Adhesivo de unión FPC
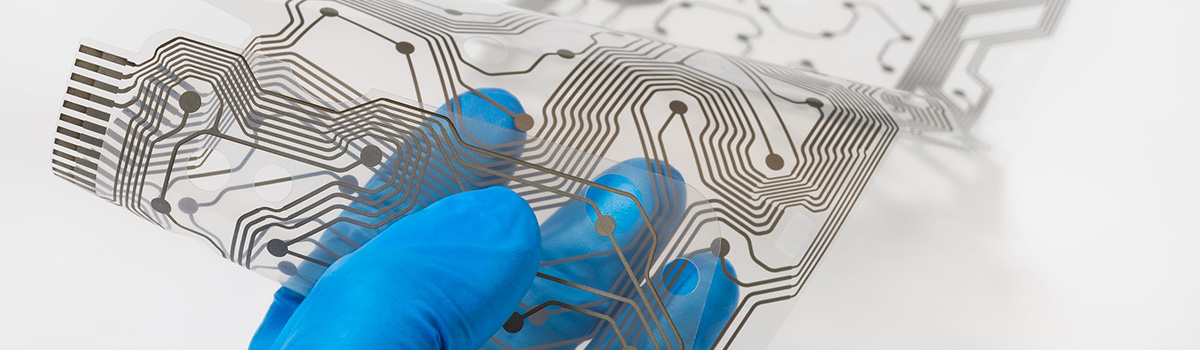
El adhesivo de unión FPC es un componente crucial en la fabricación y el ensamblaje de placas de circuito impreso flexible (FPC), que se utilizan ampliamente en varios dispositivos electrónicos, incluidos teléfonos inteligentes, dispositivos portátiles y aplicaciones automotrices. Estos adhesivos brindan fuertes capacidades de unión, aislamiento eléctrico y protección contra factores ambientales al tiempo que garantizan la flexibilidad y durabilidad de las placas FPC. A medida que crece la demanda de dispositivos electrónicos flexibles y confiables, la importancia de los adhesivos de unión FPC confiables y de alto rendimiento se ha vuelto más crítica. Este artículo explorará los diversos tipos, aplicaciones y desafíos de los adhesivos de unión FPC, destacando su papel crucial para permitir la flexibilidad y la confiabilidad en los dispositivos electrónicos.
Tipos de adhesivos de unión FPC
Los adhesivos de unión FPC (Flexible Printed Circuit) son esenciales para ensamblar y conectar circuitos flexibles en varios dispositivos electrónicos. Estos adhesivos aseguran una unión confiable y duradera entre el circuito flexible y el sustrato de destino. Hay varios tipos de adhesivos de unión FPC disponibles en el mercado, cada uno con características y aplicaciones únicas. Esta respuesta proporcionará una descripción general de algunos tipos comunes de adhesivos de unión FPC.
- Adhesivos a base de acrílico: los adhesivos de unión a base de acrílico son populares debido a su excelente adhesión a varios sustratos, incluidos metales, plásticos y vidrio. Ofrecen flexibilidad, estabilidad térmica y resistencia a la humedad y los productos químicos. Los adhesivos acrílicos están disponibles en varias formas, como cintas, películas y adhesivos líquidos, lo que los hace versátiles para diferentes aplicaciones de unión FPC.
- Adhesivos a base de epoxi: los adhesivos a base de epoxi brindan una alta fuerza de unión y se usan ampliamente para la unión de FPC. Ofrecen una excelente adherencia a varios sustratos y proporcionan buenas propiedades de aislamiento eléctrico. Los adhesivos epoxi están disponibles en diferentes formulaciones, incluidos sistemas de uno y dos componentes, lo que brinda opciones para múltiples procesos de unión y condiciones de curado.
- Adhesivos a base de silicona: los adhesivos a base de silicona son conocidos por su flexibilidad, resistencia a altas temperaturas y excelentes propiedades de aislamiento eléctrico. Pueden soportar temperaturas extremas y ofrecen una buena resistencia a la humedad, lo que las hace adecuadas para entornos exigentes. Los adhesivos de silicona se usan comúnmente en aplicaciones con gestión térmica y confiabilidad críticas.
- Adhesivos sensibles a la presión (PSA): los PSA son materiales adhesivos que forman una unión instantánea cuando se aplica presión. Eliminan la necesidad de otros procesos de curado, haciéndolos convenientes para aplicaciones de unión FPC. Los PSA ofrecen una buena adhesión a varios sustratos y se pueden quitar fácilmente sin dejar residuos, lo que los hace ideales para la unión temporal o el retrabajo.
- Adhesivos curables por UV: Los adhesivos curables por UV son adhesivos líquidos que curan rápidamente cuando se exponen a la luz ultravioleta. Ofrecen tiempos de curado rápidos, alta fuerza de unión y excelente adhesión a diferentes sustratos. Los adhesivos curables por UV se usan comúnmente en aplicaciones de unión FPC donde se requiere un ensamblaje rápido y una mayor productividad.
- Adhesivos conductivos: Los adhesivos conductivos están especialmente formulados para unión y conductividad eléctrica. Contienen rellenos conductores, como plata o carbón, que permiten que el adhesivo establezca conexiones eléctricas entre los componentes del circuito. Los adhesivos conductores se utilizan ampliamente en la unión de FPC para aplicaciones como blindaje EMI, conexión a tierra e interconexiones eléctricas.
- Adhesivos termoconductores: los adhesivos termoconductores están diseñados para proporcionar propiedades de unión y transferencia de calor eficientes. Se utilizan en aplicaciones de unión FPC donde la gestión térmica es fundamental, como la unión de circuitos flexibles a disipadores de calor u otros sustratos termoconductores.
Es importante tener en cuenta que la elección de un adhesivo de unión FPC depende de varios factores, incluidos los requisitos específicos de la aplicación, los materiales del sustrato, las condiciones ambientales y los procesos de fabricación. Consultar a los fabricantes o proveedores de adhesivos puede proporcionar información más detallada y orientación sobre cómo seleccionar el adhesivo más adecuado para una aplicación de unión FPC específica.
Adhesivos acrílicos: la opción más común
Los adhesivos acrílicos son populares en varias industrias debido a su versatilidad, fuerte capacidad de unión y facilidad de uso. Estos adhesivos están compuestos por polímeros acrílicos, que brindan una excelente adherencia a una amplia gama de sustratos. Aquí exploraremos por qué los adhesivos acrílicos son la opción más común en 450 palabras.
Una de las ventajas críticas de los adhesivos acrílicos es su capacidad para unir diferentes materiales. Los adhesivos acrílicos pueden crear uniones duraderas y confiables, ya sea para unir plásticos, metales, cerámica, madera o incluso vidrio. Esta versatilidad los hace adecuados para diversas aplicaciones de automoción, construcción, electrónica y señalización.
Los adhesivos acrílicos también ofrecen una excelente fuerza de unión y pueden formar uniones sólidas que resisten grandes tensiones, variaciones de temperatura y condiciones ambientales. Esto los hace ideales para aplicaciones donde la durabilidad y el rendimiento a largo plazo son cruciales.
Otra razón de la popularidad de los adhesivos acrílicos es su rápido tiempo de curado. En comparación con otros tipos de adhesivos, los adhesivos acrílicos tienen tiempos de curado relativamente cortos, lo que permite ciclos de producción más rápidos. A menudo pueden lograr fuerza de manejo en minutos, reduciendo el tiempo de ensamblaje y aumentando la productividad.
Además, los adhesivos acrílicos son conocidos por resistir la humedad, los productos químicos y la radiación ultravioleta. Tienen una excelente resistencia al agua y pueden mantener sus propiedades adhesivas incluso en ambientes húmedos. Esta característica los hace adecuados para aplicaciones al aire libre y entornos donde se espera exposición a condiciones adversas.
Los adhesivos acrílicos también proporcionan una excelente estabilidad térmica. Pueden soportar un amplio rango de temperatura, desde el frío extremo hasta el calor intenso, sin comprometer su fuerza de unión. Esta resistencia térmica los hace adecuados para aplicaciones donde las fluctuaciones de temperatura son comunes, como en las industrias automotriz y electrónica.
Además de sus propiedades físicas, los adhesivos acrílicos son fáciles de manejar y aplicar. Están disponibles en varias formas, incluidos líquidos, pastas, películas y cintas, lo que ofrece flexibilidad en los métodos de aplicación. Se pueden aplicar utilizando sistemas de dosificación automatizados o manualmente, según los requisitos específicos de la aplicación.
Además, los adhesivos acrílicos son generalmente inodoros y tienen un bajo contenido de compuestos orgánicos volátiles (COV). Esto los hace más seguros que los adhesivos a base de solventes, que pueden emitir olores fuertes o contener químicos dañinos.
Adhesivos de silicona: resistencia ambiental superior
Los adhesivos de silicona son una clase de adhesivos conocidos por su resistencia ambiental superior. Ofrecen un rendimiento y una durabilidad excepcionales en diversas aplicaciones, lo que los hace muy buscados en las industrias automotriz, electrónica, aeroespacial, de construcción y médica.
Una de las ventajas críticas de los adhesivos de silicona es su capacidad para soportar temperaturas extremas. Pueden resistir altas y bajas temperaturas sin perder sus propiedades adhesivas ni volverse quebradizos. Esto los hace adecuados para aplicaciones donde las fluctuaciones de temperatura son comunes, como en motores de automóviles o dispositivos electrónicos.
Los adhesivos de silicona también exhiben una excelente resistencia a la humedad y al agua. A diferencia de muchos otros tipos de adhesivos, pueden mantener la fuerza y la integridad incluso cuando se exponen al agua o ambientes húmedos. Esta propiedad es crucial en aplicaciones que requieren resistencia al agua, como juntas de sellado, unión de componentes bajo el agua o protección de circuitos electrónicos contra daños por humedad.
Además, los adhesivos de silicona ofrecen una resistencia excepcional a la radiación UV ya la intemperie. Pueden resistir la exposición prolongada a la luz solar, la lluvia, la nieve y otros factores ambientales sin degradarse ni perder sus propiedades adhesivas. Esto los hace ideales para aplicaciones al aire libre, como sellar letreros al aire libre, unir paneles solares o proteger dispositivos electrónicos al aire libre.
La resistencia química es otra área en la que sobresalen los adhesivos de silicona. Pueden resistir varios productos químicos, incluidos solventes, aceites, combustibles y ácidos. Esta resistencia es significativa en industrias como la automotriz y aeroespacial, donde la exposición a múltiples productos químicos es diaria. Incluso en productos químicos agresivos, los adhesivos de silicona pueden mantener su integridad y adhesión, lo que garantiza un rendimiento y una fiabilidad a largo plazo.
Además de su resistencia ambiental, los adhesivos de silicona ofrecen excelentes propiedades de aislamiento eléctrico. Tienen una alta rigidez dieléctrica y pueden proporcionar aislamiento contra corrientes eléctricas. Esto los hace ideales para unir y sellar componentes electrónicos, donde el aislamiento eléctrico y la protección son cruciales.
Los adhesivos de silicona están disponibles en varias formas, incluidos sistemas de una o dos partes, así como diferentes mecanismos de curado como curado por calor, curado por humedad o curado por UV. Esta versatilidad permite una amplia gama de aplicaciones y requisitos de unión.
Vale la pena señalar que, si bien los adhesivos de silicona ofrecen una resistencia ambiental excepcional, es posible que no tengan la misma fuerza de unión inicial alta que otros tipos de adhesivos. Sin embargo, compensan esto con su flexibilidad, durabilidad y rendimiento a largo plazo en condiciones adversas.
Adhesivos de curado UV: unión rápida y precisa
Los adhesivos de curado por UV, también conocidos como adhesivos de curado por ultravioleta, han ganado una popularidad significativa en varias industrias debido a su capacidad para proporcionar una unión rápida y precisa. Estos adhesivos ofrecen numerosas ventajas sobre los sistemas adhesivos tradicionales, lo que los convierte en la opción preferida para aplicaciones que requieren una adhesión rápida y confiable.
Los adhesivos de curado UV están formulados con fotoiniciadores especiales que inician el proceso cuando se exponen a la luz ultravioleta. La reacción de curado ocurre casi instantáneamente, lo que permite una rápida formación de enlaces. A diferencia de los adhesivos convencionales que usan calor o reacciones químicas para curar, los adhesivos de curado UV brindan una unión prácticamente instantánea, lo que ahorra un valioso tiempo de producción y aumenta la eficiencia.
Una de las ventajas críticas de los adhesivos de curado UV es su capacidad de unión precisa. La reacción de curado está altamente controlada y localizada, lo que garantiza que el adhesivo solo se cure en el área deseada. Esto permite un posicionamiento y una alineación precisos de los componentes, incluso en ensamblajes complejos. Los fabricantes pueden lograr tolerancias estrictas y mantener una alta calidad del producto utilizando adhesivos de curado UV.
El tiempo de curado rápido de los adhesivos UV es particularmente ventajoso en industrias donde el tiempo de producción rápido es crucial. Por ejemplo, en la fabricación de productos electrónicos, los adhesivos de curado UV permiten la unión rápida de componentes, lo que reduce el tiempo de ensamblaje y aumenta la productividad. De manera similar, en la industria de dispositivos médicos, los adhesivos UV brindan una unión rápida y confiable de varios materiales, lo que permite un montaje rápido de dispositivos médicos complejos.
Los adhesivos de curado UV ofrecen una excelente fuerza de unión y durabilidad. Una vez curados, estos adhesivos forman uniones fuertes que resisten diversas condiciones ambientales, incluidas las fluctuaciones de temperatura, la humedad y los productos químicos. Los bonos muestran una alta resistencia al amarillamiento o la degradación con el tiempo, lo que garantiza un rendimiento y una fiabilidad a largo plazo.
Los adhesivos de curado UV son versátiles y compatibles con varios sustratos, incluidos plásticos, metales, vidrio y cerámica. Pueden unir materiales diferentes, ampliando la gama de aplicaciones en las que se pueden utilizar. Desde hacer clic en componentes de plástico en la industria automotriz hasta ensamblar dispositivos electrónicos, los adhesivos de curado UV ofrecen una solución confiable para diversas necesidades de unión.
Además, los adhesivos de curado UV no contienen solventes, lo que elimina la necesidad de compuestos orgánicos volátiles (COV) y reduce el impacto ambiental. También ofrecen beneficios para la salud y la seguridad al minimizar la exposición a productos químicos peligrosos. La ausencia de disolventes y COV contribuye a un entorno de trabajo más limpio y saludable para los operadores.
Adhesivos epóxicos: Alta fuerza de unión y resistencia química
Los adhesivos epoxi son populares en varias industrias debido a su alta fuerza de unión y sus excelentes propiedades de resistencia química. Ofrecen numerosas ventajas sobre otras opciones de adhesivos, lo que los hace versátiles y confiables para múltiples aplicaciones.
Uno de los beneficios críticos de los adhesivos epoxi es su fuerza de unión excepcional. Crean uniones poderosas que pueden soportar un estrés y una carga significativos cuando se aplican correctamente, lo que los hace adecuados para aplicaciones que requieren una unión duradera y duradera. Los adhesivos epoxi pueden unir diferentes materiales, incluidos metales, plásticos, cerámica, vidrio y compuestos, lo que brinda una solución de unión confiable para diversas industrias.
Además de su alta fuerza de unión, los adhesivos epoxi exhiben una excelente resistencia química. Pueden resistir varios productos químicos, incluidos solventes, ácidos, bases, aceites y combustibles. Esta resistencia al ataque químico asegura que el adhesivo permanezca estable y mantenga su fuerza de unión incluso en ambientes hostiles. En consecuencia, los adhesivos epoxi se usan comúnmente en las industrias automotriz, aeroespacial, electrónica y de procesamiento químico, donde la exposición a productos químicos es una preocupación.
La resistencia química de los adhesivos epoxi se atribuye a su estructura molecular única. Los adhesivos epoxi consisten en una resina y un endurecedor que reaccionan químicamente para formar una red reticulada. Esta estructura reticulada proporciona al adhesivo su fuerza y resistencia a los productos químicos. El proceso de curado de los adhesivos epoxi se puede ajustar para lograr diferentes niveles de resistencia química, lo que permite la personalización según los requisitos específicos de la aplicación.
Además, los adhesivos epoxi ofrecen una excelente resistencia a la temperatura, otro factor crucial en muchas industrias. Pueden mantener su fuerza de unión e integridad a altas y bajas temperaturas, lo que los hace adecuados para aplicaciones expuestas a variaciones extremas de temperatura. Esta propiedad es fundamental en industrias como la aeroespacial y la automotriz, donde los componentes pueden experimentar fluctuaciones de temperatura significativas.
Otra ventaja de los adhesivos epoxi es su versatilidad en términos de métodos de aplicación. Se pueden aplicar varias técnicas, que incluyen la dispensación manual, la dispensación con jeringa, la aplicación por pulverización y los sistemas de dispensación automatizados. Esta flexibilidad en los métodos de aplicación permite una unión eficiente y precisa en diferentes entornos de producción.
Es importante tener en cuenta que la preparación adecuada de la superficie y las técnicas de aplicación del adhesivo son esenciales para lograr una fuerza de unión y una resistencia química óptimas con los adhesivos epoxi. Las superficies deben estar limpias, secas y libres de contaminantes para garantizar la máxima adherencia. Además, el adhesivo debe mezclarse de acuerdo con las instrucciones del fabricante, considerando la proporción correcta de resina a endurecedor y las condiciones de curado apropiadas.
En conclusión, los adhesivos epoxi ofrecen una alta fuerza de unión y una excelente resistencia química, lo que los convierte en una opción ideal para diversas aplicaciones. Su capacidad para unir diferentes materiales, resistir productos químicos agresivos y funcionar bien bajo temperaturas extremas los hace indispensables en las industrias automotriz, aeroespacial, electrónica y de procesamiento químico. Con la preparación adecuada de la superficie y las técnicas de aplicación, los adhesivos epoxi pueden proporcionar uniones duraderas y confiables, lo que contribuye al rendimiento general y la longevidad de los componentes ensamblados.
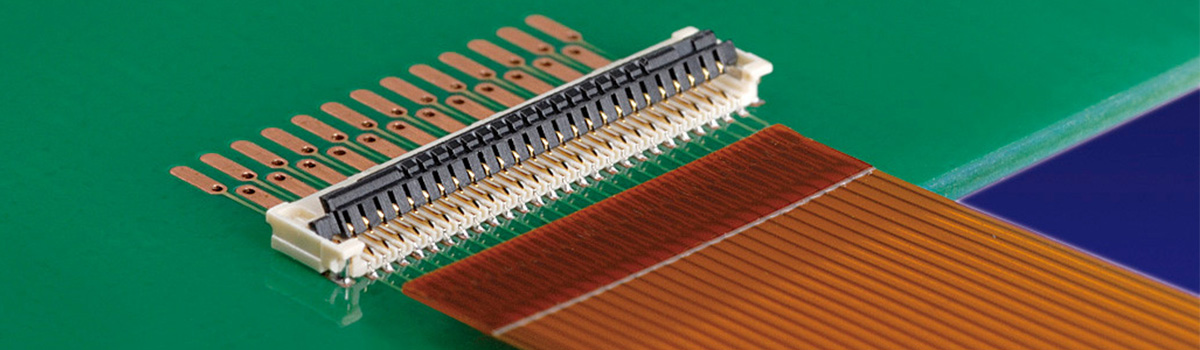
Adhesivos Conductores: Permitiendo la Conectividad Eléctrica
Los adhesivos conductores juegan un papel crucial al permitir la conectividad eléctrica en diversas aplicaciones. Estos materiales innovadores brindan una alternativa eficaz a los métodos tradicionales de soldadura o fijación mecánica al ofrecer una excelente conductividad eléctrica, facilidad de uso y versatilidad. Este artículo explorará las características y aplicaciones clave de los adhesivos conductores.
Los adhesivos conductores se formulan utilizando una combinación de rellenos conductores, como plata, cobre o carbono, y un aglutinante polimérico. Los rellenos conductores facilitan el flujo de corriente eléctrica, mientras que el aglutinante asegura la adhesión a diferentes sustratos. Esta composición única permite que los adhesivos conductores proporcionen conexiones eléctricas confiables incluso en entornos difíciles.
Una de las principales ventajas de los adhesivos conductores es su compatibilidad con una amplia gama de materiales. Pueden unir metales, cerámica, vidrio, plásticos e incluso sustratos flexibles, lo que los hace adecuados para diversas industrias. La conexión de materiales diferentes es particularmente ventajosa en la industria electrónica, donde se deben unir componentes con diferentes coeficientes de expansión térmica.
Los adhesivos conductivos ofrecen una excelente conductividad eléctrica, comparable a la soldadura tradicional. Esta propiedad les permite reemplazar juntas de soldadura en aplicaciones específicas de manera efectiva. Además, los adhesivos conductores exhiben una mejor resistencia a los ciclos térmicos, el estrés mecánico y la vibración que las conexiones soldadas. Estos atributos los hacen ideales para aplicaciones con fluctuaciones frecuentes de temperatura o movimientos automáticos.
La facilidad de aplicación es otra ventaja importante de los adhesivos conductores. Por lo general, están disponibles en formas convenientes, como jeringas, o se dispensan como películas o cintas. Esto permite una dosificación precisa y controlada, lo que los hace aptos para procesos de montaje automatizados y manuales. A diferencia de la soldadura, que requiere experiencia y equipo especializado, los adhesivos conductores se pueden aplicar fácilmente con una capacitación mínima.
Los adhesivos conductores encuentran aplicaciones en diversas industrias. En el sector de la electrónica, se utilizan para la unión de componentes, la unión de troqueles, la unión de cables y como alternativa a la soldadura en el ensamblaje de placas de circuito impreso (PCB). También se emplean en la fabricación de componentes electrónicos flexibles, donde los métodos de soldadura tradicionales no son viables debido a la flexibilidad de los sustratos.
En la industria automotriz, los adhesivos conductores se utilizan para unir sensores, antenas y sistemas de iluminación. Ofrecen una excelente adhesión a los materiales utilizados en aplicaciones automotrices, incluidos plásticos y compuestos. Además, su capacidad para soportar condiciones ambientales adversas, como variaciones de temperatura, humedad y exposición química, los convierte en una opción ideal para la electrónica automotriz.
Los adhesivos conductores también juegan un papel importante en el campo médico. Ensamblan dispositivos médicos, como sensores, electrodos y dispositivos implantables. Las variantes biocompatibles de los adhesivos conductores garantizan que sean seguros para el contacto con los tejidos humanos.
Adhesivos de baja emisión de gases: críticos para aplicaciones espaciales
Los adhesivos de baja emisión de gases desempeñan un papel fundamental en las aplicaciones espaciales en las que los materiales deben soportar las condiciones extremas del entorno espacial. La desgasificación se refiere a la liberación de compuestos volátiles de los materiales cuando se exponen al vacío o a altas temperaturas. En el espacio, estos compuestos volátiles pueden presentar riesgos significativos para la funcionalidad y confiabilidad de equipos e instrumentos sensibles.
En el vacío del espacio, los materiales desgasificados pueden condensarse en superficies cercanas, como lentes ópticos o sensores, causando contaminación y degradación del rendimiento. La contaminación puede afectar la precisión de las mediciones, reducir la calidad de la señal e incluso provocar la falla de componentes críticos. Además, los materiales desgasificados condensados pueden acumularse con el tiempo, formando una capa que puede absorber o dispersar la luz, afectando los sistemas ópticos y los dispositivos de imagen.
Los adhesivos de baja emisión de gases están específicamente formulados para minimizar la liberación de compuestos volátiles. Están diseñados para tener baja presión de vapor, lo que significa que liberan menos gases y vapores cuando se exponen a condiciones de vacío. Esta característica ayuda a prevenir la contaminación y degradación de superficies y componentes sensibles.
Las naves espaciales y los satélites dependen de adhesivos de baja emisión de gases para diversas aplicaciones. Un uso importante es en la unión y encapsulación de componentes electrónicos. Estos adhesivos brindan uniones sólidas y confiables entre diferentes materiales al tiempo que minimizan el riesgo de contaminación y problemas relacionados con la desgasificación. Garantizan la integridad estructural y la conectividad eléctrica de los componentes, lo que les permite soportar las vibraciones y los golpes experimentados durante el lanzamiento y la operación en el espacio.
Los adhesivos de baja emisión de gases también son esenciales para los sistemas ópticos utilizados en telescopios, cámaras y sensores espaciales. Los adhesivos utilizados en estos sistemas deben tener un impacto mínimo en la claridad y el rendimiento de lentes, espejos y detectores. Al reducir la desgasificación, estos adhesivos mantienen las propiedades ópticas y evitan la formación de capas de contaminación que podrían degradar la calidad de la imagen o interferir con mediciones precisas.
Además, la gestión térmica es una consideración fundamental en las aplicaciones espaciales. Los adhesivos de baja emisión de gases unen disipadores de calor, materiales de interfaz térmica y otros componentes involucrados en la disipación de calor. Estos adhesivos aseguran una transferencia de calor eficiente y minimizan el riesgo de contaminación que podría afectar el rendimiento de los sistemas de gestión térmica.
Para cumplir con los estrictos requisitos de las aplicaciones espaciales, los adhesivos de baja emisión de gases se someten a rigurosos procesos de prueba y certificación. Los materiales se someten a ciclos térmicos, exposición al vacío y análisis para evaluar sus características de desgasificación. Los adhesivos que cumplen con los estándares establecidos por organizaciones como los requisitos de desgasificación de la NASA (como ASTM E595) se consideran adecuados para misiones espaciales.
Adhesivos termoconductores: gestión del calor en dispositivos electrónicos
Los adhesivos termoconductores juegan un papel crucial en la gestión del calor en los dispositivos electrónicos. A medida que los componentes electrónicos continúan reduciéndose de tamaño y funcionan a densidades de potencia más altas, la disipación de calor efectiva se vuelve cada vez más esencial para garantizar un rendimiento y una confiabilidad óptimos. Los adhesivos termoconductores brindan una solución viable al transferir eficientemente el calor de los componentes generadores de calor a los disipadores de calor u otros mecanismos de disipación de calor. Este artículo explorará los aspectos críticos de los adhesivos termoconductores y su función en la gestión del calor en los dispositivos electrónicos.
Los adhesivos termoconductores son materiales especialmente formulados con propiedades adhesivas y alta conductividad térmica. Están diseñados para formar enlaces fuertes entre los componentes que generan calor, como los circuitos integrados o los dispositivos de alimentación, y los disipadores de calor u otros elementos de refrigeración. La naturaleza adhesiva de estos materiales asegura una unión confiable, mientras que su alta conductividad térmica permite una transferencia de calor eficiente.
Una de las principales ventajas de los adhesivos termoconductores es su capacidad para llenar pequeños espacios e irregularidades entre las superficies de contacto, minimizando así la resistencia térmica. Esta característica es particularmente beneficiosa cuando se unen componentes con superficies no planas o cuando se trata de espacios de aire microscópicos que dificultan el flujo de calor. Al llenar estos espacios, los adhesivos termoconductores establecen un contacto íntimo entre los personajes, lo que mejora la transferencia de calor y reduce el riesgo de puntos calientes térmicos.
Otro aspecto crítico de la gestión del calor en los dispositivos electrónicos es la capacidad de resistir los ciclos de temperatura y las tensiones mecánicas. Los dispositivos electrónicos están sujetos a diferentes condiciones de temperatura y vibraciones mecánicas durante su funcionamiento. Los adhesivos termoconductores están formulados para mantener su fuerza adhesiva y rendimiento térmico en un amplio rango de temperatura, lo que garantiza una disipación de calor confiable incluso en condiciones difíciles.
Además, los adhesivos termoconductores ofrecen propiedades de aislamiento eléctrico, evitando cortocircuitos eléctricos entre componentes. Esta característica es crucial en los dispositivos electrónicos donde varias piezas están empaquetadas densamente y existe el riesgo de contacto accidental entre elementos conductores.
Los adhesivos termoconductores se pueden aplicar mediante varios métodos, que incluyen dispensación, serigrafía o laminación con película. Estos adhesivos están disponibles en diferentes viscosidades y mecanismos de curado, lo que permite flexibilidad en el proceso de fabricación. Algunos adhesivos termoconductores curan a temperatura ambiente, mientras que otros requieren temperaturas elevadas o luz ultravioleta. Los fabricantes pueden seleccionar el bono que mejor se adapte a sus requisitos de producción específicos.
Adhesivos despegar y pegar: fáciles de usar y aplicar
Los adhesivos de despegar y pegar han revolucionado la forma en que abordamos varios proyectos y tareas que requieren materiales de unión. Estos adhesivos son increíblemente fáciles de usar y aplicar, lo que los hace populares entre los profesionales y entusiastas del bricolaje. Con su comodidad y versatilidad, los adhesivos despegar y pegar se han convertido en una solución de referencia para muchas aplicaciones.
Una de las principales ventajas de los adhesivos de pelar y pegar es su simplicidad. A diferencia de los adhesivos tradicionales que a menudo requieren mezclar o herramientas especializadas, los adhesivos despegar y pegar vienen preaplicados a un material de respaldo, listos para usar desde el paquete. Esto elimina la necesidad de equipo adicional o preparación extensa, ahorrando tiempo y esfuerzo.
El proceso de aplicación de los adhesivos despegar y pegar es sencillo y fácil de usar. Todo lo que necesita hacer es despegar el papel de respaldo para exponer el lado adhesivo y presionarlo firmemente sobre la superficie deseada. El adhesivo se adhiere de forma rápida y segura, proporcionando una adhesión instantánea sin abrazaderas ni tiempo de secado. Esto hace que los adhesivos despegar y pegar sean ideales para reparaciones rápidas, instalaciones temporales o proyectos sensibles al tiempo.
Otra ventaja de los adhesivos de pelar y pegar es su versatilidad. Están disponibles en varias formas, como cintas, hojas o puntos, para adaptarse a diferentes aplicaciones y materiales. Ya sea que necesite colocar objetos livianos, montar decoraciones o ciertos artículos pesados, un adhesivo despegar y pegar es adecuado para la tarea. Se adhieren bien a varias superficies, como madera, metal, vidrio, plástico y tela, y ofrecen flexibilidad y compatibilidad con diferentes materiales.
Los adhesivos de despegar y pegar también son conocidos por su aplicación limpia. A diferencia de los adhesivos tradicionales que pueden ensuciar y requieren limpieza, los adhesivos despegar y pegar no dejan residuos cuando se aplican y retiran correctamente. Esto es especialmente ventajoso cuando se trabaja en superficies delicadas o acabadas que desea proteger contra daños.
Además de su facilidad de uso, los adhesivos para despegar y pegar a menudo exhiben fuertes capacidades de unión. Los adhesivos están diseñados para proporcionar una unión confiable y duradera, lo que garantiza que los elementos adjuntos permanezcan en su lugar de forma segura. Sin embargo, es esencial elegir el tipo de adhesivo adecuado para su proyecto y seguir las instrucciones del fabricante para obtener resultados óptimos.
Películas adhesivas: mejora de la eficiencia y la consistencia
Las películas adhesivas son materiales versátiles que ofrecen diversas aplicaciones en diversas industrias. Son capas delgadas de sustancias pegajosas que recubren un material de respaldo, como papel, plástico o tela. Estas películas brindan numerosos beneficios, mejorando la eficiencia y la consistencia en varios procesos. Este artículo explorará cómo las películas adhesivas mejoran la eficiencia y la consistencia en diferentes aplicaciones.
Una ventaja clave de las películas adhesivas es su facilidad de aplicación. A diferencia de los adhesivos tradicionales, que pueden requerir mezcla o equipo especializado, las películas adhesivas vienen listas para usar. Se pueden cortar fácilmente en las formas y tamaños deseados, lo que los hace ideales para una aplicación rápida y precisa. Esto ahorra tiempo y recursos en los procesos de fabricación y ensamblaje, lo que aumenta la eficiencia general.
Además, las películas adhesivas ofrecen un rendimiento de unión constante. Su espesor uniforme y sus propiedades adhesivas controladas aseguran una adhesión fiable entre diferentes materiales. Ya sea que se unan dos superficies, se laminen capas o se adhieran componentes, las películas adhesivas brindan una fuerza de unión consistente, lo que minimiza el riesgo de fallas o reprocesos. Esta consistencia mejora la calidad del producto, reduce el desperdicio y aumenta la productividad.
Otra forma en que las películas adhesivas mejoran la eficiencia es a través de su compatibilidad con los sistemas de automatización. Con la creciente tendencia de automatización en varias industrias, las películas adhesivas están diseñadas para ser compatibles con los procesos de ensamblaje y empaque robóticos. Se pueden integrar fácilmente en líneas de producción automatizadas, lo que permite operaciones de unión precisas y de alta velocidad. Esto no solo mejora la eficiencia, sino que también reduce los costos de mano de obra y los errores humanos.
Además, las películas adhesivas ofrecen una mayor eficiencia en las aplicaciones de sellado y protección. Proporcionan una barrera contra la humedad, el polvo y los contaminantes, evitando daños a componentes o productos sensibles. Ya sea para sellar dispositivos electrónicos, empacar productos alimenticios o proteger superficies contra la corrosión, las películas adhesivas ofrecen una protección confiable y consistente. Esto contribuye a la longevidad y confiabilidad de los productos, reduciendo la necesidad de mantenimiento o reemplazos frecuentes.
Además, las películas adhesivas permiten una personalización eficiente y flexibilidad de diseño. Se pueden adaptar a requisitos específicos, como diferentes fuerzas de unión, resistencia a la temperatura o propiedades ópticas. Esto permite a los fabricantes optimizar las propiedades del adhesivo en función de sus necesidades de aplicación, lo que garantiza el mejor rendimiento y fiabilidad. Además, las películas adhesivas se pueden imprimir o decorar fácilmente, lo que ofrece oportunidades de marca y atractivo estético.
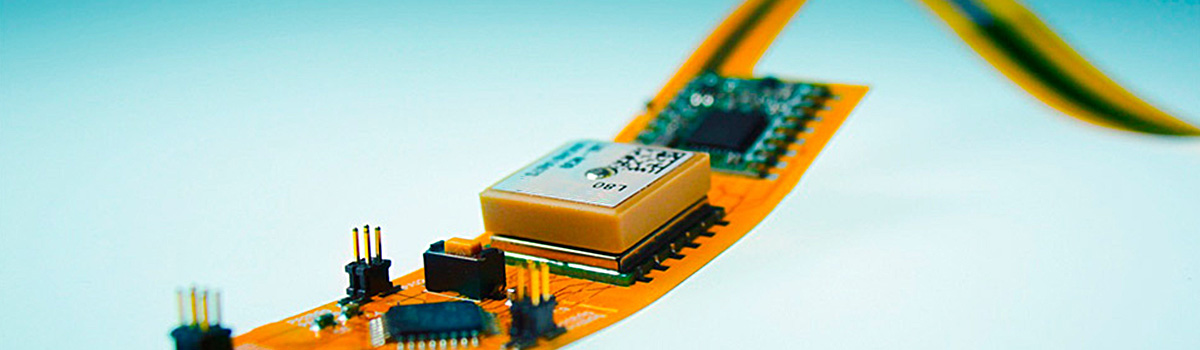
Adhesivos termofusibles: unión rápida y duradera
Los adhesivos termofusibles (HMA) son adhesivos versátiles que ofrecen soluciones de unión rápidas y duraderas en diversas industrias y aplicaciones. Estos adhesivos, o cola caliente, son materiales termoplásticos que se funden a estado líquido y se aplican fundidos. Al enfriarse, se solidifican y crean una fuerte unión entre los sustratos. Aquí hay una mirada más cercana a las características, beneficios y aplicaciones de los adhesivos de fusión en caliente.
Una de las ventajas críticas de los HMA es su capacidad de unión rápida. Estos adhesivos se licúan rápidamente cuando se calientan, lo que permite una aplicación eficiente y de alta velocidad. Eliminan la necesidad de evaporación de solventes o reacciones químicas, a diferencia de otros tipos de adhesivos. La rápida solidificación de los adhesivos de fusión en caliente da como resultado tiempos de montaje y producción más cortos, lo que aumenta la productividad y ahorra costos.
Además, los adhesivos de fusión en caliente brindan una durabilidad excepcional en las juntas unidas. Exhiben una excelente resistencia a la humedad, los productos químicos y las fluctuaciones de temperatura. Esta resiliencia los hace adecuados para entornos exigentes y aplicaciones que requieren una unión confiable y duradera. Los HMA también ofrecen flexibilidad y resistencia al impacto, lo que les permite soportar vibraciones y golpes sin comprometer la integridad de la unión.
Los HMA encuentran aplicaciones en diversas industrias, que incluyen embalaje, carpintería, automotriz, electrónica, textiles y construcción. Los adhesivos de fusión en caliente se utilizan ampliamente en el embalaje para el sellado de cajas y cajas de cartón, cierres a prueba de manipulaciones y etiquetas y cintas adhesivas. Proporcionan sellos seguros y resistentes a la manipulación, lo que garantiza la integridad del producto y evita el hurto.
Las aplicaciones de carpintería de los HMA incluyen operaciones de canteado, enchapado y laminado. La naturaleza de fraguado rápido de los adhesivos de fusión en caliente facilita procesos de línea de montaje eficientes. Crean fuertes lazos en las uniones de madera, mejorando la integridad estructural y la longevidad de los muebles y gabinetes.
Los fabricantes de automóviles confían en los adhesivos de fusión en caliente para unir molduras interiores y exteriores, mazos de cables y sellado de juntas. La durabilidad y la resistencia al calor de estos adhesivos los hacen ideales para aplicaciones automotrices, donde el rendimiento en condiciones extremas es esencial.
El ensamblaje y la fabricación de productos electrónicos a menudo utilizan adhesivos de fusión en caliente para unir componentes, unir cables y encapsular. Su capacidad para unir materiales diferentes, como plásticos, metales y vidrio, los hace adecuados para diversas aplicaciones electrónicas.
Las aplicaciones de los adhesivos de fusión en caliente para la industria textil incluyen laminación de telas, dobladillo y unión de apliques. Permiten una unión precisa y limpia sin costuras, cosidos u otros métodos mecánicos de fijación.
En el sector de la construcción, los HMA se utilizan para la instalación de pisos, paneles, aislamiento y unión de losetas. Sus características de fraguado rápido facilitan procesos de construcción rápidos y aseguran una adhesión confiable en varios materiales de construcción.
Adhesivos sensibles a la presión: asegurando una adherencia consistente
Los adhesivos sensibles a la presión (PSA) son materiales versátiles que se utilizan en diversas industrias, desde la automotriz y la electrónica hasta el embalaje y los dispositivos médicos. Estos adhesivos ofrecen ventajas únicas, como la facilidad de aplicación, la unión inmediata y la capacidad de adherirse a una amplia gama de superficies. Sin embargo, garantizar una adhesión consistente puede ser un desafío cuando se trabaja con PSA. Estas son algunas consideraciones clave para lograr una adhesión confiable y consistente con adhesivos sensibles a la presión.
- Preparación de la superficie: la preparación adecuada de la superficie es crucial para lograr una adhesión consistente con los PSA. Las superficies deben estar limpias, secas y libres de polvo, aceite, grasa y contaminantes de humedad. La limpieza de la superficie con solventes o limpiadores adecuados y el uso de técnicas como la abrasión o el tratamiento con plasma pueden mejorar la adhesión al mejorar la energía de la superficie y eliminar las barreras potenciales para la unión.
- Compatibilidad del material: es esencial asegurarse de que el PSA sea compatible con el material del sustrato. Algunos PSA pueden exhibir problemas de adhesión o compatibilidad deficientes con ciertas superficies. Comprender la composición química y las propiedades tanto del adhesivo como del sustrato puede ayudar a seleccionar el adhesivo adecuado para la aplicación específica, lo que garantiza una adhesión uniforme.
- Técnica de aplicación: La técnica de aplicación juega un papel importante en el logro de una adhesión consistente. La presión, la temperatura y el tiempo de permanencia durante la aplicación pueden afectar la fuerza de la unión. Es fundamental seguir las recomendaciones del fabricante con respecto a los parámetros de aplicación, incluida la presión adecuada para aplicar y el rango de temperatura recomendado para la unión.
- Tiempo de curado: los PSA generalmente requieren una cierta cantidad de tiempo para desarrollar su fuerza adhesiva completa. Este tiempo de curado o “permanencia” permite que el adhesivo fluya y forme fuertes enlaces con el sustrato. Es esencial permitir un tiempo de curado suficiente antes de someter el conjunto adherido a tensión o carga. Apurar el proceso puede resultar en una adhesión más débil o incluso en una falla del adhesivo.
- Factores ambientales: las condiciones ambientales pueden afectar el rendimiento de los PSA. Factores como la temperatura, la humedad y la exposición a productos químicos o radiación UV pueden afectar las propiedades del adhesivo y el rendimiento de la adhesión. Comprender las condiciones ambientales específicas a las que estará expuesto el adhesivo y seleccionar un adhesivo con la resistencia adecuada a estos factores puede ayudar a garantizar una adhesión constante a lo largo del tiempo.
- Pruebas y control de calidad: las pruebas periódicas y las medidas de control de calidad son esenciales para garantizar una adhesión uniforme. Varios métodos de prueba, como la adherencia al pelado, la resistencia al corte y la pegajosidad, pueden evaluar el rendimiento del adhesivo. Establecer protocolos de prueba adecuados y realizar controles de calidad regulares durante la producción puede ayudar a identificar cualquier inconsistencia o problema desde el principio y garantizar una adhesión uniforme en el producto final.
- Almacenamiento y vida útil: Las condiciones de almacenamiento adecuadas y el cumplimiento de las pautas de vida útil son esenciales para mantener el rendimiento del adhesivo. Los PSA pueden degradarse con el tiempo debido a la exposición al calor, la luz o el aire, lo que afecta sus propiedades adhesivas. Almacenar los bonos en ambientes controlados y usarlos dentro de su vida útil recomendada puede ayudar a mantener una adhesión consistente.
Técnicas de dosificación de adhesivos: precisión y eficiencia
Las técnicas de dosificación de adhesivos son cruciales en varias industrias, ya que garantizan la precisión y la eficiencia en las aplicaciones de unión. Ya sea para la fabricación, el ensamblaje o las reparaciones, el método de dosificación adecuado puede afectar significativamente la calidad y la confiabilidad de las uniones adhesivas. Este artículo explorará técnicas críticas que ayudan a lograr precisión y eficiencia en la aplicación de adhesivos dentro de un número limitado de palabras.
- Dosificación manual: La dosificación manual de adhesivo se emplea comúnmente en operaciones a pequeña escala o aplicaciones complejas. Implica el uso de dispositivos portátiles como jeringas, botellas exprimibles o cepillos para aplicar el adhesivo con precisión. Si bien este método ofrece flexibilidad y control, depende de la habilidad y consistencia del operador.
- Dosificación por tiempo/presión: La dosificación por tiempo/presión es una técnica ampliamente utilizada que proporciona una aplicación de adhesivo constante y controlada. Se trata de utilizar dosificadores neumáticos o eléctricos con reguladores de presión y temporizadores. Al ajustar el tiempo y la presión de dosificación, los operadores pueden controlar con precisión la cantidad de adhesivo aplicada. Esta técnica es adecuada para adhesivos de viscosidad media a alta.
- Jetting: Jetting es una técnica de dosificación que utiliza una corriente de adhesivo de alta velocidad para aplicar cantidades pequeñas y precisas de adhesivo sobre la superficie objetivo. Se usa comúnmente en aplicaciones que requieren una colocación rápida y precisa, como ensamblaje electrónico o microunión. Los sistemas de inyección utilizan accionamiento piezoeléctrico o neumático para crear gotas de adhesivo controladas.
- Dispensación por aspersión: La dosificación por aspersión es una técnica eficiente para cubrir grandes áreas o lograr una cobertura uniforme. Se trata de atomizar el adhesivo en finas gotas y dirigirlas a la superficie utilizando presión de aire o una pistola de pulverización automática. La dosificación en aerosol se usa comúnmente en las industrias automotriz, de carpintería o de empaque, donde se requiere una cobertura rápida y uniforme.
- Dosificación robótica: Los sistemas de dosificación robótica ofrecen aplicaciones adhesivas precisas y repetibles a través de la automatización programable. Están equipados con sensores avanzados y válvulas dispensadoras que se pueden programar para seguir patrones y contornos complejos. La dosificación robótica garantiza la consistencia y la precisión, lo que la hace ideal para líneas de producción de alto volumen y procesos de ensamblaje complejos.
- Revestimiento de película/remolino: El revestimiento de película o remolino es una técnica utilizada para aplicar una capa uniforme de adhesivo sobre un sustrato. Implica el uso de un mecanismo giratorio o aplicador para extender el adhesivo en una película delgada y continua. Este método se emplea comúnmente en las industrias automotriz, aeroespacial y de la construcción, donde el espesor del adhesivo controlado es fundamental para un rendimiento óptimo.
Desafíos en la aplicación de adhesivos de unión FPC
La aplicación de adhesivos de unión FPC (circuito impreso flexible) plantea varios desafíos que deben abordarse para una unión exitosa y un rendimiento confiable. Estos desafíos se derivan principalmente de las propiedades y requisitos únicos de los FPC. En esta respuesta, describiré algunos desafíos clave que se encuentran en la aplicación de adhesivos de unión FPC.
- Compatibilidad de sustratos: los FPC están hechos de materiales flexibles como poliimida, poliéster o cobre delgado, con características de superficie diferentes a las de los sustratos rígidos. El adhesivo de unión debe ser compatible con el material FPC para asegurar una adhesión adecuada sin causar delaminación o daño al sustrato.
- Preparación de la superficie: la preparación adecuada de la superficie es fundamental para la unión adhesiva. Las superficies de FPC a menudo tienen residuos, aceites o contaminantes que pueden dificultar la adhesión. El desafío radica en seleccionar el método de limpieza o tratamiento de superficie correcto para eliminar estas impurezas sin comprometer la integridad del FPC.
- Control del grosor de la línea de unión: Lograr un grosor uniforme de la línea de unión es esencial para un rendimiento confiable. El grosor del adhesivo inconsistente puede provocar variaciones en la conductividad eléctrica, la resistencia mecánica y la gestión térmica. Asegurar un control preciso sobre el grosor de la línea de unión puede ser un desafío debido a la naturaleza flexible de los FPC.
- Gestión térmica: los FPC se utilizan a menudo en aplicaciones en las que se esperan variaciones de temperatura. El adhesivo utilizado para la unión debe tener una buena conductividad térmica para disipar el calor de manera efectiva, evitando puntos calientes localizados que podrían dañar el FPC o sus componentes. Lograr una gestión térmica óptima sin comprometer la flexibilidad y las propiedades eléctricas del FPC es un desafío.
- Curado de adhesivos: los adhesivos de unión FPC generalmente requieren procesos de curado como calor o UV. El desafío consistía en garantizar un curado uniforme y completo en toda la línea de unión, especialmente en diseños de FPC complejos o densamente empaquetados. Un curado inadecuado puede dar como resultado una adhesión más fuerte o una unión incompleta, lo que genera problemas de confiabilidad.
- Flexibilidad y durabilidad: los FPC están diseñados para ser flexibles y el adhesivo de unión debe adaptarse a esta flexibilidad sin comprometer su integridad. La unión debe resistir la flexión, la flexión y el estiramiento repetidos sin agrietarse, deslaminarse o perder la fuerza de adhesión. Encontrar un enlace que pueda mantener tanto la flexibilidad como la durabilidad puede ser un desafío.
- Conductividad eléctrica: los FPC a menudo transportan señales eléctricas, lo que hace que la conductividad eléctrica sea un requisito crítico. El adhesivo de unión no debe presentar alta resistencia que pueda interferir con el desempeño del circuito. Lograr una buena conductividad eléctrica a lo largo de la línea de enlace mientras se garantiza la integridad mecánica plantea un desafío.
- Automatización de procesos: la automatización del proceso de aplicación de adhesivo se vuelve necesaria en industrias donde la unión FPC se realiza a escala. El desafío radica en desarrollar sistemas automatizados que puedan aplicar el adhesivo de manera constante con precisión y eficiencia, teniendo en cuenta las variaciones en los tamaños, formas y diseños de FPC.
Abordar estos desafíos requiere una comprensión integral de los materiales FPC, los adhesivos de unión y los requisitos específicos de la aplicación. A menudo implica una cuidadosa selección de materiales, optimización de procesos y pruebas para garantizar la compatibilidad, el rendimiento y la confiabilidad del adhesivo en las aplicaciones de unión FPC.
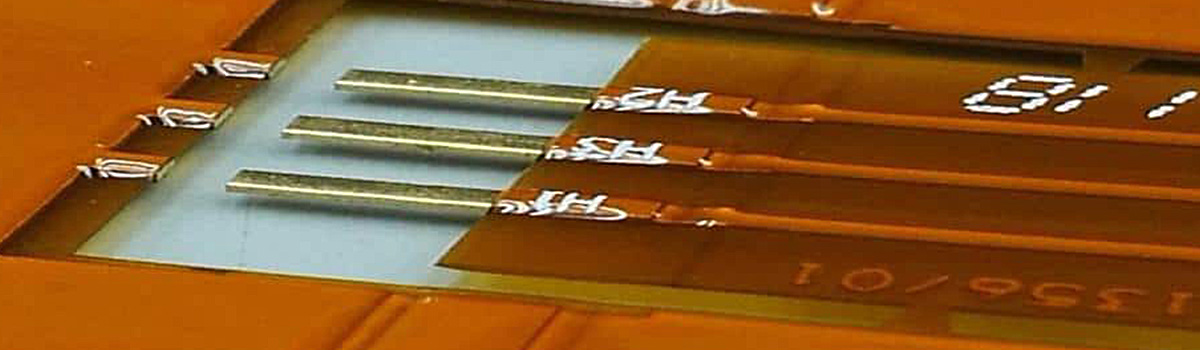
Pruebas de confiabilidad: evaluación del rendimiento del adhesivo
Las pruebas de confiabilidad son un paso crucial para evaluar el desempeño de los adhesivos. Los adhesivos se utilizan ampliamente en diversas industrias, incluidas la automotriz, aeroespacial, electrónica y de construcción, para unir diferentes materiales. La confiabilidad de las uniones adhesivas es esencial para garantizar la seguridad, la durabilidad y el rendimiento general del producto final.
Las pruebas de confiabilidad implican someter las uniones adhesivas a diversas condiciones y factores estresantes que simulan entornos y escenarios de uso del mundo real. El objetivo es evaluar la capacidad del adhesivo para mantener su fuerza de unión e integridad a lo largo del tiempo. Estos son algunos aspectos clave a tener en cuenta al evaluar el rendimiento del adhesivo en las pruebas de confiabilidad:
- Fuerza de unión: La fuerza de unión inicial del adhesivo se evalúa mediante pruebas estandarizadas, como pruebas de cizallamiento, desprendimiento o tracción. Estas pruebas miden la fuerza requerida para romper la unión adhesiva. Proporciona una línea de base para la comparación con la fuerza de unión después de la exposición a diferentes condiciones.
- Exposición ambiental: los adhesivos suelen estar expuestos a condiciones ambientales adversas, como temperaturas extremas, humedad, radiación ultravioleta y productos químicos. Las pruebas de confiabilidad implican someter muestras de adhesivo a pruebas de envejecimiento acelerado que simulan estas condiciones durante un período prolongado. Esto ayuda a evaluar la resistencia del adhesivo a la degradación ambiental y su capacidad para mantener la fuerza de unión en condiciones adversas.
- Ciclo térmico: las variaciones de temperatura pueden causar la expansión y contracción de los materiales, lo que puede estresar las uniones adhesivas. Las pruebas de ciclos térmicos implican someter muestras de adhesivo a ciclos de temperatura repetidos, desde extremos bajos hasta extremos altos, para evaluar la resistencia del adhesivo al estrés térmico y su capacidad para mantener la integridad de la unión.
- Esfuerzo mecánico: las uniones adhesivas pueden experimentar diferentes tipos de estrés mecánico durante el servicio, como tensión, compresión, corte y vibración. Las pruebas de confiabilidad implican someter las muestras de adhesivo a tensión mecánica a través de pruebas de fatiga cíclica, impacto o flexión. Estas pruebas ayudan a evaluar la capacidad del adhesivo para resistir la carga automática sin que falle la unión.
- Durabilidad y envejecimiento: se espera que las uniones adhesivas tengan una durabilidad a largo plazo y resistan la degradación con el tiempo. Las pruebas de confiabilidad incluyen pruebas de envejecimiento a largo plazo que simulan la vida útil anticipada del producto. Esto puede implicar someter las muestras de adhesivo a una exposición prolongada a factores ambientales, como la temperatura, la humedad y la radiación ultravioleta, y evaluar periódicamente la fuerza y la integridad de la unión.
- Compatibilidad: los adhesivos deben ser compatibles con los materiales a los que están destinados a unir. Las pruebas de confiabilidad implican evaluar la compatibilidad del adhesivo con diferentes sustratos, incluidos metales, plásticos, compuestos y otros materiales comúnmente utilizados en la industria. Las pruebas de compatibilidad evalúan la fuerza de unión del adhesivo, la resistencia a la interacción química y cualquier efecto adverso sobre el sustrato.
Las pruebas de confiabilidad brindan información valiosa sobre el rendimiento y las limitaciones de los adhesivos en diversas condiciones. Ayuda a los fabricantes a seleccionar el adhesivo más adecuado para su aplicación y garantiza su fiabilidad y durabilidad en escenarios del mundo real. Al realizar rigurosas pruebas de confiabilidad, los fabricantes pueden mitigar el riesgo de fallas en la unión adhesiva, mejorar la calidad del producto y mejorar la satisfacción del cliente.
Consideraciones ambientales en el adhesivo de unión FPC
Los adhesivos de unión FPC (Circuito impreso flexible) juegan un papel fundamental en el ensamblaje y la confiabilidad de los dispositivos electrónicos. A medida que la conciencia ambiental y la sustentabilidad se vuelven cada vez más importantes, es esencial considerar el impacto ecológico de estos adhesivos. Aquí hay algunas consideraciones ambientales críticas relacionadas con los adhesivos de unión FPC:
- Toxicidad: una de las principales preocupaciones es la toxicidad del adhesivo y sus componentes. Los adhesivos pueden contener sustancias químicas nocivas, como compuestos orgánicos volátiles (COV) o contaminantes peligrosos del aire (HAP). Estas sustancias pueden tener efectos perjudiciales para la salud humana y el medio ambiente. Los fabricantes deben esforzarse por minimizar o eliminar los productos químicos tóxicos en sus formulaciones adhesivas.
- Emisiones y calidad del aire: durante los procesos de fabricación y aplicación, los adhesivos de unión FPC pueden liberar COV y otros contaminantes del aire a la atmósfera. Estas emisiones contribuyen a la contaminación del aire y pueden afectar negativamente la calidad del aire. Los fabricantes de adhesivos conscientes del medio ambiente tienen como objetivo reducir estas emisiones mediante la formulación de adhesivos de bajo VOC o cero VOC.
- Consumo de energía: la producción de adhesivos de unión FPC requiere energía, que a menudo proviene de fuentes no renovables. Para minimizar el impacto ambiental, los fabricantes deben implementar procesos de eficiencia energética y explorar el uso de fuentes de energía renovables.
- Generación de residuos: los procesos de aplicación de adhesivos pueden generar residuos, incluido el exceso de material adhesivo, embalaje y materiales de limpieza. Deben seguirse prácticas adecuadas de gestión de residuos, como el reciclaje o la reutilización de materiales de desecho siempre que sea posible. Además, los fabricantes deben explorar el desarrollo de adhesivos con una vida útil más larga para reducir el desperdicio de productos vencidos o sin usar.
- Consideraciones sobre el final de la vida útil: La eliminación de dispositivos electrónicos que contienen adhesivos de unión FPC es una preocupación ambiental importante. Los adhesivos que no se degradan fácilmente o que tienen componentes peligrosos pueden contribuir a la contaminación cuando se desechan los dispositivos. Los fabricantes de adhesivos deben esforzarse por desarrollar productos respetuosos con el medio ambiente que sean compatibles con los procesos de reciclaje o eliminación, como adhesivos que se puedan separar fácilmente de las placas de circuitos durante el reciclaje.
- Sostenibilidad e iniciativas ecológicas: los fabricantes de adhesivos deben incorporar la sostenibilidad en sus prácticas comerciales. Esto puede incluir el uso de materias primas renovables, la implementación de procesos de fabricación ecológicos y el cumplimiento de estándares y certificaciones ambientales reconocidos. Además, las empresas pueden participar en iniciativas ecológicas, como programas de devolución de productos o asociaciones con instalaciones de reciclaje.
- Evaluación del ciclo de vida: realizar una evaluación integral del ciclo de vida (LCA) de los adhesivos de unión FPC es crucial para comprender su impacto ambiental desde la extracción de la materia prima hasta su eliminación. Los LCA ayudan a identificar áreas en las que se pueden realizar mejoras, como la reducción de las emisiones de gases de efecto invernadero, la minimización del consumo de recursos y la mejora de la reciclabilidad.
Tendencias e innovaciones en el adhesivo de unión FPC
Los adhesivos de unión FPC (Circuito Impreso Flexible) evolucionan constantemente, impulsados por la demanda de mayor rendimiento, miniaturización y mayor confiabilidad en los dispositivos electrónicos. Aquí hay algunas tendencias e innovaciones notables en los adhesivos de unión FPC:
- Miniaturización y delgadez: a medida que los dispositivos electrónicos se vuelven más pequeños y delgados, existe una necesidad creciente de adhesivos de unión FPC para adaptarse a estos requisitos de factor de forma. Los fabricantes están desarrollando adhesivos ultradelgados y de bajo perfil que brindan una unión fuerte y minimizan el grosor total del ensamblaje.
- Resistencia a altas temperaturas: muchos dispositivos electrónicos, en particular los de aplicaciones automotrices, aeroespaciales e industriales, funcionan en entornos de alta temperatura. Se están desarrollando adhesivos de unión FPC con mayor resistencia al calor para garantizar un rendimiento confiable en condiciones de temperatura extrema, evitando la delaminación o la falla de la unión.
- Curado a baja presión: los procesos de curado de adhesivos tradicionales a menudo requieren altas temperaturas o largos tiempos de curado, lo que puede ser un desafío para los componentes sensibles al calor o los sustratos delicados. Las innovaciones en las técnicas de baja presión, como los adhesivos de curado por UV o por humedad, ofrecen opciones de curado más suaves, lo que permite la compatibilidad con componentes y sustratos sensibles a la temperatura.
- Adhesivos conductivos: La demanda de adhesivos de unión FPC con conductividad eléctrica está aumentando en aplicaciones que requieren conexiones eléctricas entre elementos de circuitos. Los adhesivos conductivos eliminan la necesidad de diferentes procesos de soldadura, lo que permite un ensamblaje más rápido y reduce el riesgo de daño térmico a los componentes sensibles.
- Flexibilidad y durabilidad mejoradas: la flexibilidad y la durabilidad son cruciales para que los adhesivos de unión FPC resistan la flexión, la torsión y la vibración en dispositivos electrónicos flexibles. Los avances en la química de polímeros y las técnicas de formulación dan como resultado adhesivos con mayor flexibilidad, elongación y resistencia a la tensión mecánica, lo que garantiza una unión fiable en entornos dinámicos.
- Respeto al medio ambiente: Las consideraciones ambientales, incluido el uso de materias primas sostenibles y la reducción de sustancias tóxicas, son cada vez más importantes en el desarrollo de adhesivos. Los fabricantes están explorando materiales renovables y de base biológica como alternativas a los ingredientes derivados del petróleo. Además, se están desarrollando procesos de fabricación ecológicos y formulaciones de adhesivos reciclables para minimizar el impacto ambiental.
- Dispensación y aplicación mejoradas: la aplicación de adhesivo eficiente y precisa es crucial para lograr uniones consistentes y confiables. Las innovaciones en las tecnologías de dosificación, como los sistemas de dosificación automatizados y los métodos de inyección, permiten una deposición controlada y precisa de adhesivos, incluso en diseños complejos de FPC con componentes de paso delicados.
- Tecnología de película adhesiva: las películas adhesivas están ganando popularidad en la unión FPC debido a su fácil manejo y colocación precisa. Estas películas preformadas ofrecen un espesor de adhesivo uniforme, excelentes propiedades humectantes y procesos de ensamblaje simplificados. Los fabricantes mejoran continuamente las formulaciones de películas adhesivas para mejorar su rendimiento de unión y compatibilidad con varios sustratos.
- Mejoras en la confiabilidad: para garantizar la confiabilidad a largo plazo, los adhesivos de unión FPC se están desarrollando con una mayor resistencia a factores como la humedad, los productos químicos y el envejecimiento. Estos adhesivos se someten a pruebas rigurosas para evaluar su rendimiento en condiciones ambientales adversas, lo que garantiza una funcionalidad uniforme y la integridad de la unión durante la vida útil del producto.
- Personalización y soluciones para aplicaciones específicas: los adhesivos de unión FPC se están adaptando para cumplir con los requisitos específicos de diferentes aplicaciones, como la automotriz, la electrónica de consumo, los dispositivos médicos y la tecnología portátil. Los fabricantes están colaborando estrechamente con los diseñadores y fabricantes de dispositivos para desarrollar soluciones adhesivas personalizadas que aborden los desafíos únicos y las demandas de rendimiento de cada aplicación.
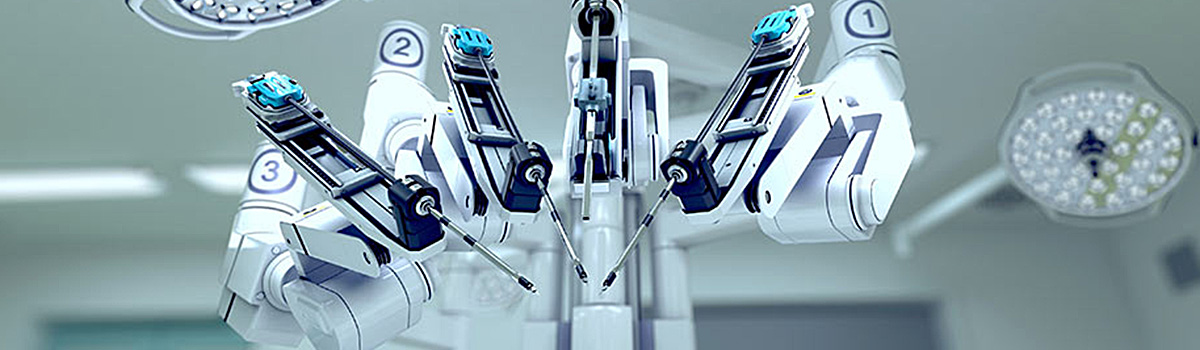
Áreas de aplicación: electrónica de consumo, automotriz, dispositivos médicos y más
Electrónica de consumo: Los productos electrónicos de consumo abarcan una amplia gama de productos diseñados para uso personal y entretenimiento. Estos incluyen teléfonos inteligentes, tabletas, computadoras portátiles, consolas de juegos, televisores inteligentes, dispositivos domésticos inteligentes, dispositivos portátiles y más. La aplicación de la electrónica de consumo ha revolucionado la forma en que las personas se comunican, trabajan y se entretienen. Los avances tecnológicos han hecho que los productos electrónicos de consumo sean más potentes, compactos y asequibles, proporcionando a los usuarios una conectividad perfecta, experiencias inmersivas y comodidad.
Automotor: La industria automotriz ha sido testigo de avances significativos en los últimos años, impulsados principalmente por la integración de tecnología. Desde vehículos eléctricos (EV) hasta sistemas de conducción autónomos, las aplicaciones automotrices han transformado la forma en que viajamos. Los coches eléctricos están ganando popularidad debido a su naturaleza ecológica y la reducción de las emisiones de carbono. Además, los fabricantes de automóviles están incorporando características innovadoras como sistemas avanzados de asistencia al conductor (ADAS), conectividad, sistemas de información y entretenimiento y telemática para mejorar la experiencia de conducción, mejorar la seguridad y permitir una gestión eficiente del vehículo.
Dispositivos médicos: Los dispositivos médicos han jugado un papel crucial en el diagnóstico, seguimiento y tratamiento de diversas afecciones médicas. Van desde dispositivos simples como termómetros y monitores de presión arterial hasta equipos avanzados como máquinas de resonancia magnética y sistemas quirúrgicos robóticos. Los dispositivos médicos permiten a los profesionales de la salud proporcionar diagnósticos precisos, realizar procedimientos mínimamente invasivos y monitorear la salud del paciente de forma remota. Han revolucionado la industria de la atención médica, mejorando los resultados de los pacientes, reduciendo las estadías en el hospital y mejorando la calidad general de la atención.
Internet de las cosas (IoT): El Internet de las cosas (IoT) es una red de dispositivos interconectados integrados con sensores, software y capacidades de conectividad. Permite el intercambio de datos y la comunicación entre dispositivos, lo que lleva a la automatización, el análisis de datos y una mejor toma de decisiones. IoT tiene aplicaciones en varias industrias, incluida la atención médica, la agricultura, la fabricación y la energía. En el cuidado de la salud, los dispositivos IoT pueden monitorear los signos vitales de los pacientes, rastrear la adherencia a los medicamentos y permitir el monitoreo remoto de pacientes. Los dispositivos IoT pueden optimizar el riego, monitorear las condiciones del suelo y mejorar el manejo de cultivos en la agricultura. IoT tiene el potencial de revolucionar las industrias haciéndolas más eficientes, sostenibles y basadas en datos.
Automatización industrial: La automatización industrial implica el uso de tecnología y sistemas de control para automatizar procesos y tareas industriales. Esto incluye robótica, sistemas de visión artificial, sensores y controladores lógicos programables (PLC). La automatización industrial aumenta la productividad, mejora la seguridad, reduce los costos operativos y encuentra aplicaciones en la fabricación, la logística, la energía y otros sectores. Con la integración de inteligencia artificial (IA) y aprendizaje automático (ML), la automatización industrial puede optimizar procesos, detectar anomalías y permitir el mantenimiento predictivo, mejorando la eficiencia y reduciendo el tiempo de inactividad.
Perspectivas y oportunidades futuras
El adhesivo de unión FPC (Circuito Impreso Flexible) es un componente crítico en la fabricación de dispositivos electrónicos. Es crucial para garantizar conexiones fiables y robustas entre los circuitos flexibles y otras partes. A medida que miramos hacia el futuro, vale la pena considerar varias perspectivas y oportunidades para el adhesivo de unión FPC.
- Avances en electrónica flexible: el campo de la electrónica flexible está evolucionando rápidamente, con una demanda creciente de pantallas flexibles, dispositivos portátiles y textiles inteligentes. Los adhesivos de unión FPC seguirán estando en orden para permitir el montaje y la interconexión de circuitos flexibles en estas aplicaciones innovadoras.
- Miniaturización y dispositivos más delgados: A medida que los productos electrónicos de consumo se vuelven cada vez más compactos y delgados, las soluciones de interconexión más delgadas y flexibles son primordiales. Los adhesivos de unión FPC pueden facilitar el montaje de circuitos flexibles ultrafinos, creando dispositivos más elegantes y ligeros.
- Rendimiento de unión mejorado: los fabricantes buscan continuamente soluciones adhesivas que ofrezcan un rendimiento de unión superior, como alta resistencia al corte, excelente conductividad eléctrica y estabilidad térmica. Es probable que los futuros adhesivos de unión FPC incorporen materiales y formulaciones avanzados para cumplir con estos exigentes requisitos.
- Integración con procesos de fabricación avanzados: las tecnologías de fabricación emergentes como la impresión 3D, el procesamiento de rollo a rollo y la integración híbrida abren nuevas posibilidades para producir circuitos flexibles. Los adhesivos de unión FPC deben adaptarse y ser compatibles con estos procesos de fabricación, ofreciendo una adherencia y fiabilidad optimizadas.
- Electrónica híbrida flexible (FHE): FHE combina la electrónica rígida tradicional con componentes adaptables, creando dispositivos con factores de forma y funcionalidades únicos. Los adhesivos de unión FPC serán fundamentales para ensamblar estos sistemas híbridos, conectando a la perfección elementos flexibles y rígidos.
- Consideraciones ambientales y de sustentabilidad: El creciente enfoque en la sustentabilidad y la responsabilidad ambiental presenta una oportunidad para desarrollar adhesivos de unión FPC ecológicos. Las futuras formulaciones pueden incorporar materiales renovables o reciclables, reduciendo el impacto ambiental de los desechos electrónicos.
- Integración de funciones inteligentes: con el auge del Internet de las cosas (IoT) y los dispositivos interconectados, los adhesivos de unión FPC pueden incorporar funciones inteligentes como sensores integrados, capacidades de autorreparación o propiedades de gestión térmica. Estos avances mejorarían la funcionalidad y la confiabilidad de los dispositivos electrónicos.
- Aplicaciones médicas y de atención médica: el campo médico está experimentando un aumento en los dispositivos portátiles, los sensores implantables y las tecnologías inteligentes de atención médica. Los adhesivos de unión FPC que son biocompatibles, esterilizables y capaces de adherirse a varios sustratos encontrarán aplicaciones significativas en este dominio.
- Industrias automotriz y aeroespacial: Los sectores automotriz y aeroespacial adoptan cada vez más circuitos flexibles por sus ventajas de ligereza y ahorro de espacio. Los adhesivos de unión FPC que pueden soportar temperaturas extremas, vibraciones y tensiones mecánicas tendrán una gran demanda en estos entornos exigentes.
- Investigación y desarrollo: Los continuos esfuerzos de investigación y desarrollo en los adhesivos de unión FPC conducirán a nuevos avances. Las innovaciones en la química de los adhesivos, las técnicas de fabricación y la optimización de procesos impulsarán a la industria hacia adelante, permitiendo nuevas aplicaciones y un rendimiento mejorado.
Importancia de la colaboración en el avance de la tecnología adhesiva de unión FPC
La colaboración es fundamental en el avance de la tecnología de adhesivos de unión FPC (Flexible Printed Circuit). Permite el intercambio de conocimientos, recursos y experiencia entre diferentes partes interesadas, lo que conduce a una innovación y un progreso acelerados. Estas son las razones clave que destacan la importancia de la colaboración en el avance de la tecnología de adhesivos de unión FPC:
- Experiencia interdisciplinaria: la tecnología de adhesivos de unión FPC involucra varios dominios, incluida la ciencia de los materiales, la química, la fabricación de productos electrónicos y la ingeniería. La colaboración reúne a expertos de estos diversos campos, fomentando enfoques interdisciplinarios para la resolución de problemas. Al combinar sus conocimientos y perspectivas, los investigadores y los profesionales de la industria pueden abordar desafíos complejos y desarrollar soluciones novedosas de manera más efectiva.
- Intercambio de conocimientos: la colaboración facilita el intercambio de información, los resultados de la investigación y las mejores prácticas entre diferentes entidades. Los fabricantes, proveedores, investigadores e instituciones académicas pueden colaborar para difundir información valiosa y conocimientos técnicos sobre la tecnología de adhesivos de unión FPC. Este conocimiento compartido ayuda a evitar esfuerzos redundantes, promueve la estandarización y acelera el desarrollo general.
- Acceso a recursos: los esfuerzos de colaboración permiten el acceso a una gama más amplia de recursos, incluidos fondos, equipos, instalaciones y materiales. Asociarse con organizaciones, institutos de investigación o agencias gubernamentales puede proporcionar acceso a recursos especializados que pueden no estar disponibles individualmente. Este acceso permite una experimentación, prueba y creación de prototipos más amplias, lo que lleva a mejores formulaciones de adhesivos de unión FPC y procesos de fabricación.
- Innovación acelerada: la colaboración fomenta un entorno de innovación abierta y creatividad. Al reunir diversas perspectivas y conocimientos, pueden surgir nuevas ideas y conceptos, ampliando los límites de la tecnología de adhesivos de unión FPC. Los proyectos colaborativos también pueden aprovechar las fortalezas de cada socio, combinando sus capacidades y recursos únicos para desarrollar soluciones innovadoras a un ritmo acelerado.
- Información del mercado y tendencias de la industria: la colaboración con socios de la industria y usuarios finales proporciona información valiosa sobre las demandas del mercado, las tendencias emergentes y los requisitos de los clientes. Esta comprensión ayuda a alinear el desarrollo de la tecnología de adhesivos de unión FPC con las necesidades cambiantes de la industria. Los esfuerzos de colaboración permiten una retroalimentación y validación tempranas, lo que garantiza que las soluciones desarrolladas sean prácticas, relevantes y comercialmente viables.
- Garantía de calidad y estandarización: la colaboración facilita el establecimiento de medidas de garantía de calidad y estándares de la industria para la tecnología de adhesivos de unión FPC. La asociación con organizaciones de estándares y organismos reguladores garantiza que los adhesivos desarrollados cumplan con los requisitos de seguridad, confiabilidad y rendimiento. La colaboración también permite compartir metodologías de prueba y protocolos de validación, lo que lleva a procesos de vinculación más consistentes y estandarizados.
- Validación y aplicación en el mundo real: la colaboración con usuarios finales, fabricantes e integradores de sistemas permite la confirmación de la tecnología de adhesivos de unión FPC en aplicaciones del mundo real. Al trabajar juntos, los fabricantes de adhesivos pueden obtener valiosos comentarios sobre el rendimiento, la usabilidad y la capacidad de fabricación. Este circuito de retroalimentación ayuda a refinar y mejorar las formulaciones adhesivas, asegurando su idoneidad para diversas aplicaciones y entornos.
- Mitigación de riesgos: la colaboración distribuye los riesgos asociados con los esfuerzos de investigación y desarrollo. Los socios pueden abordar los desafíos de manera colectiva y mitigar los riesgos individuales al aunar recursos y experiencia. La colaboración también permite compartir la propiedad intelectual y los derechos de patente, fomentando un entorno más cooperativo y menos competitivo.
Conclusión
El adhesivo de unión FPC es vital para permitir la flexibilidad y confiabilidad en los dispositivos electrónicos. La capacidad de estos adhesivos para proporcionar fuertes capacidades de unión, aislamiento eléctrico y protección contra factores ambientales mientras aseguran la flexibilidad y durabilidad de las placas FPC es crucial en la fabricación y ensamblaje de varios dispositivos electrónicos. A medida que avanza la tecnología, el desarrollo de soluciones adhesivas innovadoras y la colaboración entre fabricantes, investigadores y usuarios finales serán cruciales para satisfacer las crecientes demandas y desafíos de la industria electrónica. Al aprovechar el potencial del adhesivo de unión FPC, podemos allanar el camino para dispositivos electrónicos aún más flexibles, duraderos y confiables que impulsen nuestro mundo moderno.