Una guía completa de adhesivos electrónicos
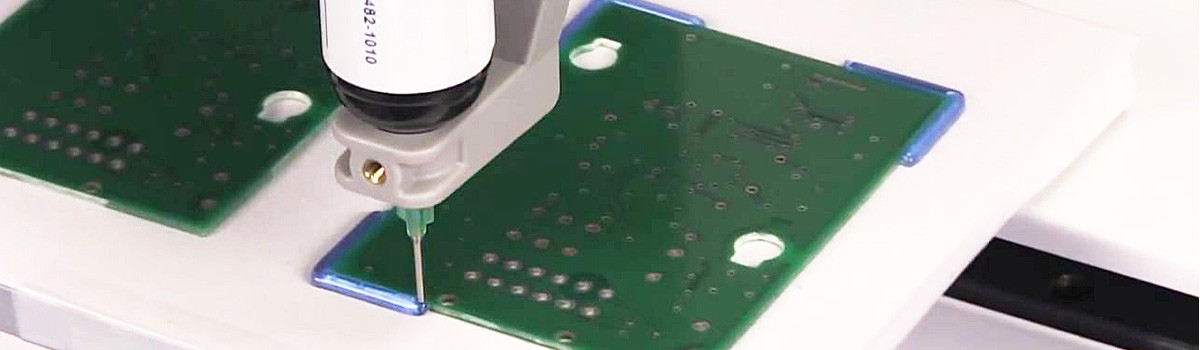
Adhesivos electrónicos
Los adhesivos electrónicos son materiales especializados que unen componentes electrónicos, como circuitos integrados, resistencias, condensadores y transistores, a placas de circuitos, sustratos y otros dispositivos electrónicos. Estos adhesivos garantizan la confiabilidad, el rendimiento y la longevidad de los productos electrónicos.
Los adhesivos electrónicos vienen en varios tipos, incluidos los adhesivos conductores y no conductores, los adhesivos conductores térmicos y eléctricos y los adhesivos curables por UV. Los formulamos para soportar temperaturas extremas, productos químicos, humedad, vibraciones y otros factores ambientales que los dispositivos electrónicos pueden encontrar durante su vida útil.
Varias industrias utilizan ampliamente adhesivos electrónicos, incluidas la automotriz, aeroespacial, de telecomunicaciones, médica y electrónica de consumo. Permiten la miniaturización, la velocidad y la funcionalidad de los dispositivos electrónicos y su resistencia a condiciones adversas.
La importancia de los adhesivos electrónicos en la tecnología moderna
Los adhesivos electrónicos son un componente esencial de la tecnología moderna. Desempeñan un papel vital para garantizar la confiabilidad y la longevidad de los dispositivos electrónicos, así como su miniaturización, velocidad y funcionalidad. Estas son algunas de las razones por las que los adhesivos electrónicos son tan importantes en la tecnología moderna:
Miniaturización: A medida que los fabricantes miniaturizan los dispositivos electrónicos, también deben miniaturizar los componentes utilizados en su construcción. Los adhesivos electrónicos permiten a los fabricantes unir estos pequeños componentes con precisión y estabilidad, lo que permite el desarrollo de dispositivos más pequeños y complejos.
Durabilidad: Las duras condiciones ambientales, incluidos los cambios de temperatura, la humedad y los golpes, a menudo exponen los dispositivos electrónicos. Formulamos adhesivos electrónicos para soportar estas condiciones, asegurando que los componentes permanezcan unidos de forma segura y que el dispositivo continúe funcionando correctamente.
Funcionalidad: También se pueden usar adhesivos electrónicos para crear caminos conductores entre los componentes, lo que permite el flujo de electricidad a través del dispositivo. Permite el desarrollo de circuitos más complejos y una mayor funcionalidad en dispositivos electrónicos.
Velocidad: El uso de adhesivos electrónicos en la fabricación puede ayudar a optimizar la producción y reducir el tiempo de montaje. Los selladores electrónicos se pueden aplicar de forma rápida y precisa, lo que ahorra tiempo y aumenta la eficiencia.
Fiabilidad: Incluso una falla menor puede causar problemas importantes en los dispositivos electrónicos. Los adhesivos electrónicos brindan una unión confiable y segura entre los componentes, lo que reduce el riesgo de pérdida y garantiza que el dispositivo funcione correctamente.
Tipos de adhesivos electrónicos: una descripción completa
Los adhesivos electrónicos vienen en varios tipos, cada uno con propiedades y ventajas únicas. La elección del adhesivo depende de la aplicación y los requisitos específicos del dispositivo, y los fabricantes deben elegir un adhesivo de dispositivo adecuado para garantizar la confiabilidad, la funcionalidad y la longevidad. Estos son los diferentes tipos de adhesivos electrónicos comúnmente utilizados en la industria:
- Adhesivos conductores:Los fabricantes de productos electrónicos utilizan adhesivos conductores para crear conexiones eléctricas entre los componentes electrónicos. Contienen partículas conductoras, como plata o cobre, que permiten el flujo de electricidad a través del pegamento. Los fabricantes suelen utilizar estos adhesivos para fabricar pantallas táctiles, sensores y otros dispositivos electrónicos.
- Adhesivos no conductores:Los fabricantes utilizan adhesivos no conductores para unir componentes electrónicos que no requieren conexiones eléctricas. A menudo se utilizan en el ensamblaje de placas de circuito, proporcionando estabilidad mecánica y aislamiento entre los miembros.
- Adhesivos Conductores Térmicos: Los adhesivos termoconductores disipan el calor de los componentes electrónicos. Contienen partículas termoconductoras, como cerámica o carbón, que permiten que el calor fluya a través del pegamento. Los fabricantes utilizan estos adhesivos para fabricar fuentes de alimentación, iluminación LED y otros dispositivos que generan cantidades significativas de calor.
- Adhesivos Conductores de Electricidad:Los adhesivos eléctricamente conductores son similares a los adhesivos conductores pero tienen una mayor conductividad eléctrica. A menudo se utilizan para ensamblar dispositivos electrónicos de alto rendimiento, como microprocesadores y chips de memoria.
- Adhesivos de curado UV: Se pueden curar adhesivos curables por UV utilizando luz ultravioleta. Son de curado rápido y brindan una excelente adhesión a una variedad de sustratos. Los fabricantes suelen utilizar estos adhesivos para fabricar dispositivos médicos, equipos ópticos y otros dispositivos que requieren tiempos de curado rápidos.
- Adhesivos Epoxi: Los adhesivos epoxi son conocidos por su alta resistencia y durabilidad. Por lo general, ensamblan dispositivos electrónicos que requieren un vínculo fuerte, como teléfonos inteligentes, tabletas y computadoras portátiles.
Adhesivos conductores: su papel en los circuitos eléctricos
Los adhesivos conductores son materiales esenciales en la fabricación de dispositivos electrónicos. Proporcionan un método para crear conexiones eléctricas entre componentes electrónicos, lo cual es crucial para la funcionalidad de estos dispositivos. Esta publicación de blog discutirá el papel de los adhesivos conductores en los circuitos eléctricos.
Los adhesivos conductores están formulados con partículas conductoras como plata, cobre o níquel, lo que permite que la electricidad fluya a través del pegamento. Estas partículas crean una vía conductora entre los componentes electrónicos, asegurando que el dispositivo funcione correctamente. Los fabricantes suelen utilizar adhesivos conductores para fabricar pantallas táctiles, sensores y otros dispositivos electrónicos.
Una ventaja de usar adhesivos conductores en los circuitos eléctricos es su capacidad para proporcionar una unión segura entre los componentes. Estos adhesivos crean una conexión robusta y estable que puede soportar las tensiones ambientales de los dispositivos electrónicos. El pegamento también puede distribuir la corriente de manera uniforme en todo el circuito, evitando puntos calientes y asegurando que todos los componentes reciban la potencia correcta.
También se pueden usar adhesivos conductores para crear circuitos flexibles, lo cual es esencial para dispositivos flexibles, como dispositivos electrónicos portátiles o dispositivos médicos. Los adhesivos conductivos se pueden aplicar a sustratos flexibles, creando cursos que se doblan, tuercen o estiran.
Uno de los desafíos del uso de adhesivos conductores es que su conductividad puede degradarse con el tiempo, especialmente cuando se exponen a condiciones ambientales adversas. Los fabricantes desarrollan continuamente nuevas formulaciones con mayor durabilidad y conductividad para abordar este problema.
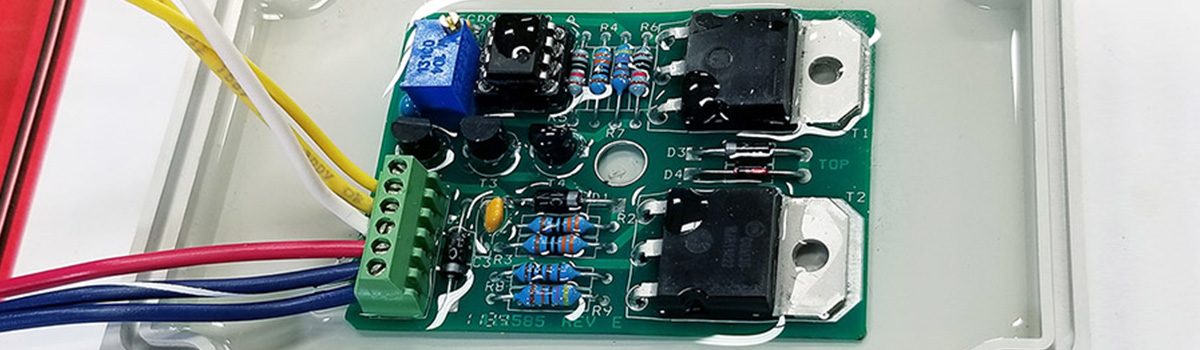
Comprensión de los adhesivos termoconductores
Los adhesivos termoconductores son un componente esencial en muchos dispositivos electrónicos modernos. Estos adhesivos unen y transfieren el calor entre dos superficies, mejorando la gestión térmica y evitando el sobrecalentamiento. En esta publicación, exploraremos qué son los adhesivos termoconductores, sus propiedades y sus aplicaciones.
Los adhesivos termoconductores son un tipo de adhesivo que tiene una alta conductividad térmica, y esto significa que pueden transferir calor de manera eficiente entre dos superficies. La composición típica de los adhesivos conductores incluye una combinación de una matriz polimérica, como epoxi o silicona, y partículas conductoras, como óxido de aluminio o nitruro de boro.
Las propiedades de los adhesivos termoconductores dependen del tipo de matriz polimérica y de las partículas conductoras utilizadas. Las propiedades fundamentales incluyen la conductividad térmica, la viscosidad y el tiempo de curado. La propiedad más crítica del adhesivo es su conductividad térmica, ya que determina la eficacia con la que se transfiere el calor entre las superficies. La viscosidad del adhesivo determina qué tan fácil es aplicarlo, y el tiempo de curado determina cuánto tarda el adhesivo en curarse y alcanzar por completo su máxima conductividad térmica.
Los adhesivos termoconductores tienen muchas aplicaciones, incluso en las industrias automotriz, aeroespacial y electrónica. En la industria electrónica, los adhesivos termoconductores unen los componentes a los disipadores y esparcidores de calor, mejorando la gestión térmica y evitando el sobrecalentamiento. También se utilizan para unir componentes de iluminación LED a sustratos, que generan mucho calor.
En la industria automotriz, los adhesivos termoconductores se utilizan para unir componentes electrónicos de potencia a disipadores de calor, lo que ayuda a mejorar la gestión térmica. También conectan sensores a los componentes del motor, que deben operar en ambientes de alta temperatura.
Adhesivos dieléctricos: asegurando el aislamiento en componentes eléctricos
Los adhesivos dieléctricos son materiales esenciales utilizados en la industria electrónica para proporcionar aislamiento y protección a los componentes eléctricos. En aplicaciones donde la conductividad eléctrica es una preocupación o se necesita un alto grado de aislamiento, se utilizan adhesivos termoconductores en lugar de los adhesivos tradicionales que no pueden cumplir con estos requisitos. Los adhesivos dieléctricos tienen excelentes propiedades de aislamiento y pueden soportar altas temperaturas, lo que los hace ideales para su uso en dispositivos electrónicos.
Estos son algunos de los beneficios de usar adhesivos dieléctricos:
- Aislamiento:Los adhesivos dieléctricos proporcionan excelentes propiedades de aislamiento, evitando que la corriente eléctrica fluya a través de ellos y asegurando que sus componentes de unión estén eléctricamente aislados.
- Resistencia al calor:Los adhesivos dieléctricos pueden soportar altas temperaturas y mantener sus propiedades a lo largo del tiempo, lo que los hace muy adecuados para aplicaciones que generan mucho calor, como motores y transformadores.
- Resistencia química: Los adhesivos dieléctricos resisten los productos químicos, lo que los hace adecuados para su uso en entornos hostiles donde otros adhesivos fallarían.
- Durabilidad: Los adhesivos dieléctricos tienen excelentes propiedades de unión y pueden soportar grandes tensiones y tensiones, lo que los hace ideales para su uso en aplicaciones con tensión mecánica.
- Fácil aplicación:Los adhesivos dieléctricos se pueden aplicar de forma rápida y eficiente, lo que permite un montaje y una producción rápidos.
- Versatilidad:Puede utilizar adhesivos dieléctricos en diversas aplicaciones, como dispositivos electrónicos, componentes de automóviles y equipos médicos.
Los adhesivos dieléctricos están disponibles en varias formulaciones, incluidos epoxis, siliconas y acrílicos. Diseñamos cada formulación con propiedades únicas que se adaptan a aplicaciones específicas.
Adhesivos de curado UV: una solución rápida para el ensamblaje electrónico
Los dispositivos electrónicos se han convertido en una parte integral de nuestras vidas. Confiamos en la electrónica para casi todo, desde teléfonos inteligentes hasta computadoras portátiles, automóviles y dispositivos médicos. El ensamblaje electrónico implica unir diferentes componentes y los adhesivos juegan un papel crucial. Los adhesivos curables por UV están ganando popularidad entre varios adhesivos debido a su rápido tiempo de curado y alta fuerza de unión.
Los adhesivos curables por UV son adhesivos reactivos que curan cuando se exponen a la luz ultravioleta. El curado se produce en cuestión de segundos, lo que los convierte en una opción ideal para entornos de producción de gran volumen. Los adhesivos de curado UV eliminan la necesidad de calentar o secar, lo que reduce el tiempo de montaje y el costo de producción.
La alta fuerza de unión de los adhesivos curables por UV los hace adecuados para diversos sustratos, incluidos metales, plásticos y vidrio. Ofrecen una excelente adhesión a materiales difíciles de unir, como polipropileno, polietileno y policarbonato. La unión adhesiva formada por los adhesivos curables por UV es sólida y duradera, y puede soportar entornos hostiles, como altas temperaturas, productos químicos y humedad.
Otra ventaja de los adhesivos curables por UV es su capacidad de curar en un área específica. El adhesivo se puede aplicar con precisión en el área de unión y el proceso de curado se puede activar al exponer el sitio a la luz ultravioleta. Esta característica los hace ideales para aplicaciones que requieren posicionamiento preciso y alineación de componentes.
Los adhesivos de curado UV también son ecológicos y no contienen solventes ni emiten compuestos orgánicos volátiles (COV) durante el curado. Los hace seguros para usar en espacios confinados y reduce el impacto ambiental.
Selección del adhesivo electrónico adecuado: factores clave a tener en cuenta
La selección de adhesivos electrónicos adecuados es fundamental para garantizar la longevidad y la fiabilidad de los dispositivos electrónicos. Los adhesivos electrónicos unen los componentes y protegen contra factores externos como la humedad, el polvo y las fluctuaciones de temperatura. Aquí discutiremos los factores clave a considerar al seleccionar un adhesivo electrónico adecuado.
Propiedades químicas
Compatibilidad: El adhesivo debe ser compatible con los materiales a los que se unirá, incluidos metales, plásticos y vidrio.
Resistencia química: El adhesivo debe resistir los productos químicos que puedan entrar en contacto con el dispositivo electrónico, como agentes de limpieza o disolventes.
Propiedades termales: El adhesivo debe soportar temperaturas de funcionamiento y fluctuaciones.
Propiedades de la aplicación
Viscosidad: Para garantizar una aplicación adecuada, debe tener en cuenta el grosor del adhesivo, ya que debe fluir uniformemente y cubrir las superficies que desea unir.
Tiempo de curado: El adhesivo debe tener un tiempo de curado compatible con el proceso de montaje. Un tiempo de curado prolongado puede ralentizar la producción, mientras que un tiempo de curado corto puede no permitir una unión adecuada.
Fuerza de adherencia: El adhesivo debe tener suficiente fuerza de adhesión para unir los componentes del dispositivo y asegurar su longevidad.
Propiedades ambientales
Resistencia a la humedad: El adhesivo debe proteger contra la humedad, que puede dañar los componentes electrónicos.
Resistencia UV: El adhesivo debe proteger contra la radiación UV, que puede causar decoloración y degradación de los materiales.
Resistencia al impacto: El adhesivo debe proteger contra impactos físicos como caídas o golpes.
La selección de adhesivos electrónicos adecuados es fundamental para garantizar la longevidad y la fiabilidad de los dispositivos electrónicos. Al considerar las propiedades químicas, de aplicación y ambientales del adhesivo, los fabricantes pueden asegurarse de que el adhesivo unirá los componentes correctamente y protegerá contra factores externos.
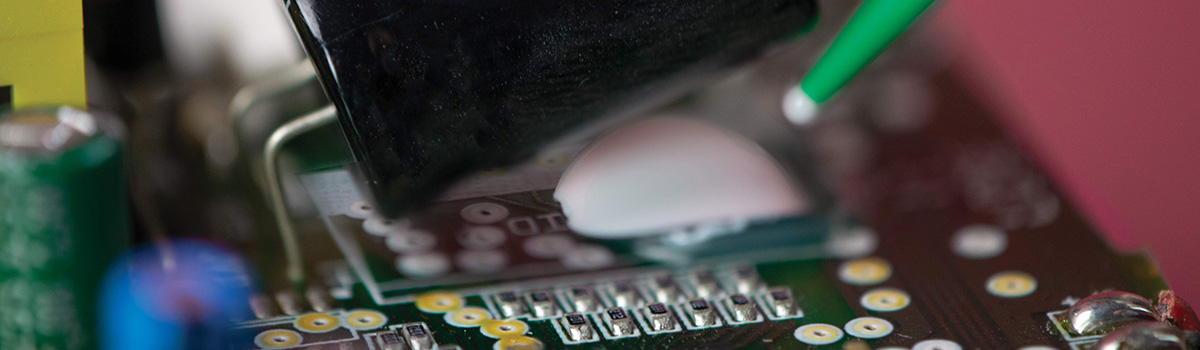
Compatibilidad con sustratos: garantizar la adherencia y la estabilidad
La compatibilidad con los sustratos garantiza la adhesión y la estabilidad en diversas industrias, como la automotriz, la construcción y el embalaje. El éxito de aplicar un recubrimiento o adhesivo a un sustrato depende de cuán compatibles sean los dos materiales. En esta discusión, enfatizaremos la importancia de garantizar la compatibilidad con los sustratos y describiremos los pasos para lograrlo.
Importancia de la compatibilidad con sustratos
Adhesión: Para garantizar que el recubrimiento o adhesivo permanezca en su lugar, debe adherirse a la superficie del sustrato cuando se aplique. La compatibilidad con los sustratos es esencial para garantizar que el revestimiento o el adhesivo se adhieran al sustrato y permanezcan estables.
Estabilidad: Un revestimiento o adhesivo incompatible con el sustrato puede provocar inestabilidad y hacer que el revestimiento o el sellador fallen. Puede dar lugar a problemas importantes, como fallas estructurales del edificio o pérdida de producto durante el uso.
Garantía de compatibilidad con sustratos
Preparación de la superficie: Para preparar la superficie del sustrato para aplicar un revestimiento o adhesivo, límpielo y elimine los contaminantes. Permitirá que el revestimiento o sellador se adhiera correctamente al sustrato.
Pruebas: Debe realizar pruebas de compatibilidad antes de aplicar un revestimiento o adhesivo para asegurarse de que los dos materiales sean compatibles. Puede utilizar varios métodos, como la prueba de corte por tracción o de traslapo, para realizar pruebas de compatibilidad.
Selección del material: Es fundamental seleccionar el recubrimiento o adhesivo adecuado para el sustrato. Considere las propiedades químicas y físicas de la capa o adhesivo y el sustrato.
Las implicaciones de la falta de compatibilidad con los sustratos pueden ser graves y provocar fallas y altos costos de tiempo y dinero. Puede lograr adherencia y estabilidad y garantizar una aplicación exitosa y duradera al garantizar la compatibilidad con los sustratos.
Resistencia ambiental: factores a considerar
La resistencia ambiental se refiere a los factores naturales que limitan el crecimiento, la distribución y la abundancia de organismos en un ecosistema. Estos factores pueden ser bióticos (vivos) o abióticos (no vivos) e incluyen una gama de condiciones físicas, químicas y biológicas. En esta publicación de blog, discutiremos los factores que contribuyen a la resistencia ambiental y las implicaciones de estos factores en la salud del ecosistema.
Factores bioticos
- Competencia: Los organismos compiten por los recursos de alimento, agua y refugio. Puede limitar el crecimiento de una población al reducir la disponibilidad de recursos.
- depredación: Los depredadores pueden restringir el tamaño de una persona al consumir individuos. También puede conducir a una disminución en el tamaño de la población general de una especie.
- Enfermedad: Las enfermedades pueden propagarse rápidamente a través de una población, causando una disminución de individuos con el tiempo.
Factores abióticos
- Temperatura:Los organismos tienen un rango de temperaturas óptimas para sobrevivir y reproducirse. Las temperaturas extremas pueden limitar el crecimiento y la distribución de organismos.
- Agua: El agua es esencial para la vida, y los organismos requieren una cierta cantidad de agua para sobrevivir. La falta de agua puede limitar el crecimiento y la distribución de organismos.
- Luz: La luz es necesaria para la fotosíntesis en las plantas, que es como producen alimentos. La falta de luz solar puede limitar el desarrollo y distribución de las plantas.
Implicaciones de la resistencia ambiental
- Mantener el equilibrio: La resistencia ambiental ayuda a mantener el equilibrio en los ecosistemas al evitar que una especie domine y cause desequilibrio.
- Biodiversidad: La resistencia ambiental promueve la biodiversidad al crear nichos para diferentes especies, aumentando así el número de especies en un ecosistema.
- Salud del ecosistema:La resistencia ambiental juega un papel crucial en el mantenimiento de la salud del ecosistema. La interrupción de estos factores puede conducir a la disminución o extinción de especies, lo que puede tener efectos en cascada en todo el ecosistema.
Método de aplicación: elección de la técnica de dosificación adecuada
Al fabricar, es crucial elegir el método de aplicación adecuado para su producto. El proceso de dosificación del revelado puede influir en gran medida en su rendimiento y apariencia.
Por eso es fundamental evaluar cuidadosamente sus opciones y elegir la técnica que mejor se adapte a sus necesidades.
Aquí hay algunos factores a considerar al elegir la técnica de dosificación adecuada:
- Viscosidad: La viscosidad del material que está dosificando es una consideración importante. Los materiales de baja viscosidad como el agua o los solventes pueden requerir diferentes estilos de dosificación que los materiales de alta viscosidad como los adhesivos o las pastas. Para materiales de baja viscosidad, las técnicas de rociado o atomización pueden ser más efectivas, mientras que los materiales de alta viscosidad pueden requerir un enfoque más controlado, como la dosificación de precisión.
- Propiedades materiales: Al seleccionar un método de dosificación, debe considerar las propiedades del material que planea dosificar. Por ejemplo, algunos materiales pueden ser sensibles al aire oa los cambios de temperatura y requieren métodos de distribución que minimicen la exposición a estos factores. De manera similar, los materiales que requieren un cierto nivel de precisión o exactitud pueden necesitar equipos de dosificación más especializados.
- Diseño de producto: El diseño de su producto también puede influir en la elección de la técnica de dosificación. Por ejemplo, si su producto tiene características complejas o delicadas, un proceso de dispensación manual puede ser más apropiado que uno automatizado. Por otro lado, si su producto requiere una salida de alto volumen, puede ser necesaria una técnica de dosificación mecánica o robótica.
- Factores medioambientales: Finalmente, los factores ambientales también pueden afectar la elección del método de dosificación. Si necesita dispensar su producto en un entorno de sala limpia, es posible que necesite un equipo especializado que cumpla determinados estándares de limpieza, por ejemplo. De manera similar, si su producto es inflamable o peligroso, es posible que deba elegir una técnica de distribución que minimice el riesgo de accidentes o incendios.
Proceso de curado: comprender el impacto del calor y el tiempo
El curado es un proceso crucial que asegura la longevidad y durabilidad de los productos en varias industrias. Desde la automoción hasta la construcción, el curado es fundamental para garantizar que los productos finales sean sólidos y resistentes a los factores ambientales. El proceso de curado involucra la aplicación de calor y tiempo al revelado, lo que afecta sus propiedades mecánicas y calidad general.
El calor es uno de los factores críticos que influyen en el proceso de curado. El rango de temperatura y la duración de la aplicación de calor afectan significativamente la resistencia y rigidez del producto. El calor activa las reacciones químicas que conducen a la formación de enlaces cruzados en el material. Estos enlaces cruzados aumentan el poder del material al crear enlaces entre las cadenas moleculares.
La duración del proceso de curado es otro factor crítico. Cuanto mayor sea el tiempo de curado, más enlaces cruzados se forman, lo que da como resultado un producto más robusto y rígido. Sin embargo, demasiado tiempo de curado puede provocar fragilidad y flexibilidad reducida. Es encontrar el equilibrio adecuado entre el tiempo de curado y la resistencia, según los requisitos del producto.
El método de curado apropiado depende del tipo de producto y de las propiedades requeridas. Por ejemplo, en la industria automotriz, se utiliza un horno de curado de pintura para aplicar calor a la carrocería del automóvil, asegurando que la pintura se seque y se adhiera al metal. En la industria de la construcción, el concreto se cura agregando agua y permitiendo que se endurezca con el tiempo, lo que aumenta su resistencia.
El proceso de curado es fundamental no solo para las propiedades mecánicas del producto sino también para su apariencia. El calor y el tiempo aplicado durante el curado afectan la textura, el color y el acabado del producto. Por lo tanto, controlar el proceso de curado es crucial para garantizar que el producto cumpla con los requisitos estéticos y funcionales deseados.
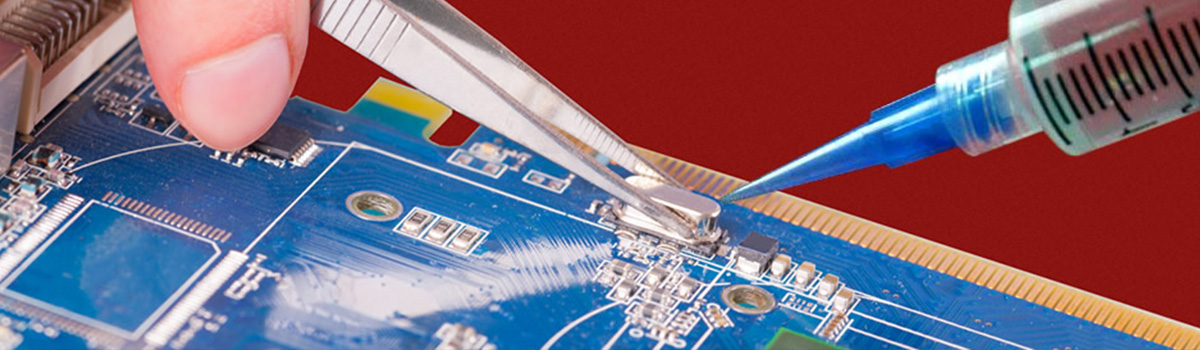
Almacenamiento y manejo: consejos para mantener la calidad del adhesivo
El almacenamiento y la manipulación adecuados son cruciales para garantizar la eficacia de los adhesivos. El almacenamiento y la manipulación inadecuados pueden conducir a la degradación de la calidad del adhesivo y, en última instancia, a la falla del producto. Estos son algunos consejos para mantener la calidad del adhesivo:
- Control de temperatura: Los materiales adhesivos son sensibles a los cambios de temperatura y la exposición a temperaturas extremas puede dañar su calidad. Las altas temperaturas pueden hacer que los materiales adhesivos pierdan su viscosidad y fuerza de adhesión, mientras que las bajas temperaturas pueden hacer que se vuelvan quebradizos y difíciles de usar. Por lo tanto, es esencial almacenar los adhesivos en un lugar fresco y seco, lejos de la luz solar directa y a una temperatura constante.
- Control de humedad: La humedad también puede afectar la calidad de los materiales adhesivos. La humedad puede hacer que los adhesivos se rompan, reduciendo su fuerza adhesiva. Para mantener la calidad del adhesivo, se deben mantener los recipientes adhesivos herméticamente cerrados y almacenarlos en un área con humedad controlada.
- Manejo adecuado: El manejo adecuado de los materiales adhesivos es crucial para su longevidad. Es fundamental evitar dejar caer o agitar los envases pegajosos, ya que esto puede dar lugar a la formación de burbujas de aire, afectando la calidad del adhesivo. Además, es esencial mezclar correctamente los adhesivos antes de usarlos, ya que una mezcla inadecuada puede provocar una calidad y un rendimiento desiguales del adhesivo.
- Vida útil: Los materiales adhesivos tienen una vida útil limitada y es esencial usarlos dentro del marco de tiempo especificado. Con el tiempo, los materiales adhesivos pueden comenzar a descomponerse, lo que hace que pierdan su fuerza adhesiva y viscosidad. Es fundamental utilizar los adhesivos antes de su caducidad para garantizar su eficacia.
- Compatibilidad: Los fabricantes diseñan diferentes materiales adhesivos para superficies y aplicaciones específicas. Es fundamental asegurarse de que el material adhesivo sea compatible con la textura y los requisitos de aplicación. El uso de materiales adhesivos incompatibles puede provocar fallas en el producto y daños en las superficies.
Aplicaciones comunes de adhesivos electrónicos
Los adhesivos electrónicos son adhesivos especializados que unen y sellan componentes y sistemas electrónicos. Las industrias aeroespacial y automotriz y la electrónica de consumo se encuentran entre las diversas aplicaciones que los utilizan. Estas son algunas de las aplicaciones más comunes de los adhesivos electrónicos:
- Electrónica de consumo:Los adhesivos electrónicos se utilizan ampliamente en productos electrónicos de consumo, incluidos teléfonos inteligentes, computadoras portátiles y tabletas. Unen y sellan componentes electrónicos como pantallas, pantallas táctiles y baterías. Los adhesivos electrónicos también protegen contra la humedad y otros factores ambientales que dañan los componentes electrónicos.
- Industria automotriz: La industria automotriz depende en gran medida de los adhesivos electrónicos para garantizar la confiabilidad y seguridad de los automóviles modernos. Los adhesivos electrónicos unen y sellan componentes electrónicos, componentes estructurales y conexiones eléctricas. Los fabricantes también los utilizan para unir y sellar materiales compuestos, como la fibra de carbono, que son cada vez más frecuentes en la construcción de automóviles modernos.
- Industria aeroespacial: La industria aeroespacial requiere adhesivos especializados que puedan soportar tensiones ambientales extremas, incluidos los cambios de alta temperatura y la exposición al agua salada. Los adhesivos electrónicos se utilizan ampliamente en la industria aeroespacial para unir y sellar componentes electrónicos, componentes estructurales y conexiones eléctricas.
- Dispositivos médicos: Los fabricantes de dispositivos médicos utilizan adhesivos electrónicos en productos como marcapasos, desfibriladores y bombas de insulina. Se utilizan para unir y sellar componentes electrónicos, asegurando que funcionen de manera correcta y confiable.
- Iluminación LED:Los fabricantes utilizan adhesivos electrónicos para producir iluminación LED, incluida la iluminación de automóviles y las farolas. Estos adhesivos unen y sellan los componentes electrónicos para protegerlos de la humedad y otros factores ambientales que pueden causar daños.
- Energía renovable: La industria utiliza adhesivos electrónicos para unir y sellar paneles solares, turbinas eólicas y baterías. Se utilizan para proteger los componentes electrónicos de la humedad y otros factores ambientales, asegurando que sigan siendo fiables y funcionales durante la vida útil del equipo.
Industria automotriz: el papel de los adhesivos electrónicos en la fabricación de automóviles
La industria automotriz está en constante evolución y los fabricantes de automóviles siempre buscan formas de mejorar la seguridad, confiabilidad y eficiencia de sus vehículos. Un componente crítico que juega un papel vital en la construcción de automóviles modernos son los adhesivos electrónicos. Los adhesivos electrónicos se utilizan ampliamente en la industria automotriz para diversas aplicaciones, que incluyen unir y sellar componentes electrónicos, componentes estructurales y conexiones eléctricas.
Los adhesivos electrónicos encuentran aplicación de varias maneras cruciales durante la fabricación de automóviles:
- Unión y sellado de componentes electrónicos:Los adhesivos electrónicos unen y rellenan detalles electrónicos como sensores, sistemas de control y pantallas. Los adhesivos electrónicos garantizan que estos componentes puedan funcionar correctamente, incluso cuando se someten a condiciones extremas.
- Unión y sellado de componentes estructurales:Los adhesivos electrónicos unen y rellenan elementos estructurales, como paneles de carrocería y chasis. El uso de adhesivos electrónicos garantiza que los componentes del automóvil permanezcan firmemente sujetos, incluso cuando se someten a las tensiones de la conducción diaria.
- Conductividad eléctrica: Los fabricantes de automóviles utilizan adhesivos electrónicos para garantizar una conductividad eléctrica confiable entre los componentes del automóvil. Las conexiones eléctricas seguras entre las piezas son particularmente cruciales en los vehículos híbridos y eléctricos, ya que garantizan la operación segura y eficiente del automóvil.
- Resistencia de vibracion:Los diseñadores electrónicos crean adhesivos electrónicos que absorben vibraciones y golpes, evitando que los componentes se suelten o fallen. Evitar que los elementos se suelten o mueran es fundamental en los vehículos de alto rendimiento, donde las piezas se someten a una gran tensión.
- Protección del medio ambiente:Los diseñadores crean adhesivos electrónicos para proteger los componentes de factores ambientales como la humedad, el polvo y otros agentes que pueden dañarlos o degradarlos. Los enlaces electrónicos garantizan que las piezas permanezcan confiables y operativas durante toda la vida útil del vehículo.
Los fabricantes de automóviles también utilizan adhesivos electrónicos durante el proceso de fabricación, además de sus aplicaciones críticas. Los fabricantes de automóviles utilizan adhesivos electrónicos para unir y sellar materiales compuestos, como la fibra de carbono, que son cada vez más comunes en la construcción de automóviles modernos. El uso de materiales compuestos da como resultado vehículos más livianos, más fuertes y más eficientes en combustible, pero también requiere sistemas adhesivos especializados para garantizar que los componentes estén correctamente adheridos y sellados.
Industria aeroespacial: cómo los adhesivos electrónicos garantizan la seguridad en las aeronaves
La industria aeroespacial es una de las industrias más complejas y exigentes del mundo. La seguridad de los pasajeros y miembros de la tripulación a bordo de las aeronaves es primordial y cualquier falla en los materiales o componentes utilizados en la construcción de aeronaves puede tener consecuencias catastróficas. Los fabricantes, diseñadores e ingenieros no pueden exagerar la importancia de los adhesivos electrónicos para garantizar la seguridad de las aeronaves.
Los adhesivos electrónicos se utilizan ampliamente en la industria aeroespacial para diversas aplicaciones. Se utilizan para unir y sellar componentes electrónicos, como sensores y sistemas de control, para garantizar que funcionen correctamente en condiciones extremas. También conectan y sellan elementos estructurales, como alas y secciones del fuselaje, para garantizar que permanezcan firmemente en su lugar durante el vuelo.
Una de las principales preocupaciones en la construcción de aeronaves es el impacto de la humedad y otros factores ambientales en la integridad de los componentes. Los diseñadores crean adhesivos electrónicos que pueden resistir las tensiones ambientales, como los cambios extremos de temperatura y la alta humedad, que pueden comprometer el rendimiento de la aeronave. Los diseñadores también diseñan adhesivos electrónicos para ofrecer una protección duradera contra la corrosión, un problema importante en aviones expuestos a entornos corrosivos como el agua salada.
Los adhesivos electrónicos también juegan un papel crucial en el proceso de fabricación de aeronaves. Los adhesivos electrónicos unen y sellan materiales compuestos, como la fibra de carbono, cada vez más comunes en la construcción de aeronaves modernas. El uso de materiales compuestos da como resultado aeronaves más livianas, más fuertes y más eficientes en combustible, pero también requiere sistemas adhesivos especializados para garantizar que los componentes estén correctamente adheridos y sellados.
Además de servir para fines estructurales y de protección, la industria aeroespacial emplea adhesivos electrónicos para la conductividad eléctrica. Se utilizan para unir y sellar circuitos y componentes electrónicos, asegurando que funcionen de manera correcta y confiable. Los adhesivos electrónicos garantizan que las conexiones eléctricas de la aeronave permanezcan seguras, minimizando el riesgo de falla eléctrica.
Industria médica: el papel de los adhesivos en dispositivos médicos
La industria médica depende de la tecnología para brindar tratamientos efectivos y eficientes a los pacientes. Los dispositivos médicos son fundamentales para diagnosticar, tratar y controlar diversas afecciones médicas. Los adhesivos son esenciales para los dispositivos médicos, ya que ofrecen una forma confiable y segura de unir componentes y garantizar la funcionalidad del dispositivo. Aquí exploraremos el papel de los adhesivos en los dispositivos médicos.
Estas son algunas de las formas en que los adhesivos juegan un papel crucial en los dispositivos médicos:
- Vinculación: Los adhesivos se utilizan para unir los componentes de los dispositivos médicos, asegurando que permanezcan en su lugar y funcionen según lo previsto. La colocación y el funcionamiento correctos de los componentes son cruciales en dispositivos como marcapasos y bombas de insulina, ya que puede ser una cuestión de vida o muerte, por lo que los adhesivos electrónicos son esenciales para garantizar una colocación segura y un funcionamiento fiable.
- Caza de focas: Los fabricantes de dispositivos médicos utilizan adhesivos para sellar dispositivos y evitar fugas y contaminación. Por ejemplo, en catéteres y líneas IV, se utilizan selladores para sellar la conexión entre el dispositivo y la piel del paciente, impidiendo la entrada de bacterias.
- Durabilidad:Los dispositivos médicos deben ser lo suficientemente duraderos para soportar las tensiones del uso diario. Los adhesivos juegan un papel crucial para garantizar la durabilidad de los dispositivos médicos al proporcionar una unión sólida y duradera entre los componentes.
- Biocompatibilidad: Los adhesivos usados en dispositivos médicos deben ser biocompatibles, lo que significa que son seguros para usar en el cuerpo humano y no causarán daño ni irritación. Los fabricantes deben utilizar adhesivos probados y aprobados para su uso en dispositivos médicos.
- Flexibilidad: Algunos dispositivos médicos deben adaptarse a la forma del cuerpo. Los fabricantes usan adhesivos para unir componentes flexibles mientras preservan la flexibilidad del dispositivo.
Electrónica de consumo: garantizar la durabilidad en los dispositivos cotidianos
Los productos electrónicos de consumo se han convertido en una parte esencial de nuestra vida diaria y dependemos de ellos para todo, desde la comunicación hasta el entretenimiento. Con un uso tan intensivo, la durabilidad es un factor fundamental para garantizar que nuestros dispositivos puedan soportar el desgaste del uso diario. Aquí exploraremos algunas formas en que los fabricantes pueden garantizar la durabilidad de los productos electrónicos de consumo.
- Diseño robusto: Uno de los factores esenciales para garantizar la durabilidad en la electrónica de consumo es el diseño. Los fabricantes deben crear dispositivos con materiales y componentes sólidos que puedan soportar las tensiones del uso diario. También deben tener en cuenta los factores de resistencia al agua, las caídas y los arañazos.
- Pruebas:Las pruebas son una parte esencial para garantizar la durabilidad en la electrónica de consumo. Los fabricantes deben realizar pruebas rigurosas de sus dispositivos para garantizar que puedan soportar diferentes condiciones ambientales y escenarios de uso. Los fabricantes pueden realizar varias pruebas, que incluyen resistencia al agua, resistencia a caídas, resistencia a la temperatura y más, para garantizar la durabilidad y confiabilidad de los productos.
- Control de calidad: El control de calidad es crucial para garantizar que cada dispositivo cumpla con los estándares de durabilidad del fabricante. Los fabricantes deben tener un riguroso proceso de control de calidad para identificar defectos o problemas que puedan afectar la durabilidad del dispositivo.
- Reparación y mantenimiento: Los consumidores también deberían poder reparar y mantener sus electrodomésticos fácilmente. Los fabricantes deben diseñar dispositivos que sean fáciles de desmontar y volver a montar, con piezas de repuesto fácilmente disponibles. Al realizar estas pruebas, los fabricantes se aseguran de que los consumidores puedan mantener las buenas condiciones de funcionamiento de sus dispositivos durante más tiempo.
- Educación del usuario: Finalmente, los fabricantes deben educar a los consumidores sobre cómo usar sus dispositivos para promover la durabilidad. Los fabricantes pueden incluir instrucciones sobre la limpieza y el mantenimiento adecuados de la máquina e información sobre cómo evitar las causas comunes de daños, como dejar caer o exponer el dispositivo al agua.
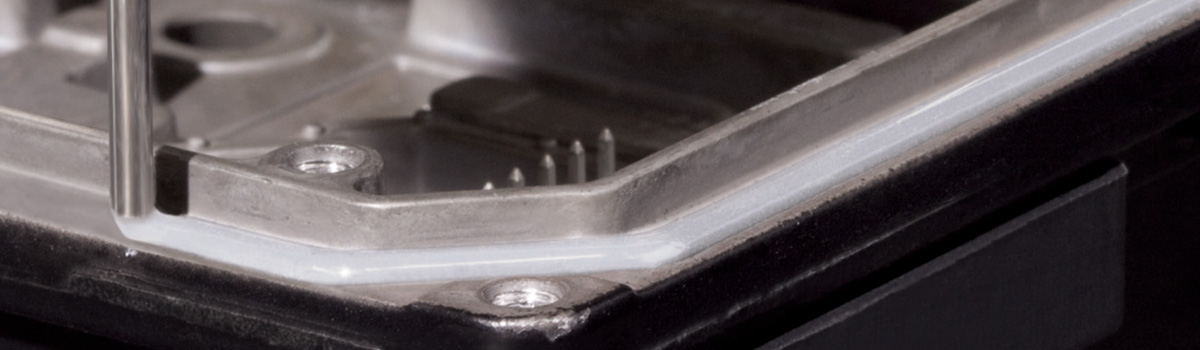
Futuro de los adhesivos electrónicos: tendencias e innovaciones emergentes
A medida que la tecnología continúa evolucionando a un ritmo sin precedentes, el futuro de los adhesivos electrónicos también se está transformando. Las tendencias e innovaciones emergentes están dando forma a la industria, ofreciendo nuevas posibilidades para que los fabricantes de dispositivos electrónicos mejoren el rendimiento y la durabilidad de sus productos. Esta publicación de blog explorará algunos de los desarrollos más prometedores en adhesivos electrónicos y su impacto potencial.
Estas son algunas de las tendencias e innovaciones emergentes en el campo de los adhesivos electrónicos:
- Adhesivos de alta conductividad térmica:Con la creciente demanda de dispositivos electrónicos de alta potencia, existe una creciente necesidad de adhesivos que puedan disipar el calor de manera efectiva. Los adhesivos de alta conductividad térmica ofrecen una solución al mejorar la gestión térmica y permitir un mayor rendimiento.
- Adhesivos Flexibles:Los selladores flexibles son cada vez más populares en electrónica flexible, dispositivos portátiles y aplicaciones médicas. Estos adhesivos ofrecen flexibilidad, resistencia y durabilidad, lo que los hace ideales para instrumentos que se doblan, tuercen o se adaptan a varias formas.
- Adhesivos Ecológicos:Con las preocupaciones ambientales cada vez más prominentes, existe una creciente necesidad de adhesivos ecológicos y sostenibles. Las innovaciones en esta área incluyen bonos hechos de materiales renovables como el caucho natural y pegamentos que se pueden reciclar o reutilizar fácilmente.
- Miniaturización: A medida que los dispositivos electrónicos continúan reduciéndose de tamaño, existe la necesidad de adhesivos que puedan mantenerse al día con la tendencia. Los selladores miniaturizados con alta fuerza de unión son cada vez más populares, lo que permite dispositivos más pequeños y compactos.
- Adhesivos innovadores:Los desarrolladores crean adhesivos innovadores con características de autocuración, memoria de forma y conductividad. Estos adhesivos permiten a los fabricantes de dispositivos electrónicos desarrollar productos más inteligentes y receptivos.
Tendencias futuras e innovaciones en la tecnología de adhesivos electrónicos
La tecnología de adhesivos electrónicos evoluciona constantemente y surgen nuevas tendencias e innovaciones para satisfacer las necesidades cambiantes de la industria electrónica. Estas son algunas de las futuras tendencias e innovaciones en la tecnología de adhesivos electrónicos:
- Miniaturización:A medida que la electrónica se vuelve más pequeña y compacta, aumenta la demanda de adhesivos que puedan funcionar a microescala. Los adhesivos que pueden unir componentes pequeños y delicados sin dañarlos son cada vez más críticos.
- Adhesivos conductores: Los fabricantes de productos electrónicos utilizan cada vez más adhesivos conductores como alternativa a la soldadura. Los beneficios incluyen temperaturas de funcionamiento más bajas, procesos de ensamblaje simplificados y confiabilidad mejorada.
- Gestión térmica: Con el aumento de la densidad de potencia de los dispositivos electrónicos, la disipación de calor se ha convertido en un desafío crítico. Los adhesivos que pueden alejar el calor de los componentes son esenciales para mejorar la longevidad y la confiabilidad de los dispositivos electrónicos.
- Adhesivos Flexibles: A medida que la electrónica se vuelve más flexible y usable, los adhesivos flexibles se vuelven más críticos. Estos adhesivos pueden resistir la flexión y la torsión sin agrietarse, lo que garantiza que los componentes electrónicos permanezcan unidos incluso bajo tensión.
- Adhesivos Ecológicos:A medida que la sostenibilidad se vuelve cada vez más importante, existe una creciente demanda de adhesivos ecológicos. Los adhesivos fabricados con materiales biodegradables o reciclados son cada vez más comunes.
- Adhesivos innovadores:Los investigadores están desarrollando adhesivos inteligentes que pueden cambiar sus propiedades en respuesta a estímulos externos como la temperatura o la luz. Estos adhesivos tienen aplicaciones potenciales en sensores, actuadores y otros dispositivos electrónicos.
Desafíos comunes que se enfrentan al usar adhesivos electrónicos y cómo superarlos
Los adhesivos electrónicos son un componente esencial en la fabricación de dispositivos electrónicos, pero también pueden presentar varios desafíos. Estos son algunos de los desafíos comunes que se enfrentan al usar adhesivos electrónicos y cómo superarlos:
- Mala adherencia:La mala adherencia puede ocurrir cuando el adhesivo no se adhiere correctamente al sustrato, lo que provoca la falla del componente. La solución es asegurarse de que la superficie esté limpia y libre de contaminantes antes de aplicar el adhesivo. Además, el uso de una imprimación o un tratamiento de superficie puede mejorar la adherencia de la unión.
- Hora de curar:Los adhesivos pueden tardar mucho en curarse, lo que provoca retrasos en la producción. La solución es utilizar adhesivos de curado rápido u optimizar las condiciones de curado, como la temperatura y la humedad, para acelerar el proceso.
- Sensibilidad a la humedad:Los adhesivos sensibles a la humedad pueden degradarse cuando se exponen a la humedad, lo que provoca una pérdida de adherencia y rendimiento eléctrico. La solución es utilizar adhesivos resistentes a la humedad o almacenar y manipular correctamente el pegamento, como mantenerlo en un ambiente seco y utilizar envases sellados.
- Expansión térmica: Los adhesivos pueden experimentar expansión y contracción térmica, lo que provoca tensión mecánica y fallas en los componentes. La solución es usar adhesivos con un bajo coeficiente de expansión térmica o diseñar un sistema electrónico para acomodar la expansión y contracción térmica.
- Compatibilidad: Los adhesivos pueden ser incompatibles con ciertos materiales, como plásticos o metales, lo que provoca una mala adherencia o una reacción química. La solución es utilizar adhesivos compatibles con los materiales del sistema electrónico o realizar pruebas de compatibilidad antes de aplicar el pegamento.
La dosificación de adhesivos puede ser un desafío, especialmente cuando se trata de componentes pequeños y delicados. Podemos resolver el problema mediante el uso de equipos de dosificación de precisión o películas o cintas adhesivas prefabricadas que las personas pueden aplicar fácilmente a las piezas.
El papel de los adhesivos electrónicos en la tecnología portátil
La tecnología portátil se ha vuelto cada vez más popular durante la última década, con una amplia gama de dispositivos ahora disponibles para los consumidores. Estos dispositivos, como los relojes inteligentes y los rastreadores de actividad física, dependen de componentes electrónicos que deben estar conectados de forma segura al dispositivo portátil. En situaciones que requieren una unión fuerte y confiable de componentes electrónicos, los adhesivos electrónicos juegan un papel crucial.
Los fabricantes utilizan adhesivos electrónicos para unir sensores, LED, baterías y otros componentes a dispositivos portátiles, asegurando que funcionen correctamente y permanezcan duraderos. Estos adhesivos deben resistir las tensiones del uso diario, incluida la exposición a la humedad, el calor y el impacto físico. Con tecnología portátil, también deben ser flexibles para permitir doblarse y estirarse.
Uno de los beneficios clave de los adhesivos electrónicos en la tecnología portátil es su capacidad para brindar una apariencia fluida y aerodinámica. Si no hubiera uniones, los fabricantes tendrían que usar tornillos u otros sujetadores mecánicos para unir los componentes, lo que podría aumentar el peso y el tamaño del dispositivo. Por otro lado, los fabricantes pueden aplicar adhesivos en una capa delgada y uniforme casi invisible a simple vista.
Otra consideración importante al elegir adhesivos electrónicos para tecnología portátil es la biocompatibilidad. Para garantizar que los dispositivos portátiles no causen irritación o reacciones alérgicas cuando se usan directamente sobre la piel, los fabricantes deben usar pegamento no irritante e hipoalergénico. Para los wearables médicos, como los monitores de glucosa o ECG utilizados por personas con condiciones de salud específicas, es especialmente crítico asegurarse de que el adhesivo no cause irritación o reacciones alérgicas, dado su contacto directo con la piel.
A medida que la tecnología portátil continúa evolucionando, la demanda de adhesivos electrónicos que puedan satisfacer las necesidades únicas de estos dispositivos seguirá creciendo. Los fabricantes de adhesivos ya están desarrollando nuevas fórmulas que pueden soportar temperaturas extremas, resistir la humedad y brindar una mayor flexibilidad. Como resultado, la tecnología portátil será aún más cómoda, confiable y funcional.
Técnicas de dosificación de adhesivos electrónicos: consejos y mejores prácticas
Los adhesivos electrónicos son esenciales en la fabricación de dispositivos electrónicos. Sin embargo, dispensarlos puede ser una tarea desafiante, especialmente cuando se trata de piezas pequeñas e intrincadas. Estos son algunos consejos y mejores prácticas para dispensar adhesivos electrónicos:
- Elija el método de dosificación adecuado: Hay varios métodos de dispensación disponibles para adhesivos electrónicos, incluida la dispensación manual, la dispensación con jeringa y la dispensación automática. Elija la forma que mejor se adapte a su aplicación.
- Utilice la punta de dosificación correcta: La punta dosificadora debe coincidir con la viscosidad del adhesivo y el tamaño de la pieza unida. La información menor es ideal para porciones más pequeñas, mientras que la información más considerable es adecuada para detalles más importantes.
- Dispensar en un ambiente limpio: Un ambiente limpio previene la contaminación y asegura una fuerte unión. Use un área de trabajo limpia y use guantes para evitar que los aceites de la piel entren en contacto con el adhesivo.
- Asegure un almacenamiento adecuado: El almacenamiento adecuado es crucial para la longevidad de los adhesivos electrónicos. Mantenga los artículos en buen estado y secos, y selle el recipiente herméticamente.
- Aplicar el adhesivo uniformemente:Asegúrese de que el adhesivo se aplique uniformemente para evitar bolsas de aire, que pueden debilitar la unión. Use una mano firme y aplique el pegamento con un movimiento continuo.
- Controle el caudal: Debe controlar la velocidad de flujo del adhesivo para evitar que el exceso de pegamento se derrame y ensucie. Utilice un caudal lento y constante, especialmente cuando trabaje con piezas pequeñas.
- Limpie la punta dosificadora regularmente:Limpie la punta dosificadora regularmente para evitar obstrucciones y garantizar un flujo uniforme de adhesivo. Utilice una solución de limpieza adecuada y siga las instrucciones del fabricante.
- Practique precauciones de seguridad:Los fabricantes suelen utilizar productos químicos en los adhesivos electrónicos que pueden suponer un peligro para la salud. Use equipo de protección como guantes y gafas cuando los manipule.
Siguiendo estos consejos y las mejores prácticas, puede dispensar con éxito adhesivos electrónicos y garantizar una unión fuerte para sus dispositivos electrónicos.
Conclusión
En conclusión, los adhesivos electrónicos juegan un papel fundamental en la tecnología moderna. Son esenciales para crear enlaces confiables y duraderos entre los componentes electrónicos, protegiéndolos de factores ambientales como la humedad, el calor y las vibraciones. Los adhesivos electrónicos también permiten la miniaturización de dispositivos electrónicos, haciéndolos más pequeños y portátiles.
A medida que la tecnología continúa avanzando, los adhesivos electrónicos serán aún más críticos. Tendrán que mantenerse al día con la creciente demanda de dispositivos electrónicos más robustos y compactos y, al mismo tiempo, abordar las preocupaciones sobre la sostenibilidad y el impacto ambiental.
Además, los adhesivos electrónicos deben cumplir con los requisitos específicos de diferentes industrias y aplicaciones, desde dispositivos médicos hasta electrónica automotriz y sistemas aeroespaciales y de defensa. Por lo tanto, la investigación y el desarrollo continuos en este campo serán necesarios para satisfacer estas demandas cambiantes.