Relleno de epoxi
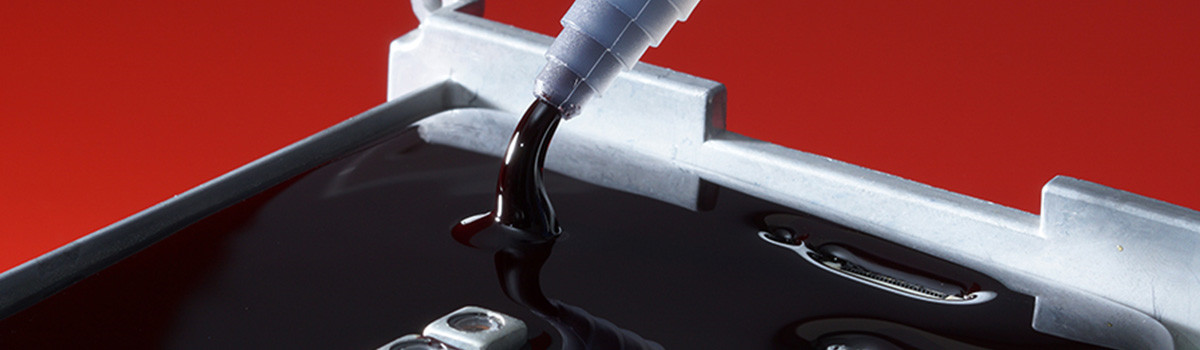
O recheo epoxi é un tipo de adhesivo usado para mellorar a fiabilidade dos compoñentes electrónicos, especialmente en aplicacións de envasado de semicondutores. Enche o oco entre o paquete e a placa de circuíto impreso (PCB), proporcionando soporte mecánico e alivio da tensión para evitar a expansión térmica e os danos por contracción. O recheo epoxi tamén mellora o rendemento eléctrico do paquete ao reducir a inductancia e a capacidade parasitarias. Neste artigo, exploramos as diversas aplicacións de recheo epoxi, os diferentes tipos dispoñibles e os seus beneficios.
A importancia do epoxi de recheo inferior nos envases de semicondutores
O recheo epoxi é crucial nos envases de semicondutores, proporcionando reforzo mecánico e protección aos delicados compoñentes microelectrónicos. É un material adhesivo especializado que se usa para cubrir o oco entre o chip semicondutor e o substrato do paquete, mellorando a fiabilidade e o rendemento dos dispositivos electrónicos. Aquí, exploraremos a importancia do recheo epoxi insuficiente nos envases de semicondutores.
Unha das funcións principais do epoxi con recheo insuficiente é mellorar a resistencia mecánica e a fiabilidade do paquete. Durante o funcionamento, os chips semicondutores están sometidos a varias tensións mecánicas, como expansión e contracción térmicas, vibracións e choques mecánicos. Estes esforzos poden levar á formación de fendas de soldadura, que poden causar fallos eléctricos e diminuír a vida útil global do dispositivo. O recheo epoxi actúa como un axente redutor de tensión distribuíndo a tensión mecánica uniformemente entre o chip, o substrato e as xuntas de soldadura. Minimiza eficazmente a formación de fendas e impide a propagación das fendas existentes, garantindo a fiabilidade a longo prazo do paquete.
Outro aspecto crítico do recheo epoxi é a súa capacidade para mellorar o rendemento térmico dos dispositivos semicondutores. A disipación de calor convértese nunha preocupación importante xa que os dispositivos electrónicos encollen o seu tamaño e aumentan a densidade de potencia, e a calor excesiva pode degradar o rendemento e a fiabilidade do chip semicondutor. O recheo epoxi ten excelentes propiedades de condutividade térmica, o que lle permite transferir de forma eficiente a calor do chip e distribuílo por todo o paquete. Isto axuda a manter as temperaturas óptimas de funcionamento e evita puntos quentes, mellorando así a xestión térmica global do dispositivo.
O recheo epoxi tamén protexe contra a humidade e os contaminantes. A entrada de humidade pode provocar corrosión, fugas eléctricas e o crecemento de materiais condutores, o que provoca un mal funcionamento do dispositivo. O recheo epoxi actúa como barreira, selando áreas vulnerables e evitando que a humidade entre no paquete. Tamén ofrece protección contra o po, a sucidade e outros contaminantes que poden afectar negativamente o rendemento eléctrico do chip semicondutor. Ao salvagardar o chip e as súas interconexións, o recheo epoxi garante a fiabilidade e a funcionalidade a longo prazo do dispositivo.
Ademais, o recheo epoxi insuficiente permite a miniaturización nos envases de semicondutores. Coa demanda constante de dispositivos máis pequenos e compactos, o recheo de epoxi permite o uso de técnicas de envasado flip-chip e a escala de chip. Estas técnicas implican montar directamente o chip sobre o substrato do envase, eliminando a necesidade de unión de fíos e reducindo o tamaño do paquete. Underfill epoxi proporciona soporte estrutural e mantén a integridade da interface chip-substrato, permitindo a implementación exitosa destas tecnoloxías de envasado avanzadas.
Como Underfill Epoxy aborda os desafíos
Os envases de semicondutores xogan un papel crucial no rendemento, fiabilidade e lonxevidade dos dispositivos electrónicos. Implica encapsular circuítos integrados (CI) en carcasas protectoras, proporcionar conexións eléctricas e disipar a calor xerada durante o funcionamento. Non obstante, os envases de semicondutores enfróntanse a varios desafíos, incluíndo estrés térmico e deformación, que poden afectar significativamente a funcionalidade e a fiabilidade dos dispositivos empaquetados.
Un dos principais retos é o estrés térmico. Os circuítos integrados xeran calor durante o funcionamento e unha disipación inadecuada pode aumentar as temperaturas dentro do paquete. Esta variación de temperatura produce estrés térmico xa que os diferentes materiais dentro do paquete se expanden e contraen a diferentes velocidades. A expansión e contracción non uniformes poden causar tensión mecánica, o que provoca fallos, delaminación e fendas das xuntas de soldadura. O estrés térmico pode comprometer a integridade eléctrica e mecánica do paquete, afectando finalmente o rendemento e a fiabilidade do dispositivo.
A deformación é outro desafío crítico no envasado de semicondutores. A deformación refírese á flexión ou deformación do substrato do paquete ou do paquete completo. Pode ocorrer durante o proceso de envasado ou debido ao estrés térmico. A deformación é causada principalmente pola falta de coincidencia no coeficiente de expansión térmica (CTE) entre os diferentes materiais do paquete. Por exemplo, o CTE da matriz de silicio, do substrato e do composto do molde pode diferir significativamente. Cando se someten a cambios de temperatura, estes materiais se expanden ou contraen a diferentes velocidades, o que provoca unha deformación.
Warpage presenta varios problemas para os paquetes de semicondutores:
- Pode producir puntos de concentración de tensión, aumentando a probabilidade de fallos mecánicos e reducindo a fiabilidade da caixa.
- A deformación pode provocar dificultades no proceso de montaxe, xa que afecta á aliñación do paquete con outros compoñentes, como a placa de circuíto impreso (PCB). Este desaxuste pode prexudicar as conexións eléctricas e causar problemas de rendemento.
- A deformación pode afectar o factor de forma global do paquete, polo que resulta difícil integrar o dispositivo en aplicacións de formato pequeno ou en PCB densamente poboados.
Empréganse diversas técnicas e estratexias na embalaxe de semicondutores para afrontar estes desafíos. Estes inclúen o uso de materiais avanzados con CTE coincidentes para minimizar a tensión térmica e a deformación. Realízanse simulacións e modelización termomecánicas para predicir o comportamento do paquete en diferentes condicións térmicas. As modificacións do deseño, como a introdución de estruturas de alivio de tensións e trazados optimizados, impléntanse para reducir a tensión térmica e a deformación. Ademais, o desenvolvemento de procesos e equipos de fabricación mellorados axuda a minimizar a aparición de deformacións durante a montaxe.
Beneficios de Underfill Epoxy
O recheo epoxi é un compoñente crítico nos envases de semicondutores que ofrece varios beneficios. Este material epoxi especializado aplícase entre o chip semicondutor e o substrato do paquete, proporcionando reforzo mecánico e abordando varios desafíos. Estes son algúns dos beneficios críticos do epoxi con recheo insuficiente:
- Fiabilidade mecánica mellorada: un dos principais beneficios do recheo epoxi é a súa capacidade para mellorar a fiabilidade mecánica dos paquetes de semicondutores. O epoxi de recheo inferior crea unha unión cohesiva que mellora a integridade estrutural xeral ao cubrir os ocos e ocos entre o chip e o substrato. Isto axuda a evitar a deformación do paquete, reduce o risco de fallos mecánicos e mellora a resistencia ás tensións externas, como vibracións, choques e ciclos térmicos. A mellora da fiabilidade mecánica leva a unha maior durabilidade do produto e unha maior vida útil do dispositivo.
- Disipación do estrés térmico: o recheo epoxi inferior axuda a disipar o estrés térmico dentro do paquete. Os circuítos integrados xeran calor durante o funcionamento e unha disipación inadecuada pode provocar variacións de temperatura dentro do recipiente. O material epoxi de recheo inferior, co seu menor coeficiente de expansión térmica (CTE) en comparación cos materiais de chip e substrato, actúa como unha capa tampón. Absorbe a tensión mecánica causada polo estrés térmico, reducindo o risco de fallos das xuntas de soldadura, delaminación e fendas. Ao disipar o estrés térmico, o recheo epoxi insuficiente axuda a manter a integridade eléctrica e mecánica do paquete.
- Rendemento eléctrico mellorado: o recheo de epoxi afecta positivamente o rendemento eléctrico dos dispositivos semicondutores. O material epoxi enche os ocos entre o chip e o substrato, reducindo a capacitancia e inductancia parasitarias. Isto dá como resultado unha mellora da integridade do sinal, unha redución das perdas de sinal e unha mellora da conectividade eléctrica entre o chip e o resto do paquete. Os efectos parasitarios reducidos contribúen a un mellor rendemento eléctrico, maiores taxas de transferencia de datos e unha maior fiabilidade do dispositivo. Ademais, o recheo de epoxi proporciona illamento e protección contra a humidade, os contaminantes e outros factores ambientais que poden degradar o rendemento eléctrico.
- Alivio do estrés e montaxe mellorada: o recheo epoxi actúa como un mecanismo de alivio do estrés durante a montaxe. O material epoxi compensa o desaxuste CTE entre o chip e o substrato, reducindo a tensión mecánica durante os cambios de temperatura. Isto fai que o proceso de montaxe sexa máis fiable e eficiente, minimizando o risco de danos ou desalineamentos do paquete. A distribución controlada do estrés proporcionada polo recheo epoxi tamén axuda a garantir o aliñamento adecuado con outros compoñentes da placa de circuíto impreso (PCB) e mellora o rendemento global da montaxe.
- Miniaturización e optimización do factor de forma: o recheo epoxi permite a miniaturización de paquetes de semicondutores e a optimización do factor de forma. Ao proporcionar reforzo estrutural e alivio da tensión, o recheo epoxi permite deseñar e fabricar paquetes máis pequenos, finos e compactos. Isto é especialmente importante para aplicacións como os dispositivos móbiles e os dispositivos electrónicos portátiles, onde o espazo é escaso. A capacidade de optimizar os factores de forma e conseguir maiores densidades de compoñentes contribúe a crear dispositivos electrónicos máis avanzados e innovadores.
Tipos de recheo epoxi
Varios tipos de formulacións epoxi de recheo inferior están dispoñibles en envases de semicondutores, cada un deseñado para cumprir requisitos específicos e abordar diferentes desafíos. Aquí tes algúns tipos de recheo epoxi comúnmente usados:
- Epoxi de recheo capilar: o epoxi de recheo capilar é o tipo máis tradicional e amplamente utilizado. Un epoxi de baixa viscosidade flúe na fenda entre o chip e o substrato por acción capilar. O recheo inferior capilar adoita dispensarse no bordo do chip e, a medida que se quenta o paquete, o epoxi flúe por debaixo do chip, enchendo os ocos. Este tipo de recheo inferior é axeitado para envases con pequenos ocos e proporciona un bo reforzo mecánico.
- Epoxi de recheo sen fluxo: o epoxi de recheo sen fluxo é unha formulación de alta viscosidade que non flúe durante o curado. Aplícase como un epoxi pre-aplicado ou como unha película entre o chip e o substrato. O epoxi de recheo sen fluxo é particularmente útil para paquetes de chip flip, onde os golpes de soldadura interactúan directamente co substrato. Elimina a necesidade de fluxo capilar e reduce o risco de danos nas xuntas de soldadura durante a montaxe.
- Recheo inferior a nivel de oblea (WLU): o recheo inferior a nivel de oblea é un epoxi de recheo inferior aplicado ao nivel da oblea antes de que as fichas individuais sexan separadas. Implica dispensar o material de recheo por toda a superficie da oblea e curalo. O recheo inferior a nivel de oblea ofrece varias vantaxes, incluíndo unha cobertura uniforme de recheo inferior, un tempo de montaxe reducido e un control do proceso mellorado. Utilízase habitualmente para a fabricación de grandes volumes de dispositivos de pequeno tamaño.
- Recheo inferior moldeado (MUF): o recheo inferior moldeado é un epoxi de recheo inferior aplicado durante o moldeado por encapsulación. O material de recheo inferior é dispensado sobre o substrato, e despois o chip e o substrato son encapsulados nun composto de molde. Durante o moldeado, o epoxi flúe e enche o oco entre o chip e o substrato, proporcionando recheo e encapsulamento nun só paso. O recheo inferior moldeado ofrece un excelente reforzo mecánico e simplifica o proceso de montaxe.
- Recheo subterráneo non condutor (NCF): o epoxi de recheo inferior non condutor está formulado especificamente para proporcionar illamento eléctrico entre as unións de soldadura do chip e o substrato. Contén cargas illantes ou aditivos que impiden a condutividade eléctrica. NCF utilízase en aplicacións nas que o cortocircuito eléctrico entre as xuntas de soldadura adxacentes é unha preocupación. Ofrece tanto reforzo mecánico como illamento eléctrico.
- Recheo de recheo de condución térmica (TCU): o epoxi de recheo de condución térmica está deseñado para mellorar as capacidades de disipación de calor do paquete. Contén recheos termocondutores, como partículas cerámicas ou metálicas, que melloran a condutividade térmica do material de recheo inferior. TCU úsase en aplicacións nas que a transferencia de calor eficiente é crucial, como dispositivos de alta potencia ou aqueles que operan en ambientes térmicos esixentes.
Estes son só algúns exemplos dos diferentes tipos de recheo epoxi utilizados nos envases de semicondutores. A selección do recheo epoxi adecuado depende de factores como o deseño do paquete, o proceso de montaxe, os requisitos térmicos e as consideracións eléctricas. Cada epoxi de recheo inferior ofrece vantaxes específicas e está adaptado para satisfacer as necesidades únicas de varias aplicacións.
Recheo capilar inferior: baixa viscosidade e alta fiabilidade
O subenchemento capilar refírese a un proceso utilizado na industria de envases de semicondutores para mellorar a fiabilidade dos dispositivos electrónicos. Implica encher os ocos entre un chip microelectrónico e o seu paquete circundante cun material líquido de baixa viscosidade, normalmente unha resina a base de epoxi. Este material de recheo proporciona soporte estrutural, mellora a disipación térmica e protexe o chip do estrés mecánico, a humidade e outros factores ambientais.
Unha das características críticas do recheo inferior capilar é a súa baixa viscosidade. O material de recheo inferior está formulado para ter unha densidade relativamente baixa, o que lle permite fluír facilmente nos espazos estreitos entre o chip e o paquete durante o proceso de recheo inferior. Isto garante que o material de recheo inferior poida penetrar e encher eficazmente todos os ocos e ocos de aire, minimizando o risco de formación de baleiros e mellorando a integridade xeral da interface do paquete de chips.
Os materiais de recheo capilar de baixa viscosidade tamén ofrecen outras vantaxes. En primeiro lugar, facilitan o fluxo eficiente do material baixo o chip, o que leva a un tempo de proceso reducido e un maior rendemento de produción. Isto é particularmente importante en ambientes de fabricación de gran volume onde o tempo e a eficiencia dos custos son críticos.
En segundo lugar, a baixa viscosidade permite mellores propiedades de humectación e adhesión do material de recheo inferior. Permite que o material se estenda uniformemente e forme fortes vínculos co chip e o paquete, creando unha encapsulación fiable e robusta. Isto garante que o chip estea protexido de forma segura contra tensións mecánicas, como ciclos térmicos, choques e vibracións.
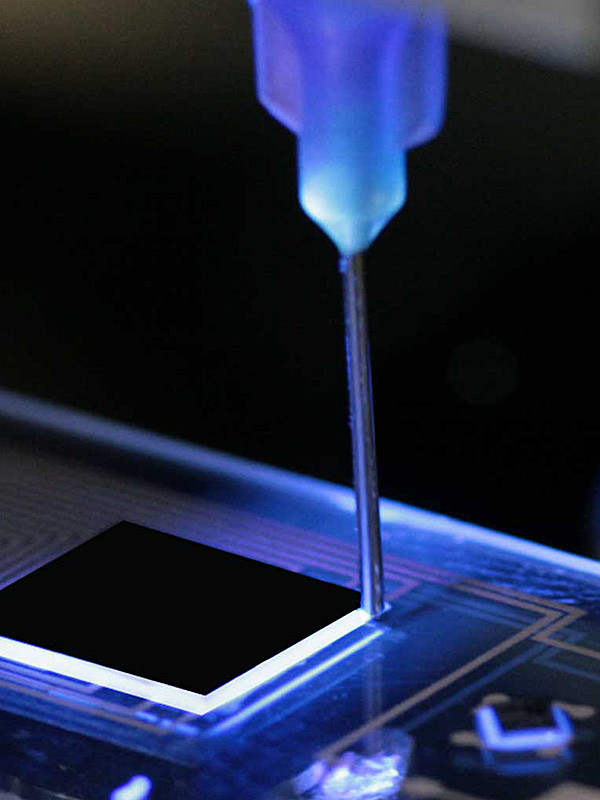
Outro aspecto crucial dos recheos capilares é a súa alta fiabilidade. Os materiais de recheo de baixa viscosidade están deseñados especificamente para mostrar unha excelente estabilidade térmica, propiedades de illamento eléctrico e resistencia á humidade e aos produtos químicos. Estas características son esenciais para garantir o rendemento e a fiabilidade a longo prazo dos dispositivos electrónicos empaquetados, especialmente en aplicacións esixentes como a automoción, a aeroespacial e as telecomunicacións.
Ademais, os materiais de recheo capilar están deseñados para ter unha alta resistencia mecánica e unha excelente adhesión a varios materiais de substrato, incluíndo metais, cerámicas e materiais orgánicos que se usan habitualmente nos envases de semicondutores. Isto permite que o material de recheo inferior actúe como un amortiguador de tensión, absorbendo e disipando eficazmente as tensións mecánicas xeradas durante a operación ou a exposición ambiental.
Underfill sen fluxo: autodispensación e alto rendemento
Non-flow underfill un proceso especializado usado na industria de envases de semicondutores para mellorar a fiabilidade e a eficiencia dos dispositivos electrónicos. A diferenza dos recheos capilares, que dependen do fluxo de materiais de baixa viscosidade, os recheos sen fluxo utilizan un enfoque de autodispensación con materiais de alta viscosidade. Este método ofrece varias vantaxes, incluíndo auto-aliñamento, alto rendemento e fiabilidade mellorada.
Unha das características críticas do subenchemento sen fluxo é a súa capacidade de autodispensación. O material de recheo inferior utilizado neste proceso está formulado cunha viscosidade máis alta, o que impide que flúe libremente. Pola contra, o material de recheo inferior é dispensado na interface do paquete de chips dun xeito controlado. Esta dispensación controlada permite a colocación precisa do material de recheo inferior, garantindo que se aplique só nas áreas desexadas sen que se desborde nin se estenda sen control.
A natureza de autodispensación do recheo insuficiente sen fluxo ofrece varios beneficios. En primeiro lugar, permite a autoalineación do material de recheo inferior. A medida que se dispensa o recheo inferior, aliñase naturalmente co chip e o paquete, enchendo os ocos e ocos de forma uniforme. Isto elimina a necesidade dun posicionamento e aliñamento precisos do chip durante o proceso de subenchemento, aforrando tempo e esforzo na fabricación.
En segundo lugar, a función de autodispensación dos recheos sen fluxo permite un alto rendemento na produción. O proceso de dispensación pódese automatizar, o que permite unha aplicación rápida e consistente do material de recheo inferior en varias fichas simultáneamente. Isto mellora a eficiencia xeral da produción e reduce os custos de fabricación, polo que é especialmente vantaxoso para ambientes de produción de gran volume.
Ademais, os materiais de recheo sen fluxo están deseñados para proporcionar unha alta fiabilidade. Os materiais de recheo de alta viscosidade ofrecen unha mellor resistencia ao ciclo térmico, tensións mecánicas e factores ambientais, garantindo o rendemento a longo prazo dos dispositivos electrónicos empaquetados. Os materiais presentan unha excelente estabilidade térmica, propiedades de illamento eléctrico e resistencia á humidade e aos produtos químicos, o que contribúe á fiabilidade global dos dispositivos.
Ademais, os materiais de recheo de alta viscosidade utilizados no recheo sen fluxo teñen propiedades de adhesión e resistencia mecánica melloradas. Forman fortes enlaces co chip e o paquete, absorbendo e disipando eficazmente as tensións mecánicas xeradas durante a operación ou a exposición ambiental. Isto axuda a protexer o chip de posibles danos e mellora a resistencia do dispositivo a golpes e vibracións externas.
Underfill moldeado: alta protección e integración
O recheo inferior moldeado é unha técnica avanzada utilizada na industria de envases de semicondutores para proporcionar altos niveis de protección e integración para dispositivos electrónicos. Implica encapsular todo o chip e o seu paquete circundante cun composto de molde que incorpora material de recheo inferior. Este proceso ofrece vantaxes significativas en canto a protección, integración e fiabilidade xeral.
Un dos beneficios críticos do recheo inferior moldeado é a súa capacidade de proporcionar unha protección completa para o chip. O composto de molde utilizado neste proceso actúa como unha barreira robusta, encerrando todo o chip e o paquete nunha capa protectora. Isto proporciona unha protección eficaz contra factores ambientais como a humidade, o po e os contaminantes que poden afectar o rendemento e a fiabilidade do dispositivo. A encapsulación tamén axuda a evitar que o chip de tensións mecánicas, ciclos térmicos e outras forzas externas, garantindo a súa durabilidade a longo prazo.
Ademais, o recheo inferior moldeado permite altos niveis de integración no paquete de semicondutores. O material de recheo inferior mestúrase directamente no composto do molde, o que permite a integración perfecta dos procesos de recheo e encapsulamento. Esta integración elimina a necesidade dun paso de recheo por separado, simplificando o proceso de fabricación e reducindo o tempo e os custos de produción. Tamén garante unha distribución coherente e uniforme do recheo por todo o paquete, minimizando os baleiros e mellorando a integridade estrutural xeral.
Ademais, o recheo inferior moldeado ofrece excelentes propiedades de disipación térmica. O composto do molde está deseñado para ter unha alta condutividade térmica, o que lle permite transferir calor lonxe do chip de forma eficiente. Isto é fundamental para manter a temperatura de funcionamento óptima do dispositivo e evitar o sobreenriquecido, o que pode provocar unha degradación do rendemento e problemas de fiabilidade. As propiedades de disipación térmica melloradas do recheo inferior moldeado contribúen á fiabilidade e á lonxevidade do dispositivo electrónico.
Ademais, o recheo inferior moldeado permite máis miniaturización e optimización do factor de forma. O proceso de encapsulación pódese adaptar para acomodar varios tamaños e formas de paquete, incluíndo estruturas 3D complexas. Esta flexibilidade permite integrar varios chips e outros compoñentes nun paquete compacto e eficiente no espazo. A capacidade de acadar niveis máis altos de integración sen comprometer a fiabilidade fai que o recheo inferior moldeado sexa particularmente valioso en aplicacións nas que as limitacións de tamaño e peso son críticas, como dispositivos móbiles, wearables e electrónica do automóbil.
Paquete de escala de chip (CSP) Underfill: miniaturización e alta densidade
O paquete de escala de chip (CSP) é unha tecnoloxía crítica que permite a miniaturización e a integración de dispositivos electrónicos de alta densidade. A medida que os dispositivos electrónicos seguen reducindo o seu tamaño ao tempo que proporcionan unha maior funcionalidade, CSP non cumpre un papel crucial para garantir a fiabilidade e o rendemento destes dispositivos compactos.
CSP é unha tecnoloxía de envasado que permite que o chip semicondutor se monte directamente no substrato ou na placa de circuíto impreso (PCB) sen necesidade de paquete adicional. Isto elimina a necesidade dun recipiente de plástico ou cerámica tradicional, reducindo o tamaño e peso global do dispositivo. CSP underfill un proceso no que se usa un material líquido ou encapsulante para cubrir o oco entre o chip e o substrato, proporcionando soporte mecánico e protexendo o chip de factores ambientais como a humidade e o estrés mecánico.
A miniaturización conséguese mediante o recheo de CSP reducindo a distancia entre o chip e o substrato. O material de recheo inferior enche o oco estreito entre o chip e o substrato, creando unha unión sólida e mellorando a estabilidade mecánica do chip. Isto permite dispositivos máis pequenos e delgados, o que permite agrupar máis funcionalidades nun espazo limitado.
A integración de alta densidade é outra vantaxe do recheo insuficiente de CSP. Ao eliminar a necesidade dun paquete separado, CSP permite que o chip se monte máis preto doutros compoñentes da PCB, reducindo a lonxitude das conexións eléctricas e mellorando a integridade do sinal. O material de recheo inferior tamén actúa como condutor térmico, disipando de forma eficiente a calor xerada polo chip. Esta capacidade de xestión térmica permite maiores densidades de potencia, permitindo a integración de chips máis complexos e potentes en dispositivos electrónicos.
Os materiais de recheo de CSP deben posuír características específicas para satisfacer as demandas de miniaturización e integración de alta densidade. Deben ter unha viscosidade baixa para facilitar o recheo de ocos estreitos, así como excelentes propiedades de fluxo para garantir unha cobertura uniforme e eliminar ocos. Os materiais tamén deben ter unha boa adherencia ao chip e ao substrato, proporcionando un soporte mecánico sólido. Ademais, deben presentar unha alta condutividade térmica para transferir calor do chip de forma eficiente.
Underfill CSP a nivel de obleas: rendible e de alto rendemento
O recheo de paquetes de escala de chip a nivel de oblea (WLCSP) é unha técnica de envasado rendible e de alto rendemento que ofrece varias vantaxes na eficiencia de fabricación e na calidade global do produto. O recheo inferior WLCSP aplica o material de recheo inferior a varios chips simultáneamente mentres aínda están en forma de oblea antes de que sexan separados en paquetes individuais. Este enfoque ofrece numerosos beneficios en canto a redución de custos, mellor control do proceso e maiores rendementos de produción.
Unha das vantaxes críticas do recheo insuficiente de WLCSP é a súa rendibilidade. A aplicación do material de recheo inferior ao nivel da oblea fai que o proceso de envasado sexa máis racional e eficiente. O material con recheo insuficiente é dispensado na oblea mediante un proceso controlado e automatizado, reducindo o desperdicio de material e minimizando os custos laborais. Ademais, a eliminación dos pasos individuais de manipulación e aliñamento de paquetes reduce o tempo e a complexidade de produción global, o que supón un aforro de custos significativo en comparación cos métodos de envasado tradicionais.
Ademais, o subenchemento de WLCSP ofrece un control mellorado do proceso e maiores rendementos de produción. Dado que o material de recheo inferior se aplica ao nivel da oblea, permite un mellor control do proceso de dispensación, garantindo unha cobertura de recheo uniforme e consistente para cada chip da oblea. Isto reduce o risco de baleiros ou de recheo incompleto, o que pode provocar problemas de fiabilidade. A capacidade de inspeccionar e probar a calidade do recheo insuficiente a nivel de obleas tamén permite a detección precoz de defectos ou variacións do proceso, permitindo accións correctoras oportunas e reducindo a probabilidade de envases defectuosos. Como resultado, o subenchemento de WLCSP axuda a conseguir maiores rendementos de produción e unha mellor calidade global do produto.
O enfoque a nivel de obleas tamén permite mellorar o rendemento térmico e mecánico. O material de recheo inferior usado no WLCSP adoita ser un material de baixa viscosidade e fluxo capilar que pode encher de forma eficiente os estreitos ocos entre as lascas e a oblea. Isto proporciona un soporte mecánico sólido aos chips, mellorando a súa resistencia ao estrés mecánico, vibracións e ciclos de temperatura. Ademais, o material de recheo inferior actúa como condutor térmico, facilitando a disipación da calor xerada polas virutas, mellorando así a xestión térmica e reducindo o risco de sobrequecemento.
Flip Chip Underfill: alta densidade de E/S e rendemento
Flip chip underfill é unha tecnoloxía crítica que permite unha alta densidade de entrada/saída (E/S) e un rendemento excepcional en dispositivos electrónicos. Desempeña un papel crucial para mellorar a fiabilidade e a funcionalidade dos envases flip-chip, que se usan amplamente en aplicacións avanzadas de semicondutores. Este artigo explorará a importancia do recheo insuficiente do chip flip e o seu impacto na consecución de alta densidade de E/S e rendemento.
A tecnoloxía Flip Chip implica a conexión eléctrica directa dun circuíto integrado (IC) ou unha matriz de semicondutores ao substrato, eliminando a necesidade de unir o cable. Isto dá como resultado un paquete máis compacto e eficiente, xa que as almofadas de E/S están situadas na superficie inferior da matriz. Non obstante, os envases flip-chip presentan desafíos únicos que deben abordarse para garantir un rendemento e unha fiabilidade óptimos.
Un dos retos críticos no envasado de chip flip é previr o estrés mecánico e o desaxuste térmico entre a matriz e o substrato. Durante o proceso de fabricación e a posterior operación, as diferenzas nos coeficientes de expansión térmica (CTE) entre a matriz e o substrato poden causar unha tensión significativa, o que provoca unha degradación do rendemento ou mesmo un fallo. Flip chip underfill é un material protector que encapsula o chip, proporcionando soporte mecánico e alivio do estrés. Reparte eficazmente as tensións xeradas durante o ciclo térmico e evita que afecten ás delicadas interconexións.
A alta densidade de E/S é fundamental nos dispositivos electrónicos modernos, onde os factores de forma máis pequenos e unha maior funcionalidade son esenciais. Flip chip underfill permite maiores densidades de E/S ao ofrecer un illamento eléctrico superior e capacidades de xestión térmica. O material de recheo inferior enche o oco entre a matriz e o substrato, creando unha interface robusta e reducindo o risco de curtocircuítos ou fugas eléctricas. Isto permite un espazamento máis próximo das almofadas de E/S, o que resulta nunha maior densidade de E/S sen sacrificar a fiabilidade.
Ademais, o recheo de chip flip contribúe a mellorar o rendemento eléctrico. Minimiza os parasitos eléctricos entre a matriz e o substrato, reducindo o atraso do sinal e mellorando a integridade do sinal. O material de recheo inferior tamén presenta excelentes propiedades de condutividade térmica, disipando de forma eficiente a calor xerada polo chip durante o funcionamento. A disipación de calor eficaz garante que a temperatura se manteña dentro dos límites aceptables, evitando o sobrequecemento e mantendo un rendemento óptimo.
Os avances nos materiais de recheo de chip flip permitiron densidades de E/S e niveis de rendemento aínda máis altos. Os recheos inferiores de nanocompostos, por exemplo, aproveitan os recheos a nanoescala para mellorar a condutividade térmica e a resistencia mecánica. Isto permite mellorar a disipación da calor e a fiabilidade, permitindo dispositivos de maior rendemento.
Ball Grid Array (BGA) Underfill: alto rendemento térmico e mecánico
Ball Grid Array (BGA) non enche unha tecnoloxía crítica que ofrece un alto rendemento térmico e mecánico en dispositivos electrónicos. Desempeña un papel crucial para mellorar a fiabilidade e a funcionalidade dos paquetes BGA, que se usan amplamente en varias aplicacións. Neste artigo, exploraremos a importancia do recheo insuficiente de BGA e o seu impacto na consecución dun alto rendemento térmico e mecánico.
A tecnoloxía BGA implica un deseño de paquete onde o circuíto integrado (IC) ou matriz de semicondutores está montado nun substrato e as conexións eléctricas realízanse a través dunha serie de bolas de soldadura situadas na superficie inferior do paquete. BGA enche por debaixo un material dispensado no espazo entre a matriz e o substrato, encapsulando as bolas de soldadura e proporcionando soporte mecánico e protección ao conxunto.
Un dos retos críticos dos envases BGA é a xestión das tensións térmicas. Durante o funcionamento, o IC xera calor, e a expansión e contracción térmicas poden causar unha presión significativa nas unións de soldadura que conectan a matriz e o substrato. A BGA non cumpre un papel crucial na mitigación destas tensións formando un enlace sólido coa matriz e o substrato. Actúa como amortiguador de tensión, absorbendo a expansión e contracción térmicas e reducindo a tensión nas unións de soldadura. Isto axuda a mellorar a fiabilidade xeral do paquete e reduce o risco de fallos das xuntas de soldadura.
Outro aspecto crítico do recheo de BGA é a súa capacidade para mellorar o rendemento mecánico do paquete. Os paquetes BGA adoitan estar sometidos a esforzos mecánicos durante a súa manipulación, montaxe e operación. O material de recheo inferior enche o oco entre a matriz e o substrato, proporcionando soporte estrutural e reforzo ás unións de soldadura. Isto mellora a resistencia mecánica global do conxunto, facéndoo máis resistente a golpes mecánicos, vibracións e outras forzas externas. Ao distribuír eficazmente as tensións mecánicas, o recheo inferior de BGA axuda a evitar a rachadura do paquete, a delaminación ou outros fallos mecánicos.
O alto rendemento térmico é esencial nos dispositivos electrónicos para garantir a correcta funcionalidade e fiabilidade. Os materiais de recheo de BGA están deseñados para ter excelentes propiedades de condutividade térmica. Isto permítelles transferir de forma eficiente a calor lonxe da matriz e distribuíla polo substrato, mellorando a xestión térmica global do paquete. A disipación de calor eficaz axuda a manter temperaturas de funcionamento máis baixas, evitando os puntos quentes térmicos e a posible degradación do rendemento. Tamén contribúe á lonxevidade da caixa ao reducir o estrés térmico dos compoñentes.
Os avances nos materiais de recheo de BGA levaron a un rendemento térmico e mecánico aínda maior. As formulacións e materiais de recheo mellorados, como os nanocompostos ou os recheos de alta condutividade térmica, permitiron unha mellor disipación de calor e resistencia mecánica, mellorando aínda máis o rendemento dos paquetes BGA.
Paquete cuádruple plano (QFP) Underfill: gran cantidade de E/S e robustez
Quad Flat Package (QFP) é un paquete de circuítos integrados (IC) moi utilizado na electrónica. Presenta unha forma cadrada ou rectangular con cables que se estenden polos catro lados, proporcionando moitas conexións de entrada/saída (E/S). Para mellorar a fiabilidade e robustez dos paquetes QFP, úsanse habitualmente materiais de recheo inferior.
Underfill é un material protector aplicado entre o IC e o substrato para reforzar a resistencia mecánica das unións de soldadura e evitar fallos inducidos polo estrés. É particularmente crucial para QFP cun gran número de E/S, xa que o alto número de conexións pode provocar esforzos mecánicos significativos durante o ciclo térmico e as condicións operativas.
O material de recheo inferior utilizado para os paquetes QFP debe posuír características específicas para garantir a robustez. En primeiro lugar, debe ter unha excelente adhesión tanto ao IC como ao substrato para crear unha unión forte e minimizar o risco de delaminación ou desprendimento. Ademais, debería ter un baixo coeficiente de expansión térmica (CTE) para coincidir co CTE do IC e do substrato, reducindo os desaxustes de tensión que poderían provocar gretas ou fracturas.
Ademais, o material de recheo inferior debe ter boas propiedades de fluxo para garantir unha cobertura uniforme e o recheo completo do espazo entre o IC e o substrato. Isto axuda a eliminar ocos, que poden debilitar as unións de soldadura e reducir a fiabilidade. O material tamén debe ter boas propiedades de curado, permitíndolle formar unha capa protectora ríxida e duradeira despois da aplicación.
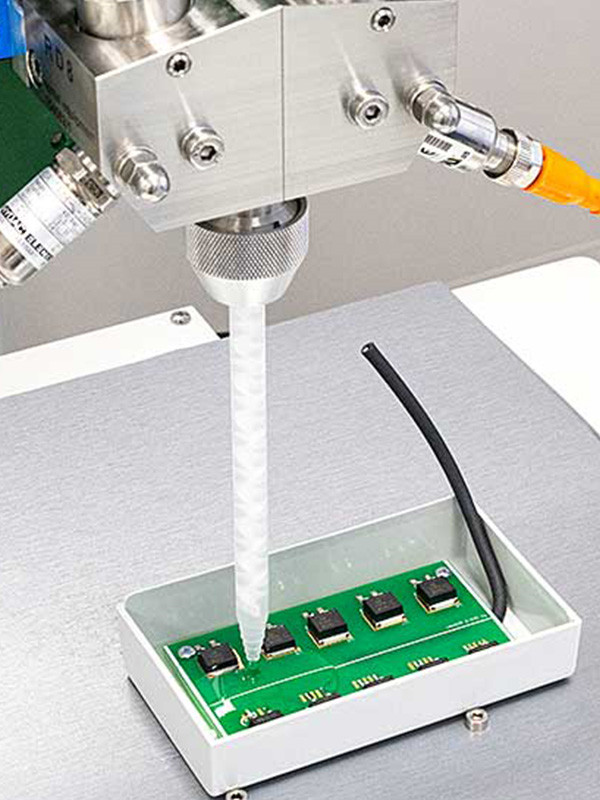
En termos de robustez mecánica, o recheo inferior debe posuír unha alta resistencia ao cizallamento e á peladura para soportar forzas externas e evitar a deformación ou separación do paquete. Tamén debe presentar unha boa resistencia á humidade e a outros factores ambientais para manter as súas propiedades protectoras ao longo do tempo. Isto é especialmente importante nas aplicacións nas que o paquete QFP pode estar exposto a condicións duras ou sufrir variacións de temperatura.
Existen varios materiais de recheo inferior para acadar estas características desexadas, incluíndo formulacións a base de epoxi. Dependendo dos requisitos específicos da aplicación, estes materiais pódense dispensar mediante diferentes técnicas, como fluxo capilar, inxección ou serigrafía.
Sistema en paquete (SiP) Underfill: integración e rendemento
System-in-Package (SiP) é unha tecnoloxía de envasado avanzada que integra múltiples chips de semicondutores, compoñentes pasivos e outros elementos nun único paquete. SiP ofrece numerosas vantaxes, incluíndo un factor de forma reducido, un rendemento eléctrico mellorado e unha funcionalidade mellorada. Para garantir a fiabilidade e o rendemento dos conxuntos SiP, úsanse habitualmente materiais de recheo inferior.
O recheo insuficiente das aplicacións SiP é fundamental para proporcionar estabilidade mecánica e conectividade eléctrica entre os distintos compoñentes do paquete. Axuda a minimizar o risco de fallas inducidas pola tensión, como fisuras ou fracturas das xuntas de soldadura, que poden ocorrer debido ás diferenzas nos coeficientes de expansión térmica (CTE) entre os compoñentes.
A integración de varios compoñentes nun paquete SiP leva a unha interconectividade complexa, con moitas unións de soldadura e circuítos de alta densidade. Os materiais de recheo inferior axudan a reforzar estas interconexións, mellorando a resistencia mecánica e a fiabilidade do conxunto. Soportan as unións de soldadura, reducindo o risco de fatiga ou danos causados por ciclos térmicos ou tensións mecánicas.
En termos de rendemento eléctrico, os materiais de recheo son fundamentais para mellorar a integridade do sinal e minimizar o ruído eléctrico. Ao cubrir os ocos entre os compoñentes e reducir a distancia entre eles, o recheo inferior axuda a reducir a capacitancia e a inductancia parasitarias, permitindo unha transmisión de sinal máis rápida e eficiente.
Ademais, os materiais de recheo inferior para aplicacións SiP deben ter unha excelente condutividade térmica para disipar a calor xerada polos compoñentes integrados de forma eficiente. A disipación de calor eficaz é esencial para evitar o sobreenriquecido e manter a fiabilidade e o rendemento global do conxunto SiP.
Os materiais de recheo inferior nos envases SiP deben ter propiedades específicas para cumprir estes requisitos de integración e rendemento. Deben ter unha boa fluidez para garantir unha cobertura completa e cubrir ocos entre os compoñentes. O material de recheo inferior tamén debe ter unha formulación de baixa viscosidade para permitir a dispensación e o recheo fáciles de orificios estreitos ou espazos pequenos.
Ademais, o material de recheo inferior debe mostrar unha forte adhesión a diferentes superficies, incluíndo chips de semicondutores, substratos e pasivos, para garantir unha unión fiable. Debe ser compatible con varios materiais de envasado, como substratos orgánicos ou cerámicas, e presentar boas propiedades mecánicas, incluíndo unha alta resistencia ao corte e á pel.
A elección do material de recheo inferior e do método de aplicación depende do deseño SiP específico, dos requisitos dos compoñentes e dos procesos de fabricación. As técnicas de dispensación como o fluxo capilar, a inxección ou os métodos asistidos por película adoitan aplicar o recheo insuficiente nos conxuntos SiP.
Underfill de optoelectrónica: aliñamento óptico e protección
O subenchemento da optoelectrónica inclúe encapsular e protexer os dispositivos optoelectrónicos ao tempo que se garante un aliñamento óptico preciso. Os dispositivos optoelectrónicos, como láseres, fotodetectores e interruptores ópticos, requiren a miúdo un aliñamento delicado dos compoñentes ópticos para conseguir un rendemento óptimo. Ao mesmo tempo, deben estar protexidos dos factores ambientais que poidan afectar a súa funcionalidade. O subfill optoelectrónico responde a ambos os requisitos proporcionando aliñamento óptico e protección nun único proceso.
O aliñamento óptico é un aspecto crítico da fabricación de dispositivos optoelectrónicos. Implica aliñar elementos visuais, como fibras, guías de ondas, lentes ou reixas, para garantir unha transmisión e recepción eficientes da luz. É necesario un aliñamento preciso para maximizar o rendemento do dispositivo e manter a integridade do sinal. As técnicas tradicionais de aliñamento inclúen o aliñamento manual mediante inspección visual ou o aliñamento automatizado mediante fases de aliñamento. Non obstante, estes métodos poden ser lentos, laboriosos e propensos a erros.
A optoelectrónica rechea unha solución innovadora ao incorporar funcións de aliñamento directamente no material de recheo inferior. Os materiais de recheo inferior son normalmente compostos líquidos ou semilíquidos que poden fluír e encher os ocos entre os compoñentes ópticos. Ao engadir características de aliñamento, como microestruturas ou marcas fiduciais, dentro do material de recheo inferior, o proceso de aliñamento pódese simplificar e automatizar. Estas características actúan como guías durante a montaxe, garantindo un aliñamento preciso dos compoñentes ópticos sen necesidade de procedementos de aliñamento complexos.
Ademais do aliñamento óptico, os materiais de recheo inferior protexen os dispositivos optoelectrónicos. Os compoñentes optoelectrónicos adoitan estar expostos a ambientes duros, incluíndo flutuacións de temperatura, humidade e estrés mecánico. Estes factores externos poden degradar o rendemento e a fiabilidade dos dispositivos co paso do tempo. Os materiais de recheo inferior actúan como unha barreira protectora, encapsulando os compoñentes ópticos e protexéndoos dos contaminantes ambientais. Tamén proporcionan reforzo mecánico, reducindo o risco de danos por golpes ou vibracións.
Os materiais de recheo inferior utilizados en aplicacións de optoelectrónica adoitan deseñarse para ter un índice de refracción baixo e unha excelente transparencia óptica. Isto garante unha interferencia mínima cos sinais ópticos que pasan polo dispositivo. Ademais, presentan unha boa adhesión a varios substratos e teñen baixos coeficientes de expansión térmica para minimizar o estrés do dispositivo durante o ciclo térmico.
O proceso de recheo inferior implica dispensar o material de recheo inferior no dispositivo, permitindo que flúa e enche os ocos entre os compoñentes ópticos e, a continuación, curalo para formar unha encapsulación sólida. Dependendo da aplicación específica, o material de recheo inferior pódese aplicar mediante diferentes técnicas, como fluxo capilar, dispensación por chorro ou serigrafía. O proceso de curado pódese conseguir mediante calor, radiación UV ou ambos.
Underfill de electrónica médica: biocompatibilidade e fiabilidade
A electrónica médica non enche un proceso especializado que consiste en encapsular e protexer os compoñentes electrónicos utilizados en dispositivos médicos. Estes dispositivos xogan un papel crucial en varias aplicacións médicas, como dispositivos implantables, equipos de diagnóstico, sistemas de monitorización e sistemas de administración de medicamentos. A subcarga da electrónica médica céntrase en dous aspectos críticos: a biocompatibilidade e a fiabilidade.
A biocompatibilidade é un requisito fundamental para os dispositivos médicos que entran en contacto co corpo humano. Os materiais de recheo inferior utilizados na electrónica médica deben ser biocompatibles, o que significa que non deben causar efectos nocivos nin reaccións adversas ao entrar en contacto con tecidos vivos ou fluídos corporais. Estes materiais deben cumprir normas e normas estritas, como a ISO 10993, que especifica os procedementos de proba e avaliación de biocompatibilidade.
Os materiais de recheo inferior para electrónica médica son coidadosamente seleccionados ou formulados para garantir a biocompatibilidade. Están deseñados para ser non tóxicos, non irritantes e non alerxénicos. Estes materiais non deben lixiviar ningunha substancia nociva nin degradarse co paso do tempo, xa que isto pode provocar danos nos tecidos ou inflamación. Os materiais de recheo biocompatible tamén teñen unha baixa absorción de auga para evitar o crecemento de bacterias ou fungos que poidan causar infeccións.
A fiabilidade é outro aspecto crítico do recheo insuficiente da electrónica médica. Os dispositivos médicos adoitan enfrontarse a condicións de funcionamento desafiantes, incluíndo temperaturas extremas, humidade, fluídos corporais e estrés mecánico. Os materiais de recheo inferior deben protexer os compoñentes electrónicos, garantindo a súa fiabilidade e funcionalidade a longo prazo. A fiabilidade é primordial nas aplicacións médicas onde a falla do dispositivo pode afectar gravemente á seguridade e ao benestar do paciente.
Os materiais de recheo para a electrónica médica deben ter unha alta resistencia á humidade e aos produtos químicos para soportar a exposición a fluídos corporais ou procesos de esterilización. Tamén deben mostrar unha boa adherencia a varios substratos, garantindo un encapsulamento seguro dos compoñentes electrónicos. As propiedades mecánicas, como os baixos coeficientes de expansión térmica e unha boa resistencia ao choque, son fundamentais para minimizar a tensión nos detalles durante o ciclo térmico ou a carga automática.
O proceso de subenchemento para a electrónica médica implica:
- Distribución do material de recheo inferior nos compoñentes electrónicos.
- Enchendo os ocos.
- Curándoo para formar unha encapsulación protectora e mecánicamente estable.
Hai que ter coidado para garantir a cobertura completa das funcións e a ausencia de baleiros ou bolsas de aire que poidan comprometer a fiabilidade do dispositivo.
Ademais, téñense en conta consideracións adicionais ao encher os dispositivos médicos. Por exemplo, o material de recheo inferior debe ser compatible cos métodos de esterilización utilizados para o dispositivo. Algúns materiais poden ser sensibles a técnicas de esterilización específicas, como o vapor, o óxido de etileno ou a radiación, e pode ser necesario seleccionar materiais alternativos.
Recheo de electrónica aeroespacial: resistencia a altas temperaturas e vibracións
A electrónica aeroespacial non enche un proceso especializado para encapsular e protexer os compoñentes electrónicos en aplicacións aeroespaciais. Os ambientes aeroespaciais presentan desafíos únicos, incluíndo altas temperaturas, vibracións extremas e tensións mecánicas. Polo tanto, o subenchemento da electrónica aeroespacial céntrase en dous aspectos cruciais: a resistencia ás altas temperaturas e a resistencia ás vibracións.
A resistencia a altas temperaturas é primordial na electrónica aeroespacial debido ás elevadas temperaturas experimentadas durante o funcionamento. Os materiais de recheo inferior utilizados en aplicacións aeroespaciais deben soportar estas altas temperaturas sen comprometer o rendemento e a fiabilidade dos compoñentes electrónicos. Deben presentar unha expansión térmica mínima e permanecer estables nun amplo rango de temperatura.
Os materiais de recheo inferior para a electrónica aeroespacial son seleccionados ou formulados para altas temperaturas de transición vítrea (Tg) e estabilidade térmica. Unha alta Tg garante que o material manteña as súas propiedades mecánicas a temperaturas elevadas, evitando a deformación ou a perda de adherencia. Estes materiais poden soportar temperaturas extremas, como durante o despegue, a reentrada atmosférica ou a operación en compartimentos do motor quentes.
Ademais, os materiais de recheo inferior para a electrónica aeroespacial deberían ter baixos coeficientes de expansión térmica (CTE). O CTE mide canto se expande ou contrae un material cos cambios de temperatura. Ao ter un CTE baixo, os materiais de recheo insuficiente poden minimizar a tensión sobre os compoñentes electrónicos causada polo ciclo térmico, o que pode provocar fallos mecánicos ou fatiga das xuntas de soldadura.
A resistencia ás vibracións é outro requisito crítico para o recheo inferior da electrónica aeroespacial. Os vehículos aeroespaciais están suxeitos a varias vibracións, incluíndo o motor, as vibracións inducidas polo voo e os choques mecánicos durante o lanzamento ou a aterraxe. Estas vibracións poden poñer en perigo o rendemento e a fiabilidade dos compoñentes electrónicos se non están protexidos adecuadamente.
Os materiais de recheo inferior utilizados na electrónica aeroespacial deberían mostrar excelentes propiedades de amortiguación de vibracións. Deben absorber e disipar a enerxía xerada polas vibracións, reducindo a tensión e a tensión dos compoñentes electrónicos. Isto axuda a evitar a formación de fendas, fracturas ou outros fallos mecánicos debido á exposición excesiva a vibracións.
Ademais, en aplicacións aeroespaciais prefírense materiais de recheo inferior con alta adherencia e resistencia cohesiva. Estas propiedades garanten que o material de recheo inferior permaneza firmemente unido aos compoñentes electrónicos e ao substrato, mesmo en condicións de vibración extremas. A forte adhesión evita que o material de recheo inferior se desprenda ou se separe dos elementos, mantendo a integridade da encapsulación e protexendo contra a humidade ou a entrada de restos.
O proceso de recheo inferior para a electrónica aeroespacial normalmente implica dispensar o material de recheo inferior nos compoñentes electrónicos, permitíndolle fluír e encher os ocos, e despois curalo para formar unha encapsulación robusta. O proceso de curado pódese realizar mediante métodos de curado térmico ou UV, dependendo dos requisitos específicos da aplicación.
Recheo de electrónica automotriz: durabilidade e resistencia ao ciclo térmico
A electrónica do automóbil non enche un proceso crítico que implica encapsular e protexer os compoñentes electrónicos en aplicacións automotrices. Os ambientes automotivos presentan desafíos únicos, incluíndo variacións de temperatura, ciclos térmicos, tensións mecánicas e exposición á humidade e aos produtos químicos. Polo tanto, o subenchemento da electrónica do automóbil céntrase en dous aspectos críticos: durabilidade e resistencia ao ciclo térmico.
A durabilidade é un requisito crucial para o recheo insuficiente da electrónica do automóbil. Durante o funcionamento normal, os vehículos automóbiles experimentan vibracións, golpes e esforzos mecánicos constantes. Os materiais de recheo que se usan en aplicacións de automoción deben protexer os compoñentes electrónicos de forma robusta, garantindo a súa durabilidade e lonxevidade. Deben soportar as duras condicións e cargas mecánicas que se atopan na estrada e resistir a entrada de humidade, po e produtos químicos.
Os materiais de recheo inferior para a electrónica do automóbil son seleccionados ou formulados para unha alta resistencia mecánica e resistencia ao impacto. Deben mostrar unha excelente adhesión aos compoñentes electrónicos e ao substrato, evitando a delaminación ou a separación baixo tensións mecánicas. Os materiais de recheo duradeiros axudan a minimizar o risco de danos aos compoñentes electrónicos debido a vibracións ou golpes, garantindo un rendemento fiable durante toda a vida útil do vehículo.
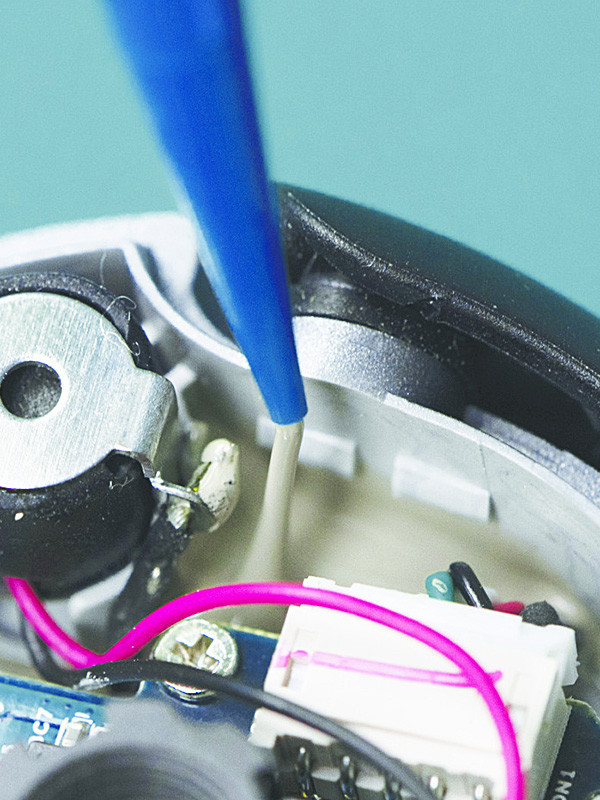
A resistencia ao ciclo térmico é outro requisito crítico para o recheo insuficiente da electrónica do automóbil. Os vehículos automóbiles sofren frecuentes variacións de temperatura, especialmente durante o arranque e o funcionamento do motor, e estes ciclos de temperatura poden inducir tensións térmicas nos compoñentes electrónicos e no material de recheo circundante. Os materiais de recheo que se usan en aplicacións de automoción deben ter unha excelente resistencia ao ciclo térmico para soportar estas flutuacións de temperatura sen comprometer o seu rendemento.
Os materiais de recheo inferior para a electrónica de automóbiles deben ter baixos coeficientes de expansión térmica (CTE) para minimizar a tensión dos compoñentes electrónicos durante o ciclo térmico. Un CTE ben combinado entre o material de recheo inferior e os ingredientes reduce o risco de fatiga das xuntas de soldadura, rachaduras ou outros fallos mecánicos causados polo estrés térmico. Ademais, os materiais de recheo inferior deben mostrar unha boa condutividade térmica para disipar a calor de forma eficiente, evitando puntos quentes localizados que poidan afectar o rendemento e a fiabilidade dos compoñentes.
Ademais, os materiais de recheo de produtos electrónicos do automóbil deben resistir a humidade, os produtos químicos e os fluídos. Deben ter unha baixa absorción de auga para evitar o crecemento de mofo ou a corrosión dos compoñentes electrónicos. A resistencia química garante que o material de recheo inferior se manteña estable cando se expón a fluídos de automóbiles, como aceites, combustibles ou axentes de limpeza, evitando a degradación ou a perda de adherencia.
O proceso de recheo inferior para a electrónica de automóbiles normalmente implica dispensar o material de recheo inferior nos compoñentes electrónicos, permitindo que flúa e enche os ocos, e despois curalo para formar unha encapsulación duradeira. O proceso de curado pódese realizar mediante métodos de curado térmico ou UV, dependendo dos requisitos específicos da aplicación e do material de recheo inferior utilizado.
Elixir o recheo epoxi correcto
Elixir o recheo epoxi correcto é unha decisión crucial na montaxe e protección dos compoñentes electrónicos. Os recheos epoxis proporcionan reforzo mecánico, xestión térmica e protección contra factores ambientais. Aquí tes algunhas consideracións fundamentais á hora de seleccionar o recheo epoxi adecuado:
- Propiedades térmicas: unha das funcións principais do recheo epoxi é disipar a calor xerada polos compoñentes electrónicos. Polo tanto, é esencial ter en conta a condutividade térmica e a resistencia térmica do epoxi. A alta condutividade térmica axuda a transferencia de calor eficiente, evitando puntos quentes e mantendo a fiabilidade dos compoñentes. O epoxi tamén debe ter unha baixa resistencia térmica para minimizar a tensión térmica sobre os compoñentes durante o ciclo de temperatura.
- Coincidencia CTE: o coeficiente de expansión térmica (CTE) do epoxi de recheo inferior debe coincidir ben co CTE dos compoñentes electrónicos e do substrato para minimizar o estrés térmico e evitar fallos das xuntas de soldadura. Un CTE moi igualado axuda a reducir o risco de fallos mecánicos debido ao ciclo térmico.
- Capacidade de recheo de fluxos e espazos: o recheo epoxi insuficiente debe ter boas características de fluxo e a capacidade de cubrir os ocos entre os compoñentes de forma eficaz. Isto garante unha cobertura completa e minimiza os baleiros ou bolsas de aire que poden afectar a estabilidade mecánica e o rendemento térmico do conxunto. A viscosidade do epoxi debe ser axeitada para a aplicación específica e o método de montaxe, xa sexa fluxo capilar, dispensación a chorro ou serigrafía.
- Adhesión: unha forte adhesión é fundamental para o recheo de epoxi para garantir unha unión fiable entre os compoñentes e o substrato. Debe mostrar unha boa adherencia a varios materiais, incluíndo metais, cerámicas e plásticos. As propiedades de adhesión do epoxi contribúen á integridade mecánica do conxunto e á fiabilidade a longo prazo.
- Método de curado: considere o método de curado que mellor se adapte ao seu proceso de fabricación. Os epoxis de recheo inferior pódense curar mediante calor, radiación UV ou unha combinación de ambos. Cada método de curado ten vantaxes e limitacións, e elixir o que se axuste aos requisitos de produción é esencial.
- Resistencia ambiental: avalía a resistencia do recheo epoxi a factores ambientais como humidade, produtos químicos e temperaturas extremas. O epoxi debe ser capaz de soportar a exposición á auga, evitando o crecemento de mofo ou corrosión. A resistencia química garante a estabilidade ao entrar en contacto con fluídos de automóbiles, axentes de limpeza ou outras substancias potencialmente corrosivas. Ademais, o epoxi debe manter as súas propiedades mecánicas e eléctricas nun amplo rango de temperatura.
- Fiabilidade e lonxevidade: considere o historial e os datos de fiabilidade do recheo epoxi. Busque materiais epoxi probados e comprobados para funcionar ben en aplicacións similares ou ter certificacións da industria e cumprimento das normas relevantes. Considere factores como o comportamento do envellecemento, a fiabilidade a longo prazo e a capacidade do epoxi para manter as súas propiedades ao longo do tempo.
Ao seleccionar o recheo epoxi correcto, é fundamental ter en conta os requisitos específicos da súa aplicación, incluíndo a xestión térmica, a estabilidade mecánica, a protección ambiental e a compatibilidade do proceso de fabricación. Consultar con provedores de epoxi ou buscar asesoramento de expertos pode ser beneficioso para tomar unha decisión informada que satisfaga as necesidades da súa aplicación e garanta un rendemento e unha fiabilidade óptimos.
Tendencias futuras en relleno epoxi
Underfill epoxi está en continua evolución, impulsado polos avances nas tecnoloxías electrónicas, as aplicacións emerxentes e a necesidade de mellorar o rendemento e a fiabilidade. Pódense observar varias tendencias futuras no desenvolvemento e aplicación de epoxi de recheo inferior:
- Miniaturización e envases de maior densidade: a medida que os dispositivos electrónicos seguen a diminuír e presentan maiores densidades de compoñentes, os epoxis de recheo inferior deben adaptarse en consecuencia. As tendencias futuras centraranse no desenvolvemento de materiais de recheo inferior que penetren e enchen os espazos máis pequenos entre os compoñentes, garantindo unha cobertura completa e unha protección fiable en conxuntos electrónicos cada vez máis miniaturizados.
- Aplicacións de alta frecuencia: coa crecente demanda de dispositivos electrónicos de alta frecuencia e alta velocidade, as formulacións epoxi de recheo insuficiente terán que abordar os requisitos específicos destas aplicacións. Os materiais de recheo inferior con baixa constante dieléctrica e tanxentes de baixa perda serán esenciais para minimizar a perda de sinal e manter a integridade dos sinais de alta frecuencia en sistemas de comunicación avanzados, tecnoloxía 5G e outras aplicacións emerxentes.
- Xestión térmica mellorada: a disipación de calor segue sendo unha preocupación crítica para os dispositivos electrónicos, especialmente co aumento da densidade de potencia. As futuras formulacións epoxi de recheo inferior centraranse na mellora da condutividade térmica para mellorar a transferencia de calor e xestionar os problemas térmicos de forma eficaz. Os recheos e aditivos avanzados incorporaranse aos epoxis de recheo inferior para acadar unha maior condutividade térmica mantendo outras propiedades desexadas.
- Electrónica flexible e estirable: o aumento da electrónica flexible e estirable abre novas posibilidades para o recheo de materiais epoxi. Os recheos epoxis flexibles deben mostrar excelentes propiedades mecánicas e de adhesión, mesmo baixo flexións ou estiramentos repetidos. Estes materiais permitirán encapsular e protexer os produtos electrónicos en dispositivos portátiles, pantallas flexibles e outras aplicacións que requiran flexibilidade mecánica.
- Solucións respectuosas co medio ambiente: a sustentabilidade e as consideracións ambientais xogarán un papel cada vez máis importante no desenvolvemento de materiais epoxi de recheo inferior. Farase un foco na creación de formulacións epoxi libres de substancias perigosas e que teñan un impacto ambiental reducido ao longo do seu ciclo de vida, incluíndo a fabricación, o uso e a eliminación. Os materiais de base biolóxica ou renovables tamén poden gañar protagonismo como alternativas sostibles.
- Procesos de fabricación mellorados: as tendencias futuras no recheo epoxi centraranse nas propiedades dos materiais e nos avances nos procesos de fabricación. Exploraranse técnicas como a fabricación aditiva, a dispensación selectiva e os métodos de curado avanzados para optimizar a aplicación e o rendemento do recheo epoxi en varios procesos de montaxe electrónica.
- Integración de técnicas avanzadas de probas e caracterización: coa crecente complexidade e requisitos dos dispositivos electrónicos, haberá que contar con métodos de proba e caracterización avanzados para garantir a fiabilidade e o rendemento do epoxi con recheo insuficiente. Técnicas como as probas non destrutivas, a vixilancia in situ e as ferramentas de simulación axudarán no desenvolvemento e control de calidade dos materiais epoxi con recheos insuficientes.
Conclusión
O epoxi de recheo inferior xoga un papel fundamental para mellorar a fiabilidade e o rendemento dos compoñentes electrónicos, especialmente nos envases de semicondutores. Os diferentes tipos de epoxi de recheo inferior ofrecen unha serie de vantaxes, incluíndo alta fiabilidade, autodispensación, alta densidade e alto rendemento térmico e mecánico. Escoller o recheo epoxi adecuado para a aplicación e o paquete garante unha unión robusta e duradeira. A medida que a tecnoloxía avanza e o tamaño dos paquetes se reduce, esperamos solucións epoxi de recheo inferior aínda máis innovadoras que ofrezan un rendemento, integración e miniaturización superiores. O epoxi Underfill terá un papel cada vez máis importante no futuro da electrónica, permitíndonos acadar maiores niveis de fiabilidade e rendemento en varias industrias.