Recubrimientos conformados para electrónica
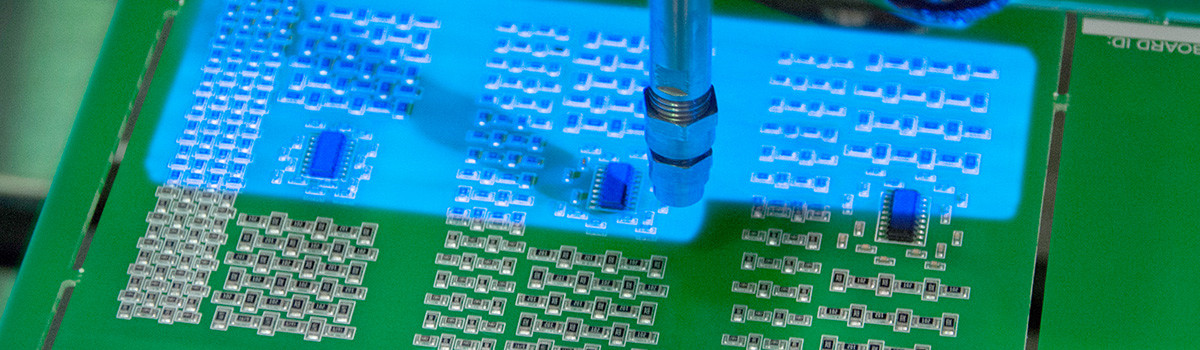
En el mundo de hoy, los dispositivos electrónicos son parte integral de nuestra vida diaria. A medida que los dispositivos electrónicos se vuelven más complejos y miniaturizados, la necesidad de protección contra factores ambientales como la humedad, el polvo y los productos químicos se vuelve más crítica. Aquí es donde entran los recubrimientos de conformación. Los recubrimientos de conformación son materiales especialmente formulados que protegen los componentes electrónicos de factores externos que pueden comprometer su rendimiento y funcionalidad. Este artículo explorará los beneficios y la importancia de los recubrimientos conformados para la electrónica.
¿Qué son los recubrimientos de conformación para la electrónica?
Los revestimientos de conformación son revestimientos protectores especializados que se utilizan en la industria electrónica para proteger los componentes electrónicos y las placas de circuitos de factores ambientales como la humedad, el polvo, los productos químicos y las temperaturas extremas. Estos recubrimientos se aplican en una capa delgada y uniforme sobre la superficie de los componentes electrónicos, adaptándose a los contornos de los componentes para brindar una cobertura y protección completas.
El objetivo principal de los recubrimientos de conformación es evitar daños o mal funcionamiento de los dispositivos electrónicos causados por elementos externos. La humedad, por ejemplo, puede causar corrosión y cortocircuitos, mientras que el polvo y la suciedad pueden afectar el rendimiento de los componentes sensibles. Un revestimiento de conformación protege el conjunto electrónico de estos peligros, asegurando su confiabilidad y longevidad.
Los recubrimientos de conformación generalmente están hechos de varias formulaciones químicas, incluidos acrílicos, siliconas, uretanos y epoxis. Cada tipo de recubrimiento ofrece distintas propiedades y ventajas. Los recubrimientos acrílicos se utilizan ampliamente debido a su versatilidad, facilidad de aplicación y rentabilidad. Proporcionan una buena resistencia a la humedad y son relativamente fáciles de quitar y volver a aplicar si es necesario. Las siliconas son conocidas por su excelente flexibilidad, estabilidad térmica y resistencia a altas temperaturas. Los recubrimientos de uretano ofrecen una excepcional resistencia química y protección contra solventes y combustibles. Los epoxis brindan dureza y durabilidad superiores, lo que los hace adecuados para entornos difíciles.
Los revestimientos de conformación requieren una atención cuidadosa para garantizar una cobertura y adhesión adecuadas. Varias técnicas incluyen cepillado, rociado, inmersión y recubrimiento selectivo. Se pueden emplear diferentes métodos dependiendo de los requisitos específicos y la complejidad del ensamblaje. Algunos recubrimientos se aplican manualmente, mientras que otros se realizan a través de procesos automatizados, como la pulverización robótica o los sistemas de recubrimiento por inmersión.
Una vez aplicado, el revestimiento de conformación crea una barrera protectora que encapsula los componentes electrónicos sin obstruir su funcionalidad. Forma una película protectora que se adhiere a la superficie y mantiene sus propiedades protectoras a lo largo del tiempo. Los recubrimientos suelen ser transparentes o translúcidos, lo que permite la inspección visual del ensamblaje.
Además de proteger contra los factores ambientales, los recubrimientos de conformación también ofrecen otros beneficios. Pueden proporcionar aislamiento eléctrico, evitando fugas de corriente y cortocircuitos. Las capas también pueden mejorar la resistencia del ensamblaje a las vibraciones y las tensiones mecánicas, lo que reduce el riesgo de daños durante el transporte o la operación. Además, pueden ofrecer protección contra hongos, moho y otros contaminantes que pueden comprometer el rendimiento de los dispositivos electrónicos.
La importancia de los recubrimientos conformados para dispositivos electrónicos
Los recubrimientos de conformación juegan un papel crucial en la mejora de la confiabilidad y durabilidad de los dispositivos electrónicos y ofrecen una variedad de beneficios esenciales para garantizar un rendimiento y una longevidad óptimos. Estas son algunas de las razones clave por las que los recubrimientos conformados son necesarios para los dispositivos electrónicos:
- Protección contra la humedad y la humedad: uno de los propósitos principales de los recubrimientos conformados es proteger los componentes electrónicos de la humedad y la humedad. El agua puede provocar corrosión, oxidación y la formación de caminos conductores, lo que puede provocar cortocircuitos y mal funcionamiento de los dispositivos. Los recubrimientos de conformación actúan como una barrera, evitando que la humedad llegue a los componentes sensibles y reduciendo el riesgo de daño.
- Prevención de la acumulación de polvo y escombros: los productos electrónicos suelen estar expuestos al polvo, la suciedad y los contaminantes del aire. Estas partículas pueden asentarse en las placas de circuito y los componentes, lo que genera problemas de aislamiento, una mayor generación de calor y posibles cortocircuitos. Los revestimientos de conformación crean una capa protectora que inhibe la acumulación de polvo y residuos, manteniendo la limpieza y el rendimiento de los componentes electrónicos.
- Resistencia química: muchos revestimientos de conformación resisten varios productos químicos, incluidos solventes, combustibles, ácidos y álcalis. Esto es particularmente importante en entornos donde los dispositivos electrónicos pueden entrar en contacto con sustancias corrosivas. Los recubrimientos actúan como escudo, previniendo reacciones químicas y asegurando la longevidad de los componentes.
- Protección térmica: los dispositivos electrónicos generan calor durante el funcionamiento y el calor excesivo puede degradar el rendimiento y la confiabilidad de los componentes. Los recubrimientos de conformación pueden proporcionar una barrera térmica, disipando el calor y reduciendo el riesgo de sobrecalentamiento. Las capas específicas, como las basadas en silicona, son conocidas por su excelente estabilidad térmica y pueden soportar altas temperaturas sin comprometer sus propiedades protectoras.
- Aislamiento eléctrico: los recubrimientos conformados pueden ofrecer aislamiento eléctrico, evitando fugas de corriente y cortocircuitos. Ayudan a mantener las características eléctricas deseadas de los componentes y reducen el potencial de fallas eléctricas causadas por factores ambientales o contaminación.
- Protección mecánica: la electrónica puede estar sujeta a tensiones mecánicas, como vibraciones, golpes o impactos. Los revestimientos de conformación mejoran la solidez mecánica de los dispositivos electrónicos al proporcionar una capa adicional de protección. Ayudan a absorber las vibraciones y las fuerzas de impacto, lo que reduce el riesgo de dañar los componentes delicados y garantiza un funcionamiento fiable.
- Resistencia ambiental: los recubrimientos de conformación permiten que los dispositivos electrónicos resistan diversas condiciones ambientales. Pueden resistir temperaturas extremas, radiación ultravioleta, niebla salina y otros elementos agresivos. Esto es particularmente importante para los dispositivos que se usan en aplicaciones industriales o al aire libre, donde pueden estar expuestos a entornos desafiantes.
Beneficios de usar recubrimientos de conformación
El uso de recubrimientos de conformación para dispositivos electrónicos ofrece varios beneficios que contribuyen a su confiabilidad y longevidad en general. Aquí hay algunas ventajas clave de usar recubrimientos de conformación:
- Protección ambiental: los recubrimientos de conformación brindan una barrera protectora que protege los componentes electrónicos de factores ambientales como la humedad, el polvo, la suciedad y los productos químicos. Evitan la entrada de agua, que puede causar corrosión y cortocircuitos, y protegen contra la acumulación de polvo y residuos que pueden afectar el rendimiento. Esta protección ambiental prolonga la vida útil de los dispositivos electrónicos.
- Mayor confiabilidad: al proteger contra los peligros ambientales, los recubrimientos de conformación mejoran la confiabilidad de los dispositivos electrónicos. Minimizan el riesgo de fallas causadas por problemas relacionados con la humedad, como daños en los componentes inducidos por la corrosión o migración electroquímica. Además, los revestimientos protegen contra el polvo y la suciedad que pueden provocar cortocircuitos eléctricos o averías en el aislamiento, lo que garantiza un rendimiento constante y fiable.
- Aislamiento eléctrico: los recubrimientos conformados ofrecen propiedades de aislamiento eléctrico, evitando fugas de corriente y cortocircuitos. Ayudan a mantener las características eléctricas deseadas de los componentes, reduciendo la posibilidad de mal funcionamiento o fallas eléctricas debido a la contaminación o absorción de humedad. El aislamiento eléctrico también ayuda a cumplir con los requisitos reglamentarios y de seguridad.
- Gestión térmica: algunos revestimientos de conformación tienen propiedades de gestión térmica, lo que les permite disipar el calor generado por los componentes electrónicos. Esta protección térmica ayuda a evitar el sobrecalentamiento, que puede degradar el rendimiento y reducir la vida útil de los dispositivos sensibles. Al manejar las temperaturas de manera efectiva, los recubrimientos de conformación contribuyen a la confiabilidad general de la electrónica.
- Resistencia química: muchos recubrimientos de conformación exhiben una excelente resistencia química. Proporcionan una barrera contra sustancias corrosivas, solventes, combustibles y otros químicos que pueden degradar los componentes electrónicos. Esta resistencia química previene las reacciones químicas, la degradación del material y las posibles fallas causadas por la exposición a entornos hostiles o el contacto con productos químicos.
- Protección contra vibraciones y golpes: los recubrimientos conformales ofrecen protección mecánica al absorber las vibraciones y reducir el impacto de los golpes y las tensiones mecánicas. Esto es particularmente beneficioso para dispositivos electrónicos sujetos a transporte o condiciones operativas adversas. Los recubrimientos de conformación ayudan a prevenir daños a componentes delicados, juntas de soldadura y conexiones al minimizar los efectos de vibraciones y golpes.
- Facilidad de inspección y reparación: los recubrimientos de conformación suelen ser transparentes o translúcidos, lo que permite la inspección visual de los componentes subyacentes. Esto facilita la detección de posibles problemas, como defectos en las juntas de soldadura, daños en los componentes o contaminación por materiales extraños. Además, los revestimientos de conformación se pueden quitar y volver a aplicar si se requieren reparaciones o modificaciones, lo que simplifica el mantenimiento.
¿Cómo funcionan los recubrimientos de conformación?
Los recubrimientos de conformación crean una barrera protectora en la superficie de los componentes electrónicos y las placas de circuitos. Estos recubrimientos generalmente se aplican como capas delgadas y uniformes que se ajustan a los contornos de los dispositivos, lo que garantiza una cobertura y protección completas. Los recubrimientos se adhieren a la superficie y forman una película continua que protege contra factores ambientales y posibles contaminantes.
La aplicación de revestimientos de conformación implica varios pasos:
- Preparación de la superficie: antes de aplicar el revestimiento de conformación, la superficie del ensamblaje electrónico debe prepararse adecuadamente. Esto generalmente implica limpiar y eliminar contaminantes como polvo, aceites y residuos. La cubierta se puede limpiar con solventes, limpieza ultrasónica u otros métodos apropiados para garantizar un sustrato limpio y suave para la adhesión del revestimiento.
- Selección del material de recubrimiento: se encuentran disponibles diferentes tipos de recubrimientos de conformación, como acrílicos, siliconas, uretanos y epoxis, cada uno con sus propiedades y ventajas. La elección del material de recubrimiento depende de factores como las condiciones ambientales, el nivel de protección deseado, los requisitos de aislamiento eléctrico y las consideraciones de aplicación específicas.
- Método de aplicación: los recubrimientos de conformación se pueden aplicar utilizando varios métodos, que incluyen cepillado, rociado, inmersión y recubrimiento selectivo. La selección del método de aplicación depende de factores como la complejidad del montaje, el tipo de material de recubrimiento y el nivel de precisión deseado. Los métodos de aplicación manual son adecuados para la producción a pequeña escala o áreas específicas que requieren un recubrimiento específico. Los procesos automatizados, como la pulverización robótica o los sistemas de recubrimiento por inmersión, a menudo se utilizan para la producción a gran escala para garantizar una cobertura de recubrimiento consistente y uniforme.
- Curado y Secado: Luego de la aplicación del recubrimiento, éste debe someterse a un proceso de curado o secado. Este proceso permite que el material de recubrimiento se solidifique y forme una película protectora. El tiempo y las condiciones de curado dependen del material de recubrimiento específico y de las recomendaciones del fabricante. Los métodos de curado pueden incluir secado al aire, curado térmico usando hornos o exposición a la luz ultravioleta para ciertos tipos de recubrimientos.
Una vez aplicado y curado, el revestimiento de conformación crea una barrera protectora que encapsula los componentes electrónicos. La capa es una barrera contra la humedad, el polvo, los productos químicos y otros factores ambientales que pueden dañar o degradar los componentes. Ayuda a prevenir la corrosión, los cortocircuitos eléctricos y la ruptura del aislamiento, lo que garantiza la confiabilidad y la longevidad de los dispositivos electrónicos.
Los recubrimientos de conformación mantienen sus propiedades protectoras a lo largo del tiempo, ofreciendo protección continua para el ensamblaje electrónico. En caso de reparaciones o modificaciones, la capa se puede quitar y volver a aplicar de manera selectiva, lo que permite el mantenimiento o el reemplazo de componentes sin comprometer la protección general que brinda el recubrimiento.
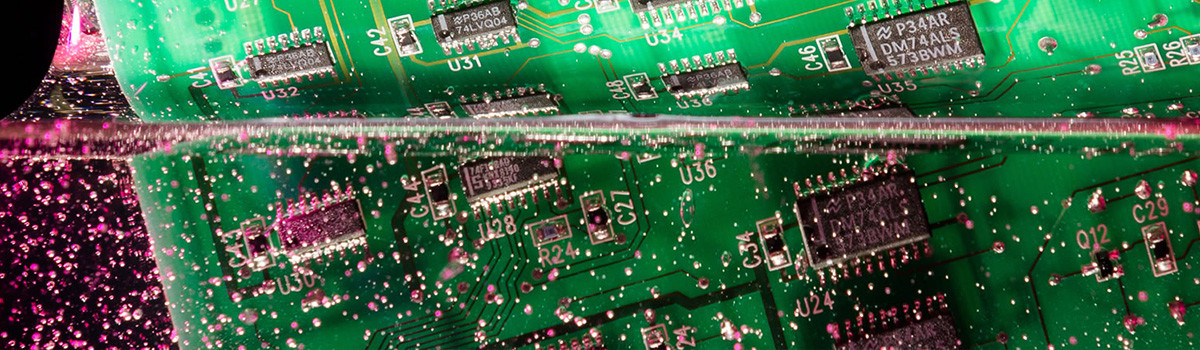
Tipos de revestimientos de conformación
Hay varios tipos de recubrimientos de conformación disponibles, cada uno con sus propiedades, ventajas y aplicaciones. La selección del tipo de recubrimiento depende de factores como los requisitos específicos del ensamblaje electrónico, las condiciones ambientales, el nivel de protección deseado y los procesos de fabricación. Estos son algunos tipos de recubrimientos de conformación de uso común:
- Recubrimientos conformados acrílicos: Los recubrimientos acrílicos son uno de los tipos más utilizados debido a su versatilidad y rentabilidad. Proporcionan buena resistencia a la humedad, aislamiento eléctrico y protección contra factores ambientales. Los recubrimientos acrílicos son fáciles de aplicar y se pueden quitar y volver a trabajar. Son adecuados para diversas aplicaciones y ofrecen una buena protección general.
- Recubrimientos de conformación de silicona: Los recubrimientos de silicona tienen una excelente flexibilidad, estabilidad térmica y resistencia a altas temperaturas. Pueden soportar variaciones extremas de temperatura sin perder sus propiedades protectoras. Los revestimientos de silicona proporcionan una excelente resistencia a la humedad y aislamiento eléctrico. A menudo se utilizan en aplicaciones en las que la alta estabilidad térmica y la flexibilidad son fundamentales, como en dispositivos electrónicos automotrices, aeroespaciales y para exteriores.
- Recubrimientos de conformación de uretano: Los recubrimientos de uretano ofrecen una resistencia química excepcional, lo que los hace adecuados para aplicaciones en las que la exposición a solventes, combustibles u otros productos químicos agresivos es una preocupación. Proporcionan una buena protección contra la humedad, aislamiento eléctrico y durabilidad mecánica. Los recubrimientos de uretano a menudo se usan en entornos exigentes, como aplicaciones automotrices, industriales y militares.
- Recubrimientos de conformación epóxicos: Los recubrimientos epóxicos son conocidos por su excelente dureza y durabilidad. Ofrecen una sólida protección mecánica y resistencia a la abrasión y al impacto. Los recubrimientos epóxicos brindan buena resistencia química y protección contra la humedad. Se utilizan comúnmente en aplicaciones que requieren una protección robusta y resistencia mecánica, como en sistemas de control industrial, electrónica robusta y entornos de alta tensión.
- Revestimientos de conformación de parileno: El parileno es un tipo único de revestimiento de conformación que se deposita como vapor y forma una película de polímero delgada y sin poros. Las capas de parileno brindan excelentes propiedades de barrera contra la humedad, aislamiento eléctrico, resistencia química y biocompatibilidad. Ofrecen un alto nivel de protección y se adaptan a geometrías complejas. Los recubrimientos de parileno se usan comúnmente en dispositivos médicos, aplicaciones aeroespaciales y electrónicas sensibles.
- Recubrimientos de conformación curables con UV: Los recubrimientos curables con UV se aplican como un líquido y luego se curan con luz UV. Ofrecen tiempos de curado rápidos, lo que puede aumentar la eficiencia de la producción. Las capas curables con UV brindan buena resistencia a la humedad, aislamiento eléctrico y resistencia química. Son adecuados para aplicaciones que requieren un curado rápido, un alto rendimiento y una calidad de recubrimiento constante.
Es importante tener en cuenta que la selección del revestimiento de conformación apropiado depende de los requisitos específicos del ensamblaje electrónico y la aplicación prevista. Las condiciones ambientales, el rango de temperatura de funcionamiento, la exposición química y el nivel de protección deseado deben tenerse en cuenta al elegir el tipo de revestimiento de conformación para garantizar un rendimiento y una vida útil óptimos de los dispositivos electrónicos.
Revestimientos acrilicos
Los conformalcoatings acrílicos se utilizan ampliamente en la industria electrónica debido a su versatilidad, rentabilidad y facilidad de aplicación. Brindan una variedad de beneficios y son adecuados para diversos ensamblajes y aplicaciones electrónicos. Estas son algunas de las características y ventajas clave de los recubrimientos conformados acrílicos:
- Protección contra la humedad: los recubrimientos acrílicos ofrecen una buena resistencia a la humedad, lo que ayuda a evitar que el agua o la humedad penetren en los componentes electrónicos. La humedad puede causar corrosión, cortocircuitos eléctricos y degradación del rendimiento. Los recubrimientos acrílicos actúan como una barrera, protegen contra problemas relacionados con la humedad y mejoran la confiabilidad y la vida útil de los dispositivos electrónicos.
- Aislamiento eléctrico: Los recubrimientos acrílicos brindan aislamiento eléctrico, evitando fugas de corriente y cortocircuitos. Ayudan a mantener las características eléctricas deseadas de los componentes y reducen el riesgo de fallas o fallas eléctricas causadas por contaminación o absorción de humedad. Esta propiedad de aislamiento eléctrico es esencial para mantener la integridad de los circuitos electrónicos.
- Protección ambiental: los recubrimientos de conformación acrílicos protegen los ensamblajes electrónicos de factores ambientales como el polvo, la suciedad, los productos químicos y las variaciones de temperatura. Crean una barrera contra los contaminantes transportados por el aire, evitando que se asienten en la superficie de los componentes. Los recubrimientos acrílicos también ofrecen cierto nivel de resistencia a los productos químicos, brindando protección adicional contra sustancias corrosivas.
- Facilidad de aplicación: los recubrimientos acrílicos son conocidos por su facilidad de aplicación. Se pueden aplicar usando varios métodos, incluyendo cepillado, rociado, inmersión o revestimiento selectivo. Esta flexibilidad permite procesos de aplicación manuales y automatizados, según los requisitos específicos y la escala de producción. Los recubrimientos acrílicos generalmente tienen una buena capacidad de humectación, lo que garantiza una cobertura y adherencia uniformes a las superficies de los componentes electrónicos.
- Capacidad de reparación y reelaboración: una de las ventajas de los recubrimientos acrílicos es su reelaboración. Si se requieren reparaciones o modificaciones, los recubrimientos acrílicos se pueden quitar fácilmente usando solventes apropiados, lo que permite reparar los componentes subyacentes. La capacidad de quitar y volver a aplicar revestimientos acrílicos simplifica el proceso de reparación y facilita las actividades de mantenimiento.
- Transparente o translúcido: los recubrimientos conformados acrílicos suelen ser transparentes o translúcidos. Esta función permite la inspección visual de los componentes subyacentes sin necesidad de retirar el revestimiento. La inspección visual identifica posibles problemas, como defectos en las juntas de soldadura, daños en los componentes o contaminación por materiales extraños.
- Rentabilidad: los recubrimientos de conformación acrílicos ofrecen una solución rentable para proteger los ensamblajes electrónicos. Equilibran bien el rendimiento y la asequibilidad, lo que los hace adecuados para una amplia gama de aplicaciones. El costo relativamente bajo de los recubrimientos acrílicos permite procesos de producción rentables sin comprometer la protección y confiabilidad deseadas de los dispositivos electrónicos.
Si bien los recubrimientos de conformación acrílicos brindan varios beneficios, es esencial tener en cuenta los requisitos específicos del ensamblaje electrónico y las condiciones ambientales al elegir un tipo de recubrimiento. Deben tenerse en cuenta factores como el rango de temperatura de funcionamiento, la exposición química y las tensiones mecánicas para garantizar una protección y un rendimiento óptimos.
Recubrimientos de silicona
Los recubrimientos de conformación de silicona se usan ampliamente en la industria electrónica debido a sus propiedades únicas y su capacidad para soportar condiciones ambientales desafiantes. Ofrecen una variedad de beneficios que los hacen adecuados para diversos ensamblajes y aplicaciones electrónicos. Estas son algunas características y ventajas clave de los recubrimientos conformados de silicona:
- Estabilidad térmica: los recubrimientos de silicona son conocidos por su excelente estabilidad térmica, lo que les permite soportar altas temperaturas de funcionamiento sin perder sus propiedades protectoras. Pueden manejar las variaciones de temperatura con mayor eficacia que muchos otros tipos de revestimientos de conformación. Esto hace que los recubrimientos de silicona sean adecuados para aplicaciones con alta estabilidad térmica, como la electrónica automotriz, aeroespacial e industrial.
- Flexibilidad y conformabilidad: los recubrimientos conformados de silicona son muy flexibles y pueden adaptarse a la forma de conjuntos electrónicos complejos. Se pueden aplicar como capas delgadas y uniformes que brindan una cobertura completa incluso en circuitos y componentes complejos. La flexibilidad y adaptabilidad de los revestimientos de silicona aseguran que las áreas críticas estén adecuadamente protegidas, lo que reduce el riesgo de daños o fallas.
- Protección contra la humedad y el medio ambiente: Los revestimientos de silicona ofrecen una excelente resistencia a la humedad, lo que los convierte en prácticas barreras contra la penetración del agua y la humedad. Esta protección contra la humedad ayuda a prevenir la corrosión, la oxidación y los cortocircuitos eléctricos causados por problemas relacionados con la humedad. Los revestimientos de silicona también resisten factores ambientales como el polvo, la suciedad y los productos químicos, lo que mejora la longevidad y la confiabilidad de los dispositivos electrónicos.
- Aislamiento eléctrico: Los revestimientos conformados de silicona brindan propiedades de aislamiento eléctrico, evitando fugas de corriente y cortocircuitos. Mantienen la integridad eléctrica de los componentes y protegen contra fallas eléctricas causadas por contaminación o absorción de humedad. El aislamiento eléctrico que ofrecen los revestimientos de silicona es fundamental para mantener la fiabilidad y el rendimiento de los circuitos electrónicos.
- Resistencia química: Los revestimientos de silicona exhiben una buena resistencia a varios productos químicos, incluidos solventes, combustibles, ácidos y álcalis. Esta resistencia química hace que los recubrimientos de silicona sean adecuados para aplicaciones donde la exposición a sustancias corrosivas es una preocupación. Las capas actúan como una barrera protectora, previniendo reacciones químicas y la degradación del material y asegurando la longevidad de los componentes electrónicos.
- Resistencia a los rayos ultravioleta ya la intemperie: Los revestimientos de silicona ofrecen una excelente resistencia a la radiación ultravioleta (UV) ya la intemperie. Pueden resistir la exposición prolongada a la luz solar y ambientes al aire libre sin una degradación significativa o pérdida de propiedades protectoras. Esto hace que los recubrimientos de silicona sean ideales para dispositivos electrónicos utilizados en aplicaciones al aire libre o expuestos a la radiación ultravioleta.
- Propiedades dieléctricas: los revestimientos conformados de silicona tienen buenas propiedades dieléctricas, lo que significa que brindan un aislamiento eléctrico efectivo sin afectar significativamente el rendimiento eléctrico de los componentes. Esta propiedad es esencial para mantener las características eléctricas deseadas y evitar averías eléctricas en los circuitos electrónicos.
Los revestimientos de conformación de silicona están disponibles en diferentes formulaciones para adaptarse a los requisitos de aplicación específicos. Se pueden aplicar usando varios métodos, incluyendo cepillado, rociado o inmersión. Los recubrimientos de silicona brindan una capa protectora confiable y duradera para los ensamblajes electrónicos, lo que garantiza su funcionalidad y confiabilidad incluso en condiciones de funcionamiento adversas.
Al considerar los revestimientos conformados de silicona, es esencial evaluar factores como el rango de temperatura de funcionamiento, la exposición a productos químicos y las tensiones mecánicas para determinar la formulación de revestimiento más adecuada para la aplicación específica.
Recubrimientos epóxicos conformes
Los recubrimientos conformados epóxicos se utilizan ampliamente en la electrónica debido a su excelente dureza, durabilidad y resistencia química. Ofrecen una variedad de beneficios que los hacen adecuados para diversos ensamblajes y aplicaciones electrónicos. Estas son algunas de las características y ventajas clave de los recubrimientos de conformación epoxi:
- Dureza y Protección Mecánica: Los recubrimientos epóxicos brindan una dureza y protección mecánica excepcionales, haciéndolos altamente resistentes a la abrasión, impacto y daño físico. Ofrecen una barrera robusta que protege los componentes electrónicos de las tensiones mecánicas, asegurando su longevidad y confiabilidad. Los recubrimientos epóxicos son particularmente adecuados para aplicaciones que requieren una protección automática mejorada, como en sistemas de control industrial y electrónica robusta.
- Resistencia química: los recubrimientos de conformación epóxicos exhiben una excelente resistencia a varios químicos, incluidos solventes, combustibles, ácidos y álcalis. Esta resistencia química protege los componentes electrónicos de la degradación o daño causado por la exposición a sustancias corrosivas. Los recubrimientos epóxicos actúan como barrera, previniendo reacciones químicas y asegurando la integridad de los componentes subyacentes.
- Protección contra la humedad y el medio ambiente: Los recubrimientos epóxicos brindan protección adecuada contra la humedad y el medio ambiente. Crean una barrera contra el agua, la humedad, el polvo y otros contaminantes ambientales que pueden dañar los componentes electrónicos. Los recubrimientos epóxicos ayudan a prevenir la corrosión, los cortocircuitos eléctricos y la degradación del rendimiento al evitar la entrada de humedad.
- Aislamiento eléctrico: los recubrimientos conformados epóxicos ofrecen excelentes propiedades de aislamiento eléctrico, evitando fugas de corriente y cortocircuitos. Mantienen las características eléctricas deseadas de los componentes, reduciendo el riesgo de mal funcionamiento o fallas eléctricas causadas por contaminación o absorción de humedad. El aislamiento eléctrico proporcionado por los recubrimientos epoxi es crucial para mantener la confiabilidad y el rendimiento de los circuitos electrónicos.
- Resistencia Térmica: Los recubrimientos epóxicos tienen buena resistencia térmica, lo que les permite soportar temperaturas elevadas sin una degradación significativa o pérdida de propiedades protectoras. Ayudan a disipar el calor generado por los componentes electrónicos, contribuyendo a la gestión térmica y evitando el sobrecalentamiento. Esta resistencia térmica hace que los recubrimientos epoxi sean adecuados para aplicaciones donde las variaciones de temperatura y la disipación de calor son consideraciones críticas.
- Adhesión y cobertura: los recubrimientos de conformación epóxicos muestran una excelente adhesión a varios sustratos, incluidos los materiales de metal, plástico y PCB. Se adhieren bien a la superficie de los ensambles electrónicos, formando una capa protectora uniforme y continua. Los recubrimientos epóxicos pueden proporcionar una cobertura completa, asegurando que todas las áreas y componentes críticos estén adecuadamente protegidos.
- Reparabilidad: Los recubrimientos epóxicos ofrecen la ventaja de ser reprocesables y reparables. Si se requieren reparaciones o modificaciones, los recubrimientos de epoxi se pueden eliminar de forma selectiva con los disolventes apropiados, lo que permite reparar los componentes subyacentes. Esta característica de reparabilidad simplifica las actividades de mantenimiento y facilita el reemplazo de componentes si es necesario.
Los recubrimientos de conformación de epoxi se aplican normalmente mediante métodos de recubrimiento con brocha, rociado o selectivos. Los recubrimientos se curan mediante una reacción química o un proceso de curado por calor, formando una película protectora duradera. Brindan protección duradera para ensamblajes electrónicos, asegurando su funcionalidad y confiabilidad en entornos desafiantes.
Al considerar los recubrimientos de conformación de epoxi, es esencial evaluar factores como el rango de temperatura de funcionamiento, la exposición a productos químicos, las tensiones mecánicas y el nivel deseado de protección mecánica y química para seleccionar la formulación de recubrimiento más adecuada para la aplicación específica.
Revestimientos conformados de uretano
Los recubrimientos conformados de uretano, también conocidos como recubrimientos de poliuretano, se utilizan ampliamente en la industria electrónica debido a su excepcional resistencia química y durabilidad mecánica. Ofrecen una variedad de beneficios que los hacen adecuados para diversos ensamblajes y aplicaciones electrónicos. Estas son algunas características y ventajas clave de los recubrimientos conformados de uretano:
- Resistencia química: Los revestimientos de uretano resisten varios productos químicos, incluidos solventes, combustibles, aceites, ácidos y álcalis. Esta resistencia química hace que los recubrimientos de uretano sean adecuados para aplicaciones donde la exposición a químicos agresivos es una preocupación. Actúan como una barrera, protegiendo los componentes electrónicos de la degradación química, la corrosión y otras formas de daño.
- Protección contra la humedad: los revestimientos conformados de uretano brindan una resistencia efectiva a la humedad, evitando que el agua o la humedad penetren en los componentes electrónicos. La humedad puede causar corrosión, cortocircuitos eléctricos y degradación del rendimiento. Los recubrimientos de uretano actúan como una barrera, protegen contra problemas relacionados con la humedad y mejoran la confiabilidad y la vida útil de los dispositivos electrónicos.
- Durabilidad mecánica: Los revestimientos de uretano ofrecen una excelente durabilidad mecánica, con resistencia a la abrasión, los impactos y los daños físicos. Proporcionan una capa protectora resistente que resiste la manipulación y las condiciones ambientales duras. Los recubrimientos de uretano son adecuados para aplicaciones donde se requiere una protección mecánica mejorada, como en entornos industriales o dispositivos expuestos a altos niveles de desgaste.
- Resistencia térmica: Los revestimientos de uretano exhiben una buena resistencia térmica, lo que les permite soportar temperaturas elevadas sin una degradación significativa o pérdida de propiedades protectoras. Ayudan a disipar el calor generado por los componentes electrónicos, contribuyendo a la gestión térmica y evitando el sobrecalentamiento. Esta resistencia térmica hace que los recubrimientos de uretano sean adecuados para aplicaciones donde las variaciones de temperatura y la disipación de calor son consideraciones críticas.
- Flexibilidad: Los recubrimientos conformados de uretano ofrecen un equilibrio entre dureza y flexibilidad. Tienen algo de elasticidad, lo que les permite adaptarse a movimientos y tensiones menores en el conjunto electrónico. Esta flexibilidad ayuda a reducir el riesgo de agrietamiento o delaminación del recubrimiento, lo que garantiza la protección a largo plazo de los componentes.
- Estabilidad UV: Los recubrimientos de uretano exhiben una buena resistencia a la radiación ultravioleta (UV), protegiendo contra los efectos potencialmente dañinos de la luz solar y otras fuentes UV. Resisten el amarillamiento o la degradación cuando se exponen a la luz ultravioleta, lo que los hace adecuados para aplicaciones al aire libre o dispositivos expuestos a la radiación ultravioleta.
- Adhesión y cobertura: Los recubrimientos de uretano demuestran una excelente adhesión a varios sustratos, incluidos metales, plásticos y materiales de PCB. Se adhieren bien a la superficie de los ensambles electrónicos, formando una capa protectora uniforme y continua. Los revestimientos de uretano pueden proporcionar una cobertura completa, asegurando que todas las áreas y componentes críticos estén adecuadamente protegidos.
Los recubrimientos de conformación de uretano se aplican normalmente mediante métodos de brocha, rociado o recubrimiento selectivo. Las capas se pueden curar mediante procesos de curado por calor o por humedad, formando una película duradera y protectora. Brindan protección duradera para ensamblajes electrónicos, asegurando su funcionalidad y confiabilidad en entornos exigentes.
Al considerar el uso de recubrimientos conformados de uretano, es esencial evaluar la exposición química específica, el rango de temperatura de funcionamiento, las tensiones mecánicas y el nivel deseado de protección química y mecánica para seleccionar la formulación de recubrimiento más adecuada para la aplicación en particular.
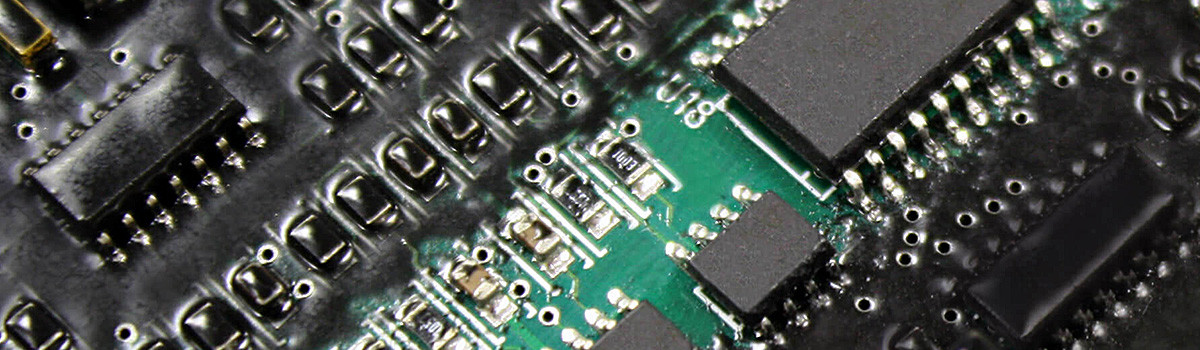
Recubrimientos conformados de parileno
Los revestimientos de conformación de parileno son únicos y brindan una protección excepcional para los dispositivos electrónicos. Los recubrimientos de parileno se depositan en forma de vapor y forman una película de polímero delgada y sin poros. Ofrecen una variedad de beneficios que los hacen muy adecuados para diversos conjuntos y aplicaciones electrónicos. Estas son algunas de las características y ventajas clave de los recubrimientos de conformación de parileno:
- Barrera contra la humedad y los productos químicos: los revestimientos de parileno proporcionan una excelente barrera contra la humedad, los gases y los productos químicos. La película delgada y uniforme formada por los revestimientos de parileno ofrece una barrera contra la humedad muy eficaz, que evita la entrada de agua y humedad en los componentes electrónicos. También brindan una resistencia excepcional a los productos químicos, incluidos los solventes, ácidos, bases y sustancias corrosivas. Esta resistencia química y a la humedad protege los dispositivos electrónicos de la corrosión, oxidación y degradación, asegurando su confiabilidad a largo plazo.
- Conformidad y cobertura: Los revestimientos de parileno tienen excelentes propiedades de conformación, lo que significa que se ajustan a la forma de superficies complejas e irregulares. El proceso de deposición de vapor permite que la capa cubra todo el conjunto electrónico de manera uniforme, incluidas las características complejas, los bordes afilados y las grietas. Los revestimientos de parileno pueden penetrar profundamente en espacios reducidos, lo que garantiza una cobertura y protección completas para todas las áreas críticas.
- Aislamiento eléctrico: Los revestimientos conformados de parileno brindan excelentes propiedades de aislamiento eléctrico. Tienen una alta rigidez dieléctrica y pueden aislar eficazmente los componentes eléctricos y evitar fugas de corriente o cortocircuitos. Los recubrimientos de parileno mantienen las características eléctricas deseadas de los detalles, lo que reduce el riesgo de mal funcionamiento o fallas eléctricas causadas por la contaminación o la absorción de humedad.
- Biocompatibilidad: los recubrimientos de parileno son biocompatibles y químicamente inertes, lo que los hace adecuados para dispositivos médicos y dispositivos electrónicos implantables. No provocan reacciones adversas en contacto con tejidos o fluidos biológicos. Los recubrimientos de parileno se utilizan en aplicaciones como marcapasos, implantes neurales y biosensores, donde la biocompatibilidad es crítica.
- Estabilidad térmica: Los revestimientos de parileno exhiben una excelente estabilidad térmica y pueden soportar un amplio rango de temperatura. Permanecen estables a bajas y altas temperaturas, manteniendo sus propiedades protectoras sin una degradación significativa. Esta estabilidad térmica hace que los recubrimientos de parileno sean adecuados para aplicaciones donde las variaciones de temperatura y la disipación de calor son consideraciones esenciales.
- Bajo coeficiente de fricción: los revestimientos de parileno tienen un bajo coeficiente de fricción, lo que proporciona lubricidad y reduce la fricción superficial entre los componentes. Este bajo coeficiente de fricción ayuda a minimizar el desgaste, evita que se adhieran o se atasquen y mejora el rendimiento general y la vida útil de los dispositivos electrónicos revestidos.
- Transparencia y trazabilidad: los recubrimientos de conformación de parileno son transparentes, lo que permite la inspección visual de los componentes subyacentes sin necesidad de retirar el recubrimiento. Esta transparencia permite evaluar e identificar posibles problemas, como defectos en las juntas de soldadura, daños en los componentes o contaminación por materiales extraños. Además, los recubrimientos de parileno se pueden dopar o marcar con elementos trazables, lo que facilita el control de calidad, el seguimiento y la identificación.
Los revestimientos de conformación de parileno se aplican normalmente mediante un proceso de deposición de vapor especializado. Las capas se forman a través de un método de deposición de vapor químico (CVD), que garantiza una cobertura uniforme y sin poros. Los recubrimientos de parileno brindan protección duradera para ensamblajes electrónicos, incluso en entornos hostiles y aplicaciones exigentes.
Al considerar los revestimientos de conformación de parileno, es esencial evaluar factores como los requisitos específicos del ensamblaje electrónico, las condiciones ambientales y el nivel de protección deseado para seleccionar el tipo de parileno y el proceso de deposición apropiados.
Factores a considerar al elegir un revestimiento de conformación
Al elegir un recubrimiento de conformación para dispositivos electrónicos, se deben considerar varios factores para garantizar que el recubrimiento cumpla con los requisitos específicos de la aplicación. Aquí hay algunos factores clave a considerar:
- Condiciones ambientales: Las condiciones ambientales en las que operará el dispositivo electrónico juegan un papel crucial en la selección del revestimiento de conformación apropiado. Considere factores tales como temperaturas extremas, niveles de humedad, exposición química, niebla salina y radiación ultravioleta. Las diferentes capas tienen distintos grados de resistencia a estos factores ambientales, y elegir un recubrimiento que pueda soportar condiciones específicas es esencial para la confiabilidad a largo plazo.
- Propiedades Eléctricas: Considere las propiedades eléctricas requeridas para el ensamble electrónico. Algunos recubrimientos ofrecen mejores propiedades de aislamiento eléctrico que otros. Evalúe la rigidez dieléctrica, la resistencia superficial y la capacidad para mantener el aislamiento incluso en presencia de humedad o contaminantes. Asegúrese de que el recubrimiento elegido no afecte negativamente el rendimiento eléctrico de los componentes.
- Espesor y cobertura: Los requisitos de espesor y cobertura del conformalcoating son consideraciones esenciales. Las capas delgadas son deseables para aplicaciones donde el espacio limitado o mantener tolerancias estrechas es crítico. Sin embargo, pueden ser necesarios recubrimientos más gruesos para aplicaciones que requieren una mayor protección contra el estrés mecánico o entornos hostiles. La capa debe poder cubrir uniformemente todas las áreas críticas, incluidas las geometrías y los componentes complejos.
- Método de aplicación: Considere los métodos disponibles y elija un recubrimiento compatible con el modo seleccionado. Los métodos de aplicación estándar incluyen rociado, cepillado, inmersión y revestimiento selectivo. Algunas capas pueden ser más adecuadas para métodos de aplicación específicos, mientras que otras pueden requerir técnicas o equipos especializados.
- Reelaboración y Reparación: Evalúe los requisitos de reelaboración y reparabilidad del revestimiento. En algunos casos, puede ser necesario quitar o reparar la capa para reemplazar, reparar o modificar componentes. Algunos recubrimientos se pueden volver a trabajar o eliminar fácilmente, mientras que otros pueden ser más difíciles o requerir métodos o solventes especializados.
- Compatibilidad del sustrato: Considere la compatibilidad del recubrimiento con los materiales y sustratos utilizados en el ensamblaje electrónico. El revestimiento debe adherirse al sustrato y exhibir una buena compatibilidad con los componentes, las juntas de soldadura y otros materiales. Los problemas de compatibilidad pueden provocar deslaminación, adhesión reducida o rendimiento deficiente del recubrimiento.
- Cumplimiento normativo: tenga en cuenta los requisitos normativos específicos que se aplican al dispositivo electrónico o la industria en la que se utilizará. Aplicaciones típicas como dispositivos médicos o electrónica aeroespacial pueden tener estándares regulatorios específicos para recubrimientos de conformación. Asegúrese de que el revestimiento elegido cumpla con los reglamentos y normas pertinentes.
- Costo y Disponibilidad: Evaluar el costo del recubrimiento y su disponibilidad en las cantidades requeridas. Considere la rentabilidad del recubrimiento, el nivel deseado de protección y el presupuesto general del proyecto. Además, asegúrese de que el recubrimiento esté fácilmente disponible de proveedores confiables para evitar demoras o problemas en la cadena de suministro.
Al considerar estos factores, puede seleccionar un revestimiento de conformación que proporcione protección, rendimiento y confiabilidad óptimos para los requisitos específicos de su dispositivo electrónico y su entorno operativo.
Métodos de aplicación para revestimientos de conformación
Los recubrimientos de conformación son capas protectoras delgadas que se aplican a las placas de circuitos y componentes electrónicos para proporcionar aislamiento y protegerlos de factores ambientales como la humedad, el polvo, los productos químicos y las fluctuaciones de temperatura. Estos recubrimientos están diseñados para “adaptarse” a la forma del sustrato, proporcionando una barrera protectora uniforme y continua. Existen varios métodos para aplicar revestimientos de conformación, cada uno con sus ventajas y consideraciones. Este artículo explorará algunos métodos de aplicación estándar para recubrimientos de conformación.
- Cepillado/Inmersión: El cepillado o inmersión es uno de los métodos más simples y tradicionales para aplicar revestimientos de conformación. El material de recubrimiento se cepilla manualmente o los componentes se sumergen en un recipiente de la solución de recubrimiento. Este método es rentable y adecuado para la producción de bajo volumen. Sin embargo, puede dar como resultado un espesor de recubrimiento inconsistente y requerir un curado posterior a la aplicación.
- Recubrimiento por aspersión: El recubrimiento por aspersión implica el uso de aire comprimido o un sistema de aspersión especializado para aplicar el material de recubrimiento como una fina niebla sobre el sustrato. Este método ofrece una aplicación más rápida y es adecuado para procesos manuales y automatizados. El recubrimiento por aspersión brinda más control sobre el espesor y la uniformidad del recubrimiento, pero requiere sistemas de filtración y ventilación adecuados para controlar el exceso de aspersión y garantizar la seguridad del operador.
- Recubrimiento selectivo: El recubrimiento selectivo se usa cuando solo áreas específicas del sustrato requieren protección. Implica el uso de un sistema de dosificación controlado o un brazo robótico con un aplicador de precisión para aplicar el material de recubrimiento con precisión en las ubicaciones deseadas. El recubrimiento selectivo minimiza el desperdicio, reduce la necesidad de enmascaramiento y permite una protección específica. Se usa comúnmente para placas de circuito complejas con componentes sensibles.
- Deposición de vapor: Los métodos de deposición de vapor, como la deposición química de vapor (CVD) y la deposición física de vapor (PVD), implican depositar una capa de revestimiento de conformación sobre el sustrato a través de una fase de vapor. Estos métodos suelen requerir equipos especializados y entornos controlados. Las técnicas de deposición de vapor ofrecen una excelente uniformidad de recubrimiento, control de espesor y cobertura en geometrías complejas. Se utilizan comúnmente para aplicaciones de alto rendimiento y dispositivos electrónicos avanzados.
- Recubrimiento de parileno: el recubrimiento de parileno es un método único que consiste en depositar una película fina de polímero conformado sobre el sustrato a través de la deposición de vapor. Los revestimientos de parileno ofrecen protección, aislamiento y biocompatibilidad excepcionales. El material de recubrimiento penetra en las grietas y cubre toda la superficie de manera uniforme, incluso en componentes intrincados. Los recubrimientos de parileno se usan comúnmente en dispositivos médicos, aplicaciones aeroespaciales y de alta confiabilidad.
Al seleccionar un método de aplicación para recubrimientos de conformación, se deben considerar varios factores, incluida la complejidad del sustrato, el volumen de producción, las propiedades del material de recubrimiento, el costo y los requisitos ambientales. Es esencial elegir el método que proporcione una cobertura, uniformidad y confiabilidad óptimas del recubrimiento al considerar las necesidades específicas de la aplicación.
Espesor del revestimiento de conformación
El espesor del revestimiento de conformación es fundamental para garantizar la eficacia y la fiabilidad del revestimiento protector aplicado a los componentes electrónicos y las placas de circuitos. El espesor del recubrimiento afecta directamente el nivel de protección brindado contra los factores ambientales, como la humedad, el polvo, los productos químicos y las variaciones de temperatura. Este artículo explorará la importancia del espesor del recubrimiento de conformación y las consideraciones involucradas para lograr el espesor de recubrimiento deseado.
El objetivo principal de los recubrimientos de conformación es crear una capa protectora uniforme y continua sobre el sustrato. El grosor del revestimiento debe ser suficiente para proporcionar aislamiento y evitar posibles cortocircuitos eléctricos o corrientes de fuga sin ser tan grueso como para causar interferencias eléctricas o problemas térmicos. El grosor ideal del revestimiento depende de factores como el material del revestimiento, la aplicación específica y las condiciones ambientales que encontrarán los componentes electrónicos revestidos.
Los recubrimientos de conformación generalmente se aplican como capas delgadas, que normalmente van desde unos pocos micrómetros (µm) hasta decenas de micrómetros de espesor. El fabricante del material de recubrimiento a menudo especifica el espesor de recubrimiento recomendado o puede definirse según los estándares de la industria, como IPC-CC-830 para recubrimientos de conformación.
Lograr el espesor de recubrimiento deseado implica considerar varios factores:
- Material de recubrimiento: Los diferentes materiales de recubrimiento de conformación tienen diferentes viscosidades y características de flujo. Estas propiedades influyen en cómo el recubrimiento se extiende y nivela sobre la superficie del sustrato, lo que afecta el espesor resultante. Es esencial comprender los requisitos específicos de la aplicación y seleccionar un material de recubrimiento que se pueda aplicar con el control de espesor deseado.
- Método de aplicación: El método de aplicación elegido también juega un papel importante en la determinación del espesor del recubrimiento. Prácticas como el cepillado o la inmersión pueden provocar variaciones en el espesor del recubrimiento debido a las técnicas de aplicación manual. Los procesos automatizados, como el rociado o el recubrimiento selectivo, pueden proporcionar más control sobre el espesor del recubrimiento, lo que da como resultado una capa más pareja y uniforme.
- Control del proceso: El control adecuado del proceso es crucial para lograr el espesor de recubrimiento deseado. Factores como la presión de rociado, el tamaño de la boquilla, la distancia de rociado y la viscosidad del material de recubrimiento deben controlarse cuidadosamente durante el proceso de aplicación. Es posible que sea necesario ajustar los parámetros del proceso según la geometría del sustrato y el espesor de recubrimiento deseado.
- Curado/Contracción: Algunos materiales de revestimiento de conformación se someten a un proceso de curado o secado después de la aplicación. El material de recubrimiento puede encogerse durante este proceso, lo que afecta el espesor final del recubrimiento. Es esencial tener en cuenta la contracción potencial al determinar el espesor inicial del revestimiento.
- Verificación e Inspección: Una vez aplicado el recubrimiento, es fundamental verificar su espesor para asegurar que cumple con las especificaciones requeridas. Se pueden utilizar diversas técnicas de inspección, como la inspección visual, el corte transversal o equipos de medición especializados como perfilómetros o microscopía óptica con software de medición calibrado.
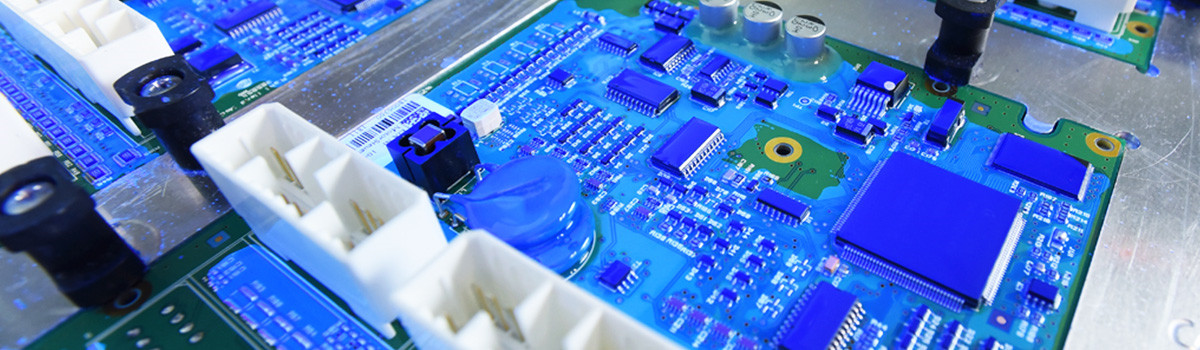
Problemas comunes con los recubrimientos de conformación
Si bien los recubrimientos de conformación son esenciales para proteger los componentes electrónicos y las placas de circuitos, a veces pueden encontrar problemas que pueden afectar su rendimiento y confiabilidad. Este artículo discutirá algunos problemas comunes con los recubrimientos de conformación y sus posibles causas.
- Cobertura inadecuada: La cobertura inadecuada ocurre cuando el revestimiento no logra cubrir toda la superficie del sustrato o deja huecos y vacíos. Este problema puede deberse a técnicas de aplicación inadecuadas, como una pulverización desigual o una viscosidad de recubrimiento insuficiente. También puede ocurrir debido a la contaminación de la superficie, secado o curado inadecuado o control inadecuado del espesor del recubrimiento.
- Variación de espesor: el espesor de recubrimiento no uniforme es otro problema común. Las técnicas de aplicación inconsistentes, como la pulverización desigual o el control inadecuado de los parámetros del proceso, pueden causarlo. Es necesario que haya más tiempo de secado o curado, la viscosidad inadecuada del material de recubrimiento o la preparación insuficiente de la superficie también pueden contribuir a las variaciones de espesor.
- Formación de ampollas y delaminación: la formación de ampollas y la delaminación se producen cuando el revestimiento de conformación forma burbujas o se separa del sustrato. Este problema puede surgir debido a una limpieza y preparación inadecuadas de la superficie, humedad o contaminación en la superficie, curado o secado inadecuado o compatibilidad inadecuada entre el material de recubrimiento y el sustrato.
- Agrietamiento y formación de puentes: el agrietamiento se refiere al desarrollo de fisuras o fracturas en el revestimiento de conformación, mientras que la formación de puentes se produce cuando el material de revestimiento se extiende por espacios o componentes adyacentes, lo que da como resultado conexiones eléctricas no deseadas. Estos problemas pueden ser causados por un espesor de recubrimiento excesivo, curado o secado inadecuado, tensión térmica, selección inadecuada del material de recubrimiento o flexibilidad de recubrimiento inadecuada.
- Adhesión deficiente: la adhesión deficiente ocurre cuando el recubrimiento no se adhiere al sustrato, lo que da como resultado una protección reducida y un posible desprendimiento del recubrimiento. La limpieza y preparación inadecuadas de la superficie, los contaminantes, los materiales de recubrimiento y sustrato incompatibles o el curado o secado insuficiente pueden causarlo.
- Migración electroquímica: la migración electroquímica es el movimiento de iones o contaminantes a través de la superficie del sustrato revestido, lo que provoca posibles cortocircuitos y corrosión. Puede ocurrir debido a un espesor de recubrimiento inadecuado, la presencia de contaminantes conductores o la presencia de humedad o humedad.
- Resistencia química insuficiente: Es posible que los revestimientos de conformación deban resistir la exposición a diversos productos químicos y solventes. Si el material de recubrimiento no tiene suficiente resistencia química, puede degradarse o disolverse cuando se expone a sustancias específicas, comprometiendo sus capacidades de protección. La selección adecuada del material es crucial para garantizar la compatibilidad con el entorno químico esperado.
Para mitigar estos problemas, es esencial seguir las mejores prácticas y pautas para la aplicación de recubrimiento conformado, incluida la limpieza y preparación adecuadas de la superficie, el control preciso de los parámetros del proceso, la selección adecuada del material de recubrimiento y el curado o secado adecuados. Se deben implementar medidas regulares de inspección y control de calidad para identificar y abordar posibles problemas de recubrimiento desde el principio. Cumplir con los estándares de la industria, como IPC-CC-830, también puede ayudar a garantizar la confiabilidad y el rendimiento de los recubrimientos de conformación.
Mantenimiento de revestimientos de conformación
Los recubrimientos de conformación protegen los componentes electrónicos y las placas de circuitos de factores ambientales como la humedad, el polvo, los productos químicos y las fluctuaciones de temperatura. Sin embargo, como cualquier revestimiento protector, los revestimientos de conformación requieren un mantenimiento adecuado para garantizar su eficacia a largo plazo. Aquí hay algunos puntos clave a considerar cuando se trata del mantenimiento de los revestimientos de conformación:
- Inspección regular: realice inspecciones de rutina de las superficies recubiertas para verificar si hay signos de daño, desgaste o deslaminación. Busque grietas, astillas o áreas donde el revestimiento se haya desgastado. Las inspecciones deben llevarse a cabo periódicamente, especialmente después de la manipulación, el transporte o la exposición a condiciones adversas.
- Limpieza: Mantenga limpias las superficies recubiertas para evitar la acumulación de contaminantes que puedan comprometer la efectividad del recubrimiento. Utilice métodos de limpieza suaves, como un cepillo suave o aire comprimido, para eliminar el polvo, los desechos o las partículas. Evite el uso de solventes fuertes o materiales abrasivos que puedan dañar el revestimiento.
- Reparación de áreas dañadas: si se detecta algún daño o desgaste durante las inspecciones, es esencial abordarlo de inmediato. Repare las áreas dañadas revistiéndolas con el mismo material de revestimiento de conformación. Asegúrese de que el área dañada esté adecuadamente limpia y preparada antes de aplicar el nuevo revestimiento. Esto ayudará a mantener la integridad de la capa protectora.
- Control de temperatura y humedad: mantenga las condiciones adecuadas de temperatura y humedad en el entorno donde se almacenan o se utilizan los componentes revestidos. Las temperaturas extremas o los altos niveles de humedad pueden afectar el rendimiento del recubrimiento y provocar delaminación o protección reducida. Siga las recomendaciones del fabricante con respecto a los rangos aceptables de temperatura y humedad para el material de revestimiento de conformación específico.
- Evite la exposición a productos químicos: evite la exposición de las superficies revestidas a productos químicos agresivos o disolventes que puedan deteriorar el revestimiento. Tenga cuidado al usar agentes de limpieza o realizar procedimientos de mantenimiento cerca de los componentes cubiertos. Tome las precauciones necesarias para proteger el conformalcoating del contacto directo con productos químicos.
- Nuevas pruebas y recertificaciones: en algunas industrias, como la aeroespacial o la médica, los recubrimientos de conformación pueden requerir nuevas pruebas y recertificaciones periódicas para garantizar que cumplan con los estándares y especificaciones necesarios. Siga las directrices de los estándares industriales pertinentes y realice las pruebas o inspecciones necesarias a intervalos regulares.
- Documentación y Mantenimiento de Registros: Mantenga registros detallados de la aplicación del conformalcoating, actividades de mantenimiento, inspecciones y reparaciones. Esta documentación ayudará a rastrear el historial de mantenimiento, identificar fallas o patrones de desgaste y garantizar el cumplimiento de las normas y estándares de la industria.
Pruebas e inspección de revestimientos de conformación
Las pruebas y la inspección de los recubrimientos de conformación son esenciales para garantizar su eficacia y confiabilidad en la protección de componentes y ensamblajes electrónicos. Estos son algunos métodos comúnmente utilizados para probar e inspeccionar recubrimientos de conformación:
- Inspección visual: La inspección visual es un paso esencial en la evaluación de la calidad de los recubrimientos de conformación. Implica examinar la superficie del recubrimiento en busca de defectos visibles, como poros, burbujas, grietas o una cobertura desigual.
- Medición del espesor: el espesor del revestimiento de conformación es crucial ya que afecta su capacidad para brindar una protección adecuada. La consistencia se puede medir utilizando técnicas de corriente de Foucault, inducción magnética o perfilometría óptica. La medida debe compararse con los requisitos de espesor de recubrimiento especificados.
- Pruebas de adhesión: las pruebas evalúan la fuerza de unión entre el revestimiento de conformación y el sustrato. Los métodos para las pruebas de adhesión incluyen pruebas de cinta, pruebas de sombreado cruzado y pruebas de extracción. Estas pruebas determinan si la capa se adhiere adecuadamente a la superficie y puede soportar las tensiones durante la operación y el manejo.
- Prueba de resistencia de aislamiento: esta prueba evalúa la resistencia eléctrica del revestimiento de conformación. Garantiza que la capa proporcione un aislamiento eléctrico eficaz para evitar fugas o cortocircuitos. La prueba de resistencia de aislamiento generalmente se realiza con un probador de alto voltaje o un megóhmetro.
- Prueba de tensión soportada dieléctrica: La prueba de tensión soportada dieléctrica, también conocida como prueba de alto potencial o hipot, verifica la capacidad del recubrimiento para soportar alta tensión sin ruptura. El revestimiento de conformación se somete a un voltaje específico durante un tiempo fijo para garantizar que cumpla con los estándares de aislamiento eléctrico requeridos.
- Pruebas de ciclos térmicos: los ciclos térmicos exponen el revestimiento de conformación a variaciones de temperatura para evaluar su resistencia al estrés térmico. La capa se somete a ciclos repetidos de temperaturas extremas y se observa cualquier cambio, como agrietamiento o delaminación.
- Pruebas de resistencia a la humedad y la humedad: estas pruebas evalúan la capacidad del revestimiento de conformación para resistir la humedad y la humedad. La capa se expone a alta humedad o condiciones de humedad durante un período específico y se evalúa su desempeño para protección contra la corrosión o fallas eléctricas.
- Pruebas de resistencia química: las pruebas de resistencia química verifican qué tan bien el revestimiento de conformación resiste la exposición a varios productos químicos, como solventes o agentes de limpieza. La capa se expone a las sustancias durante un tiempo específico y se evalúan su apariencia, adhesión y funcionalidad.
- Prueba de niebla salina: la prueba de niebla salina evalúa la resistencia del revestimiento a la corrosión en un entorno cargado de sal. El conformalcoating se expone a una neblina o niebla salina durante un período específico y se examina cualquier signo de corrosión o degradación.
Es importante tener en cuenta que los requisitos de prueba específicos pueden variar según la industria, la aplicación y los estándares aplicables al recubrimiento de conformación. Los fabricantes o las organizaciones de estándares de la industria a menudo brindan pautas o especificaciones para los procedimientos de prueba e inspección.
Estándares de la industria para recubrimientos de conformación
Existen varios estándares y especificaciones de la industria para los revestimientos de conformación para garantizar su calidad, confiabilidad y rendimiento. Estos son algunos de los estándares comúnmente referenciados:
- IPC-CC-830: Este estándar, publicado por la Asociación de Industrias Electrónicas de Conexión (IPC), se usa ampliamente para materiales de revestimiento conformado y requisitos de aplicación. Abarca las condiciones generales, las propiedades de los materiales, los métodos de aplicación y los criterios de inspección para los recubrimientos de conformación.
- MIL-STD-883: este estándar militar describe los métodos y procedimientos de prueba de dispositivos microelectrónicos, incluidos los recubrimientos de conformación. Incluye especificaciones de adhesión, resistencia de aislamiento, choque térmico, humedad y otras pruebas relevantes para los recubrimientos de conformación.
- MIL-STD-810: esta norma proporciona consideraciones de ingeniería ambiental y métodos de prueba de laboratorio para simular y evaluar el rendimiento de materiales, equipos y sistemas en diversas condiciones ambientales. Incluye procedimientos de prueba para revestimientos conformes con respecto a temperatura, humedad, vibración, choque, etc.
- IEC 61086: esta norma internacional especifica los requisitos y métodos de prueba para los recubrimientos de conformación utilizados en ensamblajes electrónicos. Abarca los materiales de revestimiento, el espesor, la adhesión, la flexibilidad, la resistencia térmica y la resistencia química.
- UL 746E: esta norma, publicada por Underwriters Laboratories (UL), se centra en la evaluación de materiales poliméricos para su uso en equipos eléctricos. Incluye requisitos de prueba para revestimientos conformes con respecto a la inflamabilidad, las características de envejecimiento y el rendimiento eléctrico.
- ISO 9001: Si bien no es específica para los recubrimientos de conformación, la ISO 9001 es una norma reconocida internacionalmente para los sistemas de gestión de la calidad. Garantiza que las organizaciones sigan procesos de control de calidad consistentes, incluida la producción e inspección de revestimientos de conformación.
Es importante tener en cuenta que diferentes industrias y aplicaciones pueden tener estándares o especificaciones específicos adaptados a sus requisitos únicos. Además, muchos fabricantes de revestimientos de conformación pueden proporcionar hojas de datos técnicos o pautas de aplicación, que pueden servir como referencias valiosas para la selección y prueba de revestimientos de conformación.
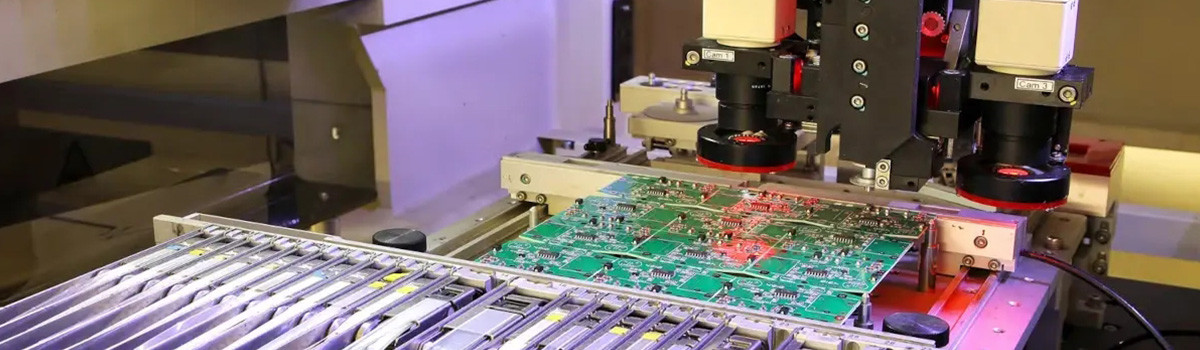
Avances en la tecnología de revestimiento de conformación
En los últimos años, ha habido avances significativos en la tecnología de revestimiento conformado, impulsados por la necesidad de mejorar la protección, la confiabilidad y el rendimiento de los componentes y ensamblajes electrónicos. Aquí hay algunas mejoras clave:
- Nano-Recubrimientos: Los nano-recubrimientos han surgido como un avance prometedor en la tecnología de recubrimiento conformado. Estos recubrimientos consisten en capas ultrafinas, generalmente a nanoescala, que brindan una excelente resistencia a la humedad y la corrosión mientras mantienen el rendimiento eléctrico. Los nanorrecubrimientos ofrecen una cobertura y adaptabilidad superiores, lo que garantiza una protección adecuada incluso en conjuntos electrónicos intrincados y densamente empaquetados.
- Recubrimientos multifuncionales: se están desarrollando recubrimientos de conformación con propiedades multifuncionales para abordar múltiples desafíos simultáneamente. Por ejemplo, algunos recubrimientos ofrecen resistencia química y a la humedad y capacidades mejoradas de conductividad eléctrica o gestión térmica. Estos recubrimientos multifuncionales reducen la necesidad de capas protectoras adicionales y mejoran el rendimiento general.
- Recubrimientos autorreparables: Los recubrimientos conformales autorreparables están diseñados para reparar daños menores automáticamente. Estos recubrimientos contienen agentes curativos encapsulados liberados sobre el daño, llenando grietas o vacíos y restaurando las propiedades protectoras del recubrimiento. Los recubrimientos de autorreparación prolongan la vida útil de los componentes electrónicos al mitigar los efectos del desgaste o las tensiones ambientales.
- Recubrimientos flexibles y estirables: con el auge de la electrónica flexible y los dispositivos portátiles, los recubrimientos de conformación deben adaptarse a la flexión, el estiramiento y la torsión de los sustratos. Se han desarrollado capas flexibles y estirables para brindar una protección robusta mientras mantienen su integridad bajo tensión mecánica. Estos recubrimientos permiten una cobertura conformada sobre sustratos flexibles, lo que amplía la gama de aplicaciones.
- Recubrimientos de bajo VOC y amigables con el medio ambiente: Hay un enfoque creciente en el desarrollo de recubrimientos de conformación con compuestos orgánicos volátiles (VOC) reducidos y formulaciones amigables con el medio ambiente. Estos recubrimientos tienen como objetivo minimizar el impacto ambiental durante la aplicación y el uso, manteniendo al mismo tiempo características de alto rendimiento. Se están desarrollando recubrimientos a base de agua o sin solventes como alternativas a los recubrimientos tradicionales a base de solventes.
- Recubrimientos curables por UV: Los recubrimientos de conformación curables por UV ofrecen tiempos de curado rápidos, lo que permite un mayor rendimiento en los procesos de fabricación. Estos recubrimientos utilizan luz ultravioleta (UV) para iniciar la reacción de curado, lo que permite ciclos de producción más rápidos y un menor consumo de energía. Los recubrimientos curables con UV también brindan una excelente cobertura y adhesión, lo que mejora la confiabilidad general de los ensamblajes recubiertos.
- Tecnologías de inspección de revestimientos de conformación: Los avances en las tecnologías de inspección ayudan a evaluar la calidad y el rendimiento de los revestimientos de conformación. Los sistemas de inspección óptica automatizada (AOI) con cámaras de alta resolución y algoritmos de análisis de imágenes pueden detectar defectos como poros, burbujas o variaciones en el grosor del revestimiento. Esto mejora la eficiencia y la confiabilidad de la inspección, lo que garantiza una calidad uniforme del recubrimiento.
- Recubrimientos más delgados y livianos: la demanda de miniaturización y diseños livianos en dispositivos electrónicos ha impulsado el desarrollo de recubrimientos conformados más delgados y livianos. Estos recubrimientos brindan suficiente protección al tiempo que minimizan el impacto en el peso y el tamaño de los componentes recubiertos. Las capas más delgadas también ofrecen una disipación de calor mejorada, fundamental para aplicaciones de alta potencia.
Estos avances en la tecnología de revestimiento conformado contribuyen al desarrollo de dispositivos electrónicos más fiables y duraderos. A medida que la industria electrónica continúa evolucionando, se espera que la investigación y la innovación en curso en los recubrimientos de conformación aborden los desafíos emergentes y permitan una protección mejorada en diversas aplicaciones.
Preocupaciones ambientales y revestimientos de conformación
Las preocupaciones ambientales juegan un papel importante en el desarrollo y uso de recubrimientos de conformación. A medida que la industria electrónica continúa creciendo, es necesario equilibrar los beneficios de los recubrimientos de conformación con sus impactos ambientales potenciales. Estos son algunos aspectos críticos relacionados con las preocupaciones ambientales y los revestimientos de conformación:
- Compuestos Orgánicos Volátiles (COV): Los recubrimientos de conformación tradicionales a base de solventes a menudo contienen altos niveles de COV, lo que contribuye a la contaminación del aire y daña la salud humana. En respuesta, existe una creciente demanda de formulaciones bajas en VOC o libres de VOC. Se están desarrollando barnices al agua y barnices con bajo contenido de VOC como alternativas para reducir el impacto ambiental.
- Sustancias peligrosas: algunos revestimientos de conformación pueden contener sustancias peligrosas, como metales pesados o contaminantes orgánicos persistentes (COP). Estas sustancias pueden tener efectos ambientales duraderos y presentar riesgos durante la fabricación, la aplicación y la eliminación al final de su vida útil. Para abordar esto, las regulaciones y estándares, como la directiva de Restricción de Sustancias Peligrosas (RoHS), restringen el uso de ciertas sustancias peligrosas en productos electrónicos.
- Evaluación del ciclo de vida (LCA): la evaluación del ciclo de vida evalúa los impactos ambientales de los recubrimientos de conformación a lo largo de todo su ciclo de vida, desde la extracción de la materia prima hasta la eliminación. Ayuda a identificar áreas de mejora y guía el desarrollo de capas respetuosas con el medio ambiente. LCA considera el consumo de energía, el agotamiento de los recursos, las emisiones y la generación de desechos.
- Formulaciones ecológicas: los fabricantes de revestimientos de conformación desarrollan activamente formulaciones ecológicas que minimizan el impacto ambiental. Esto incluye el uso de materiales de base biológica, recursos renovables y solventes ecológicos. Los recubrimientos de base biológica derivados de fuentes naturales ofrecen ventajas potenciales con respecto a una huella ecológica reducida y una mayor sostenibilidad.
- Reciclaje y manejo de desechos: La eliminación y el reciclaje adecuados de los revestimientos de conformación son esenciales para prevenir la contaminación ambiental. El reciclaje de componentes y ensamblajes electrónicos debe considerar la eliminación o separación de los revestimientos de conformación para permitir una recuperación eficiente del material. Los desarrollos en tecnologías y procesos de reciclaje están ayudando a abordar los desafíos asociados con la eliminación de recubrimientos y la gestión de desechos.
- Regulaciones ambientales: Los marcos y estándares regulatorios, como la regulación de Registro, Evaluación, Autorización y Restricción de Productos Químicos (REACH) de la Unión Europea, tienen como objetivo proteger la salud humana y el medio ambiente de sustancias potencialmente dañinas. El cumplimiento de estas reglamentaciones garantiza que los recubrimientos de conformación cumplan con los requisitos ambientales y estándares de seguridad específicos.
- Prácticas de fabricación sostenibles: la adopción de prácticas de fabricación sostenibles reduce el impacto ambiental asociado con la producción de revestimientos de conformación. Esto incluye optimizar el uso de recursos, minimizar la generación de desechos, implementar procesos de eficiencia energética y promover fuentes de energía renovable.
- Certificaciones ambientales: las certificaciones ambientales, como ISO 14001, brindan un marco para que las organizaciones administren y mejoren continuamente su desempeño ambiental. Los fabricantes de revestimientos de conformación pueden buscar la certificación para demostrar su compromiso con la responsabilidad medioambiental y las prácticas sostenibles.
A medida que la industria continúa evolucionando, hay un énfasis creciente en el desarrollo de recubrimientos de conformación que ofrecen una protección adecuada y minimizan su impacto ambiental. Los fabricantes, los organismos reguladores y los usuarios finales están trabajando juntos para promover el uso de recubrimientos ecológicos y garantizar prácticas responsables y sostenibles durante todo el ciclo de vida de los productos electrónicos.
La perspectiva futura de los recubrimientos de conformación en la electrónica
Las perspectivas futuras para los recubrimientos de conformación en la electrónica son prometedoras, impulsadas por los avances tecnológicos, la creciente demanda de dispositivos electrónicos de alto rendimiento y las tendencias emergentes en la industria. Estos son algunos aspectos clave que dan forma al futuro de los recubrimientos conformados:
- Miniaturización y mayor integración: la tendencia hacia dispositivos electrónicos más pequeños y compactos con mayores niveles de integración plantea desafíos para los recubrimientos conformados. Los recubrimientos futuros deben brindar una protección adecuada mientras mantienen su integridad en componentes miniaturizados y ensamblajes densamente empaquetados. Esto incluye el desarrollo de capas más delgadas con cobertura y adaptabilidad mejoradas.
- Electrónica flexible y estirable: el auge de la electrónica flexible y estirable, incluidos los dispositivos portátiles, requiere recubrimientos de conformación que puedan soportar la tensión mecánica y la flexión repetida sin comprometer sus propiedades protectoras. Las capas futuras se centrarán en la flexibilidad, la durabilidad y la adhesión para adaptarse a los requisitos únicos de estas aplicaciones emergentes.
- Materiales avanzados: el desarrollo de nuevos materiales con propiedades mejoradas impulsará el futuro de los recubrimientos de conformación. Esto incluye el uso de nanomateriales, como nanopartículas y nanocompuestos, para mejorar el rendimiento del recubrimiento en cuanto a resistencia a la humedad, conductividad eléctrica, gestión térmica y propiedades de barrera. Los materiales avanzados permitirán que los recubrimientos satisfagan las necesidades cambiantes de los dispositivos electrónicos.
- Recubrimientos multifuncionales: La demanda de recubrimientos multifuncionales que brinden múltiples beneficios más allá de la protección seguirá creciendo. Las capas futuras pueden incorporar capacidades de autorreparación, conductividad térmica, propiedades antiestáticas, propiedades antimicrobianas o características de recolección de energía. Los recubrimientos multifuncionales ofrecen un rendimiento mejorado, una complejidad reducida y una mayor confiabilidad en los ensamblajes electrónicos.
- Consideraciones ambientales: El enfoque en la sustentabilidad ecológica y las regulaciones con respecto a las sustancias peligrosas influirán en el futuro de los recubrimientos conformados. El desarrollo de formulaciones ecológicas con COV reducidos y el uso de materiales de base biológica se volverán más frecuentes. Las estrategias de reciclaje y gestión de residuos para los recubrimientos de conformación también jugarán un papel importante en la minimización del impacto ambiental.
- Técnicas de aplicación avanzadas: las innovaciones en las técnicas de aplicación mejorarán la eficiencia y la calidad de los procesos de recubrimiento de conformación. Esto incluye sistemas de dosificación robóticos, métodos de recubrimiento selectivo y tecnologías de pulverización avanzadas para garantizar una cobertura de recubrimiento precisa y uniforme, reducir el desperdicio de material y mejorar la productividad.
- Métodos avanzados de inspección y prueba: a medida que aumenta la complejidad de los ensamblajes electrónicos, se necesitarán métodos de inspección y prueba más sofisticados para los recubrimientos de conformación. Esto incluye el desarrollo de sistemas de inspección óptica automatizada (AOI) con capacidades avanzadas de análisis e imágenes para detectar y evaluar los defectos del revestimiento, las variaciones de espesor y la calidad de la adhesión.
- Normas y certificaciones de la industria: los desarrollos continuos en las normas y certificaciones de la industria seguirán dando forma al futuro de los recubrimientos de conformación. Los fabricantes y los usuarios finales confiarán en los estándares actualizados para garantizar la calidad, la confiabilidad y el cumplimiento de los requisitos y las reglamentaciones de las capas.
En general, el futuro de los recubrimientos de conformación en la electrónica parece prometedor, centrándose en la mejora del rendimiento, la adaptabilidad a las nuevas tecnologías, la sostenibilidad medioambiental y el desarrollo de materiales y técnicas de aplicación avanzados. Estos avances permitirán que los recubrimientos de conformación brinden una protección robusta para dispositivos electrónicos en entornos diversos y desafiantes.
Conclusión: Los recubrimientos electrónicos conformados ofrecen una excelente solución para proteger los dispositivos electrónicos de los factores ambientales que pueden provocar su falla o mal funcionamiento. A medida que avanza la tecnología, la necesidad de recubrimientos de conformación más efectivos y confiables solo aumentará. Los fabricantes, diseñadores e ingenieros deben mantenerse al día con los últimos avances en el campo para garantizar la protección óptima de sus dispositivos electrónicos. Los recubrimientos de conformación son una parte crucial del proceso de fabricación electrónica y pueden ayudar a prolongar la vida útil y el rendimiento de los dispositivos electrónicos.