Schutzlacke für die Elektronik
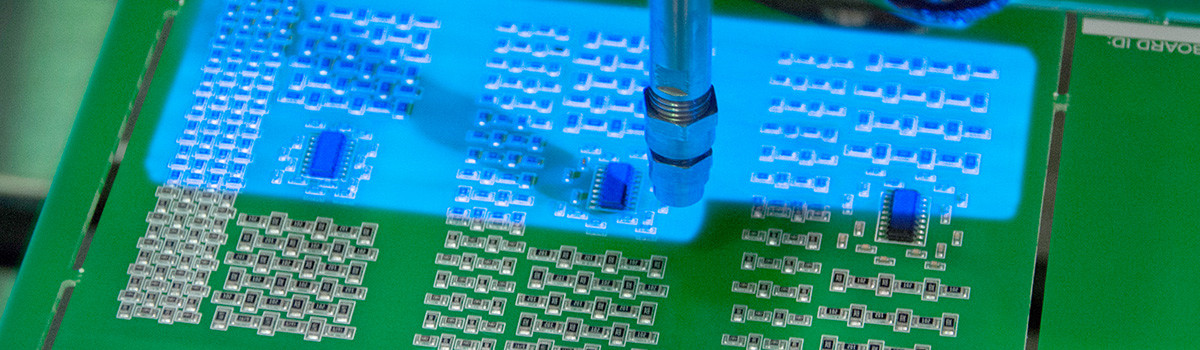
In der heutigen Welt sind elektronische Geräte aus unserem täglichen Leben nicht mehr wegzudenken. Da elektronische Geräte immer komplexer und miniaturisiert werden, wird der Schutz vor Umwelteinflüssen wie Feuchtigkeit, Staub und Chemikalien immer wichtiger. Hier kommen Schutzbeschichtungen ins Spiel. Schutzbeschichtungen sind speziell formulierte Materialien, die elektronische Komponenten vor äußeren Faktoren schützen, die ihre Leistung und Funktionalität beeinträchtigen können. In diesem Artikel werden die Vorteile und die Bedeutung von Schutzbeschichtungen für die Elektronik untersucht.
Was sind Schutzbeschichtungen für die Elektronik?
Schutzbeschichtungen sind spezielle Schutzbeschichtungen, die in der Elektronikindustrie verwendet werden, um elektronische Komponenten und Leiterplatten vor Umwelteinflüssen wie Feuchtigkeit, Staub, Chemikalien und extremen Temperaturen zu schützen. Diese Beschichtungen werden in einer dünnen, gleichmäßigen Schicht auf die Oberfläche der Elektronik aufgetragen und passen sich den Konturen der Komponenten an, um vollständige Abdeckung und Schutz zu bieten.
Der Hauptzweck von Schutzbeschichtungen besteht darin, Schäden oder Fehlfunktionen elektronischer Geräte durch äußere Einflüsse zu verhindern. Feuchtigkeit und Nässe können beispielsweise zu Korrosion und Kurzschlüssen führen, während Staub und Schmutz die Leistung empfindlicher Komponenten beeinträchtigen können. Eine konforme Beschichtung schützt die elektronische Baugruppe vor diesen Gefahren und gewährleistet so ihre Zuverlässigkeit und Langlebigkeit.
Schutzbeschichtungen werden typischerweise aus verschiedenen chemischen Formulierungen hergestellt, darunter Acryl, Silikone, Urethane und Epoxidharze. Jede Art von Beschichtung bietet unterschiedliche Eigenschaften und Vorteile. Acrylbeschichtungen werden aufgrund ihrer Vielseitigkeit, einfachen Anwendung und Kosteneffizienz häufig verwendet. Sie bieten eine gute Feuchtigkeitsbeständigkeit und lassen sich relativ einfach entfernen und bei Bedarf erneut auftragen. Silikone sind für ihre hervorragende Flexibilität, thermische Stabilität und Beständigkeit gegenüber hohen Temperaturen bekannt. Urethanbeschichtungen bieten eine außergewöhnliche chemische Beständigkeit und Schutz gegen Lösungsmittel und Kraftstoffe. Epoxidharze bieten eine überragende Härte und Haltbarkeit und eignen sich daher für raue Umgebungen.
Schutzbeschichtungen erfordern sorgfältige Aufmerksamkeit, um eine ordnungsgemäße Abdeckung und Haftung sicherzustellen. Verschiedene Techniken umfassen Bürsten, Sprühen, Tauchen und selektives Beschichten. Abhängig von den spezifischen Anforderungen und der Komplexität der Baugruppe können unterschiedliche Methoden eingesetzt werden. Einige Beschichtungen werden manuell aufgetragen, während andere durch automatisierte Prozesse wie Roboterspritzen oder Tauchbeschichtungssysteme durchgeführt werden.
Nach dem Auftragen bildet die Schutzbeschichtung eine Schutzbarriere, die die elektronischen Komponenten einkapselt, ohne deren Funktionalität zu beeinträchtigen. Es bildet einen Schutzfilm, der auf der Oberfläche haftet und seine schützenden Eigenschaften über die Zeit beibehält. Die Beschichtungen sind in der Regel transparent oder durchscheinend und ermöglichen eine visuelle Inspektion der Montage.
Neben dem Schutz vor Umwelteinflüssen bieten Schutzlacke noch weitere Vorteile. Sie können für eine elektrische Isolierung sorgen und so Leckströme und Kurzschlüsse verhindern. Schichten können auch die Widerstandsfähigkeit der Baugruppe gegenüber Vibrationen und mechanischen Belastungen erhöhen und so das Risiko von Schäden während des Transports oder Betriebs verringern. Darüber hinaus können sie Schutz vor Pilzen, Schimmel und anderen Verunreinigungen bieten, die die Leistung elektronischer Geräte beeinträchtigen können.
Die Bedeutung von Schutzbeschichtungen für elektronische Geräte
Schutzbeschichtungen spielen eine entscheidende Rolle bei der Verbesserung der Zuverlässigkeit und Haltbarkeit elektronischer Geräte und bieten eine Reihe wesentlicher Vorteile für die Gewährleistung optimaler Leistung und Langlebigkeit. Hier sind einige Hauptgründe, warum Schutzbeschichtungen für elektronische Geräte notwendig sind:
- Schutz vor Feuchtigkeit und Feuchtigkeit: Einer der Hauptzwecke von Schutzlacken besteht darin, elektronische Komponenten vor Feuchtigkeit und Nässe zu schützen. Wasser kann zu Korrosion, Oxidation und der Bildung von Leiterbahnen führen, was zu Kurzschlüssen und Fehlfunktionen der Geräte führen kann. Schutzlacke fungieren als Barriere, verhindern, dass Feuchtigkeit an die empfindlichen Bauteile gelangt und verringern das Risiko von Schäden.
- Verhinderung der Ansammlung von Staub und Schmutz: Elektronikgeräte sind häufig Staub, Schmutz und Luftschadstoffen ausgesetzt. Diese Partikel können sich auf Leiterplatten und Komponenten ablagern und zu Isolationsproblemen, erhöhter Wärmeentwicklung und möglichen Kurzschlüssen führen. Schutzbeschichtungen bilden eine Schutzschicht, die die Ansammlung von Staub und Schmutz verhindert und so die Sauberkeit und Leistung der Elektronik aufrechterhält.
- Chemische Beständigkeit: Viele Schutzbeschichtungen sind beständig gegen verschiedene Chemikalien, darunter Lösungsmittel, Kraftstoffe, Säuren und Laugen. Dies ist besonders wichtig in Umgebungen, in denen elektronische Geräte mit korrosiven Substanzen in Kontakt kommen können. Die Beschichtungen wirken als Schutzschild, verhindern chemische Reaktionen und sorgen für die Langlebigkeit der Komponenten.
- Wärmeschutz: Elektronische Geräte erzeugen während des Betriebs Wärme und übermäßige Hitze kann die Leistung und Zuverlässigkeit von Komponenten beeinträchtigen. Schutzbeschichtungen können eine Wärmebarriere bilden, die Wärme ableitet und das Risiko einer Überhitzung verringert. Bestimmte Schichten, beispielsweise auf Silikonbasis, sind für ihre hervorragende thermische Stabilität bekannt und können hohen Temperaturen standhalten, ohne ihre Schutzeigenschaften zu beeinträchtigen.
- Elektrische Isolierung: Schutzbeschichtungen können eine elektrische Isolierung bieten und so Leckströme und Kurzschlüsse verhindern. Sie tragen dazu bei, die gewünschten elektrischen Eigenschaften der Komponenten aufrechtzuerhalten und das Risiko elektrischer Ausfälle aufgrund von Umwelteinflüssen oder Verunreinigungen zu verringern.
- Mechanischer Schutz: Elektronik kann mechanischen Belastungen wie Vibrationen, Stößen oder Stößen ausgesetzt sein. Schutzbeschichtungen erhöhen die mechanische Robustheit elektronischer Geräte, indem sie eine zusätzliche Schutzschicht bieten. Sie tragen dazu bei, Vibrationen und Stoßkräfte zu absorbieren, wodurch das Risiko einer Beschädigung empfindlicher Komponenten verringert und ein zuverlässiger Betrieb gewährleistet wird.
- Umweltbeständigkeit: Schutzbeschichtungen ermöglichen es elektronischen Geräten, verschiedenen Umweltbedingungen standzuhalten. Sie widerstehen extremen Temperaturen, UV-Strahlung, Salznebel und anderen aggressiven Elementen. Dies ist besonders wichtig für Geräte, die im Freien oder in der Industrie eingesetzt werden und dort anspruchsvollen Umgebungen ausgesetzt sein können.
Vorteile der Verwendung von Schutzbeschichtungen
Die Verwendung von Schutzbeschichtungen für elektronische Geräte bietet mehrere Vorteile, die zu ihrer allgemeinen Zuverlässigkeit und Langlebigkeit beitragen. Hier sind einige wichtige Vorteile der Verwendung von Schutzbeschichtungen:
- Umweltschutz: Schutzbeschichtungen bieten eine Schutzbarriere, die elektronische Komponenten vor Umwelteinflüssen wie Feuchtigkeit, Staub, Schmutz und Chemikalien schützt. Sie verhindern das Eindringen von Wasser, das zu Korrosion und Kurzschlüssen führen kann, und schützen vor der Ansammlung von Staub und Schmutz, die die Leistung beeinträchtigen können. Dieser Umweltschutz verlängert die Lebensdauer elektronischer Geräte.
- Erhöhte Zuverlässigkeit: Durch den Schutz vor Umweltgefahren erhöhen Schutzbeschichtungen die Zuverlässigkeit elektronischer Geräte. Sie minimieren das Risiko von Ausfällen, die durch feuchtigkeitsbedingte Probleme wie korrosionsbedingte Komponentenschäden oder elektrochemische Migration verursacht werden. Darüber hinaus schützen Beschichtungen vor Staub und Schmutz, die Kurzschlüsse oder Isolationsausfälle verursachen können, und sorgen so für eine gleichbleibende und zuverlässige Leistung.
- Elektrische Isolierung: Schutzbeschichtungen bieten elektrische Isoliereigenschaften und verhindern Stromlecks und Kurzschlüsse. Sie tragen dazu bei, die gewünschten elektrischen Eigenschaften der Komponenten aufrechtzuerhalten und verringern so die Möglichkeit elektrischer Fehlfunktionen oder Ausfälle aufgrund von Verschmutzung oder Feuchtigkeitsaufnahme. Die elektrische Isolierung trägt auch dazu bei, Sicherheits- und Regulierungsanforderungen zu erfüllen.
- Wärmemanagement: Einige Schutzbeschichtungen verfügen über Wärmemanagementeigenschaften, die es ihnen ermöglichen, die von elektronischen Bauteilen erzeugte Wärme abzuleiten. Dieser Wärmeschutz verhindert eine Überhitzung, die die Leistung beeinträchtigen und die Lebensdauer empfindlicher Geräte verkürzen kann. Durch die effektive Temperaturregulierung tragen Schutzbeschichtungen zur Gesamtzuverlässigkeit der Elektronik bei.
- Chemische Beständigkeit: Viele Schutzlacke weisen eine ausgezeichnete chemische Beständigkeit auf. Sie bilden eine Barriere gegen korrosive Substanzen, Lösungsmittel, Kraftstoffe und andere Chemikalien, die elektronische Komponenten beschädigen können. Diese chemische Beständigkeit verhindert chemische Reaktionen, Materialabbau und mögliche Ausfälle, die durch die Einwirkung rauer Umgebungen oder den Kontakt mit Chemikalien verursacht werden.
- Vibrations- und Stoßschutz: Schutzbeschichtungen bieten mechanischen Schutz, indem sie Vibrationen absorbieren und die Auswirkungen von Stößen und mechanischen Belastungen reduzieren. Dies ist besonders vorteilhaft für elektronische Geräte, die einem Transport oder rauen Betriebsbedingungen ausgesetzt sind. Schutzbeschichtungen tragen dazu bei, Schäden an empfindlichen Komponenten, Lötstellen und Verbindungen zu verhindern, indem sie die Auswirkungen von Vibrationen und Stößen minimieren.
- Einfache Inspektion und Reparatur: Schutzbeschichtungen sind häufig transparent oder durchscheinend und ermöglichen eine visuelle Inspektion der darunter liegenden Komponenten. Dies erleichtert die einfachere Erkennung potenzieller Probleme wie Lötstellendefekte, Bauteilschäden oder Fremdmaterialverunreinigungen. Darüber hinaus können Schutzbeschichtungen entfernt und erneut aufgetragen werden, wenn Reparaturen oder Änderungen erforderlich sind, was die Wartung vereinfacht.
Wie funktionieren Schutzlacke?
Schutzbeschichtungen bilden eine Schutzbarriere auf der Oberfläche elektronischer Komponenten und Leiterplatten. Diese Beschichtungen werden typischerweise als dünne, gleichmäßige Schichten aufgetragen, die sich den Konturen der Geräte anpassen und so eine vollständige Abdeckung und Schutz gewährleisten. Die Beschichtungen haften auf der Oberfläche und bilden einen kontinuierlichen Film, der vor Umwelteinflüssen und potenziellen Verunreinigungen schützt.
Das Aufbringen von Schutzlacken umfasst mehrere Schritte:
- Oberflächenvorbereitung: Vor dem Auftragen der Schutzbeschichtung muss die Oberfläche der elektronischen Baugruppe ausreichend vorbereitet werden. Dabei geht es in der Regel um die Reinigung und Entfernung von Verunreinigungen wie Staub, Ölen und Rückständen. Die Abdeckung kann mit Lösungsmitteln, Ultraschallreinigung oder anderen geeigneten Methoden gereinigt werden, um einen sauberen und glatten Untergrund für die Beschichtungshaftung zu gewährleisten.
- Auswahl des Beschichtungsmaterials: Es stehen verschiedene Arten von Schutzbeschichtungen zur Verfügung, z. B. Acryl, Silikone, Urethane und Epoxidharze, jede mit ihren eigenen Eigenschaften und Vorteilen. Die Wahl des Beschichtungsmaterials hängt von Faktoren wie den Umgebungsbedingungen, dem gewünschten Schutzniveau, den Anforderungen an die elektrische Isolierung und spezifischen Anwendungsaspekten ab.
- Auftragungsmethode: Schutzbeschichtungen können mit verschiedenen Methoden aufgetragen werden, darunter Streichen, Sprühen, Tauchen und selektives Beschichten. Die Wahl der Auftragungsmethode hängt von Faktoren wie der Komplexität der Baugruppe, der Art des Beschichtungsmaterials und der gewünschten Präzision ab. Manuelle Auftragsmethoden eignen sich für kleinere Produktionsmengen oder spezielle Bereiche, die eine gezielte Beschichtung erfordern. Automatisierte Prozesse wie Robotersprüh- oder Tauchbeschichtungssysteme werden häufig für die Produktion in größerem Maßstab eingesetzt, um eine gleichmäßige und gleichmäßige Beschichtungsabdeckung sicherzustellen.
- Aushärten und Trocknen: Nach dem Auftragen der Beschichtung muss diese einem Aushärte- oder Trocknungsprozess unterzogen werden. Durch diesen Prozess verfestigt sich das Beschichtungsmaterial und bildet einen Schutzfilm. Die Aushärtungszeit und -bedingungen hängen vom jeweiligen Beschichtungsmaterial und den Empfehlungen des Herstellers ab. Zu den Aushärtungsmethoden können Lufttrocknung, thermische Aushärtung in Öfen oder die Einwirkung von UV-Licht für bestimmte Beschichtungsarten gehören.
Nach dem Auftragen und Aushärten bildet die Schutzbeschichtung eine Schutzbarriere, die die elektronischen Komponenten umschließt. Die Schicht stellt eine Barriere gegen Feuchtigkeit, Staub, Chemikalien und andere Umweltfaktoren dar, die die Komponenten beschädigen oder verschlechtern können. Es hilft, Korrosion, Kurzschlüsse und Isolationsschäden zu verhindern und sorgt so für die Zuverlässigkeit und Langlebigkeit elektronischer Geräte.
Schutzbeschichtungen behalten ihre Schutzeigenschaften im Laufe der Zeit und bieten dauerhaften Schutz für elektronische Baugruppen. Im Falle von Reparaturen oder Änderungen kann die Schicht gezielt entfernt und erneut aufgetragen werden, was eine Wartung oder den Austausch von Komponenten ermöglicht, ohne den Gesamtschutz der Beschichtung zu beeinträchtigen.
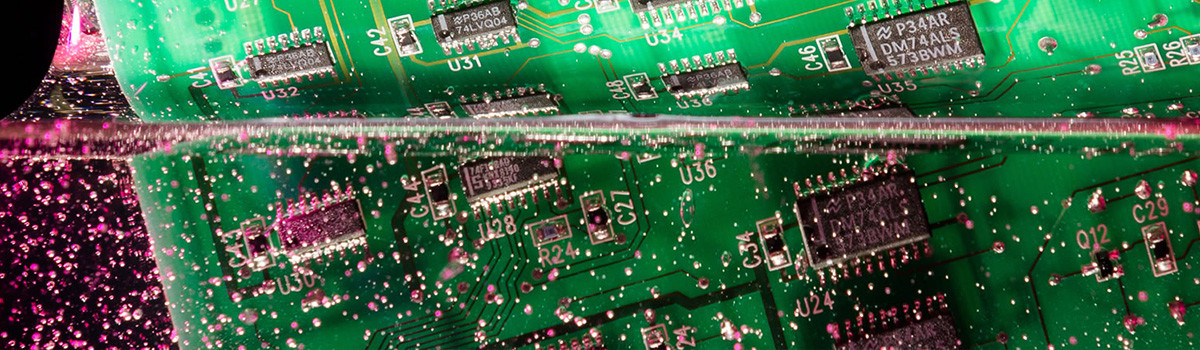
Arten von Schutzbeschichtungen
Es stehen verschiedene Arten von Schutzbeschichtungen zur Verfügung, jede mit ihren eigenen Eigenschaften, Vorteilen und Anwendungen. Die Auswahl des Beschichtungstyps hängt von Faktoren wie den spezifischen Anforderungen der elektronischen Baugruppe, den Umgebungsbedingungen, dem gewünschten Schutzniveau und den Herstellungsprozessen ab. Hier sind einige häufig verwendete Arten von Schutzbeschichtungen:
- Acryl-Schutzbeschichtungen: Acrylbeschichtungen gehören aufgrund ihrer Vielseitigkeit und Kosteneffizienz zu den am häufigsten verwendeten Arten. Sie bieten eine gute Feuchtigkeitsbeständigkeit, elektrische Isolierung und Schutz vor Umwelteinflüssen. Acrylbeschichtungen lassen sich leicht auftragen, entfernen und überarbeiten. Sie eignen sich für verschiedene Anwendungen und bieten einen guten Allzweckschutz.
- Silikon-Schutzbeschichtungen: Silikonbeschichtungen zeichnen sich durch hervorragende Flexibilität, thermische Stabilität und Beständigkeit gegenüber hohen Temperaturen aus. Sie halten extremen Temperaturschwankungen stand, ohne ihre schützenden Eigenschaften zu verlieren. Silikonbeschichtungen bieten eine hervorragende Feuchtigkeitsbeständigkeit und elektrische Isolierung. Sie werden häufig in Anwendungen eingesetzt, bei denen eine hohe thermische Stabilität und Flexibilität von entscheidender Bedeutung sind, beispielsweise in der Automobilindustrie, der Luft- und Raumfahrt sowie bei elektronischen Geräten für den Außenbereich.
- Urethan-Schutzbeschichtungen: Urethan-Beschichtungen bieten eine außergewöhnliche chemische Beständigkeit und eignen sich daher für Anwendungen, bei denen die Einwirkung von Lösungsmitteln, Kraftstoffen oder anderen aggressiven Chemikalien ein Problem darstellt. Sie bieten guten Feuchtigkeitsschutz, elektrische Isolierung und mechanische Haltbarkeit. Urethanbeschichtungen werden häufig in anspruchsvollen Umgebungen wie Automobil-, Industrie- und Militäranwendungen eingesetzt.
- Epoxidkonforme Beschichtungen: Epoxidbeschichtungen sind für ihre hervorragende Härte und Haltbarkeit bekannt. Sie bieten einen soliden mechanischen Schutz sowie Beständigkeit gegen Abrieb und Stöße. Epoxidbeschichtungen bieten eine gute Chemikalienbeständigkeit und einen guten Feuchtigkeitsschutz. Sie werden häufig in Anwendungen eingesetzt, die robusten Schutz und mechanische Festigkeit erfordern, beispielsweise in industriellen Steuerungssystemen, robuster Elektronik und Umgebungen mit hoher Belastung.
- Parylene-Schutzbeschichtungen: Parylene ist eine einzigartige Art von Schutzbeschichtung, die als Dampf aufgetragen wird und einen dünnen, lochfreien Polymerfilm bildet. Parylene-Schichten bieten hervorragende Feuchtigkeitsbarriereeigenschaften, elektrische Isolierung, chemische Beständigkeit und Biokompatibilität. Sie bieten ein hohes Maß an Schutz und passen sich komplexen Geometrien an. Parylene-Beschichtungen werden häufig in medizinischen Geräten, in der Luft- und Raumfahrt sowie in empfindlichen elektronischen Anwendungen eingesetzt.
- UV-härtende Schutzlacke: UV-härtende Lacke werden flüssig aufgetragen und anschließend mit UV-Licht ausgehärtet. Sie bieten schnelle Aushärtezeiten, was die Produktionseffizienz steigern kann. UV-härtbare Schichten bieten eine gute Feuchtigkeitsbeständigkeit, elektrische Isolierung und chemische Beständigkeit. Sie eignen sich für Anwendungen, die eine schnelle Aushärtung, einen hohen Durchsatz und eine gleichbleibende Beschichtungsqualität erfordern.
Es ist wichtig zu beachten, dass die Auswahl der geeigneten Schutzbeschichtung von den spezifischen Anforderungen der elektronischen Baugruppe und der beabsichtigten Anwendung abhängt. Umgebungsbedingungen, Betriebstemperaturbereich, chemische Belastung und gewünschter Schutzgrad sollten bei der Auswahl der Art der Schutzbeschichtung berücksichtigt werden, um optimale Leistung und Langlebigkeit der elektronischen Geräte sicherzustellen.
Acryl konforme Beschichtungen
Acrylschutzbeschichtungen werden aufgrund ihrer Vielseitigkeit, Kosteneffizienz und einfachen Anwendung häufig in der Elektronikindustrie eingesetzt. Sie bieten eine Reihe von Vorteilen und eignen sich für verschiedene elektronische Baugruppen und Anwendungen. Hier sind einige Hauptmerkmale und Vorteile von Acryl-Schutzbeschichtungen:
- Feuchtigkeitsschutz: Acrylbeschichtungen bieten eine gute Feuchtigkeitsbeständigkeit und tragen dazu bei, das Eindringen von Wasser oder Feuchtigkeit in elektronische Komponenten zu verhindern. Feuchtigkeit kann zu Korrosion, Kurzschlüssen und Leistungseinbußen führen. Acrylbeschichtungen wirken als Barriere, schützen vor feuchtigkeitsbedingten Problemen und erhöhen die Zuverlässigkeit und Lebensdauer elektronischer Geräte.
- Elektrische Isolierung: Acrylbeschichtungen sorgen für elektrische Isolierung und verhindern Stromlecks und Kurzschlüsse. Sie tragen dazu bei, die gewünschten elektrischen Eigenschaften der Komponenten aufrechtzuerhalten und das Risiko elektrischer Fehlfunktionen oder Ausfälle durch Verschmutzung oder Feuchtigkeitsaufnahme zu verringern. Diese elektrische Isolationseigenschaft ist für die Aufrechterhaltung der Integrität elektronischer Schaltkreise von entscheidender Bedeutung.
- Umweltschutz: Schutzbeschichtungen aus Acryl schützen elektronische Baugruppen vor Umwelteinflüssen wie Staub, Schmutz, Chemikalien und Temperaturschwankungen. Sie bilden eine Barriere gegen Luftschadstoffe und verhindern so, dass diese sich auf der Oberfläche von Bauteilen ablagern. Acrylbeschichtungen bieten zudem eine gewisse Chemikalienbeständigkeit und bieten so zusätzlichen Schutz vor korrosiven Substanzen.
- Einfache Anwendung: Acrylbeschichtungen sind für ihre einfache Anwendung bekannt. Sie können mit verschiedenen Methoden aufgetragen werden, darunter Streichen, Sprühen, Tauchen oder punktuelles Auftragen. Diese Flexibilität ermöglicht manuelle und automatisierte Anwendungsprozesse, abhängig von den spezifischen Anforderungen und dem Produktionsumfang. Acrylbeschichtungen haben im Allgemeinen eine gute Benetzungsfähigkeit und sorgen so für eine gleichmäßige Abdeckung und Haftung auf den Oberflächen elektronischer Komponenten.
- Reparatur- und Nacharbeitsfähigkeit: Einer der Vorteile von Acrylbeschichtungen ist ihre Nacharbeitbarkeit. Sollten Reparaturen oder Modifikationen erforderlich sein, lassen sich Acrylbeschichtungen mit geeigneten Lösungsmitteln leicht entfernen und ermöglichen so Reparaturarbeiten an den darunter liegenden Bauteilen. Die Möglichkeit, Acrylbeschichtungen zu entfernen und erneut aufzutragen, vereinfacht den Reparaturprozess und erleichtert Wartungsarbeiten.
- Transparent oder durchscheinend: Acrylschutzbeschichtungen sind typischerweise transparent oder durchscheinend. Diese Funktion ermöglicht eine visuelle Inspektion der darunter liegenden Komponenten, ohne dass die Beschichtung entfernt werden muss. Die visuelle Inspektion identifiziert potenzielle Probleme wie Lötstellendefekte, Bauteilschäden oder Fremdmaterialverunreinigungen.
- Kosteneffizienz: Acrylschutzbeschichtungen bieten eine kostengünstige Lösung zum Schutz elektronischer Baugruppen. Sie bieten ein gutes Gleichgewicht zwischen Leistung und Erschwinglichkeit und eignen sich daher für ein breites Anwendungsspektrum. Die relativ geringen Kosten von Acrylbeschichtungen ermöglichen kosteneffiziente Produktionsprozesse, ohne den gewünschten Schutz und die Zuverlässigkeit elektronischer Geräte zu beeinträchtigen.
Während konforme Acrylbeschichtungen mehrere Vorteile bieten, ist es wichtig, bei der Auswahl eines Beschichtungstyps die spezifischen Anforderungen und Umgebungsbedingungen der elektronischen Baugruppe zu berücksichtigen. Faktoren wie Betriebstemperaturbereich, chemische Belastung und mechanische Belastungen sollten berücksichtigt werden, um optimalen Schutz und Leistung zu gewährleisten.
Silikonkonforme Beschichtungen
Aufgrund ihrer einzigartigen Eigenschaften und ihrer Fähigkeit, anspruchsvollen Umgebungsbedingungen standzuhalten, werden konforme Silikonbeschichtungen in der Elektronikindustrie häufig eingesetzt. Sie bieten eine Reihe von Vorteilen, die sie für verschiedene elektronische Baugruppen und Anwendungen geeignet machen. Hier sind einige Hauptmerkmale und Vorteile von Silikon-Schutzbeschichtungen:
- Thermische Stabilität: Silikonbeschichtungen sind für ihre hervorragende thermische Stabilität bekannt, die es ihnen ermöglicht, hohen Betriebstemperaturen standzuhalten, ohne ihre Schutzeigenschaften zu verlieren. Sie können Temperaturschwankungen effektiver bewältigen als viele andere Arten von Schutzbeschichtungen. Dadurch eignen sich Silikonbeschichtungen gut für Anwendungen mit hoher thermischer Stabilität, beispielsweise in der Automobil-, Luft- und Raumfahrtindustrie sowie in der Industrieelektronik.
- Flexibilität und Anpassungsfähigkeit: Silikonkonforme Beschichtungen sind äußerst flexibel und können sich der Form komplexer elektronischer Baugruppen anpassen. Sie können als dünne, gleichmäßige Schichten aufgetragen werden, die selbst auf komplizierten Schaltkreisen und Komponenten eine vollständige Abdeckung bieten. Die Flexibilität und Anpassungsfähigkeit von Silikonbeschichtungen stellen sicher, dass kritische Bereiche ausreichend geschützt sind, wodurch das Risiko von Schäden oder Ausfällen verringert wird.
- Feuchtigkeits- und Umweltschutz: Silikonbeschichtungen bieten eine hervorragende Feuchtigkeitsbeständigkeit und sind somit praktische Barrieren gegen das Eindringen von Wasser und Feuchtigkeit. Dieser Feuchtigkeitsschutz hilft, Korrosion, Oxidation und elektrische Kurzschlüsse zu verhindern, die durch feuchtigkeitsbedingte Probleme verursacht werden. Silikonbeschichtungen widerstehen außerdem Umwelteinflüssen wie Staub, Schmutz und Chemikalien und erhöhen so die Langlebigkeit und Zuverlässigkeit elektronischer Geräte.
- Elektrische Isolierung: Silikon-Schutzbeschichtungen bieten elektrische Isoliereigenschaften und verhindern Stromlecks und Kurzschlüsse. Sie bewahren die elektrische Integrität der Komponenten und schützen vor elektrischen Ausfällen, die durch Verschmutzung oder Feuchtigkeitsaufnahme verursacht werden. Die elektrische Isolierung von Silikonbeschichtungen ist entscheidend für die Aufrechterhaltung der Zuverlässigkeit und Leistung elektronischer Schaltkreise.
- Chemikalienbeständigkeit: Silikonbeschichtungen weisen eine gute Beständigkeit gegenüber verschiedenen Chemikalien auf, darunter Lösungsmittel, Kraftstoffe, Säuren und Laugen. Aufgrund dieser chemischen Beständigkeit eignen sich Silikonbeschichtungen für Anwendungen, bei denen die Belastung durch korrosive Substanzen ein Problem darstellt. Die Schichten wirken als Schutzbarriere, verhindern chemische Reaktionen und Materialabbau und sorgen für die Langlebigkeit elektronischer Komponenten.
- UV- und Witterungsbeständigkeit: Silikonbeschichtungen bieten eine hervorragende Beständigkeit gegen ultraviolette (UV) Strahlung und Witterungseinflüsse. Sie können einer längeren Einwirkung von Sonnenlicht und Außenumgebungen standhalten, ohne dass sich die Schutzeigenschaften wesentlich verschlechtern oder verloren gehen. Dadurch sind Silikonbeschichtungen ideal für elektronische Geräte, die im Außenbereich eingesetzt werden oder UV-Strahlung ausgesetzt sind.
- Dielektrische Eigenschaften: Silikon-Schutzbeschichtungen haben gute dielektrische Eigenschaften, was bedeutet, dass sie eine wirksame elektrische Isolierung bieten, ohne die elektrische Leistung der Komponenten wesentlich zu beeinträchtigen. Diese Eigenschaft ist für die Aufrechterhaltung der gewünschten elektrischen Eigenschaften und die Verhinderung von Stromausfällen in elektronischen Schaltkreisen von entscheidender Bedeutung.
Silikonkonforme Beschichtungen sind in verschiedenen Formulierungen erhältlich, um den spezifischen Anwendungsanforderungen gerecht zu werden. Sie können mit verschiedenen Methoden aufgetragen werden, darunter Streichen, Sprühen oder Tauchen. Silikonbeschichtungen bieten eine zuverlässige und dauerhafte Schutzschicht für elektronische Baugruppen und gewährleisten deren Funktionalität und Zuverlässigkeit auch unter rauen Betriebsbedingungen.
Bei der Betrachtung von Silikon-Schutzbeschichtungen ist die Bewertung von Faktoren wie dem Betriebstemperaturbereich, der Einwirkung von Chemikalien und mechanischen Belastungen von entscheidender Bedeutung, um die am besten geeignete Beschichtungsformulierung für die spezifische Anwendung zu bestimmen.
Epoxy-konforme Beschichtungen
Aufgrund ihrer hervorragenden Härte, Haltbarkeit und chemischen Beständigkeit werden konforme Epoxidbeschichtungen häufig in der Elektronik eingesetzt. Sie bieten eine Reihe von Vorteilen, die sie für verschiedene elektronische Baugruppen und Anwendungen geeignet machen. Hier sind einige Hauptmerkmale und Vorteile von Epoxid-Schutzbeschichtungen:
- Härte und mechanischer Schutz: Epoxidbeschichtungen bieten außergewöhnliche Härte und mechanischen Schutz und machen sie äußerst widerstandsfähig gegen Abrieb, Stöße und physische Beschädigungen. Sie bieten eine robuste Barriere, die elektronische Komponenten vor mechanischer Belastung schützt und so deren Langlebigkeit und Zuverlässigkeit gewährleistet. Epoxidbeschichtungen eignen sich besonders für Anwendungen, die einen verbesserten automatischen Schutz erfordern, beispielsweise in industriellen Steuerungssystemen und robuster Elektronik.
- Chemikalienbeständigkeit: Schutzbeschichtungen aus Epoxidharz weisen eine hervorragende Beständigkeit gegenüber verschiedenen Chemikalien auf, darunter Lösungsmittel, Kraftstoffe, Säuren und Laugen. Diese chemische Beständigkeit schützt elektronische Komponenten vor Beeinträchtigung oder Beschädigung durch den Kontakt mit korrosiven Substanzen. Epoxidbeschichtungen wirken als Barriere, verhindern chemische Reaktionen und gewährleisten die Integrität der darunter liegenden Komponenten.
- Feuchtigkeits- und Umweltschutz: Epoxidbeschichtungen sorgen für ausreichenden Feuchtigkeits- und Umweltschutz. Sie bilden eine Barriere gegen Wasser, Feuchtigkeit, Staub und andere Umweltschadstoffe, die elektronische Komponenten beschädigen können. Epoxidbeschichtungen helfen, Korrosion, Kurzschlüsse und Leistungseinbußen zu verhindern, indem sie das Eindringen von Feuchtigkeit verhindern.
- Elektrische Isolierung: Epoxidkonforme Beschichtungen bieten hervorragende elektrische Isoliereigenschaften und verhindern Stromlecks und Kurzschlüsse. Sie bewahren die gewünschten elektrischen Eigenschaften der Komponenten und verringern so das Risiko elektrischer Fehlfunktionen oder Ausfälle durch Verschmutzung oder Feuchtigkeitsaufnahme. Die elektrische Isolierung durch Epoxidbeschichtungen ist entscheidend für die Aufrechterhaltung der Zuverlässigkeit und Leistung elektronischer Schaltkreise.
- Wärmebeständigkeit: Epoxidbeschichtungen verfügen über eine gute Wärmebeständigkeit, sodass sie erhöhten Temperaturen ohne nennenswerte Verschlechterung oder Verlust der Schutzeigenschaften standhalten können. Sie tragen dazu bei, die von elektronischen Bauteilen erzeugte Wärme abzuleiten, tragen zum Wärmemanagement bei und verhindern eine Überhitzung. Aufgrund dieser thermischen Beständigkeit eignen sich Epoxidbeschichtungen für Anwendungen, bei denen Temperaturschwankungen und Wärmeableitung entscheidende Faktoren sind.
- Haftung und Deckkraft: Epoxidkonforme Beschichtungen weisen eine hervorragende Haftung auf verschiedenen Substraten auf, darunter Metall, Kunststoff und PCB-Materialien. Sie haften gut auf der Oberfläche elektronischer Baugruppen und bilden eine gleichmäßige und durchgehende Schutzschicht. Epoxidbeschichtungen können eine vollständige Abdeckung bieten und sicherstellen, dass alle kritischen Bereiche und Komponenten ausreichend geschützt sind.
- Reparierbarkeit: Epoxidbeschichtungen bieten den Vorteil, dass sie überarbeitbar und reparierbar sind. Wenn Reparaturen oder Modifikationen erforderlich sind, können Epoxidbeschichtungen mit geeigneten Lösungsmitteln selektiv entfernt werden, um Reparaturarbeiten an den darunter liegenden Bauteilen zu ermöglichen. Diese Reparierbarkeitsfunktion vereinfacht Wartungsarbeiten und erleichtert bei Bedarf den Austausch von Komponenten.
Epoxidkonforme Beschichtungen werden typischerweise durch Streichen, Sprühen oder selektive Beschichtungsverfahren aufgetragen. Die Beschichtungen härten durch eine chemische Reaktion oder einen Wärmehärtungsprozess aus und bilden einen dauerhaften Schutzfilm. Sie bieten dauerhaften Schutz für elektronische Baugruppen und gewährleisten deren Funktionalität und Zuverlässigkeit in anspruchsvollen Umgebungen.
Bei der Prüfung von konformen Epoxidbeschichtungen ist die Bewertung von Faktoren wie dem Betriebstemperaturbereich, der Einwirkung von Chemikalien, mechanischen Belastungen und dem gewünschten Grad an mechanischem und chemischem Schutz von entscheidender Bedeutung, um die am besten geeignete Beschichtungsformulierung für die spezifische Anwendung auszuwählen.
Urethan-Schutzbeschichtungen
Urethan-Schutzbeschichtungen, auch Polyurethan-Beschichtungen genannt, werden aufgrund ihrer außergewöhnlichen chemischen Beständigkeit und mechanischen Haltbarkeit häufig in der Elektronikindustrie eingesetzt. Sie bieten eine Reihe von Vorteilen, die sie für verschiedene elektronische Baugruppen und Anwendungen geeignet machen. Hier sind einige Hauptmerkmale und Vorteile von Urethan-Schutzbeschichtungen:
- Chemikalienbeständigkeit: Urethanbeschichtungen sind beständig gegen verschiedene Chemikalien, darunter Lösungsmittel, Kraftstoffe, Öle, Säuren und Laugen. Aufgrund dieser chemischen Beständigkeit eignen sich Urethanbeschichtungen gut für Anwendungen, bei denen die Belastung durch aggressive Chemikalien ein Problem darstellt. Sie fungieren als Barriere und schützen elektronische Komponenten vor chemischer Zersetzung, Korrosion und anderen Formen von Schäden.
- Feuchtigkeitsschutz: Urethan-Schutzbeschichtungen bieten eine wirksame Feuchtigkeitsbeständigkeit und verhindern das Eindringen von Wasser oder Feuchtigkeit in elektronische Komponenten. Feuchtigkeit kann zu Korrosion, Kurzschlüssen und Leistungseinbußen führen. Urethanbeschichtungen wirken als Barriere, schützen vor feuchtigkeitsbedingten Problemen und erhöhen die Zuverlässigkeit und Lebensdauer elektronischer Geräte.
- Mechanische Haltbarkeit: Urethanbeschichtungen bieten eine hervorragende mechanische Haltbarkeit mit Beständigkeit gegen Abrieb, Stöße und physische Beschädigungen. Sie bilden eine robuste Schutzschicht, die rauen Handhabungs- und Umgebungsbedingungen standhält. Urethanbeschichtungen eignen sich für Anwendungen, bei denen ein verbesserter mechanischer Schutz erforderlich ist, beispielsweise in industriellen Umgebungen oder bei Geräten, die einem hohen Maß an Verschleiß ausgesetzt sind.
- Wärmebeständigkeit: Urethanbeschichtungen weisen eine gute Wärmebeständigkeit auf, sodass sie erhöhten Temperaturen ohne nennenswerte Verschlechterung oder Verlust der Schutzeigenschaften standhalten können. Sie tragen dazu bei, die von elektronischen Bauteilen erzeugte Wärme abzuleiten, tragen zum Wärmemanagement bei und verhindern eine Überhitzung. Aufgrund dieser thermischen Beständigkeit eignen sich Urethanbeschichtungen für Anwendungen, bei denen Temperaturschwankungen und Wärmeableitung entscheidende Faktoren sind.
- Flexibilität: Urethan-Schutzbeschichtungen bieten ein ausgewogenes Verhältnis von Härte und Flexibilität. Sie verfügen über eine gewisse Elastizität, sodass sie kleinere Bewegungen und Belastungen in der elektronischen Baugruppe aufnehmen können. Diese Flexibilität trägt dazu bei, das Risiko einer Rissbildung oder Delaminierung der Beschichtung zu verringern und sorgt so für einen langfristigen Schutz der Komponenten.
- UV-Stabilität: Urethanbeschichtungen weisen eine gute Beständigkeit gegen ultraviolette (UV) Strahlung auf und schützen so vor den potenziell schädlichen Auswirkungen von Sonnenlicht und anderen UV-Quellen. Sie vergilben oder zersetzen sich nicht, wenn sie UV-Licht ausgesetzt werden, und eignen sich daher für Anwendungen im Freien oder für Geräte, die UV-Strahlung ausgesetzt sind.
- Haftung und Abdeckung: Urethanbeschichtungen weisen eine hervorragende Haftung auf verschiedenen Substraten auf, darunter Metalle, Kunststoffe und PCB-Materialien. Sie haften gut auf der Oberfläche elektronischer Baugruppen und bilden eine gleichmäßige und durchgehende Schutzschicht. Urethanbeschichtungen können eine vollständige Abdeckung bieten und sicherstellen, dass alle kritischen Bereiche und Komponenten ausreichend geschützt sind.
Urethan-Schutzbeschichtungen werden typischerweise durch Streichen, Sprühen oder selektive Beschichtungsverfahren aufgetragen. Die Schichten können durch Wärmehärtung oder Feuchtigkeitshärtung ausgehärtet werden und bilden einen haltbaren und schützenden Film. Sie bieten dauerhaften Schutz für elektronische Baugruppen und gewährleisten deren Funktionalität und Zuverlässigkeit in anspruchsvollen Umgebungen.
Wenn die Verwendung von Urethan-Schutzbeschichtungen in Betracht gezogen wird, ist es wichtig, die spezifische chemische Belastung, den Betriebstemperaturbereich, die mechanischen Belastungen und das gewünschte Maß an chemischem und mechanischem Schutz zu bewerten, um die am besten geeignete Beschichtungsformulierung für die jeweilige Anwendung auszuwählen.
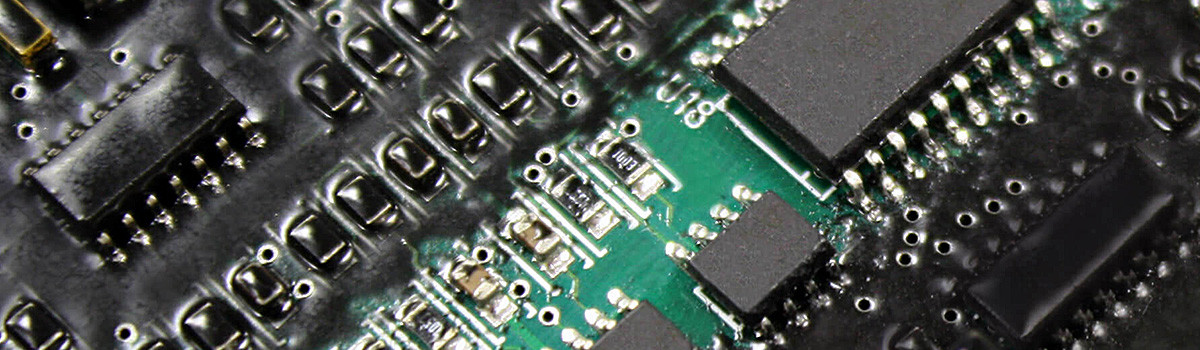
Parylene-Schutzbeschichtungen
Parylene-Schutzbeschichtungen sind einzigartig und bieten außergewöhnlichen Schutz für elektronische Geräte. Parylene-Beschichtungen werden als Dampf abgeschieden und bilden einen dünnen, lochfreien Polymerfilm. Sie bieten eine Reihe von Vorteilen, die sie für verschiedene elektronische Baugruppen und Anwendungen hervorragend geeignet machen. Hier sind einige Hauptmerkmale und Vorteile von Parylene-Schutzbeschichtungen:
- Feuchtigkeits- und Chemikalienbarriere: Parylene-Beschichtungen bieten eine hervorragende Barriere gegen Feuchtigkeit, Gase und Chemikalien. Der dünne, gleichmäßige Film, der durch Parylene-Beschichtungen gebildet wird, bietet eine hochwirksame Feuchtigkeitsbarriere und verhindert das Eindringen von Wasser und Feuchtigkeit in elektronische Komponenten. Sie bieten außerdem eine außergewöhnliche Beständigkeit gegenüber Chemikalien, einschließlich Lösungsmitteln, Säuren, Basen und ätzenden Substanzen. Diese Feuchtigkeits- und Chemikalienbeständigkeit schützt elektronische Geräte vor Korrosion, Oxidation und Zersetzung und gewährleistet so ihre langfristige Zuverlässigkeit.
- Konformität und Abdeckung: Parylene-Beschichtungen verfügen über hervorragende konforme Eigenschaften, d. h. sie passen sich der Form komplexer und unregelmäßiger Oberflächen an. Durch den Aufdampfprozess kann die Schicht die gesamte elektronische Baugruppe gleichmäßig bedecken, einschließlich komplizierter Merkmale, scharfer Kanten und Spalten. Parylene-Beschichtungen können tief in enge Räume eindringen und gewährleisten so eine vollständige Abdeckung und Schutz für alle kritischen Bereiche.
- Elektrische Isolierung: Parylene-Schutzbeschichtungen bieten hervorragende elektrische Isoliereigenschaften. Sie verfügen über eine hohe Spannungsfestigkeit und können elektrische Komponenten effektiv isolieren und Stromlecks oder Kurzschlüsse verhindern. Parylene-Beschichtungen bewahren die gewünschten elektrischen Eigenschaften der Details und verringern so das Risiko elektrischer Fehlfunktionen oder Ausfälle durch Verschmutzung oder Feuchtigkeitsaufnahme.
- Biokompatibilität: Parylene-Beschichtungen sind biokompatibel und chemisch inert, wodurch sie für medizinische Geräte und implantierbare Elektronik geeignet sind. Bei Kontakt mit biologischen Geweben oder Flüssigkeiten verursachen sie keine Nebenwirkungen. Parylene-Beschichtungen werden in Anwendungen wie Herzschrittmachern, Nervenimplantaten und Biosensoren verwendet, bei denen die Biokompatibilität von entscheidender Bedeutung ist.
- Thermische Stabilität: Parylene-Beschichtungen weisen eine hervorragende thermische Stabilität auf und können einem weiten Temperaturbereich standhalten. Sie bleiben bei niedrigen und hohen Temperaturen stabil und behalten ihre Schutzeigenschaften ohne wesentliche Verschlechterung. Aufgrund dieser thermischen Stabilität eignen sich Parylene-Beschichtungen für Anwendungen, bei denen Temperaturschwankungen und Wärmeableitung wesentliche Faktoren sind.
- Niedriger Reibungskoeffizient: Parylene-Beschichtungen haben einen niedrigen Reibungskoeffizienten, sorgen für Gleitfähigkeit und reduzieren die Oberflächenreibung zwischen Komponenten. Dieser niedrige Reibungskoeffizient trägt dazu bei, den Verschleiß zu minimieren, ein Anhaften oder Festkleben zu verhindern und die Gesamtleistung und Lebensdauer beschichteter elektronischer Geräte zu verbessern.
- Transparenz und Rückverfolgbarkeit: Parylene-Schutzbeschichtungen sind transparent und ermöglichen eine visuelle Inspektion der darunter liegenden Komponenten, ohne dass die Beschichtung entfernt werden muss. Diese Transparenz ermöglicht die Beurteilung und Identifizierung potenzieller Probleme wie Lötstellendefekte, Bauteilschäden oder Fremdmaterialverunreinigungen. Darüber hinaus können Parylene-Beschichtungen mit rückverfolgbaren Elementen dotiert oder markiert werden, was die Qualitätskontrolle, Nachverfolgung und Identifizierung erleichtert.
Parylene-Schutzbeschichtungen werden typischerweise mithilfe eines speziellen Dampfabscheidungsverfahrens aufgetragen. Die Schichten werden durch ein chemisches Gasphasenabscheidungsverfahren (CVD) gebildet, das eine gleichmäßige und lochfreie Abdeckung gewährleistet. Parylene-Beschichtungen bieten dauerhaften Schutz für elektronische Baugruppen, selbst in rauen Umgebungen und anspruchsvollen Anwendungen.
Wenn Parylene-Schutzbeschichtungen in Betracht gezogen werden, ist es wichtig, Faktoren wie die spezifischen Anforderungen der elektronischen Baugruppe, die Umgebungsbedingungen und das gewünschte Schutzniveau zu bewerten, um den geeigneten Parylene-Typ und das Abscheidungsverfahren auszuwählen.
Faktoren, die bei der Auswahl einer Schutzbeschichtung zu berücksichtigen sind
Bei der Auswahl einer Schutzbeschichtung für elektronische Geräte sollten mehrere Faktoren berücksichtigt werden, um sicherzustellen, dass die Beschichtung den spezifischen Anforderungen der Anwendung entspricht. Hier sind einige wichtige Faktoren, die Sie berücksichtigen sollten:
- Umgebungsbedingungen: Die Umgebungsbedingungen, unter denen das elektronische Gerät betrieben wird, spielen eine entscheidende Rolle bei der Auswahl der geeigneten Schutzbeschichtung. Berücksichtigen Sie Faktoren wie extreme Temperaturen, Luftfeuchtigkeit, chemische Belastung, Salznebel und UV-Strahlung. Verschiedene Schichten weisen einen unterschiedlichen Widerstandsgrad gegenüber diesen Umwelteinflüssen auf, und die Wahl einer Beschichtung, die bestimmten Bedingungen standhält, ist für die langfristige Zuverlässigkeit von entscheidender Bedeutung.
- Elektrische Eigenschaften: Berücksichtigen Sie die für die elektronische Baugruppe erforderlichen elektrischen Eigenschaften. Einige Beschichtungen bieten bessere elektrische Isolationseigenschaften als andere. Bewerten Sie die Spannungsfestigkeit, den Oberflächenwiderstand und die Fähigkeit, die Isolierung auch bei Feuchtigkeit oder Verunreinigungen aufrechtzuerhalten. Stellen Sie sicher, dass die gewählte Beschichtung die elektrische Leistung der Komponenten nicht negativ beeinflusst.
- Dicke und Abdeckung: Die Anforderungen an die Dicke und Abdeckung der Schutzbeschichtung sind wesentliche Überlegungen. Dünne Schichten sind für Anwendungen wünschenswert, bei denen begrenzter Platz oder die Einhaltung enger Toleranzen von entscheidender Bedeutung sind. Für Anwendungen, die einen besseren Schutz gegen mechanische Beanspruchung oder raue Umgebungen erfordern, können jedoch dickere Beschichtungen erforderlich sein. Die Schicht sollte in der Lage sein, alle kritischen Bereiche, einschließlich komplexer Geometrien und Komponenten, gleichmäßig abzudecken.
- Auftragungsmethode: Berücksichtigen Sie die verfügbaren Methoden und wählen Sie eine Beschichtung, die mit dem ausgewählten Modus kompatibel ist. Zu den Standardauftragsmethoden gehören Sprühen, Streichen, Tauchen und selektives Beschichten. Einige Schichten eignen sich möglicherweise besser für bestimmte Auftragungsmethoden, während für andere möglicherweise spezielle Geräte oder Techniken erforderlich sind.
- Nacharbeit und Reparatur: Bewerten Sie die Anforderungen an die Nacharbeit und Reparaturfähigkeit der Beschichtung. In einigen Fällen kann das Entfernen oder Reparieren der Schicht erforderlich sein, um Komponenten auszutauschen, zu reparieren oder zu modifizieren. Einige Beschichtungen können leicht nachbearbeitet oder entfernt werden, während andere möglicherweise schwieriger sind oder spezielle Lösungsmittel oder Methoden erfordern.
- Substratkompatibilität: Berücksichtigen Sie die Kompatibilität der Beschichtung mit den in der elektronischen Baugruppe verwendeten Materialien und Substraten. Die Beschichtung sollte auf dem Untergrund haften und eine gute Verträglichkeit mit Bauteilen, Lötstellen und anderen Materialien aufweisen. Kompatibilitätsprobleme können zu Delaminierung, verminderter Haftung oder schlechter Beschichtungsleistung führen.
- Einhaltung gesetzlicher Vorschriften: Berücksichtigen Sie alle spezifischen gesetzlichen Anforderungen, die für das elektronische Gerät oder die Branche gelten, in der es verwendet wird. Für typische Anwendungen wie medizinische Geräte oder Luft- und Raumfahrtelektronik gelten möglicherweise spezielle Regulierungsstandards für Schutzbeschichtungen. Stellen Sie sicher, dass die gewählte Beschichtung den relevanten Vorschriften und Normen entspricht.
- Kosten und Verfügbarkeit: Bewerten Sie die Kosten der Beschichtung und ihre Verfügbarkeit in den erforderlichen Mengen. Berücksichtigen Sie die Kosteneffizienz der Beschichtung, das gewünschte Schutzniveau und das Gesamtbudget des Projekts. Stellen Sie außerdem sicher, dass die Beschichtung bei zuverlässigen Lieferanten verfügbar ist, um Verzögerungen oder Probleme in der Lieferkette zu vermeiden.
Unter Berücksichtigung dieser Faktoren können Sie eine Schutzbeschichtung auswählen, die optimalen Schutz, Leistung und Zuverlässigkeit für die spezifischen Anforderungen Ihres elektronischen Geräts und seiner Betriebsumgebung bietet.
Aufbringungsmethoden für Schutzlacke
Schutzbeschichtungen sind dünne Schutzschichten, die auf elektronische Leiterplatten und Komponenten aufgetragen werden, um sie zu isolieren und vor Umwelteinflüssen wie Feuchtigkeit, Staub, Chemikalien und Temperaturschwankungen zu schützen. Diese Beschichtungen sind so konzipiert, dass sie sich der Form des Substrats „anpassen“ und eine gleichmäßige und kontinuierliche Schutzbarriere bieten. Es gibt verschiedene Methoden zum Aufbringen von Schutzbeschichtungen, jede mit Vorteilen und Überlegungen. In diesem Artikel werden einige Standard-Auftragsmethoden für Schutzbeschichtungen untersucht.
- Streichen/Tauchen: Streichen oder Tauchen ist eine der einfachsten und traditionellsten Methoden zum Auftragen von Schutzbeschichtungen. Das Beschichtungsmaterial wird manuell aufgebürstet oder die Bauteile werden in einen Behälter mit der Beschichtungslösung getaucht. Diese Methode ist kostengünstig und für die Produktion kleiner Stückzahlen geeignet. Dies kann jedoch zu einer inkonsistenten Beschichtungsdicke führen und erfordert eine Aushärtung nach dem Auftragen.
- Sprühbeschichtung: Beim Sprühbeschichten wird das Beschichtungsmaterial mithilfe von Druckluft oder einem speziellen Sprühsystem als feiner Nebel auf das Substrat aufgetragen. Diese Methode bietet eine schnellere Anwendung und eignet sich für manuelle und automatisierte Prozesse. Die Sprühbeschichtung bietet eine bessere Kontrolle über die Schichtdicke und Gleichmäßigkeit, erfordert jedoch geeignete Belüftungs- und Filtersysteme, um Overspray zu kontrollieren und die Sicherheit des Bedieners zu gewährleisten.
- Selektive Beschichtung: Die selektive Beschichtung wird verwendet, wenn nur bestimmte Substratbereiche geschützt werden müssen. Dabei wird ein gesteuertes Dosiersystem oder ein Roboterarm mit Präzisionsapplikator eingesetzt, um das Beschichtungsmaterial präzise an den gewünschten Stellen aufzutragen. Die selektive Beschichtung minimiert Verschwendung, reduziert den Bedarf an Maskierungen und ermöglicht einen gezielten Schutz. Es wird häufig für komplexe Leiterplatten mit empfindlichen Bauteilen verwendet.
- Gasphasenabscheidung: Gasphasenabscheidungsverfahren wie die chemische Gasphasenabscheidung (CVD) und die physikalische Gasphasenabscheidung (PVD) beinhalten das Abscheiden einer konformen Beschichtungsschicht auf dem Substrat durch eine Dampfphase. Diese Methoden erfordern typischerweise spezielle Ausrüstung und kontrollierte Umgebungen. Aufdampftechniken bieten eine hervorragende Gleichmäßigkeit der Beschichtung, Kontrolle der Dicke und Abdeckung komplexer Geometrien. Sie werden häufig für Hochleistungsanwendungen und fortschrittliche elektronische Geräte verwendet.
- Parylene-Beschichtung: Die Parylene-Beschichtung ist eine einzigartige Methode, bei der durch Aufdampfen ein dünner konformer Polymerfilm auf das Substrat aufgebracht wird. Parylene-Beschichtungen bieten außergewöhnlichen Schutz, Isolierung und Biokompatibilität. Das Beschichtungsmaterial dringt in Spalten ein und bedeckt die gesamte Oberfläche gleichmäßig, auch bei filigranen Bauteilen. Parylene-Beschichtungen werden häufig in medizinischen Geräten, in der Luft- und Raumfahrt sowie in hochzuverlässigen Anwendungen eingesetzt.
Bei der Auswahl einer Aufbringungsmethode für Schutzbeschichtungen müssen mehrere Faktoren berücksichtigt werden, darunter die Komplexität des Substrats, das Produktionsvolumen, die Eigenschaften des Beschichtungsmaterials, die Kosten und die Umweltanforderungen. Es ist wichtig, unter Berücksichtigung der spezifischen Anforderungen der Anwendung die Methode zu wählen, die eine optimale Beschichtungsabdeckung, Gleichmäßigkeit und Zuverlässigkeit bietet.
Dicke der konformen Beschichtung
Die Dicke der Schutzbeschichtung ist entscheidend für die Wirksamkeit und Zuverlässigkeit der Schutzbeschichtung, die auf elektronische Komponenten und Leiterplatten aufgetragen wird. Die Schichtdicke wirkt sich direkt auf den Grad des Schutzes gegen Umwelteinflüsse wie Feuchtigkeit, Staub, Chemikalien und Temperaturschwankungen aus. In diesem Artikel werden die Bedeutung der konformen Beschichtungsdicke und die Überlegungen zum Erreichen der gewünschten Beschichtungsdicke untersucht.
Der Hauptzweck von Schutzbeschichtungen besteht darin, eine gleichmäßige und kontinuierliche Schutzschicht über dem Substrat zu erzeugen. Die Beschichtungsdicke sollte ausreichend sein, um eine Isolierung zu gewährleisten und potenzielle Kurzschlüsse oder Kriechströme zu verhindern. Sie sollte jedoch nicht so dick sein, dass es zu elektrischen Störungen oder thermischen Problemen kommt. Die ideale Beschichtungsdicke hängt von Faktoren wie dem Beschichtungsmaterial, der spezifischen Anwendung und den Umgebungsbedingungen ab, denen die beschichtete Elektronik ausgesetzt ist.
Schutzbeschichtungen werden im Allgemeinen als dünne Schichten aufgetragen, deren Dicke typischerweise zwischen einigen Mikrometern (µm) und mehreren zehn Mikrometern liegt. Der Hersteller des Beschichtungsmaterials gibt häufig die empfohlene Beschichtungsdicke an oder kann durch Industriestandards wie IPC-CC-830 für Schutzbeschichtungen definiert werden.
Um die gewünschte Schichtdicke zu erreichen, müssen mehrere Faktoren berücksichtigt werden:
- Beschichtungsmaterial: Verschiedene Schutzbeschichtungsmaterialien weisen unterschiedliche Viskositäten und Fließeigenschaften auf. Diese Eigenschaften beeinflussen die Verteilung und Nivellierung der Beschichtung auf der Substratoberfläche und wirken sich auf die resultierende Dicke aus. Es ist wichtig, die spezifischen Anwendungsanforderungen zu verstehen und ein Beschichtungsmaterial auszuwählen, das mit der gewünschten Dickenkontrolle aufgetragen werden kann.
- Applikationsmethode: Auch die gewählte Applikationsmethode spielt eine wesentliche Rolle bei der Bestimmung der Schichtdicke. Techniken wie Bürsten oder Tauchen können aufgrund manueller Auftragungstechniken zu Abweichungen in der Schichtdicke führen. Automatisierte Prozesse wie Sprühen oder selektives Beschichten können eine bessere Kontrolle über die Beschichtungsdicke ermöglichen, was zu einer gleichmäßigeren und gleichmäßigeren Schicht führt.
- Prozesskontrolle: Die richtige Prozesskontrolle ist entscheidend für das Erreichen der gewünschten Beschichtungsdicke. Faktoren wie Sprühdruck, Düsengröße, Sprühabstand und Viskosität des Beschichtungsmaterials müssen während des Auftragungsprozesses sorgfältig kontrolliert werden. Abhängig von der Geometrie des Substrats und der gewünschten Beschichtungsdicke müssen die Prozessparameter möglicherweise angepasst werden.
- Aushärten/Schrumpfen: Einige Schutzbeschichtungsmaterialien durchlaufen nach dem Auftragen einen Aushärte- oder Trocknungsprozess. Das Beschichtungsmaterial kann während dieses Prozesses schrumpfen, was sich auf die endgültige Beschichtungsdicke auswirkt. Bei der Bestimmung der anfänglichen Schichtdicke ist unbedingt die mögliche Schrumpfung zu berücksichtigen.
- Überprüfung und Inspektion: Sobald die Beschichtung aufgetragen ist, ist es wichtig, ihre Dicke zu überprüfen, um sicherzustellen, dass sie den erforderlichen Spezifikationen entspricht. Es können verschiedene Inspektionstechniken wie visuelle Inspektion, Querschnittsprüfung oder spezielle Messgeräte wie Profilometer oder optische Mikroskopie mit kalibrierter Messsoftware verwendet werden.
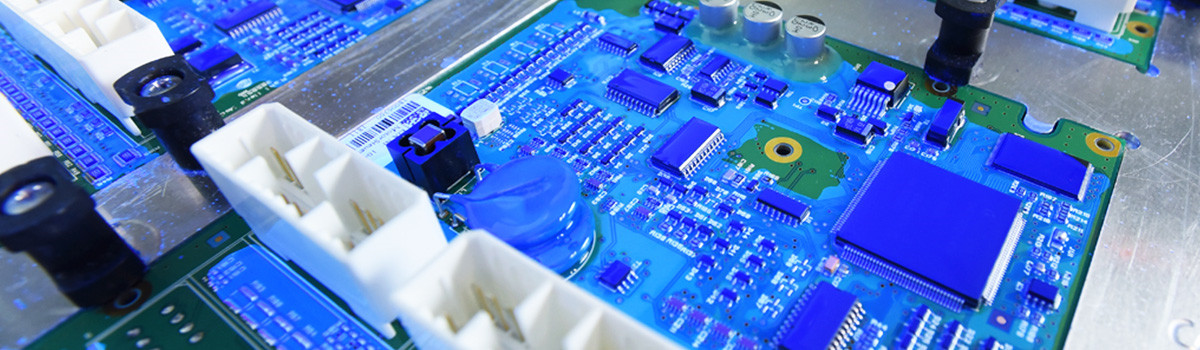
Häufige Probleme mit Schutzbeschichtungen
Während Schutzbeschichtungen für den Schutz elektronischer Komponenten und Leiterplatten unerlässlich sind, können bei ihnen manchmal Probleme auftreten, die ihre Leistung und Zuverlässigkeit beeinträchtigen können. In diesem Artikel werden einige häufige Probleme mit Schutzbeschichtungen und ihre möglichen Ursachen erläutert.
- Unzureichende Abdeckung: Eine unzureichende Abdeckung liegt vor, wenn die Beschichtung nicht die gesamte Oberfläche des Substrats bedeckt oder Lücken und Hohlräume hinterlässt. Dieses Problem kann auf unsachgemäße Auftragungstechniken zurückzuführen sein, beispielsweise auf ungleichmäßiges Sprühen oder eine unzureichende Beschichtungsviskosität. Es kann auch aufgrund von Oberflächenverunreinigungen, unzureichender Trocknung oder Aushärtung oder unzureichender Kontrolle der Schichtdicke auftreten.
- Dickenschwankungen: Ungleichmäßige Beschichtungsdicken sind ein weiteres häufiges Problem. Inkonsistente Auftragungstechniken wie ungleichmäßiges Sprühen oder eine unzureichende Kontrolle der Prozessparameter können dazu führen. Eine längere Trocknungs- oder Aushärtezeit, eine falsche Viskosität des Beschichtungsmaterials oder eine unzureichende Oberflächenvorbereitung können ebenfalls zu Dickenschwankungen führen.
- Blasenbildung und Delaminierung: Blasenbildung und Delaminierung treten auf, wenn die Schutzbeschichtung Blasen bildet oder sich vom Substrat löst. Dieses Problem kann durch unsachgemäße Reinigung und Vorbereitung der Oberfläche, Feuchtigkeit oder Verschmutzung auf der Oberfläche, unzureichende Aushärtung oder Trocknung oder unzureichende Kompatibilität zwischen Beschichtungsmaterial und Untergrund entstehen.
- Rissbildung und Brückenbildung: Unter Rissbildung versteht man die Entstehung von Rissen oder Brüchen in der Schutzbeschichtung, während Brückenbildung auftritt, wenn das Beschichtungsmaterial Lücken oder benachbarte Komponenten überspannt, was zu unbeabsichtigten elektrischen Verbindungen führt. Diese Probleme können durch eine zu hohe Beschichtungsdicke, unzureichende Aushärtung oder Trocknung, thermische Belastung, falsche Auswahl des Beschichtungsmaterials oder unzureichende Beschichtungsflexibilität verursacht werden.
- Schlechte Haftung: Eine schlechte Haftung tritt auf, wenn die Beschichtung nicht auf dem Untergrund haftet, was zu einem verringerten Schutz und einer möglichen Ablösung der Beschichtung führt. Unzureichende Oberflächenreinigung und -vorbereitung, Verunreinigungen, inkompatible Beschichtungs-Substratmaterialien oder unzureichende Aushärtung oder Trocknung können dazu führen.
- Elektrochemische Migration: Unter elektrochemischer Migration versteht man die Bewegung von Ionen oder Verunreinigungen über die Oberfläche des beschichteten Substrats, was zu möglichen Kurzschlüssen und Korrosion führen kann. Dies kann auf eine unzureichende Beschichtungsdicke, das Vorhandensein leitfähiger Verunreinigungen oder das Vorhandensein von Feuchtigkeit zurückzuführen sein.
- Unzureichende chemische Beständigkeit: Schutzlacke müssen möglicherweise verschiedenen Chemikalien und Lösungsmitteln standhalten. Wenn das Beschichtungsmaterial nicht über eine ausreichende chemische Beständigkeit verfügt, kann es bei Einwirkung bestimmter Substanzen zerfallen oder sich auflösen, wodurch seine Schutzwirkung beeinträchtigt wird. Die richtige Materialauswahl ist entscheidend, um die Kompatibilität mit der erwarteten chemischen Umgebung sicherzustellen.
Um diese Probleme zu mildern, ist die Einhaltung bewährter Verfahren und Richtlinien für die Anwendung von Schutzbeschichtungen unerlässlich, einschließlich ordnungsgemäßer Oberflächenreinigung und -vorbereitung, genauer Kontrolle der Prozessparameter, geeigneter Auswahl des Beschichtungsmaterials und angemessener Aushärtung oder Trocknung. Es sollten regelmäßige Inspektions- und Qualitätskontrollmaßnahmen durchgeführt werden, um potenzielle Beschichtungsprobleme frühzeitig zu erkennen und zu beheben. Auch die Einhaltung von Industriestandards wie IPC-CC-830 kann dazu beitragen, die Zuverlässigkeit und Leistung von Schutzbeschichtungen sicherzustellen.
Wartung von Schutzbeschichtungen
Schutzlacke schützen elektronische Komponenten und Leiterplatten vor Umwelteinflüssen wie Feuchtigkeit, Staub, Chemikalien und Temperaturschwankungen. Wie jede Schutzbeschichtung erfordern Schutzbeschichtungen jedoch eine ordnungsgemäße Wartung, um ihre langfristige Wirksamkeit sicherzustellen. Hier sind einige wichtige Punkte, die bei der Wartung von Schutzbeschichtungen zu beachten sind:
- Regelmäßige Inspektion: Führen Sie routinemäßige Inspektionen der beschichteten Oberflächen durch, um sie auf Anzeichen von Beschädigung, Abnutzung oder Delaminierung zu prüfen. Suchen Sie nach Rissen, Absplitterungen oder Stellen, an denen die Beschichtung abgenutzt sein könnte. Inspektionen sollten regelmäßig durchgeführt werden, insbesondere nach der Handhabung, dem Transport oder der Einwirkung rauer Bedingungen.
- Reinigung: Halten Sie die beschichteten Oberflächen sauber, um die Ansammlung von Verunreinigungen zu verhindern, die die Wirksamkeit der Beschichtung beeinträchtigen könnten. Verwenden Sie sanfte Reinigungsmethoden wie eine weiche Bürste oder Druckluft, um Staub, Schmutz oder Partikel zu entfernen. Vermeiden Sie die Verwendung scharfer Lösungsmittel oder scheuernder Materialien, die die Beschichtung beschädigen können.
- Beschädigte Bereiche reparieren: Wenn bei Inspektionen Schäden oder Abnutzung festgestellt werden, ist es wichtig, diese umgehend zu beheben. Reparieren Sie die beschädigten Bereiche, indem Sie sie mit demselben Schutzbeschichtungsmaterial erneut beschichten. Stellen Sie sicher, dass die beschädigte Stelle ausreichend gereinigt und vorbereitet ist, bevor Sie die neue Beschichtung auftragen. Dies trägt dazu bei, die Integrität der Schutzschicht aufrechtzuerhalten.
- Temperatur- und Feuchtigkeitskontrolle: Halten Sie die richtigen Temperatur- und Feuchtigkeitsbedingungen in der Umgebung aufrecht, in der die beschichteten Komponenten gelagert oder betrieben werden. Extreme Temperaturen oder hohe Luftfeuchtigkeit können die Leistung der Beschichtung beeinträchtigen und zu Delaminierung oder vermindertem Schutz führen. Befolgen Sie die Empfehlungen des Herstellers bezüglich der akzeptablen Temperatur- und Luftfeuchtigkeitsbereiche für das jeweilige Schutzbeschichtungsmaterial.
- Vermeiden Sie den Kontakt mit Chemikalien: Vermeiden Sie, dass die beschichteten Oberflächen aggressiven Chemikalien oder Lösungsmitteln ausgesetzt werden, die die Beschichtung angreifen können. Seien Sie vorsichtig, wenn Sie in der Nähe der abgedeckten Komponenten Reinigungsmittel verwenden oder Wartungsarbeiten durchführen. Treffen Sie die erforderlichen Vorsichtsmaßnahmen, um die Schutzbeschichtung vor direktem Kontakt mit Chemikalien zu schützen.
- Erneute Prüfung und Neuzertifizierung: In einigen Branchen, beispielsweise in der Luft- und Raumfahrt oder der Medizintechnik, müssen Schutzbeschichtungen möglicherweise in regelmäßigen Abständen erneut geprüft und zertifiziert werden, um sicherzustellen, dass sie den erforderlichen Standards und Spezifikationen entsprechen. Befolgen Sie die Richtlinien der relevanten Industriestandards und führen Sie in regelmäßigen Abständen die erforderlichen Tests oder Inspektionen durch.
- Dokumentation und Führung von Aufzeichnungen: Führen Sie detaillierte Aufzeichnungen über die Anwendung der Schutzbeschichtung, Wartungsaktivitäten, Inspektionen und Reparaturen. Diese Dokumentation hilft dabei, den Wartungsverlauf zu verfolgen, Fehler- oder Verschleißmuster zu identifizieren und die Einhaltung von Branchenvorschriften und -standards sicherzustellen.
Prüfung und Inspektion von Schutzbeschichtungen
Das Testen und Inspizieren von Schutzbeschichtungen ist unerlässlich, um deren Wirksamkeit und Zuverlässigkeit beim Schutz elektronischer Komponenten und Baugruppen sicherzustellen. Hier sind einige häufig verwendete Methoden zum Testen und Inspizieren von Schutzbeschichtungen:
- Visuelle Inspektion: Die visuelle Inspektion ist ein wesentlicher Schritt bei der Beurteilung der Qualität von Schutzbeschichtungen. Dabei wird die Beschichtungsoberfläche auf sichtbare Mängel wie Nadellöcher, Blasen, Risse oder ungleichmäßige Beschichtung untersucht.
- Dickenmessung: Die Dicke der Schutzbeschichtung ist entscheidend, da sie sich auf die Fähigkeit auswirkt, angemessenen Schutz zu bieten. Die Konsistenz kann mithilfe von Wirbelstrom-, magnetischen Induktions- oder optischen Profilometrietechniken gemessen werden. Die Messung sollte mit den angegebenen Anforderungen an die Schichtdicke verglichen werden.
- Haftungstests: Tests bewerten die Haftfestigkeit zwischen der Schutzbeschichtung und dem Substrat. Zu den Methoden zur Prüfung der Haftung gehören Klebebandtests, Kreuzschraffurtests und Abziehtests. Bei diesen Tests wird festgestellt, ob die Schicht ordnungsgemäß auf der Oberfläche haftet und den Belastungen im Betrieb und bei der Handhabung standhält.
- Prüfung des Isolationswiderstands: Dieser Test bewertet den elektrischen Widerstand der Schutzbeschichtung. Dadurch wird sichergestellt, dass die Schicht eine wirksame elektrische Isolierung bietet, um Leckagen oder Kurzschlüsse zu verhindern. Die Prüfung des Isolationswiderstands wird typischerweise mit einem Hochspannungsprüfer oder einem Megaohmmeter durchgeführt.
- Prüfung der dielektrischen Spannungsfestigkeit: Die Prüfung der dielektrischen Spannungsfestigkeit, auch als Hochspannungs- oder Hochspannungsprüfung bekannt, prüft die Fähigkeit der Beschichtung, Hochspannung ohne Durchschlag standzuhalten. Die Schutzbeschichtung wird für eine festgelegte Dauer einer bestimmten Spannung ausgesetzt, um sicherzustellen, dass sie den erforderlichen Standards für die elektrische Isolierung entspricht.
- Thermozyklische Tests: Bei thermischen Zyklen wird die konforme Beschichtung Temperaturschwankungen ausgesetzt, um ihre Widerstandsfähigkeit gegenüber thermischer Belastung zu beurteilen. Die Schicht wird wiederholten Zyklen extremer Temperaturen ausgesetzt und es werden Veränderungen wie Risse oder Delaminierung beobachtet.
- Feuchtigkeits- und Feuchtigkeitsbeständigkeitsprüfung: Diese Tests bewerten die Fähigkeit der Schutzbeschichtung, Feuchtigkeit und Nässe zu widerstehen. Die Schicht wird für einen bestimmten Zeitraum hoher Luftfeuchtigkeit oder Nässebedingungen ausgesetzt und ihre Leistung wird hinsichtlich des Schutzes vor Korrosion oder Stromausfällen beurteilt.
- Prüfung der Chemikalienbeständigkeit: Bei der Prüfung der Chemikalienbeständigkeit wird geprüft, wie gut die Schutzbeschichtung der Einwirkung verschiedener Chemikalien wie Lösungsmittel oder Reinigungsmittel standhält. Die Schicht wird für eine vorgegebene Zeit den Stoffen ausgesetzt und dabei auf Aussehen, Haftung und Funktionalität beurteilt.
- Salzsprühtest: Beim Salzsprühtest wird die Korrosionsbeständigkeit der Beschichtung in einer salzhaltigen Umgebung bewertet. Die Schutzbeschichtung wird für eine bestimmte Dauer einem Salznebel oder -nebel ausgesetzt und auf Anzeichen von Korrosion oder Zersetzung untersucht.
Es ist wichtig zu beachten, dass spezifische Testanforderungen je nach Branche, Anwendung und den für die Schutzbeschichtung geltenden Standards variieren können. Hersteller oder Industriestandardorganisationen stellen häufig Richtlinien oder Spezifikationen für Test- und Inspektionsverfahren bereit.
Industriestandards für Schutzbeschichtungen
Für Schutzbeschichtungen gibt es mehrere Industriestandards und Spezifikationen, um deren Qualität, Zuverlässigkeit und Leistung sicherzustellen. Hier sind einige der häufig zitierten Standards:
- IPC-CC-830: Dieser von der Association of Connecting Electronics Industries (IPC) veröffentlichte Standard wird häufig für konforme Beschichtungsmaterialien und Anwendungsanforderungen verwendet. Es behandelt die Rahmenbedingungen, Materialeigenschaften, Applikationsmethoden und Prüfkriterien für Schutzlacke.
- MIL-STD-883: Dieser Militärstandard beschreibt Testmethoden und -verfahren für mikroelektronische Geräte, einschließlich Schutzbeschichtungen. Es enthält Spezifikationen für Haftung, Isolationswiderstand, Thermoschock, Feuchtigkeit und andere Tests, die für Schutzbeschichtungen relevant sind.
- MIL-STD-810: Dieser Standard bietet umwelttechnische Überlegungen und Labortestmethoden zur Simulation und Bewertung der Leistung von Materialien, Geräten und Systemen unter verschiedenen Umgebungsbedingungen. Es umfasst Prüfverfahren für Schutzlacke hinsichtlich Temperatur, Feuchtigkeit, Vibration, Schock usw.
- IEC 61086: Diese internationale Norm legt die Anforderungen und Prüfmethoden für Schutzbeschichtungen fest, die in elektronischen Baugruppen verwendet werden. Es umfasst Beschichtungsmaterialien, Dicke, Haftung, Flexibilität, thermische Beständigkeit und chemische Beständigkeit.
- UL 746E: Dieser von Underwriters Laboratories (UL) veröffentlichte Standard konzentriert sich auf die Bewertung von Polymermaterialien für den Einsatz in elektrischen Geräten. Es umfasst Prüfanforderungen für Schutzlacke hinsichtlich Entflammbarkeit, Alterungseigenschaften und elektrischer Leistung.
- ISO 9001: Obwohl ISO 9001 nicht speziell auf Schutzlacke beschränkt ist, handelt es sich um einen international anerkannten Standard für Qualitätsmanagementsysteme. Es stellt sicher, dass Unternehmen konsistente Qualitätskontrollprozesse befolgen, einschließlich der Herstellung und Prüfung von Schutzbeschichtungen.
Es ist wichtig zu beachten, dass verschiedene Branchen und Anwendungen möglicherweise spezifische Standards oder Spezifikationen haben, die auf ihre individuellen Anforderungen zugeschnitten sind. Darüber hinaus stellen viele Hersteller von Schutzbeschichtungen möglicherweise technische Datenblätter oder Anwendungsrichtlinien zur Verfügung, die als wertvolle Referenz für die Auswahl und Prüfung von Schutzbeschichtungen dienen können.
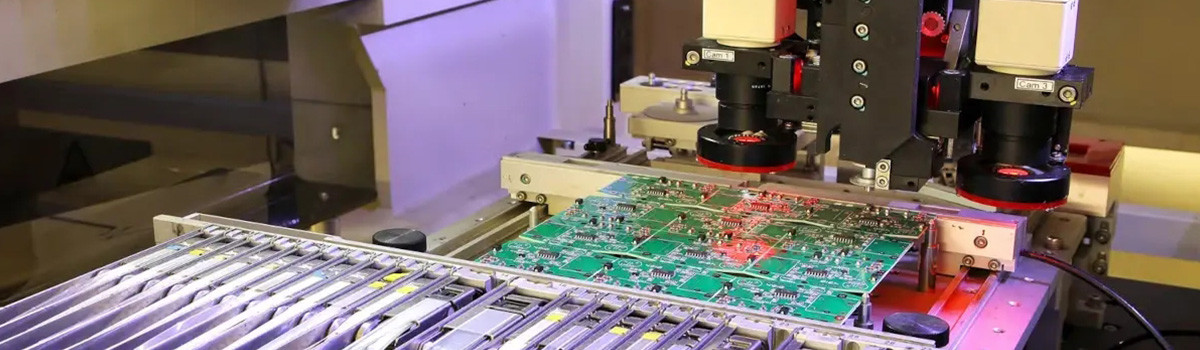
Fortschritte in der Schutzbeschichtungstechnologie
In den letzten Jahren gab es erhebliche Fortschritte in der Schutzbeschichtungstechnologie, angetrieben durch den Bedarf an verbessertem Schutz, verbesserter Zuverlässigkeit und Leistung elektronischer Komponenten und Baugruppen. Hier sind einige wichtige Verbesserungen:
- Nanobeschichtungen: Nanobeschichtungen haben sich als vielversprechender Fortschritt in der Schutzbeschichtungstechnologie herausgestellt. Diese Beschichtungen bestehen aus ultradünnen Schichten, typischerweise im Nanobereich, die eine hervorragende Feuchtigkeits- und Korrosionsbeständigkeit bieten und gleichzeitig die elektrische Leistung aufrechterhalten. Nanobeschichtungen bieten eine hervorragende Abdeckung und Anpassungsfähigkeit und gewährleisten einen angemessenen Schutz auch auf komplizierten und dicht gepackten elektronischen Baugruppen.
- Multifunktionale Beschichtungen: Es werden Schutzbeschichtungen mit multifunktionalen Eigenschaften entwickelt, um mehrere Herausforderungen gleichzeitig zu bewältigen. Einige Beschichtungen bieten beispielsweise Feuchtigkeits- und Chemikalienbeständigkeit sowie verbesserte elektrische Leitfähigkeit oder Wärmemanagementfähigkeiten. Diese multifunktionalen Beschichtungen reduzieren den Bedarf an zusätzlichen Schutzschichten und verbessern die Gesamtleistung.
- Selbstheilende Beschichtungen: Selbstheilende Schutzbeschichtungen sollen kleinere Schäden automatisch reparieren. Diese Beschichtungen enthalten eingekapselte Heilmittel, die bei der Beschädigung freigesetzt werden, Risse oder Hohlräume füllen und die Schutzeigenschaften der Beschichtung wiederherstellen. Selbstheilende Beschichtungen verlängern die Lebensdauer elektronischer Komponenten, indem sie die Auswirkungen von Verschleiß oder Umwelteinflüssen abmildern.
- Flexible und dehnbare Beschichtungen: Mit dem Aufkommen flexibler Elektronik und tragbarer Geräte müssen konforme Beschichtungen das Biegen, Dehnen und Verdrehen von Substraten ausgleichen. Flexible und dehnbare Schichten wurden entwickelt, um robusten Schutz zu bieten und gleichzeitig ihre Integrität bei mechanischer Belastung zu bewahren. Diese Beschichtungen ermöglichen eine konforme Abdeckung auf flexiblen Substraten und erweitern so das Anwendungsspektrum.
- VOC-arme und umweltfreundliche Beschichtungen: Der Schwerpunkt liegt zunehmend auf der Entwicklung von Schutzbeschichtungen mit reduzierten flüchtigen organischen Verbindungen (VOCs) und umweltfreundlichen Formulierungen. Ziel dieser Beschichtungen ist es, die Umweltbelastung während der Anwendung und Nutzung zu minimieren und gleichzeitig die Hochleistungseigenschaften beizubehalten. Als Alternativen zu herkömmlichen lösungsmittelbasierten Beschichtungen werden wasserbasierte oder lösungsmittelfreie Beschichtungen entwickelt.
- UV-härtende Beschichtungen: UV-härtende Schutzbeschichtungen bieten schnelle Aushärtezeiten und ermöglichen einen höheren Durchsatz in Herstellungsprozessen. Diese Beschichtungen nutzen ultraviolettes (UV) Licht, um die Aushärtungsreaktion einzuleiten, was schnellere Produktionszyklen und einen geringeren Energieverbrauch ermöglicht. UV-härtbare Beschichtungen bieten außerdem eine hervorragende Deckkraft und Haftung und erhöhen so die Gesamtzuverlässigkeit beschichteter Baugruppen.
- Inspektionstechnologien für Schutzbeschichtungen: Fortschritte bei Inspektionstechnologien helfen bei der Beurteilung der Qualität und Leistung von Schutzbeschichtungen. Automatisierte optische Inspektionssysteme (AOI) mit hochauflösenden Kameras und Bildanalysealgorithmen können Defekte wie Nadellöcher, Blasen oder Schichtdickenschwankungen erkennen. Dies verbessert die Inspektionseffizienz und -zuverlässigkeit und gewährleistet eine gleichbleibende Beschichtungsqualität.
- Dünnere und leichtere Beschichtungen: Der Bedarf an Miniaturisierung und Leichtbaudesigns in elektronischen Geräten hat die Entwicklung dünnerer und leichterer Schutzbeschichtungen vorangetrieben. Diese Beschichtungen bieten ausreichenden Schutz und minimieren gleichzeitig die Auswirkungen auf Gewicht und Größe der beschichteten Komponenten. Dünnere Schichten bieten außerdem eine verbesserte Wärmeableitung, was für Hochleistungsanwendungen von entscheidender Bedeutung ist.
Diese Fortschritte in der Schutzbeschichtungstechnologie tragen zur Entwicklung zuverlässigerer und langlebigerer elektronischer Geräte bei. Da sich die Elektronikindustrie weiter weiterentwickelt, wird erwartet, dass die laufende Forschung und Innovation im Bereich Schutzbeschichtungen neue Herausforderungen angeht und einen verbesserten Schutz in verschiedenen Anwendungen ermöglicht.
Umweltbelange und Schutzbeschichtungen
Umweltbelange spielen bei der Entwicklung und Verwendung von Schutzbeschichtungen eine wichtige Rolle. Da die Elektronikindustrie weiter wächst, ist es notwendig, die Vorteile von Schutzbeschichtungen mit ihren potenziellen Auswirkungen auf die Umwelt abzuwägen. Hier sind einige kritische Aspekte im Zusammenhang mit Umweltbelangen und Schutzbeschichtungen:
- Flüchtige organische Verbindungen (VOCs): Herkömmliche Schutzlacke auf Lösungsmittelbasis enthalten oft einen hohen Anteil an VOCs, die zur Luftverschmutzung beitragen und die menschliche Gesundheit schädigen. Als Reaktion darauf besteht eine wachsende Nachfrage nach VOC-armen oder VOC-freien Formulierungen. Als Alternativen zur Reduzierung der Umweltbelastung werden wasserbasierte Beschichtungen und Beschichtungen mit niedrigem VOC-Gehalt entwickelt.
- Gefährliche Substanzen: Einige Schutzbeschichtungen können gefährliche Substanzen wie Schwermetalle oder persistente organische Schadstoffe (POPs) enthalten. Diese Stoffe können langfristige Auswirkungen auf die Umwelt haben und Risiken bei der Herstellung, Anwendung und Entsorgung am Ende ihrer Lebensdauer bergen. Um diesem Problem zu begegnen, schränken Vorschriften und Standards wie die RoHS-Richtlinie (Restriction of Hazardous Substances) die Verwendung bestimmter gefährlicher Substanzen in elektronischen Produkten ein.
- Life Cycle Assessment (LCA): Die Ökobilanz bewertet die Umweltauswirkungen von Schutzlacken über ihren gesamten Lebenszyklus, von der Rohstoffgewinnung bis zur Entsorgung. Es hilft bei der Identifizierung verbesserungswürdiger Bereiche und leitet die Entwicklung umweltfreundlicher Schichten. Die Ökobilanz berücksichtigt Energieverbrauch, Ressourcenverbrauch, Emissionen und Abfallerzeugung.
- Umweltfreundliche Formulierungen: Hersteller von Schutzbeschichtungen entwickeln aktiv umweltfreundliche Formulierungen, die die Umweltbelastung minimieren. Dazu gehört die Verwendung biobasierter Materialien, nachwachsender Rohstoffe und umweltfreundlicher Lösungsmittel. Biobasierte Beschichtungen aus natürlichen Quellen bieten potenzielle Vorteile hinsichtlich eines geringeren ökologischen Fußabdrucks und einer verbesserten Nachhaltigkeit.
- Recycling und Abfallmanagement: Die ordnungsgemäße Entsorgung und Wiederverwertung von Schutzlacken ist zur Vermeidung von Umweltverschmutzung unerlässlich. Beim Recycling elektronischer Komponenten und Baugruppen sollte die Entfernung oder Trennung von Schutzbeschichtungen in Betracht gezogen werden, um eine effiziente Materialrückgewinnung zu ermöglichen. Entwicklungen bei Recyclingtechnologien und -prozessen tragen dazu bei, die Herausforderungen im Zusammenhang mit der Entfernung von Beschichtungen und der Abfallentsorgung zu bewältigen.
- Umweltvorschriften: Regulierungsrahmen und -standards wie die Verordnung zur Registrierung, Bewertung, Zulassung und Beschränkung chemischer Stoffe (REACH) der Europäischen Union zielen darauf ab, die menschliche Gesundheit und die Umwelt vor potenziell schädlichen Substanzen zu schützen. Durch die Einhaltung dieser Vorschriften wird sichergestellt, dass Schutzbeschichtungen bestimmte Umweltanforderungen und Sicherheitsstandards erfüllen.
- Nachhaltige Herstellungspraktiken: Die Einführung nachhaltiger Herstellungspraktiken reduziert die Umweltauswirkungen, die mit der Herstellung von Schutzbeschichtungen verbunden sind. Dazu gehören die Optimierung der Ressourcennutzung, die Minimierung des Abfallaufkommens, die Implementierung energieeffizienter Prozesse und die Förderung erneuerbarer Energiequellen.
- Umweltzertifizierungen: Umweltzertifizierungen wie ISO 14001 bieten Organisationen einen Rahmen für die Verwaltung und kontinuierliche Verbesserung ihrer Umweltleistung. Hersteller von Schutzbeschichtungen können eine Zertifizierung beantragen, um ihr Engagement für Umweltverantwortung und nachhaltige Praktiken nachzuweisen.
Da sich die Branche ständig weiterentwickelt, liegt der Schwerpunkt zunehmend auf der Entwicklung von Schutzbeschichtungen, die angemessenen Schutz bieten und gleichzeitig ihre Auswirkungen auf die Umwelt minimieren. Hersteller, Regulierungsbehörden und Endverbraucher arbeiten zusammen, um die Verwendung umweltfreundlicher Beschichtungen zu fördern und verantwortungsvolle und nachhaltige Praktiken während des gesamten Lebenszyklus elektronischer Produkte sicherzustellen.
Die Zukunftsaussichten für Schutzbeschichtungen in der Elektronik
Die Zukunftsaussichten für Schutzbeschichtungen in der Elektronik sind vielversprechend, angetrieben durch technologische Fortschritte, steigende Nachfrage nach leistungsstarken elektronischen Geräten und aufkommende Trends in der Branche. Hier sind einige Schlüsselaspekte, die die Zukunft von Schutzbeschichtungen prägen:
- Miniaturisierung und höhere Integration: Der Trend zu kleineren und kompakteren elektronischen Geräten mit höherem Integrationsgrad stellt konforme Beschichtungen vor Herausforderungen. Zukünftige Beschichtungen müssen einen ausreichenden Schutz bieten und gleichzeitig ihre Integrität auf miniaturisierten Bauteilen und dicht gepackten Baugruppen bewahren. Dazu gehört die Entwicklung dünnerer Schichten mit verbesserter Abdeckung und Anpassungsfähigkeit.
- Flexible und dehnbare Elektronik: Der Aufstieg flexibler und dehnbarer Elektronik, einschließlich tragbarer Geräte, erfordert konforme Beschichtungen, die der mechanischen Belastung und dem wiederholten Biegen standhalten, ohne ihre Schutzeigenschaften zu beeinträchtigen. Zukünftige Schichten werden sich auf Flexibilität, Haltbarkeit und Haftung konzentrieren, um den besonderen Anforderungen dieser neuen Anwendungen gerecht zu werden.
- Fortschrittliche Materialien: Die Entwicklung neuer Materialien mit verbesserten Eigenschaften wird die Zukunft von Schutzbeschichtungen vorantreiben. Dazu gehört die Verwendung von Nanomaterialien wie Nanopartikeln und Nanokompositen, um die Beschichtungsleistung hinsichtlich Feuchtigkeitsbeständigkeit, elektrischer Leitfähigkeit, Wärmemanagement und Barriereeigenschaften zu verbessern. Fortschrittliche Materialien werden es Beschichtungen ermöglichen, den sich verändernden Anforderungen elektronischer Geräte gerecht zu werden.
- Multifunktionale Beschichtungen: Die Nachfrage nach multifunktionalen Beschichtungen, die über den Schutz hinaus zahlreiche Vorteile bieten, wird weiter wachsen. Zukünftige Schichten können über Selbstheilungsfähigkeiten, Wärmeleitfähigkeit, antistatische Eigenschaften, antimikrobielle Eigenschaften oder Energiegewinnungsfunktionen verfügen. Multifunktionale Beschichtungen bieten eine verbesserte Leistung, eine geringere Komplexität und eine höhere Zuverlässigkeit in elektronischen Baugruppen.
- Umweltaspekte: Der Fokus auf ökologische Nachhaltigkeit und Vorschriften zu gefährlichen Stoffen wird die Zukunft von Schutzbeschichtungen beeinflussen. Die Entwicklung umweltfreundlicher Formulierungen mit reduziertem VOC-Gehalt und die Verwendung biobasierter Materialien werden zunehmend an Bedeutung gewinnen. Recycling- und Abfallmanagementstrategien für Schutzlacke werden ebenfalls eine wichtige Rolle bei der Minimierung der Umweltbelastung spielen.
- Fortschrittliche Anwendungstechniken: Innovationen in den Anwendungstechniken werden die Effizienz und Qualität von Schutzbeschichtungsprozessen verbessern. Dazu gehören Roboter-Dosiersysteme, selektive Beschichtungsmethoden und fortschrittliche Sprühtechnologien, um eine präzise und gleichmäßige Beschichtungsabdeckung zu gewährleisten, Materialverschwendung zu reduzieren und die Produktivität zu verbessern.
- Fortschrittliche Inspektions- und Testmethoden: Da die Komplexität elektronischer Baugruppen zunimmt, besteht ein Bedarf an ausgefeilteren Inspektions- und Testmethoden für Schutzbeschichtungen. Dazu gehört die Entwicklung automatisierter optischer Inspektionssysteme (AOI) mit fortschrittlichen Bildgebungs- und Analysefunktionen zur Erkennung und Bewertung von Beschichtungsfehlern, Dickenschwankungen und Haftungsqualität.
- Industriestandards und Zertifizierungen: Laufende Entwicklungen bei Industriestandards und Zertifizierungen werden die Zukunft von Schutzbeschichtungen weiterhin prägen. Hersteller und Endbenutzer werden sich auf aktualisierte Standards verlassen, um die Qualität, Zuverlässigkeit und Einhaltung der sich ändernden Anforderungen und Vorschriften der Schichten sicherzustellen.
Insgesamt sieht die Zukunft konformer Beschichtungen in der Elektronik vielversprechend aus, wobei der Schwerpunkt auf verbesserter Leistung, Anpassungsfähigkeit an neue Technologien, Umweltverträglichkeit und der Entwicklung fortschrittlicher Materialien und Anwendungstechniken liegt. Diese Fortschritte werden es konformen Beschichtungen ermöglichen, einen robusten Schutz für elektronische Geräte in vielfältigen und anspruchsvollen Umgebungen zu bieten.
Fazit: Konforme elektronische Beschichtungen bieten eine hervorragende Lösung zum Schutz elektronischer Geräte vor Umwelteinflüssen, die zu deren Ausfall oder Fehlfunktion führen können. Mit fortschreitender Technologie wird der Bedarf an wirksameren und zuverlässigeren Schutzbeschichtungen nur noch zunehmen. Hersteller, Designer und Ingenieure müssen mit den neuesten Entwicklungen auf diesem Gebiet Schritt halten, um den optimalen Schutz ihrer elektronischen Geräte zu gewährleisten. Schutzbeschichtungen sind ein entscheidender Bestandteil des elektronischen Herstellungsprozesses und können dazu beitragen, die Lebensdauer und Leistung elektronischer Geräte zu verlängern.