Underfill Epoxy
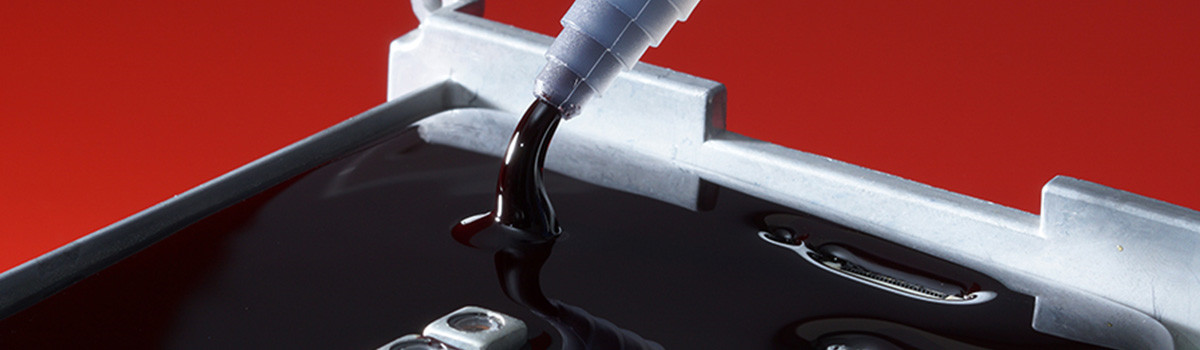
Ang underfill epoxy ay isang uri ng adhesive na ginagamit upang pahusayin ang pagiging maaasahan ng mga elektronikong bahagi, partikular sa mga aplikasyon ng packaging ng semiconductor. Pinupuunan nito ang puwang sa pagitan ng pakete at ng naka-print na circuit board (PCB), na nagbibigay ng mekanikal na suporta at nakakawala ng stress upang maiwasan ang thermal expansion at pagkasira ng contraction. Pinapabuti din ng underfill epoxy ang electrical performance ng package sa pamamagitan ng pagbabawas ng parasitic inductance at capacitance. Sa artikulong ito, tinutuklasan namin ang iba't ibang mga aplikasyon ng underfill na epoxy, ang iba't ibang uri na magagamit, at ang mga benepisyo ng mga ito.
Ang Kahalagahan ng Underfill Epoxy sa Semiconductor Packaging
Ang underfill epoxy ay mahalaga sa semiconductor packaging, na nagbibigay ng mekanikal na reinforcement at proteksyon sa mga pinong microelectronic na bahagi. Ito ay isang espesyal na materyal na pandikit na ginagamit upang punan ang puwang sa pagitan ng semiconductor chip at ng substrate ng pakete, na nagpapahusay sa pagiging maaasahan at pagganap ng mga elektronikong aparato. Dito, tutuklasin natin ang kahalagahan ng underfilled epoxy sa semiconductor packaging.
Ang isa sa mga pangunahing function ng underfilled epoxy ay upang mapabuti ang mekanikal na lakas at pagiging maaasahan ng pakete. Sa panahon ng operasyon, ang mga semiconductor chips ay sumasailalim sa iba't ibang mekanikal na stress, tulad ng thermal expansion at contraction, vibration, at mechanical shock. Ang mga stress na ito ay maaaring humantong sa pagbuo ng mga solder joint crack, na maaaring magdulot ng electrical failure at bawasan ang kabuuang habang-buhay ng device. Ang underfill epoxy ay gumaganap bilang isang stress-reducing agent sa pamamagitan ng pamamahagi ng mekanikal na stress nang pantay-pantay sa chip, substrate, at solder joints. Ito ay epektibong pinapaliit ang pagbuo ng mga bitak at pinipigilan ang pagpapalaganap ng mga umiiral na bitak, na tinitiyak ang pangmatagalang pagiging maaasahan ng pakete.
Ang isa pang kritikal na aspeto ng underfill epoxy ay ang kakayahang pahusayin ang thermal performance ng mga semiconductor device. Nagiging malaking alalahanin ang pagkawala ng init dahil lumiliit ang laki ng mga elektronikong device at tumataas ang density ng kuryente, at maaaring masira ng sobrang init ang pagganap at pagiging maaasahan ng semiconductor chip. Ang underfill epoxy ay may mahusay na thermal conductivity properties, na nagbibigay-daan dito na mahusay na maglipat ng init mula sa chip at ipamahagi ito sa buong pakete. Nakakatulong ito na mapanatili ang pinakamainam na temperatura sa pagpapatakbo at pinipigilan ang mga hotspot, sa gayon ay pinapabuti ang pangkalahatang pamamahala ng thermal ng device.
Pinoprotektahan din ng underfill epoxy laban sa moisture at contaminants. Ang pagpasok ng kahalumigmigan ay maaaring humantong sa kaagnasan, pagtagas ng kuryente, at paglaki ng mga conductive na materyales, na nagreresulta sa mga malfunction ng device. Ang underfill na epoxy ay nagsisilbing hadlang, tinatakpan ang mga lugar na mahina at pinipigilan ang kahalumigmigan na pumasok sa pakete. Nag-aalok din ito ng proteksyon laban sa alikabok, dumi, at iba pang mga contaminant na maaaring makaapekto nang masama sa electrical performance ng semiconductor chip. Sa pamamagitan ng pag-iingat sa chip at sa mga interconnection nito, tinitiyak ng underfill na epoxy ang pangmatagalang pagiging maaasahan at functionality ng device.
Higit pa rito, ang underfilled na epoxy ay nagbibigay-daan sa miniaturization sa semiconductor packaging. Sa patuloy na pangangailangan para sa mas maliliit at mas compact na device, ang underfilled na epoxy ay nagbibigay-daan sa paggamit ng flip-chip at chip-scale na mga diskarte sa packaging. Ang mga diskarteng ito ay direktang nagsasangkot ng pag-mount ng chip sa substrate ng pakete, na inaalis ang pangangailangan para sa wire bonding at binabawasan ang laki ng pakete. Nagbibigay ang underfill epoxy ng suporta sa istruktura at pinapanatili ang integridad ng interface ng chip-substrate, na nagbibigay-daan sa matagumpay na pagpapatupad ng mga advanced na teknolohiya sa packaging na ito.
Paano Tinutugunan ng Underfill Epoxy ang mga Hamon
Ang packaging ng semiconductor ay gumaganap ng isang mahalagang papel sa pagganap ng elektronikong aparato, pagiging maaasahan, at mahabang buhay. Kabilang dito ang pag-encapsulate ng mga integrated circuit (ICs) sa mga protective casing, pagbibigay ng mga de-koryenteng koneksyon, at pagwawaldas ng init na nabuo sa panahon ng operasyon. Gayunpaman, nahaharap sa ilang hamon ang semiconductor packaging, kabilang ang thermal stress at warpage, na maaaring makabuluhang makaapekto sa functionality at pagiging maaasahan ng mga naka-package na device.
Ang isa sa mga pangunahing hamon ay ang thermal stress. Ang mga pinagsama-samang circuit ay bumubuo ng init sa panahon ng operasyon, at ang hindi sapat na dissipation ay maaaring magpapataas ng temperatura sa loob ng package. Ang pagkakaiba-iba ng temperatura na ito ay nagreresulta sa thermal stress habang ang iba't ibang mga materyales sa loob ng pakete ay lumalawak at kumukuha sa iba't ibang mga rate. Ang hindi pare-parehong pagpapalawak at pag-urong ay maaaring maging sanhi ng mekanikal na strain, na humahantong sa mga pagkabigo ng solder joint, delamination, at mga bitak. Maaaring makompromiso ng thermal stress ang electrical at mekanikal na integridad ng package, na sa huli ay makakaapekto sa performance at reliability ng device.
Ang Warpage ay isa pang kritikal na hamon sa semiconductor packaging. Warpage ay tumutukoy sa baluktot o pagpapapangit ng substrate ng pakete o ang buong pakete. Ito ay maaaring mangyari sa panahon ng proseso ng packaging o dahil sa thermal stress. Ang Warpage ay pangunahing sanhi ng hindi pagkakatugma sa koepisyent ng thermal expansion (CTE) sa pagitan ng iba't ibang materyales sa pakete. Halimbawa, ang CTE ng silicon die, substrate, at mold compound ay maaaring magkaiba nang malaki. Kapag sumailalim sa mga pagbabago sa temperatura, ang mga materyales na ito ay lumalawak o kumukontra sa iba't ibang mga rate, na humahantong sa warpage.
Ang Warpage ay nagdudulot ng ilang problema para sa mga pakete ng semiconductor:
- Maaari itong magresulta sa mga punto ng konsentrasyon ng stress, pagtaas ng posibilidad ng mga mekanikal na pagkabigo at pagbabawas ng pagiging maaasahan ng kahon.
- Ang Warpage ay maaaring humantong sa mga kahirapan sa proseso ng pagpupulong, dahil nakakaapekto ito sa pagkakahanay ng pakete sa iba pang mga bahagi, tulad ng naka-print na circuit board (PCB). Ang maling pagkakahanay na ito ay maaaring makapinsala sa mga de-koryenteng koneksyon at magdulot ng mga isyu sa pagganap.
- Maaaring maapektuhan ng Warpage ang pangkalahatang form factor ng package, na ginagawang mahirap na isama ang device sa mga maliliit na form factor na application o mga PCB na maraming tao.
Iba't ibang mga diskarte at diskarte ang ginagamit sa semiconductor packaging upang matugunan ang mga hamong ito. Kabilang dito ang paggamit ng mga advanced na materyales na may katugmang CTE upang mabawasan ang thermal stress at warpage. Ang mga thermo-mechanical simulation at pagmomodelo ay isinasagawa upang mahulaan ang pag-uugali ng pakete sa ilalim ng iba't ibang mga kondisyon ng thermal. Ang mga pagbabago sa disenyo, tulad ng pagpapakilala ng mga istrukturang pampaluwag ng stress at mga naka-optimize na layout, ay ipinatupad upang mabawasan ang thermal stress at warpage. Bukod pa rito, ang pagbuo ng mga pinahusay na proseso ng pagmamanupaktura at kagamitan ay nakakatulong na mabawasan ang paglitaw ng warpage sa panahon ng pagpupulong.
Mga Benepisyo ng Underfill Epoxy
Ang underfill epoxy ay isang kritikal na bahagi sa semiconductor packaging na nag-aalok ng ilang mga benepisyo. Ang espesyal na epoxy na materyal na ito ay inilapat sa pagitan ng semiconductor chip at ng package substrate, na nagbibigay ng mekanikal na pampalakas at pagtugon sa iba't ibang hamon. Narito ang ilan sa mga kritikal na benepisyo ng underfilled epoxy:
- Pinahusay na Mechanical Reliability: Ang isa sa mga pangunahing benepisyo ng underfill epoxy ay ang kakayahang pahusayin ang mekanikal na pagiging maaasahan ng mga pakete ng semiconductor. Ang underfill epoxy ay lumilikha ng isang magkakaugnay na bono na nagpapabuti sa pangkalahatang integridad ng istruktura sa pamamagitan ng pagpuno sa mga gaps at voids sa pagitan ng chip at substrate. Ito ay nakakatulong upang maiwasan ang package warpage, binabawasan ang panganib ng mekanikal na pagkabigo, at pinahuhusay ang resistensya sa mga panlabas na stress tulad ng mga vibrations, shocks, at thermal cycling. Ang pinahusay na mekanikal na pagiging maaasahan ay humahantong sa pagtaas ng tibay ng produkto at mas mahabang buhay para sa device.
- Thermal Stress Dissipation: Ang underfill epoxy ay nakakatulong na mawala ang thermal stress sa loob ng package. Ang mga pinagsama-samang circuit ay bumubuo ng init sa panahon ng operasyon, at ang hindi sapat na pagwawaldas ay maaaring magresulta sa mga pagkakaiba-iba ng temperatura sa loob ng lalagyan. Ang underfill na materyal na epoxy, na may mas mababang koepisyent ng thermal expansion (CTE) kumpara sa mga chip at substrate na materyales, ay nagsisilbing buffer layer. Ito ay sumisipsip ng mekanikal na strain na dulot ng thermal stress, na binabawasan ang panganib ng mga pagkabigo ng solder joint, delamination, at mga bitak. Sa pamamagitan ng pag-alis ng thermal stress, ang underfilled na epoxy ay nakakatulong na mapanatili ang electrical at mechanical integrity ng package.
- Pinahusay na Pagganap ng Elektrisidad: Ang underfill na epoxy ay positibong nakakaapekto sa electrical performance ng mga semiconductor device. Pinupuno ng materyal na epoxy ang mga puwang sa pagitan ng chip at substrate, na binabawasan ang kapasidad ng parasitiko at inductance. Nagreresulta ito sa pinahusay na integridad ng signal, nabawasan ang pagkawala ng signal, at pinahusay na koneksyon sa kuryente sa pagitan ng chip at ng natitirang bahagi ng package. Ang pinababang mga parasitic effect ay nakakatulong sa mas mahusay na pagganap ng kuryente, mas mataas na rate ng paglilipat ng data, at mas mataas na pagiging maaasahan ng device. Bukod pa rito, ang underfilled na epoxy ay nagbibigay ng insulation at proteksyon laban sa moisture, contaminants, at iba pang environmental factors na maaaring magpababa ng electrical performance.
- Stress Relief at Pinahusay na Asembleya: Ang underfill epoxy ay gumaganap bilang isang mekanismo sa pagtanggal ng stress sa panahon ng pagpupulong. Binabayaran ng materyal na epoxy ang hindi pagkakatugma ng CTE sa pagitan ng chip at substrate, na binabawasan ang mekanikal na stress sa panahon ng mga pagbabago sa temperatura. Ginagawa nitong mas maaasahan at mahusay ang proseso ng pagpupulong, na pinapaliit ang panganib ng pagkasira ng package o hindi pagkakahanay. Ang kontroladong pamamahagi ng stress na ibinibigay ng underfill na epoxy ay nakakatulong din na matiyak ang wastong pagkakahanay sa iba pang mga bahagi sa printed circuit board (PCB) at pagpapabuti ng pangkalahatang resulta ng pagpupulong.
- Miniaturization at Form Factor Optimization: Ang underfill epoxy ay nagbibigay-daan sa miniaturization ng mga semiconductor packages at pag-optimize ng form factor. Sa pamamagitan ng pagbibigay ng structural reinforcement at stress relief, underfill epoxy ay nagbibigay-daan para sa pagdidisenyo at paggawa ng mas maliit, mas manipis, at mas compact na mga pakete. Ito ay partikular na mahalaga para sa mga application tulad ng mga mobile device at naisusuot na electronics, kung saan ang espasyo ay nasa isang premium. Ang kakayahang mag-optimize ng mga form factor at makamit ang mas mataas na density ng bahagi ay nag-aambag sa mas advanced at makabagong mga electronic device.
Mga Uri ng Underfill Epoxy
Maraming uri ng underfill epoxy formulation ang available sa semiconductor packaging, bawat isa ay idinisenyo upang matugunan ang mga partikular na pangangailangan at tugunan ang iba't ibang hamon. Narito ang ilang karaniwang ginagamit na uri ng underfill na epoxy:
- Capillary Underfill Epoxy: Ang Capillary underfill epoxy ay ang pinaka-tradisyonal at malawakang ginagamit na uri. Ang isang mababang-lagkit na epoxy ay dumadaloy sa puwang sa pagitan ng chip at ng substrate sa pamamagitan ng pagkilos ng maliliit na ugat. Ang capillary underfill ay karaniwang ibinibigay sa gilid ng chip, at habang ang pakete ay pinainit, ang epoxy ay dumadaloy sa ilalim ng chip, na pinupuno ang mga void. Ang ganitong uri ng underfill ay angkop para sa mga pakete na may maliliit na puwang at nagbibigay ng magandang mekanikal na pampalakas.
- No-Flow Underfill Epoxy: Ang No-flow underfill na epoxy ay isang high-viscosity formulation na hindi dumadaloy sa panahon ng curing. Ito ay inilapat bilang isang pre-apply na epoxy o bilang isang pelikula sa pagitan ng chip at ang substrate. Ang no-flow underfill epoxy ay partikular na kapaki-pakinabang para sa mga flip-chip package, kung saan direktang nakikipag-ugnayan ang solder bumps sa substrate. Tinatanggal nito ang pangangailangan para sa daloy ng maliliit na ugat at binabawasan ang panganib ng pinsala sa magkasanib na panghinang sa panahon ng pagpupulong.
- Wafer-Level Underfill (WLU): Ang wafer-level underfill ay isang underfill na epoxy na inilapat sa wafer level bago i-singulate ang mga indibidwal na chip. Kabilang dito ang paglalagay ng underfill na materyal sa buong ibabaw ng wafer at pagpapagaling nito. Nag-aalok ang wafer-level underfill ng ilang pakinabang, kabilang ang unipormeng underfill coverage, pinababang oras ng pagpupulong, at pinahusay na kontrol sa proseso. Ito ay karaniwang ginagamit para sa mataas na dami ng pagmamanupaktura ng maliliit na laki ng mga aparato.
- Molded Underfill (MUF): Ang molded underfill ay isang underfill na epoxy na inilapat sa panahon ng encapsulation molding. Ang underfill na materyal ay ibinibigay sa substrate, at pagkatapos ay ang chip at substrate ay naka-encapsulated sa isang mold compound. Sa panahon ng paghubog, ang epoxy ay dumadaloy at pinupuno ang puwang sa pagitan ng chip at substrate, na nagbibigay ng underfill at encapsulation sa isang hakbang. Ang molded underfill ay nag-aalok ng mahusay na mechanical reinforcement at pinapasimple ang proseso ng pagpupulong.
- Non-Conductive Underfill (NCF): Ang non-conductive underfill epoxy ay partikular na binuo upang magbigay ng electrical isolation sa pagitan ng solder joints sa chip at substrate. Naglalaman ito ng mga insulating filler o additives na pumipigil sa electrical conductivity. Ang NCF ay ginagamit sa mga application kung saan ang electrical shorting sa pagitan ng mga katabing solder joints ay isang alalahanin. Nag-aalok ito ng parehong mechanical reinforcement at electrical isolation.
- Thermally Conductive Underfill (TCU): Ang thermally conductive underfill epoxy ay idinisenyo upang pahusayin ang mga kakayahan sa pag-alis ng init ng package. Naglalaman ito ng mga thermally conductive filler, tulad ng mga ceramic o metal na particle, na nagpapahusay sa thermal conductivity ng underfill na materyal. Ginagamit ang TCU sa mga application kung saan mahalaga ang mahusay na paglipat ng init, gaya ng mga high-power na device o ang mga gumagana sa humihingi ng thermal environment.
Ito ay ilan lamang sa mga halimbawa ng iba't ibang uri ng underfill na epoxy na ginagamit sa semiconductor packaging. Ang pagpili ng naaangkop na underfill epoxy ay nakasalalay sa mga salik gaya ng disenyo ng pakete, proseso ng pagpupulong, mga kinakailangan sa thermal, at mga pagsasaalang-alang sa kuryente. Ang bawat underfill na epoxy ay nag-aalok ng mga partikular na pakinabang at iniakma upang matugunan ang mga natatanging pangangailangan ng iba't ibang mga application.
Capillary Underfill: Mababang Lapot at Mataas na Pagkakaaasahan
Ang capillary underfill ay tumutukoy sa isang proseso na ginagamit sa industriya ng semiconductor packaging upang mapahusay ang pagiging maaasahan ng mga elektronikong aparato. Kabilang dito ang pagpuno sa mga puwang sa pagitan ng isang microelectronic chip at ang nakapalibot na pakete nito na may mababang lagkit na likidong materyal, karaniwang isang epoxy-based na resin. Ang underfill na materyal na ito ay nagbibigay ng suporta sa istruktura, pinapabuti ang thermal dissipation, at pinoprotektahan ang chip mula sa mekanikal na stress, kahalumigmigan, at iba pang mga kadahilanan sa kapaligiran.
Ang isa sa mga kritikal na katangian ng capillary underfill ay ang mababang lagkit nito. Ang underfill na materyal ay binuo upang magkaroon ng medyo mababang density, na nagbibigay-daan sa madaling dumaloy sa makitid na mga puwang sa pagitan ng chip at ng pakete sa panahon ng proseso ng underfilling. Tinitiyak nito na ang underfill na materyal ay maaaring epektibong tumagos at punan ang lahat ng mga void at air gaps, na pinapaliit ang panganib ng void formation at pagpapabuti ng pangkalahatang integridad ng interface ng chip-package.
Ang mga low-viscosity capillary underfill na materyales ay nag-aalok din ng ilang iba pang mga pakinabang. Una, pinapadali nila ang mahusay na daloy ng materyal sa ilalim ng chip, na humahantong sa pagbawas ng oras ng proseso at pagtaas ng throughput ng produksyon. Ito ay partikular na mahalaga sa mataas na dami ng mga kapaligiran sa pagmamanupaktura kung saan ang oras at kahusayan sa gastos ay kritikal.
Pangalawa, ang mababang lagkit ay nagbibigay-daan sa mas mahusay na basa at pagdirikit ng mga katangian ng underfill na materyal. Ito ay nagpapahintulot sa materyal na kumalat nang pantay-pantay at bumuo ng matibay na mga bono sa chip at sa pakete, na lumilikha ng isang maaasahan at matatag na encapsulation. Tinitiyak nito na ang chip ay ligtas na protektado mula sa mga mekanikal na stress tulad ng thermal cycling, shocks, at vibrations.
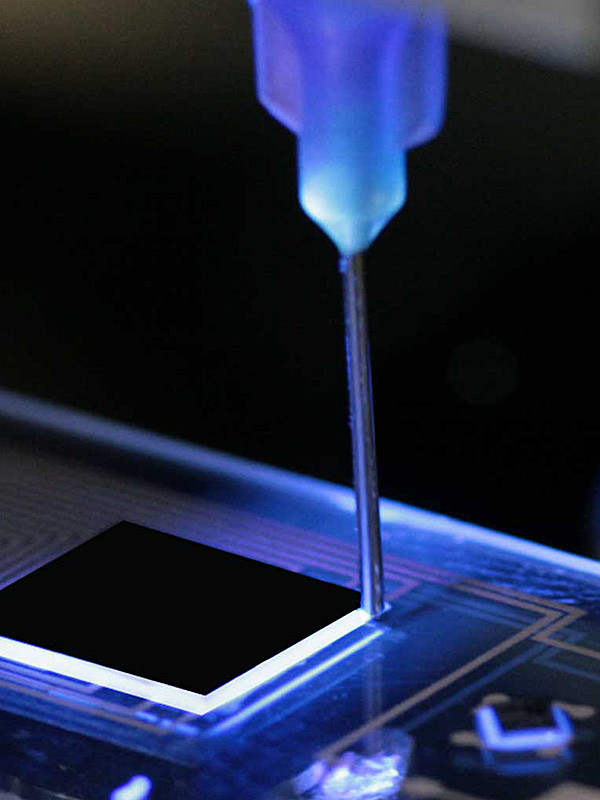
Ang isa pang mahalagang aspeto ng mga capillary underfill ay ang kanilang mataas na pagiging maaasahan. Ang mga low-viscosity underfill na materyales ay partikular na inengineered para magpakita ng mahusay na thermal stability, electrical insulation properties, at paglaban sa moisture at mga kemikal. Ang mga katangiang ito ay mahalaga para matiyak ang pangmatagalang pagganap at pagiging maaasahan ng mga naka-package na electronic device, lalo na sa mga hinihingi na aplikasyon gaya ng automotive, aerospace, at telekomunikasyon.
Bukod dito, ang mga materyal na underfill ng capillary ay idinisenyo upang magkaroon ng mataas na lakas ng makina at mahusay na pagdirikit sa iba't ibang materyal na substrate, kabilang ang mga metal, keramika, at mga organikong materyales na karaniwang ginagamit sa packaging ng semiconductor. Ito ay nagbibigay-daan sa underfill na materyal na kumilos bilang isang stress buffer, na epektibong sumisipsip at nagwawaldas ng mga mekanikal na stress na nabuo sa panahon ng operasyon o pagkakalantad sa kapaligiran.
No-Flow Underfill: Self-Dispensing at High Throughput
No-flow underfill isang espesyal na proseso na ginagamit sa industriya ng semiconductor packaging upang mapahusay ang pagiging maaasahan at kahusayan ng mga elektronikong aparato. Hindi tulad ng mga capillary underfill, na umaasa sa low-viscosity na daloy ng mga materyales, ang walang-flow na underfill ay gumagamit ng self-dispensing na diskarte sa mga high-viscosity na materyales. Ang pamamaraang ito ay nag-aalok ng ilang mga pakinabang, kabilang ang self-alignment, mataas na throughput, at pinahusay na pagiging maaasahan.
Ang isa sa mga kritikal na tampok ng walang daloy na underfill ay ang kakayahan nitong makapagbigay ng sarili. Ang underfill na materyal na ginamit sa prosesong ito ay binuo na may mas mataas na lagkit, na pumipigil sa malayang pagdaloy nito. Sa halip, ang underfill na materyal ay ibinibigay sa interface ng chip-package sa isang kinokontrol na paraan. Ang kinokontrol na dispensing na ito ay nagbibigay-daan sa tumpak na paglalagay ng underfill na materyal, na tinitiyak na ito ay inilalapat lamang sa mga gustong lugar nang hindi umaapaw o kumakalat nang hindi makontrol.
Nag-aalok ang self-dispensing na katangian ng walang daloy na underfill ng ilang benepisyo. Una, nagbibigay-daan ito para sa self-alignment ng underfill na materyal. Habang ibinibigay ang underfill, natural na umaayon ito sa chip at package, na pinupunan ang mga puwang at walang bisa nang pantay. Tinatanggal nito ang pangangailangan para sa tumpak na pagpoposisyon at pag-align ng chip sa panahon ng proseso ng underfilling, na nakakatipid ng oras at pagsisikap sa pagmamanupaktura.
Pangalawa, ang tampok na self-dispensing ng mga underfill na walang daloy ay nagbibigay-daan sa mataas na throughput sa produksyon. Ang proseso ng dispensing ay maaaring awtomatiko, na nagbibigay-daan para sa mabilis at pare-parehong paggamit ng underfill na materyal sa maraming chips nang sabay-sabay. Pinapabuti nito ang pangkalahatang kahusayan sa produksyon at binabawasan ang mga gastos sa pagmamanupaktura, na ginagawa itong partikular na kapaki-pakinabang para sa mga kapaligiran ng pagmamanupaktura na may mataas na dami.
Higit pa rito, ang mga materyal na walang daloy na underfill ay idinisenyo upang magbigay ng mataas na pagiging maaasahan. Ang mga high-viscosity underfill na materyales ay nag-aalok ng pinabuting resistensya sa thermal cycling, mechanical stresses, at environmental factors, na tinitiyak ang pangmatagalang performance ng mga naka-package na electronic device. Ang mga materyales ay nagpapakita ng mahusay na thermal stability, electrical insulation properties, at paglaban sa moisture at mga kemikal, na nag-aambag sa pangkalahatang pagiging maaasahan ng mga device.
Bukod pa rito, ang mga high-viscosity underfill na materyales na ginagamit sa no-flow underfill ay nagpahusay ng mekanikal na lakas at mga katangian ng adhesion. Bumubuo sila ng matibay na mga bono sa chip at pakete, na epektibong sumisipsip at nagwawaldas ng mga mekanikal na stress na nabuo sa panahon ng operasyon o pagkakalantad sa kapaligiran. Nakakatulong ito na protektahan ang chip mula sa potensyal na pinsala at pinahuhusay ang resistensya ng device sa mga panlabas na shocks at vibrations.
Molded Underfill: Mataas na Proteksyon at Integrasyon
Ang molded underfill ay isang advanced na pamamaraan na ginagamit sa industriya ng semiconductor packaging upang magbigay ng mataas na antas ng proteksyon at pagsasama para sa mga elektronikong device. Kabilang dito ang pag-encapsulate ng buong chip at ang nakapalibot na pakete nito na may mold compound na may kasamang underfill na materyal. Ang prosesong ito ay nag-aalok ng mga makabuluhang pakinabang tungkol sa proteksyon, pagsasama, at pangkalahatang pagiging maaasahan.
Isa sa mga kritikal na benepisyo ng molded underfill ay ang kakayahang magbigay ng komprehensibong proteksyon para sa chip. Ang mold compound na ginamit sa prosesong ito ay nagsisilbing isang matatag na hadlang, na nakapaloob sa buong chip at pakete sa isang proteksiyon na shell. Nagbibigay ito ng epektibong panangga laban sa mga salik sa kapaligiran gaya ng moisture, alikabok, at mga contaminant na maaaring makaapekto sa performance at pagiging maaasahan ng device. Nakakatulong din ang encapsulation na pigilan ang chip mula sa mga mekanikal na stress, thermal cycling, at iba pang panlabas na puwersa, na tinitiyak ang pangmatagalang tibay nito.
Bukod pa rito, ang molded underfill ay nagbibigay-daan sa mataas na antas ng pagsasama sa loob ng semiconductor package. Ang underfill na materyal ay direktang hinahalo sa mold compound, na nagbibigay-daan para sa tuluy-tuloy na pagsasama ng underfill at mga proseso ng encapsulation. Ang pagsasamang ito ay nag-aalis ng pangangailangan para sa isang hiwalay na underfill na hakbang, na pinapasimple ang proseso ng pagmamanupaktura at binabawasan ang oras at gastos ng produksyon. Tinitiyak din nito ang pare-pareho at pare-parehong pamamahagi ng underfill sa buong package, pinapaliit ang mga void at pinapahusay ang pangkalahatang integridad ng istruktura.
Bukod dito, ang molded underfill ay nag-aalok ng mahusay na thermal dissipation properties. Ang mold compound ay idinisenyo upang magkaroon ng mataas na thermal conductivity, na nagbibigay-daan dito upang ilipat ang init palayo sa chip nang mahusay. Mahalaga ito para mapanatili ang pinakamainam na temperatura ng pagpapatakbo ng device at maiwasan ang overheating, na maaaring humantong sa pagkasira ng performance at mga isyu sa pagiging maaasahan. Ang pinahusay na mga katangian ng thermal dissipation ng molded underfill ay nakakatulong sa pangkalahatang pagiging maaasahan at mahabang buhay ng electronic device.
Higit pa rito, ang molded underfill ay nagbibigay-daan sa higit pang miniaturization at form factor optimization. Maaaring iakma ang proseso ng encapsulation upang tumanggap ng iba't ibang laki at hugis ng package, kabilang ang mga kumplikadong 3D na istruktura. Ang kakayahang umangkop na ito ay nagbibigay-daan para sa pagsasama ng maraming chip at iba pang mga bahagi sa isang compact, space-efficient na pakete. Ang kakayahang makamit ang mas matataas na antas ng pagsasama nang hindi nakompromiso ang pagiging maaasahan ay ginagawang mas mahalaga ang molded underfill sa mga application kung saan ang mga hadlang sa laki at bigat ay kritikal, gaya ng mga mobile device, wearable, at automotive electronics.
Chip Scale Package (CSP) Underfill: Miniaturization at High Density
Ang Chip Scale Package (CSP) underfill ay isang kritikal na teknolohiya na nagpapagana ng miniaturization at high-density na pagsasama ng electronic device. Habang patuloy na lumiliit ang laki ng mga electronic device habang nagbibigay ng mas mataas na functionality, hindi napupunan ng CSP ang isang mahalagang papel sa pagtiyak ng pagiging maaasahan at pagganap ng mga compact na device na ito.
Ang CSP ay isang teknolohiya sa packaging na nagpapahintulot sa semiconductor chip na direktang i-mount sa substrate o printed circuit board (PCB) nang hindi nangangailangan ng karagdagang pakete. Inaalis nito ang pangangailangan para sa isang tradisyonal na plastic o ceramic na lalagyan, na binabawasan ang kabuuang sukat at bigat ng device. I-underfill ng CSP ang isang proseso kung saan ginagamit ang isang likido o encapsulant na materyal upang punan ang puwang sa pagitan ng chip at substrate, na nagbibigay ng mekanikal na suporta at pinoprotektahan ang chip mula sa mga salik sa kapaligiran tulad ng moisture at mechanical stress.
Ang miniaturization ay nakakamit sa pamamagitan ng CSP underfill sa pamamagitan ng pagbabawas ng distansya sa pagitan ng chip at ng substrate. Pinupuno ng underfill na materyal ang makitid na agwat sa pagitan ng chip at substrate, na lumilikha ng isang solidong bono at pagpapabuti ng mekanikal na katatagan ng chip. Nagbibigay-daan ito para sa mas maliit at mas manipis na mga device, na ginagawang posible na mag-pack ng mas maraming functionality sa isang limitadong espasyo.
Ang high-density integration ay isa pang bentahe ng CSP underfill. Sa pamamagitan ng pag-aalis ng pangangailangan para sa isang hiwalay na pakete, ang CSP ay nagbibigay-daan sa chip na mai-mount nang mas malapit sa iba pang mga bahagi sa PCB, na binabawasan ang haba ng mga de-koryenteng koneksyon at pagpapabuti ng integridad ng signal. Ang underfill na materyal ay gumaganap din bilang isang thermal conductor, na mahusay na nagwawaldas ng init na nabuo ng chip. Ang kakayahan ng thermal management na ito ay nagbibigay-daan para sa mas mataas na densidad ng kuryente, na nagbibigay-daan sa pagsasama ng mas kumplikado at malalakas na chips sa mga electronic device.
Ang mga materyal na underfill ng CSP ay dapat magkaroon ng mga partikular na katangian upang matugunan ang mga hinihingi ng miniaturization at high-density integration. Kailangan nilang magkaroon ng mababang lagkit upang mapadali ang pagpuno ng makitid na mga puwang, pati na rin ang mahusay na mga katangian ng daloy upang matiyak ang pare-parehong saklaw at alisin ang mga void. Ang mga materyales ay dapat ding magkaroon ng mahusay na pagdirikit sa chip at sa substrate, na nagbibigay ng solidong mekanikal na suporta. Bukod pa rito, dapat silang magpakita ng mataas na thermal conductivity upang mailipat nang mahusay ang init mula sa chip.
Wafer-Level CSP Underfill: Cost-Effective at High Yield
Ang wafer-level chip scale package (WLCSP) underfill ay isang cost-effective at high-yield packaging technique na nag-aalok ng ilang pakinabang sa kahusayan sa pagmamanupaktura at pangkalahatang kalidad ng produkto. Ang WLCSP underfill ay naglalapat ng underfill na materyal sa maraming chips nang sabay-sabay habang nasa wafer form pa rin bago sila iisa-isa sa mga indibidwal na pakete. Nag-aalok ang diskarteng ito ng maraming benepisyo tungkol sa pagbabawas ng gastos, pinahusay na kontrol sa proseso, at mas mataas na mga ani ng produksyon.
Isa sa mga kritikal na bentahe ng WLCSP underfill ay ang cost-effectiveness nito. Ang paglalapat ng underfill na materyal sa antas ng wafer ay ginagawang mas streamlined at mahusay ang proseso ng packaging. Ang underfilled na materyal ay ibinibigay sa wafer gamit ang isang kontrolado at automated na proseso, binabawasan ang materyal na basura at pinapaliit ang mga gastos sa paggawa. Bukod pa rito, ang pag-aalis ng indibidwal na mga hakbang sa paghawak at pag-align ng package ay binabawasan ang kabuuang oras at pagiging kumplikado ng produksyon, na nagreresulta sa makabuluhang pagtitipid sa gastos kumpara sa mga tradisyonal na pamamaraan ng packaging.
Bukod dito, nag-aalok ang WLCSP underfill ng pinahusay na kontrol sa proseso at mas mataas na mga ani ng produksyon. Dahil ang underfill na materyal ay inilapat sa antas ng wafer, ito ay nagbibigay-daan sa mas mahusay na kontrol sa proseso ng dispensing, na tinitiyak ang pare-pareho at pare-parehong underfill coverage para sa bawat chip sa wafer. Binabawasan nito ang panganib ng mga void o hindi kumpletong underfill, na maaaring humantong sa mga isyu sa pagiging maaasahan. Ang kakayahang mag-inspeksyon at subukan ang kalidad ng underfill sa antas ng wafer ay nagbibigay-daan din para sa maagang pagtuklas ng mga depekto o mga pagkakaiba-iba ng proseso, na nagpapagana ng mga napapanahong pagwawasto at binabawasan ang posibilidad na magkaroon ng mga sira na pakete. Bilang resulta, nakakatulong ang underfill ng WLCSP na makamit ang mas mataas na mga ani ng produksyon at mas mahusay na pangkalahatang kalidad ng produkto.
Ang diskarte sa antas ng wafer ay nagbibigay-daan din sa pinabuting pagganap ng thermal at mekanikal. Ang underfill na materyal na ginagamit sa WLCSP ay karaniwang isang low-viscosity, capillary-flowing na materyal na mahusay na makakapuno sa mga makitid na puwang sa pagitan ng mga chips at ng wafer. Nagbibigay ito ng solidong mekanikal na suporta sa mga chips, na nagpapahusay sa kanilang resistensya sa mekanikal na stress, vibrations, at temperatura ng pagbibisikleta. Bukod pa rito, ang underfill na materyal ay gumaganap bilang isang thermal conductor, na pinapadali ang pagwawaldas ng init na nabuo ng mga chips, kaya nagpapabuti ng thermal management at binabawasan ang panganib ng overheating.
Flip Chip Underfill: Mataas na I/O Density at Performance
Ang Flip chip underfill ay isang kritikal na teknolohiya na nagbibigay-daan sa mataas na input/output (I/O) density at pambihirang performance sa mga electronic device. Ito ay gumaganap ng isang mahalagang papel sa pagpapahusay ng pagiging maaasahan at functionality ng flip-chip packaging, na malawakang ginagamit sa mga advanced na semiconductor application. I-explore ng artikulong ito ang kahalagahan ng flip chip underfill at ang epekto nito sa pagkamit ng mataas na I/O density at performance.
Ang teknolohiya ng flip chip ay nagsasangkot ng direktang koneksyon sa kuryente ng isang integrated circuit (IC) o isang semiconductor die sa substrate, na inaalis ang pangangailangan para sa wire bonding. Nagreresulta ito sa isang mas compact at mahusay na pakete, dahil ang mga I/O pad ay matatagpuan sa ilalim na ibabaw ng die. Gayunpaman, ang flip-chip packaging ay nagpapakita ng mga natatanging hamon na dapat tugunan upang matiyak ang pinakamainam na pagganap at pagiging maaasahan.
Ang isa sa mga kritikal na hamon sa flip chip packaging ay ang pagpigil sa mekanikal na stress at thermal mismatch sa pagitan ng die at ng substrate. Sa panahon ng proseso ng pagmamanupaktura at kasunod na operasyon, ang mga pagkakaiba sa mga coefficient ng thermal expansion (CTE) sa pagitan ng die at substrate ay maaaring magdulot ng malaking stress, na humahantong sa pagkasira ng pagganap o kahit na pagkabigo. Ang Flip chip underfill ay isang materyal na proteksiyon na bumabalot sa chip, na nagbibigay ng mekanikal na suporta at nakakawala ng stress. Ito ay epektibong namamahagi ng mga stress na nabuo sa panahon ng thermal cycling at pinipigilan ang mga ito na maapektuhan ang mga maselan na interconnects.
Ang mataas na density ng I/O ay kritikal sa modernong mga elektronikong device, kung saan ang mas maliliit na form factor at mas mataas na functionality ay mahalaga. Ang Flip chip underfill ay nagbibigay-daan sa mas mataas na I/O density sa pamamagitan ng pag-aalok ng superior electrical insulation at thermal management na mga kakayahan. Ang underfill na materyal ay pumupuno sa puwang sa pagitan ng die at ng substrate, na lumilikha ng isang matatag na interface at binabawasan ang panganib ng mga short circuit o electrical leakage. Nagbibigay-daan ito para sa mas malapit na espasyo ng mga I/O pad, na nagreresulta sa pagtaas ng density ng I/O nang hindi sinasakripisyo ang pagiging maaasahan.
Bukod dito, ang flip chip underfill ay nag-aambag sa pinahusay na pagganap ng kuryente. Pinaliit nito ang mga electrical parasitic sa pagitan ng die at substrate, binabawasan ang pagkaantala ng signal at pagpapahusay ng integridad ng signal. Ang underfill na materyal ay nagpapakita rin ng mahusay na thermal conductivity properties, mahusay na nagwawaldas ng init na nabuo ng chip sa panahon ng operasyon. Tinitiyak ng epektibong pag-alis ng init na ang temperatura ay nananatili sa loob ng mga katanggap-tanggap na limitasyon, na pumipigil sa sobrang pag-init at pagpapanatili ng pinakamainam na pagganap.
Ang mga pag-unlad sa mga materyal na underfill ng flip chip ay nagpagana ng mas mataas na density ng I/O at mga antas ng pagganap. Ang mga nanocomposite underfill, halimbawa, ay gumagamit ng mga nanoscale filler upang mapahusay ang thermal conductivity at mekanikal na lakas. Nagbibigay-daan ito para sa pinahusay na pagkawala ng init at pagiging maaasahan, na nagbibigay-daan sa mga device na mas mahusay ang pagganap.
Ball Grid Array (BGA) Underfill: Mataas na Thermal at Mechanical Performance
Pinipuno ng Ball Grid Array (BGA) ang isang kritikal na teknolohiya na nag-aalok ng mataas na thermal at mekanikal na pagganap sa mga elektronikong device. Ito ay gumaganap ng isang mahalagang papel sa pagpapahusay ng pagiging maaasahan at paggana ng mga pakete ng BGA, na malawakang ginagamit sa iba't ibang mga aplikasyon. Sa artikulong ito, i-explore natin ang kahalagahan ng underfill ng BGA at ang epekto nito sa pagkamit ng mataas na thermal at mechanical performance.
Ang teknolohiya ng BGA ay nagsasangkot ng isang disenyo ng pakete kung saan ang integrated circuit (IC) o semiconductor die ay naka-mount sa isang substrate, at ang mga de-koryenteng koneksyon ay ginagawa sa pamamagitan ng isang hanay ng mga bolang panghinang na matatagpuan sa ilalim na ibabaw ng pakete. Kinukuha ng BGA ang isang materyal na ibinibigay sa puwang sa pagitan ng die at ng substrate, na nakakabit sa mga bolang panghinang at nagbibigay ng mekanikal na suporta at proteksyon sa pagpupulong.
Isa sa mga kritikal na hamon sa BGA packaging ay ang pamamahala ng mga thermal stress. Sa panahon ng operasyon, ang IC ay bumubuo ng init, at ang thermal expansion at contraction ay maaaring magdulot ng malaking presyon sa mga solder joints na kumukonekta sa die at sa substrate. Pinipuno ng BGA ang isang mahalagang papel sa pagpapagaan ng mga stress na ito sa pamamagitan ng pagbuo ng isang solidong bono sa mamatay at sa substrate. Ito ay gumaganap bilang isang stress buffer, sumisipsip ng thermal expansion at contraction at binabawasan ang strain sa solder joints. Nakakatulong ito na mapabuti ang pangkalahatang pagiging maaasahan ng package at binabawasan ang panganib ng mga pagkabigo ng solder joint.
Ang isa pang kritikal na aspeto ng BGA underfill ay ang kakayahang pahusayin ang mekanikal na pagganap ng package. Ang mga pakete ng BGA ay kadalasang napapailalim sa mga mekanikal na stress sa panahon ng paghawak, pagpupulong, at pagpapatakbo. Pinupuno ng underfill na materyal ang puwang sa pagitan ng die at substrate, na nagbibigay ng suporta sa istruktura at pampalakas sa mga solder joints. Pinapabuti nito ang pangkalahatang mekanikal na lakas ng pagpupulong, na ginagawa itong mas lumalaban sa mga mekanikal na shock, vibrations, at iba pang panlabas na puwersa. Sa pamamagitan ng epektibong pamamahagi ng mga mekanikal na stress, ang BGA underfill ay nakakatulong upang maiwasan ang pag-crack ng package, delamination, o iba pang mekanikal na pagkabigo.
Ang mataas na pagganap ng thermal ay mahalaga sa mga elektronikong aparato upang matiyak ang wastong paggana at pagiging maaasahan. Ang mga materyal na underfill ng BGA ay idinisenyo upang magkaroon ng mahusay na mga katangian ng thermal conductivity. Ito ay nagpapahintulot sa kanila na mahusay na ilipat ang init mula sa die at ipamahagi ito sa buong substrate, na nagpapahusay sa pangkalahatang thermal management ng package. Ang epektibong pag-alis ng init ay nakakatulong na mapanatili ang mas mababang temperatura ng pagpapatakbo, na pumipigil sa mga thermal hotspot at potensyal na pagkasira ng pagganap. Nag-aambag din ito sa mahabang buhay ng kahon sa pamamagitan ng pagbabawas ng thermal stress ng mga bahagi.
Ang mga pagsulong sa BGA underfill na materyales ay humantong sa mas mataas na thermal at mekanikal na pagganap. Ang mga pinahusay na formulation at filler materials, tulad ng mga nanocomposite o high thermal conductivity fillers, ay nagpagana ng mas mahusay na heat dissipation at mekanikal na lakas, na higit na nagpahusay sa performance ng BGA packages.
Quad Flat Package (QFP) Underfill: Malaking I/O Count at Robustness
Ang Quad Flat Package (QFP) ay isang integrated circuit (IC) package na malawakang ginagamit sa electronics. Nagtatampok ito ng isang parisukat o hugis-parihaba na hugis na may mga lead na umaabot mula sa lahat ng apat na panig, na nagbibigay ng maraming input/output (I/O) na koneksyon. Upang mapahusay ang pagiging maaasahan at katatagan ng mga pakete ng QFP, ang mga underfill na materyales ay karaniwang ginagamit.
Ang underfill ay isang proteksiyon na materyal na inilapat sa pagitan ng IC at ng substrate upang palakasin ang mekanikal na lakas ng mga solder joints at maiwasan ang mga pagkabigo na dulot ng stress. Ito ay partikular na mahalaga para sa mga QFP na may malaking bilang ng I/O, dahil ang mataas na bilang ng mga koneksyon ay maaaring humantong sa mga makabuluhang mekanikal na stress sa panahon ng thermal cycling at mga kondisyon ng pagpapatakbo.
Ang underfill na materyal na ginagamit para sa QFP packages ay dapat magkaroon ng mga partikular na katangian upang matiyak ang tibay. Una, dapat itong magkaroon ng mahusay na pagdirikit sa parehong IC at sa substrate upang lumikha ng isang malakas na bono at mabawasan ang panganib ng delamination o detatsment. Bukod pa rito, dapat itong magkaroon ng mababang coefficient ng thermal expansion (CTE) upang tumugma sa CTE ng IC at substrate, na binabawasan ang mga hindi pagkakatugma ng stress na maaaring humantong sa mga bitak o bali.
Higit pa rito, ang underfill na materyal ay dapat magkaroon ng mahusay na mga katangian ng daloy upang matiyak ang pare-parehong saklaw at kumpletong pagpuno ng puwang sa pagitan ng IC at ng substrate. Nakakatulong ito sa pag-aalis ng mga void, na maaaring magpahina sa mga solder joints at magresulta sa pagbawas ng pagiging maaasahan. Ang materyal ay dapat ding magkaroon ng mahusay na mga katangian ng paggamot, na nagpapahintulot na ito ay bumuo ng isang matibay at matibay na proteksiyon na layer pagkatapos ng aplikasyon.
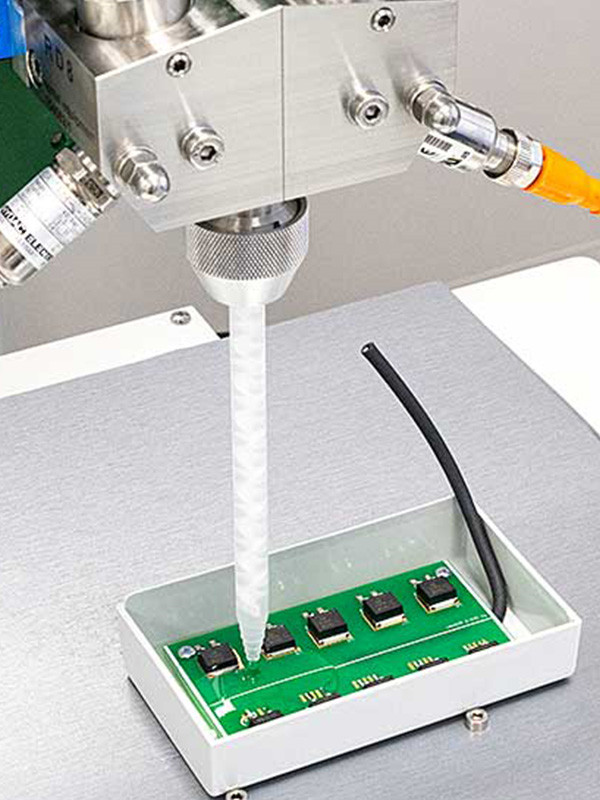
Sa mga tuntunin ng mekanikal na katatagan, ang underfill ay dapat magkaroon ng mataas na lakas ng paggugupit at pagbabalat upang mapaglabanan ang mga panlabas na puwersa at maiwasan ang pagpapapangit o paghihiwalay ng pakete. Dapat din itong magpakita ng mahusay na pagtutol sa kahalumigmigan at iba pang mga kadahilanan sa kapaligiran upang mapanatili ang mga katangian ng proteksyon nito sa paglipas ng panahon. Ito ay partikular na mahalaga sa mga application kung saan ang QFP package ay maaaring malantad sa malupit na mga kondisyon o sumailalim sa mga pagkakaiba-iba ng temperatura.
Available ang iba't ibang underfill na materyales upang makamit ang mga gustong katangiang ito, kabilang ang mga formulation na nakabatay sa epoxy. Depende sa mga partikular na kinakailangan ng application, ang mga materyales na ito ay maaaring ibigay gamit ang iba't ibang mga diskarte, tulad ng capillary flow, jetting, o screen printing.
System-in-Package (SiP) Underfill: Integration at Performance
Ang System-in-Package (SiP) ay isang advanced na teknolohiya sa packaging na nagsasama ng maraming semiconductor chips, passive na bahagi, at iba pang elemento sa isang pakete. Nag-aalok ang SiP ng maraming pakinabang, kabilang ang pinababang form factor, pinahusay na pagganap ng kuryente, at pinahusay na functionality. Upang matiyak ang pagiging maaasahan at pagganap ng mga SiP assemblies, ang mga underfill na materyales ay karaniwang ginagamit.
Ang underfill sa mga SiP application ay mahalaga sa pagbibigay ng mekanikal na katatagan at electrical connectivity sa pagitan ng iba't ibang bahagi sa loob ng package. Nakakatulong ito upang mabawasan ang panganib ng mga pagkabigo na dulot ng stress, tulad ng solder joint crack o fractures, na maaaring mangyari dahil sa mga pagkakaiba sa coefficients ng thermal expansion (CTE) sa pagitan ng mga bahagi.
Ang pagsasama ng maraming bahagi sa isang pakete ng SiP ay humahantong sa kumplikadong pagkakakonekta, na may maraming mga solder joint at high-density na circuitry. Ang mga underfill na materyales ay nakakatulong upang mapalakas ang mga pagkakaugnay na ito, na nagpapahusay sa mekanikal na lakas at pagiging maaasahan ng pagpupulong. Sinusuportahan nila ang mga solder joints, na binabawasan ang panganib ng pagkapagod o pinsala na dulot ng thermal cycling o mechanical stress.
Sa mga tuntunin ng pagganap ng kuryente, ang mga underfill na materyales ay kritikal sa pagpapabuti ng integridad ng signal at pagliit ng ingay ng kuryente. Sa pamamagitan ng pagpuno sa mga puwang sa pagitan ng mga bahagi at pagbabawas ng distansya sa pagitan ng mga ito, ang underfill ay nakakatulong upang mabawasan ang parasitic capacitance at inductance, na nagbibigay-daan sa mas mabilis at mas mahusay na paghahatid ng signal.
Bukod pa rito, ang mga underfill na materyales para sa mga aplikasyon ng SiP ay dapat na may mahusay na thermal conductivity upang maalis ang init na nabuo ng mga pinagsama-samang bahagi nang mahusay. Ang epektibong pag-alis ng init ay mahalaga upang maiwasan ang sobrang init at mapanatili ang pangkalahatang pagiging maaasahan at pagganap ng SiP assembly.
Ang mga underfill na materyales sa SiP packaging ay dapat may mga partikular na katangian upang matugunan ang mga kinakailangan sa pagsasama at pagganap na ito. Dapat silang magkaroon ng mahusay na flowability upang matiyak ang kumpletong saklaw at punan ang mga puwang sa pagitan ng mga bahagi. Ang underfill na materyal ay dapat ding magkaroon ng low-viscosity formulation upang payagan ang madaling pag-dispense at pagpuno sa mga makikitid na butas o maliliit na espasyo.
Higit pa rito, ang underfill na materyal ay dapat magpakita ng malakas na pagdirikit sa iba't ibang mga ibabaw, kabilang ang mga semiconductor chip, substrate, at mga passive, upang matiyak ang maaasahang pagbubuklod. Dapat itong tugma sa iba't ibang mga materyales sa packaging, tulad ng mga organikong substrate o keramika, at nagpapakita ng magagandang mekanikal na katangian, kabilang ang mataas na lakas ng gupit at balat.
Ang pagpili ng underfill na materyal at paraan ng aplikasyon ay depende sa partikular na disenyo ng SiP, mga kinakailangan sa bahagi, at mga proseso ng pagmamanupaktura. Ang mga diskarte sa dispensing gaya ng capillary flow, jetting, o film-assisted na pamamaraan ay karaniwang nalalapat sa underfill sa mga SiP assemblies.
Optoelectronics Underfill: Optical Alignment at Proteksyon
Kasama sa underfill ng optoelectronics ang pag-encapsulate at pagprotekta sa mga optoelectronic na device habang tinitiyak ang tumpak na optical alignment. Ang mga optoelectronic na aparato, tulad ng mga laser, photodetector, at optical switch, ay kadalasang nangangailangan ng maselan na pagkakahanay ng mga optical na bahagi upang makamit ang pinakamainam na pagganap. Kasabay nito, kailangan nilang protektahan mula sa mga kadahilanan sa kapaligiran na maaaring makaapekto sa kanilang pag-andar. Tinutugunan ng optoelectronics underfill ang parehong mga kinakailangang ito sa pamamagitan ng pagbibigay ng optical alignment at proteksyon sa isang proseso.
Ang optical alignment ay isang kritikal na aspeto ng pagmamanupaktura ng optoelectronic device. Kabilang dito ang pag-align ng mga visual na elemento, tulad ng mga fibers, waveguides, lens, o gratings, upang matiyak ang mahusay na paghahatid at pagtanggap ng liwanag. Ang tumpak na pagkakahanay ay kinakailangan upang i-maximize ang pagganap ng device at mapanatili ang integridad ng signal. Kasama sa mga tradisyunal na diskarte sa alignment ang manu-manong alignment gamit ang visual inspection o automated alignment gamit ang alignment stages. Gayunpaman, ang mga pamamaraang ito ay maaaring magtagal, matrabaho, at madaling kapitan ng mga pagkakamali.
Optoelectronics underfill ang isang makabagong solusyon sa pamamagitan ng pagsasama ng mga feature ng alignment nang direkta sa underfill na materyal. Ang mga underfill na materyales ay karaniwang likido o semi-likido na mga compound na maaaring dumaloy at punan ang mga puwang sa pagitan ng mga optical na bahagi. Sa pamamagitan ng pagdaragdag ng mga feature ng alignment, tulad ng mga microstructure o fiducial mark, sa loob ng underfill na materyal, ang proseso ng alignment ay maaaring gawing simple at awtomatiko. Ang mga tampok na ito ay kumikilos bilang mga gabay sa panahon ng pagpupulong, na tinitiyak ang tumpak na pagkakahanay ng mga optical na bahagi nang hindi nangangailangan ng mga kumplikadong pamamaraan ng pag-align.
Bilang karagdagan sa optical alignment, pinoprotektahan ng mga underfill na materyales ang mga optoelectronic na device. Ang mga optoelectronic na bahagi ay madalas na nakalantad sa malupit na kapaligiran, kabilang ang mga pagbabago sa temperatura, kahalumigmigan, at mekanikal na stress. Maaaring pababain ng mga panlabas na salik na ito ang pagganap at pagiging maaasahan ng mga device sa paglipas ng panahon. Ang mga underfill na materyales ay kumikilos bilang isang proteksiyon na hadlang, na nagpapaloob sa mga optical na bahagi at pinoprotektahan ang mga ito mula sa mga kontaminant sa kapaligiran. Nagbibigay din sila ng mekanikal na pampalakas, na binabawasan ang panganib ng pinsala dahil sa pagkabigla o panginginig ng boses.
Ang mga underfill na materyales na ginagamit sa mga aplikasyon ng optoelectronics ay karaniwang idinisenyo upang magkaroon ng mababang refractive index at mahusay na optical transparency. Tinitiyak nito ang kaunting interference sa mga optical signal na dumadaan sa device. Bukod pa rito, nagpapakita sila ng mahusay na pagdirikit sa iba't ibang mga substrate at may mababang koepisyent ng pagpapalawak ng thermal upang mabawasan ang stress ng device sa panahon ng thermal cycling.
Ang proseso ng underfill ay kinabibilangan ng paglalagay ng underfill na materyal sa device, na nagbibigay-daan dito na dumaloy at punan ang mga puwang sa pagitan ng mga optical na bahagi, at pagkatapos ay i-cure ito upang bumuo ng solidong encapsulation. Depende sa partikular na aplikasyon, ang underfill na materyal ay maaaring ilapat gamit ang iba't ibang diskarte, gaya ng capillary flow, jet dispensing, o screen printing. Ang proseso ng paggamot ay maaaring makamit sa pamamagitan ng init, UV radiation, o pareho.
Medical Electronics Underfill: Biocompatibility at Reliability
Ang mga medikal na electronics ay underfill sa isang espesyal na proseso na kinabibilangan ng pag-encapsulate at pagprotekta sa mga elektronikong sangkap na ginagamit sa mga medikal na device. Ang mga device na ito ay gumaganap ng isang mahalagang papel sa iba't ibang mga medikal na aplikasyon, tulad ng mga implantable device, diagnostic equipment, monitoring system, at mga sistema ng paghahatid ng gamot. Nakatuon ang underfill ng medikal na electronics sa dalawang kritikal na aspeto: biocompatibility at pagiging maaasahan.
Ang biocompatibility ay isang pangunahing kinakailangan para sa mga medikal na aparato na nakikipag-ugnayan sa katawan ng tao. Ang mga underfill na materyales na ginagamit sa mga medikal na elektroniko ay dapat na biocompatible, ibig sabihin, hindi sila dapat magdulot ng mga mapaminsalang epekto o masamang reaksyon kapag nadikit sa buhay na tissue o mga likido sa katawan. Ang mga materyales na ito ay dapat sumunod sa mga mahigpit na regulasyon at pamantayan, tulad ng ISO 10993, na tumutukoy sa mga pamamaraan ng pagsusuri at pagsusuri ng biocompatibility.
Ang mga underfill na materyales para sa medikal na electronics ay maingat na pinipili o binabalangkas upang matiyak ang biocompatibility. Ang mga ito ay idinisenyo upang maging hindi nakakalason, hindi nakakairita, at hindi allergenic. Ang mga materyales na ito ay hindi dapat mag-leach ng anumang nakakapinsalang substance o bumababa sa paglipas ng panahon, dahil ito ay maaaring humantong sa pagkasira ng tissue o pamamaga. Ang mga biocompatible underfill na materyales ay mayroon ding mababang pagsipsip ng tubig upang maiwasan ang pagdami ng bacteria o fungi na maaaring magdulot ng mga impeksiyon.
Ang pagiging maaasahan ay isa pang kritikal na aspeto ng medikal na electronics underfill. Ang mga medikal na device ay kadalasang nahaharap sa mga mapanghamong kondisyon sa pagpapatakbo, kabilang ang labis na temperatura, kahalumigmigan, mga likido sa katawan, at mekanikal na stress. Dapat protektahan ng mga underfill na materyales ang mga electronic na bahagi, na tinitiyak ang kanilang pangmatagalang pagiging maaasahan at functionality. Ang pagiging maaasahan ay pinakamahalaga sa mga medikal na aplikasyon kung saan ang pagkabigo ng device ay maaaring malubhang makaapekto sa kaligtasan at kapakanan ng pasyente.
Ang mga underfill na materyales para sa mga medikal na elektroniko ay dapat na may mataas na pagtutol sa kahalumigmigan at mga kemikal upang makatiis sa pagkakalantad sa mga likido sa katawan o mga proseso ng isterilisasyon. Dapat din silang magpakita ng mahusay na pagdirikit sa iba't ibang mga substrate, na tinitiyak ang secure na encapsulation ng mga elektronikong bahagi. Ang mga mekanikal na katangian, tulad ng mababang coefficient ng thermal expansion at magandang shock resistance, ay mahalaga sa pagliit ng stress sa mga detalye sa panahon ng thermal cycling o awtomatikong paglo-load.
Ang proseso ng underfill para sa medikal na electronics ay kinabibilangan ng:
- Pagbibigay ng underfill na materyal sa mga elektronikong bahagi.
- Pinuno ang mga puwang.
- Paggamot nito upang bumuo ng isang proteksiyon at mekanikal na matatag na encapsulation.
Dapat gawin ang pangangalaga upang matiyak ang kumpletong saklaw ng mga tampok at ang kawalan ng mga void o air pockets na maaaring makompromiso ang pagiging maaasahan ng device.
Higit pa rito, ang mga karagdagang pagsasaalang-alang ay isinasaalang-alang kapag kulang ang pagpuno ng mga kagamitang medikal. Halimbawa, ang underfill na materyal ay dapat na tugma sa mga pamamaraan ng isterilisasyon na ginagamit para sa device. Maaaring sensitibo ang ilang materyal sa mga partikular na pamamaraan ng isterilisasyon, gaya ng singaw, ethylene oxide, o radiation, at maaaring kailanganing pumili ng mga alternatibong materyales.
Aerospace Electronics Underfill: Mataas na Temperatura at Panlaban sa Vibration
Aerospace electronics underfill ng isang espesyal na proseso upang i-encapsulate at protektahan ang mga electronic na bahagi sa aerospace application. Ang mga kapaligiran sa aerospace ay nagdudulot ng mga natatanging hamon, kabilang ang mataas na temperatura, matinding vibrations, at mga mekanikal na stress. Samakatuwid, ang underfill ng aerospace electronics ay nakatuon sa dalawang mahahalagang aspeto: paglaban sa mataas na temperatura at paglaban sa vibration.
Ang paglaban sa mataas na temperatura ay pinakamahalaga sa aerospace electronics dahil sa mataas na temperatura na naranasan sa panahon ng operasyon. Ang mga underfill na materyales na ginagamit sa mga aplikasyon ng aerospace ay dapat makatiis sa mataas na temperatura na ito nang hindi nakompromiso ang pagganap at pagiging maaasahan ng mga elektronikong bahagi. Dapat silang magpakita ng kaunting thermal expansion at manatiling matatag sa isang malawak na hanay ng temperatura.
Ang mga underfill na materyales para sa aerospace electronics ay pinili o binuo para sa mataas na glass transition temperature (Tg) at thermal stability. Ang isang mataas na Tg ay nagsisiguro na ang materyal ay nagpapanatili ng mga mekanikal na katangian nito sa mataas na temperatura, na pumipigil sa pagpapapangit o pagkawala ng pagdirikit. Ang mga materyales na ito ay maaaring makatiis sa mga sukdulan ng temperatura, tulad ng sa panahon ng pag-alis, muling pagpasok sa atmospera, o pagpapatakbo sa mga mainit na bahagi ng makina.
Bilang karagdagan, ang mga underfill na materyales para sa aerospace electronics ay dapat na may mababang coefficients ng thermal expansion (CTE). Ang CTE ay sumusukat kung gaano kalaki ang isang materyal na lumalawak o kumukontra sa mga pagbabago sa temperatura. Sa pagkakaroon ng mababang CTE, mababawasan ng mga underfill na materyales ang stress sa mga elektronikong bahagi na dulot ng thermal cycling, na maaaring humantong sa mga mekanikal na pagkabigo o solder joint fatigue.
Ang vibration resistance ay isa pang kritikal na kinakailangan para sa aerospace electronics underfill. Ang mga sasakyan sa aerospace ay napapailalim sa iba't ibang vibrations, kabilang ang engine, flight-induced vibrations, at mechanical shocks sa panahon ng paglulunsad o paglapag. Ang mga vibrations na ito ay maaaring mapahamak ang pagganap at pagiging maaasahan ng mga elektronikong bahagi kung hindi sapat na protektado.
Ang mga underfill na materyales na ginagamit sa aerospace electronics ay dapat magpakita ng mahuhusay na katangian ng vibration-damping. Dapat nilang i-absorb at iwaksi ang enerhiya na nalilikha ng mga vibrations, na binabawasan ang stress at strain sa mga elektronikong bahagi. Nakakatulong ito na maiwasan ang pagbuo ng mga bitak, bali, o iba pang mekanikal na pagkabigo dahil sa labis na pagkakalantad sa vibration.
Bukod dito, ang mga underfill na materyales na may mataas na adhesion at cohesive strength ay mas gusto sa mga aerospace application. Tinitiyak ng mga katangiang ito na ang underfill na materyal ay nananatiling matatag na nakagapos sa mga elektronikong bahagi at substrate, kahit na sa ilalim ng matinding kondisyon ng vibration. Pinipigilan ng malakas na pagdirikit ang underfill na materyal mula sa pag-delaminate o paghihiwalay sa mga elemento, pagpapanatili ng integridad ng encapsulation at pagprotekta laban sa moisture o debris na pagpasok.
Ang proseso ng underfill para sa aerospace electronics ay karaniwang nagsasangkot ng dispensing ng underfill na materyal sa mga electronic na bahagi, na nagpapahintulot dito na dumaloy at punan ang mga puwang, at pagkatapos ay i-curing ito upang bumuo ng isang matatag na encapsulation. Ang proseso ng paggamot ay maaaring magawa gamit ang thermal o UV curing na pamamaraan, depende sa mga partikular na kinakailangan ng application.
Automotive Electronics Underfill: Durability at Thermal Cycling Resistance
Ang automotive electronics ay underfill sa isang kritikal na proseso na kinabibilangan ng pag-encapsulate at pagprotekta sa mga electronic na bahagi sa mga automotive na application. Ang mga automotive environment ay nagpapakita ng mga natatanging hamon, kabilang ang mga pagkakaiba-iba ng temperatura, thermal cycling, mechanical stresses, at exposure sa moisture at mga kemikal. Samakatuwid, ang automotive electronics underfill ay nakatuon sa dalawang kritikal na aspeto: tibay at thermal cycling resistance.
Ang tibay ay isang mahalagang kinakailangan para sa underfill ng automotive electronics. Sa regular na operasyon, ang mga sasakyang automotive ay nakakaranas ng patuloy na vibrations, shocks, at mechanical stresses. Ang mga underfill na materyales na ginagamit sa mga automotive na application ay dapat na protektahan ang mga elektronikong bahagi nang matatag, na tinitiyak ang kanilang tibay at mahabang buhay. Dapat nilang mapaglabanan ang malupit na mga kondisyon at mekanikal na kargada na nakatagpo sa kalsada at labanan ang pagpasok ng kahalumigmigan, alikabok, at mga kemikal.
Ang mga underfill na materyales para sa automotive electronics ay pinili o binuo para sa mataas na mekanikal na lakas at impact resistance. Dapat silang magpakita ng mahusay na pagdirikit sa mga elektronikong bahagi at substrate, na pumipigil sa delamination o paghihiwalay sa ilalim ng mga mekanikal na stress. Ang matibay na underfill na materyales ay nakakatulong na mabawasan ang panganib ng pinsala sa mga elektronikong bahagi dahil sa mga vibrations o shocks, na tinitiyak ang maaasahang pagganap sa buong buhay ng sasakyan.
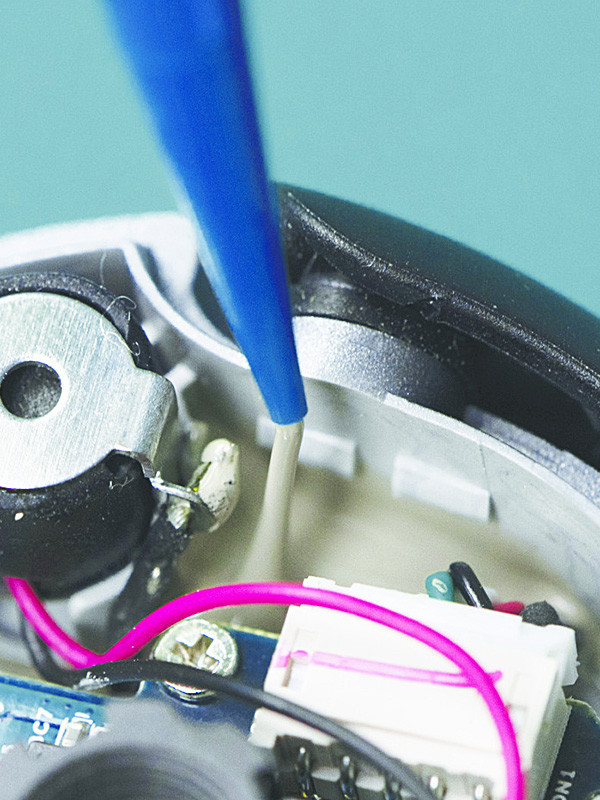
Ang thermal cycling resistance ay isa pang kritikal na kinakailangan para sa automotive electronics underfill. Ang mga sasakyang sasakyan ay dumaranas ng madalas na mga pagkakaiba-iba ng temperatura, lalo na sa panahon ng pagsisimula at pagpapatakbo ng engine, at ang mga ikot ng temperatura na ito ay maaaring magdulot ng mga thermal stress sa mga elektronikong bahagi at ang nakapalibot na underfill na materyal. Ang mga underfill na materyales na ginagamit sa mga automotive application ay dapat na may mahusay na thermal cycling resistance upang mapaglabanan ang mga pagbabago sa temperatura na ito nang hindi nakompromiso ang kanilang pagganap.
Ang mga underfill na materyales para sa automotive electronics ay dapat na may mababang thermal expansion (CTE) coefficient para mabawasan ang stress ng mga electronic component sa panahon ng thermal cycling. Ang isang mahusay na tugmang CTE sa pagitan ng underfill na materyal at ng mga sangkap ay nakakabawas sa panganib ng solder joint fatigue, crack, o iba pang mekanikal na pagkabigo na dulot ng thermal stress. Bukod pa rito, ang mga underfill na materyales ay dapat magpakita ng magandang thermal conductivity upang maalis ang init nang mahusay, na pumipigil sa mga localized hotspot na maaaring makaapekto sa performance at pagiging maaasahan ng mga bahagi.
Bukod dito, ang mga automotive electronics underfill na materyales ay dapat lumaban sa kahalumigmigan, mga kemikal, at mga likido. Dapat silang magkaroon ng mababang pagsipsip ng tubig upang maiwasan ang paglaki ng amag o kaagnasan ng mga elektronikong sangkap. Tinitiyak ng paglaban sa kemikal na ang underfill na materyal ay nananatiling stable kapag nalantad sa mga automotive fluid, gaya ng mga langis, panggatong, o mga ahente sa paglilinis, na iniiwasan ang pagkasira o pagkawala ng adhesion.
Ang proseso ng underfill para sa automotive electronics ay karaniwang nagsasangkot ng dispensing ng underfill na materyal sa mga electronic na bahagi, na nagpapahintulot dito na dumaloy at punan ang mga puwang, at pagkatapos ay i-curing ito upang bumuo ng isang matibay na encapsulation. Ang proseso ng paggamot ay maaaring maisakatuparan sa pamamagitan ng thermal o UV curing na pamamaraan, depende sa mga partikular na kinakailangan ng aplikasyon at ang underfill na materyal na ginamit.
Pagpili ng Tamang Underfill Epoxy
Ang pagpili ng tamang underfill na epoxy ay isang mahalagang desisyon sa pagpupulong at proteksyon ng mga elektronikong bahagi. Ang underfill epoxies ay nagbibigay ng mechanical reinforcement, thermal management, at proteksyon laban sa mga salik sa kapaligiran. Narito ang ilang mahahalagang pagsasaalang-alang kapag pumipili ng naaangkop na underfill na epoxy:
- Thermal Properties: Ang isa sa mga pangunahing function ng underfill epoxy ay ang pag-alis ng init na nalilikha ng mga electronic na bahagi. Samakatuwid, mahalagang isaalang-alang ang thermal conductivity at thermal resistance ng epoxy. Ang mataas na thermal conductivity ay nakakatulong sa mahusay na paglipat ng init, pinipigilan ang mga hotspot at pagpapanatili ng pagiging maaasahan ng bahagi. Ang epoxy ay dapat ding magkaroon ng mababang thermal resistance upang mabawasan ang thermal stress sa mga bahagi habang umiikot sa temperatura.
- Pagtutugma ng CTE: Ang thermal expansion coefficient (CTE) ng underfill na epoxy ay dapat na mahusay na tumugma sa CTE ng mga elektronikong bahagi at substrate upang mabawasan ang thermal stress at maiwasan ang mga pagkabigo ng solder joint. Ang isang malapit na katugmang CTE ay nakakatulong upang mabawasan ang panganib ng mga mekanikal na pagkabigo dahil sa thermal cycling.
- Kakayahang Pagpuno ng Daloy at Gap: Ang hindi napunong epoxy ay dapat magkaroon ng magandang katangian ng daloy at ang kakayahang punan ang mga puwang sa pagitan ng mga bahagi nang epektibo. Tinitiyak nito ang kumpletong coverage at pinapaliit ang mga void o air pockets na maaaring makaapekto sa mechanical stability at thermal performance ng assembly. Ang lagkit ng epoxy ay dapat na angkop para sa partikular na paraan ng aplikasyon at pagpupulong, ito man ay capillary flow, jet dispensing, o screen printing.
- Pagdirikit: Ang malakas na pagdirikit ay mahalaga para sa underfilling epoxy upang matiyak ang maaasahang pagbubuklod sa pagitan ng mga bahagi at ng substrate. Dapat itong magpakita ng mahusay na pagdirikit sa iba't ibang mga materyales, kabilang ang mga metal, keramika, at plastik. Ang mga katangian ng adhesion ng epoxy ay nakakatulong sa mekanikal na integridad ng assembly at pangmatagalang pagiging maaasahan.
- Paraan ng Paggamot: Isaalang-alang ang paraan ng paggamot na pinakaangkop sa iyong proseso ng pagmamanupaktura. Ang underfill epoxies ay maaaring gamutin sa pamamagitan ng init, UV radiation, o kumbinasyon ng dalawa. Ang bawat paraan ng paggamot ay may mga pakinabang at limitasyon, at ang pagpili ng isa na naaayon sa iyong mga kinakailangan sa produksyon ay mahalaga.
- Paglaban sa Kapaligiran: Suriin ang paglaban ng underfill na epoxy sa mga salik sa kapaligiran gaya ng moisture, kemikal, at labis na temperatura. Ang epoxy ay dapat na makatiis sa pagkakalantad sa tubig, na pumipigil sa paglaki ng amag o kaagnasan. Ang paglaban sa kemikal ay nagsisiguro ng katatagan kapag nakikipag-ugnayan sa mga automotive fluid, mga ahente ng paglilinis, o iba pang potensyal na kinakaing unti-unti na mga sangkap. Bukod pa rito, dapat panatilihin ng epoxy ang mga mekanikal at elektrikal na katangian nito sa isang malawak na hanay ng temperatura.
- Pagkakaaasahan at Tagal: Isaalang-alang ang track record at data ng pagiging maaasahan ng underfill na epoxy. Maghanap ng mga materyal na epoxy na nasubok at napatunayang mahusay na gumaganap sa mga katulad na aplikasyon o may mga sertipikasyon sa industriya at pagsunod sa mga nauugnay na pamantayan. Isaalang-alang ang mga salik tulad ng pag-uugali sa pagtanda, pangmatagalang pagiging maaasahan, at kakayahan ng epoxy na mapanatili ang mga katangian nito sa paglipas ng panahon.
Kapag pumipili ng tamang underfill na epoxy, mahalagang isaalang-alang ang mga partikular na kinakailangan ng iyong aplikasyon, kabilang ang thermal management, mekanikal na katatagan, proteksyon sa kapaligiran, at pagiging tugma sa proseso ng pagmamanupaktura. Ang pagkonsulta sa mga supplier ng epoxy o paghingi ng ekspertong payo ay maaaring maging kapaki-pakinabang sa paggawa ng matalinong desisyon na nakakatugon sa mga pangangailangan ng iyong aplikasyon at nagsisiguro ng pinakamainam na pagganap at pagiging maaasahan.
Mga Trend sa Hinaharap sa Underfill Epoxy
Ang underfill epoxy ay patuloy na umuunlad, na hinihimok ng mga pagsulong sa mga elektronikong teknolohiya, mga umuusbong na application, at ang pangangailangan para sa pinahusay na pagganap at pagiging maaasahan. Maraming mga uso sa hinaharap ang maaaring maobserbahan sa pagbuo at paggamit ng underfill epoxy:
- Miniaturization at Mas Mataas na Densidad na Packaging: Habang patuloy na lumiliit ang mga electronic device at nagtatampok ng mas mataas na density ng bahagi, ang mga underfill na epoxies ay dapat na umangkop nang naaayon. Ang mga trend sa hinaharap ay tututuon sa pagbuo ng mga underfill na materyales na tumagos at pumupuno sa mas maliliit na gaps sa pagitan ng mga bahagi, na tinitiyak ang kumpletong saklaw at maaasahang proteksyon sa lalong pinaliit na mga electronic assemblies.
- High-Frequency na Application: Sa lumalaking demand para sa high-frequency at high-speed na electronic device, ang mga underfill na epoxy formulation ay kailangang tugunan ang mga partikular na pangangailangan ng mga application na ito. Ang mga underfill na materyales na may mababang dielectric constant at low loss tangent ay magiging mahalaga upang mabawasan ang pagkawala ng signal at mapanatili ang integridad ng mga high-frequency na signal sa mga advanced na sistema ng komunikasyon, 5G na teknolohiya, at iba pang mga umuusbong na application.
- Pinahusay na Pamamahala ng Thermal: Ang pag-alis ng init ay nananatiling kritikal na alalahanin para sa mga elektronikong aparato, lalo na sa pagtaas ng mga density ng kuryente. Ang hinaharap na underfill epoxy formulation ay tututuon sa pinahusay na thermal conductivity upang mapahusay ang paglipat ng init at epektibong pamahalaan ang mga isyu sa thermal. Ang mga advanced na filler at additives ay isasama sa underfill epoxies upang makamit ang mas mataas na thermal conductivity habang pinapanatili ang iba pang gustong katangian.
- Flexible at Stretchable Electronics: Ang pagtaas ng flexible at stretchable na electronics ay nagbubukas ng mga bagong posibilidad para sa underfilling na materyales ng epoxy. Ang nababaluktot na underfill epoxies ay dapat magpakita ng mahusay na pagdirikit at mekanikal na katangian kahit sa ilalim ng paulit-ulit na pagbaluktot o pag-uunat. Ang mga materyales na ito ay magbibigay-daan sa encapsulation at proteksyon ng mga electronics sa mga naisusuot na device, nababaluktot na mga display, at iba pang mga application na nangangailangan ng mekanikal na kakayahang umangkop.
- Mga Solusyong Pangkalikasan: Ang pagpapanatili at mga pagsasaalang-alang sa kapaligiran ay magkakaroon ng lalong makabuluhang papel sa pagbuo ng mga underfill na materyal na epoxy. Magkakaroon ng pagtutok sa paglikha ng mga epoxy formulation na libre mula sa mga mapanganib na substance at nabawasan ang epekto sa kapaligiran sa kabuuan ng kanilang lifecycle, kabilang ang pagmamanupaktura, paggamit, at pagtatapon. Ang bio-based o renewable na materyales ay maaari ding maging prominente bilang napapanatiling alternatibo.
- Mga Pinahusay na Proseso sa Paggawa: Ang mga trend sa hinaharap sa underfill na epoxy ay tututuon sa mga materyal na katangian at mga pagsulong sa mga proseso ng pagmamanupaktura. Ang mga pamamaraan tulad ng additive manufacturing, selective dispensing, at advanced na mga paraan ng curing ay i-explore para ma-optimize ang application at performance ng underfill epoxy sa iba't ibang proseso ng electronic assembly.
- Pagsasama-sama ng Mga Advanced na Pagsusuri at Mga Teknik sa Pag-characterization: Sa pagtaas ng pagiging kumplikado at mga kinakailangan ng mga elektronikong aparato, magkakaroon ng pangangailangan para sa mga advanced na pamamaraan ng pagsubok at characterization upang matiyak ang pagiging maaasahan at pagganap ng underfilled na epoxy. Ang mga pamamaraan tulad ng hindi mapanirang pagsubok, in-situ na pagsubaybay, at mga tool sa simulation ay tutulong sa pagbuo at kontrol ng kalidad ng mga underfilled na materyales na epoxy.
Konklusyon
Ang underfill epoxy ay gumaganap ng isang kritikal na papel sa pagpapahusay ng pagiging maaasahan at pagganap ng mga electronic na bahagi, lalo na sa semiconductor packaging. Ang iba't ibang uri ng underfill epoxy ay nag-aalok ng hanay ng mga benepisyo, kabilang ang mataas na pagiging maaasahan, self-dispensing, mataas na density, at mataas na thermal at mekanikal na pagganap. Ang pagpili ng tamang underfill na epoxy para sa application at package ay nagsisiguro ng isang matatag at pangmatagalang bono. Habang umuunlad ang teknolohiya at lumiliit ang mga laki ng package, inaasahan namin ang higit pang makabagong mga underfill na solusyon sa epoxy na nag-aalok ng mahusay na pagganap, pagsasama, at miniaturization. Ang underfill epoxy ay nakatakdang gumanap ng lalong mahalagang papel sa hinaharap ng electronics, na nagbibigay-daan sa amin na makamit ang mas mataas na antas ng pagiging maaasahan at pagganap sa iba't ibang industriya.