اپوکسی کم پر
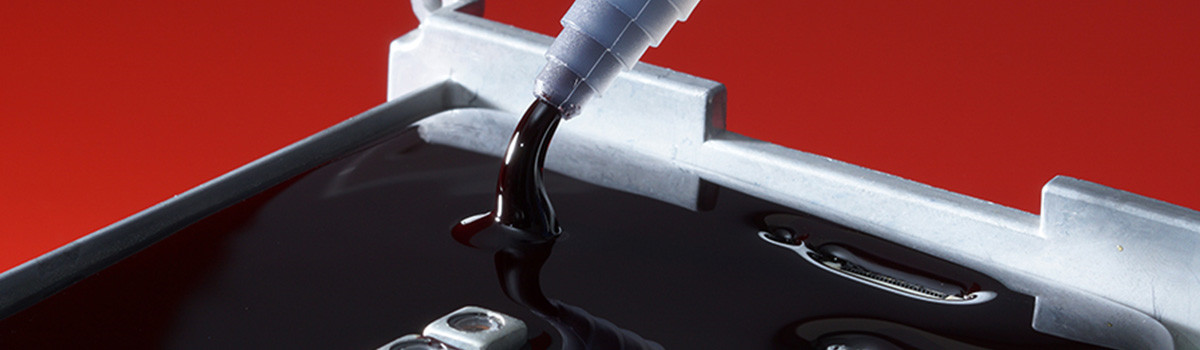
اپوکسی Underfill نوعی چسب است که برای افزایش قابلیت اطمینان قطعات الکترونیکی بخصوص در کاربردهای بسته بندی نیمه هادی استفاده می شود. شکاف بین بسته و برد مدار چاپی (PCB) را پر می کند و پشتیبانی مکانیکی و کاهش استرس را برای جلوگیری از آسیب انبساط حرارتی و انقباض فراهم می کند. اپوکسی Underfill همچنین عملکرد الکتریکی بسته را با کاهش اندوکتانس و ظرفیت انگلی بهبود می بخشد. در این مقاله، کاربردهای مختلف اپوکسی زیر پر، انواع مختلف موجود و مزایای آنها را بررسی می کنیم.
اهمیت اپوکسی کم پر در بسته بندی نیمه هادی
اپوکسی underfill در بسته بندی های نیمه هادی بسیار مهم است و تقویت مکانیکی و محافظت از اجزای ظریف میکروالکترونیک را فراهم می کند. این یک ماده چسب تخصصی است که برای پر کردن شکاف بین تراشه نیمه هادی و بستر بسته استفاده می شود و قابلیت اطمینان و عملکرد دستگاه های الکترونیکی را افزایش می دهد. در اینجا، ما اهمیت اپوکسی کم پر شده در بسته بندی نیمه هادی را بررسی خواهیم کرد.
یکی از وظایف اصلی اپوکسی کم پر شده، بهبود استحکام مکانیکی و قابلیت اطمینان پکیج است. در حین کار، تراشه های نیمه هادی تحت تنش های مکانیکی مختلفی مانند انبساط و انقباض حرارتی، لرزش و شوک مکانیکی قرار می گیرند. این تنش ها می تواند منجر به ایجاد ترک های اتصال لحیم کاری شود که می تواند باعث خرابی الکتریکی و کاهش طول عمر کلی دستگاه شود. اپوکسی underfill با توزیع یکنواخت تنش مکانیکی در تراشه، بستر و اتصالات لحیم کاری به عنوان یک عامل کاهش دهنده تنش عمل می کند. این به طور موثر تشکیل ترک ها را به حداقل می رساند و از انتشار ترک های موجود جلوگیری می کند و اطمینان طولانی مدت بسته را تضمین می کند.
یکی دیگر از جنبه های حیاتی اپوکسی کم پر، توانایی آن در افزایش عملکرد حرارتی دستگاه های نیمه هادی است. اتلاف گرما به دلیل کوچک شدن اندازه دستگاه های الکترونیکی و افزایش چگالی توان، به یک نگرانی مهم تبدیل می شود و گرمای بیش از حد می تواند عملکرد و قابلیت اطمینان تراشه نیمه هادی را کاهش دهد. اپوکسی Underfill دارای خواص هدایت حرارتی عالی است و به آن اجازه می دهد تا گرما را به طور موثر از تراشه منتقل کرده و آن را در سراسر بسته توزیع کند. این به حفظ دمای عملیاتی بهینه کمک می کند و از ایجاد نقاط داغ جلوگیری می کند و در نتیجه مدیریت حرارتی کلی دستگاه را بهبود می بخشد.
اپوکسی Underfill همچنین در برابر رطوبت و آلاینده ها محافظت می کند. نفوذ رطوبت می تواند منجر به خوردگی، نشت الکتریکی و رشد مواد رسانا شود و در نتیجه دستگاه دچار اختلال شود. اپوکسی underfill به عنوان یک مانع عمل می کند، مناطق آسیب پذیر را آب بندی می کند و از ورود رطوبت به بسته بندی جلوگیری می کند. همچنین محافظت در برابر گرد و غبار، کثیفی و سایر آلاینده هایی که می توانند بر عملکرد الکتریکی تراشه نیمه هادی تأثیر منفی بگذارند، ارائه می دهد. اپوکسی کم پر با محافظت از تراشه و اتصالات آن، قابلیت اطمینان و عملکرد طولانی مدت دستگاه را تضمین می کند.
علاوه بر این، اپوکسی کم پر شده، کوچک سازی را در بسته بندی های نیمه هادی امکان پذیر می کند. با تقاضای دائمی برای دستگاههای کوچکتر و فشردهتر، اپوکسی کم پر شده، امکان استفاده از تکنیکهای بستهبندی با فلیپ تراشه و مقیاس تراشه را فراهم میکند. این تکنیک ها شامل نصب مستقیم تراشه بر روی بستر بسته بندی، حذف نیاز به اتصال سیم و کاهش اندازه بسته بندی است. اپوکسی Underfill پشتیبانی ساختاری را فراهم می کند و یکپارچگی رابط تراشه- بستر را حفظ می کند و اجرای موفقیت آمیز این فناوری های بسته بندی پیشرفته را ممکن می سازد.
چگونه Underfill اپوکسی چالش ها را برطرف می کند
بسته بندی نیمه هادی نقش مهمی در عملکرد دستگاه الکترونیکی، قابلیت اطمینان و طول عمر دارد. این شامل کپسوله کردن مدارهای مجتمع (ICs) در محفظه های محافظ، ایجاد اتصالات الکتریکی و اتلاف گرمای تولید شده در حین کار است. با این حال، بسته بندی نیمه هادی با چالش های متعددی از جمله تنش حرارتی و تاب خوردگی مواجه است که می تواند به طور قابل توجهی بر عملکرد و قابلیت اطمینان دستگاه های بسته بندی شده تأثیر بگذارد.
یکی از چالش های اصلی استرس حرارتی است. مدارهای مجتمع در حین کار گرما تولید می کنند و اتلاف ناکافی می تواند باعث افزایش دما در بسته شود. این تغییر دما منجر به تنش حرارتی می شود زیرا مواد مختلف درون بسته بندی با سرعت های مختلف منبسط و منقبض می شوند. انبساط و انقباض غیر یکنواخت می تواند باعث ایجاد فشار مکانیکی شود که منجر به شکست اتصالات لحیم کاری، لایه لایه شدن و ترک می شود. استرس حرارتی می تواند یکپارچگی الکتریکی و مکانیکی بسته را به خطر بیندازد و در نهایت بر عملکرد و قابلیت اطمینان دستگاه تأثیر بگذارد.
Warpage یکی دیگر از چالش های مهم در بسته بندی نیمه هادی است. Warpage به خم شدن یا تغییر شکل بستر بسته یا کل بسته اشاره دارد. این می تواند در طول فرآیند بسته بندی یا به دلیل استرس حرارتی رخ دهد. تاب خوردگی در درجه اول ناشی از عدم تطابق در ضریب انبساط حرارتی (CTE) بین مواد مختلف در بسته بندی است. برای مثال، CTE قالب سیلیکونی، بستر و ترکیب قالب ممکن است به طور قابل توجهی متفاوت باشد. هنگامی که این مواد در معرض تغییرات دما قرار می گیرند، با سرعت های مختلف منبسط یا منقبض می شوند که منجر به تاب برداشتن می شود.
Warpage مشکلات متعددی را برای بسته های نیمه هادی ایجاد می کند:
- این می تواند منجر به نقاط تمرکز تنش، افزایش احتمال خرابی های مکانیکی و کاهش قابلیت اطمینان جعبه شود.
- تاب خوردگی می تواند منجر به مشکلاتی در روند مونتاژ شود، زیرا روی همسویی بسته با اجزای دیگر مانند برد مدار چاپی (PCB) تأثیر می گذارد. این ناهماهنگی می تواند اتصالات الکتریکی را مختل کند و باعث مشکلات عملکرد شود.
- Warpage می تواند بر ضریب فرم کلی بسته تأثیر بگذارد و ادغام دستگاه را در برنامه های کاربردی فرم فاکتور کوچک یا PCB های پرجمعیت چالش برانگیز کند.
تکنیک ها و استراتژی های مختلفی در بسته بندی نیمه هادی برای رفع این چالش ها استفاده می شود. اینها شامل استفاده از مواد پیشرفته با CTEهای منطبق برای به حداقل رساندن تنش حرارتی و تاب خوردگی است. شبیهسازی و مدلسازی حرارتی مکانیکی برای پیشبینی رفتار بسته تحت شرایط مختلف حرارتی انجام میشود. اصلاحات طراحی، مانند معرفی سازههای تنشزدایی و چیدمانهای بهینه، برای کاهش تنش حرارتی و تابخوردگی اجرا میشوند. علاوه بر این، توسعه فرآیندهای تولید و تجهیزات بهبود یافته به به حداقل رساندن وقوع تاب خوردگی در هنگام مونتاژ کمک می کند.
مزایای اپوکسی Underfill
اپوکسی Underfill یک جزء حیاتی در بسته بندی نیمه هادی است که مزایای متعددی را ارائه می دهد. این ماده اپوکسی تخصصی بین تراشه نیمه هادی و بستر بسته اعمال می شود و تقویت مکانیکی را فراهم می کند و چالش های مختلف را برطرف می کند. در اینجا برخی از مزایای حیاتی اپوکسی کم پر شده آورده شده است:
- قابلیت اطمینان مکانیکی بهبود یافته: یکی از مزایای اولیه اپوکسی زیر پر، توانایی آن در افزایش قابلیت اطمینان مکانیکی بسته های نیمه هادی است. اپوکسی underfill یک پیوند منسجم ایجاد می کند که یکپارچگی ساختاری را با پر کردن شکاف ها و فضاهای خالی بین تراشه و بستر بهبود می بخشد. این به جلوگیری از چروکیدگی بسته کمک می کند، خطر خرابی های مکانیکی را کاهش می دهد و مقاومت در برابر تنش های خارجی مانند لرزش، ضربه و چرخه حرارتی را افزایش می دهد. قابلیت اطمینان مکانیکی بهبود یافته منجر به افزایش دوام محصول و طول عمر بیشتر دستگاه می شود.
- اتلاف استرس حرارتی: اپوکسی کم پر به دفع تنش حرارتی درون بسته کمک می کند. مدارهای مجتمع در حین کار گرما تولید می کنند و اتلاف ناکافی می تواند منجر به تغییرات دما در ظرف شود. مواد اپوکسی کم پر، با ضریب انبساط حرارتی کمتر (CTE) در مقایسه با مواد تراشه و زیرلایه، به عنوان یک لایه بافر عمل می کند. این کرنش مکانیکی ناشی از تنش حرارتی را جذب می کند و خطر شکست اتصالات لحیم کاری، لایه لایه شدن و ترک را کاهش می دهد. با از بین بردن تنش حرارتی، اپوکسی کم پر شده به حفظ یکپارچگی الکتریکی و مکانیکی بسته کمک می کند.
- عملکرد الکتریکی بهبود یافته: اپوکسی کم پر تأثیر مثبتی بر عملکرد الکتریکی دستگاه های نیمه هادی دارد. مواد اپوکسی شکاف بین تراشه و بستر را پر می کند و ظرفیت خازنی و اندوکتانس انگلی را کاهش می دهد. این منجر به بهبود یکپارچگی سیگنال، کاهش تلفات سیگنال و افزایش اتصال الکتریکی بین تراشه و بقیه بسته میشود. کاهش اثرات انگلی به عملکرد الکتریکی بهتر، نرخ انتقال داده بالاتر و افزایش قابلیت اطمینان دستگاه کمک می کند. علاوه بر این، اپوکسی کم پر شده، عایق و محافظت در برابر رطوبت، آلایندهها و سایر عوامل محیطی است که میتوانند عملکرد الکتریکی را کاهش دهند.
- کاهش استرس و مونتاژ بهبود یافته: اپوکسی کم پر شده به عنوان مکانیزم کاهش استرس در هنگام مونتاژ عمل می کند. مواد اپوکسی عدم تطابق CTE بین تراشه و بستر را جبران می کند و تنش مکانیکی را در طول تغییرات دما کاهش می دهد. این امر فرآیند مونتاژ را قابل اعتمادتر و کارآمدتر می کند و خطر آسیب یا ناهماهنگی بسته را به حداقل می رساند. توزیع تنش کنترل شده ارائه شده توسط اپوکسی کم پر نیز به اطمینان از تراز مناسب با سایر اجزای روی برد مدار چاپی (PCB) کمک می کند و بازده کلی مجموعه را بهبود می بخشد.
- کوچک سازی و بهینه سازی فرم فاکتور: اپوکسی Underfill کوچک کردن بسته های نیمه هادی و بهینه سازی فرم فاکتور را امکان پذیر می کند. با ارائه تقویت ساختاری و کاهش تنش، اپوکسی underfill امکان طراحی و ساخت بستههای کوچکتر، نازکتر و فشردهتر را فراهم میکند. این امر به ویژه برای برنامههایی مانند دستگاههای تلفن همراه و لوازم الکترونیکی پوشیدنی، که در آن فضا در اولویت قرار دارد، مهم است. توانایی بهینه سازی فرم فاکتورها و دستیابی به تراکم اجزای بالاتر به دستگاه های الکترونیکی پیشرفته تر و نوآورانه تر کمک می کند.
انواع اپوکسی Underfill
چندین نوع فرمولاسیون اپوکسی زیر پر در بسته بندی های نیمه هادی موجود است که هر کدام برای برآوردن نیازهای خاص و رفع چالش های مختلف طراحی شده اند. در اینجا برخی از انواع رایج اپوکسی زیر پر استفاده می شود:
- اپوکسی زیر پر مویرگی: اپوکسی زیر پر مویرگی سنتی ترین و پرکاربردترین نوع اپوکسی است. یک اپوکسی با ویسکوزیته کم از طریق عملکرد مویرگی به شکاف بین تراشه و بستر جریان می یابد. کم پر شدن مویرگی معمولاً روی لبه تراشه پخش می شود و با گرم شدن بسته، اپوکسی در زیر تراشه جریان می یابد و فضاهای خالی را پر می کند. این نوع زیر پر برای بسته هایی با شکاف های کوچک مناسب است و تقویت مکانیکی خوبی را ارائه می دهد.
- اپوکسی بدون جریان: اپوکسی بدون جریان، فرمولاسیونی با ویسکوزیته بالا است که در طول پخت جریان ندارد. این به عنوان یک اپوکسی از قبل اعمال شده یا به عنوان یک فیلم بین تراشه و بستر اعمال می شود. اپوکسی بدون جریان به ویژه برای بسته های فلیپ تراشه، که در آن برآمدگی های لحیم کاری به طور مستقیم با بستر تعامل دارند، مفید است. نیاز به جریان مویرگی را از بین می برد و خطر آسیب اتصال لحیم کاری در حین مونتاژ را کاهش می دهد.
- Underfill سطح ویفر (WLU): زیر پر کردن سطح ویفر یک اپوکسی است که در سطح ویفر قبل از جداسازی تراشه های جداگانه اعمال می شود. این شامل توزیع مواد پر شده در کل سطح ویفر و پخت آن است. کم پر شدن در سطح ویفر چندین مزیت از جمله پوشش یکنواخت زیر پر، کاهش زمان مونتاژ و بهبود کنترل فرآیند را ارائه می دهد. معمولاً برای تولید دستگاه های با حجم بالا استفاده می شود.
- زیر پر کردن قالبی (MUF): زیر پر کردن قالبی یک اپوکسی زیر پر شده است که در طی قالب گیری کپسوله استفاده می شود. مواد زیر پر شده روی بستر پخش میشود و سپس تراشه و بستر در یک ترکیب قالب محصور میشوند. در طول قالبگیری، اپوکسی جریان مییابد و شکاف بین تراشه و زیرلایه را پر میکند و در یک مرحله کمپر و محصور میشود. زیرپر قالبی تقویت مکانیکی عالی را ارائه می دهد و فرآیند مونتاژ را ساده می کند.
- کم پر شدن غیر رسانا (NCF): اپوکسی پرکننده غیر رسانا به طور خاص برای ایجاد عایق الکتریکی بین اتصالات لحیم روی تراشه و زیرلایه فرموله شده است. حاوی پرکننده ها یا مواد افزودنی عایق است که از هدایت الکتریکی جلوگیری می کند. NCF در کاربردهایی استفاده می شود که در آن اتصال کوتاه الکتریکی بین اتصالات لحیم کاری مجاور یک نگرانی است. هم تقویت مکانیکی و هم عایق الکتریکی را ارائه می دهد.
- کم پر رسانای حرارتی (TCU): اپوکسی کم پر رسانای حرارتی برای افزایش قابلیت اتلاف حرارت بسته طراحی شده است. حاوی پرکننده های رسانای حرارتی مانند ذرات سرامیکی یا فلزی است که رسانایی حرارتی مواد زیر پر را بهبود می بخشد. TCU در کاربردهایی استفاده میشود که انتقال حرارت کارآمد بسیار مهم است، مانند دستگاههای پرقدرت یا آنهایی که در محیطهای حرارتی سخت کار میکنند.
اینها تنها چند نمونه از انواع مختلف اپوکسی زیر پر استفاده شده در بسته بندی نیمه هادی هستند. انتخاب اپوکسی زیر پرکننده مناسب به عواملی مانند طراحی بسته، فرآیند مونتاژ، نیازهای حرارتی و ملاحظات الکتریکی بستگی دارد. هر اپوکسی کم پر مزایای خاصی را ارائه می دهد و برای رفع نیازهای منحصر به فرد کاربردهای مختلف طراحی شده است.
کم پر شدن مویرگی: ویسکوزیته کم و قابلیت اطمینان بالا
کم پر شدن مویرگی به فرآیندی اطلاق می شود که در صنعت بسته بندی نیمه هادی برای افزایش قابلیت اطمینان دستگاه های الکترونیکی استفاده می شود. این شامل پر کردن شکاف بین یک تراشه میکروالکترونیک و بسته بندی اطراف آن با یک ماده مایع با ویسکوزیته پایین است که معمولاً یک رزین مبتنی بر اپوکسی است. این ماده پرکننده، پشتیبانی ساختاری را فراهم می کند، اتلاف حرارتی را بهبود می بخشد و از تراشه در برابر استرس مکانیکی، رطوبت و سایر عوامل محیطی محافظت می کند.
یکی از ویژگی های مهم زیرپر مویرگی ویسکوزیته کم آن است. مواد زیر پر شده به گونه ای فرموله شده است که چگالی نسبتاً کمی داشته باشد و به آن اجازه می دهد به راحتی در شکاف های باریک بین تراشه و بسته در طول فرآیند کم پر شدن جریان یابد. این تضمین میکند که مواد کمپر میتوانند بهطور مؤثری به تمام فضاهای خالی و شکافهای هوا نفوذ کرده و آنها را پر کند، خطر تشکیل فضای خالی را به حداقل میرساند و یکپارچگی کلی رابط بسته تراشه را بهبود میبخشد.
مواد کم پرکننده مویرگی با ویسکوزیته پایین چندین مزیت دیگر نیز دارند. اولا، آنها جریان کارآمد مواد را در زیر تراشه تسهیل می کنند که منجر به کاهش زمان فرآیند و افزایش توان تولید می شود. این امر بهویژه در محیطهای تولیدی با حجم بالا که در آن زمان و کارایی هزینه بسیار مهم است، مهم است.
ثانیا، ویسکوزیته پایین باعث میشود که مواد مرطوبکننده و چسبندگی بهتر مواد زیر پر شوند. این اجازه می دهد تا مواد به طور یکنواخت پخش شوند و پیوندهای قوی با تراشه و بسته ایجاد کنند و یک کپسولاسیون قابل اعتماد و قوی ایجاد کنند. این تضمین می کند که تراشه به طور ایمن در برابر تنش های مکانیکی مانند چرخه حرارتی، شوک ها و ارتعاشات محافظت می شود.
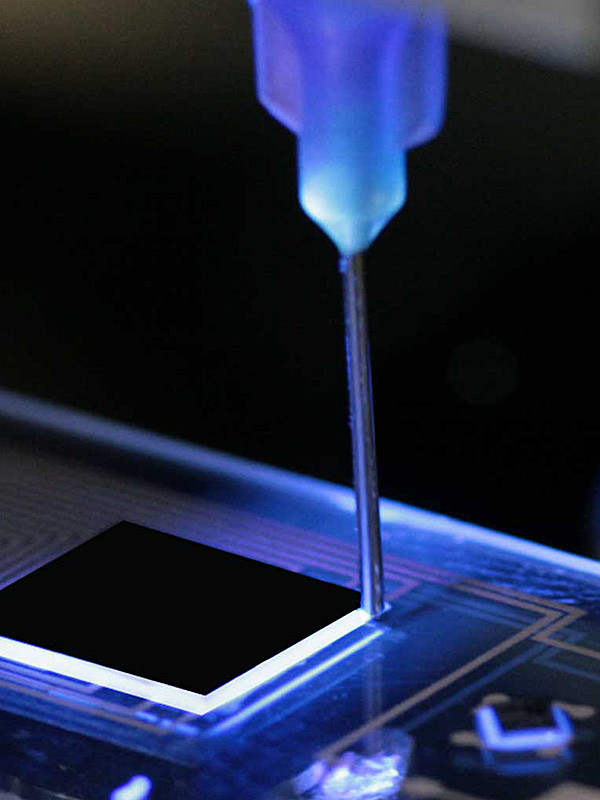
یکی دیگر از جنبه های مهم زیر پر شدن مویرگی، قابلیت اطمینان بالای آنها است. مواد کم پرکننده با ویسکوزیته پایین به طور خاص مهندسی شده اند تا پایداری حرارتی عالی، خواص عایق الکتریکی و مقاومت در برابر رطوبت و مواد شیمیایی را نشان دهند. این ویژگی ها برای اطمینان از عملکرد طولانی مدت و قابلیت اطمینان دستگاه های الکترونیکی بسته بندی شده، به ویژه در برنامه های کاربردی مانند خودرو، هوافضا، و مخابرات ضروری هستند.
علاوه بر این، مواد زیر پرکننده مویرگی به گونهای طراحی شدهاند که دارای استحکام مکانیکی بالا و چسبندگی عالی به مواد مختلف زیرلایه، از جمله فلزات، سرامیکها و مواد آلی که معمولاً در بستهبندیهای نیمه هادی استفاده میشوند، داشته باشند. این ماده را قادر می سازد تا به عنوان یک بافر تنش عمل کند و به طور موثر تنش های مکانیکی ایجاد شده در طول عملیات یا قرار گرفتن در معرض محیط را جذب و دفع کند.
بدون جریان کم: خود توزیع و توان عملیاتی بالا
بدون جریان یک فرآیند تخصصی مورد استفاده در صنعت بسته بندی نیمه هادی برای افزایش قابلیت اطمینان و کارایی دستگاه های الکترونیکی است. بر خلاف زیر پرهای مویرگی، که بر جریان مواد با ویسکوزیته پایین متکی هستند، در زیر پرهای بدون جریان از یک رویکرد خود توزیع با مواد با ویسکوزیته بالا استفاده می کنند. این روش چندین مزیت از جمله خود تراز، توان عملیاتی بالا و قابلیت اطمینان بهبود یافته را ارائه می دهد.
یکی از ویژگیهای حیاتی کمپر شدن بدون جریان، قابلیت خود توزیع آن است. مواد زیر پر استفاده شده در این فرآیند با ویسکوزیته بالاتر فرموله شده است که از جریان آزاد آن جلوگیری می کند. در عوض، مواد کم پر شده به صورت کنترل شده روی رابط بسته تراشه توزیع می شود. این توزیع کنترلشده، قرار دادن دقیق مواد زیر پر را امکانپذیر میسازد، و اطمینان میدهد که فقط در مناطق مورد نظر بدون سرریز شدن یا پخش شدن غیرقابل کنترل اعمال میشود.
ماهیت خود توزیعی کم پر شدن بدون جریان چندین مزیت دارد. در مرحله اول، این امکان را برای خود تراز کردن مواد زیر پر می کند. همانطور که زیر پر می شود، به طور طبیعی با تراشه و بسته بندی خود تراز می شود و شکاف ها و فضاهای خالی را به طور یکنواخت پر می کند. این امر نیاز به مکان یابی دقیق و هم ترازی تراشه را در طول فرآیند کم پر شدن از بین می برد و باعث صرفه جویی در زمان و تلاش در ساخت می شود.
ثانیا، ویژگی خود توزیعی کمپرهای بدون جریان، توان عملیاتی بالایی را در تولید ممکن میسازد. فرآیند توزیع را می توان به صورت خودکار انجام داد و امکان استفاده سریع و مداوم از مواد کم پر شده را در چندین تراشه به طور همزمان فراهم کرد. این کار راندمان کلی تولید را بهبود میبخشد و هزینههای تولید را کاهش میدهد و به ویژه برای محیطهای تولیدی با حجم بالا مفید است.
علاوه بر این، مواد بدون جریان کم پر شده برای ارائه قابلیت اطمینان بالا طراحی شده اند. مواد کم پرکننده با ویسکوزیته بالا مقاومت بهتری در برابر چرخه حرارتی، تنشهای مکانیکی و عوامل محیطی ارائه میدهند و عملکرد طولانیمدت دستگاههای الکترونیکی بستهبندی شده را تضمین میکنند. این مواد پایداری حرارتی عالی، خواص عایق الکتریکی و مقاومت در برابر رطوبت و مواد شیمیایی را نشان میدهند که به قابلیت اطمینان کلی دستگاهها کمک میکند.
بهعلاوه، مواد با ویسکوزیته بالا که در کمپر شدن بدون جریان استفاده میشوند، استحکام مکانیکی و خواص چسبندگی را افزایش میدهند. آنها پیوندهای قوی با تراشه و بسته ایجاد می کنند و به طور موثر تنش های مکانیکی ایجاد شده در طول عملیات یا قرار گرفتن در معرض محیط را جذب و از بین می برند. این به محافظت از تراشه در برابر آسیب های احتمالی کمک می کند و مقاومت دستگاه را در برابر ضربه ها و لرزش های خارجی افزایش می دهد.
Molded Underfill: حفاظت و یکپارچگی بالا
زیر پر کردن قالبی یک تکنیک پیشرفته است که در صنعت بسته بندی نیمه هادی برای ارائه سطوح بالایی از حفاظت و یکپارچگی برای دستگاه های الکترونیکی استفاده می شود. این شامل کپسوله کردن کل تراشه و بسته بندی اطراف آن با یک ترکیب قالبی است که مواد زیر پر شده را در خود جای داده است. این فرآیند مزایای قابل توجهی در مورد حفاظت، یکپارچگی و قابلیت اطمینان کلی ارائه می دهد.
یکی از مزایای حیاتی زیر پر کردن قالب، توانایی آن در ارائه حفاظت جامع از تراشه است. ترکیب قالب مورد استفاده در این فرآیند به عنوان یک مانع قوی عمل می کند و کل تراشه و بسته را در یک پوسته محافظ محصور می کند. این یک محافظ موثر در برابر عوامل محیطی مانند رطوبت، گرد و غبار و آلاینده هایی است که می تواند بر عملکرد و قابلیت اطمینان دستگاه تأثیر بگذارد. کپسوله سازی همچنین به جلوگیری از تنش های مکانیکی، چرخه حرارتی و سایر نیروهای خارجی تراشه کمک می کند و دوام طولانی مدت آن را تضمین می کند.
بهعلاوه، پر شدن قالبگیری شده، سطوح ادغام بالایی را در بسته نیمهرسانا امکانپذیر میسازد. مواد زیر پر شده مستقیماً در ترکیب قالب مخلوط میشوند و امکان یکپارچهسازی یکپارچه فرآیندهای پر کردن و کپسولهسازی را فراهم میکنند. این ادغام نیاز به مرحله کم پر کردن جداگانه را از بین می برد و فرآیند تولید را ساده می کند و زمان و هزینه تولید را کاهش می دهد. همچنین توزیع یکنواخت و یکنواخت کم پر را در سراسر بسته تضمین می کند، فضای خالی را به حداقل می رساند و یکپارچگی ساختاری کلی را افزایش می دهد.
علاوه بر این، زیر پر شدن قالبگیری شده، خواص اتلاف حرارتی عالی را ارائه میدهد. ترکیب قالب طوری طراحی شده است که رسانایی حرارتی بالایی داشته باشد و به آن اجازه می دهد گرما را به طور موثر از تراشه خارج کند. این برای حفظ دمای بهینه عملکرد دستگاه و جلوگیری از گرمای بیش از حد، که می تواند منجر به کاهش عملکرد و مشکلات قابلیت اطمینان شود، بسیار مهم است. خواص اتلاف حرارتی افزایش یافته زیرپر قالبی به قابلیت اطمینان کلی و طول عمر دستگاه الکترونیکی کمک می کند.
علاوه بر این، زیر پر کردن قالببندی شده، کوچکسازی و بهینهسازی فاکتور شکل بیشتری را ممکن میسازد. فرآیند کپسولهسازی را میتوان به گونهای تنظیم کرد که اندازهها و شکلهای بستهبندی مختلف، از جمله ساختارهای پیچیده سهبعدی را در خود جای دهد. این انعطافپذیری امکان ادغام چندین تراشه و سایر اجزا را در یک بسته فشرده و کارآمد در فضا فراهم میکند. توانایی دستیابی به سطوح بالاتری از یکپارچگی بدون به خطر انداختن قابلیت اطمینان باعث میشود که کمپر شدن قالبها در برنامههایی که محدودیتهای اندازه و وزن حیاتی هستند، مانند دستگاههای تلفن همراه، پوشیدنیها و لوازم الکترونیکی خودرو، ارزشمند باشد.
پکیج مقیاس تراشه (CSP): کمپر کردن: کوچکسازی و چگالی بالا
کمپر کردن بسته مقیاس تراشه (CSP) یک فناوری حیاتی است که کوچکسازی و یکپارچهسازی دستگاههای الکترونیکی با چگالی بالا را ممکن میسازد. از آنجایی که دستگاههای الکترونیکی همچنان به کوچکتر شدن از نظر اندازه و در عین حال افزایش عملکرد، CSP نقش مهمی در اطمینان از قابلیت اطمینان و عملکرد این دستگاههای جمعوجور دارد.
CSP یک فناوری بسته بندی است که به تراشه نیمه هادی اجازه می دهد بدون نیاز به بسته اضافی مستقیماً روی بستر یا برد مدار چاپی (PCB) نصب شود. این امر نیاز به یک ظرف پلاستیکی یا سرامیکی سنتی را از بین می برد و باعث کاهش اندازه و وزن کلی دستگاه می شود. CSP فرآیندی است که در آن از یک ماده مایع یا محصورکننده برای پر کردن شکاف بین تراشه و بستر استفاده میشود، که پشتیبانی مکانیکی را فراهم میکند و از تراشه در برابر عوامل محیطی مانند رطوبت و استرس مکانیکی محافظت میکند.
کوچک سازی از طریق کم پر شدن CSP با کاهش فاصله بین تراشه و بستر حاصل می شود. مواد کم پر شده، شکاف باریک بین تراشه و بستر را پر می کند و یک پیوند محکم ایجاد می کند و پایداری مکانیکی تراشه را بهبود می بخشد. این امکان را برای دستگاههای کوچکتر و نازکتر فراهم میکند و امکان بستهبندی عملکردهای بیشتری را در یک فضای محدود فراهم میکند.
ادغام با چگالی بالا یکی دیگر از مزایای کم پر شدن CSP است. با حذف نیاز به یک بسته جداگانه، CSP تراشه را قادر میسازد تا نزدیکتر به سایر اجزای PCB نصب شود و طول اتصالات الکتریکی را کاهش دهد و یکپارچگی سیگنال را بهبود بخشد. مواد پر شده همچنین به عنوان یک رسانای حرارتی عمل می کند و گرمای تولید شده توسط تراشه را به طور موثر دفع می کند. این قابلیت مدیریت حرارتی امکان چگالی توان بالاتر را فراهم می کند و ادغام تراشه های پیچیده تر و قدرتمندتر را در دستگاه های الکترونیکی امکان پذیر می کند.
مواد پرکننده CSP باید دارای ویژگیهای خاصی باشند تا نیازهای کوچکسازی و ادغام با چگالی بالا را برآورده کنند. آنها باید ویسکوزیته کم داشته باشند تا پر کردن شکاف های باریک را تسهیل کنند و همچنین خواص جریان عالی برای اطمینان از پوشش یکنواخت و از بین بردن فضای خالی داشته باشند. مواد همچنین باید چسبندگی خوبی به تراشه و بستر داشته باشند و پشتیبانی مکانیکی جامد را فراهم کنند. علاوه بر این، آنها باید رسانایی حرارتی بالایی از خود نشان دهند تا گرما را به طور موثر از تراشه دور کنند.
سطح ویفر CSP Underfill: مقرون به صرفه و بازده بالا
پکیج در مقیاس تراشه سطح ویفر (WLCSP) یک تکنیک بسته بندی مقرون به صرفه و با بازده بالا است که چندین مزیت را در کارایی تولید و کیفیت کلی محصول ارائه می دهد. WLCSP مواد underfill را روی چندین تراشه به طور همزمان اعمال می کند در حالی که هنوز به شکل ویفر هستند قبل از اینکه در بسته های جداگانه قرار گیرند. این رویکرد مزایای بی شماری را در مورد کاهش هزینه، بهبود کنترل فرآیند و بازده تولید بالاتر ارائه می دهد.
یکی از مزایای حیاتی کم پر شدن WLCSP مقرون به صرفه بودن آن است. استفاده از مواد پر شده در سطح ویفر، فرآیند بسته بندی را ساده تر و کارآمدتر می کند. مواد کم پر شده با استفاده از یک فرآیند کنترل شده و خودکار روی ویفر توزیع می شود و ضایعات مواد را کاهش می دهد و هزینه های نیروی کار را به حداقل می رساند. علاوه بر این، حذف مراحل دستکاری بستهبندی و تراز کردن، زمان و پیچیدگی کلی تولید را کاهش میدهد و در نتیجه صرفهجویی قابلتوجهی در هزینه در مقایسه با روشهای بستهبندی سنتی میشود.
علاوه بر این، کمبود WLCSP کنترل فرآیند بهبود یافته و بازده تولید بالاتر را ارائه می دهد. از آنجایی که مواد زیر پر شده در سطح ویفر اعمال می شود، کنترل بهتری بر فرآیند توزیع را امکان پذیر می کند و از پوشش کامل و یکنواخت برای هر تراشه روی ویفر اطمینان حاصل می کند. این امر خطر ایجاد فضای خالی یا پر شدن ناقص را کاهش می دهد که می تواند منجر به مشکلات قابلیت اطمینان شود. توانایی بازرسی و آزمایش کیفیت کم پر شدن در سطح ویفر همچنین امکان تشخیص زودهنگام عیوب یا تغییرات فرآیند را فراهم می کند و اقدامات اصلاحی به موقع را امکان پذیر می کند و احتمال بسته های معیوب را کاهش می دهد. در نتیجه، کم پر شدن WLCSP به دستیابی به بازده تولید بالاتر و کیفیت کلی محصول بهتر کمک می کند.
رویکرد سطح ویفر همچنین عملکرد حرارتی و مکانیکی را بهبود می بخشد. مواد زیر پر استفاده شده در WLCSP معمولاً یک ماده با ویسکوزیته کم و دارای جریان مویرگی است که می تواند شکاف های باریک بین تراشه ها و ویفر را پر کند. این امر پشتیبانی مکانیکی محکمی را برای تراشه ها فراهم می کند و مقاومت آنها را در برابر استرس مکانیکی، ارتعاشات و چرخه دما افزایش می دهد. علاوه بر این، مواد پر شده به عنوان یک رسانای حرارتی عمل میکند و اتلاف گرمای تولید شده توسط تراشهها را تسهیل میکند، بنابراین مدیریت حرارتی را بهبود میبخشد و خطر گرم شدن بیش از حد را کاهش میدهد.
Flip Chip Underfill: چگالی و کارایی I/O بالا
کم پر شدن تراشه فلیپ یک فناوری حیاتی است که تراکم ورودی/خروجی (I/O) بالا و عملکرد استثنایی را در دستگاه های الکترونیکی امکان پذیر می کند. نقش مهمی در افزایش قابلیت اطمینان و عملکرد بسته بندی فلیپ چیپ ایفا می کند که به طور گسترده در کاربردهای نیمه هادی پیشرفته استفاده می شود. این مقاله اهمیت کم پر شدن تراشه فلیپ و تاثیر آن بر دستیابی به چگالی و عملکرد ورودی/خروجی بالا را بررسی خواهد کرد.
فناوری Flip Chip شامل اتصال الکتریکی مستقیم یک مدار مجتمع (IC) یا یک قالب نیمه هادی به بستر است که نیاز به اتصال سیم را از بین می برد. این منجر به بستهبندی فشردهتر و کارآمدتر میشود، زیرا پدهای ورودی/خروجی در سطح پایینی قالب قرار دارند. با این حال، بسته بندی فلیپ تراشه چالش های منحصر به فردی را ارائه می دهد که باید برای اطمینان از عملکرد و قابلیت اطمینان بهینه مورد توجه قرار گیرد.
یکی از چالش های مهم در بسته بندی فلیپ چیپ، جلوگیری از تنش مکانیکی و عدم تطابق حرارتی بین قالب و زیرلایه است. در طول فرآیند تولید و عملیات بعدی، تفاوت در ضرایب انبساط حرارتی (CTE) بین قالب و بستر میتواند باعث تنش قابل توجهی شود که منجر به تخریب عملکرد یا حتی شکست میشود. زیر پر کردن تراشه فلیپ یک ماده محافظ است که تراشه را محصور می کند و پشتیبانی مکانیکی و کاهش استرس را فراهم می کند. این به طور موثر تنش های ایجاد شده در طول چرخه حرارتی را توزیع می کند و از تأثیر آنها بر اتصالات ظریف جلوگیری می کند.
چگالی ورودی/خروجی بالا در دستگاههای الکترونیکی مدرن، که در آن فاکتورهای شکل کوچکتر و افزایش عملکرد ضروری هستند، حیاتی است. پر شدن تراشه فلیپ تراکم ورودی/خروجی بالاتری را با ارائه عایق الکتریکی برتر و قابلیت های مدیریت حرارتی امکان پذیر می کند. مواد کم پر شده، شکاف بین قالب و بستر را پر می کند، یک رابط مستحکم ایجاد می کند و خطر اتصال کوتاه یا نشت الکتریکی را کاهش می دهد. این اجازه می دهد تا فاصله نزدیک تری از پدهای ورودی/خروجی وجود داشته باشد و در نتیجه تراکم ورودی/خروجی افزایش یابد بدون اینکه قابلیت اطمینان از بین برود.
علاوه بر این، کم پر شدن تراشه فلیپ به بهبود عملکرد الکتریکی کمک می کند. انگل های الکتریکی بین قالب و بستر را به حداقل می رساند، تاخیر سیگنال را کاهش می دهد و یکپارچگی سیگنال را افزایش می دهد. مواد زیر پر شده همچنین خواص هدایت حرارتی عالی را نشان میدهند و به طور موثر گرمای تولید شده توسط تراشه را در حین کار دفع میکنند. اتلاف موثر گرما تضمین می کند که دما در محدوده قابل قبول باقی می ماند و از گرمای بیش از حد جلوگیری می کند و عملکرد بهینه را حفظ می کند.
پیشرفتها در مواد پرکننده تراشههای فلیپ، تراکم ورودی/خروجی و سطوح عملکرد بالاتری را ممکن کرده است. به عنوان مثال، از پرکننده های نانوکامپوزیت برای افزایش رسانایی حرارتی و استحکام مکانیکی استفاده می شود. این امکان اتلاف گرما و قابلیت اطمینان را بهبود میبخشد و دستگاههای با عملکرد بالاتر را قادر میسازد.
آرایه شبکه توپ (BGA) Underfill: عملکرد حرارتی و مکانیکی بالا
آرایه شبکه توپ (BGA) یک فناوری حیاتی را که عملکرد حرارتی و مکانیکی بالایی را در دستگاههای الکترونیکی ارائه میدهد، کم پر میکند. نقش مهمی در افزایش قابلیت اطمینان و عملکرد بسته های BGA دارد که به طور گسترده در برنامه های مختلف استفاده می شود. در این مقاله، اهمیت کم پر شدن BGA و تاثیر آن در دستیابی به عملکرد حرارتی و مکانیکی بالا را بررسی خواهیم کرد.
فناوری BGA شامل طراحی بسته بندی می شود که در آن مدار مجتمع (IC) یا قالب نیمه هادی بر روی یک بستر نصب می شود و اتصالات الکتریکی از طریق آرایه ای از توپ های لحیم کاری که در سطح زیرین بسته قرار دارند انجام می شود. BGA ماده ای را که در شکاف بین قالب و زیرلایه توزیع می شود، کم پر می کند، توپ های لحیم کاری را محصور می کند و پشتیبانی مکانیکی و محافظت از مجموعه را فراهم می کند.
یکی از چالش های مهم در بسته بندی BGA مدیریت تنش های حرارتی است. در حین کار، آی سی گرما تولید می کند و انبساط و انقباض حرارتی می تواند باعث ایجاد فشار قابل توجهی بر اتصالات لحیم کاری شود که قالب و زیرلایه را به هم متصل می کند. BGA نقش مهمی در کاهش این تنش ها با ایجاد یک پیوند جامد با قالب و بستر دارد. به عنوان یک بافر تنش عمل می کند، انبساط و انقباض حرارتی را جذب می کند و فشار روی اتصالات لحیم کاری را کاهش می دهد. این به بهبود قابلیت اطمینان کلی بسته کمک می کند و خطر خرابی اتصالات لحیم کاری را کاهش می دهد.
یکی دیگر از جنبه های مهم کم پر شدن BGA، توانایی آن در افزایش عملکرد مکانیکی بسته است. بسته های BGA اغلب در حین جابجایی، مونتاژ و عملیات تحت فشارهای مکانیکی قرار می گیرند. مواد پرکننده شکاف بین قالب و زیرلایه را پر میکند و پشتیبانی ساختاری و تقویت اتصالات لحیم کاری را فراهم میکند. این امر استحکام مکانیکی کلی مجموعه را بهبود می بخشد و آن را در برابر ضربه های مکانیکی، ارتعاشات و سایر نیروهای خارجی مقاوم تر می کند. با توزیع موثر تنش های مکانیکی، کم پر شدن BGA به جلوگیری از ترک خوردگی بسته، لایه لایه شدن یا سایر خرابی های مکانیکی کمک می کند.
عملکرد حرارتی بالا در دستگاه های الکترونیکی برای اطمینان از عملکرد مناسب و قابلیت اطمینان ضروری است. مواد زیر پرکننده BGA طوری طراحی شده اند که خواص هدایت حرارتی عالی داشته باشند. این به آنها اجازه می دهد تا گرما را به طور مؤثر از قالب خارج کرده و آن را در سراسر بستر توزیع کنند و مدیریت حرارتی کلی بسته را بهبود بخشند. اتلاف موثر گرما به حفظ دمای عملیاتی پایین تر، جلوگیری از کانون های حرارتی و کاهش عملکرد بالقوه کمک می کند. همچنین با کاهش تنش حرارتی قطعات به طول عمر جعبه کمک می کند.
پیشرفتها در مواد کمپر شده BGA منجر به عملکرد حرارتی و مکانیکی بالاتری شده است. فرمولاسیون و مواد پرکننده بهبود یافته، مانند نانوکامپوزیت ها یا پرکننده های رسانایی حرارتی بالا، اتلاف گرما و استحکام مکانیکی بهتری را امکان پذیر کرده و عملکرد بسته های BGA را بیشتر افزایش داده است.
کمپر کردن بسته چهارگانه تخت (QFP): تعداد ورودی/خروجی بزرگ و استحکام
بسته چهار تخت (QFP) یک بسته مدار مجتمع (IC) است که به طور گسترده در الکترونیک استفاده می شود. دارای یک شکل مربع یا مستطیل با سرنخ هایی است که از هر چهار طرف امتداد یافته اند و بسیاری از اتصالات ورودی/خروجی (I/O) را فراهم می کند. برای افزایش قابلیت اطمینان و استحکام بستههای QFP، معمولاً از مواد پرکننده استفاده میشود.
Underfill یک ماده محافظ است که بین آی سی و زیرلایه اعمال می شود تا استحکام مکانیکی اتصالات لحیم کاری را تقویت کرده و از خرابی های ناشی از استرس جلوگیری کند. این امر به ویژه برای QFP هایی با تعداد ورودی/خروجی زیاد بسیار مهم است، زیرا تعداد زیاد اتصالات می تواند منجر به تنش های مکانیکی قابل توجهی در طول چرخه حرارتی و شرایط عملیاتی شود.
مواد زیر پر استفاده شده برای بسته های QFP باید دارای ویژگی های خاصی برای اطمینان از استحکام باشد. اولاً، باید چسبندگی عالی هم به آی سی و هم به زیرلایه داشته باشد تا یک اتصال قوی ایجاد کند و خطر لایه برداری یا جدا شدن را به حداقل برساند. علاوه بر این، باید ضریب انبساط حرارتی پایینی (CTE) داشته باشد تا با CTE IC و بستر مطابقت داشته باشد و عدم تطابق تنش را کاهش دهد که میتواند منجر به ترک یا شکستگی شود.
علاوه بر این، مواد زیر پر باید خواص جریان خوبی داشته باشند تا از پوشش یکنواخت و پر شدن کامل شکاف بین IC و بستر اطمینان حاصل شود. این به از بین بردن فضای خالی کمک می کند، که می تواند اتصالات لحیم کاری را ضعیف کرده و منجر به کاهش قابلیت اطمینان شود. این ماده همچنین باید خواص پخت خوبی داشته باشد و به آن اجازه می دهد پس از اعمال یک لایه محافظ سفت و سخت و بادوام تشکیل دهد.
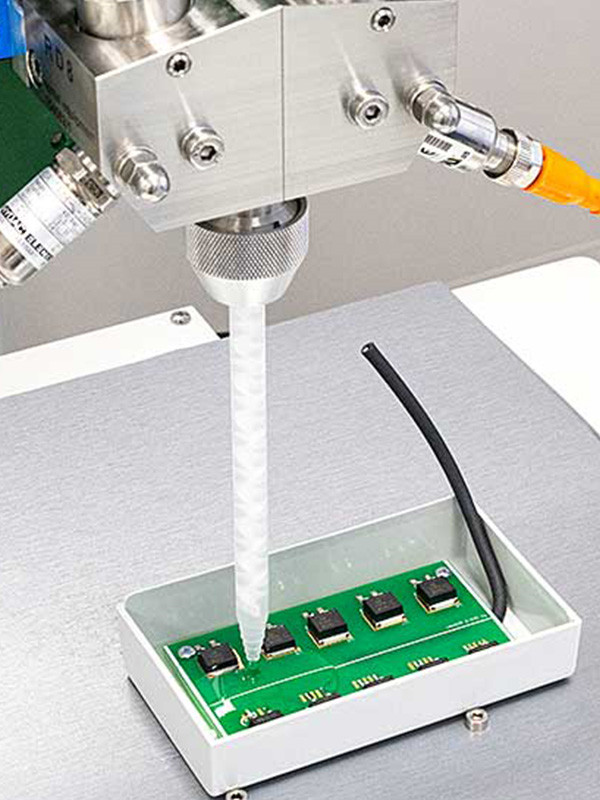
از نظر استحکام مکانیکی، زیرپر باید دارای استحکام برشی و لایه برداری بالایی باشد تا در برابر نیروهای خارجی مقاومت کند و از تغییر شکل یا جدا شدن بسته بندی جلوگیری کند. همچنین باید مقاومت خوبی در برابر رطوبت و سایر عوامل محیطی از خود نشان دهد تا خواص محافظتی خود را در طول زمان حفظ کند. این امر به ویژه در کاربردهایی که بسته QFP ممکن است در معرض شرایط سخت یا تغییرات دما قرار گیرد، اهمیت دارد.
برای دستیابی به این ویژگی های مورد نظر، مواد مختلف زیر پر در دسترس هستند، از جمله فرمولاسیون های مبتنی بر اپوکسی. بسته به نیازهای خاص برنامه، این مواد را می توان با استفاده از تکنیک های مختلف، مانند جریان مویرگی، جت کردن، یا چاپ روی صفحه توزیع کرد.
System-in-Package (SiP) Underfill: یکپارچه سازی و عملکرد
System-in-Package (SiP) یک فناوری بسته بندی پیشرفته است که چندین تراشه نیمه هادی، اجزای غیرفعال و سایر عناصر را در یک بسته ادغام می کند. SiP مزایای متعددی از جمله کاهش ضریب فرم، بهبود عملکرد الکتریکی و عملکرد بهبود یافته را ارائه می دهد. برای اطمینان از قابلیت اطمینان و عملکرد مجموعههای SiP، معمولاً از مواد پرکننده استفاده میشود.
کم پر شدن در برنامه های SiP در ارائه پایداری مکانیکی و اتصال الکتریکی بین اجزای مختلف درون بسته بسیار مهم است. این کمک می کند تا خطر شکست های ناشی از استرس، مانند ترک یا شکستگی اتصال لحیم کاری، که می تواند به دلیل تفاوت در ضرایب انبساط حرارتی (CTE) بین اجزا رخ دهد، به حداقل برسد.
ادغام چندین مؤلفه در یک بسته SiP منجر به اتصالات پیچیده با اتصالات لحیم کاری و مدارهای با چگالی بالا می شود. مواد پرکننده به تقویت این اتصالات کمک می کنند و استحکام مکانیکی و قابلیت اطمینان مجموعه را افزایش می دهند. آنها از اتصالات لحیم پشتیبانی می کنند و خطر خستگی یا آسیب ناشی از چرخه حرارتی یا استرس مکانیکی را کاهش می دهند.
از نظر عملکرد الکتریکی، مواد کم پر در بهبود یکپارچگی سیگنال و به حداقل رساندن نویز الکتریکی بسیار مهم هستند. با پر کردن شکاف بین اجزا و کاهش فاصله بین آنها، کم پر کردن به کاهش ظرفیت خازنی و اندوکتانس انگلی کمک می کند و انتقال سیگنال را سریعتر و کارآمدتر می کند.
علاوه بر این، مواد پرکننده برای کاربردهای SiP باید رسانایی حرارتی عالی داشته باشند تا گرمای تولید شده توسط اجزای یکپارچه را به طور موثر دفع کنند. اتلاف گرمای موثر برای جلوگیری از گرمای بیش از حد و حفظ قابلیت اطمینان و عملکرد کلی مجموعه SiP ضروری است.
مواد پر شده در بسته بندی SiP باید دارای ویژگی های خاصی باشند تا این الزامات یکپارچه سازی و عملکرد را برآورده کنند. آنها باید جریان پذیری خوبی داشته باشند تا از پوشش کامل و پر کردن شکاف بین اجزا اطمینان حاصل شود. مواد کم پر نیز باید دارای فرمولاسیون کم ویسکوزیته باشد تا امکان توزیع آسان و پر کردن سوراخ های باریک یا فضاهای کوچک را فراهم کند.
علاوه بر این، مواد زیر پر باید چسبندگی قوی به سطوح مختلف، از جمله تراشه های نیمه هادی، بسترها، و غیرفعال ها نشان دهند تا از اتصال قابل اطمینان اطمینان حاصل شود. این باید با مواد بسته بندی مختلف مانند بسترهای آلی یا سرامیک سازگار باشد و خواص مکانیکی خوبی از جمله مقاومت برشی و پوسته شدن بالا از خود نشان دهد.
انتخاب مواد پر شده و روش کاربرد به طراحی خاص SiP، الزامات اجزا و فرآیندهای تولید بستگی دارد. روشهای توزیع مانند جریان مویرگی، جت کردن، یا روشهای به کمک فیلم معمولاً در مجموعههای SiP به کار میروند.
Optoelectronics Underfill: تراز نوری و حفاظت
اپتوالکترونیک کم پر کردن شامل کپسوله کردن و محافظت از دستگاه های اپتوالکترونیک در حالی که از تراز نوری دقیق اطمینان می دهد. دستگاههای الکترونیک نوری، مانند لیزر، آشکارسازهای نوری و سوئیچهای نوری، اغلب برای دستیابی به عملکرد بهینه نیاز به تراز ظریف اجزای نوری دارند. در عین حال، آنها باید از عوامل محیطی محافظت شوند که می تواند بر عملکرد آنها تأثیر بگذارد. اپتوالکترونیک با ارائه همراستایی نوری و حفاظت در یک فرآیند واحد، هر دو این الزامات را برطرف می کند.
تراز نوری یک جنبه حیاتی در ساخت دستگاه های الکترونیک نوری است. این شامل تراز کردن عناصر بصری، مانند الیاف، موجبرها، لنزها، یا توری ها برای اطمینان از انتقال و دریافت نور کارآمد است. تراز دقیق برای به حداکثر رساندن عملکرد دستگاه و حفظ یکپارچگی سیگنال ضروری است. تکنیک های تراز سنتی شامل تراز دستی با استفاده از بازرسی بصری یا تراز خودکار با استفاده از مراحل تراز است. با این حال، این روش ها می توانند زمان بر، کار فشرده و مستعد خطا باشند.
اپتوالکترونیک یک راه حل نوآورانه را با ترکیب ویژگی های هم ترازی مستقیماً در مواد زیر پر می کند. مواد پرکننده معمولاً ترکیبات مایع یا نیمه مایعی هستند که میتوانند جریان داشته باشند و شکافهای بین اجزای نوری را پر کنند. با افزودن ویژگیهای همترازی، مانند ریزساختارها یا علائم اعتباری، در مواد زیر پر، فرآیند همترازی را میتوان ساده و خودکار کرد. این ویژگی ها در حین مونتاژ به عنوان راهنما عمل می کنند و از تراز دقیق اجزای نوری بدون نیاز به روش های تراز پیچیده اطمینان می دهند.
علاوه بر تراز نوری، مواد پرکننده از دستگاههای الکترونیک نوری محافظت میکنند. اجزای اپتوالکترونیک اغلب در معرض محیط های خشن از جمله نوسانات دما، رطوبت و تنش های مکانیکی قرار می گیرند. این عوامل خارجی می توانند عملکرد و قابلیت اطمینان دستگاه ها را در طول زمان کاهش دهند. مواد پرکننده به عنوان یک مانع محافظ عمل میکنند، اجزای نوری را محصور میکنند و از آنها در برابر آلودگیهای محیطی محافظت میکنند. آنها همچنین تقویت مکانیکی را فراهم می کنند و خطر آسیب ناشی از ضربه یا لرزش را کاهش می دهند.
مواد پرکننده مورد استفاده در کاربردهای اپتوالکترونیک معمولاً به گونهای طراحی میشوند که ضریب شکست پایین و شفافیت نوری عالی داشته باشند. این حداقل تداخل را با سیگنال های نوری عبوری از دستگاه تضمین می کند. علاوه بر این، چسبندگی خوبی به زیرلایههای مختلف نشان میدهند و ضریب انبساط حرارتی پایینی برای به حداقل رساندن تنش دستگاه در طول چرخه حرارتی دارند.
فرآیند زیر پر کردن شامل توزیع مواد پر شده روی دستگاه، اجازه جریان یافتن و پر کردن شکافهای بین اجزای نوری و سپس پخت آن برای تشکیل یک کپسوله جامد است. بسته به کاربرد خاص، مواد زیر پر را می توان با استفاده از تکنیک های مختلفی مانند جریان مویرگی، توزیع جت یا چاپ روی صفحه اعمال کرد. فرآیند پخت را می توان از طریق گرما، اشعه ماوراء بنفش یا هر دو به دست آورد.
تجهیزات الکترونیک پزشکی کم پر: زیست سازگاری و قابلیت اطمینان
الکترونیک پزشکی یک فرآیند تخصصی را پر می کند که شامل کپسوله کردن و محافظت از اجزای الکترونیکی مورد استفاده در دستگاه های پزشکی است. این دستگاهها در کاربردهای مختلف پزشکی مانند دستگاههای قابل کاشت، تجهیزات تشخیصی، سیستمهای مانیتورینگ و سیستمهای تحویل دارو نقش اساسی دارند. کمبود تجهیزات الکترونیک پزشکی بر دو جنبه حیاتی تمرکز دارد: زیست سازگاری و قابلیت اطمینان.
زیست سازگاری یک نیاز اساسی برای وسایل پزشکی است که با بدن انسان در تماس هستند. مواد پرکننده مورد استفاده در الکترونیک پزشکی باید زیست سازگار باشند، به این معنی که در تماس با بافت زنده یا مایعات بدن نباید اثرات مضر یا واکنش های نامطلوب ایجاد کنند. این مواد باید با مقررات و استانداردهای سختگیرانه ای مانند ISO 10993 مطابقت داشته باشند که روش های تست زیست سازگاری و ارزیابی را مشخص می کند.
مواد پرکننده برای الکترونیک پزشکی با دقت انتخاب یا فرموله می شوند تا از زیست سازگاری اطمینان حاصل شود. آنها به گونه ای طراحی شده اند که غیر سمی، غیر تحریک کننده و غیر حساسیت زا باشند. این مواد نباید هیچ گونه ماده مضری را شسته و یا در طول زمان تجزیه شوند، زیرا ممکن است منجر به آسیب بافتی یا التهاب شود. مواد زیر پرکننده زیست سازگار همچنین جذب آب پایینی برای جلوگیری از رشد باکتری ها یا قارچ هایی که می توانند باعث عفونت شوند، دارند.
قابلیت اطمینان یکی دیگر از جنبه های حیاتی کم پر شدن الکترونیک پزشکی است. دستگاه های پزشکی اغلب با شرایط عملیاتی چالش برانگیز، از جمله دما، رطوبت، مایعات بدن و استرس مکانیکی مواجه هستند. مواد پرکننده باید از قطعات الکترونیکی محافظت کنند و از قابلیت اطمینان و عملکرد طولانی مدت آنها اطمینان حاصل کنند. قابلیت اطمینان در کاربردهای پزشکی که خرابی دستگاه میتواند به شدت بر ایمنی و رفاه بیمار تأثیر بگذارد، بسیار مهم است.
مواد پرکننده برای الکترونیک پزشکی باید مقاومت بالایی در برابر رطوبت و مواد شیمیایی داشته باشند تا در برابر قرار گرفتن در معرض مایعات بدن یا فرآیندهای استریلسازی مقاومت کنند. آنها همچنین باید چسبندگی خوبی به بسترهای مختلف نشان دهند و از محصور شدن ایمن قطعات الکترونیکی اطمینان حاصل کنند. خواص مکانیکی، مانند ضرایب کم انبساط حرارتی و مقاومت در برابر شوک خوب، برای به حداقل رساندن تنش وارده به جزئیات در طول چرخه حرارتی یا بارگذاری خودکار بسیار مهم هستند.
فرآیند کم پر شدن برای الکترونیک پزشکی شامل موارد زیر است:
- توزیع مواد پر شده روی قطعات الکترونیکی.
- پر کردن جای خالی.
- پخت آن برای تشکیل یک کپسول محافظ و مکانیکی پایدار.
برای اطمینان از پوشش کامل ویژگی ها و عدم وجود حفره های خالی یا حفره های هوا که می تواند قابلیت اطمینان دستگاه را به خطر بیندازد، باید مراقب بود.
علاوه بر این، ملاحظات اضافی در هنگام کم پر کردن دستگاه های پزشکی در نظر گرفته می شود. به عنوان مثال، مواد پر شده باید با روش های استریل سازی مورد استفاده برای دستگاه سازگار باشد. برخی از مواد ممکن است به تکنیک های خاص استریلیزاسیون مانند بخار، اکسید اتیلن یا تشعشع حساس باشند و ممکن است نیاز به انتخاب مواد جایگزین باشد.
Aerospace Electronics Underfill: درجه حرارت بالا و مقاومت در برابر لرزش
الکترونیک هوافضا یک فرآیند تخصصی را برای محصور کردن و محافظت از قطعات الکترونیکی در کاربردهای هوافضا پر می کند. محیط های هوافضا چالش های منحصر به فردی از جمله دماهای بالا، ارتعاشات شدید و تنش های مکانیکی ایجاد می کنند. بنابراین، کم پر شدن الکترونیک هوافضا بر دو جنبه مهم تمرکز دارد: مقاومت در برابر دمای بالا و مقاومت در برابر لرزش.
مقاومت در برابر درجه حرارت بالا در الکترونیک هوافضا به دلیل دماهای بالا که در حین کار تجربه می شود، بسیار مهم است. مواد پرکننده مورد استفاده در کاربردهای هوافضا باید این دماهای بالا را بدون به خطر انداختن عملکرد و قابلیت اطمینان قطعات الکترونیکی تحمل کنند. آنها باید حداقل انبساط حرارتی را نشان دهند و در یک محدوده دمایی گسترده پایدار بمانند.
مواد پرکننده برای الکترونیک هوافضا برای دماهای انتقال شیشه ای بالا (Tg) و پایداری حرارتی انتخاب یا فرموله می شوند. Tg بالا تضمین می کند که مواد خواص مکانیکی خود را در دماهای بالا حفظ می کند و از تغییر شکل یا از دست دادن چسبندگی جلوگیری می کند. این مواد می توانند در برابر درجه حرارت بالا، مانند هنگام برخاستن، ورود مجدد جو، یا کار در محفظه موتور داغ مقاومت کنند.
علاوه بر این، مواد کم پر برای الکترونیک هوافضا باید ضریب انبساط حرارتی پایینی (CTE) داشته باشند. CTE میزان انبساط یا انقباض یک ماده با تغییرات دما را اندازه گیری می کند. با داشتن CTE پایین، مواد کم پر میتوانند فشار وارده بر قطعات الکترونیکی ناشی از چرخه حرارتی را به حداقل برسانند، که میتواند منجر به خرابیهای مکانیکی یا خستگی مفصل لحیم شود.
مقاومت در برابر ارتعاش یکی دیگر از نیازهای حیاتی برای پر نشدن تجهیزات الکترونیکی هوافضا است. وسایل نقلیه هوافضا در معرض ارتعاشات مختلفی از جمله موتور، ارتعاشات ناشی از پرواز و شوک های مکانیکی در هنگام پرتاب یا فرود هستند. این ارتعاشات می تواند عملکرد و قابلیت اطمینان قطعات الکترونیکی را در صورت عدم محافظت کافی به خطر بیندازد.
مواد پرکننده مورد استفاده در الکترونیک هوافضا باید خواص ارتعاشی عالی از خود نشان دهند. آنها باید انرژی تولید شده توسط ارتعاشات را جذب و از بین ببرند و استرس و فشار وارد بر قطعات الکترونیکی را کاهش دهند. این به جلوگیری از ایجاد ترک، شکستگی یا سایر خرابی های مکانیکی به دلیل قرار گرفتن در معرض ارتعاش بیش از حد کمک می کند.
علاوه بر این، مواد زیر پر با چسبندگی و استحکام چسبندگی بالا در کاربردهای هوافضا ترجیح داده می شوند. این ویژگیها تضمین میکند که مواد زیر پر شده به طور محکم به اجزای الکترونیکی و زیرلایه متصل میشوند، حتی در شرایط ارتعاش شدید. چسبندگی قوی مانع از لایه برداری یا جدا شدن مواد زیر پر شده از عناصر می شود و یکپارچگی کپسوله را حفظ می کند و در برابر نفوذ رطوبت یا زباله محافظت می کند.
فرآیند کم پر کردن برای الکترونیک هوافضا معمولاً شامل توزیع مواد پر شده روی اجزای الکترونیکی، اجازه جریان دادن به آن و پر کردن شکافها و سپس پخت آن برای تشکیل یک کپسوله قوی است. بسته به نیازهای خاص برنامه، فرآیند پخت را می توان با استفاده از روش های پخت حرارتی یا UV انجام داد.
تجهیزات الکترونیکی خودرو: دوام و مقاومت در برابر چرخش حرارتی
الکترونیک خودرو فرآیند مهمی را که شامل کپسوله کردن و محافظت از اجزای الکترونیکی در کاربردهای خودرو است، پر می کند. محیط های خودرو چالش های منحصر به فردی از جمله تغییرات دما، چرخه حرارتی، تنش های مکانیکی و قرار گرفتن در معرض رطوبت و مواد شیمیایی را به همراه دارند. بنابراین، پر کردن قطعات الکترونیکی خودرو بر دو جنبه مهم تمرکز دارد: دوام و مقاومت در برابر چرخه حرارتی.
دوام یک نیاز حیاتی برای پر نشدن وسایل الکترونیکی خودرو است. در طول کارکرد منظم، وسایل نقلیه خودرویی ارتعاشات، شوکها و تنشهای مکانیکی دائمی را تجربه میکنند. مواد پرکننده مورد استفاده در کاربردهای خودرو باید از قطعات الکترونیکی به شدت محافظت کنند و دوام و طول عمر آنها را تضمین کنند. آنها باید در برابر شرایط سخت و بارهای مکانیکی وارد شده در جاده مقاومت کنند و در برابر نفوذ رطوبت، گرد و غبار و مواد شیمیایی مقاومت کنند.
مواد پرکننده برای الکترونیک خودرو برای استحکام مکانیکی بالا و مقاومت در برابر ضربه انتخاب یا فرموله می شوند. آنها باید چسبندگی عالی به اجزای الکترونیکی و زیرلایه نشان دهند و از لایه برداری یا جدا شدن تحت تنش های مکانیکی جلوگیری کنند. مواد پر بادوام به کاهش خطر آسیب به قطعات الکترونیکی در اثر لرزش یا ضربه کمک می کند و عملکرد قابل اعتماد را در طول عمر خودرو تضمین می کند.
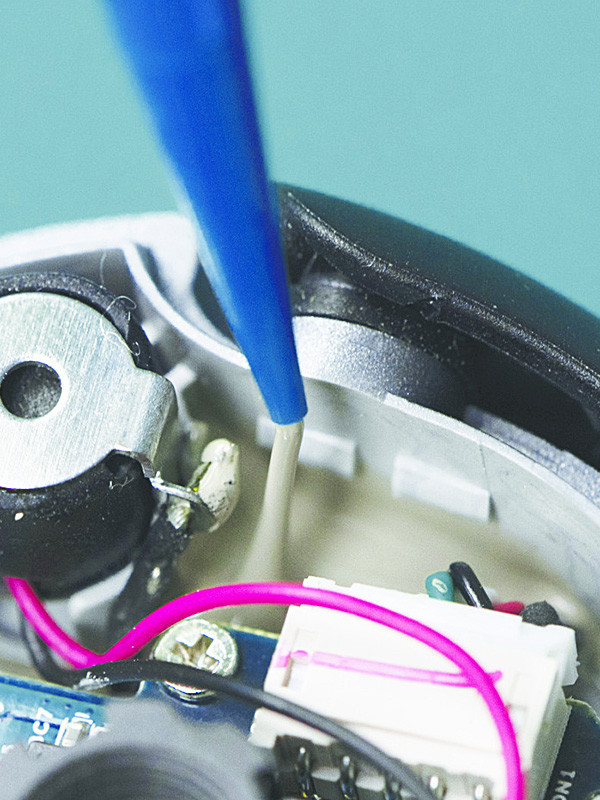
مقاومت در برابر چرخش حرارتی یکی دیگر از نیازهای حیاتی برای کم پر کردن لوازم الکترونیکی خودرو است. وسایل نقلیه خودرویی بهویژه در هنگام راهاندازی و کارکرد موتور دچار تغییرات دمایی مکرر میشوند و این چرخههای دمایی میتوانند باعث ایجاد تنشهای حرارتی بر روی قطعات الکترونیکی و مواد کمپر شده اطراف شوند. مواد پرکننده مورد استفاده در کاربردهای خودرو باید مقاومت بالایی در چرخه حرارتی داشته باشند تا بتوانند این نوسانات دما را بدون به خطر انداختن عملکردشان تحمل کنند.
مواد پرکننده برای وسایل الکترونیکی خودرو باید دارای ضرایب انبساط حرارتی پایین (CTE) باشند تا استرس قطعات الکترونیکی در طول چرخه حرارتی به حداقل برسد. یک CTE مناسب بین مواد پرکننده و مواد تشکیل دهنده، خطر خستگی مفصل لحیم کاری، ترک خوردن یا سایر خرابی های مکانیکی ناشی از تنش حرارتی را کاهش می دهد. علاوه بر این، مواد پرکننده باید رسانایی حرارتی خوبی از خود نشان دهند تا گرما را به طور موثر دفع کنند و از نقاط حساس موضعی که میتوانند بر عملکرد و قابلیت اطمینان قطعات تأثیر بگذارند، جلوگیری میکنند.
علاوه بر این، مواد پرکننده الکترونیک خودرو باید در برابر رطوبت، مواد شیمیایی و مایعات مقاومت کنند. آنها باید جذب آب کمی داشته باشند تا از رشد قالب یا خوردگی قطعات الکترونیکی جلوگیری کنند. مقاومت شیمیایی تضمین میکند که مواد پرکننده در هنگام قرار گرفتن در معرض مایعات خودرو مانند روغنها، سوختها یا مواد تمیزکننده پایدار میمانند و از تخریب یا از بین رفتن چسبندگی جلوگیری میکنند.
فرآیند کم پر کردن برای لوازم الکترونیکی خودرو معمولا شامل توزیع مواد پر شده روی قطعات الکترونیکی، اجازه جریان دادن به آن و پر کردن شکاف ها، و سپس پخت آن برای تشکیل یک کپسوله بادوام است. فرآیند پخت را می توان از طریق روش های پخت حرارتی یا UV انجام داد، بسته به نیازهای خاص برنامه و مواد کم پر استفاده شده.
انتخاب اپوکسی زیر پرکننده مناسب
انتخاب اپوکسی زیر پر کننده مناسب یک تصمیم بسیار مهم در مونتاژ و محافظت از قطعات الکترونیکی است. اپوکسیهای پرکننده، تقویت مکانیکی، مدیریت حرارتی و محافظت در برابر عوامل محیطی را فراهم میکنند. در اینجا برخی از ملاحظات کلیدی هنگام انتخاب اپوکسی زیر پر شده مناسب وجود دارد:
- خواص حرارتی: یکی از عملکردهای اولیه اپوکسی کم پر، دفع گرمای تولید شده توسط قطعات الکترونیکی است. بنابراین، در نظر گرفتن هدایت حرارتی و مقاومت حرارتی اپوکسی ضروری است. رسانایی حرارتی بالا به انتقال حرارت کارآمد کمک می کند، از ایجاد نقاط داغ جلوگیری می کند و قابلیت اطمینان قطعات را حفظ می کند. اپوکسی همچنین باید مقاومت حرارتی پایینی داشته باشد تا استرس حرارتی بر روی اجزا در طول چرخه دما به حداقل برسد.
- CTE Match: ضریب انبساط حرارتی اپوکسی کم پر (CTE) باید به خوبی با CTE قطعات الکترونیکی و زیرلایه مطابقت داشته باشد تا استرس حرارتی به حداقل برسد و از خرابی اتصالات لحیم کاری جلوگیری شود. یک CTE نزدیک به هم به کاهش خطر خرابی های مکانیکی ناشی از چرخه حرارتی کمک می کند.
- جریان و قابلیت پر کردن شکاف: اپوکسی کم پر شده باید ویژگی های جریان خوبی داشته باشد و توانایی پر کردن شکاف بین اجزا را به طور موثر داشته باشد. این پوشش کامل را تضمین می کند و فضاهای خالی یا حفره های هوا را که می تواند بر پایداری مکانیکی و عملکرد حرارتی مجموعه تأثیر بگذارد، به حداقل می رساند. ویسکوزیته اپوکسی باید برای کاربرد خاص و روش مونتاژ مناسب باشد، خواه جریان مویرگی، توزیع جت یا چاپ روی صفحه باشد.
- چسبندگی: چسبندگی قوی برای کم پر کردن اپوکسی برای اطمینان از اتصال قابل اعتماد بین اجزا و زیرلایه بسیار مهم است. باید چسبندگی خوبی به مواد مختلف از جمله فلزات، سرامیک ها و پلاستیک ها نشان دهد. خواص چسبندگی اپوکسی به یکپارچگی مکانیکی و قابلیت اطمینان طولانی مدت آن کمک می کند.
- روش پخت: روش پخت را در نظر بگیرید که به بهترین وجه برای فرآیند تولید شما مناسب است. اپوکسی های کم پر را می توان از طریق گرما، اشعه ماوراء بنفش یا ترکیبی از هر دو درمان کرد. هر روش پخت مزایا و محدودیتهایی دارد و انتخاب روشی که با نیازهای تولید شما مطابقت داشته باشد ضروری است.
- مقاومت محیطی: مقاومت اپوکسی زیر پر شده را در برابر عوامل محیطی مانند رطوبت، مواد شیمیایی و دمای شدید ارزیابی کنید. اپوکسی باید بتواند در برابر آب مقاومت کند و از رشد قالب یا خوردگی جلوگیری کند. مقاومت شیمیایی پایداری را هنگام تماس با مایعات خودرو، مواد پاک کننده یا سایر مواد بالقوه خورنده تضمین می کند. علاوه بر این، اپوکسی باید خواص مکانیکی و الکتریکی خود را در محدوده دمایی وسیعی حفظ کند.
- قابلیت اطمینان و طول عمر: سابقه اپوکسی و داده های قابلیت اطمینان آن را در نظر بگیرید. به دنبال مواد اپوکسی آزمایش شده و اثبات شده در کاربردهای مشابه باشید یا دارای گواهینامه های صنعتی و مطابقت با استانداردهای مربوطه باشند. عواملی مانند رفتار پیری، قابلیت اطمینان طولانی مدت و توانایی اپوکسی برای حفظ خواص خود در طول زمان را در نظر بگیرید.
هنگام انتخاب اپوکسی زیر پرکننده مناسب، مهم است که الزامات خاص برنامه خود را در نظر بگیرید، از جمله مدیریت حرارتی، پایداری مکانیکی، حفاظت از محیط زیست و سازگاری با فرآیند تولید. مشاوره با تامین کنندگان اپوکسی یا جستجوی مشاوره متخصص می تواند در تصمیم گیری آگاهانه که نیازهای برنامه شما را برآورده می کند و عملکرد و قابلیت اطمینان بهینه را تضمین می کند، مفید باشد.
روندهای آتی در اپوکسی کم پر
اپوکسی Underfill به طور مداوم در حال تکامل است که به دلیل پیشرفت در فناوری های الکترونیکی، برنامه های کاربردی نوظهور و نیاز به بهبود عملکرد و قابلیت اطمینان ایجاد می شود. چندین روند آینده را می توان در توسعه و کاربرد اپوکسی underfill مشاهده کرد:
- کوچکسازی و بستهبندی با چگالی بالاتر: از آنجایی که دستگاههای الکترونیکی همچنان کوچک میشوند و دارای تراکم اجزای بالاتری هستند، اپوکسیهای کمپر باید مطابق با آن سازگار شوند. روندهای آتی بر روی توسعه مواد پرکننده متمرکز خواهند بود که شکافهای کوچکتری را بین قطعات نفوذ کرده و پر میکنند و از پوشش کامل و حفاظت قابل اعتماد در مجموعههای الکترونیکی کوچکتر بهطور فزایندهای اطمینان میدهند.
- کاربردهای فرکانس بالا: با افزایش تقاضا برای دستگاههای الکترونیکی با فرکانس بالا و سرعت بالا، فرمولهای اپوکسی کمپر باید نیازهای خاص این برنامهها را برطرف کنند. مواد پرکننده با ثابت دی الکتریک کم و مماس تلفات کم برای به حداقل رساندن تلفات سیگنال و حفظ یکپارچگی سیگنالهای فرکانس بالا در سیستمهای ارتباطی پیشرفته، فناوری 5G و سایر برنامههای در حال ظهور ضروری هستند.
- مدیریت حرارتی پیشرفته: اتلاف گرما همچنان یک نگرانی اساسی برای دستگاه های الکترونیکی است، به خصوص با افزایش چگالی توان. فرمولهای اپوکسی کمپر در آینده بر بهبود هدایت حرارتی برای افزایش انتقال حرارت و مدیریت مؤثر مسائل حرارتی تمرکز خواهند کرد. پرکنندهها و افزودنیهای پیشرفته برای دستیابی به رسانایی حرارتی بالاتر و در عین حال حفظ سایر خواص مطلوب، در اپوکسیهای زیر پر گنجانده میشوند.
- الکترونیک انعطاف پذیر و قابل کشش: ظهور وسایل الکترونیکی انعطاف پذیر و قابل کشش، فرصت های جدیدی را برای کم پر کردن مواد اپوکسی باز می کند. اپوکسی های زیر پر انعطاف پذیر باید چسبندگی و خواص مکانیکی عالی را حتی در خم شدن یا کشش مکرر نشان دهند. این مواد محصورسازی و محافظت از وسایل الکترونیکی را در دستگاههای پوشیدنی، نمایشگرهای قابل خم شدن و سایر کاربردهایی که به انعطافپذیری مکانیکی نیاز دارند، ممکن میسازد.
- راه حل های دوستدار محیط زیست: ملاحظات پایداری و زیست محیطی نقش مهمی در توسعه مواد اپوکسی کم پر خواهند داشت. تمرکز بر ایجاد فرمولاسیون های اپوکسی عاری از مواد خطرناک و کاهش اثرات زیست محیطی در طول چرخه عمر آنها از جمله ساخت، استفاده و دفع خواهد بود. مواد مبتنی بر زیستی یا تجدیدپذیر نیز ممکن است به عنوان جایگزین های پایدار برجسته شوند.
- فرآیندهای تولید بهبود یافته: روندهای آتی در اپوکسی کم پر بر روی خواص مواد و پیشرفت در فرآیندهای تولید تمرکز خواهد کرد. تکنیک هایی مانند ساخت افزودنی، توزیع انتخابی، و روش های پخت پیشرفته برای بهینه سازی کاربرد و عملکرد اپوکسی کم پر در فرآیندهای مختلف مونتاژ الکترونیکی مورد بررسی قرار خواهند گرفت.
- ادغام تکنیکهای آزمایش و مشخصهسازی پیشرفته: با افزایش پیچیدگی و الزامات دستگاههای الکترونیکی، برای اطمینان از قابلیت اطمینان و عملکرد اپوکسی کمپر، نیاز به روشهای آزمایش و مشخصههای پیشرفته وجود خواهد داشت. تکنیک هایی مانند آزمایش غیر مخرب، نظارت در محل و ابزارهای شبیه سازی به توسعه و کنترل کیفیت مواد اپوکسی کم پر شده کمک می کند.
نتیجه
اپوکسی underfill نقش مهمی در افزایش قابلیت اطمینان و عملکرد قطعات الکترونیکی، به ویژه در بسته بندی های نیمه هادی ایفا می کند. انواع مختلف اپوکسی زیر پر کننده طیف وسیعی از مزایای، از جمله قابلیت اطمینان بالا، خود توزیع، چگالی بالا و عملکرد حرارتی و مکانیکی بالا را ارائه می دهد. انتخاب اپوکسی زیر پرکننده مناسب برای کاربرد و بسته بندی، اتصال قوی و طولانی مدت را تضمین می کند. با پیشرفت فناوری و کوچک شدن اندازه بستهها، ما انتظار داریم راهحلهای اپوکسی زیر پرکننده حتی نوآورانهتری با عملکرد عالی، یکپارچهسازی و کوچکسازی ارائه دهند. اپوکسی Underfill نقش مهمی را در آینده الکترونیک ایفا می کند و ما را قادر می سازد تا به سطوح بالاتری از قابلیت اطمینان و عملکرد در صنایع مختلف دست یابیم.