Adhesivo de unión eléctrica
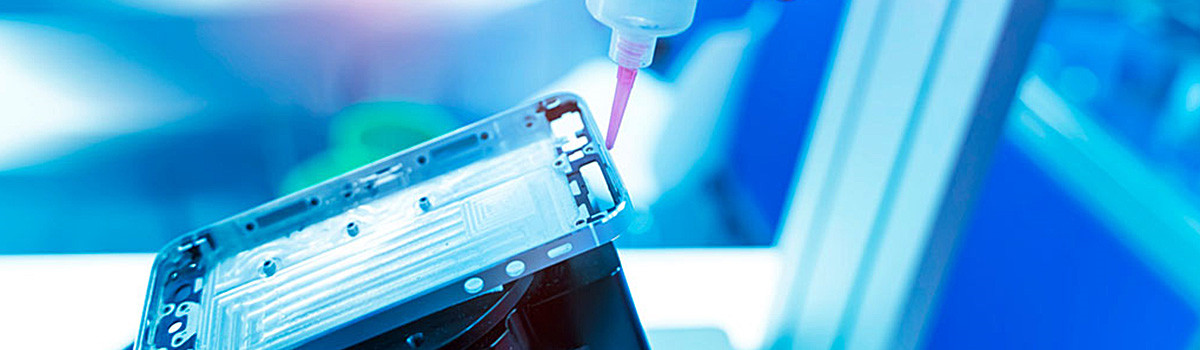
Los adhesivos de unión eléctrica son adhesivos especializados que se utilizan para unir y sellar aplicaciones eléctricas. Ellos proveen:
- Excelente conductividad eléctrica y estabilidad térmica.
- Haciéndolos ideales para dispositivos electrónicos.
- Componentes automotrices.
- Aplicaciones aeroespaciales.
Estos adhesivos desempeñan un papel fundamental para garantizar la seguridad y la fiabilidad de los sistemas eléctricos al proporcionar una unión segura y evitar la formación de arcos eléctricos o chispas.
¿Qué son los adhesivos de unión eléctrica?
Los adhesivos de unión eléctrica son adhesivos especializados que se utilizan en aplicaciones eléctricas y electrónicas para crear una unión segura entre diferentes componentes conductores. Estos adhesivos están diseñados para proporcionar conexiones eléctricas confiables, garantizar la conexión a tierra y proteger contra interferencias electromagnéticas (EMI). Son cruciales en diversas industrias, incluidas la automotriz, la aeroespacial, las telecomunicaciones y la electrónica de consumo.
La función principal de los adhesivos para conexiones eléctricas es establecer una ruta de baja resistencia entre dos o más superficies conductoras, como componentes metálicos o placas de circuitos. Esta ruta permite la transferencia eficiente de corriente eléctrica, ayuda a prevenir descargas estáticas y reduce el riesgo de fallas eléctricas. Al crear una unión sólida, estos adhesivos también ofrecen soporte mecánico y mejoran la durabilidad general de los componentes ensamblados.
Varias características vitales hacen que los adhesivos de unión eléctrica sean adecuados para las aplicaciones previstas. En primer lugar, tienen una excelente conductividad eléctrica, lo que significa que pueden conducir la electricidad de manera efectiva, minimizando la resistencia y asegurando una conexión confiable. Los rellenos conductores como plata, cobre o grafito a menudo se incorporan a la formulación del adhesivo para mejorar la conductividad.
En segundo lugar, los adhesivos de unión eléctrica suelen tener buenas propiedades de conductividad térmica. Esto les permite disipar el calor generado por los componentes eléctricos, evitando el sobrecalentamiento y posibles daños a los dispositivos electrónicos sensibles.
Además, estos adhesivos están formulados para tener alta resistencia e integridad de unión. Pueden soportar tensiones mecánicas, vibraciones y ciclos térmicos sin comprometer la conexión eléctrica. Esto es crucial, especialmente en aplicaciones donde los componentes unidos pueden estar expuestos a condiciones ambientales adversas.
Los adhesivos de unión eléctrica vienen en varias formas, incluidas pastas, películas, cintas o líquidos. La elección del adhesivo depende de factores como los requisitos de la aplicación, el tipo de materiales que se van a unir y el proceso de montaje. Por ejemplo, las películas o cintas adhesivas conductoras se usan comúnmente para ensamblar circuitos flexibles. Por el contrario, los adhesivos en pasta conductora se utilizan a menudo para unir componentes de montaje superficial en placas de circuito impreso.
Además de proporcionar unión eléctrica y mecánica, algunos adhesivos ofrecen propiedades de protección contra EMI. Contienen rellenos conductores que crean una barrera conductora, evitando que la radiación electromagnética interfiera con el funcionamiento de los componentes electrónicos cercanos.
La preparación adecuada de la superficie es crucial cuando se utilizan adhesivos de unión eléctrica para garantizar una resistencia y un rendimiento de unión óptimos. Las superficies deben limpiarse a fondo, libres de contaminantes y, en algunos casos, pueden requerir activación de la superficie o imprimación para mejorar la adhesión.
Los adhesivos de unión eléctrica son esenciales en la fabricación eléctrica y electrónica moderna. Permiten conexiones eléctricas confiables y eficientes al tiempo que ofrecen soporte mecánico y protección contra EMI. Con los avances continuos en materiales y tecnologías adhesivas, estos adhesivos juegan un papel vital en el desarrollo de dispositivos y sistemas electrónicos innovadores y confiables.
Tipos de adhesivos de unión eléctrica
Los adhesivos de unión eléctrica crean conexiones eléctricas seguras y confiables entre los componentes conductores. Estos adhesivos están diseñados para proporcionar una excelente conductividad eléctrica al mismo tiempo que ofrecen fuertes propiedades de unión mecánica. Estos son algunos tipos comunes de adhesivos para conexiones eléctricas:
- Adhesivos epóxicos conductores: Los adhesivos epóxicos conductores se utilizan ampliamente en aplicaciones de unión eléctrica. Consisten en un sistema de dos partes, normalmente una resina y un endurecedor, que deben mezclarse antes de su uso. Estos adhesivos contienen rellenos conductores, como plata, cobre o grafito, que permiten el flujo de corriente eléctrica. Los adhesivos epoxi conductivos ofrecen una excelente adhesión a varios sustratos, proporcionando conductividad eléctrica y resistencia mecánica.
- Cintas adhesivas conductoras de electricidad: Las cintas adhesivas conductoras de electricidad consisten en un material de respaldo recubierto con un adhesivo que contiene partículas conductoras. El material de respaldo proporciona soporte mecánico y aislamiento, mientras que el adhesivo conductor asegura la continuidad eléctrica. Estas cintas son fáciles de aplicar, versátiles y pueden adaptarse a superficies irregulares. Se utilizan comúnmente para unir circuitos flexibles, aplicaciones de puesta a tierra y blindaje EMI/RFI.
- Adhesivos de plata conductiva: Los adhesivos de plata conductiva están formulados con partículas de plata suspendidas en una matriz de polímero. La plata es un excelente conductor de electricidad, ofreciendo una alta conductividad eléctrica. Estos adhesivos brindan una fuerte adhesión a varios sustratos, incluidos metales, cerámica y plásticos. Se utilizan comúnmente en ensamblaje electrónico, unión de componentes eléctricos y reparación de circuitos eléctricos.
- Adhesivos de silicona eléctricamente conductores: Los adhesivos de silicona eléctricamente conductores están formulados con polímeros de silicona y rellenos conductores, como plata, níquel o carbono. Ofrecen buena conductividad eléctrica, flexibilidad y estabilidad térmica. Estos adhesivos se utilizan a menudo en aplicaciones que requieren flexibilidad y resistencia ambiental, como la unión de circuitos flexibles, el sellado de conectores y el encapsulado de componentes electrónicos.
- Adhesivos de poliuretano conductores de electricidad: Los adhesivos de poliuretano conductores de electricidad están diseñados para proporcionar tanto conductividad eléctrica como fuertes propiedades de unión. Están formulados con polímeros de poliuretano y rellenos conductores, como carbón o partículas metálicas. Estos adhesivos ofrecen buena adherencia a varios sustratos, resistencia a factores ambientales y durabilidad. Se utilizan comúnmente en la fabricación electrónica, aplicaciones de conexión a tierra y unión de materiales diferentes.
- Adhesivos instantáneos conductivos: Los adhesivos instantáneos conductivos, también conocidos como adhesivos de cianoacrilato, son adhesivos de un solo componente que curan rápidamente al entrar en contacto con la humedad. Estos adhesivos, como partículas de metal o grafito, contienen rellenos conductores que proporcionan conductividad eléctrica. Ofrecen una unión rápida y alta resistencia, lo que los hace adecuados para aplicaciones que requieren un montaje rápido y un buen rendimiento eléctrico.
Es importante tener en cuenta que la elección del adhesivo de unión eléctrica depende de los requisitos específicos de la aplicación, como los materiales del sustrato, las condiciones ambientales y la conductividad eléctrica deseada. Consultar con fabricantes de adhesivos o expertos en el campo puede ayudar a seleccionar el adhesivo más apropiado para una aplicación en particular.
Adhesivos conductivos frente a no conductivos
Los adhesivos conductores y no conductores son dos categorías distintas que se utilizan en varias aplicaciones, y la principal diferencia entre ellos radica en sus propiedades de conductividad eléctrica. Aquí hay una descripción general de los adhesivos conductores y no conductores:
Adhesivos conductores: Los adhesivos conductores están formulados para permitir el flujo de corriente eléctrica. Contienen rellenos conductores, como partículas metálicas o de carbono, que proporcionan conductividad eléctrica. Los adhesivos conductores se usan comúnmente en aplicaciones donde se requiere continuidad eléctrica. Algunas características clave de los adhesivos conductores incluyen:
- Conductividad eléctrica: Los adhesivos conductivos ofrecen una excelente conductividad eléctrica debido a la presencia de rellenos conductivos. Pueden crear conexiones eléctricas confiables entre componentes conductores, como la unión de trazas eléctricas en tableros de circuitos o aplicaciones de puesta a tierra.
- Unión y fuerza mecánica: Los adhesivos conductivos proporcionan conductividad eléctrica y propiedades mecánicas de unión sólida. Pueden crear enlaces sólidos entre sustratos, asegurando la integridad estructural y la confiabilidad a largo plazo.
- Flexibilidad de aplicación: los adhesivos conductores vienen en varias formas, que incluyen epoxi, silicona y poliuretano, lo que ofrece flexibilidad en cuanto a métodos de aplicación y sustratos. Se pueden dosificar como líquidos, películas o pastas, lo que permite versatilidad en diferentes procesos de ensamblaje.
- Blindaje EMI/RFI: Los adhesivos conductores se utilizan a menudo para proteger la interferencia electromagnética (EMI) y la interferencia de radiofrecuencia (RFI). Pueden crear caminos conductivos, minimizando efectivamente el impacto de la radiación electromagnética en componentes electrónicos sensibles.
Adhesivos no conductores: Los adhesivos no conductores o aislantes no conducen la electricidad y están formulados para proporcionar aislamiento eléctrico entre componentes o sustratos. Los adhesivos no conductores se utilizan ampliamente en aplicaciones donde se requiere aislamiento eléctrico. Aquí hay algunas características críticas de los adhesivos no conductores:
- Aislamiento Eléctrico: Los adhesivos no conductores tienen alta resistividad, impidiendo el flujo de corriente eléctrica. Se utilizan para crear barreras eléctricas, aislando componentes entre sí o del entorno circundante.
- Rigidez dieléctrica: Los adhesivos no conductores exhiben una alta fuerza dieléctrica, que puede soportar la tensión eléctrica sin romperse. Esta propiedad es crucial en aplicaciones con altos voltajes, como electrónica de potencia o aislamiento eléctrico.
- Estabilidad térmica: los adhesivos no conductores a menudo poseen una excelente estabilidad térmica, lo que les permite mantener sus propiedades de aislamiento eléctrico a temperaturas elevadas. Esta característica es esencial en aplicaciones donde la disipación de calor es una preocupación.
- Resistencia ambiental: los adhesivos no conductores están diseñados para resistir diversos factores ambientales, como la humedad, los productos químicos y las fluctuaciones de temperatura. Ofrecen confiabilidad a largo plazo en condiciones de operación desafiantes.
Los adhesivos no conductores se pueden encontrar en varias formas, como formulaciones a base de epoxi, acrílico o silicona, lo que brinda flexibilidad en la aplicación y compatibilidad con el sustrato.
Ventajas de usar adhesivos de unión eléctrica
Los adhesivos para conexiones eléctricas ofrecen varias ventajas a la hora de crear conexiones eléctricas seguras y fiables. Estos son algunos de los beneficios clave del uso de adhesivos de unión eléctrica:
- Conductividad eléctrica: Los adhesivos de unión eléctrica están formulados para proporcionar una excelente conductividad eléctrica. Permiten el flujo de corriente eléctrica, asegurando conexiones eléctricas confiables entre los componentes conductores. Esto es crucial en aplicaciones con continuidad eléctrica esencial, como ensamblaje electrónico, unión de placas de circuitos o aplicaciones de conexión a tierra.
- Fuerza de unión: además de la conductividad eléctrica, los adhesivos de unión ofrecen fuertes propiedades de unión mecánica. Pueden crear uniones sólidas y duraderas entre sustratos, lo que mejora la integridad estructural general del ensamblaje. Esto es particularmente importante en aplicaciones donde pueden ocurrir vibraciones, ciclos térmicos o estrés mecánico.
- Compatibilidad con varios sustratos: los adhesivos de unión eléctrica están diseñados para unirse a varios sustratos, incluidos metales, cerámica, plásticos y compuestos. Esta versatilidad permite conectar materiales disímiles y simplifica el proceso de montaje. Elimina la necesidad de sujetadores mecánicos adicionales, como tornillos o soldadura, lo que reduce el tiempo y los costos de ensamblaje.
- Distribución de la tensión: los adhesivos de unión distribuyen la tensión de manera más uniforme en el área unida que otros métodos de sujeción. Pueden disipar el estrés y reducir los puntos de concentración, minimizando el riesgo de fallas localizadas o grietas en el ensamblaje.
- Disipación de calor mejorada: algunos adhesivos de unión eléctrica, como los adhesivos termoconductores, pueden mejorar la disipación de calor en los dispositivos electrónicos. Proporcionan una ruta termoconductora entre los componentes que generan calor y los disipadores de calor, lo que permite una transferencia de calor eficiente y una gestión térmica mejorada.
- Resistencia ambiental: Los adhesivos para unión eléctrica están formulados para resistir varios factores ambientales, incluidas las fluctuaciones de temperatura, la humedad, los productos químicos y la exposición a los rayos UV. Ofrecen una buena resistencia al envejecimiento y la degradación, lo que garantiza una fiabilidad a largo plazo en diferentes condiciones de funcionamiento.
- Flexibilidad de diseño: los adhesivos ofrecen flexibilidad de diseño, lo que permite unir formas complejas o superficies irregulares. Pueden adaptarse a contornos, llenar espacios y crear uniones fuertes en áreas de difícil acceso, lo que permite diseños más versátiles y eficientes.
- Solución rentable: en muchos casos, el uso de adhesivos de unión eléctrica puede ser rentable en comparación con otros métodos de unión tradicionales. Eliminan la necesidad de hardware adicional o procesos de ensamblaje complejos, lo que reduce los costos de materiales y mano de obra.
- Blindaje EMI/RFI: Los adhesivos de unión conductivos pueden proporcionar un blindaje eficaz contra interferencias electromagnéticas (EMI) e interferencias de radiofrecuencia (RFI). Crean caminos conductores, minimizando el impacto de la radiación electromagnética en componentes electrónicos sensibles.
En general, los adhesivos de unión eléctrica ofrecen numerosas ventajas, incluida la conductividad eléctrica, la fuerza de unión muscular, la compatibilidad con varios sustratos, la distribución de tensiones, la disipación de calor, la resistencia ambiental, la flexibilidad de diseño, la rentabilidad y el blindaje EMI/RFI. Estos beneficios los convierten en una opción importante para muchas aplicaciones eléctricas y electrónicas.
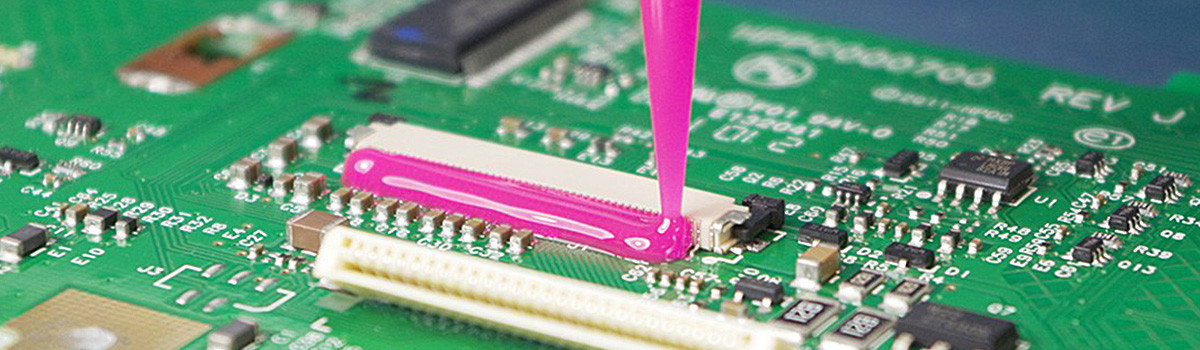
Aplicaciones de Adhesivos para Unión Eléctrica
Los adhesivos de unión eléctrica encuentran numerosas aplicaciones en diversas industrias donde se requieren conexiones eléctricas seguras y confiables. Estos adhesivos ofrecen propiedades únicas que los hacen aptos para múltiples aplicaciones. Estas son algunas aplicaciones típicas de los adhesivos de unión eléctrica:
- Fabricación de productos electrónicos: los adhesivos de unión eléctrica desempeñan un papel fundamental en el montaje y la unión de componentes electrónicos. Crean conexiones eléctricas entre tableros de circuitos, unen cables y conectan piezas montadas en la superficie y dispositivos electrónicos sensibles al encapsulado. Estos adhesivos proporcionan conductividad eléctrica y fuerza de unión mecánica, lo que garantiza el rendimiento de los dispositivos electrónicos y su durabilidad a largo plazo.
- Industria automotriz: La industria automotriz depende de los adhesivos de unión eléctrica para diversas aplicaciones. Se utilizan para unir y poner a tierra componentes eléctricos, como sensores, conectores y arneses de cableado. Estos adhesivos garantizan conexiones eléctricas seguras, soportan vibraciones y ciclos térmicos y brindan resistencia ambiental en aplicaciones automotrices.
- Aeroespacial y aviación: en los sectores aeroespacial y de aviación, los adhesivos de unión eléctrica son cruciales para unir componentes eléctricos en aeronaves, satélites y naves espaciales. Se utilizan para unir sistemas de aviónica, antenas, sensores y aplicaciones de puesta a tierra. Estos adhesivos deben ofrecer alta confiabilidad, durabilidad y resistencia a variaciones extremas de temperatura y vibraciones.
- Dispositivos médicos: los adhesivos de unión eléctrica fabrican dispositivos y equipos médicos. Se utilizan para unir electrodos, conectores, sensores y cableado en diversas aplicaciones médicas, incluidos dispositivos de monitoreo, equipos de diagnóstico y dispositivos implantables. Estos adhesivos deben cumplir estrictos requisitos de biocompatibilidad, resistencia a la esterilización y fiabilidad a largo plazo.
- Energía renovable: Los adhesivos de unión eléctrica se utilizan en el sector de las energías renovables, particularmente en la fabricación de paneles solares. Se utilizan para unir y poner a tierra las conexiones eléctricas dentro de los paneles solares, como unir células solares, unir barras colectoras y conectar cables eléctricos. Estos adhesivos deben proporcionar conductividad eléctrica confiable, resistencia a la intemperie y durabilidad a largo plazo en ambientes al aire libre.
- Telecomunicaciones: en la industria de las telecomunicaciones, los adhesivos de unión eléctrica se emplean para unir conexiones eléctricas en dispositivos de comunicación, antenas, conectores y componentes de fibra óptica. Estos adhesivos garantizan conexiones eléctricas seguras, blindaje EMI/RFI y resistencia a factores ambientales, como la humedad y las variaciones de temperatura.
- Productos electrónicos de consumo: los adhesivos de unión eléctrica ensamblan productos electrónicos de consumo, incluidos teléfonos inteligentes, tabletas, computadoras portátiles y dispositivos portátiles. Se utilizan para unir componentes eléctricos, unir pantallas, unir circuitos flexibles y aplicaciones de conexión a tierra. Estos adhesivos brindan conductividad eléctrica confiable, fuerza de unión mecánica y flexibilidad para adaptarse a diseños miniaturizados.
- Equipos industriales: los adhesivos de unión eléctrica encuentran aplicaciones en diversos equipos industriales, como paneles de control, sensores industriales, motores y transformadores. Se utilizan para unir conexiones eléctricas, componentes de puesta a tierra y blindaje EMI/RFI. Estos adhesivos deben soportar entornos industriales rigurosos, incluidas temperaturas extremas, vibraciones y exposición a productos químicos.
Estos son solo algunos ejemplos de la amplia gama de aplicaciones de los adhesivos para conexiones eléctricas. La versatilidad, confiabilidad y desempeño de estos adhesivos los hacen indispensables en industrias donde las conexiones eléctricas seguras son críticas para una funcionalidad y seguridad óptimas.
Pegado y Sellado en Dispositivos Electrónicos
La unión y el sellado son dos procesos esenciales en el ensamblaje y la fabricación de dispositivos electrónicos, y juegan un papel crucial para garantizar la confiabilidad, funcionalidad y protección de los componentes electrónicos. Aquí hay una descripción general de la unión y el sellado en dispositivos electrónicos:
La unión se refiere a unir dos o más componentes utilizando un material adhesivo. En los dispositivos electrónicos, la vinculación se utiliza para diversos fines, incluidas las conexiones eléctricas, el soporte mecánico y la gestión térmica. Estos son algunos aspectos críticos de la vinculación en dispositivos electrónicos:
- Conexiones eléctricas: los adhesivos de unión crean conexiones eléctricas entre los componentes, como la unión de cables a las almohadillas en las placas de circuitos o la unión de pistas conductoras. Estos adhesivos proporcionan conductividad eléctrica, lo que garantiza una continuidad eléctrica fiable en el dispositivo.
- Fijación de componentes: la unión une los componentes a las placas de circuito o sustratos. Los materiales adhesivos incluyen adhesivos a base de epoxi o silicona, componentes de unión como dispositivos montados en superficie (SMD), conectores, sensores o pantallas. Esto garantiza una adhesión segura y mecánicamente fuerte de los componentes.
- Soporte estructural: los adhesivos de unión brindan soporte estructural a los componentes electrónicos. Crean fuertes lazos que ayudan a resistir las tensiones mecánicas, las vibraciones y los ciclos térmicos. Esto es especialmente importante para las características que pueden experimentar tensión mecánica o fuerzas externas.
- Disipación de calor: en dispositivos con disipación de calor crítica, se utilizan adhesivos de unión con propiedades de conductividad térmica. Estos adhesivos ayudan a transferir el calor de los componentes que generan calor, como los transistores de potencia o los LED, a los disipadores de calor u otras soluciones de gestión térmica.
Caza de focas: El sellado implica la aplicación de un material protector para evitar la entrada de humedad, polvo u otros contaminantes en los dispositivos electrónicos. El sellado es esencial para mejorar la confiabilidad y la longevidad de los componentes y sistemas electrónicos. Estos son algunos aspectos críticos del sellado de dispositivos electrónicos:
- Protección ambiental: los adhesivos de sellado, como los materiales a base de silicona, crean una barrera que protege los componentes electrónicos de la humedad y los contaminantes ambientales. Esto es particularmente importante para los dispositivos expuestos a entornos hostiles, como la electrónica al aire libre o las aplicaciones automotrices.
- Impermeabilización: el sellado es fundamental para lograr la resistencia al agua o al polvo en los dispositivos electrónicos, especialmente en exteriores o entornos difíciles. Los materiales de sellado se aplican a gabinetes, conectores o aberturas para evitar la penetración de agua o polvo, lo que garantiza el rendimiento y la longevidad del dispositivo.
- Resistencia química: los adhesivos de sellado pueden resistir la exposición química, protegiendo los componentes electrónicos de sustancias corrosivas o vapores químicos. Esto es importante en aplicaciones en las que los dispositivos electrónicos pueden entrar en contacto con productos químicos o entornos agresivos.
- Propiedades de aislamiento y dieléctricas: los materiales de sellado a menudo poseen excelentes propiedades de aislamiento, proporcionando aislamiento eléctrico entre componentes o pistas. Esto ayuda a prevenir cortocircuitos y fallas eléctricas. Los adhesivos de sellado con alta rigidez dieléctrica se utilizan en aplicaciones que requieren aislamiento eléctrico.
- Resistencia a vibraciones y golpes: los adhesivos de sellado ayudan a mejorar la estabilidad mecánica de los dispositivos electrónicos al proporcionar resistencia a las vibraciones y los golpes. Evitan que los componentes internos se aflojen o se desplacen debido a la tensión mecánica, lo que garantiza la fiabilidad a largo plazo del dispositivo.
La unión y el sellado son procesos cruciales en el ensamblaje y la fabricación de dispositivos electrónicos, y aseguran conexiones eléctricas confiables, estabilidad mecánica, protección contra factores ambientales y longevidad de los dispositivos. La elección de los materiales de unión y sellado depende de la aplicación del dispositivo, las condiciones de funcionamiento y las características de rendimiento deseadas.
Aplicaciones automotrices
Los adhesivos de unión eléctrica tienen numerosas aplicaciones en la industria automotriz, donde juegan un papel crucial para garantizar conexiones eléctricas confiables, integridad estructural y rendimiento general. Aquí hay algunas aplicaciones automotrices críticas de adhesivos de unión eléctrica:
- Conjunto de arneses de cables: Los arneses de cables son componentes esenciales en los sistemas eléctricos automotrices que transmiten señales eléctricas y energía en todo el vehículo. Los adhesivos de unión eléctrica aseguran y protegen los arneses de cables, proporcionando soporte mecánico, alivio de tensión y resistencia a las fluctuaciones de vibración y temperatura. Estos adhesivos aseguran la longevidad y confiabilidad de los arneses de cables en entornos automotrices desafiantes.
- Vinculación de sensores: varios sensores se emplean en sistemas automotrices, incluidos sensores de motor, sensores de posición y sensores de proximidad. Los adhesivos de unión eléctrica unen estos sensores a sus ubicaciones de montaje, proporcionando una conexión segura y asegurando lecturas precisas y confiables del sensor. Estos adhesivos ofrecen estabilidad mecánica, protección contra vibraciones y resistencia a la temperatura y la humedad.
- Vinculación de conectores: los conectores son componentes críticos en los sistemas eléctricos automotrices, facilitando las conexiones eléctricas entre subsistemas y componentes. Los adhesivos de unión eléctrica unen los conectores a las placas de circuitos u otras superficies de montaje, lo que garantiza conexiones eléctricas seguras y estabilidad mecánica. Estos adhesivos resisten golpes, vibraciones y ciclos de temperatura, que son comunes en aplicaciones automotrices.
- Unidades de control electrónico (ECU): las ECU son componentes centrales en los sistemas automotrices modernos, responsables de controlar diversas funciones, como la gestión del motor, los frenos y los sistemas de seguridad. Los adhesivos de unión eléctrica ensamblan las ECU y brindan conexiones eléctricas, soporte mecánico y protección contra factores ambientales. Estos adhesivos ofrecen una excelente conductividad eléctrica, gestión térmica y resistencia a la humedad, los productos químicos y las variaciones de temperatura.
- Sistemas de iluminación: Los sistemas de iluminación automotriz, incluidos los faros delanteros, las luces traseras y la iluminación interior, requieren una unión segura para las conexiones eléctricas y la estabilidad mecánica. Los adhesivos de unión eléctrica unen los componentes de iluminación, como los LED, a sus ubicaciones de montaje, lo que garantiza conexiones eléctricas confiables y resistencia a las vibraciones y los ciclos térmicos. Estos adhesivos ofrecen una alta transparencia, lo que permite una transmisión óptima de la luz y una durabilidad a largo plazo.
- Ensamblaje del paquete de baterías: en los vehículos eléctricos e híbridos, los paquetes de baterías son componentes críticos que requieren una unión segura para las conexiones eléctricas y la integridad estructural. Los adhesivos de unión eléctrica se utilizan en el ensamblaje de paquetes de baterías y brindan propiedades de adhesión y sellado para garantizar una conductividad eléctrica confiable, resistencia a las vibraciones y protección contra la humedad y los ciclos térmicos. Estos adhesivos contribuyen a la seguridad y el rendimiento de las baterías de los vehículos eléctricos.
- Blindaje EMI/RFI: Los adhesivos de unión eléctrica con propiedades conductoras se utilizan para el blindaje contra interferencias electromagnéticas (EMI) e interferencias de radiofrecuencia (RFI) en aplicaciones automotrices. Crean caminos conductores, reduciendo el impacto de la radiación electromagnética en componentes electrónicos sensibles. Los adhesivos de blindaje EMI/RFI se utilizan en áreas como módulos electrónicos, antenas y cableado para garantizar el correcto funcionamiento de la electrónica automotriz.
- Unión estructural: en algunas aplicaciones automotrices, los adhesivos de unión eléctrica se utilizan con fines de unión estructural. Proporcionan una fuerte adhesión entre diferentes sustratos, lo que mejora la integridad estructural general de los componentes automotrices. Los adhesivos de unión estructural, por ejemplo, se utilizan para unir paneles de carrocería de vehículos, reforzar soportes o unir materiales compuestos, lo que contribuye a reducir el peso y mejorar el rendimiento del vehículo.
Estos son solo algunos ejemplos de la amplia gama de aplicaciones automotrices para adhesivos de unión eléctrica. Las propiedades de estos adhesivos, como la conductividad eléctrica, la resistencia mecánica, la resistencia ambiental y la gestión térmica, los hacen esenciales en el ensamblaje y el rendimiento de los sistemas y componentes eléctricos de los automóviles.
Aplicaciones aeroespaciales
Los adhesivos de unión eléctrica desempeñan un papel fundamental en las aplicaciones aeroespaciales, donde se utilizan para diversos fines, como unión eléctrica, conexión a tierra, unión estructural y protección contra factores ambientales. Aquí hay algunas aplicaciones aeroespaciales críticas de adhesivos de unión eléctrica:
- Sistemas de aviónica: Los sistemas de aviónica, incluidos los sistemas de control de vuelo, los sistemas de comunicación y los sistemas de navegación, dependen de conexiones eléctricas y puestas a tierra seguras. Los adhesivos de unión eléctrica unen y conectan a tierra los componentes dentro de los recintos de aviónica, lo que garantiza una continuidad eléctrica confiable, estabilidad mecánica y protección contra vibraciones, variaciones de temperatura e interferencias electromagnéticas.
- Cableado y arneses de aeronaves: El cableado y los arneses de aeronaves son redes complejas de cables y conectores eléctricos que transmiten energía y señales a través de la aeronave. Los adhesivos de unión eléctrica protegen el cableado y los arneses, proporcionando alivio de tensión, soporte mecánico y resistencia a la vibración y los factores ambientales. Estos adhesivos aseguran la longevidad y confiabilidad de las conexiones eléctricas en entornos aeroespaciales exigentes.
- Montaje de la antena: las antenas son cruciales en las aplicaciones aeroespaciales, ya que permiten la comunicación, la navegación y la transmisión de datos. Los adhesivos de unión eléctrica unen las antenas a sus superficies de montaje, lo que proporciona una conexión segura, continuidad eléctrica y resistencia a la tensión mecánica, las vibraciones y las variaciones de temperatura. Estos adhesivos contribuyen al rendimiento y la durabilidad de los sistemas de antenas aeroespaciales.
- Unión compuesta: Las estructuras aeroespaciales incorporan cada vez más materiales compuestos que ofrecen una alta relación resistencia-peso. Los adhesivos de unión eléctrica se utilizan para componentes compuestos, como paneles de fuselaje, sistemas de alas y superficies de control. Estos adhesivos proporcionan uniones fuertes y duraderas, lo que contribuye a la integridad estructural de la aeronave y reduce el peso.
- Electrónica de satélites y naves espaciales: los satélites y las naves espaciales requieren conexiones eléctricas confiables y protección contra las duras condiciones del espacio. Los adhesivos de unión eléctrica ensamblan componentes electrónicos de satélites y naves espaciales, como unidades de control electrónico, sensores y sistemas de comunicación. Estos adhesivos ofrecen conductividad eléctrica, estabilidad mecánica, resistencia a ciclos térmicos y condiciones de vacío, y protección contra la radiación.
- Protección contra rayos: Los rayos representan un riesgo significativo para las aeronaves. Los adhesivos de unión eléctrica y los materiales conductores se utilizan en los sistemas de protección contra rayos. Estos adhesivos ayudan a crear rutas conductoras que canalizan de forma segura la corriente del rayo lejos de los componentes críticos, lo que reduce el riesgo de daños y garantiza la seguridad de la aeronave y sus ocupantes.
- Blindaje EMI/RFI: En aplicaciones aeroespaciales, el blindaje de interferencia electromagnética (EMI) e interferencia de radiofrecuencia (RFI) es crucial para evitar la interferencia con sistemas electrónicos sensibles. Los adhesivos de unión eléctrica con propiedades conductoras se utilizan para el blindaje EMI/RFI. Proporcionan una ruta conductora, lo que reduce el impacto de la radiación electromagnética en los componentes electrónicos y garantiza una funcionalidad adecuada.
- Gestión térmica: los sistemas aeroespaciales a menudo se enfrentan a variaciones de temperatura extremas. Los adhesivos de unión eléctrica con propiedades de conductividad térmica se utilizan para una disipación de calor y una gestión térmica eficaces. Ayudan a transferir el calor lejos de los componentes que generan calor, como la electrónica de potencia o las interfaces térmicas, para mejorar el rendimiento y la confiabilidad general de los sistemas aeroespaciales.
Estos son solo algunos ejemplos de la amplia gama de aplicaciones aeroespaciales para adhesivos de unión eléctrica. Las propiedades de estos adhesivos, como la conductividad eléctrica, la resistencia mecánica, la resistencia ambiental y la gestión térmica, son fundamentales para garantizar la fiabilidad, la funcionalidad y la seguridad de los componentes y sistemas aeroespaciales.
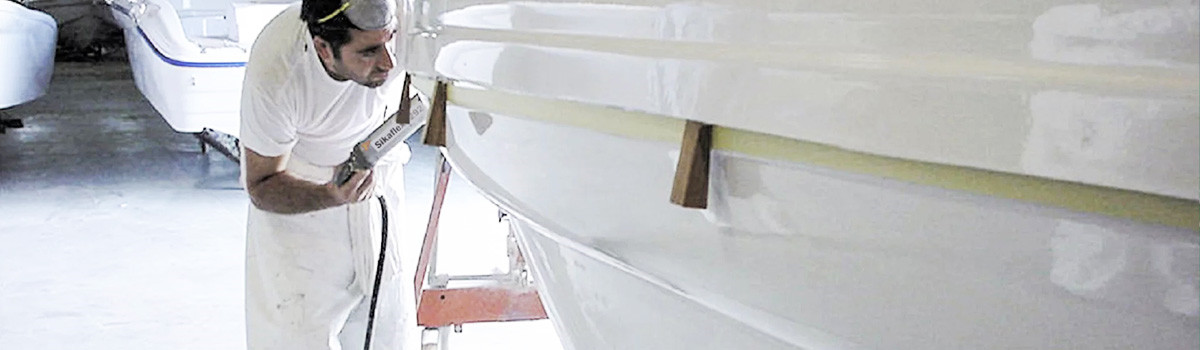
Aplicaciones marinas
Los adhesivos para conexiones eléctricas tienen aplicaciones significativas en la industria marina, donde se utilizan para varios propósitos, que incluyen conexiones eléctricas, conexión a tierra, protección contra la corrosión y sellado. Aquí hay algunas aplicaciones marinas críticas de adhesivos de unión eléctrica:
- Unión eléctrica y puesta a tierra: Los adhesivos de unión eléctrica crean conexiones eléctricas y puestas a tierra confiables en embarcaciones marinas. Unen y aseguran cables eléctricos, conectores y correas de conexión a tierra, asegurando una continuidad eléctrica adecuada y minimizando el riesgo de fallas o fallas eléctricas. Estos adhesivos brindan excelente conductividad, resistencia a la corrosión y estabilidad mecánica en ambientes marinos.
- Electrónica e instrumentación: las embarcaciones marinas dependen de sistemas electrónicos complejos para la navegación, la comunicación, el control y el monitoreo. Los adhesivos de unión eléctrica se utilizan para ensamblar e instalar componentes electrónicos, como paneles de control, sistemas de instrumentación y dispositivos de comunicación. Estos adhesivos garantizan una unión segura, conexiones eléctricas y protección contra factores ambientales como la humedad, las vibraciones y las variaciones de temperatura.
- Sistemas de iluminación: los adhesivos de unión eléctrica encuentran aplicaciones en los sistemas de iluminación marinos, incluidas las luces de navegación, las luces interiores y las luces subacuáticas. Unen accesorios de iluminación, módulos LED o componentes de iluminación a la estructura de la embarcación, lo que garantiza las conexiones eléctricas y la estabilidad mecánica. Estos adhesivos resisten la entrada de agua, la corrosión y las vibraciones, lo que contribuye a la longevidad y el rendimiento de los sistemas de iluminación marinos.
- Protección anticorrosión: las embarcaciones marinas están constantemente expuestas al agua de mar corrosiva, que puede dañar las estructuras y los componentes metálicos. Los adhesivos de unión eléctrica con propiedades anticorrosivas protegen las superficies metálicas de la corrosión. Estos adhesivos forman una barrera protectora, evitando el contacto directo con el agua de mar y ofreciendo resistencia a la corrosión. Se aplican a áreas como cascos, accesorios de cubierta y equipos submarinos para mejorar la durabilidad y la vida útil de las embarcaciones marinas.
- Sellado e impermeabilización: Los adhesivos de sellado se emplean en aplicaciones marinas para proporcionar propiedades de impermeabilización y sellado. Sellan entradas de cables, conectores, accesorios a través del casco y otras aberturas en la estructura de la embarcación. Estos adhesivos evitan la entrada de agua, protegen los componentes eléctricos sensibles y mantienen la integridad de la embarcación. Resisten el agua salada, la radiación ultravioleta y las fluctuaciones de temperatura, lo que garantiza una eficacia de sellado a largo plazo.
- Unión de componentes de fibra de vidrio y compuestos: La fibra de vidrio y los materiales compuestos se utilizan ampliamente en la construcción de embarcaciones marinas debido a sus propiedades de ligereza y alta resistencia. Los adhesivos de unión eléctrica se utilizan para unir y asegurar componentes compuestos y de fibra de vidrio, como cascos, cubiertas y refuerzos estructurales. Estos adhesivos proporcionan uniones fuertes y duraderas, mejorando la integridad estructural de la embarcación.
- Blindaje EMI/RFI: Las embarcaciones marinas a menudo tienen equipos electrónicos sensibles que requieren protección contra interferencias electromagnéticas (EMI) e interferencias de radiofrecuencia (RFI). Los adhesivos de unión eléctrica con propiedades conductoras se utilizan para el blindaje EMI/RFI en aplicaciones marinas. Crean rutas conductoras, lo que reduce el impacto de la radiación electromagnética en los componentes electrónicos y garantiza una funcionalidad y confiabilidad adecuadas.
- Reparación y mantenimiento: Los adhesivos de unión eléctrica también se utilizan con fines de reparación y mantenimiento en la industria marina. Pueden reparar conexiones eléctricas, asegurar componentes sueltos, reparar cableado dañado y reforzar estructuras debilitadas. Estos adhesivos ofrecen soluciones de unión rápidas y confiables, lo que permite reparaciones eficientes y minimiza el tiempo de inactividad.
Estos son solo algunos ejemplos de la amplia gama de aplicaciones marinas para adhesivos de unión eléctrica. Las propiedades de estos adhesivos, como la conductividad eléctrica, la resistencia a la corrosión, la efectividad del sellado y la resistencia mecánica, los hacen esenciales para garantizar conexiones eléctricas confiables, protección contra factores ambientales y el rendimiento general de embarcaciones y equipos marinos.
Aplicaciones médicas
Los adhesivos de unión eléctrica tienen aplicaciones esenciales en el campo de la medicina, donde se utilizan para diversos fines, incluida la fijación de electrodos, el montaje de dispositivos médicos, la monitorización de pacientes y la estimulación eléctrica. Aquí hay algunas aplicaciones médicas críticas de los adhesivos de unión eléctrica:
- Fijación de electrodos: Los adhesivos de unión eléctrica fijan los electrodos a la piel con fines de control y diagnóstico médico. Estos adhesivos proporcionan una unión segura, lo que garantiza un contacto eléctrico fiable entre el electrodo y la piel. Ofrecen excelentes propiedades de biocompatibilidad, adaptabilidad y adhesión para mantener la colocación adecuada de los electrodos, mejorar la calidad de la señal y minimizar la incomodidad del paciente.
- Ensamblaje de dispositivos médicos: los adhesivos de unión eléctrica son cruciales para ensamblar varios dispositivos médicos. Unen y aseguran componentes como sensores, conectores, placas de circuitos impresos y cables dentro de dispositivos médicos. Estos adhesivos brindan conductividad eléctrica, estabilidad mecánica y protección contra factores ambientales, lo que contribuye al rendimiento general y la confiabilidad de los dispositivos.
- Monitoreo de pacientes: Los adhesivos de unión eléctrica se utilizan en sistemas de monitoreo de pacientes, como dispositivos de ECG (electrocardiograma), EEG (electroencefalograma) y EMG (electromiograma). Se utilizan para conectar electrodos o sensores al cuerpo del paciente, asegurando las conexiones eléctricas adecuadas y la adquisición de la señal. Estos adhesivos ofrecen una fuerte unión, conductividad eléctrica fiable y adhesión a largo plazo, lo que permite una monitorización precisa y continua del paciente.
- Estimulación eléctrica: los adhesivos de unión eléctrica desempeñan un papel en las terapias de estimulación eléctrica, como la estimulación nerviosa eléctrica transcutánea (TENS) o la estimulación eléctrica neuromuscular (NMES). Se utilizan para unir electrodos de estimulación a la piel, suministrando corrientes eléctricas a áreas específicas. Estos adhesivos brindan una unión segura, un contacto eléctrico confiable y comodidad para el paciente durante los tratamientos de estimulación.
- Cierre de heridas: los adhesivos de unión eléctrica encuentran aplicaciones en técnicas como el cierre eléctrico de heridas (EWC) o procedimientos electroquirúrgicos. Aseguran los bordes de la herida y facilitan el flujo de corriente eléctrica durante el proceso de curación. Estos adhesivos ofrecen una fuerte unión, conductividad eléctrica y compatibilidad con los tejidos circundantes, lo que ayuda a cerrar y curar las heridas.
- Sensores médicos y dispositivos portátiles: los adhesivos de unión eléctrica ensamblan sensores médicos y dispositivos portátiles, como biosensores, monitores de glucosa y rastreadores de salud. Proporcionan una conexión segura de los sensores a la piel u otras superficies, lo que garantiza una adquisición de señal adecuada y una transmisión de datos confiable. Estos adhesivos ofrecen biocompatibilidad, flexibilidad y adhesión a largo plazo para facilitar un control cómodo y preciso.
- Rehabilitación y prótesis: los adhesivos de unión eléctrica desempeñan un papel en la reparación y los dispositivos protésicos. Se utilizan para unir electrodos, sensores o componentes de dispositivos de asistencia al cuerpo o interfaces protésicas. Estos adhesivos brindan conexiones eléctricas confiables, estabilidad mecánica y adhesión duradera, lo que contribuye a la funcionalidad y facilidad de uso de los sistemas protésicos y de rehabilitación.
- Investigación y desarrollo médicos: los adhesivos de unión eléctrica se emplean en entornos de investigación y desarrollo médicos. Se utilizan para la creación de prototipos, pruebas y montaje de circuitos electrónicos personalizados, sensores o configuraciones experimentales. Estos adhesivos ofrecen flexibilidad, facilidad de uso y conexiones eléctricas confiables, lo que permite a los investigadores crear dispositivos y sistemas médicos innovadores.
Estos son solo algunos ejemplos de la amplia gama de aplicaciones médicas de los adhesivos para conexiones eléctricas. Las propiedades de estos adhesivos, como la biocompatibilidad, la conductividad eléctrica, la fuerza de adhesión y la resistencia ambiental, son fundamentales para garantizar un rendimiento seguro y confiable en entornos médicos.
Factores a considerar al elegir adhesivos de unión eléctrica
Al elegir adhesivos de unión eléctrica, se deben considerar varios factores para garantizar la idoneidad y eficacia del adhesivo para la aplicación prevista. Aquí hay algunos factores clave a considerar:
- Conductividad eléctrica: La conductividad eléctrica del adhesivo es crucial para aplicaciones donde se requieren conexiones eléctricas o puesta a tierra. Según los requisitos específicos, como baja resistencia o niveles de conductividad específicos, el adhesivo debe tener propiedades de conductividad adecuadas para garantizar un rendimiento eléctrico confiable.
- Compatibilidad de sustratos: Considere los tipos de sustratos involucrados en la aplicación de unión. El adhesivo debe ser compatible con materiales aglomerados como metales, plásticos, compuestos o vidrio. La compatibilidad incluye tanto la compatibilidad química para evitar la degradación o corrosión del sustrato como la compatibilidad mecánica para garantizar una fuerte adhesión a la superficie del sustrato.
- Resistencia Ambiental: Evaluar las condiciones ambientales a las que estará expuesto el adhesivo. Tenga en cuenta factores como las variaciones de temperatura, la humedad, los productos químicos, la radiación ultravioleta y otras condiciones ambientales específicas relevantes para la aplicación. El adhesivo debe resistir estas condiciones para mantener su rendimiento y fuerza de adhesión a lo largo del tiempo.
- Resistencia y durabilidad de la unión: evalúe la resistencia y la durabilidad de la unión necesarias para la aplicación específica. Deben tenerse en cuenta factores como la capacidad de carga, la resistencia a las vibraciones, los impactos y los esfuerzos cíclicos. El adhesivo debe proporcionar suficiente fuerza de unión y durabilidad para garantizar la fiabilidad y el rendimiento a largo plazo en condiciones de funcionamiento.
- Tiempo y proceso de curado: Considere el mecanismo de curado del adhesivo y el tiempo de curado. Según los requisitos de la aplicación, elija entre adhesivos que curan a temperatura ambiente (curado ambiental) o aquellos que requieren exposición al calor, la humedad o los rayos UV para el curado. El tiempo de curado debe alinearse con el proceso de producción o ensamblaje para permitir una unión eficiente y minimizar el tiempo de producción.
- Método de aplicación: considere el método de aplicación y el equipo disponible para aplicar el adhesivo. Algunos adhesivos son adecuados para la aplicación manual, mientras que otros pueden requerir un equipo de aplicación o dispensación especializado. La viscosidad y las propiedades reológicas del adhesivo deben ser compatibles con el método de aplicación elegido para garantizar una cobertura y unión adecuadas del adhesivo.
- Cumplimiento normativo: es posible que se requiera el cumplimiento de normas y reglamentos específicos de la industria para ciertas aplicaciones, como dispositivos médicos o componentes aeroespaciales. Asegúrese de que el adhesivo elegido cumpla con los estándares relevantes de la industria, como biocompatibilidad, inflamabilidad o normas de seguridad, para cumplir con los requisitos específicos de la aplicación.
- Servicio y soporte: evalúe la disponibilidad de soporte técnico, documentación del producto y asistencia del fabricante o proveedor del adhesivo. Tenga en cuenta su experiencia en el campo y su capacidad para brindar orientación o abordar cualquier pregunta o inquietud relacionada con la selección, la aplicación o el rendimiento del adhesivo.
Al considerar cuidadosamente estos factores, puede seleccionar el adhesivo de unión eléctrica más adecuado para su aplicación específica, lo que garantiza un rendimiento, confiabilidad y longevidad óptimos de los componentes o sistemas unidos.
Tiempo y temperatura de curado
El tiempo y la temperatura de curado son consideraciones importantes cuando se trabaja con adhesivos para conexiones eléctricas. El tiempo de curado se refiere a la duración requerida para que la unión alcance su máxima resistencia y propiedades de unión. La temperatura, por otro lado, afecta la tasa de curado y el desempeño general del adhesivo. Aquí hay algunos puntos clave para comprender el tiempo de curado y la temperatura en los adhesivos de unión eléctrica:
Tiempo de curado:
- El tiempo de curado puede variar significativamente según el tipo de adhesivo y su formulación. Puede variar desde unos pocos minutos hasta varias horas o incluso días.
- Los tiempos de curado más rápidos son deseables en muchas aplicaciones, ya que reducen el tiempo de ensamblaje y permiten un manejo rápido y un procesamiento adicional de los componentes unidos.
- Es posible que se necesiten tiempos de curado más prolongados para aplicaciones en las que se requiera una alineación o ajustes precisos antes de que fragüe el adhesivo.
- El tiempo de curado puede verse influenciado por factores como el espesor del adhesivo, las condiciones ambientales (humedad, temperatura) y la presencia de aceleradores o agentes de curado.
Consideraciones de temperatura:
- Los fabricantes de adhesivos proporcionan rangos de temperatura de curado recomendados para sus productos. Es esencial seguir estas pautas para un desempeño óptimo del adhesivo.
- La temperatura afecta la tasa de curado. Las temperaturas más altas generalmente aceleran el proceso de curado, mientras que las temperaturas más bajas lo ralentizan. Sin embargo, las temperaturas excesivamente altas pueden provocar la degradación del adhesivo o efectos secundarios no deseados.
- Los adhesivos pueden tener un rango de temperatura mínimo y máximo para el curado. Operar fuera de estos límites de temperatura puede resultar en un curado incompleto o comprometido, lo que reduce la resistencia y la durabilidad de la unión.
- Algunos adhesivos requieren perfiles de temperatura de curado específicos que involucran un aumento o disminución gradual de la temperatura para lograr propiedades de unión óptimas.
- Es fundamental tener en cuenta las limitaciones de temperatura de los sustratos que se van a unir. Algunos materiales pueden ser sensibles a las altas temperaturas y deformarse o sufrir daños térmicos.
Curado por calor frente a curado a temperatura ambiente:
- Algunos adhesivos de unión eléctrica requieren curado por calor, sometiendo la unión a temperaturas elevadas específicas durante un período definido. El curado con calor puede proporcionar tiempos de curado más rápidos y propiedades adhesivas mejoradas.
- Los adhesivos de curado a temperatura ambiente o los adhesivos de curado a temperatura ambiente se curan naturalmente sin calor adicional. Curan a temperatura ambiente promedio y, por lo general, requieren tiempos de curado más prolongados en comparación con los enlaces curados con calor.
- La elección entre el curado con calor y el curado a temperatura ambiente depende de los requisitos específicos de la aplicación, los procesos de producción y la disponibilidad del equipo.
Es esencial seguir cuidadosamente las instrucciones y recomendaciones del fabricante con respecto al tiempo de curado y la temperatura para el adhesivo específico. Desviarse de las pautas recomendadas puede comprometer el desempeño del adhesivo, lo que resulta en uniones debilitadas o fallas del adhesivo. El tiempo de curado y el control de la temperatura adecuados contribuyen a lograr la resistencia de unión, la durabilidad y la confiabilidad general deseadas de los ensamblajes o componentes unidos.
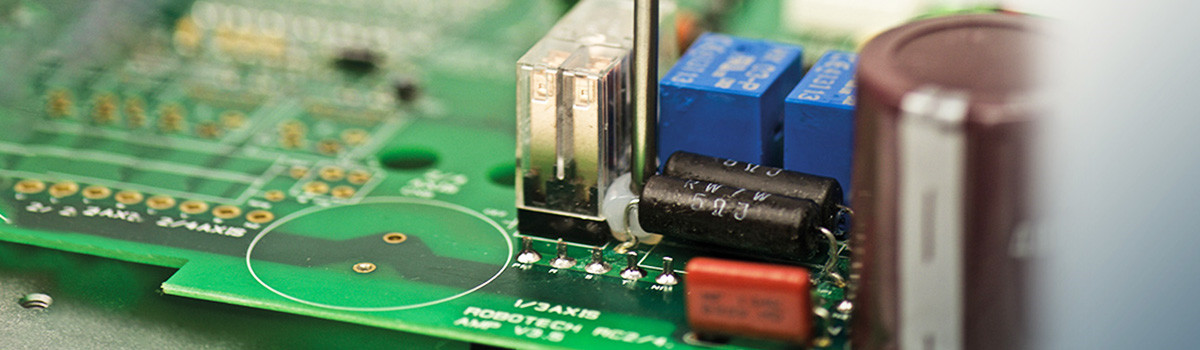
Resistencia química
La resistencia química es una consideración importante cuando se seleccionan adhesivos de unión eléctrica, especialmente en aplicaciones que exponen el adhesivo a varios químicos, solventes o ambientes agresivos. La resistencia química de un enlace determina su capacidad para mantener su integridad, fuerza de adhesión y rendimiento general cuando entra en contacto con productos químicos específicos. Aquí hay algunos puntos clave para comprender la resistencia química de los adhesivos de unión eléctrica:
- Compatibilidad química: Los distintos adhesivos tienen distintos niveles de resistencia a productos químicos específicos. Es fundamental evaluar la compatibilidad del adhesivo con los productos químicos con los que puede entrar en contacto durante su vida útil. Esto incluye considerar los tipos de productos químicos, sus concentraciones y la duración de la exposición.
- Tipos de productos químicos: la resistencia química puede variar según los tipos de productos químicos específicos, como ácidos, bases, disolventes, aceites, combustibles, agentes de limpieza o productos químicos industriales. Algunos adhesivos pueden exhibir buena resistencia a ciertos químicos pero pueden ser susceptibles a otros. Es esencial evaluar la compatibilidad del adhesivo con los productos químicos específicos relevantes para la aplicación.
- Hinchazón y degradación: cuando un adhesivo se expone a productos químicos, puede hincharse, ablandarse o degradarse, lo que provoca una pérdida de la fuerza de adhesión y el rendimiento general. Es esencial seleccionar un adhesivo que muestre una hinchazón y una degradación mínimas o nulas cuando entre en contacto con los productos químicos previstos.
- Consideraciones de temperatura: La temperatura también puede influir en la resistencia química. Algunos adhesivos pueden presentar una buena resistencia a ciertos productos químicos a temperatura ambiente, pero pueden ser menos resistentes a temperaturas elevadas. Es esencial considerar el rango de temperatura de funcionamiento y evaluar la resistencia química del adhesivo en esas condiciones.
- Pruebas y datos: los fabricantes de adhesivos suelen proporcionar hojas de datos o información técnica que especifican las propiedades de resistencia química de sus productos. Estos recursos pueden ayudar a evaluar la compatibilidad del adhesivo con productos químicos específicos y ayudar a seleccionar el adhesivo adecuado para la aplicación prevista.
- Recubrimientos y selladores: en algunos casos, se pueden aplicar recubrimientos protectores o selladores adicionales sobre el adhesivo para mejorar la resistencia química. Estos recubrimientos pueden proporcionar una capa adicional de protección contra los productos químicos y mejorar aún más la durabilidad general y la compatibilidad química del conjunto adherido.
- Requisitos específicos de la aplicación: Las diferentes aplicaciones tienen diferentes requisitos de exposición química. Por ejemplo, en la industria automotriz, los adhesivos utilizados en los componentes del sistema de combustible deben exhibir una excelente resistencia a los combustibles e hidrocarburos. Es esencial comprender las condiciones de exposición química específicas de la aplicación y elegir un adhesivo que cumpla con esos requisitos.
Tener en cuenta la resistencia química de los adhesivos de unión eléctrica es fundamental para garantizar la fiabilidad y el rendimiento a largo plazo de los conjuntos o componentes unidos. La selección de un adhesivo con las propiedades de resistencia química apropiadas para la aplicación específica ayuda a prevenir la falla del adhesivo, a mantener uniones fuertes y a garantizar la integridad general del sistema en presencia de entornos químicos agresivos.
Conductividad eléctrica
La conductividad eléctrica de los adhesivos de unión eléctrica es una propiedad crítica en aplicaciones donde se requieren conexiones eléctricas o puesta a tierra. La conductividad eléctrica se refiere a la capacidad de un material para permitir el flujo de corriente eléctrica. Aquí hay algunos puntos clave para comprender la conductividad eléctrica de los adhesivos de unión eléctrica:
Adhesivos conductivos frente a no conductivos: los adhesivos de unión eléctrica se pueden clasificar en términos generales en dos tipos según su conductividad eléctrica: adhesivos conductivos y no conductivos.
- Adhesivos Conductores: Estos adhesivos están formulados con rellenos conductores, como partículas metálicas o fibras, que facilitan el flujo de corriente eléctrica. Los adhesivos conductores ofrecen baja resistencia eléctrica, lo que permite una conducción eléctrica eficiente entre los componentes unidos. Se utilizan comúnmente en aplicaciones que requieren continuidad eléctrica, como conexión a tierra, protección contra interferencias electromagnéticas (EMI) o conexiones eléctricas.
- Adhesivos no conductores: los adhesivos no conductores, como su nombre indica, no poseen conductividad eléctrica inherente. Estos adhesivos se utilizan normalmente en aplicaciones que requieren aislamiento o aislamiento eléctrico. Evitan el flujo de corriente eléctrica entre los componentes unidos y pueden proporcionar aislamiento eléctrico o propiedades dieléctricas.
- Resistencia eléctrica: La conductividad eléctrica de un adhesivo a menudo se expresa en términos de resistencia eléctrica o resistividad. La resistencia eléctrica es una medida de la oposición al flujo de corriente eléctrica a través del material. Los valores de resistencia más bajos indican una mejor conductividad eléctrica.
- Rellenos y aditivos: Los adhesivos conductores contienen rellenos o aditivos que mejoran la conductividad eléctrica. Estos rellenos, como partículas de plata, cobre, carbono o grafito, establecen vías conductoras dentro de la matriz adhesiva, lo que facilita el flujo de corriente eléctrica. El tipo, tamaño y concentración de estos rellenos pueden influir en la conductividad eléctrica del adhesivo.
- Conexión eléctrica y puesta a tierra: los adhesivos conductores se usan comúnmente para crear conexiones eléctricas entre componentes o para la puesta a tierra. Se emplean en diversas industrias, incluidas la electrónica, la automotriz, la aeroespacial y las telecomunicaciones, donde la conductividad eléctrica confiable es esencial para la funcionalidad y el rendimiento adecuados del dispositivo.
- Blindaje EMI: Los adhesivos conductores con buenas propiedades de conductividad eléctrica se utilizan en aplicaciones de blindaje electromagnético. Proporcionan una vía conductora para la disipación de la interferencia electromagnética, protegiendo los dispositivos o circuitos electrónicos sensibles de la radiación o el ruido electromagnético externo.
- Confiabilidad de los contactos eléctricos: La conductividad eléctrica de los adhesivos de unión afecta directamente la confiabilidad de los contactos eléctricos. Los adhesivos conductores aseguran un contacto eléctrico adecuado y consistente entre las superficies unidas, minimizando la resistencia de contacto y evitando conexiones intermitentes o poco confiables.
- Espesor del adhesivo y área de contacto: La conductividad eléctrica de un adhesivo puede verse influenciada por el espesor de la capa adhesiva y el área de contacto entre las superficies unidas. Las capas adhesivas más delgadas y las áreas de contacto más grandes generalmente ofrecen una mejor conductividad eléctrica.
- Prueba y verificación: la conductividad eléctrica de los adhesivos se puede medir utilizando varias técnicas, incluidos los métodos de sonda de cuatro o dos puntos. Estas pruebas ayudan a evaluar las propiedades de conductividad del adhesivo y garantizan el cumplimiento de las especificaciones eléctricas requeridas.
Es esencial seleccionar el tipo apropiado de adhesivo de unión eléctrica en función de los requisitos específicos de conductividad eléctrica de la aplicación. Los adhesivos conductores son adecuados cuando se necesita continuidad eléctrica o puesta a tierra, mientras que los adhesivos no conductores proporcionan aislamiento o aislamiento eléctrico. Comprender las propiedades de conductividad eléctrica del adhesivo ayuda a garantizar un rendimiento, confiabilidad y seguridad óptimos en las aplicaciones de unión eléctrica.
Estabilidad térmica
La estabilidad térmica es una característica esencial de los adhesivos de unión eléctrica, particularmente en aplicaciones donde la unión estará expuesta a temperaturas elevadas. La estabilidad térmica de un adhesivo se refiere a su capacidad para mantener su integridad, fuerza de adhesión y rendimiento general en condiciones de alta temperatura. Aquí hay algunos puntos clave para comprender la estabilidad térmica de los adhesivos de unión eléctrica:
- Rango de temperatura: los adhesivos tienen temperaturas específicas para mantener su rendimiento y estabilidad. La estabilidad térmica de un adhesivo a menudo se describe por su temperatura máxima de funcionamiento continuo o su resistencia máxima a la temperatura. Es esencial elegir un enlace que pueda soportar el rango de temperatura esperado de la aplicación.
- Degradación Térmica: El calor excesivo puede causar la degradación del adhesivo, cambiando las propiedades físicas y químicas. Esto puede resultar en una fuerza de adhesión reducida, pérdida de propiedades mecánicas y rendimiento general disminuido. Un adhesivo térmicamente estable resiste la degradación incluso a altas temperaturas, manteniendo sus propiedades originales.
- Retención de la fuerza de unión: La estabilidad térmica de un adhesivo está estrechamente relacionada con su capacidad para mantener la fuerza de unión a temperaturas elevadas. Cuando se expone a altas temperaturas, un adhesivo térmicamente estable debe presentar una reducción mínima de la fuerza de unión. Debe poseer una unión sólida y duradera entre las superficies adheridas, incluso en condiciones térmicas adversas.
- Temperatura de transición vítrea (Tg): La temperatura de transición vítrea es un parámetro importante a considerar al evaluar la estabilidad térmica de un adhesivo. Es la temperatura a la que el adhesivo pasa de un estado rígido y vítreo a un estado más blando y gomoso. Los adhesivos con valores de Tg más altos generalmente ofrecen una mejor estabilidad térmica, ya que pueden soportar temperaturas más altas antes de ablandarse o perder sus propiedades mecánicas.
- Ciclos térmicos: algunas aplicaciones implican la exposición a ciclos térmicos repetidos, en los que el adhesivo experimenta temperaturas altas y bajas alternas. La estabilidad térmica es esencial en tales casos, ya que el adhesivo debe soportar estas fluctuaciones de temperatura sin una degradación significativa o pérdida de la fuerza de adhesión. Un adhesivo térmicamente estable mantiene su rendimiento incluso después de múltiples ciclos térmicos.
- Resistencia al calor: los adhesivos utilizados en aplicaciones que involucran componentes o entornos que generan calor, como la electrónica, la electrónica de potencia o los sistemas de iluminación, requieren una buena resistencia al calor. Los adhesivos resistentes al calor pueden soportar el calor generado por estos componentes y mantener su rendimiento sin ablandarse, derretirse o perder la fuerza de adhesión.
- Conductividad térmica: en algunas aplicaciones, la conductividad térmica es una consideración importante. La conductividad térmica se refiere a la capacidad de un material para conducir el calor. Los adhesivos con alta conductividad térmica pueden transferir eficazmente el calor de los componentes sensibles al calor, lo que garantiza una disipación de calor eficiente y previene el daño térmico.
- Pruebas y datos: los fabricantes de adhesivos suelen proporcionar hojas de datos técnicos que especifican las propiedades de estabilidad térmica de sus productos. Esta información incluye el rango de temperatura de funcionamiento recomendado, la resistencia térmica y otras propiedades térmicas relevantes. Es fundamental revisar estos datos para garantizar que el adhesivo cumpla con los requisitos específicos de estabilidad térmica de la aplicación.
Elegir un adhesivo térmicamente estable es fundamental para garantizar la confiabilidad y el rendimiento a largo plazo, especialmente en aplicaciones que involucran altas temperaturas o ciclos térmicos. Un adhesivo térmicamente estable mantiene su fuerza de adhesión, sus propiedades mecánicas y su rendimiento general en condiciones de alta temperatura, lo que contribuye a la durabilidad e integridad de los ensamblajes o componentes unidos.
Viscosidad
La viscosidad es una propiedad esencial de los adhesivos de unión eléctrica que determina su comportamiento de flujo y las características de aplicación. Se refiere al espesor o resistencia al flujo del adhesivo. Comprender la viscosidad es crucial para la selección adecuada del adhesivo y el proceso de aplicación. Aquí hay algunos puntos clave para comprender la viscosidad de los adhesivos de unión eléctrica:
- Definición y Medida: La viscosidad mide la resistencia de un fluido a fluir. Determina la capacidad del adhesivo para esparcirse, humedecer las superficies y llenar huecos. La viscosidad normalmente se mide en unidades como centipoise (cP) o Pascal-segundos (Pa·s).
- Rango de viscosidad: Los adhesivos de unión eléctrica pueden tener varias viscosidades, desde líquidos de baja viscosidad hasta pastas o geles de alta viscosidad. La viscosidad adecuada depende de los requisitos de la aplicación, como el tamaño de la línea de unión, la capacidad de relleno de espacios y la facilidad de aplicación.
- Comportamiento de flujo: los adhesivos pueden exhibir diferentes comportamientos de flujo dependiendo de su viscosidad. Los fluidos newtonianos tienen un espesor constante independientemente de la velocidad de corte aplicada. Por otro lado, los fluidos no newtonianos pueden presentar un comportamiento de adelgazamiento por cizallamiento (disminución de la densidad al aumentar la velocidad de cizallamiento) o espesamiento por cizallamiento (aumento de la viscosidad al aumentar la velocidad de cizallamiento). Comprender el comportamiento del flujo ayuda a predecir el comportamiento del adhesivo durante la aplicación y en diferentes condiciones.
- Métodos de aplicación: la viscosidad afecta la aplicabilidad de los adhesivos que utilizan varios métodos, como la dosificación manual, la dosificación automática, la serigrafía o la dosificación con jeringa. Los adhesivos de baja viscosidad fluyen con facilidad y son adecuados para dispensación automática, mientras que los adhesivos de alta viscosidad pueden requerir métodos de aplicación manual o equipos de dispensación capaces de manejar materiales más gruesos.
- Capacidad de relleno de espacios: La viscosidad juega un papel en la capacidad del adhesivo para llenar espacios o superficies de unión irregulares. Los adhesivos de menor viscosidad pueden fluir hacia espacios reducidos o espacios reducidos de manera más eficiente, mientras que los adhesivos de mayor viscosidad tienden a permanecer en su lugar y brindan una mejor capacidad de relleno de espacios.
- Compatibilidad del sustrato: la viscosidad también es importante cuando se considera la compatibilidad del adhesivo con los sustratos que se unen. Los adhesivos con niveles de viscosidad apropiados aseguran una buena humectación y contacto con las superficies del sustrato, promoviendo una fuerte adhesión.
- Tixotropía: algunos adhesivos exhiben un comportamiento tixotrópico, donde su viscosidad disminuye cuando se somete a esfuerzo cortante o agitación, pero se recupera cuando está en reposo. Los adhesivos tixotrópicos son fáciles de aplicar y esparcir durante la aplicación, pero recuperan espesor rápidamente después de la aplicación, lo que evita el flujo o la flacidez no deseados.
- Dependencia de la temperatura: la viscosidad puede depender de la temperatura, lo que significa que cambia con la temperatura. Algunos adhesivos pueden volverse menos viscosos a temperaturas más altas, haciéndolos más fáciles de aplicar o dispensar. Otros pueden exhibir una mayor viscosidad a temperaturas más bajas, lo que requiere precalentamiento o calentamiento para un flujo y una trabajabilidad óptimos.
- Manejo de materiales: la viscosidad afecta la facilidad de manejo de materiales, como mezclar, agitar o transferir adhesivos. Los adhesivos de mayor viscosidad pueden requerir mezclas o equipos adicionales para garantizar la uniformidad y la homogeneidad.
Comprender la viscosidad de los adhesivos de unión eléctrica es crucial para una aplicación exitosa y lograr la calidad de unión deseada. La selección adecuada de la viscosidad garantiza la humectación y la adhesión adecuadas a los sustratos, un relleno eficaz de las holguras y la facilidad de aplicación. Es fundamental tener en cuenta los requisitos específicos de la aplicación y consultar las recomendaciones del fabricante del adhesivo sobre las especificaciones de viscosidad para garantizar un rendimiento óptimo.
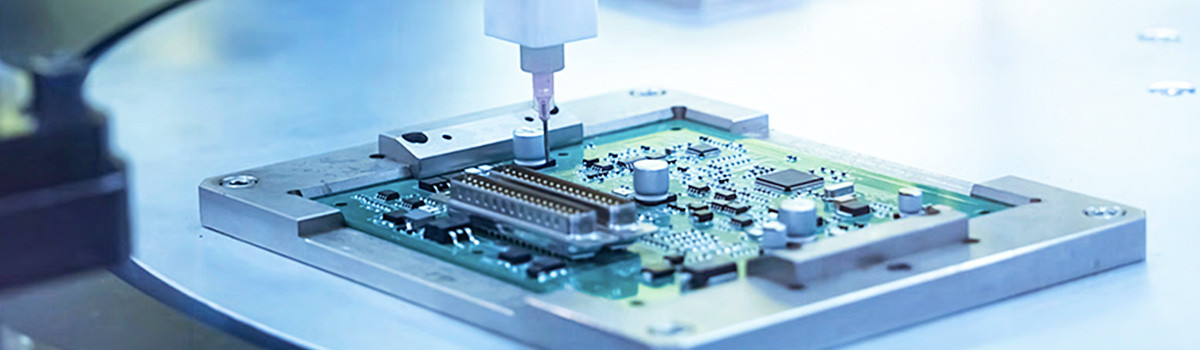
Vida útil
La vida útil de los adhesivos de unión eléctrica se refiere al período durante el cual el adhesivo se puede almacenar y permanecer apto para su uso. Es esencial comprender la vida útil de los adhesivos para garantizar su eficacia y confiabilidad cuando se aplican. Estos son algunos puntos clave que debe saber sobre la vida útil de los adhesivos de unión eléctrica:
- Definición: La vida útil es el tiempo que el adhesivo puede almacenarse en condiciones específicas sin cambios significativos en sus propiedades, rendimiento o calidad.
- Fecha de caducidad: los fabricantes de adhesivos suelen proporcionar una fecha de caducidad o una vida útil recomendada del producto. Esta fecha indica el punto a partir del cual el adhesivo puede degradarse o perder eficacia. Es fundamental respetar esta fecha de caducidad para garantizar un rendimiento óptimo.
- Factores que afectan la vida útil: varios factores pueden influir en la vida útil de los adhesivos para conexiones eléctricas:
- Condiciones de almacenamiento: Los adhesivos deben almacenarse en condiciones controladas para mantener la estabilidad. Factores como la temperatura, la humedad y la exposición a la luz pueden afectar la vida útil del adhesivo. Los adhesivos deben almacenarse en áreas frescas y secas, lejos de la luz solar directa o de las fluctuaciones extremas de temperatura.
- Empaque: El empaque apropiado es crucial para preservar la vida útil del adhesivo. Los adhesivos deben almacenarse en recipientes herméticamente cerrados para evitar la entrada de humedad, la evaporación o la contaminación. Los contenedores deben estar debidamente etiquetados con el tipo de adhesivo, el número de lote y la fecha de vencimiento para una fácil identificación.
- Estabilidad química: los adhesivos pueden sufrir reacciones químicas con el tiempo que pueden provocar cambios en sus propiedades. Factores como la humedad, el oxígeno o la exposición a sustancias reactivas pueden acelerar estas reacciones y reducir la vida útil. Los adhesivos formulados con estabilizadores o antioxidantes pueden tener una estabilidad química mejorada y una vida útil más prolongada.
- Recomendaciones de almacenamiento: los fabricantes brindan recomendaciones de almacenamiento específicas para sus productos adhesivos. Estas recomendaciones pueden incluir rangos de temperatura, niveles de humedad y contenedores o condiciones de almacenamiento transparentes. Es fundamental seguir estas pautas para garantizar la calidad y la longevidad del adhesivo.
- Prueba y verificación: si un adhesivo se almacenó durante un período prolongado o más allá de su fecha de vencimiento, se recomienda realizar pruebas de adhesivo para verificar su idoneidad. Estas pruebas pueden incluir la medición de la viscosidad y la fuerza de adhesión o la realización de pruebas de unión para evaluar el rendimiento del adhesivo.
- Segregación de productos: los adhesivos deben almacenarse y usarse según el principio de "primero en entrar, primero en salir" para garantizar que los materiales más antiguos se utilicen antes que los más nuevos. Esta práctica ayuda a prevenir adhesivos vencidos o degradados y proporciona los mejores resultados.
- Orientación del fabricante: es esencial consultar la documentación del fabricante, como hojas de datos del producto o boletines técnicos, para obtener información específica sobre la vida útil del adhesivo. La guía del fabricante considera la formulación del adhesivo, las condiciones de almacenamiento y el rendimiento esperado a lo largo del tiempo.
Comprender la vida útil de los adhesivos de unión eléctrica es fundamental para mantener su eficacia y garantizar un rendimiento adecuado. Los adhesivos que han excedido su vida útil pueden presentar una fuerza de adhesión reducida, cambios en la viscosidad u otros efectos perjudiciales. Cumplir con las prácticas de almacenamiento adecuadas, seguir las pautas del fabricante y monitorear regularmente las fechas de vencimiento de los adhesivos ayuda a garantizar su confiabilidad y rendimiento constante cuando se aplican.
Preparación de la superficie
La preparación de la superficie es un paso crítico en la aplicación de adhesivos de unión eléctrica. La preparación adecuada de la superficie garantiza una adherencia y una fuerza de unión óptimas entre el adhesivo y el sustrato. Estos son algunos puntos clave para entender acerca de la preparación de superficies para adhesivos de unión eléctrica:
- Limpieza: El primer paso en la preparación de la superficie es limpiar a fondo las superficies del sustrato. Las superficies deben estar libres de contaminantes como suciedad, polvo, grasa, aceite, humedad u oxidación. La limpieza se puede realizar con disolventes, detergentes o agentes de limpieza específicos recomendados por el fabricante del adhesivo. El proceso de limpieza puede implicar frotar, cepillar o usar técnicas de limpieza ultrasónica según el sustrato y la naturaleza de los contaminantes.
- Aspereza de la superficie: En algunos casos, puede ser necesario raspar la superficie del sustrato para mejorar la fuerza de unión del adhesivo. Normalmente, esto se realiza mediante métodos mecánicos, como lijado, esmerilado o limpieza con chorro abrasivo. La rugosidad de la superficie aumenta el área superficial y proporciona un enclavamiento mecánico, lo que permite que el adhesivo forme una unión más fuerte.
- Activación de superficie: algunos sustratos, como metales o ciertos plásticos, pueden requerir activación de superficie para promover la adhesión. Los métodos de activación de superficies incluyen tratamientos químicos, tratamientos con plasma, imprimaciones o promotores de adhesión. Estos tratamientos modifican las propiedades superficiales, mejorando las características de humectación y adherencia del adhesivo.
- Eliminación de la oxidación: La eliminación de las capas de oxidación es crucial para que los sustratos metálicos aseguren una buena adhesión. La oxidación puede dificultar la capacidad del adhesivo para unirse al sustrato. Los métodos mecánicos como el lijado o los tratamientos químicos como el decapado con ácido pueden eliminar las capas de óxido y exponer una superficie limpia para la unión.
- Secado y desengrasado: Después de la limpieza y el tratamiento de la superficie, es esencial secar bien las superficies del sustrato para eliminar la humedad o los agentes de limpieza. La humedad puede interferir con el proceso de curado del adhesivo y comprometer la fuerza de unión. Además, desengrasar las superficies ayuda a eliminar los aceites residuales o los contaminantes que pueden dificultar la capacidad del adhesivo para adherirse de manera efectiva.
- Compatibilidad de la superficie: es fundamental tener en cuenta la compatibilidad entre el adhesivo y la superficie del sustrato. Algunas uniones pueden requerir características de superficie específicas o métodos de tratamiento para garantizar una unión adecuada. Se deben seguir las recomendaciones del fabricante del adhesivo para determinar las técnicas apropiadas de preparación de la superficie para la combinación particular de adhesivo y sustrato.
- Aplicación de adhesivo: Una vez que se completa la preparación de la superficie, se puede aplicar el adhesivo a las superficies preparadas. Es fundamental seguir las instrucciones del fabricante del adhesivo en cuanto al método de aplicación, el espesor recomendado del adhesivo y el tiempo disponible. Las técnicas de aplicación adecuadas, como la distribución uniforme o la dosificación controlada, garantizan una cobertura uniforme y una fuerza de unión.
La preparación adecuada de la superficie es crucial para lograr uniones sólidas y duraderas cuando se utilizan adhesivos de unión eléctrica. Promueve una adhesión óptima, minimiza el riesgo de falla del adhesivo y garantiza la confiabilidad a largo plazo de los ensamblajes adheridos. Seguir los procedimientos de preparación de superficies recomendados especificados por el fabricante del adhesivo ayuda a maximizar el rendimiento del adhesivo y proporciona una unión exitosa.
Manipulación y almacenamiento
La manipulación y el almacenamiento adecuados de los adhesivos para conexiones eléctricas son esenciales para mantener su eficacia, calidad y vida útil. La manipulación o el almacenamiento inadecuados pueden dañar el adhesivo, comprometiendo el rendimiento y reduciendo la fuerza de unión. Aquí hay algunos puntos clave para entender sobre el manejo y almacenamiento de adhesivos de unión eléctrica:
Precauciones de manipulación: Al manipular adhesivos, es fundamental seguir ciertas precauciones para garantizar la seguridad y evitar la contaminación:
- Use el equipo de protección personal (EPP) adecuado según lo recomendado por el fabricante del adhesivo. Esto puede incluir guantes, gafas de seguridad y ropa protectora.
- Evite el contacto con la piel, los ojos o la ropa. En caso de contacto accidental, enjuague bien con agua y busque atención médica si es necesario.
- Utilice una ventilación adecuada en el área de trabajo para garantizar un flujo de aire adecuado y minimizar la exposición a humos o vapores.
- Siga las instrucciones del fabricante para las técnicas de manipulación adecuadas, incluidas las proporciones de mezcla (si corresponde) y cualquier precaución específica.
Condiciones de almacenamiento: Las condiciones de almacenamiento del adhesivo son cruciales para mantener la calidad y la eficacia. Tenga en cuenta los siguientes factores al almacenar adhesivos para conexiones eléctricas:
- Temperatura: Los adhesivos deben almacenarse dentro del rango de temperatura recomendado por el fabricante. Las temperaturas extremadamente altas y bajas pueden afectar el rendimiento y la vida útil del adhesivo. Por lo general, se recomienda mantener los adhesivos en un lugar fresco y seco, lejos de la luz solar directa y fuentes de calor.
- Humedad: La humedad puede afectar negativamente las propiedades del adhesivo y causar un curado o degradación prematuros. Los adhesivos deben almacenarse en ambientes de baja humedad para evitar la absorción de humedad. Mantenga los recipientes herméticamente cerrados para minimizar la entrada de humedad.
- Supervisión de la vida útil: los envases de adhesivo deben etiquetarse con el número de lote, la fecha de fabricación y la fecha de caducidad. Implemente un sistema de primeras entradas, primeras salidas (FIFO) para usar primero el inventario de adhesivos más antiguos y evitar el uso de materiales vencidos.
- Compatibilidad: algunos adhesivos pueden tener requisitos de almacenamiento específicos según su formulación. Siga las recomendaciones del fabricante sobre la temperatura de almacenamiento, los niveles de humedad y otras instrucciones para mantener la calidad del adhesivo.
Manipulación de contenedores: Los contenedores de adhesivo deben manipularse con cuidado para evitar fugas, derrames o contaminación:
- Asegúrese de que los recipientes estén bien cerrados después de su uso para evitar la exposición al aire y la entrada de humedad. Siga las instrucciones del fabricante para las técnicas de cierre adecuadas.
- Evite dejar caer o manipular mal los envases de adhesivo, ya que esto puede dañar el embalaje o comprometer la integridad del adhesivo.
- Limpie las superficies externas de los envases antes de abrirlos para evitar que entre contaminación al adhesivo.
- Segregación y etiquetado: almacene los adhesivos separados de los materiales incompatibles para evitar la contaminación cruzada o las reacciones. El etiquetado adecuado de los contenedores con tipo de adhesivo, número de lote y otra información relevante ayuda a identificar y rastrear el inventario con precisión.
- Transporte: Al transportar adhesivos, asegúrese de que estén debidamente embalados y asegurados para evitar fugas o daños. Siga las normas o directrices aplicables para el transporte seguro de materiales adhesivos.
La manipulación y el almacenamiento adecuados de los adhesivos para conexiones eléctricas son cruciales para mantener su calidad, rendimiento y vida útil. El cumplimiento de las condiciones de almacenamiento recomendadas, las precauciones de manejo y el seguimiento de las instrucciones del fabricante aseguran que el adhesivo siga siendo efectivo y confiable para las aplicaciones de unión.
Precauciones de Seguridad
Se deben tomar precauciones de seguridad cuando se trabaja con adhesivos de unión eléctrica para proteger a las personas y garantizar un entorno de trabajo seguro. Los adhesivos pueden contener productos químicos que pueden ser peligrosos si no se manipulan correctamente. Estas son algunas precauciones de seguridad esenciales que se deben tener en cuenta al trabajar con adhesivos para conexiones eléctricas:
- Equipo de Protección Personal (PPE): Use PPE apropiado para protegerse de peligros potenciales. Esto puede incluir guantes, anteojos o gafas de seguridad, batas de laboratorio o ropa protectora y protección respiratoria si es necesario. Los requisitos de EPP deben determinarse según la hoja de datos de seguridad del material (MSDS) del adhesivo y las recomendaciones del fabricante.
- Ventilación: Asegure una ventilación adecuada en el área de trabajo para minimizar la exposición a humos, vapores o partículas en el aire generadas durante la aplicación o el curado del adhesivo. Use ventilación de escape local o trabaje en áreas bien ventiladas para mantener la calidad del aire.
- Sustancias químicas peligrosas: Los adhesivos para conexiones eléctricas pueden contener sustancias químicas que pueden ser peligrosas para la salud. Familiarícese con la MSDS del adhesivo para comprender los peligros específicos asociados con el producto. Siga las recomendaciones del fabricante para el manejo, almacenamiento y desecho seguros del adhesivo.
- Contacto con la piel: Evite el contacto directo de la piel con el adhesivo. Algunos adhesivos pueden causar irritación de la piel o reacciones alérgicas. Use guantes de protección resistentes al adhesivo específico para evitar el contacto con la piel. En caso de contacto accidental, lave el área afectada con agua y jabón y busque atención médica si es necesario.
- Protección para los ojos: Los adhesivos pueden causar irritación o lesiones en los ojos si entran en contacto con los ojos. Use anteojos o gafas de seguridad para proteger sus ojos cuando trabaje con adhesivos. En caso de contacto accidental con los ojos, enjuague los ojos con agua durante al menos 15 minutos y busque atención médica inmediata.
- Inhalación: Minimice la inhalación de humos o vapores de adhesivo. Trabaje en un área bien ventilada o use protección respiratoria si es necesario. Siga las recomendaciones del fabricante para el equipo de protección respiratoria adecuado.
- Fuego y fuentes de ignición: Algunos adhesivos pueden ser inflamables o tener características de inflamabilidad específicas. Tome precauciones para evitar que el adhesivo entre en contacto con llamas abiertas, chispas u otras fuentes de ignición. Almacene y utilice los adhesivos lejos de fuentes de calor y siga las medidas de seguridad contra incendios adecuadas.
- Compatibilidad química: tenga en cuenta la compatibilidad del adhesivo con otros materiales o sustancias. Evite mezclar adhesivos con productos químicos o materiales incompatibles que puedan causar reacciones peligrosas.
- Almacenamiento y eliminación: almacene los adhesivos siguiendo las instrucciones del fabricante para evitar fugas, derrames o exposición accidental. Siga las pautas adecuadas para almacenar y desechar de manera segura los recipientes de adhesivo y los materiales de desecho.
- Preparación para emergencias: Esté preparado para emergencias teniendo estaciones de lavado de ojos de emergencia, duchas de seguridad y equipos de extinción de incendios disponibles en el área de trabajo. Familiarícese con los procedimientos y protocolos de emergencia apropiados.
Es imprescindible consultar los datos e instrucciones de seguridad específicos del fabricante del adhesivo. Seguir las precauciones y pautas de seguridad adecuadas ayuda a proteger a las personas, prevenir accidentes y garantizar un entorno de trabajo seguro con adhesivos de conexión eléctrica.
Conclusión
En conclusión, los adhesivos de unión eléctrica juegan un papel fundamental para garantizar la confiabilidad y seguridad de los sistemas eléctricos. Proporcionan una excelente solución de unión y sellado para diversas aplicaciones, desde dispositivos electrónicos hasta componentes aeroespaciales. La elección de un adhesivo adecuado requiere una cuidadosa consideración de varios factores, incluido el tiempo de curado, la resistencia química y la conductividad eléctrica. Con una manipulación y un almacenamiento adecuados, los adhesivos para conexiones eléctricas pueden proporcionar una unión duradera y segura, lo que garantiza el rendimiento óptimo de los sistemas eléctricos.