Underfill-Epoxy
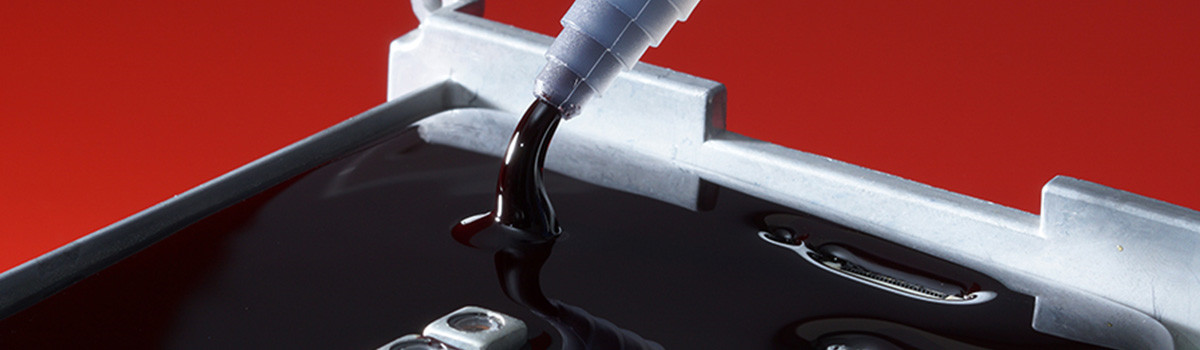
Underfill-Epoxidharz ist eine Art Klebstoff, der zur Verbesserung der Zuverlässigkeit elektronischer Komponenten, insbesondere bei Halbleiterverpackungsanwendungen, verwendet wird. Es füllt die Lücke zwischen dem Gehäuse und der Leiterplatte (PCB) und bietet mechanischen Halt und Spannungsabbau, um Schäden durch thermische Ausdehnung und Kontraktion zu verhindern. Unterfülltes Epoxidharz verbessert außerdem die elektrische Leistung des Gehäuses, indem es die parasitäre Induktivität und Kapazität reduziert. In diesem Artikel untersuchen wir die verschiedenen Anwendungen von Underfill-Epoxidharz, die verschiedenen verfügbaren Typen und ihre Vorteile.
Die Bedeutung von Underfill-Epoxidharz in Halbleiterverpackungen
Underfill-Epoxidharz ist bei Halbleiterverpackungen von entscheidender Bedeutung, da es empfindliche mikroelektronische Komponenten mechanisch verstärkt und schützt. Dabei handelt es sich um ein spezielles Klebematerial, das die Lücke zwischen dem Halbleiterchip und dem Gehäusesubstrat füllt und so die Zuverlässigkeit und Leistung elektronischer Geräte erhöht. Hier werden wir die Bedeutung von unterfülltem Epoxidharz in Halbleiterverpackungen untersuchen.
Eine der Hauptfunktionen von unterfülltem Epoxidharz besteht darin, die mechanische Festigkeit und Zuverlässigkeit der Verpackung zu verbessern. Während des Betriebs sind Halbleiterchips verschiedenen mechanischen Belastungen ausgesetzt, wie z. B. thermischer Ausdehnung und Kontraktion, Vibration und mechanischem Schock. Diese Spannungen können zur Bildung von Lötstellenrissen führen, die zu Stromausfällen führen und die Gesamtlebensdauer des Geräts verkürzen können. Underfill-Epoxid wirkt als spannungsreduzierendes Mittel, indem es die mechanische Belastung gleichmäßig auf Chip, Substrat und Lötstellen verteilt. Es minimiert effektiv die Bildung von Rissen und verhindert die Ausbreitung bestehender Risse, wodurch die langfristige Zuverlässigkeit der Verpackung gewährleistet wird.
Ein weiterer wichtiger Aspekt von Underfill-Epoxidharz ist seine Fähigkeit, die thermische Leistung von Halbleiterbauelementen zu verbessern. Die Wärmeableitung wird zu einem erheblichen Problem, da elektronische Geräte immer kleiner werden und die Leistungsdichte zunimmt. Übermäßige Wärme kann die Leistung und Zuverlässigkeit des Halbleiterchips beeinträchtigen. Underfill-Epoxidharz verfügt über hervorragende Wärmeleitfähigkeitseigenschaften, die es ihm ermöglichen, die Wärme effizient vom Chip zu übertragen und im gesamten Gehäuse zu verteilen. Dies trägt dazu bei, optimale Betriebstemperaturen aufrechtzuerhalten und Hotspots zu verhindern, wodurch das gesamte Wärmemanagement des Geräts verbessert wird.
Underfill-Epoxidharz schützt außerdem vor Feuchtigkeit und Verunreinigungen. Das Eindringen von Feuchtigkeit kann zu Korrosion, Leckströmen und dem Wachstum leitfähiger Materialien führen, was zu Fehlfunktionen des Geräts führen kann. Unterfülltes Epoxidharz fungiert als Barriere, versiegelt gefährdete Bereiche und verhindert, dass Feuchtigkeit in die Verpackung eindringt. Es bietet außerdem Schutz vor Staub, Schmutz und anderen Verunreinigungen, die die elektrische Leistung des Halbleiterchips beeinträchtigen können. Durch den Schutz des Chips und seiner Verbindungen gewährleistet Underfill-Epoxidharz die langfristige Zuverlässigkeit und Funktionalität des Geräts.
Darüber hinaus ermöglicht unterfülltes Epoxid die Miniaturisierung von Halbleitergehäusen. Angesichts der ständigen Nachfrage nach kleineren und kompakteren Geräten ermöglicht unterfülltes Epoxidharz den Einsatz von Flip-Chip- und Chip-Scale-Packaging-Techniken. Bei diesen Techniken wird der Chip direkt auf dem Gehäusesubstrat montiert, sodass kein Drahtbonden erforderlich ist und die Gehäusegröße reduziert wird. Underfill-Epoxid bietet strukturelle Unterstützung und erhält die Integrität der Chip-Substrat-Schnittstelle aufrecht, was die erfolgreiche Implementierung dieser fortschrittlichen Verpackungstechnologien ermöglicht.
Wie Underfill Epoxy die Herausforderungen bewältigt
Halbleiterverpackungen spielen eine entscheidende Rolle für die Leistung, Zuverlässigkeit und Langlebigkeit elektronischer Geräte. Dabei geht es darum, integrierte Schaltkreise (ICs) in Schutzgehäusen zu verkapseln, elektrische Verbindungen herzustellen und die im Betrieb entstehende Wärme abzuleiten. Allerdings stehen Halbleiterverpackungen vor mehreren Herausforderungen, darunter thermischer Stress und Verformung, die die Funktionalität und Zuverlässigkeit der verpackten Geräte erheblich beeinträchtigen können.
Eine der größten Herausforderungen ist die thermische Belastung. Integrierte Schaltkreise erzeugen während des Betriebs Wärme, und eine unzureichende Ableitung kann die Temperaturen im Gehäuse erhöhen. Diese Temperaturschwankung führt zu thermischer Belastung, da sich verschiedene Materialien innerhalb der Verpackung unterschiedlich schnell ausdehnen und zusammenziehen. Die ungleichmäßige Ausdehnung und Kontraktion kann zu mechanischer Belastung führen, die zu Lötstellenfehlern, Delamination und Rissen führt. Thermische Belastung kann die elektrische und mechanische Integrität des Gehäuses beeinträchtigen und letztendlich die Leistung und Zuverlässigkeit des Geräts beeinträchtigen.
Verzug ist eine weitere kritische Herausforderung bei der Halbleiterverpackung. Unter Verzug versteht man die Biegung oder Verformung des Gehäusesubstrats oder des gesamten Gehäuses. Dies kann während des Verpackungsprozesses oder aufgrund thermischer Belastung auftreten. Verzug wird hauptsächlich durch die Diskrepanz des Wärmeausdehnungskoeffizienten (CTE) verschiedener Materialien in der Verpackung verursacht. Beispielsweise kann sich der WAK des Siliziumchips, des Substrats und der Formmasse erheblich unterscheiden. Bei Temperaturschwankungen dehnen oder ziehen sich diese Materialien unterschiedlich schnell aus, was zu Verformungen führt.
Bei Halbleitergehäusen stellt der Verzug mehrere Probleme dar:
- Dies kann zu Spannungskonzentrationen führen, was die Wahrscheinlichkeit mechanischer Ausfälle erhöht und die Zuverlässigkeit der Box verringert.
- Verzug kann zu Schwierigkeiten beim Montageprozess führen, da er die Ausrichtung des Gehäuses mit anderen Komponenten, wie beispielsweise der Leiterplatte, beeinträchtigt. Diese Fehlausrichtung kann die elektrischen Verbindungen beeinträchtigen und zu Leistungsproblemen führen.
- Eine Verformung kann sich auf den gesamten Formfaktor des Gehäuses auswirken und die Integration des Geräts in Anwendungen mit kleinem Formfaktor oder dicht bestückten Leiterplatten erschweren.
Bei der Halbleiterverpackung werden verschiedene Techniken und Strategien eingesetzt, um diesen Herausforderungen zu begegnen. Dazu gehört die Verwendung fortschrittlicher Materialien mit passenden CTEs, um thermische Spannungen und Verformungen zu minimieren. Thermomechanische Simulationen und Modellierungen werden durchgeführt, um das Verhalten des Pakets unter verschiedenen thermischen Bedingungen vorherzusagen. Designmodifikationen, wie die Einführung von Entspannungsstrukturen und optimierten Layouts, werden implementiert, um thermische Spannungen und Verzug zu reduzieren. Darüber hinaus trägt die Entwicklung verbesserter Herstellungsprozesse und -ausrüstung dazu bei, das Auftreten von Verzug während der Montage zu minimieren.
Vorteile von Underfill-Epoxy
Underfill-Epoxidharz ist eine wichtige Komponente in Halbleiterverpackungen, die mehrere Vorteile bietet. Dieses spezielle Epoxidmaterial wird zwischen dem Halbleiterchip und dem Gehäusesubstrat aufgetragen, sorgt für mechanische Verstärkung und meistert verschiedene Herausforderungen. Hier sind einige der entscheidenden Vorteile von unterfülltem Epoxidharz:
- Verbesserte mechanische Zuverlässigkeit: Einer der Hauptvorteile von Underfill-Epoxidharz ist seine Fähigkeit, die mechanische Zuverlässigkeit von Halbleitergehäusen zu verbessern. Underfill-Epoxidharz schafft eine kohäsive Verbindung, die die gesamte strukturelle Integrität verbessert, indem es die Lücken und Hohlräume zwischen Chip und Substrat füllt. Dies trägt dazu bei, ein Verziehen des Gehäuses zu verhindern, das Risiko mechanischer Ausfälle zu verringern und die Widerstandsfähigkeit gegenüber äußeren Belastungen wie Vibrationen, Stößen und Temperaturschwankungen zu erhöhen. Die verbesserte mechanische Zuverlässigkeit führt zu einer erhöhten Produkthaltbarkeit und einer längeren Lebensdauer des Geräts.
- Wärmespannungsableitung: Die Unterfüllung mit Epoxidharz trägt dazu bei, die Wärmespannung innerhalb des Gehäuses abzuleiten. Integrierte Schaltkreise erzeugen im Betrieb Wärme und eine unzureichende Ableitung kann zu Temperaturschwankungen im Behälter führen. Das Underfill-Epoxidmaterial mit seinem im Vergleich zu den Chip- und Substratmaterialien geringeren Wärmeausdehnungskoeffizienten (CTE) fungiert als Pufferschicht. Es absorbiert die durch thermische Belastung verursachte mechanische Belastung und verringert so das Risiko von Lötstellenfehlern, Delamination und Rissen. Durch die Ableitung thermischer Spannung trägt unterfülltes Epoxidharz dazu bei, die elektrische und mechanische Integrität des Gehäuses aufrechtzuerhalten.
- Verbesserte elektrische Leistung: Unterfülltes Epoxidharz wirkt sich positiv auf die elektrische Leistung von Halbleiterbauelementen aus. Das Epoxidmaterial füllt die Lücken zwischen Chip und Substrat und reduziert so parasitäre Kapazitäten und Induktivitäten. Dies führt zu einer verbesserten Signalintegrität, geringeren Signalverlusten und einer verbesserten elektrischen Konnektivität zwischen dem Chip und dem Rest des Gehäuses. Die verringerten parasitären Effekte tragen zu einer besseren elektrischen Leistung, höheren Datenübertragungsraten und einer erhöhten Gerätezuverlässigkeit bei. Darüber hinaus bietet unzureichend gefülltes Epoxidharz Isolierung und Schutz vor Feuchtigkeit, Verunreinigungen und anderen Umweltfaktoren, die die elektrische Leistung beeinträchtigen können.
- Spannungsabbau und verbesserte Montage: Unterfülltes Epoxidharz dient als Spannungsabbaumechanismus während der Montage. Das Epoxidmaterial gleicht die WAK-Fehlanpassung zwischen Chip und Substrat aus und reduziert so die mechanische Belastung bei Temperaturänderungen. Dies macht den Montageprozess zuverlässiger und effizienter und minimiert das Risiko einer Beschädigung oder Fehlausrichtung der Verpackung. Die kontrollierte Spannungsverteilung durch Underfill-Epoxid trägt außerdem dazu bei, die richtige Ausrichtung mit anderen Komponenten auf der Leiterplatte (PCB) sicherzustellen und die Gesamtausbeute der Baugruppe zu verbessern.
- Miniaturisierung und Formfaktoroptimierung: Underfill-Epoxidharz ermöglicht die Miniaturisierung von Halbleitergehäusen und die Optimierung des Formfaktors. Durch die strukturelle Verstärkung und Spannungsentlastung ermöglicht Underfill-Epoxidharz die Entwicklung und Herstellung kleinerer, dünnerer und kompakterer Pakete. Dies ist besonders wichtig für Anwendungen wie mobile Geräte und tragbare Elektronik, bei denen der Platz knapp ist. Die Möglichkeit, Formfaktoren zu optimieren und höhere Komponentendichten zu erreichen, trägt zu fortschrittlicheren und innovativeren elektronischen Geräten bei.
Arten von Underfill-Epoxy
In Halbleiterverpackungen sind verschiedene Arten von Underfill-Epoxidformulierungen erhältlich, die jeweils darauf ausgelegt sind, spezifische Anforderungen zu erfüllen und unterschiedliche Herausforderungen zu bewältigen. Hier sind einige häufig verwendete Arten von Underfill-Epoxidharz:
- Kapillares Underfill-Epoxidharz: Kapillares Underfill-Epoxidharz ist der traditionellste und am weitesten verbreitete Typ. Durch Kapillarwirkung fließt ein niedrigviskoses Epoxidharz in den Spalt zwischen Chip und Substrat. Typischerweise wird Kapillarunterfüllung auf die Kante des Chips aufgetragen, und wenn das Gehäuse erhitzt wird, fließt das Epoxidharz unter den Chip und füllt die Hohlräume. Diese Art der Unterfüllung eignet sich für Pakete mit kleinen Lücken und sorgt für eine gute mechanische Verstärkung.
- No-Flow-Underfill-Epoxidharz: No-Flow-Underfill-Epoxidharz ist eine hochviskose Formulierung, die beim Aushärten nicht fließt. Es wird als vorab aufgetragenes Epoxidharz oder als Film zwischen Chip und Substrat aufgetragen. No-Flow-Underfill-Epoxidharz eignet sich besonders für Flip-Chip-Gehäuse, bei denen die Löthöcker direkt mit dem Substrat interagieren. Es macht einen Kapillarfluss überflüssig und verringert das Risiko einer Beschädigung der Lötstelle während der Montage.
- Wafer-Level-Underfill (WLU): Wafer-Level-Underfill ist ein Underfill-Epoxidharz, das auf Wafer-Ebene aufgetragen wird, bevor die einzelnen Chips vereinzelt werden. Dabei wird das Underfill-Material über die gesamte Waferoberfläche verteilt und ausgehärtet. Die Unterfüllung auf Waferebene bietet mehrere Vorteile, darunter eine gleichmäßige Unterfüllungsabdeckung, kürzere Montagezeit und eine verbesserte Prozesskontrolle. Es wird häufig für die Massenfertigung kleiner Geräte verwendet.
- Geformte Unterfüllung (MUF): Geformte Unterfüllung ist ein Unterfüllungs-Epoxidharz, das beim Verkapselungsformen aufgetragen wird. Das Unterfüllmaterial wird auf das Substrat aufgetragen und anschließend werden Chip und Substrat in einer Formmasse eingekapselt. Während des Formens fließt das Epoxidharz und füllt den Spalt zwischen Chip und Substrat und sorgt so für Unterfüllung und Verkapselung in einem einzigen Schritt. Die geformte Unterfüllung bietet eine hervorragende mechanische Verstärkung und vereinfacht den Montageprozess.
- Nichtleitende Unterfüllung (NCF): Nichtleitende Unterfüllung aus Epoxidharz wurde speziell entwickelt, um eine elektrische Isolierung zwischen den Lötstellen auf dem Chip und dem Substrat zu gewährleisten. Es enthält isolierende Füllstoffe oder Zusätze, die die elektrische Leitfähigkeit verhindern. NCF wird in Anwendungen eingesetzt, bei denen elektrische Kurzschlüsse zwischen benachbarten Lötstellen ein Problem darstellen. Es bietet sowohl mechanische Verstärkung als auch elektrische Isolierung.
- Thermisch leitfähige Unterfüllung (TCU): Die thermisch leitfähige Unterfüllung aus Epoxidharz soll die Wärmeableitungsfähigkeiten des Gehäuses verbessern. Es enthält wärmeleitende Füllstoffe wie Keramik- oder Metallpartikel, die die Wärmeleitfähigkeit des Unterfüllungsmaterials verbessern. TCU wird in Anwendungen eingesetzt, bei denen eine effiziente Wärmeübertragung von entscheidender Bedeutung ist, beispielsweise bei Hochleistungsgeräten oder solchen, die in anspruchsvollen thermischen Umgebungen betrieben werden.
Dies sind nur einige Beispiele für die verschiedenen Arten von Underfill-Epoxidharz, die in Halbleiterverpackungen verwendet werden. Die Auswahl des geeigneten Underfill-Epoxidharzes hängt von Faktoren wie dem Gehäusedesign, dem Montageprozess, den thermischen Anforderungen und elektrischen Überlegungen ab. Jedes Underfill-Epoxidharz bietet spezifische Vorteile und ist auf die individuellen Anforderungen verschiedener Anwendungen zugeschnitten.
Kapillarunterfüllung: Niedrige Viskosität und hohe Zuverlässigkeit
Unter kapillarer Unterfüllung versteht man einen Prozess, der in der Halbleiterverpackungsindustrie zur Verbesserung der Zuverlässigkeit elektronischer Geräte eingesetzt wird. Dabei werden die Lücken zwischen einem mikroelektronischen Chip und dem umgebenden Gehäuse mit einem dünnflüssigen flüssigen Material, typischerweise einem Harz auf Epoxidbasis, gefüllt. Dieses Unterfüllungsmaterial bietet strukturelle Unterstützung, verbessert die Wärmeableitung und schützt den Chip vor mechanischer Belastung, Feuchtigkeit und anderen Umweltfaktoren.
Eine der entscheidenden Eigenschaften der Kapillarunterfüllung ist ihre niedrige Viskosität. Das Underfill-Material ist so formuliert, dass es eine relativ geringe Dichte aufweist, sodass es während des Underfilling-Prozesses problemlos in die engen Lücken zwischen Chip und Gehäuse fließen kann. Dadurch wird sichergestellt, dass das Unterfüllmaterial effektiv alle Hohlräume und Luftspalte durchdringen und füllen kann, wodurch das Risiko der Hohlraumbildung minimiert und die Gesamtintegrität der Schnittstelle zwischen Chip und Gehäuse verbessert wird.
Darüber hinaus bieten niedrigviskose kapillare Underfill-Materialien mehrere weitere Vorteile. Erstens erleichtern sie den effizienten Materialfluss unter dem Chip, was zu einer kürzeren Prozesszeit und einem höheren Produktionsdurchsatz führt. Dies ist besonders wichtig in Produktionsumgebungen mit hohen Stückzahlen, in denen Zeit- und Kosteneffizienz von entscheidender Bedeutung sind.
Zweitens ermöglicht die niedrige Viskosität bessere Benetzungs- und Haftungseigenschaften des Unterfüllmaterials. Dadurch kann sich das Material gleichmäßig verteilen und starke Verbindungen mit dem Chip und dem Gehäuse bilden, wodurch eine zuverlässige und robuste Kapselung entsteht. Dadurch wird sichergestellt, dass der Chip sicher vor mechanischen Belastungen wie Temperaturschwankungen, Stößen und Vibrationen geschützt ist.
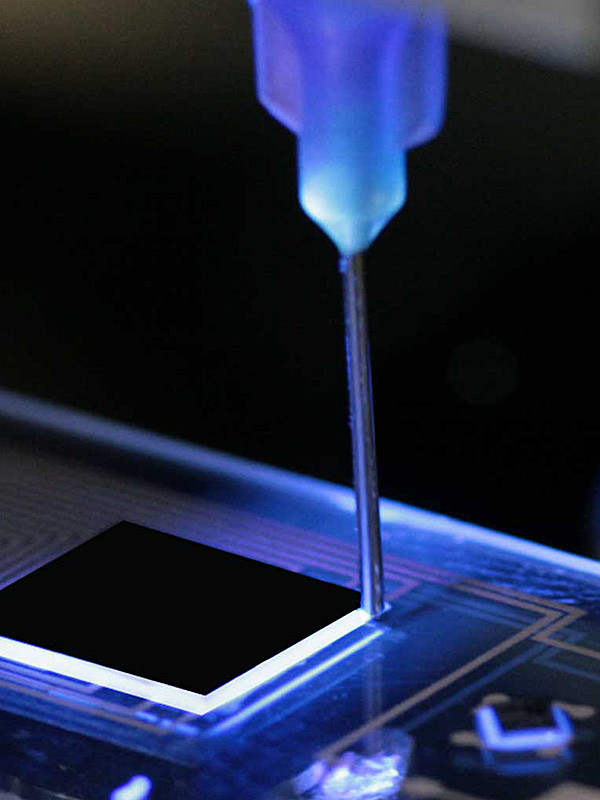
Ein weiterer entscheidender Aspekt von Kapillar-Underfills ist ihre hohe Zuverlässigkeit. Die niedrigviskosen Unterfüllungsmaterialien wurden speziell entwickelt, um eine hervorragende thermische Stabilität, elektrische Isolationseigenschaften sowie Beständigkeit gegen Feuchtigkeit und Chemikalien zu bieten. Diese Eigenschaften sind von entscheidender Bedeutung, um die langfristige Leistung und Zuverlässigkeit verpackter elektronischer Geräte sicherzustellen, insbesondere in anspruchsvollen Anwendungen wie der Automobilindustrie, der Luft- und Raumfahrt sowie der Telekommunikation.
Darüber hinaus sind kapillare Unterfüllungsmaterialien so konzipiert, dass sie eine hohe mechanische Festigkeit und eine hervorragende Haftung auf verschiedenen Substratmaterialien aufweisen, darunter Metalle, Keramik und organische Materialien, die üblicherweise in Halbleiterverpackungen verwendet werden. Dadurch kann das Unterfüllungsmaterial als Spannungspuffer fungieren und mechanische Spannungen, die während des Betriebs oder bei Umwelteinflüssen entstehen, wirksam absorbieren und ableiten.
No-Flow-Underfill: Selbstdosierung und hoher Durchsatz
No-Flow-Underfill ist ein spezielles Verfahren, das in der Halbleiterverpackungsindustrie zur Verbesserung der Zuverlässigkeit und Effizienz elektronischer Geräte eingesetzt wird. Im Gegensatz zu kapillaren Unterfüllungen, die auf dem Fluss niedrigviskoser Materialien basieren, nutzen No-Flow-Unterfüllungen einen selbstdispensierenden Ansatz mit hochviskosen Materialien. Diese Methode bietet mehrere Vorteile, darunter Selbstausrichtung, hohen Durchsatz und verbesserte Zuverlässigkeit.
Eines der entscheidenden Merkmale der No-Flow-Unterfüllung ist ihre Fähigkeit zur Selbstabgabe. Das bei diesem Verfahren verwendete Unterfüllmaterial ist mit einer höheren Viskosität formuliert, die ein freies Fließen verhindert. Stattdessen wird das Unterfüllmaterial kontrolliert auf die Schnittstelle zwischen Chip und Gehäuse verteilt. Diese kontrollierte Abgabe ermöglicht eine präzise Platzierung des Unterfüllmaterials und stellt sicher, dass es nur auf die gewünschten Bereiche aufgetragen wird, ohne überzulaufen oder sich unkontrolliert zu verteilen.
Die selbstspendende Natur der No-Flow-Unterfüllung bietet mehrere Vorteile. Erstens ermöglicht es eine Selbstausrichtung des Unterfüllmaterials. Wenn die Unterfüllung aufgetragen wird, richtet sie sich automatisch auf den Chip und das Gehäuse aus und füllt die Lücken und Hohlräume gleichmäßig. Dadurch entfällt die Notwendigkeit einer präzisen Positionierung und Ausrichtung des Chips während des Unterfüllungsprozesses, was Zeit und Aufwand bei der Herstellung spart.
Zweitens ermöglicht die Selbstdosierfunktion von No-Flow-Unterfüllungen einen hohen Durchsatz in der Produktion. Der Abgabevorgang kann automatisiert werden, was ein schnelles und gleichmäßiges Auftragen des Unterfüllmaterials auf mehrere Chips gleichzeitig ermöglicht. Dies verbessert die Gesamteffizienz der Produktion und senkt die Herstellungskosten, was es besonders vorteilhaft für Produktionsumgebungen mit hohen Stückzahlen macht.
Darüber hinaus sind No-Flow-Underfill-Materialien auf eine hohe Zuverlässigkeit ausgelegt. Die hochviskosen Unterfüllungsmaterialien bieten eine verbesserte Beständigkeit gegenüber thermischen Zyklen, mechanischen Belastungen und Umwelteinflüssen und stellen so die langfristige Leistung der verpackten elektronischen Geräte sicher. Die Materialien zeichnen sich durch hervorragende thermische Stabilität, elektrische Isolationseigenschaften sowie Beständigkeit gegen Feuchtigkeit und Chemikalien aus und tragen so zur Gesamtzuverlässigkeit der Geräte bei.
Darüber hinaus weisen die hochviskosen Underfill-Materialien, die beim No-Flow-Underfill verwendet werden, eine verbesserte mechanische Festigkeit und Haftungseigenschaften auf. Sie bilden starke Verbindungen mit dem Chip und dem Gehäuse und absorbieren und leiten mechanische Belastungen, die während des Betriebs oder bei Umwelteinflüssen entstehen, wirksam ab. Dies trägt dazu bei, den Chip vor möglichen Schäden zu schützen und erhöht die Widerstandsfähigkeit des Geräts gegenüber äußeren Stößen und Vibrationen.
Geformte Unterfüllung: Hoher Schutz und Integration
Geformte Unterfüllung ist eine fortschrittliche Technik, die in der Halbleiterverpackungsindustrie eingesetzt wird, um ein hohes Maß an Schutz und Integration für elektronische Geräte zu bieten. Dabei werden der gesamte Chip und sein umgebendes Gehäuse mit einer Formmasse verkapselt, die Unterfüllmaterial enthält. Dieses Verfahren bietet erhebliche Vorteile hinsichtlich Schutz, Integration und Gesamtzuverlässigkeit.
Einer der entscheidenden Vorteile der geformten Unterfüllung ist ihre Fähigkeit, den Chip umfassend zu schützen. Die bei diesem Verfahren verwendete Formmasse fungiert als robuste Barriere und umschließt den gesamten Chip und das Gehäuse mit einer Schutzhülle. Dies bietet eine wirksame Abschirmung gegen Umwelteinflüsse wie Feuchtigkeit, Staub und Verunreinigungen, die die Leistung und Zuverlässigkeit des Geräts beeinträchtigen könnten. Die Kapselung trägt außerdem dazu bei, den Chip vor mechanischer Beanspruchung, Temperaturschwankungen und anderen äußeren Kräften zu schützen, wodurch seine langfristige Haltbarkeit gewährleistet wird.
Darüber hinaus ermöglicht die geformte Unterfüllung einen hohen Integrationsgrad innerhalb des Halbleitergehäuses. Das Underfill-Material wird direkt in die Formmasse eingemischt, was eine nahtlose Integration der Underfill- und Verkapselungsprozesse ermöglicht. Diese Integration macht einen separaten Unterfüllungsschritt überflüssig, was den Herstellungsprozess vereinfacht und Produktionszeit und -kosten reduziert. Es sorgt außerdem für eine konsistente und gleichmäßige Unterfüllungsverteilung in der gesamten Verpackung, wodurch Hohlräume minimiert und die strukturelle Gesamtintegrität verbessert werden.
Darüber hinaus bietet die geformte Unterfüllung hervorragende Wärmeableitungseigenschaften. Die Formmasse ist auf eine hohe Wärmeleitfähigkeit ausgelegt, sodass sie die Wärme effizient vom Chip ableiten kann. Dies ist entscheidend, um die optimale Betriebstemperatur des Geräts aufrechtzuerhalten und eine Überhitzung zu verhindern, die zu Leistungseinbußen und Zuverlässigkeitsproblemen führen kann. Die verbesserten Wärmeableitungseigenschaften der geformten Unterfüllung tragen zur Gesamtzuverlässigkeit und Langlebigkeit des elektronischen Geräts bei.
Darüber hinaus ermöglicht die geformte Unterfüllung eine stärkere Miniaturisierung und Optimierung des Formfaktors. Der Verkapselungsprozess kann auf verschiedene Paketgrößen und -formen, einschließlich komplexer 3D-Strukturen, zugeschnitten werden. Diese Flexibilität ermöglicht die Integration mehrerer Chips und anderer Komponenten in ein kompaktes, platzsparendes Gehäuse. Die Fähigkeit, höhere Integrationsgrade zu erreichen, ohne die Zuverlässigkeit zu beeinträchtigen, macht geformte Unterfüllungen besonders wertvoll für Anwendungen, bei denen Größen- und Gewichtsbeschränkungen von entscheidender Bedeutung sind, wie z. B. mobile Geräte, Wearables und Automobilelektronik.
Chip Scale Package (CSP) Underfill: Miniaturisierung und hohe Dichte
Das Unterfüllen von Chip Scale Packages (CSP) ist eine entscheidende Technologie, die Miniaturisierung und die Integration elektronischer Geräte mit hoher Dichte ermöglicht. Da elektronische Geräte immer kleiner werden und gleichzeitig mehr Funktionalität bieten, spielt CSP eine entscheidende Rolle bei der Gewährleistung der Zuverlässigkeit und Leistung dieser kompakten Geräte.
CSP ist eine Verpackungstechnologie, die es ermöglicht, den Halbleiterchip direkt auf dem Substrat oder der Leiterplatte (PCB) zu montieren, ohne dass ein zusätzliches Gehäuse erforderlich ist. Dadurch entfällt die Notwendigkeit eines herkömmlichen Kunststoff- oder Keramikbehälters, wodurch sich die Gesamtgröße und das Gewicht des Geräts verringern. CSP-Unterfüllung ist ein Prozess, bei dem ein flüssiges oder einkapselndes Material verwendet wird, um die Lücke zwischen dem Chip und dem Substrat zu füllen, um für mechanische Unterstützung zu sorgen und den Chip vor Umwelteinflüssen wie Feuchtigkeit und mechanischer Belastung zu schützen.
Die Miniaturisierung wird durch CSP-Unterfüllung erreicht, indem der Abstand zwischen Chip und Substrat verringert wird. Das Underfill-Material füllt den schmalen Spalt zwischen Chip und Substrat, sorgt für eine feste Verbindung und verbessert die mechanische Stabilität des Chips. Dies ermöglicht kleinere und dünnere Geräte, wodurch mehr Funktionalität auf begrenztem Raum untergebracht werden kann.
Ein weiterer Vorteil des CSP-Underfills ist die hohe Integrationsdichte. Durch den Wegfall der Notwendigkeit eines separaten Gehäuses ermöglicht CSP die Montage des Chips näher an anderen Komponenten auf der Leiterplatte, wodurch die Länge der elektrischen Verbindungen reduziert und die Signalintegrität verbessert wird. Das Unterfüllungsmaterial fungiert auch als Wärmeleiter und leitet die vom Chip erzeugte Wärme effizient ab. Diese Wärmemanagementfähigkeit ermöglicht höhere Leistungsdichten und ermöglicht die Integration komplexerer und leistungsfähigerer Chips in elektronische Geräte.
CSP-Unterfüllungsmaterialien müssen spezifische Eigenschaften aufweisen, um den Anforderungen der Miniaturisierung und Integration hoher Dichte gerecht zu werden. Sie müssen eine niedrige Viskosität aufweisen, um das Füllen enger Lücken zu erleichtern, sowie hervorragende Fließeigenschaften, um eine gleichmäßige Abdeckung zu gewährleisten und Hohlräume zu vermeiden. Darüber hinaus sollten die Materialien eine gute Haftung auf dem Chip und dem Substrat aufweisen und so einen festen mechanischen Halt bieten. Darüber hinaus müssen sie eine hohe Wärmeleitfähigkeit aufweisen, um die Wärme effizient vom Chip abzuleiten.
CSP-Underfill auf Wafer-Ebene: Kostengünstig und mit hoher Ausbeute
Die Unterfüllung von Wafer-Level-Chip-Scale-Packages (WLCSP) ist eine kostengünstige und ertragreiche Verpackungstechnik, die mehrere Vorteile in Bezug auf die Fertigungseffizienz und die Gesamtproduktqualität bietet. WLCSP Underfill trägt Underfill-Material auf mehrere Chips gleichzeitig auf, während sie sich noch in Waferform befinden, bevor sie in einzelne Gehäuse vereinzelt werden. Dieser Ansatz bietet zahlreiche Vorteile hinsichtlich Kostenreduzierung, verbesserter Prozesskontrolle und höherer Produktionsausbeute.
Einer der entscheidenden Vorteile der WLCSP-Unterfüllung ist ihre Kosteneffizienz. Durch das Aufbringen des Unterfüllmaterials auf Waferebene wird der Verpackungsprozess rationalisiert und effizienter. Das unterfüllte Material wird mithilfe eines kontrollierten und automatisierten Prozesses auf den Wafer aufgetragen, wodurch Materialverschwendung reduziert und die Arbeitskosten minimiert werden. Darüber hinaus reduziert der Wegfall einzelner Pakethandhabungs- und Ausrichtungsschritte die Gesamtproduktionszeit und -komplexität, was zu erheblichen Kosteneinsparungen im Vergleich zu herkömmlichen Verpackungsmethoden führt.
Darüber hinaus bietet WLCSP Underfill eine verbesserte Prozesskontrolle und höhere Produktionsausbeuten. Da das Underfill-Material auf Waferebene aufgetragen wird, ermöglicht es eine bessere Kontrolle über den Dispensierungsprozess und gewährleistet eine konsistente und gleichmäßige Underfill-Abdeckung für jeden Chip auf dem Wafer. Dies verringert das Risiko von Hohlräumen oder unvollständiger Unterfüllung, was zu Zuverlässigkeitsproblemen führen kann. Die Möglichkeit, die Unterfüllungsqualität auf Waferebene zu prüfen und zu testen, ermöglicht außerdem die frühzeitige Erkennung von Defekten oder Prozessschwankungen, was zeitnahe Korrekturmaßnahmen ermöglicht und die Wahrscheinlichkeit fehlerhafter Pakete verringert. Dadurch trägt die WLCSP-Unterfüllung dazu bei, höhere Produktionsausbeuten und eine insgesamt bessere Produktqualität zu erzielen.
Der Wafer-Level-Ansatz ermöglicht auch eine verbesserte thermische und mechanische Leistung. Das bei WLCSP verwendete Unterfüllmaterial ist typischerweise ein dünnflüssiges, kapillarfließendes Material, das die engen Lücken zwischen den Chips und dem Wafer effizient füllen kann. Dies bietet den Chips eine solide mechanische Unterstützung und erhöht ihre Widerstandsfähigkeit gegenüber mechanischer Beanspruchung, Vibrationen und Temperaturschwankungen. Darüber hinaus fungiert das Unterfüllungsmaterial als Wärmeleiter und erleichtert die Ableitung der von den Chips erzeugten Wärme, wodurch das Wärmemanagement verbessert und das Risiko einer Überhitzung verringert wird.
Flip-Chip-Underfill: Hohe I/O-Dichte und Leistung
Flip-Chip-Underfill ist eine entscheidende Technologie, die eine hohe Ein-/Ausgabedichte (I/O) und außergewöhnliche Leistung in elektronischen Geräten ermöglicht. Es spielt eine entscheidende Rolle bei der Verbesserung der Zuverlässigkeit und Funktionalität von Flip-Chip-Gehäusen, die in fortschrittlichen Halbleiteranwendungen weit verbreitet sind. In diesem Artikel werden die Bedeutung der Flip-Chip-Unterfüllung und ihre Auswirkungen auf das Erreichen einer hohen I/O-Dichte und Leistung untersucht.
Bei der Flip-Chip-Technologie handelt es sich um die direkte elektrische Verbindung eines integrierten Schaltkreises (IC) oder eines Halbleiterchips mit dem Substrat, sodass kein Drahtbonden erforderlich ist. Dies führt zu einem kompakteren und effizienteren Paket, da sich die I/O-Pads auf der Unterseite des Chips befinden. Flip-Chip-Verpackungen stellen jedoch besondere Herausforderungen dar, die bewältigt werden müssen, um optimale Leistung und Zuverlässigkeit zu gewährleisten.
Eine der entscheidenden Herausforderungen beim Flip-Chip-Packaging besteht darin, mechanische Spannungen und thermische Fehlanpassungen zwischen Chip und Substrat zu verhindern. Während des Herstellungsprozesses und des anschließenden Betriebs können die Unterschiede in den Wärmeausdehnungskoeffizienten (CTE) zwischen Chip und Substrat zu erheblichen Spannungen führen, die zu Leistungseinbußen oder sogar zum Ausfall führen. Bei der Flip-Chip-Unterfüllung handelt es sich um ein Schutzmaterial, das den Chip einkapselt und so für mechanischen Halt und Spannungsabbau sorgt. Es verteilt die Spannungen, die bei Temperaturwechseln entstehen, effektiv und verhindert, dass sie die empfindlichen Verbindungen beeinträchtigen.
Eine hohe I/O-Dichte ist in modernen elektronischen Geräten von entscheidender Bedeutung, bei denen kleinere Formfaktoren und erhöhte Funktionalität unerlässlich sind. Die Flip-Chip-Unterfüllung ermöglicht höhere I/O-Dichten, indem sie hervorragende elektrische Isolations- und Wärmemanagementfähigkeiten bietet. Das Unterfüllmaterial füllt die Lücke zwischen Chip und Substrat, schafft eine robuste Schnittstelle und verringert das Risiko von Kurzschlüssen oder elektrischen Leckagen. Dies ermöglicht einen engeren Abstand der I/O-Pads, was zu einer höheren I/O-Dichte ohne Einbußen bei der Zuverlässigkeit führt.
Darüber hinaus trägt die Flip-Chip-Unterfüllung zu einer verbesserten elektrischen Leistung bei. Es minimiert die elektrischen Parasiten zwischen Chip und Substrat, reduziert die Signalverzögerung und verbessert die Signalintegrität. Das Unterfüllungsmaterial weist außerdem hervorragende Wärmeleitfähigkeitseigenschaften auf und leitet die vom Chip während des Betriebs erzeugte Wärme effizient ab. Eine effektive Wärmeableitung stellt sicher, dass die Temperatur innerhalb akzeptabler Grenzen bleibt, verhindert so eine Überhitzung und sorgt für eine optimale Leistung.
Fortschritte bei Flip-Chip-Unterfüllungsmaterialien haben noch höhere I/O-Dichten und Leistungsniveaus ermöglicht. Nanokomposit-Unterfüllungen beispielsweise nutzen nanoskalige Füllstoffe, um die Wärmeleitfähigkeit und mechanische Festigkeit zu verbessern. Dies ermöglicht eine verbesserte Wärmeableitung und Zuverlässigkeit und ermöglicht so leistungsstärkere Geräte.
Ball Grid Array (BGA) Underfill: Hohe thermische und mechanische Leistung
Ball Grid Array (BGA) ist eine wichtige Technologie, die eine hohe thermische und mechanische Leistung in elektronischen Geräten bietet. Es spielt eine entscheidende Rolle bei der Verbesserung der Zuverlässigkeit und Funktionalität von BGA-Gehäusen, die in verschiedenen Anwendungen weit verbreitet sind. In diesem Artikel werden wir die Bedeutung der BGA-Unterfüllung und ihre Auswirkungen auf das Erreichen einer hohen thermischen und mechanischen Leistung untersuchen.
Bei der BGA-Technologie handelt es sich um ein Gehäusedesign, bei dem der integrierte Schaltkreis (IC) oder Halbleiterchip auf einem Substrat montiert ist und die elektrischen Verbindungen über eine Reihe von Lötkugeln hergestellt werden, die sich auf der Unterseite des Gehäuses befinden. BGA unterfüllt ein Material, das in den Spalt zwischen Chip und Substrat aufgetragen wird, um die Lötkugeln einzukapseln und der Baugruppe mechanischen Halt und Schutz zu bieten.
Eine der entscheidenden Herausforderungen bei der BGA-Verpackung ist die Bewältigung thermischer Spannungen. Während des Betriebs erzeugt der IC Wärme, und thermische Ausdehnung und Kontraktion können einen erheblichen Druck auf die Lötverbindungen zwischen Chip und Substrat ausüben. BGA-Unterfüllungen spielen eine entscheidende Rolle bei der Minderung dieser Belastungen, indem sie eine feste Verbindung mit dem Chip und dem Substrat bilden. Es wirkt als Spannungspuffer, absorbiert die thermische Ausdehnung und Kontraktion und reduziert die Belastung der Lötstellen. Dies trägt dazu bei, die Gesamtzuverlässigkeit des Gehäuses zu verbessern und das Risiko von Lötstellenfehlern zu verringern.
Ein weiterer entscheidender Aspekt der BGA-Unterfüllung ist ihre Fähigkeit, die mechanische Leistung des Gehäuses zu verbessern. BGA-Gehäuse sind bei Handhabung, Montage und Betrieb häufig mechanischen Belastungen ausgesetzt. Das Unterfüllmaterial füllt den Spalt zwischen Chip und Substrat und sorgt für strukturelle Unterstützung und Verstärkung der Lötstellen. Dies verbessert die mechanische Gesamtfestigkeit der Baugruppe und macht sie widerstandsfähiger gegen mechanische Stöße, Vibrationen und andere äußere Kräfte. Durch die effektive Verteilung der mechanischen Spannungen trägt die BGA-Unterfüllung dazu bei, Gehäuserisse, Delaminierung oder andere mechanische Fehler zu verhindern.
Eine hohe thermische Leistung ist bei elektronischen Geräten unerlässlich, um eine ordnungsgemäße Funktionalität und Zuverlässigkeit sicherzustellen. BGA-Unterfüllungsmaterialien sind so konzipiert, dass sie hervorragende Wärmeleitfähigkeitseigenschaften aufweisen. Dadurch können sie die Wärme effizient vom Chip ableiten und über das Substrat verteilen, wodurch das gesamte Wärmemanagement des Gehäuses verbessert wird. Eine effektive Wärmeableitung trägt dazu bei, niedrigere Betriebstemperaturen aufrechtzuerhalten und so thermische Hotspots und mögliche Leistungseinbußen zu verhindern. Es trägt auch zur Langlebigkeit der Box bei, indem es die thermische Belastung der Komponenten reduziert.
Fortschritte bei BGA-Unterfüllungsmaterialien haben zu einer noch höheren thermischen und mechanischen Leistung geführt. Verbesserte Formulierungen und Füllstoffmaterialien wie Nanokomposite oder Füllstoffe mit hoher Wärmeleitfähigkeit haben eine bessere Wärmeableitung und mechanische Festigkeit ermöglicht und die Leistung von BGA-Gehäusen weiter verbessert.
Quad Flat Package (QFP) Underfill: Große I/O-Anzahl und Robustheit
Quad Flat Package (QFP) ist ein in der Elektronik weit verbreitetes IC-Gehäuse (Integrated Circuit). Es verfügt über eine quadratische oder rechteckige Form mit von allen vier Seiten ausgehenden Leitungen und bietet zahlreiche Ein-/Ausgangsverbindungen (I/O). Um die Zuverlässigkeit und Robustheit von QFP-Gehäusen zu erhöhen, werden üblicherweise Unterfüllungsmaterialien eingesetzt.
Underfill ist ein Schutzmaterial, das zwischen dem IC und dem Substrat angebracht wird, um die mechanische Festigkeit der Lötverbindungen zu verstärken und spannungsbedingte Ausfälle zu verhindern. Dies ist besonders wichtig für QFPs mit einer großen I/O-Anzahl, da die hohe Anzahl an Verbindungen zu erheblichen mechanischen Belastungen während der Temperaturwechsel- und Betriebsbedingungen führen kann.
Das für QFP-Pakete verwendete Unterfüllungsmaterial muss bestimmte Eigenschaften aufweisen, um Robustheit zu gewährleisten. Erstens sollte es eine hervorragende Haftung sowohl am IC als auch am Substrat aufweisen, um eine starke Verbindung zu schaffen und das Risiko einer Delaminierung oder Ablösung zu minimieren. Darüber hinaus sollte es einen niedrigen Wärmeausdehnungskoeffizienten (CTE) haben, der dem CTE von IC und Substrat entspricht, wodurch Spannungsunterschiede reduziert werden, die zu Rissen oder Brüchen führen könnten.
Darüber hinaus sollte das Unterfüllmaterial über gute Fließeigenschaften verfügen, um eine gleichmäßige Abdeckung und vollständige Füllung des Spalts zwischen IC und Substrat zu gewährleisten. Dies trägt dazu bei, Hohlräume zu vermeiden, die die Lötverbindungen schwächen und zu einer verringerten Zuverlässigkeit führen können. Das Material sollte zudem über gute Härtungseigenschaften verfügen, sodass es nach dem Auftragen eine feste und dauerhafte Schutzschicht bilden kann.
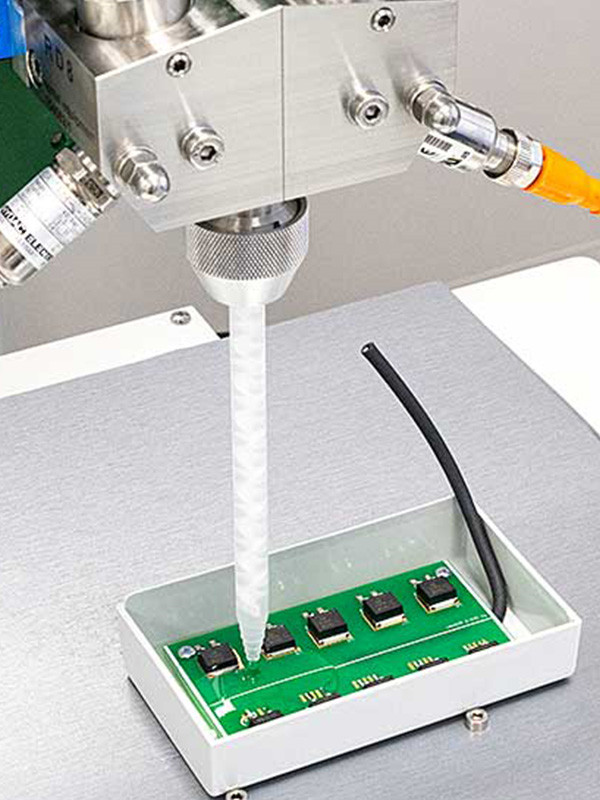
Im Hinblick auf die mechanische Robustheit sollte die Unterfüllung eine hohe Scher- und Schälfestigkeit aufweisen, um äußeren Kräften standzuhalten und eine Verformung oder Trennung der Verpackung zu verhindern. Es sollte außerdem eine gute Beständigkeit gegen Feuchtigkeit und andere Umwelteinflüsse aufweisen, um seine Schutzeigenschaften über einen längeren Zeitraum beizubehalten. Dies ist besonders wichtig bei Anwendungen, bei denen das QFP-Gehäuse rauen Bedingungen oder Temperaturschwankungen ausgesetzt sein kann.
Zur Erzielung dieser gewünschten Eigenschaften stehen verschiedene Unterfüllungsmaterialien zur Verfügung, darunter auch Formulierungen auf Epoxidbasis. Abhängig von den spezifischen Anforderungen der Anwendung können diese Materialien mit verschiedenen Techniken wie Kapillarfluss, Jetting oder Siebdruck dosiert werden.
System-in-Package (SiP) Underfill: Integration und Leistung
System-in-Package (SiP) ist eine fortschrittliche Verpackungstechnologie, die mehrere Halbleiterchips, passive Komponenten und andere Elemente in einem einzigen Gehäuse integriert. SiP bietet zahlreiche Vorteile, darunter einen reduzierten Formfaktor, eine verbesserte elektrische Leistung und eine erweiterte Funktionalität. Um die Zuverlässigkeit und Leistung von SiP-Baugruppen sicherzustellen, werden üblicherweise Unterfüllungsmaterialien verwendet.
Underfill ist bei SiP-Anwendungen von entscheidender Bedeutung für die Gewährleistung mechanischer Stabilität und elektrischer Konnektivität zwischen den verschiedenen Komponenten innerhalb des Gehäuses. Es trägt dazu bei, das Risiko spannungsbedingter Ausfälle wie Lötstellenrisse oder Brüche zu minimieren, die aufgrund unterschiedlicher Wärmeausdehnungskoeffizienten (CTE) zwischen den Komponenten auftreten können.
Die Integration mehrerer Komponenten in ein SiP-Gehäuse führt zu einer komplexen Interkonnektivität mit vielen Lötstellen und hochdichten Schaltkreisen. Unterfüllungsmaterialien tragen zur Verstärkung dieser Verbindungen bei und erhöhen so die mechanische Festigkeit und Zuverlässigkeit der Baugruppe. Sie unterstützen die Lötstellen und verringern so das Risiko von Ermüdungserscheinungen oder Schäden durch Temperaturwechsel oder mechanische Beanspruchung.
Im Hinblick auf die elektrische Leistung sind Unterfüllungsmaterialien von entscheidender Bedeutung für die Verbesserung der Signalintegrität und die Minimierung elektrischer Störungen. Durch das Füllen der Lücken zwischen Komponenten und die Verringerung des Abstands zwischen ihnen trägt die Unterfüllung dazu bei, parasitäre Kapazitäten und Induktivitäten zu reduzieren, was eine schnellere und effizientere Signalübertragung ermöglicht.
Darüber hinaus sollten Unterfüllungsmaterialien für SiP-Anwendungen eine hervorragende Wärmeleitfähigkeit aufweisen, um die von den integrierten Komponenten erzeugte Wärme effizient abzuleiten. Eine effektive Wärmeableitung ist unerlässlich, um eine Überhitzung zu verhindern und die allgemeine Zuverlässigkeit und Leistung der SiP-Baugruppe aufrechtzuerhalten.
Unterfüllungsmaterialien in SiP-Verpackungen müssen bestimmte Eigenschaften aufweisen, um diese Integrations- und Leistungsanforderungen zu erfüllen. Sie sollten eine gute Fließfähigkeit aufweisen, um eine vollständige Abdeckung zu gewährleisten und Lücken zwischen den Komponenten zu füllen. Das Unterfüllmaterial sollte außerdem eine niedrigviskose Formulierung haben, um ein einfaches Auftragen und Füllen in enge Löcher oder kleine Räume zu ermöglichen.
Darüber hinaus sollte das Unterfüllmaterial eine starke Haftung auf verschiedenen Oberflächen, einschließlich Halbleiterchips, Substraten und passiven Bauteilen, aufweisen, um eine zuverlässige Verbindung zu gewährleisten. Es sollte mit verschiedenen Verpackungsmaterialien wie organischen Substraten oder Keramik kompatibel sein und gute mechanische Eigenschaften aufweisen, einschließlich hoher Scher- und Schälfestigkeit.
Die Wahl des Unterfüllungsmaterials und der Anwendungsmethode hängt vom spezifischen SiP-Design, den Komponentenanforderungen und den Herstellungsprozessen ab. Bei Dosiertechniken wie Kapillarfluss, Jetting oder filmunterstützten Methoden wird in SiP-Baugruppen häufig eine Unterfüllung angewendet.
Optoelektronische Unterfüllung: Optische Ausrichtung und Schutz
Unterfüllungen für die Optoelektronik umfassen die Einkapselung und den Schutz optoelektronischer Geräte bei gleichzeitiger Sicherstellung einer präzisen optischen Ausrichtung. Optoelektronische Geräte wie Laser, Fotodetektoren und optische Schalter erfordern häufig eine sorgfältige Ausrichtung optischer Komponenten, um eine optimale Leistung zu erzielen. Gleichzeitig müssen sie vor Umwelteinflüssen geschützt werden, die ihre Funktionalität beeinträchtigen könnten. Die optoelektronische Unterfüllung erfüllt beide Anforderungen, indem sie optische Ausrichtung und Schutz in einem einzigen Prozess bietet.
Die optische Ausrichtung ist ein entscheidender Aspekt bei der Herstellung optoelektronischer Geräte. Dabei geht es um die Ausrichtung visueller Elemente wie Fasern, Wellenleiter, Linsen oder Gitter, um eine effiziente Lichtübertragung und -empfang sicherzustellen. Eine präzise Ausrichtung ist erforderlich, um die Geräteleistung zu maximieren und die Signalintegrität aufrechtzuerhalten. Zu den herkömmlichen Ausrichtungstechniken gehören die manuelle Ausrichtung mithilfe einer visuellen Inspektion oder die automatisierte Ausrichtung mithilfe von Ausrichtungsstufen. Allerdings können diese Methoden zeitaufwändig, arbeitsintensiv und fehleranfällig sein.
Optoelektronische Unterfüllung ist eine innovative Lösung, bei der Ausrichtungsmerkmale direkt in das Unterfüllungsmaterial integriert werden. Unterfüllungsmaterialien sind typischerweise flüssige oder halbflüssige Verbindungen, die fließen und die Lücken zwischen optischen Komponenten füllen können. Durch das Hinzufügen von Ausrichtungsmerkmalen wie Mikrostrukturen oder Referenzmarkierungen innerhalb des Unterfüllungsmaterials kann der Ausrichtungsprozess vereinfacht und automatisiert werden. Diese Merkmale dienen während der Montage als Führung und gewährleisten eine präzise Ausrichtung der optischen Komponenten, ohne dass komplexe Ausrichtungsverfahren erforderlich sind.
Zusätzlich zur optischen Ausrichtung schützen Unterfüllungsmaterialien optoelektronische Geräte. Optoelektronische Komponenten sind oft rauen Umgebungen ausgesetzt, darunter Temperaturschwankungen, Feuchtigkeit und mechanische Belastung. Diese externen Faktoren können die Leistung und Zuverlässigkeit der Geräte im Laufe der Zeit beeinträchtigen. Unterfüllungsmaterialien fungieren als Schutzbarriere, kapseln die optischen Komponenten ein und schützen sie vor Umweltverschmutzungen. Sie sorgen außerdem für eine mechanische Verstärkung und verringern so das Risiko von Schäden durch Stöße oder Vibrationen.
Unterfüllungsmaterialien, die in optoelektronischen Anwendungen verwendet werden, sind typischerweise so konzipiert, dass sie einen niedrigen Brechungsindex und eine ausgezeichnete optische Transparenz aufweisen. Dadurch wird eine minimale Beeinträchtigung der durch das Gerät fließenden optischen Signale gewährleistet. Darüber hinaus weisen sie eine gute Haftung auf verschiedenen Substraten auf und verfügen über niedrige Wärmeausdehnungskoeffizienten, um die Belastung des Geräts bei Temperaturwechseln zu minimieren.
Beim Underfill-Prozess wird das Underfill-Material auf das Gerät aufgetragen, es fließen lassen und die Lücken zwischen optischen Komponenten füllen und anschließend aushärten, um eine feste Kapselung zu bilden. Abhängig von der konkreten Anwendung kann das Underfill-Material mit unterschiedlichen Techniken aufgetragen werden, beispielsweise durch Kapillarfluss, Jet-Dispensing oder Siebdruck. Der Aushärtungsprozess kann durch Wärme, UV-Strahlung oder beides erreicht werden.
Underfill für medizinische Elektronik: Biokompatibilität und Zuverlässigkeit
Medizinische Elektronik erfordert einen speziellen Prozess, bei dem in medizinischen Geräten verwendete elektronische Komponenten eingekapselt und geschützt werden. Diese Geräte spielen eine entscheidende Rolle in verschiedenen medizinischen Anwendungen, beispielsweise bei implantierbaren Geräten, Diagnosegeräten, Überwachungssystemen und Medikamentenverabreichungssystemen. Die Unterfüllung medizinischer Elektronik konzentriert sich auf zwei entscheidende Aspekte: Biokompatibilität und Zuverlässigkeit.
Biokompatibilität ist eine Grundvoraussetzung für Medizinprodukte, die mit dem menschlichen Körper in Kontakt kommen. Die in der Medizinelektronik verwendeten Unterfüllungsmaterialien müssen biokompatibel sein, das heißt, sie dürfen bei Kontakt mit lebendem Gewebe oder Körperflüssigkeiten keine schädlichen Wirkungen oder Nebenwirkungen hervorrufen. Diese Materialien sollten strengen Vorschriften und Standards entsprechen, wie z. B. ISO 10993, die Verfahren zur Prüfung und Bewertung der Biokompatibilität festlegt.
Unterfüllungsmaterialien für medizinische Elektronik werden sorgfältig ausgewählt oder formuliert, um die Biokompatibilität sicherzustellen. Sie sind ungiftig, nicht reizend und nicht allergen. Diese Materialien sollten keine Schadstoffe auslaugen oder sich im Laufe der Zeit zersetzen, da dies zu Gewebeschäden oder Entzündungen führen könnte. Biokompatible Unterfüllungsmaterialien weisen außerdem eine geringe Wasseraufnahme auf, um das Wachstum von Bakterien oder Pilzen zu verhindern, die Infektionen verursachen könnten.
Zuverlässigkeit ist ein weiterer kritischer Aspekt der Unterfüllung medizinischer Elektronik. Medizinische Geräte sind häufig anspruchsvollen Betriebsbedingungen ausgesetzt, darunter extreme Temperaturen, Feuchtigkeit, Körperflüssigkeiten und mechanische Beanspruchung. Unterfüllungsmaterialien müssen die elektronischen Komponenten schützen und ihre langfristige Zuverlässigkeit und Funktionalität gewährleisten. Bei medizinischen Anwendungen, bei denen ein Geräteausfall die Sicherheit und das Wohlbefinden des Patienten erheblich beeinträchtigen könnte, ist Zuverlässigkeit von größter Bedeutung.
Unterfüllungsmaterialien für medizinische Elektronik sollten eine hohe Beständigkeit gegen Feuchtigkeit und Chemikalien aufweisen, um der Einwirkung von Körperflüssigkeiten oder Sterilisationsprozessen standzuhalten. Sie sollten außerdem eine gute Haftung auf verschiedenen Substraten aufweisen und so eine sichere Verkapselung der elektronischen Komponenten gewährleisten. Mechanische Eigenschaften wie niedrige Wärmeausdehnungskoeffizienten und gute Schockfestigkeit sind entscheidend für die Minimierung der Belastung der Details bei Temperaturwechseln oder automatischer Belastung.
Der Underfill-Prozess für medizinische Elektronik umfasst:
- Auftragen des Underfill-Materials auf die elektronischen Komponenten.
- Die Lücken füllen.
- Aushärten zu einer schützenden und mechanisch stabilen Kapselung.
Es muss darauf geachtet werden, dass die Funktionen vollständig abgedeckt sind und keine Hohlräume oder Lufteinschlüsse vorhanden sind, die die Zuverlässigkeit des Geräts beeinträchtigen könnten.
Darüber hinaus werden bei der Unterfüllung von Medizinprodukten zusätzliche Überlegungen berücksichtigt. Beispielsweise sollte das Unterfüllmaterial mit den für das Gerät verwendeten Sterilisationsmethoden kompatibel sein. Einige Materialien reagieren möglicherweise empfindlich auf bestimmte Sterilisationstechniken wie Dampf, Ethylenoxid oder Strahlung. Daher müssen möglicherweise alternative Materialien ausgewählt werden.
Underfill für Luft- und Raumfahrtelektronik: Hohe Temperatur- und Vibrationsbeständigkeit
Die Luft- und Raumfahrtelektronik unterliegt einem speziellen Prozess zum Einkapseln und Schützen elektronischer Komponenten in Luft- und Raumfahrtanwendungen. Luft- und Raumfahrtumgebungen stellen einzigartige Herausforderungen dar, darunter hohe Temperaturen, extreme Vibrationen und mechanische Belastungen. Daher konzentriert sich die Unterfüllung von Luft- und Raumfahrtelektronik auf zwei entscheidende Aspekte: Hochtemperaturbeständigkeit und Vibrationsbeständigkeit.
Aufgrund der hohen Temperaturen während des Betriebs ist in der Luft- und Raumfahrtelektronik die Hochtemperaturbeständigkeit von größter Bedeutung. Die in Luft- und Raumfahrtanwendungen verwendeten Unterfüllungsmaterialien müssen diesen hohen Temperaturen standhalten, ohne die Leistung und Zuverlässigkeit der elektronischen Komponenten zu beeinträchtigen. Sie sollten eine minimale Wärmeausdehnung aufweisen und über einen weiten Temperaturbereich stabil bleiben.
Unterfüllungsmaterialien für die Luft- und Raumfahrtelektronik werden im Hinblick auf hohe Glasübergangstemperaturen (Tg) und thermische Stabilität ausgewählt oder formuliert. Eine hohe Tg stellt sicher, dass das Material seine mechanischen Eigenschaften bei erhöhten Temperaturen behält und verhindert so Verformungen oder Haftungsverluste. Diese Materialien halten extremen Temperaturen stand, beispielsweise beim Start, beim Wiedereintritt in die Atmosphäre oder beim Betrieb in heißen Motorräumen.
Darüber hinaus sollten Unterfüllungsmaterialien für die Luft- und Raumfahrtelektronik niedrige Wärmeausdehnungskoeffizienten (CTE) aufweisen. Der CTE misst, wie stark sich ein Material bei Temperaturänderungen ausdehnt oder zusammenzieht. Durch ihren niedrigen CTE können Unterfüllungsmaterialien die Belastung der elektronischen Komponenten durch Temperaturwechsel minimieren, die zu mechanischen Ausfällen oder Ermüdung der Lötstelle führen kann.
Vibrationsfestigkeit ist eine weitere wichtige Anforderung an die Unterfüllung von Luft- und Raumfahrtelektronik. Luft- und Raumfahrtfahrzeuge sind verschiedenen Vibrationen ausgesetzt, darunter Triebwerksvibrationen, flugbedingte Vibrationen und mechanische Stöße beim Start oder bei der Landung. Diese Vibrationen können die Leistung und Zuverlässigkeit elektronischer Komponenten gefährden, wenn sie nicht ausreichend geschützt werden.
In der Luft- und Raumfahrtelektronik verwendete Unterfüllungsmaterialien sollten hervorragende vibrationsdämpfende Eigenschaften aufweisen. Sie sollen die durch Vibrationen erzeugte Energie absorbieren und ableiten und so die Belastung der elektronischen Komponenten verringern. Dies trägt dazu bei, die Bildung von Rissen, Brüchen oder anderen mechanischen Ausfällen aufgrund übermäßiger Vibrationseinwirkung zu verhindern.
Darüber hinaus werden Unterfüllungsmaterialien mit hoher Adhäsions- und Kohäsionsfestigkeit in Luft- und Raumfahrtanwendungen bevorzugt. Diese Eigenschaften stellen sicher, dass das Unterfüllmaterial auch unter extremen Vibrationsbedingungen fest mit den elektronischen Bauteilen und dem Substrat verbunden bleibt. Eine starke Haftung verhindert, dass sich das Unterfüllungsmaterial delaminiert oder von den Elementen löst, wodurch die Integrität der Kapselung erhalten bleibt und vor dem Eindringen von Feuchtigkeit oder Schmutz geschützt wird.
Der Underfill-Prozess für die Luft- und Raumfahrtelektronik umfasst typischerweise das Auftragen des Underfill-Materials auf die elektronischen Komponenten, das Fließen und Füllen der Lücken und das anschließende Aushärten, um eine robuste Kapselung zu bilden. Der Aushärtungsprozess kann je nach den spezifischen Anforderungen der Anwendung durch thermische oder UV-Härtungsverfahren erfolgen.
Unterfüllung der Automobilelektronik: Haltbarkeit und Temperaturwechselbeständigkeit
Die Automobilelektronik erfüllt einen kritischen Prozess, bei dem es um die Einkapselung und den Schutz elektronischer Komponenten in Automobilanwendungen geht. Automobilumgebungen stellen einzigartige Herausforderungen dar, darunter Temperaturschwankungen, Temperaturschwankungen, mechanische Belastungen sowie die Einwirkung von Feuchtigkeit und Chemikalien. Daher konzentriert sich die Unterfüllung von Automobilelektronik auf zwei entscheidende Aspekte: Haltbarkeit und Temperaturwechselbeständigkeit.
Haltbarkeit ist eine entscheidende Voraussetzung für Unterfüllungen in der Automobilelektronik. Im regulären Betrieb sind Kraftfahrzeuge ständigen Vibrationen, Stößen und mechanischen Belastungen ausgesetzt. Die in Automobilanwendungen verwendeten Unterfüllungsmaterialien müssen elektronische Komponenten robust schützen und ihre Haltbarkeit und Langlebigkeit gewährleisten. Sie sollen den rauen Bedingungen und mechanischen Belastungen im Straßenverkehr standhalten und dem Eindringen von Feuchtigkeit, Staub und Chemikalien standhalten.
Unterfüllungsmaterialien für die Automobilelektronik werden im Hinblick auf hohe mechanische Festigkeit und Schlagfestigkeit ausgewählt oder formuliert. Sie sollten eine hervorragende Haftung an den elektronischen Bauteilen und dem Substrat aufweisen und eine Delaminierung oder Trennung bei mechanischer Belastung verhindern. Langlebige Unterfüllungsmaterialien tragen dazu bei, das Risiko einer Beschädigung der elektronischen Komponenten durch Vibrationen oder Stöße zu minimieren und sorgen so für eine zuverlässige Leistung über die gesamte Lebensdauer des Fahrzeugs.
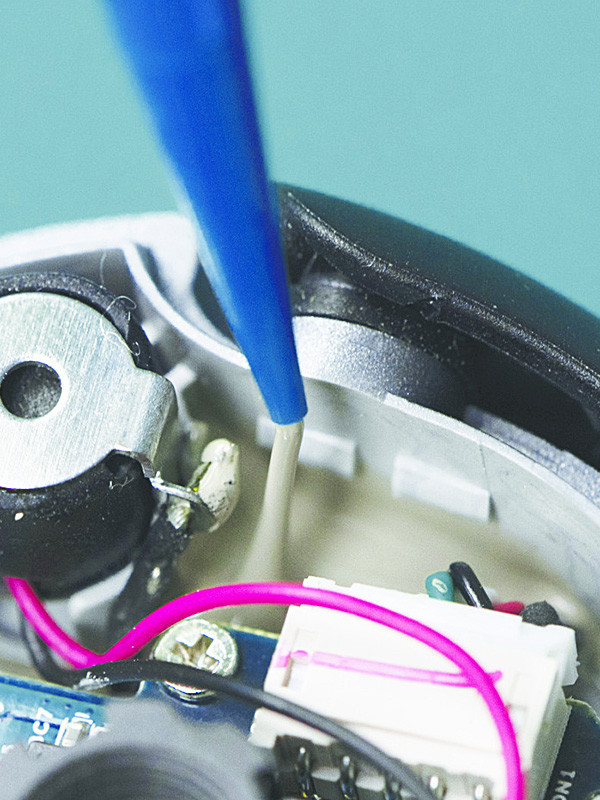
Die Temperaturwechselbeständigkeit ist eine weitere wichtige Anforderung für die Unterfüllung von Automobilelektronik. Kraftfahrzeuge unterliegen häufigen Temperaturschwankungen, insbesondere während des Motorstarts und -betriebs, und diese Temperaturzyklen können zu thermischen Belastungen elektronischer Komponenten und des umgebenden Unterfüllungsmaterials führen. Die in Automobilanwendungen verwendeten Unterfüllungsmaterialien müssen eine ausgezeichnete Temperaturwechselbeständigkeit aufweisen, um diesen Temperaturschwankungen standzuhalten, ohne ihre Leistung zu beeinträchtigen.
Unterfüllungsmaterialien für die Automobilelektronik sollten einen niedrigen Wärmeausdehnungskoeffizienten (CTE) aufweisen, um die Belastung der elektronischen Komponenten während der Temperaturwechselbelastung zu minimieren. Ein gut abgestimmter WAK zwischen dem Unterfüllungsmaterial und den Inhaltsstoffen verringert das Risiko von Ermüdungserscheinungen, Rissen oder anderen mechanischen Ausfällen der Lötstelle durch thermische Belastung. Darüber hinaus sollten die Unterfüllungsmaterialien eine gute Wärmeleitfähigkeit aufweisen, um die Wärme effizient abzuleiten und lokale Hotspots zu verhindern, die die Leistung und Zuverlässigkeit der Komponenten beeinträchtigen könnten.
Darüber hinaus sollten Unterfüllungsmaterialien für die Automobilelektronik feuchtigkeits-, chemikalien- und flüssigkeitsbeständig sein. Sie sollten eine geringe Wasseraufnahme aufweisen, um Schimmelbildung oder Korrosion der elektronischen Komponenten zu verhindern. Durch die chemische Beständigkeit bleibt das Unterfüllungsmaterial stabil, wenn es Automobilflüssigkeiten wie Ölen, Kraftstoffen oder Reinigungsmitteln ausgesetzt wird, und verhindert so eine Verschlechterung oder einen Verlust der Haftung.
Der Underfill-Prozess für die Automobilelektronik umfasst typischerweise das Auftragen des Underfill-Materials auf die elektronischen Komponenten, das Fließen und Füllen der Lücken und das anschließende Aushärten, um eine dauerhafte Verkapselung zu bilden. Der Aushärtungsprozess kann je nach den spezifischen Anforderungen der Anwendung und dem verwendeten Unterfüllmaterial durch thermische oder UV-Härtungsverfahren erfolgen.
Auswahl des richtigen Underfill-Epoxidharzes
Die Wahl des richtigen Underfill-Epoxidharzes ist eine entscheidende Entscheidung bei der Montage und dem Schutz elektronischer Komponenten. Underfill-Epoxidharze sorgen für mechanische Verstärkung, Wärmemanagement und Schutz vor Umwelteinflüssen. Hier sind einige wichtige Überlegungen bei der Auswahl des geeigneten Underfill-Epoxidharzes:
- Thermische Eigenschaften: Eine der Hauptfunktionen von Underfill-Epoxidharz ist die Ableitung der von elektronischen Bauteilen erzeugten Wärme. Daher ist es wichtig, die Wärmeleitfähigkeit und den Wärmewiderstand des Epoxidharzes zu berücksichtigen. Eine hohe Wärmeleitfähigkeit trägt zu einer effizienten Wärmeübertragung bei, verhindert Hotspots und gewährleistet die Zuverlässigkeit der Komponenten. Das Epoxidharz sollte außerdem einen geringen thermischen Widerstand aufweisen, um die thermische Belastung der Komponenten während des Temperaturwechsels zu minimieren.
- CTE-Übereinstimmung: Der Wärmeausdehnungskoeffizient (CTE) des Underfill-Epoxidharzes sollte gut auf den CTE der elektronischen Komponenten und des Substrats abgestimmt sein, um thermische Spannungen zu minimieren und Ausfälle der Lötverbindungen zu verhindern. Ein genau angepasster CTE trägt dazu bei, das Risiko mechanischer Ausfälle aufgrund thermischer Zyklen zu verringern.
- Fließ- und Lückenfüllvermögen: Das unterfüllte Epoxidharz sollte gute Fließeigenschaften und die Fähigkeit haben, Lücken zwischen Komponenten effektiv zu füllen. Dies gewährleistet eine vollständige Abdeckung und minimiert Hohlräume oder Lufteinschlüsse, die die mechanische Stabilität und thermische Leistung der Baugruppe beeinträchtigen könnten. Die Viskosität des Epoxidharzes sollte für die jeweilige Anwendung und Montagemethode geeignet sein, sei es Kapillarfluss, Strahldosierung oder Siebdruck.
- Haftung: Eine starke Haftung ist für die Unterfüllung mit Epoxidharz von entscheidender Bedeutung, um eine zuverlässige Verbindung zwischen den Bauteilen und dem Untergrund sicherzustellen. Es sollte eine gute Haftung auf verschiedenen Materialien, einschließlich Metallen, Keramik und Kunststoffen, aufweisen. Die Hafteigenschaften des Epoxidharzes tragen zur mechanischen Integrität und langfristigen Zuverlässigkeit der Baugruppe bei.
- Aushärtungsmethode: Überlegen Sie, welche Aushärtungsmethode am besten zu Ihrem Herstellungsprozess passt. Underfill-Epoxidharze können durch Hitze, UV-Strahlung oder eine Kombination aus beidem ausgehärtet werden. Jede Härtungsmethode hat Vor- und Nachteile, und es ist wichtig, diejenige zu wählen, die Ihren Produktionsanforderungen entspricht.
- Umweltbeständigkeit: Bewerten Sie die Beständigkeit des Underfill-Epoxidharzes gegenüber Umweltfaktoren wie Feuchtigkeit, Chemikalien und extremen Temperaturen. Das Epoxidharz sollte der Einwirkung von Wasser standhalten und so die Bildung von Schimmel oder Korrosion verhindern. Die chemische Beständigkeit gewährleistet Stabilität bei Kontakt mit Fahrzeugflüssigkeiten, Reinigungsmitteln oder anderen potenziell korrosiven Substanzen. Darüber hinaus sollte das Epoxidharz seine mechanischen und elektrischen Eigenschaften über einen weiten Temperaturbereich beibehalten.
- Zuverlässigkeit und Langlebigkeit: Berücksichtigen Sie die Erfolgsbilanz und Zuverlässigkeitsdaten des Underfill-Epoxidharzes. Suchen Sie nach Epoxidharzmaterialien, die in ähnlichen Anwendungen getestet wurden und nachweislich eine gute Leistung erbringen oder über Branchenzertifizierungen verfügen und die relevanten Standards einhalten. Berücksichtigen Sie Faktoren wie Alterungsverhalten, Langzeitzuverlässigkeit und die Fähigkeit des Epoxidharzes, seine Eigenschaften über die Zeit beizubehalten.
Bei der Auswahl des richtigen Underfill-Epoxidharzes ist es wichtig, die spezifischen Anforderungen Ihrer Anwendung zu berücksichtigen, einschließlich Wärmemanagement, mechanische Stabilität, Umweltschutz und Kompatibilität des Herstellungsprozesses. Die Rücksprache mit Epoxidlieferanten oder die Einholung von Expertenrat kann hilfreich sein, um eine fundierte Entscheidung zu treffen, die den Anforderungen Ihrer Anwendung entspricht und optimale Leistung und Zuverlässigkeit gewährleistet.
Zukünftige Trends bei Underfill-Epoxidharz
Underfill-Epoxidharz entwickelt sich ständig weiter, angetrieben durch Fortschritte in der elektronischen Technologie, neue Anwendungen und den Bedarf an verbesserter Leistung und Zuverlässigkeit. Bei der Entwicklung und Anwendung von Underfill-Epoxidharz sind mehrere zukünftige Trends zu beobachten:
- Miniaturisierung und Verpackung mit höherer Dichte: Da elektronische Geräte immer kleiner werden und eine höhere Komponentendichte aufweisen, müssen Underfill-Epoxidharze entsprechend angepasst werden. Zukünftige Trends werden sich auf die Entwicklung von Underfill-Materialien konzentrieren, die in kleinere Lücken zwischen Komponenten eindringen und diese füllen und so eine vollständige Abdeckung und zuverlässigen Schutz in zunehmend miniaturisierten elektronischen Baugruppen gewährleisten.
- Hochfrequenzanwendungen: Angesichts der wachsenden Nachfrage nach elektronischen Hochfrequenz- und Hochgeschwindigkeitsgeräten müssen Underfill-Epoxidformulierungen den spezifischen Anforderungen dieser Anwendungen gerecht werden. Unterfüllungsmaterialien mit niedriger Dielektrizitätskonstante und niedrigem Verlustfaktor werden von entscheidender Bedeutung sein, um Signalverluste zu minimieren und die Integrität von Hochfrequenzsignalen in fortschrittlichen Kommunikationssystemen, der 5G-Technologie und anderen neuen Anwendungen aufrechtzuerhalten.
- Verbessertes Wärmemanagement: Die Wärmeableitung bleibt ein kritisches Anliegen für elektronische Geräte, insbesondere angesichts der zunehmenden Leistungsdichten. Künftige Underfill-Epoxidformulierungen werden sich auf eine verbesserte Wärmeleitfähigkeit konzentrieren, um die Wärmeübertragung zu verbessern und thermische Probleme effektiv zu bewältigen. Fortschrittliche Füllstoffe und Additive werden in Underfill-Epoxidharze eingearbeitet, um eine höhere Wärmeleitfähigkeit zu erreichen und gleichzeitig andere gewünschte Eigenschaften beizubehalten.
- Flexible und dehnbare Elektronik: Der Aufstieg flexibler und dehnbarer Elektronik eröffnet neue Möglichkeiten für die Unterfüllung von Epoxidmaterialien. Flexible Underfill-Epoxidharze müssen auch bei wiederholtem Biegen oder Dehnen eine hervorragende Haftung und mechanische Eigenschaften aufweisen. Diese Materialien ermöglichen die Einkapselung und den Schutz von Elektronik in tragbaren Geräten, biegsamen Displays und anderen Anwendungen, die mechanische Flexibilität erfordern.
- Umweltfreundliche Lösungen: Nachhaltigkeits- und Umweltaspekte werden bei der Entwicklung von Underfill-Epoxidmaterialien eine immer wichtigere Rolle spielen. Der Schwerpunkt liegt auf der Entwicklung von Epoxidformulierungen, die frei von gefährlichen Substanzen sind und während ihres gesamten Lebenszyklus, einschließlich Herstellung, Verwendung und Entsorgung, eine geringere Umweltbelastung aufweisen. Auch biobasierte oder erneuerbare Materialien könnten als nachhaltige Alternativen an Bedeutung gewinnen.
- Verbesserte Herstellungsprozesse: Zukünftige Trends bei Underfill-Epoxidharz werden sich auf Materialeigenschaften und Fortschritte bei Herstellungsprozessen konzentrieren. Techniken wie additive Fertigung, selektives Dispensieren und fortschrittliche Aushärtungsmethoden werden erforscht, um die Anwendung und Leistung von Underfill-Epoxidharz in verschiedenen elektronischen Montageprozessen zu optimieren.
- Integration fortschrittlicher Test- und Charakterisierungstechniken: Angesichts der zunehmenden Komplexität und Anforderungen elektronischer Geräte besteht ein Bedarf an fortschrittlichen Test- und Charakterisierungsmethoden, um die Zuverlässigkeit und Leistung von unterfülltem Epoxidharz sicherzustellen. Techniken wie zerstörungsfreie Tests, In-situ-Überwachung und Simulationstools werden bei der Entwicklung und Qualitätskontrolle von unterfüllten Epoxidmaterialien helfen.
Zusammenfassung
Underfill-Epoxidharz spielt eine entscheidende Rolle bei der Verbesserung der Zuverlässigkeit und Leistung elektronischer Komponenten, insbesondere bei Halbleiterverpackungen. Die verschiedenen Arten von Underfill-Epoxidharz bieten eine Reihe von Vorteilen, darunter hohe Zuverlässigkeit, Selbstverteilung, hohe Dichte sowie hohe thermische und mechanische Leistung. Die Wahl des richtigen Underfill-Epoxidharzes für die Anwendung und Verpackung gewährleistet eine robuste und langlebige Verbindung. Da die Technologie voranschreitet und die Packungsgrößen schrumpfen, erwarten wir noch innovativere Underfill-Epoxidharz-Lösungen, die überragende Leistung, Integration und Miniaturisierung bieten. Underfill-Epoxidharz wird in der Zukunft der Elektronik eine immer wichtigere Rolle spielen und es uns ermöglichen, in verschiedenen Branchen ein höheres Maß an Zuverlässigkeit und Leistung zu erreichen.