Підзаливна епоксидна смола
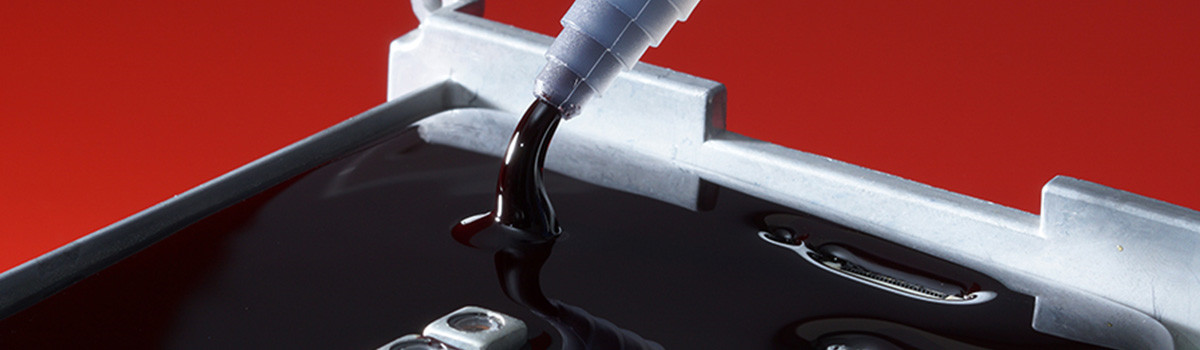
Епоксидна смола для заливки — це тип клею, який використовується для підвищення надійності електронних компонентів, зокрема для упаковки напівпровідників. Він заповнює проміжок між упаковкою та друкованою платою (PCB), забезпечуючи механічну підтримку та зняття напруги, щоб запобігти пошкодженню теплового розширення та стиснення. Епоксидна смола Underfill також покращує електричні характеристики упаковки шляхом зменшення паразитної індуктивності та ємності. У цій статті ми досліджуємо різноманітні застосування епоксидної смоли для заливки, різні доступні типи та їхні переваги.
Важливість епоксидної смоли для заливки в упаковці напівпровідників
Епоксидна смола для заповнення має вирішальне значення в упаковці напівпровідників, забезпечуючи механічне зміцнення та захист делікатних мікроелектронних компонентів. Це спеціальний клейовий матеріал, який використовується для заповнення проміжків між напівпровідниковим чіпом і підкладкою упаковки, що підвищує надійність і продуктивність електронних пристроїв. Тут ми розглянемо важливість епоксидної смоли з недостатнім наповненням для упаковки напівпровідників.
Однією з основних функцій епоксидної смоли з недостатнім наповненням є підвищення механічної міцності та надійності упаковки. Під час роботи напівпровідникові мікросхеми піддаються різним механічним навантаженням, таким як теплове розширення та стиснення, вібрація та механічні удари. Ці напруги можуть призвести до утворення тріщин паяного з’єднання, що може спричинити електричні збої та зменшити загальний термін служби пристрою. Епоксидна смола Underfill діє як засіб для зменшення напруги, рівномірно розподіляючи механічну напругу між мікросхемою, підкладкою та паяними з’єднаннями. Він ефективно мінімізує утворення тріщин і запобігає поширенню існуючих тріщин, забезпечуючи тривалу надійність упаковки.
Ще один важливий аспект епоксидної смоли для заливки — це її здатність підвищувати теплові характеристики напівпровідникових пристроїв. Розсіювання тепла стає серйозною проблемою, оскільки електронні пристрої зменшуються в розмірах і збільшують щільність потужності, а надмірне тепло може погіршити продуктивність і надійність напівпровідникової мікросхеми. Епоксидна смола Underfill має чудові властивості теплопровідності, що дозволяє їй ефективно передавати тепло від мікросхеми та розподіляти його по всій упаковці. Це допомагає підтримувати оптимальну робочу температуру та запобігає появі гарячих точок, тим самим покращуючи загальне керування температурою пристрою.
Епоксидна смола також захищає від вологи та забруднень. Попадання вологи може призвести до корозії, витоку електричного струму та розростання струмопровідних матеріалів, що призведе до несправностей пристрою. Епоксидна смола Underfill діє як бар’єр, запечатуючи вразливі ділянки та запобігаючи проникненню вологи в упаковку. Він також забезпечує захист від пилу, бруду та інших забруднень, які можуть негативно вплинути на електричні характеристики напівпровідникового чіпа. Захищаючи мікросхему та її з’єднання, епоксидна смола з нижньою заливкою забезпечує тривалу надійність і функціональність пристрою.
Крім того, недоповнена епоксидна смола забезпечує мініатюризацію напівпровідникової упаковки. Зважаючи на постійний попит на менші та компактніші пристрої, епоксидна смола з недостатнім заповненням дозволяє використовувати технології упаковки з перевернутим чіпом і чіпом. Ці методи передбачають безпосереднє встановлення мікросхеми на підкладку упаковки, що усуває потребу в з’єднанні проводів і зменшує розмір упаковки. Епоксидна смола Underfill забезпечує структурну підтримку та підтримує цілісність інтерфейсу чіп-підкладка, забезпечуючи успішне впровадження цих передових технологій упаковки.
Як Underfill Epoxy вирішує проблеми
Упаковка напівпровідників відіграє вирішальну роль у продуктивності, надійності та довговічності електронних пристроїв. Він передбачає інкапсуляцію інтегральних схем (ІС) у захисні оболонки, забезпечення електричних з’єднань і розсіювання тепла, що виділяється під час роботи. Однак упаковка напівпровідників стикається з кількома проблемами, зокрема термічною напругою та викривленням, які можуть значно вплинути на функціональність і надійність упакованих пристроїв.
Однією з основних проблем є термічний стрес. Інтегровані схеми виділяють тепло під час роботи, а недостатнє розсіювання може підвищити температуру в корпусі. Ця зміна температури призводить до термічної напруги, оскільки різні матеріали в упаковці розширюються та стискаються з різною швидкістю. Нерівномірне розширення та звуження може спричинити механічну деформацію, що призведе до руйнування паяного з’єднання, розшарування та тріщин. Термічний вплив може порушити електричну та механічну цілісність упаковки, що зрештою вплине на роботу та надійність пристрою.
Деформація є ще однією критичною проблемою для упаковки напівпровідників. Викривлення означає вигин або деформацію підкладки упаковки або всієї упаковки. Це може статися під час процесу пакування або через термічний стрес. Деформація в основному спричинена невідповідністю коефіцієнта теплового розширення (КТР) між різними матеріалами в упаковці. Наприклад, КТР кремнієвої матриці, підкладки та суміші форми може значно відрізнятися. Під впливом температурних змін ці матеріали розширюються або стискаються з різною швидкістю, що призводить до викривлення.
Деформація створює кілька проблем для корпусів напівпровідників:
- Це може призвести до концентрації напруги, збільшуючи ймовірність механічних поломок і знижуючи надійність коробки.
- Деформація може призвести до труднощів у процесі складання, оскільки впливає на вирівнювання упаковки з іншими компонентами, такими як друкована плата (PCB). Це зміщення може погіршити електричні з’єднання та спричинити проблеми з продуктивністю.
- Викривлення може вплинути на загальний форм-фактор упаковки, ускладнюючи інтеграцію пристрою в додатки малого форм-фактора або густонаселені друковані плати.
Для вирішення цих проблем у упаковці напівпровідників використовуються різні методи та стратегії. Вони включають використання передових матеріалів із відповідними КТР для мінімізації теплового стресу та викривлення. Термомеханічне моделювання та моделювання проводяться для прогнозування поведінки упаковки за різних температурних умов. Зміни конструкції, такі як введення структур для зняття напруги та оптимізоване розташування, впроваджуються для зменшення термічної напруги та короблення. Крім того, розробка вдосконалених виробничих процесів і обладнання допомагає звести до мінімуму виникнення деформації під час складання.
Переваги епоксидної смоли Underfill
Епоксидна смола для заповнення є критично важливим компонентом упаковки напівпровідників, який має кілька переваг. Цей спеціальний епоксидний матеріал наноситься між напівпровідниковим чіпом і підкладкою упаковки, забезпечуючи механічне зміцнення та вирішуючи різні проблеми. Ось деякі з найважливіших переваг епоксидної смоли з недостатнім наповненням:
- Покращена механічна надійність. Однією з головних переваг епоксидної смоли для заливки є її здатність підвищувати механічну надійність корпусів напівпровідників. Епоксидна смола Underfill створює когезійне з’єднання, яке покращує загальну структурну цілісність, заповнюючи проміжки та порожнечі між чіпом і підкладкою. Це допомагає запобігти викривленню упаковки, зменшує ризик механічних пошкоджень і підвищує стійкість до зовнішніх навантажень, таких як вібрація, удари та перегрівання. Покращена механічна надійність забезпечує підвищену довговічність виробу та подовжує термін служби пристрою.
- Розсіювання термічної напруги: епоксидна смола для заливки допомагає розсіювати термічну напругу в упаковці. Інтегровані схеми виробляють тепло під час роботи, а неадекватне розсіювання може призвести до коливань температури всередині контейнера. Епоксидний матеріал під заливку з нижчим коефіцієнтом теплового розширення (КТР) порівняно з матеріалами мікросхеми та підкладки діє як буферний шар. Він поглинає механічні навантаження, викликані термічними навантаженнями, знижуючи ризик пошкодження паяного з’єднання, розшарування та тріщин. Розсіюючи термічні навантаження, епоксидна смола з недостатнім наповненням допомагає підтримувати електричну та механічну цілісність упаковки.
- Покращені електричні характеристики: епоксидна смола для заливки позитивно впливає на електричні характеристики напівпровідникових пристроїв. Епоксидний матеріал заповнює проміжки між мікросхемою та підкладкою, зменшуючи паразитну ємність та індуктивність. Це призводить до покращення цілісності сигналу, зменшення втрат сигналу та покращення електричного зв’язку між мікросхемою та рештою корпусу. Зниження паразитних ефектів сприяє кращим електричним характеристикам, вищій швидкості передачі даних і підвищеній надійності пристрою. Крім того, недоповнена епоксидна смола забезпечує ізоляцію та захист від вологи, забруднень та інших факторів навколишнього середовища, які можуть погіршити електричні характеристики.
- Зняття напруги та покращене складання: епоксидна смола під заливкою діє як механізм зняття напруги під час складання. Епоксидний матеріал компенсує невідповідність КТР між чіпом і підкладкою, зменшуючи механічні навантаження під час змін температури. Це робить процес складання більш надійним і ефективним, зводячи до мінімуму ризик пошкодження упаковки або зміщення. Контрольований розподіл напруги, що забезпечується епоксидною смолою під заливку, також допомагає забезпечити правильне вирівнювання з іншими компонентами на друкованій платі (PCB) і покращує загальну продуктивність збірки.
- Мініатюризація та оптимізація форм-фактора: епоксидна смола Underfill забезпечує мініатюризацію корпусів напівпровідників та оптимізацію форм-фактора. Забезпечуючи структурне посилення та зняття напруги, епоксидна смола з нижньою заливкою дозволяє проектувати та виготовляти менші, тонші та компактніші упаковки. Це особливо важливо для таких додатків, як мобільні пристрої та переносна електроніка, де простір важливий. Здатність оптимізувати форм-фактори та досягти більшої щільності компонентів сприяє створенню більш досконалих та інноваційних електронних пристроїв.
Типи епоксидної смоли під заповнення
У напівпровідникових упаковках доступні кілька типів епоксидних складів для заливки, кожен з яких розроблений відповідно до конкретних вимог і вирішення різних завдань. Ось кілька типових типів епоксидної смоли для заповнення:
- Епоксидна смола для капілярного заповнення: епоксидна смола для капілярного заповнення є найбільш традиційним і широко використовуваним типом. Епоксидна смола з низькою в’язкістю проникає в щілину між мікросхемою та підкладкою через капілярну дію. Капілярне заповнення зазвичай наноситься на край чіпа, і коли упаковка нагрівається, епоксидна смола тече під чіп, заповнюючи порожнечі. Цей тип недоповнення підходить для пакетів з невеликими зазорами та забезпечує гарне механічне зміцнення.
- No-Flow Underfill Epoxy: No-Flow Underfill епоксидна смола є складом з високою в’язкістю, який не тече під час затвердіння. Його наносять у вигляді попередньо нанесеної епоксидної смоли або у вигляді плівки між чіпом і підкладкою. Епоксидна смола для нижнього заповнення, що не тече, особливо корисна для упаковок із фліп-чіпом, де виступи припою безпосередньо взаємодіють із підкладкою. Це усуває необхідність капілярного потоку та знижує ризик пошкодження паяного з’єднання під час складання.
- Заливка на рівні пластини (WLU): заливка на рівні пластини – це епоксидна смола для заливки, яка наноситься на рівень пластини перед виділенням окремих частинок. Це передбачає розподіл матеріалу підзаповнювача по всій поверхні пластини та її затвердіння. Заливка на рівні вафель має ряд переваг, включаючи рівномірне покриття заливки, скорочений час складання та покращений контроль процесу. Зазвичай використовується для великосерійного виробництва малогабаритних пристроїв.
- Формоване підзаповнення (MUF): Формоване підзаповнення – це епоксидна смола під заповнення, яка наноситься під час формування капсульованого матеріалу. Матеріал підкладки розподіляється на підкладку, а потім чіп і підкладку інкапсулюють у формувальну суміш. Під час формування епоксидна смола тече і заповнює щілину між чіпом і підкладкою, забезпечуючи заповнення та інкапсуляцію в один крок. Формована нижня частина забезпечує чудове механічне зміцнення та спрощує процес складання.
- Непровідна нижня заливка (NCF): непровідна епоксидна смола з нижньою заливкою спеціально розроблена для забезпечення електричної ізоляції між паяними з’єднаннями на мікросхемі та підкладкою. Він містить ізоляційні наповнювачі або добавки, що перешкоджають електропровідності. NCF використовується в програмах, де електричне замикання між сусідніми паяними з’єднаннями викликає занепокоєння. Він пропонує як механічне посилення, так і електричну ізоляцію.
- Теплопровідна нижня заливка (TCU): Теплопровідна епоксидна смола для нижнього заповнення призначена для покращення здатності упаковки розсіювати тепло. Він містить теплопровідні наповнювачі, такі як керамічні або металеві частинки, які покращують теплопровідність матеріалу підкладки. TCU використовується в додатках, де ефективна теплопередача має вирішальне значення, наприклад, у потужних пристроях або тих, що працюють у складних теплових середовищах.
Це лише кілька прикладів різних типів епоксидної смоли для заливки, яка використовується в упаковці напівпровідників. Вибір відповідної епоксидної смоли для заливки залежить від таких факторів, як дизайн упаковки, процес складання, вимоги до тепла та електрики. Кожна епоксидна смола для заливки має певні переваги та розроблена для задоволення унікальних потреб різних застосувань.
Капілярне заповнення: низька в'язкість і висока надійність
Капілярне заповнення відноситься до процесу, який використовується в промисловості упаковки напівпровідників для підвищення надійності електронних пристроїв. Це передбачає заповнення проміжків між мікроелектронним чіпом і навколишньою упаковкою рідким матеріалом з низькою в’язкістю, як правило, смолою на основі епоксидної смоли. Цей матеріал для заповнення забезпечує структурну підтримку, покращує розсіювання тепла та захищає чіп від механічних впливів, вологи та інших факторів навколишнього середовища.
Однією з найважливіших характеристик капілярного заповнення є його низька в'язкість. Матеріал підзаповнення має відносно низьку щільність, що дозволяє йому легко проникати у вузькі щілини між чіпом і упаковкою під час процесу заповнення. Це гарантує, що матеріал підзаповнення може ефективно проникати та заповнювати всі порожнечі та повітряні проміжки, мінімізуючи ризик утворення пустот і покращуючи загальну цілісність інтерфейсу чіп-пакет.
Матеріали для капілярного заповнення з низькою в’язкістю також мають ряд інших переваг. По-перше, вони полегшують ефективний потік матеріалу під стружкою, що призводить до скорочення часу процесу та збільшення продуктивності. Це особливо важливо в умовах великого обсягу виробництва, де економічність часу та витрат є критично важливою.
По-друге, низька в'язкість забезпечує кращі властивості змочування та адгезії матеріалу підкладки. Це дозволяє матеріалу рівномірно розподілятися та утворювати міцні зв’язки з мікросхемою та упаковкою, створюючи надійну та міцну інкапсуляцію. Це забезпечує надійний захист мікросхеми від механічних навантажень, таких як перегрівання, удари та вібрація.
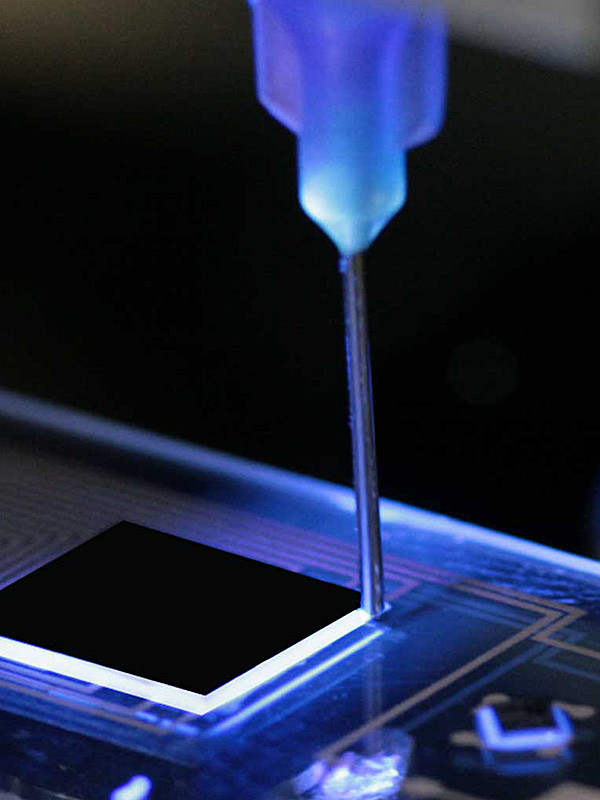
Іншим важливим аспектом капілярних заливок є їх висока надійність. Матеріали наповнювача з низькою в’язкістю розроблені спеціально для демонстрації чудової термічної стабільності, електроізоляційних властивостей і стійкості до вологи та хімічних речовин. Ці характеристики мають важливе значення для забезпечення тривалої роботи та надійності упакованих електронних пристроїв, особливо в таких вимогливих додатках, як автомобільна, аерокосмічна промисловість і телекомунікації.
Крім того, матеріали для капілярного заповнення мають високу механічну міцність і чудову адгезію до різних матеріалів підкладки, включаючи метали, кераміку та органічні матеріали, які зазвичай використовуються в упаковці напівпровідників. Це дозволяє заповнювальному матеріалу діяти як буфер напруги, ефективно поглинаючи та розсіюючи механічні навантаження, що виникають під час експлуатації або впливу навколишнього середовища.
No-Flow Underfill: самодозування та висока пропускна здатність
No-flow underfill спеціалізований процес, який використовується в промисловості упаковки напівпровідників для підвищення надійності та ефективності електронних пристроїв. На відміну від капілярних заповнювачів, які покладаються на потік матеріалів з низькою в’язкістю, заповнювачі без течії використовують підхід до самодозування матеріалів з високою в’язкістю. Цей метод пропонує кілька переваг, включаючи самовирівнювання, високу пропускну здатність і підвищену надійність.
Однією з важливих особливостей заливки без течії є її здатність до самодозування. Матеріал підзаповнення, який використовується в цьому процесі, має більш високу в’язкість, що запобігає його вільному плину. Замість цього матеріал під заповнення розподіляється на інтерфейс чіп-пакет контрольованим чином. Таке контрольоване дозування забезпечує точне розміщення матеріалу підзаповнення, забезпечуючи його нанесення лише на потрібні ділянки без переливу або неконтрольованого розтікання.
Самодозуючий характер заливки без потоку забезпечує кілька переваг. По-перше, це дозволяє самовирівнювати матеріал підкладки. Під час розподілу заповнення воно природним чином самовирівнюється з чіпом і упаковкою, рівномірно заповнюючи проміжки та порожнечі. Це усуває потребу в точному позиціонуванні та вирівнюванні чіпа під час процесу заповнення, заощаджуючи час і зусилля на виробництві.
По-друге, функція самодозування недоливних заливок забезпечує високу продуктивність виробництва. Процес дозування може бути автоматизований, що дозволяє швидко й узгоджено наносити заливний матеріал на кілька чіпів одночасно. Це покращує загальну ефективність виробництва та знижує витрати на виробництво, що робить його особливо вигідним для виробничих середовищ великого обсягу.
Крім того, матеріали для нижньої заливки, що не протікають, розроблені для забезпечення високої надійності. Високов’язкі наповнювальні матеріали пропонують покращену стійкість до термічного циклу, механічних навантажень і факторів навколишнього середовища, забезпечуючи довгострокову роботу упакованих електронних пристроїв. Матеріали демонструють чудову термічну стабільність, електроізоляційні властивості, стійкість до вологи та хімічних речовин, що сприяє загальній надійності пристроїв.
Крім того, високов’язкі наповнювальні матеріали, які використовуються в непротікаючих наповнювачах, мають підвищену механічну міцність і адгезійні властивості. Вони утворюють міцні зв’язки з мікросхемою та корпусом, ефективно поглинаючи та розсіюючи механічні навантаження, що виникають під час роботи або впливу навколишнього середовища. Це допомагає захистити мікросхему від потенційного пошкодження та підвищує стійкість пристрою до зовнішніх ударів і вібрації.
Формована нижня частина: високий захист та інтеграція
Формоване нижнє заповнення — це передова техніка, яка використовується в промисловості упаковки напівпровідників для забезпечення високого рівня захисту та інтеграції електронних пристроїв. Це включає в себе капсулювання всього чіпа та його навколишнього пакета за допомогою прес-форми, що містить матеріал підзаповнення. Цей процес пропонує значні переваги щодо захисту, інтеграції та загальної надійності.
Однією з важливих переваг формованого нижнього заповнення є його здатність забезпечувати повний захист чіпа. Формова суміш, яка використовується в цьому процесі, діє як міцний бар’єр, закриваючи весь чіп і упаковку в захисну оболонку. Це забезпечує ефективний захист від факторів навколишнього середовища, таких як вологість, пил і забруднення, які можуть вплинути на продуктивність і надійність пристрою. Інкапсуляція також допомагає захищати чіп від механічних навантажень, температурних циклів та інших зовнішніх сил, забезпечуючи його тривалу довговічність.
Крім того, формоване нижнє заповнення забезпечує високий рівень інтеграції в корпус напівпровідника. Матеріал підзаповнення змішується безпосередньо з сумішшю для форми, що дозволяє бездоганно інтегрувати процеси підзаповнення та інкапсуляції. Ця інтеграція усуває потребу в окремому етапі недоповнення, спрощуючи виробничий процес і скорочуючи час виробництва та витрати. Це також забезпечує послідовний і рівномірний розподіл заповнення по всій упаковці, мінімізуючи пустоти та підвищуючи загальну структурну цілісність.
Крім того, формований нижній наповнювач забезпечує чудові властивості розсіювання тепла. Формова суміш має високу теплопровідність, що дозволяє їй ефективно відводити тепло від мікросхеми. Це має вирішальне значення для підтримки оптимальної робочої температури пристрою та запобігання перегріву, що може призвести до погіршення продуктивності та проблем із надійністю. Покращені властивості розсіювання тепла формованого нижнього наповнення сприяють загальній надійності та довговічності електронного пристрою.
Крім того, формоване нижнє заповнення забезпечує більшу мініатюризацію та оптимізацію форм-фактора. Процес інкапсуляції можна адаптувати для упаковки різних розмірів і форм, включаючи складні 3D-структури. Ця гнучкість дозволяє інтегрувати кілька чіпів та інших компонентів у компактну, компактну упаковку. Здатність досягти більш високого рівня інтеграції без шкоди для надійності робить формовану нижню частину особливо цінною в додатках, де обмеження розміру та ваги є критичними, наприклад у мобільних пристроях, носимих пристроях та автомобільній електроніці.
Недоповнення пакета чіпів (CSP): мініатюризація та висока щільність
Chip Scale Package (CSP) underfill — це важлива технологія, що забезпечує мініатюризацію та інтеграцію електронних пристроїв високої щільності. Оскільки електронні пристрої продовжують зменшуватися в розмірах, забезпечуючи збільшену функціональність, CSP не виконує вирішальну роль у забезпеченні надійності та продуктивності цих компактних пристроїв.
CSP — це технологія упаковки, яка дозволяє монтувати напівпровідниковий чіп безпосередньо на підкладку або друковану плату (PCB) без додаткової упаковки. Це усуває потребу в традиційному пластиковому або керамічному контейнері, зменшуючи загальний розмір і вагу пристрою. CSP underfill — процес, у якому рідина або герметизуючий матеріал використовується для заповнення проміжку між чіпом і підкладкою, забезпечуючи механічну підтримку та захищаючи чіп від факторів навколишнього середовища, таких як волога та механічні навантаження.
Мініатюризація досягається за допомогою заповнення CSP шляхом зменшення відстані між чіпом і підкладкою. Матеріал підкладки заповнює вузький проміжок між чіпом і підкладкою, створюючи міцний зв’язок і покращуючи механічну стабільність чіпа. Це дозволяє створювати менші та тонші пристрої, що дає змогу розмістити більше функціональних можливостей в обмеженому просторі.
Інтеграція з високою щільністю є ще однією перевагою заповнення CSP. Усуваючи потребу в окремому корпусі, CSP дозволяє встановити мікросхему ближче до інших компонентів на друкованій платі, зменшуючи довжину електричних з’єднань і покращуючи цілісність сигналу. Матеріал підзаповнення також діє як теплопровідник, ефективно розсіюючи тепло, що виділяється мікросхемою. Ця здатність керування температурою забезпечує вищу щільність потужності, дозволяючи інтегрувати складніші та потужніші чіпи в електронні пристрої.
Матеріали підзаповнення CSP повинні мати специфічні характеристики, щоб відповідати вимогам мініатюризації та інтеграції високої щільності. Вони повинні мати низьку в'язкість, щоб полегшити заповнення вузьких щілин, а також відмінну текучість, щоб забезпечити рівномірне покриття та усунути пустоти. Матеріали також повинні мати хорошу адгезію до мікросхеми та підкладки, забезпечуючи надійну механічну підтримку. Крім того, вони повинні мати високу теплопровідність, щоб ефективно відводити тепло від мікросхеми.
CSP Underfill на рівні пластин: економічно ефективний і високий вихід
Упаковка з накипом пластинчастого рівня (WLCSP) є економічно ефективною технікою пакування з високим рівнем продуктивності, яка пропонує ряд переваг у ефективності виробництва та загальній якості продукції. WLCSP underfill наносить матеріал підзаповнення на кілька чіпів одночасно, поки вони все ще знаходяться у формі пластини, перш ніж вони будуть розділені в окремі упаковки. Цей підхід пропонує численні переваги щодо зниження витрат, покращеного контролю процесу та підвищення продуктивності.
Однією з найважливіших переваг недоповнення WLCSP є його економічна ефективність. Застосування наповнювача на рівні вафель робить процес пакування більш раціональним та ефективним. Недоповнений матеріал розподіляється на пластину за допомогою контрольованого та автоматизованого процесу, що зменшує відходи матеріалу та мінімізує витрати на робочу силу. Крім того, усунення окремих етапів обробки та вирівнювання упаковки зменшує загальний час і складність виробництва, що призводить до значної економії коштів порівняно з традиційними методами пакування.
Крім того, WLCSP underfill забезпечує покращений контроль процесу та більший вихід продукції. Оскільки матеріал підзаповнення наноситься на рівні пластини, це дає змогу краще контролювати процес дозування, забезпечуючи послідовне та рівномірне покриття під заповненням для кожної стружки на пластині. Це зменшує ризик утворення пустот або неповного заповнення, що може призвести до проблем з надійністю. Можливість перевіряти та перевіряти якість недостатнього заповнення на рівні пластини також дозволяє раннє виявлення дефектів або варіацій процесу, що дозволяє вчасно вжити коригувальних заходів і зменшити ймовірність дефектних упаковок. Як наслідок, недоповнення WLCSP допомагає досягти вищих врожаїв і кращої загальної якості продукції.
Підхід на рівні пластин також забезпечує покращені термічні та механічні характеристики. Матеріал підзаповнення, який використовується в WLCSP, як правило, є низьков’язким матеріалом з капілярною текучістю, який може ефективно заповнювати вузькі проміжки між мікросхемами та пластиною. Це забезпечує надійну механічну підтримку чіпів, підвищуючи їх стійкість до механічних навантажень, вібрації та змін температури. Крім того, наповнювач діє як теплопровідник, сприяючи розсіюванню тепла, що виділяється чіпами, таким чином покращуючи керування температурою та знижуючи ризик перегріву.
Flip Chip Underfill: висока щільність введення-виведення та продуктивність
Flip chip underfill — це важлива технологія, яка забезпечує високу щільність введення/виведення (I/O) і виняткову продуктивність електронних пристроїв. Він відіграє вирішальну роль у підвищенні надійності та функціональності фліп-чіп-пакетів, які широко використовуються в передових напівпровідникових додатках. У цій статті досліджуватиметься значення недостатнього заповнення фліп-чіпа та його вплив на досягнення високої щільності вводу-виводу та продуктивності.
Технологія фліп-чіпа передбачає пряме електричне з’єднання інтегральної схеми (ІС) або напівпровідникового кристала з підкладкою, що усуває необхідність з’єднання проводів. Це призводить до більш компактної та ефективної упаковки, оскільки майданчики введення/виведення розташовані на нижній поверхні матриці. Однак упаковка з перекидними мікросхемами створює унікальні проблеми, які необхідно вирішити, щоб забезпечити оптимальну продуктивність і надійність.
Однією з найважливіших проблем у упаковці фліп-чіпів є запобігання механічним навантаженням і термічній невідповідності між матрицею та підкладкою. Під час виробничого процесу та подальшої експлуатації відмінності в коефіцієнтах теплового розширення (CTE) між матрицею та підкладкою можуть спричинити значне навантаження, що призведе до погіршення продуктивності або навіть до поломки. Flip chip underfill — це захисний матеріал, який інкапсулює мікросхему, забезпечуючи механічну підтримку та зняття напруги. Він ефективно розподіляє навантаження, що виникають під час термічного циклу, і запобігає їх впливу на делікатні з’єднання.
Висока щільність вводу/виводу має вирішальне значення для сучасних електронних пристроїв, де важливі менші форм-фактори та розширена функціональність. Flip chip underfill забезпечує більшу щільність вводу/виводу, пропонуючи чудову електричну ізоляцію та можливості управління температурою. Матеріал підзаповнення заповнює щілину між матрицею та підкладкою, створюючи міцний інтерфейс і знижуючи ризик короткого замикання або витоку електричного струму. Це дозволяє збільшити відстань між панелями вводу-виводу, що призводить до збільшення щільності введення-виведення без шкоди для надійності.
Крім того, заливка фліп-чіп сприяє покращенню електричних характеристик. Це мінімізує електричні паразити між матрицею та підкладкою, зменшуючи затримку сигналу та підвищуючи його цілісність. Матеріал підкладки також демонструє чудові властивості теплопровідності, ефективно розсіюючи тепло, що виділяється чіпом під час роботи. Ефективне розсіювання тепла забезпечує збереження температури в допустимих межах, запобігаючи перегріву та зберігаючи оптимальну продуктивність.
Удосконалення матеріалів для заповнення фліп-чіпів забезпечило ще більшу щільність введення/виведення та рівень продуктивності. Нанокомпозитні наповнювачі, наприклад, використовують нанорозмірні наповнювачі для підвищення теплопровідності та механічної міцності. Це забезпечує покращене розсіювання тепла та надійність, створюючи пристрої з більшою продуктивністю.
Кулькова сітка (BGA) Underfill: висока теплова та механічна продуктивність
Ball Grid Array (BGA) заповнює критично важливу технологію, пропонуючи високі теплові та механічні характеристики в електронних пристроях. Він відіграє вирішальну роль у підвищенні надійності та функціональності корпусів BGA, які широко використовуються в різних додатках. У цій статті ми дослідимо значення недоповнення BGA та його вплив на досягнення високих теплових і механічних характеристик.
Технологія BGA передбачає конструкцію упаковки, у якій інтегральна схема (IC) або напівпровідниковий кристал встановлено на підкладку, а електричні з’єднання здійснюються за допомогою масиву кульок для припою, розташованих на нижній поверхні упаковки. BGA заповнює матеріал, розподілений у зазорі між матрицею та підкладкою, інкапсулюючи кульки припою та забезпечуючи механічну підтримку та захист вузла.
Однією з найважливіших проблем у упаковці BGA є керування термічними навантаженнями. Під час роботи мікросхема виділяє тепло, а теплове розширення та звуження можуть спричинити значний тиск на паяні з’єднання, що з’єднують матрицю та підкладку. BGA не виконує вирішальну роль у зменшенні цих навантажень, утворюючи міцний зв’язок із матрицею та підкладкою. Він діє як буфер напруги, поглинаючи теплове розширення та звуження та зменшуючи навантаження на паяні з’єднання. Це допомагає підвищити загальну надійність комплекту та зменшує ризик виходу з ладу паяного з’єднання.
Іншим важливим аспектом заповнення BGA є його здатність покращувати механічні характеристики упаковки. Корпуси BGA часто піддаються механічним навантаженням під час транспортування, складання та експлуатації. Матеріал підзаповнення заповнює щілину між матрицею та підкладкою, забезпечуючи структурну підтримку та зміцнення паяних з’єднань. Це покращує загальну механічну міцність вузла, роблячи його більш стійким до механічних ударів, вібрації та інших зовнішніх сил. Ефективно розподіляючи механічні навантаження, заповнення BGA допомагає запобігти розтріскування упаковки, розшарування або інші механічні пошкодження.
Високі теплові характеристики є важливими в електронних пристроях для забезпечення належної функціональності та надійності. BGA-матеріали для заповнення мають чудові властивості теплопровідності. Це дозволяє їм ефективно відводити тепло від матриці та розподіляти його по підкладці, підвищуючи загальний контроль тепла упаковки. Ефективне розсіювання тепла допомагає підтримувати низькі робочі температури, запобігаючи тепловим точкам і потенційному погіршенню продуктивності. Це також сприяє довговічності коробки, зменшуючи температурний стрес компонентів.
Удосконалення матеріалів для заповнення BGA призвело до ще кращих теплових і механічних характеристик. Покращені склади та наповнювачі, такі як нанокомпозити або наповнювачі з високою теплопровідністю, забезпечили кращий розсіювання тепла та механічну міцність, ще більше підвищивши продуктивність пакетів BGA.
Quad Flat Package (QFP) Underfill: велика кількість вводів/виводів і надійність
Quad Flat Package (QFP) — це пакет інтегральних схем (IC), який широко використовується в електроніці. Він має квадратну або прямокутну форму з проводами, що простягаються з усіх чотирьох сторін, забезпечуючи багато з’єднань входу/виводу (I/O). Для підвищення надійності та міцності пакетів QFP зазвичай використовуються матеріали для заповнення.
Underfill — це захисний матеріал, який наноситься між мікросхемою та підкладкою для посилення механічної міцності паяних з’єднань і запобігання пошкодженням, спричиненим напругою. Це особливо важливо для QFP з великою кількістю вводів/виводів, оскільки велика кількість з’єднань може призвести до значних механічних навантажень під час термоциклування та умов експлуатації.
Матеріал підзаповнення, який використовується для упаковок QFP, повинен мати певні характеристики для забезпечення міцності. По-перше, він повинен мати чудову адгезію як до IC, так і до підкладки, щоб створити міцний зв’язок і мінімізувати ризик розшарування або від’єднання. Крім того, він повинен мати низький коефіцієнт теплового розширення (КТР), щоб відповідати КТР мікросхеми та підкладки, зменшуючи невідповідність напруги, яка може призвести до тріщин або розломів.
Крім того, матеріал підзаповнення повинен мати хороші властивості текучості, щоб забезпечити рівномірне покриття та повне заповнення проміжку між IC та підкладкою. Це допомагає усунути порожнечі, які можуть послабити паяні з’єднання та призвести до зниження надійності. Матеріал також повинен мати хороші властивості твердіння, що дозволяє йому утворювати жорсткий і міцний захисний шар після нанесення.
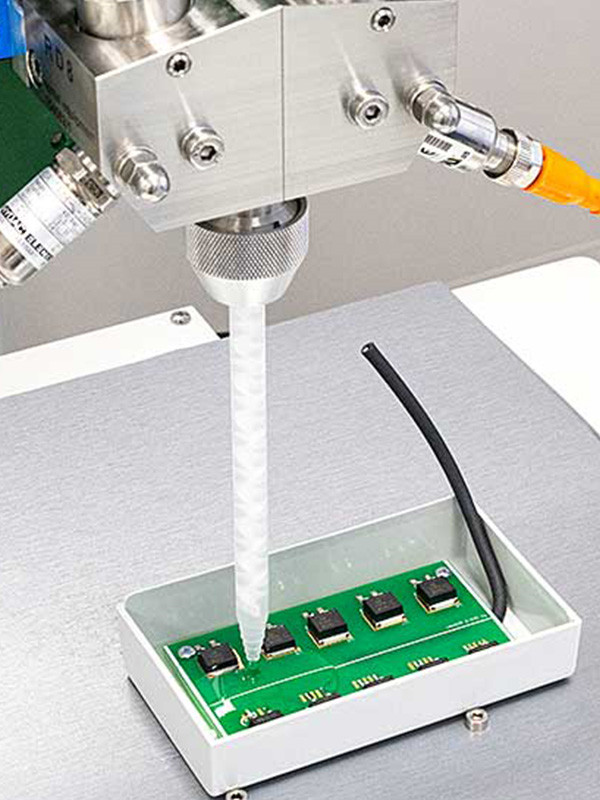
З точки зору механічної міцності, заповнювач повинен мати високу міцність на зсув і відрив, щоб протистояти зовнішнім силам і запобігати деформації або розриву упаковки. Він також повинен демонструвати хорошу стійкість до вологи та інших факторів навколишнього середовища, щоб зберегти свої захисні властивості з часом. Це особливо важливо в програмах, де пакет QFP може піддаватися впливу суворих умов або зазнавати коливань температури.
Для досягнення цих бажаних характеристик доступні різні матеріали для заповнення, включаючи склади на основі епоксидної смоли. Залежно від конкретних вимог застосування, ці матеріали можна розподіляти за допомогою різних методів, таких як капілярний потік, струменевий або трафаретний друк.
Система в упаковці (SiP) Underfill: інтеграція та продуктивність
System-in-Package (SiP) — це передова технологія упаковки, яка об’єднує кілька напівпровідникових мікросхем, пасивних компонентів та інших елементів в єдину упаковку. SiP пропонує численні переваги, включаючи зменшений форм-фактор, покращені електричні характеристики та розширену функціональність. Для забезпечення надійності та продуктивності вузлів SiP зазвичай використовуються матеріали для заповнення.
Недоповнення в системах SiP має вирішальне значення для забезпечення механічної стабільності та електричного зв’язку між різними компонентами всередині пакета. Це допомагає звести до мінімуму ризик спричинених напругою несправностей, таких як тріщини або розломи паяних з’єднань, які можуть виникнути через різницю в коефіцієнтах теплового розширення (КТР) між компонентами.
Інтеграція кількох компонентів у пакет SiP призводить до складних взаємозв’язків із багатьма паяними з’єднаннями та схемою високої щільності. Матеріали підзаповнення допомагають зміцнити ці взаємозв’язки, підвищуючи механічну міцність і надійність збірки. Вони підтримують паяні з’єднання, зменшуючи ризик втоми або пошкодження, викликаного циклічним перегріванням або механічним впливом.
З точки зору електричних характеристик, матеріали підзаповнення мають вирішальне значення для покращення цілісності сигналу та мінімізації електричного шуму. Заповнюючи проміжки між компонентами та зменшуючи відстань між ними, недостатнє заповнення допомагає зменшити паразитну ємність та індуктивність, забезпечуючи швидшу та ефективнішу передачу сигналу.
Крім того, матеріали для заповнення SiP повинні мати чудову теплопровідність, щоб ефективно розсіювати тепло, що виділяється вбудованими компонентами. Ефективне розсіювання тепла має важливе значення для запобігання перегріву та підтримки загальної надійності та продуктивності вузла SiP.
Матеріали нижнього заповнення в упаковці SiP повинні мати особливі властивості, щоб відповідати вимогам інтеграції та продуктивності. Вони повинні мати хорошу текучість, щоб забезпечити повне покриття та заповнити проміжки між компонентами. Матеріал для заповнення також повинен мати склад з низькою в’язкістю, щоб можна було легко дозувати та заповнювати вузькі отвори або невеликі простори.
Крім того, матеріал підкладки повинен мати міцну адгезію до різних поверхонь, включаючи напівпровідникові мікросхеми, підкладки та пасивні елементи, щоб забезпечити надійне зчеплення. Він повинен бути сумісним з різними пакувальними матеріалами, такими як органічні субстрати або кераміка, і мати хороші механічні властивості, включаючи високу міцність на зсув і відрив.
Вибір матеріалу підзаповнення та методу нанесення залежить від конкретної конструкції SiP, вимог до компонентів і виробничих процесів. Методи дозування, такі як капілярний потік, струминні або методи з використанням плівки, зазвичай застосовують недоповнення в збірках SiP.
Оптоелектронне заповнення: оптичне вирівнювання та захист
Оптоелектронне заповнення включає інкапсуляцію та захист оптоелектронних пристроїв, забезпечуючи при цьому точне оптичне вирівнювання. Оптоелектронні пристрої, такі як лазери, фотодетектори та оптичні перемикачі, часто потребують делікатного вирівнювання оптичних компонентів для досягнення оптимальної продуктивності. У той же час їх необхідно захистити від факторів навколишнього середовища, які можуть вплинути на їхню функціональність. Optoelectronics underfill задовольняє обидві ці вимоги, забезпечуючи оптичне вирівнювання та захист в одному процесі.
Оптичне вирівнювання є критичним аспектом виробництва оптоелектронних пристроїв. Це передбачає вирівнювання візуальних елементів, таких як волокна, хвилеводи, лінзи або решітки, щоб забезпечити ефективну передачу та прийом світла. Точне вирівнювання необхідне для максимізації продуктивності пристрою та підтримки цілісності сигналу. Традиційні методи вирівнювання включають ручне вирівнювання за допомогою візуального огляду або автоматичне вирівнювання за допомогою етапів вирівнювання. Однак ці методи можуть бути тривалими, трудомісткими та схильними до помилок.
Оптоелектроніка заповнює інноваційне рішення, використовуючи функції вирівнювання безпосередньо в матеріалі заповнення. Матеріали підзаповнення зазвичай являють собою рідкі або напіврідкі сполуки, які можуть текти та заповнювати проміжки між оптичними компонентами. Завдяки додаванню елементів вирівнювання, таких як мікроструктури або контрольні позначки, у матеріал підзаповнення процес вирівнювання можна спростити та автоматизувати. Ці функції діють як напрямні під час складання, забезпечуючи точне вирівнювання оптичних компонентів без необхідності виконання складних процедур вирівнювання.
На додаток до оптичного вирівнювання матеріали підзаповнення захищають оптоелектронні пристрої. Оптоелектронні компоненти часто піддаються впливу агресивних середовищ, зокрема коливань температури, вологи та механічного впливу. Ці зовнішні фактори можуть з часом погіршити продуктивність і надійність пристроїв. Матеріали нижньої заливки діють як захисний бар’єр, інкапсулюючи оптичні компоненти та захищаючи їх від забруднень навколишнього середовища. Вони також забезпечують механічне зміцнення, зменшуючи ризик пошкодження внаслідок ударів або вібрації.
Матеріали підзаповнення, які використовуються в оптоелектроніці, як правило, мають низький показник заломлення та чудову оптичну прозорість. Це забезпечує мінімальні перешкоди для оптичних сигналів, що проходять через пристрій. Крім того, вони демонструють хорошу адгезію до різних основ і мають низькі коефіцієнти теплового розширення, щоб мінімізувати навантаження на пристрій під час термоциклування.
Процес підзаповнення передбачає розподіл матеріалу підзаповнення на пристрій, що дозволяє йому текти та заповнювати проміжки між оптичними компонентами, а потім затверджувати його для утворення твердої інкапсуляції. Залежно від конкретного застосування матеріал підзаповнення можна наносити різними техніками, такими як капілярний потік, струменеве дозування або трафаретний друк. Процес затвердіння може бути досягнутий за допомогою тепла, УФ-випромінювання або обох.
Медична електроніка Underfill: біосумісність і надійність
Медична електроніка виконує спеціалізований процес, який передбачає інкапсуляцію та захист електронних компонентів, що використовуються в медичних пристроях. Ці пристрої відіграють вирішальну роль у різних медичних додатках, таких як імплантовані пристрої, діагностичне обладнання, системи моніторингу та системи доставки ліків. Недостатнє заповнення медичної електроніки зосереджується на двох найважливіших аспектах: біосумісності та надійності.
Біосумісність є основною вимогою до медичних виробів, які контактують з тілом людини. Матеріали підзаповнення, які використовуються в медичній електроніці, повинні бути біосумісними, тобто вони не повинні викликати шкідливих наслідків або побічних реакцій при контакті з живими тканинами або рідинами організму. Ці матеріали мають відповідати суворим нормам і стандартам, таким як ISO 10993, який визначає процедури тестування та оцінки біосумісності.
Матеріали для заливки для медичної електроніки ретельно відібрані або розроблені для забезпечення біосумісності. Вони розроблені таким чином, щоб бути нетоксичними, не подразнювальними та не викликати алергію. Ці матеріали не повинні вимивати шкідливі речовини або розкладатися з часом, оскільки це може призвести до пошкодження тканин або запалення. Біосумісні матеріали для наповнення також мають низьке водопоглинання, щоб запобігти росту бактерій або грибків, які можуть спричинити інфекції.
Надійність є ще одним критичним аспектом недостатнього заповнення медичної електроніки. Медичні пристрої часто стикаються з складними умовами експлуатації, включаючи екстремальні температури, вологість, рідини організму та механічні навантаження. Матеріали підзаповнення повинні захищати електронні компоненти, забезпечуючи їх довгострокову надійність і функціональність. Надійність має першорядне значення в медичних програмах, де збій пристрою може серйозно вплинути на безпеку та благополуччя пацієнта.
Матеріали нижнього наповнювача для медичної електроніки повинні мати високу стійкість до вологи та хімічних речовин, щоб протистояти впливу біологічних рідин або процесів стерилізації. Вони також повинні демонструвати хорошу адгезію до різних підкладок, забезпечуючи надійну герметизацію електронних компонентів. Механічні властивості, такі як низькі коефіцієнти теплового розширення та хороша ударостійкість, мають вирішальне значення для мінімізації навантаження на деталі під час термічного циклу або автоматичного навантаження.
Процес заповнення медичної електроніки передбачає:
- Дозування заливного матеріалу на електронні компоненти.
- Заповнення прогалин.
- Затвердіння для утворення захисної та механічно стабільної капсули.
Необхідно подбати про те, щоб забезпечити повне охоплення функцій і відсутність пустот або повітряних кишень, які можуть поставити під загрозу надійність пристрою.
Крім того, при недоповненні медичних виробів враховуються додаткові міркування. Наприклад, матеріал підзаповнення має бути сумісним із методами стерилізації, які використовуються для пристрою. Деякі матеріали можуть бути чутливими до певних методів стерилізації, таких як пара, етиленоксид або випромінювання, тому, можливо, потрібно вибрати альтернативні матеріали.
Аерокосмічна електроніка Underfill: стійкість до високих температур і вібрації
Аерокосмічна електроніка виконує спеціалізований процес для інкапсуляції та захисту електронних компонентів в аерокосмічних програмах. Аерокосмічне середовище створює унікальні проблеми, зокрема високі температури, екстремальні вібрації та механічні навантаження. Тому недостатнє заповнення аерокосмічної електроніки зосереджується на двох ключових аспектах: стійкість до високих температур і стійкість до вібрації.
Стійкість до високих температур має першорядне значення в аерокосмічній електроніці через високі температури під час роботи. Матеріали для заповнення, які використовуються в аерокосмічних додатках, повинні витримувати такі високі температури без шкоди для продуктивності та надійності електронних компонентів. Вони повинні демонструвати мінімальне теплове розширення і залишатися стабільними в широкому діапазоні температур.
Матеріали нижнього наповнювача для аерокосмічної електроніки вибираються або складаються з урахуванням високих температур склування (Tg) і термічної стабільності. Високий Tg гарантує, що матеріал збереже свої механічні властивості при підвищених температурах, запобігаючи деформації або втраті адгезії. Ці матеріали можуть витримувати екстремальні температури, наприклад під час зльоту, входу в атмосферу або роботи в гарячих моторних відсіках.
Крім того, матеріали підзаповнення для аерокосмічної електроніки повинні мати низькі коефіцієнти теплового розширення (КТР). КТР вимірює, наскільки матеріал розширюється або стискається при зміні температури. Маючи низький КТР, матеріали для заповнення можуть мінімізувати навантаження на електронні компоненти, викликане циклічним перегріванням, що може призвести до механічних пошкоджень або втоми паяного з’єднання.
Стійкість до вібрації є ще однією важливою вимогою для недозаповнення аерокосмічної електроніки. Аерокосмічні апарати піддаються різним вібраціям, включаючи вібрацію двигуна, вібрацію, спричинену польотом, і механічні удари під час запуску чи посадки. Ці вібрації можуть поставити під загрозу продуктивність і надійність електронних компонентів, якщо їх не захистити належним чином.
Матеріали нижнього заповнення, які використовуються в аерокосмічній електроніці, повинні демонструвати чудові віброгасильні властивості. Вони повинні поглинати та розсіювати енергію, що генерується вібрацією, зменшуючи напругу та навантаження на електронні компоненти. Це допомагає запобігти утворенню тріщин, розломів або інших механічних пошкоджень через надмірну вібрацію.
Крім того, в аерокосмічному застосуванні перевагу надають матеріалам підзаповнення з високою адгезією та когезійною міцністю. Завдяки цим властивостям заповнювач міцно з’єднується з електронними компонентами та підкладкою навіть за умов екстремальної вібрації. Сильна адгезія запобігає розшаруванню або відокремленню матеріалу підзаповнення від елементів, зберігаючи цілісність герметичності та захищаючи від проникнення вологи чи сміття.
Процес нижнього заповнення для аерокосмічної електроніки зазвичай передбачає розподіл матеріалу нижньої заливки на електронні компоненти, що дозволяє йому текти та заповнювати проміжки, а потім затверджувати його для формування міцної інкапсуляції. Процес затвердіння можна здійснити за допомогою методів термічного або УФ-затвердіння, залежно від конкретних вимог застосування.
Автомобільна електроніка Underfill: довговічність і термоциклічна стійкість
Автомобільна електроніка не виконує критично важливий процес, який включає герметизацію та захист електронних компонентів в автомобільних додатках. Автомобільні середовища створюють унікальні виклики, включаючи коливання температури, температурні цикли, механічні навантаження та вплив вологи та хімікатів. Тому недоповнення автомобільної електроніки зосереджується на двох важливих аспектах: довговічності та стійкості до циклічного перегріву.
Довговічність є важливою вимогою до автомобільної електроніки. При постійній експлуатації автомобіль відчуває постійні вібрації, удари, механічні навантаження. Матеріали для заливки, які використовуються в автомобільних додатках, повинні надійно захищати електронні компоненти, забезпечуючи їх міцність і довговічність. Вони повинні витримувати суворі умови та механічні навантаження, що виникають на дорозі, а також протистояти проникненню вологи, пилу та хімікатів.
Матеріали для заливки для автомобільної електроніки вибрано або розроблено з урахуванням високої механічної міцності та стійкості до ударів. Вони повинні демонструвати відмінну адгезію до електронних компонентів і підкладки, запобігаючи розшаруванню або відриву під механічними навантаженнями. Міцні матеріали підзаповнення допомагають мінімізувати ризик пошкодження електронних компонентів через вібрацію або удари, забезпечуючи надійну роботу протягом усього терміну служби автомобіля.
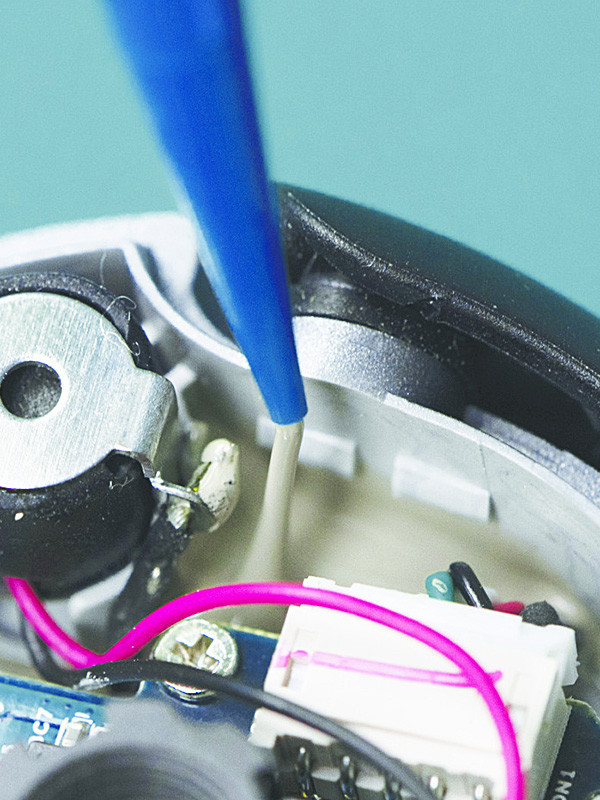
Стійкість до термічних циклів є ще однією важливою вимогою для недоповнення автомобільної електроніки. Автомобілі зазнають частих коливань температури, особливо під час запуску та роботи двигуна, і ці температурні цикли можуть викликати термічні навантаження на електронні компоненти та навколишній матеріал підзаповнення. Матеріали підзаповнення, які використовуються в автомобільних додатках, повинні мати чудову стійкість до термічних циклів, щоб протистояти цим температурним коливанням без шкоди для своїх характеристик.
Матеріали нижньої заливки для автомобільної електроніки повинні мати низькі коефіцієнти теплового розширення (КТР), щоб мінімізувати напругу електронних компонентів під час термоциклування. Добре узгоджений КТР між матеріалом підзаповнення та інгредієнтами зменшує ризик втоми паяного з’єднання, розтріскування або інших механічних пошкоджень, спричинених термічним впливом. Крім того, матеріали підзаповнення повинні демонструвати хорошу теплопровідність, щоб ефективно розсіювати тепло, запобігаючи локальним гарячим точкам, які можуть вплинути на продуктивність і надійність компонентів.
Крім того, матеріали для наповнення автомобільної електроніки повинні бути стійкими до вологи, хімікатів і рідин. Вони повинні мати низьке водопоглинання, щоб запобігти утворенню цвілі або корозії електронних компонентів. Хімічна стійкість гарантує, що матеріал підзаповнення залишається стабільним під час впливу автомобільних рідин, таких як масла, паливо або засоби для чищення, уникаючи деградації або втрати адгезії.
Процес заливки для автомобільної електроніки зазвичай включає розподіл матеріалу для заповнення на електронні компоненти, що дозволяє йому текти та заповнювати проміжки, а потім затверджувати його для утворення міцної інкапсуляції. Процес затвердіння можна здійснити за допомогою методів термічного або УФ-затвердіння, залежно від конкретних вимог застосування та використовуваного матеріалу для заповнення.
Вибір правильної епоксидної смоли для заливки
Вибір правильної епоксидної смоли для заповнення є вирішальним рішенням у складанні та захисті електронних компонентів. Епоксидні наповнювачі забезпечують механічне зміцнення, теплорегулювання та захист від факторів зовнішнього середовища. Ось кілька ключових міркувань при виборі відповідної епоксидної смоли:
- Теплові властивості. Однією з основних функцій епоксидної смоли для заповнення є розсіювання тепла, що виділяється електронними компонентами. Тому важливо враховувати теплопровідність і термостійкість епоксидної смоли. Висока теплопровідність сприяє ефективній теплопередачі, запобігаючи гарячим точкам і зберігаючи надійність компонентів. Епоксидна смола також повинна мати низьку термостійкість, щоб мінімізувати термічне навантаження на компоненти під час зміни температури.
- Відповідність CTE: Коефіцієнт теплового розширення (CTE) епоксидної смоли для заливки має добре узгоджуватися з CTE електронних компонентів і підкладки, щоб мінімізувати термічне навантаження та запобігти виходу з ладу паяного з’єднання. Чітко підібраний КТР допомагає зменшити ризик механічних пошкоджень через термоциклування.
- Текучість і здатність заповнювати щілини: недоповнена епоксидна смола повинна мати хороші характеристики текучості та здатність ефективно заповнювати щілини між компонентами. Це забезпечує повне покриття та мінімізує порожнечі або повітряні кишені, які можуть вплинути на механічну стабільність і термічну продуктивність вузла. В’язкість епоксидної смоли має відповідати конкретному застосуванню та методу складання, будь то капілярний потік, струменеве дозування або трафаретний друк.
- Адгезія: міцна адгезія має вирішальне значення для наповнення епоксидної смолою для забезпечення надійного зчеплення між компонентами та основою. Він повинен мати хорошу адгезію до різних матеріалів, включаючи метали, кераміку та пластик. Адгезійні властивості епоксидної смоли сприяють механічній цілісності вузла та довгостроковій надійності.
- Метод затвердіння: оберіть метод затвердіння, який найкраще відповідає вашому виробничому процесу. Епоксидні смоли під заливку можна затвердіти за допомогою тепла, ультрафіолетового випромінювання або їх комбінації. Кожен метод затвердіння має переваги та обмеження, тому вибір того, який відповідає вашим виробничим вимогам, є важливим.
- Стійкість до навколишнього середовища: Оцініть стійкість епоксидної смоли під заливку до факторів навколишнього середовища, таких як вологість, хімічні речовини та екстремальні температури. Епоксидна смола повинна витримувати вплив води, запобігаючи розвитку цвілі або корозії. Хімічна стійкість забезпечує стабільність під час контакту з автомобільними рідинами, очисними засобами чи іншими потенційно корозійними речовинами. Крім того, епоксидна смола повинна зберігати свої механічні та електричні властивості в широкому діапазоні температур.
- Надійність і довговічність: враховуйте послужний список і дані про надійність епоксидної смоли для заповнення. Шукайте епоксидні матеріали, перевірені та підтверджені як ефективні в аналогічних застосуваннях, або мають галузеві сертифікати та відповідність відповідним стандартам. Враховуйте такі фактори, як поведінка старіння, довгострокова надійність і здатність епоксидної смоли зберігати свої властивості з часом.
Вибираючи правильну епоксидну смолу для заливки, важливо враховувати конкретні вимоги вашої програми, включаючи терморегулювання, механічну стабільність, захист навколишнього середовища та сумісність виробничого процесу. Консультації з постачальниками епоксидних смол або пошук експертної поради можуть бути корисними для прийняття обґрунтованого рішення, яке відповідає потребам вашої програми та забезпечує оптимальну продуктивність і надійність.
Майбутні тенденції в епоксидній смолі для заливки
Епоксидна смола для заповнення безперервно розвивається завдяки прогресу в електронних технологіях, новим застосуванням і потребам у покращенні продуктивності та надійності. Можна спостерігати кілька майбутніх тенденцій у розробці та застосуванні епоксидної смоли для заповнення:
- Мініатюризація та упаковка з більшою щільністю: оскільки електронні пристрої продовжують зменшуватися та мають більшу щільність компонентів, епоксидні смоли для заливки повинні відповідним чином адаптуватися. Майбутні тенденції будуть зосереджені на розробці матеріалів для заповнення, які проникають і заповнюють менші проміжки між компонентами, забезпечуючи повне покриття та надійний захист у все більш мініатюрних електронних вузлах.
- Високочастотні застосування: Зі зростаючим попитом на високочастотні та високошвидкісні електронні пристрої, епоксидні склади для заливки повинні відповідати конкретним вимогам цих застосувань. Матеріали нижнього заповнення з низькою діелектричною проникністю та малим тангенсом втрат будуть необхідними для мінімізації втрат сигналу та підтримки цілісності високочастотних сигналів у передових системах зв’язку, технології 5G та інших нових додатках.
- Покращене управління температурою: розсіювання тепла залишається критичною проблемою для електронних пристроїв, особливо зі збільшенням щільності потужності. Майбутні склади епоксидної смоли для нижнього заповнення будуть зосереджені на покращенні теплопровідності для покращення теплопередачі та ефективного вирішення теплових проблем. Удосконалені наповнювачі та добавки будуть включені в нижню епоксидну смолу для досягнення вищої теплопровідності при збереженні інших бажаних властивостей.
- Гнучка та розтяжна електроніка: розвиток гнучкої та розтяжної електроніки відкриває нові можливості для епоксидних матеріалів для заливки. Гнучка епоксидна смола повинна демонструвати чудову адгезію та механічні властивості навіть при багаторазовому згинанні чи розтягуванні. Ці матеріали дозволять герметизувати та захистити електроніку в пристроях, що носяться, дисплеях, що згинаються, та інших додатках, які потребують механічної гнучкості.
- Екологічно чисті рішення: Екологічність та екологічні міркування відіграватимуть усе більш важливу роль у розробці епоксидних матеріалів для заповнення. Основна увага буде приділена створенню епоксидних складів, які не містять шкідливих речовин і мають знижений вплив на навколишнє середовище протягом усього життєвого циклу, включаючи виробництво, використання та утилізацію. Біологічні або відновлювані матеріали також можуть отримати популярність як стійкі альтернативи.
- Удосконалені виробничі процеси: майбутні тенденції в епоксидній смолі для заливки будуть зосереджені на властивостях матеріалів і вдосконаленні виробничих процесів. Будуть досліджені такі методи, як адитивне виробництво, вибіркове дозування та передові методи затвердіння, щоб оптимізувати застосування та продуктивність епоксидної смоли під заливку в різних процесах складання електроніки.
- Інтеграція вдосконалених методів тестування та визначення характеристик: із зростанням складності та вимог до електронних пристроїв виникне потреба у передових методах тестування та визначення характеристик, щоб забезпечити надійність та ефективність епоксидної смоли з недостатнім наповненням. Такі методи, як неруйнівний контроль, моніторинг на місці та інструменти моделювання, допоможуть у розробці та контролі якості епоксидних матеріалів з недоповненим наповненням.
Висновок
Епоксидна смола Underfill відіграє вирішальну роль у підвищенні надійності та продуктивності електронних компонентів, особливо в упаковці напівпровідників. Різні типи епоксидної смоли для заливки мають низку переваг, включаючи високу надійність, самодозування, високу щільність і високі термічні та механічні характеристики. Вибір правильної епоксидної смоли для заливки для застосування та упаковки забезпечує міцне та довговічне з’єднання. У міру розвитку технологій і зменшення розмірів упаковок ми очікуємо ще більше інноваційних епоксидних рішень для заливки, які забезпечуватимуть чудову продуктивність, інтеграцію та мініатюрність. Епоксидна смола Underfill відіграватиме дедалі важливішу роль у майбутньому електроніки, дозволяючи нам досягти вищих рівнів надійності та продуктивності в різних галузях промисловості.