底部填充環氧樹脂
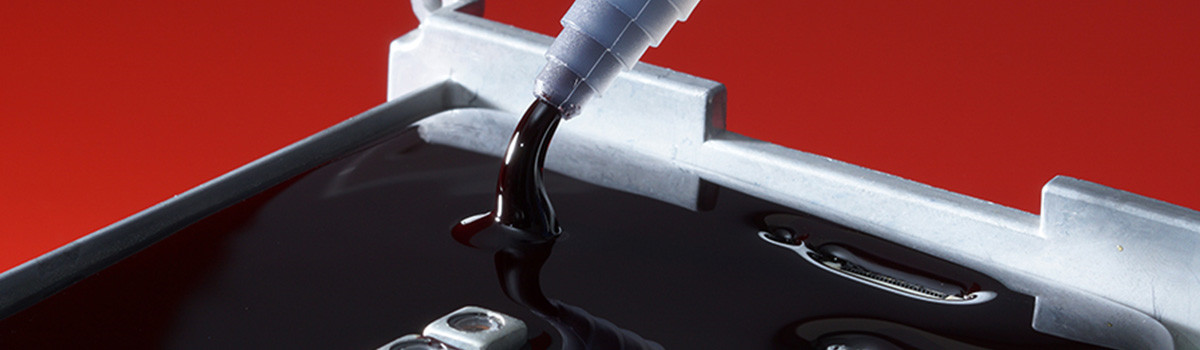
底部填充環氧樹脂是一種用於增強電子元件可靠性的粘合劑,特別是在半導體封裝應用中。 它填充封裝和印刷電路板 (PCB) 之間的間隙,提供機械支撐和應力釋放,以防止熱膨脹和收縮損壞。 底部填充環氧樹脂還可以通過降低寄生電感和電容來提高封裝的電氣性能。 在本文中,我們探討了底部填充環氧樹脂的各種應用、可用的不同類型及其優點。
底部填充環氧樹脂在半導體封裝中的重要性
底部填充環氧樹脂在半導體封裝中至關重要,可為精密的微電子元件提供機械加固和保護。 它是一種特殊的粘合材料,用於填充半導體芯片和封裝基板之間的間隙,提高電子設備的可靠性和性能。 在這裡,我們將探討底部填充環氧樹脂在半導體封裝中的重要性。
底部填充環氧樹脂的主要功能之一是提高封裝的機械強度和可靠性。 在工作過程中,半導體芯片會受到各種機械應力,例如熱膨脹和收縮、振動和機械衝擊。 這些應力可能導致焊點裂紋的形成,從而導致電氣故障並縮短設備的整體使用壽命。 底部填充環氧樹脂通過將機械應力均勻分佈在芯片、基板和焊點上,充當應力降低劑。 它有效地最大限度地減少裂紋的形成並防止現有裂紋的擴展,確保封裝的長期可靠性。
底部填充環氧樹脂的另一個重要方面是其增強半導體器件熱性能的能力。 隨著電子設備尺寸縮小和功率密度增加,散熱成為一個重要問題,過多的熱量會降低半導體芯片的性能和可靠性。 底部填充環氧樹脂具有優異的導熱性能,使其能夠有效地從芯片傳遞熱量並將其分佈到整個封裝中。 這有助於保持最佳工作溫度並防止熱點,從而改善設備的整體熱管理。
底部填充環氧樹脂還可以防止潮濕和污染物。 濕氣進入會導致腐蝕、漏電和導電材料的生長,從而導致設備故障。 底部填充環氧樹脂充當屏障,密封脆弱區域並防止濕氣進入封裝。 它還可以防止灰塵、污垢和其他污染物,這些污染物可能會對半導體芯片的電氣性能產生不利影響。 通過保護芯片及其互連,底部填充環氧樹脂可確保設備的長期可靠性和功能。
此外,底部填充環氧樹脂可實現半導體封裝的小型化。 隨著對更小、更緊湊設備的持續需求,底部填充環氧樹脂允許使用倒裝芯片和芯片級封裝技術。 這些技術涉及將芯片直接安裝到封裝基板上,從而消除了引線鍵合的需要並減小了封裝尺寸。 底部填充環氧樹脂提供結構支撐並保持芯片-基板界面的完整性,從而能夠成功實施這些先進的封裝技術。
底部填充環氧樹脂如何應對挑戰
半導體封裝在電子設備的性能、可靠性和壽命方面發揮著至關重要的作用。 它涉及將集成電路 (IC) 封裝在保護殼中、提供電氣連接以及散發運行過程中產生的熱量。 然而,半導體封裝面臨著一些挑戰,包括熱應力和翹曲,這會嚴重影響封裝器件的功能和可靠性。
主要挑戰之一是熱應力。 集成電路在工作過程中會產生熱量,散熱不充分會導致封裝內的溫度升高。 由於封裝內的不同材料以不同的速率膨脹和收縮,這種溫度變化會導致熱應力。 不均勻的膨脹和收縮會導致機械應變,導致焊點故障、分層和裂紋。 熱應力會損害封裝的電氣和機械完整性,最終影響器件的性能和可靠性。
翹曲是半導體封裝的另一個關鍵挑戰。 翹曲是指封裝基板或整個封裝的彎曲或變形。 它可能在封裝過程中或由於熱應力而發生。 翹曲主要是由封裝中不同材料之間的熱膨脹係數 (CTE) 不匹配引起的。 例如,矽芯片、基板和模塑料的 CTE 可能顯著不同。 當受到溫度變化時,這些材料會以不同的速率膨脹或收縮,從而導致翹曲。
翹曲給半導體封裝帶來了幾個問題:
- 它會導致應力集中點,增加機械故障的可能性並降低盒子的可靠性。
- 翹曲可能會導致組裝過程中的困難,因為它會影響封裝與其他組件(例如印刷電路板(PCB))的對齊。 這種不對中可能會損害電氣連接並導致性能問題。
- 翹曲會影響封裝的整體外形尺寸,使得將器件集成到小外形尺寸應用或人口密集的 PCB 中具有挑戰性。
半導體封裝採用了各種技術和策略來應對這些挑戰。 其中包括使用具有匹配 CTE 的先進材料來最大限度地減少熱應力和翹曲。 進行熱機械模擬和建模以預測封裝在不同熱條件下的行為。 實施設計修改,例如引入應力消除結構和優化佈局,以減少熱應力和翹曲。 此外,改進的製造工藝和設備的開發有助於最大限度地減少組裝過程中翹曲的發生。
底部填充環氧樹脂的好處
底部填充環氧樹脂是半導體封裝中的關鍵成分,具有多種優點。 這種特殊的環氧樹脂材料應用於半導體芯片和封裝基板之間,提供機械加固並解決各種挑戰。 以下是底部填充環氧樹脂的一些關鍵優勢:
- 提高機械可靠性:底部填充環氧樹脂的主要優點之一是能夠提高半導體封裝的機械可靠性。 底部填充環氧樹脂可形成內聚力,通過填充芯片和基板之間的間隙和空隙來提高整體結構完整性。 這有助於防止封裝翹曲,降低機械故障的風險,並增強對振動、衝擊和熱循環等外部應力的抵抗力。 機械可靠性的提高可提高產品的耐用性並延長設備的使用壽命。
- 熱應力消散:底部填充環氧樹脂有助於消散封裝內的熱應力。 集成電路在工作過程中會產生熱量,散熱不充分會導致容器內的溫度變化。 與芯片和基板材料相比,底部填充環氧樹脂材料具有較低的熱膨脹係數 (CTE),可充當緩衝層。 它可以吸收熱應力引起的機械應變,降低焊點故障、分層和裂紋的風險。 通過消散熱應力,底部填充的環氧樹脂有助於保持封裝的電氣和機械完整性。
- 增強電氣性能:底部填充環氧樹脂對半導體器件的電氣性能產生積極影響。 環氧樹脂材料填充芯片和基板之間的間隙,減少寄生電容和電感。 這可以提高信號完整性、減少信號損失並增強芯片與封裝其餘部分之間的電氣連接性。 寄生效應的減少有助於改善電氣性能、提高數據傳輸速率並提高設備可靠性。 此外,底部填充的環氧樹脂可提供絕緣和保護,防止潮濕、污染物和其他可能降低電氣性能的環境因素。
- 應力消除和改進的裝配:底部填充環氧樹脂在裝配過程中起到應力消除機制的作用。 環氧樹脂材料可補償芯片和基板之間的 CTE 不匹配,從而減少溫度變化期間的機械應力。 這使得組裝過程更加可靠和高效,最大限度地降低封裝損壞或錯位的風險。 底部填充環氧樹脂提供的受控應力分佈還有助於確保與印刷電路板 (PCB) 上的其他組件正確對齊,並提高整體裝配良率。
- 小型化和外形優化:底部填充環氧樹脂可實現半導體封裝的小型化和外形優化。 通過提供結構加固和應力消除,底部填充環氧樹脂可以設計和製造更小、更薄、更緊湊的封裝。 這對於移動設備和可穿戴電子產品等空間非常寶貴的應用尤其重要。 優化外形尺寸和實現更高元件密度的能力有助於打造更先進和創新的電子設備。
底部填充環氧樹脂的類型
半導體封裝中有多種類型的底部填充環氧樹脂配方,每種配方都旨在滿足特定要求並應對不同的挑戰。 以下是一些常用的底部填充環氧樹脂類型:
- 毛細管底部填充環氧樹脂:毛細管底部填充環氧樹脂是最傳統和最廣泛使用的類型。 低粘度環氧樹脂通過毛細作用流入芯片和基板之間的間隙。 毛細管底部填充通常被分配到芯片的邊緣上,並且當封裝被加熱時,環氧樹脂在芯片下方流動,填充空隙。 這種類型的底部填充適用於間隙較小的封裝,並提供良好的機械加固。
- 不流動底部填充環氧樹脂:不流動底部填充環氧樹脂是一種高粘度配方,在固化過程中不會流動。 它作為預塗環氧樹脂或作為芯片和基板之間的薄膜來應用。 無流動底部填充環氧樹脂對於倒裝芯片封裝特別有用,其中焊料凸塊直接與基板相互作用。 它消除了毛細管流動的需要,並降低了組裝過程中焊點損壞的風險。
- 晶圓級底部填充 (WLU):晶圓級底部填充是在單個芯片被分割之前在晶圓級應用的底部填充環氧樹脂。 它涉及將底部填充材料分配到整個晶圓表面並將其固化。 晶圓級底部填充具有多種優勢,包括均勻的底部填充覆蓋、減少組裝時間和改進的工藝控制。 它通常用於小型設備的大批量製造。
- 模製底部填充膠 (MUF):模製底部填充膠是在封裝成型過程中應用的底部填充環氧樹脂。 將底部填充材料分配到基板上,然後將芯片和基板封裝在模塑料中。 在成型過程中,環氧樹脂流動並填充芯片和基板之間的間隙,從而在一個步驟中提供底部填充和封裝。 模製底部填充膠可提供出色的機械加固並簡化裝配過程。
- 非導電底部填充膠 (NCF):非導電底部填充環氧樹脂經過專門配製,可在芯片和基板上的焊點之間提供電氣隔離。 它含有絕緣填料或防止導電的添加劑。 NCF 用於需要考慮相鄰焊點之間電氣短路的應用。 它提供機械加固和電氣隔離。
- 導熱底部填充膠 (TCU):導熱底部填充環氧樹脂旨在增強封裝的散熱能力。 它含有導熱填料,例如陶瓷或金屬顆粒,可提高底部填充材料的導熱率。 TCU 用於高效傳熱至關重要的應用,例如高功率設備或在要求嚴格的熱環境中運行的設備。
這些只是半導體封裝中使用的不同類型底部填充環氧樹脂的幾個示例。 選擇合適的底部填充環氧樹脂取決於封裝設計、組裝工藝、熱要求和電氣考慮等因素。 每種底部填充環氧樹脂都具有特定的優勢,並且經過定制,可以滿足各種應用的獨特需求。
毛細管底部填充:低粘度和高可靠性
毛細管底部填充是指半導體封裝行業中用於增強電子設備可靠性的工藝。 它涉及用低粘度液體材料(通常是環氧基樹脂)填充微電子芯片與其周圍封裝之間的間隙。 這種底部填充材料提供結構支撐,改善散熱,並保護芯片免受機械應力、潮濕和其他環境因素的影響。
毛細管底部填充膠的關鍵特性之一是其低粘度。 底部填充材料被配製為具有相對較低的密度,使其在底部填充過程中能夠容易地流入芯片和封裝之間的狹窄間隙中。 這確保了底部填充材料能夠有效地滲透和填充所有空隙和氣隙,從而最大限度地降低空隙形成的風險並提高芯片封裝界面的整體完整性。
低粘度毛細管底部填充材料還具有其他一些優點。 首先,它們促進了芯片下材料的高效流動,從而減少了處理時間並提高了生產量。 這在時間和成本效率至關重要的大批量製造環境中尤其重要。
其次,低粘度使底部填充材料具有更好的潤濕和粘合性能。 它使材料能夠均勻分佈並與芯片和封裝形成牢固的結合,從而形成可靠且堅固的封裝。 這可確保芯片受到安全保護,免受熱循環、衝擊和振動等機械應力的影響。
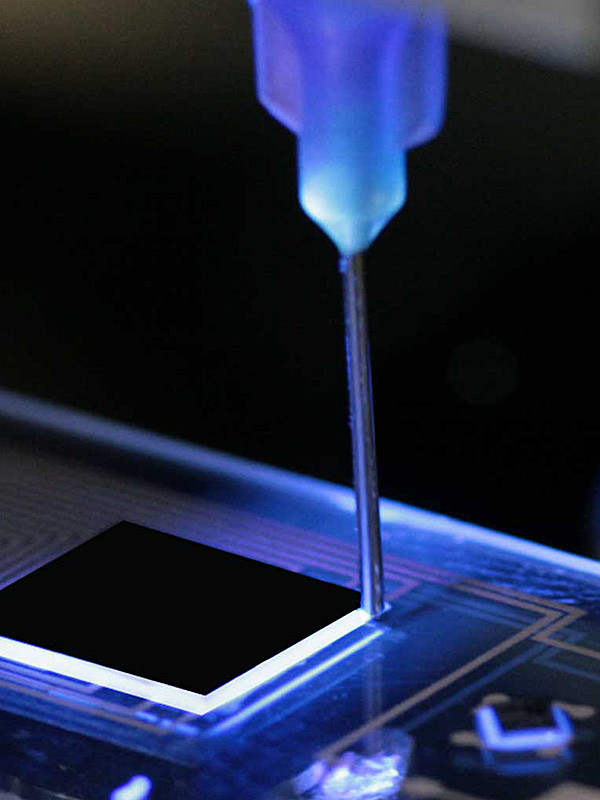
毛細管底部填充的另一個重要方面是其高可靠性。 低粘度底部填充材料經過專門設計,具有出色的熱穩定性、電絕緣性能以及防潮和耐化學品性能。 這些特性對於確保封裝電子設備的長期性能和可靠性至關重要,特別是在汽車、航空航天和電信等要求苛刻的應用中。
此外,毛細管底部填充材料被設計為具有高機械強度和對各種基材材料的優異粘合力,包括半導體封裝中常用的金屬、陶瓷和有機材料。 這使得底部填充材料能夠充當應力緩衝器,有效吸收和消散操作或環境暴露期間產生的機械應力。
無流動底部填充:自分配和高吞吐量
無流動底部填充是一種用於半導體封裝行業的專門工藝,可提高電子設備的可靠性和效率。 與依賴低粘度材料流動的毛細管底部填充不同,無流動底部填充採用高粘度材料的自分配方法。 該方法具有多種優點,包括自對準、高通量和更高的可靠性。
無流動底部填充膠的關鍵特性之一是其自點膠能力。 該工藝中使用的底部填充材料的配方具有較高的粘度,這會阻止其自由流動。 相反,底部填充材料以受控方式分配到芯片封裝界面上。 這種受控分配可以精確放置底部填充材料,確保其僅應用於所需區域,而不會溢出或不受控制地擴散。
無流動底部填充膠的自分配特性具有多種優勢。 首先,它允許底部填充材料的自對準。 當底部填充膠被分配時,它會自然地與芯片和封裝自動對齊,均勻地填充間隙和空隙。 這樣就無需在底部填充過程中對芯片進行精確定位和對準,從而節省了製造時間和精力。
其次,無流動底部填充膠的自點膠特性可實現高生產量。 點膠過程可以實現自動化,從而可以同時在多個芯片上快速、一致地應用底部填充材料。 這提高了整體生產效率並降低了製造成本,使其特別有利於大批量製造環境。
此外,非流動底部填充材料旨在提供高可靠性。 高粘度底部填充材料可提高對熱循環、機械應力和環境因素的抵抗力,確保封裝電子設備的長期性能。 這些材料表現出優異的熱穩定性、電絕緣性能以及耐濕氣和耐化學性,有助於提高設備的整體可靠性。
此外,用於非流動底部填充的高粘度底部填充材料具有增強的機械強度和粘合性能。 它們與芯片和封裝形成牢固的結合,有效吸收和消散操作或環境暴露期間產生的機械應力。 這有助於保護芯片免受潛在損壞,並增強設備對外部衝擊和振動的抵抗力。
模製底部填充膠:高保護性和集成度
模塑底部填充是半導體封裝行業中使用的一項先進技術,可為電子設備提供高水平的保護和集成。 它涉及使用包含底部填充材料的模塑料封裝整個芯片及其周圍封裝。 該工藝在保護、集成和整體可靠性方面具有顯著的優勢。
模製底部填充的關鍵優勢之一是它能夠為芯片提供全面的保護。 該工藝中使用的模塑料充當堅固的屏障,將整個芯片和封裝封裝在保護殼中。 這可以有效屏蔽可能影響設備性能和可靠性的環境因素,例如濕氣、灰塵和污染物。 封裝還有助於防止芯片受到機械應力、熱循環和其他外力的影響,確保其長期耐用性。
此外,模製底部填充可實現半導體封裝內的高集成度。 底部填充材料直接混合到模塑料中,從而實現底部填充和封裝工藝的無縫集成。 這種集成消除了單獨的底部填充步驟的需要,從而簡化了製造工藝並減少了生產時間和成本。 它還確保整個封裝中底部填充的一致和均勻分佈,最大限度地減少空隙並增強整體結構完整性。
此外,模製底部填充膠具有出色的散熱性能。 模塑料被設計為具有高導熱性,使其能夠有效地將熱量從芯片上傳導出去。 這對於維持設備的最佳工作溫度和防止過熱至關重要,過熱可能導致性能下降和可靠性問題。 模製底部填充膠增強的散熱性能有助於提高電子設備的整體可靠性和使用壽命。
此外,模製底部填充可以實現更加小型化和外形優化。 封裝工藝可以定制以適應各種封裝尺寸和形狀,包括複雜的 3D 結構。 這種靈活性允許將多個芯片和其他組件集成到一個緊湊、節省空間的封裝中。 在不影響可靠性的情況下實現更高水平的集成的能力使得模製底部填充在尺寸和重量限制至關重要的應用中特別有價值,例如移動設備、可穿戴設備和汽車電子產品。
芯片級封裝 (CSP) 底部填充:小型化和高密度
芯片級封裝 (CSP) 底部填充是實現電子器件小型化和高密度集成的關鍵技術。 隨著電子設備尺寸不斷縮小,功能不斷增加,CSP 在確保這些緊湊型設備的可靠性和性能方面發揮著至關重要的作用。
CSP是一種封裝技術,允許將半導體芯片直接安裝在基板或印刷電路板(PCB)上,而不需要額外的封裝。 這消除了對傳統塑料或陶瓷容器的需要,從而減小了設備的整體尺寸和重量。 CSP 底部填充是一種使用液體或密封劑材料填充芯片和基板之間間隙的工藝,提供機械支撐並保護芯片免受濕氣和機械應力等環境因素的影響。
通過 CSP 底部填充,通過減小芯片與基板之間的距離來實現小型化。 底部填充材料填充芯片和基板之間的狹窄間隙,形成牢固的結合併提高芯片的機械穩定性。 這使得設備變得更小、更薄,從而可以在有限的空間中容納更多的功能。
高密度集成是CSP底部填充的另一個優勢。 通過消除對單獨封裝的需求,CSP 使芯片能夠安裝得更靠近 PCB 上的其他組件,從而縮短了電氣連接的長度並提高了信號完整性。 底部填充材料還充當熱導體,有效散發芯片產生的熱量。 這種熱管理功能可實現更高的功率密度,從而能夠將更複雜、更強大的芯片集成到電子設備中。
CSP底部填充材料必須具備特定的特性,以滿足小型化和高密度集成的需求。 它們需要具有低粘度以促進狹窄間隙的填充,以及優異的流動性能以確保均勻覆蓋並消除空隙。 這些材料還應對芯片和基板具有良好的粘附力,提供堅實的機械支撐。 此外,它們必須表現出高導熱性,以有效地將熱量從芯片中轉移出去。
晶圓級 CSP 底部填充:經濟高效且高良率
晶圓級芯片尺寸封裝 (WLCSP) 底部填充是一種經濟高效且高產量的封裝技術,在製造效率和整體產品質量方面具有多種優勢。 WLCSP 底部填充將底部填充材料同時應用於多個芯片,同時仍處於晶圓形式,然後將它們分割成單獨的封裝。 這種方法在降低成本、改進過程控制和提高產量方面具有諸多優勢。
WLCSP 底部填充的關鍵優勢之一是其成本效益。 在晶圓級應用底部填充材料使封裝過程更加簡化和高效。 使用受控的自動化流程將底部填充材料分配到晶圓上,從而減少材料浪費並最大限度地降低勞動力成本。 此外,消除單獨的包裝處理和對齊步驟可減少總體生產時間和復雜性,與傳統包裝方法相比可顯著節省成本。
此外,WLCSP 底部填充可改善工藝控制並提高產量。 由於底部填充材料是在晶圓級應用的,因此可以更好地控制點膠工藝,確保晶圓上每個芯片的底部填充覆蓋一致且均勻。 這降低了可能導致可靠性問題的空隙或不完全底部填充的風險。 在晶圓級檢查和測試底部填充質量的能力還可以及早發現缺陷或工藝變化,從而能夠及時採取糾正措施並減少封裝故障的可能性。 因此,WLCSP 底部填充有助於實現更高的產量和更好的整體產品質量。
晶圓級方法還可以提高熱性能和機械性能。 WLCSP 中使用的底部填充材料通常是一種低粘度、毛細管流動材料,可以有效填充芯片和晶圓之間的狹窄間隙。 這為芯片提供了堅實的機械支撐,增強了它們對機械應力、振動和溫度循環的抵抗力。 此外,底部填充材料充當熱導體,有助於散發芯片產生的熱量,從而改善熱管理並降低過熱風險。
倒裝芯片底部填充:高 I/O 密度和性能
倒裝芯片底部填充是一項關鍵技術,可在電子設備中實現高輸入/輸出 (I/O) 密度和卓越性能。 它在增強倒裝芯片封裝的可靠性和功能方面發揮著至關重要的作用,倒裝芯片封裝廣泛應用於先進半導體應用。 本文將探討倒裝芯片底部填充的重要性及其對實現高 I/O 密度和性能的影響。
倒裝芯片技術涉及將集成電路 (IC) 或半導體芯片直接電連接到基板,從而無需引線鍵合。 由於 I/O 焊盤位於芯片的底面,因此封裝更加緊湊、高效。 然而,倒裝芯片封裝提出了必須解決的獨特挑戰,以確保最佳性能和可靠性。
倒裝芯片封裝的關鍵挑戰之一是防止芯片和基板之間的機械應力和熱失配。 在製造過程和後續操作過程中,芯片和基板之間的熱膨脹係數 (CTE) 差異可能會產生顯著的應力,從而導致性能下降甚至失效。 倒裝芯片底部填充是一種封裝芯片的保護材料,提供機械支撐和應力釋放。 它有效地分散了熱循環過程中產生的應力,並防止它們影響脆弱的互連。
高 I/O 密度對於現代電子設備至關重要,更小的外形尺寸和更強的功能至關重要。 倒裝芯片底部填充通過提供卓越的電氣絕緣和熱管理功能來實現更高的 I/O 密度。 底部填充材料填充芯片和基板之間的間隙,形成堅固的界面並降低短路或漏電的風險。 這使得 I/O 焊盤的間距更近,從而在不犧牲可靠性的情況下提高 I/O 密度。
此外,倒裝芯片底部填充有助於提高電氣性能。 它最大限度地減少了芯片和基板之間的電寄生,減少了信號延遲並增強了信號完整性。 底部填充材料還表現出優異的導熱性能,有效散發芯片在工作過程中產生的熱量。 有效的散熱可確保溫度保持在可接受的範圍內,防止過熱並保持最佳性能。
倒裝芯片底部填充材料的進步實現了更高的 I/O 密度和性能水平。 例如,納米複合材料底部填充膠利用納米級填料來增強導熱性和機械強度。 這可以改善散熱和可靠性,從而實現更高性能的設備。
球柵陣列 (BGA) 底部填充:高熱性能和機械性能
球柵陣列 (BGA) 底部填充是一項關鍵技術,可在電子設備中提供高熱性能和機械性能。 它在增強 BGA 封裝的可靠性和功能方面發揮著至關重要的作用,BGA 封裝廣泛應用於各種應用。 在本文中,我們將探討 BGA 底部填充的重要性及其對實現高熱性能和機械性能的影響。
BGA 技術涉及一種封裝設計,其中集成電路 (IC) 或半導體芯片安裝在基板上,並通過位於封裝底部表面上的焊球陣列進行電氣連接。 BGA 對分配在芯片和基板之間的間隙中的材料進行底部填充,封裝焊球並為組件提供機械支撐和保護。
BGA 封裝的關鍵挑戰之一是熱應力的管理。 在工作過程中,IC 會產生熱量,熱膨脹和收縮會對連接芯片和基板的焊點造成巨大壓力。 BGA 底部填充通過與芯片和基板形成牢固的結合,在減輕這些應力方面發揮著至關重要的作用。 它充當應力緩衝器,吸收熱膨脹和收縮並減少焊點上的應變。 這有助於提高封裝的整體可靠性並降低焊點故障的風險。
BGA 底部填充的另一個重要方面是其增強封裝機械性能的能力。 BGA 封裝在搬運、組裝和操作過程中經常會受到機械應力。 底部填充材料填充芯片和基板之間的間隙,為焊點提供結構支撐和加固。 這提高了組件的整體機械強度,使其更能抵抗機械衝擊、振動和其他外力。 通過有效分佈機械應力,BGA 底部填充有助於防止封裝破裂、分層或其他機械故障。
高熱性能對於電子設備來說至關重要,以確保正常的功能和可靠性。 BGA 底部填充材料被設計為具有優異的導熱性能。 這使得他們能夠有效地將熱量從芯片轉移出去,並將其分佈到整個基板上,從而增強封裝的整體熱管理。 有效的散熱有助於保持較低的工作溫度,防止出現熱熱點和潛在的性能下降。 它還可以通過減少組件的熱應力來延長盒子的使用壽命。
BGA 底部填充材料的進步帶來了更高的熱性能和機械性能。 改進的配方和填充材料,例如納米複合材料或高導熱性填充物,可以實現更好的散熱和機械強度,進一步增強 BGA 封裝的性能。
四方扁平封裝 (QFP) 底部填充:大量 I/O 數量和穩健性
四方扁平封裝 (QFP) 是一種廣泛應用於電子領域的集成電路 (IC) 封裝。 它具有正方形或矩形形狀,引線從所有四個側面延伸,提供許多輸入/輸出 (I/O) 連接。 為了提高 QFP 封裝的可靠性和堅固性,通常採用底部填充材料。
底部填充膠是一種應用於 IC 和基板之間的保護材料,可增強焊點的機械強度並防止應力引起的故障。 這對於具有大量 I/O 數量的 QFP 尤為重要,因為大量連接可能會在熱循環和操作條件下導致顯著的機械應力。
用於 QFP 封裝的底部填充材料必須具有特定的特性,以確保堅固性。 首先,它應該對 IC 和基板具有出色的粘合力,以形成牢固的粘合併最大限度地減少分層或脫離的風險。 此外,它還應具有較低的熱膨脹係數 (CTE),以匹配 IC 和基板的 CTE,從而減少可能導致裂紋或斷裂的應力不匹配。
此外,底部填充材料應具有良好的流動性能,以確保均勻覆蓋並完全填充IC和基板之間的間隙。 這有助於消除空隙,空隙會削弱焊點並導致可靠性降低。 該材料還應具有良好的固化性能,使其在應用後形成堅固耐用的保護層。
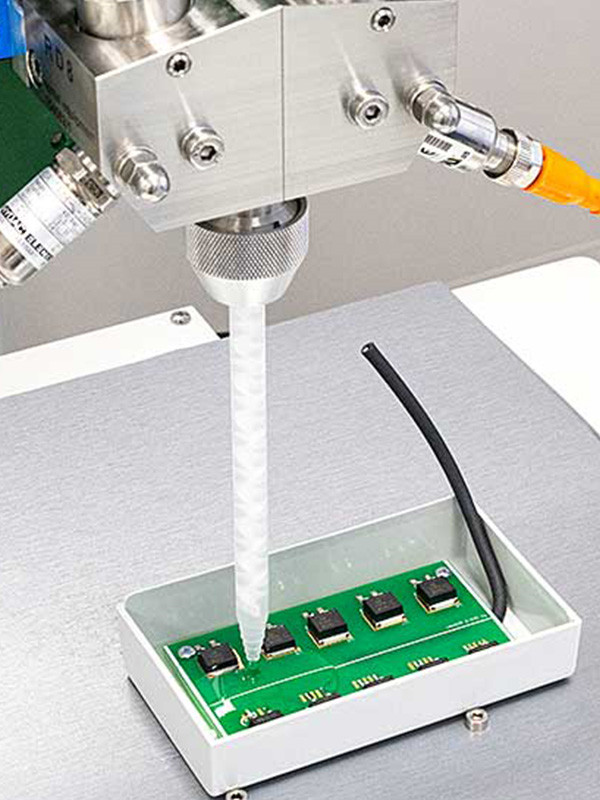
在機械堅固性方面,底部填充膠應具有高剪切強度和剝離強度,以承受外力並防止封裝變形或分離。 它還應表現出良好的耐濕氣和其他環境因素的能力,以隨著時間的推移保持其保護性能。 這對於 QFP 封裝可能暴露在惡劣條件或經歷溫度變化的應用中尤其重要。
可以使用各種底部填充材料來實現這些所需的特性,包括環氧基配方。 根據應用的具體要求,這些材料可以使用不同的技術進行點膠,例如毛細管流動、噴射或絲網印刷。
系統級封裝 (SiP) 底部填充:集成和性能
系統級封裝 (SiP) 是一種先進的封裝技術,將多個半導體芯片、無源元件和其他元件集成到一個封裝中。 SiP 具有許多優點,包括縮小的外形尺寸、改進的電氣性能和增強的功能。 為了確保 SiP 組件的可靠性和性能,通常使用底部填充材料。
SiP 應用中的底部填充對於提供封裝內各個組件之間的機械穩定性和電氣連接至關重要。 它有助於最大限度地降低應力引起的故障風險,例如由於組件之間的熱膨脹係數 (CTE) 差異而可能發生的焊點裂紋或斷裂。
在 SiP 封裝中集成多個組件會導致複雜的互連性,並具有許多焊點和高密度電路。 底部填充材料有助於加強這些互連,從而提高組件的機械強度和可靠性。 它們支撐焊點,降低熱循環或機械應力引起的疲勞或損壞的風險。
就電氣性能而言,底部填充材料對於提高信號完整性和最小化電氣噪聲至關重要。 通過填充元件之間的間隙並縮短元件之間的距離,底部填充有助於減少寄生電容和電感,從而實現更快、更高效的信號傳輸。
此外,SiP 應用的底部填充材料應具有出色的導熱性,以有效散發集成組件產生的熱量。 有效的散熱對於防止過熱並保持 SiP 組件的整體可靠性和性能至關重要。
SiP 封裝中的底部填充材料必須具有特定的屬性才能滿足這些集成和性能要求。 它們應具有良好的流動性,以確保完全覆蓋並填充組件之間的間隙。 底部填充材料還應具有低粘度配方,以便在狹窄的孔或狹小的空間中輕鬆分配和填充。
此外,底部填充材料應對不同表面(包括半導體芯片、基板和無源器件)表現出很強的粘附力,以確保可靠的接合。 它應該與各種包裝材料兼容,例如有機基材或陶瓷,並表現出良好的機械性能,包括高剪切和剝離強度。
底部填充材料和應用方法的選擇取決於具體的 SiP 設計、組件要求和製造工藝。 毛細管流動、噴射或薄膜輔助方法等點膠技術通常應用於 SiP 組件中的底部填充。
光電底部填充:光學對準和保護
光電底部填充包括封裝和保護光電器件,同時確保精確的光學對準。 激光器、光電探測器和光開關等光電設備通常需要對光學元件進行精密對準才能實現最佳性能。 同時,需要保護它們免受可能影響其功能的環境因素的影響。 光電底部填充通過在單一工藝中提供光學對準和保護來滿足這兩個要求。
光學對準是光電器件製造的一個關鍵方面。 它涉及對齊光纖、波導、透鏡或光柵等視覺元素,以確保高效的光傳輸和接收。 為了最大限度地提高設備性能並保持信號完整性,必須進行精確對準。 傳統的對準技術包括使用目視檢查的手動對准或使用對準台的自動對準。 然而,這些方法可能非常耗時、費力並且容易出錯。
光電底部填充是一種創新解決方案,將對準功能直接融入底部填充材料中。 底部填充材料通常是液體或半液體化合物,可以流動並填充光學元件之間的間隙。 通過在底部填充材料內添加對準特徵,例如微結構或基準標記,可以簡化和自動化對準過程。 這些特徵在組裝過程中起到引導作用,確保光學元件的精確對準,而無需複雜的對準程序。
除了光學對準之外,底部填充材料還可以保護光電器件。 光電元件經常暴露在惡劣的環境中,包括溫度波動、潮濕和機械應力。 隨著時間的推移,這些外部因素可能會降低設備的性能和可靠性。 底部填充材料充當保護屏障,封裝光學元件並保護它們免受環境污染物的影響。 它們還提供機械加固,降低因衝擊或振動而損壞的風險。
光電應用中使用的底部填充材料通常設計為具有低折射率和優異的光學透明度。 這確保了對通過設備的光信號的干擾最小。 此外,它們對各種基材表現出良好的附著力,並具有較低的熱膨脹係數,可最大限度地減少熱循環過程中器件的應力。
底部填充工藝包括將底部填充材料分配到器件上,使其流動並填充光學元件之間的間隙,然後將其固化以形成固體封裝。 根據具體應用,可以使用不同的技術來施加底部填充材料,例如毛細管流動、噴射點膠或絲網印刷。 固化過程可以通過熱、紫外線輻射或兩者來實現。
醫療電子底部填充:生物相容性和可靠性
醫療電子底部填充是一種專門的工藝,涉及封裝和保護醫療設備中使用的電子元件。 這些設備在各種醫療應用中發揮著至關重要的作用,例如植入設備、診斷設備、監測系統和藥物輸送系統。 醫療電子底部填充關注兩個關鍵方面:生物相容性和可靠性。
生物相容性是與人體接觸的醫療器械的基本要求。 醫療電子產品中使用的底部填充材料必須具有生物相容性,這意味著它們在與活體組織或體液接觸時不應造成有害影響或不良反應。 這些材料應符合嚴格的法規和標準,例如 ISO 10993,其中規定了生物相容性測試和評估程序。
用於醫療電子產品的底部填充材料經過精心挑選或配製,以確保生物相容性。 它們被設計為無毒、無刺激性和無過敏性。 這些材料不應濾出任何有害物質或隨著時間的推移而降解,因為這可能導致組織損傷或炎症。 生物相容性底部填充材料還具有低吸水性,可防止可能引起感染的細菌或真菌的生長。
可靠性是醫療電子底部填充的另一個重要方面。 醫療設備經常面臨具有挑戰性的操作條件,包括極端溫度、濕度、體液和機械應力。 底部填充材料必須保護電子元件,確保其長期可靠性和功能。 在醫療應用中,可靠性至關重要,設備故障可能會嚴重影響患者的安全和福祉。
用於醫療電子產品的底部填充材料應具有高耐濕性和耐化學性,以承受體液暴露或滅菌過程。 它們還應該對各種基材表現出良好的附著力,確保電子元件的安全封裝。 機械性能,例如低熱膨脹係數和良好的抗衝擊性,對於最大限度地減少熱循環或自動加載過程中細節上的應力至關重要。
醫療電子產品的底部填充工藝包括:
- 將底部填充材料分配到電子元件上。
- 填補空白。
- 將其固化以形成保護性且機械穩定的封裝。
必須小心確保功能的完全覆蓋,並且不存在可能損害器件可靠性的空隙或氣穴。
此外,在對醫療器械進行底部填充時還需要考慮其他因素。 例如,底部填充材料應與設備所使用的滅菌方法兼容。 有些材料可能對特定的滅菌技術敏感,例如蒸汽、環氧乙烷或輻射,並且可能需要選擇替代材料。
航空航天電子底部填充膠:耐高溫、耐振動
航空航天電子產品底部填充採用專門的工藝來封裝和保護航空航天應用中的電子元件。 航空航天環境帶來了獨特的挑戰,包括高溫、極端振動和機械應力。 因此,航空電子底部填充關注兩個關鍵方面:耐高溫和耐振動。
由於運行過程中會經歷高溫,因此耐高溫對於航空航天電子產品至關重要。 航空航天應用中使用的底部填充材料必須能夠承受這些高溫,同時又不影響電子元件的性能和可靠性。 它們應表現出最小的熱膨脹並在較寬的溫度範圍內保持穩定。
用於航空航天電子產品的底部填充材料經過選擇或配製,具有高玻璃化轉變溫度 (Tg) 和熱穩定性。 高 Tg 可確保材料在高溫下保持其機械性能,防止變形或失去附著力。 這些材料可以承受極端溫度,例如在起飛、重返大氣層或在熱發動機艙中運行時。
此外,航空航天電子產品的底部填充材料應具有較低的熱膨脹係數 (CTE)。 CTE 測量材料隨溫度變化而膨脹或收縮的程度。 由於熱膨脹係數較低,底部填充材料可以最大限度地減少熱循環對電子元件造成的應力,這種應力可能導致機械故障或焊點疲勞。
抗振性是航空航天電子底部填充膠的另一個關鍵要求。 航空航天器會受到各種振動的影響,包括發動機振動、飛行引起的振動以及發射或著陸過程中的機械衝擊。 如果沒有充分保護,這些振動可能會危及電子元件的性能和可靠性。
航空航天電子產品中使用的底部填充材料應表現出優異的減振性能。 它們應該吸收和耗散振動產生的能量,減少電子元件上的應力和應變。 這有助於防止由於過度振動而形成裂紋、斷裂或其他機械故障。
此外,在航空航天應用中,具有高粘附力和內聚強度的底部填充材料是首選。 這些特性確保底部填充材料即使在極端振動條件下也能牢固地粘合到電子元件和基板上。 強大的附著力可防止底部填充材料分層或與元件分離,從而保持封裝的完整性並防止水分或碎片進入。
航空航天電子產品的底部填充工藝通常涉及將底部填充材料分配到電子元件上,使其流動並填充間隙,然後將其固化以形成堅固的封裝。 根據應用的具體要求,可以使用熱固化或紫外線固化方法來完成固化過程。
汽車電子底部填充膠:耐久性和熱循環耐受性
汽車電子底部填充是涉及汽車應用中的電子元件封裝和保護的關鍵工藝。 汽車環境提出了獨特的挑戰,包括溫度變化、熱循環、機械應力以及暴露於濕氣和化學品。 因此,汽車電子底部填充關注兩個關鍵方面:耐久性和耐熱循環性。
耐久性是汽車電子底部填充的關鍵要求。 在正常運行過程中,機動車輛會經歷持續的振動、衝擊和機械應力。 汽車應用中使用的底部填充材料必須牢固地保護電子元件,確保其耐用性和使用壽命。 它們應能承受道路上遇到的惡劣條件和機械載荷,並能抵抗濕氣、灰塵和化學品的侵入。
汽車電子產品的底部填充材料經過選擇或配製,具有高機械強度和抗衝擊性。 它們應該對電子元件和基板表現出優異的粘附力,防止在機械應力下分層或分離。 耐用的底部填充材料有助於最大程度地降低電子元件因振動或衝擊而損壞的風險,確保車輛在整個使用壽命期間具有可靠的性能。
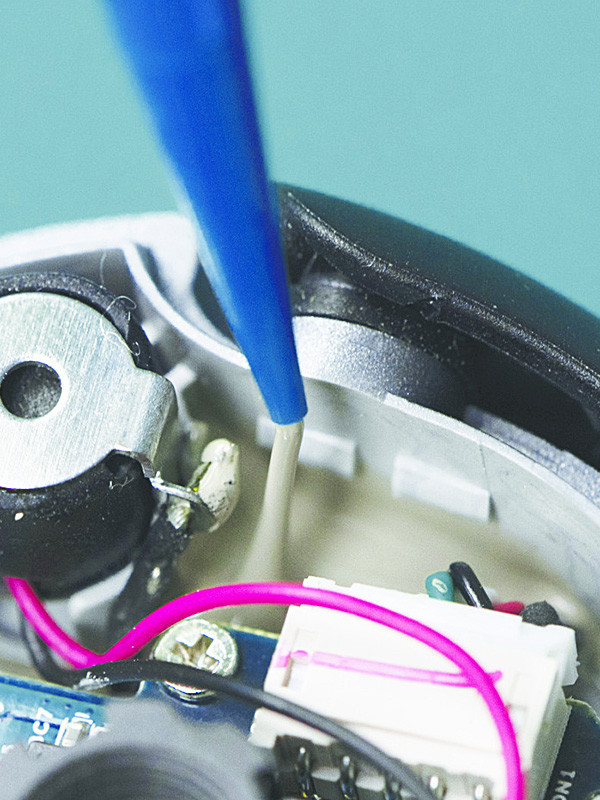
耐熱循環性是汽車電子底部填充膠的另一個關鍵要求。 汽車會經歷頻繁的溫度變化,特別是在發動機啟動和運行期間,這些溫度循環會對電子元件和周圍的底部填充材料產生熱應力。 汽車應用中使用的底部填充材料必須具有出色的耐熱循環性,以承受這些溫度波動而不影響其性能。
汽車電子產品的底部填充材料應具有較低的熱膨脹 (CTE) 係數,以最大限度地減少電子元件在熱循環過程中的應力。 底部填充材料和成分之間良好匹配的 CTE 可以降低焊點疲勞、開裂或由熱應力引起的其他機械故障的風險。 此外,底部填充材料應具有良好的導熱性,以有效散熱,防止出現可能影響組件性能和可靠性的局部熱點。
此外,汽車電子底部填充材料應耐濕氣、耐化學品和耐液體。 它們應該具有低吸水性,以防止黴菌生長或電子元件腐蝕。 耐化學性確保底部填充材料在暴露於汽車液體(例如油、燃料或清潔劑)時保持穩定,避免降解或失去附著力。
汽車電子產品的底部填充工藝通常涉及將底部填充材料分配到電子元件上,使其流動並填充間隙,然後將其固化以形成耐用的封裝。 固化過程可以通過熱固化或紫外線固化方法來完成,具體取決於應用的具體要求和所使用的底部填充材料。
選擇正確的底部填充環氧樹脂
選擇正確的底部填充環氧樹脂是電子元件組裝和保護中的關鍵決策。 底部填充環氧樹脂可提供機械增強、熱管理和針對環境因素的保護。 以下是選擇合適的底部填充環氧樹脂時的一些關鍵考慮因素:
- 熱性能:底部填充環氧樹脂的主要功能之一是散發電子元件產生的熱量。 因此,必須考慮環氧樹脂的導熱率和熱阻。 高導熱率有助於高效傳熱,防止熱點並保持組件可靠性。 環氧樹脂還應具有低熱阻,以最大限度地減少溫度循環過程中元件上的熱應力。
- CTE 匹配:底部填充環氧樹脂的熱膨脹係數 (CTE) 應與電子元件和基板的 CTE 良好匹配,以最大限度地減少熱應力並防止焊點故障。 緊密匹配的 CTE 有助於降低因熱循環而導致機械故障的風險。
- 流動和間隙填充能力:底部填充的環氧樹脂應具有良好的流動特性和有效填充組件之間間隙的能力。 這可確保完全覆蓋並最大限度地減少可能影響組件機械穩定性和熱性能的空隙或氣穴。 環氧樹脂的粘度應適合特定的應用和組裝方法,無論是毛細管流動、噴射點膠還是絲網印刷。
- 粘合力:強粘合力對於底部填充環氧樹脂至關重要,以確保元件和基板之間的可靠粘合。 它應該對各種材料表現出良好的附著力,包括金屬、陶瓷和塑料。 環氧樹脂的粘合性能有助於提高組件的機械完整性和長期可靠性。
- 固化方法:考慮最適合您的製造工藝的固化方法。 底部填充環氧樹脂可以通過熱、紫外線輻射或兩者的組合來固化。 每種固化方法都有優點和局限性,選擇符合您生產要求的方法至關重要。
- 耐環境性:評估底部填充環氧樹脂對濕氣、化學品和極端溫度等環境因素的耐受性。 環氧樹脂應該能夠耐受水,防止黴菌生長或腐蝕。 耐化學性可確保與汽車液體、清潔劑或其他潛在腐蝕性物質接觸時的穩定性。 此外,環氧樹脂應在較寬的溫度範圍內保持其機械和電氣性能。
- 可靠性和壽命:考慮底部填充環氧樹脂的跟踪記錄和可靠性數據。 尋找經過測試並證明在類似應用中表現良好或具有行業認證並符合相關標準的環氧材料。 考慮老化行為、長期可靠性以及環氧樹脂隨時間推移保持其性能的能力等因素。
選擇正確的底部填充環氧樹脂時,考慮應用的具體要求至關重要,包括熱管理、機械穩定性、環境保護和製造工藝兼容性。 諮詢環氧樹脂供應商或尋求專家建議有助於做出明智的決定,滿足您的應用需求並確保最佳的性能和可靠性。
底部填充環氧樹脂的未來趨勢
在電子技術進步、新興應用以及提高性能和可靠性的需求的推動下,底部填充環氧樹脂不斷發展。 底部填充環氧樹脂的開發和應用可以觀察到幾個未來趨勢:
- 小型化和更高密度的封裝:隨著電子設備不斷縮小並具有更高的元件密度,底部填充環氧樹脂必須相應地適應。 未來的趨勢將集中於開發底部填充材料,這些材料能夠滲透並填充組件之間較小的間隙,確保在日益小型化的電子組件中實現完全覆蓋和可靠的保護。
- 高頻應用:隨著對高頻和高速電子設備的需求不斷增長,底部填充環氧樹脂配方將需要滿足這些應用的特定要求。 具有低介電常數和低損耗角正切的底部填充材料對於最大限度地減少信號損失並保持先進通信系統、5G 技術和其他新興應用中高頻信號的完整性至關重要。
- 增強的熱管理:散熱仍然是電子設備的一個關鍵問題,特別是隨著功率密度的增加。 未來的底部填充環氧樹脂配方將側重於提高導熱性,以增強傳熱並有效管理熱問題。 先進的填料和添加劑將被納入底部填充環氧樹脂中,以實現更高的導熱率,同時保持其他所需的性能。
- 柔性和可拉伸電子產品:柔性和可拉伸電子產品的興起為底部填充環氧樹脂材料開闢了新的可能性。 即使在反复彎曲或拉伸的情況下,柔性底部填充環氧樹脂也必須表現出優異的附著力和機械性能。 這些材料將使可穿戴設備、可彎曲顯示器和其他需要機械靈活性的應用中的電子器件能夠封裝和保護。
- 環保解決方案:可持續性和環境考慮將在底部填充環氧材料的開發中發揮越來越重要的作用。 重點是創造不含有害物質的環氧樹脂配方,並減少其整個生命週期(包括製造、使用和處置)對環境的影響。 生物基或可再生材料也可能作為可持續替代品而受到關注。
- 改進的製造工藝:底部填充環氧樹脂的未來趨勢將集中在材料特性和製造工藝的進步上。 將探索增材製造、選擇性點膠和先進固化方法等技術,以優化底部填充環氧樹脂在各種電子組裝工藝中的應用和性能。
- 先進測試和表徵技術的集成:隨著電子設備的複雜性和要求不斷增加,需要先進的測試和表徵方法來確保底部填充環氧樹脂的可靠性和性能。 無損檢測、現場監測和模擬工具等技術將有助於底部填充環氧材料的開發和質量控制。
結論
底部填充環氧樹脂在提高電子元件的可靠性和性能方面發揮著關鍵作用,特別是在半導體封裝中。 不同類型的底部填充環氧樹脂具有一系列優點,包括高可靠性、自分配、高密度以及高熱性能和機械性能。 為應用和封裝選擇正確的底部填充環氧樹脂可確保牢固且持久的粘合。 隨著技術的進步和封裝尺寸的縮小,我們期望更多創新的底部填充環氧樹脂解決方案能夠提供卓越的性能、集成度和小型化。 底部填充環氧樹脂將在電子行業的未來發揮越來越重要的作用,使我們能夠在各個行業實現更高水平的可靠性和性能。