Underfill Epoxy
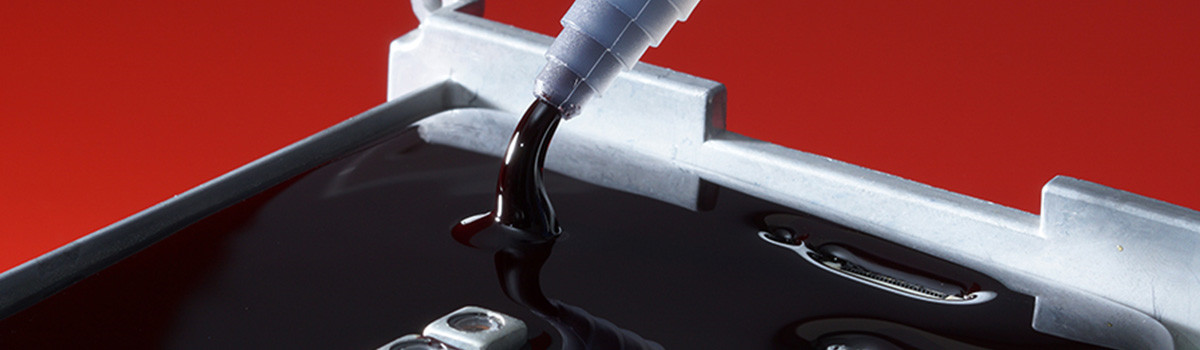
Underfill epoksi je vrsta lepila, ki se uporablja za izboljšanje zanesljivosti elektronskih komponent, zlasti pri pakiranju polprevodnikov. Zapolnjuje vrzel med paketom in tiskanim vezjem (PCB), zagotavlja mehansko podporo in razbremenitev napetosti, da prepreči poškodbe zaradi toplotnega raztezanja in krčenja. Underfill epoksi tudi izboljša električno zmogljivost paketa z zmanjšanjem parazitske induktivnosti in kapacitivnosti. V tem članku raziskujemo različne uporabe epoksi smole za polnilo, različne vrste, ki so na voljo, in njihove prednosti.
Pomen epoksida za polprevodnike v embalaži polprevodnikov
Epoksi za polnilo je ključnega pomena pri embalaži polprevodnikov, saj zagotavlja mehansko ojačitev in zaščito občutljivih mikroelektronskih komponent. To je specializiran lepilni material, ki se uporablja za zapolnjevanje vrzeli med polprevodniškim čipom in substratom paketa, kar povečuje zanesljivost in učinkovitost elektronskih naprav. Tukaj bomo raziskali pomen premalo polnjenega epoksida v embalaži polprevodnikov.
Ena od glavnih funkcij premalo polnjenega epoksida je izboljšanje mehanske trdnosti in zanesljivosti paketa. Med delovanjem so polprevodniški čipi izpostavljeni različnim mehanskim obremenitvam, kot so toplotno raztezanje in krčenje, vibracije in mehanski udarci. Te obremenitve lahko povzročijo nastanek razpok spajkalnih spojev, kar lahko povzroči električne okvare in skrajša celotno življenjsko dobo naprave. Epoksi za polnilo deluje kot sredstvo za zmanjševanje napetosti z enakomerno porazdelitvijo mehanske obremenitve po čipu, substratu in spajkanih spojih. Učinkovito zmanjšuje nastajanje razpok in preprečuje širjenje obstoječih razpok, kar zagotavlja dolgoročno zanesljivost paketa.
Drugi kritični vidik epoksi smole s premajhnim polnilom je njegova sposobnost izboljšanja toplotne učinkovitosti polprevodniških naprav. Odvajanje toplote postane pomembna skrb, saj se elektronske naprave manjšajo in povečujejo gostoto moči, prekomerna toplota pa lahko poslabša delovanje in zanesljivost polprevodniškega čipa. Underfill epoksi ima odlične lastnosti toplotne prevodnosti, kar mu omogoča učinkovit prenos toplote iz čipa in njeno porazdelitev po celotnem paketu. To pomaga vzdrževati optimalne delovne temperature in preprečuje vroče točke ter s tem izboljša splošno toplotno upravljanje naprave.
Podfill epoksi tudi ščiti pred vlago in onesnaževalci. Vdor vlage lahko povzroči korozijo, uhajanje električnega toka in rast prevodnih materialov, kar povzroči okvaro naprave. Underfill epoksi deluje kot pregrada, tesni ranljiva področja in preprečuje vlagi vstop v paket. Ponuja tudi zaščito pred prahom, umazanijo in drugimi onesnaževalci, ki lahko negativno vplivajo na električno zmogljivost polprevodniškega čipa. Z zaščito čipa in njegovih medsebojnih povezav epoksid s premajhnim polnjenjem zagotavlja dolgoročno zanesljivost in funkcionalnost naprave.
Poleg tega premalo napolnjen epoksid omogoča miniaturizacijo polprevodniške embalaže. Zaradi nenehnega povpraševanja po manjših in bolj kompaktnih napravah premalo polnjeni epoksi omogoča uporabo tehnik pakiranja z obračanjem čipov in čipov. Te tehnike vključujejo neposredno montažo čipa na substrat embalaže, s čimer se odpravi potreba po žičnem povezovanju in zmanjša velikost embalaže. Underfill epoksi zagotavlja strukturno podporo in ohranja celovitost vmesnika čip-substrat, kar omogoča uspešno implementacijo teh naprednih tehnologij pakiranja.
Kako se Underfill Epoxy spopada z izzivi
Embalaža polprevodnikov igra ključno vlogo pri delovanju, zanesljivosti in dolgoživosti elektronskih naprav. Vključuje enkapsulacijo integriranih vezij (IC) v zaščitna ohišja, zagotavljanje električnih povezav in odvajanje toplote, ki nastane med delovanjem. Vendar se polprevodniška embalaža sooča z več izzivi, vključno s toplotno obremenitvijo in zvijanjem, kar lahko znatno vpliva na funkcionalnost in zanesljivost zapakiranih naprav.
Eden glavnih izzivov je toplotna obremenitev. Integrirana vezja med delovanjem ustvarjajo toploto, neustrezno odvajanje pa lahko zviša temperature v paketu. Posledica te temperaturne spremembe je toplotna obremenitev, saj se različni materiali v paketu širijo in krčijo z različnimi hitrostmi. Neenakomerno širjenje in krčenje lahko povzroči mehansko obremenitev, kar povzroči okvare spajkalnih spojev, razslojevanje in razpoke. Toplotna obremenitev lahko ogrozi električno in mehansko celovitost paketa, kar na koncu vpliva na delovanje in zanesljivost naprave.
Zvitost je še en kritičen izziv pri pakiranju polprevodnikov. Zvitost se nanaša na upogibanje ali deformacijo substrata embalaže ali celotne embalaže. Pojavi se lahko med postopkom pakiranja ali zaradi toplotne obremenitve. Zvijanje je predvsem posledica neusklajenosti koeficienta toplotnega raztezanja (CTE) med različnimi materiali v embalaži. Na primer, CTE silicijeve matrice, substrata in mase kalupa se lahko bistveno razlikuje. Ko so izpostavljeni temperaturnim spremembam, se ti materiali širijo ali krčijo z različnimi stopnjami, kar povzroči zvijanje.
Warpage predstavlja več težav za polprevodniške pakete:
- Posledica so lahko točke koncentracije napetosti, kar poveča verjetnost mehanskih okvar in zmanjša zanesljivost škatle.
- Zvitost lahko povzroči težave v procesu sestavljanja, saj vpliva na poravnavo paketa z drugimi komponentami, kot je tiskano vezje (PCB). Ta neporavnanost lahko poslabša električne povezave in povzroči težave z delovanjem.
- Zvitost lahko vpliva na celotno obliko paketa, zaradi česar je integracija naprave v aplikacije majhne oblike ali gosto poseljena tiskana vezja zahtevna.
Za reševanje teh izzivov se v embalaži polprevodnikov uporabljajo različne tehnike in strategije. Ti vključujejo uporabo naprednih materialov z ustreznimi CTE za zmanjšanje toplotne obremenitve in zvijanja. Termomehanske simulacije in modeliranje se izvajajo za napovedovanje obnašanja embalaže v različnih toplotnih pogojih. Spremembe načrta, kot je uvedba struktur za razbremenitev napetosti in optimizirane postavitve, so izvedene za zmanjšanje toplotne obremenitve in zvijanja. Poleg tega razvoj izboljšanih proizvodnih procesov in opreme pomaga zmanjšati pojav zvijanja med sestavljanjem.
Prednosti epoksi smole Underfill
Epoksi pod polnilom je kritična komponenta polprevodniške embalaže, ki ponuja številne prednosti. Ta specializirani epoksi material se nanese med polprevodniški čip in substrat paketa, zagotavlja mehansko ojačitev in obravnava različne izzive. Tukaj je nekaj kritičnih prednosti premalo polnjenega epoksida:
- Izboljšana mehanska zanesljivost: Ena od glavnih prednosti epoksi smole s premajhnim polnilom je njegova sposobnost izboljšanja mehanske zanesljivosti polprevodniških paketov. Underfill epoksi ustvari kohezivno vez, ki izboljša celotno strukturno celovitost tako, da zapolni vrzeli in praznine med čipom in substratom. To pomaga preprečevati zvijanje embalaže, zmanjšuje tveganje mehanskih okvar in povečuje odpornost na zunanje obremenitve, kot so vibracije, udarci in termični cikli. Izboljšana mehanska zanesljivost vodi do povečane vzdržljivosti izdelka in daljše življenjske dobe naprave.
- Odvajanje toplotnih obremenitev: epoksid za polnilo pomaga pri odvajanju toplotnih obremenitev znotraj paketa. Integrirana vezja med delovanjem ustvarjajo toploto, neustrezno odvajanje pa lahko povzroči nihanje temperature v posodi. Epoksi material pod polnilom z nižjim koeficientom toplotnega raztezanja (CTE) v primerjavi z materiali za čipe in podlago deluje kot vmesni sloj. Absorbira mehanske obremenitve, ki jih povzroča toplotna obremenitev, s čimer se zmanjša tveganje za okvare spajkalnih spojev, razslojevanje in razpoke. Z razpršitvijo toplotne obremenitve premalo polnjeni epoksi pomaga ohranjati električno in mehansko celovitost paketa.
- Izboljšana električna zmogljivost: Underfill epoksi pozitivno vpliva na električno zmogljivost polprevodniških naprav. Epoksi material zapolni vrzeli med čipom in substratom ter zmanjša parazitsko kapacitivnost in induktivnost. Posledica tega je izboljšana celovitost signala, zmanjšane izgube signala in izboljšana električna povezljivost med čipom in ostalim paketom. Zmanjšani parazitski učinki prispevajo k boljši električni zmogljivosti, višji hitrosti prenosa podatkov in povečani zanesljivosti naprave. Poleg tega premalo polnjeni epoksid zagotavlja izolacijo in zaščito pred vlago, onesnaževalci in drugimi okoljskimi dejavniki, ki lahko poslabšajo električno zmogljivost.
- Razbremenitev in izboljšano sestavljanje: epoksidna smola deluje kot mehanizem za razbremenitev med sestavljanjem. Epoksi material kompenzira neusklajenost CTE med čipom in substratom, kar zmanjša mehansko obremenitev med temperaturnimi spremembami. Zaradi tega je postopek sestavljanja bolj zanesljiv in učinkovit, kar zmanjša tveganje za poškodbe paketa ali neporavnanost. Nadzorovana porazdelitev obremenitev, ki jo zagotavlja epoksid s premajhnim polnilom, prav tako pomaga zagotoviti pravilno poravnavo z drugimi komponentami na tiskanem vezju (PCB) in izboljša celoten izkoristek sestavljanja.
- Miniaturizacija in optimizacija faktorja oblike: Epoxy Underfill omogoča miniaturizacijo paketov polprevodnikov in optimizacijo faktorja oblike. Z zagotavljanjem strukturne ojačitve in razbremenitvijo napetosti epoksid s premajhnim polnilom omogoča načrtovanje in proizvodnjo manjših, tanjših in bolj kompaktnih paketov. To je še posebej pomembno za aplikacije, kot so mobilne naprave in nosljiva elektronika, kjer je prostor omejen. Zmožnost optimizacije faktorjev oblike in doseganja večje gostote komponent prispeva k naprednejšim in inovativnejšim elektronskim napravam.
Vrste epoksi smole za polnilo
V polprevodniških embalažah je na voljo več vrst epoksidnih formulacij pod polnilom, od katerih je vsaka zasnovana tako, da izpolnjuje posebne zahteve in obravnava različne izzive. Tukaj je nekaj pogosto uporabljenih vrst epoksi smole za polnilo:
- Epoksi za kapilarno polnilo: Epoksi za kapilarno polnilo je najbolj tradicionalna in pogosto uporabljena vrsta. Epoksi z nizko viskoznostjo teče v režo med čipom in podlago s kapilarnim delovanjem. Kapilarna polnila se običajno nanesejo na rob čipa in ko se embalaža segreje, epoksi steče pod čipom in zapolni praznine. Ta vrsta spodnjega polnila je primerna za pakete z majhnimi režami in zagotavlja dobro mehansko ojačitev.
- No-Flow Underfill epoksi: No-flow underfill epoksi je formula z visoko viskoznostjo, ki med strjevanjem ne teče. Nanaša se kot predhodno nanešen epoksi ali kot film med čipom in podlago. Epoksid brez pretoka pod polnilom je še posebej uporaben za ohišja s preklopnimi čipi, kjer spajkalne izbokline neposredno vplivajo na podlago. Odpravlja potrebo po kapilarnem pretoku in zmanjšuje tveganje poškodbe spajkalnega spoja med montažo.
- Podpolnilo na ravni rezin (WLU): Podpolnilo na ravni rezin je epoksid za podpolnitev, ki se nanese na ravni rezin, preden se posamezni čipi izolirajo. Vključuje doziranje materiala za polnilo po celotni površini rezin in njegovo strjevanje. Podpolnjenje na ravni oblatov nudi več prednosti, vključno z enakomerno pokritostjo spodnjega polnila, skrajšanim časom sestavljanja in izboljšanim nadzorom procesa. Običajno se uporablja za velikoserijsko proizvodnjo majhnih naprav.
- Ulito podpolnilo (MUF): Ulito podpolnilo je epoksi podpolnilo, ki se nanese med vlivanjem v kapsulo. Material za polnilo se nanese na substrat, nato pa se odrezki in substrat inkapsulirajo v zmes za kalupe. Med oblikovanjem epoksid teče in zapolnjuje vrzel med čipom in substratom, kar zagotavlja podpolnitev in inkapsulacijo v enem koraku. Oblikovano spodnje polnilo nudi odlično mehansko ojačitev in poenostavlja postopek montaže.
- Neprevodno polnilo (NCF): Neprevodno epoksidno polnilo je posebej oblikovano za zagotavljanje električne izolacije med spajkanimi spoji na čipu in substratom. Vsebuje izolacijska polnila ali dodatke, ki preprečujejo električno prevodnost. NCF se uporablja v aplikacijah, kjer je zaskrbljujoč električni kratki stik med sosednjimi spajkanimi spoji. Ponuja mehansko ojačitev in električno izolacijo.
- Toplotno prevodno podpolnilo (TCU): Toplotno prevodno podpolnilo epoksi je zasnovano za izboljšanje zmogljivosti odvajanja toplote paketa. Vsebuje toplotno prevodna polnila, kot so keramični ali kovinski delci, ki izboljšajo toplotno prevodnost materiala pod polnilom. TCU se uporablja v aplikacijah, kjer je učinkovit prenos toplote ključnega pomena, kot so naprave z visoko močjo ali tiste, ki delujejo v zahtevnih toplotnih okoljih.
To je le nekaj primerov različnih vrst epoksi smole za polnilo, ki se uporablja v embalaži polprevodnikov. Izbira ustreznega epoksida za polnilo je odvisna od dejavnikov, kot so zasnova paketa, postopek sestavljanja, toplotne zahteve in električni vidiki. Vsak epoksid za polnilo ponuja posebne prednosti in je prilagojen edinstvenim potrebam različnih aplikacij.
Kapilarna podpolnitev: nizka viskoznost in visoka zanesljivost
Kapilarno premajhno polnjenje se nanaša na postopek, ki se uporablja v industriji polprevodniške embalaže za povečanje zanesljivosti elektronskih naprav. Vključuje zapolnjevanje vrzeli med mikroelektronskim čipom in njegovim okoliškim paketom s tekočim materialom z nizko viskoznostjo, običajno smolo na osnovi epoksida. Ta material za polnilo zagotavlja strukturno podporo, izboljša odvajanje toplote in ščiti čip pred mehanskimi obremenitvami, vlago in drugimi okoljskimi dejavniki.
Ena od kritičnih lastnosti kapilarnega polnila je njegova nizka viskoznost. Material za polnilo je oblikovan tako, da ima sorazmerno nizko gostoto, kar mu omogoča, da zlahka teče v ozke reže med čipom in paketom med postopkom polnjenja. To zagotavlja, da lahko material pod polnilom učinkovito prodre in zapolni vse praznine in zračne reže, kar zmanjša tveganje za nastanek praznin in izboljša splošno celovitost vmesnika čip-paket.
Nizko viskozni materiali za kapilarno polnilo ponujajo tudi številne druge prednosti. Prvič, olajšajo učinkovit pretok materiala pod čipom, kar vodi do skrajšanega časa postopka in povečanega pretoka proizvodnje. To je še posebej pomembno v okoljih velike količine proizvodnje, kjer sta čas in stroškovna učinkovitost kritični.
Drugič, nizka viskoznost omogoča boljše omočilne in adhezijske lastnosti materiala za polnilo. Omogoča, da se material enakomerno porazdeli in oblikuje močne vezi s čipom in paketom, kar ustvarja zanesljivo in robustno inkapsulacijo. To zagotavlja, da je čip varno zaščiten pred mehanskimi obremenitvami, kot so termični cikli, udarci in vibracije.
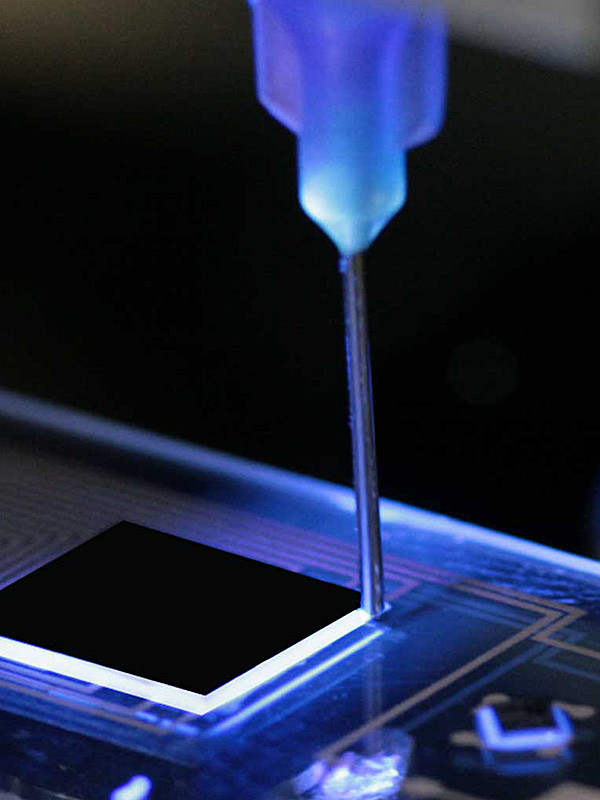
Še en pomemben vidik kapilarnih polnil je njihova visoka zanesljivost. Materiali za polnilo z nizko viskoznostjo so posebej zasnovani tako, da kažejo odlično toplotno stabilnost, električne izolacijske lastnosti ter odpornost proti vlagi in kemikalijam. Te značilnosti so bistvene za zagotavljanje dolgoročne učinkovitosti in zanesljivosti pakiranih elektronskih naprav, zlasti v zahtevnih aplikacijah, kot so avtomobilska, vesoljska in telekomunikacijska industrija.
Poleg tega so materiali za kapilarno polnilo zasnovani tako, da imajo visoko mehansko trdnost in odličen oprijem na različne substratne materiale, vključno s kovinami, keramiko in organskimi materiali, ki se običajno uporabljajo v embalaži polprevodnikov. To omogoča, da material pod polnilom deluje kot blažilnik napetosti, ki učinkovito absorbira in razprši mehanske napetosti, ki nastanejo med delovanjem ali izpostavljenostjo okolju.
No-Flow Underfill: samodoziranje in visoka zmogljivost
No-flow underfill specializiran postopek, ki se uporablja v industriji polprevodniške embalaže za povečanje zanesljivosti in učinkovitosti elektronskih naprav. Za razliko od kapilarnih spodnjih polnil, ki temeljijo na pretoku materialov z nizko viskoznostjo, podporna polnila brez pretoka uporabljajo pristop samodoziranja z materiali z visoko viskoznostjo. Ta metoda ponuja več prednosti, vključno s samoporavnavo, visoko prepustnostjo in izboljšano zanesljivostjo.
Ena od kritičnih lastnosti polnila brez pretoka je njegova sposobnost samodoziranja. Material za polnilo, ki se uporablja v tem procesu, je formuliran z višjo viskoznostjo, kar mu preprečuje prost pretok. Namesto tega se material pod polnilom nadzorovano razdeli na vmesnik čip-paket. To nadzorovano doziranje omogoča natančno namestitev materiala za polnilo in zagotavlja, da se nanese samo na želena področja brez prelivanja ali nenadzorovanega širjenja.
Samodozirna narava polnila brez pretoka nudi številne prednosti. Prvič, omogoča samoporavnavo materiala za polnilo. Ko se podpolnilo razdeli, se naravno samo poravna s čipom in paketom ter enakomerno zapolni vrzeli in praznine. To odpravlja potrebo po natančnem pozicioniranju in poravnavi čipa med postopkom polnjenja, kar prihrani čas in trud pri izdelavi.
Drugič, funkcija samodoziranja spodnjih polnil brez pretoka omogoča visoko zmogljivost v proizvodnji. Postopek doziranja je mogoče avtomatizirati, kar omogoča hitro in dosledno nanašanje materiala za polnilo na več čipov hkrati. To izboljša splošno proizvodno učinkovitost in zmanjša proizvodne stroške, zaradi česar je še posebej ugoden za proizvodna okolja z velikimi količinami.
Poleg tega so materiali za polnilo brez pretoka zasnovani tako, da zagotavljajo visoko zanesljivost. Materiali za polnilo z visoko viskoznostjo nudijo izboljšano odpornost na termično kroženje, mehanske obremenitve in okoljske dejavnike, kar zagotavlja dolgoročno delovanje pakiranih elektronskih naprav. Materiali izkazujejo odlično toplotno stabilnost, električne izolacijske lastnosti ter odpornost na vlago in kemikalije, kar prispeva k splošni zanesljivosti naprav.
Poleg tega imajo materiali za polnilo z visoko viskoznostjo, ki se uporabljajo pri polnilu brez pretoka, izboljšano mehansko trdnost in adhezijske lastnosti. Tvorijo močne vezi s čipom in paketom ter učinkovito absorbirajo in razpršijo mehanske obremenitve, ki nastanejo med delovanjem ali izpostavljenostjo okolju. To pomaga zaščititi čip pred morebitnimi poškodbami in poveča odpornost naprave na zunanje udarce in tresljaje.
Ulito spodnje polnilo: visoka zaščita in integracija
Ulito spodnje polnilo je napredna tehnika, ki se uporablja v industriji polprevodniške embalaže za zagotavljanje visoke ravni zaščite in integracije za elektronske naprave. Vključuje inkapsulacijo celotnega čipa in njegove okolice z zmesjo kalupa, ki vsebuje material za polnilo. Ta postopek nudi pomembne prednosti glede zaščite, integracije in splošne zanesljivosti.
Ena od ključnih prednosti oblikovanega spodnjega polnila je njegova sposobnost zagotavljanja celovite zaščite za čip. Masa kalupa, uporabljena v tem procesu, deluje kot robustna pregrada, ki zapre celoten čip in paket v zaščitni ovoj. To zagotavlja učinkovito zaščito pred okoljskimi dejavniki, kot so vlaga, prah in onesnaževalci, ki bi lahko vplivali na delovanje in zanesljivost naprave. Enkapsulacija prav tako pomaga preprečevati čip pred mehanskimi obremenitvami, toplotnimi cikli in drugimi zunanjimi silami, kar zagotavlja njegovo dolgotrajno vzdržljivost.
Poleg tega ulito spodnje polnilo omogoča visoko stopnjo integracije znotraj polprevodniškega paketa. Material za polnilo se vmeša neposredno v zmes kalupa, kar omogoča brezhibno integracijo postopkov polnila in kapsulacije. Ta integracija odpravlja potrebo po ločenem koraku premajhnega polnjenja, kar poenostavi proizvodni proces in zmanjša proizvodni čas in stroške. Zagotavlja tudi dosledno in enakomerno porazdelitev spodnjega polnila po celotni embalaži, kar zmanjšuje praznine in povečuje splošno strukturno celovitost.
Poleg tega oblikovano spodnje polnilo ponuja odlične lastnosti toplotne disipacije. Zmes kalupa je zasnovana tako, da ima visoko toplotno prevodnost, kar ji omogoča učinkovit prenos toplote stran od čipa. To je ključnega pomena za vzdrževanje optimalne delovne temperature naprave in preprečevanje pregrevanja, ki lahko povzroči poslabšanje delovanja in težave z zanesljivostjo. Izboljšane lastnosti odvajanja toplote oblikovanega spodnjega polnila prispevajo k splošni zanesljivosti in dolgoživosti elektronske naprave.
Poleg tega ulito spodnje polnilo omogoča večjo miniaturizacijo in optimizacijo faktorja oblike. Postopek enkapsulacije je mogoče prilagoditi za različne velikosti in oblike paketov, vključno s kompleksnimi 3D strukturami. Ta prilagodljivost omogoča integracijo več čipov in drugih komponent v kompakten, prostorsko učinkovit paket. Zaradi zmožnosti doseganja višjih stopenj integracije brez ogrožanja zanesljivosti je ulito spodnje polnilo še posebej dragoceno v aplikacijah, kjer so omejitve velikosti in teže kritične, kot so mobilne naprave, nosljivi izdelki in avtomobilska elektronika.
Podpolnitev paketa čipov (CSP): miniaturizacija in visoka gostota
Chip Scale Package (CSP) underfill je kritična tehnologija, ki omogoča miniaturizacijo in integracijo elektronskih naprav z visoko gostoto. Ker se elektronske naprave še vedno manjšajo v velikosti, hkrati pa zagotavljajo večjo funkcionalnost, CSP premalo igra ključno vlogo pri zagotavljanju zanesljivosti in zmogljivosti teh kompaktnih naprav.
CSP je tehnologija pakiranja, ki omogoča, da se polprevodniški čip neposredno namesti na podlago ali tiskano vezje (PCB), ne da bi potrebovali dodatno embalažo. To odpravlja potrebo po tradicionalni plastični ali keramični posodi, kar zmanjša celotno velikost in težo naprave. CSP underfill postopek, pri katerem se za zapolnitev vrzeli med čipom in substratom uporablja tekočina ali material za kapsuliranje, ki zagotavlja mehansko podporo in zaščito čipa pred okoljskimi dejavniki, kot sta vlaga in mehanske obremenitve.
Miniaturizacija je dosežena s premajhnim polnjenjem CSP z zmanjšanjem razdalje med čipom in podlago. Material za polnilo zapolni ozko režo med čipom in podlago, s čimer ustvari trdno vez in izboljša mehansko stabilnost čipa. To omogoča manjše in tanjše naprave, kar omogoča pakiranje več funkcionalnosti v omejen prostor.
Integracija z visoko gostoto je še ena prednost CSP underfill. Z odpravo potrebe po ločenem paketu CSP omogoča namestitev čipa bližje drugim komponentam na tiskanem vezju, kar zmanjša dolžino električnih povezav in izboljša integriteto signala. Material za polnilo deluje tudi kot toplotni prevodnik in učinkovito odvaja toploto, ki jo proizvaja čip. Ta zmožnost toplotnega upravljanja omogoča večjo gostoto moči, kar omogoča integracijo kompleksnejših in zmogljivejših čipov v elektronske naprave.
Materiali za polnilo CSP morajo imeti posebne lastnosti, da izpolnjujejo zahteve po miniaturizaciji in integraciji z visoko gostoto. Imeti morajo nizko viskoznost, da olajšajo zapolnjevanje ozkih rež, kot tudi odlično pretočnost, da zagotovijo enakomerno pokritost in odpravijo praznine. Materiali morajo imeti tudi dober oprijem na čip in podlago, kar zagotavlja trdno mehansko podporo. Poleg tega morajo imeti visoko toplotno prevodnost za učinkovit prenos toplote stran od čipa.
CSP Underfill na ravni rezin: stroškovno učinkovit in visok izkoristek
Nezadostno polnjenje paketa z lestvico rezin (WLCSP) je stroškovno učinkovita tehnika pakiranja z visokim izkoristkom, ki ponuja številne prednosti pri učinkovitosti proizvodnje in splošni kakovosti izdelka. WLCSP underfill nanese material za podpolnitev na več čipov hkrati, medtem ko so še vedno v obliki rezin, preden so ločeni v posamezne pakete. Ta pristop ponuja številne prednosti glede znižanja stroškov, izboljšanega nadzora procesa in višjih proizvodnih donosov.
Ena od ključnih prednosti WLCSP underfill je njegova stroškovna učinkovitost. Uporaba materiala za polnilo na nivoju rezin naredi postopek pakiranja bolj poenostavljen in učinkovit. Premalo napolnjen material se na rezino nanese z nadzorovanim in avtomatiziranim postopkom, kar zmanjša odpad materiala in zmanjša stroške dela. Poleg tega odprava individualnega ravnanja s paketi in korakov poravnave skrajša celoten proizvodni čas in zapletenost, kar povzroči znatne prihranke pri stroških v primerjavi s tradicionalnimi metodami pakiranja.
Poleg tega WLCSP underfill nudi izboljšan nadzor procesa in višje proizvodne donose. Ker se material za polnilo nanese na ravni rezin, omogoča boljši nadzor nad postopkom doziranja, kar zagotavlja dosledno in enotno pokritost s spodnjim polnilom za vsak čip na rezini. To zmanjša tveganje za nastanek praznin ali nepopolnega premajhnega polnjenja, kar lahko povzroči težave z zanesljivostjo. Zmožnost pregledovanja in testiranja kakovosti premajhnega polnjenja na ravni rezin omogoča tudi zgodnje odkrivanje napak ali variacij procesa, kar omogoča pravočasne korektivne ukrepe in zmanjšuje verjetnost napačnih paketov. Kot rezultat, WLCSP underfill pomaga doseči višje proizvodne donose in boljšo splošno kakovost izdelka.
Pristop na ravni rezin omogoča tudi izboljšano toplotno in mehansko učinkovitost. Material za polnilo, ki se uporablja v WLCSP, je običajno nizko viskozen, kapilarno tekoč material, ki lahko učinkovito zapolni ozke vrzeli med čipi in rezino. To zagotavlja trdno mehansko podporo za čipe, kar povečuje njihovo odpornost na mehanske obremenitve, vibracije in temperaturne cikle. Poleg tega material pod polnilom deluje kot toplotni prevodnik, kar olajša odvajanje toplote, ki jo ustvarijo čipi, s čimer se izboljša upravljanje toplote in zmanjša tveganje pregrevanja.
Flip Chip Underfill: visoka V/I gostota in zmogljivost
Flip chip underfill je kritična tehnologija, ki omogoča visoko gostoto vhoda/izhoda (I/O) in izjemno zmogljivost v elektronskih napravah. Ima ključno vlogo pri povečanju zanesljivosti in funkcionalnosti embalaže flip-chip, ki se pogosto uporablja v naprednih polprevodniških aplikacijah. Ta članek bo raziskal pomen premajhnega polnjenja flip chip in njegov vpliv na doseganje visoke gostote V/I in zmogljivosti.
Tehnologija flip chip vključuje neposredno električno povezavo integriranega vezja (IC) ali polprevodniške matrice s substratom, kar odpravlja potrebo po žični vezavi. Posledica tega je bolj kompakten in učinkovit paket, saj so V/I ploščice nameščene na spodnji površini matrice. Vendar pa embalaža s preklopnimi čipi predstavlja edinstvene izzive, ki jih je treba obravnavati, da zagotovimo optimalno delovanje in zanesljivost.
Eden od ključnih izzivov pri pakiranju flip čipov je preprečevanje mehanskih obremenitev in toplotnega neskladja med matrico in substratom. Med proizvodnim procesom in kasnejšim delovanjem lahko razlike v koeficientih toplotnega raztezanja (CTE) med matrico in substratom povzročijo znatno obremenitev, kar povzroči poslabšanje delovanja ali celo okvaro. Flip chip underfill je zaščitni material, ki oklepa čip, zagotavlja mehansko podporo in razbremenitev. Učinkovito porazdeli napetosti, ki nastanejo med termičnim kroženjem, in prepreči, da bi vplivale na občutljive medsebojne povezave.
Visoka gostota V/I je kritična v sodobnih elektronskih napravah, kjer so bistvenega pomena manjše oblike in večja funkcionalnost. Flip chip underfill omogoča večjo gostoto V/I s ponudbo vrhunske električne izolacije in zmožnosti upravljanja toplote. Material za polnilo zapolnjuje vrzel med matrico in substratom, ustvarja robusten vmesnik in zmanjšuje tveganje kratkega stika ali uhajanja električnega toka. To omogoča večji razmik med V/I ploščicami, kar ima za posledico večjo gostoto V/I brez žrtvovanja zanesljivosti.
Poleg tega flip chip underfill prispeva k izboljšani električni učinkovitosti. Zmanjša električne parazite med matrico in substratom, zmanjša zakasnitev signala in izboljša celovitost signala. Material pod polnilom ima tudi odlične lastnosti toplotne prevodnosti, saj učinkovito odvaja toploto, ki jo ustvari čip med delovanjem. Učinkovito odvajanje toplote zagotavlja, da temperatura ostane v sprejemljivih mejah, preprečuje pregrevanje in ohranja optimalno delovanje.
Napredek pri materialih za polnilo flip chip je omogočil še višje gostote V/I in ravni zmogljivosti. Nanokompozitna podpolnila, na primer, izkoriščajo polnila v nanometrskem merilu za povečanje toplotne prevodnosti in mehanske trdnosti. To omogoča izboljšano odvajanje toplote in zanesljivost, kar omogoča naprave z večjo zmogljivostjo.
Podpolnilo s kroglično mrežo (BGA): visoka toplotna in mehanska zmogljivost
Ball Grid Array (BGA) izpolnjuje kritično tehnologijo, ki ponuja visoko toplotno in mehansko zmogljivost v elektronskih napravah. Ima ključno vlogo pri povečanju zanesljivosti in funkcionalnosti paketov BGA, ki se pogosto uporabljajo v različnih aplikacijah. V tem članku bomo raziskali pomen nezadostnega polnjenja BGA in njegov vpliv na doseganje visoke toplotne in mehanske učinkovitosti.
Tehnologija BGA vključuje zasnovo ohišja, kjer je integrirano vezje (IC) ali polprevodniška matrica nameščena na substrat, električne povezave pa so izvedene prek niza spajkalnih kroglic, ki se nahajajo na spodnji površini ohišja. BGA zapolni material, razporejen v režo med matrico in substratom, inkapsulira spajkalne kroglice ter zagotavlja mehansko podporo in zaščito sklopa.
Eden kritičnih izzivov pri embalaži BGA je obvladovanje toplotnih obremenitev. Med delovanjem IC ustvarja toploto, toplotno raztezanje in krčenje pa lahko povzročita znaten pritisk na spajkalne spoje, ki povezujejo matrico in podlago. BGA ima premalo ključno vlogo pri zmanjševanju teh napetosti z oblikovanjem trdne vezi z matrico in substratom. Deluje kot blažilnik napetosti, absorbira toplotno raztezanje in krčenje ter zmanjšuje obremenitev spajkalnih spojev. To pomaga izboljšati splošno zanesljivost paketa in zmanjša tveganje za okvare spajkalnih spojev.
Drugi kritični vidik nezadostnega polnjenja BGA je njegova sposobnost izboljšanja mehanske učinkovitosti paketa. Paketi BGA so med rokovanjem, sestavljanjem in delovanjem pogosto izpostavljeni mehanskim obremenitvam. Material za polnilo zapolnjuje vrzel med matrico in substratom ter zagotavlja strukturno podporo in ojačitev spajkalnih spojev. To izboljša celotno mehansko trdnost sklopa, zaradi česar je bolj odporen na mehanske udarce, vibracije in druge zunanje sile. Z učinkovito porazdelitvijo mehanskih obremenitev BGA underfill pomaga preprečiti pokanje paketa, razslojevanje ali druge mehanske okvare.
Visoka toplotna zmogljivost je bistvenega pomena pri elektronskih napravah za zagotovitev pravilne funkcionalnosti in zanesljivosti. Materiali za polnilo BGA so zasnovani tako, da imajo odlične lastnosti toplotne prevodnosti. To jim omogoča, da učinkovito prenašajo toploto stran od matrice in jo porazdelijo po substratu, s čimer izboljšajo splošno toplotno upravljanje embalaže. Učinkovito odvajanje toplote pomaga vzdrževati nižje delovne temperature, preprečuje vroče točke in morebitno poslabšanje delovanja. Prav tako prispeva k dolgoživosti škatle z zmanjšanjem toplotne obremenitve komponent.
Napredek pri materialih za polnilo BGA je privedel do še višje toplotne in mehanske učinkovitosti. Izboljšane formulacije in polnilni materiali, kot so nanokompoziti ali polnila z visoko toplotno prevodnostjo, so omogočili boljše odvajanje toplote in mehansko trdnost, s čimer so dodatno izboljšali učinkovitost paketov BGA.
Quad Flat Package (QFP) Underfill: veliko število V/I in robustnost
Quad Flat Package (QFP) je paket integriranih vezij (IC), ki se pogosto uporablja v elektroniki. Ima kvadratno ali pravokotno obliko z vodniki, ki se raztezajo z vseh štirih strani in zagotavljajo številne vhodno/izhodne (I/O) povezave. Za povečanje zanesljivosti in robustnosti paketov QFP se običajno uporabljajo materiali za polnilo.
Underfill je zaščitni material, ki se nanese med IC in podlago za okrepitev mehanske trdnosti spajkalnih spojev in prepreči okvare zaradi napetosti. Še posebej je ključnega pomena za QFP-je z velikim številom V/I, saj lahko veliko število povezav privede do znatnih mehanskih obremenitev med termičnimi cikli in pogoji delovanja.
Material za polnilo, ki se uporablja za pakete QFP, mora imeti posebne lastnosti, da se zagotovi robustnost. Prvič, imeti mora odličen oprijem tako na IC kot na podlago, da se ustvari močna vez in zmanjša tveganje razslojevanja ali ločitve. Poleg tega mora imeti nizek koeficient toplotnega raztezanja (CTE), da se ujema s CTE IC in podlage, kar zmanjša neskladje napetosti, ki bi lahko povzročilo razpoke ali zlome.
Poleg tega mora imeti material za polnilo dobre pretočne lastnosti, da zagotovi enakomerno pokritost in popolno zapolnitev vrzeli med IC in substratom. To pomaga pri odpravljanju praznin, ki lahko oslabijo spajkalne spoje in povzročijo zmanjšano zanesljivost. Material mora imeti tudi dobre lastnosti utrjevanja, kar mu omogoča, da po nanosu tvori trdo in trajno zaščitno plast.
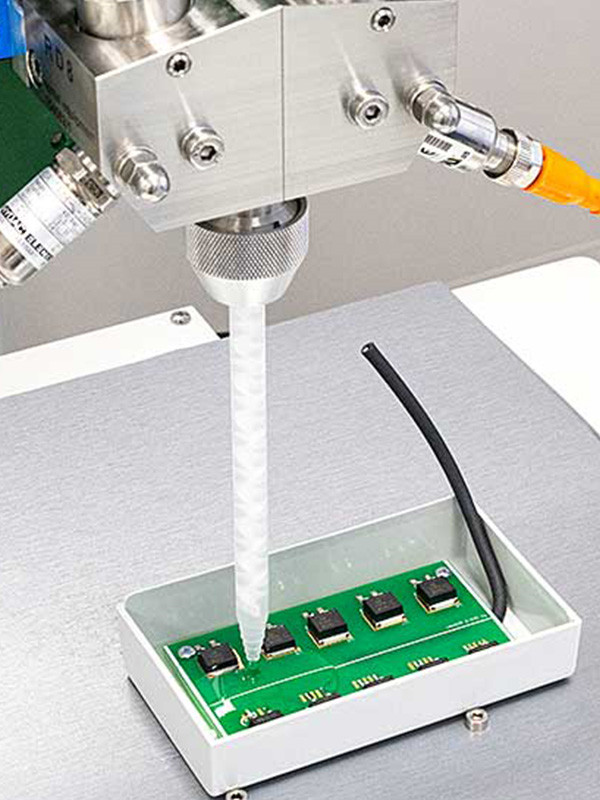
Kar zadeva mehansko robustnost, mora imeti podpolnilo visoko strižno trdnost in trdnost pri lupljenju, da prenese zunanje sile in prepreči deformacijo ali ločevanje paketa. Prav tako mora biti odporen proti vlagi in drugim okoljskim dejavnikom, da ohrani svoje zaščitne lastnosti skozi čas. To je še posebej pomembno pri aplikacijah, kjer je paket QFP lahko izpostavljen težkim pogojem ali temperaturnim nihanjem.
Za dosego teh želenih lastnosti so na voljo različni materiali za polnilo, vključno s formulacijami na osnovi epoksida. Odvisno od posebnih zahtev aplikacije je mogoče te materiale razdeliti z različnimi tehnikami, kot so kapilarni tok, brizganje ali sitotisk.
Sistem v paketu (SiP) Underfill: integracija in zmogljivost
System-in-Package (SiP) je napredna tehnologija pakiranja, ki vključuje več polprevodniških čipov, pasivnih komponent in drugih elementov v en sam paket. SiP ponuja številne prednosti, vključno z zmanjšanim faktorjem oblike, izboljšano električno zmogljivostjo in izboljšano funkcionalnostjo. Za zagotovitev zanesljivosti in učinkovitosti sklopov SiP se običajno uporabljajo materiali za polnilo.
Underfill v aplikacijah SiP je ključnega pomena za zagotavljanje mehanske stabilnosti in električne povezave med različnimi komponentami znotraj paketa. Pomaga zmanjšati tveganje za okvare zaradi napetosti, kot so razpoke ali zlomi spajkalnih spojev, do katerih lahko pride zaradi razlik v koeficientih toplotnega raztezanja (CTE) med komponentami.
Vključevanje več komponent v paket SiP vodi do kompleksne medsebojne povezljivosti s številnimi spajkanimi spoji in vezjem z visoko gostoto. Materiali za polnilo pomagajo okrepiti te medsebojne povezave, s čimer povečajo mehansko trdnost in zanesljivost sklopa. Podpirajo spajkalne spoje in zmanjšujejo tveganje za utrujenost ali poškodbe zaradi termičnega cikliranja ali mehanske obremenitve.
Kar zadeva električno zmogljivost, so materiali za polnilo ključnega pomena pri izboljšanju celovitosti signala in zmanjševanju električnega šuma. Z zapolnitvijo vrzeli med komponentami in zmanjšanjem razdalje med njimi premajhno polnjenje pomaga zmanjšati parazitsko kapacitivnost in induktivnost, kar omogoča hitrejši in učinkovitejši prenos signala.
Poleg tega morajo imeti materiali za polnilo za aplikacije SiP odlično toplotno prevodnost za učinkovito odvajanje toplote, ki jo ustvarjajo integrirane komponente. Učinkovito odvajanje toplote je bistvenega pomena za preprečevanje pregrevanja in ohranjanje splošne zanesljivosti in učinkovitosti sklopa SiP.
Materiali za polnilo v embalaži SiP morajo imeti posebne lastnosti, da izpolnjujejo te zahteve glede integracije in učinkovitosti. Imeti morajo dobro pretočnost, da zagotovijo popolno pokritost in zapolnijo vrzeli med komponentami. Material za polnilo mora imeti tudi formulacijo z nizko viskoznostjo, ki omogoča enostavno doziranje in polnjenje ozkih lukenj ali majhnih prostorov.
Poleg tega mora material za polnilo imeti močan oprijem na različne površine, vključno s polprevodniškimi čipi, substrati in pasivi, da se zagotovi zanesljiva vezava. Biti mora združljiva z različnimi embalažnimi materiali, kot so organski substrati ali keramika, in mora imeti dobre mehanske lastnosti, vključno z visoko strižno trdnostjo in trdnostjo na lupljenje.
Izbira materiala za polnilo in metode nanosa je odvisna od specifične zasnove SiP, zahtev glede komponent in proizvodnih postopkov. Tehnike doziranja, kot so kapilarni tok, brizganje ali metode s pomočjo filma, običajno uporabljajo premajhno polnjenje v sklopih SiP.
Optoelektronika Underfill: Optična poravnava in zaščita
Optoelektronsko premalo polnjenja vključuje kapsuliranje in zaščito optoelektronskih naprav, hkrati pa zagotavlja natančno optično poravnavo. Optoelektronske naprave, kot so laserji, fotodetektorji in optična stikala, pogosto zahtevajo občutljivo poravnavo optičnih komponent za doseganje optimalne učinkovitosti. Hkrati jih je treba zaščititi pred okoljskimi dejavniki, ki bi lahko vplivali na njihovo funkcionalnost. Optoelectronics underfill izpolnjuje obe zahtevi z zagotavljanjem optične poravnave in zaščite v enem samem procesu.
Optična poravnava je kritičen vidik proizvodnje optoelektronskih naprav. Vključuje poravnavo vizualnih elementov, kot so vlakna, valovod, leče ali rešetke, da se zagotovi učinkovit prenos in sprejem svetlobe. Natančna poravnava je potrebna za povečanje učinkovitosti naprave in ohranjanje celovitosti signala. Tradicionalne tehnike poravnave vključujejo ročno poravnavo z vizualnim pregledom ali avtomatsko poravnavo z uporabo stopenj poravnave. Vendar so lahko te metode dolgotrajne, delovno intenzivne in nagnjene k napakam.
Optoelektronika zapolni inovativno rešitev z vključitvijo funkcij za poravnavo neposredno v material za zapolnitev. Materiali za polnilo so običajno tekoče ali poltekoče spojine, ki lahko tečejo in zapolnijo vrzeli med optičnimi komponentami. Z dodajanjem funkcij poravnave, kot so mikrostrukture ali referenčne oznake, znotraj materiala za polnilo je mogoče postopek poravnave poenostaviti in avtomatizirati. Te funkcije delujejo kot vodila med sestavljanjem in zagotavljajo natančno poravnavo optičnih komponent brez potrebe po zapletenih postopkih poravnave.
Poleg optične poravnave materiali za polnilo ščitijo optoelektronske naprave. Optoelektronske komponente so pogosto izpostavljene težkim okoljem, vključno s temperaturnimi nihanji, vlago in mehanskimi obremenitvami. Ti zunanji dejavniki lahko sčasoma poslabšajo delovanje in zanesljivost naprav. Materiali za polnilo delujejo kot zaščitna pregrada, zapirajo optične komponente in jih ščitijo pred onesnaževalci iz okolja. Zagotavljajo tudi mehansko ojačitev, ki zmanjšuje tveganje poškodb zaradi udarcev ali vibracij.
Materiali za polnilo, ki se uporabljajo v aplikacijah optoelektronike, so običajno zasnovani tako, da imajo nizek lomni količnik in odlično optično preglednost. To zagotavlja minimalne motnje optičnih signalov, ki prehajajo skozi napravo. Poleg tega izkazujejo dober oprijem na različne podlage in imajo nizke koeficiente toplotnega raztezanja, da zmanjšajo obremenitev naprave med toplotnim ciklom.
Postopek nezadostnega polnjenja vključuje doziranje materiala pod polnilom na napravo, ki mu omogoča, da teče in zapolni vrzeli med optičnimi komponentami, nato pa ga strdi, da tvori trdno inkapsulacijo. Odvisno od posebne uporabe se lahko podpolnilni material nanaša z različnimi tehnikami, kot so kapilarni tok, doziranje s curkom ali sitotisk. Postopek strjevanja lahko dosežemo s toploto, UV sevanjem ali oboje.
Medicinska elektronika Underfill: biokompatibilnost in zanesljivost
Medicinska elektronika je del specializiranega postopka, ki vključuje kapsuliranje in zaščito elektronskih komponent, ki se uporabljajo v medicinskih napravah. Te naprave imajo ključno vlogo v različnih medicinskih aplikacijah, kot so naprave za vsaditev, diagnostična oprema, sistemi za spremljanje in sistemi za dostavo zdravil. Medicinska elektronika premalo se osredotoča na dva kritična vidika: biokompatibilnost in zanesljivost.
Biokompatibilnost je temeljna zahteva za medicinske pripomočke, ki pridejo v stik s človeškim telesom. Materiali za polnilo, ki se uporabljajo v medicinski elektroniki, morajo biti biokompatibilni, kar pomeni, da ne smejo povzročati škodljivih učinkov ali neželenih reakcij v stiku z živim tkivom ali telesnimi tekočinami. Ti materiali morajo biti skladni s strogimi predpisi in standardi, kot je ISO 10993, ki določa postopke testiranja in ocenjevanja biokompatibilnosti.
Materiali za polnilo za medicinsko elektroniko so skrbno izbrani ali oblikovani tako, da zagotavljajo biokompatibilnost. Zasnovani so tako, da niso strupeni, ne dražijo in ne povzročajo alergij. Ti materiali ne smejo izpirati nobenih škodljivih snovi ali se sčasoma razgraditi, saj lahko to povzroči poškodbe tkiva ali vnetje. Biokompatibilni materiali za polnilo imajo tudi nizko absorpcijo vode, da preprečijo rast bakterij ali gliv, ki bi lahko povzročile okužbe.
Zanesljivost je še en kritičen vidik premajhnega polnjenja medicinske elektronike. Medicinske naprave se pogosto srečujejo z zahtevnimi pogoji delovanja, vključno s skrajnimi temperaturami, vlago, telesnimi tekočinami in mehanskimi obremenitvami. Materiali za polnilo morajo zaščititi elektronske komponente ter tako zagotoviti njihovo dolgoročno zanesljivost in funkcionalnost. Zanesljivost je najpomembnejša v medicinskih aplikacijah, kjer lahko okvara naprave resno vpliva na varnost in dobro počutje pacienta.
Materiali za polnilo za medicinsko elektroniko morajo imeti visoko odpornost na vlago in kemikalije, da prenesejo izpostavljenost telesnim tekočinam ali postopkom sterilizacije. Prav tako morajo imeti dober oprijem na različne podlage, kar zagotavlja varno inkapsulacijo elektronskih komponent. Mehanske lastnosti, kot so nizki koeficienti toplotnega raztezanja in dobra odpornost na udarce, so bistvenega pomena za zmanjšanje obremenitev detajlov med toplotnim ciklom ali samodejnim nalaganjem.
Postopek podpolnjenja za medicinsko elektroniko vključuje:
- Doziranje materiala za polnilo na elektronske komponente.
- Zapolnjevanje vrzeli.
- Utrjuje, da se oblikuje zaščitna in mehansko stabilna kapsula.
Paziti je treba, da zagotovite popolno pokritost funkcij in odsotnost praznin ali zračnih žepov, ki bi lahko ogrozili zanesljivost naprave.
Poleg tega se pri premajhnem polnjenju medicinskih pripomočkov upoštevajo dodatni vidiki. Na primer, material za polnilo mora biti združljiv z metodami sterilizacije, ki se uporabljajo za napravo. Nekateri materiali so lahko občutljivi na posebne tehnike sterilizacije, kot so para, etilen oksid ali sevanje, zato bo morda treba izbrati alternativne materiale.
Aerospace Electronics Underfill: odpornost na visoke temperature in vibracije
Letalska elektronika izpolnjuje specializirani postopek za enkapsulacijo in zaščito elektronskih komponent v vesoljskih aplikacijah. Vesoljska okolja predstavljajo edinstvene izzive, vključno z visokimi temperaturami, ekstremnimi vibracijami in mehanskimi obremenitvami. Zato se premajhna izpolnitev vesoljske elektronike osredotoča na dva ključna vidika: odpornost na visoke temperature in odpornost na vibracije.
Odpornost na visoke temperature je najpomembnejša v vesoljski elektroniki zaradi povišanih temperatur med delovanjem. Materiali za polnilo, ki se uporabljajo v vesoljskih aplikacijah, morajo prenesti te visoke temperature, ne da bi pri tem ogrozili delovanje in zanesljivost elektronskih komponent. Izkazovati morajo minimalno toplotno raztezanje in ostati stabilni v širokem temperaturnem območju.
Materiali za polnilo za vesoljsko elektroniko so izbrani ali oblikovani za visoke temperature posteklenitve (Tg) in toplotno stabilnost. Visoka Tg zagotavlja, da material obdrži svoje mehanske lastnosti pri povišanih temperaturah, kar preprečuje deformacijo ali izgubo oprijema. Ti materiali lahko prenesejo ekstremne temperature, na primer med vzletom, ponovnim vstopom v atmosfero ali delovanjem v vročih motornih prostorih.
Poleg tega morajo imeti materiali za polnilo za vesoljsko elektroniko nizke koeficiente toplotnega raztezanja (CTE). CTE meri, koliko se material razširi ali skrči s temperaturnimi spremembami. Z nizkim CTE lahko materiali za polnilo zmanjšajo obremenitev elektronskih komponent zaradi termičnega kroženja, kar lahko povzroči mehanske okvare ali utrujenost spajkalnega spoja.
Odpornost na vibracije je še ena kritična zahteva za premajhno polnilo letalske elektronike. Letalska vozila so podvržena različnim tresljajem, vključno z tresljaji motorja, tresljaji, ki jih povzroči let, in mehanskimi udarci med vzletom ali pristankom. Te vibracije lahko ogrozijo delovanje in zanesljivost elektronskih komponent, če niso ustrezno zaščitene.
Materiali za polnilo, ki se uporabljajo v vesoljski elektroniki, morajo imeti odlične lastnosti dušenja vibracij. Absorbirati in razpršiti morajo energijo, ki nastane zaradi tresljajev, s čimer se zmanjša obremenitev in obremenitev elektronskih komponent. To pomaga preprečiti nastanek razpok, zlomov ali drugih mehanskih okvar zaradi čezmerne izpostavljenosti vibracijam.
Poleg tega so v vesoljskih aplikacijah prednostni materiali za polnilo z visoko oprijemljivostjo in kohezijsko trdnostjo. Te lastnosti zagotavljajo, da material pod polnilom ostane trdno vezan na elektronske komponente in podlago, tudi v pogojih ekstremnih vibracij. Močan oprijem preprečuje razslojevanje ali ločevanje materiala za polnilo od elementov, ohranja celovitost ovoja in ščiti pred vdorom vlage ali smeti.
Postopek nezadostnega polnjenja za letalsko in vesoljsko elektroniko običajno vključuje doziranje materiala za nezadostno polnilo na elektronske komponente, ki mu omogoča, da teče in zapolni vrzeli, nato pa ga strdi, da tvori robustno inkapsulacijo. Postopek strjevanja je mogoče izvesti s termičnimi ali UV metodami strjevanja, odvisno od posebnih zahtev aplikacije.
Avtomobilska elektronika Underfill: vzdržljivost in odpornost na toplotne cikle
Avtomobilska elektronika premalo zapolnjuje kritičen proces, ki vključuje kapsuliranje in zaščito elektronskih komponent v avtomobilskih aplikacijah. Avtomobilska okolja predstavljajo edinstvene izzive, vključno s temperaturnimi nihanji, termičnimi cikli, mehanskimi obremenitvami ter izpostavljenostjo vlagi in kemikalijam. Zato se premajhna izpolnitev avtomobilske elektronike osredotoča na dva kritična vidika: vzdržljivost in odpornost na termične cikle.
Vzdržljivost je ključna zahteva za premajhno polnilo avtomobilske elektronike. Med rednim delovanjem se avtomobilska vozila soočajo s stalnimi vibracijami, udarci in mehanskimi obremenitvami. Materiali za polnilo, ki se uporabljajo v avtomobilskih aplikacijah, morajo robustno zaščititi elektronske komponente, kar zagotavlja njihovo vzdržljivost in dolgo življenjsko dobo. Prenesti morajo težke pogoje in mehanske obremenitve na cestišču ter biti odporni na vdor vlage, prahu in kemikalij.
Materiali za polnilo za avtomobilsko elektroniko so izbrani ali oblikovani za visoko mehansko trdnost in odpornost na udarce. Izkazovati morajo odličen oprijem na elektronske komponente in podlago ter preprečiti razslojevanje ali ločevanje pod mehanskimi obremenitvami. Vzdržljivi materiali za polnilo pomagajo zmanjšati tveganje poškodb elektronskih komponent zaradi tresljajev ali udarcev, kar zagotavlja zanesljivo delovanje skozi celotno življenjsko dobo vozila.
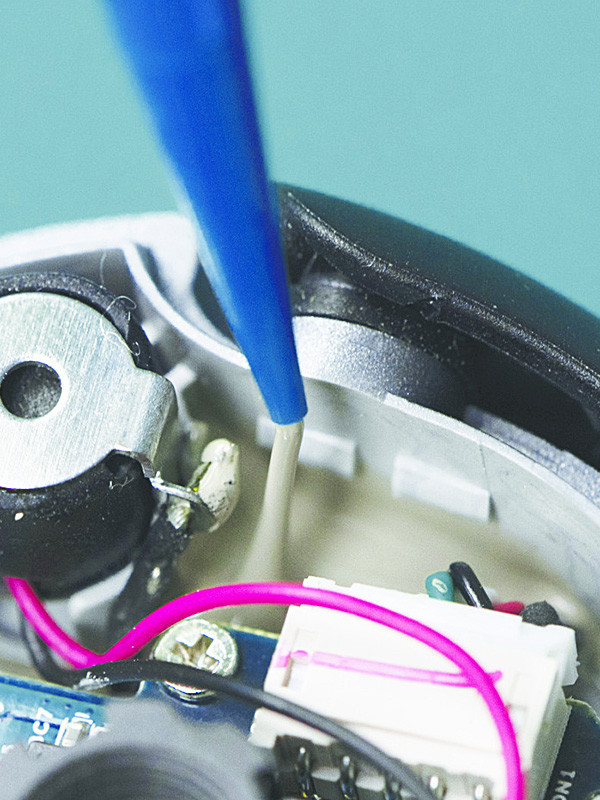
Odpornost na toplotne cikle je še ena kritična zahteva za premajhno polnjenje avtomobilske elektronike. Avtomobilska vozila so podvržena pogostim temperaturnim nihanjem, zlasti med zagonom in delovanjem motorja, ti temperaturni cikli pa lahko povzročijo toplotne obremenitve elektronskih komponent in materiala pod polnilom. Materiali za polnilo, ki se uporabljajo v avtomobilskih aplikacijah, morajo imeti odlično toplotno ciklično odpornost, da prenesejo ta temperaturna nihanja brez ogrožanja njihove učinkovitosti.
Materiali za polnilo za avtomobilsko elektroniko morajo imeti nizke koeficiente toplotnega raztezanja (CTE), da se zmanjša obremenitev elektronskih komponent med toplotnim ciklom. Dobro usklajen CTE med materialom za polnilo in sestavinami zmanjša tveganje za utrujenost spajkalnega spoja, razpoke ali druge mehanske okvare, ki jih povzroči toplotna obremenitev. Poleg tega morajo materiali za polnilo izkazovati dobro toplotno prevodnost za učinkovito odvajanje toplote in preprečevanje lokaliziranih vročih točk, ki bi lahko vplivale na delovanje in zanesljivost komponent.
Poleg tega morajo biti materiali za polnilo avtomobilske elektronike odporni na vlago, kemikalije in tekočine. Imeti morajo nizko absorpcijo vode, da se prepreči rast plesni ali korozija elektronskih komponent. Kemična odpornost zagotavlja, da material pod polnilom ostane stabilen, ko je izpostavljen avtomobilskim tekočinam, kot so olja, goriva ali čistilna sredstva, pri čemer se izogne razgradnji ali izgubi oprijema.
Postopek nezadostnega polnjenja za avtomobilsko elektroniko običajno vključuje doziranje materiala pod polnilom na elektronske komponente, ki mu omogoča, da teče in zapolni vrzeli, nato pa ga strdi, da tvori trajno inkapsulacijo. Postopek strjevanja je mogoče izvesti s termičnimi ali UV metodami strjevanja, odvisno od posebnih zahtev aplikacije in uporabljenega materiala za polnilo.
Izbira pravega epoksi smole za polnilo
Izbira pravega epoksida za polnilo je ključna odločitev pri sestavljanju in zaščiti elektronskih komponent. Podpolnilni epoksidi zagotavljajo mehansko ojačitev, toplotno upravljanje in zaščito pred okoljskimi dejavniki. Tukaj je nekaj ključnih premislekov pri izbiri ustreznega epoksi smola za podpolnilo:
- Toplotne lastnosti: Ena od primarnih funkcij epoksi smole za polnilo je odvajanje toplote, ki jo ustvarjajo elektronske komponente. Zato je bistveno upoštevati toplotno prevodnost in toplotno odpornost epoksida. Visoka toplotna prevodnost pomaga pri učinkovitem prenosu toplote, preprečevanju vročih točk in ohranjanju zanesljivosti komponent. Epoksi mora imeti tudi nizko toplotno odpornost, da zmanjša toplotno obremenitev komponent med temperaturnimi cikli.
- Ujemanje CTE: Koeficient toplotne razteznosti (CTE) epoksi smole pod polnilom se mora dobro ujemati s CTE elektronskih komponent in podlage, da zmanjšamo toplotno obremenitev in preprečimo okvare spajkalnega spoja. Tesno usklajen CTE pomaga zmanjšati tveganje mehanskih okvar zaradi termičnega kroženja.
- Sposobnost pretoka in zapolnjevanja rež: premalo napolnjen epoksi mora imeti dobre lastnosti pretoka in sposobnost učinkovitega zapolnjevanja rež med komponentami. To zagotavlja popolno pokritost in zmanjšuje praznine ali zračne žepke, ki bi lahko vplivali na mehansko stabilnost in toplotno učinkovitost sklopa. Viskoznost epoksida mora biti primerna za specifično uporabo in način sestavljanja, ne glede na to, ali gre za kapilarni tok, doziranje s curkom ali sitotisk.
- Oprijem: močan oprijem je ključnega pomena za epoksidno smolo za polnilo, da se zagotovi zanesljiva vezava med komponentami in podlago. Imeti mora dober oprijem na različne materiale, vključno s kovinami, keramiko in plastiko. Adhezijske lastnosti epoksida prispevajo k mehanski celovitosti in dolgoročni zanesljivosti sklopa.
- Metoda strjevanja: Razmislite o metodi strjevanja, ki najbolj ustreza vašemu proizvodnemu procesu. Podfill epoksi se lahko strdijo s toploto, UV sevanjem ali kombinacijo obojega. Vsaka metoda strjevanja ima prednosti in omejitve, zato je bistvenega pomena, da izberete tisto, ki je v skladu z vašimi proizvodnimi zahtevami.
- Odpornost na okolje: Ocenite odpornost epoksi smole pod polnilom na okoljske dejavnike, kot so vlaga, kemikalije in ekstremne temperature. Epoksi mora biti odporen na vodo, kar preprečuje rast plesni ali korozije. Kemična odpornost zagotavlja stabilnost pri stiku z avtomobilskimi tekočinami, čistilnimi sredstvi ali drugimi potencialno jedkimi snovmi. Poleg tega mora epoksid ohraniti svoje mehanske in električne lastnosti v širokem temperaturnem območju.
- Zanesljivost in dolgoživost: Upoštevajte dosežke in podatke o zanesljivosti epoksi smole s podpolnilom. Poiščite epoksidne materiale, ki so testirani in dokazano delujejo dobro v podobnih aplikacijah ali imajo industrijske certifikate in skladnost z ustreznimi standardi. Upoštevajte dejavnike, kot so staranje, dolgoročna zanesljivost in sposobnost epoksida, da skozi čas ohrani svoje lastnosti.
Pri izbiri pravega epoksida za polnilo je ključnega pomena upoštevati posebne zahteve vaše aplikacije, vključno s toplotnim upravljanjem, mehansko stabilnostjo, zaščito okolja in združljivostjo proizvodnega procesa. Posvetovanje z dobavitelji epoksidov ali iskanje strokovnega nasveta je lahko koristno pri sprejemanju informirane odločitve, ki ustreza potrebam vaše aplikacije in zagotavlja optimalno delovanje in zanesljivost.
Prihodnji trendi v epoksi smoli z zapolnitvijo
Underfill epoksi se nenehno razvija, ki ga poganjajo napredek v elektronskih tehnologijah, nastajajoče aplikacije in potreba po izboljšani učinkovitosti in zanesljivosti. Pri razvoju in uporabi epoksi smole za polnilo je mogoče opaziti več prihodnjih trendov:
- Miniaturizacija in embalaža z večjo gostoto: Ker se elektronske naprave še naprej krčijo in imajo večjo gostoto komponent, se morajo epoksidi s premajhnim polnilom ustrezno prilagoditi. Prihodnji trendi se bodo osredotočali na razvoj materialov za polnilo, ki prodrejo in zapolnijo manjše reže med komponentami, kar zagotavlja popolno pokritost in zanesljivo zaščito v vedno bolj miniaturiziranih elektronskih sklopih.
- Visokofrekvenčne aplikacije: Z naraščajočim povpraševanjem po visokofrekvenčnih in hitrih elektronskih napravah bodo morale epoksidne formulacije s premajhnim polnilom ustrezati posebnim zahtevam teh aplikacij. Materiali za polnilo z nizko dielektrično konstanto in nizkimi tangentami izgub bodo bistveni za zmanjšanje izgube signala in ohranjanje integritete visokofrekvenčnih signalov v naprednih komunikacijskih sistemih, tehnologiji 5G in drugih nastajajočih aplikacijah.
- Izboljšano upravljanje toplote: Odvajanje toplote ostaja kritična skrb za elektronske naprave, zlasti z naraščajočo gostoto moči. Prihodnje epoksidne formulacije pod polnilom se bodo osredotočale na izboljšano toplotno prevodnost za izboljšanje prenosa toplote in učinkovito obvladovanje toplotnih težav. Napredna polnila in dodatki bodo vgrajeni v epokside pod polnilom za doseganje višje toplotne prevodnosti ob ohranjanju drugih želenih lastnosti.
- Fleksibilna in raztegljiva elektronika: Vzpon fleksibilne in raztegljive elektronike odpira nove možnosti za epoksidne materiale pod polnilom. Fleksibilni epoksidi za polnilo morajo pokazati odličen oprijem in mehanske lastnosti tudi pri ponavljajočem se upogibanju ali raztezanju. Ti materiali bodo omogočili inkapsulacijo in zaščito elektronike v nosljivih napravah, upogljivih zaslonih in drugih aplikacijah, ki zahtevajo mehansko prilagodljivost.
- Okolju prijazne rešitve: Trajnost in okoljski vidiki bodo igrali čedalje pomembnejšo vlogo pri razvoju epoksi materialov za polnilo. Poudarek bo na ustvarjanju epoksidnih formulacij brez nevarnih snovi in z zmanjšanim vplivom na okolje v celotnem življenjskem ciklu, vključno s proizvodnjo, uporabo in odlaganjem. Biološki ali obnovljivi materiali lahko prav tako postanejo pomembnejši kot trajnostne alternative.
- Izboljšani proizvodni procesi: Prihodnji trendi pri epoksidu s premajhnim polnilom se bodo osredotočali na lastnosti materiala in napredek v proizvodnih procesih. Tehnike, kot so proizvodnja dodatkov, selektivno doziranje in napredne metode strjevanja, bodo raziskane za optimizacijo uporabe in učinkovitosti epoksi smole v različnih postopkih elektronskega sestavljanja.
- Integracija naprednih tehnik testiranja in karakterizacije: Z naraščajočo kompleksnostjo in zahtevami elektronskih naprav bo potrebna napredna metoda testiranja in karakterizacije, da se zagotovi zanesljivost in učinkovitost premalo polnjenega epoksida. Tehnike, kot so neporušitveno testiranje, spremljanje in situ in orodja za simulacijo, bodo pomagale pri razvoju in nadzoru kakovosti epoksidnih materialov s premajhnim polnilom.
zaključek
Underfill epoksi ima ključno vlogo pri povečanju zanesljivosti in učinkovitosti elektronskih komponent, zlasti v polprevodniški embalaži. Različne vrste epoksi smola za polnilo nudijo vrsto prednosti, vključno z visoko zanesljivostjo, samodoziranjem, visoko gostoto ter visoko toplotno in mehansko zmogljivostjo. Izbira pravega epoksida za polnilo za aplikacijo in paket zagotavlja robustno in dolgotrajno vez. Ker tehnologija napreduje in se velikosti embalaže zmanjšujejo, pričakujemo še več inovativnih epoksidnih rešitev pod polnilom, ki ponujajo vrhunsko zmogljivost, integracijo in miniaturizacijo. Underfill epoksi naj bi imel vse pomembnejšo vlogo v prihodnosti elektronike, kar nam bo omogočilo doseganje višjih stopenj zanesljivosti in učinkovitosti v različnih panogah.