Isolierende Epoxidbeschichtung
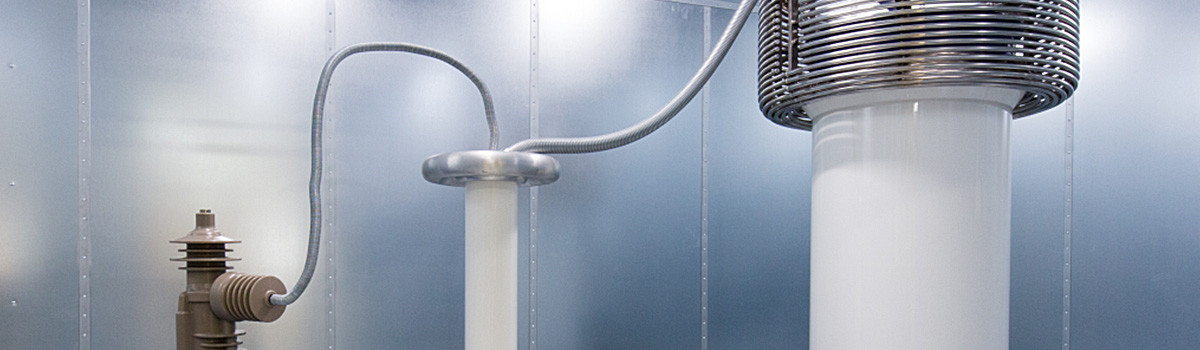
Isolierende Epoxidbeschichtungen sind ein vielseitiges und weit verbreitetes Material mit hervorragenden elektrischen Isoliereigenschaften. Verschiedene Branchen setzen es häufig ein, um elektrische Komponenten, Leiterplatten und andere empfindliche Geräte vor Feuchtigkeit, Staub, Chemikalien und physischen Schäden zu schützen. Ziel dieses Artikels ist es, sich mit der isolierenden Epoxidbeschichtung zu befassen und ihre Anwendungen, Vorteile und kritischen Überlegungen für die Auswahl der geeigneten Schicht für bestimmte Anforderungen hervorzuheben.
Isolierende Epoxidbeschichtung verstehen
Eine isolierende Epoxidbeschichtung ist eine Schutzbeschichtung, die verschiedenen Oberflächen Isolierung und elektrischen Leitfähigkeitswiderstand verleiht. Es wird häufig in der Elektronik-, Elektro-, Automobil- und Luft- und Raumfahrtindustrie verwendet, um elektrische Komponenten zu schützen und deren Leistung zu verbessern.
Der Hauptzweck isolierender Epoxidbeschichtungen besteht darin, den Fluss von elektrischem Strom zwischen leitfähigen Materialien zu verhindern. Diese Beschichtungen werden auf Oberflächen aufgetragen, die anfällig für elektrische Kurzschlüsse, Korrosion oder Schäden durch Umwelteinflüsse sind. Das Epoxidmaterial wirkt als Isolator, verhindert die Übertragung von Elektronen und minimiert das Risiko von Stromausfällen oder Fehlfunktionen.
Isolierende Epoxidbeschichtungen bestehen typischerweise aus einer Kombination aus Epoxidharz, einem duroplastischen Polymer und einem Härter. Das Epoxidharz bietet hervorragende Haftung, chemische Beständigkeit und mechanische Festigkeit, während der Härter die Vernetzungsreaktion auslöst, die das flüssige Epoxidharz in eine feste, dauerhafte Beschichtung umwandelt.
Das Aufbringen isolierender Epoxidbeschichtungen umfasst mehrere Schritte. Zunächst wird die zu beschichtende Oberfläche gründlich gereinigt und vorbereitet, um eine gute Haftung zu gewährleisten. Um eine saubere Klebefläche zu schaffen, müssen jeglicher Schmutz, Fett oder Verunreinigungen entfernt werden. Anschließend wird die Epoxidharzbeschichtung nach Herstellerangaben angemischt und im Sprüh-, Streich- oder Tauchverfahren auf die Oberfläche aufgetragen.
Nach dem Auftragen durchläuft die Epoxidbeschichtung einen Aushärtungsprozess, bei dem sie aushärtet und eine Schutzbarriere bildet. Die Aushärtung kann durch verschiedene Methoden erreicht werden, darunter Hitze, Chemikalien oder beides. Durch die Aushärtung werden die mechanischen Eigenschaften, die Haftfestigkeit und die chemische Beständigkeit der Beschichtung verbessert.
Isolierende Epoxidbeschichtungen bieten mehrere Vorteile:
- Sie sorgen für elektrische Isolierung, verhindern den Fluss von elektrischem Strom und verringern das Risiko von Kurzschlüssen oder Stromausfällen.
- Diese Beschichtungen bieten einen hervorragenden Schutz vor Umwelteinflüssen wie Feuchtigkeit, Chemikalien und Abrieb und verlängern so die Lebensdauer beschichteter Komponenten.
- Isolierende Epoxidbeschichtungen können die thermische Stabilität und Flammwidrigkeit von Oberflächen verbessern und sie für Anwendungen in Umgebungen mit hohen Temperaturen geeignet machen.
Die Bedeutung der elektrischen Isolierung
Die elektrische Isolierung spielt eine entscheidende Rolle bei der Aufrechterhaltung der Sicherheit, Zuverlässigkeit und Effizienz elektrischer Systeme. Dabei werden Materialien und Techniken eingesetzt, um den Fluss elektrischen Stroms zwischen leitenden Komponenten oder Oberflächen zu verhindern. Hier sind einige Hauptgründe, die die Bedeutung der elektrischen Isolierung hervorheben:
- Schutz vor Stromschlägen: Die elektrische Isolierung verhindert den direkten Kontakt mit stromführenden Leitern und verringert so das Risiko eines Stromschlags. Es fungiert als Barriere, die den Fluss von elektrischem Strom durch nichtleitende Materialien verhindert und so Personen vor möglichen Schäden schützt.
- Verhinderung von Kurzschlüssen und elektrischen Bränden: Durch die Isolierung wird ein unbeabsichtigter elektrischer Kontakt zwischen leitfähigen Materialien verhindert, der zu Kurzschlüssen und elektrischen Bränden führen kann. Durch die Isolierung von Drähten, Kabeln und elektrischen Komponenten wird die Wahrscheinlichkeit von Lichtbögen, Funken und Überhitzung minimiert, wodurch das Risiko von Bränden und Geräteschäden erheblich verringert wird.
- Verbesserte elektrische Leistung: Isoliermaterialien mit hoher Durchschlagsfestigkeit und geringer elektrischer Leitfähigkeit verbessern die Gesamtleistung elektrischer Systeme. Sie halten die richtigen Spannungspegel aufrecht, verhindern Leckströme und reduzieren Signalstörungen oder -verzerrungen, wodurch die optimale Funktion elektrischer Schaltkreise und Geräte gewährleistet wird.
- Schutz vor Umwelteinflüssen: Elektrische Isoliermaterialien widerstehen Feuchtigkeit, Chemikalien, Staub und anderen Verunreinigungen. Dieser Schutz trägt dazu bei, Korrosion, Beeinträchtigung und Isolationsversagen durch äußere Faktoren zu verhindern und sorgt so für die Langlebigkeit und Zuverlässigkeit elektrischer Komponenten.
- Erhöhte Energieeffizienz: Isolierung reduziert Energieverluste und verbessert die Effizienz elektrischer Systeme. Durch die Verhinderung von Leckströmen minimiert die Isolierung die Energieverschwendung und verbessert die Übertragung und Verteilung elektrischer Energie, was zu einem geringeren Energieverbrauch und niedrigeren Betriebskosten führt.
- Einhaltung von Sicherheitsstandards und -vorschriften: Elektrische Isolierung ist für die Einhaltung von Sicherheitsstandards und -vorschriften von Behörden und Branchenorganisationen unerlässlich. Durch die Einhaltung dieser Anforderungen wird sichergestellt, dass elektrische Anlagen und Geräte so konzipiert und betrieben werden, dass Risiken für Personal, Eigentum und Umwelt minimiert werden.
- Schutz empfindlicher Geräte: Die Isolierung ist entscheidend für den Schutz empfindlicher elektrischer und elektronischer Geräte vor elektrischen Störungen und Spannungsspitzen. Isoliermaterialien wie Lacke oder Beschichtungen schützen empfindliche Komponenten vor elektromagnetischen Störungen (EMI) und elektrostatischen Entladungen (ESD), bewahren so ihre Funktionalität und verlängern ihre Lebensdauer.
Anwendungen der isolierenden Epoxidbeschichtung
Bei der isolierenden Epoxidbeschichtung handelt es sich um eine spezielle Beschichtung, die hervorragende elektrische Isoliereigenschaften bietet und sich daher für verschiedene Anwendungen eignet. Diese Beschichtung besteht typischerweise aus einem Epoxidharz, das isolierende Eigenschaften und Schutzeigenschaften bietet. Hier sind einige der kritischen Anwendungen einer isolierenden Epoxidbeschichtung:
- Elektronik und elektrische Komponenten: Isolierende Epoxidbeschichtungen werden in der Elektronik- und Elektroindustrie häufig verwendet. Es wird auf Komponenten wie Leiterplatten, Transformatoren, Kondensatoren und Spulen aufgetragen, um eine elektrische Isolierung zu gewährleisten, Kurzschlüsse zu verhindern und die Gesamtzuverlässigkeit und Lebensdauer dieser Komponenten zu verbessern. Die Beschichtung schützt außerdem vor Feuchtigkeit, Staub und anderen Umweltverschmutzungen.
- Stromerzeugung und -übertragung: Isolierende Epoxidbeschichtungen sind in Stromerzeugungs- und -übertragungssystemen von entscheidender Bedeutung. Sie werden an Isolatoren, Schaltanlagen, Sammelschienen und anderen Hochspannungsgeräten angebracht, um elektrische Kriechströme, Koronaentladungen und Überschläge zu verhindern. Durch die Bereitstellung einer hohen dielektrischen Festigkeit trägt die Beschichtung dazu bei, die Integrität und Sicherheit der elektrischen Infrastruktur aufrechtzuerhalten.
- Motoren und Generatoren: Elektromotoren und Generatoren benötigen eine Isolierung, um Stromausfälle zu verhindern und eine effiziente Leistung sicherzustellen. Auf die Wicklungen und andere kritische Teile dieser Maschinen werden isolierende Epoxidbeschichtungen aufgetragen. Die Beschichtung verbessert die elektrische Isolierung, verbessert die Wärmeableitung und bietet Schutz vor Chemikalien, Feuchtigkeit und mechanischer Beanspruchung.
- Automobilindustrie: Isolierende Epoxidbeschichtungen finden im Automobilbereich vielfältige Anwendungen. Sie isolieren elektrische Verbindungen, Klemmen und Kabelbäume in Fahrzeugen. Die Schicht trägt zur Aufrechterhaltung der elektrischen Integrität bei, verhindert Kurzschlüsse und schützt vor Korrosion, Vibration und Temperaturschwankungen. Es wird auch zur Isolierung von Bauteilen in Hybrid- und Elektrofahrzeugen eingesetzt.
- Luft- und Raumfahrt und Verteidigung: Isolierende Epoxidbeschichtungen sind im Luft- und Raumfahrt- und Verteidigungssektor von entscheidender Bedeutung. Sie werden auf elektronische Systeme, Avionik, Radargeräte und Kommunikationssysteme angewendet, um eine zuverlässige Leistung in anspruchsvollen Umgebungen sicherzustellen. Die Beschichtung schützt vor elektrischen Störungen, Strahlung, Feuchtigkeit und extremen Temperaturen.
- Beschichtung für Leiterplatten (PCBs): Leiterplatten sind das Rückgrat elektronischer Geräte. Epoxidbeschichtungen schützen die Schaltkreise und Lötstellen von Leiterplatten vor Feuchtigkeit, Staub und anderen Verunreinigungen. Die Beschichtung sorgt außerdem für eine Isolierung zwischen den leitenden Schichten, verhindert Kurzschlüsse und erhöht die Gesamthaltbarkeit der Platinen.
- Chemikalien- und Korrosionsbeständigkeit: Isolierende Epoxidbeschichtungen bieten eine hervorragende Chemikalienbeständigkeit und können Oberflächen vor korrosiven Substanzen schützen. Sie werden in der chemischen Verarbeitung, in der Öl- und Gasindustrie sowie in der Abwasseraufbereitung eingesetzt. Die Beschichtung verhindert chemische Angriffe, erhöht die Lebensdauer der Geräte und minimiert den Wartungsaufwand.
- Elektrische Kapselung: Isolierende Epoxidbeschichtungen werden zur elektrischen Kapselung verwendet, insbesondere bei Anwendungen, bei denen Feuchtigkeit oder andere Verunreinigungen ein Risiko darstellen. Es wird häufig zum Vergießen und Einkapseln elektronischer Komponenten, Sensoren und Steckverbinder verwendet. Die Beschichtung bildet eine Schutzbarriere gegen Umwelteinflüsse und mechanische Beanspruchung.
Schutz für elektronische Komponenten
Der Schutz elektronischer Komponenten ist von entscheidender Bedeutung, um deren ordnungsgemäße Funktion und Langlebigkeit sicherzustellen. Elektronische Komponenten reagieren häufig empfindlich auf Umweltfaktoren wie Temperatur, Feuchtigkeit, elektrisches Rauschen und körperliche Belastung. Mit einem angemessenen Schutz können diese Komponenten geschützt und sogar funktionsunfähig gemacht werden. Hier sind einige Standardmethoden und -techniken zum Schutz elektronischer Komponenten:
- Gehäuse: Elektronische Komponenten können in Schutzgehäusen wie Koffern, Schränken oder Kästen untergebracht werden. Abschnitte bieten physischen Schutz vor Staub, Feuchtigkeit und anderen Verunreinigungen. Sie schützen die Komponenten außerdem vor unbeabsichtigten Stößen oder unsachgemäßer Handhabung.
- EMI/RFI-Abschirmung: Elektromagnetische Störungen (EMI) und Hochfrequenzstörungen (RFI) können den regulären Betrieb elektronischer Komponenten stören. Bei der EMI/RFI-Abschirmung werden leitfähige Materialien wie Metallbeschichtungen oder leitfähige Dichtungen verwendet, um einen Faradayschen Käfigeffekt zu erzeugen. Diese Abschirmung verhindert, dass externe elektromagnetische Signale die empfindliche Elektronik stören.
- Wärmemanagement: Elektronische Komponenten erzeugen während des Betriebs Wärme, und übermäßige Hitze kann ihre Leistung und Zuverlässigkeit beeinträchtigen. Wärmemanagementtechniken wie Kühlkörper, Lüfter und Wärmeleitpads helfen dabei, Wärme abzuleiten und optimale Betriebstemperaturen aufrechtzuerhalten. Kühlkörper absorbieren und leiten Wärme ab, während Lüfter die Luftzirkulation fördern. Wärmeleitpads bilden eine thermische Schnittstelle zwischen der Komponente und dem Kühlkörper für eine effiziente Wärmeübertragung.
- Überspannungsschutz: Durch Blitzeinschläge, elektrische Fehler oder Schalttransienten verursachte Überspannungen können elektronische Komponenten beschädigen. Überspannungsschutzgeräte wie Überspannungsableiter oder Metalloxid-Varistoren (MOVs) leiten überschüssige Spannung ab, um die Mitglieder zu schützen. Diese Geräte begrenzen die Spannungspegel und verhindern, dass vorübergehende Spannungsspitzen die empfindlichen Komponenten erreichen.
- Umweltabdichtung: In bestimmten Anwendungen müssen elektronische Komponenten vor rauen Umgebungsbedingungen wie Feuchtigkeit, Chemikalien oder extremen Temperaturen geschützt werden. Umgebungsabdichtungstechniken wie Schutzbeschichtungen, Vergussmassen oder hermetische Versiegelung schaffen eine Barriere, die die Komponenten vor diesen Elementen schützt.
- Schaltkreisschutz: Elektronische Komponenten können anfällig für Überspannung, Überstrom und elektrostatische Entladung (ESD) sein. Schaltkreisschutzgeräte wie Sicherungen, Leistungsschalter, Überspannungsschutz (TVS-Dioden) und ESD-Schutzdioden werden eingesetzt, um übermäßige Ströme, Spannungen oder statische Ladungen von den Komponenten abzuleiten.
- Erdung und Potentialausgleich: Um elektronische Komponenten vor elektrischem Rauschen zu schützen und die Sicherheit zu gewährleisten, sind geeignete Erdungs- und Potentialausgleichstechniken unerlässlich. Die Erdung bietet einen Weg zur Ableitung unerwünschter elektrischer Ladungen. Im Gegensatz dazu werden durch das Kleben potenzielle Unterschiede reduziert, die zu Schäden führen könnten. Zu den Erdungs- und Verbindungstechniken gehört die Verwendung von Erdungsplatten, Drähten und typischen Erdungsverbindungen.
- Filterung: Elektrisches Rauschen und Interferenzen aus verschiedenen Quellen können die Leistung elektronischer Komponenten beeinträchtigen. Filter wie Tiefpass-, Hochpass- oder elektromagnetische Interferenzfilter können unerwünschte Signale eliminieren oder reduzieren und eine saubere Stromversorgung der Mitglieder gewährleisten.
- Antistatische Maßnahmen: Elektrostatische Entladung (ESD) kann zu erheblichen Schäden an elektronischen Bauteilen führen. Antistatische Maßnahmen wie ESD-sichere Arbeitsplätze, Armbänder und Verpackungsmaterialien verhindern, dass sich statische Aufladungen ansammeln und in empfindliche Teile entladen.
- Regelmäßige Wartung und Prüfung: Regelmäßige Wartung, Inspektion und Prüfung sind unerlässlich, um potenzielle Probleme mit elektronischen Komponenten zu erkennen. Durch regelmäßige Kontrollen wird sichergestellt, dass die Schutzmaßnahmen ordnungsgemäß funktionieren und eventuelle Störungen oder Ausfälle zeitnah behoben werden.
Durch den Einsatz dieser Schutztechniken können elektronische Komponenten vor Umweltgefahren, elektrischen Störungen und physischen Schäden geschützt werden. Dies gewährleistet ihren zuverlässigen Betrieb und verlängert ihre Lebensdauer, was zu einer verbesserten Leistung und geringeren Ausfallzeiten führt.
Leiterplattenbeschichtung
Die Leiterplattenbeschichtung ist ein entscheidender Prozess in der Elektronikfertigung, bei dem eine Schutzschicht auf die Leiterplatte (PCB) aufgetragen wird. Diese Beschichtung bietet Isolierung, Schutz vor Umwelteinflüssen und erhöht die Zuverlässigkeit und Langlebigkeit der Schaltung. In diesem Artikel werden wir die Bedeutung der Leiterplattenbeschichtung und die verschiedenen Arten der verwendeten Beschichtungen untersuchen.
Der Hauptzweck der Leiterplattenbeschichtung besteht darin, die empfindlichen elektronischen Komponenten vor verschiedenen Umwelteinflüssen zu schützen. Zu diesen Belastungen zählen Feuchtigkeit, Staub, Schmutz, Chemikalien und Temperaturschwankungen, die zu Korrosion, Kurzschlüssen und anderen Ausfällen führen können. Die Beschichtung fungiert als Barriere und verhindert, dass diese schädlichen Elemente die Schaltkreise erreichen und Schäden verursachen.
Für Leiterplatten stehen verschiedene Arten von Beschichtungen zur Verfügung, die je nach Anwendungsanforderungen jeweils spezifische Vorteile bieten. Eine gängige Art ist die Schutzbeschichtung, bei der es sich um einen dünnen Schutzfilm handelt, der direkt auf die Leiterplattenoberfläche aufgetragen wird. Schutzbeschichtungen können aus verschiedenen Materialien hergestellt werden, darunter Acryl, Urethane, Silikone und Epoxidharze. Diese Beschichtungen passen sich der Form der Leiterplatte an, decken alle Komponenten und freiliegenden Leiterbahnen ab und bieten hervorragenden Schutz vor Feuchtigkeit, Staub und chemischen Verunreinigungen.
Eine andere Art der Beschichtung ist die Verguss- oder Vergussmasse, ein dickeres Material, das die gesamte Leiterplatte bedeckt und sie vollständig verkapselt. Vergussmassen bestehen typischerweise aus Epoxidharz oder Polyurethan und bieten hervorragenden Schutz vor mechanischer Beanspruchung, Vibration und extremen Temperaturen. Sie werden häufig in Anwendungen eingesetzt, bei denen die Leiterplatten rauen Umgebungen oder hohen physischen Belastungen ausgesetzt sind.
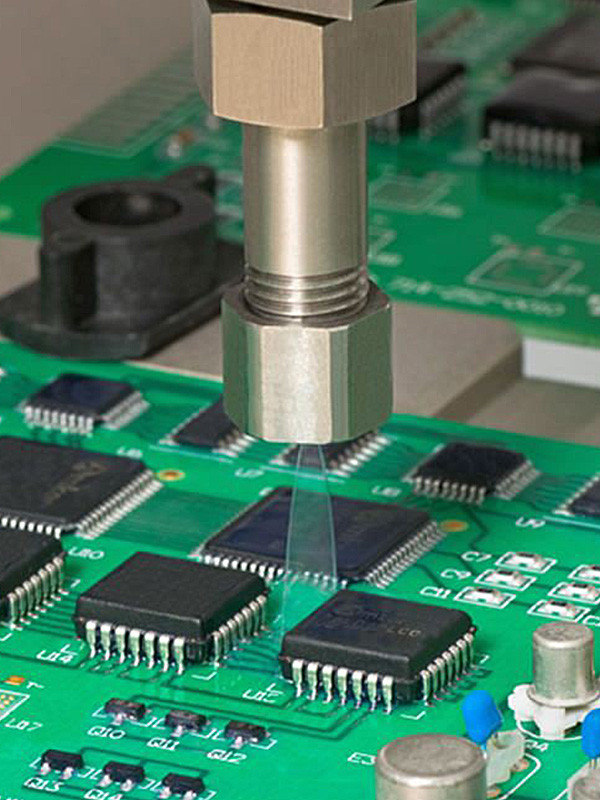
Der Beschichtungsprozess selbst erfordert sorgfältige Auftragstechniken, um eine gleichmäßige Abdeckung und gute Haftung zu gewährleisten. Es können verschiedene Methoden eingesetzt werden, wie zum Beispiel Sprühbeschichten, Tauchbeschichten oder selektives Beschichten. Beim Sprühbeschichten wird mit einer Spritzpistole oder einem Zerstäuber ein feiner Nebel des Beschichtungsmaterials auf die Leiterplatte aufgetragen. Beim Tauchbeschichten hingegen wird die Leiterplatte in ein Bad des Beschichtungsmaterials getaucht, wodurch die Leiterplatte vollständig beschichtet wird. Bei der selektiven Beschichtung handelt es sich um eine präzise Methode, bei der die Beschichtung nur auf bestimmte Bereiche der Leiterplatte aufgetragen wird, während andere Komponenten aus Gründen der Zugänglichkeit unbeschichtet bleiben.
Neben dem Umweltschutz bieten Leiterplattenbeschichtungen auch elektrische Isolationseigenschaften. Das Beschichtungsmaterial verfügt über eine hohe Durchschlagsfestigkeit, die den Leckstrom zwischen eng beieinander liegenden Leiterbahnen oder Komponenten verhindert. Dies ist besonders wichtig bei Hochspannungsanwendungen, bei denen die elektrische Isolierung von entscheidender Bedeutung ist.
Motor- und Transformatorisolierung
Der Schutz elektronischer Komponenten ist von entscheidender Bedeutung, um deren ordnungsgemäße Funktion und Langlebigkeit sicherzustellen. Elektronische Komponenten reagieren häufig empfindlich auf Umweltfaktoren wie Temperatur, Feuchtigkeit, elektrisches Rauschen und körperliche Belastung. Mit einem angemessenen Schutz können diese Komponenten geschützt und sogar funktionsunfähig gemacht werden. Hier sind einige Standardmethoden und -techniken zum Schutz elektronischer Komponenten:
- Gehäuse: Elektronische Komponenten können in Schutzgehäusen wie Koffern, Schränken oder Kästen untergebracht werden. Abschnitte bieten physischen Schutz vor Staub, Feuchtigkeit und anderen Verunreinigungen. Sie schützen die Komponenten außerdem vor unbeabsichtigten Stößen oder unsachgemäßer Handhabung.
- EMI/RFI-Abschirmung: Elektromagnetische Störungen (EMI) und Hochfrequenzstörungen (RFI) können den regulären Betrieb elektronischer Komponenten stören. Bei der EMI/RFI-Abschirmung werden leitfähige Materialien wie Metallbeschichtungen oder leitfähige Dichtungen verwendet, um einen Faradayschen Käfigeffekt zu erzeugen. Diese Abschirmung verhindert, dass externe elektromagnetische Signale die empfindliche Elektronik stören.
- Wärmemanagement: Elektronische Komponenten erzeugen während des Betriebs Wärme, und übermäßige Hitze kann ihre Leistung und Zuverlässigkeit beeinträchtigen. Wärmemanagementtechniken wie Kühlkörper, Lüfter und Pads tragen dazu bei, Wärme abzuleiten und optimale Betriebstemperaturen aufrechtzuerhalten. Kühlkörper absorbieren und leiten Wärme ab, während Lüfter die Luftzirkulation fördern. Wärmeleitpads bilden eine thermische Schnittstelle zwischen der Komponente und dem Kühlkörper für eine effiziente Wärmeübertragung.
- Überspannungsschutz: Durch Blitzeinschläge, elektrische Fehler oder Schalttransienten verursachte Überspannungen können elektronische Komponenten beschädigen. Überspannungsschutzgeräte wie Überspannungsableiter oder Metalloxid-Varistoren (MOVs) leiten überschüssige Spannung ab, um die Mitglieder zu schützen. Diese Geräte begrenzen die Spannungspegel und verhindern, dass vorübergehende Spannungsspitzen die empfindlichen Komponenten erreichen.
- Umweltabdichtung: In bestimmten Anwendungen müssen elektronische Komponenten vor rauen Umgebungsbedingungen wie Feuchtigkeit, Chemikalien oder extremen Temperaturen geschützt werden. Umgebungsabdichtungstechniken wie Schutzbeschichtungen, Vergussmassen oder hermetische Versiegelung schaffen eine Barriere, die die Komponenten vor diesen Elementen schützt.
- Schaltkreisschutz: Elektronische Komponenten können anfällig für Überspannung, Überstrom und elektrostatische Entladung (ESD) sein. Schaltkreisschutzgeräte wie Sicherungen, Leistungsschalter, Überspannungsschutz (TVS-Dioden) und ESD-Schutzdioden werden eingesetzt, um übermäßige Ströme, Spannungen oder statische Ladungen von den Komponenten abzuleiten.
- Erdung und Potentialausgleich: Um elektronische Komponenten vor elektrischem Rauschen zu schützen und die Sicherheit zu gewährleisten, sind geeignete Erdungs- und Potentialausgleichstechniken unerlässlich. Die Erdung bietet einen Weg zur Ableitung unerwünschter elektrischer Ladungen. Im Gegensatz dazu werden durch das Kleben potenzielle Unterschiede reduziert, die zu Schäden führen könnten. Zu den Erdungs- und Verbindungstechniken gehört die Verwendung von Erdungsplatten, Drähten und typischen Erdungsverbindungen.
- Filterung: Elektrisches Rauschen und Interferenzen aus verschiedenen Quellen können die Leistung elektronischer Komponenten beeinträchtigen. Filter wie Tiefpass-, Hochpass- oder elektromagnetische Interferenzfilter können unerwünschte Signale eliminieren oder reduzieren und eine saubere Stromversorgung der Mitglieder gewährleisten.
- Antistatische Maßnahmen: Elektrostatische Entladung (ESD) kann zu erheblichen Schäden an elektronischen Bauteilen führen. Antistatische Maßnahmen wie ESD-sichere Arbeitsplätze, Armbänder und Verpackungsmaterialien verhindern, dass sich statische Aufladungen ansammeln und in empfindliche Teile entladen.
- Regelmäßige Wartung und Prüfung: Regelmäßige Wartung, Inspektion und Prüfung sind unerlässlich, um potenzielle Probleme mit elektronischen Komponenten zu erkennen. Durch regelmäßige Kontrollen wird sichergestellt, dass die Schutzmaßnahmen ordnungsgemäß funktionieren und eventuelle Störungen oder Ausfälle zeitnah behoben werden.
Durch den Einsatz dieser Schutztechniken können elektronische Komponenten vor Umweltgefahren, elektrischen Störungen und physischen Schäden geschützt werden. Dies gewährleistet ihren zuverlässigen Betrieb und verlängert ihre Lebensdauer, was zu einer verbesserten Leistung und geringeren Ausfallzeiten führt.
Kabel- und Drahtisolierung
Kabel- und Leitungsisolierungen spielen in elektrischen Systemen eine entscheidende Rolle, indem sie Schutz, Isolierung und Sicherheit bieten. Es bezieht sich auf die äußere Hülle oder Ummantelung, die elektrische Leiter umgibt, den Fluss von elektrischem Strom in unbeabsichtigte Bereiche verhindert und die Leiter vor Umwelteinflüssen schützt. Die Wahl des Isoliermaterials hängt von Faktoren wie Nennspannung, Temperaturbereich, Umgebungsbedingungen und der beabsichtigten Anwendung ab.
Eines der am häufigsten verwendeten Isoliermaterialien ist Thermoplast. Thermoplastische Isolierung ist flexibel, langlebig sowie abrieb- und chemikalienbeständig. Polyvinylchlorid (PVC) ist ein beliebtes thermoplastisches Material, das für seine Erschwinglichkeit und sein breites Anwendungsspektrum bekannt ist. Es wird häufig in Niederspannungsanwendungen wie Haushaltsverkabelungen und Allzweckkabeln verwendet. PVC-Isolierung bietet gute elektrische Eigenschaften und ist schwer entflammbar.
Ein weiteres weit verbreitetes Isoliermaterial ist Duroplast. Im Gegensatz zu Thermoplasten kann eine duroplastische Isolierung nach dem Aushärten nicht wieder geschmolzen oder umgeformt werden. Vernetztes Polyethylen (XLPE) ist ein häufig verwendetes duroplastisches Material, das für seine hervorragenden elektrischen Eigenschaften, Beständigkeit gegen hohe Temperaturen sowie Beständigkeit gegen Feuchtigkeit und Chemikalien bekannt ist. XLPE-Isolierung wird häufig in Mittel- und Hochspannungskabeln verwendet, einschließlich unterirdischer Übertragungs- und Verteilungssysteme.
Neben Thermoplasten und Duroplasten sind auch andere spezielle Isoliermaterialien für spezifische Anwendungen konzipiert. Isolierungen aus Silikonkautschuk sind beispielsweise für ihre hohe Temperaturbeständigkeit bekannt und eignen sich daher für Anwendungen in extremen Umgebungen wie der Luft- und Raumfahrt- und Automobilindustrie. Fluorpolymere wie Polytetrafluorethylen (PTFE) werden aufgrund ihrer hervorragenden elektrischen Eigenschaften und Beständigkeit gegenüber Chemikalien und Hitze in Hochtemperatur- und Hochfrequenzanwendungen eingesetzt.
Die Nennspannung und der Verwendungszweck des Kabels oder Drahts bestimmen die Dicke der Isolierschicht. Anwendungen mit höherer Spannung erfordern dickere Isolationsschichten, um den höheren elektrischen Feldern standzuhalten und einen elektrischen Durchschlag zu verhindern. Die Isolationsdicke beeinflusst auch den Gesamtdurchmesser und die Flexibilität des Kabels.
Um ihre Leistungsfähigkeit und Sicherheit sicherzustellen, werden Dämmstoffe verschiedenen Tests unterzogen. Diese Tests können die Messung elektrischer Eigenschaften wie Durchschlagsfestigkeit und Isolationswiderstand, die Bewertung der Beständigkeit gegenüber Temperaturschwankungen, der Flammwidrigkeit und mechanischer Eigenschaften wie Flexibilität und Abriebfestigkeit umfassen. Die Einhaltung von Industriestandards und -vorschriften ist für die Gewährleistung der Zuverlässigkeit und Sicherheit elektrischer Systeme von entscheidender Bedeutung.
Luft- und Raumfahrt- und Automobilindustrie
Isolierende Epoxidbeschichtungen finden wichtige Anwendungen sowohl in der Luft- und Raumfahrt- als auch in der Automobilindustrie. Diese Beschichtungen bieten zahlreiche Vorteile, darunter elektrische Isolierung, Korrosionsbeständigkeit und Wärmeschutz. In dieser Antwort werden die kritischen Einsatzmöglichkeiten von isolierenden Epoxidbeschichtungen in der Luft- und Raumfahrt sowie im Automobilsektor unter Einhaltung der 450-Wörter-Grenze untersucht.
Luft-und Raumfahrtindustrie:
- Flugzeugstrukturen: Isolierende Epoxidbeschichtungen schützen Flugzeugstrukturen vor Umwelteinflüssen wie Feuchtigkeit, Chemikalien und UV-Strahlung. Diese Beschichtungen wirken als Barriere, verhindern Korrosion und verlängern die Lebensdauer kritischer Komponenten. Darüber hinaus sorgen sie für elektrische Isolierung, wodurch das Risiko elektrischer Störungen verringert und die Sicherheit erhöht wird.
- Elektronische Komponenten: Isolierende Epoxidbeschichtungen werden auf elektronische Komponenten in Luft- und Raumfahrtsystemen aufgetragen, darunter Leiterplatten, Steckverbinder und Sensoren. Diese Beschichtungen bieten hervorragende elektrische Isolationseigenschaften und schützen empfindliche Elektronik vor statischer Entladung, Feuchtigkeit und Verunreinigungen. Die Schichten helfen auch bei der Wärmeableitung und sorgen so für optimale Leistung und Zuverlässigkeit elektronischer Systeme.
- Radome: Radome, bei denen es sich um Schutzgehäuse für Radarantennen handelt, erfordern isolierende Epoxidbeschichtungen, um Signaltransparenz und Schutz vor Umwelteinflüssen zu gewährleisten. Diese Beschichtungen bieten Isolierung gegen elektromagnetische Störungen (EMI) und bewahren gleichzeitig die strukturelle Integrität des Radoms. Sie bieten außerdem Erosions- und Witterungsbeständigkeit und sorgen so für die Aufrechterhaltung der Radarsystemleistung.
Automobilindustrie:
- Batterien für Elektrofahrzeuge (EV): Isolierende Epoxidbeschichtungen sind für den Schutz der Batterien von Elektrofahrzeugen von entscheidender Bedeutung. Diese Beschichtungen verhindern das Eindringen von Feuchtigkeit und Verunreinigungen und gewährleisten so die Integrität und Langlebigkeit der Batteriezellen. Sie sorgen außerdem für elektrische Isolierung, minimieren das Risiko von Kurzschlüssen und erhöhen die Sicherheit von Elektrofahrzeugen.
- Motorkomponenten: Isolierende Epoxidbeschichtungen werden auf Motorkomponenten verwendet, um sie vor Korrosion, Hitze und chemischer Einwirkung zu schützen. Diese Beschichtungen verbessern die Haltbarkeit und Leistung von Motorteilen wie Zylinderköpfen, Ansaugkrümmern und Abgassystemen. Die Schichten sorgen außerdem für eine Wärmedämmung, reduzieren die Wärmeübertragung und verbessern die Motoreffizienz.
- Elektrische Systeme: Isolierende Epoxidbeschichtungen werden auf elektrische Systeme in Fahrzeugen aufgetragen, einschließlich Kabelbäumen, Steckverbindern und Leiterplatten. Diese Beschichtungen bieten elektrische Isolierung, verhindern Kurzschlüsse und gewährleisten eine zuverlässige Leistung. Sie schützen außerdem vor Feuchtigkeit, Chemikalien und Temperaturschwankungen und erhöhen so die Lebensdauer elektrischer Komponenten.
- Fahrgestell- und Unterbodenschutz: Isolierende Epoxidbeschichtungen schützen das Fahrgestell und den Unterboden von Fahrzeugen vor Korrosion durch Feuchtigkeit, Salz und Straßenschmutz. Diese Beschichtungen bilden eine robuste Barriere, die das Eindringen korrosiver Substanzen verhindert und die Lebensdauer des Fahrzeugs verlängert. Darüber hinaus sorgen sie für Wärmedämmung, reduzieren die Wärmeübertragung und verbessern den Fahrgastkomfort.
Marine- und Offshore-Anwendungen
Isolierende Epoxidbeschichtungen spielen eine entscheidende Rolle bei Schiffs- und Offshore-Anwendungen, indem sie eine Schutzbarriere gegen Korrosion, Abrieb und elektrische Leitfähigkeit bieten. Diese Spezialbeschichtungen bieten zahlreiche Vorteile und werden häufig in Meeres- und Offshore-Umgebungen eingesetzt.
- Seeschiffe: Isolierende Epoxidbeschichtungen werden häufig auf Seeschiffen, einschließlich Schiffen, Lastkähnen und Offshore-Plattformen, verwendet. Diese Beschichtungen schützen die Rümpfe vor der korrosiven Wirkung von Salzwasser, Chemikalien und Meeresorganismen. Sie bilden eine dauerhafte Schutzbarriere, die die Lebensdauer des Schiffs verlängert und den Wartungsaufwand reduziert.
- Offshore-Öl- und Gasplattformen: Bei der Offshore-Öl- und Gasexploration und -produktion sind isolierende Epoxidbeschichtungen für die Aufrechterhaltung der Integrität von Plattformen und Geräten unerlässlich. Sie schützen die Bauwerke vor rauen Umgebungsbedingungen, einschließlich korrosivem Salzwasser, hohen Temperaturen und Chemikalieneinwirkung. Isolierbeschichtungen sorgen auch für elektrische Isolierung, verhindern so, dass elektrische Ströme empfindliche Geräte beeinträchtigen und sorgen für Sicherheit.
- Pipelines und Unterwasseranwendungen: Isolierende Epoxidbeschichtungen werden auf Kanäle und Unterwasserausrüstung aufgetragen, um sie vor Korrosion durch Meerwasser, Feuchtigkeit und Chemikalien zu schützen. Diese Beschichtungen wirken als Barriere, verhindern das Eindringen korrosiver Substanzen und wahren die Integrität der Infrastruktur. Sie sorgen außerdem für eine elektrische Isolierung und verringern so das Risiko elektrischer Störungen oder Schäden.
- Offshore-Windparks: Isolierende Epoxidbeschichtungen werden beim Bau und der Wartung von Offshore-Windparks eingesetzt. Sie schützen Windkraftanlagen, einschließlich Türme, Fundamente und Unterseekabel, vor Korrosion und Umweltschäden. Diese Beschichtungen sorgen auch für eine elektrische Isolierung und sorgen so für eine sichere und effiziente Stromübertragung.
- Schiffs- und Offshore-Ausrüstung: Epoxidbeschichtungen werden auf verschiedene Schiffs- und Offshore-Geräte wie Pumpen, Ventile, Tanks und Verankerungssysteme aufgetragen. Diese Beschichtungen schützen die Geräte vor Korrosion, Abrieb und Chemikalieneinwirkung, verlängern ihre Lebensdauer und senken die Wartungskosten. Die isolierenden Eigenschaften dieser Beschichtungen verhindern außerdem Probleme mit der elektrischen Leitfähigkeit und verbessern so die Sicherheit und Zuverlässigkeit der Geräte.
- Floating Production Storage and Offloading (FPSO)-Schiffe: FPSOs werden häufig in der Offshore-Öl- und Gasförderung eingesetzt. Isolierende Epoxidbeschichtungen werden auf die Rümpfe und Innenstrukturen von FPSOs aufgetragen, um sie vor Korrosion, Abrieb und chemischer Einwirkung zu schützen. Diese Beschichtungen bieten langfristigen Schutz und gewährleisten die strukturelle Integrität des Schiffes.
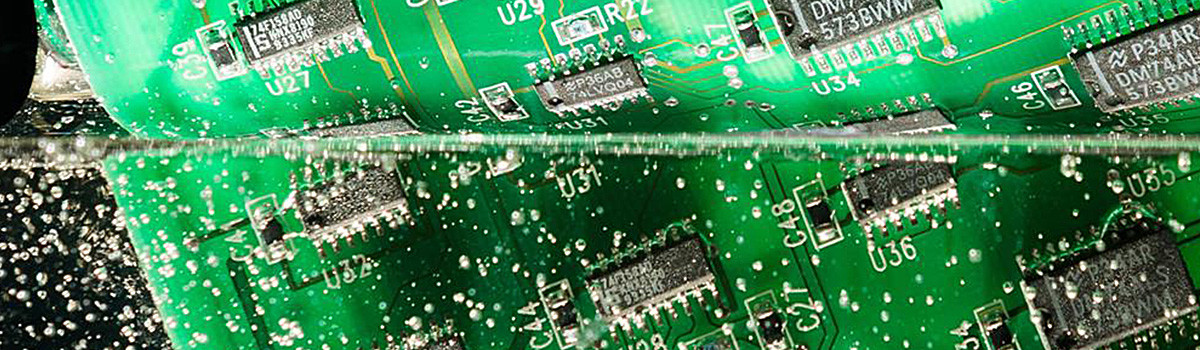
Chemikalien- und Korrosionsbeständigkeit
Isolierende Epoxidbeschichtungen werden in verschiedenen Branchen häufig zum Schutz vor Korrosion und zur elektrischen Isolierung eingesetzt. Diese Beschichtungen bieten eine hervorragende chemische Beständigkeit und eignen sich daher für raue Umgebungen, in denen die Belastung durch korrosive Substanzen ein Problem darstellt.
Die chemische Beständigkeit ist für isolierende Epoxidbeschichtungen von entscheidender Bedeutung, da sie häufig einer Vielzahl von Chemikalien ausgesetzt sind, darunter Säuren, Laugen, Lösungsmittel und Kraftstoffe. Epoxidbeschichtungen widerstehen aufgrund ihrer dichten Molekularstruktur und ihres vernetzten Polymernetzwerks vielen korrosiven Substanzen. Diese Struktur bildet eine Barriere, die das Eindringen von Korrosionsmitteln verhindert und so den darunter liegenden Untergrund schützt.
Einer der Hauptfaktoren für die chemische Beständigkeit von Epoxidbeschichtungen ist ihre hohe Vernetzungsdichte. Unter Vernetzung versteht man die chemische Bindung zwischen den Epoxidmolekülen, wodurch ein dreidimensionales Netzwerk entsteht. Dieses Netzwerk erhöht die Widerstandsfähigkeit der Beschichtung gegenüber chemischen Angriffen, indem es eine Barriere bildet, die die Diffusion korrosiver Substanzen verhindert. Dadurch bleibt das beschichtete Substrat vor Korrosion geschützt.
Darüber hinaus können Epoxidbeschichtungen mit verschiedenen Zusatzstoffen und Verstärkungen formuliert werden, um ihre chemische Beständigkeit zu verbessern. Beispielsweise kann der Zusatz von Korrosionsinhibitoren die Schutzeigenschaften der Beschichtung weiter verbessern, indem sie den Korrosionsprozess hemmen und den Abbau des Epoxidharzes verringern. Auch Verstärkungen wie Glasfasern oder Nanopartikel können die mechanische und chemische Beständigkeit der Beschichtung erhöhen.
Zusätzlich zur chemischen Beständigkeit bieten isolierende Epoxidbeschichtungen eine hervorragende Korrosionsbeständigkeit. Korrosion tritt auf, wenn ein Material mit seiner Umgebung reagiert, was zu seiner Verschlechterung und einem möglichen Ausfall führt. Epoxidbeschichtungen wirken als Barriere zwischen der korrosiven Umgebung und dem Untergrund und verhindern den Kontakt von Feuchtigkeit, Sauerstoff und anderen korrosiven Stoffen mit der darunter liegenden Metalloberfläche.
Epoxidbeschichtungen bieten außerdem eine hervorragende Haftung auf verschiedenen Untergründen und gewährleisten so einen langfristigen Korrosionsschutz. Die starke Verbindung zwischen der Schicht und dem Untergrund verhindert das Eindringen von Feuchtigkeit und korrosiven Substanzen und verringert so die Wahrscheinlichkeit der Entstehung und des Fortschreitens von Korrosion.
Es ist wichtig zu beachten, dass die Chemikalien- und Korrosionsbeständigkeit isolierender Epoxidbeschichtungen durch die Temperatur, die Einwirkungszeit und die spezifische chemische Umgebung beeinflusst werden kann. Während Epoxidbeschichtungen eine hervorragende Beständigkeit gegen verschiedene Chemikalien bieten, können hochaggressive Substanzen über längere Zeiträume oder unter extremen Bedingungen dennoch Schäden verursachen.
Um eine optimale Leistung zu gewährleisten, ist die Auswahl der geeigneten Epoxidbeschichtungsformulierung basierend auf den spezifischen Anwendungsanforderungen von entscheidender Bedeutung. Bei der Auswahl des richtigen Epoxidbeschichtungssystems sollten die Betriebsumgebung, die chemische Belastung, die Temperatur und die erwartete Lebensdauer berücksichtigt werden.
Wärmeleitfähigkeit und Wärmeableitung
Wärmeleitfähigkeit und Wärmeableitung sind in verschiedenen Bereichen von entscheidender Bedeutung, darunter im Ingenieurwesen, in der Elektronik und in den Materialwissenschaften. Sie sind entscheidend für die Effizienz und Zuverlässigkeit von Systemen, die Wärme erzeugen oder verarbeiten. Lassen Sie uns diese Konzepte innerhalb der vorgegebenen Wortgrenze weiter untersuchen.
Unter Wärmeleitfähigkeit versteht man die Fähigkeit eines Materials, Wärme zu leiten. Sie ist eine Eigenschaft, die angibt, wie leicht Wärme durch einen Stoff übertragen werden kann. Materialien mit hoher Wärmeleitfähigkeit ermöglichen einen schnellen Wärmefluss, während Materialien mit geringer Wärmeleitfähigkeit die Wärmeübertragung behindern. Die Maßeinheit für die Wärmeleitfähigkeit ist Watt pro Meter Kelvin (W/mK).
Verschiedene Faktoren beeinflussen die Wärmeleitfähigkeit eines Materials. Einer der entscheidenden Faktoren ist die molekulare oder atomare Struktur. Stoffe mit dicht gepackten Atomen oder Molekülen weisen tendenziell eine höhere Wärmeleitfähigkeit auf. Metalle wie Kupfer und Aluminium sind aufgrund ihrer metallischen Bindung und dicht gepackten Kristallstruktur für ihre hohe Wärmeleitfähigkeit bekannt.
Andererseits weisen Materialien mit komplexen Molekülstrukturen oder großen Hohlräumen, wie etwa Polymere oder Isolatoren wie Holz oder Gummi, eine relativ geringere Wärmeleitfähigkeit auf. Luft und andere Gase sind schlechte Wärmeleiter, weshalb Materialien mit eingeschlossenen Lufteinschlüssen, wie z. B. Isoliermaterialien, eine geringe Wärmeleitfähigkeit aufweisen.
Unter Wärmeableitung versteht man jedoch die Übertragung oder Ableitung von Wärme von einem System oder einer Komponente, um eine Überhitzung zu verhindern und optimale Betriebsbedingungen aufrechtzuerhalten. Eine effiziente Wärmeableitung ist entscheidend für die Langlebigkeit und Leistung von Geräten, insbesondere von Geräten, die große Mengen Wärme erzeugen, wie z. B. elektronische Komponenten, Stromversorgungssysteme und Motoren.
Je nach Anwendungsfall gibt es unterschiedliche Methoden zur Wärmeableitung. Einige Standardtechniken umfassen Leitung, Konvektion und Strahlung.
Bei der Wärmeleitung handelt es sich um die Übertragung von Wärme durch direkten physischen Kontakt zwischen Objekten. Effiziente wärmeleitende Materialien wie Metalle oder Materialien mit hoher Wärmeleitfähigkeit erleichtern die Wärmeübertragung zwischen wärmeerzeugenden Komponenten und Kühlkörpern oder Kühlsystemen.
Bei der Konvektion handelt es sich um die Übertragung von Wärme durch die Bewegung von Flüssigkeiten wie Luft oder Flüssigkeit. Dieser Prozess beruht auf der Zirkulation der Flüssigkeit, entweder auf natürliche Weise oder mit Ventilatoren oder Pumpen, um Wärme von der Quelle abzutransportieren. Kühlkörper mit erweiterten Oberflächen werden häufig verwendet, um die Oberfläche für die konvektive Wärmeübertragung zu vergrößern.
Unter Strahlung versteht man die Emission und Absorption von Wärmestrahlung, also elektromagnetischer Strahlung, die von Objekten aufgrund ihrer Temperatur abgegeben wird. Alle Objekte oberhalb des absoluten Nullpunkts emittieren Wärmestrahlung. Wärmeableitung durch Strahlung erfolgt, wenn die emittierte Strahlung Wärme von der Quelle in eine entspanntere Umgebung transportiert.
Zur Verbesserung der Wärmeableitung werden verschiedene Techniken und Technologien eingesetzt, darunter Kühlkörper, Wärmerohre, Wärmeschnittstellenmaterialien, Lüfter, Flüssigkeitskühlsysteme und fortschrittliche Wärmemanagementlösungen.
Elektrische Isolationsleistung
Isolierende Epoxidbeschichtungen sind für die elektrische Isolierung in verschiedenen Branchen, einschließlich Elektronik, Elektrogeräten und Energiesystemen, von entscheidender Bedeutung. Diese Beschichtungen sollen den Fluss von elektrischem Strom verhindern und vor Stromausfällen oder Kurzschlüssen schützen. Lassen Sie uns die elektrische Isolationsleistung isolierender Epoxidbeschichtungen innerhalb der angegebenen Wortgrenze untersuchen.
Eine der grundlegenden Eigenschaften, die zur elektrischen Isolationsleistung von Epoxidbeschichtungen beitragen, ist ihre hohe Durchschlagsfestigkeit. Unter Durchschlagsfestigkeit versteht man das maximale elektrische Feld, dem ein Material standhalten kann, ohne dass es zu einem elektrischen Durchschlag kommt. Isolierende Epoxidbeschichtungen sind so formuliert, dass sie eine hohe dielektrische Festigkeit aufweisen, sodass sie hohen Spannungen standhalten und elektrische Kriechströme oder Lichtbögen verhindern können.
Mehrere Faktoren, darunter die Harzformulierung, der Aushärtungsprozess und die Füllmaterialien, beeinflussen die Durchschlagsfestigkeit isolierender Epoxidbeschichtungen. Epoxidharze mit hohem Molekulargewicht und hoher Vernetzungsdichte weisen eine höhere Durchschlagsfestigkeit auf. Auch der Aushärtungsprozess spielt eine Rolle, denn durch die richtige Aushärtung entsteht eine dichte und gleichmäßige Beschichtung, die elektrischen Belastungen standhält.
Epoxidbeschichtungen können Füllmaterialien zugesetzt werden, um die elektrische Isolationsleistung zu verbessern. Füllstoffe wie Glasfasern oder mineralische Füllstoffe können die Durchschlagsfestigkeit erhöhen, indem sie das Auftreten von Hohlräumen oder Schwachstellen innerhalb der Beschichtung verringern. Diese Füllstoffe verbessern die Gesamthomogenität und strukturelle Integrität der Beschichtung und minimieren das Risiko eines Stromausfalls.
Isolierende Epoxidbeschichtungen bieten außerdem einen guten elektrischen Widerstand, was sich auf die Fähigkeit des Materials bezieht, dem Fluss von elektrischem Strom zu widerstehen. Ein hoher elektrischer Widerstand ist entscheidend für die Vermeidung von Leckströmen und die Aufrechterhaltung der Integrität der elektrischen Isolierung. Epoxidbeschichtungen weisen typischerweise hohe Widerstandswerte auf, was zu ihrer Wirksamkeit als elektrische Isolatoren beiträgt.
Ein weiterer wichtiger Aspekt der elektrischen Isolationsleistung ist die Fähigkeit isolierender Epoxidbeschichtungen, Umwelteinflüssen zu widerstehen, die sich auf ihre elektrischen Eigenschaften auswirken können. Faktoren wie Feuchtigkeit, Temperaturschwankungen und die Einwirkung von Chemikalien können die Durchschlagsfestigkeit und den spezifischen Widerstand der Beschichtung beeinflussen. Daher ist es wichtig, Epoxidbeschichtungen mit geeigneten Formulierungen und Zusatzstoffen auszuwählen, um unter bestimmten Umgebungsbedingungen eine langfristige elektrische Isolationsleistung zu gewährleisten.
Darüber hinaus sollten isolierende Epoxidbeschichtungen eine gute Haftung auf dem Untergrund aufweisen, um eine dauerhafte elektrische Isolierung zu gewährleisten. Eine starke Verbindung zwischen der Schicht und der darunter liegenden Oberfläche verhindert die Bildung von Hohlräumen oder Lücken, die die elektrische Isolationsleistung beeinträchtigen könnten. Die Oberflächenvorbereitung, die Aufbringungstechniken der Beschichtung und die Kompatibilität zwischen Beschichtung und Untergrund beeinflussen die Haftung.
Zusammenfassend lässt sich sagen, dass isolierende Epoxidbeschichtungen eine hervorragende elektrische Isolationsleistung bieten, indem sie eine hohe Durchschlagsfestigkeit, einen elektrischen Widerstand und eine gute Haftung auf dem Substrat bieten. Ihre Formulierung, der Aushärtungsprozess und die Verwendung von Füllstoffen tragen dazu bei, dass sie elektrischen Belastungen standhalten und Stromausfälle verhindern können. Die richtige Auswahl und Anwendung isolierender Epoxidbeschichtungen ist von entscheidender Bedeutung, um eine wirksame elektrische Isolierung in verschiedenen Anwendungen sicherzustellen, von der Elektronik bis hin zu Energiesystemen.
Arten von isolierenden Epoxidbeschichtungen
Es stehen verschiedene Arten von isolierenden Epoxidbeschichtungen zur Verfügung, die jeweils auf spezifische Anforderungen zugeschnitten sind und unterschiedliche Grade an elektrischer Isolierung bieten. Hier sind einige gängige Arten von schützenden Epoxidbeschichtungen:
- Standardisolierende Epoxidbeschichtungen: Dabei handelt es sich um Allzweck-Epoxidbeschichtungen, die für eine primäre elektrische Isolierung konzipiert sind. Sie bieten eine gute Durchschlagsfestigkeit und einen guten elektrischen Widerstand, wodurch sie für verschiedene Anwendungen geeignet sind.
- Hochtemperaturisolierende Epoxidbeschichtungen: Diese Beschichtungen wurden speziell entwickelt, um erhöhten Temperaturen standzuhalten, ohne ihre elektrische Isolationsleistung zu beeinträchtigen. Sie können in Anwendungen eingesetzt werden, bei denen eine hohe Hitzeeinwirkung zu erwarten ist, beispielsweise bei Motoren, Transformatoren oder elektrischen Komponenten in der Automobil- oder Luft- und Raumfahrtindustrie.
- Wärmeleitende isolierende Epoxidbeschichtungen: Diese Beschichtungen bieten elektrische Isolierung und verfügen zusätzlich über die Eigenschaft der Wärmeleitfähigkeit. Sie sind so konzipiert, dass sie die Wärme effizient ableiten und gleichzeitig die elektrische Isolierung aufrechterhalten. Diese Beschichtungen werden häufig in Anwendungen eingesetzt, die eine elektrische Isolierung und eine effektive Wärmeableitung erfordern, beispielsweise in der Leistungselektronik.
- Flammhemmende, isolierende Epoxidbeschichtungen: Flammhemmende Epoxidbeschichtungen sind so formuliert, dass sie elektrische Isolierung bieten und gleichzeitig Widerstand gegen Flammenausbreitung und Verbrennung bieten. Diese Beschichtungen werden häufig in Anwendungen verwendet, bei denen der Brandschutz eine Rolle spielt, beispielsweise bei Schalttafeln, Schaltanlagen oder Kabeln.
- Chemikalienbeständige isolierende Epoxidbeschichtungen: Diese Beschichtungen dienen der elektrischen Isolierung und bieten gleichzeitig eine hervorragende Beständigkeit gegen verschiedene Chemikalien und korrosive Substanzen. Sie eignen sich für Anwendungen, bei denen eine Belastung durch aggressive Chemikalien oder korrosive Umgebungen zu erwarten ist, beispielsweise in chemischen Verarbeitungsanlagen oder bei Schiffsanwendungen.
- UV-beständige isolierende Epoxidbeschichtungen: UV-beständige Beschichtungen sind so formuliert, dass sie elektrische Isolierung bieten und gleichzeitig Schutz vor den schädlichen Auswirkungen ultravioletter (UV) Strahlung bieten. Diese Beschichtungen werden häufig in Außenanwendungen oder Umgebungen verwendet, in denen die Sonneneinstrahlung erheblich ist, wie z. B. Sonnenkollektoren oder elektrische Geräte im Freien.
- Flexible isolierende Epoxidbeschichtungen: Flexible Epoxidbeschichtungen dienen der elektrischen Isolierung bei Anwendungen, bei denen das beschichtete Substrat mechanischer Belastung oder Bewegung ausgesetzt ist. Diese Beschichtungen bieten eine gute Haftung und Flexibilität, sodass sie Biegungen oder Dehnungen standhalten, ohne zu reißen oder die elektrische Isolierung zu beeinträchtigen.
Es ist wichtig zu beachten, dass die Auswahl des geeigneten isolierenden Epoxidbeschichtungstyps von den spezifischen Anwendungsanforderungen, Umgebungsfaktoren und Leistungserwartungen abhängt. Die Beratung mit Beschichtungsherstellern oder Branchenexperten kann dabei helfen, die am besten geeignete isolierende Epoxidbeschichtung für eine bestimmte Anwendung zu ermitteln.
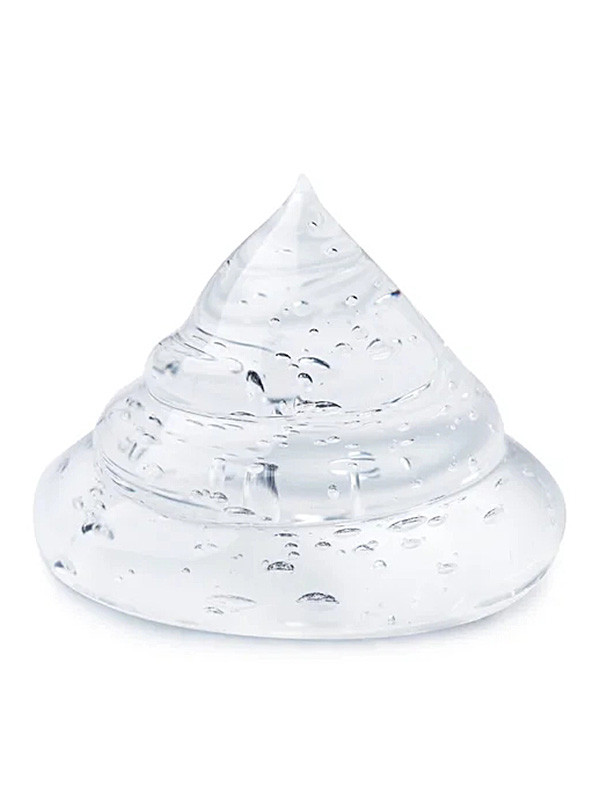
Zweikomponentige Epoxidbeschichtungen
Zweikomponenten-Epoxidbeschichtungen werden aufgrund ihrer außergewöhnlichen Haltbarkeit, chemischen Beständigkeit und Vielseitigkeit in verschiedenen Branchen häufig eingesetzt. Diese Beschichtungen bestehen aus zwei Komponenten: einem Harz und einem Härter. Wenn sie im richtigen Verhältnis kombiniert werden, kommt es zu einer chemischen Reaktion, die als Aushärtung bezeichnet wird, wodurch eine feste und schützende Beschichtung entsteht. Hier werden wir die wichtigsten Eigenschaften, Anwendungen und Vorteile von zweiteiligen Epoxidbeschichtungen untersuchen.
Charakteristik: Zweikomponenten-Epoxidbeschichtungen bieten mehrere Schlüsselmerkmale, die sie für viele Anwendungen äußerst wünschenswert machen. Erstens bieten sie eine hervorragende Haftung auf verschiedenen Untergründen, darunter Beton, Metall, Holz und Glasfaser. Diese Haftung gewährleistet eine lang anhaltende Leistung und verhindert Probleme wie Abblättern oder Delaminierung. Darüber hinaus weisen Epoxidbeschichtungen eine hohe chemische Beständigkeit auf und eignen sich daher für den Einsatz in Umgebungen, die korrosiven Substanzen, Chemikalien oder Lösungsmitteln ausgesetzt sind. Sie sind außerdem für ihre außergewöhnliche Härte, Abriebfestigkeit und Schlagfestigkeit bekannt, was zu ihrer Langlebigkeit und Haltbarkeit beiträgt. Darüber hinaus können Epoxidbeschichtungen je nach den gewünschten ästhetischen und funktionalen Anforderungen so formuliert werden, dass sie verschiedene Oberflächen aufweisen, darunter glänzend, matt oder strukturiert.
Sondermaschinen: Zweikomponenten-Epoxidbeschichtungen finden aufgrund ihrer Vielseitigkeit und Leistungsmerkmale in verschiedenen Branchen Anwendung. Im industriellen Bereich werden sie häufig zum Schutz von Betonböden in Produktionsanlagen, Lagerhallen und Garagen eingesetzt. Durch die Epoxidbeschichtung entsteht eine nahtlose, haltbare Oberfläche, die starkem Verkehr, Stößen und verschütteten Chemikalien standhält. In der Schifffahrtsindustrie werden Epoxidbeschichtungen für Bootsrümpfe, Decks und andere Strukturen verwendet und schützen vor dem Eindringen von Wasser, UV-Strahlung und Korrosion. Diese Beschichtungen werden auch in der Automobilindustrie eingesetzt, um Autokarosserien, Motorkomponenten und Unterbodenbeschichtungen mit einer Schutzschicht zu versehen und so deren Widerstandsfähigkeit gegen Abrieb, Chemikalien und Witterungseinflüsse zu erhöhen. Darüber hinaus werden zweikomponentige Epoxidbeschichtungen im Bausektor häufig für Abdichtungen, Betonreparaturen und dekorative Bodensysteme verwendet.
Vorteile: Der Einsatz zweikomponentiger Epoxidbeschichtungen bietet zahlreiche Vorteile für industrielle und gewerbliche Anwender. Erstens sorgen ihre außergewöhnliche Haltbarkeit und Verschleißfestigkeit für eine längere Lebensdauer beschichteter Oberflächen und reduzieren so die Wartungs- und Austauschkosten. Epoxidbeschichtungen lassen sich außerdem relativ einfach auftragen, was eine effiziente Installation ermöglicht und Ausfallzeiten in industriellen Umgebungen minimiert. Ihre nahtlose und porenfreie Beschaffenheit macht sie hygienisch und leicht zu reinigen, ideal für Umgebungen, die ein hohes Maß an Sauberkeit erfordern, wie z. B. Gesundheitseinrichtungen oder Lebensmittelverarbeitungsbetriebe. Darüber hinaus können Epoxidbeschichtungen an spezifische Anforderungen angepasst werden, darunter Rutschfestigkeit, Hitzebeständigkeit oder elektrische Leitfähigkeit. Diese Vielseitigkeit ermöglicht maßgeschneiderte Lösungen für verschiedene Anwendungen. Schließlich sind zweikomponentige Epoxidbeschichtungen umweltfreundlich, da sie wenig flüchtige organische Verbindungen (VOCs) enthalten, was sie für Arbeitnehmer und die Umwelt sicherer macht.
Einkomponentige Epoxidbeschichtungen
Einkomponentige Epoxidbeschichtungen sind Einkomponentenbeschichtungen, die viele Vorteile gegenüber herkömmlichen zweiteiligen Epoxidbeschichtungen bieten, jedoch über vereinfachte Auftragsverfahren verfügen. Diese Beschichtungen werden mit einem Harz formuliert, das sowohl Epoxidharz als auch Härter enthält, sodass kein separater Härter erforderlich ist. In diesem Artikel werden die Eigenschaften, Anwendungen und Vorteile von einteiligen Epoxidbeschichtungen untersucht.
Charakteristik: Einkomponentige Epoxidbeschichtungen verfügen über mehrere Hauptmerkmale, die sie in verschiedenen Branchen beliebt machen. Diese Beschichtungen weisen eine hervorragende Haftung auf verschiedenen Untergründen, einschließlich Beton, Metall und Holz, auf und gewährleisten so eine solide Verbindung und langanhaltenden Schutz. Sie bieten eine gute chemische Beständigkeit und bieten Schutz vor korrosiven Substanzen, Chemikalien und Lösungsmitteln. Darüber hinaus bieten einteilige Epoxidbeschichtungen eine gute Abriebfestigkeit und Haltbarkeit, sodass sie für Oberflächen geeignet sind, die starkem Verkehr oder Verschleiß ausgesetzt sind. Sie können auch mit unterschiedlichen Finishs formuliert werden, beispielsweise glänzend oder matt, um den gewünschten ästhetischen Reiz zu erzielen.
Sondermaschinen: Einkomponentige Epoxidbeschichtungen finden in verschiedenen Branchen und auf verschiedenen Oberflächen Anwendung. In der Bauindustrie werden sie häufig zum Schutz und zur Verbesserung von Betonböden eingesetzt und sorgen für eine nahtlose und dauerhafte Abdeckung in Umgebungen wie Lagerhallen, Einzelhandelsflächen und Gewerbegebäuden. Diese Beschichtungen finden auch Anwendung in der Automobilindustrie, wo sie zum Korrosionsschutz von Fahrzeugfahrgestellen, Fahrwerkskomponenten und anderen Metalloberflächen eingesetzt werden. Darüber hinaus werden einkomponentige Epoxidharzbeschichtungen in der Schifffahrtsindustrie für Bootsdecks, Schwimmbäder und Schiffskonstruktionen verwendet und sorgen für Beständigkeit gegen Wasser, UV-Strahlung und Chemikalien. Sie können auch auf Metalloberflächen wie Maschinen, Geräten oder Lagertanks zum Schutz vor Korrosion und Verschleiß eingesetzt werden.
Vorteile: Einkomponentige Epoxidbeschichtungen bieten mehrere Vorteile, die sie für viele Anwendungen vorteilhaft machen. Einer der Hauptvorteile ist ihre einfache Handhabung und Anwendung. Da sie vorgemischt geliefert werden, ist das Abmessen und Mischen mehrerer Komponenten nicht erforderlich, was den Beschichtungsprozess vereinfacht und das Fehlerpotenzial verringert. Dadurch sind sie ideal für kleinere Projekte oder Anwender mit begrenzter Erfahrung mit Epoxidbeschichtungen. Darüber hinaus haben Einkomponenten-Epoxidbeschichtungen häufig eine längere Topfzeit als Zweikomponentensysteme, was eine längere Verarbeitungszeit und eine einfachere Anwendung ermöglicht. Sie bieten außerdem eine hervorragende Haftung, Haltbarkeit und chemische Beständigkeit und gewährleisten so einen langanhaltenden Schutz beschichteter Oberflächen. Darüber hinaus enthalten Einkomponenten-Epoxidbeschichtungen in der Regel wenig flüchtige organische Verbindungen (VOCs), was sie umweltfreundlicher und sicherer für den Anwender macht.
Auswahl der richtigen isolierenden Epoxidbeschichtung
Die Auswahl der isolierenden Epoxidbeschichtung ist entscheidend, um eine angemessene Isolierung und Schutz für verschiedene Anwendungen sicherzustellen. Isolierende Epoxidbeschichtungen sollen elektrische Isolierung und Wärmebeständigkeit bieten und elektrische Leitfähigkeit und Wärmeübertragung verhindern. Hier sind einige Schlüsselfaktoren, die bei der Auswahl der geeigneten isolierenden Epoxidbeschichtung zu berücksichtigen sind:
- Elektrische Eigenschaften: Die Hauptfunktion einer isolierenden Epoxidbeschichtung besteht darin, für elektrische Isolierung zu sorgen. Daher ist es wichtig, die elektrischen Eigenschaften der Beschichtung wie Durchschlagsfestigkeit, Volumenwiderstand und Oberflächenwiderstand zu berücksichtigen. Die Durchschlagsfestigkeit bestimmt die maximale Spannung, die die Beschichtung vor dem Durchschlag aushalten kann, während der spezifische Widerstand die Fähigkeit des Materials misst, dem Fluss von elektrischem Strom zu widerstehen. Stellen Sie sicher, dass die Schicht den erforderlichen elektrischen Standards für Ihre spezifische Anwendung entspricht.
- Wärmebeständigkeit: Von isolierenden Epoxidbeschichtungen wird auch erwartet, dass sie Wärmebeständigkeit bieten, um eine Wärmeübertragung zu verhindern. Berücksichtigen Sie die Fähigkeit der Beschichtung, hohen Temperaturen standzuhalten und eine wirksame Wärmedämmung zu bieten. Suchen Sie nach Schichten mit geringer Wärmeleitfähigkeit, um die Wärmeübertragung zu minimieren und die Temperaturstabilität aufrechtzuerhalten.
- Untergrundkompatibilität: Bewerten Sie die Kompatibilität der Epoxidbeschichtung mit dem Untergrundmaterial. Isolierende Epoxidbeschichtungen werden üblicherweise auf Kupfer-, Aluminium- oder Stahlmetallen verwendet. Stellen Sie sicher, dass die Beschichtung so formuliert ist, dass sie gut auf dem jeweiligen Substratmaterial haftet und eine starke Bindung und langfristige Leistung bietet.
- Auftragungsmethode: Berücksichtigen Sie die Auftragungsmethode und die einfache Anwendung der gewählten isolierenden Epoxidbeschichtung. Einige Beschichtungen eignen sich zum Auftragen durch Sprühen, während andere eher zum Auftragen mit Pinsel oder Rolle geeignet sind. Wählen Sie eine Ebene, die mit der verfügbaren Anwendungsausrüstung und den Projektanforderungen übereinstimmt.
- Umweltbeständigkeit: Bewerten Sie die ökologischen Bedingungen, denen die Beschichtung ausgesetzt sein wird, wie z. B. Feuchtigkeit, Nässe, Chemikalien oder UV-Strahlung. Isolierende Epoxidbeschichtungen sollten diesen Umwelteinflüssen hervorragend standhalten, um langfristige Leistung und Schutz zu gewährleisten. Erwägen Sie Beschichtungen mit hoher chemischer Beständigkeit und UV-Stabilität, wenn Sie rauen Umgebungen ausgesetzt sind.
- Zertifizierungen und Standards: Je nach Anwendung können bestimmte Zertifizierungen oder Standards erforderlich sein. Beispielsweise müssen isolierende Epoxidbeschichtungen möglicherweise bestimmte elektrische Standards oder Zertifikate in der Elektroindustrie erfüllen. Stellen Sie sicher, dass die gewählte Beschichtung den Industriestandards und Zertifizierungen entspricht, um Konformität und Leistung sicherzustellen.
- Leistung und Haltbarkeit: Berücksichtigen Sie die Gesamtleistung und Haltbarkeit der isolierenden Epoxidbeschichtung. Suchen Sie nach Schichten mit hervorragender Haftung, Abriebfestigkeit und Langzeitbeständigkeit, um eine dauerhafte Isolierung und Schutz zu gewährleisten. Bewerten Sie die Widerstandsfähigkeit der Beschichtung gegenüber physischen Beschädigungen wie Stößen oder Kratzern, die die Isoliereigenschaften beeinträchtigen könnten.
- Kosten und Wert: Bewerten Sie abschließend die Kosten und den Wert der isolierenden Epoxidbeschichtung. Berücksichtigen Sie Faktoren wie die Anschaffungskosten, die erwartete Lebensdauer der Schicht und die potenziellen Wartungs- oder Austauschkosten im Laufe der Zeit. Das Abwägen der Vorabinvestition mit der langfristigen Leistung und Haltbarkeit wird dabei helfen, den Gesamtwert der Beschichtung zu bestimmen.
Umwelterwägungen
Umweltaspekte spielen bei der Auswahl und Verwendung isolierender Epoxidbeschichtungen eine wichtige Rolle. Es ist von entscheidender Bedeutung, Beschichtungen zu wählen, die eine angemessene Isolierung bieten und die Umweltbelastung während ihres gesamten Lebenszyklus minimieren. Hier sind einige wichtige ökologische Aspekte, die Sie bei der Auswahl isolierender Epoxidbeschichtungen berücksichtigen sollten:
- VOC-Gehalt: Flüchtige organische Verbindungen (VOCs) sind Chemikalien, die zur Luftverschmutzung beitragen und potenzielle gesundheitliche Auswirkungen haben können. Entscheiden Sie sich bei der Auswahl isolierender Epoxidbeschichtungen für VOC-arme oder VOC-freie Formulierungen. Diese Beschichtungen geben beim Auftragen weniger schädliche Dämpfe ab und tragen zu einer besseren Luftqualität im Innen- und Außenbereich bei.
- Gefährliche Substanzen: Bewerten Sie das Vorhandensein gefährlicher Substanzen in der Epoxidbeschichtungsformulierung. Bestimmte Zusatzstoffe, Lösungsmittel oder Schwermetalle können die menschliche Gesundheit oder die Umwelt schädigen. Suchen Sie nach Beschichtungen, die frei von gefährlichen Stoffen sind oder deren Gehalt reduziert ist, um eine sicherere Handhabung und Entsorgung sowie eine langfristige Umweltbelastung zu gewährleisten.
- Biologische Abbaubarkeit: Berücksichtigen Sie die biologische Abbaubarkeit der isolierenden Epoxidbeschichtung. Biologisch abbaubare Beschichtungen zersetzen sich im Laufe der Zeit auf natürliche Weise und verringern so ihre Auswirkungen auf die Umwelt. Suchen Sie nach Schichten, die aus nachwachsenden Rohstoffen stammen oder auf ihre biologische Abbaubarkeit getestet und zertifiziert wurden.
- Energieeffizienz: Isolierende Epoxidbeschichtungen verbessern häufig die Energieeffizienz, indem sie die Wärmeübertragung reduzieren. Durch die Auswahl von Beschichtungen mit hoher Wärmebeständigkeit können Sie die Energieeffizienz in Anwendungen wie Elektroisolierung, Gebäudeisolierung oder Wärmebarrieren verbessern. Dies kann zu einem geringeren Energieverbrauch und einer geringeren Umweltbelastung führen.
- Haltbarkeit und Langlebigkeit: Wählen Sie isolierende Epoxidbeschichtungen mit ausgezeichneter Haltbarkeit und Langlebigkeit. Beschichtungen, die widerstandsfähiger gegen Verschleiß, Korrosion oder Zersetzung sind, müssen seltener gewartet, erneut aufgetragen und entsorgt werden. Dadurch wird die Gesamtumweltbelastung, die mit der Verwendung der Beschichtungen einhergeht, reduziert.
- Verpackung und Abfall: Berücksichtigen Sie die Verpackung der isolierenden Epoxidbeschichtungen und die Abfallerzeugung bei deren Verwendung. Entscheiden Sie sich für Beschichtungen, die in recycelbaren oder umweltfreundlichen Materialien verpackt sind. Darüber hinaus können Beschichtungen, die die Abfallerzeugung während der Anwendung minimieren, z. B. solche mit weniger Overspray oder minimalen Mischanforderungen, dazu beitragen, die Umweltbelastung zu verringern.
- Umweltzertifizierungen: Suchen Sie nach isolierenden Epoxidbeschichtungen, die Umweltzertifizierungen erhalten haben oder anerkannten Umweltstandards entsprechen. Beispiele hierfür sind Zertifikate wie LEED (Leadership in Energy and Environmental Design) oder die Einhaltung der Umweltmanagementnormen ISO 14001. Diese Zertifizierungen stellen sicher, dass die Beschichtungen strengen Tests unterzogen wurden und bestimmte Umweltleistungskriterien erfüllen.
- Ordnungsgemäße Entsorgung und Recycling: Erwägen Sie die geeigneten Entsorgungs- und Recyclingmöglichkeiten für isolierende Epoxidbeschichtungen. Überprüfen Sie die örtlichen Vorschriften und Richtlinien, um sicherzustellen, dass die Beschichtungen am Ende ihres Lebenszyklus ordnungsgemäß entsorgt oder recycelt werden können. Für einige Beschichtungen stehen möglicherweise spezielle Recyclingprogramme oder -optionen zur Verfügung.
Unter Berücksichtigung dieser Umweltaspekte können Sie isolierende Epoxidbeschichtungen auswählen, die eine ausreichende Isolierung bieten und ihre ökologischen Auswirkungen minimieren. Die Wahl umweltfreundlicher Beschichtungen trägt zu Nachhaltigkeitsbemühungen bei, reduziert die Umweltverschmutzung und fördert ein gesünderes Ökosystem.
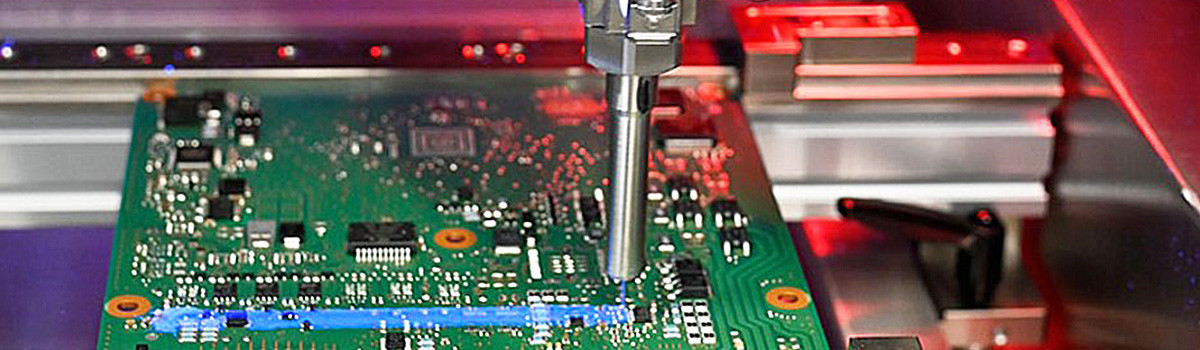
Anwendungstechniken und Tipps
Um optimale Ergebnisse bei der Isolierung von Epoxidbeschichtungen zu erzielen, sind die richtigen Anwendungstechniken unerlässlich. Die folgenden Tipps helfen dabei, eine erfolgreiche Anwendung sicherzustellen und die Leistung der Schicht zu verbessern:
- Oberflächenvorbereitung: Reinigen und bereiten Sie die Oberfläche gründlich vor, bevor Sie die isolierende Epoxidbeschichtung auftragen. Entfernen Sie Schmutz, Staub, Fett oder vorhandene Beschichtungen, die die Haftung beeinträchtigen könnten. Zu den Techniken zur Oberflächenvorbereitung können Schleifen, Entfetten oder die Verwendung geeigneter Reinigungsmittel gehören. Befolgen Sie die Richtlinien des Herstellers zur Oberflächenvorbereitung speziell für die Beschichtung und den Untergrund.
- Mischungsverhältnisse und Topfzeit: Befolgen Sie sorgfältig die Anweisungen des Herstellers bezüglich Mischungsverhältnissen und Topfzeit. Isolierende Epoxidbeschichtungen sind typischerweise zweiteilige Systeme, die eine genaue Mischung der Harz- und Härterkomponenten erfordern. Unsachgemäßes Mischen kann zu unvollständiger Aushärtung oder beeinträchtigter Leistung führen. Achten Sie auf die Topfzeit und die verfügbare Verarbeitungszeit nach dem Mischen der Zutaten. Vermeiden Sie eine Überschreitung der Topfzeit, um eine ordnungsgemäße Anwendung zu gewährleisten.
- Auftragungsmethode: Wählen Sie die geeignete Auftragungsmethode für die isolierende Epoxidbeschichtung basierend auf der Oberfläche und den Projektanforderungen. Zu den Standardauftragsmethoden gehören Pinsel-, Rollen- oder Sprühauftrag. Für kleinere Flächen oder wenn Präzision erforderlich ist, verwenden Sie Pinsel und Rollen. Die Sprühanwendung eignet sich für größere Räume oder eine gleichmäßigere Oberfläche. Befolgen Sie die Empfehlungen des Herstellers für die jeweilige Beschichtung hinsichtlich der Auftragungsmethode und -ausrüstung.
- Temperatur und Luftfeuchtigkeit: Berücksichtigen Sie bei der Anwendung die Umgebungstemperatur und die Luftfeuchtigkeit. Für eine optimale Leistung können isolierende Epoxidbeschichtungen bestimmte Temperatur- und Feuchtigkeitsanforderungen stellen. Befolgen Sie die Richtlinien des Herstellers bezüglich des empfohlenen Temperaturbereichs und der Luftfeuchtigkeitsbedingungen während der Anwendung und Aushärtung. Extreme Temperaturen oder hohe Luftfeuchtigkeit können die Aushärtezeit und die Gesamtleistung der Beschichtung beeinträchtigen.
- Auftragsdicke: Tragen Sie die isolierende Epoxidbeschichtung in der empfohlenen Dicke auf, um die gewünschte Isolierung und den gewünschten Schutz zu erzielen. Eine ausreichende Beschichtungsdicke kann die Isoliereigenschaften beeinträchtigen, während eine zu große Schichtdicke zu Aushärtungsproblemen oder unzureichender Haftung führen kann. Verwenden Sie ein Nassfilmdickenmessgerät, um während der gesamten Anwendung eine gleichmäßige und genaue Beschichtungsdicke sicherzustellen.
- Belüftung und Sicherheit: Sorgen Sie für eine ausreichende Belüftung im Anwendungsbereich, um das Einatmen von Dämpfen oder Dämpfen zu minimieren. Verwenden Sie geeignete persönliche Schutzausrüstung (PSA), wie vom Hersteller empfohlen, wie Handschuhe, Schutzbrillen oder Atemschutz. Befolgen Sie die Sicherheitsrichtlinien und -vorschriften, um sich und andere während des Bewerbungsprozesses zu schützen.
- Aushärte- und Trocknungszeit: Lassen Sie der isolierenden Epoxidbeschichtung ausreichend Aushärte- und Trocknungszeit. Befolgen Sie die Anweisungen des Herstellers hinsichtlich der empfohlenen Aushärtungszeit und Umgebungsbedingungen, um eine ordnungsgemäße Haftung und Leistung zu gewährleisten. Vermeiden Sie übermäßige Feuchtigkeit oder mechanische Beanspruchung der beschichteten Oberfläche, bis die Beschichtung vollständig ausgehärtet ist.
- Inspektion und Wartung: Überprüfen Sie die beschichtete Oberfläche regelmäßig auf Anzeichen von Beschädigung oder Abnutzung. Führen Sie routinemäßige Wartungsarbeiten durch, um die dauerhafte Wirksamkeit der isolierenden Epoxidbeschichtung sicherzustellen. Beheben Sie alle Probleme umgehend, um weitere Verletzungen oder eine Verschlechterung zu verhindern.
Wenn Sie diese Anwendungstechniken und Tipps befolgen, können Sie beim Auftragen isolierender Epoxidbeschichtungen erfolgreiche Ergebnisse erzielen. Eine ordnungsgemäße Oberflächenvorbereitung, genaues Mischen, geeignete Anwendungsmethoden und die Einhaltung der Aushärtungsrichtlinien tragen dazu bei, die gewünschte Isolierung und den gewünschten Schutz Ihrer Anwendung sicherzustellen.
Aushärte- und Trocknungsprozess
Der Härtungs- und Trocknungsprozess für isolierende Epoxidbeschichtungen ist ein entscheidender Schritt, der die endgültigen Eigenschaften und Leistung der Beschichtung bestimmt. Eine ordnungsgemäße Aushärtung gewährleistet eine starke, dauerhafte und vollständig isolierende Schicht. Hier sind die Schlüsselfaktoren und Überlegungen für den Aushärtungs- und Trocknungsprozess von isolierenden Epoxidbeschichtungen:
- Befolgen Sie die Anweisungen des Herstellers: Beachten Sie immer die Anweisungen und das technische Datenblatt des Herstellers, um spezifische Hinweise zu Aushärte- und Trocknungszeiten sowie zu den für die Beschichtung erforderlichen Umgebungsbedingungen zu erhalten. Verschiedene Epoxidbeschichtungen können unterschiedliche Aushärteprozesse und empfohlene Trocknungszeiten haben.
- Umgebungstemperatur: Der Aushärtungsprozess von Epoxidbeschichtungen ist temperaturabhängig. Die meisten Epoxidbeschichtungen erfordern für eine ordnungsgemäße Aushärtung einen minimalen und maximalen Umgebungstemperaturbereich. Stellen Sie sicher, dass die Umgebungstemperatur während des gesamten Aushärte- und Trocknungsprozesses innerhalb des angegebenen Bereichs liegt. Extreme heiße und kalte Temperaturen können den Aushärtungsprozess und die endgültige Leistung der Beschichtung beeinträchtigen.
- Relative Luftfeuchtigkeit: Die Luftfeuchtigkeit kann sich auch auf die Aushärtung und Trocknung isolierender Epoxidbeschichtungen auswirken. In Umgebungen mit hoher Luftfeuchtigkeit kann sich die Aushärtezeit aufgrund der langsamen Verdunstung der Feuchtigkeit aus der Schicht verlängern. Umgekehrt kann eine niedrige Luftfeuchtigkeit dazu führen, dass die Beschichtung zu schnell aushärtet und ihre Integrität beeinträchtigt wird. Halten Sie für eine optimale Aushärtung die vom Hersteller empfohlene Luftfeuchtigkeit ein.
- Belüftung: Eine ausreichende Belüftung ist während des Aushärtens und Trocknens von entscheidender Bedeutung, um eine ordnungsgemäße Luftzirkulation und die Ableitung von Dämpfen oder Dämpfen sicherzustellen. Eine gute Belüftung erleichtert den Aushärtungsprozess und verringert das Risiko von Lösungsmitteleinschlüssen, die die Leistung der Beschichtung beeinträchtigen könnten.
- Aushärtezeit: Die Aushärtezeit für isolierende Epoxidbeschichtungen kann je nach spezifischer Formulierung, Dicke der aufgetragenen Schicht und Umgebungsbedingungen variieren. Um eine vollständige Vernetzung und die Entwicklung der gewünschten Eigenschaften zu gewährleisten, ist es unbedingt erforderlich, die vom Hersteller empfohlene Aushärtezeit einzuhalten. Eine vorzeitige Einwirkung von Feuchtigkeit, Staub oder mechanischer Beanspruchung während des Aushärtungsprozesses kann die Leistung der Beschichtung beeinträchtigen.
- Trocknungszeit: Die Trocknungszeit bezieht sich auf die Zeit, in der das Lösungsmittel aus der Beschichtung verdunstet. Die Trocknungszeit kann je nach Schichtdicke, Temperatur, Luftfeuchtigkeit und Belüftung variieren. Es ist wichtig, die empfohlene Trocknungszeit für die Beschichtung einzuhalten, um eine ordnungsgemäße Filmbildung zu erreichen und eine vorzeitige Handhabung oder Belichtung zu vermeiden.
- Vollständige Aushärtung: Auch wenn sich die Beschichtung nach der empfohlenen Trocknungszeit trocken anfühlt, ist es wichtig zu beachten, dass die vollständige Aushärtung länger dauern kann. Unter vollständiger Aushärtung versteht man die vollständige chemische Vernetzung und Aushärtung der Epoxidbeschichtung. Befolgen Sie die Anweisungen des Herstellers bezüglich der empfohlenen vollständigen Aushärtungszeit, bevor Sie die beschichtete Oberfläche starker Belastung, Abrieb oder anderen Belastungen aussetzen.
- Nachhärtung: Einige isolierende Epoxidbeschichtungen können von einer Nachhärtung profitieren, um ihre Eigenschaften weiter zu verbessern. Bei der Nachhärtung wird die ausgehärtete Schicht für eine bestimmte Dauer erhöhten Temperaturen ausgesetzt. Durch diesen Prozess können die chemische Beständigkeit, Härte und Haftung der Beschichtung verbessert werden. Beachten Sie gegebenenfalls die Richtlinien des Herstellers bezüglich des empfohlenen Nachhärtungsprozesses.
Durch sorgfältiges Befolgen der Herstelleranweisungen, Aufrechterhaltung geeigneter Umgebungsbedingungen, ordnungsgemäße Aushärte- und Trocknungszeiten sowie Gewährleistung einer ausreichenden Belüftung können Sie optimale Ergebnisse bei der Isolierung von Epoxidbeschichtungen erzielen. Richtig ausgehärtete und getrocknete Beschichtungen sorgen für die gewünschte elektrische Isolierung und Wärmebeständigkeit für die beabsichtigte Anwendung.
Wartung und Reparatur von isolierenden Epoxidbeschichtungen
Isolierende Epoxidbeschichtungen werden in verschiedenen Branchen häufig zum Schutz und zur Isolierung elektrischer Geräte und Infrastruktur eingesetzt. Diese Beschichtungen bilden eine dauerhafte Schutzbarriere, die verhindert, dass Feuchtigkeit, Chemikalien und andere Verunreinigungen die darunter liegenden Oberflächen erreichen. Allerdings können isolierende Epoxidbeschichtungen wie jedes andere Beschichtungssystem Wartung und Reparatur erfordern, um ihre Wirksamkeit und Langlebigkeit sicherzustellen.
Die Wartung isolierender Epoxidbeschichtungen umfasst in erster Linie eine regelmäßige Inspektion und Reinigung. Überprüfen Sie die beschichteten Oberflächen regelmäßig auf Anzeichen von Schäden wie Risse, Blasenbildung oder Abblättern. Bitte achten Sie besonders auf Bereiche, die rauen Bedingungen oder mechanischer Belastung ausgesetzt sind, da diese anfälliger für Beschädigungen sind. Wenn Probleme festgestellt werden, beheben Sie diese umgehend, um eine weitere Verschlechterung zu verhindern.
Die Reinigung der beschichteten Oberflächen ist unerlässlich, um Schmutz, Staub, Öle und andere Verunreinigungen zu entfernen, die sich im Laufe der Zeit ansammeln können. Verwenden Sie milde, nicht scheuernde Reinigungsmittel und weiche Bürsten oder Tücher, um die Oberflächen schonend zu reinigen. Vermeiden Sie aggressive Chemikalien oder abrasive Materialien, die die Beschichtung zerkratzen oder beschädigen. Regelmäßige Reinigung trägt dazu bei, die isolierenden Eigenschaften der Epoxidbeschichtung aufrechtzuerhalten und verhindert die Ansammlung leitfähiger Materialien, die ihre Wirksamkeit beeinträchtigen könnten.
Bei der Reparatur kann die Vorgehensweise je nach Ausmaß des Schadens unterschiedlich ausfallen. Sie können Epoxid-Reparatursets verwenden, die speziell für die Isolierung von Beschichtungen bei kleineren Verletzungen wie kleinen Rissen oder Absplitterungen entwickelt wurden. Diese Kits enthalten normalerweise Epoxidfüller und Anweisungen zum korrekten Auftragen. Reinigen Sie den beschädigten Bereich gründlich, befolgen Sie die mit dem Gerät gelieferten Anweisungen und tragen Sie den Epoxidspachtel auf den beschädigten Bereich auf. Lassen Sie es gemäß den Empfehlungen des Herstellers aushärten.
In Fällen, in denen der Schaden schwerwiegender ist, kann es erforderlich sein, den beschädigten Teil der Beschichtung zu entfernen und eine neue Schicht isolierenden Epoxidharzes aufzutragen. Dies erfordert eine sorgfältige Oberflächenvorbereitung, einschließlich Reinigen und Aufrauen des Bereichs um die Beschädigung herum, um eine ordnungsgemäße Haftung der neuen Beschichtung sicherzustellen. Befolgen Sie die Richtlinien des Herstellers zum Auftragen der neuen Epoxidbeschichtung, einschließlich Aushärtezeiten und Temperaturanforderungen.
In manchen Fällen kann es praktischer sein, professionelle Hilfe bei der Wartung und Reparatur isolierender Epoxidbeschichtungen in Anspruch zu nehmen. Erfahrene Auftragnehmer oder Beschichtungsspezialisten können das Ausmaß des Schadens beurteilen, die am besten geeignete Reparaturmethode empfehlen und sicherstellen, dass die verbesserte Beschichtung den erforderlichen Standards und Anforderungen entspricht.
Denken Sie daran, dass regelmäßige Inspektionen und vorbeugende Wartung entscheidend für die Verlängerung der Lebensdauer isolierender Epoxidbeschichtungen sind. Indem Sie kleinere Probleme frühzeitig beheben und die richtigen Reinigungsverfahren befolgen, können Sie die Notwendigkeit umfangreicher Reparaturen minimieren und die anhaltende Wirksamkeit der Beschichtung beim Schutz und der Isolierung elektrischer Geräte und Infrastruktur sicherstellen.
Zusammenfassung
Isolierende Epoxidbeschichtungen sind entscheidend für den Schutz elektrischer Komponenten und Geräte vor verschiedenen äußeren Einflüssen. Bei Anwendungen, die von elektronischen Bauteilen bis hin zu Leiterplatten, Motoren und Kabeln reichen, bieten diese Beschichtungen einen wesentlichen Schutz vor Feuchtigkeit, Chemikalien und physischen Schäden. Die richtige Auswahl einer isolierenden Epoxidbeschichtung hängt von den Umgebungsbedingungen, Leistungsanforderungen und Anwendungstechniken ab. Durch das Verständnis der Vorteile und Überlegungen im Zusammenhang mit isolierenden Epoxidbeschichtungen können Branchen fundierte Entscheidungen treffen, um die Haltbarkeit, Zuverlässigkeit und Langlebigkeit ihrer elektrischen Systeme und Geräte zu verbessern.