Adhesivo MEMS
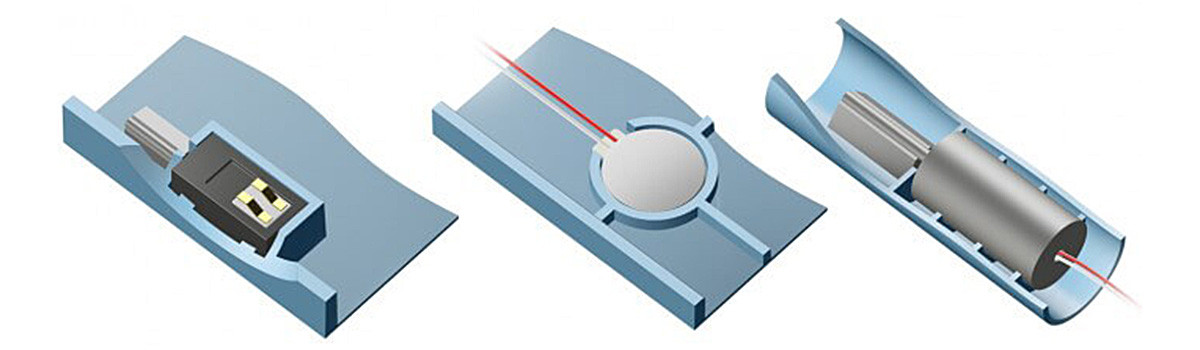
Los sistemas microelectromecánicos (MEMS) han revolucionado varias industrias al permitir el desarrollo de dispositivos más pequeños y eficientes. Un componente crítico que ha contribuido al éxito de la tecnología MEMS es el adhesivo MEMS. El adhesivo MEMS juega un papel crucial en la unión y fijación de microestructuras y componentes en dispositivos MEMS, asegurando su estabilidad, confiabilidad y rendimiento. En este artículo, exploramos la importancia del adhesivo MEMS y sus aplicaciones, destacando los subtítulos clave que arrojan luz sobre sus diversos aspectos.
Comprender el adhesivo MEMS: fundamentos y composición
Los sistemas microelectromecánicos (MEMS) han revolucionado varias industrias al permitir la producción de dispositivos diminutos con capacidades poderosas. El adhesivo MEMS juega un papel fundamental en el montaje y embalaje de estos dispositivos en miniatura. Comprender los fundamentos y la composición del adhesivo MEMS es esencial para lograr una unión fiable y sólida en la fabricación de MEMS. Este artículo profundiza en el adhesivo MEMS para arrojar luz sobre su importancia y consideraciones críticas.
Los fundamentos del adhesivo MEMS
El adhesivo MEMS está diseñado específicamente para facilitar uniones sólidas y duraderas entre varios componentes de microdispositivos. Estos adhesivos poseen propiedades únicas para cumplir con los estrictos requisitos de las aplicaciones MEMS. Una de las propiedades fundamentales del adhesivo MEMS es su capacidad para soportar condiciones ambientales adversas, incluidas las fluctuaciones de temperatura, la humedad y la exposición a sustancias químicas. Además, los adhesivos MEMS deben exhibir excelentes propiedades mecánicas, como alta fuerza de adhesión, baja contracción y mínima fluencia, para garantizar la confiabilidad a largo plazo.
Composición del adhesivo MEMS
La composición del adhesivo MEMS está cuidadosamente formulada para satisfacer las necesidades específicas de los envases MEMS. Por lo general, los adhesivos MEMS constan de varios componentes clave, cada uno con un propósito particular:
Matriz de polímero: La matriz polimérica forma la mayor parte del adhesivo y proporciona la integridad estructural necesaria. Los polímeros comunes utilizados en los adhesivos MEMS incluyen epoxi, poliimida y acrílico. Estos polímeros ofrecen excelentes propiedades de adhesión, resistencia química y estabilidad mecánica.
Materiales de relleno: Para mejorar las propiedades adhesivas, se incorporan rellenos a la matriz polimérica. Los rellenos como sílice, alúmina o partículas de metal pueden mejorar la conductividad térmica, la conductividad eléctrica y la estabilidad dimensional del adhesivo.
Agentes de curado: Los adhesivos MEMS a menudo requieren un proceso de curado para alcanzar sus propiedades finales. Los agentes de curado, como aminas o anhídridos, inician reacciones de reticulación en la matriz polimérica, lo que da como resultado una fuerte unión adhesiva.
Promotores de adhesión: Algunos adhesivos MEMS pueden incluir promotores de adhesión para mejorar la unión entre el adhesivo y los sustratos. Estos promotores suelen ser compuestos a base de silano que mejoran la adhesión a varios materiales, como metales, cerámica o polímeros.
Consideraciones para la selección de adhesivos MEMS
El adhesivo MEMS adecuado garantiza el rendimiento y la fiabilidad a largo plazo de los dispositivos MEMS. Al elegir un bono, se deben considerar varios factores:
Compatibilidad: El adhesivo debe ser compatible con los materiales que se unen, así como con el entorno operativo del dispositivo MEMS.
Compatibilidad de procesos: El adhesivo debe ser compatible con los procesos de fabricación involucrados, como los métodos de aplicación, curado y unión.
Propiedades térmicas y mecánicas: El adhesivo debe exhibir una estabilidad térmica adecuada, un bajo coeficiente de expansión térmica (CTE) y excelentes propiedades mecánicas para soportar las tensiones encontradas durante el funcionamiento del dispositivo.
Fuerza de adherencia: El adhesivo debe proporcionar la fuerza suficiente para garantizar una unión sólida entre los componentes, evitando la delaminación o fallas.
Tipos de adhesivo MEMS: descripción general
Los dispositivos MEMS (sistemas microelectromecánicos) son dispositivos en miniatura que combinan componentes mecánicos y eléctricos en un solo chip. Estos dispositivos a menudo requieren técnicas de unión precisas y confiables para garantizar una funcionalidad adecuada. Los adhesivos MEMS juegan un papel crucial en el montaje y empaquetado de estos dispositivos. Proporcionan una unión sólida y duradera entre diferentes componentes mientras se adaptan a los requisitos únicos de la tecnología MEMS. Aquí hay una descripción general de algunos tipos comunes de adhesivos MEMS:
- Adhesivos epoxi: Los adhesivos a base de epoxi se utilizan ampliamente en aplicaciones MEMS. Ofrecen una excelente fuerza de unión y buena resistencia química. Los adhesivos epoxi suelen ser termoendurecibles y requieren calor o un agente de curado endurecedor. Proporcionan una alta integridad estructural y pueden soportar condiciones de funcionamiento adversas.
- Adhesivos de silicona: los adhesivos de silicona son conocidos por su flexibilidad, resistencia a altas temperaturas y excelentes propiedades de aislamiento eléctrico. Son particularmente adecuados para dispositivos MEMS que se someten a ciclos térmicos o requieren amortiguación de vibraciones. Los adhesivos de silicona ofrecen una buena adhesión a diversos sustratos y pueden mantener sus propiedades en un amplio rango de temperaturas.
- Adhesivos acrílicos: los adhesivos a base de acrílico son populares debido a sus rápidos tiempos de curado, buena fuerza de unión y transparencia óptica. A menudo se utilizan en aplicaciones que requieren claridad visual, como dispositivos MEMS ópticos. Los adhesivos acrílicos brindan una unión confiable y pueden adherirse a diferentes sustratos, incluidos vidrio, metales y plásticos.
- Adhesivos curables por UV: Los adhesivos curables por UV están diseñados para curar rápidamente cuando se exponen a la luz ultravioleta (UV). Ofrecen tiempos de curado rápidos, lo que puede mejorar la eficiencia de la producción. Los adhesivos UV se usan comúnmente en aplicaciones MEMS donde es necesaria una alineación precisa porque permanecen líquidos hasta que se exponen a la luz UV. Proporcionan una excelente adherencia y son adecuados para unir componentes delicados.
- Adhesivos conductores anisotrópicos (ACA): Los adhesivos ACA están diseñados para unir componentes microelectrónicos que requieren soporte mecánico y conductividad eléctrica. Consisten en partículas conductoras dispersas dentro de una matriz adhesiva no conductora. Los adhesivos ACA brindan conexiones eléctricas confiables mientras mantienen la estabilidad mecánica, lo que los hace ideales para dispositivos MEMS que involucran interconexiones eléctricas.
- Adhesivos sensibles a la presión (PSA): Los adhesivos PSA se caracterizan por su capacidad para formar una unión tras la aplicación de una ligera presión. No requieren calor ni agentes de curado para la unión. Los adhesivos PSA ofrecen facilidad de uso y se pueden reposicionar si es necesario. Se usan comúnmente en dispositivos MEMS que requieren unión temporal o donde se desea una separación no destructiva.
Los adhesivos MEMS están disponibles en varias formas, incluidos adhesivos líquidos, películas, pastas y cintas, lo que permite flexibilidad para elegir la opción más adecuada para procesos específicos de ensamblaje y empaque. La selección de un adhesivo en particular depende de factores como los materiales del sustrato, las condiciones ambientales, los requisitos térmicos y las consideraciones de conductividad eléctrica.
Es esencial considerar la compatibilidad del adhesivo con los materiales MEMS y los requisitos y limitaciones de procesamiento para garantizar la integración exitosa y la confiabilidad a largo plazo de los dispositivos MEMS. Los fabricantes suelen realizar extensos procesos de prueba y calificación para validar el rendimiento y la idoneidad del adhesivo para aplicaciones MEMS específicas.
Técnicas de Unión: Energía Superficial y Adhesión
La energía superficial y la adhesión son conceptos fundamentales en las técnicas de unión, y comprender estos conceptos es crucial para lograr uniones sólidas y confiables entre materiales. Aquí hay una descripción general de la energía superficial y la adhesión en la unión:
Energía superficial: La energía superficial es una medida de la energía requerida para aumentar el área superficial de un material. Es una propiedad que determina cómo un material interactúa con otras sustancias. La energía superficial surge de las fuerzas cohesivas entre átomos o moléculas en la superficie de un material. Se puede considerar como la tendencia de un material a minimizar su área superficial y formar una forma con la menor cantidad de energía superficial.
Diferentes materiales exhiben diferentes niveles de energía superficial. Algunos materiales tienen una alta energía superficial, lo que significa que tienen una gran afinidad por otras sustancias y forman enlaces fácilmente. Los ejemplos de materiales de alta energía superficial incluyen metales y materiales polares como el vidrio o ciertos plásticos. Por otro lado, algunos materiales tienen una energía superficial baja, lo que los hace menos propensos a unirse con otras sustancias. Los ejemplos de materiales de baja energía superficial incluyen polímeros específicos, como el polietileno o el polipropileno.
Adhesión: La adhesión es el fenómeno de atracción molecular entre diferentes materiales que hace que se peguen entre sí cuando entran en contacto. La fuerza mantiene unidas dos superficies, y la adhesión es esencial para lograr uniones sólidas y duraderas en las técnicas de unión.
La adhesión se puede clasificar en varios tipos según los mecanismos involucrados:
- Adhesión mecánica: la adhesión mecánica se basa en el enclavamiento o el enclavamiento físico entre superficies. Ocurre cuando dos materiales tienen superficies ásperas o irregulares que encajan entre sí, creando una unión sólida. La adhesión mecánica a menudo se mejora con adhesivos o técnicas que aumentan el área de contacto entre los caracteres, como cintas adhesivas con alta adaptabilidad.
- Adhesión química: La adhesión química ocurre cuando hay una interacción química entre las superficies de dos materiales. Implica la formación de enlaces químicos o fuerzas atractivas en la interfase. La adhesión química se logra comúnmente a través de adhesivos que reaccionan químicamente con las superficies o mediante tratamientos superficiales que promueven la unión química, como el tratamiento con plasma o las imprimaciones.
- Adhesión electrostática: La adhesión electrostática se basa en la atracción entre cargas positivas y negativas en diferentes superficies. Ocurre cuando un carácter se carga eléctricamente, atrayendo la superficie con carga opuesta. La adhesión electrostática se utiliza comúnmente en técnicas de sujeción o unión electrostática que involucran partículas cargadas.
- Adhesión molecular: La adhesión molecular implica las fuerzas de van der Waals o interacciones dipolo-dipolo entre moléculas en la interfaz de dos materiales. Estas fuerzas intermoleculares pueden contribuir a la adhesión entre superficies. El enlace molecular es particularmente relevante para materiales con baja energía superficial.
Para lograr una adhesión adecuada, es fundamental considerar la energía superficial de los materiales que se van a unir. Los materiales con energías superficiales similares tienden a exhibir una mejor adhesión; sin embargo, cuando se unen materiales con energías superficiales significativamente diferentes, pueden ser necesarios tratamientos superficiales o promotores de adhesión para mejorar la adhesión.
Beneficios del adhesivo MEMS en miniaturización
Los sistemas microelectromecánicos (MEMS) han revolucionado el campo de la miniaturización, permitiendo el desarrollo de dispositivos compactos y sofisticados en diversas industrias. El adhesivo MEMS juega un papel crucial en la integración y el ensamblaje exitosos de los dispositivos MEMS, y ofrece varios beneficios que contribuyen a su miniaturización. En esta respuesta, resumiré las ventajas clave del adhesivo MEMS en miniaturización en 450 palabras.
- Unión precisa: el adhesivo MEMS ofrece capacidades de unión precisas y confiables, lo que permite la unión segura de microcomponentes con alta precisión. Con dispositivos miniaturizados, donde el tamaño de los componentes individuales suele estar en la escala de micras o submicras, el adhesivo debe poder formar uniones fuertes y consistentes entre estructuras delicadas. Las formulaciones de adhesivos MEMS están diseñadas para proporcionar excelentes propiedades de adhesión, asegurando la integridad estructural y la funcionalidad de los dispositivos MEMS ensamblados.
- Baja desgasificación: los dispositivos miniaturizados a menudo funcionan en entornos sensibles o de alto rendimiento, como aplicaciones aeroespaciales, automotrices o médicas. En tales casos, el adhesivo utilizado debe presentar una mínima desgasificación para evitar la contaminación, la degradación o la interferencia con los componentes o las superficies circundantes. Los adhesivos MEMS están formulados para tener características de baja desgasificación, lo que minimiza la liberación de compuestos volátiles y reduce el riesgo de efectos adversos en el rendimiento del dispositivo.
- Estabilidad térmica: los dispositivos MEMS frecuentemente encuentran condiciones de temperatura variables durante su funcionamiento. Los materiales adhesivos MEMS están diseñados para exhibir una excelente estabilidad térmica, soportando temperaturas extremas y ciclos térmicos sin comprometer la fuerza de unión. Esta característica es esencial en sistemas miniaturizados donde el espacio es limitado y el adhesivo debe soportar ambientes térmicos exigentes sin degradación.
- Flexibilidad mecánica: la capacidad de soportar el estrés mecánico y la vibración es crucial para los dispositivos miniaturizados que pueden estar sujetos a fuerzas externas. Las formulaciones de adhesivos MEMS ofrecen flexibilidad mecánica, lo que les permite absorber y disipar el estrés, lo que reduce la probabilidad de daños o fallas estructurales. Esta flexibilidad garantiza la confiabilidad y durabilidad a largo plazo de los dispositivos MEMS miniaturizados, incluso en entornos dinámicos.
- Aislamiento eléctrico: muchos dispositivos MEMS incorporan componentes eléctricos, como sensores, actuadores o interconexiones. Los materiales adhesivos MEMS poseen excelentes propiedades de aislamiento eléctrico, lo que previene eficazmente los cortocircuitos o las interferencias eléctricas entre diferentes componentes. Esta característica es particularmente importante en dispositivos miniaturizados, donde la proximidad de vías eléctricas puede aumentar el riesgo de acoplamiento eléctrico no deseado.
- Compatibilidad química: las formulaciones adhesivas de MEMS están diseñadas para ser químicamente compatibles con una amplia gama de materiales comúnmente utilizados en la fabricación de MEMS, como silicona, polímeros, metales y cerámica. Esta compatibilidad permite una integración versátil de diferentes componentes, lo que permite la miniaturización de sistemas MEMS complejos. Además, la resistencia química del adhesivo garantiza la estabilidad y longevidad de las interfaces unidas, incluso cuando se exponen a entornos operativos hostiles o sustancias corrosivas.
- Compatibilidad del proceso: los materiales adhesivos MEMS se desarrollan para que sean compatibles con varios procesos de ensamblaje, incluida la unión de chip invertido, el empaque a nivel de obleas y la encapsulación. Esta compatibilidad facilita los procesos de fabricación optimizados para dispositivos miniaturizados, lo que mejora la productividad y la escalabilidad. Las formulaciones de adhesivos MEMS se pueden adaptar para cumplir con los requisitos de procesamiento específicos, lo que permite una integración perfecta en las técnicas de fabricación existentes.
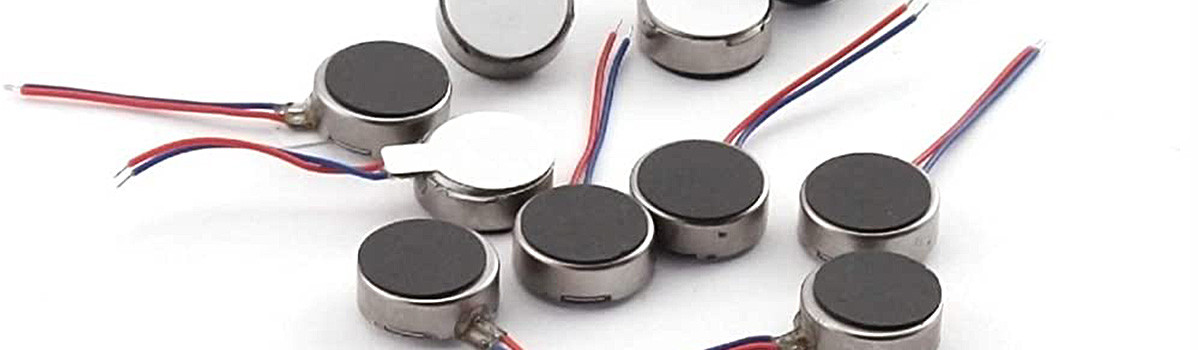
Adhesivo MEMS para aplicaciones de sensores
Los sensores MEMS (Micro-Electro-Mechanical Systems) se utilizan ampliamente en diversas aplicaciones, como la automoción, la electrónica de consumo, la sanidad y los sectores industriales. Estos sensores suelen ser dispositivos miniaturizados que combinan componentes eléctricos y mecánicos para medir y detectar fenómenos físicos como presión, aceleración, temperatura y humedad.
Un aspecto crítico de la fabricación e integración de sensores MEMS es el material adhesivo utilizado para unir el sensor al sustrato objetivo. El adhesivo garantiza un rendimiento fiable y robusto del sensor, proporcionando estabilidad mecánica, conectividad eléctrica y protección contra factores ambientales.
Cuando se trata de seleccionar un adhesivo para aplicaciones de sensores MEMS, se deben considerar varios factores:
Compatibilidad: el material adhesivo debe ser compatible con el sensor y el sustrato para garantizar una adhesión adecuada. Diferentes sensores MEMS pueden tener distintos materiales, como silicio, polímeros o metales, y el adhesivo debe adherirse de manera efectiva a estas superficies.
Propiedades mecánicas: el adhesivo debe poseer propiedades mecánicas adecuadas para adaptarse a las tensiones encontradas durante el funcionamiento del sensor MEMS. Debe exhibir buena resistencia al corte, resistencia a la tracción y flexibilidad para resistir la expansión térmica, la vibración y los choques mecánicos.
Estabilidad térmica: los sensores MEMS pueden estar expuestos a temperaturas variables durante el funcionamiento. El material adhesivo debe tener una alta temperatura de transición vítrea (Tg) y mantener su fuerza adhesiva en un amplio rango de temperatura.
Conductividad eléctrica: en algunas aplicaciones de sensores MEMS, es necesaria la conectividad eléctrica entre el sensor y el sustrato. Un adhesivo con buena conductividad eléctrica o baja resistencia puede garantizar una transmisión de señal confiable y minimizar las pérdidas eléctricas.
Resistencia química: el adhesivo debe resistir la humedad, los productos químicos y otros factores ambientales para brindar estabilidad a largo plazo y proteger los componentes del sensor de la degradación.
Los adhesivos a base de silicona se usan comúnmente en aplicaciones de sensores MEMS debido a su excelente compatibilidad con varios materiales, baja desgasificación y resistencia a factores ambientales. Ofrecen una buena adhesión a los dispositivos MEMS basados en silicio y proporcionan aislamiento eléctrico si es necesario.
Además, los adhesivos a base de epoxi son ampliamente utilizados por su alta resistencia y excelente estabilidad térmica. Ofrecen una unión sólida a varios sustratos y pueden soportar diferentes temperaturas.
En algunos casos, se utilizan adhesivos conductores cuando se requiere conectividad eléctrica. Estos adhesivos están formulados con rellenos conductores como plata o carbón, lo que les permite proporcionar tanto unión mecánica como conducción eléctrica.
Es fundamental tener en cuenta los requisitos específicos de la aplicación del sensor MEMS y consultar a los fabricantes o proveedores de adhesivos para seleccionar el adhesivo más adecuado. También se deben considerar factores como el tiempo de curado, la viscosidad y el método de aplicación.
Adhesivo MEMS en Dispositivos Médicos: Avances y Desafíos
La tecnología MEMS (Sistemas Micro-Electro-Mecánicos) tiene aplicaciones significativas en dispositivos médicos, permitiendo avances en diagnóstico, monitoreo, administración de medicamentos y dispositivos implantables. Los materiales adhesivos utilizados en los dispositivos médicos basados en MEMS desempeñan un papel crucial para garantizar la confiabilidad, la biocompatibilidad y el rendimiento a largo plazo de estos dispositivos. Exploremos los avances y desafíos de los adhesivos MEMS en dispositivos médicos.
Avances:
- Biocompatibilidad: los materiales adhesivos utilizados en dispositivos médicos deben ser biocompatibles para garantizar que no provoquen reacciones adversas ni causen daño al paciente. Se han logrado avances significativos en el desarrollo de materiales adhesivos con biocompatibilidad mejorada, lo que permite una integración más segura y confiable de sensores MEMS en dispositivos médicos.
- Miniaturización: la tecnología MEMS permite la miniaturización de dispositivos médicos, haciéndolos más portátiles, mínimamente invasivos y capaces de monitoreo en tiempo real. Los materiales adhesivos diseñados para aplicaciones MEMS han avanzado para adaptarse a la tendencia de miniaturización, proporcionando una unión sólida y confiable en espacios reducidos.
- Sustratos flexibles: los dispositivos médicos flexibles y estirables han ganado prominencia debido a su capacidad para adaptarse a superficies curvas y mejorar la comodidad del paciente. Se han desarrollado materiales adhesivos con alta flexibilidad y capacidad de estiramiento para permitir la unión segura entre sensores MEMS y sustratos flexibles, ampliando las posibilidades de dispositivos médicos portátiles e implantables.
- Biodegradabilidad: en aplicaciones médicas específicas en las que se utilizan dispositivos temporales, como sistemas de administración de fármacos o andamios de tejidos, los adhesivos biodegradables han llamado la atención. Estos adhesivos pueden degradarse gradualmente con el tiempo, lo que elimina la necesidad de procedimientos de extracción o explantación del dispositivo.
Desafíos:
- Pruebas de biocompatibilidad: garantizar la biocompatibilidad de los materiales adhesivos utilizados en dispositivos médicos basados en MEMS es un proceso complejo que requiere pruebas exhaustivas y cumplimiento normativo. Los fabricantes de adhesivos enfrentan desafíos para cumplir con los estrictos estándares establecidos por los organismos reguladores para garantizar la seguridad del paciente.
- Confiabilidad a largo plazo: los dispositivos médicos a menudo requieren una implantación a largo plazo o un uso continuo. Los materiales adhesivos deben exhibir una unión confiable y mantener sus propiedades mecánicas y adhesivas durante períodos prolongados, considerando las condiciones fisiológicas y los posibles factores de degradación presentes en el cuerpo.
- Estabilidad química y térmica: los dispositivos médicos basados en MEMS pueden encontrarse con entornos químicos hostiles, fluidos corporales y fluctuaciones de temperatura durante el funcionamiento. Los adhesivos deben poseer una excelente resistencia química y estabilidad térmica para mantener su integridad y fuerza de unión.
- Compatibilidad de esterilización: los dispositivos médicos deben someterse a procesos de esterilización para eliminar posibles patógenos y garantizar la seguridad del paciente. Los materiales adhesivos deben ser compatibles con los métodos de esterilización estándar, como el autoclave, la esterilización con óxido de etileno (EtO) o la radiación gamma sin comprometer sus propiedades adhesivas.
Adhesivo MEMS para microfluidos: mejora del control de fluidos
La microfluídica, la ciencia y la tecnología de manipular pequeños volúmenes de fluidos, ha ganado una atención significativa en varios campos, incluida la investigación biomédica, el diagnóstico, la administración de fármacos y el análisis químico. La tecnología MEMS (Micro-Electro-Mechanical Systems) permite un control de fluidos preciso en dispositivos microfluídicos. Los materiales adhesivos utilizados en estos dispositivos son fundamentales para lograr conexiones fluídicas confiables y mantener el control de fluidos. Exploremos cómo los adhesivos MEMS mejoran la potencia de los fluidos en la microfluídica y los avances asociados.
- Sellado sin fugas: los dispositivos de microfluidos a menudo requieren múltiples canales fluídicos, válvulas y depósitos. Los materiales adhesivos con excelentes propiedades de sellado son cruciales para conexiones sin fugas, evitando la contaminación cruzada y asegurando un control de fluidos preciso. Los adhesivos MEMS proporcionan un sellado sólido, lo que permite el funcionamiento fiable de los dispositivos de microfluidos.
- Unión de materiales diferentes: los dispositivos de microfluidos pueden constar de varios materiales, como vidrio, silicona, polímeros y metales. Los adhesivos MEMS están formulados para tener una buena adhesión a diferentes materiales de sustrato, lo que permite unir materiales diferentes. Esta capacidad permite la integración de diversos componentes y facilita la fabricación de estructuras microfluídicas complejas.
- Alta compatibilidad química: los adhesivos MEMS utilizados en microfluidos deben exhibir una alta compatibilidad química con los fluidos y reactivos manipulados. Deben resistir la degradación química y permanecer estables, asegurando la integridad de los canales fluídicos y evitando la contaminación. Los adhesivos MEMS avanzados están diseñados para resistir varios productos químicos comúnmente utilizados en aplicaciones de microfluidos.
- Características de flujo óptimas: en los dispositivos de microfluidos, el control preciso del flujo de fluido y la minimización de las interrupciones del flujo son esenciales. Los adhesivos MEMS se pueden adaptar para que tengan propiedades de superficie lisas y uniformes, lo que reduce la aparición de burbujas, gotitas o patrones de flujo irregulares. Esta optimización mejora el control de fluidos y mejora la precisión de las operaciones microfluídicas.
- Replicación de características a microescala: los dispositivos de microfluidos a menudo requieren la replicación de características complejas a microescala, como canales, cámaras y válvulas. Los adhesivos MEMS con baja viscosidad y altas propiedades de humectación pueden rellenar características de microescala de manera efectiva, asegurando la reproducción precisa de estructuras fluídicas complejas y manteniendo el control de fluidos a pequeña escala.
- Resistencia a la temperatura y la presión: los dispositivos de microfluidos pueden experimentar variaciones de temperatura y fluctuaciones de presión durante el funcionamiento. Los adhesivos MEMS diseñados para microfluidos ofrecen estabilidad a altas temperaturas y pueden soportar las presiones experimentadas dentro del sistema de microfluidos, lo que garantiza la durabilidad y confiabilidad del control de fluidos.
- Integración con componentes funcionales: los dispositivos de microfluidos a menudo incorporan sensores, electrodos y actuadores adicionales. Los adhesivos MEMS pueden facilitar la integración de estos elementos funcionales, proporcionando conexiones seguras y confiables, permitiendo la funcionalidad multimodal y mejorando el rendimiento general de los sistemas de microfluidos.
Los avances en la tecnología de adhesivos MEMS continúan mejorando la precisión, confiabilidad y versatilidad del control de fluidos en dispositivos microfluídicos. La investigación en curso se centra en el desarrollo de adhesivos con propiedades personalizadas, como bioadhesivos para microfluidos biocompatibles, adhesivos que responden a estímulos para potencia dinámica de fluidos y adhesivos de autorreparación para mejorar la longevidad del dispositivo. Estos avances contribuyen a mejorar la microfluídica y su amplia gama de aplicaciones.
Gestión térmica y adhesivo MEMS: abordar la disipación de calor
La gestión térmica es fundamental para los dispositivos MEMS (Sistemas Micro-Electro-Mecánicos), ya que a menudo generan calor durante el funcionamiento. La disipación de calor eficiente es esencial para mantener un rendimiento óptimo, evitar el sobrecalentamiento y garantizar la confiabilidad y la longevidad de los dispositivos MEMS. Los adhesivos MEMS son vitales para abordar los desafíos de disipación de calor al proporcionar soluciones de gestión térmica efectivas. Exploremos cómo los adhesivos MEMS pueden ayudar a abordar la disipación de calor en los dispositivos MEMS.
- Conductividad térmica: los adhesivos MEMS con alta conductividad térmica pueden transferir calor de manera eficiente desde los componentes generadores de calor a los disipadores de calor u otros mecanismos de enfriamiento. Estos adhesivos actúan como puentes térmicos efectivos, reduciendo la resistencia térmica y mejorando la disipación del calor.
- Unión a disipadores de calor: los disipadores de calor se usan comúnmente en dispositivos MEMS para disipar el calor. Los adhesivos MEMS brindan una unión confiable entre los componentes que generan calor y los disipadores de calor, lo que garantiza una transferencia de calor eficiente al disipador. El material adhesivo debe tener buenas propiedades de adhesión para resistir los ciclos térmicos y mantener una fuerte unión a temperaturas elevadas.
- Resistencia térmica baja: los adhesivos MEMS deben tener una resistencia térmica baja para minimizar la impedancia térmica entre la fuente de calor y la interfaz de enfriamiento. La baja resistencia térmica permite una transferencia de calor eficiente y mejora la gestión térmica en dispositivos MEMS.
- Estabilidad térmica: los dispositivos MEMS pueden operar a altas temperaturas o experimentar fluctuaciones de temperatura. El material adhesivo debe exhibir una excelente estabilidad térmica para resistir estas condiciones sin degradarse o perder sus propiedades adhesivas. Esta estabilidad garantiza un rendimiento constante de disipación de calor durante la vida útil del dispositivo MEMS.
- Propiedades dieléctricas: en algunos casos, los dispositivos MEMS pueden requerir aislamiento eléctrico entre los componentes que generan calor y los disipadores de calor. Los adhesivos MEMS con propiedades dieléctricas apropiadas pueden proporcionar conductividad térmica y aislamiento eléctrico, lo que permite una disipación de calor efectiva mientras se mantiene la integridad eléctrica.
- Capacidad de relleno de espacios: Los adhesivos MEMS con una buena capacidad de relleno de espacios pueden eliminar espacios de aire o vacíos entre los componentes que generan calor y los disipadores de calor, mejorando el contacto térmico y minimizando la resistencia térmica. Esta capacidad garantiza una transferencia y disipación de calor más eficientes dentro del dispositivo MEMS.
- Compatibilidad con materiales MEMS: los dispositivos MEMS incorporan silicio, polímeros, metales y cerámica. Los adhesivos MEMS deben ser compatibles con estos materiales para garantizar una adhesión y una gestión térmica adecuadas. La compatibilidad también evita las interacciones químicas adversas o la degradación que afectan el rendimiento de la disipación de calor.
Los avances en la tecnología de adhesivos MEMS se centran en el desarrollo de materiales con conductividad térmica mejorada, estabilidad térmica mejorada y propiedades adaptadas para abordar los requisitos específicos de gestión térmica. Los investigadores están explorando nuevas formulaciones de adhesivos, como los adhesivos de nanocompuestos que contienen rellenos termoconductores, para mejorar aún más las capacidades de disipación de calor.
Adhesivo MEMS en sistemas ópticos: garantizar una alineación precisa
En los sistemas ópticos, la alineación precisa es crucial para lograr un rendimiento y una funcionalidad óptimos. Un componente clave que desempeña un papel fundamental para garantizar una alineación precisa es el adhesivo de sistemas microelectromecánicos (MEMS). El adhesivo MEMS se refiere al material de unión utilizado para unir dispositivos MEMS, como espejos, lentes o microaccionadores, a sus respectivos sustratos en sistemas ópticos. Permite el posicionamiento y la alineación precisos de estos dispositivos, lo que mejora el rendimiento general y la confiabilidad del sistema visual.
Cuando se trata de garantizar una alineación precisa en los sistemas ópticos, se deben considerar varios factores al seleccionar y aplicar adhesivos MEMS. En primer lugar, el material adhesivo debe poseer excelentes propiedades ópticas, como un índice de refracción bajo y una mínima dispersión o absorción de la luz. Estas características ayudan a minimizar los reflejos o distorsiones no deseados, que pueden degradar el rendimiento del sistema óptico.
Además, el adhesivo MEMS debe exhibir una alta estabilidad mecánica y durabilidad. Los sistemas ópticos a menudo se someten a diversas condiciones ambientales, incluidas las fluctuaciones de temperatura, los cambios de humedad y las tensiones mecánicas. El material adhesivo debe soportar estas condiciones sin comprometer la alineación de los componentes ópticos. Además, debe tener un bajo coeficiente de expansión térmica para minimizar el impacto de los ciclos térmicos en la estabilidad de la alineación.
Además, el adhesivo debe ofrecer un control preciso sobre el proceso de unión. Esto incluye baja viscosidad, buenas propiedades humectantes y tiempo de curado o endurecimiento controlado. La baja densidad garantiza una cobertura adhesiva uniforme y confiable entre el dispositivo MEMS y el sustrato, lo que facilita un mejor contacto y alineación. Las buenas propiedades humectantes permiten una adhesión adecuada y evitan la formación de vacíos o burbujas de aire. El tiempo de curado controlado permite un ajuste y una alineación suficientes antes de que se fije el adhesivo.
En cuanto a la aplicación, se debe prestar especial atención a las técnicas de aplicación y manipulación del adhesivo. Los adhesivos MEMS generalmente se aplican en pequeñas cantidades con alta precisión. Se pueden emplear sistemas de dosificación automatizados o herramientas especializadas para garantizar una aplicación precisa y repetible. Las técnicas de manejo adecuadas, como el uso de salas limpias o entornos controlados, ayudan a prevenir la contaminación que podría afectar negativamente la alineación y el rendimiento óptico.
Para validar y garantizar la alineación precisa de los componentes ópticos que utilizan adhesivos MEMS, son esenciales las pruebas y la caracterización exhaustivas. Se pueden emplear técnicas como la interferometría, la microscopía óptica o la perfilometría para medir la precisión de la alineación y evaluar el rendimiento del sistema visual. Estas pruebas ayudan a identificar desviaciones o desalineaciones, lo que permite ajustes o mejoras para lograr la alineación deseada.
Adhesivo MEMS en electrónica de consumo: Habilitación de diseños compactos
Los adhesivos MEMS se han vuelto cada vez más importantes en la electrónica de consumo, lo que permite el desarrollo de diseños compactos y delgados para varios dispositivos. Estos adhesivos son fundamentales para unir y asegurar componentes de sistemas microelectromecánicos (MEMS) dentro de dispositivos electrónicos de consumo, como teléfonos inteligentes, tabletas, dispositivos portátiles y electrodomésticos inteligentes. Al garantizar una fijación fiable y una alineación precisa, los adhesivos MEMS contribuyen a la miniaturización y al rendimiento mejorado de estos dispositivos.
Una ventaja clave de los adhesivos MEMS en la electrónica de consumo es su capacidad para proporcionar una unión sólida y duradera ocupando un espacio mínimo. A medida que los dispositivos electrónicos de consumo se vuelven más pequeños y portátiles, los materiales adhesivos deben ofrecer una alta fuerza de adhesión en una capa delgada. Esto permite diseños compactos sin comprometer la integridad estructural. Los adhesivos MEMS están diseñados para proporcionar una excelente adhesión a diversos sustratos comúnmente utilizados en la electrónica de consumo, incluidos metales, vidrio y plásticos.
Además de sus capacidades de unión, los adhesivos MEMS ofrecen beneficios en términos de gestión térmica. Los dispositivos electrónicos de consumo generan calor durante el funcionamiento, y la disipación eficiente del calor es crucial para evitar la degradación del rendimiento o la falla de los componentes. Los adhesivos MEMS con alta conductividad térmica pueden unir componentes que generan calor, como procesadores o amplificadores de potencia, a disipadores de calor u otras estructuras de refrigeración. Esto ayuda a disipar el calor de manera efectiva, mejorando la gestión térmica general del dispositivo.
Además, los adhesivos MEMS contribuyen a la fiabilidad y durabilidad general de los dispositivos electrónicos de consumo. Estos adhesivos resisten factores ambientales como variaciones de temperatura, humedad y tensiones mecánicas, y pueden soportar las condiciones rigurosas que se encuentran durante el uso diario, incluidas caídas, vibraciones y ciclos térmicos. Al proporcionar una unión sólida, los adhesivos MEMS ayudan a garantizar la longevidad y la confiabilidad de los productos electrónicos de consumo.
Otra ventaja de los adhesivos MEMS es su compatibilidad con los procesos de fabricación automatizados. Dado que los dispositivos electrónicos de consumo se fabrican en masa, los métodos de ensamblaje eficientes y confiables son cruciales. Los adhesivos MEMS se pueden dosificar con precisión utilizando sistemas de dosificación mecánicos, lo que permite un ensamblaje preciso y de alta velocidad. Los materiales adhesivos están diseñados para tener características adecuadas de viscosidad y curado para el manejo automatizado, lo que permite procesos de producción optimizados.
Además, la versatilidad de los adhesivos MEMS permite su uso en una amplia gama de aplicaciones de electrónica de consumo. Ya sea para conectar sensores, micrófonos, parlantes u otros componentes MEMS, estos adhesivos ofrecen la flexibilidad para adaptarse a varios diseños y configuraciones de dispositivos. Se pueden aplicar a diferentes materiales de sustrato y acabados superficiales, proporcionando compatibilidad con varios productos electrónicos de consumo.
Adhesivo MEMS para aplicaciones aeroespaciales y de defensa
La tecnología adhesiva MEMS ha demostrado ser muy valiosa en aplicaciones aeroespaciales y de defensa, donde la precisión, la confiabilidad y el rendimiento son primordiales. Las propiedades únicas de los adhesivos MEMS los hacen ideales para unir y asegurar componentes de sistemas microelectromecánicos (MEMS) en sistemas aeroespaciales y de defensa, que van desde satélites y aeronaves hasta equipos y sensores militares.
Un aspecto crítico de las aplicaciones aeroespaciales y de defensa es la capacidad de los adhesivos para soportar condiciones ambientales extremas. Los adhesivos MEMS están diseñados para ofrecer estabilidad a altas temperaturas, soportando las temperaturas elevadas experimentadas durante misiones espaciales, vuelos supersónicos u operaciones en entornos hostiles. Exhiben una excelente resistencia a los ciclos térmicos, lo que garantiza la confiabilidad y el rendimiento a largo plazo de los componentes unidos.
Además, los sistemas aeroespaciales y de defensa a menudo se enfrentan a grandes tensiones mecánicas, incluidas vibraciones, golpes y fuerzas de aceleración. Los adhesivos MEMS proporcionan una estabilidad mecánica y una durabilidad excepcionales, manteniendo la integridad de la unión en estas exigentes condiciones. Esto garantiza que los componentes de MEMS, como sensores o actuadores, permanezcan conectados de forma segura y operativos, incluso en entornos de trabajo desafiantes.
Otro factor crucial en las aplicaciones aeroespaciales y de defensa es la reducción de peso. Los adhesivos MEMS ofrecen la ventaja de ser livianos, lo que permite minimizar el peso total del sistema. Esto es particularmente importante en aplicaciones aeroespaciales, donde la reducción de peso es esencial para la eficiencia del combustible y la capacidad de carga útil. Los adhesivos MEMS permiten unir materiales livianos, como compuestos de fibra de carbono o películas delgadas, manteniendo la integridad estructural.
Además, los adhesivos MEMS son cruciales para miniaturizar los sistemas aeroespaciales y de defensa. Estos adhesivos permiten la unión y el posicionamiento exclusivos de los componentes MEMS, que suelen ser pequeños y delicados. Al facilitar diseños compactos, los adhesivos MEMS contribuyen a la optimización del espacio dentro de áreas limitadas de aeronaves, satélites o equipos militares. Esto permite integrar más funcionalidades y mejorar el rendimiento del sistema sin comprometer las limitaciones de tamaño o peso.
La capacidad de los adhesivos MEMS para mantener una alineación precisa también es fundamental en las aplicaciones aeroespaciales y de defensa. El material adhesivo debe garantizar un posicionamiento preciso, ya sea alineando componentes ópticos, sensores basados en MEMS o microaccionadores. Esto es crucial para lograr un rendimiento óptimo, como una navegación precisa, orientación o adquisición de datos. Los adhesivos MEMS con excelente estabilidad dimensional y propiedades de baja desgasificación ayudan a mantener la alineación durante períodos prolongados, incluso en entornos de vacío o de gran altitud.
Los estrictos estándares de calidad y los procedimientos de prueba son primordiales en las industrias aeroespacial y de defensa. Los adhesivos MEMS se someten a pruebas rigurosas para garantizar su cumplimiento con los requisitos de la industria. Esto incluye pruebas mecánicas de resistencia y durabilidad, pruebas térmicas de estabilidad en temperaturas extremas y pruebas ambientales de humedad, productos químicos y resistencia a la radiación. Estas pruebas validan el rendimiento y la confiabilidad del material adhesivo, asegurando su idoneidad para aplicaciones aeroespaciales y de defensa.
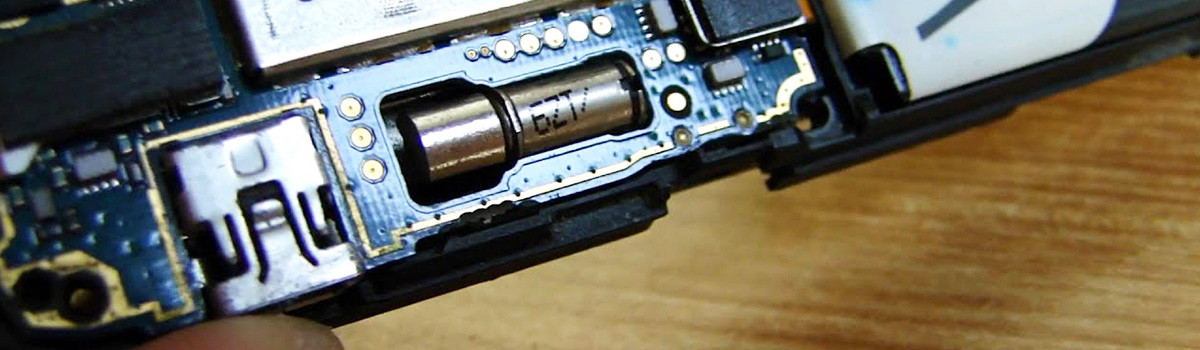
Adhesivo MEMS para la industria automotriz: mejora de la seguridad y el rendimiento
La tecnología adhesiva MEMS se ha convertido en un activo valioso en la industria automotriz, fundamental para mejorar la seguridad, el rendimiento y la confiabilidad. Con la creciente complejidad y sofisticación de los sistemas automotrices, los adhesivos MEMS proporcionan soluciones de unión y seguridad cruciales para los componentes de los sistemas microelectromecánicos (MEMS), contribuyendo a la funcionalidad y eficiencia general de los vehículos.
Una de las principales áreas en las que los adhesivos MEMS mejoran la seguridad automotriz es en las aplicaciones de sensores. Los sensores MEMS, como los que se utilizan en el despliegue de bolsas de aire, el control de estabilidad o los sistemas avanzados de asistencia al conductor (ADAS), requieren una conexión precisa y confiable. Los adhesivos MEMS garantizan la unión segura de estos sensores a varios sustratos dentro del vehículo, como el chasis o la estructura de la carrocería. Esto proporciona un rendimiento preciso del sensor, lo que permite la adquisición de datos oportunos y precisos para funciones críticas de seguridad.
Además, los adhesivos MEMS contribuyen a la durabilidad y confiabilidad general de los componentes automotrices. Resisten los factores ambientales, incluidas las variaciones de temperatura, la humedad y las vibraciones. En aplicaciones automotrices donde los detalles están sujetos a tensiones continuas y variables, los adhesivos MEMS brindan una unión sólida, lo que evita que los componentes se desprendan o fallen. Esto mejora la longevidad y el rendimiento de los sistemas automotrices, lo que lleva a una mayor confiabilidad general del vehículo.
Los adhesivos MEMS también ayudan en la reducción de peso y la optimización del diseño en la industria automotriz. A medida que los fabricantes de automóviles se esfuerzan por mejorar la eficiencia del combustible y reducir las emisiones, se utilizan cada vez más materiales ligeros. Los adhesivos MEMS ofrecen la ventaja de ser livianos, lo que permite una unión eficiente de materiales livianos como compuestos o películas delgadas. Esto ayuda a reducir el peso total del vehículo sin comprometer la integridad estructural o los requisitos de seguridad.
Además, los adhesivos MEMS contribuyen a la miniaturización de los sistemas automotrices. A medida que los vehículos incorporan tecnologías y funcionalidades más avanzadas, los diseños compactos se vuelven cruciales. Los adhesivos MEMS permiten la fijación y el posicionamiento precisos de componentes pequeños y delicados, como microsensores o actuadores. Esto facilita la optimización del espacio dentro del vehículo, lo que permite la integración de características adicionales mientras se mantiene un factor de forma más pequeño.
En términos de eficiencia de fabricación, los adhesivos MEMS ofrecen ventajas en los procesos de ensamblaje dentro de la industria automotriz. Se pueden aplicar utilizando sistemas de dosificación automatizados, lo que garantiza una unión precisa y consistente, y esto agiliza los procesos de producción, reduce el tiempo de ensamblaje y mejora los rendimientos de fabricación. Las propiedades de los adhesivos MEMS, como el tiempo de curado controlado y las buenas propiedades de humectación, contribuyen a una unión eficiente y confiable durante la producción de alto volumen.
Por último, los adhesivos MEMS se someten a estrictos procesos de prueba y control de calidad para cumplir con los estándares de la industria automotriz. Las pruebas mecánicas aseguran la resistencia y durabilidad de la unión adhesiva, mientras que las pruebas térmicas evalúan su estabilidad bajo variaciones de temperatura. Las pruebas ambientales evalúan la resistencia del adhesivo a los productos químicos, la humedad y otros factores. Al cumplir con estos rigurosos requisitos, los adhesivos MEMS brindan la confiabilidad y el rendimiento necesarios para las aplicaciones automotrices.
Adhesivo MEMS biocompatible: habilitación de dispositivos implantables
La tecnología de adhesivo MEMS biocompatible ha revolucionado el campo de los dispositivos médicos implantables al permitir la unión segura y confiable de componentes de sistemas microelectromecánicos (MEMS) dentro del cuerpo humano. Estos adhesivos desempeñan un papel fundamental para garantizar el éxito y la funcionalidad de los dispositivos implantables al proporcionar soluciones de unión biocompatibles compatibles con tejidos y fluidos humanos.
Uno de los requisitos críticos para los dispositivos implantables es la biocompatibilidad. Los adhesivos MEMS utilizados en tales aplicaciones están cuidadosamente formulados para que no sean tóxicos ni irriten los tejidos circundantes. Se someten a pruebas exhaustivas de biocompatibilidad para garantizar que no provoquen reacciones adversas ni perjudiquen al paciente. Estos adhesivos están diseñados para ser estables en entornos fisiológicos y mantener la integridad sin liberar sustancias nocivas en el cuerpo.
Los dispositivos implantables a menudo requieren uniones sólidas y duraderas para garantizar la estabilidad y la funcionalidad durante períodos prolongados. Los adhesivos MEMS biocompatibles ofrecen una excelente adhesión a varios sustratos, incluidos metales, cerámicas y polímeros biocompatibles que se usan comúnmente en dispositivos implantables. Estos adhesivos brindan una unión segura de los componentes MEMS, como sensores, electrodos o sistemas de administración de medicamentos, al dispositivo o al tejido circundante, lo que permite un rendimiento preciso y confiable.
Además de la biocompatibilidad y la fuerza de unión, los adhesivos MEMS biocompatibles poseen excelentes propiedades mecánicas. Los dispositivos implantables pueden experimentar tensiones mecánicas, como doblarse, estirarse o comprimirse, debido al movimiento o los procesos naturales dentro del cuerpo. El material adhesivo debe soportar estas tensiones sin comprometer la integridad de la unión. Los adhesivos MEMS biocompatibles ofrecen alta estabilidad mecánica y flexibilidad, lo que garantiza la durabilidad de la unión adhesiva en el entorno dinámico del cuerpo humano.
Además, los adhesivos MEMS biocompatibles permiten un posicionamiento y alineación precisos de los componentes MEMS dentro del dispositivo implantable. La colocación precisa es crucial para la funcionalidad y el rendimiento óptimos del dispositivo. El material adhesivo permite el ajuste fino y la fijación segura de funciones, como biosensores o microaccionadores, lo que garantiza el posicionamiento y la alineación adecuados en relación con el tejido u órgano objetivo.
Los dispositivos implantables a menudo requieren un sellado hermético para proteger los componentes sensibles de los fluidos corporales circundantes. Los adhesivos MEMS biocompatibles pueden proporcionar un sello fiable y biocompatible, evitando la entrada de líquidos o contaminantes en el dispositivo. Estos adhesivos exhiben excelentes propiedades de barrera, asegurando la integridad a largo plazo del dispositivo implantable y minimizando el riesgo de infección o falla del dispositivo.
Finalmente, los adhesivos MEMS biocompatibles se someten a pruebas rigurosas para garantizar su idoneidad para aplicaciones implantables. Están sujetos a evaluaciones de biocompatibilidad de acuerdo con estándares internacionales, incluidas evaluaciones de citotoxicidad, sensibilización e irritación. Los materiales adhesivos también se someten a pruebas de estabilidad en condiciones fisiológicas, incluidas variaciones de temperatura, pH y humedad. Estas pruebas garantizan la seguridad, la fiabilidad y el rendimiento a largo plazo del adhesivo dentro del dispositivo implantable.
Pruebas de adhesivo MEMS y consideraciones de confiabilidad
Las pruebas de adhesivo MEMS y las consideraciones de confiabilidad son cruciales para garantizar el rendimiento y la longevidad de los dispositivos de sistemas microelectromecánicos (MEMS). Estos dispositivos a menudo funcionan en entornos exigentes y están sujetos a diversas tensiones y condiciones. Las pruebas exhaustivas y la consideración cuidadosa de los factores de confiabilidad son esenciales para validar el desempeño del adhesivo y garantizar la confiabilidad de los dispositivos MEMS.
Un aspecto crítico de las pruebas de adhesivos es la caracterización mecánica. Las uniones adhesivas deben evaluarse en cuanto a su resistencia mecánica y durabilidad para resistir las tensiones encontradas durante la vida útil del dispositivo. Pruebas como las pruebas de cizallamiento, tracción o pelado miden la resistencia del adhesivo a diferentes fuerzas mecánicas. Estas pruebas brindan información sobre la capacidad del adhesivo para mantener una unión fuerte y resistir las tensiones mecánicas, lo que garantiza la confiabilidad del dispositivo MEMS.
Otro factor crucial en las pruebas de adhesivos es el rendimiento térmico. Los dispositivos MEMS pueden experimentar variaciones de temperatura significativas durante el funcionamiento. Los materiales adhesivos deben probarse para garantizar su estabilidad e integridad en estas condiciones de temperatura. Las pruebas de ciclos térmicos, en las que el adhesivo se somete a ciclos de temperatura repetidos, ayudan a evaluar su capacidad para soportar la expansión y contracción térmica sin delaminación ni degradación. Además, las pruebas de envejecimiento térmico evalúan la estabilidad y confiabilidad a largo plazo del adhesivo bajo una exposición prolongada a temperaturas elevadas.
Las pruebas ambientales también son esenciales para evaluar la resistencia del adhesivo a diversos factores ambientales. La humedad, los productos químicos y los gases que se encuentran comúnmente en las aplicaciones del mundo real pueden afectar el rendimiento y la integridad del adhesivo. Las pruebas de envejecimiento acelerado, en las que el enlace se expone a condiciones ambientales adversas durante un período prolongado, ayudan a simular los efectos a largo plazo de estos factores. Estas pruebas brindan información valiosa sobre la resistencia del adhesivo a la degradación ambiental, asegurando su confiabilidad en diferentes condiciones de operación.
Las consideraciones de confiabilidad van más allá de las pruebas, incluidos factores como los modos de falla de la adhesión, los mecanismos de envejecimiento y el rendimiento a largo plazo. Comprender los modos de falla de la unión adhesiva es crucial para diseñar dispositivos MEMS robustos. Las técnicas de análisis de fallas, como la microscopía y la caracterización de materiales, ayudan a identificar los mecanismos de falla, como la delaminación del adhesivo, la falla cohesiva o la falla de la interfaz. Este conocimiento guía la mejora de las formulaciones adhesivas y los procesos de unión para mitigar los riesgos de falla.
Los mecanismos de envejecimiento también pueden afectar el rendimiento a largo plazo del adhesivo, y factores como la absorción de humedad, las reacciones químicas o la exposición a los rayos UV pueden degradar el adhesivo. Como se mencionó anteriormente, las pruebas de envejecimiento acelerado ayudan a evaluar la resistencia del adhesivo a estos mecanismos de envejecimiento. Los fabricantes pueden diseñar dispositivos MEMS con una vida útil operativa extendida y un rendimiento confiable al comprender y abordar los posibles problemas de envejecimiento.
Además, las consideraciones de confiabilidad incluyen la selección de materiales adhesivos apropiados para aplicaciones MEMS específicas. Los diferentes adhesivos tienen propiedades variables, como la viscosidad, el tiempo de curado y la compatibilidad con los sustratos, y estos factores deben considerarse cuidadosamente para garantizar una unión óptima y una confiabilidad a largo plazo. Los fabricantes de adhesivos proporcionan datos técnicos y pautas de aplicación para ayudar en la selección de materiales, teniendo en cuenta los requisitos específicos y las condiciones de funcionamiento de los dispositivos MEMS.
Procesos y técnicas de fabricación de adhesivos MEMS
Los procesos y técnicas de fabricación de adhesivos MEMS implican una serie de pasos para producir materiales adhesivos de alta calidad para aplicaciones de sistemas microelectromecánicos (MEMS). Estos procesos aseguran la consistencia, la confiabilidad y el rendimiento del adhesivo y cumplen con los requisitos específicos de los dispositivos MEMS. A continuación se muestran los pasos críticos involucrados en la fabricación de adhesivos MEMS:
- Formulación: El primer paso en la fabricación de adhesivos es formular el material adhesivo. Esto implica seleccionar la resina base y los aditivos apropiados para lograr las propiedades deseadas, como fuerza de adhesión, flexibilidad, estabilidad térmica y biocompatibilidad. La formulación considera los requisitos de la aplicación, los materiales del sustrato y las condiciones ambientales.
- Mezclado y Dispersión: Una vez determinada la formulación del adhesivo, el siguiente paso es el mezclado y dispersión de los ingredientes. Esto normalmente se hace usando un equipo de mezcla especializado para asegurar una mezcla homogénea. El proceso de mezcla es crucial para la distribución uniforme de los aditivos y el mantenimiento de propiedades constantes en todo el material adhesivo.
- Aplicación del Adhesivo: El adhesivo se prepara para su aplicación después de las etapas de formulación y mezcla. La técnica de aplicación depende de los requisitos y características específicas del adhesivo. Los métodos de aplicación estándar incluyen dispensación, serigrafía, revestimiento por rotación o pulverización. El objetivo es aplicar uniformemente el adhesivo a las superficies o componentes deseados con precisión y control.
- Curado: El curado es un paso crítico en la fabricación de adhesivos, transformando el adhesivo de un estado líquido o semilíquido a una forma sólida. El curado se puede lograr a través de varias técnicas, como calor, UV o curado químico. El proceso de curado activa reacciones de reticulación dentro del adhesivo, desarrollando propiedades de resistencia y adhesión.
- Control de calidad: A lo largo del proceso de fabricación del adhesivo, se implementan estrictas medidas de control de calidad para garantizar la consistencia y confiabilidad del material adhesivo. Esto incluye monitorear parámetros como la viscosidad, la fuerza adhesiva, el tiempo de curado y la composición química. Los procedimientos de control de calidad ayudan a identificar desviaciones o inconsistencias, lo que permite realizar ajustes o acciones correctivas para mantener la integridad del producto.
- Empaque y almacenamiento: una vez que se fabrica el adhesivo y se prueba su calidad, se empaqueta y prepara para su almacenamiento o distribución. El embalaje adecuado protege el adhesivo de factores externos como la humedad, la luz o los contaminantes. Las condiciones de almacenamiento del adhesivo, incluidas la temperatura y la humedad, se consideran cuidadosamente para mantener la estabilidad y el rendimiento del adhesivo durante su vida útil.
- Optimización y ampliación de procesos: los fabricantes de adhesivos se esfuerzan continuamente por optimizar el proceso de fabricación y escalar la producción para satisfacer la creciente demanda. Esto implica refinamiento de procesos, automatización y mejoras de eficiencia para garantizar una calidad constante, reducir los costos de producción y mejorar la productividad general.
Vale la pena señalar que los procesos y técnicas de fabricación específicos pueden variar según el tipo de adhesivo, la aplicación prevista y las capacidades del fabricante. Los fabricantes de adhesivos a menudo tienen métodos patentados y experiencia para adaptar el proceso de fabricación a las formulaciones de sus productos específicos y los requisitos del cliente.
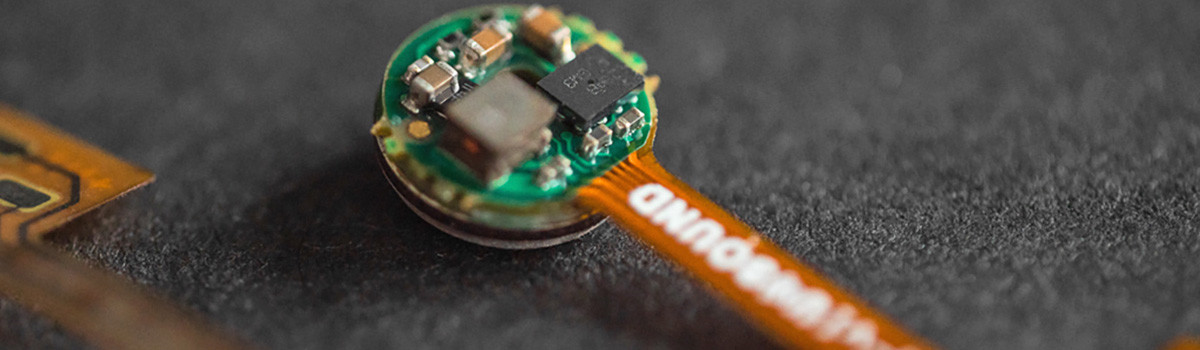
Desafíos en la unión adhesiva de MEMS: compatibilidad de materiales y manejo del estrés
La unión adhesiva MEMS presenta varios desafíos, particularmente en lo que respecta a la compatibilidad de materiales y el manejo del estrés. Estos desafíos surgen debido a la diversa gama de materiales utilizados en los dispositivos de sistemas microelectromecánicos (MEMS) y las complejas condiciones de estrés que experimentan. Superar estos desafíos es crucial para garantizar uniones adhesivas confiables y duraderas en aplicaciones MEMS.
La compatibilidad del material es una consideración crítica en la unión adhesiva MEMS. Los dispositivos MEMS a menudo se componen de varios materiales, como silicio, vidrio, polímeros, metales y cerámica, cada uno con propiedades únicas. El adhesivo debe ser compatible con estos materiales para establecer una unión fuerte y confiable. La selección del adhesivo implica considerar factores como los coeficientes de expansión térmica, la adhesión a diferentes materiales y la compatibilidad con las condiciones de funcionamiento del dispositivo.
Las diferencias en los coeficientes de expansión térmica pueden provocar tensiones y tensiones significativas durante los ciclos de temperatura, lo que provoca delaminación o agrietamiento en la interfaz del adhesivo. El manejo de estas tensiones térmicas requiere una cuidadosa selección de materiales y consideraciones de diseño. Los adhesivos con módulos más bajos y coeficientes de expansión térmica más cercanos a los materiales unidos pueden ayudar a reducir el desajuste de la tensión y mejorar la confiabilidad a largo plazo de la unión.
Otro desafío en la unión adhesiva MEMS es la gestión de las tensiones mecánicas experimentadas por el dispositivo. Los dispositivos MEMS pueden estar sujetos a diversas tensiones mecánicas, como flexión, estiramiento y compresión. Estas tensiones pueden resultar de las condiciones ambientales, el funcionamiento del dispositivo o los procesos de ensamblaje. Los materiales adhesivos deben poseer suficiente resistencia y flexibilidad para soportar estas tensiones sin deslaminación ni fallos.
Para abordar los desafíos del manejo del estrés, se pueden emplear varias técnicas. Un enfoque utiliza adhesivos flexibles o elastoméricos que absorben y distribuyen las tensiones en el área adherida. Estos adhesivos brindan una mayor flexibilidad, lo que permite que el dispositivo resista deformaciones mecánicas sin comprometer la unión del adhesivo. Además, la optimización del diseño de los dispositivos MEMS, como la incorporación de características de alivio de tensión o la introducción de interconexiones flexibles, puede ayudar a aliviar las concentraciones de tensión y minimizar el impacto en las uniones adhesivas.
Asegurar la preparación adecuada de la superficie también es fundamental para abordar los desafíos de compatibilidad de materiales y manejo del estrés. Los tratamientos superficiales, como la limpieza, el endurecimiento o la aplicación de imprimadores o promotores de adhesión, pueden mejorar la adhesión entre el adhesivo y los materiales del sustrato. Estos tratamientos promueven una mejor humectación y unión en la interfaz, mejorando la compatibilidad del material y la distribución de tensiones.
Además, el control preciso de la aplicación del adhesivo es vital para una unión exitosa. Factores como la técnica de aplicación del adhesivo, las condiciones de curado y los parámetros del proceso pueden influir en la calidad y el rendimiento de la unión del adhesivo. La consistencia en el espesor del adhesivo, la cobertura uniforme y el curado adecuado son esenciales para lograr uniones confiables que puedan resistir los desafíos de compatibilidad de materiales y las tensiones mecánicas.
Superar los desafíos de compatibilidad de materiales y manejo del estrés en la unión adhesiva MEMS requiere un enfoque multidisciplinario que involucre la ciencia de los materiales, el diseño de dispositivos y la optimización de procesos. La colaboración entre los fabricantes de adhesivos, los diseñadores de dispositivos MEMS y los ingenieros de procesos es esencial para abordar estos desafíos de manera efectiva. A través de una cuidadosa selección de materiales, consideraciones de diseño, preparación de superficies y control de procesos, la unión adhesiva en aplicaciones MEMS se puede optimizar para lograr uniones confiables y duraderas, lo que garantiza el rendimiento y la longevidad de los dispositivos MEMS.
Avances en la tecnología de adhesivos MEMS: nanomateriales y adhesivos inteligentes
Los avances en la tecnología de adhesivos MEMS han sido impulsados por la necesidad de mejorar el rendimiento, la miniaturización y la funcionalidad mejorada en aplicaciones de sistemas microelectromecánicos (MEMS). Dos áreas significativas de avance en la tecnología de adhesivos MEMS incluyen la integración de nanomateriales y el desarrollo de adhesivos inteligentes. Estos avances ofrecen capacidades únicas y un rendimiento mejorado en la vinculación de dispositivos MEMS.
Los nanomateriales han jugado un papel crucial en el avance de la tecnología de adhesivos MEMS. La integración de nanomateriales, como nanopartículas, nanofibras o nanocompuestos, en formulaciones adhesivas ha mejorado las propiedades y funcionalidades. Por ejemplo, la adición de nanopartículas puede mejorar la resistencia mecánica, la estabilidad térmica y la conductividad eléctrica del material adhesivo. Las nanofibras como los nanotubos de carbono o el grafeno pueden proporcionar un mayor refuerzo y mejores propiedades eléctricas o térmicas. El uso de nanocompuestos en adhesivos ofrece una combinación única de propiedades, que incluyen alta resistencia, flexibilidad y compatibilidad con diversos materiales de sustrato. La integración de nanomateriales en adhesivos MEMS permite el desarrollo de soluciones de unión de alto rendimiento para aplicaciones MEMS exigentes.
Otro avance significativo en la tecnología de adhesivos MEMS es el desarrollo de adhesivos inteligentes. Los adhesivos innovadores están diseñados para exhibir propiedades o funcionalidades únicas en respuesta a estímulos externos, como la temperatura, la luz o el estrés mecánico. Estos adhesivos pueden sufrir cambios reversibles o irreversibles en sus propiedades, lo que permite respuestas dinámicas y adaptabilidad en diferentes condiciones de operación. Por ejemplo, los adhesivos con memoria de forma pueden cambiar de forma o recuperar su forma original al exponerse a variaciones de temperatura, ofreciendo capacidades de unión reversibles. Los adhesivos activados por luz se pueden activar para que se unan o se despeguen mediante longitudes de onda de luz específicas, lo que proporciona un control y una reelaboración precisos. Los adhesivos innovadores pueden habilitar funcionalidades avanzadas en los dispositivos MEMS, como la reconfigurabilidad, la autorreparación o las capacidades de detección, mejorando su rendimiento y versatilidad.
La integración de nanomateriales y tecnologías adhesivas innovadoras ofrece beneficios sinérgicos en aplicaciones MEMS. Los nanomateriales se pueden incorporar en adhesivos inteligentes para mejorar aún más sus propiedades y funcionalidades. Por ejemplo, los nanomateriales se pueden utilizar para desarrollar adhesivos de nanocompuestos sensibles a estímulos que muestren un comportamiento único basado en estímulos externos. Estos sistemas adhesivos pueden proporcionar capacidades de autodetección, lo que permite la detección de tensión mecánica, temperatura u otros cambios ambientales. También pueden ofrecer propiedades de autorreparación, donde el adhesivo puede reparar microfisuras o daños tras la exposición a condiciones específicas. La combinación de nanomateriales y tecnologías adhesivas innovadoras abre nuevas posibilidades para dispositivos MEMS avanzados con rendimiento, durabilidad y adaptabilidad mejorados.
Estos avances en la tecnología de adhesivos MEMS tienen implicaciones en varias industrias. Permiten el desarrollo de dispositivos MEMS más pequeños y fiables con una funcionalidad mejorada. En el cuidado de la salud, los adhesivos mejorados con nanomateriales pueden respaldar la fabricación de dispositivos implantables con biocompatibilidad mejorada y confiabilidad a largo plazo. Los adhesivos innovadores pueden habilitar dispositivos autoreparables o reconfigurables en la electrónica de consumo, mejorando la experiencia del usuario y la longevidad del producto. Los enlaces mejorados con nanomateriales pueden ofrecer soluciones de unión ligeras con mayor resistencia y durabilidad en aplicaciones automotrices y aeroespaciales.
Consideraciones ambientales: Adhesivo MEMS para la sostenibilidad
Las consideraciones ambientales son cada vez más importantes en el desarrollo y uso de materiales adhesivos para dispositivos de sistemas microelectromecánicos (MEMS). A medida que la sostenibilidad y la conciencia ecológica continúan ganando terreno, es crucial abordar el impacto de los materiales adhesivos MEMS a lo largo de su ciclo de vida. Estos son algunos factores clave a tener en cuenta cuando se aspira a la sostenibilidad en las aplicaciones de adhesivos MEMS:
- Selección de materiales: la elección de materiales adhesivos respetuosos con el medio ambiente es el primer paso hacia la sostenibilidad. Optar por adhesivos con bajo impacto ambiental, como formulaciones a base de agua o sin solventes, puede ayudar a reducir las emisiones y minimizar el uso de sustancias peligrosas. Además, la selección de bonos con una vida útil más larga o derivados de recursos renovables puede contribuir a los esfuerzos de sostenibilidad.
- Procesos de fabricación: Evaluar y optimizar los procesos de fabricación asociados con la producción de adhesivos MEMS es vital para la sostenibilidad. El empleo de técnicas de fabricación energéticamente eficientes, la minimización de la generación de residuos y la implementación de prácticas de reciclaje o reutilización pueden reducir significativamente la huella ambiental de la fabricación de adhesivos. La optimización de procesos también puede generar ahorros de recursos y una mayor eficiencia, lo que contribuye a los objetivos de sostenibilidad.
- Consideraciones sobre el final de la vida útil: comprender las implicaciones del final de la vida útil de los materiales adhesivos MEMS es esencial para la sostenibilidad. Los adhesivos compatibles con los procesos de reciclaje o que se eliminan fácilmente durante el desmontaje del dispositivo promueven la circularidad y reducen los desechos. Tener en cuenta la reciclabilidad o la biodegradabilidad de los materiales adhesivos permite la eliminación o recuperación ambientalmente responsable de componentes valiosos.
- Evaluación de impacto ambiental: la realización de una evaluación integral de impacto ambiental de los materiales adhesivos MEMS ayuda a identificar posibles riesgos ecológicos y evaluar el desempeño de la sustentabilidad. Las metodologías de evaluación del ciclo de vida (LCA) se pueden emplear para analizar el impacto ambiental de los materiales adhesivos a lo largo de todo su ciclo de vida, incluida la extracción, fabricación, uso y eliminación de materias primas. Esta evaluación proporciona información sobre puntos críticos y áreas de mejora, guiando el desarrollo de soluciones adhesivas más sostenibles.
- Cumplimiento de la normativa: El cumplimiento de las normativas y estándares pertinentes relacionados con la protección del medio ambiente es fundamental para las aplicaciones de adhesivos sostenibles. El cumplimiento de leyes como REACH (Registro, Evaluación, Autorización y Restricción de Productos Químicos) garantiza el uso y la manipulación seguros de los materiales adhesivos, lo que reduce el daño potencial al medio ambiente y la salud humana. Además, adherirse a esquemas de etiquetado ecológico o certificaciones puede demostrar un compromiso de sostenibilidad y brindar transparencia a los usuarios finales.
- Investigación e innovación: la investigación y la innovación continuas en la tecnología de adhesivos pueden impulsar la sostenibilidad en las aplicaciones de MEMS. La exploración de materiales adhesivos alternativos, como los adhesivos de base biológica o inspirados biológicamente, puede ofrecer opciones más sostenibles. El desarrollo de materiales adhesivos con reciclabilidad mejorada, biodegradabilidad o menor impacto ambiental puede conducir a dispositivos MEMS más ecológicos y sostenibles.
Tendencias futuras en el desarrollo de adhesivos MEMS
En los últimos años, la tecnología de sistemas microelectromecánicos (MEMS) ha ganado una atención significativa y se ha convertido en una parte integral de varias industrias, incluidas la electrónica, la atención médica, la automotriz y la aeroespacial. Los dispositivos MEMS generalmente consisten en componentes mecánicos y eléctricos miniaturizados que requieren una unión precisa para garantizar la confiabilidad y la funcionalidad. Los materiales adhesivos son cruciales en el ensamblaje de MEMS, ya que proporcionan uniones fuertes y duraderas entre las piezas.
Mirando hacia el futuro, se pueden identificar varias tendencias en el desarrollo de adhesivos para aplicaciones MEMS:
- Miniaturización e integración: se espera que continúe la tendencia de miniaturización en dispositivos MEMS, lo que generará la demanda de materiales adhesivos que puedan unir componentes más pequeños y complejos. Los adhesivos con capacidades de alta resolución y la capacidad de crear enlaces fuertes en superficies a microescala serán cruciales para fabricar dispositivos MEMS miniaturizados. Además, los materiales adhesivos que permitan la integración de múltiples componentes dentro de un solo dispositivo MEMS tendrán una gran demanda.
- Confiabilidad y durabilidad mejoradas: los dispositivos MEMS a menudo están expuestos a condiciones de operación severas, incluidas fluctuaciones de temperatura, humedad y estrés mecánico. Los futuros desarrollos de adhesivos se centrarán en mejorar la fiabilidad y la durabilidad de las uniones en tales condiciones. Los adhesivos con mayor resistencia a los ciclos térmicos, la humedad y las vibraciones mecánicas serán esenciales para garantizar el rendimiento y la estabilidad a largo plazo de los dispositivos MEMS.
- Curado a baja temperatura: muchos materiales MEMS, como polímeros y componentes electrónicos delicados, son sensibles a las altas temperaturas. En consecuencia, existe una creciente demanda de adhesivos que puedan curar a bajas temperaturas sin comprometer la fuerza de unión. Los adhesivos de curado a baja temperatura permitirán el ensamblaje de componentes MEMS sensibles a la temperatura y reducirán el riesgo de daño térmico durante la fabricación.
- Compatibilidad con múltiples sustratos: los dispositivos MEMS a menudo implican la unión de diferentes materiales, como metales, cerámica y polímeros. Se buscarán mucho materiales adhesivos que muestren una excelente adhesión a diversos sustratos. Además, el desarrollo de adhesivos que puedan unir materiales diferentes con coeficientes de expansión térmica no coincidentes ayudará a mitigar el potencial de fallas inducidas por el estrés en los dispositivos MEMS.
- Adhesivos biocompatibles: el campo de los MEMS biomédicos avanza rápidamente, con aplicaciones en la administración de fármacos, la ingeniería de tejidos y los dispositivos implantables. Los materiales adhesivos, biocompatibles y no tóxicos serán cruciales para estas aplicaciones, ya que garantizarán la seguridad y la compatibilidad de los dispositivos MEMS con los sistemas biológicos. Los desarrollos futuros se centrarán en el diseño y la síntesis de adhesivos que muestren una excelente biocompatibilidad mientras mantienen una fuerte adhesión y propiedades mecánicas.
- Adhesivos liberables y reutilizables: en algunas aplicaciones de MEMS, es deseable la capacidad de liberar y reposicionar o reutilizar componentes después de la unión. Los adhesivos liberables y reutilizables brindarán flexibilidad durante los procesos de fabricación y ensamblaje de MEMS, lo que permitirá realizar ajustes y correcciones sin dañar las piezas o los sustratos.
Conclusión: el adhesivo MEMS como fuerza impulsora en el avance de la microelectrónica
Los materiales adhesivos MEMS se han convertido en una fuerza impulsora en el avance de la microelectrónica, desempeñando un papel fundamental en el ensamblaje y la funcionalidad de los dispositivos MEMS. Estos diminutos componentes mecánicos y eléctricos requieren una unión especial para garantizar la fiabilidad y el rendimiento. Se espera que las tendencias futuras en el desarrollo de adhesivos MEMS mejoren aún más las capacidades y aplicaciones de estos dispositivos.
La miniaturización y la integración seguirán ampliando los límites de la tecnología MEMS. Los materiales adhesivos con capacidades de alta resolución serán cruciales para unir componentes más pequeños y complejos. Además, los adhesivos que permiten la integración de múltiples componentes dentro de un solo dispositivo MEMS impulsarán la innovación en este campo.
La confiabilidad y la durabilidad son primordiales en las aplicaciones MEMS, ya que estos dispositivos están expuestos a condiciones de funcionamiento adversas. Los futuros desarrollos de adhesivos mejorarán los ciclos térmicos, la humedad y la resistencia a la tensión mecánica. El objetivo es garantizar el rendimiento y la estabilidad a largo plazo de los dispositivos MEMS en diversos entornos.
Los adhesivos de curado a baja temperatura abordarán la sensibilidad de los materiales MEMS a las altas temperaturas. El curado a temperaturas más bajas sin comprometer la fuerza de unión facilitará el ensamblaje de componentes sensibles a la temperatura, reduciendo el riesgo de daño térmico durante la fabricación.
La compatibilidad con múltiples sustratos es crucial en el ensamblaje de MEMS, ya que a menudo se involucran diferentes materiales. Los materiales adhesivos que exhiben una excelente adhesión a una amplia gama de sustratos permitirán la unión de materiales diferentes y ayudarán a mitigar las fallas inducidas por el estrés en los dispositivos MEMS.
En MEMS biomédicos, la demanda de adhesivos biocompatibles está creciendo rápidamente. Estos adhesivos deben ser no tóxicos y compatibles con los sistemas biológicos manteniendo una fuerte adherencia y propiedades mecánicas. El desarrollo de dichos enlaces ampliará las aplicaciones de MEMS en áreas como la administración de fármacos, la ingeniería de tejidos y los dispositivos implantables.
Por último, los adhesivos liberables y reutilizables brindarán flexibilidad durante los procesos de fabricación y ensamblaje de MEMS. La capacidad de liberar y reposicionar componentes o incluso reutilizarlos después de la unión admite ajustes y correcciones sin dañar las piezas o los sustratos.
En conclusión, los materiales adhesivos MEMS están impulsando los avances en microelectrónica al permitir el ensamblaje y la funcionalidad de los dispositivos MEMS. Los desarrollos futuros en los adhesivos MEMS mejorarán aún más la miniaturización, la confiabilidad, el curado a baja temperatura, la compatibilidad del sustrato, la biocompatibilidad y la flexibilidad de los procesos de ensamblaje. Estos avances desbloquearán nuevas posibilidades y aplicaciones para la tecnología MEMS, revolucionando varias industrias y dando forma al futuro de la microelectrónica.