Subpreenchimento Epóxi
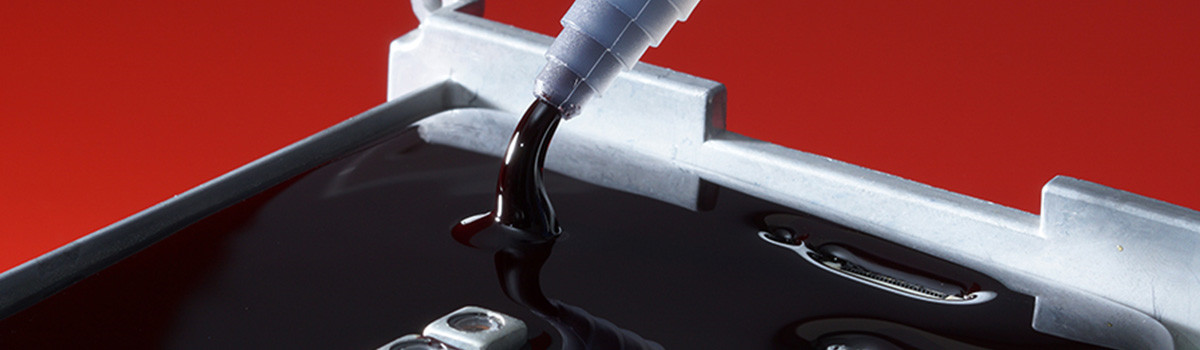
Underfill epóxi é um tipo de adesivo usado para aumentar a confiabilidade dos componentes eletrônicos, particularmente em aplicações de embalagens de semicondutores. Ele preenche a lacuna entre a embalagem e a placa de circuito impresso (PCB), fornecendo suporte mecânico e alívio de tensões para evitar expansão térmica e danos por contração. O preenchimento epóxi também melhora o desempenho elétrico do pacote, reduzindo a indutância e a capacitância parasitas. Neste artigo, exploramos as várias aplicações do epóxi subpreenchido, os diferentes tipos disponíveis e seus benefícios.
A importância do subpreenchimento de epóxi na embalagem de semicondutores
O preenchimento epóxi é crucial na embalagem de semicondutores, fornecendo reforço mecânico e proteção para componentes microeletrônicos delicados. É um material adesivo especializado usado para preencher a lacuna entre o chip semicondutor e o substrato da embalagem, aumentando a confiabilidade e o desempenho dos dispositivos eletrônicos. Aqui, exploraremos a importância do epóxi subpreenchido na embalagem de semicondutores.
Uma das principais funções do epóxi subpreenchido é melhorar a resistência mecânica e a confiabilidade da embalagem. Durante a operação, os chips semicondutores são submetidos a várias tensões mecânicas, como expansão e contração térmica, vibração e choque mecânico. Essas tensões podem levar à formação de rachaduras nas juntas de solda, que podem causar falhas elétricas e diminuir a vida útil geral do dispositivo. O epóxi de subpreenchimento atua como um agente redutor de estresse, distribuindo o estresse mecânico uniformemente pelo chip, substrato e juntas de solda. Ele efetivamente minimiza a formação de rachaduras e evita a propagação de rachaduras existentes, garantindo a confiabilidade da embalagem a longo prazo.
Outro aspecto crítico do epóxi underfill é sua capacidade de melhorar o desempenho térmico de dispositivos semicondutores. A dissipação de calor torna-se uma preocupação significativa à medida que os dispositivos eletrônicos diminuem de tamanho e aumentam a densidade de potência, e o calor excessivo pode degradar o desempenho e a confiabilidade do chip semicondutor. O epóxi de enchimento tem excelentes propriedades de condutividade térmica, permitindo que ele transfira o calor do chip de forma eficiente e o distribua por toda a embalagem. Isso ajuda a manter as temperaturas operacionais ideais e evita pontos de acesso, melhorando assim o gerenciamento térmico geral do dispositivo.
Underfill epóxi também protege contra umidade e contaminantes. A entrada de umidade pode levar à corrosão, vazamento elétrico e crescimento de materiais condutores, resultando em mau funcionamento do dispositivo. O preenchimento epóxi atua como uma barreira, selando áreas vulneráveis e impedindo a entrada de umidade na embalagem. Ele também oferece proteção contra poeira, sujeira e outros contaminantes que podem afetar adversamente o desempenho elétrico do chip semicondutor. Ao proteger o chip e suas interconexões, o epóxi subpreenchido garante a confiabilidade e funcionalidade de longo prazo do dispositivo.
Além disso, o epóxi subpreenchido permite a miniaturização em embalagens de semicondutores. Com a demanda constante por dispositivos menores e mais compactos, o epóxi subpreenchido permite o uso de técnicas de embalagem flip-chip e chip-scale. Essas técnicas envolvem a montagem direta do chip no substrato da embalagem, eliminando a necessidade de colagem de fios e reduzindo o tamanho da embalagem. O epóxi de subpreenchimento fornece suporte estrutural e mantém a integridade da interface chip-substrato, permitindo a implementação bem-sucedida dessas tecnologias avançadas de embalagem.
Como o Underfill Epoxy aborda os desafios
A embalagem de semicondutores desempenha um papel crucial no desempenho, confiabilidade e longevidade de dispositivos eletrônicos. Envolve o encapsulamento de circuitos integrados (CIs) em invólucros protetores, fornecendo conexões elétricas e dissipando o calor gerado durante a operação. No entanto, a embalagem de semicondutores enfrenta vários desafios, incluindo estresse térmico e empenamento, que podem afetar significativamente a funcionalidade e a confiabilidade dos dispositivos embalados.
Um dos principais desafios é o estresse térmico. Os circuitos integrados geram calor durante a operação e a dissipação inadequada pode aumentar as temperaturas dentro da embalagem. Essa variação de temperatura resulta em estresse térmico, pois diferentes materiais dentro da embalagem se expandem e se contraem em taxas diferentes. A expansão e contração não uniformes podem causar tensão mecânica, levando a falhas nas juntas de solda, delaminação e rachaduras. O estresse térmico pode comprometer a integridade elétrica e mecânica do pacote, afetando o desempenho e a confiabilidade do dispositivo.
O empenamento é outro desafio crítico na embalagem de semicondutores. Empenamento refere-se à flexão ou deformação do substrato da embalagem ou de toda a embalagem. Pode ocorrer durante o processo de embalagem ou devido ao estresse térmico. O empenamento é causado principalmente pela incompatibilidade no coeficiente de expansão térmica (CTE) entre diferentes materiais na embalagem. Por exemplo, o CTE da matriz de silício, substrato e composto de molde pode diferir significativamente. Quando submetidos a mudanças de temperatura, esses materiais se expandem ou se contraem em taxas diferentes, levando ao empenamento.
Warpage apresenta vários problemas para pacotes de semicondutores:
- Pode resultar em pontos de concentração de tensões, aumentando a probabilidade de falhas mecânicas e reduzindo a confiabilidade da caixa.
- O empenamento pode trazer dificuldades no processo de montagem, pois afeta o alinhamento da embalagem com outros componentes, como a placa de circuito impresso (PCB). Esse desalinhamento pode prejudicar as conexões elétricas e causar problemas de desempenho.
- O empenamento pode afetar o fator de forma geral do pacote, dificultando a integração do dispositivo em aplicativos de fator de forma pequeno ou PCBs densamente povoados.
Várias técnicas e estratégias são empregadas na embalagem de semicondutores para enfrentar esses desafios. Isso inclui o uso de materiais avançados com CTEs correspondentes para minimizar o estresse térmico e o empenamento. Simulações termomecânicas e modelagem são realizadas para prever o comportamento da embalagem sob diferentes condições térmicas. Modificações de projeto, como a introdução de estruturas de alívio de tensão e layouts otimizados, são implementadas para reduzir o estresse térmico e o empenamento. Além disso, o desenvolvimento de processos e equipamentos de fabricação aprimorados ajuda a minimizar a ocorrência de empenamento durante a montagem.
Benefícios do Underfill Epóxi
O preenchimento epóxi é um componente crítico na embalagem de semicondutores que oferece vários benefícios. Esse material epóxi especializado é aplicado entre o chip semicondutor e o substrato da embalagem, fornecendo reforço mecânico e abordando vários desafios. Aqui estão alguns dos benefícios críticos do epóxi subpreenchido:
- Confiabilidade mecânica aprimorada: um dos principais benefícios do epóxi de subenchimento é sua capacidade de aumentar a confiabilidade mecânica dos pacotes de semicondutores. O epóxi de subpreenchimento cria uma ligação coesiva que melhora a integridade estrutural geral, preenchendo as lacunas e vazios entre o chip e o substrato. Isso ajuda a evitar o empenamento da embalagem, reduz o risco de falhas mecânicas e aumenta a resistência a tensões externas, como vibrações, choques e ciclos térmicos. A confiabilidade mecânica aprimorada leva a uma maior durabilidade do produto e uma vida útil mais longa para o dispositivo.
- Dissipação de estresse térmico: o epóxi de subenchimento ajuda a dissipar o estresse térmico dentro da embalagem. Os circuitos integrados geram calor durante a operação, e a dissipação inadequada pode resultar em variações de temperatura dentro do recipiente. O material epóxi subpreenchido, com seu menor coeficiente de expansão térmica (CTE) em comparação com os materiais de cavaco e substrato, atua como uma camada tampão. Absorve a tensão mecânica causada pelo estresse térmico, reduzindo o risco de falhas nas juntas de solda, delaminação e rachaduras. Ao dissipar o estresse térmico, o epóxi subpreenchido ajuda a manter a integridade elétrica e mecânica da embalagem.
- Desempenho elétrico aprimorado: o epóxi subenchido afeta positivamente o desempenho elétrico de dispositivos semicondutores. O material epóxi preenche as lacunas entre o chip e o substrato, reduzindo a capacitância e a indutância parasitas. Isso resulta em integridade de sinal aprimorada, perdas de sinal reduzidas e conectividade elétrica aprimorada entre o chip e o restante do pacote. Os efeitos parasitas reduzidos contribuem para um melhor desempenho elétrico, maiores taxas de transferência de dados e maior confiabilidade do dispositivo. Além disso, o epóxi subpreenchido fornece isolamento e proteção contra umidade, contaminantes e outros fatores ambientais que podem degradar o desempenho elétrico.
- Alívio de tensão e montagem aprimorada: o epóxi de subenchimento atua como um mecanismo de alívio de tensão durante a montagem. O material epóxi compensa a incompatibilidade CTE entre o chip e o substrato, reduzindo o estresse mecânico durante as mudanças de temperatura. Isso torna o processo de montagem mais confiável e eficiente, minimizando o risco de danos ou desalinhamento da embalagem. A distribuição de tensão controlada fornecida pelo epóxi underfill também ajuda a garantir o alinhamento adequado com outros componentes na placa de circuito impresso (PCB) e melhora o rendimento geral da montagem.
- Miniaturização e otimização do fator de forma: o epóxi subpreenchido permite a miniaturização de pacotes de semicondutores e a otimização do fator de forma. Ao fornecer reforço estrutural e alívio de tensões, o epóxi subenchido permite projetar e fabricar embalagens menores, mais finas e mais compactas. Isso é particularmente importante para aplicações como dispositivos móveis e eletrônicos vestíveis, onde o espaço é valioso. A capacidade de otimizar fatores de forma e atingir densidades de componentes mais altas contribui para dispositivos eletrônicos mais avançados e inovadores.
Tipos de subpreenchimento epóxi
Vários tipos de formulações de epóxi de enchimento estão disponíveis em embalagens de semicondutores, cada uma projetada para atender a requisitos específicos e enfrentar diferentes desafios. Aqui estão alguns tipos comumente usados de epóxi underfill:
- Subpreenchimento capilar epóxi: O epóxi subpreenchimento capilar é o tipo mais tradicional e amplamente utilizado. Um epóxi de baixa viscosidade flui para o espaço entre o chip e o substrato por meio de ação capilar. O subenchimento capilar é normalmente dispensado na borda do chip e, à medida que a embalagem é aquecida, o epóxi flui sob o chip, preenchendo os espaços vazios. Este tipo de subenchimento é adequado para embalagens com pequenos vãos e proporciona um bom reforço mecânico.
- Epóxi de subenchimento sem fluxo: O epóxi de subenchimento sem fluxo é uma formulação de alta viscosidade que não flui durante a cura. É aplicado como um epóxi pré-aplicado ou como um filme entre o cavaco e o substrato. O epóxi de preenchimento sem fluxo é particularmente útil para pacotes flip-chip, onde os solavancos de solda interagem diretamente com o substrato. Elimina a necessidade de fluxo capilar e reduz o risco de danos nas juntas de solda durante a montagem.
- Enchimento de nível de wafer (WLU): O preenchimento de nível de wafer é um epóxi de enchimento aplicado no nível de wafer antes que os chips individuais sejam individualizados. Envolve a distribuição do material de subenchimento sobre toda a superfície do wafer e sua cura. O subenchimento no nível do wafer oferece várias vantagens, incluindo cobertura uniforme do subenchimento, tempo de montagem reduzido e controle de processo aprimorado. É comumente usado para fabricação de alto volume de dispositivos de pequeno porte.
- Underfill moldado (MUF): Underfill moldado é um epóxi de underfill aplicado durante a moldagem por encapsulamento. O material de preenchimento é dispensado no substrato e, em seguida, o chip e o substrato são encapsulados em um composto de molde. Durante a moldagem, o epóxi flui e preenche a lacuna entre o cavaco e o substrato, fornecendo subpreenchimento e encapsulamento em uma única etapa. O underfill moldado oferece excelente reforço mecânico e simplifica o processo de montagem.
- Enchimento não condutivo (NCF): O epóxi de enchimento não condutivo é especificamente formulado para fornecer isolamento elétrico entre as juntas de solda no chip e o substrato. Contém cargas isolantes ou aditivos que impedem a condutividade elétrica. O NCF é usado em aplicações onde o curto-circuito elétrico entre juntas de solda adjacentes é uma preocupação. Oferece reforço mecânico e isolamento elétrico.
- Subenchimento termicamente condutivo (TCU): o epóxi de subenchimento termicamente condutivo é projetado para melhorar as capacidades de dissipação de calor do pacote. Ele contém enchimentos termicamente condutores, como partículas de cerâmica ou metal, que melhoram a condutividade térmica do material de preenchimento. O TCU é usado em aplicações onde a transferência de calor eficiente é crucial, como dispositivos de alta potência ou aqueles que operam em ambientes térmicos exigentes.
Estes são apenas alguns exemplos dos diferentes tipos de epóxi de subpreenchimento usados em embalagens de semicondutores. A seleção do epóxi de subenchimento apropriado depende de fatores como o projeto da embalagem, processo de montagem, requisitos térmicos e considerações elétricas. Cada subpreenchimento epóxi oferece vantagens específicas e é adaptado para atender às necessidades exclusivas de várias aplicações.
Subpreenchimento Capilar: Baixa Viscosidade e Alta Confiabilidade
Subpreenchimento capilar refere-se a um processo usado na indústria de embalagens de semicondutores para aumentar a confiabilidade dos dispositivos eletrônicos. Envolve preencher as lacunas entre um chip microeletrônico e sua embalagem circundante com um material líquido de baixa viscosidade, geralmente uma resina à base de epóxi. Este material de preenchimento fornece suporte estrutural, melhora a dissipação térmica e protege o chip contra estresse mecânico, umidade e outros fatores ambientais.
Uma das características críticas do underfill capilar é sua baixa viscosidade. O material de subenchimento é formulado para ter uma densidade relativamente baixa, permitindo que flua facilmente para os espaços estreitos entre o cavaco e a embalagem durante o processo de subenchimento. Isso garante que o material de subenchimento possa penetrar e preencher com eficiência todos os vazios e lacunas de ar, minimizando o risco de formação de vazios e melhorando a integridade geral da interface chip-pack.
Os materiais de preenchimento capilar de baixa viscosidade também oferecem várias outras vantagens. Em primeiro lugar, eles facilitam o fluxo eficiente do material sob o cavaco, o que leva à redução do tempo de processo e ao aumento do rendimento da produção. Isso é particularmente importante em ambientes de fabricação de alto volume, onde o tempo e a eficiência de custos são críticos.
Em segundo lugar, a baixa viscosidade permite melhores propriedades de umectação e adesão do material de subenchimento. Ele permite que o material se espalhe uniformemente e forme ligações fortes com o chip e a embalagem, criando um encapsulamento confiável e robusto. Isso garante que o chip esteja protegido com segurança contra tensões mecânicas, como ciclos térmicos, choques e vibrações.
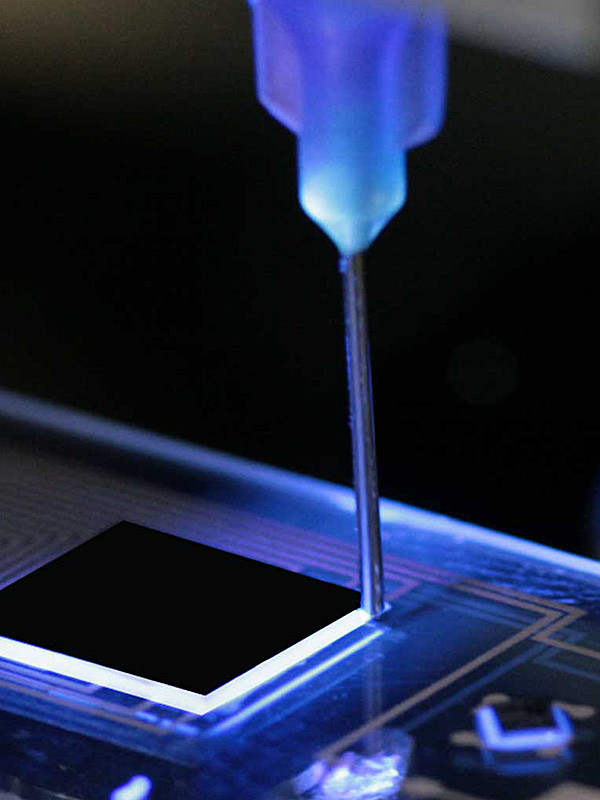
Outro aspecto crucial dos underfills capilares é sua alta confiabilidade. Os materiais de preenchimento de baixa viscosidade são projetados especificamente para exibir excelente estabilidade térmica, propriedades de isolamento elétrico e resistência à umidade e produtos químicos. Essas características são essenciais para garantir o desempenho e a confiabilidade de longo prazo dos dispositivos eletrônicos embalados, especialmente em aplicações exigentes, como automotiva, aeroespacial e de telecomunicações.
Além disso, os materiais de preenchimento capilar são projetados para ter alta resistência mecânica e excelente adesão a vários materiais de substrato, incluindo metais, cerâmica e materiais orgânicos comumente usados em embalagens de semicondutores. Isso permite que o material de subenchimento atue como um amortecedor de tensão, absorvendo e dissipando efetivamente as tensões mecânicas geradas durante a operação ou exposição ambiental.
Subenchimento sem fluxo: dispensação automática e alto rendimento
No-flow underfill, um processo especializado usado na indústria de embalagens de semicondutores para aumentar a confiabilidade e a eficiência de dispositivos eletrônicos. Ao contrário dos subenchimentos capilares, que dependem do fluxo de materiais de baixa viscosidade, os subenchimentos sem fluxo utilizam uma abordagem de autodistribuição com materiais de alta viscosidade. Este método oferece várias vantagens, incluindo auto-alinhamento, alto rendimento e maior confiabilidade.
Uma das características críticas do subenchimento sem fluxo é sua capacidade de auto-dispensação. O material de subenchimento usado neste processo é formulado com uma viscosidade mais alta, o que o impede de fluir livremente. Em vez disso, o material de preenchimento é distribuído na interface chip-pack de maneira controlada. Essa distribuição controlada permite a colocação precisa do material de subenchimento, garantindo que seja aplicado apenas nas áreas desejadas, sem transbordar ou espalhar descontroladamente.
A natureza de auto-dispensação do subenchimento sem fluxo oferece vários benefícios. Em primeiro lugar, permite o auto-alinhamento do material de enchimento. À medida que o subenchimento é dispensado, ele naturalmente se auto-alinha com o chip e a embalagem, preenchendo as lacunas e vazios uniformemente. Isso elimina a necessidade de posicionamento e alinhamento precisos do cavaco durante o processo de subenchimento, economizando tempo e esforço na fabricação.
Em segundo lugar, o recurso de autodistribuição de subenchimentos sem fluxo permite alto rendimento na produção. O processo de distribuição pode ser automatizado, permitindo a aplicação rápida e consistente do material de preenchimento em vários chips simultaneamente. Isso melhora a eficiência geral da produção e reduz os custos de fabricação, tornando-o particularmente vantajoso para ambientes de fabricação de alto volume.
Além disso, os materiais de subenchimento sem fluxo são projetados para fornecer alta confiabilidade. Os materiais de subenchimento de alta viscosidade oferecem maior resistência a ciclos térmicos, tensões mecânicas e fatores ambientais, garantindo o desempenho de longo prazo dos dispositivos eletrônicos embalados. Os materiais apresentam excelente estabilidade térmica, propriedades de isolamento elétrico e resistência à umidade e produtos químicos, contribuindo para a confiabilidade geral dos dispositivos.
Além disso, os materiais de subenchimento de alta viscosidade usados no subenchimento sem fluxo têm maior resistência mecânica e propriedades de adesão. Eles formam ligações fortes com o chip e a embalagem, absorvendo e dissipando com eficiência as tensões mecânicas geradas durante a operação ou exposição ambiental. Isso ajuda a proteger o chip de possíveis danos e aumenta a resistência do dispositivo a choques e vibrações externas.
Underfill moldado: alta proteção e integração
O underfill moldado é uma técnica avançada usada na indústria de embalagens de semicondutores para fornecer altos níveis de proteção e integração para dispositivos eletrônicos. Envolve o encapsulamento de todo o chip e seu pacote circundante com um composto de molde incorporando material de enchimento. Este processo oferece vantagens significativas em relação à proteção, integração e confiabilidade geral.
Um dos benefícios críticos do subenchimento moldado é sua capacidade de fornecer proteção abrangente para o chip. O composto do molde usado neste processo atua como uma barreira robusta, envolvendo todo o chip e a embalagem em um invólucro protetor. Isso fornece proteção eficaz contra fatores ambientais, como umidade, poeira e contaminantes que podem afetar o desempenho e a confiabilidade do dispositivo. O encapsulamento também ajuda a evitar que o chip sofra tensões mecânicas, ciclos térmicos e outras forças externas, garantindo sua durabilidade a longo prazo.
Além disso, o underfill moldado permite altos níveis de integração dentro do pacote de semicondutores. O material de preenchimento é misturado diretamente no composto do molde, permitindo a integração perfeita dos processos de preenchimento e encapsulamento. Essa integração elimina a necessidade de uma etapa separada de subenchimento, simplificando o processo de fabricação e reduzindo o tempo e os custos de produção. Ele também garante uma distribuição consistente e uniforme do subenchimento em toda a embalagem, minimizando os vazios e melhorando a integridade estrutural geral.
Além disso, o underfill moldado oferece excelentes propriedades de dissipação térmica. O composto do molde é projetado para ter alta condutividade térmica, permitindo que ele transfira o calor para longe do cavaco com eficiência. Isso é crucial para manter a temperatura operacional ideal do dispositivo e evitar o superaquecimento, que pode levar à degradação do desempenho e problemas de confiabilidade. As propriedades de dissipação térmica aprimoradas do subenchimento moldado contribuem para a confiabilidade geral e a longevidade do dispositivo eletrônico.
Além disso, o underfill moldado permite mais miniaturização e otimização do fator de forma. O processo de encapsulamento pode ser adaptado para acomodar vários tamanhos e formas de embalagem, incluindo estruturas 3D complexas. Essa flexibilidade permite a integração de vários chips e outros componentes em um pacote compacto e eficiente em termos de espaço. A capacidade de alcançar níveis mais altos de integração sem comprometer a confiabilidade torna o subenchimento moldado particularmente valioso em aplicações onde as restrições de tamanho e peso são críticas, como dispositivos móveis, vestíveis e eletrônicos automotivos.
Subpreenchimento do Chip Scale Package (CSP): miniaturização e alta densidade
O underfill Chip Scale Package (CSP) é uma tecnologia crítica que permite a miniaturização e a integração de dispositivos eletrônicos de alta densidade. À medida que os dispositivos eletrônicos continuam diminuindo de tamanho e oferecem maior funcionalidade, o CSP desempenha um papel crucial ao garantir a confiabilidade e o desempenho desses dispositivos compactos.
CSP é uma tecnologia de empacotamento que permite que o chip semicondutor seja montado diretamente no substrato ou na placa de circuito impresso (PCB) sem a necessidade de um pacote adicional. Isso elimina a necessidade de um recipiente tradicional de plástico ou cerâmica, reduzindo o tamanho e o peso total do dispositivo. Subpreenchimento CSP um processo no qual um líquido ou material encapsulante é usado para preencher a lacuna entre o chip e o substrato, fornecendo suporte mecânico e protegendo o chip de fatores ambientais, como umidade e estresse mecânico.
A miniaturização é obtida através do subpreenchimento CSP, reduzindo a distância entre o chip e o substrato. O material de preenchimento preenche o espaço estreito entre o cavaco e o substrato, criando uma ligação sólida e melhorando a estabilidade mecânica do cavaco. Isso permite dispositivos menores e mais finos, possibilitando a inclusão de mais funcionalidades em um espaço limitado.
A integração de alta densidade é outra vantagem do subpreenchimento CSP. Ao eliminar a necessidade de um pacote separado, o CSP permite que o chip seja montado mais próximo de outros componentes no PCB, reduzindo o comprimento das conexões elétricas e melhorando a integridade do sinal. O material de subenchimento também atua como um condutor térmico, dissipando eficientemente o calor gerado pelo chip. Esta capacidade de gerenciamento térmico permite maiores densidades de energia, permitindo a integração de chips mais complexos e poderosos em dispositivos eletrônicos.
Os materiais de preenchimento CSP devem possuir características específicas para atender às demandas de miniaturização e integração de alta densidade. Eles precisam ter baixa viscosidade para facilitar o preenchimento de lacunas estreitas, além de excelentes propriedades de fluxo para garantir uma cobertura uniforme e eliminar os vazios. Os materiais também devem ter boa adesão ao cavaco e ao substrato, proporcionando suporte mecânico sólido. Além disso, eles devem exibir alta condutividade térmica para transferir o calor do chip de forma eficiente.
Subenchimento CSP em nível de wafer: econômico e de alto rendimento
O subenchimento do pacote de escala de chip em nível de wafer (WLCSP) é uma técnica de embalagem econômica e de alto rendimento que oferece várias vantagens na eficiência de fabricação e na qualidade geral do produto. O subenchimento WLCSP aplica material de subenchimento a vários chips simultaneamente enquanto ainda está na forma de wafer antes de serem separados em embalagens individuais. Essa abordagem oferece inúmeros benefícios em relação à redução de custos, melhor controle do processo e maiores rendimentos de produção.
Uma das vantagens críticas do subenchimento WLCSP é sua relação custo-benefício. A aplicação do material de subenchimento no nível do wafer torna o processo de embalagem mais simplificado e eficiente. O material subpreenchido é dispensado no wafer usando um processo controlado e automatizado, reduzindo o desperdício de material e minimizando os custos de mão de obra. Além disso, a eliminação do manuseio de pacotes individuais e das etapas de alinhamento reduz o tempo e a complexidade geral da produção, resultando em economia significativa de custos em comparação com os métodos de embalagem tradicionais.
Além disso, o subenchimento WLCSP oferece melhor controle de processo e maiores rendimentos de produção. Uma vez que o material de subenchimento é aplicado no nível do wafer, ele permite um melhor controle sobre o processo de distribuição, garantindo uma cobertura consistente e uniforme do subenchimento para cada chip no wafer. Isso reduz o risco de vazios ou subpreenchimento incompleto, o que pode levar a problemas de confiabilidade. A capacidade de inspecionar e testar a qualidade do subenchimento no nível do wafer também permite a detecção precoce de defeitos ou variações do processo, permitindo ações corretivas oportunas e reduzindo a probabilidade de embalagens defeituosas. Como resultado, o subenchimento WLCSP ajuda a alcançar maiores rendimentos de produção e melhor qualidade geral do produto.
A abordagem em nível de wafer também permite desempenho térmico e mecânico aprimorado. O material de preenchimento usado no WLCSP é tipicamente um material de fluxo capilar de baixa viscosidade que pode preencher com eficiência as lacunas estreitas entre os cavacos e o wafer. Isso fornece suporte mecânico sólido para os chips, aumentando sua resistência ao estresse mecânico, vibrações e ciclos de temperatura. Além disso, o material underfill atua como um condutor térmico, facilitando a dissipação do calor gerado pelos cavacos, melhorando assim o gerenciamento térmico e reduzindo o risco de superaquecimento.
Flip Chip Underfill: alta densidade de E/S e desempenho
Flip chip underfill é uma tecnologia crítica que permite alta densidade de entrada/saída (E/S) e desempenho excepcional em dispositivos eletrônicos. Ele desempenha um papel crucial no aprimoramento da confiabilidade e funcionalidade do encapsulamento flip-chip, que é amplamente utilizado em aplicações avançadas de semicondutores. Este artigo explorará a importância do subpreenchimento do flip chip e seu impacto na obtenção de alta densidade e desempenho de E/S.
A tecnologia flip chip envolve a conexão elétrica direta de um circuito integrado (IC) ou uma matriz semicondutora ao substrato, eliminando a necessidade de ligação de fios. Isso resulta em um pacote mais compacto e eficiente, pois os blocos de E/S estão localizados na superfície inferior da matriz. No entanto, a embalagem flip-chip apresenta desafios únicos que devem ser enfrentados para garantir desempenho e confiabilidade ideais.
Um dos desafios críticos na embalagem flip chip é evitar o estresse mecânico e a incompatibilidade térmica entre a matriz e o substrato. Durante o processo de fabricação e operação subsequente, as diferenças nos coeficientes de expansão térmica (CTE) entre a matriz e o substrato podem causar estresse significativo, levando à degradação do desempenho ou até mesmo à falha. Flip chip underfill é um material protetor que encapsula o chip, fornecendo suporte mecânico e alívio de tensão. Ele distribui efetivamente as tensões geradas durante os ciclos térmicos e evita que afetem as delicadas interconexões.
Alta densidade de I/O é crítica em dispositivos eletrônicos modernos, onde fatores de forma menores e maior funcionalidade são essenciais. O subpreenchimento do chip flip permite densidades de E/S mais altas, oferecendo isolamento elétrico superior e recursos de gerenciamento térmico. O material de subenchimento preenche o espaço entre a matriz e o substrato, criando uma interface robusta e reduzindo o risco de curto-circuito ou vazamento elétrico. Isso permite um espaçamento menor dos blocos de E/S, resultando em maior densidade de E/S sem sacrificar a confiabilidade.
Além disso, o subpreenchimento do flip chip contribui para melhorar o desempenho elétrico. Ele minimiza os parasitas elétricos entre a matriz e o substrato, reduzindo o atraso do sinal e melhorando a integridade do sinal. O material de preenchimento também exibe excelentes propriedades de condutividade térmica, dissipando eficientemente o calor gerado pelo chip durante a operação. A dissipação de calor eficaz garante que a temperatura permaneça dentro dos limites aceitáveis, evitando o superaquecimento e mantendo o desempenho ideal.
Avanços em materiais de subpreenchimento de flip chip permitiram densidades de E/S e níveis de desempenho ainda maiores. Subpreenchimentos de nanocompósitos, por exemplo, aproveitam os enchimentos em nanoescala para melhorar a condutividade térmica e a resistência mecânica. Isso permite uma melhor dissipação de calor e confiabilidade, permitindo dispositivos de maior desempenho.
Subpreenchimento Ball Grid Array (BGA): alto desempenho térmico e mecânico
Ball Grid Array (BGA) preenche uma tecnologia crítica que oferece alto desempenho térmico e mecânico em dispositivos eletrônicos. Ele desempenha um papel crucial no aprimoramento da confiabilidade e funcionalidade dos pacotes BGA, que são amplamente utilizados em vários aplicativos. Neste artigo, exploraremos a importância do subenchimento BGA e seu impacto na obtenção de alto desempenho térmico e mecânico.
A tecnologia BGA envolve um projeto de embalagem em que o circuito integrado (IC) ou matriz semicondutora é montado em um substrato e as conexões elétricas são feitas por meio de uma matriz de esferas de solda localizadas na superfície inferior da embalagem. O BGA preenche um material dispensado no espaço entre a matriz e o substrato, encapsulando as esferas de solda e fornecendo suporte mecânico e proteção ao conjunto.
Um dos desafios críticos na embalagem BGA é o gerenciamento de tensões térmicas. Durante a operação, o IC gera calor e a expansão e contração térmica podem causar pressão significativa nas juntas de solda que conectam a matriz e o substrato. O BGA desempenha um papel crucial na mitigação dessas tensões, formando uma ligação sólida com a matriz e o substrato. Atua como um amortecedor de tensão, absorvendo a expansão e contração térmica e reduzindo a tensão nas juntas de solda. Isso ajuda a melhorar a confiabilidade geral do pacote e reduz o risco de falhas nas juntas de solda.
Outro aspecto crítico do subenchimento BGA é sua capacidade de melhorar o desempenho mecânico da embalagem. Os pacotes BGA são frequentemente submetidos a tensões mecânicas durante o manuseio, montagem e operação. O material de preenchimento preenche o espaço entre a matriz e o substrato, fornecendo suporte estrutural e reforço às juntas de solda. Isso melhora a resistência mecânica geral do conjunto, tornando-o mais resistente a choques mecânicos, vibrações e outras forças externas. Ao distribuir eficazmente as tensões mecânicas, o underfill BGA ajuda a evitar rachaduras, delaminação ou outras falhas mecânicas na embalagem.
O alto desempenho térmico é essencial em dispositivos eletrônicos para garantir funcionalidade e confiabilidade adequadas. Os materiais de subenchimento BGA são projetados para ter excelentes propriedades de condutividade térmica. Isso permite que eles transfiram com eficiência o calor para longe da matriz e distribuam-no pelo substrato, aprimorando o gerenciamento térmico geral da embalagem. A dissipação de calor eficaz ajuda a manter temperaturas operacionais mais baixas, evitando pontos quentes térmicos e possível degradação do desempenho. Também contribui para a longevidade da caixa ao reduzir o estresse térmico dos componentes.
Os avanços nos materiais de subenchimento BGA levaram a um desempenho térmico e mecânico ainda maior. Formulações e materiais de enchimento aprimorados, como nanocompósitos ou enchimentos de alta condutividade térmica, permitiram melhor dissipação de calor e resistência mecânica, melhorando ainda mais o desempenho dos pacotes BGA.
Subpreenchimento Quad Flat Package (QFP): grande número de E/S e robustez
Quad Flat Package (QFP) é um pacote de circuito integrado (IC) amplamente utilizado em eletrônica. Possui uma forma quadrada ou retangular com condutores que se estendem de todos os quatro lados, fornecendo muitas conexões de entrada/saída (E/S). Para aumentar a confiabilidade e a robustez dos pacotes QFP, materiais de subenchimento são comumente empregados.
Underfill é um material de proteção aplicado entre o IC e o substrato para reforçar a resistência mecânica das juntas de solda e evitar falhas induzidas por estresse. É particularmente crucial para QFPs com uma grande contagem de E/S, pois o alto número de conexões pode levar a tensões mecânicas significativas durante os ciclos térmicos e as condições operacionais.
O material de subenchimento utilizado para embalagens QFP deve possuir características específicas para garantir robustez. Em primeiro lugar, deve ter excelente adesão tanto ao IC quanto ao substrato para criar uma ligação forte e minimizar o risco de delaminação ou desprendimento. Além disso, deve ter um baixo coeficiente de expansão térmica (CTE) para corresponder ao CTE do IC e do substrato, reduzindo as incompatibilidades de tensão que podem levar a rachaduras ou fraturas.
Além disso, o material de preenchimento deve ter boas propriedades de fluxo para garantir cobertura uniforme e preenchimento completo do espaço entre o IC e o substrato. Isso ajuda a eliminar vazios, que podem enfraquecer as juntas de solda e resultar em confiabilidade reduzida. O material também deve ter boas propriedades de cura, permitindo formar uma camada protetora rígida e durável após a aplicação.
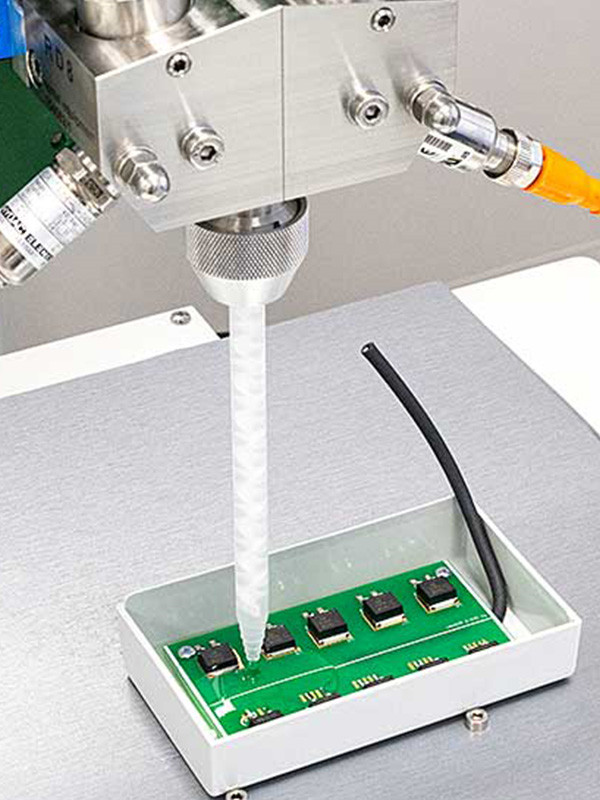
Em termos de robustez mecânica, o subenchimento deve possuir alto cisalhamento e resistência ao descascamento para suportar forças externas e evitar deformação ou separação da embalagem. Também deve apresentar boa resistência à umidade e outros fatores ambientais para manter suas propriedades protetoras ao longo do tempo. Isso é particularmente importante em aplicações onde o pacote QFP pode ser exposto a condições adversas ou sofrer variações de temperatura.
Vários materiais de subenchimento estão disponíveis para atingir essas características desejadas, incluindo formulações à base de epóxi. Dependendo dos requisitos específicos da aplicação, esses materiais podem ser dispensados usando diferentes técnicas, como fluxo capilar, jateamento ou serigrafia.
Subpreenchimento do System-in-Package (SiP): integração e desempenho
System-in-Package (SiP) é uma tecnologia de empacotamento avançada que integra vários chips semicondutores, componentes passivos e outros elementos em um único pacote. O SiP oferece inúmeras vantagens, incluindo fator de forma reduzido, desempenho elétrico aprimorado e funcionalidade aprimorada. Para garantir a confiabilidade e o desempenho dos conjuntos SiP, materiais de subenchimento são comumente usados.
O subpreenchimento em aplicações SiP é crucial para fornecer estabilidade mecânica e conectividade elétrica entre os vários componentes dentro do pacote. Ajuda a minimizar o risco de falhas induzidas por tensão, como rachaduras ou fraturas nas juntas de solda, que podem ocorrer devido a diferenças nos coeficientes de expansão térmica (CTE) entre os componentes.
A integração de vários componentes em um pacote SiP leva a uma interconectividade complexa, com muitas juntas de solda e circuitos de alta densidade. Os materiais de subenchimento ajudam a reforçar essas interconexões, aumentando a resistência mecânica e a confiabilidade da montagem. Eles suportam as juntas de solda, reduzindo o risco de fadiga ou danos causados por ciclos térmicos ou estresse mecânico.
Em termos de desempenho elétrico, os materiais de subenchimento são essenciais para melhorar a integridade do sinal e minimizar o ruído elétrico. Ao preencher as lacunas entre os componentes e reduzir a distância entre eles, o subpreenchimento ajuda a reduzir a capacitância e a indutância parasita, permitindo uma transmissão de sinal mais rápida e eficiente.
Além disso, materiais de subenchimento para aplicações SiP devem ter excelente condutividade térmica para dissipar o calor gerado pelos componentes integrados de forma eficiente. A dissipação de calor eficaz é essencial para evitar o superaquecimento e manter a confiabilidade e o desempenho geral do conjunto SiP.
Materiais de subenchimento em embalagens SiP devem ter propriedades específicas para atender a esses requisitos de integração e desempenho. Eles devem ter boa fluidez para garantir cobertura completa e preencher lacunas entre os componentes. O material de subenchimento também deve ter uma formulação de baixa viscosidade para facilitar a distribuição e enchimento em orifícios estreitos ou pequenos espaços.
Além disso, o material de preenchimento deve apresentar forte adesão a diferentes superfícies, incluindo chips semicondutores, substratos e passivos, para garantir uma ligação confiável. Deve ser compatível com vários materiais de embalagem, como substratos orgânicos ou cerâmicos, e apresentar boas propriedades mecânicas, incluindo alto cisalhamento e resistência ao descascamento.
A escolha do material de subenchimento e do método de aplicação depende do projeto específico do SiP, dos requisitos do componente e dos processos de fabricação. Técnicas de dispensação, como fluxo capilar, jato ou métodos assistidos por filme, geralmente aplicam subenchimento em montagens SiP.
Preenchimento Optoeletrônico: Alinhamento Óptico e Proteção
O subpreenchimento optoeletrônico inclui o encapsulamento e a proteção de dispositivos optoeletrônicos, ao mesmo tempo em que garante um alinhamento óptico preciso. Dispositivos optoeletrônicos, como lasers, fotodetectores e interruptores óticos, muitas vezes requerem um alinhamento delicado dos componentes óticos para atingir o desempenho ideal. Ao mesmo tempo, eles precisam ser protegidos de fatores ambientais que possam afetar sua funcionalidade. O subpreenchimento optoeletrônico atende a esses dois requisitos, fornecendo alinhamento e proteção óticos em um único processo.
O alinhamento óptico é um aspecto crítico da fabricação de dispositivos optoeletrônicos. Envolve o alinhamento de elementos visuais, como fibras, guias de onda, lentes ou grades, para garantir transmissão e recepção de luz eficientes. O alinhamento preciso é necessário para maximizar o desempenho do dispositivo e manter a integridade do sinal. As técnicas tradicionais de alinhamento incluem alinhamento manual usando inspeção visual ou alinhamento automatizado usando estágios de alinhamento. No entanto, esses métodos podem ser demorados, trabalhosos e propensos a erros.
O subpreenchimento optoeletrônico é uma solução inovadora incorporando recursos de alinhamento diretamente no material do subenchimento. Os materiais de subenchimento são compostos tipicamente líquidos ou semilíquidos que podem fluir e preencher as lacunas entre os componentes ópticos. Ao adicionar recursos de alinhamento, como microestruturas ou marcas de referência, dentro do material de preenchimento, o processo de alinhamento pode ser simplificado e automatizado. Esses recursos atuam como guias durante a montagem, garantindo o alinhamento preciso dos componentes ópticos sem a necessidade de procedimentos complexos de alinhamento.
Além do alinhamento óptico, os materiais de subenchimento protegem os dispositivos optoeletrônicos. Os componentes optoeletrônicos são frequentemente expostos a ambientes hostis, incluindo flutuações de temperatura, umidade e estresse mecânico. Esses fatores externos podem degradar o desempenho e a confiabilidade dos dispositivos ao longo do tempo. Os materiais de subenchimento atuam como uma barreira protetora, encapsulando os componentes ópticos e protegendo-os de contaminantes ambientais. Também fornecem reforço mecânico, reduzindo o risco de danos por choque ou vibração.
Os materiais de preenchimento usados em aplicações optoeletrônicas são normalmente projetados para ter baixo índice de refração e excelente transparência óptica. Isso garante interferência mínima com os sinais ópticos que passam pelo dispositivo. Além disso, eles exibem boa adesão a vários substratos e possuem baixos coeficientes de expansão térmica para minimizar o estresse do dispositivo durante os ciclos térmicos.
O processo de preenchimento envolve a aplicação do material de preenchimento no dispositivo, permitindo que ele flua e preencha as lacunas entre os componentes ópticos e, em seguida, cure-o para formar um encapsulamento sólido. Dependendo da aplicação específica, o material de preenchimento pode ser aplicado usando diferentes técnicas, como fluxo capilar, dispensação de jato ou serigrafia. O processo de cura pode ser obtido através de calor, radiação UV ou ambos.
Subpreenchimento de eletrônicos médicos: biocompatibilidade e confiabilidade
A eletrônica médica é um processo especializado que envolve encapsular e proteger componentes eletrônicos usados em dispositivos médicos. Esses dispositivos desempenham um papel crucial em várias aplicações médicas, como dispositivos implantáveis, equipamentos de diagnóstico, sistemas de monitoramento e sistemas de administração de medicamentos. O subpreenchimento de eletrônicos médicos concentra-se em dois aspectos críticos: biocompatibilidade e confiabilidade.
A biocompatibilidade é um requisito fundamental para dispositivos médicos que entram em contato com o corpo humano. Os materiais de preenchimento usados em eletrônicos médicos devem ser biocompatíveis, o que significa que não devem causar efeitos nocivos ou reações adversas quando em contato com tecidos vivos ou fluidos corporais. Esses materiais devem cumprir regulamentos e padrões rígidos, como o ISO 10993, que especifica testes de biocompatibilidade e procedimentos de avaliação.
Os materiais de preenchimento para eletrônicos médicos são cuidadosamente selecionados ou formulados para garantir a biocompatibilidade. Eles são projetados para serem não tóxicos, não irritantes e não alergênicos. Esses materiais não devem liberar nenhuma substância nociva ou degradar com o tempo, pois isso pode levar a danos nos tecidos ou inflamação. Os materiais de subenchimento biocompatíveis também têm baixa absorção de água para evitar o crescimento de bactérias ou fungos que podem causar infecções.
A confiabilidade é outro aspecto crítico do subpreenchimento de eletrônicos médicos. Os dispositivos médicos geralmente enfrentam condições operacionais desafiadoras, incluindo temperaturas extremas, umidade, fluidos corporais e estresse mecânico. Os materiais de preenchimento devem proteger os componentes eletrônicos, garantindo sua confiabilidade e funcionalidade a longo prazo. A confiabilidade é fundamental em aplicações médicas em que a falha do dispositivo pode afetar gravemente a segurança e o bem-estar do paciente.
Os materiais de preenchimento para eletrônicos médicos devem ter alta resistência à umidade e produtos químicos para resistir à exposição a fluidos corporais ou processos de esterilização. Eles também devem apresentar boa adesão a vários substratos, garantindo o encapsulamento seguro dos componentes eletrônicos. As propriedades mecânicas, como baixos coeficientes de expansão térmica e boa resistência ao choque, são cruciais para minimizar o estresse nos detalhes durante o ciclo térmico ou o carregamento automático.
O processo de subpreenchimento para eletrônicos médicos envolve:
- Dispensar o material de subenchimento nos componentes eletrônicos.
- Preenchendo as lacunas.
- Curando-o para formar um encapsulamento protetor e mecanicamente estável.
Deve-se ter cuidado para garantir a cobertura completa das características e a ausência de espaços vazios ou bolsões de ar que possam comprometer a confiabilidade do dispositivo.
Além disso, considerações adicionais são levadas em consideração ao subencher dispositivos médicos. Por exemplo, o material de subenchimento deve ser compatível com os métodos de esterilização usados para o dispositivo. Alguns materiais podem ser sensíveis a técnicas específicas de esterilização, como vapor, óxido de etileno ou radiação, e materiais alternativos podem precisar ser selecionados.
Subpreenchimento de Eletrônica Aeroespacial: Resistência a Alta Temperatura e Vibração
A eletrônica aeroespacial é um processo especializado para encapsular e proteger componentes eletrônicos em aplicações aeroespaciais. Os ambientes aeroespaciais apresentam desafios únicos, incluindo altas temperaturas, vibrações extremas e tensões mecânicas. Portanto, o underfill da eletrônica aeroespacial concentra-se em dois aspectos cruciais: resistência a altas temperaturas e resistência à vibração.
A resistência a altas temperaturas é fundamental na eletrônica aeroespacial devido às temperaturas elevadas experimentadas durante a operação. Os materiais de preenchimento usados em aplicações aeroespaciais devem suportar essas altas temperaturas sem comprometer o desempenho e a confiabilidade dos componentes eletrônicos. Eles devem exibir expansão térmica mínima e permanecer estáveis em uma ampla faixa de temperatura.
Os materiais de subenchimento para eletrônicos aeroespaciais são selecionados ou formulados para altas temperaturas de transição vítrea (Tg) e estabilidade térmica. Uma alta Tg garante que o material mantenha suas propriedades mecânicas em temperaturas elevadas, evitando deformações ou perda de adesão. Esses materiais podem suportar temperaturas extremas, como durante a decolagem, reentrada na atmosfera ou operação em compartimentos de motor quentes.
Além disso, materiais de subenchimento para eletrônicos aeroespaciais devem ter baixos coeficientes de expansão térmica (CTE). O CTE mede o quanto um material se expande ou se contrai com as mudanças de temperatura. Por ter um CTE baixo, os materiais de subenchimento podem minimizar o estresse nos componentes eletrônicos causado pelo ciclo térmico, o que pode levar a falhas mecânicas ou fadiga da junta de solda.
A resistência à vibração é outro requisito crítico para subenchimento de eletrônicos aeroespaciais. Os veículos aeroespaciais estão sujeitos a várias vibrações, incluindo motor, vibrações induzidas pelo voo e choques mecânicos durante o lançamento ou pouso. Essas vibrações podem comprometer o desempenho e a confiabilidade dos componentes eletrônicos se não forem adequadamente protegidos.
Materiais de subenchimento usados em eletrônica aeroespacial devem exibir excelentes propriedades de amortecimento de vibração. Eles devem absorver e dissipar a energia gerada pelas vibrações, reduzindo o estresse e a tensão nos componentes eletrônicos. Isso ajuda a evitar a formação de rachaduras, fraturas ou outras falhas mecânicas devido à exposição excessiva à vibração.
Além disso, materiais de subenchimento com alta adesão e resistência coesiva são preferidos em aplicações aeroespaciais. Essas propriedades garantem que o material de enchimento permaneça firmemente ligado aos componentes eletrônicos e ao substrato, mesmo sob condições de vibração extremas. A forte adesão evita que o material do subenchimento se delamine ou se separe dos elementos, mantendo a integridade do encapsulamento e protegendo contra a entrada de umidade ou detritos.
O processo de subenchimento para eletrônicos aeroespaciais geralmente envolve a aplicação do material de subenchimento nos componentes eletrônicos, permitindo que ele flua e preencha as lacunas e, em seguida, cure-o para formar um encapsulamento robusto. O processo de cura pode ser realizado usando métodos de cura térmica ou UV, dependendo dos requisitos específicos da aplicação.
Preenchimento de componentes eletrônicos automotivos: durabilidade e resistência à ciclagem térmica
A eletrônica automotiva preenche um processo crítico que envolve encapsular e proteger componentes eletrônicos em aplicações automotivas. Os ambientes automotivos apresentam desafios únicos, incluindo variações de temperatura, ciclos térmicos, tensões mecânicas e exposição à umidade e produtos químicos. Portanto, o underfill da eletrônica automotiva se concentra em dois aspectos críticos: durabilidade e resistência ao ciclo térmico.
A durabilidade é um requisito crucial para subenchimento de componentes eletrônicos automotivos. Durante a operação regular, os veículos automotores experimentam vibrações, choques e tensões mecânicas constantes. Os materiais de subenchimento usados em aplicações automotivas devem proteger os componentes eletrônicos de forma robusta, garantindo sua durabilidade e longevidade. Eles devem suportar as duras condições e cargas mecânicas encontradas na estrada e resistir à entrada de umidade, poeira e produtos químicos.
Os materiais de subenchimento para eletrônicos automotivos são selecionados ou formulados para alta resistência mecânica e resistência ao impacto. Devem apresentar excelente adesão aos componentes eletrônicos e ao substrato, evitando delaminação ou separação sob esforços mecânicos. Os materiais de preenchimento duráveis ajudam a minimizar o risco de danos aos componentes eletrônicos devido a vibrações ou choques, garantindo um desempenho confiável ao longo da vida útil do veículo.
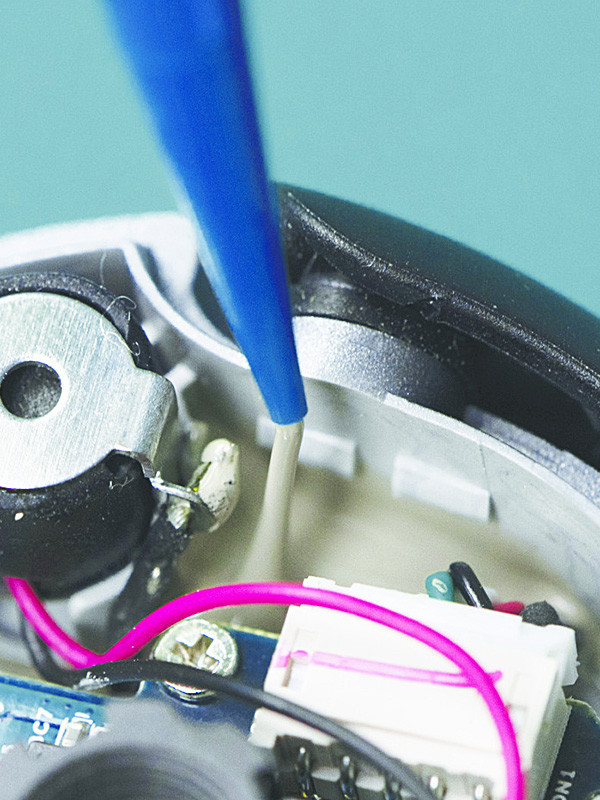
A resistência à ciclagem térmica é outro requisito crítico para subenchimento de componentes eletrônicos automotivos. Veículos automotivos sofrem variações frequentes de temperatura, especialmente durante a partida e operação do motor, e esses ciclos de temperatura podem induzir tensões térmicas em componentes eletrônicos e no material de subenchimento circundante. Os materiais de subenchimento usados em aplicações automotivas devem ter excelente resistência ao ciclo térmico para suportar essas flutuações de temperatura sem comprometer seu desempenho.
Os materiais de subenchimento para eletrônicos automotivos devem ter coeficientes de expansão térmica (CTE) baixos para minimizar o estresse dos componentes eletrônicos durante os ciclos térmicos. Um CTE bem combinado entre o material de preenchimento e os ingredientes reduz o risco de fadiga da junta de solda, rachaduras ou outras falhas mecânicas causadas por estresse térmico. Além disso, os materiais de subenchimento devem apresentar boa condutividade térmica para dissipar o calor com eficiência, evitando pontos quentes localizados que possam afetar o desempenho e a confiabilidade dos componentes.
Além disso, os materiais de subenchimento da eletrônica automotiva devem resistir à umidade, produtos químicos e fluidos. Eles devem ter baixa absorção de água para evitar o crescimento de fungos ou corrosão dos componentes eletrônicos. A resistência química garante que o material de preenchimento permaneça estável quando exposto a fluidos automotivos, como óleos, combustíveis ou agentes de limpeza, evitando degradação ou perda de aderência.
O processo de subenchimento para eletrônicos automotivos normalmente envolve a aplicação do material de subenchimento nos componentes eletrônicos, permitindo que ele flua e preencha as lacunas e, em seguida, cure-o para formar um encapsulamento durável. O processo de cura pode ser realizado por métodos de cura térmica ou UV, dependendo dos requisitos específicos da aplicação e do material de subenchimento utilizado.
Escolhendo o subpreenchimento certo de epóxi
Escolher o epóxi correto é uma decisão crucial na montagem e proteção de componentes eletrônicos. Os epóxis de preenchimento fornecem reforço mecânico, gerenciamento térmico e proteção contra fatores ambientais. Aqui estão algumas considerações importantes ao selecionar o epóxi de subenchimento apropriado:
- Propriedades Térmicas: Uma das principais funções do epóxi underfill é dissipar o calor gerado pelos componentes eletrônicos. Portanto, é essencial considerar a condutividade térmica e a resistência térmica do epóxi. A alta condutividade térmica ajuda na transferência de calor eficiente, evitando pontos quentes e mantendo a confiabilidade do componente. O epóxi também deve ter baixa resistência térmica para minimizar o estresse térmico nos componentes durante os ciclos de temperatura.
- Correspondência de CTE: O coeficiente de expansão térmica (CTE) do epóxi de enchimento deve ser bem combinado com o CTE dos componentes eletrônicos e do substrato para minimizar o estresse térmico e evitar falhas nas juntas de solda. Um CTE estreitamente combinado ajuda a reduzir o risco de falhas mecânicas devido ao ciclo térmico.
- Fluxo e capacidade de preenchimento de lacunas: o epóxi subpreenchido deve ter boas características de fluxo e a capacidade de preencher lacunas entre os componentes de forma eficaz. Isso garante uma cobertura completa e minimiza vazios ou bolsões de ar que podem afetar a estabilidade mecânica e o desempenho térmico do conjunto. A viscosidade do epóxi deve ser adequada para a aplicação específica e método de montagem, seja fluxo capilar, dispensação de jato ou serigrafia.
- Adesão: A adesão forte é crucial para o preenchimento de epóxi para garantir uma ligação confiável entre os componentes e o substrato. Deve apresentar boa adesão a vários materiais, incluindo metais, cerâmicas e plásticos. As propriedades de adesão do epóxi contribuem para a integridade mecânica e a confiabilidade de longo prazo do conjunto.
- Método de Cura: Considere o método de cura que melhor se adapta ao seu processo de fabricação. Os epóxis de subenchimento podem ser curados por meio de calor, radiação UV ou uma combinação de ambos. Cada método de cura tem vantagens e limitações, e escolher aquele que se alinha com seus requisitos de produção é essencial.
- Resistência Ambiental: Avalie a resistência do epóxi do subenchimento a fatores ambientais, como umidade, produtos químicos e temperaturas extremas. O epóxi deve ser capaz de resistir à exposição à água, evitando o crescimento de mofo ou corrosão. A resistência química garante estabilidade quando em contato com fluidos automotivos, agentes de limpeza ou outras substâncias potencialmente corrosivas. Além disso, o epóxi deve manter suas propriedades mecânicas e elétricas em uma ampla faixa de temperatura.
- Confiabilidade e Longevidade: Considere o histórico do epóxi de subenchimento e os dados de confiabilidade. Procure materiais epóxi testados e com bom desempenho em aplicações semelhantes ou tenham certificações do setor e conformidade com os padrões relevantes. Considere fatores como comportamento de envelhecimento, confiabilidade a longo prazo e a capacidade do epóxi de manter suas propriedades ao longo do tempo.
Ao selecionar o epóxi de subenchimento correto, é crucial considerar os requisitos específicos de sua aplicação, incluindo gerenciamento térmico, estabilidade mecânica, proteção ambiental e compatibilidade do processo de fabricação. Consultar fornecedores de epóxi ou buscar aconselhamento especializado pode ser benéfico para tomar uma decisão informada que atenda às necessidades de sua aplicação e garanta desempenho e confiabilidade ideais.
Tendências Futuras em Epóxi Underfill
O epóxi de subpreenchimento está em constante evolução, impulsionado por avanços em tecnologias eletrônicas, aplicações emergentes e a necessidade de desempenho e confiabilidade aprimorados. Várias tendências futuras podem ser observadas no desenvolvimento e aplicação de epóxi underfill:
- Miniaturização e embalagem de maior densidade: Como os dispositivos eletrônicos continuam a encolher e apresentam densidades de componentes mais altas, os epóxis de subpreenchimento devem se adaptar de acordo. As tendências futuras se concentrarão no desenvolvimento de materiais de subenchimento que penetram e preenchem lacunas menores entre os componentes, garantindo cobertura completa e proteção confiável em montagens eletrônicas cada vez mais miniaturizadas.
- Aplicações de alta frequência: Com a crescente demanda por dispositivos eletrônicos de alta frequência e alta velocidade, as formulações de epóxi de subpreenchimento precisarão atender aos requisitos específicos dessas aplicações. Materiais de preenchimento com baixa constante dielétrica e tangentes de baixa perda serão essenciais para minimizar a perda de sinal e manter a integridade dos sinais de alta frequência em sistemas avançados de comunicação, tecnologia 5G e outras aplicações emergentes.
- Gerenciamento térmico aprimorado: a dissipação de calor continua sendo uma preocupação crítica para dispositivos eletrônicos, especialmente com o aumento das densidades de energia. As futuras formulações de epóxi de subenchimento se concentrarão na condutividade térmica aprimorada para melhorar a transferência de calor e gerenciar problemas térmicos de forma eficaz. Cargas e aditivos avançados serão incorporados aos epóxis de subenchimento para obter maior condutividade térmica, mantendo outras propriedades desejadas.
- Eletrônicos Flexíveis e Elásticos: A ascensão de eletrônicos flexíveis e elásticos abre novas possibilidades para materiais epóxi de preenchimento insuficiente. Os epóxis de preenchimento flexível devem demonstrar excelente adesão e propriedades mecânicas, mesmo sob dobras ou alongamentos repetidos. Esses materiais permitirão o encapsulamento e proteção de eletrônicos em dispositivos vestíveis, monitores dobráveis e outras aplicações que requerem flexibilidade mecânica.
- Soluções ecológicas: Sustentabilidade e considerações ambientais desempenharão um papel cada vez mais significativo no desenvolvimento de materiais epóxi de subenchimento. Haverá um foco na criação de formulações de epóxi livres de substâncias perigosas e com impacto ambiental reduzido em todo o seu ciclo de vida, incluindo fabricação, uso e descarte. Materiais de base biológica ou renovável também podem ganhar destaque como alternativas sustentáveis.
- Processos de fabricação aprimorados: as tendências futuras em epóxi de subpreenchimento se concentrarão nas propriedades do material e nos avanços nos processos de fabricação. Técnicas como manufatura aditiva, distribuição seletiva e métodos avançados de cura serão exploradas para otimizar a aplicação e o desempenho do epóxi de subenchimento em vários processos de montagem eletrônica.
- Integração de técnicas avançadas de teste e caracterização: Com a crescente complexidade e requisitos de dispositivos eletrônicos, haverá a necessidade de métodos avançados de teste e caracterização para garantir a confiabilidade e o desempenho do epóxi subpreenchido. Técnicas como testes não destrutivos, monitoramento in-situ e ferramentas de simulação ajudarão no desenvolvimento e controle de qualidade de materiais epóxi subpreenchidos.
Conclusão
O epóxi de subpreenchimento desempenha um papel crítico no aprimoramento da confiabilidade e do desempenho de componentes eletrônicos, principalmente em embalagens de semicondutores. Os diferentes tipos de epóxi de subenchimento oferecem uma série de benefícios, incluindo alta confiabilidade, auto-distribuição, alta densidade e alto desempenho térmico e mecânico. A escolha do epóxi de subenchimento correto para a aplicação e a embalagem garante uma união robusta e duradoura. À medida que a tecnologia avança e os tamanhos das embalagens diminuem, esperamos soluções epóxi de subenchimento ainda mais inovadoras, oferecendo desempenho, integração e miniaturização superiores. O epóxi de enchimento está definido para desempenhar um papel cada vez mais importante no futuro da eletrônica, permitindo-nos alcançar níveis mais altos de confiabilidade e desempenho em vários setores.