Adhesivo semiconductor
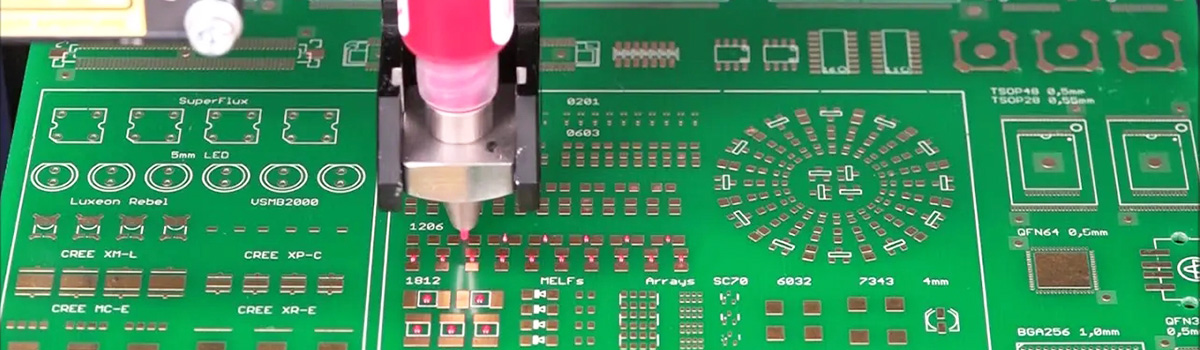
O adhesivo semicondutor é un compoñente crítico na fabricación e montaxe de dispositivos semicondutores, como microprocesadores, chips de memoria e outros circuítos integrados. Estes adhesivos proporcionan capacidades de unión robustas e fiables e protección contra factores ambientais e estrés térmico. Coa crecente demanda de dispositivos semicondutores máis pequenos, rápidos e complexos, as solucións de adhesivos fiables e de alto rendemento volvéronse máis importantes que nunca. Este artigo explorará os distintos tipos, aplicacións e desafíos dos adhesivos semicondutores, destacando o seu papel crucial para permitir a miniaturización e o alto rendemento dos dispositivos semicondutores.
Tipos de adhesivos semicondutores
Os adhesivos semicondutores xogan un papel crucial nos procesos de fabricación e montaxe de dispositivos electrónicos. Estes adhesivos están deseñados para proporcionar unha unión robusta e fiable entre varios compoñentes en dispositivos semicondutores, como chips, substratos e paquetes. Poden soportar condicións ambientais duras, ciclos térmicos e esforzos mecánicos. No mercado están dispoñibles varios tipos de adhesivos semicondutores, cada un con propiedades e aplicacións únicas. Exploremos algúns dos adhesivos semicondutores de uso común:
- Adhesivos epoxi: os adhesivos a base de epoxi son amplamente utilizados en aplicacións de semicondutores debido á súa excelente forza de unión, alta resistencia química e boas propiedades de illamento eléctrico. Ofrecen unha forte adhesión a varios materiais, incluíndo metais, cerámicas e plásticos. Os adhesivos epoxi curan a temperatura ambiente ou baixo calor, formando unha unión ríxida e duradeira.
- Adhesivos de silicona: os adhesivos a base de silicona son coñecidos pola súa flexibilidade, estabilidade térmica e resistencia a temperaturas extremas. Dependendo da formulación, poden soportar un amplo rango de temperaturas de -50 °C a 200 °C ou incluso superior. Os adhesivos de silicona presentan excelentes propiedades de illamento eléctrico e úsanse habitualmente en aplicacións nas que a xestión térmica é crucial, como os dispositivos electrónicos de potencia.
- Adhesivos acrílicos: os adhesivos acrílicos proporcionan un curado rápido, alta forza de adhesión e boa resistencia á temperatura e á humidade. Son coñecidos pola súa versatilidade e poden unirse a varios substratos, incluíndo metais, plásticos e vidro. Os adhesivos acrílicos, como a electrónica de automóbiles e a montaxe LED, úsanse a miúdo en aplicacións que requiren alta resistencia e durabilidade.
- Adhesivos de poliuretano: os adhesivos a base de poliuretano ofrecen un equilibrio entre flexibilidade e resistencia. Proporcionan unha boa adherencia a varios materiais, incluíndo metais, plásticos e vidro. Os adhesivos de poliuretano son resistentes ao impacto, ás vibracións e aos ciclos térmicos, polo que son axeitados para aplicacións nas que interveñen tensións mecánicas, como a electrónica da automoción e a aeroespacial.
- Adhesivos condutores: os adhesivos condutores están formulados con recheos condutores, como prata, cobre ou carbono, para permitir a condutividade eléctrica nas unións unidas. Utilízanse habitualmente para a conexión de matrices de dispositivos electrónicos, a unión de chip flip e os compoñentes de interconexión. Os adhesivos condutores ofrecen baixa resistencia e excelente adhesión, proporcionando conexións eléctricas fiables.
- Adhesivos de recheo inferior: os adhesivos de recheo inferior están deseñados explícitamente para aplicacións de chip flip-chip, onde o chip está montado boca abaixo sobre un substrato. Estes adhesivos flúen baixo o chip durante o curado, enchendo os ocos entre o chip e o substrato. Os adhesivos de recheo inferior proporcionan soporte mecánico, melloran a condutividade térmica e evitan os fallos das xuntas de soldadura causados polo estrés térmico.
- Adhesivos curables UV: os adhesivos curables UV curan rapidamente cando se exponen á luz ultravioleta. Ofrecen alta forza de unión, claridade óptica e resistencia química. Os adhesivos curables por UV úsanse a miúdo en aplicacións que requiren un procesamento rápido e unión de precisión, como o conxunto de pantallas, fibras ópticas e dispositivos optoelectrónicos.
Adhesivos epoxi: a opción máis común
Os adhesivos epoxi son amplamente recoñecidos como un dos tipos máis comúns e versátiles. Son amplamente utilizados en varias industrias e aplicacións debido á súa excepcional forza de unión, durabilidade e versatilidade. Aquí, exploraremos por que os adhesivos epoxi son a opción máis común dentro dun número limitado de palabras.
- Resistencia de unión: os adhesivos epoxi ofrecen unha forza de unión excepcional, polo que son axeitados para varios materiais. Xa se trate de metais, plásticos, cerámica, madeira ou compostos, os adhesivos epoxi proporcionan unións sólidas e fiables, garantindo a lonxevidade e estabilidade das pezas unidas.
- Versatilidade: os adhesivos epoxi presentan unha excelente versatilidade nos seus métodos de aplicación e opcións de curado. Están dispoñibles en diferentes formas, como sistemas dunha ou dúas partes, o que permite flexibilidade no seu uso. Ademais, os adhesivos epoxi pódense curar a temperatura ambiente ou con calor, dependendo dos requisitos específicos da aplicación.
- Resistencia química: os adhesivos epoxi posúen unha resistencia química excepcional, polo que son idóneos para aplicacións onde a exposición a produtos químicos ou disolventes agresivos é unha preocupación. Manteñen a súa integridade estrutural mesmo cando están expostos a diversos produtos químicos, aceites, combustibles e ácidos, o que garante a durabilidade dos conxuntos unidos.
- Resistencia á temperatura: os adhesivos epoxi poden soportar un amplo rango de temperaturas, polo que son axeitados para aplicacións que requiren resistencia a altas ou baixas temperaturas. Xa sexa na industria automotriz, aeroespacial ou electrónica, os adhesivos epoxi proporcionan unha unión fiable mesmo a temperaturas extremas.
- Capacidade de recheo de espazos: outra vantaxe dos adhesivos epoxi é a súa capacidade para cubrir ocos e irregularidades entre as superficies de acoplamento. Esta característica garante unha unión forte mesmo cando as superficies de contacto non están perfectamente combinadas, proporcionando unha maior integridade estrutural ás pezas unidas.
- Propiedades mecánicas: os adhesivos epoxi ofrecen excelentes propiedades mecánicas, como unha alta resistencia á tracción e ao corte e unha boa resistencia ao impacto. Estas propiedades fanos axeitados para aplicacións de soporte de carga, onde o adhesivo necesita soportar un esforzo ou impacto significativo sen comprometer a forza de unión.
- Illamento eléctrico: os adhesivos epoxi presentan excelentes propiedades de illamento eléctrico, polo que son populares en aplicacións electrónicas e eléctricas. Proporcionan un illamento eficaz, protexendo os compoñentes electrónicos sensibles de correntes eléctricas ou curtocircuítos.
- Facilidade de uso: os adhesivos epoxi son relativamente fáciles de usar e aplicar. Pódense dispensar con precisión, permitindo unha aplicación controlada e minimizando o desperdicio. Ademais, os adhesivos epoxi teñen un tempo aberto longo, proporcionando tempo de traballo suficiente para montar as pezas antes de que o adhesivo se fixe.
Adhesivos condutores: habilitando a conectividade eléctrica
Os adhesivos condutores son un tipo especializado de material adhesivo con propiedades tanto adhesivas como condutoras. Están deseñados para permitir a conectividade eléctrica en varias aplicacións onde os métodos tradicionais de soldadura poden non ser viables ou desexables. Estes adhesivos ofrecen numerosas vantaxes, incluíndo facilidade de uso, compatibilidade co medio ambiente e versatilidade.
Un dos principais beneficios dos adhesivos condutores é a súa facilidade de uso. A diferenza da soldadura, que require calor e pode ser complexa, os adhesivos condutores pódense aplicar simplemente distribuíndo ou estendendo o adhesivo nas superficies desexadas. Isto fai que sexan axeitados para unha ampla gama de usuarios, desde profesionais ata afeccionados e elimina a necesidade de equipamento especializado.
A compatibilidade co medio ambiente é outra vantaxe dos adhesivos condutores. A diferenza da soldadura, que normalmente implica soldaduras a base de chumbo, os adhesivos condutores pódense formular con materiais non tóxicos. Isto fai que sexan máis respectuosos co medio ambiente e máis seguros de manexar, reducindo os riscos para a saúde dos usuarios. Ademais, a ausencia de chumbo fai que estes adhesivos cumpran coa normativa que restrinxe o uso de substancias perigosas.
Os adhesivos condutores tamén ofrecen versatilidade nos materiais que poden unir. Poden unir materiais condutores como metais e materiais non condutores como plásticos, cerámicas e vidro. Esta ampla compatibilidade permite crear conxuntos multimateriais con conectividade eléctrica integrada, abrindo novas posibilidades de deseño en varias industrias.
A condutividade destes adhesivos conséguese incluíndo cargas condutoras, como partículas de prata ou de carbono, dentro da matriz adhesiva. Estes recheos forman vías condutoras que permiten o fluxo de corrente eléctrica a través das superficies unidas. A elección do material de recheo e a concentración pódense adaptar para cumprir requisitos específicos de condutividade, o que permite axustar con precisión as propiedades eléctricas do adhesivo.
As aplicacións de adhesivos condutores están moi estendidas. Utilízanse habitualmente na industria electrónica para unir compoñentes, substituíndo ou complementando procesos de soldadura. Os adhesivos condutores son particularmente beneficiosos para unir compoñentes electrónicos delicados que non poden soportar as altas temperaturas asociadas á soldadura. Tamén se utilizan para fabricar circuítos flexibles, etiquetas RFID e pantallas táctiles, onde a súa capacidade de unirse a varios substratos é vantaxosa.
Na industria do automóbil, os adhesivos condutores ensamblan sensores, unidades de control e sistemas de iluminación. As súas capacidades de unión non mecánica reducen os puntos de concentración de tensión, mellorando a fiabilidade e a lonxevidade da conexión eléctrica. Ademais, os adhesivos condutores permiten reducir o peso dos vehículos eliminando a necesidade de conectores de metais pesados.
Ademais de aplicacións electrónicas e automotrices, os adhesivos condutores atopan uso en dispositivos médicos, compoñentes aeroespaciais e mesmo en produtos de consumo como produtos electrónicos portátiles. A súa versatilidade, facilidade de uso e vantaxes ambientais fan que sexan atractivos para os deseñadores e enxeñeiros industriais.
Adhesivos de fixación de matrices: unión de chips de semicondutores a substratos
Os adhesivos de fijación de matrices desempeñan un papel crucial na industria de semicondutores ao proporcionar un método fiable e eficiente para unir chips de semicondutores a substratos. Estes adhesivos serven de interface entre o chip e o substrato, garantindo unha conexión segura e eléctricamente condutora.
A función principal dos adhesivos adheridos á matriz é proporcionar soporte mecánico e conectividade eléctrica entre o chip e o substrato. Deben posuír excelentes propiedades de adhesión para garantir que o chip permanece firmemente unido ao substrato en varias condicións de funcionamento, incluíndo ciclos térmicos, estrés mecánico e exposición ambiental.
Un requisito crítico para os adhesivos adhesivos é a súa capacidade para soportar altas temperaturas. Durante os procesos de ensamblaxe de chips, como o refluxo de soldadura ou a unión por termocompresión, o adhesivo debe manter a súa integridade e forza de adhesión. Normalmente, os adhesivos adhesivos están deseñados para soportar temperaturas superiores a 200 °C, garantindo a fiabilidade da unión.
Os adhesivos de fijación de matrices clasifícanse habitualmente en adhesivos a base de epoxi e de soldadura. Os adhesivos a base de epoxi son materiais termoestables que se curan ao exponerse á calor. Ofrecen unha excelente adherencia, alta condutividade térmica e illamento eléctrico. Por outra banda, os adhesivos a base de soldadura consisten nunha aliaxe metálica que se funde durante o proceso de unión. Proporcionan un camiño eléctrico de baixa resistencia e alta condutividade térmica, o que os fai axeitados para aplicacións de disipación de alta potencia.
A selección do adhesivo adherido depende de varios factores, incluíndo a aplicación específica, as condicións de funcionamento e o material do substrato. O adhesivo debe ser compatible cos materiais aos que se vai unir, garantindo unha correcta adhesión e evitando calquera interacción adversa. O adhesivo tamén debe ter boas características de dispensación e fluxo para facilitar a unión e minimizar os baleiros ou ocos entre o chip e o substrato.
Para conseguir unha unión fiable, a preparación da superficie é esencial. O substrato e as superficies das virutas deben limparse a fondo para eliminar contaminantes, óxidos e outras impurezas que impidan a adhesión. As técnicas de tratamento de superficies, como a limpeza con plasma, o gravado químico ou a limpeza por ultrasóns, úsanse habitualmente para mellorar o rendemento de unión do adhesivo.
Unha vez que se aplica o adhesivo de fijación da matriz, o chip colócase coidadosamente e aliñase sobre o substrato. Pódese empregar presión ou calor para garantir a humectación e o contacto adecuados entre o adhesivo e as superficies que se están a unir. A continuación, o adhesivo cura ou solidifica, completando o proceso de unión.
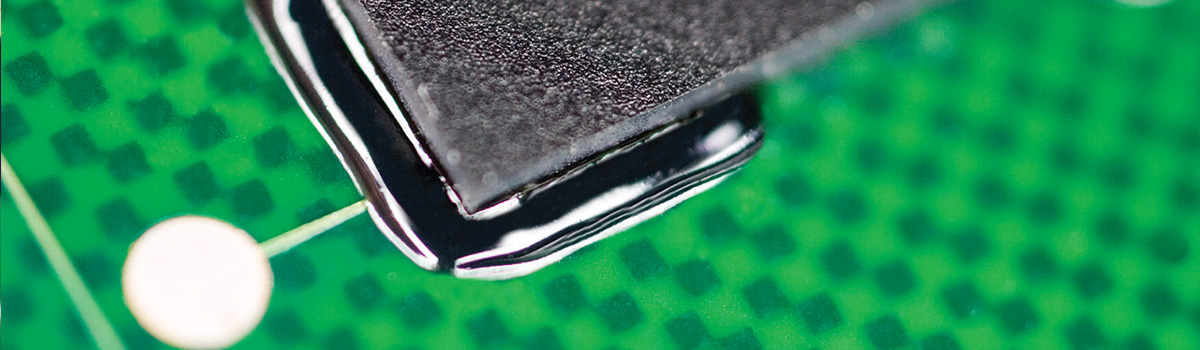
Adhesivos de recheo inferior: protección contra a tensión térmica
Os adhesivos de recheo son materiais esenciais utilizados nos envases electrónicos para protexer contra o estrés térmico. Proporcionan reforzo mecánico e melloran a fiabilidade dos dispositivos electrónicos minimizando o impacto do ciclo térmico e dos choques mecánicos.
O estrés térmico é unha preocupación importante nos conxuntos electrónicos debido á falta de coincidencia dos coeficientes de expansión térmica (CTE) entre diferentes materiais. Cando un dispositivo sofre flutuacións de temperatura, os materiais se expanden e contraen a diferentes velocidades, desenvolvendo tensións que poden fallar. Os adhesivos de underfill axudan a mitigar este problema actuando como un amortiguador entre o chip e o substrato, absorbendo e distribuíndo o estrés causado polo ciclo térmico.
A función principal dos adhesivos de recheo inferior é reforzar as unións de soldadura que conectan o chip de circuíto integrado (IC) co substrato. Durante a fabricación, o chip está montado no substrato mediante soldadura, o que crea unha unión entre os dous compoñentes. Non obstante, o desaxuste CTE entre o chip e o substrato pode causar concentracións de tensión nas unións de soldadura. Os adhesivos de recheo inferior inxéctanse no espazo entre o chip e o substrato, enchendo os ocos e formando unha capa robusta e elástica. Esta capa reduce a concentración de tensión, mellorando a integridade mecánica global do conxunto.
Os adhesivos de recheo inferior tamén ofrecen unha excelente condutividade térmica, fundamental para disipar a calor xerada polos compoñentes electrónicos. A disipación de calor eficiente é vital para evitar o sobreenriquecido e manter o rendemento e a lonxevidade do dispositivo. Ao facilitar a transferencia de calor do chip ao substrato, os adhesivos de recheo inferior axudan a manter unha temperatura de funcionamento estable e evitan que o estrés térmico dane o IC.
Ademais, os adhesivos de recheo inferior protexen contra a humidade e os contaminantes. Os dispositivos electrónicos adoitan estar expostos a ambientes duros, incluíndo humidade e diversos produtos químicos, que poden degradar o seu rendemento e fiabilidade. Os materiais de recheo inferior son unha barreira, evitando a entrada de humidade e a difusión de substancias nocivas no paquete de chip. Esta protección axuda a manter o rendemento eléctrico e prolonga a vida útil do dispositivo.
Adhesivos Flip Chip: habilitando a miniaturización
Os adhesivos flip chip son cruciais para permitir a miniaturización en varios dispositivos electrónicos. A medida que avanza a tecnoloxía, hai unha demanda constante de máquinas máis pequenas, lixeiras e potentes. A unión flip-chip xurdiu como un método preferido para conseguir interconexións de alta densidade nestes dispositivos. Estes adhesivos facilitan a conexión eléctrica e mecánica directa entre o chip e o substrato, ofrecendo numerosos beneficios á miniaturización.
Unha das vantaxes críticas dos adhesivos flip-chip é a súa capacidade para reducir o tamaño total dos paquetes electrónicos. As técnicas tradicionais de unión de fíos requiren espazo para bucles de fíos, o que limita o tamaño do dispositivo alcanzable. Pola contra, a unión flip-chip elimina a necesidade de bucles de arame, reducindo significativamente o tamaño do paquete. A menor pegada é significativa nos dispositivos electrónicos portátiles, como teléfonos intelixentes, tabletas e wearables, onde o espazo é un premio.
Ademais, os adhesivos flip-chip permiten un maior rendemento do dispositivo. A conexión eléctrica directa entre o chip e o substrato reduce a lonxitude do camiño do sinal e a inductancia, mellorando o rendemento eléctrico. Isto é especialmente importante para aplicacións de alta velocidade, como microprocesadores e chips de memoria, onde é fundamental minimizar o atraso e a perda de sinal. A unión de chip flip contribúe a velocidades de transferencia de datos máis rápidas, un menor consumo de enerxía e unha maior fiabilidade do dispositivo ao reducir os efectos parasitarios.
Ademais, os adhesivos flip-chip ofrecen excelentes capacidades de xestión térmica. Xestionar a disipación de calor convértese nun reto importante a medida que os compoñentes electrónicos se fan máis potentes e densamente embalados. A unión do chip flip permite unha unión directa do chip ao substrato, o que mellora a eficiencia da transferencia de calor. Isto permite unha disipación eficiente da calor, evitando o sobreenriquecido e mellorando a fiabilidade e a vida útil do dispositivo. A xestión térmica eficaz é esencial para dispositivos de alto rendemento como as unidades de procesamento gráfico (GPU) e as unidades de procesamento central (CPU).
Outra vantaxe dos adhesivos flip-chip é a súa estabilidade mecánica. Os materiais adhesivos utilizados na unión de chip flip proporcionan interconexións sólidas e fiables. A ausencia de enlaces de fío elimina o risco de rotura ou fatiga do fío, garantindo a integridade mecánica a longo prazo. A robustez dos adhesivos flip-chip fainos axeitados para aplicacións sometidas a duras condicións de funcionamento, como a electrónica do automóbil ou os sistemas aeroespaciais.
Ademais, os adhesivos flip-chip admiten interconexións de alta densidade. Coa conexión flip-chip, é posible conseguir un gran número de conexións nunha pequena área, o que permite a integración de máis funcionalidades nun espazo limitado. Isto é especialmente beneficioso para dispositivos electrónicos complexos que requiren numerosas conexións de entrada/saída, como circuítos integrados, sensores ou sistemas microelectromecánicos (MEMS). As interconexións de alta densidade habilitadas por adhesivos flip-chip contribúen á miniaturización global do dispositivo.
Adhesivos de encapsulación: protección de compoñentes sensibles
Os adhesivos de encapsulación son esenciais para protexer os compoñentes electrónicos sensibles de varios factores ambientais, estrés mecánico e exposición química. Estes adhesivos proporcionan unha barreira protectora, encapsulando os elementos e garantindo a súa lonxevidade e fiabilidade. Este artigo explorará a importancia dos adhesivos de encapsulación e o seu papel na salvagarda de compoñentes sensibles.
Os compoñentes electrónicos sensibles, como circuítos integrados, sensores e cableados delicados, son vulnerables aos danos causados pola humidade, o po, as flutuacións de temperatura e o impacto físico. Os adhesivos de encapsulación ofrecen unha solución fiable formando unha capa protectora arredor destes compoñentes. Actúan como unha barreira, protexendo os compoñentes de elementos externos que poidan comprometer a funcionalidade ou provocar fallos prematuros.
Unha das propiedades críticas dos adhesivos de encapsulación é a súa capacidade para resistir a entrada de humidade. A humidade pode causar corrosión, curtocircuítos e fugas eléctricas, o que provoca un mal funcionamento do dispositivo. Os adhesivos de encapsulación proporcionan unha excelente resistencia á humidade, evitando a entrada de auga ou vapor de humidade nos compoñentes sensibles. Esta característica é crucial en aplicacións expostas a ambientes ricos en humidade ou alta humidade, como a electrónica de automóbiles ou os equipos industriais ao aire libre.
Ademais da protección contra a humidade, os adhesivos de encapsulación tamén ofrecen unha excelente resistencia química. Poden soportar a exposición a diversos produtos químicos, incluíndo disolventes, ácidos, bases e axentes de limpeza. Esta resistencia garante que os compoñentes sensibles non se vexan afectados polas interaccións químicas, preservando a súa integridade e funcionalidade.
Os adhesivos de encapsulación tamén proporcionan protección mecánica aos compoñentes sensibles. Actúan como amortiguadores, disipando as tensións mecánicas e as vibracións que poden danar os compoñentes. Esta función é vital en aplicacións sometidas a movementos frecuentes, como aeroespacial, automoción e electrónica de consumo.
Ademais, os adhesivos de encapsulación ofrecen excelentes propiedades de xestión térmica. Posúen unha alta condutividade térmica, o que permite unha disipación eficiente da calor dos compoñentes sensibles. Estes adhesivos axudan a manter as temperaturas óptimas de funcionamento disipando a calor de forma eficaz, evitando o estrés térmico e garantindo a fiabilidade a longo prazo.
Outra vantaxe dos adhesivos de encapsulación é a súa capacidade para mellorar a integridade estrutural dos conxuntos electrónicos. O encapsulamento e a unión de varios compoñentes proporcionan resistencia e estabilidade adicional ao sistema global. Esta característica é especialmente beneficiosa en aplicacións onde a robustez mecánica é esencial, como os sistemas de control industrial ou a electrónica de grao militar.
Os adhesivos de encapsulación veñen en varias formulacións para atender a diferentes requisitos de aplicación. Poden ser adhesivos líquidos que curan a temperatura ambiente ou compostos termocondutores usados para aplicacións de alta potencia. A selección do adhesivo axeitado depende de factores como o nivel de protección desexado, as condicións de funcionamento, o tempo de curado e o proceso de montaxe.
Adhesivos de baixa desgasificación: críticos para aplicacións espaciais
Os adhesivos de baixa emisión de gases xogan un papel fundamental nas aplicacións espaciais nas que é esencial manter un ambiente limpo e controlado. A desgasificación refírese á liberación de compostos orgánicos volátiles (COV) e outros contaminantes dos materiais, incluídos os adhesivos, en condicións de baleiro ou de baixa presión. A desgasificación pode danar equipos sensibles, sistemas ópticos e superficies das naves espaciais en condicións extremas do espazo, onde non hai presión atmosférica. Polo tanto, o uso de adhesivos de baixa emisión de gases é primordial para garantir o rendemento fiable e a lonxevidade das misións espaciais.
Unha das principais preocupacións coa desgasificación é a deposición de contaminantes en superficies críticas, como lentes ópticas e sensores. As impurezas poden formar unha fina película nestas superficies, reducindo a súa transparencia, degradando o rendemento e interferindo coas medicións científicas. No caso dos sistemas ópticos, incluso unha lixeira redución da apertura pode afectar significativamente a calidade das imaxes e os datos recollidos do espazo. Os adhesivos de baixa emisión de gases están deseñados para minimizar a liberación de compostos volátiles, reducindo o risco de contaminación e preservando a funcionalidade dos instrumentos sensibles.
Outro aspecto crítico dos adhesivos de baixa emisión de gases é o seu impacto nos compoñentes electrónicos e nos circuítos. Os COV liberados durante a desgasificación poden corroer ou degradar sistemas electrónicos delicados, o que provoca un mal funcionamento ou un fallo total. Isto é especialmente preocupante para as naves espaciais, onde os compoñentes electrónicos están expostos ao baleiro do espazo, ás variacións extremas de temperatura e á radiación. Os adhesivos de baixa emisión de gases están formulados con materiais de baixa presión de vapor, minimizando a liberación de compostos corrosivos e protexendo a integridade dos sistemas electrónicos.
Ademais, a desgasificación tamén pode ameazar a saúde dos astronautas e a habitabilidade das naves espaciais tripuladas. En ambientes pechados como as cápsulas espaciais ou as estacións espaciais, a acumulación de COV pola desgasificación pode crear unha atmosfera desagradable ou perigosa. Os adhesivos de baixa emisión de gases axudan a mitigar este risco ao reducir a emisión de compostos volátiles, garantindo un ambiente seguro e saudable para os astronautas durante as súas misións.
Para conseguir baixas propiedades de desgasificación, os adhesivos utilizados en aplicacións espaciais son sometidos a rigorosos procesos de proba e cualificación. Estes procesos implican someter os adhesivos a condicións espaciales simuladas, incluíndo cámaras de baleiro, temperaturas extremas e diversas tensións ambientais. Os adhesivos que cumpren os estritos requisitos de baixa emisión de gases están certificados e aprobados para o seu uso en misións espaciais.
Adhesivos de unión a nivel de obleas: reducindo custos e mellorando o rendemento
A unión a nivel de obleas é un proceso crucial na industria de semicondutores, onde se interconectan múltiples chips ou obleas para formar circuítos integrados complexos. Tradicionalmente, este proceso de unión implicaba golpes de soldadura ou técnicas de unión de fíos, que requiren un aliñamento preciso e unha unión individual de cada chip, o que resulta en custos máis altos e menores rendementos. Non obstante, os avances nas tecnoloxías de adhesivos abriron o camiño para adhesivos de unión a nivel de obleas que ofrecen unha redución de custos e un maior rendemento na fabricación de semicondutores.
Os adhesivos de unión a nivel de obleas están deseñados para proporcionar unha unión fiable e robusta entre as obleas ou chips a nivel de obleas, eliminando a necesidade de procesos de unión individuais. Estes adhesivos aplícanse normalmente como unha fina capa entre as obleas e curan en condicións controladas para acadar a forza de unión desexada. Aquí están algúns factores clave que contribúen á redución de custos e á mellora do rendemento:
- Simplificación do proceso: os adhesivos de unión a nivel de obleas simplifican o proceso de unión ao permitir a unión simultánea de múltiples chips ou obleas nun só paso. Isto elimina a necesidade dun aliñamento complicado e a unión individual de cada chip, aforrando tempo e reducindo os custos de produción. Ademais, o adhesivo pódese aplicar uniformemente nunha gran área, garantindo unha adhesión consistente na oblea.
- Alta resistencia e fiabilidade de unión: os adhesivos de unión a nivel de obleas ofrecen excelentes propiedades de adhesión, o que resulta nunha alta resistencia de unión entre as obleas. Esta conexión robusta garante unha interconectividade fiable e minimiza o risco de delaminación ou fallo durante os pasos posteriores de fabricación ou o funcionamento do dispositivo. As propiedades mecánicas, térmicas e eléctricas do adhesivo pódense adaptar para cumprir requisitos específicos de aplicación, mellorando aínda máis a fiabilidade.
- Materiais rendibles: os adhesivos de unión a nivel de obleas adoitan utilizar materiais rendibles en comparación coas técnicas de unión tradicionais. Estes adhesivos pódense formular utilizando unha variedade de polímeros, como epoxi, poliimidas ou acrilatos, que están facilmente dispoñibles e ofrecen un bo rendemento a un custo razoable. Escoller entre varios materiais permite aos fabricantes optimizar a selección de adhesivos en función do rendemento, o prezo e a compatibilidade con diferentes substratos.
- Mellora do rendemento: os adhesivos de unión a nivel de obleas contribúen a mellorar o rendemento na fabricación de semicondutores. A aplicación uniforme do adhesivo na oblea minimiza o risco de ocos, atrapamento de aire ou unión irregular, o que pode provocar defectos ou fallos. Ademais, a eliminación da unión de chips individuais reduce as posibilidades de desalineación ou danos durante o proceso de unión, resultando en maiores rendementos e reducindo as taxas de chatarra.
- Compatibilidade con tecnoloxías de envasado avanzadas: os adhesivos de unión a nivel de obleas son compatibles con varias tecnoloxías de envasado avanzadas, como o envasado a escala de chip a nivel de oblea (WLCSP), o envasado a nivel de oblea (FOWLP) ou os procesos de integración 3D. Estes adhesivos permiten a integración de múltiples chips ou compoñentes diversos nun factor de forma compacto, facilitando a miniaturización e posibilitando unha funcionalidade avanzada en dispositivos electrónicos.

Adhesivos de curado UV: unión rápida e precisa
Os adhesivos de curado UV son adhesivos revolucionarios que ofrecen capacidades de unión rápida e precisa. Eles gañaron popularidade en varias industrias debido ás súas propiedades únicas e vantaxes sobre os adhesivos tradicionais. Os adhesivos de curado UV normalmente están compostos por un monómero, un fotoiniciador e un estabilizador. Cando se expón á luz ultravioleta (UV), estes adhesivos sofren unha reacción fotoquímica que conduce a un rápido curado e unión.
Un dos beneficios críticos dos adhesivos de curado UV é o seu rápido tempo de curado. A diferenza dos adhesivos tradicionais que requiren horas ou incluso días para curarse completamente, os adhesivos de curado UV curan en segundos ou minutos. Este tempo de curado rápido aumenta significativamente a eficiencia da produción e reduce os tempos de espera da cadea de montaxe, o que supón un importante aforro de custos para os fabricantes. A formación de unión instantánea tamén permite a manipulación inmediata e o procesamento posterior dos compoñentes unidos.
A capacidade de unión precisa dos adhesivos de curado UV é outra vantaxe significativa. O adhesivo permanece líquido ata que se expón á luz UV, proporcionando moito tempo para o aliñamento e o posicionamento das pezas a unir. Unha vez que o adhesivo está exposto á luz UV solidificase rapidamente, creando unha unión sólida e duradeira. Esta capacidade de unión precisa beneficia ás aplicacións que requiren alta precisión e tolerancias estreitas, como electrónica, óptica e dispositivos médicos.
Os adhesivos de curado UV tamén ofrecen unha excelente resistencia e durabilidade. O adhesivo curado forma unha forte unión que pode soportar varios factores ambientais, incluíndo temperaturas extremas, humidade e produtos químicos. Isto garante a lonxevidade e fiabilidade dos compoñentes unidos, facendo que os adhesivos de curado UV sexan axeitados para aplicacións esixentes.
Ademais, os adhesivos de curado UV non teñen disolventes e teñen baixas emisións de compostos orgánicos volátiles (COV). A diferenza dos adhesivos a base de disolventes que requiren secado e liberan vapores potencialmente nocivos, os adhesivos de curado UV son respectuosos co medio ambiente e son seguros. Isto convérteos nunha opción atractiva para as industrias que pretenden reducir a súa pegada ambiental e cumprir coa normativa.
A versatilidade dos adhesivos de curado UV é outro aspecto notable. Poden unir varios materiais, incluíndo vidro, metais, plásticos, cerámica e mesmo substratos diferentes. Esta ampla compatibilidade fai que os adhesivos de curado UV sexan axeitados para diversas aplicacións nas industrias automoción, aeroespacial, electrónica e médica.
Adhesivos de pasta condutora: habilitando produtos electrónicos flexibles e impresos
Os adhesivos de pasta condutor xurdiron como unha tecnoloxía habilitante fundamental para o desenvolvemento de produtos electrónicos flexibles e impresos. Estes materiais innovadores combinan as propiedades dos adhesivos tradicionais coa condutividade dos metais, abrindo novas posibilidades para a fabricación e integración de dispositivos electrónicos en diversos substratos.
Unha das principais vantaxes dos adhesivos en pasta condutora é a súa capacidade de proporcionar tanto adherencia mecánica como condutividade eléctrica. Os adhesivos tradicionais son normalmente illantes, o que limita o seu uso en aplicacións electrónicas. Os adhesivos en pasta condutora, pola contra, conteñen partículas condutoras como prata, cobre ou carbono que facilitan o fluxo de electricidade. Esta dobre funcionalidade permítelles servir tanto de adhesivo como de vía condutora, polo que son ideais para unir compoñentes electrónicos ou crear trazos condutores en substratos flexibles.
A flexibilidade dos adhesivos de pasta condutora é outra característica crítica que os fai axeitados para a electrónica flexible. Estes adhesivos poden manter a súa condutividade eléctrica mesmo cando están sometidos a flexión, estiramento ou torsión. Esta flexibilidade é crucial para aplicacións como dispositivos wearable, pantallas flexibles e electrónica conforme, onde os circuítos ríxidos tradicionais serían pouco prácticos ou imposibles de implementar. Os adhesivos de pasta condutor permiten a creación de conexións eléctricas robustas e fiables en substratos flexibles, garantindo o rendemento e a durabilidade dos dispositivos electrónicos flexibles.
Ademais, os adhesivos en pasta condutor son compatibles con varias técnicas de impresión, como a serigrafía, a impresión inxección de tinta e a impresión flexográfica. Esta compatibilidade permite a fabricación de alto volume e rendible de produtos electrónicos impresos. Os procesos de impresión permiten a deposición de adhesivos en pasta condutora en patróns precisos, o que permite crear circuítos complexos e deseños electrónicos cun mínimo desperdicio de material. A capacidade de imprimir trazos condutores directamente sobre substratos flexibles simplifica o proceso de fabricación e reduce o tempo de produción, facendo da electrónica impresa unha solución viable para a fabricación a gran escala.
Os adhesivos en pasta condutora tamén ofrecen vantaxes en termos de xestión térmica. A presenza de partículas condutoras nestes adhesivos facilita a disipación da calor xerada polos compoñentes electrónicos. Esta propiedade é fundamental para garantir a fiabilidade e o rendemento dos dispositivos que xeran calor importante, como a electrónica de potencia ou os LED de alta potencia. Usando adhesivos de pasta condutora como interfaces térmicas, a calor pódese transferir de forma eficiente desde o compoñente xerador de calor ata un disipador de calor, mellorando o rendemento e a lonxevidade do dispositivo en xeral.
Pastas de soldadura: alternativa á unión adhesiva
As pastas de soldar, tamén coñecidas como pastas de soldar, ofrecen unha alternativa á unión adhesiva en varias aplicacións. Aínda que a unión adhesiva implica o uso de adhesivos para unir materiais, as pastas de soldar utilizan un mecanismo diferente para lograr unha unión robusta e fiable. Nesta resposta, exploraremos as pastas de soldar como alternativa á unión adhesiva nun límite de 450 palabras.
As pastas de soldar consisten nunha mestura de partículas de aliaxe metálica, fundente e un aglutinante. As partículas de aliaxe metálica normalmente consisten en estaño, chumbo, prata ou unha combinación destes metais. O cambio axuda no proceso de soldadura eliminando os óxidos das superficies metálicas e favorecendo a humectación e a adhesión. O aglutinante mantén a pasta xunta e permite que se aplique facilmente.
Unha das principais vantaxes das pastas de soldar fronte á unión adhesiva é a resistencia e durabilidade da unión. A soldadura crea unha unión metalúrxica entre os materiais unidos, dando como resultado unha unión forte que pode soportar diversas tensións mecánicas, térmicas e eléctricas. A unión soldada adoita ser máis robusta e fiable que as unións adhesivas, que poden degradarse co paso do tempo ou en determinadas condicións.
As pastas de soldar tamén ofrecen un proceso de unión máis rápido e eficiente. A pasta pódese aplicar con precisión ás áreas desexadas e a unión pódese formar quentando o conxunto á temperatura de fusión da soldadura. Este proceso adoita ser máis rápido que a unión adhesiva, que pode requirir tempos de curado ou secado. Ademais, as pastas de soldar permiten a unión simultánea de múltiples compoñentes, reducindo o tempo de montaxe e aumentando a produtividade.
Outra vantaxe é a versatilidade das pastas de soldar na unión de diferentes materiais. A unión adhesiva pode ter limitacións ao unir materiais diferentes ou materiais con diferentes coeficientes de expansión térmica. As pastas de soldar poden formar xuntas fiables entre diversos materiais, incluíndo metais, cerámicas e algúns plásticos, polo que son aptas para diversas aplicacións.
Ademais, as pastas de soldar poden mellorar a condutividade térmica e eléctrica en comparación coa unión adhesiva. Esta propiedade é especialmente beneficiosa en aplicacións nas que a disipación de calor ou a continuidade eléctrica é crucial, como os conxuntos electrónicos: a unión soldada forma unha vía metálica directa, facilitando a transferencia de calor eficiente e a condución eléctrica.
Non obstante, é esencial ter en conta que as pastas de soldar tamén teñen algunhas consideracións e limitacións. Por exemplo, algunhas aliaxes de soldadura conteñen chumbo, que pode estar restrinxido debido a problemas ambientais e de saúde. Como alternativas desenvolvéronse pastas de soldar sen chumbo, pero poden ter características diferentes e requirir consideracións de proceso específicas.
Técnicas de dispensación de adhesivos: precisión e eficiencia
As técnicas de dispensación de adhesivos son cruciais en varias industrias, desde a fabricación ata a construción. Conseguir precisión e eficiencia na aplicación de adhesivos é esencial para garantir unións fiables, minimizar o desperdicio e mellorar a produtividade xeral. Este artigo explorará técnicas críticas que axudan a lograr precisión e eficiencia na dispensación de adhesivos.
- Sistemas de dispensación automatizados: os sistemas de dispensación automatizados utilizan brazos robóticos ou equipos controlados por ordenador para aplicar adhesivos con precisión. Estes sistemas ofrecen unha alta repetibilidade, precisión e velocidade, garantindo unha aplicación consistente do adhesivo en varias pezas ou produtos. Ao eliminar o erro humano, os sistemas automatizados minimizan o desperdicio e melloran a eficiencia nos procesos de dispensación de adhesivos.
- Sistemas de medición e mestura: Algunhas aplicacións requiren dispensar dous ou máis compoñentes que deben mesturarse nunha proporción específica. Os sistemas de dosificación e mestura miden e combinan con precisión os compoñentes adhesivos antes de distribuílos, garantindo proporcións precisas e calidade consistente. Estes sistemas son particularmente beneficiosos para epoxis de dúas partes, poliuretanos e outros adhesivos reactivos.
- Dispensación controlada por presión: as técnicas de dispensación controladas por presión implican o uso de sistemas pneumáticos ou hidráulicos para controlar o caudal e a presión do adhesivo. O adhesivo dispensase a un ritmo controlado mantendo unha forza consistente, garantindo unha aplicación precisa e minimizando o exceso de adhesivo. A dispensación controlada por presión úsase habitualmente para aplicacións que requiren liñas finas, puntos ou patróns complicados.
- Inyección e dispensación de agullas: as técnicas de inxección e dispensación de agullas son adecuadas para aplicacións que requiren unha colocación de adhesivo precisa e de alta velocidade. Os sistemas de chorro usan pulsos de presión para dispensar pequenas gotas ou liñas adhesivas continuas. Por outra banda, a dispensación de agullas implica o uso dunha agulla ou boquilla para depositar adhesivo en cantidades controladas. Estas técnicas utilízanse habitualmente na montaxe de produtos electrónicos, onde se requiren depósitos de adhesivo pequenos e precisos.
- Sistemas de pulverización e revestimento: para aplicacións de unión ou revestimento de grandes áreas, os sistemas de pulverización e revestimento proporcionan unha dispensación eficiente de adhesivo. Estes sistemas utilizan técnicas de atomización para crear unha fina néboa ou pulverización de adhesivo, garantindo unha cobertura uniforme e un desperdicio mínimo. Os sistemas de pulverización e revestimento son amplamente utilizados na industria automotriz, aeroespacial e de fabricación de mobles.
- Válvulas e boquillas de dispensación: a elección das válvulas e boquillas de dispensación é fundamental para lograr a precisión na dispensación de adhesivo. Diferentes tipos de válvulas e boquillas, como válvulas de agulla, válvulas de diafragma ou boquillas cónicas, ofrecen un control variable sobre o caudal, o patrón e o tamaño das gotas. A selección da válvula ou boquilla adecuada para os requisitos específicos de adhesivo e aplicación é esencial para conseguir unha dispensación precisa e eficiente.
- Sistemas guiados pola visión: os sistemas de dispensación guiados pola visión usan cámaras e software avanzado para detectar e rastrexar a posición de pezas ou substratos. Analizando as imaxes capturadas, o sistema axusta os parámetros de dispensación de adhesivo en tempo real, garantindo unha colocación precisa incluso en superficies irregulares ou dimensións variables das pezas. Os sistemas guiados pola visión melloran a precisión e a eficiencia ao mesmo tempo que se adaptan ás variacións do proceso.
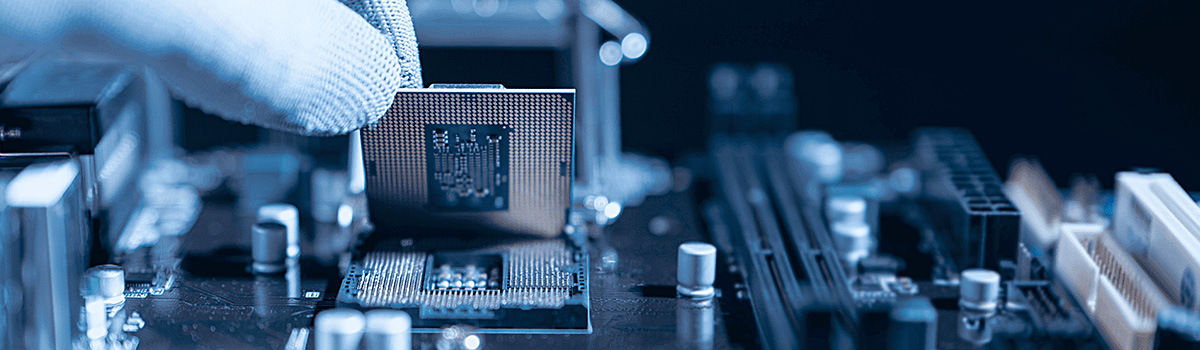
Retos na aplicación de adhesivos semicondutores
A aplicación de adhesivos de semicondutores enfróntase a varios retos que poden afectar o rendemento e a fiabilidade dos dispositivos electrónicos. Estes desafíos xorden debido aos requisitos e características únicas dos semicondutores e ás esixentes condicións de funcionamento ás que están sometidos. Estes son algúns dos desafíos críticos na aplicación de adhesivos semicondutores:
- Xestión térmica: os semicondutores xeran calor durante o funcionamento, e unha xestión térmica eficaz é fundamental para evitar o sobreenriquecido. Os materiais adhesivos utilizados nos semicondutores deben ter unha excelente condutividade térmica para transferir calor do dispositivo de forma eficiente. Garantir unha adhesión adecuada sen comprometer o rendemento térmico é un reto importante.
- Compatibilidade química: os semicondutores están expostos a varios produtos químicos durante a súa vida útil, incluíndo axentes de limpeza, disolventes e fluxos. Os materiais adhesivos deben ser químicamente compatibles con estas substancias para evitar a degradación ou a perda de adherencia co paso do tempo. A selección de materiais adhesivos que poidan soportar a exposición a produtos químicos específicos é unha tarefa complexa.
- Esfuerzo mecánico: os dispositivos electrónicos adoitan experimentar estrés mecánico debido á expansión térmica, vibracións e forzas externas. Para soportar estas tensións, os materiais adhesivos deben ter propiedades mecánicas adecuadas, como flexibilidade e resistencia. O mal rendemento do adhesivo pode provocar a delaminación do dispositivo semicondutor, rachaduras ou fallos mecánicos.
- Miniaturización: coa tendencia actual de miniaturización, os dispositivos semicondutores son cada vez máis pequenos e complexos. A aplicación de adhesivo en tales estruturas en miniatura require unha alta precisión e control. Garantir unha cobertura uniforme, evitar baleiros e manter un grosor constante da liña de unión convértense en retos críticos.
- Compatibilidade de procesos: a fabricación de semicondutores implica múltiples pasos de procesamento, incluíndo limpeza, deposición e envasado. Os materiais adhesivos deben ser compatibles con estes procesos sen afectar negativamente o seu rendemento. Os retos xorden para atopar adhesivos que poidan soportar procesos de alta temperatura, resistir a humidade e manter a estabilidade durante todo o ciclo de fabricación.
- Fiabilidade e envellecemento: espérase que os dispositivos semicondutores teñan unha longa vida útil e un rendemento fiable en varias condicións de funcionamento. Os materiais adhesivos deben mostrar estabilidade a longo prazo, resistencia ao envellecemento e adhesión fiable durante períodos prolongados. O reto reside en predicir e mitigar os posibles mecanismos de degradación que poidan afectar o rendemento e a fiabilidade do dispositivo semicondutor.
- Consideracións ambientais: os materiais adhesivos utilizados en aplicacións de semicondutores deben cumprir as normas e normas ambientais.
- Isto inclúe limitar as substancias perigosas, como o chumbo e outros materiais tóxicos. Desenvolver solucións adhesivas respectuosas co medio ambiente que cumpran os requisitos regulamentarios sen comprometer o rendemento pode ser un reto.
- Custo e escalabilidade: os materiais adhesivos deben ser rendibles e escalables para satisfacer as demandas da produción de semicondutores de gran volume. Equilibrar as consideracións de custo cos requisitos de rendemento supón un reto para seleccionar materiais adhesivos axeitados e optimizar o proceso de aplicación.
Probas de fiabilidade: avaliación do rendemento do adhesivo
As probas de fiabilidade son un proceso esencial para avaliar o rendemento dos adhesivos. Os adhesivos úsanse habitualmente en varias industrias, incluíndo a automoción, a aeroespacial, a electrónica e a construción, onde xogan un papel fundamental na unión de diferentes materiais. A fiabilidade dos adhesivos é fundamental para garantir a durabilidade e a funcionalidade a longo prazo dos conxuntos adheridos.
Un aspecto clave das probas de fiabilidade é a avaliación da resistencia e propiedades de adhesión do adhesivo. Isto implica someter mostras de adhesivo a diferentes condicións de estrés para simular escenarios do mundo real e determinar o seu rendemento baixo diversas cargas, temperaturas e condicións ambientais. As probas de tracción, cizallamento e pelado realízanse habitualmente para avaliar as propiedades mecánicas do adhesivo e a capacidade de soportar forzas en diferentes direccións.
Ademais das probas mecánicas, os factores ambientais xogan un papel importante no rendemento do adhesivo. Os adhesivos poden estar expostos a temperaturas extremas, humidade, substancias químicas e radiación UV durante a súa vida útil. Polo tanto, as probas de fiabilidade implican someter mostras pegajosas a probas de envellecemento acelerado, onde están expostas a duras condicións ambientais durante un período prolongado. Isto axuda a predicir o rendemento a longo prazo do adhesivo e a avaliar a súa resistencia á degradación, como a perda de forza de adhesión ou o deterioro químico.
Outro aspecto importante das probas de fiabilidade é a avaliación da durabilidade do adhesivo baixo carga cíclica. En moitas aplicacións, os adhesivos están sometidos a tensións mecánicas repetidas, como vibracións ou ciclos térmicos. As probas de fatiga avalían a resistencia do adhesivo ao fallo baixo estas cargas cíclicas. As mostras son normalmente sometidas a un número especificado de ciclos de carga, e o seu rendemento é supervisado para detectar calquera signo de deficiencias do adhesivo, como a propagación de gretas ou a delaminación da unión.
Ademais, as probas de fiabilidade implican avaliar o rendemento do adhesivo en condicións reais. Isto pode incluír probar a capacidade do adhesivo para unir diferentes materiais de uso habitual na industria, como metais, plásticos, compostos ou vidro. As mostras prepáranse mediante procedementos normalizados e sométense a protocolos de proba que simulan os requisitos específicos da aplicación. Isto permite aos enxeñeiros avaliar a compatibilidade do adhesivo con diferentes substratos e avaliar a súa forza de unión, flexibilidade e resistencia aos factores ambientais.
As probas de fiabilidade tamén inclúen a avaliación da compatibilidade química do adhesivo con outras substancias coas que poida entrar en contacto durante a súa aplicación ou vida útil. Isto implica realizar probas de compatibilidade para determinar se o adhesivo reacciona negativamente con disolventes, axentes de limpeza, combustibles ou outros produtos químicos que poidan estar presentes no ambiente. As probas de compatibilidade química axudan a identificar problemas potenciais que poidan provocar fallos ou degradación do adhesivo.
En conclusión, as probas de fiabilidade son un paso crucial para avaliar o rendemento do adhesivo. Implica avaliar as propiedades mecánicas, realizar probas de envellecemento acelerado, avaliar a durabilidade baixo carga cíclica, avaliar o rendemento en condicións reais e probar a compatibilidade química. Ao realizar probas exhaustivas de fiabilidade, os fabricantes e enxeñeiros poden garantir a idoneidade dos adhesivos e o rendemento a longo prazo nas súas aplicacións previstas.
Consideracións ambientais en adhesivos semicondutores
Os adhesivos semicondutores xogan un papel fundamental na montaxe e envasado de dispositivos electrónicos, especialmente na industria de semicondutores. Aínda que estes adhesivos proporcionan funcións esenciais como a unión e a xestión térmica, é vital ter en conta o seu impacto ambiental ao longo do seu ciclo de vida. Aquí están algunhas consideracións ambientais cruciais no adhesivo semicondutor:
- Toxicidade: moitos adhesivos semicondutores conteñen substancias perigosas, incluíndo compostos orgánicos volátiles (COV), metais pesados e outros produtos químicos tóxicos. Estas substancias poden ter efectos negativos sobre a saúde humana e o medio ambiente. Minimizar ou eliminar ingredientes nocivos nas formulacións de adhesivos é fundamental para reducir o seu impacto ambiental.
- Emisións: durante a fabricación e aplicación de adhesivos semicondutores, pódense liberar compoñentes volátiles ao aire, contribuíndo á contaminación do aire. As emisións de COV, por exemplo, poden contribuír á formación de ozono troposférico e á formación de partículas nocivas. Os fabricantes deben esforzarse por desenvolver formulacións de adhesivos con baixo contido de COV e implementar medidas rigorosas de control de emisións para mitigar estes impactos ambientais.
- Consumo de enerxía: a produción de adhesivos semicondutores require procesos intensivos enerxéticos, incluíndo a síntese, a mestura e o curado. Reducir o consumo de enerxía mediante a optimización do proceso e o uso de tecnoloxías eficientes enerxéticamente pode minimizar a pegada ambiental asociada á fabricación de adhesivos.
- Xeración de residuos: a industria de semicondutores xera residuos significativos e os adhesivos contribúen a este fluxo de residuos. Os residuos poden incluír adhesivos non utilizados ou caducados, materiais de embalaxe e subprodutos de fabricación. Implementar prácticas de xestión de residuos como a reciclaxe, a reutilización ou a eliminación segura dos residuos de adhesivos é esencial para minimizar a contaminación ambiental e o esgotamento dos recursos.
- Análise do ciclo de vida: considerar todo o ciclo de vida dos adhesivos semicondutores é crucial para avaliar de forma exhaustiva o seu impacto ambiental. Esta análise inclúe a avaliación da pegada ecolóxica da extracción de materias primas, fabricación, transporte, aplicación e eliminación ao final da súa vida útil. Identificar oportunidades de mellora en cada etapa pode levar a solucións adhesivas máis sostibles.
- Alternativas sostibles: explorar e adoptar alternativas sostibles é esencial para reducir o impacto ambiental dos adhesivos semicondutores. Isto pode implicar o uso de materias primas de base biolóxica ou renovables, o desenvolvemento de formulacións a base de auga ou sen disolventes e o emprego de procesos de fabricación respectuosos co medio ambiente. A promoción da reciclaxe de adhesivos ou a implementación de prácticas de economía circular tamén poden contribuír á conservación dos recursos.
- Conformidade normativa: os fabricantes de adhesivos deben cumprir as normas e normas ambientais que regulan o uso, a eliminación e a etiquetaxe de produtos químicos. Para garantir a protección ecolóxica e da saúde humana, é fundamental manterse actualizado coas normativas relevantes, como REACH (Rexistro, Evaluación, Autorización e Restricción de Substancias Químicas) na Unión Europea e normativas similares en diferentes rexións.
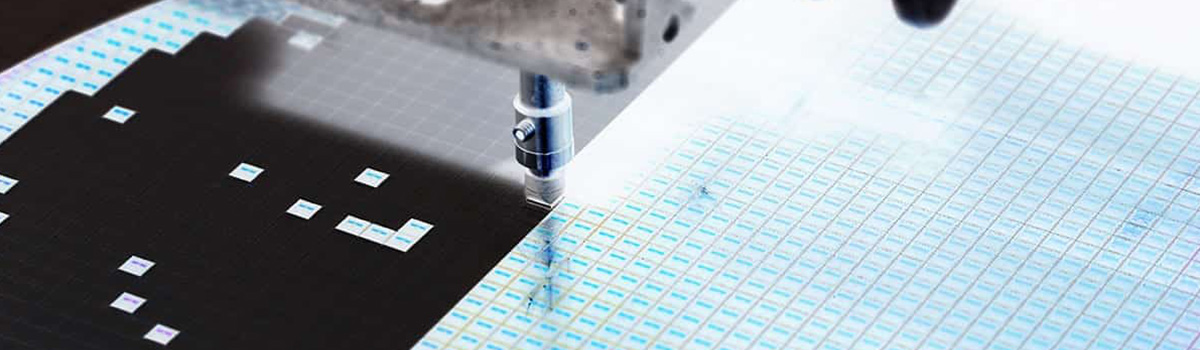
Tendencias e innovacións en adhesivos semicondutores
O adhesivo de semicondutores xoga un papel crucial na montaxe e envasado de dispositivos electrónicos, garantindo a unión e estabilidade adecuadas dos compoñentes de semicondutores. A medida que avanza a tecnoloxía, xorden varias tendencias e innovacións clave no campo dos adhesivos de semicondutores.
- Miniaturización e maior complexidade de dispositivos: unha tendencia significativa na industria de semicondutores é a miniaturización en curso dos dispositivos electrónicos e a crecente complexidade dos seus deseños. Esta tendencia require adhesivos con propiedades melloradas, como unha viscosidade máis baixa, unha maior forza de unión e unha condutividade térmica mellorada, para acomodar compoñentes máis pequenos e máis densamente embalados.
- Técnicas de envasado avanzadas: as técnicas de envasado avanzadas, como o sistema en paquete (SiP), o envasado a nivel de oblea en fan-out (FOWLP) e o envasado en 3D, están gañando popularidade debido á súa capacidade para mellorar o rendemento do dispositivo e reducir o factor de forma. Estas técnicas adoitan necesitar adhesivos especializados que poidan xestionar os desafíos únicos de interconectar múltiples matrices e compoñentes nunha pequena pegada.
- Xestión térmica: a medida que os dispositivos electrónicos se fan máis potentes e compactos, a xestión térmica eficaz faise cada vez máis crítica. Están a desenvolverse adhesivos semicondutores con excelentes propiedades de condutividade térmica para facilitar a disipación da calor dos dispositivos semicondutores, evitando o sobrequecemento e garantindo un rendemento óptimo.
- Curado a baixa temperatura: os adhesivos semicondutores tradicionais adoitan necesitar procesos de curado a alta temperatura, que poden ser problemáticos para compoñentes ou substratos sensibles á temperatura. As innovacións en adhesivos de curado a baixa temperatura permiten a unión a temperaturas significativamente máis baixas, reducindo o risco de danos térmicos en materiais semicondutores delicados.
- Novas formulacións de materiais: os investigadores están a explorar novas formulacións de materiais para adhesivos semicondutores para cumprir os requisitos en evolución. Isto inclúe o desenvolvemento de adhesivos condutores de electricidade (ECA) que proporcionan unión e condutividade eléctrica, eliminando a necesidade de soldar en aplicacións específicas. Ademais, estanse introducindo novos materiais como adhesivos flexibles para dar cabida á crecente demanda de dispositivos electrónicos flexibles e flexibles.
- Consideracións ambientais: a sustentabilidade e o impacto ambiental están a gañar máis atención na industria de semicondutores. Os fabricantes de adhesivos céntranse no desenvolvemento de formulacións ecolóxicas con compostos orgánicos volátiles (COV) reducidos e substancias perigosas mantendo excelentes características de rendemento.
- Optimización e automatización de procesos: coa crecente demanda de dispositivos semicondutores, hai unha necesidade crecente de procesos de fabricación eficientes e automatizados. Os fabricantes de adhesivos colaboran cos provedores de equipos para optimizar os procesos de dispensación e curado de adhesivos, garantindo resultados consistentes e fiables ao tempo que reducen os tempos do ciclo de produción.
- Fiabilidade e durabilidade: espérase que os dispositivos semicondutores funcionen de forma fiable durante períodos prolongados, a miúdo en ambientes duros. As innovacións de adhesivos teñen como obxectivo mellorar a fiabilidade do dispositivo mellorando a forza de adhesión, a resistencia á humidade, a temperatura e varios factores ambientais.
Áreas de aplicación: electrónica de consumo, automoción, aeroespacial e moito máis
Electrónicos de consumo:
A electrónica de consumo é unha das áreas de aplicación máis destacadas dos avances tecnolóxicos. Abarca moitos dispositivos como teléfonos intelixentes, tabletas, portátiles, televisores intelixentes, dispositivos portátiles e electrodomésticos. Nos últimos anos, a electrónica de consumo experimentou importantes desenvolvementos de rendemento, funcionalidade e conectividade. Por exemplo, os teléfonos intelixentes fixéronse máis poderosos, ofrecendo funcións avanzadas como cámaras de alta resolución, integración de intelixencia artificial e capacidades de realidade aumentada. Os televisores intelixentes agora admiten resolución 4K e incluso 8K e a integración do fogar intelixente para mellorar as experiencias de entretemento. Os dispositivos que se poden levar como reloxos intelixentes e rastreadores de fitness gañaron popularidade polas súas capacidades de seguimento da saúde e de seguimento da condición física.
Automoción:
A industria do automóbil experimentou avances notables, impulsados principalmente pola tecnoloxía. Os vehículos modernos teñen sistemas electrónicos e software sofisticados que melloran a seguridade, a eficiencia e a experiencia do usuario. Unha das áreas críticas de desenvolvemento é a condución autónoma, sendo os coches autónomos unha realidade. Estes vehículos confían en sensores avanzados, algoritmos de intelixencia artificial e conectividade para navegar polas estradas e tomar decisións intelixentes. Ademais, as aplicacións de automoción inclúen:
- Sistemas de infoentretemento.
- Sistemas avanzados de asistencia ao condutor (ADAS).
- Conectividade no coche.
- Tecnoloxía de vehículos eléctricos.
- Comunicación vehículo a vehículo.
Aeroespacial:
A industria aeroespacial depende en gran medida das tecnoloxías avanzadas para mellorar a seguridade, a eficiencia e o rendemento. As aplicacións aeroespaciais inclúen o deseño e fabricación de aeronaves, a exploración espacial, os sistemas de satélites e a xestión do tráfico aéreo. As ferramentas de deseño asistido por ordenador (CAD) e de simulación axudan aos enxeñeiros a crear aeronaves máis aerodinámicas e eficientes no deseño de aeronaves. Os sistemas de satélite proporcionan servizos de comunicación global, vixilancia meteorolóxica e navegación. A industria aeroespacial tamén aproveita materiais avanzados, como compostos e aliaxes lixeiras, para reducir o peso e aumentar a eficiencia do combustible. Na exploración espacial, a robótica, a teledetección e os sistemas de propulsión permiten realizar misións para explorar corpos celestes e reunir datos científicos.
Asistencia sanitaria:
A tecnoloxía xoga un papel crucial na saúde, transformando a industria de varias maneiras. Os dispositivos e equipos médicos, como as máquinas de resonancia magnética, os escáneres de ultrasóns e os sistemas de cirurxía robótica, revolucionaron os procedementos de diagnóstico e tratamento. Os rexistros sanitarios electrónicos (EHR) e a telemedicina permiten aos profesionais sanitarios acceder á información do paciente e proporcionar atención remota. Os dispositivos portátiles e os sistemas de vixilancia da saúde permiten aos individuos rastrexar os seus signos vitais e recibir recomendacións de atención sanitaria personalizadas. A intelixencia artificial e os algoritmos de aprendizaxe automática empréganse para o diagnóstico de enfermidades, o descubrimento de fármacos e as análises preditivas, o que permite mellorar os resultados dos pacientes e unha medicina personalizada.
Automatización industrial:
A automatización industrial implica o uso de tecnoloxías avanzadas para automatizar os procesos de fabricación e mellorar a produtividade. A robótica e os brazos robóticos úsanse amplamente para tarefas como a montaxe, a soldadura e a manipulación de materiais. Os dispositivos e sensores de Internet das Cousas (IoT) están implantados para recoller datos en tempo real e optimizar a eficiencia operativa. Os sistemas de visión artificial permiten o control e a inspección de calidade, garantindo que os produtos cumpran estándares estritos. Os sistemas de control avanzados e os algoritmos de mantemento preditivo axudan a minimizar o tempo de inactividade e maximizar a produción. A automatización industrial pode aumentar a eficiencia, reducir custos e mellorar a seguridade en varias industrias, incluíndo a fabricación, a loxística e a enerxía.
Perspectivas e oportunidades de futuro
O futuro está cheo de perspectivas e oportunidades interesantes, impulsadas polos rápidos avances tecnolóxicos, as necesidades sociais cambiantes e as tendencias globais en evolución. Aquí, exploramos algunhas áreas clave con potencial de crecemento e desenvolvemento significativo.
- Intelixencia artificial (IA) e automatización: a IA está a transformar as industrias en todos os ámbitos, mellorando a eficiencia, a produtividade e a toma de decisións. A medida que as tecnoloxías de IA madurezan, haberá cada vez máis oportunidades para especialistas en IA, científicos de datos e enxeñeiros. A automatización seguirá axilizando os procesos, o que levará á creación de emprego en robótica, aprendizaxe automática e sistemas intelixentes.
- Enerxías renovables e sustentabilidade: coa crecente preocupación polo cambio climático, hai unha demanda masiva de solucións enerxéticas renovables. A transición a fontes máis limpas como a enerxía solar, eólica e hidroeléctrica presenta numerosas perspectivas. As carreiras en enxeñaría de enerxías renovables, xestión da enerxía e desenvolvemento sostible serán fundamentais para dar forma a un futuro máis verde.
- Saúde e biotecnoloxía: os avances na investigación médica, a medicina personalizada e a edición de xenes están a revolucionar a industria sanitaria. As oportunidades abundan en bioinformática, asesoramento xenético, telemedicina e desenvolvemento farmacéutico. A intersección da tecnoloxía e a asistencia sanitaria impulsará a innovación, o que levará a unha mellor atención ao paciente e resultados mellores.
- Ciberseguridade e privacidade de datos: a medida que a nosa dependencia dos sistemas dixitais segue aumentando, tamén o fai a necesidade de medidas sólidas de ciberseguridade. As ameazas cibernéticas son cada vez máis sofisticadas, o que xera unha demanda de expertos en ciberseguridade, hackers éticos e especialistas en privacidade de datos. Protexer a información confidencial e desenvolver unha infraestrutura segura será crucial para as organizacións e os individuos.
- Comercio electrónico e mercadotecnia dixital: o comercio electrónico transformou a forma na que compramos, creando novas vías para as empresas. As plataformas de venda polo miúdo en liña, o marketing dixital e a publicidade en redes sociais convertéronse en esenciais para as empresas prósperas. As carreiras de xestión de comercio electrónico, creación de contido dixital e optimización da experiencia do cliente seguirán tendo unha gran demanda.
- Exploración e comercialización espacial: a exploración espacial pasou de iniciativas dirixidas polo goberno a empresas comerciais, abrindo oportunidades en enxeñería aeroespacial, tecnoloxía de satélites e turismo espacial. As empresas privadas están a investir en viaxes espaciais, minería de recursos e comunicacións por satélite, abrindo o camiño para unha nova era de exploración espacial.
- Agricultura e sistemas alimentarios sostibles: se espera que a poboación mundial alcance os 9 millóns en 2050, é fundamental garantir a seguridade alimentaria e as prácticas agrícolas sostibles. A agricultura vertical, a agricultura de precisión e as fontes alternativas de proteínas ofrecen potencial de innovación. As carreiras en tecnoloxía agrícola, agronomía e ciencia dos alimentos desempeñarán un papel vital para satisfacer as futuras demandas alimentarias.
- Realidade Virtual (VR), Realidade Aumentada (AR) e Realidade Estendida (XR): Estas tecnoloxías teñen o potencial de revolucionar o entretemento, a educación, a formación e varias industrias. Os desenvolvedores de RV/AR, os creadores de contido e os deseñadores de experiencias inmersivas darán forma ao futuro do entretemento, dos xogos e da colaboración virtual.
- Tecnoloxía financeira (Fintech): a integración da tecnoloxía e as finanzas deu lugar ao auxe da Fintech, que ofrece novos servizos financeiros, solucións de pago dixitais e tecnoloxía blockchain. Espérase que as carreiras en analítica financeira, ciberseguridade na banca e desenvolvemento de blockchain teñan unha gran demanda.
- Consultoría de sustentabilidade e arquitectura verde: a medida que a sustentabilidade se converte nunha prioridade, as empresas e os individuos buscan orientación para reducir a súa pegada de carbono e adoptar prácticas ecolóxicas. Os consultores sostibles, os arquitectos ecolóxicos e os enxeñeiros ambientais serán fundamentais no deseño e implementación de solucións sostibles.
Importancia da colaboración no avance da tecnoloxía adhesiva de semicondutores
A colaboración é vital para avanzar na tecnoloxía de adhesivos de semicondutores, impulsar a innovación e garantir a súa implantación exitosa en varias industrias. A industria dos semicondutores é moi complexa e está en rápida evolución, polo que require coñecementos interdisciplinarios e cooperación entre as partes interesadas.
- Experiencia diversa: a tecnoloxía de adhesivos de semicondutores abarca múltiples disciplinas, incluíndo a ciencia dos materiais, a química, a enxeñaría e a fabricación. A colaboración reúne a expertos de diversos campos, cada un aportando coñecementos e habilidades especializadas. Ao combinar diversos coñecementos, a asociación permite o desenvolvemento de novos materiais e técnicas adhesivas que poden mellorar o rendemento, a fiabilidade e a durabilidade dos dispositivos semicondutores.
- Intercambio de coñecemento: a colaboración facilita o intercambio de coñecemento e información entre investigadores, enxeñeiros e profesionais do sector. A través de esforzos de colaboración, os individuos poden compartir os seus coñecementos, experiencias e resultados de investigación, o que leva a unha comprensión máis profunda dos materiais adhesivos e das súas aplicacións. Este intercambio de coñecemento pode axudar a identificar tendencias emerxentes, abordar desafíos técnicos e acelerar o desenvolvemento de solucións innovadoras.
- Investigación e desenvolvemento mellorados: os esforzos de investigación e desenvolvemento colaborativos permiten a posta en común de recursos en termos de financiamento e equipamento. Isto permite unha experimentación, probas e análises máis amplas, o que leva a un descubrimento e unha innovación máis rápidos. Ao traballar xuntos, os investigadores poden acceder a instalacións especializadas, tecnoloxías de punta e ferramentas de caracterización avanzadas que poden non estar dispoñibles individualmente. Tales recursos poden contribuír significativamente ao avance da tecnoloxía adhesiva de semicondutores.
- Colaboración industria-universidade: a colaboración entre a industria e a academia é fundamental para traducir os resultados da investigación en aplicacións prácticas. As universidades poden realizar investigacións fundamentais e explorar novos conceptos, mentres que os socios da industria achegan perspectivas do mundo real e consideracións prácticas. Esta colaboración garante que os desenvolvementos da tecnoloxía de adhesivos se aliñan coas necesidades do mercado e poidan integrarse nos procesos industriais. A asociación industria-universidade tamén promove a transferencia de tecnoloxía, o que permite que a investigación académica teña un impacto tanxible nas aplicacións comerciais.
- Normalización e garantía de calidade: a colaboración entre os axentes da industria fomenta o desenvolvemento de estándares e directrices para a tecnoloxía de adhesivos de semicondutores. Os estándares axudan a garantir a coherencia, compatibilidade e fiabilidade en diferentes produtos e procesos de fabricación. Os esforzos de colaboración poden establecer mellores prácticas, metodoloxías de proba e procedementos de control de calidade, que son esenciais para garantir o rendemento e a fiabilidade a longo prazo dos dispositivos semicondutores.
- Expansión do mercado e competitividade: a colaboración entre as empresas que operan na industria de semicondutores pode levar á expansión do mercado e ao aumento da competitividade. As empresas poden combinar os seus recursos, coñecementos e coñecementos de mercado traballando xuntos para desenvolver solucións adhesivas que cumpran os requisitos específicos do sector. Os esforzos de colaboración tamén poden facilitar a adopción da tecnoloxía adhesiva en novas aplicacións e mercados emerxentes, impulsando aínda máis o crecemento da industria de semicondutores.
Conclusión:
O adhesivo de semicondutores xoga un papel vital para permitir a miniaturización e o alto rendemento dos dispositivos semicondutores. A capacidade destes adhesivos para proporcionar fortes capacidades de unión, protección contra factores ambientais e estrés térmico e condutividade eléctrica é crucial na fabricación e montaxe de microprocesadores, chips de memoria e outros circuítos integrados. A medida que a tecnoloxía continúa avanzando, o desenvolvemento de solucións adhesivas innovadoras e a colaboración entre fabricantes, investigadores e usuarios finais serán cruciales para satisfacer as crecentes demandas e desafíos da industria de semicondutores. Ao aproveitar o potencial do adhesivo semicondutor, podemos preparar o camiño para dispositivos semicondutores aínda máis pequenos, rápidos e complexos que impulsen o noso mundo moderno.