Adhesivo MEMS
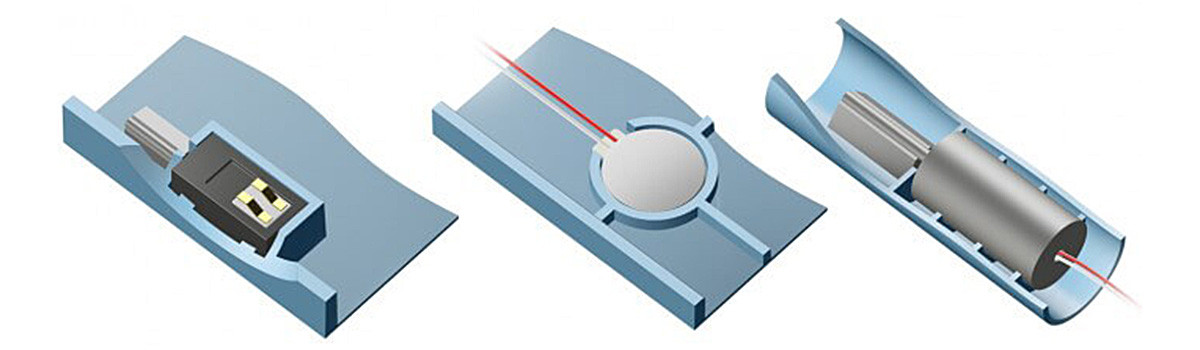
Os sistemas microelectromecánicos (MEMS) revolucionaron varias industrias ao permitir o desenvolvemento de dispositivos máis pequenos e eficientes. Un compoñente crítico que contribuíu ao éxito da tecnoloxía MEMS é o adhesivo MEMS. O adhesivo MEMS xoga un papel crucial na unión e na fixación de microestruturas e compoñentes en dispositivos MEMS, garantindo a súa estabilidade, fiabilidade e rendemento. Neste artigo, exploramos a importancia do adhesivo MEMS e as súas aplicacións, destacando os subtítulos clave que arroxan luz sobre os seus diversos aspectos.
Comprensión do adhesivo MEMS: fundamentos e composición
Os sistemas microelectromecánicos (MEMS) revolucionaron varias industrias ao permitir a produción de pequenos dispositivos con poderosas capacidades. O adhesivo MEMS xoga un papel fundamental na montaxe e embalaxe destes dispositivos en miniatura. Comprender os fundamentos e a composición do adhesivo MEMS é esencial para lograr unha unión fiable e robusta na fabricación de MEMS. Este artigo afonda no adhesivo MEMS para arroxar luz sobre a súa importancia e consideracións críticas.
Fundamentos do adhesivo MEMS
O adhesivo MEMS está deseñado especificamente para facilitar vínculos robustos e duradeiros entre varios compoñentes dos microdispositivos. Estes adhesivos posúen propiedades únicas para cumprir os estritos requisitos das aplicacións MEMS. Unha das propiedades fundamentais do adhesivo MEMS é a súa capacidade de soportar condicións ambientais duras, incluíndo flutuacións de temperatura, humidade e exposición química. Ademais, os adhesivos MEMS deben mostrar excelentes propiedades mecánicas, como unha alta resistencia de adhesión, baixa contracción e un mínimo de fluencia, para garantir a fiabilidade a longo prazo.
Composición do adhesivo MEMS
A composición do adhesivo MEMS está coidadosamente formulada para satisfacer as necesidades específicas dos envases MEMS. Normalmente, os adhesivos MEMS constan de varios compoñentes clave, cada un deles cun propósito particular:
Matriz de polímero: A matriz polimérica forma a maior parte do adhesivo e proporciona a integridade estrutural necesaria. Os polímeros comúns utilizados nos adhesivos MEMS inclúen epoxi, poliimida e acrílico. Estes polímeros ofrecen excelentes propiedades de adhesión, resistencia química e estabilidade mecánica.
Materiais de recheo: Para mellorar as propiedades adhesivas, incorpóranse cargas á matriz polimérica. Os recheos como a sílice, a alúmina ou as partículas metálicas poden mellorar a condutividade térmica, a condutividade eléctrica e a estabilidade dimensional do adhesivo.
Axentes de curación: Os adhesivos MEMS a miúdo requiren un proceso de curado para acadar as súas propiedades finais. Os axentes de curado, como aminas ou anhídridos, inician reaccións de reticulación na matriz de polímero, o que dá lugar a unha forte unión adhesiva.
Promotores de adhesión: Algúns adhesivos MEMS poden incluír promotores de adhesión para mellorar a unión entre o adhesivo e os substratos. Estes promotores son normalmente compostos a base de silano que melloran a adhesión a diversos materiais, como metais, cerámicas ou polímeros.
Consideracións para a selección de adhesivos MEMS
O adhesivo MEMS adecuado garante o rendemento e a fiabilidade a longo prazo dos dispositivos MEMS. Ao elixir un vínculo, hai que ter en conta varios factores:
compatibilidade: O adhesivo debe ser compatible cos materiais que se van unir, así como co ambiente operativo do dispositivo MEMS.
Compatibilidade de procesos: O adhesivo debe ser compatible cos procesos de fabricación implicados, como os métodos de dispensación, curado e unión.
Propiedades térmicas e mecánicas: O adhesivo debe presentar unha estabilidade térmica adecuada, baixo coeficiente de expansión térmica (CTE) e excelentes propiedades mecánicas para soportar as tensións que se atopan durante o funcionamento do dispositivo.
Forza de adhesión: O adhesivo debe proporcionar unha resistencia suficiente para garantir unha unión robusta entre os compoñentes, evitando a delaminación ou a falla.
Tipos de adhesivos MEMS: unha visión xeral
Os dispositivos MEMS (Sistemas Microelectromechanical) son dispositivos en miniatura que combinan compoñentes mecánicos e eléctricos nun único chip. Estes dispositivos adoitan necesitar técnicas de unión precisas e fiables para garantir unha funcionalidade adecuada. Os adhesivos MEMS xogan un papel crucial na montaxe e embalaxe destes dispositivos. Proporcionan un vínculo sólido e duradeiro entre os diferentes compoñentes á vez que se adaptan aos requisitos únicos da tecnoloxía MEMS. Aquí tes unha visión xeral dalgúns tipos comúns de adhesivos MEMS:
- Adhesivos epoxi: os adhesivos a base de epoxi son amplamente utilizados en aplicacións MEMS. Ofrecen unha excelente forza de unión e boa resistencia química. Os adhesivos epoxi son normalmente termoestables, requirindo calor ou un axente de curado endurecedor. Proporcionan unha gran integridade estrutural e poden soportar condicións de operación duras.
- Adhesivos de silicona: os adhesivos de silicona son coñecidos pola súa flexibilidade, resistencia ás altas temperaturas e excelentes propiedades de illamento eléctrico. Son especialmente axeitados para dispositivos MEMS que sofren ciclos térmicos ou requiren amortiguación de vibracións. Os adhesivos de silicona ofrecen unha boa adhesión a varios substratos e poden manter as súas propiedades nun amplo intervalo de temperatura.
- Adhesivos acrílicos: os adhesivos a base de acrílico son populares debido aos seus rápidos tempos de curado, boa forza de adhesión e transparencia óptica. Adoitan usarse en aplicacións que requiren claridade visual, como dispositivos MEMS ópticos. Os adhesivos acrílicos proporcionan unha unión fiable e poden unirse con diferentes substratos, incluíndo vidro, metais e plásticos.
- Adhesivos curables UV: os adhesivos curables UV están deseñados para curar rapidamente cando se exponen á luz ultravioleta (UV). Ofrecen tempos de curado rápidos, o que pode mellorar a eficiencia da produción. Os adhesivos UV úsanse habitualmente en aplicacións MEMS onde é necesario un aliñamento preciso porque permanecen líquidos ata que se expoñan á luz UV. Proporcionan unha excelente adhesión e son axeitados para unir compoñentes delicados.
- Adhesivos condutores anisotrópicos (ACA): os adhesivos ACA están deseñados para unir compoñentes microelectrónicos que requiren soporte mecánico e condutividade eléctrica. Consisten en partículas condutoras dispersas dentro dunha matriz adhesiva non condutora. Os adhesivos ACA proporcionan conexións eléctricas fiables mantendo a estabilidade mecánica, polo que son ideais para dispositivos MEMS que impliquen interconexións eléctricas.
- Adhesivos sensibles á presión (PSA): os adhesivos PSA caracterízanse pola súa capacidade para formar un enlace ao aplicar unha lixeira presión. Non requiren calor nin axentes de curado para a unión. Os adhesivos PSA ofrecen facilidade de uso e pódense reposicionar se é necesario. Utilízanse habitualmente en dispositivos MEMS que requiren unión temporal ou onde se desexa unha separación non destrutiva.
Os adhesivos MEMS están dispoñibles en varias formas, incluíndo adhesivos líquidos, películas, pastas e cintas, o que permite flexibilidade na elección da opción máis adecuada para procesos específicos de montaxe e envasado. A selección dun adhesivo particular depende de factores como os materiais do substrato, as condicións ambientais, os requisitos térmicos e as consideracións de condutividade eléctrica.
É esencial considerar a compatibilidade do adhesivo cos materiais MEMS e os requisitos e restricións de procesamento para garantir a integración exitosa e a fiabilidade a longo prazo dos dispositivos MEMS. Os fabricantes adoitan realizar extensas probas e procesos de cualificación para validar o rendemento e a idoneidade do adhesivo para aplicacións MEMS específicas.
Técnicas de unión: Enerxía superficial e adhesión
A enerxía superficial e a adhesión son conceptos fundamentais nas técnicas de unión, e comprender estes conceptos é fundamental para unhas unións sólidas e fiables entre materiais. Aquí tes unha visión xeral da enerxía superficial e da adhesión na unión:
Enerxía de superficie: A enerxía superficial é unha medida da enerxía necesaria para aumentar a superficie dun material. É unha propiedade que determina como interactúa un material con outras substancias. A enerxía superficial xorde das forzas de cohesión entre átomos ou moléculas na superficie dun material. Pódese considerar como a tendencia dun material a minimizar a súa superficie e formar unha forma coa menor cantidade de enerxía superficial.
Os distintos materiais presentan diferentes niveis de enerxía superficial. Algúns materiais teñen unha gran enerxía superficial, o que significa que teñen unha forte afinidade por outras substancias e forman facilmente enlaces. Exemplos de materiais de alta enerxía superficial inclúen metais e materiais polares como o vidro ou certos plásticos. Por outra banda, algúns materiais teñen baixa enerxía superficial, polo que son menos propensos a unirse con outras substancias. Exemplos de materiais de baixa enerxía superficial inclúen polímeros específicos, como o polietileno ou o polipropileno.
Adhesión: A adhesión é o fenómeno de atracción molecular entre diferentes materiais que fai que se peguen entre si cando entran en contacto. A forza mantén dúas superficies xuntas, e a adhesión é esencial para conseguir vínculos sólidos e duradeiros nas técnicas de unión.
A adhesión pódese clasificar en varios tipos segundo os mecanismos implicados:
- Adhesión mecánica: a adhesión mecánica depende do enclavamento ou entrelazamento físico entre superficies. Prodúcese cando dous materiais teñen superficies rugosas ou irregulares que encaixan, creando unha unión sólida. A adhesión mecánica adoita mellorarse mediante adhesivos ou técnicas que aumentan a área de contacto entre os personaxes, como cintas adhesivas con alta conformabilidade.
- Adhesión química: a adhesión química prodúcese cando hai unha interacción química entre as superficies de dous materiais. Implica a formación de enlaces químicos ou forzas de atracción na interface. A adhesión química conséguese habitualmente mediante adhesivos que reaccionan quimicamente coas superficies ou mediante tratamentos de superficie que favorecen a unión química, como o tratamento con plasma ou as imprimacións.
- Adhesión electrostática: a adhesión electrostática depende da atracción entre cargas positivas e negativas en diferentes superficies. Ocorre cando un personaxe se carga eléctricamente, atraendo a superficie con carga oposta. A adhesión electrostática utilízase habitualmente en técnicas de suxeición ou unión electrostáticas que inclúen partículas cargadas.
- Adhesión molecular: a adhesión molecular implica as forzas de van der Waals ou interaccións dipolo-dipolo entre moléculas na interface de dous materiais. Estas forzas intermoleculares poden contribuír á adhesión entre superficies. O enlace molecular é particularmente relevante para materiais con baixa enerxía superficial.
Para conseguir unha adhesión adecuada, é fundamental ter en conta a enerxía superficial dos materiais que se van unir. Os materiais con enerxías de superficie similares tenden a mostrar unha mellor adhesión, porén, cando se unen materiais con enerxías de superficie significativamente diferentes, poden ser necesarios tratamentos de superficie ou promotores de adhesión para mellorar a adhesión.
Beneficios do adhesivo MEMS na miniaturización
Os sistemas microelectromecánicos (MEMS) revolucionaron o campo da miniaturización, permitindo o desenvolvemento de dispositivos compactos e sofisticados en varias industrias. O adhesivo MEMS xoga un papel crucial na integración e montaxe exitosas dos dispositivos MEMS, ofrecendo varios beneficios que contribúen á súa miniaturización. Nesta resposta, describirei as principais vantaxes do adhesivo MEMS na miniaturización en 450 palabras.
- Unión precisa: o adhesivo MEMS ofrece capacidades de unión precisas e fiables, permitindo a fixación segura de microcompoñentes con alta precisión. Con dispositivos miniaturizados, onde o tamaño dos compoñentes individuais adoita estar nunha escala de micras ou submicras, o adhesivo debe ser capaz de formar vínculos fortes e consistentes entre estruturas delicadas. As formulacións de adhesivos MEMS están deseñadas para proporcionar excelentes propiedades de adhesión, garantindo a integridade estrutural e a funcionalidade dos dispositivos MEMS montados.
- Baixa desgasificación: os dispositivos miniaturizados adoitan funcionar en ambientes sensibles ou de alto rendemento, como aplicacións aeroespaciais, automotivas ou médicas. Nestes casos, o adhesivo utilizado debe presentar unha mínima desgasificación para evitar a contaminación, degradación ou interferencia cos compoñentes ou superficies circundantes. Os adhesivos MEMS están formulados para ter baixas características de desgasificación, minimizando a liberación de compostos volátiles e reducindo o risco de efectos adversos sobre o rendemento do dispositivo.
- Estabilidade térmica: os dispositivos MEMS adoitan atoparse con condicións de temperatura variables durante o seu funcionamento. Os materiais adhesivos MEMS están deseñados para mostrar unha excelente estabilidade térmica, soportando temperaturas extremas e ciclos térmicos sen comprometer a forza de unión. Esta característica é esencial nos sistemas miniaturizados onde o espazo é limitado, e o adhesivo debe soportar ambientes térmicos esixentes sen degradación.
- Flexibilidade mecánica: a capacidade de soportar estrés mecánico e vibracións é fundamental para os dispositivos miniaturizados que poden estar sometidos a forzas externas. As formulacións de adhesivos MEMS ofrecen flexibilidade mecánica, o que lles permite absorber e disipar a tensión, reducindo a probabilidade de danos ou fallas estruturais. Esta flexibilidade garante a fiabilidade e durabilidade a longo prazo dos dispositivos MEMS miniaturizados, mesmo en ambientes dinámicos.
- Illamento eléctrico: moitos dispositivos MEMS incorporan compoñentes eléctricos, como sensores, actuadores ou interconexións. Os materiais adhesivos MEMS posúen excelentes propiedades de illamento eléctrico, evitando eficazmente curtocircuítos ou interferencias eléctricas entre diferentes compoñentes. Esta característica é particularmente importante nos dispositivos miniaturizados, onde a proximidade das vías eléctricas pode aumentar o risco de acoplamento eléctrico non desexado.
- Compatibilidade química: as formulacións de adhesivos MEMS están deseñadas para ser químicamente compatibles cunha ampla gama de materiais que se usan habitualmente na fabricación de MEMS, como silicio, polímeros, metais e cerámicas. Esta compatibilidade permite a integración versátil de diferentes compoñentes, permitindo a miniaturización de sistemas MEMS complexos. Ademais, a resistencia química do adhesivo garante a estabilidade e lonxevidade das interfaces unidas, mesmo cando se expón a ambientes operativos duros ou a substancias corrosivas.
- Compatibilidade de procesos: os materiais adhesivos MEMS desenvólvense para ser compatibles con varios procesos de montaxe, incluíndo a unión de chip flip, o envasado a nivel de obleas e a encapsulación. Esta compatibilidade facilita os procesos de fabricación racionalizados de dispositivos miniaturizados, mellorando a produtividade e a escalabilidade. As formulacións de adhesivos MEMS pódense adaptar para cumprir requisitos específicos de procesamento, permitindo unha integración perfecta nas técnicas de fabricación existentes.
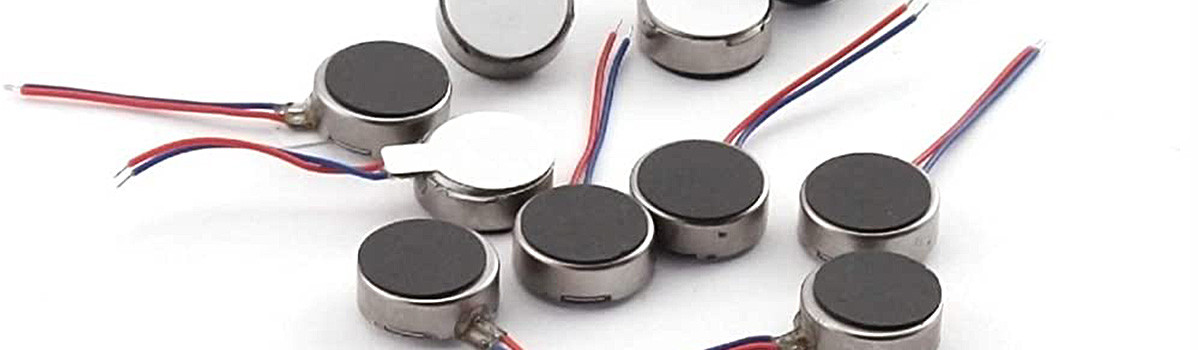
Adhesivo MEMS para aplicacións de sensores
Os sensores MEMS (Sistemas Micro-Electro-Mecánicos) úsanse amplamente en varias aplicacións como a automoción, a electrónica de consumo, a saúde e os sectores industriais. Estes sensores son normalmente dispositivos miniaturizados que combinan compoñentes eléctricos e mecánicos para medir e detectar fenómenos físicos como presión, aceleración, temperatura e humidade.
Un aspecto crítico da fabricación e integración do sensor MEMS é o material adhesivo utilizado para unir o sensor ao substrato obxectivo. O adhesivo garante un rendemento fiable e robusto do sensor, proporcionando estabilidade mecánica, conectividade eléctrica e protección contra factores ambientais.
Cando se trata de seleccionar un adhesivo para aplicacións de sensores MEMS, hai que ter en conta varios factores:
Compatibilidade: o material adhesivo debe ser compatible co sensor e o substrato para garantir a correcta adhesión. Diferentes sensores MEMS poden ter materiais distintos, como silicio, polímeros ou metais, e o adhesivo debe unirse eficazmente con estas superficies.
Propiedades mecánicas: o adhesivo debe posuír propiedades mecánicas adecuadas para acomodar as tensións atopadas durante o funcionamento do sensor MEMS. Debe presentar unha boa resistencia ao corte, resistencia á tracción e flexibilidade para soportar a expansión térmica, as vibracións e os choques mecánicos.
Estabilidade térmica: os sensores MEMS poden estar expostos a temperaturas variables durante o funcionamento. O material adhesivo debe ter unha alta temperatura de transición vítrea (Tg) e manter a súa forza adhesiva nun amplo intervalo de temperatura.
Condutividade eléctrica: nalgunhas aplicacións de sensores MEMS, é necesaria a conectividade eléctrica entre o sensor e o substrato. Un adhesivo cunha boa condutividade eléctrica ou baixa resistencia pode garantir unha transmisión fiable do sinal e minimizar as perdas eléctricas.
Resistencia química: o adhesivo debe resistir a humidade, os produtos químicos e outros factores ambientais para proporcionar estabilidade a longo prazo e protexer os compoñentes do sensor da degradación.
Os adhesivos a base de silicona utilízanse habitualmente en aplicacións de sensores MEMS debido á súa excelente compatibilidade con diversos materiais, baixa emisión de gases e resistencia aos factores ambientais. Ofrecen unha boa adhesión aos dispositivos MEMS baseados en silicio e proporcionan illamento eléctrico se é necesario.
Ademais, os adhesivos a base de epoxi son amplamente utilizados pola súa alta resistencia e excelente estabilidade térmica. Ofrecen unha unión sólida a varios substratos e poden soportar diferentes temperaturas.
Nalgúns casos, utilízanse adhesivos condutores cando se require conexión eléctrica. Estes adhesivos están formulados con recheos condutores como prata ou carbono, o que lles permite proporcionar tanto unión mecánica como condución eléctrica.
É fundamental ter en conta os requisitos específicos da aplicación do sensor MEMS e consultar aos fabricantes ou provedores de adhesivos para seleccionar o adhesivo máis axeitado. Tamén se deben considerar factores como o tempo de curado, a viscosidade e o método de aplicación.
Adhesivo MEMS en dispositivos médicos: avances e desafíos
A tecnoloxía MEMS (Sistemas Micro-Electro-Mecánicos) ten aplicacións importantes en dispositivos médicos, permitindo avances no diagnóstico, seguimento, entrega de medicamentos e dispositivos implantables. Os materiais adhesivos utilizados nos dispositivos médicos baseados en MEMS xogan un papel crucial para garantir a fiabilidade, a biocompatibilidade e o rendemento a longo prazo destes dispositivos. Exploremos os avances e retos dos adhesivos MEMS en dispositivos médicos.
Avances:
- Biocompatibilidade: os materiais adhesivos utilizados en dispositivos médicos deben ser biocompatibles para garantir que non provoquen reaccións adversas nin causen danos ao paciente. Realizáronse avances significativos no desenvolvemento de materiais adhesivos cunha biocompatibilidade mellorada, o que permite unha integración máis segura e fiable dos sensores MEMS en dispositivos médicos.
- Miniaturización: a tecnoloxía MEMS permite a miniaturización de dispositivos médicos, facéndoos máis portátiles, mínimamente invasivos e capaces de monitorizar en tempo real. Os materiais adhesivos deseñados para aplicacións MEMS avanzaron para adaptarse á tendencia da miniaturización, proporcionando unión robusta e fiable en espazos reducidos.
- Substratos flexibles: os dispositivos médicos flexibles e elásticos gañaron protagonismo debido á súa capacidade de adaptarse a superficies curvas e mellorar o confort do paciente. Desenvolvéronse materiais adhesivos con alta flexibilidade e elasticidade para permitir unha unión segura entre os sensores MEMS e os substratos flexibles, ampliando as posibilidades de dispositivos médicos que se poden levar e implantar.
- Biodegradabilidade: en aplicacións médicas específicas onde se usan dispositivos temporais, como sistemas de administración de fármacos ou armazóns de tecidos, os adhesivos biodegradables chamaron a atención. Estes adhesivos poden degradarse gradualmente co paso do tempo, eliminando a necesidade de procedementos de eliminación ou explantación do dispositivo.
Desafíos:
- Probas de biocompatibilidade: garantir a biocompatibilidade dos materiais adhesivos utilizados nos dispositivos médicos baseados en MEMS é un proceso complexo que require probas exhaustivas e cumprimento normativo. Os fabricantes de adhesivos afrontan retos para cumprir os estritos estándares establecidos polos organismos reguladores para garantir a seguridade do paciente.
- Fiabilidade a longo prazo: os dispositivos médicos a miúdo requiren implantación a longo prazo ou uso continuo. Os materiais adhesivos deben mostrar unha unión fiable e manter as súas propiedades mecánicas e adhesivas durante períodos prolongados, tendo en conta as condicións fisiolóxicas e os posibles factores de degradación presentes no organismo.
- Estabilidade química e térmica: os dispositivos médicos baseados en MEMS poden atoparse con ambientes químicos duros, fluídos corporais e flutuacións de temperatura durante o funcionamento. Os adhesivos deben posuír unha excelente resistencia química e estabilidade térmica para manter a súa integridade e forza de unión.
- Compatibilidade de esterilización: os dispositivos médicos deben someterse a procesos de esterilización para eliminar potenciais patóxenos e garantir a seguridade do paciente. Os materiais adhesivos deben ser compatibles cos métodos estándar de esterilización como a autoclave, a esterilización con óxido de etileno (EtO) ou a irradiación gamma sen comprometer as súas propiedades adhesivas.
Adhesivo MEMS para microfluídica: mellorando o control de fluídos
A microfluídica, a ciencia e a tecnoloxía de manipular pequenos volumes de fluídos, gañou unha atención significativa en varios campos, incluíndo a investigación biomédica, o diagnóstico, a administración de fármacos e a análise química. A tecnoloxía MEMS (Sistemas Micro-Electro-Mecánicos) permite un control preciso de fluídos en dispositivos microfluídicos. Os materiais adhesivos utilizados nestes dispositivos son fundamentais para conseguir conexións fluídicas fiables e manter o control do fluído. Exploremos como os adhesivos MEMS melloran o poder fluído na microfluídica e os avances asociados.
- Selado sen fugas: os dispositivos microfluídicos a miúdo requiren múltiples canles, válvulas e depósitos de fluidos. Os materiais adhesivos con excelentes propiedades de selado son fundamentais para conexións sen fugas, evitando a contaminación cruzada e garantindo un control preciso do fluído. Os adhesivos MEMS proporcionan un selado robusto, permitindo o funcionamento fiable dos dispositivos microfluídicos.
- Unión de materiais disímiles: os dispositivos microfluídicos poden consistir en varios materiais como vidro, silicio, polímeros e metais. Os adhesivos MEMS están formulados para ter unha boa adherencia a diferentes materiais de substrato, permitindo unir materiais diferentes. Esta capacidade permite a integración de diversos compoñentes e facilita a fabricación de estruturas microfluídicas complexas.
- Alta compatibilidade química: os adhesivos MEMS utilizados en microfluídica deben mostrar unha alta compatibilidade química cos fluídos e reactivos manipulados. Deben resistir a degradación química e permanecer estables, garantindo a integridade das canles fluídicas e evitando a contaminación. Os adhesivos MEMS avanzados están deseñados para soportar diversos produtos químicos usados habitualmente en aplicacións microfluídicas.
- Características do fluxo óptimo: nos dispositivos microfluídicos, é esencial un control preciso do fluxo do fluído e minimizar as interrupcións do fluxo. Os adhesivos MEMS pódense adaptar para ter propiedades de superficie lisas e uniformes, reducindo a aparición de burbullas, gotículas ou patróns de fluxo irregulares. Esta optimización mellora o control de fluídos e mellora a precisión das operacións microfluídicas.
- Replicación de características a microescala: os dispositivos microfluídicos a miúdo requiren replicar características complexas a microescala, como canles, cámaras e válvulas. Os adhesivos MEMS con baixa viscosidade e altas propiedades de humectación poden encher características de microescala de forma eficaz, garantindo a reprodución precisa de estruturas fluídicas complexas e mantendo o control do fluído a pequenas escalas.
- Resistencia á temperatura e á presión: os dispositivos microfluídicos poden atopar variacións de temperatura e flutuacións de presión durante o funcionamento. Os adhesivos MEMS deseñados para microfluídicos ofrecen estabilidade a altas temperaturas e poden soportar as presións experimentadas no sistema microfluídico, garantindo a durabilidade e fiabilidade do control de fluídos.
- Integración con compoñentes funcionais: os dispositivos microfluídicos adoitan incorporar sensores, electrodos e actuadores adicionais. Os adhesivos MEMS poden facilitar a integración destes elementos funcionais, proporcionando conexións seguras e fiables, posibilitando a funcionalidade multimodal e mellorando o rendemento global dos sistemas microfluídicos.
Os avances na tecnoloxía de adhesivos MEMS seguen mellorando a precisión, fiabilidade e versatilidade do control de fluídos nos dispositivos microfluídicos. A investigación en curso céntrase no desenvolvemento de adhesivos con propiedades adaptadas, como bioadhesivos para microfluídicos biocompatibles, adhesivos sensibles a estímulos para o poder dinámico do fluído e adhesivos de autocuración para mellorar a lonxevidade do dispositivo. Estes avances contribúen a mellorar a microfluídica e a súa ampla gama de aplicacións.
Xestión térmica e adhesivo MEMS: abordando a disipación de calor
A xestión térmica é fundamental para os dispositivos MEMS (Sistemas Micro-Electro-Mecánicos), xa que adoitan xerar calor durante o funcionamento. A disipación de calor eficiente é esencial para manter un rendemento óptimo, evitar o sobrequecemento e garantir a fiabilidade e a lonxevidade dos dispositivos MEMS. Os adhesivos MEMS son vitais para abordar os desafíos de disipación de calor proporcionando solucións eficaces de xestión térmica. Exploremos como os adhesivos MEMS poden axudar a abordar a disipación de calor nos dispositivos MEMS.
- Condutividade térmica: os adhesivos MEMS con alta condutividade térmica poden transferir de forma eficiente a calor dos compoñentes xeradores de calor aos disipadores de calor ou outros mecanismos de refrixeración. Estes adhesivos actúan como pontes térmicas eficaces, reducindo a resistencia térmica e mellorando a disipación da calor.
- Unión aos disipadores de calor: os disipadores de calor úsanse habitualmente nos dispositivos MEMS para disipar a calor. Os adhesivos MEMS proporcionan unha unión fiable entre os compoñentes xeradores de calor e os disipadores de calor, garantindo unha transferencia de calor eficiente ao pía. O material adhesivo debe ter boas propiedades de adhesión para soportar o ciclo térmico e manter unha unión forte a temperaturas elevadas.
- Baixa resistencia térmica: os adhesivos MEMS deben posuír unha baixa resistencia térmica para minimizar a impedancia térmica entre a fonte de calor e a interface de refrixeración. A baixa resistencia térmica permite unha transferencia de calor eficiente e mellora a xestión térmica nos dispositivos MEMS.
- Estabilidade térmica: os dispositivos MEMS poden funcionar a altas temperaturas ou experimentar flutuacións de temperatura. O material adhesivo debe presentar unha excelente estabilidade térmica para soportar estas condicións sen degradar nin perder as súas propiedades adhesivas. Esta estabilidade garante un rendemento constante de disipación de calor durante toda a vida útil do dispositivo MEMS.
- Propiedades dieléctricas: nalgúns casos, os dispositivos MEMS poden requirir illamento eléctrico entre os compoñentes xeradores de calor e os disipadores de calor. Os adhesivos MEMS con propiedades dieléctricas adecuadas poden proporcionar condutividade térmica e illamento eléctrico, permitindo unha disipación eficaz da calor mantendo a integridade eléctrica.
- Capacidade de recheo de ocos: os adhesivos MEMS cunha boa capacidade de recheo de ocos poden eliminar ocos ou ocos entre os compoñentes xeradores de calor e os disipadores de calor, mellorando o contacto térmico e minimizando a resistencia térmica. Esta capacidade garante unha transferencia e disipación de calor máis eficientes dentro do dispositivo MEMS.
- Compatibilidade con materiais MEMS: os dispositivos MEMS incorporan silicio, polímeros, metais e cerámica. Os adhesivos MEMS deben ser compatibles con estes materiais para garantir unha correcta adhesión e xestión térmica. A compatibilidade tamén evita interaccións químicas adversas ou a degradación que afectan o rendemento da disipación de calor.
Os avances na tecnoloxía de adhesivos MEMS céntranse no desenvolvemento de materiais con condutividade térmica mellorada, estabilidade térmica mellorada e propiedades adaptadas para atender os requisitos específicos de xestión térmica. Os investigadores están a explorar novas formulacións de adhesivos, como adhesivos nanocompostos que conteñen cargas condutoras térmicamente, para mellorar aínda máis as capacidades de disipación da calor.
Adhesivo MEMS en sistemas ópticos: garantindo unha aliñación precisa
Nos sistemas ópticos, o aliñamento preciso é fundamental para conseguir un rendemento e unha funcionalidade óptimos. Un compoñente clave que xoga un papel crítico para garantir un aliñamento preciso é o adhesivo de sistemas microelectromecánicos (MEMS). O adhesivo MEMS refírese ao material de unión utilizado para unir dispositivos MEMS, como espellos, lentes ou microactuadores, aos seus respectivos substratos en sistemas ópticos. Permite o posicionamento e o aliñamento precisos destes dispositivos, mellorando así o rendemento xeral e a fiabilidade do sistema visual.
Cando se trata de garantir un aliñamento preciso nos sistemas ópticos, hai que ter en conta varios factores na selección e aplicación de adhesivos MEMS. En primeiro lugar, o material adhesivo debe posuír excelentes propiedades ópticas, como un baixo índice de refracción e unha mínima dispersión ou absorción da luz. Estas características axudan a minimizar as reflexións ou distorsións non desexadas, que poden degradar o rendemento do sistema óptico.
Ademais, o adhesivo MEMS debe presentar unha alta estabilidade mecánica e durabilidade. Os sistemas ópticos a miúdo sofren varias condicións ambientais, incluíndo flutuacións de temperatura, cambios de humidade e tensións mecánicas. O material adhesivo debe soportar estas condicións sen comprometer o aliñamento dos compoñentes ópticos. Ademais, debe ter un baixo coeficiente de expansión térmica para minimizar o impacto do ciclo térmico na estabilidade da aliñación.
Ademais, o adhesivo debe ofrecer un control preciso sobre o proceso de unión. Isto inclúe baixa viscosidade, boas propiedades de humectación e tempo de curado ou endurecemento controlado. A baixa densidade garante unha cobertura adhesiva uniforme e fiable entre o dispositivo MEMS e o substrato, facilitando un mellor contacto e aliñamento. As boas propiedades de humectación permiten unha adhesión adecuada e evitan que se formen ocos ou burbullas de aire. O tempo de curado controlado permite un axuste e un aliñamento suficientes antes de que o adhesivo se fixe.
En termos de aplicación, débese considerar coidadosamente as técnicas de dispensación e manipulación de adhesivos. Os adhesivos MEMS adoitan aplicarse en pequenas cantidades con alta precisión. Pódense empregar sistemas de dispensación automatizados ou ferramentas especializadas para garantir unha aplicación precisa e repetible. As técnicas de manipulación adecuadas, como o uso de salas limpas ou ambientes controlados, axudan a evitar a contaminación que pode afectar negativamente o aliñamento e o rendemento óptico.
Para validar e garantir o aliñamento preciso dos compoñentes ópticos mediante adhesivos MEMS, son esenciais probas exhaustivas e caracterización. Pódense empregar técnicas como a interferometría, a microscopía óptica ou a perfilometría para medir a precisión do aliñamento e avaliar o rendemento do sistema visual. Estas probas axudan a identificar desviacións ou desaxustes, permitindo axustes ou perfeccionamentos para conseguir o aliñamento desexado.
Adhesivo MEMS en electrónica de consumo: habilitando deseños compactos
Os adhesivos MEMS teñen cada vez máis importancia na electrónica de consumo, o que permite o desenvolvemento de deseños compactos e finos para varios dispositivos. Estes adhesivos son fundamentais para unir e asegurar compoñentes dos sistemas microelectromecánicos (MEMS) dentro de dispositivos electrónicos de consumo, como teléfonos intelixentes, tabletas, wearables e electrodomésticos intelixentes. Ao garantir unha fixación fiable e un aliñamento preciso, os adhesivos MEMS contribúen á miniaturización destes dispositivos e á mellora do rendemento.
Unha vantaxe fundamental dos adhesivos MEMS na electrónica de consumo é a súa capacidade de proporcionar unión robusta e duradeira mentres ocupa un espazo mínimo. A medida que os dispositivos electrónicos de consumo fanse máis pequenos e portátiles, os materiais adhesivos deben ofrecer unha alta resistencia de adhesión nunha capa fina. Isto permite deseños compactos sen comprometer a integridade estrutural. Os adhesivos MEMS están deseñados para proporcionar unha excelente adherencia a varios substratos usados habitualmente en produtos electrónicos de consumo, incluíndo metais, vidro e plásticos.
Ademais das súas capacidades de unión, os adhesivos MEMS ofrecen beneficios en termos de xestión térmica. Os dispositivos electrónicos de consumo xeran calor durante o funcionamento e unha disipación eficiente da calor é fundamental para evitar a degradación do rendemento ou a falla dos compoñentes. Os adhesivos MEMS con alta condutividade térmica poden unir compoñentes xeradores de calor, como procesadores ou amplificadores de potencia, a disipadores de calor ou outras estruturas de refrixeración. Isto axuda a disipar a calor de forma eficaz, mellorando a xestión térmica global do dispositivo.
Ademais, os adhesivos MEMS contribúen á fiabilidade e durabilidade dos dispositivos electrónicos de consumo. Estes adhesivos resisten factores ambientais como as variacións de temperatura, a humidade e as tensións mecánicas, e poden soportar as condicións rigorosas que se atopan durante o uso diario, incluíndo caídas, vibracións e ciclos térmicos. Ao proporcionar unha unión robusta, os adhesivos MEMS axudan a garantir a lonxevidade e a fiabilidade dos produtos electrónicos de consumo.
Outra vantaxe dos adhesivos MEMS é a súa compatibilidade cos procesos de fabricación automatizados. Como os dispositivos electrónicos de consumo son producidos en masa, os métodos de montaxe eficientes e fiables son cruciais. Os adhesivos MEMS pódense dispensar con precisión mediante sistemas de dispensación mecánicos, o que permite unha montaxe precisa e de alta velocidade. Os materiais adhesivos están deseñados para ter unhas características de viscosidade e curado adecuadas para a manipulación automatizada, o que permite axilizar os procesos de produción.
Ademais, a versatilidade dos adhesivos MEMS permite o seu uso nunha ampla gama de aplicacións electrónicas de consumo. Xa se trate de conectar sensores, micrófonos, altofalantes ou outros compoñentes MEMS, estes adhesivos ofrecen a flexibilidade para acomodar varios deseños e configuracións de dispositivos. Pódense aplicar a diferentes materiais de substrato e acabados de superficie, proporcionando compatibilidade con diversos produtos electrónicos de consumo.
Adhesivo MEMS para aplicacións aeroespaciais e de defensa
A tecnoloxía de adhesivo MEMS demostrou ser moi valiosa en aplicacións aeroespaciais e de defensa, onde a precisión, a fiabilidade e o rendemento son primordiales. As propiedades únicas dos adhesivos MEMS fan que sexan moi axeitados para unir e asegurar compoñentes de sistemas microelectromecánicos (MEMS) en sistemas aeroespaciais e de defensa, que van desde satélites e avións ata equipos e sensores militares.
Un aspecto crítico das aplicacións aeroespaciais e de defensa é a capacidade dos adhesivos para soportar condicións ambientais extremas. Os adhesivos MEMS están deseñados para ofrecer estabilidade a altas temperaturas, soportando as elevadas temperaturas experimentadas durante misións espaciais, voos supersónicos ou operacións en ambientes duros. Presentan unha excelente resistencia ao ciclo térmico, o que garante a fiabilidade dos compoñentes unidos e o rendemento a longo prazo.
Ademais, os sistemas aeroespaciais e de defensa adoitan enfrontarse a grandes esforzos mecánicos, incluíndo vibracións, choques e forzas de aceleración. Os adhesivos MEMS proporcionan unha estabilidade e durabilidade mecánicas excepcionais, mantendo a integridade da unión nestas condicións esixentes. Isto garante que os compoñentes MEMS, como sensores ou actuadores, permanezan conectados de forma segura e operativos, mesmo en ambientes de traballo desafiantes.
Outro factor crucial nas aplicacións aeroespaciais e de defensa é a redución de peso. Os adhesivos MEMS ofrecen a vantaxe de ser lixeiros, o que permite minimizar o peso total do sistema. Isto é especialmente significativo nas aplicacións aeroespaciais, onde a redución do peso é esencial para a eficiencia do combustible e a capacidade de carga útil. Os adhesivos MEMS permiten unir materiais lixeiros, como compostos de fibra de carbono ou películas finas, mantendo a integridade estrutural.
Ademais, os adhesivos MEMS son cruciais na miniaturización dos sistemas aeroespaciais e de defensa. Estes adhesivos permiten a unión e o posicionamento únicos dos compoñentes MEMS, que adoitan ser pequenos e delicados. Ao facilitar deseños compactos, os adhesivos MEMS contribúen á optimización do espazo dentro de áreas limitadas de avións, satélites ou equipos militares. Isto permite integrar máis funcionalidades e mellorar o rendemento do sistema sen comprometer as restricións de tamaño ou peso.
A capacidade dos adhesivos MEMS para manter un aliñamento preciso tamén é fundamental en aplicacións aeroespaciais e de defensa. O material adhesivo debe garantir un posicionamento preciso, xa sexa aliñando compoñentes ópticos, sensores baseados en MEMS ou microactuadores. Isto é fundamental para conseguir un rendemento óptimo, como a navegación precisa, a orientación ou a adquisición de datos. Os adhesivos MEMS cunha excelente estabilidade dimensional e baixas propiedades de desgasificación axudan a manter o aliñamento durante períodos prolongados, mesmo en ambientes de baleiro ou de gran altitude.
Os estritos estándares de calidade e procedementos de proba son fundamentais nas industrias aeroespacial e de defensa. Os adhesivos MEMS son sometidos a probas rigorosas para garantir o seu cumprimento cos requisitos da industria. Isto inclúe probas mecánicas de resistencia e durabilidade, probas térmicas de estabilidade a temperaturas extremas e probas ambientais de humidade, produtos químicos e resistencia á radiación. Estas probas validan o rendemento e a fiabilidade do material adhesivo, garantindo a súa idoneidade para aplicacións aeroespaciais e de defensa.
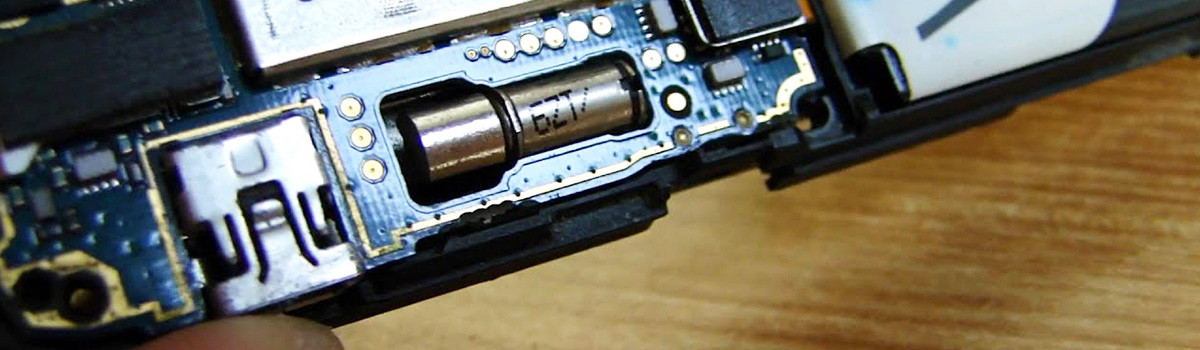
Adhesivo MEMS para a industria do automóbil: mellorando a seguridade e o rendemento
A tecnoloxía de adhesivos MEMS emerxeu como un activo valioso na industria do automóbil, fundamental para mellorar a seguridade, o rendemento e a fiabilidade. Coa crecente complexidade e sofisticación dos sistemas de automoción, os adhesivos MEMS proporcionan solucións cruciais de unión e suxeición para os compoñentes dos sistemas microelectromecánicos (MEMS), contribuíndo á funcionalidade e eficiencia xeral dos vehículos.
Unha das áreas principais onde os adhesivos MEMS melloran a seguridade dos automóbiles é nas aplicacións de sensores. Os sensores MEMS, como os utilizados no despregamento de airbags, control de estabilidade ou sistemas avanzados de asistencia ao condutor (ADAS), requiren un accesorio preciso e fiable. Os adhesivos MEMS garanten a unión segura destes sensores a varios substratos dentro do vehículo, como o chasis ou o marco da carrocería. Isto proporciona un rendemento preciso do sensor, permitindo a adquisición de datos oportuna e precisa para funcións de seguridade críticas.
Ademais, os adhesivos MEMS contribúen á durabilidade e fiabilidade xeral dos compoñentes dos automóbiles. Resisten factores ambientais, incluíndo variacións de temperatura, humidade e vibracións. En aplicacións de automoción onde os detalles están sometidos a tensións continuas e variables, os adhesivos MEMS proporcionan unha unión robusta, evitando que se desprendan ou fallen os compoñentes. Isto mellora a lonxevidade e o rendemento dos sistemas automotivos, o que leva a unha mellora da fiabilidade global do vehículo.
Os adhesivos MEMS tamén axudan á redución de peso e á optimización do deseño na industria do automóbil. A medida que os fabricantes de automóbiles se esforzan por mellorar a eficiencia do combustible e reducir as emisións, úsanse cada vez máis materiais lixeiros. Os adhesivos MEMS ofrecen a vantaxe de ser lixeiros, permitindo unha unión eficiente de materiais lixeiros como compostos ou películas finas. Isto axuda a reducir o peso total do vehículo sen comprometer a integridade estrutural nin os requisitos de seguridade.
Ademais, os adhesivos MEMS contribúen á miniaturización dos sistemas de automoción. A medida que os vehículos incorporan tecnoloxías e funcionalidades máis avanzadas, os deseños compactos vólvense cruciais. Os adhesivos MEMS permiten a fixación e o posicionamento precisos de compoñentes pequenos e delicados, como microsensores ou actuadores. Isto facilita a optimización do espazo dentro do vehículo, permitindo a integración de funcións adicionais mantendo un factor de forma máis pequeno.
En termos de eficiencia de fabricación, os adhesivos MEMS ofrecen vantaxes nos procesos de montaxe dentro da industria do automóbil. Pódense aplicar mediante sistemas de dispensación automatizados, garantindo unha unión precisa e consistente, e isto axiliza os procesos de produción reduce o tempo de montaxe e mellora os rendementos de fabricación. As propiedades dos adhesivos MEMS, como o tempo de curado controlado e as boas propiedades de humectación, contribúen a unha unión eficiente e fiable durante a produción de gran volume.
Por último, os adhesivos MEMS son sometidos a rigorosos procesos de proba e control de calidade para cumprir os estándares da industria do automóbil. As probas mecánicas garanten a resistencia e durabilidade da unión adhesiva, mentres que as probas térmicas avalían a súa estabilidade ante as variacións de temperatura. As probas ambientais avalían a resistencia do adhesivo a produtos químicos, humidade e outros factores. Ao cumprir estes rigorosos requisitos, os adhesivos MEMS proporcionan a fiabilidade e o rendemento necesarios para as aplicacións de automoción.
Adhesivo MEMS biocompatible: habilitación de dispositivos implantables
A tecnoloxía de adhesivos MEMS biocompatibles revolucionou o campo dos dispositivos médicos implantables ao permitir a fixación segura e fiable de compoñentes dos sistemas microelectromecánicos (MEMS) no corpo humano. Estes adhesivos xogan un papel fundamental para garantir o éxito e a funcionalidade dos dispositivos implantables proporcionando solucións de unión biocompatibles compatibles con tecidos e fluídos humanos.
Un dos requisitos críticos dos dispositivos implantables é a biocompatibilidade. Os adhesivos MEMS utilizados nestas aplicacións están coidadosamente formulados para non ser tóxicos e non irritantes para os tecidos circundantes. Sométense a exhaustivas probas de biocompatibilidade para garantir que non induzan reaccións adversas nin danan ao paciente. Estes adhesivos están deseñados para ser estables en ambientes fisiolóxicos e manter a integridade sen liberar substancias nocivas no corpo.
Os dispositivos implantables adoitan necesitar vínculos sólidos e duradeiros para garantir a estabilidade e a funcionalidade durante períodos prolongados. Os adhesivos MEMS biocompatibles ofrecen unha excelente adhesión a varios substratos, incluíndo metais, cerámicas e polímeros biocompatibles usados habitualmente en dispositivos implantables. Estes adhesivos proporcionan unha fixación segura de compoñentes MEMS, como sensores, electrodos ou sistemas de administración de fármacos, ao dispositivo ou ao tecido circundante, o que permite un rendemento preciso e fiable.
Ademais da biocompatibilidade e da forza de unión, os adhesivos MEMS biocompatibles posúen excelentes propiedades mecánicas. Os dispositivos implantables poden experimentar tensións mecánicas, como flexión, estiramento ou compresión, debido ao movemento ou aos procesos naturais dentro do corpo. O material adhesivo debe soportar estas tensións sen comprometer a integridade da unión. Os adhesivos MEMS biocompatibles ofrecen unha alta estabilidade mecánica e flexibilidade, garantindo a durabilidade da unión adhesiva no ambiente dinámico do corpo humano.
Ademais, os adhesivos MEMS biocompatibles permiten o posicionamento e o aliñamento precisos dos compoñentes MEMS dentro do dispositivo implantable. A colocación precisa é fundamental para unha funcionalidade e un rendemento óptimos do dispositivo. O material adhesivo permite o axuste fino e a fixación segura de características, como biosensores ou microactuadores, garantindo un posicionamento e un aliñamento axeitados en relación ao tecido ou órgano obxectivo.
Os dispositivos implantables a miúdo requiren un selado hermético para protexer os compoñentes sensibles dos fluídos corporais circundantes. Os adhesivos MEMS biocompatibles poden proporcionar un selado fiable e biocompatible, evitando a entrada de fluídos ou contaminantes no dispositivo. Estes adhesivos presentan excelentes propiedades de barreira, que garanten a integridade a longo prazo do dispositivo implantable e minimizan o risco de infección ou fallo do dispositivo.
Finalmente, os adhesivos MEMS biocompatibles son sometidos a probas rigorosas para garantir a súa idoneidade para aplicacións implantables. Están sometidos a avaliacións de biocompatibilidade segundo estándares internacionais, incluíndo avaliacións de citotoxicidade, sensibilización e irritación. Os materiais adhesivos tamén son probados para determinar a estabilidade en condicións fisiolóxicas, incluíndo variacións de temperatura, pH e humidade. Estas probas garanten a seguridade, a fiabilidade e o rendemento a longo prazo do adhesivo dentro do dispositivo implantable.
Consideracións de proba e fiabilidade de adhesivos MEMS
As probas de adhesivo MEMS e as consideracións de fiabilidade son cruciais para garantir o rendemento e a lonxevidade dos dispositivos de sistemas microelectromecánicos (MEMS). Estes dispositivos adoitan funcionar en ambientes esixentes e están sometidos a varias tensións e condicións. As probas exhaustivas e a consideración coidadosa dos factores de fiabilidade son esenciais para validar o rendemento do adhesivo e garantir a fiabilidade dos dispositivos MEMS.
Un aspecto crítico das probas de adhesivo é a caracterización mecánica. As unións adhesivas deben ser avaliadas pola súa resistencia mecánica e durabilidade para soportar as tensións encontradas durante a vida útil do dispositivo. Probas como as probas de corte, tracción ou pelado miden a resistencia do adhesivo a diferentes forzas mecánicas. Estas probas proporcionan información sobre a capacidade do adhesivo para manter unha unión forte e soportar esforzos mecánicos, garantindo a fiabilidade do dispositivo MEMS.
Outro factor crucial nas probas de adhesivo é o rendemento térmico. Os dispositivos MEMS poden experimentar variacións significativas de temperatura durante o funcionamento. Os materiais adhesivos deben ser probados para garantir a súa estabilidade e integridade nestas condicións de temperatura. As probas de ciclos térmicos, onde o adhesivo está sometido a ciclos de temperatura repetidos, axudan a avaliar a súa capacidade para soportar a expansión e contracción térmicas sen delaminación nin degradación. Ademais, as probas de envellecemento térmico avalían a estabilidade e fiabilidade a longo prazo do adhesivo baixo unha exposición prolongada a temperaturas elevadas.
As probas ambientais tamén son esenciales para avaliar a resistencia do adhesivo a varios factores ambientais. A humidade, os produtos químicos e os gases que se atopan habitualmente nas aplicacións do mundo real poden afectar o rendemento e a integridade do adhesivo. As probas de envellecemento acelerado, onde o enlace está exposto a duras condicións ambientais durante un período prolongado, axudan a simular os efectos a longo prazo destes factores. Estes ensaios proporcionan información valiosa sobre a resistencia do adhesivo á degradación ambiental, garantindo a súa fiabilidade en diferentes condicións de funcionamento.
As consideracións de fiabilidade van máis alá das probas, incluíndo factores como os modos de falla de adhesión, os mecanismos de envellecemento e o rendemento a longo prazo. Comprender os modos de falla da unión adhesiva é fundamental para deseñar dispositivos MEMS robustos. As técnicas de análise de avarías, como a microscopía e a caracterización de materiais, axudan a identificar mecanismos de falla, como a delaminación do adhesivo, a falla cohesiva ou a falla da interface. Este coñecemento orienta a mellorar as formulacións de adhesivos e os procesos de unión para mitigar os riscos de falla.
Os mecanismos de envellecemento tamén poden afectar o rendemento a longo prazo do adhesivo e factores como a absorción de humidade, as reaccións químicas ou a exposición aos UV poden degradar o adhesivo. Como se mencionou anteriormente, as probas de envellecemento acelerado axudan a avaliar a resistencia do adhesivo a estes mecanismos de envellecemento. Os fabricantes poden deseñar dispositivos MEMS cunha vida útil prolongada e un rendemento fiable ao comprender e abordar os posibles problemas de envellecemento.
Ademais, as consideracións de fiabilidade inclúen a selección de materiais adhesivos axeitados para aplicacións específicas de MEMS. Os diferentes adhesivos teñen propiedades variables, como a viscosidade, o tempo de curado e a compatibilidade cos substratos, e estes factores deben considerarse coidadosamente para garantir unha unión óptima e unha fiabilidade a longo prazo. Os fabricantes de adhesivos proporcionan datos técnicos e directrices de aplicación para axudar na selección de materiais, tendo en conta os requisitos específicos dos dispositivos MEMS e as condicións de funcionamento.
Procesos e técnicas de fabricación de adhesivos MEMS
Os procesos e técnicas de fabricación de adhesivos MEMS implican unha serie de pasos para producir materiais adhesivos de alta calidade para aplicacións de sistemas microelectromecánicos (MEMS). Estes procesos garanten a consistencia, fiabilidade e rendemento do adhesivo, cumprindo os requisitos específicos dos dispositivos MEMS. Abaixo amósanse os pasos críticos implicados na fabricación de adhesivos MEMS:
- Formulación: o primeiro paso na fabricación de adhesivos é a formulación do material adhesivo. Isto implica seleccionar a resina base e os aditivos axeitados para acadar as propiedades desexadas, como resistencia de adhesión, flexibilidade, estabilidade térmica e biocompatibilidade. A formulación considera os requisitos de aplicación, os materiais do substrato e as condicións ambientais.
- Mestura e dispersión: unha vez que se determina a formulación do adhesivo, o seguinte paso é a mestura e dispersión dos ingredientes. Normalmente, isto faise usando equipos de mestura especializados para garantir unha mestura homoxénea. O proceso de mestura é crucial para a distribución uniforme dos aditivos e para manter as propiedades consistentes en todo o material adhesivo.
- Aplicación do adhesivo: o adhesivo prepárase para a súa aplicación despois das fases de formulación e mestura. A técnica de aplicación depende dos requisitos específicos e das características do adhesivo. Os métodos de aplicación estándar inclúen dispensación, serigrafía, revestimento por centrifugado ou pulverización. O obxectivo é aplicar uniformemente o adhesivo ás superficies ou compoñentes desexados con precisión e control.
- Curado: o curado é un paso crítico na fabricación de adhesivos, transformando o adhesivo dun estado líquido ou semilíquido a un sólido. O curado pódese conseguir mediante varias técnicas como o curado por calor, UV ou químico. O proceso de curado activa reaccións de reticulación dentro do adhesivo, desenvolvendo propiedades de resistencia e adhesión.
- Control de calidade: ao longo do proceso de fabricación do adhesivo, aplícanse medidas estritas de control de calidade para garantir a consistencia e fiabilidade do material adhesivo. Isto inclúe parámetros de control como a viscosidade, a forza adhesiva, o tempo de curado e a composición química. Os procedementos de control de calidade axudan a identificar desviacións ou inconsistencias, permitindo axustes ou accións correctoras para manter a integridade do produto.
- Embalaxe e almacenamento: unha vez que o adhesivo está fabricado e comprobada a calidade, encádase e prepárase para o seu almacenamento ou distribución. O embalaxe axeitado protexe o adhesivo de factores externos como a humidade, a luz ou os contaminantes. As condicións de almacenamento do adhesivo, incluídas a temperatura e a humidade, considéranse coidadosamente para manter a estabilidade e o rendemento do adhesivo durante a súa vida útil.
- Optimización e ampliación do proceso: os fabricantes de adhesivos esfórzanse continuamente por optimizar o proceso de fabricación e escalar a produción para satisfacer a crecente demanda. Isto implica perfeccionamento dos procesos, automatización e melloras de eficiencia para garantir unha calidade consistente, reducir os custos de produción e mellorar a produtividade xeral.
Paga a pena notar que os procesos e técnicas de fabricación específicos poden variar dependendo do tipo de adhesivo, a aplicación prevista e as capacidades do fabricante. Os fabricantes de adhesivos adoitan ter métodos propietarios e experiencia para adaptar o proceso de fabricación ás súas formulacións específicas de produtos e aos requisitos do cliente.
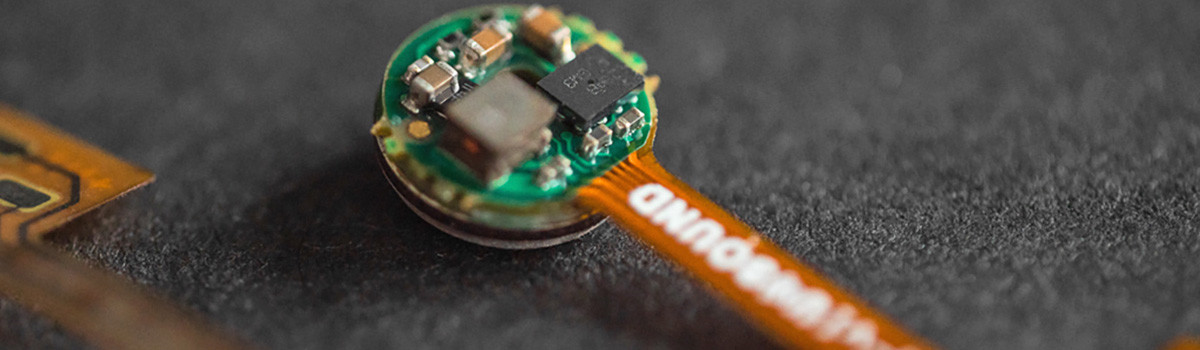
Retos na unión adhesiva MEMS: compatibilidade de materiais e xestión de tensións
A unión adhesiva MEMS presenta varios desafíos, especialmente no que se refire á compatibilidade dos materiais e á xestión do estrés. Estes desafíos xorden debido á diversa gama de materiais utilizados nos dispositivos de sistemas microelectromecánicos (MEMS) e ás complexas condicións de tensión que experimentan. Superar estes desafíos é fundamental para garantir unións adhesivas fiables e duradeiras nas aplicacións MEMS.
A compatibilidade dos materiais é unha consideración crítica na unión adhesiva MEMS. Os dispositivos MEMS adoitan estar formados por diversos materiais, como silicio, vidro, polímeros, metais e cerámica, cada un con propiedades únicas. O adhesivo debe ser compatible con estes materiais para establecer unha unión forte e fiable. A selección de adhesivos implica considerar factores como os coeficientes de expansión térmica, a adhesión a diferentes materiais e a compatibilidade coas condicións de funcionamento do dispositivo.
As diferenzas nos coeficientes de expansión térmica poden levar a tensións e tensións importantes durante o ciclo de temperatura, causando delaminación ou rachaduras na interface adhesiva. Xestionar estas tensións térmicas require unha selección coidadosa do material e consideracións de deseño. Os adhesivos con menor módulo e coeficientes de expansión térmica máis próximos aos materiais unidos poden axudar a reducir o desajuste de tensión e mellorar a fiabilidade a longo prazo da unión.
Outro desafío na unión adhesiva MEMS é xestionar as tensións mecánicas experimentadas polo dispositivo. Os dispositivos MEMS poden estar suxeitos a varias tensións mecánicas, incluíndo flexión, estiramento e compresión. Estes esforzos poden ser consecuencia das condicións ambientais, o funcionamento do dispositivo ou os procesos de montaxe. Os materiais adhesivos deben posuír a suficiente resistencia e flexibilidade para soportar estes esforzos sen delaminación ou falla.
Para abordar os retos de xestión do estrés, pódense empregar varias técnicas. Un enfoque utiliza adhesivos compatibles ou elastoméricos que absorben e distribúen as tensións pola área unida. Estes adhesivos proporcionan unha maior flexibilidade, permitindo que o dispositivo resista deformacións mecánicas sen comprometer a unión adhesiva. Ademais, a optimización do deseño dos dispositivos MEMS, como a incorporación de funcións de alivio da tensión ou a introdución de interconexións flexibles, pode axudar a aliviar as concentracións de tensión e minimizar o impacto nas unións adhesivas.
Asegurar unha preparación adecuada da superficie tamén é fundamental para abordar os desafíos da compatibilidade dos materiais e da xestión do estrés. Os tratamentos de superficie, como a limpeza, a rugosidade ou a aplicación de imprimacións ou promotores de adhesión, poden mellorar a adhesión entre o adhesivo e os materiais do substrato. Estes tratamentos promoven unha mellor humectación e unión na interface, mellorando a compatibilidade do material e a distribución de tensións.
Ademais, o control preciso sobre a aplicación do adhesivo é vital para unha unión exitosa. Factores como a técnica de dispensación de adhesivo, as condicións de curado e os parámetros do proceso poden influír na calidade e o rendemento da unión adhesiva. A consistencia no grosor do adhesivo, a cobertura uniforme e o curado axeitado son esenciais para lograr unións fiables que poidan soportar os desafíos de compatibilidade de materiais e as tensións mecánicas.
Superar os retos de compatibilidade de materiais e xestión de estrés na unión adhesiva MEMS require un enfoque multidisciplinar que implique a ciencia dos materiais, o deseño de dispositivos e a optimización de procesos. A colaboración entre os fabricantes de adhesivos, os deseñadores de dispositivos MEMS e os enxeñeiros de procesos é esencial para abordar estes desafíos de forma eficaz. Mediante unha coidadosa selección de materiais, consideracións de deseño, preparación da superficie e control do proceso, a unión adhesiva en aplicacións MEMS pódese optimizar para lograr unións fiables e duradeiros, garantindo o rendemento e a lonxevidade dos dispositivos MEMS.
Avances na tecnoloxía de adhesivos MEMS: nanomateriais e adhesivos intelixentes
Os avances na tecnoloxía de adhesivos MEMS foron impulsados pola necesidade de mellorar o rendemento, a miniaturización e a funcionalidade mellorada nas aplicacións de sistemas microelectromecánicos (MEMS). Dúas áreas importantes de avance na tecnoloxía de adhesivos MEMS inclúen a integración de nanomateriais e o desenvolvemento de adhesivos intelixentes. Estes avances ofrecen capacidades únicas e un rendemento mellorado na conexión de dispositivos MEMS.
Os nanomateriais desempeñaron un papel crucial no avance da tecnoloxía de adhesivos MEMS. A integración de nanomateriais, como nanopartículas, nanofibras ou nanocompostos, en formulacións de adhesivos mellorou as propiedades e as funcionalidades. Por exemplo, a adición de nanopartículas pode mellorar a resistencia mecánica, a estabilidade térmica e a condutividade eléctrica do material adhesivo. As nanofibras como os nanotubos de carbono ou o grafeno poden proporcionar un reforzo mellorado e propiedades eléctricas ou térmicas melloradas. O uso de nanocompostos en adhesivos ofrece unha combinación única de propiedades, incluíndo alta resistencia, flexibilidade e compatibilidade con varios materiais de substrato. A integración de nanomateriais en adhesivos MEMS permite o desenvolvemento de solucións de unión de alto rendemento para aplicacións MEMS esixentes.
Outro avance significativo na tecnoloxía de adhesivos MEMS é o desenvolvemento de adhesivos intelixentes. Os adhesivos innovadores están deseñados para mostrar propiedades ou funcionalidades únicas en resposta a estímulos externos, como temperatura, luz ou estrés mecánico. Estes adhesivos poden sufrir cambios reversibles ou irreversibles nas súas propiedades, o que permite respostas dinámicas e adaptabilidade en diferentes condicións de funcionamento. Por exemplo, os adhesivos con memoria de forma poden cambiar de forma ou recuperar a súa forma orixinal ao exporse a variacións de temperatura, ofrecendo capacidades de unión reversible. Os adhesivos activados pola luz pódense activar para unirse ou separarse mediante lonxitudes de onda específicas de luz, proporcionando un control preciso e reelaborabilidade. Os adhesivos innovadores poden habilitar funcionalidades avanzadas nos dispositivos MEMS, como a reconfigurabilidade, a autocuración ou as capacidades de detección, mellorando o seu rendemento e versatilidade.
A integración de nanomateriais e tecnoloxías adhesivas innovadoras ofrece beneficios sinérxicos nas aplicacións MEMS. Os nanomateriais pódense incorporar a adhesivos intelixentes para mellorar aínda máis as súas propiedades e funcionalidades. Por exemplo, os nanomateriais pódense usar para desenvolver adhesivos nanocompostos sensibles aos estímulos que presentan un comportamento único baseado en estímulos externos. Estes sistemas adhesivos poden proporcionar capacidades de autodetección, permitindo a detección de estrés mecánico, temperatura ou outros cambios ambientais. Tamén poden ofrecer propiedades de autocuración, onde o adhesivo pode reparar microfechas ou danos tras a exposición a condicións específicas. A combinación de nanomateriais e tecnoloxías adhesivas innovadoras abre novas posibilidades para os dispositivos MEMS avanzados cun rendemento, durabilidade e adaptabilidade mellorados.
Estes avances na tecnoloxía de adhesivos MEMS teñen implicacións en varias industrias. Permiten o desenvolvemento de dispositivos MEMS máis pequenos e fiables cunha funcionalidade mellorada. Na asistencia sanitaria, os adhesivos mellorados con nanomateriais poden apoiar a fabricación de dispositivos implantables cunha biocompatibilidade mellorada e unha fiabilidade a longo prazo. Os adhesivos innovadores poden permitir que se auto-reparan ou se reconfiguren dispositivos en produtos electrónicos de consumo, mellorando a experiencia do usuario e a lonxevidade do produto. As unións melloradas con nanomateriais poden ofrecer solucións de unión lixeiras con resistencia e durabilidade melloradas en aplicacións automotivas e aeroespaciais.
Consideracións ambientais: adhesivo MEMS para a sustentabilidade
As consideracións ambientais son cada vez máis importantes no desenvolvemento e uso de materiais adhesivos para dispositivos de sistemas microelectromecánicos (MEMS). A medida que a sustentabilidade e a conciencia ecolóxica seguen gañando forza, é fundamental abordar o impacto dos materiais adhesivos MEMS ao longo do seu ciclo de vida. Aquí tes algúns factores clave que hai que ter en conta ao pretender a sustentabilidade nas aplicacións de adhesivos MEMS:
- Selección de materiais: a elección de materiais adhesivos respectuosos co medio ambiente é o primeiro paso cara á sustentabilidade. Optar por adhesivos de baixo impacto ambiental, como formulacións a base de auga ou sen disolventes, pode axudar a reducir as emisións e minimizar o uso de substancias perigosas. Ademais, a selección de bonos cunha vida útil máis longa ou derivados de recursos renovables pode contribuír aos esforzos de sustentabilidade.
- Procesos de fabricación: avaliar e optimizar os procesos de fabricación asociados á produción de adhesivos MEMS é vital para a sustentabilidade. Empregar técnicas de fabricación eficientes enerxéticamente, minimizar a xeración de residuos e implementar prácticas de reciclaxe ou reutilización poden reducir significativamente a pegada ambiental da fabricación de adhesivos. A optimización do proceso tamén pode levar a un aforro de recursos e unha maior eficiencia, contribuíndo aos obxectivos de sustentabilidade.
- Consideracións ao final da vida útil: comprender as implicacións ao final da vida útil dos materiais adhesivos MEMS é esencial para a sustentabilidade. Os adhesivos compatibles cos procesos de reciclaxe ou que se eliminan facilmente durante a desmontaxe do dispositivo favorecen a circularidade e reducen os residuos. Considerar a reciclabilidade ou a biodegradabilidade dos materiais adhesivos permite unha eliminación responsable co medio ambiente ou a recuperación de compoñentes valiosos.
- Avaliación de impacto ambiental: a realización dunha avaliación exhaustiva do impacto ambiental dos materiais adhesivos MEMS axuda a identificar os riscos ecolóxicos potenciais e a avaliar o desempeño da sustentabilidade. As metodoloxías de avaliación do ciclo de vida (ACV) pódense empregar para analizar o impacto ambiental dos materiais adhesivos ao longo de todo o seu ciclo de vida, incluíndo a extracción de materias primas, a fabricación, o uso e a eliminación. Esta avaliación proporciona información sobre os puntos quentes e as áreas de mellora, orientando o desenvolvemento de solucións adhesivas máis sostibles.
- Cumprimento da normativa: o cumprimento das normativas e estándares relevantes relacionados coa protección ambiental é fundamental para aplicacións de adhesivos sostibles. O cumprimento de leis como REACH (Rexistro, Evaluación, Autorización e Restricción de Substancias Químicas) garante o uso e a manipulación seguras dos materiais adhesivos, reducindo os posibles danos ao medio ambiente e á saúde humana. Ademais, a adhesión aos sistemas de etiquetaxe ecolóxica ou certificacións pode demostrar un compromiso coa sustentabilidade e proporcionar transparencia aos usuarios finais.
- Investigación e innovación: a investigación e innovación continuadas na tecnoloxía de adhesivos poden impulsar a sustentabilidade nas aplicacións MEMS. Explorar materiais adhesivos alternativos, como adhesivos de base biolóxica ou de inspiración biolóxica, pode ofrecer opcións máis sostibles. Desenvolver materiais adhesivos con reciclabilidade, biodegradabilidade ou menor impacto ambiental mellorada pode levar a dispositivos MEMS máis ecolóxicos e sostibles.
Tendencias futuras no desenvolvemento de adhesivos MEMS
Nos últimos anos, a tecnoloxía de Sistemas Microelectromecánicos (MEMS) gañou unha atención significativa e converteuse nunha parte integrante de varias industrias, incluíndo a electrónica, a saúde, a automoción e a aeroespacial. Os dispositivos MEMS normalmente consisten en compoñentes mecánicos e eléctricos miniaturizados que requiren unha unión precisa para garantir a fiabilidade e a funcionalidade. Os materiais adhesivos son fundamentais na montaxe de MEMS, xa que proporcionan unións fortes e duradeiras entre as pezas.
De cara ao futuro, pódense identificar varias tendencias no desenvolvemento de adhesivos para aplicacións MEMS:
- Miniaturización e integración: espérase que a tendencia de miniaturización nos dispositivos MEMS continúe, levando á demanda de materiais adhesivos que poidan unir compoñentes máis pequenos e complexos. Os adhesivos con capacidades de alta resolución e a capacidade de crear enlaces fortes en superficies a microescala serán cruciais para fabricar dispositivos MEMS miniaturizados. Ademais, os materiais adhesivos que permiten a integración de múltiples compoñentes nun único dispositivo MEMS terán unha gran demanda.
- Fiabilidade e durabilidade melloradas: os dispositivos MEMS adoitan estar expostos a duras condicións de funcionamento, incluíndo flutuacións de temperatura, humidade e estrés mecánico. Os futuros desenvolvementos de adhesivos centraranse en mellorar a fiabilidade e durabilidade das unións en tales condicións. Os adhesivos con maior resistencia ao ciclo térmico, á humidade e ás vibracións mecánicas serán esenciais para garantir o rendemento e a estabilidade a longo prazo dos dispositivos MEMS.
- Curado a baixa temperatura: moitos materiais MEMS, como polímeros e compoñentes electrónicos delicados, son sensibles ás altas temperaturas. En consecuencia, hai unha demanda crecente de adhesivos que poidan curar a baixas temperaturas sen comprometer a forza de unión. Os adhesivos de curado a baixa temperatura permitirán a montaxe de compoñentes MEMS sensibles á temperatura e reducirán o risco de danos térmicos durante a fabricación.
- Compatibilidade con varios substratos: os dispositivos MEMS adoitan implicar unir diferentes materiais, como metais, cerámicas e polímeros. Os materiais adhesivos que presenten unha excelente adhesión a varios substratos serán moi buscados. Ademais, o desenvolvemento de adhesivos que poidan unir materiais diferentes con coeficientes de expansión térmica non coincidentes axudará a mitigar o potencial de falla inducida polo estrés nos dispositivos MEMS.
- Adhesivos biocompatibles: o campo dos MEMS biomédicos avanza rapidamente, con aplicacións na administración de medicamentos, enxeñería de tecidos e dispositivos implantables. Os materiais adhesivos, biocompatibles e non tóxicos serán fundamentais para estas aplicacións, garantindo a seguridade e compatibilidade dos dispositivos MEMS cos sistemas biolóxicos. Os desenvolvementos futuros centraranse en deseñar e sintetizar adhesivos que presenten unha excelente biocompatibilidade mantendo unha forte adhesión e propiedades mecánicas.
- Adhesivos desprendibles e reutilizables: nalgunhas aplicacións MEMS, é desexable a capacidade de liberar e reposicionar ou reutilizar compoñentes despois da unión. Os adhesivos desprendibles e reutilizables proporcionarán flexibilidade durante os procesos de fabricación e montaxe de MEMS, permitindo axustes e correccións sen danar as pezas ou substratos.
Conclusión: o adhesivo MEMS como forza motriz no avance da microelectrónica
Os materiais adhesivos MEMS convertéronse nunha forza impulsora no avance da microelectrónica, xogando un papel fundamental na montaxe e na funcionalidade dos dispositivos MEMS. Estes pequenos compoñentes mecánicos e eléctricos requiren unha unión especial para garantir a fiabilidade e o rendemento. Espérase que as tendencias futuras no desenvolvemento de adhesivos MEMS melloren aínda máis as capacidades e aplicacións destes dispositivos.
A miniaturización e a integración seguirán impulsando os límites da tecnoloxía MEMS. Os materiais adhesivos con capacidades de alta resolución serán cruciais para unir compoñentes máis pequenos e complexos. Ademais, os adhesivos que permiten a integración de múltiples compoñentes nun único dispositivo MEMS impulsarán a innovación neste campo.
A fiabilidade e a durabilidade son primordiales nas aplicacións MEMS, xa que estes dispositivos están expostos a duras condicións de funcionamento. Os futuros desenvolvementos de adhesivos mellorarán o ciclo térmico, a humidade e a resistencia ao estrés mecánico. O obxectivo é garantir o rendemento e a estabilidade a longo prazo dos dispositivos MEMS en varios ambientes.
Os adhesivos de curado a baixa temperatura abordarán a sensibilidade dos materiais MEMS ás altas temperaturas. O curado a temperaturas máis baixas sen comprometer a forza de unión facilitará a montaxe de compoñentes sensibles á temperatura, reducindo o risco de danos térmicos durante a fabricación.
A compatibilidade con múltiples substratos é crucial na montaxe de MEMS, xa que moitas veces interveñen diferentes materiais. Os materiais adhesivos que presentan unha excelente adhesión a unha ampla gama de substratos permitirán a unión de materiais diferentes e axudarán a mitigar a falla inducida polo estrés nos dispositivos MEMS.
Nos MEMS biomédicos, a demanda de adhesivos biocompatibles está a crecer rapidamente. Estes adhesivos deben ser non tóxicos e compatibles cos sistemas biolóxicos mantendo unha forte adhesión e propiedades mecánicas. O desenvolvemento destes enlaces ampliará as aplicacións dos MEMS en áreas como a entrega de medicamentos, a enxeñería de tecidos e os dispositivos implantables.
Por último, os adhesivos liberables e reutilizables proporcionarán flexibilidade durante os procesos de fabricación e montaxe de MEMS. A capacidade de liberar e reposicionar compoñentes ou incluso reutilizalos despois da unión permite axustes e correccións sen danar as pezas ou substratos.
En conclusión, os materiais adhesivos MEMS están impulsando avances na microelectrónica ao permitir a montaxe e a funcionalidade dos dispositivos MEMS. Os desenvolvementos futuros en adhesivos MEMS mellorarán aínda máis a miniaturización, a fiabilidade, o curado a baixa temperatura, a compatibilidade do substrato, a biocompatibilidade e a flexibilidade dos procesos de ensamblaxe. Estes avances desbloquearán novas posibilidades e aplicacións para a tecnoloxía MEMS, revolucionando varias industrias e configurando o futuro da microelectrónica.