Membranklebstoff
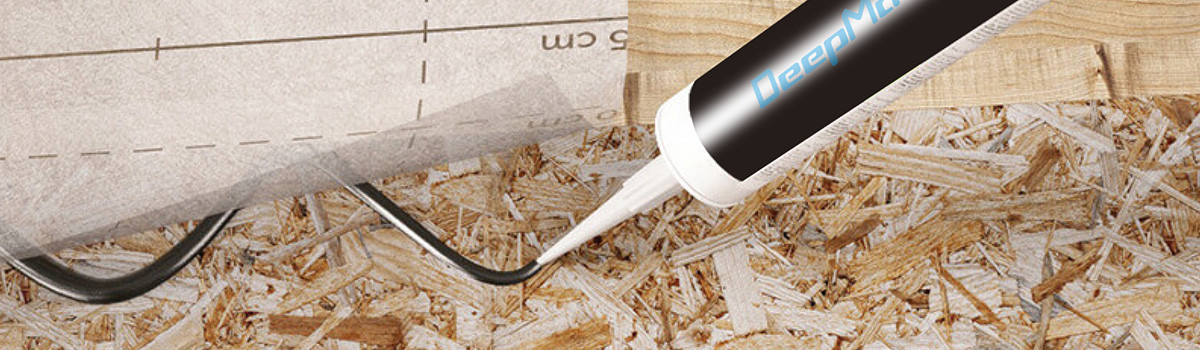
Membranverklebung ist ein Spezialklebstoff, der in verschiedenen Industriezweigen von entscheidender Bedeutung ist, darunter im Baugewerbe, in der Automobilindustrie und in der verarbeitenden Industrie. Es wurde speziell zum Verkleben und Befestigen verschiedener Arten von Membranen entwickelt, z. B. Abdichtungsbahnen, Dachbahnen und Automobilmembranen. Dieser Artikel befasst sich mit der Welt der membranverbindenden Klebstoffe, ihren Anwendungen, Vorteilen und Überlegungen zur Auswahl geeigneter Klebstoffe für spezifische Anforderungen an die Membranverklebung.
Membranklebstoff verstehen
Unter Membranklebstoff versteht man einen Klebstofftyp, der speziell zum Verkleben oder Verbinden verschiedener Arten von Membranen entwickelt wurde. Membranen sind dünne Platten oder Filme aus Materialien wie Kunststoff, Gummi oder Stoffen und werden in verschiedenen Branchen häufig für Anwendungen wie Abdichtung, Luftbarrieren, Isolierung und Dacheindeckung verwendet.
Die Hauptfunktion von Membranklebstoffen besteht darin, eine feste und dauerhafte Verbindung zwischen zwei oder mehr Membranen herzustellen und so deren effektive Leistung als zusammenhängendes System sicherzustellen. Diese Klebstoffe sind so formuliert, dass sie eine hervorragende Haftung auf einer Vielzahl von Membranmaterialien bieten, darunter Polyethylen, Polypropylen, PVC, EPDM, TPO und modifiziertes Bitumen.
Zu den wichtigsten Merkmalen und Eigenschaften von Membranklebstoffen gehören:
- Haftfestigkeit: Membranklebstoffe sind so konzipiert, dass sie eine hohe Haftfestigkeit zwischen Membranen bieten und so eine zuverlässige und dauerhafte Verbindung gewährleisten. Die Haftfestigkeit wird typischerweise unter verschiedenen Umgebungsbedingungen wie Temperaturschwankungen, Feuchtigkeit und Einwirkung von UV-Strahlung getestet, um die Leistung in realen Anwendungen sicherzustellen.
- Flexibilität: Da Membranen aufgrund von Temperaturänderungen oder strukturellen Spannungen häufig Bewegungen, Ausdehnungen und Kontraktionen ausgesetzt sind, muss der Klebstoff flexibel sein, um solchen Aktivitäten standzuhalten, ohne die Verbindung zu beeinträchtigen. Die Flexibilität trägt außerdem dazu bei, Spannungen und Lasten gleichmäßig über die Klebefläche zu verteilen und so die Gesamthaltbarkeit des Systems zu verbessern.
- Chemische Beständigkeit: Membranen sind je nach Anwendung häufig Chemikalien, Wasser oder anderen Substanzen ausgesetzt. Ein geeigneter Membranklebstoff sollte gegen diese Chemikalien beständig sein, um die Langlebigkeit und Integrität der Verbindung zu gewährleisten. Die chemische Beständigkeit verhindert, dass sich der Klebstoff zersetzt oder schwächt, wenn er rauen Umgebungen ausgesetzt wird.
- Wetterbeständigkeit: Für Außenanwendungen von Membranen sind Klebstoffe erforderlich, die extremen Wetterbedingungen wie Temperaturschwankungen, UV-Strahlung, Regen, Schnee und Wind standhalten. Witterungsbeständige Dichtstoffe behalten ihre Haftfestigkeit und Gesamtleistung auch in rauen Außenumgebungen und schützen die Membranen vor vorzeitigem Versagen.
- Einfache Anwendung: Membranklebstoffe sind benutzerfreundlich formuliert und ermöglichen eine einfache und effiziente Anwendung. Abhängig von den spezifischen Anwendungsanforderungen können sie in verschiedenen Formen vorliegen, einschließlich Flüssigkeiten, Bändern oder Blättern. Die einfache Anwendung verbessert die Produktivität und sorgt für eine gleichmäßige Verbindung aller Membranen.
- Kompatibilität: Membranklebstoffe müssen mit den zu verklebenden Materialien kompatibel sein. Hersteller stellen häufig Richtlinien und Kompatibilitätstabellen zur Verfügung, um die richtige Klebstoffauswahl für bestimmte Membranmaterialien sicherzustellen. Die Kompatibilität sorgt für eine optimale Haftung und minimiert das Risiko eines Klebeversagens.
Um die besten Ergebnisse bei der Verwendung von Membranklebstoffen zu erzielen, ist es wichtig, die Anweisungen des Herstellers zur Oberflächenvorbereitung, zum Auftragen des Klebstoffs und zur Aushärtezeit zu befolgen. Insbesondere bei komplexen Anwendungen oder speziellen Membranen kann eine professionelle Beratung oder Unterstützung erforderlich sein.
Insgesamt sind Membranklebstoffe von entscheidender Bedeutung für die Herstellung starker, dauerhafter und zuverlässiger Verbindungen zwischen Membranen. Ihre einzigartigen Eigenschaften ermöglichen effektive Membransysteme, die Vorteile wie Wasserdichtigkeit, Isolierung und Luftbarrierefunktionen in verschiedenen Branchen und Anwendungen bieten.
Die Bedeutung einer effektiven Membranbindung
Eine ausreichende Membranverklebung ist in verschiedenen Branchen und Anwendungen von größter Bedeutung. Hier sind einige Hauptgründe, warum es so wichtig ist:
- Strukturelle Integrität: Membranen werden häufig in Anwendungen eingesetzt, die zur strukturellen Integrität eines Systems beitragen. Durch eine ausreichende Verklebung wird sichergestellt, dass die Membranen sicher an Ort und Stelle bleiben und die allgemeine Stabilität und Festigkeit der Struktur erhalten bleibt. Beispielsweise verhindert die ordnungsgemäße Verklebung von Abdichtungsbahnen in Dachsystemen das Austreten von Wasser und schützt die darunter liegende Struktur vor Schäden.
- Wasserdichtigkeit und Feuchtigkeitskontrolle: Die Membranverklebung ist für eine wirksame Wasserdichtigkeit und Feuchtigkeitskontrolle von entscheidender Bedeutung. Wenn Membranen ordnungsgemäß miteinander verbunden sind, bilden sie eine kontinuierliche Barriere, die das Eindringen von Wasser, Feuchtigkeit oder Dampf verhindert. Dies ist in Gebäudehüllen, Tunneln und Kellern von entscheidender Bedeutung, wo das Eindringen von Feuchtigkeit zu strukturellen Schäden, Schimmelbildung und einer Beeinträchtigung der Raumluftqualität führen kann.
- Luft- und Dampfsperren: Membranen werden häufig als Luft- und Dampfsperren verwendet, um den Luft- und Feuchtigkeitsfluss in Baugruppen zu kontrollieren. Eine angemessene Verklebung gewährleistet die Kontinuität und Integrität des Barrieresystems, minimiert Luftlecks und verhindert feuchtigkeitsbedingte Probleme wie Kondensation. Die ordnungsgemäße Leistung der Luft- und Dampfsperre trägt zur Energieeffizienz, zum Wohnkomfort und zur langfristigen Haltbarkeit von Gebäuden bei.
- Energieeffizienz: In Anwendungen wie Isoliersystemen steigern Membranen die Energieeffizienz, indem sie die Wärmeübertragung oder Luftleckage reduzieren. Durch eine angemessene Verklebung wird sichergestellt, dass die Isoliermembranen ordnungsgemäß installiert werden, wodurch Lücken oder Hohlräume vermieden werden, die die Wärmeleistung beeinträchtigen könnten. Dies führt zu einer verbesserten Energieeffizienz, geringeren Heiz- und Kühlkosten und einem angenehmeren Raumklima.
- Haltbarkeit und Langlebigkeit: Die Membranverklebung wirkt sich direkt auf die Haltbarkeit und Langlebigkeit des Systems aus. Eine gut verklebte Membrankonstruktion kann äußeren Kräften wie Wind, Temperaturschwankungen und Gebäudebewegungen standhalten, ohne die Leistung zu beeinträchtigen. Es widersteht einer Verschlechterung und behält seine Integrität im Laufe der Zeit bei, wodurch die Notwendigkeit häufiger Reparaturen oder Austausche verringert und die Lebensdauer des Systems verlängert wird.
- Sicherheit und Zuverlässigkeit: Bei bestimmten Anwendungen, beispielsweise bei Membranen, die in gefährlichen Umgebungen oder kritischen Infrastrukturen eingesetzt werden, ist eine angemessene Verbindung für Sicherheit und Zuverlässigkeit von entscheidender Bedeutung. Eine zuverlässige Verklebung sorgt beispielsweise dafür, dass die Membranen die Stoffe sicher einschließen und minimiert so das Risiko von Leckagen oder Umweltkontaminationen in Rückhaltesystemen für Chemikalien oder gefährliche Abfälle.
Eine angemessene Membranbindung ist entscheidend für die Erzielung der gewünschten Leistung, Funktionalität und Langlebigkeit in verschiedenen Anwendungen. Es gewährleistet strukturelle Integrität, Wasserdichtigkeit, Feuchtigkeitskontrolle, Energieeffizienz, Haltbarkeit und Sicherheit. Die Auswahl geeigneter Klebstoffe und die Befolgung geeigneter Installationstechniken sind entscheidend für die Erzielung robuster und zuverlässiger Verbindungen zwischen Membranen und tragen letztendlich zum Erfolg des Gesamtsystems oder der gesamten Struktur bei.
Anwendungen von Membranklebstoffen
Membranklebstoffe finden in verschiedenen Branchen ein breites Anwendungsspektrum. Hier sind einige typische Anwendungen:
- Dacheindeckung: Membranklebstoffe werden häufig in Dachsystemen verwendet, insbesondere für einlagige Membranen wie EPDM, TPO und PVC. Diese Klebstoffe sorgen für eine starke Verbindung zwischen den Membranbahnen und sorgen so für ein wasserdichtes und langlebiges Dach. Sie bieten eine hervorragende Beständigkeit gegen Witterungseinflüsse, UV-Strahlung und Temperaturschwankungen und erhöhen so die Langlebigkeit des Dachsystems.
- Abdichtung: Membranklebstoffe sind für Abdichtungsanwendungen im Bauwesen unerlässlich. Sie dienen zur Verbindung von Abdichtungsbahnen wie Bitumenbahnen oder Flüssigbahnen und schaffen so eine fugenlose und zuverlässige Barriere gegen eindringendes Wasser. Diese Klebstoffe sorgen für eine dichte und sichere Verbindung, verhindern Undichtigkeiten und schützen Bauwerke vor feuchtigkeitsbedingten Schäden.
- Luft- und Dampfsperren: Membranklebstoffe sind bei der Installation von Luft- und Dampfsperrsystemen in Gebäuden von entscheidender Bedeutung. Sie werden verwendet, um Membranschichten zu verbinden und so eine kontinuierliche Barriere zu schaffen, die das Austreten von Luft verhindert und die Bewegung von Wasserdampf kontrolliert. Diese Klebstoffe tragen dazu bei, die Energieeffizienz aufrechtzuerhalten, die Raumluftqualität zu verbessern und vor feuchtigkeitsbedingten Problemen wie Kondensation und Schimmelbildung zu schützen.
- Automotive: Membranklebstoffe werden in der Automobilindustrie für verschiedene Anwendungen eingesetzt. Sie verkleben Innenverkleidungen, Dachhimmel, Teppiche und andere Komponenten mit Fahrzeugstrukturen. Diese Klebstoffe sorgen für solide und zuverlässige Verbindungen, die Vibrationen, Temperaturschwankungen und anderen Belastungen im Automobilumfeld standhalten.
- Luft- und Raumfahrt: In der Luft- und Raumfahrtindustrie werden Membranklebstoffe für Klebe- und Dichtungsanwendungen eingesetzt. Sie verkleben leichte Verbundwerkstoffe in Flugzeugstrukturen, etwa kohlenstofffaserverstärkte Polymere. Diese Klebstoffe bieten hohe Festigkeit, leichte Eigenschaften und Beständigkeit gegenüber extremen Temperaturbedingungen und gewährleisten so die strukturelle Integrität und Leistung von Luft- und Raumfahrtkomponenten.
- Medizinische Geräte: Membranklebstoffe finden Anwendung bei der Montage medizinischer Geräte. Sie verkleben Membranen oder Folien in Geräten wie Kathetern, Wundauflagen und transdermalen Pflastern. Diese Klebstoffe bieten Biokompatibilität, sterile Verbindung und Flexibilität und erfüllen die strengen Anforderungen der medizinischen Industrie.
- Industrielle Anwendungen: Membranklebstoffe werden in verschiedenen industriellen Anwendungen eingesetzt, bei denen Membranen oder Folien verbunden werden müssen. Sie produzieren beispielsweise flexible Verpackungen, laminierte Materialien, aufblasbare Strukturen und Stoffverbundstoffe. Diese Klebstoffe sorgen für eine zuverlässige Verbindung verschiedener Materialien, darunter Kunststoffe, Stoffe und Elastomere.
Es ist zu beachten, dass die spezifischen Klebstoffanforderungen je nach Anwendung und zu verklebenden Materialien variieren können. Hersteller bieten Klebesysteme an, die auf verschiedene Membrantypen zugeschnitten sind und so Kompatibilität und optimale Leistung in bestimmten Anwendungen gewährleisten.
Abdichtungsbahnen im Bauwesen
Abdichtungsbahnen spielen eine entscheidende Rolle beim Schutz von Bauwerken vor eindringendem Wasser und feuchtigkeitsbedingten Schäden in der Bauindustrie. Diese Membranen werden in verschiedenen Anwendungen eingesetzt, beispielsweise in Kellern, Dächern, Fundamenten und unterirdischen Strukturen. Hier sind einige kritische Aspekte von Abdichtungsbahnen im Bauwesen:
- Arten von Abdichtungsmembranen: Für Bauanwendungen stehen verschiedene Arten von Abdichtungsmembranen zur Verfügung. Zu den gängigen Typen gehören Bitumenmembranen (modifiziertes Bitumen oder APP/SBS-modifiziert), flüssig aufgetragene Membranen (auf Polyurethan- oder Acrylbasis), thermoplastische Membranen (PVC, TPO oder EPDM) und zementäre Membranen. Jeder Typ bietet Vorteile, Installationsmethoden und Kompatibilität mit verschiedenen Untergründen.
- Funktion und Vorteile: Abdichtungsbahnen bilden eine kontinuierliche Barriere, die das Eindringen von Wasser, Feuchtigkeit und Dampf in die Gebäudestruktur verhindert. Sie schützen vor Wasserschäden, Schimmelbildung und dem Verfall von Baumaterialien. Auch Abdichtungsbahnen tragen zur Energieeffizienz bei, da sie den Verlust klimatisierter Luft verhindern und die Gefahr von Kondensation verringern.
- Anwendungsgebiete: In verschiedenen Baubereichen werden Abdichtungsbahnen eingesetzt, um einen ausreichenden Feuchtigkeitsschutz zu gewährleisten. Diese beinhalten:
- Dächer: Abdichtungsbahnen werden zum Schutz flacher oder geneigter Decken angebracht und sorgen dafür, dass sie wasserdicht und witterungsbeständig sind. Membranen wie EPDM, TPO oder PVC werden häufig in Dachanwendungen verwendet.
- Fundamente: Abdichtungsmembranen werden an der Außenseite von unterirdischen Fundamenten angebracht, um das Eindringen von Wasser zu verhindern. Sie tragen dazu bei, das Fundament trocken zu halten und verringern so das Risiko von Rissen, Schimmel und Strukturschäden.
- Keller: Um Durchsickern und Feuchtigkeit zu verhindern, sind Abdichtungsbahnen für Keller unerlässlich. Sie werden an Innen- oder Außenwänden und Böden angebracht, um eine Barriere gegen Grundwasser und Feuchtigkeit zu schaffen.
- Nassbereiche: Abdichtungsmembranen werden in Nassbereichen wie Badezimmern, Duschen und Schwimmbädern verwendet, um Wasserlecks und -sickern zu verhindern. Sie sorgen für eine dauerhafte und wasserdichte Umgebung.
- Installationsmethoden: Die Installation von Abdichtungsbahnen hängt von der Art der verwendeten Membran ab. Einige Membranen sind selbstklebend, während andere zum Verkleben die Anwendung von Klebstoff oder Hitze erfordern. Flüssig aufgetragene Membranen werden typischerweise auf die Oberfläche aufgesprüht, gerollt oder aufgestrichen. Eine ordnungsgemäße Oberflächenvorbereitung, einschließlich Reinigen, Grundieren und Nivellieren, sorgt für eine sichere und dauerhafte Verbindung.
- Qualitätssicherung: Qualitätssicherung ist bei Abdichtungsmembraninstallationen von wesentlicher Bedeutung, um die Wirksamkeit und Haltbarkeit des Systems sicherzustellen. Dazu gehören die ordnungsgemäße Oberflächenvorbereitung, das genaue Anbringen der Membran und die gründliche Inspektion von Nähten und Überlappungen. Zur Validierung der Leistung des Abdichtungssystems sollten Qualitätskontrollmaßnahmen wie Dichtheitsprüfungen und die Einhaltung der Herstellerrichtlinien befolgt werden.
- Wartung und Reparatur: Regelmäßige Wartung und rechtzeitige Reparatur sind erforderlich, um die Integrität von Abdichtungsbahnen zu bewahren. Es sollten Inspektionen durchgeführt werden, um Anzeichen von Schäden oder Abnutzung, wie Risse, Blasen oder Risse, festzustellen. Um das Eindringen von Wasser zu verhindern und die Wirksamkeit des Abdichtungssystems aufrechtzuerhalten, sollten zeitnahe Reparaturen unter Verwendung kompatibler Materialien und Techniken durchgeführt werden.
Dachbahnen zum Wetterschutz
Dachbahnen sind wesentliche Bestandteile der Gebäudehülle und bieten entscheidenden Wetterschutz. Diese Membranen bilden eine Barriere gegen eindringendes Wasser, Windschäden und andere Umwelteinflüsse. Sie sollen eine wasserdichte, wetterbeständige Schicht bilden, die die darunter liegende Struktur, Isolierung und Innenräume schützt. In diesem Artikel wird die Bedeutung von Dachmembranen untersucht und einige gängige Arten besprochen, die zum Wetterschutz verwendet werden.
Der Hauptzweck von Dachbahnen besteht darin, das Eindringen von Wasser in das Dachsystem zu verhindern. Das Eindringen von Wasser kann zu erheblichen Schäden führen, darunter strukturelle Schäden, Schimmelbildung und eine beeinträchtigte Isolierung. Dachbahnen fungieren als Schutzschild und sorgen dafür, dass Wasser von der Dachoberfläche abfließt, ohne in die darunter liegenden Schichten einzudringen.
Eine beliebte Art von Dachbahnen ist die Membran aus thermoplastischem Olefin (TPO). TPO-Membranen bestehen aus einer Mischung aus Polypropylen und Ethylen-Propylen-Kautschuk. Sie bieten eine hervorragende Beständigkeit gegen ultraviolette (UV) Strahlung, Ozon und chemische Einwirkung. TPO-Membranen sind äußerst flexibel und eignen sich daher für Dachdesigns und -formen. Sie sind außerdem heißschweißbar, was eine nahtlose Installation gewährleistet und das Risiko von Undichtigkeiten verringert.
Eine weitere häufig verwendete Dachbahn ist die Ethylen-Propylen-Dien-Terpolymer-Membran (EPDM). EPDM ist eine Synthesekautschukmembran, die eine hervorragende Witterungsbeständigkeit aufweist und extremen Temperaturen, UV-Strahlung und Ozoneinwirkung standhält, ohne sich zu verschlechtern. EPDM-Membranen sind in großen Platten erhältlich, wodurch die Anzahl der Nähte und Verbindungen, die gefährdete Bereiche für das Eindringen von Wasser sind, minimiert wird. Sie sind außerdem sehr langlebig und haben eine lange Lebensdauer.
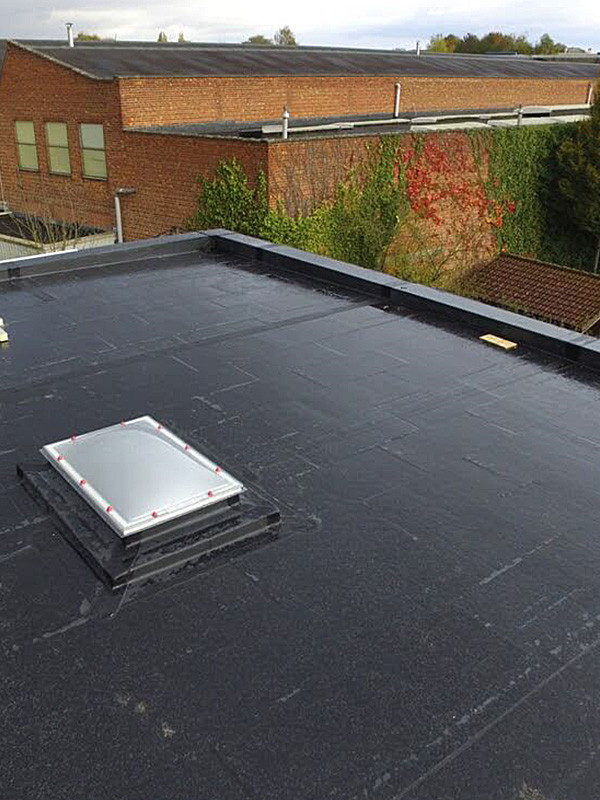
Auch Dachbahnen aus Polyvinylchlorid (PVC) erfreuen sich in der Branche großer Beliebtheit. PVC-Membranen sind mit Polyester oder Glasfaser verstärkt und bieten hervorragende Festigkeit und Haltbarkeit. Sie weisen eine hohe Beständigkeit gegen Chemikalien, UV-Strahlung und Feuer auf. PVC-Membranen sind für ihre Energieeffizienz bekannt, da sie Wärme reflektieren und die Kühllast eines Gebäudes reduzieren. Sie sind in verschiedenen Farben erhältlich und können für eine wasserdichte Versiegelung heißverschweißt werden.
Darüber hinaus werden modifizierte Bitumenbahnen häufig zum Wetterschutz eingesetzt. Diese Membranen bestehen aus mit Polymeren modifiziertem Asphalt, um ihre Leistungseigenschaften zu verbessern. Modifizierte Bitumenbahnen sind flexibel, einfach zu verlegen und bieten eine hervorragende Beständigkeit gegen Wasser, UV-Strahlung und thermische Belastungen. Sie sind in verschiedenen Formen erhältlich, einschließlich selbstklebender Folien, die die Installation vereinfachen und den Einsatz offener Flammen minimieren.
Automobilmembranen zur Geräusch- und Vibrationskontrolle
Geräusch- und Vibrationskontrolle sind für die Konstruktion und Herstellung von Fahrzeugen von entscheidender Bedeutung, da sie den Komfort und das gesamte Fahrerlebnis erheblich beeinflussen. Automobilmembranen haben sich als wirksame Lösung zur Reduzierung von Fahrzeuggeräuschen und -vibrationen erwiesen. Diese speziell entwickelten Membranen sollen Vibrationen und Geräusche absorbieren und dämpfen, die von verschiedenen Quellen im Fahrzeug erzeugt werden.
Automobilmembranen werden typischerweise aus hochwertigen Materialien wie Gummi, Elastomeren oder Verbundwerkstoffen hergestellt. Sie sind strategisch in verschiedenen Bereichen des Fahrzeugs platziert, einschließlich Motorraum, Türen, Boden und Innenverkleidungen, um Geräusche und Vibrationen wirksam zu dämpfen.
Eine der Hauptfunktionen von Automobilmembranen ist die Vibrationsdämpfung. Wenn ein Fahrzeug in Bewegung ist, können verschiedene Komponenten und Systeme wie Motor, Getriebe und Straßenkontakt Vibrationen erzeugen. Diese Vibrationen können sich auf die gesamte Fahrzeugstruktur übertragen, was zu unerwünschtem Lärm und Unbehagen für die Insassen führt. Automobilmembranen wirken als Schwingungsisolatoren, indem sie diese Schwingungen absorbieren und ableiten und verhindern, dass sie sich auf andere Fahrzeugteile ausbreiten. Dies trägt dazu bei, den Gesamtgeräuschpegel zu reduzieren und die Laufruhe zu verbessern.
Neben der Vibrationsdämpfung spielen Automobilmembranen eine entscheidende Rolle bei der Geräuschreduzierung. Sie sollen Luft- und Körperschall im Fahrzeug absorbieren und dämpfen. Unter Luftschall versteht man Geräusche, die von externen Quellen wie Straße und Wind erzeugt werden, während die mechanischen Komponenten des Fahrzeugs Körperschall erzeugen. Durch den Einbau von Membranen in die Fahrzeugkonstruktion kann die Übertragung dieser Geräusche deutlich reduziert werden. Die Membranen absorbieren die Schallenergie und wandeln sie in Wärme um, wodurch die Auswirkungen auf die Insassen minimiert werden.
Darüber hinaus bieten Automobilmembranen zusätzliche Vorteile, die über die Geräusch- und Vibrationskontrolle hinausgehen. Sie können die strukturelle Integrität des Fahrzeugs insgesamt verbessern, indem sie die Belastung und Beanspruchung der Komponenten, die Vibrationen ausgesetzt sind, reduzieren. Dies wiederum kann die Haltbarkeit und Lebensdauer verschiedener Teile erhöhen und so zu einer verbesserten Fahrzeugzuverlässigkeit führen.
Darüber hinaus tragen Automobilmembranen zu Initiativen zur Gewichtsreduzierung in modernen Fahrzeugen bei. Durch den Ersatz traditioneller schwerer Materialien durch leichte Membranen können Hersteller Gewicht einsparen, ohne Kompromisse bei Leistung oder Sicherheit einzugehen. Diese Gewichtsreduzierung trägt dazu bei, die Kraftstoffeffizienz zu verbessern und den COXNUMX-Ausstoß zu reduzieren, was im Einklang mit den kontinuierlichen Bemühungen der Branche um Nachhaltigkeit steht.
Industrie- und Fertigungsanwendungen
Membranklebstoffe spielen eine entscheidende Rolle in verschiedenen Industrie- und Fertigungsanwendungen, bei denen das Verbinden und Kleben von Membranen erforderlich ist. Diese Klebeprodukte wurden speziell entwickelt, um robuste und dauerhafte Verbindungen zwischen verschiedenen Membrantypen herzustellen und so zuverlässige und langlebige Strukturen zu schaffen. Hier sind einige wichtige Anwendungen von Membranklebstoffen:
- Bauwesen und Dachdecker: Die Bauindustrie verwendet in großem Umfang Membranklebstoffe, hauptsächlich für Dachdeckeranwendungen. Es ermöglicht die sichere Befestigung von Dachbahnen wie EPDM (Ethylen-Propylen-Dien-Monomer), PVC (Polyvinylchlorid), TPO (thermoplastisches Olefin) und modifiziertem Bitumen. Der Kleber sorgt für wasserdichte Versiegelungen und Beständigkeit gegen Witterungseinflüsse, UV-Strahlung und extreme Temperaturbedingungen.
- Automobilbau: In der Automobilindustrie wird Membranklebstoff für verschiedene Anwendungen eingesetzt, einschließlich der Verklebung von Innen- und Außenverkleidungsteilen. Diese Klebstoffe ermöglichen die sichere Befestigung von Membranen für Dachhimmel, Türverkleidungen, Armaturenbretter und andere Elemente im Fahrzeuginnenraum. Die Eigenschaften des Klebstoffs sorgen für starke Verbindungen, die Vibrationen, Temperaturschwankungen sowie der Einwirkung von Chemikalien und Feuchtigkeit standhalten.
- Luft- und Raumfahrt: Membranklebstoffe werden in der Luft- und Raumfahrtindustrie häufig für Anwendungen wie Flugzeuginnenräume, Isoliersysteme und Verbundklebungen eingesetzt. Es sorgt für eine zuverlässige Haftung von Membranen in Flugzeugkabinen und gewährleistet so strukturelle Integrität und Feuerbeständigkeit. Die leichten Eigenschaften des Klebstoffs kommen besonders bei Anwendungen in der Luft- und Raumfahrt zum Einsatz, bei denen es auf eine Gewichtsreduzierung ankommt.
- Schifffahrtsindustrie: Membranklebstoff wird in der Schifffahrtsindustrie für Anwendungen wie Bootsbau, Deckverklebung und Abdichtung eingesetzt. Es ermöglicht die Verklebung von Membranen für Decks, Rümpfe, Schotte und andere Schiffsbauteile. Die Beständigkeit des Klebstoffs gegenüber Wasser, Salz und Umwelteinflüssen gewährleistet eine langfristige Haltbarkeit und Wasserdichtigkeit.
- Herstellung medizinischer Geräte: In der medizinischen Industrie werden Membranklebstoffe zum Zusammenbau verschiedener medizinischer Geräte und Geräte verwendet. Es erleichtert das Verkleben von Membranen in chirurgischen Instrumenten, Diagnosegeräten und tragbaren medizinischen Sensoren. Die Biokompatibilität und Sterilisationsbeständigkeit des Klebstoffs machen ihn für medizinische Anwendungen geeignet und sorgen für Sicherheit und Zuverlässigkeit.
- Elektronik- und Elektroindustrie: Membranklebstoff wird in der Elektronik- und Elektrobranche zum Verkleben von flexiblen Leiterplatten, Touchscreens und Anzeigetafeln eingesetzt. Der Klebstoff ermöglicht die Befestigung von Membranen an elektronischen Bauteilen und sorgt für elektrische Leitfähigkeit, Schutz vor Feuchtigkeit und Staub sowie mechanische Stabilität.
- Filtrationssysteme: Membranklebstoff ist bei der Herstellung von Filtersystemen in Branchen wie der Wasseraufbereitung, der Pharmaindustrie und der Lebensmittelverarbeitung von entscheidender Bedeutung. Der Klebstoff verbindet Membranen sicher mit Filtergehäusen, gewährleistet eine effiziente Filtrationsleistung und verhindert Bypass oder Leckagen.
- Energiesektor: Membranklebstoffe finden Anwendung im Bereich der erneuerbaren Energien, insbesondere bei der Herstellung und Installation von Photovoltaikmodulen (PV). Die Verbindung erleichtert die Verbindung von Membranen, wie z. B. Verkapselungsfolien, mit PV-Zellen und Rückseitenfolienmaterialien und gewährleistet so eine ordnungsgemäße Abdichtung, Wetterbeständigkeit und elektrische Isolierung.
Dies sind nur einige Beispiele für die vielfältigen Industrie- und Fertigungsanwendungen, bei denen Membranklebstoffe zum Einsatz kommen. Die Eigenschaften des Klebstoffs, wie z. B. feste Bindung, Haltbarkeit, Beständigkeit gegenüber Umwelteinflüssen und Kompatibilität mit verschiedenen Materialien, machen ihn zu einer wertvollen Lösung in verschiedenen Branchen und tragen zur Herstellung zuverlässiger und leistungsstarker Strukturen und Produkte bei.
Arten von Membranklebstoffen
Membranklebstoffe spielen eine entscheidende Rolle in verschiedenen Industrie- und Fertigungsanwendungen, bei denen das Verbinden und Kleben von Membranen erforderlich ist. Diese Klebeprodukte wurden speziell entwickelt, um robuste und dauerhafte Verbindungen zwischen verschiedenen Membrantypen herzustellen und so zuverlässige und langlebige Strukturen zu schaffen. Hier sind einige wichtige Anwendungen von Membranklebstoffen:
- Bauwesen und Dachdecker: Die Bauindustrie verwendet in großem Umfang Membranklebstoffe, hauptsächlich für Dachdeckeranwendungen. Es ermöglicht die sichere Befestigung von Dachbahnen wie EPDM (Ethylen-Propylen-Dien-Monomer), PVC (Polyvinylchlorid), TPO (thermoplastisches Olefin) und modifiziertem Bitumen. Der Kleber sorgt für wasserdichte Versiegelungen und Beständigkeit gegen Witterungseinflüsse, UV-Strahlung und extreme Temperaturbedingungen.
- Automobilbau: In der Automobilindustrie wird Membranklebstoff für verschiedene Anwendungen eingesetzt, einschließlich der Verklebung von Innen- und Außenverkleidungsteilen. Diese Klebstoffe ermöglichen die sichere Befestigung von Membranen für Dachhimmel, Türverkleidungen, Armaturenbretter und andere Elemente im Fahrzeuginnenraum. Die Eigenschaften des Klebstoffs sorgen für starke Verbindungen, die Vibrationen, Temperaturschwankungen sowie der Einwirkung von Chemikalien und Feuchtigkeit standhalten.
- Luft- und Raumfahrt: Membranklebstoffe werden in der Luft- und Raumfahrtindustrie häufig für Anwendungen wie Flugzeuginnenräume, Isoliersysteme und Verbundklebungen eingesetzt. Es sorgt für eine zuverlässige Haftung von Membranen in Flugzeugkabinen und gewährleistet so strukturelle Integrität und Feuerbeständigkeit. Die leichten Eigenschaften des Klebstoffs kommen besonders bei Anwendungen in der Luft- und Raumfahrt zum Einsatz, bei denen es auf eine Gewichtsreduzierung ankommt.
- Schifffahrtsindustrie: Membranklebstoff wird in der Schifffahrtsindustrie für Anwendungen wie Bootsbau, Deckverklebung und Abdichtung eingesetzt. Es ermöglicht die Verklebung von Membranen für Decks, Rümpfe, Schotte und andere Schiffsbauteile. Die Beständigkeit des Klebstoffs gegenüber Wasser, Salz und Umwelteinflüssen gewährleistet eine langfristige Haltbarkeit und Wasserdichtigkeit.
- Herstellung medizinischer Geräte: In der medizinischen Industrie werden Membranklebstoffe zum Zusammenbau verschiedener medizinischer Geräte und Geräte verwendet. Es erleichtert das Verkleben von Membranen in chirurgischen Instrumenten, Diagnosegeräten und tragbaren medizinischen Sensoren. Die Biokompatibilität und Sterilisationsbeständigkeit des Klebstoffs machen ihn für medizinische Anwendungen geeignet und sorgen für Sicherheit und Zuverlässigkeit.
- Elektronik- und Elektroindustrie: Membranklebstoff wird in der Elektronik- und Elektrobranche zum Verkleben von flexiblen Leiterplatten, Touchscreens und Anzeigetafeln eingesetzt. Der Klebstoff ermöglicht die Befestigung von Membranen an elektronischen Bauteilen und sorgt für elektrische Leitfähigkeit, Schutz vor Feuchtigkeit und Staub sowie mechanische Stabilität.
- Filtrationssysteme: Membranklebstoff ist bei der Herstellung von Filtersystemen in der Wasseraufbereitungs-, Pharma- und Lebensmittelindustrie von entscheidender Bedeutung. Der Klebstoff verbindet Membranen sicher mit Filtergehäusen, gewährleistet eine effiziente Filtrationsleistung und verhindert Bypass oder Leckagen.
- Energiesektor: Membranklebstoffe finden Anwendung im Bereich der erneuerbaren Energien, insbesondere bei der Herstellung und Installation von Photovoltaikmodulen (PV). Die Verbindung erleichtert die Verbindung von Membranen, wie z. B. Verkapselungsfolien, mit PV-Zellen und Rückseitenfolienmaterialien und gewährleistet so eine ordnungsgemäße Abdichtung, Wetterbeständigkeit und elektrische Isolierung.
Dies sind nur einige Beispiele für die vielfältigen Industrie- und Fertigungsanwendungen, bei denen Membranklebstoffe zum Einsatz kommen. Die Eigenschaften des Klebstoffs, wie z. B. feste Bindung, Haltbarkeit, Beständigkeit gegenüber Umwelteinflüssen und Kompatibilität mit verschiedenen Materialien, machen ihn zu einer wertvollen Lösung in verschiedenen Branchen und tragen zur Herstellung zuverlässiger und leistungsstarker Strukturen und Produkte bei.
Membranklebstoff auf Wasserbasis
Membranklebstoff auf Wasserbasis ist ein Klebstofftyp, der mit Wasser als Hauptträger formuliert ist. Es wird häufig in verschiedenen Industrie- und Fertigungsanwendungen eingesetzt, bei denen das Verkleben und Verbinden von Membranen erforderlich ist. Klebstoffe auf Wasserbasis bieten mehrere Vorteile, darunter Umweltfreundlichkeit, Benutzerfreundlichkeit und Vielseitigkeit. Hier sind einige kritische Aspekte des wasserbasierten Membranklebstoffs:
- Umweltfreundlichkeit: Einer der wesentlichen Vorteile wasserbasierter Klebstoffe ist ihre geringere Umweltbelastung. Klebstoffe auf Wasserbasis enthalten weniger flüchtige organische Verbindungen (VOCs), die bekanntermaßen zur Luftverschmutzung beitragen, als Klebstoffe auf Lösungsmittelbasis. Als Hauptträger dieser Klebstoffe minimiert Wasser die Emission von Schadstoffen beim Auftragen und Aushärten. Dies macht wasserbasierte Klebstoffe zu einer umweltfreundlicheren Option, insbesondere bei Anwendungen, bei denen die Reduzierung von VOC-Emissionen Priorität hat.
- Nicht brennbar: Klebstoffe auf Wasserbasis sind nicht brennbar und daher sicherer in der Handhabung und Lagerung als Klebstoffe auf Lösungsmittelbasis. Diese nicht brennbare Beschaffenheit macht zusätzliche Sicherheitsvorkehrungen im Zusammenhang mit brennbaren Klebstoffen überflüssig und verringert so das Risiko von Unfällen und Brandgefahren am Arbeitsplatz.
- Einfache Reinigung: Klebstoffe auf Wasserbasis ermöglichen eine einfache Reinigung und Entfernung. Sie können leicht mit Wasser gereinigt werden, sodass keine aggressiven Lösungsmittel oder Chemikalien erforderlich sind. Dies vereinfacht die Wartung und Reinigung und trägt zu einer sichereren und effizienteren Arbeitsumgebung bei.
- Gute Hafteigenschaften: Klebstoffe auf Wasserbasis bieten zuverlässige Klebeeigenschaften für verschiedene Membranmaterialien. Sie bieten eine gute Haftung auf verschiedenen Oberflächen, einschließlich Metallen, Kunststoffen, Stoffen und Verbundmaterialien. Klebstoffe auf Wasserbasis können Membranen wie EPDM, PVC, TPO und modifiziertes Bitumen, die üblicherweise in der Dach-, Bau- und anderen Industrieanwendung verwendet werden, effektiv verkleben.
- Vielseitigkeit: Klebstoffe auf Wasserbasis können in verschiedenen Auftragungsmethoden verwendet werden, darunter Sprühen, Rollenauftrag und Pinselauftrag. Sie können leicht an spezifische Klebeanforderungen angepasst und optimiert werden, was Flexibilität in verschiedenen Herstellungsprozessen ermöglicht. Darüber hinaus können wasserbasierte Klebstoffe mit Additiven formuliert werden, um bestimmte Eigenschaften wie Flexibilität, Hitzebeständigkeit oder verbesserte Klebkraft zu verbessern und so den besonderen Anforderungen verschiedener Anwendungen gerecht zu werden.
- Geringerer Geruch: Klebstoffe auf Wasserbasis haben im Allgemeinen einen geringeren Geruch im Vergleich zu lösungsmittelbasierten Gegenstücken. Dadurch eignen sie sich besser für Innenanwendungen, insbesondere in Bereichen, in denen starke Gerüche, wie z. B. bewohnte Gebäude oder Produktionsanlagen, ein Problem darstellen.
- Breites Anwendungsspektrum: Membranklebstoff auf Wasserbasis findet in verschiedenen Branchen und Sektoren Anwendung. Es wird häufig im Bau- und Dachbereich zum Verkleben von Dachbahnen verwendet und sorgt für eine wirksame Abdichtung und Witterungsbeständigkeit. Wasserbasierte Klebstoffe werden auch im Automobilbau für die Verklebung von Innenverkleidungen, in Schiffsanwendungen für die Verklebung von Decks und anderen industriellen Anwendungen eingesetzt, bei denen eine zuverlässige und dauerhafte Membranverklebung erforderlich ist.
Membranklebstoffe auf Wasserbasis bieten mehrere Vorteile, darunter Umweltfreundlichkeit, Nichtentflammbarkeit, einfache Reinigung und gute Klebeeigenschaften. Seine Vielseitigkeit und Eignung für verschiedene Anwendungen machen es zur bevorzugten Wahl in Branchen, in denen Leistung und Nachhaltigkeit im Vordergrund stehen. Der Einsatz wasserbasierter Klebstoffe entspricht der wachsenden Nachfrage nach umweltfreundlichen und sicheren Klebelösungen in Industrie- und Fertigungsprozessen.
Lösungsmittelbasierter Membranklebstoff
In verschiedenen Branchen sind starke und dauerhafte Verbindungslösungen von größter Bedeutung. Beim Verbinden von Membranen und anderen flexiblen Materialien haben sich lösungsmittelbasierte Membranklebstoffe als praktische Wahl erwiesen. Dieser Klebstofftyp bietet hervorragende Haftung, Vielseitigkeit und Zuverlässigkeit in verschiedenen Anwendungen. In diesem Artikel werden die wichtigsten Merkmale, Vorteile und Anwendungen von lösungsmittelbasierten Membranklebstoffen untersucht.
Hauptmerkmale Lösungsmittelbasierte Membranklebstoffe bestehen aus hochwertigen synthetischen Polymeren, die in Lösungsmitteln gelöst sind. Diese Zusammensetzung bietet mehrere Hauptmerkmale, die sie ideal für Klebeanwendungen machen:
- Starke Haftung: Klebstoffe auf Lösungsmittelbasis weisen eine außergewöhnliche Klebekraft auf und sorgen für zuverlässige und dauerhafte Verbindungen zwischen Membranen. Sie stellen auch unter anspruchsvollen Bedingungen eine dauerhafte Verbindung her und gewährleisten die strukturelle Integrität.
- Vielseitigkeit: Diese Klebstoffe sind mit verschiedenen Membranmaterialien kompatibel, darunter PVC, EPDM, TPO und modifiziertes Bitumen. Diese Vielseitigkeit ermöglicht den Einsatz in verschiedenen Branchen, beispielsweise in der Dachdecker-, Bau-, Automobil- und Verpackungsindustrie.
- Schnelle Trocknungszeit: Klebstoffe auf Lösungsmittelbasis verdunsten schnell und ermöglichen so ein schnelles Trocknen. Diese Eigenschaft verbessert die Produktivität, indem sie die Montagezeit verkürzt und eine schnellere Verarbeitung ermöglicht.
- Hervorragende Hitze- und Chemikalienbeständigkeit: Die durch lösungsmittelbasierte Klebstoffe erzeugten ausgehärteten Verbindungen weisen eine außergewöhnliche Beständigkeit gegenüber hohen Temperaturen und Chemikalien auf. Dadurch eignen sie sich für Anwendungen, bei denen extreme Bedingungen oder raue Umgebungen zu erwarten sind.
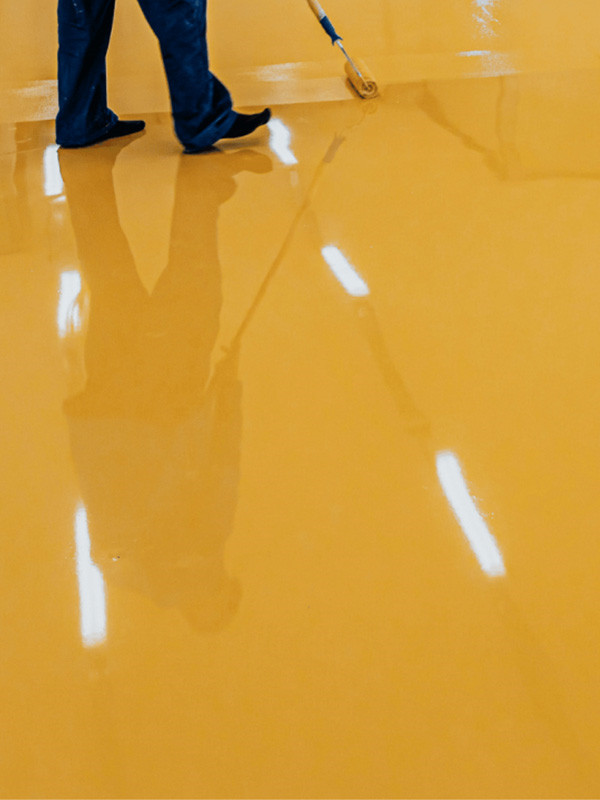
Vorteile: Die Verwendung von lösungsmittelbasierten Membranklebstoffen bietet mehrere bemerkenswerte Vorteile:
- Erhöhte Haltbarkeit: Die starken und belastbaren Bindungen, die diese Klebstoffe bilden, gewährleisten eine lang anhaltende Leistung und halten den Strapazen des täglichen Gebrauchs und Umweltbelastungen stand. Diese Haltbarkeit trägt zu einer längeren Produktlebensdauer bei und reduziert die Notwendigkeit häufiger Reparaturen oder Austausche.
- Verbesserte Wasserdichtigkeit: Membranklebstoffe tragen zur Schaffung wasserdichter Abdichtungen bei, verhindern das Eindringen von Wasser und schützen darunter liegende Strukturen. Dies ist besonders bei Dachanwendungen von entscheidender Bedeutung, bei denen die Wasserbeständigkeit für die Aufrechterhaltung der Integrität der Gebäudehülle von entscheidender Bedeutung ist.
- Kostengünstige Lösung: Lösungsmittelbasierte Klebstoffe bieten aufgrund ihrer effizienten Anwendung und langlebigen Leistung eine kostengünstige Klebelösung. Ihre Fähigkeit, auf einer Vielzahl von Materialien zu haften, macht den Einsatz mehrerer Klebstofftypen überflüssig und senkt die Lagerhaltungskosten.
Anwendungen: Lösungsmittelbasierte Membranklebstoffe finden umfangreiche Anwendungen in verschiedenen Branchen:
- Dacheindeckung: Diese Klebstoffe werden häufig in der Dacheindeckung verwendet, um einlagige Membranen wie PVC und TPO zu verkleben und so sichere und leckagesichere Abdichtungen zu gewährleisten.
- Bauwesen: Lösungsmittelbasierte Klebstoffe werden zum Verkleben von Architekturmembranen, Dampfsperren und Dämmmaterialien in Bauprojekten eingesetzt und sorgen so für strukturelle Integrität und Energieeffizienz.
- Automobil: Sie werden im Automobilsektor zum Verkleben flexibler Komponenten wie Türverkleidungen, Dachhimmel und Teppiche eingesetzt und bieten Festigkeit und Haltbarkeit auch unter schwierigen Fahrbedingungen.
- Verpackung: Lösungsmittelbasierte Klebstoffe bieten effektive Klebelösungen für flexible Verpackungsmaterialien wie Folien und Laminate und sorgen für sichere Versiegelungen und Produktschutz.
Zweikomponentiger Membranklebstoff
Für die Verklebung von Membranen und anderen flexiblen Materialien ist eine zuverlässige und robuste Klebelösung unerlässlich. Zweikomponenten-Membranklebstoffe erfreuen sich aufgrund ihrer außergewöhnlichen Festigkeit, Vielseitigkeit und Zuverlässigkeit in verschiedenen Branchen großer Beliebtheit. In diesem Artikel werden die wichtigsten Merkmale, Vorteile und Anwendungen von Zweikomponentenklebstoffen für Membranklebstoffe erläutert.
Hauptmerkmale Zweikomponenten-Membranklebstoffe bestehen aus zwei separaten Komponenten, typischerweise einem Harz und einem Härter, die unmittelbar vor dem Auftragen gemischt werden. Diese einzigartige Zusammensetzung bietet mehrere Hauptmerkmale, die sie äußerst wirksam machen:
- Überlegene Festigkeit: Zweikomponentenklebstoffe bieten eine außergewöhnliche Klebefestigkeit und sorgen für robuste und dauerhafte Membranverbindungen. Sie halten erheblichen Belastungen stand und sorgen für dauerhafte und zuverlässige Verbindungen.
- Einstellbare Aushärtezeit: Die Aushärtezeit von Zweikomponentenklebstoffen kann durch Veränderung des Verhältnisses von Harz zu Härter oder durch die Auswahl verschiedener Härter angepasst werden. Diese Vielseitigkeit ermöglicht eine maßgeschneiderte Anwendung und gewährleistet eine ausreichende Verarbeitungszeit und die gewünschte Aushärtungsgeschwindigkeit.
- Hohe chemische Beständigkeit: Diese Klebstoffe weisen eine ausgezeichnete chemische Beständigkeit auf und eignen sich daher für Anwendungen, bei denen eine Belastung durch aggressive Substanzen zu erwarten ist. Sie können ihre Integrität auch in chemisch aggressiven Umgebungen bewahren.
- Vielseitige Substratkompatibilität: Zweikomponentenklebstoffe sind mit verschiedenen Membranmaterialien kompatibel, darunter PVC, EPDM, TPO und Polyurethan. Diese Vielseitigkeit macht sie für verschiedene Branchen und Anwendungen geeignet.
Vorteile: Die Verwendung von zweikomponentigen Membranklebstoffen bietet mehrere bemerkenswerte Vorteile:
- Außergewöhnliche Haftfestigkeit: Die durch Zweikomponentenklebstoffe gebildeten soliden und dauerhaften Verbindungen gewährleisten strukturelle Integrität und Langlebigkeit. Sie halten extremen Bedingungen und hohen Belastungen stand und eignen sich daher für anspruchsvolle Anwendungen.
- Erhöhte Flexibilität: Diese Klebstoffe bieten Flexibilität hinsichtlich Aushärtezeit und Klebeeigenschaften. Sie können an die spezifischen Anforderungen eines Projekts angepasst werden und ermöglichen so eine verbesserte Individualisierung und Optimierung.
- Erhöhte Beständigkeit: Zweikomponentenklebstoffe widerstehen Temperaturschwankungen, Feuchtigkeit, UV-Strahlung und anderen Umweltfaktoren. Dieser Widerstand gewährleistet eine langfristige Leistung und minimiert das Risiko eines Versagens der Bindung.
- Vielseitige Anwendungen: Diese Klebstoffe finden in verschiedenen Branchen Anwendung. Sie werden häufig in der Dach-, Bau-, Automobil- und Schifffahrtsbranche eingesetzt, wo eine starke und zuverlässige Verbindung von Membranen von entscheidender Bedeutung ist.
Anwendungen: Zweikomponentige Membranklebstoffe haben ein breites Anwendungsspektrum:
- Dacheindeckung: Sie werden häufig in Dacheindeckungssystemen zum Verkleben von Membranen, einschließlich EPDM, TPO und PVC, verwendet und sorgen für sichere und wetterbeständige Dichtungen, die rauen Umgebungsbedingungen standhalten.
- Bauwesen: Zweikomponentenklebstoffe werden zum Verkleben von Architekturmembranen wie Dampfsperren und Abdichtungsbahnen eingesetzt und sorgen für stabile Verbindungen und Schutz vor dem Eindringen von Feuchtigkeit.
- Automobil: Sie finden in der Automobilindustrie Anwendung zum Verkleben flexibler Komponenten wie Innenverkleidungen, Polster und schalldämmender Materialien und bieten Festigkeit, Haltbarkeit und Vibrationsbeständigkeit.
- Marine: Diese Klebstoffe verkleben Membranen und Materialien in Marinequalität wie Bootsrümpfe, Decks und Innenverkleidungen und sorgen so für wasserdichte Abdichtungen und strukturelle Integrität in anspruchsvollen Meeresumgebungen.
Flexibler Membranklebstoff
Flexible Membranen werden aufgrund ihrer Vielseitigkeit und Leistung häufig in der Bau-, Automobil- und Verpackungsindustrie eingesetzt. Um eine sichere und dauerhafte Verbindung zwischen flexiblen Membranen zu erreichen, ist ein spezieller Klebstoff erforderlich. Flexible Klebstoffe für die Membranverklebung sind so formuliert, dass sie eine hervorragende Haftung und Flexibilität bieten und so solide und zuverlässige Verbindungen gewährleisten. In diesem Artikel werden die wichtigsten Merkmale, Vorteile und Anwendungen flexibler Membranklebstoffe untersucht.
Hauptmerkmale Klebstoffe für die Verklebung flexibler Membranen sind mit spezifischen Eigenschaften ausgestattet, um den Anforderungen beim Verkleben flexibler Materialien gerecht zu werden. Hier sind einige Hauptmerkmale dieser Klebstoffe:
- Flexibilität: Diese Klebstoffe weisen ein hohes Maß an Flexibilität auf, sodass sie sich den natürlichen Bewegungen und Ausdehnungen flexibler Membranen anpassen können, ohne die Verbindung zu beeinträchtigen. Diese Flexibilität trägt dazu bei, ein Versagen der Verbindung zu verhindern und gewährleistet eine langfristige Haltbarkeit.
- Gute Haftung auf flexiblen Substraten: Flexible Membranklebstoffe sind so formuliert, dass sie eine starke Haftung auf einer Vielzahl flexibler Materialien herstellen. Sie haften effektiv auf Substraten wie PVC, EPDM, TPO, Polyurethan und anderen Elastomermembranen, die üblicherweise in verschiedenen Branchen verwendet werden.
- Wetterbeständigkeit: Diese Klebstoffe widerstehen Witterungseinflüssen wie UV-Strahlung, Feuchtigkeit, Temperaturschwankungen und chemischer Einwirkung. Diese Witterungsbeständigkeit gewährleistet die Langlebigkeit der Verbindung auch in rauen Umgebungen.
- Einfache Anwendung: Flexible Membranklebstoffe sind für eine einfache Anwendung konzipiert. Sie können je nach den spezifischen Anforderungen der Anwendung mit verschiedenen Methoden aufgetragen werden, darunter Pinsel, Rolle oder Spray. Ihre Formulierung ermöglicht eine reibungslose und gleichmäßige Anwendung.
Vorteile: Die Verwendung flexibler Membranklebstoffe bietet mehrere wesentliche Vorteile:
- Feste und dauerhafte Verbindungen: Diese Klebstoffe schaffen starke und dauerhafte Verbindungen zwischen flexiblen Membranen und gewährleisten so die Integrität und Langlebigkeit der Baugruppe. Sie halten Belastungen, Bewegungen und Umgebungsbedingungen stand und bieten zuverlässige Leistung.
- Verbesserte Flexibilität: Durch die Beibehaltung der Flexibilität auch nach dem Aushärten ermöglichen diese Klebstoffe, dass sich die verklebten Membranen bewegen und ausdehnen, ohne dass es zu Rissen oder Ausfällen kommt. Diese Flexibilität verbessert die Gesamtleistung und Lebensdauer der Verbundbaugruppe.
- Verbesserte wasserdichte Dichtungen: Flexible Membranklebstoffe tragen zur Schaffung wasserdichter Dichtungen zwischen Membranen bei und bieten ausreichenden Schutz gegen das Eindringen von Wasser. Dies ist besonders wichtig bei Anwendungen wie Dacheindeckungen und Abdichtungen, bei denen es auf Wasserbeständigkeit ankommt.
- Vielseitige Anwendungen: Flexible Membranklebstoffe finden in verschiedenen Branchen Anwendung. Sie werden häufig in Dachsystemen, im Automobilbau, bei flexiblen Verpackungen und anderen Anwendungen eingesetzt, bei denen flexible Membranen und Materialien miteinander verbunden werden müssen.
Anwendungen: Flexible Membranklebstoffe haben ein breites Anwendungsspektrum in allen Branchen:
- Dacheindeckung: Diese Klebstoffe werden häufig in Dachsystemen zum Verkleben von flexiblen Dachmembranen wie TPO, PVC und EPDM verwendet und sorgen für zuverlässige und dauerhafte Wasserdichtigkeit und Witterungsbeständigkeit.
- Automobil: Sie finden in der Automobilindustrie Anwendung zum Verkleben flexibler Komponenten wie Dichtungsstreifen, Türdichtungen, Innenverkleidungen und Polsterungen und sorgen so für solide und dauerhafte Verbindungen, die den dynamischen Bewegungen von Fahrzeugen standhalten.
- Verpackung: Flexible Membranklebstoffe werden in der Verpackungsindustrie zum Verkleben flexibler Folien und Laminate verwendet, sorgen für sichere Versiegelungen und bewahren die Unversehrtheit der verpackten Produkte.
- Bauwesen: Diese Klebstoffe werden in der Bauindustrie zum Verkleben von Architekturmembranen, Dampfsperren und Isoliermaterialien eingesetzt, um luftdichte und witterungsbeständige Baugruppen zu gewährleisten.
Schnellhärtender Membranklebstoff
Schnell aushärtende Klebstofflösungen sind in Branchen, in denen Effizienz und Produktivität von entscheidender Bedeutung sind, sehr gefragt. Schnell aushärtende Membranklebstoffe sind so formuliert, dass sie eine schnelle Montage und Verklebung von Membranen und flexiblen Materialien ermöglichen. In diesem Artikel werden die wichtigsten Merkmale, Vorteile und Anwendungen schnell aushärtender Membranklebstoffe untersucht.
Hauptmerkmale Schnell aushärtende Membranklebstoffe bieten einzigartige Eigenschaften, die schnelle und effiziente Klebeprozesse ermöglichen. Hier sind einige Hauptmerkmale dieser Klebstoffe:
- Schnelle Aushärtezeit: Diese Klebstoffe sind so konzipiert, dass sie schnell aushärten und starke Verbindungen erzielen. Sie bieten im Vergleich zu herkömmlichen Klebstoffen deutlich kürzere Aushärtezeiten und ermöglichen so schnellere Produktionszyklen und eine verbesserte Produktivität.
- Hohe Anfangsfestigkeit: Schnell aushärtende Klebstoffe weisen kurz nach dem Auftragen eine hohe Anfangsfestigkeit auf. Dies ermöglicht eine schnellere Handhabung und Montage verklebter Komponenten und minimiert den Bedarf an längeren Spann- oder Aushärtezeiten.
- Vielseitige Anwendungsmethoden: Diese Klebstoffe können mit verschiedenen Methoden aufgetragen werden, einschließlich Sprüh-, Rollen- oder Pinselauftrag. Diese Vielseitigkeit ermöglicht eine effiziente und präzise Anwendung, um unterschiedlichen Klebeanforderungen und Produktionsprozessen gerecht zu werden.
- Kompatibilität mit mehreren Substraten: Schnell aushärtende Membranklebstoffe sind für die Verklebung einer Vielzahl von Substraten konzipiert, darunter PVC, EPDM, TPO und andere flexible Materialien, die üblicherweise in Branchen wie Dachdeckerarbeiten, Baugewerbe und Automobilindustrie verwendet werden.
Vorteile: Die Verwendung schnell aushärtender Membranklebstoffe bietet mehrere bemerkenswerte Vorteile:
- Erhöhte Effizienz: Die schnelle Aushärtezeit dieser Klebstoffe verkürzt den Montage- und Produktionszyklus erheblich, was zu einer verbesserten Effizienz und kürzeren Durchlaufzeiten führt. Dies ermöglicht es Herstellern, die Produktion zu steigern, ohne Kompromisse bei der Klebkraft oder Qualität einzugehen.
- Zeit- und Kosteneinsparungen: Eine schnellere Aushärtung reduziert Arbeitskosten und Energieverbrauch. Die Möglichkeit, schnell zum nächsten Produktionsschritt oder Versand überzugehen, kann zu erheblichen Zeit- und Kosteneinsparungen bei Herstellungsprozessen führen.
- Verbesserte Produktivität: Schnell aushärtende Klebstoffe steigern die Produktivität, indem sie Warte- oder Leerlaufzeiten minimieren. Sie ermöglichen eine schnelle Montage, verkürzen die Produktionsvorlaufzeiten und halten enge Fristen ein.
- Zuverlässige Haftfestigkeit: Trotz ihrer schnellen Aushärtungseigenschaften behalten diese Klebstoffe eine hohe Haftfestigkeit und Haltbarkeit bei. Sie sorgen für zuverlässige und dauerhafte Verbindungen und gewährleisten die strukturelle Integrität und Leistung der zusammengebauten Komponenten.
Anwendungen: Schnell aushärtende Membranklebstoffe finden in verschiedenen Branchen Anwendung:
- Dacheindeckung: Diese Klebstoffe werden häufig in Dacheindeckungsanwendungen verwendet, beispielsweise zum Verkleben von einlagigen Membranen wie TPO, PVC oder EPDM. Die schnelle Aushärtung ermöglicht eine effiziente Installation und gewährleistet wasserdichte Abdichtungen, wodurch die Geschwindigkeit und Qualität von Dachprojekten erhöht wird.
- Bauwesen: Schnell aushärtende Klebstoffe werden im Bauwesen zum Verkleben von Architekturmembranen, Dämmstoffen und Dampfsperren eingesetzt. Ihre kurze Aushärtezeit ermöglicht schnellere Bauprozesse und hilft, Projektfristen einzuhalten.
- Automobil: Sie finden in der Automobilindustrie Anwendung zum Verkleben flexibler Komponenten wie Türverkleidungen, Dachhimmel und Teppiche. Die schnelle Aushärtungszeit gewährleistet eine effiziente Montage in der Produktionslinie, ohne die Klebefestigkeit oder -qualität zu beeinträchtigen.
- Allgemeine Fertigung: Schnell aushärtende Klebstoffe werden in verschiedenen Herstellungsprozessen mit flexiblen Klebematerialien eingesetzt. Sie ermöglichen eine schnelle Montage und Verklebung von Gegenständen wie flexiblen Verpackungen, Membranen für aufblasbare Strukturen und flexiblen Verbundteilen.
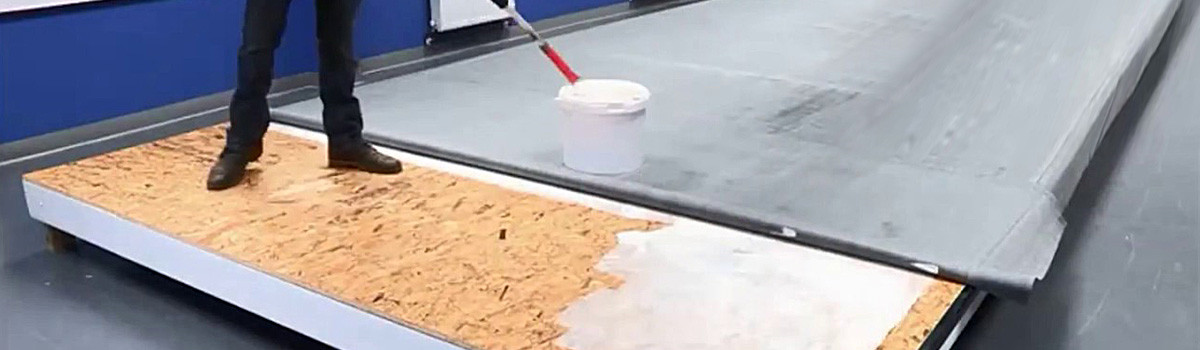
Überlegungen zur Auswahl eines Membranklebstoffs
Bei der Auswahl eines Membranklebstoffs sollten mehrere wichtige Überlegungen berücksichtigt werden, um eine erfolgreiche und dauerhafte Verbindung sicherzustellen. Zu diesen Überlegungen gehören Substratkompatibilität, Umgebungsbedingungen, Anwendungsanforderungen und Klebeeigenschaften. Hier sind einige wesentliche Punkte, die es zu beachten gilt:
- Untergrundkompatibilität: Bewerten Sie die verklebten Materialien, um die Kompatibilität mit dem Klebstoff sicherzustellen. Verschiedene Klebstoffe haben unterschiedliche Affinitäten zu anderen Substraten wie Metallen, Kunststoffen, Gummi oder Verbundwerkstoffen. Berücksichtigen Sie die Oberflächenenergie, Rauheit und chemische Zusammensetzung des Substrats, um die Eignung des Klebstoffs zu bestimmen.
- Umgebungsbedingungen: Bewerten Sie die Bedingungen, denen die Verbundmembran ausgesetzt sein wird, einschließlich extremer Temperaturen, Feuchtigkeit und Einwirkung von UV-Strahlung, Chemikalien oder Wasser. Wählen Sie einen Klebstoff, der diesen Bedingungen standhält, ohne dass seine Klebkraft oder Haltbarkeit darunter leidet.
- Haftfestigkeit und Haltbarkeit: Bestimmen Sie die erforderliche Stärke der Bindung basierend auf der mechanischen Beanspruchung und den Belastungsanforderungen der Anwendung. Berücksichtigen Sie Faktoren wie Scher-, Zug- und Schälfestigkeit sowie die voraussichtliche Lebensdauer der geklebten Baugruppe. Stellen Sie sicher, dass der ausgewählte Klebstoff die erforderliche Festigkeit und langfristige Haltbarkeit bietet.
- Auftragungsmethode: Berücksichtigen Sie die verfügbaren Methoden zum Auftragen des Klebstoffs. Einige Klebstoffe werden als Flüssigkeiten, Filme oder Bänder geliefert, während andere möglicherweise Misch- oder Aushärteprozesse erfordern. Wählen Sie eine Verbindung, die mit der Auftragungsmethode kompatibel ist und sich leicht auf die Membran und den Untergrund auftragen lässt.
- Aushärtezeit und -prozess: Machen Sie sich mit der Aushärtezeit und dem Aushärteprozess des Klebstoffs vertraut. Einige Klebstoffe benötigen Wärme, UV-Licht oder Feuchtigkeit, um den Aushärtungsprozess einzuleiten oder zu beschleunigen, während andere bei Raumtemperatur aushärten. Berücksichtigen Sie die verfügbaren Aushärtungsgeräte und Zeitbeschränkungen, um einen Klebstoff auszuwählen, der den Anforderungen der Anwendung entspricht.
- Chemische Beständigkeit: Bewerten Sie die Beständigkeit des Klebstoffs gegenüber Chemikalien oder Lösungsmitteln, die mit der verklebten Baugruppe in Kontakt kommen könnten. Bei bestimmten Anwendungen kann es zu einer Belastung durch Kraftstoffe, Öle, Säuren oder Reinigungsmittel kommen. Bitte stellen Sie sicher, dass der Klebstoff solchen Substanzen standhält, ohne dass die Klebkraft abnimmt oder beeinträchtigt wird.
- Flexibilität und Elastizität: Berücksichtigen Sie die Flexibilitäts- und Elastizitätsanforderungen der Klebebaugruppe. Bei einigen Anwendungen kann es zu erheblicher thermischer Ausdehnung, Kontraktion oder Vibration kommen. Wählen Sie einen Klebstoff, der diese Bewegungen aufnehmen kann, ohne Spannungskonzentrationen oder ein Versagen der Verbindung zu verursachen.
- Einhaltung gesetzlicher Vorschriften: Stellen Sie fest, ob für die Anwendung bestimmte gesetzliche Anforderungen oder Industriestandards gelten. Stellen Sie sicher, dass der ausgewählte Klebstoff den Compliance-Standards für Entflammbarkeit, Toxizität oder Lebensmittelkontakt entspricht.
- Kosten und Verfügbarkeit: Bewerten Sie die Kosteneffizienz des Klebstoffs unter Berücksichtigung von Faktoren wie der benötigten Menge, der Haltbarkeitsdauer und der einfachen Beschaffung. Berücksichtigen Sie die Verfügbarkeit des Klebstoffs bei seriösen Lieferanten und seine langfristige Verfügbarkeit für mögliche Reparaturen oder Ersatzlieferungen.
- Tests und Validierung: Führen Sie gründliche Tests und Validierungen des Klebstoffs unter relevanten Bedingungen und anwendungsspezifischen Szenarien durch. Führen Sie Haftungs- und Haltbarkeitstests durch und simulieren Sie die voraussichtlichen Betriebsbedingungen, um sicherzustellen, dass die Verbindung wie erwartet funktioniert.
Durch sorgfältige Berücksichtigung dieser Faktoren können Sie einen Membranklebstoff auswählen, der mit den Materialien, Anwendungsanforderungen und Umgebungsbedingungen kompatibel ist und eine robuste und zuverlässige Verbindung für Ihre spezifische Anwendung gewährleistet.
Membrankompatibilität und Substratvorbereitung
Membrankompatibilität und Untergrundvorbereitung sind entscheidende Aspekte bei der Auswahl eines Klebstoffs für die Membranverklebung. Die richtige Oberflächenvorbereitung und Kompatibilitätsbeurteilung spielt eine wichtige Rolle bei der Erzielung einer festen und dauerhaften Verbindung. Hier finden Sie eine detaillierte Erklärung dieser Faktoren:
- Membrankompatibilität: Es ist wichtig sicherzustellen, dass der Klebstoff mit dem Membranmaterial kompatibel ist. Membranen können aus verschiedenen Materialien wie PVC, EPDM, TPO oder PTFE bestehen. Jedes Material kann unterschiedliche Oberflächeneigenschaften, chemische Zusammensetzung oder Oberflächenenergie haben. Einige Klebstoffe funktionieren bei bestimmten Membranmaterialien besser, während andere möglicherweise nicht effektiv haften. Konsultieren Sie die Richtlinien des Herstellers oder führen Sie Kompatibilitätstests durch, um den besten Klebstoff für das spezifische Membranmaterial zu ermitteln.
- Untergrundvorbereitung: Die richtige Untergrundvorbereitung ist entscheidend für eine gute Haftung. Der Untergrund sollte sauber, trocken und frei von Verunreinigungen sein, die den Klebevorgang behindern könnten. Befolgen Sie diese Schritte zur Untergrundvorbereitung:
- Reinigung: Staub, Schmutz, Fett oder Öle von der Untergrundoberfläche entfernen. Verwenden Sie geeignete Lösungsmittel oder Reinigungsmittel und achten Sie auf gründliches Spülen, um Rückstände zu entfernen.
- Aufrauen der Oberfläche: In manchen Fällen kann es notwendig sein, die Oberfläche des Untergrundes aufzurauen, um die Klebeverbindung zu verbessern. Dies kann durch Methoden wie Schleifen, Sandstrahlen oder den Einsatz chemischer Ätzmittel erreicht werden. Ziel ist es, eine aufgeraute Oberfläche zu erzeugen, die die mechanische Verzahnung zwischen Klebstoff und Untergrund verbessert.
- Grundierung: Je nach Untergrundmaterial kann zur Verbesserung der Haftung eine Grundierung erforderlich sein. Primer tragen dazu bei, die Benetzung und Bindungsfähigkeit des Klebstoffs auf dem Untergrund zu verbessern. Sie können nach Herstellerangaben durch Streichen, Sprühen oder Tauchen aufgetragen werden.
- Membranoberflächenbehandlung: Ähnlich wie bei Substraten muss die Membranoberfläche möglicherweise behandelt werden, um die Haftung zu verbessern. Einige Membranen haben eine glatte oder nicht poröse Oberfläche, wodurch es für Klebstoffe schwierig ist, effektiv zu haften. Erwägen Sie die folgenden Behandlungen:
- Membranreinigung: Reinigen Sie die Membranoberfläche gründlich, um Schmutz, Staub oder Öle zu entfernen, die die Klebeverbindung beeinträchtigen könnten.
- Oberflächenaktivierung: Einige Membranen können von Oberflächenaktivierungstechniken wie Korona- oder Flammenbehandlung profitieren. Diese Methoden modifizieren die Oberflächenenergie der Membran und verbessern so die Benetzbarkeit und die Bindungseigenschaften.
- Oberflächengrundierung: Bestimmte Membranmaterialien erfordern möglicherweise die Anwendung einer Grundierung, um die Haftung zu verbessern. Der Primer sorgt für eine bessere Haftung zwischen Membran und Kleber. Stellen Sie sicher, dass die Grundierung sowohl mit der Membran als auch mit dem Kleber kompatibel ist.
- Klebstoffauswahl: Berücksichtigen Sie die Membrankompatibilität des Klebstoffs und Empfehlungen zur Untergrundvorbereitung. Klebstoffhersteller stellen häufig Richtlinien und Empfehlungen für Oberflächenvorbereitungstechniken, Grundierungen oder Reinigungsmittel zur Verfügung, die mit ihren Produkten verwendet werden sollen. Befolgen Sie diese Empfehlungen genau, um eine optimale Klebeleistung sicherzustellen.
Indem Sie die Kompatibilität der Membran berücksichtigen und geeignete Techniken zur Untergrundvorbereitung anwenden, können Sie die Chancen auf eine solide und dauerhafte Verbindung verbessern. Die Einhaltung der Herstellerrichtlinien, die Durchführung von Kompatibilitätstests und die Befolgung der empfohlenen Methoden zur Oberflächenvorbereitung tragen dazu bei, die Wirksamkeit des Klebstoffs zu maximieren und eine dauerhafte Membranbindung sicherzustellen.
Umweltfaktoren und Widerstandseigenschaften
Umweltfaktoren spielen eine entscheidende Rolle für die Leistungs- und Widerstandseigenschaften von Membranklebstoffen. Membranklebstoffe werden in verschiedenen Branchen eingesetzt, darunter im Baugewerbe, in der Automobilindustrie und in der Elektronikindustrie, um Membranen sicher auf unterschiedlichen Substraten zu verkleben. Die Fähigkeit des Klebstoffs, Umweltbelastungen standzuhalten, ist entscheidend für die Aufrechterhaltung der Integrität und Haltbarkeit der verklebten Membranen.
Einer der kritischen Umweltfaktoren, die sich auf Membranklebstoffe auswirken, ist die Temperatur. Klebstoffe sind häufig unterschiedlichen Temperaturen ausgesetzt, von extremer Kälte bis hin zu großer Hitze. Temperaturschwankungen können die Viskosität, Aushärtezeit und Klebkraft des Klebstoffs beeinflussen. Klebstoffe für kalte Umgebungen müssen auch bei niedrigen Temperaturen flexibel bleiben und ihre Klebeeigenschaften behalten. Andererseits müssen Klebstoffe, die bei Hochtemperaturanwendungen verwendet werden, eine ausgezeichnete Hitzebeständigkeit aufweisen, um ein Versagen oder eine Verschlechterung der Bindung zu verhindern.
Auch Feuchtigkeit und Luftfeuchtigkeit haben einen wesentlichen Einfluss auf die Widerstandseigenschaften von Membranklebstoffen. Übermäßige Feuchtigkeit kann sich negativ auf die Leistung des Klebstoffs auswirken, indem sie die Klebkraft verringert und zum Versagen des Klebstoffs führt. Wasser kann bei bestimmten Klebstoffen auch chemische Reaktionen oder Quellungen auslösen, die zu Dimensionsänderungen oder zum Verlust der Haftung führen. Daher werden feuchtigkeitsbeständige Eigenschaften wie feuchtigkeitshärtende oder wasserfeste Klebstoffe häufig für Anwendungen bevorzugt, bei denen mit einer Einwirkung von Wasser oder hoher Luftfeuchtigkeit zu rechnen ist.
Die Belastung durch Chemikalien ist ein weiterer wichtiger Umweltfaktor, den es zu berücksichtigen gilt. Abhängig von der Anwendung können Klebstoffe mit verschiedenen Chemikalien wie Lösungsmitteln, Säuren oder Laugen in Kontakt kommen. Bestimmte Chemikalien können den Klebstoff zersetzen und zu einem Versagen der Verbindung führen. Es ist wichtig, Klebstoffe mit chemischen Beständigkeitseigenschaften auszuwählen, die der Belastung durch bestimmte in der Umwelt vorkommende Substanzen standhalten.
Auch ultraviolette (UV) Strahlung der Sonne kann die Widerstandseigenschaften von Membranklebstoffen beeinträchtigen. Eine längere Einwirkung von UV-Strahlen kann zur Zersetzung des Klebstoffs führen, was zu einer verringerten Klebefestigkeit und einem Versagen des Klebstoffs führt. UV-beständige Dichtstoffe, oft mit speziellen Additiven oder Polymeren formuliert, können vor UV-Strahlung schützen und ihre Leistung bei Außenanwendungen aufrechterhalten.
Mechanische Belastungen wie Vibrationen, Stöße oder Scherkräfte sind häufige umweltbedingte Herausforderungen, denen Membranklebstoffe ausgesetzt sind. Klebstoffe, die in Anwendungen eingesetzt werden, in denen mechanische Belastungen vorherrschen, wie beispielsweise in der Automobil- oder Luft- und Raumfahrtindustrie, erfordern eine hohe Widerstandsfähigkeit gegenüber diesen Kräften. Häufig werden gehärtete Klebstoffe oder flexible Formulierungen eingesetzt, um die Widerstandsfähigkeit des Klebstoffs gegenüber mechanischer Beanspruchung zu erhöhen und ein Versagen der Verbindung zu verhindern.
Anwendungstechniken und -methoden
Die korrekte Anwendung von Membranklebstoffen ist für die Erzielung fester und dauerhafter Verbindungen von entscheidender Bedeutung. Die Anwendungstechnik und -methode kann die Leistung des Klebstoffs und die Gesamtqualität der verklebten Membran erheblich beeinflussen. Hier sind einige wichtige Überlegungen und Strategien für die effektive Anwendung von Membranklebstoffen:
- Oberflächenvorbereitung: Um eine gute Haftung zu gewährleisten, ist eine ordnungsgemäße Oberflächenvorbereitung von entscheidender Bedeutung. Die zu verklebenden Oberflächen sollten sauber, trocken und frei von Verunreinigungen wie Staub, Öl, Fett oder losen Partikeln sein. Je nach Untergrundmaterial können Oberflächenreinigungsmethoden das Abwischen mit Lösungsmittel, das Schleifen oder die Verwendung einer Oberflächengrundierung zur Verbesserung der Haftung umfassen.
- Klebstoffmischung: Wenn der Membranklebstoff gemischt werden muss, befolgen Sie sorgfältig die Anweisungen des Herstellers, um das richtige Verhältnis und eine gründliche Durchmischung zu erreichen. Unzureichendes Mischen kann zu unvollständiger Aushärtung, verminderter Klebkraft oder ungleichmäßigen Klebeeigenschaften führen.
- Auftragungsmethode: Die Wahl der Auftragungsmethode hängt vom jeweiligen Klebstoff sowie der Größe und Form der Klebefläche ab. Zu den Standardanwendungsmethoden für Membranklebstoffe gehören:
- Pinsel/Rolle: Geeignet für große Klebeflächen. Mit einem Pinsel oder einer Rolle kann der Kleber gleichmäßig auf der Oberfläche verteilt werden. Diese Methode wird häufig im Bau- oder Dachbereich eingesetzt.
- Sprühen: Die Verwendung eines Sprühsystems ermöglicht einen schnellen und gleichmäßigen Klebstoffauftrag. Dies ist bei großen Flächen von Vorteil oder wenn eine dünne und gleichmäßige Klebeschicht erforderlich ist.
- Kelle/Zahnkelle: Ideal für dickere Klebstoffe oder wenn eine bestimmte Klebstoffdicke erforderlich ist. Die Zahnspachtel sorgt für eine gute Deckung und gleichmäßige Verteilung des Klebers.
- Extrusion: In einigen Fällen werden Klebstoffe mithilfe von Extrusionsgeräten, beispielsweise einer Kartuschenpistole oder speziellen Dosiersystemen, aufgetragen. Diese Methode ermöglicht ein präzises Auftragen und die Kontrolle der Kleberraupengröße.
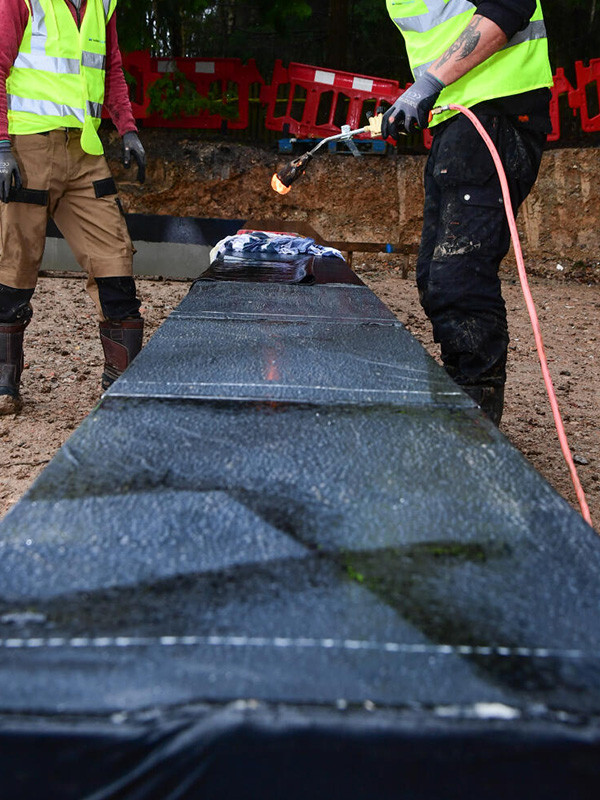
- Offene Zeit und Topfzeit: Die verfügbare Zeit bezieht sich auf die Zeit, in der der Klebstoff nach dem Auftragen noch verarbeitbar ist und die Membran positioniert und angepasst werden kann. Es ist wichtig, die offene Zeit des Klebstoffs zu kennen und innerhalb dieses Zeitrahmens effizient zu arbeiten. Unter Topfzeit versteht man die Zeit, die der angemischte Klebstoff noch verwendbar bleibt, bevor er auszuhärten beginnt. Klebstoffe sollten innerhalb der angegebenen Topfzeit aufgetragen und verwendet werden.
- Kleben und Anpressen: Nach dem Auftragen des Klebers die Membran vorsichtig auf der mit Kleber beschichteten Oberfläche positionieren. Verwenden Sie geeignete Werkzeuge wie Rollen oder Presspads, um einen gleichmäßigen Druck auf die gesamte Klebefläche auszuüben. Dieser Schritt trägt dazu bei, den richtigen Kontakt und die Haftung zwischen der Membran und dem Untergrund sicherzustellen.
- Aushärten und Trocknen: Klebstoffe haben bestimmte Aushärte- oder Trocknungszeiten, die für eine optimale Verbindung eingehalten werden sollten. Lassen Sie dem Kleber entsprechend den Empfehlungen des Herstellers ausreichend Zeit zum Aushärten bzw. Trocknen, bevor Sie die verklebte Membran einer Belastung oder Belastung aussetzen.
- Qualitätskontrolle und Tests: Es ist von entscheidender Bedeutung, Qualitätskontrollkontrollen und Tests durchzuführen, um die Stärke und Integrität der Verbindung zu überprüfen. Dies kann die Durchführung von Zug-, Scher- oder anderen relevanten Tests umfassen, um sicherzustellen, dass der Klebstoff die gewünschte Leistung erreicht hat.
Beachten Sie immer die Richtlinien und Anweisungen des Herstellers des jeweils verwendeten Membranklebstoffs. Die Einhaltung geeigneter Anwendungstechniken und -methoden sowie eine entsprechende Oberflächenvorbereitung tragen dazu bei, eine erfolgreiche Verklebung sicherzustellen und die Langlebigkeit und Leistung der verklebten Membran zu verbessern.
Haltbarkeit und Langlebigkeit von Verbundmembranen
Verbundmembranen werden aufgrund ihrer außergewöhnlichen Haltbarkeit und Langlebigkeit häufig in verschiedenen Branchen und Anwendungen eingesetzt. Diese Membranen bilden eine Schutzbarriere, verbessern die strukturelle Integrität und verhindern das Eindringen von Feuchtigkeit oder anderen schädlichen Substanzen. Hier werden wir die Schlüsselfaktoren untersuchen, die zur Haltbarkeit und Langlebigkeit von Verbundmembranen beitragen.
- Materialauswahl: Die Wahl der Materialien für Verbundmembranen ist entscheidend für deren Haltbarkeit. Aufgrund ihrer hervorragenden Beständigkeit gegen Witterungseinflüsse, UV-Strahlung und chemische Einwirkung werden häufig hochwertige Materialien wie synthetische Kautschuke, modifizierte Bitumen oder thermoplastische Olefine (TPO) verwendet. Diese Materialien bieten überragende Festigkeit, Flexibilität und Belastbarkeit und gewährleisten langfristige Leistung und Langlebigkeit.
- Klebetechnik: Die bei der Verlegung von Membranen eingesetzte Klebetechnik hat erheblichen Einfluss auf deren Haltbarkeit. Die richtige Oberflächenvorbereitung, Klebstoffauswahl und Anwendungstechniken sind entscheidend für eine solide und dauerhafte Verbindung zwischen der Membran und dem Untergrund. Fortschrittliche Verbindungsmethoden wie Heißschweißen oder Lösungsmittelschweißen schaffen robuste, nahtlose Verbindungen, die sich im Laufe der Zeit nicht lösen, reißen oder abblättern.
- Strukturelles Design: Das Design von Verbundmembranen ist für ihre Langlebigkeit von entscheidender Bedeutung. Verstärkungsschichten wie Polyester oder Glasfaser werden häufig in die Membranstruktur eingearbeitet, um deren Festigkeit und Reiß- oder Durchstoßfestigkeit zu erhöhen. Die Dicke und Zusammensetzung der Membran sind außerdem auf spezifische Leistungsanforderungen unter Berücksichtigung der Tragfähigkeit, der zu erwartenden Bewegung und der Umgebungsbedingungen zugeschnitten.
- Wetterbeständigkeit: Die Haltbarkeit im Außenbereich hängt stark von der Fähigkeit einer Verbundmembran ab, extremen Wetterbedingungen standzuhalten. Hochwertige Membranen sind so konstruiert, dass sie Temperaturschwankungen, thermischen Zyklen und ultravioletter (UV) Strahlung standhalten. Der Membranoberfläche können UV-Stabilisatoren und reflektierende Beschichtungen hinzugefügt werden, um ihre Beständigkeit gegen UV-Zersetzung zu erhöhen und so das Risiko von Rissen, Versprödung oder Farbverblassung zu verringern.
- Wartung und Inspektionen: Um die langfristige Haltbarkeit von Verbundbahnen sicherzustellen, sind regelmäßige Wartungen und Inspektionen unerlässlich. Durch Bewertungen können frühzeitig Anzeichen von Schäden oder Verschlechterungen erkannt werden, was eine rechtzeitige Reparatur ermöglicht und schwerwiegendere Probleme verhindert. Richtige Reinigungs- und Wartungsverfahren, wie vom Membranhersteller empfohlen, tragen dazu bei, die Leistungsmerkmale der Membran zu erhalten und ihre Lebensdauer zu verlängern.
- Qualitätssicherung: Die Einhaltung von Branchenstandards und -vorschriften sowie die Beauftragung seriöser Hersteller und Auftragnehmer ist von entscheidender Bedeutung, um die Haltbarkeit von Verbundmembranen sicherzustellen. Zuverlässige Lieferanten bieten qualitativ hochwertige Produkte mit strengen Test- und Zertifizierungsprozessen an und geben Vertrauen in ihre langfristige Leistung.
Wartung und Reparatur von Membranklebstoffen
Um die optimale Leistung und Langlebigkeit von Membranklebstoffen zu gewährleisten, sind eine ordnungsgemäße Wartung und rechtzeitige Reparaturen von entscheidender Bedeutung. Diese Klebstoffe werden verwendet, um feste und dauerhafte Verbindungen zwischen Membranen und Substraten herzustellen. Ihre Wirksamkeit kann durch verschiedene Faktoren wie Umgebungsbedingungen, Alterung und Abnutzung beeinträchtigt werden. Hier besprechen wir die kritischen Aspekte der Wartung und Reparatur von Membranklebstoffen.
- Regelmäßige Inspektionen: Die Durchführung von Routineinspektionen ist unerlässlich, um Anzeichen von Schäden, Verschleiß oder Klebefehlern zu erkennen. In regelmäßigen Abständen sollten Inspektionen gemäß den Empfehlungen des Herstellers durchgeführt und etwaige Probleme umgehend behoben werden, um weitere Schäden oder Beeinträchtigungen des Verbundmembransystems zu verhindern.
- Reinigung: Eine ordnungsgemäße Reinigung des Verbundmembransystems kann dazu beitragen, die Leistung des Klebstoffs aufrechtzuerhalten und seine Lebensdauer zu verlängern. Entfernen Sie Ablagerungen, Schmutz oder Verunreinigungen von der Membranoberfläche und dem Untergrund mit geeigneten Reinigungsmitteln oder den vom Klebstoffhersteller empfohlenen Methoden. Dies gewährleistet einen sauberen und glatten Charakter für eine optimale Klebeleistung.
- Klebstoffkompatibilität: Wenn Reparaturen erforderlich sind, ist die Verwendung eines Klebstoffs, der mit dem vorhandenen Klebesystem kompatibel ist, von entscheidender Bedeutung. Überprüfen Sie die Richtlinien des Klebstoffherstellers, um die Kompatibilität mit dem spezifischen Membranmaterial und Untergrund sicherzustellen. Die Verwendung inkompatibler Klebstoffe kann zu schlechter Haftung, verringerter Haltbarkeit oder sogar zu Schäden an der Membran oder dem Untergrund führen.
- Oberflächenvorbereitung: Vor dem Auftragen des Klebers für Reparaturen ist eine ordnungsgemäße Oberflächenvorbereitung unerlässlich. Reinigen Sie die Klebeflächen gründlich und entfernen Sie Verunreinigungen, lose Partikel oder alte Klebereste. Abhängig von der spezifischen Bindung und dem Untergrund können zusätzliche Schritte zur Oberflächenvorbereitung wie Schleifen, Grundieren oder Auftragen eines Haftvermittlers erforderlich sein. Die Einhaltung der Herstelleranweisungen ist für eine optimale Klebefestigkeit und Haltbarkeit von entscheidender Bedeutung.
- Anwendungstechniken: Befolgen Sie beim Auftragen von Klebstoff für Reparaturen sorgfältig die vom Hersteller empfohlenen Anwendungstechniken. Tragen Sie den Klebstoff gleichmäßig und in der empfohlenen Dicke auf, um eine ordnungsgemäße Verklebung zu gewährleisten und einen übermäßigen oder unzureichenden Klebstoffauftrag zu vermeiden. Auch beim Auftragen sollten angemessene Temperatur- und Feuchtigkeitsbedingungen eingehalten werden, wie vom Klebstoffhersteller angegeben.
Zukünftige Entwicklungen bei Membranklebstoffen
Der Bereich der Membranklebstoffe entwickelt sich ständig weiter, angetrieben durch Fortschritte in der Materialwissenschaft, den Herstellungsprozessen und den Anforderungen der Industrie. Zukünftige Entwicklungen bei Membranklebstoffen zur Verbesserung der Leistung, Nachhaltigkeit und Benutzerfreundlichkeit sind zu erwarten. Hier sind einige mögliche Auswirkungen, auf die Sie achten sollten:
- Umweltfreundliche Formulierungen: Mit der zunehmenden Betonung der Nachhaltigkeit besteht eine steigende Nachfrage nach Membranklebstoffen mit minimaler Umweltbelastung. Zukünftige Entwicklungen könnten sich auf die Formulierung von Klebstoffen mit reduzierten flüchtigen organischen Verbindungen (VOCs) und gefährlichen Substanzen konzentrieren, um die Einhaltung von Umweltvorschriften sicherzustellen. Es könnten auch biologisch abbaubare oder biobasierte Klebstoffe entwickelt werden, die eine umweltfreundlichere Alternative darstellen.
- Verbesserte Haltbarkeit und Leistung: Die Suche nach langlebigeren und leistungsstarken Klebeklebstoffen wird fortgesetzt. Forschungs- und Entwicklungsbemühungen können sich auf die Verbesserung von Klebstoffformulierungen konzentrieren, um die Widerstandsfähigkeit gegenüber extremen Wetterbedingungen, UV-Strahlung, chemischer Belastung und Alterung zu stärken. Dies würde zu Klebstoffen führen, die auch in rauen Umgebungen über längere Zeiträume ihre Festigkeit und Bindungsintegrität beibehalten.
- Neuartige Klebetechnologien: Fortschritte in der Klebetechnologie können zur Entwicklung innovativer Klebesysteme führen. Beispielsweise könnte die Einführung intelligenter Klebstoffe, die sich selbst heilen oder sich an veränderte Bedingungen anpassen können, den Bereich revolutionieren. Die Integration von Nanotechnologie in Klebstoffformulierungen kann die Klebefestigkeit, Flexibilität und andere gewünschte Eigenschaften verbessern.
- Schnellere Aushärtezeiten: Herkömmliche Klebstoffsysteme benötigen oft eine lange Aushärtezeit, bevor sie ihre maximale Festigkeit erreichen. Zukünftige Entwicklungen könnten den Aushärtungsprozess durch neuartige Aushärtungsmechanismen beschleunigen, beispielsweise durch UV- oder feuchtigkeitsaktivierte Klebstoffe. Dies würde eine schnellere Installation ermöglichen und Ausfallzeiten in verschiedenen Anwendungen reduzieren.
- Verbesserte Kompatibilität: Membranklebstoffe müssen mit verschiedenen Membranmaterialien, Substraten und Oberflächenbedingungen kompatibel sein. Zukünftige Entwicklungen zielen darauf ab, die Kompatibilität von Klebstoffen zu verbessern und solide und zuverlässige Verbindungen für verschiedene Anwendungen sicherzustellen. Dies könnte die Entwicklung von Klebstoffen mit breiteren Haftfähigkeiten oder spezifischen Formulierungen umfassen, die auf verschiedene Materialien und Substrate zugeschnitten sind.
- Einfache Bewerbung: Die Vereinfachung des Bewerbungsprozesses ist ein weiterer Bereich mit potenziellem Entwicklungspotenzial. Klebstoffhersteller konzentrieren sich möglicherweise auf die Entwicklung von Klebstoffen mit verbesserter Benutzerfreundlichkeit, z. B. vorgemischte oder voraufgetragene Klebstoffsysteme. Diese Fortschritte würden den Installationsprozess rationalisieren, das Risiko von Anwendungsfehlern verringern und es möglicherweise auch weniger erfahrenen Arbeitern ermöglichen, eine qualitativ hochwertige Verklebung zu erzielen.
- Erweiterte Qualitätskontrolle: Da die Anforderungen an Zuverlässigkeit und Konsistenz steigen, können zukünftige Entwicklungen erweiterte Qualitätskontrollmaßnahmen für die Klebstoffproduktion erfordern. Dazu könnte die Implementierung automatisierter Inspektionssysteme, die Echtzeitüberwachung der Klebstoffeigenschaften während der Anwendung sowie der Einsatz fortschrittlicher Analyse- und maschineller Lernalgorithmen zur Optimierung von Klebstoffformulierungen gehören.
Zusammenfassung
Membranklebstoffe sind vielseitig und in verschiedenen Branchen unverzichtbar und sorgen für eine sichere und zuverlässige Verbindung von Membranen, die in Bau-, Automobil- und Fertigungsanwendungen verwendet werden. Durch die Auswahl des geeigneten Klebstoffs auf der Grundlage von Faktoren wie Membrankompatibilität, Umgebungsbedingungen und Anwendungstechniken können Industrieunternehmen die dauerhafte und effektive Leistung verklebter Membranen sicherstellen. Mit fortschreitenden Fortschritten wird erwartet, dass zukünftige Entwicklungen bei Membranklebstoffen die Klebefestigkeit, Haltbarkeit und Anwendungseffizienz verbessern werden.