Adhesivo semiconductor
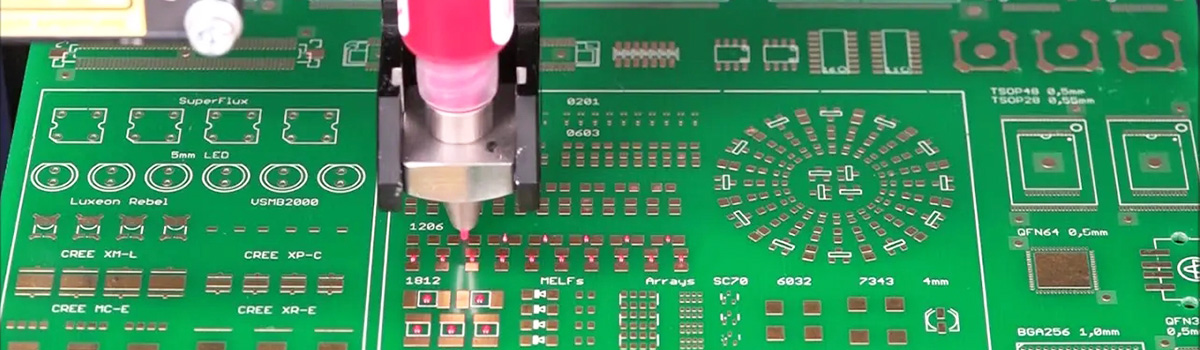
El adhesivo semiconductor es un componente fundamental en la fabricación y el montaje de dispositivos semiconductores, como microprocesadores, chips de memoria y otros circuitos integrados. Estos adhesivos brindan capacidades de unión robustas y confiables y protección contra factores ambientales y estrés térmico. Con la creciente demanda de dispositivos semiconductores más pequeños, rápidos y complejos, las soluciones adhesivas confiables y de alto rendimiento se han vuelto más críticas que nunca. Este artículo explorará los diversos tipos, aplicaciones y desafíos de los adhesivos semiconductores, destacando su papel crucial para permitir la miniaturización y el alto rendimiento de los dispositivos semiconductores.
Tipos de adhesivos semiconductores
Los adhesivos semiconductores desempeñan un papel fundamental en los procesos de fabricación y montaje de dispositivos electrónicos. Estos adhesivos están diseñados para brindar una unión sólida y confiable entre varios componentes en dispositivos semiconductores, como chips, sustratos y paquetes. Pueden soportar condiciones ambientales adversas, ciclos térmicos y tensiones mecánicas. Hay varios tipos de adhesivos semiconductores disponibles en el mercado, cada uno con propiedades y aplicaciones únicas. Exploremos algunos de los adhesivos semiconductores de uso común:
- Adhesivos epoxi: Los adhesivos a base de epoxi se utilizan ampliamente en aplicaciones de semiconductores debido a su excelente fuerza de unión, alta resistencia química y buenas propiedades de aislamiento eléctrico. Ofrecen una fuerte adhesión a varios materiales, incluidos metales, cerámica y plásticos. Los adhesivos epoxi se curan a temperatura ambiente o bajo calor, formando una unión rígida y duradera.
- Adhesivos de silicona: los adhesivos a base de silicona son conocidos por su flexibilidad, estabilidad térmica y resistencia a temperaturas extremas. Dependiendo de la formulación, pueden soportar un amplio rango de temperatura de -50 °C a 200 °C o incluso más. Los adhesivos de silicona exhiben excelentes propiedades de aislamiento eléctrico y se usan comúnmente en aplicaciones donde la gestión térmica es crucial, como los dispositivos electrónicos de potencia.
- Adhesivos acrílicos: los adhesivos acrílicos brindan un curado rápido, alta fuerza de unión y buena resistencia a la temperatura y la humedad. Son conocidos por su versatilidad y pueden adherirse a varios sustratos, incluidos metales, plásticos y vidrio. Los adhesivos acrílicos, como la electrónica automotriz y el ensamblaje de LED, a menudo se usan en aplicaciones que requieren alta resistencia y durabilidad.
- Adhesivos de poliuretano: los adhesivos a base de poliuretano ofrecen un equilibrio entre flexibilidad y resistencia. Proporcionan una buena adherencia a varios materiales, incluidos metales, plásticos y vidrio. Los adhesivos de poliuretano son resistentes al impacto, la vibración y los ciclos térmicos, lo que los hace adecuados para aplicaciones en las que intervienen tensiones mecánicas, como en la electrónica automotriz y aeroespacial.
- Adhesivos conductivos: los adhesivos conductivos están formulados con rellenos conductivos, como plata, cobre o carbono, para permitir la conductividad eléctrica en las uniones unidas. Se utilizan comúnmente para componentes de interconexión y unión de chips invertidos de dispositivos electrónicos. Los adhesivos conductores ofrecen baja resistencia y excelente adherencia, proporcionando conexiones eléctricas confiables.
- Adhesivos de relleno inferior: los adhesivos de relleno inferior están diseñados explícitamente para aplicaciones de flip-chip, donde el chip se monta boca abajo sobre un sustrato. Estos adhesivos fluyen debajo del chip durante el curado, llenando los espacios entre el chip y el sustrato. Los adhesivos de relleno proporcionan soporte mecánico, mejoran la conductividad térmica y evitan fallas en las uniones de soldadura causadas por estrés térmico.
- Adhesivos de curado UV: Los adhesivos de curado UV curan rápidamente cuando se exponen a la luz ultravioleta. Ofrecen alta fuerza de unión, claridad óptica y resistencia química. Los adhesivos curables por UV se utilizan a menudo en aplicaciones que requieren un procesamiento rápido y una unión de precisión, como ensamblaje de pantallas, fibra óptica y dispositivos optoelectrónicos.
Adhesivos Epoxi: La Elección Más Común
Los adhesivos epoxi son ampliamente reconocidos como uno de los tipos más comunes y versátiles. Se utilizan ampliamente en diversas industrias y aplicaciones debido a su excepcional fuerza de unión, durabilidad y versatilidad. Aquí, exploraremos por qué los adhesivos epoxi son la opción más común dentro de un número limitado de palabras.
- Fuerza de unión: Los adhesivos epoxi ofrecen una fuerza de unión excepcional, lo que los hace adecuados para varios materiales. Ya se trate de metales, plásticos, cerámica, madera o compuestos, los adhesivos epoxi brindan uniones sólidas y confiables, lo que garantiza la longevidad y la estabilidad de las partes unidas.
- Versatilidad: Los adhesivos epoxi muestran una excelente versatilidad en sus métodos de aplicación y opciones de curado. Están disponibles en diferentes formas, como sistemas de una o dos partes, lo que permite flexibilidad en su uso. Además, los adhesivos epoxi se pueden curar a temperatura ambiente o con calor, según los requisitos específicos de la aplicación.
- Resistencia química: los adhesivos epóxicos poseen una resistencia química excepcional, lo que los hace ideales para aplicaciones donde la exposición a solventes o productos químicos agresivos es una preocupación. Mantienen su integridad estructural incluso cuando se exponen a diversos productos químicos, aceites, combustibles y ácidos, lo que garantiza la durabilidad de los ensamblajes unidos.
- Resistencia a la temperatura: los adhesivos epoxi pueden soportar un amplio rango de temperatura, lo que los hace adecuados para aplicaciones que requieren resistencia a temperaturas altas o bajas. Ya sea en la industria automotriz, aeroespacial o electrónica, los adhesivos epoxi brindan una unión confiable incluso en temperaturas extremas.
- Capacidad de relleno de espacios: otra ventaja de los adhesivos epoxi es su capacidad para llenar espacios e irregularidades entre las superficies de contacto. Esta característica asegura una fuerte unión incluso cuando las superficies de contacto no coinciden de manera ideal, proporcionando una mayor integridad estructural a las partes unidas.
- Propiedades mecánicas: Los adhesivos epoxi ofrecen excelentes propiedades mecánicas, como alta resistencia a la tracción y al corte y buena resistencia al impacto. Estas propiedades los hacen adecuados para aplicaciones de soporte de carga, donde el adhesivo debe soportar una tensión o un impacto significativos sin comprometer la fuerza de la unión.
- Aislamiento eléctrico: Los adhesivos epoxi muestran excelentes propiedades de aislamiento eléctrico, lo que los hace populares en aplicaciones electrónicas y eléctricas. Proporcionan un aislamiento eficaz, protegiendo componentes electrónicos sensibles de corrientes eléctricas o cortocircuitos.
- Facilidad de uso: los adhesivos epoxi son relativamente fáciles de usar y aplicar. Se pueden dispensar con precisión, lo que permite una aplicación controlada y minimiza el desperdicio. Además, los adhesivos epoxi tienen un tiempo abierto prolongado, lo que proporciona suficiente tiempo de trabajo para ensamblar las piezas antes de que fragüe el adhesivo.
Adhesivos Conductores: Permitiendo la Conectividad Eléctrica
Los adhesivos conductores son un tipo especializado de material adhesivo con propiedades adhesivas y conductoras. Están diseñados para permitir la conectividad eléctrica en varias aplicaciones donde los métodos de soldadura tradicionales pueden no ser factibles o deseables. Estos adhesivos ofrecen numerosas ventajas, incluida la facilidad de uso, el respeto por el medio ambiente y la versatilidad.
Uno de los beneficios críticos de los adhesivos conductores es su facilidad de uso. A diferencia de la soldadura, que requiere calor y puede ser compleja, los adhesivos conductores se pueden aplicar simplemente dispensando o extendiendo el adhesivo sobre las superficies deseadas. Esto los hace adecuados para una amplia gama de usuarios, desde profesionales hasta aficionados, y elimina la necesidad de equipos especializados.
El respeto al medio ambiente es otra ventaja de los adhesivos conductores. A diferencia de la soldadura blanda, que generalmente implica soldaduras a base de plomo, los adhesivos conductores se pueden formular con materiales no tóxicos. Esto los hace más amigables con el medio ambiente y más seguros de manejar, reduciendo los riesgos para la salud de los usuarios. Además, la ausencia de plomo hace que estos adhesivos cumplan con las normas que restringen el uso de sustancias peligrosas.
Los adhesivos conductores también ofrecen versatilidad en los materiales que pueden unir. Pueden unir materiales conductores como metales y materiales no conductores como plásticos, cerámica y vidrio. Esta amplia compatibilidad permite crear ensamblajes de múltiples materiales con conectividad eléctrica integrada, lo que abre nuevas posibilidades de diseño en diversas industrias.
La conductividad de estos adhesivos se logra al incluir rellenos conductores, como partículas de plata o carbón, dentro de la matriz adhesiva. Estos rellenos forman vías conductoras que permiten el flujo de corriente eléctrica a través de las superficies unidas. La elección del material de relleno y la concentración se puede adaptar para cumplir con los requisitos de conductividad específicos, lo que permite un ajuste fino de las propiedades eléctricas del adhesivo.
Las aplicaciones de adhesivos conductores están muy extendidas. Son comúnmente utilizados en la industria electrónica para unir componentes, reemplazando o complementando procesos de soldadura. Los adhesivos conductores son particularmente beneficiosos para unir componentes electrónicos delicados que no pueden soportar las altas temperaturas asociadas con la soldadura. También se utilizan para fabricar circuitos flexibles, etiquetas RFID y pantallas táctiles, donde su capacidad para adherirse a varios sustratos es ventajosa.
En la industria automotriz, los adhesivos conductores ensamblan sensores, unidades de control y sistemas de iluminación. Sus capacidades de unión no mecánica reducen los puntos de concentración de tensión, lo que mejora la confiabilidad y la longevidad de la conexión eléctrica. Además, los adhesivos conductores permiten reducir el peso de los vehículos al eliminar la necesidad de conectores de metal pesado.
Más allá de las aplicaciones electrónicas y automotrices, los adhesivos conductores encuentran uso en dispositivos médicos, componentes aeroespaciales e incluso productos de consumo como dispositivos electrónicos portátiles. Su versatilidad, facilidad de uso y ventajas ambientales los hacen atractivos para los diseñadores e ingenieros industriales.
Adhesivos Die Attach: unión de chips semiconductores a sustratos
Los adhesivos Die Attach juegan un papel crucial en la industria de los semiconductores al proporcionar un método confiable y eficiente para unir chips semiconductores a sustratos. Estos adhesivos sirven como interfaz entre el chip y el sustrato, asegurando una conexión segura y conductora de electricidad.
La función principal de los adhesivos adheridos al troquel es proporcionar soporte mecánico y conectividad eléctrica entre el chip y el sustrato. Deben poseer excelentes propiedades de adhesión para garantizar que el chip permanezca firmemente adherido al sustrato en diversas condiciones de funcionamiento, incluidos los ciclos térmicos, el estrés mecánico y la exposición ambiental.
Un requisito fundamental para los adhesivos de fijación por matriz es su capacidad para soportar altas temperaturas. Durante los procesos de ensamblaje de chips, como el reflujo de soldadura o la unión por termocompresión, el adhesivo debe mantener su integridad y fuerza de adhesión. Por lo general, los adhesivos de fijación por matriz están diseñados para soportar temperaturas superiores a 200 °C, lo que garantiza la fiabilidad de la unión.
Los adhesivos de fijación por troquel se clasifican comúnmente en adhesivos basados en epoxi y basados en soldadura. Los adhesivos a base de epoxi son materiales termoendurecibles que curan al exponerse al calor. Ofrecen una excelente adherencia, alta conductividad térmica y aislamiento eléctrico. Por otro lado, los adhesivos a base de soldadura consisten en una aleación de metal que se funde durante el proceso de unión. Proporcionan una ruta eléctrica de baja resistencia y alta conductividad térmica, lo que los hace adecuados para aplicaciones de disipación de alta potencia.
La selección del adhesivo de matriz depende de varios factores, incluida la aplicación específica, las condiciones de funcionamiento y el material del sustrato. El adhesivo debe ser compatible con los materiales a los que se unirá, lo que garantiza una adhesión adecuada y evita interacciones adversas. El adhesivo también debe tener buenas características de distribución y flujo para facilitar la unión y minimizar los vacíos o espacios entre el chip y el sustrato.
Para lograr una unión confiable, la preparación de la superficie es esencial. Las superficies del sustrato y del chip deben limpiarse a fondo para eliminar contaminantes, óxidos y otras impurezas que dificultan la adhesión. Las técnicas de tratamiento de superficies, como la limpieza con plasma, el grabado químico o la limpieza ultrasónica, se emplean comúnmente para mejorar el rendimiento de unión del adhesivo.
Una vez que se aplica el adhesivo de fijación del troquel, el chip se coloca y alinea con cuidado en el sustrato. Se puede usar presión o calor para garantizar la humectación adecuada y el contacto entre el adhesivo y las superficies que se unen. Luego, el adhesivo se cura o solidifica, completando el proceso de unión.
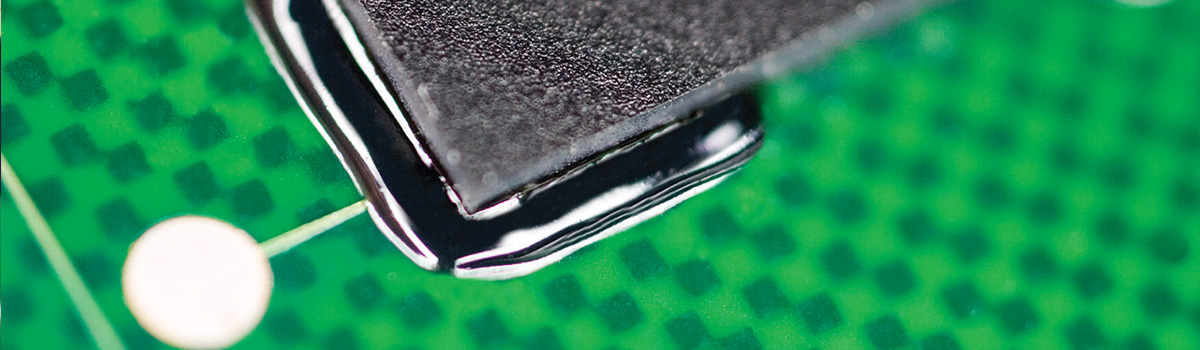
Adhesivos de relleno inferior: protección contra el estrés térmico
Los adhesivos de relleno son materiales esenciales que se utilizan en los embalajes electrónicos para proteger contra el estrés térmico. Proporcionan refuerzo mecánico y mejoran la confiabilidad de los dispositivos electrónicos al minimizar el impacto de los ciclos térmicos y los choques mecánicos.
El estrés térmico es una preocupación importante en los ensamblajes electrónicos debido a la falta de coincidencia en los coeficientes de expansión térmica (CTE) entre diferentes materiales. Cuando un dispositivo sufre fluctuaciones de temperatura, los materiales se expanden y contraen a diferentes velocidades, desarrollando tensiones que pueden fallar. Los adhesivos de relleno ayudan a mitigar este problema al actuar como un amortiguador entre el chip y el sustrato, absorbiendo y distribuyendo el estrés causado por los ciclos térmicos.
La función principal de los adhesivos de relleno es reforzar las juntas de soldadura que conectan el chip del circuito integrado (IC) al sustrato. Durante la fabricación, el chip se monta sobre el sustrato mediante soldadura, lo que crea una unión entre los dos componentes. Sin embargo, el desajuste de CTE entre el chip y el sustrato puede causar concentraciones de tensión en las uniones de soldadura. Los adhesivos de relleno se inyectan en el espacio entre el chip y el sustrato, llenando los vacíos y formando una capa resistente y elástica. Esta capa reduce la concentración de tensiones y mejora la integridad mecánica general del conjunto.
Los adhesivos de relleno también ofrecen una excelente conductividad térmica, crucial para disipar el calor generado por los componentes electrónicos. La disipación de calor eficiente es vital para evitar el sobrecalentamiento y mantener el rendimiento y la longevidad del dispositivo. Al facilitar la transferencia de calor del chip al sustrato, los adhesivos de relleno ayudan a mantener una temperatura de funcionamiento estable y evitan que la tensión térmica dañe el circuito integrado.
Además, los adhesivos de relleno protegen contra la humedad y los contaminantes. Los dispositivos electrónicos a menudo están expuestos a entornos hostiles, que incluyen humedad y diversos productos químicos, que pueden degradar su rendimiento y confiabilidad. Los materiales de relleno son una barrera que evita la entrada de humedad y la difusión de sustancias nocivas en el paquete de chips. Esta protección ayuda a mantener el rendimiento eléctrico y prolonga la vida útil del dispositivo.
Adhesivos Flip Chip: Habilitación de la miniaturización
Los adhesivos Flip Chip son cruciales para permitir la miniaturización en varios dispositivos electrónicos. A medida que avanza la tecnología, existe una demanda constante de máquinas más pequeñas, livianas y potentes. La unión flip-chip se ha convertido en el método preferido para lograr interconexiones de alta densidad en dichos dispositivos. Estos adhesivos facilitan la conexión eléctrica y mecánica directa entre el chip y el sustrato, ofreciendo numerosos beneficios a la miniaturización.
Una de las ventajas fundamentales de los adhesivos flip-chip es su capacidad para reducir el tamaño total de los paquetes electrónicos. Las técnicas tradicionales de unión de cables requieren espacio para los bucles de cables, lo que limita el tamaño del dispositivo alcanzable. Por el contrario, la unión flip-chip elimina la necesidad de bucles de alambre, lo que reduce significativamente el tamaño del paquete. La huella más pequeña es significativa en dispositivos electrónicos portátiles, como teléfonos inteligentes, tabletas y dispositivos portátiles, donde el espacio es primordial.
Además, los adhesivos flip-chip permiten un mayor rendimiento del dispositivo. La conexión eléctrica directa entre el chip y el sustrato reduce la longitud de la ruta de la señal y la inductancia, mejorando el rendimiento eléctrico. Esto es particularmente importante para aplicaciones de alta velocidad, como microprocesadores y chips de memoria, donde es fundamental minimizar el retraso y la pérdida de la señal. Flip chip bonding contribuye a velocidades de transferencia de datos más rápidas, menor consumo de energía y mayor confiabilidad del dispositivo al reducir los efectos parásitos.
Además, los adhesivos flip-chip ofrecen excelentes capacidades de gestión térmica. La gestión de la disipación de calor se convierte en un desafío importante a medida que los componentes electrónicos se vuelven más potentes y compactos. La unión Flip Chip permite una unión directa del chip al sustrato, lo que mejora la eficiencia de la transferencia de calor. Esto permite una disipación de calor eficiente, evitando el sobrecalentamiento y mejorando la confiabilidad general y la vida útil del dispositivo. La gestión térmica eficaz es esencial para los dispositivos de alto rendimiento, como las unidades de procesamiento de gráficos (GPU) y las unidades de procesamiento central (CPU).
Otra ventaja de los adhesivos flip-chip es su estabilidad mecánica. Los materiales adhesivos utilizados en la unión flip-chip brindan interconexiones sólidas y confiables. La ausencia de uniones de cables elimina el riesgo de rotura o fatiga del cable, lo que garantiza la integridad mecánica a largo plazo. La robustez de los adhesivos flip-chip los hace adecuados para aplicaciones sujetas a condiciones de operación severas, como la electrónica automotriz o los sistemas aeroespaciales.
Además, los adhesivos flip-chip admiten interconexiones de alta densidad. Con flip-chip bonding, es posible lograr una gran cantidad de conexiones en un área pequeña, lo que permite la integración de más funciones dentro de un espacio limitado. Esto es particularmente beneficioso para dispositivos electrónicos complejos que requieren numerosas conexiones de entrada/salida, como circuitos integrados, sensores o sistemas microelectromecánicos (MEMS). Las interconexiones de alta densidad habilitadas por los adhesivos flip-chip contribuyen a la miniaturización general del dispositivo.
Adhesivos de encapsulación: protección de componentes sensibles
Los adhesivos de encapsulación son esenciales para proteger los componentes electrónicos sensibles de varios factores ambientales, estrés mecánico y exposición química. Estos adhesivos proporcionan una barrera protectora, encapsulan los elementos y aseguran su longevidad y confiabilidad. Este artículo explorará la importancia de los adhesivos de encapsulación y su papel en la protección de componentes sensibles.
Los componentes electrónicos sensibles, como los circuitos integrados, los sensores y el cableado delicado, son vulnerables al daño causado por la humedad, el polvo, las fluctuaciones de temperatura y el impacto físico. Los adhesivos de encapsulación ofrecen una solución confiable al formar una capa protectora alrededor de estos componentes. Actúan como una barrera, protegiendo los componentes de elementos externos que podrían comprometer la funcionalidad o provocar fallas prematuras.
Una de las propiedades críticas de los adhesivos de encapsulación es su capacidad para resistir la entrada de humedad. La humedad puede causar corrosión, cortocircuitos y fugas eléctricas, lo que puede provocar un mal funcionamiento del dispositivo. Los adhesivos de encapsulación brindan una excelente resistencia a la humedad, evitando la entrada de agua o vapor de humedad en los componentes sensibles. Esta característica es crucial en aplicaciones expuestas a alta humedad o ambientes ricos en humedad, como electrónica automotriz o equipos industriales al aire libre.
Además de la protección contra la humedad, los adhesivos de encapsulación también ofrecen una excelente resistencia química. Pueden resistir la exposición a varios productos químicos, incluidos solventes, ácidos, bases y agentes de limpieza. Esta resistencia asegura que los componentes sensibles no se vean afectados por las interacciones químicas, preservando su integridad y funcionalidad.
Los adhesivos de encapsulación también brindan protección mecánica a los componentes sensibles. Actúan como amortiguadores, disipando tensiones mecánicas y vibraciones que podrían dañar los componentes. Esta función es fundamental en aplicaciones sujetas a movimientos frecuentes, como la industria aeroespacial, la automoción y la electrónica de consumo.
Además, los adhesivos de encapsulación ofrecen excelentes propiedades de gestión térmica. Poseen alta conductividad térmica, lo que permite una eficiente disipación del calor de los componentes sensibles. Estos adhesivos ayudan a mantener temperaturas operativas óptimas al disipar el calor de manera efectiva, prevenir el estrés térmico y garantizar la confiabilidad a largo plazo.
Otra ventaja de los adhesivos de encapsulación es su capacidad para mejorar la integridad estructural de los ensamblajes electrónicos. Encapsular y unir varios componentes juntos proporciona fuerza y estabilidad adicionales al sistema general. Esta característica es especialmente beneficiosa en aplicaciones donde la robustez mecánica es esencial, como los sistemas de control industrial o la electrónica de grado militar.
Los adhesivos de encapsulación vienen en varias formulaciones para satisfacer los diferentes requisitos de aplicación. Pueden ser adhesivos líquidos que curan a temperatura ambiente o compuestos termoconductores utilizados para aplicaciones de alta potencia. La selección del adhesivo adecuado depende de factores como el nivel de protección deseado, las condiciones de funcionamiento, el tiempo de curado y el proceso de montaje.
Adhesivos de baja emisión de gases: críticos para aplicaciones espaciales
Los adhesivos de baja emisión de gases desempeñan un papel fundamental en las aplicaciones espaciales en las que es esencial mantener un entorno limpio y controlado. La desgasificación se refiere a la liberación de compuestos orgánicos volátiles (COV) y otros contaminantes de los materiales, incluidos los adhesivos, en condiciones de vacío o baja presión. La desgasificación puede dañar equipos sensibles, sistemas ópticos y superficies de naves espaciales en las condiciones extremas del espacio, donde no hay presión atmosférica. Por lo tanto, el uso de adhesivos de baja emisión de gases es fundamental para garantizar el rendimiento y la longevidad fiables de las misiones espaciales.
Una de las principales preocupaciones con la desgasificación es la deposición de contaminantes en superficies críticas, como lentes ópticos y sensores. Las impurezas pueden formar una película delgada en estas superficies, reduciendo su transparencia, degradando el rendimiento e interfiriendo con las mediciones científicas. En el caso de los sistemas ópticos, incluso una ligera reducción en la apertura puede afectar significativamente la calidad de las imágenes y los datos recopilados desde el espacio. Los adhesivos de baja emisión de gases están diseñados para minimizar la liberación de compuestos volátiles, reduciendo el riesgo de contaminación y preservando la funcionalidad de los instrumentos sensibles.
Otro aspecto crítico de los adhesivos de baja emisión de gases es su impacto en los componentes y circuitos electrónicos. Los COV que se liberan durante la desgasificación pueden corroer o degradar sistemas electrónicos delicados, lo que puede provocar fallas en el funcionamiento o fallas completas. Esto es especialmente preocupante para las naves espaciales, donde los componentes electrónicos están expuestos al vacío del espacio, las variaciones extremas de temperatura y la radiación. Los adhesivos de baja emisión de gases están formulados con materiales de baja presión de vapor, lo que minimiza la liberación de compuestos corrosivos y protege la integridad de los sistemas electrónicos.
Además, la desgasificación también puede amenazar la salud de los astronautas y la habitabilidad de las naves espaciales tripuladas. En entornos cerrados como cápsulas espaciales o estaciones espaciales, la acumulación de COV por desgasificación puede crear una atmósfera desagradable o peligrosa. Los adhesivos de baja emisión de gases ayudan a mitigar este riesgo al reducir la emisión de compuestos volátiles, lo que garantiza un entorno seguro y saludable para los astronautas durante sus misiones.
Para lograr propiedades de baja desgasificación, los adhesivos utilizados en aplicaciones espaciales se someten a rigurosos procesos de prueba y calificación. Estos procesos implican someter los adhesivos a condiciones de espacio simuladas, incluidas cámaras de vacío, temperaturas extremas y diversas tensiones ambientales. Los adhesivos que cumplen con los estrictos requisitos de baja emisión de gases están certificados y aprobados para su uso en misiones espaciales.
Adhesivos de unión a nivel de oblea: reducción de costos y aumento del rendimiento
La unión a nivel de oblea es un proceso crucial en la industria de los semiconductores, donde se interconectan múltiples chips u obleas para formar circuitos integrados complejos. Tradicionalmente, este proceso de unión involucraba técnicas de soldadura por golpes o unión por cable, que requieren una alineación precisa y una unión individual de cada chip, lo que resulta en costos más altos y rendimientos más bajos. Sin embargo, los avances en las tecnologías de adhesivos allanaron el camino para los adhesivos de unión a nivel de obleas que ofrecen reducción de costos y mayor rendimiento en la fabricación de semiconductores.
Los adhesivos de unión a nivel de oblea están diseñados para proporcionar una unión fiable y sólida entre obleas o chips a nivel de oblea, eliminando la necesidad de procesos de unión individuales. Estos adhesivos normalmente se aplican como una capa delgada entre las obleas y se curan en condiciones controladas para lograr la fuerza de unión deseada. Estos son algunos factores clave que contribuyen a la reducción de costos y al aumento del rendimiento:
- Simplificación del proceso: los adhesivos de unión a nivel de obleas simplifican el proceso de unión al permitir la unión simultánea de múltiples chips u obleas en un solo paso. Esto elimina la necesidad de alineación compleja y unión individual de cada chip, lo que ahorra tiempo y reduce los costos de producción. Además, el adhesivo se puede aplicar de manera uniforme sobre un área grande, lo que garantiza una adhesión uniforme en toda la oblea.
- Alta fuerza de unión y confiabilidad: los adhesivos de unión a nivel de obleas ofrecen excelentes propiedades de adhesión, lo que da como resultado una alta fuerza de unión entre las obleas. Este vínculo sólido garantiza una interconectividad confiable y minimiza el riesgo de delaminación o falla durante los pasos de fabricación posteriores o la operación del dispositivo. Las propiedades mecánicas, térmicas y eléctricas del adhesivo se pueden adaptar para cumplir con los requisitos específicos de la aplicación, mejorando aún más la confiabilidad.
- Materiales rentables: los adhesivos de unión a nivel de oblea a menudo utilizan materiales rentables en comparación con las técnicas de unión tradicionales. Estos adhesivos se pueden formular utilizando una variedad de polímeros, como epoxis, poliimidas o acrilatos, que están fácilmente disponibles y ofrecen un buen rendimiento a un costo razonable. Elegir entre varios materiales permite a los fabricantes optimizar la selección del adhesivo en función del rendimiento, el precio y la compatibilidad con diferentes sustratos.
- Mejora del rendimiento: los adhesivos de unión a nivel de obleas contribuyen a mejorar el rendimiento en la fabricación de semiconductores. La aplicación uniforme de adhesivo en la oblea minimiza el riesgo de vacíos, atrapamiento de aire o unión desigual, lo que puede provocar defectos o fallas. Además, la eliminación de la unión de chips individuales reduce las posibilidades de desalineación o daño durante el proceso de unión, lo que da como resultado mayores rendimientos y menores tasas de desechos.
- Compatibilidad con tecnologías de empaquetado avanzadas: los adhesivos de unión a nivel de oblea son compatibles con diversas tecnologías de empaquetado avanzadas, como el empaquetado a escala de chip a nivel de oblea (WLCSP), el empaquetado a nivel de oblea con abanico (FOWLP) o los procesos de integración 3D. Estos adhesivos permiten la integración de múltiples chips o diversos componentes dentro de un factor de forma compacto, lo que facilita la miniaturización y permite una funcionalidad avanzada en dispositivos electrónicos.

Adhesivos de curado UV: unión rápida y precisa
Los adhesivos de curado UV son adhesivos revolucionarios que ofrecen capacidades de unión rápidas y precisas. Han ganado popularidad en varias industrias debido a sus propiedades y ventajas únicas sobre los adhesivos tradicionales. Los adhesivos de curado UV suelen estar compuestos por un monómero, un fotoiniciador y un estabilizador. Cuando se exponen a la luz ultravioleta (UV), estos adhesivos experimentan una reacción fotoquímica que conduce a un curado y unión rápidos.
Uno de los beneficios críticos de los adhesivos de curado UV es su rápido tiempo de curado. A diferencia de las uniones tradicionales que requieren horas o incluso días para curarse por completo, los adhesivos de curado UV curan en cuestión de segundos o minutos. Este rápido tiempo de curado aumenta significativamente la eficiencia de la producción y reduce los tiempos de espera en la línea de montaje, lo que genera importantes ahorros de costos para los fabricantes. La formación instantánea de enlaces también permite la manipulación inmediata y el procesamiento posterior de los componentes unidos.
La capacidad de unión precisa de los adhesivos de curado UV es otra ventaja significativa. El adhesivo permanece líquido hasta que se expone a la luz ultravioleta, lo que proporciona suficiente tiempo para la alineación y el posicionamiento de las piezas que se van a unir. Una vez que el adhesivo se expone a la luz ultravioleta, se solidifica rápidamente, creando una unión sólida y duradera. Esta capacidad de unión precisa beneficia a las aplicaciones que requieren alta precisión y tolerancias estrictas, como la electrónica, la óptica y los dispositivos médicos.
Los adhesivos de curado UV también ofrecen una excelente fuerza de unión y durabilidad. El adhesivo curado forma una unión fuerte que puede soportar varios factores ambientales, incluidas temperaturas extremas, humedad y productos químicos. Esto asegura la longevidad y confiabilidad de los componentes unidos, lo que hace que los adhesivos de curado UV sean adecuados para aplicaciones exigentes.
Además, los adhesivos de curado UV no contienen disolventes y tienen bajas emisiones de compuestos orgánicos volátiles (COV). A diferencia de los adhesivos a base de solventes que requieren secado y liberan vapores potencialmente dañinos, los adhesivos de curado UV son amigables con el medio ambiente y seguros. Esto los convierte en una opción atractiva para las industrias que buscan reducir su huella ambiental y cumplir con las regulaciones.
La versatilidad de los adhesivos de curado UV es otro aspecto destacable. Pueden unir varios materiales, incluidos vidrio, metales, plásticos, cerámica e incluso sustratos diferentes. Esta amplia compatibilidad hace que los adhesivos de curado UV sean adecuados para diversas aplicaciones en las industrias automotriz, aeroespacial, electrónica y médica.
Adhesivos de pasta conductora: posibilitando la electrónica impresa y flexible
Los adhesivos de pasta conductora se han convertido en una tecnología habilitadora fundamental para el desarrollo de productos electrónicos flexibles e impresos. Estos materiales innovadores combinan las propiedades de los adhesivos tradicionales con la conductividad de los metales, abriendo nuevas posibilidades para la fabricación e integración de dispositivos electrónicos en diversos sustratos.
Una de las principales ventajas de los adhesivos en pasta conductora es su capacidad para proporcionar tanto adherencia mecánica como conductividad eléctrica. Los adhesivos tradicionales suelen ser aislantes, lo que limita su uso en aplicaciones electrónicas. Los adhesivos en pasta conductora, por el contrario, contienen partículas conductoras como plata, cobre o carbono que facilitan el flujo de electricidad. Esta doble funcionalidad les permite servir tanto como adhesivo como conductor, lo que los hace ideales para unir componentes electrónicos o crear pistas conductoras en sustratos flexibles.
La flexibilidad de los adhesivos de pasta conductora es otra característica crítica que los hace adecuados para la electrónica flexible. Estos adhesivos pueden mantener su conductividad eléctrica incluso cuando se doblan, estiran o tuercen. Esta flexibilidad es crucial para aplicaciones tales como dispositivos portátiles, pantallas flexibles y electrónica conformada, donde los circuitos rígidos tradicionales serían poco prácticos o imposibles de implementar. Los adhesivos en pasta conductiva permiten la creación de conexiones eléctricas robustas y confiables en sustratos flexibles, lo que garantiza el rendimiento y la durabilidad de los dispositivos electrónicos flexibles.
Además, los adhesivos en pasta conductora son compatibles con diversas técnicas de impresión, como la serigrafía, la impresión por inyección de tinta y la impresión flexográfica. Esta compatibilidad permite la fabricación rentable y de gran volumen de productos electrónicos impresos. Los procesos de impresión permiten la deposición de adhesivos de pasta conductora en patrones precisos, lo que hace posible crear circuitos complejos y diseños electrónicos con un mínimo desperdicio de material. La capacidad de imprimir trazas conductoras directamente sobre sustratos flexibles simplifica el proceso de fabricación y reduce el tiempo de producción, lo que hace que la electrónica impresa sea una solución viable para la fabricación a gran escala.
Los adhesivos en pasta conductora también ofrecen ventajas en términos de gestión térmica. La presencia de partículas conductoras en estos adhesivos facilita la disipación del calor generado por los componentes electrónicos. Esta propiedad es crucial para garantizar la fiabilidad y el rendimiento de los dispositivos que generan una cantidad significativa de calor, como la electrónica de potencia o los LED de alta potencia. Al usar adhesivos de pasta conductora como interfaces térmicas, el calor se puede transferir de manera eficiente desde el componente generador de calor a un disipador de calor, lo que mejora el rendimiento general y la longevidad del dispositivo.
Pastas para soldar: alternativa a la unión adhesiva
Las pastas para soldar, también conocidas como pastas para soldar, ofrecen una alternativa a la unión adhesiva en diversas aplicaciones. Mientras que la unión adhesiva implica el uso de adhesivos para unir materiales, las pastas para soldar utilizan un mecanismo diferente para lograr una unión sólida y confiable. En esta respuesta, exploraremos las pastas para soldar como alternativa a la unión adhesiva dentro de un límite de 450 palabras.
Las pastas para soldar consisten en una mezcla de partículas de aleación de metal, fundente y un aglutinante. Las partículas de aleación de metal típicamente consisten en estaño, plomo, plata o una combinación de estos metales. El cambio ayuda en el proceso de soldadura al eliminar los óxidos de las superficies metálicas y promover la humectación y la adhesión. El aglutinante mantiene unida la pasta y permite que se aplique fácilmente.
Una de las principales ventajas de las pastas para soldar sobre la unión adhesiva es la resistencia y durabilidad de la unión. La soldadura crea una unión metalúrgica entre los materiales unidos, lo que da como resultado una unión fuerte que puede soportar diversas tensiones mecánicas, térmicas y eléctricas. La unión soldada suele ser más robusta y confiable que las uniones adhesivas, que pueden degradarse con el tiempo o bajo ciertas condiciones.
Las pastas para soldar también ofrecen un proceso de unión más rápido y eficiente. La pasta se puede aplicar con precisión en las áreas deseadas y la unión se puede formar calentando el ensamblaje a la temperatura de fusión de la soldadura. Este proceso suele ser más rápido que la unión adhesiva, que puede requerir tiempos de curado o secado. Además, las pastas para soldar permiten la unión simultánea de múltiples componentes, lo que reduce el tiempo de montaje y aumenta la productividad.
Otra ventaja es la versatilidad de las pastas de soldar para unir diferentes materiales. La unión adhesiva puede tener limitaciones cuando se unen materiales diferentes o materiales con diferentes coeficientes de expansión térmica. Las pastas para soldar pueden formar uniones confiables entre varios materiales, incluidos metales, cerámica y algunos plásticos, lo que las hace adecuadas para diversas aplicaciones.
Además, las pastas para soldar pueden mejorar la conductividad térmica y eléctrica en comparación con la unión adhesiva. Esta propiedad es especialmente beneficiosa en aplicaciones donde la disipación de calor o la continuidad eléctrica son cruciales, como ensambles electrónicos: la unión soldada forma una vía metálica directa, lo que facilita la transferencia de calor y la conducción eléctrica eficientes.
Sin embargo, es esencial tener en cuenta que las pastas para soldar también tienen algunas consideraciones y limitaciones. Por ejemplo, algunas aleaciones de soldadura contienen plomo, que puede estar restringido debido a problemas ambientales y de salud. Se han desarrollado pastas para soldar sin plomo como alternativas, pero pueden tener características diferentes y requerir consideraciones de proceso específicas.
Técnicas de dosificación de adhesivos: precisión y eficiencia
Las técnicas de aplicación de adhesivos son cruciales en varias industrias, desde la fabricación hasta la construcción. Lograr precisión y eficiencia en la aplicación de adhesivos es esencial para garantizar uniones confiables, minimizar el desperdicio y mejorar la productividad general. Este artículo explorará técnicas críticas que ayudan a lograr precisión y eficiencia en la aplicación de adhesivos.
- Sistemas de dosificación automatizados: Los sistemas de dosificación automatizados utilizan brazos robóticos o equipos controlados por computadora para aplicar adhesivos con precisión. Estos sistemas ofrecen alta repetibilidad, precisión y velocidad, lo que garantiza una aplicación uniforme del adhesivo en múltiples piezas o productos. Al eliminar el error humano, los sistemas automatizados minimizan el desperdicio y mejoran la eficiencia en los procesos de dispensación de adhesivos.
- Sistemas de dosificación y mezcla: Algunas aplicaciones requieren dispensar dos o más componentes que deben mezclarse en una proporción específica. Los sistemas de dosificación y mezcla miden y combinan con precisión los componentes del adhesivo antes de distribuirlos, lo que garantiza proporciones precisas y una calidad uniforme. Estos sistemas son particularmente beneficiosos para epoxis de dos partes, poliuretanos y otros adhesivos reactivos.
- Dosificación controlada por presión: las técnicas de dosificación controladas por presión implican el uso de sistemas neumáticos o hidráulicos para controlar el caudal y la presión del adhesivo. El adhesivo se dispensa a un ritmo controlado manteniendo una fuerza constante, asegurando una aplicación precisa y minimizando el exceso de adhesivo. La dosificación controlada por presión se usa comúnmente para aplicaciones que requieren líneas finas, puntos o patrones intrincados.
- Jetting y dispensación con aguja: las técnicas de inyección y dispensación con aguja son adecuadas para aplicaciones que requieren una colocación precisa y de alta velocidad del adhesivo. Los sistemas de inyección utilizan pulsos de presión para dispensar pequeñas gotas o líneas continuas de adhesivo. Por otro lado, la dosificación con aguja implica el uso de una aguja o boquilla para depositar adhesivo en cantidades controladas. Estas técnicas se utilizan comúnmente en el ensamblaje de componentes electrónicos, donde se requieren depósitos adhesivos pequeños y precisos.
- Sistemas de recubrimiento y rociado: para aplicaciones de recubrimiento o unión de áreas grandes, los sistemas de recubrimiento y rociado brindan una dispensación de adhesivo eficiente. Estos sistemas utilizan técnicas de atomización para crear una fina niebla o rociado de adhesivo, lo que garantiza una cobertura uniforme y un desperdicio mínimo. Los sistemas de rociado y recubrimiento se utilizan ampliamente en las industrias automotriz, aeroespacial y de fabricación de muebles.
- Válvulas y Boquillas Dosificadoras: La elección de las válvulas y boquillas dosificadoras es crucial para lograr precisión en la dosificación del adhesivo. Los diferentes tipos de válvulas y boquillas, como válvulas de aguja, válvulas de diafragma o boquillas cónicas, ofrecen un control variable sobre el caudal, el patrón y el tamaño de las gotas. La selección de la válvula o boquilla adecuada para el adhesivo específico y los requisitos de aplicación es esencial para lograr una dosificación precisa y eficiente.
- Sistemas guiados por visión: los sistemas de dosificación guiados por visión utilizan cámaras y software avanzado para detectar y rastrear la posición de piezas o sustratos. Al analizar las imágenes capturadas, el sistema ajusta los parámetros de aplicación del adhesivo en tiempo real, lo que garantiza una colocación precisa incluso en superficies irregulares o piezas de diferentes dimensiones. Los sistemas guiados por visión mejoran la precisión y la eficiencia mientras se adaptan a las variaciones del proceso.
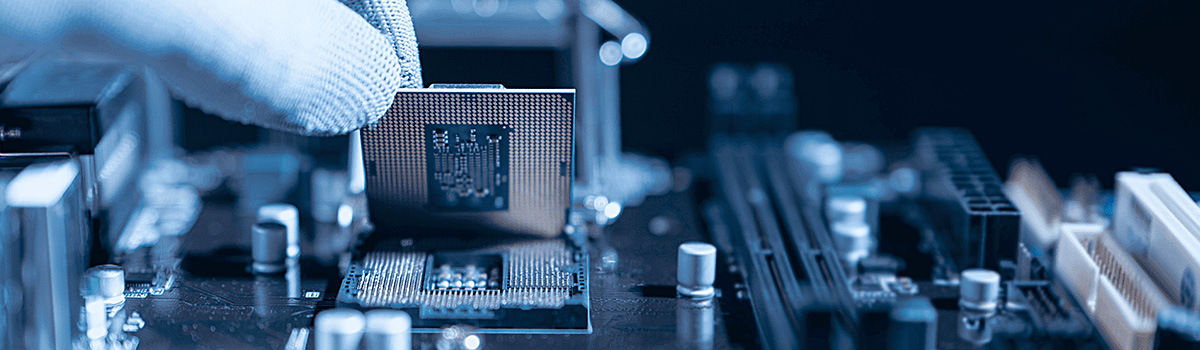
Desafíos en la aplicación de adhesivos semiconductores
La aplicación de adhesivos semiconductores enfrenta varios desafíos que pueden afectar el rendimiento y la confiabilidad de los dispositivos electrónicos. Estos desafíos surgen debido a los requisitos y características únicos de los semiconductores y las exigentes condiciones de operación a las que están sujetos. Estos son algunos de los desafíos críticos en la aplicación de adhesivos semiconductores:
- Gestión térmica: los semiconductores generan calor durante el funcionamiento, y una gestión térmica eficaz es fundamental para evitar el sobrecalentamiento. Los materiales adhesivos utilizados en los semiconductores deben tener una excelente conductividad térmica para transferir calor desde el dispositivo de manera eficiente. Garantizar una adhesión adecuada sin comprometer el rendimiento térmico es un desafío importante.
- Compatibilidad química: los semiconductores están expuestos a varios productos químicos durante su vida útil, incluidos agentes de limpieza, solventes y fundentes. Los materiales adhesivos deben ser químicamente compatibles con estas sustancias para evitar la degradación o pérdida de adherencia con el tiempo. Seleccionar materiales adhesivos que puedan soportar la exposición a productos químicos específicos es una tarea compleja.
- Estrés mecánico: los dispositivos electrónicos a menudo experimentan estrés mecánico debido a la expansión térmica, las vibraciones y las fuerzas externas. Para soportar estas tensiones, los materiales adhesivos deben tener propiedades mecánicas adecuadas, como flexibilidad y resistencia. El desempeño deficiente del adhesivo puede conducir a la delaminación, agrietamiento o falla mecánica del dispositivo semiconductor.
- Miniaturización: con la tendencia actual de miniaturización, los dispositivos semiconductores son cada vez más pequeños y complejos. La aplicación de adhesivos en tales estructuras en miniatura requiere una gran precisión y control. Garantizar una cobertura uniforme, evitar los vacíos y mantener un grosor uniforme de la línea de unión se convierten en desafíos críticos.
- Compatibilidad de procesos: la fabricación de semiconductores implica múltiples pasos de procesamiento, que incluyen limpieza, deposición y empaque. Los materiales adhesivos deben ser compatibles con estos procesos sin afectar negativamente su desempeño. Los desafíos surgen al encontrar adhesivos que puedan soportar procesos de alta temperatura, resistir la humedad y mantener la estabilidad durante todo el ciclo de fabricación.
- Confiabilidad y envejecimiento: se espera que los dispositivos semiconductores tengan una vida útil prolongada y un rendimiento confiable en diversas condiciones de funcionamiento. Los materiales adhesivos deben exhibir estabilidad a largo plazo, resistencia al envejecimiento y adhesión confiable durante períodos prolongados. El desafío radica en predecir y mitigar los posibles mecanismos de degradación que podrían afectar el rendimiento y la confiabilidad del dispositivo semiconductor.
- Consideraciones ambientales: los materiales adhesivos utilizados en aplicaciones de semiconductores deben cumplir con las regulaciones y normas ambientales.
- Esto incluye limitar las sustancias peligrosas, como el plomo y otros materiales tóxicos. Desarrollar soluciones adhesivas ecológicas que cumplan con los requisitos reglamentarios sin comprometer el rendimiento puede ser un desafío.
- Costo y escalabilidad: los materiales adhesivos deben ser rentables y escalables para satisfacer las demandas de producción de semiconductores de alto volumen. Equilibrar las consideraciones de costos con los requisitos de rendimiento plantea un desafío en la selección de materiales adhesivos adecuados y la optimización del proceso de aplicación.
Pruebas de confiabilidad: evaluación del rendimiento del adhesivo
La prueba de confiabilidad es un proceso esencial para evaluar el desempeño de los adhesivos. Los adhesivos se usan comúnmente en varias industrias, incluidas la automotriz, aeroespacial, electrónica y de construcción, donde juegan un papel fundamental en la unión de diferentes materiales. La confiabilidad de los adhesivos es crucial para garantizar la durabilidad y la funcionalidad a largo plazo de los ensamblajes adheridos.
Un aspecto clave de las pruebas de confiabilidad es evaluar la resistencia y las propiedades de adhesión del adhesivo. Esto implica someter muestras de adhesivo a diferentes condiciones de estrés para simular escenarios del mundo real y determinar su desempeño bajo diversas cargas, temperaturas y condiciones ambientales. Las pruebas de tracción, cizallamiento y pelado se realizan comúnmente para evaluar las propiedades mecánicas del adhesivo y su capacidad para soportar fuerzas en diferentes direcciones.
Además de las pruebas mecánicas, los factores ambientales juegan un papel importante en el desempeño del adhesivo. Los adhesivos pueden estar expuestos a temperaturas extremas, humedad, sustancias químicas y radiación ultravioleta durante su vida útil. Por lo tanto, las pruebas de confiabilidad implican someter muestras pegajosas a pruebas de envejecimiento acelerado, en las que se exponen a condiciones ambientales adversas durante un período prolongado. Esto ayuda a predecir el rendimiento a largo plazo del adhesivo y evaluar su resistencia a la degradación, como la pérdida de fuerza de adhesión o el deterioro químico.
Otro aspecto importante de las pruebas de confiabilidad es evaluar la durabilidad del adhesivo bajo carga cíclica. En muchas aplicaciones, los adhesivos están sujetos a esfuerzos mecánicos repetidos, como vibraciones o ciclos térmicos. Las pruebas de fatiga evalúan la resistencia del adhesivo al fallo bajo estas cargas cíclicas. Las muestras normalmente se someten a un número específico de ciclos de carga y se controla su rendimiento para detectar cualquier signo de deficiencia del adhesivo, como la propagación de grietas o la delaminación de la unión.
Además, las pruebas de confiabilidad implican evaluar el rendimiento del adhesivo en condiciones reales. Esto puede incluir probar la capacidad del adhesivo para unir diferentes materiales comúnmente utilizados en la industria, como metales, plásticos, compuestos o vidrio. Las muestras se preparan utilizando procedimientos estandarizados y se someten a protocolos de prueba que simulan los requisitos específicos de la aplicación. Esto permite a los ingenieros evaluar la compatibilidad del adhesivo con diferentes sustratos y evaluar su fuerza de unión, flexibilidad y resistencia a factores ambientales.
Las pruebas de confiabilidad también incluyen la evaluación de la compatibilidad química del adhesivo con otras sustancias con las que puede entrar en contacto durante su aplicación o vida útil. Esto implica realizar pruebas de compatibilidad para determinar si el adhesivo reacciona negativamente con solventes, agentes de limpieza, combustibles u otros productos químicos que puedan estar presentes en el medio ambiente. Las pruebas de compatibilidad química ayudan a identificar problemas potenciales que podrían provocar fallas o degradación del adhesivo.
En conclusión, las pruebas de confiabilidad son un paso crucial para evaluar el desempeño del adhesivo. Implica evaluar las propiedades mecánicas, realizar pruebas de envejecimiento acelerado, evaluar la durabilidad bajo carga cíclica, evaluar el rendimiento en condiciones reales y probar la compatibilidad química. Al realizar pruebas integrales de confiabilidad, los fabricantes e ingenieros pueden garantizar la idoneidad y el rendimiento a largo plazo de los adhesivos en las aplicaciones previstas.
Consideraciones ambientales en el adhesivo semiconductor
Los adhesivos semiconductores desempeñan un papel fundamental en el montaje y empaquetado de dispositivos electrónicos, especialmente en la industria de los semiconductores. Si bien estos adhesivos brindan funciones esenciales como la unión y la gestión térmica, es vital considerar su impacto ambiental a lo largo de su ciclo de vida. Aquí hay algunas consideraciones ambientales cruciales en el adhesivo semiconductor:
- Toxicidad: muchos adhesivos semiconductores contienen sustancias peligrosas, incluidos compuestos orgánicos volátiles (COV), metales pesados y otros productos químicos tóxicos. Estas sustancias pueden tener efectos adversos sobre la salud humana y el medio ambiente. Minimizar o eliminar los ingredientes dañinos en las formulaciones adhesivas es crucial para reducir su impacto ambiental.
- Emisiones: Durante la fabricación y aplicación de adhesivos semiconductores, los componentes volátiles pueden liberarse al aire, lo que contribuye a la contaminación del aire. Las emisiones de COV, por ejemplo, pueden contribuir a la formación de ozono troposférico y partículas dañinas. Los fabricantes deben esforzarse por desarrollar formulaciones de adhesivos con bajo VOC e implementar medidas estrictas de control de emisiones para mitigar estos impactos ambientales.
- Consumo de energía: la producción de adhesivos semiconductores requiere procesos que consumen mucha energía, como la síntesis, la mezcla y el curado. La reducción del consumo de energía a través de la optimización de procesos y el uso de tecnologías de eficiencia energética pueden minimizar la huella ambiental asociada con la fabricación de adhesivos.
- Generación de residuos: la industria de los semiconductores genera una cantidad importante de residuos y los adhesivos contribuyen a este flujo de residuos. Los residuos pueden incluir adhesivos sin usar o caducados, materiales de embalaje y subproductos de fabricación. La implementación de prácticas de gestión de residuos como el reciclaje, la reutilización o la eliminación segura de los residuos de adhesivos es esencial para minimizar la contaminación ambiental y el agotamiento de los recursos.
- Análisis del ciclo de vida: tener en cuenta el ciclo de vida completo de los adhesivos semiconductores es crucial para evaluar exhaustivamente su impacto ambiental. Este análisis incluye la evaluación de la huella ecológica de la extracción, fabricación, transporte, aplicación y disposición final de la materia prima. La identificación de oportunidades de mejora en cada etapa puede conducir a soluciones adhesivas más sostenibles.
- Alternativas sustentables: Explorar y adoptar alternativas sustentables es esencial para reducir el impacto ambiental de los adhesivos semiconductores. Esto puede implicar el uso de materias primas renovables o de base biológica, el desarrollo de formulaciones a base de agua o sin disolventes y el empleo de procesos de fabricación respetuosos con el medio ambiente. Promover el reciclaje de adhesivos o implementar prácticas de economía circular también puede contribuir a la conservación de los recursos.
- Cumplimiento normativo: los fabricantes de adhesivos deben cumplir con las reglamentaciones y normas ambientales que rigen el uso, la eliminación y el etiquetado de productos químicos. Para garantizar la protección ecológica y de la salud humana, es fundamental mantenerse actualizado con las reglamentaciones pertinentes, como REACH (Registro, Evaluación, Autorización y Restricción de Productos Químicos) en la Unión Europea y reglamentaciones similares en diferentes regiones.
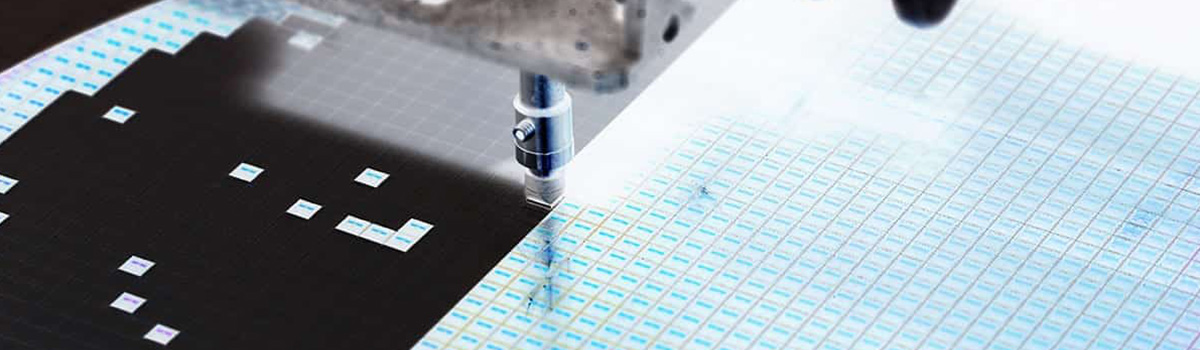
Tendencias e innovaciones en adhesivos semiconductores
El adhesivo semiconductor desempeña un papel fundamental en el montaje y el empaquetado de dispositivos electrónicos, ya que garantiza la unión y la estabilidad adecuadas de los componentes semiconductores. A medida que avanza la tecnología, surgen varias tendencias e innovaciones clave en el campo de los adhesivos para semiconductores.
- Miniaturización y mayor complejidad de los dispositivos: una tendencia significativa en la industria de los semiconductores es la miniaturización continua de los dispositivos electrónicos y la creciente complejidad de sus diseños. Esta tendencia requiere adhesivos con propiedades mejoradas, como menor viscosidad, mayor fuerza de unión y conductividad térmica mejorada, para acomodar componentes más pequeños y más densamente empaquetados.
- Técnicas de empaquetado avanzadas: las técnicas de empaquetado avanzadas, como system-in-package (SiP), empaquetado a nivel de oblea de abanico (FOWLP) y empaquetado 3D, están ganando popularidad debido a su capacidad para mejorar el rendimiento del dispositivo y reducir el factor de forma. Estas técnicas a menudo requieren adhesivos especializados que puedan manejar los desafíos únicos de interconectar múltiples troqueles y componentes dentro de un espacio reducido.
- Gestión térmica: a medida que los dispositivos electrónicos se vuelven más potentes y compactos, la gestión térmica eficaz se vuelve cada vez más crítica. Se están desarrollando adhesivos semiconductores con excelentes propiedades de conductividad térmica para facilitar la disipación de calor de los dispositivos semiconductores, evitando el sobrecalentamiento y asegurando un rendimiento óptimo.
- Curado a baja temperatura: los adhesivos semiconductores tradicionales a menudo requieren procesos de curado a alta temperatura, lo que puede ser problemático para componentes o sustratos sensibles a la temperatura. Las innovaciones en los adhesivos de curado a baja temperatura permiten la unión a temperaturas significativamente más bajas, lo que reduce el riesgo de daño térmico en materiales semiconductores delicados.
- Nuevas formulaciones de materiales: los investigadores están explorando nuevas formulaciones de materiales para adhesivos semiconductores para cumplir con los requisitos en evolución. Esto incluye el desarrollo de adhesivos eléctricamente conductores (ECA) que brindan unión y conductividad eléctrica, eliminando la necesidad de soldadura en aplicaciones específicas. Además, se están introduciendo nuevos materiales, como adhesivos flexibles, para adaptarse a la creciente demanda de dispositivos electrónicos flexibles y flexibles.
- Consideraciones ambientales: la sostenibilidad y el impacto ambiental están ganando más atención en la industria de los semiconductores. Los fabricantes de adhesivos se enfocan en desarrollar formulaciones ecológicas con compuestos orgánicos volátiles (COV) reducidos y sustancias peligrosas mientras mantienen excelentes características de rendimiento.
- Optimización y automatización de procesos: con la creciente demanda de dispositivos semiconductores, existe una necesidad creciente de procesos de fabricación eficientes y automatizados. Los fabricantes de adhesivos colaboran con los proveedores de equipos para optimizar los procesos de aplicación y curado de adhesivos, lo que garantiza resultados consistentes y confiables al tiempo que reduce los tiempos del ciclo de producción.
- Confiabilidad y durabilidad: se espera que los dispositivos semiconductores funcionen de manera confiable durante períodos prolongados, a menudo en entornos hostiles. Las innovaciones adhesivas tienen como objetivo mejorar la confiabilidad del dispositivo al mejorar la fuerza de adhesión, la resistencia a la humedad, la temperatura y varios factores ambientales.
Áreas de aplicación: electrónica de consumo, automotriz, aeroespacial y más
Electrónica de consumo:
La electrónica de consumo es una de las áreas de aplicación más destacadas de los avances tecnológicos. Abarca muchos dispositivos, como teléfonos inteligentes, tabletas, computadoras portátiles, televisores inteligentes, dispositivos portátiles y electrodomésticos. En los últimos años, la electrónica de consumo ha experimentado importantes desarrollos en cuanto a rendimiento, funcionalidad y conectividad. Por ejemplo, los teléfonos inteligentes se han vuelto más poderosos y ofrecen funciones avanzadas como cámaras de alta resolución, integración de inteligencia artificial y capacidades de realidad aumentada. Los televisores inteligentes ahora admiten resolución 4K e incluso 8K e integración de hogar inteligente para experiencias de entretenimiento mejoradas. Los dispositivos portátiles, como los relojes inteligentes y los rastreadores de actividad física, han ganado popularidad por sus capacidades de control de la salud y seguimiento de la actividad física.
Automotor:
La industria automotriz ha experimentado avances notables, principalmente impulsados por la tecnología. Los vehículos modernos tienen sofisticados sistemas electrónicos y de software que mejoran la seguridad, la eficiencia y la experiencia del usuario. Una de las áreas críticas de desarrollo es la conducción autónoma, con los coches autónomos convirtiéndose en una realidad. Estos vehículos se basan en sensores avanzados, algoritmos de inteligencia artificial y conectividad para navegar por las carreteras y tomar decisiones inteligentes. Además, las aplicaciones automotrices incluyen:
- Sistemas de infoentretenimiento.
- Sistemas avanzados de asistencia al conductor (ADAS).
- Conectividad en el coche.
- Tecnología de vehículos eléctricos.
- Comunicación vehículo a vehículo.
Aeroespacial:
La industria aeroespacial depende en gran medida de tecnologías avanzadas para mejorar la seguridad, la eficiencia y el rendimiento. Las aplicaciones aeroespaciales incluyen el diseño y la fabricación de aeronaves, la exploración espacial, los sistemas satelitales y la gestión del tráfico aéreo. El diseño asistido por computadora (CAD) y las herramientas de simulación ayudan a los ingenieros a crear aeronaves más aerodinámicas y eficientes en combustible en el diseño de aeronaves. Los sistemas satelitales brindan comunicaciones globales, monitoreo del clima y servicios de navegación. La industria aeroespacial también aprovecha materiales avanzados, como compuestos y aleaciones ligeras, para reducir el peso y aumentar la eficiencia del combustible. En la exploración espacial, la robótica, la teledetección y los sistemas de propulsión permiten que las misiones exploren cuerpos celestes y recopilen datos científicos.
Cuidado de la salud:
La tecnología juega un papel crucial en el cuidado de la salud, transformando la industria de varias maneras. Los dispositivos y equipos médicos, como las máquinas de resonancia magnética, los escáneres de ultrasonido y los sistemas de cirugía robótica, han revolucionado los procedimientos de diagnóstico y tratamiento. Los registros de salud electrónicos (EHR) y la telemedicina permiten a los profesionales de la salud acceder a la información del paciente y brindar atención remota. Los dispositivos portátiles y los sistemas de monitoreo de la salud permiten a las personas realizar un seguimiento de sus signos vitales y recibir recomendaciones de atención médica personalizadas. Los algoritmos de inteligencia artificial y aprendizaje automático se emplean para el diagnóstico de enfermedades, el descubrimiento de fármacos y el análisis predictivo, lo que conduce a mejores resultados para los pacientes y medicina personalizada.
Automatización industrial:
La automatización industrial implica el uso de tecnologías avanzadas para automatizar los procesos de fabricación y mejorar la productividad. La robótica y los brazos robóticos se utilizan ampliamente para tareas como ensamblaje, soldadura y manipulación de materiales. Los dispositivos y sensores de Internet de las cosas (IoT) se implementan para recopilar datos en tiempo real y optimizar la eficiencia operativa. Los sistemas de visión artificial permiten el control y la inspección de calidad, lo que garantiza que los productos cumplan con los estándares más estrictos. Los sistemas de control avanzados y los algoritmos de mantenimiento predictivo ayudan a minimizar el tiempo de inactividad y maximizar la producción. La automatización industrial puede aumentar la eficiencia, reducir los costos y mejorar la seguridad en varias industrias, incluidas la fabricación, la logística y la energía.
Perspectivas y oportunidades futuras
El futuro está lleno de perspectivas y oportunidades emocionantes, impulsadas por los rápidos avances tecnológicos, las necesidades sociales cambiantes y las tendencias globales en evolución. Aquí, exploramos algunas áreas clave con un importante potencial de crecimiento y desarrollo.
- Inteligencia artificial (IA) y automatización: la IA está transformando industrias en todos los ámbitos, mejorando la eficiencia, la productividad y la toma de decisiones. A medida que maduren las tecnologías de IA, aumentarán las oportunidades para los especialistas en IA, los científicos de datos y los ingenieros. La automatización continuará agilizando los procesos, lo que conducirá a la creación de empleos en robótica, aprendizaje automático y sistemas inteligentes.
- Energía renovable y sostenibilidad: con la creciente preocupación por el cambio climático, existe una demanda masiva de soluciones de energía renovable. La transición a fuentes más limpias como la energía solar, eólica e hidroeléctrica presenta numerosas perspectivas. Las carreras en ingeniería de energías renovables, gestión de energía y desarrollo sostenible serán fundamentales para dar forma a un futuro más verde.
- Atención médica y biotecnología: los avances en la investigación médica, la medicina personalizada y la edición de genes están revolucionando la industria de la atención médica. Abundan las oportunidades en bioinformática, asesoramiento genético, telemedicina y desarrollo farmacéutico. La intersección de la tecnología y la atención médica impulsará la innovación, lo que conducirá a una mejor atención al paciente y mejores resultados.
- Ciberseguridad y privacidad de datos: a medida que aumenta nuestra dependencia de los sistemas digitales, también aumenta la necesidad de medidas sólidas de ciberseguridad. Las ciberamenazas son cada vez más sofisticadas, lo que crea una demanda de expertos en ciberseguridad, hackers éticos y especialistas en privacidad de datos. La protección de la información confidencial y el desarrollo de una infraestructura segura serán cruciales para las organizaciones y las personas.
- Comercio electrónico y marketing digital: el comercio electrónico ha transformado la forma en que compramos, creando nuevas vías para las empresas. Las plataformas minoristas en línea, el marketing digital y la publicidad en las redes sociales se han vuelto esenciales para las empresas prósperas. Las carreras en administración de comercio electrónico, creación de contenido digital y optimización de la experiencia del cliente seguirán teniendo una gran demanda.
- Exploración y comercialización del espacio: la exploración del espacio ha pasado de ser iniciativas dirigidas por el gobierno a empresas comerciales, lo que abre oportunidades en la ingeniería aeroespacial, la tecnología satelital y el turismo espacial. Las empresas privadas están invirtiendo en viajes espaciales, extracción de recursos y comunicación por satélite, allanando el camino para una nueva era de exploración espacial.
- Agricultura y sistemas alimentarios sostenibles: dado que se espera que la población mundial alcance los 9 2050 millones para XNUMX, es fundamental garantizar la seguridad alimentaria y las prácticas agrícolas sostenibles. La agricultura vertical, la agricultura de precisión y las fuentes alternativas de proteínas ofrecen potencial para la innovación. Las carreras en tecnología agrícola, agronomía y ciencia de los alimentos desempeñarán un papel vital para satisfacer las futuras demandas de alimentos.
- Realidad virtual (VR), realidad aumentada (AR) y realidad extendida (XR): estas tecnologías tienen el potencial de revolucionar el entretenimiento, la educación, la capacitación y varias industrias. Los desarrolladores de VR/AR, los creadores de contenido y los diseñadores de experiencias inmersivas darán forma al futuro del entretenimiento, los juegos y la colaboración virtual.
- Tecnología financiera (Fintech): la integración de la tecnología y las finanzas ha resultado en el surgimiento de Fintech, que ofrece nuevos servicios financieros, soluciones de pago digital y tecnología blockchain. Se espera que las carreras en análisis financiero, ciberseguridad en la banca y desarrollo de blockchain tengan una gran demanda.
- Consultoría de sostenibilidad y arquitectura ecológica: a medida que la sostenibilidad se convierte en una prioridad, las empresas y las personas buscan orientación para reducir su huella de carbono y adoptar prácticas ecológicas. Los consultores sostenibles, los arquitectos ecológicos y los ingenieros ambientales serán fundamentales para diseñar e implementar soluciones sostenibles.
Importancia de la colaboración en el avance de la tecnología de adhesivos semiconductores
La colaboración es vital para hacer avanzar la tecnología de adhesivos de semiconductores, impulsar la innovación y garantizar su implementación exitosa en diversas industrias. La industria de los semiconductores es muy compleja y evoluciona rápidamente, lo que requiere experiencia interdisciplinaria y la cooperación de las partes interesadas.
- Experiencia diversa: la tecnología de adhesivos de semiconductores abarca múltiples disciplinas, incluidas la ciencia de los materiales, la química, la ingeniería y la fabricación. La colaboración reúne a expertos de diversos campos, cada uno de los cuales contribuye con conocimientos y habilidades especializados. Al combinar experiencia diversa, la asociación permite el desarrollo de técnicas y materiales adhesivos novedosos que pueden mejorar el rendimiento, la confiabilidad y la durabilidad de los dispositivos semiconductores.
- Intercambio de conocimientos: la colaboración facilita el intercambio de conocimientos e información entre investigadores, ingenieros y profesionales de la industria. A través de esfuerzos de colaboración, las personas pueden compartir sus conocimientos, experiencias y hallazgos de investigación, lo que lleva a una comprensión más profunda de los materiales adhesivos y sus aplicaciones. Este intercambio de conocimientos puede ayudar a identificar tendencias emergentes, abordar desafíos técnicos y acelerar el desarrollo de soluciones innovadoras.
- Investigación y desarrollo mejorados: los esfuerzos colaborativos de investigación y desarrollo permiten la puesta en común de recursos en términos de financiación y equipo. Esto permite una experimentación, prueba y análisis más extensos, lo que conduce a un descubrimiento e innovación más rápidos. Al trabajar juntos, los investigadores pueden acceder a instalaciones especializadas, tecnologías de punta y herramientas de caracterización avanzadas que pueden no estar disponibles individualmente. Dichos recursos pueden contribuir significativamente al avance de la tecnología de adhesivos semiconductores.
- Colaboración entre la industria y la universidad: la colaboración entre la industria y la academia es crucial para traducir los hallazgos de la investigación en aplicaciones prácticas. Las universidades pueden realizar investigaciones fundamentales y explorar nuevos conceptos, mientras que los socios de la industria aportan perspectivas del mundo real y consideraciones prácticas. Esta colaboración garantiza que los desarrollos de tecnología de adhesivos se alineen con las necesidades del mercado y puedan integrarse en los procesos industriales. La asociación industria-universidad también promueve la transferencia de tecnología, lo que permite que la investigación académica tenga un impacto tangible en las aplicaciones comerciales.
- Estandarización y garantía de calidad: la colaboración entre los actores de la industria fomenta el desarrollo de estándares y pautas para la tecnología de adhesivos semiconductores. Los estándares ayudan a garantizar la coherencia, la compatibilidad y la confiabilidad entre diferentes productos y procesos de fabricación. Los esfuerzos de colaboración pueden establecer mejores prácticas, metodologías de prueba y procedimientos de control de calidad, que son esenciales para garantizar el rendimiento y la confiabilidad a largo plazo de los dispositivos semiconductores.
- Expansión del mercado y competitividad: la colaboración entre empresas que operan en la industria de los semiconductores puede conducir a la expansión del mercado y una mayor competitividad. Las empresas pueden combinar sus recursos, conocimientos y conocimientos del mercado trabajando juntas para desarrollar soluciones adhesivas que cumplan con los requisitos específicos de la industria. Los esfuerzos de colaboración también pueden facilitar la adopción de tecnología adhesiva en nuevas aplicaciones y mercados emergentes, impulsando aún más el crecimiento de la industria de los semiconductores.
Conclusión:
El adhesivo semiconductor juega un papel vital al permitir la miniaturización y el alto rendimiento de los dispositivos semiconductores. La capacidad de estos adhesivos para brindar fuertes capacidades de unión, protección contra factores ambientales y estrés térmico, y conductividad eléctrica es crucial en la fabricación y ensamblaje de microprocesadores, chips de memoria y otros circuitos integrados. A medida que la tecnología continúa avanzando, el desarrollo de soluciones adhesivas innovadoras y la colaboración entre fabricantes, investigadores y usuarios finales serán cruciales para satisfacer las crecientes demandas y desafíos de la industria de los semiconductores. Al aprovechar el potencial del adhesivo semiconductor, podemos allanar el camino para dispositivos semiconductores aún más pequeños, rápidos y complejos que impulsan nuestro mundo moderno.