Adhesivo de unión de membranas
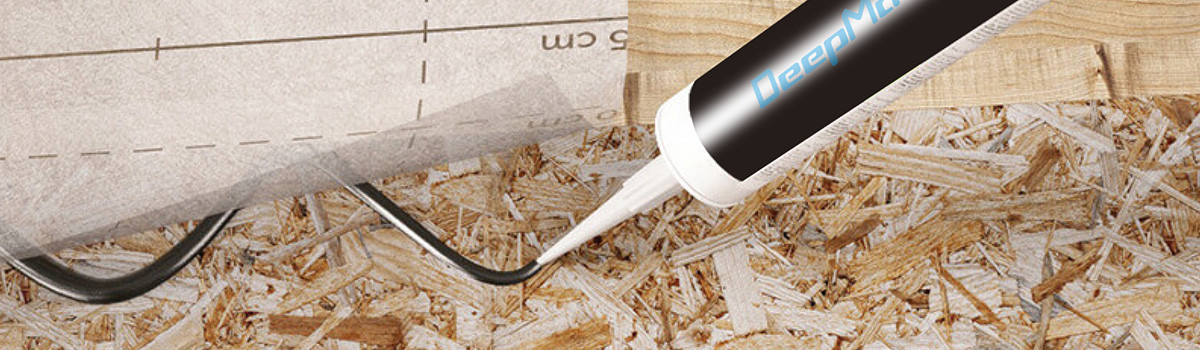
La unión de membranas es un adhesivo especializado fundamental en varias industrias, incluidas la construcción, la automoción y la fabricación. Está diseñado específicamente para unir y asegurar diferentes tipos de membranas, como membranas impermeabilizantes, membranas para techos y membranas para automóviles. Este artículo explorará el mundo de los adhesivos que se comunican con membranas, sus aplicaciones, beneficios y consideraciones para seleccionar los adhesivos adecuados para las necesidades específicas de unión de membranas.
Comprender el adhesivo de unión de membranas
El adhesivo de unión de membranas se refiere a un tipo de adhesivo diseñado específicamente para unir o unir diferentes tipos de membranas. Las membranas son láminas o películas delgadas hechas de materiales como plásticos, caucho o telas, y se usan comúnmente en varias industrias para aplicaciones como impermeabilización, barreras de aire, aislamiento y techado.
La función principal de los adhesivos para la unión de membranas es crear una unión sólida y duradera entre dos o más membranas, asegurando su desempeño efectivo como un sistema cohesivo. Estos adhesivos están formulados para brindar una excelente adhesión a una amplia gama de materiales de membrana, incluidos polietileno, polipropileno, PVC, EPDM, TPO y betún modificado.
Las características y propiedades clave de los adhesivos para la unión de membranas incluyen:
- Fuerza de adhesión: los adhesivos para la unión de membranas están diseñados para proporcionar una alta fuerza de unión entre las membranas, lo que garantiza una conexión confiable y duradera. La fuerza de adhesión generalmente se prueba en diversas condiciones ambientales, como cambios de temperatura, humedad y exposición a la radiación ultravioleta, para garantizar el rendimiento en aplicaciones del mundo real.
- Flexibilidad: dado que las membranas a menudo están sujetas a movimiento, expansión y contracción debido a cambios de temperatura o tensiones estructurales, el adhesivo debe ser flexible para adaptarse a tales actividades sin comprometer la unión. La flexibilidad también ayuda a distribuir el estrés y la carga de manera uniforme en el área adherida, lo que mejora la durabilidad general del sistema.
- Resistencia química: las membranas suelen estar expuestas a productos químicos, agua u otras sustancias, según la aplicación. Un adhesivo de unión de membrana adecuado debe mostrar resistencia a estos productos químicos para garantizar la longevidad y la integridad de la unión. La resistencia química evita que el adhesivo se degrade o debilite cuando se expone a entornos hostiles.
- Resistencia a la intemperie: las aplicaciones de membranas en exteriores requieren adhesivos que puedan soportar condiciones climáticas extremas, como variaciones de temperatura, radiación ultravioleta, lluvia, nieve y viento. Los selladores resistentes a la intemperie mantienen su fuerza de unión y su rendimiento general incluso en ambientes exteriores hostiles, protegiendo las membranas de fallas prematuras.
- Facilidad de aplicación: los adhesivos de unión de membranas están formulados para ser fáciles de usar, lo que permite una aplicación fácil y eficiente. Según los requisitos específicos de la aplicación, pueden presentarse en diferentes formas, incluidos líquidos, cintas o láminas. La facilidad de aplicación mejora la productividad y asegura una unión uniforme a través de las membranas.
- Compatibilidad: Los adhesivos de unión de membranas deben ser compatibles con los materiales adheridos. Los fabricantes a menudo brindan pautas y tablas de compatibilidad para garantizar la selección adecuada del adhesivo para materiales de membrana específicos. La compatibilidad garantiza una adhesión óptima y minimiza el riesgo de falla de la unión.
Seguir las instrucciones del fabricante para la preparación de la superficie, la aplicación del adhesivo y el tiempo de curado es esencial para lograr los mejores resultados cuando se utilizan adhesivos para la unión de membranas. Puede ser necesaria una consulta o asistencia profesional, especialmente para aplicaciones complejas o membranas especializadas.
En general, los adhesivos para la unión de membranas son fundamentales para crear uniones fuertes, duraderas y confiables entre las membranas. Sus propiedades únicas permiten sistemas de membrana efectivos que brindan beneficios tales como funciones de impermeabilización, aislamiento y barrera de aire en diversas industrias y aplicaciones.
La importancia de una unión eficaz de membranas
La unión adecuada de la membrana es de suma importancia en diversas industrias y aplicaciones. Aquí hay algunas razones clave por las que es crucial:
- Integridad estructural: las membranas se utilizan a menudo en aplicaciones que contribuyen a la integridad estructural de un sistema. La unión adecuada garantiza que las membranas permanezcan en su lugar de manera segura, manteniendo la estabilidad y la resistencia generales de la estructura. Por ejemplo, adherir correctamente las membranas impermeabilizantes en los sistemas de techado previene la fuga de agua y protege la estructura subyacente de daños.
- Impermeabilización y control de la humedad: la unión de la membrana es fundamental para lograr una impermeabilización y un control de la humedad efectivos. Cuando las membranas se unen correctamente, crean una barrera continua que evita la entrada de agua, humedad o vapor. Esto es crucial en la construcción de envolventes, túneles y sótanos, donde la intrusión de humedad puede provocar daños estructurales, crecimiento de moho y comprometer la calidad del aire interior.
- Barreras de aire y vapor: las membranas se utilizan a menudo como barreras de aire y vapor para controlar el flujo de aire y humedad en los conjuntos de construcción. Una unión adecuada garantiza la continuidad y la integridad del sistema de barrera, minimizando las fugas de aire y evitando problemas relacionados con la humedad, como la condensación. El desempeño adecuado de la barrera de aire y vapor contribuye a la eficiencia energética, la comodidad de los ocupantes y la durabilidad a largo plazo de los edificios.
- Eficiencia energética: en aplicaciones como los sistemas de aislamiento, las membranas mejoran la eficiencia energética al reducir la transferencia de calor o las fugas de aire. La unión adecuada asegura que las membranas de aislamiento se instalen correctamente, eliminando espacios o vacíos que podrían comprometer el rendimiento térmico. Esto conduce a una mayor eficiencia energética, menores costos de calefacción y refrigeración y un ambiente interior más confortable.
- Durabilidad y longevidad: la unión de la membrana afecta directamente la durabilidad y la longevidad del sistema. Un ensamblaje de membrana bien adherido puede soportar fuerzas externas, como el viento, las fluctuaciones de temperatura y el movimiento de edificios, sin comprometer el rendimiento. Resiste la degradación y mantiene su integridad a lo largo del tiempo, lo que reduce la necesidad de reparaciones o reemplazos frecuentes y prolonga la vida útil del sistema.
- Seguridad y confiabilidad: en aplicaciones específicas, como membranas utilizadas en entornos peligrosos o infraestructura crítica, la unión adecuada es esencial para la seguridad y la confiabilidad. Por ejemplo, una unión fiable garantiza que las membranas contengan las sustancias de forma segura, minimizando el riesgo de fugas o contaminación ambiental en los sistemas de contención de productos químicos o residuos peligrosos.
La unión adecuada de la membrana es crucial para lograr el rendimiento, la funcionalidad y la longevidad deseados en diversas aplicaciones. Garantiza la integridad estructural, la impermeabilización, el control de la humedad, la eficiencia energética, la durabilidad y la seguridad. La elección de los adhesivos adecuados y el seguimiento de las técnicas de instalación adecuadas son cruciales para lograr uniones sólidas y fiables entre las membranas, lo que en última instancia contribuye al éxito de la estructura o el sistema en general.
Aplicaciones del adhesivo para unión de membranas
Los adhesivos para la unión de membranas encuentran una amplia gama de aplicaciones en diversas industrias. Aquí hay algunas aplicaciones típicas:
- Techado: Los adhesivos para la unión de membranas se utilizan ampliamente en sistemas de techado, especialmente para membranas de una sola capa como EPDM, TPO y PVC. Estos adhesivos crean una fuerte unión entre las láminas de la membrana, lo que garantiza un techo resistente al agua y duradero. Proporcionan una excelente resistencia a la intemperie, la radiación ultravioleta y las fluctuaciones de temperatura, lo que mejora la longevidad del sistema de techado.
- Impermeabilización: Los adhesivos de unión de membranas son esenciales para aplicaciones de impermeabilización en la construcción. Se utilizan para unir membranas impermeabilizantes, como membranas bituminosas o membranas de aplicación líquida, creando una barrera confiable y sin costuras contra la intrusión de agua. Estos adhesivos aseguran una unión firme y segura, evitando fugas y protegiendo las estructuras de daños relacionados con la humedad.
- Barreras de aire y vapor: Los adhesivos de unión de membranas son vitales en la instalación de sistemas de barrera de aire y vapor en edificios. Se utilizan para unir capas de membrana, creando una barrera continua que evita la fuga de aire y controla el movimiento del vapor de agua. Estos adhesivos ayudan a mantener la eficiencia energética, mejoran la calidad del aire interior y protegen contra problemas relacionados con la humedad, como la condensación y el crecimiento de moho.
- Automoción: Los adhesivos para la unión de membranas se utilizan en la industria del automóvil para diversas aplicaciones. Unen paneles de molduras interiores, revestimientos de techo, alfombras y otros componentes a las estructuras del vehículo. Estos adhesivos brindan uniones sólidas y confiables que resisten las vibraciones, los cambios de temperatura y otras tensiones de los entornos automotrices.
- Aeroespacial: En la industria aeroespacial, los adhesivos de unión de membranas se emplean para aplicaciones de unión y sellado. Unen materiales compuestos livianos en estructuras de aeronaves, como polímeros reforzados con fibra de carbono. Estos adhesivos ofrecen alta resistencia, características de ligereza y resistencia a condiciones de temperatura extrema, lo que garantiza la integridad estructural y el rendimiento de los componentes aeroespaciales.
- Dispositivos médicos: Los adhesivos de unión de membranas encuentran aplicación en el montaje de dispositivos médicos. Unen membranas o películas en dispositivos como catéteres, apósitos para heridas y parches transdérmicos. Estos adhesivos brindan biocompatibilidad, unión estéril y flexibilidad, y cumplen con los estrictos requisitos de la industria médica.
- Aplicaciones industriales: Los adhesivos para la unión de membranas se utilizan en diversas aplicaciones industriales en las que se deben unir membranas o películas. Por ejemplo, producen empaques flexibles, materiales laminados, estructuras inflables y compuestos de tela. Estos adhesivos brindan una unión confiable para varios materiales, incluidos plásticos, telas y elastómeros.
Vale la pena señalar que los requisitos adhesivos específicos pueden variar según la aplicación y los materiales que se unen. Los fabricantes ofrecen sistemas adhesivos adaptados a diferentes tipos de membranas, lo que garantiza la compatibilidad y un rendimiento óptimo en aplicaciones específicas.
Membranas Impermeabilizantes en la Construcción
Las membranas impermeabilizantes juegan un papel crucial en la protección de las estructuras contra la intrusión de agua y los daños relacionados con la humedad en la industria de la construcción. Estas membranas se utilizan en diversas aplicaciones, como sótanos, techos, cimientos y estructuras subterráneas. Estos son algunos aspectos críticos de las membranas impermeabilizantes en la construcción:
- Tipos de Membranas Impermeabilizantes: Hay diferentes tipos de membranas impermeabilizantes disponibles para aplicaciones de construcción. Algunos tipos comunes incluyen membranas bituminosas (betún modificado o modificado con APP/SBS), membranas de aplicación líquida (poliuretano o a base de acrílico), membranas termoplásticas (PVC, TPO o EPDM) y membranas cementosas. Cada tipo tiene ventajas, métodos de instalación y compatibilidad con diferentes sustratos.
- Función y beneficios: Las membranas impermeabilizantes crean una barrera continua que evita la penetración de agua, humedad y vapor en la estructura del edificio. Protegen contra daños por agua, crecimiento de moho y deterioro de los materiales de construcción. Las membranas impermeabilizantes también contribuyen a la eficiencia energética, ya que evitan la pérdida de aire acondicionado y reducen el potencial de condensación.
- Áreas de aplicación: Varias áreas de construcción utilizan membranas impermeabilizantes para proporcionar una protección adecuada contra la humedad. Éstas incluyen:
- Cubiertas: Las membranas impermeabilizantes se aplican para proteger techos planos o inclinados, asegurando su estanqueidad y resistencia a la intemperie. Las membranas como EPDM, TPO o PVC se usan comúnmente en aplicaciones de techado.
- Cimientos: Las membranas impermeabilizantes se aplican al exterior de los cimientos subterráneos para evitar la infiltración de agua. Ayudan a mantener los cimientos secos, lo que reduce el riesgo de grietas, moho y daños estructurales.
- Sótanos: Para evitar filtraciones y humedades, las membranas impermeabilizantes son esenciales para los sótanos. Se aplican a las paredes y pisos interiores o exteriores para crear una barrera contra el agua subterránea y la humedad.
- Áreas húmedas: las membranas impermeabilizantes se utilizan en áreas húmedas como baños, duchas y piscinas para evitar fugas y filtraciones de agua. Garantizan un entorno duradero y estanco.
- Métodos de instalación: La instalación de membranas impermeabilizantes depende del tipo de membrana utilizada. Algunas membranas son autoadhesivas, mientras que otras requieren la aplicación de adhesivo o calor para unirlas. Las membranas de aplicación líquida generalmente se rocían, se enrollan o se cepillan sobre la superficie. La preparación adecuada de la superficie, incluida la limpieza, imprimación y nivelación, garantiza una unión segura y duradera.
- Garantía de calidad: La garantía de calidad es esencial en las instalaciones de membranas impermeabilizantes para garantizar la eficacia y durabilidad del sistema. Esto incluye la preparación adecuada de la superficie, la aplicación precisa de la membrana y la inspección minuciosa de las costuras y superposiciones. Se deben seguir medidas de control de calidad, como pruebas de fugas y cumplimiento de las pautas del fabricante, para validar el desempeño del sistema de impermeabilización.
- Mantenimiento y Reparación: El mantenimiento regular y la reparación oportuna son necesarios para preservar la integridad de las membranas impermeabilizantes. Se deben realizar inspecciones para identificar cualquier signo de daño o deterioro, como grietas, ampollas o rasgaduras. Las reparaciones inmediatas deben llevarse a cabo utilizando materiales y técnicas compatibles para evitar la infiltración de agua y mantener la eficacia del sistema de impermeabilización.
Membranas para techos para protección contra la intemperie
Las membranas para techos son componentes esenciales de la envolvente de un edificio y brindan una protección climática crucial. Estas membranas son una barrera contra la infiltración de agua, daños por viento y otros elementos ambientales. Están diseñados para crear una capa impermeable y resistente a la intemperie que protege la estructura subyacente, el aislamiento y los espacios interiores. Este artículo explorará la importancia de las membranas para techos y analizará algunos tipos comunes utilizados para la protección contra la intemperie.
El propósito principal de las membranas para techos es evitar que el agua penetre en el sistema del techo. La infiltración de agua puede provocar daños significativos, incluido el deterioro estructural, el crecimiento de moho y el aislamiento comprometido. Las membranas para techos actúan como un escudo protector, asegurando que el agua se drene de la superficie del techo sin filtrarse a las capas subyacentes.
Un tipo popular de membrana para techos es la membrana de olefina termoplástica (TPO). Las membranas TPO están hechas de una mezcla de polipropileno y caucho de etileno-propileno. Ofrecen una excelente resistencia a la radiación ultravioleta (UV), el ozono y la exposición química. Las membranas de TPO son muy flexibles, lo que las hace adecuadas para diseños y formas de techos. También son termosoldables, lo que garantiza una instalación perfecta y reduce el riesgo de fugas.
Otra membrana para techos comúnmente utilizada es la membrana de terpolímero de etileno propileno dieno (EPDM). EPDM es una membrana de caucho sintético que exhibe una excelente resistencia a la intemperie y puede soportar temperaturas extremas, radiación ultravioleta y exposición al ozono sin degradación. Las membranas de EPDM están disponibles en láminas grandes, lo que minimiza la cantidad de costuras y juntas, que son áreas vulnerables a la penetración del agua. También son muy duraderos y tienen una larga vida útil.
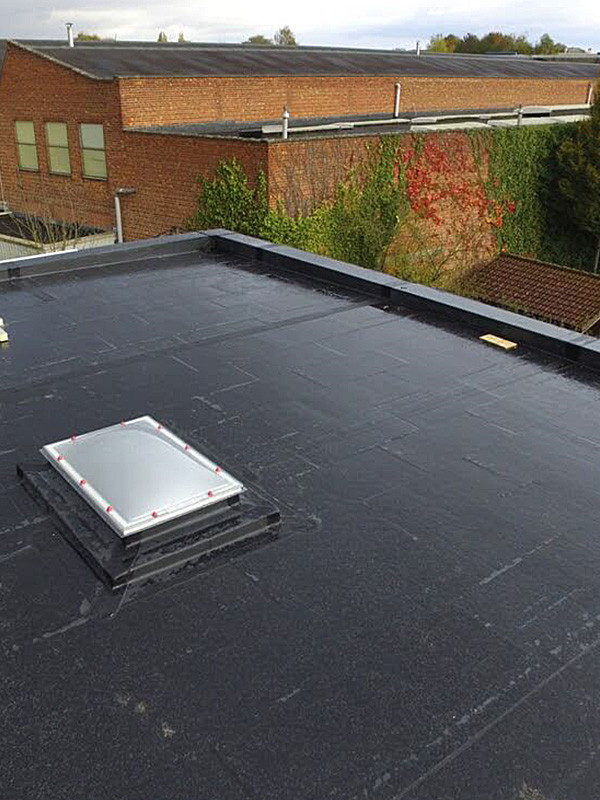
Las membranas para techos de cloruro de polivinilo (PVC) también son populares en la industria. Las membranas de PVC están reforzadas con poliéster o fibra de vidrio, proporcionando una excelente resistencia y durabilidad. Tienen una alta resistencia a los productos químicos, a la radiación UV y al fuego. Las membranas de PVC son conocidas por su eficiencia energética, ya que reflejan el calor y reducen la carga de refrigeración de un edificio. Están en diferentes colores y se pueden soldar con calor para un sello hermético.
Además, las membranas bituminosas modificadas se utilizan ampliamente para la protección contra la intemperie. Estas membranas consisten en asfalto modificado con polímeros para mejorar sus características de desempeño. Las membranas bituminosas modificadas son flexibles, fáciles de instalar y ofrecen una excelente resistencia al agua, a la radiación UV y al estrés térmico. Están disponibles en varias formas, incluidas láminas autoadhesivas, que simplifican la instalación y minimizan el uso de llamas abiertas.
Membranas Automotrices para Control de Ruido y Vibración
El control del ruido y las vibraciones es esencial para el diseño y la fabricación de vehículos, ya que tienen un impacto significativo en la comodidad y la experiencia general de conducción. Las membranas automotrices han surgido como una solución eficaz para reducir el ruido y las vibraciones de los vehículos. Estas membranas especialmente diseñadas están diseñadas para absorber y amortiguar las vibraciones y el ruido generado por diversas fuentes dentro del vehículo.
Las membranas automotrices generalmente están hechas de materiales de alta calidad como caucho, elastómeros o materiales compuestos. Están ubicados estratégicamente en diferentes áreas del vehículo, incluido el compartimiento del motor, las puertas, el piso y los paneles interiores, para mitigar el ruido y las vibraciones de manera efectiva.
Una de las funciones principales de las membranas automotrices es el control de vibraciones. Cuando un vehículo está en movimiento, varios componentes y sistemas, como el motor, la transmisión y el contacto con la carretera, pueden generar vibraciones. Estas vibraciones pueden transmitirse por toda la estructura del vehículo, dando como resultado ruidos indeseables e incomodidad para los ocupantes. Las membranas automotrices actúan como aisladores de vibraciones absorbiendo y disipando estas vibraciones, evitando que se propaguen a otras partes del vehículo. Esto ayuda a reducir los niveles generales de ruido y mejora la suavidad del viaje.
Además del control de vibraciones, las membranas automotrices son cruciales en la reducción del ruido. Están diseñados para absorber y amortiguar el ruido aéreo y estructural dentro del vehículo. El ruido aéreo se refiere a los sonidos generados por fuentes externas, como la carretera y el viento, mientras que los componentes mecánicos del vehículo producen ruido estructural. Al incorporar membranas en la construcción del vehículo, la transmisión de estos ruidos se puede reducir significativamente. Las membranas absorben la energía del sonido y la convierten en calor, minimizando su impacto sobre los ocupantes.
Además, las membranas automotrices ofrecen beneficios adicionales más allá del control del ruido y las vibraciones. Pueden mejorar la integridad estructural general del vehículo al reducir el estrés y la tensión en los componentes sujetos a vibraciones. Esto, a su vez, puede mejorar la durabilidad y la vida útil de varias piezas, lo que lleva a una mayor confiabilidad del vehículo.
Además, las membranas automotrices contribuyen a las iniciativas de reducción de peso en los vehículos modernos. Al reemplazar los materiales pesados tradicionales con membranas livianas, los fabricantes pueden ahorrar peso sin comprometer el rendimiento o la seguridad. Esta reducción de peso ayuda a mejorar la eficiencia del combustible y reduce las emisiones de carbono, alineándose con los esfuerzos continuos de la industria hacia la sostenibilidad.
Aplicaciones industriales y de fabricación
El adhesivo para la unión de membranas desempeña un papel fundamental en diversas aplicaciones industriales y de fabricación en las que se requiere unir y unir membranas. Estos productos adhesivos están específicamente formulados para brindar uniones sólidas y duraderas entre diferentes tipos de membranas, creando estructuras confiables y duraderas. Aquí hay algunas aplicaciones críticas del adhesivo de unión de membranas:
- Construcción y techado: La industria de la construcción utiliza ampliamente el adhesivo de unión de membranas, principalmente para aplicaciones de techado. Permite la fijación segura de membranas para techos, como EPDM (monómero de etileno propileno dieno), PVC (cloruro de polivinilo), TPO (olefina termoplástica) y betún modificado. El adhesivo asegura sellos herméticos y resistencia contra la intemperie, la radiación UV y las condiciones de temperatura extrema.
- Fabricación de automóviles: en la industria automotriz, el adhesivo de unión de membranas se utiliza para diversas aplicaciones, incluida la unión de componentes de molduras interiores y exteriores. Estos adhesivos permiten la fijación segura de membranas para revestimientos de techos, paneles de puertas, tableros y otros elementos del interior del vehículo. Las propiedades del adhesivo aseguran uniones fuertes que soportan vibraciones, cambios de temperatura y exposición a productos químicos y humedad.
- Aeroespacial y aviación: el adhesivo de unión de membranas encuentra un amplio uso en los sectores aeroespacial y de aviación para aplicaciones tales como interiores de aeronaves, sistemas de aislamiento y unión compuesta. Proporciona una adhesión fiable de las membranas en las cabinas de los aviones, asegurando la integridad estructural y la resistencia al fuego. Las propiedades de ligereza del adhesivo son particularmente beneficiosas en aplicaciones aeroespaciales donde la reducción de peso es crucial.
- Industria marítima: El adhesivo para unión de membranas se emplea en la industria marítima para aplicaciones como la construcción de embarcaciones, la unión de cubiertas y el sellado. Permite la adhesión de membranas para cubiertas, cascos, mamparos y otros componentes marinos. La resistencia del adhesivo al agua, la sal y los elementos ambientales garantiza durabilidad e impermeabilización a largo plazo.
- Fabricación de dispositivos médicos: en la industria médica, el adhesivo de unión de membranas se utiliza para ensamblar varios dispositivos y equipos médicos. Facilita la unión de membranas en instrumentos quirúrgicos, dispositivos de diagnóstico y sensores médicos portátiles. La biocompatibilidad y la resistencia a la esterilización del adhesivo lo hacen adecuado para aplicaciones médicas, lo que garantiza seguridad y confiabilidad.
- Industria electrónica y eléctrica: el adhesivo de unión de membranas se utiliza en los sectores de la electrónica y la electricidad para unir placas de circuitos flexibles, pantallas táctiles y paneles de visualización. El adhesivo permite la unión de membranas a componentes electrónicos, proporcionando conductividad eléctrica, protección contra la humedad y el polvo y estabilidad mecánica.
- Sistemas de filtración: el adhesivo de unión de membranas es crucial en la producción de sistemas de filtración en industrias como la de tratamiento de agua, farmacéutica y de procesamiento de alimentos. El adhesivo une de forma segura las membranas a las carcasas de los filtros, lo que garantiza un rendimiento de filtración eficiente y evita el desvío o las fugas.
- Sector energético: El adhesivo para la unión de membranas encuentra aplicaciones en el sector de las energías renovables, en particular para la fabricación e instalación de módulos fotovoltaicos (PV). La unión facilita la unión de membranas, como películas encapsulantes, a celdas fotovoltaicas y materiales de lámina posterior, asegurando un sellado adecuado, resistencia a la intemperie y aislamiento eléctrico.
Estos son solo algunos ejemplos de la amplia gama de aplicaciones industriales y de fabricación que utilizan adhesivos de unión de membranas. Las propiedades del adhesivo, como unión sólida, durabilidad, resistencia a factores ambientales y compatibilidad con diferentes materiales, lo convierten en una solución valiosa en diversas industrias, contribuyendo a la producción de estructuras y productos confiables y de alto rendimiento.
Tipos de adhesivos para unión de membranas
El adhesivo para la unión de membranas desempeña un papel fundamental en diversas aplicaciones industriales y de fabricación en las que se requiere unir y unir membranas. Estos productos adhesivos están específicamente formulados para brindar uniones sólidas y duraderas entre diferentes tipos de membranas, creando estructuras confiables y duraderas. Aquí hay algunas aplicaciones críticas del adhesivo de unión de membranas:
- Construcción y techado: La industria de la construcción utiliza ampliamente el adhesivo de unión de membranas, principalmente para aplicaciones de techado. Permite la fijación segura de membranas para techos, como EPDM (monómero de etileno propileno dieno), PVC (cloruro de polivinilo), TPO (olefina termoplástica) y betún modificado. El adhesivo asegura sellos herméticos y resistencia contra la intemperie, la radiación UV y las condiciones de temperatura extrema.
- Fabricación de automóviles: en la industria automotriz, el adhesivo de unión de membranas se utiliza para diversas aplicaciones, incluida la unión de componentes de molduras interiores y exteriores. Estos adhesivos permiten la fijación segura de membranas para revestimientos de techos, paneles de puertas, tableros y otros elementos del interior del vehículo. Las propiedades del adhesivo aseguran uniones fuertes que soportan vibraciones, cambios de temperatura y exposición a productos químicos y humedad.
- Aeroespacial y aviación: el adhesivo de unión de membranas encuentra un amplio uso en los sectores aeroespacial y de aviación para aplicaciones tales como interiores de aeronaves, sistemas de aislamiento y unión compuesta. Proporciona una adhesión fiable de las membranas en las cabinas de los aviones, asegurando la integridad estructural y la resistencia al fuego. Las propiedades de ligereza del adhesivo son particularmente beneficiosas en aplicaciones aeroespaciales donde la reducción de peso es crucial.
- Industria marítima: El adhesivo para unión de membranas se emplea en la industria marítima para aplicaciones como la construcción de embarcaciones, la unión de cubiertas y el sellado. Permite la adhesión de membranas para cubiertas, cascos, mamparos y otros componentes marinos. La resistencia del adhesivo al agua, la sal y los elementos ambientales garantiza durabilidad e impermeabilización a largo plazo.
- Fabricación de dispositivos médicos: en la industria médica, el adhesivo de unión de membranas se utiliza para ensamblar varios dispositivos y equipos médicos. Facilita la unión de membranas en instrumentos quirúrgicos, dispositivos de diagnóstico y sensores médicos portátiles. La biocompatibilidad y la resistencia a la esterilización del adhesivo lo hacen adecuado para aplicaciones médicas, lo que garantiza seguridad y confiabilidad.
- Industria electrónica y eléctrica: el adhesivo de unión de membranas se utiliza en los sectores de la electrónica y la electricidad para unir placas de circuitos flexibles, pantallas táctiles y paneles de visualización. El adhesivo permite la unión de membranas a componentes electrónicos, proporcionando conductividad eléctrica, protección contra la humedad y el polvo y estabilidad mecánica.
- Sistemas de filtración: El adhesivo de unión de membranas es crucial en la producción de sistemas de filtración en las industrias de tratamiento de agua, productos farmacéuticos y procesamiento de alimentos. El adhesivo une de forma segura las membranas a las carcasas de los filtros, lo que garantiza un rendimiento de filtración eficiente y evita el desvío o las fugas.
- Sector energético: El adhesivo para la unión de membranas encuentra aplicaciones en el sector de las energías renovables, en particular para la fabricación e instalación de módulos fotovoltaicos (PV). La unión facilita la unión de membranas, como películas encapsulantes, a celdas fotovoltaicas y materiales de lámina posterior, asegurando un sellado adecuado, resistencia a la intemperie y aislamiento eléctrico.
Estos son solo algunos ejemplos de la amplia gama de aplicaciones industriales y de fabricación que utilizan adhesivos de unión de membranas. Las propiedades del adhesivo, como unión sólida, durabilidad, resistencia a factores ambientales y compatibilidad con diferentes materiales, lo convierten en una solución valiosa en diversas industrias, contribuyendo a la producción de estructuras y productos confiables y de alto rendimiento.
Adhesivo de unión de membranas a base de agua
El adhesivo de unión de membranas a base de agua es un tipo de adhesivo formulado con agua como vehículo principal. Es ampliamente utilizado en diversas aplicaciones industriales y de fabricación donde se requiere la unión y unión de membranas. Los adhesivos a base de agua ofrecen varias ventajas, como el respeto al medio ambiente, la facilidad de uso y la versatilidad. Estos son algunos aspectos críticos del adhesivo de unión de membranas a base de agua:
- Respeto al medio ambiente: una de las ventajas significativas de los adhesivos a base de agua es su impacto ambiental reducido. Los adhesivos a base de agua tienen niveles más bajos de compuestos orgánicos volátiles (COV), que se sabe que contribuyen a la contaminación del aire, que los adhesivos a base de solventes. Como principal portador de estos adhesivos, el agua minimiza la emisión de sustancias nocivas durante la aplicación y el curado. Esto hace que los adhesivos a base de agua sean una opción más respetuosa con el medio ambiente, especialmente en aplicaciones en las que la reducción de las emisiones de COV es una prioridad.
- No inflamabilidad: los adhesivos a base de agua no son inflamables, lo que los hace más seguros de manejar y almacenar que los adhesivos a base de solventes. Esta naturaleza no inflamable elimina la necesidad de precauciones de seguridad adicionales asociadas con los adhesivos inflamables, lo que reduce el riesgo de accidentes y peligros de incendio en el lugar de trabajo.
- Fácil limpieza: los adhesivos a base de agua ofrecen una fácil limpieza y eliminación. Se pueden limpiar fácilmente con agua, eliminando la necesidad de solventes o productos químicos agresivos. Esto simplifica el mantenimiento y la limpieza, contribuyendo a un entorno de trabajo más seguro y eficiente.
- Buenas propiedades de adhesión: los adhesivos a base de agua brindan propiedades de unión confiables para varios materiales de membrana. Ofrecen una buena adherencia a diferentes superficies, incluidos metales, plásticos, telas y materiales compuestos. Los adhesivos a base de agua pueden unir de manera efectiva membranas como EPDM, PVC, TPO y betún modificado, comúnmente utilizados en techado, construcción y otras aplicaciones industriales.
- Versatilidad: los adhesivos a base de agua se pueden usar en varios métodos de aplicación, que incluyen rociado, recubrimiento con rodillo y aplicación con brocha. Se pueden ajustar y optimizar fácilmente para requisitos de unión específicos, lo que permite flexibilidad en diferentes procesos de fabricación. Además, los adhesivos a base de agua se pueden formular con aditivos para mejorar propiedades específicas, como flexibilidad, resistencia al calor o fuerza de unión mejorada, para satisfacer las necesidades únicas de diferentes aplicaciones.
- Menos olor: los adhesivos a base de agua generalmente tienen menos olor en comparación con sus contrapartes a base de solventes. Esto los hace más adecuados para aplicaciones en interiores, especialmente en áreas donde los olores fuertes, como edificios ocupados o instalaciones de fabricación, son una preocupación.
- Amplia gama de aplicaciones: el adhesivo de unión de membranas a base de agua encuentra aplicaciones en diversas industrias y sectores. Se utiliza comúnmente en la construcción y el techado para unir membranas de techado, brindando una impermeabilización efectiva y resistencia a la intemperie. Los adhesivos a base de agua también se utilizan en la fabricación de automóviles para la unión de molduras interiores, aplicaciones marinas para la unión de cubiertas y otras aplicaciones industriales donde se requiere una unión de membrana confiable y duradera.
El adhesivo de unión de membranas a base de agua ofrece varios beneficios, que incluyen respeto por el medio ambiente, no inflamabilidad, facilidad de limpieza y buenas propiedades de adhesión. Su versatilidad e idoneidad para diversas aplicaciones lo convierten en la opción preferida en industrias que priorizan el rendimiento y la sostenibilidad. El uso de adhesivos a base de agua se alinea con la creciente demanda de soluciones de unión seguras y ecológicas en los procesos industriales y de fabricación.
Adhesivo de unión de membranas a base de solvente
En varias industrias, las soluciones de unión fuertes y duraderas son primordiales. En cuanto a la unión de membranas y otros materiales flexibles, los adhesivos de unión de membranas a base de solventes han demostrado ser una opción práctica. Este tipo de adhesivo ofrece excelente adherencia, versatilidad y confiabilidad en diversas aplicaciones. Este artículo explorará las características clave, los beneficios y las aplicaciones de los adhesivos de unión de membranas a base de solventes.
Características Clave: Los adhesivos de unión de membranas a base de solventes están formulados con polímeros sintéticos de alta calidad disueltos en solventes. Esta composición proporciona varias características clave que los hacen ideales para aplicaciones de unión:
- Fuerte adherencia: los adhesivos a base de solventes exhiben una fuerza de unión excepcional, creando uniones confiables y duraderas entre las membranas. Forman una conexión duradera, incluso en condiciones exigentes, lo que garantiza la integridad estructural.
- Versatilidad: estos adhesivos son compatibles con varios materiales de membrana, incluidos PVC, EPDM, TPO y betún modificado. Esta versatilidad les permite ser utilizados en múltiples industrias, como techado, construcción, automotriz y empaque.
- Tiempo de secado rápido: los adhesivos a base de solventes tienen una tasa de evaporación rápida, lo que permite un secado rápido. Esta característica mejora la productividad al reducir el tiempo de montaje y permitir un procesamiento más rápido.
- Excelente resistencia al calor y a los productos químicos: las uniones curadas creadas por los adhesivos a base de solventes exhiben una resistencia excepcional a las altas temperaturas y los productos químicos. Esto los hace adecuados para aplicaciones en las que se espera exposición a condiciones extremas o entornos hostiles.
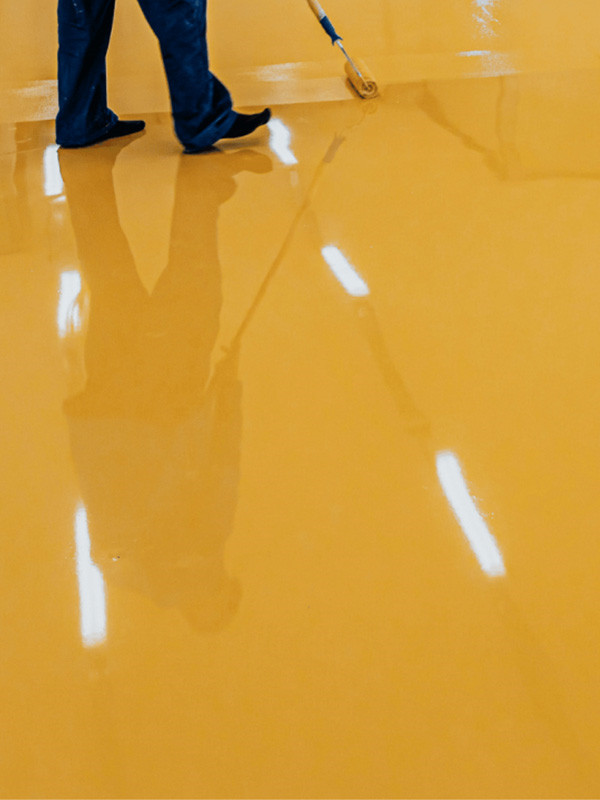
Beneficios: La utilización de adhesivos de unión de membranas a base de solventes proporciona varios beneficios notables:
- Durabilidad mejorada: las uniones fuertes y resistentes que forman estos adhesivos garantizan un rendimiento duradero, soportando los rigores del uso diario y las tensiones ambientales. Esta durabilidad contribuye a mejorar la vida útil del producto y reduce la necesidad de reparaciones o reemplazos frecuentes.
- Impermeabilización mejorada: los adhesivos de unión de membrana ayudan a crear sellos herméticos, evitando la infiltración de agua y protegiendo las estructuras subyacentes. Esto es particularmente crucial en aplicaciones de techado, donde la resistencia al agua es esencial para mantener la integridad de la envolvente del edificio.
- Solución rentable: los adhesivos a base de solventes ofrecen una solución de unión rentable debido a su aplicación eficiente y su rendimiento duradero. Su capacidad para adherirse a una amplia gama de materiales elimina la necesidad de múltiples tipos de adhesivos, lo que reduce los costos de inventario.
Aplicaciones: Los adhesivos de unión de membranas a base de solventes encuentran amplias aplicaciones en varias industrias:
- Techos: estos adhesivos se usan ampliamente en techos para unir membranas de una sola capa, como PVC y TPO, proporcionando sellos seguros y resistentes a fugas.
- Construcción: Los adhesivos a base de solventes se emplean para unir membranas arquitectónicas, barreras de vapor y materiales aislantes en proyectos de construcción, asegurando la integridad estructural y la eficiencia energética.
- Automoción: se utilizan en el sector de la automoción para unir componentes flexibles, como paneles de puertas, revestimientos de techos y alfombras, y ofrecen resistencia y durabilidad incluso en condiciones de conducción exigentes.
- Empaque: Los adhesivos a base de solventes brindan soluciones de unión efectivas para materiales de empaque flexibles, como películas y laminados, lo que garantiza sellos seguros y protección del producto.
Adhesivo para unión de membranas de dos componentes
Una solución adhesiva confiable y robusta es esencial para unir membranas y otros materiales flexibles. Los adhesivos de unión de membranas de dos componentes se han convertido en una opción popular en varias industrias debido a su excepcional resistencia, versatilidad y confiabilidad. Este artículo profundizará en las características clave, los beneficios y las aplicaciones de los adhesivos de unión de membranas de dos componentes.
Características Clave: Los adhesivos de unión de membranas de dos componentes constan de dos componentes separados, normalmente una resina y un endurecedor, que se mezclan justo antes de la aplicación. Esta composición única proporciona varias características clave que los hacen altamente efectivos:
- Resistencia superior: los adhesivos de dos componentes ofrecen una fuerza de unión excepcional, creando conexiones de membrana robustas y duraderas. Pueden soportar un estrés significativo, lo que garantiza uniones duraderas y confiables.
- Tiempo de curado ajustable: el tiempo de curado de los adhesivos de dos componentes se puede ajustar alterando la proporción de resina a endurecedor o seleccionando diferentes agentes de curado. Esta versatilidad permite una aplicación personalizada, lo que garantiza un tiempo de trabajo suficiente y la velocidad de curado deseada.
- Alta resistencia química: estos adhesivos exhiben una excelente resistencia química, lo que los hace adecuados para aplicaciones en las que se espera exposición a sustancias agresivas. Pueden mantener su integridad incluso en ambientes químicamente agresivos.
- Compatibilidad de sustrato versátil: los adhesivos de dos componentes son compatibles con varios materiales de membrana, incluidos PVC, EPDM, TPO y poliuretano. Esta versatilidad los hace adecuados para diversas industrias y aplicaciones.
Beneficios: El uso de adhesivos de unión de membranas de dos componentes proporciona varios beneficios notables:
- Fuerza de unión excepcional: Las uniones sólidas y duraderas formadas por los adhesivos de dos componentes aseguran la integridad estructural y la longevidad. Pueden soportar condiciones extremas y cargas pesadas, lo que los hace adecuados para aplicaciones exigentes.
- Mayor flexibilidad: estos adhesivos ofrecen flexibilidad en cuanto al tiempo de curado y las propiedades adhesivas. Se pueden ajustar para que coincidan con los requisitos específicos de un proyecto, lo que permite una mejor personalización y optimización.
- Resistencia mejorada: los adhesivos de dos componentes resisten las variaciones de temperatura, la humedad, la exposición a los rayos UV y otros factores ambientales. Esta resistencia asegura un rendimiento a largo plazo y minimiza el riesgo de falla de la unión.
- Aplicaciones versátiles: estos adhesivos encuentran aplicaciones en diversas industrias. Se utilizan comúnmente en los sectores de techado, construcción, automotriz y marino, donde la unión fuerte y confiable de las membranas es crucial.
Aplicaciones: Los adhesivos de unión de membranas de dos componentes tienen una amplia gama de aplicaciones:
- Techado: se utilizan ampliamente en sistemas de techado para unir membranas, incluidos EPDM, TPO y PVC, lo que garantiza sellos seguros y resistentes a la intemperie que soportan condiciones ambientales adversas.
- Construcción: Los adhesivos de dos componentes se emplean para unir membranas arquitectónicas, como barreras de vapor y membranas impermeabilizantes, proporcionando conexiones sólidas y protección contra la entrada de humedad.
- Automotriz: encuentran aplicaciones en la industria automotriz para unir componentes flexibles, como molduras interiores, tapicería y materiales insonorizantes, que ofrecen fuerza, durabilidad y resistencia a las vibraciones.
- Marina: estos adhesivos unen membranas y materiales de grado marino, como cascos de embarcaciones, cubiertas y paneles interiores, lo que garantiza sellos herméticos e integridad estructural en entornos marinos desafiantes.
Adhesivo de unión de membrana flexible
Las membranas flexibles se utilizan ampliamente en las industrias de la construcción, la automoción y el embalaje por su versatilidad y rendimiento. Se requiere un adhesivo especializado para lograr una unión segura y duradera entre las membranas flexibles. Los adhesivos de unión de membranas flexibles están formulados para proporcionar una excelente adhesión y flexibilidad, asegurando uniones sólidas y confiables. Este artículo explorará las características clave, los beneficios y las aplicaciones de los adhesivos de unión de membranas flexibles.
Características Clave: Los adhesivos de unión de membranas flexibles están diseñados con propiedades específicas para cumplir con los requisitos de unión de materiales flexibles. Estas son algunas de las características clave de estos adhesivos:
- Flexibilidad: estos adhesivos exhiben un alto grado de flexibilidad, lo que les permite adaptarse a los movimientos y expansiones naturales de las membranas flexibles sin comprometer la unión. Esta flexibilidad ayuda a prevenir fallas en la unión y asegura una durabilidad a largo plazo.
- Buena adherencia a sustratos flexibles: Los adhesivos de unión de membranas flexibles están formulados para establecer una fuerte adherencia a una amplia gama de materiales flexibles. Se adhieren de manera efectiva a sustratos como PVC, EPDM, TPO, poliuretano y otras membranas elastoméricas comúnmente utilizadas en diversas industrias.
- Resistencia a la intemperie: estos adhesivos resisten los elementos de la intemperie, como la radiación ultravioleta, la humedad, las variaciones de temperatura y la exposición química. Esta resistencia a la intemperie asegura la longevidad de la unión, incluso en entornos hostiles.
- Fácil aplicación: los adhesivos de unión de membranas flexibles están diseñados para facilitar su uso. Se pueden aplicar con varios métodos, que incluyen brocha, rodillo o rociador, según los requisitos específicos de la aplicación. Su formulación permite una aplicación uniforme y uniforme.
Beneficios: El uso de adhesivos de unión de membranas flexibles proporciona varias ventajas significativas:
- Uniones sólidas y duraderas: estos adhesivos crean uniones fuertes y duraderas entre membranas flexibles, lo que garantiza la integridad y la longevidad del ensamblaje. Pueden soportar el estrés, el movimiento y las condiciones ambientales, proporcionando un rendimiento confiable.
- Flexibilidad mejorada: al mantener la flexibilidad incluso después del curado, estos adhesivos permiten que las membranas unidas se muevan y expandan sin causar grietas ni fallas. Esta flexibilidad mejora el rendimiento general y la vida útil del conjunto unido.
- Sellos herméticos mejorados: Los adhesivos de unión de membranas flexibles ayudan a crear sellos herméticos entre las membranas, proporcionando una protección adecuada contra la infiltración de agua. Esto es particularmente crucial en aplicaciones como techado e impermeabilización, donde la resistencia al agua es esencial.
- Aplicaciones versátiles: Los adhesivos de unión de membranas flexibles encuentran aplicaciones en diversas industrias. Se utilizan comúnmente en sistemas de techado, fabricación de automóviles, empaques flexibles y otras aplicaciones que requieren la unión de membranas y materiales flexibles.
Aplicaciones: Los adhesivos de unión de membranas flexibles tienen una amplia gama de aplicaciones en todas las industrias:
- Techado: estos adhesivos se utilizan ampliamente en sistemas de techado para unir membranas de techado flexibles, como TPO, PVC y EPDM, proporcionando impermeabilización confiable y duradera y resistencia a la intemperie.
- Automotriz: encuentran aplicaciones en la industria automotriz para unir componentes flexibles como burletes, sellos de puertas, molduras interiores y tapicería, asegurando conexiones sólidas y duraderas que pueden soportar los movimientos dinámicos de los vehículos.
- Empaque: Los adhesivos de unión de membranas flexibles se utilizan en la industria del empaque para unir películas y laminados flexibles, proporcionando sellos seguros y manteniendo la integridad de los productos empacados.
- Construcción: estos adhesivos se emplean en la industria de la construcción para unir membranas arquitectónicas, barreras de vapor y materiales de aislamiento, asegurando ensamblajes herméticos y resistentes a la intemperie.
Adhesivo de unión de membranas de curado rápido
Las soluciones adhesivas de curado rápido son muy buscadas en industrias donde la eficiencia y la productividad son críticas. Los adhesivos de unión de membranas de curado rápido están formulados para proporcionar un montaje y unión rápidos de membranas y materiales flexibles. Este artículo explorará las características clave, los beneficios y las aplicaciones de los adhesivos de unión de membranas de curado rápido.
Características Clave: Los adhesivos de unión de membranas de curado rápido ofrecen características únicas que permiten procesos de unión rápidos y eficientes. Estas son algunas características clave de estos adhesivos:
- Tiempo de curado rápido: estos adhesivos están diseñados para curar rápidamente y lograr uniones fuertes. Ofrecen tiempos de curado significativamente reducidos en comparación con los adhesivos tradicionales, lo que permite ciclos de producción más rápidos y una productividad mejorada.
- Alta resistencia inicial: los adhesivos de curado rápido muestran una alta resistencia inicial poco después de la aplicación. Esto permite una manipulación y un montaje más rápidos de los componentes unidos, lo que minimiza la necesidad de tiempos prolongados de sujeción o curado.
- Métodos de aplicación versátiles: estos adhesivos se pueden aplicar mediante varios métodos, incluida la aplicación con rociador, rodillo o brocha. Esta versatilidad permite una aplicación eficiente y precisa, atendiendo a diferentes requisitos de unión y procesos de producción.
- Compatibilidad con múltiples sustratos: los adhesivos de unión de membranas de curado rápido están formulados para unir una amplia gama de sustratos, incluidos PVC, EPDM, TPO y otros materiales flexibles que se usan comúnmente en industrias como techado, construcción y automotriz.
Beneficios: El uso de adhesivos de unión de membranas de curado rápido ofrece varios beneficios notables:
- Mayor eficiencia: el rápido tiempo de curado de estos adhesivos reduce significativamente el ciclo de ensamblaje y producción, lo que da como resultado una mayor eficiencia y tiempos de respuesta más rápidos. Esto permite a los fabricantes aumentar la producción sin comprometer la fuerza o la calidad de la unión.
- Ahorro de tiempo y costos: un curado más rápido reduce los costos de mano de obra y el consumo de energía. La capacidad de pasar rápidamente al siguiente paso de producción o envío puede generar ahorros sustanciales de tiempo y costos en los procesos de fabricación.
- Productividad mejorada: los adhesivos de curado rápido mejoran la productividad al minimizar los tiempos de espera o inactividad. Permiten un montaje rápido, reducen los plazos de producción y cumplen plazos ajustados.
- Fuerza de unión confiable: a pesar de sus propiedades de curado rápido, estos adhesivos mantienen una alta resistencia y durabilidad de la unión. Proporcionan uniones fiables y duraderas, lo que garantiza la integridad estructural y el rendimiento de los componentes ensamblados.
Aplicaciones: Los adhesivos de unión de membranas de curado rápido encuentran aplicaciones en diversas industrias:
- Techado: estos adhesivos se usan comúnmente en aplicaciones de techado, como la unión de membranas de una sola capa como TPO, PVC o EPDM. El curado rápido permite una instalación eficiente y asegura sellos herméticos, lo que mejora la velocidad y la calidad de los proyectos de techado.
- Construcción: Los adhesivos de curado rápido se emplean en la construcción para unir membranas arquitectónicas, materiales aislantes y barreras de vapor. Su tiempo de curado rápido permite procesos de construcción más rápidos y ayuda a cumplir con los plazos del proyecto.
- Automotriz: encuentran aplicaciones en la industria automotriz para unir componentes flexibles, como paneles de puertas, revestimientos de techos y alfombras. El rápido tiempo de curado asegura un ensamblaje eficiente en la línea de producción sin comprometer la fuerza o la calidad de la unión.
- Fabricación general: Los adhesivos de curado rápido se utilizan en varios procesos de fabricación que involucran materiales de unión flexibles. Permiten el montaje y la unión rápidos de elementos como embalajes flexibles, membranas para estructuras inflables y piezas compuestas flexibles.
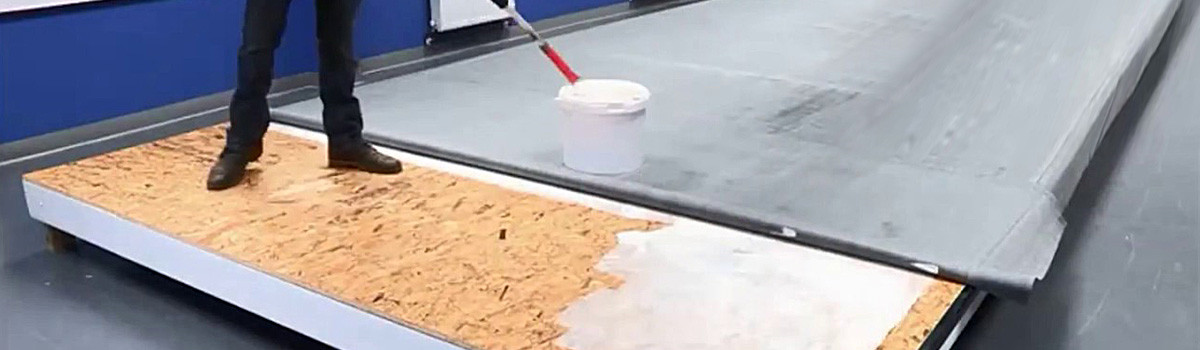
Consideraciones para seleccionar el adhesivo de unión de membranas
Al seleccionar un adhesivo para la unión de membranas, se deben tener en cuenta varias consideraciones clave para garantizar una unión exitosa y duradera. Estas consideraciones incluyen la compatibilidad del sustrato, las condiciones ambientales, los requisitos de aplicación y las propiedades adhesivas. Aquí hay algunos puntos esenciales a considerar:
- Compatibilidad del sustrato: evalúe los materiales adheridos para garantizar la compatibilidad con el adhesivo. Los diferentes adhesivos tienen distintas afinidades por otros sustratos, como metales, plásticos, caucho o compuestos. Tenga en cuenta la energía superficial, la rugosidad y la composición química del sustrato para determinar la idoneidad del adhesivo.
- Condiciones ambientales: evalúe las condiciones que encontrará la membrana adherida, incluidas las temperaturas extremas, la humedad y la exposición a la radiación ultravioleta, los productos químicos o el agua. Seleccione un adhesivo que pueda soportar estas condiciones sin comprometer su fuerza de unión o durabilidad.
- Fuerza y durabilidad de la unión: determine la fuerza requerida de la unión en función de los requisitos de carga y tensión mecánica de la aplicación. Tenga en cuenta factores como la resistencia al corte, a la tracción y al desprendimiento, así como la vida útil anticipada del conjunto adherido. Asegúrese de que el adhesivo seleccionado pueda proporcionar la resistencia necesaria y la durabilidad a largo plazo.
- Método de Aplicación: Considere los métodos disponibles para aplicar el adhesivo. Algunos adhesivos se suministran como líquidos, películas o cintas, mientras que otros pueden requerir procesos de mezcla o curado. Elija una unión compatible con el método de aplicación y que se aplique fácilmente a la membrana y al sustrato.
- Tiempo y proceso de curado: comprenda el tiempo y el proceso de curado del adhesivo. Algunos adhesivos requieren calor, luz ultravioleta o humedad para iniciar o acelerar el proceso de curado, mientras que otros curan a temperatura ambiente. Considere el equipo de curado disponible y las limitaciones de tiempo para seleccionar un adhesivo que cumpla con los requisitos de la aplicación.
- Resistencia química: Evalúe la resistencia del adhesivo a los productos químicos o solventes que puedan entrar en contacto con el ensamblaje unido. Las aplicaciones específicas pueden implicar la exposición a combustibles, aceites, ácidos o agentes de limpieza. Verifique que el adhesivo pueda soportar dichas sustancias sin degradarse ni comprometer su fuerza de unión.
- Flexibilidad y elasticidad: considere los requisitos de flexibilidad y elasticidad del ensamblaje unido. Algunas aplicaciones pueden experimentar una expansión, contracción o vibración térmica significativa. Elija un adhesivo que pueda acomodar estos movimientos sin causar concentraciones de tensión o fallas en la unión.
- Cumplimiento normativo: determine si se aplican requisitos normativos específicos o estándares de la industria a la aplicación. Asegúrese de que el adhesivo seleccionado cumpla con los estándares de inflamabilidad, toxicidad o contacto con alimentos.
- Costo y disponibilidad: evalúe la rentabilidad del adhesivo, teniendo en cuenta factores como la cantidad requerida, la vida útil y la facilidad de adquisición. Considere la disponibilidad del adhesivo de proveedores acreditados y su disponibilidad a largo plazo para posibles reparaciones o reemplazos.
- Pruebas y validación: realice pruebas y validaciones exhaustivas del adhesivo en condiciones relevantes y escenarios específicos de la aplicación. Realice pruebas de adhesión y durabilidad, y simule las condiciones de servicio anticipadas para garantizar que la unión se desempeñe como se espera.
Al considerar cuidadosamente estos factores, puede seleccionar un adhesivo de unión de membranas compatible con los materiales, los requisitos de la aplicación y las condiciones ambientales, lo que garantiza una unión sólida y confiable para su aplicación específica.
Compatibilidad de membranas y preparación de sustratos
La compatibilidad de la membrana y la preparación del sustrato son consideraciones cruciales al seleccionar un adhesivo para la unión de membranas. La preparación adecuada de la superficie y la evaluación de la compatibilidad juegan un papel importante para lograr una unión sólida y duradera. Aquí hay una explicación detallada de estos factores:
- Compatibilidad de la membrana: Es esencial asegurarse de que el adhesivo sea compatible con el material de la membrana. Las membranas pueden estar hechas de varios materiales como PVC, EPDM, TPO o PTFE. Cada material puede tener diferentes propiedades superficiales, composición química o energía superficial. Algunos adhesivos funcionan mejor con ciertos materiales de membrana, mientras que otros pueden no adherirse de manera efectiva. Consulte las pautas del fabricante o realice pruebas de compatibilidad para determinar el mejor adhesivo para el material de membrana específico.
- Preparación del sustrato: la preparación adecuada del sustrato es fundamental para garantizar una buena adhesión. El sustrato debe estar limpio, seco y libre de contaminantes que puedan dificultar el proceso de unión. Siga estos pasos para la preparación del sustrato:
- Limpieza: Retire el polvo, la suciedad, la grasa o los aceites de la superficie del sustrato. Use solventes o detergentes de limpieza apropiados y asegúrese de enjuagar a fondo para eliminar los residuos.
- Aspereza de la superficie: en algunos casos, puede ser necesario raspar la superficie del sustrato para mejorar la unión del adhesivo. Esto se puede lograr a través de métodos como el lijado, el granallado o el uso de agentes de grabado químico. El objetivo es crear una superficie rugosa que mejore el enclavamiento mecánico entre el adhesivo y el sustrato.
- Imprimación: según el material del sustrato, es posible que se requiera una imprimación para mejorar la adhesión. Los imprimadores ayudan a mejorar la capacidad de humectación y unión del adhesivo al sustrato. Siguiendo las instrucciones del fabricante, se pueden aplicar con brocha, rociado o inmersión.
- Tratamiento de la superficie de la membrana: Al igual que los sustratos, la superficie de la membrana puede requerir un tratamiento para mejorar la unión. Algunas membranas tienen una superficie lisa o no porosa, lo que dificulta que los adhesivos se adhieran de manera efectiva. Considere los siguientes tratamientos:
- Limpieza de la membrana: limpie bien la superficie de la membrana para eliminar la suciedad, el polvo o los aceites que puedan interferir con la unión del adhesivo.
- Activación de la superficie: algunas membranas pueden beneficiarse de técnicas de activación de la superficie, como el tratamiento de corona o de llama. Estos métodos modifican la energía superficial de la membrana, mejorando la humectabilidad y las características de unión.
- Imprimación de superficie: Ciertos materiales de membrana pueden requerir la aplicación de una imprimación para mejorar la adhesión. La imprimación promueve una mejor adhesión entre la membrana y el adhesivo. Asegúrese de que la imprimación sea compatible tanto con la membrana como con el adhesivo.
- Selección del adhesivo: considere la compatibilidad de la membrana del adhesivo y las recomendaciones de preparación del sustrato. Los fabricantes de adhesivos a menudo brindan pautas y recomendaciones para las técnicas de preparación de superficies, imprimaciones o limpiadores que se utilizarán con sus productos. Siga atentamente estas recomendaciones para garantizar un rendimiento de unión óptimo.
Al considerar la compatibilidad de la membrana e implementar las técnicas adecuadas de preparación del sustrato, puede mejorar las posibilidades de lograr una unión sólida y duradera. Cumplir con las pautas del fabricante, realizar pruebas de compatibilidad y seguir los métodos de preparación de superficies recomendados ayudará a maximizar la eficacia del adhesivo y garantizará una unión duradera de la membrana.
Factores ambientales y propiedades de resistencia
Los factores ambientales juegan un papel crítico en el rendimiento y las propiedades de resistencia de los adhesivos de unión de membranas. Los adhesivos de unión de membranas se utilizan en diversas industrias, incluidas la construcción, la automoción y la electrónica, para unir membranas a diferentes sustratos de forma segura. La capacidad del adhesivo para resistir los factores estresantes ambientales es crucial para mantener la integridad y durabilidad de las membranas unidas.
Uno de los factores ambientales críticos que afectan a los adhesivos de unión de membranas es la temperatura. Los adhesivos suelen estar sujetos a diversas temperaturas, desde el frío extremo hasta el calor intenso. Las fluctuaciones de temperatura pueden afectar la viscosidad del adhesivo, el tiempo de curado y la fuerza de unión. Los adhesivos diseñados para ambientes fríos deben permanecer flexibles y conservar las propiedades de unión incluso a bajas temperaturas. Por otro lado, los adhesivos utilizados en aplicaciones de alta temperatura deben tener una excelente resistencia al calor para evitar la degradación o falla de la unión.
Los niveles de humedad y humedad también influyen significativamente en las propiedades de resistencia de los adhesivos para la unión de membranas. La humedad excesiva puede afectar negativamente el rendimiento del adhesivo al reducir la fuerza de unión y causar fallas en el adhesivo. El agua también puede desencadenar reacciones químicas o hinchazón en ciertos adhesivos, lo que provoca cambios dimensionales o pérdida de adherencia. Por lo tanto, las propiedades de resistencia a la humedad, como los adhesivos impermeables o de curado por humedad, a menudo se prefieren para aplicaciones en las que se espera exposición al agua o alta humedad.
La exposición química es otro factor ambiental importante a considerar. Según la aplicación, los adhesivos pueden entrar en contacto con diversos productos químicos, como disolventes, ácidos o álcalis. Ciertos productos químicos pueden degradar el adhesivo y provocar fallas en la unión. Es esencial seleccionar adhesivos con propiedades de resistencia química que puedan soportar la exposición a sustancias específicas que se encuentran en el medio ambiente.
La radiación ultravioleta (UV) del sol también puede afectar las propiedades de resistencia de los adhesivos de unión de membranas. La exposición prolongada a los rayos UV puede hacer que el adhesivo se degrade, lo que reduce la fuerza de unión y falla el adhesivo. Los selladores resistentes a los rayos UV, a menudo formulados con aditivos o polímeros especiales, pueden proteger contra la radiación UV y mantener su rendimiento en aplicaciones al aire libre.
Los estresores mecánicos, como la vibración, el impacto o las fuerzas de cizallamiento, son desafíos ambientales comunes que enfrentan los adhesivos para la unión de membranas. Los adhesivos utilizados en aplicaciones en las que prevalecen las tensiones mecánicas, como las industrias aeroespacial o de automoción, requieren una alta resistencia a estas fuerzas. A menudo se emplean adhesivos endurecidos o formulaciones flexibles para mejorar la resistencia del adhesivo al estrés mecánico y evitar fallas en la unión.
Técnicas y Métodos de Aplicación
La aplicación correcta de adhesivos para la unión de membranas es crucial para lograr uniones sólidas y duraderas. La técnica y el método de aplicación pueden afectar significativamente el rendimiento del adhesivo y la calidad general de la membrana adherida. Estas son algunas consideraciones y estrategias importantes para la aplicación efectiva de adhesivos para la unión de membranas:
- Preparación de la superficie: La preparación adecuada de la superficie es vital para garantizar una buena adhesión. Las superficies a unir deben estar limpias, secas y libres de contaminantes, como polvo, aceite, grasa o partículas sueltas. Dependiendo del material del sustrato, los métodos de limpieza de la superficie pueden incluir limpieza con solvente, lijado o el uso de una imprimación de superficie para promover la adhesión.
- Mezcla de adhesivos: Si es necesario mezclar el adhesivo para unir membranas, siga cuidadosamente las instrucciones del fabricante para lograr la proporción correcta y una mezcla completa. Una mezcla inadecuada puede dar como resultado un curado incompleto, una fuerza de unión reducida o propiedades adhesivas desiguales.
- Método de aplicación: La elección del método de aplicación depende del adhesivo específico y del tamaño y la forma del área de unión. Los métodos de aplicación estándar para adhesivos de unión de membranas incluyen:
- Brocha/Rodillo: Adecuada para áreas de unión grandes, una brocha o rodillo puede esparcir uniformemente el adhesivo sobre la superficie. Este método se usa comúnmente en aplicaciones de construcción o techado.
- Rociado: El uso de un sistema de rociado permite una aplicación rápida y uniforme del adhesivo. Es beneficioso para áreas grandes o cuando se requiere una capa adhesiva delgada y uniforme.
- Llana/llana dentada: Ideal para adhesivos más gruesos o cuando se necesita un espesor de adhesivo específico. La llana dentada asegura una cobertura adecuada y una distribución uniforme del adhesivo.
- Extrusión: en algunos casos, los adhesivos se dosifican mediante equipos de extrusión, como una pistola de calafateo o sistemas de dosificación especializados. Este método permite una aplicación y un control precisos del tamaño del cordón de adhesivo.
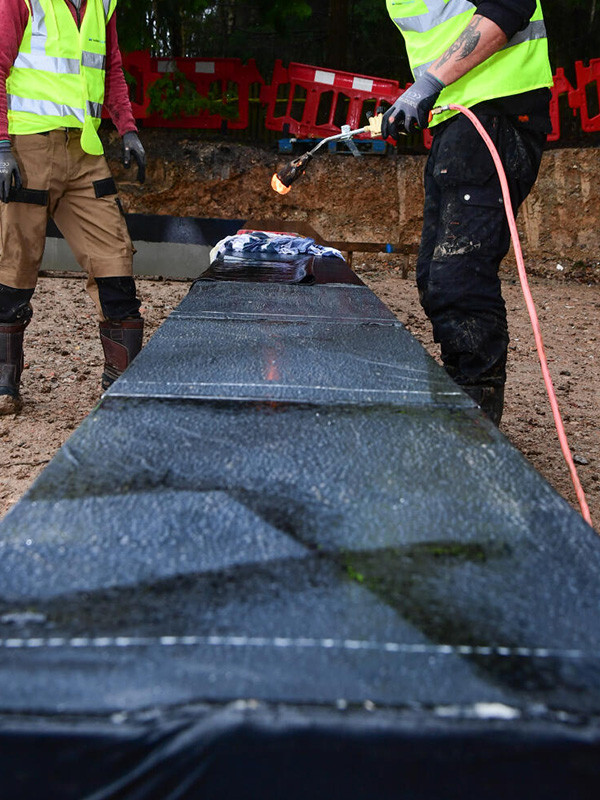
- Tiempo abierto y vida útil: el tiempo disponible se refiere a cuando el adhesivo permanece trabajable después de la aplicación, lo que permite colocar y ajustar la membrana. Es fundamental conocer el tiempo abierto del adhesivo y trabajar eficientemente dentro de ese tiempo. La vida útil se refiere al tiempo que el adhesivo mezclado permanece utilizable antes de que comience a curar. Los adhesivos deben aplicarse y usarse dentro de la vida útil especificada.
- Unión y prensado: Después de aplicar el adhesivo, coloque con cuidado la membrana sobre la superficie recubierta con adhesivo. Use herramientas adecuadas, como rodillos o almohadillas de presión, para aplicar una presión uniforme en toda el área adherida. Este paso ayuda a garantizar el contacto y la adhesión adecuados entre la membrana y el sustrato.
- Curado y secado: los adhesivos tienen tiempos específicos de curado o secado, que se deben seguir para lograr una unión óptima. Permita suficiente tiempo para que el adhesivo cure o seque de acuerdo con las recomendaciones del fabricante antes de someter la membrana adherida a tensión o carga.
- Control de calidad y pruebas: es crucial realizar controles de calidad y pruebas para verificar la fuerza y la integridad de la unión. Esto puede implicar la realización de pruebas de tracción, corte u otras pruebas relevantes para garantizar que el adhesivo haya alcanzado el rendimiento deseado.
Siempre consulte las pautas e instrucciones del fabricante para el adhesivo de unión de membrana específico que se está utilizando. Cumplir con las técnicas y métodos de aplicación adecuados, junto con la preparación adecuada de la superficie, ayudará a garantizar una unión exitosa y mejorará la longevidad y el rendimiento de la membrana adherida.
Durabilidad y longevidad de las membranas adheridas
Las membranas adheridas se utilizan ampliamente en diversas industrias y aplicaciones debido a su excepcional durabilidad y longevidad. Estas membranas proporcionan una barrera protectora, mejoran la integridad estructural y evitan la infiltración de humedad u otras sustancias nocivas. Aquí, exploraremos los factores clave que contribuyen a la durabilidad y longevidad de las membranas adheridas.
- Selección de materiales: la elección de los materiales para las membranas adheridas es crucial para determinar su durabilidad. Los materiales de alta calidad, como los cauchos sintéticos, los betunes modificados o las olefinas termoplásticas (TPO), se utilizan comúnmente debido a su excelente resistencia a la intemperie, la radiación ultravioleta y la exposición química. Estos materiales ofrecen resistencia, flexibilidad y resiliencia superiores, lo que garantiza un rendimiento y una longevidad a largo plazo.
- Tecnología de unión: La tecnología de unión empleada durante la instalación de membranas afecta significativamente su durabilidad. La preparación adecuada de la superficie, la selección del adhesivo y las técnicas de aplicación son fundamentales para lograr una unión sólida y duradera entre la membrana y el sustrato. Los métodos de unión avanzados, como la soldadura por calor o la soldadura por solvente, crean conexiones sólidas y sin costuras que resisten la separación, el agrietamiento o el pelado con el tiempo.
- Diseño estructural: el diseño de las membranas adheridas es vital para su longevidad. Las capas de refuerzo, como poliéster o fibra de vidrio, a menudo se incorporan dentro de la estructura de la membrana para mejorar su fuerza y resistencia al desgarro o perforación. El grosor y la composición de la membrana también se adaptan para cumplir con los requisitos de rendimiento específicos, teniendo en cuenta la capacidad de carga, el movimiento anticipado y las condiciones ambientales.
- Resistencia a la intemperie: la durabilidad en ambientes al aire libre depende en gran medida de la capacidad de una membrana adherida para soportar condiciones climáticas extremas. Las membranas de alta calidad están diseñadas para resistir las fluctuaciones de temperatura, los ciclos térmicos y la exposición a la radiación ultravioleta (UV). Se pueden agregar estabilizadores UV y revestimientos reflectantes a la superficie de la membrana para mejorar su resistencia a la degradación UV, reduciendo el riesgo de agrietamiento, fragilización o decoloración.
- Mantenimiento e inspecciones: el mantenimiento y las inspecciones regulares son esenciales para garantizar la durabilidad a largo plazo de las membranas adheridas. Las evaluaciones pueden identificar signos tempranos de daño o deterioro, lo que permite reparaciones oportunas y previene problemas más importantes. Los procedimientos adecuados de limpieza y mantenimiento, tal como lo recomienda el fabricante de la membrana, ayudan a preservar las características de rendimiento de la membrana y prolongan su vida útil.
- Garantía de calidad: Cumplir con los estándares y regulaciones de la industria e involucrar a fabricantes y contratistas acreditados es crucial para garantizar la durabilidad de las membranas adheridas. Los proveedores confiables ofrecen productos de alta calidad con rigurosos procesos de prueba y certificación, lo que brinda confianza en su desempeño a largo plazo.
Mantenimiento y Reparación de Adhesivo de Unión de Membranas
El mantenimiento adecuado y las reparaciones oportunas son cruciales para garantizar el rendimiento y la longevidad óptimos de los adhesivos para la unión de membranas. Estos adhesivos se utilizan para crear uniones sólidas y duraderas entre membranas y sustratos, y su eficacia puede verse afectada por diversos factores, como las condiciones ambientales, el envejecimiento y el desgaste. Aquí, discutiremos los aspectos críticos del mantenimiento y la reparación de los adhesivos para la unión de membranas.
- Inspecciones regulares: La realización de inspecciones de rutina es esencial para identificar cualquier signo de daño, deterioro o falla del adhesivo. Las inspecciones deben llevarse a cabo periódicamente, siguiendo las recomendaciones del fabricante, y cualquier problema debe abordarse de inmediato para evitar más daños o comprometer el sistema de membrana unida.
- Limpieza: La limpieza adecuada del sistema de membrana unida puede ayudar a mantener el rendimiento del adhesivo y prolongar su vida útil. Elimine cualquier residuo, suciedad o contaminante de la superficie de la membrana y el sustrato utilizando agentes de limpieza adecuados o métodos recomendados por el fabricante del adhesivo. Esto asegura un carácter limpio y suave para un rendimiento de unión óptimo.
- Compatibilidad del adhesivo: cuando se necesitan reparaciones, es crucial usar un adhesivo compatible con el sistema de unión existente. Consulte las pautas del fabricante del adhesivo para garantizar la compatibilidad con el material de membrana y el sustrato específicos. El uso de adhesivos incompatibles puede provocar una adhesión deficiente, una durabilidad reducida o incluso daños en la membrana o el sustrato.
- Preparación de la superficie: La preparación adecuada de la superficie es esencial antes de aplicar el adhesivo para reparaciones. Limpie a fondo las superficies de unión, eliminando contaminantes, partículas sueltas o residuos de adhesivo antiguo. Es posible que se requieran pasos adicionales de preparación de la superficie, como lijado, imprimación o aplicación de un agente adhesivo, según la unión y el sustrato específicos. Seguir las instrucciones del fabricante es crucial para una resistencia y durabilidad óptimas de la unión.
- Técnicas de aplicación: Al aplicar adhesivo para reparaciones, siga cuidadosamente las técnicas de aplicación recomendadas proporcionadas por el fabricante. Aplique el adhesivo uniformemente y con el espesor recomendado para asegurar una correcta unión y evitar una aplicación excesiva o insuficiente del adhesivo. También se deben mantener condiciones adecuadas de temperatura y humedad durante la aplicación, según lo especifique el fabricante del adhesivo.
Desarrollos futuros en adhesivos para unión de membranas
El campo de los adhesivos para la unión de membranas está en constante evolución, impulsado por los avances en la ciencia de los materiales, los procesos de fabricación y las demandas de la industria. Se pueden esperar futuros desarrollos en los adhesivos de unión de membranas para mejorar el rendimiento, la sostenibilidad y la facilidad de uso. Aquí hay algunos efectos potenciales a tener en cuenta:
- Formulaciones respetuosas con el medio ambiente: con un énfasis creciente en la sostenibilidad, existe una demanda creciente de adhesivos para la unión de membranas con un impacto medioambiental mínimo. Los desarrollos futuros pueden enfocarse en la formulación de adhesivos con compuestos orgánicos volátiles (COV) reducidos y sustancias peligrosas, asegurando el cumplimiento de las regulaciones ambientales. También se pueden desarrollar adhesivos biodegradables o de base biológica, que ofrecen una alternativa más ecológica.
- Durabilidad y rendimiento mejorados: Continuará la búsqueda de adhesivos de unión más duraderos y de alto rendimiento. Los esfuerzos de investigación y desarrollo pueden enfocarse en mejorar las formulaciones adhesivas para fortalecer la resistencia contra condiciones climáticas extremas, radiación ultravioleta, exposición química y envejecimiento. Esto daría como resultado adhesivos que mantienen la fuerza y la integridad de la unión durante períodos prolongados, incluso en entornos hostiles.
- Nuevas tecnologías de unión: Los avances en las tecnologías de unión pueden conducir al desarrollo de sistemas adhesivos innovadores. Por ejemplo, la introducción de adhesivos inteligentes que puedan autorrepararse o adaptarse a condiciones cambiantes podría revolucionar el campo. La integración de la nanotecnología en las formulaciones adhesivas puede mejorar la fuerza adhesiva, la flexibilidad y otras propiedades deseadas.
- Tiempos de curado más rápidos: los sistemas adhesivos tradicionales a menudo requieren un tiempo de curado significativo antes de alcanzar su máxima resistencia. Los desarrollos futuros pueden acelerar el proceso de curado a través de nuevos mecanismos de curado, como los adhesivos UV o activados por humedad. Esto permitiría una instalación más rápida y reduciría el tiempo de inactividad en varias aplicaciones.
- Compatibilidad mejorada: los adhesivos de unión de membranas deben ser compatibles con varios materiales de membrana, sustratos y condiciones de superficie. Los desarrollos futuros apuntan a mejorar la compatibilidad de los adhesivos, asegurando uniones sólidas y confiables en diversas aplicaciones. Esto podría implicar el desarrollo de adhesivos con capacidades de adhesión más amplias o formulaciones específicas diseñadas para diferentes materiales y sustratos.
- Facilidad de solicitud: simplificar el proceso de solicitud es otra área de desarrollo potencial. Los fabricantes de adhesivos pueden enfocarse en crear adhesivos con mayor facilidad de uso, como sistemas adhesivos premezclados o preaplicados. Estos avances agilizarían el proceso de instalación, reducirían el riesgo de errores de aplicación y, potencialmente, permitirían que los trabajadores menos experimentados logren una unión de alta calidad.
- Control de calidad avanzado: A medida que aumenta la demanda de confiabilidad y consistencia, los desarrollos futuros pueden implicar medidas de control de calidad avanzadas para la producción de adhesivos. Esto podría incluir la implementación de sistemas de inspección automatizados, el monitoreo en tiempo real de las propiedades del adhesivo durante la aplicación y el uso de análisis avanzados y algoritmos de aprendizaje automático para optimizar las formulaciones adhesivas.
Conclusión
El adhesivo de unión de membranas es versátil y esencial en diversas industrias, ya que proporciona una unión segura y confiable para membranas utilizadas en aplicaciones de construcción, automoción y fabricación. Al seleccionar el adhesivo adecuado en función de factores como la compatibilidad de la membrana, las condiciones ambientales y las técnicas de aplicación, las industrias pueden garantizar el rendimiento efectivo y duradero de las membranas adheridas. A medida que continúan los avances, se espera que los desarrollos futuros en el adhesivo de unión de membranas mejoren la fuerza de unión, la durabilidad y la eficiencia de la aplicación.