගස්වා ඇති බව සහ PCB වෙත ආරක්ෂිතව සම්බන්ධ කර ඇති බව සහතික කිරීමට මැලියම් උපකාරී වේ. මෙය චලනය හෝ කම්පනය හේතුවෙන් සංරචක අසමත් වීමේ හෝ අක්රිය වීමේ අවදානම අඩු කරයි.
SMT මැලියම් සමඟ ශක්තිමත් සහ විශ්වාසනීය බන්ධන ලබා ගැනීම
SMT (Surface Mount Technology) මැලියම් සමඟ ඝන සහ විශ්වාසනීය බන්ධන ලබා ගැනීම ඉලෙක්ට්රොනික නිෂ්පාදනයේ සාර්ථකත්වය සඳහා ඉතා වැදගත් වේ. SMT ඇලවුම් ද්රව්ය මුද්රිත පරිපථ පුවරුවක (PCB) ඒවා පෑස්සීමට පෙර ස්ථානගත කරයි. SMT මැලියම් සමඟ ඝන සහ විශ්වාසනීය බන්ධන ලබා ගැනීම සඳහා උපදෙස් කිහිපයක් මෙන්න:
- නිවැරදි මැලියම් තෝරන්න: සුදුසු SMT මැලියම් තෝරාගැනීම අත්යවශ්ය වේ. මැලියම් තෝරාගැනීමේදී සලකා බැලිය යුතු සාධක වන්නේ උපස්ථර ද්රව්ය, පාරිසරික තත්ත්වයන්, සුව කිරීමේ කාලය, දුස්ස්රාවීතාවය, තික්සොට්රොපි, රසායනික හා තාප ප්රතිරෝධය සහ යෙදුම් ක්රමය ඇතුළත් වේ. ව්යාපෘතියේ නිශ්චිත අවශ්යතා සමඟ ගැලපෙන සීලන්ට් එකක් තෝරා ගැනීම ශක්තිමත් සහ විශ්වාසනීය බැඳීමක් සහතික කිරීමට උපකාරී වේ.
- මතුපිට සකස් කරන්න: PCB මතුපිට පිරිසිදු විය යුතු අතර තෙල්, අපිරිසිදු සහ දූවිලි වැනි දූෂක වලින් තොර විය යුතුය. පිරිසිදු කිරීමේ කාරකයක් සහ ලින්ට් රහිත රෙදි හෝ ප්ලාස්මා ක්ලීනර් භාවිතයෙන් මෙය සාක්ෂාත් කරගත හැකිය. ශක්තිමත් සහ විශ්වාසනීය බැඳීමක් සාක්ෂාත් කර ගැනීම සඳහා නිසි මතුපිට සකස් කිරීම ඉතා වැදගත් වේ.
- මැලියම් නිවැරදිව යොදන්න: මැලියම් නිවැරදි ප්රමාණයෙන් සහ නිවැරදි ස්ථානයේ යෙදිය යුතුය. මැලියම් යෙදීම සඳහා සිරින්ජ, ඉඳිකටු සහ ඩිස්පෙන්සර් වැනි බෙදා හැරීමේ උපකරණ භාවිතා කළ හැකිය. සංරචක ආරක්ෂිතව තබා ඇති බව සහතික කිරීම සඳහා මැලියම් ඒකාකාරව හා නිවැරදි ප්රමාණයෙන් යෙදිය යුතුය.
- නිසි සුව කිරීම සහතික කරන්න: සංරචක පෑස්සීමට පෙර මැලියම් වලට සුව කිරීමට ප්රමාණවත් කාලයක් ලබා දිය යුතුය. ඇලවුම් සහ පාරිසරික තත්ත්වයන් අනුව සුව කිරීමේ කාලය වෙනස් විය හැක. නිසි පිළියමක් සහතික කිරීම සඳහා නිෂ්පාදකයාගේ උපදෙස් අනුගමනය කරන්න.
- පාරිසරික තත්ත්වයන් නිරීක්ෂණය කරන්න: නිෂ්පාදන පරිසරයේ පාරිසරික තත්ත්වයන් මැලියම්වල ක්රියාකාරිත්වයට බලපෑම් කළ හැකිය. උෂ්ණත්වය, ආර්ද්රතාවය සහ රසායනික ද්රව්යවලට නිරාවරණය වීම යන සියල්ල බන්ධනයේ ශක්තියට සහ විශ්වසනීයත්වයට බලපෑම් කළ හැකිය. මෙම තත්ත්වයන් නිරීක්ෂණය කර ඒවා නිර්දේශිත පරාසය තුළ ඇති බව සහතික කිරීමට සුදුසු පියවර ගන්න.
- ගුණාත්මක සංරචක භාවිතා කරන්න: ශක්තිමත් සහ විශ්වාසනීය බැඳීමක් සාක්ෂාත් කර ගැනීම සඳහා ගුණාත්මක සංරචක අත්යවශ්ය වේ. දුර්වල ගුණාත්මක සංරචක බන්ධන ක්රියාවලියට බලපෑම් කළ හැකි අක්රමිකතා හෝ නොගැලපීම් තිබිය හැක. අවශ්ය පිරිවිතරයන් සපුරාලන සහ පිළිගත් සැපයුම්කරුවන්ගෙන් ලබා ගන්නා අමුද්රව්ය භාවිතා කරන්න.
- බන්ධනය පරීක්ෂා කරන්න: ඇලවුම් ද්රව්ය ශක්තිමත් සහ විශ්වාසදායක බන්ධනයක් සාදා ඇති බව සහතික කර ගැනීම සඳහා බන්ධනය පරීක්ෂා කිරීම අත්යවශ්ය වේ. ඇදීමේ පරීක්ෂණය, ෂියර් පරීක්ෂණය සහ තාප පාපැදි පරීක්ෂාව ඇතුළුව බන්ධනය පරීක්ෂා කිරීමට විවිධ ක්රම භාවිත කළ හැක. බන්ධන ක්රියාවලියේ කිසියම් ගැටළුවක් හඳුනා ගැනීමට සහ අවසාන නිෂ්පාදනය විශ්වාසදායක සහ කල් පවතින බව සහතික කිරීමට පරීක්ෂණයට උපකාර කළ හැක.
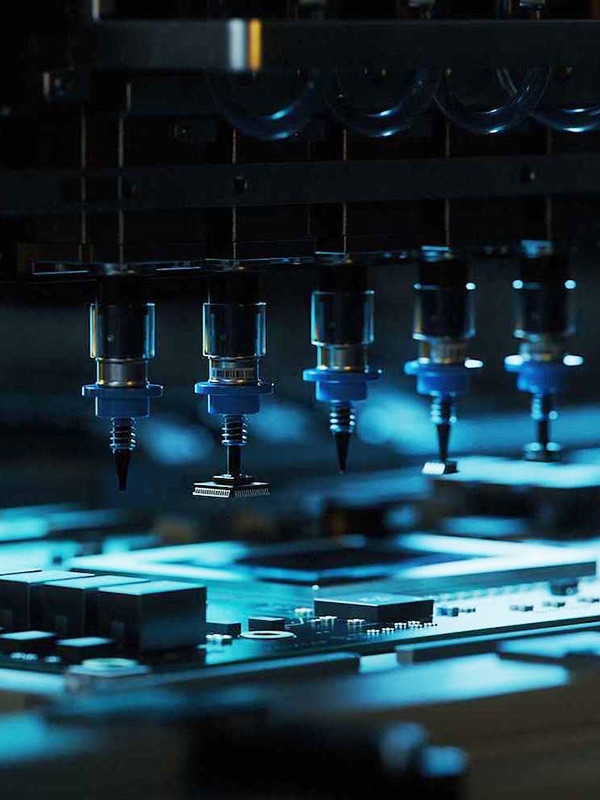
SMT මැලියම් බෙදා හැරීමේ තාක්ෂණික ක්රම සහ හොඳම භාවිතයන්
SMT (Surface Mount Technology) ඇලවුම් බෙදා හැරීම ඉලෙක්ට්රොනික නිෂ්පාදනයේදී ඉතා වැදගත් වේ. ඇලවුම් ද්රව්ය පෑස්සීමට පෙර මුද්රිත පරිපථ පුවරුවක (PCB) සංරචක රඳවා තබා ගනී. SMT මැලියම් සඳහා බෙදා හැරීමේ ක්රම කිහිපයක් සහ හොඳම භාවිතයන් මෙන්න:
- අතින් බෙදා හැරීම: අතින් බෙදා හැරීම යනු දක්ෂ ක්රියාකරුවෙකු අවශ්ය වන ලාභදායී තාක්ෂණයකි. අතින් බෙදා හැරීම සිරින්ජයක් හෝ පෑනක් භාවිතයෙන් සිදු කළ හැකිය. මෙම තාක්ෂණය මඟින් නිකුත් කරන ලද මැලියම් ප්රමාණය පිළිබඳ නිරවද්ය පාලනයට ඉඩ සලසයි, එය කුඩා පරිමාණ ව්යාපෘති සඳහා වඩාත් සුදුසු වේ.
- ස්වයංක්රීය බෙදා හැරීම: ස්වයංක්රීය බෙදාහැරීම මහා පරිමාණ නිෂ්පාදනය සඳහා වඩාත් වේගවත් හා කාර්යක්ෂම තාක්ෂණයකි. PCB වෙත මැලියම් යෙදීම සඳහා ස්වයංක්රීය බෙදාහැරීමේ පද්ධති රොබෝවරු, පොම්ප සහ කපාට වැනි උපකරණ භාවිතා කරයි. මෙම තාක්ෂණය ස්ථාවර බෙදාහැරීම සඳහා ඉඩ ලබා දෙන අතර නිෂ්පාදන කාර්යක්ෂමතාව වැඩි කළ හැක.
- ජෙට් ඩිස්පෙන්සින්: ජෙට් ඩිස්පෙන්සිං යනු ඇලවුම් ද්රව්ය සියුම් ප්රවාහයක යෙදීම සඳහා වායුමය ඩිස්පෙන්සරයක් භාවිතා කරන අධිවේගී බෙදා හැරීමේ තාක්ෂණයකි. මෙම තාක්ෂණය ඉහළ පරිමාවකින් නිෂ්පාදනය සඳහා වඩාත් සුදුසු වන අතර ඉහළ නිරවද්යතාවයකින් කුඩා මැලියම් ප්රමාණයක් නිකුත් කළ හැකිය.
- තිර මුද්රණය: තිර මුද්රණය යනු ස්ටෙන්සිල් හරහා මැලියම් යෙදීම ඇතුළත් බහුලව භාවිතා වන බෙදා හැරීමේ තාක්ෂණයකි. මෙම තාක්ෂණය PCB සඳහා බොහෝ මැලියම් යෙදීම සඳහා සුදුසු වේ. තිර මුද්රණය යනු කුඩා පරිමාණ සහ මහා පරිමාණ නිෂ්පාදන සඳහා භාවිතා කළ හැකි පිරිවැය-ඵලදායී සහ කාර්යක්ෂම බෙදා හැරීමේ ක්රමයකි.
- හොඳම භාවිතයන්: SMT මැලියම් බෙදා හැරීම සඳහා හොඳම භාවිතයන් අනුගමනය කිරීම අත්යවශ්ය වේ. සමහර හොඳම භාවිතයන් ඇතුළත් වේ:
- බෙදා හැරීමේ උපකරණ පිරිසිදු හා දූෂක වලින් තොර බවට සහතික වන්න.
- භාවිතා කරන මැලියම් සඳහා නිවැරදි බෙදා හැරීමේ ඉඟිය හෝ තුණ්ඩය භාවිතා කරන්න.
- බෙදා හැරීමේ තොරතුරු හෝ තුණ්ඩය බන්ධිත සංරචකය සඳහා ප්රමාණයෙන් ඇති බව සහතික කර ගන්න.
- බෙදා හැරීමේ ඉඟිය හෝ තුණ්ඩය සහ PCB අතර නිසි දුරක් පවත්වා ගන්න.
- බෙදා හැරීමේ ඉඟිය හෝ තුණ්ඩය PCB මතුපිටට ලම්බකව තබා ගන්න.
- නොනවත්වා අඛණ්ඩ චලනයකින් මැලියම් විසුරුවා හරින්න.
- මැලියම් ඒකාකාරව සහ නිවැරදි ප්රමාණයෙන් බෙදා හරින බවට සහතික වන්න.
- නිසි ලෙස බෙදා හැරීම සහතික කිරීම සඳහා මැලියම්වල දුස්ස්රාවීතාවය සහ තික්සොට්රොපි නිරීක්ෂණය කරන්න.
SMT ඇලවුම් යෙදුමේ අභියෝග ජය ගැනීම
SMT (Surface Mount Technology) ඇලවුම් යෙදුම මැලියම්වල දුස්ස්රාවීතාව, සංරචකවල ප්රමාණය සහ හැඩය සහ PCB පිරිසැලසුමේ සංකීර්ණත්වය වැනි විවිධ සාධක හේතුවෙන් අභියෝගාත්මක විය හැක. SMT ඇලවුම් යෙදුමේ පොදු අභියෝග කිහිපයක් සහ ඒවා ජය ගන්නේ කෙසේද යන්න මෙන්න:
- මැලියම්වල දුස්ස්රාවීතාව: SMT මැලියම් විවිධ දුස්ස්රාවීතාවයන්ගෙන් ලබා ගත හැකි අතර, අඩු සිට ඉහළ දක්වා පරාසයක පවතී. මැලියම්වල අනුකූලතාව බෙදා හැරීමේ ක්රියාවලියට සහ බන්ධන ශක්තියට බලපෑම් කළ හැකිය. අඩු දුස්ස්රාවීතාවයෙන් යුත් ඇලවුම් වඩාත් කාර්යක්ෂමව ගලා යන අතර, අධික දුස්ස්රාවීතාවයෙන් යුත් මැලියම් සඳහා ඉහළ බෙදාහැරීමේ පීඩනයක් අවශ්ය විය හැකිය. මෙම අභියෝගය ජය ගැනීම සඳහා, නිෂ්පාදකයින් විසින් නිශ්චිත යෙදුම සඳහා සුදුසු දුස්ස්රාවීතාවය සහිත මැලියම් තෝරාගෙන ඒ අනුව බෙදා හැරීමේ පරාමිතීන් සකස් කළ යුතුය.
- සංරචක ප්රමාණය සහ හැඩය: SMT සංරචක විවිධ ප්රමාණවලින් සහ හැඩවලින් පැමිණේ, සමහරක් ඒවායේ කුඩා ප්රමාණය හෝ අක්රමවත් හැඩය නිසා බන්ධනයට අපහසු විය හැක. මීට අමතරව, ඉතා සමීපව ඇති ලක්ෂණ ඇලෙනසුලු ලේ ගැලීම හෝ පාලම් වළක්වා ගැනීම සඳහා විශේෂ බෙදා හැරීමේ ක්රම අවශ්ය විය හැකිය. මෙම අභියෝගය ජය ගැනීම සඳහා, නිෂ්පාදකයින් විසින් කුඩා විශේෂාංග සඳහා සියුම් බෙදා හැරීමේ ඉඟියක් හෝ තුණ්ඩයක් හෝ සමීප සාමාජිකයින් සඳහා ජෙට් බෙදා හැරීමේ පද්ධතියක් වැනි සංරචකවල ප්රමාණය සහ හැඩය හැසිරවිය හැකි බෙදාහැරීමේ තාක්ෂණයක් තෝරාගත යුතුය.
- PCB පිරිසැලසුම: PCB පිරිසැලසුමේ සංකීර්ණත්වය SMT ඇලවුම් යෙදුමට ද බලපෑ හැකිය. PCB හි මායිමට ඉතා ආසන්නව තබා ඇති සංරචක මැලියම් පිටාර ගැලීම වැළැක්වීම සඳහා විශේෂ බෙදා හැරීමේ ක්රම අවශ්ය විය හැකිය. මීට අමතරව, ඉහළ සංඝටක ඝනත්වයක් සහිත PCB සඳහා නිශ්චිත සහ පාලිත ආකාරයෙන් මැලියම් යෙදිය හැකි බෙදාහැරීමේ ප්රවේශයක් අවශ්ය විය හැකිය. මෙම අභියෝගය ජය ගැනීම සඳහා, නිෂ්පාදකයින් විසින් PCB පිරිසැලසුම ප්රවේශමෙන් සමාලෝචනය කර පිරිසැලසුම සඳහා ඉඩ සැලසිය හැකි බෙදාහැරීමේ තාක්ෂණයක් තෝරාගත යුතුය.
- පාරිසරික සාධක: උෂ්ණත්වය, ආර්ද්රතාවය සහ වායු පීඩනය වැනි පාරිසරික සාධක SMT ඇලවුම් ක්රියාවලියට බලපෑ හැකිය. උදාහරණයක් ලෙස, අධික ආර්ද්රතාවය නිසා මැලියම් ඉතා ඉක්මනින් සුව විය හැක. ඊට ප්රතිවිරුද්ධව, අඩු ආර්ද්රතාවය මැලියම් ඉතා සෙමින් සුව කිරීමට හේතු විය හැක. මෙම අභියෝගය ජය ගැනීම සඳහා නිෂ්පාදකයින් පාරිසරික තත්ත්වයන් හොඳින් නිරීක්ෂණය කළ යුතු අතර ඒ අනුව බෙදා හැරීමේ පරාමිතීන් සකස් කළ යුතුය.
- ඇලවුම් සුව කිරීම: SMT මැලියම් වලට අපේක්ෂිත බන්ධන ශක්තිය ලබා ගැනීම සඳහා සුව කිරීම අවශ්ය වේ. උෂ්ණත්වය, ආර්ද්රතාවය සහ ඇලවුම් ස්ථරයේ ඝනකම වැනි සාධක මගින් සුව කිරීමේ ක්රියාවලිය බලපෑ හැකිය. මෙම අභියෝගය ජය ගැනීම සඳහා, නිෂ්පාදකයින් විසින් මැලියම් නිෂ්පාදකයාගේ සුව කිරීමේ කාලය සහ උෂ්ණත්ව නිර්දේශයන් අනුගමනය කළ යුතු අතර පාරිසරික තත්ත්වයන් නිර්දේශිත පරාසය තුළ ඇති බවට සහතික විය යුතුය.
තාප කළමනාකරණය මත SMT මැලියම්වල බලපෑම
මතුපිට සවි කිරීමේ තාක්ෂණය (SMT) මැලියම් ඉලෙක්ට්රොනික උපාංගවල තාප කළමනාකරණය සඳහා අත්යවශ්ය කාර්යභාරයක් ඉටු කරයි. ඉලෙක්ට්රොනික උපාංගවල තාප කළමනාකරණය ඉතා වැදගත් වන්නේ යන්ත්රය කාර්යක්ෂමව සහ විශ්වාසනීය ලෙස ක්රියාත්මක වන බව සහතික කරන අතර අධික තාපය නිසා සිදුවන හානිය වළක්වයි. පහත සාකච්ඡා කර ඇති පරිදි SMT ඇලවුම් තාප කළමනාකරණයට ආකාර කිහිපයකින් බලපෑම් කළ හැකිය.
පළමුව, SMT මැලියම් මගින් තාපය විසුරුවා හැරීම සඳහා තාප සන්නායක මාර්ගයක් සැපයිය හැකිය. මෙම අලවන ද්රව්ය නිර්මාණය කර ඇත්තේ ඉහළ තාප සන්නායකතාවක් ඇති වන පරිදි වන අතර එමඟින් තාප උත්පාදක සංරචක වලින් තාපය උපාංගයේ තාප සින්ක් වෙත මාරු කිරීමට ඉඩ සලසයි. මෙම තාප හුවමාරුව ආරක්ෂිත මෙහෙයුම් සීමාවන් තුළ උපාංගයේ උෂ්ණත්වය පවත්වා ගැනීමට උපකාරී වේ.
දෙවනුව, SMT මැලියම් තාප බාධකයක් සැපයීමෙන් තාප කළමනාකරණයට ද බලපෑම් කළ හැකිය. මෙම මැලියම් තාප පරිවාරකයක් ලෙස ක්රියා කළ හැකි අතර, උපකරණයෙන් තාපය පිටවීම වැළැක්වීම. වෛද්ය උපකරණ හෝ විද්යාත්මක උපකරණ වැනි ස්ථාවර උෂ්ණත්වයක් පවත්වා ගැනීම ඉතා වැදගත් වන විට මෙය ප්රයෝජනවත් විය හැක.
තෙවනුව, SMT මැලියම් ඔවුන්ගේ සුව කිරීමේ ලක්ෂණ හරහා තාප කළමනාකරණයට බලපෑම් කළ හැකිය. සමහර මැලියම් වැඩි උෂ්ණත්වවලදී සුව වන අතර එමඟින් උපාංගයේ තාප ආතතිය ඇති විය හැක. මෙය මැලියම්වල ඉරිතැලීම් හෝ දිරාපත්වීම වැනි යාන්ත්රික අසමත්වීම් වලට හේතු විය හැක. එබැවින්, උපාංගයේ ක්රියාකාරී උෂ්ණත්වය ඉක්මවා නොයන උෂ්ණත්වයකදී සුව කරන මැලියම් තෝරාගැනීම අත්යවශ්ය වේ.
සිව්වනුව, ඇලවුම් ඝණකම තාප කළමනාකරණයට ද බලපෑ හැකිය. ඝන ඇලවුම් ස්ථරයක් තාප විසර්ජනයට බාධා කළ හැකි තාප බාධකයක් නිර්මාණය කළ හැකිය, උපාංගයේ උෂ්ණත්වය වැඩි කිරීම. අනෙක් අතට, තුනී ඇලවුම් ස්ථරයක් තාප කළමනාකරණය වැඩිදියුණු කිරීම සඳහා තාපය වඩා කාර්යක්ෂමව මාරු කිරීමට ඉඩ සලසයි.
අවසාන වශයෙන්, SMT මැලියම් උපාංගයේ සමස්ත තාප ක්රියාකාරිත්වයට බලපෑම් කළ හැකිය. විවිධ බන්ධනවල විවිධ තාප සන්නායකතා, සුව කිරීමේ ලක්ෂණ සහ ඝනකම ඇත. තාප කළමනාකරණය සඳහා විෙශේෂෙයන් නිර්මාණය කර ඇති මැලියම් තෝරාගැනීම උපාංගයේ ප්රශස්ත කාර්ය සාධනය සහතික කිරීමට උපකාරී වේ.
SMT මැලියම් සහ කම්පන සහ කම්පන ප්රතිරෝධයට එහි දායකත්වය
මතුපිට සවි කිරීමේ තාක්ෂණය (SMT) මැලියම් තාප කළමනාකරණයට බලපාන අතර ඉලෙක්ට්රොනික උපාංග කම්පනය සහ කම්පන ප්රතිරෝධයට සැලකිය යුතු ලෙස දායක වේ. කම්පනය සහ කම්පනය ඉලෙක්ට්රොනික උපාංගවලට හානි සිදු කළ හැකි අතර, මෙම අවදානම අවම කිරීම සඳහා SMT මැලියම් අත්යවශ්ය වේ.
SMT මැලියම් මගින් පෑස්සුම් කරන ලද සංරචක සඳහා යාන්ත්රික ආධාරක සහ ශක්තිමත් කිරීම සපයයි. ඒවා විස්තර සහ උපස්ථරය අතර බෆරයක් ලෙස ක්රියා කරයි, පුළුල් ප්රදේශයක් හරහා කම්පන සහ කම්පන බලවේග බෙදා හරිනු ලැබේ. මෙය පෑස්සුම් සන්ධිවල ආතතිය අඩු කරන අතර යොදන පීඩනය යටතේ ඒවා කැඩීම හෝ කැඩීම වළක්වයි.
SMT යෙදුම්වල භාවිතා කරන ඇලවුම් ද්රව්ය කම්පනය සහ කම්පන ප්රතිරෝධය සඳහා තීරණාත්මක කාර්යභාරයක් ඉටු කරයි. මැලියම් කැඩීම හෝ කැඩීමකින් තොරව උපාංගයට යොදන බලවේගවලට ඔරොත්තු දීමට තරම් ඝන සහ කල් පවතින විය යුතුය. අතිරේකව, එහි ව්යුහාත්මක අඛණ්ඩතාවයට හානියක් නොවන පරිදි යන්ත්රයේ චලනය සහ නම්යශීලීභාවය සඳහා මැලියම් වලට යම් ප්රත්යාස්ථතාවයක් තිබිය යුතුය.
SMT මැලියම් උපාංගයේ කම්පන අඩු කිරීමට ද දායක විය හැකිය. ඩම්ප් කිරීම යනු පද්ධතියේ කම්පන විස්තාරය අඩු කරන ශක්තිය විසුරුවා හැරීමයි. ඇලවුම් වලට කම්පන වලින් යම් බලයක් අවශෝෂණය කර විසුරුවා හැරීම, දෝලනය වීමේ විස්තාරය අඩු කිරීම සහ උපාංගයට හානි වීම වැළැක්වීම.
ඇලවුම් ස්ථරයේ ඝණකම උපාංගයේ කම්පන සහ කම්පන ප්රතිරෝධයට ද බලපෑ හැකිය. ඝන ඇලවුම් ස්ථරයක් කුෂන් සහ කම්පන අවශෝෂණය සැපයිය හැකිය. තුනී ස්ථරයක් වඩාත් දෘඩ විය හැකි අතර අඩු කම්පන ප්රතිරෝධයක් ලබා දෙයි. උපාංගයේ නිශ්චිත අවශ්යතා මත පදනම්ව ඇලවුම් ස්ථරයේ ඝණකම තෝරා ගත යුතු අතර එය කම්පන සහ කම්පන මට්ටමට යටත් වේ.
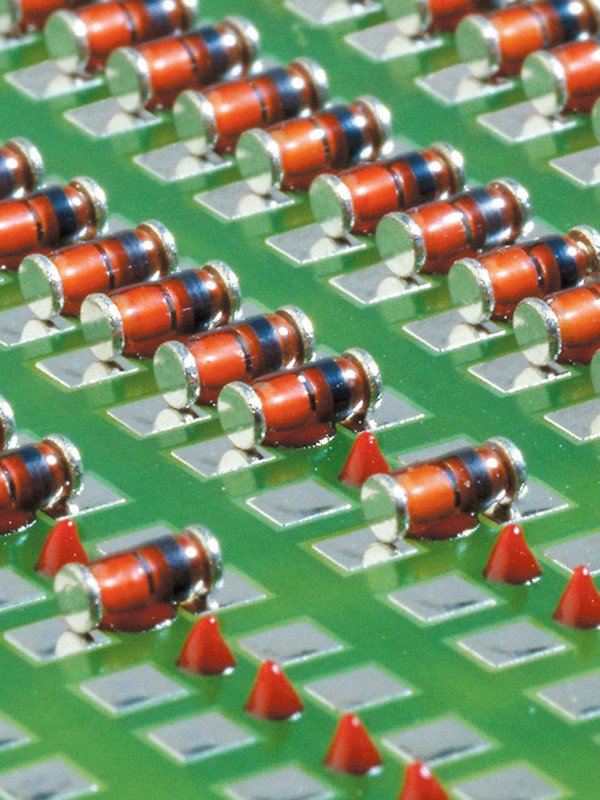
SMT මැලියම්වල වාසි
මතුපිට සවි කිරීමේ තාක්ෂණය (SMT) ඇලවුම් යනු ඉලෙක්ට්රොනික උපාංග නිෂ්පාදනයේදී අත්යවශ්ය අංගයකි. එය නිෂ්පාදනය කිරීමේදී මතුපිට සවි කරන කොටස් මුද්රිත පරිපථ පුවරු (PCBs) වෙත බන්ධනය කිරීම සඳහා විශේෂයෙන් නිර්මාණය කර ඇති මැලියම් වර්ගයකි. SMT මැලියම් භාවිතා කිරීමේ වාසි කිහිපයක් මෙන්න:
- වැඩිදියුණු කළ විශ්වසනීයත්වය: SMT මැලියම් මතුපිට සවිකිරීම් සංරචක සහ PCB අතර ශක්තිමත් බැඳීමක් සපයයි, ඉලෙක්ට්රොනික උපාංගවල විශ්වසනීයත්වය සහ ක්රියාකාරිත්වය වැඩි දියුණු කරයි. ක්රියාකාරීත්වයේ දී සංරචක විස්ථාපනය වීම හෝ හානි වීම, අසාර්ථක වීම් හෝ අක්රමිකතා ඇති වීම වැළැක්වීමට එය උපකාරී වේ.
- අඩු කරන ලද ප්රතිනිර්මාණය සහ අළුත්වැඩියා කිරීම්: ආරක්ෂිත සංරචක සඳහා SMT මැලියම් භාවිතා කිරීමෙන්, නිෂ්පාදකයින්ට නැවත සකස් කිරීම සහ අලුත්වැඩියා කිරීමේ අවශ්යතාවය අඩු කළ හැකිය. මෙමගින් නිෂ්පාදන ක්රියාවලියේදී කාලය සහ මුදල් ඉතිරි කර ගත හැකි අතර නිමි භාණ්ඩයේ සමස්ත ගුණාත්මක භාවය වැඩි දියුණු කළ හැක.
- වැඩි දියුණු කළ තාප කළමනාකරණය: සංරචක සහ PCB අතර තාප සින්ක් ලබා දීමෙන් ඉලෙක්ට්රොනික උපාංග තාප කළමනාකරණය වැඩිදියුණු කිරීමට SMT මැලියම් උපකාරී වේ. මෙය තාපය විසුරුවා හැරීමට සහ උනුසුම් වීම වැළැක්වීමට උපකාරී වේ, අසමත්වීම් හෝ අක්රියවීම් වලට මග පාදයි.
- කුඩාකරණය: SMT මැලියම් කුඩා හා වඩා සංයුක්ත ඉලෙක්ට්රොනික උපාංග නිෂ්පාදනය කිරීමට ඉඩ සලසයි. එය කුඩා සංරචක භාවිතා කිරීමට ඉඩ සලසයි. එය සංරචක ස්ථානගත කිරීම සඳහා අවශ්ය ඉඩ ප්රමාණය අඩු කරයි, එමඟින් වඩාත් කාර්යක්ෂම හා ලාභදායී සැලසුම් ඇති කළ හැකිය.
- වැඩිදියුණු කළ විද්යුත් ක්රියාකාරිත්වය: SMT මැලියම් මඟින් සංරචක සහ PCB අතර ප්රතිරෝධය අඩු කිරීමෙන් ඉලෙක්ට්රොනික උපාංගවල විද්යුත් ක්රියාකාරිත්වය වැඩි දියුණු කළ හැකිය. මෙය වැඩිදියුණු කළ සංඥා අඛණ්ඩතාව, ශබ්දය අඩු කිරීම සහ වඩා හොඳ සමස්ත කාර්ය සාධනය ඇති කළ හැක.
- බහුකාර්යතාව: විවිධ යෙදුම්වල නිශ්චිත අවශ්යතා සපුරාලීම සඳහා විවිධ සූත්රගත කිරීම් සහ දුස්ස්රාවීතාවයන් තුළ SMT මැලියම් ලබා ගත හැකිය. මෙය පාරිභෝගික ඉලෙක්ට්රොනික උපකරණ, වෛද්ය උපකරණ සහ මෝටර් රථ ඉලෙක්ට්රොනික උපකරණ ඇතුළු බහු ඉලෙක්ට්රොනික උපාංග සඳහා බහුවිධ බන්ධනයක් බවට පත් කරයි.
සමස්තයක් වශයෙන්, SMT මැලියම් භාවිතය ඉලෙක්ට්රොනික උපාංග නිෂ්පාදනයේ බොහෝ වාසි සපයයි. මතුපිට සවිකිරීම් සංරචක සහ PCB අතර ශක්තිමත් සහ විශ්වාසනීය බැඳීමක් සැපයීම මගින් ඉලෙක්ට්රොනික උපාංගවල ක්රියාකාරිත්වය, විශ්වසනීයත්වය සහ කාර්යක්ෂමතාව වැඩි දියුණු කළ හැකි අතරම නැවත සකස් කිරීම සහ අලුත්වැඩියා කිරීමේ අවශ්යතාවය අඩු කරයි. එය ඉලෙක්ට්රොනික කර්මාන්තයේ අත්යවශ්ය අංගයක් බවට පත් කරමින් විවිධ යෙදුම්වල භාවිතා කරන බහුකාර්ය මැලියම් වේ.
SMT මැලියම්වල අවාසි
Surface Mount Technology (SMT) මැලියම් යනු ඉලෙක්ට්රොනික පරිපථ සහ උපාංග නිෂ්පාදනයේදී බහුලව භාවිතා වන මැලියම් වර්ගයකි. එය පෑස්සුම් කිරීමේදී මතුපිට සවිකිරීම් සංරචක රඳවා තබා ගන්නා මැලියම් වේ. SMT මැලියම් එහි වාසි ඇති අතර, මෙම වර්ගයේ මැලියම් භාවිතා කිරීමේ අවාසි කිහිපයක් ද ඇත.
- ඉවත් කිරීමේ අපහසුව: SMT මැලියම්වල ඇති ප්රධාන අවාසියක් නම් එය ඉවත් කිරීමට අපහසු වීමයි. මැලියම් සුව වූ පසු, පරිපථ පුවරුවට හානියක් නොවන පරිදි මතුපිට සවි කිරීමේ සංරචකය ඉවත් කිරීම අභියෝගාත්මක විය හැකිය. මෙය අනාගතයේදී කොටස් අලුත්වැඩියා කිරීම හෝ ප්රතිස්ථාපනය කිරීම අභියෝගාත්මක විය හැක.
- පිරිවැය: SMT මැලියම් මිල අධික විය හැකි අතර, එය ඉහළ පරිමාවකින් යුත් නිෂ්පාදන පරිසරයක භාවිතා කිරීමට අපහසු වේ. සංරචකවල විශ්වසනීය ඇලවීම සහතික කිරීම සඳහා අවශ්ය වන මැලියම් උසස් තත්ත්වයේ නම් මෙය විශේෂයෙන්ම සත්ය වේ.
- පදම් කිරීමේ කාලය: SMT මැලියම් වලට කෑලි පෑස්සීමට පෙර සුව කිරීමට යම් කාලයක් අවශ්ය වේ. මෙය ඉලෙක්ට්රොනික උපාංග සහ පරිපථවල සමස්ත නිෂ්පාදන කාලය වැඩි කළ හැකිය.
- කල් තබා ගත හැකි කාලය: SMT මැලියම් සීමිත ආයු කාලයක් ඇත, එබැවින් එය නිශ්චිත කාල රාමුවක් තුළ භාවිතා කළ යුතුය. මැලියම් කල් ඉකුත් වීමට පෙර භාවිතා නොකළහොත් මෙය නාස්තියට හේතු විය හැක.
- තත්ත්ව පාලනය: SMT මැලියම් ඉහළ පරිමාණ නිෂ්පාදන පරිසරයන් තුළ අභියෝගාත්මක විය හැක. බන්ධන යෙදීමෙහි ඇති වෙනස්කම්, සංරචකවල ඇලවීමෙහි නොගැලපීම් ඇති විය හැකි අතර, අවසාන නිෂ්පාදනයේ දෝෂ ඇති විය හැක.
- පාරිසරික ගැටළු: SMT මැලියම්වල නිසි ලෙස බැහැර නොකළහොත් පරිසරයට හානි කළ හැකි රසායනික ද්රව්ය අඩංගු වේ. මෙය තිරසාර හා පාරිසරික වශයෙන් වගකිවයුතු නිෂ්පාදන පිළිවෙත් සඳහා කැපවී සිටින සමාගම් ගැන සැලකිලිමත් විය හැක.
- සංරචක වලට හානි කිරීමේ විභවය: SMT මැලියම් එය රඳවා තබා ගැනීමට අදහස් කරන විශේෂාංග වලට හානි කළ හැකිය. අලවන ද්රව්යය ඉතා ඝන ලෙස යොදන්නේ නම් හෝ ඒකාකාරව යොදන්නේ නැතිනම් මෙය සිදු විය හැක.
- නම්යශීලී බව නොමැතිකම: SMT මැලියම් අස්ථාවර විය හැක, එයින් අදහස් වන්නේ නම්යශීලී බව අවශ්ය සංරචක සඳහා එය සුදුසු නොවිය හැකි බවයි. මෙමගින් ඉලෙක්ට්රොනික උපාංග සහ පරිපථවල භාවිතා වන විශේෂාංග වර්ග සීමා කළ හැක.
පාරිසරික සලකා බැලීම්: ඊයම්-නිදහස් SMT ඇලවුම් විසඳුම්
පාරිසරික ගැටළු හේතුවෙන් ඊයම් රහිත මතුපිට සවිකිරීමේ තාක්ෂණය (SMT) ඇලවුම් විසඳුම් වඩ වඩාත් වැදගත් වී ඇත. EU හි RoHS (අනතුරුදායක ද්රව්ය සීමා කිරීම) නියෝගය සහ අනෙකුත් රටවල සමාන රෙගුලාසි මගින් ඉලෙක්ට්රොනික උපාංගවල ඊයම් භාවිතය සීමා කර ඇත. එබැවින්, ඊයම්-නිදහස් SMT මැලියම් සාම්ප්රදායික ඊයම් අඩංගු බැඳුම්කර සඳහා ජනප්රිය විකල්පයක් බවට පත්ව ඇත.
ඊයම් රහිත SMT මැලියම්වල සාමාන්යයෙන් රිදී, තඹ හෝ ටින් වැනි වෙනත් ලෝහ අඩංගු වන අතර ඒවා ඊයම් වලට වඩා පරිසරයට හානිකර නොවන බව සැලකේ. නිෂ්පාදකයින් උසස් තත්ත්වයේ නිෂ්පාදන කාර්ය සාධනයක් පවත්වා ගනිමින් ඔවුන්ගේ පාරිසරික බලපෑම අඩු කිරීමට උත්සාහ කරන බැවින් මෙම විකල්ප ලෝහ වඩාත් ප්රචලිත වී ඇත.
ඊයම්-නිදහස් SMT මැලියම් නිෂ්පාදනය සම්ප්රදායික ඊයම් අඩංගු බැඳුම්කරවලට වඩා අඩු පාරිසරික බලපෑමක් ඇත. ඊයම් අඩංගු අලවන ද්රව්ය නිෂ්පාදනය සඳහා බොහෝ විට විෂ සහිත රසායනික ද්රව්ය භාවිතා කිරීම අවශ්ය වන අතර එය කම්කරුවන්ට සහ පරිසරයට අහිතකර විය හැකිය. ඊට වෙනස්ව, ඊයම් රහිත මැලියම් නිෂ්පාදනය කරනු ලබන්නේ පිරිසිදු, වඩාත් පරිසර හිතකාමී ක්රම භාවිතා කරමිනි.
ඊයම් රහිත SMT මැලියම් සඳහා තවත් පාරිසරික සලකා බැලීමක් වන්නේ ඒවා බැහැර කිරීමයි. සාම්ප්රදායික ඊයම් අඩංගු මැලියම් අන්තරායකර අපද්රව්ය ලෙස සලකනු ලබන අතර විශේෂ බැහැර කිරීමේ ක්රියා පටිපාටි අවශ්ය වේ. ඊට ප්රතිවිරුද්ධව, ඊයම්-නිදහස් මැලියම් අන්තරායකර අපද්රව්ය ලෙස වර්ගීකරණය කර නොමැත. සම්මත අපද්රව්ය බැහැර කිරීමේ ක්රම භාවිතයෙන් ඒවා බැහැර කළ හැකිය.
ඊයම් රහිත SMT මැලියම් තාප කළමනාකරණය, කම්පනය සහ කම්පන ප්රතිරෝධය සම්බන්ධයෙන් සාම්ප්රදායික ඊයම් අඩංගු බන්ධනවලට සමාන ලෙස ක්රියා කරන බව පෙන්වා දී ඇත. එමනිසා, ඒවා උපාංගයේ කාර්ය සාධනයට හානි නොකර ඊයම් අඩංගු මැලියම් සඳහා සෘජු ආදේශකයක් ලෙස භාවිතා කළ හැකිය.
කුඩා ඉලෙක්ට්රොනික උපකරණවල SMT මැලියම්: නිරවද්යතාවය සහතික කිරීම
මතුපිට සවි කිරීමේ තාක්ෂණය (SMT) මැලියම් කුඩා ඉලෙක්ට්රොනික උපකරණවල නිරවද්යතාවය සහතික කිරීම සඳහා තීරණාත්මක කාර්යභාරයක් ඉටු කරයි. ඉලෙක්ට්රොනික උපාංග දිගින් දිගටම ප්රමාණයෙන් හැකිලෙන බැවින්, සංරචක ස්ථානගත කිරීම සහ බන්ධනය වඩ වඩාත් තීරණාත්මක වේ. SMT මැලියම් මගින් පෑස්සුම් කරන ලද කොටස් වලට යාන්ත්රික ආධාරක සහ ශක්තිමත් කිරීම් සපයන අතර, ක්රියාත්මක වන විට ඒවා මාරු කිරීම හෝ චලනය වීම වළක්වයි.
කුඩා ඉලෙක්ට්රොනික උපකරණවල, නිසි ක්රියාකාරීත්වය සහතික කිරීම සඳහා සංරචක ස්ථානගත කිරීම ඉතා වැදගත් වේ. SMT මැලියම් එකලස් කිරීමේදී සහ ක්රියාත්මක කිරීමේදී කොටස් සුරක්ෂිත කිරීමට ක්රමයක් සපයයි. සංරචක නිවැරදි ස්ථානයේ සහ දිශානතියේ ඇති බව සහතික කිරීම සඳහා මැලියම් නිශ්චිතවම යෙදිය යුතුය. කුඩාම නොගැලපීම පවා කාර්ය සාධන ගැටළු ඇති කිරීමට හෝ උපාංගය භාවිතයට නුසුදුසු බවට පත් කළ හැකිය.
උසස් බෙදාහැරීමේ තාක්ෂණයන් හරහා SMT ඇලවුම් යෙදුමේ නිරවද්යතාවය වැඩිදියුණු කළ හැක. මෙම තාක්ෂණයන් එක් එක් සංරචක සඳහා අවශ්ය නිශ්චිත ප්රමාණය සහ ස්ථානයෙහි මැලියම් යෙදීම සඳහා ඉහළ නිරවද්ය ඩිස්පෙන්සර් භාවිතා කරයි. එකලස් කිරීමේදී විස්තර නිවැරදිව සුරක්ෂිත කර ඇති බව මෙය සහතික කරයි.
කුඩා ඉලෙක්ට්රොනික උපකරණවල නිරවද්යතාවය සඳහා ඇලවුම් ද්රව්ය තෝරාගැනීම ද අත්යවශ්ය වේ. මැලියම් අඩු දුස්ස්රාවීතාවයක් සහ එහි ස්ථානගත කිරීමේදී ඉහළ නිරවද්යතාවක් තිබිය යුතුය. එය ඉක්මන් සුව කිරීමේ කාලයක් ද තිබිය යුතුය, ඉක්මන් එකලස් කිරීම සහ හැරවුම් කාලය සඳහා ඉඩ ලබා දේ.
ස්ථානගත කිරීමේදී නිරවද්යතාවයට අමතරව, SMT ඇලවුම් කුඩා ඉලෙක්ට්රොනික උපකරණවල ක්රියාකාරිත්වයට ද බලපෑම් කළ හැකිය. සංරචක වලින් උපස්ථරයට කාර්යක්ෂම තාප හුවමාරුව සහතික කිරීම සඳහා මැලියම් විශිෂ්ට තාප සන්නායකතාවක් තිබිය යුතුය. කෙටි පරිපථ සහ අනෙකුත් කාර්ය සාධන ගැටළු වළක්වා ගැනීම සඳහා මැලියම්වල ඉහළ විදුලි පරිවාරක ගුණ ද තිබිය යුතුය.
සමස්තයක් වශයෙන්, කුඩා ඉලෙක්ට්රොනික උපකරණවල නිරවද්යතාවය සහ ක්රියාකාරීත්වය සහතික කිරීම සඳහා SMT මැලියම් තීරණාත්මක කාර්යභාරයක් ඉටු කරයි. මැලියම් නිශ්චිතවම, ඉහළ නිරවද්යතාවයකින් යෙදිය යුතු අතර, යෙදුමේ නිශ්චිත අවශ්යතා සපුරාලීම සඳහා ද්රව්ය තෝරා ගැනීම ප්රවේශමෙන් සලකා බැලිය යුතුය. උසස් බෙදාහැරීමේ තාක්ෂණයන්ට මැලියම් යෙදුමේ නිරවද්යතාවය වැඩි දියුණු කළ හැකි අතර, එකලස් කිරීමේදී සංරචක නිසි ලෙස ආරක්ෂිතව සහ පෙළගැසී ඇති බව සහතික කරයි. සුදුසු අලවන ද්රව්ය තෝරාගැනීමෙන්, නිෂ්පාදකයින්ට ඔවුන්ගේ කුඩා ඉලෙක්ට්රොනික උපාංගවල ක්රියාකාරීත්වය සහ කල්පැවැත්ම සහතික කළ හැකිය.
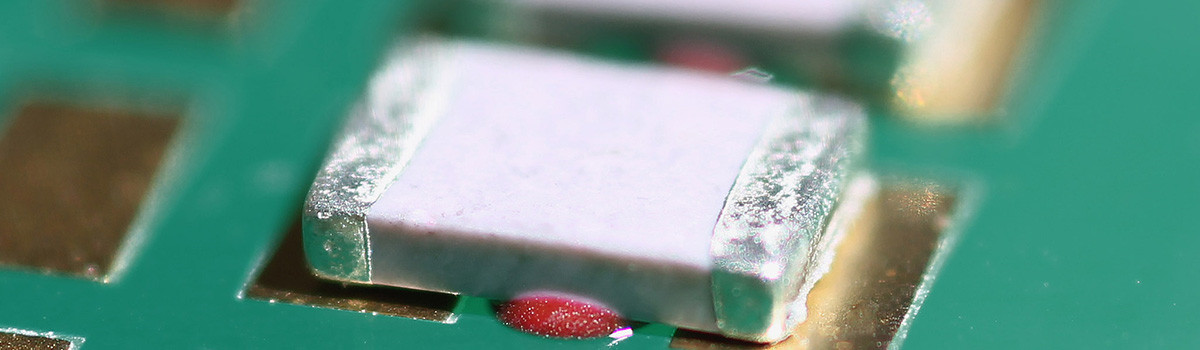
SMT මැලියම් සමඟ අස්වැන්න සහ කාර්යක්ෂමතාව වැඩි දියුණු කිරීම
මතුපිට සවි කිරීමේ තාක්ෂණය (SMT) මැලියම් කුඩා ඉලෙක්ට්රොනික උපකරණවල නිරවද්යතාවය සහතික කිරීම සඳහා තීරණාත්මක කාර්යභාරයක් ඉටු කරයි. ඉලෙක්ට්රොනික උපාංග දිගින් දිගටම ප්රමාණයෙන් හැකිලෙන බැවින්, සංරචක ස්ථානගත කිරීම සහ බන්ධනය වඩ වඩාත් තීරණාත්මක වේ. SMT මැලියම් මගින් පෑස්සුම් කරන ලද කොටස් වලට යාන්ත්රික ආධාරක සහ ශක්තිමත් කිරීම් සපයන අතර, ක්රියාත්මක වන විට ඒවා මාරු කිරීම හෝ චලනය වීම වළක්වයි.
කුඩා ඉලෙක්ට්රොනික උපකරණවල, නිසි ක්රියාකාරීත්වය සහතික කිරීම සඳහා සංරචක ස්ථානගත කිරීම ඉතා වැදගත් වේ. SMT මැලියම් එකලස් කිරීමේදී සහ ක්රියාත්මක කිරීමේදී කොටස් සුරක්ෂිත කිරීමට ක්රමයක් සපයයි. සංරචක නිවැරදි ස්ථානයේ සහ දිශානතියේ ඇති බව සහතික කිරීම සඳහා මැලියම් නිශ්චිතවම යෙදිය යුතුය. කුඩාම නොගැලපීම පවා කාර්ය සාධන ගැටළු ඇති කිරීමට හෝ උපාංගය භාවිතයට නුසුදුසු බවට පත් කළ හැකිය.
උසස් බෙදාහැරීමේ තාක්ෂණයන් හරහා SMT ඇලවුම් යෙදුමේ නිරවද්යතාවය වැඩිදියුණු කළ හැක. මෙම තාක්ෂණයන් එක් එක් සංරචක සඳහා අවශ්ය නිශ්චිත ප්රමාණය සහ ස්ථානයෙහි මැලියම් යෙදීම සඳහා ඉහළ නිරවද්ය ඩිස්පෙන්සර් භාවිතා කරයි. එකලස් කිරීමේදී විස්තර නිවැරදිව සුරක්ෂිත කර ඇති බව මෙය සහතික කරයි.
කුඩා ඉලෙක්ට්රොනික උපකරණවල නිරවද්යතාවය සඳහා ඇලවුම් ද්රව්ය තෝරාගැනීම ද අත්යවශ්ය වේ. මැලියම් අඩු දුස්ස්රාවීතාවයක් සහ එහි ස්ථානගත කිරීමේදී ඉහළ නිරවද්යතාවක් තිබිය යුතුය. එය ඉක්මන් සුව කිරීමේ කාලයක් ද තිබිය යුතුය, ඉක්මන් එකලස් කිරීම සහ හැරවුම් කාලය සඳහා ඉඩ ලබා දේ.
ස්ථානගත කිරීමේදී නිරවද්යතාවයට අමතරව, SMT ඇලවුම් කුඩා ඉලෙක්ට්රොනික උපකරණවල ක්රියාකාරිත්වයට ද බලපෑම් කළ හැකිය. සංරචක වලින් උපස්ථරයට කාර්යක්ෂම තාප හුවමාරුව සහතික කිරීම සඳහා මැලියම් විශිෂ්ට තාප සන්නායකතාවක් තිබිය යුතුය. කෙටි පරිපථ සහ අනෙකුත් කාර්ය සාධන ගැටළු වළක්වා ගැනීම සඳහා මැලියම්වල ඉහළ විදුලි පරිවාරක ගුණ ද තිබිය යුතුය.
සමස්තයක් වශයෙන්, කුඩා ඉලෙක්ට්රොනික උපකරණවල නිරවද්යතාවය සහ ක්රියාකාරීත්වය සහතික කිරීම සඳහා SMT මැලියම් තීරණාත්මක කාර්යභාරයක් ඉටු කරයි. මැලියම් නිශ්චිතවම, ඉහළ නිරවද්යතාවයකින් යෙදිය යුතු අතර, යෙදුමේ නිශ්චිත අවශ්යතා සපුරාලීම සඳහා ද්රව්ය තෝරා ගැනීම ප්රවේශමෙන් සලකා බැලිය යුතුය. උසස් බෙදාහැරීමේ තාක්ෂණයන්ට මැලියම් යෙදුමේ නිරවද්යතාවය වැඩි දියුණු කළ හැකි අතර, එකලස් කිරීමේදී සංරචක නිසි ලෙස ආරක්ෂිතව සහ පෙළගැසී ඇති බව සහතික කරයි. සුදුසු අලවන ද්රව්ය තෝරාගැනීමෙන්, නිෂ්පාදකයින්ට ඔවුන්ගේ කුඩා ඉලෙක්ට්රොනික උපාංගවල ක්රියාකාරීත්වය සහ කල්පැවැත්ම සහතික කළ හැකිය.
SMT මැලියම් සමඟ විශ්වසනීයත්වය පිළිබඳ සැලකිල්ල යොමු කිරීම
මතුපිට සවි කිරීමේ තාක්ෂණය (SMT) ඉලෙක්ට්රොනික උපාංගවල විශ්වසනීයත්වය සහතික කිරීම සඳහා මැලියම් අත්යවශ්ය කාර්යභාරයක් ඉටු කරයි. මැලියම් මඟින් සංරචක ස්ථානගත කිරීම, චලනය වැළැක්වීම සහ ක්රියාත්මක වන විට හානි හෝ අසාර්ථක වීමේ අවදානම අවම කරයි. කෙසේ වෙතත්, නිෂ්පාදකයින් තම නිෂ්පාදනවල දිගුකාලීන කාර්ය සාධනය සහතික කිරීම සඳහා අවධානය යොමු කළ යුතු SMT මැලියම් හා සම්බන්ධ විශ්වසනීයත්වය පිළිබඳ ගැටළු කිහිපයක් තිබේ.
SMT මැලියම් සමඟ ඇති ප්රධාන විශ්වසනීයත්වය වන්නේ එහි දිගුකාලීන කල්පැවැත්මයි. මැලියම් උෂ්ණත්ව වෙනස්වීම්, ආර්ද්රතාවය සහ යාන්ත්රික ආතතිය වැනි විවිධ පාරිසරික සාධකවලට ඔරොත්තු දිය යුතුය. කාලයාගේ ඇවෑමෙන්, මෙම සාධකවලට නිරාවරණය වීමෙන් මැලියම් නරක් වීමට හේතු විය හැක, සංඝටක චලනය හා විභව අසාර්ථකත්වයට මග පාදයි. එබැවින්, නිෂ්පාදකයින් දිගුකාලීන විශ්වසනීයත්වය සහතික කිරීම සඳහා පාරිසරික සාධකවලට විශිෂ්ට කල්පැවැත්මක් සහ ප්රතිරෝධයක් සහිත මැලියම් තෝරාගත යුතුය.
SMT මැලියම් සමඟ ඇති තවත් සැලකිල්ලක් වන්නේ යෙදුම අතරතුර හිස් හෝ වායු බුබුලු සෑදීමේ හැකියාවයි. මෙම හිස් තැන් තාප හුවමාරුව සමඟ ගැටළු ඇති කළ හැකි අතර නොමේරූ සංරචක අසාර්ථක වීමට හේතු විය හැක. නිශ්පාදකයින් විසින් රික්තය සෑදීම වැළැක්වීම සහ විශ්වසනීය තාප හුවමාරුව පවත්වා ගැනීම සඳහා ඔවුන්ගේ ඇලවුම් යෙදුම් ක්රියාවලිය ප්රවේශමෙන් පාලනය කළ යුතුය.
ගබඩා තත්ත්වයන් සහ හැසිරවීම SMT මැලියම්වල විශ්වසනීයත්වය කෙරෙහි ද බලපෑම් කළ හැකිය. නිෂ්පාදනයේදී මැලියම් නිවැරදිව ගබඩා කර නොමැති හෝ වැරදි ලෙස හසුරුවා නොමැති බව සිතමු. එම අවස්ථාවේ දී, එය දූෂිත හෝ පිරිහීමට ලක් විය හැක, කාර්ය සාධනය සහ විශ්වසනීයත්වය අඩු කරයි.
මෙම විශ්වසනීයත්වය පිළිබඳ ගැටළු විසඳීම සඳහා නිෂ්පාදකයින්ට පියවර කිහිපයක් ගත හැකිය. පාරිසරික සාධකවලට ඔප්පු කළ කල්පැවැත්ම සහ ප්රතිරෝධය සහිත මැලියම් තෝරා ගත හැකි අතර, එය දිගු කාලීන භාවිතයේ දෘඩතාවන්ට ඔරොත්තු දෙන බව සහතික කරයි. රික්තය සෑදීම වැළැක්වීම සහ විශ්වසනීය තාප හුවමාරුව පවත්වා ගැනීම සඳහා ඇලවුම් යෙදුම් ක්රියාවලිය ද ප්රවේශමෙන් පාලනය කළ හැකිය. මැලියම් නිසි ලෙස ගබඩා කිරීම සහ හැසිරවීම ද එහි කාර්ය සාධනය සහ විශ්වසනීයත්වය පවත්වා ගැනීමට උපකාරී වේ.
මීට අමතරව, නිෂ්පාදකයින්ට ඔවුන්ගේ නිෂ්පාදනවල විශ්වසනීයත්වය සහතික කිරීම සඳහා පුළුල් පරීක්ෂණ සහ තත්ත්ව පාලන පියවරයන් සිදු කළ හැකිය. විභව ගැටළු හඳුනා ගැනීමට සහ මැලියම් අපේක්ෂිත පරිදි ක්රියාත්මක වන බව සහතික කිරීම සඳහා වේගවත් වයස්ගත පරීක්ෂණ, පාරිසරික පරීක්ෂණ සහ ක්රියාකාරී පරීක්ෂණ ඇතුළත් විය හැකිය.
SMT මැලියම් සහ නැවත සකස් කිරීම සහ අලුත්වැඩියා කිරීමේ ක්රියාවලීන්හි එහි කාර්යභාරය
ඉලෙක්ට්රොනික උපාංග ප්රතිනිර්මාණය කිරීමේදී සහ අලුත්වැඩියා කිරීමේදී මතුපිට සවි කිරීමේ තාක්ෂණය (SMT) මැලියම් අත්යවශ්ය වේ. ඉලෙක්ට්රොනික කර්මාන්තය තුළ ප්රතිනිර්මාණය කිරීම සහ අලුත්වැඩියා කිරීමේ ක්රියාවලීන් සම්මත වේ, මන්ද නිෂ්පාදනයේදී හෝ භාවිතයේදී දෝෂ සහ ගැටලු මතුවිය හැක. SMT මැලියම් ලිහිල් හෝ වෙන් වී ඇති සංරචක නැවත සුරක්ෂිත කිරීමට හෝ හානියට පත් කොටස් අලුත්වැඩියා කිරීමට භාවිතා කළ හැක.
SMT මැලියම් සමඟ නැවත සකස් කිරීම හෝ අලුත්වැඩියා කිරීමේදී, යෙදුම සඳහා සුදුසු මැලියම් තෝරාගැනීම අත්යවශ්ය වේ. සංරචකයට සහ උපස්ථරයට ශක්තිමත් ඇලීම සහතික කිරීම සඳහා මැලියම් සුදුසු ගුණාංග තිබිය යුතුය. ඊට අමතරව, අලවන ද්රව්යය යෙදීමට පහසු විය යුතු අතර, අක්රිය කාලය අවම කිරීම සහ අලුත්වැඩියා වියදම් අඩු කිරීම සඳහා වේගවත් සුව කිරීමේ කාලයක් ඇත.
ප්රතිනිර්මාණය කිරීමේදී සහ අළුත්වැඩියා කිරීමේදී SMT අලවන එක් දෛනික භාවිතයක් වන්නේ ලිහිල් හෝ වෙන් වී ඇති කොටස් නැවත ඇමිණීමයි. මෙය යාන්ත්රික ආතතිය, උෂ්ණත්ව උච්චාවචනයන් හෝ වෙනත් පාරිසරික සාධක නිසා සිදු විය හැක. අලවන ද්රව්යයට එම කොටස නැවත එම ස්ථානයේම සුරක්ෂිත කළ හැකි අතර තවදුරටත් චලනය වීම හෝ වෙන්වීම වැළැක්විය හැකිය. මෙය ඉලෙක්ට්රොනික උපාංගයේ ආයු කාලය දීර්ඝ කිරීමට සහ ප්රතිස්ථාපනය කිරීමේ අවශ්යතාවය අඩු කිරීමට උපකාරී වේ.
SMT මැලියම් මගින් ඉරිතලා ඇති හෝ කැඩුණු පෑස්සුම් සන්ධි වැනි හානියට පත් සංරචක අලුත්වැඩියා කළ හැකිය. අමතර ආධාරකයක් සහ ශක්තිමත් කිරීමක් ලබා දීම සඳහා හානියට පත් ප්රදේශයට මැලියම් යෙදිය හැකි අතර, සංරචකය එහි මුල් ක්රියාකාරිත්වයට යථා තත්වයට පත් කිරීමට උපකාරී වේ. සමහර අවස්ථාවලදී, SMT ඇලවුම් ද හානි වූ පරිපථ පුවරු අලුත්වැඩියා කිරීමට භාවිතා කළ හැක, සුළු හානි හෝ ගැටළු සඳහා ඵලදායී විසඳුමක් සපයයි.
නැවත සකස් කිරීම සහ අළුත්වැඩියා කිරීමේ ක්රියාවලීන්හි එය භාවිතා කිරීමට අමතරව, SMT මැලියම් ප්රථමයෙන් නැවත සකස් කිරීම හෝ අලුත්වැඩියා කිරීමේ අවශ්යතාවය වළක්වා ගත හැකිය. නිසි සංරචක ස්ථානගත කිරීම සහතික කිරීම සහ චලනය හෝ වෙන්වීම වැළැක්වීම සඳහා මුල් නිෂ්පාදන ක්රියාවලියේදී මැලියම් භාවිතා කළ හැකිය. මෙය නැවත සකස් කිරීම හෝ අලුත්වැඩියා කිරීම අවශ්ය විය හැකි දෝෂ හෝ ගැටළු වල අවදානම අවම කර ගැනීමට උපකාරී වේ.
SMT මැලියම්වල අනාගතය: දියුණු කිරීම් සහ නවෝත්පාදන
මතුපිට සවි කිරීමේ තාක්ෂණය (SMT) ඇලවුම් වෙළඳපොළ ඉදිරි වසරවලදී සැලකිය යුතු ලෙස වර්ධනය වනු ඇතැයි අපේක්ෂා කෙරේ, මැලියම් තාක්ෂණයේ දියුණුව සහ නවෝත්පාදනයන් මගින් මෙහෙයවනු ලැබේ. දිනෙන් දින වැඩි වන ඉලෙක්ට්රොනික කර්මාන්තයේ ඉල්ලුම සපුරාලීම සඳහා නිෂ්පාදකයින් නිරන්තරයෙන් නව සහ වැඩිදියුණු කළ ඇලවුම් විසඳුම් සොයමින් සිටිති.
SMT මැලියම්වල නවෝත්පාදනයේ එක් අංශයක් වන්නේ වඩාත් පරිසර හිතකාමී විසඳුම් සංවර්ධනය කිරීමයි. තිරසාරභාවය සහ අඩු පාරිසරික බලපෑම කෙරෙහි වැඩි අවධානයක් යොමු කිරීමත් සමඟ නිෂ්පාදකයින් මෙම අවශ්යතා සපුරාලන මැලියම් සොයමින් සිටිති. අඩු හානිකර රසායනික ද්රව්ය භාවිතා කරන සහ ප්රතිචක්රීකරණය කිරීමට පහසු, අපද්රව්ය අවම කර තිරසාර බව වැඩි දියුණු කරන නව ඇලවුම් විසඳුම් සංවර්ධනය වෙමින් පවතී.
නවෝත්පාදනයේ තවත් අංශයක් වන්නේ වැඩිදියුණු කළ තාප කළමනාකරණ ගුණාංග සහිත මැලියම් සංවර්ධනය කිරීමයි. කුඩා, වඩාත් සංයුක්ත ඉලෙක්ට්රොනික උපාංග වෙත නැඹුරු වීමත් සමඟ ඵලදායී තාප කළමනාකරණය වඩ වඩාත් වැදගත් වෙමින් පවතී. තාපය විසුරුවා හැරීම සහ මාරු කිරීම වැඩිදියුණු කළ හැකි බන්ධන ඉලෙක්ට්රොනික උපාංග කාර්ය සාධනය සහ විශ්වසනීයත්වය වැඩිදියුණු කිරීමට උපකාරී වේ.
මීට අමතරව, වැඩි දියුණු කරන ලද විද්යුත් ගුණාංග සහිත මැලියම් සඳහා වැඩි උනන්දුවක් දක්වයි. සන්නායකතාව වැඩි දියුණු කළ හැකි හෝ විදුලි පරිවාරකයක් සැපයිය හැකි බන්ධන ඉලෙක්ට්රොනික උපාංග කාර්ය සාධනය සහ විශ්වසනීයත්වය වැඩිදියුණු කිරීමට උපකාරී වේ. මෙයට ඉහළ පාර විද්යුත් ශක්තියක් හෝ අඩු විද්යුත් ප්රතිරෝධයක් සහිත බන්ධන ඇතුළත් විය හැක.
නැනෝ තාක්ෂණයේ දියුණුවත් SMT මැලියම්වල නවෝත්පාදනයට හේතු වේ. තාප සන්නායකතාවය, ඇලවුම් ශක්තිය සහ විද්යුත් සන්නායකතාවය වැනි ගුණාංග වැඩිදියුණු කිරීම සඳහා මැලියම් වලට නැනෝ අංශු එකතු කළ හැක. මෙය විවිධ යෙදුම්වල වැඩිදියුණු කළ කාර්ය සාධනය සහ විශ්වසනීයත්වය සහිත මැලියම් වලට හේතු විය හැක.
අවසාන වශයෙන්, බෙදා හැරීම සහ යෙදුම් තාක්ෂණ දියුණුව ද SMT මැලියම්වල නව්යකරණයට හේතු වේ. නව බෙදා හැරීමේ උපකරණ සහ ක්රම මඟින් ඇලවුම් යෙදුම් නිරවද්යතාවය සහ අනුකූලතාව වැඩිදියුණු කිරීමට උපකාරී වන අතර, ඉලෙක්ට්රොනික උපාංගවල ගුණාත්මකභාවය සහ විශ්වසනීයත්වය වැඩි දියුණු කිරීමට මග පාදයි.
කර්මාන්ත අවධානය: සිද්ධි අධ්යයනය සහ සාර්ථක කතා
බොහෝ සාර්ථක කථා සහ සිද්ධි අධ්යයනයන් ඉලෙක්ට්රොනික කර්මාන්තයේ SMT මැලියම්වල වැදගත්කම සහ සඵලතාවය ඉස්මතු කරයි. මෙන්න උදාහරණ කිහිපයක්:
- ජංගම දුරකථන නිෂ්පාදනය: ප්රධාන ජංගම දුරකථන නිෂ්පාදකයෙක් ලිහිල් උපාංග සහ අධික උෂ්ණත්වයේ දුර්වල ක්රියාකාරීත්වය ඇතුළු උපාංග ගැටලුවලට මුහුණ දෙමින් සිටියේය. ඔවුන් කොටස් සුරක්ෂිත කිරීමට සහ තාප කළමනාකරණය වැඩිදියුණු කිරීමට ඉහළ කාර්යසාධනයක් සහිත SMT මැලියම් භාවිතා කිරීමට පටන් ගත්හ. මෙය උපාංගයේ විශ්වසනීයත්වය සහ කාර්ය සාධනය සැලකිය යුතු ලෙස වැඩිදියුණු කිරීමට මෙන්ම නැවත සකස් කිරීම සහ අලුත්වැඩියා කිරීමේ අවශ්යතාව අඩු කිරීමට හේතු විය.
- ඔටෝමෝටිව් ඉලෙක්ට්රොනික්ස්: මෝටර් රථ ඉලෙක්ට්රොනික උපකරණ නිෂ්පාදකයෙකු කම්පන සහ කම්පන හේතුවෙන් සංරචක විසන්ධි වීම සම්බන්ධයෙන් ගැටළු අත්විඳිමින් සිටියේය. ඔවුන් මෙම පාරිසරික සාධකවලට ඔරොත්තු දීම සඳහා විශේෂයෙන් නිර්මාණය කර ඇති ඉතා ඔරොත්තු දෙන SMT මැලියම් භාවිතා කිරීමට පටන් ගත්හ. මෙය සංරචක අසමත්වීම් සැලකිය යුතු ලෙස අඩු කිරීමට සහ ඉලෙක්ට්රොනික පද්ධතිවල සමස්ත විශ්වසනීයත්වය වැඩි කිරීමට හේතු විය.
- වෛද්ය උපකරණ: වෛද්ය උපකරණ නිෂ්පාදකයෙකු නිෂ්පාදන ක්රියාවලියේදී සංරචක ඇලවීම සම්බන්ධ ගැටළු අත්විඳිමින් සිටියේය. ඔවුන් ඉහළ ඇලවුම් ශක්තියක් සහ විශිෂ්ට විද්යුත් ගුණාංග සැපයීම සඳහා විශේෂිත SMT මැලියම් භාවිතා කිරීමට පටන් ගත්හ. මෙය වෛද්ය උපකරණවල ගුණාත්මකභාවය සහ විශ්වසනීයත්වය වැඩිදියුණු කිරීමට මෙන්ම නිෂ්පාදන දෝෂ සහ නැවත සකස් කිරීම අඩු කිරීමට හේතු විය.
- පාරිභෝගික ඉලෙක්ට්රොනික උපකරණ: දුර්වල තාප කළමනාකරණය හේතුවෙන් පාරිභෝගික ඉලෙක්ට්රොනික නිෂ්පාදන නිෂ්පාදකයෙකු තම උපාංග උනුසුම් වීම සම්බන්ධ ගැටළු වලට මුහුණ දෙමින් සිටියේය. ඔවුන් තාපය විසුරුවා හැරීම සහ මාරු කිරීම වැඩි දියුණු කිරීම සඳහා ඉහළ කාර්යසාධනයක් සහිත SMT මැලියම් භාවිතා කිරීමට පටන් ගත්හ. මෙය උපාංගයේ ක්රියාකාරීත්වය සහ විශ්වසනීයත්වය වැඩිදියුණු කිරීමට මෙන්ම අලුත්වැඩියාව සහ ප්රතිස්ථාපනය කිරීමේ අවශ්යතාවය අඩු කිරීමට හේතු විය.
මෙම සිද්ධි අධ්යයන සහ සාර්ථක කථා ඉලෙක්ට්රොනික කර්මාන්තය තුළ විවිධ යෙදුම්වල SMT මැලියම්වල වැදගත්කම සහ සඵලතාවය ඉස්මතු කරයි. යෙදුම සඳහා සුදුසු මැලියම් තෝරාගැනීමෙන් සහ නිසි ලෙස යෙදීම සහ සුව කිරීම සහතික කිරීමෙන්, නිෂ්පාදකයින්ට ඔවුන්ගේ ඉලෙක්ට්රොනික උපාංගවල විශ්වසනීයත්වය සහ ක්රියාකාරිත්වය වැඩි දියුණු කළ හැකි අතරම නැවත සකස් කිරීම සහ අලුත්වැඩියා කිරීමේ අවශ්යතාවය අඩු කරයි.
SMT මැලියම් හැසිරවීම, ගබඩා කිරීම සහ බැහැර කිරීම සඳහා හොඳම භාවිතයන්
මතුපිට සවිකිරීමේ තාක්ෂණය (SMT) මැලියම් නිසි ලෙස හැසිරවීම, ගබඩා කිරීම සහ බැහැර කිරීම එහි සඵලතාවය සහතික කිරීම සහ විය හැකි අනතුරු අවම කිරීම සඳහා අත්යවශ්ය වේ. අනුගමනය කළ යුතු හොඳම භාවිතයන් කිහිපයක් මෙන්න:
- හැසිරවීම: SMT මැලියම් හැසිරවීමේදී, අත්වැසුම්, ආරක්ෂිත වීදුරු සහ ශ්වසන යන්ත්රයක් වැනි සුදුසු පුද්ගලික ආරක්ෂක උපකරණ (PPE) පැළඳීම අත්යවශ්ය වේ. මෙය ඕනෑම හානිකර රසායනික ද්රව්යයකට නිරාවරණය වීම අවම කර ගැනීමට උපකාරී වේ. නිසි ලෙස මිශ්ර කිරීම, යෙදීම සහ සුව කිරීම ඇතුළුව භාවිතය සඳහා නිෂ්පාදකයාගේ උපදෙස් අනුගමනය කිරීම අත්යවශ්ය වේ.
- ගබඩා කිරීම: SMT මැලියම් සෘජු හිරු එළිය, තාපය සහ තෙතමනය සිට සිසිල්, වියළි ස්ථානයක ගබඩා කළ යුතුය. මැලියම් ඵලදායීව පවතින බව සහතික කිරීම සඳහා නිෂ්පාදකයාගේ නිර්දේශයන් අනුව උෂ්ණත්වය සහ ආර්ද්රතා තත්ත්වයන් විය යුතුය. මීට අමතරව, SMT මැලියම් දූෂණය හෝ වාෂ්පීකරණය වැළැක්වීම සඳහා තදින් මුද්රා තැබූ පියනක් සමඟ එහි මුල් බහාලුම්වල ගබඩා කළ යුතුය.
- බැහැර කිරීම: විභව පාරිසරික බලපෑම් අවම කිරීම සඳහා SMT මැලියම් නිසි ලෙස බැහැර කිරීම අත්යවශ්ය වේ. භාවිතයට නොගත් හෝ කල් ඉකුත් වූ ඕනෑම මැලියම් දේශීය රෙගුලාසි සහ මාර්ගෝපදේශ අනුව බැහැර කළ යුතුය. අනතුරුදායක අපද්රව්ය බැහැර කිරීමේ මධ්යස්ථානයකට ගෙන යාම හෝ නිසි ලෙස බැහැර කිරීම සඳහා විශේෂිත අපද්රව්ය කළමනාකරණ සමාගමක් සම්බන්ධ කර ගැනීම මෙයට ඇතුළත් විය හැකිය.
- කාන්දුවීම් සහ කාන්දුවීම්: වැටීමක් හෝ කාන්දුවක් සිදු වූ විට, තවදුරටත් දූෂණය වීම වැළැක්වීම සඳහා වහාම එම ස්ථානය පිරිසිදු කිරීම අත්යවශ්ය වේ. මෙයට වැලි හෝ මැටි වැනි අවශෝෂක ද්රව්ය භාවිතයෙන් කාන්දුව පාලනය කිරීම සහ සුදුසු ද්රාවකයක් හෝ පිරිසිදුකාරකයකින් එම ප්රදේශය පිරිසිදු කිරීම ඇතුළත් විය හැක.
- පුහුණුව: SMT මැලියම් හසුරුවන සේවකයින්ට නිසි පුහුණුවක් සහ අධ්යාපනයක් ලබා දිය යුතුය. මෙම මැලියම් නිසි ලෙස හැසිරවීම, ගබඩා කිරීම සහ බැහැර කිරීම සහ PPE නිසි ලෙස භාවිතා කිරීම සහ හදිසි අනතුරක් හෝ කාන්දු වීමකදී හදිසි ප්රතිචාර දැක්වීමේ ක්රියා පටිපාටි පිළිබඳ තොරතුරු ඇතුළත් විය යුතුය.
SMT මැලියම් හැසිරවීම, ගබඩා කිරීම සහ බැහැර කිරීම සඳහා මෙම හොඳම භාවිතයන් අනුගමනය කිරීමෙන්, නිෂ්පාදකයින්ට ඕනෑම විභව උපද්රව හෝ පාරිසරික බලපෑමක් අවම කරන අතරම මැලියම්වල ආරක්ෂාව සහ කාර්යක්ෂමතාව සහතික කළ හැකිය. නිශ්චිත නිර්දේශ සහ අවශ්යතා සඳහා නිෂ්පාදකයාගේ උපදෙස්, දේශීය රෙගුලාසි සහ මාර්ගෝපදේශ උපදෙස් ලබා ගැනීම අත්යවශ්ය වේ.
නිගමනය:
නිෂ්පාදන විශ්වසනීයත්වය වැඩිදියුණු කිරීම සහ නිශ්චිත සංරචක ස්ථානගත කිරීම සක්රීය කිරීම මගින් SMT මැලියම් ඉලෙක්ට්රොනික නිෂ්පාදනයේ විප්ලවීය වෙනසක් සිදු කර ඇත. පවතින මැලියම් විකල්පයන්, බෙදාහැරීමේ ශිල්පීය ක්රමවල දියුණුව සහ පාරිසරික සලකා බැලීම් නිසා SMT මැලියම් නවීන නිෂ්පාදන ක්රියාවලීන්හි අත්යවශ්ය අංගයක් බවට පත් කර ඇත. කර්මාන්තය විකාශනය වන විට, නිෂ්පාදකයින් කාර්යක්ෂමතාව, අස්වැන්න සහ සමස්ත නිෂ්පාදන ගුණත්වය උපරිම කිරීම සඳහා SMT මැලියම් සමඟ සම්බන්ධ නවතම වර්ධනයන් සහ හොඳම භාවිතයන් සමඟ යාවත්කාලීනව සිටිය යුතුය. SMT මැලියම්වල බලය උපයෝගී කර ගැනීමෙන්, නිෂ්පාදකයින්ට ඉලෙක්ට්රොනික නිෂ්පාදන නිෂ්පාදනයේ නව හැකියාවන් විවෘත කළ හැකි අතර, එය වැඩිදියුණු කළ කාර්ය සාධනය සහ පාරිභෝගික තෘප්තියට මග පාදයි.